

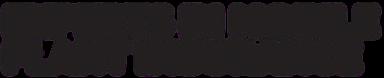
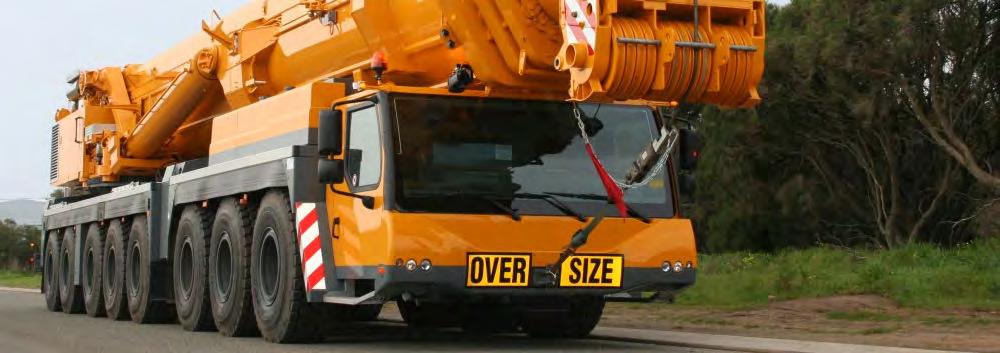
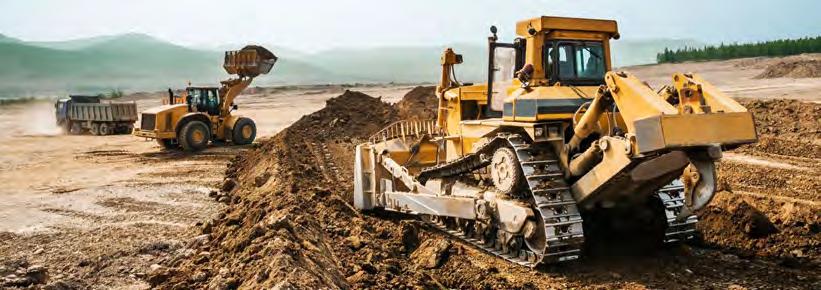

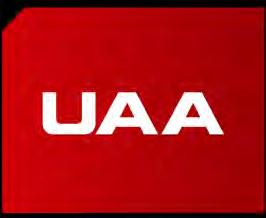
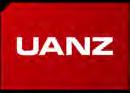

6 Tadano
Freo Group celebrates its 50th birthday with a signifcant order of Tadanos.
10 CICA CEO Report
Brandon Hitch provides insights into the Crane Code of Practice. The liaison of the NHVR and CICA has come to fruition for mobile cranes.
15 Crane Lif t Supervisor Course
GBP Cranes and Heavy Haulage host CICA Crane Lift Supervisor Course.
20 Komp Cranes
Danny Toohey talks the history of his business and new developments.
23 Vic/ Tas Industry Day
Recapping the key discussions and takeaways from the start of May.
24 CICA ISO Updates
Standards Australia and CICA host International Standards forum.
28 TRT
Avopiling take delivery of more Kobelco tele crawlers from TRT.
WA Feature
32 Freo Group
The Australian crane hire and logistics company celebrates 50 years in business.
37 Ronco
An overview of the diverse crane ser vices supplied by Ronco.
40 AEC
Reviewing work ethic and competency in engineering and lif t planning.
43 DRA
HHI completes complex four crane Humma lif t.
46 WATM
Leading crane distributor celebrates 50th birthday with major news.
49 Cranecorp
Joy Krige sits down for an exclusive interview to discuss the company’s future direction.
52 Ashbur ton Crane Hire
ACH helps launch ‘Ladies in Lifting’ initiative and continue commitment to service excellence.
54 Women in Industry
GM of Monadelphous – Heavy Lift, Lorna Rechichi, discusses the benefits of diversity of thought in the heavy lift and shift industries.
57 XCMG
YEM Technology purchases a new 160-tonne all-terrain.
58 Andromeda Industries
63 The Baden Davis Crane Connection
deliver fully refurbished Link-Belt to Strait Up Cranes & Rigging.
66 LEEA
Registrations for LiftEx Gold Coast now open.
68 Grove
McKay United deploys two Groves for some large dual lifts.
71 Potain
A new tower crane is launched to the Australian market.
73 UA A
Important advice from Team UAA.
76 Preston Hire
Preston Hire receives new battery powered Maeda from Pace Cranes.
78 Franna
McMahon Services purchases a new Franna AT40.
80 Mammoet
The APAC division of the global heavy lif ting specialist goes large in Brisbane.
82 Lif t of the Month
What our industry does best.
Tunnelling Solutions puts Andromeda’s rubber blast mats to the test.
60 Liebherr
The first LR12500 is set to land in the APAC region.
Published by:
AS OF MID APRIL, OUR INDUSTRY IS adhering to a new Crane Industry Code of Practice which has been developed by the National Heavy Regulator (NHVR) in partnership with the Crane Industry Council of Australia (CICA). The new code is set to focus more on the transportation side of mobile cranes rather than the lifting element.
The code contains a summary of control measures to control the risks in transporting mobile cranes.
However, as Alice Edwards CICA’s Technical Project Engineer, stresses, the Code of Practice differs to other models, in the sense that it gives equal weight to all of the varying risks and that it is not something to follow explicitly; rather, the model is in place to advise companies on situations they deem applicable to their situations. More details on the new code are included in this issue.
Upskilling the work force is a key
industry topic and the CICA’s Crane Lift Supervisor’s Course has proved extremely popular in regional New South Wales with GBP Cranes and Haulage hosting the course on an ongoing basis.
We take another focused look at the Western Australian crane industry and help celebrate the 50th birthdays of Freo Group and major crane distributor WATM.
As always, the team at Cranes and Lifting has worked hard to bring you the industry’s latest developments, projects and lifts, and as always we hope you enjoy the read.
379 Docklands Drive,
Docklands VIC 3008
T: 03 9690 8766
www.primecreativemedia.com.au
CEO
John Murphy
E: john.murphy@primecreative.com.au
Chief Operating Officer
Christine Clancy E: christine.clancy@primecreative.com.au
Managing Editor
Andrew Hobbs
E: andrew.hobbs@primecreative.com.au
Editor
Simon Gould
E: simon.gould@primecreative.com.au
T: 0404 865 109
Assistant Editor
Jack Alfonso
E: jack.alfonso@primecreative.com.au
Business Development Manager
Emily Schlegel
E: emily.schlegel@primecreative.com.au
T: 0466 317 555
Client Success Manager
Glenn Delaney
E: glenn.delaney@primecreative.com.au
Art Director
Bea Barthelson
Imaging Assistant
Paul Breen
Subscriptions
Frank Rapone
T: 03 9690 8766
E: frank.rapone@primecreative.com.au
The Publisher reserves the right to alter or omit any article or advertisement submitted and requires indemnity from the advertisers and contributors against damages or liabilities that may arise from material published.
© Copyright – No part of this publication may be reproduced, stored in a retrieval system or transmitted in any means electronic, mechanical, photocopying, recording or otherwise without the permission of the publisher.
From a single, second-hand ‘Wobbly’, the last 50 years have seen Freo Group evolve to become Australia’s largest crane and logistics company.
We are a proud Australian business backed by Marmon Crane Services Inc.; a Berkshire Hathaway owned company.
We operate a well-maintained, modern crane fleet of more than 497 cranes across 21 branches throughout Australia, ranging from 3T to 800T in lifting capacity.
Our Cultural and Social Responsibility Management Plan provides equal employment opportunities and respect for Indigenous Australians. We encourage diversity in our workforce, and our Community Sponsorship program supports the towns and communities where we work.
We have access to research and development on the cutting edge of innovation and safety and are committed to “The Journey to Zero Road Map” regarding safe work practices.
‘Home without harm. Everyone. Every day.’
Tadano has been a significant supplier to Freo Group for well over a decade and recently helped celebrate Freo’s 50th with the supply of 10 cranes, including three designed for wind farm construction and maintenance, in a multimillion-dollar package. Darryl Reeves, Tadano’s Western Australian Sales Manager, and Freo Group’s Chief Operating Officer Darren Rodwell detail the relationship between the organisations and the recent contract.
“THE RELATIONSHIP BETWEEN TADANO and Freo Group dates back well over a decade, because Freo Group had been buying the Demag brand for some time. Over the years, Freo Group has purchased 140 Tadano and Demag cranes, including Rough Terrains, All Terrains and Truck Cranes, with capacities ranging from 12 tonnes to 400 tonnes. Over this extended period, Tadano has developed into a
significant supplier to Freo Group,” said Darren.
Darryl explains how Tadano can continually supply Freo Group with the right cranes at the right time.
“Freo Group has a continual fleet planning process subject to the projects they and their customers are tendering for. Freo Group’s fleet management will come to us a year or so out and discuss the
projects they are working on, which cranes should be replaced, and with what.
“Models become obsolete, and models change, as do their capabilities. They sit down with us, and we’ll discuss the models that might be obsolete in the fleet and what they have been replaced with or which model might do a better job for a specific application. We have a strong working relationship with Freo Group’s Fleet Management, which includes Ray Martinez, Procurement Manager; Darren Rodwell, Chief Operating Officer; General Manager Fleet; Mike Celenza; and General Manager Assets & Maintenance Marcus Piggott. We must work closely with our customers to ensure we deliver on their expectations and needs for a successful long-term partnership,” said Darryl.
Freo Group is focused on the fleet’s sustainability and continues to examine the latest technology being developed by Tadano and other crane OEMs, says Darren.
With Tadano’s recent slogan, “Our True Mission: Zero Emissions,” Tadano is highlighting its commitment to reducing CO2 emissions from its business activities by 25 per cent and from the use
of its products by 35 per cent by 2030. Tadano’s goal is to be completely climate neutral by 2050 – zero emissions. To achieve these objectives, the company has grouped together its solutions for greater sustainability under the name of Tadano Green Solutions (TGS).
“Tadano understands the importance of the role we play in the global sustainability movement. Our research and development team puts their efforts towards alternative power solutions as well as software features that help reduce the impact on the environment while ensuring that our product and technologies align seamlessly with the needs of both the industry and our customers,” said Darryl.
“We are aware of the latest technology being developed by Tadano and are actively examining these capabilities to ensure they’re ready and prepared to enter the marketplace once these capabilities have matured,” said Darren.
“Freo Group is fully aware of the battery electric developments Tadano is working with and understands that all-electric rough terrain will be available locally from the end of next year. Like all large fleet operators, we want to be aware
of developments and timing to be confident we are investing in the right technology at the right time. We work closely and transparently with Tadano, so we are actively aware of the changes in the market, what technology will be available, and when they will be available,” said Darren.
The most recent contract was awarded due to Tadano’s depth of understanding of Freo Group’s requirements, the quality and performance of Tadano products, Tadano’s ability to deliver products on time and Tadano’s commitment to ‘second to none’ after-sales service and support, says Darryl.
“Tadano has been heavily involved in the fleet planning process with Freo Group for some time, and Freo Group has been able to make full use of its existing long-term relationships with all aspects of the organisation. The recent acquisition resulted from Tadano’s indepth understanding of Freo Group’s fleet planning process,” he said.
The multi-million-dollar package involves 10 cranes with capacities ranging between 100t and 300t. The package is a key element of Freo Group’s drive to maintain a sustainable and renewable fleet, says Darren.
“There are multiples of the same models in the package; some are replacing older models in the fleet, but there has also been growth in our fleet and capabilities. The
“We are aware of the latest technology being developed by Tadano and are actively examining these capabilities to ensure they’re ready and prepared to enter the marketplace once these capabilities have matured.”
last year, and the last of them should be delivered hopefully by the end of April,” said Darren.
Darryl has worked with Freo Group for many years.
“I’ve been fortunate to have a long relationship with Freo Group. When I started in the industry, I received advice, direction, and encouragement from Tony Canci, Nic Celenza and Mike Celenza. Over the years, and in various roles with various companies, I have had much to do with Freo Group.
“The relationship with Freo Group is strong and built on mutual respect. They understand we’ll always do our very best for them, and we’re always willing to listen and work together on solutions,” he said.
Tadano’s commitment to after-sales service and product support is a key
Over the years, Freo Group has purchased 140 Tadano and Demag cranes, including Rough Terrains, All Terrains and Truck Cranes, with capacities ranging from 12 tonnes to 400 tonnes.
Tadano products. With the number of customers continuing to increase and a growing population of cranes across the country, Tadano Oceania invests in strategies designed to deliver the highest levels of product support, service and parts availability.
Tadano continues to improve its customer service and support capabilities. Key elements of this strategy include continued investment in workshop capabilities and key personnel across the country.
Across the industry, there is a shortage of skilled and experienced labour, and the management team at Tadano has prioritised the upskilling of mechanics and technicians to ensure the organisation has the depth of skill to manage the growing population of cranes.
Tadano technicians are based in workshops nationwide and Field Service Teams assist customers with breakdown issues, conducting regular servicing requirements and assisting with the setup of machines on site where necessary.
Service and support are nationwide, with technicians ready at a moment’s notice to jump on a plane if required and fly to a breakdown, or assist the customer with
whatever support is needed on site.
Tadano’s workshop facilities and Field Service Teams work closely with the Tadano parts department, which is critical. Tadano is creating efficiencies in the procurement, distribution and availability of parts and planning with the Parts Department, helping each workshop and Field Service Team expedite the servicing
recommendations, but if there’s anything more significant that we can’t handle or a shortage of resources, Tadano steps up and puts people in when and where they are needed.
“Maintaining the fleet is a key objective because crane safety, reliability and cost savings come with maintenance. We operate an extensive maintenance
“We service our cranes as per OEM recommendations, but if there’s anything more significant that we can’t handle or a shortage of resources, Tadano steps up and puts people in when and where they are needed.”
and maintenance processes, minimising the downtime of the crane for customers like Freo Group.
“As with any large fleet operator, we must be confident in the crane OEMs’ capabilities to support product in terms of service, maintenance and parts availability. We operate our maintenance teams, supplemented with the Tadano team, wherever and whenever required,” said Darren.
“We service our cranes as per OEM
planning program, and with the number of Tadanos in the fleet, we talk to their team daily. There has always been open communication between the organisations and departments and a lot of cooperation along the way,” he said.
“Remote diagnostics and telematics assist Tadano’s product support teams in understanding what issues the crane might be experiencing, which enables them to dispatch the right part and support at the right time,” said Darren.
CICA has been working with the NHVR to put together a Mobile Crane Code of Practice, and I wanted to take this opportunity to give some context about what the code means for you as members of our industry.
WHAT IS AN INDUSTRY CODE OF PRACTICE?
Industry codes of practice are documents, created in consultation with members of industry, that identify risks and hazards common to that industry. They provide consistent, authoritative frameworks to mitigate risks to public and private safety by recommending controls for each risk listed in the code.
An industry code of practice is not a legally binding document, but it can be used as evidence of what members in the Chain of Responsibility (CoR) should know about hazards, risks and controls related to their industry activities.
WHAT ARE MY RESPONSIBILITIES?
The CoRis an existing part of the Heavy Vehicle National Law (HVNL) that makes parties other than drivers responsible for the safety of heavy vehicles on the road. All parties in the CoR are required to exercise Due Diligence to ensure they comply with all duties under the CoR.
The CoR recognises that different parties have different levels of influence on the safety of a heavy vehicle on the road. CoR parties for a heavy vehicle each have different functions, different degrees of control over what happens, and different risk profiles. They aren’t all expected to do the same things, or to go the same lengths to ensure safety. Each must still do what is reasonably practicable for them individually to do. In the code there are four relevant parties in the CoR for mobile cranes that are not loading or unloading a heavy vehicle.
They are
• The Employer The person or business that employs the driver of a mobile crane. This can include crane hire companies and agencies doing dry
services. This includes anyone who hires a crane, for example builders contracting wet hire cranes to work on a job site.
• The Operator The person or business responsible for directing or controlling the use of a mobile crane. Whoever owns the crane is considered The Operator. It could be a sole owner/driver, or a larger scale crane hire company.
• The Scheduler A person or business that schedules a mobile crane. This could be someone within the crane company in charge of dictating where and when the cranes are deployed, or a person on a construction site that decides when the crane can arrive. Note here that The Operator under
high-risk work licence and heavy vehicle licence to drive and operate the lifting controls of a mobile crane) are instead referred to as Crane Driver/Operator.
Unless they are loading or unloading a heavy vehicle, an employed Crane Driver/ Operator is not a party in the CoR and the Primary Duty does not apply to them. They do need to be trained in systems and procedures to satisfy the requirements of the CoR, and will be involved in the implementation of many of the controls recommended in this code.
When a mobile crane is used to load or unload a heavy vehicle there are more applicable parties, and Section 12 of the code describes some of the hazards relating to the loading of heavy vehicles using mobile cranes and proposes measures to manage the associated risks.
In some situations, the same person or business might be employer, operator, and scheduler. In others the employer and operator might be different entities. There may be more than one person or business that is scheduling a crane.
