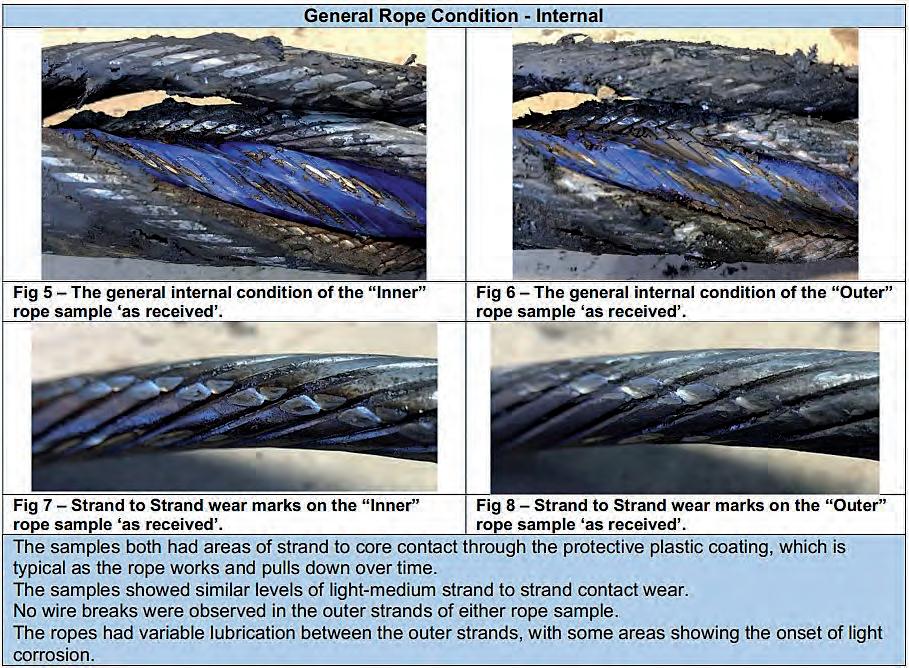
6 minute read
Forensic testing extends life of wire rope
WIRE ROPE ANALYSIS AND FORENSIC TESTING
Industry leading wire rope manufacturer, Bridon-Bekaert The Ropes Group (BBRG) recently invested in a state-of-the-art Service Centre. The new centre operates in conjunction with their NATA certified testing laboratory to provide customers with specialised services including rope analysis and forensic testing.
JAMES MACKIE IS BBRG’S PRODUCT
Applications and Testing Engineer. Starting in the steel making and casting business back in 1996 with BHP Steel in the Whyalla plant in South Australia, Mackie now has over 25 years of experience with steel.
“I worked as a Process Engineer in the casting plant and then moved across to the OneSteel Wire business and spent a decade working in process and quality engineering. I then moved to the Wire Ropes business in a customerfacing technical and testing role. In effect I’ve moved through the chain of production gaining experience in the metallurgy and technical aspects of the steel wire and now the ropes production processes.
Over the last five years I’ve been heavily involved in the testing, inspection & forensic analysis of ropes and that is where a lot of the focus is for our business right now. BBRG is focused on its Services business globally and they see the Australian business playing a key role for this part of the region,” he said.
Mackie explains more about his role within the Bridon-Bekaert business and what forensic rope analysis entails.
“I am BBRG’s local technical engineer supporting the industrial and crane rope sectors. I work closely with our Technical Sales Manager, Rhys Hughes, and Service Center team led by Stuart Coxon. I am also responsible for maintaining BBRG’s NATA accreditation for the Newcastle testing facility.
“We offer a full range of testing and inspection services both on customer sites with our locally based technical team and for rope samples which are sent back to our testing laboratory for analysis. We are able to assess the rope’s
“We offer a full range of testing and inspection services both on customer sites with our locally based technical team and for rope samples which are sent back to our testing laboratory for analysis. We are able to assess the rope’s performance and explore possibilities of life extension in consultation with customers.”
performance and explore possibilities of life extension in consultation with customers” he said.
BBRG’s goal with Rope Services is to work closely with our customers to achieve the lowest Total Cost of Ownership (TCO) for their ropes says Mackie.
