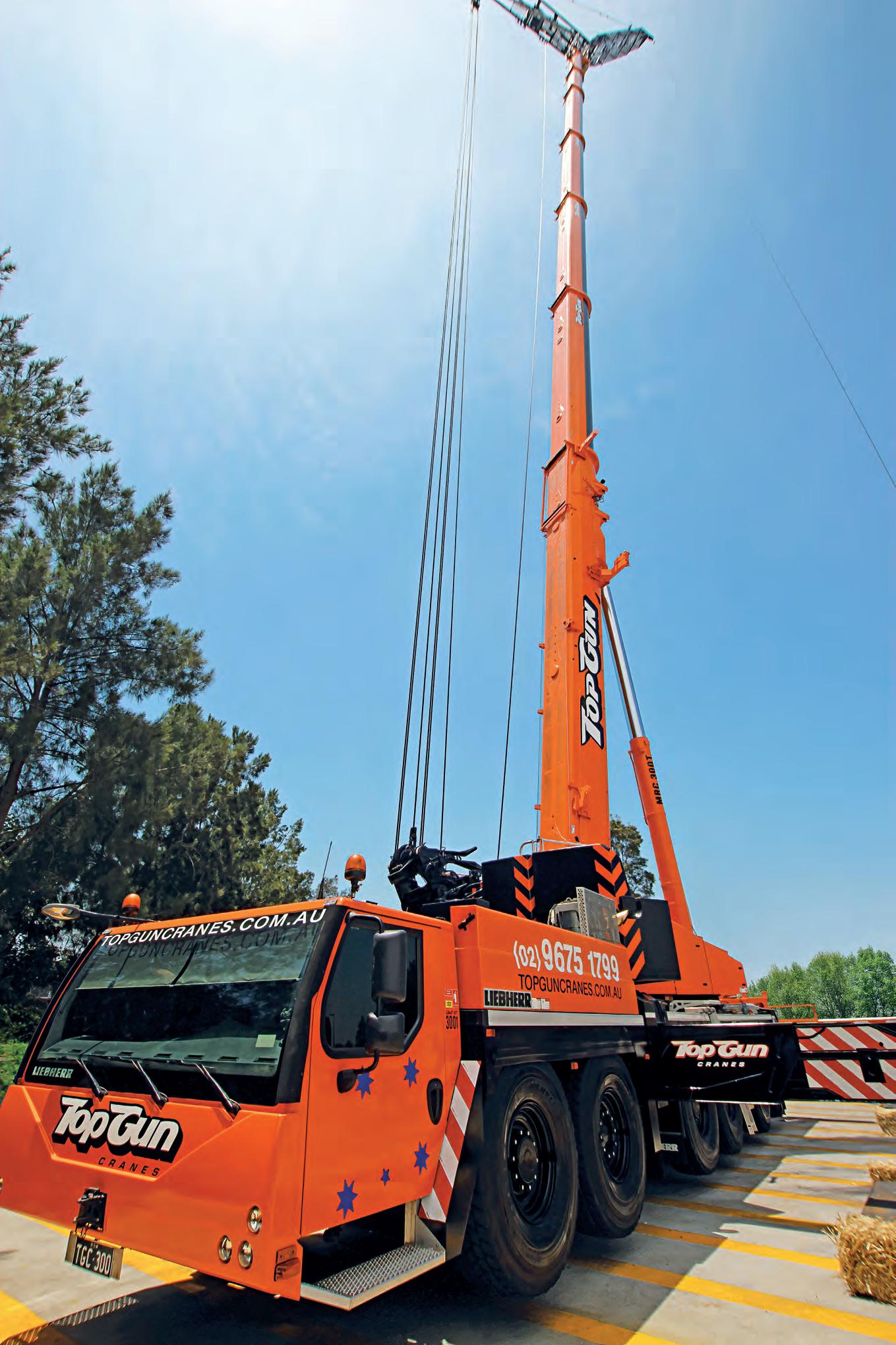
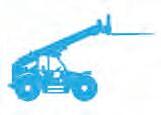
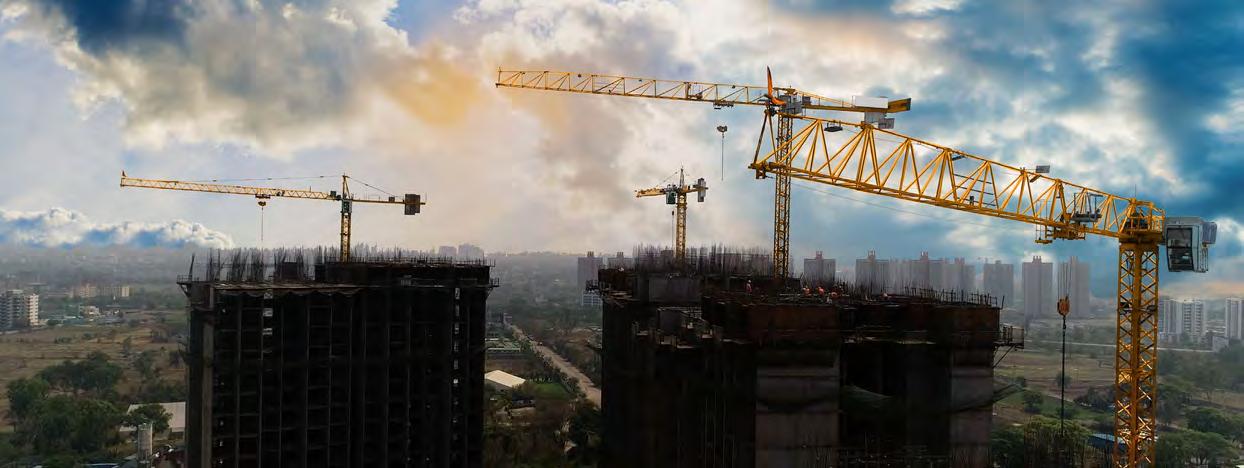
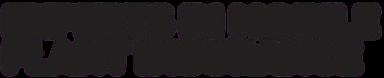

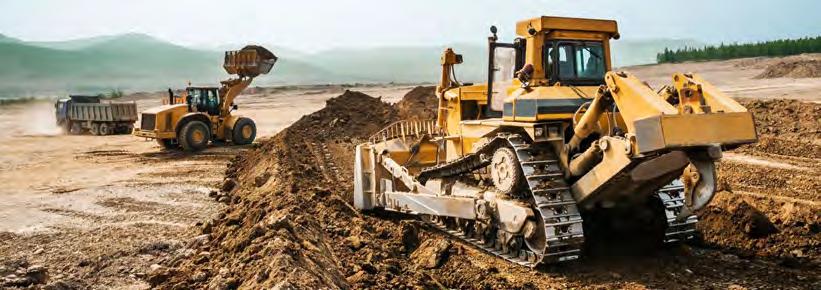
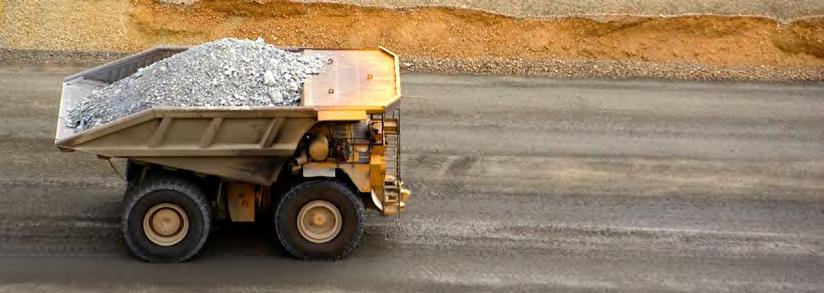

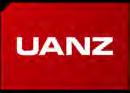
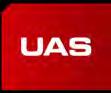
Cranes and Lifting Magazine cranes_and_lifting Cranes and Lifting
Up Front with Liebherr and TopGun TopGun steps it up with 300t Liebherr.
CICA CEO report New initiatives from CICA.
CICA StartSafe Marr Contracting implements Star tSafe.
CICA training
A close look at training for articulated pick and carr y operations.
CANZ CEO report Coping in a difficult economic environment. 18 LEEA report
LEEA launches LiftCon25.
28 Andromeda Industries What makes Andromeda products so innovative.
33 Sennebogen Celebrating 40 years of collaboration.
EWP & TELE-HANDLER feature
35 Integral role of Elevated Work Platforms & Tele-Handlers
36 Dieci Australia
Dieci’s continued investment in innovation.
39 Boom Logistics Boom’s wind farm capabilities.
42 LinCon Hire and Sales LinCon highlights broad range of access solutions.
47 Nif tylift
Niftylift continues to lead development of hybrid equipment.
50 Skyjack
Tutt Bryant Heavy Lift & Shift puts Sany crawler through its paces.
25 Manitowoc and Urban Cranes Urban Cranes dramatically increases capabilities.
New E-Drive scissor lift range arrives.
52 A1A Sof tware A1A significantly upgrades Product Suite.
UAA’s 50 year heritage with the crane
Zoomlion releases world’s largest all
Crane Connection delivers for Coehn
erex Franna and Hook and Haul New Franna MAC25 for Hook and Haul
utt Bryant, TRT and The Crane Tutt Bryant take new TIDD.
XCMG continue to build momentum.
Another Liebherr model released
New Operations Manager, renewed
82 Kobelco and GBP Cranes GBP Cranes receive new Kobelco crawler.
86 Marr Contracting Complex project for Marr Contracting.
88 Kito Crosby Working safely with powerlines.
ONE OF THE MOST, IF NOT THE MOST utilised crane in our industry is the articulated pick and carry crane. In almost any and every application, an articulated pick and carry crane will be the work horse, helping to mobilise and de mobilise larger cranes, and lifting in areas where access for larger cranes is impossible.
Almost every crane hire company operates articulated pick and carry cranes and in the major cities it is a very common sight to see them motoring between jobs. For all crane hire businesses, the articulated pick and carry crane is an extremely well utilised asset.
It is common practice for crane hire companies to introduce novice operators to crane operating via an articulated pick and carry. The irony
here is they can be one of the more difficult cranes to operate. That is why The Crane Industry Council of Australia (CICA) is urging members and anyone operating a ‘pick and carry’ or articulated mobile crane to take decisive action to address their unique and serious safety challenges.
With strong support from the National Heavy Vehicle Regulator (NHVR), CICA has developed a comprehensive training initiative aimed at ensuring every articulated mobile crane driver is properly educated on the distinct handling characteristics of these machines.
The importance of specialised training for articulated mobile cranes cannot be overstated. A rigid truck licence is currently sufficient to drive an articulated mobile crane – this is despite the stark differences in handling and operation between these vehicles. It is critically important that the industry support this training initiative. You will read more about the course in the CICA-related pages.
As always, the team at Cranes and Lifting has worked hard to bring you the very latest news and information from our industry. Once again, we explore the important role EWPs play in our industry, we take a look behind the scenes at Andromeda Industries to understand how they continue to design and manufacture innovative lifting solutions and Tutt Bryant
Heavy Lift and Shift put a large capacity SANY through its paces.
We hope you enjoy the read.
Simon Gould Editor, Cranes and Lifting
Published by:
379 Docklands Drive, Docklands VIC 3008
T: 03 9690 8766
www.primecreativemedia.com.au
CEO
John Murphy
E: john.murphy@primecreative.com.au
Chief Operating Officer
Christine Clancy
E: christine.clancy@primecreative.com.au
Publisher Sarah Baker
E: sarah.baker@primecreative.com.au
Managing Editor Lisa Korycki
E: lisa.korycki@primecreative.com.au
Editor
Simon Gould
E: simon.gould@primecreative.com.au
T: 0404 865 109
Business Development Manager
Emily Schlegel
E: emily.schlegel@primecreative.com.au
T: 0466 317 555
Client Success Manager
Louisa Stocks
E: louisa.stocks@primecreative.com.au
Art Director Bea Barthelson
Designers
Laura Drinkwater and Danielle Harris
Imaging Assistant Paul Breen
Subscriptions
Frank Rapone
T: 03 9690 8766
E: frank.rapone@primecreative.com.au
The Publisher reserves the right to alter or omit any article or advertisement submitted and requires indemnity from the advertisers and contributors against damages or liabilities that may arise from material published.
© Copyright – No part of this publication may be reproduced, stored in a retrieval system or transmitted in any means electronic, mechanical, photocopying, recording or otherwise without the permission of the publisher.
Please refer to our Mobile Cranes Customer Training programme for course descriptions and general terms and conditions.
For more information and bookings, please contact our training department via email LAS-MCTraining@liebherr.com or call us on +61 (2) 9852 1800. Please note bookings close 4 weeks prior to courses start dates.
The LTM 1300-6.2 was the first to incorporate an innovative drive concept – the engine in the undercarriage powers
TopGun Cranes recently took a huge step forward by taking delivery of a Liebherr LTM 1300-6.2 300 tonne capacity all terrain. General Manager Phill Martin and Director Barry Ramm, provide the background to the crane’s arrival.
“AT TOPGUN CRANES, WE ARE CONSTANTLY setting ourselves objectives as a business. The acquisition of this crane was part of a three-stage strategy we devised post the COVID pandemic. We achieved the first two objectives, the third was a larger capacity crane,” said Phill.
“The decision to purchase such a large capacity crane was driven by customer demand. We had regular customers tell us that they weren’t calling us for the bigger lifts because they knew we didn’t have a crane to service the work, so we knew there was a market that we were missing out on.”
TopGun Cranes went about its due diligence and looked at what was available.
“We went to the market, but it was clear Liebherr was able to offer a more complete package deal, which offered us an overall better ‘bang for buck’,” said Phill.
TopGun purchased the LTM 1300-6.2 through Tom Grady, Liebherr’s National
Used Crane Manager, Mobile and Crawler cranes.
“The relationship with Tom and Liebherr has been great. We couldn’t speak more highly about the service we have received from Liebherr,” said Phill.
“They have gone over and above to get us and that included a hand over ‘open day’ at their Erskine Park facility. They rolled out the red carpet for TopGun Cranes and we could not be happier. It’s been a real buzz from our perspective and Liebherr understand how important, and how big this step is for us.”
The LTM 1300-6.2 was the first to incorporate an innovative drive concept – the engine in the undercarriage powers the superstructure using a mechanical shaft. This eliminates the need for a second engine. This means one less engine and therefore significantly reduced maintenance costs. The lower weight can be used to increase lifting capacity. On the one hand it is a simple, classic folding
jib crane while on the other, it is a small luffing jib crane on the market for crane operators with a low cost entry point into the luffing jib crane class. It also features high performance, economy and variable boom systems.
The six axle all terrain features 78m of main boom, 114m maximum hoist height and a maximum lifting radius of 94m.
“The LTM 1300-6.2 is a unique bit of kit with multiple boom combinations, including fixed fly, luffing fly and strong lifting charts in all configurations. We bought it because it’s a grunty lifter,” said Phill.
The LTM 1300-6.2 has been based at Erskine Park, New South Wales for a number of weeks and during this time, Liebherr completely repainted the crane and conducted training sessions with TopGun’s crews.
“Liebherr utilised painting experts in their paint shop, and it took a few weeks to complete the job. The finish is amazing,
you’d think it was a brand-new crane. There were a few little issues which were fixed quickly and then we had a number of weeks getting the dolly prepped. This was designed and manufactured by BTE Engineering in Melbourne. Wherever possible we like to support local businesses,” said Phill.
“We’ve had two weeks of training with the technical experts at Liebherr and that has been invaluable and very educational for the crews. It’s meant the guys can trial and test the crane in every configuration. We also had a couple of jobs while the crane was based in the Liebherr yard, so it’s already been out there working,” he said.
Tom Grady provides more detail about TopGun’s Liebherr LTM 1300-6.2.
“It’s a 2020 model with 40,000 kilometres and 3,700 upper hours. It was in excellent condition and already a well specked unit with 70m luffing fly, adapter for 42m fixed jib, Vario-base,
TopGun ordered new support vehicles for the LTM 1300-6.2 including a purpose-built Dolly.
full counterweight and three hooks. As per Barry and Phill’s request we added some new major components: 21m double swing away jib with hydraulic offset, 14 metres of extensions to use in configuration TK and TNZK which then takes the swing away jib out to a length of 35m.
“The crane went through our new purpose-built used crane facility at BergEhingen in Germany where it received a thorough inspection and testing. AQIS (Australian Quarantine and Inspection Service) cleaning, various repairs, mods, servicing, updates, load testing in various configurations, road testing and reinspection were all carried out before shipping to Aus,” said Tom.
“Because of the tight time frame, the crane was then shipped out to our Sydney facility. Our team fitted the dolly preparation RFK and carried out TopGun’s livery painting. Pre-Delivery Inspection (PDI), dolly testing, weigh up, New South Wales road registration, 10 yearly major inspection certification, crane safe, and TopGun’s sign writing were all completed, prior to final detailing and quality assurance being carried out.
This completed our Liebherr certified Used Cranes process which includes our six-month manufacturer’s warranty.
