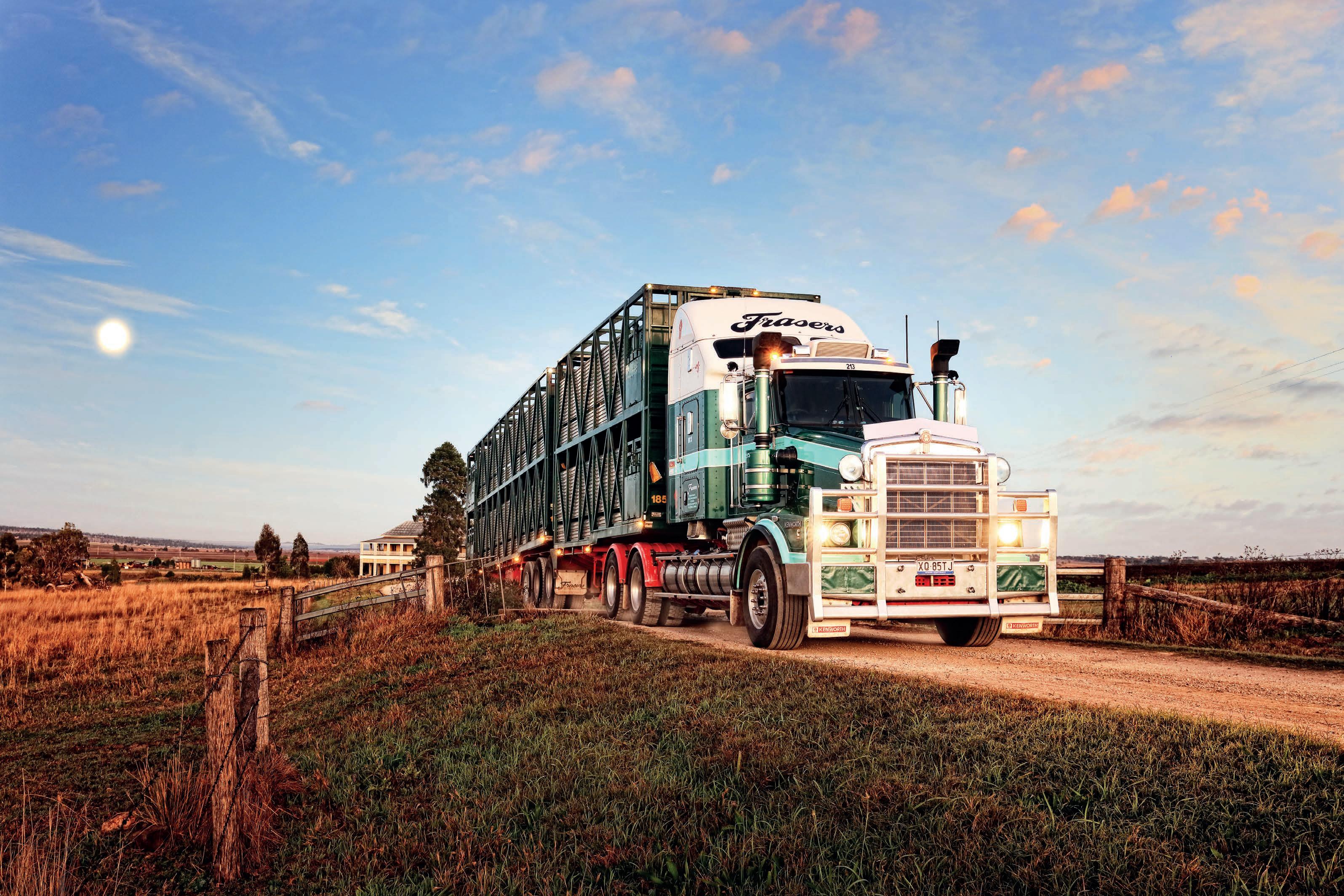
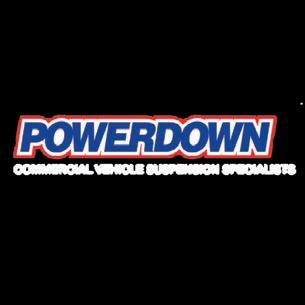


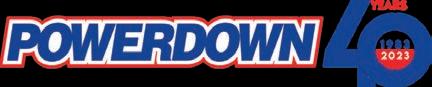
Address:
Subscriptions:
Address:
Subscriptions:
BY KAYLA WALSH
WA freight operator Campbell Transport has praised two of its drivers, who recently stopped to help a family that had run into trouble on the road.
Truckies Damien Elliot and Chris Kantor were out on a run when they noticed that a man, his pregnant wife and two young kids were in need of assistance, after their car had hit a cow south of the Kimberley Mineral Sands Thunderbird turnoff.
The couple were in distress as the woman was suffering abdominal pain following the impact, but had reportedly been told by ambulance services that the situation was “non-critical”.
Kantor told Big Rigs that when he came across the scene, the family’s car was still halfway on the road and had lost power.
“The car was a write-off,” he said. “The cow had hit the car on the passenger front and
smashed the windscreen.
“The woman would have got the main brunt of the crash, you could see the airbags had deployed on her side.
“They were obviously pretty shaken and upset at the situation.”
Kantor said his first priority was making sure the family were okay, before helping them to move the car off the road.
He and Elliot then contacted RAC on their behalf, and continued to check on them after the incident.
Kantor said he was happy to help, because it was simply the right thing to do.
“You’d hate to be in that situation yourself,” he said.
“It was a horrible area for this to happen, because there’s a fair distance between towns and not much around.
“What was disappointing was that there were about five or six vehicles that went past us while we were there, and no-one else stopped.”
Kantor and Elliot’s kindness prompted the family in question to write a letter to Campbell Transport, which the company shared on their Facebook page.
“Contacting RAC for us and the proceeding vigilance of [Kantor and Elliot] gave us a great deal of reassurance in the hours we waited,” the letter read.
“We just want to say thank you so much to them for their kind words, reassurance and care.
“You’re an awesome group and we always hold dear what you did for us.”
As a reward for being highway heroes, Campbell’s has gifted its two drivers 18 holes of golf at the Broome Golf Club.
Loki Campbell, the company’s people and culture manager, said: “It’s the least we could do.
“We’re very proud of Chris and Damien, and happy we’ve got such good blokes on board.
“They exemplify those oldschool trucking values that we really support. It’s getting out there, it’s the camarade-
rie with the people you’re on road with, and it’s the recognition that we’re all in this together.”
A $1.75 million upgrade to a rest area between Walgett and Brewarrina in north-west NSW – on the eastbound shoulder of the Kamilaroi Highway – is set to begin next year. The works at the Yambie Lagoon Rest Area will involve building toilet and
shelter facilities, as well as picnic tables and extended parking for heavy and light vehicles.
The project will also provide similar facilities in a new heavy vehicle rest area on the westbound shoulder of the highway, providing facilities for traffic in both directions.
The Yambie Lagoon Rest Area is about 60 kilometres east of Brewarrina on the Kamilaroi Highway, a key rural f reight route.
Currently there are no toilet or rest facilities for more t han 120 kilometres, or 75 minutes of travel time, in this remote location.
The renovations are intended to encourage rest breaks for heavy vehicle drivers on long trips – however they’ll also be accessible to other motorists too.
Heavy vehicle industry representatives were consulted i n early 2020 to provide input into the proposed loca-
tions of future rest stop opportunities on the Kamilaroi H ighway between Walgett and Bourke.
The project is jointly funded by the Australian Government, under the Heavy Vehicle Safety and Productivity Program, and the NSW Government.
TRUCKIES should not have to take 45 minutes out of their workday to comply with the NHVR’s 12-week safety blitz, believes a frustrated Queensland operator who spoke out in protest of the campaign that started last month.
Operators in all states and territories are now on notice to organise the time into the drivers’ scheduling to allow for the random roadside inspections.
Billed as the National Roadworthiness Survey (NRS), the regulator says the stops are necessary to “drive safety and efficiency improvements” to the mechanical condition of Australia’s heavy vehicle fleet.
“I’m trying to embrace this new age of fairness,” said the angry veteran who asked not to be named because “I don’t want a target on my back”.
“But I would like the NHVR to explain how do you all of a sudden manufacture three-quarters of an hour of extra work activity into a driver’s roster when you don’t know when you’re going to be intercepted?
“We’ve got mass and main-
tenance accreditations but if they’re going to do audits, and I’ve had them done, they notify you.
“It lets you know that you’ve got to be prepared to drop everything, like you should.
“But why is this the drivers’ problem, to be part of this, to make sure that the operator is compliant?
“The poor old driver has to find three-quarters of an hour just because the regulator wants to do a baseline on roadworthies.
“Do whatever you like, but why put them out?”
The operator can’t see why the regulator couldn’t instead just give truckies more of an idea of where and when they might be pulled over.
“All I’m suggesting is commonsense. They could say, ‘listen, we’re going to do the Hume to the Queensland border between July 10-21’, for example.”
Further west, the operator believes you’ve almost got to have a standby truck ready for a changeover.
“There comes great expense because you’ve got to go and get another truck out of your
arse. Have they unpacked this enough and really looked at the ramifications?
“The drivers over there are on 14-hour books as it is and cannot manufacture 45 minutes “for love or money”.
NHVR operations manager Tamie Haley said the NHVR recognises the survey may cause disruption for drivers and operators whose vehicles are stopped and inspected and understands the importance of keeping the supply chain moving.
“Inspections can average around 45 minutes depending on the vehicle type and if there are defects identified, so it’s important for drivers to factor adequate time into their schedule to accommodate for this,” Haley explained.
“We understand industry works to tight schedules and where possible, all NHVR officers will ensure minimal disruption occurs – we will carry out these inspections effectively and efficiently.
“I encourage industry to prepare for the NRS by reading the NHVR Daily Safety Checklist – by taking a few minutes before each trip to
check basic safety items on your vehicle, you can identify any issues and ensure the vehicle is safe and ready for the journey.”
NHVR safety and compliance officers, alongside police and authorised officers, will undertake random visual and mechanical inspections of around 8500 trucks, buses, and other special purpose vehicles to “identify existing and emerging risk trends,
with the aim of enhancing road safety across the heavy vehicle industry”.
The regulator says the results of the survey will be compared to the first one held in 2016 and the follow-up in 2021 to determine where both the NHVR and industry are making improvements in vehicle safety, and the areas that need more focus.
“Results from NRS 2021 showed the rate of non-con-
formities had dropped significantly in comparison to 2016, and we are hoping this downward trend continues,” added NHVR chief operations officer Paul Salvati.
“The results of NRS 2024 will help inform the NHVR’s modern approach to regulation, that uses data and intelligence to address the greatest safety risks on our roads and keep our heavy vehicle industry productive and efficient.”
ONE of the country’s peak trucking bodies is continuing its push to allow 4.6 metre high trucks to have general access to the road network without needing special notices or permits.
ATA CEO Mathew Munro said that allowing higher trucks would increase the industry’s productivity and remove the need for operators to apply for more than 1100 permits a year.
Under the Heavy Vehicle National Law, the general access height limit for trucks is 4.3 metres.
“National Transport Commission analysis shows it would save the industry $95,000 per year in permit fees and deliver time savings worth $91,000 per year,” explained Munro.
“It would also deliver a pro-
ductivity boost for operators that transport bulky products like retail and refrigerated goods.”
He added that the risk of trucks hitting overhead infrastructure could be managed through signage, enforcement and targeted awareness campaigns.
“Our 4.3 metre high trucks must already navigate the many road structures that are less than 4.3 metres high. Plus, there are already standard vehicles such as car carriers, livestock trucks and some containers that routinely move around the network at 4.6 metres in height.
“The low prevalence of strikes across the tens of thousands of truck movements every single day demonstrates
that operators can manage this risk safely.”
Munro believes that in high er risk or higher consequence situations, targeted awareness campaigns can be very effec tive.
“For example, strong collab oration between Road Freight NSW, the NHVR, Trans port for NSW, police and the T WU achieved a dramatic fall in incidents involving overheight trucks in the Syd ney tunnel network. There were only four overheight in cidents in November 2023, compared to 25 in November 2022,” he said.
The governments that use the HVNL must agree unanimously to any amendments, with Munro urging governments to agree to the reform,
even if they don’t proceed to apply it in their own state.
“We ask every government using the HVNL to agree to
reform so Australia and the trucking industry can benefit, even if they decide to derogate from the law in their
BY KAYLA WALSH
FEBRUARY 2025 has been proposed as the date for work to begin on the $336 million Tiaro Bypass north of Gympie in Queensland.
The project, which involves building a new four-lane section of the Bruce Highway to the east of Tiaro, is expected to be completed within two years of commencing construction. The bypass is intended to increase the flood immunity,
safety and efficiency of the Bruce Highway and remove “a significant number” of heavy vehicles from the Tiaro township.
Its long-awaited start time was revealed as part of a Federal Environment Department request for public comment on the project.
The referral document from TMR Queensland, dated April 2024, stated that detailed design for the $336 mil-
lion project was about 50 per cent complete.
However, the proposed start and end dates could be delayed by anything from bad weather to design issues to “unforeseen community, political or project funding issues”, it says.
Detailed design work will include further investigations including environmental, hydraulics, noise, geotechnical, pavement, traffic and safety assessments.
A health check of Australia’s heavy vehicle fleet
The National Roadworthiness Survey is underway and will run into September 2024 across all states and territories.
Authorised officers from the NHVR and partner agencies are conducting mandatory random mechanical inspections of approximately 8,500 of Australia’s trucks, buses and other Special Purpose Vehicles.
The National Roadworthiness program aims to drive safety and efficiency improvements to the mechanical condition of Australia’s heavy vehicle fleet.
For more information visit nhvr.gov.au/nrs
It also involves the development of detailed road and bridge design drawings including drainage, lighting, signage, property accesses and public utility relocations, and the preparation of detailed cost estimates, construction drawings and contract and procurement documents for the construction phase.
The project is awaiting the green light on its environmental controls, after it was found
that construction will likely have a significant impact on species including koalas, yellow-bellied gliders, and greater gliders.
The Bruce Highway at Tiaro contains three flood zones, variable speed limits (including a 40km/h school zone), a signalised pedestrian crossing, over 50 direct property accesses and intersections and a mix of local and through highway traffic.
TMR says that flood-related
highway closures at Tiaro lead to disruption of freight and passenger traffic, with no diversion route.
“These closures have a significant impact on the national road transport network and result in the isolation of the Tiaro township during significant flood events,” they said.
“Delays at Tiaro during peak travel times result in substantial queues on the highway in both directions.”
A PROPOSAL to increase the toll burden on heavy vehicle operators on the Sydney toll network was the last news that Scott Hannah needed to hear.
Speaking soon after an independent toll review recommended the heavy vehicle toll multiplier increase from 3 to 3.5 times higher than light vehicle tolls, Sydney-based Hannah revealed that four of his trucks had recently had their rego plates stolen.
He suspects the culprits were trying to dodge the crippling toll charges heavy vehicle operators already have to pay – and a further increase will only exacerbate the situation.
“They put the stolen one on their truck, go through the tolls and then take it off again and finish the rest of the trip off,” said Hannah, who is the boss of Hannah’s Haulage.
“They don’t pay rego on them [their own trucks] because there’s such a big downturn in the market at the moment. I haven’t seen it like this since the GFC – it’s that bad.”
Hannah said stories of other theft – such as trailers, fuel and freight – are also at an alltime high as a result.
“That’s going to kill the smaller subbies,” said Hannah of the proposed toll spike.
“The smaller subbie hasn’t got the option to go back to
THE SUGGESTED INCREASE IS UNJUSTIFIED AND MOCKS THE ESSENTIAL ROLE OF TRUCKING.” WARREN CLARK
his customer to say the tolls have gone up; he just gets a price.
“For the amount of money we’re paying, sometimes you just can’t justify it.”
Hannah said trucks running from Brisbane to Melbourne on the coast road, are already looking at upwards of $250 in tolls for a one-way trip.
“That’s why a lot of them [other operators] are using the back road still because there are no tolls, but it’s a shitty road, it’s a one-lane goat track, and there are a lot more accidents out there now.”
The National Road Transport Association (NatRoad) slammed the toll review proposal, saying that the review had failed to heed the concerns of the transport industry.
“This report is a setback for trucking businesses, which operate on extremely tight margins,” said NatRoad CEO Warren Clark.
“The suggested increase is unjustified and mocks the
essential role of trucking in our economy and our supply chain.
“Our industry simply cannot absorb these unfair and unnecessary costs, nor can we simply pass them on to customers.”
Clark said the recommendation to apply a toll to Sydney Harbour crossings for trucks, using the new higher multiplier, further exacerbates the financial burden on truck operators.
“These moves are in stark contrast to the fairer tolling system the report claims to call for.”
