
4 minute read
Streamlining heavy lifting and haulage How to streamline a heavy lifting and haulage business through digitisation
Leading German heavy lifting and haulage specialist recognised the impact paper-based administration was having on the business and streamlined processes by implementing the E.P.O.S. modular software system. Cranes and Lifting explains.
GUSTAV SEELAND GMBH is one of the largest providers of heavy goods logistics in Germany, providing solutions across the entire area of heavy and special transports, mobile cranes, industrial assembly and heavy goods storage.
Jan Gaarz, operations manager at Gustav Seeland GmbH explains how far-reaching the implementation of the E.P.O.S system has been, and how important the digitisation of paper processes will be to the future ofthe business.
“We recently integrated the E.P.O.S. Online Application which replaces existing job dockets, delivery notes and optimises the processing of orders. This information is now sent directly to tablets being operated by drivers, supervisors, operators and other staffonsite.
“The Online Application compliments the digital processes already operating in the office which are a result of
implementing E.P.O.S. the deployment, planning and organisational system modular software system. We are already seeing positive results from these implementations and we see the digitisation processes as a crucial step forward in the future development of our business,” said Gaarz.
Recently, Gustav Seeland GmbH completed a project which tested the resources and the expertise of the business. An 85m ferry had to be brought from the port of Hamburg to Fußach in Austria - by road. In order to transport the ferry to its destination, it was dismantled into 17 parts in Hamburg. The ship sections, which are almost 14m long and up to 5m wide and around 4m high, were then loaded onto the special vehicles by crane. The elements, which weigh around 33t were transported on the flatbed trucks from Hamburg via Hanover, Magdeburg, Leipzig, Nuremberg, Munich and Memmingen to Fußach within three nights. At the shipyard they are then reassembled into a ship. After completion, the ferry was the first LNG ship on Lake Constance.
Details relating to complex projects like this are available to everyone involved, including administrative staff in the office and the drivers and operators involved. With E.P.O.S., it is possible to attach numerous amounts of supporting documentation and images to every activity such as quotes, jobs and invoices in E.P.O.S.
For example, pictures from a site inspection, freight lists or ground plans from the customer are accessible for everyone at any time. It’s a simple case of dragging and dropping the documentation or images and sending the files as an email attachment. E.P.O.S. has transformed business processes for Gustav Seeland, and the integration process was relatively seamless says Gaarz.
“The integration process went very well. We ran both the paper and digital systems in parallel for the first three months and then we completely did away the paper system. Employees were initially sceptical about the E.P.O.S. system but quickly saw the benefits it brings and were soon fully accepting.
“With the Online Application , orders can be settled immediately after c ompletion. Order documents such as work plans, driving permits etc. are digitally assigned to the orders,” he said.
Job data is exported directly from E.P.O.S. to the tablet operated by the driver, crane operator or onsite staff. Job related documents can also be sent directly to the tablet. The customer is able to read the detail relating to the job and confirm it is correct by signing off on the completed job with a digital signature.
“We’ve been able to streamline the whole reporting system with the Online Application feature. It has provided a number of benefits including flexibility with digital orders, dispatch and prompt billing,” said Gaarz.
“Documents come directly back to the office via the online proof of performance which can include delivery notes and photos. Drivers are able to report back on issues relating to vehicle defects and these reports are immediately stored in the system to ensure the vehicle is inspected at the first available opportunity.
“After a very short start-up period, the digital performance records were very well received, with customers also immediately receiving a digital copy by email,” he said.
Christian Matusch, director of leading German business software company Matusch, developer of E.P.O.S. says the experience of Gustav Seeland GmbH exemplifies the importance of digitising all operational processes.
“If you are in the heavy-lift or heavy haulage industry, future-proofing your business with flexible and functional software is an important pillar to ensure your company’s future success.
“The Equipment Planning and Organisation System, (E.P.O.S.) functions as the information centre for the entire company. The software provides a standardised and transparent process, from the preparation of the quote through to the planning and execution of the project,” he said.
“Complex orders with any combination of transport, assembly and lifting services can be calculated, processed, checked and invoiced with the software, and despite the wide range of functions and complex processes, E.P.O.S. is simple and userfriendly to operate,” said Matusch.
4
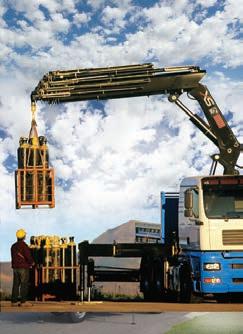
4
4
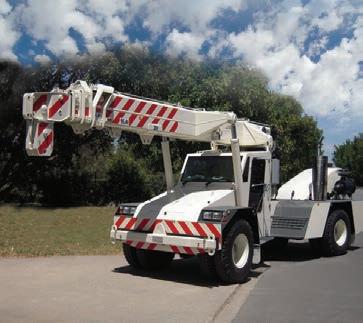
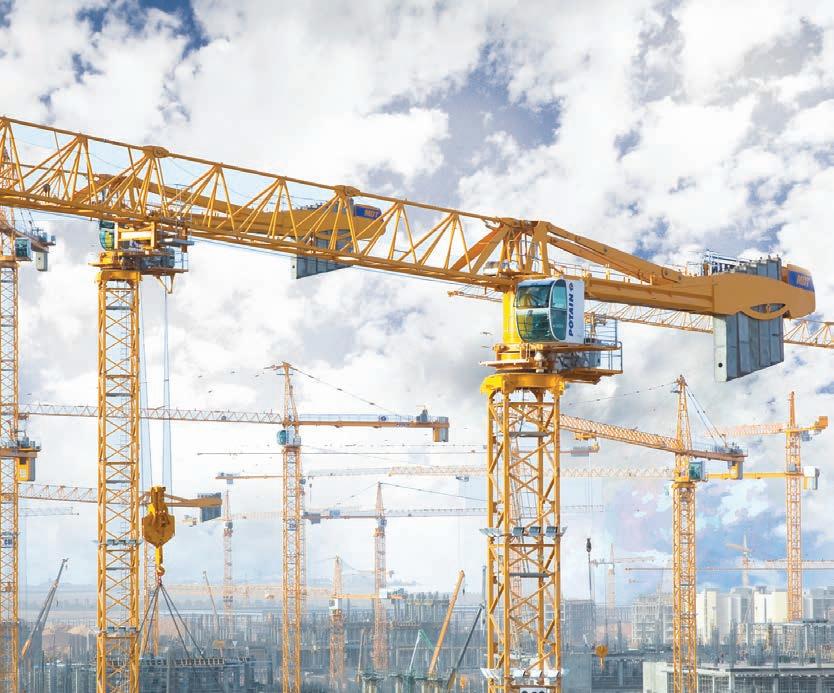
4
4
4
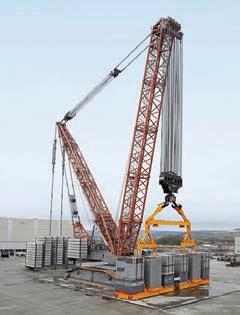
4
4
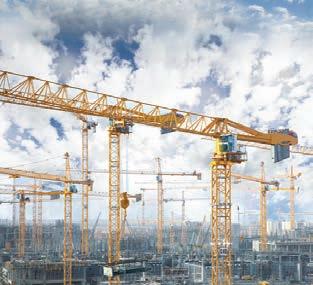
4
4