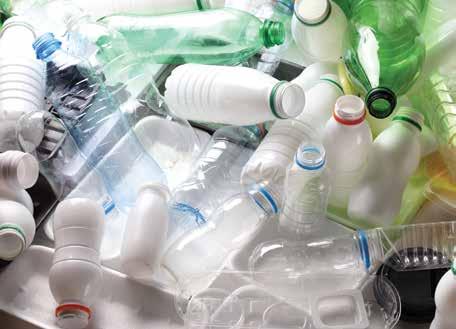
12 minute read
AIP
Redesigning packaging with reduce, reuse, recycle in mind
Author Nerida Kelton MAIP, Executive Director, Australian Institute of Packaging (AIP)
The AIP’s executive director, Nerida Kelton, explains why the 5Rs are important for consumers.
Reduce, reuse and recycle are the three most important areas for long-term changes when it comes to packaging design.
As a consumer, you might have heard about the “Waste Hierarchy” and the 5Rs. From a consumer perspective they are: • Refuse – do not purchase unwanted items. • Reduce – eliminate single-use packaging wherever possible. This means declining plastic coffee cups, shopping bags, straws and buying products that are sustainable. • Reuse products more than once.
Purchase reusable water bottles, keep-a-cups, and recyclable shopping bags • Recycle – ensure that you place your products in the recycling bins and purchase products that are recyclable. Look for products that are using the new Australasian Recycling Label (ARL) to better understand the true recyclability of the materials. • Repurpose – purchase products that are made from recycled materials – consciously purchase bags, shoes, furniture, jewellery that you know is made from recycled content.
Mindsets have shifted over the last few years, and globally consumers are actively driving brands and their packaging departments to supplement sustainable packaging design to incorporate the 5Rs and to redesign with environmental impacts in mind.
Packaging technologists are being asked to reconsider the outcomes of their packaging design all the way across the supply chain from manufacturing to recycling, and also consider a closed-loop and more circular approach. Packaging
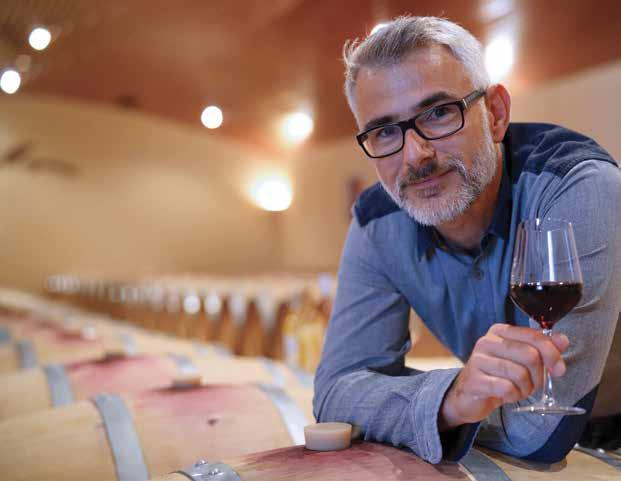
design can no longer be linear.
When discussing the waste hierarchy from a packaging design perspective, reduce, reuse and recycle are the three most important areas for long-term changes as they are the preventative measures with the highest level of impact.
Achievable steps for packaging technologists can include redesigning the shape and size of a product, reducing thickness and weight of materials, shifting to recyclable materials, and developing a closed-loop system for products. However, any adaptations to the packaging design, structure and form must not compromise the ultimate purpose of packaging, which is maintain the ability to protect, preserve, contain, communicate and transport a product to the consumer. First and foremost, packaging must remain fit-for-purpose before any structural changes are made to a pack. The AIP encourages all packaging teams to undertake a lifecycle assessment where possible before any pack is altered. A redesign feature of packaging that consumers are embracing is reuse whereby a customer can refill their products using the same packaging.
It is important to note that reusable containers have less impact on the environment than one that is single use. Packaging technologists need to re-imagine their packaging for continued use and the ability to have multiple uses for the consumer.
Consumers are also driving the focus to what is really happening with packaging and the end of life. Packaging technologists are now being asked to stop and review their packaging and find out whether it is actually being recycled or landfilled in the country it is sold in. The availability of the APCO PREP tool enables this decision making. In addition, if the material is capable of being recycled in the country in which it is sold, then consumer waste and greenhouse gas emissions will be reduced across the lifespan of the product. This in turn achieves the 2025 National Packaging Targets that all brands are working towards.
