POWER AND VERSATILITY
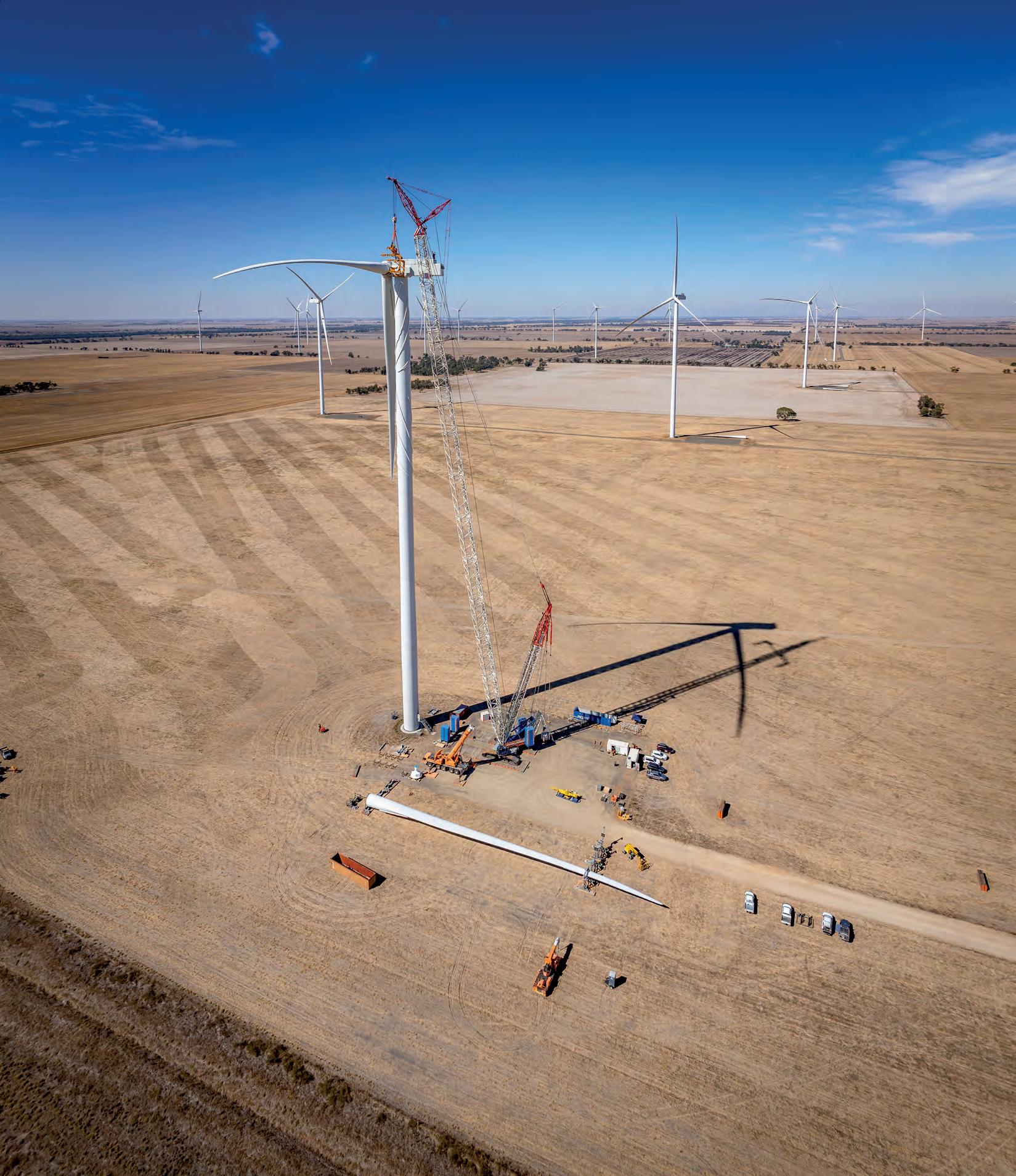
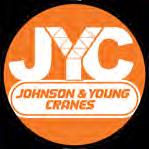
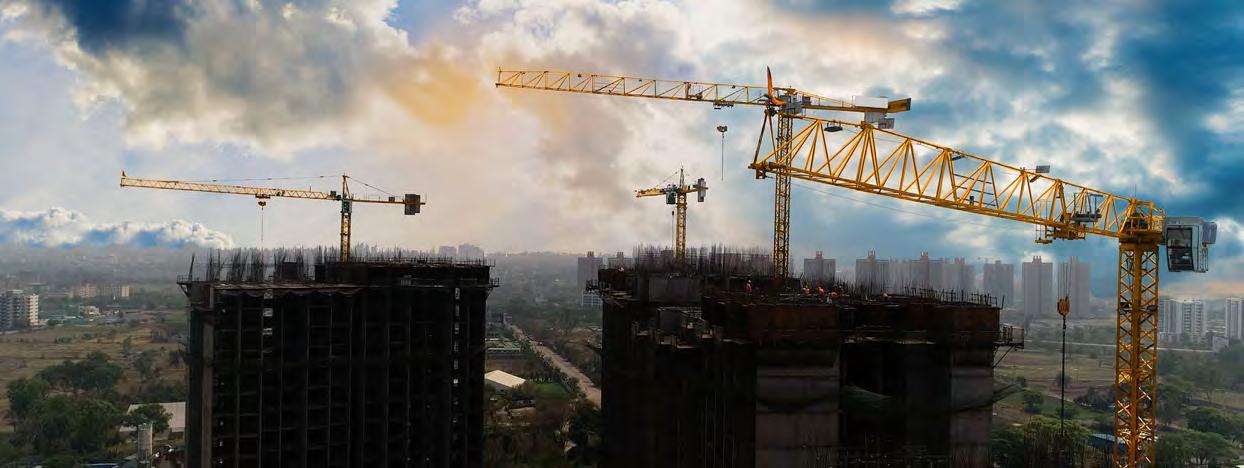


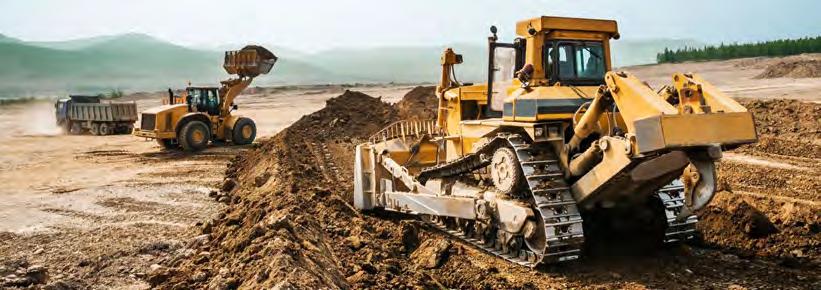
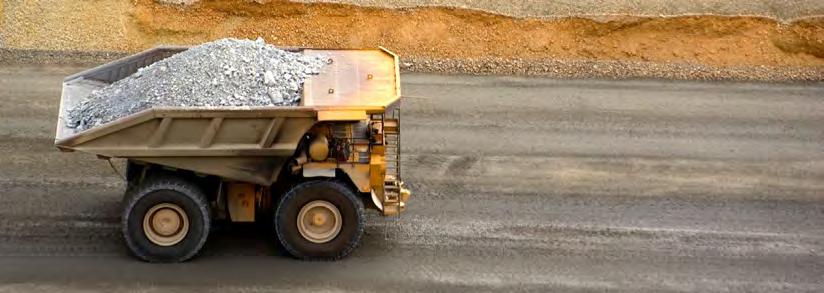
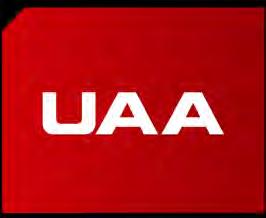
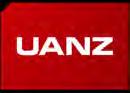

Cranes and Lifting Magazine cranes_and_lifting Cranes and Lifting
16 CANZ CEO report Vita technology lands in NZ.
20 LEEA
Importance of compliance.
22 Membrey’s mammoth project
Moving a family of elephants from Melbourne Zoo to new home.
25 Visual Dispatch Visual Dispatch and RapidWorks.
Between Hook and Load features
29 All Lif ting
Proudly Australian providing world class lif ting equipment.
32 Legend Lif ting
Creating and maintaining a legend in lif ting.
34 Lif ting business for sale
37 Delphi Measurement
Price load measurement for Super Shackles.
Pace Cranes
Spider Crane Hire impressed with knuckle boom technology.
XCMG
Crane pads for all sizes of cranes.
Tutt Bryant and Sany New crawler for Direct Cranes.
Borger Crane Hire
Aerial crane ballet at its finest.
CICA’s ‘Launch Into Work’ Program
Building Careers in the Crane Industry.
Liebherr
Liebherr deliver for Goodline.
Manitowoc factory visit
International visitors impressed with factory’s technology.
UA A
Importance of safety and competence when it comes to insurance.
Borger Crane Hire
New CEO with a familiar face.
70 Mammoet
Mammoet manage logistics for huge rig move.
72 Sennebogen Sennebogen and Deutz strengthen ties.
Over
14 CICA On-Road Articulated Steering Mobile Crane Training Course
Quicklift Crane Hire and Access Hire put operators through the course.
40 Andromeda Industries Ready to take on the world.
43 BAB Engineering
Launching a new 4.2m loading deck.
48 Manitowoc
New home for leading brands.
IT WAS GREAT TO ATTEND THE CICA Wind Forum in Melbourne and join over 120 industry professionals for a productive day of discussion, knowledgesharing, and networking. The event provided a comprehensive look into the evolving wind energy landscape, covering global trends, transportation challenges and emerging crane technology.
The broad overview of the Australian wind turbine market confirmed that maintenance on wind farms will evolve to be a very sizeable market and cranes will play an integral role in this space. The dedicated expert panel brought together OEMs and crane industry representatives for an interactive session that reinforced a universal message: early involvement is crucial for efficient project execution. The panel engaged in valuable discussions on optimising workforce deployment and maintaining site efficiency, with a strong consensus on improving collaboration from the outset of wind farm projects.
In this issue we acknowledge Quicklift Crane Hire and Access Hire for taking the initiative and putting
their operators through the CICA OnRoad Articulated Steering Mobile Crane Training Course. Cranes and Lifting will continue an awareness campaign for this course as we recognise the critical nature of safely driving and operating articulated pick and carry cranes.
As always, the team at Cranes and Lifting has worked hard to bring you the very latest developments from our industry. We highlight some big moves from Borger Crane Hire and Rigging and also Manitowoc. We highlight the importance of lifting equipment in our regular Between Hook and Load feature and we take a look at a recent project for Membrey’s Transport and Cranes where they moved a family of elephants for Melbourne Zoo.
As always, we hope you enjoy the read.
Simon Gould Editor, Cranes and Lifting
Published by:
379 Docklands Drive, Docklands VIC 3008
T: 03 9690 8766
www.primecreativemedia.com.au
CEO John Murphy E: john.murphy@primecreative.com.au
Chief Operating Officer
Christine Clancy E: christine.clancy@primecreative.com.au
Publisher Sarah Baker
E: sarah.baker@primecreative.com.au
Managing Editor Lisa Korycki E: lisa.korycki@primecreative.com.au
Editor
Simon Gould
E: simon.gould@primecreative.com.au T: 0404 865 109
Assistant Editor
Danny D’Cruze
E: danny.dcruze@primecreative.com.au
Busiiness Development Manager
Emily Schlegel
E: emily.schlegel@primecreative.com.au
T: 0466 317 555
Client Success Manager
Louisa Stocks
E: louisa.stocks@primecreative.com.au
Art Director Bea Barthelson
Designers
Laura Drinkwater and Danielle Harris
Imaging Assistant Paul Breen
Subscriptions
Frank Rapone
T: 03 9690 8766
E: frank.rapone@primecreative.com.au
The Publisher reserves the right to alter or omit any article or advertisement submitted and requires indemnity from the advertisers and contributors against damages or liabilities that may arise from material published.
© Copyright – No part of this publication may be reproduced, stored in a retrieval system or transmitted in any means electronic, mechanical, photocopying, recording or otherwise without the permission of the publisher.
Johnson & Young Cranes (JYC) has built its fleet with a clear focus on servicing both the renewable energy and the civil infrastructure sectors and given the substantial investment required to achieve this – whether a crawler crane or a wheeled carrier with outriggers – it is essential that each machine is capable of handling a diverse range of tasks.
JYC’S TADANO-DEMAG CC3800 RECENTLY demonstrated its versatility following a two-year assignment lifting and traversing girders and beams for Melbourne’s West Gate Tunnel Project. The crane was recently redeployed for a wind turbine main bearing replacement –140 metres in the air. This challenging lift involved the precise removal of three blades, a hub, and the turbines drivetrain, with the heaviest component weighing over 80 tonnes. Once the main bearing was replaced at ground level, the entire process was reversed, requiring ten separate lifts to reassemble the turbine.
A key factor in the success of this project was the CC3800’s extensive boom configuration options. JYC’s strategic investment in two CC3800 units allowed one crane to remain in Melbourne lifting 450 tonne steel girders, while the second was fitted with ‘Boom Booster’ sections to achieve an impressive 120-tonne lifting capacity
at 160 metres above the vast western Victorian plains.
The crane’s 21-metre superlift tray radius minimised the counterweight required to lift the boom, while the flexframe system enabled real-time adjustments to the counterweight position mid-lift. Additionally, the split tray option is available to leave the unrequired boom erection counterweight out of the way and slew, luff and crawl with only the counterweight required to hold the load.
Further enhancing the crane’s adaptability is its 175-tonne-rated LF
“Efficiency is paramount in the wind maintenance and construction market, where rapid setup, pack-up, and movement between sites are essential.”
Specialist windfarm tooling and equipment requires extra head height and extra clearance.
wind jib attachment. This provides the strength to handle heavy wind turbine components, such as powertrains and complete nacelles, while also offering crucial jib clearance with 15- and 20-degree offset options.
position. With the right combination of boom, backmast, counterweight, and split superlift tray configurations, the CC3800 can transition between turbine sites in a comparable timeframe to some rubber tyre cranes.
increasing complexity and unique lifting challenges. Selecting the right crane for the job is never a simple decision, but in this case, the CC3800 crawler crane proved to be the perfect solution –delivering the precision, strength, and
Efficiency is paramount in the wind maintenance and construction market, where rapid setup, pack-up, and movement between sites are essential. The CC3800’s wide-track crawler configuration offers a distinct advantage over some other machines, in that it’s main component, the 90t carbody, can lift itself off it’s own trailer and install it’s own 43t crawler tracks in a matter of hours and then crawl/relocate into whatever position is required without a support crane.
The machine’s low-to-the-ground boom build, enabled by its boom pivot and slew ring height, further enhances safety and efficiency and once the boom is assembled, the crane can then crawl/track in any direction with the boom in the air, to an optimised lifting
“The CC3800’s wide-track crawler configuration offers a distinct advantage over some other machines, in that it’s main component, the 90t carbody, can lift itself off it’s own trailer and install it’s own 43t crawler tracks in a matter of hours and then crawl/relocate into whatever position is required without a support crane.”