Exercising Due Diligence as defined by the NHVR means
• G etting and maintaining knowledge about carrying out transport activities safely
• Understanding the nature of the business’s transport activities, including the hazards and risks of those activities
• E nsuring the business has, and uses, the resources needed to eliminate or minimise the hazards and risks created by its transport activities
• E nsuring the business has, and uses, processes to eliminate or minimise the hazards and risks created by its transport activities - and that information about hazards, risks and incidents is received, considered and responded to quickly.
If you are an Executive of a business that is a party in the CoR, you have a Due Diligence Duty. It requires executives of businesses in the CoR to ensure that business is complying with the Primary Duty, of ensuring safe transport activities.
Ben Pieyre – President
Marcus Ferrari – Vice President
Danny Adair – Director
Danny Black – Director
Andrew Esquilant – Director
David Solomon – Director
Karli Sutherland– Director
Brandon Hitch Chief Executive Officer 03 8320 0444 0428 228 048 ceo@cica.com.au
Paul Arztenhofer Membership Engagement/ Business Development Specialist 04 9093 9274 paul@cica.com.au
Alice Edwards Road Technical Engineer 03 8320 0440 alice@cica.com.au
Patrick Cran CraneSafe and CrewSafe Technical Advisor 0488 004 274 pat@cranesafe.com.au
Damien Hense CICA Road Policy Advisor 03 8320 0460 0488 007 575 damien@cica.com.au
Julie Turner CICA Executive Assistant/ Board Secretariat 03 8320 0411 julie@cica.com.au
Kate Galloway Traineeship Coordinator 0491 047 118 Kate@cica.com.au
Shane Coupe CraneSafe & CrewSafe Administrative Assistant Officer shane@cica.com.au 0491 047 134
Madeleine Flynn Senior Marketing Communications Officer madeleine@cica.com.au
Justina Blackman
Member Events and Engagement 0403 717 626 justina@cica.com.au
Ashleigh Gould Office Operations Coordinator, ashleigh@cica.com.au 03 8320 0466
Unit 10, 18–22 Lexia Place, Mulgrave Vic 3170
Phone: 03 9501 0078
Fax: 03 9501 0083
Email: admin@cica.com.au
Website: www.cica.com.au
For information, please visit our website or call the CICA office.
• Th e term Executive includes an executive officer, a manager, or another person who takes part in the management of a business. It also includes a director of a company and a partner in a partnership.
Executives overseeing a business relevant to the activities and hazards listed in the code have a duty to familiarise themselves with the contents of the code.
The Primary Duty requires a party in the CoR to ensure the safety of its transport activities in relation to a heavy vehicle. It is a duty to eliminate public risk so far as is reasonably practicable, and if a risk cannot be eliminated then to minimise the risk. It also includes the risk of damage to property, including vehicles and loads, damage to road infrastructure, and harm to the environment.
Each party in the CoR must spend a proportionate amount of time, effort, and resources, to meet their obligations to the Primary Duty. What is or is not proportional is weighed against the function a party performs, the public risk created by its activities, and its capacity to control, eliminate or minimise the risk.
You should choose the controls, or combination of controls, from the Crane Code that will eliminate each risk. If it is not reasonably practicable to eliminate a risk, you must take measures to minimise it. You also need to manage other hazards and risks in your business that are not identified by the code.
You do not have to use every control recommended by the code.
You can use different controls altogether, provided you can show that they eliminate or minimise risk just as well as those recommended by the code. Differences between businesses will mean different risk profiles, and variation in how practicable some control measures will be to implement. When considering implementing a control measure the assessment must be based on what a reasonable member of the community would think is proportional relative to the seriousness of the risk or hazard, not what is convenient to the business.
A code of practice is not exhaustive. There may be additional risks and hazards not identified. For unidentified risks, members of the CoR must take proactive steps to mitigate them.
It also isn’t intended to be a step-by-step manual for actions needed to be taken to satisfy your legal requirements. It’s an enormously valuable resource, and I strongly suggest you take the time to read through it.
Brandon Hitch Chief Executive OfficerAre you ready to take charge on construction sites, oversee critical lifts, and ensure safety at every turn? Step into the role of a Crane Lift Supervisor with CICA's comprehensive and specialised training course.
The course instructors are seasoned professionals who will mentor course participants through real-life scenarios, preparing them for the challenges and responsibilities of a Crane Lift Supervisor.
The curriculum covers a wide range of topics, including lift planning, load calculations, safety protocols, communication strategies, and legal compliance.
The CICA Lift Supervisor Course emphasises safety practices, risk assessment, and emergency response, enabling participants to create a secure work environment for their team and equipment.
Graduates from the CICA Lift Supervisor Course will receive a prestigious certification recognised by industry leaders. This credential validates their expertise and demonstrates their commitment to excellence.
After seven years, the code has overcome a range of challenges to be released to the crane industry.
THE NATIONAL HEAVY VEHICLE REGULATOR (NHVR) has published a new Crane Industry Code of Practice as of April 15.
The Code, developed in partnership with the Crane Industry Council of Australia (CICA), is being produced to assist the crane industry and associated businesses in complying with the primary duty, of ensuring safety as far as reasonably practicable. according to the NHVR. According to CICA’s Technical Project Engineer, Alice Edwards, the new code is set to focus more on the transportation side of mobile cranes rather than the lifting element.
“What’s been produced between the NHVR and CICA is a good document for the safety elements of transporting a mobile crane,” she said. “It’s important for our members to read the industry code when it comes out and implement the safety practices advised.”
The new code is set to contain a summary of control measures to control the risks in transporting mobile cranes. However, as Alice stresses, the Code of Practice differs to other models, in the sense that it gives equal weight to all of the varying risks and that it is not something to follow explicitly; rather, the
model is in place to advise companies on scenarios applicable to their situations.
“The onus is on any key stakeholder involved in the chain of conducting business with a mobile crane to deem what is related to their business,” she said. “We’ve developed this code to service the entirety of the supply chain – whether that be a Tier One builder, or a local crane hire company – and it’s imperative that companies examine the Code of Practice to deem what is relevant to them.”
Should a mishap occur with the transportation of mobile cranes, the Code of Practice will be referred back to to deem what went wrong and what control measures were in place.
Once the initial draft was published, the NHVR invited industry participants and members of the public to review the code and provide feedback. The code was open for feedback from Monday April 15 through to Wednesday May 15.
The new industry Code has been in development since early 2017, having gone through a series of meetings between CICA and the NHVR to get to the point it is at today.
The New GMK5150XL is the latest sibling of the GMK5150L-1, with longest boom (69m) and most versatile road weights in class
• Reach further with 69m boom and 30m hydraulic luffing fly
• 50t GVM with outriggers in situ for reduced cost legal travel in all Australian states and territories
• 10.2t counterweight in situ at 12t per axle
• Increased safety and flexibility with MAXbase variable outrigger positioning
• Faster, intuitive set-up with CCS (Crane Control System)
• Grove Connect Telematics
• Capacity: 150t
• Main boom: 68.7m pinned*
• Maximum Jib: 30.2m (40O hyd luff)
• Maximum tip height: 99m
Early April saw Gunnedah’s GBP Crane and Haulage host the two-day CICA Crane Lift Supervisor Course. Derek Hamilton was the RTO and Damien Roman, GBP’s General Manager, the host. Both discuss the content and aims and objectives of the course and what it means to the local community.
DEREK IS A CHARTERED CIVIL ENGINEER, Qualified Arbitrator and a Federal Safety Officer.
“I’ve been working in both the private and public sectors of civil construction, in Australia and overseas, for over 30 years.
“I worked with Fulton Hogan for 18 years and that’s where I met Tom Clark a leading specialist in cranes and lifting. Together we wrote the cranes and lifting procedure for Fulton Hogan. I understand the responsibilities of Tier One Builders and how Contractors, Crane Operators, Riggers, Doggers and other High-Risk License operators are involved in lifting processes.
“I have been lecturing Civil Engineering and Construction at Monash University for 20 years and that’s where I met Brandon Hitch, CEO of CICA. Brandon lectures the cranes and lifting topic within civil engineering construction, and we’ve been doing this for five or six years,” said Derek.
Derek goes on to explain more about the course content.
“In many respects, the course deals with the gaps in the industry around training for high-risk licenses, including Dogging and Rigging. It provides a fundamental understanding for Tier Ones and Supervisors who, on completion of the course, have the ability to ask open-ended questions or request information on issues relating to the lifts they are planning.
“When it comes to Work Health and Safety, everyone in the Chain of Responsibility needs to be aware of their Duty of Care. Whether you are a Tier One builder or the Contractor conducting the
work, you need to understand your Duty of Care, have good processes in place and implement the processes to Australian Standard requirements,” he said.
The two day course covers three modules. The first covers engineering principles and brings the students back to basics including: what is the load? How much does it weigh? How do you calculate the weight? Basically, the fundamentals of understanding volumes, working out volumes and areas and knowing densities and materials per cubic metre. The module also covers wind, understanding center of gravity and rigging requirements.
“We cover wind calculations, understanding the effect of wind and requirements around that. On the second
day, we look at more complex lifting. Understanding what the key requirements around complex lifting are, working out forces in different cranes based on where the centre of gravity is.
“Fundamentally practical as well as theoretical topics including lifting precast elements, making sure you have the correct certification and confirmation for the lifting arrangements from the manufacturer so you can lift that particular precast element into place. That’s what we go over,” said Derek.
“There are assessments for the guys. There’s a bench level mark they need to attain to pass and get a certificate for their learning. When you pass, you are accredited to Crane Supervision based
on what The Crane Industry Council of Australia believes is a fair benchmark,” he said.
Derek goes on to explain how the course attracts individuals from various areas and roles in industry.
“For this course we have Mining Supervisors from Whitehaven Coal and with other courses we have attracted foremen, boiler makers riggers and crane operators. The course is designed to be challenging.
“The content isn’t so challenging for crane operators and riggers because they will be across the material, for them it’s a case of reinforcing the information. But for the Mine Supervisors for example, it is challenging because we’re asking them to focus on maths and understand what included angles mean and how to calculate sling loads based on what the shared load might be on an anchorage point, these types of topics. But at the end of the course, the feedback is overwhelmingly positive and everyone takes something away,” said Derek.
Damien Roman is the General Manager at GBP Crane and Haulage. He explains how he got the business involved with the Crane Supervisor course and the reason why.
“As a regionally based member of CICA it was obvious that most of the training activities were taking place on the East Coast revolving around the major cities. For our business, it would be too expensive and disruptive to send our teams to Sydney
for a few days, for example, but we could see the benefits of upskilling our teams.
“So, I reached out to Paul Artzenhofer CICA’s Membership, Conference & Business Development Manager, to explore the opportunity of bringing the training courses to Gunnedah and suggested we could network with other crane companies in the region to fill the spots.
“The courses, including CICA’s On-Road Articulated Steering Mobile Crane Training Course are professional development courses. That’s important
Within a one-month period between mid-October and mid-November 2022, there were seven lifting-related dangerous incidents, with four occurring over five days. The incidents involved cranes, chain/ lever hoists and self-propelled jigs, with a range of causes and contributing factors.
“With the significant increase in the number of incidents and close calls, the CICA Crane Lift Supervisors Course became relevant to Supervisors on the ground in the mines. Various coal mines including Maules Creek, Whitehaven Coal and Boggabri Coal jumped on board and collectively we’ve had close to 80 people attending the course and in between that interest we are trying to fit our guys in as well,” said Damien.
“The interest has been good and with the NSW Resources Regulator Forum covering lifting and unplanned movements, the mines pro-actively put their supervisors through some form of formal training. This is where the course has become a godsend and that’s why they’ve jumped on board. Maules Creek, for example, have used this course as a replied action of improvement and a way to mitigate the risks around lifting,” he said.
The fees for booking the training room are donated to community charities.
“For this course we have Mining Supervisors from Whitehaven Coal and with other courses we have attracted foremen, boiler makers riggers and crane operators. The course is designed to be challenging.”
for our more senior team members who have high-risk work licenses, they are competent, but we are always looking to up skill their abilities which in turn reduces our insurance premiums, so it’s a win win,” said Damien.
“As we were speaking to Paul, the New South Wales Resources Regulator put out a statement confirming a significant rise in the number of dangerous incidents involving lifting equipment which prompted the NSW Resources Regulator to review recent events in the NSW mining industry,” he said.
“As a family business, we strongly support local businesses and charities, and I don’t think there’s much in town we don’t support. When we developed the new yard and facilities including the training room, we partnered with Boggabri Coal, who book it out annually.
“We save the room hire fees and donate it to local charities and we’ve got two university scholarships in there as well. In 2023 we donated just over $7000 and with the CICA courses now on board we have already passed $10,000 and it is only April,” said Damien.
The Crane Industry Council of Australia (CICA) recognises excellence and innovation in the Australian crane industry with the CICA Lift Of The Year Awards. To enter the 2024 awards visit cica.com.au/awards-lift-of-the-year
CICA PHOTO OF THE YEARUniversal Cranes won for a complex lift of a Geodesic Dome Roof.
THE INNOVATION AWARD went to Bullivants for the ADAPTA Adjustable HMPE Lifting Sling.
LIFT OF THE YEAR LESS THAN 20 TONNE WINNER –McMahon Services won for removal of the Heritage Listed Copper Kettle during demolition of the West End Brewery.
Co-director of Komp Cranes, Danny Toohey, and new Operations Manager, Rob Burns, discuss the company’s history, newest investments and the steady trajectory of the Melbourne-based business.
AS WE’RE SITTING AROUND A TABLE IN Glenroy in Melbourne’s inner north, the sound of a rumbling engine starts to come into the vicinity. Not a minute has passed and in comes a 16-tonne Tadano bubble crane, parking itself in the garage to get refuelled and prepared for its next day of work.
Out jumps the operator who, after a quick discussion about what happened on the job that day, proceeds to pull up a stool at the table and join the discussion. At this point a deafening silence descends upon the warehouse and, Danny Toohey, seasoned veteran of the crane industry, leans back in his chair, slings one arm over the seat, and looks at his operator from across the table.
“You blokes,” he says, “would have struggled back in my day.”
A pause ensues; a laugh follows; a series of choice words round out the exchange, and its business as usual in the Komp Cranes warehouse. However, the story for Danny begins well before Komp Cranes, going back to Coburg Truck Parts in the mid 1980s that saw his first foray into heavy vehicles and machinery before moving into cranes in the mid 90s. With a career that has seen him work for the now defunct companies Elite Cranes and Independent Cranes while operating machines possessing a capacity of 300 tonnes, Danny has witnessed the comings and goings of many events, businesses, and trends in
the industry, before eventually finding himself at the helm as Director of Komp Cranes in 2011 – or, as he puts it online, the “Maker of Money”.
“Basically, I got sick of working for people who always rubbed me up the wrong way, and I wanted to work for myself,” he says. “I heard from my mate Paul Keinhuis that he was looking to sell the business, and I figured that I should back myself in and have a go at running a business for myself.”
Today, Komp Cranes runs a fleet containing its two Maeda mini crawler cranes, a 13-tonne Kato, a 16-tonne Tadano, a 40-tonne and 55-tonne Liebherr and a 20-tonne Franna pick and carry crane. Co-owning the business with his wife, Barbara, Danny says the duo keep the business ticking over by knowing exactly what they do best: looking after the smaller, lighter jobs for the residential, commercial, and industrial aspects of the general crane hire market.
“Some days, we’ll be booked in the entire day and packed to the rafters trying to allocate machinery to certain jobs, and others we’ll have one booking in before
it just explodes randomly with everyone needing a taxi crane or city crane solution,” he says. “It’s the nature of general crane hire, and we’re very comfortable operating in our own market.”
To aid the company in its endeavours, Komp Cranes has made two major acquisitions recently, with both being indicative of the future direction the company wants to head in. Komp Cranes has hired a new Operations Manager in Rob Burns, a seasoned campaigner in the asphalting and road management industries.
Rob details his new role, looking after the allocation of Komp’s machinery and personnel, ensuring Komp’s day-to-day activities run as smoothly as possible. Beginning his new position three months ago, he says he’s ready to embrace his new role head on, and that he’s keen to get “stuck in” in the crane industry, as it presented a new challenge, a new project, and a chance for personal growth – as well as giving Danny and Barbara some hardearned time off.
“I’ve got a long history in managing people, machinery and job allocation across multiple different roles in traffic management in Melbourne,” he says. “A lot of those skills are highly transferrable to an Operations Manager role, so I’m looking forward to learning as much about the crane hire industry as possible and helping drive Komp Cranes forward in its future endeavours.”
“Our tracked carrier comes with an A-frame that complements our two vacuum lifters that also go well with our two Maedas, which are all compounded by our fleet of mobile cranes. We want to really prioritise those smaller lifts and help out in any way we can – whether that’s working on an insurance job at a shopping centre or helping out a neighbouring business with some general cranage solutions.”
CICA does for its members.”
