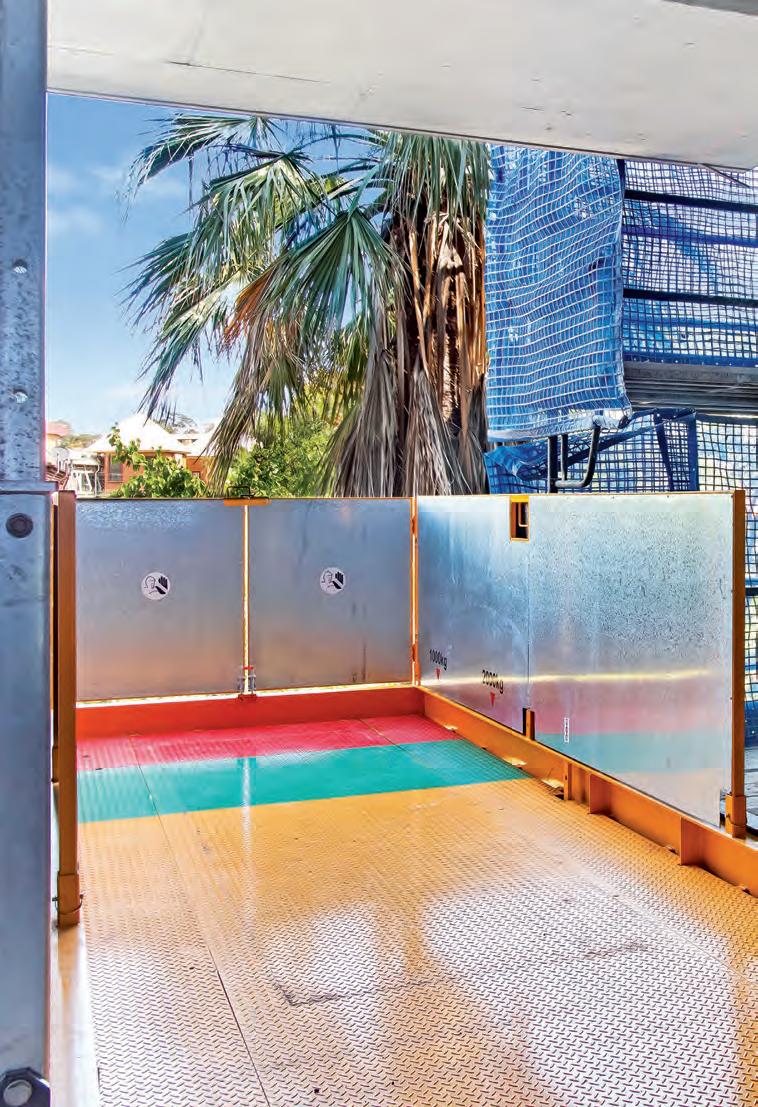
12 minute read
Up Front
GAME CHANGER FOR CRANE DECKS
Active Crane Hire celebrates its 21st birthday with the launch of a range hydraulic loading decks.
ACTIVE CRANE HIRE STARTED IN 2001
hiring Potain self-erecting cranes. Hermann Buchberger has had various business partnerships over the years but streamlining the decision-making process enabled the business to grow with the fleet including both self-erecting and tower cranes. Again, the brand was mainly Potain.
In 2011, Buchberger solely took over the helm of Active Crane Hire and continued to build the business adding more cranes to the fleet. The construction industry experienced a considerable up turn at the time and the fleet quickly grew to 150 cranes. In 2019, he was planning the next stage of the Active Crane Hire’s evolution, and decided he needed a partner back in the business, one which knew and understood the crane sector inside and out. He sold 50 per cent of the business to Shawn and Nathan Borger from Borger Cranes and Rigging Services.
“Since then, we have increased the fleet further and we now have 160 cranes. Both the Borger’s and I like to take an innovative approach to the crane sector and our business, and so we have taken a slightly direction by introducing electric luffing cranes to the fleet,” said Buchberger.
Active Crane Hire specialises in supplying cranes to the small to medium size section of the construction market including the construction of luxury housing in the Eastern Suburbs of Sydney and medium high rise residential construction projects, up to 18 floors.
