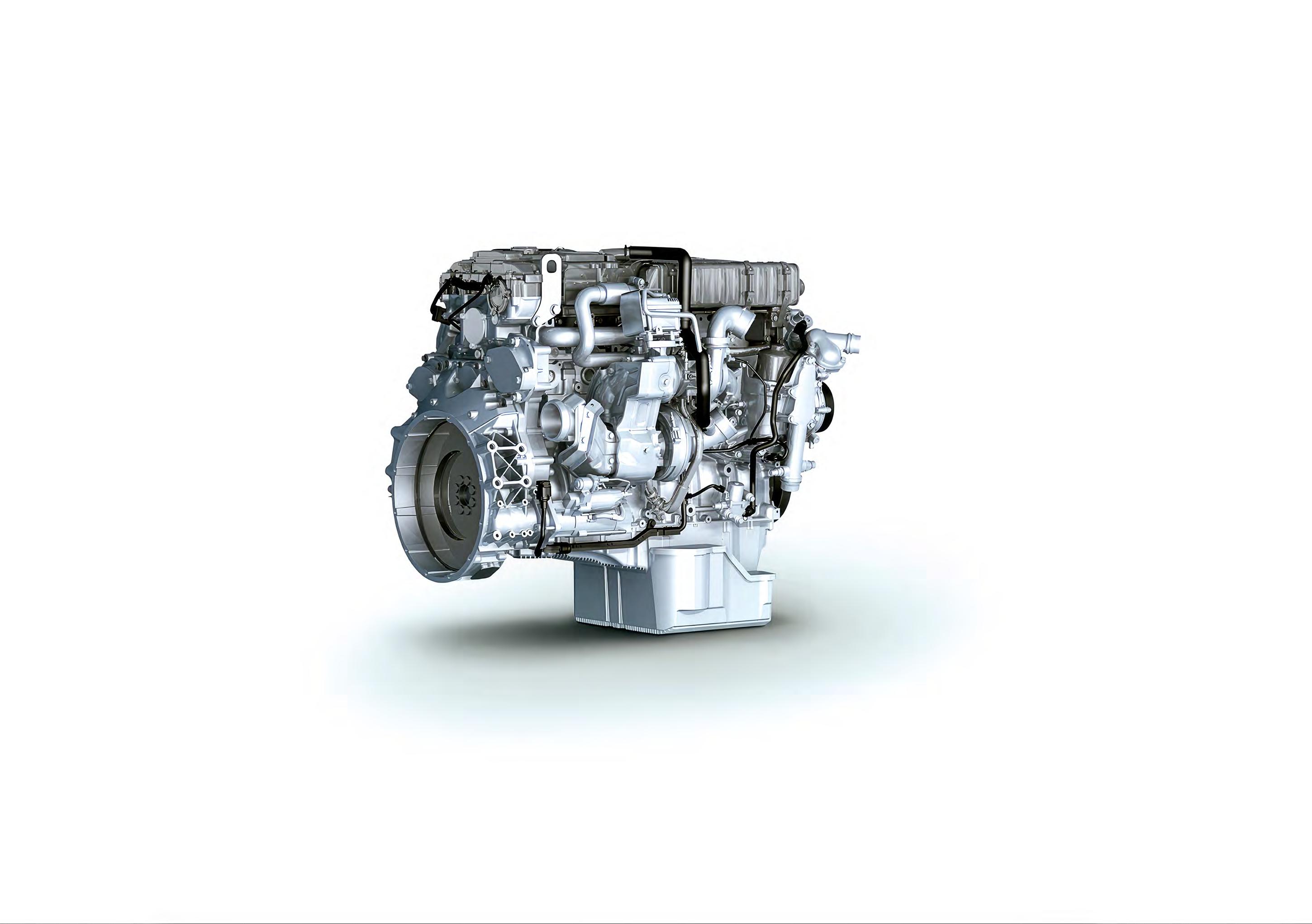
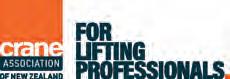
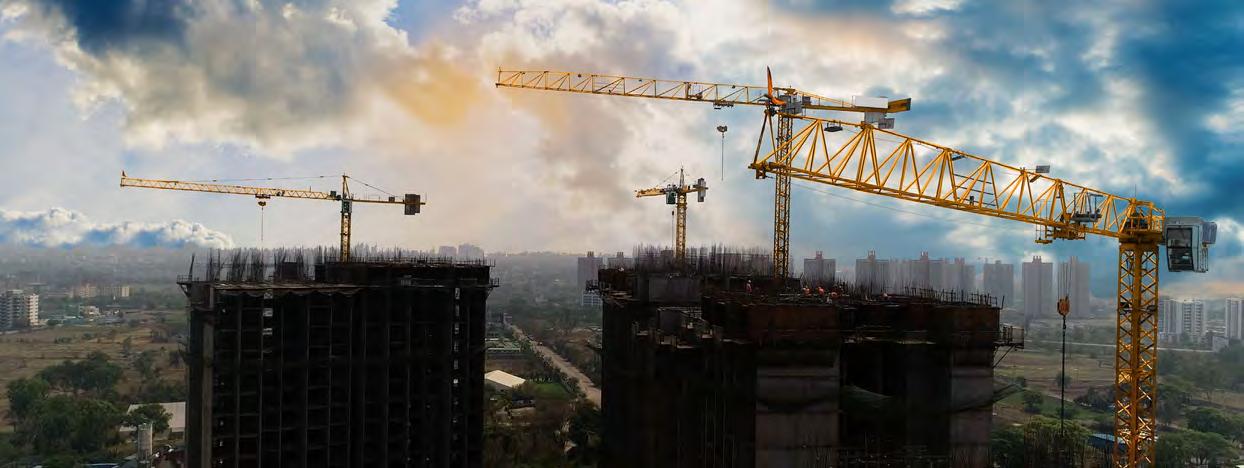
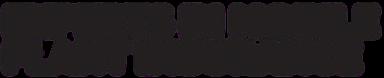
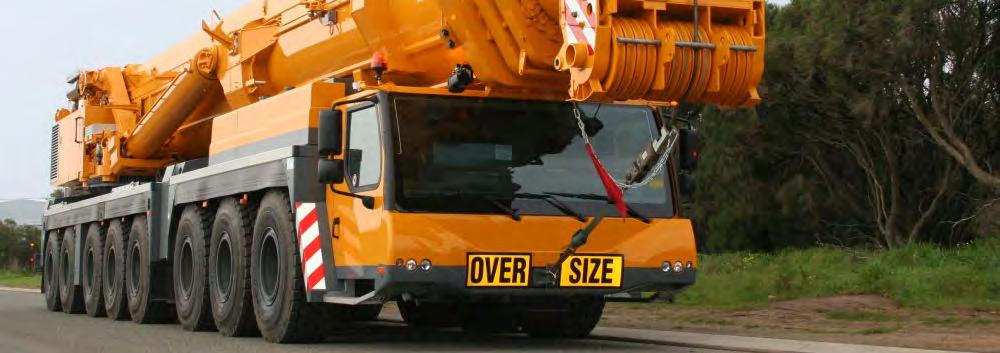
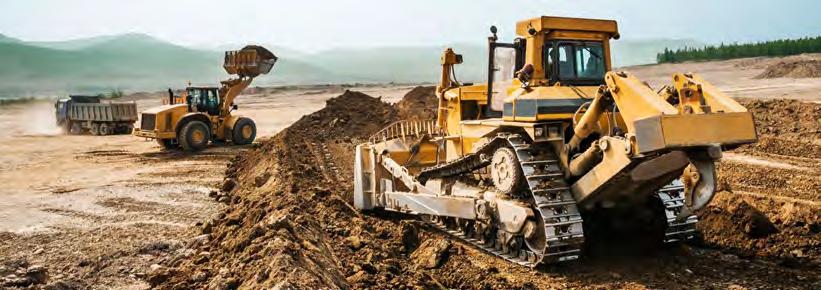
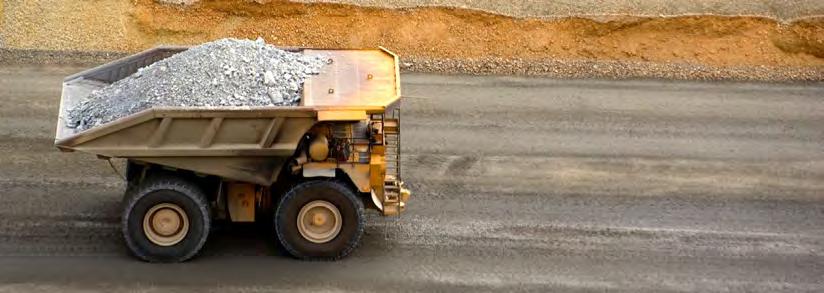
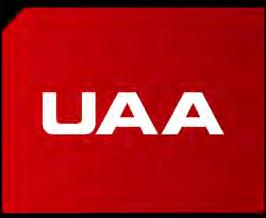
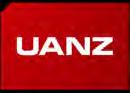
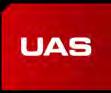
6 Franna
The Australian manufacturer reveals its next generation of ADR-compliant pick and carry cranes.
8 CICA CEO Report
Brandon Hitch examines the success of The Lif t Supervisor Course.
11 CICA Charity
Attendees at NSW CICA Regional meeting bid high for the Touched by Olivia Foundation.
14 NSW Regional Meeting
NSW CICA Regional Meeting well attended with excellent presentations delivered.
19 Soft Sling Compliance
CICA cracks down on non-compliant sof t slings entering the Australian market.
21 Monadelphous
The largest new crane officially arrives Down Under.
22 Tadano
Tadano and Boom Logistics demonstrate commitment to a sustainable industry.
27 MCT Equipment
45 Pace Cranes
Scott McLeod discusses his purchase of a Track Carrier from Pace Cranes.
48 UA A
The WA dealer has revealed a new, purpose-built machine set to enter the market.
28 Tutt Bryant
TBHLS showcases its turnkey capabilities in a massive showing in WA.
30 Sany Australian contingent attends SANY
Crane Global Key Account Summit
CANZ Feature
35 CANZ CEO Report
CEO Sarah Toase provides insights into how NZ’s crane sector is performing in 2024.
37 Ian Roebuck Crane Hire
Ian Roebuck celebrates 45 years in cranes and lifting.
40 APS Equipment
Clyde Services purchases the largest telehandler in the Southern Hemisphere.
42 Liebherr
A changing of the Liebherr guard with Tom Curran’s imminent retirement.
Matt Ziegler, UANZ Head of New Zealand and Pacific, takes a deep dive into the insurance of mobile plant in NZ.
50 Allcrane
Allcrane sales and service delivers NZ’s largest FASSI knuckleboom
52 Visual Dispatch
Scott McIntosh discusses how Visual Dispatch has streamlined his crane scheduling and allocation.
55 Preston Hire NZ
A brief look at Preston Hire’s NZ capabilities.
56 TRT
MD Bruce Carden reflects on the recent TRT Customer Day.
61 Pace Cranes
Pace Cranes confirm commitment to Apprenticeship Program
64 Potain
New model Potains released.
67 Grove
Pfeiffer Cranes takes delivery of largest all terrain in Tasmania.
70 SpanSet Australia
SpanSet’s game changing investment in testing and certification.
73 Penske
Penske goes in depth on the new Mercedes engine in the Franna cranes.
75 LEEA
Justin Boehm questions the quality of lif ting equipment and announces training partners.
79 Liebherr
The manufacturer reveals its global sustainability rank.
80 Mammoet
Mammoet breaks a record in Lithuania with a first for the Baltic nation
83 Zoomlion
A colossal, world-record breaking lift.
84 Tutt Bryant
Exploring mobile power storage units and what they mean for battery electric cranes.
86 Lift of the month What our industry is all about.
Optimal Partners for Wind Turbine Hoisting and Large-scale Foundation Construction
Excellent Lifting Performance
· The maximum lifting capacity of the fully extended main boom is 15.6t, and the maximum single-rope pulling force is 8.6t
· The maximum lifting moment of the basic boom is 352 t.m, and the maximum lifting moment of the fully extended boom is 192.6 t.m
Superior Adaptability
· Larger chassis dimensions with a wheelbase distance of 5530 mm and a track center distance of 4470 mm provide strong operational stability
· With a maximum gradeability 45%, it has excellent off-road capabilities, suitable for muddy, swampy, and other harsh terrains."
Efficient transportation
· Compact transportation dimensions: 3.49m wide with tracks intact and 3m wide with tracks removed
· The minimum transport weight of the main unit is 52t (with counterweights and ballast removed), resulting in low transportation costs
Rough terrain crane
ZRT400V
ZRT400V
ZRT600V
ZRT700V
ZRT900V
ZRT1100V
ZRT1300V
ZCC850V-1
ZCC850V-1EV
ZCC1500V-1
ZCC2600-2
ZCC3200V-1
ZCC7200
ZCT160V
ZCT300V
ZCT300V
ZCT600V
ZCT1000V
ZCT1200V
ZCT1500V
Published by:
Work Done data from the Australian Bureau of Statistics provided some interesting insights as to how the Australian construction sector is travelling. The data revealed residential building activity slipped in the first quarter of 2024, falling 1.2 per cent to $19.58 billion (chain volume measure) in seasonally adjusted terms. This was marginally below expectations, pointing to the recent weakness in new dwelling demand.
Trade labour shortages remain a central issue. Construction vacancies have softened, but remain elevated at a level nearly 70 per cent above the pre-pandemic base. Meanwhile, bottlenecks continue towards the fitout stage at which a lot of value is put in place. This is slowing the rollover onto new projects and contributing to the challenges being faced in terms of housing supply.
Non-residential construction slid in the first quarter of 2024, down 7 per cent to $13.73 billion. Public works led the way, down 9.4 per cent despite a sizeable pipeline of public projects underway. Private activity also fell (-6 per cent) as the slowdown in commercial construction continues to play through.
The approvals lead for non-residential building continues to soften, with the March quarter 2024 maintaining the
recent downward trend in project approvals. Compounding the slowdown in approvals, a higher dropout rate to commencement is also evident.
Engineering (non-building) construction activity declined 2.1 per cent seasonally adjusted over the March quarter to $30.72 billion. This result was led by public works, offsetting the step up in Q4.
Recent Federal and State Budgets delivered few surprises, although the Victorian Budget did flag changes to specific projects and resulted in a slight downgrade to our long-term profile for publicly funded civil engineering construction in the state. At a federal level, support has been announced for the development of Australia’s critical minerals and hydrogen industries – including funding to map Australia’s resource endowments.
As always, the team at Cranes and Lifting has worked hard to bring you the latest developments from the Australian and New Zealand crane sectors. We hope you enjoy the read.
Simon Gould Editor, Cranes and Lifting
379 Docklands Drive, Docklands VIC 3008
T: 03 9690 8766
www.primecreativemedia.com.au
CEO
John Murphy E: john.murphy@primecreative.com.au
Chief Operating Officer
Christine Clancy E: christine.clancy@primecreative.com.au
Managing Editor
Andrew Hobbs E: andrew.hobbs@primecreative.com.au
Editor
Simon Gould
E: simon.gould@primecreative.com.au
T: 0404 865 109
Assistant Editor
Jack Alfonso E: jack.alfonso@primecreative.com.au
Business Development Manager
Emily Schlegel
E: emily.schlegel@primecreative.com.au
T: 0466 317 555
Client Success Manager
Glenn Delaney
E: glenn.delaney@primecreative.com.au
Art Director
Bea Barthelson
Imaging Assistant
Paul Breen
Subscriptions
Frank Rapone
T: 03 9690 8766
E: frank.rapone@primecreative.com.au
The Publisher reserves the right to alter or omit any article or advertisement submitted and requires indemnity from the advertisers and contributors against damages or liabilities that may arise from material published.
© Copyright – No part of this publication may be reproduced, stored in a retrieval system or transmitted in any means electronic, mechanical, photocopying, recording or otherwise without the permission of the publisher.
Franna reveals that the AT40, MAC25 and AT22 are to receive upgrades and new series designation.
FRANNA CRANES HAVE CARVED A legendary reputation in the Australian crane industry, consistently praised for their unwavering reliability, exceptional performance and remarkable adaptability. Franna is proud to unveil the next chapter in Franna’s history - the all new Franna AT40 Series 2, AT22 Series 2 and MAC25 Series 5.This comprehensive upgrade represents a transformative leap forward, encompassing not only a more powerful and environmentally sustainable engine but a multitude of advancements designed to elevate customers’ lifting experience in every aspect.
Mercedes-Benz OM936 Engine during extensive testing of the prototype AT40-2.
At the core of the Series upgrade lies the Mercedes-Benz OM936 engine. This Stage V and Tier 4 Final compliant engine surpasses the latest Australian Design Rules (ADR) for cleaner emissions and future-proofs customers’ investment by also meeting planned future engine ADR. This means customers’ Franna cranes operate sustainably, minimising their environmental impact while ensuring seamless compliance with evolving environmental regulations.
The benefits extend far beyond mere compliance. The OM936 boasts a
well-established track record, having undergone over a decade of refinements to achieve exceptional reliability. Our dedicated engineering team collaborated closely with Penske Power Systems, the authorised distributor of MercedesBenz engines in Australia, to ensure seamless integration of the OM936 into the Franna range. This collaboration included extensive aftermarket treatments, a power increase and fine tuning of the gearbox to provide a greater driving experience, as well as providing optimal performance and efficiency within the demanding environment of pick and carry cranes.