NatRoad has made the following points in regard to the increase in the toll multiplier:
1. The report overlooks substantial evidence that the current truck toll multiplier is unsupported by data.
2. A 1.5 times multiplier is sufficient to recover the cost of heavy vehicle road wear while still generating additional revenue.
NatRoad’s recommended 2 times multiplier is more than reasonable and equitable. Ramping it to 3.5 times is simply using the trucking sector as a cash cow.
3. Over 90 per cent of trucking operators are small and family businesses with profit margins averaging
SYDNEY
510 Victoria Street, Wetherill Park NSW 2164
Ph. 02 9756 6199, email: isri@isri.com.au, www.isri.com.au
BRISBANE
just 2 per cent. Increasing the multiplier to 3.5 times places an undue burden on these operators, who already struggle with limited ability to pay and pass on costs. In a time when the sector is struggling to find drivers, this action could put the supply chain into crisis.
4. The 2022 NSW Parliamentary Inquiry into road tolling found it already inequitable to charge trucks three times as much as cars, especially where trucks are compelled to use toll roads.
“We are calling on NSW Government to reject the proposed toll multiplier increase and to engage in meaningful dialogue with the trucking industry to develop a more realistic tolling system,” Clark said.
NatRoad is also asking for variable lower truck toll rates, discounts for multiple truck journeys, and exemptions for zero-emission heavy vehicles.
NatRoad does, however, agree with some aspects of the report, such as the establishment of an independent regulator and the move to -
wards a unified and simplified tolling system, including the introduction of peak and off-peak tolls. Meanwhile, the Transport Workers’ Union of NSW welcomed the report’s recommendation to implement a middle-class heavy vehicle classification for trucks that are 3m or less in height and 5m or less in length. The union said this classification would provide fairer pricing for heavy vehicles using Sydney’s toll network by lowering drivers’ toll multiplier from three times that of a car to two times.
3/120 Gardens Drive, Willawong QLD 4110 Ph. 07 3275 2044, email: sales@isribrisbane.com.au, www.isribrisbane.com.au
MELBOURNE
Unit 1/569 Somerville Rd, Sunshine West VIC, 3020 Ph. 03 9311 5544, email: sales@isrisunshine.com.au, www.isri.com.au
MACKAY
110 – 120 Maggiolo Drive, Paget QLD 4740 Ph. 07 4952 1844, email: admin@isrimky.com.au, www.isriseatsmackay.com.au
PERTH
408 Welshpool Rd, Welshpool WA 6106
Ph. 08 9362 6800, email: info@mmtisri.com.au, www.mmtisri.com.au
DARWIN
Mobile Sales and Service
Ph. 08 8927 0986, email: info@isridarwin.com.au, www.isridarwin.com.au
ADELAIDE
TAMDELE, 21 Hakkinen Road, Wingfield SA 5013
Ph. 08 8347 1222, email: sales@gitsham.com.au, www.gitsham.com.au
NEWCASTLE/HUNTER VALLEY
Unit 2/13 Hinkler Ave, Rutherford NSW 2320
Ph 02 4932 0600, email: sales@hvss.com.au www.isri.com.au
Cause close to heart
An incredible $483,000 has been raised for motor neurone disease (MND) research thanks to the restoration and raffle of a 1946 Ford Jailbar truck, named Bonnie.
Hundreds crowded around the NTI Supercars in Townsville last month as the winner was announced – Redland local Beverly Smith.
Smith received the winning call, after buying a single ticket in the raffle. “I lost my mum to MND nearly 20 years ago, so it’s a cause that’s very close to my heart,” she said.
“I always try to support the foundation in any way that I can, but never in my wildest dreams did I expect to actually win the truck.”
Bonnie was the seventh truck to be restored and raffled by Australia’s largest transport and logistics insurance specialists, bringing the total raised for MND research by NTI to over $2.5 million.
Sealing works in NT
As part of a $7.6 million project, over 5 kilometres of Fleming Road will be upgraded to “sealed road standards”, funded by the NT Government.
“Fleming Road is a key access road for the cattle industry in the Douglas Daly region who use the road to transport livestock to Darwin Port and interstate,” said Minister for Infrastructure, Planning and Logistics Joel Bowden.
“Sealing our roads will improve connectivity, reduce travel time and provide better protection from flooding.”
The upgrades are due to begin this month and be completed by July 2025.
A parliamentary inquiry has confirmed what truckies have known for months – the controversial $3.9 billion Rozelle Interchange in Sydney was not built in their “best interests”.
In a critical report handed down last month, a NSW parliamentary committee was scathing in its findings, saying there was a “concerning lack of clarity and transparency” around contractual arrangements between the NSW government and Transurban over the interchange’s delivery.
The committee made 17 recommendations, that also proposed a review of consultation practices and policies for projects of this type to ensure “meaningful and genuine consultation” moving forward.
An official response to the recommendations from the government is due by October 15.
Plans are in the works to upgrade a 10km stretch of the Logan Motorway in Queensland, to slash travel times by 20 minutes during peak periods – but not until 2031.
An upgrade proposal from Transurban Queensland and the state government includes a new lane in each direction, enhancements to on and off ramps, and the installation of smart motorway technology.
The goal of the proposal is to unclog one of the South East’s most congested freight routes and improve travel reliability.
BY DANIELLE GULLACI
WHEN the idea was first floated to mandate new pictorial length signage on road trains in Western Australia, John Mitchell says his immediate first thought was, “How bloody stupid!”
Mitchell is a third generation transport operator and the CEO of Mitchell’s Livestock Transport, operating a fleet of 32 trucks, and 140 trailers and dollies from his Waroona base, in WA’s south-west.
He’s slammed the decision by Main Roads WA that will require operators to transition to new road train signage for heavy vehicle combinations ranging from 22 to 60 metres in length.
When the news came on July 1, operators were told they’ll have just six months to transition to the new signs – at their own expense.
It’s a move that has been heavily criticised by transport operators and industry groups across WA.
When Mitchell was asked to
weigh in on the issue, he didn’t hold back, labelling the deci sion ignorant and misguided; and “part of a bigger systemic problem”.
“Since this idea actually ma terialised, there’s been quite a bit of industry push-back.
Main Roads WA has decided not to listen to the collective industry in Western Austra lia,” he said.
“I’ve lived this industry for the past 30 years and there are a lot of people who won’t stick around for much longer. As an industry, we could all walk in united on the same issue, and we’d just get chased out.
“This is part of a systematic problem within the Depart ment of Transport and Main Roads WA. There are too many poor decisions being made – they do it all the time and it’s second nature to them.
“People are affected every day by their decisions that are collectively much bigger than road train signs!”
The new pictorial signs are being touted as being all about
But Mitchell isn’t buying it.
“How many prangs are being caused by people overtaking heavy vehicles?” he asked.
what the industry thinks, that destroys people’s emotional and mental wellbeing, when they’re working in an industry
The issue regarding the new signs is now slated to go to an industry working group. “There is a national problem
BY JAMES GRAHAM
LONG-TIME truckie Dean Skuse dreads the weekly runs he makes along the treacherous southern tip of the Mount Lindesay Highway near the Queensland/NSW border.
The narrow, windy pass was hammered by rainfall in early 2022 and with increased heavy vehicle traffic in the area, particularly from the logging sector, Skuse fears that’s it’s only a matter of time before there’s a serious accident on one of the 30 or so hairpin bends.
“There’s some terrible bloody turns in there,” said Skuse who drives a DAF rigid from Brisbane to Kyogle carrying heavy pipe. He added, “It scares the shit outta me whenever I run through lately.
“I’ve had way too many close calls. You just come up to a corner and all of a sudden there’s someone who has cut the corner, could be a B-double, could be anything coming down that hill – way too close.
“There are a lot of newcomers using this road now and they don’t know to call up.”
All he wants is for simple UHF call-up signs to be in stalled on both sides of the border to remind the new comers to warn other truckies of their presence.
The need is already so great for warnings, that Skuse said other drivers have taken it upon themselves to draw their own call-up reminders [on channel 29] on existing signage along the stretch.
“All the ones who travel that road know the points to call-up, but it needs better sign posting to remind oth ers,” he said.
The D port and Main Roads (TMR) said it appreciates feedback from the Big Rigs reader regarding the request for Call UHF on the southern section of the Mount Lindesay Highway.
“Please be assured this feedback will be considered,” a spokesperson said.
“In relation to current and upcoming roadworks, we can advise that work is underway on the Mount Lindesay Highway between Beaudesert and the Queensland/New South Wales border to repair
vehicles entering and exiting work sites and by traffic controllers to manage traffic.
“The Call UHF signage is not included in the signage scheme for this work for through traffic. All road users, including heavy vehicle operators are required to follow the directions of traffic controllers and signage.”
Heavy vehicle operators should continue to use UHF Channel 40 to communi-
cate with other drivers, the spokesperson added.
Meanwhile, construction of the 1.5km, $95 million, Mount Lindesay Highway upgrade – Johanna Street to South Street, is set to commence in late 2024. The project is currently in market for tender.
TMR said the upgrade will
improve safety, ease congestion, and reduce travel times by widening the highway from two to four lanes, including construction of a new southbound bridge over the disused rail corridor. The Call UHF signage is being reviewed for this section of the Mount Lindesay Highway upgrade project.
EDITOR JAMES GRAHAM
never read such a pile of nonsensical rhetoric as the NSW Government responses to the parliamentary inquiry into the pressures heavy vehicle drivers are under in the state.
We’ve done our best to summarise this on page 12 because if you waded through the lot, that’s 20 minutes of wasted time you can’t get back.
What I can’t understand is that the government asked for the inquiry in the first place.
Unless I’m missing something in the nine responses to the committee’s recommendations, nothing will change for the better any time soon.
A cynical person might argue it was only convened to appease motorists stuck in traffic after a spate of overheight incidents in the Sydney tunnel network.
Do they really care about the pressures you are under and what can be done to fix them?
TRUCK driver and social media star Aaron Farquhar’s hopes to end the “us vs them” dynamic between truckies and the NHVR got a huge reaction when we posted the story on Facebook.
Many of our readers criticised Farquhar’s ambition to collaborate with the regulator, calling it “naive”.
“It ignores the real facts, that the regulator exists purely on the KPI of punishment and enforcement,” wrote Peter Mark.
“In theory this sounds like a plan, but the NHVR are justifying their jobs,” added Pete Hughes. “While they can make up their own rules to suit themselves, it’s an
endless money pit.”
Others defended Farquhar’s positive attitude and his attempts to make a difference.
“Plenty of people here commenting against him, but who has a better solution?” asked Brett Oh. “Who’s sticking their hand up to have a go?”
Farquhar thinks many truckies have an unfair attitude towards the NHVR.
Image: Aaron Farquhar
WHEN Walgett Highway Patrol released the results of a two-day heavy vehicle operation on both directions of the Castlereagh Highway in Walgett, NSW, our readers weren’t impressed.
Some of them thought the police weren’t qualified to be carrying out truck inspections.
“In my 44 years of driving to date, I have never had highway patrol show me their fatigue qualification or mechanic certificate,” wrote Phil Benson. “They can’t chase criminals because they would rather check our logbooks to see if we’re tired.”
be doing heavy vehicle in spections,” wrote Regan Bow.
Ashley Brown agreed: “This bloke is trying to help you get a fairer system, and all you do is talk him down and call him names. You might think this [collaboration] won’t happen –well it won’t with this attitude. Both sides need to change here, not just one.” drugs?” asked Niell Graham. “It’s not the good old bad old days anymore, the days of being pushed are over. We don’t need these types of drivers in the industry, it just makes it harder for the rest of us as we all get looked at the same way.”
BIG RIGS’ recent interview with Casuarina Smith, a truck driver who shares her day-to-day life, safety messages and more with her almost 80k Instagram followers, got a great reaction online.
CJ works for Merkanooka Haulage in Western Australia’s Goldfields region, hauling raw unprocessed gold ore from the mine to a processing plan – and she’s loving the job so far.
Her hard-working attitude and tenacity won a lot of praise from our readers, with James Atkins applauding her for overcoming barriers.
“That’s absolutely great,” he said. “There are a few small
physical jobs associated with big trucks that females may find a little bit difficult, but there’s always the way to overcome that.”
Tristan Michael agreed that CJ is an inspiration, adding: “A great role model for younger people. Well done.”
Casuarina Smith is popular with our readers.
Images: Trucking with CJ
Russell J Iles said: “CJ is doing great and showing her initiative. She’s on the right track.”
Meanwhile Dallas Johnson echoed: “To see a young person having a go and being proud to be productive is great. It’s a 10/10 from me.”
“Sorry but police shouldn’t
“They have no idea.”
Others were disappointed to read about one of the intercepted drivers being found with drugs in his system.
“I don’t understand why these drivers keep taking
WE recently ran a story on Big Rigs’ website about Vic toria’s shadow minister for Roads and Road Safety, Dan ny O’Brien, slamming the lack of action on the state’s “crumbling” road network – and readers were quick to chime in.
Many agreed that Victoria’s roads are in a terrible con dition and woefully under funded.
“Victoria’s state-owned regional roads are the worst they have ever been and are getting worse daily!” said Mick Debenham.
“Victoria is broke,” added Garry McPhee. “They’re building tunnels for nothing.”
Stephen Alexander agreed: “Victoria will end up the
Cuba or Venezuela of the Australian continent.”
While Craig Masefield said that it isn’t just Victoria that needs more funding for roads and infrastructure.
“Australia as a whole is so underfunded when it comes to our roads. Just ask any truck driver cris-crossing Aussie. But bugger me, there seems to be endless amounts of money spent on 50 kilometre circles in and around the main CBDs. This is a major thing in the transport industry. We have to abide by all the rules and not have defective equipment, but they can’t supply sufficient roads for us to drive on.”
BY KAYLA WALSH
THE Department for Infrastructure and Transport in South Australia has told a developer to “get a move on” and finish a roundabout on a major freight route which is causing issues for truckies.
The Roseworthy roundabout is intended to be an egress point to the new Hickinbotham development at Roseworthy Gardens, and onto the busy Horrocks Highway.
However, transport operators have said the roundabout is too small for bigger trucks to pass through safely, with sharply raised edges – and it’s killing their business.
Malcolm Heinrich, owner of transport company S.C Heinrich & Co, told Big Rigs: “This roundabout is an absolute menace.
“If you go through it with a B-double, a road train or even a normal semi, you have to go
down to about five or ten kilometres an hour.
“If you had a really high load and you were going too fast around it, the wrong movements could be catastrophic.”
Heinrich said the roundabout has forced him and his drivers to take lengthy detours, wasting time and money.
“We have quite big low loaders and the Department for Transport was telling us to go over round Two Wells and then come back.
“But Two Wells has a roundabout there with the same circumstances... So that means we would have to go right out to Dublin and then back across, or invent some other route.
“That creates a financial strain for us, as well as safety concerns, because we don’t want our drivers to get fatigued from these detours.”
Heinrich said he knows of several cases where the roundabout has damaged truck
t yres, suspensions and undercarriages.
“It’s affecting all road transport companies in the area,” he added.
“This should never have happened.”
The business owner is calling for the roundabout, which has a completion deadline of October this year, to be fixed as soon as possible.
“This was basically railroaded through, with no consultation with the heavy vehicle industry,” he said.
“The Hickinbotham development, once it’s in its final stage, is meant to have 100,000 people in it.
“This roundabout just doesn’t cut it, even for smaller traffic.”
Steve Shearer, executive director of the South Australian Road Transport Association (SARTA), said that the developers of the Roseworthy Gardens estate, the Hickinbotham
Group, have been dragging their feet.
“Because this issue has had some attention in the media, the DIT have cracked the whip and told them they have to get on with it,” he said.
Shearer said finishing the roundabout will make a difference to transport operators, but it won’t solve everything.
“There is currently an eight-centimetre drop at the edge, and when they finish the roundabout and put on the next layer of bitumen, this will be reduced to 30 millimetres.
“That will solve one of the issues with trucks going up over that ridge, but it won’t fix everything.”
He said the roundabout is fine in some directions, for some trucks and some configurations, but not all of them.
“Depending on whether you’re traveling south or north, you can almost go straight through in one direction, but about.
key freight routes.”
A spokesperson for the Department for Infrastructure and Transport for South Australia told Big Rigs that they will “continue to assess” the roundabout and its impact on traffic.
“Horrocks Highway is a state-maintained road, and the design was independently verified and subsequently approved by the Department for Infrastructure and Transport,” they said.
“Heavy vehicles will be able to freely use the roundabout once construction is complete. In the meantime, a slip lane commodate heavy vehicles for
“The roundabout is due to be completed in October 2024.”
A spokesperson for the Hickinbotham Group said: “The Roseworthy roundabout was designed in accordance with required specifications. Its design was independently reviewed and approved by the Department for Infrastructure and Transport. Construction is progressing as planned via a staged approach to avoid closing the road and to maintain access for all road users.”