JYC benefits from the best of both worlds however, also operating a 750-tonne lattice boom crane on a wheeled carrier. This diversity ensures JYC is prepared for a range of lifting scenarios, in both renewables to infrastructure projects.
As the renewables sector continues to expand, wind turbines are evolving with
versatility required by the client, while also reinforcing its status as a true allrounder within JYC’s diverse fleet. With a proven track record across multiple industries, including road, rail, tunnel infrastructure, and petrochemical projects, JYC’s investment in adaptable lifting solutions ensures it remains at the forefront of the industry.
WELCOME TO ANOTHER ISSUE OF Cranes and Lifting Magazine. Simon, Emily and the team at Prime Creative always do such an amazing job keeping our industry connected and informed through this publication.
Like many of you, it was great to catch up at the CICA Cranes in Wind Forum in February which was an outstanding success. I remember a conversation at the end of 2023 I had with Nick Morris about creating an event like this. Together with Nick and others, our objective of bringing together key industry stakeholders, experts, and contributors to discuss the vital role of cranes in both the construction and maintenance of wind farms has really taken shape. This forum is now a yearly event that highlights the growing importance of lifting solutions in renewable energy projects, reinforcing the indispensable role our industry plays in Australia’s clean energy transition.
As Australia seeks to diversify its energy mix, discussions like these are crucial. The insights shared at the forum underscored the challenges and opportunities in crane operations for wind energy projects, from logistical complexities to technological advancements. The engagement and expertise on display were a testament to our industry’s capability and commitment to supporting a sustainable energy future.
A big thank you to Karli from Quicklift Crane Hire and Access Hire for her dedication and approach in guiding her team through the Articulated Mobile Crane Driving (AMCD) Course. Her authentic experience highlights the challenges and successes of workforce development, and we hope you take the time to read her story.
Recognising the importance of employer support in this process, we are currently developing a Familiarisation
“The
CICA calendar for 2025 is filling up fast, offering a wealth of opportunities for members to participate in branch meetings and industr y events.”
owners and managers. This initiative will be rolled out across every state, equipping leaders with the knowledge and tools to better support their teams in navigating the AMCD Course. Stay tuned for upcoming course dates!
The shortage of skilled crane operators, doggers, and riggers has been a welldocumented challenge within our
workforce and increasing demand for skilled professionals, CICA has been actively lobbying the government to include Cranes, Hoist, and Lift Operators (ANZSCO 7121) in the National Skilled Occupation List.
At the same time, sourcing local talent remains a major priority. The Launch into Work initiative provides a valuable pathway for engaged and willing participants to enter our industry with the necessary support and training.
By investing in workforce development, we are not only addressing skill shortages but also ensuring the long-term sustainability and growth of our sector. This program represents a significant step forward in attracting new talent and equipping them with the skills needed to thrive in crane operations.
The CICA calendar for 2025 is filling up fast, offering a wealth of opportunities for members to participate in branch meetings and industry events. These meetings provide a crucial platform for you to raise concerns, share insights, and stay informed on key developments impacting your industry and businesses.
CICA is continually striving to deliver valuable resources to its members. Two key initiatives you may not be aware of are:
• C ICA Business Essentials – Our monthly online sessions feature expert presenters covering essential business topics such as HR matters, finance, insurance, and regulatory compliance, to name a few. These sessions are designed to provide practical, relevant advice to help businesses navigate the complexities of running a business.
• Fortnightly Safety Bulletins – These bulletins address crucial crane safety topics and are widely used in toolbox talks on worksites across Australia and internationally. Keeping safety at the forefront of our operations is a priority, and these bulletins serve as an essential resource for industry professionals.
To stay up to date with upcoming events and initiatives, head to the CICA website and follow CICA on LinkedIn, Facebook, and Instagram. If you’re not already receiving our fortnightly safety bulletins, please email michelle@cica.com.au to be added to the list.
We look forward to seeing you at our events this year and working together to strengthen our industry. Stay safe!
Brandon Hitch CICA CEO
CICA BOARD
Ben Pieyre – President
Marcus Ferrari – Vice President
Danny Adair – Director
Danny Black – Director
David Solomon – Director
Karli Sutherland– Director
Tom Clark – Director
Anthony Grosser – Director
Brandon Hitch Chief Executive Officer 0428 228 048 ceo@cica.com.au
Alice Edwards Road Technical Engineer 03 8320 0440 alice@cica.com.au
Patrick Cran
CICA Site Operations Advisor 0488 004 274 pat@cranesafe.com.au
Sharon Pearce
Crane Crew Competency Officer 0491 134 533 sharon@cica.com.au
Damien Hense
CICA Road Policy Advisor 0488 007 575 damien@cica.com.au
Thomas Webber Communications Coordinator thomas@cica.com.au
Kate Galloway Traineeship & Industry Engagement Coordinator
0491 047 118 kate@cica.com.au
Michelle Verkerk Communications and Special Projects Advisor michelle@cica.com.au
Just ina Blackman Member Events and Engagement 0403 717 626 justina@cica.com.au
Ashleigh Gould Office Operations Coordinator 0490 356 041 ashleigh@cica.com.au
Shane Coupe
CraneSafe & CrewSafe Administrative Assistant Officer 0491 047 134 shane@cica.com.au
Unit 10, 18–22 Lexia Place, Mulgrave Vic 3170
Phone: 03 9501 0078
Email: admin@cica.com.au
Website: www.cica.com.au
For information, please visit our website or call the CICA office.
The presenters and panellists.
THE RECENT CICA WIND FORUM HELD ON 19 February 2025 in Melbourne brought together over 120 industry professionals for a highly beneficial day of discussion, knowledge-sharing, and networking. The event provided a comprehensive look into the evolving wind energy landscape, covering global trends, transportation challenges and crane technology.
The XCMG keynote address set the tone for the day, offering a detailed overview of wind power solutions and trends in China. As a global leader in wind power generation, with over 470 million KW of installed capacity, China’s advancements in turbine size and crane technology served as a compelling case study.
Nick Morris provided a broad overview of the Australian wind turbine market, providing context on
Wind Turbine Generators (WTG’s) and that maintenance on wind farms is shaping up to be a very sizeable market. He also covered the crucial role cranes play in this space. Qube examined the logistical challenges of transporting turbine components from ports to installation sites. Real-world case studies emphasised the importance of meticulous transport planning, the necessity of spotters for safety, and the value of conducting dry runs before each journey. The industry was urged to involve transporters at the earliest stages of project development to mitigate costly delays.
A dedicated expert panel brought together OEMs and crane industry representatives for an interactive session that reinforced a universal message: early involvement is crucial for efficient project execution. The panel engaged
in valuable discussions on optimising workforce deployment and maintaining site efficiency, with a strong consensus on improving collaboration from the outset of wind farm projects.
Technical sessions throughout the day by Axzion and Borger delved into specialised lifting solutions, highlighting the critical role of hook technologies for wind turbine erection (Axzion) and lessons learned from a Vesta installation (Borger). A presentation by iCube explored geotechnical engineering considerations, underscoring the necessity of site preparation to ensure turbine stability.
Attendees were also treated by Tadano to a historical perspective on the Demag CC-2800-1 crane, a key player in numerous wind farm projects worldwide. Insights into wind turbine stand challenges and specialised crane
adaptations for diverse environments. and Universal Cranes provided a case study of a recent installation success – the Harapaki Wind Farm – further enriched the discussions.
Liebherr provided an overview of the climate crisis, highlighting the global push to expand wind and energy installations, and they discussed the role of their cranes in wind turbine projects worldwide and the scale of these installations. It concluded with insights into the history of the LG1550 and LG 1750 and how the development of LG 1800 drew on their experience of operating in Australia, specifically in a specialised tyre design tailored for the challenging conditions in Australia and the United States.
The day was punctuated with networking breaks, allowing participants to engage in valuable one-on-one discussions, exchange insights, and forge new partnerships. Each presentation sparked lively and insightful conversations, reinforcing the importance of cross-industry collaboration in advancing wind energy projects.
A dedicated expert panel of crane industry representatives contributed to interactive sessions that reinforced a universal message, early involvement is crucial for efficient project execution.
“The panel engaged in valuable discussions on optimising workforce deployment and maintaining site efficiency, with a strong consensus on improving collaboration from the outset of wind farm projects.”
As wind energy installation efforts ramp up both nationally in Australia and globally, forums like this serve as vital platforms for aligning strategies, addressing challenges, and embracing innovation. The event underscored the collective commitment of industry leaders to drive crane efficiency, safety,
and sustainability in wind power development.
A huge thank you again to everyone who attended and contributed to the 2025 CICA Wind Forum conversation on the vital role cranes play in the wind industry, we look forward to carrying on the conversation next year.
Quicklift Crane and Access Hire recently had each of its Franna operators complete The Crane Industry Council of Australia’s (CICA) On-Road Articulated Steering Mobile Crane Training Course. Quicklift’s Karli Sutherland discusses the results, her take-outs from the course and why it’s important that every CICA member ensures their operators take the course.
THE DEVELOPMENT OF THE COURSE STEMS from a tragic incident in 2013, where a mother and son lost their lives due to an articulated crane accident. This incident forever changed the lives of all involved and their families.
“For the road managers across the country, we recognise that the articulated pick and carry crane has it’s own unique operational characteristics and associated risks. CICA has taken the initiative and developed this adaptive learning opportunity specific to articulated mobile cranes to address aspects of the operation or specific risks which are unique to this type of crane,” said Karli.
“Being a regional crane hire business, Quicklift operates a little differently to our Metro counterparts. If our operators have the necessary competency and experience, they will operate anything from our small mini crawlers, through to our fleet of Frannas and slewing cranes, all the way up to our 250 tonne capacity Liebherr all terrain crane. Each piece of equipment has its own unique operational characteristics, requiring our operators to have a broad knowledge of all types of mobile cranes.
“When CICA offered this course free of charge to members we were quick to take advantage of the offer. Although there was no direct financial cost to our business, there is still a significant investment in terms of the operators’ time. When you have been operating a business in this industry for 26 years, you
understand the operational risks and for us it was really important to support this CICA initiative. It helped reinforce to our operators, the safety aspects of operating this type of crane while providing them with additional training which we like to do wherever possible.”
Karli goes on to discuss how Quicklift’s operators approached the course and the learning they took away from it.
“Like most crews in our industry, our team are practical thinkers, and they have learned their skills in a practical and hands-on manner. As a result, a significant percentage of our staff found the theoretical element of the training a little overwhelming.
“Following our first staff members completion of the theory component of the course I made contact with Pat Cran, CICA’s Site Operations Manager. Pat is such an important resource for our company. He’s been out to our yard on numerous occasions, and we rely on his advice to get these types of initiatives up and running and at the best levels of efficiency as well.
business was to pair our more technology challenged team members with our younger operators who are more familiar with the technology behind this type of training model.
“We discussed how long it was taking our guys to complete the online component and at that point, I realised that we did need a better approach to this component of the course. We had to consider the varying ages of our operators. We have operators completing the course who are 70 years old and others as young as 21. The best approach for our
“Our son Ty is 23 and he operates up to our 250t Liebherr. He finds the technology relatively easy. He has been in front of computers from a young age, something that is consistent with his age group. Whereas our operator Rod is 70 and he’s probably a bit more technologically challenged,” said Karli. “It just made sense to pair our operators from the online component through to the on road requirement to complete the course.
“By pairing people, you get a better outcome because one is helping the other. Rod’s experience far outweighs
Ty’s, yet Ty’s knowledge of technology is considerably better than Rods. We wanted to put them through the theoretical training without the levels of frustration of our first couple of guys and in turn they had a better experience and learnt more.
“Some went in with a mindset that it’s going to be like a regular induction, it’s a tick and flick. They took the approach that they don’t really have to listen to what this video is telling them because they are going to know the answer at the other end, which just simply wasn’t the case.”
Karli goes on to explain the varying degrees of experience Quicklift’s operators have and how they develop within the business.
“We have a few guys with 20 plus years’ experience of operating pick and
carry cranes, a couple with five and others with only two years’ experience. There’s a big range in age and competency. In our yard they typically get a dogman’s ticket and then a rigger’s ticket and then the natural progression to crane operator of a Franna crane. From there they will move into the slew cranes. That is how we naturally progress the team and the process can take years,” said Karli.
She said the practical component to the course is also a commitment from both the operators and the business.
“It is a reasonable commitment of time to complete both components of the training. As an owner of a crane company we understand the financial cost to have a staff member spend a couple of hours completing training.
“However we also understand the considerable cost in lost time if an incident occurs. It’s not just the financial cost but the potential for serious injury if something goes wrong in a high risk industry such as ours.
“Our operators can complete a one week course to obtain their crane ticket but nothing substitutes for training and experience on the job. You can’t buy it, you have to do the hard work to ensure at the end of the day everyone gets to go home safely. For all of these reasons, we prioritise training for our staff,” she said.
With the on-road element of the course Karli again contacted Pat Cran.
“I spoke to Pat about how we should go about it and he provided us with a list
The course instructors are seasoned professionals who will mentor course participants through real-life scenarios, preparing them for the challenges and responsibilities of a Crane Lift Supervisor.
Crane Lift Supervisors are in high demand globally. Completing this course enhances employability and opens doors to a wide array of job opportunities and career growth.
The curriculum covers a wide range of topics, including lift planning, load calculations, safety protocols, communication strategies, and legal compliance.
Scan the QR code to book in now
Melbourne 5-6 February 2025
Sydney 19-20 February 2025
Brisbane 5-6 March 2025
Perth 19-20 March 2025
Melbourne 4-5 June 2025
Brisbane 10-11 July 2025
Perth 16-17 July 2025
Sydney 17-18 September 2025
of actions that really should be undertaken while they completed the on-road training. I went onto Google Maps and I plotted a course, which every one of our staff members would navigate and complete.
“They’d go through a school crossing, complete a hill start, change lanes, this type of thing. We paired them up again and one person filmed while the other was driving, they’d get back to our yard and swap over. This meant that we didn’t have one guy taking half an hour, and not getting every aspect required, and another taking an hour or so, still trying to tick off the list. That was important, half an hour per operator and they were done and dusted.”
For Karli, one of the biggest takeaways from the course was an assumption that everyone has the same understanding about the operation and risks associated with a particular type of equipment such as an articulated mobile crane.
“A prime example occurred when two of our operators, each with five years’ experience, were among the first to tackle the training. They were asked whether an articulated mobile crane was rear or front wheel driven. They repeatedly answered this question incorrectly, which significantly extended the time required to complete the theory section.
“We assumed that was a basic knowledge question about how the crane worked. But it turned out that even an experienced operator may not have that fundamental understanding. This reinforced the lesson that you never assume that someone knows everything or that everyone has the same understanding of something,” said Karli.
Karli has this message for other CICA members considering putting their operators through the course.