The Series upgrade goes beyond just a new engine. Franna has implemented a series of additional enhancements across all Franna models, designed to streamline customers’ lifting operations across useability, productivity and safety:
Meets current and future ADR Compliance: in addition to the OM936 engine, the cranes have been upgraded to ensure they are compliant with all current and near future ADR compliance standards, including through headlights, visibility, noise levels, ABS and emission standards, along with a suite of safety standards. Safety Radar as standard: Safety remains an unwavering priority at Franna. The Series upgrade elevates safety standards by incorporating the Franna Safety Radar as a standard feature. This radar system adds an additional layer of protection and awareness for operators. Rear Body Upgrade: The rear body of all the models has been reworked to improve serviceability of the cranes. ABS, battery isolators and larger capacity batteries have been added as standard, along with the below model-specific enhancements that recognise the unique strengths of each Franna model, tailoring the features to maximise their potential:
“This comprehensive upgrade represents a transformative leap forward, encompassing not only a more powerful and environmentally sustainable engine but a multitude of advancements designed to elevate customers’ lifting experience in every aspect.”
AT40-2: The flagship AT40 receives a power boost with a 230kW version of the OM936 engine, further solidifying its position as the industry leader in lifting capacity and performance. Efficiency has also been considered with the AT40 receiving new deck panels to facilitate serviceability.
MAC25-5: The MAC25 receives a model designation upgrade to MAC255, reflecting its continuous evolution and improvement. In addition to the above range improvements, the MAC25-5 includes an engine power boost to 210kW, improved boom and steering response, an additional step for the rear body and the relocation
of the isolators to outside of the articulation zone for enhanced safety.
AT22-2: These versatile models are equipped with a 210 kW OM936 engine, an additional step for the rear body, and improved efficiency and power for a wide range of lifting tasks. The AT22-2 also receives the winch handrail as standard, for safer rear body deck access.
Franna understands that customers’ cranes are a pivotal component of operations. The Series upgrade represents the combination of
improved power, efficiency and safety. Here’s what customers can expect:
• I mproved Efficiency: Fuel efficiency is a concern for any operator. The Series upgrade introduces optimisations that contribute to lower fuel consumption, resulting in reductions in operating costs.
• S treamlined Maintenance: We’ve implemented improvements that simplify maintenance procedures, saving customers’ valuable time and resources. This translates into increased uptime and improved productivity.
• A dvanced Safety: The suite of advanced safety features, including the Franna Safety Radar 360-degree camera, creates a safer working environment for both the operator and those on site.
• C omprehensive Training and Support: Our commitment extends beyond the crane itself. Our entire team, from engineering and service technicians to our 24/7 product support team, has undergone rigorous training on the Series upgrades. This ensures Franna can provide customers with the highest level of support, maximising customers’ productivity and minimising downtime. Our team is here to answer customer questions, address any concerns, and ensure customers get the most out of the Franna cranes.
The launch of the new series of Franna Cranes reflects the company’s unwavering commitment to innovation. Franna is dedicated to providing customers with the most advanced, efficient and user-friendly cranes on the market. With the Series upgrade, customers will experience industry-leading performance, future-proof compliance, enhanced safety features, streamlined maintenance and a renewed focus on efficiency, that has made Franna Australia’s number one choice for over 40 years.
WE’VE COME A LONG WAY FROM OUR initial pilot for The Lift Supervisor Course in August last year. 13 course sessions, spread over 4 states, with over 200 participants. The feedback has been fantastic, and training days are being filled as fast as we can schedule them.
Opportunity is a fundamental aspect of what we want to create with our programs. Opportunity for professional development for members of industry that already have experience but want to reach for something more. Opportunities to learn for new blood coming in, and opportunities to understand other teams operationally within a business.
The Lift Supervisor Course is an example of a single course that can meet all those needs. Experienced operators can see their knowledge grow, and skills validated. Newer operators looking to build on the foundations they already have in place can do so in a structured environment.
Even staff members that may never see an active site can benefit from going through the course to understand what it’s like to be in the field – the language and terminology, the considerations that go into a lift, communication and protocol, how it all fits together.
We’re not an RTO, and not in the business of becoming one.
But part of our commitment to our industry is giving avenues for growth. Not just in the literal sense of more cranes and more jobs, but in developing the skills and knowledge of the people already in it. Our resources are specific, shaped to fit our niche, and undiluted by a need to satisfy multiple potential stakeholders. They’re for our industry, by our industry.
Being a leader is more than a title, it’s a skillset that needs to be learned and shaped. Knowing what kind of leader you want to be, and how to become that person, can be a hard transition without guidance. We’re working with leadership experts to bring two courses to our industry that can provide that support – the Women’s
actively accepting registrations, and the Emerging Dynamic Leaders Program, which is currently accepting expressions of interest.
ON-ROAD DRIVING FOR PICK AND CARRY CRANES
Many seasoned Pick and Carry crane operators have never been formally
assessed, and the safety of these cranes on the road has been a point of concern from within and outside of our industry. The On-Road Articulated Steering Mobile Crane Training Course was created in response to the ongoing conversation around the future of these cranes in Australia, funded through a grant from the NHVR Heavy Vehicle Safety Initiative. More information about our courses and programs can be found on the CICA website under Resources, and if you have questions, our team is happy to help.
As our industry evolves, and CICA evolves, our programs will too. They’re designed to fill the gap between what’s learned during a High Risk Work License and what’s done in the field. They’re relevant, contemporary, and practical – informed by experience and collaboration between industry experts.
We hope to see you in them.
Brandon Hitch CEO
“Even staff members that may never see an active site can benefit from going through the course to understand what it’s like to be in the field – the language and terminology, the considerations that go into a lift, communication and protocol, how it all fits together.”
Ben Pieyre – President
Marcus Ferrari – Vice President
Danny Adair – Director
Danny Black – Director
Andrew Esquilant – Director
David Solomon – Director
Karli Sutherland– Director
Brandon Hitch Chief Executive Officer
03 8320 0444 0428 228 048
ceo@cica.com.au
Paul Arztenhofer
Membership Engagement/ Business Development Specialist 04 9093 9274 paul@cica.com.au
Alice Edwards Road Technical Engineer 03 8320 0440 alice@cica.com.au
Patrick Cran CraneSafe and CrewSafe Technical Advisor 0488 004 274 pat@cranesafe.com.au
Damien Hense CICA Road Policy Advisor 03 8320 0460 0488 007 575 damien@cica.com.au
Julie Turner CICA Executive Assistant/ Board Secretariat 03 8320 0411 julie@cica.com.au
Kate Galloway Traineeship Coordinator 0491 047 118 Kate@cica.com.au
Shane Coupe CraneSafe & CrewSafe Administrative Assistant Officer shane@cica.com.au 0491 047 134
Madeleine Flynn
Senior Marketing Communications Officer madeleine@cica.com.au
Justina Blackman
Member Events and Engagement 0403 717 626 justina@cica.com.au
Ashleigh Gould Office Operations Coordinator, ashleigh@cica.com.au 03 8320 0466
Unit 10, 18–22 Lexia Place, Mulgrave Vic 3170
Phone: 03 9501 0078
Fax: 03 9501 0083
Email: admin@cica.com.au
Website: www.cica.com.au
For information, please visit our website or call the CICA office.
The New GMK5150XL is the latest sibling of the GMK5150L-1, with longest boom (69m) and most versatile road weights in class
• Reach further with 69m boom and 30m hydraulic luffing fly
• 50t GVM with outriggers in situ for reduced cost legal travel in all Australian states and territories
• 10.2t counterweight in situ at 12t per axle
• Increased safety and flexibility with MAXbase variable outrigger positioning
• Faster, intuitive set-up with CCS (Crane Control System)
• Grove Connect Telematics
• Capacity: 150t
• Main boom: 68.7m pinned*
• Maximum Jib: 30.2m (40O hyd luff)
• Maximum tip height: 99m
second child, Olivia, was a healthy baby up until the age of seven months, when her lymphatic system went into battle against her. Her diagnosis with Lymphatic Malformation at eight months old was too late, and she spent her last two weeks in hospital, never coming home.
A time that is usually cherished, with summer and Christmas festivities approaching, became a time for the Perkins family to dig deep and mask their unhappiness, as every living breath became focussed on building Olivia’s legacy to bring hope to others through their loss.
Within six weeks of Olivia’s death, Touched by Olivia was created in her memory. Thanks to her little life, the charity has changed the lives of families around Australia. This has been achieved by connecting with families through play with the creation of its LIVVI’s Place National Network of Inclusive Playspaces.
John and Justine continued their connection with the Sydney Children’s Hospital, Randwick, by investing in medical support to help other children living with similarly rare medical
conditions. The equipment purchased for the Hospital and clinical trial and research conducted have leveraged the Hospital as a Centre of Excellence in the area of Vascular Malformations, the family of diseases that took Olivia’s life.
In the play arena, Touched by Olivia’s work has really taken flight. The LIVVI’s Places that have opened around Australia have shone a light on the importance of play, as not only a fundamental building block in a child’s development, but as a medium by which people of all ages can connect. With social connection so important to a person’s wellbeing, these spaces are
happy places where difference is not a factor. Everyone feels safe, welcome and that they belong. Everyone can play!
Touched By Olivia has partnered with government, developers, corporates and community groups to create more than 48 inclusive playspaces across Australia. Over half of these are in regional and remote areas. These communities would simply not have access to the expertise or funding for inclusive playspaces, where every child can play, without the support of the foundation. In 2017, the NSW Government’s release of the Everyone Can Play guidelines was
a direct endorsement of Touched by Olivia’s work in inclusive play, and the charity is proud of its role in securing these standards for others to follow suit both nationally and internationally.
Touched by Olivia continues to work within communities to connect people together and has expanded into disability employment with the opening of its social enterprise LIVVI’s Cafe at Five Dock in Sydney and recently launched a new initiative in Australia building on the Community Circles model from the UK.
Justine Perkins, founder and Olivia’s mum, explains more.
“We know that there are so many good people who want to do good things, and there are also many people who need a bit of support and kindness, but the two rarely meet. For the past 18 years we have brought communities
together to do good things. Now more than ever we need diverse, strong, connected communities and that’s what our LIVVIng Room Social Enterprise Project is going to do. It’s a space where all in a community will come together to celebrate difference, contribute with purpose and be valued for who they are and what they bring”.
Listening to Justine and Kim Becherand’s presentation, and understanding more about the work the charity does to improve the well-being of individuals and communities though inclusion and belonging, the audience was primed with open hearts for the auction.
“We are overwhelmed at the incredible generosity and kindness of CICA NSW Regional members,” said Justine.
“It really was an amazing night.
We loved sharing our story and work with such genuine people who really wanted to listen and help to achieve our dream of a truly inclusive world”.
Auction items were generously donated by Liebherr, Tadano and Pace Cranes, sporting memorabilia included a boxing glove signed by Mike Tyson, signed photographs of motor racing greats including Jack Brabham, and a signed Don Bradman bat. As always, the bidding from individuals was incredibly generous and over $43,000 was raised for the charity.
“I know ‘Cranies’ in the industry, are the salt of the earth. They work together, through differences and challenges, to get things done. So, I knew CICA members and the work of Touched by Olivia would be a good match in that way,” said Kim Becherand, Head of Inclusive Play.
“But the support on the night was incredible. Our work is hard, and it sometimes feels like we are pushing it up hill alone. That night filled our cup, figuratively and financially! To have so many there validate and support our work is just as important as the funds raised, and we thank everyone who bid at the auction with all our hearts.
“We promise to share with you the impact your generosity will achieve in the coming months and hope this is just the start of new friendships and achieving more together,” she said.
The Foundation’s next big initiative is to build the LIVVIng Room. A social hub that expands their track record of success of the social enterprise LIVVI’s Café where real relationships blossom, real work experience and on the job training is received and real jobs are attained for young people with disability.
If you or your organisation would like to contribute support, either financially or in kind, or be part of contributing to greater inclusive employment in Australia and making a real difference, please reach out to Justine or Kim via the Touched by Olivia website https://www. touchedbyolivia.com.au/
In early May, CICA held its New South Wales Regional meeting in the Hunter Valley.
REPRESENTATIVES OF MORE THAN 50 crane hire companies and Crane OEMs enjoyed listening to topics delivered by leaders in our industry. Presentations included updates on the state of the economy from Chris Burke of Finlease and insurance insights from UAA’s George Grasso – which also included the announcement of a major Safety Award for the industry. CICA’s Damien Hense and Scott Greenow from Transport for NSW delivered updates on crane roadability, and Michael Selinger from Holding Redlich also dialled in with an industrial relations presentation.
For many the highlight of the day was the fundraising auction. Each year a charity is nominated by CICA’s NSW committee and this year the chosen charity was Touched by Olivia. More information about the charity is included in the next article.
The day kicked off with a question and answer session with the Crane OEM Panel which included Andrew Esquilant from Liebherr, Jay Gower from Tadano,
John Stewart from Manitowoc, Phil White from Sany and Michael Cawston from Pace Cranes.
Topics were varied and included the Federal Government’s amended legislation requiring special purpose vehicles to become compliant with Australian Design Rules (ADRs) for road registered vehicles.
From July 2024, cranes need to be compliant to the rest of the ADRs, including engine emissions. The 2024 standards are significantly impacting the importation of certain types of new and used cranes, including City Cranes, and the cost of engine technology is increasing the cost of new cranes significantly. The panel agreed that for the best part, the major manufacturers have the ADRs covered because Europe and America have already adopted the standards and all new cranes will be compliant.
Another interesting topic involved the unprecedented shipping disruptions which are posing a significant risk to global trade. 2024 has seen unparalleled attacks on commercial vessels in the Red Sea severely
affect shipping through the Suez Canal. The panel agreed that whilst there were still significant delays in the delivery of new cranes and spare parts, the situation appears to be easing and supply chains are not under the significant strain they were immediately post COVID-19.
As construction companies strive to lower carbon footprints and by reducing emissions on construction sites, the panel discussed the emergence of battery electric powered cranes – especially large capacity battery powered crawlers. The panel discussed how the Australian market isn’t quite ready for these products, with sites running diesel generators to provide the electricity for these cranes and with some of the larger capacity cranes not finding work at all. As always, the audience was highly engaged during the panel discussions with a number of informed and challenging questions being asked.
Chris Burke’s presentation on the economy confirmed interest rate predictions from last year have been extended.
“The expectation now is that we will not see rate reductions until very late 2024 or early 2025. This is being driven by higherthan-expected inflation data and resilient household consumption.
“Interest rates in Australia are still low, relative to other developed countries. This is placing continued downward pressure on our exchange rate. The depreciating exchange rate, coupled with increasing cost of goods, has impacted the crane industry given they are subject to importation,” he said.
“Labour markets are easing. Unemployment is forecast to rise over the next 12-24 months to a more stable 4.5 per cent. This is being driven by increased migration and a spike in company insolvencies. Finally, business confidence appears to be on the rebound post COVID-19. It is believed that as we enter a
rate cutting cycle, business conditions and therefore confidence will improve,” said Chris.
The CICA NSW Regional meeting provided a great opportunity to get the latest road related updates directly from TfNSW. Scott Greenow (Executive Director) and Alison Chisholm (Senior Stakeholder Engagement Officer) provided a wide-ranging update on the future of special purpose vehicle (SPV) access in NSW. System improvements related to key projects including telematics monitoring application (TMA), alternate configurations and automated asset assessment were welcomed by the attendees. CICA members are looking forward to the rollout of the Heavy Vehicle Access Management System (HVAMS) for SPVs in 2025, which will result in a more streamlined approach to road access across the state. It was also announced that TMA will soon be available in NSW, allowing members to switch from the more costly IAP platform. One of the many benefits of switching will be increased flexibility when it comes to travelling on different SPV levels of access on the NSW road network.
Updates were also provided by CICA on the ROVER (Road Vehicle Standards Act) transition due to occur on July 1, 2024. As of this date, all cranes that are imported into Australia must demonstrate compliance with the full suite of Australian Design
Rules (ADRs). CICA has been working closely with the federal department as well as manufacturers and importers to ensure that the industry is prepared for this significant change. With July 1 fast approaching we expect to see an influx of applications into the system to make sure that cranes move quickly from the docks to crane yards across the country.
Finally, an update was provided on the NHVR Crane Code of practice, a project that CICA has been working on for some years. The document is now finally available for public comment. All members of the industry are encouraged to read the draft and provide a submission either directly to the NHVR or though CICA. A formal CICA response will be composed which will include comments and suggestions received from members. This is an opportunity for members to ensure that any changes to current practices are discussed and understood prior to its final publication later this year.
George Grasso’s update on all things relating to insurance covered a number of topics.
