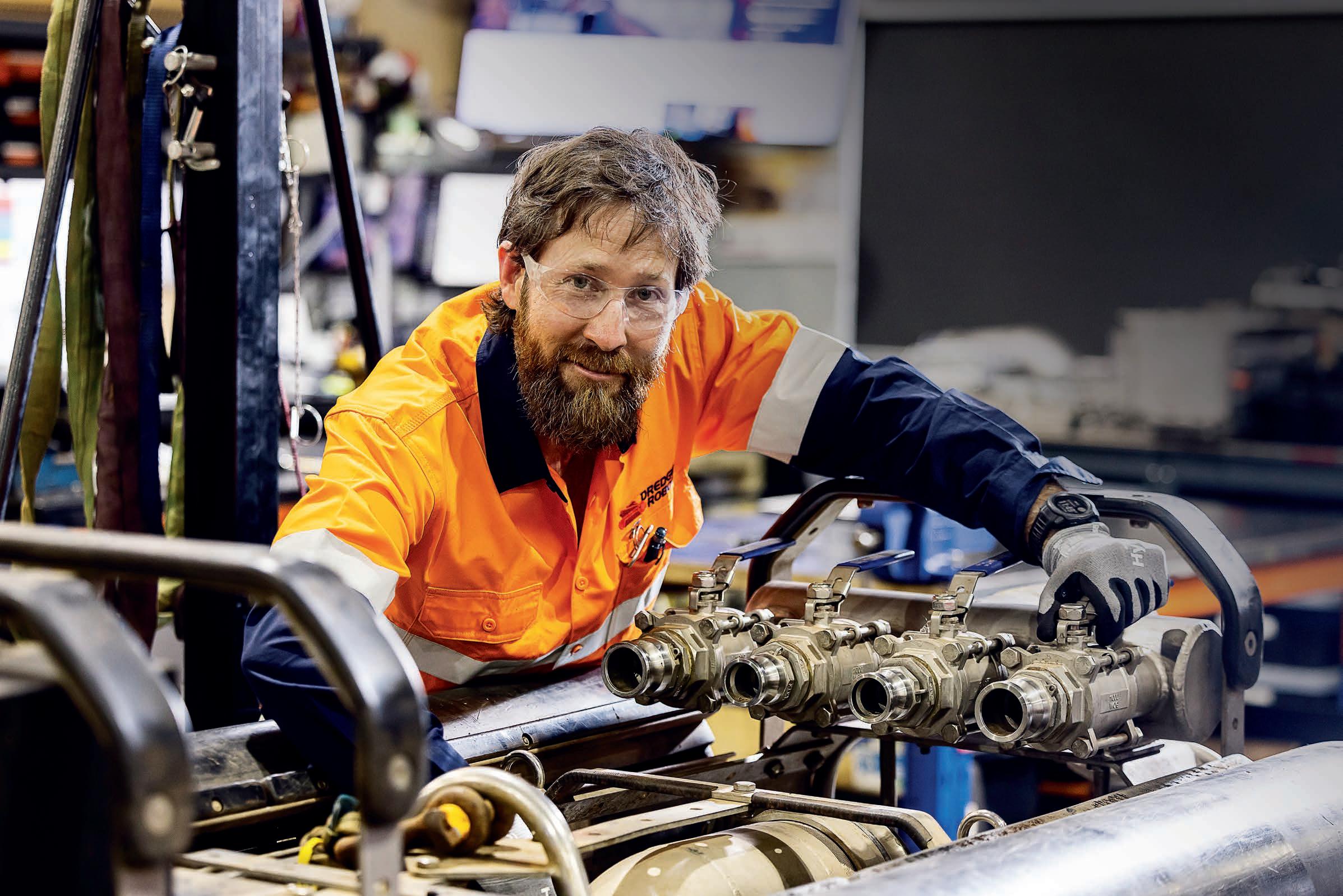
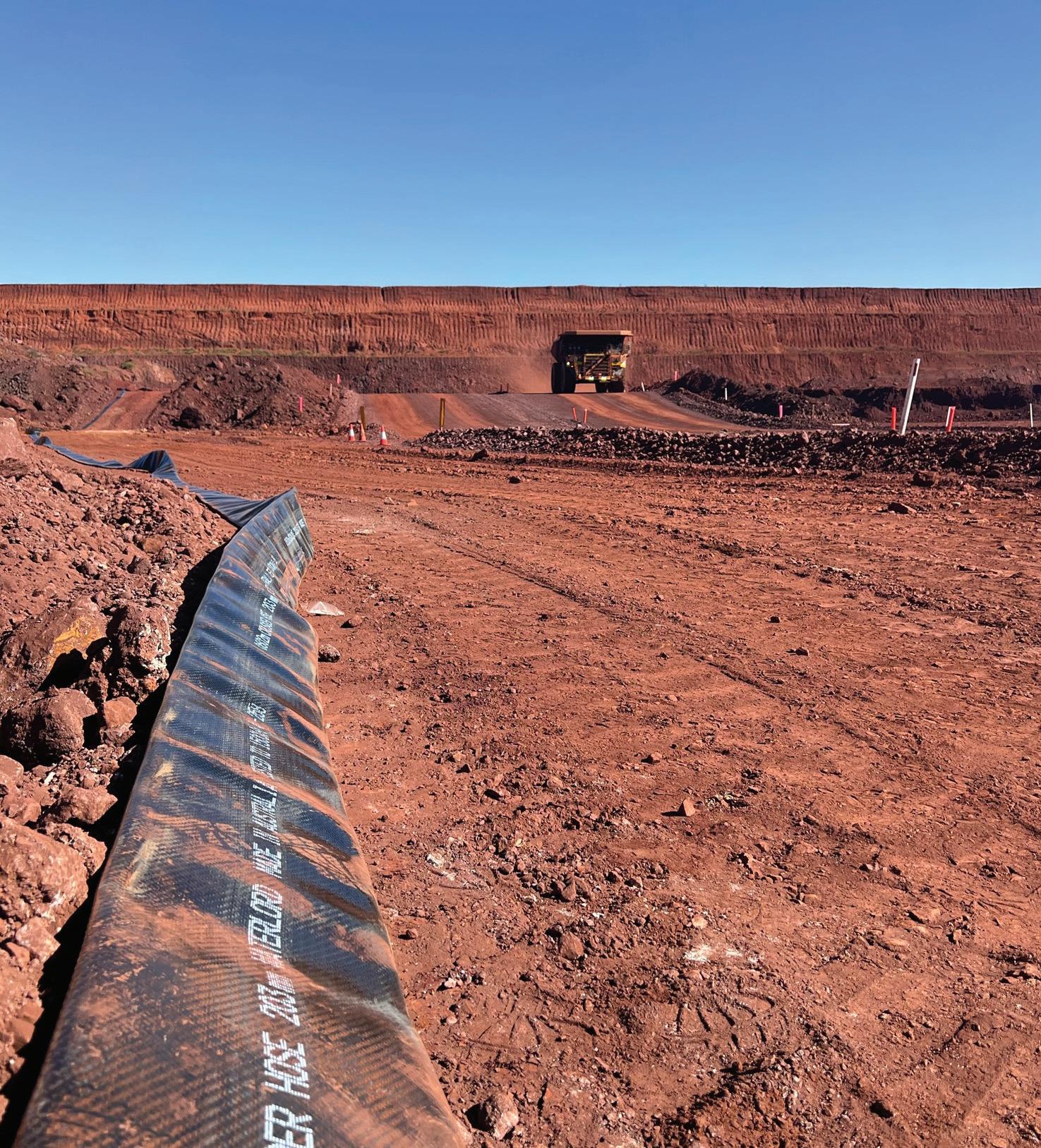
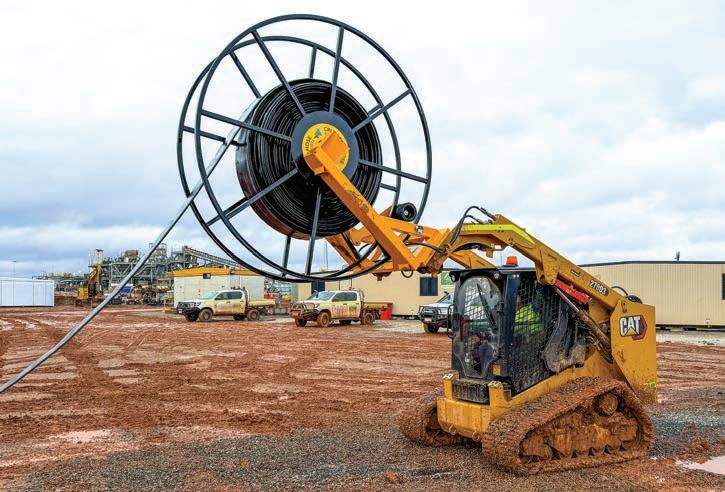
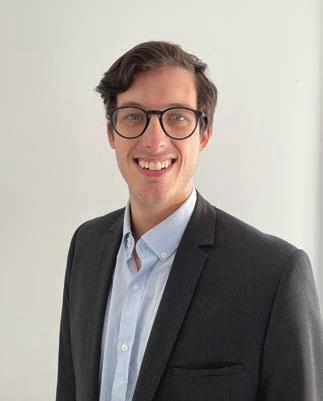
Big trucks and novel innovations quickly capture our gaze, but without adequate maintenance processes in place, the resources industry would fall apart.
Proactive maintenance is not only central to keeping machinery on the park but also unlocking efficiency and productivity gains.
The best-performing mining operations prioritise predictive and preventive maintenance to limit costly downtime, enabling them to shift more tonnes more often.
While preventive maintenance is a routine practice, predictive maintenance is made possible by condition monitoring and data analysis.
This could involve sensor-based solutions, machine learning, parts and attachments, or inherent maintenance attributes built into existing equipment, enabling operators to anticipate pain points or breakdowns before they arise.
Such solutions are not possible without contributions from the mining equipment, technology and services (METS) sector.
The March edition of Australian Mining sees us celebrate the original equipment manufacturers (OEMs), suppliers and service providers supporting more proactive and intelligent maintenance practices.
Cummins shares its unique maintenance approach. The company’s PrevenTech solution has become an important analyser of engine and equipment health.
CHIEF EXECUTIVE OFFICER
JOHN MURPHY
CHIEF OPERATING OFFICER
CHRISTINE CLANCY
MANAGING EDITOR PAUL HAYES
EDITOR
TOM PARKER
Email: tom.parker@primecreative.com.au
ASSISTANT EDITOR
ALEXANDRA EASTWOOD
Email: alexandra.eastwood@primecreative.com.au
JOURNALISTS
OLIVIA THOMSON
Email: olivia.thomson@primecreative.com.au
Elsewhere, we learn of how Hastings Deering helped save a Queensland coal miner thousands of dollars in operating costs through its innovative ground engaging tools.
We also spotlight maintenance solutions from DomeShelter, Bedeschi, MAX Plant, Nivek Industries and Veyex, to name a few.
Through its novel dredging technology, Dredge Robotics is en route to international stardom, which is why the company graces the cover of the March edition.
Dredge has developed a fleet of robots to help clean lined ponds at all ends of the pH spectrum. Just as Dredge thinks it’s completed its technology development, more use cases are discovered, demonstrating the company’s significant upside.
“What we keep finding is that clients, and potential clients, are approaching us with new niche applications that are ideal for our tech,” Dredge chief executive officer Antony Old told Australian Mining. “We keep expanding into that rather than contracting.”
This edition also sees us spotlight the future of green iron and vanadium, and analyse what Northern Star’s acquisition of De Grey Mining will look like.
Happy reading.
Tom Parker Editor
KELSIE TIBBEN
Email: kelsie.tibben@primecreative.com.au
DYLAN BROWN
Email: dylan.brown@primecreative.com.au
CLIENT SUCCESS MANAGER
JANINE CLEMENTS
Tel: (02) 9439 7227
Email: janine.clements@primecreative.com.au
SALES MANAGER
JONATHAN DUCKETT
Mob: 0498 091 027
Email: jonathan.duckett@primecreative.com.au
BUSINESS DEVELOPMENT MANAGERS
JAMES PHIPPS
Mob: 0466 005 715
Email: james.phipps@primecreative.com.au
ROB O’BRYAN Mob: 0411 067 795
Email: robert.obryan@primecreative.com.au
ART DIRECTOR MICHELLE WESTON michelle.weston@primecreative.com.au
SUBSCRIPTION RATES Australia (surface mail) $120.00 (incl
Dredge Robotics creates unique, cost-effective robotic cleaning solutions that deliver significant savings to clients by keeping water assets online during the dredging process.
As an Australian-owned and -operated company, Dredge understands what’s required to provide superior quality dredging across the Australian mining, industrial, manufacturing, processing and wastewater industries. Dredge Robotics is backed by an extensive asset base, comprehensive management systems and over 35 years of experience.
With the demand for safe and effective dredging solutions rapidly rising and diversifying in the mining industry, Dredge is constantly evolving its platform and adding new tooling to support specific applications.
Cover image: Dredge Robotics
game-changer
Green Iron SA is working to transform the steel industry with the help of the Razorback iron ore project.
12 CRITICAL MINERALS
Vanadium: A critical player
Australian Mining highlights four projects vying to deliver the country’s first active vanadium mine.
14 COVER STORY
A burgeoning international success
Dredge Robotics is rapidly expanding its profile at home and overseas as mining companies recognise the value in its unique solution.
28 MAINTENANCE
Intelligent filtration management
FleetguardFIT is a filtration intelligence monitoring system that helps prevent costly equipment damage and downtime.
52 MAINTENANCE
Keeping a lid on leaks
Compressed air leaks can wreak havoc on a mine site. Luckily, FLIR has a solution.
56 M&A
Reaching for the Northern Star
What does Northern Star Resources’ potential acquisition of De Grey Mining mean for the WA gold sector?
58 DECARBONISATION
Mastering the path to decarbonisation
As mining companies look to slash emissions, robust and reliable renewable energy solutions are key.
64 DRILL AND BLAST
Go-go gadget
The narrow vein drilling solution Brokk developed for a South African mining company is now attracting attention in Australia.
AUSTRALIAN MINING PRESENTS THE LATEST NEWS FROM THE BOARDROOM TO THE MINE AND EVERYWHERE IN BETWEEN. VISIT WWW.AUSTRALIANMINING.COM.AU TO KEEP UP TO DATE WITH WHAT IS HAPPENING.
Native Mineral Resources (NMR) is ramping up refurbishment at its Blackjack gold processing plant in Queensland, with targeted for the third quarter of 2025 (Q3 2025).
NMR acquired 17 granted mining leases, one mineral development license, six exploration permits, and the Blackjack processing plant from Collins St convertible notes for $18.9 million in November 2024.
The tenements are situated in the Ravenswood-Charters Towers region, an area known to be rich with minerals.
Since the acquisition’s finalisation, NMR has advanced works to pave the way for gold production to recommence at Blackjack.
Such works include process plant refurbishment, regulatory compliance, site establishment and an assessment of the tailings storage facility. Ball mill inspections were also completed, with a report issued in late January.
NMR’s maintenance team has reviewed the draining of the carbonin-leach (CIL) tanks and assessed the process pumps, ensuring the systems are functioning as normal ahead of the targeted restart.
NATIVE MINERAL RESOURCES IS TARGETING FIRST GOLD POUR IN THE THIRD QUARTER OF 2025.
refurbishment team comprising 14 personnel to Blackjack in mid-January.
The team carried out demolition, equipment removal and cladding works in Goldroom Area 05, and ventilation and further electrical and
MEET THE WORLD’S LARGEST LITHIUM RESOURCE
Australia might be the largest lithium producer globally, producing 52 per cent of the world’s total, but Lithium Americas has laid claim to the world’s largest lithium resource.
Lithium Americas is currently advancing its Thacker Pass asset in Nevada, US, to production to meet the growing lithium demand in North America.
In a major milestone for Thacker Pass, the mineral reserve estimate has increased to 14.3 million tonnes (Mt) of lithium carbonate equivalent at an average grade of 2540 parts per million (ppm). This represents a 286 per cent jump from Lithium
Americas’ November 2022 feasibility study and paves the way for an expansion of up to five phases with an 85-year mine life.
Thacker Pass’ measured and indicated mineral resource estimate now sits at 44.5Mt lithium carbonate equivalent at an average grade of 2230ppm, representing a 177 per cent increase from the November 2022 feasibility study.
Lithium Americas president and chief executive officer Jonathan Evans said Thacker Pass’ new mineral reserve and mineral reserve estimate “demonstrates the multigenerational opportunity
AUSTRALIAN MINING GETS THE LATEST NEWS EVERY DAY, PROVIDING MINING PROFESSIONALS WITH UP-TO-THE-MINUTE INFORMATION ON SAFETY, NEWS AND TECHNOLOGY FOR THE AUSTRALIAN MINING AND RESOURCES INDUSTRY.
to pour first gold at our Queensland projects in Q3 2025,” NMR managing director Blake Cannavo said.
“With key milestones set to be achieved this month and essential activities progressing as planned, the company is focused on continuing this momentum and looks forward to providing further updates.”
television (CCTV), access control, and security systems were completed in early February.
“Our process plant refurbishment tasks are continuing to progress on schedule and we remain on track
for transformational growth the project creates”.
“Thacker Pass is now the largest measured lithium reserve and resource in the world and has the potential to become an unmatched district, generating American jobs and helping the US regain independence of its energy supply,” Evans said.
“We are committed to safely and sustainably developing Thacker Pass while engaging with our stakeholders to increase domestic production of critical minerals.”
Thacker Pass’ first phase is expected to reach a final investment decision by early 2025.
NMR is also progressing its mining tenements, environmental reporting, and regulatory submissions for the projects.
MEC Mining has also signed on to help with the process.
Phase one is projected to create nearly 2000 jobs during the construction stage, approximately 350 full-time jobs once operational and an average of about 1100 fulltime employees over Thacker Pass’ total mine life.
The project’s first four phases will target 40,000 tonnes (t) of batterygrade lithium carbonate per annum, with the overall expansion plan targeting 160,000t per annum.
Thacker Pass is indirectly owned by Lithium Nevada Ventures, a 62:38 joint venture between Lithium Americas and General Motors, a motor vehicle manufacturer.
BHP has awarded a contract worth approximately $40 million to support the proposed expansion of its Olympic Dam copper smelter and refinery facilities in South Australia.
A joint venture between Fluor Australia and Hatch have been granted the engineering, procurement and construction management (EPCM) contract following engagement with BHP’s major projects, procurement, commercial and Copper South Australia teams.
The contract will be executed in stages as BHP progresses towards
MINRES DELIVERED ITS FINAL TRAINLOAD OF IRON ORE FROM ITS YILGARN OPERATIONS IN WA BACK IN JANUARY.
“Fluor and Hatch are experienced EPCM partners with significant shared experience in delivering mega projects, who will bring the right level of scale and expertise to help BHP progress its copper growth plans in South Australia,” BHP Group procurement officer Rashpal Bhatti said. “The growth potential for Copper SA is exciting and this first stage of EPCM works will be key as we progress the proposal for an expanded copper smelter and refinery at the heart of South Australia’s growing copper province towards a
copper production in South Australia over the next decade.
The Big Australian would introduce a phased approach to increase refined copper cathode production to 500,000 tonnes (t) annually by the early 2030s, with a possible boost to 650,000t by the mid-2030s. This would be a significant jump from the approximately 322,000t produced in FY24.
Phase one of the strategy would involve upgrading the existing copper smelter and refinery at Olympic Dam to a two-stage smelter and extension
“It is critical that we prudently manage our spending to achieve the vision that BHP shares with many others to grow copper production in South Australia, and we have worked closely with Fluor and Hatch on a contract structure that supports this,” Bhatti said.
BHP’s Copper South Australia business comprises Olympic Dam, the Carrapateena and Prominent Hill mines, and the Oak Dam deposit, the latter of which has 13 rigs currently carrying out exploration in a bid to advance its studies.
Mineral Resources (MinRes) delivered its final trainload of iron ore from its Yilgarn operations in WA in January, signalling the end of the company’s involvement in the region.
MinRes faced limited remaining mine life, significant capital cost and lead time to develop new resources at Yilgarn, prompting the company to finish up and focus on other projects.
Many of the MinRes’ Yilgarn workers are set to work at the company’s emerging Onslow Iron operation in WA.
As one of the largest iron ore projects currently under development, Onslow Iron is set to unlock billions of tonnes of stranded deposits.
to 35 million tonnes per year, with an expected mine life of more than 30 years.
Onslow Iron is being developed by MinRes on behalf of Red Hill Iron joint venture (RHIJV), including partners Baowu, AMCI and POSCO.
“Our teams have done a tremendous job in delivering this world-class transport infrastructure, which highlights the capability within our business,” MinRes chief executive engineering and construction Darren Killeen said.
transport operations from the Ken’s Bore mine through to the Port of Ashburton and enabling Onslow Iron’s ongoing production ramp-up to nameplate capacity.
The haul road has been specifically designed to support the planned conversion of MinRes road trains to autonomous operation via a series of roadside monitoring bases positioned alongside the roadway.
While MinRes has finished up in the historic Yilgarn iron ore region, which has been a source of iron ore since the
project in the region through her company Hancock Magnetite.
A pre-feasibility study (PFS) exploring Mt Bevan’s development was completed in July 2024, with more than $5 billion of capital expenditure set to be invested in the magnetite project.
According to the PFS, Mt Bevan, which boasts a mineral resource estimate of 1.29 billion tonnes, has the potential to achieve a direct reduction iron (DRI) product grade of more than 70 per cent iron.
Maximise performance with MASPRO’s high-quality components for underground and surface mining machinery. Using cutting-edge technology and rigorous testing, we engineer solutions that extend asset life, enhance reliability, and improve safety - helping you drill deeper, haul more, and tackle the toughest mining challenges.
MAGNETITE MINES IS WORKING TO TRANSFORM THE STEEL INDUSTRY THROUGH ITS RAZORBACK IRON ORE PROJECT IN SOUTH AUSTRALIA.
South Australia is helping reshape the world’s steel industry and its economic future as the state ambitiously works toward decarbonisation.
And there’s one project that stands out as a critical pillar in this green transition: the Razorback iron ore mine.
The project has the backing of Green Iron SA, a consortium comprising its owner Magnetite Mines, construction and engineering company GHD, freight rail transport company Aurizon and Flinders Ports.
The days of utilising carbon-based materials to create steel may soon be behind us, as Green Iron SA looks
Tim Dobson said Australia holds lots of magnetite, which hasn’t been economic up until now.
“South Australia finds itself in a very fortunate position in that it already hosts the biggest magnetite reserves in Australia and has three different regions that contain massive amounts,” he said.
The state’s commitment to renewable energy has already positioned it towards a sustainable future and by 2027, SA plans to power its entire grid with 100 per cent renewable energy, having already reached 75 per cent through wind and solar.
“It’s then that you have the ability to make the magnetite concentrate and producers can use the renewable energy
A key player in this emerging green iron industry is the Razorback project, located in the Braemar region of SA.
Razorback is Magnetite Mines’ flagship project, containing 3.2 billion tonnes of magnetite ore and two billion tonnes of probable ore reserves.
“It’s quite a large and spectacular project that will sustain 50 to 60 years of operations just on its first reserve,” Dobson said. “We’re expecting at least 100 years of production ahead at a very substantial scale. This project is set to be an economic game-changer not only for the region, but for the state.
“It will add significantly to Australia’s balance of trade and export incomes as
So how exactly will Razorback support sustainable steelmaking?
Dobson said magnetite can produce an almost-pure iron oxide product by processing it at the mine site using its magnetic properties.
He explained the plan is to dig the magnetite out of the ground, move it into a processing plant, remove all of the impurities using magnetic separation to produce a pure product, and use that to make green iron using hydrogen.
“There are no impurities involved, and this is the differentiator between magnetite and hematite (a traditional steelmaking material) which uses copious amounts of coal and hence emits copious amounts of carbon dioxide,” he said.
“This is the shift to magnetite. It’s not new, it’s been processed for 150 years and there’s five magnetite mining operations already in Australia.
