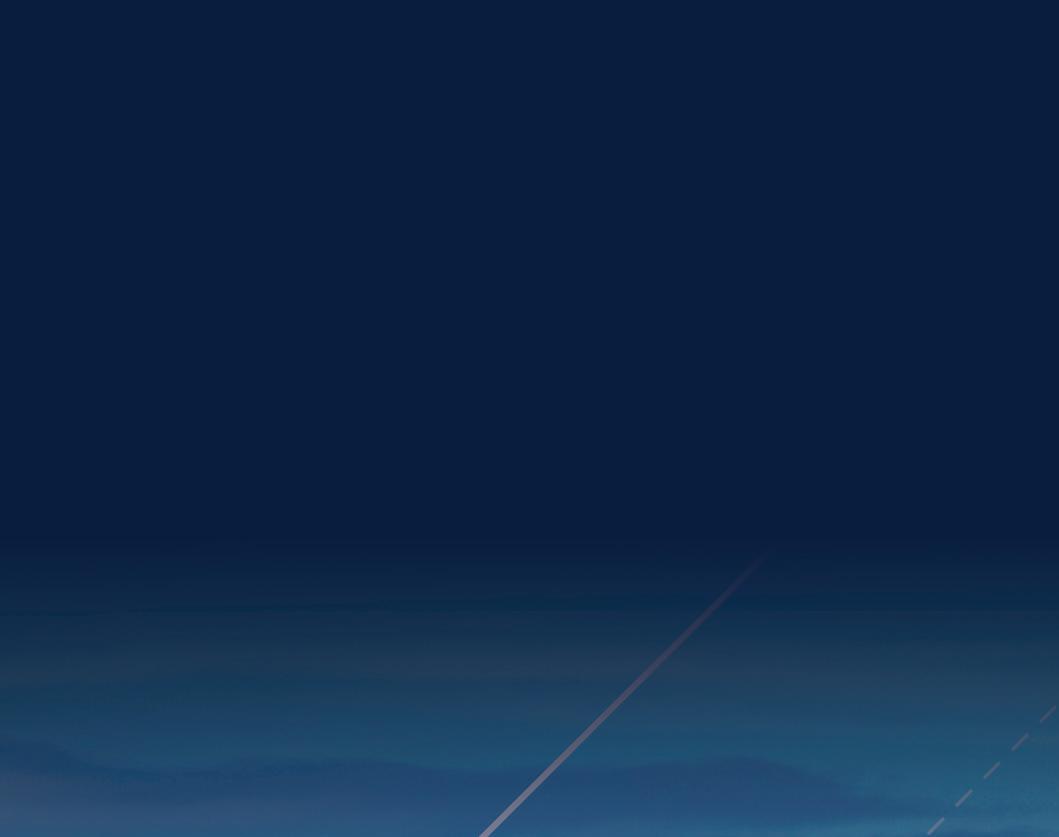

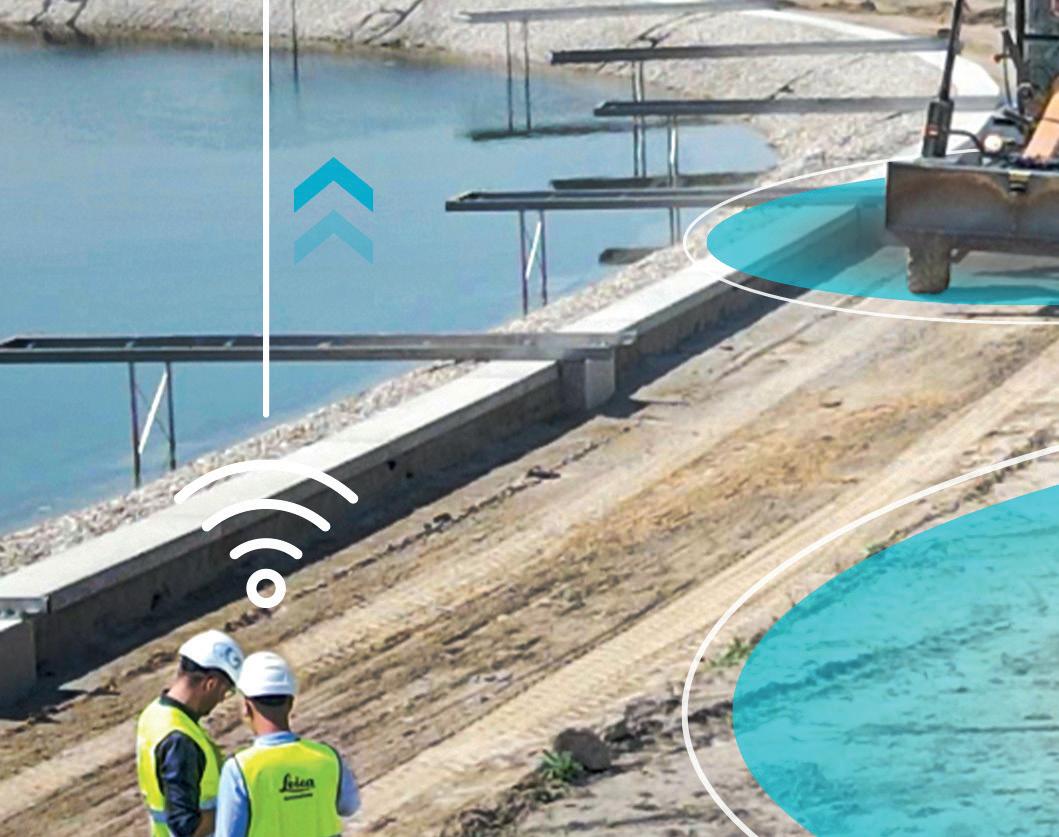
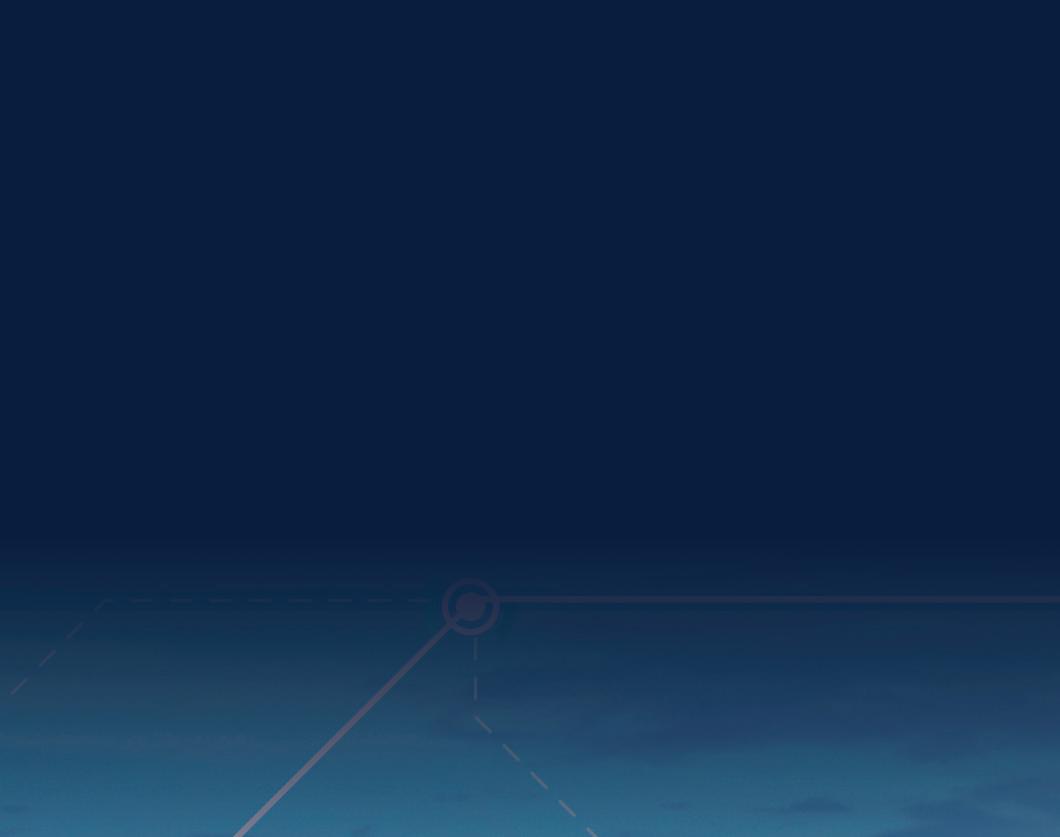

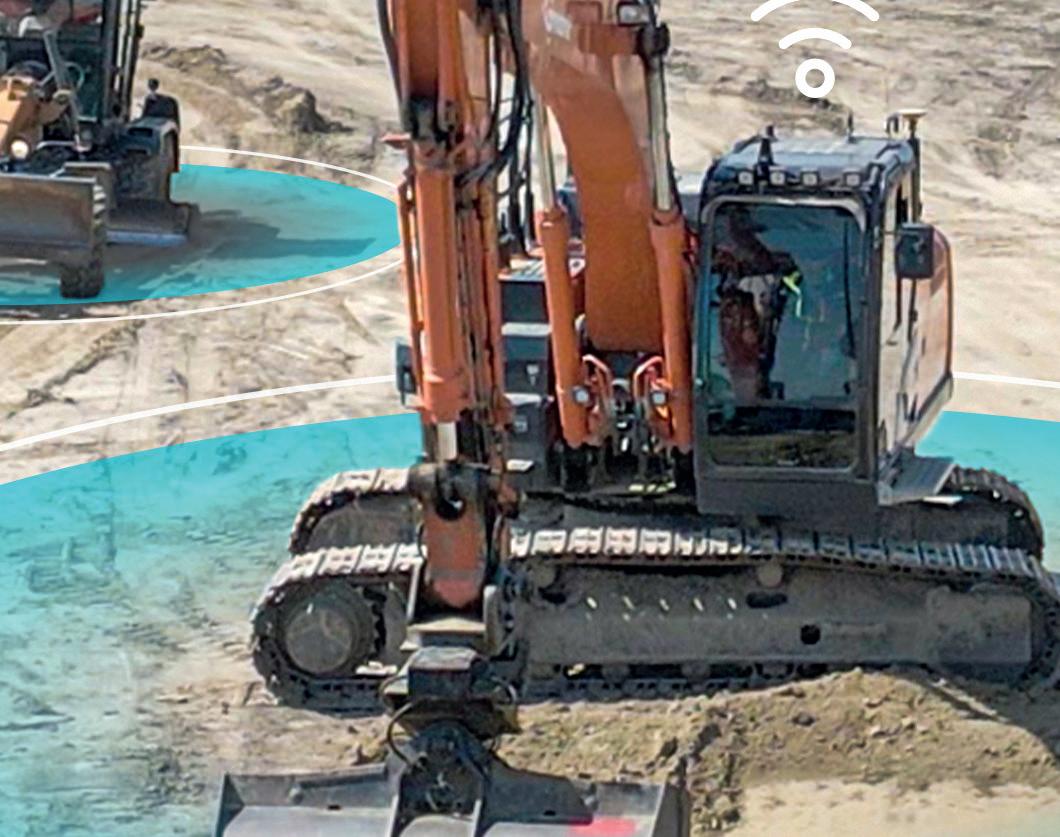


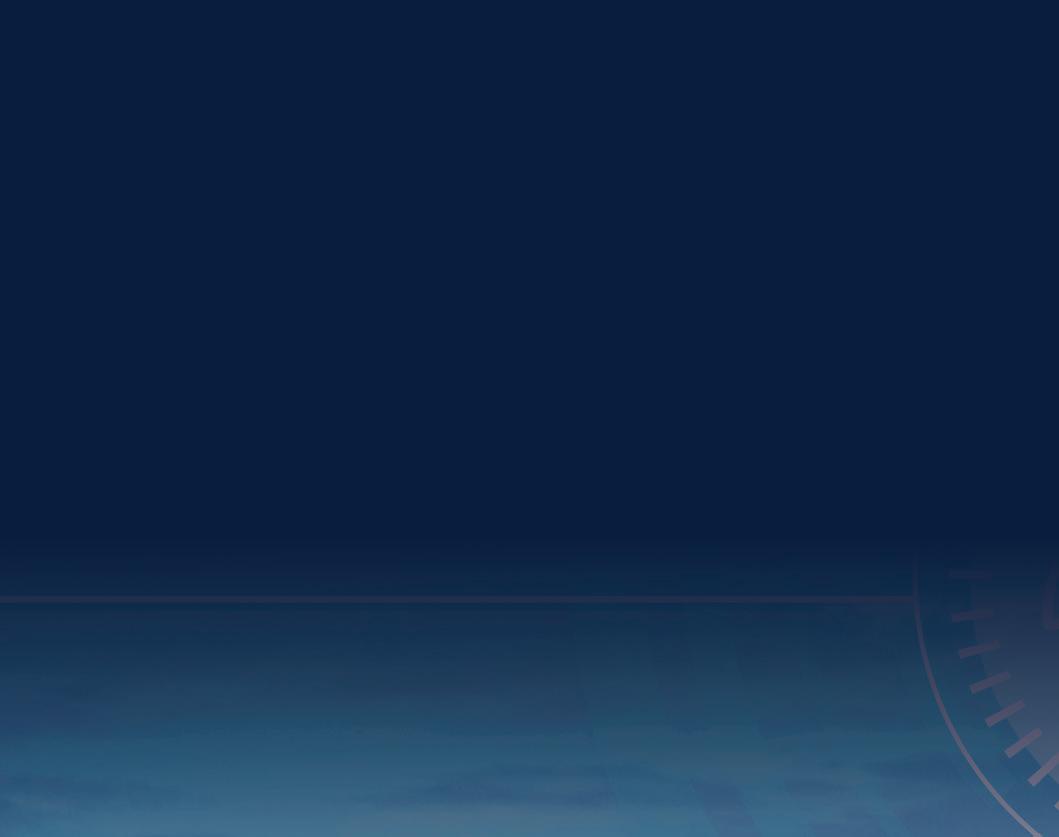
Editor: Mike Woof
Contributing Editors: David Arminas, Kevin O'Shea
Designers: Simon Ward, Andy Taylder
Production Manager: Nick Bond
Of ce Manager: Kelly Thompson
Internet, IT & Data Services Director:
James Howard
Publisher: Geoff Hadwick
Managing Director: Andrew Barriball
Chairman: Roger Adshead
Digitalisation and modelling for the Lower Thames Crossing: Kristina Smith reports
Transformative power of standardisation: Christian Luttenberger of Hexagon Geosystems
Autonomous compacting: Dynapac, Trimble in British Columbia, Canada
The Maybach mining heap: Onsite with Komatsu in Germany
Improved machine maintenance for Liebherr
Interview: Looking into the future with Topcon Positioning
New technology solutions from OEMs: Bomag, Komatsu, Volvo CE
Update: Hexagon, Leica Geosystems expand offerings
Data for generating connected sites: Jennifer Thomson of MachineMax
Data & Marketing Manager: Alan Cansick
Web Manager: Sarah Biswell
Social Media Manager: Tatyana Mechkarova
ADVERTISEMENT SALES
Head of Construction Sales: Graeme McQueen
Tel: +44 1322 612069
Email: gmcqueen@ropl.com
Bentley’s OpenBridge for Cebu-Cordova Link
Unlocking ef ciency with B2W: Villager Construction’s digital journey
Advances in machine control: John Lawrence of UK Volvo CE dealer SMT GB
Virtual worlds for road planning: Lee Shinkin of AtkinsRéalis 58 Wacker Neuson’s digital solutions
Leica Geosystems deal with JCB
Trimble’s updated mapping system
Cybersecurity for machines: Update from the CECE
Get Smart in Construction: Richard Clement of Smart Construction
Trimble package for Mincon Attachments
Sales Director: Philip Woodgate Tel: +44 1322 612067
Email: pwoodgate@ropl.com
Sales Director & Classi ed: Dan Emmerson Tel: +44 1322 612068
Email: demmerson@ropl.com
Italy: Fulvio Bon glietti Tel: +39 339 1010833
Email: bon glietti@tiscali.it
Asia/Australasia: Roger Adshead Tel: +44 7768 178163
Email: radshead@ropl.com
Published by
ADDRESS
Route One Publishing Ltd, Second Floor, West Hill House, West Hill, Dartford, Kent, DA1 2EU, UK
Tel: +44 (0) 1322 612055
Fax: +44 (0) 1322 788063
ONLINE: ISSN 3033-3342
Kristina Smith reports
The handover of London’s Silvertown Tunnel next year will involve digital assets as well as physical ones. Enabling the flow of information from designers to constructors to asset managers has thrown up some complex challenges for the project’s small but resourceful BIM team. Digitalisation of the processes involved has played a key role.
The Silvertown Tunnel in London will be the first new road crossing of the river Thames to be built for 30 years. Running close to the existing Blackwall Tunnel, it crosses from the Greenwich Peninsula on the South side of the river to Silvertown in Newham on the North, so that traffic heading North on the A102 will have a choice of two tunnels.
A visit to the project, where construction started in 2020, reveals that it is well advanced. Almost all the civil works have been complete; some sections of road at either end of the scheme and a new footbridge have already been brought into use. With installation of services and systems underway, testing and commissioning is due to begin at the end of 2024 with the new crossing planned for mid-2025.
As that date approaches, the BIM team at contractor Riverlinx CJV (Bam Nuttall, Ferrovial and SK Ecoplant) is moving into a final, intense phase of work: assembling, gathering and converting the data that is needed for the as-built digital model, at BIM Level 2, that will be handed over to the operator Riverlinx Special Purpose Vehicle (SPV) and TfL which will be responsible
for traffic controls and flows towards and through the tunnel.
With some models containing up to 40,000 elements making up buildings, structures, highways, and MEP, and each of those elements having multiple parameters, this project boasts around 6 million pieces of data. Over 140 3D models created by multiple design disciplines and specialist suppliers are integrated into a federated BIM model.
The as-built information must be extracted from these models and put into a form that is compatible with Salesforce - the asset management software Riverlinx SPV will work with - as well as
Maximo and BridgeStation, TfL’s preferred system management software.
Although the transfer of data from design and construction into the operation phase of an asset was one of the core aims of BIM when it was first imagined, this rarely happens in practice. There are many reasons why it is so difficult to do, including lack of compatibility or interoperability between software, different levels of maturity among those contributing information, and asset owners not specifying how they want the information.
"Including not only ‘traditional asset data,’ but more than 140 native 3D models from more than five different types of software in the same asset management system, will be a huge challenge I think," says Riverlinx CJV BIM manager María Fuentes Crespo.
TfL awarded the £1bn, 30-year design-build-finance-operate (DBFO) contract for the Silvertown Tunnel to Riverlinx SPV in 2019. TfL will introduce tolls on both the Silvertown and Blackwall Tunnels, once Silverlink is open, and will pay Riverlinx SPV for agreed service levels in the Silvertown crossing.