There is no doubt the construction and machinery insurance market has been impacted by rising costs, along with the rest of the market and most other industries
across the globe. The insurance market is dynamic and has had to adapt to rising claims costs by countering with premium increases along with cost management in order to remain sustainable in supporting their customers, this is influenced by various factors, such as;
a) Increased Inflation Costs: The rising costs of commodities post COVID-19, along with a lack of supply in comparison to demand has had a huge impact on the value of assets along with claims costs. Claims costs have been mainly impacted by increasing costs in materials, parts, freight, labour, and technology enhancements.
b) Risk Management Focus: Insurers emphasise risk management practices. Clients who demonstrate effective risk mitigation strategies and lower claims costs and frequency may receive more favourable terms.
c) Claims and Litigation: Mobile plant and machinery, construction, civil and mining projects can be complex, leading to potential claims, invariably high claims with cost exposure along with complex litigated matters when other parties have been impacted after an incident. The litigation practices and associated costs in Australia are extraordinary high, particular as there is no cap or ceiling in terms of the types of claims entering litigation. This includes
third party property damage along with personal injury and worker-toworker claims. Insurance companies specialising in liability insurance have no option to consider increasing in premiums; and or reducing cover; or exiting the market as it has become extremely unviable as costs in liability matters continue to far outweigh the premium pool collected.
d) Capacity and Competition: New entrants and existing insurers continue to compete for market share, however the capacity of insurance limits of cover for entities is vast from one insurer to another. Many have difficulty in finding appropriate coverage to protect the value of their assets along with risks associated with the industry.
a) Insurance rates have been adjusting to accommodate the growing claims trends
b) Underwriters evaluate industry and entity risks, including occupation hazards, construction type, location, claims history and frequency, safety protocols and value of machines. Valuations of machines both in the second hand and new market has seen values of assets soar. Amongst many of the algorithms that determines the insurance premium, value of assets is a key factor. In addition, the growth of claims costs is also following the same increasing trend. Commercial and responsible underwriting becomes challenging with this continuous growth in all areas.
a) Climate Change: Insurers assess climate-related risks (e.g., extreme weather events, sea-level rise) impacting the projects clients are involved in. Natural disaster frequency continues to increase and are now becoming Business as Usual – occurring on an annual basis as opposed to once being considered as infrequent and one-off events.
b) Infrastructure Investments: Government infrastructure spending influences demand for construction insurance.
c) Technology Adoption: Insurtech solutions streamline underwriting, claims processes and cyber risk mitigation. In addition, as an everchanging industry there is a greater emphasis of moving from conventional machines to other alternate energy such as battery, hydrogen and other power sources. Thus, there is an unknown territory on how this impacts on asset value and cost of loss’s.
d) Increasing Regulatory Compliance: Additional process and resource to comply with the ever-changing regulatory requirements.
Globally there has been instability, with insurers less keen on supporting the construction industry, particularly in Australia, due to its unsustainable litigated practices and the high exposure of material damage costs of individual assets.
Market competition will continue between the insurers that have remained in the market and new entrants, though with insurers balancing risk appetite and profitability.
Clients should collaborate with their brokers and insurers to tailor coverage to their specific needs and continue to improve their risk mitigation strategies.
*The presentation by Executive Director of Freight, Scott Greenow was entitled:
TELEMATICS OPTIONS TO DELIVER OPERATIONAL
Operators of large mobile cranes will have a choice in telematics applications under proposed changes by Transport for NSW (TfNSW).
In response to industry feedback about the closure of the 3G Network and desire for greater harmonisation of telematics between jurisdictions, TfNSW is introducing flexible telematics options. By the end of 2024, operators will be able to choose between using the Intelligent Access Program (IAP) or the Telematics Monitoring Application (TMA), with a self-declaration feature to capture configuration and axle mass information. The introduction of TMA with the selfdeclaration feature is expected to deliver operational efficiencies and encourage productivity. This will provide road managers with movement data to support expanded network access and improve assurance and visibility of network use. This in turn informs data driven network maintenance and investment decisions.
Existing IAP enabled devices are compatible with TMA, however operators should discuss their needs and existing contractual arrangements with their application service provider. A list of service providers can be found at https://tca.gov.au/service-providers/.
Flexible on the construction site
• Short set up time
• Easy to transport
• Travel under 100 % load
Sennebogen 6133E
Telescopic Crawler Crane
130 Tonne Capacity
52m Main Boom 15m Fly Jib
Following a comprehensive tour of SpanSet Australia’s facility, CICA has made moves to alert the Australian crane industry to potentially non-compliant, defective soft slings from manufacturers.
SPANSET AUSTRALIA HAS UNDERTAKEN a sustained examination of the synthetic slings flooding Australia’s rigging equipment market following a comprehensive demonstration to The Crane Industry Council of Australia (CICA).
Earlier in April, Kristian Pritchett, the Managing Director of SpanSet Australia, welcomed Brandon Hitch, the CEO of CICA, and representatives from Cranes and Lifting Magazine to SpanSet’s stateof-the-art manufacturing facility in Emu Plains, Western Sydney.
Brandon’s keen interest in Australian manufacturing led him to see the creation of synthetic slings at the SpanSet facility, where he witnessed firsthand the meticulous processes involved in ensuring that SpanSet slings exceed the highest
quality standards. Each sling undergoes individual in-house proof testing, adhering strictly to the Australian Standards AS4497:2018.
SpanSet’s multimillion-dollar testing facility includes a 45m long, 600-tonne capacity testbed, providing assurance to those prioritising safety and compliance. Through live testing demonstrations, Brandon gained insight into the significant disparities among suppliers of commercially available slings in terms of quality and compliance, debunking claims on compliance tags. As was evidenced by the live demonstrations, not all slings are created equal.
In the ensuing weeks, CICA released a series of CICA/Incolink safety bulletins – all of which can be found online –
pertaining to how to spot faulty and defective slings, proper practices to adopt to ensure no faulty slings are purchased, and proper maintenance of soft slings for operations, procurement, and safety teams.
“Synthetic slings used widely for lifting operations involving cranes offer several advantages over traditional steel wire or alloy chain slings, including being lighter and less likely to cause damage to sensitive loads. However, recent testing has shone a spotlight and raised concerns about the variability in quality and safety compliance of synthetic slings supplied by some manufacturers,” CICA wrote in safety bulletin #335. “Non-compliance could lead to catastrophic lifting failures, risking damage to property and serious injury to personnel.”
PROJECT OF THE YEAR
WINNER 2023 - John Holland for the Batemans Bay Bridge replacement project.
The Crane Industry Council of Australia (CICA) recognises excellence and innovation in the Australian crane industry with the CICA Lift Of The Year Awards.
PROJECT OF THE YEAR
INNOVATION OF THE YEAR
LIFT OF THE YEAR –UNDER 20T
LIFT OF THE YEAR –OVER 20T
THE INNOVATION AWARD went to Bullivants for the ADAPTA Adjustable
LIFT OF THE YEAR
LESS THAN 20 TONNE WINNER –
McMahon Services won for removal of the Heritage Listed Copper Kettle during demolition of the West End Brewery.
LIFT OF THE YEAR MORE THAN 20 TONNE WINNER -
Walz Group won for several Triple Crane Lifts completed to extract the 60m-long DN500 Jacketed Pipe Units at an alumina refinery.
The 1600-tonne monster has officially been delivered and ready for deployment onto a major mining engineering construction project.
MONADELPHOUS HAS OFFICIALLY TAKEN stock of Australia’s equal largest crane, the 1600-tonne capacity Tadano CC88.1600-1.
Delivered and handed over on Tuesday, May 21 in Port Hedland, Monadelphous executives, local team members, Rubino family members and customers were joined by Tadano President and CEO, Toshiaki Ujiie, as well as Executive Officer, Takashi Fukui, who all bore witness to the crane being named ‘Rubino’ after former Monadelphous chairman, John Rubino, who passed away last year.
“We are thrilled to see “Rubino” find its home with Monadelphous,” said Ujiie. “Our collaboration with Monadelphous showcases the strength of our partnership
and our shared commitment to advancing the industry.”
‘Rubino’can lift 1600 tonnes, with its design enabling the crane to lift 561 tonnes at a radius of 42m.
The crane can hold 1155 tonnes of counterweight and can be configured with a maximum lifting height of 205m as well as a maximum lifting radius of 174m. the unique features of this particular crane include the 800t super lift and boom booster preparation.
Monadelphous’ Managing Director Zoran Bebic said the acquisition marked a “significant milestone” for the engineering construction group as its single largest investment in heavy lift equipment.
“This crane not only represents our
commitment to delivering what we promise, but also honours the legacy of our much-loved former Chairman, John Rubino, with the naming of the giant of our fleet,” he said. “We’re pleased to continue our long-term partnership with Tadano, which began over 25 years ago, and appreciate the team joining us in Port Hedland to unveil ‘Rubino’.”
The crane has been commissioned to work on the BHP Car Dumper 3 (CD3) project in Port Hedland, that will see the delivery of structural, mechanical, and piping works.
According to Monadelphous, CD3 is a “critical piece of equipment” used for unloading iron ore from trains at BHP’s Nelson Point facility in Port Hedland.
BOOM Logistics recently demonstrated its commitment to a sustainable future, and community engagement, with a significant presence at the Perth Garden and Outdoor Living Festival. With Environmental, Social and Governance (ESG) paramount to the organisation, BOOM Logistics continues to prioritise environmental and social issues as well as corporate governance, says CEO Ben Pieyre.
“WE CHOSE TO DISPLAY OUR CAPABILITIES at the Perth Garden and Outdoor Living Festival because ESG and community engagement are very important to us as an organisation. BOOM Logistics is the only ASX-listed crane service provider in the Australian market. We are owned by Australians, we employ Australians, and we service Australian industry,” said Ben.
“The event provided us with an opportunity to explain how BOOM Logistics has been providing comprehensive project services and significant benefits to customers across a range of industries for 20 plus years.
“Our commitment to sustainability and reducing operational carbon emissions was at the forefront of this showcase. We wanted to demonstrate to our clients, suppliers, industry peers and the broader community that we are dedicated to minimising our environmental impact. We were focused on promoting the use of equipment that will help us de-carbonise the industries we service, like the crane we had on display, the fully hybrid Tadano AC 4.080-1, which is the first of its kind in the country,” said Ben.
The industry is changing and there is increasing expectation that leading service providers like BOOM Logistics
Boom Logistics’ Tadano AC 4.080-1 is equipped with Tadano’s E-pack, a mobile electric crane power system – and the first in Australia with one.
“Boom Logistics is always looking at innovative ways to reduce its carbon footprint. We thought the show was perfect to showcase the features of the AC 4.80-1 and the e-PACK technology.”
will provide customers with the latest technology, which will contribute to the reduction of carbon footprints.
Showcasing its commitment to a sustainable future, Boom Logistics displayed its fully hybrid Tadano AC 4.080-1. This commitment was further solidified by a “Sundowner” event. on Friday, May 10th.
“Boom Logistics is always looking at innovative ways to reduce its carbon footprint. We thought the show was perfect to showcase the features of the
AC 4.80-1 and the e-PACK technology. With the e-PACK connected, the functions of the crane were perfect, with the only difference being how quiet it was in the cabin,” said Ben.
“On the Friday evening, we invited visitors to attend our Sundowners event which was a significant milestone event for BOOM Logistics. We were able to demonstrate that as the world is changing, so is BOOM Logistics. By showcasing our fully hybrid Tadano AC4.080-1, we were demonstrating our
commitment to leading the industry to a carbon neutral future.
“As we move forward with our customers, we are committed to finding new ways to reduce our environmental footprint and we are investing in technology that allows greener operations. We are also developing new ways to service our customers that align with their sustainable goals,” said Ben.
“We were delighted with the response to the Sundowner event and also our presence at the Perth Garden and Outdoor Living Festival. For many visitors, seeing a crane up close and personal for the first time was quite an experience. We underestimated the interest we would generate.
“As part of message regarding a sustainable future we planned to give
As part of the message regarding a sustainable future, Boom Logistics gave away 1000 Australian native saplings.
away 1000 Australian native saplings, thinking this would cover the duration of the event. They were in high demand, and we ran out by the third day,” he said.
The Tadano AC 4.080-1 was lifting an Evergreen Oak tree which had a height of 14.4m, a weight of one tonne and lifting at a radius of approximately five metres, says Anthony Hunt, Maintenance Manager for Boom Logistics.
“The configuration we used for this lift included 9.2t of counterweight, with 14.4m of boom, which meant the crane was lifting at about 45 per cent of its charts. The only challenge we had with this job was actually freeing the crane up, it’s a very popular crane within our fleet,’ he said.
“When Tadano heard we were having the AC 4.80-1 on display at
the Perth Garden and Outdoor Living Festival, they couldn’t do enough for us. They were the first ones to reach out and provide training for our operators to ensure that the e-PACK and was connected correctly and operating properly. They also offered transport and assistance in getting the cranes and associated equipment to the show.
“The professionalism and commitment to customer service is really apparent throughout Tadano’s departments. This includes parts through to repairs, maintenance and technical support. I can’t say enough good things about Tadano,” said Anthony.
Boom Logistics’ Tadano AC 4.080-1 is equipped with Tadano’s e-pack, a mobile electric crane power system – and the first in Australia to have one. The E-pack
is capable of powering the superstructure of a Tadano crane without using its diesel engine, instead using a 400v/63a connection to connect to the power grid at a worksite.
Furthermore, the electro-hydraulic e-pack can be quickly connected to certain Tadano all terrain models, featuring an integrated electric motor that allows for zero-emission crane operation while significantly reducing noise levels.
The Tadano AC 4.080-1 features a maximum lifting capacity of 80 tonnes, a maximum tip height of 69m, and a maximum load radius of 48m.
Boom Logistics possesses a large fleet of mobile crawler, and pick and carry cranes ranging from five tonnes through to 800 tonnes in capacity.
The 4.9t CK series mini crawlers have high specifications, practical capacities and features designed to be a priority utility crane. Where working space is restricted, such as road and rail tunneling, underground infrastructure, trenches for utilities, foundation work or work on elevated bridges and rail tracks, these high-performance mini crawlers can be relied upon to get the job done.
TRT are the Asia-Pacific agents for Kobelco providing a full comprehensive end to end solution. Service and parts support 24/7, 365 days a year during the entire life of your crane.
Troy Hand 1800 595 576
sales@trtaust.com.au
www.trtaustralia.com.au
MCT EQUIPMENT AND CME BOILERMAKING Services have announced the launch of Magni by LIFTR, unveiling the HTH 16.10U heavy telehandler.
Announced on May 21, 2024, the HTH 16.10U telehandler represents the intersection of MCT Equipment and CME Boilermaking Services’ knowledge of the Western Australian environment and Magni’s global expertise with its telehandler range. According to a press release from MCT Equipment, the HTH 16.10U is purpose-built for the toughest mining environments in Australia.
This machine is fitted with a Strenex 700 Exo Skeleton for high impact protection, along with an array of features including a fitted work basket, OEMapproved design and a whopping 1250kg maximum capacity at a 12m height. With front and rear high-impact frames, a 360-degree camera view and remote-
control capabilities, the Magni HTH 16.10U sets a new standard for safety and efficiency, according to the manufacturers and distributors.
Partnering with Magni, LIFTR has enhanced the HTH 16.10U’s durability without altering its core systems. This collaboration has resulted in a machine that excels in underground environments, paired with heavy-duty attachments to match its robust capabilities. LIFTR’s mission is clear: to deliver specialised equipment and ancillary projects to the mining industries of Australia and Indonesia, utilising Magni’s global expertise and LIFTR’s local innovation.
The HTH 16.10U meets full OEM specifications and Australian design compliance ensuring the machine’s integrity and enhancing safety. LIFTR is developing a range of attachments and applications to expand its capabilities.
LIFTR is a Western Australian owned and operated company that designs, manufactures, delivers and supports specialised equipment and ancillary projects for the underground and mining industries throughout Australia and Indonesia, designing key products in conjunction with OEMs to ensure that industry safety and innovation is continually evolving.
MCT Equipment supplies, designs, supports and hires mobile lifting equipment throughout Western Australia and the Northern Territory. Across construction, mining, infrastructure and marine lifting settings, MCT Equipment’s key focus is on innovation, safety and efficiency.
CME Boilermaking Services is an established and reputable engineering and fabrication company based in Perth, Western Australia.
Tutt Bryant Heavy Lift & Shift has been busy showcasing its transport, logistical and engineering expertise on a project in Western Australia that saw the delivery and assembly of Western Australia’s new Causeway Pedestrian and Cyclist Bridges project.
100 TRUCKLOADS TO TRANSPORT A CRANE, liaison with the Civil Aviation Safety Authority, and placing 100-tonne loads at radii of over 100m doesn’t fall under the banner of every day work.
Yet, for Felix Marquez Jr, Engineering Team Lead at Tutt Bryant Heavy Lift & Shift, every day work is not what he and his team perform – and this was on show for all to see with the assembly of a new bridge in Perth, Western Australia.
The national heavy lift division of Tutt Bryant Group was contracted by the Causeway Link Alliance – comprising of Civmec Construction and Engineering Pty Ltd., Seymour Whyte, WSP Australia and Main Roads WA – to supply a turnkey logistical solution for the new Causeway Pedestrian and Cyclist Bridges that spans from Victoria Park to Perth’s CBD.
At the heart of the project is the goal of completely separating path users from traffic, enhancing safety for both cyclists and pedestrians traversing the bridge.
To achieve this, Main Roads WA began planning and development for the bridge to be built connecting McCallum Park and Heirisson Island over the Swan River, before continuing to connect Heirisson Island to Point Fraser.
TBHLS was tasked with solving the problem of installing components that weighed up to 100 tonnes in capacity
at distances of over 100m in radius; serendipitously, Australia’s largest crane –the Demag CC8800-1 – became available in Perth after a start delay on another project meant there was a small window of opportunity to use it on the Causeway Pedestrian and Cyclist Bridges project. With a lifting capacity of 1600-tonnes and a maximum radius of 174m at which it can lift 14 tonnes, the crane lent itself well to the job.
Before the crawler crane could arrive and commence its assembly process, however, the subgrade of the operating areas needed to be addressed. With the crawler exerting 800kPa, TBHLS worked closely with Geotech engineering companies FSG Geotechnics & Foundations and WSP Australia to ensure the subgrade became strong enough to place the crawler crane on top of. Ultimately, TBHLS and the Geotech companies determined that a crane pad needed to be constructed involving steel beams and crawler mats and thus, the area reinforced, before the crawler was delivered to the site and began assembly.