“The difference now is that our project is massive. It will support up to 100 years of production and has the ability to produce this very high quality concentrate.”
One of Razorback’s key advantages is its proximity to existing rail and port infrastructure, with the project located only 50km from an open access railway line.
Dobson described this as a fortunate coincidence as iron ore projects typically need to be moving very large tonnages to be profitable.
“Building rail into mining projects is usually one of the most expensive capital items, so the fact we only have to move our material 50km to get it onto a railway line and then move it to port is great,” he said.
The material will then be transported to either Port Pirie or Whyalla, two critical export hubs in SA.
To fast track the development of the Razorback project, a consortium has been launched with Magnetite Mines, Aurizon Holdings, Flinders Port Holdings and GHD.
Australia’s largest rail operator, Aurizon, is tasked with transporting the magnetite. Flinders Port will then facilitate the export of the material with GHD providing essential technical and engineering support. Magnetite Mines is the downstream customer of not only the magnetite, but also future green iron.
The consortium aims to supply high-purity magnetite to produce green iron. The project will then progress to the production of direct reduction (DR) grade pellets, before manufacturing and exporting direct reduced iron (DRI) in the form of hot briquetted iron (HBI) from Port Pirie.
The creation of a new green iron industry will deliver economic benefits to the Upper Spencer Gulf region, including long-term job creation and community revitalisation.
Magnetite Mines’ product will be in high demand from international
steelmakers, including JFe Shoji, the trading arm of Japan’s second largest steelmaker, with which the company recently signed an offtake partnership.
“They are seeking new a supply chain to decarbonise their steel operations in Japan as one of the bigger and more successful steelmaking nations,” Dobson said.
“With our first partnership being solidified now, we’re also talking with other Japanese partners, and other partners from countries such as Taiwan, Korea, India and China.
“They’re our logical partners, and all of them are trying to decarbonise, and therefore all of them need magnetite.”
The SA Government has shown strong support for the Razorback project, with both State and Federal Governments recognising its economic and environmental potential.
Magnetite Mines is set to hand its mining lease proposal into the SA Government, which will trigger the formal regulatory and approvals process to receive permission to mine.
“The government is quite enthusiastic because the economic shift that we’ll get from building a green iron industry is phenomenal and necessary,” Dobson said.
While the support remains strong thus far, Dobson and his team hope for more backing, particularly in the form of material support.
“We’ve been talking with the Federal Government to support this
new industry by providing funding infrastructure so the SA Government,” he said. “This can help build things like roads, rail, power lines and port facilities, which can move these projects along and help get them to market.
“This is a shared responsibility between government and the private sector – one that will provide thousands of jobs and help keep our standard of living in Australia where it should be: at a very high level.”
For Australia to seize its green iron opportunity, Dobson believes it will take strong collaboration between miners, Australian industry providers, downstream international steelmaking customers and all levels of government to move projects forward.
Looking toward the future, Magnetite Mines’ priorities include securing the necessary mining approvals to formalise partnerships and at least one other partner to support funding and offtake agreements.
These priorities will allow a feasibility study to be completed to enable the Razorback project to progress from construction and into operations.
Green Iron SA is ushering in an exciting opportunity for South Australia and the country, and as the world transitions away from fossil fuels, the consortium has the chance to lead a new era of green innovation. AM
Vanadium has firmly positioned itself as an emerging critical mineral in Australia.
Used in steel production, batteries and electronics, vanadium is set to play a key role in the global energy transition, where renewables such as vanadium redox flow batteries (VRFB) will become primary energy sources.
According to the United States Geological Survey (USGS), vanadium demand – like for many ferroalloys – largely depends on the global steel market, specifically China’s.
But the winds are changing.
“Vanadium redox flow battery technology continue to be an increasingly important part of large-scale energy storage as it allows for high-safety, large-scale, environmentally friendly, mediumand long-term energy storage,” USGS said in its 2024 vanadium mineral commodity summary.
“Installations of VRFB projects continued to increase worldwide as energy companies looked to support renewable energy projects as many countries attempt to lower their carbon emissions.”
As of December 31, 2022, Australia had 8.5 million tonnes (Mt) of vanadium economic demonstrated resources and 2.97Mt in vanadium ore reserves, making up 32 per cent of the world’s vanadium resources.
While there are currently no active vanadium mines in Australia, the commodity is there for the taking, with four companies vying to take the top spot.
Australian Vanadium
Recognised as one of the largest and highest-grade vanadium deposits being developed in the world, the Australian Vanadium project is located in the Murchison province of Western Australia.
The project comprises a vanadium mine and a crushing, milling and beneficiation (CMB) plant.
Australian Vanadium Limited (AVL), the project’s owner, finalised its $217 million merger with Technology Metals Australia in February 2024 and has been undertaking an optimised feasibility study (OFS) to enable an integrated project across an 18km-long orebody.
The first phase of the OFS has been completed, delivering several key outcomes including an updated mineral resource estimate (MRE), identifying the optimal location to commence mining and build a processing plant.
Australian Vanadium’s MRE now sits at 395.4Mt at 0.77 per cent vanadium oxide, with 105.4Mt falling under the measured or indicated categories – a 39 per cent increase from the previous MRE.
“Our ongoing work on the OFS underscores the project’s strength and long-term viability, supported by high-quality engineering that establishes a foundation for excellence in both construction and production,” AVL chief executive officer (CEO)
Graham Arvidson said in the company’s September 2024 quarterly report.
Australian Vanadium also received a grant from the Federal Government’s Modern Manufacturing Initiative for up to $49 million.
“The indication of support from the US EXIM bank and our Federal Government grants demonstrate the project’s significance and the calibre of the parties that we are attracting,” Arvidson said.
AVL is currently working on the OFS’ next phase, which includes finalising the detailed mining plan using the updated MRE, optimising project infrastructure, and completing the layout and key design criteria for the CMB plant at Gabanintha and processing plant at Tenindewa.
Barrambie
Situated approximately 80km northwest of Sandstone in WA, the Barrambie titanium-vanadium project has already been granted a mining lease and
proposal to mine approximately 1.2Mt per annum.
According to owner Neometals, Barrambie is one of the world’s largest vanadiferous-titanomagnetite resources.
It currently holds 280.1Mt at 9.18 per cent titanium dioxide and 0.44 per cent vanadium oxide and contains the world’s second highest-grade hard-rock titanium mineral resource of 53.6Mt.
“Barrambie is a large and unique ‘mine-ready’ development opportunity benefiting from exceptionally high titanium resource/ reserve grades in a Tier 1 jurisdiction,” Neometals said.
“Securing access to large, high-grade chloride feedstock sources is a strategic imperative to downstream users for sustainable production of pigments and metal alloys.”
Neometals has released three pre-
one in 2015, 2022 and most recently in 2023.
The 2023 PFS estimated that Barrambie has a 13-year mine life, a project pre-tax net present value (NPV) of $374.9 million and an internal rate of return of 45 per cent.
The Australian Critical Minerals Prospectus states Barrambie will produce 1Mt of direct shipping ore in its first year, followed by 1Mt per annum of more than 35 per cent mixed titaniumvanadium-iron gravity concentrate from year two to five.
It’s then expected to produce over 30 per cent mixed titanium-vanadium-iron gravity concentrate for the rest of its mine life.
While Neometals revealed in August 2024 it was advancing discussions to divest Barrambie to prioritise the progression of Primobius, its lithium-
with GmbH, the project remains essential in feeding Australia’s vanadium aspirations.
The Victory Bore vanadium project is tipped to be a key critical minerals asset.
Located roughly 450km north of Perth in WA, Victory Bore is described as “one of the largest advanced critical mineral projects in Australia” by owner Surefire Resources.
Victory Bore’s 2023 PFS states the project has a 24-year mine life, a NPV of $1.7 billion, and is expected to produce 2580t of high-purity vanadium and 5760t of ferrovanadium per annum.
“The project is one of the largest vanadium resources in Australia with a mineral resource estimate of 464Mt and an ore reserve of 93Mt at 0.35 per cent vanadium oxide, 5.2 per cent titanium dioxide, (and) 19.8% iron,” Surefire said in its September 2024 quarterly report.
Surefire has secured three agreements with the Ministry of Investment Saudi Arabia, AJLAN Bros, Mining and Metals, and RASI Investment Company, all of which concern processing vanadium from Victory Bore.
The company has received expressions of interest from several parties for vanadium offtake agreements and is currently progressing these discussions.
Unlike many vanadium projects in Australia, QEM’s Julia Creek vanadium and energy project is located in the North West Minerals Province of Queensland.
Covering a 250km2 landholding, Julia Creek is considered to be a unique,
The project will comprise a greenfield vanadium and oil shale mine, alongside processing facilities. It aims to produce 10,571t of high-purity vanadium pentoxide per annum over a 30-year mine life.
Julia Creek currently holds a vanadium resource made up of approximately 2.9 billion tonnes, with 461Mt falling under the indicated category, making it one of the largest vanadium deposits in the world.
In recognising this significance, Queensland Coordinator-General Gerard Coggan declared Julia Creek a ‘coordinated project’ in December 2024, allowing the environmental approvals process with the Queensland and Federal Governments to commence.
“The adoption of vanadium flow batteries is accelerating around the world and Queensland is uniquely positioned to establish a ‘pit to battery’ manufacturing industry,” QEM managing director Gavin Loyden said.
“QEM will expand its participation in the value chain by processing its vanadium pentoxide into vanadium electrolyte for flow batteries.”
Julia Creek was also named a controlled action by the Department of Climate Change, Energy, the Environment and Water in January 2025, providing certainty on the approval pathway for the project.
According to the International Energy Agency, vanadium demand is set to soar to 773,100t by 2050 under a net-zero emissions by 2050 scenario.
And with several local vanadium projects aiming to come online, Australia is readying itself as key partner in a green future underpinned by vanadium-driven energy
DREDGE ROBOTICS IS RAPIDLY EXPANDING ITS PROFILE AT HOME AND OVERSEAS AS MINING COMPANIES RECOGNISE THE VALUE IN ITS UNIQUE SOLUTION.
When Dredge Robotics attended MINExpo in Las Vegas last year, the company made a somewhat unlikely discovery.
“We were expecting we might find other players emerging into our market or having a crack at it, but we really couldn’t identify anyone else that was even remotely in our realm,” Dredge chief executive officer Antony Old told Australian Mining Dredge Robotics is generating significant interest in its novel dredging technology, which can safely clean lined ponds containing contaminants at both ends of the pH spectrum.
new clients at the event but also to visit nearby mining operations and gauge the appetite for its solution.
During his time in the US, Old pondered what could be perceived as a ‘good problem to have’, something that validates the unbridled growth potential of Dredge’s technology.
“We’re certainly more broadly capable than we were seven years ago (when Dredge Robotics was founded),” he said. “But I did envisage back then that if we did get to this point, we would be largely close to completing our development.
“But what we keep finding is that clients, and potential clients, are approaching us with new niche applications that are ideal for our tech
tonne, they all run the same software platforms and they run the same computational architecture.
“Everything is consistent and repeatable, so if you’re going to create a relatively bespoke solution you’re not starting from zero. A lot of the AI architecture and electrical and programming software is all embedded and very versatile.”
Old said Dredge is increasingly getting to a point where it’s developing bespoke tooling to accompany an established dredging platform.
“Where we have clients with a particular type of sediment or a particular challenge they want to execute with our robot, we design and build a customised tooling head for the
Old explained how developing an acid dredging solution created a ripple effect of interest.
“We were originally approached by one of our major clients five years ago about whether we could remove the human element from dredging a pond that had a very low pH with sulfuric acid in it,” Old said.
“At the time, this was a perplexing challenge that required a lot of day-one thinking. But as soon as we started engaging with the client, and the market became marginally aware of what we were doing, we started to find use cases everywhere.
“When you look around in mining and manufacturing, it’s amazing how
balloon depending on the pH and liquor being dredged.
In these situations, it could be said that Dredge, which needs to quickly adapt, is only as good as its research and development (R&D) team.
Luckily for the company, it has one of the best R&D teams in the business, boasting robotics engineers who conduct physical rendering of robot designs and stress testing, as well as an electrical team to take care of the software design and hardware configuration.
This is complemented by a few specialist engineers and a fitting and fabrication team that assembles the robots for site.
While there are sub-divisions within the company, Dredge employees work international success story.”
DOMESHELTER AUSTRALIA’S FABRIC SHELTERS HAVE BECOME AN ESSENTIAL PART OF MINE SITES ACROSS THE GLOBE.
According to Maslow’s Hierarchy of Needs, a key physiological need for humans is shelter.
This is especially true in the Australian mining industry, where workers operate under challenging weather conditions daily.
Enter DomeShelter Australia, a leading fabric shelter manufacturing company based in multiple locations across Australia.
“Our mission is to protect people and assets from the elements, quickly, simply and effectively,” DomeShelter Australia’s director of global sales Roy Fawkes told Australian Mining.
“Mine sites are dynamic environments, with commodity prices, expanding and contracting operations, and the weather all dictating what a site looks like and needs. Our semipermanent DomeShelter Structures adapt to these changes.
“Our shelters are relocatable, reusable, repairable, and resellable, meeting the needs of evolving mine sites.”
As a mining operation expands, its design and infrastructure scope changes. A site might require a maintenance facility to be built close to the mining
area, to eliminate travel time and operational downtime.
This is where DomeShelter Australia comes to the fore, with its fabric shelters offering an array of benefits, including the ability to be swiftly installed, disassembled and relocated.
“Instead of heavy vehicles travelling to a maintenance facility off-site, they can visit a purpose-built DomeShelter nearby,” Fawkes said.
“Then as the mine changes or expands, the mining company can easily relocate as needed. Being semipermanent, our structures can adapt to suit the evolving nature of a mine site.”
The mobility of the shelters also has environmental advantages.
“Getting approval to build a large permanent facility can take months if not years, whereas one of our semipermanent structures can be designed, engineered, manufactured and shipped within five or six weeks,” Fawkes said.
“The structures make less of an environmental impact, because we’re not installing deep concrete footings or concrete pads which is often the case with permanent structures.
“All the material needed to build the structure can be packed up in a light, compact kit when transported to site.
And once the mine has reached its end of life, the shelter can be easily packed up again and moved on, making things easy for mine-closure teams and post-mining land use.”
Having a fabric structure on-site for maintenance can also increase staff retention and satisfaction, leading to increased productivity.
“If you have a permanent shelter, when equipment breaks down it can take too long to get the machine back to the main facility,” Fawkes said. “This means maintenance crews will often complete their work out in the open for long hours, exposed to the sun, rain, and snow –conditions that can be challenging.
“Workers can be put at risk of heat stress, sunburn and dehydration, and even frostbite if they’re working in snow.
“By having our semi-permanent structures closer to the mining pit, workers can safely carry out maintenance under shelter and away from the elements.”
DomeShelter Australia follows its unique six-element design methodology – dubbed DomeShelter Logic – to manage the thinking, processes and outputs that go into delivering tailored shelter solutions to the mining industry.
Fawkes said by maintaining the DomeShelter Logic, the company ensures the shelter does what it’s designed to do.
“The orientation and design are extremely critical to the success of our structures, so we’re committed to assisting our customers from the very start of a shelter’s creation,” Fawkes said.
“We work closely on the initial design, ensuring the shelters always meet the unique requirements of our clients’ sites.”
DomeShelter Australia ensures all material used is the highest-grade material sourced in Australia. This ensures the facilities adhere to international quality assurance standards such as ISO 9001, AS 4801 and OHSAS 18001.
The company also recommends regular site audits, which involves a DomeShelter representative visiting site to make sure fabric structures are continually maintained.
“Our after-sales service gives customers peace of mind that structures are doing what they’re meant to be doing and abide by the standards they were designed against,” Fawkes said.
DomeShelter Australia utilises its multiple manufacturing facilities across Australia to ship fabric shelters from various ports, guaranteeing fast and efficient delivery to even the most remote locations.
“We have an in-house design and engineering team that collaborates with customers to ensure we’re building a structure that meets clients’ needs,” Fawkes said.
DomeShelter fabric structures are in high demand locally and internationally.
In 2022, the Bald Hill lithium mine in WA required several shelter solutions to use as on-site maintenance workshops.
The operation reached out to DomeShelter Australia with its specifications and the end result comprised three interconnected container-mounted structures with end walls, which are used as workshops
DOMESHELTER FABRIC STRUCTURES ACT AS A PROTECTOR TO ENSURE A SAFE WORKING ENVIRONMENT.
for heavy vehicles, light vehicles and drill maintenance.
Soon after, the Kibali gold mine in Africa asked DomeShelter Australia to create a solution that could be quickly transported and installed without compromising size and durability.
Several DomeShelter structures were provided for purposes such as maintenance, boilermaker workshops, lubrication and tyre bays.
Fawkes said these case studies illustrate how DomeShelter Australia puts customers first.
PROTECTING MACHINERY WITH A FABRIC SHELTER CAN PROLONG THE LIFE OF EQUIPMENT.
“We’re looking forward to strengthening existing partnerships and building new ones across Australia and the rest of the world,” he said.
Backed by over 30 years’ experience, and with over 8000 shelters installed across 50 countries,
DomeShelter Australia builds quality fabric shelters tailor-made for the mining industry.
“We’re creating an oasis for workers to go in and service their vehicles to ensure they get what they need out of their equipment,” Fawkes said. AM
KalPRO TireSight: autonomous tyre inspections and a 24/7 Condition Monitoring Team to validate and prioritize tire service work. TireSight sees it sooner to enhance safety, tyre performance and fleet productivity.
MASPRO HAS ESTABLISHED A REPUTATION FOR HANDLING THE MOST DIFFICULT MINING QUANDARIES.
As today’s mining equipment evolves, so too does the sector’s problem-solvers, with inspired solutions being engineered to respond to the most sophisticated site challenges.
MASPRO is one such problemsolver, leveraging deep domain expertise to significantly prolong asset life and bolster company balance sheets.
A partnership with a Tier 1 mining client in WA saw MASPRO extend the life of a drill gearbox by thousands of hours, boosting its reliability and reducing the need for scheduled downtime. It did this by reverse engineering the underperforming gearbox to isolate the problem, before reengineering it into a new solution.
This is not a singular case, with MASPRO unlocking significant productivity gains right across the Australian mining sector through its precise quality assurance (QA) processes and commitment to quality.
MASPRO head of engineering and quality Tony Waterman shared insight into the company’s QA approach.
“In-process inspection sees our staff check parts as they’re being machined to ensure tooling is behaving as expected,” Waterman told Australian Mining
“This ensures that if we’re making 500 of something, that we don’t face an issue with tooling halfway through which wasn’t picked up prior.”
MASPRO inspects parts on a percentage basis: how often and how
much of a part gets checked depends on what it is, its history, its application, and how critical the part is.
“If the part is something that’s difficult to access and replace, like a bush located inside a drill, which can only be accessed by pulling a whole drill apart, it will get a higher percentage of checks,” Waterman said.
“Our percentage of checks changes depending on the production output. If we’re consistently producing the same quality parts, we can reduce the number of checks as we can depend on the part
Waterman provided an example to back up his point.
“For pistons inside a drifter, where the pistons are getting smashed all day every day, every part will get 100 per cent checked because they are important components of the drifter and need to hold up against high stress,” he said.
“The customer can’t afford a failure, as it could lead to a breakdown and potential downtime. Completing a higher percentage of checks ensures that part is less likely to fail.
“In this instance, we would check everything at every stage of the manufacturing process, from the raw materials coming in to every heat treatment process.”
MASPRO conducts destructive
through its paces. This can be done on the raw materials prior to construction, on heat treatment processes, and on the final product.
This helps to ensure MASPRO can discover a problem at the earliest possible stage. Because a part can be a single component of a larger machine, problems that aren’t picked up right away can create much bigger headaches down the road.
“We treat every single part as if we’re only selling that one part,” Waterman said. “It doesn’t get skipped because it’s part of an assembly – everything gets checked the same.”
This meticulous approach to engineering is seeing MASPRO win many new clients in the Australian mining industry, where high-quality, long-lasting components can unlock millions of dollars of revenue.
MASPRO’s testing and QA processes underpin the company’s constant pursuit of quality, something Waterman believes is critical to the success of any company servicing the Australian mining industry.
“Our clients have a strict need for parts that perform,” Waterman said. “At the end of the day, everything we do is in our name, and if we make parts that fail and put our clients out, it isn’t good for the client or our brand.”
Whether it’s overhauling failing parts for drills, trucks or loaders, MASPRO can turn any mining quandary into a solution, no matter how niche it may be.
Such solutions can’t be achieved without MASPRO’s commitment to quality, highlighting the company’s unique value proposition in local and international mining sectors. AM
CUMMINS’ PREVENTECH FOR MINING IS A PROVEN MAINTENANCE SOLUTION OFFERING AN ARRAY OF BENEFITS FOR THE INDUSTRY.
Sensor-based solutions are becoming an important part of modern-day maintenance systems.
The trend, which sees mining equipment of all shapes and sizes attached with devices to measure critical metrics, is only going one way, with a growing number of reports from around the world acknowledging the rapid onset and importance of digitalisation in mining.
By predicting potential equipment ‘health’ issues before they occur, the bottom line for digital monitoring is obvious – reduced downtime and production costs.
Cummins’ PrevenTech for Mining is a proven real-time, data-driven digital solution to improve equipment reliability and reduce lifecycle costs.
Mining companies around the world testify to its effectiveness.
PrevenTech works by applying telematics, big data, advanced analytics and IoT (Internet of Things) technology to a machine’s engine hardware, helping a mine identify and diagnose issues faster and more accurately.
Features include real-time engine data logging and graphing, equipment mapping, and customised fault code management.
engine, securely transmitting alerts
A
for urgent and potential problems and recommendations for actions and servicing.
Miners can optimise maintenance intervals for each site individually, see the status of equipment in real time, and plan downtime and repair work to minimise disruption.
Alerts and recommendations are sent to the customer by the Cummins Care
remotely without the need for technician/engine interaction.
A logical step for Whitehaven
In Australia, PrevenTech is connected to around 100 Cummins-powered trucks and excavators at Whitehaven coal mines in New South Wales.
saw PrevenTech as a “logical step” for integration in the fleet while the system was being trialled at the mine.
“During the trial period we only had 10 engines connected but still prevented a couple of potentially significant downtime events,” Irwin said. “The machines were diagnosed and then repaired in a short period so as not to disrupt production. Anything that helps us trend data and get ahead of issues is important.
“We’ve gone from looking in the rearview mirror to learn from the past, to looking forward and making informed decisions with the real-time data we’re getting from PrevenTech. In other words, we’re now being more proactive, and less reactive, with our maintenance practices and that means reduced operational and maintenance costs.”
Another important element of PrevenTech is the ability to integrate it with FleetguardFIT, which monitors oil, air and fuel filters as well as oil conditions.
This allows Cummins to report on the condition of oil and engine filters on mining equipment, thus reducing reliance on standardised maintenance schedules and minimising unnecessary costs.
Customers have reported extended filter servicing intervals – for example, from 500 hours to 2000 hours –by combining PrevenTech with FleetguardFIT. AM
AMCAP IS ON A MISSION TO REVOLUTIONISE ITS PARTS SERVICES TO THE MINING INDUSTRY, EXPANDING ITS HEAVY MOBILE EQUIPMENT PORTFOLIO.
Wthe company is always looking to take its offerings a step further.
heavy mobile equipment (HME) service exchange components to AMCAP’s portfolio, the company seized it without hesitation.
components category about three years ago and never looked back,” AMCAP general manager Kevin Yap told Australian Mining
individual components that were utilised to fit these larger assets, so it made sense to expand that into its own category. Now, we supply large components for haul trucks, dozers, graders, wheel loaders and any other machinery that a mine uses for its operations.”
components work hand-in-hand with its maintenance service kits, providing customers with a superior level of reliability by having the replacement parts and components available when required.
AMCAP HAS EXPANDED ITS PORTFOLIO TO INCLUDE HEAVY MOBILE EQUIPMENT SERVICE EXCHANGE COMPONENTS.
their components will perform to original equipment manufacturer (OEM) specifications.