THE Lake Coolmunda Roadhouse in Queensland has reopened under new ownership – and it’s had an impressive revamp.
Apart from the structure of the old building, everything is essentially brand new, from the toilets and showers to the kitch-
The new owner, Abdul Syed, told Big Rigs that he was delighted to be able to bring the roadhouse back to life.
“This used to be a very popular roadhouse, and the previous owner closed it down to rebuild it,” he said.
“He never got to do the re-
had great potential.”
Syed’s team has spent the last nine months renovating the site.
“We basically gutted it, keeping the skeleton of the old building because it was still in good condition and we would have had to apply for development approval if we got rid of that,” he said.
“Then we put in all new showers, kitchen – you name it.”
The parking bay can fit up to 20 B-doubles, with another rest area for trucks just across the road.
“The government’s rest stop is right opposite the roadhouse,
and that can fit about eight B-doubles as well,” Syed added.
“Trucks can easily turn in and out.”
With no other truck stops close by, Syed said the roadhouse is in a prime location.
“There are no other proper stops about 100km either side,” he said. “The closest one is probably Goondiwindi.
“We’ve got the lake here as well, which is very popular.”
Hot and cold food is available at the roadhouse, with a full restaurant menu as well as takeaway sandwiches and coffees.
Syed has made a point of supporting the local community
through his business.
“From the staff to the bread to the meat and produce, everything is local where possible,” he said.
The roadhouse, which was formerly a Caltex, is now a Shell dealership open from 5am to 9pm daily.
Fuel will be available 24/7, after a brief testing period, with an outdoor payment terminal on site.
Syed brings years of experience managing supermarkets and truck stops to his new venture.
“I have been a franchisee all my career, dealing with fuel,” he said.
“I used to operate the M4 motorway truck stops, which are probably the biggest ones in New South Wales.
“So this isn’t new to me!”
When Big Rigs spoke to Syed, he had just opened the roadhouse the day before.
“It’s going well so far,” he said.
“I’m expecting it to get busier after 5pm because of the trucks.
“We’re running a deal this week to get the truckies in, and the town seems to be talking about the place, with people wanting to come and try the food.
“We’re very excited to be open.”
A RESOUNDING yes to more rest areas for truckies –from the Sydney metro area to the regions – but no to making RTOs part of the chain of responsibility.
They were two of the main takeaways from the recently released NSW Government response to the parliamentary inquiry into the pressures on heavy vehicle drivers and their impact in NSW.
A parliamentary committee was hastily convened in August last year after a spike in overheight incidents in the Sydney tunnel network.
The committee received just 24 submissions from associations, drivers and other stakeholders which informed nine recommendations it tabled in January this year.
Below is an edited summary of the recommendations, the state government’s response (either ‘noted’ or ‘supported’) and Big Rigs reaction.
Recommendation 1
That the NSW Government fund and construct more heavy vehicle rest areas, whether they be formal or informal rest areas, in metropolitan and regional areas in NSW in consultation with the transport and freight industry, to ensure heavy vehicle drivers can effectively manage their fatigue and comply with relevant regulations.
NSW Government response – supported: Transport for NSW has several projects underway which includes investigation, planning, design and delivery phases to deliver new formal and informal rest areas. Industry feedback is guiding this work to ensure it meets the current and future needs of heavy vehicle drivers and the growing freight task. Some of this work includes:
• A $30 million commitment to investigate and plan for a Western Sydney Rest Area.
• A Heavy Vehicle Rest Stop Improvement Program to prepare a Strategic Business Case to propose funding for, research, audit, plan and prioritise new heavy vehicle rest area opportunities across the regional and outer metropolitan network.
• A Heavy Vehicle Rest Stop Implementation Plan, which brings together the broad range of work under-
way across the agency for visibility, including funding and constructing more heavy vehicle rest areas, whether they be formal or informal rest areas.
• Commercial partnerships with industry to develop Highway Service Centres on land owned by TfNSW.
• Submission of rest stop improvement projects to the Australian Government’s Heavy Vehicle Safety and Productivity Program for up to 80 per cent funding.
Big Rigs reaction: More reviews, plans and studies. Same old tired tune and still no action for truckies.
Recommendation 2
That the NSW Government consider the rules and regulations for industrial development in metropolitan Sydney to determine if there should be requirements for particular developments or types of business to include a dedicated percentage of land to allow trucks to be parked overnight.
Response – noted: The government said the regulatory “burden” of requiring preservation of land for the purpose of rest areas may not meet the Better Regulation Principles given the shortage of industrial land in Sydney, with reportedly the lowest vacancy rate in the world. “This may have unintended consequences in terms of the impact on availability and use of industrial land.”
Big Rigs reaction: Another cop-out tangled in red tape. Truckies would have been happy just to have an area in a quiet industrial space where they could park without the threat of a fine.
Recommendation 3
That the NSW Government fund and construct more adequate heavy vehicle parking bays and sites in metropolitan and regional areas in NSW, in consultation with the transport and freight industry, to ensure heavy vehicle drivers can effectively manage their fatigue and regulation compliance.
Response – supported: See recommendation one.
Big Rigs reaction: They must have been short on recommendations. They basically repeated the response to
number one but added in the words ‘parking bays’ instead of ‘rest areas’.
Recommendation 4
That the NSW Government require Transport for NSW to take all necessary steps to:
• Find alternative heavy vehicle rest areas, and parking bays when roadworks or closures are undertaken that result in existing rest stops being accessible.
• Notify the heavy vehicle industry as early as possible prior to the changes occurring.
Response – supported: To support this recommendation, Transport for NSW will undertake a two-stage approach:
1. Transport will issue internal communications to project and maintenance teams to ensure that impacts to heavy vehicle rest areas and parking bays are considered as part of the Road Occupancy Licence1 process. The communication will also require teams to notify industry as soon as possible, a fter the impact is identified and where no alternative is available.
2 Transport will develop and introduce mandatory requirements to ensure planning for all road works assess and identify the impacts to heavy vehicle rest stops. This includes indirect impacts where the existence of any road works has the potential to impact fatigue management plans as part of a heavy vehicle journey.
Big Rigs reaction: They should have been better at communication from the outset. But we’ll take this as a win.
That the NSW Government fund and run a targeted community education campaign for light vehicle drivers on the importance of rest areas for heavy vehicle drivers to discourage their use by cars and caravans.
Response – noted: A campaign discouraging use is inconsistent with existing fatigue management campaigns, the government said. However, it will provide ac-
tive education directly to caravan and motorhome associations on best practice use of rest stops.
As part of the heavy vehicle rest stop program, Transport for NSW will also investigate signage at appropriate rest stop locations to focus on the inappropriate use of rest stops by caravans for long stays. All rest stops in NSW are designated for use by both heavy and light vehicles, it added.
Big Rigs reaction: It reads like they intend to provide more facilities for truckies, but only ones they still have to share with caravanners.
Recommendation 6
That the NSW Government consult with relevant national bodies regarding the possibility of requiring RTOs to be included as part of the chain of responsibility framework to ensure the provision of quality training.
Response – noted: The NSW Government said it supports the need to raise safety standards by addressing poor-quality RTO practices that may arise. But requiring them to be part of the RTO is a bridge too far.
TfNSW is concerned that expanding the CoR to capture RTOs may dilute responsibility from those with day-to-day oversight of the transport task.
“It could be foreseen that adding CoR status could dissuade some providers from delivering training in this field and could impact the number of training providers in the market,” the government added.
Big Rigs reaction: So, they
want to improve training standards just as long as they don’t discourage newcomers from entering the sector? We don’t follow the logic.
Recommendation 7
That the NSW Government consider whether the current heavy vehicle licencing regime, based on a knowledge test and a competency a ssessment is adequate in the absence of a compulsory education/training component.
Response – supported: The current Heavy Vehicle Competency Based Assessment (HVCBA) system for new licensees isn’t about to change anytime soon, based on the government’s response.
Any changes to the current system would result in “access and equity issues” for regional and remote drivers.
Big Rigs reaction: Based on your feedback, the government needs to start auditing more RTOs if they think the training system we have is adequate.
That the NSW Government endorse the introduction of competency-based driver training programs for new heavy vehicle drivers and ensure drivers issued with a heavy vehicle licence have the various skill sets and experience to drive, and manage, a heavy vehicle.
Response – supported: See recommendation 7. State government feels that the HVCBA “aligns with Australian best practice” and already contains up to 14 compulsory competency-based criteria.
That the NSW Government work with transport and freight industry stakeholders to design, develop and implement a cadetship or apprenticeship pathway program that allows or encourages people to access the workforce as a heavy vehicle driver to help alleviate some of the pressure stemming from workforce shortages in the industry.
Response – supported: The government said a cadetship or apprenticeship pathway program will be considered as part of a suite of options to address workforce shortages, but it is not the only solution that will be considered.
“Consultation with industry and other stakeholders will inform development of options and the final recommended policy approach.”
The government said a current traineeship pathway is a lready in place to support heavy vehicle drivers (Certificate III in Driving Operations), and that the Department of Education can work with industry partners to investigate ways to increase participation and completion rates under the Apprenticeship and Traineeship Roadmap 2024-2026.
The government said it is also considering a “range of options” focusing on improving workforce diversity, but didn’t elaborate on what they were.
Big Rigs reaction: All sounds grand but how does it help the industry today?
For many, the chain of responsibility laws and how they apply to the industry are just as confusing today as they were when they first launched.
BY JOHN-ANTHONY HODGENS AND LOUISA COOK
THE intricacies of the Heavy Vehicle National Law (HVNL) and the Chain of Responsibility (CoR) can be tricky to understand, so law firm Macpherson Kelley has put together this explainer.
The article details who is a party in the CoR, what are the duties of everyone in the CoR and what duties executives play.
It also explores how the hierarchy of control can be implemented by businesses to manage and mitigate risk.
What is the Chain of Responsibility?
It’s been six years since the introduction of the HVNL established the CoR obligations for all parties who play a role in the logistics supply chain.
In more recent times, we have seen an increase in enforcement activities at a national level which has resulted in jail sentences for individuals, other than drivers and this trend looks set to continue.
In March this year, we
produced an Insight that delves into how the National Heavy Vehicle Regulator has changed. At a high level, in May 2017 the National Heavy Vehicle Regulator (NHVR) established the CoR which legislated a primary duty of safety for vehicles that are 4.5 tonnes or more.
Many vehicles have a Gross Vehicle Mass (GVM) of 4.5 tonnes. By way of example, some of the larger utility vehicles have a GVM nudging in at 4.5 tonnes, and many vehicles towing a caravan or carrying a heavy load will have a GVM of more than 4.5 tonnes.
The obligation requires all parties in the CoR to ensure so far as reasonably practicable, the safety of transport activities (Primary Duty). These changes affect any state or territory in Australia, except Western Australia and the Northern Territory. Recent case law has highlighted the extent of the Primary Duty reaching managers and executives. The maximum penalties for breaches of the Primary Duty for executives are:
1. $300,000 and/or up to five years imprisonment for conduct that recklessly exposes a person to risk of injury;
2. $150,000 for conduct that exposes a person to risk of injury; and
3. $50,000 for conduct that breaches the executive duty.
A ‘party’ is any person who is involved in the operation of vehicles weighing in excess of 4.5 tonnes that transport goods. The legislation focuses on a granular examination of the everyday duties of the employee rather than the job title or position description in isolation.
For executives of businesses, the HVNL imposes a positive duty of due diligence (Positive Duty). Under section 5 of the HVNL, an ‘executive’ extends to any person who is concerned with or takes part in the management of a corporation.
The Positive Duty requires executives to perform their due diligence and ensure that the business is complying with their Primary Duty.
What are the duties of everyone in the COR?
The NHVL requires parties of the COR to ensure, so far as reasonably practicable, that their vehicles and drivers are
Vehicles should be consistently monitored to ensure that they are maintained in working order and meet the minimum design and safety requirements before being
‘Reasonably practicable’ is he likelihood of a risk to safety and/or road infrastructure and the potential harm;
• the party’s knowledge of
• the practicability of implementing the control strategies to eliminate or minimise the hazards and risks arising.
It is critical that all parties in the COR consult with each other about the risks and undertake a comprehensive risk assessment (on a continuous basis) of the current hazards and risks, and verify and validate the implementation of any risk controls.
What are the duties of executives?
The Positive Duty imposed on executives requires them to ensure:
• they have sufficient and upto-date knowledge on:
risks involved in transport activities; and
• how to implement safe transport activities;
• access to resources regarding eliminating and minimising the risks and hazards associated with transport activities are easily accessible by the business and any employees in the COR;
• the business is implementing processes to eliminate or minimise the risks and hazards and have the information available for the steps involved if there is an incident.
For example, executives can assist in reducing the risk of drivers in the business feeling pressure to speed or to drive
while fatigued by allowing for adequate timeframes when preparing schedules for loading and dispatching the vehicles.
It is recommended that businesses implement a control system to effectively manage and minimise risks. The ‘Hierarchy of Control’ (Hierarchy) methodology ranks the control methods by reference to the level of protection and reliability of each elimination/minimisation process. The Hierarchy of Controls is shown on the panel below.
• For more on CoR and why prosecutions must go further along the chain, turn to Jodie Broadbent’s column on page 48.
Key Takeaways
• It is not just the party operating the vehicle that is liable for safety contraventions, executives and other decision-makers in the business need to ensure that they are also taking steps to ensure the business is discharging its positive duties.
• It is important to ensure that your risk management practices are fit for purpose and that you are continuously monitoring processes and looking for ways to improve on the elimination and minimisation of risk (adopting a Hierarchy will assist you to do so).
• In the event that a crisis occurs, you and your employees need to be adequately informed on the extent of incident reporting obligations and evidence management processes, including when to seek legal advice, which is almost always, early.
When Sharna Chapman’s marriage broke down, the mum-of-four found herself running an interstate transport company alone.
Buying the K200s has been a major highlight for Sharna, but she admits her life is so hectic that she hasn’t had the opportunity to stop and think about how far she’s come.
“I don’t get a lot of time to sit back and look at what I have achieved. I just have to keep going!”
When people ask her how she’s managed to make the business work on her own, she says she never had a choice.
“I don’t know anything else. If I was to give it all away, there’s no way I would get another job that pays well enough to support my family.
“I needed to feed my kids and pay the rent, so they have a house to live in.
love for trucking.
“Driving is what does it for me,” she said. “Every time I get behind the wheel, it changes my whole attitude.
“I’ve just picked up a new Pearlcraft steering wheel for my K108, and I’ve switched the outside lights so they turn from amber to purple.
“You’ve got to have a bit of fun with it, don’t you?”
Sharna grew up around trucks – her dad was a driver for most of his life and used to tell her stories about his adventures on the road.
“One day when I was about ten years old, I was out with him when he was loading some hay,” she said.
“He asked me what I wanted
‘Livestock is in our DNA’
What started with a single four-tonne truck 80 years ago has grown into one of the country’s largest livestock transport companies, now in its third generation.
BY DANIELLE GULLACI
FROM shipments of cattle, sheep and pigs to the occasional donkeys, camels and even circus animals, it’s been one hell of a ride for family-owned and operated business Frasers Livestock Transport.
Based in the town of Warwick, Queensland, which the family has called home since 1888, the livestock transport business was founded in 1944 and has depots across the state. Frasers tranship between 2.5-3 million stock and travel more than 7 million kilometres each year.
The company is run by directors Ross and Les Fraser, who represent the second generation, and Warwick (son of Les), bringing the business into a third generation.
In 1944, when Charlie and Edna Fraser first got the keys to their little red Ford, they could not have imagined this would mark the beginning of something so successful.
“Dad had a friend in Warwick who had a small truck; and he said ‘why don’t you buy one and start carting livestock. I think there’s a future in it’,” recalled eldest son Ross. So Charlie did just that, borrowing 100 pounds from his grandfather.
Back then, it was Charlie’s grandfather who said: “Who knows, one day you might have a fleet of trucks.”
The Ford was used to cart grain, then chickens, before moving into general livestock. And as the saying goes, the rest is history.
One truck grew to two, and then three. “The first few trucks were only about 15ft long. Then they progressed to 20-footers.
“It was all body trucks for the first 12 to 15 years,” said Ross. “Those were the days when the only bitumen west of Warwick was through the towns.”
I REMEMBER DRIVING MY FIRST LOADED BODY TRUCK ON MY OWN, LOADED WITH SHEEP, WHEN I WAS 13, WITH DAD TRAVELLING BEHIND ME.”
ROSS FRASER
from the family business, got involved very early on. “Dad never made any secret of the fact: ‘Your mother and I are setting-up the business for you boys’,” said Ross.
“Fortunately, we were interested, particularly in the livestock aspect. We love working with livestock. Livestock is in our DNA.”
From just 13 years of age, Ross was working in the business with his parents, while still going to school.
“I remember driving my first loaded body truck on my own, loaded with sheep, when I was 13, with dad
travelling behind me.”
