BORGER CRANES’
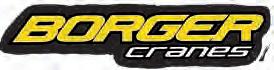

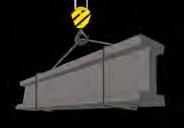
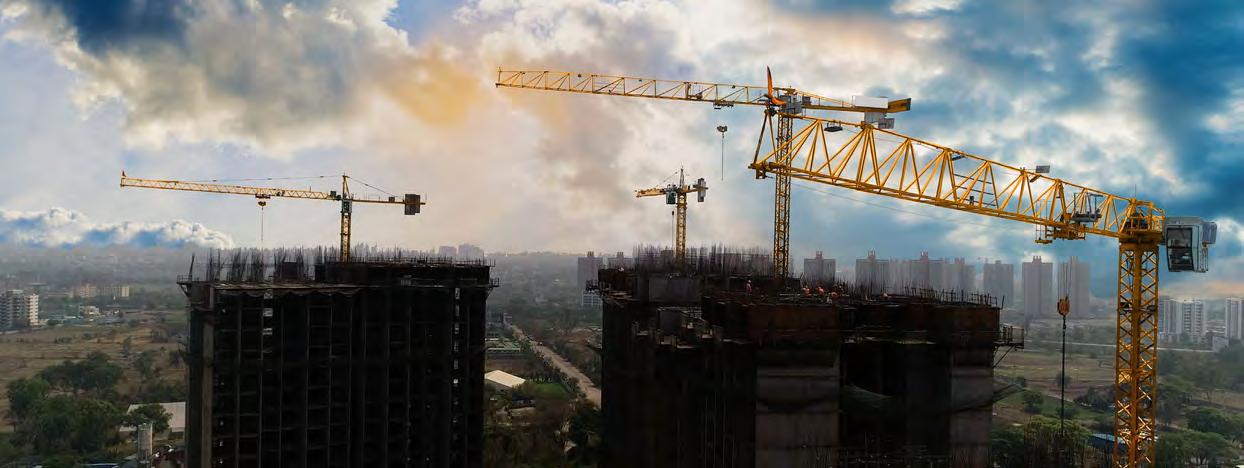
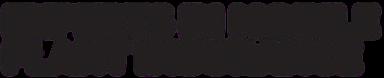

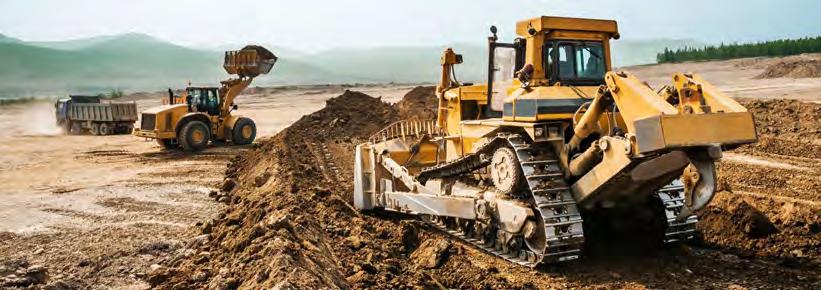
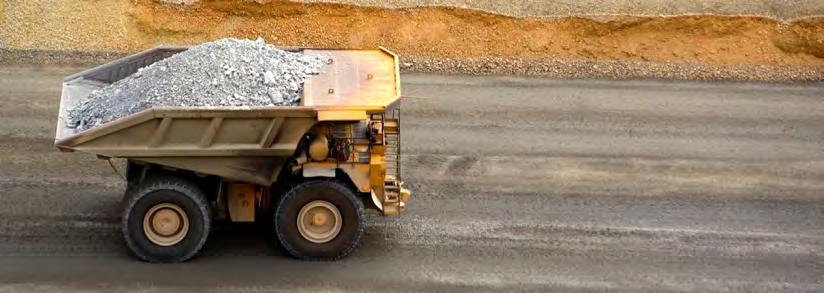



6 Up Front with Borger Crane Hire and Rigging
Borger Crane Hire and Rigging’s complex bridge lift.
10 CICA CEO report
Brandon Hitch reviews CICA’s 2024 achievements.
12 CICA’s safety award CICA’s Damien Hense recognised with Safety Pioneer Award.
13 CANZ CEO report Sarah Toase looks to the future.
16 Harvey Norman Technology for Business Cyber Attacks a real threat for crane sector.
19 Terex Franna
New capacity Rough Terrains released.
22 TRT trailers TRT launches new trailer.
Between Hook & Load features
26 Lif ting Equipment Engineers Association LEEA’s 2024 highlights.
33 Titan Lifting Technologies Titan’s quality control approach reflected in extensive product range.
36 Queensland Rigging Hire New premises, more products, bigger team.
41 Modulif t’s power lifts Modulift supplies bespoke spreader bars for nuclear lifts.
43 Alliance Engineering Consultants (AEC) AEC looks back on 30 successful years in the industry.
’s plans for Australia Zoomlion’s bold plans for Australian crane sector.
53 Managing Liebherr’s supply chain Alex Coleman provides insights into Liebherr ’s supply chain strategies.
56 Grove upgrades Significant upgrades to Grove heavy lif ters.
60 Tutt Bryant Tutt Bryant’s Go Green range proves to be a sustainable option for crane sector.
63 The Buddie System Crane sector’s very positive response to Buddie System launch.
66 Sany Crawlers
The Sany SCC3200A-1 crawler duo is playing a pivotal role in major WA infrastructure project.
69 Sino Distribution Milleen Constructions recently bought two Zoomlion machines for a rural NSW infrastructure project.
72 TRT and QUBE QUBE goes large with TRT Trailers.
74 Lif t of the Month What our industry does best.
Published by:
GENERALLY SPEAKING, A GOOD thermometer on how the health of the construction industry, and therefore the crane sector, is the number of tower cranes seen on city sky lines.
The 25th edition of the Rider Levett Bucknall (RLB) Crane Index® reveals there are 863 cranes on sites nationally. The RLB Crane Index® has recorded more than 800 cranes nationally for the past six editions.
The non-residential index has reached 322 points, the highest index value since commencement, primarily due to the many government-funded civil projects across the country. The highest number of fixed cranes on a site was the Amazon Fulfillment Centre in Melbourne, with seven cranes.
With 30 long-term crawler cranes in operation, Melbourne’s $36 billion North East Link project has the largest crane deployment in the country. The Gold Coast increased crane numbers to reach a record 62 cranes across the region.
New South Wales accounted for 49.5%
of all cranes across Australia; Melbourne accounted for 22.8%; and South-East Queensland for 16.5% of all cranes. The gap between Sydney and Melbourne’s crane numbers continues to be significant at 191 cranes, with Sydney hosting 387 cranes and Melbourne 196. So, it does appear that the construction sector will be bouncing back in 2025.
This issue is very much a review of 2024 with many articles taking a quick glimpse at 2025. The team at Cranes and Lifting magazine takes this opportunity to thank the crane sector for the unwavering support you have afforded us over the last 12 months and we wish everyone the very best for the Festive Season and the year ahead.
Simon Gould Editor, Cranes and Lifting
379 Docklands Drive, Docklands VIC 3008
T: 03 9690 8766
www.primecreativemedia.com.au
CEO
John Murphy
E: john.murphy@primecreative.com.au
Chief Operating Officer
Christine Clancy E: christine.clancy@primecreative.com.au
Managing Editor
Andrew Hobbs
E: andrew.hobbs@primecreative.com.au
Editor Simon Gould
E: simon.gould@primecreative.com.au
T: 0404 865 109
Journalist
Jacob Lynch
E: jacob.lynch@primecreative.com.au
Business Development Manager
Emily Schlegel
E: emily.schlegel@primecreative.com.au
T: 0466 317 555
Client Success Manager
Louisa Stocks
E: louisa.stocks@primecreative.com.au
Art Director
Bea Barthelson
Imaging Assistant
Paul Breen
Subscriptions
Frank Rapone
T: 03 9690 8766
E: frank.rapone@primecreative.com.au
The Publisher reserves the right to alter or omit any article or advertisement submitted and requires indemnity from the advertisers and contributors against damages or liabilities that may arise from material published.
© Copyright – No part of this publication may be reproduced, stored in a retrieval system or transmitted in any means electronic, mechanical, photocopying, recording or otherwise without the permission of the publisher.
For five decades, Gamuda has been a global leader in delivering complex infrastructure projects that connect cities and communities.
It’s our people who make the difference. They bring their expertise to help deliver critical projects to our clients in the roads, rail, and energy sectors. With a workforce of over 2,000 people across five states, the Gamuda Group of Companies offers a full end-to-end solution in design, construction, and project management.
To find out more about Gamuda, visit gamuda.com.au
Borger Crane Hire and Rigging, in conjunction with joint venture partners Ferrovial and Gamuda, recently lifted into place the Luke Bowen Bridge, a key element of the Coffs Harbour Bypass project in New South Wales. The new pedestrian bridge spans a total eight lanes over the Pacific Highway and two local roads.
BOTH THE AUSTRALIAN AND NSW
Governments are investing in the 14-kilometre project which is designed to boost the regional economy and improve connectivity, road transport efficiency and safety for local and interstate motorists.
The Gamuda and Ferrovial joint venture is delivering the major package of work through a collaborative Design and Construct contract with Transport for NSW. With a focus on innovation, efficiency and value for money, the project includes three tunnels, about 11 kilometres of new road and about 3.5 kilometres of upgraded highway.
The Luke Bowen Bridge lift was not without its challenges, explains Dean Tauasa - better known as “Dingo” in the
industry - who is the National Lifting and Rigging Manager for Gamuda. Dean has been with Gamuda for two and a half years, having worked with John Holland and Melrose Crane Hire on projects such as the Rozelle Interchange, Waterloo Station, WestConnex (M8) and Northwest Rapid Transit (NRT) just to name a few.
“For this project, we went with Borger Cranes for all of our big lifts, we did look at local providers, but the largest capacity crane available was a 250t and that simply would not cut it when it came to the Super T girders and big lifts. We needed a large capacity crane, mainly due to the size of the bridge, and so we decided on Borger’s 650t capacity LTM 1650-8.1. We’ve had the LTM 1650-8.1 up here quite a few times for majority of our bridges, we even had the LTM 1750-9.1 on the project for the very first bridge girder installation back in May,” said Dean.
“When it comes to craneage, Borger
engaged as a supplier for the Rozelle Interchange project. With branches in Sydney, Newcastle and South East Queensland, and with the location of this project, Borgers have been able to supply us with large capacity cranes, from both sides of the border. Nathan and Shawn Borger as well as Matt Steain, Borger Cranes Heavy Lift Supervisor, have been very supportive and accommodating, working in with the requirements of the project to help meet specific and tight deadlines,” he said.
With the Pacific Highway being the main arterial road between New South Wales and Queensland, disruption to traffic had to kept to a minimum - which required meticulous planning, explains Dean.
“We were given a window from 7pm until midnight for the closure of the
northbound lanes, to allow us to set up the crane. From midnight we closed the entire highway, and we had until 3am (max) to complete the installation. Heavy vehicles were parked up both north and south of the crane setup, with light vehicles and emergency services being diverted via a local road. By 6am we had to have everything packed away and off the road for the highway to open to the full four lanes again,” he said.
The set up for the crane wasn’t ideal as it was on a significant incline, and the dimensions of the bridge were also a complicating factor, said Dean.
“Weight wise, the bridge was quite manageable, coming in at about 80 tonnes, but the bridge was a single span construction 61 metres long, 4.5 metres tall and 5 metres wide. We also had to set the crane up on a hill, which meant
“We needed a large capacity crane mainly due to the size of the bridge, and so we decided on Borger’s 650t capacity LTM 1650-8.1.”
set
packing the underside of the front of the crane with TRT mats and timbers. We used a 100t capacity all terrain and a Franna from Coffs City Cranes to assist in the build of the crane and the preparation for the lift,” said Dean.
The lift was more than 18 months in the planning, says Dean, with Tom Patterson (FGJV Senior Project Engineer) leading the charge alongside Transport for NSW project team members.
“There were all sorts of factors influencing the timing of the lift. Obviously, Tom and his team worked closely with the fabricator of the bridge to understand when it would be ready for transporting and examine the best ways of getting it to site and ready for lifting. We also had to factor in constraints including the NSW and Queensland school holidays so as to minimise the disruption for road users,” he said.
Dean explains how detailed the planning had to be and how closely he and the team at Borger Cranes worked on planning every aspect of the lift.
“A week before the lift we met the Borger Cranes’ team on site, and we went through an hour-by-hour planning session. The bridge was already on site
“A week before the lift we met the Borger Cranes’ team on site, and we went through an hour-by-hour planning session.”
sitting on stands so we were able to get a good look at what we were lifting.
“When the Liebherr LTM 1650-8.1 got to site the following week, we picked up the bridge and loaded it onto the Jinker which would get it into position for lifting. This loading process proved a good option,” said Dean.
“Because the lift wasn’t scheduled for a couple of days, moving it to the Jinker provided a good opportunity for us to work with the rigging and make adjustments if required. There was a Crossfall on the bridge and we needed to ensure that the rigging was in the correct positions to get the Crossfall right. We made some adjustments and got the bridge onto the Jinker. When it came to the actual lift, we hooked down and got the rigging back on the hook and proceeded with the lift,” he said.
“The rigging featured a spreader bar the width of the bridge and that was right at the top of the rigging and then we had
some very long slings which attached to engineered lifting points on top of the bridge. The LTM Liebherr 1650-8.1 proved ideal. Although the bridge only weighed 80t, we needed a lot of ‘boom out’ to allow for the rigging lengths as well as the required head height to get the bridge into position,” said Dean.
Dean paid tribute to all parties involved.
“The success of this lift is the result of the tireless work put in by everyone, including the client (Transport for NSW), subcontractors including Borger Cranes, Goldsprings Heavy Haulage, Coffs City Cranes, Coates Hire and Civmec. We are grateful to the expertise from the Ferrovial Gamuda Joint Venture Project and Site teams including Adrian Hawkins, Tom Patterson, Borja Llanos and Jamie Mason along with their respective teams. With the support of the Project Safety Team and Senior Management, this complex lift was completed and delivered safely and successfully,” said Dean.
At Harvey Norman Technology for Business, we hear it all the time from small business owners —
We don’t need Cyber Security. They won’t target us, we’re too small.
The reality is, cyber threats don’t discriminate. We’ve helped many small businesses who thought they were safe — until they weren’t.