This form of procurement, where Riverlinx will only get a return on its investment once the link is operational, drives the way the project is being managed from top to bottom. “It's not just about the technical assurance or the operational risk mitigation, but the commercial realities of not wanting to delay the project and the time scales involved,” says Nicholas BootHandford, programme delivery manager for TfL of his team’s governance role. “There are three strands to the risk: operational, technical, and commercial. The role of my team is to make sure all those three strands are held in tension, whilst supporting
“ Including not only ‘traditional asset data,’ but more than 140 native 3D models from more than five different types of software in the same asset management system, will be a huge challenge I think ”
María Fuentes Crespo, Riverlinx CJV BIM manager
“
There was a massive amount of work to divert all the utilities that used to run under Dock Road which has moved towards the bank on the Silvertown side ”
Nicholas Boot-Handford, programme delivery manager for TfL
Riverlinx in making sure standards of safety are as high as possible.”
As well as two huge, bored tunnels, the project involves cut-and-cover sections of tunnel, portal and control buildings at either side, approaches, a new pedestrian bridge and overbridge on the Greenwich side, and changes to road layouts on either side. There will also be a new storage yard for the Docklands Light Railway and a new river wall to enable future housing development.
“There was a massive amount of work to divert all the utilities that used to run under Dock Road which has moved towards the bank on the Silvertown side, adds Boot-Handford. “And there were also two massive Thames Water rising mains to lift up and put over the cut and cover section, whilst doing it all under the DLR and keeping the DLR operational. It was an enormous challenge.”
The installation of services involves mechanical and electrical equipment, plumbing and drainage, ventilation, firefighting, and security systems and all the associated controls. By the end of February 2024, manholes and drainage had been installed in the tunnel and the invert infilled to road level. The next step was to lay the asphalt.
In selecting the asphalt mix, Riverlinx SPV aims to limit maintenance – and hence costly closures – as well as meeting the specification, says Boot-Handford. “There's a technical specification for the pavement but ultimately there are commercial implications. Were we a traditional client using an NEC contract, the contractor would look to see what the most efficient way is of delivering the client requirement. But Riverlinx also has an O&M requirement to meet. There are
financial consequences if there are too many closures. That has fed into the design and safety critical infrastructure.”
For instance, says Boot-Handford, there are hydrocarbon detectors in the drains to pick up fuel spillages quickly and
automatically alert incident responses. “A lot of the tunnel control is automated to ensure a fast response,” he says.
Unlike the Blackwall Tunnel, whose two tunnels were completed in 1897 and 1967, the Silvertown Tunnel will be able to accommodate double-decker buses. This has meant that the Silvertown project required the UK’s largest-diameter tunnel, with an internal diameter of 10.66m and hence the UK’s largestever tunnel boring machine (TBM) too: a 10.91m-diameter
Herrenknecht earth pressure balance (EPB) machine, named Jill after the UK’s first female bus driver, Jill Viner.
Herrenknecht’s data management and visualisation software,
Herreknecht Connected – something that could be deployed
Herreknecht Connected, allowed engineers to monitor what was happening remotely at the same time as the pilot driving the TBM. On Silvertown, a first for Herrenknecht and the project team was incorporating data from the conveyor, which carries excavated earth away from the TBM, into Herreknecht Connected – something that could be deployed on future projects.
The TBM’s systems have measured and recorded making a U-turn in a huge shaft at Greenwich and boring
thousands of data points as it bored North to South, before making a U-turn in a huge shaft at Greenwich and boring back again. Fuentes Crespo has automated the extraction of some of the information recorded by the TBM during its journey. As well as helping to create the as-built model, this could also be useful for the construction team in analysing
could also be useful for the construction team in analysing how the build has gone.
“ Unlike the Blackwall Tunnel, whose two tunnels were completed in 1897 and 1967, the Silvertown Tunnel will be able to accommodate double-decker buses ”
“ The BIM team also presents data to their colleagues in the operations team through Microsoft’s Power BI which visualises data and presents information and graphics ”
In the earlier phases of the project, Fuentes Crespo, and her small BIM team of three people had to grapple with the use of multiple types of BIM software. Designers were using Bentley for the highways and landscape design which accounted for around 35percent of the models and Autodesk (Revit and Civil 3D) for buildings, civil structures, and MEP.
