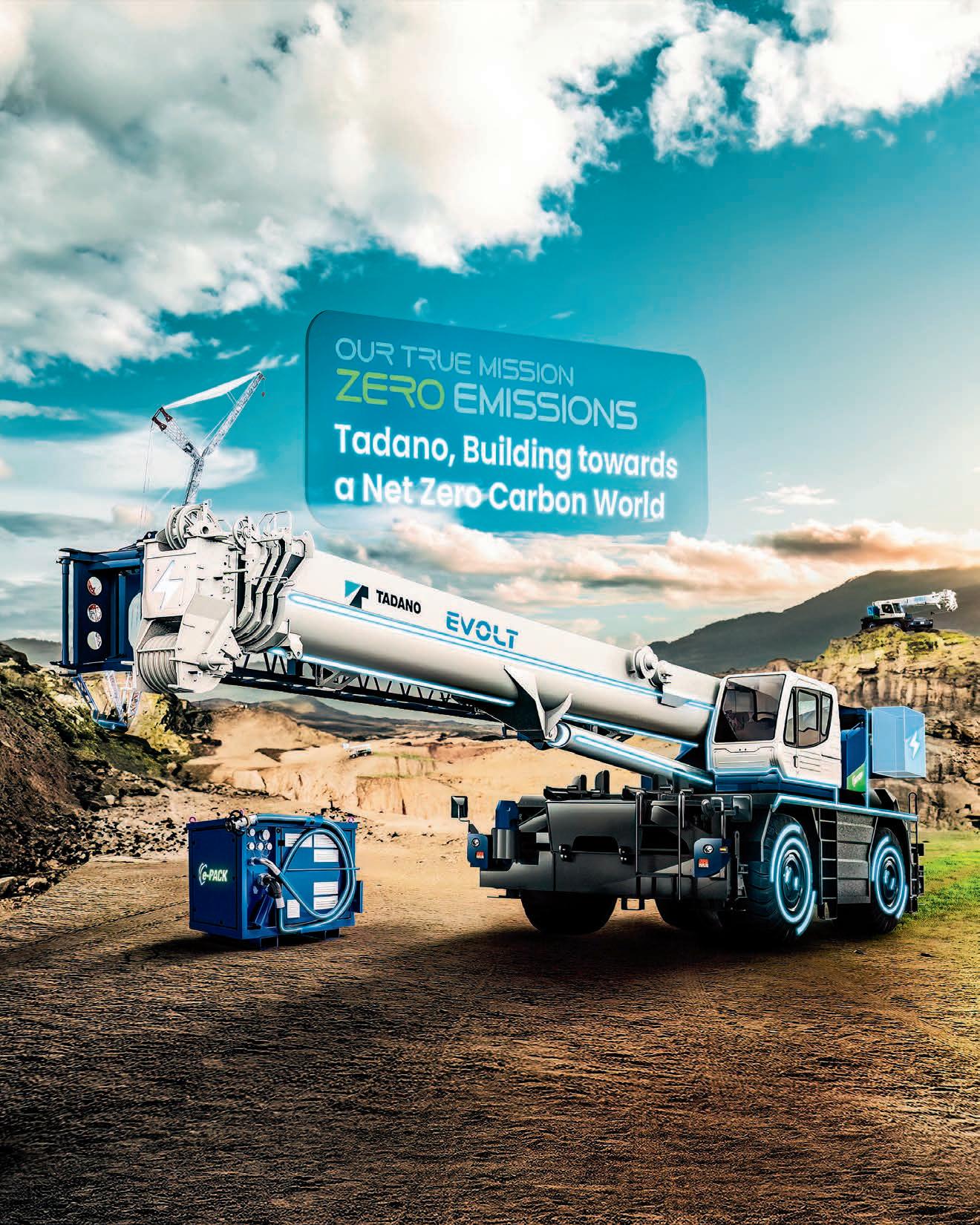

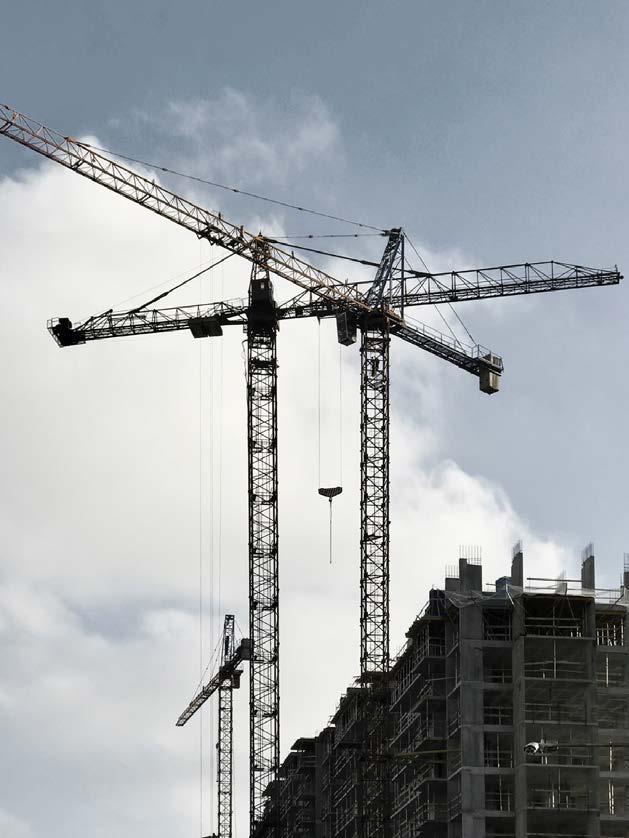

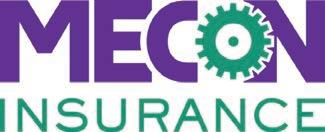
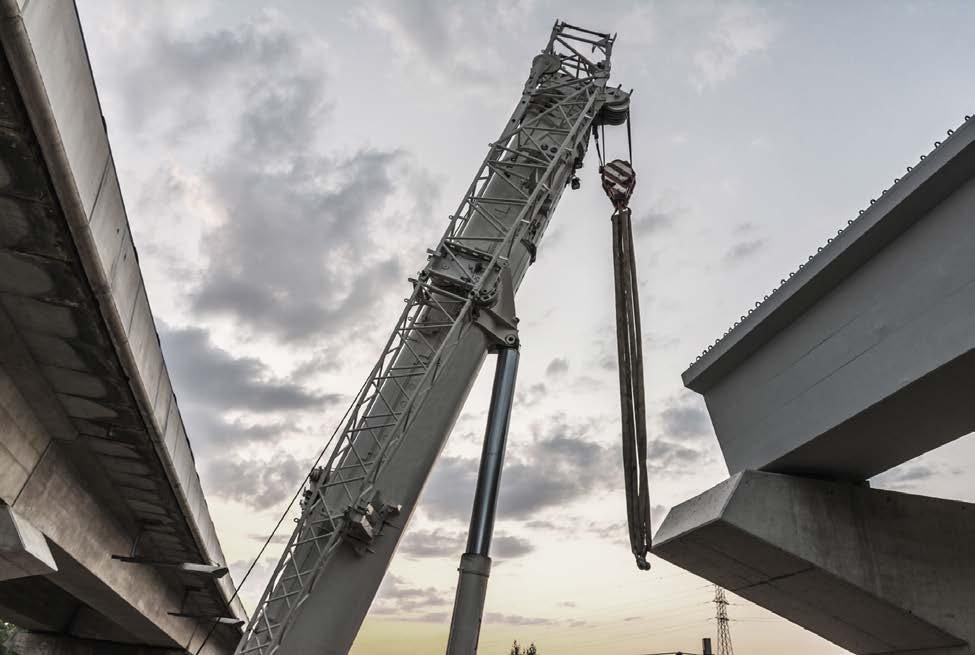
10 Industry News
Mammoet’s helping hand at a Queensland renewable hub, and Multiplex’s innovative solution to a unique site location.
14 Up Front: Tadano Tadano’s commitment net zero emissions.
18 CICA President’s Report
As technology advances at an unprecedented pace, the crane industry must adapt to remain relevant and attractive to the next generation.
20 Holding Redlich
Holding Redlich examines the proposed reforms to Australia’s fair work laws
22 CICA Lift Supervisor Course
CICA introduces Crane Lift Supervisor Course.
24 CICA Member Profile
Landmark first for MAX Academy.
28 JYC
The Victorian-based company goes in depth about a dual lift it completed on a windfarm recently.
32 Sarens Sarens examines local capabilities and recent local projects.
36 Dynamic Rigging
The lifting equipment hire company announces a big new acquisition.
39 Borger Crane and Rigging
Borger’s Liebherr LG 1750 arrives, and gets put straight to work on a windfarm.
43 WA Feature
How the crane industry is lifting the Western Australian economy.
44 Freo Group
Freo Group provides an overview of its services and capabilities.
48 Ashburton Crane Hire
ACH Managing Director Guy Black gives an update on the company’s operations out west.
52 Boom Logistics
Founder Jack Hebiton takes Cranes and Lifting through the history of the ASXlisted company.
57 Lift Plan Australia
LPA’s founder Guy McGowan discusses the importance of an engineered lift plan and his experience in the crane industry.
60 Joyce Krane Hire
Pioneer of the Pilbara details the remarkable career of Mick Joyce.
68 Alliance Engineering Consultants
The team at AEC examine instances where lift plans haven’t been followed or even engaged, and how they’ve gone wrong.
72 Ronco Operations Manager Mark Turner discusses Ronco’s workshop capabilities and what the company offers its customers.
76 Norwest Group
Norwest Group is a proud family business and the leading crane service provider in the North West region of Western Australia.
81 DRA Engineering
Burralga Industries Director Andrew Pretlove discusses the revolutionary new Humma UG series and its applications in underground mining sites.
84 XCMG
The Chinese manufacturer has made a big Boom out west, with an ASX-listed company the latest to jump aboard its products.
87 Verton Technologies
BDM Marcio Casagranda elaborates on the company’s game-changing gyroscopic, load-stabilising technology and its efficacy in mining and offshore environments.
90 MCT Equipment
The alternative lifting company details its close relationship with CICA.
92 WATM
Recently WATM achieved a significant milestone, by winning the prestigious Manitowoc Crane Refurbishment Award.
96 Rigging Rentals
General Manager Craig O’Dowd details the lifting and rigging equipment company’s newest addition: the MegaTest facility.
98 Franna General Crane Services (WA) tracks down and refurbishes an earlier investment, a Franna 12T 4WD.
102 JYC
JYC put its crawler division to full use on the West Gate Tunnel Project on another dual lift.
106 Unilift
The Orange-based lifting and rigging equipment specialist goes in depth about the Diepa wire rope it distributes and other items in its inventory.
111 Liebherr Tower Cranes
Liebherr Tower Cranes’ renewed approach to the market.
114 Ranger Lifting
Ranger Lifting launches LEEA-accredited ‘Safe Lifting Learning Hub’.
118 LEEA
LEEA’s Regional Manager Justin Boehm provides an association-wide update after its inaugural LiftEx Australia event.
Freo Group, including WGC Cranes, is Australia’s largest crane hire company. With 23 strategically-positioned depots across Australia, we’re never far away when you need us. Having an on-theground presence in so many locations makes it easy to access equipment and support, and ensures we bring local knowledge to each job.
With over 49 years of experience providing safe, efficient services across Australia, Freo Group has the knowledge and the know how to make even the toughest jobs simple. With a modern fleet of over 480 cranes, Freo Group has the lifting capacity to tackle the biggest and the smallest of jobs.
122 Andromeda Industries
Borger Crane Hire and Rigging’s Yard Supervisor Hennie Geyser goes in depth about the benefits of Andromeda’s Superflex cable.
124 UAA
The problems with under-insuring or overinsuring equipment.
128 Pace Cranes
Komp Cranes owner Danny Toohey goes in depth about his new Maeda crawler crane.
132 Hevway
Brothers Tom and Bernie Peoples provide an update on how they’re changing the road-access game.
134 Manitowoc
Manitowoc examines a different approach to major inspections.
139 Crane History
The team at Cranes and Lifting was recently privy to a collection of archived books about cranes from centuries gone by.
143 Pickles
Pickles National Sales Manager James Chauncy talks business closures and the booming used crane industry.
146 Liebherr
Fleurieu Cranes recently took delivery of a Liebherr LTM 1650-8.1 and celebrated the arrival with a launch party.
150 Baden Davis
The NSW Kobelco distributor has sold six new Kobelco crawler cranes to Borger Crane Hire and Rigging.
154 RUD Chains
SureLift owner Mark Read goes in depth about the superiority he’s seen from RUD’s lifting and lashing solutions.
156 Melrose Cranes
To celebrate its 25th anniversary, owner and founder Gregg Melrose details the NSW company’s journey to date and looks forward to the next 25 years.
162 Queensland Rigging Hire
Company owner Ben Fitzgerald gives an update on the company’s operations and recent investments.
167 Precision Rigging
Owner and founder Luke Williams discusses Precision’s involvement on a job in Uluru and how it reflects the company’s can-do attitude.
171 TRT
TRT announces the launch of the PC28-3G at the CICA National Conference and Exhibition.
174 TopGun Cranes
New additions to the fleet increases capabilities for TopGun Cranes.
179 Bremco
Owner Brett Moody discusses what the metalworks company can offer the crane industry.
182 WireCo
Sales representative Kath Darr discusses the range of wire ropes and services the company stocks.
184 Two Way Cranes
New Two Way Cranes operation opens in Newcastle area and gains immediate traction.
188 Tutt Bryant
The leading equipment distributor goes in depth about the new Kato CR-130RV.
190 Women in Industry Awards
Following the resounding success of the 2023 edition, nominations are now open for the 2024 Women in Industry Awards.
192 Gleason Cranes
Sales Manager Chris Logan discusses the new Zoomlion products coming to Gleason Cranes.
196 Quicklift
Jarrod Sutherland provides an update on the company’s operations and the latest additions to the fleet.
Josh and John Handley detail the company’s history and how it became a towering success.
RANGER-R45XS
4X4 EXTRA STABILITY
35 Tonne pick and carry / 45 tonne stationary on outriggers.
Advanced stabiliser system providing better safety
Fast out and down outriggers increases stability by 200%
Standard 3 tonne counterweight for longer range lifts
25m long reach 5 stage full power booms
Published by:
WITH PERTH HOSTING CICA’S NATIONAL Conference and Exhibition, and with this issue being widely distributed during the event, the team at Cranes and Lifting took the opportunity to report on the booming crane sector in Western Australia.
Its 2023-24 State Budget shows Western Australia’s economy remains strong despite global economic headwinds. Exports reached a record $272 billion in the year to March 2023, accounting for 45 per cent of the national total. Strong economic activity has seen the state’s employment climb to a historic high of 1.53 million people with record full-time employment. Of note, full-time employment for women has grown by more than 10 per cent over the 12 months to March.
WA’s resources sector is the key driver of the economy and in 2022 it achieved its highest ever sales of $246 billion. There were a record 117,970 full-time equivalent jobs in the mining industry and with exploration continuing to prosper with critical minerals leading the way, regional WA is set to benefit from ongoing
investment and construction.
The Western Australian crane industry is closely aligned with the resources sector and the Cranes and Lifting team is privileged to have had unparalleled access to a number of leading crane businesses to discuss their heritage and capabilities today.
As well as the dedicated WA feature, this bumper edition includes numerous updates from crane manufacturers and covers significant investments made by crane hire businesses, news and updates from crane suppliers and hirers of associated equipment.
The Cranes and Lifting team has worked hard to provide you with a magazine full of interesting and local content and as always, we hope you enjoy the read.
379 Docklands Drive, Docklands VIC 3008
T: 03 9690 8766
www.primecreativemedia.com.au
CEO
John Murphy
E: john.murphy@primecreative.com.au
Chief Operating Officer Christine Clancy
E: christine.clancy@primecreative.com.au
Managing Editor Andrew Hobbs
E: andrew.hobbs@primecreative.com.au
Editor Simon Gould
E: simon.gould@primecreative.com.au
T: 0404 865 109
Journalist
Jack Alfonso
E: jack.alfonso@primecreative.com.au
Business Development Manager Emily Schlegel
E: emily.schlegel@primecreative.com.au
T: 0466 317 555
Client Success Manager
Glenn Delaney
E: glenn.delaney@primecreative.com.au
Art Director Bea Barthelson
Imaging Assistant Paul Breen Subscriptions Frank Rapone
T: 03 9690 8766
E: frank.rapone@primecreative.com.au
The Publisher reserves the right to alter or omit any article or advertisement submitted and requires indemnity from the advertisers and contributors against damages or liabilities that may arise from material published.
© Copyright – No part of this publication may be reproduced, stored in a retrieval system or transmitted in any means electronic, mechanical, photocopying, recording or otherwise without the permission of the publisher.
Mammoet Australia has installed 28 wind turbines at a 149-metre hub height at Queensland’s Kaban Green Power Hub.
Working alongside mechanical and electrical installation teams from Vestas, Mammoet’s scope of work focused on the offloading, preassembly and main installation of the 28 Vestas EnVentus V162-5.6 wind turbines.
“Through our collaborative efforts with Neoen, Vestas and the other project stakeholders, we played a part in driving the transition to clean and green energy in Far North Queensland,” said Sales Executive Manager of Mammoet Australia Bjorn-Evert Eck Rasmussen.
The global heavy lifting specialists used a Terex Demag AC700 crane, a Liebherr LG 1750SX lattice boom crane and a fleet of Scheuerle SPMT and Goldhofer THP multi-axle trailers to complete its work on the $373 million project.
One of the main challenges posed to the conglomerate of teams was the remote nature of the site, which they could only gain access to via narrow access roads and steep slopes. Working on a renewable energy project, the team aimed to keep its carbon footprint as minimal as possible while operating in as safe and efficient a manner as possible.
To offload and preassemble the crane, Mammoet utilised its Demag AC700 hydraulic crane. Establishing the machine in a single, optimal position enabled a two-stage offloading process with intermediate preassembly, meaning the number of staff required was reduced by a third and minimised crane movements between lifts, resulting in large resource savings.
For the installation of the turbines, Mammoet employed its Liebherr lattice boom LG1750SX crane. Using the SPMTs to
manoeuvre 400 tonnes of superlift counterweight, the lattice boom crawler crane was configured with a 151-metre main boom and 12 metres of fixed fly-jib attachment. What this ensured was that the crane could lift the wind turbines, each weighing 92 tonnes, to a hub height of 149 metres.
“The company’s long-established presence in Australia, extensive fleet of equipment and vast expertise in onshore wind farm projects, positioned us as the ideal partner for the project,” said Eck Rasmussen. “With a strong focus
on sustainability, we brought a new level of expertise to the table.”
Based in the Atherton Tablelands, Queensland, Neoen’s Kaban Green Power Hub aims to harness the region’s wind resources to help Queensland hit its target of 50 per cent renewable electricity by 2030.
The $373 million wind farm is expected to power up to 100,000 homes by generating 460,000 megawatts of clean energy annually.
MAMMOET’S WIND TURBINE
TO POWER 100,000 HOMES
“Through our collaborative efforts with Neoen, Vestas and the other project stakeholders, we played a part in driving the transition to clean and green energy in Far North Queensland.”Mammoet’s LG1750 crane works on one of the 28 wind turbines installed in rural Queensland.
Our HC-L series luffing jib cranes enable quick, safe and reliable operation almost anywhere. Maximum lifting capacities of up to 64 tonnes, hook heights of more than 1,000 metres and a small slewing radius ensure efficient construction site work, even in the tightest spaces and under extreme conditions. Contact
Australian construction company Multiplex has completed the installation of three tower cranes above the water at its New Sydney Fish Market site.
Undertaking the project with Marr Contracting’s supplied tower cranes and SMC Marine, Multiplex’s crane installation and associated support systems required complex planning and engineering because of the site’s location and exposure to marine conditions – inclusive of “tidal waters”, according to Multiplex
Project Manager Paul Couani.
“The first two tower cranes were installed within the waters of the Bay and before the cofferdam was closed off, which meant we were exposed to tidal changes,” he said.
“We undertook detailed planning in partnership with Marr Contracting and SMC Marine, and the complexity required four times the typical amount of time needed to complete a dry land installation.”
The companies could only install the third tower crane after Multiplex
successfully dewatered 100 million litres of water from the cofferdam. This created a watertight enclosure and a dry working environment for the structural build to commence. Because of the unique site location, a specialist marine barge was required to be anchored in Blackwattle Bay to operate from.
The tower cranes used are among the first in Australia to use HVO100 renewable diesel, with sustainability being a key pillar of Multiplex’s future. HVO100 diesel is a 100 per cent renewable fuel with up to 90 per cent reduction in overall emissions when compared to fossil fuel.
Once complete, the Sydney Fish Market will have a 100-year structural design life with energy efficient services and systems to achieve a 30 per cent reduction in energy use. Construction is set to be complete in late 2024.
“The companies could only install the third tower crane after Multiplex successfully dewatered 100 million litres of water from the cofferdam. This created a watertight enclosure and a dry working environment for the structural build to commence.”
WITH ITS NEW SLOGAN, “OUR TRUE Mission: Zero Emissions,” the company is highlighting its commitment to reducing CO2 emissions from its business activities by 25 per cent and from the use of its products by 35 per cent by 2030. Moreover, the goal is to be completely climate neutral by 2050 – zero emissions. To achieve these objectives, the company has grouped together its solutions for greater sustainability under the name of Tadano Green Solutions (TGS). The result of all this was presented at ConExpo, and the message is crystal clear:
Tadano told the world it was working on a fully electric rough terrain crane in April 2021. That crane was showcased at this year’s ConExpo to industry members for the first time ever as a fully functional prototype. Its name? The GR-1000XLL EVOLT.
Since making its debut at the major Las Vegas event, Tadano has been busy preparing for an official launch - and 2024 is the year to do it.
Tadano says the GR-1000XLL EVOLT will be launched in 2024first in the USA and in Canada with additional releases in other countries such as Australia to follow.
“This crane will make an invaluable contribution to achieving our goal of reducing the CO2 emissions from our products by 35 per cent by 2030,”
underscores Toshiaki Ujiie, President and CEO of Tadano Ltd.
This should come as no surprise, as the GR-1000XLL EVOLT can travel to work sites and take care of all lifting operations there using energy supplied by its batteries exclusively, making fully zero-emission operation possible.
Also remarkable is the fact that a single battery charge is enough for up to nine hours of crane operation, or five hours of crane operation with a travel distance of up to 20 km.
As a result, the battery’s capacity is enough to cover an entire typical workday for this crane model.
Moreover, the integrated regenerative braking function lengthens both running time and range.
On top of this, the engineers at Tadano have also achieved something
With its green solutions, Tadano is making a worldwide contribution to the goal of a decarbonised society. Tadano’s commitment to protecting our environment and contributing to the fight against climate change is manifesting itself in increasingly tangible ways.The GR-1000XLL EVOLT was showcased during this year’s ConExpo. The crane can travel to work sites and take care of all lifting operations there with energy exclusively supplied by its batteries, making fully zero-emission operation possible. The Tadano APU auxiliary power unit reduces fuel consumption and CO2 emissions by 25 percent.
fast charging on a US-COMBO CCS1 connection and only about seven hours with normal charging on a three-phase 240 VAC, 100 A commercial power supply connection.
In addition, unlimited operation with the crane plugged into a power outlet is available as well.
It is worth mentioning that the crane’s lifting performance is exactly the same as that of its diesel-driven counterpart, the GR-1000XLL-4.
But where the GR-1000XLL EVOLT truly stands apart from its
diesel counterpart is environmental friendliness, with Tadano calculating savings of around 8,328 litres of diesel and a resulting reduction of close to 22t of CO2 emissions a year for an average crane usage scenario.
Its powerful electric motor delivers a maximum output of 194 kW, ensuring that the GR-1000XLL EVOLT has the exact same lifting capacity and operating speed. It offers a top speed of 18 km/h, and its dimensions are exactly the same as those of the GR1000XLL-4.
The electric motor not only provides the rough terrain crane with environmentally friendly operation, but also with significantly lower noise levels during work, all while eliminating exhaust emissions. These two factors come with considerable advantages for customers in a multitude of scenarios, including projects in urban areas with noise regulations, nighttime lifting work, and indoor assignments.
The development of the GR-1000XXL EVOLT is clearly tied to Tadano’s sustainability philosophy and its long-term environmental goals, which Toshiaki said was so important for the company.
“In our role as the Tadano Group, we are deeply aware of our social responsibility for the environment and climate. This is why we’ve committed ourselves to actively and significantly contributing to making a decarbonized society a reality with our products and manufacturing processes,” he said.
“With the GR-1000XXL EVOLT as an important tech demo, we’ve taken a crucial step towards that goal.”
During ConExpo, Tadano also introduced its diesel-driven APU auxiliary power unit on a GR800XL-4 rough terrain crane for the first time.
The unit is already currently approved for use as an optional accessory for new orders of Tadano RT models GR-1000XLL and GT1000XL-4 in the USA and Canada.
The unit’s nine horsepower, twocylinder engine has an extremely low fuel consumption rate of only 0.75 litres of diesel fuel per hour.
Moreover, by producing an output of 972 W, the APU is able to supply electric power for numerous important crane functions while the onboard engine is off.
This includes the floodlights and aviation obstruction beacon, the wipers for the windshield and roof, the HVAC system, the USB outlet, and, of course, all important display functions inside the cockpit.
Tadano calculates that the APU can reduce fuel consumption and CO2 emissions by around a fourth when compared to the onboard diesel engine’s idle running.
It is worth mentioning that the flagship of the Tadano CC range of cranes will also be available with an electric drive in the future. The engineers at Tadano are working on giving the CC 88.1600-1, the company’s biggest crane, an electrified sibling.
An electrical cable connection will ensure that the giant will be able to run with absolutely zero CO2 emissions, with the lattice boom crawler crane’s electric motor planned to have a power of 2 x 390 kW so that it can deliver the same lifting capacity as its diesel-driven counterpart. In addition, there will be flexible options for supplying power, with 6,000 V and 6,600 V 50 Hz connections and 6,600V 60 Hz connections all working for this purpose.
A truck-based electric aerial work platform for the Japanese market is
“I’m confident that we’ll be able to achieve our sustainability goals in our role as a highly innovative company that is aware of its responsibility towards our world, and that we’ll take on a trailblazer role in our industry with our technologically leading solutions.”
also currently in development, and in fact is already undergoing prototype testing. Both its travel and lifting operation with a maximum working height of 56 ft (17.1 m) will be purely electric. It is also worth adding that the development partner for this Tadano Green Solutions project is Australian company SEA Electric, which specialises in electrifying trucks and buses.
With its compact dimensions, the electrically driven vehicle is being explicitly designed for travelling and working on tight Japanese roads.
Nevertheless, the compact truck wheelbase of only 2.515m has not kept the developers from integrating a suitably large and powerful battery into the unit: Its capacity will be around 100 kW/h, ensuring that a single battery charge will be enough for a travel distance of around 100 km and five hours of operation. In addition, the vehicle’s top speed is also remarkable, as it is just under 100 km/h. The vehicle is planned to be presented for the first time in 2024, with its launch to follow in 2025.
Tadano introduced its e-PACK in Europe all the way back in 2019. It is an electro-hydraulic system featuring an integrated 32-kW electric motor that works with zero emissions and nearly zero noise – and without any loss in lifting capacity to boot. All that is needed is for the crane to set down the e-PACK where it will be used so that it can be connected to an external 400 V / 63 A or 400 V / 32 A power supply.
The e-PACK is currently available for all new Tadano AC cranes with lifting capacities of up to 80 tonnes, as well as a retrofit for existing cranes.
Both Tadano customers and the entire industry were thrilled at last year’s
electrified superstructure. The special thing about it: The crane was fully functional and completely self-sufficient under all operating conditions thanks to a flexible power supply concept. More specifically, the electric superstructure was able to run on any of the three following options: the integrated battery, an external power connection, or a generator on the diesel engine that delivered power for the electric motor.
The electric motor’s working speed and delivered lifting capacity were exactly at the same level as those of a diesel engine, not to mention that its sound emissions were much lower under all lifting conditions. Also remarkable was the fact that the tech demo achieved a system efficiency of around 85 per cent, which is more than double the energy efficiency of an efficient diesel
of up to 50 per cent when compared to diesel-operated superstructures.
Toshiaki says these changes show that Tadano is making real change happen. “This all shows that we’re on the right path with Our True Mission: Zero Emissions and our Tadano Green Solutions,” he said.
“I’m confident that we’ll be able to achieve our sustainability goals in our role as a highly innovative company that is aware of its responsibility towards our world, and that we’ll take on a trailblazer role in our industry with our technologically leading solutions.”
AS OUR WORLD EVOLVES AND technology advances at an unprecedented pace, industries of all kinds must adapt to remain relevant and attractive to the next generation. The crane industry is no exception, facing a pressing need to draw in fresh talent to sustain its growth, replace retiring operators and ensure a prosperous future. To achieve this, an approach that combines innovation, education and diversity is crucial.
The crane industry holds immense potential for people seeking a dynamic career path. However, traditional notions of heavy machinery and construction may not immediately align with the aspirations of many young people, women, new and diverse Australians - especially if they have never been exposed to it. The CICA 2023 National Conference being held in Perth, Western Australia, from 2628 October 2023 is themed ‘The Next Generation’ and will address how to bridge this gap.
As industry leaders attending the conference, we have an opportunity to facilitate a transformative journey to make the crane sector more alluring and inclusive to a more diverse demographic.
1. Raising Awareness: It begins with education. Many people are unaware of the diverse and rewarding career opportunities the crane industry has to offer. At the various career expos that CICA has displayed at this year, many young people have told us ‘I didn’t realise that you could get a job doing that!’. CICA is collaborating with training providers to introduce crane-related curricula that will prepare the next generation to work with cranes. Equipping school career counsellors with information and providing information evenings are another way CICA is working to pique students’ interest and
present the industry as a high-tech, environmentally responsible and impactful field.
2. Embracing Technology: Modernising the crane sector with cutting-edge technology is a surefire way to attract tech-savvy millennials and Gen Z, but also making equipment more accessible for everyone to access and operate. Remote-controlled and autonomous cranes, augmented reality training programs and digital platforms for crane management
carbon footprints; or working on renewable projects (like wind farms and solar panel installation) the industry can appeal to environmentally minded individuals who seek meaningful work that contributes positively to the planet.
4. Promoting Diversity and Inclusion: Creating a more diverse and inclusive work environment will not only foster creativity and innovation but also make the industry more appealing to a wide range of talent.
“As industry leaders attending the conference, we have an opportunity to facilitate a transformative journey to make the crane sector more alluring and inclusive to a more diverse demographic.”
not only increase efficiency and safety but also portray the industry as innovative and future-focused. The crane simulators that CICA has invested in are proving useful in skill development and attracting keen interest at expos.
3. Sustainable Practices: We are becoming increasingly environmentally conscious. By promoting green initiatives within the crane industry, such as the implementation of electric or hybrid crane models and reducing
Encouraging women and individuals from underrepresented groups to pursue careers in the crane industry can be achieved through mentorship programs, networking opportunities and by dismantling stereotypes. CICA’s recent Diversity breakfast launch was a well-attended and highly successful event, and CICA is committed to keeping up the momentum.
5. Collaboration with Tech Companies: Partnering with technology, CICA
has been working with Area9 Lyceum on an adaptive learning module for its courses, which provides customised training to individuals, employing reliable data analysis and intelligent tools to make real-time adjustments. Adaptive learning recognises the existing knowledge of each learner and modifies the training to specifically address areas where they lack understanding, including those areas they might not be aware of.
6. Showcasing Success Stories: Highlighting success stories of individuals thriving in the crane industry can inspire others and challenge misconceptions. CICA’s presence on platforms such as social media, the Cranes and Lifting magazine and e-newsletter, and industry events showcase these achievements and generates enthusiasm among potential newcomers. If you haven’t seen CICA’s new Traineeship video yet, head to the CICA YouTube channel.
7. Offering Attractive Incentives: Opportunities for career growth, such as the Traineeship (in the states that offer one) are essential in attracting new talent. Additionally, offering mentorship programs, the Lifeworks EAP (that CICA offers to members and their employees) and skill development courses (like the Articulated Crane On-Road Course) can demonstrate a commitment to nurturing employees’ long-term aspirations.
Attracting the next generation of people (young or a bit older) to the crane industry necessitates a comprehensive approach that embraces innovation, education, and inclusivity.
If you are attending the 2023 CICA National Conference, I look forward to seeing you there and thank you for your continued support of CICA. Together, we can work on equipping the ‘Next Generation’ to elevate the industry to new heights.
Ben Pieyre CICA Board PresidentBen Pieyre – President
Marcus Ferrari – Vice President
Tom Smith – Director
Danny Adair – Director
Danny Black – Director
Andrew Esquilant – Director
David Solomon – Director
Karli Sutherland– Director
CICA OFFICE
Brandon Hitch Chief Executive Officer 03 8320 0444 0428 228 048
ceo@cica.com.au
Paul Arztenhofer Membership Engagement/ Business Development Specialist 04 9093 9274 paul@cica.com.au
Alice Edwards Road Technical Engineer 03 8320 0440 alice@cica.com.au
Patrick Cran CraneSafe and CrewSafe Technical Advisor 0488 004 274 pat@cranesafe.com.au
Damien Hense CICA Road Policy Advisor 03 8320 0460 0488 007 575 damien@cica.com.au
Julie Turner CICA Executive Assistant / Office Manager
03 8320 0411
julie@cica.com.au
Kate Galloway Traineeship Coordinator 0491 047 118
Kate@cica.com.au
Ashleigh Gould Cranesafe and Crewsafe Administration Officer Phone: 03 8320 0466
Email: ashleigh@cica.com.au
Michelle Verkerk Marketing Communications Officer 0404 938 714 michelle@cica.com.au
Justina Blackman
Member Events and Engagement 0403 717 626 justina@cica.com.au
Unit 10, 18–22 Lexia Place, Mulgrave Vic 3170
Phone: 03 9501 0078
Fax: 03 9501 0083
Email: admin@cica.com.au
Website: www.cica.com.au
For information, please visit our website or call the CICA office.
In the August edition of the Cranes and Lifting magazine, our article discussed the changes to the enterprise bargaining regime introduced by the Secure Jobs, Better Pay Act. In this edition, we take a look at a round of proposed reforms to Australia’s fair work laws, with a particular focus on changes affecting businesses that enter into labour hire arrangements.
Since the passage of the Secure Jobs, Better Pay Act in December 2022, the Federal Government has undertaken public consultation on a further round of proposed reforms aimed at addressing the following issues:
1. L abour hire loopholes.
2. Wage theft.
3. C haracterising a person as an employee or independent contractor.
4. Discrimination.
This article focuses on the proposed reforms addressing ‘labour hire loopholes’ and implications of the reforms for businesses that enter into labour hire arrangements.
Labour hire is where a business has agreements in place with other businesses to supply workers. The business supplying the labour is the labour hire provider and the business being supplied with the labour is the host. The employment relationship is between the labour hire provider and the labour hire worker, and there is usually no direct contractual or employment relationship between the labour hire worker and the host.
The labour hire industry in Australia is rapidly growing and many businesses, particularly in construction, enter into labour hire arrangements and use externally sourced labour. For businesses, labour hire is predominantly utilised for its flexibility and to meet urgent demand for more labour in peak periods. For workers, labour hire provides additional flexibility to working arrangements, tailored working
the same paid leave entitlements as, employees despite performing the same or similar duties. This is because the terms and conditions of employment may be set by different instruments.
For example, a labour hire worker may be paid pursuant to a Modern Award, while a directly engaged employee may be paid pursuant to an Enterprise Agreement. This means that the labour hire worker would not have access to the more generous bargained
loophole, the Federal Government is seeking to introduce legislation to ensure that, among other things, labour hire workers are paid at least the same as directly engaged employees.
The Same Job, Same Pay legislation aims to strike the balance between protecting labour hire workers from exploitation while not affecting a business’ ability
to access labour hire to meet genuine surges in demand for labour and shortterm needs. Key considerations for the proposed legislation include:
• E stablishing a criteria to determine when a labour hire worker and a directly engaged employee will be deemed to be performing the ‘same job’.
• Measures to calculate the ‘same pay’ payable to the labour hire worker.
• A mendments to the Fair Work Act 2009 (Cth) to introduce (a) a requirement for labour hire workers to receive at least the same pay as directly engaged employees and (b) a positive obligation on labour hire providers and hosts to take reasonable steps to ensure the direct entitlement is paid to the labour hire worker. This is subject to the ‘same job’ criteria being met.
The legislation is also proposed to include a mechanism for dispute resolution (including powers for the Fair Work Commission to deal with disputes), enforcement provisions (including for civil penalties and compliance to be enforced by the Fair Work Ombudsman) and anti-avoidance
The proposed legislation, if passed, is likely to have significant implications for crane industry employers and other organisations that enter into labour hire arrangements as a host. We note the proposed legislation may not apply to all hosts as there may be exceptions, including based on the size of the host. The significant implications include:
1. P otential increases to labour costs, limiting the flexibility benefits labour hire arrangements provide, particularly for those that utilise labour hire to respond to market fluctuations and to manage unexpected downturns in business.
2. F rom a practical perspective, the host will need to consider the actual steps to take to ensure the correct entitlement is paid to the labour hire worker, including how it will determine what pay and conditions are required. This may be challenging where the host does not have employees performing the same work.
3. Th ere may implications for the contractual relationship between the labour hire supplier and the host, including how the parties will work together to ensure they both discharge the positive obligation.
4. Th e administrative implications and changes required in that regard to ensure labour hire workers are being paid appropriately.
Following public consultation on the further round of proposed reforms, on 4 September 2023, the Federal Government introduced the Fair Work Legislation Amendment (Closing Loopholes) Bill 2023 (Cth). In relation to the Same Job, Same Pay measures, the Closing Loopholes Bill empowers the Fair Work Commission to make an order that would require a labour hire employee to be paid at least the same as a direct employee of the host who performs the same work. For the Fair Work Commission to make an order of this kind, they must be satisfied that the labour hire worker would be covered by the host’s enterprise agreement (or other employment instrument) if the labour hire worker was direct employee of the host.
Recognising there are short periods where businesses require labour hire workers for surges in demand and/or to address temporary labour vacancies, labour hire workers engaged for a period of 3 months or less are exempt and parties can seek to extend or shorten that period with the Fair Work Commission. Small businesses (in this case the labour hire provider), being businesses who employ fewer than 15 employees, are also exempt from these changes. The passing of the Closing Loopholes Bill has been delayed until early 2024, and, if passed, a labour hire provider could not be required to pay the protected rate of pay until on or after 1 November 2024.
Authors: Michael Selinger and Adrian Zagami
THE CICA LIFT SUPERVISOR COURSE IS A proactive initiative designed to enhance the safety and efficiency of crane operations on construction sites and industrial projects. This program introduces the role of a crane lift supervisor, who acts as a dedicated overseer of crane-related lifting activities.
A Pilot Lift Supervisor Course (Level 1) was held in August 2023 in Sydney. The aim of the pilot course was to engage with the industry and create an opportunity for participants to provide feedback on the complexity of the course contents and the course delivery methods. Nine participants from a variety of industry sectors (including crane hirers, principal
complement to the safety of the crane industry. Considering the suggestions and advice received from the pilot course, CICA has made some adjustments to the format of the course content. Improvements have been made, such as increasing the use of visual examples to demonstrate how to integrate engineering calculation principles into various site lifting tasks.
With the completion of the review process, CICA is now ready to formally launch the course in early 2024.
THE CICA LIFT SUPERVISOR COURSE: AN OVERVIEW
pre-operational checks, including equipment inspection, load capacity assessment and safety system verification. Risk Assessment: Before any lift, the supervisor evaluates potential risks and develops a comprehensive lift plan that accounts for variables such as weather conditions, terrain and nearby structures. Operator Communication: The supervisor maintains constant communication with the crane operator, providing real-time guidance and adjustments as needed during the lift.
Safety Oversight: Safety protocols and regulations are strictly enforced by the crane lift supervisor. They ensure that the entire work area remains clear, personnel are properly trained and all safety measures are adhered to.
Emergency Response: In the event of unforeseen circumstances or emergencies, the crane lift supervisor is trained to respond swiftly, ensuring the safety of personnel, equipment, and the surrounding environment.
The lift supervisor course contents were developed aiming at covering all the above
The three parts of the course are: work health and safety; leadership and frontline management; and lift supervision and transport activities. These will assist course attendees to: vide supervision for crane crews on crane related activities and ensure that they could play an important role in assisting the relevant parties to fulfil their compliance obligations if required by the work health and safety regulations.
Recognising the need to elevate lifting safety standards and streamline operations, CICA worked extensively with lifting experts to introduce a Crane Lift Supervisor Course.The overall feedback from the pilot course was exceptional; all the participants recommended that this course will be a complement to the safety of the crane industry.
Lift supervision and transport activities
To deliver the program efficiently and effectively, the Level 1- Lift and Transport portion of the program was split into two parts, an online self-learning program and a face-to-face classroom teaching program.
The online learning modules of the CICA Lift Supervisor Course focus on reviewing the knowledge and skills learnt from the High-Risk Work (HRW) Licence training, plus some basic crane-related knowledge that is useful and practical for providing guidance as a lift supervisor for crane operations.
CICA Lift Supervisor program includes five modules:
• Engineering principal basics;
• Sling and rigging basics;
• Different types of cranes and crane charts;
• Specific lifting operations (powerline, workbox, marine lift); and
• Transport safety
The face-to-face classroom teaching aspect incorporates three modules and a final assessment:
• Engineering principles and rigging stability;
• Crane loads and lift planning; and
development, write and develop SWMS on site;
• Guidance on High-Risk Workshop participation;
• Skillsets to liaise with regulatory authorities; and
• Training on incident/accident response and investigation
Lift supervisors are leaders of the crane crew, they need to possess the necessary skills and knowledge to communicate with their team members and make informed decisions and solve problems effectively. To help the attendees achieve these, the leadership and frontline management portion of the course will be delivered via face-to-face classroom teaching sessions and covers topics such as how to:
• Communicate effectively as a workplace leader;
• Implement operational plans;
• Exercise self-awareness and behavioural management;
• Show leadership in the workplace;
• Conduct mentoring and coaching in the workplace;
• Conduct work within a compliance framework; and
• Carry out workplace assessments;
The introduction of the CICA Lift Supervisor Course is poised to enhance crane operations in the construction and heavy machinery sectors. It has the potential to become a hallmark of responsible and forward-thinking construction practices, influencing regulations and guidelines.
Although HRW training organisations follow the content set out in the regulations, they may focus on some aspects and overlook others, or some of the knowledge learnt from HRW training may not be used frequently enough for the crew member to have consolidated the skills to be competent a few years after the training. It is imperative that the lift supervisor be familiar with all aspects and provide guidance if required.
To better equip the Lift Supervisor, the online self-learning component of the
• Complex lift (multi-crane/multi-hook lift, precast lift)
The work health and safety portion of the program will be delivered via face-to-face classroom teaching sessions. Through case studies and work examples, this part will equip students with:
• A basic understanding of crane related work health and safety regulations;
• A basic understanding of crane related Australian Standards;
• Knowledge to participate in SWMS
The ideal candidate for Level 1 of the program is someone with C6 or above, an HRWL crane license and Intermediate Rigging License with at least two years of crane industry-related experience.
As the program gains momentum and potentially becomes standard practice, it will undoubtedly set new benchmarks for operational and safety protocols, ensuring a safer and more efficient crane industry.
CICA will commence running the Lift Supervisor Course in early 2024, to register your interest head to www.cica.com.au/ lift-supervisor w
“The three parts of the course are: work health and safety; leadership and frontline management; and lift supervision and transport activities.”The face-to-face classroom teaching aspect incorporates
threemodules and
a final assessment
LOU FIRST ENGAGED WITH MAX SERVICES five years ago as the company was entering a significant growth phase and operating with around 100 staff. The business was tendering for major contracts and, being both regionally based and expanding, there were obvious issues in terms of attracting both the right labour, and local labour with the right skill sets.
The business was also decentralising and instead of equipment, staff and decisions coming out of the Port Augusta head office, each depot was going to operate on its own.
“There were a lot of changes happening to the business, changes to systems and changes to leadership styles which required a huge amount of development,” Lou said.
“Max Services was operating its own internal trainee program which was good, and it met the needs at the time, but they didn’t realise there was a qualification for the
industry. I found the relevant qualification to the industry and began asking why it was so problematic and why there wasn’t a huge uptake for Cert III and Cert IV Mobile Crane Operations nationally.”
As a result, Lou began investigating training options and discovered there are approximately 5,000 training providers across the country.
At that time, there were only eight training providers promoting the qualification, but they weren’t actually providing the qualification. They were providing high-risk tickets out of the qualification and only had the qualification on their scope of registration.
That made things problematic, and that’s one of the biggest issues locally, said Lou.
“Everyone goes off and completes a one- or two-week ticket course in dogging, non-slew crane and other relevant courses,
thinking they are competent and believing they can get a job, of course that’s not the case,” he said.
“We basically decided to bring the Cert III and Cert IV training program inhouse and then form a relationship with a national training provider gaining approvals at a State and a Commonwealth level.
“That was the time-consuming part. Over a 15-month period, we engaged a training provider, that was State and Commonwealth approved, and then we were in a position to sign up our first trainee,” said Lou.
“By December 2021, we had a Safe Work Assessor onboard and we also had an immigration strategy in place which involved bringing in multiple migrants over a fiveyear period,” he said.
“With the Max Academy, we are able to send learning resources overseas and by the time they got to Australia, we are able to provide them with an Australian driver’s license, a bank account and the high-risk tickets required to operate in Australia, all within 12 days. Basically, they land and by the time they’re questioning why they’ve come to remote South Australia, straight away they’re out working and making money, it makes a huge difference,” he said.
According to Lou, a large part of bringing in migrants is because the skillset doesn’t exist in Australia, it’s been exhausted. That’s because construction, infrastructure and other industry sectors have grown exponentially, and they’ve sucked in all the available labour resources.
“The only way you can introduce younger people into the industry is to make sure you increase your supervision rate. Since we started the Max Academy our supervision rates have probably doubled in size.
“We have the technical advisory group that oversees all subject matter, verification of competencies, and the level of training
Lou Sapio helped establish the Max Academy back in 2021. On a quest to see better training standards across the industry, he and the Max Services team were delighted to see the first trainee recently graduate from the Max Academy with a Cert IV in Mobile Cranes Operations.The Max Academy is engaging schoolchildren at a young age.