When the big IT companies won’t help because you’re too small, that’s where we come in. We specialise in robust, affordable cyber security for businesses like yours.
24/7/365 Monitoring: Continuous protection through our Security Operations Centre (SOC)
Managed Threat Detection & Response: Non-stop defence against ransomware and malware
Proactive Monitoring & Management: Fixing potential issues before they impact your business
Security Awareness Training: Keep your staff one step ahead of cyber threats
Compliance Management: Stay legally compliant with industry standards
Not sure if your business is Cyber Compliant?
Sign up for a Free Cyber Security Assessment. Protect your business with enterprise-level solutions at unbeatable prices. Contact us today to secure your business’s future.
Scan to arrange your FREE Cyber Security Assessment
Email info@harveynormanbusiness.com.au or call 1300 781 865 for assistance.
installation and setup on all Technology Service and Security Packages during December 2024!
AS WE APPROACH THE END OF 2024, it’s a fitting time to reflect on a transformative year for the crane industry in Australia, marked by significant advancements in safety, regulatory reform and innovation. Throughout the year, CICA has continued to pioneer initiatives that support our members and the industry more broadly nationwide, ensuring safer, more compliant and supportive work environments.
Raising the Bar on Safety: The CICA Lift Supervisor Course
This year saw attendees in the CICA Lift Supervisor Course, reach record numbers. This course has been designed to elevate safety standards and operational oversight by supporting the crucial role of the Crane Lift Supervisor, who oversees all lifting activities to maintain high safety and coordination standards on construction sites. It’s heartening to see this initiative so positively embraced across the industry, emphasising the importance of specialised oversight in complex lift operations. Dates for 2025 are now available on the CCA website.
“CICA continues to lobby for the adoption of HVAMS, so that crane owners and operators can look forward to more efficient access to roads nationwide.”
Supporting Regulatory Reform: A Modernised High-Risk Work Licence Framework
In 2024, CICA has been a key contributor to Safe Work Australia’s review of the High-Risk Work (HRW) licence. This initiative is central to modernising licensing standards, ensuring they meet the needs of today’s equipment and work practices.
forward are essential in enhancing both safety and competence within our industry.
Transforming Access: The Heavy Vehicle Access Management System (HVAMS) CICA continues to lobby for the adoption of HVAMS, so that crane owners and operators can look forward to more efficient access to roads
The introduction of the ROVER (Road Vehicle Certification System) by the Federal Labor Government has brought about new standards for crane compliance with Australian Design Rules (ADRs). CICA has worked closely with manufacturers and government bodies to facilitate smooth transitions under the ROVER system and this work is also ongoing,
As we look to 2025, we remain committed to supporting our members with continuous professional development, advocating for industry-led reforms, and ensuring a safer, more efficient operational framework for crane operators across Australia. This holiday season let’s celebrate the progress we’ve made and look forward to a productive new year ahead.
On a personal level, I hope you’ll have the opportunity to take a step back from your daily routine and take time out to be with the people who matter most. In the midst of work commitments, deadlines, and responsibilities, it’s easy to lose sight of what truly matters. Taking a pause to reconnect with loved ones allow us to reflect on the blessings in our lives and recharge for the year ahead.
To all our members, partners, and stakeholders, thank you for your dedication and shared commitment to advancing our industry. On behalf of the Board and everyone at CICA, I wish you a Merry Christmas and a New Year filled with safety, success, and continued growth.
Brandon Hitch Chief Executive Officer
CICA BOARD
Ben Pieyre – President
Marcus Ferrari – Vice President
Danny Adair – Director
Danny Black – Director
Andrew Esquilant – Director
David Solomon – Director
Karli Sutherland– Director
CICA OFFICE
Brandon Hitch Chief Executive Officer 0428 228 048 ceo@cica.com.au
Alice Edwards Road Technical Engineer 03 8320 0440 alice@cica.com.au
Patrick Cran
CICA Site Operations Advisor 0488 004 274 pat@cranesafe.com.au
Sharon Pearce
Crane Crew Competency Officer, 0491 134 533 sharon@cica.com.au
Damien Hense
CICA Road Policy Advisor 0488 007 575 damien@cica.com.au
Julie Turner CICA Executive Assistant/ Board Secretariat 03 8320 0411 julie@cica.com.au
Kate Galloway Traineeship & Industry Engagement Coordinator 0491 047 118 kate@cica.com.au
Michelle Verkerk Communications and Special Projects Advisor michelle@cica.com.au
Just ina Blackman Member Events and Engagement 0403 717 626 justina@cica.com.au
Ashleigh Gould Office Operations Coordinator, 0490 356 041 ashleigh@cica.com.au
Shane Coupe
CraneSafe & CrewSafe Administrative Assistant Officer 0491 047 134 shane@cica.com.au
Unit 10, 18–22 Lexia Place, Mulgrave Vic 3170
Phone: 03 9501 0078
Email: admin@cica.com.au
Website: www.cica.com.au
For information, please visit our website or call the CICA office.
and Safety Show in Sydney, Damien Hense was awarded the prestigious Safety Pioneer Award for his groundbreaking work on The Crane Industry Council of Australia (CICA) On-Road Articulated Steering Mobile Crane Training Course.
This honour highlights his dedication to workplace health and safety (WHS) and the positive impact of his efforts on keeping mobile cranes safely on the road across the country.
Damien Hense was part of the Australian Road Research Board (ARRB), focusing on research-based applications development, innovation and industry consultation activities, including interaction with Australian governments and municipal bodies across key road transport projects.
Damien has been involved in programs of work related to road infrastructure management, including intermodal solutions, network operations, road safety (including risk assessment technology) and the operation of high productivity freight vehicles.
workplace health and safety (WHS) and the positive impact of his efforts on keeping mobile cranes safely on the road across the country
Damien Hense engaged and worked with numerous stakeholders to find a workable solution to keep articulated mobile cranes on the road. This is the CICA On-Road Articulated Steering Mobile Crane Training Course.
Being part of the team planning the solution, the implementation and the feedback - Damien has worked to make the workplace and Australian roads safer. This will continue as more and more operators complete both elements of the CICA on-road articulated steering crane program.
Training is being provided to an industry that has been overlooked in both the heavy vehicle road licence and high-risk work licence.
By developing this standardised training, it also assists small and medium businesses that would otherwise not have resources to create this training in-house.
The greatest outcomes to date have been: aising awareness on the issue in such a way, without crippling the industry
Damien joined CICA in 2018 and works with CICA’s members and key stakeholders to focus on road safety, access and mutually beneficial network operations outcomes.
In Australia, articulated or “pickand-carry” cranes are widely used —they’re a go-to for many jobs across different industries. But with high usage comes high risk, especially since these cranes are often moving on roads to different sites or moving loads through busy, uneven job sites.
The Mobile Articulated Crane on Road Safety course is a specialised program developed by CICA to
“Damien Hense engaged and worked with numerous stakeholders to find a workable solution to keep articulated mobile cranes on the road.”
address the unique challenges of operating articulated mobile cranes on Australian roads.
Many experienced pick-and-carry crane operators haven’t actually been formally trained or assessed in how to safely operate these articulated cranes.
Because of current licence frameworks, operators with a general slewing crane licence can legally operate pick-and-carry cranes— without needing any specific training to do so.
• Helping operators, employers and companies meet their obligations under the Heavy Vehicle National Law (HVNL) by addressing specific hazards and risks associated with articulated crane operation.
• C ustomising the delivery to the user in a way that is easily accessible and encourages participation.
For more information on the CICA On Road Articulated Steering Mobile Crane Training Course go to: https:// www.cica.com.au/The-CICA-OnRoad-Course
AS I WRITE MY LAST MESSAGE IN Cranes and Lifting Magazine for 2024, my mind is already looking to 2025. Next year holds special significance for the Crane Association of New Zealand (CANZ), as it will mark our 50th anniversary. This milestone not only gives us a chance to honour the Association’s legacy but also propels us toward an exciting future.
Reflecting on the journey we’ve taken together since I joined four years ago, I am reminded daily of the importance of our history and the legacy of those who have laid the foundation for where we stand today.
Our association’s heritage is something I deeply respect. Every time I glance at the name board in my office, I’m reminded of the numerous individuals who’ve contributed to the crane industry in New Zealand. These are people who have invested their heart and soul—not just for personal or professional gain but to uplift and strengthen the entire industry.
I felt this legacy profoundly when we honoured Tony Gibson with a life membership at this year’s conference. Tony was the President of the Association when I first came on board, and his support has been instrumental in my own journey.
I am now beginning to see my own story woven into the fabric of this Association. I am proud of the progress we’ve made together, and I feel a profound responsibility to serve our members with the same passion and commitment as those who came before me.
This shared journey and dedication to our members are what make this
industry such a pleasure to be part of. I know how challenging the last 12 months have been economically for many of our members. We are all still waiting for those first signs of recovery, and that tough reality sharpens my focus on what the Association needs to do to elevate the New Zealand crane industry. We are here to be both a support and an advocate, ensuring that our industry is resilient and forwardthinking.
Our commitment to the future is firmly grounded in our four strategic
priorities, which provide a roadmap for everything we do:
These pillars guide our actions, and I am proud to say that our council lives by them. We have ensured that all our activities are aligned with these priorities to create a strong, thriving industry for our members.
The emphasis on training has been especially important over the past two years. We have invested heavily in training initiatives, setting up our private training enterprise (PTE) to
“CANZ’s vision for the future is one of innovation, resilience, and unwavering commitment to our members.”
provide gold standard training resources for crane operators. When I first joined, one of the most significant concerns from members was the availability and quality of training. Today, we have made enormous strides in addressing that concern, and this will continue to be a vital focus as we move forward.
Looking ahead to the next 12-24 months, we are turning our attention to
another critical area in our strategic vision: regulatory updates and industry guidance. During our recent AGM, this focus resonated with our members, affirming that we are on the right path. They expressed the need for updated regulations and guidance to reflect the realities and challenges of our industry today. It’s clear that our regulatory framework needs to evolve to keep pace with the industry’s growth and the complexity of modern crane operations.
To achieve this, CANZ is already working closely with the government. Recently, we met with both WorkSafe and the Ministry of Business, Innovation and Employment (MBIE) to chart a path forward for crane regulations. Our goal is to create a regulatory environment that enhances safety, supports professionalism and fosters growth within the industry.
Additionally, we’re exploring operator licensing and a crane-specific pre-qualification process to establish a consistent industry standard. Reducing duplication and ensuring high standards across the board will benefit both operators and businesses, making the industry safer and more efficient.
This regulatory and standards initiative aligns closely with CANZ’s founding purpose: to support the success of our members. As we continue this work, I’m excited and motivated because I know it will make a difference where it counts. It’s my hope that the efforts of everyone involved—whether in the President’s chair, in council seats, or as part of our dedicated team—will leave a legacy that our members value and appreciate.
A wireless instant safety alert device designed for crane operators and dogmen enabling rapid alarm activation in emergencies.
The true measure of our success as an Association lies in what we deliver for our members. As our PTE gains traction and we update industry guidance, the value of these initiatives will become apparent in the form of higher standards, better training, and a stronger industry overall. I am confident that these actions will lead to a tangible improvement in the quality of our industry, positioning New Zealand’s crane sector to thrive in the years to come.
Our work is far from over, and as we enter our 50th year, we remain as committed as ever to raising the bar. By focusing on the critical areas of training, regulation, and industry standards, we aim to build a future where New Zealand’s crane industry is recognised for its professionalism, expertise and excellence. As I look back on the progress we’ve made and ahead to the work still to be done, I am filled with both pride and anticipation. CANZ stands on the shoulders of the giants who have shaped this Association, and I am honoured to be part of this legacy.
As we move into 2025, we will continue to serve as the voice of the industry, advocating for the needs of our members and ensuring that they have the resources and support they need to succeed. CANZ’s vision for the future is one of innovation, resilience, and unwavering commitment to our members. Thank you to everyone who has been part of this journey, and here’s to the next 50 years of growth, progress and shared success in the New Zealand crane industry.
The TBS device overcomes the shortfalls of two-way radio failure and often-inaudible backup whistles. The TBS device allows a dogman to instantly transmit an alarm signal to a crane operator to stop.
A quick snap on the TBS the alarm.
Rutland Smith, Director of Harvey Norman Technology For Business (HNTFB) spoke at The Crane Industry Council of Australia’s (CICA) National Conference and Exhibition. From the feedback he received, it is apparent that Cyber Attacks are viewed as a genuine threat to the crane industry.
“I WAS GRATEFUL FOR THE OPPORTUNITY to present during CICA’s National Conference and Exhibition and from the feedback I received, Cyber Attacks do pose a genuine risk to the crane industry. This doesn’t surprise me as the criminals behind these attacks do not discriminate, they carefully plan their deception and implement their attacks with precision with any industry seen as fair game.
CYBER CRIMINALS POSE A VERY REAL RISK TO YOUR BUSINESS
“The subject of Cyber Security was even raised during the Crane Owners panel and the CEO of a national crane hire business shared how his business was only just getting back to normal following an attack five years ago,” said Rutland.
“During the conversations I had with crane businesses, there were many misconceptions about how vulnerable businesses are to Cyber Attacks. A lot of small business owners make the assumption that big businesses are at risk and their business is too small to be a target. The reality is it’s the other way around. Cyber criminals tend to focus on smaller businesses, and that’s because they are more vulnerable and have much lower defenses.
“We know from the Australian Cyber Security Centre (ACSC) statistics that 43 per cent of attacks in Australia actually happen to small businesses. So the first thing I’d say is the assumption that ‘I’m too small to be attacked’ is actually incorrect. The second thing I’d
say is small businesses have the most to lose,” said Rutland.
Every industry is a target but criminals target different industries for different reasons, he added. The crane industry is particularly appealing to cyber criminals for fake invoice scams because of the larger size of the amounts transacted between crane businesses and their customers. The crane industry is also targeted for ransomware attacks because of the enormous costs associated with the business being unable to operate for days or even weeks.
The average cost of an attack on a small business in Australia is a
involved in government work such as Tier One projects.
“The issue to be aware of is that most large government departments, and certainly most large corporations, are now insisting that you have a certain level of cybersecurity before they’ll allow you to tender for their business. If you don’t meet the requirements, you won’t be allowed to tender or quote for the business. You’ll simply be prevented from even participating.”
The Federal Government’s Australian Cyber Security Centre has published a cybersecurity risk mitigation framework called the Essential Eight.
