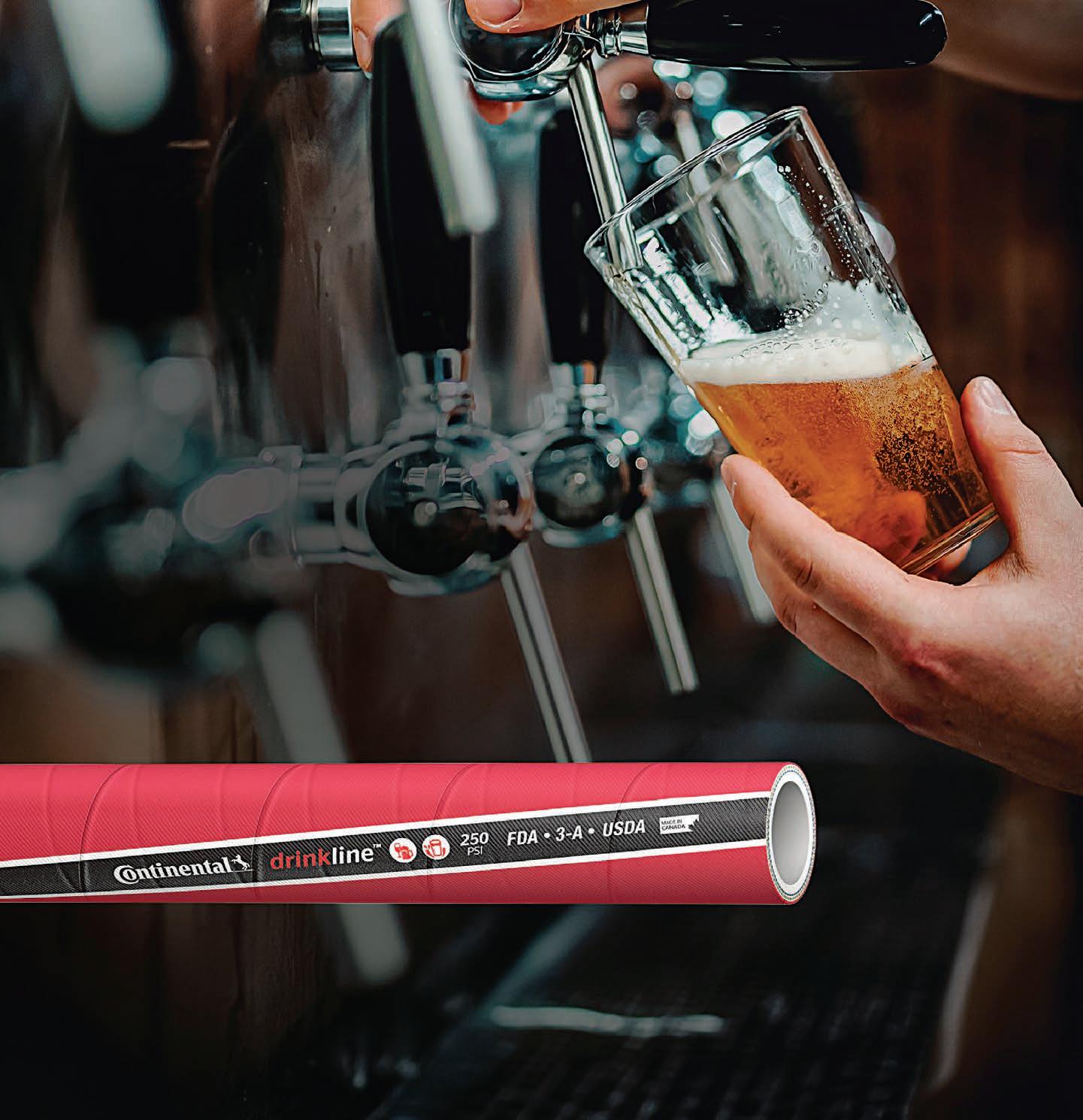
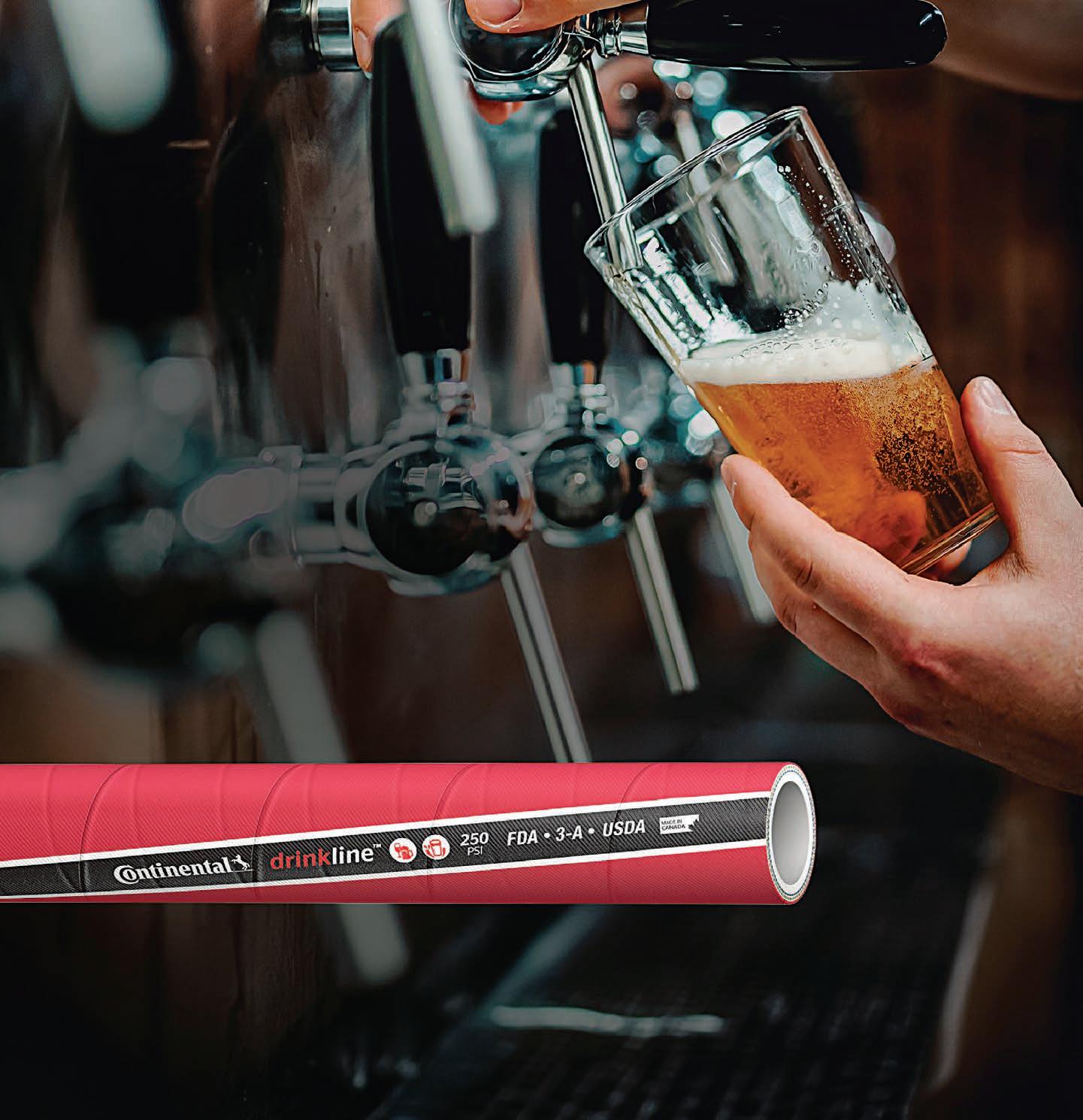
DRINKLINE:
TIGHT SITUATIONS easily handles
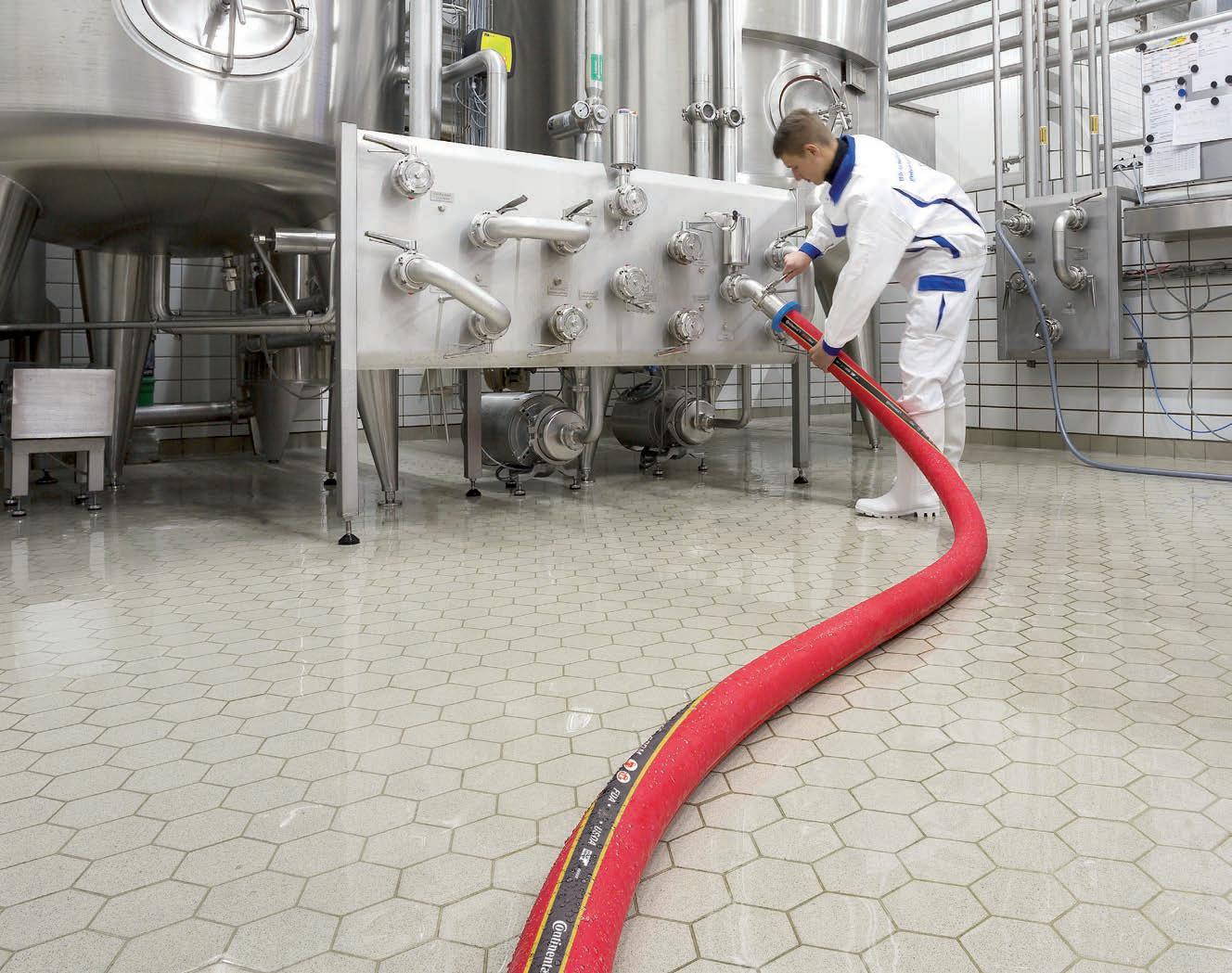
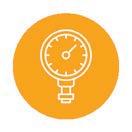
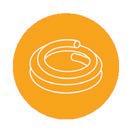

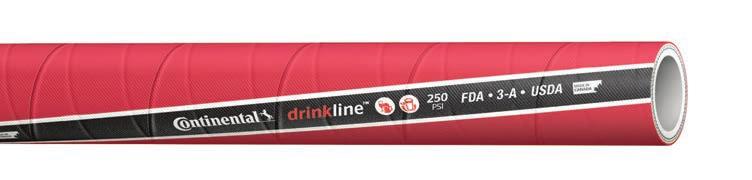
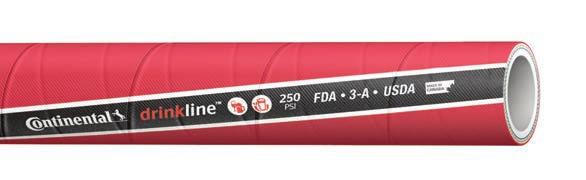
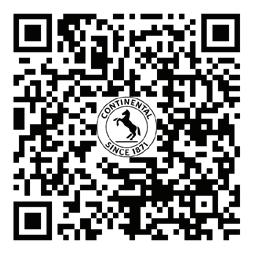
CEO: John Murphy
COO: Christine Clancy
Managing Editor: Mike Wheeler
Editor: Adam McCleery
Ph: (02) 9439 7227
adam.mccleery@primecreative.com.au
Art Director: Michelle Weston
michelle.weston@primecreative.com.au
Sales/Advertising: Franck Casili
Ph: 0434 785 611
franck.casili@primecreative.com.au
Production Coordinator:
Salma Kennedy
Ph: (03) 9690 8766
salma.kennedy@primecreative.com.au
Subscriptions AUS NZ O/S
1 year subscription 99 109 119
2 year subscription 189 199 209
For subscriptions enquiries please email subscriptions@primecreative.com.au
Copyright Food & Beverage Industry News is owned by Prime Creative Media and published by John Murphy. All material in Food & Beverage Industry News is copyright and no part June be reproduced or copied in any form or by any means (graphic, electronic or mechanical including information and retrieval systems) without written permission of the publisher. The Editor welcomes contributions but reserves the right to accept or reject any material. While every effort has been made to ensure the accuracy of information, Prime Creative Media will not accept responsibility for errors or omissions or for any consequences arising from reliance on information published.
The opinions expressed in Food & Beverage Industry News are not necessarily the opinions of, or endorsed by the publisher unless otherwise stated.
© Copyright Prime Creative Media, 2024
Articles
All articles submitted for publication become the property of the publisher. The Editor reserves the right to adjust any article to conform with the magazine format.
Cover Image: Koko Black Head Office
379 Docklands Drive
Docklands VIC 3008
Ph: +61 3 9690 8766
enquiries@primecreative.com.au
http://www.primecreative.com.au
Sydney Office
Suite 303,
1-9 Chandos Street
Saint Leonards NSW 2065, Australia
Ph: (02) 9439 7227
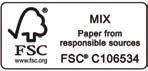
Ph: (03) 9794 8337
Embracing the future of manufacturing
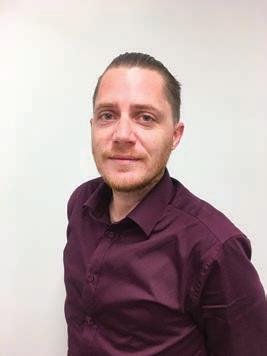
AEditor: Adam McCleery
ustralian food and beverage manufacturing has been undergoing a transformation in recent years, thanks to many factors, including innovation.
Traditionally known for its high-quality produce and innovative spirit, Australia is now at the forefront of a resurgence in food and beverage manufacturing, driven by technological advancements, sustainable practices, and a burgeoning export market.
One of the most significant drivers of this transformation is the integration of advanced technologies, as we have covered extensively in the pages of this publication.
From automated processing lines to precision agriculture and block chain for supply chain transparency, technology is helping revolutionise just about every aspect of food and beverage manufacturing.
Companies are investing heavily in research and development to create smarter, more efficient production methods.
For instance, the use of artificial intelligence in predictive maintenance and quality control ensures consistent product quality and reduces downtime, leading to increased productivity and cost savings.
Moreover, the adoption of the Internet of Things (IoT) enables real-time monitoring and data collection, providing valuable insights into production processes.
This data-driven approach allows manufacturers to optimise operations, reduce waste, and improve sustainability.
Sustainability is no longer just a buzzword, it’s a fundamental part of modern manufacturing.
Australian food and beverage manufacturers are increasingly recognising the importance of sustainable practices, both as a moral obligation and a strategic advantage.
With consumers becoming more environmentally conscious, the demand for sustainably produced goods is on the rise. Companies that prioritise sustainability are not only contributing to the preservation of the environment but also appealing to a broader, more discerning customer base.
Innovations in packaging, energy-efficient production methods, and the reduction of food waste are just a few key examples of how the industry is embracing sustainability.
Initiatives such as the Australian Packaging Covenant Organisation’s (APCO) target to make all packaging reusable, recyclable, or compostable by 2025 highlight the industry’s commitment to a circular economy.
Meanwhile, the demand for Australian products, particularly in Asia, is growing rapidly.
The country’s clean and green image, combined with stringent food safety standards, makes Australian products highly desirable in international markets. This presents a significant opportunity for local manufacturers to expand their reach and increase their export volumes.
Government support through trade agreements and export grants further bolsters the industry’s potential. By leveraging these opportunities, Australian manufacturers can tap into new markets, diversify their revenue streams, and mitigate the risks associated with domestic market fluctuations.
Despite the promising outlook, the industry also faces several challenges. From rising production costs, labour shortages, and the impacts of climate change. However, these challenges can be addressed through a collaborative approach involving government, industry bodies, and educational institutions. Investment in workforce development, research, and infrastructure will be crucial in overcoming these obstacles and ensuring the industry’s continued growth.
The resurgence of Australian food and beverage manufacturing is a testament to the industry’s resilience and adaptability.
By embracing technological advancements, prioritising sustainability, and seizing export opportunities, Australian manufacturers are well-positioned to lead the way in the global market.
The future of the industry lies in its ability to innovate, collaborate, and adapt to changing market dynamics, ensuring a prosperous and sustainable future for all stakeholders involved.
Until next time, happy reading!
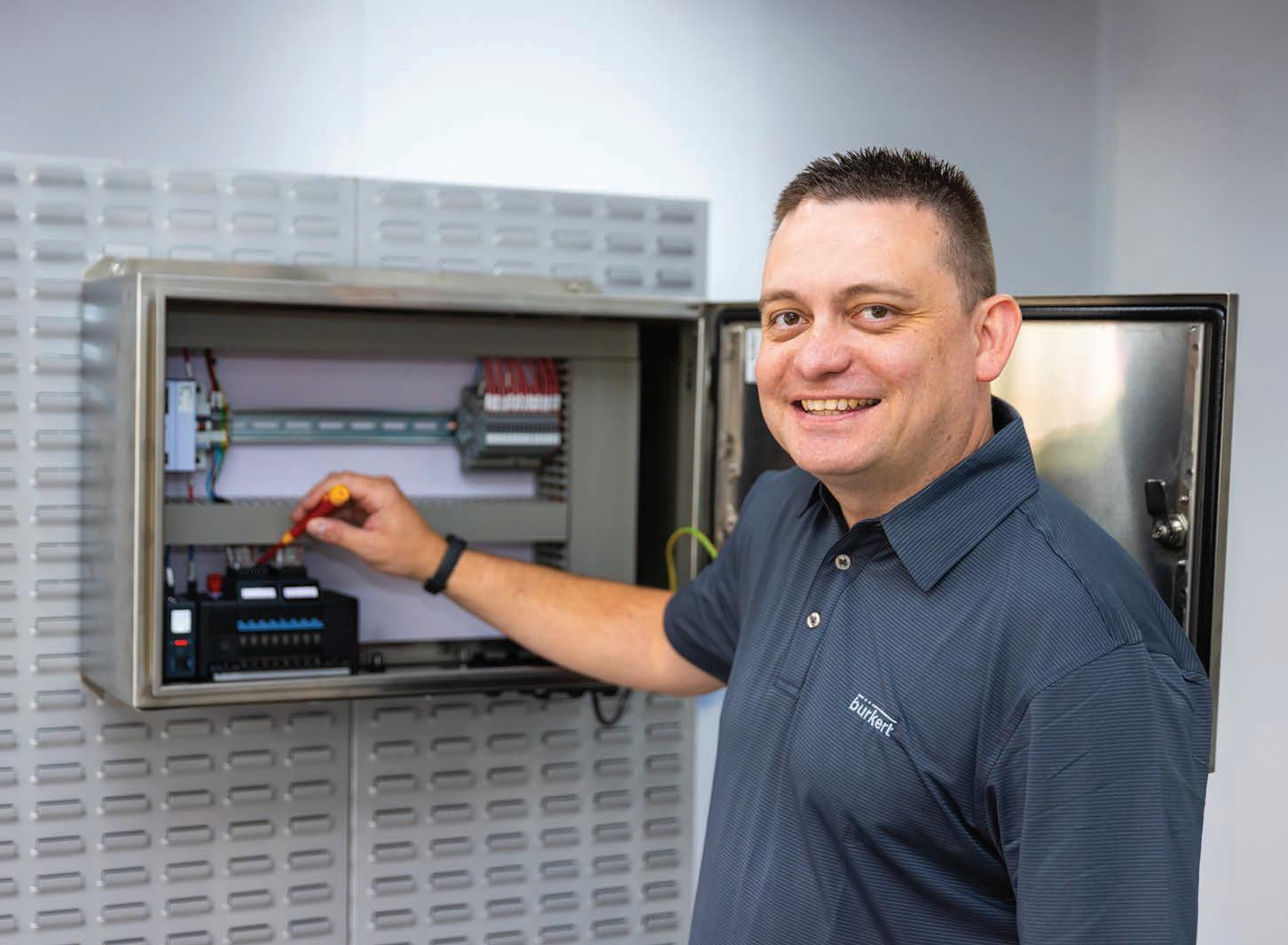
Boost Food & Beverage
Manufacturing Reliability with Bürkert’s Valve Island Type 8652 and PROFINET
// Discover why F&B prefer to partner with us >

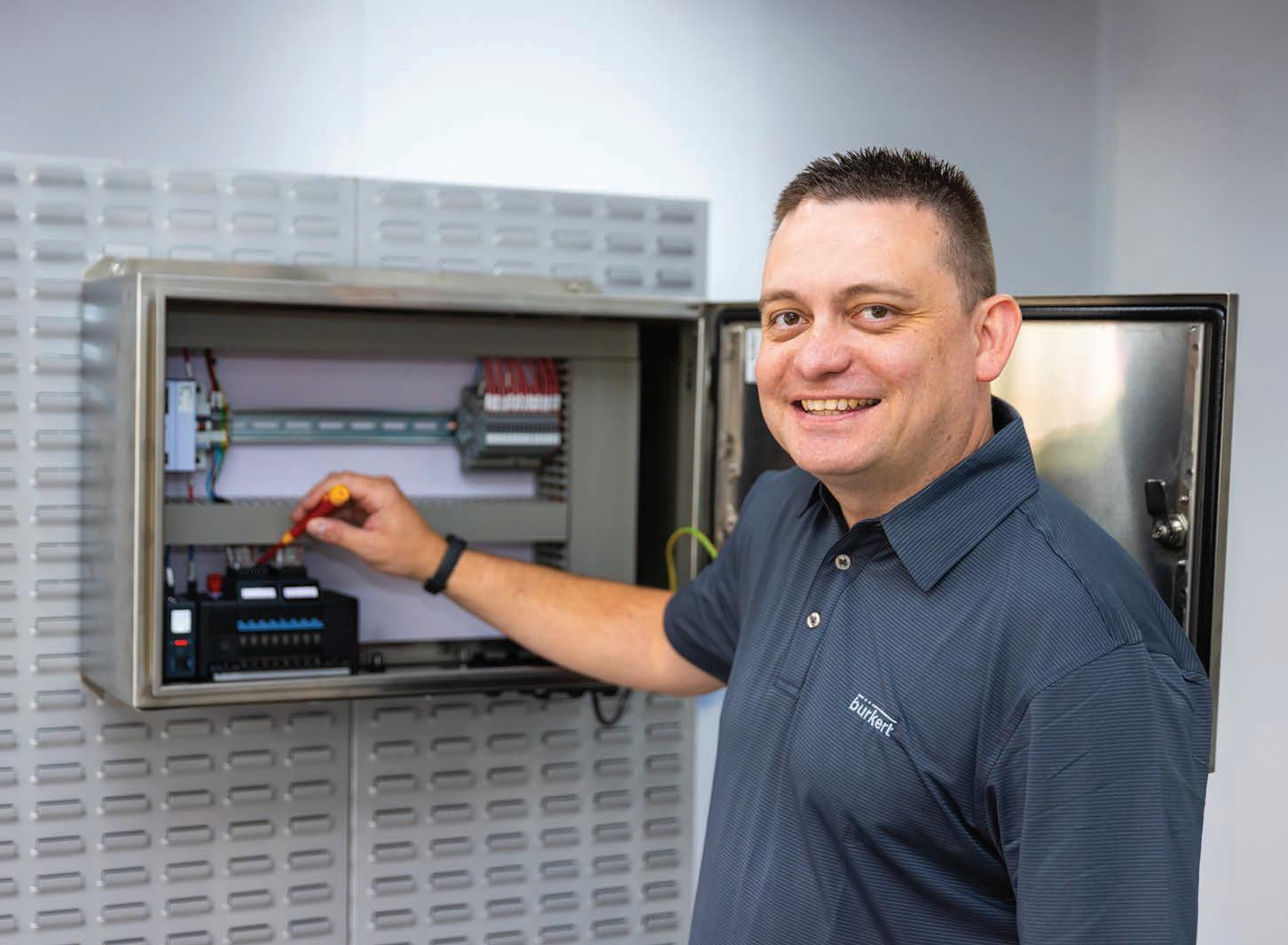
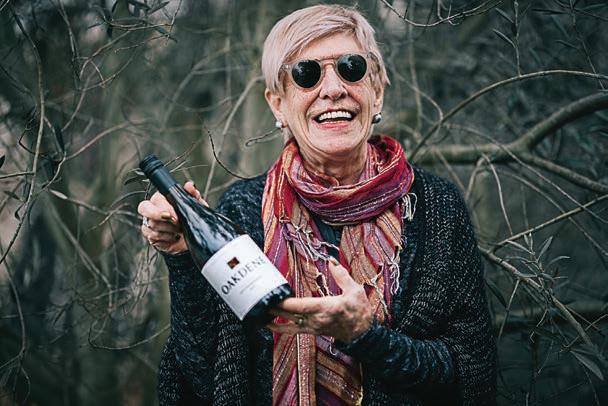
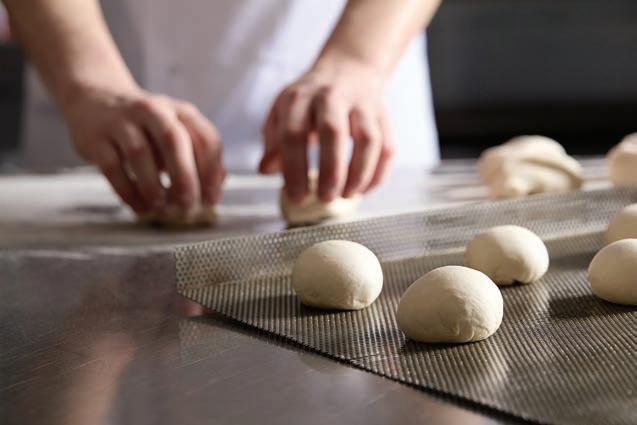