“With the Max Academy, we are able to send learning resources overseas and by the time they got to Australia, we are able to provide them with an Australian driver’s license, a bank account and the high-risk tickets required to operate in Australia, all within 12 days.”
and development that we’re providing is first class. We have that governing body, so there’s no tick and flick, we’ve got the training provider, we’ve got good trainers and assessors that know how to mark somebody as competent,” he said.
Lou added the Max Academy also has documentation that supports the approach.
“We’re checking the VOC process because ours is at a really high standard. We’ve seen incident rates drop, we’ve seen all the metrics you’d want to measure operationally head in the right directions,” he said.
“Michael Kuhn, who is a Technical Advisory Manager, is the first guy to get his Cert IV Mobile Cranes Operations. The rest of our trainees are probably around 80 per cent to 90 per cent there and by the end of this year, we’ll have our full first group of 20 young people go through with Cert III and or Cert IV,” said Lou.
The other significant part to this story is that the Max Academy is open to all staff now.
“It’s not only for young people. Age doesn’t matter, it’s available for anyone in the business. We currently have a supervisor
who is enrolled, it’s open to anyone who wants to have their skills recognised.
“As the business has grown, the skill sets required throughout the business have too. We’ve got our first Cert III in driving operations training, our first Cert III in mobile heavy trailer mechanic technician and our first Cert III in supply chain operations and we’ve had our first Cert III business trainees complete for the first time in 21 years of operations at Max Services,” Lou said.
“It has become part of the culture as a business. The managers and supervisors are on board, and any development is very much structured to a national training framework which helps build career paths.
“We are 80 per cent completed on our Crane Technician program. How do you take a diesel mechanic as such, through to becoming a crane technician? Normally with a huge amount of OEM training and a lot of on-the-job experience, but we’ve been
able to build a training package for that as well,” said Lou.
He goes on to discuss the importance of engaging youth.
“In our experience, you’ve got to get to the schools, and if you’re waiting for year 11 or 12, it’s too late, you’ve got to engage at the year seven level.
“We arrange field days and barbecue days where we bring the kids in, show them around and get them all over the crane.
“We have a lot of trainees available on the day and the kids can talk to them about their experience in our industry. That’s what enterprise needs to do now, if you’re waiting for someone to do it for you, you’ve missed the boat. I know it’s resource intensive, but as an industry group there should be a real
focus on this approach.
“In August we held three field days, one at our Adelaide yard, one in Port Augusta and one in Whyalla. We invited groups from schools and up to 100 young people attended each event. They came from various backgrounds to experience our industry and we didn’t just present opportunities in specialist lifting, we showed them how they can get into transport, into business generally and procurement. It’s about providing pathways into the various aspects of the business and demonstrating there are more opportunities rather than pulling levers and throwing chains,” said Lou.
Lou confirms that neurodivergent individuals are proving to be very successful in the Max Academy. Neurodivergent individuals may have a brain that works differently from the average or “neurotypical” person. There may be differences in social preferences, ways of learning, ways of communicating and/or ways of perceiving the environment.
“Because we have a scholarship program with the high school, we’ve taken four
trainees over five years. All of them highly successful, probably some of the best in the business but most of our trainees are great! At MAX, if you have the right attitude, we will develop you to become successful. We don’t set diversity targets; all people are accepted equally.
“We have one trainee with very distinct behaviours that people in the wrong business might struggle with and he might not be given the same opportunities as a ‘nuerotypical’ person.”
“Through work experience opportunities and partnering him with the right mentors in the business, he’s just gone ahead in leaps and bounds,” Lou says.
“He’s a good hard worker, if he’s standing around, he’ll grab a broom or wash a vehicle. He’s got to be doing something all of the time.
“That’s the benefit of having neurodivergent individuals in the business, when they see something that’s not right out on site, they’ll be the first to report it and those behaviours are actually extremely beneficial in a high-risk environment.
“They’ll follow everything to the letter of the law, whatever’s written into our policies, procedures and client requirements. They won’t deviate and they won’t be pressured by poor behaviour out in the workplace,” said Lou.
Max Academy recently brought in a new trainer, Todd Davidson, to work with the trainees. Todd started his career as a motor mechanic and moved into scaffolding in the mines. From there, he got involved in plant operation, and then with MAX in Moomba where he constantly worked on developing himself and his skill sets. He was working two weeks on, two weeks off, on a FIFO arrangement.
“Todd was signed up in our Cert IV qualification, and he went off and did his own Certificate IV in WHS, and Certificate IV in Training and Assessing. After having a newborn child, he came back and we crossed paths and whilst on paternity leave, he completed the assessor skillset, and now he’s part of the Max Academy,” said Lou.
“Todd is 37 with a huge amount of experience and personal drive and all the trainees love him. He can connect with them, because he hasn’t been ‘institutionalised’ by the training sector, he’s very much here for the right reason. Todd is really the future of the crane industry and specialist lifting training environment. It’s unique opportunity to bring a guy like Todd into the Max Academy, he’s like a unicorn, a very rare breed of person,” said Lou.
“That’s the benefit of having neurodivergent individuals in the business, when they see something that’s not right out on site, they’ll be the first to report it and those behaviours are actually extremely beneficial in a high-risk environment.”
The New GMK5150XL is the latest sibling of the GMK5150L-1, with longest boom (69m) and most versatile road weights in class
• Reach further with 69m boom and 30m hydraulic luffing fly
• 50t GVM with outriggers in situ for reduced cost legal travel in all Australian states and territories
• 10.2t counterweight in situ at 12t per axle
• Increased safety and flexibility with MAXbase variable outrigger positioning
• Faster, intuitive set-up with CCS (Crane Control System)
• Grove Connect Telematics
• Capacity: 150t
• Main boom: 68.7m pinned*
• Maximum Jib: 30.2m (40O hyd luff)
• Maximum tip height: 99m
Contracted by a market leading wind farm operator to refurbish two wind turbines in Central Victoria, Johnson & Young Cranes (JYC) provided an innovative, cost-saving, emission-reducing alternative to the historical method of undertaking this scope of dual lifting work with two lattice boom crawler cranes: a dual lift with two hydraulic mobile cranes. Engineer John Humphries talks technicalities, fleet mobilisation, logistical challenges and the performance of JYC’s Liebherrs.
AS OF OCTOBER 2022, THERE WERE 94 operational wind farms in Australia playing host to over 2,700 wind turbines. Currently, the wind accounts for just over nine gigawatts of energy per year. By 2035, that number is expected to hit 32 gigawatts per year.
And so, with a large, forecasted growth in the wind industry comes the need for equipment capable of erecting, maintaining, and repairing the turbines themselves.
Based out of locations in Melbourne’s North and Southeast, JYC – ‘Team Orange’, as it’s colloquially known –performs a range of lifts in the construction and renewables industries across Australia.
JYC runs a fleet of over 30 machines ranging from its three-tonne mini-Maeda through to its monstrous 800-tonne capacity Liebherr mobile cranes. In and among those cranes are two 650-tonne Tadano crawler cranes and three 350-tonne crawlers operated through a joint venture, and a range of supporting equipment including 13 prime movers and 30 trailers.
So, when JYC’s valued client presented the company with an opportunity to participate in this unique project, the JYC team knew it held the perfect fleet capacity to complete the project at hand: the restoration of two wind turbines.
JYC was contracted by a large wind farm operator to undertake major component exchanges on two wind turbines. To achieve this, the Melbourne-based crane hire company needed to remove the three blades, the hub, the gearbox and drivetrain, to swap the required parts, and then replace everything it removed from the turbine.
The heaviest item the crane hire company would be lifting weighed in at nearly 40t. On the other hand, however, wind turbine blades – despite falling well within the selected cranes’ capacity – are designed to catch a lot of wind at higher altitudes, which was something for the team to factor in as they completed their works nearly 120m above the ground.
Traditionally, the client that contracted JYC used lattice boom crawler cranes to complete this kind of work in other regions, but as John says: “big crawlers can be difficult and slow, pieces of equipment to move, that often end up holding more capacity than what is required for component changeouts”.
“Sometimes, a customer prefers the use of a lattice boom crawler crane in these scenarios because it provides them with a little bit more leeway in terms of capacity,” he says.
“Our case for winning the contract was different; we believe that contracts can be won and lost on the mobilisation strategy, and so we pitched a different case.”
The business case pitched to the wind farm operator was clear: instead of using a large crawler crane that would take longer to transport and require many more trucks, why not use two hydraulic cranes operating within their maximum capacity, providing a much more economical, time efficient, environmentally conscious lift?
The choice was clear for JYC on which machines were going to be selected from its diverse fleet; the company is in possession of two 800-tonne Liebherr LTM 1750-9.1 all terrain cranes and, thanks to its V2E boom extension system, the machines thrive on jobs that require high lifting capacity at substantial hook heights.
Needing to complete its repairs on the turbine in question at a height approaching 120m, JYC’s LTM1750 Liebherr cranes, with maximum hoist heights of 152m each, safely completed the three blade dual lifts while then allowing the lead crane to remove the heavier driveline components without changing position or reconfiguring the boom or fly.
“The reason why we chose this crane is because it’s optimal for this kind of travel,” says John. “If you combine the lifting power of the LTM1750-9.1 with roadability benefits, overall, it’s the best crane by far. Our LTM1750 crane is the perfect point of lifting power, versatility, and roadability.”
One of John’s biggest challenges and indeed favourite personal moments to come out of JYC’s recent refurbishment of two wind turbines in Central Victoria was obtaining access for two 800-tonne hydraulic cranes to complete a 1200km round trip with their booms still attached.
Travelling from its Campbellfield depot in Melbourne’s north, the road access team at JYC needed to be realistic about axle loads for the journey to the wind farm while still achieving an efficient mobilisation
compliant with Victoria’s complex heavy vehicle road rules.
John relied on his past experience at CICA and alongside the Department of Transport to achieve a feat he says he’s “really quite proud of”: moving both cranes to the jobsite without needing to remove either boom.
This ‘European style’ scenario is unique to Victoria where this level of crane access is allowed to exist, and John pays tribute the progressiveness and pragmatism of the Victorian Department of Transport.
Citing the complexities of navigating the bureaucracy involved in moving the machines, John says the team at JYC needed to lobby with local governments to gain access to certain bridges so they could bypass other bridges on the main highways that they weren’t allowed to cross.
“Being able to be part of a lift involving in such a significant mobilisation strategy involving our two biggest cranes travelling at a heavy weight that we would not normally be able to do in the past is a logistical milestone for us,” he says.
“It helps us reduce time and operational costs because now we don’t need to spend time putting the boom back on the cranes.”
“Additionally, it helps the construction industry shift toward more leaner and efficient practices,” he continues.
“By being able to move the cranes with their booms on, we reduce our logistical/ carbon footprint because now we don’t need a second crane in support, and we don’t need as many trucks and trailers carrying counterweight and equipment.”
Transporting the machines to the jobsite in an efficient manner is one thing; erecting the cranes at the wind farm is another.
JYC’s LTM1750-9.1 cranes possess a telescopic boom that extends out to 52m.
What it also features, however, is a lattice jib extension that can provide the crane with an additional 91m of boom.
For its job in removing and lifting the blades into position, and replacing the generator, JYC needed to configure its machines with the over 50m of boom extension to provide maximum reach to its 114m tall job.
To assemble the cranes, a 40-tonne
Franna pick and carry crane was deployed to build and attach the crane’s boom extension and luffing fly.
There was a problem, however; the crane pad was, in a rough estimate from John, “75m by 45m and on the side of a steep hill” – a significant issue when both crane’s booms extended nearly 90m each.
“When they build these wind towers, they just typically put erect one big crane in the middle, and so the crane pads is are designed to accommodate just that,” says John.
“For repair and maintenance work, there are portable sheds and all sorts of equipment along with two big cranes (in this case) all on the crane pad at the same time. There is not a lot of room, so we played a Tetris-like game fitting the two LTM1750s on the crane pad with all the blades and components.”
After equipping the primary crane with 124 tonnes of counterweight and the secondary one with 94 tonnes, the team was ready to start their dual lift on the wind turbines.
THE LIFT:
A team of six people was constantly on site to complete the job: two operators, one in the tower, and three on the ground. Using rigging equipment supplied by the client – thanks to the fragile nature of the wind turbines themselves – the job also required multiple engineers working for JYC’s client watching both from the tower and from afar to help maintain the balance of the turbine as it was being lifted.
One of the complexities in the dual lift that John points out was navigating the small dimensions of the crane pad for the cranes to be able to operate in their working range. In their configurations, the machines needed to be operating at a minimum radius of around 30m. Without these inbuilt limitations, the crane could fall over backwards with no load on the hook.
“The whole point of a crane is usually to lift heavier items at a larger radius,” he says. “Our challenge here was not so much maximum radius but minimum radius due to the 56m and 59m fly jibs.
“At times we had a very narrow working
range as moving out from our minimum radius meant capacity dropped off very quickly, pushing our lead crane well above 90 per cent capacity to complete the lift.”
Further difficulties arose with the very essence of a wind turbine blade; as a 60m long component designed to catch wind in a purposely selected windy area, a max wind speed of 30km an hour was something that needed to be factored in when removing and lifting the blades back into place.
“With a dual lift, you’ve got to derate the capacity of the cranes,” says John. “There’s a lot at stake lifting these blades back to their positions. Everything needed to be kept dead level, or else the blade may slip out at either end of the supplied rigging.”
To accommodate this, JYC sent one of its team members away to watch the lift from a vantage point to keep an eye on the horizontal alignment of the cranes, with a radio on standby to sound the alarm should anything look out of place.
“To ensure these were safe, efficient dual lifts, we needed every single member out there keeping an eye on things and making sure that everything was proceeding exactly as it was designed,” says John.
And so, having successfully completed this project with 12 successful dual lifts and 12 single lifts, providing resource-saving solutions to a complex logistical problem, the team at JYC promptly demobilised the machines and sent them straight back to resume work in Melbourne.
The success JYC enjoyed on the project was the result of close collaboration with the client, communication among stakeholders in the mobilisation process, and the “professionalism” of the crane, the transport and the client’s MCE crews according to John.
“These factors were pivotal to ensuring that our methodology for this project came to life, which resulted in reduced overall costs by performing the dual lift with our two largest cranes,” says John. “Additionally, we were able to minimise truck movements and emissions with a lean logistical footprint, and collectively we demonstrated that it can all be done safely, compliantly, reliably and efficiently.”
IT IS AN EXCITING TIME FOR SARENS, locally and globally, with a strong team of experienced heavy lift professionals helping support its focus on strengthening its presence within the region.
Regional Manager for Oceania Isabella Burke stated “Sarens is making investments in its people and equipment within the region to ensure we can provide the best solutions for our clients. Our engineering and operational team’s detailed planning and precise engineering calculations have allowed us to minimise risk and meet our clients’ timelines in key civil and mining projects across Australia.”
Sarens recently completed works on the Sydney Gateway Project, for the John Holland Seymour Whyte Joint Venture in conjunction with Transport for New South Wales. This project involved the installation of girders for several new bridges that will connect the Sydney Motorway Network with the Sydney Airport and Port Botany precinct. This was a complex project due to the proximity to the Airport, height restrictions were imposed, and there several site constraints during the transport and installation manoeuvres. The most complex installation was conducted across Alexandra Canal located besides the Sydney Airport.
Main bridge sections were approximately 120m long, 20m wide and weighed approx 700 metric tonnes as a final weight. Operations design led to an extensive and collaborated engineering design between Sarens and the client. A key design detail
addressed during the planning phase was the challenge involved when handling the bridge sections without inducing significant stresses. At the same time, the bridge transport operation involved crossing over a public bridge and roads, where special care to ground loads applied by Sarens equipment had to be considered and determined.
The equipment selected for this project were the Kamag K2400ST self-propelled modular trailers (SPMT) for transport, an in-house developed jacking system, the Sarens CS250 as well as additional support structure and a hydraulic gantry, the Enerpac SBL1100 as a secondary installation method. Sarens overcame very challenging and narrow time frames for the bridge installation as the operations had to adhere to strict permits and restrictions.
On the other side of the country, Western Australia has always been a strong base for Sarens, with over 15 years experience in the mining and gas projects locally. Strong relationships have been built with
clients during these years. Their focus on collaborating with their clients over the years has allowed Sarens to provide end-to-end engineering solutions that will help clients carry out the construction, maintenance, repairs, refurbishment and extensions on all types of projects, no matter the size.
One such collaboration is occurring at a cement plant expansion in Kwinana for SIMPEC. Sarens worked closely with SIMPEC throughout the year, supplying several heavy lift cranes and engineering support for its lifting requirements. The fleet of cranes Sarens has onsite include a CC2800, LR1350 in superlift configuration, two SCX 2800s and a variety of all-terrain cranes.
“These specialised cranes are rigged with various configurations ie. luffer, superlift and fixed fly, to accommodate our clients numerous requirements to install materials at various heights and radiuses” Isabella said.
“Our engineering team has supplied solutions for challenges that our client has
In the world of heavy lifting and engineered transport, Sarens has established itself as a global leader. The company’s success can be attributed to a combination of cutting-edge design tools, a massive inventory of cranes, transporters and specialist rigging equipment, and a team of highly qualified professionals.Sarens Regional Manager for Oceania, Isabella Burke. SPMT’s in action during August on a Sydney project.
encountered during the various stages of the plant construction and installation.
“Sarens is well positioned to provide engineered solutions to clients in the current civil and infrastructure boom across Australia. This is expected to continue into the future and looking towards 2032 Brisbane Olympics. Sarens experience in the construction industry and the proofed expertise of our engineers, will ensure that Sarens can help clients delivery on their projects for the Olympics and beyond,” said Isabella.
Looking to the future, with benefits beyond 2032, Australia has committed to clean energy - and offshore wind is an integral part of Australia’s energy future.
As global green energy faces bigger and bigger challenges, the realisation has come that critical infrastructure relies on the timely delivery of these massive projects, and that’s where Sarens comes in.Globally Sarens is powering tomorrows world through its ability to deliver critical transport, construction and installation solutions.
Whether it be loading gravity based
foundations or transporting wind farm jackets, Sarens has the equipment that can make it happen.
Sarens is committed to the green energy transition. Sarens Senior Offshore Wind Advisor Dirk Verwimp was a keynote speaker at the Australian Wind Energy Conference in Melbourne in July 2023, sharing Sarens global experiences in offshore wind and marshalling activities in ports & marshalling yards.
Sarens Technical Solutions Sales Manager, Michiel De Bodt, said it was a wonderful opportunity.
“It was great to engage with key stakeholders as Australia moves progressively towards further developing the offshore wind market, in Australia” he said.
“With our global experience in offshore wind generation we want to share our knowledge and work with our customers to create similar successes.”
“Sarens are a one-stop solution for everything offshore. Our extensive fleet of SPMTs can deliver precision transport for truly enormous loads. We operate a world-
As global green energy faces bigger and bigger challenges, there is a realisation that critical infrastructure relies on the delivery of massive projects.
leading selection of cranes, gantries, and climbing, jacking, and skidding systems. By combining equipment and services, Sarens has the capability to execute even the most complex of projects - from onshore logistics to offshore installations, handling massive concrete foundations and installing the latest generation of wind turbines on floating structures, ready for load-out.”
“We know our world depends on new sources of energy, and we will do everything we can to be a key part of the journey that will take us into a bright future. Sarens is proud of its decades of heavy lifting experience, and even more proud of its vision into centuries still to come,” said Michiel.
Overall, Sarens success can be attributed to its focus on innovation, expertise, and quality. By combining the latest design tools with a massive inventory of equipment and a team of highly skilled professionals, the company has established itself as the global leader in the heavy lifting and engineered transport industry. Sarens is committed to excellence in everything it does.
Australia’s safest pick and carry crane is now powered by the Cummins Euro 6 Engine, the highest emission control diesel engine available with significantly more horsepower. Including more powerful front suspension cylinders, lifting capacity has increased by an average of 17% when articulated or working on a side slope and in some cases by over 40% in lifting performance.
The latest Allison Transmission with retarder provides superior downhill braking, delivering increased safety and control, lowered operational expenses, and reduced noise in urban areas.
The new TIDD PC28-3G is driven by our continuous focus on innovation and actively exceeding expectations for our customers.
Talk to us today to learn more about the TIDD PC28-3G Pick and Carry Crane.
IT’S 2013, AND GENERAL MANAGER OF Dynamic Rigging Ross Johnson is sitting in his office, reflecting on all the services Dynamic Rigging offers.
Since its inception, the Melbournebased lifting and rigging equipment hire company has provided products to lift all types of loads, including bridges, trains, tanks, excavators, MRI machines and an even a house.
The conversation he’s just held over the phone presents a new challenge, however. On the other end of the line, the Melbourne Zoo had come to Dynamic Rigging with a very specific request.
It needed to lift and position a baby elephant for surgery.
“We supplied the rigging equipment for that job,” he reflects. “Really, whenever someone needs our products, we will always supply them – no matter the job.”
Having been in his position for just over 13 years, Ross has seen Dynamic Rigging’s products thrive in multiple different aspects of the lifting industry. Operating as a hire company for lifting and rigging equipment out in the industrial north-west Melbourne suburb of Sunshine, its products can be found in the maritime, construction and mining industries.
Holding a CICA membership and employing LEEA trained lifting gear inspectors, safety and due process are always at the core of Dynamic Rigging’s operations. As we’re conducting the interview, Ross stops to take a call –ensuring the right lifting procedures are in place for the equipment the company supplies.
“It’s imperative that we get it right,” he says. “Lifting and handling heavy loads is a dangerous game, and we need to make sure our equipment is certified to work
and that it is being operated in the way it is intended to.”
With an array of products featuring spreader beams, lifting beams, pre-cast rigging gear, ducting, materials and personnel cages, winches, air hoists, chain blocks and load cells, Ross is certain that Dynamic’s services can comfortably supply anyone in the industry, should they need their help for any period – whether that be one day or, in some cases, one year.
“Our products are substantially involved in the Metro Tunnel and West Gate Tunnel projects,” he says. “We’re starting to enter the North-East Link as well, but we’ve also got your regular crane hire companies calling us in the early morning to hire out equipment for
a day when they realise they don’t have the right equipment for the job they need to do.”
It’s in the name of being a hire company that can provide immediate solutions to any customer demand –no matter how pressing – that Ross tells Cranes and Lifting that Dynamic Rigging has purchased the assets to steel fabrication and engineering company GTC Engineering.
Taking possession of 26 offset beams, Ross knows Dynamic’s latest acquisition will only enhance the Sunshine-based company’s capabilities within the lifting and rigging equipment sphere.
Where a traditional lifting beam functions by evenly distributing the weight of a load across a wider range than
Dynamic Rigging holds a range of equipment that can fulfil any customer’s needs at any time, thanks to its large inventory and dry-hire business model. The Sunshine-based company’s latest acquisition of offset lifting beams from GTC seeks only to enhance that.Dynamic Rigging has purchased 26 offset lifting beams, essential lifting equipment for lifts in tight spaces that are difficult to access.
just the hook and thus providing stability, offset lifting beams hold a counterweight at one end. This allows for a load to be located further to one side of the bar than the other, providing a new scope of accessibility in tight construction projects.
Predominantly used by tower cranes, Ross is keen to highlight the important, holistic role they play in lifting.
“They’re also used by the mobile crane industry, particularly in things to do with some of the major projects now such as the Metro tunnel,” he says.
“These beams allow the crane to place the load outside of the reach of a crane. One example is when the roof on a structure has already been installed, and some larger object like an escalator needs to be carefully lifted in.”
“We see instances like that regularly in the construction industry, hence our decision to acquire these 26 offset beams.”
And it’s not just bigger, bulkier items where the offset beams thrive; with the range of beams holding a working load limit as low as 400kg through to 13 tonnes and spanning anywhere between 3-12 metres, Ross says the newest additions to Dynamic’s inventory will take the construction sector by storm due to the flexibility these beams provide.
“The smaller ones are used for glass panels and the like, because they can lift suction vacuums holding a sheet of glass up the side of a building with a reduced risk of hitting the existing structure,” he says.
On top of positioning escalators, lifting staircases and finessing glazing work, the beams also thrive when it comes to lifting delicate pieces of equipment in buildings such as a laboratory or a hospital. Using the example of MRI machines that can be fed through a hole in the side of a building, Ross again emphasises the practicality of the beams for the entire lifting industry.
“We really do see these being useful for the smaller crane hire companies and, simultaneously, the biggest crane yards and large-scale construction companies.”
“A lot of these beams will end up travelling well outside of Melbourne,” he continues. “We’re looking at targeting some of the major construction projects in Queensland and NSW, because we now hold the largest inventory of offset beams in Australia.”
Additional to its 26 offset lifting beams, Dynamic Rigging also holds 50 regular spreader beams available for dry hire in its inventory. Featuring modular, telescopic, end cap and lifting spreader beams, the equipment hire company also holds “one of the biggest” inventories of materials lifting cages.
With products ranging from 250kg tool cages through to 3 tonne material lifting and side loading cages, Ross says the Sunshine-based lifting and rigging company is firmly placed to supply to any industry that needs stable, safe lifting equipment.
“Whether it’s loads coming off ships, construction jobs, or mining jobs, they all come to us to provide,” he says. “They’ve got the crane, and they’ve got the customer and the customer has got the job, but we’ve got the gear that connects the crane, to the cargo with the load.”
“We’re LEEA accredited, all our products are tested vigorously, we supply a range of lifting equipment for specific applications across a range of time frames, and we supply to all facets of the lifting industry,” he continues.
“With the latest addition of these offset lifting beams, we’re actively expanding our capacity to aid our customers’ requirements.”
Borger Crane Hire and Rigging Services recently took delivery of its first Liebherr LG 1750. As soon as commissioning was completed it headed straight to a New South wind farm. Shawn Borger, General Manager at Borger Crane Hire is particuarly pleased with the latest addition to the fleet.
“THIS CRANE IS THE ULTIMATE FOR THE wind farm sector, and with the extra lifting capacity and boom length it will enable Borger Crane Hire to work on the larger taller turbines - featuring increased hub weights that are being installed on wind farms today,” he said.
More powerful and stable in the wind – that is a rough summary of the main benefits that Liebherr has delivered for its customers in the form of its innovative SX2 and SX3 boom systems for crawler and lattice boom cranes. The reinforced booms are particularly helpful for wind power crane operations. The SX3 version delivers a major increase in lifting capacity of 20 per cent and significantly higher wind tolerance compared to the conventional SX version.
“This crane with its SX3 boom enables us to increase our capacities, so that we can also erect these very large turbines. Its 165 metre of main boom and 12 metre jib gives us a lifting capacity of 127 tonnes. That is really enormous,” said Shawn.
While the lower section of the lattice boom has been extended to a width of six metres, the boom system upgrades are not simply Liebherr’s reaction to an ongoing increase in the weights of components and hoist
heights for erecting wind turbines. The 28 or 42 metre boom reinforcement (which is also fully compatible with the Liebherr LR 1750/2 crawler crane) delivers significantly greater rigidity in the boom design and therefore results in less crane downtime due to wind.
The earlier systems used on the LG 1750 were calculated on the basis of a maximum wind speed of nine metres per second. The SX system now allows work to continue in wind speeds of up to ten, or in some cases even 11.2 metres per second. This is not only a major benefit for cranes working in wind farms, but is certainly a big plus for them.
The 8-axle LG 1750 is viewed by many crane businesses as the ‘go to’ crane for the wind energy industry in the 750-tonne
class. The LG 1750 lattice boom mobile crane offers the flexibility of a 750 tonne crawler crane combined with the mobility of a high-speed truck crane. It thus combines the advantages of both crane types in one concept. For the LG 1750, Liebherr uses the crane slewing platform and boom system of the LR 1750 crawler crane as well as an eight-axle chassis of the latest design with speed-dependent rear-axle steering. The lattice boom mobile crane is therefore ideal for fast assembly operations in wind power, industrial construction or infrastructure. The chassis travels to the construction site with all four outriggers at a total weight of 96 tonnes. If required, the outriggers of the LG 1750 can be removed, thus reducing the weight to 48 tonnes.
Liebherr also offers a wide range of special wind power boom systems for the LG 1750, which are optimised for smaller and medium-sized turbines as well as for the latest generation of wind turbines with tower heights of more than 160 metres.
The LG 1750 is powered by an eight cylinder, water-cooled, 868 horsepower Mercedes Benz engine. This engine will finish any job with ease and easily manoeuvre around the jobsite.
The transmission system is a ZF TCTRONIC automatic transimission with 12 forward speed and two backward.
The suspension system is an all axle system with hydropneumatic suspension. It has automatic leveling control, limiting the shift of weight from one axle to another, therefore limiting the amount of maintenance required. The suspension is also able to be hydraulically blocked. The steering system of the LG 1750 is a ZF semiintegral power steering two circuit system, with a hydraulic servo mechanism.
The brake system is made up of a service brake, an all-wheel servo brake, an exhaust pipe retarded, and hand brake acting on the 3rd, 6th and 8th axle. By including this many brakes, the Liebherr team makes sure that even if one fails, it is easily possible to stop the crane in a different way, limiting potentially dangerous situations.
Liebherr is dedicated to safety. For this reason, there are many features on the LG 1750 to combat dangerous situations. These features include a hoist limit switch, safety valves to prohibit hose and pipe rupture, a drum switch limit, a wind speed gauge, an inclination indicator and an aircraft warning control light.
Shawn says that while the Liebherr LG 1750 is a significant investment for the business, it also allows Borger to keep providing its clients with an ever-increasing fleet of high-tech cranes.
“Although this crane went straight to a wind farm project, it is designed to be equally comfortable on the large
infrastructure projects where it could be lifting large bridge beams or Tunnel Boring Machines,” he said.
“As we are seeing, these infrastructure projects are demanding much faster construction times which means larger components, leading to fewer but heavier lifts, with larger capacity cranes.
“The Liebherr LG 1750 is an investment in the work we have today and the projects we will be tendering for and winning in the future. This crane enables Borger Crane Hire to provide our clients with a whole package of lifting solutions, whatever the size of the project,” said Shawn.
He goes on to discuss the Liebherr product in the fleet and why his operational team likes the brand.
“Renewing and reinvigorating our fleet is a continual process and we will always assess what is available from the crane OEMs and purchase what we see as being the best solution for our clients and our business at the time.
“The Liebherr LG 1750 is a fairly unique purchase for us as there really isn’t another crane quite like on the market. It combines the mobility of a large capacity all terrain with the lifting capacity of a large lattice boom crawler.
“When we get up into the larger capacity all terrains, we tend to lean towards the Liebherr brand. One of the reasons for this is that our operators are very comfortable with the LICCON crane control system which enables them to move easily between various capacity cranes,” said Shawn.
The LICCON3 crane control system has future-oriented power. Thanks to its completely new software and programming language as well as the faster data bus, significantly more memory and higher computer performance, the control system can be further developed more quickly in the future. This may be the case, for example, with complex applications such as VarioBase® which require high performance data.
One thing was important in the development: Crane operators who already work with Liebherr cranes should quickly get to grips with the new control system. In this way, the new was combined with the tried and tested. The information on the displays has been revised and even simplified. At the same time, familiar features such as the BTT remote control terminal have remained. So anyone who has previously operated one of the LICCON2 cranes, will quickly find their way around.
All LICCON3 cranes are prepared for telematics and fleet management as standard. Via the MyLiebherr customer portal, registered customers can view, monitor and evaluate all relevant data of their Liebherr mobile cranes - and even pass it on as an operational report if they wish.
Another feature of the Liebherr brand which impresses Shawn are the enhanced safety features and performance provided by Liebherr’s VarioBase®. With the space available on many construction sites often
constricted, it is frequently impossible to extend all the outriggers of the mobile crane evenly.
VarioBase® from Liebherr allows the crane to be used safely and flexibly in these difficult conditions. The increased safety and ease of use take the strain off the crane driver who can concentrate fully on the hoist. The enhanced range and lifting capacity means that the system’s capacity has also been improved. VarioBase® enables work to be carried out safely in constricted areas. The maximum lifting capacities are calculated individually and precisely for every situation. This ensures safe working practice with any chosen support base.
“Crane technology is developing at a rapid rate and as a leading crane hire company and lifting partner of choice, we need to ensure we are investing in the right cranes. A key part of our purchasing decisions is the service and support we receive from the crane manufacturer.
“We have an excellent relationship with local Liebherr teams, and this has been developing over the last 20 years. The product support and service is excellent and they continue to invest locally in this side of the business. We also know the teams very well in Germany and they keep us informed regarding new product developments which they think might interest us.
“We believe the arrival of the Liebherr LG 1750 heralds a new phase for Borger Crane Hire and Rigging Services and our teams are excited to welcome the crane into our fleet,” said Shawn.
“The Liebherr LG 1750 is a fairly unique purchase for us as there really isn’t another crane quite like on the market. It combines the mobility of a large capacity all terrain with the lifting capacity of a large lattice boom crawler.”The 8-axle LG 1750 is viewed by many crane businesses as the ‘go to’ crane for the wind energy industry in the 750-tonne class.
FREO GROUP IS A PROUD BUSINESS, backed by the systems, ingenuity, and dependability of Marmon Crane Services Inc., a Berkshire Hathaway-owned company. Cranes & Lifting discussed the capabilities of the business with Freo Group CEO Sven Gade.
From the mining and resource sectors to civil construction and renewable energy, Freo Group provides a complete range of crane hire, heavy lifting and logistics services – including oversize transport, materials handling, warehousing and storage.
“With 23 branches across Australia and a fleet of over 480 state-of-the-art mobile cranes, we have the right equipment for the job when and where you need it. Our people are locally based, our reach global and our experience unmatched,” Sven said.
“Since 1974, the Freo Group name has been synonymous with reliability and customer service. It’s what sets us apart from the rest and a key reason why we are a trusted partner to some of the world’s largest companies.
“Family values, a commitment to supporting local communities and a focus on environmental stewardship are key pillars of how we operate. Our culture is founded on the highest professional, ethical and safety standards, and we take pride in nurturing long-term relationships,” Sven said.
The culture of Freo Group’s business is made up of three fundamental aspects:
To build a successful and profitable business by:
• Engaging employees and suppliers in a
safe and focused culture;
• Providing superior customer service and to develop long-term, mutually beneficial relationships with our clients; and
• Leading the way in technical excellence and innovation in the crane industry.
To be the supplier of choice and be:
• The safest supplier of crane services;
• Recognised as the market leader in providing superior service and bestpractice technical solutions to industry;
• The preferred choice for repeat work on future contract; and
• The employer of choice.
• Working safely is at the forefront of our operations;
• Our people are our foundatio;
• Customer service is our focus;
• Performance excellence is how we strive for the best; and
• Innovation and improvement drive us forward.
“Health, safety, environment, and quality are central to all we do. It’s a commitment we uphold with pride and is the cornerstone of our reputation,” Sven said.
Freo Group’s goal is to operate in a workplace free from harm or loss. The 2zero Roadmap is an organisational strategic improvement plan that details how Freo Group will meet its vision: Home without harm. Everyone. Every Day.
The Roadmap is supported, led, and driven by senior leadership and is made visible and regularly communicated to all personnel, ensuring every person in the team is aware of, engaged with, and supports the plan.
Freo Group’s HSE Management system is certified to ISO 45001, with the accreditation achieved in 2011.
“HSE is an extremely important aspect of our operation, and our HSE Management plan ensures Freo Group meets all relevant statutory requirements and standards while promoting the continuation of our safety-first culture,” Sven said.
“We achieved ISO 14001 accreditation in 2021 and we endeavour to operate as an
Freo Group continues to grow and expand into the renewable energy sector with an ability to leverage from its WGC business, which was an acquisition in 2018.
Freo Group is Australia’s largest crane hire company, offering an unrivalled capacity to meet clients’ needs whatever the job, no matter the industry.
environmentally sustainable company. This is demonstrated in our commitment to continuous policy, equipment and technology improvement, along with procedures that reduce noise and vehicle pollution,” Sven said.
Freo Group has an ISO 9001 accredited Quality Management system, certified in 1996. This certification is accompanied by a robust Quality Management plan.
The plan uses an integrated management system to incorporate all components of the business into one coherent system. This system adopts a ‘process model approach’ and is part of its continual improvement process.
In the current challenging labour market, the company has devised a range of strategies to attract and retain the best talent.
A prominent example is the Freo Advanced Skills Training initiative. This program is aimed at individuals who are new to the rigging industry and have recently obtained their High Risk Work Licence (HRWL).
Freo Group engages them in a comprehensive two-week Freo
Advanced Skills Training program. This intensive course serves to build upon foundational skills and offers a controlled environment to hone their abilities and learn ‘the Freo Way’.
Upon successful program completion, participants join the company’s casual shutdown pool, gaining exposure to Freo sites across Western Australia.
“This unique approach has proven instrumental in not only sourcing rigging employees but also sets us apart from our competitors. Beyond the Freo Advanced Skills Training, we have recently concluded an exhaustive Training Needs Analysis initiative. This initiative was conducted to pinpoint our future leadership requirements,” Sven said.
“We are currently in the process of formulating leadership pathways for our frontline leaders to enhance their leadership skills, knowledge and capabilities. This includes developing an understanding of available career development pathways.
“At Freo Group, we are all
accountable for the social responsibilities and expectations of our employees and stakeholders, as well as the local, Australian, and international communities,” Sven said.
Freo Group’s processes and plans are aligned with the principles of the United Nations’ Sustainable Development Goals.
“We believe in being socially responsible and doing our part to better the communities in which we live and work. We are committed to our set targets, which we have currently exceeded,” Sven said.
“We are dedicated to ensuring our people are given every possible opportunity to grow and excel both in their careers and in self-development.
“Our objective is to engage the best person to do the best possible job whilst remaining open-minded to every applicant.
Through training and development, we aim to ensure respect, equality and
“At Freo Group, we are all accountable for the social responsibilities and expectations of our employees and stakeholders, as well as the local, Australian, and international communities.”Through engagement and consultation with Indigenous peoples, Freo Group aims to establish long-term working relationships to achieve measurable and sustainable outcomes in the regions where Freo Group is situated.
inclusion are prioritised across our workforce,” Sven said.
Freo Group is an equal opportunity employer providing training, development and initiatives that are focused on engaging:
• Gender Balance;
• Indigenous Employment;
• Disabled Workers;
• Gender Diversity; and an
• Aged Workforce
Led by its National Indigenous Affairs & Community Relations Manager, Freo Group’s targeted approach to increasing the Indigenous workforce and its involvement with Indigenous businesses and communities nationally is a focus across the entire operation.
Through engagement and consultation with Indigenous peoples, Freo Group aims to establish longterm working relationships to achieve measurable and sustainable outcomes in the regions where Freo Group is situated.
Creating sustainable outcomes will be driven through four key areas of focus:
• Relationships – Social and Cultural Support
• Respect – Land, People, Rights
• Opportunity – Economic Empowerment
• Governance – Reporting and Transparency
Freo Group continues to be part of the Crane Industry Council of Australia (CICA), assisting with codes of practice, legislation, and best-practice operating procedures. Its dedicated Innovation Committee helps it stay ahead of the game and in the industry.
suite inspires the next generation of crane operators by providing our new team members with an immersive learning experience. It gives employees on-the-job training in a risk-free environment, the basics of rigging, and experience driving our cranes in realistic scenarios.”
“Innovation is ingrained in our DNA and allows us to consistently find new and better ways of operating. Freo Group’s passion for remaining innovative and dynamic allows clients to save money and have the confidence we are working to the best possible standards and practices,” Sven said.
Freo Group transitioned to a purposebuilt fleet management software system to increase efficiencies on all levels, assisting the transition to a paper-free workplace. Fleet Cost & Care (FCC) incorporates all quoting, invoicing, scheduling, dispatching and reporting needs.
Freo Group combines scoping documentation with modern analytical reporting tools to increase efficiencies across all projects.
The Crane Collision Avoidance (CCA) system is a revolutionary innovation in crane operation safety. This fully integrated system warns operators of any obstructions on the rear or sides of the crane using radar technology.
“Virtual Reality Training is one of our innovative initiatives used as a workforce training tool to complement theoretical and practical training programs,” Sven said.
“This value-add option in our training
Freo Group proudly boasts an almost 50-year heritage of servicing industries nationwide.
Next year marks Freo Group’s 50th anniversary of providing mobile crane hire and logistics services to the mining, resources, civil construction, and renewable energy industries in Australia
The journey from a family run business to become the largest crane hire company in Australia has been a great journey with some of the original employees still being in the business today.
“Freo Group proudly boasts an almost 50-year heritage of servicing industries nationwide.”Freo Group’s Head Office.
Growing up in the cranes and lifting industry, Guy Black decided to create his own destiny in 2005 with Ashburton Crane Hire. He goes into depth about his company’s history, the expanded services it offers, and what sets Ashburton Crane Hire apart from its competitors.
SERVICING THE CRANE
IS PART of Guy Black’s DNA.
Guy is a second-generation crane business owner; in 1989, his father Bill Black founded Onslow Crane Hire Services in the Pilbara region of Western Australia. From the outset, cranes and transport played a central, formative part to his life.
Commencing his career with his father and later moving to various projects in the mining and construction industries in Australia and New Zealand as a crane operator, Guy and his partner Tenille decided to start their own crane business in Perth in 2005.
“I’m very passionate about the crane industry,” he says, “and I recognised the potential for an experienced crane service provider to enter WA’s crane market. So, we took a loan out against our home, purchased our first crane, and ventured into business ownership from there.”
Established in 2005 by Guy and Tenille, Ashburton Crane Hire’s (ACH) path to the position it finds itself in now was not always so simple. Starting its operations with a 20-tonne Franna and a door-knocking approach, Guy admits that
things were “difficult” from the outset.
“At the start, we didn’t have any work – not one client,” says Guy. “But we kept on persisting, we kept on doing the right thing by people, and we kept on providing an honest, hardworking service.”
“We did it the hard way, but I believe it was the best way to do it,” he continues. “Not having everything handed to you keeps you grounded and humble and makes the taste of success sweeter.”
Today, ACH employs over 50 people in Western Australia across two depots in Perth and Port Hedland. The company prides itself on its 100 per cent employee retention rate, with operators and dogmen who joined the company back in 2005 still working at ACH today.
Additionally, it has built up its fleet size from one 20-tonne Franna pick & carry crane to over 30 cranes, plus a large transport division consisting of ten prime movers and over 50 pieces of trailing gear. With its smallest machine available being a 12-tonne Kato city crane, ACH’s fleet also possesses 25-tonne and 40-tonne Franna cranes, a variety of all-terrain cranes, and its flagship machine: a 300-tonne Demag mobile all-terrain crane.
ACH services multiple industries across Western Australia wherever cranes and heavy haulage logistics support are needed. Completing projects in the oil and gas, mining, construction, marine and civil engineering industries, the company’s reach extends across Western Australia with their Northwest depot in Port Hedland servicing Karratha, Onslow, Paraburdoo, Tom Price, Newman and surrounding areas. Its Southwest depot is responsible for servicing the Perth metro area and other surrounding regions.
One of the challenges of operating in Western Australia is its remoteness. For the team at ACH, however, that challenge is their strength; with its facility in Port Hedland, the company is equipped to serve even the most remote customers.
“It’s very isolated in the Pilbara and Kimberley regions; we are more than happy to drive those 500-800-kilometres to service the surrounding areas,” says Guy. “Clients who know we’re capable of making these trips love our service; they know we’re constantly on hand to provide back-up for their business 24/7.”
“We’ve consistently shown through our work that we’re happy to operate in any place that our customer needs us,” says Guy. “Now, we’re starting to reap
ACH has been awarded a series of major contracts recently thanks to the level of accessibility it provides across multiple regions.
local team aside, our dogmen, crane operators and truck drivers work on a rotating roster of two weeks on, one week off, FIFO from Perth. We fly permanent staff members from Brisbane and Sydney to complete our staffing requirements across our maintenance, project and adhoc works.”
Getting staffing right is imperative to running a successful business for Guy and Tenille. As Guy highlights, a crane is a crane, and a truck is a truck; what sets a company apart from others is its people and the attitudes that are fostered and nurtured to deliver good service.
“When we’re hiring, we look for a good attitude and honesty,” he says. “We want people who, when they walk through our doors for a day at work, are ready to go out of their way to do the little things that ensure our clients are happy.”
the rewards of our hard work by being awarded a series of major maintenance and construction projects for lithium and iron ore projects in the Pilbara, and infrastructure in the Perth metro.” Additionally, ACH recently formed a joint venture partnership with a local Nyamal Aboriginal Traditional Owner Company, with Guy saying the company is “proud and excited” to make such an announcement.
“I was brought up in the Pilbara, growing up in Carnarvon, Telfer, Roeburne, Karratha and Onslow, and am very proud to have a close association with the people and the country up here,” he says. “We have local Indigenous team members, and using local labour is our first priority when it comes to staffing.”
“Our management live up there in the community; they’re not FIFO workers, and they’re well immersed in the local environment. These guys really understand the challenges it presents and how to find the best solutions to the problems presented,” he continues. “Our
Hiring based on attitude is only half of the job though, as Guy says. The other aspect is creating an environment where people are respected and enjoy coming to work. Hosting regular barbecues and providing complete flexibility for whatever the personal lives of its workers demand, Guy is insistent on creating a “family-like” environment at ACH.
“We respect – and do our best to retain – very honest, hardworking, down to earth people, because that’s the culture that we want here,” he says. “There are people who are still working here from when we started the business; we want to retain our staff for as long as possible and give them ultimate longevity in their careers here.”
After all, as is the motto and a highly repeated phrase internally: “service is what sets us apart,” according to Guy.
“At the end of the day, we’re a crane and transport service,” says Guy. “But, we go to the ends of the earth for our clients, and we know we’ve got great people to back us up.”
“We’ve consistently shown through our work that we’re happy to operate in any place that our customer needs us.”
Structural Engineering Consultants to the Resource Industries. Lifting and Rigging Design Specialists.
•Detailed structural design of lifting and rigging systems
•Design/Upgrade civil and structural systems for onshore and offshore projects
•Structural engineering assessments based on inspection reports
•Independent verification of structural design and investigations of structural incidents
•Development of Lifting Equipment Management Systems
Today,
IN 1988 SENIOR STAFF FROM UNITED Transport were part of a failed management buyout for the United Transport group in Australia, Brambles was the successful bidder.
The Western Australian management team, including Allan McPherson and Frank Legena, had an opportunity presented to purchase the Bell crane assets that had been acquired by Boral Resources. The successful bid for the purchase of the assets saw the formation of Uniway Cranes on 13 April, 1989.
Uniway Cranes, under the leadership of Allan in operations and Frank in administration, formed a successful crane and transport business that traded until 2002.
In 1999 the Uniway Crane Leadership Team discussed a succession plan for the business. Unfortunately, the children in the family business, who were old enough, were not interested in getting involved in a very tough and competitive crane industry.