“We know from the Australian Cyber Security Centre (ACSC) statistics that 43 per cent of attacks in Australia actually happen to small businesses.”
little over $46,000, according to the ACSC. These costs can be crippling to a business and may even result in the business closing down.
In addition to the financial risks associated with cyber security, many crane operators will need to make themselves compliant with government guidelines for legal reasons and because larger projects will exclude non compliant businesses from their tenders.
Rutland explains the risks to small and medium sized crane businesses
In many ways, the framework has the same function as Occupational Health and Safety Guidelines, but instead of physical security, this is about cybersecurity. Rutland explains more.
“Under the findings of the courts, all businesses have a duty of care to protect their customer data, and the measurement for whether or not that duty has been discharged is whether or not the business has made the appropriate effort to implement the recommendations of the Essential Eight. The Essential Eight framework is complicated and it’s not something
that you can implement by yourself, you need someone like us help you,” he said.
CAN HARVEY NORMAN HELP Rutland explains how complicated cybersecurity can be for small to medium sized businesses and how HNTFB simplifies the process.
“One of the challenges for all businesses is to meet the standard of the courts. They have to implement the ‘Essential Eight’. That’s an incredibly complicated framework to implement, and almost no small business, that I’m aware of, is capable of implementing that by themselves.
“By getting HNTFB on board as their IT department, we are able to provide a small business with all the support that they need and ensure they are compliant with the government framework” said Rutland.
HNTFB recently partnered with The Crane Industry Council of Australia (CICA) with the aim of offering members solutions to the increasing threat from cyberattacks. Rutland explains how HNTFB can help a crane hire business in practical terms.
“We are fortunate that we’ve entered into this relationship with CICA and
we’ve created a landing page that’s been created specifically for CICA members.
“From this page, members are able to make contact with our team. They’re also able to see the special offers that are available to CICA members only, and they’re also able to learn more about cybersecurity by reading the ‘tips and tricks’ on the page.
“We are asking owners of small to medium sized businesses to imagine how much more you can achieve with Harvey Norman as your IT department? We are just like a really large IT department for a big company. But we don’t just provide IT support and services, we also provide our customers with advice on what they should be doing with their IT moving forward,” he said,
Working with CICA and its members is exciting for Rutland and his team at HNTFB.
“We’re really pleased that CICA has approached us for this partnership, it is great that they’re taking the initiative in trying to protect their members from cyberattacks. We are keen to show CICA and its members what we are capable of and, as a show of goodwill, we are offering to provide an ‘Essential
Eight Business Assessment’ free of charge. This normally retails for $499.
“There is nothing to be lost by having HNTFB conduct this assessment. We will provide members with an independent view that confirms everything is dandy and there is nothing to worry about, or we will provide you with a list of things that are missing and recommendations on how you can fix it. You don’t have to do that with us, you can go and do that with any provider you want,” said Rutland.
“With the various industry sectors we work in, there are always owners of small to medium sized businesses believing they are too small to be the subject of a cyberattack. We are here to tell you these criminals do not discriminate, they are targeting vulnerable businesses no matter the size, and as I’ve said, many businesses simply don’t recover from an attack. So, we are asking CICA members to take the FREE ‘Essential Eight Assessment’ and ask, ‘can you afford not to?’” finished Rutland.
Visit the CICA members page at https://www.harveynormanbusiness. com.au/pages/cica to find out more about what Harvey Norman can offer.
The SCX2800A-3 is designed for versatility across diverse job sites. It includes a sturdy winch that guarantees stable operations, and its ‘Eco winch mode’ boosts operational efficiency while optimising energy consumption. Created with innovative design principles for easy use, it also offers features such as wide shoes and options for reduced counterweight, making its high-performance lifting capacity of 275 tonnes ideally suited for building the future.
The Terex TRT100 has a maximum capacity of 100 tonnes and main boom length of 47 metres, with a 17m jib stowed on the crane’s side that can be easily attached to the main boom to extend reach.
New additions to Terex Rough Terrain range highlight ambitious portfolio expansion
TEREX ROUGH TERRAIN CRANES IS pleased to launch two new models from its expanding TRT Series of userfriendly, flexible, durable cranes—the TRT100 and TRT60.
These new models follow the recently launched TRT 80L, also part of the TRT Series. With advanced features including the intelligent TEOS
operating system, four steering modes, an Eco Mode function, a proportional full power telescoping boom and T-Link telematics platform, and its compact design, the TRT Series has been exceptionally well-received in the marketplace. The cranes also come fitted with LED lights, a comfortable, spacious, tiltable cabin with large glass surfaces and high-quality components throughout. Combined, these advanced features contribute to the strength and ease of operation of the TRT Series and make these cranes ideal for applications including ports, construction, infrastructure, mining, energy, yard
possesses the capacity and flexibility to address daily lifting challenges in the modern working environment,” said Giancarlo Montanari, General Manager, Terex Rough Terrain Cranes. “The marketplace is highly competitive, but I have great confidence in our dedicated team members and the superior Italian craftsmanship behind every crane produced at our Crespellano manufacturing centre of excellence.”
Specifically, the TRT100 has a maximum capacity of 100 tonnes and main boom length of 47 metres, with
counterweight aids operational efficiency, stability and transportability. On the other hand, the TRT 60 has a maximum capacity of 60 tonnes and main boom length of 42.5 metres, with a stowable jib of 8-15 metres.
These machines are the first to feature the new ‘IdeaLift’ from Terex Rough Terrain Cranes, which optimises load lifting with asymmetric outriggers. Whether fully extended or partially retracted, the crane automatically selects the best lifting capacity based on the specific formation of the outriggers.
reintroducing some past product lines that are currently in demand in certain markets,” adds Montanari. “This is an exciting development for our engineering and manufacturing teams, and we eagerly anticipate bringing these innovations to the marketplace in the coming year. I am proud of our team and believe these future advancements will strengthen our value offering and reputation in the lifting industry.”
For more information, please visit https://www.terex.com/roughterrain-cranes
Specifically designed to meet your requirements, providing you with complete control while still allowing remote operation via radio remote control, with a 25,000kg capacity for heavy-duty tasks.
Non-Marking Tyres to Prevent Floor Markings
Multiple Attachment Options Removable Counterweights Counter Rotation on Front Wheels
Evolution is a continuous process at TRT and when they’ve made their best version, they make it better. Every generation of TRT trailers builds on the innovative design engineering that came before it. The team at TRT recently staged a customer event focused on a new trailer design.
TRT’S ENGINEERING AND DESIGN TEAM have spent the last 12 months refining the design of the new 4x8 dedicated ESS Low Loader. The design is a New Zealand specification, new Low Loader build that uses TRT’s patented Electronic Steering System (ESS) technology and follows in the footsteps of its successful ESS Platform and House Trailers. Jeremy Carden, TRT Trailer Sales, explains more.
“For some time now, TRT has seen the need for an all-steering Rows of Eight Low Loader in the NZ market. The design is new but the TRT team has simply tapped into the ESS Platform design and worked out where the tare weight can be removed, while at the same time maintaining the strong chassis shape and construction. This reduction in tare weight enables the new trailer to be highly competitive within the NZ heavy haulage market.
“Over a period of time we’ve undertaken a number of changes and updates to the design and general construction of the trailer. We are now in a position where we can manufacture a four-line platform trailer with the same dimensions that previously weighed 30 tonne. The newly designed trailer comes in at 22.5 tonne, providing customers with a 7.5 tonne payload increase.
The customer benefits are numerous explains Jeremy.
• A competitive tare weight, allowing for increased payloads
• Reduced running costs – rubber stays on the rim.
• Massive advantages in manoeuvrability due to an active, intuitive steering system, along with
an increased suspension stroke.
“Customers with a four-line lead platform trailer require a dolly in the mix to be legal on the road, whereas with the new trailer, for at least 50% to 60% of the time, the customer will be able to remove the dolly from the equation.
“Dollies don’t steer and are generally
TRT’s ESS trailers follow the truck’s arc through a turn and have a pivot point that can be adjusted.
regarded as a difficult piece of equipment to operate, so eliminating the dolly is a significant benefit,” Jeremy said.
“Another benefit in New Zealand, more than in Australia I’d say, is nonsteering trailers in the heavy-haulage market have been the norm for many years. In regards to the maintenance
“Our ESS trailers follow the truck’s arc through a turn and have a pivot point that can be adjusted. Like all-terrains, our trailers can crab sideways behind the truck and can basically mirror the truck’s angle.”
of the running gear, customers are constantly wearing through tyres, breaking them off the bead and generally placing heavy strain on the trailer leading axles and the trucks chassis.”
“Another huge benefit of the ESS system design is the suspension stroke. In comparison to standard rows of eight, the new build features three and a half times a suspension stroke, which means it’s going to be a lot more user friendly on uneven terrain,” said Jeremy.
“The idea of having a trailer that is not ‘fighting’ you as you navigate corners and roundabouts because it’s actively steering behind you, has seen a large number of customers purchase our ESS Platform Trailers which has been a huge step forward in the New Zealand
market,” said Jeremy. “Kiwis are a very progressive bunch, our roads aren’t getting better any time soon, so our trailers need to be constantly evolving as the loads tend to get larger and longer.”
ESS technology is very similar to that seen in modern all-terrain and mobile cranes, enabling the trailer to actively steer behind the truck, says Jeremy. The driver can override the auto-steering as long as the truck is at an offset angle, this can be done right up to 50km/h and is probably the biggest advantage to this ESS system overall.
“Our ESS trailers follow the truck’s arc through a turn and have a pivot point that can be adjusted. Like all-terrains, our trailers can crab sideways behind the truck and can basically mirror the truck’s angle. Having been the Grove distributor since 1972, none of this technology is new to us and we’ve basically developed this technology in our trailers. In terms of software development, our partner is Bosch Rexroth with the ‘brain’ or the ‘beating heart’ of the trailer being the Rexroth controllers or RC controllers, which are mounted in an enclosure on the side of the gooseneck,” said Jeremy.
“As long as the operator has configured the trailer correctly, as the truck moves off at a different angle, it causes a rotation in the slew ring up on the fifth wheel coupling, and that transfer of angle is picked up by mechanical cogs that are mounted to two encoders inside the teeth of the slew ring. That information is then communicated through the controllers with signals being sent via CANBUS to the individual steering rams,” he said.
“For a live demonstration trailer event in New Zealand, the Customer Day was very well attended. The majority of customers in NZ are smaller owneroperators, whereas in Australia our customers tend to be larger companies,” said Jeremy.
“We were really pleased to see between 30 and 40 customers in attendance, and we had 15 of our staff on hand to talk about the development.
The course instructors are seasoned professionals who will mentor course participants through real-life scenarios, preparing them for the challenges and responsibilities of a Crane Lift Supervisor.
Crane Lift Supervisors are in high demand globally. Completing this course enhances employability and opens doors to a wide array of job opportunities and career growth.
The curriculum covers a wide range of topics, including lift planning, load calculations, safety protocols, communication strategies, and legal compliance.
Scan the QR code to book in now
Melbourne 5-6 February 2025
Sydney 19-20 February 2025
Brisbane 5-6 March 2025
Perth 19-20 March 2025
Melbourne 4-5 June 2025
Brisbane 10-11 July 2025
Perth 16-17 July 2025
Sydney 17-18 September 2025
“We were able to demonstrate how the integration between the truck, the operator and the trailer work into one cohesive unit.”
We also had a number of customers attend from the South Island, which was really impressive. The Customer Day included a static display of the trailer and staff were able to highlight the various features and benefits, but customers really wanted to see the steering.
“We were able to demonstrate how the integration between the truck, the operator and the trailer work into one cohesive unit. We demonstrated how the remote control can override the steering and how to use the truck to dictate the crab steering. I think everyone was impressed with what they saw,” said Jeremy.
“We are actively building large modular ESS platform trailer systems for companies that require this type of technology, and at the moment, it seems to be in high demand from crane companies in particular - these include Borger’s, Max Services, Pollocks Cranes and Qube Heavy Lift.
“There are plenty of others that are seeing the advantages of our trailers because of the amount of infrastructure work they are involved in. For many of these projects, the lifts are in tight and confined areas and the ESS technology is ideal for these applications.
“The next step for Australia isn’t going to be a four by eight, it will be a five by eight ESS low loader. On the east coast of Australia especially, it’s going to be a lot more useful and that design will be ready over the next six to 12 months,” said Jeremy.
Justin Boehm takes a look at LEEA’s year, highlighting a number of stand out successes.
2024 HAS TRULY BEEN A MILESTONE year for LEEA in Australia and New Zealand. We’ve continued to set the bar high with our unwavering commitment to improving standards, promoting safety and fostering collaboration within the lifting equipment industry.
A significant highlight of the year was the expansion of LEEA’s training programs into Australia. This year, we teamed up with our Licensed Training Partners (LTP) - ATC Offshore and Tower Crane Training - to deliver LEEA’s highly regarded, globally
recognised training courses. Thanks to these partnerships, LEEA members can now offer comprehensive training to their lifting industry professionals, ensuring they are equipped with the latest knowledge and skills to maintain safety and efficiency during their examinations and inspections through their local LTP.
LEEA’s dedication to enhancing industry standards remains steadfast. In 2024 we’ve made significant progress in our work to raise standards, in particular through the
development of the Australia and New Zealand Technical Committee.
The inaugural LEEA ANZ Technical Committee meeting was a pivotal event for us, symbolising a new chapter for LEEA in the region. We are thrilled to announce Ashlea Johnston from Bunzl Safety and Lifting as the new Chair of the Technical Committee. Ashlea, with her extensive industry background, is a fantastic ambassador for our field. She will lead a committee of technical experts from across our industry,
“With continued focus on training, standards, and industry collaboration, LEEA is poised to lead the lifting industry into a new era.”
whose focus will be on renewing guidance documents for the local market, providing a unified voice in our representations to Standards Australia and offering expert knowledge to our global technical advisory team based in the UK.
This year Australian members were again winners at the LEEA Awards, held at the world-famous Dorchester in London. The LEEA Awards received hundreds of nominations from across the LEEA membership globally and Bunzl Safety and Lifting took out two awards – Sustainability Excellence and the Excellence in Safety awards. This is a significant achievement for our region and we should again commend our industry leaders for their commitment.