Among those initiatives being undertaken are April’s ‘Cranes in Wind’ forum that allowed crane hire companies to openly discuss the high-risk nature of wind farm construction and maintenance, an overseas trip to explore crane manufacturing facilities with road managers at State Government levels, as well as a range of training and upskilling
“Nothing will ever substitute for operator experience, intuition and know-how, and that’s what we need to be reinforcing to the younger crane operators coming through the system.”
The second investment made by Komp Cranes is in its physical machinery: a new tracked carrier purchased through national dealer, Pace Cranes. Featuring a 1200kg capacity, 750mm carrying platform and a rotating platform, Danny says the new machine has been a brilliant addition to Komp’s line up as the company seeks to expand its offerings in the glass-handling domain of lifting. The 1200 R Pro model acquired by Komp Cranes is electrically driven, features hazard lights on the front and rear, on board diagnostics, and a switchable motion alarm – something that came in very handy when the demo was being conducted in a warehouse with high reverberations.
“Essentially, we’re building a fleet that complements itself,” says Danny.
As the Vice President of CICA’s Victorian and Tasmanian branch, camaraderie in the industry is something that Danny not only prioritises and enacts himself, but implores his fellow crane businesses to live by too. Being in his position for over four years, Danny says working with the association has been of the utmost importance to him because he is fully across all the services available to all CICA members – something he finds he’s able to disseminate to other members of the association.
“It’s reassuring to know I’ve got the capacity to give back to the industry and members trying to do the right thing,” he says. “CICA’s main objective is to support the crane industry and help it grow in the safest and most effective manner, and we’d be in a really average spot without the work
courses designed to increase safety in the crane industry as well as combatting the skills shortage.
Amid the skills shortage, a younger, more inexperienced workforce is beginning to enter the crane industry. With over 30 years of experience, Danny has some advice for newer operators.
“The industry’s changed to become a lot more focused on the technical side of the job, which is all well and good until you turn up to site,” he says. “Nothing will ever substitute for operator experience, intuition and know-how, and that’s what we need to be reinforcing to the younger crane operators coming through the system.”
Because, while no operator ever being better than him may be up for conjecture, there remains one resounding notion: there will only be one Danny Toohey.
SITUATED JUST NEXT TO MELBOURNE’S Tullamarine Airport at Essendon Fields’ Hyatt Place where the inaugural ‘Cranes in Wind’ forum was recently held, CICA’s Victorian/Tasmanian Industry Day explored a range of key issues most pertinent to the crane hire industry.
MC’d by Johnson and Young Cranes Lift Engineer John Humphries, the day’s proceedings began with a comprehensive presentation from WorkSafe Victoria representatives, Michael Nathan and James Webster, who gave speeches regarding notable crane incident patterns and the purpose as well as common issues of SWMS respectively. At the core of Nathan’s speech around crane incident patterns was a message that inadequate planning and poor change management were leading to unsafe systems of work, thereby causing incidents such as collisions with structures and plant (most commonly with mobile and pick and carry cranes) as well as load collisions – something that Nathan said WorkSafe had observed a discernible rise in, especially with tower cranes and crawler cranes. Webster, on the other hand, discussed at length the issues commonly popping up with SWMS, such as the statements being too long and containing unnecessary risks such as swooping birds, statements being too short (E.G “forklifts are dangerous”), generic, and non-site specific, and not being accessible or practical for those
The contractors panel ensued; moderated by Boom Logistics’ Nick Morris, the panel featured Duke Barac from John Holland Group, Paul Brevlin from Multiplex, Aidan Thompson from Fulton Hogan and David Waterfield from Mirvac. The topics broached consisted of crane requirements and general usage, the expected services
of crane hire companies including the diminishing role of low-cost options, the importance of involving an independent third party to review all lift plans and ensure no oversights have occurred, before it was rounded out with a technical discussion regarding how best to control risk.
Following this, CEO Brandon Hitch spoke at length about the new dogging and rigging guide available via TfNSW’s website. Soft-launched in late April as an on-site, mobile phone accessible tool, the guide contains sections for different types of loads and calculators to help establish specific rigging configurations. As Brandon was keen to stress, despite being available only from TfNSW’s website, the
CICA’s Lift Supervisor Course. The course, he said, revealed that 33 per cent of riggers with tickets possessed “unconscious incompetency”: in other words, they didn’t know that they didn’t know what they were doing was wrong. Some of the most difficult concepts, he said, related to powerline spotting, no-go-zones, centres of gravity and rigging and wire rope discard criteria.
After a brief intermission, representatives from Victoria’s Department of Transport and Planning got up on stage, discussing the August soft-launch of its HV-SAPS module that will streamline assessment results for heavy vehicle permit applications.
Finally, rounding out a day packed
“The course, he said, revealed that 33 per cent of riggers with tickets possessed “unconscious incompetency”: in other words, they didn’t know that they didn’t know what they were doing was wrong. Some of the most difficult concepts, he said, related to powerline spotting, nogo-zones, centre of gravity, and rigging and wire rope discard criteria.”
dogging and rigging guide was designed to be applied nationally.
Also on the agenda for the CICA CEO was a review of the High Risk Work Licence – especially when it comes to operating cranes. Pointing out the intrinsic flaws of an operator being able to operate machines as varied as a 25-tonne pick and carry crane, a 300-tonne mobile crane and a 600-tonne crawler crane all via the same ticket and with no demonstratable experience, Hitch said the association was moving toward a review of crane type tickets.
Furthermore, Hitch also highlighted some alarming stats derived from
full of content was Holding Redlich’s Charles Power and Jane Hall to give an industrial law and safety update. Hall discussed the new ISO45004 and how it could aid with the monitoring and auditing of contractors; Power elaborated at length on some of the key IR changes coming to Australia, such as the ‘Right to Disconnect’ laws that will see an employee not needing to respond outside of work hours, and a new agreement coming into play on July 1 this year that will see union officials possessing the capacity to go on site immediately in cases of suspected underpayments and violations of Fair Work.
The ISO Technical Committee 96 looks after the standards relating to all crane types for international standardisation. In mid-April, 50 plus ISO TC 96 Committee representatives from around the world, arrived in Sydney to attend a week-long series of meetings, presentations, updates and discussions about ISO Standards. Being a Founding Member of ISO, Standards Australia hosted the event, explains CICA CEO Brandon Hitch.
“WITH ISO BEING INTERNATIONAL standards, representatives attended from all over the world including France, the United States, India, United Kingdom, Germany, China, Japan, Republic of Korea, Sweden, Finland and Italy. Standards Australia is a Founding Member of ISO and hosted the event, the last time they hosted was in 2015. That year CICA sponsored the networking event, and we did the same this year,” he said.
ISO Technical Committee 96 is the parent technical committee and there are nine subcommittees which cover topics ranging from definitions and vocabulary to design principles for tower cranes, mobile cranes, bridge and gantry cranes. All nine subcommittees meet face-to-face once a year.
“The meetings were a combination of reporting on the progress of the working groups responsible for updating standards or creating new standards relating to cranes. Examples included the standards for the testing of stability and access to crane cabins,” said Brandon.
“Meetings also covered classifying cranes for their use, which is important to our market as it relates to major inspections. Reporting also included operator competencies for slingers, riggers, doggers or what they call signallers, all the way up to the wind effects that should be considered by different crane types.
“The objective of each subcommittee is to examine the drafting of requirements for countries to use in the design or use of the standards within the crane industry. Each country is represented by their own expert, and they will explain why they think a part of the standard needs to be updated, or which area of the standard is important for their country and the committee reaches a consensus on content that can be adopted around the world,” said Brandon.
“Australia really shone both in terms of the hospitality shown by Standards Australia and also having Sydney as the backdrop. It is an easy city to invite international visitors to because they really enjoy the scenery, the Australian
culture and relaxed behaviour and general friendliness.
“What happens in the meetings is consistent, it doesn’t matter where you are, you are resolving issues. It’s when the meetings conclude and members leave the rooms and these international delegates become tourists enjoying everything Sydney has to offer,” he said.
“In terms of hosting international meetings, uniquely, Standards Australia Bridge Street head office in Sydney, is world class.
“They were able to host more than 50 delegates for a total of 21 meetings over seven days. Our final summary meeting at the end of the week attracted 45 delegates from the countries mentioned. During the week the number of participants for each
with the detailed research and reports from institutions developed to help feed inputs into the planning and drafting of standards,” said Brandon.
CICA had a strong presence at the ISO is the body for global standards, with representatives from around the world present.
as a whole. The support of the CICA Board enables us to contribute to the standardisation of our industry and help build harmony across the different countries and contribute to the ‘Global and reacquaint with others for the week, which helps the development of relationships and rapport.
“When issues arise throughout the year or when things come up randomly, we can reference individuals and relationships that we’ve built over the time. Having the CICA board support this event, indicates the value CICA brings to the local crane sector and also the contribution it makes at a global level. It puts Australia on the
“There is what is termed a ‘Mirror Committee’ which is an Australian Standards Committee working on local standards and how they relate to the standards, processes and procedures ISO is developing internationally. Increasingly the local standards are utilising and adopting information being developed internationally to assist with the training activities here
“I think the perception of other delegates attending the ISO Technical Committee 96 meeting was that the CICA representatives were strong contributors and that is indicative of the way we approach these types of opportunities. We are focused on gaining as much information as we can regarding overseas developments and bring this back to our membership to continue to ensure our industry is at the forefront of development and remains as safe and sustainable as
The
12th – 13th September 2024
Event Centre, The Star Gold Coast
Proudly sponsored byExhibitors
Leading piling and foundation specialist Avopiling recently took delivery of four new 75 tonne capacity Kobelco telescopic crawlers. Avopiling’s Group General Manager
“THE PROCESS OF RENEWING AND expanding the capabilities of our crane fleet started two years ago and initially we invested in the larger capacity Kobleco lattice boom crawlers,” said David.
The initial order was delivered by TRT in mid 2022 and included the Kobelco CKE 900, which has a 100t capacity with a maximum boom length of 61m, and two Kobelco CKE 1100s, which feature a lifting capacity of 110t and a boom length of 70.1m. Then there is a Kobelco CKE 1350, which features a lifting capacity of 150t and a boom length of 76.2m and two Kobelco CKE 2500s, with a lifting capacity of 250t and boom lengths of 91.4m.
“I also wanted to ensure that the fleet has plenty of capabilities in lower capacity cranes and I was waiting for the Kobelco to release the TK750s, a 75 tonne capacity telescopic crawler, to the overseas markets. Following a tour of the factory in Japan, I was aware that Kobelco had done a lot with the domestic market, but they hadn’t pushed this particular model overseas.
“Finally, TRT was able to confirm pricing, delivery scope and timing, and as soon as we had this information, we quickly pushed the button on four units because we are increasingly using this capacity and type of crane in our works,” said David.
TK750s are demobilised and floated to the next project. Or if you’ve got capacity, you leave it on the project, and keep it working as a support crane.
He goes on to explain how versatile the Kobelco TK750 is and how it works with the mobilisation of the larger capacity cranes.
“To have a 75t capacity tele crawler turn up to site and be lifting in under an hour is the reason we’ve gone down this path. We took delivery of the larger lattice boom cranes, including the CKE 1350 and the CKE 2500 and they are coming to site with the tracks and counterweights off, as is the larger piling equipment.
“Again, it’s about the progression and evolution of our business and the modernisation of our fleet. Our Sumitomo SC500 and Sumitomo SC700, for example, are hitting 25 years and with all the maintenance engineering and ensuring the 10 year major inspections are up to date, it is getting increasingly expensive getting them to site.
“The Kobelcos have been a really good purchase, and the guys are really happy to have them in the fleet. I jumped in one
units. They offer over 11t of line pull which is excellent for the topping-and-tailing and you don’t get caught out with not having the capacity to be able to roll these cages up in the piling work,” he said.
The Kobelco TK750 75t capacity crawler is equipped with a Daimler 235kW diesel engine to provide the rugged power for the piling, foundation and civil work.
The TK750 has 208kN maximum line pull and 107.9kN-rated line pull on the main, auxiliary and third winch, and an operating weight of 74.8t. It also features 153kN maximum line pull and 68.7kN-rated line pull on the main and auxiliary winch, and an operating weight of 69.2 tonnes.
The telescopic crawler features a maximum lifting capacity of 75t at 3m and a telescopic boom length of 10m to 30.1m with a main hook maximum height of 30.4m.
The telescopic crawler cranes of the Kobelco TK750 Series combine the lifting power and high stability of crawler crane models with the excellent performance of an automatic boom extender/retractor.
David has been pleased with the service and support he has received from TRT Australia.
“Troy Hand and his team at TRT have been excellent to deal with. They are always there with support if there are any niggling issues with the Kobelcos. The service and support is also excellent with spare parts readily available,” he said.
David explains the types of the type of works and environments the Kobelco TK750s are suited for.
“For us the Kobelcos are working in piling work and for most of the time, the work is not pushing the crane to its capacity. We are using it for lifting ancillary equipment, drilling tools, casings and reinforcement cages.
“They are operating in tough environments, but they are not being used in a heavy-duty scenario, like our other cranes. We have Bauers and Liebherrs in our piling equipment fleet and they are specifically built for duty cycle works. They feature 25t, 30t and 35t winches, big line pull, big ropes and you are using them for grab work, driving tubes, or steel casings,” said David.
David’s father Avo Tevanian (B.Tech Civil Engineer). Avo has 48 years of diverse experience in the field of piling, foundations and ground engineering.
“The beauty of theseTK750s cranes is they come from Kobelco’s background in foundation equipment, and you can still run a vibrator, and that type of equipment on these cranes, which is fantastic for us. Now we have lots of capacity in the fleet which has made a big difference to the business.
“We are not spending money hiring in external cranes – we are managing our craneage requirement internally. It helps build our business and the profile of the business. When you drive past many of the major projects in the major cities you will see an Avopiling piling rig, in our colours, and you are also seeing an Avopiling branded crane in our colours, that’s something to be proud of,” he said.
Avopiling was established in 1989 by
“Recently, I was driving down to Gerringong with Dad, we were driving over the Fern Street Bridge and I told him we put in the piles for the project, 1,800 of them. Dad said that was great and he looks over, and 30 metres to our left is a rail bridge and he said, “Well, I did the piles for that bridge 20 years ago.” We are multi-generational business working on major projects that will service the community for generations to come and we are very proud of the legacy we are leaving,” said David.
David is one of three brothers and all now work in the business
“I’m the youngest of the three brothers. My middle brother Masis has been working in the business for 25 years and my older brother Mario has been working in the business full time for close to two years.
“Mario worked with Microsoft for 20
years, so his background is digital platforms and he’s working with us to digitise and modernise the business. Masis works on the operational side of the business and spends time setting up the projects with the right equipment and specifically the drilling tools.
“Dad is slowly stepping aside and handing over more and more of the business for us to run. I’ve been the General Manager for three years now and I personally believe you have to be in a position for five years before you can really stand on your own two feet and really understand what the role entails.
“I had a steep learning curve during COVID-19 which proved to be a really difficult time for the business, but we’ve managed to pull out of that, and we grew from 130 people to 250 in a period of 13 months,” he said.
TRT is the Oceania agents for Kobelco providing a full comprehensive end to end solution, as well as service and parts support 24/7, 365 days a year during the entire life of a crane.
P.A. Construction Equipment Pty Ltd (Pace Cranes) was established in 1987 to provide the construction industry with an independent Australian owned and operated crane sales, crane service and crane spare parts organisation.
For over 30 years Pace Cranes have offered premium quality equipment to the Australasian market with a dedicated and unrivalled service, supported by specialist technical advise across the full range of equipment sold.
Freo Group originated as a small business featuring a single, second-hand crane, bought almost by accident by a hard-working migrant. Today, Freo Group is Australia’s largest crane and logistics company, operating nearly 500 cranes and boasting one thousand employees across 21 branches.
WHEN MICHELE ‘MICK’ CANCI ARRIVED
In 1960 as a teenager in Fremantle, he initially found it hard transitioning to a new culture – but no one had to explain what hard work was. A decade later, Michele married Tina Elpitelli, a like-minded soul when it came to hard work, paving the origins for Freo’s lengthy history.
In 1973, Tina’s brother Dino Elpitelli was sent by his boss at Sabemo to an auction to look at a job lot of plant equipment, including a second-hand five-tonne BHB wobbly tractor crane. When he returned successfully, his boss changed his mind and didn’t want the equipment. Dino had
put his name on the auction slip and was obligated to pay for it, but he didn’t have the $5000 needed.
He asked his brother-in-law Michele Canci if he could help, and, along with some financial backing from Luigi Canci, they pooled enough money to buy the equipment.
They chased jobs anywhere; the hours were long, the work hard, dirty, and sometimes dangerous. The paperwork was done on weekends, and money was so tight that they regularly went without a salary for weeks.
Their first employee was Mike Celenza, who quickly became known as “Little Michael”. He arrived at Spearwood in 1978 on work experience and has stayed with the company for over 45 years.
As the company expanded, so did its workforce – including Nic Celenza, who joined his brother, Mike, working for over 40 years in various roles and retired in early 2023.
In 1982, the first “serious” road crane was purchased – an eight-tonner converted to a 10-tonne capacity.