“We’ve had the TopGun team here doing training for the past few weeks putting the crane together in various configurations. All jibs were installed, including the luffing fly, as seen on the crane at the customer day. It was an absolute pleasure dealing with Barry, Phill and the whole TopGun team throughout the complete process.”
On a hot Sydney day in early December 2024, more than 100 customers and interested parties descended on Liebherr’s Erskine Park facility to see the LTM 1300-6.2 up close and personal.
“We were pleased with the turnout and we are grateful to Liebherr for making this possible. The feedback we’ve received has been very positive,” said Barry.
“The Sydney market is very competitive, and we know this addition takes us to the next level in terms of capabilities, but we’re not interested in ‘taking on the world’.
“We have long-term relationships with our customers and with other crane hire businesses in Sydney, and this investment
will ensure we can cater to the needs of our customers more readily.”
Phill and Barry attended the Crane Industry Council of Australia’s (CICA) National Conference and Exhibition hosted by Adelaide in October 2024.
“The CICA Conference and Exhibition is always a great networking opportunity. As I said earlier, we like to support local businesses wherever we can, and I got talking to an engineering and fabricating business from Broken Hill about our requirements for crane pads. We’d been looking to source pads from the US, but it turns out they can manufacture exactly what we want and price the pads competitively. We would never have known of this company if it hadn’t been for CICA,” said Phill. “With a crane this size there’s a significant amount of transport infrastructure, including the Dolly, required to get the crane on the road. We have a Melbourne trailer company manufacturing support trailers and they can turn these around in seven weeks, which is excellent. Wherever possible, TopGun Cranes will continue to support Australian engineering, design and manufacturing.”
This year at CICA we’ve been off to a flying start, with significant progress across key industry initiatives.
important article on the articulated mobile crane driving course. I cannot stress enough the importance of this training and ensuring that your team completes it as well. Under Australia’s Chain of Responsibility (CoR) laws, all parties in the supply chain – including business owners, site managers, and employers have a legal obligation to ensure the safe operation of heavy vehicles.
The training is free to both CICA members and non-members, and no external providers are required to complete the course. Ensuring compliance with CoR laws is a critical responsibility, and this course provides essential knowledge to meet those obligations.
The article covers information on the course and how to access it.
The Launch into Work program is an initiative designed to support businesses in recruiting new staff by co-designing pre-employment projects. CICA, in partnership with the Department of Employment and Workplace Relations, officially kicked off the Launch into Work program in Adelaide at the end of January. This initiative brought together industry leaders to introduce entry-level Trainee Dogger positions, creating real career pathways and strengthening the future workforce. The program prepares job seekers for entry-level roles within the crane industry.
It was very encouraging to witness a broad range of our SA members come together, showcasing the incredible opportunities within our industry, the support and shared commitment to
program. Your dedication to fostering growth and development within the industry has a profound impact.
If you are interested in being a host employer for our next program (Australia-wide), contact kate@cica.com. au to learn more.
CICA has been actively working with the Department of Transport and Infrastructure to address ongoing
• Vehicle Stability Function (VSF ADR35)
• Advanced Emergency Braking (AEB ADR97)
• L ane Departure Warning System (LDWS ADR99) exemptions
These amendments, can be accessed via the Federal Register of Legislation under “Vehicle Standard (Australian Design Rule) Mobile Crane and Other Amendments 2025.”
While we appreciate this progress,
the changes fall short of delivering the comprehensive solution CICA has been advocating for. If our proposed solution –the mutual recognition of EU Regulation 2018/858 – is adopted it would cover not only the amended ADRs but all ADRs currently applicable to cranes.
Instead, manufacturers must still submit paperwork individually, despite already being certified under the European system. This redundancy places an unnecessary burden on our industry.
CICA is continuing to push for meaningful change, and we have made a formal submission to the Department of Infrastructure, Transport, Regional Development, Communications and the Arts 2024-25 Review on ADR Harmonisation. While this review is an important step, we are cognisant that the review process will take too long to provide practical benefits in a reasonable timeframe.
We have also addressed the urgent need to add Crane, Hoist, and Lift Operators (ANZSCO 7121) to the National Skilled Occupation List with the Minister for Immigration, Citizenship, and Multicultural Affairs with little effect.
Unfortunately to date, and at the time of writing, the Albanese Labor Government have been resistant to assisting us with the significant challenges facing the Australian construction sector, specifically fixing the major issues with ROVER and addressing the urgent need for highly skilled crane operators.
Crane operators and cranes play a pivotal role in supporting critical sectors such as construction, housing, mining, and renewable energy, all of which are fundamental to Australia’s infrastructure goals and economic growth.
CICA will continue to advocate strongly for reforms in these areas and we appreciate any support you are able to offer by raising awareness with your local Federal Member of Parliament in the leadup to the Federal election.
Brandon
Hitch CICA CEO
CICA BOARD
Ben Pieyre – President
Marcus Ferrari – Vice President
Danny Adair – Director
Danny Black – Director
David Solomon – Director
Karli Sutherland– Director
Tom Clark – Director
Anthony Grosser – Director
CICA OFFICE
Brandon Hitch
Chief Executive Officer 0428 228 048 ceo@cica.com.au
Alice Edwards Road Technical Engineer 03 8320 0440 alice@cica.com.au
Patrick Cran
CICA Site Operations Advisor 0488 004 274 pat@cranesafe.com.au
Sharon Pearce
Crane Crew Competency Officer 0491 134 533 sharon@cica.com.au
Damien Hense
CICA Road Policy Advisor 0488 007 575 damien@cica.com.au
Thomas Webber Communications Coordinator thomas@cica.com.au
Kate Galloway Traineeship & Industry Engagement Coordinator
0491 047 118 kate@cica.com.au
Michelle Verkerk
Communications and Special Projects Advisor michelle@cica.com.au
Just ina Blackman Member Events and Engagement 0403 717 626 justina@cica.com.au
Ashleigh Gould Office Operations Coordinator 0490 356 041 ashleigh@cica.com.au
Shane Coupe
CraneSafe & CrewSafe Administrative Assistant Officer 0491 047 134 shane@cica.com.au
Unit 10, 18–22 Lexia Place, Mulgrave Vic 3170
Phone: 03 9501 0078
Email: admin@cica.com.au
Website: www.cica.com.au
For information, please visit our website or call the CICA office.
Implementing StartSafe across the Marr’s fleet has made the pre-start inspection process simpler, more relevant and instantly available to those responsible for the safe operation of cranes on project sites.
The Crane Industry Council of Australia’s (CICA) StartSafe
app has proved to be a hit with world-leading heavy lift specialists Marr Contracting (Marr). Managing Director, Simon Marr, discusses the benefits of utilising the StartSafe app for daily pre-start inspections of cranes and equipment.
the Marr’s fleet has made the prestart inspection process simpler, more relevant and instantly available to those responsible for the safe operation of cranes on project sites, says Simon.
“We have been impressed with the data we have been able to collect from the cranes, which not only benefits our business but the operators of the equipment. I’ve spent many years driving cranes and am fully aware of how laborious filling out a logbook can be. I always thought there had to be a better way, so when we heard that CICA was developing a pre-start system we were keen to get on board and trial it as a more efficient way to conduct daily pre-starts.”
Marr worked with CICA for more than 12 months to refine the StartSafe app for application to its unique fleet of heavy lift tower cranes.
“We initially trialled StartSafe in our Sydney yard operations before piloting on three client project sites. As with any new system, nothing is ever perfect straight away and it was a process of continual development and refinement. We could see the potential and wanted to get the functionality of the system right so that when it was launched, it was immediately useful for our operators, clients and the broader construction industry,” said Simon.
Marr has subsequently become the first tower crane owner and operator to
adopt the use of StartSafe for rollout across all cranes in its fleet, both in Australia and globally.
StartSafe has reduced the amount of paperwork and streamlined the prestart inspection processes significantly, according to Simon.
“StartSafe has made it much easier for operators to communicate issues to the nominated person on the project responsible for lifting operations and the safe use of the crane. That information then comes back to us as the crane owner,” said Simon.
“Our teams in Australia, the UK and elsewhere in the world are now conducting pre-starts in real time with the reports automatically being available on
our portal. StartSafe has plenty of features which enable us to transfer information in real time and enable our teams to inspect different aspects of our equipment. If we do find an issue, we can focus on resolving it and then ensure we haven’t got the same issue on another crane that we might not have already identified,” said Simon.
StartSafe has also improved communication between Marr’s operators and maintenance teams.
“StartSafe has made communication between our teams a lot simpler and instantaneous. If there’s an issue with the crane they can identify it and we can be notified instantly rather than waiting for a logbook to come from the operator. With a logbook, the onus is on the crane operator
to report everything, but issues might be developing over time and not be noticed until it’s too late. If we can see an issue developing, it can be addressed before it becomes a major issue,” said Simon.
StartSafe has also provided Marr with the ability to demonstrate crane inspection history to clients on site and they, in turn, are also seeing genuine value in the app.
“The feedback from clients and operators using the StartSafe app has been extremely positive and it’s a massive step forward for the industry. As a business, we’ve had a significant internal focus on improving our systems processes and at the same time we’ve been encouraging the industry to do the same.
“As an industry we need to shift the focus from, ‘Is the crane ready to operate?’ to ‘Is the crane safe to start lifting operations?’ Safety has to be paramount because the consequences can be horrendous if we don’t conduct inspections properly.
“Pre-start inspections of cranes and rigging equipment prior to commencing work is the most safety critical task crane operators are expected to do every day. It’s not just important, but a legal responsibility that comes with a highrisk work licence (the operator). The person with management or control of the plant on a project also has the same responsibility to ensure that the crane is safe to operate before lifting commences.
“A senior client of ours at a tier one builder recently used an apt analogy about how similar the role of crane operators is to that of a pilot on a plane, and that really stuck with me. We don’t necessarily have to get up in the crane and look at everything, but you’ve got to be aware and check to ensure the piece of equipment that you’re about to operate is safe to operate. It shouldn’t be a ‘tick and flick exercise.”
“The StartSafe app prompts the operator to check tower structures, bolts, pins, retaining pins, oil levels, electrical circuits, whatever the case may be. There are all sorts of different issues that the app throws up, which keeps the operator stimulated and engaged, ensuring the safety inspections are conducted correctly,” he said.
“One thing every crane driver has in common is that they don’t want to have an incident. StartSafe is providing them with a tool that makes it easier for them to conduct their inspections which is the first, and the most important, step towards not having an incident.
“When we first introduced the StartSafe app to our teams the typical reaction was ‘What is this?’ But once they understood it and could see how simple it is to use, the response was more like,
terms of what they should be looking for, whether they are operating a crane, erecting a crane or servicing a crane,” said Simon.
The StartSafe app also provides unexpected advantages such as cost savings and efficiency gains.
“An incident on a project is the biggest cost a client can have and it’s the last thing anyone wants. If we’re conducting daily inspections properly and the client, the operator, and the responsible party on site looking after the crane respect that before we start lifting, we have to make sure the crane is safe, then the benefits are there for everyone,” said Simon.
“The other side of the conversation is if we don’t go down that path and instead take the view that ‘the crane is just there to lift and we don’t care about inspections’, then there will be consequences. We
“We encourage the industry to get behind the StartSafe app. Over many years, across multiple sites and projects we’ve experienced the pressures around programs to meet, but we’d really like to see more respect and acceptance in the industry about what an important piece of equipment a crane is on a project.”
‘Finally, some great technology that helps us complete the most important tasks we have to do every day, that is simpler and easier with a record that we’ve done it’,” he said.
According to Simon, StartSafe has also positively impacted Marr’s compliance with safety regulations and standards.
“We now have a great library of records confirming the daily inspections our teams have conducted on our machines. We’ve also expanded the app’s functionality to conduct more thorough three-monthly inspections.
“We’re offering that additional service to our clients where we go out and inspect the crane from top to toe. That’s been fantastic because we are obviously ensuring the equipment is safe, but it also provides an opportunity to educate and train our people and client teams about what ‘good looks like’ in
don’t want to see accidents and injuries or construction sites shutting down, and we believe that this technology can help prevent that happening.
“We encourage the industry to get behind the StartSafe app. Over many years, across multiple sites and projects we’ve experienced the pressures around programs to meet but we’d really like to see more respect and acceptance in the industry about what an important piece of equipment a crane is on a project.
“That means having people correctly trained to manage the safety of the crane and making sure it is safe to operate every day.
“We want to get the focus back onto safety with the understanding that all operators need the time to conduct their pre-start inspections diligently – because when it comes to site safety, it starts here,” said Simon.
THE CRANE INDUSTRY COUNCIL OF AUSTRALIA (CICA) is urging members and anyone operating a ‘pick and carry’ or articulated mobile crane to take decisive action to address their unique and serious safety challenges.
With strong support from the National Heavy Vehicle Regulator (NHVR), CICA has developed a comprehensive training initiative aimed at ensuring every articulated mobile crane driver is properly educated on the distinct handling characteristics of these machines.
CICA Chief Executive Officer Brandon Hitch urged owners, operators and site supervisors to take advantage of the free and comprehensive resources on offer.
“These tools are designed to elevate safety standards, ensure best practices, and protect not only operators but everyone sharing the road,” Brandon said. “A ‘rigid’ truck licence won’t prepare you for the unique characteristics of this type of crane.”
The importance of specialised training for articulated mobile cranes cannot be overstated. Unlike trucks, buses, and cars, which employ Ackermann steering (turning the front wheels to steer), articulated cranes use frame steering, pivoting in the middle of the vehicle. This results in the cabin and front section rotating in the direction of the turn, creating a unique sensation for the driver.
Additionally, articulated cranes lack the natural steering feedback common in other vehicles, making them more prone to oversteering. Drivers must also actively straighten the steering after turning, as the front wheels do not naturally return to alignment.
Compounding these challenges, stiff suspension required for heavy lifting results in a less forgiving ride, particularly on uneven surfaces.
A rigid truck licence is currently sufficient to drive an articulated mobile crane – this is
despite the stark differences in handling and operation between these vehicles.
Recognising this gap, the NHVR’s Heavy Vehicle Safety Initiative (HVSI) grant program funded CICA to develop an industry-first training course, which includes a theoretical online component (adaptive learning) and a practical assessment to ensure drivers are adequately equipped to manage these cranes safely on roads and on-site.
The success of this program has led to additional funding from the NHVR, with support of the Australian Government, to develop a ‘Train the Trainer’ course and promote the training further.
The ultimate goal is clear: for every articulated mobile crane operator in Australia to complete this essential training.
The development of this course stems from a tragic incident in 2013, where a mother and her son lost their lives due to an articulated crane accident.
This incident forever changed the lives of all involved and their families.
A coronial inquiry highlighted the unique handling challenges of these vehicles and recommended specialised training for drivers.
CICA’s program is a direct response to these recommendations, filling a critical gap in safety standards.
For information on how to complete the course, go to www.cica.com.au/The-CICAOn-Road-Course or reach out to Sharon Pearce, CICA Crane Crew Competency Officer: sharon@cica.com.au
CICA is also developing the curriculum for a ‘Train the Trainer’ course to equip trainers to effectively help their team complete the course and achieve their intended outcomes.
This project will be a major focus for CICA in 2025 and is funded by the National Heavy Vehicle Regulator’s Heavy Vehicle Safety Initiative supported by the Australian Government.
The crane industry is no stranger to ups and downs – just like, well, a crane. But with demand currently sagging lower than a dropped load (don’t worry, we won’t tell WorkSafe), it’s time to think smarter, work leaner, and stay positive.
HERE’S YOUR GUIDE TO KEEPING BUSINESS (and morale) elevated while the market is feeling a little… grounded.
event organisers who might need a lift. Consider:
• Tapping into new sectors – Agriculture,
Keep in marketing, a fresh website, or even some good old-fashioned word-of-mouth can go a long way.
2. Trim the fat, but keep the muscle
Cutting costs doesn’t mean cutting corners. Take a hard look at expenses and make sure you’re running as efficiently as possible. That could mean:
• Optimising fleet maintenance –Preventative care keeps your cranes running longer and avoids costly breakdowns.
• Revisiting contracts and suppliers – Are you getting the best deals? Now’s the time to negotiate.
• Smarter scheduling – Maximise uptime by ensuring your cranes are in use as much as possible.
3. Keep your team tight and motivated
Low demand doesn’t mean morale has to hit rock bottom. Keeping your crew engaged and motivated is crucial. Try:
• Upskilling and training – Use the downtime to get additional certifications or train in new crane technology.
• Open communication – Be upfront about the challenges but also share the wins. Transparency builds trust.
• A bit of fun – A team barbecue or a friendly “who can balance a spanner on their nose the longest” competition (don’t worry, insurance should cover it) can lighten the mood.
4. Stay calm and carry on (literally) Running a business in a downturn is
stressful, and stress doesn’t lift loads –it just weighs you down. Keep your head in the game by:
• Taking care of yourself – Get enough sleep, eat right, and maybe swap that fourth coffee for a glass of water.
• Talking to others – Whether it’s industry mates or professional advisors, a problem shared is a problem halved.
• Remembering it’s a cycle – The industry has bounced back before, and it will again. Keep your business in fighting shape so you’re ready when things pick up.