If the material is unable to be recycled, then look at the possibility of moving to a recycled content, and even the use of renewable resource raw materials. Once again, the AIP urges consumers to undertake a full lifecycle assessment if possible, before moving to recycled content to determine if this is in fact the best decision for a product.
A recent example of the reuse, refill and recycle concept that has considered the product all the way through the supply chain is Cif ecorefill. Unilever announced on its global website the launch of Cif ecorefill, the new at-home technology that allows consumers to refill and reuse their Cif spray bottles for life. Cif has worked to create a no-mess solution, becoming the first household cleaning brand to do so with this pioneering twist and click refill design. Made with 75 per cent less plastic, Cif ecorefill attaches to the current Cif Power & Shine bottles. Through its technology, it seamlessly releases the super-concentrated product into the bottle, which is filled with water at home. The ecorefills are 100 per cent recyclable once the plastic sleeves are removed and, by the end of 2020, the ambition is for all Cif ecorefills and spray bottles to be made from 100 per cent recycled plastic. Going smaller is certainly better – the ecorefills are lightweight and save on storage space. Diluting the product at home means 97 per cent less water is being transported, fewer trucks on the road and less greenhouse gas emissions.
Every day, more companies are announcing refillable packaging solutions including cosmetics and beauty, toiletries such as shampoo and soaps, cleaning products and beverages. The journey to sustainable packaging has only just begun and it is exciti ng to see what innovative designs packaging technologists are working on that address reduce, reuse, refill and recycle. F
Leader in Low Flow Fluidics Handling Technology
Flow ranges for gases from 0 - 0,7 ml n /min up to 0 - 11000 m 3 n /h
Flow ranges for liquids from 0 - 100 mg/h up to 0-600 kg/h
Pressure ranges from 0 - 100 mbar up to 0 - 400 bar
Laboratory, industrial (IP65), Class I Div. 2 or ATEX approved design

Analog, RS232, FLOW-BUS, PROFIBUS DP, PROFINET, DeviceNet™,

Modbus, EtherCAT®
Innovation and sustainability were the stars of the Food & Beverage Industry Awards’ night.
Thursday July 18 was a great night at Doltone House in Sydney for the 16th annual Food & Beverage Industry Awards. It was an occasion where a lot of the nominees and winners thought outside the box – whether it was a new food or beverage product, innovative packaging, or plant and machinery that made a difference to the processing of food and beverages. Over the next few pages, we list the nominees, celebrate the winners, and give a pat on the back to all those who think outside the box and make this such a fascinating industry.
BEST OF THE BEST AND INNOVATIVE TECHNOLOGY OF THE YEAR
Inox Australia Stock Processing Systems Inox supplied a Melbourne-based company with a beef, chicken, seafood and vegetable stock processing system that provided the customer with increased yield and improved processing time (from 12 hours down to two hours). It also included a heat recovery system to provide heated water for the fully automated Clean in Place (CP) system that cleans the process system ready for the next batch.
Taking about seven months to bring to fruition, features of the system include a single user operational interface; safe and ergonomic handling of the product during the process from start to finish; hygienic design of the process including zero wastage of product at end of production; and improved yield of raw materials by pressure processing instead of traditional atmospheric process.
“It’s an automatic system that allows you to run it for a couple of hours, and then come back and it’s all done,” said Inox managing director, Robert Becher. “It started off as a bespoke system, but things come up, things happen, and so we adapt the design to fit the purpose.”
All materials used are stainlesssteel 304SS and 316SS grade and built from scratch by Inox.
The system works by putting up to 1000kg of raw materials into a stainless-steel basket, which is lifted by electric hoist into the automatically opening pressure vessel. Water is filled into the vessel to the required volume set by the
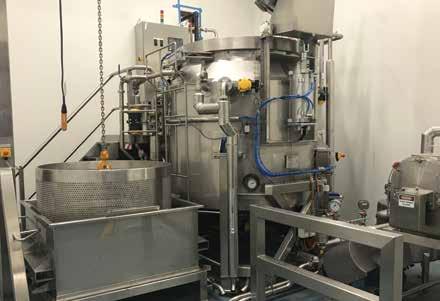
Inox Australia’s managing director Robert Becher (left) with Flavour Makers northern sales manager, Rowan Barnes.
