
4 minute read
New food calls for new technology
The latest science and technology may hold the key to solving the world’s future food sustainability goals. Food & Beverage Industry News
It is predicted that the global demand for food will increase by up to 70 per cent by 2050. We cannot meet this demand sustainably or ethically with current production methods alone.
One of the solutions being actively explored today is cellular agriculture, which uses cells and innovative biotechnologies to produce accessible, ethical, and sustainable agricultural products.
It is most commonly used to make animal-derived foods and ingredients such as meat, seafood, dairy products, fats, egg whites and gelatin.
Cellular agriculture is an innovative approach to producing animal products without traditional animal farming, and has the potential to overcome six critical challenges facing our current agricultural system:
• Food insecurity
• Deforestation
• Biodiversity loss
• Cl imate change
• Public health
• A nimal welfare
The actual impact of cellular agriculture will depend on numerous decisions biotechnology food companies will have to make as they move towards commercial scale.
Innovation and technology in a world of new food production processes
Using well-proven methods from the pharmaceutical and biotechnology sectors, cell cultivation and fermentation have emerged as game-changing technologies in food production.
Bürkert recognises the need for precise control and monitoring of these processes to achieve consistent and high-quality results, and has extensive experience in the control technologies required for these processes.
One example is Bürkert’s work with the Centre for Solar Biotechnology at University of Queensland: In 2019 Bürkert helped the Centre achieve the precise control of solar-powered bioreactors for the production of microalgae cultures in order to produce high quality biomass that is then used to develop bio-inspired green medicines, foods and nanomaterials.
At the heart of successful cell cultivation and fermentation lies the ability to create and maintain optimal growth conditions.
A bioreactor’s purpose is to provide the greatest possible product yield.
To do this, it requires precise regulation of all important parameters such as nutrient concentration, pH, temperature and oxygen content to optimally support fermentation.
However, the biochemical process reacts extremely sensitively to changed parameters.
This means that too little or too much nutrient solution must never be added, for example. If the process is disrupted, all supplemented substances are unusable, which results in unnecessary costs and time delays.
Constant monitoring of the correct feed is necessary, and contamination by foreign germs or CIP media must be avoided, as it would render the entire batch of the product unusable.
For these reasons and others, bioreactors are always equipped with numerous sensors and valves whose functions must be orchestrated with precision.
Bürkert’s advanced automation solutions provide the necessary precision, control, and reliability to achieve the required outcomes.
State-of-the-art control valves, sensors, and controllers ensure accurate monitoring and regulation of critical parameters such as temperature, pH, dissolved oxygen, and nutrient supply.
Every application will be unique, and the ability to provide a customised solution is essential.
From the lab to mass production
The complexity of such systems can lead to complex control wiring and high build costs.
While these costs may be tolerable in a small lab environment, food manufacturers hoping to engage in cellular agriculture need to look to the needs of future mass-production, once the food production method has been perfected. It is therefore essential that the engineering costs are minimised.
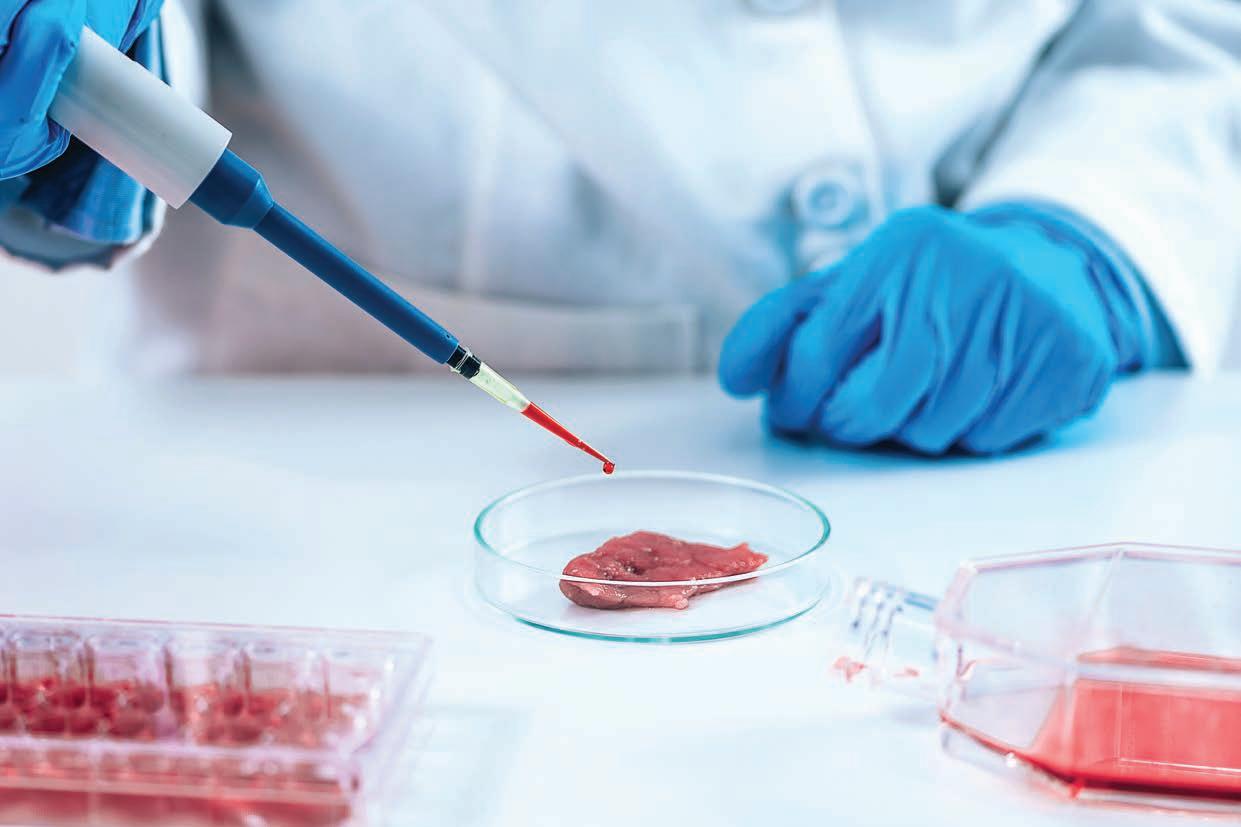
Different types of devices are needed for new foods processing, including fastacting valves and actuators, flowmeters, pH, pressure and temperature sensors.