As a small family company, it was only
a matter of time before the next generation started to join Freo Machinery. Michele and Tina’s children – Tony, Rosa, and Dominic- all have strong childhood memories of work and home, which are almost the same.
When Tony finished high school, he went to Italy to meet his extended family before returning to work for Freo, where he was soon joined by his younger brother. They helped their father and Uncle Dino by delivering scaffold and working on building and construction sites. However, when both were in their mid-20s, it became clear to Dino that the boys had larger ambitions.
In 1996, the company was split into Freo Machinery and CMS Construction. Michele was happy with a small crane hire business, but he knew his sons were not. Tony told his father that “if we don’t go into the larger cranes, this business will die”; in the late 1990s, Freo Machinery was hiring its cranes to Brambles Manford.
“They were the Godfathers, and all the other small crane mobs fed off them,” said Michele.
Freo Machinery struggled to make an impact in Perth, and Nic Celenza suggested looking at the Pilbara, where he had some contacts. It turned out to be a moment of genius because, within six months, the company had a house at Bulgarra and twenty cranes operating.
There was never any question about the passion the Canci family brought to their company, but it went to another level when they bought a crane capable of heavy lifting in 2007. It was a second-hand Liebherr 500-tonne all-terrain out of Germany – the largest crane in Australia then and a step up from anything the competitors owned.
After opening depots in Karratha (2001), Welshpool and Port Hedland (2003), there was an appetite to find work outside WA. In the Sunshine State, success came in the mid-2000s after Queensland Premier Anna Bligh announced an ambitious 20-year infrastructure plan for greater Brisbane.
Following a depot in Brisbane, Freo started a partnership to create Global Cranes in September 2005. In March 2006, Global Cranes expanded further by purchasing Millers Cranes and Transport (formerly Northside Crane Hire).
“Freo Group has a well-earned reputation for using state-ofthe-art cranes, but as part of a global conglomerate, it has access to research and development from the United States that is on the cutting edge of innovation and safety.”
As well as an opportunity to expand in the east, a company name change reflected the geographic spread by moving from Freo Machinery to Freo Group. From the mid2000s, Freo Group covered Queensland from the New South Wales border through Brisbane, the Sunshine Coast and up to Nebo.
In 2005, Woodside discovered an enormous gas field called Pluto, 190 kilometres off Karratha, and began planning to build a pipeline, processing, and export hub. The construction phase would take several years and cost $12 billion, with more than half of that earmarked for local contractors.
Nic Celenza called the job a game changer, saying it put Freo Group into a different category from its competitors. It also changed the company balance sheet
by bringing in money without requiring outgoings for new equipment.
The Canci family had occasionally received offers to be bought out but had only taken them seriously once word came that an American company had shown an interest. It originated during a game of golf in 2009 between David Snyder –the President of the Canadian crane hire company Sterling Crane – and Glen Tellock, then-president of the American crane manufacturer Manitowoc.
While playing their round of golf, David mentioned that his company wanted to enter another market because of the downturn caused by the Global Financial Crisis and was considering Australia.
His opponent told him that if he was looking down under, a company called Freo
had just placed a $20 million dollar order to fulfill a contract with Woodside.
“By placing an order with a US manufacturer rather than a German one, we got on their radar,” reflected Tony Canci, “We didn’t have the ‘For Sale’ sign up, but the price was right, and it was good for the family.”
In 2010 BHP awarded Freo Group a five-year contract to provide crane services for BHP’s iron ore operations exclusively, and in December 2023, the two companies signed off on a ten-year extension that is worth an estimated 40 per cent of Freo’s budget.
On the final day of 2011, Freo Group was acquired by Sterling Crane, a subsidiary of Marmon Crane Services belonging to Warren Buffet’s Berkshire Hathaway, one of the largest conglomerates in the world.
The acquisition by Marmon Crane Services turned Freo Group from a
regional company into a national business. Within a decade, the company doubled its workforce, expanded into New South Wales through its purchase of WGC, moved into the Northern Territory and SouthEast Asia, and enlarged its fleet to over one thousand pieces of equipment – all while being debt free.
As the world transitions from fossil fuels toward renewable energy, the infrastructure needed to harness the power of the wind is providing a valuable new opportunity for Freo Group. Freo entered the industry in 2018 at the Murra Warra Wind Farm at Horsham in Victoria. Next came Flyers Creek near Orange in New South Wales, where 38 turbines were constructed to provide 450gWh per year – enough to power 80,000 homes.
Freo Group has a well-earned reputation
Freo Group’s Cultural and Social Responsibility Management Plan provides equal employment opportunities and respect for Indigenous Australians. Freo Group encourages diversity in the workforce, and the Community Sponsorship program supports the towns and communities where Freo Group works.
for using state-of-the-art cranes, but as part of a global conglomerate, it has access to research and development from the United States that is on the cutting edge of innovation and safety.
Among the innovations are digital camera systems that use artificial intelligence to interlace images to provide a 360-degree view for operators, including seeing up above the crane as if in a drone.
Training is now carried out using virtual reality. The headsets and hand controls simulate what an operator sees and moves. These sessions can be carried out in an office rather than on-site. Notably, the space-age VR training is helping attract young people to the industry as elements of computer gaming are used.
Freo Group’s Cultural and Social Responsibility Management Plan manifests itself in various ways, from simple community sponsorship to broader aims of
that action speaks louder than words: “Successful achievements will be the real test of Freo Group’s integrity.”
Adding further to its commitment to cultural and social responsibility, in 2018 Freo Group drew up a roadmap to improve safety, asking why accidents occurred and how they could be prevented.
The roadmap was formalised as “The Journey to Zero” – a bold, stated ambition that no one should be hurt while working for Freo Group, along with an acknowledgement that it requires everyone in the company to make it a reality.
Over time, company surveys have shown that more people are buying into the progress, with staff engagement rising from 30 per cent in 2018 to 70 per cent in
accidental purchase of a five-tonne wobbly crane and continuing to this day as Australia’s largest crane and logistics company, CEO Sven Gade has a resounding message.
“This year, Freo Group has reached a significant milestone, celebrating 50 years since the company was formed. Over those five decades, Freo has grown from a single crane operation into Australia’s leading crane hire and logistics service provider,” he said.
“Thank you to everyone for making us an industry leader and a respected business across Australia. I am very honoured to lead this amazing team of people in its 50th anniversary year and beyond. Happy Birthday, Freo.”
Structural Engineering Consultants to the Resource Industries. Lifting and Rigging Design Specialists.
•Detailed structural design of lifting and rigging systems
•Design/Upgrade civil and structural systems for onshore and offshore projects
•Structural engineering assessments based on inspection reports
•Independent verification of structural design and investigations of structural incidents
•Development of Lifting Equipment Management Systems
BASED IN MADDINGTON, WESTERN Australia, Ronco Construction Equipment and Engineering provides an extensive, detailed range of crane-related services to companies in Australia’s west. Servicing all markets - from mining and resources to construction and infrastructure - Ronco prides itself on providing a comprehensive, holistic experience to those engaging with the company – whether that be purchasing a crane, or undertaking a 10-year major inspection of a machine.
The company is positioned uniquely for the crane industry in Australia’s west; appointed as distributor and dealer of the XCMG and TIDD crane brands, the HYVA loaders and EWPs, and the ‘Rolls-Royce’ of SPMTs, Scheuerle, Ronco strives to bring high quality equipment to the doorstep of the cranes and lifting industry in Western Australia, promising comprehensive postsale service and support. This is solidified by Ronco’s extensive storage capabilities; possessing a 4000sqm storage yard on top of its 12,000sqm main yard, the company is able to ensure the efficient and effective provision and delivery of spare parts,
should they need to be called on.
Ronco’s diverse offerings to the crane industry are typified by its major inspection work. Working within a combined total of 16,000sqm of space, Ronco’s major inspections are supervised by a Chartered Professional Engineer as per AS2550.5 to ensure that is involved in the process from initial test lifts through to the CraneSafe inspection at the end. On top of efficiently turning around machines, this ensures high quality servicing is the status quo for the Maddington-based construction and engineering services company – something that is further encapsulated by the company’s .
Ronco’s servicing and maintenance capabilities are driven by four apprentices and a team of 15 service department staff. Noting the importance of getting the right people on the right jobs when it comes to maintaining heavy machinery, Ronco also strives to ensure that its highly capable human resources are matched and supported by auxiliary equipment. Contained within the workshop are three overhead gantry cranes, a large wash
pad with raised walkways, and an area dedicated to the machining requirements of the team – all in place to help the servicing and repair team at Ronco’s workshop turn machines around as efficiently and effectively as possible.
Outside of its major inspection work, a significant element of Ronco’s servicing and maintenance of machines is its boomrepair operations. At Ronco, no boom is spared; every single boom type comes through their front gates. Whether it be a repair needed for a hydraulic telescoping boom or a lacing replacement for a lattice boom, Ronco has the capacity to service it all.
Since the Maddington-based company’s inception 27 years ago, cranes have been central to Ronco’s DNA. Operating at the forefront of the growing success of the TIDD and XCMG brands, as well as supplying high quality shifting machinery such as Scheuerles, Ronco’s commitment to providing a high-quality service remains as true as the day it opened its doors.
Commencing its major inspection services over 15 years ago, Ronco has finetuned its capabilities to, ultimately, provide an effective, tailored service to its customers, minimising downtime and maximising efficiency.
Longest powered boom to 20.9m with 5.5m telescopic fly extends to 26m
All Models (25T, 35T, 55T) rated @ 1.4m boom position, highest boom strength available, fully fabricated
Air-spring suspension with shock absorbers eliminating cabin noise and vibration
High Stability at all positions to 42 degrees
Low centre of gravity with rigid chassis design, safest crane available
Dynamic Load Chart and Digital Rope Compensation
Safe road speed 90-100kph with 180 degree unobstructed front vision with four cameras to sides and rear
Humma Heavy Lift Crane design, specification with proven componentry has set the new Industry standard for performance. ONE FOOTPRINT FOR ALL MODELS.
Crane owners require low operating and maintenance costs, highest level of safety in both driving and crane mode, achievable on all Humma Models.
Patented Auto-leveller on Humma 55, the largest and safest Pick and Carry available.
Highest level of safety at all articulation positions to 42 degrees using Humma low twist chassis design.
Cabin rated the safest and quietest available at 65 decibels.
Remove the removeable counterweight from 35T and 55T and you have a heavy duty 25T and 35T.
AEC emphasises the importance of its engineers going out onto site and gaining practical experience.
Alliance Engineering Consultants (AEC) Director, Jeff Kazazi, and Engineers, Ieva Dzvankute and Yasmin Santana, discuss their favourite lifting engineering studies, diversity of skills, and the importance of a strong work ethic and the willingness to learn.
DIVERSITY IN GENDER IS NOTABLY improving within the crane industry along with diversity of training and sources of talent. The following is a focus on two female engineers with overseas background who have been working at AEC.
As Australia faces one of the worst professional skills shortages seen in decades, it must look to different approaches to address the gaps that are emerging in the country’s skilled workforce. This is particularly present in the engineering discipline, with Engineers Australia releasing a detailed report that revealed the demand for skilled engineers was outpacing supply, growing at three times the rate of the general workforce.
However, just because a shortage is rife, does not mean that gaps must be filled with any qualified person. A proper work ethic must be inherent along with the willingness to learn for an engineer to be successful in their career – especially in the highstakes world of lifting engineering and lift planning for the oil & gas, infrastructure, construction, and onshore mining industries.
“We could advertise a job vacancy position online and receive a vast range of different applicants,” says Jeff. “However, we need to ensure that we will employ the
right person for the position because, what matters at the end of the day, is a good work ethic, willingness to learn and putting in the effort that reigns supreme for us. Innovative thinking and attention to detail then follow. The team spirit that develops is very satisfying.”
This, for Jeff, is typified by AEC’s engineers, Ieva Dzvankute and Yasmin Santana. Hailing from Lithuania and working at AEC for nearly 12 years, Ieva’s work has seen her complete a range of complex lifting operations – from designing a large high ropes activity course in Queensland at a local adventure park through to lifting and shifting large electrical panels into place on an offshore gas facility and the site supervision of the deconstruction of a drilling derrick on the North Rankin A platform for Woodside. Before coming to Australia, Ieva achieved an honours degree in Structural Engineering from Vilnius Gediminas Technical University in Lithuania and then worked for seven years in the United Kingdom on commercial and communications projects. Her first job in Australia was with AEC. Jeff’s usual requirement for a three-month trial before offering a permanent position was trimmed to one month!
says is needed to succeed in the industry.
“From our studies, we were always learning about engineering from a civil, hydraulic, and structural point of view,” she said. “That made our skills very transferrable, and it ensured our capacity to feel comfortable completing an array of different jobs.”
And, underscored by AEC conducting its work all across Australia and in an array of different industries, this transferability is something that comes to the fore regularly. Ieva and Yasmin’s work primarily involves structural engineering but, as mentioned before, can range from various jobs, going from adventure parks to offshore platforms. For the pair of them, working on the theory is an integral part of the job, and it is supplemented by the need to get out onto site and deal with jobs practically, to ensure that they, as engineers, know exactly what the operations teams are dealing with. This range of work and involvement in all stages of the project gives both of them rare skills not very often seen in the industry.
“Ieva’s work ethic and ‘can do’ approach was quickly recognised and fortunately for us,” says Jeff, “she is still happy here!”
Yasmin, on the other hand, came to Australia after obtaining an honours degree in Civil Engineering in Brazil and working on medium to large civil/structural projects for two years in Brazil and then nearly four years abroad, including Egypt. Yasmin attended the University of Uberlandia in
Brazil via a rarely awarded scholarship and has managed to learn English to a very high proficiency in a relatively short time while working away from her home base. Yasmin went through a similar trial period in AEC which was reduced due to Yasmin’s obvious potential. Yasmin is relatively fresh to the lifting industry having only been with AEC for over two years, but she represents the holistic, hard-working, positive attitude Jeff
“Although we are mostly in the office, we aim to get out and about as often as we can; that makes the whole difference in engineering,” says Yasmin. “I think a lot of people are just operating theoretically, but when you see these things in real life, you become much more practical and become aware of what other people are physically dealing with and how the construction and installation process works. It only enhances our ability to complete our jobs better and optimize our designs.”
For Ieva, this principle holds true too. One of the other key lessons she vouches for, and something that consistently reverberates around AEC’s operations, is the need to be involved early on in the project. Because, if AEC is involved early on, the design of the lifting systems has a better chance to be streamlined and successful. This, for Ieva, was exemplified by a job that she conducted where a prime engineering contractor for an oil and gas company couldn’t find a solution to installing a large piece of equipment in a tight space. Ieva, however, could.
“The prime contractor for the oil and gas company wasn’t able to come up with a solution,” she says. “We were able to
“I think a lot of people are just operating theoretically, but when you see these things in real life, you become much more practical and become aware of what other people are physically dealing with and how the construction and installation process works. It only enhances our ability to complete our jobs better and optimize our designs.”
come up with a design for installing this equipment with only 40mm of clearance by using roller balls that are used on aircraft cargo bays and turning them upside down to become the transfer device on a flat surface.
“We took inspiration for that one because I was watching how baggage handlers transferred suitcases,” she continues. “It’s a prime example of how being involved in the project from day one enables us to implement an innovative and efficient solution.”
This kind of practical thinking is reflected in a range of the work AEC conducts. The list of unconventional jobs and lifting solutions goes on and on; using air skates to navigate equipment successfully into position with only minimal clearance, deploying barge cranes to lift structures into place offshore, and designing 850m-long zip lines for Mount Buller in Victoria snow fields. Each of these jobs
requires creative, lateral thinking in order to successfully deliver the correct lifting and installation solution; thinking that both Yasmin and Ieva concur.
“People at AEC have the freedom to conduct their scope of work and it’s really enjoyable to have this freedom to self-manage our time,” says Yasmin. “We know that we’ve got full ownership of our own working time, and we know that it’s on us to appropriately manage our time and resources to effectively deliver engineering solutions to clients’ problems. It’s empowering, and it fosters a positive working environment for us to operate in.”
“We’ve always felt valued for our knowledge and ideas,” says Ieva. “We always aim to brainstorm and consult with the AEC team to improve ourselves and come up with the best output for our client; for me, this is fundamental to engineering, because no one can be expected to know
everything instantly. All we can do is learn from our and others’ practical experiences and keep bringing the best of ourselves to each job that we work on.”
Ultimately, for Jeff and the AEC team, practical, hands-on experience as well as a sound technical knowledge base is crucial to ensuring work gets done correctly, efficiently and effectively. Operating across the country and providing lifting solutions to such a diverse range of industries requires creative thinking and a willingness to consider new materials and methods.
“One thing that people underestimate is the need for both a very sound understanding of the physics involved plus a practical approach. If we can’t advise how to construct and install what we have designed, we can’t assume that the personnel in the field will be on the same page. All theory and little practical experience is only of limited value” says Jeff.
“Besides technical correctness and attention to detail, practicality is vital,” he continues. “Work ethic and an open mind are fundamental aspects to succeeding for us, and that is what we prioritize.”
