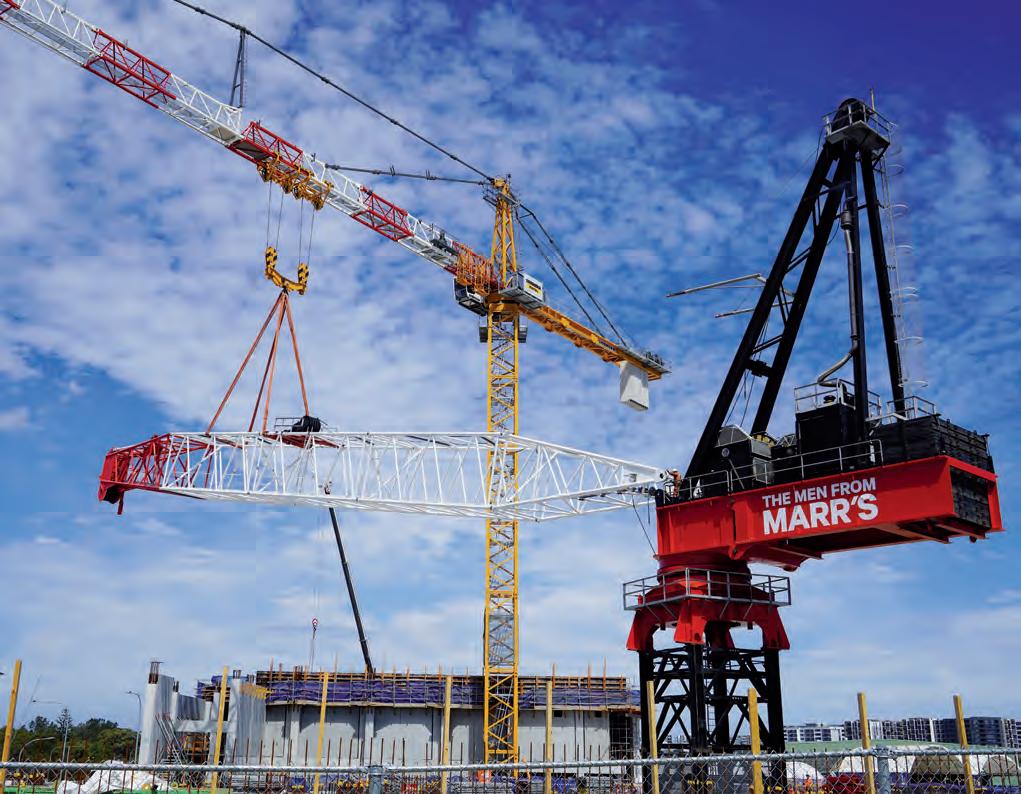
5 minute read
Liebherr delivers hammer head for infrastructure project
LIEBHERR’S LARGEST HAMMERHEAD GOES TO WORK ON WESTCONNEX
Liebherr Australia recently installed the largest Hammerhead in its range, to assist with the construction of the WestConnex M4-M5 Link Tunnels.
WESTCONNEX IS AUSTRALIA’S LARGEST
road infrastructure project. James Littler Liebherr Australia’s, National Sales & Rental Executive, Tower Cranes explains more about the crane and what it will contribute to the project.
Earlier in the year, Liebherr installed the first Liebherr 1000EC-H 50 Litronic for the Acciona Samsung Bouygues Joint Venture, to help with the construction of the WestConnex M4-M5 Link Tunnels.
Marr Contracting had a crane onsite to complete the heavy lifting of the precast elements weighing up to 80 tonnes and then due to height restrictions with Sydney Airport, they needed to change the stage two works to the Liebherr 1000ECH.
Marr’s team introduced Liebherr into the project and worked with the joint venture partners and Liebherr to develop a methodology for the safe dismantle and removal of the crane.
Simon Marr, managing director of
EC-H cranes are ideal for medium-sized and large construction projects and High-Top cranes are the best choice for handling high lifting capacities.
Marr Contracting said, “We introduced Liebherr into the project because we believe they are the best flat top hammerhead cranes in our industry.”
James Littler knew the Liebherr 1000ECH was up to the task.
“The client required a crane with a large enough capacity to dismantle Marr Contracting’s crane which had been installed for the initial construction phases. They also needed a crane which would continue to work on the project and manage the required loads which could be up to 11t at 80m. The crane will be on the project for approximately 12 months,” he said.
