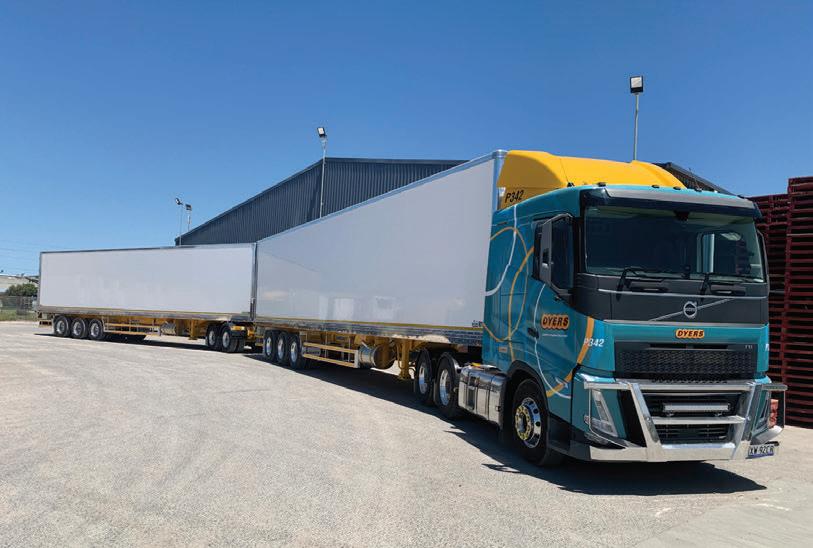
3 minute read
It all
THE Dyers family’s foray into transport started with a paddle steamer back in 1908, used to deliver goods via the Murray River. Fast forward to today and the business is 100 per cent owned and operated by the third generation of Scott, Greg, and David Dyer and operates a large fleet of prime movers and rigids in their distinctive livery. The business is an expert in linehaul, storage and distribution of refrigerated and general freight throughout Victoria, South Australia, Queensland and NSW from eight locations.
As with any efficiently run transport operation, safety is paramount and service is key.
Tony Wain, Dyers national safety and compliance manager, who has been with the company since 1998, says Dyers began using Procon for its telematics needs in 2013 and hasn’t looked back.
Ten years ago a trial of an initial 25 units with an alternate GPS supplier had stalled. “We were with another larger provider, but the reliability and customer service didn’t meet our expectations; so we went looking for another option,” he explained.
“Back then we had about 100 trucks. After talking with Procon, we initially had their Fleetlocate GPS system fitted to a few trucks. Now we have it fitted on all of our trucks.”
Dyers Transport operates a fleet of over 200 prime movers. Add to that the smaller trucks and sub-contractors and it brings the number of Procon units being used by the company to over 300.
“Today, every large vehicle in the fleet is fitted with Procon GPS devices. It comes down to the customer service. If I was to ring the owner at Procon, René Bueman, now and say I need you to fit five trucks with the system tomorrow, it would be done. It’s that simple,” said Wain.
“René still has that personal touch and still fits all the units for us. If I ring him and ask him to do something, he’ll personally oversee it. I still catch up with him in person, two to three times a month.”
Procon’s Fleetlocate software provides a wide range of reporting for Dyers, on everything from the basic time and location information, to driver behaviour, fleet utilisation, geofencing and importantly, overspeed events.
“We use it a lot on the safety side of things. It’s not just about knowing where your truck is; it’s about knowing what your truck does. Procon gives us security because if a truck is somewhere longer than it should be, or not being operated at its scheduled time, or on its correct route, we know there could be a problem.”
An added advantage provided by Procon is its ability to customise its own Fleetlocate software to suit its customers’ needs. In the case of Dyers, a variety of special scripts have been set up by Procon, helping the business stay at the forefront of safety. “The integration with our TMS provides a seamless redundancy GPS system in the event the driver’s portable device used for our ‘Customer Track and Trace’ app is not providing GPS data.
“As a safety measure, we’ve speed-limited all of our trucks to 98km/h. There are obviously situations where vehicles can exceed that limit, for example if they are going downhill an in these instances the Procon system immediately provides the driver with a visual ‘In-Cab’ alert to ensure the driver takes appropriate action. At 101 km/h there is a further audible alert and in the unlikely event the truck exceeds 104 km/h the compliance and operations team receive an SMS alert, and will contact the driver,” Wain explained.