“It is a privilege to have such a dedicated team of engineers, designers and support staff,” says Jeff, “working together at AEC.”
Hedland Harbour Industries (HHI) has been operating in the Pilbara iron ore region of Western Australia as a crane hire and mine services company for over 10 years. Recently, HHI deployed all four of its Humma pick and carry cranes to assist in the installation of a 200t dual hoist Eilbeck overhead crane.
HHI OPERATES TWO HUMMA UV 35-25 35T capacity cranes and two Humma 55-25 55t capacity cranes, the largest capacity
Allan Buchan, HHI’s Operations Manager explains there were several
“Having such a small area to work within and very limited headroom made
coupled with having to install one girder first and have that literally tied into place whilst we set up the offset lifts of the two
“These were held there with our 35t
girder into place with the dual lift off the Rhino Hook. We had to use this as the main blocks would not allow us the headroom,” said Allan.
“All of these moving parts meant that we had to ensure we had everything accounted for without error, not just the practical lifts but the preparation of the personnel in key places. We also had to ensure we had the right documentation in place to ensure all bases were covered from a safety perspective,” he said.
Detailed and meticulous planning was required to ensure the lifts were completed safely and on time, said Allan.
the lack of room, we had to manoeuvre the Hummas and the lack of headroom - we planned every eventuality with the lifts.
“Ensuring the lift plans were on point was key to the success of such a technical installation. Because we spent time assessing the site and planning and preparing the correct sequence of lifts, we were in a position to ensure we were good to go without needing our operators to go through ‘dummy runs’. The operators and crane crews were well briefed prior to the lift, ensuring we completed the install in a timely manner,” he said.
staff like about the cranes.
“We operate two 35t capacity Hummas and two 55t capacity Hummas. What HHI and our operational staff appreciate is the power and capabilities the Humma pick and carrys offer. It is second to none.
“This power, coupled with the benefits of being able to mobilise them to work in small areas, and with that lifting capability and power, HHI has significant advantages over our competitionallowing HHI to consistently work in niche areas of the market where others simply can’t,” he said.
“The strength of the Hummas provides HHI with opportunities to tender for and complete technical, out the box scopes, which means our operators and crane crews are always working on something different. They absolutely love the look of the Hummas, they are so different from the regular Frannas going around and they are certainly a head turner in the area.
“Since taking delivery of the Hummas, we have absolutely no complaints, they are a very well designed, engineered and manufactured piece of kit. The power we have in such a relatively small machine is testament to the DRA Group. Having the confidence in our fleet allows us to ensure complete compliance onsite and 100 per
“Since taking delivery of the Hummas, we have absolutely no complaints, they are a very well designed, engineered, and manufactured piece of kit. The power we have in such a relatively small machine is testament to the DRA Group.”
cent satisfaction from our clients,” said Allan.
The Humma 55-25 55 pick and carry has an impressive 55t lifting capacity with advanced dynamic hydraulic suspension, which allows the Humma to operate in places never thought possible. With automatic levelling engaged, the Humma can pick and carry over uneven ground, up to 5 degrees side slope, without need for deration charts - and is fully road registerable in all states on annual permits.
Made by privately owned company DRA Engineering, which celebrated 50 years in 2021, the Humma cranes are made entirely in Australia. All fabrication and assembly is completed in Perth with all major components – cylinders, winch, lighting, hydraulics imported from Europe, while other components are from Australia.
Humma has the same footprint for all
models. The chassis loadings are always in the same position and the design eliminates twist, which in turn eliminates weld cracking and maintains crane stability as it articulates from 0° to 42°.
Humma drivers with experience with Tidd and Franna cranes find Humma is very safe when articulating with a load.
Peter Dalla Riva, Operations Director for DRA Engineering, is rightly proud of the Humma range.
“Apart from the structural design of the chassis and booms, the performance and reliability of a pick and carry depends on using quality componentry proven in plant such as loaders, where loads are lifted, articulated and moved on rough surfaces.
“Bearings and axle selection is important, as is the engine. Humma is the only crane with ADR 80/02 automotive diesel engine with low emissions and fuel usage of up to 25 per cent lower than industrial diesel engines,” said Peter.
Ashburton Crane Hire provides a specialised selection of manned and equipment only hire services throughout Perth and the Pilbra region of Western Australia. We provide both crane and rigging services to a wide range of industries including logistics, construction, domestic, marine and vehicle, industrial, oil and gas and mining companies.
achcranes.com.au
2024 sees WATM, the Western Australian distributor for a range of products including Manitowoc, Grove and Hiab, celebrate 50 years in business. Managing Director Anthony Lazenby and CEO Adrian Wilkes cover the rich heritage of the business and the significance of recent developments.
STARTED IN 1974 BY FRANK AND MARCIA Lazenby, WATM began life as WA Truck and Machinery Repairs, says Anthony.
“Dad was a panel beater, his business partner at the time was a diesel mechanic and Mum looked after the books. They rented a shed, opened the doors and then started to chase work, with their first job being a smashed-up truck which had rolled over. They repaired the truck and away they went,” he said.
“It remained a truck and heavy machinery repair business until the mid ‘90s. By this time, we had a good reputation for not only repairing trucks but all types of heavy equipment including different types of earthmoving equipment, anything that came through the door, pretty much,” said Anthony.
He goes on to discuss the significant opportunities which presented in the late
business transformed from a general repair shop to a crane business, to the point where we were exclusively focused on the Hiab and Grove products. We also picked up Pettibone Rail Cranes and WATM became a specialised crane business from that point forward,” he
“In 2006, we built Workshop 3 and we kept developing the yard, and investing and improving our facilities. In late 2011, we bought [a workshop at] Pickett Street because we were overrun with installation of new Hiabs and we’d outgrown the main
facility, Shovelanna Street in Newman, and we’ve occupied that ever since,” Anthony said.
Adrian goes on to discuss more recent and significant developments for WATM.
“Today, WATM employs 61 people, across our three branches in Bayswater and Newman. The business has continued to develop over the years whilst managing to retain our family first culture and customer focus,” he said.
“Like from the very beginning, product support remains at the core of what we do and is our largest area of investment. As a reflection of this, we have three additional technicians starting over the next three months.”
They are experienced technicians specifically recruited from around the world, says Adrian.
“They are factory trained Grove technicians and they will complement and further add to the capability of our WATM Service team,” he says.
With the increase in number of Grove cranes in operation across the Pilbara, WATM is keeping pace and will increase its service and support capacity at its Newman facility.
Two additional trained and experienced technicians will be arriving in the Pilbara in May and June 2024, to enhance WATM’s expansion and service offering throughout the Pilbara.
it as the best rebuild completed across the Asia Pacific Region in 2023.
“That was great recognition for the excellent work our service team delivered, and which is why we are one of a limited number of Global ‘Elite’ Dealers across the Manitowoc Group,” Adrian said.
It was a logical extension, and we have access to the full suite of Port Equipment products including forklifts, reachstackers, terminal tractors and other specialised port equipment,” he said.
“WATM continues to implement our strategic plan which includes the establishment of a coastal Pilbara facility over the next six months,” Adrian said.
“Feasibility is at its final stage for a Karratha or Port Hedland depot, in order for WATM to be best positioned, to support our Pilbara customers. WATM will then be the leading and largest crane service provider, across the Pilbara.
“To ensure all crane sites are safely accessed and efficiently serviced, WATM has increased our fleet of field service trucks and light vehicles, to accommodate and support our team of trained technicians. This will ensure prompt response times and service reliability is enjoyed by our customers,” said Adrian.
The changes come after Manitowoc recognised WATM for its hard work, naming
“To be an Elite Dealer, means we have the inhouse capability to manage full crane rebuilds, maintain excellent parts availability and undertake extensive factory training for our technicians. WATM is also a leading crane service provider across WA to perform 10 Year ‘Major Inspections’ and I would like to highlight our ability to perform this on ALL makes and models of cranes – and not just Manitowocs, Groves and Frannas,” he said.
“A very exciting new development for our business was the establishment of WATM Equipment mid-way through 2023. This new business has been set up to provide diversification and allow the WATM group to provide a broader range of equipment, not only to our existing customers but also new segments such as civil and infrastructure, right through to smaller trade type businesses.
“The first major step for WATM Equipment was the appointment as a Western Australian dealer for Kalmar, which is part of the Hiab family of companies.
“The most recent very exciting news was our appointment as the exclusive Western Australian and Northern Territory dealer for SANY construction equipment. This is a new opportunity for us. Initially we will be selling and supporting the full range of excavators, rollers and graders with further new products lines to be added later in 2024. Obviously, we will not be handling cranes, we are very clear to our customers about the products we support in our new equipment business.
“We are undergoing training at the moment, and we already have excavators in our yard. We see this as an exciting opportunity to help diversify our business and it also helps to de-risk the business as well. It’s well and truly within our wheelhouse. We have experienced technicians who are very capable of swapping between the SANY equipment and the full crane service and support we offer,” he said.
“Our aftermarket support across the Pilbara, as it is currently and with our future expansion plans, will enable full remote support for the complete range of WATM group products.
beckoned again, and in 2004, Joy’s founded Cedar Cranes in Cape Town, South Africa. Joy grew Cedar from a single crane into a 20-strong fleet before selling the business in early 2013.
Joy then moved to Perth and continued her involvement in the crane industry working for the Freo Group. She then moved to Fenner Conveyors where she held the position of Executive General Manager. However, again, cranes reemerged in her career – in late 2023 she was approached by the owners of leading WA crane services provider Cranecorp, and early this year she commenced as CEO.
Joy felt the decision to join Cranecorp was an easy one to make. Cranecorp has a similar history and reflects the values of the business she built in South Africa. Cranecorp was established in 1997 by Rick Musarra who also started out with just a single crane. Cranecorp has since grown into a major Western Australian business servicing mining and industrial projects across the state.
“What I love about Cranecorp is that
it was a family-owned business that has grown, but it still retains those original customer focused values and team spirit, which is something that really resonates with me,” she says.
Joy sees an exciting future for Cranecorp and has strong views on how this growth might be achieved. She sees having a reputation as both a supplier of choice and an employer of choice as being central to Cranecorp’s growth strategy.
Joy believes that Cranecorp can provide clients and staff with the efficiencies, sophistication, systems and confidence of a large business, together with the flexibility and customer focus of a small family business. She sees the Company as already being well positioned in many ways to achieve this goal.
In her first few weeks with Cranecorp
Joy was struck by how often mining companies and other service firms call Cranecorp when they get stuck. Cranecorp has a reputation for responsiveness, safety, open communications, and transparency.
“These are attributes of the business we need to continue to focus on in the future and are a testament to the team within the business,” Joy says.
Cranecorp is backed by a highly respected Western Australian based investment management firm: the company’s largest shareholder is Viburnum Funds, who have specialised in growing private mining industrial companies for almost 20 years. Viburnum is actively involved in Cranecorp, and since Viburnum invested in Cranecorp in mid-2020, Cranecorp has expanded its crane fleet to around 100 cranes and now employs more than 200 people. Cranecorp also has strategic partnerships in place that can deliver benefits for customers. For example, Cranecorp has a joint venture with Tutt Bryant, which allows it to combine the resources of the two companies to provide an “all-in-one” solution for heavy lift and shift projects.
The customer is front and centre in Joy’s plans. Her goal is to further enhance the customer focus ethos that has long been part of Cranecorp’s approach, and she wants Cranecorp to be recognised as having an undisputed and an unwavering focus on customer service.
“Our absolute focus on the highest level of customer service, operational excellence and problem-solving skills as a key part of our strategy for differentiation in the market,” Joy says. “I want our people to feel highly motivated to go the extra mile to surpass our customers’ expectations”.
To ensure that staff feel that they are part of the business and are aligned to the goals within the business, Cranecorp has recently implemented an employee ownership program that allows all permanent staff to become a shareholder in the company. Cranecorp is also keen to attract new people to the Cranecorp business. As part of its strategy to do this, Cranecorp is developing an internal training school for operators and riggers. This initiative will not only allow Cranecorp to grow the number of crane operators and riggers but will also be good for the wider industry. A focus within this training school will be a broad-based inclusion and mentoring program to attract more females into the industry. Female representation amongst crane and hoist operators currently stands at just four per cent, according to Jobs and Skills Australia. Increasing this rate will bolster the ranks of qualified riggers and operators in the industry.
For Joy, as a working mother of two, ensuring a positive, welcoming culture is key; however, as she also notes, staff should earn their position because of their
capability, not through tokenistic gestures.
“The female crane mechanics, operators and riggers currently working at Cranecorp,” says Joy, “are all there because they are the right person for the job.”
In addition to having the right people, another key element of Cranecorp’s strategy for Cranecorp is ensuring the right mix and location of cranes, and on introducing innovations to improve the efficiency of lifts. Joy sees innovation as key to maintaining high standards of safety and increasing productivity and efficiency both for crane companies and their clients.
As part of Cranecorp’s overall focus on customer service, Joy is also identifying efficiencies and working towards a seamless backroom service for clients. Joy wants Cranecorp to be recognised in the mining industry as one of the easiest and most transparent companies to deal with.
Cranecorp’s focus is on shut down and maintenance work, primarily in the mining industry in Western Australia. Joy sees long-term growth opportunities within this market. Joy expects the industry will see changes in Cranecorp’s operating fleet and geographic focus as the company continues to enhance its service offering.
In somewhat of a ‘full-circle’ moment, given Joy’s long-time involvement in the crane industry, Joy is now driving Cranecorp’s next phase of growth and innovation, with a strategy aimed at benefiting customers and staff alike.
WATM is a Western Australian family owned and operated company that was established in 1974.
WATM sells and provides support services for cranes and lifting equipment and has distributions rights for a number of cranes and forklifts, including:
Exclusive WA distributor for Manitowoc Cranes (including Grove mobile cranes)
Exclusive WA distributor Hiab range of vehicle loading cranes
Exclusive WA Pettibone dealer across Australia and APAC region
Ashburton Crane Hire husband and wife team Guy and Tenille Black, reflect on the near 20-year journey they have been on, their future plans for the business and how they are reinvesting in the industry.
STARTED Ashburton Crane Hire with a 20-tonne Franna and a lot of doorknocking. The only way Ashburton Crane Hire (ACH) has ever known is providing an outstanding level of customer service to its clients. It has taken almost 20 years of hard work to get the business to the position it is in today, says Tenille.
“Guy has grown up around cranes with his father establishing Onslow Crane Hire in the Pilbara. Guy is very passionate about the Cranes and Transport industry. But we had little experience of running a business, we had a young family and it was all a bit crazy in the early days. Looking back, it would
have been really helpful to have some sort of support system back then, a network where we could share our experiences and learn from others in a similar situation,” said Tenille.
“Growing up, we were told not to talk about or admit if you are having troubles or if you’re failing, and you don’t ask for help. So, we never asked for help and made lots of mistakes along the way, but as we progressed with the business, we realised other business owners were going through the similar pain. The more authentic you are and talk to people about it, you connect more which leads to more business and better business relationships,” she said.
“I was a young Mum, business owner and working fulltime in the business, at times it felt as though we were muddling our way through this whole rollercoaster ride, but we muddled through successfully. We have worked hard on the culture of our business, and we are very proud of the community we have built.
“We receive so many positive comments about the energy and banter our office staff generates and we always get great feedback with our crews out in the field. I feel like we are now in a situation where it would be really good to help other people, particularly women, who find themselves in similar situations to where we have been. I wanted to create an environment where trust and sharing are key objectives and that’s how ‘Ladies in Lifting’ came about,” she said.
As the title would suggest, Ladies in
Lifting is a forum for women in the Western Australian crane industry.
“We meet monthly at our office, and we provide an environment where attendees are comfortable sharing their experiences and knowledge. Ultimately, we want women in male dominated industry to understand and feel that whatever role they have, they are not alone, and, in many instances, someone has been through the same experience and can probably help with advice and direction. We also have a bit of fun and lots of laughs.
“Sometimes it’s not possible for people to physically attend so they dial in via Teams. Ultimately, Ladies in Lifting is designed to connect the network of women in this industry, and to reassure them we all face similar challenges,” said Tenille.
As ACH turns 20 next year, Tenille discusses the plans for the next 10 years and how she and Guy will further improve on the services provided to customers. ACH is now driven by goals of building a safer, more connected, innovative future through exceptional crane hire solutions. This realignment includes balance, excellence, trust, responsibility, discipline, passion,
“Our capacity to work remotely is highlighted by our maintenance work on a lithium mine shutdown, remote camp relocations and general transportation, all in the north-west region of WA.”
perseverance, unity, innovation and achievement.
“Combining exceptional talent and a large modern fleet, we are committed to industry leadership. We aim to set new standards in service and reliability with dedication to excellence in every aspect of our operations,” she said.
ACH operates two depots covering the Northern and Southern regions of Western Australia and has both its fleet and personnel based in Perth and Port Hedland servicing multiple industries. This includes ompleting projects in the oil and gas, mining, construction, marine domestic and infrastructure industries.