16 MEET THE MANUFACTURER
Oakdene Vineyards started as a hobby farm but has since blossomed into a prominent Victorian viticulture player.
20 FLOW MEASUREMENT
Bürkert’s FLOWave is designed to accurately detect media changes without the need for sensor elements.
22 INGREDIENTS
Australian Bakels’ expert reading of market and consumer trends helps the company provide the best solutions.
24 MEGATRANS
MEGATRANS 2024 registrations are now open.
26 FORCE MEASUREMENT
AMS Instrumentation & Calibration is the exclusive Australian distributor of Interface Force Measurement Solutions.
28 CONDIMENTS
FoodFx prides itself on innovation, quality ingredients, and agile production processes.
30 FLUID TRANSFER
Continental’s Drinkline hose continues the company’s promise of reliability and innovation.
32 AUTOMATION
SIMATIC HMI Unified Basic Panels is helping set a new standard in industrial automation, streamlining data communication and visualisation.
34 SUSTAINABLE AGRICULTURE
The Natural Heritage Trust is a key investment platform for the Federal Government to provide funds for sustainable agriculture.
36 AUSTRALIAN MANUFACTURING
The Manufacturing Alliance and Manufacturing Skills Queensland (MSQ) have joined forces to leverage local intelligence.
38 CIRCULAR ECONOMY
Australia’s environment ministers have renewed their focus on the National Circular Economy Framework.
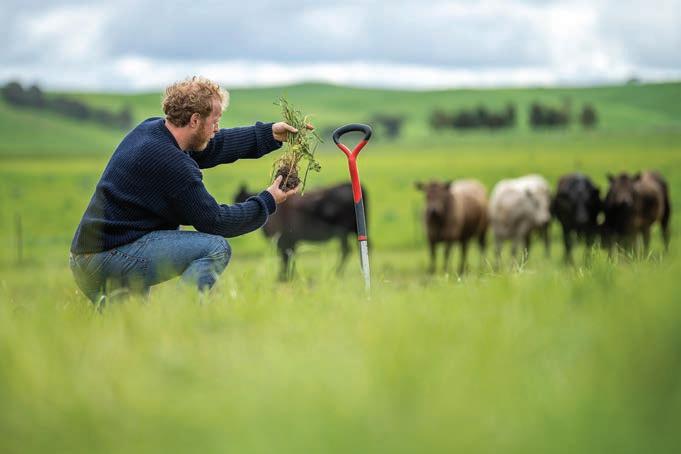
40 WINE MARKET
The Australian wine industry is already reaping the benefits of China lifting trade tariffs on wine exports into the country.
44 FOOD WASTE
State Governments, the Federal Government, and advocacy groups, continue to work hard to combat food waste.
46 DAIRY
47 AIP
48 FOOD MANUFACTURING
The AFGC has used the Diabetes Inquiry report as a chance to strengthen collaboration with Australian food manufacturers.
50 PRODUCTS

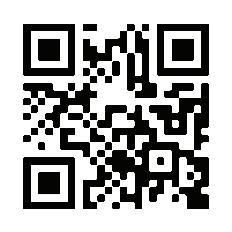

Spirits industry leaders make case for industry reforms
products – and Australia will miss out on the economic windfall that could be ours.”
Spirits & Cocktails Australia director Nicole Lestal said the Government must release the hand brake that is the current excise regime.
“While Australian spirits account for 20 per cent of alcohol consumption, it accounts for 50 per cent of alcohol taxes,” said Lestal.
“This structural disadvantage impedes innovation and opportunities to re-invest in Australian spirits manufacturing.
“Our global spirits industry experience tells us that when governments act decisively and across multiple fronts to provide coordinated support, it incentivises investment to achieve scale and unlock further opportunities for economic value-add and innovation.” F
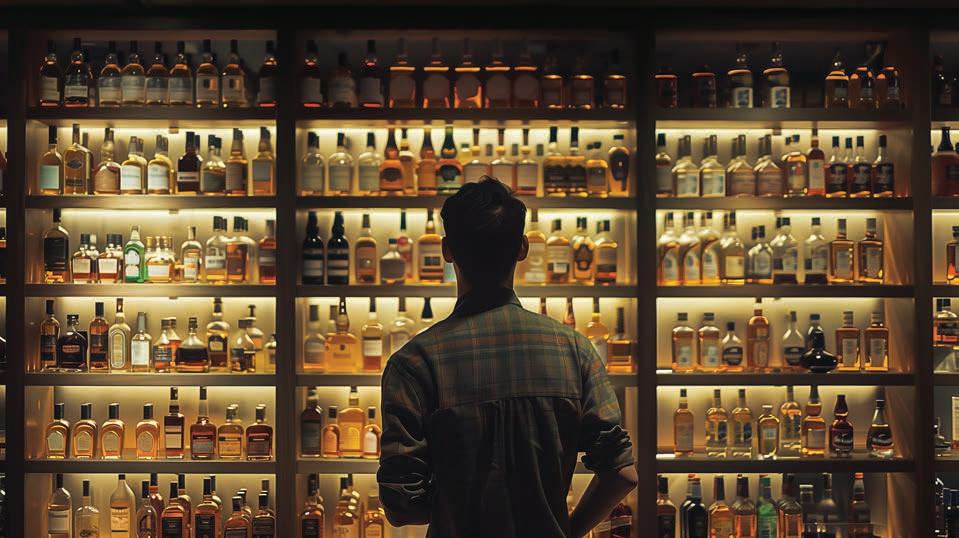
$500,000 funding for WA food and beverage businesses
“The Agrifood and Beverage Voucher Program is a real success story, lifting up WA agrifood and beverage businesses to achieve their goals and capture enduring benefits to local communities and the economy,” said Jarvis.
“Over the past six years, this program has supported a diverse range of businesses – from speciality food and baked products, to dairy, honey and seafood, to coffee and confectionery through to beer, wine, spirits and more –from the north to the south of the State.
Since its inception in 2018, 355 vouchers valued at $1.9 million have given WA businesses access to professional expertise to identify opportunities, overcome challenges and realise potential.
The program has leveraged more than $2.7 million in industry investment via co-contributions.
Applications close 5pm, Tuesday, 27 August 2024. F
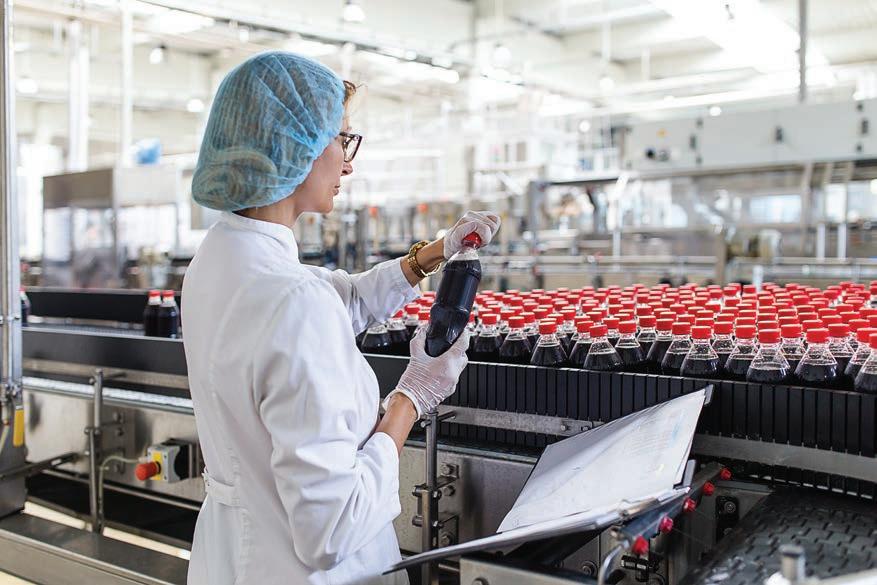
Spirits & Cocktails Australia director, Nicole Lestal, said the Government must release the hand brake the current excise regime.
Since its inception in 2018, 355 vouchers valued at $1.9 million have been granted.
NSW Government extends AgSkilled program
The NSW Government has approved a $5 million extension to AgSkilled, a program focused on upskilling the State’s agricultural workforce.
AgSkilled is an industry-led training program designed to upskill and better prepare the agricultural workforce for fast-moving changes driven by innovation, research, and technology.
Minister for Agriculture Tara Moriarty said this investment shows the NSW government is supporting a resilient and innovative agricultural sector.
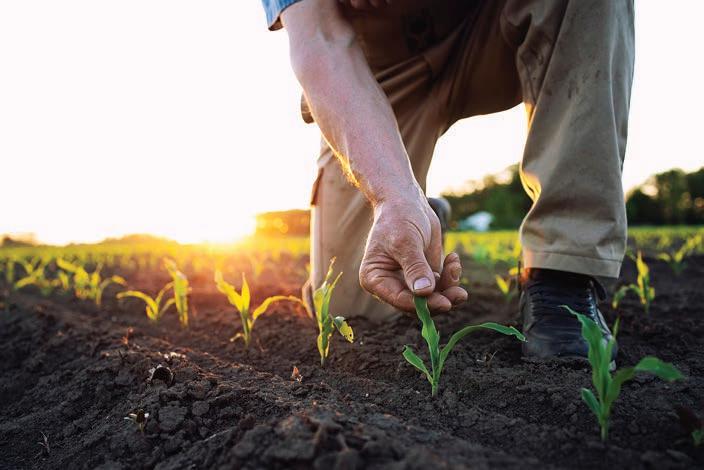
“It’s great to have programs like AgSkilled to further assist agricultural workers to stay up-to-date with research and developments, new technologies and help increase agricultural farm productivity,” said Moriarty.
In the past year, the program delivered 601 courses across 145 locations in NSW, with 2,536 participants.
95 per cent of these participants completed their courses, showcasing the program’s effectiveness and popularity.
With the extension of AgSkilled, the program aims to:
Attract, develop, and retain a productive agricultural workforce.
Support career progression, entry pathways, and employment outcomes in agriculture.
I ncrease agricultural farm efficiency,
New Coles proposition aims to transform retail media
Coles is set to super-charge its Coles Liquor retail media offering across its liquor business thanks to the introduction of Coles 360.
It means that Coles Liquor suppliers will be able to connect with their customers across a growing omnichannel network covering the three Liquor banners: First Choice Liquor Market, Liquorland and Vintage Cellars.
The introduction of Coles 360 also means the liquor brands will have the unique opportunity to connect with Coles supermarket customers by extending their advertising across the established Coles 360 retail media network.
This capability will make Coles 360 the only retail media network offering a food and drink proposition in Australia.
“We are excited to work with the Coles Liquor Group suppliers to help them connect with their customers in new ways and extend their reach to Coles supermarket customers by
leveraging our extensive existing retail media network,” said Paul Brooks, General Manager Coles 360.
Coles 360 have plans to connect food and drink suppliers to develop joint media plans based on similar audiences and objectives.
“That’s where the real opportunity lies. We have oversight of brands objectives so can help facilitate powerful partnerships that benefit both brands,” said Brooks.
Coles 360 is already seeing suppliers leveraging the power of its omni-channel network, working with Lion on the launch campaign for the James Squire Limited Edition XPA.
Customer director – Coles, Field & eComm from Lion, Chloe Gibson said it was fantastic partnering with Coles360.
Coles Liquor supplier campaigns booked through Coles 360 from August will also unlock critical insights into campaign effectiveness that Coles Liquor suppliers haven’t had access to before. F
productivity, and profitability.
• Develop industry capacity to adopt new technologies and sustainable farming practices.
• L everage research and development to ensure training is relevant, current, and meets industry needs.
Popular and priority courses, based on industry feedback, include honeybee biosecurity, chemical risk management, biosecurity training for managers/supervisors and farm workers/ employees, farm business planning and operating and managing remote pilot aircraft systems.
AgSkilled is delivered by Training Services NSW in partnership with industry associations, the NSW Department of Primary Industries, and the Agriculture, Food, and Animal Management Industry Training Advisory Body (ITAB).
This collaboration ensures the program is designed to meet the evolving needs of the agricultural sector. F
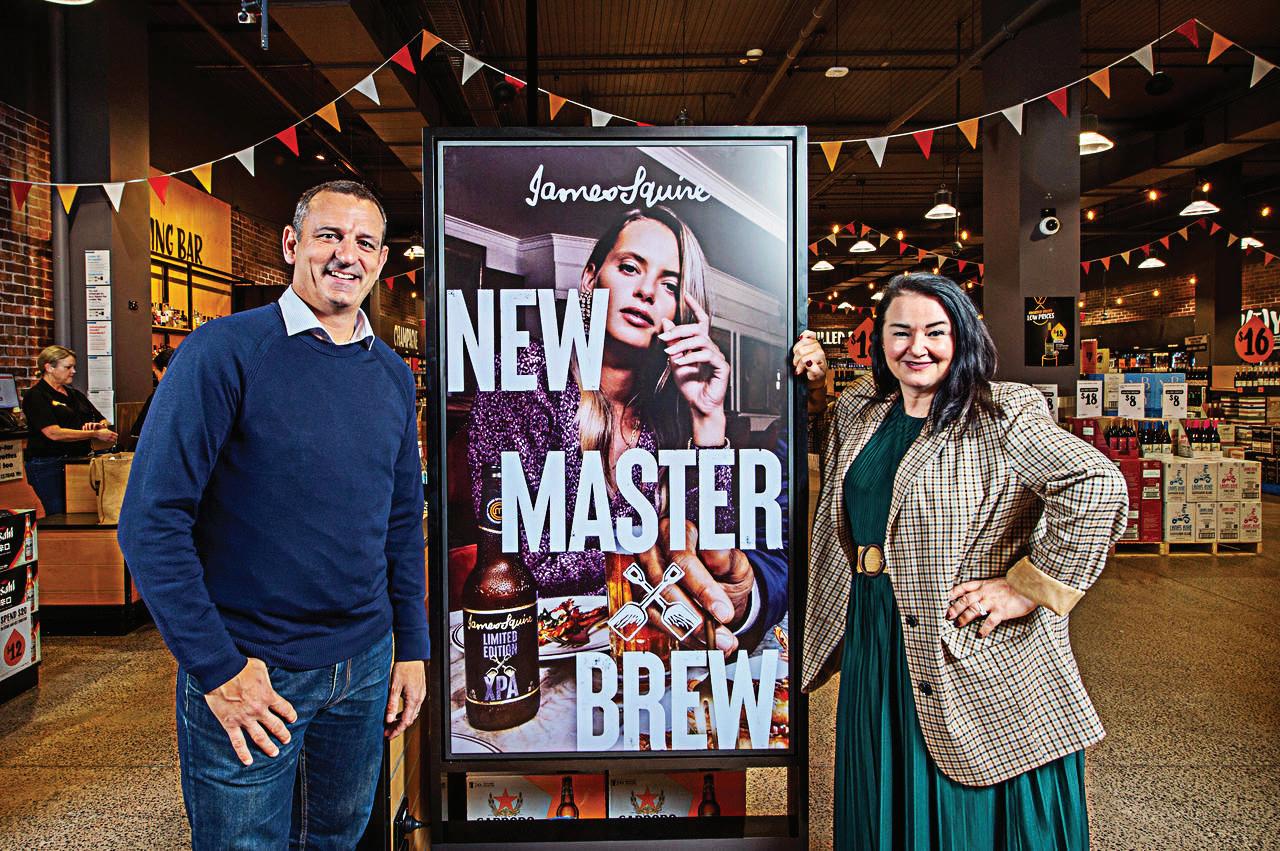
AgSkilled is an industry-led training program designed to upskill.
Image: Coles Group
The introduction of Coles 360 also means liquor brands will have the opportunity to connect with Coles customers.
Suntory Oceania appoint new sales director
Suntory Beverage & Food Oceania has announced Deb Cooper as its new sales director in New Zealand.
Cooper’s appointment comes as the company works towards the launch of its new $3 billion partnership, Suntory Oceania, with sister company Suntory Global Spirits.
“I’m thrilled to be joining the thriving New Zealand commercial team and am looking forward to fostering new partnerships and working with our customers to drive innovation and shape strategic growth,” said Cooper.
With responsibility for the New Zealand sales team, Cooper will drive the non-alcohol portfolio, working with iconic brands such as V Energy, Suntory Boss Coffee, and Gatorade.
Cooper’s appointment comes ahead of the business’s exclusive launch of American energy giant Celsius, which she calls a “game changer.”
“This provides the opportunity to strengthen our position in the category and demonstrate the expertise and leadership we have across the entire energy segment. We’re looking forward to launching this new product in New
Zealand in September,” said Cooper.
Cooper has been a part of the Suntory business for over a decade and has an impressive track record in grocery, leisure, and route channels.
Her most recent role was as head of petrol and convenience (P&C) at Suntory Beverage & Food, Australia.
This includes leading teams in global businesses Drinkworks and Fonterra, with Deb bringing her extensive knowledge and passion for the industry to the New Zealand market.
CEO at Suntory Beverage & Food Oceania, Brad Erceg, said Cooper’s appointment is a coup for the business and for New Zealand customers.
“Deb’s exceptional leadership, customer-centric approach, and energy have enabled our business to go from strength to strength in Australia, transforming category growth and delivering unrivalled recognition within the P&C channel. Her extensive FMCG experience positions her well to drive growth and innovation in this market,” said Erceg.
The Suntory Oceania partnership is set to go live in Australia in mid-2025 and in New Zealand from January 2026.
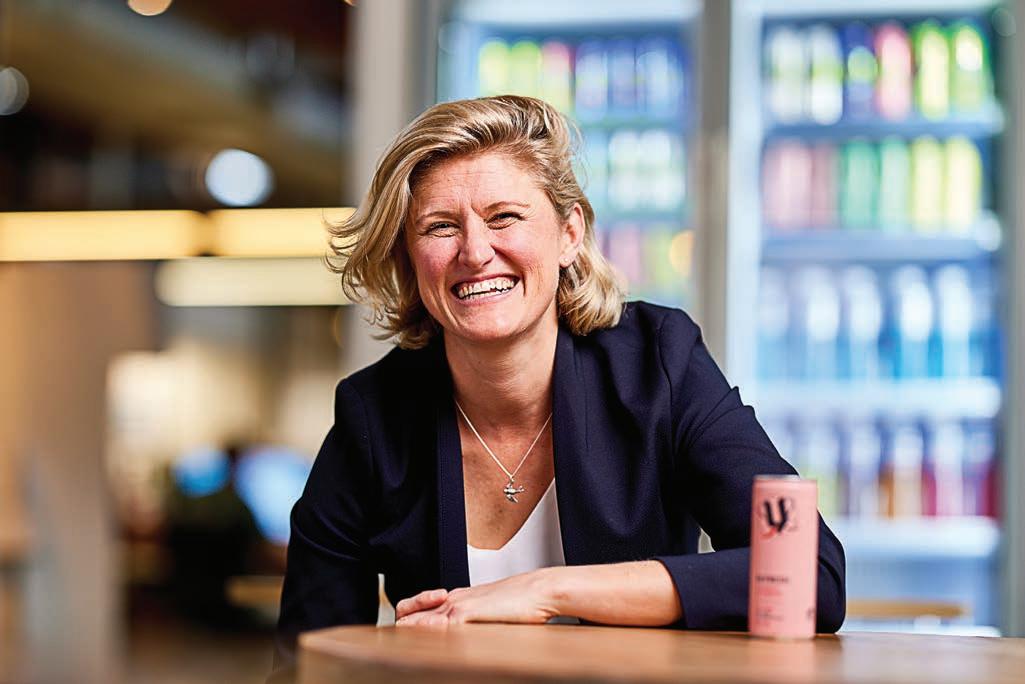
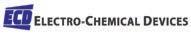
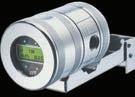
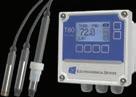
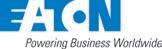
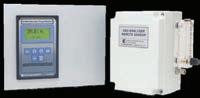

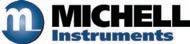
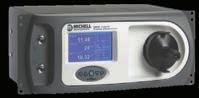
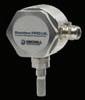
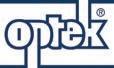
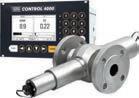