Operations have been focused on New South Wales but over the last two years, there has been a gradual and successful expansion into Queensland.
“Approximately 10 Potain cranes were purchased from MSCR (Matt Savage Crane and Rigging) as they exited the industry and this provided an immediate presence in the market,” said Buchberger.
“We are following the Borger expansion in the state where they are having plenty of success in South-East Queensland and also the Sunshine Coast. We now have 45 staff on our books, and we continue to specialise on the dry hire market. We will provide cranes with operators for some of the larger builders on major projects, but dry hire is in our DNA.
“We currently have 100 projects on the go and forward bookings are looking very solid. The highest number of cranes we had on projects was 140 and this
The genuine “game changer” is the ‘push of a button’ hydraulic platform extension.
was two years ago, so there has been a readjustment in the market, but we are confident the market is ramping up again and we are very confident as we look at the next calendar year.
“We continually examine our business activities and we realised there is a market for crane accessories including crane decks and other associated equipment. Over the years we’ve been asked about crane loading decks and when we were tendering on projects, we were referring clients to other businesses for the decks.
“With the advent of the COVID pandemic, we re-examined our business again and looked at ways of utilising our assets better, including our staff, and we decided to start manufacturing our own crane accessories,” he said.
Buchberger ventured back to the future and invited his previous business partner Gerd Altmeyer for advice and expertise in building platforms and decks. The firm BAB Engineering was established. Market research suggested the demand would be for around 100 decks a year and together they decided the best way to proceed would be to design engineer and manufacture everything inhouse.
Buchberger goes on to explain more about the range of loading decks.
“As with our crane businesses, we want to lead the market by introducing innovation with everything we do and so we have launched a range of hydraulically operating loading decks. We are marketing the range as Active Crane Deck,” he said.
There are three models in the hydraulic loading deck (HLD) range. The first is the HLD 2200 with the 2200 indicating the width of the deck which is important as it will fit between a standard scaffold bay.
“If a deck doesn’t fit between a standard scaffold bay, you are already ruling yourself out of a number of projects. The next sizes are going to be the HLD2800 and the HLD3200.
“The HLD 2800 and 3200 which is 2.8 and 3.2m wide are still in the planning stages and we are considering making the manufacturing process modular by utilising the main components from the 2200 main deck,” said Buchberger.
“From our perspective, the genuine ‘game changer’ is the hydraulic platform extension.
We are super confident in its performance and have tested it extensively with incredible results. The HLD2200 is ready for action, we have 40 units manufactured and ready for installation on our first projects which are already locked. The first decks were installed in early October,” he said.
The Active Crane Deck HLD range is being manufactured locally in Somersby, near Gosford, on the Central Coast an hour north of Sydney.
“We have purchased and completely refurbished a factory unit in the same industrial area as our main crane depot and yard. We have two overhead gantry cranes inside the factory for the heavy lifting,” said Buchberger.
Buchberger discusses the design process and the functionality of the HLD range.
“We started the design process approximately 12 months ago. I was working with Gerd, and we thought the manually handled ‘push in-push out’ loading decks were hard work on a construction site and there are inherent safe work risks with the manual process.
“Both Gerd and I drew on our previous knowledge of hydraulics which dates back to the mid 90’s when I was importing a range of hydraulic scissor lifts and elevated work platforms. The manufacturer of the range was Liftlux which, at the time, was a small company based in the south-west of Germany. Gerd was the principal of the company, and I was his only employee in Australia. Liftlux was later acquired by Potain which is how I made the transition from scissor lifts to cranes.
“We manufactured very large scissor lift platforms with some machines reaching up to 32m. A number of products featured large diameter decks
There are three models in the hydraulic loading deck (HLD) range. The first is the HLD 2200 with the 2200 indicating the width of the deck which is important as it will fit between a standard scaffold bay.