As mentioned, the Demag CC8800-1 was required to lift loads of around 100 tonnes at radii of over 100m. To complete its scope of work, TBHLS put the machine in SSL/LSL configuration with 144m of main boom and 640 tonnes of full superlift counterweight –a configuration that was devised following close liaison with the Civil Aviation Safety Authority due to the proximity of Perth airport. Also helping the Demag CC8800-1
in its endeavours was the 800-tonne Sany SCC8000A that was configured in HDB mode with 90m of boom and 390 tonnes in superlift counterweight. To help configure the two cranes, TBHLS deployed its 275-tonne HSC SCX2800-2 crawler as an auxiliary machine.
Simultaneously, while the cranes were being established in their appropriate configuration, TBHLS was showcasing the transport capabilities of its business. The project was headed by Operations Manager – Specialised Lifting and Transport, Ryan Ockenden, who possesses in excess of 20 years of experience at Tutt Bryant Heavy Lift & Shift. Having worked his way through Brambles, Kingston, and Lampson while focusing on trailer duties, Ryan holds a
wealth of experience in specialised transport. According to Ryan, the project team that is led by Greg Dunlop – Senior Project Manager, was tasked with overcoming challenges offered by this project, with access to site being limited to certain entrances that approached onto two high volume-traffic highways. Further considerations taken were the presence of nearby residences, trees and existing surfaces, with Ryan saying minimising disruption on the existing environment was at the top of the priority list. Utilising a mixture of prime movers and trailers – such as TBHLS’ Nicolas Jinker, self-propelled, and Platform trailer with 24 axle lines – Ryan says the team was able to overcome the challenges by closely collaborating with Main Roads WA and the
client to determine the most suitable pathway to accessing the job site and delivering the modules required to assemble the bridges. One such difficulty arose when transporting a 9.66m wide module, where the traditional maximum legal size transportable being 8.5m. This, too, was matched by the different shape of all loads being transported, due to the curved, modular nature of the bridge, providing more logistical and engineering issues for the team in its attempt to minimise impact on local traffic flow. However, as Ryan says, the team worked closely on traffic management, planned route surveys, notification drops, and liaised with the client through both the tendering process and the last 12-24 months, thereby ensuring any complications that ensued were overcome or managed. and, as detailed by Ryan, when transporting a 47m pylon to a job site, every millimetre and every consideration needs to be factored in. For Felix, Ryan, the engineering and operations teams, the transport part of the project highlighted that the challenges to be overcome were not just on a civil engineering level, but also on a planning and preparation level to ensure timely and effective delivery of the project. With the lifting complete on the McCallum Park side of the bridge, TBHLS’ attention
is now turned to the Point Fraser side of the bridge, where the Sany SCC8000A is set to take over the heavy lifting duties, assembling the bridge before working in tandem with the 275-tonne HSC to tandem lift the unique, project-defining boomerang shaped pylon into place.
After a long and successful stint in Melbourne before being transported to the other side of the country and placing loads at distances of over 100m in Perth, the 1600-tonne Demag is now being sent to the resources sector where it will be lifting components weighing up to 700 tonnes.
Ultimately, for Felix and the Tutt Bryant Heavy Lift & Shift team, the continued delivery of the Causeway Pedestrian and Cycling Bridges has been derived from the close liaison with relevant authorities to ensure configurations are right, restrictions are adhered to, and rules are continually abided by. The project that is set to improve safety, connectivity, as well as amenity between the Victoria Park foreshore and Perth’s CBD reflected the meticulous attention to detail the Australian engineered heavy lift and shift division provides to its transport, as well as being a prime example of the company’s capacity to provide turnkey logistical solutions.
Global manufacturer Sany showcased 36 flagship products to over 400 customers and interested parties at the annual Sany Crane Global Key Account Summit.
SANY AND TUTT BRYANT EQUIPMENT
recently organised a customer tour to Sany’s state of the art manufacturing facilities. Customers were, once again, seriously impressed with what they saw.
Philip White, Sany’s International Sales Company Sales Manager was on the tour.
Held across two days in late May, visitors from across the world gathered in Huzhou, Zhejiang province to witness the manufacturer’s showcase that included its SAC2500E, SAC600E, SAC700E, SRC1200T, STC1600T7, and SCC3200T, along with muliple electric including the SCC400TBEV,SCC1500TB-EV and heavy duty crawler cranes.
Yuan Yue, President of Sany Heavy Crane Business Group, expressed a welcome and appreciation to the visiting partners and customers from across the globe.
“We attach great importance to our
partnership,” he said, “and it is your valuable advice and trust that shape our high-quality and robust products.”
In front of the onlookers, the manufacturer showcased the the performance and capabilities of its cranes through a series of live operations.. These included unloading and loading counterweight with one button, changing outrigger span flexibly – and enhancing lifting capacity by 20 per cent, as well as the extending and retracting of the boom with one button – an “industryfirst” technology, according to Sany, that realises the intelligent cooperation between the telescopic boom and winch, ensuring that the height of the hook from the ground is always controlled within the safety range.
Also of note in the event was a speech given by Tom Liu, General Manager of the Overseas Marketing of Sany Crane. Discussing the “growth, progress, value,
and win-win” approach of Sany in the global layout, Liu also expressed his confidence in the global market.
“Sany’s manufacturing facilities are seriously impressive. Customers were amazed to see the focus Sany has on maintaining efficiencies throughout the manufacturing processes to keep overall prices down without losing quality in the products.
“They were also impressed with the total quality control Sany maintains by manufacturing all their own components and not being reliant on external manufacturers to supply parts,” said Philip.
Customers were impressed with the implementation of automation and robotic technology throughout the factories the group visited – both in the work done and in the factory itself.
Sany builds the same factory over and over, calling the enormous facilities ‘Lighthouse Factories’ because they feature a lot of glass. Inside, 80 per cent of the welds completed by robots, with the machines picking, placing and cutting the steel before it is transported on automated trolleys to the next station. It’s picked up by another robot, and welded by another, or dual robots if they need to weld at the same time to prevent distortion.
“The quality of the welding is unbelievable. In the middle of the ‘Lighthouse Factory’, there is a large strip of grass, and it is good to see a bit of nature in amongst all the mechanical automation and robots. It wasn’t just one factory, we would have seen four or five factories that were clones of each other,” said Philip.
The customers who joined the trip were “blown away” with the efficiencies
on display, Philip added.
“Customers were amazed and seriously impressed with what they saw, and there is no doubt there were high levels of confidence within the group around the purchase of Sany equipment. We took 14 customers from Australia but there were over 400 customers from all over the world. It was a significant showcase event for Sany,” said Philip.
Philip started his career in cranes in February 2012.
“I started my journey in the crane industry with Tadano. After 5 years I then moved to TRT where I was selling TIDD pick and carry cranes and Grove All-Terrains before joining Sany in January 2024.
“My role as Sany’s International Sales Company Sales Manager will basically entail continuing the momentum Tutt Bryant Equipment and Sany have built over the last few years.
“I will be responsible for selling tower cranes direct to customers and I will be directly supporting customers for all types of Sany cranes. I will be responsible for the research and development of Sany all terrains and I will be supporting sales and generating leads for the team at Tutt Bryant Equipment,” said Philip.
“Sany has come a long in terms of the quality of their products and is widely regarded as the best value for money crane on the market. A key element of my role will be to educate the crane industry regarding the entire range of Sany cranes, focusing on promoting our all-terrain cranes and introducing Sany tower cranes to the Australian market.
“As I’ve said, customer support will be a key focus as well as overseeing the introduction of new models and relaying customer feedback directly back to the technicians and engineering teams in the factory,” said Philip.
SANY displayed its comprehensive range of all terrains.
Cloud Solution
Quoting
eTickets / eDockets
Payroll / Timesheets
Reporting / Dashboard
Purchase Orders
Invoicing
Fleet Maintenance
Storage
Visual, Drag and Drop Scheduling
Form Designer
Inductions / Compliance
WELCOME BACK AGAIN
AS THE CEO OF THE CRANE ASSOCIATION of New Zealand (CANZ), I’ve had the privilege of witnessing firsthand the resilience and innovation of our industry. Since I joined CANZ, we’ve enjoyed a period of remarkable economic prosperity, with booming construction projects and a robust market that has driven growth and opportunities for all. However, as we approach the halfway mark of 2024, it’s clear that we are facing a new set of challenges. For the first time in my tenure, the economic landscape isn’t just less favourable—it’s decidedly tough.
The boom and bust cycle is something we are all familiar with. Our industry has always been subject to the ebb and flow of economic conditions. The highs bring about a surge of projects and a demand for our services, while the lows require us to tighten our belts and navigate through leaner times. It doesn’t make it any easier to bear, especially for those feeling the immediate impact on their businesses and livelihoods. Yet, it is during these challenging times that our community’s strength and solidarity become most apparent.
At CANZ, we understand the pressures that come with a downturn. Reduced project pipelines, tighter budgets and the uncertainty of what lies ahead can be daunting. That’s why I want to remind each and every one of you that we are here to support you. Whether you need advice, resources, or just a listening ear, CANZ is committed to standing by your side. Please don’t hesitate to reach out if you need assistance. Our collective experience and knowledge are powerful tools that can help us all weather this storm.
Today (at the time of writing) is Budget Day, and it’s fair to say it is the most anticipated budget in quite some time.
The government, led by the National Party, has talked a big game, and we are all expecting them to deliver. The phrase “survive until ‘25” is gaining traction globally, reflecting the widespread understanding that any significant economic recovery and green shoots of growth are expected next year. However, for our industry, those green shoots could be signalled by the government making its priorities and investment clear in today’s budget. I sincerely hope that’s what we will see.
Despite the economic headwinds, I am heartened by the response we’ve received as registrations and sponsorships flow in for the 2024 CANZ conference. It’s a testament to the trust and confidence you place in us, even in less prosperous times. Organising a successful event in the current climate is no small feat, and your support reassures us that we are on the right track.
This year’s conference will not only provide valuable insights and networking opportunities but also serve as a crucial platform for discussing the challenges we face and exploring strategies to overcome them.
In anticipation of the budget announcement, we remain hopeful that the government will recognise the critical role our industry plays in the country’s economic fabric. Clear priorities and targeted investments can provide the stability and confidence needed to navigate these turbulent times. Infrastructure projects, in particular, have the potential to drive demand for crane services, creating jobs and fostering growth in our sector. As always, we will be closely monitoring the outcomes and advocating for the best interests of our members.
focused and adaptable. While the current economic situation may be difficult, it also presents an opportunity for us to innovate and improve. Embracing new technologies, enhancing safety protocols, and investing in workforce development are key areas where we can make a difference. By doing so, we not only prepare ourselves for future growth but also ensure that we are resilient in the face of adversity.
As we gather for the 2024 CANZ conference, let’s take this opportunity to share our experiences, learn from each other, and strengthen our bonds. Our industry’s ability to come together and support one another is one of our greatest assets. Together, we can navigate these challenging times and emerge stronger.
In closing, I want to express my gratitude for your continued trust and support. It is your dedication and commitment that drive us forward. Remember, we are here for you, and together, we will overcome these challenges and seize the opportunities that lie ahead.
Thank you, and I look forward to seeing you at the conference.
Sarah Toase CEO, Crane Association of New Zealand
“Our products are undeniably great, but it is the exceptional calibre of our people that distinguishes us from others”
When it comes to cranes and lifting, Ian Roebuck has been there and done that. 2024 sees him celebrate 45 years in the industry. Ian and daughter Tania discuss
IAN BEGAN HIS CAREER AS AN APPRENTICE mechanic in Taranaki, a small town on the West Coast of New Zealand’s North Island. He worked his way up to be in charge of the garage, before moving to the family business, Roebuck Construction. This move began his love affair with cranes.
“I joined the family business in the mid 60’s and worked there for 14 years. My first experience of owning a crane came when the family business bought a Michigan TLD T20 which was an ex-Ministry of Works machine which we bought as a wreck. It had been underwater for three days before we brought it back to life. It used to lift seven tonne at 30 feet,” said Ian.
Ian decided to venture out on his own in 1979 and bought his first crane, an 18 tonne capacity Grove TMS 180.
“That crane was assembled in New
Zealand on a New Zealand built carrier.
I was very lucky, the person I bought it off, he did a deal with me, whereby, I was able to buy the crane and have enough money in the bank to last me three months.
“I drove into town the next morning letting everyone know I was in business. The next day a chap rang to say the local meat works had burnt down three days earlier and so for the first eight months of my life with that crane and business, we worked 7 days a week. Some days I was wheeling concrete, others I was helping the welders and others I was driving the crane, but I was there every day and that’s how the business started.
“It was at that point I recognised we needed a second crane and the same company had a little 12 tonne pedestal crane, so they mounted that on an old Readymix concrete truck and that gave
us two cranes,” said Ian.
The business grew in terms of staff and Ian found niches for his business that were very lucrative.
“There was a big oil and gas industry and we found work shifting drilling rigs. We had two cranes on each site and the work was taking up a lot each month. Each rig shift would be every four to six days, so it was quite a lucrative setup. And in between times, I’d bought a new 40 tonne Grove and that’s how it all started,” he said.
Tania explains there are two crane hire businesses operating in Taranaki but says Ian has a reputation for taking on the difficult work.
“There are two crane companies in town, us and Titans. We are friends and we help each other out but Ian has a reputation for taking on work which needs ‘out of the box’ solutions.
of experience,” said Tania.
Ian isn’t put off by the challenges.
“There’s an old saying in life and that is, “never worry worry until worry, worries you”. The time to worry is the day before you do the job, too much worry during the preparation beforehand, will see you end up with ulcers and I’ve got to this age ulcer free, I hope,” said Ian.
Tania joined Ian in the business 15 years ago.
“I left a job I’d been in for 20 years because I felt the need to help Dad out and try and get him to ease back a little but that kind of hasn’t worked out too well. He loves to come in every morning
Ian hasn’t been scared to take it on and work out the methodology and engineer solutions with lift plans and other tools at his disposal.
workings, we had up to 22 cranes here in New Plymouth,” said Tania.
Ian runs through the fleet.
“The smallest crane is a Unic mini crawler which will drive through a household door and lift two and a half tonne and the largest one is the 250t capacity Liebherr. That was the biggest crane, bought into New Zealand in its time. The first big crane that came to New Zealand was an 80t Kato, which I bought and then my opposition
“I had to eat humble pie for a couple of years. And then I bought 150t crane and we were down in South Taranaki with it up in the air showing all the clients what we could do and couldn’t do. We got a call from Fonterra dairy factory in Hamilton that had had an explosion. So we packed up the crane that night and went up to Hamilton and we worked on that site, from memory, for about four or five
“Over the lifespan of the business, we have conducted 14 marine salvages. The biggest one of those was 95 ton displacement, which we had to build a road for and we walked it 40km into the port to put it back in the water.
“Over the lifespan of the business, we have conducted
14 marine
salvages.
The biggest one of those was 95 ton displacement, which we had to build a road for and we walked it 40 kms into the port to put it back in the water.”
and that’s what we like to see, it’s his baby and empire that he has built up solely on his own.
“I work on the allocation and crane dispatch as well as a bit of the HR Health and Safety, although when it’s above my head we do have others to help out. Ian deals with all the financial side of the business and we have a very good Transport Manager who looks after the Trucks and Hiabs. Before we had our current government in place and they stopped all the oil and gas
There’s nothing at this stage that’s beaten us.
“A few statistics; we’ve completed over 190 bridge replacements in Taranaki, that’s on farm bridges and main bridges. We’ve managed 14 marine salvages of significance. We’ve completed nearly 350 heavy salvages, trucks on their sides blocking roads, over banks and out of rivers. There’s a different challenge every week,” he said.
Tania highlights how hands on Ian
has been with the business.
“Just north of New Plymouth there is a massive gorge which you have to navigate to go North. A lot of trucks come to grief in the area, and we are the first port of call for the police when trucks go over the bank or go over on their side blocking the entire road. You might be up in the middle of the night and moving a truck loaded with food or whatever it may be and getting that
Services, has acquired a new Magni Telescopic Handler, the Magni 6.46 – the largest telehandler in the southern hemisphere – through APS Equipment. Managing Director, Clyde Cowley, discusses his journey to business ownership, lessons learned, and how his new Magni will help him move his business forward.
his own equipment, Clyde Cowley worked laboriously as a rigger.
Doing his time for 12 years at Downer Group, he worked hard, paid his dues, committed himself to labour hire, and succeeded.
Then, however, 2019 came; and, with 2019, came the biggest sustained disruption to the global economy: COVID-19. For many, this was a time of loss and reflection – and, for Clyde, it meant losing a lot.
“COVID took everything from me,” he said. “It is not a period of life that I look back on fondly, but it taught me resilience and mental fortitude.”
It’s that mental fortitude that has stuck with Clyde throughout his journey. Beginning his business in 2011, Clyde’s time has seen him work extensively
“COVID allowed me to be reborn into a different part of the industry that I feel like I should’ve been in anyway,” he said. “We’re working across the telecommunications industry, and we’re committed to servicing that market all across New Zealand.”
In his efforts to better service the telecommunications market, Clyde announces that he’s made a significant purchase to bolster the equipment aspect of his business: the tallest telehandler in the southern hemisphere, the Magni Rotational Telehandler 6.46.
Purchased through leading New Zealand equipment distributor, APS Equipment, the Magni RTH 6.46 features a maximum lifting height of 45.6m, a maximum radius of 32m, a maximum lifting capacity of 6000kg and a full 360
degrees of rotation, allowing it to slew, or rotate, anywhere to complete its scope of work. Key features on the Magni 6.46 also include an electronically controlled hydrostatic transmission, an automatic levelling device and scissor-shaped stabilisers/outriggers.