However, on top of all that, the crowning glory of the year was undoubtedly LiftEx on the Gold Coast. This two-day exhibition brought together global manufacturers, industry leaders and professionals from across the region. LiftEx Gold Coast was our first full-scale exhibition outside the UK and set a new standard for future events. The event attracted visitors from all corners of the country, as well as international attendees, providing a platform for high-level conversations, significant business deals and valuable networking opportunities. Exhibitors and attendees alike praised the quality and quantity of inquiries received, with many confirming substantial orders during the event. This success has spurred us to plan our next major expo in 2026.
Looking ahead, we’re gearing up for an even bigger year in 2025.
We’ll be introducing new products and revamped training programs for endusers of lifting equipment. Our training courses for lifting industry professionals will receive a fresh update. Additionally, we’ll be honouring our industry legends with a new annual award and ensuring that our industry stalwarts receive the recognition they deserve for dedication to our industry.
As we move forward, LEEA remains committed to its vision of lifting and height safety industries which have eliminated accidents, injuries and fatalities. Our dedication to promoting
enhanced standards and industry best practice, through our achievements of this year, are a testament to the association’s capability and the collaborative efforts of its members. With continued focus on training, standards and industry collaboration, LEEA is poised to lead the lifting industry into a new era.
As we look ahead to 2025, we are excited to continue building on our successes, driving innovation and fostering a culture of safety and excellence in the lifting equipment industry.
Over the past 12 months, Andromeda Industries has continued to make significant inroads in the local lifting and rigging industry. Experiencing significant growth in almost every state Geoff Bower, Andromeda’s Customer Relationship Manager, highlights the reasons for the continued momentum.
“THE LAST 12 MONTHS HAVE BEEN VERY good for the business, and we have definitely experienced a significant upsurge from a number of our resellers whilst others are generating a steady flow
“With all the activity in the resources sector, Western Australia remains very strong for us, and although we have seen a slight dip in demand from Victoria, Queensland has increased in activity to fill this void. Traditionally, Victoria has been our second largest market and although it has quietened down, all signs are it will bounce back early next year,” said Geoff.
Although Andromeda Industries services the market via a network of 100-plus distributors that includes major nationals as well as independent family businesses, all specialising in rigging and lifting equipment, Geoff and the team understand the importance of increasing the profile of the Andromeda brand and product range directly with end user
“This year we exhibited at both LiftEx Gold Coast, organised by the Lifting Equipment Engineers Association (LEEA), and The Crane Industry Council of Australia’s (CICA) National Conference and Exhibition in Adelaide. Both were very successful for Andromeda Industries and our brand. We’ve already received concrete orders from attending the
“LiftEx and the CICA Conference and Exhibition attracted different audiences. At LiftEx we were talking to our distributors who were either exhibiting or
hire businesses and Tier One construction companies.
“The CICA Conference and Exhibition was more focused on end users and again we spoke to most of the large crane hire companies as well as smaller family-owned businesses. We generated all sorts of enquiries, and it was good to reinforce that our products are designed, engineered and manufactured in our facility just north of Tamworth, in the New England region of New South Wales,” said Geoff.
Although the enquiries were right across the Andromeda Industries range
proved to be most popular with the crane sector.
The Dean-O is a sling produced by Andromeda Industries especially designed to provide a single lifting point under Ramshorn Hooks on large cranes. These slings can be made very short and creates a single point load to be attached and still maintain centreline loading. Unbalanced loads can cause the Ramshorn Hooks to skew on the rig centreline, potentially damaging the block assembly and wire rope. Andromeda manufactures the Dean-O Sling in capacities ranging from 11 tonnes up to 165 tonnes.
“The Dean-O Sling has been around for a couple of years, but it’s only recently that we’ve started pushing it. We had it properly displayed at the CICA event and it drew a lot of attention from some of the major national crane companies and also smaller crane hire businesses from all over the country.
“Companies we spoke with are really keen on it and with capacities ranging from 11 tonne to 165 tonne, the Dean-O Sling covers most applications. There are already a number of the Dean-O Slings operating in WA with the large crane hire companies. We also have some large tower crane companies using them on the east coast,” said Geoff.
The demand for the Dean-O Sling is being driven by the dramatic increases in crane capacities and by the construction industry moving down the path of modular construction says Geoff.
“The construction industry is moving to modular construction methods where elements of new buildings like bathroom and kitchens are built in offsite facilities, transported to site and then lifted into place. With infrastructure, the components in bridge construction for example, are getting so much bigger and heavier requiring these large capacity cranes.
“The Dean-O Sling was a concept designed by Raymond McLaren, the founder of Andromeda Industries, many years ago. He saw the benefit of a centralised lifting point utilising the Ramshorn Hook, rather than having multiple slings or Master Shackles with soft slings and a massive rigging configuration. Basically, we were able to utilise our Double-Ended Strops with a specialised Cast Steel Thimble that we designed and developed in-house to create a central lifting point for Ramshorn Hooks,” said Geoff.
“Basically, you can keep the Dean-O Sling on the Ramshorn Hook and interchange the rigging gear. If you are lifting with a 110 tonne capacity Ramshorn, you can fit smaller shackles and rigging gear to lift a one tonne crate, for example.
“The Dean-O Sling concept also originated because there were so many new people coming into the industry.
It was designed to simplify the rigging configurations using the Ramshorn.
“Crane companies have said you don’t have to interchange your hooks, which is time-consuming, labour-intensive and comes with a number of work safety-related associated issues. As with everything we do, safety must be paramount,” said Geoff.
Andromeda Industries has been designing, engineering and manufacturing large steel cables since 1972, providing some of the largest locally manufactured steel cable in Australia, as well wire rope
The construction industry is moving to modular construction methods where elements of new buildings like bathroom and kitchens are built in offsite facilities, transported to site and the lifted into place.
“Obviously we are recognised for our lifting and rigging products, but we also operate a rubber division and it would appear not many people outside of our local area know this.”
roofing slings are extremely popular in Victoria and Queensland, however they are not as well known in NSW, so it was great to be able to showcase the range.
“We had plenty of visitors to the stand saying, ‘So you are the guys that manufacture these products,’ which is great, because they are starting to put pieces of the puzzle together. The market is understanding that Andromeda Industries products are Australian designed and manufactured,” he said.
LiftEx and CICA’s National Conference and Exhibition provided Geoff and the Andromeda team an ideal opportunity to confirm to the market that there are two distinct aspects to the business.
“Obviously we are recognised for our lifting and rigging products, but we also operate a rubber division and it would appear not many people outside of our local area know this,” said Geoff.
Andromeda Industries’ Rubber Belt division is Australia’s leading supplier of re-purposed rubber belt and rubber matting products. Repurposing used belts minimises the environmental impact of ‘hard-to-dispose of’ materials, whereas recycling uses much more energy.
The main product from this Division is SPLITBELT which is created by the process of mechanically splitting the rubber belt using specialised machinery developed through Andromeda’s engineering division. The resulting SPLITBELT rubber matting is very strong and durable, whilst remaining lighter and easier to handle. With over 100 plus different applications, SPLITBELT is available in various lengths, widths and thicknesses.
“Our re-purposed rubber belt and new rubber matting products are not as wellknown as our lifting products, but there are so many applications for them. They
are being used by large crane companies as Friction Coefficients for ‘steel on steel’ contact surfaces which is now an important issue for the National Heavy Vehicle Regulator. Increasingly crane companies are recognising our rubber products are exactly what they need,” said Geoff.
“Our rubber mats are ideal for support trailers transporting counterweights or supporting hook blocks and other heavy lifting equipment. The mats sit between the steel surfaces adding to the stability of the load as it is being transported. Once again, a simple product that is designed with safety in mind for such critical industries.”
“Our rubber products also make a positive contribution to a sustainable future because we are positively repurposing very durable rubber products which are manufactured for tough environments and notoriously difficult to recycle or dispose of. There’s no need for either with our rubber products, they are ready for a new life in these types of Friction Coefficient applications. We are proud of the fact that our overall wastage is down to just 0.4% and we are continually working to reduce this further, ensuring a sustainable future,” he said.
Quality control (QC) is at the heart of Titan Lifting Technologies’ precision hoisting and lifting equipment, with industry knowledge and traceability as its non-negotiables. Titan Chief Operating Officer John Di Michele explains how the Bundoora-based company helps the industry lift with some of the most trusted materials on the market.
that can help the industry lift high capacity loads, the science of what sits between hook and load is a speciality of Titan Lifting Technologies.
The Australian company has designed and developed an extensive product range that spans the lifting, rigging, mining, shipping, construction and transport industries.
Specialising in chain and lever hoists as well as electric chain hoists and trolleys, the company has also designed lashing and loading equipment, load and lifting chains, shackles and ratchet straps, hooks and wire cable products.
John Di Michele said much of this equipment is manufactured overseas, adding that Titan works hard to ensure the product reaches the highest of standards before it enters the market.
“At Titan, we are proud to say we purchase from best manufacturers in China for lifting gear,” he said.
As the Australian agent for Wirop International, Titan not only sells these testers, it fully utilises its own machine to carry out testing.
“The lifting industry is stronglysafety oriented, whether it’s lifting something into a high-rise building, on a construction site, on an offshore petroleum rig, on the ship or restraining something on the back of a semi-trailer, it’s all safety oriented. It’s got to be safe. It’s got to be secure; so the product has to perform how it’s meant to perform, and also in an efficient way.”
Founded in 1998 as Allan Marketing Group but known colloquially as Titan Lifting, Titan’s journey began back in 1974 when founder and current
Managing Director, Ian Allan, moved from tools manufacturing with Bosch to working with an international lifting equipment company, PWB Anchor.
Ian’s investment in high quality, safe, reliable lifting equipment organically grew, resulting in the development of Titan Lifting Technologies.
John’s expertise in hoists and slings is the result of receiving Ian’s tutelage as well as many of his own visits to China, looking for the best products to bring back to Australian shores.
“The lifting solutions we provide customers with via our products is all knowledge-based.”
“We have a policy whereby we don’t buy anything from anywhere
overseas unless either myself or Ian have met the local manufacturers on the ground and have inspected the premises, their product and their processes - particularly in quality control,” John added.
John said the cost of this exercise is worth the knowledge attained.
“There is a lot of cost and time involved when we travel to our overseas suppliers, but we pick up new ideas which then turns into new equipment that we can be proud of.”
AGENCY BRAND PARTNERSHIPS IN LIFTING AND RIGGING PRODUCTS
Apart from their own brand, Titan also has a number of overseas agency partnerships such as Wirop
markings to ensure the products comply with or exceed Australian standards,” John said.
Once a shipment has passed Titan’s Quality Assurance (QA) process, relevant test documentation is filed according to batch numbers.
International, Van Beest Green Pin from the Netherlands, Tractel from France, and Probst from Germany.
Recently back from his annual trip to China and Taiwan, John explains how regular site visits help best inform his decisions when it comes to collecting information on current and future developments.
“Most of the factories we visit in China are ISO 9000 accredited and they are well organised too, with advanced machinery and robotics. This makes us feel incredibly confident about
the products we are bringing back to Australia.”
John explained that if the products are not up to Australian standards at the overseas warehouses he visits, then it’s not worth pursuing either the factory or products at all.
But Titan’s strict testing regime is quite extensive.
Once a batch of new products arrives at its facilities, John says Titan quarantines the shipment in the first warehouse until it undergoes a battery of comprehensive tests.
“Apart from testing, we then check factors such as the packaging and the
Titan’s traceability mechanisms are in place to ensure that in the incredibly rare situation where a product seems faulty, Titan can trace back all recipients of that particular batch of product and conduct further investigations, as well as tracing the products to the overseas manufacturer.
“It’s one of our biggest litmus tests,”
“If there are any issues out in the market, we can then go back to our factory and identify the batch number. Then they trace back to see what could
With high quality control standards and a list of well-designed and innovative products, Titan products are widespread across Australia, and also overseas.
“We have over 200 distributors in Australia and supply a broad range of
“We are in the business of helping businesses ensure their haulage or lifting systems are strong with our
distributors internationally, sending its reliable Titan products to 13 other countries, such as the USA, South Africa, New Zealand, Indonesia, Thailand, Malaysia and Fiji.
John said Titan’s approach has been recognised in the industry as incredibly diligent when it comes to quality and therefore safety upkeep.
“We’ve been told that we do more than what’s required to ensure our products are reliable,” he said.
“But I want to sleep at night knowing everyone goes home at the end of the day, and I know our products allow this.”
Over the past eight years, husband and wife team Ben and Jess Fitzgerald have put their hearts and souls into the family business, Queensland Rigging Hire. Financially, they continue to put everything on the line, firstly to develop and now to maintain their reputation as a successful, highly driven ‘customer service’ business. Ben discusses recent developments, how he and Jess have never forgotten their roots and how they continue to support local communities and initiatives.
“JESS AND I STARTED THE BUSINESS WITH basically nothing, but we soon realised that by working seven days, 60 to 70 hours a week, you can achieve anything. After years of blood, sweat, tears and sacrifice we are as dedicated as ever to making something of ourselves without losing focus on what really matters, and that’s providing the best levels of service, world class equipment, industry experience and knowledge to ensure we provide the right solutions to our customers, each and every time,” said Ben.
Like any new family business, the first few years were really tough, says Ben.
“Jess and I were raising our young family, working in the business fulltime and for a long time, we didn’t have $10 to rub together. But we never strayed from our fundamental beliefs of investing in good people, world class equipment and providing customers with the best possible service we could,” he said.
“We’re a service-based business. Our business isn’t just hiring rigging equipment, it’s service. Our customers ring not because they want to use us but because they need assistance, and they need suppliers to be reliable. Providing reliability is exactly what we do, and we do it well.
“They know they can ring us at the 11th hour, and we will deliver on what we promise. This lets our customers focus on what they need to do and not worry about the rigging element of their project. They know our equipment is of the highest quality, it is well maintained and compliant to the Australian Standards,” said Ben.
Although the first few years were tough, Ben and Jess’ belief in themselves and the
business was unwavering. They continued to invest in new equipment as well as the right people and gradually the business grew. Ben says that everything went up a few gears 12 months ago.
“A year ago, we started thinking about what was next, and how we could move forward. Again, we decided to effectively put everything on the line and reinvest in more people and equipment and ‘super charge’ the growth of the business.
“It was a high-risk strategy with our costs increasing substantially, and there were no guarantees. But the strategy has really paved the way for us to capitalise on the current construction boom, particularly in South-East Queensland,” said Ben.