Competing software has not been designed to be 100 per cent compatible which means that Fuentes Crespo had to come up with a workaround. The solution was to use a package called Bexel which allowed the BIM team to combine Autodesk and Bentley models so that design review, take-offs and costings could be carried out. Bexel can extract information from IFC (International Foundation Class) files that come from both Bentley and Autodesk.
The BIM team also presents data to their colleagues in the operations team through Microsoft’s Power BI which visualises data and presents information and graphics. More recently, it has introduced the use of Dynamo which is a tool to automate modelling in updating 3D as built models and Dalux, an enormously powerful BIM tool for some on-site quality controls.
“Dalux is used by the construction and quality teams,” says Fuentes Crespo. “It’s a powerful tool and, because the model is in the cloud, I know that if I update anything, they will always be working with the latest version.”
In creating the as-built models, the BIM team is drawing on a variety of sources. For some elements, it will be the fabrication models. Survey details – such as the exact centre line of the tunnel or a laser survey of its lining to show where the joints of the precast tunnel segments are – will also be incorporated.
There is a whole new round of individual models for the mechanical, electrical, and plumbing activities which must be incorporated. “The theoretical approach is that all the suppliers are able to provide us with a fabrication design model that will plug into ours and then we will coordinate that,” says Jose Luis Rodriguez Sanchez, Riverlink CPV’s engineering manager.
“Practically, they are not all able to do that. We have two consultants working with us doing pre-coordination for the suppliers that are not mature enough to have good modellers.”
One of the issues which has yet to be resolved for the as-built data phase is how different assets will be divided up to be compatible with the Salesforce asset. This might be straightforward for a single item such as a door or a camera, but less obvious for a length of pipe or cabling.
The operational, technical, and commercial challenges highlighted by Boot-Handford are just as apparent for Fuentes Crespo and her team. The nature of this project has driven the BIM team to invest time and resource only in activities that really add value.
“BIM is sometimes about people saying, ‘look what we
can do’ but good things only happen when you really need to sharpen the pencil,” says Rodriguez Sanchez. “We don’t have a 4D model. I think we are still years away from that. The industry is not ready to pay for it.” 4D BIM looks good, but it is expensive to do and would not have contributed to driving the project forward to meet the crucial deadlines.
“I come from a pure BIM background, but in four years here, I have understood that we need to do useful things, not fancy things,” says Fuentes Crespo. “Every time I have an idea, such as automating the tunnel data, I have to ask myself whether it will be useful. We always have to find faster ways and more efficient ways to do things.”
This approach has already attracted interest from other parts of the industry. No doubt there will be more to learn from what they do in the final phases of the project.
“ The theoretical approach is that all the suppliers are able to provide us with a fabrication design model that will plug into ours and then we will coordinate that ”
Jose Luis Rodriguez Sanchez, Riverlink CPV’s engineering manager
By Christian Luttenberger, Vice President at Hexagon Geosystems
The construction industry is hardly ever at the forefront of technological innovation. However, in recent decades, digitalisation has proven to be a decisive factor for safety, quality, efficiency and sustainability. Technologies such as machine control systems, laser scanners and the latest advancements in artificial intelligence (AI) have revolutionised how construction projects are executed, promising greater accuracy, productivity and cost-effectiveness. Amidst these advancements lie challenges, particularly in managing the patchwork of proprietary systems and file formats that dominate jobsites.
The inability to easily share and integrate data from different brands across different data formats and platforms limits the benefits felt by contractors, original equipment manufacturers (OEMs) and customers alike. Standardisation is essential to overcome this lack of interoperability and reach a point where data can be used autonomously.
Historically, construction has been seen as a traditional, labourintensive field, but over the past few decades it has increasingly embraced technology to improve efficiency, safety, and sustainability. This remarkable transformation spans from the days of basic tools and manual processes through the introduction of hydraulic systems to computerised and sophisticated digital solutions.
One reason for this is the inherently complex nature of construction projects, which often involve numerous stakeholders, intricate schedules and large-scale operations. Digital tools and technologies have helped streamline project management, facilitate communication between teams and optimise resource allocation. Today, digitalisation is no longer merely a buzzword. Increased investments in technologies such as Building Information Modelling (BIM), drones, robotics and artificial intelligence are demonstrating how the industry is evolving. These technologies are transforming how construction projects are designed, planned and executed, leading to greater efficiency, cost savings and innovation.
One of the most impactful developments has been the integration of GPS and other positioning technologies into construction equipment. These sensors enable real-time tracking of machinery and materials, optimising resource allocation and
improving overall project management. Operators gained the ability to precisely control heavy machinery, leading to higher accuracy. This not only improved the quality of work but also reduced labour costs and project timelines. Additionally, they enable more accurate surveying and site mapping, leading to better decision-making and fewer errors during construction.
Yet, the path to digitalisation is not without hurdles. One of the most pressing challenges is the proliferation of proprietary systems and file formats used by different manufacturers. This patchwork of technologies creates compatibility issues, data silos and inefficiencies, hindering the seamless exchange of information between stakeholders. Contractors often find themselves grappling with fragmented data management systems, leading to delays, errors and increased project costs. Up until this year, there has been no standardisation or regulations that allow the technology to intercommunicate.
“ One of the most impactful developments has been the integration of GPS and other positioning technologies into construction equipment ”
Developed by the International Organization for Standardization (ISO), ISO standards are guidelines designed to promote uniformity and quality across a wide range of industries and activities, providing guidelines and specifications to ensure consistency, quality and safety in products, services, and processes.
For the heavy construction industry, ISO standards play a pivotal role in streamlining operations, enhancing safety measures and facilitating interoperability between different systems and equipment. Establishing a common language and guidelines fosters effective collaboration among contractors, engineers and other stakeholders. From materials and equipment specifications to quality management and
environmental practices, ISO standards set the benchmark for excellence in construction practices worldwide.
Key ISO standards, particularly relevant to heavy construction, cover project management, quality management, occupational health and safety, and environmental management. They enhance safety measures, improve project management practices and minimise errors and defects in the execution of construction projects.
Since 2010, the ISO subgroup for machine control has been working to standardise data exchange requirements between earthmoving machinery, mobile road construction machinery and worksite information systems. Streamlining data exchange
protocols and file formats across various machine control systems harmonises the communication between vehicles and external equipment. It encompasses server-to-server data communication, as well as the definition of data elements and file formats for worksite descriptions, including task execution details, periodic progress monitoring and as-built descriptions.
This year, the fourth iteration of these standards dedicated specifically to improving the interoperability of worksite data exchange is expected to be published. The new standards mark a major turning point in construction connectivity. They will provide a common, brand-agnostic framework that will enable seamless communication between machinery, sensors, software and more. By eliminating compatibility issues and streamlining data exchange, contractors can minimise downtime, boost
productivity and deliver projects with greater speed and precision.
For over six years, Hexagon has worked alongside industry partners to shape this fourth generation of the standards. As one of the global technology providers for the construction industry, there is a responsibility to support companies and contractors for this next level of connected construction.
In road construction, earthmoving and mobile road construction machinery perform a variety of tasks, from moving massive quantities of earth to laying asphalt or concrete surfaces and maintaining roads and highways. Standardised communication protocols are indispensable to
converge these operations. Therefore, the significance of ISO/ CD TS 15143-4 cannot be overstated, especially in collaborative projects involving multiple subcontractors and diverse heavy machinery.
This standard bridges the gap between disparate fleets of heavy machines, enabling seamless interoperability and data exchange. Subcontractors, each equipped with their own machinery mix, can collaborate with cohesion and efficiency. On the jobsite, subcontractors can unlock new levels of synergy and
productivity. Standardised communication protocols facilitate smooth collaboration and streamlined workflows, allowing for confident navigation of mixed fleets. Whether coordinating earthmoving activities, fine-tuning grading operations, optimising milling processes, or synchronising paving endeavours, this standard ensures every project component works in concert. Ultimately, this leads to enhanced project outcomes, reduced downtime and increased cost-effectiveness, benefiting both subcontractors and project stakeholders alike.
The adoption of machine control in construction is increasing, but it has not yet reached its full potential. Open and brand-agnostic protocols future-proof investments in job site technology, reducing reliance on specific vendors. Therefore, a huge untapped opportunity to benefit from machine control and interoperability is an important step. For construction professionals juggling mixed fleets from different OEMs and subcontractors, interoperability promises to improve and streamline workflows with the wider adoption of machine control technologies. This will reduce time wasted on data conversion and translation, improving efficiency, reducing error and increasing profit margins.
At Hexagon, we know that a mixed fleet can save contractors added investment costs, allowing them to spread their investment across more machines to build a more extensive fleet or the freedom to invest in other aspects of their business. It allows them to overlay new technologies without investing in new equipment or replacing large sections of their fleet at once to keep up.
“ The adoption of machine control in construction is increasing, but it has not yet reached its full potential”
https://www.youtube.com/watch?v=hFPg81XYFqI
To provide the most significant opportunities for contractors, we offer an agnostic approach to equipment on the jobsite with machine control and digital construction solutions from Leica Geosystems, part of Hexagon. This approach enables them to capture standardised machine and equipment data for aggregation, regardless of brand. To mix and match the tools and the equipment that works best for their needs on the jobsite allows contractors to future-proof their investments, knowing they can invest more today, and their purchase will be compatible with new technology offerings as they hit the market.
All technological advancements in that field are steps on the path to autonomy. Developing a common language of data exchange makes the coordination and automation of complex workflows possible. The ability to design once, push this design to any machine and receive data about as-built production in a common format is applicable now and yields gains far beyond convenience. Project managers can gain more centralised
“ The ability to design once, push design to any machine and receive about as-built production in a format is applicable now and far beyond convenience”
oversight, with real-time access to as-built status from all connected equipment. OEMs will be able to integrate their equipment with a wider range of technology and offer more flexibility to their customers. Contractors will see increased profit margins thanks to more efficient resource management, better error correction that avoids costly rework, and time-saving thanks to simplified data exchange. This will not just benefit construction today, but it will also encourage innovations for new applications. By reducing vendor lock-in and allowing new technology players to integrate more easily, the standards will help build the platform to develop technologies that have not yet been considered. The standards for earthmoving and road construction machinery represent only one piece of the puzzle. There will be more stages to come in the journey towards standardised automation. Embracing the open exchange of experience and expertise between industry players to develop these standards means that the construction industry is well-positioned to reap the benefits of connected machine control and, ultimately, autonomy.
Learn more about the offerings for road construction from Leica Geosystems: https://leica-geosystems.com/industries/ heavy-construction/highways
Trimble technology provided the autonomous controls for a Dynapac soil compactor working on a jobsite in Canada. This is one of the industry’s first public tests of a fully autonomous compactor on a live construction site, rather than under test at specially prepared areas.
The job is for the construction of an earth covered dam and the Dynapac compactor was used alongside conventional machines guided by operators to carry out the work. Trimble technology used in all of the soil compactors ensuring they worked as a team, covering the entire area ef ciently.
The Trimble Earthworks Grade Control Platform for Autonomous Compactors was used to guide the Dynapac CA 5000 soil compactor. The project is for the Site C Clean Energy Project on the Peace River in north-east British Columbia.
For some of the time, an operator did sit in the machine to
oversee its working while the compactor was under autonomous control. At other times the machine was used without a person in the cab when handling work close to an edge that would have posed risks for an operator. To optimise safety, the machine operated in geofenced areas on the site and was also tted with safety systems to detect the presence of personnel.
