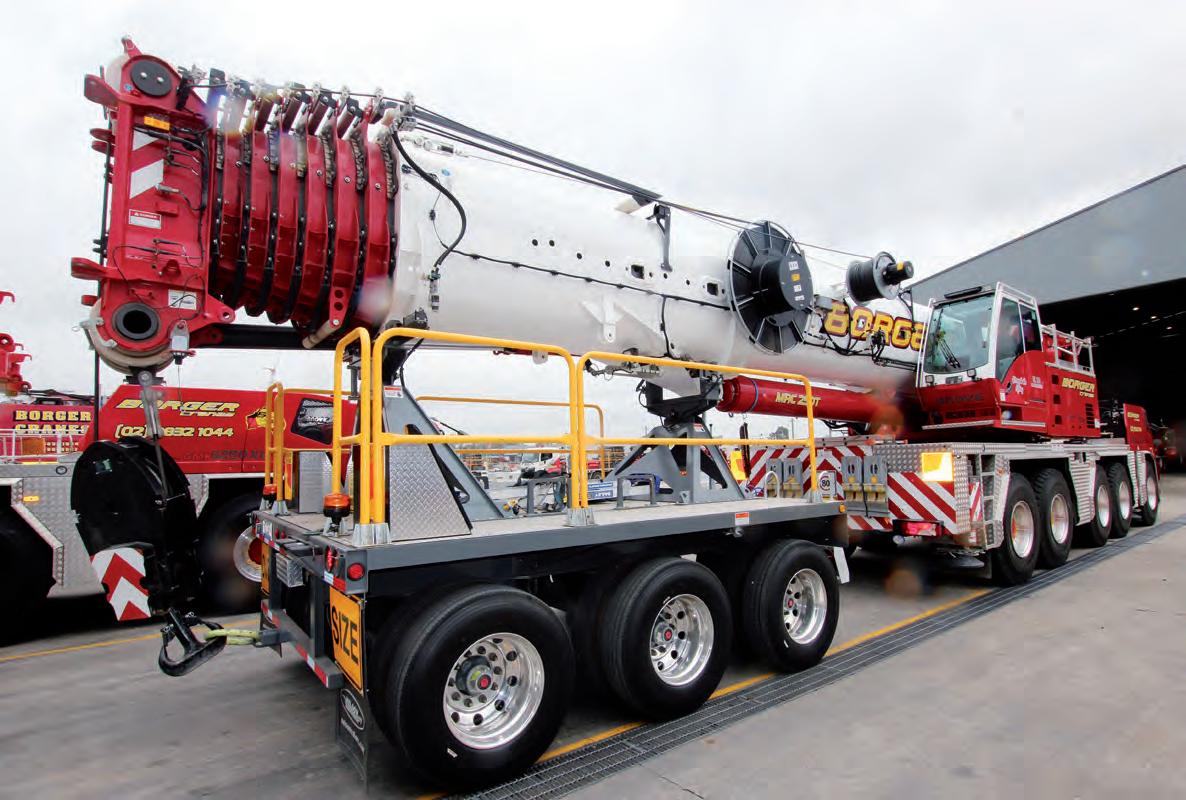
5 minute read
Five axle Groves continue to deliver
GROVE 5 AXLE CRANES CONTINUE TO DELIVER FOR BORGER
Grove all terrains are still playing an integral role in the expansion plans for Borger Cranes and Rigging Services.
FOR MORE THAN A DECADE GROVE ALL
terrains have been integral to the Borger Cranes fleet. General manager, Shawn Borger explains why Groves are popular with the business and why he continues to invest in new models.
“Grove all terrains have been integral to the success of our business since 2005. We have invested in capacities that suit the general lifting work our business is contracted to manage. You could call them the work horses of the business.
Every day, we mobilise them to help with countless projects including the construction tower cranes, work on construction sites, and to lift whatever our customers need lifting. As far as we are concerned, Groves all terrains are excellent all-rounders,” said Borger.
“Over the last 12 months, we have taken delivery of six new Groves, two GMK5250XL-1s and four GMKs 5150Ls for a total of seven 150s and four 250s overall. This takes the number of Groves in our fleet to 27. As the industry well knows, Borger Cranes and Rigging Services is expanding rapidly and these new models will be deployed across our growing number of depots including Sydney, Brisbane, the Sunshine Coast, Newcastle and the Hunter Valley,” he said.