At the 2000 CICA Annual Crane conference in Perth Allan was presented with the Con Popov award. During his acceptance speech he said that with all the changes that were occurring in the crane industry, including quality assurance, improved safety requirements and enterprise bargaining, it was hard to envisage how medium crane companies could survive.
Construction and industrial companies were demanding larger capacity cranes and capital constraints were channeling crane industry growth towards the larger players, placing financial and operational pressures on small to medium enterprises.
Jack and two investors had purchased Alpha Crane company in the late 1990s
and they soon discovered it was a pretty tough game. Jack attended the CICA 2000 conference in Perth and reported back to his fellow investors, “We’ve got two choices, we either get out and lose a lot of money or we get bigger.” They concluded getting bigger was a better outlook.
“There were two things in our favour. Number one, Brambles had decided to exit the crane industry across Australia and they had obviously been the largest player by far, and the idea of consolidating a number of small crane companies into one large one had the support of a number of businesses.
These included Frank and Allan at Uniway Cranes which operated 38 cranes, Alpha which had 8 cranes and Midland (20 cranes) all in WA, General
Contractors and Sutville Tower cranes which operated 30 plus tower and mobile cranes in Melbourne,” said Jack.
The decision to join this consolidation of smaller crane companies wasn’t straightforward. The biggest hurdle was that the owners were independent people who had successfully run their businesses for some time and there was an initial degree of pushback when changes came in - but overall, they were very supportive, said Jack.
In late 2001, Jack presented the idea of consolidating a number of small to medium crane operators into a national crane business in Australia to Uniway Cranes’ owners, Allan McPherson and Frank Legena, and he was grateful to receive their strong support for the strategy.
Boom Logistics is a publicly listed company, employs over 500 staff and operates one of the largest crane fleets in the country. 25 years ago, Boom Logistics was the joint vision of three men, Allan McPherson, Frank Legena and Jack Hebiton. They take us back to where it all began.The final consolidation involved five businesses in the Australian crane market, three in Western Australia including Uniway Cranes.
The final consolidation involved five businesses in the Australian crane market, three in Western Australia (Alpha Crane Hire, Midland Crane Hire and Uniway Cranes) and two companies in Victoria (General Contracting and Sutville Cranes).
These businesses formed Australian Crane Company. This was to facilitate the strategy to form a national crane company that would eventually list on the Australian Stock Exchange and this company was incorporated on 22nd December 2001.
Boom Logistics Pty Ltd officially started on February 7, 2002 starting out with a management team led by their Chief Executive Officer Rod Harman.
Allan McPherson and Frank Legena continued to contribute to the development and growth of Boom Logistics - with their confidence in the consolidation strategy ultimately creating the succession plan for Uniway and other crane small to medium enterprises.
Boom Logistics has made significant investments over the last few years, in both equipment and also its people, encouraging diversity and empowering employees.
• P urcell Cranes (WA); and
• Holts (Queensland)
The completion of these acquisitions provided Boom Logistics with a broad, national spread of operations and a strong presence across different industries.
The next round of acquisitions up to June 2008 included:
• Sherrin Hire (National);
• James Equipment (Victoria);
• G.M. Baden (NSW);
• D&D Crane Hire (NSW); and
• Moorland Hire (Victoria)
Jack was delighted when Ben Pieyre was appointed CEO and Managing Director of Boom Logistics.
“Ben is a very successful man in the crane business, and he is also a very fair man, he works hard and builds excellent teams around him. He has worked extensively overseas and was in Canada before he joined Boom Logistics,” said Jack.
Over its first few years Boom Logistics carried out a number of acquisitions of smaller companies around Australia.
The initial round of acquisitions:
• A lpha Crane Hire (WA);
• Uniway Crane Hire (WA);
• M idland Crane Hire (WA);
• Sutville (Victoria); and
• G eneral Contractors (Victoria)
Later:
• Brambles Perth Cranes (WA); and
• Brambles Goldfields Cranes (WA)
In October 2003 Boom Logistics Limited was successfully listed on the Australian Stock Exchange (ASX code BOL).
The listing enabled the successful raising of additional capital to acquire the next group of established businesses.
• C onmor Cranes (Victoria);
• Heavy Lift Cranes (Victoria);
• P ort Kembla Cranes (NSW);
Whilst Boom Logistics has experienced some mixed results in its first 20 years, it is now well positioned to build on its place as the largest Australian owned crane services business.
There will be a continued focus on growth, particuarly in the renewable energy sectors, as well as an ongoing commitment to providing quality, safe and efficient services across all major markets in Australia.
To support its position, Boom Logistics has made significant investments over the last few years, in equipment and in its people, encouraging diversity and empowering employees.
Since its inception, the successes of Boom Logistics have been the result of its people delivering clever and innovative solutions developed through many years of expertise and dedication.
This commitment to excellence will remain a high priority under the guidance of Ben Pieyre and his team.
“Since its inception, the successes of Boom Logistics have been the result of its people delivering clever and innovative practices developed over many years of expertise and dedication.”
Weekly rates are very competitive with reliable service.
Cranes are compliant with all documentation supplied.
Ashburton Crane Hire provides a specialised selection of manned and equipment only hire services throughout Perth and the Pilbra region of Western Australia. We provide both crane and rigging services to a wide range of industries including logistics, construction, domestic, marine and vehicle, industrial, oil and gas and mining companies.
achcranes.com.au
Perth Depot: 10 Imperial Street High Wycombe 08 9454 7000
Port Hedland Depot: 10 Yanana Street Wedgefield 08 9148 1770
Founder of Lift Plan Australia
Guy McGowan has worked in the crane industry since his early twenties. With a raft of industry experience, knowledge and connections behind him, he’s decided to bring his innovative, customised solutions to the lifting industry through meticulous planning.
LIFTING IS A HAZARDOUS GAME.
Lifting is also a legally complex game.
Logistically, and administratively, it can be a nightmare for crane hire and Tier One companies to work through the necessary planning phase to perform a safe, efficient lift. Thankfully, balancing the physics, engineering, legalities and administration of performing a lift can be outsourced –but it needs to be outsourced well.
Enter Lift Plan Australia.
Starting as a crane operator and
rigger across various companies over 25 years ago, Guy began working on the technical aspects of lifting in 2004 as a Supervisor at Boom Logistics, learning the intricacies of lift planning from some of the legends of lifting in Western Australia. Guy worked with the ASX-listed crane services company for six years advancing his technical knowledge. He has also worked at Sarens as a Depot Manager and as the Heavy Lift Superintendent at Tutt Bryant Group, before undertaking a
degree in Project Management in 2019.
“Since that time, I’ve been working across a range of different crane companies, preparing their lift plans –which is something that I love to do,” he says. “After working for a range of different people and businesses, I decided that I wanted to start my own consulting practice and make that service widely available across all industries.”
Lift Plan Australia operates out of Western Australia, boasting international affiliates and a range of industry connections that provide customers with unparalleled access to different, customised lifting solutions.
“We have a strategic partnership with Lowther Rolton based in Texas USA, who are a world-class lifting engineering company. Lowther Rolton can provide specialised expertise when it comes to logistics and engineering for the largest project challenges, including third-party assurance, structural design and modularisation aspects,” explains Guy.
“Sourcing the equipment is a feature of our work at LPA. I have longstanding relationships with materials and lifting equipment suppliers,” he says.
“Our range of industry connections is beneficial to our customers because it
means they get access to instant supply and problem solving from third parties should it be needed.”
As an independent contractor, Lift Plan Australia strives to ensure customers’ projects are delivered efficiently and effectively, minimising any associated costs and maximising productivity.
Lift Plan Australia’s services include the assessment of a lifting operation, the planning of a safe system of work when conducting lifts, completing method statements, assisting in the obtainment
of any permits required, the illustration of exclusion zones, the compilation of a lift study and the appropriate selection of cranes and rigging to ensure all the equipment can be handled effectively and within capacity.
“A lot of smaller companies don’t possess the budget to employ someone to do lift planning to the standard that’s required – that’s where we come in,” says Guy.
“Especially when it comes to Tier One customers, we’ll happily take the logistical and engineering aspect out of their hands and help them create all the documentation required to get their clients over the line with detailed and engineered lifting and rigging plans. This allows them to focus on what they do best – running the projects.”
For Guy and his team of engineers at Lift Plan Australia, a regular lift plan doesn’t exist; every lift is different, posing its own unique challenges, and therefore Lift Plan Australia’s services are tailored to what the customer needs. As he points out, a lot of Lift Plan Australia’s work is applying theory to practice, but the company is
responsive to whatever is asked of it.
“If they need onsite supervision, we’ll provide that,” he says. “We go out, see the customer, then work out exactly what they want and exactly what they’re trying to do and show them how to achieve their objectives.”
The benefit of employing an engineered lift plan, according to Guy, is that sometimes customers don’t know what they want, or don’t hold enough experience in the industry to perform the lift that faces them. That, he says, is also where Lift Plan Australia’s services come into play.
“We’ve got over 25 years of industry experience behind us,” he
says. “Sometimes customers are a bit unsure what they’re asking for, so we help them figure out what their project requires and what is needed to get their work over the line.”
Aiding clients through the murky waters of legal implications and Australian lifting standards is another facet of Lift Plan Australia’s operations. Part of this process includes raising customer awareness of compliance with the legalities of lifting. Pointing to his company’s previous experience with customers using gantry cranes for their lifting operations, Guy underscores the importance of engaging with companies to ensure correct procedure is followed.
“Helping to educate people as to what the Australian standards require, and how they will meet compliance is a big part of the work that we do,” Guy says.
“Lift planning is imperative to the industry,” he says. “Employing people who are capable of enacting a highquality lift plan is imperative to the safe, successful operations of the heavy lifting industry.”
“Helping to educate people as to what the Australian standards require, and how they will meet compliance is a big part of the work that we do.”
BORN IN A RURAL PART OF WESTERN Ireland, Mick was always a more hands on, practical person. At the age of 9, after being in trouble for skipping out on school one too many times, his father told him, “if you aren’t going to go to school, you can help me on the farm”. To this, Mick gladly accepted, marking the end of his ‘formal’ education.
Mick said, “we lived a modest life, there was no electricity or running water, we worked and lived off of the land”. With English being his second language to Irish Gaelic, it wasn’t until he moved to England at 18 that he began learning to speak English fluently. Finding himself in London at just 18 years old, he took up work as a labourer, accepting the only scraps of work that were available to an Irishman in those times.
It was in 1962 that three Irish lads landed in Australia. All had paid their fares to Melbourne but two of the trio were suffering so badly from sea sickness they threw their bags off the ship at Fremantle and stayed in Western Australia. Mick Joyce decided he’d paid his way to Melbourne and that’s where he was going.
Mick stayed in an old Irish pub called the Railway Hotel, which still exists today, in South Melbourne. There were seven lads sharing a big room on the first floor and from the first morning, Mick was up and out of bed by 5am ready to look for work.
Mick’s new roommates were unimpressed with the lights being on so early and shouted, “What are you doing with the bloody lights on so early you stupid bastard, go back to bed, there’s no jobs here,”.
“I didn’t listen. I would hop on a tram to suburbs like Carlton, which
took me about 10 miles out of town and then I’d start walking back. Anywhere I saw construction activity happening I was in. Every site had signs, ‘No Vacancies’ but they didn’t say ‘No Entry’”.
“On the third day, I was out looking for work, I found myself on Little Collins Street. There was a large site which had been excavated and the piling machines were preparing for a big build.”
“I walked onto the site and was confronted by the site foreman. ‘What do you want? he asked, ‘a job’ I told him. He then asked me what I do, which I responded ‘anything’. He then asked how long I had been in the country, “just 3 days I said. He then told me “Well lad come back tomorrow, and I’ll take care of you, as a fellow country man”
Sean smiles, “Three days, that’s probably the longest time you’ve spent unemployed hey Dad?”
The piling company was Frankipile Australia.
“I got back to the Railway Hotel and told the lads I’d got a job at Frankipile, they were impressed. I didn’t stay there long. I moved to work with a plumber but, I didn’t like that, and left to work on the Snowy Mountains Hydro scheme, tall blasting shot rock.
“I was working underground there and saw a lot of people get killed. I read afterwards that a worker lost their life for every mile of tunnelling we completed,’ said Mick.
During the 22-year construction course a total of 100,000 workers were employed, of whom 121 lost their lives in industrial accidents. Those workers were Australian-born, German, Greek, Irish, Italian, Norwegian, British,
Polish and Yugoslav.
“The tunnel was 5.5m wide by 7.3m high and we were tall blasting shot rock. There would be pockets you couldn’t see, and these would collapse on the workers. It was very dangerous work,” said Mick.
Whilst on the Snowy Hydro project Mick gets news that one of his mates who jumped off at Fremantle, was in hospital having had his appendix removed. Mick went to visit him in WA and never left.
“I decided to give Western Australia a go and started driving bull dozers in the rail sector, there was plenty of work. In the early 60’s, we had a narrow gauge rail line in the West, and it was decided we needed standard gauge railway line from East to West. Of course, this made sense, but it meant all the old gauge line needed to be ripped up and replaced.
“I started ‘spotting’ on the field for the truck and the dozer, helping them avoid the large rocks and over time the dozer operator would let me spend time in the dozer. Gradually I gained experience and ended up operating dozers for years.”
“I went to Esperance and that was hard work. Mick Caratti was an Italian man who worked you hard, but he was a good man and fair and if you did your job he looked after you.
“Being ambitious and not afraid of hard work, I decided I wanted to work for myself. I was in Port Hedland at the time and thinking about buying a dozer for myself.
“But I knew another Irish mate who was working with cranes. When I saw how the cranes were working and compared it to the pressure I put the dozer under every day, the wear and tear the work had on the tracks, buckets
Cranes and Lifting magazine had the absolute pleasure of sitting down with Mick and Sean Joyce from Joyce Krane and enjoyed the privilege of documenting the life of an absolute pioneer in the crane industry.
“The first crane, a 6t BHB crane cost $17,000 pounds and within two years Mick had saved enough money to buy his second crane, an 8t capacity BHB which cost him $27,000.”
cutting edges and teeth, I decided I wasn’t going to get a bulldozer or any other piece of earthmoving equipment. I was going to get a crane,” said Mick.
“To put things into perspective, Dad had been driving dozers for a decade and having never operated a crane, to then deciding he was going to own one was a big step, but it’s typical of Dad’s approach to work and life generally,” said Sean.
“Esperance was a good experience. I went there by myself, I had my own caravan and my own car, and we moved from place to place with the work. We were working for the Esperance Land Development. Mick Riley was managing the construction of the sites and a dam was built on each of the properties so there was a lot of dozer work”.
“Mick Carratti worked us hard. If it rained, and there’s plenty of rain around Esperance, he wouldn’t let you take the machine to the next site until the current site was finished and of course we were only paid if we were working the dozer,” said Mick.
“So, I’d be working the dozer, cloud would develop, and I would work the dozer until three or four in the morning to get the job finished. I’d work day and night if I knew rain was predicted, it was tough.
“When I told Mick I was leaving, he didn’t want me to go, and he gave me a lecture I never forgot. He told me you had to earn your money when you were young. Work hard and save your money. One of the supervisors told me why he was so keen for me to stay. ‘That machine made more money during
the six months you were operating it than it had done during the previous 12 months,’ I worked hard and saved my money,” he said.
Mick bought his first crane, a 6t BHB in 1974 and decided name the business Mick Joyce Crane Hire.
“When I met with my accountant he asked if I’d registered the business name and of course I hadn’t. He conducted a business search and someone in the US had registered Mick Joyce Cranes, so we went with Joyce Crane Hire. The K in Krane came later.
“Initially I wasn’t busy with the crane, it was tough. But the rail work was busy, and they knew I was a good construction equipment operator, so they offered me night work which I took. I was also offered accommodation, food and I was paid as well so I jumped at the opportunity,” said Mick.
By 1976 Mick had built a reputation for himself in and around the Cape Lambert area, a major port in the Pilbara region of WA. He was regarded as hard working and professional and he began working in Tom Price.
“I was moving around following the work. If I had to go to Pannawonica for example, the crane would go by train. The crane was loaded onto the flat bed and chained down in the afternoon, but they couldn’t tell me when the train was leaving because they didn’t know when it be would available.
“I’d park my car alongside the railroad and when the locomotive came in and coupled up, the noise would wake me up and I’d jump into the locomotive alongside the driver and get to Pannawonica that way. It saved me taking my car and all the wear and tear it would have suffered on that long unsealed road. I would frequently sleep with the crane if I was working on a critical job,” said Mick.
The first crane, a 6t BHB crane cost $17,000 pounds and within two years Mick had saved enough money to buy his second crane, an 8t capacity BHB which cost him $27,000. As the business grew, so did the town of Karratha, there was increasingly more
work around and Mick ensured that he employed locals. A practise that Joyce Kranes maintains to this day.
Through the 70’s and into the 80’s, he continued to work for Transfield in Tom Price. Transfield asked him to relocate to Mount Newman. He had a mate who owned a plane, and he flew over the Mount Newman and liked what he saw.
“We flew back to Tom Price, and I had pretty much made up my mind. I then had a conversation with a colleague at Rio Tinto who said there was a company called Woodside coming into Dampier that would make the projects we were currently working on look like a drop in the ocean. I thought, what am I doing going to Newman when there’s a major new player coming to the coast? That’s when I changed my mind and decided to come to Karratha,” said Mick.
Throughout the 80’s the business
continued to grow as Mick worked with Woodside and other major organisations in the resources sector. The fleet grew in size and capacity and in the mid 80’s he added a 50t Kato which was a big crane back then.
He continued to work hard but did afford himself some down time and his
travel south but there was civil unrest at the time. I read in the paper that a hand grenade had been thrown into a gathering of people and I decided I wasn’t going to go South and instead I decided to go to Cebu.
“I asked a friend where I should stay, and he said the Mercedes hotel. I
“The fleet grew in size and capacity and in the mid 80’s he added a 50t Kato which was a big crane back then.”
favourite holiday destination was the Philippines.
“I liked the Philippines and on one of my trips I became friends with a local guy named Bert who managed a fish farm. He had a boat which he used to make trips to the different islands selling his fish. Anyway, I got to know him, and we’d do the trips together.
“On one of my trips I was booked to
booked a room, arrived and checked in, then later that night there’s a knock on the door and it’s Bert,” said Mick.
“He said, ‘come, we are going to visit my relatives,’ this was Rebecca’s family. We arrived at the home and that’s the first time I saw Rebecca, my future wife. She was a seamstress, she’d been woken up and looked very sleepy.
“Over the coming days I met with
her a number of times, she was very curious about me and wanted to know where I came from, what I did, and of course her father didn’t like me at all. I came back to Australia, and we wrote to each other. Six months later I went back over.
“I asked her father Emigdio if I could take Rebecca to the movies or to a restaurant and I received a sharp no. He was very protective of his daughter. When he finally agreed he said, “wait there!” and he came back into the room with Rebeccas’ two brothers and her uncle. “They were her chaperones and I had to take them all out to dinner”.
It was only in 2007/2008 that Mick finally employed someone to manage the phone. Up until then, he used to answer all calls and write the details of jobs on his jeans. Mick was well known throughout Karratha for writing notes this way.
“Yes. I’d be driving and the mobile would ring, I’d stop the car, take the call and write the details on my jeans, a bit about the job, the number that sort of thing. I had to get Rebecca to buy light coloured jeans so I could see what I had written.
“There were many times when I called Rebecca to ask if she had done the washing. If she hadn’t, I’d ask her to read back the notes I’d written on the right knee of the jeans.”
Sean chimed in “You don’t know any different when you are young. You think it is normal for your parents to have a conversation about washing Dad’s jeans, and before they could be washed, he had to check that he had all the information from the jeans. This was a regular occurrence for our family”.
Mick continues with the family story.
“I’m not sure how Rebecca raised five children and helped me with the business which was starting to gain momentum. Fortunately, she took good care of James, our eldest, followed by Colleen, brother Michael, then Sean and Connell. She also took care of everything inside the home whilst I
worked hard on everything outside of it.
“We were constantly reinvesting in the business and didn’t spend money where we didn’t need to. We are still driving around in a Land Cruiser we bought in the late 90s and it suits us just fine,” said Mick.
Sean and his siblings were away at boarding school, but with every break they would be in the yard in Karratha. Here they spent time cleaning and greasing the machines, inspecting rigging equipment and learning more about the business from the bottom up.
“We might be lucky enough to go on a job with Dad every so often. But we would spend most of our time in the yard. Dad would put a crane on the pad, we’d clean it, he’d come along and inspect the work, point out where
were a lot of construction projects happening and the resources sector was rapidly growing.
“We had to purchase more cranes during this period, mostly Liebherrs. We were buying 100, 200 and 250 tonne capacity cranes. With our all terrains, anything above 100t capacity we have only ever bought Liebherr.
“In 2011 Dad purchased a company in Onslow (a town of 700 at the time) which is in the Pilbara. The business was Onslow Crane Hire. Dad said to me ‘I want you to go down and manage the hand over.’ I was 20 at this stage and I didn’t have much experience in the office or the running of the business, I was part of the operations team.
“But I thought I’ll get down there, get an understanding of the business,
“We might be lucky enough to go on a job with Dad every so often. But we would spend most of our time in the yard. Dad would put a crane on the pad, we’d clean it, he’d come along and inspect the work, point out where we’d missed spots, we’d fix these, and he’d move the crane and bring another one in for us to clean.”
we’d missed spots, we’d fix these, and he’d move the crane and bring another one in for us to clean. So, cranes have always been a big part of our lives,” said Sean.
The Joyce Kranes business really took a shift in the 2000’s. Sean takes up the story.
“In 2007 I left school. I had just turned 18 and started working in the yard. I would be running out rigging gear to various jobs, fuelling cranes, I wasn’t given a specific role, I simply did what needed to be done.
“And now, this is a big part of our culture at Joyce Krane. Yes, there are job titles but at the very core of the business is the philosophy, if a job needs to be done, we help each other out.
Over time Sean worked his way up to rigging and then crane operating. By 2009/2010 the business was growing with more cranes coming online. There
Dad would find someone to manage the business and they’d take over from me. I got down there and got to know the old owner, Bill Black, he was doing business from a Collins diary, very much like Dad had been doing,” said Sean.
At this stage, Joyce Krane had a team of people running this side of the business.
“I had come from an environment where we had a team running the business and the office was fairly automated, here in Onslow, I was back to a Collins diary run business,” said Sean.
“I’m calling Dad with updates and asking if he had found anyone to replace me and he would always reply, ‘Yes I’m working on it.’ I only went down with a duffle bag because in my mind I was only going to be there a couple of weeks.
“After a month, I’d call Dad and,
‘Yes I’m working on it’ was the answer. So, I decided to leave it and let him call me when he had found the replacement. After a couple of months, I realised this was now my job. I ran the Onslow operation for close to five years,” he said.
“Well, he was doing such a good job, we decided to leave him there,” smiled Mick.
Taking strategic risks with investments has been a theme within the Joyce Krane business.
“Like when you purchased the Liebherr 160t (LTM 1160/2) in 2000,” said Sean.
At that time this was considered a large crane in the North West of Western Australia.
“Yes. That crane gave me arthritis. I went to Germany to visit the Liebherr factory and to assess the crane which was second hand. It was a good looking
machine, well looked after and we agreed to take it. But the planned work we had bought the crane for, didn’t happen.
“I would be driving up the main road of Karratha to the yard and there would be this huge expensive yellow machine sitting there doing nothing, and I’d turn the Ute around, drive back into town and have a coffee with a friend. I couldn’t drive into the yard with it sitting there without any work for the crane or for myself.
“At the time my joints were sore, and the GP was draining fluid from my knees and ankles, he explained that stress can be a major cause of arthritis. That crane caused me so much stress and pain, because it had so little work at the beginning,” said Mick.
Sean reflects on the crane, and he can see how it was a positive move for the business.
Mick and Sean talk about the approach they have to the crane industry. Mick is certainly regarded by many as a pioneer of the industry and yes, he has taken risks and significantly invested in very large assets but the decisions around these investments have been based on customer requirements.
“For me, the investments we have made, over many years, have been about providing our customers with the equipment that meets their needs. Again the 160 and the LG 750 are examples of this; they were firsts for the market,” said Mick.
Mick goes on to discuss the relationship with Liebherr and why he has worked so closely with the brand over an extended period of time.
“When I first ventured into cranes, I hadn’t heard of the Liebherr name. But asking around, I knew the Liebherr
name had a good reputation, not only for cranes but for construction and mining equipment and other products.
“Initially, Liebherr cranes were represented by Gerhard Baden over in Sydney. “Gerhard made the trip to Karratha, well out of his way to introduce himself, and introduce me to the Liebherr product. I really appreciated it as I was out of my depth when it came to purchasing a machine of this size. I was dealing with him when we purchased the 160t. Then I got to meet the German management in the factories, they have been great to work with.
“When the 160t went to work we could see it was a great piece of equipment and there really weren’t any questions after that, we were and have remained a committed Liebherr crane business,” said Mick.
Sean is also a big Liebherr fan.
“In my experience, Liebherr is at the
“We stick with Liebherr and focus on the quality their machines bring to our business. Operators can move between the cranes because the operating system is fairly consistent across the entire range and so are the parts and componentry.”
forefront of technological developments in the crane industry. The cranes are extremely reliable and the service and support we receive from the team at Liebherr is second to none. Over many years, we’ve developed a great relationship with the Liebherr team.
“We stick with Liebherr and focus on the quality their machines bring to our business. Operators can move between the cranes because the operating system is fairly consistent across the entire range and so are the parts and componentry. So, from a service and maintenance point of view
the workshops don’t have to keep as many parts on the shelves,” he said.
After over 40 years in the business, Mick finally takes things easier. Living in Perth, he enjoys the company of his children and 5 grandchildren, who he hopes will one day become crane operators themselves. Turning 85 in October, it hasn’t been that long since he was last spotted in a crane. With his two sons, James and Sean at the helm of the business, he still enjoys regular reports from his sons and likes to stay in touch with old clients.
Alliance Engineering Consultants (AEC) knows that more than just a crane, a crew, and some rigging equipment are required to successfully complete a complex lift. Director Jeff Kazazi, Principal Consultant Len Sgherza and Lead Engineers Nick Birks and Steve Keating discuss the value of attention to detail in the design, understanding what’s needed for a high-quality lift plan, their lessons learned from decades in the industry and some high-profile cases where the basics have been ignored, producing near-catastrophic outcomes.
GRADUATING FROM UWA IN 1976 WITH an honours degree in Civil/Structural Engineering, Jeff spent the first five years of his career in the commercial, industrial and domestic sectors before moving into the oil, gas and resources industries. Jeff and Len have collaborated for the past 32 years and Steve and Nick have been at AEC for more than 13 years. Nick is the nominated CICA
AEC’s engineering experience has covered lifting and rigging systems, offshore, brownfield projects, front end engineering design, detailed design verification and management of structural projects.
The company also checks cranes for issuance of compliance certificates or certification for maintenance, including the 10-to-25-year major inspections required on some machines. The central aspect of its business, however, is lifting engineering, rigging design and problem solving and post failure subject matter expert (SME) incident reports for when things have gone awry.
AEC has invested considerable resources into software, surveying and inspection hardware and tooling, including an ‘engineers’ toy box’ of typical lifting gear items to ensure that the team can really understand what they are dealing with from a design and practicality point of view.
AEC personnel have developed lifting and rigging standards for a number of global energy companies. Sorting out problems
for clients by providing innovative options of lifting and rigging, Jeff says that at the core of many problems are a failure to pay attention to the core principles of lifting and engineering.
“Experience, attention to detail, collaboration and a respect and understanding of the physics involved in lifting heavy objects,” he says. “These are the fundamental aspects of getting lifting right, but we consistently see them ignored or misunderstood as recorded in our incident assessment reports.”
– Valve Access Platforms for LNG tanks: LNG tanks usually feature large valve access platforms supported on their roofs, where loads can exceed 400 tonnes. In some cases, the project team will look to save installation time by pre-assembling the complete platform at grade and then lift them into place onto the tank roof.
In one notable example, the designer of the transport frame and the valves support module made assumptions regarding the rigging stiffness that was in error by a factor of 10. To make matters worse, the designer of the rigging equipment (a separate company) also assumed loads paths that were not physically possible. The failure in communication between the original parties
and the lack of an independent thirdparty verification (which should have been considered due to the high risk) led to an initial failure that was noted at site at the start of the lift.
Thankfully the client’s reps put a halt to the lift before a potentially catastrophic outcome. Jeff says that when AEC was called in to investigate what went wrong and how it could be resolved, he and Nick were “staggered” by some of the errors uncovered.
“Nick worked on this project assessing the load, revising the rigging set out and designing custom lifting beams to resolve the issues,” Jeff says. “We found a number of what can only be described as ‘schoolboy errors’ because both the module designer
Nick, who has been in his role for nearly 13 years, says that communication is key when it comes to successfully managing lifts with multiple different parties, ensuring that everyone understands proper procedure and who is responsible for what.
“There wasn’t enough understanding between the parties involved before we came on to the project and had a look,” he says. “Each of them thought that some of the potential problems were being covered by one of the other parties, but they weren’t.” The commercial implications of the delay required to fix the problems were significant.
To the layperson the above items are the same but in reality, they are not. AEC recently became aware that a rigging crew, who were responsible for lifting a variety of heavy cargo items onto a ship, used a designated spreader beam, as specified by one person, but the team that took the job on decided to take matters into their own hands and change the rigging.
Setting up a rigging system that included three spreader beams, they used one main spreader beam with triangular rigging, and proceeded to use the other two as lifting beams.
“The spreader beam identification plate clearly outlined its working load limits, but the rigging crew picked it up in the middle of the beam, went to lift the item, just cleared it off the truck, and then it snapped and dropped the 45-tonne load back on the
“Twice we’ve had our people go down to a site to inspect the lifting procedures and be told to ‘butt out’ essentially,” he says. “Unsurprisingly, they got it wrong. So, combatting these attitudes of ‘I know better’ is something that we stumble across regularly, and they’re only fixed when people see how wrong it can go. Engineers ignoring sound advice from those more experienced does happen. Collaboration by all parties is considered key to a successful lift”.
One of the more recent high-profile out of control lifts that AEC has been contracted to resolve (for future lifts) was an out-of-control large swinging load.
Crane operations on barges or ships are subject to motions that can magnify under certain conditions which are not always apparent or foreseen. Procedures that state a maximum roll angle, period etc. are usually experience-based, and for good reason, but a rogue wave is not a predictable event.
The problem arose at a critical time of lifting when a load was about to be released from a fixed marine structure when a very long period swell passed through the operation.
Perhaps even more disconcerting was that, prior to the incident, the same crew had enacted the same rigging on a lift that was only marginally lighter – “luck”, as Melvyn calls it. AEC was called out to investigate and advise before any further lifting was undertaken.
Failure of rigging is a common theme in a lot of AEC’s incident assessment reports.
According to Jeff, however, it’s not the equipment’s fault; it’s an underlying misunderstanding for the load path and the capacities of the equipment that drives a lot of these failures.
Further to the theme of not carefully considering a lift plan, Melvyn also highlights the fundamental flaws in lifting procedures that AEC were engaged to review. Upon
discovering that the original installation of a flare tip appeared to have been “completed in a hurry” during construction, further investigation revealed that the initial operation had not been carried out according to the lift plan “at all”. When the facility came due for refurbishment works and the same lifting procedures were proposed to be used, AEC found the original rigging system procedures were “completely unacceptable”.
The original installation had been done by using a large crane and the replacement of an item at the top of the tower using the documented procedure had never been done before.
Working alongside those with practical knowledge of the cranes and other lifting equipment is at the core of AEC’s operations; after all, combining theoretical knowledge with practical experience is what produces
It’s through the experience of its engineers that AEC can provide a range of well-informed, practically proven solutions. Steve speaks of AEC’s experience at an LNG plant where the company’s services were engaged from the outset.
After being approached by the client because of its previous experience in performing engineered lift plans for the exact same type of equipment before, AEC was able to direct the client down the correct pathway to complete its lift.
“The job was for multiple large lifts in a marine environment, and the client wanted to use a heavy lift vessel for the job,” says Steve. “Immediately, we were able to show them photos and videos of a job where a heavy lift vessel was used, and that project was a near disaster. Because of the rolling motions, it was not a sufficiently stable lifting platform; for this exact job, you need a very stable lifting platform, such as a Jack-up Barge, because the last thing anyone wants is a crane that’s bobbing and moving around.”
“When the client sees what we show them, they’re instantly relieved, and thankful they’ve engaged a group that specialises in these jobs,” he continues. “Companies want to avoid delays, mistakes, incidents, and by employing AEC to complete the engineered lift plans they do exactly that.”
After all, according to Steve, who holds over 20 years of experience in the oil and gas sector specialising in lifting engineering, that’s where AEC is of most assistance; putting in recommendations for lifts and jobs that they’ve witnessed before, because they’ve investigated the exact failures before.
“When people employ our lift engineering services earlier on, we’re able to suggest certain pathways and we can design customised lifting equipment perfectly suited to the job at hand,” he says. “The result is that critical lifts go smoothly, without incident and client feedback is always positive.”
“For a typical offshore project, operators will send a team of around six-to-eight guys offshore, with the right skills in the right equipment to do that project within a specific time frame,” Nick says.
“It’s all driven by this requirement to plan really well, with extreme attention to detail,” he continues. “If you don’t have the right people planning these operations, the delays can result in cost blowouts and increased downtime; they’re just so, so common, which is why it’s so important to engage with a lift plan that pays attention to every detail.”
Steve concurs with Nick’s sentiments. Highlighting the value of engineered lift
plans in mining site shutdowns, Steve points to the millions of dollars per day that can be lost when shutdowns go over schedule.
“Every activity needs to be planned with a magnifying lens, because one day of delays could amount to millions of dollars of lost or deferred production,” he says. “Often the clients spend a lot of time in procuring various replacement components, such as mechanical components, turbines, rotating
safer, better result, whether that be offshore, onshore, or during construction.”
An important point that the AEC Team is quick to note, however, is their desire to operate in a manner that encourages participation from all parties in their associated fields of expertise. Crane hire companies possess practical experience in the field of lifting things, engineers possess a deep understanding of the physics involved in the lifting process, and OEMs hold the inside knowledge to its equipment and how it should operate.
“Engineers working with crane operators and lifting crews is the best way to go about it,” says Nick. “We don’t say we’re the experts in everything; but we are there to help avoid some very unnecessary and catastrophic failures that we have seen in our time.”
“When planning a high value lift, it is critical to ascertain the needs and expectations of everyone involved,” adds Len. “Often handling considerations for a single package need to encompass several locations including the workshop, the wharf and the installation location.”
equipment and control systems, but they sometimes give a lower priority to how they’re actually going to lift these items in and out, which is where we come in.”
After all, as Nick points out, when it comes to lift planning, crane hire companies make their money through exactly what they advertise: hiring cranes out for an hourly or daily rate. And that is where the value in AEC’s input can also come forth: applying customised, tailored, unique solutions to large and logistically complex tasks.
“There’s a difference between what we can do and what crane hire companies can do,” he says. “We come at things with a different focus and apply engineering solutions – not necessarily crane solutions – to all problems. Ultimately, we’re just trying to help our clients achieve a quicker,
“A clear understanding of the requirements of client specifications, multiple design codes, verifier focus, lifting equipment availability, site set out constraints, weather limits and site work practices is important to prevent hold ups through the various planning and execution stages,” he continues.
“It is only when you talk to the key personnel and step back and look at the whole process that you can see the best fit for the task at hand.”
“When people employ our lift engineering services earlier on, we’re able to suggest certain pathways and we can design customised lifting equipment perfectly suited to the job at hand.”
Every minute detail needs to be considered when detailing a lift plan, as seen by this derrick deconstruction completed with AEC’s help.
Based in Maddington, WA, cranes have been central to Ronco’s DNA for over 27 years. Commencing its major inspections services over 15 years ago, Operations Manager Mark Turner discusses how the company has expanded its workshop capabilities to accommodate the demands of almost any customer.
BOTH PLANT AND EQUIPMENT HAVE PLAYED a central role in Mark Turner’s life for the past 20 years. Indeed, as we’re talking, the Operations Manager at Ronco needs to pause the conversation to answer a call from a terminal manager about a crane being shipped into Fremantle Ports Berth 11.
“It’s been a challenging industry to work my way into,” he says, speaking of the cranes and lifting sector. “There’s been a lot to learn, but it’s very rewarding once you break down the initial barriers.”
“Other industries can be very exclusive and individualistic, but the crane industry provides very fulfilling relationships and is brimmed with people who want to help out. You just have to ask, and not guess. September this year marked my tenth year at Ronco and there is still a huge amount to learn; it never stops.”
Highlighting “Major Inspections” as a large proportion of the work completed at
Ronco, Mark says the range of work at the WA-based crane services company “keeps everyone quite busy”.
“We normally undertake anywhere between five-to-nine major inspections simultaneously,” he says, “and we’ll service any crane of any size – whether it be a spider crane or a crawler crane, we’ll take on the job.”
“All of our major inspections are supervised by a Chartered Professional Engineer per AS2550.5, and the engineer is involved the whole way through from our initial test lifts through to the CraneSafe inspection at the end,” he says.
Underlining his point are the eight cranes currently situated in Ronco’s 12,000 squaremetre main yard, undergoing the Major Inspection process inside its 1400 squaremetre workshop specifically designated for the repair and inspection services. With two crawler cranes, an articulated pick and carry
crane, two truck cranes, an all-terrain crane, a self-propelled EWP, and two rough-terrain cranes undergoing the Major Inspection process, Mark emphasises the importance of a quick turnaround for customers.
Ronco’s servicing capacities, which include a 4,000 square metre storage yard on the same street, can provide exactly that: a quick, efficient turnaround with a focus on minimal downtime.
“Sometimes it can take three, four, even five weeks to receive spare parts shipped in from overseas – especially since COVID-19,” he says. “There are absolutely parts that are imperative to receive from the same OEM, particularly parts pertaining to structural loads.”
However, some parts that are necessary for the operation of the crane don’t necessarily need to come from the same OEM, he says.
Citing hydraulic cylinder seals as a
“prime example”, Mark says Ronco saves its customers time and money by returning their cranes to action as soon as possible by using products that aren’t directly sourced from OEMs where applicable.
“For luffing, tele-boom, and outrigger jacking cylinders we prefer to use OEM seals. For all other cylinders we will use aftermarket seals where viable,” he says.
“If we can put the machine back in action in a more timely and equally as safe manner by using parts that we can source locally from aftermarket suppliers, we end up saving our customers time and money, and freeing up space in our workshop to help someone else. It’s a win-win.”
Helping the servicing and repair team
at Ronco’s workshop are three overhead gantry cranes, a large wash pad with raised walkways and an area dedicated to the machining requirements of the team.
In light of the massive loads cranes are capable of lifting, an aspect of their maintenance that frequently gets overlooked is their bottom half; after all, a crane still needs an engine to run, as Mark notes.
“Historically, the split in our job scope of works has been 30 per cent mechanical maintenance, compared to 70 per cent inspections or hydraulics and boom repair,” he says. “At the moment, however, we’re operating at 15 per cent mechanical versus 85 per cent inspections or upper section repairs.”
“When taking into consideration the crane as a whole, it’s the equivalent to a truck being fully loaded 100 per cent of the time,” he adds.
“When we go over crane carriers and drivetrains as part of the major inspections or servicing, we often find maintenance items that should have been addressed.”
This said, it is undeniable that boom repairs are of the utmost importance to the general maintenance of a crane. At Ronco, no boom is spared; every single boom type comes through their front gates, according to Mark. Whether it be a repair needed for a hydraulic telescoping boom, or a lacing replacement for a lattice boom, Ronco has the capacity to service all.
At the forefront of its boom repair operations is Ronco’s hydraulic boom straightening capacities. Citing the commonality of a “hook-strike” to both lattice and telescopic booms, Mark stresses the importance of dealing with these straight away, due to the fault-line they create in the boom’s structure.
“It creates an overall weakness that may result in the crane’s boom collapsing on itself at that fault line,” he says. “We employ a technique here to repair those kinds of faults in house, all per an engineer’s repair plan. Even corrosion repairs to structural surfaces can be undertaken once the engineer has provided a repair plan.”
“99 per cent of our repairs are completed in-house; being able to repair in house results
in a much quicker turnaround and much lower cost for the customer,” he continues. “There are times when we outsource our work a to specialist repairer because it’s just not feasible for us to complete some jobs. Ultimately, we want to make sure the right thing is being done by the customer, and sometimes that means sending the work to a specialist.”
That said, completing its repairs in house is a source of pride for the team at Ronco. After fulfilling any structural repairs, the team uses the ample space in its yard to complete load testing at 125 per cent capacity per the Australian Standards to ensure the structural integrity of the machine they’ve serviced is intact once again. What these operations all need, however, is competent staff to fulfil the services Ronco can offer.
Citing the pandemic as a turning point, Mark says all businesses faced the same problem: the available staff pool dramatically decreased, leaving them all chasing the same
resources. Whether it was a repairer, a hirer, or a primary contractor there “just wasn’t enough” to go around for everyone and it had “an impact”, he says.
“During COVID-19, we were looking for the ‘right’ staff: people that were experienced and had been in the industry for five or ten years,” he says. “They just weren’t there. And so, we took a step back and acknowledged that, if we weren’t training younger people, how could we expect to be finding good quality workers?”
It’s a mindset that’s paid off for the WA-based crane services company. Now employing four apprentices and a team of 15 service department staff, Mark notes
Obtaining the credentials to safely drive an articulated steering mobile crane on-road
the importance of getting the right people on the right jobs at the right time when it comes to servicing and maintenance.
“We want our staff to be fully trained up and completely comfortable with the tasks being asked of them in the workshop,” he says. “There are services that we’ll outsource to certain trusted specialists, or repairs and tests where an engineer will come in and oversee what we’re doing to ensure the safety and compliance of the process.”
“Ultimately, it comes back to a customer centric focus; how can we, at Ronco, employ our resources in the most efficient and effective manner to ensure the people who engage us leave happy.”
“99 per cent of our repairs come from in house; being able to repair in house results in a much quicker turnaround and much lower cost for the customer.”
Norwest Group specialises in the provision of integrated crane, project logistics and labour services for major mining and resources companies. Norwest Crane Hire forms part of the Norwest Group, a proud family business originating in the WA Pilbara, and is the leading crane service provider in the North West region of Western Australia.
A KEY ELEMENT OF NORWEST CRANE HIRE’S commitment is the significant investment it has made in enhanced onsite leadership and presence within its Pilbara operations to ensure its industry leading standards of safety, quality, performance and client service are maintained.
These standards have been the foundation
for the successful growth of the business. This investment by Norwest Group’s Owners and Founders, Bernie Johnson and Toni Jessop, to elevate safety, quality, connection and trust within the Group’s operations, processes and culture, has included appointment of a new Executive Management team. Graeme Parker joined in the role of Group Chief Operating
Officer, bringing a wealth of knowledge in finance, governance, commerce, leadership and strategy. Further, Travis Lee-Gowland was elevated to the role of General Manager – Cranes, Personnel and Safety.
An enhanced leadership and support team has also been appointed within its crane operations, including an increased team of
on-site Supervisors and safety resources, and two new appointments and roles in Allan Buchan (NCH Operations Manager) and Jardine Pitt (NCH Planning Manager).
Travis has been with Norwest for four years and has a wealth of experience, having worked for other large crane businesses. He spent some time in the resources sector working in the Pilbara before joining Bernie, Toni and their teams.
“I knew Bernie and Toni from our BOOM Logistics days, and I’d always kept an eye on their business and kept in contact with Bernie. When the right opportunity presented, I grabbed it.
“Ultimately, my role is to look after the operational performance across Norwest Crane Hire, including safety, which is a key element of our operations. I am also responsible for our Norwest Personnel division, which provides labour that supports
much of our work in the Pilbara, including shutdowns and other projects.
“As the business grows, we are becoming a sustainable business that looks after its people, our Norwest Family. To match the growth, we’ve altered our structure and now have a Planning Manager and an Operations Manager to each bring different areas of expertise to come together as a team,” said Travis.
There is a strong focus on safety throughout Norwest Crane Hire.
“We have the policies and procedures needed for a high-risk industry, but the difference that separates us is we really engage with our guys on the ground. Our HSEQ manager, Peter Kagioulis, and his team have done a really good job of breaking down barriers when it comes to being able to talk openly about safety.
“Most of the processes, safe work plans and work instructions have been developed in conjunction with the guys on the ground. This makes them feel connected and part of the process, they then own and trust it, and because they’ve had that ownership, this flows down to them talking to their colleagues about why it’s important. Everyone needs to do the right thing and look after each other to ensure everyone goes home safe,” said Travis.
Travis explains how his team manages personnel when it comes to high-risk work environments, high pressure, odd hours, and the time pressures involved in mining shutdowns.
“Providing people with advanced notice of what’s coming is important, our leaders and planning team take into account fatigue when planning shutdowns. Summers in the Pilbara are incredibly hot, so we do our best to look after our guys. If people are struggling
in any way, we support them and prioritise their health, safety and welfare.
“It’s a tough industry with long hours but that’s the game we’re in. Ultimately, good open communications, genuine empathy towards our people and fostering strong connections and understanding with our clients, means we all go home safely at the end of the day,” said Travis.
Travis provides an overview on the Norwest Crane Hire fleet.
“We currently operate 44 cranes, ranging from our 25t Frannas, all the way up to our Liebherr LTM 1650-8.1 All Terrain. Bernie has a strong and trusted partnership with Liebherr and we only have Liebherr cranes within our slewing crane fleet. We have a varied fleet of assets from All Terrains to Rough Terrains, and we also have hydraulic crawler cranes,” said Travis.
“The fleet provides us with the flexibility to meet the different needs of customers. We have a base in Port Hedland, with depots in Newman and Tom Price.
“Through our strong relationships with our partners, we are also able to base some of our equipment at our major partners’ sites, so that we can be flexible and efficient if we need to move and we need to move fast, which is often the way,” said Travis.
With operations across the Pilbara there is a significant labour requirement, he says.
“From a personnel point of view, we have approximately 20 full-time operators, with close to 150 people, and growing, available through our labour hire division, Norwest Personnel.
“This supports the flex of the business when major shutdowns are on and across the different customers. We have to be agile, and we have to be flexible to ensure we can
deliver the highest level of service to our clients at short notice.
“We are a truly local Pilbara business built and started in Port Hedland by Bernie and Toni. Actively, our business wants people to live in this region and we want to invest back into the local communities. We have really strong relationships which have been built over many years and these are the foundations for the business. The business succeeds through building trusted relationships, that’s how Bernie and Toni started the business and that is how it continues to run,” said Travis.