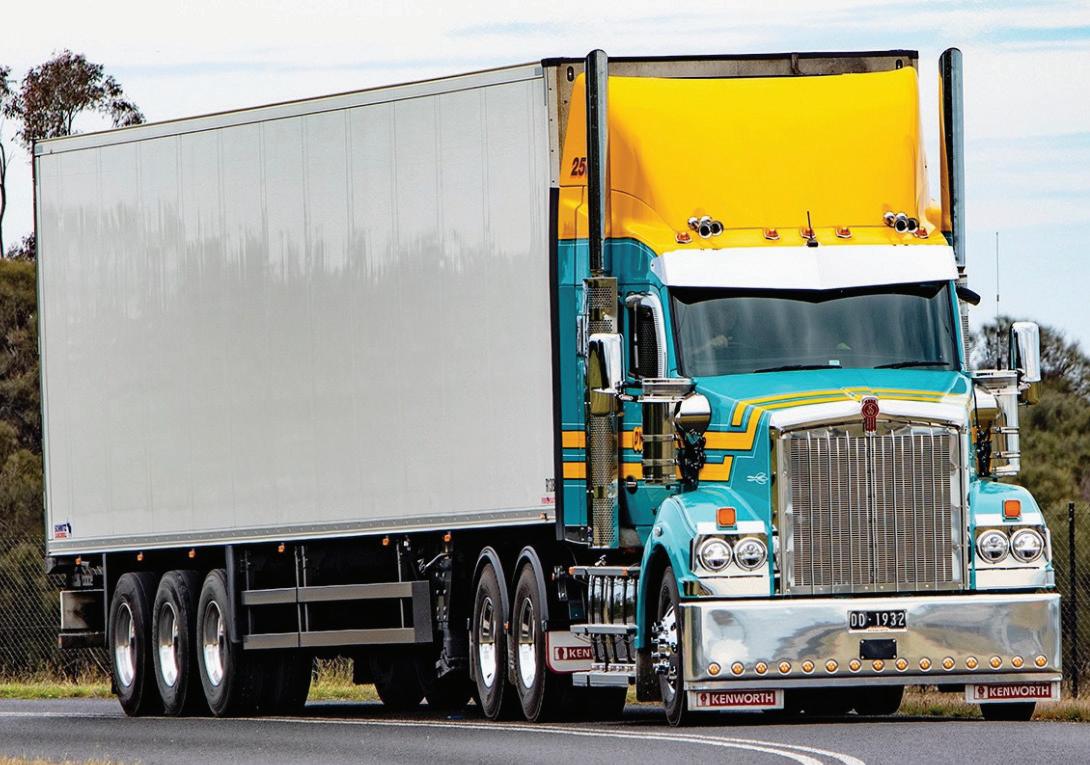
“All drivers are supplied an individual fob to log in each time a journey is commenced so that speed alerts are logged by both vehicle and driver.”
According to Wain, the Procon system helps the business keep on top of its CoR requirements too. “We always know who is in the truck, the speed of that truck and can monitor fatigue requirements. We’re set up on Basic Fatigue Management (BFM), which is 14 hours but aim to keep things to no more than 12 hours for all our drivers. We use the additional two hours as a buffer in case something goes wrong. So on the safety side, we know if our drivers are doing big days and can see every day that the driver has worked over 12 hours.
We can then change and customise our runs based on that.
“For auditing, I can pull reports out easily and see exactly what was done for the set period. The Procon system is really good for compliance. Without it, we’d go back to old pens and paper and would be working blind!”
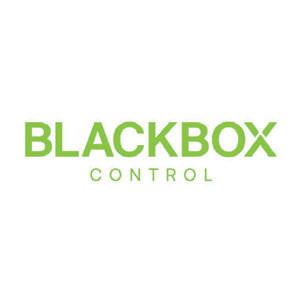
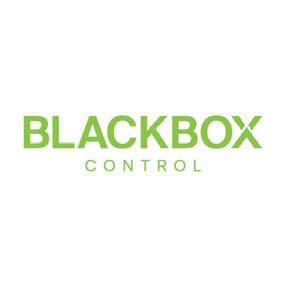
Earlier this year, Dyers set up a control room which is heavily reliant on monitoring Procon’s Fleetlocate and other systems to monitor driver welfare, on road safety, temperature compliance and customer service. “Before the monitoring was predominately done in the hours the operations team were in the office, and some issues weren’t dealt with until the operations team were onsite, but with the technology now available to the control room we can manage remotely 24/7,” Wain added.
“With some other telematics providers, the system is okay but their personal touch and service isn’t there to the same level that we value with Procon. If we need things fixed, we need it done straight away. Procon may not be the biggest telematics provider out there, but we’re not going anywhere, because the customer service is just impeccable.”
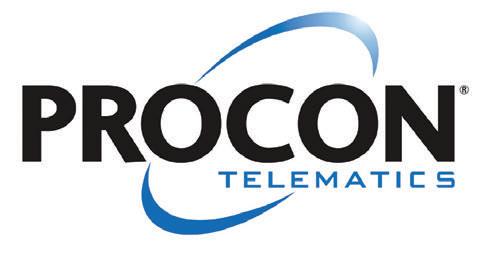