According to Trimble the fully autonomous machine completed 37 hours of real compaction work, operating alongside a mixed eet of compactors, the rest of which were running the Trimble CCS900 Compaction Control System. Data from all machines – both with and without an operator – was delivered using Trimble WorksOS Software, which is being used as the system of record for all compaction data on the jobsite.
AggNexus offers an entirely new kind of event for the industry.
AggNexus, scheduled for September 9-10, 2024, in Austin, Texas, is a landmark event for the aggregates, concrete, and construction materials industries. It provides a platform for 12 leading service providers to showcase innovative solutions that propel industry operations forward. The event invites over 150 industry leaders to explore new technologies, engage in direct discussions, and foster meaningful collaborations. Through tailored presentations, interactive vendor sessions, and expert-led panel discussions, AggNexus aims to catalyze the digital transformation of these critical sectors, offering unprecedented opportunities for networking and growth among industry professionals and service vendors alike.
Presented by
“The Site C project was the perfect place to begin live testing of the fully autonomous soil compactor because of the cost and safety bene ts autonomy will bring to large infrastructure projects like this in the future, and because of the willingness of the project owner and contractor to use new technology on their jobsite,” said Cameron Clark, earthmoving industry director for Trimble’s civil infrastructure solutions. “We are pleased that this initial testing reinforces our philosophy that autonomous technology will play an important role in delivering a cheaper, faster, safer and greener future for the construction industry.”
Clark said that operating data from the machines has also been used in the model of record for the project.
The Site C Clean Energy Project is a BC Hydro hydroelectric dam being built in north-eastern British Columbia. When complete, it will provide 1,100MW of electricity each year, enough to power 450,000 homes or 1.7 million electric vehicles. Prime contractors include ACCIONA Infrastructure Canada Inc. and Samsung C&T Canada, among others. The role of ACCIONA and Samsung includes construction of an earth ll dam, two diversion tunnels and a roller-compacted concrete foundation for the generating station and spillways.
While the mining sector has been running autonomous haul
trucks on sites for over 20 years, these have been in controlled working areas and on large machines. Using autonomous machines in construction operations poses more challenges as the sites are more dynamic. This new development is a signi cant step for the construction sector and will be followed by other applications of autonomous machine technology. According to Clark, the highly repetitive soil compactor working cycle is particularly well suited to the use of autonomous machines, although the rm is developing autonomy solutions for other types of machines that could be used in certain duties. The rm has previously demonstrated an excavator working autonomously for trenching work. But Clark explained that excavators are so versatile that only certain repetitive tasks, such as trenching, suit autonomous operation.
Clark continued, “Our compactor is our launch machine and a lot of the building blocks we can add to other machines.”
Dynapac www.dynapac.com
Trimble https://heavyindustry.trimble.com
“ Using autonomous machines in construction operations poses more challenges as the sites are more dynamic ”
https://www.youtube.com/watch?v=0lmahXYKymY&t=3s
The Komatsu PW148-11 is compact and powerful. A short rear swing radius allows safe work even in tight spaces. Features such as integrated attachment control (KIAC) or the optional trailer hitches increase productivity and versatility, while the premium comfort seat and adjustable joystick steering provide maximum operator comfort.
Located in Friedrichsthal, at the heart of Saarland’s renowned mining region in the southwestern German state, the Maybach mining heap stands as a testament to the industrial legacy dating back centuries.
Historically serving as the repository for non-coal-bearing waste rock from neighbouring coal mines, this site has long been a landmark of the local landscape.
However, with the conclusion of mining activities in Saarland on June 30, 2012, an era spanning over 250 years drew to a close and the site remained inactive until now, as an ambitious project takes shape to breathe new life into the area. This project involves the delivery of an impressive 2 million m3 of soil across 27ha, over the entire duration of 10 years.
In an exclusive interview with Smart Construction, Sina, a dedicated jobsite manager from HEITKAMP Corporate Group, shares insights into her mission overseeing the project. With
a deep-rooted connection to Saarland, she prioritises safety, conformity, ef ciency, and community welfare, all made possible with modern construction methods.
Jobsite changes everyday
“For me as a jobsite manager, the daily challenge lies in grasping the latest jobsite development. Materials are being delivered, machines are constantly running and I’m confronted with a ood of data every day! It’s crucial for me to nd an easy way to make sense of it and make use of this information effectively.”
Drawing on her expertise in Lean Construction and Building Information Modelling (BIM), Sina aims to integrate BIM methods
into earthworks by creating a constantly updated 3D digital twin of the jobsite. This innovative approach allows for realtime consultation of the latest jobsite updates by managers, operators, surveyors, and clients.
Now the pressing question is, how can we ef ciently collect high-quality eld data for the digital twin?
As-built data for daily progress monitoring Drone surveying was the rst solution Sina’s team put in place. It’s a great method to gain comprehensive terrain insights once every few months. However, the logistical challenge of daily drone ights and the need for more detailed information on speci c jobsite areas and material deliveries required them to explore alternative solutions.
Introduced to the Intelligent Machine system by Smart Construction Partner AP Deutschland GmbH, Sina was impressed by its versatile capabilities. Not only renowned for its ef ciency, precision, and productivity, the system can also serve as a data collection tool while the machine operates. While
doing its lling job onsite, the intelligent dozer can also capture actual height and position data as a by-product during the lling process and then transmit this data to the cloud as a point cloud automatically.
This dataset can then be agglomerated with the drone point clouds, creating a 3D digital twin of the jobsite terrain. Sina remarks, “With all this data available at my ngertips on Smart Construction Dashboard, I am able to track the amount of soil delivered at any given time and compare it with the data recorded on the weighbridge. This forms the basis for invoicing, providing me with real-time insights into the ll levels and inventory on the heap.”
For more information on Smart Construction, visit smartconstruction.io to explore the full solution suite.
Liebherr says that its new MyAssistant for Earthmoving app provides all relevant information about earthmoving and material handling machines in a digital format. Bundled in a mobile application, the app combines numerous features that offer added value, especially for machine operators. The MyAssistant for Earthmoving app provides contextual data from various databases around the world relating to the operation and maintenance of machines – simply, quickly and intelligently.
The app is said to provide signi cant support for construction machinery operators in their daily work. The mobile application is available for wheeled excavators, material handling machines and wheeled loaders of generation 6.0 and higher as well as for crawler excavators, graders and crawler loaders, pipelayers and articulated trucks of generation 8.0 and higher. The new mobile app can be downloaded now free of charge from the Apple App Store and the Google Play Store.
After successful authentication via the MyLiebherr portal, the full range of features is available to the user. Once logged in, MyLiebherr makes all Liebherr earthmoving and material handling machines in the company’s eet available to the user via a drop-down menu. The machines can then be selected via the model designation and serial number. The resulting menu tiles: “Operating instructions”, “Spare parts catalogue” and “Scan operating symbol” that are displayed in the app refer exclusively to the machine selected by the user.
In addition, the entire Liebherr operator’s manual is available to the user digitally via the app. Required spare parts can be selected in the menu tile of the same name and placed in the shopping cart. Depending on the user’s authorisation level in MyLiebherr, a corresponding order can then be triggered.
The function “Scan operating symbol” can be used to identify unknown symbols on operating panels, keyboards and switches as well as on the control panel in the cab. The user can scan the symbol using the camera on their smartphone. Following a match in the symbol database, the user is shown the suggested solutions that t the context as well as corresponding links to the Liebherr operator’s manual. This quick analysis of the symbol in question not only saves the machine operator valuable time – by displaying and describing previously unknown or new symbols, the app increases clarity for the machine operator and thus also safety during daily operations on the construction site. Machine operators whose companies have a large eet of machines that undergoes frequent changes, as well as newcomers to the profession and inexperienced machine operators, will nd this feature useful.
Liebherr www.liebherr.com
“ The new mobile app can be downloaded now free of charge from the Apple App Store and the Google Play Store ”
Optimised maintenance procedures can be achieved with the new tool from
Liebherr
Topcon Positioning’s Yassir Shanshal, senior vice president of Global Quality, Service and Kris Cowles, executive vice president & CIO spoke with Mike Woof of World Highways on Topcon’s view for the future.
As a technology rm, it is no surprise that Topcon Positioning is utilising some of the latest technology in delivering solutions for customers in construction (and agriculture). Nor is it a surprise that the rm is ahead of the curve when it comes to research and development, looking at how emerging technologies will impact on future advancements.
The rm uses AI to leverage trends and analyse eld data to prevent quality issues. Shanshal said, “We’ve put a lot of emphasis on AI to identify what our customers are looking for. With AI there has been an easier way of looking at trends and seeing issues before they happen.”
The rm leverages AI to understand these issues so as to address them and also use the information for new product development. Shanshal continued, “With AI you have a lot more knowledge of things you’d spend time looking for. AI does that search for you.”
Cowles commented, “In the last 12 months there has been a massive explosion of AI.” She added that areas such as professional services and support will change faster through the use of AI, adding that there will be new roles for people to create the information that the necessary algorithms will
utilise. “We are going to make major moves in technical support,” she said and added, “The value is being able to change how we do things.”
But she cautioned that when someone asks a question of an AI tool (such as Chat GPT), will it give a good answer and who will decide what is a good answer versus what is the best answer?
Meanwhile, Shanshal explained that a new generation of operators is coming that is more aware of technology than in previous times. However, there is also a shortage of machine operators, which is why there is a growing need for machine control systems. “Automating the industry is a gamechanger. The next step is autonomous operation,” he said.
Cowles agreed and added, “There is a shortage of workers and that is going to get worse.”
Shanshal continued, “As we automate the world of construction equipment, we also automate the manufacture of our equipment. We’re working on two elements. The rst step we’re looking at is designing our product for automation.”
The new research and development area for Topcon will offer increased space for testing of new systems for the construction (and agriculture) segment
He said that the units have been complex in the past, with many internal wires. The newest models are instead being designed with snap together components, making them easier and quicker to assemble as well as to service and maintain. “It’s also a great way to reduce the number of parts and increase durability,” he added.
Shanshal said that rm is developing robotic cells for the manufacture of its units, while AI has been used to help determine how best to manufacture the products. Testing of the products once they are assembled is also carried out using AI systems and stereo vision cameras. This learning technology has helped to boost quality and is more reliable than conventional testing by personnel.
The changes to manufacturing and testing are not intended to reduce the payroll at the Topcon facility and instead the aim is to retain personnel levels while increasing output and productivity.
Demand is growing for products and Shanshal said, “The biggest growth the industry is seeing is on compact loaders and mini excavators.”
He explained that demand is particularly strong for the MC Mobile package, which is used on smaller machines. For contractors, this technology goes part of the way to addressing the challenge in nding people to operate equipment. Technology is going through a step change and rather than the old ways of doing things, rms are using new types of tools.
This change has been seen at Topcon, which has moved from being a hardware supplier to offering a whole suite of software solutions and services. But Cowles cautioned, “A large part of the industry is not aware what technology is available.”
Topcon Positioning www.topconpositioning.com
“ Demand is growing for products and Shanshal said, “The biggest growth the industry is seeing is on compact loaders and mini excavators ”
https://vimeo.com/760843950
Construction machinery manufacturers are introducing new systems that can boost machine efficiency and site safety – Mike Woof writes
While a considerable number of the new technologies have been developed by specialist suppliers, many original equipment manufacturers (OEMs) are also introducing their own solutions. These can help boost working ef ciency as well as site safety for the industry.
Bomag says that its latest Asphalt Pro system offers new capabilities for construction. The package can provide key data to everyone involved in a project, including details of every stage of the materials being supplied and used. Users can receive the data on a tablet device or smartphone.