Two such trusted relationships are the loyal and committed relationship Norwest Crane Hire has with Liebherr, and the alliance between Norwest Crane Hire and Tambourah. “I understand the need for the best quality equipment to attract and retain the best operators, hence why we only partner with Liebherr,” Bernie said.
“It’s a commitment from both parties and leads to a higher service standard for us and our clients. Liebherr cranes have a proven reliability for the Pilbara area where some other brands struggle. Another upside is we only run one brand, which saves on a few fronts, such as VOC’ing the operators to one brand, and with maintenance it means our mechanical staff are trained by Liebherr.”
Tambourah is a 100 per cent indigenous owned and operated industrial services company. The alliance is based on the strong bonds and decades long friendship between Bernie and Toni and Tambourah owner and founder Bill Coffin. Norwest and Tambourah are in discussions to grow and enhance this alliance and form a stronger partnership going forward within the Pilbara.
Bernie takes up the story.
“Back in the mid 1990’s Bill and I worked together at Brambles and our friendship has gone on from there. When Toni and I started our own business, Bill bought a crane, which we leased off him. Our relationship developed and so did the equipment. We now lease from Bill’s company Tambourah, trucks, cranes, cars and labour. We are now having positive discussions about enhancing the alliance,” said Bernie.
Bill explains the background to Tambourah, his family’s history in the region
and how the relationship works with Bernie and Toni and the Norwest teams.
“Tambourah is an area south of Port Hedland that was an old gold mining district. That’s where my father was born, and he grew up there with his brothers and sisters. I picked the name because of that.
“I do a bit of labour hire for Norwest, and they lease equipment from me. We’re looking at extending that and getting more involved in community engagement programs as well.
“My family has been associated with this region for generations and interestingly my grandfather owned a local station which was called Redcliffe, this is now the BHP Rail Camp Redmont,” said Bill.
Broadening the alliance is particularly aimed at bringing youngsters into the industry, says Bernie.
“The labour side of Bill’s business drives cranes for us. But we are exploring with Bill another initiative around training and bringing indigenous and non-indigenous youngsters into the industry through training programs and pathways.
“We plan to present the crane industry as a viable career path and future opportunity for the next generation. Cranes is an industry that they may not know, and this program
Allan Buchan is Norwest Crane Hire Operations Manager. He highlights the priorities for onsite leadership within Norwest Crane Hire.
“Safety and client deliverables are always our priorities and also making sure our staff feel connected and are looked after, because at the end of the day, happy staff make for a safe and committed work force.
“Having the personal and professional capabilities to deliver a continuous safety-based culture within Norwest and performance deliverables to our key clients makes me strive to be better each day. Walking what I talk to my team also assists with improving our standards and setting the bar higher in the field,” he said.
“Having quality in the field, safety focused leadership, and the HSEQ team to bolster this, allows Norwest to take a proactive attitude in this space. Identifying potential risks at an early stage and mitigating these risks with JHAs etc, allows us to be one step ahead, quality pre-starts in the field daily with prior incident learnings delivered keeps our safety focus on the job.”
Allan goes on to explain how Norwest continues to succeed in an extremely competitive environment.
“All our customers have differing
could be part of the enhanced alliance.
“The idea of partnering with Bill is to make it a bigger project and to really get a footprint on the Pilbara Region generally, not just Port Hedland, but Newman, Tom Price and other communities, and to ensure we invest back in the right way to the community we operate within,” said Bernie.
Community engagement is an important strategy for the alliance, says Toni.
“A certain amount of dollars is set aside each year for local sponsorship. The community benefits from this strategy through sponsorship of sporting teams, events and charities. We believe it is important to give back to the local communities where our staff live, wherever we can.” she said.
requirements and Norwest has adapted an approach of tailoring requests to suit. This is done by making sure we have the correct equipment, including lift studies and lift plans, and that the personnel selected for the job are at the top of their game and fluent with the asset and the job-scope itself.
“Norwest sets itself apart from all the other industry competitors by delivering a quality service to all our clients, having very competitive pricing, and having the “family” feel to the business which helps us develop the best relationships with our stakeholders, staff and clients,” Allan said.
“With the outstanding HSEQ team at Norwest, our safety culture is second to none. By adapting a proactive attitude, our staff continually engage with external safety
“All our customers have differing requirements and Norwest has adapted an approach of tailoring requests to suit.”
professionals in the field and take a proactive approach to safety on the front line.”
Jardine Pitt is the Norwest Crane Hire Planning Manager, and while he has been with the organisation for four years, but he has been around cranes for over 20 years.
Explaining more about his role with Norwest, Jardine says that detailed planning for mining shutdowns is essential.
“My role plays a pivotal part in supporting the operations team, primarily through client engagement and project execution. Our process of assessing project requirements, conducting site visits, and determining crane specifications, aligns with industry best practices.
“Furthermore, the role extends beyond just planning, encompassing project quoting, scheduling and deployment, and using my site-based experience to contribute to the end outcome,” says Jardine.
“The FIFO arrangement that I work alternates between onsite, Port Hedland and with the support team in Perth, bridging the gap between field operations and the office. This approach is valuable for maintaining communication and coordination across departments.”
An additional key part of the Norwest Group is NGL Projects (NGL), which was conceived five years ago by Bernie, Toni, Jordan Rose (NGL Projects General Manager) and Niall Lucas (NGL Projects Operations Manager).
NGL is an end-to-end project logistics operation, specialising in freight forwarding of oversized, heavy-lift or time sensitive equipment and assets.
NGL specialises in moving unique equipment that doesn’t fit in containers, including oversized and heavy machinery, from various locations such as China, USA or Africa mostly into Australia. NGL’s clients are predominantly the tier one miners and their subsidiaries and suppliers.
Jordan takes up the story. “We are essentially a team of project managers specialising in supply chain management. We engage subcontractors in every phase of the operation, from the manufacturer’s facility through to the client’s end site.
“And because that changes every time, they’re buying equipment from different locations all over the world, we have a network of agents and subcontractors that we use, depending on what type of cargo it is and where in the world it needs to be moved.”
“Our largest clients are in mining, and we’re particularly strong in rail-related projects where we move a lot of rolling stock, locomotives, ore cars, ballast wagons, specialised track machines. We also work in rail infrastructure including steel rail and sleepers, with this comprising a reasonable portion of the business.”
“We are also involved in structural steel
for the same sort of clients, modular-type construction and more recently we’ve been working in the aviation space moving helicopters and aviation parts,” said Niall.
“The locomotives are probably one of the heaviest bits of kit on mine sites. They are around the 200t mark. We also facilitate the movement of mining dump trucks and trays. The structural steel attached with those projects are all oversized and definitely get up there in weight.”
NGL works closely with Norwest Crane Hire on many of the mining related projects and they are happy with the growth of the business, says Jordan.
“We will get contracts from mining companies and Norwest Crane Hire acts as a subcontractor to us. We could win a project for a mining client in Western Australia and our part would be to deliver wagons, we would hire in the best crane to lift them.
“Essentially it’s a relationship where we’re engaging the Norwest Crane Hire team to do work on our behalf, while we coordinate the overall movement and manage the site operation.
“Over the last five years, the growth of the business has been great, it’s been sustainable and consistent and we have built a strong team of skilled operators.
“Over the last few years we’ve diversified in terms of region by expanding to Queensland and South Africa, and also in the types of services that we offer. We now have a greater capacity in the general freight space in addition to the project logistics.”
“As Niall said, we’ve also diversified into aerospace and aviation equipment. We’ll look to continue to diversify in terms of the types of cargo that we are moving and clients that we’re targeting, as well as the regions we operate in.
“We’re looking very closely at further expansion internationally, potentially another office here in Australia. We are excited about the future growth opportunities and our ability to target these opportunities and deliver results for our clients.
“The repeat business and loyalty we have with our larger clients is testament to the trusted partnership we have built, the understanding and connection we have with them, and the quality service delivered by the team,” said Jordan.
WATM is a Western Australian family owned and operated company that was established in 1974.
WATM sells and provides support services for cranes and lifting equipment and has distributions rights for a number of cranes and forklifts, including:
Exclusive WA distributor for Manitowoc Cranes (including Grove mobile cranes)
Exclusive WA distributor Hiab range of vehicle loading cranes
Exclusive WA Pettibone dealer across Australia and APAC region
In 2014, mining giants BHP issued an order that no vehicles could travel underground without a wet-brake system. With the technology unavailable when BHP called for tenders for a crane that met its requirements in 2022, Burralga Industries – still only in its infancy as a business – reached out to DRA Engineering’s Humma with a six-month time frame and a very specific request. Humma delivered.
TIMES OF CRISIS BRING ABOUT INVESTMENT, and with investment comes technological development.
History corroborates this; if it weren’t for the Second World War, the world would not have accessed nuclear energy as quickly as it did. If it weren’t for the Cold War, who knows if the internet would have even been developed. Because of a global pandemic, governments threw millions into developing a vaccine as fast as they could to restore business as usual across the globe.
It is for precisely that reason that, after identifying an issue within global crane operations in underground applications, BHP issued an order in 2014 that no vehicles could travel underground if they did not possess a wet-brake system. There was one problem, however; no such crane existed.
With underground vehicle standards having been updated to minimise the risk of a fire breaking out, BHP sought to resolve the issue by contacting all known crane suppliers to see what they could come up with. However, no existing companies on
site – or even manufacturers – were willing to apply the braking system to their cranes.
“It asked all the crane companies at the site if they could supply anything that resembled its demands,” says Andrew Pretlove, Director at Burralga Cranes. “None of us held anything within our capacity; what they were asking for just didn’t exist.”
Based in WA, 12-month-old business Burralga Industries operates cranes all throughout the Australian mining industry, with a heavy focus on Central Australia, Northern Territory, and its home state. By Andrew’s own admission, the Indigenousowned company is “slowly growing”.
Andrew, with 15 years of experience behind him, saw the mining giant’s unique request for wet brakes on a mobile crane as a chance to grow with the development of new technology.
After encountering roadblocks with numerous other brands, the Olympic Dam team contacted Humma after hearing about the crane’s performance in the Iron Ore
mines in WA. Explaining the specifications, the DRA Engineering team suggested the Humma 35 Mk3 as the crane to fit the wet brake system on; within eight weeks, Humma had sourced the brake componentry from overseas, redesigned the crane’s chassis to accommodate DRA’s design of the wet brake installation and submitted its designs and pricing for the manufacturing of the Underground Series.
After the designs and pricing of the new crane were approved, tenders were sent out in August 2022; however, none of the major crane hire companies operating at Olympic Dam could responded. Burralga Industries, seeing the potential in the machines, then contacted Humma asking for a quote on supplying a Humma Mk3 that could meet the requirements outlined and could be delivered by January 1 2023.
Humma delivered. Receiving the quote in August, a crane that met and performed to the outlined specifications was provided to the Olympic Dam mining site on January 1, 2023, and the Humma 35 Mk3 Underground series commenced its career in the mining industry; and, according to Andrew, the crane is “just next level”.
“It’s revolutionary,” says Andrew. “This is the first crane that’s compliant with underground specifications, and as soon as other mining companies introduce this level of safety on site, they’ll realise that it was the Humma brand at the forefront of it all.”
With the development of this gamechanging crane, Andrew highlights the
potential for growth for both Burralga Industries and the Humma 35 Mk3 UG series, saying the company wants to “build its standing with the Humma brand”.
“We want to position ourselves as the company that contractors look to when it comes to renewing the older machines in their fleets,” he says. “Because this crane from Humma is the world’s very first crane installed with wet brakes for underground mining, we feel we can do exactly that.”
Thanks to Humma’s installation of these brakes, the chances of an event such as a fire caused by overheating brakes is reduced significantly, ensuring the safety of those working around and that production can continue reliably. At the Olympic Dam mining site, one of the world’s most significant deposits of copper, gold, and uranium, located 560km north of Adelaide in South Australia, safety, reliability, and productivity are key.
“As far as the crane’s safety features go – with its computer system that operates in tandem with the wet-brake system – the machine is simply outstanding,” Andrew says. “Additional to the safety features, our team are really enjoying the crane’s functionality: it runs really smoothly thanks to its suspension, it works faster, harder and longer than anything we’ve experienced before, and it lifts a lot for its size in tight, confined spaces which is invaluable on underground mining sites.”
As is Humma’s policy, all new developments must be field tested and debugged prior to market release. Considering that the wet brake was a ‘first’
in tandem with overall structural changes to the crane’s chassis, the engineering team wasn’t 100 per cent positive on the overall impact on the electrical system.
Humma, however, was working to a tight deadline; aiming to deliver the crane by January 1, 2023, the manufacturers agreed to supply the crane under lease conditions for the first six months of the purchase on the grounds that, should the crane not perform as expected, Humma would be able to re-
and, six months later, Burralga Industries was able to take full possession of the crane, with Andrew highly complimentary of Humma’s post-sale service.
“There’s a myriad of other features and technologies that go into producing a compliant crane for underground conditions, including different lights, speed restrictions, an underground alarm system,” he said. “Humma’s post-sale service in making sure the crane was performing exactly as it should was incredible.”
“Whenever we have any questions, we can ring up day or night, and we’re going to get some on the other end of the phone,” he continues. “It’s important to Humma that whatever issues we’re experiencing are resolved either on the phone, or a fieldtechnician comes out to help us.”
DRA’s Humma Failsafe Driveline Wet brake system can be fitted to all Humma mobile cranes providing an Emergency Failsafe Wet Brake Solution for underground mining applications. Additionally, the system can also be used for operations above ground where brake contamination or failure are notable risks.
Boom Logistics has made the decision to purchase a new XCMG XGC320. General Manager of Boom Logistics - West Coast Lester Fernandez discusses the reasons for purchasing the crane, the brand’s reputation and the allure of working for the ASX-listed company.
IN THE RAPIDLY EVOLVING WORLD OF crane services, keeping pace with industry innovations is not just an option; it’s a necessity. Companies that fail to adapt are left behind, while those that embrace change set the standards. One company embodying this is Boom Logistics.
Since its inception, Boom Logistics has been at the forefront of the crane industry in Australia. With a reputation built on trust, precision and a consistent record of selecting top-tier machinery, Boom has carved a niche as the market leaders in crane services. Boom’s recent purchase of the XCMG crawler crane underscores its commitment to stay ahead of industry trends.
The decision to invest in XCMG’s crawler crane wasn’t made overnight. Lester Fernandez, General Manager at Boom Logistics, shared the company’s rationale,
labelling the choice as “strategic”.
“Analysing all operational and financial metrics, the XGC320 emerged as the best fit for our needs,” he said. “The crane’s robust post-sales service support, outstanding quality and cost-effectiveness made it the ideal choice for the company’s fleet.”
The XCMG crawler crane’s introduction signifies more than just a machinery acquisition; it heralds Boom Logistics’ readiness to meet the future demands of the industry. As the crane industry grapples with the challenges of sustainability, costefficiency and technological advancements, the XCMG machine promises to address these issues head-on. Lester, with his broad experience in the crane industry, recognises the sector’s challenges and opportunities.
“The crane industry is demanding. It requires successful companies to operate at
their very best,” he says. “Every piece of machinery we invest in, is a testament to our unwavering commitment to excellence.”
For Boom, it’s not just about procuring new machinery; Lester speaks about the spirit of innovation that runs deep within the company.
“We don’t just acquire; we innovate,” he says. “The introduction of the XCMG crawler crane is a manifestation of our commitment to innovate and set new industry standards.”
With the XCMG crawler crane set to be operational by mid-November, industry experts are keeping a keen eye on Boom Logistics. There’s a palpable excitement about how this new addition and the other recent changes will reshape operations, not just for Boom Logistics, but for the industry at large.
In the ever-dynamic landscape of crane services, having a sturdy hand at the helm is crucial. As discussed in the August edition of Cranes and Lifting, the company is now starting to place itself at the forefront of social issues when it comes to its ESG initiatives. Lester points to the company being a “new and rejuvenated” one over the past few years, especially after changes that resulted in Ben Pieyre being appointed as permanent CEO in June this year.
“The biggest catalyst for change is working with good people,” says Lester. “For me, Boom ticks all the boxes in that space; I’m surrounded by competent, driven people who possess a good character, which I believe is very important at the leadership level.”
Being the only crane company listed on the Australian Stock Exchange is no mean feat. Boom isn’t merely seeking to maintain its market leadership; the company aspires to set the gold standard for the industry.
“Our goals stretch beyond revenue,” Lester elaborates. “We’re pioneering ESG initiatives, striving for a sustainable future while ensuring top-tier service.”
The recent introduction of the XGC320, the new XCMG crawler crane, is a testament to this forward-thinking strategy. While its European counterparts may be more recognised in the industry, the XCMG stands out not only for its competitive price point but also for its outstanding post-sales service and the robust partnership with distributor heavyweights like RONCO. It’s this focus on quality, backed by sound economic reasoning, that has allowed Boom Logistics to consistently deliver stellar results.
“What sets Ronco aside from other distributors, dealers, and service operators is that, in my hour of need, I hold full confidence in Ronco to answer my call and work with me to find a solution,” he says. “Buying a new product and knowing that there’s a warehouse and depo in Karratha, spare parts, and technical assistance on standby is really important to me,” he continues. “It’s a credit to XCMG and the thought the people in charge gave to appointing the dealers responsible for its products in Australia.”
Early adopters in the crane domain, such as Lester, alongside distribution agents like Robert Smith of RONCO, are now looking
at brands like XCMG in a new light. The trajectory of XCMG mirrors that of Asian automotive brands from decades ago, which evolved from underdogs to leaders in their respective segments.
Lester, shedding light on Boom Logistics’ decision to opt for XCMG, says: “our commitment is rooted deeply in safety, service, quality, and performance. The XGC320 choice, backed by thorough market analysis, symbolises these values.”
With its strategic affiliations and a passion-driven team, Boom Logistics is perfectly poised for growth. As the XGC320 becomes operational, all eyes will be on how this new asset performs within the crane service industry.
However, machinery is just a part of the equation. It’s the cohesive vision, shared by the leadership and every member of the Boom Logistics family, that promises a brighter future for the crane industry. This unity, combined with their tireless pursuit of innovation, ensures that Boom Logistics remains a formidable force in the sector.
“Our journey with the XGC320 is just the
beginning,” says Lester. “We’re exploring multiple avenues, pushing our boundaries, and constantly redefining what it means to be at the forefront of the crane service industry.”
Ultimately, one sentiment resounds: under Boom’s dynamic leadership and the spirit of pacesetters like Lester Fernandez, Boom Logistics is not just shaping its future, but that of the entire crane industry.
Verton Technologies has a proud history of working with and in the Western Australian economy. With plaudits received from various interest groups across the mining and offshore industries, Verton’s revolutionary load-stabilising technology is lifting the safety game to new standards.
THE TALE OF VERTON TECHNOLOGIES IS symbiotic with the story of the lifting and rigging industry in Western Australia.
Even before the company was brought into being, founder, owner and current CEO Stan Thomson began his career in the state at an iron ore construction site in the Pilbara region back in 1978. In short, the company has always held an innate understanding of the challenges posed to the mining and construction industries out west.
Verton has always sought to provide safe, stable and precise lifting solutions to whomever engages the new technologies from the Brisbane-based company, and it does so through its range of modular spreader beams.
The technology itself is revolutionary; Verton’s Everest SpinPod series does all the things expected of a modular lifting spreader. Holding capacities ranging from 5 tonnes through to 200 tonnes, depending on the
generation, Verton’s technology holds a key point of difference: remote-controlled loadstabilising, gyroscopic technology.
“The concept of removing taglines and removing people from the presence of a suspended load is central to the work that we do at Verton Technologies,” says Business Development Manager Marcio Casagranda.
Where this concept is ultimately at its most present is in the mining and offshore sectors. Encountering environments where cranes can be thrown off balance and where efficiency and safety need to be optimised together, Verton sees a lot of investment in its products come from Western Australia.
The very first recipient of Verton’s firstgeneration SpinPod came from Western Australia, as Marcio highlights. Adding that the first purchaser of the third generation of SpinPod technology was a mining company also based in WA, and it’s clear to see the close relationship Verton Technologies has
enjoyed with a range of different companies based out west.
“For Verton, we’ve always enjoyed a prosperous relationship with clients engaging our services from the mining and offshore industries,” says Marcio. “In our experience, these are the companies prepared to engage with new developments in technology and really invest in providing the newest and latest safety measures.”
In WA, the resources industry accounted for 46 per cent – or $186.8 billion – of the state’s Gross State Product (GSP) last year. In 2022, the state achieved its highest ever sales of $246 billion whilst simultaneously employing people in 117,970 full-time equivalent roles in the mining industry.
What this means is that there are a lot of moving parts with high-stake risks associated in the WA economy. Cranes are a fundamental element of shutdown maintenance, and safety is paramount, with
According to Marcio, Verton’s track record in the mining industry shows that the company’s technological solutions for removing people from around the load only substantiates the efficacy of its products.
“Our products have consistently been taken up by the likes of Roy Hill, MACA, and Mineral Resources,” he says. “In the shutdown and maintenance aspect of mining, businesses are bleeding money; everything needs to be planned accordingly, and everything needs to be executed according to
“When there’s an increase in lost revenue, more risks are taken,” he continues. “Our technologies provide a safer lifting solution in a stable manner producing precise results, in turn providing greater efficiency and less downtime.”
This, according to Marcio, is evidenced by the prominent role Verton’s gyroscopic technology played in facilitating the removal of 30 transformers for Roy Hill. Operating in the harsher climes of the Pilbara region, Roy Hill was expecting to complete the
maintenance work within eight days, as previous experience had shown this was the normal timeframe.
With Verton’s SpinPods being used, the maintenance crew only needed five days to complete the tasks at hand. Jeremy Whiting from Kutharra Cranes – the company enlisted to complete the shutdown at Roy Hill’s mining site – spoke of safety being “number one” during the process thanks to Verton’s Everest 6, as there was “no need for taglines” and riggers were able to be kept “out of the line of fire”.
“This is emblematic of the work that our technologies do,” says Marcio. “Our SpinPod series removes people from around the load and removes the need for taglines. Because of that, there’s less people involved, resulting in a much safer, streamlined process.”
It’s not just in the mining industry where Verton has seen its products thrive. Revealing the company has sold 12 units of its third generation SpinPod technology to an offshore resources company, Marcio says the load-stabilising technology underpins the level of safety involved in intensive lifting environments.
“When a crane – or other associated lifting equipment – is conducting its lifting from a barge, it’s operating in an unstable environment in hostile conditions,” he says. “The benefit of our technology is that it can hold these loads stable without anyone needing to be near them, resulting in extended, more precise lifting procedures conducted in a safer manner.”
Verton doesn’t just see its products stay local, either. Adding value in a range of industries – whether that be stabilising loads in the offshore environments, increasing safety in the maintenance of mining equipment, or lifting bridge beams or panels in the construction and infrastructure industries – Verton’s products can now be seen in Europe, North America and South America, according to Marcio.
“This exemplifies the manner in which our load-stabilising gyroscopic technology is revolutionising the crane industry,” he says. “Guided by our three principles of safety, stability and precision, we want to create as safe a lifting environment as possible to ensure that everyone can go home safely at the end of the day.”
MCT Equipment’s booth at the 2023 national CICA conference is set to feature the company’s standout products and its latest international collaborations.
THE STAGE IS SET, ANTICIPATION IS HIGH and MCT Equipment is ready to attend the much-anticipated 2023 CICA Conference.
The Perth Convention and Exhibition Centre will be buzzing with activity as MCT Equipment takes centre stage with a captivating booth showcasing a full telehandler display. The stars of the show will undoubtedly be the highly acclaimed Magni RTH 7.26 and Magni TH Fixed Boom, Winch and Basket. These groundbreaking machines have been garnering attention for their unparalleled performance and unwavering reliability while setting new industry standards.
Driving this developing enterprise is none other than the Managing Director of MCT Equipment and CICA WA Chair, Anthony Grosser. With a long-standing relationship with CICA WA, Anthony’s contributions – and those of the team at CICA WA –continue to develop the industry’s trajectory in the region. The involvement of Anthony’s son James Grosser and the team at MCT further strengthens the family alliance and reinforces confidence in a prosperous future for MCT Equipment.
Collaborations with international industry leaders have opened doors to exciting prospects, promising ground-breaking innovations for the Australian market.
These include groups such as Magni with its impressive telehandler range, JMG Cranes and its innovative electric cranes, and Cimolai Technology, a heavy machinery
giant for rubber tyre/rail gantry cranes, flat bed trolleys and self-propelled transporters.
MCT Equipment’s international network of trusted partners enables it to source required equipment, managing every phase of the process to deliver high-quality machines ready for operation. With access to an extensive range of equipment and the ability to refurbish machinery from companies such as Terex, Tadano, Liebherr and more, MCT ensures a seamless experience, from training and handovers to repairs and modifications. Its dedicated team collaborates to ensure clients receive the required equipment with minimal downtime.
A key element of MCT’s success is its workshop rebuild division, underpinned by efficient processes. Its major inspections for mobile cranes have positioned MCT as a leader in the market, driven by meticulous approaches and strategic planning.
In January 2023, MCT Equipment made a substantial investment by opening a state-
of-the-art 5000m² workshop and office facility in Henderson. This purpose-designed infrastructure bolsters the company’s agility and responsiveness to market dynamics, enabling it to cater to evolving client needs. To further increase its capability, MCT has taken on a second 6000m² yard to service larger machines – including crawler cranes.
MCT’s vision is one of a fresh perspective and an unwavering commitment to ‘Think different, lift different’. By encouraging the industry to break free from conventional practices, it aims to redefine and elevate lifting to new heights, setting a precedent for the entire Australian lifting industry.
The 2023 CICA Conference is the perfect opportunity to witness MCT Equipment’s transformative innovations firsthand.
Visitors can head over to the booth during the event to engage in discussions, explore the machinery on display and learn more about the advancements shaping the lifting landscape in Australia.
WITH A RICH LEGACY SPANNING 50 YEARS, WATM has continuously evolved to meet the ever-changing demands of the market and has proven itself as a reliable partner for crane solutions in Western Australia.
In 2023, WATM achieved a significant milestone by winning the prestigious Manitowoc Crane Refurbishment Award. The award serves as a testament to the company’s commitment to excellence in crane refurbishment and maintenance. Manitowoc, a leading name in the crane manufacturing industry, bestows this recognition on companies that demonstrate outstanding craftsmanship and dedication in refurbishing their cranes to exceptional standards.
WATM’s expertise in crane refurbishment involves a meticulous process that includes thorough inspections, repairs and component replacements to ensure that the cranes operate at their optimal performance levels. This award serves as a validation of the company’s dedication to providing top-notch service and reinforces its position as a leader in the industry.
The refurbishment of the Manitowoc M16000 started in August 2022 and was completed in January 2023 and the process was painstakingly detailed.
This was a detailed project that needed to be highly organised. WATM dedicated personnel to the project from start to finish.
The team colour coded, marked, tagged and took pictures of everything. They made “zones” for large areas and the work area was kept free of unnecessary traffic.
The majority of this work was going on simultaneously.
Taking the manufacturer’s recommendation into consideration and the customer’s concerns, the WATM team decided to replace approximately 95 per cent of the hoses. With damage caused through aging, sun and hydraulic oil temperature, over 200 hoses were removed, made and replaced.
The WATM team pulled apart all three hoist drums, replacing five planetaries with brand new assemblies. Under the whip line
the team colour coded and removed hoses from the top down to the bottom. They removed, cleaned and replaced O-rings for fittings and hard lines throughout the crane.
The team marked, tagged and removed hoses, hard pipes and pumps. After removing all seven pumps, the WATM team removed the engine with the pump drive assembly and all pumps and motors were sent out for testing.
The WATM team removed the pump drive assembly from the engine and found the shaft was worn at the pilot bearing. The team then disassembled the pump drive and had the shaft repaired.
Before the engine assembly was reinstalled, the WATM team replaced the front and rear main seals and installed a new clutch assembly. They adjusted the overhead and installed a new valve cover gasket, replaced the water pump and thermostats and installed a new alternator and two new starters. The slew was removed for Non Destructive Testing.
The team removed and resealed the superstructure outrigger jack cylinders which were then tested several times to work out the air pressures.
All electrical harnesses were replaced during the refurbishment process, which was finished safely, on time, under budget and to the complete satisfaction of the customer.
In the competitive landscape of crane sales and service, Western Australian Truck and Machinery (WATM) has emerged as a true trailblazer. Setting new standards and garnering industry recognition for its exceptional services, WATM is revolutionising crane solutions one achievement at a time.WATM’s apprenticeship program has been a great success for the organisation.
“This achievement was brought about by the commitment of the team involved, led by an experienced and accomplished female technician employed here at WATM. We believe that having a diverse workforce gives us a more rounded technical knowledge base
for the whole team to learn from,” he said.
“One of the key drivers behind our success is our dedication to recruiting and fostering talent within the business. We take pride in our comprehensive apprenticeship development program, which aims to nurture and train the next generation of crane technicians into industry professionals.
“The apprenticeship program at WATM provides aspiring individuals with hands-on experience and classroom training under the guidance of seasoned experts. By offering a structured learning environment, WATM equips these apprentices with the necessary skills and knowledge to excel.
“Currently our apprentice team of nine includes vehicle body builders, diesel mechanics and auto electricians, varying from junior to mature age with some completing their second trade qualification whilst at WATM. This commitment to nurturing talent not only benefits the apprentices but also ensures that WATM maintains a pool of skilled and qualified professionals to meet the demands of its ever-expanding clientele,” said Anthony.
Safety and reliability are paramount in the crane industry, and WATM understands this importance wholeheartedly. To ensure the safety of its team and to prolong the operational life of its customers’ cranes, WATM offers a comprehensive Major Inspection Program.
Under this program, WATM’s certified technicians conduct detailed inspections of the cranes, focusing on critical components and potential wear and tear. The inspection process involves cutting-edge diagnostic techniques and advanced testing methodologies to identify any issues or risks proactively. Once the inspection is complete, the team at WATM provides clients with a comprehensive report outlining the crane’s condition and any recommended maintenance or repairs. Transparent communication between its customers and WATM is key to its success.
By availing the Major Inspection Program, customers can rest assured that their cranes are in top-notch condition, comply with industry regulations and adhere to the highest safety standards.
WATM not only completes major inspections on the Grove mobile cranes, but the program also includes Franna cranes, Hiab vehicle mounted cranes and hook lifts and Moffett branded forklifts.
WATM Crane Sales and Service has undoubtedly made its mark in the crane industry. Winning the 2023 Manitowoc Crane Refurbishment Award is a testament to the company’s dedication to excellence, while its robust apprenticeship development program showcases its commitment to nurturing talent within the industry. The Major Inspection Program further underscores WATM’s focus on safety and reliability, ensuring that its clients’ cranes operate optimally and safely.
As the company continues to push boundaries and set new industry standards, it remains a dependable partner for crane solutions in Western Australia, reflecting its vision of revolutionising the crane industry, one achievement at a time.
Rigging Rentals recently opened its brand-new, purpose-built facility in Kenwick, in Perth’s south east, and invited industry partners and customers to both experience the company’s landmark event and explore its future capabilities.
WESTERN AUSTRALIA’S FIRST DEDICATED lifting equipment hire company was born from humble beginnings in 2003. Rigging Rentals has a rich 20-year history of servicing customers with innovative heavy lifting and rigging solutions. General Manager Craig O’Dowd discusses the company’s heritage, the services it has offered over the years and how its new MegaTest facility has the potential to propel the company’s future growth and revolutionise Western Australia’s lifting industry.
“Like all small businesses you have to start somewhere, and Rigging Rentals began with the idea of servicing the lifting and rigging industry across the country with the option to hire rather than buy, offering world class products from leading brands, an objective that hadn’t been seen before,” said Craig.
“We started with a few fleet items and a shared workshop space, knowing that it would take time for the industry to appreciate the benefit of our products and services and how these could positively impact their businesses. We worked hard alongside our
customers, we listened to their feedback, and we invested in the products we could see they needed for their projects.”
Customer service and satisfaction have been central to Rigging Rentals’ success, and by listening to customer feedback and by providing the right solutions, the business continued to grow. Continued investment in quality equipment, from leading manufacturers, attracted repeat business from customers, which enabled investment in an increased range of products, which attracted customers from different areas of industry with larger projects.
With experience in testing, inspecting, manufacturing and selling lifting equipment, Craig has been the General Manager of Rigging Rentals for 13 years and says he is ready to see the company take its next step.
“Over the last decade, the business has seen steady growth and the concept of renting lifting and rigging equipment has certainly gathered momentum over this time. A change in ownership structure in 2015 has enabled rapid growth and expansion to where the company finds itself today.
“This is our third major move to larger premises in the time I’ve been in the General Manager’s role,” said Craig.
This latest move is designed to facilitate further expansions into more diversified areas of the lifting and rigging industry. Rigging Rentals moved into the new facility with MegaTest, a business operating under the leadership of Rigging Rentals. MegaTest was established to fill a gap in the lifting and rigging industry when it comes to load testing of niche equipment such as spreader / lifting beams, winches, hoists and fabricated equipment such as baskets, cages and frames. Rather than having to hire mobile cranes and transport semi-trailer loads of test weights around town, testing can be completed much more efficiently using the overhead cranes and dead weights or slab anchors, all under cover and out of the elements.
The testing area of the new facility was nicknamed ‘The Sky Bay’ because of its imposing and colossal height. It features two 50-tonne German-made ABUS computerised cranes capable of synchronising for load tests of up to 100 tonnes. These overhead cranes operate alongside a large fleet of steel and water
test weights and, true to the driving ethos outlined by Craig earlier, are designed to cater for customer requirements with almost any lifting solution capable of being tested in the facility.
“The ‘Sky Bay testing area’ is unique. Customers can visit and see what we are doing with their lifting solution, they will have input into the testing, we can discuss various scenarios for when it is out and lifting in the field,” said Craig..
“This is ‘next level’ customer service and we are now in a position to truly partner our customers with their lifting and testing requirements. They can now see how Rigging Rentals, in conjunction with the MegaTest Sky Bay facility, is offering a lifting, rigging and testing package unsurpassed anywhere in the country.”
Although still in its formative stages, Craig is keen to highlight the flexibility the facility offers and the open approach MegaTest will be adapting to anyone making use of the new testing centre.
“We’ll make additions to the facility where customers request them, and where we can see benefit. We are completely open and receptive to the requirements of our customers and this facility is designed to evolve as the industry evolves.
“For example, we can see that cranes are only going to get bigger and lifts heavier, which will lead to heavier lifting equipment and more complex lifting solutions. Our testing capabilities will continually reflect this evolution,” said Craig.
At the forefront of the MegaTest facility is the high bay, measuring in at 31.3m long by 13.3m wide, with a floor-to-hook height of 18.5m. The concrete slab is 1.3 metres thick,
consisting of 1,355 tonnes of concrete and 47 tonnes of steel reinforcing. The slab-anchors embedded in the structure total 144, reflected in a grid pattern of 18m by 6m at one-metre spacings. Each slab-anchor is capable of withstanding 50t of force. Additionally, the MegaTest facility features dead weights ranging from 20kg through to 10t, a 16-tonne Kone forklift to assist with the handling of the dead weights and equipment for testing, and four 15 kilowatt air compressors in parallel.
“The MegaTest facility has dramatically increased our certified testing and servicing capabilities and we now have the capacity to further tailor solutions to the specific demands of our customers,” said Craig.
The Rigging Rentals and MegaTest facility provide the businesses with an ideal launch platform for its next stages of growth. This will include continued investment in inventory for the rental business and investment in the latest testing equipment with NATA accreditation on the horizon.
Rigging Rentals operates as a dry-hire company offering its services Australiawide. Industries serviced include mining and construction companies, utility providers, shipping companies, defence contractors, engineering contractors, crane companies, offshore oil and gas and testing organisations.
The company offers water load bags ranging from 1 tonne to 55 tonnes to complete load-testing, especially for offshore oil and gas installations and local and remote land-based installations. With a large inventory consisting of spreader beams spanning from 1-1,000 tonnes, JDN air hoists from 500kg to 30 tonnes and a large fleet of load cells and round slings to 200t
“We see a lot of our air hoists go into the oil and gas industry working on offshore projects and we have one of the largest and broadest range of spreader beams available. You’d be hard pressed to find many other companies across the country with a 1000-tonne spreader beam,” Craig said.
With such a large inventory of stock and array of products, Craig says Rigging Rentals plays a central role in making the lifting industry more sustainable.
“For some projects equipment is purchased for one-time use, they buy cheap products and discard them immediately after the project is completed. A key focus for Rigging Rentals is to negate this practice. We possess large quantities of stock for our customers to hire, use on their projects, mark-up if they are damaged, and return to us. We don’t want to discard our assets; we want to maintain, regularly re-certify, and re-deploy them. Sustainability is an issue we need to address as an industry, not to mention the financial benefits that come with hiring as opposed to buying,” he said.
Working across a range of industries with each possessing their own demands and requirements requires a flexible attitude and service. Ensuring communication lines are constantly open is imperative to the success of Rigging Rentals, says Craig.
“We have always listened to our customers, and we will continue to do so. Their feedback is paramount and ensures we are investing in the right products and equipment for their projects today and for those in the future,” said Craig. “We work in a high-risk industry, and we all have responsibilities to each other. Rigging Rentals’ responsibility is to continually invest in quality products in the first place. MegaTest ensures the equipment is capable of managing the lift. Both are responsible for maintaining the product so it is always fit for purpose when it leaves our facility.”
Rigging Rentals would like to recognise the efforts and expertise of Built Ink and Alliance Engineering Consultants for helping bring the Megatest dream to reality and welcomes anyone to contact them to discuss how the Sky Bay can be utilised for their project.
GENERAL CRANE SERVICES (WA) HAS a rich history of embracing cuttingedge crane technology, but recently, they embarked on a more sentimental journey – the restoration of one of their earliest acquisitions, the Terex Franna 12T 4WD. This crane holds a special place in the company’s heart as it was one of the first in their fleet, purchased in December 1989 by Tony Bucciarelli.
“My wife and I purchased the Franna 12T 4WD in December 1989 as the first of the Anten Cranes Fleet, primarily because it was the biggest Franna around at the time. It was the first crane I bought because we needed it to be available for all and any work we could get,” said Tony.
The Terex Franna 12T 4WD was a pioneering crane back in its day, designed and built in Australia and the ideal all terrain articulated lift and carry mobile crane for general hire and crane work. With impressive lifting capabilities and exceptional versatility, it could manoeuvre through rugged sites and also achieve highway speeds of up to 85kmph. Spare parts were readily available due to the use of mainly conventional truck components and were easily accessible from the manufacturing plants in Brisbane and Perth and agents in each state.
Tony owned this Franna crane for approximately two decades, and it played a pivotal role in the company’s growth. Eventually, he sold it to a contractor on a BGC Mine Site near York, WA. Tony’s son, Eric Bucciarelli, took up the quest to locate this cherished piece of the company’s
history. After some detective work and an unexpected discovery on an online auction site, Eric went up there the next day and put in an offer in and he managed to reclaim the Franna.
Ironically, Tony had previously told his boys not to worry about locating the Franna.
“I didn’t think it was worth the headache, it was an old crane, but now we have it and its being restored, I’m
“It was the first crane I bought because we needed it to be available for all and any work we could get.”Despite the number of hours, the engine was in great condition and didn’t need a thing done to it.
Themain refurbishments needed were on the interior, which is understandable after 21,451 operator hours.
happy we did it, it’s a great reminder of where it all started,” he said.
While the crane had clocked over 21,541 hours and showed signs of wear and tear, its spirit remained intact.
“It was pretty knocked up. There was no apparent rust at all, but it had seen better days. That said, the tyres were the same ones I sold it with, and they were still in a reasonable state. The main refurbishments needed were on the interior, understandably after all those operator hours. The crane’s paint work needed serious attention but the engine was in great condition and didn’t need a thing doing to it,” Tony said.
The Franna 12T 4WD is powered
by a Hino, 163HP, 6 Cylinder diesel engine. The axle loadings featured 5,700 kg at the front and 9,000 kg at the rear, a total weight of 14,700 tonnes and the crane boasts a turning circle from the outside wheels of 6.2 metres. The overall length of the crane is 8.89 metres with a width 2.40 metres and height 2.82 metres.
There was some structural work required on the Franna but not much explains Tony.
“The boom has been pulled apart, inspected and repaired, and we fitted new ropes. Terex Franna were very responsive with our parts requirements on this part of the refurbishment but as I’ve said, most of the work has been
mainly cosmetic on the interior and exterior. I engaged Terry from T & H Custom Panel and Paint for the bulk of the refurbishment program, and he has done a great job.
“The refurbishment process had been handled in house, but when Terex Franna heard about the story and suggested we display the crane at the CICA National Conference and Exhibition in our home town, we decided to get it finished and sent it to Terry for the final touches”.
“We are grateful to Terex Franna for this opportunity to display an important part of our company’s history. Personally, I am delighted that my sons ignored my instruction and went in search of the first crane I purchased, found it and refurbished it for me. We have always been strong supporters of the Franna pick and carry crane and remain so,” said Tony.
“It was pretty knocked up. There was no apparent rust at all, but it had seen better days.”Tony’s original Franna 12T 4WD.
Sarens is the global leader and reference in crane rental services, heavy lifting, and engineered transport. With state of the art equipment, value engineering, one of the world’s largest inventories of cranes, transporters, and specialty rigging equipment, Sarens o ers creative and intelligent solutions to today’s heavy lifting and engineered transport challenges. With more than 100 entities in 65 countries, Sarens is the ideal partner for small- scale to mega-scale projects. In Australia, we are a crew of over 50 experts, powered by a wide-ranged fleet in lifting, transport, and rigging solutions.
sarens.com
Address: 2/34 Navigator Place, Hendra, QLD 4011
T: 1800 SARENS (1800 727 367), 1300 SARENS (1300 727 367)
E: australia@sarens.com
We are fluent in FEED studies and work closely with your project team during the FEED, pre-design, and engineering execution phase. With a strong in-house engineering department to select equipment, perform risk analysis, conduct method statements, and respect budgets, Sarens is an experienced partner with nationwide service centres for quick mobilisation for our clients. The Australian division is ISO9001, ISO14001, and ISO45001 certified. Our commitment to cater to the needs of our clients and our willingness for continuous improvement is unwavering.
Address: 1 Marion Road, Maddington, WA 6109
T: 1800 SARENS (1800 727 367), 1300 SARENS (1300 727 367)
E: australia@sarens.com
Engaged at Victoria’s West Gate Tunnel Project to help lift a range of girders and steel portals, JYC’s two Tadano CC3800s have been put to the test over the past 18 months. JYM Heavy Lift Manager Ben Musson provides an update on the project, its difficulties, and a range of the heavy lifts completed by the joint venture.
WITH BIG INVESTMENT IN INFRASTRUCTURE projects comes the need for big investment in large machinery capable of completing the task at hand.
Victoria’s A$10 billion West Gate Tunnel project fits that bill. As part of the state’s ‘Big Build’ that seeks to improve current infrastructure such as regional rail, urban rail connections and urban connecting roads, the West Gate Tunnel project is one of the major infrastructure projects taking place nationally, with cranes and other heavy machinery dominating the suburbs of Port Melbourne, Footscray and Docklands.
One of the companies at the forefront is Johnson & Young Cranes, putting its joint venture with McKay United, ‘JYM’, to full
use. After the two businesses noticed a gap in the market for larger capacity crawler cranes, they decided to put their assets together to form the JYM brand circa 2020. The joint venture’s fleet contains three Tadano CC2200s and two Tadano CC3800s that possess full SSL, boom boost and split tray capabilities.
JYM’s two CC3800s have now been operating on the West Gate Tunnel Project for the last 18 months, working under the JYC banner during the joint venture’s contract for the installation of the heavier components of the numerous bridges that make up the intersection of Footscray Road and CityLink. Ben Musson, seconded as JYM’s Heavy Lift Manager for the project since 2021, says the JYC and WGTP engineering departments worked “hand in glove” in producing concepts to ensure machine program was consistent with an efficient workflow.
“On top of my role, we added JYC’s Lift Designer Brendan Thorne to the team so we could work together on
creating CC3800 concepts for all girders in this area to ensure operational change management and program changes can be facilitated to suit machine availability within the project,” he said.
The main scope of work for the CC3800s so far has been the installation of the girders that, to date, have topped out at 289 tonnes. The CC3800s, however, have also installed a range of steel portals that were responsible for transitioning the girders from their steel berths to the precast segment above the Footscray Road area and Dynon Road area. The Tadano crawler cranes completed lifts on steel portals of up to 459 tonnes.
One of the main challenges for the team at JYC was transporting the crane from site to site in a congested, dense, urban area, with lots of traffic surrounding the operations. Using such a large crane as the Tadano CC3800, a lot of counterweight and boom sections were needed for the job. This presented a “logistically difficult” challenge, according to Ben, as the team
wanted to establish the cranes in the right configuration for each lift to ensure optimal efficiency ensued.
“To fully derig, reassemble, and relocate the cranes, we needed to deploy 30+ semi loads, two floats for the tracks of the crane and a seven-line platform for the main car body,” said Ben. “Additionally, thanks to the tight nature of the jobsite, we needed to make full use of the limited space we had to lay components down. At times, this entailed the delivery of components for the crane in reverse order and sometimes take possession of the roads to allow space for the boom and SL mast to be assembled.”
Helping in the assembly and disassembly of the Tadano crawlers was any one of JYC’s numerous LTM1250 all-terrain cranes, with some mobilisation processes requiring the use of JYC’s
LTM1400 all-terrain crane. Further complicating the project, however, was the prevalence of Coode Island silt – a young sedimentary soil in the Yarra Delta that is known for being highly compressible. To overcome this, the team at JYC worked closely with the West Gate Tunnel Project to ensure crane platforms were not constructed any thicker than necessary, according to Ben.
“On multiple occasions, we used the SL tray for the pick operation because it produces a far lower and more uniform track pressure,” says Ben. “This especially helpful in the ‘Bridge 70’ areas of the project, as the pick of the load became more precise with the use of the tray, resulting in less margin for error.”
“As an engineering team, we reduced the complication by placing the SL tray at a lesser radius than was required for
“As most of the lifts on Bridge 70 held some interface with the road, rail, CityLink, or bike paths, ensuring the loads were precisely trimmed and efficiently enacted was imperative, as the location made the lifts “extremely time critical.”
the lifted load, which resulted in the tray floating before the load is raised, assisting the operator with any fine adjustments during the lift,” he continued. “In many cases we also returned the tray to a lesser radius as we lost weight on the placing of the load. This saved additional costs on platforms as the dimensions of the overall platform could be reduced to support the tray.”