“Liebherr Australia is the only crane manufacturer to rent tower cranes directly to the Australian market. We also employ directly our technicians, riggers, crane crews and project management teams. Our technicians also include fully qualified electricians and fitters. In addition to their trade qualifications, they regularly attend Liebherr training in one of our facilities, including factory training in Germany. Our local facility is positioned in Caringbah, and as a manufacturer we carry full availability of spare parts for all our equipment,” said Littler.
Liebherr has pioneered the manufacture of tower cranes for over 70 years and continues to surpass other manufacturers with triple level EU standard redundancy safety systems. The integrated Litronic system ensures the reliability of the Liebherr EC-H range and enhances features including superior speed and efficient energy use. All Liebherr tower cranes are manufactured in Germany facilities which operate to the highest European environmental standards.
LITRONIC HIGH-TOP
EC-H cranes are ideal for medium-sized and large construction projects and High-Top cranes are the best choice for handling high lifting capacities.
The Liftronic system ensures the heaviest components can be moved into place and positioned with millimetre precision. This ensures the greatest possible safety – for the building site, components and construction workers.
The Load-Plus function increases the lifting capacity of the crane for individual hoisting – at the push of a button. This means a smaller tower crane is often adequate with Litronic, as infrequent hoisting of heavy parts is nevertheless possible.
The level luffing function makes the crane operator’s work easier, as he does not have to readjust the height of the load manually. This allows him to concentrate on positioning the load. That makes work on the construction site more efficient and enhances safety for everyone involved.
High-speed slewing and braking manoeuvres can cause loads to swing. The integrated oscillation damping system compensates automatically – a major step forward for site safety since it increases the crane operator’s control of the load.
LiDAT is a data transfer and positioning system for Liebherr machines and machines from other manufacturers. Based on state-of- the-art data transfer technology, LiDAT supplies information for positioning and operation.
The operating range limiting system allows you to automatically exclude areas requiring protection. This enhances safety enormously and also lets you utilise the free areas with metre precision – thereby boosting efficiency on the construction site.
The monitored system increases safety during climbing. The clear release for the next step prevents unnecessary interruptions.
Litronic cranes are equipped with wind force moment control. The control registers the movements of the jib via high-resolution sensors and counteracts the movements caused by the wind. In this way, the effect of the wind can also be reduced with large-area loads. As a result, safety and precision are increased on the construction site.
Crane operators need to stay informed about the crane’s operating parameters for their work. Here the EMS helps them to keep an overview of everything – even in difficult conditions. The personalised mask also provides precise information that is important in special situations.
The newly developed LiUP crane driver elevator is designed to transport two people or a payload of 200kg. This allows the crane driver to get to his workplace quickly and safely. Service fitters are also saved the job of having to climb up the crane to complete maintenance work.
“As I have mentioned, the Liebherr 1000 EC-H 50 is the largest Hammerhead we have in the country and this project provides us with an opportunity to show customers how well it copes with infrastructure projects. The first task for the 1000 EC-H 50 was to dismantle the Marr Contracting’s crane.
“This was an involved project which required the close collaboration of Two Way Cranes and Liebherr. Two Way Cranes provided a Liebherr LTM 13506.1 along with a couple of Frannas for the project,” said Littler.
The LTM 1350-6.1 sets standards in the 6-axle class with outstanding load capacities and boom lengths. Its Y guying significantly increases its lifting capacities when used with the telescopic boom and lattice jibs, in some cases even doubling it. The LTM 1350-6.1 can set up the Y-guying during its self-erection, in other words without an auxiliary crane. As it is the smallest crane to feature Y-guying, it is the perfect entry level machine for Y-guying for many crane contractors. Overall, it features many of our outstanding technologies to ensure reliable, safe and economical crane operation.
“As a result of excellent planning involving the site, Liebherr Australia, Two Way Cranes, and other subcontractors, the crane build went exceptionally well. Once constructed and as we expected, the 1000 EC-H 50 performed outstandingly. We used the crane to its maximum capacities during the dismantle of the other crane. Builders, contractors and other crane companies respect Liebherr Australia for our safety, large and varied fleet, as well as the quality and productivity of our machinery,” said Littler.