5. Innovate and adapt
Now might be the perfect time to look at
diversification. Could you offer additional lifting services? Rent out equipment? Get into training? If necessity is the mother of invention, then a slow market is the weird uncle who forces you to think outside the box.
Yes, things are tough, but tough times don’t last – tough crane operators do. With a mix of smart strategy, cost management, and a healthy dose of humour, you can weather this downturn and come out even stronger on the other side. So, keep your boom high and your spirits higher–better days are on the horizon!
“With a mix of smart strategy, cost management, and a healthy dose of humour, you can weather this downturn and come out even stronger on the other side.”
We have the capability to heavy lift and shift loads from 30 tonnes through to 3,000 tonnes, enabling us to efficiently support our clients.
•Heavy Lift
•Project Hire
•Quality Endorsed
•Specialised Engineering
•Heavy & Oversized Transport
in Sydney in May, and the LEEA regional events will play a crucial role in promoting safety through professional development.
of over 1200 companies large and small. LEEA contributes significantly to the industry’s standards and practices in key global markets including the UK and Europe, the Middle East, South East Asian hubs like Singapore and Malaysia, and emerging markets in Asia and Africa.
However, in Australia and New Zealand, the full extent of LEEA’s expertise and value is not always widely recognised.
LEEA has always been renowned for training programs as a way for members to easily benchmark highly skilled industry technicians against those who promote their competency, but cannot compare with the global strength of LEEA’s training program. So, in 2025 we’re sharing our extensive capabilities
in, not only training, but technical excellence via an extensive events program. Scheduled for 20 and 21 May, LiftCon25 will take place in Sydney. This premier event is set to attract a diverse array of participants, including manufacturers, suppliers, and end-users of lifting equipment. LiftCon25 will be our key event, providing a platform for showcasing the latest innovations, discussing emerging trends, in-depth technical sessions and networking opportunities with peers.
This year, attendees can look forward to a comprehensive program that includes keynote speeches from leading manufacturers, interactive panel sessions, and an exhibition featuring cutting-edge products and services. The event will also offer
multiple networking sessions, providing participants opportunities to forge new connections and strengthen existing relationships.
But further to LiftCon25, we’re kicking off our series of LEEA Regional Events on 6 March in Brisbane. The LEEA regional events are designed to extend the association’s reach and impact. Our regional events aim to address a knowledge gap, by providing both LEEA members and companies outside our membership with a deeper understanding of the association’s highvalue work.
These events will serve as a platform for industry partners to gain insights into LEEA’s contributions and how they benefit from the association’s ongoing work and why we’re trusted
experts to global firms, regulators and governments the world over.
LEEA’s commitment to the industry is evident through its rigorous standards, comprehensive training programs, and advocacy efforts. By attending the regional events, industry partners will have the opportunity to learn about LEEA’s initiatives in areas such as safety, compliance, and innovation. These events will feature presentations from LEEA experts,
case studies showcasing successful implementations, and interactive sessions where attendees can ask questions and share their experiences.
Both LiftCon and the LEEA regional events underscore the importance of collaboration and knowledge-sharing in the lifting and crane industry. By bringing together stakeholders from users, procurement, safety and management, these events foster an environment where ideas
can be exchanged, challenges can be addressed, and solutions can be developed.
For companies in Australia and New Zealand, participating in these events offers a unique opportunity to connect with global leaders, stay updated on industry advancements, and gain valuable insights that can drive their businesses forward. Whether it’s through the innovative showcases at LiftCon or the informative sessions at the LEEA regional events, attendees are sure to leave with a wealth of knowledge and new connections.
As we look ahead to 2025, the lifting and cranes’ industry is poised for growth and innovation. Events like LiftCon in Sydney and the LEEA regional events starting in Brisbane are crucial in driving this progress. By highlighting the value of these gatherings, we can encourage broader participation and ensure that the industry continues to thrive.
Join the must-attend event for manufacturers, suppliers, and end-users of lifting equipment.
Scan the QR code to secure your place
u Discover the latest innovations
u Gain insights on emerging trends
u Engage in in-depth technical sessions
u Network with industry leaders
Leading foundation machine manufacturer Fundex Equipment recently announced it has intentions to increase support, sales and service in Australia. Sales Manager Arjan Roubos spoke to Cranes and Lifting magazine to explain more.
WITH 60 YEARS OF EXPERIENCE IN THE field, Fundex Equipment produces and supplies multifunctional foundation machines and sells them all over the world.
“Fundex Equipment is an original equipment manufacturer (OEM) of multifunctional foundation equipment,” Arjan said. “With 70 employees, we are a relatively small company compared to some of our competitors, but we do have a rich heritage in the industry.
“A significant advantage for Fundex Equipment is the fact that we manage all the design engineering and
manufacturing in-house. We operate our own engineering, R&D and software development departments and we manage the construction, assembly and service in-house.
“Whilst we offer a wide range of machines, we also manufacture a broad range of auxiliary equipment which includes rotary heads and ring vibrators. We also provide leading software solutions including intelligent data acquisition systems for piling installations, and GPS systems for monitoring the quality of the piles customers are working with.
“We manage the information from these software solutions via our online portal, MYRIX. We’re not just about designing, engineering and manufacturing world class machines, we have a very strong focus on the software systems required to intelligently run and service them,” he said.
Being based in the Netherlands, understandably the main countries serviced by Fundex Equipment include the Netherlands, Belgium, Germany, France, United Kingdom and Switzerland, but Australia is also a significant focus, confirms Arjan.
“We sell a lot of machines into the USA and Australia. We recently visited a number of customers in Australia to understand how we can better service the market. During our visit we could see the industry is a deep Continuous Flight Auger (CFA) market and our rigs are perfectly suitable for the CFA installation method.
“We service our Australian customers through our online portal, MYRIX. Our rigs are full of sensors which enable our customers to monitor the technical condition of the rig every day in real time which helps to determine maintenance programs. If a customer has issues with our equipment, we log into the MYRIX portal, see what’s happening and can advise on the appropriate actions to take,” said Arjan.
In nine out of 10 instances, technical issues can be sorted through the MYRIX portal and by phone, but if it can’t be, Fundex Equipment will have a technical engineer on the first available flight. As far as parts are concerned, customers have access to the spare parts department at Fundex and if a part is required urgently it will be airfreighted on the first available flight.
“Most of our Australian customers operate their own technical department and before we deliver one of our rigs we train these departments. We have a simulator for the operator, and we provide technical training, including hydraulics and electrical training. We also train them how to mobilise and demobilise the rig. We frequently have Australian customers here in the Netherlands for one week, or
two weeks, to familiarise them with our company and people and also with their rig,” said Arjan.
“I encourage Australian foundation and piling companies to engage with us. We are a Dutch manufacturer of deep foundation rigs specialised in (amongst others) CFA. We encourage companies to get to know us, see how we work and understand our ‘can do’ culture.
“We are not a big company, and we always focus on customer-specific solutions. We do not build all models for stock, we build when we have the order and this provides the customer with opportunities to customise our products to meet their specific requirements,” said Arjan.
Fundex Equipment will be exhibiting at bauma, the world’s leading trade fair for construction machinery, in Munich in April where it will be displaying the most popular model in its range – the FUNDEX F3500 – and demonstrating how this is now capable of working emissions free.
“I encourage all Australian visitors to bauma, to visit our stand (FN 721/2). Although the uptake of emission free machines is slower in Australia, compared to Europe for example, we can see that government legislation and requirements in construction and other industry sectors will accelerate the uptake. We would like to demonstrate how our most popular model, the FUNDEX F3500 can operate
emission free and how this technology can be retrofitted to older models,” said Arjan.
The FUNDEX F3500 features a diesel engine and a power pack on the back which is also powered by a conventional diesel engine. The power pack provides the hydraulic oil flow for the tool on the front side. In terms of the bauma display, this will be a special tool, said Arjan.
Fundamentally, Fundex has replaced the power pack on the back with the Fundex Power Switch. The FUNDEX FPS803 is an electric/hydraulic power pack allowing the user to switch between conventional drive and zero emission drive, for both the foundation machine and tool functions.
“The FUNDEX FPS803 is an electric hydraulic-driven power pack which provides the flow for both the machine and tool functions on the front side of the rig which means you can use your conventional diesel rig emission-free with this setup. Of course, the electric engines on the back also require power, so we have two battery packs developed which are on the rig as well, meaning less cables on the job site,” said Arjan.
“We have a lot of interest in this technology, and we’ve already delivered the first complete setup, including the Fundex Battery Packs and Fundex Power Switch, to a very happy customer”
Tutt Bryant Heavy Lift and East Coast Cranes recently removed a dry dock gate weighing more than 300 tonnes at a historic World War II - era dry dock on behalf of Cairncross Dockyard in Brisbane.
THE DRY DOCK GATE, MEASURING 37 METRES in width and 14 metres in height (with 10 metres submerged), has a rich history.
Cairncross Dry Dock, the second largest in Australia, was constructed for wartime ship repair. Post-war, it continued operations as a major hub for ship repair, accommodating Panamax-class vessels and as a base for heavy infrastructure projects.
The gate was not designed to be lifted and had no original lifting points or precise weight specifications, making planning of the lift an engineering feat. Adding to the challenge, the gate held approximately 180 tonnes of water as ballast and was located beneath Brisbane Airport’s flight path.
Scott De La Rue, Tutt Bryant’s Heavy Lift and Shift, Projects & Heavy Lifting Manager East Coast discusses the project.
“For this job our client was East Coast Cranes and the land owner and the dock owner were East Coast Cranes’ customer. We were initially contracted to lift a pontoon into the water, it was one of the little riverside stations used to catch ferries. This weighed 180 tonnes. Then, at relatively short notice, the customer decided that while the large capacity cranes were onsite and given the cost of getting them there, it provided an ideal opportunity to lift the dock gate. They hadn’t done anything with this for many years and in the end we had approximately two weeks to plan the dock gate element of the lifts,” said Scott.
Tutt Bryant Heavy Lift and Shift deployed its Sany SCC4500A 450t capacity lattice crawler crane for the lifts.
This lattice boom crawler is powered by a Cummins diesel engine with rated power of 298kW/1800rpm and maximum torque of 1898N.m/1400rpm. SYIC-I integrated control system – power, engine,
main control, LMI, auxiliary and safety monitoring systems. The operating weight is about 380t including the upperworks, lowerworks, rear counterweight of basic machine, carbody counterweight, 24m basic boom and 450t hook.
The SCC4500A lattice crawler crane is built with enhanced safety features including load moment limiter, over-hoist protection of the main and auxiliary hooks, over-release protection device of the main and auxiliary hook, brake of hoisting mechanism, CCTV monitoring system, fault auto-diagnosis system, anemometer and many more.
The Sany SCC4500A was in HDB/Super Lift configuration with 66 metres of main boom and lifting at a radius of 17 metres.
Scott goes on to discuss the site and the complexities of the lift.
“We were operating on one of the best sites I’ve seen in years. There was plenty of room to mobilise and demobilise the Sany and it only took us two and a half days to build it. The support crane was East Coast Cranes’ GROVE GMK7450, 450t capacity all terrain.
“Basically, there were four stages to this project. The first was lifting and placing of the pontoon into the water, the second was the lifting of the dock gate out of the water and the third was landing the dock gate and re-arranging the rigging, and the fourth was laying the dock gate over on its side. The GROVE was also the support crane when we laid the dock gate over.
The performance of the Sany was all the more impressive when Tutt Bryant started to lift the dock gate it weighed 500t with 270t of water inside it.
“What made the performance of the Sany all the more impressive was that when we started to lift the dock gate we expected it weighed around 500t with 270t of water inside it. We got as much water out of it as we could and then lifted it as far as we could, while still being capacity. We didn’t get it all the way out of the water, but it gave us an opportunity to put holes on the side of the dock gate to release more water.
“We were expecting the lift to come in at about 230t but it didn’t. Even when we got all the water out of it, it still came in at 308t. That was dead weight and didn’t include anything else like the rigging,” said Scott.
The lift required a complex rigging configuration, which included a Modulift MOD® 400 and two MOD® 250 spreader beams in a one-over-two rig configuration.
In such high-stakes projects, Modulift’s versatile spreader beams demonstrate their engineering excellence. The MOD® 400 was deployed at a 16-metre span, while the two MOD® 250 beams operated at 4-metre spans each.
Together, they distributed the load evenly, ensuring optimal stability and safety throughout the lift.
“We had a series of slings basketing under the dock gate and once we had it out of the water, and onto land, we connected East Coast Cranes’ 450t Grove to the top of the load taking over 100t of weight to stabilise the gate vertically,” Scott said.
“We then de-rigged the basketing slings, and then re-rigged with two, 150t equalising sheeves and a series of 100 grade 32mm chains to lay it over.
“At this stage there was a load moment where the gate shifts from vertical to starting to lay over, and there’s a shock load that we needed to eliminate. This shock load would have been above the capacity for the rigging gear that we had on the load.
“The Grove ensured there was no shock load in the load moment as it shifted perfectly through 90 degrees into rolling over.”
As a member, you have exclusive access to:
Empower your team with industry-leading skills and safety expertise. Industry Networking
Join the exclusive network shaping the future of lifting.
Stay ahead with exclusive access to international standards and expert guidance.
Perth-based Urban Crane’s fleet just got a whole lot bigger following the acquisition of FG Cranes (FGC) assets. Cranes and Lifting spoke to Urban Cranes directors Drew Wright and Anthony Ivanhoe about the development.
DREW STARTED IN CRANES AND RIGGING and Anthony in construction in 2006 and they worked together for a number of years in the Perth construction game. Drew went on to fly-in-fly-out projects working at Barrow Island and iron ore construction projects, while Anthony went on to establish Urban Cranes in 2014.
“I approached Drew at the end 2015 to join the Urban Cranes team as our operations manager,” Anthony states. “Initially, we started with mobile cranes and in 2016 when Drew joined, we purchased our first tower crane.
“Wherever we could we purchased the Potain tower cranes as well as Grove mobile cranes, and between 2016 and 2024, we built the tower crane fleet up to 20 with varying capacities.
“Our reason for aligning ourselves with Potain and Grove goes back several years, the support and trust we have experienced sealed a bond between us early.
“We focused the tower crane fleet on the small end of the market. At that time the market was dominated by FGC and we didn’t want to compete,” said Anthony.
Drew explains where the mobile crane side of the business sits.
“Since 2018, we have been working directly on the Government Alliance infrastructure projects in Western Australia, this work includes bridges and noise walls, horizontal construction on the freeways and the major highways that are local to Perth. We’ve established a proven track record working for major clients such as ACCIONA, BMD, NRW and Georgiou.
“In the early days, our strategy was focused on staying diversified in multiple areas which ultimately created multiple
large opportunities for our business, and as a result our rate of growth has been rapid”, said Drew. “We are seeking the right people, the right clients and the right projects. We want to work with clients who see value in us, and we see value in them. We have a strong set of core values and we’re focused on providing a service that exceeds our client expectations.
“Infrastructure projects work well for us. We are in partnership with our clients and are both focused on getting the job done”.
Anthony explains how the FGC development came about.
“John Stewart from Manitowoc put FGC and us together. We didn’t know them prior to the deal, and he understood the owners were thinking it was time to exit, which presented us with the opportunity to talk.
“We sat down with the owners, and we could see both parties were aligned and committed to making a deal work.
“Over the next four months we worked on valuations and finance terms which
ultimately resulted in the deal being settled in October. We had the smaller tower cranes in the market, and FGC typically had the bigger cranes, and it was the same with our mobiles. We could see their assets would plug the holes that we didn’t have across our crane fleet,” he said.
“There were huge synergies in combining the fleet. It was the same with the staff, the capabilities of their staff versus the capabilities of ours showed it would be a relatively seamless integration.
Manitowoc Finance played an integral role in the acquisition, massaging the package and providing strong support to ensure the best ‘cranes and finance package’.
As everyone knows, cashflow is key and Manitowoc Finance has been very creative to get us an initial footing in the industry and then enable us to financially manage this massive influx of cranes. They are great to work with,” said Anthony.
Since the acquisition of FGC’s assets Urban Cranes fleet has increased significantly and includes:
• 13 mobile cranes including the Grove GMK6400
• 60 plus tower cranes
• C rane Deck loading Platforms
• Transport equipment
• Access equipment
“We’ve got a decent-sized fleet of mobiles and we are focused on project work. If we have the cranes available we will take on the taxi hire work, but it’s not our core business,” said Drew “We have our mobiles and we have our tower cranes, we install and dismantle with all our own plant, equipment and personnel.
“We don’t have the largest mobile fleet, but we do have the largest tower crane fleet in Western Australia, including 33 luffing cranes.
“We also have a really strong management and leadership team, for the tower crane division – Andrea Baravelli – a structural engineer who has been working with Potain tower cranes for 20 plus years. Andrea plays a key role in the tower crane division, Urban Cranes being the only tower crane provider in WA that has an in-house engineer.
“We had the smaller tower cranes in the market, and FGC typically had the bigger cranes, and it was the same with our mobiles. We could see their assets would plug the holes that we didn’t have across our crane fleet.”