For Ben and the team at JYC, the Vario SL feature – which ensures the finetuning of the floating of the tray – has been pivotal across the team’s work on the West Gate Tunnel Project. Able to assist in avoiding any obstacles encountered during the slewing of the crane, the feature also allows the luffing of the back mast and tray from 11m to 21m, dependent on the load’s weight and radius.
“Though many older machines can change SL mast or derrick radius, not all can stay ‘on chart’ when adjusting the mast radius, and so they should not conduct this under lifting conditions,” says Ben. “Without the Vario SL ability,
many of the lifts would not have been able to be performed.”
Further to the precise nature of the lifts JYC completed, georeferenced CAD files were also provided for the project so that accurate survey marks for the cranes, the SL tray, and the load’s centre of gravity could be accurately recorded, which further assisted the team on site in their accuracy when lifting and configuring.
To provide additional reduction in platform thickness, the project engaged RBG to design some heavy-duty mats for the crane, at a width of 7.5m and a weight just short of 10t each. Constructed from 310UC sections – larger than what is generally found under a 650-tonne crawler crane – a minimum of 10 mats were required under each setup, according to Ben.
“We have also performed pick and carry operations on the heaviest girder to date at 289 tonnes, which required a runway of 20 mats,” he says. “This brought the gross weight of the crane up to around 1500 tonnes once the load,
rigging and fabricated mats had all been added together. It was important that we produced georeferenced CAD files to know the impact we would be having on the ground around the project, allowing us to ensure precision throughout the lift.”
A key part to the successful lifts completed over the past 12 months for JYC and its two Tadano CC3800s was the rigging equipment supplied. Because of the confined, precise nature of the tasks at hand, the West Gate Tunnel Project supplied several Enerpac sync hoists to help with the load stabilisation and exact positioning of the loads. As most of the lifts on Bridge 70 held some interface with the road, rail, CityLink or bike paths, ensuring the loads were precisely trimmed and efficiently enacted was imperative, as the location made the lifts “extremely time critical”.
“It was essential that we completed the work required of us in the allotted timeframe, or else the project could have seen delays for weeks on end,” says Ben. “Ultimately, this collaborative approach between the JYC team and the West Gate Tunnel team has thus far served both parties well and provided the desired outcomes for the project.”
The dual lift:
The difficulty of the lifts required of JYC were encapsulated by the dual lift completed at the intersection of Appleton
Dock Road and Footscray Road. Requiring the use of both CC3800s in and amongst the four rail lines, three roads and one bike path that all needed to be fully closed down by the WGTP, JYC needed to employ all its engineering nous to work within the parameters of the project’s lifting procedures.
“In this instance, the main challenge
was ensuring the SL tray would float while maintaining less than 90 per cent of capacity, with the addition of the 20 per cent dual lift factor,” says Ben.
JYC deployed both cranes in SSL_2 with 84m of boom and 325 tonnes of SL counterweight, and SSL_3 with 90m of boom and 325 tonnes of SL counterweight respectively. In accordance with the approved lift study, both cranes required the 325 tonnes of SL counterweight at an SL radius of 21m. However, because of the 20 per cent dual lift factor not being “actual”, the SL tray “would not raise with the actual load on the hook in reality”, according to Ben.
“To overcome this issue, we once again turned to the versatile Vario SL option,” he said. “We started with the SL trays at 13m and 15m respectively, which meant that the tray would rise with a smaller percentage of the total hoisted load. As the cranes took more of the load, the SL vario mast radius was increased while ensuring that the crane did not exceed 90 per cent of capacity.”
Overall, in lifting the girder, the first crane had a load share of 74.454 tonnes,
picking at a radius of 63.38m and placed at 66.98m and the SL positioned between 15m and 17.8m. The second crane had a load share of 70.64 tonnes working at 63.9m to 70.9m and the tray at 13.2m to 17.9m at to maintain the under 90 per cent operational capacity required and ensure the tray floated throughout.
To ensure there were no unforeseen clashes, JYC also produced a full threedimension model to simulate the lift manually and engaged with the crew in a collaborative manner to agree on how the lift should proceed.
“On the day of the lift we had two crews of six, consisting of one operator, one rigger observing the tray, two ground riggers for the rig up and pick, and two riggers up on the scaffold for the placement of the girder, with the lead rigger controlling the lift switched between ground and scaffold crew as required,” says Ben.
“Ultimately it’s the team on the ground who make it happen, and JYC are fortunate enough to have the best in the industry in both engineering and crane crew departments.”
Orange-based lifting and rigging equipment company Unilift takes pride in offering durable, sustainable, quality products to the crane industry. General Manager Ben Scott and brother Caleb Scott discuss the company’s position as the exclusive distributor for European brands Diepa and Extreema, and Unilift’s attitude to reducing waste in the industry.
Setting aside spiralling worldwide crane prices, machine acquisition at any stage of a company’s life can range from hundreds of thousands of dollars to well into the millions. This naturally takes up the main budget of crane hire companies and larger scale construction, mining or port businesses.
But the machine itself is not the only component responsible for completing safe and successful lifts; high-quality rigging must go together with high-quality machinery.
After crane purchase, one of the largest long-term investments a business will make in its machines are the ropes that are installed. Potentially costing tens or even hundreds of thousands of dollars, these ropes need to be designed to provide many years of flawless service. Unilift, as the sole distributor for Diepa Special Wire Ropes, provides exactly that.
The stalwart rope for some of Germany’s biggest crane manufacturers, Diepa’s rotation-resistant B-series winch ropes possess “excellent” anti-spin characteristics, with a fully encapsulated compacted structure and rugged outer strands. Manufactured to a tighter nominal tolerance of +3.5 per cent, installing these ropes also reduces initial wear on sheaves and drum while the rope is bedding in.
Damage in this area is to be avoided at all costs, as premature wear of drum or sheaves is very expensive to rectify, as many crane owners would know.
Above and beyond Diepa’s reputation for precision rope design, the highest quality wire and various corrosion-resistant coatings, it is its manufacturing technology that really sets Diepa apart from the crowd. A patented manufacturing process—unique to Diepa—provides not only highly accurate
strand formation but exceptional lubricant impregnation right to the rope’s core.
“This is one of the key factors behind the exceptional life of Diepa crane ropes” says Caleb Scott, from Unilift’s wire rope division. “During testing and certification, we often break-down and test-to-destruction a whole range of ropes from all the big manufacturers. What many customers don’t realise is that we see lots of ropes that display very few visible signs of damage to the outer strands, but failure can still occur without warning from extensive, invisible issues within the core. Sometimes the lubricant and even the plastic core sheath has been squeezed out through the outer strands, leaving the core to corrode and break. In a crane setting, this can be disastrous.”
“But Diepa ropes are manufactured in such a way to allow visual wear to occur on the outer layers (where they can be seen
upon inspection) well and truly before any extensive wear can impact upon the core.”
“Part of the way they manage to achieve this is by maintaining a high level of internal lubrication even after many years of hard use. When in use, a rope’s inner strands are constantly being stretched, compressed, twisted and flexed – all at the same time. If these strands are well protected by internal lubrication from both friction and corrosion, they’re far more likely to last the distance. Only Diepa has really managed to offer this high level of internal protection for the long haul through great rope design and precision manufacture.”
Diepa ropes come in a range of sizes and alternative rope designs that can be tailored to suit specialised usage. Their X-series and H-series offer ideal luffing ropes with their parallel lay option and superior plasticated core.
“As you’d expect, it’s the parallel lay design that gives these ropes their greater flexibility for luffing use,” says Caleb, “but it’s the addition of the plasticated innersheath that allows Diepa to achieve the same great service life on a more flexible rope. If this plastic sheath wasn’t up to the
task, cracks would very quickly form and moisture—then corrosion—could find its way inside, often tracking up and down the core leading to strand breakage and eventually failure. But it’s very rare to see this happen with a Diepa rope.”
Further to its exclusive distribution of Diepa’s wire ropes, Unlift is also in the unique position of being the sole distributor of Extreema soft slings in the Australian heavy-lifting industry. As the world pushes toward renewable energy, projects such as wind farms—both onshore and offshore—are gaining further investment. With that investment comes the need for lifting products and construction equipment tailored to the demands of wind turbines themselves.
“Wind components are both huge and fragile, which requires some very careful planning and specialist equipment,” says Ben Scott, Unilift’s General Manager. “We were privileged to play a part in a recent Wind Energy conference and were reminded again just how far heavy-lift technology has come in the last decade to meet the needs of the growing renewables sector, and just how important it will be for crane companies to
be ahead of the curve when it comes to these types of lifts.”
According to the Unilift team, this is where Extreema’s soft slings thrive. As Ben points out, these products were developed in the Netherlands and are distributed across Europe, an area with significant wind energy investment that has seen Extreema’s reputation boom. As part of a significant shift in the lifting and rigging industry, these soft slings weigh less, are immensely strong, are quieter and softer and as a result cause much less damage to the products being lifted.
The scope for Extreema slings is just as large as the projects they excel in, featuring lifting capacities ranging from 0.5 tonnes through to 8000 tonnes, with some of the slings extending up to 80 metres long. Additionally, it is not just the wind energy industry where these slings thrive: capable of floating on—and being repellent to— water, they are suitable for a range of port and offshore lifting practices. And thanks to its new ‘Inferno’ range, Extreema now also offers a heat resistant range that maintains its working load limit in temperatures up to 200 degrees Celsius, making them a perfect option for many factory operations as well.
With the industry-wide push towards long-term sustainability, Extreema slings are part of Unilift’s own driving motivation to offer long-term, sustainable products to the lifting industry.
Not only is genuine Dyneema (and the newer Bio-based Dyneema) exceptionally strong and hard-wearing, but the wide range of protection options available—from velcro attached edge or pinch-point protection to full double- or even triple-layer Dyneema or Cordura sleeves—allow for exceptional longevity.
“It’s frustrating to still wander past the ‘corner of the yard’ in some businesses where piles of used soft slings curl up to rot,” says Ben. “If treated well by the end user, our Extreema slings will give a company many years of excellent service and can be repaired upon damage. Simultaneously, this saves money and benefits the environment.”
Speak to anyone on the team, and they will all tell you that supplying high-quality equipment is only part of the job at Unilift.
With substantial fabrication and machining resources in its Orange facility, Unilift also provides servicing and repair for hook and sheave blocks as well as other engineered lifting products. These big-ticket items can be a lifetime investment, so ‘care and repair’ is a mantra encouraged by Unilift.
Part of Unilift’s fabrication and machining resources is its 1000-tonne test-bed. One of the largest in Australia, this test-bed allows for the destruction testing of large diameter ropes and load testing of all hardware, chains, slings, and spreader systems, whether manufactured by Unilift or not. Aligning with the company’s ethos of providing smarter, safer and sustainable solutions, Unilift’s maintenance, repair and testing work underlines its commitment to ensuring the certainty and safety of its products.
Outside of slings and ropes, Unilift also holds an inventory of fixed, telescopic and modular spreader beams for hire (as well as all related slings and hardware to suit).
“Hire is a steadily growing part of our work here” says Ben. “To be able to offer specialised rigging to a range of companies for a range of applications is very rewarding. In these times of rising prices when lifts are getting more technical and storage space for many businesses is at a premium, some time investing in large capacity resources might be overkill for a ‘one-off’ job.”
Unilift also designs, engineers and manufactures many custom lifting assemblies to suit the needs of various lifts and customers. While its range of smaller telescopic spreaders is gaining in popularity—spanning a 5-30-tonne capacity and possessing 2.0-3.5-metre or 3.5-6.0-metre spread options—its modular spreaders are an entity all of their own. With weight classes spanning from 12-tonne through to a mammoth 3000-tonne capacity, Unilift’s 1-50-metre spreaders are highly applicable for complex, heavy lifts on rail, bridge, and offshore projects.
Less exotic but much more frequently utilised are Unilift’s triangle, delta, and droplink plates. Lighter than many competitors’ products due to their platform-style design, these plates are also highly compatible with Unilift’s range of lifting and spreader beams, manufactured wire rope slings and grommets and its extensive range of shackles, fittings and other hardware.
“At Unilift, our desire is to be the Australian go-to for complete heavylift solutions – and not just heavy-lift components,” says Ben. “There’s been a steadily growing reliance upon overseas manufacture, but as we’ve seen in recent years that can very quickly be disrupted by world events.
“At Unilift we want to play our part in ensuring the success of the heavy-lift sector by continuing to offer these specialised products and services at a local level.”
AVAILABLE
Thurs 20 June, 2024
The Women in Industry Awards recognise outstanding women leaders from across Australia’s industrials sector.
With over a decade’s experience in the tower crane sector, Executive General Manager Damien Laforest joined the Liebherr organisation earlier this year - and he is keen to build on the reputation the brand has in this sector.
“LIEBHERR TOWER CRANES HAS ALWAYS had an excellent reputation as a premium product in the tower crane sector. Since I started, we have focused on what Liebherr rental can provide its clients and expand on our offering,” Damien says.
“With the rental side of the business, the most significant change is offering crane crews on construction projects in NSW. This has created new opportunities to broaden our customer base and showcase what Liebherr is
about. Our QLD branch has been offering crane crews for a little longer and has a presence on many notable projects in the region.
“I always knew the strength of the Liebherr brand, what I know now (since joining), is that it is matched by the incredible people in this company. We are fortunate to have some talented employees, many with a long association with Liebherr.”
“We have been busy this year optimising the rental fleet to answer
the Australian market’s needs; which means we have removed older traditional trolley-jib cranes from the fleet and have added mostly larger luffing-jib cranes.”
“Our investment focus has been on larger models with fast hoist winches, namely 357 HC-L and 542 HC-L, although we recently took delivery of another 1000 EC-H for a project in Sydney. This one is a 40-tonne version and can be installed with a maximum 91.4
metre jib. We are also excited to take delivery of our largest luffing crane, the 710 HC-L 32/64 Litronic which will be erected on a project in mid2024,” said Damien.
Creating a long term viable rental option means packaging up more than just the tower cranes.
“We continue to invest in our sizable fleet of Alimak hoists along with generators, hook cameras, anticollision systems as well as a variety of lifting equipment. A popular rental item currently is a product called LiUP. This is an operator lift that is designed for the crane driver or even a technician with some tooling.
“It can lift a payload of 200 kg and other than time saved on the crane climb, it runs internally within the tower sections, great for penetrations
market. The crane has a maximum lifting capacity of 12 tonnes and has a maximum jib length of 55 metres.”
“Aside from the rental business, we seek to increase the volume of Liebherr cranes both here and in New Zealand. The two markets differ greatly for us, as we do not rent cranes in New Zealand, instead we support the many owners of Liebherr Tower Cranes in the region. We are thankful to have many builders’ own machines and we would like to translate the benefits of Liebherr ownership to some more companies in Australia.
“We seek to expand the number of builders and subcontractors in Australia to incorporate Liebherr in their own fleets. Many builders in New Zealand have purchased Liebherr tower cranes to make us one of the most dominant brands in the country. Buyers can leverage off the local support with parts, servicing, technicians, engineering support and rigging works. As a manufacturer, Liebherr has an enviable ability to support its customers locally in Australia and New Zealand and we want more customers to experience these benefits,” he said.
The focus for Liebherr Tower
“It can lift a payload of 200 kg and other than time saved on the crane climb, it runs internally within the tower sections, great for penetrations and space constraints on site.”
and space constraints on site. Set up time is very fast as components are installed during crane preparation in the yard and is ready to go the same day as the crane is erected,” said Damien.
“Having been showcased at Bauma 2022, we will be installing the world’s first unit of Liebherr’s hydraulic luffing-jib crane on a project in Q4 2023. We opted for the 2/4-falls version which is called the NC-LH 12-55 because it is more suited to meet the needs of the Australian
Cranes includes a very transparent relationship with clients and prospective clients, says Damien.
“We are approaching the market with an open agenda, which is along the lines of ‘here we are, this is what Liebherr is about, and this is what we can offer,’ and we’ll follow through on our promises. We’re going to grow in Australia, there’s no doubt about that. The Liebherr brand is very strong, and we want to capitalise on that and reach customers like we haven’t before,” he said.
The ‘Safe Use of Lifting Equipment’ training course is an online program aimed at equipping participants with the confidence, knowledge and practical skills to ensure the safe operation and conduct of pre-use inspections.
Leading lifting equipment experts Ranger Lifting recently launched a comprehensive online training program designed to increase safe work practices in the lifting sector. This innovative course is the first of its kind in Australia and sets a new benchmark in the industry.
THE SAFE USE OF LIFTING EQUIPMENT training program available via Ranger Lifting’s ‘Learning Hub,’ has received Accredited Training Scheme (ATS) accreditation from The Lifting Equipment Engineers Association (LEEA).
Now fully established after three years in the making, the ‘Safe Use of Lifting Equipment’ training course does just what its name suggests.
It is an online program aimed at equipping participants with the confidence, knowledge and practical skills to ensure the safe operation and conduct of pre-use inspections. The course contains different
modules which cover topics like Chain Slings and Components, Wire Rope, Shackles, Lifting Beams, Chain and Lever Blocks to name a few.
Ashley Thacker, general manager for Ranger Lifting, says there had been a significatn gap in the market for end-user training for some years.
“There really hasn’t been anything that teaches end users how to use lifting equipment safely. Individuals can take their Dogman and Rigger tickets, but under Australian Standards, that’s not enough to deem them competent. We’d been examining this gap in the training market,
but there was never enough time to focus on it properly.”
“We took COVID-19 as the opportunity to really examine the gap and what we could do to fill it. We put a framework for what we thought a course could cover. We also realised that if it was to carry weight in the industry it needed to be underpinned by LEEA certification,” said Ashley.
For a long time, half-day and whole-day face-to-face slinging awareness courses have been available, but the content hasn’t been vetted by an industry body and a significant amount of the content is outdated. There is a Certified Course
for Lifting Inspectors but in terms of the Australian Standards, there has been ambiguity around what they expect a competent person to do.
The online course caters to all end users and professionals within the lifting, rigging, and construction sectors – in fact, it is essential for anyone using lifting equipment in any industry. Upon completion, participants receive a LEEA accreditation and a certificate of completion. The accreditation and collaboration with LEEA ensures that this course and its content materials and are of the highest standard, aligning with Australian industry regulations.
“We could see the benefit of a training program which was broken into modules enabling people to learn at their own pace. We could see a crane hire company for example, putting teams through an online course by fitting in the modules around their work loads. They can spend two hours on the course and then they come back to it a week later,” said Ashley.
Ranger Lifting works with Tier One Contractors
and builders doing everything to meet their compliance obligations in terms of work health and safety, to make sure their workplaces are safe workplaces and that they’re identifying risks as they go.
“Obviously, there is a requirement for a Certified Lifting Inspector to conduct periodic inspections on the equipment, but from the beginning, our concept was to teach the end user how to safely use the equipment, how to select the right piece of equipment, how to conduct pre-use inspections, how to use the equipment safely and how to maintain it correctly,” said Ashley.
“There are too many accidents happening day to day. I did my advanced rigger’s course at TAFE, and we wouldn’t have spent more than five minutes on lifting gear. Today, they spend more time on this during the Dogman’s ticket, but they’re not going to spend more than an hour and they just cover the basics. Australian standards go into so much detail around competency requirements. They actually state that the person using the piece of lifting equipment should be able to identify the standard that it relates to, I doubt you would find many people capable of doing that,” said Ashley.
LEEA has always been accredited to provide training courses for lifting and rigging equipment companies. In other countries, you don’t necessarily need to be a Registered Training Organisation (RTO). In the UK, LEEA has hundreds of Accredited Training Schemes (ATS) members which provide training on slinging and rigging and the safe use of lifting equipment.
“LEEA thoroughly examined our program, vetting every module making sure it was relevant, and that all the standards were correct. We had to submit a training needs analysis, which included the course outline, the lesson plans, which included the objectives, all the key learning points. LEEA also went through our application process for the Ranger Lifting to become an accredited training company. Minimal changes were required to the program which was very satisfying,” said Ashley.
Accredited Training Schemes (ATS) have been around for decades, it’s just that none of these training opportunities have been available in Australia, says Justin Boehm, LEEA’s Regional ManagerAustralia and New Zealand.
“ATS is a mature, well-known product in the UK as well as the Middle East and Southeast Asia, but until now there has been no one locally. Ranger Lifting is a leader in our industry.
“ I’ve had a close look at the course content and it’s awesome, it really is.”
“This is a fantastic development for our region and having LEEA’s first Accredited Training Scheme partner in Ranger is excellent news for end users in our Industry,” said Justin.
“Ranger is one of the leading businesses in our industry and it is testament to their commitment to safety and their clients’ safety. This course, backed by LEEA’s high standards, will help keep job sites safe by identifying potential issues that could be missed during a pre-use inspection.
companies that they can’t come through our channels and they should consider this program which is endorsed by LEEA,” said Justin.
Ashley says that the market is ready for the Safe Use of Lifting Equipment training program.
“Because there was no gap between the Dogman ticket and a LEEA course, the larger companies were frequently asking to put their people through a LEEA course. If we allowed that to happen, the industry
“LEEA has struggled with getting end users to understand how to complete a pre-use check, everyone says they do it, but do they really know what to look for? To have the opportunity for them to complete this course which is backed by LEEA is a massive, massive win. This is a fantastic development for our region and having LEEA’s first Accredited Training Scheme partner in Ranger is excellent news for end users in our industry,” he said.
“LEEA is there for the members of the association, and we’ve had pathways for people to do some training, but the courses are not designed to just train everyone. This program allows us to advise interested
would fall apart, because we would have no inspection body.
“We see the Safe Use of Lifting Equipment program as a happy medium, it teaches them the basics. They get a certificate from Ranger Lifting and we log into LEEA’s system, confirm who has completed the course, and they receive a printed LEEA accredited certificate,” he said.
The program is a testament to Ranger Lifting’s pursuit and commitment to safety. It will act as a trusted and reliable resource for end-users seeking to learn how to safely use and inspect lifting equipment based on Australian Standards guidelines.
“Ranger is one of the leading businesses in our industry and it is testament to their commitment to safety and their clients safety.”
AUSTRALIA’S ONLY LEEA ACCREDITED END-USER TRAINING COURSE
and conduct pre-use inspections
Can you correctly select and conduct pre-use inspections of lifting equipment according to Australian Standards? Do you keep accurate training records and can prove competency?
Ensure you and your team are competently trained according to Australian Standards. Enrol in Ranger’s online LEEA-certified training course in the safe use of lifting equipment and receive a LEEA accredited certificate on completion.
Relevant industry training delivered online in 10 learning modules
Lifting Industry Overview
Chain Slings & Components
Wire Rope
Shackles
Synthetic Slings
Chain & Lever Blocks
Lifting Points
Turnbuckles
Lifting Beams & Spreader Bars
Lifting Clamps and Trolleys
Ready to get certified in the safe use of lifting equipment
Enrol now > learning.ranger.com.au
EARLIER THIS YEAR WE LAUNCHED
our inaugural LiftEx event in Sydney, where we celebrated the dedication of our members in the lifting equipment industry. This event held special significance as it was the first time LiftEx had ventured beyond the UK. The resounding success of this LiftEx 2023 has paved the way for an even larger and more impactful event scheduled for September 2024.
Making use of LiftEx as a platform, we introduced the Certificate IV in Lifting Equipment Testing and Inspection to the industry. This achievement has marked a significant shift in the industry’s landscape. Professionals within the lifting equipment sector now have access to a nationally accredited training program, which serves as a platform for industry recognised competence. This education
initiative stands as a testament to the industry’s commitment to practical expertise and is a recognition of professionalism.
An additional significant stride taken this year is the launch of the Accredited Training Scheme (ATS) in Australia and New Zealand, with the first member being accredited to this program recently. The ATS has been instrumental in providing essential training to end-users worldwide for several years. Originally focused on the UK, the ATS now has active members in Europe, Asia, The Middle East and now Australia.
In recognition of the global significance of lifting equipment training, training providers seek LEEA’s accreditation for their programs. These programs complement the renowned industryspecific training offered by LEEA. All ATS members undergo rigorous audits of their course materials, trainers, and facilities to ensure consistency and quality. Trainers are appropriately qualified and experienced, while facilities are reviewed to ensure a comfortable and conducive learning environment.
This is a significantly important development, as research conducted by LEEA has revealed a common cause behind many lifting equipment-related incidents is failure to identify defects and risks prior to use. Given the critical nature of safety in industries that involve heavy lifting, addressing these issues is of paramount importance.
Ensuring safety within the lifting industry is non-negotiable. The consequences of failed lifting equipment can be catastrophicaccidents, injuries, property damage
Throughout 2023, the Lifting Equipment Engineers Association (LEEA) has taken significant strides to increase its presence and impact.Justin Boehm from LIFTEX.
and fatalities are unfortunately the outcome, at times, of poor training. Comprehensive training programs, particularly those offered through LEEA’s framework, play a pivotal role in equipping industry technicians with the requisite knowledge and skills to inspect equipment thoroughly during statutory and periodic inspection, but with the addition of the ATS, end users can now look at proactive, industrybacked training to assist mitigation of risks and promote a safer working environment prior to each lift.
The training programs offered by LEEA’s ATS members create a mechanism through which hazards, and risks can be highlighted, explored, explained and therefore, we hope, removed before use. LEEA’s vision—
to eliminate accidents, injuries and fatalities in the lifting and height safety industries—is no small feat. This ambitious objective is underpinned by a strong mission statement: To educate, influence and enable so that best practice is everyday action. LEEA firmly believes that achieving these objectives is within reach, and the ATS is a strategic tool that will push us forward in that mission.
The ATS program is designed to address a recurring concern shared across many of our affiliated industry associations: pre-use inspections being overlooked - a gap that has been left open by degraded high risk licence training. With ATS members taking on the role of influential trainers, they will shed light on crucial aspects to watch out for during pre-use inspections. The aim of the ATS is to instil knowledge
“LEEA’s vision—to eliminate accidents, injuries, and fatalities in the lifting and height safety industries—is no small feat. This ambitious objective is underpinned by a strong mission statement: To educate, influence and enable so that best practice is everyday action.”The launch of the Accredited Training Scheme (ATS) in Australia and New Zealand has been a significant step. LEEA’s Justin Boehm congratulates Ranger’s Ashley Thacker for being the first member accredited to this program.
that becomes an integral part of daily operations, thereby enhancing industry-wide safety. In a region where the “she’ll be right” mentality regularly creeps in, we must ensure pre-use checks and safe-use is built in to every day practice and we must foster regular training to ensure safety is constantly the top priority.
Adhering to standards, regulations and legislations are not merely legal obligations but moreso, these are a moral responsibility to safeguard the well-being of people on-site. Ill-trained operators pose a threat to those around them, shirking regulatory compliance, potentially leading to hefty fines, jail time and significant reputational damage for companies who run the site. These practices should be a thing of the past – they are however very present. Thorough training ensures that end-user operators remain updated
on the latest industry standards and regulations, facilitating a culture of safety and compliance industry wide.
In industries where heavy lifting is an integral part of daily operations, conducting thorough pre-use checks on lifting equipment assumes paramount importance. Professionals in liftingrelated roles are tasked with complex lifts that impact both productivity and safety. The value of comprehensive training for these professionals cannot be overstated. Therefore, comprehensive training before utilising lifting equipment is not just important—it’s an
absolute necessity for end-users.
The Lifting Equipment Engineers Association’s strides in 2023 have brought about changes in the industry. The LiftEx event in Sydney, the introduction of nationally accredited training and the launch of the ATS program all stand as testament to LEEA’s commitment to safety, professionalism, and excellence. As industries involving heavy lifting navigate intricate challenges, LEEA’s contributions continue to shape a safer and more responsible landscape for everyone involved.
A modern fleet of Lifting equipment ranging from 3 tonne - 250 tonnes. With 25 years of experience in the Crane Industry we are dedicated to providing safe & reliable lifting solutions for our customers.
www.quicklift.com.au
“Professionals in lifting related roles are tasked with complex lifts that impact both productivity and safety. The value of comprehensive training for these professionals cannot be overstated.”
Andromeda’s Superflex steel is highly effective and holds an unrivalled structural integrity and efficacy in hot environments according to Hennie Geyser.
BORGER CRANE HIRE AND RIGGING IS A name synonymous with the Australian crane industry.
As detailed in Cranes and Lifting magazine, the company has been rapidly expanding and performing an array of dexterous lifts across the east coast of the country. What everyone notices is the crane picking up Hard Rock Café’s guitar, precast concrete, a hot water tank – you name it, Borger’s probably lifted it.
But there’s an equally imperative piece of equipment facilitating those lifts; lifting and rigging equipment. As Queensland Yard Supervisor at Borger Cranes Hennie Geyser says: “good, quality rigging is a substantial investment into a company that will provide abundant returns”.
Holding over 15 years of experience in the crane industry, Hennie Geyser was initially a yard manager for a wellestablished crane hire company in Queensland until October 2021. From there, he joined the rapid expansion of
NSW-based company Borger Cranes to find himself in his current position as a Queensland Yard Supervisor.
Throughout his career, Hennie has operated cranes up to 250 tonnes in size and worked in the nitty gritty when it comes to the procurement and managing of rigging equipment. So when he says the Superflex steel cable range from Andromeda Industries is up there with the best, there’s an added element of legitimacy to his words.
“Throughout my time, I’ve seen a lot of different rigging methods and applications,” he says. “Andromeda’s Superflex series provide structural integrity, versatility and capacity that other brands just can’t match.”
Superflex cable is a steel cable of plaited configuration; it is not laid or twisted like wire rope, which gives Superflex its unique flexible and set resistant cable. The plaiting of the steel cords creates a very tough and set resistant cable composed of many more wires than is possible with laid wire rope.
Andromeda Industries is the only producer of Superflex steel cable. The Australian-owned and operated
Andromeda Industries is the only producer of Superflex steel in Australia. With heightened emphasis on safety in lifting, the importance of investing in high quality lifting and rigging equipment is being consistently underscored –and Borger Cranes is right on board with Andromeda’s quality.
manufacturer from Moonbi, NSW, specialises in the research, development, and sale of its products to markets both nationally and internationally through a distributor network that totals over 100. With such strong structural integrity, Andromeda’s Superflex range embodies the company’s sustainable ethos: where others create single-use items that can be easily discarded, Andromeda’s range of plaited and woven steel slings and cables are built to last, possessing the benefit of being fully recyclable at the end of its lifting life.
With his vast experience in the lifting and rigging industry, Hennie says he first stumbled across Andromeda’s Superflex products on a demolition job roughly 10 years ago. After seeing the product’s performance, he was convinced to invest in the rigging equipment.
“From that point, we used the Superflex a lot as well on a high application where you might not be able to use a soft sling,” he says. “These steel cables were capable of lifting incredible amounts of capacity; we’ve used them for lifting applications of up to 100 tonnes.”
Operating up and down the East Coast of Australia, Borger Cranes finds itself in some unique lifting environments. What this means is that the company needs flexible lifting equipment – and not just from the different cranes in its fleet. Another key point of difference for Hennie with Andromeda’s Superflex range is its ability to work at different capacities at different temperatures.
“These slings really prove their worth in hot environments; soft and synthetic slings hold their own unique uses, but Andromeda’s products come in clutch for jobs that require equipment capable of handling high temperatures,” he says. “In hot environments, synthetic slings are a little bit more vulnerable to load failure; Andromeda’s Superflex steel cable is not.”
Citing the product’s recent performance for Borger Cranes in work
for refineries, Hennie also highlights the slings’ capacity when it came to lifting a hot water vessel for a brewery, citing the importance of “structural integrity” and “good quality rigging equipment”.
“At Borgers, a lot of our work pertains to roofing; if we don’t use the right rigging equipment, we run the risk of damaging the equipment, losing the client, and losing face,” he continues. “Sustainable, flexible, versatile rigging equipment is a significant investment towards our business; with quality rigging comes ease of use in a durable manner.”
“Good quality rigging makes such a big difference on a job,” he says. “Using the right equipment for the right application is imperative to a successful lift. Investing in good quality equipment like the Superflex range from Andromeda ensures safety and practicality ensues.”
“Using the right equipment for the right application is imperative to a successful lift. Investing in good quality equipment like the Superflex range from Andromeda ensures safety and practicality ensues.”
The sum insured you set can influence multiple aspects of your insurance, including premium and potential claims payout. As the sum insured for your equipment is set by you (and not the insurer), it is important that sums insured are reviewed with your broker at renewal to ensure your equipment is adequately covered for its current market value.
FOR EXAMPLE, YOU MAY HAVE PURCHASED a machine at a fire sale or an auction, and the price paid was an absolute bargain, but if the unit needed to be replaced with the exact same item tomorrow, how much would it really cost in the market?
To get an idea of the current value of your equipment, consideration should be given to its age, make, capacity and hours, as well as any permanent attachments or modifications made to the machine. Your experience in purchase or sale of your equipment plus any machinery trader websites may also assist with establishing your sum insured.
The nominated sum insured will also determine:
• the premium payable per machine
• the maximum amount that will be paid in the event of a loss
• excess applicable in the event of a claim – usually calculated as a percentage of the sum insured (however subject to any minimum excess applicable)
As the premium payable for a machine is influenced by the nominated sum insured, if this value is not reviewed there is potential that premium is being overpaid (i.e. if the current market value is in fact much lower than nominated). Conversely, if the current market value is higher than the nominated sum insured, premium is being underpaid which may result in
indemnity payable for damages to your machine. UAA utilises independent qualified and experienced machinery assessors with a trade background to determine the cause and severity of the damages. Utilising the experience levels of the assessor, the assessor will determine if the machine can be safely and adequately repaired within the indemnity levels or if the vehicle is an economic total loss, meaning the cost of repairs outweigh the total loss value of the machine, or the machine is a statutory total loss and cannot be safely repaired.
When determining if the vehicle can be repaired or if it is an economic total loss, UAA’s independent assessing panel will seek to obtain the market value of a machine immediately before the incident. This is provided through independent and certified valuation firms. Once obtained, the assessor will appeal to the market for salvage tenders, being the value of the machine in its damaged state. In order to be a successful repair, the costs of the assessed amount must be less than the
market value of the machine immediately before the incident, less its salvage value in its damaged state.
If the item can be successfully repaired for less than its total loss value, the machine is considered a repairable option. If the costs of repairs outweigh the total loss value, the machine is considered to be an economic total loss.
Of course, machine values can change over time for a number of reasons (e.g. supply restrictions, increased demand, inflation, depreciation). UAA’s insurance product allows for scenarios where there may be a difference between the sum insured and the market value immediately preceding a loss:
• Market value plus
• Appreciation in value
• Replacement provision
• Average clause
However, these benefits, and the extent to which they could apply, depend on the nominated sum insured being
accurate at renewal.
Market value plus is an automatic benefit included within UAA policies. As UAA insureds set their own sums insured, if the market value of the machine is determined to be less than the sum insured, UAA deploys a free additional benefit within its policy. This policy benefit means that in the event of a total loss, if the Market Value immediately preceding a loss is determined as being at least 85 per cent of the Sum Insured, the settlement amount will be the amount you’ve nominated as the sum insured (scenario 1). If the market value of a machine is determined by the valuer to be less than 85 per cent of your declared sum insured, the settlement amount will be the market value and add an additional 15 per cent on top (scenario 2).
Market value plusScenario 1Scenario 2
Sum insured$100,000$100,000
Market value$85,000$80,000
Settlement amount$100,000 $92,000
This is an excellent allowance provided by UAA, however this could mean that the over insurance of your machine does not see the expected return of the sum insured at a total loss settlement. On the contrary, other insurers may only pay up to the market value of equipment in the event of a total loss.
Appreciation in value – this policy provision allows for circumstances where the value of equipment increases during the period of insurance, but the sum insured was adequate at the beginning of the period. In this instance, claim settlement could be increased by up to 25 per cent above your nominated sum insured (scenario 1). If the nominated sum insured was not adequate to begin with, this benefit may not be applicable (scenario 2).
Appreciation in Value Scenario 1Scenario 2
Sum insured$100,000$100,000
Replacement benefit – where a machine is within two* years of age and is deemed a total loss, UAA may replace the item with a new machine. Claim settlement could be increased by a maximum of 15 per cent above the nominated sum insured for a new replacement machine. *increased to three years in Nov 23 policy wording.
Average clause - If a machine has been significantly under-insured (the sum insured is significantly below the market value), claim settlement for repairing a machine may be reduced proportionally due to this under insurance, meaning that whilst a machine is technically repairable, the value of the sum insured requires UAA to economically total loss the machine.
UAA would then consider two factors – a total loss payment to the insured or the application of the average clause as noted in the policy, meaning reduced indemnity.
The average clause applies a calculation to settlement which in its simple forms means that for a machine that has been under insured and is only an economical
total loss by nature of its sum insured, UAA would contribute a percentage of the repair, representing the percentage of the partial insurance of the machine.
Over insurance can create a perception of additional security if the machine were to be deemed a total loss, however settlement will always be determined using aforementioned principals.
UAA has seen an increasing trend in the number of machines being total lossed as a result of inadequate insurance. This not only has an effect on the settlement amount of your claim, but also flows onto potential financial impacts - given the scarcity of readily available replacement machines. Supply chain issues are still prevalent in both the parts and purchase sector of our industry.
To maximise policy benefits available with UAA, the nominated sum insured for every machine should be as accurate as possible at the beginning of every policy period. This leads to a smoother claims process with both UAA and our Insureds aligned on the value of the machines insured.
Servicing
With an experienced team that are passionate and committed, a comprehensive mobile crane fleet ranging from 3t to 800t in capacity, complimented by a wide variety of truck & trailer combinations, you can be assured that your job will be completed safely and on time.
Melbourne-based crane services company Komp Cranes recently took delivery of a new Maeda MC305C mini crawler crane. Director Danny Toohey and Pace Cranes’ National Sales Manager Michael Cawston discuss the Maeda brand, Japanese manufacturing and the importance of post-sale service.
IT’S WEDNESDAY, JUNE 28, 2023.
Melbourne’s winter sun is shining as a chill 12-degree day encompasses Danny Toohey, who stands out the front of his Glenroy warehouse expectantly. This Wednesday was like no other Wednesday he’d experienced yet; today was a significant milestone.
It was the day he was receiving his second Maeda mini crawler crane.
“It was also my 15-year wedding anniversary,” laughs Danny, “but we don’t really talk about that.”
Sitting in his warehouse with Pace Cranes’ National Sales Manager Michael Cawston and the Cranes and Lifting team, he assures us the new crane was not an anniversary present for his wife and business partner Barbara – in his own words, she just “wasn’t as excited with the new purchase as much as I was”. Instead, the director of Melbourne-based crane hire and services company Komp Cranes is in a relaxed mood as he discusses the history of his business.
Commencing operations in the early 2000s, Komp Cranes was once owned by Danny’s friend Paul, and the name ‘Komp’ is derived from the initials of Paul and his family, as Danny explains.
“Paul was finished with the industry by 2011,” he says. “He didn’t really have the drive or desire to keep running a business. At that point, I’d gotten sick of working for people, so I figured it would be nice to run my own business and work for myself essentially.”
And, 22 years later, it’s hard to disagree with the choice Danny’s made in forging ahead for Komp Cranes.
The crane hire company specialises in domestic construction and commercial developments, including tasks such as pool, spa and jacuzzi installations, as well as steel and panel erections.
It’s nifty projects such as these where compact, lightweight machinery capable of performing dexterous lifts in confined
areas is required and, as Danny discovered, the Maeda mini crawlers are the perfect answer to his needs.
“I first came across the Maeda brand when I had a customer who I completed a lot of façade work for,” he says.
“There weren’t a lot of Maedas around at the time, but it really opened up a whole new market for me with new access to steel jobs, domestic jobs and glass jobs that my other, bigger machines could not get access to.”
It was that kind of access to new markets that spurred Danny to purchase his second Maeda, which also conveniently arrived close to his anniversary date.
He highlights the “quality” that’s been apparent for “so long” in his experience with the Maeda brand and the service he’s received from national distributors Pace Cranes as key factors in making his decision to acquire the MC305C.
With a lifting capacity of three tonnes at a range of 2.5 metres, the MC305C has a maximum lifting height of 12.52m in tandem with a maximum working radius of 12.16m.
Also featuring a maximum belowground reach of -64.36m, the machine is 4.285m long, 1.28m wide, 1.695m tall and weighs 3.9 tonnes – indicative of its superiority in more compact lifting areas.
“It’s such a unique crane,” explains Danny. “There’s always increasing demand from customers for a crane of its size and, by buying this second Maeda, I’m investing in the business; I want to create another line of income for my staff and our business.”
“Additionally, I know that they’ve got an agent down here who’s willing to help with any issue I encounter, which is why I feel confident about going through Pace Cranes.”
As Danny points out, other brands are not necessarily his “cup of tea” because of their lack of post-sale servicing support. Michael, nearly 10 years into his role as the National Sales Manager at Pace Cranes, believes this is what “differentiates” the company from
other dealers.
Having been associated with the Maeda brand for over 30 years as the distributor of the Japanese manufacturer’s equipment and machinery, the team at Pace Cranes is well acquainted with what is required from its stock of spare parts and their servicing departments.
“We invest in our service agents,” he says. “We know which spare parts are needed on hand to avoid any downtime, so we do our best to keep those items in stock.”
“Ultimately, we’ve invested a lot to ensure that we can provide a thorough post-sale service for our customers.”
And, as Danny highlights, Pace Cranes is a family business, meaning there’s a constant emphasis on providing a high level of personalised support to those choosing to go through them – or, in Danny’s words: “you can sit down and have a bloody beer with him!”.
“I’ve always felt really valued as a customer at Pace,” he says. “It’s never felt as though it was just a transaction; there’s a genuine level of care displayed in their follow-up service.”
When it comes to the technology involved in the safe operation of Maeda’s mini-crawler, Danny is nothing but complimentary.
“I’ve been working with cranes for a long time now,” he says, “and I know how to operate a crane safely.”
“But there are some guys out there who need the extra technology because they’re newer to the industry.”
“With cranes like the Maedas, not only do I know the crane is going to come back in one piece, I know – most importantly – the operator is going to go back home that night.”
As Michael adds, Maeda does its best to ensure the crane is borderline “failsafe”.
And so, for a seasoned crane operator owning a local business out in the north of Melbourne for the best part of 13 years, the future remains undefined for Danny Toohey and Komp Cranes – but his two Maeda mini-crawlers are set to play a major role in what the next target will be.
“These are almost my semiretirement plan,” he reflects. “I want to move into more local, smaller work, servicing the community around me.”
“I’ve got no interest in the bigger jobs, and these two cranes are the future of my business.”
Combining the reliability of steel and ultra-flexibility for all lifting applications
Superflex Slings
Size Range 10mm - 96mm
Capacity 1t - 168t
Flat Woven Slings
Size range 50mm - 250mm
Capacity 1t - 48t
Often involving long routes through unfamiliar areas and trips to construction sites deep within the city, getting a crane to where it needs to be takes up time and resources. This doesn’t even factor in the different road regulations, axle limits and road access restrictions that change from state to state, bridge to bridge, road to road, day to day.
Bernie Peoples has over ten years of experience working in the crane industry. His time has seen him operate machines for Boom Logistics, Advanced Crane Hire, Mammoet and, currently, Metcalf Cranes in Melbourne. During his early years in the mobile crane industry
operating all over Victoria, he saw the need for a better way to navigate between worksites.
“There just were no good tools for planning your route or navigating to or from sites,” he says. “I’d have spent a lot of my own time looking up where I could go and making a route to suit, which may not have been the best way.”
At that point, he reached out to his brother. Tom has an extensive career in software development, working in various industries, from telecommunications to embedded vehicle systems.
Highlighting the problem to his brother over Christmas lunch, Bernie posed the idea of a mobile app allowing
crane drivers to select their machine and destination. Then, the app would develop the quickest available route that complied with regulations while avoiding delays and low bridges.
“I wasn’t too keen on the idea initially,” admits Tom. “All the information was open source; anyone could access it online. I thought that surely someone has tried this before.”
Bernie could see how valuable a tool like this would be to the mobile crane industry and persisted in getting Tom to work on a prototype. Tom eventually came around, and the duo launched ‘Hevway’ in October 2022.
Hevway, when it was launched, focused on making driving a crane
A crane operator and a software developer are an unlikely business duo.
Bernie and Tom Peoples, their app Hevway combines the best of their talents. It is set to transform how crane drivers and operators navigate the complexities of road access rules.
efficient, practical, and safe for operators. However, as Bernie says, he began to see an increasing value in the business side of things the more Hevway developed.
“It minimises business expenses by reducing time travelling to site, delays due to traffic and fines,” he says. “Reducing operational costs and saving the crane operators time is where Hevway produces the most value.”
The last year for Hevway has been one of learning, growth, and development. After its initial launch, Tom and Bernie focused on improving the stability of Hevway and adding features requested by their customers to make Hevway fit into operators’ existing work processes.
“Hevway features maps with Approved, Conditionally Approved, and Restricted roads for each mobile crane class in Victoria up to nine-axle cranes with a GVM of 109 tonnes,” he says. “Hevway is currently moving towards routing on NHVR permits and expanding to the rest of Australia, starting with New South Wales.”
Initially, Hevway only displayed the red, orange and green roads and planned routes. It has now expanded to showing all the information an operator needs, like low structures over roads, traffic disruptions and road closures.
“Within Hevway, the user can click on any red or orange road displayed on a map to see the conditions for that road,” Tom continues. “The other aspect that we’ve streamlined is the filtering of hazards during route planning so the operators can see only what will affect the suggested route. The data is updated every 30 seconds, giving the operator real-time information relevant to the route.”
Another improvement the duo has focused on over the past 12 months is simplifying Hevway’s interface to create a more user-friendly app. Hevway now features password remembering, the option to turn the audio off and filter the information displayed on the map.
“Essentially, we’re trying to create a user-friendly product that can be tailored to the operator’s needs,” says Tom. “This last year has been about refining our product to make Hevway more valuable
to the operators and businesses using it.”
Bernie’s experience in the industry has provided access and insights into how operators worked before Hevway, allowing them to design Hevway in a way that fits smoothly into the industry. Listening to their customers across Victoria, they continue to refine Hevway to have as much value as possible.
“Operators see the value in not having to spend their own time the night before a job figuring out which roads they can access and which roads they can’t,” says Bernie. “Being able to plug in your crane and destination and have the route readily available instantly is
invaluable to drivers.”
As the creators of Hevway are keen to highlight, the app is growing; it holds more information with less noise and irrelevant data than other resources available online and turns results around quickly. The future, while indefinite, is starting to become clearer in terms of where they want to go.
“The next stage of our growth will be including the operations teams, as that is an area where we can compound Hevway’s value,” says Tom. “The more people we get on, the quicker we will grow, and all our growth is being invested in creating a better product.”