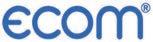

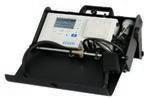
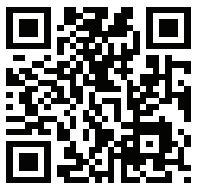
Deb Cooper has been a part of the Suntory family for more than a decade.
Image:
Suntory Beverage & Food Oceania
New funding set to lower energy and equipment costs for SMEs
Small and medium businesses in sectors such as agriculture will be able to obtain cheaper finance for solar, batteries and more energy efficient vehicles and equipment, with a new $50 million Federal Government investment to support discounted loans.
Assistant minister for Climate Change and Energy, Jenny McAllister, said the loans will mean savings on energy bills and financing.
“We want to help small businesses across industries and across the country make every watt count. These lower cost energy performance upgrades mean more control over energy use and emissions, especially in hard to abate sectors,” said McAllister.
“From farmers to local grocers, the Albanese Government is helping take pressure off small businesses bills. Lower cost financing for solar and electric machinery will save small businesses on
energy bills and loan repayments.”
This investment through the Clean Energy Finance Corporation (CEFC) will go towards discounted finance worth $250 million by non-bank lender Metro for electric vehicles, rooftop solar and batteries.
Small businesses will also be able to access discounted finance for more energy efficient farm and building machinery such as tractors, harvesters, earthmovers and cranes.
Minister for Climate Change and Energy, Chris Bowen said the investment will help Australian businesses in reducing their operating costs.
“Clean technologies like EVs, solar, batteries and electric machinery are a great way for businesses to save on energy bills and decarbonise,” said Bowen.
Eligible customers financing a
Small businesses will also be able to access discounted finance for more energy-efficient farm and building machinery.
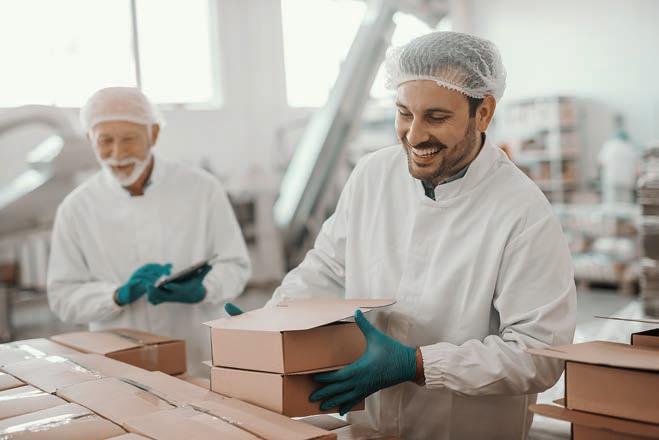
$60,000 electric vehicle, for example, could save about $1,700 in interest over 5 years.
Metro is an independent Australian
non-bank lender specialising in auto and equipment finance for businesses, car finance for consumers, and novated leasing. F
Boost to Western Australia Shellfish industry
The WA Government has announced the first sublicences for the second stage of the Albany Aquaculture Development Zone (Albany Zone), to boost aquaculture production along the south coast.
At full capacity, the Albany Zone is expected to produce around 1500 tonnes of shellfish at an estimated value of $30 million per year, creating more than 200 direct jobs.
The sublicences will support Harvest Road Oceans to expand its rock oyster aquaculture operations.
The Cook Government has invested $1.3 million into identifying and establishing aquaculture development zones along the south coast of Western Australia.
Aquaculture development zones provide ‘investment-ready’ platforms for large scale aquaculture operators, with environmental approvals and management frameworks already in place.
Fisheries minister, Don Punch, said the State Government is committed to supporting the growth of the aquaculture industry in WA.
“The Albany Aquaculture Development Zone builds on Albany’s long history of shellfish aquaculture and premium seafood production, and this latest development will further boost local opportunity going forward,” said Punch.
“Combined with the Cook Government’s recent investment in the Albany Shellfish Hatchery, this latest milestone will facilitate increased local shellfish output while also supporting industry diversification and regional economic growth.”
Stage one of the Albany Zone was announced in August 2020, covering 500 hectares in the Oyster Harbour area.
Stage two, covering around 310 hectares of Princess Royal Harbour and King George Sound combined, was declared in December 2021.
The Department of Primary Industries and Regional Development (DPIRD) worked closely with the Southern Ports Authority (SPA) to finalise tenure arrangements for stage two of the Albany Zone.
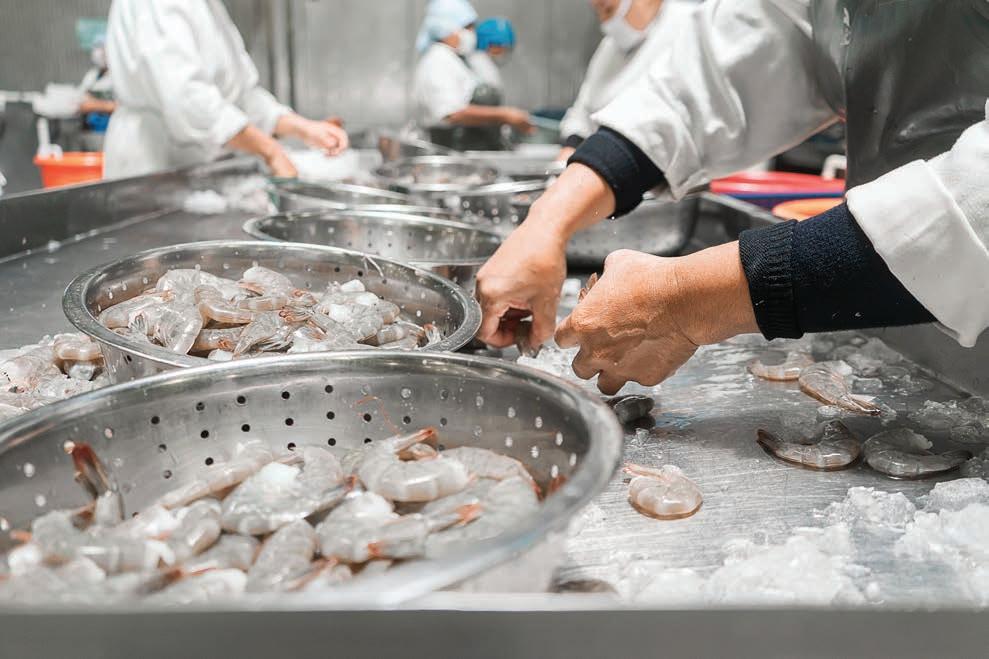
Aquaculture development zones provide ‘investment-ready’ platforms for large scale aquaculture operators.
Inghams converts debt into Sustainability Linked Loan
Ingham’s Group has announced that it has completed a transaction to convert its entire $545 million of debt facilities into a Sustainability Linked Loan (SLL).
The move is believed to be the first transaction of its kind for a poultry company in Australia.
Inghams’ CEO and managing director, Andrew Reeves, announced the company’s inaugural Sustainability Linked Loan.
“This ground-breaking transaction reaffirms our sustainability leadership position within the Australasian poultry industry and demonstrates our ongoing commitment to achieving our ambitious environmental goals which will directly benefit our key stakeholders,” said Reeves.
The SLL is governed by Inghams’ Sustainable Finance Framework, which expands Inghams’ capability to deliver its commitment of ‘Always Good.’
The SLL incorporates three key
sustainability performance targets, which incentivise greenhouse gas (GHG) emissions intensity, water intensity, and landfill intensity reductions.
Ingham’s has also appointed ANZ as sustainability coordinator to assist with the transaction.
Executive director sustainable finance at ANZ, David Simmons, said the deal is an encouraging step for the poultry sector.
“The sustainability performance targets within this loan help incentivise Inghams on a pathway towards reducing greenhouse gas emissions, water use, and waste,” said Simmons.
“The transaction also acted as a catalyst for discussions on developing and finalising Inghams’ Sustainable Finance Framework. The deal is an encouraging step for the broader poultry sector and one which we hope will inspire others in the industry along a similar pathway.”

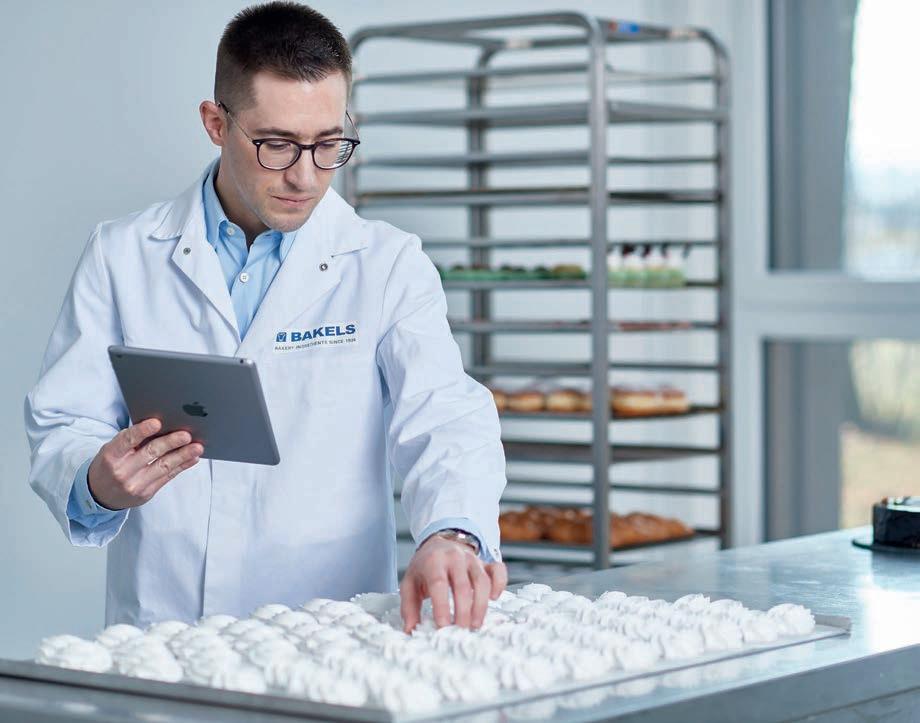
Bakels has been offering customers high quality food ingredients for more than 100 years, and operating in Australia since 1952. Our expertise in the industrial sector goes beyond the development of ingredients; our manufacturing capabilities allow us to partner with customers from concept formation, through to finished product launch.
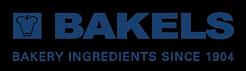
Assurance Statement covering the Linked Loan Principles. F
The SLL is believed to be the first transaction of its kinds for an Australian poultry company.
Image:
Ingham’s
Wine Australia launches new educational tool
Wine Australia has launched a transformational asset for students, teachers, and primary and high schools that provides a real-world connection from the vineyard to education.
Careers in Viticulture and Wine is a site that provides age-appropriate information and supports the exploration of the diverse range of careers available and the pathways to them.
It also supplies national school curriculum-aligned teaching resources and various activities that connect key school subjects with areas of the sector’s production and operations.
For the grape and wine sector, the resource offers an opportunity to connect with local and regional schools.
The aim is to provide budding viticulturists, winemakers, innovators, agtech specialists, and marketers, cellar door managers with the opportunity to hear directly from those with expertise.
Wine Australia CEO Dr Martin Cole said the resource was developed as a direct response to feedback from the grape and wine sector.
“From sustainability to creativity, investigation to innovation, there are careers across the length and breadth of the sector that support the interests, values, and aspirations of our youth,” said Cole.
“We are aiming to inspire the next generation by demonstrating the breadth of, and the pathways to, careers across the wine sector value chain.”
A central component of the site is a virtual tour that allows students to choose their own adventure by matching values and aspirations, strengths, and subjects to a career in the sector.
Nuriootpa High School in the Barossa is featured on Careers in Viticulture and Wine, showcasing the school’s hands-on wine program and its connection to practical skills and experience for students. F
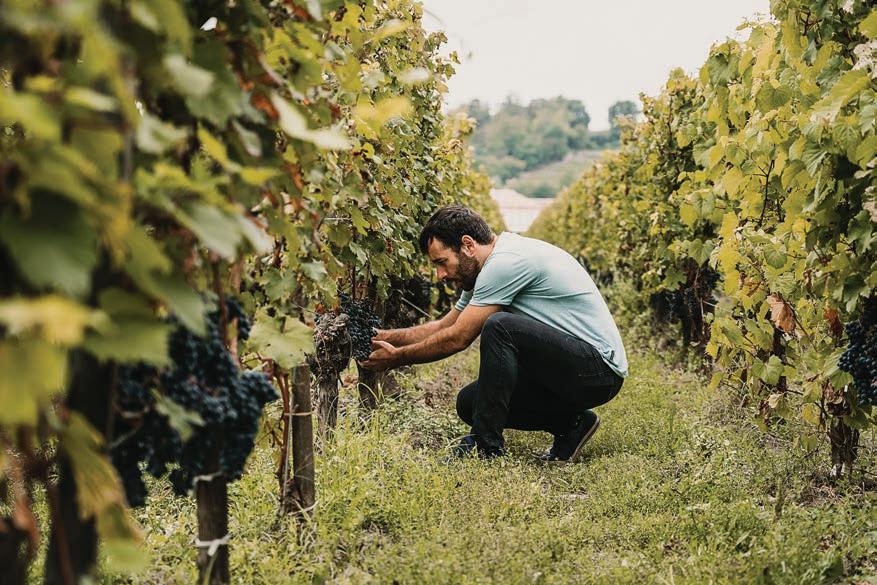
New biosecurity precinct to help SA fresh produce
Construction has commenced on a new $50 million biosecurity precinct at the SA Produce Market in Pooraka to help create a more affordable, competitive, and sustainable fresh produce industry for the state.
the first multi-treatment and inspection facility to support the South Australian
horticultural industry in its fight against the invasive fruit fly plant pest.
The current fruit fly outbreaks in the Riverland and Salisbury North have meant that produce cannot be sent from
provide treatment and pressure cooling technology to eliminate pests.
CEO of SA Produce Market, Angelo Demasi, said he is delighted that the project has come to fruition.
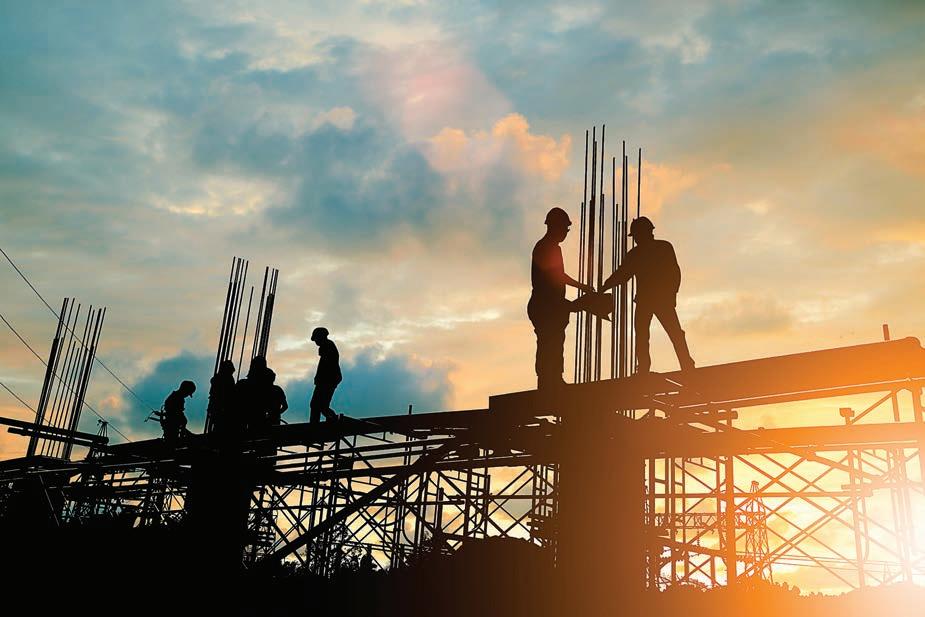
and treat produce from affected areas, safeguarding our industry and ensuring a stable supply chain,” said Demasi.
“The new facilities will enable the industry to use advanced post-harvest treatment technology, essential for exporting South Australian produce globally. It is a significant step towards making our produce more competitive and sustainable.”
Currently, producers can only send untreated produce to the eastern states.
Once in operation, the new facility will reduce transport costs, time delays, and subsequent wastage, which will improve affordability for consumers and profitability for local producers.
In addition to creating savings for consumers by helping to reduce the cost of produce at local supermarkets, the precinct will encourage a boom in exports.
The precinct is expected to unlock an estimated additional $100 million of fresh produce exports over a fiveyear period. F
Image: lubero/AdobeStock
Image: Yuttana Studio/AdobeStock
Wine Australia CEO Dr Martin Cole said the resource was developed as a direct response to feedback.
Coles has launched its annual appeal for national food rescue charity SecondBite to help feed Aussies doing it tough this winter.
The Coles SecondBite Winter Appeal starts as new SecondBite research conducted by YouGov reveals that just over three quarters of Australians struggle more financially in winter.
SecondBite CEO Daniel Moorfield said the need for food relief is heightened during the winter months and urged shoppers to support the appeal.
“The need for food relief is exacerbated this winter as many vulnerable Aussies are faced with choosing between heating or eating, finding they can no longer make their budget work to cover the necessities,” said Moorfield.
“The funds raised at Coles will help SecondBite to meet the increased
Coles and SecondBite partner for food rescue initiative Costa group calls for changes to fresh produce exports
Costa Group has reiterated calls for a whole of government approach to ensuring new export market access opportunities for Australia’s fresh produce.
Costa CEO Marc Werner, who was
demands and will help us to continue to rescue and deliver nutritious food free of charge to more than 1,000 community food partners.”
This most common reasoning is high electricity or energy bills, with those living in South Australia, Victoria and NSW struggling the most.
Until Tuesday 30 July, customers can help support SecondBite in more than 1,800 supermarkets and Coles Liquor stores nationally.
To help, customers can purchase a $2 donation card at a Coles supermarket or by donate at any Vintage Cellars, Liquorland or First Choice Liquor Market store.
Donations can also be made via Coles Online.
There are also more ways to support SecondBite at Coles this winter with brands Chobani, Mount Franklin,
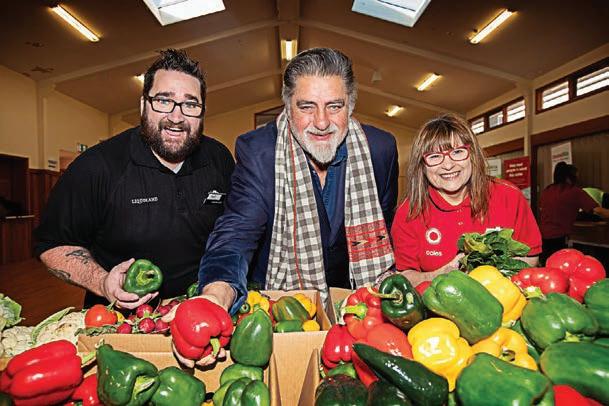
A portion of sales from these selected products sold in all Coles supermarkets or on Coles Online going towards the appeal.
customers and suppliers will enable SecondBite to deliver unsold, edible fruit, vegetables, bread, and other grocery staples to more than 1,000 charities and community partners. F
today, highlighted the challenges the fresh produce sector faces in getting access to crucial markets in China and Japan, for some of its key produce lines.
“Free trade agreements have been very beneficial for Australian
Costa and many others have benefitted from free trade agreements with Japan, China, United States, Korea and India,” said Werner.
“However, free trade agreements only address tariffs, they do not
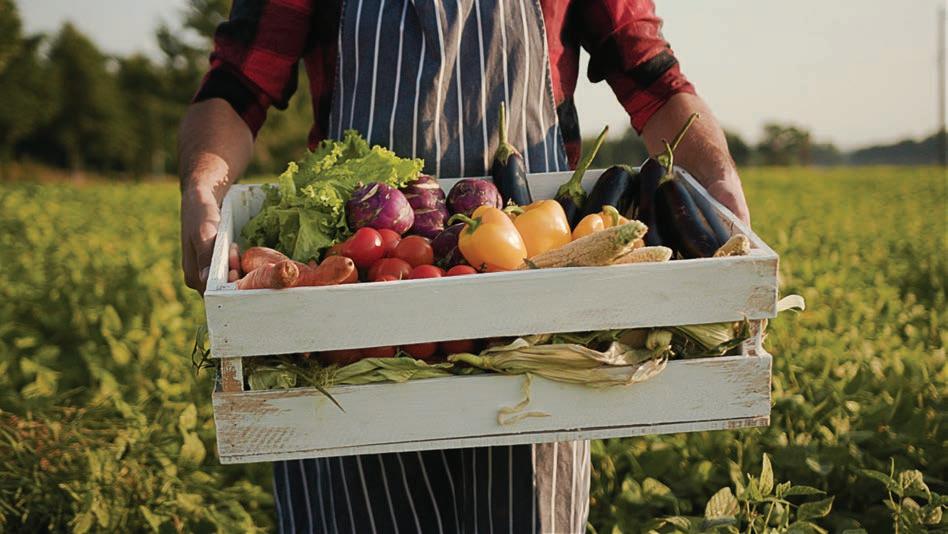
of export protocols, which are often related to the treatment of fresh produce for fruit fly.”
Werner said these negotiations for fresh produce often took many years, leaving Australian produce well behind compared with other countries such as Mexica, Peru, Chile, and Argentina.
“Our Australian fresh produce does not seem to attract the same trade priority and political support at the highest levels that other agricultural items, such as wine, meat, grain and more recently lobster, seem to benefit from,” said Werner.
“In the instance of blueberries, for example, Australia is a global leader in the development and growing of premium varieties, yet we have had to sit by over the last decade and watch other countries with inferior product gain access to China.”
Gaining access to Japan for Queensland grown avocados is another key opportunity which has yet to come to fruition. F
Nando’s and the Natural Chip Co. also joining the cause.
Gaining access to Japan for Queenslandgrown avocados is one key opportunity.
All funds raised by Coles will enable SecondBite to deliver unsold, edible, grocery staples to more than 1,000 charities.
AMA advocates for toddler milk revamp
The Australian Medical Association urges the government to abolish current marketing guidelines for infant formula and toddler drinks and align them with international best practices.
The call is one of the AMA’s recommendations in a submission to the Australian Competition and Consumer Commission’s (ACCC) consultation on reauthorising the current voluntary and self-regulated code — ‘Marketing in Australia of Infant Formulas: Manufacturers and Importers (MAIF) Agreement’ for another five years.
The submission says Australia needs a marketing code of practice for breastmilk substitutes that mirrors the World Health Organisation’s (WHO) international code.
“We need to scrap this voluntary code and replace it with the evidencebased best practice code. The good news is this code already exists in the WHO’s Code,” said Professor Steve Robson, AMA President.
The AMA is concerned the current code allows unnecessary and potentially
The AMA is concerned the current code allows unnecessary and potentially unhealthy products to be marketed.
unhealthy products to be marketed to parents under the guise of infant formula.
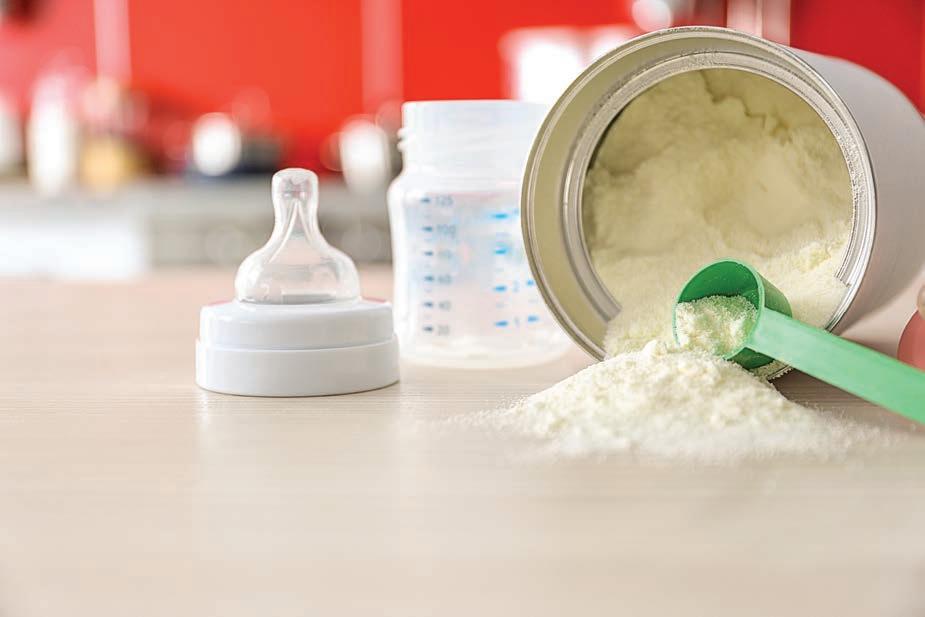
make informed decisions about their babies by having an evidence-based approach to health,” said Robson.
The current agreement only covers infant formulas to 12 months of age,
to 36 months and classifies toddler milk as a breastmilk substitute.
”Toddler milks are unnecessary, unhealthy and deceptively marketed as beneficial — they are a milk myth that
National Food Donation Tax incentive tabled
WA Senator Dean Smith has introduced an incentive that aims to amend the tax system to offer deductions for businesses donating food and essential services, such as refrigeration and transportation, to food rescue organisations.
The National Food Donation Tax Incentive was tabled as a private Senator’s Bill in federal parliament and, if passed, has the potential to revolutionise Australia’s approach to food donation.
The bill, a result of extensive collaboration and research from the End Food Waste Cooperative Research Centre, KPMG, food rescue organisations Foodbank Australia and OzHarvest, as well as the Queensland and New South Wales state governments, has the potential to provide millions of additional meals each year to those in need.
This initiative is a significant step towards achieving Australia’s goal of halving food waste by 2030.
CEO of End Food Waste Australia, Dr Steven Lapidge, said the bill is critical
to combat Australian food waste and hunger.
“With more than 7.6 million tonnes of food wasted annually in Australia – 70 per cent of which is edible – this initiative is not just timely but essential,” said Lapidge.
“This tax incentive will encourage businesses to donate surplus food and essential services, dramatically increasing the support for food rescue organisations and ensuring that surplus food reaches those who need it most.”
Lapidge said the End Food Waste Cooperative Research is proud to have supportive partners that include KPMG, Foodbank Australia, OzHarvest and the Queensland and New South Wales state governments.
The proposed tax incentive not only addresses food insecurity but also aligns with environmental sustainability goals by reducing the volume of waste sent to landfills.
Businesses will benefit from tax deductions, creating a win-win situation for both the economy and society.