They also provide logistical cost savings through handling and transport of a single material line item, as well as the accuracy of having all parts consolidated within the kit. The kits are packaged appropriately in bespoke cabinets and containers, ensuring they are securely delivered on-site.
“Large component changeouts like engine replacements require longterm planning because they can cause a considerable amount of downtime,” Yap said.
“Most companies will give us a schedule to work with to ensure minimal downtime for assets that need component replacement, and we’ll make sure they get the required parts on that date maintaining as close to 100 per cent delivery in full.”
AMCAP’s services operate under three key pillars: minimising downtime, maximising efficiency, and maximising safety and sustainability. AMCAP offers a service exchange program to exchange old components for a remanufactured component that is both cost effective and efficient.
All of the company’s service exchange components are rebuilt
“We plan our inventory six months in advance, so if we’re due to provide a maintenance service kit to a customer in April and they bring forward the shut to February, we will have it ready to go,” Yap said.
“In addition to the efficiency gains our customers experience by working with us, we also take safety and sustainability incredibly seriously.”
In 2021, AMCAP was awarded ‘Best solution to a work health and safety risk’ at the Work Health and Safety Excellence Awards hosted by the Western Australian Government. This was followed by the AIM WA Pinnacle Award in the RAC Environmental Sustainability Excellence category in 2024.
“We’re committed to supplying our kits in a sustainable manner, including reducing waste by cutting down on packaging,” Yap said.
“We have also partnered with key charities including Aboriginal crisis line 13YARN, Lifeline WA and the National Breast Cancer Foundation, creating awareness of their messaging by printing it on our kits that travel around WA.”
The company has supplied service kits to major iron ore miners since 2018, supplying around 4000 kits per month.
Its partnerships with mining companies have enabled AMCAP to further research and develop its kitting services, providing an opportunity to implement different parts from both OEM and non-OEM products to optimise the cost of the finished product.
“Since we were already supplying many of the individual parts needed to fit larger components, it was natural to expand kitting these parts into a fitting kit for major components, e.g. complete corners, nose cones and total plug and play option,” Yap said.
“Whatever we can do to innovate our offerings is worthwhile investing in.” AMCAP assembles its kits and components out of its modern, purposebuilt storage and distribution facility in Welshpool, WA – but this doesn’t restrict them to only WA customers.
“We have the capability and capacity to supply nationally,” Yap said. “The maintenance service kits and components category is a fairly new and innovative market for us, and we’re excited to take that around the country.” AM
Certified Rebuild programs help you benefit from the multiple lives designed into Cat® machines, power trains and major components. They are “built to be rebuilt” for maximum value and longer life. Maximise the investment in your asset with full utilisation of a second life, at a fraction of the cost of buying new.
Access to advanced condition monitoring service with HDAdvantage™ program
Sustainability – reducing waste by reusing and recycling quality material
Finance options available
Call Hastings Deering on 131 228 or scan here to find out more
*Terms & Conditions apply.
THROUGHOUT ITS LIFECYCLE. BEDESCHI DELIVERS JUST THAT.
The Australian mining industry is replete with unforgiving terrain, meaning equipment is constantly put to the test.
As a trusted original equipment manufacturer (OEM), Bedeschi not only delivers state-of-theart machinery, but also builds lasting partnerships with its clients to ensure assets remain at their peak performance throughout the lifecycle.
Bedeschi chief executive officer (CEO) Uwe Zulehner said the company has been focused on creating a successful aftermarket business in recent years.
“We now support the mining industry with services such as maintenance and shutdown support, delivery of critical spare parts, fabrication and parts repair,” he told Australian Mining
“We have cemented our position as a full-line OEM delivering not only new machines but also providing lifecycle support to mines and port operations.”
Bedeschi’s maintenance services are more than routine fixes; they represent a full-circle approach, with qualified technicians and field engineers readily available to respond to needs 24–7.
From integrating a new part into an existing machine, to removing parts and completing repairs, as well as the quick delivery of premium spare parts, mines can rely on Bedeschi for service support long after the machines have been initially deployed.
Bedeschi’s maintenance services have evolved in response to the everchanging needs of the Australian mining industry.
Zulehner said Bedeschi’s close relationship and proximity to its customers has helped it better understand service and maintenance demands.
“Our close proximity to customers has helped us develop a pool of experts and specialised services in the right places,” he said. “And our presence continues to expand, positioning Bedeschi in closer proximities to mine sites and ports.
“We will continue expanding our business within Western Australia and on the east coast of Australia.”
Holding close customer relationships provides Bedeschi with invaluable insights into their operational needs.
“Our client’s operational knowledge sparks ideas of improvement and development,” Zulehner said. “Backed by our deep experience of designing and developing technologies and products, we convert these ideas into physical solutions.”
Bedeschi has built a reputation for enhancing the longevity and performance of mining equipment.
Aftermarket general manager Marco Ringe explained how one Bedeschi customer had realised significant availability gains from the company’s solutions.
“One site experienced a seven per cent increase in machine availability across a 12-month period after Bedeschi undertook mechanical engineering inspections and servicing,” he said.
“Specialty tooling and methodologies were also implemented, creating safer, repeatable, and accurate testing
doesn’t come without its challenges, expecially when shutdowns occur with little-to-no notice, giving little time to mobilise labour.
Bedeschi overcomes unscheduled downtime by staying closely connected to its customers.
Longer-term partnerships see
enabling them to get on with the job.
To accompany its established maintenance offerings, Bedeschi is looking at new innovation techniques, including the use of digitalisation through discrete element method (DEM) modelling, which optimises equipment performance before costly modifications are made.
Though still early in its implementation, this technology can significantly improve maintenance processes and enable operators to work smarter by better understanding asset wear and performance.
As Bedeschi continues to expand its customer base, which includes a new order from a major mining company in recent months, Zulehner is proud of the company’s growth journey.
“We will continue to build on the back of our close relationships and regular order intake,” he said. “We’re also aiming to expand into new mining areas and assist new customers with maintenance services and aftermarket support.”
Bedeschi’s full lifecycle approach ensures Australian mining operations have the tools and support they need to thrive in one of the world’s most demanding industries.
It’s this commitment that will help shape the future of mining maintenance.
Hexagon is the global leader in precision technologies at any scale. We partner with customers for transformative improvements across the workflows that define a mine’s safety, value, reputation, and life expectancy. Designed by mining professionals for mining professionals, our solutions are backed by
AFTER CONSULTING WITH ITS CUSTOMERS, DONALDSON AUSTRALIA HAS INTRODUCED A SOLUTION THAT REVOLUTIONISES AIR-CLEANER MAINTENANCE ON MINE SITES.
As Australian mining companies seek to reduce personnel exposure to dusts, they aren’t always receiving the right solutions.
Ironically, some practices introduced to help minimise dust are counterproductive and result in the need for additional primary filter services.
Today’s modern diesel engines can consume up to 20,000 litres of heavily contaminated air for every litre of diesel fuel burned, meaning air intake systems can be overwhelmed by vast volumes of dust, threatening these high-performing diesel engines.
A dual SSG Radial Seal air housing can separate and filter out more than 200kg of test dust prior to reaching the maximum allowable intake restriction common to modern engines.
It’s a reasonable assumption that the filter housings on your heavy mining equipment will have protected your engines from similar weights of dust between every primary filter change out.
While laboratory data is a valuable tool to make theoretical comparisons between competitor products, it does not always reflect real-world challenges.
SSG housings incorporate two-stage filtration to protect engines from vast amounts of dust.
The first stage of inertial pre-cleaning separates a high percentage of the heavy dust, which drops down to the lower dust cups for evacuation through the vacuator valves when the engine returns to idle or shuts down.
The dust evacuation process is highly effective in the laboratory, however, can experience challenges in the real world. Static and moisture can make some dusts stick or cling, preventing them from readily leaving the air housing.
Many sites have experimented with various approaches to address these challenges, but with limited or no success. These methods include installing earth straps, wiring in scavenge fans, installing reverse pulse units, replacing Donaclone tubes with centrifugal pre-cleaners, and even removing the vac valves.
To minimise personnel dust exposure, various pre-cleaner maintenance practices have also been trialled.
Some sites open the quick-release dust cups prior to the vehicle entering the wash pad. Water cannons blast the lower bodies to remove built-up dust, occasionally damaging the pre-cleaning tubes and always saturating the tubes with water.
Other sites will open the dust cups on the apron and utilise a high-pressure hose to wash out the lower bodies, while some remove the filters altogether and flush from the top down.
In a modern world of increased vehicle availability demands and pit stop servicing, pre-cleaning tubes don’t have adequate time to dry before the
returns to service. Water and fine dusts will make mud and set hard like concrete, preventing dust evacuation shortly after the vehicle returns to work.
With reduced pre-cleaning and no ability to evacuate dust, usable element life and service intervals are unacceptably shortened, resulting in additional labourintensive air intake maintenance events.
Donaldson Australia listened to its customers and initiated trials on a range of alternate dust evacuation systems.
The final concept is simple, replace the OEM (original equipment manufacturer) dust cups with a fixed cup that doesn’t include the quick release lower cup, additional gasket and threeinch vacuator valve fitting.
The trickle valve assembly features a tapered cup with an integrated six-inch trickle valve port, eliminating the need for an additional gasket.
Donaldson’s six-inch injection moulded EPDM (ethylene propylene diene monomer) trickle valve underwent rigorous testing in the company’s Minnesota air laboratories and was
extensively trialled at several Australian mine sites. The successful field trials confirmed the laboratory findings.
Donaldson’s trickle valve eliminates unnecessary mine-vehicle maintenance and can remain in position and function effectively without labour input for more than 6000 hours. This innovation transforms what was once routine maintenance to an annual task.
The soft, pliable trickle valve prevents water ingress during vehicle washdowns, preventing dust cup caking and preserving the integrity of essential precleaner tubes.
Combined with best practice maintenance procedures, the trickle valve prolongs element life, reduces high restriction events, minimises dust caking, eliminates service steps, and reduces workshop personnel’s exposure to nuisance dusts.
Leave your dust where it belongs, on the haul road and not in the workshop. AM
Optimising Sustainable Mining Operations: Your Partner for Shutdowns, Logistics and Maintenance
Scan the QR code to find out more!
Empowering Industries. Building Futures. One lift at a time.
FLEETGUARDFIT IS A FILTRATION INTELLIGENCE MONITORING SYSTEM THAT HELPS PREVENT COSTLY EQUIPMENT DAMAGE AND DOWNTIME.
Fleetguard is transforming equipment maintenance in the mining sector with Filtration Intelligence Technology (FleetguardFIT), a predictive maintenance solution that enhances asset reliability, optimises service intervals, and improves environmental sustainability.
With filtration issues among the leading causes of avoidable engine failures, FleetguardFIT provides real-time monitoring of air, fuel, oil condition and oil filters, reducing unplanned downtime and preventing costly equipment damage.
The system is already deployed globally, operating in 25 countries, and continues to gain traction in the highhorsepower mining market.
FleetguardFIT comprises a suite of sensors connected to a microcontroller known as the filtration monitoring system, which processes raw data via advanced analytics and algorithms to provide actionable insights to customers.
“We are the only commerciallyavailable filtration monitoring solution that actually measures the real-time health of filters and oil rather than relying on preset fault codes,” Fleetguard chief engineer Matthew Ferguson told Australian Mining
“Customers are able to reduce unplanned failures by taking action at the right time and establish predictive condition-based maintenance practices.
“It helps customers optimise their spend on engine consumables, and it gives them the peace of mind that the maintenance that was supposed to be done, was done at the right time.”
Unlike traditional mining service intervals that rely on miles covered or a designated date, FleetguardFIT delivers condition-based maintenance, ensuring consumables are replaced at the optimal time.
Ferguson compared the difference between FleetguardFIT and conventional car maintenance alerts.
“If you drive a late-model car, and a light comes on the dash telling you to change your oil, that’s a systemgenerated alert based on kilometres, hours or time – it doesn’t actually analyse the physical condition of oil,” he said.
“FleetguardFIT, on the other hand, physically determines the oil’s condition in real time and provides an actual assessment every time the engine is running.”
FleetguardFIT helps miners avoid costly equipment failures by providing early warnings of potential issues.
This was demonstrated when the FleetguardFIT system detected a fuel dilution event well before the next scheduled service interval, where traditionally an oil sample would have been taken.
The system identified that the oil viscosity had fallen below the lower threshold limit on QSK60 MCRS (modular common-rail system) engines and automatically alerted the customer.
This early warning allowed the customer to prevent potential catastrophic engine damage.
Upon investigation, it was confirmed the fuel pump had failed, allowing the customer to make the repair in a timely manner. The data then returned to normal confirming the correct repair.
The FleetguardFIT system is sophisticated enough to not only detect when an air filter is approaching the end of its useful life but also features an anomaly detection function.
In one instance, the system identified abnormal air filter behaviour in a QSK78 haul truck containing six air filters.
One of the air filters was performing abnormally, triggering an alert and notifying the customer of a pending issue that would have otherwise gone undetected.
It was discovered that due to a lack of maintenance, the pre-cleaner was severely blocked but not enough to affect performance yet.
Further inspections revealed that nine other haul trucks at the site had the same issue.
Uncovering this issue early was only possible through FleetguardFIT’s anomaly alerts, preventing potential performance degradation and increased operational costs.
Before any catastrophic damage could occur, FleetguardFIT sent a critical air-filter alert, notifying a customer of a sudden spike in air filter differential pressure, exceeding the customer’s maximum custom threshold for air restriction.
Further investigation found that a technician had improperly installed the air filters on a dualengine QSK60-powered CAT 6090 Excavator, allowing dust to bypass the outer element.
This led to rapid loading of the safety (inner) element, causing a sharp rise in differential pressure.
By catching the mistake early, FleetguardFIT prevented a costly failure, enabling the engine to achieve its maximum expected life. FLEETGUARD
FleetguardFIT detected rapid loading of the fuel water separators (FWS) on two bulldozers operating at the same site.
The automated system alerted the customer in real-time, allowing them to investigate the issue.
It was discovered that the on-site bulk fuel tank was too low, allowing sediment and contaminants to reach multiple pieces of equipment.
Thanks to FleetguardFIT’s early detection, the customer was able to prevent a larger and more costly issue.
One of FleetguardFIT’s invaluable attributes is its ability to extend service intervals safely.
Ferguson said that over 80 per cent of customers were changing their filters too early, leading to unnecessary costs and waste.
“In industry terms, we’ve helped customers extend service intervals, in some cases from 500 hours to 2000 hours, all while ensuring filtration performance is maintained,” Ferguson said.
By leveraging FleetguardFIT analytics, customers can safely maximise filter life, reducing the frequency of replacements and lowering overall maintenance expenses.
Another often-overlooked advantage is that air filters perform better when they have a dust layer.
“Air filter performance is optimised after a certain amount of time because the filter builds up a ‘dust cake’ on the outside, which actually improves filtration,” FleetguardFIT sales manager Brandon Brinton said.
“If you swap them out too frequently, you’re removing the opportunity for that layer to form, making the filter less efficient.”
FleetguardFIT ensures air filters are changed only when necessary, improving efficiency and longevity.
FleetguardFIT also aligns with the mining industry’s environmental, social, and governance (ESG) goals by minimising waste and optimising maintenance operations.
“By ensuring filters and oil are used for their full lifecycle, we help customers
transport emissions from maintenance activities,” Brinton said.
“Reducing unnecessary maintenance trips also plays a role in sustainability.
“If a company doesn’t have to deploy a maintenance truck unnecessarily, that’s less fuel burned, less wear on tyres, and less overall impact on the environment.”
FleetguardFIT offers flexible integration options, ensuring compatibility with existing asset management systems.
Customers can choose between a cloud-based solution or edge computing
Recognising the importance of data security, FleetguardFIT can integrate with customers’ existing telematics service providers (TSPs), ensuring compliance with industry security standards.
“We simply provide the filtration intelligence layer without introducing additional cybersecurity concerns,” Brinton said.
advantage
FleetguardFIT provides a significant competitive edge by improving fleet efficiency and reducing unexpected failures.
However, due to its strategic benefits, some mining companies choose to keep their FleetguardFIT implementation confidential.
This exclusivity highlights the system’s game-changing potential in the mining industry.
With increasing pressure to enhance efficiency, reliability, and sustainability, FleetguardFIT is proving to be a critical tool for modern mining operations.
As Fleetguard continues to evolve, the company is continually working on new advancements, including more sophisticated oil condition monitoring and further integrations into predictive maintenance platforms.
“FleetguardFIT isn’t just a monitoring tool, it’s an intelligent maintenance solution that empowers mining companies to operate smarter, safer, and more sustainably,” Ferguson said.
For miners looking to reduce costs, prevent failures and improve ESG performance, FleetguardFIT offers
ELPHINSTONE IS SETTING THE STANDARD IN UNDERGROUND HAUL ROAD MAINTENANCE WITH THE RECENTLY RELEASED EG20 UNDERGROUND GRADER.
The role of the underground grader is to prepare and maintain quality haul and access roads with adequate drainage throughout the tunnel network.
The added benefit is a significant increase in haulage productivity, reduced tyre wear, increased component life, and higher speed on grade.
In 2018, Elphinstone identified an opportunity to expand its range of underground mining support vehicles by including a purpose-built underground grader based on the Caterpillar 120K and 120M surface grader platform.
Elphinstone UG20K and UG20M underground graders operate all around the world including Canada, Argentina, Chile, the Democratic Republic of Congo, India, Mongolia, Mali, Mexico, Peru, Burkino Faso, Kazakhstan, Tanzania, Saudi Arabia, South Africa, and the US.
Superseding the K&M series, the new EG20 series incorporates all Cat 120 standard upgrades and redesigned Elphinstone modifications, improving operator safety, ergonomics, comfort, and view of the blade.
When conditions get tough, the robust frame, work tools and powertrain of the EG20 gets the work done.
The EG20 drawbar is designed with hardened circle teeth for increased durability. Rippers (factory fit options) are available to assist with the grading of underground roadway surfaces.
The blade lift cylinder accumulators assist in reducing blade bounce and damage to the blade components.
Powered by the C7.1 ACERT Tier 3 engine arrangement, the EG20 meets the standard for regions with more stringent emission regulations and those without access to ultra-low sulphur fuel.
The Cat C7.1 uses Caterpillar’s breakthrough ACERT technology to meet exhaust emission-reduction standards. The engine boasts efficient fuel delivery and air management to provide outstanding performance and lower emissions, and electronic control for high productivity and longer service life.
The C7.1 ACERT Tier 4 Final Stage V engine arrangement is available as an option, adhering to EU Stage V exhaust emission standards.
The electronic throttle control provides easier, more precise and consistent throttle operation. Engine over-speed protection prevents downshifting until an acceptable safe travel speed has been established.
Variable horsepower plus (VHP Plus) comes standard providing more power in the higher gears.
All powertrain components are made to be rebuilt, adding value to the total cost and lifecycle of the machine.
The EG20 enclosed cab has been redesigned to improve ergonomics, machine control adjustability and visibility.
The cab, which features a rollover protection system (ROPS) or falling object protection system (FOPS), provides a quiet environment with low vibration levels, reducing operator fatigue.
Cab features include low-effort pedals and controls, adjustable implement controls, an adjustable steering wheel angle, and an adjustable seat, all providing a comfortable work environment.
Operator comfort is further enhanced with improved leg room across the spine and additional storage areas including cup holders located on both sides of the cab.
The digital instrument panel, with easy-to-read, high-visibility gauges and warning lamps, places vital machine information and diagnostic capability in direct view of the operator. Working in the dark is much easier with backlit transmission shifter and rocker switches.
The instrument cluster includes gauges for engine coolant temperature, articulation, voltage, and fuel level, along with a speedometer, tachometer, and an hour meter.
The air conditioning (HVAC) system dehumidifies and pressurises the cab, circulates fresh air, removes dust, and prevents the windows from fogging.
The EG20 is engineered to protect the operator and others on the job site, featuring a ground-level engine shutoff switch and refuelling, laminated glass windows, and door and seat belt park brake interlocks with visual and
THE NEW ELPHINSTONE EG20 UNDERGROUND GRADER IS PURPOSEBUILT TO THRIVE IN HARSH HARDROCK MINING ENVIRONMENTS.
audible detection alarms. Other features include a seat belt cutter, robust rearguard, and a front counterweight for machine balance.
Emergency stops and fire suppression actuators are conveniently located at ground level and inside the cab. Hydraulic brakes replace air brakes that were previously standard on the UG20K.
High-visibility green grab rails and steps for three-point contact, brake and back up lights, alarms, and blade and rear-view cameras with dedicated display all combine to ensure a safe work environment.
The ground level fuel fill system prevents the need to climb onto the machine for refuelling. An optional fast fill is also available at ground level.
Grouped service points make daily maintenance easier and faster while enhanced diagnostics and monitoring help reduce downtime.
Ground level access to service points reduces risk and time spent checking the machine’s status, while next-generation filters help reduce filtration costs.
OPTIONAL FEATURES INCLUDING RIPPERS CAN BE ADDED TO THE EG20 UNDERGROUND GRADER TO SUIT SPECIFIC APPLICATIONS.
providing location, machine hours, fuel usage, productivity, idle time, and other machine data on-demand through the VisionLink online interface, improving efficiency and lowering operating costs.
The Elphinstone EG20 can be optioned with a wide range of additional features to suit each specific mine site application, including fire suppression, automatic lubrication, and rippers.
All Elphinstone products, technical assistance, support, and access to spare parts are available through the global Cat dealer network with additional support available from the Elphinstone regional sales and support team. AM
HASTINGS DEERING HAS HELPED SOJITZ CORPORATION SAVE THOUSANDS OF DOLLARS IN OPERATING COSTS AT ITS GREGORY COAL MINE IN QUEENSLAND’S BOWEN BASIN.
For more than 40 years, the Gregory mine located 60km northeast of Emerald in Queensland has been known as one of Australia’s premier coking coal operations.
Gregory has a three-million-tonneper-annum production capacity and a mine life of more than 20 years, and boasts a fleet of 20 mining trucks, 80 per cent of which are Caterpillar (Cat) branded.
Since Sojitz Corporation acquired Gregory in 2019, the mine has utilised Cat’s ground engaging tools (GET) on its ancillary fleet, specifically using the EWL (extended wear life) cutting edges on its Cat D11 large track-type tractors (LTTT).
While using this system, Sojitz was flipping cutting edges at an average of 350 hours and changing a new set of cutting edges at approximately 700 hours.
The company manages its D11 tractors on a 500-hour preventive maintenance (PM) interval and wasn’t changing its GET in the field due to safety concerns.
This saw the machines trammed long distances to the workshop to both flip and change the GET, leading to two additional trips to the workshop within a 1000-hour operating period.
This had a ripple effect on Gregory’s operating costs, labour hours and reduction in physical availability.
As a long-standing and loyal customer, Sojitz reached out to Cat’s Queensland dealer Hastings Deering to implement an alternative solution that decreased operating costs and aligned with its 500-hour PM strategy.
The trial
Hastings Deering commenced a trial where three D11s operated under similar conditions.
Each dozer was equipped with different GET systems. The first, DZ38, was fitted with extended wear life (EWL) cutting edges and applied by Hastings Deering.
The second, DZ39, was set with extreme extended wear life (EEWL) middle edges and high abrasion (HA) end bits, while the third dozer, DZ40, was fitted with offset edges.
Each system was examined on a regular basis, specifically inspecting
the wear trends. To gather the results, Hastings Deering designed an inspection sheet and Microsoft Excel spreadsheet.
The original equipment manufacturer (OEM) also created a ‘Go-No Go’ gauge to analyse the wear on each system.
outcome
The trial concluded that the DZ40 fitted with offset edges offered the longest wear life, delivering 1385 hours.
Despite this, Sojitz was concerned the solution wouldn’t align with its 500-hour PM strategy due to the offset wear material.
Following further evaluation, the company implemented the EEWL middle edges and HA end bits method to its LTTT fleet, which achieved 1086 hours and was the second best of the three trialled.
This solution is projected to save Sojitz approximately $70,000 per annum in material and labour costs per annum.