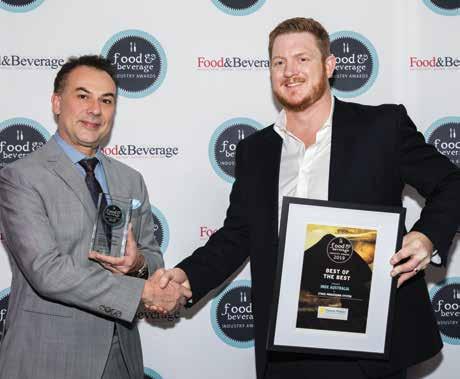
touchscreen operational interface.
The process is fully automatic to the set parameters and alarmed when the process is completed. Following the cooking procedure, the CIP water is circulated through the vessel heating jacket, which serves two purposes. The first is to cool the cooking vessel to a temperature that allows the product to be discharged. Second, the heat recovered from the cooking vessel is used to heat up the cleaning water, therefore no external heating of the cleaning water is needed.
The liquid stock is then pumped through a special design filtration system to a holding tank that is ready for the product to be received by the external filling line. The basket is removed from the vessel, the waste product is dumped into a hopper underneath the basket ready to be removed by forklift to the external waste disposal bin.
Following this, the basket is cleaned within the vessel during the CIP process and does not exit the food processing room at any point ensuring that the equipment is cleaned and cannot be contaminated externally.
“I am speaking to several companies about a similar system both in Australia and Asia,” said Becher. “One of the things that opens peoples’ eyes is the cleaning part of it. Also, the energy efficiency part of it has impressed people whereby we use heat that usually dissipates into the atmosphere for another purpose. The second thing is, we reduce the production time drastically. They used to run two shifts to do every batch, but now they are doing it in half a shift. This means they can double their output in half the time.”
INNOVATIVE TECHNOLOGY OF THE YEAR FINALISTS
Operations Feedback Systems – OFS-X & OFS-Flow Pollen Consulting Group – Digital Twin Trust Codes – QR/NFC codes that provide traceability CSIRO – shockwave technology
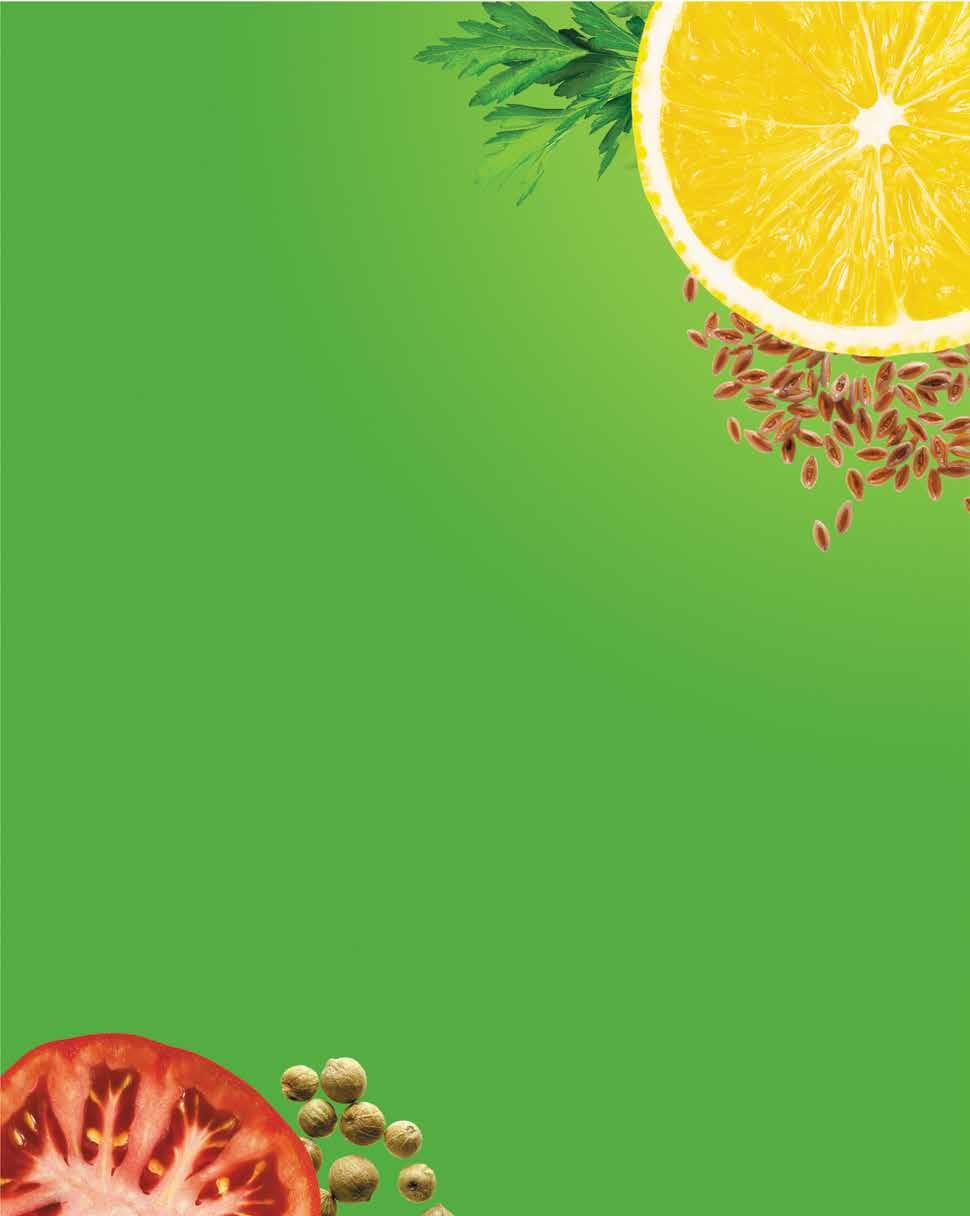
CEO of AquaBotanical, David Driver (left), and Kevin Cole, territory manager for New South Wales and Queensland for Rockwell Automation.
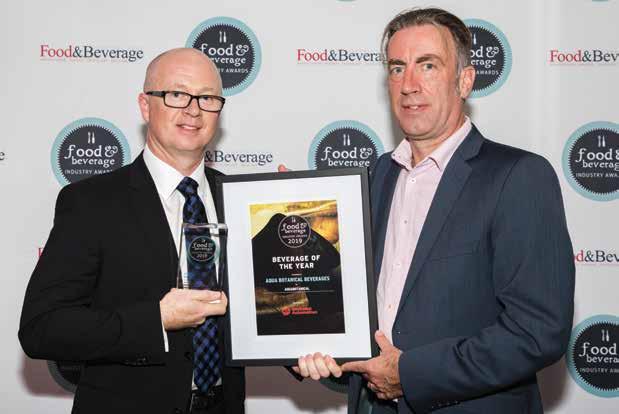
BEVERAGE OF THE YEAR