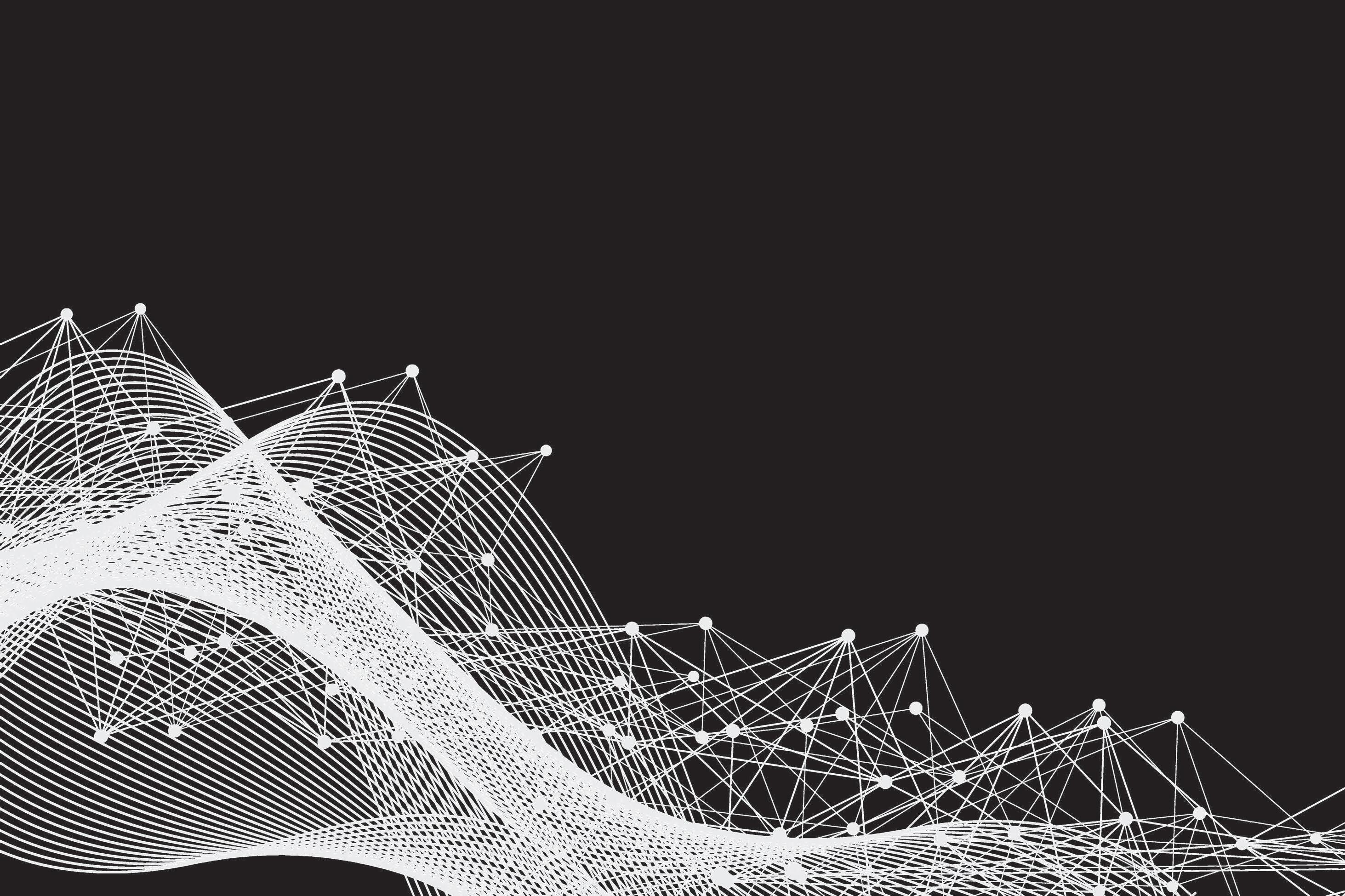
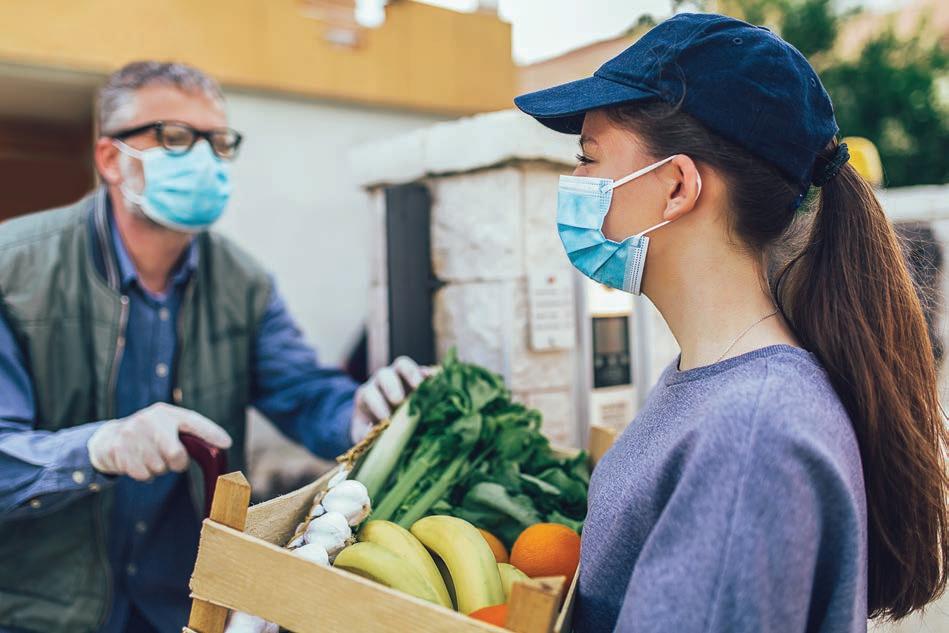
The tax incentive not only addresses food insecurity but also aligns with environmental sustainability goals.

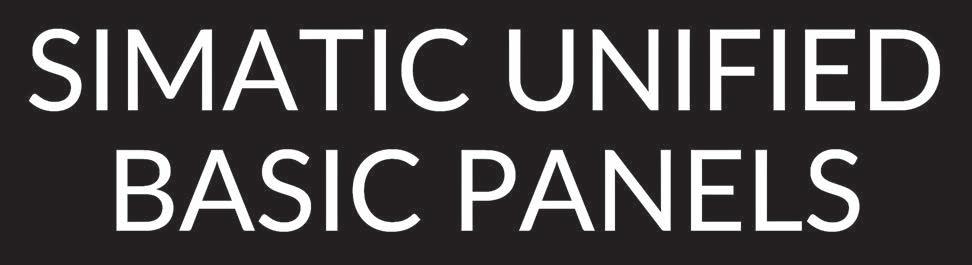
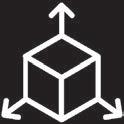
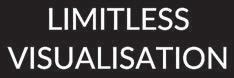
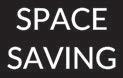
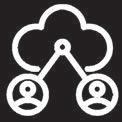
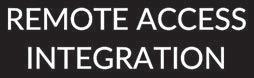
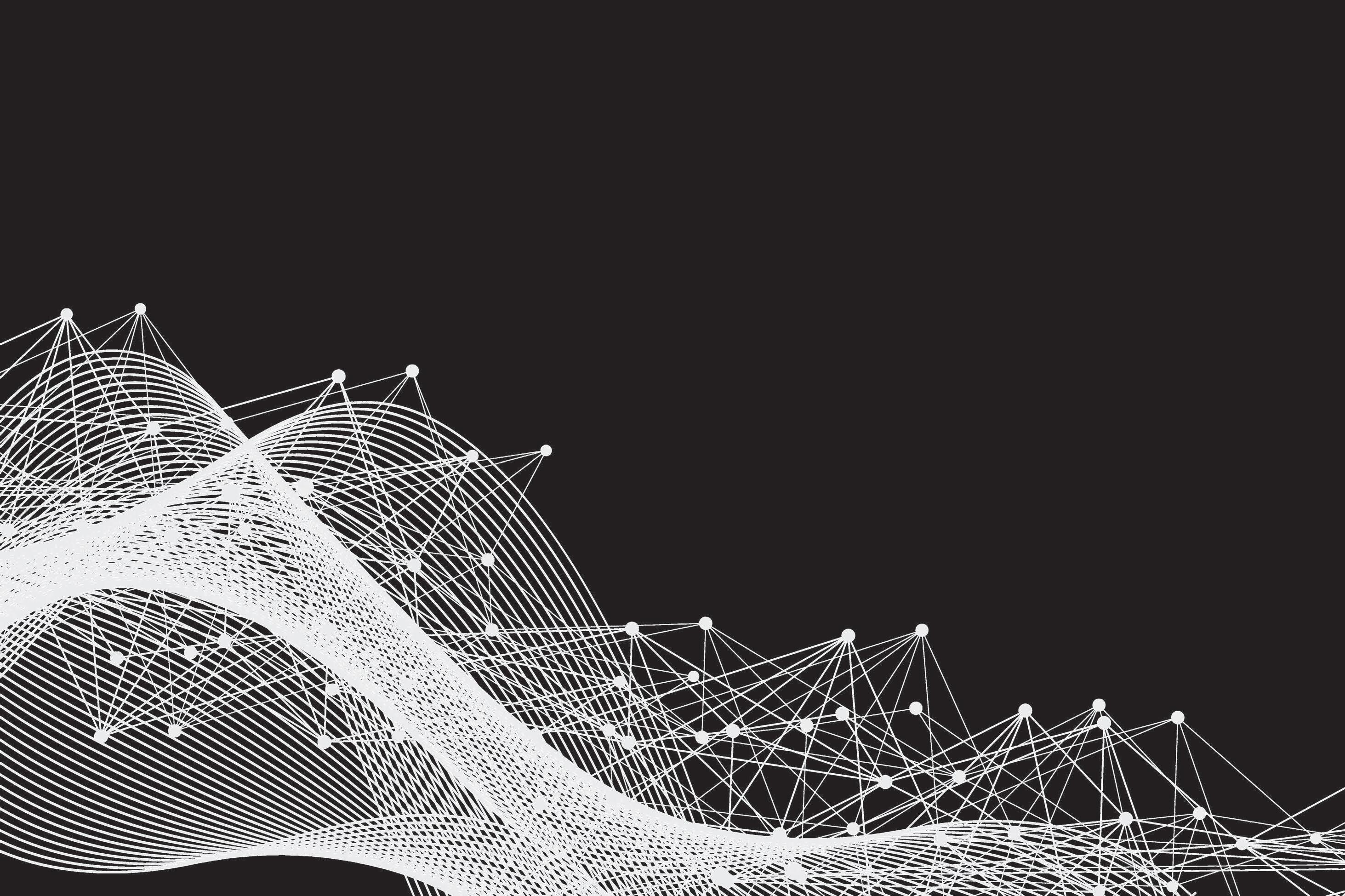


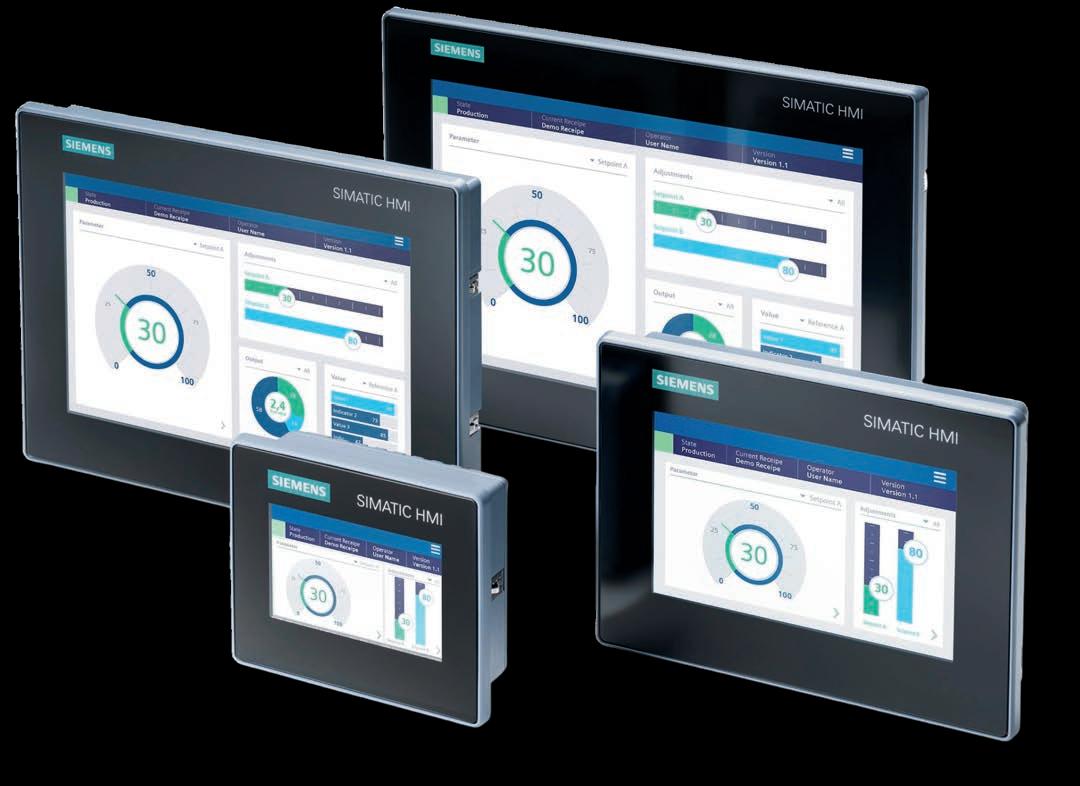
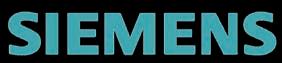