The package can supply data on materials from the mixing plant through truck distribution and also on parameters for the paver and compaction.
Should a paver fail onsite, a warning is sent to the mix plant for example, so that truck loads can be stopped and costly material wastage minimised. Similarly, the paver operator will know when trucks will arrive with asphalt for paving.
Useful information includes comparing theoretical asphalt tonnage supplied with actual tonnage used. If the theoretical quantities match the actual tonnages used, this highlights paving ef ciency. But if there is a large disparity, the paver operator realises that the screed needs adjustment.
The sophisticated digitalisation package also allows users to reduce CO2 emissions as it helps to minimise energy use.
Komatsu is offering its Smart Construction 3D Machine Guidance kit for a broad range of standard Komatsu machines
as well as mixed eets. The 3D Machine Guidance kit provides an accessible way to add 2D and 3D machine guidance to any crawler or wheeled excavator from 13-120tonnes.
The kit can be customised with options such as a tilt bucket and couplers kit, a two-piece boom kit, a super long front kit, and a SATEL radio kit. A 3D safety zone feature has been integrated into the system, allowing customers to generate avoidance zones. The feature alerts operators when they are near hazards such as powerlines, underground utilities or public roads.
The 3D Machine Guidance system’s automatic le conversion is compatible with common design le formats. This ensures integration with existing 3D systems from different manufacturers.
In addition, the 3D Machine Guidance kit has an integrated payload meter option for Komatsu machines. This feature allows for dynamic material weighing, boosting productivity by ensuring trucks are loaded optimally.
The kit is also integrated into the Smart Construction suite as a rst step towards optimising earthmoving. It automatically collects terrain and payload data, which can be visualised and analysed using Smart Construction solutions.
Volvo CE says that its Connected Map provides visibility of the jobsite by giving a real-time visual overview of the position of every machine, vehicle and visitor. The intelligent positioning service can be accessed by all site personnel, both in the machine (via Volvo Co-Pilot or an Android/iOS device) and in the of ce (via the Of ce portal).
Connected Map can display site features and landmarks, including roads, to help operators navigate the site, loading zones, unloading zones, speed zones and restricted areas. Points of interest such as of ces, workshops, and service stations can also be visualised. Single-lane (narrow road) sections can be de ned as warning the operator if another machine is approaching in a single-lane section, helping to avoid traf c jams.
Connected Map users also stay informed about the location of machines, due to Connected Map’s search functionality, which
“ Volvo CE says that its Connected Map provides visibility of the job site by giving a real-time visual overview of the position of every machine, vehicle and visitor”
will search and nd users or machines in real time, with the machine’s last position visible for 30 days. Away from the of ce, Connected Map makes it easier for the operator to familiarise themselves with the site and know where everyone is, boosting safety.
BOMAG www.bomag.com
Komatsu www.komatsu.com
Volvo CE www.volvoce.com
Hexagon is expanding its capabilities, with an array of new technologies under its own name and for its Leica Geosystems brand also.
The rm’s Reality Cloud Studio package delivers automated digital reality to the cloud. The Reality Cloud Studio is powered by HxDR (Hexagon Digital Reality). This SaaS application is said to make reality capture data accessible, combining advanced Hexagon technologies with automation to make data processing simpleto-use.
Customers can upload reality capture data to the cloud for automated processing, storing and visualisation to create photorealistic digital twins, and to share data quickly and securely. These functions enable fast extraction of vital information from reality capture data and make it readily available to stakeholders in any industry or trade.
Reality Cloud Studio can be accessed from any computer or mobile device with a web browser. Users in the eld can upload data directly from compatible reality sensors to create registered and meshed digital twins for use onsite.
“We are at a point in reality capture where a uni ed, scalable and simpli ed digital reality experience is necessary to make digital twins and their value accessible to everyone,” said Thomas Harring, President, Hexagon’s Geosystems division. “Reality Cloud Studio provides a space where anyone can access and build digital twins and share their vital information, using valuable communication tools that bring people and data together in a centralised space for digital reality.”
Powered by HxDR, Hexagon’s cloud-native platform for geospatial solutions at any scale, Reality Cloud Studio
provides an intuitive, user-centric interface that performs tasks such as automated registration and meshing of point clouds captured by any sensor that produces a compatible le type. Users can collaborate in real time with measurements, annotations, attachments, comments and virtual tours.
Experienced professionals stream data directly from Reality Cloud Studio into the Cyclone 3DR desktop software for detailed analysis and reporting – with more Leica Geosystems reality capture software connections coming soon.
Reality Cloud Studio enables streamlined end-to-end work ows for everyone. With essential tasks automated for simplicity and ease of use, users can expect further functionalities and features to be deployed in the application.
Reality Cloud Studio is available for purchase in subscription tiers, billed monthly. Customers can choose how many seats they require and which functions they would like to use. They can also control data access and user roles, and directly manage their account through the application. Software development kits for custom applications are also available by contacting Hexagon directly.
The new PA10 system from Leica Geosystems will help boost site safety for personnel
Meanwhile, Leica Geosystems is offering a new system that is said to help boost safety for personnel on construction sites. Safety is a key issue on busy sites where there may be numerous items of construction machinery in use. Personnel on foot can be at risk if they are close to working machines and the industry does need to boost its safety record.
Leica Geosystems says it has a new tool to tackle this issue in the shape of the innovative PA10 system that utilises new technology to identify when personnel may be walking around a jobsite. The system then alerts machine operators to the presence as well as the location of construction personnel. At the same time, the system will warn any personnel walking around a site that construction machines are operating in the immediate vicinity.
Thomas Bonvalot of Leica Geosystems explained, “It’s a personnel awareness system. Everybody onsite will know where a machine is working and the machine operator will know there is a pedestrian.”
Leica Geosystems www.leica-geosystems.com
https://www.youtube.com/watch?v=BDQLbrrmvA0
The construction industry nds itself at an interesting juncture, where in March 2023, insolvencies in construction represented 18% of all companies that failed. It was the worst performing month that the industry has faced since the nancial crisis, according to data from the UK government’s Insolvency Service. Materials and labour costs are increasing too. Research from construction data specialist Barbour ABI found that in ation added £23 billion to the cost of construction in 2022.
When it comes to construction digital strategies, often the primary focus within construction is the BIM model, which underpins a successful project. However, what is often overlooked in the short term is the digitalising of the actual construction site and a full understanding of the end-to-end process from a data perspective.
By applying the same rigour to the data and information ow on projects as is applied to the project management of the build, the industry stands to make huge gains in terms of optimisation and a “live view” of risk, alterations, and what-if scenarios.
Connected sites can connect machines, people, and materials and collect and process the data to generate a usable digital twin. This digital version of the site enables and improves decisionmaking. With advancements in technology, such as automation, arti cial intelligence, and machine learning, construction has an opportunity to gather and analyse vast amounts of data to allow this to be done ef ciently in real time.
It is not simply about connecting and generating data. It is about providing the right data at the right time to the right people. The goal should not be to gather in nite amounts of data, but to analyse the data and make faster and more accurate decisions. To achieve this, the data collected needs to be relevant, timely, and of suf cient quality.
The key to a successful connected site is being able to combine data coming from a site, pairing it with contextual data and understanding how the variables interact to anticipate an outcome.
The bene ts of data are vast, the McKinsey Global Institute found that making a digital transformation can result in productivity gains of about 15% and cost reductions in the range of 4-6%.
More than productivity gains, a connected site could use existing data, enrich it, and provide additional bene ts, moving towards net-zero and promote collaboration across a site. Is it too far-fetched to imagine a resource of past issues/risks and the
context behind them that could be analysed for future projects at the design stage?
This was achieved working with the SMP Alliance along a 16km stretch of the M6. The machines onsite were generating data and through this, it was established that the baseline idling rate was 50% of operating hours. Enriching the data and ensuring it was provided to the right people at the right time enabled personnel to change behaviour. They were alerted to issues as soon as they arose, identifying training and engaging operators with the data. The result was a 36% decrease in idling time, saving 3,500litres of fuel each month, cutting CO emissions by nearly 1tonne.
On the surface, connecting everything on a site has been made easier with the evolution of the IoT, smart sensors, and visual AI. The exciting part is using optical sensing to address multiple issues with vision rather than device-based solutions. However, diving deeper reveals practical challenges.
The UK’s construction industry faces a signi cant challenge due to a fragmented supply chain. Data is scattered among clients, contractors, subcontractors, consultants and equipment hirers. For instance, excavator data owned by hirers is valuable to contractors and clients.
Data lacks standardisation, complicating data consolidation across different project tiers. Focusing on connecting plant machinery highlights challenges in data retrieval, including connectivity, frequency of OEM data transmission and data type. Comparing data across machines is dif cult. Furthermore, the data’s primary users, typically vendors providing onsite services, are not the ultimate bene ciaries of insights.
A practical solution is for the project client to set data requirements and tools in contracts from the outset. However, parties hesitate due to concerns about disadvantaging others. Collaboration is needed to determine what bene ts the entire supply chain for the common good.
collaborative supply chain efforts. The industry must be
It is vital to prioritise understanding the data in connected sites and establish clear data expectations for a productive and sustainable construction future. Digitisation can boost productivity, sustainability, and cut costs, but requires collaborative supply chain efforts. The industry must be encouraged to challenge data-related questions and ensure data supply consistency.
The tolled Cebu-Cordova Link Expressway is a bridge and causeway stretching almost 9km across it the Philippines’ longest and tallest bridge. It connects the city of Cebu, which has nearly one greater Central Visayas area, to the smaller municipality of Cordova, around 75,000 people on the
The OpenBridge solution, by Bentley, features automated post-processing that helped reduce time and costs on the Cebu-Cordova Link Expressway by almost 30% (image courtesy of SENER)
across the Mactan Channel, making million inhabitants within the the island of Mactan.
Before the four-lane, 27m-wide expressway opened in 2022, Cebu was connected to Mactan by only two bridges to the north. This third inter-island connection to the south is relieving traf c congestion on the two original bridges and improving regional tourism and the economy. Importantly, the expressway has reduced travel time between Mactan Island and Cebu International Airport by 40 minutes.
As part of a temporary design joint venture, SENER, a private engineering and technology group founded in Spain in 1956, led detailed engineering design, managed the multiorganisational design teams and provided technical assistance during construction. The overall project features several bridges and access viaducts connecting to the main cable-stayed bridge, explained Jordi Revoltós, bridges and viaducts discipline head at SENER.
The project presented several challenges, including extreme seismic conditions and an extremely sensitive marine environment. The area is prone to typhoons with winds as strong as 250km/h. On top of this, with design teams across multiple organisations working on the project, SENER faced design compatibility issues when connecting the viaducts to the main bridge structure.
“Since the approach viaducts connect with support at the mid-span of the bridge, special coordination [needed to be] developed to ensure a joint and compatible design,” said Revoltós. Effective interaction was a key factor in obtaining a balanced design.
Another challenge was that the project needed to be
https://www.youtube.com/watch?v=KdC3TqHeGV8
constructed entirely over water on a tight timeline. This complex construction sequence required software that could integrate with all design parameters to develop models that incorporated modi cations from the construction site.
SENER realised that they needed exible, interoperable bridge modeling software. “An [unsuitable] choice of calculation software [would lead to] increased time and costs during the design phase, while jeopardising nal approvals needed before construction,” said Revoltós.