“I would say: don’t delay. Set aside time each week to ensure your team can complete the training and allow you to accurately assess their competency level. It provides an opportunity to address any knowledge gaps, as the adaptive training process naturally highlights areas of weakness.
“In a high-risk industry, I would say to any crane owner, safety has to be our top priority. Everyone that comes to work has a right to go home at the end of the day and the financial impact to the business should never outweigh this as a priority.
“You have to do everything you can within your power to ensure that everybody is equipped with the best knowledge and, in particular, be aware of the risks associated with this type of vehicle, because they are unique. As an owner of a crane business, if you don’t try and minimise the risk of injury to people or damage to property, you’re not doing your job. You have a responsibility.”
MAXbase Equipped
The GMK4080L is an outstanding four-axle taxi crane that, with its 60-meter-long boom, offers both the longest boom and the lowest gross vehicle weight in its class. Within 10 t per axle, the crane can carry 5.2 t counterweight and even 13.3 t counterweight with 12 t axle load.
•60 m boom length and capacity matches the 90-100t class (4.8 t @ 60 m)
•Main boom: 11,3m - 60m, 7-section
•Bifold swingaway jib: 8,7 m /15 m (optional)
•Minimum width 2,55 m and overall length 12,82 m
•Carrier cab: Latest generation of Grove carrier cabs
•Increased safety and flexibility with MAXbase variable outrigger system
•Faster Intuitive set-up with CCS (Crane Control System)
•Engine: Mercedes-Benz OM470LA, 300kW
•Capacity: 80 t
•Main boom: 60 m
•Maximum jib: 15 m (0°-40° luff)
•Maximum tip height: 77 m
•GVW: 48000 kg
Crane operations are constantly evolving. CANZ CEO Sarah Toase recently had the chance to see a new technology that could significantly improve safety and efficiency. During a visit to Concretec (its Director Stefan Young is one of three people involved in bringing this to New Zealand) she saw the Vita Load Navigator (VLN) in action – and had the opportunity to operate it.
THE VLN IS AN AUTONOMOUS LOAD stabilisation system that eliminates the need for taglines, using sensors and electric motors to actively control swing and rotation. This means crane operators can stabilise and position loads remotely, without workers needing to stand near the load. It’s an impressive step forward in lifting safety.
The VLN attaches directly to the load, using real-time monitoring and adjustments to keep it stable, even in challenging conditions such as high winds or confined spaces. Instead of relying on workers manually pulling on ropes, the VLN’s sensors detect movement and instantly correct it.
Key features include:
• Automatic load stabilisation
• Wireless remote operation
• 360° rotation capability
• 8+ hours of battery life
• Capacity for loads between 20-40 tons
A pioneering device, the Vita Load Navigator uses aviation sensors to detect load position, wind speed and hundreds of other data points per second. Highpowered air thrusters dynamically adjust loads within milliseconds with up to one degree of accuracy. The unit can be controlled via remote for precise lifting applications.
What impressed me most was how simple the system is to use. It doesn’t require any modifications to cranes –just a straightforward attachment to the rigging.
For years, crane operators have relied on taglines – ropes used by workers to control loads. The VLN removes these risks and in the right environment will certainly provide a safer, more efficient way to manage load movement. It’s particularly valuable for industries handling precast concrete, steel structures, and large mechanical components.
I was enthralled to hear the story behind the creation of the VLN. In 2009, Vita Inclinata founder Caleb Carr lost his friend and mentor in a search and rescue mission when a helicopter couldn’t stabilise its rescue basket due to high winds. The helicopter ultimately failed to rescue Don, and he didn’t survive. Determined to prevent similar tragedies, Carr worked with engineers to develop a stabilisation system for lifting operations – first for rescue helicopters, and later for cranes.
This cutting-edge technology has now arrived in New Zealand, thanks to LNZ – Lifting New Zealand, a new company focused on bringing innovative lifting solutions to the industry. The VLN has already been specified in a tender and is available for lease.
I’m also working to bring the VLN to the CANZ conference, so more industry professionals can see its potential first-hand.
I’ve had my ear to the ground this year, waiting to hear signs of the industry picking up following the sharp and painful downturn Kiwis have endured in almost all sectors for the past 18 months. I am starting to hear and see signs of it.
The economic indications are there with reduced inflation, official cash rate and interest rates. There is growth in property lending, both commercial and residential. And more telling is the feedback from multiple members that they are starting to see early signs of things picking up. This is both through a small increase in enquiries/jobs, emptier yards and significant tender activity.
This is a watching brief, however there are indications that this year will indeed see a turn for the better.
I DON’T HAVE TO TELL ANYONE reading this but when it comes to purchasing lifting equipment, safety is paramount. Year in, and year out I continue to see that ‘price’ is the main driver and yet everyone is saying that safety is their number one priority. Don’t they know we can see they’re lying through their wallets? It’s easy to ‘talk the safety talk’ but it’s much hard to ‘walk the safety walk’ and execute genuine actions that will actually protect people.
Recently I travelled to Malaysia, and during our Regional Event in Kuala Lumpur, I heard from a number of South East Asia-based LEEA members. What absolutely resonated, was the fact they face exactly the same challenges as our Australian members. Safety is spoken about lots, but actions fail to translate into outcomes.
In a past life, I did some sales training that showed the Value Triangle. Products can be two of three things – fast, cheap or quality. If you want a product fast and cheap, you have to forgo quality. If you want a product of high quality, you’ll probably have to forgo it being cheap. Most people understand that using the right equipment, for the right application can significantly enhance productivity and safety, but there is cost associated in gaining that efficiency. Yet, so many firms are willing to choose the cheapest product over something that is obviously going to be better suited to the application. In a high risk industry, firms continue to say that people are their greatest asset, yet they risk accidents, injuries and even fatalities by purchasing products on price.
LEEA has a bold vision of Lifting and Height Safety industries which have eliminated accidents, injuries and fatalities. I know it’s a huge task,
and some think an over ambitious and ridiculous one, but it gets me out of bed every day. Every worker that leaves their family for work in the morning has the right to expect to return home safe and sound that night. Sadly too many don’t.
Recent LEEA research confirmed that products in our industry are of high quality with factors of safety built in, to ensure that they perform to the highest of standards. However, there are always times where situations go ‘pearshaped’, and this is often as a result of inappropriate application of products.
One of the important services that LEEA offers to the wider industry is the opportunity to undertake training. For people in the critically important role of purchasing lifting equipment, we offer the End User Guidance training. This is
correct equipment is selected and is fit for purpose.
As we see the proliferation of lifting equipment as a retail item, we continually highlight the importance working with reputable suppliers, who have a proven track record of providing highquality lifting equipment. Continued investment in their own product development is crucial as is the servicing, maintenance and regular checking of the product.
We want users to look for suppliers who are members of recognised industry associations, such as LEEA. LEEA members adhere to strict standards and codes of practice, ensuring that the equipment they supply meets the highest standards of safety and quality.
We also urge trainees to ensure lifting
“Remember, the right equipment not only enhances productivity but also plays a vital role in protecting the health and safety of your workforce.”
free to everyone, and provides end-users of lifting equipment the required tools to ensure their teams know they have an integral role in providing a safe working environment for their workmates.
The End User Guidance training clearly defines the requirements for the lifting equipment, based on the specific tasks and the environment in which it will be used. It helps users consider factors such as load capacity, lifting height, frequency of use, and working in special conditions such as corrosive environments or in extreme temperatures. This will help narrow down the options and ensure that the
equipment complies with all relevant safety standards and regulations, request certification and documentation from the supplier to verify compliance. This includes certificates of conformity, test reports, and maintenance records. Compliance with standards is essential for ensuring the safety and reliability of the equipment.
As highlighted above, when evaluating lifting equipment, consider the total cost of ownership, not just the initial purchase price. This includes factors such as maintenance, inspection, training, and potential downtime. Investing in highquality equipment may have a higher
upfront cost but can result in long-term savings through reduced maintenance and increased reliability.
Finally, we ask the trainees to engage with experts who can provide guidance on selecting the right lifting equipment for your specific needs. LEEA members are a valuable resource in this regard. They have extensive knowledge and experience in the lifting industry and can offer advice on equipment selection, compliance, and best practices.
Utilising their expertise can help ensure that you are making informed decisions and select equipment that meets all safety and operational requirements.
The end user guidance training highlights the requirement to conduct a detailed risk assessment before purchasing equipment. This involves identifying potential hazards, evaluating the risks associated with different types of equipment, and determining the necessary safety measures.
Proper planning ensures that the equipment selected is suitable for the intended application and that all safety requirements are met.
Additionally, we need people to be educated. Proper training and competency of personnel involved in lifting operations are vital for maintaining safety. We all need to ensure operators are adequately trained in the safe use of lifting equipment and to follow established procedures and any variation from procedures put lives at risk. Regular training and assessments help ensure operators remain competent and up-todate with the latest safety practices.
In recent months many of us have seen accidents as a result of plans not being followed and products being selected for applications they weren’t designed for. Pre-use checks clearly weren’t done, and in the worst cases, someone simply said ‘she’ll be right’!
Purchasing and using lifting
equipment is a critical decision that requires careful consideration around safety, compliance, and operational requirements. Everyone should be following best practices and engaging with reputable suppliers, such as LEEA members, to ensure that you have selected equipment that meets the highest safety standards and delivers reliable performance.
Remember, the right equipment not only enhances productivity but also plays a vital role in protecting the health and safety of your workforce.
If LEEA’s vision to provide ‘Lifting and Height Safety Industries which have eliminated accidents, injuries and fatalities is something you are striving for in your business, then please, reach out to me, I’d like to hear from you.
Justin Boehm
LEEA’s Regional Manager Australia and New Zealand
Membrey’s Transport and Crane Hire and Linfox Group recently completed a sensitive logistical project transferring a herd of elephants from Melbourne Zoo to their new residence at Werribee Open Range Zoo. Craig Membrey and his team are no strangers to managing this type of project. Having managed the transferring of animals to and from Melbourne Zoo for 56 years they were up to the ‘tusk’.
WHEN YOU ARE MOVING A 23 TONNE FAMILY to new digs the logistics and planning are mammoth. They involved nine elephants, 21 elephant keepers, three cranes, three Riggers, three trucks, three specially modified elephant containers, and two police escorts. Special all green traffic light controls allowed the 40 kilometre trip from Parkville to Werribee to go off without a hitch delivering Melbourne Zoo’s entire herd to their $88 million new enclosure, which is the same size as the entire footprint of Melbourne Zoo.
Craig Membrey takes up the story.
“We’ve been discussing the project with the Zoo for some time, and we’ve been planning in detail for the past 12 months. With the transportation of such sensitive cargo, the plans for the lifts and transportation have to 100 per cent,” said Craig.
“Two years ago, we lifted the crates into the enclosure and the keepers walked the elephants in and out, gradually getting them accustomed to how they felt. Obviously, there were numerous meetings involving the Zoo, the keepers, Linfox, us. The Police were also involved because on the days of transporting them, we had a full police escort.
“We provided detailed lift plans to ensure we had everything covered. With Mums travelling with their babies, we had
to cater for the uneven weight distribution. The Linfox Group had specially prepared air conditioning units which controlled the atmosphere in each of the containers,” he said.
Craig and his team determined the best way to lift the containers onto the low loaders was with two MAC25 Super Lift Frannas to dual lift the containers.
“It was difficult, but it all went to plan,” said Craig. “One Franna went backwards and one forward. Tolerances were an issue and in some instances, we only had millimetres of area between benches and trees. We folded the crane’s mirrors in so we could navigate the tight areas which meant the operators were being
guided via UHF radio. Because the containers were already tall, Linfox had arranged for some extremely low loaders ensuring height restrictions were not an issue and the prime movers were all Volvos,” said Craig.
The bull elephant was in the first container with the Zoo wanting him in the new enclosure first. After a couple of days, they moved more of the herd in two containers during the second trip and three containers in the third. When the containers arrived at Werribee Open Range Zoo, Membrey’s dual lifted them from the
With Mums travelling with their babies, Membrey’s had to cater for the uneven weight distribution in the containers.
low loader with a Liebherr LTM 11204.1 and a MAC25 Super Lift Franna. The containers were placed in the holding area behind the new enclosure.
“When the containers were safely on the ground the keepers opened the doors, and you could see the elephants were inquisitive but cautious. We turned the crane’s engines off and after a few minutes they nudged out slowly, touching each other with their trunks for reassurance, they were vocalising and there was lots of trumpeting, rumbling, squeaking, and then ear flapping, and just engaging with each other.
“They were all solid signs the crew was feeling settled, reassuring their dedicated keepers that years of training and preparation had paid off and that the meticulous planning by all parties ensured everything went perfectly,” said Craig.
“We’ve been working with Melbourne Zoo for 56 years with my late father, Jack Membrey Senior, beginning the relationship in the ’70s. Over that time, we’ve moved many animals to and from the Zoo including elephants, giraffes, tigers and rhinos.”
Craig tells a story about an elephant he helped move a few years ago.
“One of the young bull elephants we helped move I remember very clearly. It was
2018, and we moved him from Melbourne Zoo and took him to Melbourne airport. Ironically a 747 ‘jumbo’ had been chartered, and he was the only passenger on the plane, headed to Miami Zoo.
“About nine months ago my family and I visited the Miami Zoo. Having introduced myself, the keepers were very welcoming and took us behind the scenes. When they brought the young bull out he wasn’t very friendly at all, he made a huge noise,
threw his trunk in the air, trumpeted and flapped his ears in a threatening manner. I could see he was looking at me and the elephant keeper turned to me and said, ‘He remembers you’,” said Craig.
“It was quite an experience and I’m glad I was on the outside of the enclosure. He remembered that I’d taken him from his family and interestingly, his Mother and Father were in the herd that we moved with this project,” he said.
Crane scheduling software company, Visual Dispatch has been acquired by United States-based RapidWorks. While the product and team at Visual Dispatch remains the same, the new ownership will add to the momentum of increased
AFTER ACQUIRING THE CRANE SCHEDULING software company in July of 2024, RapidWorks, a heavy equipment solutions provider, will support the Visual Dispatch team in managing the growing demand for its product.
Daniel McBride, Visual Dispatch Australia and New Zealand Cranes Manager, said keeping the brand current and agile is important in the crane services software market. RapidWorks will assist the company with creative consulting and communications support.
Visual Dispatch is a one-stop-shop developed specifically for the crane hire industry. The software optimises quoting processes, crane and support equipment scheduling, dispatch workflow and invoicing systems.
The company has grown from 20 customers in the early 2000s to now helping about 135 companies – an estimated 5000 users – in Australia and New Zealand realise their fleet systemisation potential.
“The leadership team and I identified that our customer base was growing exponentially,” Daniel said.
“In light of the positive trend, we decided it would be beneficial to join forces with a company that has experience in this space.”
RapidWorks’ services include, Rapid Enterprise Resource Planning (ERP), Telematics Global Positioning System (GPS) and the Rapid On-the-Go mobile applications.
The applications enable companies to dispatch and manage the complex requirements for crane services dispatch, construction work involving concrete pumping, hydrovac excavation, and other types of heavy construction jobs.