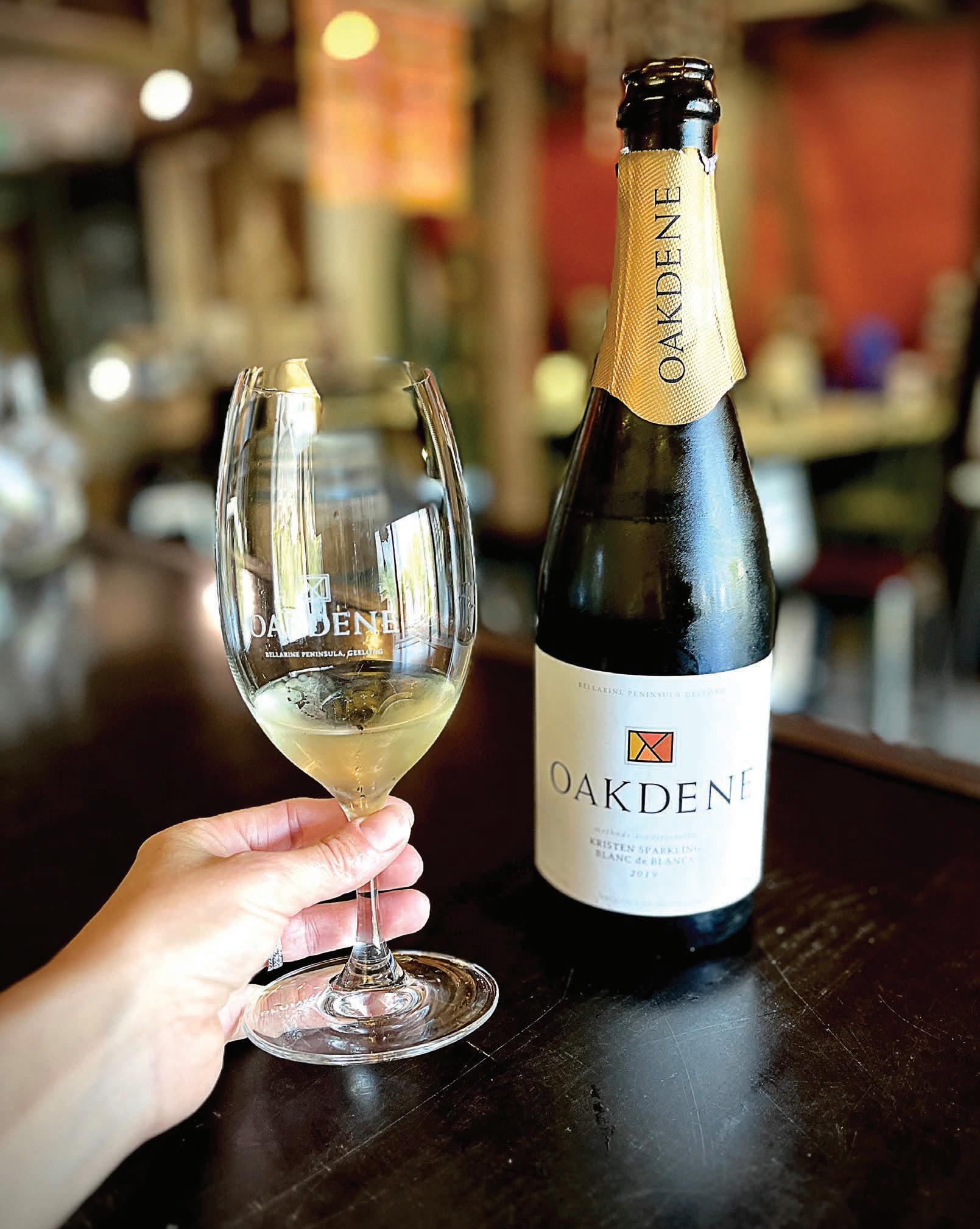
From humble beginnings to statewide recognition
Oakdene Vineyards started as a hobby farm but has since blossomed into a prominent Victorian viticulture player, who this year earnt the prestigious 2024 Premier’s Trophy.
Demand for Oakdene’s benchmark sparkling offerings is quickly rising.
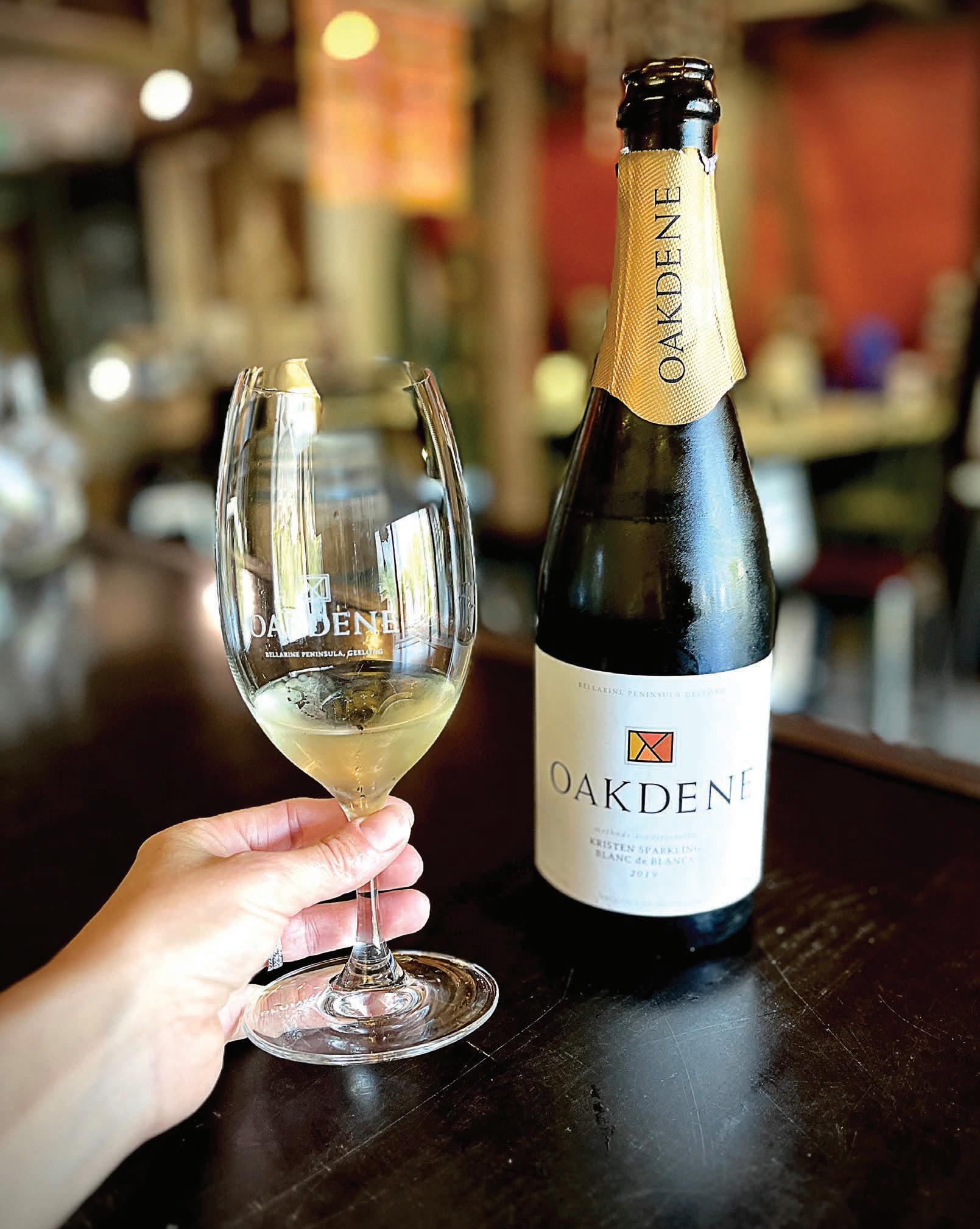
Located in Wallington, Oakdene is a family-owned vineyard that sits on coastal farmland east of Geelong on the Bellarine Peninsula.
In recent years, Oakdene’s benchmark wines have garnered awards from major wine shows and maintained a 5-star rating in the Halliday Wine Companion.
However, the vineyard’s beginnings were humbler. General manager and director of Oakdene Vineyards, Steven Paul, talked to Food and Beverage Industry News to discuss the story behind one of Victoria’s most acclaimed wine labels.
In 2001, Bernard and Liz Hooley discovered an old dairy farm named Oakdene. Initially treated as a hobby farm, its beginnings mirrored those of many other boutique wineries.
“Most wineries like ours, probably started with someone that wanted a hobby type farm… and then decided, hey, let’s put some grapes in,” said Paul.
The location of the farm was perfect for a vineyard. Located in the ‘dress circle’ of Victoria, Oakdene is placed in among the state’s premier wine locations.
Situated on the Bellarine Peninsula near Geelong, Oakdene is followed by iconic winery locations, such as Macedon, Yarra Valley and Gippsland.
The cold climate in these areas allows producers to specialise in developing high-quality wine in several categories.
“Cold climate regions for viticulture focus on pinot noir and chardonnay and probably shiraz to a lesser extent and pinot gris,” said Paul.
Recognising these advantages for viticulture, the Hooleys decided to develop Oakdene into a fully-fledged vineyard. Starting with just a few grapevines, the Hooleys went on to adopt the necessary capabilities to produce wine and even opened a restaurant.
wine at Oakdene, most of the fruit from the original 30-acre vineyard was sold to other wineries. This changed when Paul joined Oakdene in 2009 and began enhancing the vineyards commercial appeal.
“I joined…from another winery in the Bellarine and I moved Oakdene into more of a commercial business,” said Paul.
“We decided to sort of keep everything ourselves and start to expand.”
Paul’s decision to expand Oakdene as its own independent vineyard would result in Oakdene selling more than 12,000 cases of wine in one year. Prior to the expansion in 2005, they sold just 700 cases. Oakdene’s expansion was further evident when the vineyard
“Cold climate regions for viticulture focus on pinot noir and chardonnay and probably shiraz to a lesser extent and pinot gris.”
“They decided to piece together an old homestead and turn that into a restaurant. And then from a restaurant, decided to produce wine,” said Paul.
While the Hooleys did produce
purchased a new 160-acre property.
“We purchased a new property in 2014 or 15 and planted immediately. And now we’ve gotten 70 acres under vine, and a 160-acre property about 11
km from the original block,” said Paul.
Since then, the site has evolved into a fully operational vineyard with accompanying facilities that not only include the restaurant but a cellar door and café.
“We work between the two sites now with both in the same region,” said Paul.
Oakdene wine-making production and processes
While most wineries adhere to a standard production process involving grape harvesting, grape crushing, fermentation, aging, blending, and bottling, Oakdene incorporates unique twists into this process.
Paul said part of Oakdene’s success can be attributed to how the vineyard focuses on what occurs long before the grapes are harvested. He also emphasised that Oakdene’s small, boutique and family-owned nature presents an advantage over larger producers.
“We focus on the people that grow the grapes a little bit more, because that’s where the quality comes from,” he said.
“You’ve got to have a great site. But you’ve also got to have a good viticulture
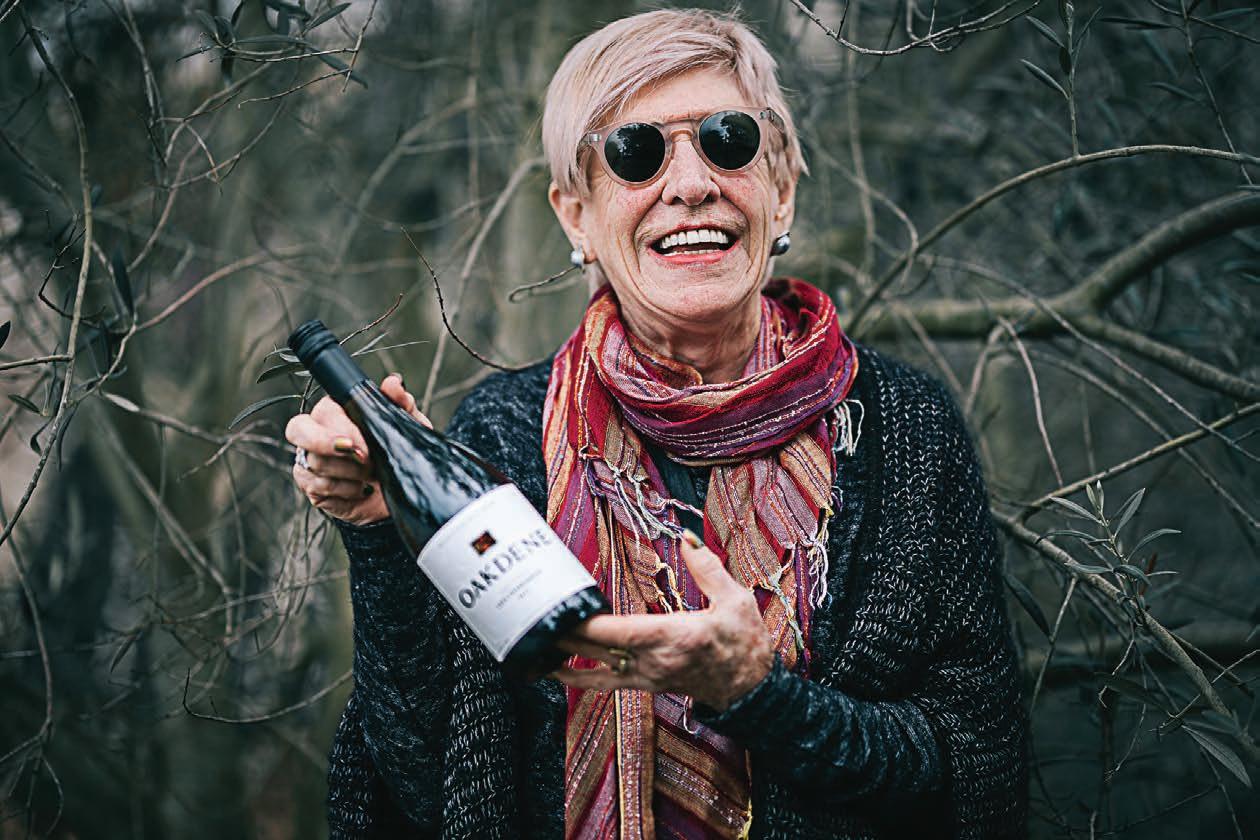
Images: Oakdene Winery
The winner of the 2024 Premier’s Trophy, the 2022 Liz Chardonnay, was named after co-founder Liz Hooley.
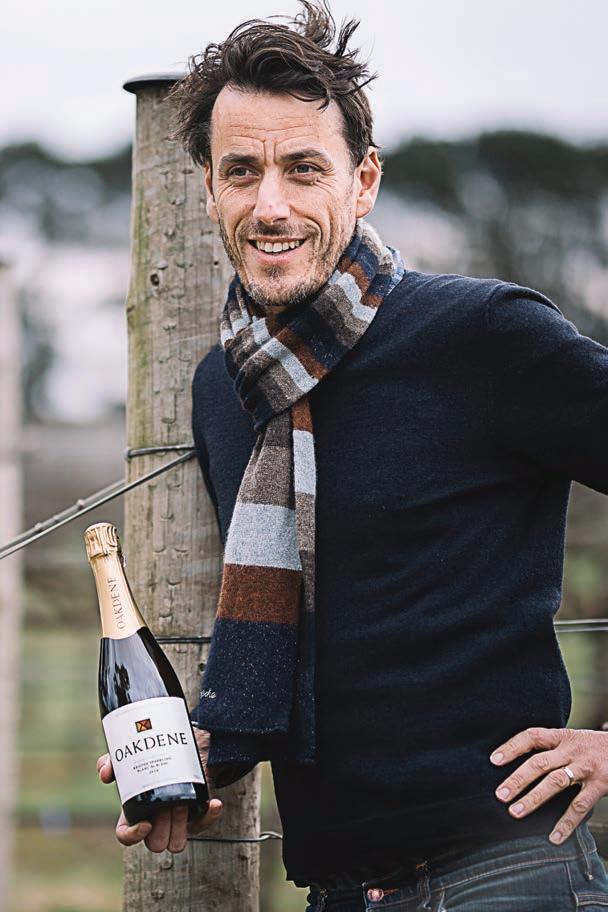
team that focuses on 100 per cent quality.”
Furthermore, Oakdene utilises key manufacturing principles that other producers may view as risky. For its benchmark wines, Oakdene uses 100 per cent wild yeast to help express a unique palate.
“The idea with wild yeast is to maybe express your vineyard or your winery a little more than you would if you use a cultured yeast from a packet. It is a little bit riskier because you don’t exactly know what you’re going to get,” said Paul.
Oakdene’s ability to give premium treatment to its benchmark wines is supported by its second-level wine offerings. The tier has a low production cost and therefore offers an affordable option for consumers.
“These are the ones who sit below. With those we’re using cultured yeasts and old oak to try and manage the production costs because you’re also trying to bring a line to the market that’s ready to drink immediately,” said Paul.
Paul couldn’t describe Oakdene’s wine production without acknowledging that the vineyard is blessed by the iconic Australian sun.
“The Australian touch is that we get a whole lot more sun than people do in Europe,” said Paul.
“Our Chardonnay probably ripens a little bit quicker than it would in a longer period and we have lower natural acidity because we’re warmer.”
Paul further attributes the success of Oakdene’s wines to ensuring that the wine matches current market dynamics. Oakdene has implemented a benchmark tasting system to gauge competition and align with seasonal preferences.
“I think with winemaking, you’re certainly making a wine for a market,” said Paul.
“Five years ago, we just couldn’t make enough shiraz. Now, we can’t make enough chardonnay. Sauvignon blanc is sort of waning, and pinot gris is still strong. Rose has gone through the roof, and sparkling is huge,” said Paul.
To further predict seasonal preferences, Oakdene utilises its cellar door which itself attracts tourism and draws attention to its products. This is essential, as the company doesn’t have a traditional distributor.
“We make trial batches of small runs and run those through our cellar door.
“The idea with wild yeast is to maybe express your vineyard or your winery a little more than you would if you use a cultured yeast from a packet. It is a little bit riskier because you don’t exactly know what you’re going to get."
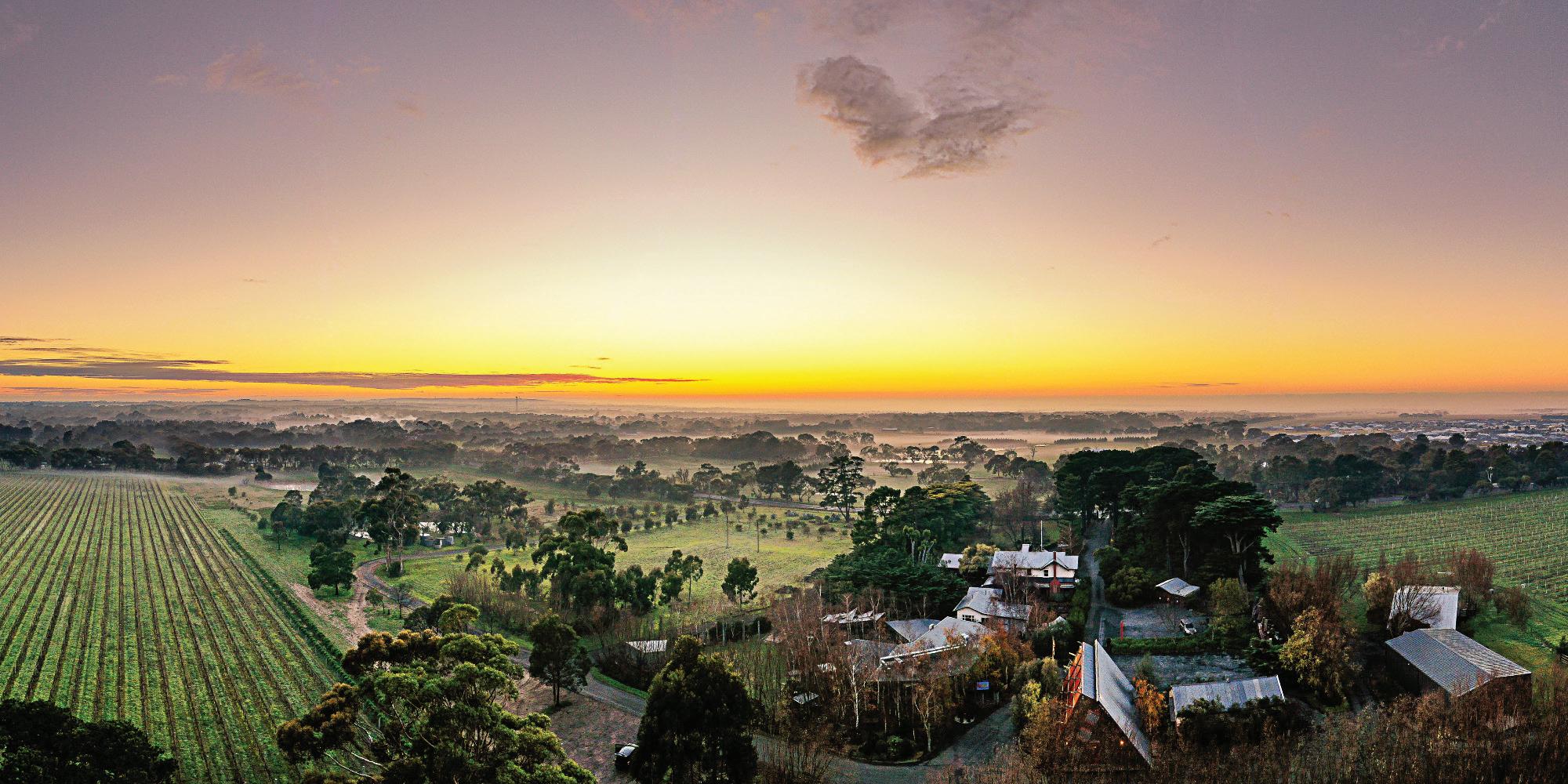
Oakdene is a family-owned vineyard that sits on a coastal farmland east of Geelong on the Bellarine Peninsula.
GM and Director of Oakdene Vineyards, Steven Paul, joined the wine producer in 2009.
They then appear as a more commercial wine the following year and get released. If they don’t work, they disappear,” he said.
“Our cellar door is a huge part of our business because we’re in a busy region. The bulk of our sales go directly through the cellar door.”
Achievements and recognition
These unique production quirks and testing strategies have moulded Oakdene into the boutique powerhouse it is today. Just this year, Oakdene’s 2022 Liz Chardonnay clinched the 2024 Premier’s Trophy at the Victorian Wine Show. Awarded at Parliament House in Victoria by the Premier Jacinta Allan, the achievement was bigger than Paul initially thought.
“We have never won an award that big before. There was a lot of media press, and there were a lot of online orders almost immediately,” he said.
The Premier’s Trophy is one of the
highest honours in the Victorian wine industry, as the award requires finalists to have already won an award in one of the 14 wine shows across Victoria.
Leading up to the Victorian Wine Show, the Liz Chardonnay took home three different awards at two highly respected wine shows. At the Geelong Wine Show 2023, the chardonnay took home the Trophy for Wine and the Trophy for Best Chardonnay. It also took home the Trophy for Best Chardonnay at the 2023 Ballarat Wine Show.
Paul said that the wine not only resonated with Oakdene but also impressed judges and consumers alike with its price point and quality.
“I know a lot of people out there buy what they love. It’s nice to think that this is the one that a lot of the people in the region certainly love us for,” he said.
“Liz retails at $45, we have another chardonnay for $30, and we sell more Liz Chardonnay than we do the second label.”
The winning 2022 Chardonnay was named justifiably after co-founder Liz Hooley and was planted on what they now call the ‘mature block,’ where Oakdene was founded all those years ago.
Alongside Oakdene’s proudest product, demand for its pinot noir and sparkling benchmark offerings is quickly rising.
Challenges
While Oakdene’s wine production system appears airtight, Paul said at each stage of the vineyard’s journey, challenges have emerged. He said the biggest challenge in viticulture is lead time, especially when establishing a vineyard.
“The hardest thing I think with viticulture and winemaking is that there is a very long lead time between establishing a vineyard and then getting your first crop. It’s probably three years,” he said.
“And then from that first crop, working out what parts of the vineyard
are working best, what varieties you’ve got in the ground, and whether the general public actually wants those wines.”
Paul explained that these long lead times mean if trends change, you have a lot of leftover wine that “you’re pretty proud of.” Instead of panicking, Paul emphasised that Oakdene strives to be a vineyard that practices confidence, foresight, and flexibility.
“Having the foresight and flexibility across certain wine styles is crucial. For example, pinot noir and chardonnay allow you to make sparkling, rose, dry red or dry white,” he said.
Going Forward
Paul said Oakdene will continue to focus on projects aimed at further enhancing the reach of the brand. Partaking in an Australian sustainability program is currently a priority. Oakdene has also fitted out a new cellar door and is in the process of constructing a second restaurant and an art gallery. F
Oakdene’s cellar door plays a vital role in attracting tourism and drawing attention to its products.
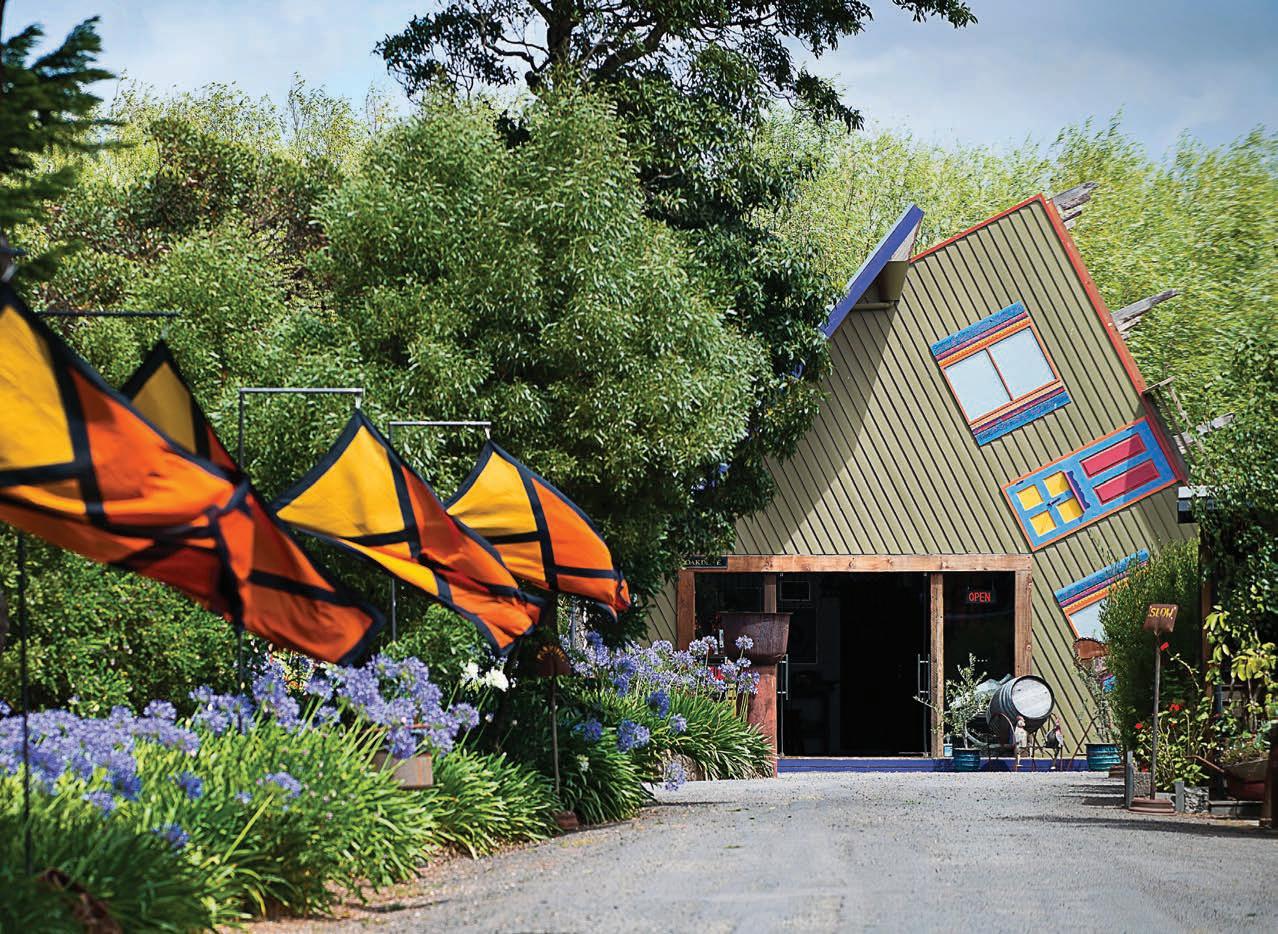
Streamlining production transitions with FLOWave
Bürkert’s innovative FLOWave, a multiparameter flowmeter solution, is designed to accurately detect media changes without the need for sensor elements in the measuring tube. Food & Beverage Industry News reports.
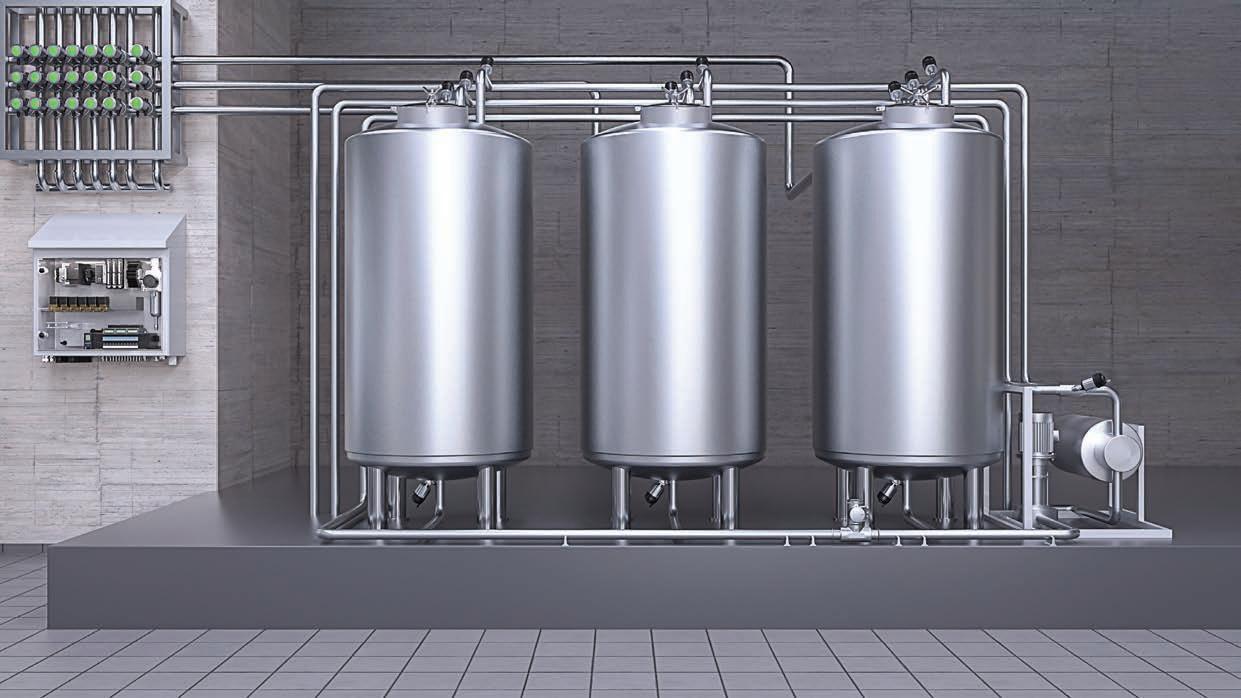
at maximum efficiency and minimise waste while maintaining product quality and consistency. However, this goal is challenged every time a media changeover or cleanin-place (CIP) cycle occurs. These transitions, if not managed effectively, can lead to product contamination, wastage, and costly downtime.
To achieve minimal waste and avoid contamination, timing is everything.
If the valve to the drain opens too late, product will be contaminated. If it opens too soon, product will be wasted.
For example, 100 litres of liquid per minute flow through a DN50 pipeline, and if the valve opens 15 seconds too early, then with five media changeovers per day, around 125 litres of product end up in the drain.
To minimise these risks, it is imperative that media changeovers are detected accurately.
In most cases conventional flowmeter solutions may measure flow
media stream, raising hygiene and maintenance issues. Coriolis flowmeters offer more advantages, but are costly and bulky, and may be more sensitive to blockage from viscous fluids.
A flowmeter that can see media changes
Fortunately, an innovative solution in FLOWave, a multiparameter flowmeter solution from Bürkert, is revolutionising how manufacturers address this challenge, offering unprecedented precision and reliability.
Because FLOWave leverages advanced Surface Acoustic Wave (SAW) technology, it dispenses with sensor elements in the measuring tube, which means no leaks, no material incompatibility, no maintenance, no pressure drops and easy cleaning. Instead, it acoustically measures the volume flow independently of the conductivity of the medium with an
accuracy of ≤ 1°C.
Its Density Factor function allows FLOWave to detect fluid changeovers very quickly, while the Acoustic Transmission Factor function detects bubbles, particles or solids in the liquid. This allows the user to intervene quickly as soon as defined process variables are exceeded or undercut.
All this means that FLOWave offers unparalleled accuracy and reliability in detecting changes in fluid composition in real time. This means that manufacturers can now transition between different media more quickly, without the risk of contamination and minimising product loss – leading to significant improvements in efficiency and cost savings.
FLOWave solutions are built on the Bürkert device platform EDIP, ensuring quick and efficient integration into existing fieldbus systems.
A Wi-Fi module provides remote access to measurement parameters via a web browser, facilitating monitoring
This system solution requires calibration and installation by an approved Bürkert service provider, ensuring precise setup and reliable performance. This collaborative approach promotes a successful partnership between the customer and Bürkert.
Special offer
At Bürkert, we understand the challenges that food and beverage manufacturers face in optimising their production processes.
Bürkert also announced a limited time offer for FLOWave, with prices starting from just $5,800.
This presents a unique opportunity for manufacturers to invest in cuttingedge technology that can revolutionise operations and drive business growth. Whether you’re looking to improve efficiency, ensure product quality, or reduce operational costs, FLOWave offers a comprehensive solution that delivers tangible results. F
FLOWave solutions are built on the Bürkert device platform EDIP, ensuring quick and efficient integration into existing fieldbus systems.
Image:
Bürkert
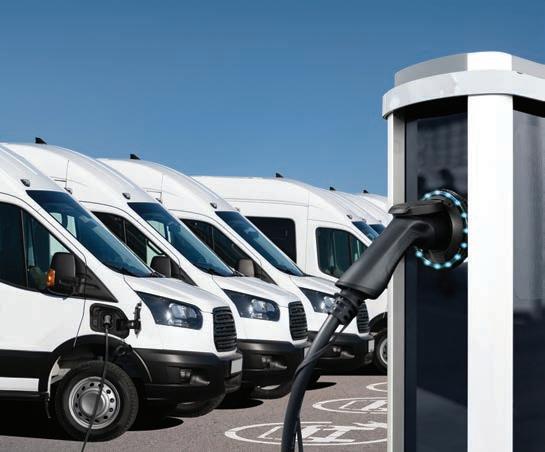
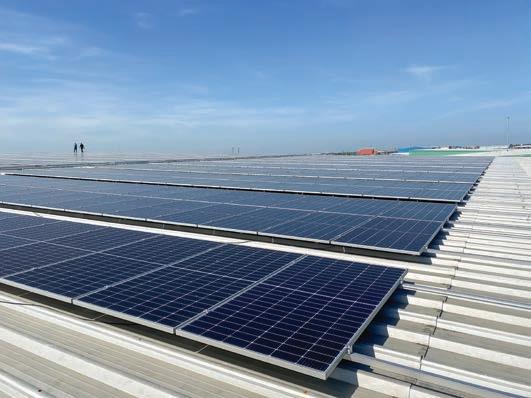
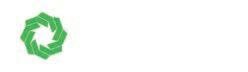
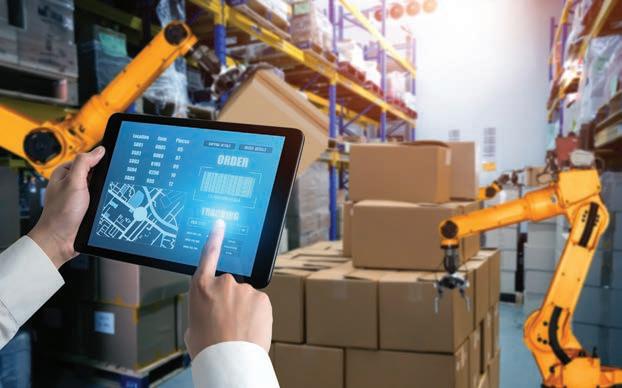
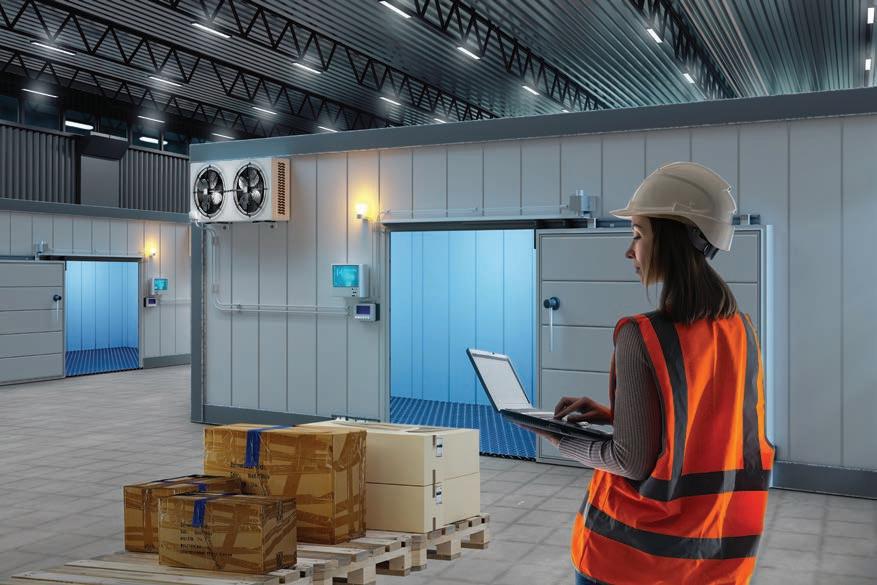
Innovating on the back of market trends
Australian Bakels’ expert reading of market and consumer trends helps the company provide the best solutions for an ever-evolving baking industry. Food & Beverage Industry News reports.
At Australian Bakels, staying ahead of industry trends isn’t just a strategy, it’s a commitment.
This dedication to trend-watching is rooted in a deep understanding of their customers’ needs and the broader market dynamics.
To achieve the best results, market experts at Australian Bakels keep a close eye on trends, ensuring they are always in sync with consumer preferences, helping their clients develop products and solutions that resonate with current demands.
“I think it’s important for us to keep an eye on trends because that’s what our customers do, and we like to work closely with our customers to help them develop products and solutions that appease those trends,” said Angelique Schmidt, development and application manager, Australian Bakels.
“A customer may come across a trend that is of interest to them, and we can then help with making that a reality. It’s not just flavours and textures in products, but also packaging solutions.”
Schmidt said tracking consumer behaviour was a critical part of recognising emerging and possibly future trends.
Kristen Kuan, marketing coordinator, Australian Bakels says that tracking consumer behaviour is a critical part of recognising emerging and possibly future trends.
“Consumer behaviour is very important when it comes to tracking trends and what products we can help our customers develop,” she said.
“We provide products that appeal to those trends.”
Australian Bakels ensures it has access to both national and international
trends to inform its decision making.
“It creates a great overview of the market for us and if there is a gap we can fill, or a pain point that is trending,” said Schmidt.
“If there is anything we can do to help our customers find success through those trends, then that’s what we do.”
This holistic approach includes tracking consumer behaviour meticulously, identifying market gaps, and filling those voids with innovative solutions.
By leveraging both local and international market trend reports, their marketing department maintains a keen awareness of evolving trends, ensuring they stay ahead of the curve.
In today’s digital age, social media has become an increasingly important platform for trend identification.
“Everyone wants to go viral these
days, whether it’s a long-term trend is up to the business to identify,” said Kuan.
“Digital is everywhere these days and usually social media/digital is where those trends tend to originate.
“There’s been a significant trend in recent years around cleaner labels in terms of colours, flavours, and also preservative free products,” said Schmidt.
“We’ve responded by modifying existing products and developing new ones to meet the trends. Through doing that we face our own challenges because it can be more costly than removing preservatives impacts the product’s shelf life.
However, this shift presents challenges, such as managing shelf life without preservatives.
To achieve this, the expert Australian Bakels team looks at several ways to extend shelf life.
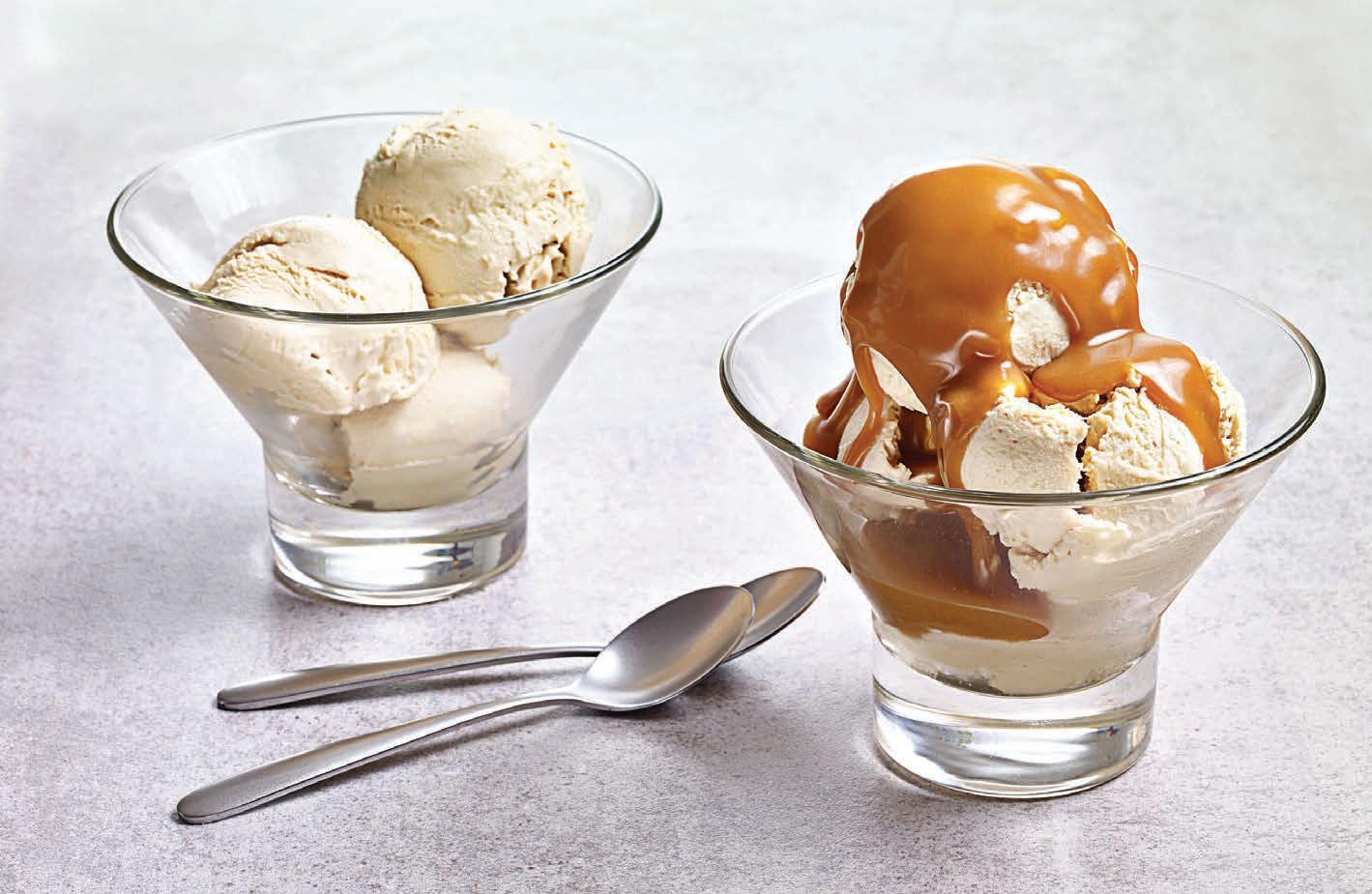
To achieve the best results, the expert team at Australian Bakels keep a close eye on market and consumer trends.
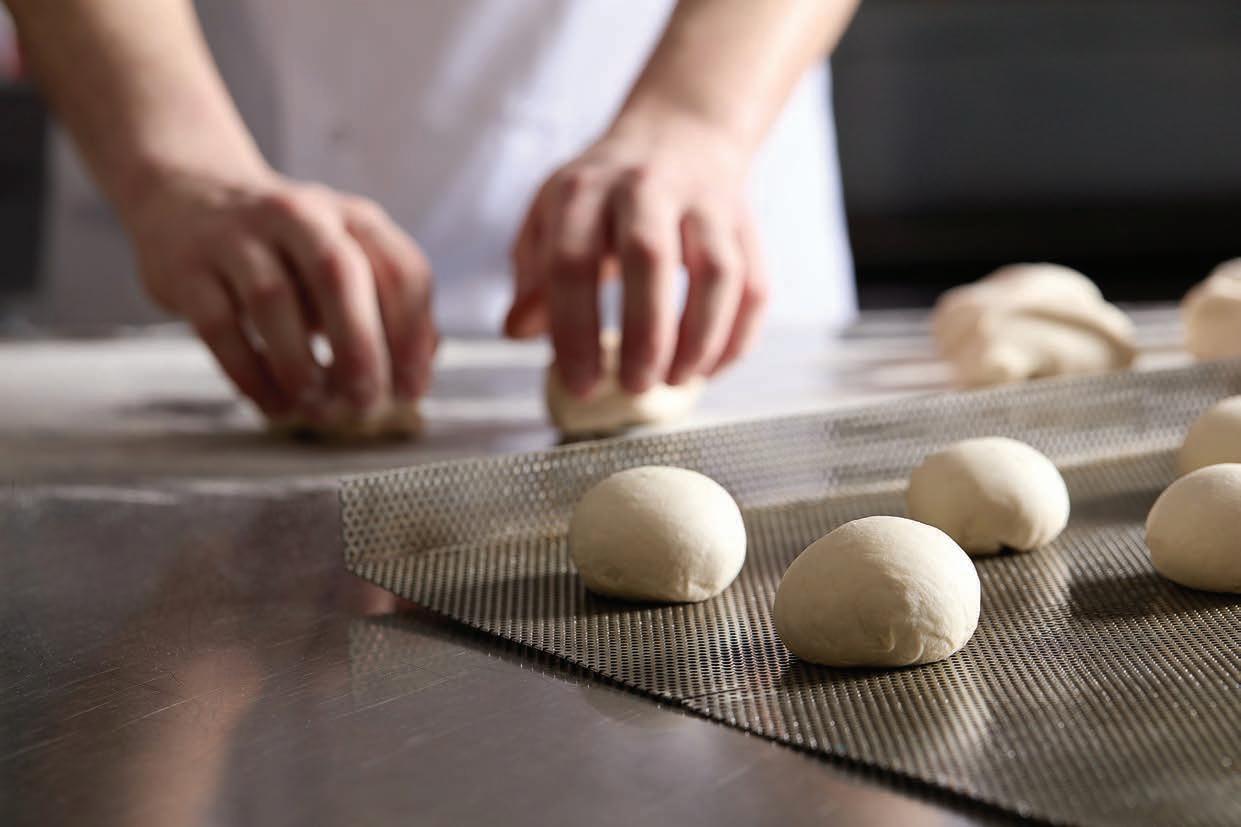
shelf life of a product either through formulation, processing or packaging. For example, it might be around something like the customers packaging, there are many ways to increase the shelf life of a product,” said Schmidt.
“This is all important because of consumers becoming much more holistic in the way they purchase their food now.
Understanding this dynamic, Australian Bakels cater to customers who are keen on making their products go viral, adapting quickly to the fastpaced changes in digital trends.
Customer feedback is another invaluable tool for Australian Bakels.
“We receive requests from customers, and we recognise the commonality between those needs,” said Schmidt
They pay close attention to requests and by recognising commonalities in customer needs, can craft the best solutions available.
This feedback loop allows them to refine their offerings continuously, ensuring they meet the expectations of their clientele.
Modern consumers are also more health-conscious and environmentally aware than ever.
“Consumers have also become more aware of health and their environmental footprint.
Not compromising on the quality
trends, We do our own blue-sky work and come up with our own innovation based on the trends we see, but we also respond to customer requirements and come up with tailored solutions,” said Schmidt.
“They may have limitations or particular requirements, so we develop specially for them, and our turnaround is relatively short compared to others.”
Sustainability is another crucial area, with consumers being willing to invest in sustainable packaging and proof of provenance for ingredients.
“Sustainability is very important, many customers are more conscious of their environmental footprint and some consumers might be willing to invest in a product that has sustainable packaging or ingredients, or proof of provenance for its ingredients,” said Schmidt.
“Premium ingredients also have a similar impact and is a growing trend.
This trend towards premium ingredients is significant, with consumers increasingly checking product ingredients. Highlighting provenance and premium quality has become essential.
The clean label trend has gained significant traction, emphasising natural ingredients, colours, flavours, and preservative-free products.
in three consumers globally always look for ingredients of interest and calling out that provenance or premium ingredient is important in that case,” said Schmidt.
“For example, percentage of fruit, the filling. We’ve really tried to focus on that with some of our products and a high fruit percentage.”
Another key driver behind this trend is the growing awareness around the environmental footprint of brands and products.
Australian Bakels has responded by modifying existing products and developing new ones to align with these trends.
“People are so much more conscious now of supporting the environment and I think as a business we have taken that into consideration,” said Schmidt.
“We look at sustainability of ingredients, on top of provenance. And it’s not just about packaging, we look at that, but it’s also about reducing footprints on the environment in several areas.”
“You have to look at other ways where you can manage that. People still have the same expectation of the product at the end of the day,” said Schmidt.
Australian Bakels prides itself on its agility in responding to market trends and customer requests. Their sales team
tailored products, often conducting trials and providing samples to ensure customer satisfaction.
Open communication and a crossfunctional team approach, involving sales, marketing, procurement, development, quality control, and compliance, ensure a smooth and efficient process.
“One of the trends we have seen is around convenience and consistency in quality and supply, especially post COVID,” said Schmidt.
Australian Bakels has leveraged new technology, such as their batch process vacuum cooker, to expand their product range, offering true caramels, sweet and savoury sauces, and various fillings.
This innovation has opened new product categories.
“We are unique in this way, because we also have the capability to do dry and wet manufacturing,” said Schmidt.
By staying attuned to trends and maintaining a flexible, responsive approach, Australian Bakels continue to meet and exceed the expectations of their clients.
Their dedication to quality, sustainability, and innovation ensures they remain a key player in the baking industry, well-prepared for the evolving demands of the market.
Australian Bakels prides itself on its agility in responding to market trends and customer requests.
Shaping the future of transport and logistics
Registrations are open for Australia’s largest integrated conference and exhibition dedicated to the logistics sector, MEGATRANS. Food & Beverage Industry News reports.
In the constantly evolving landscape of transport and logistics, staying ahead of the curve is crucial. Enter MEGATRANS, the biennial event that brings together industry professionals from across the world.
MEGATRANS2024, being held in Melbourne, from September 18 and 19, is a must-attend event for anyone looking to immerse themselves in the cutting-edge advancements and emerging trends of the sector.
Registration for the event is now open, and free. And tickets can also be purchased for the Mercury Awards Gala Dinner during the registration process
“MEGATRANS is not just an opportunity to witness innovation, it’s an interactive experience, and I encourage people to engage with everything the event will have to offer,” says Lauren Chartres, show director.
Spanning several days, MEGATRANS is a celebration of technology, innovation, and collaboration. With this year’s event set
solutions, the expo floor is a treasure trove of ground-breaking innovations.
The event boasts an expansive exhibition hall where hundreds of companies showcase their latest products and services, including logistics experts Combilift and Schmitz Cargobull.
Chris Littlewood, Combilift country manager, Australia, said MEGATRANS provides excellent business opportunity for both exhibitors and visitors.
“We have been involved with MEGATRANS since its inception and are looking forward to showcasing our products and innovations,” said Littlewood.
“Because we’ve had such a longstanding relationship with its parent company, it has been a no brainer for us to be involved with MEGATRANS.”
Littlewood said Combilift has always had a strong emphasis on being present at industry trade events across the world.
“Each year we probably attend around 90 trade shows globally, and at least 10 within Australia,” he said.
experience firsthand the tools that are set to revolutionise the way we move goods and people.
For Combilift, the opportunity to showcase its biggest innovations in person is invaluable in terms of generating business and recognising emerging industry trends.
“Our display will cover 72 square metres, so it’s a large stand, which allows us to display several our models,” said Littlewood.
“Such as our Multi-Directional Forklift, and our Pedestrian Stackers. We will also be able to talk extensively about our Mobile Gantries, which are designed for handling containerised, bulky, or oversized loads.”
The Combi-CS electric Pedestrian Stacker has already proven popular in the food and beverage manufacturing industry, due in no small part to its patented, award-winning, multiposition tiller arm.
The Combi-CS can navigate very narrow aisles whilst managing loads of
improved safety but was simple enough for any operator, we knew it was our gap to fill,” said Littlewood.