“We invested in a lot of equipment, and we started saying yes to everything our customers were asking in terms of hiring rigging equipment. Today, there are
very few jobs we can’t help with. Because we were saying yes and employing more people, our previous premises could not accommodate the business.
“We have a few emerging industry leaders developing in our business, with our operations Manager Trey Yee currently studying a Certificate IV in Leadership and Management at the Australian Institute of Management to up his level of skills. We hope at some stage Trey can take over the running of the business. We also have Claire who over the last 12 months has project managed the integration of our hire program Syrinx, which has enabled us to control our assets much more efficiently, including maintenance and delivery scheduling. Claire is quickly becoming a huge part of our business, and we can see a very bright future for her at Queensland Rigging Hire,” said Ben.
“We had grown to a team of nine and we were literally on the top of each other and with so much equipment we were aware that we needed to minimise the Occupational Health and Safety risks and started looking for a larger premises,” said Ben.
It took approximately eight months for Ben and Jess to find the right facility.
“We looked at building a bespoke premises with overhead cranes etc., but we’re self-funded and it is our bank account that has to pay for it all, so we had to find a compromise with a facility that provided a lot more space but was still economically affordable.
“We’ve moved into a much larger facility in Willawong which is only nine minutes from our old location. It features 1200 square metres of warehouse and we have already added an additional 160
square metres of mezzanine as a part of the fit out. The new facility provides a much safer working environment and enables us to continue to grow and fill the gaps in the market,” said Ben.
Jess and Ben are committed to the continued investment in the team and new equipment.
“We have always recognised the importance of training our team and over the next three months, we’ll have another four team members taking their Dogging and Rigging tickets. It’s important for the team to understand who we are and what we do. Training helps them understand how our business works and the challenges our customers face,” said Ben.
“We treat our team like family, and it is no coincidence that in our eight years only one member has left us, and he came back! We look after them, we organise barbecues and lunches, celebrate birthdays and go on camping trips together. We attend social events and have big Christmas parties, we try to make it feel like a ‘work family’.”
more accurate, which is really important to square things up,” said Ben.
“We’ve also invested in a 40m lattice beam spreader bar which is the first in Queensland available for rent to the open market. It’s taken me many years to finalise the design and the best part about it, is that it’s designed to fit in an open top 40 foot shipping container and can be transported on one single trailer. No other lattice beam spreader bar in Australia can do that. It is Australian designed and Australian manufactured by Maxirig in Geelong.
“We’ve also added some more JDN air hoists in 16 and 20 tonne capacities and they’ve all been converted to wireless remote control, in-house by our own technicians. We’ve also added a couple of Ingersoll Rand five tonne air winches to the fleet,” he said.
Social responsibility and local community engagement remain high priorities for Jess and Ben. Because they come from humble, working class backgrounds, ‘battling’ is in their DNA and wherever possible
“We’ve also invested in a 40m lattice beam spreader bar which is the first in Queensland available for rent to the open market.”
Investing in the latest technology remains a key business strategy for Ben and Jess. A recent and significant investment has been in an Enerpac Synchronous Hoist System. The Synchronous Hoist System is a below-the-hook sling adjuster (hydraulic turnbuckle) which typically includes multiple specialised hydraulic cylinders mounted directly in-line with the rigging which provides the operator the freedom to precisely monitor and adjust each lifting point independently. The system enables a single crane to precisely position heavy and unbalanced loads.
“This system will open up so many doors around in the engineered heavy lifts space, where accuracy is absolutely essential. In a nutshell, they’re hydraulic turn buckles that can be extended or retracted under load, so that you can adjust your rigging weights up to a metre and a half before you position your load. You can get things balanced, and
communities and deserving causes. An example of this is the support they offer Justin Clements, a Masters boxer who works on the Cross River Rail project.
“We see Justin a lot through business and he’s competing in the Pan Pacific Masters Boxing next year. We’ve sponsored him over the last three or four years, basically since we’ve known him, and we’ve provided a healthy donation to help pay for his costs and enable him to concentrate on his training.
“He’s 53, and he gets the gloves on, and pushes hard. He’s actually fighting later this month for Men’s Mental Health raising money for charity. He’s bloody upstanding, decent person and it’s easy to get behind someone who’s a likable fella and good person. He always wants the best for people and wears his heart on his sleeve, and we are very happy to get behind him,” said Ben.
Jess and Ben have just renewed their sponsorship relating to the Beaudesert Kingfishers Rugby League Club footy shirts. Beaudesert is a working-class country town, where little things go a long way. The footy club is an important part of the community, says Ben.
“A few years back, we donated over 400 training shirts to the club so that every single kid had one to train in. It was a really
big success. As a kid personally growing up, we didn’t have a lot of money, so when I played footy, and we got a shirt, that was the only shirt that I wore for a whole year, because you valued it so much. You’re part of a club, part of a team. I think it’s really important for kids to have that feeling as well,” said Ben.
“For the last couple of years, we’ve sponsored three age groups with jerseys including the little fellas, the juniors, and we’re going to sponsor them for the next couple of years. We also sponsoring the under-16 girls, and couple of the other teams. They’re the ones that are the underdogs and coming up in sport and we want to give them a hand as well,” said Ben. Sailing program Sailability is another cause close to Ben and Jess’s hearts.
“One of our best mates’ family is part of the Warwick community (about 130 kilometres south-west of Brisbane) I doubt
there is anyone in that community who would not know his brother Leigh, he’s a bloody legend. Leigh has Down Syndrome and their family have been strong advocates for disability support for the 25-plus years we’ve know them
“We were talking one night and he mentioned the charity Sailability and how it was designed to get people with disabilities onto the water, and teach them how to sail. He explained they needed shipping containers to store the boats in. We instantly organised and paid for one, had it painted to their specifications and had it delivered to the Leslie Dam near Warwick.
“Sailability is a national program with lots of different locations and having one in the bush on the Leslie Dam provides a lot of people with challenges, who live nowhere near the ocean, the opportunity to learn to sail. we think it’s a great thing,” said Ben.
MAXbase Equipped
The GMK4080L is an outstanding four-axle taxi crane that, with its 60-meter-long boom, offers both the longest boom and the lowest gross vehicle weight in its class. Within 10 t per axle, the crane can carry 5.2 t counterweight and even 13.3 t counterweight with 12 t axle load.
•60 m boom length and capacity matches the 90-100t class (4.8 t @ 60 m)
•Main boom: 11,3m - 60m, 7-section
•Bifold swingaway jib: 8,7 m /15 m (optional)
•Minimum width 2,55 m and overall length 12,82 m
•Carrier cab: Latest generation of Grove carrier cabs
•Increased safety and flexibility with MAXbase variable outrigger system
•Faster Intuitive set-up with CCS (Crane Control System)
•Engine: Mercedes-Benz OM470LA, 300kW
•Capacity: 80 t
•Main boom: 60 m
•Maximum jib: 15 m (0°-40° luff)
•Maximum tip height: 77 m
•GVW: 48000 kg 3
Bylor partners with Modulift to supply custom lifting equipment to Hinkley Point C.
manufacturer Modulift is facilitating civil engineering installation works at Hinkley Point C, the first nuclear power station to be built in the United Kingdom in over a generation.
One milestone moment saw the 730-tonne reactor cavity precast pool installed with Modulift underslung
beams and “Big Carl,” the world’s largest crane, at the Somerset worksite.
BYLOR, a joint venture of Bouygues Travaux Publics and Laing O’Rourke, is the contractor delivering Hinkley Point C’s main civil engineering works. Appointed in 2022 due to its ability to innovate and modify beyond standard lifting equipment, Modulift
has delivered bespoke lifting systems tailored to the unique demands of this major infrastructure project. Sarah Spivey, Managing Director at Modulift, said “All lifting equipment is precisely designed using state-ofthe-art engineering technology and Finite Element Studies. By leveraging our engineering expertise and 20+
“Modulift custom lifting beams play a crucial role in the ongoing construction of Hinkley Point C, supporting the installation of key infrastructure elements.”
years of experience in the nuclear sector, we ensure all lifting equipment adheres to rigorous UK compliance standards such as BS EN. We are proud to be part of such a critical energy infrastructure project”.
Artur Osicki, Temporary Works Lead at Bylor said “Modulift custom lifting beams play a crucial role in the ongoing construction of Hinkley Point C, supporting the installation of key infrastructure elements. Modulift’s reputation for precision engineering and quality assurance
provides us with the confidence that all equipment complies with regulations for the UK market. Each custom piece of equipment comes with comprehensive User Instructions ensuring safe and efficient operations on site.”
Once complete, Hinkley Point C is expected to deliver zerocarbon electricity to approximately 6 million homes, solidifying its place at the forefront of the UK’s clean energy transition.
For more information about Modulift visit https://www.modulift.com/
Big and intricate lifts across major Australian infrastructure projects is the strength of Alliance Engineering Consultants (AEC). The AEC team joins Cranes and Lifting to look at some of the greatest moments and challenges that have shaped this Western Australian company.
WITH ABOUT 150 YEARS OF COMBINED experience, the talented team at Perthbased Alliance Engineering Consultants (AEC) specialises in the design and installation of innovative structures and lifting equipment in the offshore oil and gas and onshore civil construction industries.
This covers everything from the engineering of lifting and rigging systems for offshore and onshore brownfield projects, as well as front-end engineering design, detailed design and verification of diverse systems and management of civil/ structural projects.
Since AEC Director and Chief Engineer Jeff Kazazi founded AEC 30 years ago, the consultancy has worked with major civil construction companies such as Laing O’Rourke and resources companies including Woodside, BHP, Inpex, Santos, Shell and Rio Tinto on some of Australia’s most important projects.
In recent years, alongside work on the Inpex-run Ichthys LNG plant in Darwin and many of Woodside’s offshore facilities, there has also been a wide list of unconventional jobs and lifting solutions that have come AEC’s way.
Surprisingly, adventure parks and ziplines are now in the AEC portfolio.
The team has used air skates to navigate equipment successfully into position with
only minimal clearance, designed remedial rigging to lift large odd-shaped structures into place at gas plants and concept designed 860m-long zip lines proposed for Mount Buller in Victoria’s snow fields.
AEC started off with Jeff alone in a small office, but today boasts nation-wide recognition with a strong staff list of 15, 11
of whom are university qualified engineers.
As with most start-ups, cash flow was a challenge in the very early days, he recalls, with the cost of securing a commercial property and fitting it out with the latest equipment another hurdle “that required steady nerves.”
“Technology changes – including regular IT upgrades – rising office and insurance costs and the odd client who goes
he said.
But one of the hardest lessons came when Jeff decided to help an old friend with the installation of some equipment into his fourth-floor apartment.
“I detailed a bespoke lifting system, bought the steel and rigging units and used my team to install it all. And just as we finished installing the lifting structures, the client called me and said, ‘take it all away!’. We suspected that he had not advised the strata manager regarding approval from the system.”
Jeff said the friend ‘had found another option’ after AEC had installed all the necessary gear. “We were left ‘holding the baby’.”
“You end up moving on, despite it being a bit painful… I moved on fairly quickly and realised that it’s all a lesson for later; I pass on these lessons to my team,” Jeff explained.
“I’ve learnt that if you really want to make sure you’re not going to get caught out, you’ve got to have a purchase order in place before progressing. Most reputable companies insist on this process anyway.”
The structural engineering design
Today’s range and scale of jobs is an indication of how far AEC has come since those early days.
AEC was engaged to perform verification works for the installation of four large valve platforms on the roofs of the liquefied natural gas (LNG), butane and propane tanks at the Ichthys LNG plant in Darwin.
The US$67 billion project required AEC’s expertise to help lift the valve access platforms onto big concrete tanks listed at approximately 30 metres high and 60m in diameter. The initial design by others had failed and the client was in need of urgent help.
These valve access platforms can exceed 400 tonnes and their shapes are not symmetrical.
“The whole project involved highly critical lifting and engineering procedures, so we had to make sure the physics was perfect and the tolerances carefully chosen,” said Jeff.
The project was a highlight for AEC, as the engineering team leant on its high-performing problem solving skills
to resolve the issues in front of them and provide solutions to safely execute the lifts.
Jeff said he is very proud of the team’s efforts pertaining to those lifts.
“Our team in the office and onsite executed everything to the highest standard, they did a really good job,” Jeff said.
“At AEC, we’ve got a bit of a reputation for ‘pulling a rabbit out of a hat’. We believe there is no job too technically difficult that cannot be solved.”
For AEC’s Principal Structural Engineer Len Sgherza, who has been with the company since 2005, the consultancy’s willingness to take on new opportunities is an ongoing gift.
“The company is at an optimum size to be able to provide a rapid response to clients in need and we are often their first call in preference over much larger consultants who can be slower to engage and activate, and they don’t work on weekends!” Len said.
“AEC’s ‘can do’ approach, led by Jeff’s drive and enthusiasm for a challenge, has brought countless diverse and rewarding jobs to our playbook.”
While this has included work as far afield as China, Canada, Singapore and
“At AEC, we’ve got a bit of a reputation for ‘pulling a rabbit out of a hat’. We believe there is no job too technically difficult t hat cannot be solved.”
as rewarding, especially those where the team is involved every step of the way.
“One example of this was the Cliff Head A Platform offshore from Dongara, Western Australia, where I was involved in the initial offshore survey then development, design, fabrication inspection, onshore trials and offshore installation of a large skidding and pulling system,” he said.
AEC designed and supported the fabrication and installation of a bidirectional skidding system for a temporary hydraulic workover unit (HWU) and laydown area onto the Cliff Head A platform off the coast of Dongara.
The entire system was installed using the platform’s existing 20t WLL crane, with AEC providing full implementation support including detailed installation workpacks, lift plans and attendance during fabrication,
trial assembly and offshore installation.
The HWU system was installed on the facility over a period of three weeks, operating for another 10 until it successfully completed its work scope and was demobilised to Dongara for storage until it is next required. The client was able to increase production due to this system.
Reflecting on the strength of the wider AEC team, Len can’t help but look back to the early days of his career.
“I first worked with Jeff Kazazi way back in 1990 when he hired me as a graduate structural engineer, when he was Supervising Engineer at Dawson Engineering,” he said.
“Way back then he was already known to be very generous in sharing his patience, work ethic and wisdom with his team.”
Len says little has changed with the way the wider AEC team has evolved since he joined the team in 2005.
“Jeff has built a dedicated and diverse team at AEC, taking each new member under his wing and bringing them into the fold,” he says.