Daniel said RapidWorks will assist the team in developing the Visual Dispatch software interface, upgrade branding (including a revamped logo and graphics) and external communication processes and employ more staff. 100 per cent of Visual Dispatch’s staff were retained in the acquisition.
Visual Dispatch’s story could be considered a symbiotic journey with the crane and rental industry. It was founded
in the mid-1990s to address the flood of paperwork that crane hire companies were confronted with.
“Before the turn of the century, crane company operators were attempting to manage a surge in demand for machinery and the paperwork associated with that demand, including scheduling, timesheets and monitoring machine usage,” Daniel said.
“Visual Dispatch emerged to provide a solution for many crane companies.”
Since 2002, Visual Dispatch has been servicing Australian and New Zealand customers, helping them improve productivity, reduce costs, optimise workflows and increase customer service.
Visual Dispatch allows companies to manage resources from a single screen with a drag and drop functionality on a computer, tablet or smartphone. New jobs can be allocated to equipment and employee schedules. Shared resources
between company branches means any changes are instantly communicated between field and office personnel via email and text.
The software also tracks employee certifications ensuring qualified staff are operating the right machinery on jobsites.
“Our customers love how easy it is to use the Visual Dispatch software solution, particularly for getting job dockets signed at the start and end of shifts,” Daniel said.
“Timesheets are easily input too, as the Visual Dispatch system’s easy-tonavigate interface allows users to quickly and accurately confirm their hours worked with only a couple of clicks.”
Fleet safety is one of the key features of the software. Regularly generated reports identify any heavy equipment due for servicing or major inspections.
“In this instance, staff using Visual Dispatch will receive a notification, so that no worker steps foot in a crane that
is deemed to be unsafe due to equipment non-compliance,” Daniel said.
“Visual Dispatch also notifies the company and crane managers when any heavy lifting equipment linked to the software is compliant. It essentially records in real-time when each piece of equipment or vehicle has passed its compliance testing phase.”
Quoting is another advantage Visual Dispatch brings to a jobsite.
Daniel and the Visual Dispatch team are working to optimise and grow the product. He believes the software will be suitable for a wide range of customers across the globe.
“After seeing the rapid growth of Visual Dispatch, I feel that the sky’s the limit.” Daniel said.
“One day I’d like every crane yard in Australia and New Zealand using our product; that would make me happy.
Cloud Solution
Quoting
eTickets / eDockets
Payroll / Timesheets
Reporting / Dashboard
Purchase Orders
Invoicing
Fleet Maintenance
Storage
Visual, Drag and Drop Scheduling
Form Designer
ERP Integration
Inductions / Compliance
The Lifting Equipment Experts since 1974
The wireless aluminium super cells are supplied in kit form, which includes a load cell with integral wireless transmitter, hand-held readout, battery charger, 2 x super shackles, and carry case with foam cut outs.
All Lifting and Safety has been servicing Australian industry for more than 40 years and is proud to be an Australian owned and operated lifting, rigging and height safety supplier. It’s also a leading industrial brand when it comes to chain hoists, rigging equipment, lifting slings, lifting beams and much more.
WITH OVER 1,500 PRODUCT LINES available, the team at All Lifting and Safety is committed to meeting customers’ lifting, rigging, and height safety needs with precision and expertise. Managing Director Jason Warner explains more about the company’s offerings.
“All Lifting and Safety also provides high-quality lifting and rigging products. Our dedicated team of safety specialists offers comprehensive onsite inspections, in-house testing and certification, as well as tailored height safety solutions designed specifically for
a customer’s business environment,” said Jason.
“We are a specialist distributor of many of the world’s leading brands, including RUD, KITO PWB, Gunnebo, PEWAG, Andromeda Industries, and more. Additionally, we specialise in providing comprehensive inspections, as well as load and destruct testing services.
“Our in-house testing and certification procedures are conducted by a team of specialists with extensive experience in the lifting and rigging industry. All equipment tested adheres to Australian Standards, and each item is accompanied by a test certificate, ensuring compliance and quality assurance,” he added.
INTRODUCING THE ATEAM INSPECTION MANAGEMENT SYSTEM FROM ALL LIFTING Managing lifting gear inspections has never been easier.
“With ATEAM, All Lifting’s latest inspection management system, we are eliminating piles of paperwork and tedious processes,” said Jason. “Staying compliant and organised is now simple, efficient, and accessible wherever you are.
“ATEAM is designed to take the stress out of managing lifting gear inspections. This online platform provides our customers with quick access to reports, inspection scheduling, automatic reminders, and gear compliance tracking, all from any device, at any time.”
Here’s how ATEAM will transform your inspection management:
• Access inspection reports anytime, anywhere Forget searching through filing cabinets or emails! With ATEAM, your inspection reports are securely stored online and available whenever you need them.
• Request inspections with just a few clicks
Scheduling inspections has never been easier. Whether it’s a regular check or a one-off, ATEAM streamlines the process so you can set it up quickly and get on with your day.
• S tay ahead with due inspections Avoid missed deadlines with ATEAM’s automated reminders, helping you keep track of inspection dates and ensuring your lifting gear remains compliant.
• G ain real-time performance insights ATEAM monitors your equipment’s
performance and compliance status, providing real-time insights so you can make informed decisions about maintenance or replacements.
• E ffortless gear management From reducing paperwork to compliance tracking, ATEAM simplifies every step of managing your lifting gear, giving you peace of mind and more time for day-today operations.
All Lifting’s highly trained staff inspect and identify any possible repairs needed, carry out the necessary repairs, and perform proof load tests.
“We repair, service, and refurbish a wide range of lifting equipment, including chain slings, plate clamps, lever hoists, lifting magnets, lever and chain blocks, fabricated items, magnetic particle testing, fall arrest blocks, crane hook blocks, and reswagging of wire ropes,” said Jason.
With an extensive product line-up t hat includes wire ropes, shackles, slings, hooks, crane accessories, and more, All Lifting ensures that every piece of equipment meets the highest standards of safety and performance. In addition to these essential products, the company specialises in the fabrication of Australian-made lifting equipment, offering custom-designed spreader bars, lifting beams, kibbles, man cages, and much more, all manufactured inhouse at their state-of-the-art facility.
What sets All Lifting apart is its deep commitment to Australian manufacturing, which ensures all products are crafted locally. This
focus on local production allows the company to maintain strict control over quality, ensuring that every piece of lifting equipment is built to last and perform in the toughest environments. By supporting local jobs and the Australian economy, All Lifting continues to uphold its reputation as a leader in the lifting and rigging industry.
When it comes to fabricating lifting equipment, such as man cages, kibbles, and spreader beams, All Lifting’s expertise is unparalleled. The company’s in-house engineering and fabrication teams work closely with clients to design and create tailored lifting solutions that meet specific project needs. Whether the task is handling heavy machinery or transporting large components, All
Lifting’s products are engineered to ensure maximum safety, efficiency, and durability.
“When it comes to fabricating lifting equipment like man cages, kibbles, and spreader beams, our focus is always on safety, precision, and meeting the specific needs of our clients. Each piece of equipment is designed with the end-user in mind, ensuring it performs under the toughest conditions. We’ve built a reputation for producing robust, reliable lifting solutions that help our clients succeed, no matter the scale or complexity of their projects,” said Jason.
All Lifting also recognises the importance of competitive pricing. Understanding that every project comes with its budgetary constraints, the company offers cost-effective solutions without sacrificing the quality or
reliability of its products. Whether a client needs a standard piece of lifting equipment or requires a custombuilt solution, All Lifting delivers with precision and care, ensuring every project is completed to the highest standards.
By offering both off-the-shelf and custom lifting solutions, All Lifting has positioned itself as a trusted partner for businesses requiring durable, reliable, and safe lifting equipment. All products are designed and manufactured with a focus on performance, compliance with Australian safety standards, and the satisfaction of each customer’s unique requirements. With a proud Australian legacy,
All Lifting continues to be the go-to provider for lifting equipment that is built to last.
PREMIUM LIFTING, RIGGING, AND TOWING SOLUTIONS FOR
Our extensive range includes Grade 100 Chain and Fittings, Lifting Points, Container Hooks, Concrete Lifting Clutches, Round Slings, Webbing Slings, Load Restraint Solutions, and Recovery Equipment.
Our partnership with globally renowned manufacturers ensures we deliver equipment that stands out in durability, reliability, and safety.
As the lifting and rigging industry continues to evolve, having access to premium-quality, compliant, and readily available equipment is critical to ensuring safety and efficiency.
LIFTING IS AN AUSTRALIANowned and operated importer and wholesaler specialising in lifting, rigging, towing, and recovery products that is quickly becoming a trusted name in the industry.
Legend Lifting was founded with a clear purpose: to provide the market with high-quality lifting and rigging products backed by expertise, rigorous testing, and exceptional service.
Managing Director Ben McIlroy has spent more than a decade in the industry, working across sales, branch management, and national account management roles before taking the leap to establish his own business.
“I’ve been in the lifting and rigging industry for a long time, and I’ve built strong relationships with distributors across the country. I understand the challenges they face, from product availability to ensuring compliance with industry standards,” Ben said.
“With Legend Lifting, my goal has always been to offer a product range that meets those needs while providing the highest level of support.”
One of the key differentiators of Legend Lifting is its focus on partnering exclusively with distributors rather than selling directly to end users. This ensures that lifting and rigging professionals across Australia have access to high-quality products through trusted suppliers.
“We work closely with our distributors, helping them secure jobs by providing
quick turnaround times on quotes, technical support, and access to a growing range of lifting, rigging, and recovery products. Our success is built on their success,” Ben explains.
Legend Lifting has made significant investments to expand its product range, ensuring distributors have access to a broad selection of lifting and rigging solutions. The company now carries an extensive range of Grade 100 chain from 6 millimetres (mm) to 22mm, Grade 100 fittings from 6mm to 32mm, container hooks, weld on lifting points, concrete lifting clutches, round slings, flat webbing slings, recovery towing strops and soft shackles, as well as a range of load restraint products.
In addition to its lifting and rigging products, Legend Lifting has established strong partnerships with international manufacturers to supply crane ropes and wire rope slings. These partnerships ensure that distributors have access to high-performance wire rope solutions for cranes and other heavy lifting applications, providing an extended range of products that meet industry demands.
“We understand the critical role wire rope plays in lifting operations, and we only work with manufacturers who meet the highest quality and safety standards,” Ben said.
One of the biggest pain points in the lifting and rigging industry is lead times. Many products – particularly specialty items – are manufactured to order, leading to delays that can impact job timelines. Recognising this challenge, Legend Lifting has structured its business to ensure faster access to essential lifting and towing products.
“When I launched Legend Lifting, I knew that having the right stock available
when distributors needed it would set us apart,” said Ben. “That’s why we’ve built a strong inventory across multiple product lines, reducing wait times and ensuring our customers can get what they need, when they need it.”
He said this approach has been particularly beneficial in the recovery towing sector, where delays in obtaining equipment can create costly disruptions.
“We introduced a comprehensive range of recovery towing strops and soft shackles up to 300 tonne minimum breaking load (MBL), available off the shelf. Before, these products were often made to order, causing delays. Now, our customers know they can rely on us to have the stock on hand.”
Legend Lifting sources most of its products from reputable overseas manufacturers, working closely with factories that produce for global markets. Ben personally visits these facilities annually to oversee production, maintain quality standards, and explore new innovations.
“We don’t just source products and hope for the best. I travel to our
Having the right stock available when distributors need it sets Legend Lifting apart from competitors.
“We don’t just source products and hope for the best. I travel to our manufacturing partners regularly to ensure the quality and compliance of our products. It’s about being proactive – making sure we’re offering the best possible lifting and rigging solutions to the market.”
manufacturing partners regularly to ensure the quality and compliance of our products. It’s about being proactive – making sure we’re offering the best possible lifting and rigging solutions to the market,” he said.
While China is a primary sourcing region, Legend Lifting also works with European manufacturers for specialised items, ensuring that distributors have access to the right equipment for any job.
Beyond product availability and quality assurance, Legend Lifting prides itself on
its customer service and technical support, understanding that time is money.
“Our customers don’t have the luxury of waiting days for a response. When a distributor reaches out with an inquiry, they get an answer the same day. If we need to confirm freight pricing or work through technical specifications, we keep the communication flowing so they know exactly what’s happening,” Ben said.
This level of responsiveness has helped the business establish itself as a reliable partner for distributors, giving them the confidence to offer Legend Lifting products to their customers.
With a strong foundation in place, Legend Lifting is focused on building brand awareness within the crane and lifting industries. By ensuring that end users can trust the products they see in the field, the company aims to become a go-to name in lifting, rigging, and recovery solutions.
“Our vision is simple: when someone sees a Legend Lifting product in use, we want them to have complete confidence that it’s high-quality, compliant, and reliable,” Ben said.
“Legend Lifting’s continued investment in its product range, commitment to quality, and strong distributor partnerships are setting the stage for long-term growth.
“We’re in this for the long haul. Legend Lifting isn’t just a supplier – it’s a trusted partner for lifting and rigging professionals. We’ll continue to grow, innovate, and provide the best possible solutions for the industry.”
An opportunity has arisen to acquire a highly reputable rigging supply business located in Tasmania. This well-established business, with a market share of 40-45 per cent of the Tasmanian rigging industry, specialises in the supply of high-quality rigging, height safety supply, service and installation, and safety equipment.
TASMANIAN RIGGING SUPPLIES PTY LTD
is a Tasmanian-owned and operated business, supplying rigging and lifting equipment to customers throughout the state.
The business is committed to providing expert service and quality products to customers, so they can safely and efficiently manage lifting and rigging applications in their business.
With more than 45 years combined experience, Tasmania Rigging Supplies’ workforce is one of the most experienced in Tasmania’s lifting equipment industry. Professional development and continued training has been an important focus for the company.
Tasmanian Rigging Supplies is the only company within Tasmania that is a full member of the Lifting Equipment Engineering Association (LEEA) which, like NATA (National Association of Testing Authorities), has a strict procedure within Work Health and Safety and Management Systems that require compliance and
constant upgrading. The company strives to offer a service and a product range that complies with AS17025, AS4801, ISO9001, AS14001, and all relevant Australian Standards within the lifting and engineering industry.
Tasmanian Rigging Supplies has a system in place which provides full traceability of all products from its vast supply base, plus a program that can be accessed from the website seven days a week 24 hours a day.
Extensive product range: The business offers a comprehensive selection of rigging supplies, and safety equipment, catering to diverse sectors including construction, mining, and manufacturing.
Industry expertise: With more than 45 years of combined experience, the team is highly knowledgeable, providing valuable advice and support to customers.
Strategic location: Situated in Southern Tasmania, the business is well-positioned to
serve a broad client base across the region. Solid customer base: The business maintains strong relationships with top clients, including major players in the crane, industrial lifting, and civil construction industries.
Growth opportunities: The business is well-positioned to capitalise on Tasmania’s ongoing infrastructure development and the growing emphasis on workplace safety and regulatory compliance.