SENER selected Bentley’s OpenBridge solution because of its exibility, collaborative design capabilities and automated calculation features. “The high exibility of OpenBridge to develop models with modi cations requested from the construction site, together with the short time required to adapt previous bridge models to new structures, led us to choose this software to design all bridges and viaducts,” said Revoltós.
Using Bentley’s application, they performed coordinated multidiscipline modeling and analysis that enabled the geometry adjustments that would ensure design compatibility between the structures.
Working in an open digital environment allowed the geotechnical and bridge design and construction teams to share information and determine the optimal bored pile diameters for the main bridge and viaducts. They also ensured that the structural solutions could withstand the seismic conditions and extreme winds.
SENER also used OpenBridge to conduct detailed structural checks to ensure that each structural element was correctly developed and veri ed. Meanwhile, automating post-processes allowed the team to completely control the design schedule and to adjust resources and tasks as necessary. The software’s versatility, interoperability and intelligent modeling and analysis facilitated a fast-track design process and model-based
construction work ows to address the complex construction sequence and constrained project schedule.
Implementing collaborative digital modeling and analysis processes using OpenBridge streamlined work ows, enabling SENER to timely develop the models and meet the project schedule. OpenBridge’s exibility to update models simpli ed the geometry adjustments required for design compatibility. This capability reduced coordination time between design teams and allowed them to achieve high-quality digital designs.
Based on the detailed calculations, the design teams reduced the dimensions of the foundations and minimised the impact on the coral seabed. Having highly accurate models in an open digital platform facilitated collaboration with the construction team, optimising time onsite.
Furthermore, Bentley’s application automated post-processes, allowing SENER to generate calculation reports exibly and ef ciently, saving additional time and costs by almost 30%, explained Revoltós. Working in Bentley’s connected digital
environment also improved review and approval ef ciencies, accelerating approvals of different parts of the project, enabling construction to begin in the shortest possible time.
The intermediate control steps enabled by the software, together with the quality control sheets, made internal veri cation ef cient and traceable. “The use of OpenBridge, in conjunction with internal quality control processes, minimised potential errors in the nal product,” said Revoltós.
Bentley Systems is an American software development company that manufactures, licenses, sells and supports computer software and services for the design, construction and operation of infrastructure.
Material was supplied by Amy Heffner, director of product marketing at Bentley Systems.
Bentley Systems www.bentley.com
Volvo Construction Equipment’s (Volvo CE) Site Operations tool, which is independent of the brand, helps customers with mixed eets control their safety, productivity and ef ciency in all their operations. It’s a simple but highly effective concept that takes complex data and transforms it into easy-to-use,
easy-to-understand information les to improve day-to-day operations.
Designed for site owners, site managers, eet owners and operators, Site Operations is a collaborative technology platform where various data from a mixed eet is brought together with the position and movement of each piece of
equipment on a con gurable site map. It focuses on site safety through connected map functionality, site information through the compilation and analysis of daily work cycle data and site management through work order planning. The result is greater safety for drivers and anyone else in the vicinity, greater exibility thanks
to the ability to choose the optimum working areas in real time and improved ef ciency, productivity and sustainability by analysing machine performance and making incremental improvements as customers work.
Volvo CE www.volvoce.com
Your work matters.
Whether building new highways, roads, or bridges, the things you build are vital to improving the lives of people and communities now and in the future. We provide solutions that bring increased accuracy, e ciency, and sustainability to your projects, allowing you to do more with less.
Learn more at topconpositioning.com
efficiency
As heavy construction projects become increasingly competitive, Villager Construction is among the many contractors seeking ways to unlock its most underutilised asset: data.
More than ever, profitability hinges on the ability to collect, access, analyse and act on the vast amounts of data available. Yet many contractors still rely on spreadsheets and disconnected systems. While this way of working may be comfortable, it is not very efficient, resulting in contractors having to waste countless hours trying to capture, find and organise data.
Villager Construction realised that it does not have to be this way. Technology has helped the company unify and connect its data and people, streamline workflows, enhance profit margins and simplify how projects are run.
Villager Construction is based in Rochester, New York and specialises in milling and paving, civil construction and aggregates. The company had deployed technology solutions as a way to overcome its challenges for years, starting with president Tim Lawless, who was hired to install the company’s first computer system for accounting in 1992. Technology has been part of the growth strategy ever since, helping the company grow from 35 to 250 employees and expand its reach from New York
to over 14 states today.
software applications provided a better way to connect people, data and workflows across the company as well as the growing workforce and volume of data associated with those workflows.
“We knew specialised and connected software would be a vast improvement over paper and spreadsheets,” said Lawless. “So when our chief estimator, Adam Kohn, suggested that we upgrade our existing estimating software to B2W because it was more powerful and would allow us to work faster and turn out competitive bids, we were ready.”
Focusing first on estimating accelerated the company’s time to bid. “In 20 minutes, we can build an estimate for a job that would have taken six hours to build in our previous estimating software,” said Hunter Nelson, a construction project manager at Villager Construction.
Moving to B2W gave Villager Construction a centralised database of up-to-date costing information for labour, tasks, materials and equipment. Templates pre-populated with costs eliminate the time estimators would spend searching for figures, making it quicker and easier to complete project bids. “We can pull pre-built templates and cost structures into our bids, which makes it much more streamlined,” said Nelson.
The company’s estimators now have the flexibility to bid with as much or as little detail as required. “We can break down our bids in much better detail,” said Casey Smith, vice president of milling and paving at Villager Construction. “Access to data from previous bids means we spend less time
Villager Construction’s growth was a big reason the company began steadily and methodically implementing the B2W platform in 2018 to replace spreadsheets to manage estimating, resource scheduling and dispatching and performance tracking. As projects became more complex and competitive, the unified
down our bids in much better detail,” said Casey Smith, “Access to data from previous bids means we spend less time chasing numbers and more time on strategy. I like to bid for a job the same way I would build it, and now I can.”
“ We knew specialised and connected software would be a vast improvement over paper and spreadsheets
Tim Lawless also liked the fact that B2W enabled the company to generate and evaluate multiple bid scenarios quickly. “Being able to do multiple scenarios was a huge benefit. We can then look at them as a team and try to build the job out of it, and then take that to the field.”
With efficiency gains in estimating, Villager Construction implemented B2W Track, a construction progress tracking solution. Today, the company can capture job performance information and compare it to the bid. This ability to link field data with estimating helps manage costs. “I’m in the software every day looking at the cost summary reports and checking our daily performance on multiple projects across 14 states,” said Smith.
Bid information and phase codes are used to establish field logs that capture real-time data on productivity, labour, materials and equipment. “All of our foremen track quantities, equipment hours, material usage, trucking, and capture notes and pictures from the field,” said George Lynch, paving project manager at Villager Construction. “Daily, we can easily see if the quantities in the estimate match what is happening in the field. We track progression on production account items to see if we’re at 50 or 60% and how the job is coming along.”
Access to real-time data from the field allows teams in the office to make informed decisions and streamline communication. “We’re getting a full picture of what’s going on daily so we can make smarter adjustments more quickly – for example, on labour or equipment, that allow us to meet or beat production targets,” said Mike Lawless, who coordinates IT systems at Villager Construction.
“Sharing data with the people that are doing the work is really important because it enables everyone to have the same information at the same time. It also makes it easier to have a conversation with a foreman or PM about their job because we’re all looking at the same information,” said Tim Lawless.
With real-time visibility into production, Villager Construction turned its attention to real time, online scheduling to get the right resources to the right place at the right time.
“Before, we sent hundreds of texts every week or made calls
to get crews where they needed to be,” said Smith. “Now, once we get the schedule set and personnel in place, we click one button, and everyone is notified. Moving away from spreadsheets has made us 10 times more efficient with scheduling.”
Using B2W Schedule helps the company maximise resources to keep jobs on schedule and within budget. Schedulers can also be alerted of conflicts with labour, equipment or materials to prevent last-minute scheduling emergencies and minimise interruptions or downtime. With access to the same information in real time, employees can work together and keep projects running at optimal efficiency.
“I view the schedule based on jobs, employees, equipment, and can schedule 1-2 months in advance,” said Lynch. “With real-time visibility into our jobs and resources, I can make adjustments on the fly and borrow resources from another department, or if I have too many workers, I can shift them to another job. It’s much more efficient.”
While the anticipated pushback and the desire to do things the way that they have always been done may stop some contractors from modernising workflows and operations,
Villager Construction is thriving in an increasingly complex and demanding environment.
“People we thought would never open an iPad transitioned to it with no issues,” said Steve Verdine, vice president of construction at Villager Construction. “It’s been great. Once they started using B2W, everybody realised how much easier it was.”
Bringing teams, workflows and data together across the company has been transformative and led to greater efficiencies, quality and profitability. “You can’t get complacent about using what you have,” said Tim Lawless. “You have to continue to look for better and more advanced ways of doing things in order to not just keep pace, but to help your company continue to prosper and grow.”
l Tom Willey is a solution engineering manager for Trimble. He assists heavy civil construction companies in assessing estimating, operations and ERP workflows and in evaluating software solutions, including the B2W and Viewpoint platforms. B2W Software is a Trimble company with unified applications to manage estimating, resource scheduling, performance tracking and equipment maintenance.
B2W Software www.bswsoftware.com
Trimble www.trimble.com
Softree’s new software offers optimised road alignment planning
Civil engineering software specialist Softree Technical Systems is offering a new version of its RoadEng Version 11 Software. This latest version includes AIbased technologies to find low-cost, constructable road and corridor locations and is suited to use for greenfield road projects.
Research and development for Path Explorer has been ongoing for years, guided by collaboration and dialogue with clients. “We continually engage with our customers to better understand their challenges, this helps us focus our R&D effort on features that matter to them.” said Matt Dickie, Applications
Specialist & Training Manager Softree Technical Systems. For greenfield road projects. Path Explorer AI enables users to explore multiple route options from Point A to Point B within minutes, offering optimised alignment solutions while considering various constraints such as grade limits, side slopes, and environmental factors. This innovation accelerates decision-making and optimises costs.
This is especially pertinent in wind farm development, where swift planning and analysis of proposed roads and road networks are required. The placement of roads is
often influenced by project factors like turbine locations. The ability to account for those factors and quickly determine lower-cost, feasible road locations accelerates project initiation, reducing capital expenses and the project timeline.
“Path Explorer integrates into our established earthwork optimisation workflow within RoadEng, where the potential for savings is substantial,” explains Erin Wasney, Business Development Manager at Softree. “Minor adjustments to the vertical alignment, aimed at minimising cuts and fills, yield rapid and significant results. Just recently, one of
our Australian clients shared an impressive success story from one of their windfarm projects: US$1.9 million in savings. That’s a 19% reduction in subgrade costs.” Version 11 introduces additional features aimed at reducing environmental impact and increasing user efficiency, including a hydrology toolkit, improvements in lidar processing and corridor design, automated horizontal and vertical curve generation and drafting and output improvements.
Softree Technical Systems www.softree.com
John Lawrence, product manager for Site Technology Solutions at UK Volvo CE dealer SMT GB, shares how the machine control landscape has evolved and how the firm is supporting customers to leverage technology.
Machine control systems have taken construction by storm in recent years. The tools have changed earthmoving and construction contractors, bringing new levels of productivity, ef ciency, and precision, as well as contributing to greater sustainability. While these systems may feel new, the technological principles have been around for a long time in site surveying.
Back in the day, land surveying meant someone behind a tripod watching another person with a stick, moving about the site. Now, robotic optical instruments automate tracking. This shift means greater accuracy and fewer people on a potentially hazardous site.