“We don’t just sell high performance ropes, we back that up with expert technical support and rope assessments to ensure our customers get reliable and consistently longer service lives. That results in predictable rope changeouts and less downtime to maximise machine operating times.
“Our Rope Services team currently works closely across major industry sectors including port operations, crane and industrial, underground mining and oil and gas markets. The team is currently working with a key port crane operator on a life extension program for their STS hoist ropes. We are also conducting Ton-Mile programs in the offshore oil and gas segment. Both of those programs are conducted in accordance with BBRG’s global MORE program,” he said.
MORE stands for Maximum Operating Rope Efficiency and Mackie explains how the MORE program works.
“The MORE Program was designed by BBRG to deliver savings to our customers without compromising on product, quality or safety. It is an iterative process of maximising the service life of BBRG ropes in high cycle applications.”
A MORE Analysis consists of: • Detailed rope inspection, analysis and testing which is undertaken in
BBRG’s Newcastle Test Laboratory. • Rope condition is compared with
Discard Criteria specific to the application using Australian and/or
International Standards. • A comprehensive report is prepared, then reviewed by the respective
Application Specialist within the
BBRG global business. • The final report provided to the customer will typically include recommendations for optimisation of rope cycle life, followed by further analysis and testing. • The process is repeated a number of
times until the optimum rope life is achieved for the specific customer and application. • “The key to the whole process is to find the root cause of the rope deterioration. We look at the equipment, the application is it operating in, the conditions and the rope itself. • “We can identify improvements and make recommendations around rope design to better suit the equipment the customer is using or to better cope with the environment within which the ropes are operating. Our local technical team works closely with the BBRG global technical teams to draw on experience and expertise in the many industry sectors BBRG services around the world,” he said. • Mackie goes onto illustrate how the new Service Centre positively impacts on BBRG’s ability to better service customers and help with their wire rope demands and questions. • “The Service Centre has really opened up our local business to the crane and industrial sector. It has allowed us to offer a more complete set of rope supply options and our services are also about to be expanded. • “BBRG has invested in an AMC Non-
Destructive Testing (NDT) unit and
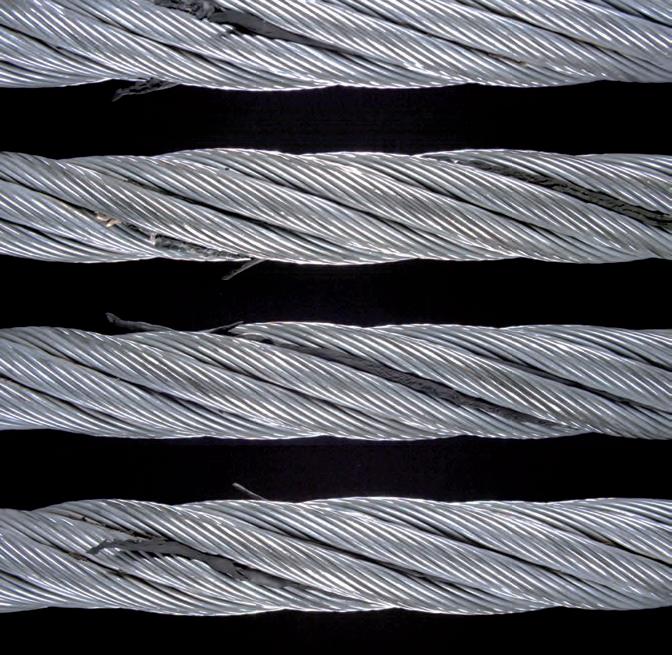

BBRG follows a structured process to optimize rope life for all customer applications.
a VisionTek unit which is the most advanced 3D rope measurement and visual analysis device available. The two units can be used together to provide an online, non-destructive testing, full analysis of rope condition throughout its length. The VisionTek unit takes highresolution images of the rope surface while taking continual optical measurements of rope diameter, lay length and ovality. When used alongside the NDT unit, this allows for full analysis and reporting of rope condition including highresolution images of the rope at points where the NDT has detected
LMA (Loss of Metallic Area) or LF (Local Fault). • This new equipment gives us the ability to provide a full suite of rope services which we haven’t been able
to provide in the past. Our goal is to provide a market-leading range of services from the birth to the death of our wire ropes and to provide guidance on wire rope life extension throughout that process,” he said. • “A number of our customers are working with local BBRG agents and distributors and we are now stepping up as the leading wire rope manufacturer to say ‘this is what you have seen in the past and this is the level of service you can expect from our brand into the future’. • “Essentially, we see ourselves as increasing our services for the customer through our existing channels to market. This whole strategy is designed to improve the support our customers receive, both technically and operationally with
BBRG wire products,” he said.