“This stacker really sums up what Combilift is about – we listen, we learn, and we give the people exactly what they want.”
to advanced warehouse management systems and sustainable supply chain
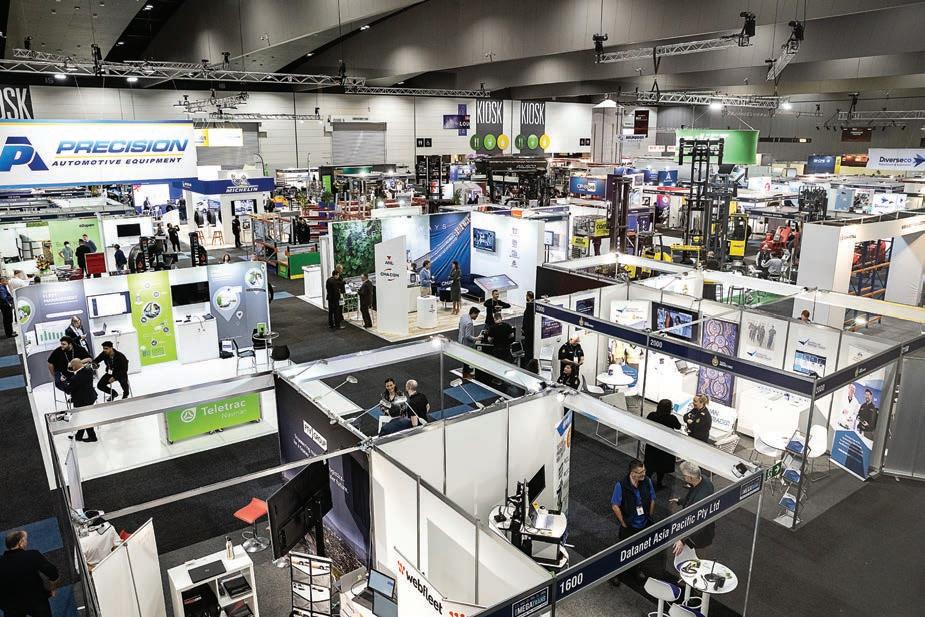
MEGATRANS is more than just an exhibition. It is also a platform for knowledge sharing and professional development, as mentioned by Littlewood.
The conference component features a series of seminars, panel discussions, and keynote addresses from industry leaders and visionaries.
Topics cover the full spectrum of transport and logistics, including the integration of artificial intelligence, the impact of e-commerce on supply chains, and strategies for reducing carbon footprints.
Speakers have been confirmed from companies such as ANL, Toll Group, Prological, Deloitte, Jones Land LaSalle, Mosaic Brands, OneStop, and the Victorian Government.
Attendees can also look forward to engaging with exhibitors showcasing various products and services. From state-of-the-art transportation technologies to innovative warehousing solutions, the exhibition floor will have something for everyone.
“I urge people to come and experience MEGATRANS firsthand
MEGATRANS returns to Melbourne from September 18 to 19, 2024.
Spanning several days, MEGATRANS is a celebration of technology, innovation, and collaboration.