IT HAS LONG BEEN ACCEPTED THAT 10-YEAR major inspections are the benchmark for crane maintenance. While it is convenient to have a measurable time frame to schedule a major inspection, this method is now under scrutiny. Time-based maintenance (TBM) also called “clock-based” maintenance, or “condition-independent” maintenance is an asset maintenance schedule based on a strict timetable.
In line with ISO 9927-1:2013, AS2550.5-2016, AS2550.11-2016, AS2550.1- 2011 and AS2550.102006, CICA recommends considering an alternative condition monitoring approach to the existing default practice of conducting a major inspection at 10 years. Responsibilities under workplace
legislation can be met in many ways. There is no “one-size-fits all” position in relation to safety issues and workplace safety legislation explicitly allows for this as a way of encouraging safety measure innovation.
The team at Manitowoc led by Garry Barker, Product Support Director, working in conjunction with Mike Percy from IDEAS Cranes, a crane engineering and major inspection specialist, are proposing a new monitoring system based on data captured on all Grove products which could dramatically extend the period before a major inspection is required.
Mike has been working on major inspections for 20 years and collaborating with Grove for five. Together, they are currently completing between 15 and 20
inspections per year along with other engineering services.
“Garry and I have always seen the benefits of the current CraneSafe inspection criteria which provides third party reviews, however it doesn’t consider proactive assessment of time monitoring of components, in that they don’t account for the total life span of the crane. A requirement of the standards for extending the trigger point for a major inspection beyond seven years is an annual design life assessment. By combining with OEM guidelines we can monitor the usage of the crane so owners know what the future of the crane will look like, instead of getting to the 10th year of ownership and being forced to pay a large sum on a major inspection.
The major inspection for cranes is easy to monitor, but if crane owners can demonstrate a willingness to fulfil requirements of a system that bases maintenance on usage, it may be able to eliminate the need for expensive and time prohibitive inspections.Data regarding the crane’s history is combined with data captured from the telematics system on the crane.
“Our monitoring systems use data from the CraneSafe process, and then tying that in with the maintenance records and Telematics data we can get from Grove. We’ll then complete a review and provide an annual engineers report including upcoming maintenance requirements and anything else which is getting picked up in the CraneSafe process,” Mike said.
“We’ll complete an annual review of this information, and we can tell the owner, ‘You’re tracking it, it’s year three and you’re at 22 per cent of winch use, for example, and we want oil changed or something done at this date, and we want a service completed at this date.’ And your projected major works are going to happen in 14 years time or whatever the extended period might be.”
“Because of the way the industry is set up, sites demand paperwork at 10 years, so part of our process will be to complete a rigorous inspection at 10 years anyway, basically to validate that the condition matches up with the life span we’ve calculated for the crane. As long as the owners are tracking these maintenance and service requirements along the way, that should be achievable,” he said.
Garry takes up the story.
“From our perspective, we give the crane a use expectancy from day one, like a birth certificate and then annually, or more frequently if the crane is clocking up the hours, we gather the data from CICA via the CraneSafe inspections, with the owners’ approval.
“We can grab the data regarding the crane’s history and combine this with the data we are capturing from the telematics system on the crane. Then each year, or more frequently, depending on usage, the customer knows what their usage of that crane is and what the expected usage of that machine will be,” he said.
“Essentially, crane owners are going to be able to project expenditure on the crane a lot more accurately than at the moment. The idea is that we’re regularly reporting the utilisation of the machine which enables them to better plan what needs to be
done and adopt preventative maintenance program for their assets.
“If crane owners are looking after the machines properly, they might not have to touch that machine for 15 years. At the moment, they’re spending between $20K and $25K on a deferred major, or more on a full major inspection at the 10 year mark.
“This will become part of the sale of the crane and if they’re using the machines on average 1000 hours a year, they’re going to get 15 years very easily before they need to do a major inspection.”
“Another big win for the owner is residual value of the crane. Because they can predict the usage of the crane, when a major inspection is due, if they want to change out their machine out at eight or 10 years, normally the value of the crane will drop at this point because it’s going to need a major inspection, whereas now, that won’t dip to 13-15 years,” he said.
“Depending on the usage of the crane we can generate reports from the telematics and make a call on what we are seeing and what might need servicing.”
According to Mike there will be flexibility in the inspection process.
“Depending on the usage of the crane we can generate reports from the telematics and make a call on what we are seeing and what might need servicing. An ongoing benefit is that we’ve worked on an extensive number of Grove machines,” he said.
“Partnering with Manitowoc we have a large data set and extensive understanding of the product to base projected maintenance, inspection and replacement schedules on. We can plug that data back in and tell the owner what we’re finding and that tele-cylinders are OK for another on average amount of hours, or whatever it is. The annual reporting is essentially an annualised utilisation report.
“The issue was that the 10 year major inspection was adopted and no one said, “The life cycle for cranes is 10 years.” It just said, “The nominal life of a crane is 10 years depending on how you use it, and the industry just defaulted to the 10 years. Our data shows that the typical design life for an average crane is closer to 15 years. However, some higher utilized cranes could reach this point much earlier than 10 years.”
Garry concurs with this observation.
“For example, we have data on how many times the pins go in and out on the tele-cylinder, how many hours each winch has completed, detailed data on all of the components and now with telematics, all that data is available without actually being on the grid.”
“This is a historical issue in Australia and a number of other countries. There are 10 year and 25 year inspections, with inspections starting to be more serious after 10 years because that’s when things start to fall apart depending on the utilisation. At 25 years some countries, like Singapore, simply say the crane is done, take it out of service and get rid of it.
“With our Grove GMKs we can download the information and see all of the component movements in our operating systems over the 20 plus years. That gives us a really great handle on exactly the hours and the functionality of each of the components and I’m pretty certain we’re the only manufacturer that can do this.
“For example, we have data on how many times the pins go in and out on the tele-cylinder, how many hours each winch has completed, detailed data on all of the
components and now with telematics, all that data is available without actually being on the grid. Before you’d have to open up the right page and take a picture of it. Now, all that information is in telematics and for the servicing of those components, you can actually zero in and set timers for the servicing,” he said.
“Through telematics we can see actual hours on the machine, the winch and engine hours, we can then work out what percentage of the winch life remains given its utilisation. We’ve got cranes out there today that are 10 years old and the auxiliary winch has only got 100 hours on it. I mean that’s probably only reached three or four per cent of its utilisation.
“Our reporting system is going to provide far more accurate information than anyone has ever delivered before,” said Garry.
HMPE has revolutionized the lifting, rigging, and towing cultures. The HMPE fibre is 15 times stronger than steel wire rope of the same weight. This highly advanced synthetic fibre allows you to achieve the same WLL with a sling that is about 80% lighter.
WEIGHT AND SIZE REDUCTION
•8 to 10 times lighter than wire rope
•Up to 2.5 times lighter than standard polyester round slings
• Significantly smaller and lighter than polyester round slings
FLEXIBILITY
• Easier to handle and transport
• Superior load control
• Floats on water
SUPERIOR D/d RATIO
• Greater D/d ratio and compatibility with other rigging gear
• D:d = 1:1 for round slings up to 200t, above 200t D:d = 1:1.5
DURABILITY
• Impervious to environmental conditions
• Excellent UV Resistance
• Good chemical resistance
CIRCA 2670 BCE, UNDER THE REIGN OF King Djoser, the very first pyramid in ancient Egypt was built by Imhotep: an Egyptian polymath, responsible for the design of the famous ‘Step Pyramid’.
A massive structure it was too: made purely out of limestone, the ancient Egyptian structure once stood at 64.5 metres tall, with a (nearly) square base of 109 metres x 121 metres and, up until 1997, was considered to be the earliest largescale cut stone construction made by man.
So, unless we account for aliens or some other extra-terrestrial being, then it is evident that cranes have been around for a very long time – nearly 5000 years, in fact.
During that elapsed time, they’ve managed to evolve in numerous ways, through technology, safety, load capacity, raw materials and every other imaginable way possible. Ultimately, however, their core purpose remains the exact same: cranes lift stuff up, and put it somewhere else.
The team at Cranes and Lifting was fortunate enough to witness part of this history firsthand courtesy of retired builder Peter Rodger, who supplied the magazine with historic content detailing cranes from the late 1800s and major construction projects in Australia in the early 1900s.
most iconic landmarks across the country.
Completed in 1910, the brothers were selected by architects Fawcett & Ashworth to construct the original Flinders Street station in Melbourne – an instantly recognisable building across the nation. Further to that, the two also played pivotal parts in constructing country landmarks such as the Bairnsdale courthouse, the Camperdown clocktower and some other city constructions such as Hobart’s GPO and the massive St John’s Cathedral in Brisbane.
Their machines of choice, however, were generally derived from Scotland, according to Peter.
“They really enjoyed the Scotch product,” he says. “It was where our heritage lay, and we held a rich history with the Scottish building industry: Sir William Arrol, a Scottish civil engineer who supplied cranes for the Titanic, was an ‘Uncle’ figure to both Peter and David”.
A Scottish civil engineer and bridge builder, Arrol worked on several projects in the latter years of the 19th century that still hold firm today. Reconstructing monuments such as the Tay Bridge in 1883, Arrol also led the construction of the Tower Bridge travelling over the Thames in London, and the Firth of Forth in Edinburgh.
Most notably, however, he played a significant role in creating the Titan Crane which was eventually used in the construction of many notable ships as well as lifting engines and boilers on battle ships. Furthermore, he built the Arrol Gantry in Belfast in 1908, a machine that was used for the construction of the RMS Titanic and RMS Olympic.
With three of the catalogues supplied to Cranes and Lifting originating from Butters Brothers, a Scottish crane manufacturing company originating in 1867, it’s not difficult to see the infatuation; however, other – also defunct – companies do make an appearance too, such as Scottish-based McDowall & Sons, and the midlandsbased Thomas Smith & Sons.
Throughout, the catalogues feature an array of cranes from the past – whether they’re electric, steam powered, the original gantry cranes, or locomotives – and provide an intriguing insight into what construction, mining, and port work looked like before the technological advancements that we’re so familiar with arrived.
Ultimately, we can talk about the history these catalogues hold for as long as we want, but the reality is it’s just better to see them for yourself. So, without further ado, here’s our selection of the best images from the material supplied to Cranes and Lifting.
“The catalogues feature an array of cranes from the past –whether they’re electric, steam powered, the original gantry cranes, or locomotives – and provide an intriguing insight into what construction, mining, and port work looked like before the technological advancements that we’re so familiar with arrived.”
Precision Rigging and Logistics provides an end to end solution for any lifting job in Queensland. Precision Rigging and Logistics can visit your site at any time to suit you, to conduct a comprehensive, cost free site evaluation and consult with you to provide you with a cost effective, efficient solution to all your logistical needs.
• On Site Mechanical Rigging
• Relocation and final positioning of sensitive and heavy equipment
• Removal of redundant equipment/debris from site
• Comprehensive crane, transport and traffic control logistics packages
• Demolition and removal of mechanical equipment
• Commercial and residential equipment removal & relocations
Precision Rigging and Logistics service a range of industries including:
• Mechanical Air-Conditioning
• Electrical
• Medical
• Heavy Industrial factory equipment
• Telecommunication and I.T Equipment
• Universities and Hospitals
• Heavy Art
businesses from Australia’s industrial sector have found it increasingly difficult to source new equipment - none moreso than crane operators. With new assets sparse and slow to reach Australian shores, the demand for quality used cranes has grown steadily into and throughout 2023. This has created a thriving hub of both buyers and sellers looking for solutions to their business needs for used asset specialists like Pickles.
For Pickles’ National Sales Manager of Trucks & Machinery James Chauncy, this increased demand for cranes has led to the creation of a specialised marketplace where both buyers and sellers win.
Interestingly for James, the most important aspect of establishing a thriving crane marketplace has been in guiding sellers through the seemingly daunting process of
closing. For many long established crane businesses who have decided to retire in 2023, the idea of ‘shutting up shop’ feels too final and intimidating an undertaking.
However, with the recent success in sales, James has seen the value in helping businesses with tailored solutions and proverbially holding their hand through the process. This can mean helping businesses offload one or two cranes to free up capital for new purchases, instead of offloading their whole fleet.
Given the current market, James knows that offloading crane assets in 2023 can create fortuitous results for businesses and inject much-needed equipment into the industry. That’s why Pickles is structured to assist businesses that are considering selling equipment. Throughout 2023, Pickles has successfully hosted a number of crane
specific auctions and found operators to be satisfied with not just the results, but also the service. Its most recent sale, a huge auction on behalf of Tolsaf Cranes, generated results that had vendors, bidders and Pickles satisfied.
“The Tolsaf Cranes Business Closure Auction was our most recent sale, and that was really successful. It took place just before the end of the financial year and it generated $6.3 million plus in sales. We had a 96 per cent clearance rate and the family (vendors) just kept one small truck to run around town in. Probably the most expensive asset was a 130t Lieberr and there was a range of all terrains, Frannas, prime movers and tilt trays,” said James.
In order to guide businesses through an auction, he and his team go to great lengths to organise every facet of the sale and make
the auction as seamless and painless as possible for their vendors.
“The process is sparked by a conversation with one of our 50+ sales executives. They handle different regions around the country. For Tolsaf Cranes, we had one sales executive, Tosh, work exclusively with them for 12 months leading up to the sale.
“When the family decided they were ready to retire, Tosh and I met with them to get a better understanding of what their expectations were, what they could and couldn’t do and what their timeline was. Our aim is to take the pressure off the customers, particularly during times of heightened stress like shutting down a business after so many years. We know that when a client comes to us for a business closure sale, they already have their plates full with organising their final months of operation. So we like to take the whole reins for the auction, including dedicating a full team to helping their closure. This can sometimes entail sending a project team to unpack up to 50 years worth of crane ancillary gear and paperwork. We then manage everything from a chain to a crane - and we’ve got the experts that do it,” said James.
James goes on to explain the emphasis that Pickles places on the details. From
inspecting and presenting assets down to the smallest detail to help their bidders complete online inspections, to carefully ensuring they get the right specifications of each and every single item, Pickles takes care of every detail.
All this happens before Pickles’ team of marketing specialists begins a tailored digital campaign specifically for the one auction.
“If a crane has two winches, we make sure it’s listed with two winches and has photos to reflect this. We focus on adding value for potential buyers, particularly for bidders who might be on the other side of
top quality images of the asset. Some buyers are so desperate for assets that they plan on putting the equipment to work as soon as the auction finishes. And in some workplaces, you’ve got to show previous service and maintenance history to put an asset into operation,” he said.
For businesses deciding whether to take the leap, the first question is often about the timeline. How quickly assets can be offloaded greatly impacts businesses, specifically for those looking to retire.
Luckily, from the initial conversation with a Pickles Sales Executive to the auction day, the whole process can be completed in roughly six to seven weeks. During the lead up to the sale, several Pickles’ departments will move like cogs in a clock to ensure maximum sales results and ultimate convenience for the vendor.
the country or even overseas in the UAE, Egypt, or Asia who won’t be coming to inspect the equipment before the auction,” James said.
As a digital-first auction house, Pickles is meticulous about its online listings and pays close attention to sourcing all of the details needed for buyers to make informed purchases from an online auction. For crane sales this can include annual crane certificates, 10 yearly and major rebuild reports and any service and maintenance history for individual assets.
“It’s really important that we upload all the details onto the auction listing, alongside
The finance department will make sure the funds and details are organised so the vendor can be paid as quickly as possible, and the marketing team will create a huge pre-sale campaign to reach a huge audience of potential buyers.
Most importantly, Pickles places an emphasis on post-sale care for their vendors. This aftercare includes quick payment and asset management while the equipment makes its way to new homes.
“At the end of the day, we’re in partnership with businesses and buyers to help everyone find what they need. Anything to do with trucks, cranes, trailers, earthmoving, ag, whatever the industry is, we can help,” James said.
Manager, Trucks and Machinery, James Chauncy.
As a digital-first auction house, Pickles is meticulous about its online listings and pays close attention to sourcing all of the details needed for buyers to make informed purchases from an online auction.
“It’s really important that we upload all the details onto the auction listing, alongside top quality images of the asset. Some buyers are so desperate for assets that they plan on putting the equipment to work as soon as the auction finishes.”
Fleurieu Cranes recently took delivery of a Liebherr LTM 1650-8.1. To celebrate the arrival of the crane, both Liebherr and Fleurieu
Cranes organised an official reception which attracted close to 200 from local South Australian crane companies and general industry representatives combined.
IT’S A BIG STEP FOR A RELATIVELY SMALL company - the new crane is only the fourth Liebherr LTM 1650-8.1 delivered in the country and the second largest capacity crane in South Australia.
Brandon Freer, Managing Director of Fleurieu Cranes, provides the background to the purchase and explains why the business has taken such a significant step.
Fleurieu Cranes has been operating for over 18 years, but the decision was made following the passing, in November 2021, of one of Fleurieu Cranes’ three original owners, Philip ‘Snowy’ Allen.
“I’d been General Manager with the business for nine years and following Snowy’s passing I was approached by the other owners to buy into the business,” Brandon said.
“Since that time, we’ve bought a number of assets to satisfy growth, along
with refreshing the fleet to best service our customers with a focus on new equipment and technology.”
Fleurieu Cranes was started by Snowy and a couple of friends who both initially worked in the business and then left to focus on their own fields unrelated to cranes. The business began with a 30t capacity truck mount crane - and whilst this crane is no longer in the fleet, a picture of this crane is proudly displayed in their head office.
“Today, we are 130 people strong, having grown 25 per cent in the last couple of years. In terms of cranes, we have probably grown the fleet by a similar percentage and we have been freshening up the fleet too, which is something we have always tried to do. By refreshing the fleet, we offer our operational teams the opportunity to work with the latest technology whilst ensuring we’ve got the best fleet available,” he said.
Brandon goes on to discuss the profile of his customers, the industry sectors Fleurieu Cranes services and his team’s experience.
“We are fortunate enough to service Tier One companies, right through to mum and dad projects, we are not too proud to service that section of the market,” he said.
“We do plenty of infrastructure cranage typical work throughout South Australia, however we do quite a bit of work in the wind farm space as well. The Liebherr LTM 1650-8.1 is ideal for wind farm construction and maintenance. Obviously, in South Australia we’re well positioned to service a lot of wind farms,” he said.
“We are also exposed to the resources sector where we work for all the major players. We do a fair bit of mining related work, including project work and shutdowns, and we’re also in the renewables sector with solar farms and wind farms.
“People want to work for Fleurieu Cranes, we are like a family, we treat our people well and they in turn treat the business well. We invest time and money in training and upskilling our people which they value, and this leads to high retention rates,” he said.
“We have apprentices in our workshop, and years ago we had apprentices with boiler maker backgrounds in the field, but we’re not in that space now. We really focus our efforts on cranes and lifting with
many associated value-add services. We employ people based on their drive, how they conduct themselves, we can train skills, that’s our philosophy,” said Brandon.
Fleurieu Cranes operates from a purposebuilt facility with workshop capabilities.
“With our large workshop, we have sufficient facilities to complete all general servicing, maintenance and repair work, and all works necessary in managing major inspections for ourselves and others. We regularly work on cranes from other companies - you will see their cranes in our yard all of the time. Our workshop features four full time technicians, and each has some form of factory training,” said Brandon.
Brandon also discussed the renewal of the fleet and its importance for the business.
“In terms of brands, we have a mixed fleet, and we are continually renewing this through a dedicated fleet strategy. We operate Terex Franna, TIDD, Grove, Tadano, and Liebherr cranes. We ran a Demag AC350 for some time and we sold that crane, replacing it with a Tadano Demag AC300 which features 80m of main boom,” he said.
“We are always looking at the advances being made with technology and bringing this into our fleet wherever possible. The Tadano Demag AC300 is a great example of technological advancement, it’s charts compete well with the AC350 and in many places it exceeds it.”
“When you talk about wind farms and replacement of generators and that type
of application on some of the lesser hub height wind farms around South Australia, it services them really well. It is more efficient to get there and more economical as well with less fuel burn,” he said.
Brandon goes on to discuss the process which led to the purchase of the Liebherr LTM 1650-8.1.
“I first saw the crane at bauma in 2019 where Liebherr unveiled the crane for the first time. Snowy and I had many conversations about the best configurations for our customers. Importantly, the Liebherr LTM 1650-8.1 was not a brandnew style of crane, it is effectively the evolution of the LTM 1500-8 axle crane.
“I believe that when a new crane is a result of this type of evolution it just gets better. Whenever a totally new model is released with a new shape, engine, new everything, there are bound to be bugs that require ironing out. Because the Liebherr LTM 1650-8.1 is a result of this evolution, I believe it will hit the ground running,” said Brandon.
Fleurieu Cranes has never been afraid to invest in new cranes explains Brandon.
“Ten years ago, we invested in the Grove GMK6400, which at the time was a big step-up for us. It has proved to be a very good lifter at height, and we bought that crane to service the wind farm industry where we’re changing out gear boxes in 80m hub height wind turbines. That crane did really well for us, and still does today in fact.
The Liebherr LTM 1650-8.1 might seem like a big step, but it’s natural for this business to continue investing in what we see as the best fit for our customers’ requirements at the time,” he said.
He then talks about the personnel within Fleurieu Cranes and how they plan for major projects like mining shutdowns.
“We obviously have a pool of individuals whilst focusing our energies on having the same regular operators in the same cranes wherever possible. When you have shutdowns and 24 hour operations, that’s
moved to Melbourne where she is now working for JYC,” said Brandon.
Brandon adds that he focuses on building the engineering and lift planning capabilities within Fleurieu Cranes.
“We have four engineers in the business, which sounds pretty top-heavy for our size, but we see that as really important. This investment enables our supervisors to stay out on the road and spend as little time in the office as possible.
“Our supervisors are also our safety people as well, so they’re out on site looking
not always possible, but we certainly try and keep the teams familiar with the assets that we’re running.
“We also have a significant pool of casuals in the business which enables us to increase and decrease our workforce as we need. Within our workforce we also have a few female operators and riggers.
“One of our operators who had been with us for a long time introduced his daughter to us and she went on to become a great asset for the business. She worked on FIFO mining work for us and recently
at tomorrow’s jobs but also managing today’s jobs, which is important. We actually run more supervisors per staffer in the state by far, probably double any of our competitors. We see this as a way to manage our safety and our people and also stay close to our customers,” he said.
A sustainable future and reducing carbon footprints are key topics for many crane companies, and it is no different for Fleurieu Cranes.
“About 12 months ago we made a decision to partner with Trees for Life and
“Importantly, the Liebherr LTM 1650-8.1 was not a brand-new style of crane, it is effectively the evolution of the LTM 1500-8 axle crane. I believe that when a new crane is a result of this type of evolution it just gets better.”Andrew Esquilant, General Manager Liebherr Mobile Cranes hands Brandon Freer, Managing Director of Fleurieu Cranes the key to the LTM 1650.
today we offset 100 per cent of fuel burn carbon emissions from all our cranes, trucks and vehicles,” said Brandon.
“Effectively the way that we achieve this is we contribute money to Trees for Life and they plant trees across the country. This is an initiative we’ve chosen to do, we want to lead the industry in this regard, not be pushed by government to do it,” said Brandon.
“We are also speaking to all the crane manufacturers and asking them what are they doing in terms of electrifying machines or green energy and what’s the best way forward? I’ve seen firsthand what Liebherr is doing in terms of having electric superstructures, however currently the necessary size of cable (volts or amps) makes that solution unrealistic on many of our sites.
“The next step is to look at hydrogen as a fuel source and I know all the manufacturers are working very hard on
these concepts. Hopefully this new fuel technology won’t just be on new machines, it will be great if we can retrofit this to older engines as well.
“I was driving in Europe recently where they have green zones where only low or zero emission vehicles can enter; that’s the future and Australia is going to be adopting similar environmental policies, so if we don’t have these green vehicles and machines, we won’t be able to service customers,” he said.
The South Australian crane sector is very competitive and the team at Fleurieu Cranes is comfortable competing with the best of them.
“I enjoy the fact that we have a competitive market, a healthy and competitive industry keeps everyone on their toes and service levels high. We are always working on projects in the city, large infrastructure works, and we are also working out bush, particuarly in the resources sector - including renewables.
“We compete with the likes of Max Cranes, they are a very good outfit including provision of most of the value adds like engineering, etc that we have.
“I’m happy to compete with them. It is, however, difficult when we compete against the smaller players as they don’t have all the background costs that we would have, but then that’s our selling point, isn’t it?” said Brandon.
“The future will include letting our people continue to flourish. For some time, we have been working on a strategic plan for the business.
“We tell our teams the direction in which we are headed and where we want to be, and we let our people take their natural direction to get there.
“Our business has grown over a long period not as a result of micromanaging our people, they understand and appreciate this style of management and respond accordingly,” he said.
Borger Crane Hire and Rigging Services recently took delivery of the first of six Kobelco lattice boom crawler cranes from TRT’s distributor of Kobelco crawler cranes, Baden Davis Crane Connection. The new cranes include four Kobelco CKS2500s - 250t capacity crawlers and two CKE1800s - 180t capacity crawlers.
SHAWN BORGER, GENERAL MANAGER
at Borger Crane Hire, provides some background to the purchases.
“As our business grows, we are working more closely with all our clients particuarly the Tier One builders, and we are increasingly involved on the major infrastructure projects in Sydney and Brisbane. These new Kobelcos are ideal for projects liken the Sydney Gateway, Sydney Metro Tunnelling and the Western Sydney Airport Station works. They will increase our ability to supply complete crane packages, providing our clients with the ability to program their works more effectively.
“The Kobelco brand has always impressed our organisation. Their cranes are well designed and include traditional Japanese engineering values which lead to a robust crane well suited to Australian conditions,” said Shawn.
The CKS2500 has a maximum lifting capacity of 250t and a long boom length of 91.4m. This model is part of the S series from Kobelco. The S series consists of crawler cranes with lifting capacities ranging from 60t 250t.
The S series was designed, upgraded and improved for the customer with safety, reliability and efficiency in mind.
The design of the CKS2500 is based on end-user feedback and real jobsite experiences. The design makes the model “transportation friendly,” “assembly friendly” and “operator friendly.” All are essential to fulfil the satisfaction of owners and operators. New features of Kobelco’s S Series are consistent with these key concepts.
The new models can be adapted for both bucket and lifting applications. The
hydraulic circuit can be set to dual-pump flow or single-pump flow, so that the circuit can be perfectly adequate for both applications. The newly designed circuit can be switched to choose the best circuit for the job application.
Available as an option, the new counterweight amount detection device always tells the correct amount of the counterweight. The swing angle detection device prevents over-swinging, and the ground level sensor prevents operations on uneven ground.
Machine status is displayed on a new wide monitor in the cabin, now newly redesigned for comfortable operation.
The new models have an improved
counterweight self-installation mechanism. Counterweights can be stacked up on the ground and installed on the machine by vertical cylinders. Safety and work efficiency have been greatly improved.(* Counterweights of 80 tons and 90 tons are optional specifications.)
The Kobelco CKE1800 features a maximum lifting capacity of 180t and a maximum boom length of 85.3m.
The crawler is powered by a Hino diesel engine P11C-UN, a water-cooled, direct fuel injection model, equipped with turbocharger and compliant with NRMM (Europe) Tier III and USA EPA Tier III standards.
Four variable displacement piston pumps are driven by heavy duty pump drive. Two are used in the main hook hoist circuit, auxiliary hook hoist circuit, third hoist circuit and each propel circuit. One of the other two pumps is used in the boom hoist circuit, and the other is used in
the swing circuit.
The Kobelco CKE offers full-flow hydraulic control system for infinitely variable pressure to front and rear drums, boom hoist brakes and clutches. Controls respond instantly to the touch, delivering smooth function operation.
The boom hoist system is powered by a hydraulic motor through a planetary reducer and the brake is a spring-set, hydraulically released multiple-disc brake which is mounted on the boom hoist motor and operated through a counter-balance valve. The load hoist system features front and rear drums for load hoist powered by a hydraulic variable plunger motors, driven
through planetary reducers. A springset, hydraulically released multiple- disc brake is mounted on the hoist motor and operated with a counter-balance valve.
The Swing system is powered by hydraulic motor driving spur gears through two sets of planetary reducers and the swing system provides 360 degree rotation.
The upper structure features a torsionfree precision machined upper frame. All components are located clearly and service friendly.
The full vision cab features safety glass, a fully adjustable, high backed seat with a head-rest and armrests, and intermittent
wiper and window washer (skylight and front window) as well as four adjustable levers for front drum, rear drum, boom drum and swing controls, and a boom hoist pedal.
The lower structure is a steel-welded carbody with axles. Crawler assemblies are designed with quick disconnect feature for individual removal as a unit from the axles. Crawler belt tension is maintained by hydraulic jack force on the trackadjusting bearing block. The carbody weight is 20t.
Independent hydraulic propel drive is built into each crawler side frame. Each drive consists of a hydraulic motor propelling a driving tumbler through a planetary gear box. Hydraulic motor and gear box are built into the crawler side frame within the shoe width and spring-set, hydraulically released parking brakes are built into each propel drive. A hydraulic propel system provides both
“The design makes the model “transportation friendly,” “assembly friendly” and “operator friendly. All are essential to fulfil the satisfaction of owners and operators.”The first of four Kobelco CKS2500, 250t capacity crawlers ready to be shipped.
each track in opposite directions). The track rollers are sealed track rollers for maintenance-free operation.
Borger Crane Hire and Rigging Services continues to invest in the fleet, says Shawn.
“Our continued investment in today’s crane technology is critical to our business. By investing in the latest technology, we are able to provide our clients with a complete package of cranage options. From our latest large capacity acquisition, the Liebherr LG 1750, to these new Kobelcos, we have the solution whatever the application. We see this as critical for our clients.
“We also invest in the latest and safest cranes for the benefit of our employees. Our operators and operational crews love the new equipment and always look after the gear as if it was their own. Our investment strategy also helps to attract new staff and retain existing crews. With the new technology, our crews are confident of completing the task safely because new equipment minimises breakdowns, eliminating the frustrations
of not finishing the job on time. Wherever possible, our crews take pride in delivering our projects on time and in full,” said Shawn.
Borger Crane Hire and The Baden Davis Crane Connection have a long and rich relationship which is based on much more than business, says Shawn.
“The Borgers and Badens have had a friendship for over 20 years. It dates back to 2000 when we purchased our first 80t Liebherr through Anthony. Since then, we have gone on to purchase
many more cranes and we always have our repairs completed by Ben Baden and his team.
“Ben and Anthony are extremely knowledgeable, what they don’t know about cranes isn’t worth knowing. It’s always reassuring when you buy a crane, you know the support and back up are going to be there.
“We know this will absolutely be the case with the Baden Davis Crane Connection and TRT Australia supporting the Kobelco product,” said Shawn.
Originating in Germany in 1875 as a small family business, RUD now supplies its products to a range of clients across a variety of industries – including mining in Queensland. Director of SureLift Crane Hire Mark ‘Chopper’ Read discusses his business and why the company consistently chooses RUD’s products.
IT REQUIRES SOME ‘MENTAL GYMNASTICS’ to take a business from Germany in 1875 to Moranbah, Queensland, 2023, but that is exactly what German manufacturer RUD has done; according to SureLift owner Mark ‘Chopper’ Read, it’s for good reason.
“They’re the best chains in the industry,” says Chopper. “All of RUD’s lifting and lashing equipment consistently performs on safety and durability measures; it’s because of the way we’ve seen RUD’s products perform that we don’t buy anything but RUD.”
Chopper himself holds an extensive career in the mining industry; working
in and around shutdowns in the mining industry before starting Surelift, he’s seen it all; and that’s why when he labels RUD’s lifting chains and slings as the “best” he’s worked with, there’s an added element of legitimacy to his words.
SureLift Crane Hire was conceived in the mining town of Moranbah and began its operations with just one 20-tonne Franna crane. Since then, the Queenslandbased company has expanded its fleet to include seven Franna P&C cranes, seven all terrain cranes, a 280-tonne crawler crane and a variety of truck and trailer combinations.
“Initially, when I started the business,
I reflected on my time in the shutdown industry and I saw the potential for more crane hire in the market,” he says. “I decided to try it out, and we’ve eventually grown into the business we are today.”
At the core of its operations, SureLift provides crane hire and transport services to businesses and individuals in Moranbah and its surrounding regions. Frequently employed by contractors working in the mining, construction, maintenance and industrial sectors, Surelift’s team of 48 full-time employees is well-versed in the crane and logistics industry, thanks to the company’s 17 years of experience.
“The biggest problem that we
experienced when starting SureLift was just attracting the work,” says Chopper. “But we kept our heads down and worked hard and eventually things fell our way; today, we own over 16 cranes and operate across a range of projects.”
Part of working across a range of projects in the crane industry requires versatile, durable, safe lifting and rigging equipment. As Chopper mentioned before, that is precisely what he feels SureLift receives when purchasing from RUD.
“Although we’re general hire, the chains consistently stand up for us no matter what environment they’re placed in,” he says. “I initially came across RUD’s products early on in my career and they have not disappointed me.”
The other blatant testimony to the working capacities of the German manufacturer’s products is the industries they appear in. Working with a range of clients in the defence, infrastructure, energy and engineering industries, RUD’s technologies offer “capacity, versatility, and unique features” that other chains “just don’t have”, according to Chopper.
Where this is most prevalent is with its ICE Grade 120 range of lifting chains. Weighing 30 per cent less than the next nominal grade chain, RUD’s ICE Grade 120 chain also possesses a 60 per cent
chains and slings, Chopper is also highly complimentary of the lifting and lashing points that RUD supplies to SureLift. The German manufacturer offers more than 700 tested boltable and weldable lifting point variants with load ranges all the way up to 250 tonnes. Stringently tested and certified according to LEEA and NATA standards, Chopper says the versatility offered by the products is “incomparable”.
“Working in the shutdown industry,
“Their post-sale service is excellent; anything you need to talk to them about – whether it be maintenance of the product, a new range that’s just come out, or different lifting solutions – they’re there,” he says. “Additionally, if we need any advice for setting up new slings or purchasing any new items, RUD are always on the other end of the phone ready and willing to give us a helping hand – or, in this case, a sling.”
higher breaking force than a grade 80 chain. Furthermore, as manufacturers, RUD holds the capacity to customise its lifting chains to provide customers with tailor-made solutions, dependent on their site requirements. On top of the aforementioned ICE Grade 120 chains, a RUD ICE 16mm chain – when used with a balancer – can lift up to 48 tonnes, the highest in its class.
“The balancer is a huge point of difference when compared to other options on the market,” says Chopper. “It allows us to lift at a higher capacity with the same level of safety.”
Aside from using its range of lifting
it’s imperative to get things right with dependable, durable products,” he says. “The weld on lift-points that we use are exactly that; having versatile gear that holds many applications at many ranges is essential.”
What all these products collectively feature for Chopper are two things: safety, and excellent post-sale service and support. Talking about his relationship with RUD Chains and its after-sale service, Chopper says no stone is left unturned for RUD when it comes to making sure the company supplies the right product in accordance with Surelift’s needs.
As mentioned above, all RUD’s products are manufactured, tested and maintained in accordance with Australian Quality, Environmental, and OH&S standards, as well as holding both LEEA and NATA accreditation. For the team at Surelift, this is even more important than RUD’s highquality post-sale service: the lifting and rigging industry needs to be consistently flooded with safe, highquality, sustainable products; with all of its products assembled and proof load tested in the company’s Brisbanebased facilities, Chopper believes RUD’s products tick all these boxes.
“At the start of the day, everyone’s got a right to go to work; at the end of the day, everyone’s got the right to go home safely,” says Chopper. “We feel that using RUD’s products embodies that message of safety.”
“The weld on lift-points that we use are exactly that; having versatile gear that holds many applications at many ranges is essential.”
Melrose Cranes & Rigging recently celebrated 25 years in business. Gregg Melrose, the 66 year old Managing Director of Melrose Cranes & Rigging takes us back to where it all began and highlights some major milestones along his 25 years of developing the business.
GREGG WAS A GREEN 18 YEAR OLD WHEN HE started in his Uncle Ronnie’s heavy transport business, Royan Truck and Trailer Repairs, which rebuilt trucks, trailers and other heavy equipment.
“Uncle Ronnie gave me a start on a gas axe at his truck wrecking yard when I left school and over the next 12 years he and his many varied tradesmen taught me everything. I ended up running his East Coast divisions in Sydney, Melbourne and Dubbo and I managed about 150 people.
“At 30 years of age, I left the business to expand my career and I was lucky enough to get a start with Kerry Adair at Glenrelle Cranes who ran seven or eight cranes based in Blacktown. I worked there as his logistics coordinator, and although cranes were new to me, the basics were very similar to trucks and trailers and I picked it up quickly. In that yard he also had subcontractors including Benny Cruse and Santo Rapisarda.
“Kerry later wanted to semi retire, so he employed a manager who for some reason resented me. For the first and only time in my entire career I was sacked. It was a blessing in disguise in many ways,” said Gregg.
The late Brian Callaghan owned Mobile Concrete Pumping at Wetherill Park and in 1988 Gregg went for an interview to operate one of their mobile concrete pumps. During the interview he was offered the alternate role of Logistics Coordinator, which he quickly accepted.
“After about six months, Brian said, “You know all about cranes, don’t you?” And of course, I said yes, even though I’d only worked for Kerry for a couple of years. He said, “We pump these big concrete tilt panels for people and I’m sick of watching Brambles and Wilson put them up with their 130t cranes. I’m going to buy an AC615 Demag.” I said, “How’s that involve me?” and he replied, “You’re going to manage it.” Next
thing we were on a plane to Zweibrücken in Germany to have a look at a 200 tonner, which he ordered immediately.
“On the way back, we stopped off in Japan and he bought a Kato 50 tonner just for good measure. Brian had around 40 concrete pumps and he also built concrete pumping systems. That was my first real experience with bigger equipment,” said Gregg. Mobile Crane Company Pty Ltd was born.
The first 200t and the 50t went into service in 1989 and Brian was so happy with how things were going, he ordered another Demag AC615, which arrived in 1990. These twins were the two biggest roadable cranes in Australia at that point in time, and Brambles and Wilson Cranes were not pleased. It was a great experience until Brian once again had a ‘light bulb moment’,” he said.
Unbeknown to Gregg, Brian had already agreed with Laurie Wilson, of Wilson Cranes, to sell him the three cranes and also employ Gregg and the crane crews. Wilson Cranes and Gillespies Crane Services were the largest independent operators and family businesses at the time and both were competing with Brambles in the Sydney market.
“Brian was a great mentor to me, and the most important thing he taught me was to always have ‘a bench’, that is, a Plan B. Whilst I was disappointed at Brian’s decision I offered to stay as his Logistics Manager, but he said ‘No, I’m going to change direction and employ a smart CAD engineer to design and build bigger concrete pumps of all types in opposition to the Germans,’ which he successfully did,” said Gregg.
Gregg and the crane crews moved to Wilson Cranes in 1991, which was a very reputable crane business. Over many years Laurie had also fostered many dedicated subcontractors that only worked for him. Many of these people went on to open successful crane businesses, including
Gordon Henderson, Kerry Adair, Jon Borger, Larry Fuller and Ari Debner.
“Working for Laurie was a great experience and I learned a lot. I was there until 1998 when he decided to retire and sell his business to Brambles. At the time Brambles was a large, listed company and everybody transferred except me. I had made it clear I didn’t want to work for them.
“This is where Brian’s advice to always have a bench was critical. Laurie had an outside subcontractor called Davis Cranes, which was owned by Alan Caspers, who is also unfortunately no longer with us. He was based in Pendle Hill and any ‘overflow’ work that Laurie had, went to Alan.
“Alan operated a small fleet which went up to a 50t Kato and his company was a reputable second tier operator. Effectively Alan was my client. I was a project manager for Wilsons, and I managed Alan and his larger crane requirements. I spent a lot of time in his office, which was a converted triple garage on the back of his property. Alan was another mentor who taught me about life and how to manage people,” said Gregg.
At the time Alan was looking to improve his golf handicap at Leonay Golf Club and wanted to spend less time running the business.
“I said to Alan, “I can’t afford to buy you upfront but I’m willing to offer you a deal. I’ll buy you for an agreed amount in the year 2000. In the meantime, I’ll manage your company, I get paid as the manager and I’ll try to develop the company into something better. As your credit rating is very high and I don’t have one, you’re going to have to cosign loans etc. and I will become responsible for them in 2000.”
“We agreed on the proposal, he didn’t want any paper, there were a few notes written on the back of a scribble book which were photocopied, and we each took a copy.
I formed Melrose Industries Pty Ltd with my wife Debbie as our family company. Melrose Industries owns half of Melrose Cranes & Rigging and my brother Tony owns the other half,” said Gregg.
It was an eventful and stressful two years for Gregg. He was focused on developing the company, getting a credit rating and trying to gain credibility in the market. The business initially stayed as Davis Cranes, which made sense as it been around for 30 years. Melrose Industries then bought a 50 per cent stake in a new 50t Kato with Mark Muir and formed Melmar Pty Ltd, Gregg’s first dedicated subcontractor.
“Mark was a mate from Parramatta Rugby, a client from Wilsons, and most importantly, I trusted him. I was determined to get more business and I had a potential client list that was massive, so I attacked it.
“But I knew I wouldn’t be successful unless I had access to more and larger machines. I made calls to people I knew including Stan Beard, who was a major local steel erector at that time. He had a new 30t Kato which was doing nothing, so he put it in the fleet. Benny Cruse, who was a very reputable crane driver, brought a 50 tonner and a 30 tonner to the fleet,” said Gregg.
Although this boosted the fleet Gregg was not in a position to take on all of the larger capacity work he wanted, and the business was missing out.
“I said to Alan we needed to get a bigger crane and I also pointed out that we didn’t have any Frannas. A new AC205 80t Demag and an AT18t Franna were ordered. I had to sell my holiday home in Mollymook and put up half the family home as my contribution, with Alan signing off on the other half.
“The Commonwealth Bank was very good to us, and we worked with Bruce Coggins who I had played footy with at Parramatta Rugby. He was a good mate, but I didn’t realise he was also Alan’s banker. This was a massive advantage as Bruce and I trusted each other,” said Gregg.
With the 200t capacity Demags at its disposal, Brambles continued as the number one crane company in the Sydney market, but Gregg wasn’t about to concede anything.
Fred Wheeler (who recently passed away) owned Wheeler Cranes and he also designed and built factories and lifted tilt panels. He
had two 200t capacity Liebherrs. Gregg had helped Fred when he was busy, and Fred reciprocated.
Gregg approached Fred saying he needed a 200t crane in the fleet and Fred advised he’d just ordered a 300 tonne Liebherr.
“He said ‘I’ll put a 200 tonner in your fleet, but I want a percentage of every dollar, and all cranes are to be branded as Wheelers. Again, this was all done on a handshake agreement,” said Gregg.
“Alan didn’t care; ‘just stick to our deal and I’m happy. If you want to put Wheeler stickers on these cranes, that’s fine.’” So, I’m still Melrose Industries, everyone’s still there. All the subbies are still there, but in 1999 they all became Wheelers Hydraulic Cranes,” he said.
Wheelers Hydraulic Cranes lasted for about a year until Fred was approached by a South Australian power station which needed a 300t and 200t Liebherr for a two year project.
“Fred delivered the news that he was moving on and I didn’t quite know what I
birthday,” he said.
There was not enough space for the expanding fleet in the Pendle Hill yard, so the rebranded Melrose Cranes & Rigging company leased 2,500 metres at 16 Foundry Road, Seven Hills. In the background he had been talking to the Lindores brothers (LCR). They were a tower crane company from Queensland with a 200t Liebherr and 30t Kato for their own use. They needed increased utilisation so Gregg made a ‘Hire to Buy’ agreement where he managed the 200t crane for two years, paid them money for every dollar it earned and bought it for an agreed amount at the end of the two years.
“They offered me their 30t Kato and all of the counterweight trailers as well. In return we agreed to give them first preference to put up their tower cranes. That was the arrangement and once again, there was never a piece of paper between me and the Lindore brothers,” said Gregg.
The 200t Liebherr became our new ‘pinnacle’ machine. I was managing a lot of cranes. We were getting busier and we took
was going to do. I was approaching the time to pay Alan out, and effectively I would have been reduced to a minnow in the market. I pondered how I was going to survive and service my expanding client base. The year 2000 arrived and Alan put his hand out, which was fair enough, but I didn’t quite have all of the money.
“I rang my brother Tony and told him the whole story and why I needed his help. I reminded him that our old man had always said you can’t break a promise and after listening to me he said, ‘Yeah, all right’”, said Gregg.
“Tony had a very successful accountancy business. I’m his big brother and he looked after me and put in 50 per cent. Alan was paid out and Melrose Cranes & Rigging Pty Ltd was officially born, in the Olympic year. We are celebrating 25 years because I started on June 28th 1998, the day after my 41st
on more subcontractors. Mark Muir bought my 50 per cent share of the 50 tonner and became solely responsible for that crane. (Mark only retired mid-August.) He was my most loyal subby, and a good friend.
“Noel Fairweather, who’s still with me to this day, came in a little bit later and various subbies followed. We ended up outgrowing that yard and bought next door, number 18 Foundry Road. Not long after that, we leased a big yard, 5,000+ square metres, out at Mulgrave,” said Gregg.
“Over the years you could say we experienced progressive growth, and many subcontractors helped me grow the company with the volume and capacity of cranes. We weren’t Brambles and we weren’t Gillespies but we developed Melrose Cranes & Rigging into probably the number three position at the time. It was very different in those days, we didn’t have the WHS conformity,
“Over the years you could say we experienced progressive growth, and many subcontractors helped me grow the company with the volume and capacity of cranes.”
ticketing, registrations, NHVAS compliances and CAD drawings etc etc that we have to do these days”, said Gregg.
Melrose Cranes & Rigging is a true family business. Gregg reflects, “My wife Debbie was with me from the start running all administration, and only retired after 21 years of unwavering service. Simply put, we wouldn’t exist as we do today without her contribution.
“Our son Ryan joined us straight out of school in early 2003 after passing up the opportunity to go to university. He started sweeping floors before learning to dog and later drive cranes. After 20 years he is now following in my footsteps and I value not only his contribution to our growth, but his entire skillset every single day,” said Gregg proudly. Gregg and Tony’s youngest brother Mick started in 2008 after a successful international career as a construction manager, heading up multi-million-dollar construction projects around the world. “Mick’s experience and insight into how the ‘other side’ works has proven invaluable when tendering tier one projects locally,” said Gregg.
Others may not share the Melrose name
but have become family through their years of loyal service. Deb Rudd joined the company in 2007 and quickly earned the monicker ‘Lefty’, as the left arm of Gregg. “I don’t function properly without her, it’s as simple as that; she’s invaluable,” said Gregg.