“Geoff Brown is our operations manager for the tower crane division. Geoff also has 20 plus years’ experience in the tower crane industry and with Potain Cranes, his experience is passed onto our team as well as our clients and their projects.
“Adam Hills is our operations manager for mobile cranes and project work and he’s been with us for three years. He’s a great asset to the team with 18 years construction experience. We do a lot of precast lifting, which requires a specialised team that includes lift planners,
supervisors and riggers to execute in a safe and efficient way.
“We have Liam Gazey, our asset manager whose role is to make sure all our plant and equipment is compliant and maintained at all times,” said Drew.
We have tower crane riggers, technicians and mechanics. Across the board, we have a great team with a very positive attitude and strong harmonised culture focused on successfully delivering projects for our customers. As with any business, without good people, we wouldn’t be where we are today.”
• 9.5 m
Andromeda’s Steel Cable & Slings Division manufactures Superflex steel cables and slings, as well as the flat woven steel slings. These are used in a wide range of lifting applications in many industries.
SUPERFLEX CABLES AND THE MACHINES used to manufacture them, as well as the termination systems, have been invented and designed by Raymond McLaren, who is still involved in the business today as a technical advisor. Over the years the machines and process equipment have been manufactured by his team of engineers in Andromeda’s engineering workshops. Central to Andromeda’s manufacturing facilities is the Orbital Square Plaiting Machine. Geoff Bower, Andromeda’s Customer Relationship Manager discusses the various manufacturing processes.
“The Orbital Square Plaiting Machine produces our feedstock cable which goes on to create our Superflex by plaiting the cables together around a central core wire.
“For the majority of the time our plaiting machine is producing our Superflex steel cable in a variety of sizes from 10mm through to 40mm, however we have also produced speciality cable of stainless-steel configuration which is used as mine sweeping rope as well as plaited wire rope used exclusively in the electrical industry for the drawing of powerlines,” said Geoff Raymond McLaren and his
engineering team designed the Orbital Square Plaiting Machine.
“Raymond and the engineering team designed and developed the first version in the late seventies and our current version came on board in the midnineties. It is a testament to Raymond’s innovative approach to design and engineering that it works as well as it ever has,” said Geoff.
“Output capacity depends on the diameter of the cables we are manufacturing. With the smaller 10mm and 12mm we have the capability to produce up to a two kilometre continuous length and with the larger diameters like 40mm, it’ll punch out 180 metres at a time. The machines’ design and capabilities are completely flexible and we are continually changing the diameters produced as required.
“Michael Sipple is our machine operator and he’s been with the organisation for three years. He works closely with this machine. When the finished Superflex cable has been manufactured it is wound onto one of our standard cutting reels or our storage reels. Ready to produce our range of Superflex Slings and Strops. Obviously, we manufacture a huge
the arms move inwards and outwards producing a unique steel cable that has unparalleled flexibility. Andromeda also manufactures flat woven steel strapping on a weaving machine which is the only one of its kind.
“Raymond and his engineers designed and developed the machine
“At the end of the day, because we’re creating such a critical product you have to ensure that it’s on point and that our customers are assured of quality. That’s why we’re members of LEEA and CICA, that’s why we have our NATA accreditation.”
number of slings and the bulk of the Superflex we manufacture remains on site, however we do have a number of resellers who produce their own slings using Andromeda’s Superflex Cables which we supply on various size reels as requested,” said Geoff.
The process of plaiting Superflex Cable involves 12 bobbins with different lay cable on each, (left hand and right hand lays). There’s a core wire that runs up through the middle of the machine and the bobbins turn clockwise and counter-clockwise whilst
which produces strapping with diameters between 50mm and 250mm. The strapping products are designed predominantly for lifting applications, it’s nearly all below the hook. However, we do produce a range of flat woven slings used as lashing points in the transportation of heavy and difficult loads. This is due to the extreme cut resistance the flat woven slings have.
“We manufacture a lot of flat woven slings which are used as roofing slings, so they’re predominantly flat woven choker slings with applications in civil
construction. The 250mm flat woven sling will lift 25t in a straight pull,” said Geoff.
The team at Andromeda continue to hand make slings.
“Steve Harrison (sling maker) is responsible for our handwoven slings. The sling he is working on only has ferrules or a termination on one end, the other end features a soft hand plaited eye. The entire webbing of the slings is made by hand.
“Originally, all of Andromeda’s products were handmade until Raymond and his team designed and developed the weaving machines. The reason why we still manufacture handmade products is because you’ve only got a termination on one end. If you are trying to fit it in between a really tight space, you don’t have ferrules or anything that’s going to catch, it’s a smooth soft finish at one end,” said Geoff.
Andromeda Industries has National Association of Testing Authorities (NATA) accreditation, they are active members of The Lifting Equipment Engineers Association (LEEA) and they are also a member of The Crane Industry Council of Australia (CICA).
“At the end of the day, because we’re creating such a critical product you have to ensure that it’s on point and that our customers are assured of quality. That’s why we’re members of LEEA and CICA, that’s why we have our NATA accreditation.
“Every product that leaves our facility has been tested; as per the Australian Standards it’s been certified and it has that backing behind it. We go through our NATA audit
every two years to ensure we remain compliant. Jumping on board with CICA has well and truly opened our eyes and we continue to make sure we are manufacturing the best lifting equipment available not just in Australia, but from any manufacturer worldwide,” said Geoff.
Andromeda Industries continues to remain active with LEEA and CICA attending both LiftEx on the Gold Coast and the CICA
National Conference and Exhibition in Adelaide.
“The response from these events has been wonderful. Although we’ve been around for such a long time it is surprising the amount of people who one; didn’t know we existed and two; didn’t know we are an Australian company. One major crane hire business thought because of our product was such high quality, it had to be coming in from Europe.
“These events provide us with the opportunity to connect with our resellers and with the guys that are using our products on a daily basis.
“Getting positive feedback from them and suggestions on how we can make improvements is invaluable. As a result of the events, we’ve organised a couple of factory tours where we’ve had our resellers and crane guys through the facilities and we could see it was a real eye-opener for them,” said Geoff.
MAXbase Equipped
The GMK4080L is an outstanding four-axle taxi crane that, with its 60-meter-long boom, offers both the longest boom and the lowest gross vehicle weight in its class. Within 10 t per axle, the crane can carry 5.2 t counterweight and even 13.3 t counterweight with 12 t axle load.
•60 m boom length and capacity matches the 90-100t class (4.8 t @ 60 m)
•Main boom: 11,3m - 60m, 7-section
•Bifold swingaway jib: 8,7 m /15 m (optional)
•Minimum width 2,55 m and overall length 12,82 m
•Carrier cab: Latest generation of Grove carrier cabs
•Increased safety and flexibility with MAXbase variable outrigger system
•Faster Intuitive set-up with CCS (Crane Control System)
•Engine: Mercedes-Benz OM470LA, 300kW
•Capacity: 80 t
•Main boom: 60 m
•Maximum jib: 15 m (0°-40° luff)
•Maximum tip height: 77 m
•GVW: 48000 kg
THE ZERO-EMISSION SOLUTION WITH A CONVENTIONAL RIG
In 1984, Lower Bavarian machine manufacturer
SENNEBOGEN and Lower Franconian machine manufacturer
ABI GmbH laid the foundations for a successful collaboration for sophisticated solutions in the field of piling, extracting and other applications in special civil engineering.
SENNEBOGEN
Maschinenfabrik can look back on 73 years of success. With a wide range of solutions for the construction industry and material handling, the Lower Bavarian company, which now has more than 2,200 employees, plays a leading role in various sectors. With carriers, material handlers, telescopic handlers, cranes and duty cycle cranes (up to an operating weight of 420 tonne), SENNEBOGEN offers its customers the greatest variety of industry and customer-specific solutions.
ABI GmbH is a medium-sized family business with a passion for special civil engineering machines. Since 1974, the Lower Franconian company has grown steadily to more than 250 employees. Management is
committed to the innovative further development of the company and pursues a clear vision: “With our efficient machines, we offer our customers the best possible conditions as a solution for their projects in special civil engineering and support them as a reliable partner throughout the entire service life of the machine,” emphasises Christian Heichel, shareholder of ABI GmbH.
Co-operation between the two companies steadily expanded.
As early as the 1980s, both companies knew that complementing each other’s core competencies would lead to successful solutions on the market.
The SENNEBOGEN carrier machines of the time – known as SR19T, SR20T, SR26T, SR28T, also built as mobile machines – were completed by ABI with a leader system and attachments to form the well-known MOBILRAM systems, which increasingly made a name for themselves on the national and international market.
In November 2024, the two companies celebrated 40 years of cooperation. Both company representatives emphasised
Modern specialist foundation engineering machines such as the MOBILRAM TM17 are shaping the market in specialist foundation engineering worldwide today, thanks to the customer-oriented co-operation between ABI and SENNEBOGEN.
“We understand a lot about the construction of carrier equipment, ABI is an expert in special civil engineering applicat ions. Together, we now offer customers market-leading solutions.”
that working together and complementing each other has always led to better solutions.
“We have always challenged and encouraged each other over the years. The number of solutions that we have realised together testifies to the great success of this constellation,” said Erich Sennebogen, Managing Partner, in his laudatory speech.
“We understand a lot about the construction of carrier equipment, ABI
is an expert in special civil engineering applications. Together, we now offer customers market-leading solutions.”
With many years of experience behind them, both companies are looking to the future with confidence, as there are major challenges and opportunities for the joint products in many markets.
The pursuit of customer-oriented solutions will continue to be the driving force behind their joint development.
“The synergies from our collaboration never cease to inspire me. If I could describe an ideal cooperation, it would be exactly as it is today between our companies, ABI GmbH and SENNEBOGEN,” said Christian.
Dieci Australia has been selling its range of Italian designed and manufactured telescopic handlers for over 25 years. The company’s continued investment in facilities, parts, service and support will enhance the longterm prospects for growth according to National Sales Manager Bob Mules.
WITH OVER 40 YEARS OF EXPERIENCE in equipment sales, hire, service and support, Bob is well qualified to discuss the company’s strategies for growth while maintaining the levels of support customers have become accustomed to.
“As a proud, privately owned and operated Australian company, Dieci Australia continues to grow from strength to strength by ensuring our customers receive the highest quality, fit for purpose telehandlers, to accommodate a broad range of industry applications, operations and requirements,” said Bob. “We back this with a strong national after-sales network to ensure customers are happy long after their purchase is made.”
Evidence of the company’s growth trajectory came last year with the opening of a new purpose-built 5,500 square metre flagship facility in the Sydney suburb of Prestons, which provides a “significant stake in the ground”.
“Opening a brand-new, purpose-built facility, in our 25th year of operation was a milestone event for the business,” Bob said. “We have been focused on how we can improve our customers’ experience and better support our network of Authorised Parts and Service Agents, and this facility is a key part of that improvement. Further to this, we are moving into a new larger facility in Melbourne in March of this year, once
again highlighting our commitment to our customers and to the market.
“The new facilities will enable us to increase the supply of both spare parts and machinery inventory, supporting customers right across the country, thanks to the national footprint including branches in each of Australia’s capital cities. From a parts point of view, a significant advantage with Dieci is an 85 per cent commonality of parts across the range.”
Customer service has always been a strong focus for Dieci Australia, and this is emphasised as a point of difference when it comes to the competitive market of telehandlers, but the machines themselves and their performance are also a critical part of the equation.
Dieci’s telehandlers are manufactured in the same region of northern Italy as Ferrari, Lamborghini, Maserati, so customers know they are going to get a quality, reliable machine.
Every machine and every attachment has design verifications and meet or exceed the relevant Australian Standards.
Dieci offers a range of fixed boom and rotational telehandlers with lifting capacities ranging from two tonne up to 23 tonne. With its broad range of machines, Dieci is servicing numerous industry sectors including construction, mining, agriculture, infrastructure and renewables.
Dieci’s construction range of telehandlers can be equipped with a wide selection of attachments, including, jibs, hooks, winches, pipe grabs and man baskets to name a few, allowing them to perform all necessary construction site operations using a single telehandler.
The telehandler is very versatile and is generally one of the first pieces of equipment onto a construction site and one of the last off it. The wide range of Dieci telehandlers and attachments allows customers to choose the best machine suited to their individual needs.
“For the customer, our focus on the ‘Total Cost of Ownership’ (TCO) is a valued part of the partnership. The 85 per cent parts commonality throughout our range of telehandlers is a key factor in the cost of ownership throughout the life of a
Dieci Telehandler. Add to this our industry leading 3 YEAR – 3000 HOUR warranty on all machines and over $3 million of spare parts on the ground in Australia through our state-of-the-art facilities.
“Our range of attachments also enhances the overall cost of ownership as one machine can complete multiple tasks that may otherwise need multiple machines. We don’t just talk about ‘Total Cost of Ownership’ and ‘After Sales Service and Support’, we live it every day.
“With assistance from the factory, certainly post-COVID, our focus has been to ensure the availability of all models throughout our range and we now have a good selection of most models either on the ground or continually arriving,” said Bob
“I joined Dieci Australia to provide a single focus for our sales team and to ensure the customer experience we provide is industry leading. We operate a national sales team with sales representatives in each of the states looking after our customers. We have a nationally approved Parts and Service Agent (APSA) agreement with AWD Australia, who operate in each state, as well as a broad net of regional APSA’s we are adding to all the time, to ensure our customers continue to be supported once they have bought their Dieci. It doesn’t matter what industry our customers are from, our approach is exclusively on how we can best service our customers and provide that industry leading customer experience.”
Bob goes on to discuss how industry sectors, including construction and
mining, are focused on reducing the carbon footprint of projects by using sustainable materials, equipment and construction techniques that help mitigate climate change.
“In Europe, Dieci recently launched a new battery electric model, the E26.6 which will be available locally by the middle of 2025. This is an exciting development and I believe this will be game-changing technology for the telehandler market, and we can’t wait for it to arrive,” said Bob.
Dieci Australia’s comprehensive range of telehandlers, mixers, and dumpers is accessible nationwide through flagship branches in Sydney, Brisbane, Melbourne and Perth.
For more information, visit: www.dieciaustralia.com.au
skyjack.com/en-au/simply-more
Boom Logistics’ Travel Towers division is powering wind farm maintenance projects across Australia, ensuring critical infrastructure stays operational.
WITH A FLEET OF OVER 35 TRAVEL towers, including several newly acquired 70-metre units. Boom Logistics continues to expand its capabilities in the renewable energy sector.
Shane McLaughlin, Boom’s National Business Manager for Travel Towers, shares insights into the busy summer season and the company’s growing role in the industry.
A significant strength for Boom Logistics is its integrated crane and travel tower operations.
“Summer is a critical period for wind farm maintenance,” Shane explains. “Providers worldwide schedule major servicing during the warmer months when wind speeds tend to be lower. Maintenance teams fly in, complete their work, and then move to the northern hemisphere for their summer season.”
A key focus during these shutdowns is blade repairs, which are necessary due to wear and tear from constant motion or occasional bird strikes. This year, Boom’s team has been engaged in multiple programs across various wind farms, keeping its 65 skilled workers busy across the country.
Boom Logistics operates an extensive fleet of over 35 aerial platforms, strategically located across Australia. “Our reach starts at 38 metres and extends up to 70 metres, which allows us to cater to diverse wind farm and infrastructure projects,” said Shane.
The latest additions to the fleet, new 70-metre Bronto units, reinforce Boom’s commitment to supporting Australia’s renewable energy sector with industryleading equipment. These heavy-duty aerial work platforms provide increased workload capacity, compact design, and a state-of-theart control system, ensuring maximum safety and efficiency.
Beyond equipment, Boom Logistics takes pride in its experienced crews. “We have 65 dedicated personnel who bring a wealth of expertise to the job. Many of them have been with us for years, which speaks to the strong culture we’ve built,” Shane notes.
“Working in wind farm maintenance requires a ‘can-do’ attitude, long hours, and a commitment to working away from home.
“Despite the demands of the job, our teams remain highly motivated. They support each other, work seamlessly as a unit, and their loyalty is a testament to the great culture we foster at Boom.”
Boom Logistics follows strict OEM service guidelines, ensuring every unit performs at
Boom Logistics follows strict OEM service guidelines, ensuring every unit performs at peak efficiency.
peak efficiency. “We service each unit every 250 hours, with major servicing at 800 hours. Our technicians understand the product inside out, which helps maintain high standards across the fleet,” Shane said.
He highlights that Boom applies this rigorous maintenance philosophy across all business divisions. “We don’t cut corners – whether it’s cranes, travel towers, or any other equipment, everything is maintained to OEM standards. It’s a key part of our business strategy.”
One of Boom Logistics’ strengths is its integrated crane and travel tower operations.
“We work hand in hand with our crane division, particularly on transmission line projects where both travel towers and cranes are needed,” Shane said. “We’re unique in this space as the only company offering both services at scale, providing clients with a one-stop solution.”
With an expanding fleet, growing team and industry expertise, Boom Logistics continues to be a trusted partner in wind farm maintenance and renewable energy projects.
QR CODE FOR MORE INFORMATION
The course instructors are seasoned professionals who will mentor course participants through real-life scenarios, preparing them for the challenges and responsibilities of a Crane Lift Supervisor.