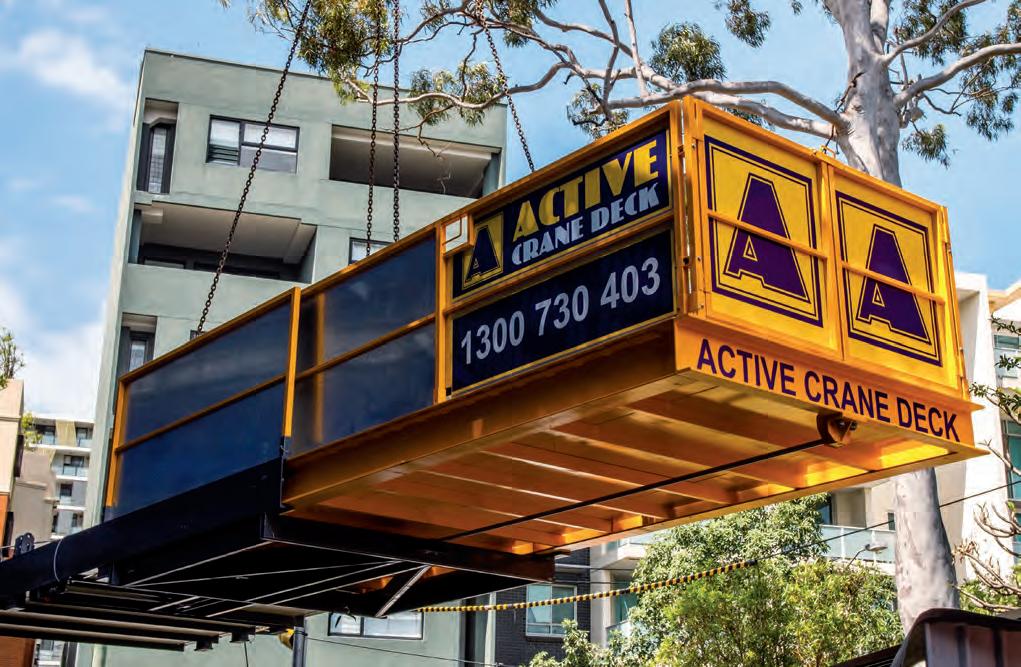
which were hydraulically extendable and retractable. When we sat down to discuss the loading decks, we examined the possibility of using the hydraulic concept for the ‘roll in roll out’ mechanism.
“This was the broad design concept and then we began working on questions around the weight of the decks, what profiles are currently available, so we started with a fair idea of what would and wouldn’t work. And because of our experience with the scissors lifts we had a fair idea of the best way to extend and retract the platform,” he said.
“After all our research and development, which included examining electric motors and rack and pinion systems, our overwhelming conclusion was a hydraulic cylinder placed under the deck would be the best option. Fundamentally, this was the starting point for the design process.
BAB Engineering then teamed up with Matthew O’Hearn and O’Hearn Consulting. Matthew is a long-term partner of Active Crane Hire, and his work has been around crane base designs. Today, he and his team are gurus when it comes to structural engineering and construction says Buchberger.
“A year ago, we produced the first deck which featured a manual ‘roll in roll out’ mechanism which enabled us to work through the various design and engineering challenges. When we had overcome these, we incorporated the hydraulic mechanism into the structure, and this was the ‘game changer’ for us,” he said.
Buchberger explains how the hydraulics of the HLD range works and the benefits the system will provide.
“In the fully retracted position, the depth of the deck is 2.25m and we can extend the deck in sections. The first position takes the deck to 4.5m x 1.8m, these are the internal dimensions, the second position takes the deck out to 5.2m x 1.8m.
“The extending of the deck is managed by a hydraulic cylinder which is under the deck. With the deck fully extended the cylinder is at 3m. The concept is uncomplicated and the sizes we are offering seem to be where the demand will be in the market and what the construction companies are used to.
“Another key feature is we can hydraulically extend and retract the decks when they are fully loaded. When the deck is fully extended and a crane places a pallet of tiles (for example), the deck structure is loaded to its maximum capacity. When the load is landed, with the push of a button, we can retract the load and bring the whole structure back to a much safer position. I don’t want to know how many decks on any given day are actually permanently overloaded. With a conventional deck, the load is landed and then has to be retrieved from the tip of the deck before it can be retracted,” he said.