and register to attend,” said Chartres.
Another of the key attractions of MEGATRANS is the unparalleled networking opportunities provided by the event.
The expo draws a diverse crowd, from logistics managers and engineers to CEOs and policymakers.
Throughout the expo, there are numerous networking opportunities, including luncheons, cocktail receptions, and roundtable discussions, designed to foster connections and collaborations.
These interactions often lead to new partnerships, business deals, and the exchange of ideas that drive the industry forward.
In recent years, sustainability has become a central theme at MEGATRANS. The transport and logistics sectors are under increasing pressure to reduce their environmental impact, and MEGATRANS provides a forum for discussing and promoting sustainable practices.
Exhibitors and speakers highlight innovations in electric and hydrogenpowered vehicles, eco-friendly packaging, and green logistics strategies.
The expo underscores the importance of balancing efficiency and profitability with environmental responsibility.
The Innovation Awards, a highlight of the event, celebrate the most groundbreaking advancements in the industry.
Companies and individuals are recognised for their contributions to technology, sustainability, and operational excellence.
These awards not only honour achievements but also inspire others to push the boundaries of what is possible.
MEGATRANS Expo is not just about the present; it’s about envisioning the future.
The event serves as a window into the future of the sector, offering insights into the trends and technologies that will shape the transport and logistics landscape in the coming years.
From smart logistics and digital twins to blockchain and IoT, the expo provides a glimpse into how these innovations will enhance efficiency, transparency, and customer satisfaction.
Meanwhile, for young professionals and students, MEGATRANS is an invaluable learning experience.
It provides exposure to the latest technologies and practices, as well as opportunities to engage with industry veterans. Educational workshops and hands-on demonstrations offer practical knowledge that can be applied in their careers.
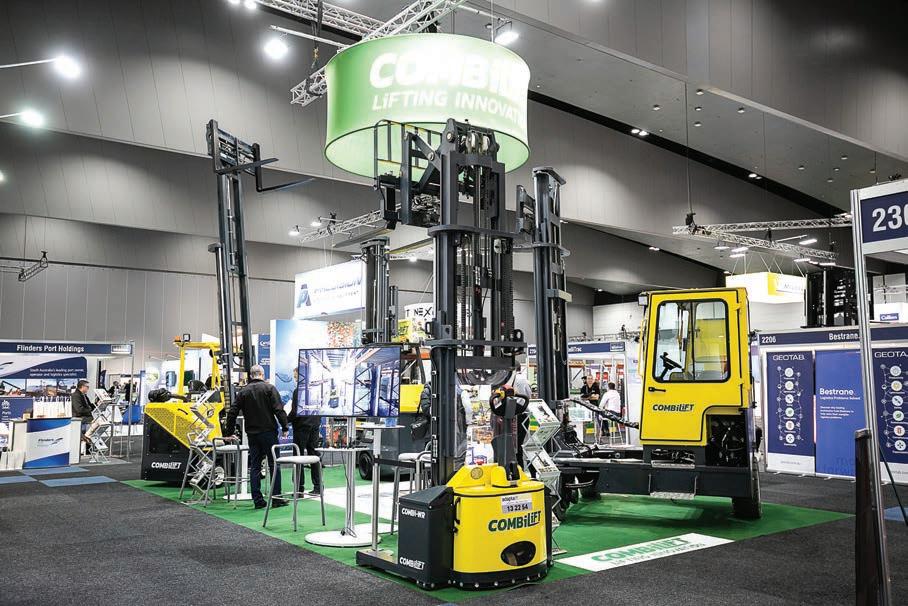
All of this is designed for MEGATRANS to support the transport and logistics sectors. It is a place where ideas are born, connections are made, and the future is mapped out.
For industry professionals,
attending MEGATRANS is not just an opportunity to stay current, it is a chance to be at the forefront of innovation and to contribute to the evolution of an industry that is fundamental to our global economy.
Whether you are a seasoned professional, a tech enthusiast, or a newcomer to the field, MEGATRANS
offers something for everyone. It is a celebration of the ingenuity and resilience of an industry that keeps the world moving.
As the transport and logistics sectors continue to evolve, MEGATRANS will undoubtedly remain a pivotal event, driving the industry towards a smarter, more sustainable future. F
Chris Littlewood, Combilift country manager, was full of praise for MEGATRANS and the opportunities it provides the business.
Accurate and robust solutions for top results
As the exclusive Australian distributor of Interface Force Measurement Solutions, Melbourne-based AMS Instrumentation & Calibration knows firsthand the benefits of these premium products.
AMS Instrumentation & Calibration specialises in industrial instrumentation including flow, pressure, level, temperature, and analytical equipment. They also offer calibration services to ensure the accuracy and reliability of these instruments.
Their extensive product range and technical expertise enable them to cater to diverse industrial needs, not only in Australia but also in New Zealand, Papua New Guinea, and the Pacific Region.
A great example of AMS’ expert role in the market is its partnership with American company Interface, to supply its force measurement products to the Australian market.
Founded in 1968, Interface Force Measurement Solutions manufactures industry solutions at its 60,000-squarefoot multi-facility campus in Scottsdale, Arizona. AMS Instrumentation & Calibration imports these solutions into
AMS Instrumentation & Calibration offer a range of cutting edge solutions to the food and beverage manufacturing industry.
Australia for local industries, including food and beverage manufacturing. Interface’s products can measure from grams to millions of pounds in hundreds of models and physical sizes,
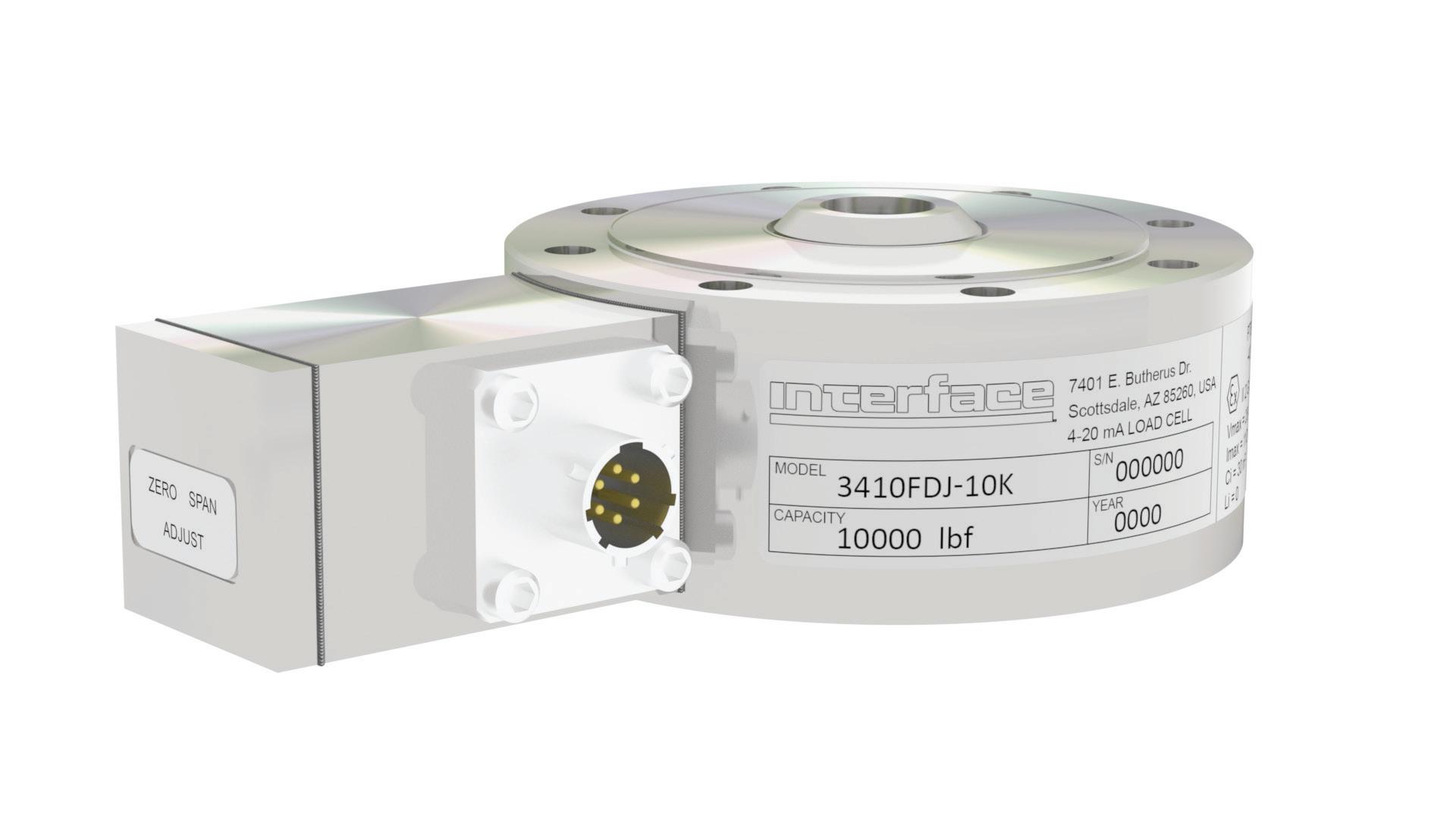
the entire process, from design, machining, strain gauge manufacturing, and assembly. In our own facilities, we ensure the highest degree of performance possible.
“Any
area within the food sector which requires a measurement of force is where Interface products and solutions are used.”
meaning the company has solutions to meet most, if not all, the needs of clients in the industrial space.
This is achieved by maintaining
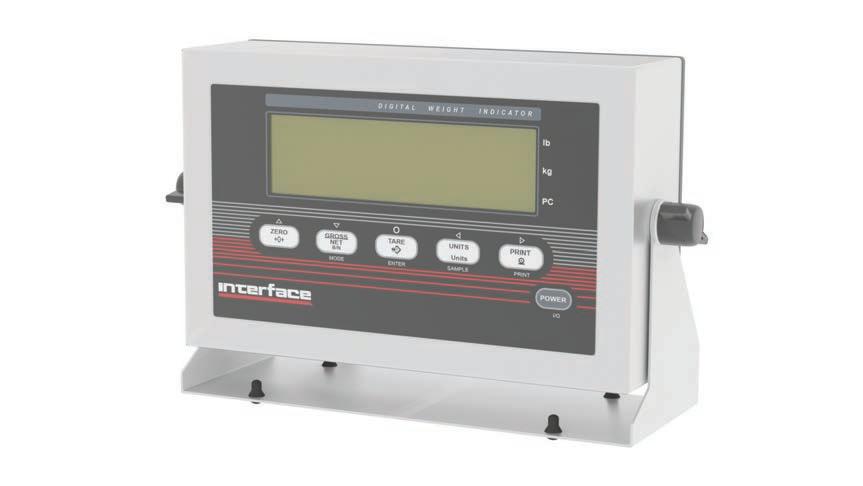
specialist, AMS Instrumentation & Calibration.
“It prevents excess force being used, especially for machinery that needs protection.
“Anywhere you need to have an accurate scale then Interface can be used.” Among Interface’s string of solutions is a variety of load cells.
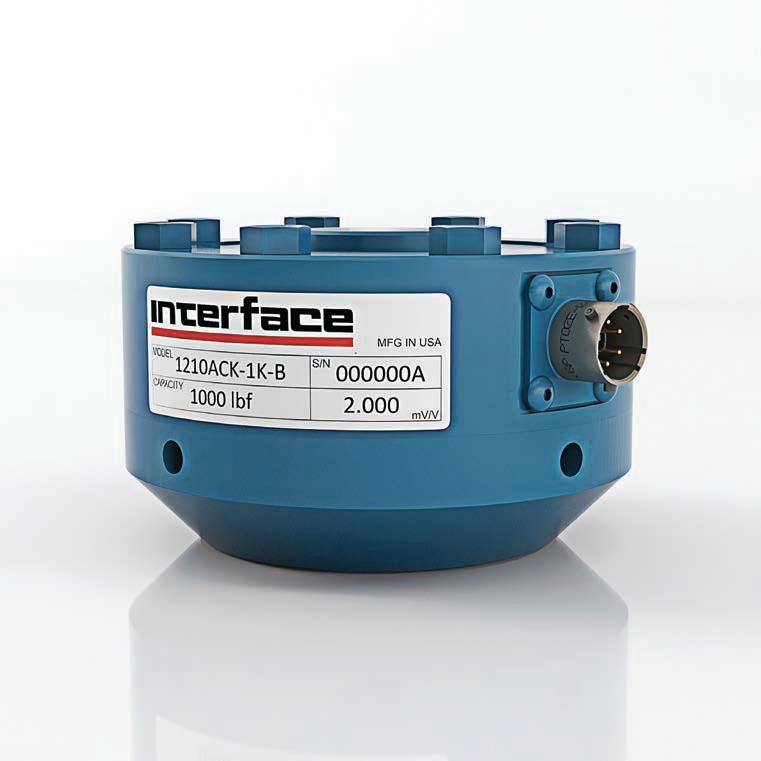
AMS Instrumentation & Calibration’s has partnered with American company, Interface, to supply force measurement solutions.
AMS Instrumentation & Calibration’s has partnered with American company, Interface, to supply force measurement solutions.
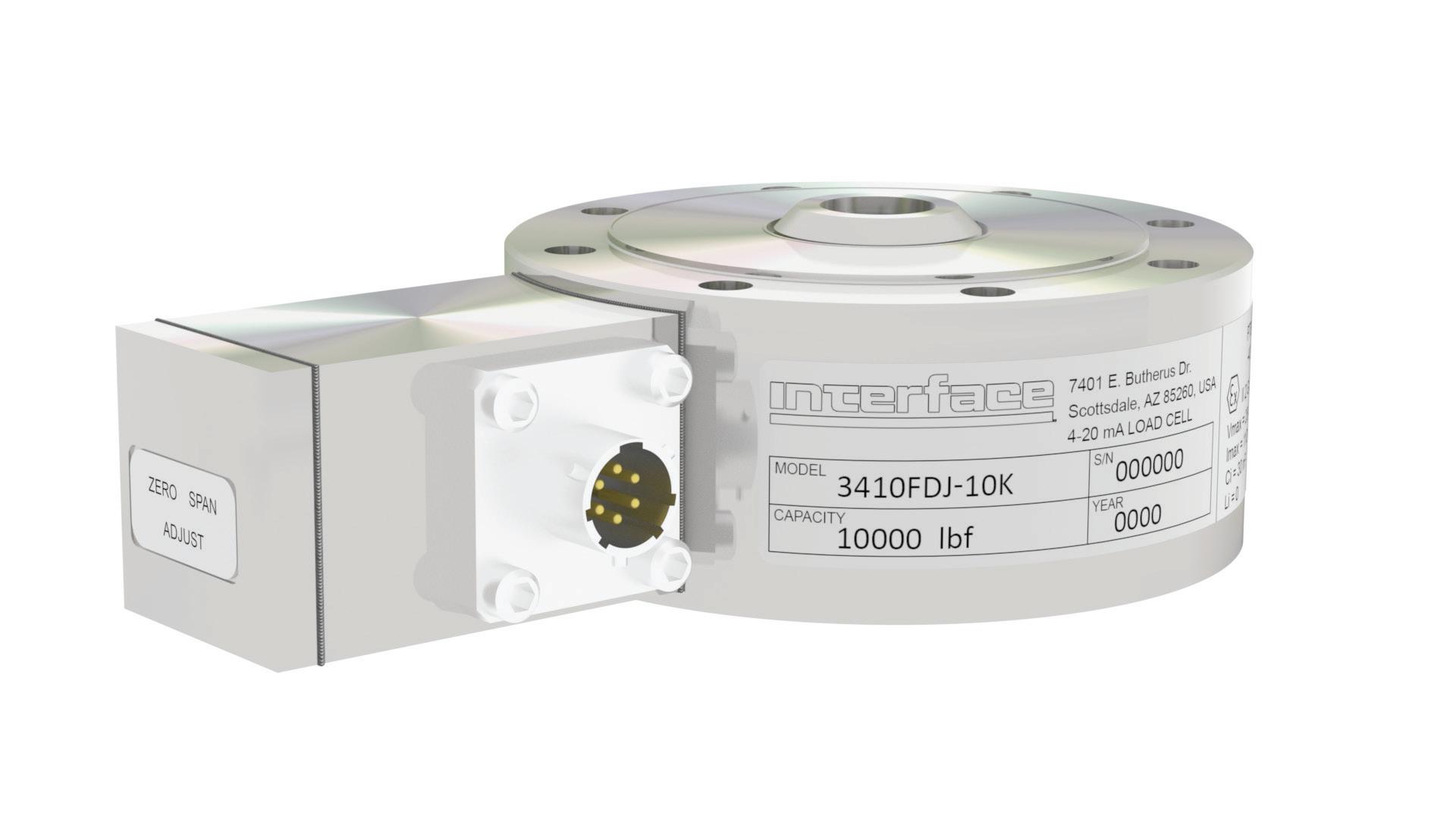
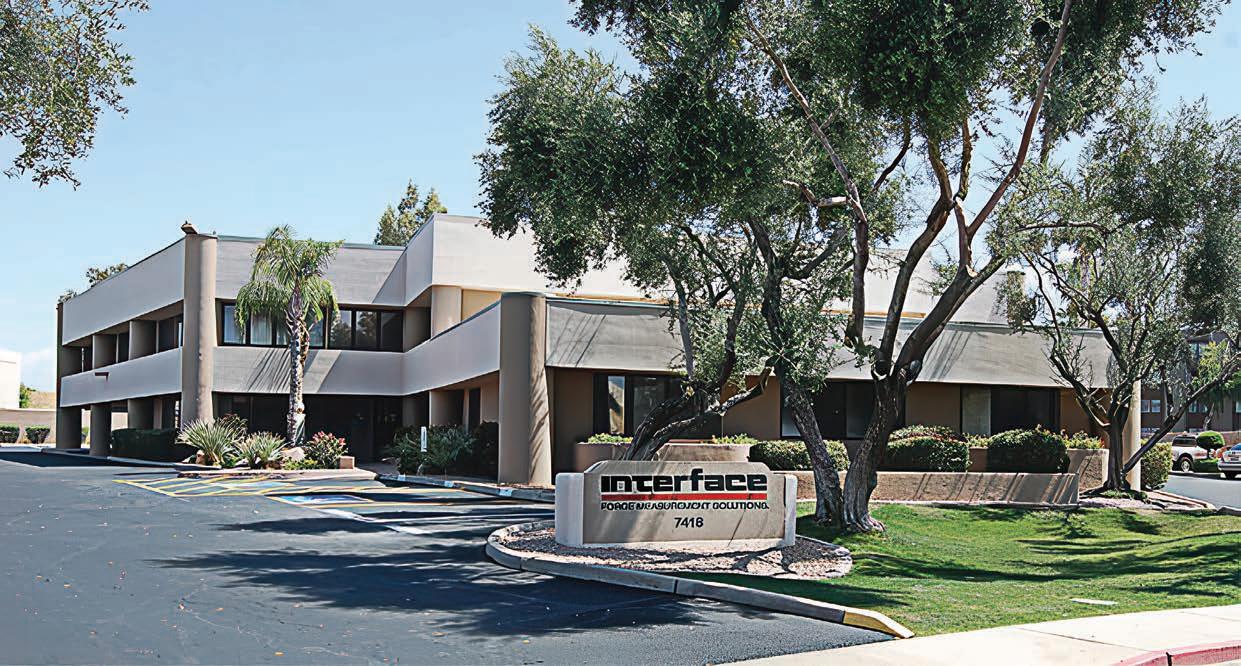
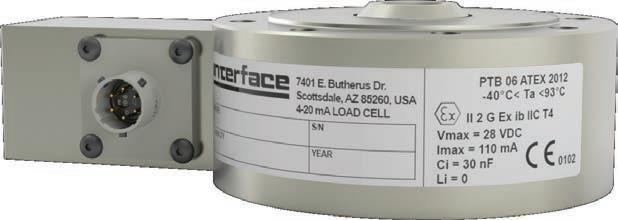

Interface is one of many suppliers in partnership with AMS Instrumentation & Calibration.
measurement sector,” said Grey.
“The principle behind the load cells is not too complicated, it’s just about having the right materials and that’s something Interface did.”
“For example, the wire they used was purchased in the 1960s, it filled a warehouse, and that has given them better repeatability and accuracy. It shows a forward-thinking mentality to do something like that.”
The force measurement solutions from Interface are also easy for customers to install and use.
“It is pretty much plug and play, it’s not a complicated system,” added Grey.
“Anything purchased from Interface will be set up in the factory and is sent out operational ready. It just needs to be installed when sent to the client.
“Load cells are a pretty simple construction, there is nothing complicated about them. It is all about the quality of the Interface product, the accuracy, and the repeatability.
“They are also durable; they are
tested for repeated and continuous use.”
Grey said the product catalogue from Interface Force Measurement Solutions was created to address all critical areas that require force measurement products.
European-made solutions to the product catalogue.
“They started as a small family business and have managed to retain the family business side of things while also
“Load cells are a pretty simple construction, there is nothing complicated about them. It is all about the quality of the Interface product, the accuracy, and the repeatability.”
“Everything from the measuring to the reading of those measurements they offer, whether it be wired or wireless or Bluetooth,” he said.
“They cover all the important areas. For example, you can have four load cells and they are averaged out for a single reading of the total weight.”
“They have a wide range of sizes to help address the needs of customers.”
AMS imports the solutions into Australia before distributing them to the local industrial markets where force measurement is required. A recent acquisition by Interface will also add
experiencing a lot of growth,” said Grey.
“The company has grown into more of a corporate organisation now, which demonstrated their growth. Just recently they acquired another force measurement company, LCM, which is part of the plan to expand their range.”
Interface CEO Greg Adams said he was thrilled with the acquisition.
“LCM Systems is an established and recognized leader in the design and manufacture of specialized load cells and instrumentation, and we are proud to officially welcome them to the Interface family,” he said
“Adding their quality, proficiency and long history, the LCM team further bolsters our global capabilities in meeting the rapidly growing demands for exceptional products including their load pins, load shackles, load cells and other sensor technologies.”
Because of the North American, and now European Interface manufacturing centres, turnaround times for orders vary depending on the requirements of customers.
“Turnaround times depend on what type of load cell is needed, some of the smaller stuff might already be on the shelf but the bigger stuff is made to order,” said Grey.
“It could be anything from four to six weeks to 20 weeks, it all depends on what the requirements of the solution are.
“Some cases where it’s a bit more technical we have Interface engineers involved to help consult with the customer to come up with the best solution for them.” F
AMS imports solutions into Australia before distributing them to the local industrial markets.
Images: AMS Instrumentation & Calibration
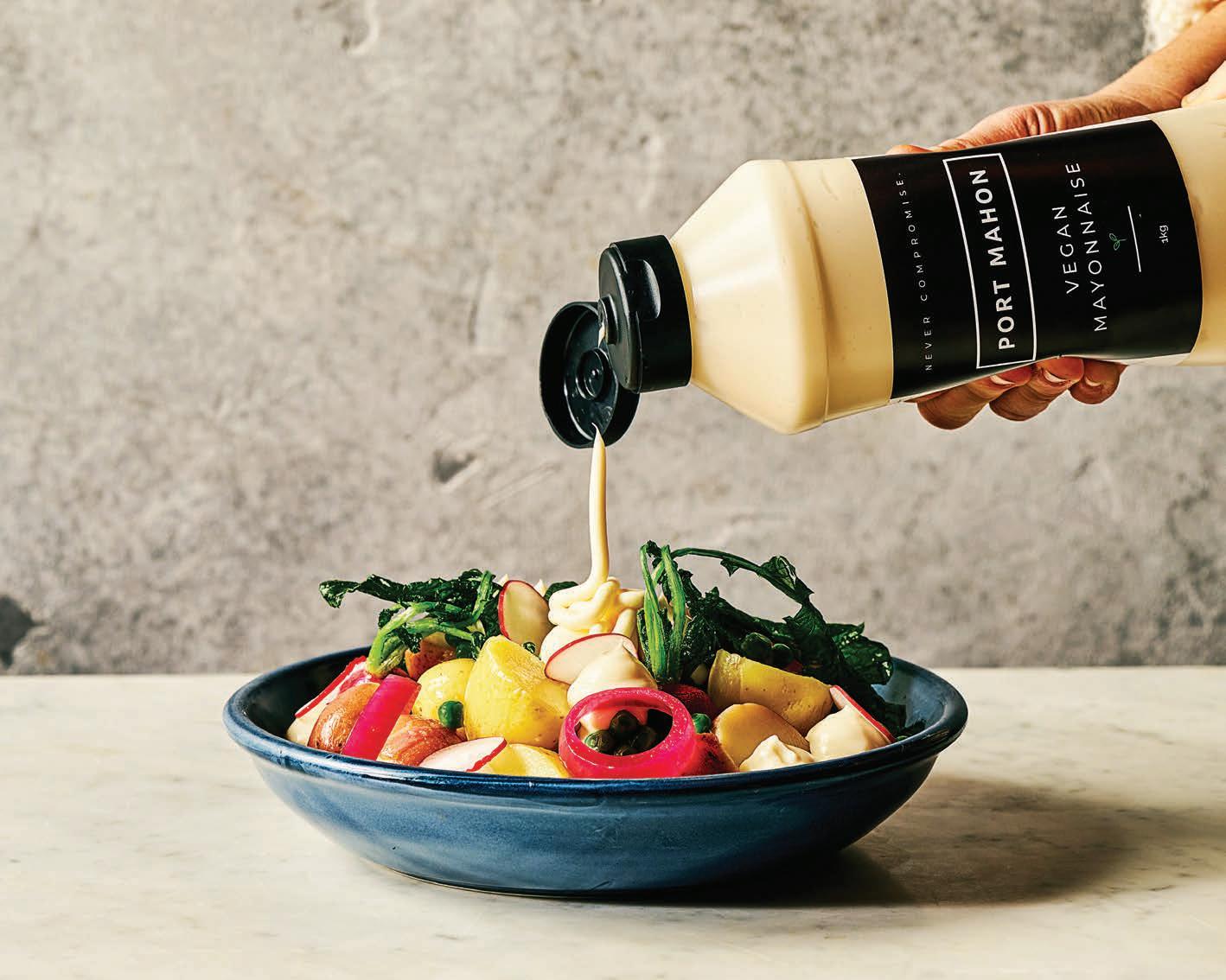
Remaining agile to meet market demands and disruptions
FoodFx prides itself on innovation, quality ingredients, and agile production processes. This makes them an ideal partner in the ever-evolving condiments space. Here’s why.
FoodFx is an Australian-owned food manufacturing company specialising in creating highquality condiments, mayonnaises, sauces, and meal bases.
The company has a strong focus on the use of fresh local Australian ingredients to produce premium products. In this role, FoodFx serves a range of clients, including QSRs, cafes and restaurants of all sizes.
Founded on the principles of quality and consistency, FoodFx has built a reputation for its custom manufacturing capabilities and its three distinct brands: Port Mahon, batch No.5, and Hermans Homemade.
Because of their dedication to custom manufacturing, FoodFx has the capability to meet the unique requirements of each client, ensuring each product is crafted to specific needs.
Another key area of focus for the brand is its commitment to dietary inclusivity, such as offering gluten-free and vegan options.
FoodFx also emphasises the agility to keep on top of, and ahead of, emerging market trends and innovations, with an example being the rise in plant-based/ vegan products.
“Increased consumer demand has led to a wider variety of products, including meat substitutes, dairy alternatives,
snacks, and ready-to-eat meals,” said Andrew Casley, Sales and Marketing Manager at FoodFx.
“Advances in food technology have also improved the taste and texture of these products, making them more appealing to a broader audience.
“Nutritional enhancements, such as fortification with essential nutrients, have also become common, creating balanced and wholesome options that cater to health-conscious consumers.”
As a result of these factors, mainstream adoption has surged. With plant-based products now available in supermarkets, restaurants, and fastfood chains.
A growing focus on sustainability has also played a key role in the rise of plantbased and vegan products.
“[That] focus and the environmental benefits of plant-based diets has attracted eco-conscious consumers, while celebrity and influencer endorsements have further boosted popularity,” said Casley.
“Increased investment and innovation in the sector have driven continuous research and development, leading to ground-breaking new products.
“Additionally, the sector has expanded culturally and regionally, adapting traditional dishes to suit diverse local tastes.”
Port Mahon Vegan Mayonnaise provides an example of how the experts at FoodFx are helping manufacturers capitalise on trends.
Images: FoodFx
Casley said health consciousness is another driver, with consumers seeking out plant-based foods perceived as healthier alternatives to animal products.
“Environmental concerns are also significant, as more people recognise the lower carbon footprint and reduced resource consumption associated with plant-based diets,” he said.
“Ethical considerations, such as animal welfare, have further fuelled the shift towards veganism.”
“Additionally, advances in food technology have made plant-based products more appealing by improving their taste and texture, thus attracting a broader consumer base.”
The FX vegan range also helps address allergen risks and concerns at the point of sale.
“Allowing for end user outlets to reduce allergens via the Port Mahon, batch No.5 and Hermans Homemade Vegan ranges and manage less products, for example, one vegan mayonnaise across all recipes or meals, has been great to see. This is also the case with ensuring all our products are gluten free,” said Casley.
“FoodFx, through our brands Port Mahon, batch No.5, and Hermans Homemade, plays a crucial role in helping the sector respond to these trends.
“By producing a range of vegan mayonnaises and condiments, we can cater to the growing demand for plant-based alternatives without compromising on flavour and quality.”
The egg shortage being experienced in Australia, due to the recent bird flu outbreak, has also highlighted in real time the benefits of providing alternatives for the market.
“This presents a unique opportunity for restaurants to switch to vegan mayonnaises,” said Casley.
“With traditional egg-based products becoming scarcer and more expensive, vegan alternatives offer a reliable and cost-effective solution.”
“Port Mahon and batch No.5’s range of vegan mayonnaises provides high-quality, flavourful options that can seamlessly replace conventional mayonnaise in various dishes.”
This shift not only addresses supply chain challenges, but also aligns with the growing consumer demand for plantbased options. Casley says this allows the food and beverage industry to cater to a broader audience while maintaining menu quality.
FoodFx also leans into these trends
by diversifying existing offerings, such as its new branch of the Port Mahon product range.
“While Port Mahon has always had a vegan offering, our revamped Vegan product line includes an initial launch of Vegan Mayonnaise and Vegan Aioli in 1kg squeezy bottles, with the plan to expand the range in additional flavours in coming months,” said Nelson Fanelli, Category Manager at FoodFx.
“This range addresses the growing demand for healthier, sustainable, and ethical food choices, and provides a reliable solution amidst the current egg shortage.”
“Our product development capabilities allow us to create a vegan product that matches the flavour, quality and consistency of our egg-based products. This is something rarely accomplished in the market, and something we are very proud of.
“The revamped Port Mahon Vegan line in 1kg squeezy bottles also allows for precise dispensing and provides a more economical solution for businesses by maximising product usage before use by dates”.
Fanelli said the decision to adopt this new packaging format was driven by several factors.
“Predominantly, the need to enhance operational efficiency in commercial kitchens by simplifying the use of condiments and reducing preparation
and cost-effective products, aligning with broader market trends toward efficiency and sustainability.”
“Our customers, that at times post COVID have struggled to source available labour back of house, can now rely on the high-quality Port Mahon 1kg squeezy bottles to potentially reduce significant labour in store, for example, less de canting and preparation time.”
FoodFx develops its products with a focus on quality, innovation, and market responsiveness, as exemplified by the Port Mahon 1kg Vegan line.
“The development process begins with extensive market research to identify emerging trends and consumer preferences,” said Andrew Casley.
“Understanding the growing demand for vegan and plant-based options,
that cater to customer demand.”
Key drivers behind product development decisions include innovation, sustainability, convenience, and cost-effectiveness.
“This and ongoing feedback from our current customer base on what they see in the market and what they require also allows Foodfx to develop products that the market needs,” said Casley
“FoodFx’s commitment to continuous research and development ensures that its products meet high standards of taste and quality while addressing the evolving needs of consumers and businesses.
“Our agile approach allows us to adapt quickly to market changes and deliver innovative solutions that enhance both customer satisfaction and