One of the major selling points of the Magni Telescopic Handler range is its wide applicability to a variety of different projects. For example, the Magni RTHs can be fitted with multiple attachments depending on the job required of them – something that Clyde and the team took full advantage of, ordering the new machine with wide forks, a three and six tonne winch, a telescopic platform and a 500kg extendable platform with its own 600kg winch.
“The 600kg winch is going to come in really useful for our façade work, with the rotating aspect of the machine being a very attractive feature of the machine because of
the accessibility it provides,” said Clyde. “Furthermore, the TP O/U-R platform allows us to access undersides of bridges, which has allowed us to line up a range of different projects for installing fibre under bridges.”
And, when discussing the service received from APS Equipment and Darren Boon, Clyde is nothing but complimentary of the manner in which things were conducted.
“I met Darren at the CANZ Conference in Hamilton two years ago, where he introduced the Magni machines to me,” he said. “Since then, we’ve worked closely together, and I intend on purchasing many more Magnis in the future as we continue expanding our business.”
Darren, equally, was effusive in his praise for the Magni machines, highlighting the versatility of the Magni 6.46 and how it will help its latest owner.
“The ability to quickly change from crane mode with winch to pick and carry mode with forks makes it extremely valuable around any modernday construction site,” said Darren. “Having the Magni telehandler in their fleet allows companies to enhance their capabilities, improve efficiency and offer a broader range of services to their clients while minimising downtime due to the telehandler’s flexibility and versatility.”
This, for Clyde, is essential as he continues his post-COVID comeback. Embodying a story of resilience and perseverance in the face of adversity, Clyde’s work ethic, his attitude and his new machinery are setting Clyde’s Services in good stead for the future.
“Anything that’s classically been ‘too hard to do’ is my bread and butter,” he said. “We’re looking to expand our work, and we’re keen to utilise our Magni to do so.”
Drilling rig maintenance and shifting
Site maintenance
Truck and boat salvaging
Tree removal
Structural steel placement
Container carting and placement
Pre-cast panel carting and erection
Swimming pool placements
Tiny home carting and placement
Certified load pilots
Over-dimensional transport
Tom Curran, Liebherr’s Sales Manager Mobile and Crawler Cranes New Zealand retires in August with Andrew Cameron replacing the industry stalwart. Tom started his career with Liebherr 20 years ago.
“I FIRST JOINED THE LIEBHERR Earthmoving Equipment Division as the Warranty Manager, moved to Service Manager and then Sales Manager. In 2011 I moved into the role of Sales Manager for Mobile and Crawler Crane Division where I’ve been ever since,” said Tom.
He discusses the changes he has seen during his time with Liebherr’s crane division.
“From an organisational point of view, there have been massive changes. The levels of service and support have been dramatically improved as have our facilities and the numbers of staff. In turn, this had led to the number of machines sold doubling on average each year.
“The increase in Liebherr’s share of the market in New Zealand has also been quite dramatic. When I first started, we probably had no more than nine machines working in the North Island and now we have 170 plus, that’s pretty phenomenal growth. If you look at the class of machines that we’re in, we would currently have between 80 per cent to 90 per cent market share,” said Tom.
He goes on to talk about why Liebherr has experienced so much growth and how his team has managed to maintain these
levels of growth for an extended period.
“First of all, New Zealand customers appreciate quality, there’s no doubt about that, they are looking for good, reliable machines. Liebherr is the number one product for a very good reason, it is reliable and performs well. Product has been available, and we’ve been prepared to fully support the market,” he said.
“We are carrying stock machines in Australia/New Zealand which means product is available, and we’ve put the service and support infrastructure in place locally with mobile technicians in both islands and parts personnel servicing the growing numbers of machines. As we’ve increased the number of new machines, customers have self-imported used machines knowing we have the required service and parts support locally,” said Tom.
“The industry’s recognition of Liebherr’s commitment to parts support and service has been a big plus for us. I believe we do go the extra mile in parts and service support, there’s no doubt about it. The industry has recognised this and supported us because of it.
“Ultimately, the machines have performed as have the Liebherr people
supporting them. We have great Service Technicians and parts personnel within Liebherr New Zealand and the factory works very hard, supporting us with technical information and if there’s ever a significant issue, as an organisation we are very quick to get on top of it and sort things out,” he said.
Tom discusses the culture at Liebherr and how individuals develop their skills and progress through the organisation.
“A key element of Liebherr’s culture is the development our own people. We recognise their capabilities and give them every opportunity to progress and build a career here at Liebherr. From any level or from any position you can progress, if you want to take on the training and the hard work, there’s no ceiling. It doesn’t matter, male or female, it’s open for everybody. It’s a very positive culture for individuals who are serious about their work,” said Tom.
Andrew Esquilant, Liebherr’s General Manager Mobile Cranes has played a significant role in Tom’s career.
“Andrew is a major reason for the success of Liebherr Mobile Cranes in both Australia and New Zealand. We really couldn’t have succeeded as we have
without his attitude and the fresh air he leaves in front of you to go and play the game how you want to.
“He’s a humble leader and that’s what I admire about the leadership culture at Liebherr. It starts at the top and Andrew gives everybody full rein and works as hard as anybody else. He’s always available and that’s been a big part of our success over the years. He’s always there and he talks to everybody, and he’s always available 24/7 which is probably too much. We don’t want to burn him out too early,” said Tom.
Tom has immediate plans for his retirement and he won’t be sitting around and relaxing.
“My wife Helen and I are currently building another house. I’m not quite sure what we’ll do when it’s finished, live in it or sell it. We also have a bit of land development tied to that, so that’s the immediate project. I like working, so I’ll be doing something,” he said.
Over the years, Tom has made a lot of friends, in both the New Zealand and Australian markets. He explains how he feels about saying sayonara to them.
“I’ve made lifelong friends over the years, and I’m going to really miss them and I’m sure I’ll see a few on my travels. What an industry, really. You find a place in the crane industry and that’s quite special and difficult to put into words,” he said.
Tom is confident Liebherr has the right succession plan with Andrew Cameron taking over the reins.
“With Andrew I decided to take Elon Musk’s advice, “When you want to get replaced, find someone smarter than you,” and that’s pretty much the case with Andrew. He’s very sharp and he’s well liked by the customers. He’s a terrific technician, and commercially sound, hardworking and helpful. I know he’ll be a big success,” said Tom.
Andrew has been with Liebherr for nine years and started as a Service Technician.
“I worked mostly out of Christchurch as a mechanic, and I was traveling all around the country getting to know customers and learn about the Liebherr business. Being the only Service
Technician I was travelling everywhere, now there are four of us based around New Zealand.
“Obviously with Tom retiring I was offered the opportunity to step up into sales which I see as a different challenge and opportunity within the Liebherr business. I’ll be responsible for selling mobile cranes and crawler cranes over 300 tonne capacity,” said Andrew.
Andrew’s technical understanding of cranes will help in the sales role.
“Knowing the cranes inside and out and getting to know the customers over the last nine years and having to earn their trust will also be a massive help. The business is definitely growing, it’s a different beast to when I started with new customers popping up around the country,” he said.
Andrew has worked with Tom for some time and explains how he has been prepared to share his knowledge and experience and mentor those around him.
“Tom has been brilliant, he comes from a similar background to me having worked in the service side of the business before moving into sales. He’s since taken the Liebherr crane business in New Zealand to the next level. Our customers only have good things to say about Tom, they love
him and have great respect for him.
“Liebherr and Tom have done such a good job that my approach doesn’t need to change a great deal. I’ll definitely bring a new lease of life and a new energy to the role.
“My technical knowledge will be a big help in terms of walking customers through the purchasing process, being able to discuss the different configurations including counterweight and boom configurations will help customers make the right decisions on which crane will best suit their purpose.
“We’ve always had great support from everyone in the Australian operation. The team in the factory provide great support from the ground up and nothing is ever a problem.
“Tom has done a great job for the New Zealand crane industry and deserves the respect he has from everyone. He’s going to be a sore loss to the company, but we have the team in place to pick up the slack and hopefully we will catch up with him every now and then. The Liebherr organisation and everyone in the New Zealand crane industry wish Tom the very best for his well deserved retirement,” said Andrew.
McLeod Cranes continues to invest in new technology and innovation. A recent example of this strategy is the purchase of a remote controlled Track Carrier 1200 PRO from Pace Cranes. Managing Director Scott McLeod explains more.
MCLEOD CRANES HAS SEEN STEADY growth in recent times - today it boasts a team of 180, operates a fleet which includes 50 Hiabs and 30 plus cranes and a fleet of transport vehicles.
“Business has been outstanding, we have seen really exciting times. Even as we see the economy change gear, we’re still seeing lots of exciting projects coming through and lots of opportunity,” said Scott.
“We’ve always approached the business in an innovative way, and we are prepared to embrace new technologies. The Track Carrier 1200 Pro is a good example of this. More recently we’ve introduced spider cranes and mini crawlers into the fleet because we want to be the best taxi crane company in the field. When a customer talks to us, we want to be in a position to offer the right machine for the job, as my father would have said, ‘we want to play with the full deck of cards, not just the one,’” he said.
“For Mcleod Cranes it is important that when we conduct a site inspection, we are looking to provide the best solution for the customer because we have a broad range of equipment available to us. We want the customer to walk away from the job saying ‘McLeod Cranes? They’re good bastards, they did an awesome job,” said Scott.
The process of investing in diverse equipment started some time ago, explains Scott.
“We started looking at areas of work that we were missing out on and looking at jobs where we probably had the wrong gear. A clear weakness in our offering was smaller equipment like mini crawlers and spider cranes. We started
purchasing these which has led to a lot of earthquake strengthening work inside buildings where the working area is tight and confined. It is this type of application where a spider crane or a mini crawler are absolutely leaps and bounds ahead, they are incredible little machines.
“The move to smaller equipment led to us examining heavy manual lifting of building products (for example) where site personnel are involved. We prepared a task analysis and a process around
this, and it was clear that it is a high risk activity where someone could be harmed. This analysis led us to the Track Carrier which is an outstanding tool,” he said.
“We bought the dolly with the carrier and also the mini crane, as we see this eliminating a massive amount of risk. When you are working with steel beam or a piece of equipment for example, you lift it onto the carrier and strap it down.
“The Track Carrier features very
which enhances the safety of the product. We can drive the carrier with the load, to the crane without anyone needing to touch it which is incredibly logical to me,” said Scott.
The Track Carrier 1200 PRO is an incredibly versatile machine with huge capabilities and many uses. With the ability to carry heavy loads of up to 1200kg or 2000kg with the dolly, which would usually require multiple persons, Tracked Carriers are a safe and cost effective solution that can provide material handling in the tightest of situations.
The rotating turntable can be locked or unlocked depending on the task. Unlocking the turntabling allows unmatched manoeuvrability and the ability to steer the load in awkward or tight spaces.
Perfect for transporting long, heavy loads, the dolly is manually steerable and adds an additional 1000kg capacity to the machine.
With a maximum gradient of 45 degrees, this machine excels on uneven terrain. It even has the capacity to climb stairs.
This makes it ideal for moving large sheets of glass or thin material over steep or uneven terrain. The A-frame remains under 2m tall when fitted.
“When you are talking big cranes, you’d maybe need a semi-trailer to bring a steel or concrete beam to lift. I don’t see it as being any different with a mini crawler or a spider crane. We need to have the right tools to make the handling of these types of materials safe and efficient for our customers.
“Increasingly, customers are thinking first and foremost about completing the job safely and efficiently and its then up to us to have the right tools in our deck of cards. We present these opportunities to them, and they chose the cards they want,” said Scott.
Scott discusses how the conversation about Track Carriers started with Pace Cranes.
“Some time ago, David ‘Chalky’ White from Pace Cranes and I were chatting and I’d been looking at the
“When you are talking big cranes, you’d maybe need a semi-trailer to bring a steel or concrete beam to lift. I don’t see it as being any different with a mini crawler or a spider crane. We need to have the right tools to make the handling of these types of materials safe and efficient for our customers.”
carriers for a while. We had a great discussion around the couple of products that they offer. One of the things about this particular option is that it has some really clever features especially the crane attachment.
“As our first machine, it provides a wide field of abilities and it hit the spot. With mini cranes, we are adding smaller and larger capacity cranes to make sure we are offering a broad range of options. It will be same with tracked carrier space. I think the Track Carrier 1200 Pro
is an outstanding starting carrier for us.
“Track Carriers offer all sorts of opportunities. Being a large Taxi Crane business we might be sending a 350 tonne all terrain to a wind farm and on the same day get a call from a Mum and Dad who want large pot plants moved, or sculptures lifted into place in their backyard.
“This type of work might mean we put a big crane on the street with traffic management out the front which is expensive. We can now throw a little
bit of equipment or whatever they want, onto the Track Carrier, drive it down the side path and conduct the lift from there. As a taxi crane company, we need to be about solutions, and you can only provide these solutions if you’ve got that range and breadth of equipment. I feel like without this machine, we were only going half the distance, now we have it, we are playing with a full deck of cards,” said Scott.
“Before we received the machine, customers were talking about jobs they have coming up and they were already writing the Track Carrier into the job because of the labour costs, the time it would save and the safety aspects it brings. The Track Carrier sells itself and when you add the green element - it’s battery driven - to me this equipment is the future. It’s a great match for McLeod Cranes,” he said.
Matt Ziegler, UANZ Head of New Zealand and Pacific, explains how the economy is impacting the insurance sector for cranes and other types of mobile plant.
“OVER THE 10 YEARS WE HAVE BEEN operating in New Zealand we have grown with the industry to become one of the largest mobile plant insurers in the country. We are backed by QBE which has an A-Plus credit rating, so we are very strong in that sense. The crane industry has been a cornerstone for the success of our New Zealand business UANZ and together we will continue to support the crane industry into the future in every way we can,” said Matt.
UANZ works with a national network of insurance brokers, says Matt.
“We work with brokers on a national basis. We’re a specialist insurer in mobile plant equipment and part of our value proposition is to provide help, advice and give guidance on accounts with cranes, earthmoving equipment and all those types of heavy plant and equipment.
“Another major part of our value proposition is our claims handling. Because we specialise in this area, we have vast experience managing claims for mobile plant and we work with assessors and reviewers that have in-depth knowledge of this sector.
“Insurance brokers tend to be ‘Jacks of all Trades’ and there are only a few brokers that specialise in heavy plant and mobile equipment. We have good relationships with the larger brokers that have a construction department, and they call on us for advice on matters knowing this is all we see all day every day,” said Matt.
UANZ has plenty of experience in insurance, with Matt clocking up 37 years this year and the underwriting team providing 60 years of combined experience.
“Our claims department is headed up by Dana Van Tiel. She’s been handling heavy plant equipment claims for 15 years here and in Australia. Dana came on board not long after we first started the company in NZ, so she’s highly experienced in mobile plant equipment claims,” he said.
Matt raises some interesting points regarding the insurance of tower cranes in the earthquake prone Shaky Isles.
“I’m not an expert in tower cranes and I’m certainly not a technical engineer, but it’s my understanding that the tower crane bases are engineered to the New Zealand earthquake code/standard. We have tower
cranes in Wellington and Christchurch and there have been shakes but we’ve had no issues with that. In fact, we don’t charge extra levies for earthquakes. We are in the Shaky Isles and there’s always that possibility and that risk. And if you get a big one, no amount of engineering is going to stop a tower crane being damaged or God forbid falling over. It’s worth noting that the earthquake standards are designed to protect people not property,” he said.
Matt explains how important it is for customers to work closely with their brokers to ensure their policies are not under insuring or over insuring their plant and equipment.
“Under insuring is not a major issue today, although it has been in the past. Nowadays, we have affordability with the equipment and the perception that if you underinsure something you’ll pay less in premiums doesn’t apply so much.
“Why insure for half the cost if something goes wrong with the plant, you are then left facing losses anyway. In my opinion, it you’re going to insure, it makes no sense to underinsure unless you’re prepared to wear that loss. I think you are better off insuring fully, taking a higher excess and be prepared to have some skin in the game and receive a premium discount that way, rather than under insuring. There are a lot of ways to skin a cat,” said Matt.
He goes on to discuss how UANZ manages an incident and how responsive his team is to assess the damage and have the crane repaired.
“We recently had an unfortunate incident with a machine on its side. As soon as we found out, our assessor contacted the insured to discuss next steps and triage the incident. We use various assessors but there a couple that we value the most and prefer to use. They actually had our client’s number and got onto them straight away. Fortunately crane hire businesses are pretty good at salvaging because they have most of the heavy equipment needed in their fleet. We provide our brokers and our larger clients our assessor’s details, and they are available 24/7, should there be an incident,” he said.
continue doing what you do,” he said.
UANZ has a network of preferred repairers, says Matt.
“We do have a network of specialised repairers, but a lot of this work tends to be under warranty, so we also rely on the Original Equipment Manufacturers (OEMs). There are some very good repairers in New Zealand, and we’d love to use them but sometimes it’s not possible.
“Each type of plant goes to a different type of repairer because they specialise in specific fields. Our assessors have access to this network, and our clients know these
“Time is money in the crane industry. It’s high value, heavily financed equipment and it needs to be back working. We are very much reliant on the repair networks and overseas parts coming in which puts us at the mercy of supply chains, but we do everything we can to turn our claims around as quickly as possible.”
“Time is money in the crane industry. It’s high value, heavily financed equipment and it needs to be back working. We are very much reliant on the repair networks and overseas parts coming in which puts us at the mercy of supply chains, but we do everything we can to turn our claims around as quickly as possible. We do have the capacity to help out in those in-between times with some of the features of our policy including financial protection. But at the end of the day, you want to get the machine either replaced or repaired and carry on with your contract and
networks as well. A forestry product, for example, will go to a specialist repairer who knows the machine and they can repair it safely and within warranty specifications. You have strict health and safety issues with repairs, and they need to be certified by independent engineers to ensure they are fit for purpose.