Some AEC staff are out on site most days, assisting with directing major lifts performed by cranes and gantries.
If they’re not there, they are in the office, designing lift plans for incredibly large objects.
These include energy production topsides, steel trusses and most major components of infrastructure involved with mining and oil and gas shutdowns in Western Australia.
AEC Lead Designer Lee Ferguson says that finding safe and effective solutions to tasks “deemed practically impossible” is one of his favourite aspects of the job.
“Each team member has strengths they bring to the challenge which have been honed through decades of experience and each has a true passion for the technical and practical aspects of our engineering, 3D modelling and laser
scanning skills,” he said.
Lee also praised the extra opportunities that come with being part of a smaller team – allowing greater exposure to the entire engineering process which, he said, has helped him develop as a designer.
AEC Senior Structural Engineer Melvyn Lim agreed, saying working at AEC has given him access to myriad work scopes and experiences.
“At AEC, we are given the autonomy to fully manage our projects from cradle to grave. We take ownership of the work scope in all aspects of the job from quoting to close-out,” he said.
“Rather than just focussing on the engineering aspects, this provides opportunities for a holistic development of the individual not only on technical engineering expertise but also critical thinking and management.
“Assistance and advice are also readily provided by seniors at AEC when help is sought, often obliging and setting aside precious time during the day amidst their workload to assist – whether it be meetings to bounce off ideas for a complex engineering design, carrying out independent design checks or queries on engineering analysis software, just to name a few,” he said.
For AEC Civil and Structural Engineer Yasmin Santana, her two and a half years at the company so far has seen her participate
in the initial scope of work, advise clients on the most effective approaches and engage in the design and calculation phases of a series of projects.
“I’ve also had the opportunity to be hands-on during the installation and fabrication stages, where we manage the delivery of proposed materials, conduct proof load tests and assist clients through the installation and construction phases,” she said.
“For an engineer, there’s nothing more rewarding than seeing your designs come to life. This experience has not only helped refine my design approach but has also given me valuable insights into overcoming construction challenges. It also allows us to apply lessons learned and drive improvements in future projects.
“AEC is a truly multicultural company, and as a young female migrant engineer, I’ve always felt welcomed and supported. The word ‘team’ perfectly captures the spirit of AEC—collaboration and mutual support are at the core of our work,” she added.
Among the AEC team, Jeff’s generous attitude as a mentor, advisor and supporter are mentioned repeatedly – with staff praising his passion and dedication to the job.
“He fosters a culture of openness, where new ideas are welcomed, and experimentation and innovation are
encouraged,” Yasmin said.
“We don’t work for him; we work with him.”
For Jeff, building a successful company has been a joy in and of itself, with many of the team having worked there for over ten years.
“Growing a team of valued and competent people has been very satisfying – and seeing their families grow over time is also rewarding,” he said.
“My trepidation over starting an engineering consultancy 30 years ago was soon overcome by the rewards that came from successes - and also the learnings from inevitable challenges.”
“I was warned early in the process that if a company cannot survive the first three years, then it was likely to fail. It is not by ‘luck’ that AEC has continued to operate for 30 years!
Instead, it’s the ability to learn from the past, to embrace the future and to always look for new challenges – and set out to meet them.
“Having a broad range of clients who appreciate what we do and are willing to work with us enables positive outcomes,” he said.
“The flexibility to take on very varied work scopes by choice is liberating. I’m also very proud of every member of the team who contribute at AEC and also lucky to have their support.”
Excellent Lifting Performance
· Max. lifting capacity of fully extended 6-section 65 m main boom is 15.5T
Innovative plate boom head and compact boom tail features the optimized overlap ratio and stronger lifting capacity.
· Max. load moment of basic boom is 5220kN.m, max. load moment of fully extended boom is 2840kN.m, both of which leads the industry
Great Adaptability
· Adaptable to various uneven ground construction sites, capable of construction on terrain with a maximum slope of 4°
· Equipped with four-stage grading counterweight function, providing a no-counterweight operation mode, more suitable for soft ground auxiliary hoisting in wind power field
Convenient & Cost-effective Transportation
· The crane width is less than 3.6m when fully retracted, allowing it to self-load onto and unload from a flatbed truck
· Only 2 flatbed trucks are required for short-distance transportation, involving disassembly of counterweights with no vehicle body pressure
Telescopic crawler crane
TELESCOPIC CRAWLER CRANE
ZCT160V5
ZCT300V4
ZCT300V5-1
ZCT600V5
ZCT1000V5
ZCT1200V6
ZCT1500V6
The Crane Industry Council of Australia’s (CICA) National Conference and Exhibition saw the management team from Zoomlion Mobile Cranes in attendance. Cranes and Lifting spoke to Mr
“FOR THE PAST FEW YEARS WE HAVE BEEN designing, engineering and manufacturing our products, including all terrain crane products, crawler cranes and truckmounted cranes, specifically for the Australian and New Zealand markets,” Mr Chen said.
“We see these markets as being very important because they have the highest levels of compliance requirements and meeting these will provide a pathway to the Australian markets. We are determined to show the Australian and New Zealand markets that Zoomlion is committed for the long term and we are confident our products will be recognised for their quality, performance and reliability.”
Mr Chen went on to discuss how Zoomlion intends to service the growing
population of products in the Australian market. In the past, Zoomlion has relied on distributors for market presence and product support - but recently Zoomlion has invested directly in new facilities and its own direct-to-market representatives.
“For the past few years, we have been proactively seeking distributors locally to be our business partners, and this includes partners like Nationwide Machinery and Gleason Cranes. We will continue with this strategy and support our distributors by appointing technical sales staff to help educate the market about the quality and diversity of Zoomlion products.
“We are also investing in facilities across the country where we will hold spare parts to ensure we are providing the best possible support for our products. Zoomlion and
our distributor partners have the same goal and that is to grow market share. We understand this will take time, but as I’ve said, we are here for the long haul,” said Mr Chen.
With the crane industry evolving and manufacturers examining alternate fuel options, Stone Su, Deputy Director of the Marketing Department for Zoomlion’s Mobile Cranes Overseas Company, explains how Zoomlion is engineering and manufacturing mobile cranes designed to contribute to a carbon-free environment.
“We are all working towards Zero Emissions 2050 and Zoomlion has been designing and manufacturing mobile cranes with all types of new energy sourcesincluding battery powered electric, electric plug-in and also hybrid.
“We have launched our 40 tonne battery electric Rough Terrain crane and we have already received orders for our 85 tonne Crawler crane. We have been working on new energy solutions for some time and we have sold units into overseas markets. For Zoomlion, it is not a problem to design and manufacture cranes with ‘green power’ technologies,” said Stone.
Stone explains how Zoomlion has manufactured battery electric all-terrains whilst managing the extra weight a battery brings.
“Our design engineers have been working with the battery as a counterweight to reduce the overall weight of the cranes and they are also working on technologies
that will reduce the whole weight of the machine. We are also developing movable batteries which will be transported to a site and will charge and recharge the EV cranes.
“We are also working with the manufacturers of industrial batteries and seek a new generation of advanced batteries which will enable the EV cranes to travel to site and work for longer hours without the need to be recharged,” said Stone.
“As Mr Chen mentioned, our commitment isn’t just from a design and technological perspective relating to our products. We are investing in new technologies in our manufacturing processes which will reduce our carbon footprints. Zoomlion has a clear 10-year plan relating
to our manufacturing processes as we aim for zero emissions by 2050,” Stone said.
“An example of this are the solar energy systems we have installed on the roofs of our 1,000 acre ‘Smart City’ manufacturing facilities. These systems are generating enough energy for Zoomlion products to be manufactured by renewable energy rather than energy generated by burning fossil fuels. We have a surplus of energy which we sell back to the grid. We have invested the equivalent of A$7 billion in our state of the art ‘Smart City’ manufacturing facilities,” said Mr Chen.
Deputy General Manager of Zoomlion International Mrs Freya Huang said the company planned to provide the Australian
and New Zealand markets with products and capacities they are familiar with.
“We want them to see the quality and experience the performance of our products. Once we have customers comfortable with the brand, we will bring in larger capacity cranes.
“We will demonstrate our capabilities to the market. We recently released a 4,000 tonne capacity all terrain which I’m sure would impress many in Australia. We will be using the local media to highlight these developments and we need customers to really feel and see the products.
“We will have product in our premises across the country. We have just opened a new facility, our head office in Melbourne and we are opening a branch in Adelaide next year. This means we will be operating five branches in Australia.
“We will also invite customers to our ‘Smart City’ manufacturing facilities where they can witness our comprehensive product range first hand. We will also encourage them to visit our stands at Shanghai bauma and Munich bauma. For these international events, Zoomlion has large stands where we display the latest products and technologies. Obviously, the other major manufacturers are there -
as a research institute owned by the state, today Zoomlion is the home of construction machinery in China. For the past few decades, our efforts have been focused on the Chinese market because, as you will have seen, the Chinese economy has experienced rapid growth year on year for the past three to four decades.
“With our focus on the Chinese domestic market we didn’t really examine the global opportunities until relatively recently. But since we decided to expand our global presence, we have established more than 30 subsidiaries around the world that could cover more than 140 countries and we have over 5,000 employees overseas,” said Freya.
“We have been establishing our global footprint for the last 20 years and over the last three years, our sales revenue from overseas markets has been growing by 50% every year - and in some years, like last year, it has grown by 100%,” she said.
“This growth is as a result of our ‘Localisation Strategy’ where we engineer and manufacture products that are compliant to Australian Standards, for example, and we employ local people to support this product. This year, as you know, we have established branches in Melbourne, Perth, Sydney, and Brisbane
Managing a supply chain is complex. With shipping delays still causing significant issues, it takes a cool head to manage the day-to-day challenges. Alex Coleman is the man for Liebherr Mobile Cranes.
HAVING STUDIED ECONOMICS AT university and majored in Supply Chain Management, Alex joined Liebherr on an internship two years ago. It was meant to be for six months, but seeing the difference Alex was making to the business, Liebherr’s General Manager Mobile Cranes, Andrew Esquilant, quickly decided to make the position permanent. Alex takes up the story.
“Because we had such a large quantity of machines coming into the country, Andrew recognised the need for someone to manage the transport, logistics and shipping elements of the business. 2020, 2021 and 2022 saw significant delays due to the COVID-caused shipping congestion issues all around the world, and with these issues now easing Andrew wanted our supply
chain to be as streamlined as possible,” said Alex.
He goes on to explain what the role entails on a day to day basis and how Liebherr and its customers benefit.
“Basically, I track where everything is, every single day. I know when a crane is about to leave the factory and when it does, I know where it is from that point on. This enables me to confidently advise the sales team about how the crane’s shipping journey is progessing, and they relay this information to their clients which enables them to better plan for the arrival of the crane,” said Alex.
“I also work closely with our Customs Brokers to see how we can lower our overall costs of importing machines and what are the best ways to do this. I liaise with the
Port Authorities on how we can effectively move our machines off the port as well.
“The last 12 months has seen a transition to our new Custom Brokers, and we have also implemented new transport partners to ensure we are dealing with the right service providers most experienced to handle our machines. Obviously, they are expensive pieces of equipment and we want them to be in the best hands as possible at all times,” he said.
When a crane leaves the German factory and is loaded onto the ship, all the relevant documentation is sent to Alex. He forwards this paperwork to the Customs Brokers and to Government Authorities including quarantine officials.
“From that point it’s about engaging our transport partners. If it’s a larger crane
we are engaging with the port to ensure we have right crane teams onsite when the crane arrives. We try to ensure our customers have a say in how the larger cranes are handled when they arrive at the port. If a customer has bought a really large crawler or all terrain, we’ll make sure they’re engaged to see if they want to manage the cranage. The whole process is designed to ensure the new crane is delivered to one of our facilities in perfect condition,” said Alex.
Alex explains how he works in with Liebherr spare parts team when required.
“There are occasions where I work with the spare parts team. Although they have their own system and a lot of their parts are containerised, there are scenarios where we work hand in hand. This has happened with the arrival of a crane where a large component has been shipped with it. The sales team also orders in large parts on behalf of customers who have bought a new crane and they get a project where additional boom sections might be needed, for example, or additional counterweights are required,” said Alex.
Alex goes on to discuss the challenges presented by the Department of Agriculture, Fisheries and Forestry’s
machines and we’ve introduced a number of strategies recently to better comply with the regulations. We had a really good result recently in Queensland, where we bought in a large machine with over 50 line items. Only eight ended up requiring a re-clean, which was really positive.
“That is as a result of the reports and strategies we’ve developed as the Government and DAFF are increasingly putting more pressure on this side of the ledger. They are flagging for the smallest little bit of dirt and dust or anything like that around. So, we do have a pretty extensive cleaning regime occurring in Europe. We also have some really good cleaning suppliers here in Australia and we can mobilise them to make sure machines are quickly cleaned if there is an issue with DAFF,” said Alex.
Overall, Alex is happy with the feedback he is getting from customers.
“At the end of the day, customers now know they can call Liebherr and get a definite answer on when their crane is going to arrive. Customers enjoy the fact that Liebherr is actively working with the ports to bring these machines in and that they’re not left in the dark. I think customers enjoy seeing their machine in
“Customers
enjoy the fact that Liebherr is actively working with the ports to bring these machines in and t hat they’re not left in the dark.”
Alex tracks where everything is every single day. He knows when a crane is about to leave the factory and when it does, he knows where it is from that point on.
The Grove GMK6400-1 will be upgraded to the GMK6450-1 and carry an increased maximum capacity rating of 450 tonnes, which is 50t more than the previous GMK6400-1
“OVER THE PAST TWO YEARS, WE HAVE seen a growing demand for a name change from our global customer base. We reviewed the crane’s performance, which resulted in a new model, the GMK6450-1,” explained Andreas Cremer, Vice President Product and Project Management for Mobile Cranes at Manitowoc.
The addition of the MAXbase™ variable outrigger positioning system on the GMK6400-1 in 2021 allowed customers to further capitalise on the
all-terrain crane’s strong performance. This feature allows the use of asymmetrical outrigger setups and results in enhanced load charts. In addition, MAXbase can be used in conjunction with the capacityincreasing MegaWingLift™. The selfrigging attachment can be deployed in less than 20 minutes and does not require an assist crane. MAXbase increases lifting capacity by up to 70% on the main boom and by up to 400% when using the luffing jib. These enhancements led to customer requests to rename the crane.