Traditionally each device has an individual cable connection back to a control cabinet, and has the limitation of only providing the basic necessary functionality, with no diagnostic data.
But the biggest issue is the complexity of wiring and the associated build and maintenance costs: discrete wiring leads to higher installation expenditure.
The solution to reducing costs and improving maintainability is to use a decentralised, digital solution.
Bürkert’s automation solutions reduce the number of cables to four, and at the same time only one type of IO-Link master serves all devices.
All relevant data is available digitally, and significantly more parameters can be utilised than in traditional systems.
This enables permanent diagnostics to ensure system availability at all times. In addition, all push-in connectors are replaced by M12 connections, making the assembly process of electrical devices is very fast, safe and simple.
The conversion from analogue to digital devices also eliminates the need for recalibration after a certain operating time.
Digital communication and simplified wiring also improve future fault-finding and maintenance, making a system that is faster to diagnose and faster to repair or maintain.
Within this highly regulated and pharmaceutical-style manufacturing food space, reliability and precision will be essential to operators.
Bürkert’s solutions and industry experience, along with its fit-for-purpose product range, will ensure peace of mind for manufacturers seeking to be part of the new generation of food manufacturing.
Sustainability and customisation
Sustainability is also a cornerstone of the new food movement.

Through precise control and efficient use of energy and water resources, fast acting and precise Bürkert technology can help food producers achieve their sustainability goals while maintaining product integrity and quality.
The new food landscape also encompasses a wide array of applications, each with its own set of challenges and requirements.
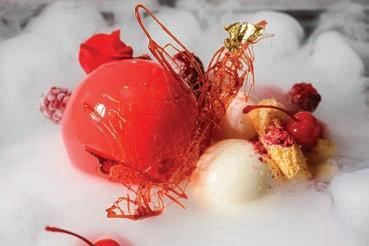
Bürkert’s portfolio of products and services can be customised to suit diverse applications within the food and beverage industry.
Whether the application is plantbased protein production, precision fermentation, or alternative dairy products, Bürkert can provide expertise and experience to provide tailor-made solutions, from small-scale pilot projects to large-scale industrial facilities.
Staying ahead of the curve
Cutting-edge science may well hold the key to solving many of the world’s food sustainability problems, and the future of food lies in the latest in technology to provide precision, efficiency, and innovation.
As the new food industry continues to evolve, it is essential to remain at the forefront of innovation.
Bürkert not only offers cutting-edge solutions but also collaborates closely with industry partners and experts to drive progress and shape the future of food.
Through Bürkert’s participation in research and development projects, it stays abreast of emerging trends and technologies, ensuring that manufacturers benefit from the latest advancements in the field. F
Held at the Melbourne Convention and Exhibition Centre, MICE routinely hosts more than 170 exhibitors representing all sectors of the global supply chain, including coffee producers and green importers, equipment manufacturers, roasters, café owners, and baristas.

With plans well underway, the 2023 event, scheduled for August 17-19, is already looking to meet, and even exceed, expectations after a bumper 2022.
Since its inception in 2012, MICE is recognised as the largest dedicated coffee show in the Southern Hemisphere.
Organisers reiterate the purpose of the expo is to connect buyers and sellers and bring industry members together in the one space annually to do business. It’s a one-stop-shop to the latest and greatest technology circulating the global coffee industry.
A strong of key brands that have already committed to the 2023 event, including BioPak, specialists in sustainable packaging, which is taking the coffee industry by storm as consumers move towards more sustainable practices.
BioPak combines innovative material design with a business model that is