According to Sojitz, the EEWL middle edges and HA end bits method was $0.79 per hour cheaper than the EWL cutting edges fitment. This totals $27,650 savings per year in materials across the company’s mining fleet.
CORPORATION’S GREGORY FLEET INCLUDES CAT D11 LARGE TRACK-TYPE TRACTORS.
Reduced worn undercarriage and labour hours were also estimated to save $200 per hour, or $40,000 per year across the fleet.
Increased productivity was another highlight. By limiting additional travels to the workshop for GET changes, Sojitz’s machinery is estimated to gain an additional 200 operating hours per annum.
Since its inception more than 90 years ago, Hastings Deering has prioritised forming and maintaining long-term relationships with its customers.
This commitment is clearly illustrated in its work at the Gregory coal mine. By working alongside Sojitz with care, integrity and transparency, Hastings Deering has upheld its reputation as a leading OEM in Queensland that not only provides premier mining equipment but tailored solutions that meet customer specifications. AM
CORPORATION HAS UTILISED CAT’S GROUND ENGAGING TOOLS AT THE GREGORY MINE SINCE 2019.
AusProof has been committed to providing the industry with safe, reliable and high-quality cable coupler solutions since 1994. Offering a variety of high and low voltages, AusProof aims to boost safety and efficiency, create long-term cost benefits, and reduce downtime for all sites, from hazardous to open-cut.
Over the years, through the hard work and dedication of our Research and Development team, AusProof has released a number of innovative products and accessories, such as the world’s first 35kV coupler, an Ex-certified 11kV coupler featuring a Removable Flange, our aluminium Restrained Ranges, the re-designed LED Live Line Indicator, a ‘mix & match’ style CAT Skid suitable for both new and old AusProof couplers, and more. Why not get in touch and chat to the AusProof team about finding the right cable coupler solution for your site?
CRUSADER HOSE BREAKS DOWN THE DIFFERENCES BETWEEN RIGID AND LAYFLAT HOSE SYSTEMS.
CRUSADER HOSE’S HOSE SYSTEMS ARE BUILT TO WITHSTAND HARSH ENVIRONMENTAL CONDITIONS.
ine dewatering is a critical process in mining operations, ensuring water doesn’t interfere with excavation and
There are two primary pipeline systems used for dewatering and water transfer: rigid hose systems and layflat
While both systems get water from A to B, they differ significantly in their
manufacturer of layflat hose systems for mine dewatering, offers a comparison.
Rigid hose systems, typically made from steel or HDPE (high-density polyethylene), have long been used in
Although these pipes provide a stable water transport system, they also offer extensive maintenance challenges.
Rigid hoses comprise metal pipes, which are prone to corrosion due to constant exposure to water, chemicals,
Scaling and mineral deposits can build up inside the pipes, reducing
Another challenge is the structural integrity of traditional hose systems.
Rigid hose systems are vulnerable to cracking, denting, and joint failures due to the movement of heavy equipment and ground shifts.
Repairing a damaged rigid hose often requires welding, specialised fittings, or complete section replacements, leading to downtime.
Switching to a layflat hose system eliminates these issues.
Rigid hose systems also pose installation and handling challenges due to the fact these systems require heavy machinery for transportation, installation, and repositioning.
Handling and relocating rigid pipe is labour-intensive, increasing maintenance-related costs and time.
Rigid hose systems also rely on multiple joints and couplings, which are prone to leaks and require downrating in high temperature.
Improperly sealed joints can lead to water loss and inefficiencies in the dewatering process.
Maintenance requirements of layflat hoses
Crusader Hose’s Waterlord and Waterlord Extra layflat hose systems offer a more modern and efficient alternative for mine dewatering.
Their textile reinforcement is woven from high-tenacity polyester fibres, which handle the hose’s high-pressure and tensile loads.
The hose is then extruded with thermoplastic polyurethane, providing durability.
Used across mines and up high pit walls, the maintenance requirements of layflat hose systems are significantly lower than rigid systems, and they are unaffected by temperature.
Other benefits of layflat hose systems
Corrosion and chemical resistance
Unlike metal pipes, layflat hoses don’t corrode, even when exposed to acidic or mineral-heavy water. The woven hose slightly dilates under pressure, eliminating the risk of scaling or internal buildup. There is no need to clean out the hose.
Durability and damage resistance
When handled properly, layflat hoses are highly resistant to abrasion and punctures. The Waterlord and Waterlord Extra hose systems are UV-stabilised and can handle harsh environmental conditions. The textile reinforcement ensures hose pressure is unaffected by the hot sun and doesn’t need to be derated due to temperature. If damage occurs, repairs are simpler and quicker compared to rigid pipes, often requiring only patching or coupling attachment.
fraction of the time compared to HDPE.
Fewer connection points
Layflat hoses can be deployed in long continuous sections up to their standard 200m lengths, reducing the number of joints and potential
dewatering, layflat hoses offer a more efficient, cost-effective, and lowmaintenance solution.
Their resistance to corrosion, ease of handling, durability, and minimal joint attachment make them an ideal choice for modern mining operations.
mining environments.
For companies looking to optimise their dewatering operations while reducing maintenance costs and downtime, Crusader Hose’s layflat hose systems provide a clear advantage. AM
After narrowly escaping a serious workplace injury in 2008, Nivek Industries founder Kevin Cant knew something needed to be done to improve the safety of mining personnel carrying out site maintenance.
Cant was inspired to begin development of what would become the company’s flagship Tracked Elevated Device (TED), a remote-controlled all-terrain hydraulic belly plate jack designed for applications where a crane or forklift isn’t viable.
Since it was launched in 2011, the TED was quickly adopted by mining and quarry sites across the country and internationally, inspiring Nivek to implement multiple upgrades and enhancements so that it now has more than 40 versatile attachments available.
From fork tines and front jibs to extension blocks and even a dedicated trailer for easy transportation, the TED continues to help fitters finish every shift safely.
“At Nivek, we’re committed to developing innovative and safe products for mining and heavy industry that enhance workplace safety, efficiency and productivity,” Nivek general manager Derrick Cant told
After many years of success being used across various heavy industries, including rail, mining and civil construction, Nivek decided to level up and innovate its renowned product even further, developing the aptly named Big TED.
Fondly known as the ‘bigger brother’ of Nivek’s debut release, Big TED comes with an increased lifting capacity while embodying the same low profile and manoeuvrability capabilities of the original TED.
With joystick remote operation, extreme precision and a rechargeable battery offering up to two hours of continuous operation, the Big TED is also compatible with a range of Nivek’s specially designed attachments.
Not only has Nivek’s TED range helped to reduce the number of injuries on mine sites, but the ensuing development of the Lift Assist (LA40 and LA80) equipment has also made the industry more accessible to workers of all body types and capabilities.
The LA40, which can be attached to the TED, aims to reduce muscle strain and fatigue, as well as chronic musculoskeletal injuries in workers, by taking the weight of equipment like rattle guns, impact drivers and torque tooling.
“When you consider the tools themselves weigh 30kg to 40kg just to do up a nut or a bolt, our equipment has taken the weight out of the job –that physical requirement has been eliminated,” Cant said.
The success of the TED and Lift Assist ranges inspired the Nivek team to continue improving the experience of mine workers through its solutions.
This led to the development of the company’s Beast of Burden (BOB), an all-terrain remote-controlled carrier with the ability to track loads across long distances of rough terrain.
“The BOB was developed to complement the TED range to provide a long-distance carrying option, something the TED is unable to provide,” Cant said.
NIVEK’S LA40 MAKES COMPONENT REPLACEMENT SAFER AND MORE EFFICIENT FOR EVERY FITTER.
“BOB is more than just a carrier – it’s essentially a mobile, adaptable powerhouse capable of undertaking a wide variety of jobs.”
Currently available in 500kg (the 0.5T model), 1500kg (the 1.5T model) and 5000kg (the 5T model), each BOB carrier has been built to comply with three key Australian standards: AS1170.0, AS1170.1 and AS4100.
Able to be adapted to a range of situations, BOB is rapidly becoming an industry mainstay.
“Nivek designs and builds products that can be adapted to suit customer requirements,” Cant said. “This has been done deliberately to allow us to develop specific attachments to meet individual customer needs without having to fully develop an entirely new machine.”
All of this innovation is coming out of the company’s research and development
(R&D) facility in Singleton, New South Wales.
“Most of our ideas for attachments and developments come from our end users,” Cant said. “There’s probably a million jobs BOB, TED or the Lift Assist can do, and we’re only thinking of 20 of them.
“It’s through our customers using our equipment that we are able to see all the ways they can make an impact on-site and drive that impact even further.” AM
MICHAEL COLVIN ON HOW MAX PLANT CAN HELP MINERS ACHIEVE SUCCESS IN A NEW ERA.
Over the years, familyowned business MAX Plant has built a name for itself for developing tailored solutions to the most unique mining conundrums.
A major focus for the company has been on supporting mining contractors and junior miners that need to get from the feasibility study stage to production in the shortest possible timeframe and within tight budgets.
Specialising in modular, mobile, and fixed crushing and screening plants, MAX Plant has always focused on differentiation by providing tailored, turnkey solutions designed to meet the unique needs of each project.
The company has spent the last 20 years working with Australian mining and contracting companies to forge longlasting relationships.
This has seen MAX Plant become a trusted project partner, delivering fully integrated, end-to-end solutions.
Australian Mining sat down with MAX Plant general manager Michael Colvin to discuss the company’s path to success.
He discussed how MAX Plant has been on an upward trajectory for the last 10 years, and how the company’s future is just as bright.
How has MAX Plant evolved?
Since its inception, MAX Plant has grown from a small, family-owned business into an internationally recognised provider of complete mineral processing solutions.
We focus on solving client’s problems, simply finding the best solution that fits their criteria. This involves providing reliable, high-quality equipment for both the mining and quarrying industries, with a strong emphasis on innovation, sustainability and customercentric solutions.
How do MAX Plant solutions adapt?
One of MAX Plant’s key strengths is its flexibility. Every plant we design is fully customisable, allowing us to adapt equipment layouts, components, and configurations to fit unique processes or site requirements.
Whether it’s iron ore, gold or copper mining, rare earth processing, or a simple quarry plant, we collaborate with clients to ensure plant integrates seamlessly into existing or new operations.
Additionally, our modular systems allow for scalability, so plants can evolve alongside a growing project.
Can you tell us more about modular MAX Plants?
One of the challenges we’ve faced over the years is customers coming to us with traditional fixed plant layouts and wanting the process and layout replicated with modular equipment that can be customised and relocated.
So we came up with a range that can be easily adapted, with the ability to add plant components to increase capacities for the future or remove sections of plant should the goal posts change.
Modular designs reduce lead times, streamline installation, and offer unmatched versatility for sites with fluctuating requirements. They also align with sustainability goals by enabling efficient resource utilisation and reducing site disruptions.
the downtime challenge. The second is addressed by designing equipment with common components across our product range, allowing for easier sourcing of spare parts and faster replacements, reducing delays caused by unique or hard-to-find components.
How is MAX Plant equipment maintenance-friendly?
Our equipment is designed with maintenance in mind. It has many fixed plant maintenance features, but stands alone with our design philosophy of common parts.
clients as it reduces spare parts stock. Other maintenance features include
How does MAX Plant prioritise collaboration?
Collaboration is at the core of our approach. From the initial consultation to final commissioning, we work closely with clients to understand their unique
Our focus for the next 12–24 months is a simple approach: keep supporting existing clients and focus on further expansion of the MAX Plant in-house design and technical team to support the mining industry’s transition to more sustainable practices.
With MAX Plant, it’s never just about equipment, it’s about creating lasting solutions and relationships that drive success.
We’re proud to be an Australian, family-
USED IN ROLLERS, WIND AND CONVEYOR GUARDS, COMPOSITE MATERIALS ARE BECOMING VIABLE ALTERNATIVES TO STEEL AND ALUMINIUM.
In 2019, a maintenance task at a port operation took a dangerous turn when a 24mm threaded bar sheared off during a bucket pin removal, shooting through the front and rear windscreen of a forklift.
Fortunately, no one was inside the vehicle at the time, but the incident stressed the risks of traditional maintenance practices.
Following the event, the port explored safer alternatives, trialling the replacement of carbon-manganese steel bushes with Veyex’s composite bushes in bucket pin assemblies.
The results were significant, with the composite bushes requiring significantly less force for removal, eliminating the need for hydraulic pulling equipment and reducing the risk of high-energy failures and the potential for fatal injury.
These composite bushes have now replaced all existing steel bushes across a fleet of bucket wheel reclaimers for one of the world’s largest iron ore miners.
This shift towards safer, lightweight materials is something Veyex, formerly known as Lorbrand Australia, has been pioneering for years.
Through its innovative composite solutions, Veyex is helping to redefine mining maintenance by improving safety, reducing weight, and minimising downtime.
safer, lighter
Veyex’s composite rollers represent a breakthrough in bulk handling maintenance, providing a modern alternative to traditional steel rollers.
“Traditionally, steel rollers have been the way of the industry, but over the last 10 years, there’s been a transition to composite,” Veyex general manager David Massarotto told Australian Mining
“There’s several drivers behind the change, weight being one. A composite roller will weigh anywhere from 30 to 60 per cent less than a steel roller.”
By reducing weight, these components decrease manual handling risks and physical strain on workers.
Veyex has taken this concept even further with its ultra-light rolls, specifically designed to keep iron ore components under 20kg, something not achievable with steel.
“Miners and exporters are always looking at ways they can put more tonnes
on their conveyors,” Massarotto said. “So every kilogram we take off a balance machine means an added kilogram to their throughput.”
The company’s patented ultra-light rolls contain composite shafts that are 50 per cent lighter than steel.
Reducing maintenance costs
With downtime being one of mining’s most expensive challenges, Veyex’s composite rollers play a crucial role in preventing unscheduled stoppages.
Unlike steel rollers, which can seize and cause extensive conveyor belt damage, composite rollers fail in a way that allows operations to continue safely until scheduled maintenance.
“If a composite roller is to seize or fail, it won’t damage the conveyor belt in the way a steel roller would, allowing belt crews to plan a roll changeout or slot it into scheduled conveyor downtime rather than having to stop the conveyor immediately.” Massarotto said.
This design principle mirrors the approach taken with bucket wheel bushes, where replacing traditional materials with composite options has made maintenance tasks more predictable and safer.
Veyex has also developed composite wind guards, a solution that not only protects conveyor systems from environmental exposure but also enhances workplace safety.
While they were originally introduced to combat corrosion and weight issues, composite wind guards have unlocked additional benefits such as noise reduction.
“Noise pollution can be deadened with composite rollers because there isn’t the shell resonance that you get with steel or aluminium rollers,” Massarotto said. “Replace traditional steel wind guards with composite wind guards and you can further reduce conveyor resonance.”
This noise-dampening feature has made a significant difference for mine sites operating near residential areas, such as in the Hunter Valley or ports, where large conveyors run close to communities.
As Veyex continues to push innovation under its new branding, the company remains committed to providing
solutions that prioritise safety, efficiency, and cost-effectiveness.
From ultra-light rolls and bucket wheel bushes to composite wind and conveyor guarding, Veyex is ensuring mining operations across Australia are not only more productive but
“This highlights the advantages of using composite componentry around conveyors,” Massarotto said. “They are safer, can drive down weight and noise, and enable operators to avoid costly unscheduled downtime.”
By leading a new era of composite
AS MINES PUSH FOR FASTER BELTS TO DIRECT INCREASED TONNAGES, A NEW CUSHION IS SET TO SUPPORT EXTENDED SHUTDOWN CYCLES AND REDUCE DOWNTIME.
Flexco has engineered an innovative solution to address the demands of high-speed conveyor belts with its patented Flextreme PXT cushion for the P-Type secondary belt cleaner.
As mines increasingly require faster, heavier, and thicker belts to manage higher tonnages, the PXT cushion is rising to the challenge to provide longer life and reduced maintenance.
The traditional P-Type cushion, designed decades ago, has served the industry well but the increase in demand for extended shutdown cycles and faster belt speeds requires more durable belt cleaning solutions.
“The belts these days are thicker, faster, and handling larger tonnages,” Flexco conveyor specialist Jason Coe told Australian Mining
“The original P-Type cushion design, with its two plates bonded together, was at risk of delamination issues under these more extreme conditions.”
Flexco’s new Flextreme PXT cushion was developed to eliminate this problem. Encased in stainless steel and paired with a polyurethane dampener pressed into the cushion, the innovative design ensures durability while removing the risk of delamination.
“This design enables us to deliver unmatched longevity and reliability for high-speed belts operating at up to 7.5 metres per second,” Coe said.
Its compatibility with existing P-Type setups means it can be seamlessly implemented, minimising downtime.
“The footprint is the same as the original, so it’s essentially a slot-in replacement,” Coe said.
This design also extends shutdown cycles for operations using highspeed belts.
“Previously, mines had to replace both the cushion and the tungsten carbide tip every 20 weeks, but now with the PXT cushion, only the tips need replacement during that period,” Coe said.
“This can save significant time and costs during scheduled maintenance.”
Flexco isn’t stopping there as the company continues to refine its belt cleaning systems in response to customer
The stainless-steel encasement of the cushion isn’t just about durability; it’s also about reducing fatigue for workers handling the cleaner.
“These new cushions are 15 per cent lighter than their predecessors,” Coe said. “The reduced weight means less strain on workers.”
This lightweight design also simplifies maintenance, with easier installation and reduced handling effort.
Extensive internal and field testing of the PXT cushion highlights its unmatched resilience, with the seamless ability to adapt to diverse operational conditions.
“The new cushions lasted beyond any current shut cycles and showed no signs of failure during trials conducted in mines across Australia and internationally,” Coe said.
From high-speed environments to extreme temperatures, the PXT cushion has been proven to maintain its performance and reliability.
Beyond durability, the PXT cushion supports efficient maintenance processes.
feedback and evolving industry demands.
“We’re constantly evaluating new materials and designs to further improve performance, with future iterations of the Flextreme product line already in
THE PXT IS THE IDEAL BELT CLEANER CUSHION TO PAIR WITH AGGRESSIVE HIGH-SPEED BELTS.
THE PXT FEATURES FLEXCO’S PROPRIETARY POLYURETHANE, ACTING AS A DAMPENER TO MITIGATE VIBRATION.
Flextreme PXT is more than a simple upgrade; it’s a solution designed for modern conveyor systems that delivers increased longevity, reduced maintenance, and ergonomic benefits.
YOUR CHALLENGE: Minimise maintenance costs related to filters and oil, as well as equipment downtime in your mining operation.
A SOLUTION: Through intelligent sensing and advanced data analytics, FleetguardFIT gives you full visibility of filters and oil health on your equipment.
YOUR RESULT: By monitoring your filters and oil health with FleetguardFIT, you can reduce your spend on filters and oil service only as needed, synchronize filter and oil change intervals alongside equipment service intervals, and proactively turn breakdowns into planned maintenance events. For more information:
Monitor Fleetguard Filters & Oil Health
MAINTENANCE COSTS LOWER Reduce Spend & Optimize Maintenance
PROACTIVELY PREVENT BREAKDOWNS Sync Service Intervals & Prevent Breakdowns
IN 2013, AUSPROOF MANUFACTURED THE WORLD’S FIRST 35KV COUPLER FOR A MINING CLIENT IN AFRICA – A PRODUCT THE COMPANY CONTINUES TO EVOLVE TO THIS DAY.
AusProof couplers aren’t your everyday plugs for household appliances. Instead, they are scaled up to meet the high demands of the mining industry.
Spanning more than 14 different models, AusProof couplers cover a vast spectrum of voltages, from 660, 11,000, 22,000, all the way up to 35,000 volts.
What sets these products apart isn’t just their size and capacity, but their continuous evolution.
Speaking with Australian Mining, AusProof managing director Aston Marks reflected on how the company’s culture is driven by endless improvement.
“Over the years we’ve constantly tried to make our products better,” he said. “It’s always been in our nature and DNA to give our products a fresh look and ask ourselves what new features are needed to meet the evolving demands of the industries we serve.”
In making improvements, AusProof listens closely to its clients to identify changes that need to be made.
This saw AusProof add a handle to its heavier couplers to make them easier to carry, which came about purely because of client feedback.
However, as Marks explained, what works for one customer might not work for another.
“Some customers prefer the coupler without the handle, so we adapt the coupler to suit them,” he said. “Other customers might want to add extra features, which we can easily facilitate for them.
“We are constantly taking on customer feedback and making adjustments, which sees us regularly release new models and product iterations.”
As it constantly evolves its product portfolio, AusProof is also pushing the boundaries of what’s possible in the mining sector through its coupler design and development.
Just take AusProof’s record-setting 35-kilovolt (kV) coupler .
After being approached by an overseas sand mining operation, AusProof was tasked to develop a product to float a wash plant in the middle of a dam.
“No one in the world had developed a coupler capable of doing what this project needed,” Marks said. “The client knew about us and trusted our products.
So we developed the world’s first 35kV coupler.”
With no other product on the market able to handle this level of power, AusProof was able to push the boundaries, and after 15 weeks in development, the coupler was released.
In the 10 years since its development, AusProof’s 35kV coupler remains the only product of its kind in the world.
“Ten years has passed and AusProof remains uniquely capable of supplying a coupler of this rating, which is proof that we know what we’re doing,” Marks said. “We’ve established a niche market here in Australia, which means we can support the Australian mining industry with high-quality homegrown products.”
The 35kV coupler is just one of AusProof’s many offerings.
To complement its range of low and high-voltage couplers, AusProof is currently working on a new product to support longwall mining.
Marks said these are valuable opportunities for AusProof and can create further awareness around what the company offers.
“There’s only half a dozen products like this in Australia, so this is a really exciting opportunity and will see us further assist the mining industry,” Marks said.
AusProof not only manufactures and supplies cable couplers and accessories for the mining industry, but the company also takes great pride in its after-market support and services.
The company offers a training scheme, ideal for toolbox talks, that aims to improve AusProof product understanding to increase asset longevity, prevent damage and boost site safety.
AusProof customers are treated as partners, whereby both parties
MANUFACTURED IN 2013, AUSPROOF’S 35KV COUPLER REMAINS A FIRSTOF-ITS-KIND PRODUCT.
are constantly communicating to get the best out of a product. This open exchange can inform the creation of new parts and solutions.
So what’s next for AusProof?
While Marks was tight-lipped about future projects, he made it clear there are more innovations to come, with several products poised to reach the next level.
As the mining industry demands more power and reliability, AusProof will continue to forge ahead and explore the unknown. AM
WHILE LUBRICATION IS A NECESSITY IN THE MINING INDUSTRY, IT’S NOT ALWAYS EASY TO ACCESS. TRADESALES IS LOOKING TO CHANGE THIS.
The efficient operation of mining machinery relies heavily on proper lubrication, yet such a solution can be difficult to access and maintain.
Tradesales recognised this and developed the Lubestation, designed to expedite maintenance processes for fixed and mobile machinery on mine sites.
The Lubestation centralises the storage and handling of vital fluids like oils, greases, and coolants into one contamination-free, fit-for-purpose unit.
“Everywhere you look on a mine site, there’s machinery that depends on fluids to function,” Tradesales national sales manager Jay McEwen told Australian Mining
“Just like your daily drive, mining machinery, from 400-tonne haul trucks through to forklifts and fixed plant facilities, require engine and gearbox oils, greases, coolants and more.
“Without these fluids, at best machinery will soon start underperforming, and at worst machinery will break down and require an off-schedule rebuild, costing both time and money.”
The Lubestation combines all the necessary fluids into one secure unit, eliminating contamination risks while streamlining maintenance.
Contamination, whether caused by dust, water, or process chemicals, is responsible for the lion’s share of
lubrication-related failures, significantly shortening equipment life.
Lubricant contamination can occur at any time, whether during transport, storage, or in operation, costing mining companies millions of dollars in downtime.
“Reducing contamination has been a priority in our design,” McEwen said.
“The Lubestation features replaceable dust filters, ventilated enclosures, and bunding compliant with Australian Standards. This keeps fluids secure and contamination-free while protecting the environment.”