While the first trucks were Fords, during the 1960s and 1970s, the fleet was largely made up of Commer ‘Knockers’, before progressing to Kenworths. The first Kenworth in the fleet was sec
ond-hand, purchased in the 1980s. This was followed by the first new Kenworth in 1987.
Today, the fleet of 50 prime movers is all Kenworth T659s.
“We achieve a lot of efficiencies in having one brand
and one model. Plus, we see the Kenworth product as the number one for what we do in our industry, particularly in our business. They’re all Australian made and a very good vehicle backed by good service. The T659s are easy
TO HAVE ANOTHER GENERATION INVOLVED IN THE LIVESTOCK TRANSPORT BUSINESS WOULD BE THE FAIRYTALE.” WARWICK FRASER
for our mechanics to work on too,” explained Ross.
through to the 150-strong trailer fleet, built by Byrne Trailers, based in Wagga Wag ga, NSW.
workshop crews, it makes it as efficient as possible to have one brand of truck and one brand of trailer. Those products just fit everything we need,” added Warwick.
years in the family business, Ross has witnessed much change first-hand. “One of the major differences is in the mul tiple trailer combinations we now use. The level of innova tion, improvements in equip ment and the way we do things is just incredible,” he said.
ing and internet communica tion with drivers. It was not so many years ago that drivers would have to find a phone box to ring-in to head office.
“The other change is the distance we cart the livestock.
Loading densities are so im portant in this industry, par ticularly when carting long distances. The quality of the equipment and of our drivers means we get the job done,” said Ross.
“In the days I was driving, we’d do a 600-700-kilometre trip and it would take two to three days – pulling one trail er. Now our drivers can do the same job (pulling three trail ers) in one day. It’s testament to the quality of the equip ment we’re using, the quality of the roads and the expertise and experience of our drivers.
“In spite of some sectors of the trucking industry criti cising the road network, the roads have improved over the years and that’s really opened up this country. Our drivers can do the work more effi ciently. Our company motto ‘in time, on time’ is something we’re really proud of.”
Frasers’ biggest logistical move to date came in 1986, when the company was tasked with moving 6500 pigs from the Darling Downs to Dar win in an exercise that would take several months to com plete. “They were live export pigs and that was a huge un dertaking for us. We did it in four trips, carrying around 1600 pigs per trip,” recalled Ross.
“We started in the middle of winter and the last lift was in
Queensland, into central and southern New South Wales, as well as into the Northern Territory,” said Warwick.
can be said of many of their customers.
“We have a lot of long-standing loyal customers who have
“My father, grandfather and uncles would often talk about working for families, and then working for their sons and daughters. We’ve been lucky
“We recently had a job booked in by a company which was one of Frasers first customers in 1944. They’re
“This is also true of some of Ross believes a good business
“We’ve been fortunate to have really good people in ond and third-generation – a lot of long-serving staff,” he said. “Some have been with us more than 35 years. We’re
volves a lot of time on the road and time away from family.”
Just like his father and uncles, Warwick grew up around trucks.
constant for as long as I can remember, in particular the ‘going’s on’ in Short Street.
School holidays spent helping out on the truck wash and at the sheep sale; grandparents and cousins living close-by; riding my bike to school and looking down Short Street to see trucks, trailers and plenty of activity.
“I went to uni and worked elsewhere for 10 years. Back then, there was no intention of joining the family business. As those years progressed though, the business fire was idling away.
“My grandparents are undoubtedly the reason I’m involved in this business. They had so much time for all of their children and grandchildren,” continued Warwick.
“There have been a lot of great people who have brought the business to where it is today – but it all started with my grandparents Charlie and Edna and the fortitude they must have had in 1944.
“They were newly married
years that they had the guts to buy a truck and say, ‘let’s do this’.
“That can-do attitude is something that has continued in our business. It’s been a great effort by so many people to get the business to where it is today. Our business is about family, and not just the Fraser family, but all the families who are involved.
“I’m incredibly humbled to be a part of what has been a pretty amazing family business and legacy built over the last 80 years.
“I love being part of it and love being able to do my bit to see the family business move forward through the ages.
“I hope that, in 80 years from now, there will be plenty of green Frasers trucks on the road - doing what we do best,” Warwick said. “I also hope my kids develop that passion for the business. To have another generation involved in the livestock transport business would be the fairytale.
“Our family passion for this
Since coming into the industry, this north Queensland truckie has tried his hand at various types of roles – and says that’s what keeps things interesting.
BY DANIELLE GULLACI
AFTER spending 16 years in the army, where he progressed from a medium rigid through to a multi combination driver’s licence, Steve Beasy moved straight into the transport industry – and he hasn’t looked back.
Aged 46, Steve grew up in Victoria and the Northern Territory. He joined the army in Victoria in 1995 and after completing his training, transferred to Townsville, which he has called home ever since.
“Even though I got my MC licence in the army, I never used it. I had my fuel ticket though so when I left I got into fuel tankers, starting out in the heavy rigids and eventually working my way up to road trains,” he explained.
“I’ve moved around a fair bit because I like to try something different. I’ve done local and interstate. I’ve done refrigerated, general, side tip pers, and quad side tippers while I was doing FIFO work for Toll out of Cloncurry.”
Another transport business Steve worked for was Hillman’s Transport, doing refrigerated and general transport – and it was here that he met his partner, fellow road train driver Hope Mogg.
In June, Steve began a new role at Hawkin’s Transport, doing a mixture of freight including cement powder, flat top and general work, mostly in triples.
Steve is currently behind the wheel of a 2013 Kenworth C509, which is a big change from the previous truck he was in at Morgan Transport, where he spent the last two years carrying refrigerated freight.
“I came out of an automatic Volvo and into the C509, so it’s a bit different to driving that. I don’t mind it though. Now that I’m back in the long bonnet, it’s been pretty good,” he said. “It’s a bit like riding a bike, you never forget how to
Transport was a great compa ny to work for, he was keen to get back into road train work and daytime driving rather than overnight express. “Dave Morgan was a great boss. I al ways got along with him, and he’s helped me out whenever I’ve needed work.”
When Steve chatted with Big Rigs, he was just weeks into the new role at Hawkin’s and said it was a perfect fit. “I’m enjoying all the different types of loads and the versa tility of the work. The runs change so you get to go to places you don’t normally go and it’s a mix of gravel work and highway.”
So far the runs have seen Steve away anywhere up to five days at a time. When he chatted with Big Rigs, he had just arrived at the outback Queensland town of Nor manton, carrying a cement ISO on the lead trailer and two dongas on the rear.
IT’S
A BIT LIKE RIDING A BIKE, YOU NEVER FORGET HOW TO DRIVE A ROADRANGER!”
STEVE BEASY
Though Steve says Morgan
Steve prefers to bring his own food and drinks where he can and has his truck set up well for the long runs, with two fridges, a freezer and a 12-volt meal warmer. “I think it’s important to set up your truck so you can travel in comfort,” he said.
In terms of rest areas, Steve says he hasn’t had too much trouble finding somewhere to stop, though many don’t have facilities. “I just try and pull up wherever there’s a decent amount of parking. Out here it’s pretty good, and even from Townsville to Mt Isa there are a few places you can stop,” Steve added.
In terms of tough roads, Steve says a stretch between Millaa Millaa and Ravenshoe in Queensland can be quite the challenge. “It’s a B-double route but it’s up the steepest hill and sharpest bends and it’s really foggy out there because it’s all dairy country.
cated but I don’t reckon it’ll ever happen. Not at this end anyway.”
But all in all, Steve says he enjoys his work as a truck driver. “It’s the freedom of not being told what to do every 5 minutes like when you’re doing the around-town work – you can do your own thing and pull up when you want to pull up.
“I know sometimes people push themselves to get there but at the end of the day, what’s an extra half an hour? If I’m tired, I’ll pull over and have a little sleep, and then I feel good again. I know a lot of guys will have a rest in their seat but I like to get in the bunk where it’s comfortable, even if it is just for 15 minutes.”
Steve added that he’d like to see a lot more young people coming into the industry.
“There are a lot of drivers who are in their sixties or older and unfortunately we don’t have any real recruitment path for young people to come into the industry when they finish school.”
He added that there are also
cars just brake checking and doing stupid stuff or cutting in front of you and then slow
come into the industry think
ing they know everything, which is why there are a lot of accidents now. They come in a bit cocky and don’t listen to the older guys. There seems to
BY DAVID VILE
“I WENT and had a look at it the first chance I got, bought it and then thought ‘What am I doing?’, but I have no regrets now!” Despite those initial reservations, Dale Twyford reckons the investment he made taking the plunge on a 1997 Kenworth T601 as a project truck has been a worthwhile one. He was running the polishing cloth over the Kenworth earlier this year at the Rutherglen Rumble, with the T601 originally put into service as a fleet workhorse for Francis Transport just over the Murray River at Corowa.
Having been on the lookout for a Kenworth to tinker with, the T601 may not have been his first choice, but when it came across his radar in April last year he was soon making a move. “I guess I was more a fan of the square bonnet Ken worths, like the T650s and so
forth, but they are a bit of an iconic truck, the old ‘Anteaters’ – there aren’t a lot of 601s getting around and I thought ‘I could make something of that’. My brother was talking to one of the Francis employees at the servo in Corowa one day and he said there was one for sale. I said, ‘You’d better chase that up, and see if they are serious about selling it,’ and here we are!”
With Francis Transport running out of Corowa to the major centres, the Kenworth had been a fleet truck, running the highway on general freight. Powered by a Cummins N14 Celect at 525 horsepower running through to a 13-speed transmission, the T601 was in a pretty sound condition both mechanically and structurally when Dale took possession. He explained: “It’s only been up and down the highway with a single trailer, it hasn’t been outback or anything like
that. It has done 2.4 million kilometres all up. When I bought it last year, it had only done 90,000km on a rebuild in eight years. They were just using it on local, pulling a trailer between Corowa and Albury, so it hadn’t done a lot of work in that time. It has been well looked after. I took it for a roadworthy straight after and was panicking a bit as I had put my money down for it, but it pretty much nailed that.”
Dale works as a mechanic at Dawson’s Haulage in Wodonga, so his skills were soon put to use on the T601, at both his parents’ place at Table Top and at his home in Howlong. The Cummins had a blown head gasket, which Dale soon rectified, before he started making a few changes to the appearance of the Kenworth. “It had spider rims, so we changed that to 10-studs on the steer,” he said. “We put on the extra exhaust stack, and inside I have replaced the sound deadening stuff in the cabin and put a new floor in it, which has made a heck of a difference to the heat coming through into the cabin. We got a bull bar for it that had been on a log truck, it was absolutely buggered but it got blasted and polished up and it has come up a treat.”
With Dale’s brother Jake working as a spray painter at Complete Body Craft, the brothers soon put their heads together to work on the paint, to give it somewhat of an identity change from the Francis paint design. “It is all the original paint, so we touched it up as we went, but we decided to put the stripe on it,” he continued. “We just taped it up in the backyard in all the dirt! I would like to do a bit of a custom paint job on it one day; our family truck colours are usually blue so I wouldn’t mind doing the chassis blue and maybe doing the cab white with a blue stripe or something, but we will look at that in good time.”
Dale took the T601 to the Kenworth Klassic at Clarendon last year and is looking at making a return visit this September. Having missed
just taped it up
the Crawlin’ the Hume heritage run the day before, he wheeled the T601 out for the Show and Shine at the Rutherglen event on the same weekend. “I haven’t done a hell of a lot with it in terms of taking it to shows, as I want things to be right on it before I take it too far, so thought I would give it a run over here today.”
Having drilled holes in the chassis, Dale is on the lookout for a set of round tanks to affix to the T601.
He plans to keep chipping away, making some more improvements with a view to having the truck making a dollar or two for its owner. “We are slowly getting there with it… I wouldn’t mind if it did a bit of local work around the place, just to say it’s done it, and then put it on club rego. As it is now it’s a pretty expensive garden ornament, but it’s all good fun!” he concluded with a grin.
TRAILER giant MaxiTRANS has partnered with Triple Eight Race Engineering/Red Bull Ampol Racing. MaxiTRANS said the new partnership, which promotes the company’s Freighter brand, marks a significant milestone in its “commitment to promoting excellence, durability and quality as it continues through t he exciting transformation of its trailer manufacturing business”.
Launching at last month’s SuperNight at Sydney Motorsport Park, the partnership aims to enhance engagement with fans of Australian motorsport and to help create memorable experiences for our customers.
“We are excited to join forces with Red Bull Ampol Racing,” said Greg L’Estrange, MaxiTRANS executive chairman.
“This partnership brings together two brands that both reflect a shared dedication and commitment to high performance, innovation and delivering excellence. Particularly at a time as the MaxiTRANS business is forging ahead with its plans to transform the trailer manufacturing industry in Australia.
“We are certainly thrilled to be part of supporting a high performing team, collaborating and working towards achieving great things together.”
Jamie Whincup, managing director of Triple Eight R ace Engineering, said he couldn’t be prouder to announce Triple Eight’s partnership with the team at MaxiTRANS, representing their Freighter brand for the remainder of the season and into next year.
“Their focus and drive towards strong, durable, and top-tier equipment is a quality we love at Triple Eight,” Whincup said.
“There is no doubt in my mind our partnership with Freighter is a brilliant chance to merge our thinking and processes moving forward, and I can’t wait to see what the future holds between our two brands.”
BY KAYLA WALSH
THERE are so many great truck shows and events that are coming up soon – here are some dates to add to your diaries.
AUGUST
Casino Truck Show
August 3, 2024
Casino, NSW casinotruckshow.com.au
One of the biggest truck shows in the southern hemisphere, the Casino Truck Show is back – with over 600 trucks expected from all over Australia. Truck registrations ($30 each) will take place from 6am to 9.45am. The popular street parade is at 10am, and award presentations will take place at 3pm, with over 70 trophies up for grabs. Entertainment will include Mossy Rocks and the Tony Q Band, who will be rocking out tunes from two separate stages. There will also be plenty of kid-friendly activities such as amusement rides and face painting, and a range of exhibitors showcasing industry-related products and services. Plus J&J Rodeo will put on a spectacular Bull Ride under the roof of the new arena at the Casino Showground and Racecourse. For more info email info@casinotruckshow. com.au or call (02) 6660 0300.
TechDrive 2024
August 7 Braybrook, VIC marketing.whgsolutions. team/techdrive-eoi
Following its successful launch event in Melbourne in 2023, WHG is taking TechDrive on the road again this year. The event will showcase the latest in technology and innovation, with announcements on new product releases, developments in telematics, IoT, location data and more.
Lowood Truck Show
August 17
Lowood Showgrounds, QLD
Facebook: The Lowood Truck Show
Held at the Lowood Showgrounds in Queensland, this local show features a display of trucks, bikes and cars. A
through Main Steet, Lowood, at 11am. Other attractions on the day include kids’ entertainment, trade stands, live music and food and drink. Entry is free, with donations for charity welcome. For more information email lowoodtruckshow@ yahoo.com.au, or call Robert on 0467 530 349.
Australian Festival of Transport
August 22-25 Alice Springs, NT roadtransporthall.com
The Australian Festival of Transport is back! Held at the Road Transport Hall of Fame in Alice Springs, the induction ceremony for the Shell Rimula Wall of Fame will be held on August 24, honouring transport heroes who have been in the industry for at least 25 years. Attendees at the festival can also look forward to welcome drinks, a breakfast hosted by Transport Women Australia Limited, and a museum open day on August 25 with mini train rides.
Thallon Truck Pull
August 31
Thallon, QLD
Facebook: Thallon Team Truck Pull
The main attraction at this event is the Team Truck Pull competition, where a team of six people pull a prime mover over 25 metres. The winner is the fastest team! Attendees at the event can also enjoy a kids’ zone, market stalls, food and drink and more. For more info, email thallonpandctreasurer@ gmail.com.
SEPTEMBER
American Iron Echuca Truck Display
September 7-8, 2024
Echuca Rotary Park, VIC campaspe.vic.gov.au
All makes and models of trucks are welcome at the American Iron Echuca Truck Display. Attendees can look forward to modified tractor/ mini tractor pull demonstrations, on-site camping and catering, club merchandise and trade stalls, as well as live music by Van-yt.
September 12-13
Pacific Bay Resort, Coffs Harbour, NSW natroad.com.au
NatRoad Connect 24 is an event where truck operators, industry suppliers, and sector stakeholders can network and attend sessions on practical and operational information and advice. The event also includes the Cummins and PACCAR and its Dealer Industry Fund Gala Dinner, where the NatRoad Annual Awards will be presented. Early Bird registrations are open until August 9, 2024.