Crane Lift Supervisors are in high demand globally. Completing this course enhances employability and opens doors to a wide array of job opportunities and career growth.
The curriculum covers a wide range of topics, including lift planning, load calculations, safety protocols, communication strategies, and legal compliance.
Scan the QR code to book in now
Melbourne 5-6 February 2025
Sydney 19-20 February 2025
Brisbane 5-6 March 2025
Perth 19-20 March 2025
Melbourne 4-5 June 2025
Brisbane 10-11 July 2025
Perth 16-17 July 2025
Sydney 17-18 September 2025
LinCon Hire and Sales is a leading provider of high standard access equipment hire as well as offering repairs, servicing and sales. With an extensive and diverse range of nearly 150 truckmounted Elevating Work Platforms, and with a team of skilled personnel across six states, LinCon ensures exceptional service with a focus on global safety standards.
TONY FISH IS RESPONSIBLE FOR TECHNICAL
Sales at LinCon. With close to 40 years’ experience in cranes and access equipment, he is well qualified to talk about LinCon’s capabilities when it comes to Elevated Work Platforms (EWPs) and access equipment.
“Throughout my career I’ve been in cranes and access equipment. I started at Lindore Cranes and Rigging in 1988 and
stayed in cranes for quite a while, then moved into EWPs when Colleen Lindores started this business. I was the workshop manager for 13 of the 20 years that I’ve been here, and now I’m in technical sales,” said Tony.
“LinCon Hire and Sales is the agent for Palfinger Platforms and Barin under bridge inspection equipment in Australia and New Zealand. I’m currently part of
the Australian Standards Committee to add some extra knowledge of the truckmounted platforms and also on the board of the Elevated Work Platform Association (EWPA) Board so we can provide additional knowledge with the truckmount platforms.
“During my time selling truckmounted elevated work platforms, I was also receiving enquiries for scissor
lifts, boom lifts, tow-behinds etc., and so we started the Access Equipment Sales website. Although focusing on the Palfinger and Barin products this website generates general enquiries for selfpropelled machines.
“We have created relationships with all the major EWP suppliers including the Chinese manufacturers now in the Australian market. With the website we’re not stuck to one brand of machine. We can source the type of machine the customer wants or alternatively offer a machine suitable to their budget,” said Tony.
“A lot of the solutions offered via the website are for smaller family businesses, we also get a lot of second-hand enquiries via the website. With the second-hand market I’ll speak to manufacturers regarding their trade-ins or to access equipment providers about their older machines which might not suit their requirements anymore but still have value. We’ll buy and sell them. With the Palfinger and the Barin products, we are working with more of the larger utility companies and government organisations,” he said.
Tony goes on to explain how LinCon manages the national fleet of access equipment.
“We have managers in each state managing after the operations of the machines plus business development managers based in Queensland and New South Wales putting the LinCon name forward while looking for new work. Repairs and maintenance is taken care of by Mick freeman, he has over 20 years of experience in the crane and access equipment industry. Mick is the National Workshop Manager based in Brisbane however has the overview of the workshops in New South Wales, Victoria, South Australia, Tasmania and Western Australia. Nationally Mick manages the servicing and quality of the Lincon fleet plus maintaining equipment sold to other customers,” said Tony.
He explains how enquiries for the Palfinger access platforms are managed.
“The smaller Palfinger units, are supplied as kits to be fitted here in
“With the website we’re not stuck to one brand of machine. We can source the type of machine the customer wants or alternatively offer a machine suitable to their budget.”
Australia. Palfinger provide us with comprehensive engineering drawings of the subframe for each build. The customers have the option to select the truck of their choice, the build from subframe to mounting and testing is all done in house, this even comes down to the painting in our certified paint booth. Once complete, all builds are tested and signed off by an independent registered engineer.
“Generally speaking, the kits are up to 30 metres for external customers, but we’ve recently built a couple of 48-metres and a 75-metre kits. Initially Palfinger didn’t offer the platforms as kits, but after
years of us lobbying, they are now moving towards this type of business model,” said Tony.
LinCon also operates a fleet of insulated access platforms.
“The larger insulated machines are from Bronto Skylift. They are live line machines that are rated to 500,000 volts. We also have a Palfinger live line machine that’s rated to 750,000 volts,” said Tony.
“These machines are compliance tested every six months. They have to go down to the National Measurement Institute in Sydney, which is the only place in Australia that can test them now. Part of the testing involves one million volts
through them to make sure that they are fit for purpose. When you consider we have 10 of these units in the fleet, this is a significant cost for the business,” said Tony.
“But there’s a significant amount of high voltage work coming up over the next decade or so and we are well positioned for that work. The work revolves around the renewable sector, including wind and solar farms. The companies that own them don’t want power lines shut down, because if they’re not producing power, they’re not making money. If the lines can stay up and we can work on them while they’re live, they’re making money, so these machines are busy all of the time.”
Tony explains a bit more about the Palfinger range of aerial platforms.
“The smallest in the range is 13 metres and this will fit on a Ford Ranger or an Isuzu truck. This size has been quite popular with mines in New South Wales; they’ve got them on little trucks. With the Ranger, they’re pretty much at their capacity. The 13-metre weighs 3.2 tonne however with a GVM upgrade the ute is good for 3.5 tonne. But by the time you put a bloke in the basket, you can’t carry too many tools.
“We go up to 103 metre units that are mounted to a Tadano Crane Carrier which is specially built, they weigh 60 tonne. It’s not like a crane, you can’t take counter weight off, they weigh 60 tonne and that’s it.
“A lot of the times they’re moving around on a low loader,” he said.
“We’ve recently got approval from the National Heavy Vehicle Regulator (NHVR) to road them in Queensland. It’ll be a single trip permit and whatever road it travels on will be decided by NHVR. With six of these in the fleet, with a reach of 103 metres, we’ll be managing lot of wind turbine work.
“Initially, when we first got the machine, it was working on drag line. Before the mine had the machine, they were using a 300 tonne crane with a man box to work on the drag line. We got in there with our 100-metre machine with 530 kilos in the basket. You can have five people up there doing the greasing, inspecting the sheaves and ropes,” said Tony. “We were able to manage 35 metres of horizontal outreach which meant we could set up in one spot and inspect 70 metres of the pendant ropes. They conduct non-destructive testing (NDT) and run along the ropes, testing them. We’ve taken the machine out to Tanami Desert to a gold mine out there and we’ve also had some wharf work on the container cranes. It’s a very flexible machine.”
“We go up to 103 metre units that are mounted to a Tadano Crane Carrier which is specially built – they weigh 60 tonne. It’s not like a crane, you can’t take counter weight off, they weigh 60 tonne and that’s it. A lot of the times they’re moving around on a low loader.”
When it comes to efficiency, adaptability, and raw lifting power, the Dieci Pegasus 40.18 stands in a league of its own. Designed to handle the toughest jobs with ease, this rotational telehandler offers 400° non-continuous rotation, transforming how you work on-site. Whether you need the capabilities of a telehandler, an aerial platform, or a crane, the Pegasus 40.18 seamlessly adapts with its diverse range of attachments—one machine, limitless possibilities.
Max Capacity: 4,000 kg
Max Lift Height: 18.00 m Total Weight: 13,700 kg
Max Power: 73.4 kW (98 hp)
Niftylift was the first Elevated Work Platform (EWP) manufacturer to introduce the hybrid engine concept. Niftylift’s Managing Director John King discusses the continued commitment to a carbon neutral future.
teams developed the first hybrid engine for an Elevated Work Platform (EWP) in 2017. The team has continued to develop the efficiencies of the system and today, these feature in the HR 21 Hybrid MK2.
In designing the first hybrid system, Niftylift’s teams learned a lot of lessons, and in the ensuing years set about redesigning the system to be even more efficient. The regen system now features a Stage V engine with electric boost which reduces fuel consumption by up to 50 per cent.
“Today, this is really important, because job sites are now asking, ‘what is your
carbon footprint?’,” said John King, Niftylift Managing Director. “The Stage V diesel engine is under 19 kilowatts which doesn’t require particulate filters or diesel additives such as AdBlue, and it’s a lot quieter.”
There are three stages of operating the machine. When the HR 21 Hybrid is running on diesel, whether that’s driving the machine or operating the boom, and not all power is being used, the system will automatically turn the electric motor on and store the extra energy in the batteries.
There is boost mode, which is used when operators are faced with really steep or boggy ground and need extra drive. The system will
bring the electric motor in to back up the diesel engine, providing a combined power of about 26 kilowatts. The machine can operate in electric mode which will provide 22 kilowatts of power.
The efficiency of the hybrid system is demonstrated with the Niftylift Standard Duty Cycle (SDC), explained John.
“With the SDC we start with fully charged batteries and the safe working load (SWL) and cage, which is 250 kilograms with the HR 21. We drive the machine 30 metres forward, 30 metres backwards, we take the boom all the way up, slew it through 90 degrees, bring it back down.
All cycles start with the machine in a fully charged state with the battery charger showing an indication that the charge is complete. The full safe working load of the machine must be present in the cage throughout the test, and all machine functions are operated at the maximum possible speed.
The cycle is repeated until the point at which the machine can no longer operate, or the battery display is showing zero per cent.
“The industry standard for a full day’s work is a minimum of 16 repetitions of our standard duty cycle or an SDC rating of 16. Most new electric-only Niftylifts have an SDC rating of 32, which means they could comfortably perform two full working days on one charge,” said John.
“The performance of the HR-21 is 26 cycles, at which point the batteries are flat. We then start the diesel engine and run the machine on diesel, but you are also ‘regening’ at the same time. With this combination you are looking at around 67 cycles.
“We then run it back on electric again, receiving another 24 cycles. We then run the diesel engine again as a hybrid and regen for another 51 cycles. Then back on electric the machine manages 18 cycles. So, with 33 litres of diesel and fully charged batteries, we received 188 cycles from the machine. In terms of CO2, the machine runs at 458 grams of CO2 per cycle running on diesel. All the information is there, and we can tell our customers exactly what’s happening with the machine and how they can best benefit from its efficiencies.”
Niftylift uses Absorbent Glass Matte (AGM) batteries which are maintenance free.
“We have found them to be really good batteries. Everything on the electric machine is very similar to the other models in the range, including the console layouts. Our booms now have the same console so once you’ve operated one Nifty, you can get straight onto the next one. It’s obvious how it all works,” said John.
“The new electric machines have an SDC rating of 66 cycles which is the equivalent of four days’ work, probably more if you are
realistic. There’s no diesel consumption and the battery is fully recharged in 10 hours. All our booms now feature telematics which enable a customer to monitor the machine from their computer or tablet, they can fault find, understand when it was last charged, what the diesel consumption is, how much fuel is on board and how many times the boom has been used… all the information is there,” he said.
The Niftylift range also features an override system enabled by the operator.
“If there is an emergency the operator can override the safety system which leaves the function open to abuse,” said John.
“With the Niftylift range, there is an override button in the cage. If this is pushed a small electric motor will bring the boom down very slowly and a light will come on in the console and stay on. When that machine returns to the yard and management is happy that there was a problem and they weren’t abusing the machine, they can ring us and we will give them a one-time code to clear the warning light.”
maintenance solutions provider.
Building the future of infrastructure through wind farms, telecommunications, and utilities, one tower at a time.
Scan the QR code to find out more!
Empowering Industries.
Building Futures. One lift at a time.
Skyjack has expanded its E-Drive scissor range with a complete line available for the Australian, New Zealand and European markets.
IT FOLLOWS THE SUCCESSFUL LAUNCH OF AC brushless electric drive scissors in the North American market in 2023. The new models feature a designation carrying “E” to signify E-Drive, for example “SJ3219 E”.
cent gradeability, so that climbing loading ramps is easy.
The simply electric range is designed to give users more, with improved efficiency, controllability, and torque. The innovative drive system provides exceptional duty cycles and fully proportional controls, which offer a superior drive experience. This means that productivity is boosted with an improvement of up to 20 per cent in runtime per charge.
E-Drive provides consistent power, traction and torque, with more than 25 per
Below: E-Drive models boast exceptional maneuverability, while Skyjack’s unique scissor stack design makes them suitable for a wide range of indoor and outdoor construction, maintenance, and industrial applications.
E-Drive models boast exceptional maneuverability, while Skyjack’s unique scissor stack design makes them suitable for a wide range of indoor and outdoor construction, maintenance, and industrial applications.
“We’re proud to offer the latest expansion of our E-Drive line,” said Charlie Patterson, Skyjack President. “With this latest launch we now offer both our DC scissor range and our rough terrain articulated booms with E-Drive technology, allowing us to empower users with more.”
Mark Trowman, Product Development and Project Manager EAME, Skyjack Europe, said that throughout the development of the latest line the company focused on giving users more.
“For example, cost of ownership is reduced significantly with maintenancefree, brushless AC electric drive motors; while uptime is maximised with more runtime per charge with less power consumption and lower battery maintenance.”
In addition, the new range will carry Skyjack’s ECO mark, introduced to provide products that deliver benefits in environmental performance and long-term sustainability.
Skyjack’s E-Drive scissors ECO benefits include;
• Up to 16 per cent operational carbon
saving compared to previous models,
• Up to 20 per cent improvement in duty cycle,
• Zero emissions,
• I nherently quiet machines, white noise alarm optional,
• L eak containment (ECOTRAY) optional,
• Biodegradable oil optional.
Skyjack provides rental companies globally with engineered, simple and reliable access and telehandler equipment so that they maximise use and their return on investment.
Skyjack began manufacturing scissor lifts in 1985 and through the 1990s grew to become a world leader in the aerial lift industry. It remains a dominant player that has adapted rapidly to the changing face of the industry.
The product range now includes vertical mast lifts, DC electric scissors, rough terrain scissors, telescopic booms, articulating booms, telehandlers, and ELEVATE, Skyjack’s OEM-delivered telematics solution.
In 2002 Skyjack became part of the Linamar Corporation, a diversified manufacturing company that operates in the industrial and mobility segments.
• Family-owned business
• Largest Truck Mounted EWPs in Australia
• Market Leader
• Project Specialists
Honesty | Reliability | Punctuality
A1A Software LLC has released its newest version of the A1A Product Suite, which eliminates the need to import Sketch Pad or Jobsite Designer plans while using the apps. Further, it allows the user to seamlessly use the power of the individual apps to complete their industry-leading lift plans in the 3D Lift Plan app.
A1A FIRST INTRODUCED THE A1A PRODUCT Suite at Con-Expo 2023. The driving factors toward app-based lift planning are enabling several new features not possible with the web browser version; and protecting the customer and company’s investments in the lifting platform, ensuring changes or probation within web browsers don’t disrupt service platform.
3D Lift Plan is the foundation of A1A Product Suite. The industry’s best-known software for creating bids, critical lifts, rigging documentation, lift simulations, and more, is made more powerful with the addition of stand-alone tools that can be used by themselves or in combination with 3D Lift Plan app.
“The A1A Product Suite applicationbased tools open up features of 3D Lift Plan to people who may not need the full lift planning program,” said Tawnia Weiss, President of A1A Software, LLC.
“The idea is to enable estimators, salespeople, project managers, and others to accomplish the level of lift planning that makes sense for their role, improving communication, and streamlining digital documentation.”
The A1A Product Suite includes the following apps. All apps will be available through Microsoft, Google Play, or the Apple App Store.
• SKETCHPAD eliminates the need for paper when gathering preliminary jobsite information. Establish crane location, travel path, location of 3D objects on top of a scaled Google Map image by drawing a sketch on a tablet
Key features include scaled jobsite with the touch of a button or simple address; superior annotation tools, great for sales teams.
• RIGGING DESIGNER is a faster way to create custom rigging plans for cranes,
gantries, forklifts, and other equipment using hundreds of pre-built 3D rigging loads and objects.
Key features include Point/Click/Drag/ Drop rigging components; Snap to points for easy addition of items; create, save simple or complex rigging for any lift equipment.
• JOBSITE DESIGNER allows users to greatly enhance the jobsite and simplify creation and editing of jobsite objects. Key features include 1-Click scaled building creation from Google imagery; Draw any custom shape; Import CAD objects; Move/Edit jobsite objects with mouse.
• 3D LIFT PLAN brings all functionality of apps together to create lift plans with ease with all the current web-based
features plus more … Key features include use on any device mobile or PC; Full screen interface; Integrated access to other apps in the suite; Intuitive controls layout for easy use; Drag increments for dimensions, rotation and other input parameters.
• 3D LIFT VISION is the only virtual crane simulator based on actual lift plans. Great for sales communications, training and risk management/ assurance. It allows the user to be immersed into created lift plans; Users virtually operate in the specific crane on a jobsite they’ve created with all the sounds and controls of an actual crane; CCO practical test are included, along with ability to add weather/wind etc.