Tasmanian Rigging Supplies represents an outstanding investment for those looking to enter or expand within the rigging industry. With a strong market position, an experienced team, and ample growth potential, this is a rare opportunity to acquire a leading business in Tasmania’s rigging industry.
For more information contact:
Morgan Business Sales: Licence #597 M: 0419 422 124
kat@morganbusinesssales.com
For more than 20 years Delphi Measurement has designed and manufactured a huge variety of tension loadcells for the Australian lifting industry. These simple yet rugged designs make them suitable for the harshest environments, said Mike Leonard, Delphi Measurement’s Managing Director.
DELPHI MEASUREMENT’S LOAD CELLS
are manufactured from aircraft-grade aluminium, and the ongoing development of the designs has resulted in lightweight load cells with high safety factors, making them suitable for numerous lifting applications.
Tension load cells are used in many industries, where measurement of a pulling force is required. Delphi’s tension cells are available in stainlesssteel and aluminium. The stainlesssteel cells are available in wired or wireless variants, while the aluminium cells are wireless only. Wired (cabled) versions are predominantly used in permanent installations, like conveyor belt tensioning, mine shaft winders and conveyances, dead end rope load monitoring and many more industrial applications. The wireless variants are typically used in portable applications such as crane testing, load weighing, anchor point verification etc.
The combination of wireless technology and high strength materials make the 103TWK series a lightweight, highly versatile and portable load measuring solution.
“The Delphi 103TWK range of load cells have been very popular for many years, and many of The Crane Industry Council of Australia (CICA) inspectors own or use, one or more of our load cells. They use them for conducting crane certification, Major Inspections, and other applications like load weighing, pulling anchor point testing etc,” said Mike.
“Delphi Measurement has manufactured a range of wireless aluminium load cells for a very long time and there would be many hundreds, if not
thousands, of them being used throughout industry every day, both within Australasia and many other locations around the globe.”
The development of Super Shackles over the past few years by some of the world leaders in shackle manufacture have
meant that shackles are now capable of higher ratings for the same size.
The advancement of materials, and manufacturing methods, has given rise to smaller, stronger shackles, for example a 30 tonne super shackle is the same size as a 17t safety shackle. This advancement
opens an opportunity for tension cells to do the same, i.e. to make smaller, stronger loadcells. Delphi Measurement has seized this opportunity and developed a range of tension cells, specifically for Super Shackles.
“We’ve engineered a new series of products and called the range the 104TWK to differentiate it from the existing 103TWK loadcell kits. To my knowledge, there is nobody else in the world doing this right now,” said Mike.
Super Shackles are available in various sizes and Delphi Measurement has focused on five sizes; 5 tonne, 9.5 tonne, 15 tonne, 21 tonne and 30-tonne. They’ve designed a ‘kit’ which comprises the load cell, the mating shackles, handset and charger, all in one case. With everything in the one case, there is no
Delphi Measurement’s 150t Tension Cell kit, the 103TWK-150.
geographical range in Australia, we have entered into an exclusive distribution agreement with the Global Lifting Group for the 104TWK series. They are selling lifting and rigging gear to a very large base of end users, and have a solid understanding of the various industry sectors that are relevant to this product range. It made total sense for us to partner with them.”
Mark Heath, General Manager of All-Rig Lifting and Engineering Supplies, and Chairman of The Global Lifting Group, is pleased to ‘partner’ with Delphi Measurement for the 104TWK Series Super Shackle tension load cells.
“This is a new concept in tension cells making them lighter, more manageable and featuring super shackles specifications,” Mark said. “The Global Lifting Group members look forward to supplying the market with this industry-first tension cell design, and are proud to be recognised as the Australian agents for this unique product, designed and manufactured by the team at Delphi Measurement.”
Mike explains how the combination of the 103TWK and 104TWK provides a broad spectrum of load cells to choose from.
“Between the 103TWK Safety Shackle
“Between the 103TWK Safety Shackle load cells, and the 104TWK Super Shackle load cells we have load cell kits available that start at five tonne and go up to 250 tonne, we have also made 103 Series cells up to 300 tonne.”
need to have shackles elsewhere, so when you get to site everything is with you to get started.
According to Mike, the 104TWK is aimed at the end user, providing them with the benefit of a complete lightweight kit.
“Kilogram per tonne of carrying capacity, these will be the lightest kits in the world, certainly others will follow, but Australian ingenuity got there first,” he said. “With the end user in mind, and knowing they are spread over a huge
load cells, and the 104TWK Super Shackle load cell kits available that start at five tonne and go up to 250 tonne, we have also made 103TWK Series cells up to 300 tonne. The most common capacities range from five to 120 tonnes.
“For under the hook applications we have typically provided the wireless aluminium 103TWK Series. While this range is among the lightest in the world, the 104TWK Super Shackle cells will be lighter again, lighter than any load cell on the market per capacity. Another
Super Shackles are available in various sizes and Delphi Measurement has focused on five sizes; 5 tonne, 9.5 tonne, 15 tonne, 21 tonne and 30-tonne.
advantage of the 104TW series is the reduced overall length, meaning that they take up less headroom.
“Delphi has been manufacturing load cells for 40 plus years. We only use European and United States aluminium and steel. We use world-class electronics
from the United Kingdom and we’ve been partnered with Mantracourt Electronics for over 15 years.
“Delphi Measurement has the capability to provide quality products, service and repairs, without the need to send products overseas. We offer open
For more information about this business opportunity contact:
calibration, enabling any calibration facility to calibrate our load cells. Other manufacturers may have locked calibration software, limiting end users to specific service providers. We pride ourselves on responding timeously and professionally to our customers’ requirements providing complete custom load measuring solutions.”
Mike said the new ‘partnership’ with the Global Lifting Group will benefit both parties, but more importantly it will increase the collective ability to provide existing and future customers with a range of high-quality products, including the 103TWK and 104TWK load cells, to manage their lifting requirements well into the future.
For further information on Delphi Measurement’s 104TWK Super Shackle cells contact The Global Lifting Group 1300 454 768.
Andromeda Industries’ innovative approach to the design and manufacture of steel cable and lifting products has seen the crane and lifting industry respond in a very positive manner. Combined, the rich innovation produced at Andromeda, and strict testing procedures, makes for compliant and quality products, fit for purpose.
GEOFF BOWER, ANDROMEDA INDUSTRIES Customer Relationship Manager, explains how the company’s manufacturing process doesn’t stop at assembly but expands into the precise testing regime.
“When each product reaches the end of the production line, they are put through our 600 tonne capacity Swaging press operated by Jason Waterhouse. The Swaging press ‘swages’ the ferrule which basically means it terminates the cable before we test the product. These products are then tested in our vertical testing bed which is capable of testing products up to 450 kilonewtons,” Geoff explains.
With a wide range of products manufactured at Andromeda, the majority of the testing procedures are completed within this area.
“There are a number of different products and configurations which are tested in this area which go up to and include our Eight-0 cable (32mm). We have our standard Superflex Slings, Strops, Double-Ended Strops, Flat Woven Slings both in cradle and choker configuration. We also test our smaller Dean-0 slings and Counterweight Strops here as well.” Geoff said.
Andromeda’s manufacturing doesn’t stop there but branches into lifting slings on a much larger scale that requires much larger testing beds and gear.
“The cable manufactured for our XL sling division are produced by our horizontal braider. This braider produces Superflex Cable from 12 mm to 24 mm feedstock and once braided makes our largest 96mm cable. These products are assembled in a similar way to the smaller range, it’s just that everything’s much bigger.”
For Andromeda’s XL division, this includes the 10-0 (40mm) up to 24-0 (96mm) cable.
“We have heavier machinery to help us move and assemble the larger slings. From the Superflex cable through the whole assembly process, machinery is used due to the sheer size of the products. Our ‘XL’ divisions as we call it, is completed with our larger Swaging press with a capacity of 4200 tonnes and tested in our 300 tonne horizontal Wirop Test bed. “Geoff explained”
Andromeda has its very own engineering division, headed up by Mark O’Neill. Geoff explains how this division makes a critical contribution to each and every product.
“Mark is one of our machinists and he actually produces our fittings for the lifting range. Mark and the team manufacture our U-Terminations and our steel ferrules. They are all produced in-house starting from standard bar stock. With the use of our CNC machines to mill the bar stock and machine it down, we also have a unique range of benders and other special machines to bend it into shape. This means we’ve got quality control not only on the cable but our fittings as well,” said Geoff.
He said some termination designs are completely unique to Andromeda.
“We produce our steel, low deformation ferrules as a two swaging process. They feature an inner tube that presses the cable to begin with, and then there’s an outer tube that goes over the top, it’s a steel ferrule rather than aluminium, so it can be used in caustic environments.
“These are unique to us here at Andromeda, and we’ve designed them with a tapered end which gives a much smoother and clean finish. These steel ferrules hide the tail of the pressed cable but leave you with inspection holes.
“When you are conducting your sling inspections the tail is still there, which you can see through the previous mentioned ‘inspection holes’. There you can see there’s been no damage or slippage to the tail that could affect the integrity of the sling. The development of our steel ferrules, from the idea to implementation, was a 10 year process for the founder, Raymond McLaren and the engineering team,” Geoff said.
To finish the production line, all products are compliant and certified with relevant standards providing Andromeda Industries with a great opportunity to expand into new markets.
“We are members of the Lifting Equipment Engineers Association (LEEA) and also the National Association of Testing Authorities (NATA) certified for the wire ropes. Our products conform to AS 1666.1 which is the wire rope standard
in Australia. We recently joined the Associated Wire Rope Fabricators (AWRF) which is the industry body in the United States,” Geoff said.
“We are attending an AWRF event in Denver later in the year. We have ventured in the US market previously and believe there is a strong calling for Flat Woven Slings and it’s a market that really interests us. The US is heavily focused in the wire rope market which makes us interested in getting back there and having a look.
“We’re also attending an event in Riyadh, Saudi Arabia, as part of an initiative by Investment NSW. They’ve taken a stand at the Saudi Big 5 Construct, which is a two-week event for the construction sector. As we manufacture in New South Wales, we’ve been fortunate to be invited for the second week, which will be huge. We already export to the UAE and we are starting to get enquiries from Saudi Arabia.” said Geoff.
“It’s going to be a massive step up and it’ll give us a better understanding of what’s happening there, because the construction industry is next level. The money being
spent is astronomical and because our lifting and rigging gear has been designed to suit the civil construction space, we think there will be plenty of interest. The idea is to hopefully set up meetings with potential distributors and discuss projects with some of the major builders.”
Geoff will also be in New Zealand later in 2025 to celebrate the Crane Association of New Zealand’s 50th birthday during its National Conference and Exhibition.
“We are already working closely with a couple of the larger distributors in New Zealand and it’s a market that we’d like to grow,” he said.
“I was speaking to a couple of contacts recently. I think there could be a really good market for our Dean-0 sling, especially on the ports. The Dean-0 in particular has the potential for a lot of traction over there.
“It’s going to be another event, like the Crane Industry Council of Australia’s National Conference and Exhibition and also LEEA’s LiftCon. These events are a great opportunity to network with our industries and showcase who we are and what we do.”
As a member, you have exclusive access to:
Empower your team with industry-leading skills and safety expertise. Industry Networking
Join the exclusive network shaping the future of lifting.
Stay ahead with exclusive access to international standards and expert guidance.
BAB Engineering, a leading manufacturer of electrohydraulically powered loading decks, recently announced a number of changes to the business as well as launching a brand new 4.2 metre deck designed to help builders with the boom in modular construction.
GERD ALTMEYER AND EVELYN KLEIN relocated BAB Engineering’s manufacturing facility to Geelong following conversations with Peter Zeirzer, Director at HPS Tech, a leading process engineering provider specialising in manufacturing of dairy, brewery, beverage, foods, liquids, powders and more. A partnership with Peter was formed to further develop the range of electro-hydraulic loading decks.
Peter takes up the story.
“With a strong background in manufacturing, I was impressed with the innovation and quality of the decks, and having a specialised fabrication division also aligned with a new patent development that Gerd and I were separately working on,” he said. “I could see the benefits of utilising my experience within manufacturing and 9x5 Consulting, an IT business I’m also involved in to further expand the decks functionalities, capabilities and safety, so it is a great match.”
BAB Engineering’s electro-hydraulic control and operations are safer, more efficient and provide the convenience of having a single person manage operation of the loading deck effortlessly. Gerd explains more.
“From a work, health and safety perspective, the reduction in physical
repetitive tasks and the reduction of risk to personal injury are probably the main advantages of our powered decks.
“We can hydraulically extend and retract the decks when they are fully loaded. When the deck is fully extended and a crane places a pallet of tiles (for example), the deck structure is loaded to its maximum capacity. When the load is landed, with the push of a button, we can retract the load and bring the whole structure back to a much safer position.
“With a conventional deck, the load is landed and then has to be retrieved from the tip of the deck before it can be retracted,” he said. “Our decks are safer and designed to increase the productivity
of a construction site. Over time, the mechanisms on manual decks begin to wear and it becomes increasingly difficult to push them in and out. It can take up to three people to manage the process –which couldn’t be completed in under five minutes.
“It doesn’t sound a lot, but if this is required two or three times a day, that is one and a half hours per week just to rearrange a deck. Multiply this time over the course of a project and factor in the costs of three people, and the onsite crane being not productive, we are talking serious money.”
BAB Engineering is manufacturing three sizes of electro-hydraulic controlled
decks starting at 2.2 metre, then 3.2 metre, and now the 4.2 metre deck.
“The 4.2 metre deck is unique, it’s not a prototype, it’s not just an image in a brochure, it physically exists and works perfectly,” Peter said.
“We have designed the 4.2 metre deck to accommodate the move towards modular construction. Increasingly we are seeing a move towards modules for high-rise construction which are being prefabricated offsite. The modules require larger installation windows and so the 4.2 has been designed to accommodate this trend.
“We have a transport solution for this deck and we encourage interested builders to give us a call to discuss this.
“Being a fabricator based in Geelong, we design and manufacture with Australian steel and ship Australia-wide. We’ve got custom fabrication options available which include accessories like ramps. It also means if a customer wants a base to the deck, we have the capabilities to engineer these, but ultimately, we are a fabrication company, which means our customers have customisation options available if they want them,” he said.
Charlie Turner, Workshop and Floor Manager, moved with the BAB Engineering team to the new manufacturing facility in Geelong. Evelyn explains the advantages of securing his services.
“Charlie is young, enthusiastic and extremely knowledgeable about the product. He knows every single part that goes into the decks off by heart,” said Evelyn.
“He knows where every bracket and every bolt goes, which obviously makes it a lot easier when you hire new people –you have somebody who already knows how it’s done, and how to organise everything.”
BAB Engineering understands that building sites are tough on products like loading decks and expects the occasional bang and dent, but she is not concerned about structural damage because the range is ‘built tough’.
“The hydraulic system is designed to push up to 60 bars and our system requires less than 10 bars to extend and retract the deck. So, we’ve deliberately over engineered capabilities into every aspect of the product.