With its 78.5m main boom, the Grove GMK5250XL-1 has the longest main boom in the 250t class. Combining high capacities up to 250t with excellent manoeuvrability, the GMK5250XL-1 can perform a multitude of jobs, ensuring high return on investment. With its single engine design and EUROMOT emission levels, the all terrain crane meets the latest regulation. This is especially important as construction companies are increasing their efforts to reduce their carbon footprint. The

The five-axle Grove GMK5150 and GMK5150L cranes have the best combination of axle weights and load charts in their class.
GMK5250XL-1 also delivers lower operating costs due to the 30 per cent decrease in diesel consumption compared to previous generation models.
“We continue to invest in the latest technology because we have always taken an innovative approach to our business and our industry. Our customers expect the best from Borger Cranes and Rigging Services and this latest investment in our fleet demonstrates our intention to provide the best available cranes for every project,” said Borger.
GMK5150L cranes feature a compact design for improved manoeuvrability and an overall load chart increase of 20 per cent compared to the old 130t class.
The five-axle Grove GMK5150 and GMK5150L cranes have the best combination of axle weights and load charts in their class, both when working in their taxi configuration at 50t or 60t GVM - for the most convenient road travel - and when configured with their maximum counterweight for optimal capacity.
The GMK5150L, features a 60 m boom while the GMK5150 has a 51 m boom which is ideal for panel work. The GMK5150L replaced the GMK5130-2 and the GMK5150 replaced GMK5110-1 in Grove’s product line.
Maximum counterweight is an impressive 45t and helps the cranes achieve an overall load chart increase of 20 per cent over the GMK5130-2. Up to 10.2 t of counterweight can be carried but the crane can also travel comfortably at 50t GVM in QLD and NSW.
With a capacity of 11.6t with its boom fully extended to 60m, the GMK5150L is ideal for tower crane assembly or other applications where strength at height is required. Boosting both cranes’ overall reach is an 18m bi-fold swing-away jib which can be extended with an 8m boom extension and an 8m jib extension for a total jib length of 34m. The jib also offers an improved offset of 50 degrees and comes with an integral heavy-duty jib
The GMK5150L and GMK5150 are powered by a single engine, reducing their overall weight and allowing them to carry more counterweight. This in turn delivers superior lifting ability. The engine is a Tier IV Final/EUROMOT 4 Mercedes-Benz OM471LA 6-cylinder diesel engine with a 390 kW rating at 1,700 rpm and a maximum torque rating of 2,460 Nm at 1,300 rpm. With 16-in. tires and an overall width of 2.75 m, the compact five-axle cranes can be easily maneuvered on congested job sites.
Operator efficiency is maximised through the inclusion of Manitowoc’s Crane Control System (CCS), a standardized and user-friendly interface whose components and operating software have been designed, developed and tested by Manitowoc to ensure the highest standards of reliability. It includes the highly intuitive Boom Configurator Mode which makes it quick and easy to select the optimum boom position for a specific lift. The operator simply inputs lift parameters such as radius, load or required distance the boom should be moved, and the system
Combining high capacities of up to 250t with excellent manoeuvrability, the GMK5250XL-1 can perform a multitude of jobs, ensuring a high return on investment.
calculates the best configuration. Once the operator selects the preferred option, the boom automatically extends to the required length.
As expected, trademark Grove features such as the Twin-Lock boom pinning system, Megaform boom shaping and Megatrak independent active suspension are all included. The cranes’ booms also benefit from the laser-hybrid welding technology in place at the Wilhelmshaven plant, which increases welding precision and creates booms that both weigh less and perform better.
There are a number of benefits to having so many cranes of the same brand in the fleet say Borger.
“Our operators like the Groves, they like the way they handle on the road and on site. They can easily move between the different models and capacities because the operating system is similar across the range. We have excellent relationships with the crane OEMs and it is no different with the Grove team. They are always responsive to our requests and answer any questions we might have.
“They are also quick to deal with any issues we might have. You need that level of support from your supplier. If we can’t get a crane to site, for whatever reason, we let the customer down and we don’t want this to happen. Working closely with the team at Manitowoc ensures we are onto issues quickly and our assets are in good shape all of the time.