The safety of workers is another key focus of the Lubestation’s design, which eliminates the need for manual handling of fluids.
Tradesales offers multiple Lubestation configurations to meet the diverse needs of the mining industry, including mobile, fixed plant, and workshop options.
Mobile equipment lubestations
Mobile Lubestations are designed for field operations, enabling seamless lubrication for trucks, excavators, and other heavy equipment.
These relocatable units, featuring hoses and user-friendly handpieces, allow operators to top up fluids directly in the field without returning to service bays.
“We were approached to design and manufacture several 20-foot, five-IBC (intermediate bulk container) mobile
plant Lubestations for Roy Hill,” McEwen said.
“Four of the IBCs will dispense oils, while the fifth will be used to top up the coolant of mobile equipment.”
The unit was fitted out with five fiveto-one pneumatically operated Meclube piston pumps, while a Graco Husky pump was also added, which will be used to dispense the coolant.
Fixed plant Lubestations cater to the needs of stationary equipment like conveyors and crushers that run around the clock.
With dedicated decanting areas, they allow maintenance crews to efficiently transfer large volumes of fluids while safeguarding against spills and contamination.
In collaboration with Talison, which operates the Greenbushes lithium mine in WA, Tradesales designed a 20-foot fixed plant Lubestation tailored to the miner’s specific needs.
The Lubestation accommodates six different oils pumped from 1000-litre IBCs using Graco Husky pumps, offering an efficient solution while preventing manual handling issues by transitioning from 205-litre drums to IBCs.
Fluids are channelled through stainless-steel pipes to a series of taps, allowing easy dispensing into smaller 20-litre oil-safe containers used by the maintenance team on-site.
For workshops, the Lubestation connects directly to hose reels via gantries or bulkheads, ensuring maintainers have quick and easy access to fluids.
This setup eliminates time wasted retrieving and handling fluids, boosting productivity and safety.
“At BHP Jimblebar, our custom Lubestation was integrated into the site’s MEM (mobile equipment maintenance) workshop,” McEwen said.
“With six IBCs and external plumbing, maintainers could top up fluids quickly without entering the storage area.
“It was even painted to match the workshop infrastructure, demonstrating how we can customise units to fit seamlessly into existing operations.”
The Lubestation is more than a tool, it’s an investment in productivity and safety. Boasting modular designs and bunded and ventilated cyclone-rated builds, the units can be deployed across mines, pits, and workshops.
Each Lubestation is a reusable asset with minimal maintenance requirements and a long design life.
Tradesales prides itself on tailoring Lubestations to meet clients’ unique needs.
“We offer standard designs, but every project is customisable,” McEwen said.
TRADESALES DESIGNED THIS 20-FOOT FIXED PLANT LUBESTATION TAILORED TO A MINER’S
“Our aim is to deliver solutions that address specific operational challenges while maximising efficiency.”
Proven results in the sector Tradesales’ Lubestations have been implemented by many Tier 1 mining companies, including Fortescue, Rio Tinto, BHP, and Northern Star.
From mobile operations to fixed facilities, Lubestations are helping these companies save time, reduce downtime, and minimise costs.
“The feedback from our clients has been overwhelmingly positive,” McEwen said. “They see tangible benefits in terms of efficiency and reduced contamination risks, which translate to
extended equipment lifespans and lower maintenance costs.”
With its innovative design and versatile applications, Tradesales’ Lubestation range is setting new standards for maintenance in the mining sector.
By addressing critical challenges like contamination, safety, and downtime, the Lubestation ensures operations run
smoothly keeping machinery in peak condition and miners focused on the job at hand.
“Our goal has always been to provide practical, cost-effective solutions,” McEwen said.
“The Lubestation is proof of how innovative thinking can make a tangible difference in the industry.” AM
• Complex projects
• Systematic planning
• Manage timelines
• Monitoring
• Coordinate resources
• Extensive expertise with all igus products
• Specialised knowledge on mining applications
• Tailored solutions ensuring optimal performance
• Comprehensive range of igus products
• Readily available
• Products specifically for mining including cables and connectors
• Local supply in all states
• Trained personnel
• Systematic approach to planning
• Executing, monitoring and completing projects efficiently and effectively.
• Treotham provides support to all projects.
• Dedicated team of support personnel on call.
MAINTAINING AND SERVICING MINING TYRES CAN BE A DAUNTING TASK. FOR KAL TIRE, IT’S SOMETHING THE COMPANY LIVES AND BREATHES.
Kal Tire is proud of its legacy of service to the mining industry, especially when it comes to tyre and rim management and maintenance.
A core part of its business, Kal Tire develops tyre and rim management plans for its customers to capitalise on their mining tyres and keep things running in tip-top shape. The tyre and rim management plans detail the key metrics that trigger and determine tyre maintenance activities.
“Given the importance of tyres to mining equipment, we’ve always offered tyre and rim management plans for our customers,” Kal Tire general manager, Australia, Wes Woodroffe told Australian Mining
“It’s an integral part of our mining partnerships, and we set clients up in such a way that the plan aligns fully with their desired outcome.”
There are many different outcomes a customer might like to achieve from their tyres.
They might like to see an increase in tyre kilometres per hour, or they may want to reduce downtime.
Whatever the outcome, Kal Tire can tailor a plan to suit.
“The first step in enacting a tyre and rim management plan is to sit with the customer and work out what their site objectives are,” Woodroffe said. “We find out any previous issues, what they understand about their sites, and then we tailor a plan to focus on those objectives, whether it is maximising tyre life or production, or minimising downtime.
“It’s a team effort, both from the Kal Tire side and the customer side.”
One of the key benefits of having a comprehensive tyre and rim management plan is the sense of comfort it affords mine operators.
“Tyres can be a high-risk part of the industry, so it’s important to ensure every person on the team knows what their role is,” Woodroffe said. “The plan is the single source of knowledge each member can come back to.
“It can be seen as a real conduit between the corporate level and
the operational level of a mine as it translates the overall mine strategy into specific and supportive tyre maintenance actions.”
As well as any special requests a customer might have, Kal Tire’s maintenance plans also include regular tyre servicing like pressure checks, rotation strategies and tread wear principles.
Like all of Kal Tire’s team members, Woodroffe is very hands-on in his level of service. He enjoys connecting with his customers face-to-face to learn about their tyre needs.
“A typical site visit might start out by sitting with the team and answering their questions, or talking about what’s been happening on-site,” Woodroffe said.
“We inspect the tyre bay to make sure everything is safe and up to spec, and above all, we make sure we’re doing what we said we were going to. If a customer is looking to reduce downtime, for instance, we make sure the maintenance and servicing we give their tyres matches that goal.”
The key to tyre management, Woodroffe said, is partnering with a specialist tyre management company with the necessary experience to achieve what customers want to achieve.
“There’s a lot of people out there that can just put boots on the ground, but for Kal Tire it’s about having the support network behind tyre maintenance that will help customers achieve their goals,” he said.
“Wherever there’s mining, you’ll find us. We have a dedicated team, and we’ll often have over 100 years of combined experience sitting around one table.
“Whenever that happens, our customers are always in great hands. We all care about what we do, and that not only gives me a level of comfort but the customer as well.”
Global technology for Australian conditions backed by local support
FLUKE’S ACOUSTIC IMAGERS MAKE SURE NO LEAK IS LEFT UNCHECKED, POTENTIALLY SAVING MINERS THOUSANDS – IF NOT MILLIONS – OF DOLLARS IN AVOIDED DOWNTIME.
Even the smallest of compressed gas leaks can put a mine out of action, leading to hours of lost time and lost revenue.
Pinpointing these leaks can be a challenging process, especially on a busy site with many pieces of equipment operating at once. Whether from material spillage or hydraulic and fluid seepage, leaks can stop an operation in its tracks.
Luckily, Fluke has come through with a solution.
Fluke’s high-quality acoustic imagers have been designed to allow users to visualise the sound of a leak while identifying partial discharge and spotting mechanical deterioration.
Not only does this enable operators to fix any leaks before they worsen, but it also makes predictive maintenance a breeze.
“We launched our three acoustic imagers in 2024: the ii500, ii905, and the ii915,” Fluke product manager Max Malik told Australian Mining
“The imagers scan an area for any leaks and provide a visual indication for where the leak is. There’s no need for training; anyone can use them.”
The imagers work by capturing soundwaves emitting from a leak; soundwaves that, without the imagers’ 64 micro-electronic microphones, would be inaudible to the human ear.
Software converts the sound signals into an image for the operator, giving them a picture of the exact area the leak is coming from. Once the operator has an image of the source of the leak, they can add annotations and tags to ensure the issue is followed up on.
The advantages of using the imagers on a mine site are far-reaching. Easy to deploy, they require minimal training and seamlessly integrate into routine predictive maintenance programs, ensuring quick adoption across the team.
“Of the three models, the ii915 is best suited to most mining operations,” Malik said. “Not only does the ii915 have the highest frequency range (two to 100 kilohertz), but it also includes MecQ Mode (for potential mechanical deterioration) and PDQ Mode (for partial discharge).”
Partial discharge can pose serious issues to mine sites, potentially causing
arc flash fires and blackouts. Enter PDQ Mode, which turns partial discharge sounds into visuals to give the operator a pinpoint view of a fault’s location.
“At Fluke, we’re passionate about advancing operations for our customers while keeping them safe,” Malik said.
An extended frequency range from two to 100 kilohertz means the imagers detect leaks at the earliest possible moment, and with the press of a button, the leak’s location and data can be shared to the wider team to enable a quick fix.
There’s no need to worry about the leak getting lost in a noisy environment either. The imagers’ 73.2-decibel delta performance means leaks don’t go unnoticed.
“Predictive maintenance goes handin-hand with safety on-site,” Malik said. “It’s important to ascertain if there’s a potential problem, like a compressed gas leakages, partial discharges and mechanical deterioration, before they become catastrophic.
“Downtime costs start mounting from the first minute a piece of machinery is offline, let alone the first hour. Having knowledge and awareness of leaks before they spread and get worse is imperative to the wellbeing of both the mine and its employees.”
With the potential cost of downtime often exceeding $100,000 each hour, tools like Fluke’s acoustic imagers are becoming imperative to the modern mine. AM
Conveying Excellence in Heavy-Duty Conveyor Components. At Veyex, we design and manufacture high-performance conveyor components built to withstand the harshest environments. Our solutions are trusted worldwide in mining, quarrying, agriculture, ship loading, utilities, bulk material handling, and more.
Built for performance, designed for reliability. Our high-quality components keep your conveyor systems running efficiently, reducing downtime and maximising productivity.
Durable. Reliable. Engineered to Perform. 1300 70 70 67 veyex.com.au
Contact us today to optimise your conveyor system.
COMPRESSED AIR LEAKS CAN WREAK HAVOC ON A MINE SITE. LUCKILY, FLIR HAS A SOLUTION.
Air compressors are widely used in the mining industry, especially in the underground sector.
Underground mining employs a wide range of drilling methods, which are heavily reliant on compressed air systems to flush debris and cuttings.
Air compressor systems also play a large part in blasting, producing high-velocity streams that trigger explosives safely.
In fact, they have become such a staple in the mining industry that they can be found in almost every corner of a mine.
But while compressed air has made mining safer and more efficient, it is not without its challenges.
Compressed air systems can be prone to leaks, which can drive up a mine’s energy costs due to wasted air. In fact, a compressed air system can lose 25–30 per cent of their air to leaks.
In response, FLIR Systems, a Teledyne Technologies company, has engineered a solution: acoustic imaging cameras.
“To meet the mining industry’s challenges, mining companies can turn to technology with a particular emphasis on condition monitoring,” FLIR said.
“The FLIR Si2 acoustic imaging camera offers a powerful solution for condition monitoring and is specifically designed to discover compressed air leaks and partial discharges as well as bearing issues and detection of some gases.”
The FLIR Si2 detects ultrasonic frequencies of a compressed air system leak through its 124 low-noise MEMS (micro-electromechanical system) microphones and real-time sound visualisation.
And with the complimentary FLIR acoustic camera viewer, images of the problem can be visualised quickly and uploaded for immediate analysis.
“This service provides users with valuable insights, such as the energy costs of compressed air leaks and the classification, severity assessment, and recommended corrective actions,” FLIR said. “The camera requires minimal training and is easy to incorporate into the maintenance cycle
of a mining operation, even in the noisiest environments.”
The FLIR Si2 is known for its one-handed ease-of-use operation, and the acoustic imaging camera also enables operators to complete inspections up to 10 times faster than traditional methods.
“By employing acoustic imaging cameras to promptly detect and
address leaks, mining operations can enhance their energy efficiency and decrease overall energy consumption,” FLIR said.
This leads to reduced operational expenses and an improved environmental footprint, enhancing a mine’s safety.
“The FLIR Si2 hosts 124 sensitive microphones, which are advantageous for high-voltage systems and substations, enabling operators to maintain a safe distance when inspecting energised equipment,” FLIR said.
“The non-contact camera works from an operational distance from 0.3m up to 200m, allowing conditionbased maintenance to occur in large areas safely and efficiently and without halting operation.
“As a result, mines can promptly mitigate safety risks while optimising the performance of their equipment.”
Compressed air leaks can translate to a costly problem for a mine site, so getting on top of them is essential.
“Leaks in compressed air systems can be detrimental to the mining process, increasing energy costs, reducing tool efficiency, and increasing maintenance requirements,” FLIR said.
“The FLIR Si2 acoustic imaging camera offers a powerful solution for condition monitoring in mining facilities, detecting compressed air leaks early on and improving operational continuity.”
Dependable testing and troubleshooting for critical applications. Built for hazardous environments.
• Completely sealed, IP67-rated, intrinsically safe digital multimeter (ATEX and ANZEZ) with CAT III 1000V and CAT IV 600V rating
• True RMS AC voltage and current allow for accurate measurement of non-linear signals
• Measures AC and DC voltage and current up to 1000V and 10A
• Low-pass filter ensures accurate voltage and frequency measurements on variable speed drives (VSD)
MST GLOBAL IS HELPING THE MINING INDUSTRY UNLOCK GREATER EFFICIENCY AND PRODUCTIVITY THROUGH ITS CUSTOMER-FOCUSED SOLUTIONS.
The rapidly evolving mining industry is increasingly looking for innovative solutions to optimise operations, ensure compliance with regulatory standards, and bolster safety.
Through its HELIX platform, MST Global, a global leader in mining solutions, provides cutting-edge tools to be ahead of the game, improving mine efficiency and safety.
This includes the integration of tracking systems, Internet of Things (IoT), ventilation sensors, and predictive analytics, revolutionising underground mining practices in the process.
HELIX Dispatch, a core module of MST’s HELIX platform, serves as a fleet management system (FMS) tailored to underground mining.
MST Global product manager Nick Rebeiro said HELIX Dispatch is fundamentally focused on productivity, with advanced tools designed to execute shift plans more effectively.
“It’s an operations tool that helps collect data and provides dispatchers with insights they can use to better execute the shift plan,” he told Australian Mining.
“The primary features of HELIX Dispatch include automated cycle tracking, or production tracking, which is where we automatically track truck and loader dumps underground and on the surface, without any operator input.”
The system automates processes such as cycle tracking, including real-time data capture of loads and dumps.
For mining equipment such as drills, HELIX Dispatch tracks drilling productivity to provide actionable insights into efficiency.
HELIX Dispatch also extends beyond productivity and offers critical tools for maintenance management.
“The system enables mining operators to manage the availability of mining vehicles in real time, providing updates on statuses like ‘ready’, ‘delay’, ‘down’ or ‘standby’,” Rebeiro said.
“We provide a simplified interface for being able to analyse these equipment statuses in the field, with the insights enabling mining operations to swiftly respond to operational upsets or maintenance requirements.”
Clients can also digitise pre-start checklists. Through onboard tablets, operators can conduct equipment safety checks in real time.
The HELIX Telemetry module offers a comprehensive system for asset health monitoring by gathering OEM (original equipment manufacturer) data directly from vehicles.
The module provides detailed dashboards and trend analysis, enabling users to detect early signs of mechanical issues and prevent costly breakdowns.
Rebeiro emphasised the module’s capability to generate real-time alarms and notifications for vehicle health issues, delivering this data directly to maintenance teams.
By identifying problems before they escalate, HELIX Telemetry minimises unplanned downtime, optimising asset lifecycle management and enhancing overall operational performance.
Given the complexity of underground mines, safety is paramount. MST’s integrated solutions ensure safety is not just a regulatory box to tick but a streamlined part of daily operations.
MST Global product manager Shaun Newton discussed the company’s ultra-wideband (UWB) tracking technology, which offers GPS-level accuracy underground.
“Our UWB technology is similar to Apple’s AirTag in that it acts as a tracking device,” he told Australian Mining.
“It’s ruggedised for mining and has additional functionality so it can also be a precision monitoring, safety and productivity solution to connect people and assets underground, creating a more interconnected mining operation.
“We can monitor vehicle and ventilation emissions and unlock cost savings by realising efficiencies at various points of a mine.”
This precision enhances evacuation planning, enabling operations teams to quickly and accurately locate personnel during emergencies, and help guide them to safety.
MST’s automated ventilation systems incorporate real-time monitoring of people and assets to regulate ventilation systems. If a section of a mine is unoccupied, the system reduces ventilation flow, saving energy and costs.
Airflow adjusts automatically when personnel enter, creating a safer environment without wasting resources.
MST’s refuge chamber monitoring is an emergency response tool that identifies and monitors occupancy in refuge chambers, facilitating faster decision-making and ensuring personnel safety during critical situations.
MST’s UWB tracking technology, automated ventilation systems and refuge chamber monitoring are all incorporated into the company’s HELIX platform.
Unlike competitors that offer standalone systems, HELIX stands apart by combining FMS, telemetry, tracking, and environmental monitoring into the one platform.
MST Global product manager Ramodh Rangasamy highlighted scenarios where this multi-functionality has a tangible impact.
“HELIX ensures a mine is evacuated before blasting operations occur,” he told Australian Mining. “Once the system verifies that no personnel remain, it issues clearance for blasting to proceed.
“The platform monitors environmental conditions to ensure air quality meets safety standards, enabling personnel to re-enter quickly and safely.”
By merging capabilities, HELIX ensures operations remain not only compliant but also become more efficient and resilient.
One of HELIX’s key advantages is its ability to mitigate downtime – both planned and unplanned.
Digital tools are used for tracking delays or stoppages, fostering transparency and quicker issue resolution.
These features empower mines to optimise their workflows and reduce operational disruptions.
MST recognises that adopting advanced systems such as HELIX requires robust onboarding and support, so the company works closely with clients to identify specific challenges and tailor solutions.
Beginning with network deployment and gradually integrating modules like Telemetry or Dispatch, MST ensures HELIX scales to meet evolving requirements.
MST collaborates with clients to establish custom workflows, empowering operators to leverage HELIX effectively from day one.
This tailored approach minimises the learning curve while maximising return on investment from the technology.
With a focus on smarter, datadriven decision-making, through HELIX, MST bridges the gap between traditional mining challenges and future safety, compliance, and operational excellence demands.
This seamless blend of tracking, predictive analytics, and real-time monitoring positions MST Global as a critical partner in the drive towards more efficient, safer, and sustainable mining practices. AM
Increased production demands have resulted in faster, wider, more
Carry-back leads to excessive wear on conveyor components, buildup on return idlers, misalignment of the belt, adverse effects on the conveyor operation and plant efficiency, and increased OH&S risks.
The ESS IPS Cleaners deliver superior belt cleaning performance
The IPS is an upgraded version of the ESS InLine 20-Ten Premium Cleaner & the original ESS InLine cleaner, which set the standard – reduces jamming for easier service
• Stainless steel manufacture – to resist product wear and suitable for corrosive environments
• New tensioning bracket design – increases the cleaners sensitivity to belt movement to maintain optimal cleaning pressure and angle
• New Air and Spring Tensioner design – interchangeable to offer flexibility as the requirements of the client evolves
• Same footprint as the 20Ten Premium InLine cleaner - as a client 20Ten Premium cleaner comes to the end of its service life, a new IPS Cleaner can be retrofitted.
WHAT DOES NORTHERN STAR RESOURCES’ POTENTIAL ACQUISITION OF DE GREY MINING MEAN FOR THE WESTERN AUSTRALIAN GOLD SECTOR?
The Australian gold industry saw multiple mergers and acquisitions (M&A) take place in 2024.
Red 5 merged with Silver Lake Resources to create Vault Minerals, Westgold Resources and Karora Resources joined forces, while Greatland Gold took the helm of Newmont’s Telfer gold mine and gained full ownership over the Havieron goldcopper project.
Also joining the fray in December was Northern Star Resources’ play for De Grey Mining.
Northern Star holds the title as the largest ASX-listed gold miner, while De Grey is the owner of the Hemi gold project in WA, one of the world’s largest undeveloped gold projects.
For these reasons and more, the potential $5 billion acquisition has set the mining industry abuzz. But how will it shape WA’s gold sector?
Hemi
of gold per annum over its first 10 years, Hemi is considered to be a Tier 1 project that, once production has commenced, will be a top five Australian gold mine. Its first gold is expected in mid-2026.
By acquiring De Grey, Northern Star will add a globally significant
shareholders,” Northern Star managing director and chief executive officer Stuart Tonkin said in December 2024.
“De Grey’s Hemi development project will deliver a low-cost, long-life and large-scale gold mine in the Tier 1 jurisdiction of Western Australia,
the combined entity and De Grey shareholders will own the balance. The scheme has been unanimously recommended by the De Grey board.
“Given the high-quality nature of Hemi, De Grey is in the fortunate position to have had many avenues to progress the asset, including M&A,” De Grey managing director Glenn Jardine said in December 2024.
“The transaction that we have entered with Northern Star (on December 2) is a highly attractive opportunity for De Grey shareholders in terms of the upfront premium, as well as retaining ongoing exposure to Hemi and gaining exposure to the broader Northern Star portfolio.”
Northern Star’s current portfolio comprises three production centres situated in iconic gold mining regions: the Kalgoorlie and Yandal centres in WA and the Pogo centre in Alaska, US.
The Kalgoorlie centre includes the Kalgoorlie Consolidated Gold Mines (KCGM) operations, one of the largest open pit gold mines in Australia, as well as the Carosue Dam operations and the Kalgoorlie operations.
The Yandal centre comprises the Jundee operations, the Thunderbox operations and the Bronzewing operations.
By acquiring Hemi, Northern Star will have a third production centre in WA – its fourth overall.
Northern Star will leverage its extensive exploration, mine development
and operating expertise to unlock Hemi’s long-term value, increasing its growth pathway to approximately 2.5Moz per annum by the 2028–29 financial year.
“This reinforces Northern Star’s position as the leading Australian ASXlisted gold company and a top 10 global gold major,” Tonkin said.
“The addition of the Hemi project leverages Northern Star’s inbuilt project capability with the project team expected to transition from the mill expansion to Hemi.
“The 27Mtpa (million tonnes per annum) KCGM mill expansion is the largest Australian gold project in over 10 years and provides Northern Star with the unique opportunity to de-risk the Hemi development pathway through our experience and relationships with contractors and suppliers.”
De Grey is currently advancing Hemi
70% of lubrication-related failures are caused by contamination.
LUBESTATION® packs all your lube, oil, and fluids under one portable roof so it can be moved to different areas of a mine site, saving on capital costs while protecting your pumps, reels, and hoses from the harsh Australian elements. LUBESTATION® also prevents cross-contamination of oil, grease and coolant, giving you peace of mind that you’re putting fresh fluids into your expensive mobile equipment.
AS MINING COMPANIES LOOK TO SLASH EMISSIONS, ROBUST AND RELIABLE RENEWABLE ENERGY SOLUTIONS ARE KEY.
While a new year has begun, the global energy transition is only just heating up.
According to the Climate Change Authority’s 2024 ‘Sector Pathway Review’, emissions from Australia’s resources sector equalled 99 million tonnes of carbon dioxide equivalent in 2022, representing 23 per cent of the country’s total emissions in that year.
For Australia to achieve netzero greenhouse gas emissions by 2050, decarbonising the mining sector is key.