“There are two props, one on each side of the deck, and these can be placed in three different positions. We also have an option where props are not required with the deck bolted to the concrete floor. Some builders might prefer this because it means decks can be installed without having to wait for the concrete floor above to cure,” she said.
The decks feature a control panel which is a standalone unit and features a 10 amp power outlet for a normal 240 volt standard power supply. It also features a number of safety mechanisms including a VC drive making it fully proportional.
“Everywhere in the world, construction sites are looking for better utilisation from site cranes and wherever possible they are
making the sites safer for the construction workers. Our crane decks address these requirements and in terms of costing we are only marginally more expensive than manual ‘roll in roll out’ decks,” said Gerd.
“On the larger construction sites, where safety is a main aspect, only the crane crews are able to extend and retract the decks. You can imagine what a dogman, who has been extending and retracting a deck several times a day, is going to say when he sees this can be done with the push of a button. The builder will also see the financial benefits of our system because he is paying for the crane crew as well as the hire of the crane.
“The better utilised the cranes are, the more return the builder sees on his investment. If a crane is made available for an additional four hours a week due to the time saved with our decks, that is a huge bonus,” he said.
The Crane Industry Council of Australia (CICA) recognises excellence and innovation in the Australian crane industry with the CICA Lift Of The Year Awards.
LIFT OF THE YEAR –UNDER 20T
LIFT OF THE YEAR –OVER 20T
LIFT OF THE YEAR MORE THAN 20 TONNES WINNERBMS Heavy Cranes Australia & CPB Contractors & John Holland Joint Venture. Girder GSR-08 Install of Bridge 80 of the West Gate Tunnel Project.
To enter the 2025 awards visit cica.com.au/awards-lift-of-the-year PROJECT OF THE YEAR INNOVATION OF THE YEAR
PROJECT OF THE YEAR WINNERSydney Gateway Project John Holland - Seymour Whyte JV.
AWARD WINNERAlevro. LNG Compressors Jack Down with Jacking System.
LIFT OF THE YEAR LESS THAN 20
TONNES WINNER - John Holland and Johnson & Young Cranes. Relocation of the heritage-listed Nissen Hut.
BILL SHAW MEMORIAL CUP WINNERBMS Heavy Cranes Australia and CPB Contractors & John Holland Group Joint Venture.
For several years Manitowoc has been trying to find the right location to grow and expand the business. Manitowoc’s John Stewart VP Sales & Support / General Manager and Paul Churchill, Customer Service Director, provide details about their new premises.
“OUR BLACKTOWN FACILITY HAS served us well, but we have known for some time that a larger facility was required if we are to grow the business and significantly expand our services supporting the large population of Groves and Potains we have in the industry,” said John.
“For us to take the next step we needed to find the right facility and our
options included having something purpose-built. We know we have to expand our service capabilities as well as having enough room to accommodate our growing product range, especially the new eight axle that will be arriving in Australia. We’ve been looking for some time.
“Since Paul came on board over 18 months ago, he has had a lot of contact
with our customers, and having worked for them for three years, he’s had even closer contact with Melrose Cranes. With the recent Borger Crane Hire and Rigging acquisition of Melrose Crane Hire, Paul was made aware that the Melrose facility in Seven Hills would be vacated, and we were given first option to take up residence.”
Paul explains what a difference the new facility will make to the Manitowoc business.
“It’s basically tripled the amount of hard stand we had at Blacktown and it’s more than tripled the undercover warehousing and workshop space. We will have far more space to house spare parts and, with the expanded service capabilities, we will be employing
“We know we have to expand our service capabilities as well as having enough room to accommodate our growing product range, especially the new eight axle that will be arriving in Australia.”
extra technicians to significantly grow the levels of support we are providing our customers.
“The facility enables us to manage a much wider scope of larger projects. I joined Manitowoc tasked with improving and expanding our after sales capabilities for the Grove and Potain products, and this facility will enable us to do just that.”
Pace Cranes recently introduced Maeda’s MK3053CB knuckle boom mini crawlers with crane hire businesses and industrial glaziers responding quickly and positively. One of the early adopters of the technology is Spider Crane Hire.
SPIDER CRANE HIRE WAS LAUNCHED in 2023 by business partners and trade qualified glaziers Brendan Crew and Blair Brough of BKB Gazing, both with 25 years’ experience in the glazing industry.
“Working together in the glazing trade we had a continuous requirement for spider cranes and instead of hiring the
mini crawlers in all of the time we decided to purchase our first Maeda 285C,” said Brendan.
“With our combined 50 years of glazing experience, being on the end of the spider crane hook and working closely with operators, our transition into being an owner-operator has been seamless.
“Following continued growth in the business, we purchased the Maeda MC305C a year ago. Then Michael Cawston, National Sales Manager at Pace Cranes, advised that the battery-powered Maeda MK305CB was about to arrive so we sold that model and bought the MK3053CB knuckle boom.”
The MK3053CB features a telescopic boom with a knuckle that folds out from underneath the main boom. The knuckle features a telescoping luffing with a telescoping jib attached. The 12-metre main boom features four falls hook mode as well as a detachable negative angle jib with a maximum height of 16.95m. The model also features automatic and stepless multi outrigger settings, variable crawler gauge, diesel/electric and battery electric options as well fully proportional radio remote control.
Maeda has designed this model like the other machines in its range and offer a standard diesel engine option, diesel-electric or full battery lithiumpowered for those companies wanting a 100 per cent ‘green machine’. The battery-powered option is designed to work a full day, but it has the capability of running from the mains for unlimited working hours.
“The jib is very simple to operate and easy, it’s a one-man operation to take on and off and all functions are remotely controlled,” said Michael.
“Depending on what you are lifting, you might need the winch application. You can pre-rig the jib with the single fall hook fitted and then pull the boom out and you’re ready to go, or you can take the jib off, depending on what is required.
“Everything is remote controlled, which comes as standard. The MK3053CB features an expandable undercarriage for the stability of the machine, but the undercarriage also retracts enabling the machine to fit through doorway access.”
The MK3053CB features the next generation of outriggers which are stepless, meaning there’s no pinning system. If there is an obstacle in the way, you can stop the outriggers at any angle and the machine automatically sets up
the load chart to suit. The controls feature a one touch setup, and from one button you can completely set the machine up. It swings the outriggers, extends them and puts them down, and it also self-levels the machine.
“The load charts are set up to work at multiple angles. The Load Moment Indicator (LMI) will read that setup and tell the operator before the lift what they’re good for and at what particular angle, so it features very smart technology,” Michael said.
Brendan is excited by the opportunities a battery powered machine offers.
“Battery-powered equipment is the way forward for Spider Crane Hire. Builders and Tier one and Tier two projects are specifying zero emissions and so the MK3053CB ticks all their boxes,” he said.
“With glass installations, the knuckle boom on the MK3053CB helps us get inside the building a lot further, which is important. We can now go up with the boom and push inside which is a game changer for us.
“With the new Maeda being battery operated we have opened up new scope of works and we can work in areas where diesel engine cranes can’t go. We are also
finding the knuckle boom provides more versatility in the places we can reach and it allows for horizontal lifting over objects at zero degrees where a straight boom is restricted. For example we can now lift an object into a balcony area with limited head height and the reduced size, with no loss of capacity. It provides amazing access to the tightest of sites.
“The remote control provides us with the opportunity to be close to the load while operating the crane, providing precision placement. The remote control is brilliant for fine-tuning and adjusting the speed at which the crane lifts, it’s all very user-friendly,” said Brendan.
He goes on to discuss other industry sectors serviced by Spider Crane Hire, battery life of the crane and the support provided by Pace Cranes.
“Although we don’t have anything to compare it with, the charge in the battery manages everything we are asking the crane to do, and the ability to charge from a 10amp power source, means we haven’t experienced any limiting effects on usage. With our contacts and experience in commercial glazing a large majority of our work is providing spider cranes, glass
lifting equipment as well as sharing our knowledge to many glazing companies in both Queensland and New South Wales.
“However our work is not limited to glass, we also provide our services to metal fabrication companies, tile and stone companies, we install spas and basically any heavy item that requires lifting on sites with tight access.”
Spider Crane Hire also operates glass vacuum rigs ranging from 0 to 1000 kilograms in lifting capacity, bremner glass equipment as well as Kappel vacuum rig, Uplifter vacuum rig, Abaco glass grabber and utilise NFK glass equipment hire. It has also purchased a tilting A-Frame which is attached to a Tracked Carrier 1200R/PRO, from Pace Cranes.
“Even before the purchase of the Maeda mini crawlers, Michael and the team at Pace Cranes provided us with outstanding product knowledge and customer service. Now that we own a couple of crane their advice and support is ongoing. It’s obvious they care about what they do, the training during the handover of the MK3053C was informative and gave us the confidence to put the crane straight to work and it hasn’t stopped.”
For more than 30 years, XCMG has been manufacturing outrigger crane pads that are used in many applications around the globe. XCMG first used the pads in its own crane test yards to spread the heavy loads, and when customers came to view the cranes, they enquired about purchasing the pads. The rest, as they say, is history. Stephen Broomfield, General Manager XCMG Oceania Crane Center, explains more.
“XCMG MANUFACTURE THE LARGEST cranes in the world, so it makes sense that they have an extensive range of pads, and they do,” Stephen said. “But the range is broad and many of the pads are ideal for the Australian crane industry. We still use wooden planks for outriggers but overseas, where the ground is not well prepared, they use these extra-large outrigger pads.”
XCMG pads were previously
manufactured with fork pockets enabling a forklift or telehandler to load and unload them from a trailer. Today, they are manufactured with lifting trunnions providing a more effective means of loading and unloading with a crane.
Stephen said the original design of the pads included two pockets for fork tines, but the XCMG design team, which included an Australian engineer, conducted an extensive review and
realised the cavities weakened the weight bearing capabilities of the pads. They also realised that removing the fork pockets and adding lifting trunnions was more cost effective to manufacture.
“Our newest size pads in the XCMG range are manufactured to match the footprint of a 20-foot container and feature two twist-lock pockets vertically in each corner, enabling the pads to be locked together in a stack. There are
advantages with this size of pad and twist-lock feature,” said Stephen.
“XCMG crane pads can be of immense benefit when it comes to transporting all the necessary equipment when you mobilise a crane of any description. Let’s take a flat-bed trailer. You’ve already got the weight of the trailer and when you put the pads on and maybe your fly jibs and counterweights you will be at the permitted weight limits.
“If you take a 40-foot Skel trailer, which is the lightest form of trailer, you can lock two of these pads together which become the 40ft base of the trailer. You then have a flat-bed trailer on which you put the counterweights, hooks and fly jibs, significantly reducing your transport costs.
“You could put a stack of these, four high, and they would be half the height of a 20-foot container. You might need to
move a 20-foot container full of rigging gear. You can twist lock one of these pads to the trailer and put the container on top of your pad, then twist lock again. That’s the idea behind the 20-foot container size option. Also using ‘pigs ears’ on the corner of the pad, which are the lifting devices that work with twist locks, you can lift like a conventional container weighing 40 tonnes or even more.”
Stephen said XCMG is in the process of arranging to destructively test one of these new style pads to understand what they are capable of. The plan is to put weight, probably five times more than expected, and lift it off the ground and destroy it.
Stocks of XCMG crane pads are in the country and ready to be shipped to interested customers.
“We’ve been selling outrigger crane pads for some time, and they’ve been
“Our newest size pads in the XCMG range are manufactured to match the footprint of a 20-foot container and feature two twist-lock pockets vertically in each corner, enabling the pads to be locked together in a stack.”
delivered all over the country. To date we have been selling the smaller end of the range to all manner of crane hire businesses, but we do encourage interested businesses to give us a call to discuss the range,” Stephen said.
“We receive regular deliveries from the factory, so availability isn’t a problem. If you are interested in the larger pads, it will take the factory 25 days to manufacture with the in-house cutting and welding robots and have them ready for dispatch. Then there’s the shipping time.
“Compared to other brands on the market, XCMG pads are extremely competitively priced, and a significant number of enquiries have come from businesses that have seen them being operated out in the field. They’ve seen the quality and the capabilities of the pads, made an enquiry and bought them.”
Gary Sheppard, Founder and Director of Direct Cranes, is ambitious and passionate about what he does. Aiming to be a trailblazer in the field of helicopter lifting, he tells his story.
“MY WIFE AND I HAVE BEEN OPERATING Direct Cranes for almost three years now. I started out in construction as a form worker and I left the industry to pursue my career in aviation in 2017. I came back into construction in 2019 and started my first business, Sheppard Cranes and Rigging which was a labour business focused on rigging.”
Direct Cranes has been steadily adding to its fleet and now runs two Franna MAC 25s with SuperLift, which have been working on windfarm projects and general hire, a 60t Liebherr all terrain, as well as the 100t. Gary recently purchased a 60t Sany telescopic crawler.
“Apart from our first Liebherr, everything we have bought has been brand new and our latest addition is a new 60-tonne Sany telescopic crawler which arrived in early March. We had several brands to choose from, but we went with Sany for a number of reasons, most of them fairly obvious.
“Over the past few years, I’ve noticed with interest how much momentum international brands like Sany have been gaining. When it comes to the crawler market, lattice boom and telescopic, Sany has been proving itself for a number of years, and Tutt Bryant Equipment is supporting the product well with service, parts and after sales support.
“The 60t Sany will be working on a fairly ‘ugly job’ where the work will be tough. It’s not there to look pretty, it’s there to turn a profit from the get-go,” said Gary.
“To me, the Sany made sound business sense. The European, United States and Japanese brands have been around a lot longer, but when you examine the business proposition and compare the prices of some European brands to the quality and pricing of a Sany, and then factor in you’re not going to get higher rates because your providing a more expensive crane for the work, then the decision was a no brainer for me.”
The Sany SCC600TB telescopic boom crawler is built to work. The main
The block-type counterweight tray and blocks are stacked in a way that is easy to assemble, disassemble and transport.
“Realistically we’ve got the best of both worlds. With Sany and Tutt Bryant we’ve secured a cost-effective entry into the crawler market, knowing the support and parts support is going to be there when needed.
boom is made of high-strength steel with five sections, of which the basic boom is 11.88 metres and the maximum boom length is 46 metres.
The super structure features a high strength steel frame structure, no torsional deformation with a layout of components designed to enhance convenient maintenance and service.
The block-type counterweight tray and blocks are stacked in a way that is easy to assemble, disassemble and transport.
The ergonomically designed cab has the operator’s comfort and the safe operation of the crane as priorities. Large glass windows provide excellent vision of the work area, the position of the seat provides comfortable access to the joystick controls, various control
buttons and mechanisms. The cab also features a large integrated touch screen, and multiple cameras can be presented on the monitor at the same time to realise real-time monitoring of wire rope on each winch, conditions behind the counterweight and surrounds of the machine.