· 6×6 full wheel drive steering mode, the overall length is less than 12 meters and features six steering modes
· Automatic boom telescoping by a single press for all OMs
· Highly integrated remote control technology
· Allison 4500SP 6-speed automatic transmission, 525/80R25 tires
· Equipped with multiple detection technologies, including outrigger length, outrigger pressure, and boom head
· Central lubricating system
For over 50 years, Underwriting Agencies of Australia (UAA) has been the number one provider of insurance for the crane and mobile plant and machinery sectors. Over this time UAA has stood as a pillar of strength and reliability in the crane insurance industry, providing comprehensive coverage tailored to the unique challenges of these sectors.
AS UAA CONTINUES TO EVOLVE ALONGSIDE industry advancements and shifting market dynamics, it remains committed to delivering best-in-class solutions that safeguard crane operators, businesses, and their critical assets. UAA’s deeprooted expertise, strong partnerships, and forward-thinking approach position it as the premier choice for crane insurance today and into the future.
From nothing to $450 million per annum in 50 years, the growth of UAA has been exceptional. The history of UAA starts with humble beginnings in 1972 as Sanderson Insurance Brokers based in Newcastle, founded by Phillip Duncan. As an insurance brokerage, it identified that sourcing specialised crane insurance for customers was difficult and further investigation uncovered a need to develop a product for the Australian crane industry.
Phillip Duncan packed his suit and flew to England to visit the global insurance market Lloyds of London, to see if he could source a product for crane insurance. He
found a syndicate with a very basic product that developed into Contractors Plant Insurance (CPI) in Australia and went on to build an incredible relationship with Lloyds of London.
There was an aspiration to further develop this product and further service the needs of the entire Australian insurance industry through a broader distribution and a specialised underwriting approach that assessed and correctly priced the risk. To do this it was identified that the next step was to become a recognised niche underwriting
UAA continues to evolve alongside industry advancements and shifting market dynamics, it remains committed to delivering best-in-class solutions that safeguard crane operators, businesses, and their critical assets.
agency that specialised in crane and machinery insurance and to utilise the national insurance brokers network to distribute the product to their clients.
In 1988, UAA was born, maintaining a strong relationship with the Lloyds of London syndicate who provided the security that backed UAA. This meant that UAA was able to autonomously underwrite its own crane and machinery risks, and importantly also allowed to manage claims and service its customers. UAA became the first niche underwriter in its class
to pioneer such a specific product in the Australian market.
THE NOW: Evolving with industry needs UAA, understands the ever-changing nature of the crane industry and the importance of adapting insurance offerings to meet the demands of clients. UAA’s current policy enhancements reflect this commitment, ensuring comprehensive protection that aligns with modern risks and operational realities.
1. Unrestricted Coverage for Large Capacity Cranes – Unlike other insurers that impose capacity and value restrictions, UAA continues to provide coverage without such limitations, ensuring businesses operating high-value, high-capacity cranes are fully protected.
2. Extended New-for-Old Replacement – UAA has increased the eligibility period for new-for-old replacement from two years to three years for equipment suffering total loss, providing greater financial security for owners investing in new machinery.
3. Enhanced Tower Crane Coverage –Recognising the unique challenges associated with tower cranes, UAA now cover additional costs for commissioning, erecting, and reinstalling on the same site following a total loss, reducing financial and operational burdens.
4. Automatic Multi/Dual Lift Coverage – When Australian Standards are adhered to, multi/dual lifts are automatically covered without the need for prior declaration, simplifying the insurance process while ensuring compliance.
5. Industry Leadership in Recovery Cost Awareness – UAA actively works with the industry to educate and promote safe recovery practices for specialised and heavy equipment, helping prevent further damage and ensuring assets are salvaged efficiently.
6. Specialised Assessors for Tailored Loss Management – Each claim is unique, which is why UAA engages specialised assessors suited to the specific circumstances of a loss, drawing on
expert advice from within the industry to ensure fair and accurate assessments.
7. Coverage for Crane Accessories –UAA’s policies extend to essential crane accessories such as ropes, bog mats, and counterweights, recognising the financial impact of these components being damaged or stolen when the crane is not in operation.
8. Coverage for High-Risk Occupations and Lifts – UAA continues to lead in providing insurance solutions for highrisk industries and lifting scenarios, including wind farms, barge lifts, and sensitive equipment transportation, where traditional policies often fall short.
THE FUTURE: Pioneering tomorrow’s crane insurance
As the crane industry evolves with new technologies and operational challenges, UAA is committed to staying ahead of the curve. UAA’s forward-looking initiatives are designed to address emerging risks, ensure ongoing education, and improve overall industry safety and efficiency.
in Australia, UAA is considering the implications of importation and expediting costs to ensure its policies adequately support businesses needing rapid equipment replacement.
4. Expanding Recovery Cost Coverage –In some cases, equipment may require recovery efforts even in the absence of physical damage. UAA is exploring expanded coverage options for recovery costs in such scenarios, reducing financial exposure for businesses.
5. Education and Broker Collaboration – Many cranes are currently insured under contract works policies with significantly higher deductibles and fewer industry-specific benefits. UAA is dedicated to educating brokers and working with MECON to ensure businesses receive tailored coverage that includes critical elements such as damage to lifted goods, recovery costs, and dismantling/re-erection
“UAA, understands the ever-changing nature of the crane industry and the importance of adapting insurance offerings to meet the demands of clients.”
1. Understanding Emerging Technologies – With innovations such as lithium battery-powered cranes entering the market, UAA is investing in research to understand the risks and mitigation strategies associated with these advancements, ensuring that our policies evolve to accommodate new technology.
2. Monitoring Crane Brands and Models – Recognising that different crane manufacturers and models present unique risk profiles, UAA is actively tracking industry developments to refine its pricing and coverage options accordingly.
3. Addressing Importation and Expediting Challenges – With certain crane models not readily available
6. Enhancing Industry Safety – UAA remains committed to working with industry bodies such as CICA to support initiatives like Franna licensing and walking crane endorsements, reinforcing its leadership in safety advocacy and education.
UAA’s long-standing presence in the crane insurance sector is a testament to its expertise, adaptability, and unwavering commitment to its clients. As UAA navigates the future, it remains focused on providing superior coverage, driving industry education, and innovating in response to emerging risks.
With UAA, businesses can trust that they have a partner who not only understands the intricacies of crane operations but also leads the way in shaping a safer, more resilient industry for years to come.
Zoomlion’s ZAT4000H763 is equipped with a 10-axle chassis with a width of only three metres and a length of just 22.5 metres, which is comparable to a
Zoomlion recently revealed the ZAT4000H763. With a lifting capacity of 4000 tonnes it is claimed to be the most powerful all terrain crane on Earth.
ZOOMLION’S ZAT4000H763 HAS BEEN designed and engineered to keep pace with the predicted increase of requirements in wind farm construction over the next ten years.
The massive crane is designed to handle the lifting for 15.XMW wind turbines on land for the next 10 years.
The ZAT4000H763 is capable of lifting 10.0MW wind turbines at a height of 160 metres and 7.0MW wind turbines at a height of 190 metres.
The lifting capabilities of Zoomlion’s ZAT4000H763 are impressive:
• At a height of 125 metres and a radius of 20 metres, the lifting capacity is 317 tonnes.
• At a height of 140 metres and a radius of 22 metres, the lifting capacity is 281 tonnes.
• At a height of 160 metres and a radius of 24 metres, the lifting capacity is 236 tonnes.
• At a height of 170 metres and a radius
of 26 metres, the lifting capacity is 218 tonnes.
• At a height of 180 metres and a radius of 28 metres, the lifting capacity is 190 tonnes.
FLEXIBLE MANEUVERABILITY ENHANCING MOBILISATION AND DE-MOBILISATION
Equipped with a 10-axle chassis with a width of only three metres and a length of just 22.5 metres, which is comparable to a nine-axle equivalent,
“Dual motors on a single winch enable rope threading in just 40 minutes per session. In 180m working conditions, the crane can be fully set up in just 30 minutes.”
the ZAT4000H763 can travel on highways and is more suitable for operations in narrow areas such as mountainous wind farms. With the full boom attached, the overall height of the crane is six metres, featuring a low centre of gravity for excellent ground clearance and enhanced safety during heavy-load travel. The 6+2 drive system enables the crane to climb gradients exceeding 20 per cent even with the main boom under heavy loads.
The 95.4m ultra-long main boom with dual-side pins requires minimal assembly space for wind turbine installation and other similarly limited working conditions such as infrastructure projects. Autonomous boom raising is possible without the need for auxiliary cranes in wind turbine installation scenarios up to 160m.
Dual motors on a single winch enable rope threading in just 40 minutes per session. In 180m working conditions, the crane can be fully set up in just 30 minutes.
The 1.4m large-distance counterweight displacement reduces the need for two transport trailers, enhancing economic efficiencies. For wind turbine installation scenarios up to 160m, only 22 trailers are needed for large-scale relocations.
Zoomlion’s ZAT4000H763 has been designed and engineered to keep pace with the predicted increase of requirements in wind farm construction over the next ten years.
I’VE ALWAYS WORKED IN STEEL FABRICATION and erection. The steel shop I worked at for 21 years had a crane so 20 years ago I started operating a 1974 Coles 30 tonne model to put up our steel work and manage a bit of general hire around town.
“Two years ago, I decided it was time to do something for myself and the family and I found a 30t Liebherr close by in Tumut (New South Wales). I liked the look of the crane and bought it, and Coen Cranes was born,” Andrew said.
With the 30-tonner, Andrew was managing general crane hire work for anyone and everyone, lifting anything and everything. He was used for man box work for a fabrication business, was servicing silos and grain augers, lifting
roof trusses for builders, putting in pools, as well as working in the local railway workshop, lifting engines, locomotive components and moving containers on and off railway wagons.
Andrew worked the Liebherr hard and soon realised the demand was a lot higher than anticipated. He wanted to research if an upgrade to a slightly newer and larger crane was on the table so early in the business’s startup phase.
“I was pushing the Liebherr to its limits and decided I needed to upgrade to a 40 tonner. I called Anthony Davis and Andrew Whyte at The Crane Connection, and they had one for sale. Unfortunately, by the time I’d sorted the finances with the bank and went back to the guys, it had been sold a couple of days earlier.
“They had a 55t capacity Liebherr LTM1055-3.2 available, which they said would be great for me. I never wanted to go that big – 40 tonnes was as big as I wanted – but I had a number of conversations with Andrew, he invited
me to look over the crane in their yard, which I did and bought it there and then. The service from Andrew and Anthony has been unbelievable, they are old-school, with traditional business values. I’ll never go anywhere else now,” said Andrew.
He said Andrew Whyte joining The Crane Connection has been a great development.
“When it comes to cranes, Andrew is very knowledgeable, and he has the time to work closely with you, one-on-one, which has been the best thing ever. We’ve become good friends and if anything happens, or there is a niggling issue, I get straight onto him, and he sorts it for me. He’s brilliant, I can’t fault him or his service,” he said.
The three-axle Liebherr LTM 10553.2 mobile crane provides high flexibility through its outstanding lifting capacities with full and part ballast. The fully automated support levelling and ballasting systems with advanced keyhole technology ensure that the crane can be ready for use very quickly.
With hours on the crane, Andrew decided to have Ben Baden Services conduct a 10-year major inspection while it was in the yard.
“When I purchased the crane, I had Ben and his team manage a 10-year major
inspection. They pulled it apart and put it back together which meant it was an eight-week period from the purchase through to me collecting the crane. When it was ready, I spent a couple of days with Andrew, Anthony and Ben, and they showed me all over the crane. I drove and tested it, I unloaded my old crane, loaded the new one, floated it home and we haven’t stopped working since,” he said.
had the 55, with nearly every job I do now, I think ‘how did I do this before?’ Another benefit is I can run it without counterweights as a 40t machine and then load it with counterweights and charge it out as a 55t. It works really well,” said Andrew.
While Andrew does the heavy lifting, wife Lauren is the brains behind the Coen Cranes name, keeping the administrative
CAD (computer-aided design) drawings and make the calculations for the lifts. We focus on the personal touch, so a customer can ring and deal with the person that’s going to do the job for them.
“We explain ‘this is what we do and won’t do’ and they know they are not going through two or three pairs of hands to get the job done. When you are operating in a regional town like Junee, we think it’s important to provide a personal service, where agreements are on a handshake, and you deliver on your promise.”
Andrew finds the recently launched CRANGLE App a useful tool for lift planning.
“The Crangle App is really useful for lift planning, and I use it nearly every day. Two brothers have created it, one was a computer designer the other a crane operator, and it is unbelievably brilliant,” said Andrew.
Coen Cranes is a member of The Crane Industry Council of Australia (CICA).
“We might be a small business, but from the beginning we could see the importance of being a member of a strong industry body like CICA. We joined when the business was new, mainly for CraneSafe (a crane assessment program) and then we progressed to using their logbooks.
“Once we got into it, we could see how handy the information and documents are on their website. Things like their dry hire agreement are excellent and we used this early on when I dry hired the crane to a few people. The website is a good resource and they’re very proactive as an industry group, with the best interest of the members at heart,” said Andrew.
Lauren understands the importance of creating and then maintaining a positive profile for Coen Cranes.
“We’re still trying to get our name out
More than just a pre-start checklist
StartSafe is comprehensive tool designed to streamline your crane operations, enhance safety, and ensure accountability.
there in the region and have been doing our best to have a strong social media presence. We get a lot of positive feedback from people following our journey on Facebook and they are always looking forward to seeing what we are lifting next.
“We also know the power of Google and employed the services of our good friend Liz to build and launch our website. We keep the activity on the website current which has been the attraction for those making contact after a Google search,” said Lauren.
“With a small advertising budget like a lot of startups, we decided to enlist the support of our friends, family and community members to help spread the word about Coen Cranes. With a run of T-shirts and hoodies, we have walking billboards around the community and can’t thank them enough for their ongoing support. You can’t beat the community spirit of a small town.”
Machine specific checklists are in line with the CraneSafe program.
StartSafe streamlines the process for collecting pre-start information, with instant data retention to a central location for the crane owner to access.
Photos tell the story.
When a faulty item is recorded by the operator, the maintenance team is notified of the issue by email, which includes photo evidence of the fault. This also assists with gathering major inspection data.
Hook & Haul’s Rick Mathews and partner Melinda have been dry hiring cranes for the best part of a decade. They recently took delivery of a new Franna MAC25-5. Rick provides background to the purchase and the history relating to the business.
“WHEN WE STARTED HOOK & HAUL in 2015, I was doing crane maintenance for various crane companies and dealers out of a $2000 Falcon ute, but the intention was always to be a dry hire crane business,” said Rick.
“Back in the ’90s I completed my diesel mechanic apprenticeship for a tower company and their business model was to hire tower cranes to crane companies and builders. This provided me with the concept of a dry hire business.
“From there I worked in crane maintenance and rigging and spent 10 years in workshop and equipment management. During this time, I was fortunate enough to receive a significant level of management
training, including being sent to INSEAD Business School in France and studying lean manufacturing at various Komatsu facilities in Japan.”
The business name Hook & Haul is a nod to the Franna pick and carry range which dominates the fleet, said Rick.
“We predominantly hire our cranes to crane hire companies; we don’t offer any form of wet hire so our customers can be confident we won’t be approaching their customers directly.
“Given that we are often partnering with our customers, the fleet is tailored to meet their requirements. We typically like to have around 15 Franna MAC 25 Super Lifts in the fleet. While the fleet is dominated by Frannas, we also hire city cranes and a couple of all terrains.
“We are currently working with customers around Australia, so pretty much where there’s cranes you may see one of ours too. Even though it may be painted in our customers colours.”
Strategies for sustainability and lowering Australia’s carbon footprint are being implemented across all industry sectors and, as highlighted at the Crane Industry Council of Australia’s 2024 National Conference and Exhibition in Adelaide, the crane industry is becoming increasingly focused on reducing emissions.
Rick said more of his customers, and their customers, are talking about this aspect of crane hire. Across the board, crane manufacturers are moving towards lowering emissions and the Franna MAC 25-5 is a perfect example of sustainable innovation.
“With the new Australian Design Rules (ADR) compliance regulations now in effect, Terex Franna has taken the opportunity to incorporate new technology across the entire Franna range, including the AT22-2, MAC25-5 and AT40-2,” he said.
“Each model in the line-up has received significant upgrades designed to reduce environmental impact and improve operational efficiency.”
Although this is new technology for Franna, it is technology that has been powering European all terrains and other special purpose vehicles for many years.
The technology has been implemented as a result of regulatory compliance requirements, but Franna has taken the opportunity to also improve performance – the Mercedes OM936 is a proven 7.7 litre engine versus the outgoing OM906’s 6.4 litre displacement, power and torque are up across the range (up to 230kW and 1300Nm respectively) as fitted to the AT402. The OM936 boasts a well-established track record, having undergone more than a decade of refinements to achieve exceptional reliability.
Franna’s dedicated engineering team collaborated directly with the German manufacturer, MTU, in conjunction with Penske Power Systems, the authorised distributor of Mercedes Benz engines in Australia, to ensure seamless integration of the OM936 into the range.
The Series upgrade goes beyond just the new OM936 engine. Franna has implemented a series of additional enhancements across all models, designed to streamline customers’ lifting operations enhancing useability, productivity and safety. All Franna models have been upgraded to ensure they are compliant
with current ADR compliance standards, including lights, visibility, noise levels, ABS braking and emission standards, along with a suite of safety features.