This will see solutions such as battery energy storage systems (BESS), wind farms, and solar microgrids implemented across both brownfield and greenfield sites.
Aggreko head of energy solutions Asia-Pacific Greg Lunt said there has been a substantial increase in the number of mines looking for renewables and hybrid power stations in recent years.
“Several mid-tier miners are leading the way,” Lunt told Australian Mining
“The Tier 1 miners are probably a little bit slower, but they are definitely looking to decarbonise their operations. I think it’s due to the decision-making timeframes, approval processes, and the number of studies larger companies tend to go through.
“Current fuel sources being used at mine sites have a big impact on the economic benefits of renewables. Some Tier 1 miners have assets connected to gas pipelines and depending on their location, their fuel cost can be very low, making the shift to renewables less financially attractive.
“Most new mines these days generally end up implementing a hybrid power station as it provides the lowest cost of energy.”
Hybrid technology refers to one renewable energy system being integrated with another.
Aside from reducing emissions, benefits of a hybrid solution include having the ability to scale to meet different energy demands, being cheaper to run compared to standalone gas or diesel systems and being able to provide uninterrupted power during outages.
Lunt provided insight into the kinds of hybrid plants being installed throughout Australia.
“The hybrid solutions being installed at the moment are pushing the boundaries of technological advances,” he said.
“ Power stations are going completely thermal off, meaning they’re just running
on renewable energy at portions of the day with no gas or diesel engines running. That requires a bit more engineering than what we’ve seen in the past.
“Wind turbines are also being implemented at various mines, so you’ve got a combination of wind, solar, battery and thermal providing energy with a large portion coming from the renewables.”
If a mine site is yet to move away from fossil fuels and embrace renewable energy, there can be challenges.
These include the cost of investing in low-carbon energy sources and its associated infrastructure.
To help make the jump, mining companies can work with an independent power producer (IPP).
Aggreko, a leading IPP in Australia, has over 60 years’ experience and provides a wide range of innovative and flexible modular energy solutions.
such as Aggreko, they can rely on the engineering and analysis capability we have built up and solutions can be developed far quicker than if they were to go and undertake the studies themselves,” Lunt said.
“Accessing energy ‘experts’ that understand these projects can also be challenging for clients.
“An IPP model allows the client to avoid upfront capital and enter into a service agreement for power supply. These agreements include the necessary drivers to ensure that a hybrid power station optimises the use of renewable energy and runs efficiently. The fuel savings alone can often pay for the power station.
swiftly devise the optimal solution that provides the lowest cost of energy.
they’ve got the land and approvals.”
Aggreko has seen significant success in the mining industry, both in Australia and internationally.
The company has worked with Gold Fields extensively to implement various energy solutions at its Granny Smith gold mine in Western Australia.
Following the installation of a gas power station in 2016, Gold Fields
existing gas supply to create a hybrid power station.
The package comprises more than 20,000 solar panels, 2MW of battery storage and 27MW of gas power.
The assets produce around 18GWh of energy per annum, with carbon emissions at Granny Smith expected to be reduced by approximately 9500 tonnes of carbon dioxide equivalent
AGGREKO
particularly the batteries and the understanding of how batteries are used,” Lunt said. “There’s been learnings from this and other projects.
“Aggreko has other hybrid projects under construction, including two 5.25MW solar farms at Rio Tinto’s Gove operation in the Northern Territory, and a 12.4MW solar farm being added to a diesel power station at the company’s Amrun bauxite project in Weipa.”
An 8.8MW/2.1MWh BESS will also be installed at Amrun. Once operational, the solar farm and BESS are expected to reduce Amrun’s diesel electricity consumption by 37 per cent or approximately 5.5 million litres of diesel fuel per annum. This will reduce annual carbon dioxide emissions by approximately 14,000 tonnes.
Aggreko’s key value propositions include its mobile and modular energy solutions, the constant investment in new renewable technologies, and its ability to leverage global expertise.
“We can lean on our global engineering resources and capability,” Lunt said.
“We have developed expertise in analysing and optimising the use of renewable energy over time, contributing to market development and supporting our customers’ evolving needs.”
As the world shifts towards a greener economy, Aggreko is here to help mine sites embrace renewables and reduce emissions. AM
BOOM LOGISTICS IS LEADING THE AUSTRALIAN RESOURCES INDUSTRY INTO A NEW ERA OF SUSTAINABILITY AND DECARBONISATION.
As the Australian mining industry increasingly embraces sustainability and decarbonisation, Boom Logistics is leading the charge by integrating innovative technologies that prioritise environmental, social and governance (ESG).
This has seen the company make significant strides in reducing its environmental footprint, underscoring its dedication to a sustainable mining future.
Reflecting on Boom Logistics’ ESG journey, chief executive officer Ben Pieyre highlighted the importance of actionable change.
“Last year was transformative for us,” Pieyre said. “We focused heavily on reducing our carbon footprint. As we continue to seek advancement in
hybrid and electric cranes remain central to our decarbonisation mission.”
A new era of cranes
A standout in Boom Logistics’ sustainability efforts has been the introduction of the Tadano AC 4.080-1 hybrid crane, the first of its kind in Australia.
Now fully operational in Western Australia, the AC 4.080-1 features Tadano’s innovative electro-hydraulic e-PACK, enabling zero-emission crane operation and significantly reducing noise pollution. This hybrid crane is a game-changer, demonstrating that sustainability and productivity can go hand-in-hand.
Complementing this is the fully electric MC85, a groundbreaking crane designed for zero-emission performance. With its transportable design,
flexibility, enabling seamless relocation between job sites without sacrificing environmental responsibility.
The MC85 sets a powerful precedent, proving the viability of electric solutions in the mining sector – a traditionally energy-intensive industry.
The integration of hybrid and electric cranes into Boom’s fleet has already yielded measurable results. These technologies have not only reduced the company’s diesel consumption but have also improved operational efficiency, demonstrating that sustainability initiatives can deliver tangible benefits across multiple fronts.
further embedding sustainability into our operations.”
“Our hybrid and electric cranes are proof that innovation drives results,” Pieyre said. “But the journey doesn’t end here. Working with our
Beyond the environmental benefits, Boom’s investments are setting a new industry standard. By adopting advanced, energy-efficient solutions, the company is paving the way for other mining service providers to follow suit.
Collaboration
Despite Boom’s achievements, Pieyre emphasised that real progress requires industry-wide cooperation.
“Sustainability is a shared responsibility,” he said. “As a service provider, our ability to support decarbonisation depends on collaboration with our clients and suppliers, and the need for operational transformation and infrastructural readiness. Together, we can align our efforts and turn shared goals into
Boom’s proactive approach highlights the importance of partnerships in driving meaningful environmental change. By aligning its ESG goals with its clients’ sustainability initiatives, the company is fostering a culture of shared accountability and mutual progress.
Boom Logistics’ commitment to sustainability extends beyond technology. The company actively supports community engagement and industry initiatives that promote sustainable practices, solidifying its reputation as a leader in responsible business.
“Our goal is to inspire others in the mining industry to adopt innovative, sustainable solutions,” Pieyre said. “Together, we can create a greener, more
As the Australian mining sector continues its net-zero transition, Boom Logistics exemplifies how innovation, collaboration and bold leadership can drive the change needed for a sustainable tomorrow.
HEXAGON HAS EXPANDED ITS AUTONOMOUS MINING DIVISION THROUGH A KEY ACQUISITION.
Companies like Hexagon are continually challenged to not just innovate, but to also ensure systems work together in harmony.
The company has embraced that challenge since launching its mining business 10 years ago.
Hexagon’s recent acquisition of indurad and its autonomous haulage subsidiary, xtonomy, marked a significant step towards realising the company’s vision of fully connected and integrated
indurad’s unique offering of 1D, 2D, and 3D radars and RTLS (real-time locating systems) solutions expands Hexagon’s solutions in collision avoidance, positioning, digitalisation, process optimisation and automation.
The ability to understand unique problems from pit to port, complemented by its radar expertise, enables indurad to deliver digital twins that are otherwise next to impossible to achieve with other sensors.
Hexagon plans to release the fifth version of indurad’s collision avoidance and proximity detection system,
The fourth version of iProximity uses hardware at a gate or entry point, hardware in vehicles and equipment, and personal transponders installed in helmets, which transmit to each other and to dedicated antennae.
An in-cab processor alerts operators using a red, yellow and green light system. Green indicates no transponders within 100m, yellow means a transponder is within 100m, and red indicates a transponder is within 25m.
An in-cab display gives additional information, such as direction or position and distance. System data is transmitted to a server, which can use a mine’s pre-existing Wi-Fi or LTE (long term evolution) network.
iProximity’s technology integrates multiple frequencies and concurrent algorithm processing, creating a simple, low-cost, precise, and reliable solution deployed in mines worldwide.
The next generation of iProximity goes one step further using ultra-wideband. New features will be based on new timeof-flight and phase difference of arrival (PDoA) measurement capabilities. The upgrades will help improve tracking performance and reduce the false positives that annoy operators.
Historically, the system can generate a significant amount of data that is often left unused. Now the goal is to liberate
the data and better understand what is going on underground.
Coming to the market in 2025, iProximity G5 features an event replayer, which, supported by cameras, enables users to see exactly what happened around a piece of equipment.
The system operates mostly peer-topeer and in most cases requires no new infrastructure. Hexagon expects the reliability of the system to help increase operator acceptance.
“The whole idea is to get the right information at the right time to the people operating the machines,” Hexagon senior product manager Florent Garin said. “What we want is a system that warns you and shows what is around you but is not intrusive.
“I see iProximity G5 as a platform, and our adoption of the system represents a commitment to the future. Today it is a collision avoidance system, but tomorrow we will have the possibility to do more.”
The indurad acquisition is part of a greater safety journey Hexagon is on with its customers.
The company began 2025 with 65,000 collision avoidance systems deployed in more than 100 open-pit and underground mine sites worldwide, the largest global install base on the market.
As Hexagon expands its portfolio, customers can expect an integrated ecosystem of safety solutions that unify collision avoidance, operator alertness and intervention systems. AM
TED and BIG TED are essential pieces of safety gear for anyone working on dozers, graders, dump trucks and other mining and earth-moving machinery.
Remote-controlled operation eliminates the need for personnel near suspended loads, reducing the risk of crush injuries and enhancing safety.
Streamlined field maintenance increases productivity and reduces the need for personnel to move loads between sites.
Quick and easy deployment to the pit, meeting the demands of the toughest sites with the addition of a purpose-built Pit Rescue Trailer.
Both TED and BIG TED offer an ever-increasing range of practical attachments designed to enhance safety and efficiency in a variety of workplace operations.
Can be used in tight spaces beneath machinery to remove and replace belly guards and other heavy components.
Aggreko - your power partner for the long-term.
At Aggreko, we help you progress your business with better – and cleaner –energy solutions for the life of your mine.
THE NARROW VEIN DRILLING SOLUTION BROKK DEVELOPED FOR A SOUTH AFRICAN MINING COMPANY IS NOW ATTRACTING ATTENTION IN AUSTRALIA.
Inspector Gadget captured the world’s imagination with his multitude of high-tech gadgets and capabilities.
Just as the inspector was able to quickly activate a device by saying “go-go gadget”, the same can be said for Brokk’s suite of attachments and offerings.
Brokk has become known as a problem-solver in the various industries it serves, with its robots able to expertly complete a range of tasks, from drilling to rock-breaking to loading to splitting to shotcreting and vacuuming, to name a few.
Attachments can be quickly and easily replaced, limiting operational downtime and enabling operators to carry out a range of tasks with minimal footprint.
Significant drilling power and flexibility are achieved by combining a Brokk machine with TEI’s hydraulic rock drill attachment. This solution has proven its worth in countries like South Africa and is now being applied to underground mining in Australia.
“A Brokk armed with a rock drill has the ability to drill with rollover and many degrees of freedom,” Brokk Australia managing director Will Visser told Australian Mining. “The machine can drill left-hand stope, right-hand stope,
footwall and handwall with very little angle deviation.”
Visser said the goal was to deliver a mechanised solution in a narrow vein drilling application, making the Brokk and TEI combination the perfect option.
“Normal mechanisation ends at around seven or eight degrees of angle,” Visser said. “We could move our Brokk machine unassisted at 30 degrees incline, so we could go more than three times what normal equipment could handle in an underground mine.”
The addition of hydraulic clamps to the front end of the drill enabled rod extension and the ability to complete extended drilling up to 10m away.
When it came to deploying a Brokk machine into a WA gold mine, the robot was tasked with drilling and rock-splitting in narrow underground confines, with quick hitches enabling the rapid switching of attachments.
“Without using explosives, the Brokk robot could drill, perforate rock and split it,” Visser said. “This proved to be an effective way of doing controlled rock excavation in that shaft.”
Fitted with the TEI attachment, the Brokk machine was able to complete face drilling, support drilling and anchor drilling at extended distances.
As power specialists, we understand the energy you need to oper ate ef fectively – regardless of your mine’s location or how complex your operation’s practical challenges of reducing your
“The TEI hydraulic rock drill has proven itself as a very versatile attachment for the Brokk machine, creating a balanced and reliable system that is more powerful than traditional handheld drilling methods,” Visser said.
That is why we will work with you and use our deep expertise to develop the right choice of solutions and services
“Fitted with the TEI rock drill, the Brokk robot can enter confined underground mining environments, and the machine can be moved up narrow inclines and down declines, enabling underground miners to carry out drilling in previously inaccessible areas.
We have been providing energy services across a variet y of industries for over 60 years. From humble beginnings, we have grown to be the world’s leading provider of mobile modular power and temperature control now operating
“And because it’s remote controlled and can be operated from a safe distance, operators are removed from hazardous environments where there’s the risk of rock falls.”
In mining, our histor y is just as rich having first entered the industry over the only company to put 1MW of power
Whether it be construction, tunnelling or mining, Visser said owners and operators “love the flexibility”.
“Operators are usually impressed with ease of use and the versatility,” he said. “The machine is easy to move around in confined areas – it’s not a big, cumbersome machine that creates headaches for operators.
“You can drive it into small, compact tunnelling applications and conduct the desired drilling tasks.”
Brokk robots are nimble and able to navigate the narrowest of
underground spaces, as opposed to other drilling equipment.
“Production drills are unlikely to be able to run up 30-degree angles in stopes like the Brokk machine can,” Visser said. “So we can enter really compact areas and drill in areas previously deemed too steep.”
Over time, our solutions have grown from initially supporting mines with bridging power to now providing fully hybridised micro-grids that we build, own and operate throughout the mine’s life. Where we once supported mines operationally with their short-term energy needs, we organically developed into an investment partner now active at more than
Visser provided another example to further illustrate his point.
“In a maintenance area where underground mining equipment is serviced, these areas are typically seven, eight metres in the air,” he said. “These are confined areas that are not suitable to traditional drilling machines.
“You might not be able to fit traditional rock support equipment in these environments, meaning underground teams would need to build scaffolds. This could take X number of weeks to construct, and this is before drilling has even begun.
We understand that mining is a business of uncertaint y, requiring quick response to changing circumstances, and the flexibility and agilit y to keep pace with a constantly shif ting market in order to maximise opportunities and minimise losses. We understand this kind of working environment and have built our business and operations around serving and supporting customers with these unique needs.
We know that power is critical to miners, and we are ready and able to be a key mining project partner, providing reliable your op eration.
“We can enable underground mining teams to be more productive in confined areas and give them the right tools to perform the jobs they need too.
“The production machines are too big, and the handheld drill is too slow, but you can drive a Brokk machine in, drill the holes, put the support in, and your job’s done.” AM
At Aggreko, we help you progress your business with better – and cleaner – energy solutions for the life of your mine.
As power specialists, we understand the energy you need to operate effectively – regardless of your mine’s location or how complex your operation’s needs are. We also understand the practical challenges of reducing your carbon emissions. That is why we will work with you and use our deep expertise to develop the right choice of solutions and services to give you the energy you require. Talk to our mining specialists today to power your operation.
IN THE LESS THAN A YEAR, NEWMONT SUCCESSFULLY OFFLOADED EIGHT NON-CORE GOLD PROJECTS. AUSTRALIAN MINING TAKES A CLOSER LOOK AT THE DIVESTED MINES.
In February 2024, Newmont, still working out the kinks from its $26.2 billion acquisition of Newcrest Mining, announced its plans to divest eight gold projects.
The move was not without thought. In acquiring Newcrest in November 2023, Newmont had become a world-leading gold miner and needed to keep the momentum going.
So it was decided that the company would divest mines that didn’t meet its criteria of a ‘Tier 1 asset’.
“We have a number of Tier 2 assets that are very good assets, run by very good people, but that don’t make our Tier 1 category,” Newmont president and chief executive officer Tom Palmer said in February 2024.
“With the acquisition of Newcrest now complete, our principal focus for 2024 is to integrate and transform our leading portfolio of Tier 1 assets into a unique collection of the world’s best gold and copper operations and projects.”
The last project on the list, the Porcupine gold operation in Canada, was sold in January 2025.
Australian Mining takes a look at the year of divestments and profiles the new owners of these emerging mines and projects.
Havieron and Telfer
One of the first transactions to take place saw Newmont part ways with the Telfer gold-copper mine and the Havieron project in Western Australia.
Telfer holds the title as one of Australia’s largest gold-copper mines, while Havieron is one of the largest copper-gold deposits to have been discovered in the Paterson region of WA.
In September 2024, Greatland Gold confirmed it had entered into negotiations with Newmont to acquire Telfer and, less than 24 hours later, that an agreement had been struck.
Newmont officially sold Telfer, its 70 per cent stake in Havieron, and any other related interests in the Paterson region, to Greatland for $734 million in December.
Newmont and Greatland already owned the Havieron project in a 70–30 joint venture.
And while Telfer is not strictly part of Havieron, the assets were considered by most potential buyers to be a package deal, making Greatland an obvious choice as its new owner.
“I am pleased that Telfer and Havieron are being sold to Greatland, a company with a highly experienced management team and
board of directors,” Palmer said at the time. “I have full confidence that the Greatland team will be outstanding stewards of these assets.”
Greatland managing director Shaun Day said the company was delighted by the acquisition.
“It is a credit to the exceptional efforts of the Greatland, Newmont and Telfer teams that we have been able to move efficiently and quickly towards completion well inside our target of the December 2024 quarter,” he said.
As one of only two Newmont-owned operations in Africa, the Akyem gold mine in Ghana was always going to be a hot topic when it came to divestments.
Zijin Mining Group emerged as the new owner of Akyem in October 2024, paying $1.5 billion for the 422,000-ounce gold mine.
“We believe the proposed transaction results in the greatest overall value for Newmont shareholders and is the best strategic fit for Akyem,” Palmer said.
“We are confident that Akyem will continue to thrive under new ownership with long-term benefits for local stakeholders and surrounding communities.”
Newmont managing director for Africa Rahman Amoadu said the successful completion of the transaction strengthens Ghana as a favourable mining jurisdiction, with Newmont committed to supporting the growth and development of the region.
“We ensured that our robust divestment process provided equal opportunity for all potential buyers, Ghanaian and international, to participate,” Amoadu said.
Orla Mining became the new owner of the Musselwhite gold operation in Ontario, Canada, when it purchased the project for $1.3 billion in November.
The deal more than doubles Orla’s annual gold production to over 300,000 ounces and positions the company as a North American-focused, multi-asset gold company.
“This acquisition is a significant milestone for Orla Mining,” Orla president and chief executive officer Jason Simpson said.
“We have been impressed with the operating team at Musselwhite, which runs an exceptional mine and has developed positive and strong ties
NEWMONT DIVESTED ITS STAKE IN THE HAVIERON GOLD-COPPER PROJECT IN SEPTEMBER 2024.
with First Nations, local partners, and community members. We are fully committed to respecting and growing these relationships.”
Finalisation of the deal is ongoing as of February 5, with Orla shareholders voting in favour of the acquisition on January 21.
Éléonore
Another Canadian asset, the Éléonore gold operation was sold to UKbased Dhilmar, a company that had previously joined forces with Newmont to acquire the Batu Hijau mine in Indonesia.
Dhilmar paid $1.2 billion for Éléonore in November, contributing to the $5.5 billion in gross proceeds Newmont is expecting from its divestitures.
Since the Indonesian acquisition closed in 2016, the two companies have worked closely together, and Palmer said he was pleased by the sale.
“They have a wealth of experience in gold and copper mining and we believe Dhilmar will be excellent stewards of this asset,” Palmer said.
“Proceeds from this transaction will support Newmont’s comprehensive approach to capital allocation, which includes strengthening our investmentgrade balance sheet and returning capital to shareholders.”
The Éléonore underground operation currently produces around 246,000 ounces of gold per year.
The open pit Cripple Creek and Victor (CC&V) gold operation in Colorado, US, was purchased by SSR Mining for up to $430 million.
CC&V boasts the title of the richest gold mine in Colorado history, producing 322,000 troy ounces of gold in 2019.
The operation is expected to add approximately 170,000 ounces in annual gold production to SSR Mining’s platform, with SSR’s total US gold production tipped to hit between 300,000–400,000 ounces annually.
“The acquisition of the CC&V gold mine represents a rare opportunity to add a high-quality producing asset in a Tier 1 jurisdiction at an accretive valuation,” SSR Mining executive chairman Rod Antal said.
“The transaction structure helps ensure our balance sheet remains a strength of our business, with CC&V expected to immediately contribute meaningful cash flow that facilitates an attractive payback.
“In addition to its strategic merits, CC&V employs many highly regarded mining professionals that will complement our current team, and we look forward to welcoming them all into SSR Mining.”
The final project in Newmont’s divestment program, the Porcupine gold operation in Ontario, was sold to Discovery Silver Corp in January.
Porcupine, which has produced over 68 million ounces of gold since 1910, was sold for $675 million.
The transaction comprises a cash consideration of $US200 million, equity consideration of $US75 million in the form of Discovery Silver Corp shares, and a deferred cash
consideration of $US150 million.
“Today’s announcement represents a significant milestone for Newmont as we have agreed to sell the final noncore operation from our divestiture program,” Palmer said.
“We have full confidence that Discovery’s leadership team will continue to operate Porcupine responsibly, leveraging their extensive experience and history in the area.
“Including the Porcupine divestiture, we expect to generate up to $US4.3
billion ($6.8 billion) in total proceeds from the announced sales of our high-quality non-core assets and investments, enabling us to further reduce debt and return capital to shareholders.”
With the final divestment now complete, Newmont is turning its attention to its core assets across Australia, South America, North America and beyond, positioning 2025 as another year of growth and profits for the major miner. AM
AFTER A TOUGH 2024, WHAT CAN WE EXPECT FROM LITHIUM IN 2025, AND WHAT ROLE DOES AUSTRALIA HAVE TO PLAY?
The global lithium market is set for a recovery in 2025, as the supply–demand thematic regulates and electric vehicle (EV) demand continues to rise.
The Australian mining sector, with its abundance of active lithium mines and reserves, will be at the forefront of this opportunity.
Australian Mining takes a closer look at the global lithium dynamic.
A demand surge
Global lithium consumption is projected to rise by 26 per cent to 1.46 million tonnes in 2025, an increase from 1.15 million tonnes in 2024, according to Benchmark Source.
This increase will be fuelled by accelerated EV adoption and expanding renewable energy infrastructure, both heavily reliant on lithium-ion battery technology.
In terms of pricing, the Federal Government’s Office of the Chief Economist predicts a rebound in spodumene prices, estimating a rise to $US1156 per tonne by 2025 from a low of $US750 per tonne in 2024. This recovery signals renewed confidence in the industry, providing a potential revenue boost for Australian miners.
Australia leading the way Australian miners are capitalising on lithium’s positive long-term outlook
with strategic investments and innovative technologies.
Pilbara Minerals, one of the nation’s leading lithium producers, announced in August 2024 its ambitious plans to expand to two million tonnes per annum of spodumene production, with its recently acquired Colina project in Brazil set to play a critical role.
Mineral Resources’ (MinRes) lithium business is characterised by strategic joint ventures and high-grade mines.
In partnership with Albemarle, MinRes oversees the Wodgina operation in Western Australia, while the company also operates the Mt Marion mine in WA alongside Jiangxi Gangfeng Lithium.