Machine control systems simply took that survey toolkit
– GPS, a screen, and data – and brought it to construction equipment. So now, instead of a person pacing around with strings, lines and spray paint, machine operators get all the site design information they need on a screen in the cab, preventing costly or dangerous mistakes like digging too deep.
Construction contractors are beginning to experience the bene ts of digitalisation and automation, but governments are pushing for it too. Public bodies want machine control systems in their construction projects. For example, the National Highways (formerly Highways England) Connected and Autonomous Plant (CAP) Roadmap to 2035 lays out plans for smarter, automated construction throughout the UK by 2035, with machine control playing a signi cant part.
There are two big reasons for this push: safety and productivity. The government wants to reduce injury risks to workers by having fewer staff on construction sites, close to machinery. With machine control systems, projects are completed faster and with less disturbance to the public. Automation also helps to mitigate environmental impact and the labour shortage and skills gap.
As a human machine interface (HMI), machine control systems are not fully automated, but they are an important step. As a step up from the Volvo Dig Assist machine control system, for example, Volvo Active Control automates some boom and bucket movements to improve excavation ef ciency. The sensors and processes that form part of machine control systems will be an enabler for further automation in the future.
https://www.youtube.com/watch?v=uhUeouvYaow
As well as automating certain movements, Volvo Active Control allows operators to set depth and height limits as well as a swing fence.
As public bodies back these systems, there is a trickle-down effect from the Tier 1 contractors to the rest of the industry, which has led to a surge in demand. Volvo CE dealers have been offering Volvo Co-Pilot with Dig Assist for a while, which is an integrated machine control system from the Volvo factory that stays on the excavator as it is sold.
Dig Assist offers many bene ts. However, it may not be suitable for everyone, in countries with very strong machine rental markets. Equipment is rented for project durations, aligning with a focus on operational expenses. Given this preference to
minimise upfront capital expenditures, retro t systems provide customers with the exibility to move systems between machines and get long-term value from their investments.
Retro t machine control systems rst appeared on bulldozers and motor graders about 20 years ago. Fast-forward to today, and contractors are running these systems on all sorts of equipment from different manufacturers. Many customers have mixed eets and appreciate the convenience of standardisation in their systems.
Customers buying excavators may ask if machine dealers can work with a third-party provider. To meet this need SMT has become a dealer for Unicontrol machine control systems. Unicontrol is a new player in the industry, founded in Denmark in 2018 with a mission to create a simple, user-friendly 3D machine control system that ts into existing routines. The technology is agnostic, using the same machine les and hardware, so it can work with any machine. In theory, a user could even move it between different types of machines within a eet. SMT GB can now deliver machines ready to use with a Unicontrol machine control system. The rm installs the hardware, sets up the software and ensures its precision. The dealer also provides support and a warranty covering both parts and labour. Volvo CE www.volvoce.com
SMT now covers the Unicontrol system in addition to the Volvo CE tools
Lee Shinkin, Highways Sector Lead at AtkinsRéalis, explores how synthetic environments and simulation are helping organisations capitalise on the value of their data to gain insight and drive forward-planning.
The challenges facing highway authorities and the organisations managing the UK’s roads are immense. The challenges include managing traf c ow and assessing the impact of interventions to ease ow, ranging from congestion charging zones to considering the mitigation of emissions. Overall, there a myriad of complex issues and data underlying the planning and building of road infrastructure.
Advances in technology, however, make it possible to use synthetic data techniques to visualise this complex data better, simplifying data sources and exposing unknown interrelationships. For example, this can reveal the effect traf c calming measures might have on traf c on residential roads.
Using synthetic data to create virtual worlds that decisionmakers can explore and interact with, helps them better understand the effects of potential interventions and changes upon future outcomes. Synthetic environments and simulation also enable highway infrastructure developers and planners to better use data to understand risk. These provide a picture of the current status quo of the road networks and help to predict how networks may change in the near and longer-term.
Using simulation to produce visualisations of data, of traf c ow for example, helps to contextualise it, meaning broader groups of key stakeholders can understand it, improving their engagement with potential change proposals. The images convey the story underlying the data to a wider audience – not just those with engineering or scienti c backgrounds – and can assist with securing buy-in for proposed activities. Visualisations show the possible bene ts and drawbacks of different interventions, allowing for greater understanding of future risk, and supporting more informed decision-making.
By applying synthetic data techniques during the early stages of a road project, numerous solutions can be analysed in simulated environments, with teams immersed in the virtual world during the feasibility stage.
Highways’ organisations capture extensive amounts of accurate, real-time data from their sensors, operational and information technology and asset management systems. Simulation and visualisation can capitalise on this data, delivering interpretation and insights that drive forward-planning.
For example, information on the key routes taken by vehicles within cities could underpin decisions on the introduction of congestion charging zones (CCZ) or other interventions to reduce traf c emissions. Simulations can be used to see the effect the introduction of CCZ might have on traf c on other routes in the short-, mid- and longer-term. They might also be used to identify how the building of a roundabout would affect traf c ow, mapping current data on vehicle ow against predicted ow, and showing where any bottlenecks might occur.
“ By applying synthetic data techniques during the early stages of a road project, numerous solutions can be analysed in simulated environments, with teams immersed in the virtual world during the feasibility stage ”
Further, sensor data from motorways could be used to create visualisations of managed motorways’ ow at rush hour and, in the long term, help assess the impacts from the introduction of automated vehicles. By predicting the different futures that might result from different interventions, simulations could allow highways authorities to make integrated, cohesive plans for these outcomes.
The techniques can also be applied as part of the highway design process, with synthetic environments forming part of a successful communications’ engagement strategy – helping to resolve issues which could threaten investment or delay highway improvements.
To plan for a future that will see smart cities, automated vehicles, and interconnected Industry 5.0 technology transforming our society, highways organisations will need to adopt innovative approaches. Through simulation and visualisation they can create a picture of potential futures, allowing them to develop, maintain and, if necessary, change their long-term visions as they move towards their goals.
By allowing highways authorities to ‘picture’ the journey, it will help them understand the effect each choice of route can have upon their destination. This foresight empowers these organisations to reduce costs, vehicle emissions and improve journeys for customers.
In the UK, a project undertaken by AtkinsRéalis for Wiltshire Council used simulation and visualisation to demonstrate the bene ts of proposed capacity and safety improvement works taking place on the A350 ‘Farmers’
roundabout in Melksham. It is an important transport link for towns in the west of Wiltshire, but was a bottleneck for traf c. Poor performance of the highway was perceived to be holding back local economic prosperity.
As part of an initial analysis, the design team utilised simulation tools to aid in the development of a solution. The results identi ed that, to speed up traf c, traf c lights would need to be introduced – a suggestion
negatively received both by project stakeholders and the local press.
To explain the rationale behind the design decisions, reduce future concerns and highlight the potential positive effects of the proposed traf c
lights to a non-technical audience, an interactive virtual twin of the roundabout was created. Built with a user interface, the synthetic world made it possible for stakeholders to independently navigate around the scene, and gave them the ability to switch elements on and off, to compare traf c ow at particular times for example.
Two datasets were used to create the virtual world: one showing current vehicle behaviour; and the the other highlighting the proposed changes to the design.
Green and red ‘cubes’ were attached to represent vehicles, which allowed stakeholders to directly compare both the existing and recommended designs. The virtual world clearly communicated the bene ts of the new design, displaying
improvements in traf c ow between the current and proposed layouts.
Once created, the roundabout application was used as part of the stakeholder consultation for the works. By comparing the original and proposed simulation data, the reasoning behind the complex changes became understandable. The model was also brought into play as part of the public consultation process. Site operations toimprove the roundabout started in early February 2019 and concluded in October 2019, when the traf c lights were activated. The project has been widely held to be a success, receiving favourable press coverage and public opinion.
AtkinsRéalis www.atkinsrealis.com/
Synthetic media is a catch-all term for the arti cial production, manipulation and modi cation of data and media by automated means.
Synthetic data is information that is arti cially manufactured rather than generated by real-world events.
Synthetic Worlds, Virtual Worlds or Metaverse are computer simulated environments that users can simultaneously and independently explore. The computer simulation provides users with perceptual stimuli they can manipulate, giving them a sense of presence.
Virtual worlds could be used across numerous areas within the highway’s estate including real-time control centres and training for workers, to familiarise themselves with onsite risks. Meetings to engage with stakeholders about forward strategies can also leverage virtual worlds to simulate ‘what-if’ scenarios based on current live data feeds.
Wacker Neuson is offering digital tools to assist its customers
The Wacker Neuson Group has expanded its digital strategy to develop new business models. Technologies such as the Internet of Things (IoT) are being used in the Wacker Neuson Group to offer customers in the construction solutions that deliver real added value. “We use digital technologies strategically to make our customers’ day-to-day work easier and more ef cient,” said Alexander Greschner, chief sales of cer of the Wacker Neuson Group. “In order to be able to offer the best solution for our customers, we have positioned ourselves in such a way that we can develop and operate digital products based on our own IoT backend. We have built up the relevant expertise in-house. In addition, we work with partners who are established on the market and can quickly develop suitable solutions together with us.”
An important partner is Trackunit which has been supporting the Wacker Neuson Group for several years in offering EquipCare, the customerfocused platform for eet and data management. The cooperation has now
been extended for another ve years. In this context, the Wacker Neuson Group is using Trackunit’s Kin technology to integrate non-powered equipment and attachments into the ecosystem via Bluetooth and gain a better overview of their usage. “Trackunit is an important partner for us that understands the direction in which our industries and customers are developing,” said Greschner. “As another strategic partner, we have entered into a longterm cooperation agreement with OneStop Pro.”
OneStop Pro helps the Wacker Neuson Group in developing additional
solutions for its digital product portfolio, connecting with customers more directly and thus responding even more exibly to market needs. One of the rst integrated products is the cloud-based EquipCare Pro software solution. It enables the management, scheduling and evaluation of all machines, equipment and bulk items, regardless of manufacturer or brand. EquipCare Pro helps customers to signi cantly increase the productivity of their machinery.
Wacker Neuson www.wackerneuson.com
“ Trackunit is an important partner for us that understands the direction in which our industries and customers are developing ”
JCB and Leica Geosystems are now offering factory- tted 2D and 3D-ready semiautomated excavator control solutions.
The INTELLIGRADE solutions are offered on the JCB 220X tracked excavator in the UK before being offered across the whole JCB X Series range in additional regions.
Leica Geosystems 2D and 3D-ready machine control solutions are available with semi-auto con guration to enhance productivity, accuracy and safety by automating functions such as boom, bucket and tilt rotator control, and to reduce human error in construction operations.
Working to predetermined site plans, the 2D machine control system provides real-time guidance and accuracy for tasks such as grading and levelling, ensuring the excavator’s bucket or blade achieves the desired slope or elevation. This solution is ideal for projects that involve simple terrain or require basic grading.
Customers looking for greater accuracy, precision and additional semi-auto functionality on earthmoving applications can choose the 3D-ready option to retain the exibility of upgrading to 3D in the future. To upgrade the factory solution to a 3D version, customers can contact their local Leica Geosystems sales of ce or
dealer, who will support with calibration and installation at the JCB dealership or at the customer’s premises.
JCB Business Head – Excavators, Paul Swallow said: “We are committed to innovation with our X Series range and
this introduction will mean new levels of ef ciency and reduced operating costs. In addition, it gives operators greater levels of accuracy when using X Series machines, delivering consistently high standards on construction sites. It also reduces the need for additional surveyors onsite, leading to enhanced levels of safety.
“Customers can achieve all the bene ts of semi-auto machine control without the disruption or complexity of retro tting in the eld.”
