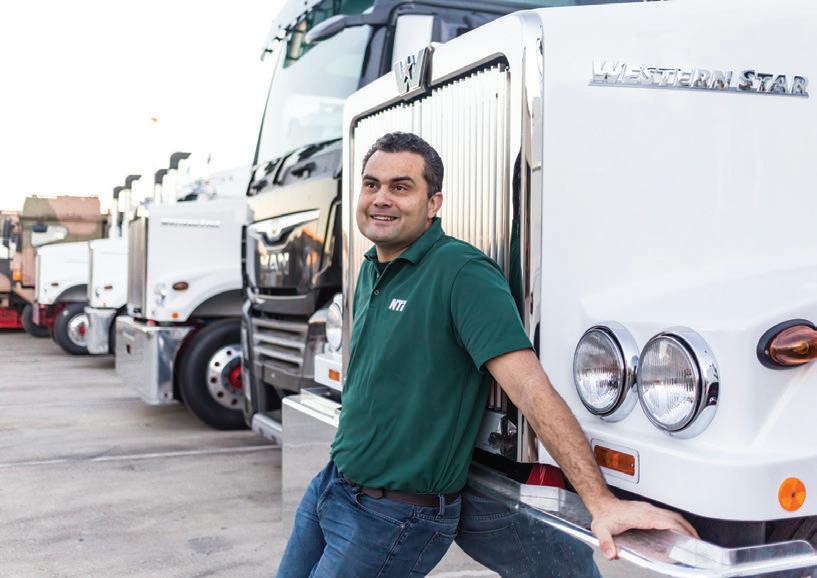
4 minute read
Landmark project aims to reduce tanker rollovers
DAIRY supply chain stakeholders – including consignors, carriers and processors – have shown enthusiasm and commitment to the initial phase of a landmark new project aimed at improving the safety performance of milk tankers.
Funded through the National Heavy Vehicle Regulator’s (NHVR) Heavy Vehicle Safety Initiative, the ‘Spilt Milk: A National Crash Reduction Program’ is being led by Australia’s leading transport and logistics specialist insurer, NTI.
NTI identified a proportionally higher frequency of crashes, compared to their peers in other industries. This is due to the challenging operating environment in bulk dairy collection, including challenging geography, winding country roads and regions with high rainfall. All of this contributing to dairy tankers being 2.4 times more likely to be involved in a major crash than other freight transport.
In response, work has begun on a new program of discovery, materials development and education to improve road safety in the industry.
“While the dairy industry has a history of excellent, but isolated, initiatives to improve the safety performance of milk tankers, the aim of the ‘Spilt Milk’ project is to bring together key stakeholders, expertise, and initiatives, to deliver whole-of-industry solutions to this whole-of-industry issue,” said NTI chief sustainability officer, Chris Hogarty.
“The goal is to reduce dairy tanker rollovers and improve road safety by working with drivers, fleet managers and consignors,” he says, noting a similar education program in Victoria’s forestry industry resulted in a 65 per cent reduction in rollovers, from 29 in a year to FY20 being rollover free.
“For the dairy industry it is about improving road safety and protecting the environment because dairy tanker crashes not only put drivers and road users at risk but can cause milk and diesel spills.”
Recruitment and identifying best practice
Phase one of this project is focused on recruiting and out- reach to top carriers and consignors and third parties in the dairy transportation industry. The response from industry has been exceptional, with four of the largest dairy carriers and three of the largest processors all signing on to participate in phase two.
In the second phase of the project, the team – headed by NTI transport research manager Adam Gibson and Australian Trucking Safety Services & Solutions director Alan Pincott – has travelled the country speaking with participants to identify current ‘best practice’ as well as known safety concerns.
“The key is making sure everyone is part of the pro- cess, understands what we are doing, and understands how it is going to be impactful for them. We need to ensure it works for everyone,” said Gibson.
“A lot of people are doing great things in the dairy space. The opportunity is to find individual pockets of brilliance and share them more widely.
“There is a net benefit to all participants to share things they don’t compete on such as safety.”
Pincott – a former VicRoads transport inspector who has developed similar programs for the Victorian forestry industry – has also jumped in the cab and spent time with farm pick-up milk tank drivers.