MinRes is also backing new technologies such as Livium’s LieNA technology, which has the potential to boost lithium extraction yields by up to
Global mining giant Rio Tinto has also rapidly expanded its lithium efforts by acquiring Arcadium Lithium and its suite of hard-rock and lithium-brine projects. These assets will accompany Rio’s Rincon development project
Environmental, social and governance (ESG) considerations are driving the transformation of the lithium mining sector, with sustainability emerging as a
Australian miners are increasingly moving towards renewable energy solutions and resource-efficient methods to align with global carbon
Pilbara Minerals has embraced ESG frameworks as it looks to limit diesel-based thermal generation at its Pilgangoora lithium operation, replacing it with natural gas and battery energy storage.
These energy sources will fuel the company’s P1000 project, which aims to produce one million tonnes per annum of spodumene concentrate from Pilgangoora.
The company is also looking to supply a midstream “green lithium” product in the future, with a demonstration plant being constructed alongside environmental technology company Calix. This venture will harness Calix’s patented electric calcination technology to produce lithium-phosphate salts.
Lithium’s strategic importance
Beyond commercial interests, lithium’s growing importance to global energy security cannot be understated.
As countries such as the United States and members of the European Union push for greater security of supply chains amid China’s dominance, Australia has positioned itself as a key partner.
The nation’s abundance of highgrade lithium resources, coupled with its stable political environment, makes it an indispensable player in international lithium markets.
The Federal Government is introducing more incentives for the production of value-added lithium products. A 10 per cent tax break for the processing of 31 critical minerals, including lithium, was recently passed
in the Senate as part of the Future Made in Australia bill.
The term for the incentive is between 2027–28 and 2039–40, for up to 10 years per project.
This shift is not only creating local jobs but also increasing Australia’s longterm competitiveness by extending its role beyond raw material exports.
Technological advancements
On the technology front, the emergence of solid-state batteries, which are expected to enhance energy density and safety compared to traditional lithiumion batteries, poses both challenges and opportunities for the lithium market.
While still in development, this innovation could alter demand for certain lithium compounds, requiring adaptability from producers.
It must be noted that lithium-ion batteries still dominate the renewable energy market, and are likely to for quite some time yet.
The likes of lithium nickel manganese cobalt oxide (NMC), lithium iron phosphate (LFP), lithium nickel cobalt aluminum oxide (NCA) and lithium cobalt oxide (LCO) are just some of the lithium-ion chemistries being implemented.
Outlook for the future
at a compound annual growth rate (CAGR) of 7.2 per cent from 2025 to 2035.
Future Market Insights predicts the global lithium mining market to grow
Australian miners are positioned to play a pivotal role, with a pricing resurgence to help greenfield projects enter production and brownfield sites expand operations.
As the world increasingly shifts to cleaner energy solutions, Australian miners are not only producing valuable raw materials but also setting new benchmarks in innovation and sustainability, exemplified by Pilbara Minerals’ efforts to produce new ‘green’ products and drive down emissions.
With the lithium market poised to recover, Australia has the potential to not only deliver more spodumene to satiate demand, but also explore new technologies underpinning the future of lithium mining and processing.
EV manufacturers are no doubt watching. AM
Built to perform in harsh environments, ELGi air compressors deliver maximum uptime and reliability. With an industry-leading 10-YEAR WARRANTY* and LOW COST OF OWNERSHIP, the ELGi 90 kW SP range offers best-in-class energy efficiency and unmatched performance.
ASIA-PACIFIC’S INTERNATIONAL MINING EXHIBITION HAS NAMED THE ROYAL FLYING DOCTOR SERVICE SA/NT AS ITS OFFICIAL CHARITY PARTNER FOR 2025.
For over 90 years, the Royal Flying Doctor Service (RFDS) has provided leading health care and 24-hour emergency and retrieval services to those in rural Australia.
Known as one of the largest aeromedical organisations, the RFDS delivers healthcare when and where mainstream services aren’t available by using the latest in aviation, medical and communications technology, and a broad-reaching ground-service fleet.
The RFDS has held a significant presence within the Australian mining industry for decades, with the organisation servicing the remote areas that several mine sites call home.
It’s for this reason and many more that Asia-Pacific’s International Mining Exhibition (AIMEX) has welcomed the RFDS as its charity partner for 2025.
With AIMEX set to call South Australia home for the next 10 years, the RFDS’ South Australia/Northern Territory section was seen as the perfect choice.
“We wanted to showcase an Australian charity at this year’s AIMEX,” Prime Creative Media marketing manager – mining events Rebecca Todesco told Australian Mining
“The RFDS is a well-known and respected institution that has been trusted across Australia for decades, and has made an impact across the mining sector and its rural sites.
“We want to showcase the great work the RFDS has done and continues to do across Australia.”
In SA and the NT, the RFDS supports and assists more than 56,000
patients annually. According to the organisation, that equates to one patient every 10 minutes.
This impressive reach is made possible by the RFDS’ four aeromedical bases in Adelaide, Alice Springs, Darwin and Port Augusta, as well as its three remote primary healthcare facilities in Andamooka, Marla and Marree in outback SA.
“We provide support to the industry in two main ways,” RFDS SA/NT executive general manager – strategy, brand and reputation Charlie Paterson told Australian Mining
“First, we provide an on-call emergency aeromedical response to mining employees in the field when they need it the most. Secondly, we deliver whole-of-life care to the communities that directly and indirectly support mining operations.
“In South Australia, where AIMEX will be held this year, these include communities like Roxby Downs, Innamincka and Andamooka.”
Over the years, the RFDS has received direct funding from several mining companies, as well as government support and donations from local communities.
“In regions where mines operate, many workers are often active participants in their community and they assist as a first responder either directly or through voluntary state emergency service roles,” Paterson said.
“The first responder role is often overlooked but essential for the wellbeing and resilience of these communities.
“As our work in digital healthcare expands, so too does our collaborative
work with the mining sector as we trial new technologies and explore innovative pathways for the finest patient care.”
The RFDS sees AIMEX as an opportunity to showcase its premier services to the larger Asia-Pacific region.
The organisation will be exhibiting a simulator at the event that showcases a mock-up of one of their planes. Staff members of the RFDS SA/NT section will also be available to answer questions from attendees.
“We are delighted to partner with the inaugural AIMEX conference in South Australia and look forward to meeting with attendees at our exhibition stand where there will be an opportunity to step into the RFDS simulator to
see what it’s like inside one of our aeromedical aircraft,” Paterson said.
Todesco said she is excited to showcase the RFDS’ passion for providing critical assistance such as emergency aeromedical services, outback community health services, interhospital patient transfers, remote oral healthcare, mental health and wellbeing services, and education and training.
“We are keen to further connect the RFDS with the Australian mining industry and the larger Asia-Pacific, and to support a charity that helps those working in remote areas,” she said. AM
AIMEX 2025 will take place at the Adelaide Showgrounds from September 23–25.
SUSTAINABILITY
Cleaner air can reduce the rate of engine wear, providing lower overall air intake restriction, resulting in less fuel burn. Longer filter life compared to the competitor element
The Trusted Choice in Mining Filtration
OPERATORS CONFERENCE KEYNOTE SPEAKER LAURA TYLER HAS MADE INNOVATION HER BREAD AND BUTTER.
As ore grades reduce and underground mines get deeper, the need for innovative underground practices has never been more important.
Adriatic Metals chief executive officer and managing director Laura Tyler has over three decades of experience in the underground mining sector and knows the industry’s recent challenges and triumphs first-hand.
That’s why Tyler has signed on to make a keynote speech at AusIMM’s upcoming Underground Operators Conference (UgOps 2025), held in Adelaide from April 7–9.
“Underground Operators is a great opportunity for people to come together, share ideas, do things differently, and really learn from each other,” Tyler told Australian Mining
“Being able to discuss ideas and make sure we deliver safer, more productive operations with the right technologies and innovation is an amazing opportunity.”
UgOps 2025 will be a meeting place for leaders from across the globe, keen to discuss not only the Australian
UNDERGROUND OPERATORS 2025 WILL FEATURE OVER 30 TECHNICAL PRESENTATIONS.
underground mining sector but also operations across the world.
“We only learn by taking a global view,” Tyler said. “We need to be looking at what’s being tested and tried in every corner of the world and what we can learn from those operations and vice versa.
“Australia sits in a global commodity market, and we must be able to compete. To be able to compete means we must constantly strive to be better.”
Tyler is one of three keynote speakers taking the stage at UgOps 2025. She will be joined by Vale Base Metals chair Mark Cutifani and resolution88 director and principal Bruce Harvey.
“There’s something for everyone in the 2025 conference program,” Tyler said. “Whether you’re interested in the geotechnical aspect of the sector, or if you’re more into the safety and sustainability side, you’ll find something that peaks your interest.”
UgOps 2025 will be feature over 30 technical presentations and a dynamic panel discussion covering the key conference themes from technology and innovation to the journey towards net-zero.
“UgOps is a conference where, after you’ve come together to share ideas, you can take those ideas back to your operation and implement them,” Tyler said.
“Within an underground operation, everyone works together from the operator to the technician. We have to work together to deliver safe and predictable operations.
“So when we look at who should attend UgOps, it has to be a full range of people that all contribute to the diversity of ideas that can help solve challenges and open up opportunities for new orebodies.”
UgOps 2025 will cover a wide range of topics, from health and safety to the global decarbonisation journey, with Adelaide providing the perfect backdrop.
“Australia is a mature mining environment,” Tyler said. “There’s a need to not only embrace technologies to find orebodies, but to also embrace technologies to extract them, because they will be undercover, they will be at depth, and they will be more difficult to reach.
“Environmentally, we also must be able to make sure that we’re minimising
our footprint and committing to netzero operations.
“These are the things that allow us to have community engagement from the broader Australian underground mining population. Every little bit matters.” AM
UgOps 2025 will take place at Adelaide Convention Centre from April 7–9.
Global air compressor manufacturer ELGi Equipments has built a reputation for its compressor technology breakthroughs and product range, delivering performance and energy efficiency.
ELGi’s ethos of ‘always better’ is a testament to the company’s portfolio of over two million compressors running across more than 100 countries, which includes an extensive dealer network across Australia.
ELGi strives to ensure its customers achieve their productivity goals and keep the total cost of ownership low. To that end, the company offers a complete range of compressed air solutions, from oil-free rotary screw compressors to oil-lubricated reciprocating compressors to dryers, filters, and downstream accessories.
This makes up a portfolio of over 400 products to suit different applications across a range of industries.
With the world facing environmental challenges, the transition to renewable energy sources, and demand to manufacture more energy-efficient products, ELGi is focused on improving its specific power consumption (SPC) and free air delivery (FAD).
Keeping best-in-class lifecycle costs (including power) in mind, ELGi has developed a new air-cooled, direct drive series with a permanent magnet synchronous motor (PMSM). Available in models ranging from 11–45 kilowatts (kW), the upgraded EG Series range has welcomed the EG PM oil-lubricated screw air compressors.
This compressor is set to deliver up to 15 per cent higher efficiency gains, aside from an incremental FAD of 16 per cent.
The EG PM Series is tailored to deliver superior performance and energy efficiency, providing unmatched lifecycle value across varying load capacities.
According to ELGi Equipments product manager Khyati Acharya, the EG PM Series offers customers a range of intelligent features engineered to minimise energy consumption and reduce environmental impact.
“The high-efficiency drive system incorporates a proprietary ultra-efficient IE5+ permanent magnet synchronous motor tailored specifically for ELGi air ends,” Acharya said.
“The motor’s efficiencies (between 96.5 and 97.6 per cent) are well above the IE5 levels at IE7, resulting in maximised energy efficiency and carbon footprint reduction.”
The directly coupled system provides optimised lower motor and airend speeds, ensuring synchronous operation and optimal performance, which is particularly effective in variable speed applications. An intelligent thermal valve with an ambient temperature sensor maintains oil at ideal operating temperatures, preventing excessive heating in colder months and improving energy efficiency.
“The compressor is also equipped with the Neuron 4 controller, which offers a comprehensive solution for superior
and reliable compressor operation,” Acharya said.
“With an industrial-grade seven-inch touchscreen interface and intelligent algorithms, the Neuron 4 is designed to optimise energy usage, enhance overall operational efficiency, ensure safe and controlled operations, and facilitate proactive maintenance.”
ELGi has also introduced its new EG SP (Super Premium) oil-lubricated screw air compressors for larger kW units. These machines represent an advancement in compressed air technology, delivering significant energy efficiency gains of up to 15 per cent, best-in-class warranty and performance, and low lifecycle costs in the 90–160kW compressor range.
“The upgraded EG SP units embody newly configured two-stage air ends, featuring the proven η-V profile, which optimises the overall compression process, resulting in up to 15 per cent savings in specific power consumption,” Acharya said.
“The low-speed airends and a lighter load on each stage extend component life. The IE4 motors also enable a seamless integration of advanced design and cutting-edge technology for increased energy efficiency.”
All EG SP machines are equipped with Neuron 4 industrial controllers
and feature a unique oil filter designed for prolonged 4000-hour lifespans. The filter efficiently removes contaminants from the compressor’s lubrication system, contributing to longer operational life.
The compressor units are also compatible with ELGi’s add-on internet of thing (IoT) solution, Air-Alert, a monitoring and alert system compatible with ELGi’s range of air compressors.
Data analysed and delivered by AirAlert from a compressor enables users to improve their compressor’s energy efficiency and uptime. Air-Alert also allows 24–7 remote monitoring from anywhere in the world.
For peace of mind, the entire EG range, including the EG PM range and SP range, comes with ELGi’s warranty package, which includes a 10-year warranty on the airend, five years on key compressor components, and three years on the VFD.
ELGi’s compressed air technology solutions, like the EG Series, reflect the company’s unwavering commitment to technological progress, energy efficiency and compressed air performance.
These compressors are tailored for manufacturing enterprises seeking energy efficiency and environmental stewardship, promising substantial energy savings bundled into a highly competitive total cost of ownership package. AM
AMCAP Industrial is a leading parts distributor servicing the Australian Mining, Commercial and Industrial sectors. With AMCAP Industrial’s kitting service, only one part number is required for each complete kit, with all items arriving in one package, delivered in full and on time. Our kits cover a wide range of machinery, some examples include:
Excavators | Haul Trucks | Loaders | Graders | Locomotive | Auxiliary Generators | Light Vehicles | Lighting & Material Handling | Mobile Cranes On Highway Trucks & Hauling | Drills | Power Generation | Compressors
AMCAP’s Components and Parts Supply Solutions are also flexible, providing our customers with a superior level of reliability of having the replacement parts and components available to you on time, saving you money and maximising asset availability and increasing your productivity. We can supply the complete powertrain of service exchange components including Engines, Torque Convertors, Transmissions, Final Drives, Front Corner Assemblies, Hydraulic Pumps and Cylinders and HV Alternators, all rebuilt to zero-hour to ensure full life.
Speak to our team about tailoring a solution for your business.
ATLAS COPCO IS HELPING MINERS OVERCOME AIR COMPRESSOR CHALLENGES WITH THE AIRCUBE.
Compressed air plays an essential role in powering equipment and improving safety outcomes in the Australian mining industry.
Understanding the challenges of securely storing and operating compressed air on mine sites, Atlas Copco developed the AIRCUBE, a modular, containerised compressor room designed to overcome the limitations of traditional plant infrastructure.
The AIRCUBE was created to provide a flexible, efficient solution for sites where building permanent plant rooms is impractical or cost prohibitive.
“Suitable covered areas or plant rooms are not always available to house compressors, blowers, or gas generation equipment close to applications,” Atlas Copco product manager Dilllon Smith told Australian Mining
“The AIRCUBE is a modular solution that safely contains and protects your compressed air equipment in any location or environment without the need for new or upgraded plant rooms, removing cost and safety implications.”
Available in 20-foot or 40-foot models, the AIRCUBE can be adapted to each site’s specific requirements.
“An AIRCUBE is selected by Atlas Copco’s engineering team based on the compressed air equipment required to meet a site’s flow and pressure needs,” Smith said.
“All other design, cooling, and safety requirements for the AIRCUBE can then be tailored to meet your specific site regulations and expectations.”
As sustainability becomes an everincreasing focus for the mining industry, the AIRCUBE rises to the task by removing the need to build permanent facilities. This minimises material transport, labour, and site disruptions, limiting a site’s carbon footprint.
Atlas Copco also selects and implements the latest technology to ensure the AIRCUBE keeps pace with industry trends and always meets sites’ unique efficiency and operational requirements.
The AIRCUBE is versatile in other ways, too.
“A standard AIRCUBE can function reliably in temperatures from 0°C to 45°C,” Atlas development manager Roshan Kumbla told Australian Mining
“However, as an option, we can also design it to withstand very extreme ambient conditions from -40°C to +45°C (even to -50°C to +50°C upon demand).”
Smart technology enhances the AIRCUBE’s appeal, with Atlas Copco offering advanced central controllers, such as the Optimizer 4.0, to optimise compressed air systems.
Integrated digital solutions enable remote monitoring and real-time operational feedback via SCADA or Ethernet networks, improving maintenance schedules and minimising downtime.
“Network feedback is also available via a SCADA or industrial Ethernet network to suit the site’s specific communication system,” Smith said. “This provides valuable real-time data of the equipment’s operation.”
Compared to traditional compressor rooms, the AIRCUBE offers significantly reduced installation times and costs.
Designed, built, and tested to meet precise specifications, the AIRCUBE arrives ready for operation. This eliminates production disruptions caused by site construction and delivers immediate benefits in cost-effectiveness and productivity.
Customisation is a cornerstone of the AIRCUBE’s design. Clients can select from features such as dust trap filtration for dusty environments, special paints for corrosive atmospheres, fire alert systems, or additional service doors.
Mining clients have embraced the AIRCUBE for its operational efficiency, cost-saving capabilities, and environmental benefits, with early adopters experiencing
notable productivity and sustainability improvements.
All in all, the AIRCUBE is a modular, itinerant all-in-one solution that safely houses compressed air equipment.
“It can be designed to meet the specific environmental and safety requirements of your site, while providing the quality compressed air or industrial gases you expect of Atlas Copco,” Smith said.
“For a seamless, sustainable approach to compressed air needs, the AIRCUBE is an unmatched asset for Australian mining operations.”
For those interested in experiencing the AIRCUBE first-hand, Atlas Copco offers a virtual tour showcasing its key features and product layout. A userfriendly selector tool helps clients easily configure and customise an AIRCUBE to fit their site’s specific requirements. With its versatility, reliability and plug-and-play functionality, the AIRCUBE is setting a new standard for compressed air solutions in the Australian mining industry.
By David Brown, AVP, Geotab, Asia Pacific
Australia’s mining industry is currently grappling with a labour crunch and increasing regulatory and political challenges, which means managers need to be more cost-conscious than ever.
Your vehicles are an obvious place to start. Geotab’s innovative open platform for fleet and asset management helps project managers track assets, increase equipment uptime and lower operating costs seamlessly. Here are three reasons why Geotab’s telematics technology can benefit your mining operations.
Track and locate equipment, while ensuring maximum utilization
Effective cost control in mining operations begins with clear visibility of your equipment. Mining sites are bustling environments and the use of telematics enables data collection from any vehicle on-site. Our technology connects directly to the vehicle’s computer, monitoring metrics like fuel consumption and engine hours. This ensures each piece of equipment is optimally utilised and cost is accurately measured. Knowing the precise location of your equipment at all times helps avoid unnecessary leasing of additional machinery due to misplacement. Furthermore, real-time equipment tracking, which seamlessly switches between cellular and satellite networks, guarantees continuous monitoring and cost tracking, even on remote sites.
Enjoy Fuel Tax Credit Rebates with our data automation
Fuel Tax Credit Rebates can offer substantial savings for mining businesses, especially if they use a lot of fuel. However, those savings could be far less if an accountant had to spend valuable hours collecting and untangling the data in order to get the payment processed. Geotab’s solutions can make the process much easier. Our telematics technology can accurately measure on and off-road usage, which is essential data used to claim fuel tax credit rebates. On mining sites, where the focus is on engine hours rather than distance travelled, our devices effectively tracks fuel usage and economy, even when vehicles are stationary and idling, ensuring you can maximise your rebate claims.
Access everything seamlessly on our single platform
Geotab offers the greatest possible flexibility for any kind of project. Our device can be attached easily to any vehicle—regardless of manufacturer—and send the data to the same platform. Installation is simple, giving you visibility over the whole project and enabling you to track fuel efficiency, fuel burn, RPM, battery oil, engine health, and other key indicators.
Furthermore, through the multi-streaming function, contractors can be granted access to a database for a fixed duration. When the contract ends, their visibility to the site will cease, and the contractor can reassign it to someone else.
Our devices are built to withstand tough conditions on work sites. They are ideal for heavy mining equipment, construction, utilities, powered assets and trucks. Also, selected models are IP68 and IP69K rated with impact, water and humidity-resistant housing.
Begin your journey with Geotab today and move into a future where every trip is safe, and every operation is efficient. With our help, you can track your valuable assets, increase equipment uptime and lower your operating costs.
For more information, visit geotab.com/au/
National Group’s human resources team, led by Scott Tobin and Erin O’Sullivan, are spearheading the largest recruitment campaign in the company’s history.
In the past two years, National Group’s workforce has doubled to more than 200 employees in response to rising demand for the company’s services.
National Group recruitment manager Scott Tobin expects that figure to be almost 300 within 12 months as staff are hired for contract wins and extensions.
“Mining-services recruitment is not easy in a tight labour market,” Scott said. “But we’ve been able to recruit really good people who fit National Group’s culture, are customer-focused and want to build long-term careers here.”
National Group talent acquisition specialist Erin O’Sullivan said the company can interview up to 10 candidates in a day to find the right person for a job.
A recruitment specialist, O’Sullivan relocated from Adelaide this year to join National Group.
NATIONAL GROUP IS RAPIDLY EXPANDING ITS WORKFORCE IN RESPONSE TO NEW CONTRACT WINS AND EXTENSIONS.
“A lot of work goes into National Group recruitment,” O’Sullivan said. “In addition to job interviews, there’s reference checking and then the onboarding process to ensure new employees hit the ground running and understand the company’s values.”
Word-of-mouth is still the firm’s key recruitment tool, O’Sullivan said.
“A lot of job candidates hear that National Group is a great place to work or they know people who work here,” she said. “They like that the business is founder-led and privately owned, and
can see how their career can grow here over the long term.”
O’Sullivan has enjoyed the transition from white-collar recruitment to mining-services recruitment.
“It’s a been a great experience so far,” she said. “Mining recruitment is faster paced and there are more issues to consider. I’m learning every day in this role.”
National Group’s recruitment strategy has several parts. A HR project last year focused on streamlining and digitising the job application process to make it faster and easier for job candidates, and more efficient for National Group.
This included the implementation of candidate-management software.
“There’s less paperwork and more time to speak to more job candidates,” Tobin said. “The digital application process also makes it much easier for
candidates who don’t want to waste time printing and sending forms.”
Paying airfares for fly-in, fly-out workers has been another key HR initiative this year. National Group introduced its new airfare policy to attract diesel mechanics who live in south-east Queensland and can fly to the Bowen Basin for work.
Scott said National Group’s significant investment in airfares is already paying off.
“We’ve had a lot of interest and have already recruited some staff from Brisbane because of the new policy,” he said. “It’s a point of difference for National Group in the labour market at a time when many firms are cutting back on airfares.”
Expanding National Group’s apprenticeship program is another HR priority. The company reintroduced its apprenticeship program in 2020 to develop more diesel mechanics internally and bolster its future workforce.
The apprenticeship program has since grown to 14 with plans to increase it further.
“We’ve had some terrific male and female apprentices go through the program,” Scott said.
“The program’s success encouraged us to double the size of it in the past 12 months and take it much further over the next few years. It’s a great way to train people in our way and address industry shortages in diesel mechanics.”
A new marketing campaign to assist National Group’s recruitment strategy is also part of the HR strategy.
Developed by National Group head of marketing and partnerships Kain Ford, the recruitment campaign will feature geo-targeted online advertising to attract job candidates.