The integrated load moment indicator (LMI) system is provided as standard, offering high levels of safety when lifting. The LMI system can automatically detect the suspended load weight, working radius of the crane and the angle of boom, and compare rated load weight and actual load, working radius and boom angle.
Under normal operating conditions, it can intelligently judge and automatically cut off the crane’s action if it gets into a dangerous situation and features a black box function to record any information relating to overloading.
Tutt Bryant being the national distributor for Sany was also a key factor in Gary’s decision to purchase the Sany.
“Tutt Bryant Equipment has a national footprint and a commitment to service and support as well as spare parts availability,” he said.
“Realistically we’ve got the best of both worlds. With Sany and Tutt Bryant we’ve secured a cost-effective entry into the crawler market, knowing the support and parts support is going to be there when needed.
“The crawler went straight to work and the ‘bang for the buck’ is obvious, these cranes go out for the same money, it’s just that we’ve just taken a huge chunk of dollars off the price tag.”
Gary and his team are innovative, continuing to examine ways of improving the service Direct Cranes provides its customers.
“We have been busy developing a lifting plan program that’s specifically for cranes with lifting capacities up to 250 tonne. We’ll release this to the general industry shortly and we can see it will benefit similar sized businesses. It is targeted to generate lift plans for Tier one projects.
“Larger crane companies can afford to spend the 140K and have a lift planner sitting in office waiting for a lift plan to come through, we can’t, we’ve got to keep our boots on the ground,” said Gary.
Lifting with helicopters is Gary’s passion. “Our helicopter will lift up to 550 kilos and for anything heavier we hire in larger helicopters. Obviously, you’ve got to build a portfolio to be able to finance the bigger machines. But that’s the direction in which we are headed, that’s the space I’m going to live in, and the cranes, including the Sany, are helping me to get there, they are a stepping stone towards the future of lifting.”
Borger Crane Hire and Rigging recently completed the construction of two Potain tower cranes with a Grove GMK6400. The project wasn’t without its challenges as it was in the heart of Bondi Junction, one of Sydney’s most densely populated suburbs. Adam Little, Technical Supervisor at Borger Crane Hire and Rigging was responsible for project.
ACCORDING TO ADAM, THE LIFTS required months of detailed planning.
“Because of the situation of the site and where we had to position the crane, as well as the traffic logistics involved in setting up a crane in Bondi Junction, we undertook months of detailed planning for these lifts,” he said.
“A key consideration was the crane’s configuration and the fact that the outriggers were on pile caps which required a significant amount of engineering detail to be completed. We chose our Grove GMK6400 400 tonne capacity, because of its ability to get into tight spaces and its exceptional lifting capabilities.”
The Grove GMK6400 is a six axle, class-leading all terrain crane with exactly the same footprint as 300 and some 220 tonne capacity cranes. It also
features outstanding lifting capabilities across a broad spectrum.
Main features of the Grove GMK6400 include:
• M ain boom: 15.39m – 60m
• Auxiliary equipment includes self rigging MegaWingLift™ and auxiliary hoist and up to 12m-79m of Luffing Fly and up to 64m of Fixed Fly.
• New designed carrier cabin
• M EGATRAK suspension system with MegaDrive
• A ll wheel steering
• Steer by wire technology
• E COS EKS5 full graphic display
• Mercedes-Benz OM 502 LA
8-cylinder engine
• F ive outrigger positions
• L ength: 17.536m and Width: 3.0m
Bondi Junction is a densely populated suburb with 88.7 per cent of dwellings either medium or high density, and the population density of approximately 10,018 people per square kilometre, so there wasn’t much room to mobilise a 400 tonne capacity all terrain. Adam and his team went through a detailed lift planning process, to ensure the lifts went off without a hitch.
“Obviously we developed a lift plan that took into account the various scenarios of lifting in a densely populated area. The tower cranes had
to be set down in definite positions on the job site due to the position of the lift shafts within the overall project,” said Adam.
“Positioning the crane off the street to enable traffic to flow in one direction towards Bondi Junction was a major consideration and the configuration of the crane was based around all of these factors. We had to conduct the lifts safely, leaving lanes open so as not to restrict traffic flow too much, it’s a very busy area.
“We configured the Grove GMK 6400 with main boom and 37 metres of luffing fly and 95 tonnes of
configured the Grove GMK 6400 with main boom and 37 metres of luffing fly and 95 tonnes of counterweight.
slew deck on the second crane. We had approximately three and a half hours of lifting and then four hours to pack up the crane and get it out of there. We were back the following night to do the whole complete setup again. We installed the slew turret to boom install, counterweights install, and then packed up again,” said Adam.
counterweight. We were lifting at a radius of 39 metres, lifting loads at a little over 13 tonnes. We were lifting at night to avoid major traffic congestion and disruption.”
On the first night the team had to set up the Grove GMK 6400. Mobilising the crane involved five semi-trailers of counterweights, two semi-trailers of luffing fly components. Borgers had a Franna AT 40 onsite as the assist crane.
“It took approximately four hours to set up the crane and we able to install one of the cranes on the first night. We set up the tower to the
The lifting spectacles attracted a number of the Bondi Junction locals on both nights with one commenting to Adam that he thought it was “aerial crane ballet at its finest”.
Because of meticulous planning everything went to plan.
“We were pleased with the outcome. Everything went to plan. We didn’t disrupt the local traffic too much and the tower cranes were in place and ready for action on time,” said Adam.
“The Grove GMK 6400 performed outstandingly. It’s a great lifter and has been a well utilized asset within the Borger Crane Hire fleet for an extended period of time.”
·
THE CRANE INDUSTRY COUNCIL OF Australia (CICA), in partnership with the Department of Employment and Workplace Relations, officially launched the Launch Into Work program in Adelaide on 21 January 2025. This exciting initiative brings together industry leaders and employers to introduce entry-level trainee dogger positions, creating real career pathways and helping to strengthen the future workforce in the crane industry.
With the growing demand for skilled workers, Launch Into Work provides participants with structured training, handson experience, and industry-recognised qualifications to set them up for success. The program ensures newcomers receive
mentoring and practical workplace exposure, helping them transition smoothly into employment while addressing workforce shortages in the crane sector.
The launch event in Adelaide saw an incredible show of support from South Australian CICA members, highlighting the many career opportunities available within the crane and associated industries. The strong sense of collaboration and commitment to workforce development was evident, as key industry players came together to invest in the next generation of skilled workers.
Participants completed their accredited training and successfully obtained their dogging licences – an important step towards their careers in the crane industry. But as we
Above: Participants completed their accredited training and successfully obtained their dogging licence, an important step towards their careers in the crane industry.
and mentor the participants, who greatly benefitted from this opportunity. In a gesture of appreciation for the work of Kate Galloway, Traineeship & Industry Engagement Co-ordinator, the participants presented her with a beautiful bouquet, and even more valuable were the comments, that this opportunity will change their lives.
Thank you to Bolzon Constructions Pty Ltd, Crane Services Pty Ltd, Hooked ON
CRANES & RIGGING, Load 28 Crane Hire | Construction | Access, Fleurieu Cranes Pty Ltd for their support of the Launch Into Work program. Dedication to fostering growth and development within the industry makes initiatives like this truly impactful.
If you are interested in being a host employer for the next program, contact kate@cica.com.au. You can follow program updates via CICA’s social media channels.
Goodline provides construction and maintenance services to Australia’s major resource companies across the country. Goodline recently took delivery of a Liebherr LTM 1090-4.2 from Tom Grady, National Used Crane Manager, Mobile and Crawler cranes.
GOODLINE IS AN AUSTRALIAN OWNED company started by John and Catherine Kennedy in 1999 for the provision of engineering, construction and maintenance services nationwide. Today, Goodline has operations in South Australia, Western Australia, the Northern Territory and the Sunshine Coast and boasts a work force of 700 plus. Thomas Kennedy discusses the purchase of the Liebherr.
“In 1999 we started out as a rigging company but since then, we’ve seen significant growth and now provide services for almost everything from domestic electrical and refrigeration to major projects, crane work and automotive fabrications and repairs,” he said. “Obviously, with our locations we are heavily focused on the mining and resources sector.”
He goes on to discuss Goodline’s crane fleet.
“The size and structure of the fleet has fluctuated and at one point, it was massive.
I’ve trimmed it right back to get the right usage and right now, we run a number of Frannas of varying capacities. We have two 60 tonne and a 30 tonne truck-mounted cranes, a 55 tonne rough terrain, two 130 tonne capacity all terrains and now the 90 tonne Liebherr.
“This is the first Liebherr in our fleet. We’ve always run Tadanos and we still have a great relationship with the brand, Over the past couple of years we’ve seen crane prices and the values of secondhand equipment increase significantly. Tom Grady and I have spoken over the past couple of years and Liebherr has been keen to secure our business. The purchase of the Liebherr LTM 1090-4.2 fell into place perfectly.
“Generally speaking, when you want something, you want it straight away and this was a quick turnaround process. Tom and his team were very easy to deal with, he was in regular contact, keeping us up to date
with times and what was happening to the crane,” said Thomas.
LIEBHERR’S REFURBISHMENT AND DELIVERY PROCESS
The Liebherr LTM 1090-4.2 was first sold to a German customer in August 2018 with Liebherr-Werk Ehingen (LWE) trading it back in November 2023. Liebherr Australia purchased the crane for stock in December 2023 and it arrived in the Melbourne yard in August 2024.
Goodline purchased the crane in September and the official handover was in Nhulunbuy Northern Territory in November 2024, with operator familiarisation taking place in January 2025.
Liebherr-Werk Ehingen (LWE) conducted an extensive process of inspections, cleaning, refurbishing and testing of the crane prior to it being shipped to Australia. On receipt, the Liebherr LTM 1090-4.2 was subject to a complete
inspection followed by six days of washing. Liebherr’s Tom Grady explains how much detail the Liebherr refurbishing team goes into.
“The inspection includes testing of the engine, clutch, transmission and hydraulic pressures. Electrical, brakes, steering, suspension and cylinder tests also are carried out. All failed or suspect components are replaced with new.
“Welds and welding joints are inspected, including NDT (Non-destructive testing), if and where required. The slewing ring assembly is inspected. Ropes are run out, inspected, measured and rewound. If any issues are found, they are replaced,” said Tom.
“The telescopic boom is removed, inspected, and tested on the horizontal bench tester. The carrier then moves into the refurbishment process. They examine steering components, axle assemblies, chassis, outriggers, cabin, check for any leaks and for everything else that was noted during the inspection.”
ALL NEW COMPONENT UPGRADES ARE NOW INSTALLED
In the case of Goodline’s Liebherr LTM 1090-4.2 the crane required upgrades to the double swing-away jib with hydraulic luffing, second winch, rooster, 20.5 alloy wheels and tyres including guard extensions, rear timber box, five sheave, single sheave and crane hooks.
“After the refurbishment and component upgrades took place, the crane was taken outside for a 40 kilometre test drive,” said Tom.
“It is then driven straight back over the inspection tunnel for a final inspection
and adjustments. After successfully passing the road test, the crane was driven outside onto the factory test area, supported with complete counterweight and the super structure features/movements are tested.
“All possible jib and boom configurations are tested; this extensive testing took around 10 days. A high load test is conducted overnight to see how the winches, luffing cylinders, telescopic cylinder and outrigger cylinders perform.
“The measurements taken include checking that the height of the load from the ground up, radius, etc, hadn’t changed. A document is produced confirming all deviations found during this process.”
Once the testing is completed the crane goes through a thorough wash for Australian Quarantine and Inspection Service (AQIS) requirements. This includes, but is not limited to, radiators, coolers, cab floors, all guards, toolboxes removed and cleaned. The outriggers and boom were cleaned during removal during the repair process.
The crane then moves into LWE’s paint shop immediately after the preparation work is completed. Once the paint job is completed the crane goes through the final
stages which includes Liebherr decals, customer branding, etc. The last part of the process includes inspection of oils, filters and Quality Assurance (QA) prior to its 900 kilometre road test to the German port for shipping Down Under.
“Once the crane had arrived into Port Melbourne, Australia and was purchased by Goodline, we transported it up to our Yatala branch where they carried out the roadability, safety items, fitment of seat covers, cameras, winch hr metres, window tinting, and Engel fridge.
“They finalised the 10-year inspection recertification, crane safe, plant registration, Pre-Delivery Inspection, final quality assurance and Queensland road registration. Six months factory warranty was included upon handover.
“The customer then transported the crane by road to Darwin where it went onto a barge to Gove port. It was then driven to Goodline’s premises in Nhulunbuy. We carried out operator familiarisation at Goodline in Nhulunbuy, Northern Territory,” said Tom.
Thomas is happy with the performance of the crane.
“The Liebherr has only been out on a couple of jobs because we have the big wet up here in the Northern Territory at this time of year and that slows down the cranage work. But the guys have been impressed with the crane and everything Liebherr brings to the party.
“The training and familiarisation were excellent, as was the service from Tom and his team.
“A little twist of fate with Goodline celebrating its 25 years in business by purchasing a quality second-hand all terrain from Liebherr.
Borger Cranes is a family owned and operated crane hire and rigging business servicing New South Wales and Queensland.
Borger cranes maintain a modern fleet of cranes and equipment and our fleet boasts some of the largest cranes on the east coast
2 x LG1750,1 X LTM 750, 2 X LTM 650 2 X LTM 500 2 X GMK 400 4 X GMK 300
With every job, our experienced and industry trained team delivers high quality performance and nothing but excellence.
Borger Cranes getting the job done for you.
SYDNEY
HEAD OFFICE
40 Kilto Crescent, Glendenning NSW 2761
P: 02 9832 1044
BOTANY
46 McCauley Street
Matraville NSW 2036
P: 02 9666 6366
NEWCASTLE
209 Old Maitland Road
Hexham 2322
P: 02 4961 3002
CENTRAL COAST
8 Ainslie Close, Somersby NSW 2250
P: 02 4346 4262
HUNTER VALLEY
10 Rosedale Close
McDougalls Hill NSW 2330
P: 02 5504 5525
MUSWELLBROOK
20 Strathmore Road, Muswellbrook NSW 2333
P: 02 5542 0077
BRISBANE
119 Brownlee Street, Pinkenba QLD 4008
P: 07 3333 5513
SUNSHINE COAST
65 Enterprise Drive
Kunda Parl QLD 4556
P: 07 5445 4900
GOLD COAST
52 City Link Drive
Carrara QLD 4211
P: 5588 5158
The event provided an opportunity for attendees to witness the high-quality standards and efficiency of local manufacturing processes and to understand some
Manitowoc hosted a diverse group of customers from around the world at its tower crane factory in Zhangjiagang, China.
THE EVENT PROVIDED AN OPPORTUNITY for attendees to witness the highquality standards and efficiency of local manufacturing processes and to understand some of the latest manufacturing innovations from Potain.
The VIP customer tour showcased Manitowoc’s commitment to collaboration and customer engagement and won praise from visiting delegates for offering a transparent view of its manufacturing processes and exclusive insights into its latest innovations and investments.
“It was great to welcome customers and dealers from all over the world to our factory in Zhangjiagang,” said Brian Wang, SVP – Emerging Markets, Manitowoc.