MAEDA MINI CRANES spider cranes knuckle boom crawler cranes
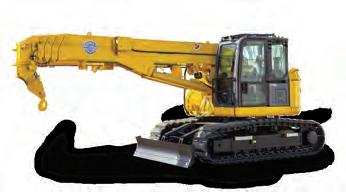
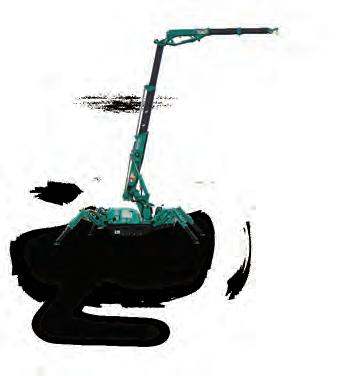
MC174C MC285C MK1033C

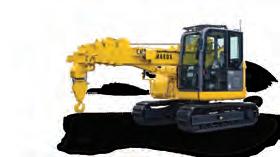
CC1908S CC985S
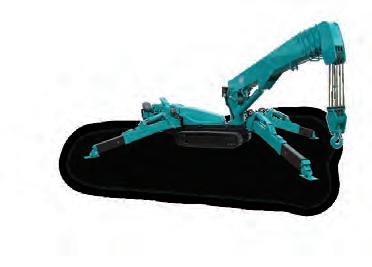
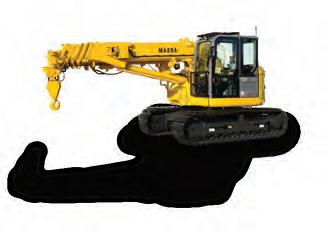
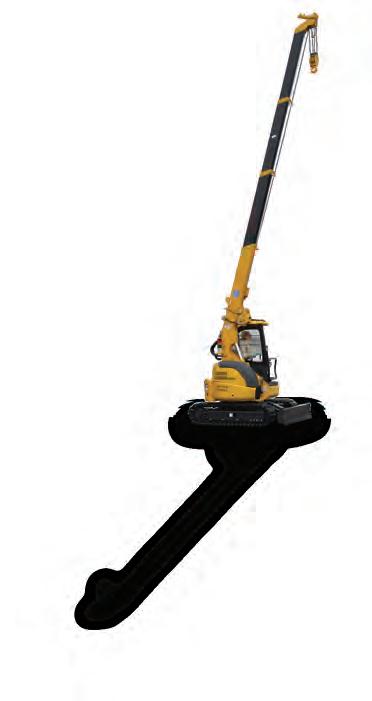
MC305C MC405C
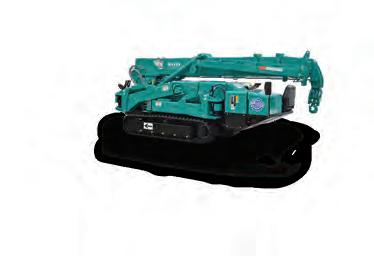
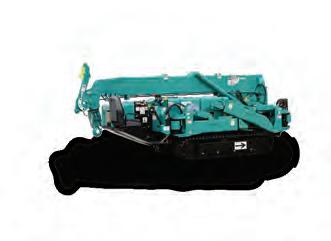
Pace Cranes is the sole distributor of Maeda Cranes in Australia and New Zealand. We provide a dedicated and unrivalled service, supported by specialist technical advice across the full range of Maeda Cranes.
MC815C CC1485S CC423S
P.A Construction Equipment Pty Ltd 5-7 Lorraine Street, Peakhurst NSW 2210 Tel: 02 9533 5411 sales@pacecranes.com.au www.pacecranes.com.au