“Our aim is to get this equipment, back out and working for the customer as quickly as possible, so they have their asset back doing what it’s supposed to do, earning money,” said Matt.
AllCrane Sales and Service recently delivered the largest capacity standard registered knuckle boom in New Zealand. The crane was delivered to long standing customer KT Cartage. Allcrane’s Karl Leonard Technical Manager and Mobile Crane Sales explains more.
“WE DELIVERED THE FASSI F1150RA.2.27 which had a few modifications to suit our customer, KT Cartage’s requirements. These modifications include a low subbase for lower mounting points and integration of the local subframe and the outriggers were offset to the cab which helps to increase stability to a greater angle forward of the outriggers,” said Karl.
The FASSI F1150 RA.2.27 features seven hydraulic boom extensions to 4730kg @17.55m and two manual extensions to 2500kg @ 22.5m. It also features V20 2000kg linepull winch with three parts of line to the hook and V20 was chosen for lighter weight. Three parts of line give a maximum lift of 6000kg @ 11m.
KT Cartage is a family business run by husband and wife team Kelvin and Emily Fitzpatrick. The business specialises in truck mounted loader cranes.
“We use a well-known and trusted range of hydraulic lifting equipment such
as Fassi, and we offer lifting, loading and transport solutions for small mum and dad type lifts through to large commercial projects,” said Kelvin.
Allcrane Sales and Service has represented the FASSI range of products since 2017. The range includes FASSI knucklebooms, Jecko mini crawler cranes, large glass handling attachments and also the Marrel hooklift product.
“We represent a range of quality products with the Fassi range and also Tadano. Having a broad range of products is important for the business as we are able to offer a number of lifting solutions to meet the specific requirements of our customers. We have had huge success with the Fassi product which has allowed us to become a top player in the NZ market,” said Karl.
The new FASSI features the FX900 Fassi V7S radio remote control system which displays on a colour screen all the relevant information as to how the crane is performing. The Internet of Cranes (IOC) allows remote access to the crane and all data points can be monitored. Service scheduling can be checked, and the parameters of the crane can be modified by Allcrane Sales and Service.
In case of a sensor failure/damage there is a sensor shut off to which allows the crane to pack up safely. If a part is supplied, it can be programmed remotely by a technician without the need for a callout.
If an issue arises during a job, an Allcrane technician can login to the crane (only with the permission and activation of the owner) and monitor the crane, providing advice and assistance in real time. The ACF feature for automatic unfold and folding of the crane is managed with one lever.
KT Cartage is a significant customer for Allcranes Sales and Service confirms Karl.
“Kelvin and Emily have been working with Allcrane since 2016 when they purchased a Cormach 275000E8. Because of the support and service we provided for that product, they have continued the relationship and gone on to purchase a Fassi F185A.2.25, F710RA.2.26, F120B.2.23 which are all new crane purchases,” said Karl.
Product support is a major focus for the entire Allcrane Sales and Service organisation.
“We support the Fassi product throughout New Zealand and we receive huge support by from the Fassi factory in Italy,” said Karl. “We understand that if there is an issue with a crane, it needs to be fixed ASAP so that asset is back out and earning money for the customer. As a business, we have invested in a major parts holding for the products we represent. But if for some reason we don’t have the part available, parts supply from Fassi is fast and expedient,” said Karl.
“Over the years Allcrane has also invested in its people and many key staff members have been with the business for many years. This experience has led to a deep understanding and knowledge of the products we represent which is second to none in our industry. Relationships with customers include our technicians and workshop staff and as a result crane owners and crane operators have a high level of trust in our business.
“Allcrane continues to invest heavily in new staff, we recently opened a larger workshop and we have increased parts stock and warehouse space. Factory direct training of the various products, at all levels, is a priority and this includes the training of key service agents around across New Zealand.
POTAIN MCT565
• Fast and easy erection
• Variable speeds and operator profile for smooth operating
• 90.9m max Free-standing on 2.45m Mast
• New display: Visu + data logging and built-in zone protection as standard
“It’s an exciting time for Allcranes Sales and Service,” said Karl.
“The ongoing investment is important for the future of the business and customers understand that we represent a range of World Class products and we back
Manager at McIntosh Cranes, Scott McIntosh, discusses how the Visual Dispatch Software has helped streamline the New Zealand crane hire company’s quoting, scheduling, invoicing and utilisation of its assets.
MUDDY PAPERS FRESH BACK FROM THE site, illegible handwriting, crumpled up pieces of important information – you name it, and Scott McIntosh has probably seen it when it comes to administrative paperwork.
Throughout his career in the family business, Scott has consistently sought out opportunities for growth and development. Starting out as an equipment operator, he progressed through various roles, including dispatch and operations. In his current position, Scott is constantly striving to optimise processes and enhance efficiency. His commitment to continuous improvement drives him to explore innovative solutions and adopt best practices to elevate the company’s performance and exceed customer expectations.
Across its more than 70 years of experience in the crane hire and transport industries, McIntosh Cranes has accumulated a vast fleet of cranes, hiabs, and truck and trailer units to uphold its operations. Now into its third generation of family ownership under the eye of Scott, the business has been steadily expanding both its fleet and industries serviced, with the company almost doubling its fleet capacity since 2017 to expand its operations in –among others – precast concrete and steel work and wind farm maintenance.
As of today, the company possesses a diverse fleet of around 30 assets, with its crane hire fleet spanning from the TIDD PC25 pick and carry crane through to a Liebherr LR 1300 before capping out at a Grove GMK6400. As mentioned, the company possesses a
range of Hiab cranes and transport machinery that, in all, as operated and serviced by 33 employees. What it doesn’t have is the intensive paperwork flow brought on by administrative procedures. Aligning with Scott’s move to fleet management and dispatching, the company has been using Visual Dispatch’s crane scheduling and allocation software since 2017.
Every lift at McIntosh is scheduled, allocated, and invoiced through Visual Dispatch’s
According to Scott, McIntosh Cranes’ back-of-house procedures have been made so much simpler and effective since the implementation of the software that was developed especially for the crane industry.
And, since updating and moving to a newer version of the software in
“We’ve moved to e-tickets for all our operations team, all our invoicing is done through the program, and everything can easily be controlled by opening a new job and monitoring everything within that job,” says Scott. “Before we implanted the system, we would use a big pad to allocate everything. Now, we use Visual Dispatch to streamline the entire package for employees, and scheduling everything, for every bit of our machinery, from quoting through to invoicing.”
The story of Visual Dispatch is symbiotic with the crane industry. Developed in the mid-90s specifically for the industry, the software optimises the quoting process, the crane and support equipment scheduling and dispatching process, and the invoicing
equipment and employee schedules scheduling is as efficient and effective as possible. Intuition and practicality were at the forefront of mind when developing the system that is accessible via mobile phone, tablet, computer – anything electronic, essentially – with the process
To undertake the process, companies start with a quote or a rental/booking within the software; from that point on, the information is permanently maintained meaning less time wasted by duplicating or copying information between systems/process and also consistent across what the customer receives(Quote, eTicket & Invoice) until it is closed, information is never lost –whether that be job hours worked by a machine or employee, or equipment allocation and distribution. For Scott, Visual Dispatch’s intertwined nature with the crane industry was the major selling point for McIntosh Cranes, saying the crane hire company felt comfortable using a software that was so
“With the quoting system including resource package’s, we knew that the
software was designed for the cranes and heavy lifting industry,” he says. “For us, the software is holistic, comprehensive, detailed, and has solved a lot of our issues as we look to continue growing our fleet and operations.”
Naturally, for Scott, a major aspect of Visual Dispatch is the software system, its integration, its practicality of use, and how it has streamlined the company’s administrative procedures. What he and McIntosh Cranes have also been taken by, however, is the responsiveness and willingness to help provided by the Visual Dispatch team, headed up in Australia and New Zealand by Daniel McBride, the manager for the ANZ
The software helps all machines of all kinds across every sector.
region with an extensive history in the crane industry as operations manager.
“When we implemented the latest version of Visual Dispatch back in November 2023, Daniel ensured he was over here with us, walking us through the processes and training everyone in the team to ensure we all understood how to effectively utilise the system,” says Scott.
“Since working with Visual Dispatch, we’ve consistently had a responsive team backing us for any questions, queries or issues that we’ve had, and the system has helped us streamline our entire administration process.”
PRESTON HIRE NEW
Preston Hire has a range of Sennebogen telescopic crawlers available for hire.
Preston Hire New Zealand is a company that specialises in providing hire solutions for construction, infrastructure, and industrial projects.
PRESTON HIRE NEW ZEALAND OFFERS
a variety of equipment and services designed to support different stages of construction. These include:
1. SuperDeck Retractable Loading Platform System Hire: A retractable loading platform that provides safe and efficient material handling for multi-story construction projects.
2. M ini & Hydraulic Crawler Crane Hire: Apart of the SuperCrane range
of cranes designed to meet lifting requirements on construction sites, enhancing productivity and safety.
3. C onstruction Hoist Hire: The SuperHoist fleet plays a major role in the vertical transportation of workers, materials, and tools on construction sites, particularly for multi-storey buildings.
Preston Hire is home to the worldrenowned SuperDeck – the market
leader in retractable loading platform systems. In the SuperCrane range Preston Hire offers an extensive fleet of Maeda, Sennebogen and UNIC mini cranes and larger hydraulic tele-crawler cranes, as well as highly reliable and safe personnel and construction hoists by world-class vertical access solutions provider, Raxtar, which feature in the SuperHoist product category.
Over 57 years, TRT has worked hard to be recognised as a progressive engineering and manufacturing business specialising in the crane sector. Managing director Bruce Carden says it’s a busy time for the business, not only manufacturing the TIDD pick and carry crane, bespoke crane trailers and crane pads but representing Manitowoc products, including Grove all terrains, in New Zealand and Queensland, as well as the Kobelco range of crawlers throughout Oceania.
INVITING EXISTING AND POTENTIAL customers to visit the manufacturing facility in Hamilton, New Zealand is an important strategy which enables customers to better understand TRT’s DNA, said Bruce.
“Over the last three years we have focused on getting customers to our factory and demonstrating what TRT stands for. For us, it’s imperative that we bring groups of potential buyers to view the business and show them firsthand how TRT goes about its business. There is no doubt that all visitors are impressed when they see raw steel entering one end of our facility and rolling stock, which could be either cranes,
trailers or crane pads, rolling out the other. Understanding how we do things helps customers better understand TRT’s DNA,” said Bruce.
“Our approach has always been to understand the customer’s business and then look at what solutions we can offer to help make their business A: more profitable, and B: fix the issues the customer is experiencing.
“This approach is something our team does very well, we ‘deep dive’ into customer enquiries and really get to the bottom of what it is that they are looking for in terms of lifting or transportation solutions. When we understand what the
customer requires, we can provide the best solution,” he said.
TRT’s specialist and bespoke crane trailers have been extremely successful over recent years, said Bruce.
“One area where we’ve had good success in is our specialist crane trailers. Customers can come to us with a particular model of crane, and it doesn’t matter what brand or type, we’ll look at the specific product and figure out the best transport solution for that particular crane.
“We now have a significant number of
customers who see our trailers in the marketplace, they can see how they would benefit their businesses, and they are coming to us also,” said Bruce.
Borger Crane Hire is a major purchaser of TRT crane trailers.
“It’s been a nice long-standing relationship with both Shawn and Nathan [Borger] and their father Jon, although
have helped them get there. They came to me almost 14 years ago when their first crane required purpose-built trailers – a 500t capacity Liebherr all-terrain and wanted crane trailer solutions for that. And since that time, we’ve built over 100 crane trailers for all the various cranes that they have in their fleet.
“It’s now got to the point that virtually
every time they buy a new all-terrain crane, they order a set of TRT engineered ground pads to go with it because they’ve realised that the engineering behind the pads and the certification we provide can be presented to Tier One sites which is beneficial for their business,” said Bruce.
A key element of the recent factory visit was the demonstration of the all-new TIDD PC28-3G.
“We wanted to reinforce to the market that the development of our new TIDD PC28-3G Pick and Carry Crane has been
From an operator’s perspective, there is a significant step up in drivability of the TIDD
driven by a continuous focus on innovation and actively exceeding expectations for customers.
“For the factory visit we had our second production 3G unit, as we call it, ready for demonstrations. During the two days that they were on site, they witnessed both the build quality of the product through the manufacturing and assembly processes, but just as importantly, we put on a live demonstration, which showed them a lot of the safety features that are with the crane,” said Bruce.
“And one thing that came out loud and clear is that from an operator’s perspective, there is a significant step up in drivability compared to the PC28-2. The new Euro 6 Cummins engine is a lot quieter than the old Mercedes engine and another feature they love is the retarder that’s put on the transmission for helping the crane with
its braking. All in all, we had a really good response to the 3G, and we’ve now got a number of customers talking about placing orders as a result of the tour,” said Bruce.
TRT’s range of crane pads were also on display.
“We’ve been designing and manufacturing crane pads for 10 years and we have a customer in Empire Cranes who has taken a position in the market to dry hire these crane pads. Their business model’s a little bit different to others and we’ve supplied them with a number of these pads. The attraction for Empire Cranes and others, is that the pads come with certified engineering documentation so that when they go onto a Tier One site, they provide the Geotech Engineer with all the ground pressures that these pads are going to produce. That allows Empire Cranes to supply not just the pads to the
market, but a complete engineered lifting solution, which is again, part of TRT’s DNA,” said Bruce.
Bruce goes on to discuss the business philosophy in terms of design, engineering and manufacturing and the investment in robotic manufacturing.
“About 15 years ago, we decided to bring a lot more of these processes in house. And the reason for that is that we were having issues with our subcontractors, both from a quality point of view, but just as importantly from a delivery point of view.
“One thing we pride ourselves on is when we give a customer a delivery date, we want to stick with it. Particularly as a company manufacturing in New Zealand and exporting to Australia, we need to ensure that the product is ready on the day the ship sails. And by having a lot of these processes in-house, we manage to do that.
“One thing we pride ourselves on is when we give a customer a delivery date, we want to stick with it. Particularly as a company manufacturing in New Zealand and exporting to Australia, we need to ensure that the product is ready on the day the ship sails.”
We’ve invested heavily in high-definition plasma cutters, we’ve invested in robotic welding. And the learning curve with the robotic welding has been a steep one because of the range of product that we manufacture.
“It’s a very complex solution. It’s not like we’re building hundreds and hundreds of small repeat parts as happens in the automotive industry. Our robot can build two of a kind and then immediately have a totally different product put on it and build two of that kind. So, it’s certainly wellsuited for our industry now that we have it up and running well.
Neil Webb joined TRT Australia a little over two years ago. Bruce discusses the
TRT Australia operation with Neil at the helm.
“We made a decision back in early 2021 that we wanted to get someone within our business that had cranes in their blood. We were looking for someone that had general manager skills, had that background and could manage a team of people.
“I got put in touch with Neil during the days of COVID-19, and that was an interesting joining of our two paths. We offered 20 per cent shares in our business over a number of teams calls and signed Neil as the General Manager to run our Australian operations.
“I’ve got to say, it’s been one of the
best things that TRT has done in the last 10 years and certainly set TRT Australia up for success. Neil understands exactly what is required in the crane industry to make a successful business. And that’s not just selling product, it involves offering the best possible product support which makes the business model work,” said Bruce.
Bruce looks to the future and confirms his vision for the business.
“My vision for the business is to carry what we have built on for the last 57 years and to take TRT into the future as a family-owned business. My wife Mary, our son Jeremy and myself are working in the business and we see that TRT is well positioned for the future. We’ve got some great agencies and we’ve got great people – and without the people behind us, it wouldn’t be the business that it is today. We’re planning for, and looking forward to, the next 10 plus years with the intention of taking the business to new levels without losing sight of the values that have helped the business succeed for the last 57 years,” he said.
Before Pace Cranes became the National Distributor for major crane brands including Maeda and Sennebogen, the business was recognised for its crane service capabilities. Managing Director Anthony Heeks and Service Manager Patrick Mardaymootoo explain how workshop capabilities remain a key element of Pace Cranes’ DNA.
“SOMETIMES I BELIEVE WE ARE A ‘VICTIM of our own success’. With the successful sales of the Maeda product, many customers are not aware of our history and especially our service and maintenance capabilities, and think we only work with mini cranes. The other perception is we only work on the brands we represent, which is not true,” said Anthony Patrick, who has worked at Pace Cranes for close to 30 years, has seen many changes to the industry. “Over this time, we have steadily increased the service
work year on year and a lot of this work is major inspections. This work involves Maeda and Sennebogen, but we also work on other brands and pieces of equipment including telescopic handlers, forklifts and access equipment,” he said.
“Many of our Maeda and Sennebogen customers have asked us to service and maintain other types of equipment in their fleet. We look after our customers and the work is always varied.
“We’ve been representing Sennebogen for 14 years now. With many reaching the
10-year age, these cranes are coming up to their major inspection period. Customers are starting to book these in which is increasing the workload. Many of the cranes are working nationally but they are still preferring to bring them back to us for the major inspections,” said Patrick.
Anthony explains more about the servicing heritage of Pace Cranes and the company’s commitment to an apprenticeship program.
Some of the key areas of focus for the service department are employment, staff
training and more importantly, staff retention.