“We’re proud of the cranes we build here and many of our visitors have benefited from their high level of productivity for years. Several customers saw the facility for the first time, and it was great to show them our manufacturing processes. And for those returning to Zhangjiagang, there were multiple updates and investments to share.”
The tour began with a warm welcome from the Zhangjiagang leadership team. Attendees were then treated to an exclusive presentation of the Potain MCT 2205
tower crane, which was launched at the end of 2024 and is now in production in the Zhangjiagang factory. In addition, there were presentations on the Grove range of TMC truck cranes, including the TMC 550, for emerging markets,
Customers were guided through the production facility, where they saw the precision at each stage of the manufacturing process – from component testing to final assembly and quality control. The tour concluded with a visit to the test yard, where attendees witnessed two cranes being operated via remote control from Shanghai: approximately 150 kilometres away.
For many attendees, this visit marked their first time at the factory, and they talked enthusiastically of their admiration for the state-of-the-art facilities and the manufacturing quality of the cranes.
Returning visitors were quick to highlight the advancements that have been made and commended the local team for their progress and dedication to excellence. The tour was both informative and engaging, with many attendees recommending the experience to others.
Manitowoc plans to host similar visits in the future to further strengthen customer connections.
With the renewed focus on the safe operation of articulated pick and carry cranes, especially with The Crane Industry Council of Australia (CICA) now offering the On-Road Articulated Steering Mobile Crane Training Course, leading crane insurer UAA is reinforcing the importance of safety and the impact continued incidents have from a claims perspective. George Grasso, UAA’s Executive General Manager, Claims and Procurement speaks on the topic.
UAA INSURES ALL TYPES OF CRANES AND the articulated pick and carry invariably features strongly in every customer’s fleet one way or another.
“The articulated pick and carry crane is a versatile machine. It works in many industry sectors in Australia and New Zealand and other parts of the world. UAA respects the machine, we respect their capabilities and the countless number of application’s they operate in.
“However, in terms of the losses in cranes, the most frequent claims involve pick and carries. They are not necessarily the most expensive, any one incident of a larger crane can be far more expensive than the cost of a repair or total loss of a pick and carry crane, but they are certainly far more frequent in terms of losses and those losses occur while the machine is being operated as a tool of trade or on the road,” said George.
“On the road, an operator can lose stability and control, particularly at higher speeds. When on site and articulating when lifting, we’ve seen instances where they have turned over as a result of a lack of training, and also a lack of experience in operating this type of machine, particularly on the road.
“From a ‘tool of trade’ perspective, we see various instances resulting from a potential lack of experience and also work site pressures about getting the job done quickly. We have also seen a number of injuries and sadly, fatalities over the years involving pick and carry cranes.
“UAA will always support and work very closely with the industry around
presenting the losses and the trends of the losses that we see and working together to try and mitigate those risks as an industry by further reinforcing the importance of training, further reinforcing the importance of not letting your inexperienced staff operate these machines,” he said.
Invariably pick and carry cranes are
more difficult to operate and drive on the road than your other conventional all terrain cranes, for example. They are a machine that doesn’t lift with outriggers.
“There so many different variables to the types of instances we see, and it is difficult to see them cause injuries and fatalities. We’re working very closely with the OEMs around the frequency of
Incidents involving articulated pick and carry cranes are the highest frequency claims in UAA’s portfolio.
“From UAA’s perspective it is encouraging to see CICA and other industry groups, including regulatory bodies, recognising that there is a definite need for training due to the risk associated with pick and carry cranes.”
these losses ensuring there is continuous improvement and corrective actions taken on these machines improving their engineering to further reinforce safety. Workers leave home for work and have the right to return home safe and sound. Too many don’t.
UAA welcomes CICA’s new training initiative.
“From UAA’s perspective it is encouraging to see CICA and other industry groups, including regulatory bodies, recognising that there is a definite need for training due to the risk associated with pick and carry cranes. UAA supports these initiatives and certainly supports other regulatory bodies taking notice and getting involved with funding etc. Part of
the answer is how do we work together to reduce the associated risks?,” said George.
“From an insurance sustainability perspective and costs aspect, there are significant benefits with these training courses. We don’t penalise a business that doesn’t take up this type of training, but there is an element within insurance products, and not just from UAA, whereby if it’s evident that there are systemic issues within the business that create losses, that could have been preventable, there is the possibility of an incident being heavily investigated, systemic issues being identified within the business, and businesses potentially being penalised.
“This may impact indemnity because there wasn’t enough effort done by the
entities or by the insureds themselves. So there could be an element of penalty if nothing is done in terms of appropriate training and procedures and processes. In terms of the regulatory bodies getting involved, the benefit will be if there’s greater uptake of this training and in turn the industry actually participates to reduce the risk,” said George.
“That will allow insurance companies like us to then start changing our profile around the risks associated with this particular type of machine. And if we see a more sustainable loss ratio, that allows insurance companies like UAA to be more sustainable with premiums for these types of machines. So that’s the ultimate benefit.
“The ‘proof is in the pudding’. Proof will be in the industry’s action and the uptake of the course, proof is in the action in terms of reduction in losses, and those reductions in losses become an immediate benefit to the industry in terms of better sustainable premiums on those particular machines,” he said.
+ 80t Lifting Capacity
+ 47m Boom
+ Cummins L9-C325
Diesel Engine (EU stage V)
+ 87,700kg Operating Mass
The new Sany SCE800TB telescopic crawler crane has now arrived in Australia. The SCE800TB can deliver an 80-tonne lift capacity and is fitted with a 47-metre boom and 17.5-metre fly jib.
The Sany is fitted with top quality components right across the board. From Bosch Rexroth hydraulics to a 242Kw Stage V compliant Cummins engine this crane is manufactured to ensure maximum reliability and performance. The hydraulic counterweight selfassembly is a brilliant feature. This can be employed in just 15 minutes, reducing down time and maximising productivity.
Borger Crane Hire and Rigging, Australia’s largest family-owned and operated crane hire business, recently announced the appointment of Andrew Esquilant as Chief Executive Officer.
Shawn Borger, General Manager, and Nathan Borger, Technical Manager, had this to say.
“WE ARE PLEASED TO INFORM YOU THAT Andrew Esquilant has joined the Borger Group of Companies as Chief Executive Officer (CEO) effective Monday, 3 February. Over the past 30 years, Andrew has developed his career in the crane industry, working for two global companies, Morrow Equipment LLC and the Liebherr Group of Companies,” said Shawn.
Andrew brings a wealth of experience in terms of the rental and manufacturing aspects of the crane industry. Most recently, he served as General Manager for Liebherr Mobile Cranes across Australia and New Zealand, and held a seat as a Board Member of Liebherr Australia Pty Ltd. He brings significant expertise to the Borger Crane Hire and Rigging team.
“With Borger Group of Companies operating 11 depots across New South Wales and Queensland, our next steps
will be to secure best-practice customer service, explore new markets and industries, and embark on the next chapters of our business,” said Nathan.
“Borger Group of Companies takes great pride in being a one-stop supply solution,
a vision inspired by our founders, Jon and Barbara Borger.
“We would like to wish Andrew the very best as he leads Borger Group of Companies forward in our evolving market.”
Heavy lifting expertise shortens project schedule and provides contingency planning. The N05-A platform is the first offshore gas platform in the Dutch North Sea to be powered entirely by wind power – harnessing electricity via cable from the nearby 113.4 MW Riffgat offshore wind farm.
THE PLATFORM IS PART OF THE GEMS (‘Gateway to the Ems’) project, whose focus is the development of field N05-A and other fields in the area, situated in the waters on the border of Netherlands and Germany. The electrification of the N05-A platform is expected to reduce carbon emissions by over 85 per cent during the project’s duration.
Mammoet was approached by HSM Offshore to support the load-out of the 3,050 tonne N05-A topside, and 3,150t jacket, at HSM’s quayside fabrication facility in Schiedam, Rotterdam.
Mammoet’s scope for the project was to successfully load-out both components onto a barge for shipping to sea. Offshore sailing
and installation were managed by ONEDyas, the owner of the platform.
Mammoet’s engineering approach allowed the jacket to be assembled more efficiently, close to its installation location, and reduced the lead time for construction.
Assembly and weighing of the jacket and topside realised with mobile cranes, conventional trailers and SPMTs
The first operational phase of the project was to support the movement and assembly of the jacket, which was fabricated and assembled in two parts.
Mammoet supported the heavy transport and upending of the jacket’s rows with four
mobile cranes carrying out the lifts: two LTM 1650 (650t) cranes and two LTM 1450 (450t) cranes. The installation of its pile sleeves was completed using a 750t mobile crane.
Once in the correct position, the top section of the jacket was moved to the quayside where heavy lifting was performed by two sheerlegs. This created the space for the bottom section to be driven underneath so the two parts could be joined.
Self-Propelled Modular Transporters (SPMTs) were driven underneath the topside. These SPMTs drove the structure outside the fabrication facility and onto the quay. Mammoet then supported the
installation of a pedestal crane onto it using conventional trailers and mobile cranes.
With both the jacket and topside complete, both were picked up by SPMTs and their final weights were determined by using Mammoet load cells. The load-out operation could begin after the weighing of both structures.
Shipping together both parts of the offshore gas platform to meet the schedule
One of the biggest challenges of the project was the load-out phase. Normally, for loadouts of this type, a barge would receive either a topside or a jacket; not both together. However, for this project both structures needed to be loaded-out onto the same vessel, to shorten the overall schedule.
This created space and engineering challenges, as the team had to also allow room to install pumps and winches onto the transport vessel. It also meant conventional mooring methods couldn’t be applied.
“The mooring was quite critical, and we had to do a lot of engineering,” explains Sven Segeren, Project Manager at Mammoet. “Normally, we would use a configuration of winches to moor and stabilise the vessel, but that wasn’t possible because of the force of the considerable loads.
“The loads on the winches were too high and the bollards not strong enough, so a small spud leg barge was used to secure the vessel and keep it in position prior to, during and after load-out.”
It took five days to prepare the main barge – to install the ballast equipment, perform the pre-ballasting, and check the sailing conditions to the final location.
The load-out operation of the jacket foundation and topside was completed in just two days. Four trains of 32 axle line SPMT trailer were used for the movements.
Due to factors beyond the project’s control, the date of execution was unknown for a significant period of time. Therefore,
Mammoet was asked if it could prepare a temporary load-in venue, so the next project at the HSM Offshore yard could continue unimpeded.
The team prepared Mammoet’s own yard in Schiedam, next door to HSM Offshore, to perform a load-in of the topside and jacket. An area was prepared to temporarily house the components, equipment was reserved, and necessary engineering plans made.
This space was ultimately not required. However, Mammoet was able to react and adapt to a changing operational environment.
“We work a lot with HSM Offshore. They always involve us at the beginning of projects, so we can help them with smart solutions for assembly,” said Sven.
“Through strong co-operation and our early involvement, we were able to help them come up with a smart approach for the assembly of the jacket and reduce the lead time for construction.”
Since the 1950s, renowned German manufacturers, SENNEBOGEN Maschinenfabrik GmbH and DEUTZ AG, have worked together in the field of drive technology for construction machiner y and material handlers. The co-operation is being expanded to exploit synergies between the two companies.
AS A TRADITIONAL, FAMILY-RUN COMPANY, SENNEBOGEN Maschinenfabrik can look back on 73 years of success. With a wide range of solutions for the construction industry and material handling, the company plays a leading role in various sectors.
With material handlers, telescopic handlers, cranes and duty cycle crawler cranes up to an operating weight of 420 tonne, SENNEBOGEN offers its customers a variety of industry and customer-specific solutions.
With 161 years of tradition, DEUTZ AG is one of the world’s leading manufacturers of innovative drive systems. The Colognebased manufacturer develops, produces, sells and services drive solutions in the power range up to 620 kW for offhighway applications.
The Deutz brand has successfully established itself globally, particularly in the areas of increasing efficiency and
reducing emissions and, in addition to high-quality diesel technology, is advanced in the development of hydrogen engines and electrification.
Even in the early years, the then senior partner Erich Sennebogen was aware of the good strategic fit between the Bavarian machines and the Cologne engines. He installed the Deutz two-cylinder diesel engine with 22 HP in the early S802 and S803 duty cycle crawler cranes. Later, the first hydraulic excavator from SENNEBOGEN, the SH40, was equipped with the air-cooled Deutz 4-cylinder diesel engine with 49 HP.
Many visitors to the Erich Sennebogen Museum in Straubing still marvel at these drive solutions in the historic machines.
Both companies developed dynamically in the following decades. SENNEBOGEN built many machines with DEUTZ
engines, including large versions in cranes, duty cycle cranes and hydraulic excavators, and supplied them to its customers worldwide.
SENNEBOGEN, with its enthusiasm for technology, has been investing in sustainable and energy-saving technologies for decades. For example, the Green Hybrid energy recovery system has been successfully used by its customers for more than 12 years to significantly reduce fuel consumption.
SENNEBOGEN has been successfully implementing electric drive solutions in many different versions for more than 30 years.
Both companies, SENNEBOGEN and DEUTZ, have recently intensified their co-operation. This includes the installation of DEUTZ diesel engines in selected
More than just a pre-start checklist
StartSafe is comprehensive tool designed to streamline your crane operations, enhance safety, and ensure accountability.
models of the broad SENNEBOGEN product range.
SENNEBOGEN’s sales partners in the global sales regions will receive the best possible support from DEUTZ’s worldwide service network. In addition, the co-operation will focus on alternative drive concepts. Battery-electric and hydrogen-based drives offer a sustainable option for the future.
“We see many positive synergies in more intensive co-operation, especially in off-highway applications. We can realise new, future-oriented solutions together,” said Erich Sennebogen, Managing Partner at SENNEBOGEN.
Thales Maia, Chief Executive Officer DEUTZ EMEA, is also delighted about the collaboration: “It’s great to see that we are reviving a historic co-operation between two companies with a long tradition and at the same time are fully geared towards the future in terms of technology.”
Machine specific checklists are in line with the CraneSafe program.
StartSafe streamlines the process for collecting pre-start information, with instant data retention to a central location for the crane owner to access.
Photos tell the story.
When a faulty item is recorded by the operator, the maintenance team is notified of the issue by email, which includes photo evidence of the fault. This also assists with gathering major inspection data.
PLEASE SEND YOUR LIFT OF THE MONTH ENTRIES TO SIMON.GOULD@PRIMECREATIVE.COM.AU
WHO: Borger Crane Hire and Rigging. WHERE: Bondi Junction in Sydney.
PROJECT: Constructing two Potain tower cranes.
WHICH CRANE: Grove GMK 6400.
CRANE CONFIGURATION AND LIFTS : The Grove GMK 6400 was lifting with main boom, plus 37 metres of Luffing Fly and 95 tonnes of counterweight. Loads were 13 tonnes plus, lifted at a radius of 39 meters.
COMPLEXITIES: Meticulous planning required due to high density housing in the suburb.