“One of our challenges is explaining to customers why they are going to be
spending a little more per deck, but it is easy to show how they will contribute significant savings to a project. Our decks are safer and designed to increase the productivity of a construction site.
“Over time, the mechanisms on manual decks begin to wear and it becomes increasingly difficult to push them in and out and it can take up to three people to manage the process which couldn’t be completed in under five minutes. It doesn’t sound a lot, but if this is required two or three times a day, that is 1.5 hours per week just to rearrange a deck. Multiply this time over the course of a project and factor in the costs of 3 people and the onsite crane being not productive we are talking serious money,” he said.
Active Crane Decks are manufactured from Australian steel, from InfraBuild (OneSteel) and the steel is made in Whyalla in South Australia. The components are world class with the hydraulic cylinders sourced from the company that supplies Caterpillar earthmoving equipment worldwide and the hydraulics are from Bosch Rexroth.
“We are working with the best products and componentry from leading global suppliers. The decks are manufactured here in our new facility at Somersby, and we are employing local boiler makers, local electricians and other trades from the Central Coast,” said Buchberger.
Manufacturing the decks locally is the result of significant investment by the new venture says Buchberger.
“We purchased the factory for $1.5million, the investment in the two overhead gantry cranes and fit-out was and additional $500K. We have completely refurbished the factory and we’ve invested in a number of welding and fabricating machines for the manufacturing processes. Just to get started, the whole investment has been around $2million.
“Obviously this facility will be servicing and maintaining the decks which have been in service, but we are confident the decks will not require too much maintenance. During the design process we fixed the prototype deck to a test stand and subjected it to extensive testing.
“We then operated the extension and retraction system, on a fully loaded deck, continuously for a few weeks. We calculated this testing was the equivalent to several years of heavy utilisation. We checked the wear on components including the bearings and rollers, and we checked for deflection in the steel and there was nothing to cause concern.
“We understand building sites are tough on products like loading decks and we expect the occasional bang and dent, but we are not concerned about structural damage because our range is ‘built tough’. The hydraulic system is designed to push up to 60 bars and our system requires less than 10 bars to extend and retract the deck. So, we’ve deliberately over engineered capabilities into every aspect of the product,” he said.
Buchberger discusses the propping options for the decks.
“There are two props one on each side of the deck and these can be placed in three different positions. We also have an option where props are not required with the deck bolted to the concrete floor. Some builders might prefer this option because it means decks can be installed without having to wait for the concrete floor above to cure,” he said.
The decks feature a control panel which is a standalone unit. The panel features a 10 amp power outlet for a normal 240 volt standard power supply. It also features a number of safety mechanisms including a VC drive making it fully proportional.
“Everywhere in the world, construction sites are looking for better utilisation from site cranes and wherever possible they are making the sites safer for the construction workers. Our crane decks address these requirements and in terms of costing we are only marginally more expensive than manual ‘roll in roll out’ decks,” he said.
“On the larger construction sites, where safety is a keen focus, only the crane crews are able to extend and retract the decks. You can imagine what a dogman, who has been extending and retracting a deck several times a day, is going to say when he sees this can be done with the push of a button. The builder will also see the financial benefits of our system because he is paying for the crane crew as well as the hire of the crane.
“The better utilised the cranes are, the more return the builder sees on his investment. If a crane is made available for an additional 4 hours a week due to the time saved with our decks, that is a huge bonus,” said Buchberger.
The decks are manufactured in the new facility in Somersby by local boiler makers, local electricians and other trades from the NSW Central Coast.
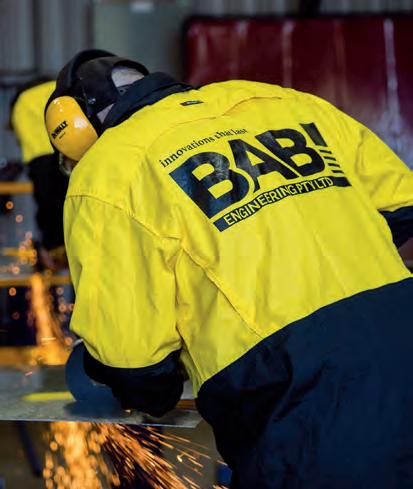