Aqua Botanical Beverages AquaBotanical Botanical Water is the world’s first natural plant-based drinking water. It is a new category of water and has won global beverage awards for Best Technology Innovation, Best CSR Initiative, Best New Water Concept, Best Sustainability Initiative and Best New Drink Concept. It is one of those concepts where people wonder, “why hasn’t anybody thought of this before?”
AquaBotanical is committed to ensuring that it can bring plant-based water to everyday Australians.
Its globally patented Botanical Water Technology (BWT) converts the aqueous liquid (waste) from fruit and vegetable concentrate and sugar-milling into clean, green and safe drinking water. It is bottled in glass under the company’s AquaBotanical brand, but importantly, the technology can be scaled through installation in existing juice extraction facilities.
After many years of research, AquaBotanical’s inventor, Dr Bruce Kambouris, found a way to harvest the naturally occurring water found in fruit and vegetables. Kambouris combined intuition with science to produce natural water made from plants and in so doing coined the term “Botanical Water” to reflect its new sustainable source.
Among his many roles in business, Terry Paule is executive chairman of AquaBotanical, the company responsible for producing the water. He was excited about the product the moment he heard about how it worked.
“As a company, we look for people like Bruce, who have a great idea, but sometimes lack the execution skills to get it over the line,” he said. “Bruce was introduced to me by a friend of mine who had heard about the invention some years. He told me that Bruce was making water out of carrots, which intrigued me. I flew up to Mildura, met Bruce, and a year later we ended up partnering in his business.
“We soon realised that this wasn’t a small idea. It was transitional and very large disruptive idea on a global scale.”
AquaBotanical is made by harvesting surplus water extracted during the juice concentration process. This aqueous liquid is filtered and mineralised and the end result is a great tasting clear, clean and environmentally green natural water made from plants.