“Over the 36 years in business we have always invested in apprentices, and we have seen 27 apprentices in our program over this time. In recent years it has proved more difficult to attract potential candidates because I believe the schools are pushing for university educations and other career opportunities,” said Anthony.
“But this focus is changing with governments recognising that together with the severe skills shortage, housing shortages and local manufacturing push, something has to change.
“Currently we have five tradespersons, three apprentices and a trade assistant in the workshop, and all are excellent. One apprentice is aiming to become a mechanical engineer and we’re helping him pursue that. We’ve got another who’s just come out of school, and he’s already completed a schooling pre-apprenticeship,” he said.
“Several apprentices have stayed with us for many years with some branching out to work for other companies. A number have started their own businesses and are now successful.
Others are in senior roles, with other manufacturers and importers,” said Anthony.
The apprentices are taught with a step-by-step approach to the work in hand says Patrick.
“The learning and improvement from the apprentices come from the support we offer and making them part of our team. We explain why we are taking the various steps and the results we are expecting,” he said.
Patrick goes on to discuss how the workflow is managed throughout the workshop.
“Recently, we promoted Chris Ryan to leading hand. His promotion is motivating for the younger staff, and he’s really taken hold of the workshop and displayed excellent leadership skills. With the amount of growth we are experiencing, and the number of apprentices we currently have, we were delighted to offer him the position.
“Every morning Chris and I meet for a toolbox session where we discuss the priorities as we walk through the workshop, what jobs need to be moved etc. We must be flexible and reactive in the workshop because customers tend
to drop off their Maedas for a service, often without notice. Many customers have the crawlers out for dry hire on projects and once that hire is up, they need them serviced before they go to the next job, which is often the next day,” said Patrick.
The Service Department also works very closely with the Sales Department, says Anthony.
“We see a lot of stock come through the workshop and we must prioritise the pre-deliveries. Every Monday, Michael Cawston, our National Sales Manager, Greg Muller, our Product Support Manager, and Patrick sit down and plan the pre-deliveries for the week ahead. The only way to manage the volume of work is to plan it, it would be mayhem otherwise,” he said.
Pace Cranes has a nationwide network of service agents who are factory trained in each product. Patrick explains how important this training is.
“The machines increasingly feature advanced technology, and ongoing factory training is a necessity. We frequently have technicians travel from Europe and Japan to conduct technical training programs and all our agents fly
in from around the country to attend.
“We have a service agency in every state and in New Zealand’s North and South Islands. From a sales perspective, we understand the importance of after sales service and support. We will sell the first crane to the customer but it’s the after sales service they receive that brings them back for the second and third,” said Patrick.
“Supporting product is critical and when we know a new model is being released, the first thing we ask for is a recommended list of parts that we should be carrying. We’ve been working with the Maeda brand for 30 years, so we have plenty of experience and understand how customers treat them. With this experience we know what parts to have on the shelf and are readily available. This helps get the customer’s crane out of the workshop and back working as quickly as possible,” he said.
Are you ready to take charge on construction sites, oversee critical lifts, and ensure safety at every turn? Step into the role of a Crane Lift Supervisor with CICA’s comprehensive and specialised training course.
®
The course instructors are seasoned professionals who will mentor course participants through real-life scenarios, preparing them for the challenges and responsibilities of a Crane Lift Supervisor.
Crane Lift Supervisors are in high demand globally. Completing this course enhances employability and opens doors to a wide array of job opportunities and career growth.
The curriculum covers a wide range of topics, including lift planning, load calculations, safety protocols, communication strategies, and legal compliance.
MANITOWOC HAS RELEASED TWO NEW Potain luffing jib tower cranes with the launch of the MR 309 and MR 329.
These models follow in the same vein as the MR 229, launched at bauma 2022 and equipped with the Potain Crane Control System and Potain Connect telematics. According to Vice President of marketing and development at Manitowoc, Thibaut Le Besnerais, the company expects these new generation luffing jib tower cranes to thrive on site in line with the MR 229.
“We’ve received excellent feedback since the debut of the MR 229, particularly for its ease of erection, minimised out-
of-service radius, and the integration of CCS,” he said. “With these achievements in mind, we have high expectations for the MR 309 and MR 329 as they round out this innovative new generation of Potain luffing jib cranes.”
Based off customer requests for quicker and simpler crane assembly, the jib on the MR 229, MR 309, and MR 329 can be mounted horizontally, section by section, while the reduced windvane spans make installation on tight jobsites easier.
Accessible platforms and steps promote secure and efficient worker movement, and the counter-jib ballast is installed at
working height. The positioning of the ballast is made easier thanks to slinging rings and a self-centring system. A redesigned luffing mechanism streamlines assembly, while an integrated jib-end basket further promotes more secure installation, inspection and maintenance. Finally, the Potain CCS decreases commissioning time, helping the cranes to get to work faster.
Additionally, according to Manitowoc, customers requested a greater height under pivot and more powerful load charts that the MR 229, MR 309, and MR 329 all deliver. The MR 309 and MR 329 have been introduced with maximum capacity variants of 16 tonnes or 25 tonnes. Despite sharing a common 60m jib and a 3.4-tonne capacity at the tip, the luffing jib tower cranes’ distinct pivot and mast configurations result in differing heights under pivot and load curves.
The MR 309, with its two-metre pivot and mast configuration, achieves a height under pivot of 49.2m, reaching
“We’ve received excellent feedback since the debut of the MR 229, particularly for its ease of erection, minimised out-of-service radius, and the integration of CCS.”
a maximum capacity of 4.3 tonnes at 55m. In contrast, the MR 329, featuring a 2.45m pivot and mast configuration, attains a height under pivot of 55.2m, with a maximum capacity of 4.7 tonnes at 55m. In addition, the new cranes address the need for a strongly reduced out-ofservice radius (9.5m to 12m) and decreased anchorage frame requirements, delivering improved efficiency and productivity on high-rise and congested construction sites where oversailing is not permitted.
12-13 September 2024
The Star Gold Coast Australia
Join the only dedicated event for the lifting and height safety industry in Australia
Key Features:
• Exhibition: See the latest in lifting equipment and innovations in action
• Conference: Hear end-user presentations on new technologies and advancements in lifting safety
• Free Training Sessions: Opportuntity to earn CPD points
• Networking: Forge connections during breaks and the drinks reception
If you are a user of lifting equipment, you should attend this event
Tasmania’s Pfeiffer Cranes recently took delivery of a new Grove GMK6450-1. With a lifting capacity
gaining work through their reputation as highly skilled operators.
Dan and Craig were recently joined by eldest brother Jack, who operates his own business, Engineering Plus, and has
and where it has been needed,” said Jack.
The Pfeiffer fleet is impressive by any standards, including 11 trucks, 18 trailers and 21 cranes consisting of brands
new Grove GMK6450-1 is important for the larger scale industrial projects we are now working on,” said Dan.
Grove’s 450-tonne, six-axle allterrain crane possesses a main boom
length of 60m which can lift 64 tonnes and has a 132m maximum lifting height with an array of extensions. Able to lift nine tonnes at that height, the highly compact crane can also be fitted with a boom removal configuration which reduces axle loads to the lowest level possible for scenarios where minimal transportation weight is required.
The MegaWing attachment is easy and quick to set up and allows for boosted lifting capacities.
Additionally, the Grove GMK6450-1 also comes with Manitowoc’s patented MegaWingLift, a self-rigging system requiring sub-20-minute setup and
dismantling times that boosts the lifting capacity of the crane. The increase in productivity and efficiency offered by the 450-tonne machine was also a major selling point for Pfeiffer Cranes, says Jack. This crane also features Grove’s famous MEGATRAK™ suspension system. All wheels are engineered with independent hydropneumatic suspension and hydraulic lockout. Simply put, this ensures a smooth ride even over challenging terrain. Driver comfort has never been better in a crane of this capacity!
The Grove GMK 6450-1’s superstructure also features a graphic
display load moment and independent two-block system. This includes an audio-visual warning and control lever lock-out. These systems provide a clear, electronic display of boom angle, length, radius, tip height, relative load moment, maximum permissible load, load indication and warning of impending two-block condition with lock-out hoist function
The Pfeiffer Cranes team is regularly challenged to undertake complex lifts which include site inspections and detailed planning and consideration of different options. Lift and engineering studies are conducted and 3D lift plan drawings take into account the lift charts of the fleet and what they can lift at various radiuses – with all the options considered to complete the job safely and succinctly.
A recent example of this level of planning was a six Grove crane lift involving a Bison Sheds, shed roof for a wool store shed owned by Wool Solutions.
Craig explains there were a number of complicating factors relating to the lift.
“Being in close proximity to the airport required the use of cranes with restricted boom lengths. This, in turn, required the deployment of more cranes and additional rigging equipment to complete the project safely and efficiently. Communication was critical during the lift, and this was maintained through private channel radios among six cranes and four riggers. The total weight of the roof and rigging etc was 100t spread over the cranes with each of the cranes derated by 50 per cent,” he said.
Jack goes on to discuss the reasons behind the purchase of the new Grove GMK6450-1 and the relationship and service the company receives.
“The business started off with Kato Cranes and quickly moved on to the first Grove. Today, all the larger cranes we own are Groves. The capacities start with the 55t GMK3055 and include the GMK3060L, GMK4080-1, GMK 4090-1, two GMK 5150-Ls, GMK
5220, GMK 6300L, GMK640 and now the GMK6450-1. A close relationship with Grove continues to this day,” said Jack.
“The crane was purchased as a result of the long-standing working relationship we have Woolnorth’s wind towers. We purchased the crane with the full accessories which are exchangeable with the 6400, which we can see will be a real bonus.
Jack explains the Pfeiffer family continues to focus mainly on Grove when it comes to all terrains.
“My parents and brothers love consistency, and our business is built on relationships. This is also true when it comes to purchasing our larger cranes. The service and reliability that Grove give our family business is second to none, and that is why we continue to work closely with the brand. They support us 100 per cent and we support them right back,” he said.
The total weight of the roof and rigging etc was 100t, spread over the cranes with each of the cranes derated by 50 per cent.
More than just a pre-start checklist
StartSafe is comprehensive tool designed to streamline your crane operations, enhance safety, and ensure accountability.
Machine specific checklists are in line with the CraneSafe program.
StartSafe streamlines the process for collecting pre-start information, with instant data retention to a central location for the crane owner to access.
When a faulty item is recorded by the operator, the maintenance team is notified of the issue by email, which includes photo evidence of the fault. This also assists with gathering major inspection data.
SpanSet, a company renowned for its unwavering dedication to global safety and quality, has invested heavily in state-of-the-art testing equipment over the years at its purpose-built manufacturing facility in Emu Plains, Western Sydney.
SpanSet, A COMPANY RENOWNED FOR ITS unwavering dedication to global safety and quality, has invested heavily in state-ofthe-art testing equipment over the years at its purpose-built manufacturing facility in Emu Plains, Western Sydney.
The centrepiece of this investment is the installation of a groundbreaking 600-tonne 45m long tensile test bed. This heavy piece of equipment ( weighing in at 65 tonnes itself ) has a 30-meter working length, thus allowing SpanSet to test up to 60 meters in a basket configuration.
The size of the test bed gives SpanSet unparalleled scope to proof test hightonnage lifting slings at exceptionally long lengths. This investment not only underscores SpanSet’s commitment to safety and compliance under the rigorous testing standards of AS4497:2018 but also positions them as the only synthetic sling manufacturer that can manufacture up to 300t round slings and proof test them to two times their Working Load Limit in accordance with AS4497:2018 “and all under one roof”, thus closing the circle of complete in-house quality control and compliance.
“Regrettably, it is not uncommon for manufacturers to outsource their hightonnage compliance-proof testing due to limited in-house testing capabilities. In some cases, they may even choose to forgo this mandatory testing altogether,” said SpanSet Managing Director Kristian Pritchett. During a joint sling destruction exercise conducted with The Crane Industry Council of Australia (CICA), significant discrepancies were discovered
between manufacturers’ claimed break strengths and actual performance. This highlighted the critical importance of purchasing synthetic slings from reputable manufacturers that maintain robust quality control systems. Additionally, it underscores the necessity of ensuring these facilities have NATA certification and the slings undergo rigorous in-house testing (CICA spotlights soft sling compliance issues).
“SpanSet stands out with its dedication to comprehensive quality control by keeping everything under one roof in Western Sydney. All SpanSet synthetic Australian Made slings are tested in the factory which is NATA certified, giving our customers certainty and confidence. SpanSet is also certified to ISO 9001:2015 ISO 45001: 2018 and ISO 14001: 2015.
“When compliance testing is outsourced to an unrelated third-party, the purchaser or end user faces significant challenges in easily verifying the compliance status of the testing house and ensuring that their testing equipment is properly calibrated in accordance with the relevant standard requirements AS2193 and further supported via NATA accreditation,” said Kristian.
“In the context of the chain of responsibility, it is highly recommended that users of synthetic slings identify the manufacturer of the slings they are purchasing and validate the claims made on the test certificates. Purchasers or end users can verify NATA testing accreditation by searching for the supplier on the NATA website,” he said. This is also highlighted in a recent CICA / Incolink Safety Bulletin titled
“Top Tips for Soft Sling Procurement and Usage,” he said,
Unlike others, SpanSet maintains complete control over the entire manufacturing and compliance testing process. This meticulous approach is not only a cornerstone of their operational philosophy but also a crucial factor that matters greatly to purchasers of SpanSet products. Crane companies globally trust in SpanSet products for safety and compliance manufactured to in-country standards.
When undertaking any lifting operation, especially in a heavy lift, there is no room for “risk”.
By managing every aspect internally, SpanSet ensures that each product meets rigorous safety and quality standards, providing unmatched assurance to its customers.
For SpanSet, the ability to oversee and execute every stage of production and testing is essential. It exemplifies their commitment to excellence and exceeds the benchmark in this country.
“In my professional opinion, it is crucial for purchasers of high-tonnage lifting slings, or lifting slings in general, to conduct thorough due diligence. This includes verifying whether the brand indicated on the compliance tag is a legitimate manufacturer or merely a trader, as well as ensuring the authenticity of the supplied test certificate,” said Kristian.
“Don’t take risks with unknown brands; opt for a SpanSet Australian Made and Tested Synthetic Slings, ensuring peace of mind and reliability.
“Our objective is to educate customers and users about our products and the supplied test certificates, providing guidance on how to interpret and understand the information contained. Furthermore, we extend an open invitation to our users to visit our facility, offering them the opportunity to observe firsthand our meticulous manufacturing processes and rigorous testing procedures for every SpanSet sling,” he said.
When purchasing a crane, selecting a brand with a history of manufacturing safe and reliable machines is essential. A brand with a proven track record in the industry offers assurance of quality and
The size of the test bed gives SpanSet unparalleled scope to proof test hightonnage lifting slings at exceptionally long lengths.
dependability. The same principle applies to purchasing synthetic lifting slings. It is crucial to choose a manufacturer that specializes in its field and has full circle quality assurance and understands the complexities of the technical aspects of textile lifting slings says Kristian.
“At SpanSet, we have over 50 years of global experience in synthetic lifting sling manufacturing. As a result, we provide all the technical information relevant to heavy lifts, including details about sling thickness under load, sling width under load, and the appropriate sling for various shackles.
SpanSet Australia manufactures lifting slings that meet the highest safety and performance standards, ensuring the reliability and efficiency of your lifting operations. With decades of experience, SpanSet has honed its expertise in producing high-quality lifting slings designed to handle
the most demanding tasks.
Moreover, SpanSet’s dedication to quality is evident in its comprehensive range of lifting solutions, which cater to various industries and applications Lifting, Load Restrain and Height Saftey. By choosing SpanSet, you are investing in a product backed by extensive global research, advanced manufacturing techniques, and a deep understanding of the industry’s needs. This translates to greater peace of mind, knowing that your SpanSet product is built to perform as intended under the AS Standards.
“In addition, SpanSet offers excellent customer support and training resources, helping you maximize the use and longevity of their products. Their commitment to customer satisfaction ensures that you receive high quality products fully backed by the manufacturer,” said Kristian.
28t
300t
220t
32t
9m
1.5m
5t
PENSKE AUSTRALIA AND FRANNA recently reached a new agreement for the supply of OM936 engines to power Franna’s pick-and-carry crane.
Seriously powerful, the OM936 engine delivered by Penske is the only dual-certified Stage V and Tier 4 EPA- labelled engine on the
The 7.7L six-cylinder industrial OM936 off-highway engine is specifically designed and certified for special-purpose vehicles such as Franna cranes, delivering a bespoke
A highly efficient and lowemission off-highway product, the OM936 meets the stringent Australian Design Rule (ADR) 80/04 regulation in addition to the Tier 4 US EPA requirements, the most stringent engine emission regulation globally.
“The USA and Europe appoint far more rigorous standards than we do locally in Australia,” said Lloyd Dilger, Diversified Products National Sales Manager at Penske Australia.
“The US currently requires Tier 4 standards for off-highway vehicles. Europe complies with Euro 6 standards for on-highway vehicles and Stage V
“The OM936 engine complies with both the rigorous European off-highway standards and the strict
“Rated to an impressive 300 kW brake power and boasting long maintenance intervals, the OM936 is the ultimate solution for cranes in terms of emissions, power and customisation for the off-
ADR 80/04 will come into effect for newly approved heavy vehicles from November 1, 2024. ADR 80/04 aims to decrease emissions from heavy
“Rated to an impressive 300 kW brake power and boasting long maintenance intervals, the OM936 is the ultimate solution for cranes in terms of emissions, power, and customisation for the off-highway market.”
vehicles and is based on the European Union Stage VI emissions standards, with which the OM936 complies.