“We want to get the message out there that lots of good opportunities are available at National Group,” Tobin said. “We want people from all walks of life to consider a career in mining services through National Group.”
As O’Sullivan and Tobin implement the firm’s HR strategy, an immediate focus has been on onboarding 65 employees who have joined National Group since June 2024.
About 40 of them are operators who joined the company on a full-time basis through its project at the Moorlaben coal mine in New South Wales.
“That transition has gone smoothly,” Tobin said. “We’ve done a lot of work in the past few years to build deeper HR foundations and enable National Group to accommodate a much larger workforce and recruit more people. It’s an ongoing process, but we’re pleased with the results so far and the quality of new hires.” AM
FORMERLY KNOWN AS BG&E RESOURCES, AGILITUS HAS AMICABLY SEPARATED FROM BG&E GROUP AND LAUNCHED A NEW NAME AND BRAND.
Established in 2017, Agilitus has rebranded, representing a new era for the multidisciplinary engineering business.
With shares predominately owned by employees, the privately-owned business is expanding into new geolocations and widening its service scope to better assist mining projects and operations.
Maximising client value throughout a project’s lifecycle, Agilitus specialises in customised design, EPCM (engineering, procurement and construction management) and rehabilitation capabilities.
This is not to mention the company’s ability to support process plants, rail systems, haul roads, ports and marine, non-process infrastructure, power systems, water and wastewater solutions.
Agilitus contains all engineering disciplines in-house, enabling the company to leverage different skills and expertise for innovative outcomes.
The company also recently expanded its offerings to help clients decarbonise their brownfield operations or develop and deliver low-carbon greenfield projects.
Agilitus co-founder and managing director Craig Bloxham explained the reasoning behind the company’s rebrand.
“In seven years, we’ve grown to more than 450 people,” he told Mining. “We’re not surprised by our growth and would like to recognise the clients that have entrusted us with their engineering and project management needs along the way.
“With this change, our team has the opportunity to own shares in Agilitus, and we can launch ourselves into new markets with expanded services.”
When exploring a new name and brand, Bloxham wanted a word that represented how the company worked with clients.
“Clients have always told us we are agile, so this name is ideal for us. Agilitus combines ‘us’ with ‘agility’,” he said.
Bloxham said he first envisioned a brand representing agility more than a decade ago.
“We when started, we felt the industry had lost the agility commonly associated with a privately-owned company, one that’s not risk-averse and can respond to client needs quickly and efficiently,” Bloxham said.
people have remained the same.
“Operationally, we are expanding into geolocations such as Newcastle, Brisbane and Townsville to leverage our full skillset across all disciplines,” he said.
“We can now control our destiny, and this transformation means more of the exceptional work we already do and an introduction of new services.”
One of the most transformative aspects of Agilitus’ creation is the opportunity for staff to acquire equity in the company.
Bloxham said this change has already ignited excitement within the company and people feel like they are part of the family.
“In a competitive environment, the best way to stand out is to capture the discretionary effort of your people,” he said. “When our people feel a vested interest in the business, they give their best effort, which benefits our clients through better quality, stronger partnerships, and innovative solutions.”
Despite the change, some things remain the same, including Agilitus remaining steadfast in its customer-centric approach.
Bloxham emphasised the company’s unwavering commitment to ensuring client needs are met.
“Our message to clients is that being owned by our people will drive us to provide the best service possible,” he said.
“At the end of the day, we are a customer-focused business and if you don’t keep your clients happy, you don’t have a business.”
Looking back on the journey, Bloxham explained the transition as a dream come true.
“If somebody told me seven years ago that we’d be where we are today, with our team owning part of the business and us seeing this level of success, I wouldn’t have believed it,” he said.
Agilitus is now poised to take on new challenges, backed by a motivated workforce, an agile business model, and a fresh brand identity that speaks to its commitment to innovation and excellence.
The rebranding signals an exciting chapter not just for the company but its clients and the resources sector. AM
AUSTRALIAN MINING TAKES A LOOK AT THE 2025 OUTLOOK FOR SOME OF THE COUNTRY’S MOST VITAL COMMODITIES.
Australia’s mining sector is showing no signs of slowing down as the industry readies for another busy year.
The Federal Government’s ‘Resources and Energy Quarterly’ (REQ) from December 2024 is predicting the next couple of years to be promising ones for the sector, with strong demand and growth expected across several key commodities.
Australia is the world’s largest iron ore producer and the commodity is perhaps one of the most integral parts of the Australian mining sector, with 892 million tonnes exported in 2023.
Over the second half of 2024, Australian iron ore export volumes continued to increase, and are expected to rise steadily, increasing by around 1.7 per cent a year over the next two years, demonstrating an improvement in productivity and the ongoing ramp-up of new mines.
However, iron ore export earnings are set to drop due to lower prices projected over the outlook period, from $138 billion in 2023–24 to $108 billion in 2024–25 and $96 billion in 2025–26.
Despite falling steel demand, China’s iron ore imports have remained strong, rising 6.8 per cent in the year to September 2024.
China’s iron ore imports from Australia increased by three per cent year-on-year in the September quarter 2024, down from a 6.6 per cent year-onyear rise in the June quarter.
Renewed stimulus measures from China, including greater investment in its ailing property sector, will also provide support for steel and iron ore prices in the coming years.
“As the world’s largest exporter of key commodities required for steel production, Australia is well placed to benefit from the demand growth projected in global markets in 2025 and 2026,” the REQ said.
“Australia’s production volumes are forecast to increase by 2.6 per cent a year over the next two years, to an estimated 1.01 billion tonnes by 2025–26.”
The additional tonnage reflects the ramp-up of Mineral Resources’ Onslow Iron and Fortesuce’s Iron Bridge projects, plus incremental tonnes from new replacement projects.
Onslow Iron in Western Australia is one of the largest iron ore projects currently under development in the country.
The project has an expected mine life of more than 30 years and will ramp up production to 35 million tonnes per year.
The Iron Bridge project will deliver a high-grade 67 per cent magnetite concentrate product to support sustainable steelmaking.
AUSTRALIA’S IRON ORE EXPORTS ARE PROJECTED TO REACH 1.01 BILLION TONNES BY 2025–26.
Iron ore exploration expenditure cost $216 million in the September quarter, 10 per cent higher than the September quarter in 2023 and the highest level since the 2013 September quarter.
Australia’s strong growth in its gold export sector was a notable highlight from 2024, driven by rising global prices and ongoing project expansions.
In the September quarter, the value of Australia’s gold exports rose by 4.5 per cent year-on-year to $8.4 billion.
A drop in the volume of exports –from 67.3 tonnes to 50.9 tonnes – was more than offset by a rise in Australian dollar gold prices.
“High gold prices are expected to drive Australia’s gold export earnings to $34 billion (in 2024–25), representing an increase of 4.7 per cent year-on-year from 2023–24,” the REQ said.
“Export earnings are then forecast to grow slightly to $35 billion in 2025–26, as higher export volumes more than offset lower forecast prices.”
The September quarter saw an increase in Australian gold production to 74 tonnes, an increase of 0.5 tonnes. However, Australian gold production is predicted to fall by 0.8 per cent to 286 tonnes in 2024–25, due to start-up delays in some mines.
Production is forecast to grow by 7.9 per cent to 309 tonnes in 2025–26, driven by new projects and expansions at existing mines.
Upcoming projects include the Great Fingall mine in WA which continues to be developed and is expected to achieve first production in the first half of 2025.
Great Fingall, being developed by Westgold Resources, is expected to have an initial eight-year mine life.
The gold price recently scaled $US2900 ($4603) per ounce for the first time ever, having notched record after record in 2024.
Due to global economic uncertainty and major central banks easing monetary policy, prices are set to remain elevated in 2025 before falling in 2026.
Australia’s copper sector is rapidly growing. In 2023 it was the fifth largest exporter and ninth largest producer globally.
In 2024–25, Australia’s copper export earnings are forecasted to reach around $15.3 billion and hit $16.2 billion in 2025–26.
Export volumes are expected to reach 924,000 tonnes in 2024–25. This would see export revenue rise by more than a third compared to 2023–24, reaching $15.3 billion in 2024–25.
In 2025, several projects could begin operations, including Develop Global’s Woodlawn project in New South Wales and Anax Metals’ Whim Creek asset in WA.
Having resumed progress on its Woodlawn mine underground development, and due to rapid progress on the processing plant, Develop hopes to deliver first production ore from Woodlawn in the March quarter of 2025.
Whim Creek, with which Develop Global owns a 20 per cent stake in, includes crushing and heap leach infrastructure, offices, workshops, established water supplies, and a regional exploration package with gold and base metal prospectivity.
Copper prices have surged to begin 2025, nudging $US10,400 per tonne as the US Government introduced a range of tariffs on raw materials such as aluminium.
The REQ expects copper prices to nudge an average of $US9700 a tonne in 2025 and reach an average of $US9700 a tonne by 2026.
This comes as global copper demand is set to grow by around three per cent in 2025 and 2026, with growth primarily
Uranium’s export values in Australia are expected to lift from $1.4 billion in 2024–25 to $1.7 billion by 2025–26, thanks to the reopening of the Honeymoon uranium mine in South Australia.
From a historical high of over $US100 a pound in early 2024, uranium prices fell to around $US80 a pound as the market stabilised from a major supply shock in the March quarter.
Due to rising demand and supply issues, prices are likely to push back up to $US88 a pound in 2025 and $US94 a pound in 2026, as reactors continue to draw from inventory to meet requirements.
“Many countries are seeking to expand their nuclear power capability to meet increasing energy demand and net-zero climate goals,” the REQ said.
“As global demand for uranium is driven by demand for reactor fuel, expanding nuclear power capability will increase long-term uranium demand.
“India and China remain the predominant drivers of demand from new reactors.”
Forecasts for uranium demand are 99,000 tonnes in 2025 and 102,000 tonnes in 2026.
driven by data-centre deployment and low-emission technologies.
“China’s electric vehicle (EV) market remains robust, with 1.1 million EVs and plug-in hybrids sold in the first nine months of 2024 – over 30 per cent higher than sales in the same period last year,” the REQ said.
“EVs are copper intensive, so transitioning from internal combustion
URANIUM’S EXPORT VALUES IN AUSTRALIA ARE EXPECTED TO LIFT TO $1.7 BILLION BY 2025–26.
vehicles to EVs and plug-in hybrids is also contributing to Chinese copper demand growth.”
By the end of 2024, China is projected to achieve its 2030 renewable energy target of 1200 gigawatts of wind and solar capacity.
As 2025 approaches, the mining industry stands on the cusp of exciting opportunities and continued growth.
Although the future is unpredictable, the local resources sector is well positioned to overcome challenges and capitalise on rising global demand for its raw materials.
While obstacles like fluctuating prices may arise, strong global demand remains across key commodities, providing a strong basis for Australia’s export earnings now and into the future. AM
THE WA MINING CONFERENCE WILL OPEN ITS DOORS TO IMPRESSIVE NEW TECH LATER THIS YEAR, WITH KOMATSU’S MC51 CONTINUOUS MINER IN THE SPOTLIGHT.
Komatsu, which has pushed the boundaries of heavyequipment technology for more than 100 years, sees WA Mining Conference & Exhibition (WA Mining) as the perfect opportunity to showcase its latest solutions.
At the 2025 event, the global original equipment manufacturer (OEM) will focus on its MC51, a hard-rock continuous miner that could redefine safety, efficiency, and environmental sustainability within the mining sector.
“Western Australia is an important mining region which Komatsu sees as a key growth market for the MC51,” Komatsu business development manager Manie Swanepoel told Australian Mining.
“WA is a hub for mining innovation, and participating in this conference allows us to engage directly with industry leaders, stakeholders and operators to understand their challenges and share solutions.”
The MC51 is part of Komatsu’s commitment to achieving a cleaner, greener future by 2050. At only 12.5m long, the machine harnesses a fully electric and remote-controlled system to complete 100 per cent of material cleanup itself.
“We’re keen to reveal the MC51 at WA Mining as it’s a powerhouse in terms of automation and ease-of-use,” Swanepoel said.
“The operator only needs to review the cut cycles to ensure the machine is operating at the best possible utilisation. Machine data can be uploaded and then analysed to ensure the best productivity is achieved.”
While WA Mining provides a great platform to display new products and generate new leads, the benefits go beyond that for Komatsu.
“It’s an opportunity to receive direct feedback from customers, ensuring we continue to align our solutions with the evolving needs of the mining industry,” Swanepoel said.
Komatsu marketing manager Shannon Perney agreed that the intention isn’t just to showcase technology at WA Mining, but to foster collaboration and build deeper connections within the industry.
“We are able to gain valuable insights into emerging trends and challenges (at the conference), while also demonstrating our commitment to supporting the Australian mining sector with innovative, sustainable and efficient solutions tailored to their needs,” she told Australian Mining.
The MC51 is part of a larger range of hard-rock machines Komatsu is developing that aim to eliminate diesel usage in the mining industry.
The company also offers electric excavators (such as the PC210E), electric-drive haul trucks (such as the 980E-5SE) and electric rope shovels (such as the 4800XPC), to name a few.
As Komatsu leads the way in creating more sustainable and efficient technology, WA Mining provides the perfect platform to showcase the company’s vision.
“Conferences are vital for staying competitive on a global scale and ensuring a sustainable future,” Swanepoel said.
“The WA Mining Conference, in particular, brings together diverse stakeholders to exchange knowledge,
explore emerging trends and showcase advancements.”
For Komatsu, WA Mining 2025 can help shape the future and enable the Australian mining industry to remain competitive globally.
The conference will not only highlight Komatsu’s innovations, but provide a glimpse of mining’s sustainable future. AM
WA
2025 will take place in Perth from October 8–9.
PROUDLY HOSTED BY AUSTMINE IN PARTNERSHIP WITH AUSIMM, THE GLOBAL RESOURCES INNOVATION EXPO 2025 IS SET TO SHOWCASE THE BEST OF MINING INNOVATION AND TECHNOLOGY.
Since its first iteration two decades ago, the Global Resources Innovation Expo (GRX) – previously known as the Austmine Conference – has grown to become a leading industry innovation event.
An expo “by industry, for industry”, GRX brings people working across the global resources sector together to network, drive important conversations about the latest trends, and showcase cutting-edge innovation. Reflecting on the last 20 years, Austmine chief
executive officer Christine Gibbs Stewart shed light on how GRX has evolved.
“Mining innovation was somewhat of an oxymoron 20 years ago,” Gibbs Stewart told Australian Mining. “The fact we were doing a conference involving technology and innovation in mining was new and rare, people weren’t really buying into the idea at the time. Fast forward to now, innovation is discussed in every boardroom and is part of every strategy.
“The use of technology such as machine learning and artificial
intelligence is powering the mining industry forward in several ways, including increasing efficiency, productivity and safety, but also through sustainability and the global energy transition.”
To keep up with the ever-changing technology and innovation space, GRX will be held annually beginning in 2025.
The event’s name was changed to reflect its larger international audience.
“We really want to attract everyone throughout the mining value chain,” Gibbs Stewart said.
“By combining the strengths of Austmine and AusIMM, we are coming together to set the strategic direction at GRX25 and carry forward the insights to better define policies and lead where the industry is heading from a strategic perspective.”
The central theme for GRX25 is ‘embracing a new era’. Gibbs Stewart said the theme symbolises the mining industry’s need to embrace change and evolve with the times.
“This includes adopting new technologies, looking at environmental impacts and ensuring there is a shared value with communities,” she said.
“It’s looking at an exciting future through the lens of harnessing technologies, which are impacting not only the mining industry, but our daily lives as well. We can’t afford to hold progress back; we have to embrace it.”
GRX25’s program will delve into the digital revolution and explore pioneering collaborations that break the mould.
“We have an exciting conference program lined up, which commences alongside the exhibition on May 20,” Stewart said. “We’ll have several pre-
conference workshops, one of which is the Global Open Innovation Collab.
“We’ve invited innovation hubs, mining innovation teams and some of our collaboration partners from around the world to talk about how we can be more aligned as an industry in moving innovation forward, and what some of those key priorities are.”
Several speakers from around the world will also take the stage to foster a future-focused dialogue.
“One of the exciting speakers kicking off the conference is Katherine BennellPegg, Australia’s first female astronaut and the director of space technology at the Australian Space Agency,” Stewart said.
“Other ideas to be explored over the three-day event include ‘pioneering changes across the globe’, ‘trailblazing technologies’, ‘shattering the boundaries’, and ‘paving the way to our bold future’.”
GRX25 will host an Industry Leaders and Awards Dinner, where excellence in innovation will be celebrated.
Five awards will also be presented:
• T he Craig Senger Excellence in Export award (supported by Austrade)
• T he Outstanding Innovative METS Company award
• T he Exceptional Innovation in Mining award
• T he Champion of Innovation award
• T he Excellence in Resources by a New Professional award
With 150 exhibitors locked in and a plethora of networking opportunities, GRX25 is set to be bigger and better than ever before. AM
GRX25 will take place at the Brisbane Convention and Exhibition Centre from May 20–22.
8-9
waminingexpo.com.au
THE 2025 PNG EXPO IS JUST AROUND THE CORNER. AUSTRALIAN MINING LOOKS AT SOME OF THE HOT TOPICS BEING DISCUSSED IN THE PACIFIC NATION.
The Papua New Guinea Industrial and Mining Resources Exhibition and Conference (PNG Expo) is set to return to Port Moresby from July 2–3, highlighting the latest technologies, products and services transforming the Pacific nation.
With so much going on in the country’s resources sector at any one time, Australian Mining takes a look at what attendees can expect from the 2025 iteration.
Some of PNG’s major miners are gearing up for a year of drilling as they look to expand their sites.
One of these miners is K92, a company looking to increase its production by over 35,000 ounces in 2025, a jump of 23.7 per cent.
Production is expected to hit 185,000 ounces of gold equivalent this year, up from the 149,515 ounces reported in 2024, an increase driven by the commissioning and ramp-up of the new 1.2-million-tonne-per-annum processing plant.
“There is tremendous enthusiasm internally, among our various stakeholders including in Papua New Guinea for the year ahead as K92 transforms into a Tier 1 mid-tier producer with the delivery of the stage three expansion,” K92 chief executive officer John Lewins said.
“In the second half of Q2 (the second quarter), the stage three expansion process plant is scheduled to commence commissioning, marking the beginning of a step-change in our throughput and production capabilities.”
K92 is planning a large exploration program in 2025, projecting $17–20 million for the year. Growth capital is forecasted to hit $110 million.
St Barbara’s Simberi gold mine is also seeing some exploration gains.
The company uncovered a promising new oxide discovery in January, with drilling showing “significant” drill intercepts up to 2.1 grams per tonne of gold at 25m.
“The identification of this new oxide mineralisation between Pigibo North and Sorowar is a real boost for the current Simberi oxide operations,” St Barbara managing director and chief executive officer Andrew Strelein said.
“These significant results from trenching and the near surface drilling results are now being followed up
with grade control drilling with the objective of commencing mining in the third quarter.”
outreach
Keeping the communities around mine sites profitable, safe and knowledgeable is a key part of any mining activity in PNG.
In January, some of Papua New Guinea’s most remote villages were registered by the National Identity Project (NID) thanks to Frieda River Limited (FRL).
The NID is a registry office that records births, deaths, marriages, divorces and adoptions in PNG.
The goal of the department is to have every PNG citizen accounted for, recognised and given mandatory individual identity to contribute
The drive saw over 2300 people registered, with those over 18 undertaking biometric testing and receiving NID cards. The registration will allow these individuals to participate in state-led processes like the creation of landowner associations near mine sites.
PNG Prime Minister James Marape has long been vocal about the need to prioritise sustainability and climate action in the country.
“Papua New Guinea is at the frontline of climate change,” he said in January.
“As custodians of vast forests and marine biodiversity, we are committed to partnering with global leaders to ensure sustainable solutions for our planet.”
This statement has been backed by miners like Ok Tedi Mining Limited
OTML manager Bige operation Naimen Kepan said it is important to the company to meet or exceed these targets.
“Reaching our rehabilitation targets brings us closer to restoring the East Bank stockpile in accordance with OTML’s Mine Area Rehabilitation and Closure Plan, ensuring a sustainable environment for the local community after mine closure,” he said.
Achieving its targets helps OTML to minimise the impact of riverine sediments on the environment while continuing to support local communities.
Dredging at Bige removes approximately 85 per cent of sediment load each year to prevent it from travelling further downstream. Once dredged, the materials are rehabilitated with vegetation cover.
As Australia’s longest running mining show, Asia-Pacific’s International Mining Exhibition (AIMEX) has a long, established history of showcasing and supporting the latest trends and developments in the industry.
AIMEX is relocating and will call South Australia home for the next 10 years, following market feedback and strong support from the local government and key mining players.
The move marks an exciting new chapter for the event and the region’s resource sector, with the state leading the way in future-focused mining.
AIMEX offers unparalleled opportunities to connect with Australia’s largest community of mining suppliers and professionals in an environment that stimulates innovation and collaboration.
The Atlas Copco HiLight BI+4 is an innovative and easy-to-use light tower that delivers energy-efficient light coverage to boost operational productivity, minimise environmental impact and meet stringent safety standards.
Featuring a state of-the-art surface mount device, LED lighting technology and lithium-phosphate batteries, the HiLight BI+4 provides excellent performance and efficiency enabling operators to utilise four modes, offering users maximum flexibility while reducing their carbon footprint and operating costs.
With an innovative, fully directional, LED lens, the HiLight BI+4 also maximises light coverage while reducing lighting waste. A single BI+4 tower can cover an area of up to 4000m2 with an average of 20 luxes of brightness ensuring a brighter, safer and more productive site.
Sandvik Mining and Rock Solutions has introduced its new Sandvik DD312i, joining the company’s i-series range of development drills.
The new compact and automated single-boom jumbo, which capitalises on 20 years of drilling legacy from Axera D05 to Sandvik DD311, can be used for applications such as face drilling, cross cutting, bolting, development and production drilling in room and pillar, cut and fill, stoping or caving applications.
The Sandvik DD312i is suitable for medium-to-large sized underground drifts and can fit into narrow confines due to its compact carrier and small cornering profile.
Its new intelligent control system with torque optimised drilling is designed for mines seeking more tonnes with maximum profitability.
Miners can enjoy up to 50 per cent higher drilling accuracy, up to 26 per cent more drilling coverage and up to 20 per cent more productivity when the DD312i is combined with Sandvik’s scalable automation packages for drills.
• rocktechnology.sandvik
and leaching, enabling the production of high purity concentrates for marketable products.
However, the quality and availability of water significantly influence both the performance and cost of mining operations.
While some mines use high-salinity water, it can negatively impact recovery rates and require specialised materials to handle the corrosive environment.
This is where FLS, a global mining technology leader, can help.
The company provides comprehensive flowsheet solutions for copper, gold, zinc, iron and lithium operations, among others.
FLS’ filtered tailings technology solution extracts water from tailings to achieve solids content of 75–90 per cent or more, enabling significant water reclamation. This reduces water costs, minimises tailings storage facility footprints, and cuts closure expenses at the end of a mine’s life.
FLS’ filtered tailings technology solution is an example of the company’s commitment to innovation, efficiency and sustainability.
• fls .com
The mining industry is energy-intensive, with power consumption accounting for 15 to 40 per cent of a mine’s total operating budget.
Most mines – especially in remote, off-grid regions – rely heavily on diesel or gas generators. Mines are also under severe scrutiny to follow local and international environmental regulations while working towards achieving net-zero emissions from their operations.
Hitachi Energy helps customers utilise battery energy storage systems (BESS) to address several challenges converging at once.
These include minimising OPEX (operational expenditure) through the reduced use of fossil fuels such as diesel and gas, ensuring high power quality to supply off-grid mines with renewables, maximising productivity, and minimising dependency on the grid power supply. Hitachi Energy also helps clients comply with environmental regulations and become energy self-sufficient.
BESS solutions can be implemented to improve overall generator efficiency or create a virtual spinning reserve, the latter having one of the most compelling business cases for storage and paybacks under five years.