
5 minute read
McKay United’s Groves to the rescue Two Groves were required for major dual lift at automated container handling facility
UNITED GROVES TO THE RESCUE
Leading Melbourne crane hire business McKay United, recently completed the company’s largest “all Grove” dual-lift utilising Grove all terrains. Cranes and Lifting finds out more.
VICTORIA INTERNATIONAL CONTAINER
TERMINAL (VICT) is Melbourne’s newest container terminal. It features a state-of-the-art container handling system including 20 Automatic Stacker Crane (ASC). When one of the ASCs derailed, McKay United deployed two Grove all terrains, a GMK7450 and GMK5250L to assist.
VICT is located north of Port Phillip Bay at the mouth of the Yarra River, at the Port of Melbourne’s Webb Dock East. The 35-hectare terminal has an annual capacity of over a million TEU (twenty-foot equivalent unit) and a straight berth of 660 meters that can accommodate two vessels along-side.
The OneTerminal deployment at VICT includes a Kalmar Automatic Stacking Crane (ASC) system comprising 20 ASCs, and it was one ofthese that had derailed.
“We are talking about an automated system for handling containers and because the ASC had come off its rails, it was holding up the whole container handling process and the production of the port in a fairly major way,” said Simon Atkins, general manager, at McKay United.
“The ASC had actually twisted so this proved a challenge and it was difficult to locate the twisted wheels back on the tracks. The ability for both the GMK7450
and GMK5250L to work at nearly maximum chart was a very positive and rewarding outcome for our client.
“They had tried to jack the crane initially which proved unsuccessful, so I went down and had a look. There was an issue getting into the area due to a water runway which we had to fill in with crushed rock and a steel plate to provide access for both the GMK 7450 and GMK5250L.
“We prepared the cranes in the yard and the GMK7450 got to the
port within two hours. We conducted an extensive examination of lifting procedures with Kalmar, to understand where the lift points were on the crane. There were two points on the top of the crane, and it was important to know if these were designed to take the whole load. We set both cranes up and came back the next morning to start the lift,” said Atkins.
The ASCs run on train tracks and one of the crane’s legs had stayed on the track following the incident.
“The 250t lifted one leg whilst the 450t lifted two, it had a weight of about 157t. We made one attempt at the lift which didn’t work and after some consultation, I said I thought the mechanical grab, which handles the containers, was throwing a bit of weight. The grab weighs about 45t and I said if we could get that weight off the legs, it would help. They got into the grab, released the brake and moved the it further along the gantry of crane. We came back the next day and that’s when we conducted the lift,” said Atkins.
For the first phase of the project the GMK7450 and GMK5250L placed the gantry crane back on the tracks. For the second phase of the project, the GMK7450 picked up one side and slewed the gantry crane away from the damaged rail and onto the straight part of the track, with assistance of winches controlling the other side of the load.
“We suspended the ASC while they did a bit of work on the track close to the 250t. This track wasn’t too badly damaged so that it could sit the stacker crane back down. Then the 250t took the weight off the 450t and slewed it because that’s where all the damage to the track was.
“There was a 10m section of damaged track and we couldn’t put it back down. We were able to get one wheel back on a piece of straight track. We lowered it down again then hooked up one leg. We slewed it gain and we were able to put the other leg on the straight track and they went to work on getting the damaged track out. That was us done, they were able to access
The cranes conducted four separate dual lifts of the gantry crane, with the GMK7450 lifting between 160t and 175t of the total load, and the GMK5250L lifting around 84t.
the bent track, replace it and run it from there,” said Atkins.
The GMK7450 was configured with 120t of counterweight, with 25.7m of main boom extended to lift at a 7m radius. The GM5250L was configured with 80t of counterweight, and it had 37.9m of main boom extended to lift at a 7m radius.
The 450t GMK7450 has a maximum main boom length of 60 m and a maximum tip height of 136m. The crane also features MEGATRAK suspension on a seven-axle carrier, a removable rear outrigger box and the Twin-Lock boom pinning system.
The 250t capacity GMK5250L has a main boom length of 70m and a maximum tip height of 110m. It is one of the most powerful and versatile five-axle cranes on the market with the highest-rated capacity and the quickest set-up time in its class.
“As far as the rigging equipment for the lift was concerned, we were lucky enough that the available spreader bar was the one used by Kalmar to assemble
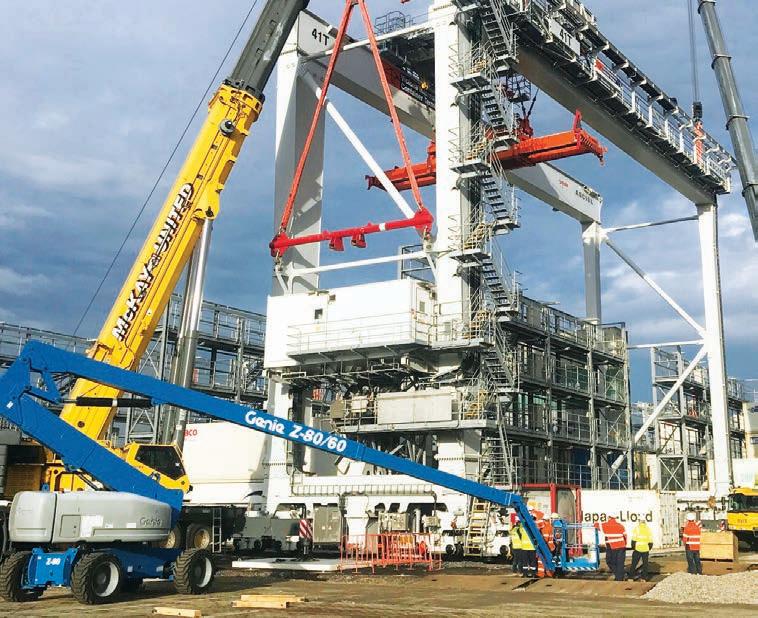
the crane and it was in test.
“We used our 100t slings, but the spreader bar was made for the assembly process. VICT were really happy with our ability to get there quickly. I said if the machines had been working, we wouldn’t have been able to respond so quickly, but because they happened to be in the yard, we are more than happy to help day or night.
“The brand new 250t is a great a machine and it performed perfectly. It was able to get right in and close to the ASC and we ended with 28.5m of main boom and we were able to get an 84t lift because it was up pretty straight. We were lucky that both machines were available and certainly Kalmar and VICT were pleased with the work we did and the outcome,” said Atkins.
In total, McKay United used the two cranes for four separate dual lifts of the gantry crane, with the GMK7450 lifting between 160t and 175t of the total load, and the GMK5250L lifting around 84t. The whole project lasted 16 hours, 8 hours on two consecutive days.