Shaun Russell was running a small engineering shop in Brookvale when Gregg convinced him to change career paths in 2008.
He started under the tutelage of the master allocator, the late, great Steve Smith. “Shaun is instrumental not only in the success of our day-to-day operations, but he continues to foster and maintain very important relationships with some of our most valued clients”, said Gregg.
One of Melrose Cranes’ most versatile employees is Ennio la Cioppa, or Ernie, as he is known. “Ernie started with us as a crane operator way back in 2002 and has proven to be one of the most reliable and capable drivers I’ve ever employed. A couple years ago he made the choice to hang up his hard hat and is now proving himself as a successful project manager out in the field”, said Gregg.
“There are many valued crew members who have been around for a long time, like
Jason O’Brien and Frank Richens, who both have over 20 years of service. There’s also Marco D’Intino and Rick Foster, who have both given over 15 years of service to the company, not to mention Rick’s dad Steve, who’s not only been here since 2007, but has been affiliated with me for 35 years.” Gregg hired Steve to drive the first MCC 200 tonner in 1989.
“The loyalty of these people has been instrumental in the ongoing growth and success of our company. In fact, almost 50 per cent of my employees have been with the company for over five years and my hope is that they too become long serving members of the Melrose team.
“Over time, we kept growing and we had yards everywhere. We had two in Foundry Road and one at Mulgrave. Then we had another 2,500 metres in Station Road before we bit the bullet five years ago and moved into a 20,000 square metre facility at Seven Hills. It’s been great having everyone in the same space,” said Gregg.
As far as the fleet is concerned, there have been some significant milestones as the business has developed says Gregg.
“In smaller cranes, the first ‘milestone
crane’ was the 50 tonner I bought with Mark in 1998. It was brand new and cost $550,000. It has to be number one because it’s the first crane I ever bought. Then there was my new AT18 Franna, which only finished its service as our yard crane earlier this year, on its third engine. It was here the full 25 years and I actually sold it to one of my crane drivers to use on his farm. But pound for pound, the Demag AC205 was the best smaller crane I ever owned, it was so reliable,” he said. “It did 25,000 hours and the pumps were never off it. I got a photo of it last month, still working on an Indian dock!”
Tony and Gregg were planning the next purchase as they always did and Tony asked, ‘What do we buy next?’
“The best local big crane that worked down as well as up in tonnage class, was Gillespie’s 160t Liebherr. I was envious of that crane because I knew his operator and a couple of his managers, and they were impressed. It has 60 metres of boom on a five axle carrier. It had to have a dolly, but it was a great crane.
“I said to Tony that’s what we’re targeting next, and I bought one out of Houston, Texas. It was 2002 and I bought a 2000 model crane with only 175 hours on the clock. It was basically brand new. That was a great crane and we had that for a very long time. It is still running around Germany. The Grove 450t was the next great highlight,” said Gregg.
In 2006, Tony and Gregg were again
planning, and Tony asked what’s next?
“I told him about the Grove GMK7450 that had been in production since 2001 and that they were proven performers. I went on to explain the technical side of the Grove and told him no one’s got anything like it, up or down the East Coast.
“At the time John Gillespie still had his eight axle Liebherr 400 tonner, which had set the benchmark for many years.
“Tony said we need to be the biggest and
thing is your commitment to put everything on the line. You’ve got to bet on the fact that work is going to come in a market where you don’t have assurances and millions of dollars have to be outlaid with no guaranteed workload.
“You’ve got to back yourself and the people around you, to put it into the market and make the income day by day, month by month, year by year. It’s the same for every mobile crane owner, they’ve got to
they’ve got
back themselves and their employees to get it done.”
we ordered the 450 and it arrived in 2007. I don’t mean to be flippant about these purchases. We’ve bought a lot of good cranes since then, but nothing compared to the 450. It’s still going to work every day. Finally, purchasing the fully factory refurbished 2017 Liebherr LTM 1500-8.1 in 2019 was the biggest step ever for the business. It is a fully spec’d crane with 84m of main boom,” said Gregg.
Companies come and go in the crane industry. Gregg provides insights into how his approach to business has stood the strength of time.
“I mentioned earlier the importance of ‘the bench’; my ‘Plan B’. But the biggest
back themselves and their employees to get it done.
“Another major advantage in our success is that Tony is a very successful accountant. He lets me run with what we’re buying, when we’re buying it, the models and makes, but with the financial side of the company, he’s very particular about budgets, forecasts and cashflow etc etc.
“The first 25 years of Melrose Cranes & Rigging has seen us meet the demands of our customers by investing in the very latest technology our industry has to offer. If the first 25 years are any gauge, I’m excited for my entire team as there is so much more to achieve over the next 25,” said Gregg.
“You’ve got to back yourself and the people around you, to put it into the market and make the income day by day, month by month, year by year. It’s the same for every mobile crane owner,
toMark and Gregg when all the cranes were branded Wheelers.
With a new premises, significant investment in heavy lifting equipment and a strong focus on the team, leading lifting equipment and hire specialist Queensland Rigging Hire is on the move.
QUEENSLAND RIGGING HIRE STOCKS the highest quality lifting and rigging equipment, fully tested and certified to ensure it meets customer needs and the relevant Australian Standards. Managing director Ben Fitzgerald takes up the story.
“For the past year or so, we’ve been focused on building our fleet, increasing the numbers in our team, upskilling our team and improving our new premises to accommodate the growth we have been experiencing,” Ben said.
“Like all rigging hire businesses, we are seeing a dramatic change in the way projects are handled. Cranes are getting bigger, lifts are getting heavier and we need to invest in the right equipment to meet the demands of the industry. Larger equipment requires more space so we are now in the
hunt to purchase a second premises to house our larger equipment.
“The new premises is in Archerfield, where we have been based for the past 18 months. We basically gutted the place and rebuilt it to accommodate our specific requirements. We have new offices, new reception area, new bathrooms, we’ve even built in a studio apartment for when we work late hours.
“We also installed a mezzanine and below this we have both fabrication and mechanical workshops. This dedicated area is designed to service and repair in house, and have full control over the process throughout the job, this makes our turnaround times much faster” he said.
Bringing youngsters into the business is a major focus for Ben and his wife Jess.
“We all know our industry is faced with the challenges of an ageing demographic. Jess and I have always wanted to invest in today’s youth, show them what our business and industry has to offer and hopefully that will have a knock-on effect in their circle of friends for example.
“We went through a pretty lengthy interviewing process, and we found a young fellow, Lachlan Leal. Lachie has left school early to compete a Traineeship in Supply Chain Operations at Queensland Rigging Hire and has a lot to offer, and has slotted in perfectly to our business. He’s been with us for six months and I don’t think he’s missed a day,” said Ben.
Ben highlights some of the products Queensland Rigging Hire has invested in.
“We recently took delivery of a Modulift
MOD 400/600, it’s a 600t modular spreader bar and there are only a handful of them in the country. This particular spreader bar has a maximum capacity of 600 tonnes at 18 metres, scaling down to 300 tonnes at 24 metres. We’ve also invested in a large range of wide body shackles.
“It’s important that rigging is to code and the code states that you’ve got to have the correct D/d ratio. The D/d ratio ensures your slings are used correctly and not pinched around the shackles. These wide body shackles are designed to spread the load over your slings for a safer lift. Most of our wide body shackles are from Van Beest, which are forged in Holland. The best of European quality,” said Ben.
Ben and Jess visited ConExpo in Las Vegas earlier in the year and they were impressed with some of what they saw.
“We spoke to a number of suppliers during the show, and we came away with some great ideas. We have already brought some new products into Australia that we think the market will need”.
“The first is a Quick Release Hook and the benefits of this product are easy to demonstrate. Imagine you are working on a project in Far North Queensland. You’re working on a barge with big cages full of rocks which are being lifted into position to stop erosion in a riverbed. To unhook the cage, someone will need to get into
keep
need the right rigging and equipment to manage the heavier lif ts. With a bigger crane, there’s lot less lifting of fewer but much heavier pieces. We want to be the hire industry leaders in Australia by investing in this larger equipment.”
crocodile infested river and unhook the rigging. With this system you can lift, put the cage into position and then pull a rope and it disconnects automatically. Much safer than dealing with crocs we reckon!,” said Ben.
“Like I said earlier, cranes will keep getting bigger and they need the right rigging and equipment to manage the
heavier lifts. With a bigger crane, there’s lot less lifting of fewer but much heavier pieces. We want to be the hire industry leaders in Australia by investing in this larger equipment. It is a huge investment to procure heavy lift rigging in Australia, and a risk for us to invest in an area which we haven’t yet taken a market share in, but we are confident the market is there and that
we will be ready when the calls come in.
Queensland Rigging Hire has the largest range of adjustable spreader bars in Queensland and one of the largest hire fleets in the country.
“We own one of the biggest range adjustable spreader bars nationally. They’re the most common spreader bar used, they are easy, they are quick, they are easy to mobilise, easy to adjust and easy to use.
“We’ve also invested in a range of oversized Load Transfer Triangles which assist in passing a load from crane to crane.
“A lot of the time you can’t get access to unload the trailer and position the load in the one pass. So quite often, they need to set up a crane to unload the equipment from the trailer and then pass it to another crane and then that crane will put it into position.
“Like I said earlier, cranes will
getting bigger and theyQueensland Rigging Hire conducts on-hire inspections for every piece of equipment that goes out, keeping equipment registers and ensuring every piece of equipment that goes out has a fresh certification.
These Load Transfer Triangles are designed to efficiently and effectively pass a load between two cranes,” said Ben.
Converting the range of electric and pneumatic hoists and winches to wireless remote is another significant investment.
“We’ve had to put in a full-time mechanic to take on this task and there’s very few people in the industry doing it. It’s our way of putting our mark in the market. We want to be the best with the products that we stock and by going wireless, it’s a significant safety improvement which keeps the operator in a safe place, away from the suspended load.
“The remotes have a 100-metre range on them and we’ve done a lot of work in power stations and mining where risk mitigation and safety are paramount. We’re getting regular repeat business because of the wireless remote controls.
“With a traditional powered hoist, you
connect it to the load, and you lift with the pendant or rope control. You’re only a couple of meters away and right in the danger zone.
“The wireless remotes mean you don’t need to be unsafe anymore, you can overcome that with technology,” said Ben.
The growing team at Queensland Rigging Hire is also a significant focus for Ben and Jess, with the company now puttting staff through a series of courses.
“Jess and I recently completed a mental health first aid course, so we’re qualified mental health first aiders and we are putting the guys through their dogging and rigging tickets at the moment,” he said.
“We want our team to really understand the products that we work with. We don’t use them on the job, and we don’t physically do the rigging, but we do have to understand what rigging products we have, and how they are used in the real world so
that they can better understand how to maintain it and warehouse it.
“We conduct on-hire inspections for every piece of equipment that goes out. We keep equipment registers and every piece of equipment that goes out has a fresh certification, which will last anywhere between three months and 12 months depending on the product. The team does exactly the same inspections when the equipment is returned.”
Sustainability is key for the future of the industry, says Ben.
“Sustainability is becoming more and more important in the world. Our type of equipment is involved in a lot of project work and at the end of the project, we know the gear is chopped up and sent to landfill.
“Because we rent this specialist equipment, it comes back to us and it gets a second, third life and fourth life.
Environmentally, it is so much better to have equipment that’s reused, refurbished, recommissioned and recertified and extending the lifespan and minimising the amount of the same product that needs to be rebuilt or remade.
“Sustainability is an issue we’re really going to push in our marketing. We know this will resonate with Tier One Builders and Contractors, they are all looking to reduce carbon footprints and work towards a sustainable future,” said Ben.
Company culture is also a significant focus for Ben and Jess.
“Being a small family business we are focused on the wellbeing of our team, we like to share the wins and at every opportunity we want to reinforce to our team that this is a safe place to come and to enjoy the work. We celebrate milestones and birthdays and all of that.
“We go camping as a team. This started when Chris, our warehouse manager confessed he had all the gear, but he’d never been camping in his life. So, we got everyone together and their partners and spent the weekend camping. We had some beers and lit a big bonfire, it was really great and everyone had fun. We’re going to make this a regular outing for the team,” said Ben.
“Sustainability is an issue we’re really going to push in our marketing. We know this will resonate with our Tier One Builder and Contractors, they are all looking to reduce carbon footprints and work towards a sustainable future.”Queensland Rigging Hire understands cranes will keep getting bigger and they need the right rigging and equipment to manage the heavier lifts.
Borger Cranes is a family owned and operated crane hire and rigging business servicing New South Wales and Queensland.
Borger Cranes maintain a modern fleet of cranes and equipment and our fleet boasts two of the largest all terrain cranes on the east cost, the Liebherr 750 tonne and Liebherr 650 tonne all terrain.
With every job, our experienced and industry trained team delivers high quality performance and nothing but excellence.
Borger Cranes getting the job done for you.
Precision Rigging & Logistics holds a companywide ethos of providing an innovative solution to the impossible tasks. Managing Director Luke Williams talks about the company’s inception, its capabilities, and a recent job undertaken in Uluru, Central Australia.
Queensland-based lifting solutions company
PRECISION RIGGING & LOGISTICS WILL provide an innovative solution if there’s a seemingly impossible task at hand.
It could be transporting equipment to complete a job out in Rockhampton; it could be going to the far-northern, warmer climes of Cairns; it could even be a range of helicopter lifts, because that’s what the situation requires. For Luke Williams, the Managing Director at Precision Rigging & Logistics, there’s regularly been a unique solution to a range of problems presented to his company by clients.
“That’s our bread and butter, really,” he says. “The unusual stuff.”
Backed by a 14-year career in the mining and construction industries, Luke’s career has seen him specialise in rigging equipment and heavy mechanical relocations. Having been at his current role for nearly eight years, Luke’s time running the Brisbane-based logistics company has seen it grow from humble beginnings operating out the back of a hatchback to working with some of the largest crane companies in Australia.
“There’s a lot of unusual solutions that we provide,” he says. “Whether it’s a crane, rigging, or a helicopter lift, we strive to be as efficient as possible, which is what we’ve built our success on as a company.”
As he acknowledges, all the jobs completed at Precision are “dependent” on the restraints imposed on the business; but, as he also highlights, the team at Precision Rigging & Logistics do what they do to “make sure the job gets done” in the safest, most professional, and efficient way.
Precision Rigging commenced operations in 2015 specialising in innovative mechanical rigging solutions. The company prides itself on providing an end-to-end solution for lifting jobs on
and positioning of a range of different equipment; and a craneage, transport, and logistics package that can be tailored to customers’ demands.
Operating for a full four years before the pandemic sunk its claws into the Australian economy, Luke says the pandemic was an opportune moment for Precision to “restructure the business” and get its ducks in a row.
Choosing to spend the company’s downtime investing in staff and back of house procedures, Luke says the goal at Precision was to make sure the company was prepared for whatever the future may entail. Inclusive of upskilling the people working there and reinvesting in training procedures to ensure staff were able to achieve the most out of themselves, Luke says being prepared on all fronts was necessary because not knowing what was
down on our efforts,” he says. “We put Chris Finch, a rigger with 25 years of experience, into an estimation role; we hired our administration star, Michelle Disiot, to add further experience and support to our backend operating systems; and from there, we’ve been going in leaps and bounds in terms of our operational capacities.”
For Luke, the “leaps and bounds” were evidenced by a job to replace an obsolete large water chiller recently undertaken in one of the most environmentally harsh, remote areas to travel to in Australia: Uluru.
The first point to note, as Luke says, is the nature of transporting machinery to such a remote area.
“One of our points of difference was that we could source all the equipment we needed to use ourselves without relying
heavily on the supply chain, which increased our capacity to complete the job efficiently and effectively,” he says.
“Then, we were able to pull all the componentry apart and lift it out using our crane truck,” he continues. “We then proceeded to put together a gantry so the machine could get rebuilt manually inside the room.”
After all, at the core of Precision Rigging’s unique, innovative, customised solutions, is maintaining charge of the situation. Luke highlights the company’s capacity to be in control of the logistical processes they’re involved with from start to finish as a reason why the company is in such high demand across the industry.
“This replacement and removal of an obsolete chiller typifies the kind of work that we do,” he says. “We want to maintain a firm sense of control on what we can, so we ensure efficiency and minimise delays for whoever engages our service. Generally, this means providing tailored, outside-of-the-box solutions.”
With business, market, and logistical nous comes awareness, and the team at Precision Rigging & Logistics are aware of exactly what they can achieve – which means also knowing the company’s limitations. This isn’t a problem for Luke, however; enjoying a solid, stable, prosperous working relationship with the team at Borger Cranes, Luke says Precision Rigging are all about finding the right solutions for its customers, which can sometimes mean working in partnership with neighbouring businesses.
“We know what we’re good at, and we know that we’ve got friends such as Borger Cranes in the industry who are more than capable of providing craneage,” he says. “We focus on providing complete logistical solutions packages, and that’s what we want to specialise in.”
Precision Rigging & Logistics’ pedigree only substantiates this. Providing customised, tailor-made solutions – no matter how unique or innovative – is the company’s strong suit, as Luke says.
“We’ve completed well over 3000 jobs in our eight-year history, and we pride ourselves on providing innovative solutions for seemingly impossible jobs.”
Hevway has turn-by-turn navigation for all vehicles listed in VicRoads Class 1 All Terrain Cranes
Hevway will allow you to check the conditions or restrictions on any road for the selected vehicle
Hevway has all of your low bridges marked clearly on the map
Hevway will alert you when a delay is found on the route currently being navigated
Hevway will alert you when the proposed route includes traffic delays
Hevway updates new traffic data every 30 seconds
With the 18.65m full power boom, a 75 per cent stationary chart for heavy lifts and a 66 per cent pick and carry chart, the TIDD PC28-3G packs a massive punch. Made from high-tensile steel, telescope sections one and two are fully synchronised and provide hook compensation. Telescope sections three and four are independently operated with their own hydraulic cylinder.
With a 28t maximum lift on the lug and 27.6t on the hook block, the TIDD PC283G delivers outstanding lifting capacities for improved efficiency and greater lift options, setting a new benchmark in the industry. Moving from the stationary chart to the pick and carry chart is as simple as turning off the hold brake. Operators can now lift more and move more safely without compromise. With its new powerful front suspension cylinders, the TIDD PC28-3G delivers increasing load capacity by an average of 17 per cent more capacity when articulated or working on a side slope. In some comparisons, we have seen an over 40 per cent increase in lifting performance. The optional 1.1t Superlift counterweight will increase lift capacity.
The Superlift counterweight allows operators to lift up to 12 per cent heavier loads in both pick and carry and on stationary charts. When fitted to the base of the 2.3t roadable counterweight, the optional 1.1t Superlift Counterweight simply and effectively increases the capacity of the crane.
• 1.1t allows transport to site under 3.5t with car licence
• Operator-friendly loading system using the crane
• Proximity sensor, auto-sensing for safety
• Fast and easy to set up
• Simple to use
Designed to maximise operational safety, the TIDD PC28-3G will minimise risk on the work site and the road. Safety features include Dynamic LMI with a deadlock switch inside the cabin and an LMI bridging switch outside the cabin. Slew Safe® is a critical safety component that is included with all TIDD PC28-3G Cranes.
The innovative safety features of the TIDD Crane, including the LMI bridging switch as standard, enable the TIDD PC283G to legitimately operate under EN13000 standards. This also means that the TIDD PC28-3G is the only Pick and Carry Crane in its class with a 75 per cent stationary lift chart.
When the crane in operation moves from green and amber to red, there is an overload notification (based on the lifting chart). This will activate Slew Safe®. When the crane is operated in the green and amber areas of the lifting chart, Slew Safe® will remain inactive.
• Reduce the speed of the steering to 15 per cent in the unsafe direction
• Makes steering harder with instant feedback through the steering wheel to the operator
• The engine will “load up” making an audible sound change for the operator
• Constant audible alarm inside and outside the cabin to warn the operator and dogman of overload
• Retains the ability to move back to the safe direction for normal operation in green.
Traction Air® manages tyre pressure to the standard 130psi on all four front and rear tyres, creating a stable lift platform and improving crane safety.
Incorrect tyre pressure, overinflation or punctured tyres can put operators at risk.
Constant tyre pressure monitoring with Traction Air allows operators to lift safely, and correctly every time. From a simple to use touch screen in the cab, instant leak and puncture alarms notify the operator of a change, reducing the risk of serious incidents.
There is no need for manual tyre pressure checks on start-up, increasing valuable uptime. No matter the surface temperature, even on bitumen, tyres on TIDD PC28-3G will remain at 130psi.
Based on more than 25 years of product innovation and exclusive to TIDD PC28-3G, Traction Air has a three year/500,000km warranty*.
Traveling between sites is effortless with a maximum speed of 80km per hour (speed limited) with reduced ambient noise, and
The Cummins IS6.7 is certified to the world’s toughest enission standard calling for near zero emissions.
ABS braking for improved safety whether the crane is operating while stationary or at speed.
It is driven by a Cummins Engine Allison Transmission. With its superior suspension, the TIDD PC28-3G is 12 tonne per axle on the road including its 2.3 tonne removable counterweight. No IAP and no permits in NSW.
From the ergonomically designed forwardmounted ROPS style cabin, with two-door configuration and ducted air conditioning, to the 150kg rated air suspension seats and three point safety belts, this crane is designed for comfort over long hours, helping to reduce operator fatigue.
Brendan ‘Cookie’ Cook has been in the pick and carry crane industry for over 30 years, working for TIDD’s closest competitor and being responsible for a large percentage of the cranes sold across the country.
He moved to TRT Australia 12 months ago being impressed with what he has seen.
“What has impressed me most about TRT is their innovative approach to improving the TIDD product, they are constantly working
of market demands and it will not be long before all crane operations will need to be cleaner, safer and sustainable,” said Cookie.
According to Cookie, TIDD is gradually changing the industry’s opinion on pick and carry cranes.
“We cannot emphasise the importance of our SlewSafe® system enough. We recently presented to a significant Tier One company with zero pick-and-carry cranes in their fleet for nearly a decade. They recently purchased
Many of the TIDD PC28-3G features are designed based on industry and operator feedback, improving safety, lift control, and capability and by drawing on technology and knowledge from not only its own manufacturing ability but also its experienced team. TRT’s manufacturing operation is ISO9001-2015 accredited.
TRT has developed an exclusive and comprehensive operator familiarisation program for training operators. The program is designed to suit your schedule and location. Your team is supported by experienced TIDD Crane experts 24/7 with a new comprehensive video which is included with the TIDD Crane. Conditions apply.
on new designs. For example, they recently upgraded the suspension cylinder with the release of the TIDD PC28-2 which has increased the lifting capacity by an average of 17 per cent, and in some cases 40 per cent, which is massive,” he said.
“The release of the TIDD PC28-3G is a major step forward in my opinion. For many of the Tier One builders, sustainability, low emissions, quieter engines, and continued safe lifting practices are going to be paramount.
“With the new emission standards coming online next year, TRT has taken the initiative by moving to the Cummins Euro 6-compliant engine. It sends a message to the industry that we are always thinking ahead
two TIDDs due to our safety innovations and service.
“We also delivered a TIDD to McMahon Services in South Australia recently. Initially, there was staunch opposition from some very senior operators, but once they jumped in, drove it down the road, and operated it, the response was “How good is this?” The roadability and new lifting capability of the TIDD are exceptional,” he said.
TRT has been designing and manufacturing heavy equipment, cranes, and trailers for over 56 years. With real expertise in crane design and manufacture, TRT is the home of the TIDD Crane.
TRT makes upgrading a fleet to include TIDD PC28-3G simple and efficient for all operators and owners. TRT’s service and spare parts support, warehouse facilities, and network of experienced dealers throughout Australia and New Zealand are second to none. TRT is committed to supporting operations and uptime, 24/7.
The TIDD PC28-3G will be officially unveiled during the Crane Industry Council of Australia (CICA) National Conference and Exhibition which will be held at the Perth Convention and Exhibition Centre, from October 26th to 28th.
TRT welcomes all to come and see the new PC28-3G – saying it is cleaner,stronger and safer.
“The release of the TIDD PC28-3G is a major step forward in my opinion. For many of the Tier One builders, sustainability, low emissions, quieter engines, and continued safe lifting practices are going to be paramount.”PC28-3G features the Allison Transmission with retarder, for superior braking.
Like so many owners of crane hire businesses, TopGun Cranes’ Barry Ramm, is a modest, no-nonsense man. He is very hands on with his business, and wants the very best for the people he employs. Barry loves nothing better than getting behind the controls of his cranes and putting them through their paces.
“OUTSIDE OF WORK, PEOPLE KNOW I’M IN cranes, but I don’t tell them I’m a crane owner, I like to keep things simple” says Barry.
“When I was a youngster, I saw a crane set up in a weird and wonderful way, and I remember thinking ‘That’s very interesting,’ said Barry.
He swapped directions in his career moving from landscaping to become
an auto electrician, and worked for a company called Hunter Valley Cranes, which, at that time did similar work to Johnston’s Transport, specializing in moving machinery and rigging. Barry was driving trucks and learning to Rig L oads.
“I got my semi-trailer license a couple of years prior and I made out I knew what I was doing, although I had no experience,
and the owner took me for a drive around the block”.
“I drove the truck like I would a car using the clutch to change gears. When we got back to the yard, the owner said “Mate, there’s not many people that use the clutch, and I’m always telling them that’s the best way to drive, but they don’t listen”. That’s where I got my start in the crane industry,” Barry said.
Barry went on to work at Stephensons Cranes where he met Phill Martin, Operations Manager, and others. This was his introduction to running a fleet of mobile cranes. Barry started the TopGun Cranes brand with a business partner Trevor Sweeney.
“Trevor was our business partner in the beginning. We had some highs and lows, and as time went on, it was clear that Trevor was going to head in a different direction”. “Five years ago, we bought Trevor’s stake in the business”.
“We have restructured the business over time. We were a tower crane company with some mobile cranes, as we pursued the tower crane market for a while. But our philosophy has been
to concentrate on one thing, and do it well. So we got out of tower cranes and progressed with our mobile crane business to meet the requirements of our customers”.
“We operate a diversified fleet and our range and capacities let us compete with much bigger yards. We provide a personalized service for our customers and I like to catch up with clients when I go to a site. I still occasionally operate cranes to understand what’s actually happening, and happy to get out on the tools whenever I can. I wouldn’t expect our teams to do anything that I wouldn’t do or haven’t already done safely,” said Barry.
The business continues to evolve, and professional development is a key focus for TopGun Cranes.
“Peter Willmott recently started with us as a Draftsman and Heavy Lift
Specialist. Pete’s been in the industry a long time and his experience and skill set is something we’ve been wanting to bring in-house for some time. He joins Graham “Butch” Cooper planning solutions for every challenge.
“We are also keen to see people progress in the business, and Nathan McNeill is a good example of this. Nathan has stepped up through the ranks having started out as a Dogman, progressed to Crane Operator and now to an Allocations Role,” said Barry.
“We really appreciate what everyone puts into the business,” he added. “I take great pride in saying I employ a team of 40 plus individuals, that’s my biggest reward. Life and working with cranes is a hard balance, the odd hours and being away from home can take a toll on families. I really appreciate what our teams do for
“We really appreciate what everyone puts into the business. I take great pride in saying I employ a team of 40 plus individuals, t hat’s my biggest reward.”TopGun Cranes is a growing business, focused on expanding its capabilities.
the business.”
TopGun Cranes recently took delivery of new cranes including a Grove GMK 3060L-1, the first Grove in the fleet and a Terex Franna AT40.
Renewing and refreshing the fleet is not a straight forward process for any crane business and it is no different for TopGun Cranes. Fluctuating exchange rates, the strength of the Euro and extended wait times on delivery are issues being dealt with, industry wide.
“We are really happy with the latest additions. It is a good feeling knowing we are buying new cranes and that they
feature all the latest safety developments. As we move forward as an industry, we believe it’s the newer cranes featuring the latest technology, which will lead to less risk and this is the direction in which we all need to be headed,” said Barry.
“There are a number of new purchases in the pipeline, big and small, and these offer challengers we look forward to,” he continued. “We are a growing business and expanding the capabilities of the fleet has its pros and cons. Our biggest hurdle at the moment is our facility and yard space in Glendenning.”
“Renewing the fleet and buying
new equipment is one thing, but accommodating it is proving to be an even bigger challenge. It’s a problem facing all businesses in major cities, especially Sydney, which has one of the highest land values in the country. If we want more space, we are going to be pushed further away from the geographic center of Sydney which increases road travel, working hours, fatigue levels, to name a few but we will manage,” said Barry.
We are seeing positive results from our apprenticeship program. Attracting youngsters to the business is a key element of TopGun Cranes’ growth strategy.
“We recently started two new apprentices. After the success of our first apprentice John Markantonatos has worked really well and was my dogman on a recent project. I’m still learning the different disciplines they are being taught, one being customer relations, which can only benefit the individuals, our business and customers,” said Barry.
“We believe our teams are ‘Next Level,’ when it comes to their approach to work. We pair the youngsters with our experienced guys who have been in the industry a long time, and they are good enough to share their knowledge and experiences.
Like all crane hire businesses, the backroom staff are critical to the business.
“We wouldn’t operate if it wasn’t for our backroom staff. My wife Emma Ramm is on top of the financial side of the business. I appreciate what Emma does and wouldn’t be here without her support. Our Office Manager, Katelyn Duffy works tirelessly keeping the books balanced, there is a lot involved,” Barry said.
“There are always stresses as a business owner, and retaining good staff is really important.
For the businesses that have retired, it’s unfortunate because a lot of them had been around for a long time. The industry has witnessed change, but change provides opportunity and that is certainly the case for us. It definitely opens new avenues and provides us with more opportunities to keep moving forward. “TopGun Cranes is here for the long haul!” said Barry.
LIFTING RIGGING HOISTING WINCHING LOAD TESTING EQUIPMENT HIRE SPECIALISTS
ON THE SHELF. FULLY CERTIFIED. READY TO USE.
Bremco has always prided itself on being a 100 per cent authentically local company. Managing Director Brett Moody discusses the company’s crane attachments capabilities, local manufacturing and the importance of safe, quality products in the lifting and rigging industry.
BREMCO METAL PRODUCTS HAS BEEN operating in the Australian marketplace for over 27 years. Starting its journey in 1996, founder and director Brett Moody was set on providing a locally sourced, locally manufactured service to the local market.
In-house, Australian manufacturing has always been at the core of Bremco’s operations; 100 per cent Australian owned and operated, the Brisbane based company commenced its operations as a sole trader business working in general and structural metal fabrication.
What the company did need to find, however, was areas to grow the business in. After identifying a gap in the forklift market early into its journey, Bremco moved quickly to begin working with products in the crane industry by manufacturing custom-made lifting attachments.
Some of Bremco’s products appear in industries such as warehouses, manufacturing, mining, construction, and transport. Now, working in a close capacity with a range of lifting and rigging suppliers such as Bullivants and Independent Rigging Stores – as reported in the November issue of
Cranes and Lifting – Bremco is seeing its products perform in the lifting industry on a regular basis.
“We have been exceptionally happy servicing the crane industry and working within the manufacturing guidelines of the relevant Australian Standards,” says Brett.
“This allows Bremco to better inform our clients rather than purchasing cheap imported products that do not meet the required code.”
Today, the crane attachments division at Bremco consists of a significant portion of the company’s portfolio. Its general crane attachments feature a range of combination beams, crane bulk bag lifters, crane lift pallet hooks, equaliser plates, lifting beams,
and spreader beams, along with a variety of site cages and bins.
Additionally, Bremco assists with design, manufacture and test tagging of custom lifting products through close collaboration between in-house engineers and external rigging teams, according to Brett.
“One of our customers was needing to lift roof sheets at 30m long and weighing up to 1.5 tonnes per pack, within their factory,” he says. “Bremco was pleased to work closely with our design team to solve the issues at hand and produce a lifting beam that would offer fixed and telescoping lifting options on sheets from 12m through to 30m.”
Bremco has consistently prided itself on custom-manufacturing crane attachments from initial design through to its attachment on the crane itself. With all its bespoke products featuring
fully welded construction, Bremco also designs and load-tests its products in accordance with the Australian Standard AS4991 (AS1418.17 for its crane man boxes).
“Bremco is exceptionally proud of the stocked and customised products we manufacture in-house,” says Brett. “We feel that there is nothing better than good old Aussie-made that leaves a certain amount of security when out there lifting people and products on the end of a crane.”
The way the company achieves this is through regular consultation with its
engineering partners to ensure every product meets every standard. Part of Bremco’s stringent testing requirements include weld testing to ensure structural integrity, testing its products on site with testbeds up to 100-tonne capacity, hydraulic testing rigs, load cells and using dead weights to formulate a testing regime for each product.
With crane lifting equipment designed to offer more versatile lifting operations, Bremco strives to supply the Australian market with safe, durable, effective lifting equipment that supports local business.
“Bremco has consistently prided itself on custom-manufacturing crane attachments from initial design through to its attachment on the crane itself.”Part of Bremco’s inventory includes an array of lifting pallets and crane bins.
WireCo Australia has undergone a significant expansion and rebranding over the past 24 months to better reflect its affiliation with all WireCo’s manufacturing facilities and brands owned and supplied by WireCo Globally. National Crane Division Account Manager Kathryn Darr elaborates on the global leading products and services supplied by the company.
FOLLOWING A 35-YEAR CAREER IN THE wire rope, lifting and cranes industry, Kathryn’s engagements then allowed her to work in multiple roles on a national platform. This widespread experience in wire rope, hoisting and lifting applications saw her arrive at WireCo Australia in 2017 where she is currently servicing the Australian market as the National Cranes Division Manager. Within the significant expansion of its national network, WireCo also
ensure when recruiting, the company seeks out highly experienced personnel with significant industry experience. This was shown with the onboarding of Adrian Paull, a well-known name in the Australian wire rope industry. This is a distinctive feature that sets WireCo Australia apart from the rest.
WireCo’s specialised rope services is supplied directly to all Australian industries. With a one stop shop related to cranes, mining, maritime, hoisting,
synthetic and lifting products. WireCo Australia also ensures it has the ability to assist its valued clients and stakeholders with any support they may need when it comes to their hoisting applications and products. This is especially prevalent in WireCo’s crane rope division, according to Kath, because when it comes to cranes and lifting, it’s important to note that “not one rope or product design can complete every single task”.
“WireCo Australia stock a wide variety of Casar and Oliveria wire rope constructions, as every application is different,” she says. “We strive to ensure the correct choice of crane rope is selected from installation, this ensures minimal maintenance requirements once our specialised rope products are in service and their intended unmatched rope service life is fully achieved. Diameter, construction, lay, tensile grade, and finish all need to be carefully considered to match the application they are intended for.”
Further to its sales, WireCo also offers a range of specialized servicing options for customers utilising their Casar, Oliveria and WireCo Branded products. WireCo Australia ensures the availability of experienced staff for any post-sale and product support.
“Our highly experienced team will assist our customers through every facet of any challenge they may have with their applications,” says Kathryn.
The reason for doing this, she says, is because in the crane rope industry challenges will always need solutions. WireCo’s servicing team assists with locating the root cause of these challenges. As Kathryn says: “Other than just a supplier of products, we are also a ‘solutions provider’”.
To ensure the highest of quality solutions WireCo Australia’s services, supplied nationally provide utilising its NATA accredited facilities. Tony Duricin, WireCo’s National Mining Division and Services Manager, helps to assist with any specialised services required.
Assembly of WireCo’s products as per customer specifications is also within
the facility’s capabilities. WireCo Australia has the ability to install and assemble wire rope end fittings in the form of ferrule secured thimble eyes, open and closed spelter sockets, WireCo’s resin buttons for all cranes, and hoisting applications. These products are also provided with NATA accredited certification. This ensures not only the quality of the fitting’s installation and testing, but the certification to keep customers’ applications working as intended.
WireCo Australia, formally known as Casar Australia and Lankhorst Euronete Australia, were amalgamated on January 01, 2021. This was to provide its customer network full access to the entire global brand and product range from a localised destination. WireCo Australia now encompasses the product ranges of Casar, Oliveira, Union, Camesa, Lankhorst, and Euronete.
WireCo Australia’s direction is to ensure that its current and future valued client base knows that its high-quality product line and brands align with the new face of WireCo Australia.
Further to branding changes, Kathryn Darr gives a further break down of the inner workings of WireCo Australia.
”Our Crane division focuses on our two main stocked brands for the Tower Crane, Crawler Crane, Mobile Crane, Port Crane, Vessel Crane and Offshore cranes industry Nationally
these well-known brands are the Casar and Oliveria product range. WireCo Australia holds over 600 Tonne of crane ropes stock in our facility at and one given time. This allows our facility to hold multiple rope diameters from 5mm – 54mm and above. Our facility holds the longer lengths from 0 metres to 3000 metres in any individual length to service all applications. We keep multiple constructions and specialised designs to service our national network and all available industries.”
WireCo Australia holds an extensive range of top tier high quality Casar specialised wire ropes. Casar wire ropes are one of the most well-known German manufactured products seen
in applications throughout Australia. These products continue to meet and exceed our customers’ expectations. The Casar product has continued to excel in regard to rope life longevity across all applications reducing customers maintenance costs and servicing needs.”
Kathryn Darr is also proud that WireCo Australia has significantly increased its stock holding of the high quality Oliveira crane rope produced in Portugal. Oliveria is one of WireCo’s European manufactured options, also held in high regard by its customers as a cost effective product alternative. This product range has also allowed Kathryn Darr to increase the WireCo Australia product portfolio.
In a move worthy of attention for the Newcastle and Hunter Valley regions of New South Wales, Two Way Cranes has made a significant expansion into the region. With Branch Manager Blake Furner seizing the opportunity, the new business has immediately gained considerable momentum.
started as a boilermaker, gained his crane tickets, went straight into driving cranes and operated for 15 years before beginning his career in management eight years ago. Blake takes up the story.
“I’ve had the luxury of working with some good clients and good companies and because I’ve featured in articles before, most will know my history. About two years ago I was watching the news with my wife, and it was a story about extending the Warragamba Dam near Sydney. There
was a Two Way all terrain on the dam and I remember saying “Wow, Two Way Cranes seem to be popping up everywhere.”
“A month or so later, I attended the CICA Regional meeting in Newcastle and introduced myself to Frank Zammit and his wife Nichole. I was immediately impressed with both, how humble they are regarding the success with the business.
“From the conversation, I learned that Nichole was the Owner and Director of Two Way Cranes and she is a proud indigenous woman. The conversation left me impressed with both Frank and Nichole and their business and when this opportunity presented, myself and my team were quick to come on board. We only started in May with the branch progressing rapidly,” said Blake.
Nichole is also an advocate for the Supply Nation community, regularly attending events in support of other fellow verified Indigenous businesses. She is also very proactive in providing pathways within the business for indigenous and non-indigenous youngsters. A great example of this is Riarna Anderson, Nichole’s cousin. Riarna had been working
in the office but showed genuine interest in getting her Dogging ticket, she recently received her HR licence and now she is working and learning on the cranes and couldn’t be happier.
“I left my previous employer because I could see this was going to be a really good opportunity and then my team of 20 crane operators and office staff followed. It’s been the same with the businesses I’ve worked for over the last 10 years, we’re a good and solid team and we stick together.
“The Two Way Cranes brand has certainly helped and the local Newcastle market has responded to the business positively. In a short period of time, we’ve achieved what has probably taken double or triple the amount of time to achieve previously, and that growth was deemed impossible back then,” he said.
“This is now my third company in a decade and Two Way Cranes is where I call home and I’m here to stay. I didn’t leave the previous companies because I wanted to leave, it wasn’t the company or the people, in large corporations you don’t always see eye to eye with management,” said Blake.
Clients have been quick to come on board, some of which have worked with Blake and his team for 20 plus years.
“Obviously, I gave clients the courtesy of letting them know I was moving on, because I didn’t want to walk out leaving them high and dry, but I didn’t actively pitch for their business either. Recently, we’ve lost a few crane hire companies in the region so there’s quite a demand for crane services. This led to a number of clients moving across straight away, and our crane crews and office staff following. More clients have come on board in a short amount of time compared to any company I’ve ever worked for, which is brilliant,” said Blake.
Frank and Blake spent some time deciding on the location for Two Way Cranes’ new yard, with Frank keen to see the yard in Newcastle.
“I discussed with Frank the fact that we’ve lost two or three crane companies in the Hunter Valley and two recently in Newcastle and we decided the best place for the yard would be Kurri Kurri. It is central, with the Hunter Valley 25 minutes up the road and Newcastle 20 minutes
down the road.
“We’ve picked up some significant works already with the local power stations and major engineering services companies like UGL. We haven’t really ventured too hard into the mines as yet, but the mines are very keen to get us onboard.
“By mid-August we’ll have a 250t housed here permanently. We’ve currently got 2 x 150t, 2 x 100t, 1 x 90t, 2 x 60t , 2 x 40t Frannas, 25t and 20t Frannas as well as a 20t City crane.
“But we have been several cranes short for the work we are generating and that’s an indicator of what’s ahead. Frank has 12 more new cranes coming in the next two months, this will certainly help us to continue our rapid growth. One thing I can say is we have never let a client down with supply and we are not about to start, when we have too much work in Newcastle our Sydney depot backfills and we also do the same when they are busy.
“John Holland have won a lot of work locally and there are other big players up here that Two Way Cranes works for in Sydney and with their relationships and my relationships, we’re certainly going to be busy. I can see us doubling in the next six months.
“Crane crews are the biggest struggle for most companies but we’re not having a problem attracting good people. I’ve had calls from a number of people with 10 years to 15 years plus experience and they are good names, so we have exciting times
ahead,” said Blake.
He goes on to discuss the lift planning and engineering capabilities of Two Way Cranes and how this works on some of the larger, more complex projects.
“We obviously have access to our drafting and engineering teams in Sydney, but my team and I have been doing this for a long time, so we manage our own lift designs as well, we manage 60 per cent in-house with Sydney managing the large-scale projects which need a lot of preparation and time,” Blake said.
A positive work culture, a focus on safety and customer service have long been
never guaranteed work, but they took a gamble which they’ve done before, this is the third time we’ve done this. I’ve got a lot of respect for my team, and I think the feeling is mutual, they wouldn’t follow if that wasn’t the case. We’re delivering an excellent service and that’s full credit to my team,” said Blake.
“Frank and I agree, we are always going to be in general hire, We can see a lot of works out there in the infrastructure space, with some seriously big projects, where there’s a lack of supply. We are also in the process of securing some major contracted work in the Hunter also.
associated with Two Way Cranes and it is no different for the Kurri Kurri operation. Blake also confirms he and Frank have high expectations for the business.
“We couldn’t ask for a better crew. I’ve known all of them for quite some time, some for over 15 years and they suit the Two Way Cranes culture really well. They are dedicated, they are meticulous with their planning, with safety always front of mind, and they are respectful of our clients when they get to site.
“They are the reason for our success. We started from nothing, and they were
“For now, we are not going to focus on one particular area. We’re going to focus on all areas and deliver excellence. Two Way Cranes is delivering excellence in Sydney and that’s what I’ve been delivering for the past 15 years.
“We’re delivering maintenance projects to the power stations, and we have some work in the mines, our 450t crane will be commencing in Newcastle soon, we’ll work them back and forth between Newcastle and the Hunter Valley where we’ve got some large builds coming on. It’s small but solid steps for now,” said Blake.
“We’ve picked up some significant works already with the local power stations and major engineering services companies like UGL.”
Tutt Bryant Equipment, national distributor of KATO Cranes recently announced the release of the new KATO City Crane, the KATO CR-130RV - to come with additional technical support from Liang Song, Tutt Bryant Equipment’s National Technical Support Manager, Cranes.
WITH A LENGTH OF UNDER 7.5M, 2M WIDE and under 3m in height, the CR-130RV is one of the most compact mobile cranes on the market and approaches confined spaces like no other mobile crane.
Its 4x4 steering provides a compact turning radius and manoeuvrable travelling abilities. It is ideally suited for work not only on construction sites but also for moving plant and machinery around warehouses and factories.
The gross weight of the vehicle (GVW) is only 13,825kg which makes the CR-130RV
ideal for works on sites that have low load bearing capabilities, such as bridges or building floors under construction.
The strong and powerful main boom features simultaneous telescoping which enables the operator to start and finish lifting easily and smoothly.
The fly jib measures up to 5.5 m and is hydraulically operated. The reach of the CR130RV with the fly jib is ideal even with the crane set up close to a building.
One of its most important features is its compact tail slewing radius. It is only
1.60m, ensuring the CR-130RV can lift right alongside the building.
The CR-130RV is typically suited to very confined job sites. However, this new CR130RV features an applied electronic control system. Outrigger operation is now available by remote control which enables the operator to check the outrigger’s position closely. Outriggers have various positions that support suitable lifting to each job site.
Outriggers start at a completely retracted distance of 1.64m to a fully extended distance of 4.74m.
When lifting in areas with height limitations such as a warehouse or factory, the CR-130RV has a Searcher Hook option available. The Searcher Hook is easy to install and able to select from two positions. With a maximum lifting weight of 3t, it is useful for lifting heavy loads such as manufacturing equipment.
The high rigidity six section Superboom is a key feature of the new KATO CR-130RV. The boom has a 13t lifting capacity at 1.7m, a maximum boom length of 24m and a maximum lifting height of 24.8m. The CR-130RV also features 2 section hydraulic luffing power jib which has a maximum length of 5.5m and increases the maximum lifting height to 30.3m.
The CR-130RV is powered by a Hino JO5E-VA which is Euro Stage V compliant. It has Selective Catalytic Reduction and DPF to reduce NOx and PM in the emissions.
The CR-130RV has an ABS braking system as a standard feature, ensuring safer braking, especially on slippery surfaces.
The electronic joystick control is ergonomically designed and easy to operate, making it more functional and comfortable for the operator.
Thanks to the electronic control system, the operator is able to set and record the crane speeds.
The operator can monitor left or rear blind spot and winch conditions from the cab with KATO’s multiple view colour monitor option.
The touch screen control COR information display provides an ECO function which supports economical crane operation.
It also limits the maximum engine speed to reduce fuel consumption and noise.
The new outrigger system facilitates the process of outrigger setting. The vertical cylinders extend and automatically stop at the horizontal positions while operating semi-automatic levelling switch.
The touch screen control ACS moment limiter provides a range of limiting functions designed to increase safety during operation. It limits the load factor to between 80 and
100 per cent of the rated lifting capacity to keep a safe margin. It also limits the working range to avoid collisions.
Hill Start Assistance is a new function for KATO CR-130RV. This function provides the brake at the point of acceleration on a hill and an activate and deactivate option is selectable for the operator.
