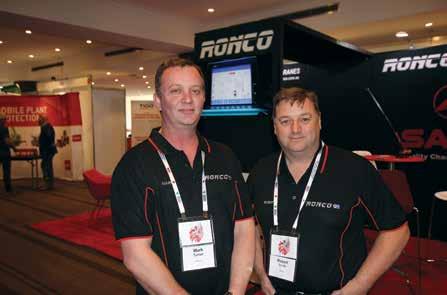
8 minute read
Sany announces new regional dealer Sany makes major announcement about local representation
Ronco Group, specialising in construction equipment and engineering, was recently appointed as the regional dealer for Sany cranes. Cranes and Lifting magazine spoke to Ronco managing director, Robert Smith, about the development.
RONCO HAS BEEN OPERATING FOR over 25 years and was recognised for manufacturing its own crane the Ronco R6000. The company was originally founded by Ron Downie and in 2011 Robert Smith, Ronco’s then general manager, purchased the company from Downie.
“When we first purchased Ronco, it was a family business with a small facility in Midland that featured three maintenance bays and a wash bay. We quickly grew the business and moved to a 4000 sqm site including a large workshop but it wasn’t big enough to receive large pieces of equipment such as full crawler cranes with booms for assembly, so four years ago we moved to the current facility in Maddington,” said Smith.
“This is a much better facility in terms of its ability to service cranes. We have a 12,000 sqm facility with a 4000 sqm storage facility in the same street and we are equipped with twin overhead cranes, a 100t press, sand blasting facilities, EPA wash down and more equipment and appliances to ensure we meet customer’s needs,” he said.
Smith discusses the recent appointment as the regional dealer for Sany cranes.
“Currently, our distribution foot-print is understandably focused in Western Australia. The recent CICA conference provided an ideal opportunity to present our plans to the industry and we expect to make announcements in the near future,” said Smith.
“Sany product has been on the Australian market for approximately 10 years and the focus has been on crawler.
Mark Turner, Ronco’s operations manager and managing director, Rob Smith, at the recent CICA Conference and Exhibition
Eight years ago, Sany had a strong relationship with James Equipment, which became part of the Boom Logistics Group,” said Smith.
“Back then I was the service and parts manager for James Equipment and we mainly sold crawler cranes. James Equipment was also handling the Tadano product and the Sany crawler cranes filled the gap in the range that we had. Through this relationship, units were delivered to customers like Tutt Bryant, Boom Logistics and various others,” he said.
The management at Ronco has been working very closely with the Sany factories to ensure specification of the cranes and the manufacturing processes will meet the demands of the Australian market.
“Mark Turner, Ronco operations
manager and Neil Holroyd, Ronco service manager, have just arrived back from the factories in China where they have been measuring up the all terrains and inspecting some of the models that are currently on their way to us. Some units be will arriving before Christmas and some just after,” said Smith.
“We will be bringing in a range of crawler cranes with capacities from 55t to 650t and also a range of telescopic crawler cranes with models from 55t and 80t. There’s also a range of rough terrains from 25t to 120t and from there we will move steadily and in stages.
Mark Turner and Neil Holroyd talk about their experiences during the recent factory visit.
“We measured two of the all terrains, the more popular sizes in the market, a 5 axle 130t all terrain and a 5 axle 220t.
The 220t was overweight on its axles for Australian roads, fine for Europe and China but just not compliant with Australian requirements and the 130t and 300t met Australian requirements. The all terrain range goes up to over 1000t,” said Turner.
“We have learnt from the errors made by other distributors over the years in terms of getting product here and then realising it isn’t roadable. We want it to come from the factory ready to go.
“We’ve established that the 110t and 130t all terrain will be fine and they’re the first two we’ve measured and confirmed. They come on the 20.5’s and they’ll be within the road regulations for West Australia at the moment. At this stage, we haven’t looked in depth at all the other states. That’s the next stage of the development,” he said.
Sany’s brief is very clear, they’re here for the long term, they want it right with Ronco right from the very beginning and into the future. According to Smith, this strategic approach allows time to research the Sany range to ensure the right models arrive.
“We will be checking every machine one by one and it may be that we can’t bring in some models from a range, but others might be fine. We will literally measure and weigh every crane because Australian requirements are stringent,” said Smith.
“We will also bring in Sany truck cranes probably the 25t and the 60t models to start with. We are starting slowly, we’re not going to swamp the market by bringing in the huge Sany range of machines, we are under strict instructions to approach and ensure our approach to the market is right,” he said.
Smith is aware that a certain stigma is still attached to the manufacture of Chinese products but argues the Sany production line is what he sees as world class and in the same class as other leading manufacturers.
“The Sany production lines are as good as any I’ve seen around the world. The factories employ 3,500 workers, all componentry is checked prior to production, the production lines are automated with every step of the manufacturing process carefully checked. They use robotic welding technology wherever possible. Simply put, the quality of Sany product is as good as its competitors and in some cases better.
“The main slogan for Sany is ‘Quality Changes the World’, and the president of Sany believes he will change the world’s perception of China by producing top quality equipment,” he said.
According to service manager, Neil Holroyd, the Sany factories are technologically advanced and producing very good quality equipment.
“I’ve been to four of the factories and all are very similar in terms of concept and execution. They are using a ‘rolling road assembly’ method where they assemble all the major components prior to assembly and put together the finished machine on a rolling road which takes a very short period of time to assemble a machine.