One of the challenges of operating in Western Australia is its remoteness. For the team at ACH, however, that challenge is its strength; with its facility in Port Hedland,
the company is equipped to serve even the most remote customers, as Guy underscores.
“Our capacity to work remotely is highlighted by our maintenance work in lithium and iron ore mining, remote camp relocations and general transportation, all in the north-west region of WA,” he says. “Additionally, we’ve also completed the replacement of water tanks in remote indigenous communities as far as Fitzroy Crossing, replacing trays on haul packs, completing building works at Onslow, Karratha and Parraburdoo and the rest of the Pilbara,” he said.
Servicing the mining and resources industries represents only a fraction of ACH’s true capabilities, with the company working on the Western Australian Government’s $10.5 billion Metronet infrastructure projects throughout Perth
and
showcase its diversity in the wide range of projects run from its Perth depot.
Ashburton Crane Hire is a name synonymous with A Grade crane hire solutions in the Western Australian lifting and craneage industry. And, with a crane hire fleet of over 30 machines with capacities ranging from the 20-tonne Franna that started the company through to its 300-tonne Demag, it’s not hard to see why. But, as Guy stresses, an aspect of its business that often flies under the radar is its heavy haulage service offering that it supplies to its customers. Additionally, ACH operates a substantial transport division, equipped to handle customers’ needs for, road trains or oversize combinations.
“Should customers have any upcoming requirements for crane or transport services from a proudly Western Australian owned and run family business, please do not hesitate to reach out.
“We are here to provide competetive quotes and assist with all your logistical challenges,” said Guy.
GM of Monadelphous – Heavy Lift, Lorna Rechichi, elaborates on her career, the fundamental aspects of the Crane Operations Pathway Traineeship program, and the team-first attitude at Monadelphous allowing the company to create a more diverse and inclusive workforce.
BACK IN 2017, DAKOTA COMMENCED HER FIFO journey starting in utilities and moving through catering, becoming a bar manager, then onto site and safety administration.
By her own admission, she was always interested in and fascinated by the crane industry and so, the natural progression was obvious. Four years after entering FIFO, she obtained her dogging and riggers tickets to progress onto site. Simply working around the machines wasn’t enough, however; Dakota wanted to be the person operating them. Through Monadelphous’ Crane Operations Pathway Traineeship program, she is on a pathway to achieve her wish.
And, for Monadelphous’ General Manager (GM)– Heavy Lift, Lorna Rechichi, Dakota’s experience exemplifies the nature of the innovative program.
“It’s not only about getting training and receiving qualifications,” she says, “but it’s very much about the onsite pace, the team environment and building knowledge of safety and operations by working in different crews and across different work scopes.”
“Monadelphous operates a very large fleet, including pick and carry, rough terrains, all terrains and crawlers, one of the largest for a construction company in the country. This large fleet and a sustainable customer base provide the basis to successfully deliver this program.”
Having recently won an award from the Chamber of Minerals and Energy of Western Australia’s Women in Resources Awards 2024 in the ‘Outstanding Company Initiative’ category, Monadelphous’ Crane Operations Pathway Traineeship program reflects
the ASX-listed engineering construction company’s commitment to fostering a more diverse and equitable crane and heavy haulage industry – or, as Lorna puts it, the “problem-solving” industry. The Pathway program was established in 2021 as a direct outcome of the company’s ‘Gender Diversity and Inclusion Plan 2021 – 2024’, which places a focus on removing barriers to women entering trade roles. At face value, it represents an opportunity for workers to undertake a 36-month course to earn nationally recognised tickets and operate cranes with capacities up to 100-tonnes; dig a little deeper, and the program seeks to address the gender disparity that sees only three per cent female representation in the crane operating profession. It achieves this by actively promoting the participation of women and Indigenous peoples in the crane industry, providing training,
Rechichi, GM of Monadelphous –Heavy Lift.support, mentorship, real life experience and – most importantly – a permanent role and a long-term career pathway at Monadelphous.
“It’s been a great success in terms of being able to attract and retain people, and it comes with a large amount of focus on making sure they’ve got access to mentors, the correct teams to support them, and our onsite leadership’s motivation and engagement to deliver the program,” says Lorna. “We’re providing real-world training and skill development, and the trainees are embracing the opportunities it creates and building a career for themselves. During that process, we’re also building a more diverse and inclusive workforce.”
The program only represents one part of Monadelphous’ team efforts to foster a more diverse and inclusive working environment. Lorna’s professional career
extends beyond Australia’s borders, beginning with PwC in the United Kingdom in 1997 before shifting to Australia in 2002, working in the USA - in Portland, Oregon - in and among her travels. Throughout her time, she’s worked across multiple sectors including power, utilities, manufacturing and retail, before moving to the resources and energy sector, working and collaborating with blue-collar and white-collar teams. It’s this diverse and different experience across multiple organisations that provides her with the key understanding of the complexity of international, multi-faceted businesses.
“Different countries, and different companies, hold very different cultures,” she says. “I think that the ability to be able to understand, engage and motivate people from different backgrounds so they respect that everybody is different, is one of the challenges I’ve enjoyed most throughout my career.”
For Lorna, and the wider team at
inclusive and embrace the benefits of diversity. This is entrenched within the culture at Monadelphous. Citing the company’s ‘Respect at Monadelphous’ program to guide a notolerance approach to harassment, Lorna says the entire team at Monadelphous is committed to addressing the first sign of any potential behavioural problems to ensure everyone that comes to work feels respected, valued, and so they can bring the best
“We’re providing real-world training and skill development, and the trainees are embracing the opportunities it creates and building a career for themselves. During that process, we’re also building a more diverse and inclusive workforce.”
Monadelphous, embracing the diverse cultures, ideas and thinking is what fosters progress. Empirically, this notion is substantiated by global research firm, the McKinsey Institute, whose 2023 ‘Diversity Matters Even More’ report found that the business case for inclusion and diversity was “stronger than ever” after it revealed that companies in the top quartile of gender diversity and ethnic and cultural diversity were 39 per cent more likely to experience above-average profitability than peer companies in the fourth quartile.
Importantly, however, for Lorna and the team at Monadelphous, it’s about driving the fundamental behavioural attitudes that demonstrate respect, which allows companies to become more
of themselves as an individual in both a skilled and social sense. The industry has a duty to build respectful cultures where inclusive behaviours are the norm.
“Fundamentally, it’s a behavioural driven thing,” she says. “We have all experienced behaviours at some point in life that we do not agree with. The industry needs to be addressing behaviours relating to bullying, harassment, intimidation, abuse, anything like that, at the first sign of its appearance,” she says. “And I think the important thing is that when we address these issues, we’ve got the greater good of the industry, workforce, and society in mind – not just a stop-gap solution.”
Holistic solutions must be what drive social change for the better in the crane
and heavy haulage industries because, according to Lorna, people must be celebrated for their differences and what they can bring to the job. At the core of fdiversity is not just gender; it’s embracing different cultures, thought patterns, experiences and practices.
“For me, I want to celebrate being a woman because of the unique set of values we bring to any workforce,” she says. “The advice to a young person –male, female, or non-binary – is have confidence in your unique self, be true to yourself and the values and the passion that you can bring, because your team will be all the better for it.”
It’s these attitudes that permeate through the operations, recruitment, training and support teams at Monadelphous that, in turn, allows initiatives such as the ‘Respect at Monadelphous’ and Crane Operations Pathway Traineeship Program to succeed, paving the way for people such as Dakota to enter the industry and be celebrated for who they are and what they bring.
Aptonymically named ‘Monadelphous’, meaning the unity of filamens and stamens in a flower to create a better collective, the company prides itself on its ability to grow careers from different backgrounds. As Lorna points out, for every Dakota, there’s also a Sophia, a Jillian, and a Norma that also flourish because of their own personal drive and the surrounding team’s commitment to enhancing their prospects.
“It’s not ever down to any individual,” she says. “Really everybody you work with is all about the team, and the team is what drives success.”
440A output from a 32A input
Power cranes and hoists from a small supply
Utilise regenerative power for the next lift
Zero emission power for cranes
Plug and Play drop in solution
Eliminate diesel generators
Up to 200 tonnes of CO2 emissions reduction per year
YEM Technology’s Material and Store Supervisor, Sait Ucal, discusses YEM’s latest purchase of an XCA160_AU, a crane designed specifically to thrive in Australian mining conditions.
XCMG AUSTRALIA HAS SOLD A 160-TONNE all-terrain crane into Australia’s mines, with APAC construction, maintenance and development of mining processing plant company, YEM Technology, announcing its purchase of the machine.
Acquired to expand the company’s fleet and help advance its operations, the XCA160_AU will be deployed on Australia’s largest magnetite mining and processing operation in Australia, Sino Iron, located 100km south west of Karratha in Western Australia. According to YEM Technology’s Material and Store Supervisor, Sait Ucal, the crossover between affordability and performance presented a business case that was too strong to ignore.
“We needed a new crane in this capacity range to expand our capabilities at the Sino Irone site,” he said. “We’ve worked with XCMG’s products before, and this machine features better technology, new inputs and an ergonomic cabin design for operator comfort.”
On top of its 160-tonne lifting capacity, the XCA160_AU possesses a six-section, U-shaped 62m main boom that comes with jib extensions of 10.5m, 17.5m, and 40m.
The crane is powered by a Mercedes Benz Engine that is compliant with the upcoming ADR 80/03 standards, can reach a road speed of up to 80km per hour and falls under the public road limit of 12 tonnes per axle with its main boom on, making the machine highly transportable and efficient at travelling from site to site.
Furthermore, the drive of the crane features ZF transmission with 12-speed forward gears and two-speed reverse gears and is road registerable in all states across Australia and New Zealand. The crane also possesses axle load monitoring technology, where the proper gear and axle driving mode are matched automatically, providing further safety for the crane and driver when travelling.
The specifications and technical features only represent one side of the equation, however: one of the major selling points of the XCA160_AU for Sait was the post-sale service and support offered by the Chinese manufacturer with its machines.
“In our experience, XCMG technicians have been fantastic, providing good follow up support and in constant attendance for any servicing requirements that we
needed,” he said. “Ultimately, the product is good, compliant, and presents a much more cost-effective solution than some of its European counterparts.”
News of YEM Technology’s purchase comes after the manufacturer showcased an extensive range of “Australia-ready” machines at the CICA Conference in October last year that were designed specifically for operations in rainy, hot and humid environments. The XCA160_AU was among those, with the manufacturer saying the crane was capable of performing optimally in temperatures of up to 50 degrees Celsius.
XCMG’s ANZ Crane Manager Stephen Broomfield said YEM Technology’s purchase was reflective of the quality that he “knows” is prevalent within XCMG’s products.
“We are bringing cranes over to the country that are fully compliant with upcoming ADR changes and can comfortably withstand the harsh Australian climate,” he said. “XCMG is committed to providing the Australian market with European standard cranes at affordable prices with shorter lead times.”
Senior Project Engineer on the Coffs Harbour Bypass, Jean-Luc Lejeune, discusses the efficacy of Andromeda Industries’ rubber blast mats when it comes to tunnelling in hard-rock areas in urban environments.
LOCATED SIX HOURS FROM SYDNEY ON the North Coast of New South Wales, Coffs Harbour possesses an abundance of beautiful sights to go and see. Ranging from its beautiful beaches to the Big Banana, from the fantastic Forest Sky Pier to the magnificent Muttonbird Island Nature Reserve, the residents have plentiful wildlife, coral reefs and seasonal animals coming virtually to their doorstep, to enjoy in tandem with scenic sunrises on Australia’s East Coast. And, better yet, the town is set to be enhanced by a new 14km long bypass that will improve road safety and road freight efficiency for heavy
in short, it seems as though the residents have it all. What they don’t have, however, is repetitive blasting noises caused by tunnelling on the new Coffs Harbour Bypass – and it’s down to Andromeda Industries’ unique rubber blast mats.
“Andromeda’s blast mats have been extremely helpful for us,” says Senior Project Engineer, Jean-Luc Lejeune. “We can’t erect our permanent attenuation structures straight away which are to keep the noise down for the residents because they would be blown up – Andromeda’s rubber blast mats have been a perfect temporary fill in for us to manage flyrock and air overpressure.”
Working for Tunnelling Solutions, Jean-Luc’s six-year-career in civil construction and, more specifically, providing tunnelling solutions to
infrastructure problems, has seen him work on Brisbane’s Cross River Rail using tunnel boring machines and the Kidston Pumped Storage Hydro Project in Kidston, FNQ – just to name a few. Across these projects, he’s used an array of different tunnelling techniques to get the job done. The Coffs Harbour Bypass being delivered by the Ferrovial Gamuda JV, however, presented a unique challenge; hard rock drill and blast tunnelling in an urban environment.
“What’s unique about this road tunnel is that we need to drill and blast as the ground is exceedingly hard” he says. “Tunnels in Brisbane, Sydney or in Melbourne typically use roadheaders for tunnels of this diameter, or even a TBM (tunnel boring machine) – which is a massive logistical operation and difficult to justify for our shorter tunnels.”
“Drill and blast is the more suitable excavation method for shorter tunnels with very hard rock,” he continues. “What we’ve got here is really, really hard rock that you can’t just dig with an excavator or roadheader: you’ve got to blow it up.”
And, as Jean-Luc says, that’s where Andromeda enters the picture. Australian standards are very stringent with air overblast requirements. Further complicating matters is the presence of residents just 200m away from the job.
“Andromeda’s mats assist in suppressing fly-rock from our blasts, and then we’ve also got the air overpressure or sound,” he says. “What we’re doing is using the blast mats as attenuation; as that force wave of sound pressure comes from the blast, it hits the mats and dissipates.”
Andromeda’s rubber blast mats are designed to specifically counter these
forces. Labelled as a “niche” product by Jean-Luc, the mats come in three different sizes: 6000mm x 3000mm, 3000mm x 3000mm, and 2000mm x 1500mm. Also factored in is the respective weight of the products: 630kg, 300kg, and 90kg. According to the manufacturer, the high density and weight of the rubber provides mass to absorb the energy of flying rocks while slowly releasing the gas pressure that comes from the blasting.
The blast mats are used in a variety of industries and applications such as ground
blast mats, suspended blast curtains in mining and construction, or as protection curtains in civil and demolition. The blast mats can be lifted and hung from their load rated plaited wire rope cable handles or bolted together using their unique eyelet design. The products lend themselves well to sustainability and the concept of reusing. The mats recycle conveyor belts that have becoming obsolete, using a special technique to fix the weft and warps together. As they are made from recycled materials with minimum embodied energy,
they provide a high level of durability under “normal conditions”, according to the manufacturer, with the mats allowing for multiple control blasts creating a greater ROI.
What’s more, on top of providing a niche solution, the service that ensued was also of a high level, with JeanLuc praising the availability of the Moonbi-based company when it came to providing solutions.
“Andromeda were super responsive and quick to help out with anything,” he says. “Whatever they couldn’t get us, they came up with an alternative, and that really helped us a lot.”
Because, despite the plethora of delights the residents of Coffs Harbour possess at their doorstep, it’s a “very quiet place”, as Jean-Luc says.
“Nobody wants to disturb the peace here,” he says. “And, with Andromeda’s blast mats, we certainly won’t be either.”
Denzai’s new LR12500 undergoes load testing.
The mammoth LR12500 that can lift 951 tonnes at a 48m radius is set to get busy on a petrochemical facility before aiding Japan’s offshore wind farms.
THE FIRST LIEBHERR LR12500 CRAWLER crane has landed in the APAC region, with Japanese company, Denzai, purchasing the 2,500 tonne machine. Set to be shipped from Germany in July this year, the Japanese engineered heavy lifting and specialised transport company intends to immediately deploy the crane at S-Oil’s Shaheen Project in Ulsan, South Korea, an underconstruction petrochemical facility that, upon completion, is expected to produce up to 3.2 million tonnes
of petrochemicals per year. Upon completion of its scope of work at the project, Denzai anticipates the crane will be used predominantly in offshore wind construction, helping to assemble offshore wind components in a manner complicit with Japanese wharves.
“The working radius of the cranes is expected to be larger than in Europe, because some Japanese ports have less strong wharves than those in Europe, and the cranes must be installed further away from the wharves,” said a press
release from Denzai. “Furthermore, if the nacelle weight exceeds 800 tonnes, it will be impossible to lift the nacelle at the far side of the vessel with a single 1350-tonne crane, and we estimate that two 1350-tonne cranes will be required.
“On the other hand, the LR12500 to be introduced this time can lift up to 951 tonnes with a working radius of 48m, thus satisfying the requirement with only one crane.”
The giant that is the Liebherr LR12500 possesses a maximum load capacity of 2,500 tonnes at a radius of 10m, a maximum hoisting height of 200m and a maximum operating radius of 168m. Furthermore, the crane can hold 320 tonnes of counterweight at its superstructure, 100 tonnes of central ballast and a derrick boom of 54m that works in tandem with a derrick ballast of 1400 tonnes.
According to Liebherr, the LR12500 possesses a concept called “HighPerformance” boom – a feature
derived from a modernised slewing platform and main boom system to provide the crane with a “uniquely wide main boom” that gives the crane the stability of a PowerBoom.