“We also continue to invest in support vehicles for the cranes. For the new Groves we have purchased more TRT trailers to carry the counterweights. We are focused on safety and efficiency and these specialist trailers are ideal for our needs. We can mobilise and demobilise the cranes quicker and in a safer manner. This saves the customer money and ensures the safety of our teams is front and central at all times,” said Borger.
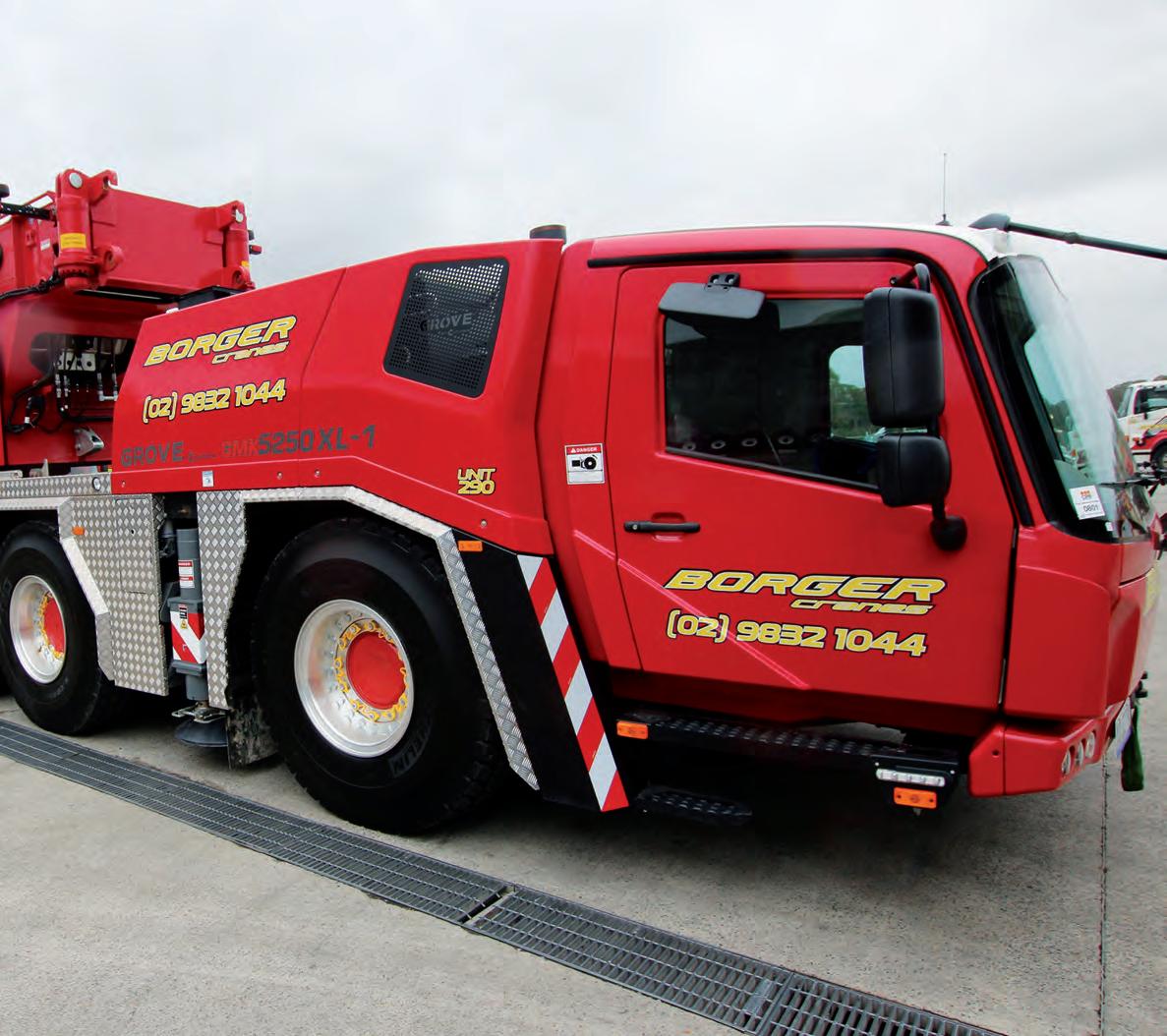