Safety remains an unwavering priority for Franna. The Series upgrade elevates safety standards by incorporating Franna’s patent pending Safety Radar as a standard feature.
Hook & Haul has always taken a sustainable approach to Frannas operating in the fleet, said Rick.
“The Franna is an incredibly ‘rebuildable’ crane with most parts still available or there is a retrofit solution even dating back to the early models. It’s important to our business that our cranes have good resale value when we determine it is time for them to leave the business.
“With the customer base we supply to, we tend to divest cranes by the time they are 15 years old. Companies that have bought our used cranes will attest to the condition of the Frannas when they leave our fleet. We avoid treating cranes as disposable items. We prioritise sustainability by maintaining and reusing cranes rather than treating them as disposable assets. Franna’s are a great practical example of renewable principles.
“Conversely, we have bought Franna cranes in the past from larger companies, which have been physically and financially depreciated. Given my crane maintenance background, we have been able to fully rebuild them, returning them to compliant and reliable cranes. So, in our own way we have always taken a sustainable approach to our crane fleet. Customers know they are going to get a no ‘BS’ approach from Hook & Haul and well-maintained quality cranes,” he said.
Currently the capacities in Hook and Haul fleet look like this:
• Franna Cranes capacities 12t, 25t and 40t
• City Cranes capacities 13t, 16t and 20t
• Liebherr All Terrains 55t and 60t
• Abbey hoist 2t
Rick goes on to discuss why the Franna pick and carry remains so popular with operators.
“Our industry has significantly evolved, and operators appreciate that engineering controls have taken away the pressure there once was to push the crane past its designed lifting capabilities. The latest Safety Radar LMI upgrade provides a visual guide to the operator of what articulating the crane will have on the capacity, before the crane is articulated.
“While driving a Franna might be a little daunting at first, due to the width and the articulation point being behind the driver’s cab, if an operator is taken to a quiet area and given the opportunity to get a feel for how the crane steers and how it sits in a lane, they soon become comfortable with driving in traffic.
“As our industry continues its safety journey, we now understand that there is more need for on road training around articulating cranes. CICA has developed the Articulated Crane On-Road Course, which consists of both an on-line adaptive learning course and a practical on road component, which promotes information and experience sharing amongst peers. Maintenance-wise, adherence to OEM guidelines around articulation and steering cylinder wear also aid the operator to feel more relaxed while driving the crane on road,” said Rick.
He goes on to discuss Hook & Haul’s relationship with Terex Franna.
“I work closely with Robin Ghosh, Regional Sales Manager at Terex Franna from whom I have bought four brand new and a number of used Frannas. Robin has always listened to my requirements and made sure the deal has worked for both parties. Our relationship with Franna’s product support and service managers around Australia has also been integral to ongoing performance of our Franna fleet and the relationships with Quentin Bourke (Product Support Technician) and Andrew Howe (Service Manager Vic) have been pivotal to our success. If you follow the
OEM service guidelines, they are the most sturdy and reliable tools of the industry,” he said. “I am not one to cold call companies or impose myself by turning up on a customer’s doorstep. Our cranes are not heavily branded and whilst we have a social media presence, we don’t post pictures of our cranes on a customer site. And if one of our cranes is posted with a customer name on it, we do not feel the need to make the post about us, so Hook & Haul does not have a particularly high profile. That said, I’d like to thank our customers and well-wishers, many of which I’ve never met, for the constant support and confidence they have shown in us.”
TRT cranes set the standard for excellence, combining strength, safety, and innovation. Designed for the harshest environments, they feature:
Unrivaled Engineering: Durable ROPS stlye cabins for ultimate operator safety.
Premium Components: Equipped with Red Dot Air Conditioners, ensuring comfort even in the extreme Australian heat.
Precision Wiring: Robotic cable protection and uniquely labelled wires for easy maintenance—no other manufacturer matches our attention to detail.
Experience unmatched quality and durability with TRT cranes - built to exceed expectations.
new assets, we always consult with the team, especially our operators, and their
them now operating on AdBlue (a diesel exhaust fluid that reduces emisions from in safety, emissions control, capability, comfort, and value.
“The new TIDD PC28-3G is equipped with the Cummins ISB6.7 Euro 6 on-road engine, a strategic choice as Euro 6 is set to become the new Australian Design Rule (ADR) standard by November 2025.”
Neil Webb, General Manager at TRT Australia, discusses the features and benefits of the new TIDD PC283G and what sets TRT apart from the competition.
“The new TIDD PC28-3G is equipped with the Cummins ISB6.7 Euro 6 on-road engine, a strategic choice as Euro 6 is set to become the new Australian Design Rule (ADR) standard by November 2025,” said Neil.
“We opted for the Cummins engine due to its extensive after-sales service and support network across Australia.
This upgrade from our previous standard Mercedes package brings an additional 34 units of horsepower, making a significant difference in operational performance.
“Obviously Slew Safe is a key safety feature and has featured in our cranes from the beginning. Developed and patented by TRT, Slew Safe serves as a significant standard for safety and is
specifically designed to assist operators in preventing rollovers. A preventative tool, it alerts the operator when they are slewing in an unsafe direction, prompting them to slew back towards safety. This ensures a clear understanding of the operator’s role in maintaining safety standards. The feedback from our customers on the PC28-3G, especially from Tier One builders, has been fantastic.”The new TIDD PC28-3G also features the TRT patented Traction Air System.
“The Traction Air System is currently operating in approximately 10 countries around the world as a CTI (central tyre inflation) system. It was initially designed for logging equipment, and we moved it into our TIDD pick and carry crane. It’s an option but we see more and more safety requirements from sites, and from customers, which means it is almost a standard option that’s ticked by our customers.
“The Traction Air System provides a management system for tyre pressure. It allows the tyre pressure to increase or deflate to ensure optimal pressure of 130 PSI is maintained. It’s a great safety feature for the crane. Because the tyres are always at the correct pressure you also get better usage and less wear and tear. During lifting, the tyres are maintained at optimal pressure, ensuring that each lift is performed safely,” said Neil.
TRT has long prioritised advanced braking systems, starting with ABS brakes in our original TIDD PC25 models. While ABS has only recently become a requirement for ADR compliance, our commitment goes beyond meeting standards—we integrate these systems because ensuring the safety of our products is our highest priority.”
When TRT began redesigning to comply with the new ADR emission standards it assessed areas for improvement and focused on the exhaust brake system, switching to a Retarder. While very similar to the technology used in a lot of heavy equipment, such as large all terrains, the Allison transmission with Retarder puts TRT ahead of the competition, said Neil.
“It’s essentially an additional safety feature for our crane. Our customers recognise that TRT doesn’t just aim to meet standards; we consistently exceed them and continue to innovate. We are highly customer-focused, incorporating their feedback into our product designs,” said Neil.
Traction Air manages tyre pressure to the standard 130psi on all four front and rear tyres, creating a stable lift platform and improving crane safety. Incorrect tyre pressure, overinflation or punctured
tyres can put operators at risk. Constant tyre pressure monitoring with Traction Air allows operators to lift safely, and correctly every time.
From a simple to use touch screen in the cab, instant leak and puncture alarms notify the operator of a change, reducing the risk of serious incidents.
There is no need for manual tyre pressure checks on start-up, increasing valuable uptime. No matter the surface temperature, even on bitumen, tyres on TIDD PC28-3G will remain at 130psi. Based on more than 25 years of product innovation and exclusive to TIDD PC28-3G, Traction Air has a three year/500,000km warranty. “Traction Air is an excellent safety feature, especially when the crane is running around gas plants, they absolutely love it. It makes life so much easier for our guys with the computer maintaining the tyre pressure. There’s no need to get out and check the pressure with a tyre gauge, it’s a great safety feature and very helpful for the guys,” said Wayne. Consider moving this paragraph to under where Wayne first introduces Traction Air.
Wayne goes on to discuss Tutt Bryant’s relationship with Anthony Davis and The Crane Connection and his impressions of TRT.
“Over the years we have developed a fantastic relationship with Anthony and The Crane Connection, and we’ve moved to them to buy all our parts for
the TIDDs. We had a small issue with one of the TIDDs and Anthony and his team’s approach to rectify the situation was second to none. They are very focused on customer relationships and operate on traditional business values and do what they say they are going to do.
“The TRT guys in New Zealand were fantastic. It was an absolute eye-opener to visit the factory and watch the machines being made from scratch through to the finished product. TRT employs over 300 people in the factory and the manufacturing technology is state of the art. I learned a lot about steel and now realise, ‘Steel is not just steel’.
“I was really interested to talk to one of their manufacturing engineers about how grades of steel vary. Some steels are rolled one way and others rolled another, some are easier to bend and that’s why certain steels are used on different parts of the crane. The steel used in the powered boom is a lot different to the steel used in the chassis for example,” said Wayne.
“TRT is a family-owned business, and the people are very welcoming. Everyone we spoke to was well informed and passionate about what they do. It’s a massive facility manufacturing two TIDDs a month, which is impressive when you consider they are hand built. They are also manufacturing their specialised trailers and crane pads, and they are selling and servicing the Grove brand. It’s a very impressive set up indeed.”
A dramatic rise in profile of XCMG mobile cranes has led to a significant increase in interest and sales. Stephen Broomfield, General Manager, XCMG Oceania Crane Centre, explains.
“DURING THE PAST 18 MONTHS XCMG and our distributors, D&D Diesel Services and Ronco Construction Equipment & Engineering, have concentrated on the ‘customers’ experience’ and monitoring their feedback. This has entailed inviting crane hire companies, including Tier Ones from Australia and New Zealand, to visit the XCMG factories in China,” Stephen said.
“Customers have gone to examine our large crawlers, with capacities from 300 tonne up to 4000t, and our large capacity all terrains, with capacities from 750 to 4000t. The large capacity all terrains have been designed with wind farm construction and maintenance work in mind. They feature 170 metres of boom and are capable of lifting more than 170t which the wind farm designers are calling for today.
“Seeing the XCMG factories up close and personal has led to a lot of enquiries and orders. We’ve had a lot of interest in the smaller capacity telescopic crawler, and are in the process of delivering three of these to the East Coast, where the demand is. There’s been a lot of interest in the rough terrains, and we have two – a 90t and a 120t – arriving in Perth soon.”
XCMG has sold a number of truck cranes, and has a new model about to be released which has lifting capacity of 30t.
Stephen said truck cranes are popular with structural steel erectors because they are robust, easy to use, and meet all new Australian Design Regulations (ADR) that were introduced in 2024.
“We don’t have any problems with the ADRs moving forward and the customers are taking up on that really well. Overall, the feedback from crane
Market demands are changing and XCMG is tailoring its product range to accomodate these changes.
“The large capacity all terrains have been designed with wind farm construction and maintenance work in mind. They feature 170 metres of boom and are capable of lifting more than 170t which the wind farm designers are calling for today.”
hire companies following the factory visits has been very positive,” he said.
Despite the positive feedback, he said there is still room for improvement.
“The important point is customers are understanding and prepared to wait and support us, which is great. We are seeing customers wanting to engage with us. We’ve had more XCMG enquiries in the past nine months than we had during the previous 18 months,” he said.
Market demands are changing and
XCMG is tailoring its product range to accommodate the changes.
“We’ve got a 60t all terrain coming in the latest shipment and, this is basically a European crane. It features European technology including the hydraulic systems, the LMI (load moment indicator), the engine, the gearbox and the axles. These components are shipped from Europe and are assembled in China to the highest international standards,” Stephen said.
“The 60-tonne class of all terrain is the most popular size in Australia and it’s dominated by one supplier. Customers have explained that they are unable to charge higher rates in the current financial climate.
“That’s why they are talking to us. The 60t all terrain is a unique size for us, so we’ll be putting this into the marketplace for trialling. We’ll monitor customer feedback and provide this to the factory so the product can be refined. We’re bringing a diesel version initially and this meets the new ADR requirements, but there is also a hybrid version to come in due course.”
Stephen goes on to discuss the feedback customers have given him following the XCMG factory tour.
“Customers who have visited the factory have also been to European and
Japanese factories, and every single one has said XCMG are light years ahead.
“The next 18 to 24 months is going to be a very interesting period. Customers are really examining their options, and they are understanding that XCMG product compares favourably with the United States, European and Japanese product in terms of technology, performance and the service and spare parts support we provide. However, the key issue is return on investment. There is a massive segment in the market where cranes are operating at fixed rates, no matter what brand of crane you are operating. It’s the sector where we are having the most success and it’s a sector that is growing exponentially,” said Stephen.
He goes on to discuss the industry’s approach to sustainability and how industry sectors are closely examining ways to reduce carbon footprints.
“The markets are changing and it’s a very dynamic situation. Over the past 50 years, the Australian and New Zealand crane industries have been dominated by the Japanese, Europeans and US Original Equipment Manufacturers (OEMs), with no alternative. But I think the evolution of EV (electric vehicle), hybrids and alternative powered cranes, has brought each of the OEMs to a sort of reset in developments and to a new chapter in the crane market. Pricing and performance are important issues, and I think that’s the most exciting part about the crane industry at the moment,” he said.
“Europe is a positive market for XCMG. We are designing to EN-13,000 standards so the cranes can be used in Europe, as well as Australia and New Zealand. We’re designing cranes to meet the Americans, the Europeans, and the Australian standards.
“XCMG are designing and manufacturing cranes for the western markets global crane company, a western crane for the western market and that’s how we are positioned. We are now making significant inroads. We have a wide range of cranes operating in Australia including 40t, 60t, 160t and 300t all terrains as well as a number of crawler cranes,” said Stephen.
XCMG is the third-biggest mining solutions provider in the world, and this helps when it comes to mine specced cranes.
“Mine requirements in Australia are much higher than the general construction market, and customers need to be aware of that,” Stephen said. “XCMG import a crane for the mining sector, the crane has been built to BSI EN13000 and the extremely strict performance requirements of the mine operator.”
Liebherr recently released another crane model with the new LICCON3 control system. The LTM 1120-4.1 becomes the LTM 1120-4.2. The four axle 120-tonne crane is also characterised by the new future-oriented crane design.
equipped with the TraXon DynamicPerform oil-cooled starting clutch and new driver assistance systems for increasing driving safety on the road. Liebherr will be exhibiting the LTM 1120-4.2 at bauma 2025, the world’s leading construction machinery trade fair, in Munich.
The family of Liebherr mobile cranes boasting the latest crane design and
system is growing. Not only will all completely new crane types receive the new control system, but Liebherr will also successively be converting its existing crane types. To signify the changes, the last digit of the type designation is incremented by one: the LTM 1120-4.1 is now the LTM 11204.2. Performance parameters and lifting capacities remain unchanged.
With what is now the third generation of the LICCON control system (Liebherr Computed Control), Liebherr is taking proven operating concepts to a new technological level – completely new software and programming language, faster data bus, significantly more memory and higher computing power. The changeover remains child’s play for crane operators: the familiar
operating concept ensures a high recognition value, so that the switch to the new control system is seamless.
Proven hardware components, such as the mobile operating and display unit BTT, have been adopted. The touchscreen function on the new large display in the superstructure cab means that it is now easier and more comfortable to control. The way in which the information is shown has also been revised and simplified. In addition, LICCON3 cranes are prepared for telemetry and fleet management as standard. In the future, crane contractors will be able to view and evaluate all the relevant data using the MyLiebherr customer portal.
As a result of the high synergy effects involved, Liebherr is launching the new driver’s cabin at the same time as the LICCON3 control system. The modern design features premium materials and timeless lines as well as delivering a host of improvements for the crane driver. These include the new multi-function steering wheel, side roller blind on the driver’s door, improved instruments and modules as well as new displays. Additional convenience is offered by options such as a central locking system with remote key and the “Coming and Leaving Home” function.
A completely new, modern automatic heating and air-conditioning system in both the driver’s cab and the crane operator’s cab ensure a high level of comfort. A sun sensor detects strong sunshine and automatically adjusts the heating settings. The lighting packages for the crane cab, the superstructure, the rear of the vehicle, the front headlights and the telescopic boom, as well as the lattice fly jib, have been optimised and can be operated with LEDs. The benefits of LED technology include a longer service life and superior lighting performance.
LTM 1120-4.2 – THERE’S NOTHING MORE ON 4!
In 2020, Liebherr set new standards
in the field of all terrain cranes and launched the LTM 1120-4.1 – a 120-tonne crane that caused a stir with the slogan “There’s nothing more on 4!” Its concept – maximum performance on four axles. This made it the most powerful four-axle all terrain crane ever built and pushed the boundaries of its class. It pushed forward into performance ranges that were previously reserved for the larger five-axle cranes and thus completely redefined the possibilities of a compact crane.
As far as boom length is concerned, the LTM 1120-4.2 is on a par with 200-tonne class cranes: its 66-metre telescopic boom is the longest ever to be installed on a four-axle mobile crane. The LTM 1120-4.2 delivers outstanding lifting capacity values, particularly with the boom fully raised. Its lifting capacity of nine tonnes on the 66 metre telescopic
millimetres – ideally suited for confined spaces. The larger ballast radius, on the other hand, increases performance and often reduces costs, as many operations can be carried out with less counterweight, eliminating the need for additional ballast transport.