“With the OM936, we are able to future-proof power solutions for the offhighway market,”Dilger said.
“Franna can confidently count on a power solution that will deliver for years to come.”
Franna customers can count on Penske’s extensive national footprint across the country, delivering support
where and when customers need it.
Furthermore, in addition to the OM936 engine, Penske also supplies OM engines rated between 170kW and 460kW for various applications, including agriculture, industrial, rail, and mining.
The mtu engine range, also represented by Penske, is rated up to 650kW and is ideal for powering cranes, haul trucks, industrial mining equipment and forestry machinery.
In announcing the appointment of two new Licenced Training Centres, Justin Boehm, LEEA’s Regional General Manager for Australia and New Zealand, emphasises the need for lifting businesses to better understand the quality of the products they are lifting with.
I SAY THIS WITH MY HAND ON MY HEART – Cranes and Lifting equipment are the backbone of all industrials. What multistorey building could be completed without lifting apparatus? Commerce relies on shipping, so how would a port lift and shift containers? How can we transition to renewable energy by 2050, with the thousands of wind turbines that need to be erected, without bigger, better, lighter and more efficient products to gain more efficiencies from wind generation.
Pushing the limits of product design is something that has happened throughout human history - we wouldn’t have landed on the moon if we didn’t. We’re seeing this now with specifically designed products in the renewables space. The height of cranes needed to lift turbines into place, along with their exceptionally long blades and the specific products needed to hold them at their exact angles, are now the norm. As we push these limits, it’s important that any new products are designed, manufactured and tested to the standards with which they are said to comply.
Recently I had the pleasure of speaking to an Australian manufacturer about their world class products. One of the key components to that success, they said, was the testing that takes place to ensure it complies to the relevant Australian Standard. This was an eye opener, but something members have raised for the entirety of my time with LEEA. It’s interesting to ponder - Do procurement teams understand the risks associated with the equipment they’re buying, and if price is always the deciding factor - when will the next fatality occur?
Knowledge is power goes the adage. In our industry it’s called competence – a fuzzy word that is bandied about regularly,
LEEA’s Regional Manager, Australia and New Zealand, Justin Boehm.
but adding knowledge and skills to this discussion needs to be a high priority. Competence takes numerous forms, and in LEEA’s case is usually used to highlight someone’s ability to inspect lifting equipment. However, procurement must be discussed. When ordering product with relatively low value, is there a level of “competence” needed, so there is a true understanding of what that product is required to do and what standard it’s manufactured to? When lifting operations
• May marked the beginning of a new era for LEEA’s globally renowned training via our Licensed Training Centres (LTC). Both Tower Crane Training in Sydney and ATC Offshore in Perth, our LTC Partners, ran their first full Face to Face Foundation courses.
LEEA has long been at the forefront of promoting safety and excellence in the lifting industry and our training is seen as minimum requirement for those inspecting Lifting Equipment. Now, the LTCs are taking this commitment to a new level by delivering our specialised courses, to empower lifting equipment inspection professionals through local face to face training.
The LTCs are delivering Foundation, Lifting Accessories and Manual Lifting Machines training to our industry specialists. These three courses form the backbone of LEEAs Certificate IV in Lifting Equipment Testing and Inspection. The LTCs are Registered Training Organisations, meaning their delivery is in accordance with the Australian Skills Quality Authority framework.
Tracy and Warwick from Tower Crane
“When ordering product with relatively low value, is there a level of “competence” needed, so there is a true understanding of what that product is required to do and what standard it’s manufactured to?”
take place the value of the products being lifted is high, so why are decisions to purchase lifting equipment usually based on the lowest bid?
In researching for this article, I visited Australia’s favourite hardware store –“Hammerbarn” (thanks Bluey), and looked at who was the signatory on a selection of slings that I purchased. It was the same signatory over five different varieties. LEEA’s End User Guidance Training is a good opportunity for procurement professionals to understand the nuances of the lifting equipment industry and how to identify quality products that comply to LEEA’s global standards.
Training are an exceptional team, who have a total of three trainers inducted into the LTC program. TCT has been training in the construction industry for over eight years, but Warwick has been a SafeWork NSW Accredited Assessor in Crane Operator and Rigging skills since 2011
Peter Schwarz and the team at ATC Offshore in Perth have been training professionals in the oil and gas industry for 12 years. The industry skills and knowledge of their LTC accredited trainers tallies over 150 years.
We’re excited to have them both onboard and delivering this game changing training for our industry.
•
•
•
Introducing the SCX1500A-3 crane, engineered by HSC for unmatched precision, efficiency, and power to elevate any job site’s performance. This crane combines flexible operation and user-friendly controls, ensuring optimal functionality regardless of the operator’s experience. Its design prioritizes comfort and visibility, reducing fatigue and enhancing daily productivity worldwide.
FEATURES:
Engine - Cummins QSB 6.7 (Stage IV / Tier 4f) or Isuzu 6HK1 (Stage IIIA / Tier 3)
Capacity at Full Reach - 1.4t x 63.3m
Max Lift Capacity - 150t x 4.5m
Max Boom Length - 75.0m
The ranking was granted following sustained efforts by the Group to decarbonise its machinery and operations across the entire company.
LIEBHERR-MCCTEC HAS RETAINED ITS gold medal status courtesy of global sustainability rating agency EcoVadis.
The award is reserved for the top five per cent of companies assessed across the world. The Liebherr division, responsible for business activities in the field of crawler, duty cycle and maritime cranes, as well as piling and drilling rigs, landed itself in the top one per cent of companies rated in its own industry.
“Being awarded the EcoVadis gold medal once again is a confirmation of our efforts to further improve in terms of sustainability and social responsibility,” said Tatjana Grissemann-Peter, Manager of Corporate Responsibility at LiebherrMCCtec GmbH. “We are proud of our progress and remain committed to developing innovative solutions to make a positive contribution to our society and the environment.”
According to Liebherr, significant improvements and initiatives in sustainability were implemented in 2023. These include the introduction or expansion of ISO certifications in the areas of occupational safety and information security at LiebherrMCCtec’s four European sites and the definition of new quantitative targets in the Corporate Responsibility policy. New targets have been defined up to 2030, including certification to the highest standards for quality, occupational safety, energy, environment and information security.
human rights, labour standards, environmental protection and anti- corruption.
Additionally, as part of its commitment to the UN Global Compact, Liebherr-MCCtec published an extended report in 2023 detailing information on governance,
The division also developed a greenhouse gas management and decarbonisation strategy by 2030 based on the identification of various CO2 reduction measures with corresponding targets. According
to Liebherr, in the production plants this includes converting the heating systems, electrifying the vehicle fleet and using alternative fuels such as HVO for testing the cranes produced. For example, 95 per cent of the electricity used at all four production plants is already generated from renewable energies.
Mammoet has showcased its extensive transport and engineered heavy lifting capabilities by shifting and installing a 1500-tonne Residue Hydrocracking Unit (RHCU) at a Lithuanian refinery, breaking a Lithuanian record in the process.
WORKING ON THE ORLEN LIETUVA REFINERY in Mažekiai – the only one of its kind in the Baltic states – Mammoet was contracted to bring the unit in from Italy and then moved into the refinery. Planning on the project began in 2016, according to Mammoet’s Global Sales Director, Edvinas Ivanauskas, working closely with multinational oil refiner ORLEN and the Lithuanian Transport Authority to investigate different methods, technologies and solutions to complete the job.
“We looked at all kinds of different options,” said Global Sales Director, Edvinas Ivanauskas. “We considered bringing it by water and by a neighbouring country. We also considered building a temporary jetty close to the refinery; however, this was not feasible due to the
“A port is usually six or seven tonnes per square metre for standard operation,” said Ivanauskas. “Basically, we took the approach to strengthen the quay and the areas around it to be able to handle the vessel. We sought special permission from the terminal owner and port authority to get approval.”
After successfully unloading the RHCU, Mammoet began transporting the unit by road on its 145km journey. The reactor was transported using 88 axle lines of PST and conventional trailer, pulled by two prime movers.
environmental impact assessment. When selecting the best route, you must carry out a lot of investigation in terms of the ground, the bridges and the weather conditions.”
Breaking the RHCU apart and transporting it in parts was also investigated. However, this approach would require welding it back together at the site using a specialist welding machine, of which there are only two in Europe. The team therefore took the decision to transport it in one piece.
Constructed in Italy, the unit was shipped to the Lithuanian port city of Klaipeda on a heavy lift Jumbo vessel equipped with two 900-tonne cranes to lift it into its port. Preparations had to be made to get the correct load introductions and ensure that the port could receive such a heavy vessel and cargo.
The journey took around 17 days, with the convoy travelling at an average speed of three to five kilometres per hour, with movements mostly at night. This was to avoid damaging the asphalt in the summer heat and to minimise disruption for traffic and the public.
Despite this, the route still posed its challenges: summer in Lithuania can bring heavy rainfall and, in the weeks leading up to the transportation, there was a downpour. To prevent the convoy from getting stuck in the ground, steel plates were laid across the gravel routes to spread the loads.
Electric cables also needed to be temporarily disconnected, and a permanent bridge constructed for the convoy to use. Five existing bridges also needed to be reinforced, as well as culverts bridged, and several bypasses erected.
At one stage, the team had to overcome an 8 per cent slope in a small valley. With the ground unstable, sheet piling was used and two additional prime movers called in, to support the convoy.
Transporting the mammoth RHCU gained much media attention and as such, drew quite a crowd of onlookers. People would arrive as early as 4am to see the convoy, and around 500 people flocked to
witness it perform one turn and capture the moment on their phone cameras.
Transportation of the unit was the most difficult part; by comparison, installation of the unit was much more straightforward, according to Mammoet. The lifting of the unit was carried out using a gantry crane and LR11350 tailing crane.
The cranes first performed a tandem lift of the unit, so that operators could drive the trailers out from underneath it. The gantry crane then lifted the top of it, whilst the LR11350 followed its movements to keep the hook of the gantry straight.
The operation was completed in roughly seven hours, and to schedule, meaning work elsewhere on the site could continue promptly.
Mammoet’s transportation of the RHCU made record books for being the heaviest load ever transported in Lithuania; additionally, the lift was the first time that a gantry crane had ever been used to perform a lift in the country.
A 3600-tonne crawler crane went absolutely massive on a petrochemical project in Zhejiang, China, earlier this year, to take home the record for the biggest lift by a single crane.
ZOOMLION’S ZCC89000 CRAWLER CRANE has broken two world records for the heaviest crane lift for a single crane and fastest lifting speed in Zhejiang, China.
The 3600-tonne crawler crane completed the feats between January 3 and January 8, 2024, when it was installing three slurry bed reactors for the construction of a new slurry bed residue hydrogenation plant that forms an integral part of the Zhejiang Petroleum & Chemical Co.’s 300-million-tonne-peryear New Material Engineering Project.
With the slurry bed reactor being the world’s largest single-weight forging and welding hydrogenation reactor, the heaviest crane lift the ZCC89000 was responsible for weighed in at 3037 tonnes and was lifted to a height of 67.57m.
The scope of work for the 3600-tonne capacity Zoomlion crawler crane required the hoisting of three reactors that, collectively, weighed over 10,000 tonnes, in a timeframe of just six days. For the job, the crane was equipped with a counterweight of 3160 tonnes and,
throughout the lift, reached a maximum load moment of 92,800 torque-metres. According to Zoomlion, the scope of work conducted by its crawler crane advanced the construction schedule by two months.
Upon completion of the new project, the plant will become a “super petrochemical industrial base”, according to Zoomlion, and will possess an annual refining capacity of 40 million tonnes of oils, 11.8 million tonnes of aromatics, and 4.2 million tonnes of ethylene.
A functional engineer and an electrician by trade, Tutt Bryant’s National Business Manager for Sustainable Products and Innovation, Chris Leahy, discusses what the leading equipment distributor is doing in partnership with Sany to support the operations of its electric products.
AS THE WORLD PROGRESSES TOWARDS A decarbonised future, so too must the worlds of infrastructure, construction, mining and renewables.
Simple decarbonisation processes such as telematics have already been employed; where the true challenge lies, however, is with decarbonising heavy construction equipment.
For most, this means electrification of the equipment. But, in a country as geographically vast as Australia, battery technology comes with its own challenges, with the worries equivalent to those presented with electric vehicles: what if I get stuck somewhere without a charging station? What if there’s a drastic compromise on performance? What if I
need to charge my vehicle and wait for eight hours in one spot?
The solution? According to Tutt Bryant’s National Business Manager for Sustainable Products and Innovation, Chris Leahy, the go-to choice will be mobile battery storage systems, a belief he says was reinforced by his recent trip to Sany’s factory in China, where he got to witness the efficacy of these products firsthand.
“The one that will be probably the low hanging fruit for everybody is going to be the mobile battery energy storage systems,” he says. “Ultimately, what that’s going to provide industry is the capability to tow a power source behind a standard commercial vehicle to where the crane is, so that crane can then have fast charging capabilities.
“Rather than bringing the crane to the power supply, we’re bringing the power supply in a mobile form to the crane.”
With a lengthy history in power generation that saw him begins his career as an electrician in 1996 and, recently, join Tutt Bryant as National Power Generation Manager in 2020, Chris’ current role will see him look to actively support and seek out battery technology as well as mobile power storage systems to bring into Tutt Bryant and distribute to its customers.
For him, this was on show in the models he saw at Sany’s factory –especially by Sany’s mobile power storage units. With rapid charge capabilities, the 210kWhr/100kW Sany BESS is a mobile charging station, compatible with equipment that can charge while in operation – such as the Sany EV cranes. Taking its design from the same infrastructure as the EV Cranes, the Sany Power Port will also operate as Prime or Standard power while adaptable to commercial and industrial application.
The 210kWhr/100kW BESS from Sany possesses rapid charge capabilities.
The way they work is simple: the units are plugged in and charged, taken to where the crane is, and then they charge up the crane’s battery as it needs it – and so, rather than relying on bringing a crane to and from a power source 500m away from where it is needed, the power can be brought to the crane. With crane charge times of under four hours from a traditional 63A socket outlet, the mobile BESS can reduce the overall charge time by 50 per cent – based on a 50 per cent state of charge – making it a genuine power solution on site.
Moreover, while charging, Sany cranes continue to operate with full functionality with tracking the only exclusion. Charging
between the BESS and crane occurs via the connection of a three-phase cable plugged into the lower track assembly, maintaining 360-degree slewing. Other advantages include extended periods between services, out to 2000 hours, increasing utilisation and productivity. Zero emissions are a significant factor with the elimination of diesel fuel and the overall reduction in noise pollution.
“The battery technology is scientifically proven to work,” says Chris. “We’ve seen LiFePO batteries thrive consistently in any environment they’re applied in, and the chemistry that has proven itself time and again is the same in cranes.”
The element of familiarity is one that construction, mining, and infrastructure companies alike will find reassuring, on top of costs saved via carbon credit savings and reduced resources spent on maintenance and refuelling of diesel products. What Chris is keen to stress as well is that the products being brought in by Tutt Bryant are fully compliant to every relevant Australian standard.
Sany’s battery technology and mobile energy storage systems operate directly
with the mandated AS 3000 pertaining to electrical installations and wiring rules; AS 3012 for electrical installations on construction and demolition sites; AS 5139 specifying requirements for general installation and safety requirements for battery energy storage systems; AS IEC 62619, which specifies requirements and tests for the safe operation of lithium cells and batteries; and IEC 62477 that revolves around powering electronic systems.
As Chris says, every one of these standards is met by the technology Tutt Bryant and Sany is bringing into Australia, ensuring that powering of its electric machinery, such as the Sany SCC400TBEV and the SCC800TB-EV, is conducted as safely as possible.
“There’s no hesitation from companies in wanting to work with us on these mobile battery storage systems,” says Chris. “A lot of these products are driven by the demand of the market and, once companies have been convinced of the compliance and quality of these products, we’ve seen great positivity towards these units.
At the end of the day, however, despite its proven capabilities, battery-electric
products still face a certain stigma due to their relative newness. This, for Chris, is allayed by Tutt Bryant’s provision of the product. Because of the company’s standing in Australia as a leading equipment distributor, and thanks to its vast network across the country, customers can feel reassured that Tutt Bryant will be on standby to assist with any qualms or queries.
“Innovation is never perfect, but Tutt Bryant is a reputable, well-established company, and we are committed to providing electric, sustainable, efficient construction machinery,” says Chris. “We believe in the quality of Sany’s electric cranes, and we’re always going to be standing behind the product to help whenever we need to.”
Because, as Chris says anecdotally, the demand to take up high-performing electrical equipment is gathering speed at a rapid rate.
“As a functional engineer and an electrician by trade, I want to share my textbook knowledge with prospective clients to talk about real world application,” he says, “and there’s never any resistance to these meetings, which is brilliant.”
PLEASE SEND YOUR LIFT OF THE MONTH ENTRIES TO SIMON.GOULD@PRIMECREATIVE.COM.AU
WHO: Pfeiffer Cranes
WHERE: Launceston, Tasmania
LIFTING WHAT: Massive shed roof.
CRANES: Six Grove crane lift
WEIGHT OF THE ROOF: 100t with rigging
COMPLICATIONS OF THE LIFT: Due to the proximity of the airport, the lift required the use of cranes with restricted boom lengths. The total weight of the roof and rigging was 100t, spread over the cranes with each of the cranes derated by 50 per cent.
It’s our competitive ethos of solving the unsolvable, finding a way, and just getting on with it, that helps us make things possible for ourselves, our partners, and our customers.
It’s this drive that has led to our new generation TIDD Pick and Carry Crane. See for yourself and talk to us today about the TIDD PC28-3G.