“We’ve been through the welding and fabrication areas which feature robotic welding systems. I deliberately spent time watching each station and as soon as the welding was finished, the engineers were there with appropriate measuring appliances, checking right angles and checking and measuring for straightness after the weld. Sany is doing it right, there are no short cuts, they’re putting serious quality control into every product manufactured,” said Holroyd.
“Every station in the production process is timed and large LCD screens highlights the progress of each machine down the assembly line. Each station has a team and they have goals to meet and they are meeting them,” he said.
Sany has implemented leading edge and intelligent manufacturing processes throughout its factories ensuring a high quality, finished product. Automated processes include: • Sany was the first in Asia to introduce 3000t bending machines. • Key welding joints on the boom, slewing platform, frame and other structures are 100 per cent robotically processed. • CNC equipment features in a multifunction machining centre. • Welding quality is managed in a simulated control network. • Automatic paint systems feature electrostatic coating and electrophoresis technology enhancing anti-corrosion capabilities. • Assembly lines are digitally controlled with manufacturing process completed in a single line. • Assembly is mechanised with high precision sensors managing processes including the automatic tightening of U-axle bolts.
Smith confirms Sany is not only investing in the best manufacturing technology, but also the best crane people from around the world.
“When it comes to the attention to detail and general presentation, the Sany manufacturing facilities are right up there. All crew members on the production line are dressed as you would expect from a world class manufacturer, they all have the same uniform, safety glasses, hard hats etc. when you watch the Sany factory operating it’s not far off watching a world-class industrialised western facility. It’s a very developed company compared to Chinese manufacturers of the past,” he said.
“Last year, Stephen and I toured the crawler crane factory with a prospective customer, and we were focussing on the SCC2600A. The customer inspected the whole production process of the crawler, including the assembly and welding processes and the crane was presented to him for a test with the full boom and full luffing fly. The crane’s performance was effortless and faultless, and the customer commented on how reassured he was to see overseas people in the factory, with a wealth of experience in the product. The chap overseeing the boom and fly construction was from the US.
“I worked with Sany equipment here in Australia a number of years ago, and the equipment was purchased by a number of major Australian based crane companies. We’re currently working on the imminent delivery of a number of products including a 300t all terrain, a 90t rough terrain, a couple of 260t crawlers and a number of material handlers. There’s no doubting the quality and the durability of Sany products but I think a lack of support and back up has let the product down in the past.
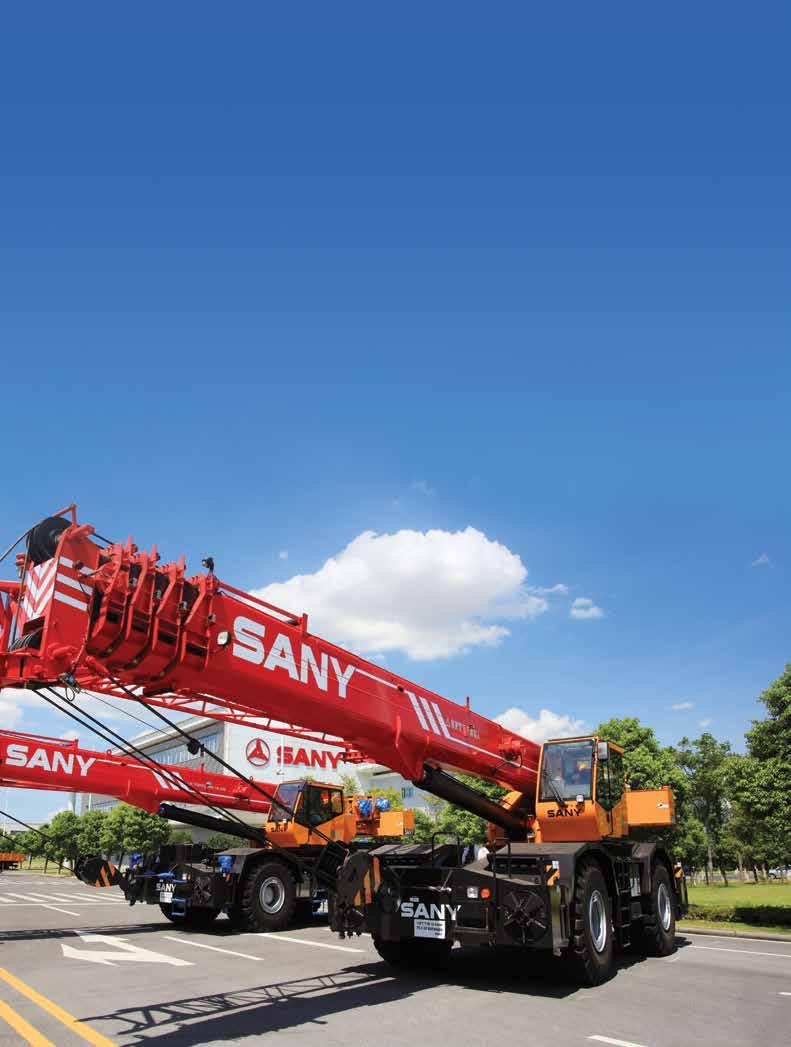
“Our role, with Sany’s management team, is to change this perception, to put in place a national footprint of partners that understand cranes, clearly understand after service and support and reflect the true quality of the Sany product and what the brand stands for,” said Smith.
“In the next month or so, we will have cranes here in stock which will include a 35t rough terrain and a 55t telescopic boom crawler crane. The equipment is well priced to keep the accountant smiling and supported by the Sany mandate of ‘Quality Products with First Class After Service,’” he said.
If prospective customers are in the market for a new crane of any style, they can visit www.ronco.com.au, email sany@ronco.com.au or call 1800 CRANES.