This “HighPerformance” boom gives the crane the power and stability of a “PowerBoom” while also reducing its weight, resulting in the high lifting capacities of the powerful 2,500-tonne machine. For Liebherr, the key attribute of the “HighPerformance” boom is the fact that the forces are transferred in the full width to the slewing platform.
The crane was predominantly designed for the loading of heavyweight goods such as offshore wind power components at ports or for industrial applications – both settings Denzai is set to utilise its latest asset.
Following its introduction to the crane market in April 2022, the crane won the Innovation Award at Heavy Lift Awards in 2023. The jury awarded the Liebherr the award for the LR12500-
1.0, a machine it described as a “master of innovation” for combining several concepts into one solution, including the “HighPerformance” boom.
However, the high power of the crane’s boom is not the only feature that caused judges to single the crane out for the Innovation Award, with Liebherr’s ‘fold-up’ transport solution taking the German manufacturer clear from the rest of the field.
Requiring a “sophisticated mechanism” to fold the ten-metre boom sections for economical transport, the sections can then be unfolded and assembled on site using a special device that stabilises the lattice type sections during the assembly process.
The first Liebherr LR12500 was received by Sarens back in 2023, where it undertook lifting tasks for monopiles in Rostock.
Denzai is a global engineered heavy lifting and specialised transport company based in Japan.
The service Strait Up Cranes has received from the
and the roadability of the
have been quite exceptional.
Strait Up Cranes & Rigging recently took delivery of a fully refurbished Link Belt from The Baden Davis Crane Connection. It’s the second Link Belt in the fleet, says Grant Gjessing, Strait Up’s Managing Director.
STRAIT UP STARTED OPERATIONS 15 years ago, working on a major contract building the Moolarben Coal Mine in New South Wales.
“We had the crane contract to completely build the infrastructure for the mine,” said Grant. “I was not an owner back then, I was only working for the company. I came back to Strait Up as a Supervisor 11 years ago and within six months I had bought half of the business,” he said.
“Back then we were running an old
Tadano 50 tonne truck mount crane. We had a new 2010 Franna as well as a 1998 18 tonne capacity Franna. Ours were the first cranes on site for the construction of Moolarben Coal, we then secured a service contract across the road at Glencore, which was Xstrata Coal at the time.
“When I bought into the business, we bought our first Link Belt, a HTC86100 from the Baden Davis Crane Connection. That’s where our relationship with Ben Baden
and Anthony Davis started and we’ve continued to buy cranes from them ever since.
Grant and Strait Up Cranes have been impressed with the performance of the Link Belt.
“The service we’ve received from the Link Belt and the roadability of the crane have been quite exceptional. We’ve had good service from The Crane Connection, in terms of parts perspective, as well as backup servicing around breakdown issues.
Image:Strait Up Cranes has received good service from The Baden Davis Crane Connection, in terms of parts perspective as well as backup servicing around breakdown issues.
“They service us out of Sydney which is a three-hour trip from their yard to our front gate, but they have been here a couple of times to resolve any issues, and they’ve completed the work very efficiently. They provide a great service and Ben, Anthony, Shawn and the team have been really good to us. We’ve developed a very good working relationship with them over the last 11 years,” said Grant.
He goes on to explain the background to receiving the latest Link Belt.
“This is the third crane we’ve bought from Ben and Anthony, we bought the first Link Belt 11 years ago and then a secondhand 130 tonne capacity Grove, that was six years ago. I’m always keeping an eye on what’s coming up for sale or what Anthony is importing.
“The Crane Connection put the crane through a complete Major inspection and full paint job, it looks and feels brand new. It arrived in March and went straight to work on a solar farm project near Mudgee and it also completed a couple of jobs at Glencore.”
I keep up-to-date via his monthly newsletter.
“He will also call and let me know if something is coming up and that’s how the second Link Belt came about. He knew we were in the market for another slew crane at the time and he had the Link Belt HTT86100 in the workshop for a repair.
“It is slightly different to our first crane as it features a rear steer function
so it can get into tighter spots. It was previously owned by GBP Cranes and Haulage. The Crane Connection put the crane through a complete major inspection and full paint job, it looks and feels brand new. It arrived in March and went straight to work on a solar farm project near Mudgee and it also completed a couple of jobs at Glencore,” said Grant.
Anthony Davis speaks about the
10-year inspection process the company recently completed on the Link Belt.
“We originally sold the machine to GBP Cranes and Haulage in Gunnedah in 2014. They bought two of them, and when they got to their 10-year mark it was time for them to upgrade. So, we traded that machine in on a second hand 2020 90 tonne Liebherr that we had in stock. I let Grant know we had the crane coming and he took it,” said Anthony.
“We completed a 10-year inspection on the crane, the boom came out, all the boom sections were crack tested, all the hydraulic rams were tested, the out riggers came out and were crack tested. We also checked all the rams internally and they were crack tested and checked as well.
“We had to replace the sprag clutch on the winch brake and we also checked the slew ring. The majority of the major inspections we turn around in a month,
if they are in pretty good condition. Then it goes into the paint shop.
“When all of this is completed, we arrange for an engineer to come in and they complete their independent overload testing. In this instance it was Findlay Consulting Engineers. We also complete the CraneSafe on the crane and we look after the registration transfer for them. Grant is bringing his first Link Belt back for a 10-year inspection and for painting as well,” said Anthony.
Grant is happy the Baden Davis Crane Connection can provide a one stop shop when it comes to used cranes.
“They provide a great service when it come to new and used cranes. They are the National Distributor for Link Belt and the New South Wales distributor for the Tidd pick and carry and also Kobelco crawlers. They source used cranes from all over the world, they
manage major inspections, and they operate their own paint shop all from the one yard. These are big advantages for a business like ours,” said Grant.
“I’m also sending my original Link Belt to them. We’ve just completed a one-year life extension on it a few months ago, but we’re sending it down for its Major Inspection. It’s going down for a complete overhaul with Ben,” he said.
There has been a lot happening for Strait Up Cranes & Rigging, explains Grant.
“We recently moved into a new premises which features new offices and a big yard which is already filling up like every other crane yard in the country. There are shipping containers and flies, and inserts and everything else to do with cranes, spare winches, spare hooks. It’s a very professional looking space and it serves us well,” said Grant.
Machine specific checklists are in line with the CraneSafe program. StartSafe streamlines the process for collecting pre-start information, with instant data retention to a central location for the crane owner to access.
Photos tell the story. When a faulty item is recorded by the operator, the maintenance team is notified of the issue by email, which includes photo evidence of the fault. This also assists with gathering major inspection data.
An additional app. (StartSafe Maintenance) is available, for your company’s maintenance team to close the fault loop once the repair is complete.
The Lifting Industry will come together this September for the eagerly anticipated LiftEx, the only event in the region wholly dedicated to lifting equipment and height safety, which takes place at The Star Hotel Gold Coast. Across two days, the industry will meet to network, exchange knowledge and showcase the latest advancements in lifting equipment and safety solutions.
LIFTEX
The Lifting Engineers Association (LEEA), offering a unique platform for lifting equipment suppliers to demonstrate their latest products to an audience of end-user professionals who are engaged in operating, inspecting and testing equipment across diverse sectors such as Mining, Oil & Gas, Infrastructure, Construction, Ports & Marine and Renewable Energy. Whether a rigger on a construction site, a WHS (Work Health and Safety) officer in mines or a purchasing manager in Oil and Gas,
attendees will find products, services and content tailored to their specific needs and interests.
Visitors can expect to see a comprehensive overview of cutting-edge technologies showcased by leading industry suppliers with LEEA-accredited expertise. From a variety of hoists and rigging equipment including slings, shackles, hooks and lifting chains, as well as lifting accessories to safety harness systems, there will be an array of products and technologies designed to drive excellence and elevate industry standards in lifting.
In addition to exploring the show floor of lifting technology, attendees will enjoy complimentary access to the conference sessions providing a platform for knowledge exchange and discussion. Justin Boehm, LEEA’s Regional Manager for Australia and New Zealand, says “At LiftEx Gold Coast 2024, we will be highlighting advancements in technology and safety from some of the leading brands and professionals at the forefront of this incredible industry, with speakers highlighting safe practice and new products”. The speaker program will include vertical-market case studies presenting examples of real-world challenges in the mining, construction, renewables and oil & gas sectors, offering attendees solutions and actionable takeaways. Additionally, thoughtprovoking panel sessions and professional development training workshops will be offered by LTC (Licensed Training Centre) member organisations, further enriching the learning experience. A session on LEEA’s Military Transition Scheme will detail how LEEA is connecting skilled and experienced individuals transitioning from the armed forces into civilian life and potential employment. The military trains and employs many personnel with direct experience of lifting engineering – think of swapping an engine out of an aircraft, or a tank, or changing a propeller shaft on a ship. Many service personnel therefore have the qualities craved by the lifting industry.
Day two will culminate in an appearance by Beaconsfield Mining Survivor Brant Webb, who will talk about how his experience has given him a unique perspective on safety, resilience and the human capacity to endure. His story aligns well with the lifting industry, being a stark reminder of the importance of safety protocols and procedures in high-risk environments.
LiftEx Gold Coast serves as a regional counterpart to LEEA’s renowned flagship show, which is now in its 19th year. Justin adds, “After the successful launch of LiftEx in Sydney in 2023, this year’s fully-fledged event marks a significant milestone. It will unite industry professionals from
across the globe to delve into cuttingedge technologies and best practices in lifting equipment. Be sure to register your attendance because LiftEx on the Gold Coast is set to redefine industry standards in 2024”.
Registration is now available. The premium visitor ticket not only grants access to the two-day exhibition but also includes admission to all the presentations and training sessions in the conference. Additionally, attendees will receive an invitation to the networking drinks reception on the evening of day one. Uniquely, the ticket covers all lunch and coffee breaks over the course of the two days.
LiftEx Gold Coast takes place at the Event Centre at The Star Hotel Gold Coast, 12-13 September. For more information, and to register for a free visitor ticket, visit https://events.leeaint.com/liftex-goldcoast.
YOUR MUST-READ INDUSTRY RESOURCE
• The only independent trade magazine dedicated to the ANZ crane sector.
• Each issue contains a mix of equipment news, product stories, and coverage of hot topics.
• 11 annual issues, delivered to your door.
McKay United has deployed two of its Grove all-terrain cranes to execute a series of complex tandem lifts on a major Victorian infrastructure project.
MCKAY UNITED HAS DEPLOYED TWO OF its Grove all-terrain cranes to complete a series of dual lifts on the new Parkdale Station as part of Victoria’s Level Crossing Removal Project.
Contracted to lift and install bridge beams, the Melbourne-based crane outfit mobilised its Grove GMK7450 and GMK6400 to lift the bridge beams into place to further the development of the new Parkdale Station.
The Parkdale Station project involves the installation of 38 spans, each consisting of four L-beams weighing 127 tonnes, and 12 super-T beams weighing 86 tonnes.
McKay United executed the tandem lift using its GMK7450 with megawing-lift, featuring a 35.3m boom and 160-tonne counterweight configuration,
as well as its GMK6400 with a 30.1m main boom and 115-tonne counterweight configuration.
The project faced numerous challenges, including height restrictions, NBN wires, electrical wires and electrical cabinets and pits that couldn’t be removed at the time of the lift.
To address these challenges, McKay United performed lift simulations for all spans and provided real-time input from the site to keep the lift plans updated. This dynamic approach allowed the crane hire company to adapt to changing conditions on-site and implement lift plans effectively.
To help configure the two Groves, McKay United also mobilised its Franna AT40 as an auxiliary crane, its 100-tonne hydraulic telescopic crawler
crane and an LTM1120-4.1.
The seven-axle Grove GMK7450 possesses a maximum lifting capacity of 450-tonnes on a seven-axle carrier, making it the flagship all-terrain crane in Grove’s inventory. Further to its lifting capacities, the crane possesses a five-section main telescopic boom length of 60m that can be enhanced by Manitowoc’s trademarked MegaWingLift technology that provides extra lifting capacity. The crane can reach a maximum hook height of 136m thanks to its optional add-ons of a 79m luffing jib and 70m fixed jib, and is capable of carrying 160-tonnes of counterweight.
The GMK6400, on the other hand, is one of the newest all-terrain cranes in Grove’s line up, and presents the
best load chart in its six-axle class – an achievement underscored by the machine earning Manitowoc the ESTA award for innovation in 2013. The crane’s 400-tonne lifting capacity is bolstered by a similar boom configuration to the aforementioned 450-tonner, with a 60m main boom length and 136m main hook
McKay United comprises Williamstown Crane Hire, East Side Crane Hire and Tasmanian company Elliot’s Crane Hire. The company possesses a fleet size ranging from its 13-tonne Kato through to its 650-tonne Demag crawler crane.
The new $450 million Parkdale Station is being delivered by an alliance of Acciona, Coleman Rail, WSP and Metro Trains Melbourne.
The new model possesses a significantly reduced out-ofservice radius compared to its other MCR counterparts.
The latest luffing jib crane from Potain can reach a height of 190m with almost half the anchorage points required by similar models.
MANITOWOC HAS LAUNCHED ITS ALL-NEW Potain MCR 305 luffing jib tower crane. Customer feedback harnessed through the company’s extensive Voice of the Customer process helped optimise the new design, offering several improvements over earlier models.
With two units already on the way to Australia, this model is set to be a crowd favourite in the construction industry.
One of the most impressive advances of the MCR 305 is its optimised design, which significantly reduces the number of points where the crane must be secured to a building as construction grows upwards. Requiring fewer anchorage points means more efficient assembly and less expense for contractors, saving precious time on the tight schedules high-rise projects demand.
For example, with the existing MCR 295 A configured with a 60m jib, 11 anchor points are required to reach a height of 192.6m. However, with the new MCR 305 with the same jib, just six anchor points are needed to reach 194.3 m.
Equally important for contractors is the MCR 305’s reduced out-of-service radius. For example, with a 60m jib the out-ofservice radius of the MCR 305 is just 12.5m, compared with 22m for the MCR 295 A in the same configuration. Lowering the out-of-service radius allows contractors to place more cranes on constrained jobsites, making more lifting options available and delivering better space optimisation. It could mean projects considering a highrise build with just one crane may now be able to accommodate two, delivering huge
productivity advantages.
The new crane’s increased load charts make the MCR 305 more attractive for high-rise construction, as it can handle heavier loads, said Leong Kwong-Joon, regional product manager for Potain tower cranes at Manitowoc.
“We’ve had extensive conversations with customers and the insights we gained have helped us develop an impressive new luffing jib crane,” he said. “Strength gains are realised along the entire length of the jib. There are also great savings for customers in climbing higher faster, and better productivity with a substantially reduced out-of-service radius. We’re excited to launch this new model to market.”
There are two versions of the MCR 305: the 20-tonne capacity MCR 305 H20, and the 25-tonne capacity MCR 305 H25. With a 60m jib length, maximum tip loads are 3.1 tonnes for the H20 version and three tonnes for the H25 version. There are multiple winch options, depending on customer preference, including High-Performance Lifting (HPL) options, with up to 1200m of wire rope available.
The cranes are built at the Manitowoc factory in Zhangjiagang, China, and will be sold across Asia, Australia and New Zealand, Africa, the Middle East and Latin America.
12-13 September 2024 The Star Gold Coast Australia
THE ONLY DEDICATED REGIONAL EXHIBITION FOR LIFTING INDUSTRY PROFESSIONALS
• Show floor of lifting and height safety equipment
• End user presentations discussing the latest technologies, advancements in safety, and industry best practices in Oli & Gas, Mining, Ports, Infrastructure and Construction industries
Members of the UAA team - including Keith Palmer, Regional Manager East; Kathy Leech, Claims Operations Manager QLD; Vivian Rivero, Claims Operations Manager NSW; Luani Guglielmin, Regional Manager North; and Martyn Shirley, Regional Manager West - take time to discuss issues relating to insurance premiums, claims and what clients can do to ensure they have the right levels of insurance.
KEITH PALMER HAS SPENT 44 YEARS IN in the insurance industry and worked for UAA for 17 years.
In his experience, clients make mistakes with insurance policies because they don’t understand that the basis of a settlement is the market value of the equipment at the time of loss, (excluding the replacement cover benefits provided under the policy).
“Clients also make mistakes by not reviewing sums insured at renewal in consideration of market conditions, they sometimes also under insure to save money. Not setting the replacement sum insured on newer equipment in line with the policy benefits, is also an issue and not realising there are financial protection covers such as Loss of Revenue and
the policy for damage,” said Keith.
He goes on to explain what clients can do to stop premiums rising.
“There are a number of relatively simple ways to assist in keeping a lid on premiums. These include the deployment of suitably qualified and licensed drivers to drive and operate machines.
The installation of dashcams in vehicles which may assist in defending any third-party claim for damages. Installing anti-theft security devices and GPS tracking units on machines and vehicles which may assist in prevention of theft claims.