In addition to the new crane control and design, the LTM 1120-4.2 has other technical features that increase efficiency, comfort and safety. The DynamicPerform clutch module provides almost wear-free starting and manoeuvring for the modular ZF TraXon gearbox without overheating, because it transmits the engine output via an oil-cooled multi-disc package.
New assistance systems, such as Blind Spot Information System and
“In addition, the LTM 1120-4.2 will be prepared for the use of RemoteDrive as standard. This allows the mobile crane to be driven from the outside with wireless remote control – a major benefit on cramped construction sites.”
boom makes it suitable for erecting tower cranes and radio masts. Lattice extensions enable the 120-tonne crane to achieve hook heights of up to 91 metres and radii of up to 64 metres.
The compact design of a four-axle crane makes the LTM 1120.4.2 the ideal choice for applications where there is simply no room for larger cranes. Liebherr’s VarioBase ® and VarioBallast® innovations come into their own on tight construction sites and ensure increased performance, flexibility and safety.
With its VarioBallast® system, the crane’s ballast radius can be adjusted between 3.83 and 4.77 metres. Thanks to the standard, mechanically swivelling ballast cylinders, the radius can be easily reduced by 940
Moving Off Information System, increase driving safety in road traffic.
In addition, the LTM 11204.2 will be prepared for the use of RemoteDrive as standard. This allows the mobile crane to be driven from the outside with wireless remote control – a major benefit on cramped construction sites. Liebherr has also decided to equip the new crane with the popular VarioBase® variable supporting base as standard.
Liebherr now also offers new options for the LTM 1120-4.2 that are popular with other crane types, such as the central lubrication system for the chassis or the digital tyre inflation pressure display, supporting its customers in operating a wellserviced and fail-safe crane.
SPECIALIST IN HARD CHROME PLATING
• Long stroke & large bore specialists
• Large turning work up to 1500mm in diameter, 10 metres between centres and 530mm spindle for extra length
• Cylinders manufactured to specifications
• Complete cylinder repair facility
• Quality service with experienced & qualified staff
Contact Sermet Gurisik
Email: sales@athydraulics.com.au
Phone: (02)9756 3077
Gleason Cranes recently announced the appointment of Rob Solomon as Operations Manager to continue to drive support services including after sales, servicing, parts and accessories and paint.
ROB STARTED HIS CAREER AS A QUALIFIED motor mechanic, moving into service management more than 20 years ago. He has worked for several leading industrial equipment brands garnering a wealth of experience in equipment sales, service and support.
“I have tended to focus on the support aspect of these businesses and have been appointed the National Service Manager role for a number of large organisations.
“Previous to this role, I was working in sales and service for Zoomlion, which facilitated conversations with Chris Logan and ultimately the move to Gleason Cranes. With my role at Zoomlion, I was
helping the various distributors with questions and issues relating to the products. I was dealing with Chris (Sales Director at Gleason Cranes) and the team. I guess they were happy with my approach and the service I provided and presented this opportunity, which was too good to pass,” said Rob.
He goes on to discuss his role and what his objectives will be for the business.
“Initially, I’m handling all the issues relating to service, support and spare parts as well as a strong focus on the paint shop. Once these aspects of the business are organised, then combining this with a sales role will help progress the company.
“It has been full-on from day one and the phone hasn’t stopped ringing. My first priority is the paint shop, and to get that side of the business really happening. Gleason’s has a very professional paint booth and mixing bay and I am tasked to see this fully utilised. I’m also restructuring the layout of the workshop for efficiency for the field service requirements for all pre-deliveries, warranty and any infield breakdowns that might occur,” he said.
Rob’s first impressions of Gleason Cranes has him very excited about the potential for the business and his role.
“Like I said, from day one my phone hasn’t stopped ringing with enquiries about
service work and particularly the capabilities of the paint shop. Businesses are hearing about this for the first time, and they are wanting quotes for all types of equipment.
“So yes, there is heaps of potential and it is all very dynamic at the moment. We’ll service and repair all brands of cranes, and we’ll work on any type of machinery. When it comes to painting, we’ll paint all types of equipment, not just cranes,” he said.
Gleason Cranes continues its reputation as a trusted crane seller, both new and used, and is a supplier of Zoomlion cranes. Zoomlion is an increasingly recognised brand across numerous industry sectors with many types of products delivering excellent value for money.
“Increasingly, Zoomlion products are proving their value through performance and providing customers with an excellent return on investment,” Rob said. “For many years, Gleason Cranes has had a strong and successful relationship with Zoomlion Cranes and basically created the market for the brand in Australia.
“Coming from Zoomlion, I understand the organisation and have strong connections with the business. We will continue to work closely with Zoomlion on behalf of our customers and the growing population of Zoomlion equipment out in the market. With these relationships Gleason Cranes
will continue to deliver the high standards of service and support our customers have come to expect and we will be helping them understand how investing in Zoomlion product can significantly benefit their business.”
“Currently, Gleason Cranes is handling a significant number of sales enquiries, and a key element of my role will be to ensure we are able to deliver product within the timelines expected by our customers. Having stock available and on the ground is an issue for all OEMs at the moment, and we will be working closely with Zoomlion on stock availability,” he said.
A significant amount of interest is coming from the smaller crane hire companies closely examining their options when it comes to their return on investment.
“I recently had a conversation with a smaller operator who was considering Zoomlion and other international brands. He was saying, ‘Look, from my perspective, I’m going to get a fixed rate on a 90 tonne crawler, and my return on investment is
going to be a lot quicker with an international brand compared to brands from Europe, Japan or the US’, and he is 100 per cent correct.
“But when you are offering an international brand like Zoomlion, or any other brand, the key is being able to offer the right levels of after-sales support, making sure you can back it up from a service perspective, support the warranty, and provide the spare parts as well.
“In the big scheme of things, that’s huge. You can sell anything but without after-sales, you’ve got nothing. That’s why after sales service and support is a priority. My main focus right now is to have in place a state-ofart customer service.
“Gleason Cranes boasts a long and proud heritage of servicing the crane industry and we encourage businesses to contact us for new and pre owned crane sales, service and support as well as major inspections, refurbishments and tailored paint work on all types of equipment. Visit: www.gleason.com. au or email operations@gleason.com.au
“Increasingly, Zoomlion products are proving their value through performance and providing customers with an excellent return on investment.”
Zoomlion has been designing and manufacturing mobile cranes with all types of new energy sources including battery powered electric, electric plug-in and hybrid.
The Baden Davis Crane Connection recently delivered a new Kobelco CKS1350 lattice boom crawler to Gunnedah-based GBP Cranes and Heavy Haulage. GBP’s Managing Director Dan Hawkins provides background to the purchase and elaborates on recent developments for the business.
DAN IS THE THIRD GENERATION TO WORK in the family business. He joined after leaving school.
“The business was initially started by my Grandfather, John Gibson with my Father Bruce Hawkins, Stuart Grosser and another business partner joining as the business progressed,” said Dan.
“I learnt about the business from the ground up, as an apprentice in the engineering shop working on the maintenance of the cranes. I progressed through to operating the cranes and then eventually moved into management roles.”
The addition of the new Kobelco is a key element of GBP’s commitment to renewing the fleet, ensuring clients are receiving the very latest technology when it comes to their craneage requirements.
“We have continually renewed our fleet of Liebherr all terrains and pick and carry cranes,” said Dan. “With our connection and long-term relationship with Anthony Davis and Ben Baden at the Baden Davis Crane Connection and National Distributor TRT, we decided to explore the opportunity of bringing a new Kobelco into the fleet.
“We’ve had crawlers in the fleet before and this purchase is for a specific long-term project for a client.”
The Kobelco CKS1350 features a maximum lifting capacity of 150 tonne at 4.4 metres and 36t at 12m with luffing jib. There are several other configurations available including maximum luffing boom length of 47.9m, maximum long boom length of 82.3m, maximum fixed jib combination 61m +30.5m and maximum luffing jib combination 47.9 + 32m and 44.8m +53.3m.
The upper structure is torsion-free precision-machined with all components
The boom hoisting system is powered by a hydraulic motor through a planetary reducer. A spring-set hydraulicallyreleased multiple-disc brake is mounted on the boom hoist motor and operated through a counter-balance valve.
consists of a hydraulic motor propelling a driving tumbler through a planetary gear box. Hydraulic motor and gear box are built into the crawler side frame within the shoe width. Crawler brakes are spring-set, with hydraulically released parking brakes
The lower structure features independent hydraulic propel drives built into each crawler side frame.
built into each propel drive. The steering mechanism features a hydraulic propel system which provides both skid steering (driving one track only) and counterrotating steering (driving each track in opposite directions). Track rollers are sealed for maintenance-free operation.
The cab and controls are totally enclosed within a full vision cab with safety glass, fully adjustable, high-backed seat with a headrest and armrests, and intermittent wiper and window washer (skylight and front window).
Dan discusses how the relationship with The Baden Davis Crane Connection dates back many years.
“We’ve had a very long business relationship with Anthony and Ben from The Crane Connection, and this dates back to when Gerhard Baden was the Liebherr distributor. Over the years we have bought multiple cranes from Anthony through the various dealerships he was working for at the time. The last crawler we purchased was from Anthony when he was working for the Grove and Manitowoc dealership.
“There were a number of reasons for purchasing the Kobelco and these included price, availability and the
support we receive from The Baden Davis Crane Connection and TRT, the national distributor for Kobelco.
“Availability was a key factor because our client brought the project to us with relatively short notice. We know from Anthony that the service and product support from TRT has proven to be excellent over a long period,” said Dan.
“Anthony is always available via phone or email if and when additional support is required. His knowledge of the Kobelco brand would be among the most extensive in the country. He has a long history and association with Kobelco, and he knows the product inside and out. It’s great to be able to call him, even out of hours, if there are niggly issues, and most times he can walk us through the problem and provide a resolution.
“With this knowledge and TRT’s commitment to service, support, and parts availability the Kobelco package is very hard to pass on. When you factor in the performance of the Kobelco, operator acceptance, transportability, and lifting charts you can see why we decided to invest in the brand,” said Dan.
GBP Cranes and Heavy Haulage
continues a major development of the company’s new complex with the completion of stage two of the project. Stage one included the construction and fitout of the administration building and stage two the construction of a huge mechanics workshop. The building is massive, 30m x 42m, and accommodates plant and equipment from GBP’s big inventory of cranes, trucks and other plant. Dan explains more.
“There has always been a long-term development plan for this yard. The family has owned this block of land since the ’70s and there have been multiple attempts to develop it. Riding with the ups and downs of the coal industry, it has been difficult to predict what will happen and when the industry is not booming there has been a reluctance to invest. We’re on our third design for the yard and facilities. We could see the way cranes and other machinery is only going to get bigger. So, after much discussion and planning we’ve managed to pull the trigger on the project and get it underway,” he said.
The development of the new complex is a significant investment and further underwrites GBP’s status as one of the largest providers of crane service in regional New South Wales. GBP now operates from sites in Narrabri and Tamworth as well as the Gunnedah hub, with clients statewide across mining, agriculture, renewable energy and gas industries.
GBP Cranes and Heavy Haulage continues to invest in new cranes and technology to help run the business.
“We have new pick and carry cranes coming, and we are looking to add more capacity to our fleet of all terrains. We recently implemented the Assignar cloud-based construction management solution which is specifically designed for self-performing contractors and subcontractors. This will help in automating scheduling, asset management, time sheets, compliance management, invoicing and payroll for the business,” said Dan.
If you would like more information on Kobelco Cranes visit the TRT website: www.trtaustralia.com.au/cranes/ kobelco-crawler-cranes
The benefits of Potain CONNECT™ include:
• Remote access to crane data: Monitor a crane’s performance metrics and status anytime, anywhere.
• Real-time crane availability: View the availability of every crane on site, in real-time, no matter the location.
• Guided troubleshooting assistant:
Quickly identify and resolve issues with step-by-step support.
• Local smartphone service tool: Enable a team to manage crane operations and maintenance directly from mobile devices.
• Monitor jobsite progress: Track jobsite progress using crane activity data for real-time project insights.
• Fleet management integration: Seamlessly import crane data into a fleet management system for
streamlined oversight and planning.
Potain CONNECT™ will be among the aftermarket products shown by Manitowoc at bauma 2025 in Munich, Germany.
Manitowoc has also released a video highlighting some typical applications of the digital tool in real-time.
Below: Potain CONNECT is an intuitive, Cloud-based platform from Manitowoc that is transforming tower crane ownership and operation.
The BlueScope No. 6 Blast Furnace (6BF) Reline Project has reached a major milestone with Marr Contracting’s M2480D heavy lift luffing tower crane successfully removing the 6BF downcomer in a carefully planned engineering feat at the Port Kembla Steelworks (PKSW).
THE REMOVAL OF THE 170-TONNE, 54-metre long downcomer was safely completed using the 330-tonne capacity M2480D, with Marr’s 400-tonne Grove mobile crane used to assist with rotating the downcomer once it had been lowered to ground level.
Once removed and lowered to the ground by the M2480D, the downcomer was horizontally rotated
and placed on Marr-supplied supports and reconfigured to be transported for refurbishment and replacement.
Engineered and planned by the BlueScope Reline Project team in collaboration with Marr, the innovative heavy lifting solution provided a less complex and safer alternative to using a traditional heavy lift crawler approach.
With previous experience removing
similar sections of plant on a similarly congested worksite during the Blast Furnace No.5 Reline Project, BlueScope’s team knew that using a large crawler crane and superlift combination would present numerous challenges due to the location of the project and the restricted space available on the site.
According to PKSW Project
“By engaging us early in the planning stages, BlueScope’s team unlocked the possibility to develop a simple solution that helped to reduce complexity and secure the tight construction program.”
Director, Justin Reed, “Marr’s team have challenged our traditional thinking by enabling large sections of equipment that were previously maintained in situ to be lifted to ground for repairs or replacement.”
“The capability and capacity of the M2480D is a true game-changer for our project. At vertical industrial sites like a blast furnace we have always wished there was a ‘sky-hook’ that could deliver a lift at any point on the plant, and now we have a solution with significant lifting capacity,” Justin said.
With safety and minimising disruption to production at PKSW a priority, Marr’s solution is also helping to mitigate risk to critical path by providing BlueScope with an instant cranage solution for a large volume of smaller lifts at site during the relining process.
Installed on a specifically-design 7.5 x 7.5m piled foundation, the M2480D provides the heavy lifting capacity required with the additional benefits of a small footprint and long reach across the project.
“By engaging us early in the planning stages, BlueScope’s team unlocked the possibility to develop a simple solution that helped to reduce complexity and secure the tight construction program,” said Marr’s Managing Director, Simon Marr.
The refurbished downcomer will be reinstalled in another major lifting operation using Marr’s M2480D in mid-2025.
BlueScope anticipates that the 6BF will be recommissioned in mid-2026.
- Use any device with apps
- Brand new user interface with, integrated access to other apps
- Intuitive controls layout for easy use
JOBSITE DESIGNER
- 1-Click scaled building creation
- Import CAD object capability
- Draw custom shapes
- Bring in a scaled jobsite with touch of button
- Superior annotation tools
- Great for field sales teams
RIGGING DESIGNER
- Point, click, drag, and drop rigging components
-Create save simple or complex rigging for any lift equipment
PLEASE SEND YOUR LIFT OF THE MONTH ENTRIES TO SIMON.GOULD@PRIMECREATIVE.COM.AU
WHO: Tutt Bryant Heavy Lift & Shift and East Coast Cranes
WHAT: were they lifting: Massive dry dock gate
WHERE: Cairncross Dockyard Brisbane
WHAT CRANES: Sany SCC4500A 450t capacity lattice crawler and GROVE GMK7450, 450t capacity all terrain.
COMPLEXITIES: The dry dock gate, measuring 37 metres in width and 14 metres in height (with 10 metres submerged) weighed 500t with 2 70t of water inside it.
Longest powered boom to 20.9m with 5.5m telescopic fly extends to 26m
All Models (25T, 35T, 55T) rated @ 1.4m boom position, highest boom strength available, fully fabricated
Air-spring suspension with shock absorbers eliminating cabin noise and vibration
High Stability at all positions to 42 degrees
Low centre of gravity with rigid chassis design, safest crane available
Dynamic Load Chart and Digital Rope Compensation
Safe road speed 90-100kph with 180 degree unobstructed front vision with four cameras to sides and rear
Humma Heavy Lift Crane design, specification with proven componentry has set the new Industry standard for performance. ONE FOOTPRINT FOR ALL MODELS.
Crane owners require low operating and maintenance costs, highest level of safety in both driving and crane mode, achievable on all Humma Models.
Patented Auto-leveller on Humma 55, the largest and safest Pick and Carry available.
Highest level of safety at all articulation positions to 42 degrees using Humma low twist chassis design.
Cabin rated the safest and quietest available at 65 decibels.
Remove the removeable counterweight from 35T and 55T and you have a heavy duty 25T and 35T.