September 18 -19, 2024
Melbourne Convention & Exhibition Centre, VIC megatrans.com.au
Leaders from across the supply chain will gather in Melbourne to discuss the future of the logistics industry at MegaTrans, an integrated trade expo and conference reserved for companies offering advanced technologies and services. Experts will discuss the issues that are shaping the future of the sustainable supply chain, including workplace diversity and real estate planning.
Clarendon Classic Machinery Rally
September 21-22
Clarendon, NSW sydneyantique machineryclub.com
Held at the Hawkesbury Showgrounds on Racecourse Road in Clarendon over two days, this event offers something for everyone. Check out some classic rigs at the Kenworth Klassic Truck Show, hop on an old double decker bus to Richmond Station, or explore the displays of vintage machinery, including stationery engines, tractors, steam engines, models and more.
Entry for the general public is from 9am to 4pm Saturday, and 8am to 3pm Sunday. Ad mission is $10 for adults and $5 for childr enjoy free admission, compli mentary camping, a welcome BBQ on F gold coin donation, and a two-
course rally dinner on the Saturday evening.
Young Big Rigs Truck Show September 22 Young, NSW youngshow.com.au
The Young Truck & Bike Show is back for its third year, with prime movers and rigids, cars and motorbikes all welcome. Prizes are up for grabs for the best-looking rigs. For more information and entry forms email youngshowsoci ety1@gmail.com or phone 0435 953 580.
Gold Coast Truck Show
September 29
Mudgeeraba Showgrounds, Worongary, QLD Facebook: Gold Coast Truck Show
The Gold Coast Truck Show combines with the GC Car & Bike Show to form three exhibitions in one at Mudgeeraba Showgrounds (exit 77 off the M1). All trucks enter Gate 3 at the back gate of the Showgrounds on Worongary Rd, Worongary from 6:30am Sunday September 29, 2024. Trophy presentations from 12.45pm at the centre stage.
OCTOBER
Wauchope Yesteryear Truck & Machinery Show
October 5-6, 2024
with plans to make the event bigger and better. There will be no Saturday night dinner this year, but there will be additional food outlets and a bar in operation. Set up and a tractor run will take place on Friday October 4. For more info email wytmc.inc@hotmail.com.
Lights on the Hill
Memorial Convoy
October 5-6, 2024
Gatton, Queensland
This year’s Lights on the Hill event will see twin convoys leaving from Brown & Hurley
Toowoomba and Mica St, Carole Park in Brisbane on Octo
event, attendees can look forward to live music, kids’ rides, markets, trade and food stalls.
NOVEMBER
Illawarra Convoy November 17, 2024 Illawarra, NSW illawarraconvoy.com.au
The Illawarra Convoy is celebrating 20 years in 2024, so this year is going to be a big one! Attendees can expect a colourful convoy, live music, kids’ entertainment, food, a raffle and more. All funds raised will be distributed via the Illawarra Community Foundation to charities and families in need within the Illawarra and South
SHELL Rimula has partnered with Big Rigs in a big way – so there are even more reasons to send in your best truck shots.
Each month, the Big Rigs team will choose a #PicOfTheMonth, with the lucky winner receiving a $500 Shell Coles Express Gift Card.
Keep an eye out for our regular posts on the Big Rigs National Road Transport Newspaper Facebook page, calling
for your best truck photos and add yours in the comments, or email them to kayla.walsh@ primecreative.com.au.
Don’t forget to include a brief note about the truck and where the photo was taken. We’ll feature some of the best photos in each edition of Big Rigs Newspaper, with one winner announced each month. Keep those amazing truck pics coming!
When the going gets tough, truckies keep everyone going
THE Lowood Truck Show is back on August 17 and promises to be even bigger and better than ever.
Located around 60km west of Brisbane, the small regional town comes to life as trucks make their way to the grand event.
Show organiser and veteran truckie Rob Liston, who’s been behind the wheel for about 40 years, started Lowood Truck Show 13 years ago, together with his wife Kassie.
That first rendition was put together in just three weeks, with 20 trucks gathering at the local RSL Club.
“It was all organised through word of mouth. And then things went from there,” said Rob. “People kept saying you should do this every year, so here we are.”
est that by the following year,
the decision was made to move the event to the Lowood Showgrounds, where 65 trucks took part.
The Lowood Truck Show has called the Showgrounds home ever since, with the last event – held in 2022 – involving 256 trucks, along with a selection of cars and bikes too.
Rob made the decision not to hold the event in 2023, as he and his wife had moved out of the town and relocated to Chinchilla, some 230 kilometres away.
Due to popular demand, it’s back!
“There was a big call asking us to get the Lowood Truck Show back up and running, so here it is,” Rob said. “This time around, we’re expecting in excess of 300 trucks.
donate something for our auction, which will also be raising money for Dementia Australia.”
“We’ve been doing the event for so long that everything falls into place nicely now. A lot
more sponsors have come on board this year – even sponsors from interstate, including Victoria and New South Wales. It’s really taken off!
“Jon from Heavy Haulage Assets (HHA) has remained as one of our great sponsors."
Each year, Rob chooses a charity for the event to partner with. This year all proceeds from the Lowood Truck Show will be donated to Dementia Australia.
“General entry and truck registration is free, however donations are welcome,” added Rob. “There is also no fee for stall holders, instead we just ask for a donation. Most stall holders will
The day will begin with a parade at 11am. Vehicles will do a loop through Lowood, departing from the Showgrounds, heading through Main Street, before making their way back for a host of activities and awards.
“We create a bit of a traffic jam through Lowood for about an hour or so. In the past we have had road trains in the parade, so we’re hoping to get a permit to get road trains in there again this year,” explained Rob.
The parade will follow behind the ‘Lead Truck’, with those hoping to score the hotly con-
tested spot invited to place a bid by messaging Rob through The Lowood Truck Show Facebook page. “The highest bidder will be taking prime position,” he said.
There will also be around 30 trophies presented on the day, with a trophy presentation kicking off at around 3.30pm.
“Truck of the Show and the Charity’s Choice are our two big awards for the day. We like to involve the charity we partner with each year, so someone from Dementia Australia will be there to present the Charity’s Choice award,” explained Rob.
Attracting up to 5000 people, the Lowood Truck Show really is an event for the whole family.
be
August. The impressive and heavily modified Western
has become known as “the world’s fastest diesel truck”. It’s become a regular sight on the truck show circuit and always draws in crowds.
Adding to that there will be plenty of stalls, food and a bar. While entertainment will include live music, a rock and roll dance group from Brisbane, a jumping castle for the kids and a mechanical bull. To find out more, visit The Lowood Truck Show Facebook page.
The family-run operation launches the start of a new chapter in its proud history by cutting the ribbon at a new premises in Unanderra.
BY GRAHAM HARSANT
PUTTING in the hard yards while growing up on a farm in NSW, to learning a trade and selling trucks, the Gerace family is celebrating the opening of its newest truck dealership.
Located in NSW’s South Coast region, the new Daimler Truck dealership officially opens this month and will be operated by STM Trucks and Machinery.
Initially it will operate from STM’s existing site at Unanderra, with a purpose-built facility soon to be constructed.
Dealer principal Michael Gerace is the son of Italian immigrants who came to Australia after the war with the dream of creating a better life. Francesco and Maria Gerace had a strong work ethic that meant long, hard hours of labour to cement a future for themselves and their family.
In the late 1950s they bought a parcel of land in the Liverpool region of NSW and ran dairy cows and a market garden. This was where sons, Michael and Ralph, and their sister Cathy learnt the meaning of hard work and the positive results it could bring.
“We worked 24/7,” quipped Michael. “If it wasn’t on the garden, it was milking the cows twice a day. Dad sold that property in the 60s and bought an orchard and chicken farm at Campbelltown. We dressed the chickens and sold those, eggs and the orchard produce in a small retail shop. The work didn’t get any easier, it was just different.”
Leaving school in year 10, Ralph gained an apprenticeship as a panel beater, whilst Michael became an apprentice diesel mechanic, working for Glen Motors who had an International Harvester franchise selling trucks and agricultural equipment.
In the last year of his apprenticeship, Michael had a soccer injury and wound up
with his leg in a plaster.
“I couldn’t work on the farm and was bored at home, so I would hobble in to work. The mechanical repairs side was out, so I sat behind the parts counter instead. I really enjoyed it, and I became a parts interpreter for four or five years.”
Jim Glen had a partner who wanted out of his share. With 50 per cent of the company up for sale, Michael saw an opportunity but didn’t have the means to jump into the deep end – so he approached his father for financial assistance.
Francesco also realised a good opportunity when he saw it and, as well as loaning Michael the money to buy in,
he also purchased the property the dealership was on, thereby becoming the landlord.
A decade later, in the early 1990s, Michael bought Jim Glen out and asked his brother Ralph and brother-in-law Nick Papallo to come in as partners.
“As part of the buyout we inherited a substantial amount of property which Jim and I had purchased over the years. We had DA approval for a new dealership on Camden Valley Way. Once Jim was gone, we built a brand-new dealership and thought we would retire there,” said Michael.
“Another decade passed, and a property developer approached us about buying
the land and premises. It was a good offer, so we did the deal. Dad suggested that we all had the opportunity to retire young, but we had 45 employees whose livelihood depended on us. So, from the proceeds of the sale, I bought the block of land where we are now at Smeaton Grange, figuring this would be the last move – except it’s not!”
The family had held the International Truck business since 1975 and added a Mitsubishi (later to become Fuso) franchise in the early 1980’s. Then around 2006 they were offered a New Holland Construction franchise, a business they felt was complimentary as a lot of their customers had tippers, prime movers, and floats and many had construction equipment.
New Holland morphed into the Japanese owned Kobelco Construction Equipment and the Gerace family have not looked back, moving into yet another premises, purchasing another Kobelco franchise at Oak Flats near Wollongong as well as a construction equipment branch at Queanbeyan.
Unlike many others, the business thrived during the Covid years with the company able to procure stock – not only of construction machinery, but also of the Fuso product.
“Throughout that period, we reached our targets with Fuso. We were proactive in
that we built trucks with bodies on them – tippers, beaver tails, whatever was needed. We were also active with our marketing and were able to increase our volumes across the dealership,” Michael explained.
Many customers had asked the business, now known as STM Trucks and Machinery, when they were going to take on a new franchise. STM has won Fuso Metro Dealer of the Year for the past two years and Michael had a good relationship with Daimler Truck Australia.
“We’ve had a sales, parts and services outlet for Fuso in Sydney for a number of years and I’d expressed our interest in expanding our franchises. Then the opportunity arose to expand with the full Daimler Truck brands on the South Coast,” said Michael.
“So, yet again we’ll be building a new purpose-built premises over an hour down the road at Kembla Grange, just south of Wollongong. We expect this to happen sometime in 2026,” said Michael.
Meanwhile he said the team is proud to be officially opening at the existing facility in Unanderra this month.
“This facility will offer the Mercedes-Benz and Freightliner product, with the Fuso brand joining them there on January 1 next year. And I
THAT WE ALL HAD THE OPPORTUNITY TO RETIRE YOUNG, BUT WE HAD 45 EMPLOYEES WHOSE LIVELIHOOD DEPENDED ON US.”
MICHAEL GERACE
can also announce that these next moves will definitely be our last!”
As well as Michael, Ralph and Nick Papallo, the family continues to involve other members, with Nick’s son Rocco as general manager and Ralph’s son Bruno as sales manager for trucks. Michael’s son Francesco has also come into the fold in the past year on the admin side and is learning the business from the ground up.
And so, the family moves onto another stage in their lives with the acquisition of the full range of Daimler Truck product.
The ‘wider family’ of employees have grown to nearly 150 and Michael says he is always cognisant that they all rely on him and his fellow directors for their livelihoods. That work ethic instilled in the brothers from an early age has paid off – not only in spades, but in trucks for Michael Gerace and co.
The new Daimler dealership is located at 7-9 Glastonbury Avenue, Unanderra, NSW.
BORDERTOWN Haulage has been choosing JOST every time for the past 30 years, for all of its trailer component requirements.
Started in 1980 and based in South Australia, Bordertown Haulage is now in its second generation – providing efficient transport services to the highest standards, to both local and interstate communities.
Company founder Peter Karger went from a single truck owner-operator to a fleet of over 10 in an instant. Today Bordertown Haulage is headed up by his son Angus.
so I’m running the compa ny now,” Angus said. “We’ve
mostly got bulk tippers, some drop decks, truck and dog combinations, B-doubles and Performance-Based Standards (PBS) A-doubles.”
Bordertown Haulage’s trucks travel anywhere between South Australia, New South Wales, Queensland and Victoria, carting grain and fertiliser into ports, feed mills and dairies.
Angus, who also uses all of the fleet’s equipment himself, looks for the best technology possible to do the job efficiently. He says that’s why he has always chosen JOST for the fleet’s fifth wheels, couplings
JOST landing legs on a lot of our gear,” he said. “We’ve pretty much been using all JOST turntables for 25 years, and everything new that we get has something from JOST on it.”
Angus specs JOST’s greaseless nylon top fifth wheels across the fleet due to them being very user-friendly, durable, reliable and environmentally friendly.
“They’re simple to use, you don’t break your back using them,” he explained. “With the nylon, their pads last hundreds of thousands of kilometres and are a lot cleaner without grease. We don’t need to replace them unless a driver damages them, -
time with care.”
A ngus added that JOST’s landing legs also get the job done. “The legs are trouble-free and they’re essentially maintenance-free. They’re easy to use, lightweight and they’re very simple.”
JOST’s Modul landing legs have increased lifting force and are easy to change between high and low gears, making the drivers’ job more efficient.
In using JOST’s fifth wheels, Angus has also become familiar with JOST’s Sensor Coupling system, which makes the process of coupling and uncoupling a trailer very simple by giving drivers both visual and audible warnings in the event
tem will alert the driver that something is wrong and that the coupling process needs to be revisited.
“We don’t do a lot of unhooking and hooking up like people who do changeovers every day,
Angus says JOST is exceptional when it comes to aftersales service and is always available if a situation arises.
“You don’t need much when it’s a reliable product, but if you do, they’re very quick to assist,”
AIR CTI’s Central Tyre Inflation System is an important tool allowing you to adjust your tyre pressures from the cab as you drive. The cold tyre pressure you commence your journey with changes as your tyres heat and/or conditions change.
A ll properties of a tyre are influenced by its pressure, e.g. the vertical stiffness, the handling performance, ride comfort, rolling resistance, speed at which aquaplaning occurs, etc. With the correct inflation pressure, the vehicle and tyres achieve their optimum performance.
A n optimally inflated tyre improves safety, reduces wear and decreases fuel consumption by reducing rolling resistance. Under inflation reduces lateral grip, increases aquaplaning, and increases fuel consumption.
Extreme under-inflation of a tyre leads to large deflections that cause excessive heat build-up and internal structural damage that will eventually lead to tyre failure, often catastrophic.
Over-inflation increases stopping distance, reduces traction, cornering grip, vibration and driver stress.
Tyre grip is defined as the maximum horizontal force
that can be transmitted be tween the tyre and road sur face. A higher level of grip allows the driver to stop quicker, avoid accidents, re duces the chance of losing control over the vehicle, and improves the steering and braking potential of vehicles. If involved in an accident, it enables the driver to reduce speed before the collision to achieve a lower impact speed, which reduces the risk of in jury.
With increased tyre grip, the risk of directional vehi cle instability during steering and braking manoeuvres is also reduced.
Lightly loaded or empty semi trailers are considered to be the most dangerous, by insurance company reports, with jack-knifes a regular oc currence. Tyre inflations in these conditions are severely over-inflated, reducing the tyre footprint to 25 per cent of the correct footprint. Stopping distance was reduced by at least 15 per cent with optimal tyre pressures in tests done by ARTSA in 2013.
Jack-knifes happen when the drive tyres lose traction and the trailer pushes them offline. Trailer swing happens when the trailer tyres lose traction and slide outwards.
Both conditions happen when the truck is braking heavily, or when the traction level is low. Loss of traction of one set of tyres is the underlying cause. Bad brake balance, that over-brakes one or the other set of tyres and/or poor loading are the main causes. Over-inflated tyres increase the risk.
An example of poor loading
is a tip or dump truck towing a plant trailer with an excavator. A heavy trailer, with no weight on the over-inflated truck drive tyres, is a common site on most roads. Almost all cases happen on empty trucks, where braking is overpowering, on severely over-inflated tyres, that provide minimal grip or traction. Poor conditions make
life even riskier. Modern electronic braking systems virtually eliminate these accidents, although stopping distances increase considerably.
Optimal tyre pressure would substantially improve both cases, while reducing stopping distances.
The tyre road interface produces all the forces and moments used to alter the vehicle state through cruising, accelerating, braking and cornering. The footprint or contact patch with the road surface provides the traction required. The ideal footprint will have almost identical pressure on all points, limiting tread squirm while providing the best traction and tread life. To obtain the ideal footprint, the air pressure must balance the load correctly.