“Depots where equipment is kept should have good security perimeter fencing and good quality gate locks. There should be good lighting and CCTV cameras with machine and vehicle keys
a back to base alarm system. Clients could undertake toolbox meeting to discuss near miss accidents and put in place procedures to prevent the same from happening. Clients could review sums insured to ensure they are not over inflated and therefore paying over inflated premiums,” he said.
Kathy Leech spent 20 plus years in the Insurance and Financial sectors before joining UAA 10 months ago. She had this to say about common mistakes.
“Clients may not fully consider the replacement cost of their equipment, including factors like depreciation or new technology. As a result, they may end up under-insuring their equipment. Equipment values can change over time due to factors such as inflation, market
fluctuations or upgrades. Clients may forget to update their insurance coverage to reflect these changes,” she said.
Clients need to work closely with their insurance broker,s confirms Kathy.
“Working closely with the insurance broker is essential. Overall, it is the broker who enables clients to make informed decisions about their insurance coverage, receive personalised advice and support and effectively manage their insurance needs to protect their business interests,” she said.
Martyn Shirley has been in insurance for close to 25 years and with UAA for 16 years. He had this to say.
“Clients need to understand the importance of ensuring the equipment is insured for a fair market value. There have been instances where the insured has purchased an item of equipment at a fire sale price and only insured for what they have paid for it when the fair market value is substantially higher.
“It is also very important for clients to work closely with their broker, so the broker is well aware of the clients’ current activities. They need to ensure that they have the correct insurance in place for not only their equipment and property risks but also to ensure they are not putting themselves at risk contractually,” said Martyn.
Vivian Rivero has been in the insurance industry for six years and working with UAA for five. She has this to say about over or under insuring equipment and their approach to processing claims.
“We often see clients over-insuring their assets, which can lead to unnecessarily high premiums. To avoid this, it’s important that clients stay updated on the market value of their machines and other insured items. Ensuring that machinery and equipment are insured at the correct value can help reduce costs while still providing the necessary coverage,” said Vivian.
“When claims do occur, UAA adopts a proactive approach to claim management. When an incident is reported, we promptly assign an expert to assist the insured by overseeing the inspection and assessment of the damage. We aim to keep
communication seamless and efficient, ensuring that the insured and their brokers are informed within 48 hours of the expert’s first contact to arrange inspections and manage repairs.
“We maintain regular follow-up every 15 days to track the progress of repairs and keep the insured and brokers updated about any potential delays. We work closely with assessors to ensure the appropriate professionals are assigned to repair insured equipment, leveraging our deep understanding of their areas of expertise to allocate resources effectively. Our close relationship with our panel of assessors allows us to select the best-suited experts for each claim, guaranteeing that their strengths align with the task at hand,” she said.
Luani Guglielmin has been with UAA for nine and a half years. She has some interesting insights on how to keep a
“We often see clients over-insuring their assets, which can lead to unnecessarily high premiums. To avoid this, it’s important that clients stay updated on the market value of their machines and other insured items. Ensuring that machinery and equipment are insured at the correct value can help reduce costs while still providing the necessary coverage.”
cap on premiums and the importance of working with insurance brokers.
“Being tactful with claiming is important. I have seen many times clients lodge claims for each and every occurrence, sometimes resulting in tens of incidents a year - all low cost but have resulted in an overall large sum in claims which has affected the policies’ gross loss ratio dramatically, without the client understanding the impact as there were no large singular claims.
“Brokers are the bridging force between clients and their insurance. Working closely and transparently with a broker gives clients the best chance at a thorough risk analysis and comprehensive insurance cover,” she said.
Thurs 20 June, 2024
JOIN US TO CELEBRATE THE BEST OF THE BEST FROM ACROSS THE AUSTRALIAN INDUSTRIALS SECTOR Celebrate the women who work tirelessly to advance the mining, engineering, road transport, logistics, rail, bulk handling, infrastructure and waste management industries.
PROUDLY
“WE HAVE OVER 70 MEADAS IN OUR national fleet and we have been operating the smaller hybrid cranes with three-phase capabilities for some time. More recently we took delivery of two MC285CB-3s which were the first fully electric powered battery operated machines manufactured by Maeda.
“The arrival of the Maeda MC305CB confirms how focused we are on our environmental responsibilities and this addition to the fleet will make a significant contribution to reducing our carbon emission footprint,” said Stephan.
“Obviously, there is a significant demand from our clients for zero emission machines for a range of different applications including indoor environments such as shopping centres, where customers are handling fresh food produce, or where the crane is operating in a processing plant or in environments where combustion engines and related emissions are a definite no go.
“Increasingly we are seeing demand for battery electric mini crawler cranes in the construction sector where they are working in confined spaces, such as tunnelling applications, or high-rise construction projects where construction workers are working alongside the crane - requiring the work environment to be totally emission free,” he said.
Preston Hire is aware of its responsibility to provide customers with state-of-the-art craneage solutions which are also environmentally friendly, says Stephan.
“We are committed to an ongoing investment in our fleet which will see us working closely with the various crane OEMs to ensure we are transitioning our capabilities by upgrading and expanding with the latest technology and green options. There is a terrific amount of development in this area, and it is important for a national crane hire business like Preston Hire to understand when these developments are realistically going to be available.
“Customer demand for the two Meada MC285CB-3s has been very high and they are well-utilised assets, this gave us the confidence to invest in the MC305CB. The
crane was delivered by Pace Cranes on the Friday, the following Monday it went to site where it stayed for almost three weeks - so the early signs are promising that it will be an equally well utilised asset.
“The investment in battery electric powered Maeda mini crawlers will continue in various capacities and we will introduce other models and types of cranes when we are confident they fit the needs of our customers,” said Stephan.
The performance and lifting capabilities of the Maeda battery powered mini crawlers are not impacted compared to diesel or hybrid powered equivalents says Stephan.
“The productivity and the capabilities of the machine are the equivalent to a diesel powered or hybrid machine. Customers are able to get a full eight to 10-hour shift from one battery charge and this includes lifting and tracking. From the operators’ perspective, the responsiveness of the controls and the lifting capabilities of the crane are the same, the only difference they notice with the battery electric powered cranes is how quiet they are and the lack of emissions,” he said.
Preston Hire works closely with Maeda’s National Distributor Pace Cranes. Stephan goes on to discuss this relationship and how responsive they are in terms of sales, service and product support.
“We have been working closely with Pace Cranes for over 20 years and developed an excellent working relationship over this time.
“In our experience Anthony, Michael and the Pace Cranes commitment to the Maeda product is unconditional. They have a national presence which is critical for an organisation like Preston Hire and their understanding of the technical aspects of the Maeda product range is excellent.
“We have unconditional access to the technical department as well as the parts department. If there are ever any niggling issues with the cranes or we need a spare part in a hurry, the Pace Cranes team is always super responsive. They understand the critical nature of our business and will help get a crane up and running as quickly as they possibly can,” said Stephan.
While it is small, Stephan says he is
impressed with the robust nature of the Maeda range and how well the cranes are designed, engineered, and manufactured.
“For me, Maeda mini crawlers are a high-quality product based on traditional Japanese engineering and manufacturing values. They are built with high quality steel, making them highly robust and capable of operating in harsh conditions like tunnelling operations.
“With the new MC305CB, the first thing you notice is the quality of the crane’s finish. It shines and having had Maedas in our fleet for such a long time, we know the quality of the components, we know how reliable they are and how popular they are with our customers.
“Because they are so well produced and high quality, Maedas have longevity. We manage our fleet of Maedas very carefully, servicing them, checking them after each rental and before they go out on the next job and relying on Pace Cranes to assist when needed. They are extremely well utilised assets in our fleet and will continue
to be so,” said Stephan.
The new Maeda MC305CB has remote control capabilities standard via a cable remote (wireless optional) which Stephan is happy about.
“The MC305CB features a wired remote as opposed to a wireless remote which I’m quite happy about. We are dry hiring these cranes to various customers all of the time and they find themselves on numerous projects across the country.
“What tends to happen with wireless remotes on these jobs? They get lost, and to replace a wireless remote is not a cheap exercise. We have had cranes return from projects and when it’s time for the next rental we can’t find the remote, it’s not with the crane…”
“With the cabled option the operator has the ability to operate the crane remotely so he can a better view of the lift site for example, and we have the peace of mind that the remote control will be returned with the crane at the end of the rental period. It’s a win-win,” said Stephan.
Australian company McMahon Services has continued its crane fleet expansion strategy, acquiring a new Franna AT40. Crane & Rigging Manager, Simon Laird-Barrington, discusses the new avenues of business the AT40 will open up for the company.
AS THE CRANE & RIGGING MANAGER at McMahon Services, Simon LairdBarrington has seen his fair share of machines walk through the door.
And, as the company looks to continue expanding its services, he’s also well and truly across what machinery is needed to broaden the national company’s already diverse capabilities.
“We want to explore what more we can do to service the civil construction, engineering and demolition industries,” he says. “Recently, we’ve seen the opportunity to expand our crane fleet size and modernise some of the equipment in there.”
With its head office in Adelaide, McMahon Services has 20 offices across Australia and New Zealand. The company holds over 30 years of experience as an industrial, construction and environmental services provider, today employing more than 1,100 staff as it seeks to service remote locations and deliver projects in any part of Australia from a central, city base. As a testimony to the company’s level of safety, McMahon Services was awarded Federal Safety Accreditation in 2009 – the first multi-disciplinary construction firm in Australia to attain the award.
McMahon Services operates in an array of disciplines, ranging all the way from asbestos and hazardous material removal through to marine contracting, with a detour in multiple engineering and construction services. Within those disciplines is the ‘Crane & Rigging Services’, an arm of the company that offers technical expertise for a range of different crane lifts, working with structural engineering teams around
Australia to plan and execute lifts in some of the harshest environments and capable of mobilising to any location Australia-wide – or, as Simon puts it: “we’ve got work all over the place!”
“We’re currently working in Perth at the Kwinana Power Station, we’ve got jobs in Adelaide, remote South Australia,” he says. “We’re even looking at a job over in New Zealand – things are getting really busy for us.”
With an abundance of work coming through the company’s doors comes the need to expand the company’s crane fleet. With such a diverse portfolio of work undertaken comes the need for a diverse range of machinery, and it’s because of this that Simon has purchased a new Franna AT40 on top of two new mobile cranes. Previously owning three Franna MAC25 cranes, Simon says the company is renewing its fleet of pick and carry machines to help expand the business; with the larger capacity AT40, he says, there’s a real opportunity for internal growth in the jobs McMahon Services can undertake.
The AT40 is the largest capacity pick and carry crane in Franna’s portfolio and the largest pick and carry crane in Australia. The crane, released in 2019, has fast become a staple of many a crane hire company’s fleet thanks to its 44 per cent lifting capacity increase on its predecessor, the MAC25. The AT40 features a threeaxle design that eliminates the need for a removable counterweight, while the third axle control system allows the third axle to be raised when operating on a work site, enhancing the crane’s manoeuvrability.
It’s with this feature that Simon sees the crane setting itself apart from the rest of the
field. He posits McMahon Services’ desire to use the crane as an auxiliary crane to help with the assembly of some of its largescale diggers, such as its 85-tonne and 120-tonne excavators, where some of the removable features weigh up to 18 tonnes.
“Through its extra lifting capacities compared to the other pick and carry cranes in our fleet, there’s a chance for us to be more ambitious in the work that we undertake,” he says. “The range of jobs the crane can perform efficiently in lessens the need for slewing cranes in our fleet which, considering the transportability of the Franna brand and lack of need for counterweight on the AT40, saves a lot of costs in the logistical and configuration aspects of cranage.”
Furthermore, the crane comes with Franna’s patented Dynamic Load Moment Indicator (LMI), a ‘real-time’ system that calculates the crane’s anticipated path and whether the load being carried will exceed the crane’s maximum rated capacity –whether it be on rough, hilly terrains in rural Australia, or a regular construction site. The Dynamic LMI is a feature Simon was very partial to, praising the practicality and comprehensive nature of the safety system and highlighting the high level of accessibility it provided to people of all
different learning persuasions.
“The technology, while advanced, is very easy to understand and reduces the risk of human error as much as it possible can, making the chance for an accident very low,” he says. “The system is good for people who learn in a more practical and visual way, as it visibly shows the operator what they can and can’t do before they’ve done it.
With the provision of a crane, however, comes the need for good follow-up service – an aspect of its business that Franna has not left wanting more. With service
workshops based in Melbourne, Brisbane, Perth and Sydney, as well as two remote field-service depots in Rockhampton and Mackay and over 70 support staff, the renowned Australian manufacturer is doing its utmost to ensure that, should anything go wrong, its expansive support network will be on hand as soon as it possibly can to help restore the crane to its peak performance. Working in remote locations across Australia, Simon knows of the need to keep downtime at a minimum – something he feels will be ensured because of Franna’s support
network and one of his recent encounters with them. Citing his experience with Franna’s support team in the Northern Territory after a rope snapped on one of the MAC25s, he said the support team could not done more to ensure the crane was back up and running in no time – something he says is emblematic of Franna’s support network.
“Our experiences with Franna have always been the same,” he says. “The team is always responsive, we enjoy a good relationship with them, and we’ve never had any issues.”
The lateral thinking and creativity of Mammoet’s APAC division was on show in a unique roll on, roll off operation.
GLOBAL ENGINEERED HEAVY LIFTING specialist Mammoet has successfully installed the 300-tonne Breakfast Creek Bridge in Brisbane, Queensland.
Commissioned by Brisbane City Council and being delivered by the Brady Marine and Civil and Georgiou Group joint venture (GBJV), Mammoet was subsequently subcontracted to install the 300-tonne, 80m-long structure, following on from its works on the Matagarup Bridge over the Swan River in Perth, Danube Bridge in Linz, Austria and the Wellsburg Bridge in Western Virginia.
The main challenge for this project was ensuring the stability of the structure was maintained during transport and installation. Furthermore, as the structure needed to be moved from the Port of Brisbane, along the Brisbane River, and then installed onto its foundation over Breakfast Creek, minimal disruption to marine traffic, adherance to tight schedules and upholding the stringent safety and environmental standards were top of the agenda for the engineered heavy lifting specialist.
To complete its scope of work, Mammoet utilised climbing jacks, 32 axle lines of SPMT and a barge. Mammoet’s engineers conducted extensive feasibility studies to determine the best approach for bridge installation and tailored a solution precisely to the project’s unique requirements, analysing weight, dimensions and the configuration of the bridge to determine the most appropriate equipment.
The project unfolded in a carefully planned sequence of phases. Mobilisation and equipment setup at the Port of Brisbane marked the beginning, where the structure was raised to a suitable transport height using a series of climbing jacks, ranging from 100 tonnes to 150 tonnes and placed onto an SPMT configuration.
With the structure safely secured on 32 axle lines of SPMT, it was transferred onto a barge via a Roll On Roll Off operation, ready for marine transport from the Port of Brisbane upriver to Breakfast Creek.
Upon arrival and positioning of the barge, timed to coincide with the beginning of the outgoing tide, the load was carefully
lowered onto pre-set temporary supports using the SPMTs. Leveraging the SPMTs’ manoeuvrability, the team ensured seamless positioning and facilitated the lowering onto Mammoet’s temporary supports, enabling the release of the barge. Employing 150-tonne climbing jacks, the bridge was then carefully lowered onto a tailor-made alignment frame, ensuring precise positioning of the structure onto its bearings. Once the surveyor gave the sign-off, confirming the positioning, the 250-tonne low-profile jacks lowered the bridge onto its foundation. Throughout all phases of the project, according to Mammoet, safety and compliance remained paramount, ensuring stability even amid fluctuating tides.
The result was a successful installation, completed on time with minimal disruption to local marine traffic and no impact on adjacent road traffic. The bridge, now
officially inaugurated as the Breakfast Creek / Yowoggera Bridge, serves as a vital link in Brisbane’s infrastructure. Thousands of residents and visitors are now privy to the extended Lores Bonney Riverwalk, enjoying enhanced commuting and leisure opportunities along the riverbanks.
It will also play a major role during the Brisbane 2032 Olympic and Paralympic Games, providing a key active transport connection to the athletes’ village at Northshore Hamilton.
The bridge, part of the city’s bridges program, aims to bolster pedestrian and cycling links across the river and enhance transport connections between the inner city and its growing northern suburbs. With the bridge serving as a key connection to the local community, the pressure was on to ensure swift, yet seamless construction, according to the global heavy lifting powerhouse.
PLEASE SEND YOUR LIFT OF THE MONTH ENTRIES TO SIMON.GOULD@PRIMECREATIVE.COM.AU
WHO: McKay United.
PR OJECT: Level Crossing Removal Project, Parkdale Station.
CLI ENT: Acciona, Coleman Rail, WSP, Metro Trains Melbourne.
CR ANES: Grove GMK7450 and Grove GMK6400
LOAD: 120-tonne bridge beams.
It’s our competitive ethos of solving the unsolvable, finding a way, and just getting on with it, that helps us make things possible for ourselves, our partners, and our customers.
It’s this drive that has led to our new generation TIDD Pick and Carry Crane. See for yourself and talk to us today about the TIDD PC28-3G.