The Grove GMK6450-1 offers segmentleading lifting capabilities and has been used on projects in place of seven-axle - or even eight-axle - all-terrain cranes. For example, it can lift 8.9 tonnes between 38 metre and 50 metre radii when working with its full boom and jib system length of
With amaximum capacity rating of 450 tonnes, the Grove GMK6450-1 can carry 50 t more than the previous GMK6400-1.
136m. When working with 120 m of boom and jib, the crane handles an impressive 12.8 t at distances between 36 m and 52 m. Furthermore, the GMK6450-1 is particularly well suited to wind power projects that require flexible set-up distances to the turbine and the ability to lift heavy loads at steep vertical angles. It can lift in wind speeds of up to 9 m/s with its 79 m luffing jib.
The Grove GMK6450-1 also offers the exciting Grove CONNECT digital platform that provides owners with real-time access to fleet data. Through Grove CONNECT, fleet managers can get instant insights into the crane’s performance with just a couple of taps on a screen. Service technicians are supported with remote, optimised troubleshooting, reducing the frequency of onsite trips and strengthening preventative maintenance programs.
The digital platform enables remote monitoring through an app-based system, providing owners and operators with the ability to view real-time crane information.
The versatile platform advances fleet management, boosts sustainability, streamlines service and maintenance for users and improves connectivity to cranes with the easy-to-use platform working across smartphones, tablets and laptops.
The GMK6450-1 remains the strongest all-terrain crane available on six-axles and renaming it better reflects its true capabilities.
Helping crane and heavy lift companies get closer to decarbonisation on the jobsite, Tutt Bryant offers three types of power systems through its Go Green Initiative: including battery energy storage systems in both mobile and containerised form factors, supported by renewable charge capabilities or the latest in Tier V Emission Compliant diesel generators. Tutt Bryant’s National Business Manager for Sustainable Products and Innovation, Chris Leahy, explains more.
FOR THOSE IN THE LIFTING INDUSTRY searching for a way to reduce emissions, Tutt Bryant’s Go Green range offers a series of cost-effective and solution-based options.
The LifePO4D Hybrid Power System, the Sany Mobile Battery Energy Storage System (BESS) and the AJ Power Tier V generator range give customers the best of both worlds – offering high levels of power with a reduced carbon output, complete with synchronisation capabilities.
With the primary advantage of delivering power to where it is needed, rather than bringing the crane to the power source, Chris explains the impressive benefits generated from Tutt Bryant’s Go Green trio of sustainable products when paired with the electric cranes currently in the market.
“Previously, if you wanted to buy the equivalent electric crane you might need to pay a significant price premium, which came with limited autonomous movement before you need to recharge,” he said.
“Today, the price delta has been greatly reduced and importantly, the crane will provide the same level of output; same operational hours and same levels of power as they would receive from a diesel hydraulic crane. The numbers are impressive, for just 2.1 hours of charge time, the Sany 40T EV crawler crane will operate for nine hours.”
allows customers to save significantly on their diesel costs, Chris said, if switching entirely to electric powered units is not an option.
“Based on the proven efficiency of the Go Green rage, we know this is a strong commercial proposition for our crane customers.
Charging these electric cranes with either AJ Power’s Tier V cleaner diesel generators, the LifePO4D hybrid power system or the Sany BESS complements that greener approach, he said.
“From my experience with our Go Green range, we’ve found that noise pollution and emissions pollution are significantly reduced when using these products,” he says.
Go Green product efficiency also
“We’ve seen construction sites running diesel generators, 24/7, 365 days a year and what we’re saying to them is, there are solutions to ‘turn your generators off,’ – as some of these generators could be using 100 litres of diesel an hour,” he said.
Chris also explained how reducing diesel consumption can lead to significant cost reductions, especially for metro Melbourne sites.
“In metro Melbourne we can save up to about $800,000 in diesel alone on
Above: With rapid charging capabilities, the 210 kilowatt hour/110 kilowatt Sany BESS is a mobile charging station, compatible with equipment that can charge while in operation, such as the Sany EV Cranes.
tower cranes over two years, by integrating sustainable products,” he said.
SANY BATTERY POWERS YOUR EV CRANE
Tutt Bryant customers get the opportunity to purchase a Sany BESS mobile charging station when they buy a Sany EV crane, such as the SCE800TB-EV.
With rapid charging capabilities, the 210 kilowatt hour/100 kilowatt Sany BESS is a mobile charging station, compatible with equipment that can also charge while in operation, such as the Sany EV Cranes.
The principle is to charge the BESS at a fixed power location, then deploy the mobile
For companies looking for a safe
“Whether it’s a charging plant, running site offices, running small communities, that’s the idea. It’s one box turns up, you drop it on site, and you’ve got a full solution to your powerless problem.”
BESS in field as required by the crane or other mobile plant.
To encourage carbon abatement activities, the Australian Government provides incentives called Australian Carbon Credit Units (ACCUs), which are a tradable financial product.
Eligible Australian Carbon Credit Unit (ACCU) Scheme projects can earn ACCUs when they reduce or avoid emissions –incentivising carbon abatement activities through projects ranging from reforestation to energy efficiency.
ACCUs are an additional income source for individuals and businesses running ACCU Scheme projects – and systems like the Sany BESS jump off the page as a feature crane and heavy lift professionals would not want to go without.
“Charging your Sany crane with a
mobile battery will contribute to the carbon offset, allowing operators to work within their carbon limit without having to purchase carbon credits,” Chris said.
The AJ Power generator system is ideal for those who have partial-to-no access to the power grid in their area, off-grid or fringegrid customers, such as those on a farm or for remote projects.
“The upside to AJ Power’s generator range is that AJ Power is a progressive brand that has really bought into sustainable products,” said Chris.
Tutt Bryant’s AJ Power range comprises 48 different diesel generators boasting different power options – from 10 kilovoltamperes (kVa) through to 3 megavolt-
amperes (MVA) – to suit a variety of applications.
All the generators are powered by class leading engines renowned for their durability and low fuel consumption, such as Mecc Alte, Mitsubishi, Perkins and Scania.
AJ Power also offers options for specific installation requirements, including acoustic canopies, bunded fuel tanks, advanced controllers and remote controlling, while its weather protective unit is fully galvanised in a steel enclosure, coated in highly durable polyester powder paint.
Chris said that in his experience, most crane, construction and heavy lift companies are aiming to use products that are more environmentally friendly – and despite the desire for batteries, there is always a need for diesel backup support.
“AJ Power helps bring all the hybrid technologies together,” he said.
Chris also explained that in most cases, customers cannot make an instant switch from fully diesel-powered units to completely electrical-powered operations, as there is still a need in many cases for diesel power to support either the transport or mobilisation of sustainable products.
“With customers that want to quickly make the switch, we tend to remind them that it is a journey, and that AJ Power products are very good at contributing to the transition.”
LIFEPO4D: COMBINING THE OLD AND NEW WITH SOLAR ENERGY
For companies looking for a safe and sustainable solar power generator, the LifePO4D Hybrid Power System ticks all the boxes.
LifePO4D is a rapidly deployable standalone power system, which Chris lauds as the ideal choice to quickly generate power in high-paced and off-grid natural disaster scenarios, such as floods and fires.
Locally manufactured by by Tutt Bryant Equipment, LifePO4D allows for automatic switching between photovoltaics (PV) selfconsumption (solar power), battery supply and Tier V diesel power.
The LifePO4D micro grid design mandate was to create a single person, rapid deployment, scalable solution which can
integrate into existing infrastructure with complete remote connectivity.
For larger systems, the user has the flexibility to increase both generator and battery density or simply add additional LifePO4D modules, ultimately increasing PV production and reducing diesel support.
Its robust construction is fundamental in maintaining the full term of each component’s design life whilst simplifying logistics.
With its bespoke design, the container has an inbuilt long range bunded fuel tank, external replaceable acoustic panels with a particular layout focused on serviceability and expansion.
“The operator feedback has been really good and the ease with which the product can be set up is a big drawcard,” said Chris.
LifePO4D is also suited for events and erecting infrastructure at festivals – a job where a crane or elevated work platform is often needed, he said.
“Whether it’s a charging plant, running site offices, running small communities, that’s the idea. It’s one box turns up, you drop it on site, and you’ve got a full solution to your powerless problem,” Chris said.
Chris said LifePO4D isn’t just for offgrid sites, it can certainly save customers money on telecommunications projects, events and major commercial metro jobs too.
“Passenger lifts for cranes are generally powered by diesel, but what if we replaced the diesel, or swapped out most of it with battery power? We believe the result will be
a commercial scenario for our tower crane customers,” Chris said.
Chris said the feedback regarding Tutt Bryant’s Go Green product range has been favourable, and he is seeing increasing industry buy-in, when it comes to sustainable machines in general.
“Our customers are genuinely pushing us for solutions in the sustainable space; they’re pushing us and they’re motivated through their own corporate strategies, and that’s excellent.”
For crane hire companies looking to buy multiple Go Green products in one order, Chris explains how Tutt Bryant’s specialised services team consults with the customer, to ensure they walk away satisfied.
“We talk to customers about their
Above: The Sany Battery Energy Storage system provides 210kWhrs or energy storage with a One-toMany 100kW output, its ideal for both construction sites and applications which require mobile power.
projects and discuss all aspects from base loads to site location, operational requirements and load profiles. And once we gather all the information, we employ our formula and apply the suitable energy system arrangement that suits the customer,” said Chris.
Tutt Bryant service and support centres are strategically placed in capital cities and regional areas in New South Wales, Victoria, Queensland, Western Australia South Australia and Tasmania.
To explore the opportunity to go greener with Tutt Bryant, chat with a member of the Tutt Bryant team on 1300 658 888.
The Buddie System, a wireless, instant safety alert device designed for Dogmen by Dogmen was officially launched at The Crane Industry Council of Australia’s (CICA) National Conference and Exhibition held in Adelaide. Designers of The Buddie System, Jade Harris and Gary Panagiotidis, have been blown away by the industry’s response to the product.
“WE KNEW THERE WOULD BE INTEREST IN the product, but we have been amazed at how quickly the industry has responded to The Buddie System. Jade and I visited LiftEx Gold Coast in September and that was really interesting. We had a number of conversations with crane hire businesses and suppliers to the lifting industry and the response was overwhelmingly positive,” said Gary.
Given this response, Gary and Jade were really excited to officially launch the product at CICA’s National Conference and Exhibition and it didn’t disappoint.
“In the lead up to the event we sent an email advising customers that we would be officially launching The Buddie System and invited them to visit our stand, and we were surprised with the response,” said Jade.
“We received enquiries from crane hire businesses in America and Europe and
from all over Australia. We know from Cranes and Lifting magazine that our article received over 1,000 page views in the first week and all this translated to a very busy stand at the CICA event.
“We had crane hire businesses from all over the country visit the stand, as well as Tier One builders and suppliers to the industry. Everyone commented on the simplicity yet effectiveness of the The Buddie System and what a great idea it was, how simple it was to use and why hadn’t something like this been designed before,” he said.
Just about everything has an emergency stop button on it these days, so Jade and Gary developed one for Dogmen – part of a system that overcomes the potential shortfalls of two-way radio failure while providing Dogmen with another form of communication.
In the case of an emergency, the Lanyard Device is designed to separate.
Both Dogmen and crane operators rely heavily on two-way radio communication in many scenarios – but alternatives are not always so well developed.
In circumstances where something goes wrong with the two-way – such as a flat battery, frequency drop out, dropped radio or accidental channel change, or if the dogman is unable to access his or her two-way radio – often the only way to communicate with the crane operator is through a whistle and, on large scale
projects, the whistle is often inaudible for the crane operator.
The Buddie System is designed to be even more attention-grabbing than a whistle, but with the convenience of the lanyard on which the whistle is so often attached.
“The Buddie System is designed to be a redundancy safety system in case communication via the two-way radio fails,” says Gary.
“We’ve all experienced interference on two ways and on occasions there can be delays in the transmission. Batteries can start beeping and go flat halfway through a lift, which can delay the signal, that’s if the signal gets through at all,” he said.
“You might have told the crane operator to bring the load down and then you’ve dropped your hand mic and you can’t get to it. Or you could be slinging a load and your handset gets caught somewhere in the load, which has probably happened to most of us. You then have to try to get back to that mic as quickly as you can to say stop.
“With The Buddie System, you have the device around your neck, you just pull it, the alarm goes off in the cab and the operator immediately stops the crane,” said Gary.
With The Buddie System, the Dogman wears a lanyard around their neck, fitted with an alarm mechanism called the ‘Lanyard Device’.
The Lanyard Device is paired with a Crane Device which sits with the tower crane or mobile crane operator and the two communicate via the long range (LoRa) radio frequency.
In the case of an emergency, the Lanyard Device is designed to separate and when it does, it triggers an audible alarm and flashing lights in the cabin, immediately alerting the operator to the problem.
“That’s the signal for crane operator to stop all motions and he’ll get on his two-way to check if everything is OK,” Jade said.
“It could be that the Dogman’s lanyard had accidently been caught on something
and it separated that way, setting off the alarm, or it could be that something has gone wrong.”
The process of pairing the Lanyard Device and Crane Device is simple, with The Buddie System selling its units in sets.
When a company buys a tower crane set, for example, they will receive one Crane Device and three Lanyard Devices.
The devices are charged and then paired in one of two ways – either by physically plugging the Lanyard Device into the Crane Device, or wirelessly connecting the devices together by pressing the pair button at the same time. Once the two devices are paired, the lanyard’s unique ID number will be displayed on the crane device.
Once confident everyone is paired, the crane operator can climb up into the crane and plug the Crane Device into the main power source. As with a radio check, there will be a lanyard check – with each Dogman pulling the lanyard and setting off The Buddie System’s alarm. One simple check that it’s all working and the day begins.
If there is a morning and afternoon shift, operators can pair up to 10 lanyards with the Crane Device. The user-friendly system also allows dogmen to unpair their lanyard from one crane and take it to another, if they are going to work with either another crane or to another job.
Gary can see plenty of interest from Tier One builders and crane hire companies.
“There already has been interest from crane hire companies because of the safety aspect of The Buddie System,” he said.
“Although there is a little initial outlay to purchase the system, this could be a large saving when The Buddie System prevents an accident.
“We are thinking the construction, infrastructure, mining, wind energy and oil and gas industries will embrace The Buddie System and implement its use in their standard operating procedures,” Gary said.