Pincott said engaging frontline staff, especially drivers, is critical to the project’s success.
So too is senior management, added Gibson: “Frontline leaders inside dairy processing businesses represent a small part of a very large, complex machine.
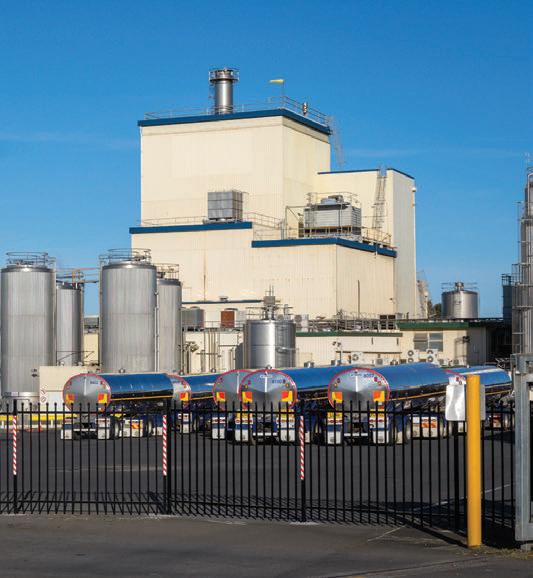
“One of the opportunities of the project is to share transport knowledge and insight to those higher up in dairy processing businesses.”
Research to date has identified the major issue as the “exceedingly challenging operating environment” for dairy tankers.
A dairy tanker has unique engineering and physical attributes, as well as a unique operating environment, that make them particularly susceptible to rollovers – and difficult for even an experienced driver to predict.
By the time the driver feels the trailer rolling, it is often too late. This poses significant risk to the safety of dairy tanker drivers, other road users and the public.

In this context, Gibson said they’ve been surprised by the limited availability of material to explain vehicle design and capabilities, especially relatively new technologies such as stability control.
“Limited operators appeared to have integrated data from vehicle electronic stability controls into their broader business processes. We need to make sure there is an opportunity for that data to be explained and made available to everyone in the organisation,” he said.
“All the gear is reasonably new, what is missing is the support to extract maximum value from it.”
What’s also missing is adequate education and training resources, the research has found.
“When we talked to driver trainers, and how they trained on vehicle dynamics, they either had VicRoads rollover training or very hands-on driver trainers. Formalised resources and materials were very limited,” Gibson said.
“It’s prohibitively expensive, there’s a lot of tooling up, creating resources, so they rely on face-to-face training.”
Program development
‘Spilt Milk’ aims to fix that. The next stage of the project commenced last month and focuses on developing resources – or what Gibson and Pincott call “artefacts”. It’s predicted to take five months to complete.
Pincott says the development of training resources will be crucial to getting a “holistic approach” through all elements of the supply chain.
“That’s not there at the moment,” he said.
The intention is to include templates and instructional videos, as well as share best practice.
“For example, a tanker driving around with cameras, in the cabin and inside the tank, to see what the load looks like going around s-bends, when you do an emergency stop, or when you go direct from a country dirt road to a highway,” Gibson explained.
They also plan to engage a leader in braking systems to run through the process with carriers and turn this into “artefacts” for their use.
Pincott adds: “One of the challenges you’ve got is you may do eight pick-ups from hundreds to thousands of litres over challenging and changing routes, and you have limited guidance on how the changing volume of milk affects vehicle dynamics.
“One of our key goals is to support drivers to understand the specific risk profile of the task, as it changes both day-today and across the course of a single run.
“Anything to increase awareness of the risks improves the ability of our already highly skilled drivers to manage them.”
Pincott said buy-in from all supply chain participants will be crucial to success – especially drivers.
“Individually they all know a lot. With my experience in a similar project in the logging industry, if you involve the guys you get ownership and you get engagement,” he said.
What’s Next?
The program will continue to engage leaders in the dairy industry during the duration of program development to identify ways these new program materials can be distributed to key stakeholders as early as Q1/Q2 23/24 FY. If you would like to learn more or participate, contact the team at spiltmilk@nti.com.au.
AFTER 290,000KM WE CAN SAY THE CASCADIA IS CLEARLY