Vice President Heavy Construction, Machine Control Field Solutions at Leica Geosystems, Tommi Kauppinen said: “By leveraging our respective strengths and expertise, we aim to create a seamless integration of easy-to-use machine control technology into JCB’s excavators.”
JCB www.jcb.com
Leica Geosystems www.leica-geosystems.com
Machine control technology from Leica Geosystems can now be speci ed for JCB machines at the factory https://www.youtube.com/
Trimble and Radiodetection have established a collaboration to improve the technology used in the utility measurement and mapping process.
Through the integration of the Trimble Catalyst DA2 GNSS system and Radiodetection’s RD MapTM+ application and precision locator products, the software and hardware integration streamlines utility-locating work ows. This can provide highaccuracy measurement capabilities for the generation of underground utilities maps in a single eld operation.
Traditionally, eld technicians mark their measurements onsite manually or rely on data entries to provide to of ce staff for map creation after a site visit. Data collected with the Trimble Catalyst DA2 GNSS system can now be simultaneously synced with Radiodetection RD Map+ and precision locators that nd and mark buried utilities. By streamlining this connection, workers can ef ciently and accurately digitise utility-line locations and reduce costly reporting errors.
“Accurate geolocation is critical to the operation and maintenance of underground utilities and public infrastructure,”
said Stephanie Michaud, strategic marketing manager, Trimble Surveying & Mapping Field Solutions. “By adding survey-grade capabilities to existing utility work ows, this collaboration creates a connected solution that provides con dence and reliability during the data capture process.”
This integration advances utility measurement work ows by giving workers the capability to accurately represent the utility asset in a digital format. This streamlines the operation, maintenance and construction process whenever utilities are involved.
“We are excited to bring to the market this solution alongside Trimble as part of the Radiodetection ‘Map It Your Way’ initiative,” said Tom Turner, product management and marketing director, Radiodetection. “The Map It Your Way initiative is launching a range of solutions combining our latest digitallyenabled hardware with mobile applications to allow customers to
Trimble and Radiodetection have collaborated to develop better digital maps of underground utilities
Trimble has updated its Viewpoint Spectrum and Viewpoint Vista construction enterprise resource planning (ERP) software, which now includes Automatic Invoicing capability. The integration of Azure AI Document Intelligence delivers ef cient Automatic Invoicing, helping turn paper and PDF invoices into validated, unapproved invoice entries within Spectrum and Vista automatically. This allow for faster, more accurate work ows and can save time and money for users.
“ Accurate geolocation is critical to the operation and maintenance of underground utilities and public infrastructure ”
accurately map underground utilities.”
Trimble Catalyst DA2 GNSS solutions are available through Trimble Geospatial Distribution Partners. Trimble Catalyst GNSS solutions are also available through the Radiodetection Distributor Network alongside Radiodetection’s precision locators and RD Map+.
“In an industry where projects operate on tight schedules and margins, every second and every dollar counts,” said Lawrence Smith, vice president and general manager of Construction Management Solutions at Trimble. “Trimble’s Automatic Invoicing/Document Intelligence integration was created to take the manual burden of data entry and veri cation off the accounting department and automates it using arti cial intelligence. The result is a more accurate process and a higher level of productivity, while also freeing accounting departments to focus on more strategic tasks.”
One signi cant advantage of the integration is the reduction in errors. Construction projects involve intricate nancial
processes, and even minor inaccuracies in invoices can lead to major setbacks. Trimble’s Automatic Invoicing/Document Intelligence integration automates data extraction, delivering greater accuracy, improved nancial work ows, and streamlined project management overall.
Eric Boyd, corporate vice president, AI Platform, Microsoft said, “By integrating Microsoft’s AI capabilities into their solution, Trimble is helping troubleshoot unique challenges faced by the construction company further demonstrating the power of AI to rede ne and elevate essential business processes.”
“We know that accounting teams spend an inordinate amount of time inputting, approving and paying invoices,” said Smith. “Additional steps are then added if mistakes are made, which happens about 10% of the time and takes an average of 15 minutes to correct, according to a recent poll in our customer community, The Network. If a contractor processes 200 invoices a week and 10% of them have errors, that equates to ve hours/week spent correcting invoices - if the errors are caught - which could be the difference between a project being pro table or not.”
Trimble www.trimble.com
Europe’s construction equipment manufacturing association, CECE has been monitoring important moves with regard to machinery regulations.
An ad-hoc group of PT Data members recently exchanged views on the expected implications for construction equipment manufacturers stemming from the nal text of the Cyber Resilience Act (CRA) – the new EU cybersecurity law for connected products, including machinery.
ambassadors. To become law, the CRA nal text requires formal adoption by Parliament and Council.
The CRA nal compromise text has achieved stability following the vote of the parliamentary Committee on Industry, Research and Energy (ITRE). In addition, the political agreement reached in trilogues had already been endorsed by the EU
During the meeting, PT Data members went through the key aspects of the nal text with a view to assessing the potential implications for construction equipment manufacturers in terms of cybersecurity requirements and manufacturers obligations to be ful lled.
CECE members welcomed the improvements introduced in relation to the determination of the product support
period, which explicitly refers to the expected use time of the product. This is further substantiated by the reference to the proportionality element and the support period of integrated components. The latter represents a good addition for the industry since machinery products’ support period is dependent on their components.
Members appreciated the alignment of the vulnerability reporting mechanism with the NIS2 directive timeframe and obligations.
In addition, the Commission’s guidelines to facilitate the CRA implementation is also considered a positive development, especially when it comes to the determination of what constitutes substantial modi cation under the regulation. According to the nal wording, digital products should be considered substantially modi ed by a software change where, inter alia, the software update modi es the intended purpose of that product. Interpretative guidelines would be welcomed.
“ Members appreciated the alignment of the vulnerability reporting mechanism with the NIS2 directive timeframe and obligations ”
The interpretation of substantial modi cation could play a key role to identify in which cases the new requirements apply also to products placed on the market before the CRA application date. As a matter of fact, the CRA regulation will apply only to new products placed on the market after its application date, unless those products placed before that are subject to substantial modi cations.
In the context of the CRA nal text analysis, members identi ed a number of controversial aspects requiring further clari cation in the coming months. Speci cally, the reference to the interplay with the new Machinery Regulation (MR) as concerns were raised from a functional standpoint. According to a preliminary assessment, future CRA standards for the security elements included under the MR will be developed in such a way that would also allow for compliance with the functional safety aspects. This should be addressed by the Commission’s guidelines when it comes to manufacturers that are subject to this Regulation who are also subject to other related Union harmonisation legislation. Additionally, further clari cation should be provided on the spare parts exemption with reference to components. Finally, the interpretation of product functions as regards remote data processing seems problematic and needs further clarity.
CECE Secretariat will continue to closely monitor the developments on this crucial legislation and provide members with assistance throughout the implementation phase.
Richard Clement, deputy general manager of Smart Construction explained the digital transformation of the construction industry and how applying IoT tools and software technologies will improve jobsite efficiency.
Smart Construction is a digital transformation strategy designed to optimise the earthmoving process, developed by the expert team at Komatsu.
As the developed world moves towards digital transformation, the construction industry must tackle one of our biggest challenges: the introduction and implementation of smart systems and technology. The construction industry must embrace and utilise technology to increase jobsite productivity and enable
the completion of safe, ef cient and accurate jobs.
By introducing and implementing digital technology into the construction journey, there is a huge opportunity for us to revisit the modern-day jobsite.
Research shows that the construction industry is falling behind other sectors when it comes to digital transformation. However, many processes could be improved by digital changes that can be incorporated into current operations, and that is why
Smart Construction will allow the industry to progress in the future
https://www.youtube.com/watch?v=TxTMlN7y_aQ https://www.youtube.com/watch?v=TxTMlN7y_aQ
as an industry, it is time to act and consider how to improve the adoption of digital tools and skills across the sector. This bene ts the end customer as well as construction teams and contractors thanks to potential cost-saving, upskilling and more accurate monitoring and tracking.
Machine guidance for excavators is an advanced technology that helps excavator operators perform their tasks with greater precision and ef ciency. It uses GPS and sensors to track an
excavator’s position and orientation in real time. A digital design model of the project is created beforehand, and the system guides the operator to follow it accurately. This leads to increased precision, faster completion of projects, cost savings and improved safety. It is a versatile tool that bene ts construction projects of all kinds.
An example of machine guidance is the Smart Construction Retro t, a 3D guidance kit that is easily installed and compatible with crawler and wheeled excavators, across a wide range of weight classes, con gurations and manufacturers. The hardware kit is compact and designed for easy installation, and its 3D Guidance system including multi-constellation GNSS delivers centimetre precision. Based on the jobsite and the project needs, the operator can switch between 2D and 3D Guidance. The Retro t Kit’s automatic le conversion for Land XML, DXF, Topcon, and Trimble formats ensures seamless integration with customers’ existing 3D systems from other manufacturers.
Besides the standard 3D guidance functionality, the Retro t kit also comes with an integrated payload meter option for Komatsu machines. This feature allows for real-time weighing of material, eliminating the need to stop and weigh each truck load. This boosts productivity by ensuring each truck is loaded to its maximum capacity without risking overload.
Real-time data and information streams from the machines doing the work are invaluable to contractors and managersand until recently, this has not been something the industry has been able to harness. Moving towards a fully connected future for construction, reliance on precise data will only strengthen and allow us to make positive changes for the better industrywide, resulting in improved productivity and ef ciency.
There are multiple bene ts to investing in IoT tools and software technologies. From upskilling the workforce, reducing the amount of time required at site or remotely to gather information and communicate changes, to providing tracking data to the customer. No more should we spend valuable time manually collecting data, where IoT tools can instead collect information, also allowing the user to control the devices remotely over a network.
Beyond functioning as a standard 3D Machine Guidance kit, the Smart Construction Retro t also integrates into the Smart Construction solution suite, serving as a gateway towards optimising earthmoving processes. As an IoT tool, it automatically gathers terrain and payload data, which can be visualised and analysed using other Smart Construction solutions, such as Dashboard, fostering data-driven decisionmaking.
There are a host of solutions working to offer construction teams an amalgamated approach to connected construction. Machine guidance is one of these processes and while it may only be a small change for the teams on the ground, it shows a wider willingness from the industry to adapt to new technologies to strategically improve jobsite processes.
This movement has the potential to transform the approach to earthmoving and groundworks. In order to best prepare for the future, the industry needs to ensure that it is able to harness data at the jobsite, making the small steps to begin what will be a total transformation.
Smart Construction www.smartconstruction.io
High accuracy positioning is achievable for users of Mincon drilling and piling attachments using a Trimble Ready factory option
A Trimble Ready factory option is now available for new Mincon piling and drilling attachments. Customers for Mincon Drill Mast Attachments for skid steers and excavators now have an option for the installation of the Trimble Groundworks Machine Control System. This can reduce the cost and complexity of the installation for the contractor.
Mincon Solar Installation Drills and Pile Drivers can pre-drill through rock, install ground screws and drive piles. Trimble Groundworks is a machine control solution that boosts the speed and accuracy of drilling and piling operations. Fitting Trimble Groundworks systems to Mincon drilling units provides stakeless navigation, positioning accuracy and as-built data so that contractors can boost
installation ef ciency.
The integration of Trimble Business Center Software design capabilities in the of ce and Trimble Groundworks machine control in the eld increasea the ef ciency and productivity of drilling and piling. Trimble WorksManager Software also enables the syncing of data from of ce to eld, reducing site visits and providing a single source of truth.
Mincon www.mincon.com
Trimble www.trimble.com