Botanical water is 100 per cent natural, clean, green and safe to drink. The globally patented process guarantees that the natural water is free from sugars, toxins, microorganisms and additives. In addition, the manufacturer believes that its plant-based Botanical Water is a healthy alternative and considered the most suitable water for vegetarians and vegans as it does not come into contact with animals or animal by-products.
The company estimates that there’s an opportunity to produce over one trillion litres of Botanical Water around the world.
“A lot of industries, such as the sugar cane industry, literally extract billions of litres of water a year from the cane plants, and throw it away,” said Paule. “Often in places like India, it is pumped out into the water to the detriment to the environment. All of this water that is coming out of these plants can be cleaned up and converted into clean, green drinking water.”
More than 70 per cent of the Earth is covered in water, and of this water, 2 per cent is trapped in glaciers, and only 0.4 per cent is drinkable and needs to be shared across seven billion people, which is why this product can make a difference in developing countries where clean drinking water is not readily available.
Some of the world’s largest aquifers are now polluted and overused and are drying up faster than they are being replenished. Botanical water taps into an otherwise unused and often discarded new source of water, making it one of the world’s most sustainable, cost effective and environmentally friendly water source.
BEVERAGE OF THE YEAR FINALISTS
Maltra Foods – Brod Kvas Ginscato – Ginscato Herbal Fix – herbal fix beverages Bowled Over Beverages – kȯ-fē tonic syrup Kombucha Me – Kombucha beverages Nutra Organics – Lunar Latte Margaret River Kombucha Co Pty Ltd – rok Kombucha MateCo2 – Sparkling Yerba Mate drink Brouhaha Brewery – Strawberry Rhubarb Sour
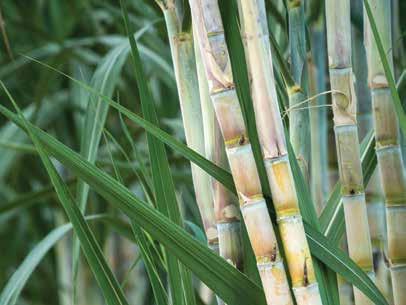
we make sweet surprises at lunch time possible because we make the software that ensures every cookie is perfectly baked, filled and packaged, every time... learn how by attending Rockwell Automation TechEd - Gold Coast, QLD 3-5 September 2019
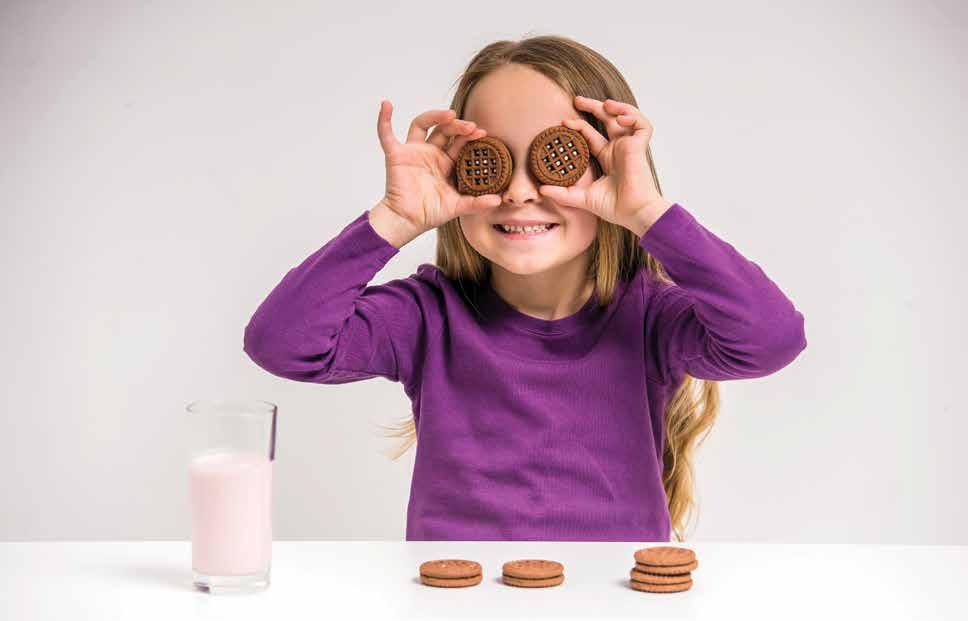