A Surround View camera provides a 360° view of the crane and aids safer stopping and or parking. It also features a Human Detect Assist System with safety cameras detecting humans in blind spots alerting the operator with visual and audible alarms.
After an extensive period working with construction equipment and cranes in Japan, Liang Song joined Tutt Bryant Equipment as National Technical Support Manager, Cranes earlier in the year.
Liang worked for KATO as the Assistant Senior Staff of Overseas Support Group, which was where he met the Tutt Bryant Equipment team.
During his six years at KATO, Liang promoted the software development of new crane models for Oceania market, so that it could comply with local regulations. He
coordinated the work of improving painting quality for Taiwan market where rusting had been an obstinate problem.
Liang also organised regular visits to Oceania, Taiwan and Hong Kong for product delivery, technical training and market research, hence strong connections with overseas distributors and prompt responses in case of a problem or emergency.
He performed as the contact person in Japan for KATO Europe regarding service issues, supporting them with any information needed by communicating with relevant departments.
Liang acquired technical expertise required for service engineering for mobile cranes and hydraulic excavators, including rough terrain cranes of 10~80 tonnes, all terrain cranes of 100~130 tonnes, truck cranes of 30~60 tonnes, hydraulic excavators of 8~45 tonnes, and miniexcavators of 3~8 tonnes.
He also attained an advanced level of trouble shooting for hydraulic, electrical and pneumatic system, and diesel engines of various manufacturers.
Tutt Bryant Equipment’s technical support for KATO and HSC products is in good hands.
In a male-dominated workforce, the achievements of female counterparts can occasionally be suppressed due to a lack of diversity and inclusivity. After consecutive successes in 2022 and 2023, Prime Creative Media’s Women in Industry Awards is returning to platform the important role all women play across every industry.
ACCORDING TO THE AUSTRALIAN Government’s 2022 labour market insights, 13.3 per cent of the construction industry – which holds 1,322,100 workers – are female; a total of 176,000 workers.
Put plainly, the construction industry –in which the crane industry resides – is an industry heavily dominated by males.
With over 100,000 jobs in construction currently going unfilled, industry leaders such as the Australian Constructors Association (ACA) are highlighting the urgent need to create a more diverse, accepting and inclusive workforce to address these shortfalls. In turn with accounting for the lack of skilled labour in the construction industry, a recent report by global management consultants McKinsey stated companies are likely to be profitable if they display a diverse, equitable and inclusive workforce.
With this objective in mind, Prime Creative Media launched its annual Women
in Industry Awards night in 2013 to acknowledge the exceptional women who have achieved success in their respective industries through leadership, innovation and commitment.
The Women in Industry Awards recognise outstanding women across a range of industrial sectors – such as mining, transport, manufacturing, engineering, logistics, bulk handling, waste management, rail and construction and infrastructure – that are traditionally maledominated.
2023 sponsor Fulton Hogan Australia’s CEO Graeme Johnson spoke of his “pride” in his company’s role in being involved with the initiative for a second year running.
“This sponsorship demonstrates our commitment to supporting and driving change within predominantly male industries, doing what we can to make heavy industry more attractive and accessible for women to join and
stay,” he said. “Fulton Hogan recognises that diversity is not only essential for us to change, adapt and grow, but it also good for business and results in happier workplaces with a better culture, leading to better retention of our people.”
Supported by over 30 different media mastheads and publications, the 2023 Women in Industry Awards saw a 95 per cent increase on its 2022 counterpart for nominations across 10 different categories, with the number hitting a record 160 nominations in the 2023 edition. The gala dinner that accompanies the event sold out for the first time in the event’s history, recording a 55 per centattendance increase compared to the 2022 edition.
2023’s winners for their respective categories included:
• Business Development Success of the Year: Stefanie Frawley from TMX Global.
• Excellence in Construction: Trudy Grimshaw, Department of Finance, WA.
• Excellence in Engineering: Elsa Antunes, James Cook University.
• Excellence in Manufacturing: Kristi Riordan, Harvest B.
PACCAR highlighted the importance of “championing inclusion and diversity in the
“PACCAR has a long and proud history of supporting women in all areas of its global businesses,” said Director of Sales and Marketing Michael Long, “and recognises programs such as Women in Industry Awards help promote women more broadly than its own company and industry.”
After its roaring success in 2023, Prime Creative Media’s ‘Women in Industry Awards’ event is set to be held on June 20, 2024, in Sydney. With nominations opening up for the eleventh edition online, now is the time recognise the women who are driving change in the industry and creating barriers for the next generation.
Nominations will close on Friday 19 April 2024.
Nominations are unable to be wn once nominations are closed.
• Nominations must be completed in one sitting; a partially completed form cannot be saved and reopened at a later date.
• All nominees must reside and work in Australia.
• Please have any supporting documentation (i.e. references, photographs, resumes) ready to upload; file sizes shouldn’t exceed 5MB.
• All nominations must be accompanied by a high-resolution image (at least 1MB in size) suitable and approved for print publication.
• All finalists are required to have a representative at the Gala Awards evening should they be successful. To assist with this, all finalists will be provided with one complimentary ticket to attend.
Sponsorship opportunities are available for the forthcoming event. If interested in sponsoring Women in Industry Awards 2024, please visit https:// womeninindustry.com.au/sponsors/.
“The Women in Industry Awards recognise outstanding women across a range of industrial sectors – such as mining, transport, manufacturing, engineering, logistics, bulk handling, waste management, rail and construction and infrastructure – that are traditionally male-dominated.”2023’s edition of the event saw a spike in attendance numbers and nominations for awards.
The new machines available now are hydraulic boom crawler cranes with capacities of up to 30, 60, 90, and 150 tonnes, as well as a full range of truck cranes with extras in the 25 and 55 tonne capacity classes.
Additionally, the Melbourne-based new crane dealer for Zoomlion is also expecting to take stock of a new 120-tonne capacity all-terrain crane, a range of new rough terrain cranes between 40 tonnes and 110 tonnes and new crawler cranes.
Sales Manager at Gleason Cranes Chris Logan says the latest acquisitions are indicative of the company’s desire to hold enough stock and spare parts when the demand comes for its services, labelling it a “big part of the company’s philosophy” when it came to selling machinery and providing ongoing customers support.
our staff work together, and we know if we do that, then we’ll sell more cranes because we’ve provided a good service that everyone’s happy with.”
Having seen the product stand up in some of Australia’s harshest environments including the mines up north and in the colder climes of the Snowy Hydro project, Chris says the quality in the Zoomlion brand is there for all to see.
“A lot of brands that expanded outside of Asia have successfully completed what Zoomlion is currently doing now,” he says.
“If you go back to the 70’s and 80’s, all the Asian brands really struggled with their reputations in Australia. We know that if we continue supplying a highquality product to the Australian market, people will continue to see the positive performance of the Zoomlion brand.”
a compromise on quality but, rather, a combination of available stock and relatively cheaper raw materials and labour.
“The quality is right up there,” he says. “Any customer we speak to is loving their cranes, irrespective of whether it’s a hydraulic crawler crane, truck crane, anything.”
“The Zoomlion brand is consistently our best-seller, and that’s because of the quality they display.”
Gleason Cranes is based in Melbourne, Victoria, and has been providing the Australian market with lifting machinery at cost-effective prices for over 50 years.
As well as being the national distributor for the Zoomlion brand, Gleason Cranes also represents the Ormig and Mi-jack brands nationally.
Looking
As
Quicklift Crane Hire celebrated its 25th year in business with the arrival of several new cranes. The last 18 months have been busy for the business, explains owner and director Jarrod Sutherland.
“LIKE MOST CRANE HIRE COMPANIES, we’ve been busy for some time now, working on all types of projects. General crane hire including commercial and residential construction, factory maintenance, irrigation and concrete panel erection work through to power line maintenance with Powercor and Ausnet. There has also been some work in the infrastructure space as well with some new bridges going in locally,” said Jarrod.
With that, he said, there have necessarily been some additions to the fleet.
“The new additions to the fleet have been fantastic. We recently took delivery of a new Franna AT40 and we are pretty excited to have it out and working. The AT40 will make life a lot easier for us being able to pick and carry with the extra lifting capacity. We currently run eight Frannas in the fleet.
“Our second Liebherr LTM 1060-3.1 60t capacity all terrain arrived in early August and our new Liebherr LTM 1150-5.3 arrived later in the month. Ordering the second Liebherr LTM 1060-3.1 was an easy decision for us, as we’ve been really impressed with the first one.
“Liebherr have a great machine in the 60T all terrain. They are really versatile and an excellent option for work in tight areas. Being a three-axle crane, even without
counterweight the lifting capacities are fabulous. With 48 metres of main boom we do a lot of work with this crane, where in the past we would have utilised a 80t machine. They’re a very popular machine and that’s why there is quite a few of them around,” said Jarrod.
With 48m of telescopic boom, Liebherr’s LTM 1060-3.1 offers enormous load capacities. At a total weight of 36 t and with a 12t axle load, it includes a 5.5 t ballast, 16.00 tyres, eddy current brake, 6 x 6 drive and a hook block. To offer the widest range of driving conditions, in particular at an axle load of 12t, a special ballast plate configuration has been implemented in the design. Depending on the crane equipment and the required vehicle payload, the ballast carried may be 3.7 t, 4.3 t, 4.9 t or 5.5 t.
To increase the load capacity, 7.3t of additional ballast is available so that the 60 tonne machine can be used with a maximum ballast of 12.8t.
Thanks to its compact dimensions, the threeaxle machine can be manoeuvred easily, even if on-site space is tight. The 9.44 m long chassis is just 2.55 m wide, even with the 445/95 R 25 (16.00 R 25) tyres. The turning
radius measured over the driver’s cab is just 7.58 m and the ballast radius remains within 3.54 m. A support width of 6.3 m is achieved with single telescoping sliding beams. Where space is tight, however, a reduced support width of 4.5 m or 2.3 m can also be used. At the touch of a button, the crane is levelled completely automatically during the support process.
The air activated disk brake developed by Liebherr for a mobile crane provides for increased safety and efficiency on the 60 tonne crane. In comparison to conventional drum brakes, they offer a considerably greater braking force that remains consistent even at high brake temperatures. The much longer service life durations also contribute to efficiency. Another advantage of disc brakes is that changing the brake linings - equipped with wear indicators - is faster and easier.
The active, speed-dependent rear axle steering system from Liebherr, tried and tested many times over, is used in the LTM 1060-3.1. This reduces tyre wear considerably. The driver has five different steering programs available that can be selected easily for a variety of situations.
The six-cylinder Liebherr in-line engine in the chassis achieves 367hp (270kW) and reaches a maximum torque of 1700 Nm.
The force is transferred to the crane axles via the 12-speed ZF-AS-TRONIC gear box. A two-stage distributor gear permits minimal creeper speeds in manoeuvring mode. The ABS (anti-lock braking system) improves driving safety significantly.
The six-part 48 m long telescopic boom on the LTM 1060-3.1 is telescoped in and out easily via the tried and tested rapid action TELEMATIK telescoping system. With the 9.5 m to 16 m long swing-away jib, the 60 tonne machine achieves hoisting heights up to 63 m and boom radii up to 48 m. The swing-away jib can be attached at an inclination of 0°, 20° or 40°. For work in two hook operation, a second hoist gear and a 2.5 m assembly jib and a rooster sheave is available.
In the hydraulic system, the electric “LoadSensing” control ensures accurate work operations. Up to four movements can be actuated simultaneously. Depending on the requirements for the lifting task and of the crane driver, the slewing gear can be easily switched from “open” to “hydraulic locked”.
The Liebherr LICCON2 crane control is used in the LTM 1060-3.1. Thanks to its modern and future-oriented control architecture, it facilitates adaptation to the continually growing needs of the market. A mobile, multifunctional control and display unit - BTT Bluetooth terminal - is provided for upgrade functions. This means that the crane can be supported easily and safely. The crane driver also has the option of attaching and removing the hook block on the crane bumper with visual contact via remote control of the hoist winch and the luffing cylinder of the telescopic boom.
The Liebherr LICCON2 mobile crane control also offers the option of simple and thus cost-effective conversion into a complete remote control system for the crane. Other than the relevant software on the crane, all that is required is a console with two master switches, which the existing BTT plugs into. A significant advantage for the crane operator is that the console can also be used for other cranes with LICCON2 controls programmed for remote control operation.
Liebherr’s LTM 1150-5.3 is a flexible all-rounder featuring the longest boom in this crane class, at 66 metres, and able to compete with crane models in the 200 tonne
lifting capacity class. It delivers outstanding lifting capacities when fully raised and at large radii.
And it is immediately ready for use once it reaches the site. This is because the new 150 tonne crane carries nine tonnes of a ballast with a gross weight of 60 tonnes. That means it can complete lots of jobs without requiring additional ballast transport vehicles. That saves time and money and makes the crane even more valuable to crane hire companies.
When fully extended to 66 metres, the LTM 1150-5.3 has a lifting capacity of over 9 tonnes, which makes it perfect for erecting tower cranes and radio masts.
Lattice extensions enable the new 150-tonne crane to achieve hook heights of up to 92 metres and radii of up to 72 metres. For this, one 7 metre lattice section as boom extension and a 10.8 to 19 metre double folding jib are used. The latter can be adjusted hydraulically between 0° and 40°. A 2.9 metre erection jib and a runner, which can be swung to the side, round off the equipment list. Particularly economical – the lattice jibs are compatible for many crane models in the 100 to 180 tonne class within the Liebherr portfolio.
The time-tested six-cylinder Liebherr diesel engine in the undercarriage provides all the drive power the LTM 1150-5.3 needs. It develops 400 kW / 544 bhp and a torque of a 2516 Nm. The engine satisfies the new stage V emissions directive and can also be configured to comply with the regulations which apply in countries outside of Europe, for example Tier 4 for the USA or stage IIIA for low regulated countries.
The ZF-TraXon gearbox is used to transfer the power to the crane’s axles. ECOdrive is particularly economical and convenient – the additional eco mode delivers enhanced drive properties which save fuel and reduce both noise and CO2 emissions. In addition, Hillstart Aid makes starting on gradients easier.
Liebherr has continued its single-engine strategy on this crane with a mechanical drive unit for the superstructure. The weight
reduction created by the elimination of the superstructure engine from the previous model is used to deliver a longer boom and more lifting capacity.
In keeping with the latest developments from the Liebherr mobile crane series, the new 150 tonne crane also features ECOmode for crane operations to reduce fuel consumption and emissions of both noise and CO2. Firstly, the complete pump drive can be disconnected automatically when the engine is idling and then reconnected by the intelligent controller in a matter of seconds when it is required. And secondly, the crane controller automatically calculates the perfect engine speed for the working speed selected using the control lever, helping to avoid unnecessarily high engine speeds.
Hook blocks have to be heavy to ensure that the hoisting winch spools reliably. However, they should be as light as possible for being transported on the crane and for high net loads during hoists. Liebherr has designed a completely new range of hook blocks to satisfy these contradictory requirements –weight plates are attached to both sides of the hook block to change the weight of the block so that it is perfect for the current situation.
As Leibherr’s mobile and crawler cranes division’s sales director Christoph Kleiner says: “Our engineers have produced a simple, but brilliant design as it means that operators can react even more flexibly to every job.”
For example, a 3-roller hook block, which previously has weighed 700 kg in this crane class, now only weighs 500 kg, but can be upgraded to 700 kg quickly and easily when necessary. The new system is available for 1 to 7-roller hook blocks. These can be used on cranes with both 19 mm and 21 mm ropes. The weights can be interchanged to ensure simple handling.
For Quicklift, Jarrod said his operators love to make the most of the cranes’ abilities.
the same operating system across the board,” said Jarrod.
The positive feedback from the team has been welcomed by Jarrod and his business partner - and wife, Karli - saying without the support of the great people in their team, their success wouldn’t have been possible.
“This October, we celebrate 25 years in business, and Karli and I are fortunate enough to have had some of our team with us for most of this time. We are lucky to have a great operations team, with Dion Canty celebrating 20 years with Quicklift last year, and Gary “Wiz” Gerada celebrating 20 years next year. We’ve got a great team, good people right across the board and we genuinely appreciate everything they do for the business,’ he said.
Jarrod and Karli are invested in the crane industry and not just with Quicklift Crane Hire. Karli is the Chair of the recently launched CICA Diversity Network which is designed to attract diverse groups to the industry, especially women.
“Anyone running or working in a crane hire business is busy and we are no different, but sometimes you do need to take a step back and look at where we are at as an industry and make a contribution where
“We have over 20 cranes, ranging from mini crawler cranes through the Frannas and into the all terrains where our largest capacity is the Liebherr LTM 1250-5.1 250t machine,” he said.
“Our operators love the Liebherrs and they think the VarioBase is magnificent. Its functionality means you can short jack a leg where you need to and know you’re safe with the LMI telling you where you are as far as your limits go.
“Thy also love the LICCON control system. It is a straightforward and easy to operate system. The benefit of having a number of Liebherr cranes in our fleet, makes it easier for the operators to move between machines because they’ve utilised
you can; and that’s what we’ve done. The CICA Diversity Network is a great initiative and Karli is very happy with the reception it has received. The recent Sydney launch was fantastic with close to 100 in attendance. It’s important to be able to contribute to your industry and what you in turn learn from the experiences of other people that are involved is also a benefit. It’s a two-way street and you get back what you put in,” said Jarrod.
“Karli has been heavily involved in the Diversity Network initiative, and she’s pretty happy with how it’s been received. For a long period of time, our industry has been male dominated, however we are gradually seeing more women enter the industry, which can only be a good thing,” said Jarrod.
“We have over 20 cranes, ranging from mini crawler cranes through the Franna’s and into the all terrains where our largest capacity is the Liebherr LTM 1250-5.1 250t machine.”
LCR, a crane and transport company dating back to the 80’s, has been reborn under the Qube Holdings Banner. Through the acquisition of the LCR brand, Qube now delivers enhanced broad spectrum industrial services to customers, expanding its reach and dominance within the logistics market. With 160 locations throughout Australia, New Zealand and Southeast Asia and an appetite for major projects, Qube is a player to watch. Garry Kearney, General Manager at Qube, walks us through how the rebranding is going, the company’s key market focus and an insight into Qube’s sustainability ambitions.
AS AUSTRALIA’S LARGEST INTEGRATED provider of import and export logistics services, Qube understands that versatility and adaptability in the market are critical for growth and longevity, Garry says.
“Acquiring and rebranding LCR allows us to align with our goal of providing a full end-to-end service package within key markets such as renewable energy,” he adds.
“Our Heavy Lift Team now provides the specialised transport and craneage scope that complements our port, stevedoring, storage and distribution services – allowing us to provide the first true end-to-end project service offering within the Australian market.”
Qube Heavy Lift’s project services extend across Australia and Papua New
Guinea. Service locations also include general hire crane facilities located in Brisbane (QLD), Chinchilla (QLD), Port Moresby (PNG) and Lae (PNG).
As part of its renewable energy project focus, Qube Heavy Lift has also establihed Australia’s first purpose-built renewable energy storage facility known as the “Qube Renewables Hub” at the Port of Brisbane (QLD).
“Whilst we continue our focus on end-to-end renewable energy services, we are also committed to sustaining a market share in other sectors such as construction, infrastructure, power transmission and mining,” Garry says.
“Our specialised transport equipment and cranage fleet will continue to grow and develop to align with market requirements”.
The Heavy Lift Team regularly deals with the enterprises and organisations that form Qube’s client and stakeholder basis, and when it comes to dealing with the change in structure, he insists there have been “no issues”.
While Qube first acquired LCR in 2019, the official rebrand to Qube only
commenced in May this year, with Garry saying all company assets – in terms of cranes, trucks, trailers and other machines – would be rebranded within the next 12 months.
“We want this to be a positive experience for everybody, including our employees that have been a part of the LCR brand for years,” he says.
“We want them to be proud to put on that uniform that reads Qube and wear it with as much pride as before. It’s about us creating an environment whereby everybody feels that they have more opportunities to thrive than ever before”.
“Change when conducted correctly is beneficial to all parties,” he adds.
“Our clients and stakeholders are happy and excited to see how the LCR legacy will develop into the future and go from strength to strength under the Qube namesake.”
Garry says these stakeholders understand the benefits that come from the integration of the companies, which include their larger and more robust service offering.
“Whilst the extended service offerings
of the Qube brand were previously available to clients and stakeholders under the LCR name, there was a mindset that it was two separate companies,” he says.
“Now we can focus on promoting and selling ourselves under the one brand name, leaving no doubt in anybody’s minds about the extent of our capabilities and our willingness to lead the market.”
As for the internal changes occurring, Garry adds that having people of varying experiences in their working backgrounds adds a level of professional diversity within the company. “Diversity within our business is the key to driving innovation and expanding the skillsets we have to offer our client basis,” he says.
Qube Heavy Lift is currently operating a fleet of 84 cranes across its project services and general hire operations, including the Demag AC-1000-9: 1200t capacity crane – the largest all-terrain crane on the east coast of Australia.
The fleet also includes a range of all-terrain cranes (60-t-1200t), Franna cranes, truck mounted cranes and hydraulic crawler cranes. Services also extend to project specific transport equipment including jinker and bolster set ups for infrastructure works, heavy transport trailers and modular style trailers.
Speaking about the supply of cranes in Qube’s fleet, Garry says the company has “a solid working relationship with
key OEMs that are keen to support our growing business operations”.
“They understand our business and our business goals and are aligning themselves to provide the equipment we require to achieve those. They also understand the rate at which Qube Heavy Lift is capable of expanding and want to be a part of the journey with us,” he says.
The newest fleet purchases include some Tadano GTC-2000 telescopic
crawler cranes as well as the new era wing max blade trailers, which were bought to expand Qube’s transport capabilities within the renewable sector.
Garry says Qube Heavy Lift’s goals are simple – to be the leading provider of integrated crane and specialised transport solutions within the Australian and PNG markets.
“To be a leading provider within our industry we are also conscious that
we need to lead by example in terms of sustainability and environmental impact, ensuring we are leaving a positive mark on our surrounding communities”.
With a key focus by government and clients on sustainability, Qube has developed a roadmap towards decarbonisation ahead of industry. This includes electrification of MHE, trucks and mining equipment within the Qube brand and clear goals towards emission and energy reduction.
As the Qube brand continues to grow into the future, the Heavy Lift Team is committed to providing an innovative and diverse service offering, including both customised and turnkey end-to-end lifting and transport solutions to all sectors.
“Our clients and stakeholders are happy and excited to see how the LCR legacy will develop into the future and go from strength to strength under the Qube namesake.”
With the instant asset writeoff scheme being modified by the Federal Government and a new financial year commencing, one might think there would be a cooling-off phase in the crane sector.
“AFTER THE END OF THE FINANCIAL YEAR, you would expect that a lot of businesses had taken advantage of the instant asset write-off and had bought forward their purchases to maximise the tax incentives that were on offer.
“Now that we are into the new financial year and we’ve been through the winter school holiday period, people have taken time to catch their breath, consolidate and regroup on what was a very big year for a lot of businesses in general. Many crane companies have come to the realisation that the work is still there more than ever,” said Jeff.
“We are now seeing the impact of those companies that did shut their doors last financial year, companies are realising there’s still all of this work out there and this means more cranes are needed”.
“Because of the business closures there are more staff out there, but the labour
shortage is still real. If we took away the media and the rhetoric about interest rate rises, home loan pressures, I think Australia is in a very good position. Yes, there are some sectors that are hurting, but overall, the feedback we get from business owners is upbeat” he said.
Jeff doesn’t think there is going to be a negative rebound with the instant asset write-off finishing.
“For the companies that have ordered new cranes which are going to be arriving in the next three, six months or 12 months, because of the projected amount of work across the country, the industry is going to need these cranes,” he said.
“If new cranes aren’t available, people are still looking at the secondhand market.”
“Post instant asset write off, we’re starting to see a change in the way that the cranes are being financed. Before June
30, most owners were financing cranes as chattel mortgages because that’s how they got their maximum tax deductions out of it.
“Today, depending on the size of the business, it may be that we need to rethink about how this is done and consider financing future cranes under a method called Finance Leasing,” said Jeff.
Finlease has prepared the following examples. With the window for the 100 per cent depreciation tax incentive having now been reduced to $20,000 assets from July 1, 2023, is a chattel mortgage still the right structure for financing equipment?
The answer depends on the size of your company.
For organisations with an annual turnover of less than $10 million, Chattel Mortgage is still seen as the preferred structure, especially if your organisation has entered the Simplified Tax System –where all relevant assets acquired after July
Jeff Wilson, Senior Partner with Finlease doesn’t see it this way.
1, 2023, can be placed into a Depreciation Pool.
Under this structure, relevant assets can be appreciated at 30 per cent diminishing value (15 per cent for the initial year, as the asset has not been held for the full 12 months).
For organisations with an annual turnover greater than $10 million, any asset acquired after July 1, 2023, will be subject to the usual depreciation allowances available under the Effective Life categorisation provided by the ATO.
By way of example, if an asset is deemed by the ATO to have an effective life of 10 years, the annual depreciation allowance will be 10 per cent of its Prime Cost, or 20 per cent Diminishing Value.
Is a Finance Lease a better option for these larger (greater than $10 million turnover) companies?
As an alternative for those larger organisations, we expect to see a return to some assets being financed under a Finance Lease, where the actual lease payment is claimed as the deduction, provided the
lease structure (term and residual) fits ATO guidelines.
As an example, where an excavator has an effective life of 10 years, the depreciation claimed after five years may be as little as 50 per cent, whereas under a finance lease (funding the asset over a five-year term with a 25 per cent residual), the lease has allowed the client to claim deductions (via the lease payments) for 75 per cent of the asset value. (Always seek advice from your accountant as to the correct structure.)
There is no doubt that the 2024 financial year and beyond is a very different landscape to the COVID-19-induced tax incentives of the past few years. Companies should speak with their brokers and accountants to ensure they structure their future equipment debt in the most appropriate tax effective manner.
Jeff thinks the transitioning period for the industry hasn’t finished just yet and we can expect to see more changes in the coming 12 to 36 months.
“As a result of companies closing, other companies are continuing to weigh up their options. Larger businesses continue to grow and the feeling is smaller businesses continue to fill the “smaller niche” markets with less competition,” said Jeff.
Jeff is always a good barometer for how the various states are travelling. He has many high-level conversations with crane hire businesses about future investments. He is bullish about the foreseeable future.
“I think every state is still optimistic about its future. It will be interesting to see what happens in Victoria with the Commonwealth Games being abandoned and the massive infrastructure projects running well over budget. That being said, the projects need to be completed and the state government will have to see these projects through to completion.
“The renewables sector is really moving, so there should be plenty of work nationally for those crane owners who do work in this space.”
“Queensland with its resources activities and with the Olympics coming online is going to remain a busy state. Western Australia continues to do what Western Australia does and the mining sector there is still strong,” said Jeff.
“As a result of companies closing, other companies are continuing to weigh up their options. Larger businesses continue to grow and the feeling is smaller businesses continue to fill the “smaller niche” markets with less competition.”
Reid Lifting holds a 100-year history supplying lifting and rigging solutions to the Australian mining, construction and manufacturing sectors. The company’s position as one of the leaders in concrete reinforcement and lifting solutions was recently underscored by the role Reid’s grout sleeves played in the erection of 20 precast lift modules for the NEXTDC Merlot 3 Project in West Footscray.
ESTABLISHED IN 1921 BY ALAN REID IN New South Wales, the company began its proceedings providing wire rope to prospective clients.
Fast forward to 2023, and the company’s portfolio now features an array of lifting clutches, anchors and plates, as well as a host of products in the concrete reinforcement, connections, and formwork aspects of manufacturing.
With numerous developments internally allowing the company to widen its target audience for its products over the last 50 years, Reid’s lifting systems centre around providing safe and robust solutions for concrete lifting and anchoring applications.
This was evidenced recently when Reid’s lifting anchors were used in conjunction with its ReidBar GroutSleeve vertical connection system, to erect 20 precast concrete lift modules that weighed approximately 25 tonnes each. It was the precast contractor Hollowcore that made the decision to use Reid’s grout sleeves – a system which provides a full-strength splicing solution for reinforcing bars, allowing reinforcing continuity between loadbearing precast concrete elements.
Completing the work for the NEXTDC Merlot 2 project, all of the lifting modules were constructed off-site before being transported to site where they were installed adjacent to the existing buildings.
“We chose Reid’s products to allow for quick installation turnarounds on
site, which was a strict requirement from the client,” a Hollowcore engineer said.
“The sleeves require short dowels that are cast in; hence the lift modules could be installed on top of each other without the need for feeding in long dowels through conventional grout ducts.”
Challenges arose and were quickly overcome for both Reid and Hollowcore, as the lifting of the modules needed effective communication and collaboration between Reid’s R&D & lifting design teams, as well as Hollowcore’s on-site construction crew.
This was mainly down to of the spacing of the grout sleeves, the critical nature of which meant the lifter positions needed to be coordinated precisely so clashes could be avoided.
“The main challenge was coordination of the short dowels in the lower modules with the grout sleeves in the succeeding modules,” said the Hollowcore engineer. “The REID grout ducts provide minimal tolerances and hence every dowel had to be surveyed for as-builts so that the succeeding module would accurately fit on top. Additionally, steel templates were made to hold the top dowels and the bottom grout sleeves in place.”
Furthermore, due to the wall panels being thinner than the typical permissible wall thickness for the lifting anchors, further communication was needed between all departments involved to confirm the anchor capacity. This flowed with carefully detailed rigging diagrams that were needed because of a six-point lift being required for multiple sections of the precast modules.
“Overall, the installation was really smooth and hassle free; 3D modelling software was intensively used to ensure that the grout sleeves fitted adequately in the precast modules amid reinforcing congestion,” said the Hollowcore engineer.
“Lifting configurations were optimised to avoid unnecessary high costs while ensuring safety in the precast yard as well as on site, and a big part of that were the grout sleeves Reid supplied.”
Select Plant Australia offers the construction industry the most technically advanced cranes and services available. In line with Select’s dedication to a sustainable future, the most recent addition to its crane fleet is the first TIDD PC28-3G from TRT. Nathan Mitschuinig, Select’s Business Unit Leader, provides insight into the organisation and the purchase of the new TIDD PC28-3G.
WITH OVER 30 YEARS OF GLOBAL EXPERIENCE, Select takes pride in delivering forward thinking, innovative, top-tier construction solutions. Select offers customers the latest in technology, ranging from plant hire to logistics and on-site solutions, including the provision and installation of on-site accommodations, facilities, transport management and services.
Select Plant Australia aspires to be the recognised leader in sustainable, safe, and innovative plant solutions and a true integrated solutions provider.
“We service clients in the construction, civil, rail, infrastructure and utilities industries. We have depots in New South Wales, Victoria and Western Australia but our industrial transportation services enable us to deliver plant and equipment to every corner of the country,” said Nathan.
Together with its parent company Laing O’Rourke, Select is committed to leading the
market toward a sustainable future.
“We have committed to reducing scope 1 and 2 carbon emissions, reaching operational emissions to net zero by 2030 and being a net zero company by 2050,” said Nathan.
“As a leader in sustainability within the Australian hire and rental industry, we are dedicated to investing in building a modern, innovative and environmentally sustainable fleet that incorporates electric, solar and hybrid-powered solutions. We already have two site compounds operating off solar energy and our fleet is expanding weekly with low and zero-emissions equipment,” he said.
The health and safety of its people, customers and suppliers has always been the number one priority for Select.
“Our dedicated safety team is committed to improving our safety performance and minimising incidents. Safety is more than just our physical welfare; it is about our psychological wellbeing. We promote a culture where everyone is included and has the courage to stand up if something doesn’t feel right,” said Nathan.
“At Select, we are committed to continuing our journey of inclusivity and diversity. We pride ourselves on reaching our targets, particularly around gender
is to ensure equality of genders across all levels and locations of the Select business by 2033,” he said.
Across much of the business, Select has already reached this target with 65 per cent of salaried positions occupied by women. The next step is to encourage, train and mentor these women to ensure they’re confident
to apply for senior positions within the organisation. As for our cultural diversity commitment, Select proactively encourages and supports positive relationships with Aboriginal and Torres Strait Islander peoples.
“We have collaborated with more than 40 Aboriginal and Torres Strait Islander enterprises, contributing more than $32m across a range of diverse businesses. As we engage with Indigenous communities across the nation, our intention is to continue to build on these relationships of respect. This year we are focused on increasing our early learning talent with Aboriginal and Torres Strait Islander peoples,” said Nathan.
Nathan goes on to discuss the Select Plant crane fleet.
“We manage a fleet of crawlers, mobile and tower cranes. Our mobile and crawler cranes range from 60-tonne rough terrain cranes up to 350-tonne crawler cranes with Superlift capability. We also offer a range of tower cranes, from small, flat-top type hammerheads, such as the CTT332-16, to larger capacity luffing types, such as our CTL430-24. Excitingly, we have recently added the first two 250t electric crawler cranes in the Australian construction
industry to our growing sustainable fleet,” he said.
Select took delivery of its first TIDD PC28-2 in February 2023 which is currently operating on a project in Western Australia says Nathan.
“One of the fundamental principles shaping our plant investment strategy is a strong focus on safety. It’s worth highlighting that the TIDD PC28-2 demonstrates great safety features, including TRT’s exclusive Slew Safe® system, a critical safety component specifically designed to help prevent rollovers.
“Other advanced safety features included Traction Air® for regulated tyre pressure, ROPs style safety frame, the latest Allison Transmission with retarder and full ABS Brakes tested and compliant with the 2023 ADR35/06 standard. Coupled with the strategic positioning of LMI controls, seamlessly accessible from both the interior and exterior confines of the operator cabin.
“As we assessed the new TIDD as part of our evaluation process, another critical factor that influences our decision is our commitment to sustainability. TRT has manufactured the TIDD PC28-3G with the latest Cummins Euro 6 engine, offering the
highest emission control diesel engine in the pick and carry crane market,” he said.
Nathan explains what initially attracted Select to TRT’s products and services.
“What initially attracted us to TRT’s products and services was that they have key product support with both the parent manufacturer TRT in New Zealand and the Australian subsidiary. TRT also offers extensive industry experience to support Select’s ventures. We have dealt with Neil and the Australian team who have been supportive throughout the whole process,” he said.
Neil Webb, General Manager of TRT Australia, provides insights into the advancements in the latest TIDD PC28-3G model. While the ADR emission standards will be enforced starting next year, TRT has gone above and beyond by adopting the state-of-the-art Cummins Euro 6 emission engine, making TRT’s TIDD Pick and Carry Crane the cleanest available in the market.
“Our design and engineering teams didn’t stop there. As well as including the Euro 6 Emission Cummins engine, they wanted to improve the safety innovations
on the new TIDD to meet the demands of Tier One builders and contractors. In this quest they’ve managed to engineer a retarder into the new unit which provides superior downhill braking, delivering increased safety and control, lowered operational expenses, less wear and tear on the crane and reduced noise in urban areas.
“We conducted extensive tests on the retarder system, and it performed above expectations. Operators rarely needed to use the brakes as the retarder system was doing all the work as expected. The TIDD PC283G takes operator control to the next level, reflecting our commitment to innovation and safety,” said Neil.
“The construction industry is showing a growing interest in enhancing sustainability and diminishing carbon footprints and emissions. Tier One builders and contractors are not only assessing the environmental impact of the end product but are also examining the sustainability of the product’s manufacturing process.”
“While a manufacturer may claim to produce an environmentally friendly machine, their manufacturing facility may not necessarily adhere to sustainable practices. TRT’s manufacturing facility in Hamilton, New Zealand, is 33,000 square metres with 9,000 square metres under the roof line.
“A recent initiative from the board focuses on cutting the organisation’s carbon
footprint not only through our product but throughout the entire organisation.
“We have installed a complete solar system on two of our manufacturing sheds from which we generate enough power to run all our machinery plant and equipment. It’s so successful we are looking into installing similar systems on the other sheds,” Neil said.
“We prioritise sustainability, which is why Select is an excellent partner. They’ve recently made significant investments in two all-electric Liebherr crawlers, showcasing their strong commitment to zero emissions.
“They hold a strong commitment to investing in an environmentally sustainable fleet and we’ve supplied them with what we consider to be the highest emission control diesel engine available in the Australian market,” Neil explained.
When Select decided to re-introduce pick and carry cranes into its fleet, Neil said TRT needed to showcase its qualities.
“Undoubtedly, was a significant step. We had to demonstrate that our machine’s safety and innovations set the TIDD apart as the best choice for excellence, safety, and innovation. This involved extensive months of on-site operations, thorough examination of specifications, and close collaboration with the entire Select team.
“They were highly impressed by our safety features, particularly Slew Safe. They are especially enthusiastic about the audible
and visual warning notifications, as well as the tactile feedback provided through the steering wheel by our Slew Safe System,” he said.
“The CTI system was another notable safety feature (for Select), managing tyre pressure to the standard 130psi on all four tyres. This is a crucial safety feature that ensures you have the correct pressure during lifting operations and includes warning devices through visual and audible alarms to promptly alert the operator of any tyre pressure issues. During on road operations CTI also reduces tyre wear and tear.
“At TRT, we are committed to environmental responsibility and safety, but we are also dedicated to manufacturing strong and reliable lifting equipment, as demonstrated by the PC28-2. With more powerful front suspension cylinders, lifting capacity has increased up to 17 per cent (on average) when articulated or working on a side slope, and in some cases, by over 40 per cent, which is an incredible improvement,” he said.
“The fantastic aspect of this upgrade is that we’re not leaving any of our customers behind. Everyone who has purchased the PC28 can take advantage of this upgrade allowing them to access the same load chart as our latest model, part of our continuous focus on innovation and actively exceeding expectations for our customers.” Neil explained.
The Ultra-Maxx HMPE (High Modulus Polyethylene) Round Slings are a game-changer for the Lifting and Rigging industry. They are transforming the way of approaching lifting tasks. These slings, made from continuous loops of HMPE fibres encased in a durable, double-layer cover, bring a host of benefits that make them stand out in a crowded field of lifting equipment. Ashley Thacker, General Manager of Ranger Lifting, explains more about Ultra-Maxx HPA slings.
HMPE FIBRES ARE A POWERHOUSE IN THE world of materials science. Classified as one of the strongest fibres globally, HMPE is significantly lighter than traditional materials like polyester and wire rope. This unique combination of strength and weight makes HMPE slings a top choice for rigging professionals. The material’s inherent strength allows HMPE slings to exhibit 75 per cent less elongation than their polyester counterparts. This reduced stretch enhances manoeuvrability and control, contributing to a safer and more efficient work environment.
Ashley Thacker, general manager of leading lifting equipment supplier Ranger Lifting, says HMPE has revolutionised lifting, rigging and towing cultures.
“HMPE round slings have much greater residual strength long into the life of the slings, and when used properly, can outlast other types of slings,” he said.
“In my opinion Australian manufacturing of round slings has basically gone, with almost everything now being imported, but there are still plenty of HMPE slings manufactured here.”
Ashley said Ranger spent “some
plenty of stock. I’m going to be stocking up to 200 tonne, 15 metre slings and to get a 200 tonne, 15 metre HPME sling from a local manufacturer or imported is going to be weeks. That’s why we wanted to be in this market,” said Ashley.
From a weight perspective, the HMPE fibre is 15 times stronger than steel wire rope of the same weight.
“HMPE round slings have much greater residual strength long into the life of the slings, and when used properly, can outlast other types of slings.”
“We’ve got D/D ratios so we know what you can, and can’t do, with the various sling weights. We’re setting out the specifics which you won’t see from local manufacturers either, typically they don’t like providing that information in case something’s wrong.”
This highly advanced synthetic fibre allows the operator to achieve the same working load limit (WLL) with a sling that is about 80 per cent lighter.
This means that it is easy to handle lifting slings made of HMPE, even when compared to standard polyester slings. HMPE slings are about 60 per cent lighter than standard polyester slings with the same WLL.
The reduction in size and weight leads to increased portability and easier handling, and their flexibility allows for the precise positioning of loads –
reducing the likelihood of accidents.
In addition, HMPE also has high resistance to UV radiation and chemicals and withstands cutting wear better than polyester and other synthetic fibres.
Together, these improve rig productivity by requiring fewer personnel and being easier to use as a result of their smaller size, when compared to polyester slings.
“HMPE slings are four times the price of a round sling, but in the long run they prove to be far more
economical,” Ashley says.
“We’ve got D/D ratios so we know what you can, and can’t do, with the various sling weights. We’re setting out the specifics which you won’t see from local manufacturers either, typically they don’t like providing that information in case something’s wrong.”
“We’ve completed a lot of testing and we’re building our stocks on a daily basis. That’s a process that can’t be rushed. If you buy 30 slings that’s going to be $200,000 worth of stock,” said Ashley.
Servicing the Major Infrastructure, Construction, Rail & Renewable Energy sectors, Johnson & Young McKay Cranes provide both wet and dry crawler crane hire solutions Australia wide.
JYM can provide full engineering solutions and site support with our growing fleet of 2x CC3800’s and 3x CC2200’s, all have full superlift capabilities with full boom booster, vario and wind kits for the CC3800’s.
Complemented by a vast fleet of all terrain hydraulic units up to 800t from our parent companies, you can be assured your requirements are within our capabilities.
To get in touch to discuss your next project, email us at info@jymcranes.com.au or call us anytime on 0427 294 022
Certex Lifting Pty Ltd is now one of the country’s largest lifting equipment and service companies, following the announcement of its significant expansion into the Australian market in November last year. Unifying a host of Australian brands under the Certex name, the lifting and rigging equipment specialists will continue its close collaboration with parent company Axel Johnson to distinguish itself in the Australian market.
certexlifting.com.au
Port Hedland 08 9406 9933
23 Pinnacles St, Wedgefield WA 6721
Bibra Lake 08 9494 5800
Unit 2/34 Discovery Dr, Bibra Lake WA 6163
Kalgoorlie 08 9022 8600
25 Darcy Ln, West Kalgoorlie WA 6430
Adelaide 1800 724 455
41 Second St, Wingfield SA 5013
Newcastle 02 4932 9979
20 Farrier Pl, Rutherford NSW 2320
Coffs Harbour 02 6651 9980
Unit 3/19 Forge Dr, North Boambee Valley NSW 2450
Melbourne North 1300 437 842
68 Commercial Dr, Thomastown VIC 3074
Melbourne West 03 8360 7923
8/151 Dohertys Rd, Laverton North VIC 3026
Geelong 03 5229 9508
19 Industrial Pl, Breakwater VIC 3219
2023 sees Cosmo Cranes celebrate 20 years in business. John and Josh Handley talk about their development, the business and why their staff are their real key to success.
IT STARTED WITH THE FAMILY BUSINESS importing tower cranes from Italy. John and Josh flew to various parts of the world, including Italy, Russia, Dubai and Singapore for factory training on the cranes and building solid relationships with the various manufacturers and suppliers.
By 2010 the fleet had increased to 15 cranes and six years later it grew to 30. In 2014 Cosmo bought its first mobile crane, a 20t Franna, closely followed by at 220t Grove. Today, the team at Cosmo tops 120 personnel and there are 50 plus tower cranes in the fleet.
The success and growth of the business is in no small part due to the professionalism of the entire Cosmo Cranes team, says John.
“We have always been very selfsufficient as a business. We like to bring people into the business, train them in our ways of doing things and provide them with growth opportunities and career pathways.
“Damien Blanch is a great example of how we work at Cosmo Cranes. He started off as a rigger, moved to be our yards person, and now he’s Project Manager. We like to retain our people as much as possible and train them to be versatile so they can move throughout the company.
“We give our staff the opportunity to take on more responsibility and to grow within the organisation. We have a core
team that has been with us for around ten years and has moved into Team Leader roles, helping us to maintain the high standard that has been set and continue to develop the good working relationships that we have built over the years,” said John.
“This growth and experience has also led to us being engaged by other crane companies. We regularly carry out servicing, maintenance and refurbishment of tower cranes, as well as installation and dismantle operations,” he said.
Cosmo Cranes services Sydney’s very competitive commercial and residential construction sector. Josh explains how the business has succeeded in such a competitive environment.
“We have long term relationships with our clients which are high end
construction companies building quality projects. Most of our business is repeat business because our clients know the quality of our service and quality of the teams that deliver it,” said Josh.
Cosmo Cranes offers turnkey solutions to clients including tower cranes, mobile cranes and also crane decks. Josh provides insights into the package.
“We introduced our range of crane decks in 2015, shortly after we started our mobile crane fIeet. We could see a demand for a ‘One Stop Shop’ approach where a builder could get everything from the one supplier.
“Obviously, there’s a lot of materials handled on a construction site, and we could see opportunities to package everything together. By providing our clients with a turnkey package we are
enhancing the safety of the site with our teams working together, understanding each other and the products they are working with. We now have 180 crane decks in our hire fleet which go hand in hand with our tower cranes. We also sell to exclusive distributors round Australia and New Zealand,” said Josh.
“On site, our Crane Decks are inspected by our Crane crews and a daily logbook record is kept. This ensures we are closing out any maintenance issues that come up, as well as committing to site compliance requirements,” he said.
Maintaining the crane fleet is a major priority for Cosmo Cranes.
“We have a team of soon to be four fulltime technicians and they maintain the fleet to the manufacturers’ recommendations, conducting periodical servicing, attending to breakdowns, installation, dismantles and climbing operations,” said John.
The team at Cosmo Cranes has spent a significant amount of time automating the maintenance and scheduling side of the business.
“We now run a cloud-based system which automatically captures all the data relating to the maintenance and scheduling of the fleet. It’s been a significant investment in terms of time and outlay but these processes are now paperless, and we are beginning the see the benefits of the system,” said John.
The Cosmo tower crane fleet features an equal split of Luffing Tower and Hammerheads, but the market is increasingly turning to Luffing tower cranes due to the ever-changing requirements of local authorities and air rights issues. The fleet is 100 per cent electric.
“We are committed to replenishing our fleet to ensure we are offering our customers the very latest technology. This program includes both the tower cranes and mobiles,” he said.
“To celebrate 20 years in business we added a 160t capacity Tadano and we have just taken delivery of a third Franna AT40 which we are excited about.”
Keeping the fleet fresh and modern is a priority for the business, said John.
The only Australian made range of Pick and Carry Cranes
Fully fabricated in Australia using robotic welding
Australian owned by the DRA Group established in 1971
Field proven lowest operating costs of all Pick and Carry Cranes
Field proven highest level of safety with class leading innovation
2 year/2,000 hours warranty, 15 year/15,000 hours to major inspection based on established historic data
Fully powered and compensated boom to 20.7m – longest in its class
Humma 35 UG series – the only Pick and Carry approved meeting underground specifications
HUMMA 25 – HUMMA 35 – HUMMA 55
YOU START SAVING MONEY THE DAY YOU BUY A HUMMA