If the pressure is too high for the load, the footprint area will reduce, and the load distribution will be concentrated toward the centre of the tyre, reducing pressure near the edge, further reducing tread life. Tyre radial deflection will reduce, reducing absorption of impact, increasing vibration and shock transferral to the suspension and the rest of the truck.
Impact from sharp stones or edges are much higher, in-
creasing punctures, cuts, and staking.
Casing life reduces when over-inflated too. As retreading is a proven method of reducing costs, casing life is important. Traditional over-inflated tyre use increases tyre costs even further. Dual tyres suffer a major design fault. Various factors increase the running temperature on one tyre more than the other, yet both are firmly bolted together and must rotate at the same speed. Any discrepancy in tyre diameters and/or pressures causes one tyre to attempt to travel farther than the other.
A IR CTI Central Tyre Inflation System is an important tool allowing you to adjust your tyre pressures from the cab as you drive. The cold tyre pressure you commence your journey with changes as your tyres heat and/or conditions change.
A IR CTI has been operational for decades as a family run business, developing and implementing improvements routinely to ensure the best customer outcomes. This continues. We are always happy to assist with any queries. For more information, please contact sales@aircti.com or call AIR CTI’s sales manager Peter on 0409 899 916.
TOUGH & RELIABILE
DEALERS THROUGHOUT AUSTRALIA
Phone: (03) 5127 6128 (Australia) or +61 3 5127 6128
Phone Sales: 0409 899 916 (Australia) or +61 409 899 916
Email: Admin@aircti.com, Accounts@aircti.com, Sales@aircti.com PO Box 218 Yinnar 3869 10 Holmes Road Morwell, Victoria Australia 3840 www.aircti.com
LELOX has long been synonymous with quality and innovation in the heavy transport industry. Our range of trailer products, including quarter mudguards, straight chassis pipes, and mounting brackets, showcases our commitment to excellence and Australian manufacturing. Designed with both performance and ease of installation in mind, LELOX trailer products stand out as the preferred choice for professional installers and trucking enthusiasts alike.
At LELOX, we understand that time is of the essence for installers. That’s why our quarter mudguards are engineered to offer unparalleled ease of installation. Made from premium stainless steel or aluminium, our quarter mudguards are durable
and designed to withstand the rigours of the road while maintaining an aesthetically pleasing appearance.
One of the standout features of LELOX quarter mudguards is the pre-punched holes for brackets and mudflaps. This innovative design drastically reduces installation time, allowing installers to simply bolt the components together without the need for additional drilling. The pre-punched holes ensure precise alignment and a secure fit, making the installation process straightforward and efficient. Whether it’s the standard version or the provision-for-mudflap version, our quarter mudguards are designed to meet diverse needs with ease.
Understanding the varied
offer
requirements of our customers, LELOX also offers a provision-for-mudflap version of our quarter mudguards. This design allows for the attachment of a small mudflap to the top of the mudguard, providing additional protection and enhancing the functionality of the trailer. The provision-for-mudflap version is crafted with the same high-quality materials and attention to detail, ensuring that it meets the rigorous standards that LELOX is known for.
LELOX straight chassis pipes are another testament to our commitment to quality and innovation. Cast in Australia at our in-house foundry in Sydney, these pipes are available with DuraGal or 304 stainless steel tubes. For those seeking a touch of elegance, we offer a marine-grade cast aluminium boss polished to a high shine.
The installation of our straight chassis pipes is simplified through the use of LELOX sub plates. These sub plates are drilled and tapped, allowing them to be easily welded to the trailer chassis. Once the sub plates are in place, the straight chassis pipe can be bolted on effortlessly. This system not only ensures a secure fit but also significantly reduces installation time, making it a favourite among professional installers.
Our mounting brackets
our quarter mudguards and straight chassis pipes perfectly. The brackets slide on and bolt directly to the pre-punched quarter mudguards, ensuring a secure and precise fit. This seamless integration of components further enhances the ease of installation, allowing for a streamlined process that minimises downtime and maximises efficiency.
At LELOX, we take immense pride in our commit
products. Each component, from our quarter mudguards to our straight chassis pipes and mounting brackets, is crafted with the highest standards of quality and precision. This dedication to local manufacturing supports the Australian economy and ensures that our products are built to last.
LELOX trailer products are designed with the installer in mind, offering unmatched
installation. Our innovative designs, such as pre-punched holes and versatile sub plates, simplify the installation process, saving time and effort. With a commitment to Australian-made excellence, LELOX continues to set the standard in the heavy transport industry, providing products that deliver superior performance and reliability on the road. Choose LELOX for trailer products that are easy
AUSTRALIAN owned and Australian made, Trailer Gates Australia (TGA) is a specialist when it comes to all kinds of truck and trailer gates. All made-to-measure gates, as well as their range of offthe-shelf gates, are expertly designed and manufactured at the TGA’s Thomastown facility in the northern suburbs of Melbourne – just off the M80 Ring Road, which has easy access, even for B-doubles.
Owner of TGA, Duncan Stewart, took over the business in January 2023. Since then, he’s remained fully committed to creating top quality products using the highest quality materials.
Under his leadership, TGA has moved away from using inferior imported steel.
Instead, TGA exclusively uses high quality Australian made Bluescope Steel and Capral Aluminium for all its products.
Duncan says that by using this locally produced steel and aluminium, it not only ensures he can maintain the highest quality products, it also helps to support the Australian economy, by keeping more jobs here in Australia.
All of TGA’s products are manufactured by its in-house team of highly qualified master welders, who bring decades of experience – specialising in gates made from galvanised steel and alloy. Their exper-
tise helps ensure high quality is maintained through every stage of production.
“Some of our competitors are offering inferior products imported from overseas. These trailer gates might be a little cheaper at the outset but they don’t have the same level of quality and durability that you’ll find in every gate that leaves TGA’s warehouse,” explained Duncan.
While TGA’s truck and trailer gates are typically made to order, to suit clients’ varying needs, TGA also has a range of off-the-shelf gate sizes available – with no wait time.
“TGA can custom make any sort of gate for trucks and trailers, from heavy duty load racks to lightweight alloy gates, or flat tray tautliners. We build gates for everyone,” added Duncan.
TGA has customers who are located all over Australia, from owner operators through to some of the country’s largest trailer manufacturers. Each and every week, the company ships out hundreds of truck and trailer gates.
Its extensive list of clientele includes major trailer manufacturers such as Krueger, MaxiTrans, MaxiParts, Hunter Express, North-East Engineering, Drake Group, Alltruck Bodies, Shepparton Body Builders, Beavertail Trailers, Border Express, Mainfreight, West-Trans, TR Group, Combined
TGA’s products are manufactured by its in-house team of master welders. Images: TGA
Truck Bodies.
With its list of satisfied customers continuing to grow, TGA has exciting plans in store for the future.
Duncan revealed that in 2025, there are plans to build on its existing capabilities through the deployment of robotics.
“This will lead to even greater precision, as well as a greater capacity to deal with larger clients,” said Duncan.
In addition, TGA offers gate measure-ups and installation services at its factory, and can also install its steel or alloy
a competitive price.
Standing by every gate that comes out of its factory, TGA offers a 12-month warranty on all its products.
TGA is ready and capable to take on new clients, including fleet managers and major trailer and truck body builders. Wholesalers are also welcome to get in touch with the team.
For more information, please call 03 9465 3225 or visit trailergatesaustralia. com.au.
THIS is something we’ve heard hundreds (if not thousands) of times: “I’m sick of polishing my wheels.”
For as long as we’ve had trucks, we’ve had wheels that need to be polished. It is part of driving a truck or owning a fleet, and it is the status quo that has never been questioned.
However, it takes around 30 minutes, on average, to polish a single truck wheel. And when you multiply that by the total number of wheels on your rig, and then by the number of trucks in your
fleet… that’s a whole lot of time spent scrubbing wheels just to keep presentation standards up to scratch.
More often than not, fleet owners and truck drivers spend too much of their time off the road polishing their wheels. Think about the opportunity cost – polishing wheels means vehicle downtime. Downtime of your vehicles means they’re not on the road. Not being on the road means your business is not making money. It’s simple. The knock-on effect is real
That time and effort should be going elsewhere. In a world where we have GPS helping us get to destinations faster, technology automating our logistics, and even cars that can drive themselves, doesn’t it make sense that there would be a more efficient way to polish your wheels?
It’s time to question the status quo.
The good news is it doesn’t take any fancy technology, high-powered washers or expensive systems. It doesn’t ven require big upfront costs
Chrome wheels are resistant to stone chips, gravel and dirt scratch marks and are designed to hold up in harsh environments. More than that, each chrome wheel can be cleaned in about 40 seconds. That means hours back in your day, dollars back in your pocket and a rig that can meet high presentation standards every single day, no matter what you’ve put it through. If it sounds too simple, that’s because it is.
Superchrome started providing chrome wheels to truck drivers and fleet owners over 20 years ago to help them improve business efficiency
rence Transport shared the cost and time-saving impact of chrome wheels: “Since we’ve been using Superchrome, the amount of money and time saved is unbelievable. Our trucks are in and out of the wash bay in no time. You get a shine in a matter of minutes.”
Superchrome’s use of the latest technology in chrome steel and alloy truck wheels guarantees top-quality wheels that have surpassed stringent quality control testing and extend the working life of your wheels. When it comes down to it, the chore of polishing truck wheels is more about the mo-
valuable, the wasted earning potential and the knowledge that no matter how hard you polish, eventually, those wheels will lose their shine. At Superchrome, we’ve made it our mission to ensure you stay on the road longer while turning heads along the way with wheels that never stop shining.
See how much you could save by making a switch from polished to chromed alloy wheels by checking out our Lifetime Savings Calculator. Head to superchrome.com. au/life-savings-calculator and see how much you could save today.
BASED in Brisbane, RTP Transport Repairs specialises in delivering quality repair and maintenance services for semi-trailers.
A family run business established by father and son Paul and Ryan Laylock, it officially opened last month in July.
RTP’s service offering includes routine trailer maintenance through to complex repairs. The business also provides engineering design services, including updating customers’ existing trailer designs or developing entirely new concepts, to suit their needs.
Paul has held various engineering roles within the trailer space over the past 10 years, including most recently as production manager for a premier trailer builder. He also has close to 40 years of experience in manufacturing heavy equipment, includ ing everything from under ground mining equipment to heavy cranes, four-wheel drive equipment and of course, trailers.
As Paul explained, RTP Transport was opened after identifying a market for high quality trailer repairs within the area. “I was getting a lot of enquiries from friends and people I knew who had trailers
owner operator, fleet or for insurance work.
“Our aim is to get our customers back on the road as soon as possible,” added Paul. “We offer a quality service and take a great deal of pride in our work.”
Along with its repair services, RTP also manufactures a range of trailer parts and accessories for trailer and truck body builders, including toolboxes, tyre carriers, ladders, handrails and steps.
RTP is located at 36 Crockford Street, Northgate, with asy access off the Gateway Motorway (near the Nudgee
For more information, call 0438 694 879 or visit www. pairs.com.au.
IN the bustling Australian transport industry, ABS Trailquip stands out for its dedication to innovation, quality, and affordability. Renowned for its extensive range of Australian-made converter dollies, air brake equipment, axles, and suspension systems for trucks and trailers, it reinforces its position as a market leader.
Established with a vision to provide top-tier transport solutions at an affordable price, ABS Trailquip has steadily built a reputation for reliability and superior engineering. Each product in the line-up reflects a deep understanding of the unique challenges faced by the Australian transport industry, where long distances and tough terrain demand robust and dependable equipment.
ABS Trailquip’s dollies are a testament to their commitment to excellence. Designed with advanced technology
and built to withstand the rigours of heavy transport, these dollies offer unparalleled performance. Whether it’s for freight, agricultural transport, or specialised hauling, ABS Trailquip has a dolly to meet the specific needs of its customers.
Locally made using high-quality materials, ABS Trailquip’s dollies are built to last, ensuring long-term performance and reliability. These dollies incorporate advanced braking systems and safety features to ensure the highest standards of operational safety.
With a variety of configurations available, dollies can be tailored to suit a wide range of transport applications, making them a versatile choice for many industries.
ABS Trailquip’s commitment to customer satisfaction is evident in its approach to product development and service. By listening to customer
feedback and staying ahead of industry trends, they continually refine their products to meet the evolving needs of the market.
The Rocklea facility is a hub of innovation, where skilled engineers and technicians work tirelessly to ensure each product meets the highest standards of quality and performance. This dedication to excellence has earned ABS Trailquip a loyal customer base and a strong reputation. ABS Trailquip is not just a manufacturer but a partner in the success of its customers. Through its innovative and reliable dolly solutions, ABS Trailquip plays a crucial role in the Australian transport sector, ensuring safety, efficiency and affordability. For those looking for the best in transport equipment, ABS Trailquip remains a trusted name, committed to excellence in every product it delivers.
EVER since I saw the movie Red Dog, I’ve had a special appreciation for the Pilbara in north-western Australia. Red Dog tells the story of the real-life red kelpie that became an icon in the Pilbara region in the late 1970s. It is believed he travelled hundreds of kilometres to places like Roebourne, Point Samson, Port Hedland, Broome, and Tom Price – he was also taken to Perth on at least two occasions. In the movie, Red Dog impacts everyone through loyalty; he is a friend to everyone.
Like Red Dog, truck drivers and operators in the Pilbara travel vast distances, and it is a hard country. Large, dry, and thinly populated, in the north of Western Australia, the Pilbara is known for its ancient landscapes, the red earth, and its vast mineral deposits, in particular, iron ore.
Today we spoke with Phil Gibbs at Jamieson Transport in the Pilbara. Jamieson Transport is a fast-growing trucking company with a long-established reputation for having a proactive, well-maintained fleet.
Jamieson Transport has
over 70 quads/super quads/ quins, and fully equipped mechanical and engineering workshops that have the latest equipment.
They operate out of Wedgefield, WA, running 24/7 to deliver iron ore to Utah Point in Port Hedland conservatively running 90 loads every day.
The company has a fleet of 75 Western Stars and Macks. And 40 of those are fitted with Atlas Balance Rings.
When Phil from the fleet workshop came on board at Jamieson’s to look after consumables, his main focus was on saving tyres. He took the unusual step of fitting Atlas Balance Rings onto trucks whose tyres were already in very worn condition, with scalloping and lots of edge wear – and he noticed the rings were flattening out the tyre wear and he managed to get another 20 to 30,000 kilometres of use out of them.
A nd that’s loading and unloading side tippers full of iron ore with the trucks pulling up to five trailers. A very tough assignment indeed. If you are a truck owner,
a workshop technician or a fleet manager, and you are tired of sky-high fuel and tyre costs, Atlas Balance Rings are designed to cut your run-
ning costs and improve your vehicle’s performance. Enjoy smoother rides, better fuel efficiency, and longer-lasting tyres. Plus, we guarantee
a 25 per cent extended tyre life and offer a 365-day money-back guarantee if you’re not satisfied with the savings. Sceptical? Take the Atlas Bal
ance challenge and experience the benefits risk-free! For more
Cut running costs
Improve your vehicle’s performance
Enjoy smoother rides
Better fuel efficiency
Longer-lasting tyres
WE GUARANTEE extended tyre life and a 365-day money-back guarantee if you’re not satisfied.
SKEPTICAL? Experience the benefits risk-free!
TRANSPORT operator Linfox has taken a delivery of 250 custom-built semi-trailers from Krueger Transport Equipment.
This is the largest project Linfox and Krueger have undertaken over the course of their 30-year partnership, with Linfox investing in the manufacturing experience of Krueger to deliver 150 temperature-controlled and 100 ambient trailers.
The trailers will transport groceries and other consumer goods, meeting growing demand for Linfox’s services.
The temperature-controlled trailers feature integrated tracked and monitored cooling systems to maintain a specific temperature range throughout the journey.
They also include advanced safety systems, aerodynamic designs and smart technologies to enhance overall effi-
ciency and reduce fuel consumption.
Linfox president of fleet and procurement Ray Gamble said: “Linfox always makes its fleet decisions in line with its commitment to safety and compliance, service excellence and sustainability.
“Linfox has trusted relationships with fleet suppliers like Krueger, along with an unwavering commitment to invest in the very best fleet.
“These customised trailers suit Linfox’s evolving logistics requirements and ensure optimal conditions for transporting perishable and non-perishable goods over long distances.”
Linfox and Krueger combined their expertise with the engineering capabilities of leading German semi-trailer manufacturer, Schmitz Cargobull, to produce the most thermally and energy efficient
refrigerated trailer available globally.
The curtain-side trailers also feature Krueger’s SlideA-Gate barrier system to enhance operator safety.
These systems are built to withstand high-impact forces from forklifts during loading and unloading and to minimise the risks to forklift drivers while operating inside the trailer.
Krueger founder and managing director, John Krueger, said the customised trailers are a blend of German engi-
neering and Australian innovation and stand as a testament to the strength of the partnership between Krueger and Linfox.