“The conversations we are having with people high up in these type of organisations have been very positive with comments like ‘If the Buddie System was ready now we’d take it right away’.”
The Buddie System will be in mass production within the next quarter of the 2024/2025 financial year.
⊲ Mercedes-Benz OM936
⊲ Stage V and Tier 4 Final compliant engine
⊲ Surpasses the latest Australian Design Rules (ADR) for cleaner emissions
⊲ Exceptional reliability and has been meticulously integrated for optimal performance and efficiency.
Not only compliant with current ADRs but also anticipates future regulations. ety as Standard Safety remains paramount. All machines incorporate the Franna Safety Radar as a standard feature, adding an extra layer of protection and awareness for operators.
Redesigned to improve user experience. Each model has recieved upgrades to streamline your operations, from simplifying maintenance tasks to providing safer and more streamlined access.
For more information contact the Franna team today: T: 1800 837 395 E: franna@terex.com
www.terex.com/franna
The Sany SCC3200T-1crawler duo plays a pivotal role in the two main phases of the Fremantle Traffic Bridge replacement.
Two new Sany SCC3200T-1 crawler cranes are showcasing their capabilities on the replacement of Fremantle’s historic Traffic Bridge. Select‘s National Cranes Manager Paul Marshall outlines the immediate impact the versatile pair is having on the Western Australian project.
TWO SANY SCC3200T-1 CRAWLER CRANES were the perfect choice for a challenging task on a major WA infrastructure project, Select’s Paul Marshall said.
With a 320 tonne lifting capacity and a 75 metre main boom, which includes a 43m luffing jib and a Tier 5 dual slew Cummins QSL8.9-C325 motor, Paul saw the value in deploying the pair to help rebuild a famous Western Australian crossing – the Fremantle Traffic Bridge.
“The cranes are perfect for this job. The SCC3200T-1 will play a pivotal role in assisting with building the new bridge and then removing the existing older bridge,” said Paul.
Known as the Swan River Crossings
Project, the ageing Fremantle Traffic Bridge is being replaced with Australia’s first extradosed bridge.
Incorporating both cantilevers and cable support, the new bridge will have two lanes in each direction and a higher clearance for watercraft, creating a striking gateway to Fremantle.
The project is being carried out by the Fremantle Bridges Alliance, a consortium between Arup, WSP and Laing O’Rourke, in partnership with Main Roads Western Australia.
It is understood to be one of Main Roads WA’s most complex and challenging projects, involving road, port, freight, river, walking, cycling, heritage, and environmental considerations.
Paul said most of the construction work would occur while the original bridge is still open.
“The first 12 months will mainly compile of temporary jetty construction, from which the two Sany SCC3200T-1 crawlers and another two Sany SCE4800As will operate, into permanent piling and the start of the bridge tower construction. The second phase of construction will consist of the demolition of superstructure assembly works,” he said.
Construction parallel to the functioning bridge using four cranes provides greater safety and less traffic impact, setting the stage for efficient removal of the old bridge
and completion of the new crossing during a 12-month closure, he added.
The four temporary jetties have been designed to accommodate Sany cranes of SCC3200T-1 and the SCE4800A in their standard configuration.
The final temporary jetty end span will accommodate the 480 tonne SCE4800A crane in super lift configuration which is required to install the central precast elements.
The SCC3200T-1s will work from the jetties to install piles for the construction of the bridge.
Once piles are installed and mucked out, a precast concrete shell is installed around the piles and suspended on hanger beams as underwater grout is installed to seal the shell from the water underneath it before the area around the piles is dewatered and additional foundation works installed.
Paul identified the SCC3200T-1’s ability to operate without outriggers as a key benefit for the project, as the 8.18 metre wide crawler is ideal for operation whilst sitting on narrow jetties.
“The ground-bearing aspect of a job like this is sensitive, as the SCC3200T-1s are basically going to be working over water,” he said.
Paul also lauds how the cab design enhances operator comfort and said that “all the cab features are user friendly and it’s not over complicated.”
The Sany SCC3200T-1 boasts multiple cameras that can present on the monitor at the same time, allowing operators real-time monitoring of hook working, travel area, winch and wire rope reeving conditions from both front and rear cameras.
“The enhanced dash screen magnifies all the vision from the multiple crane cameras, including the hook block camera too; operators can see from the tip down to their load,” he said.
Considering previous positive operator feedback regarding Sany’s upgraded cab features, Paul recognises the importance of a highly technical but comfortable cab, as a dry hire business.
The impressive operator cab includes a large window glass, which can tilt up by 20 degrees to provide a panorama view, as well as an integrated 10.4-inch touch screen
The SCC3200T-1s will work from the jetties to install piles for the construction of the bridge.
with programmable smart buttons and optional vibration handle.
The multi-way and multi-level floating adjustable seat, control buttons and handles in the cabin are ergonomically designed to make work more comfortable for the operator.
There are low and high-beam lights, a back-view mirror, heater and air conditioning, radio and other functions to provide superior comfort for the operators, especially for longer days sitting in the cab.
Select also recently purchased another four Sany tele-crawlers and a Sany Battery Energy Storage System (BESS), as Paul has confidence in the technology and aftersales care Sany provides its customers, through local distributor Tutt Bryant
“Sany is a very reliable provider – they communicate with you very quickly if you need any technical advice or assistance.”
Paul said despite the Swan River Crossings Project only commencing in September this year, the SCC3200T-1s are already generating positive sentiments.
“We have received positive feedback regarding the two SCC3200T-1s, not only from the construction workers working in and around the project, but also from the operators who are in the cranes every day.”
The purchase of the Sany BESS highlights Paul’s confidence in Sany’s sustainable products set to be used within Select’s electric crane fleet, he added.
“Sany is pioneering with us in sustainability, not only by supporting our goals but by listening to our needs in sustainable technology, to best power our EV cranes. Their back-up power generation services are second to none.”
Paul is excited by the future of the two SCC3200T-1s within the local fleet of Select Plant Australia, which offers a diverse range of hire equipment, - modular site buildings and services - for the construction industry.
“The SCC3200T-1 can be perfect for many different construction jobs such as rail, viaducts, rail platforms and can also be active in the resources space and assist in gas refinery construction/maintenance.”
Paul is passionate about the Sany SCC3200T-1, and encourages crane and heavy lifting customers to learn more about Sany’s crawler range.
“In the crawler market, Sany combines a competitive price-point with a great balance of technological strengths, which I believe present a healthy proposition to those the crane market,” he said.
Milleen Constructions’ brand-new Zoomlion crane and drill, delivered by Ganz International, combine for civil infrastructure works at a new solar power farm in rural New South Wales.
the substation, and the solar farm does its thing, turns back out 90 degrees, and then continues on down, down the line to the next tower and so on,” he said.
Owner Andrew Stones said the poles he and his company are helping to install are “like putting a PowerPoint into the high voltage line to allow connection to the solar farm.”
Under the umbrella of Milleen Group, Milleen Constructions has been a regional leader in the application of piling methods and technology for 38 years, building a company on its ability to provide a solution for any situation and any environment.
Andrew said the company’s point of difference is leveraging its engineering expertise to provide the best solution for
which excite us,” he said.
“We get enjoyment through the harder, more challenging, more complex types of work, but in doing that, we are then providing solutions for our clients that others may not necessarily be able to. “
“We are able to do that efficiently at a good price point and leave our customer base happy,” he said.
In the past, Milleen Constructions would sub-contract out its craneage needs for
The
Pushed to upgrade the fleet, Andrew reached out to Ganz to purchase not only the ZCT 300V5 but also the ZR140 drilling rig – a choice Andrew said has paved new ground for his team of over 50.
“This way we have control of the picture; if we are approached for a civil infrastructure project, which needs to be done as soon as possible, we’re able to put our hand up and say we’re available now,” he said.
“This is as opposed to then having to make another dozen phone calls to find out that everybody else is available to ensure
lifting capacity with a 42m main boom and travels with a narrow width of 3m.
Replacing the now retired 16 tonne capacity crawler, the new ZCT 300V5 has received positive feedback from the crane operators, said Andrew. “Traditionally, our old crawler formed the backbone of our pile driving capabilities, however, let’s be honest –the young fellas who are operating our cranes don’t want to drive old bits of gear... One of the main crane operators out on site says he loves the new ZCT 300V5, and the same goes for the ZR140
drilling rig – those who have operated it have loved it.”
Chemistry between both the crane and drill is pivotal in ensuring the crane can perform its role. The ZCT 300VT works closely with the ZR140 to prevent precarious sand layers, which are usually sited about 4m down the 8m hole, from caving in and taking the drill with it.
The ZCT 300VT works closely with the ZR140 to manage potential sand and water laden layers. In this project these were located approximately 5m deep.
Typically, installing the reinforcing steel cages would be completed by a drilling rig, however the diameter of these holes was too wide, Andrew said.
“Also, due to the sand and water present onsite, we needed to install permanent liners. The ZCT300V5 was utilised to install these too.”
“The ZCT uses a vibrating hammer that is powered by an independent hydraulic power pack,” he said.
When the power pack fires up, rotating weights inside the hammer spin, creating the vibrationary force required to drive the sleeve into the ground.
“This supports the surrounding ground to stop it collapsing into this hole,” he said.
Ganz International is a rapidly expanding crane and piling rig dealer in Australia, providing exceptional support for civil construction and crane hiring businesses. The Ganz team has a combined 30 years of experience in handling new and used equipment sales within the construction, haulage and foundation industries.
Ganz Managing Director David James and Ganz ANZ Technical and Sales Manager Tony Pugh are right by their clients’ sides, according to Andrew.
“Tony and David have been great right from the get-go, when I first reached out to them, they were very accommodating and provided a high level of support and training for those who are in and around the Zoomlion machines at Milleen – this makes me feel comfortable that we were talking to the right people,” Andrew said.
Andrew is excited about the next venture for his brand new pair of Zoomlion products, as they will both join each other on another similar project.
“Both the ZCT 300VT and the ZR140 will head to a new transmission line for another battery farm at the Eraring Power Station site (in NSW). And then the crane will either get utilised as required on our other civil projects to support those, as well as other piling projects similar to those ones that we have in the pipeline currently.”
Milleen Construction doesn’t just silo itself to regional New South Wales; Andrew said the growing company is up for the challenge interstate.
“We are based New South Wales but he will travel pretty much anywhere in the state.
“We’re open to most opportunities interstate, provided they align with our key values and core business,” said Andrew.
The ZCT 300V5 boasts an impressive 30 tonne maximum lifting capacity with 42m of main boom and travels with a narrow width of 3m.
Qube Heavy Lift’s new TRT ESS Platform Trailer showed its versatility when it was put through its paces recently, using its Electronic Steering System (ESS) steering capability.
THE TRAILER’S ESS OFFERS ALL AXLE steering up to 45 degrees from the centre for maximum control and manoeuvrability.
Together with the ESS Quick Connect system for easy module clip-on mounting, and with various module configurationsthis platform trailer suits Qube’s multifunctional heavy transport requirements.
The trailer is shown here transporting the 30m upper tower section of a wind turbine made by Vestas, a global leader in sustainable energy solutions. Destined for the Wambo Wind Farm outside of Dalby, Queensland, this section was loaded directly onto the trailer from the ship at port.
The trailer’s ESS offers all axle steering up to 45 degrees from the centre for maximum control and manoeuvrability.
The trailer also shows its versatility piggybacking a GTC2000 TeleCrawler
- both of these items were transported to Qube’s transitional yard within Port of Brisbane Limits, ready in preparation for vessel discharge.
The Platform Trailer can Quick Connect into different module configurations, adapting to multiple transportation requirements:
• 5 - Line (Lead Trailer)
• 8 - Line (5+3)
• 9 - Line (5+2+2)
• 10 - Line (5+3+2)
• 12 - Line (5+3+2+2
Qube is also expecting delivery of its second 12-line TRT ESS Platform Trailer which includes specialised equipment that specifically targets their work in the renewable sector.
“Together with the ESS Quick Connect system for easy module clip-on mounting, and with the various module configurations - this platform trailer suits Qube’s multi-functional heavy transport requirements.”
More than just a pre-start checklist
More than just a pre-start checklist
More than just a pre-start checklist
StartSafe is comprehensive tool designed to streamline your crane operations, enhance safety, and ensure accountability.
StartSafe is comprehensive tool designed to streamline your crane operations, enhance safety, and ensure accountability.
StartSafe is comprehensive tool designed to streamline your crane operations, enhance safety, and ensure accountability.
TAILORED VISIBLE
TAILORED VISIBLE
Machine specific checklists are in line with the CraneSafe program.
Machine specific checklists are in line with the CraneSafe program.
Machine specific checklists are in line with the CraneSafe program.
StartSafe streamlines the process for collecting pre-start information, with instant data retention to a central location for the crane owner to access.
StartSafe streamlines the process for collecting pre-start information, with instant data retention to a central location for the crane owner to access.
StartSafe streamlines the process for collecting pre-start information, with instant data retention to a central location for the crane owner to access.
When a faulty item is recorded by the operator, the maintenance team is notified of the issue by email, which includes photo evidence of the fault. This also assists with gathering major inspection data. TAILORED VISIBLE
Photos tell the story.
Photos tell the story.
Photos tell the story.
When a faulty item is recorded by the operator, the maintenance team is notified of the issue by email, which includes photo evidence of the fault. This also assists with gathering major inspection data.
When a faulty item is recorded by the operator, the maintenance team is notified of the issue by email, which includes photo evidence of the fault. This also assists with gathering major inspection data.
PLEASE SEND YOUR LIFT OF THE MONTH ENTRIES TO SIMON.GOULD@PRIMECREATIVE.COM.AU
WHERE: Coffs Harbour bypass
WHO: Borger Crane Hire and Rigging
CRANE: Liebherr LTM1650-8.1
WHAT WERE THEY LIFTING: Luke Bowen
pedestrian bridge weighing 80 tonnes, single span construction 61 metres long, 4.5 metres tall and 5.0 metres wide.
DIFFICULTIES: Limited room to set up and lift and time pressures due to road closure.
Freo Group’s Principal Assessor, Chris Everleigh, conducted a comprehensive two-day inspection of the TIDD Crane, evaluating its drivability, manoeuvrability, comfort, and operational lifting capability. Chris rated the crane a perfect 10/10 across all categories, stating:
“The TIDD Crane is very comfortable with the latest technology advancements, all coupled with TRT’s team of great knowledge. The TIDD is a very well-refined crane, 10/10.”