“Thank you to Linfox for trusting us to deliver on time and with such specific requirements,” he added.
“Our local manufacturing was completed in record time and the team in Germany successfully developed the first ever fully imported freezer van, ready to go into service within days of arriving in Australia.”
HOW can we survive for more than 70 years in the transport industry? The truth is it’s no easy feat. It takes a mix of toughness, smarts and a strong dedication to doing things right.
With the crazy challenges thrown at businesses worldwide, companies had to shake things up, adapt, and figure out new ways to do things. Among those that not only kept going, but actually did better, Alcoa Wheels and Holmwood Highgate really shine as examples of reliability and fresh ideas.
One big reason they’ve stayed successful is that they listen hard to what customers want, teamed up with good partners, and innovate with new ideas. Even when things got tough, Alcoa Wheels and Holmwood Highgate stayed ahead of the game, setting high standards and showing
what can be possible.
The story of these companies is all about bouncing back, especially in the rough and tumble world of transportation. Since the 1950s, Holmwood Highgate has been all about changing how we move liquids in bulk.
Starting from an idea to create the ultimate reliable bulk liquid transport systems, Holmwood Highgate is a third generation family owned and operated company.
Expanding from fuel, the company now manufactures bitumen, ammonium nitrate emulsion, military and aviation spec tanker transport systems.
Ian Williamson, who works in sales at Holmwood Highgate, said: “Our steadfast dedication to quality and customer satisfaction has resulted in a fleet of Holmwood tankers still in operation across the
globe, a testament to their durability and longevity.”
You can see Holmwood Highgate’s drive to keep things fresh in how they’ve expanded into other kinds of tankers, recently adding dry bulk and LPG tankers to their portfolio. Plus, they have one of the largest laser cutters in the southern hemisphere that makes production faster and more precise, proof they’re all about being the best.
Alcoa Wheels began its journey in 1948 by revolutionising the industry with aluminium wheels. But their innovation didn’t stop there. Today, they continue to advance, crafting lightweight wheels for trucks, trailers, and buses that enhance fuel efficiency and overall performance. Their commitment to improvement has resulted in numerous breakthroughs, including the development of the Dura-
Bright Surface Treatment –an innovative solution created by the forward-thinkers at Alcoa Wheels. Unlike traditional coatings, Dura-Bright minimises the time and money spent on cleaning, allowing you to get your truck back on the road faster.
A big part of what’s kept both Alcoa Wheels and Holmwood Highgate going strong is their knack for making great partnerships. Teaming up with top brands like Alcoa has been key to their success.
“I’ve always gone with Alcoa wheels because they’re topnotch, reliable, and leaders in the field,” added Ian.
Looking back on more than 70 years of hard work, we can see the values that kept Alcoa Wheels and Holmwood Highgate going strong. In a business where things can change fast, they’re like anchors, always dependable and full of new ideas. Their story shows us the power of bouncing back, being flexible, and never settling for anything less than excellence.
In a world that is always
breaking new ground, they’re showing us all how to keep striving for greatness, no matter what challenges come our way. Contact us at the Howmet Wheel System: 1800 955 191.
You can also drop us an email at alcoawheels.sales@ howmet.com or visit alcoa wheels.com.au. Don’t forget to follow Alcoa on Facebook at alcoawheelsaustralia for all the latest updates.
BY HUBFLEET
THE National Heavy Vehicle Accreditation Scheme (NHVAS) is an essential component for fleet managers striving for compliance and efficiency in the heavy vehicle industry. Among its various standards, the Fatigue Management Accreditation Standard 7, which focuses on Workplace Conditions, is critical to ensuring the safety and wellbeing of drivers.
Here at Hubfleet, we’ve partnered with Glyn Castanelli, who is an NHVR approved auditor from Transport Health and Safety, to delve into the seven fatigue man-
these standards mean and how transport companies can implement practical systems to fulfill their obligations under the Heavy Vehicle National Law (HVNL). In this article, we’ll explore the significance of Standard 7, provide insights into meeting its requirements, and discuss how innovative solutions like Hubfleet software can assist.
The essence of Fatigue Management Accreditation Standard 7
Fatigue Management Accreditation Standard 7 emphasises the importance of appropriate age driver fatigue effectively. This standard mandates that
operators must provide a safe and conducive working environment, addressing factors such as:
• Workplace safety: Ensuring that drivers have a safe place to rest and recover between shifts.
• Amenities: Providing access to basic amenities, such as clean restrooms, sleeping quarters, and dining facilities.
• Work schedules: Designing work schedules that allow adequate rest periods and comply with fatigue management regulations.
• Health and wellness programs: Implementing programs that promote the physical and mental wellbeing of drivers.
Glyn Castanelli has spent over 30 years in the heavy vehicle transport industry in many roles, including his current role as an NHVR accredited auditor at Transport Health and Safety. Glyn has the following practical tips for fleet managers to help meet Fatigue Management Accred-
itation Standard 7:
• Conduct regular safety audits: Regularly inspect workplace conditions to identify and mitigate any safety hazards. Ensure that rest areas are clean, safe, and equipped with necessary amenities.
• Optimise work schedules: Design work schedules that comply with fatigue management regulations. Ensure that drivers have sufficient rest breaks and do not exceed maximum work hours.
• Implement health and wellness programs: Promote programs focused on the physical and mental health of drivers. Encourage regular medical check-ups, provide resources for stress management, and offer healthy eating options.
• Provide adequate amenities: Ensure that drivers have access to clean and comfortable rest areas. Amenities should include proper sleeping facilities, dining areas, and clean restrooms.
• Training and awareness: Conduct regular training sessions to educate drivers and staff about the impor-
tance of fatigue management and how to maintain a safe working environment.
Hubfleet software can be an invaluable tool for fleet managers aiming to comply with NHVAS Fatigue Management Accreditation Standard 7. Here’s how Hubfleet can assist:
• Scheduling: Hubfleet’s advanced scheduling tool helps create compliant work schedules that optimise driver rest periods and prevent fatigue.
• Real-time monitoring: The software offers real-time monitoring of driver hours, ensuring that no driver exceeds the legal limits and gets adequate rest.
• Safety audits and reporting: Hubfleet provides tools for conducting regular safety audits and generating detailed reports for hazards and incidents, helping managers identify and address potential workplace hazards promptly.
• Driver feedback and communication: Hubfleet facilitates
communication between drivers and management, allowing for timely feedback on workplace conditions and help facilitate rapid resolution of any issues.
Ensuring compliance with the NHVAS Fatigue Management Accreditation Standard 7 is crucial for the safety and wellbeing of drivers. By focusing on creating safe and conducive workplace conditions, fleet managers can significantly reduce the risks associated with driver fatigue. Leveraging tools like Hubfleet software can streamline compliance efforts, making it easier to monitor, manage, and improve workplace conditions. Ultimately, a well-implemented fatigue management strategy not only ensures regulatory compliance but also enhances overall fleet performance and driver satisfaction.
Disclaimer: This article offers general guidance. For specific legal advice and detailed information on Fatigue Management Accreditation, always consult the National Heavy Vehicle Regulator (NHVR) website or an accredited legal advisor.
BASED at Armidale in NSW, Ben Robinson had travelled far and wide in his Isuzu 550 when Big Rigs saw him recently.
He’d fuelled up at the Calcium Puma Roadhouse between Townsville and Charters Towers at around
their children Tilly and baby River, aged six months old.
“We have been as far away as WA and have carried horses, cattle, dogs, and other things. It is a good truck,” he said.
Before I saw them, Ben had been in Townsville helping to load the livestock boat from
and he travels anywhere.
His wife and children were travelling behind him in a support vehicle.
The couple has also done a lot of stock work such as droving, cattle and sheep work, fencing, yard building, welding, farrier jobs and shed
JOSHUA Carlton was driving one of two Mack Superliners which were heading along the Flinders Highway.
One was hauling an Army tank which I was following as it cruised along and the other was carrying a truck.
They had pulled up at the Calcium Roadhouse, which is 50km west of Townsville.
Both Macks had wide loads and pilot escorts.
Joshua is in the Army at the giant Lavarack Barracks base in Townsville and is part of
3SSB. He revealed that they were taking part in a training run.
“We have come out here and will be heading back to base soon,” Joshua said.
From Mannila in NSW, Joshua has been in the Army for eight years and loves it.
Mannila is a small town located 45km north-west of the regional city of Tamworth, and 27km northeast of the historic village of Somerton.
“These are great trucks. The
owner operator
Brian Smith was parked at the Puma Gold City Roadhouse, sitting in his new Kenworth C509 when Big Rigs got to
Based at Mt Garnet on the Atherton Tablelands, the 61-year-old truckie had been hauling cattle in the triple
powered by a 600hp motor and with an 18 speed gearbox, had already done plenty of work when I saw Brian recently on his travels.
“It is just over a month since we got it and has already done 26,000km,” he said.
Brian had picked up livestock from Collinsville and delivered them to Clermont.
other Mack has an M88 tank on the trailer and I have a military truck,” Joshua said. There was a support crew with them. Some of the soldiers walked over to the roadhouse for a snack and a call of nature.
The trucks sure turned heads as they negotiated the highway, especially the tank load.
The two drivers also observed all of the road rules and were both safety conscious.
rain, it needed lots of care in the triple,” he said. Brian was ready to pick up a load of cattle at Charters Towers for delivery to the Atherton Tablelands. He also mentioned that there was not enough good rest areas for drivers but did single out one for praise. “It is at Christmas Creek, out from Brian added that he didn’t mind stopping at the Puma
WA roadhouse is a great find
The remote Paynes Find Roadhouse and Tavern, along the Great Northern Highway in WA has been popular with truckies Spy has yarned to.
Located 420km north of Perth, the family owned and operated business has many truck driver customers who stop there.
However it was not accessible to trucks while work was underway over the past two months to upgrade the truck parking bay, but owner Katherine Taylor is relieved that the wait is now over, welcoming truckies back with open arms.
When Spy contacted the roadhouse, Kathrine said, “A
few hundred truckies a day usually stop here.
“We have free hot showers for truck drivers and toilets, as well as free tea and coffee in the dining room. We also have a little ‘Trucky Room’ in the cottage next door with tea and coffee as well as a microwave for drivers.”
The truckies Spy spoke to said that the food was great so I asked Kathrine what their favourite meals were.
“Most truckies stop here for our amazing food and generous portions for a good price. And for the lovely home feeling, I guess. We offer homestyle cooked food and have daily specials: Sunday is roast night, Tuesday rump steak night and Friday fish and chip
night. We have a little bar open daily and a fire bucket burning every night in winter so we are a great overnight stop,” she said.
More driver friendly rest areas urgent
One of the questions Spy poses to the many truckies he yarns to is whether they believe there are enough rest areas around Australia which meet their needs.
The answer by the majority is a resounding “no” and these include drivers from every state and territory.
I would estimate that 90 per cent want more.
These are rest areas with facilities such as toilets, seats and tables under shade, rubbish bins, and water taps.
As well as enough parking space if they pull up at any hour for a fatigue break.
Often when I ask truckies what are the major obstacles they face, the lack of such rest areas is near the top of their list.
Wide loads
There are lots of reports meandering their way to Spy about the huge number of wide loads travelling along the highways.
A lot of my truckie mates around the country have been sending me pics of these wide loads.
One of them, who I refer to as Fabulous Phil, emailed one to me showing heavy mining equipment being transported west on the Dawson Highway towards Rolleston.
He said that lots of people who were warned of the oncoming load had pulled over to snap some pics.
Hold ups from boats
How many truckies have faced delays because of boats passing by?
Old Spy suspects it would not occur in the states and territories that often.
One such place where it does
though is at Dunalley which is along the Arthur Highway between Hobart and Port Arthur in Tasmania.
That is because the world’s shortest canal, which is just 400m long, is at Dunalley.
By comparison with the Suez and Panama canals it is teeny.
The road between Hobart and Port Arthur is a busy route for trucks.
Spy was there recently in a long queue of traffic waiting for the road bridge to open after the boat passed.
It cuts many hours off the sea trip for vessels and is used each January by yachts returning home after the Sydney to Hobart race.
Just up the highway is the Murdunna Store and Road-
Skin cancer awareness
In recent months Spy has spoken to at least 12 truckies who had been diagnosed with Squamous Cell Carcinoma (SCC) skin cancers.
In each instance these had been surgically removed by doctors.
Eight of these drivers said their SCC, as they are known medically, were found on the
upper leg under where the bottom of shorts would normally cover.
These SCC are located near the surface of the skin and form when there has been excessive skin exposure to ultraviolet radiation.
They can take decades to form, with their origins often from when they were young.
Each of the drivers who had their SCC on an area mostly covered by parts of their pants, questioned how that could be.
Apparently the reason is that the pants roll up the leg a bit when they have been driving and the sun comes through the windscreen or side windows.
So if you see a sore or mark in that area which won’t heal, go and see your doctor.
Drive-offs prevalent
Cost of living pressures have been responsible for increased cases of drive-offs without paying for fuel at roadhouses. Especially at those in remote locations.
I haven’t heard of any truckies being responsible however some have been fuelling up nearby when somebody did a runner.
Spy knows of one instance in which a truck driver identified one such attempted fuel thief.
Of course the culprits have little chance of escaping prosecution as most establishments have surveillance cameras.
Even so, at the bigger service centres in NSW and Victoria, it can take months for the businesses to recover their money.
That’s because the culprit drives off and police take ages to track down those responsible.
In some cases, roadhouse operators won’t activate a bowser if a passenger leaves a vehicle to fill up but the driver remains in his seat.
Tombstone scam foiled Scams are prevalent in our world but this incident in
would rate as one of the lowest acts Spy has heard of.
A much loved family member died just over a year ago and a tombstone was ordered from a reputable monument company.
When the monument was completed, the man paid for it electronically.
A day before he received an email from what he thought was the masonry company advising the payment banking details had been changed.
The payment was made and the man phoned the company to ask if the payment had come through.
To his horror the answer was “no”. It came to light that the company email had been hacked by scammers.
The tombstone cost around $5000 and numerous other family members had contributed to the amount.
Fortunately the victim contacted the bank and as the
Soon after the money was paid to the correct account.
You would have to be a real low life to scam somebody after a death.
Show trucks create interest
At this time of year there are lots of trucks of various sizes hauling show equipment around Australia.
It can be heavy trucks transporting machinery for rides big and small, or lighter rigs towing things such as merry go rounds or dagwood dog vans.
Spy recently stopped at a huge roadhouse and saw stacks of show trucks parked up.
However all of the drivers were either in the roadhouse eatery or having a rest.
Soon after I was driving along a nearby highway and spotted one carrying the Sky Flyer ride.
The little town of Mingela which is just off the Flinders Highway and 43km from Charters Towers is generally a sleepy little place.
It once used to have shops, a school, post office, a police station and other buildings but now just has a pub.
Some reckon it resembles a ghost town during the week with little traffic driving though the main street.
However Spy was sitting outside the Mingela Hotel a few weeks ago on a Wednesday arvo and a procession of trucks thundered past the hotel.
Being a curious type I took particular notice of where they were headed.
Each one was turning off to Ravenswood about 45km away where there are several mining projects.
I even saw some heavy vehicles turning the corner from Ravenswood heading for the Flinders Highway.
Publican Ivan has been there for 30 years and is a wealth of knowledge and a friendly fellow.
Many truckies will remember a former publican there named Bill Archer who used to play a practical joke on patrons.
On the wall in the public bar was a wolf whistle which customers were invited to blow to hear the sound.
However when they did, they were sprayed with talcum powder and victims included many truckies – as well as Spy.
A group of drivers were sitting in a roadhouse eatery having a yarn about serious matters and also on subjects which seemingly contained a degree of melodrama.
One conversation centred around dementia and the affects the ailment had on some of their family members.
When the roadhouse worker delivered a meal to one of them and asked if it was his, he replied, “I can’t think what I ordered and perhaps I am losing a few brain cells.”
It was a joke and the rest of the lads had a good chuckle.
But one of them who in his seventies and is switched on offered this little gem.
“I may be getting older physically but refuse to lose my mind mentally,” he said.
The others said they hoped that was true in coming years and one even referred to him as Einstein.
Come the weekend, the Mingela Hotel is a popular place for people wanting to get away from the bigger centres and enjoy some peace.
Truckies through Ararat
with Darryl Edwards
IF THERE’S a more colourful character in the trucking industry, I’m yet to meet them.
Enter Jack Blake, a man with a story longer than the bible – and more interesting too.
But today it’s all about his trucking story. More on the rest at a later date.
Jack tells me he grew up in the industry and spent every weekend washing trucks for John Carson Transport.
It was just something that he did with pride, being around the trucks, and as a young fella he was hooked.
Eventually, as it usually goes, Jack progressed to driving them for a career.
The first truck he ever drove was John Carson’s G89 Volvo, carting hanging meat from Melbourne to Adelaide, which kept him busy for a few years on the highways.
Jack was driving from the age of 19, doing mainly inter-
state, and spent most of the 80s and 90s running over to Perth and back.
I have heard from good sources that Jack has done more kilometres in reverse than some have in drive, but I’ll leave that for the campfire conversation.
Once he’d done interstate, he sought a sea change and went over to the UK for 11 years, doing all kinds of things.
Jack was a regular on the Neil Mitchell radio show, where he’d ring in from the UK with updates on his travels.
Currently driving a Kenworth T909 for Graham McKay Earthworths, he carts gravel, stone and pre coat all over Victoria and the lower parts of NSW.
According to Jack, the best place to eat would be, without a doubt, at the George and Kids fish and chip shop in Stawell.
They have excellent food
I HAVE HEARD FROM GOOD SOURCES THAT JACK HAS DONE MORE KILOMETRES IN REVERSE THAN SOME HAVE IN DRIVE, BUT I’LL LEAVE THAT FOR THE CAMPFIRE CONVERSATION.“
and you’ll always get a yarn out of George, he assures us.
The best part of his job is that he is left alone to get the job done, which he says helps as you get older.
The advice Jack gives new drivers is to listen to experi enced drivers who try to give you advice. If blokes or ladies have been in the industry a long time and they want to help you, and if they have tak en time to pass their knowl edge on, then you should give them respect, he says.
Out on the road, female truckies are competent, resourceful, lateral thinkers. They can tackle and solve most things the job throws at them and the WiTA team are no different. A close-knit bunch, happy to roll up our sleeves and get the job done, there was just one problem –- truckies we are, event planners we’re not!
I’m always in awe of those who utilise and pool cumulative skills and resources to bring about great things seemingly effortlessly and thankfully – I knew one such woman!
Reaching out to well-known and highly respected industry event planner Imelda Bergin
– the board were delighted when this powerhouse of de termination and resource fulness answered our call to arms!
Hundreds of hours of metic ulous planning later and with Imelda’s guidance, National Female Truckies’ Day 2024 dovetailed into our inaugural WiTA bp 2024 Toots Awards. It was a symphony of wonder ful moments that exceeded all of our wildest expectations.
“Connecting and inspiring women” was the theme of this highly acclaimed, unique event that saw female drivers converge on Adelaide to catch up, learn, explore opportuni ties and share their knowledge and experience with women interested in pursuing truck ing careers.
The event also showcased the critical role women play – not only as truck drivers, but also more widely the work they do in their communities as the primary caregivers –keeping the home fires burning from out on the road.
The WiTA board also resolved to launch the day with a fundraising event to support children with a cancer diagnosis and their families, so there was huge excitement when Camp Quality agreed to join forces with WiTA and host their inaugural Adelaide Convoy.
Saturday July 6 dawned
foggy and cold as female truckies joined their male colleagues in a 150-truck convoy through the streets of Adelaide. The convoy obliterated the initial goal of $90,000, raising $142,000 for Camp Quality. A stunning result and an exhilarating way to start the day.
After enjoying a family fun morning, including a show and shine for big and little kids, guests gathered at the stunning Victoria Park Social Club to enjoy some informal networking over lunch before settling in to enjoy the WiTA bp 2024 Toots Awards.
We were treated to a refreshingly candid panel interview facilitated by former Women’s Weekly editor-in-chief and Camp Quality CEO Deborah Thomas who extracted the good, the bad, and the hilarious side of life on the road from four inspirational remote area female heavy vehicle drivers.
Keynote speaker Donna Vawdrey, author and daughter of iconic female truckie Toots Holzheimer, spoke about the life and incredible legacy of her mum. This was followed by the WiTA bp Australia Toots Awards – established to celebrate and showcase the diversity and tenacity of the nation’s female heavy vehicle drivers – with the ultimate goal of fostering a more inclusive and diverse trucking industry.
The Linde Toots Diversity and Inclusion Award went to QUBE Adelaide transport manager Matt Newman. Matt’s support of WiTA’s Foot in the Door program has resulted in an afternoon shift with eight female drivers and a 60 per cent to 40 per cent gender ratio – almost 2000 per cent above the national average.
I DON’T know about you, but I am getting tired of see ing NHVR prosecutions that o ators, and don’t travel any f responsibility.
If the NHVR is serious about the Heavy Vehicle National Law (HVNL), then an investigation into the consignee receiving these overweight trucks [see Melbourne company fined $180k for mass limit breaches, July 19 issue] is, without a shadow of a doubt, the only next step the investigation team can take; not patting themselves on the back about stopping the ‘serious risk to public safety’.
If it is such a serious risk, and the 69 offences occurred over a two-year period, then any investigator with half a brain cell must think: “That freight went to a consignee, and evidently, the consignee does not have ‘systems and procedures in place to ensure drivers and loaders are adequately trained’, otherwise the transport operator would not have continued doing this…”
THE Victorian Transport Association (VTA) has long championed the cause of road safety, advocating tirelessly for the interests and wellbeing of freight operators across Victoria. Our recent regional forums have underscored the critical importance of engaging directly with regional Victorian freight operators.
These forums, part of our popular Regional Road Safety initiative, have returned with renewed vigour, bringing together a diverse array of transport industry stakeholders. This year’s theme, “Safety On Our Roads: Reducing The Risk Around Heavy Vehicles,” is particularly pertinent, reflecting our commitment to addressing the multifaceted challenges facing the freight and logistics industry.
The July Forums in Portland, Wodonga and Sale,
Why do I say that? Because if the consignee had ‘systems and procedures in place to ensure drivers and loaders are adequately trained’ then it would have: notified the transport operator they had breached he mass limits; asked for a reason why that had occurred; completed a corrective action, maybe:
o asked for the people involved to be re-trained; a nd
o provide evidence of that, before allowing them back on site;
• had a process in place whereby overloaded trucks dump their overloaded freight into a separate area, where that overloaded freight is sold, and the f unds given to charity rather than the transport operator (which is what happens in the grain industry);
• told the operator they were banned from entering the site for X days as a penalty for overloading (occurs in the timber industry); and
• have evidence of all of the above being done.
As it stands it would appear the consignee doesn’t have anything like this in place, and instead, is encouraging the operator to continue to breach – they were obviously paid for the over mass incidents, because they kept doing it!
Therefore, why is there no indication in the media re-
saw significant participation from key partners, including WorkSafe Victoria, the Trans port Accident Commission, the Victorian Department of Transport and Planning, National Heavy Vehicle Reg ulator, and Victoria Police. Their insights and expertise were invaluable, providing a comprehensive overview of the current landscape and the pressing issues at hand. Road safety remains at the forefront of our agenda.
The transportation of goods across vast distances is fraught with inherent risks, and the safety of heavy vehicle operations is paramount. The forums facilitated vital discussions on best practices, emerging technologies, and regulatory updates designed to enhance road safety. With presentations from the Transport Accident Commission, we were able to delve into the latest statistics and strategies aimed at reducing road incidents involving heavy vehicles. The involvement of Victoria Police further highlighted the importance of enforcement and compliance, ensuring that operators understand and adhere to the laws designed to keep our roads safe.
lease from the NHVR that the consignee is being investigated? Failure to conduct such an investigation makes a mockery of the system, and places a target squarely on the backs of those the COR laws were designed to protect.
The industry doesn’t need to know who is being investigated in such instances, but we do need to know it is being done.
A simple line in at the bottom of the NHVR’s successful prosecution media releases stating, ‘investigations into parties in the chain of responsibility in relation to this matter are continuing’ and a follow up when a prosecution occurs into that party will help us see the NHVR is doing what the legislation intended, and not chasing those easy targets. Otherwise, why bother having COR legislation?
Every prosecution that charges directors of a transport company must follow the chain of responsibility to complete the investigation properly – consignor, consignee, loader, unloader, loading manager, scheduler (in fatigue cases). This shouldn’t be determined by whether a prosecution is likely or not; that’s what an investigation is for, so… don’t be lazy, do the damn investigation. It should be a basic KPI: Charged a transport operator for mass breach = investigate other parties in chain. Simple.
Industry needs these investigations into COR parties to stop some of the behaviours and pressures that are still being levelled at it.
I wonder why COR parties scoff at any suggestion they might be investigated? Probably because they know a prosecution is highly unlikely; and even if it did occur, they are comfortable they’ve got the legal might to defeat any prosecution, assuming it even gets that far.
Continuing this absurd fo-
cus on transport operators makes a mockery of the entire HVNL and simply feeds the growing apathy and cynicism industry holds towards the Regulator’s prosecution tactics.
Surely, after all this time, there should be some significant, successful COR party prosecutions on the board. Is it a question of resourcing? Knowledge and capability? Or is it laziness, chasing the easy target to hit a false KPI?
In today’s digital age, cyber security has emerged as a critical concern for the freight industry. The forums included significant contributions from Gallagher and WHG Telematics, shedding light on the growing threat of cyber-attacks and the measures that can be taken to safeguard vital data. The transport sector, with its reliance on digital systems for logistics and operations, is particularly vulnerable. Understanding these risks and implementing robust cyber
security protocols is essential to protect both business interests and customer data. The issue of load restraint is another crucial area that was comprehensively addressed. Proper load restraint is not only a legal requirement but a fundamental aspect of safe transport operations. Incorrectly restrained loads can lead to accidents, posing severe risks to drivers and other road users. The forums provided practical demonstrations and updated guidelines to ensure that freight operators are well-
Fatigue management continues to be a significant challenge within the industry. Long hours on the road can lead to driver fatigue, a major factor in many road accidents involving heavy vehicles. Our forums emphasised the importance of effective fatigue management strategies. Presentations from the National Heavy Vehicle Regulator offered insights into current regulations and best practices for ensuring drivers are adequately rested and alert. By promoting a culture of safety and responsibility, we aim to reduce the incidence of fatigue-related accidents.
Enforcement and compliance were recurring themes throughout the forums. Ensuring that all operators adhere to the stringent regulations governing the industry is crucial for maintaining safety standards. WorkSafe Victoria’s involvement provided valuable perspectives on workplace safety and the importance of compliance with occupational health and safety laws. The collaborative efforts of the National Heavy Vehicle Regulator and Victoria Police
Perhaps fear, not having the guts to sink one’s teeth into a sizeable opponent, scared of the fight that might ensue, believing the risk to one’s reputation of losing a high profile (and high cost) case is not worth the effort? To which I say, what is the risk to one’s reputation of not chasing that prosecution? They say time will tell. It’s been a decade since the NHVR was first put into place. What’s time telling you?
further reinforced the message that enforcement is a key component of road safety.
The VTA’s Regional Road Safety Forums have once again proven to be an indispensable platform for dialogue and learning. By bringing together a wide range of stakeholders, we addressed the critical issues facing the freight and logistics industry comprehensively. The insights gained from these forums are instrumental in shaping our policies and initiatives, ensuring that we continue to advocate effectively for the safety and wellbeing of Victorian freight operators.
Engaging with regional operators is particularly important as it ensures that the unique challenges faced by these communities are acknowledged and addressed. As we move forward, the VTA remains committed to fostering a culture of safety, resilience, and compliance within the industry. Our continued collaboration with key partners and stakeholders will be pivotal in achieving these goals, ultimately leading to safer roads and a more secure and efficient freight industry for all Victorians.
BY DANIELLE GULLACI
Aged 62, Dave Bonello has over 40 years of experience in the trucking game – and more than a few interesting stories to tell.
A larrikin truckie, he tries to bring the fun and humour into everyone’s day, while also imparting his wisdom
to those new to the trucking game.
Dave has worked for South East Queensland Hauliers (SEQH), based at the Brisbane depot, for over three years. He drives a 700hp Volvo and A-double set-up, transporting containers up to Toowoomba and back. He also does occasional road train work into Mackay, and runs from Toowoomba into the mines.
As he explained, prior to starting at SEQH, “I had retired for about four years. I had a friend working there who said they needed drivers. I was getting lazy at home so I thought bugger it, I’ll go back and drive, doing local instead of interstate – and see how it
“I love the industry, I really do. I’ve thought about getting out of it so many times but I’ve never been able to do it.”
This year, Dave put his hand up to be part of SEQH’s professional driver mentor program, where some of the company’s most experienced truck drivers support newer drivers by providing hands on training from inside the cab.
At a time where many companies are struggling to get bums in seats, Dave believes programs such as this are invaluable to ensure people are properly trained before hit-
“Anyone can drive a truck. But too many drivers have no defensive driving skills and
I
DAVE BONELLO
can’t even change a tyre or a light globe,” said Dave.
“There are many companies out there who don’t invest in training. My philosophy is that if you train drivers properly, it’s going to save you money in the long run – less accidents, they use less fuel and do the job better.
“When I’m training people, I like to make them feel at ease and relaxed. I play little scenario games, asking what they would do if the car in front of them did this or the car to the side of them did that. It’s about helping to advance their driving skills.”
Dave is also the subject of a series of videos being released by SEQH, where he delves into his industry knowledge,
discusses training techniques and shares some of his stories.
Throughout his career, Dave has held various roles, including 19 years delivering dangerous goods interstate with TNT and five years on general freight with Toll.
He says that throughout his decades in the industry, he’s remained passionate about sharing his on-road knowledge.
“Even before officially joining the mentor program, I
was always trying to help others wherever I can. I trained many drivers at TNT too until they were skilled enough to go into the advanced driving courses,” explained Dave. He believes allowing newer drivers to learn from more experienced drivers is the way to go. “I reckon that’s the most important thing. That’s how I learnt. I got trained by experienced drivers who knew what to look out for.
“It doesn’t matter how much
experience you have though, there’s always more to learn.
For example, I’ve needed some of the younger drivers to teach me how to connect to Bluetooth and that sort of thing. I’ve had an 18 year old come up to me in a brand new truck and show me things I didn’t know. You’re always learning, that’s all part of it.
“A poor attitude is the worst thing you can have. An attitude is not for a truck driver.”
He added that he believes defensive driving is the most important thing to teach and learn. “And I don’t think enough people teach that anymore.”
For Dave, his defensive driving skills served invaluable when he was involved in the only accident he’s ever had.
That was about 20 years ago, when a mother and her young son were travelling in a car
towing a hire trailer and lost control.
“She had a 12 tonne tow ball on the back. I was in a B-double and clipped the back of her,” recalled Dave.
“I saw her as I was coming down the hill and was thinking, please don’t hit the brakes! And she hit the brakes. The car and trailer split and when she spun out in front of me, all I could see was this little boy in the back seat.
“I could have ran over the top of her car or tried to go around her and the trailer could have gone over her car. So I purposely hit her rear corner to spin her around and then drove down the gully for a couple of hundred feet. When I drove out, I blew a few air bags.
“When the police came to the scene, they found there was no nut at the bottom
of the tow ball and the clip holding the chain looked like something from a $2 shop. That’s why the car and trailer separated from each other. They weren’t connected properly.
“For five years she bought me lottery tickets as a thank you for saving her life and sent me Christmas cards.”
As a driver mentor at SEQH, some of the new drivers Dave has helped included a man named Oscar who was still learning to speak English.
“That made it a lot harder. He hadn’t driven very much so it was a challenge but I showed him and gave him confidence,” said Dave.
“There was nothing better than seeing the smile on his face when he realised he could do it. The appreciation he had at the end of it all was really good.”
Twenty newcomers to the Townsville road transport in dustry are to receive a training boost under the Queensland Trucking Association’s (QTA) Driving Townsville’s Future Program.
The scheme is funded by Jobs Queensland through the Grow Your Own (GYO) Funding Program which is designed to tackle regional workforce chal lenges in Townsville.
The QTA said the initial in take will have the opportunity to undertake five core accred ited units of competency and work experience, or on-the-job training.
The program aims to create a pathway into the Heavy Ve hicle Driving Apprenticeship, Bus Driving and Supply Chain Traineeships. Participants will enter the program as a job seeker or newly employed hire.
“The program will support the transport and logistics in dustry in North Queensland with a practical skilling and on-the-job training program that provides entry level skills for people keen to work in the sector,” said QTA CEO Gary Mahon.
“It is important to involve employers in these training programs to ensure that participants can practice what they are learning to get that true industry work experience.
“This program is an excellent starting point to encourage more people into the industry and we will continue to pursue funding options to expand the
before
actions within the 3 first
government funding programs that provide solutions to workforce and skills shortages and to support employers to fill positions now and into the future.
Jobs Queensland chair Jim Varghese said, “From north to Townsville and west to Toowoomba, these ‘Grow
liver solutions tailored to each
“We heard from industry and regional stakeholders and will now support them to deliver solutions to challenges they identified.”
Candidates and employers interested in engaging in this program can contact the QTA for more information on 07 3394 4388.
• Application specific valving for consistent performance
• High quality rubber bushings for longer life
• Premium oil provides good damping at elevated temperatures