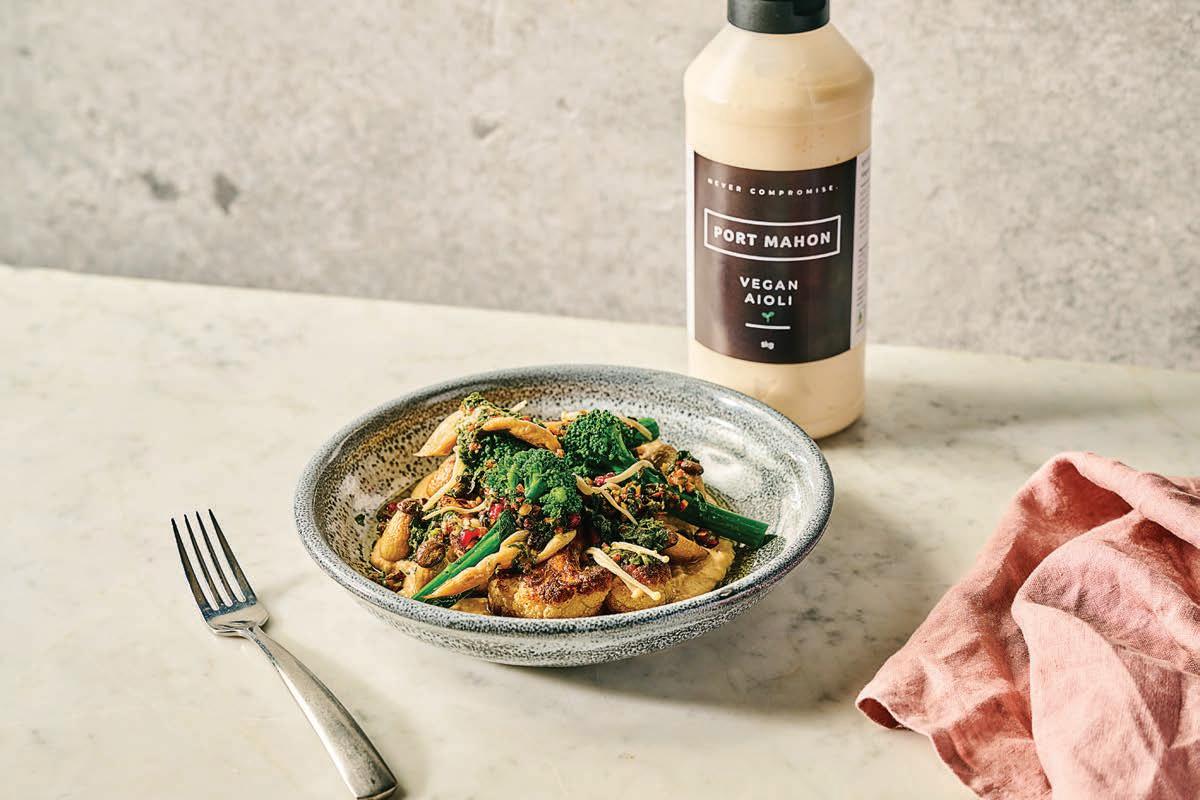
FoodFx also leans into these trends by diversifying existing offerings, such as its new branch of the Port Mahon product range.
Key drivers behind product development decisions include innovation, sustainability, convenience, and cost-effectiveness.
Introducing Drinkline to the Australian market
Continental’s Drinkline hose continues the company’s promise of reliability and innovation,
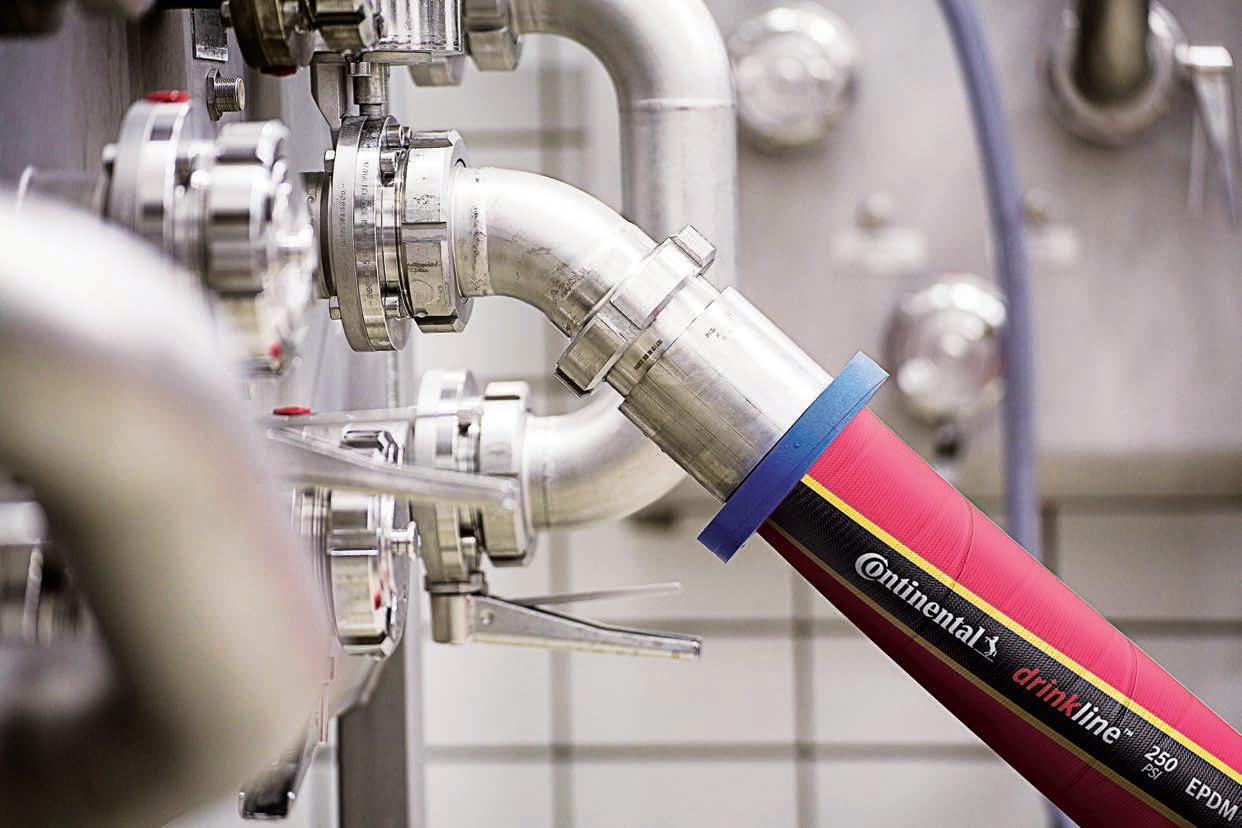
In a world where clean, safe beverages is paramount, innovation in liquid transfer technology has become increasingly important.
Enter Continental’s Drinkline hose, a game-changer in the realm of liquid transfer solutions.
Continental continues to prove its agility when it comes to meeting the unique needs of each customer. Drinkline is a direct complimentary hose to the popular Purple Snake hose no longer available, the company has provided a suitable alternative. With a blend of cutting-edge materials and meticulous engineering, the Drinkline hose is reliable and safe, making it an important addition for food and beverage manufacturers, especially in the production of beer and wine.
Wayne Rowland, sales specialist, APAC, Continental, said the Drinkline hose was relatively new to the market, just a couple of years old, and its rollout in Australia is already getting positive feedback.
“One thing about the hose is that it’s a delivery hose with reinforcement and no helix but rated to full vacuum,” said Rowland.
“In many wineries and breweries, they don’t like hoses that are susceptible to leaks because the forklifts can drive over them and crush them. Some of our other hoses have what they call a monofilament PVC helix in them, which is crush-resistant.”
Rowland said providing added peace of mind to customers was a key advantage to the Drinkline solution.
“One of its great traits is that it’s hard to damage. Of course, there are drivers who might drive off with the hoses still hooked up to the truck, and accidents do happen,” he said.
“But generally, in wineries and distilleries, where there is a bit of forklift movement, this hose will continue working even if it’s run over.
“Lightweight and Flexibility design where manoeuvrability is important in these workplaces with tight, confined areas.”
Developed with the highest standards in mind, this hose is designed to ensure that every drop of liquid that passes through it remains as pure and clean as it was intended to be, he said.
At the heart of the Drinkline hose is its material composition
“This hose has an EPDM outer cover, which is good for ozone resistance,” he said.
“The Australian ozone is aggressive compared to the US and Europe. When we manufacture hoses locally in Australia, we use a lot of UV stabilisers for our conditions.
“The hose also has an EPDM inner, which is generally very good for CIP (Clean-In-Place) cleaning processes. When cleaning the hoses after usage, especially for certain tanks, there’s an industry standard for cleaning temperatures.
“These hoses, even though their operating temperature is 104 degrees Fahrenheit, can handle up to 130 degrees for shorter periods during CIP.”” Made from FDA-approved materials,
Images: Continental
Continental’s Drinkline industrial hose provides a blend of cutting-edge materials and meticulous engineering.

the hose guarantees that no harmful chemicals leach into the liquid, safeguarding the health of its users.
This dedication to safety is further underscored by the hose’s compliance with health and safety standards for liquid transfer hoses.
The Drinkline hose is not just about safety; it’s also about performance.
Designed for flexibility, it can be easily manoeuvred in tight spaces, making it a suitable choice for a variety of applications.
The Drinkline is also robust, giving it a longer lifespan.
“I’ve had similar hoses in operation for over 10 years. Big wineries often buy cheaper alternatives that they replace every one to two years,” said Rowland.
“Sometimes quality does have its benefits, and a more expensive hose can
last a lot longer.”
A Continental customer already using Drinkline was full of praise for the solution.
“One of our customers in Tasmania, who uses a range of our food and beverage hoses, has chosen the Drinkline because it’s unique and of high quality,” said Rowland.
“The customer finds them easy to crimp with chrome fittings. The hose also has a four-to-one safety factor.”
Another key selling point for the Drinkline is the variety of sizes it’s offered in.
“The hose is available in sizes from three-quarters of an inch to four inches in diameter,” said Rowland.
“The smaller sizes are more flexible, and even the larger ones maintain a good
degree of flexibility.
“In wineries, the most common sizes are usually one and a half to two inches, and in craft breweries, one inch to one and a half inches.”
Rowland said the Continental team were optimistic about how the market will continue to react to the Drinkline hose solution.
“We’re relatively new to this product, and we received our first order either at the start of the year or the middle of last year,” he said.
“Customers are extremely happy with it so far, even after just a couple of weeks of use.”
This adaptability and flexibility of Drinkline ensures that there’s a perfect fit for every need, from small-scale installations to large-scale
industrial applications.
Additionally, the Drinkline hose incorporates innovative features such as anti-microbial linings.
This feature helps prevent the growth of bacteria within the hose, further ensuring the purity and safety of the water it transports.
Continental’s manufacturing processes are designed to be environmentally friendly, reflecting the company’s commitment to sustainability.
“The key for us now is to get the message out there that we’re still here, still good, and still doing great work,” said Rowland.
“We have some of the best food and beverage hoses globally, and we’re committed to quality and reliability.”
Made from FDA-approved materials, Continental’s Drinkline industrial hose guarantees that no harmful chemicals leach into the liquid.
Optimising manufacturing with HMI panels
SIMATIC HMI Unified Basic Panels set a new standard in industrial automation, streamlining data communication and visualisation.
SIMATIC HMI (Human-Machine Interface) Unified Basic Panels, manufactured in Europe by Siemens, enables users to streamline data communication between machines and humans.
T he panel, distributed by APS Industrial, is part of a family of ‘unified panels’ manufactured by Siemens.
These panels are part of the Siemens’ Human Machine Interface (HMI) portfolio, designed for monitoring, control and visualisation in industrial automation applications.
The interfaces are used to monitor and manage machines and systems effectively.
“Siemens has created a unified landscape for all HMIs, enabling us to access and visualise better data faster and more efficiently,” said Matthew Buser, product manager for factory automation products at APS Industrial.
“In today’s digitalisation space, this capability is essential.”
In manufacturing, HMI panels enable operators to quickly respond
to issues, subsequently improving operational efficiency and ensuring consistent product quality.
The SIMATIC Unified Basic Panels fully integrate with the Siemens family of factory automation products including S7-1500 controllers and SINAMICS
G220 variable frequency drives.
This ensures seamless visualisation of data to empower operators to make informed and effective decisions.
Data visualisations can effectively simplify complex data into visual formats, making patterns and trends easier to identify and understand, thus aiding in informed decision-making and effective communication of insights.
This can all be done in real-time with Siemens Unified Basic Panels.
These panels not only simplify data interpretation but also enhance accessibility to vital information through its intuitive touchscreen interface.
“Typically, engineers can create their own graphics to display data specific to their applications,” said Buser.
“These panels come with standard
objects that can be used to design these graphics, however engineers can customise these visuals based on the specific process data they want to display.”
Siemens, through its master distributor in Australia, APS Industrial, offers an HMI solution for every application.
Siemens Unified basic panels come with various mounting options, certifications, and device variations, which allows for use in all environmental conditions.
Available in four display sizes from 4” to 12”, all models have the same performance, the same number of hardware interfaces and the same functionality.
Information from these panels can also be accessed remotely through standard consumer devices like smartphones and tablets.
The maintenance-free web client offers flexible remote access to the visualisation, independent of on-site device operation.
This is all accessible through a web browser, with no additional software required.
“In production environments today, there’s a significant shift towards edge technology, allowing for remote access across different plants and locations,” said Buser.
“This connectivity underpins Industry 4.0 advancements across industries, enabling seamless communication and operations management from afar.
“This means businesses can efficiently monitor and control processes across their operations remotely, improving overall efficiency and responsiveness.”
Addressing cybersecurity concerns
Naturally, with connected devices, there are inherent security concerns, considering the device has access to important information.
Buser explained that Siemens, with its experience in manufacturing, has
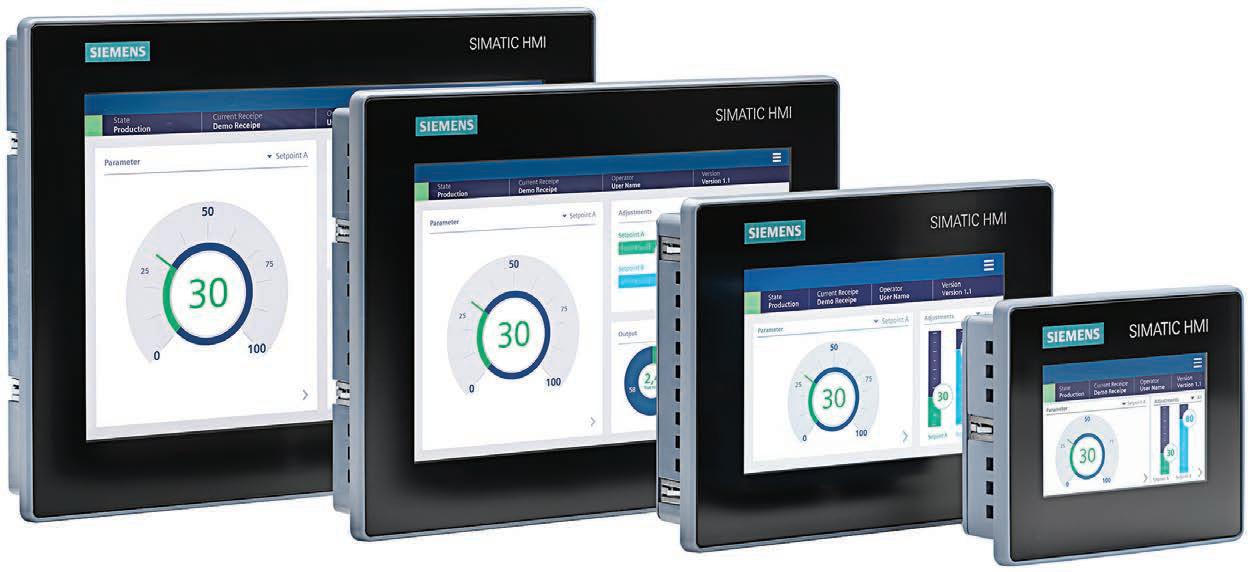
Siemens SIMATIC HMI Unified Basic Panel enhances efficiency with intuitive touchscreens, customisable, visualisations and remote access.

established itself as a global leader in cybersecurity management.
“Siemens is at the top of the tree in terms of cybersecurity management,” he said.
“They are market leaders globally, both within their own organisation and in the products they sell.
safe and secure.
“While nothing is ever 100 per cent secure, choosing Siemens gives you the best chance to mitigate those risks.”
Victoria’s Big Build with Siemens and APS
Siemens HMI panels are being utilised
northeast, transforming how people navigate the city.
As part of Victoria’s Big Build, it encompasses three major road projects.
The 6.5km Northeast Link tunnels, stretching from Watsonia to Bulleen, will address a critical gap in Melbourne’s freeway network, removing 15,000 trucks from local roads daily and reducing travel
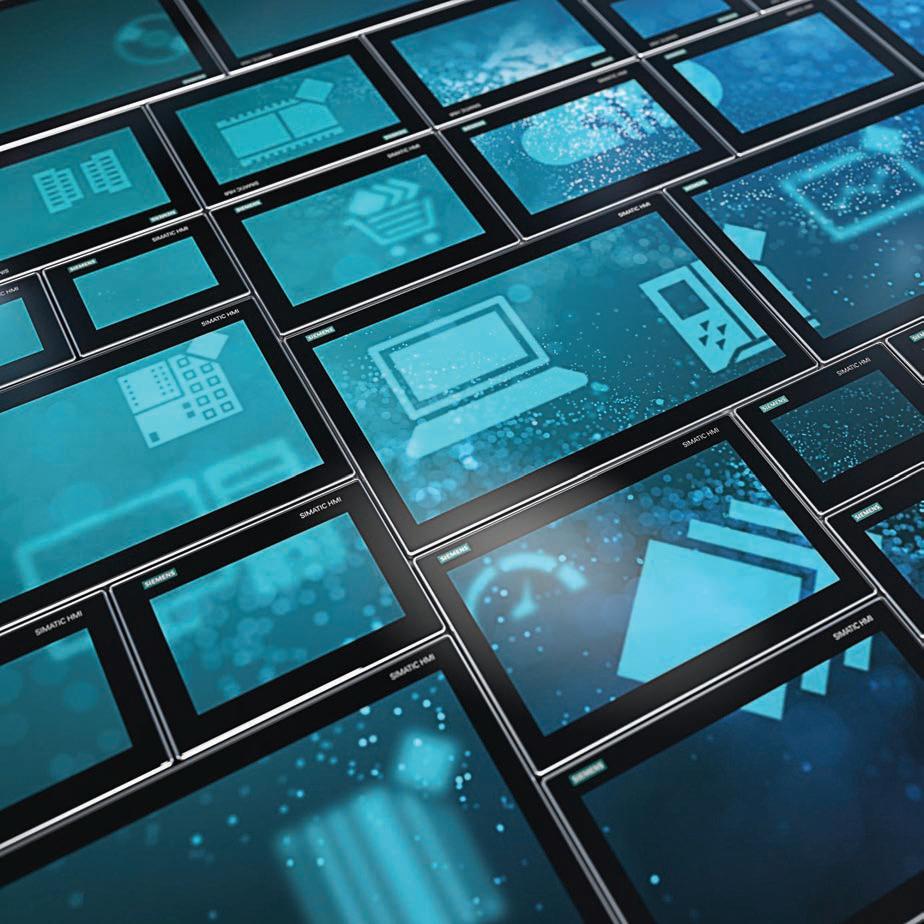
connection to the Northeast Link tunnels.
This program is meticulously planned to ensure the projects open in 2028, integrating all components of the Northeast Link.
The tunnel segments are being manufactured at the LS Precast site, which was revamped with Siemens products, with the assistance of APS Industrial.
“ The large concrete batching plant here on-site previously had two different SCADA systems running on two different PLC networks,” said Steve Bleijswijk, director at Deacam.
“We had to design the static mould vibration system from scratch, where we leaned heavily on Siemens and APS to provide us with variable speed drives, motor protection circuit breakers, and other panel accessories.”
All of which, can be interfaced with Unified Basic Panels.
As Bleijswijk explained, APS doesn’t just provide Deacam with access to high standard automation equipment from Siemens; it also provides a great service.
“APS provides us with world-class technology, along with product support for that same technology,” he said.
“Without those guys, we really wouldn’t have ended up with the solution that we’ve got here.
“We’ve got a great relationship with them, and they’re invested in our outcomes.” F
Siemens, through its distributor, APS Industrial, offers HMI solutions for almost any context.
The SIMATIC HMI Unified Basic Panel is used to monitor and manage machines and systems effectively.
Joint funding for improved agricultural practices
The Natural Heritage Trust is a key investment platform for the Federal Government to provide funds for resource management, sustainable agriculture, and environmental protection. Adam McCleery writes.
The Federal Government has announced it will be providing Landcare Australia and the National Landcare Network with $14.5 million to manage Australia’s natural resources and support the uptake of sustainable agricultural practices and environmental protection.
The funding is part of the government’s $1.1 billion commitment under the Natural Heritage Trust (NHT) and will ensure national land care organisations have capacity to deliver NHT outcomes, as well as strengthen First Nations engagement and participation in land care projects.
The Natural Heritage Trust (NHT) in Australia is a program established by the government to support the conservation and sustainable management of the country’s natural resources.
It aims to enhance the health and productivity of Australia’s environment by providing funding for projects that protect and restore the natural heritage, including land, water, and biodiversity.
organisations to protect and restore our precious places including Ramsar wetlands, World Heritage areas and threatened species habitat,” said Minister for the Environment and Water, Tanya Plibersek.
“We want to make sure our kids and grandkids can enjoy our beautiful environment – and that means acting now to protect more of what’s precious and better manage it for the future.
A Landcare Australia spokesperson said the organisation was thrilled with the funding news.
“With this substantial support, we are well-equipped to further our mission to support the land care movement,” said the spokesperson.
“We have been funded to deliver impactful programs such as the National Landcare Conference, the Landcare Awards, the NextGen Symposium, First Nations Landcare, Landcare Agriculture, and enhanced communications campaigns aimed at fostering nationwide engagement and environmental stewardship.
delivering outstanding programs on behalf of the Australian Government and achieving positive outcomes for the land care movement, our environment, vital agricultural lands and communities nationwide.”
Meanwhile, a national network of 52 Regional Delivery Partners has also been established to deliver critical environmental protection, sustainable agriculture, and natural resource management outcomes across Australia.
Regional Delivery Partners will be provided $88.3 million to support operational functions, including delivering a Natural Resource Management plan for their region, managing work, health, and safety, and ensuring appropriate governance is in place.
The panel of Regional Delivery Partners will also play a key role in implementing government commitments under the NHT by delivering on-ground projects such as planting trees to revegetate habitat for threatened species, erosion control, fire
and controlling feral animals.
“Mobilising land care groups to work with farmers and landholders as well as First Nations groups ensure a solid foundation to promote and deliver climate-smart, sustainable agriculture initiatives across Australia,” said Minister for Agriculture, Fisheries and Forestry, Murray Watt.
“This will ensure uptake of more sustainable practices, responses to
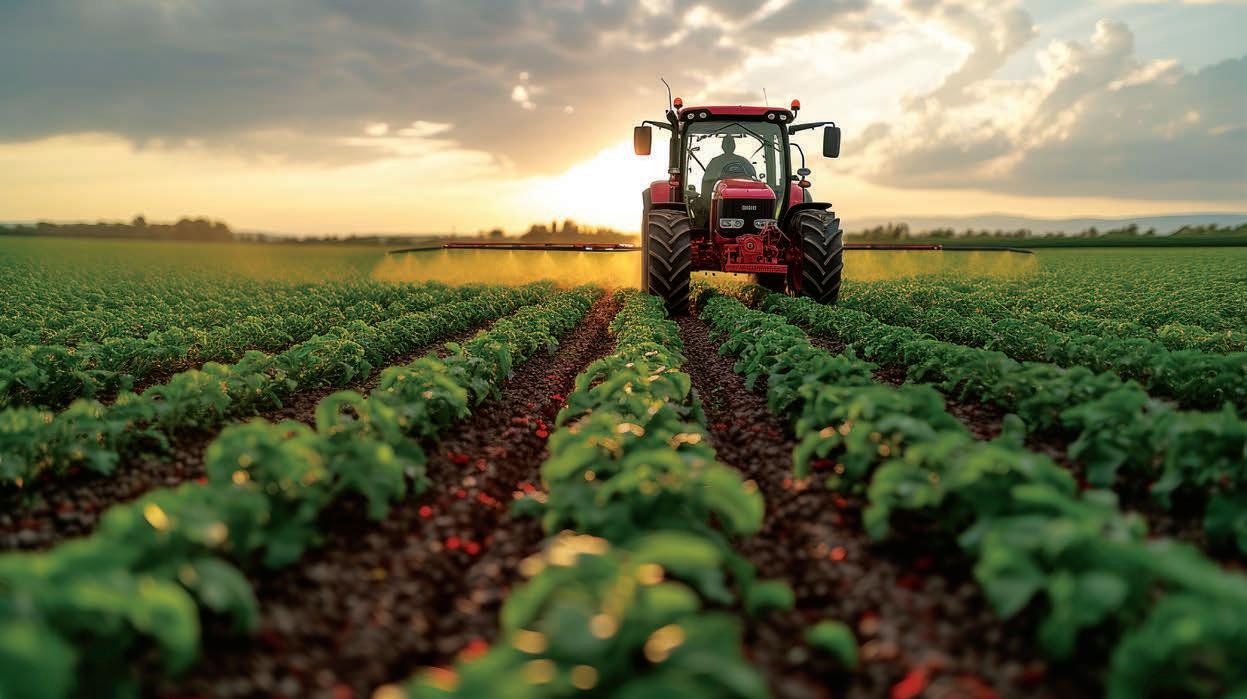

The funding is part of the government’s $1.1 billion commitment under the Natural Heritage Trust (NHT).

market demands at an international, regional and local level.”
Any Australian Government department can draw upon this valuable panel to deliver on ground natural resource management services.
The NHT is the Federal Government’s key investment platform for achieving its natural resource management, sustainable agriculture, and environmental protection outcomes.
Landcare funding also supports the goals of the Federal Government’s Climate-Smart Agriculture Program to increase the capacity of Australia’s agricultural sector to respond and adapt to climate change.
Through the NHT the Australian Government established the $302.1 million Climate-Smart Agriculture Program over five years from 2023-24. This program will drive agricultural sustainability, productivity, and competitiveness.
It supports the following program outcomes:
• T he agriculture sector is adopting practices to reduce emissions and build resilience to climate change.
• T he agriculture sector is supported to harness carbon and biodiversity incentives and implement industry sustainability frameworks.
• Farmers are supported to drive
agricultural growth, while adopting sustainable natural resource management practices that protect and conserve natural capital and biodiversity.
“Landcare organisations play a crucial role in supporting our shift to a more sustainable future for our agriculture industry by protecting our natural resources,” said Watt.
Landcare Australia, a national not-for-profit organization founded
35 years ago, supports the land care community by providing funding, capacity-building, on-ground projects, information, networking opportunities, and promoting land care achievements.
Meanwhile, the National Landcare Network serves as the peak representative body for community Landcare groups throughout Australia.
Sustainable agriculture is an approach to farming that focuses
agricultural products in ways that are environmentally sound, economically viable, and socially responsible.
It aims to meet the needs of the present without compromising the ability of future generations to meet their own needs.
Sustainable agriculture also often involves a combination of traditional knowledge and modern technology to create farming systems that are resilient,
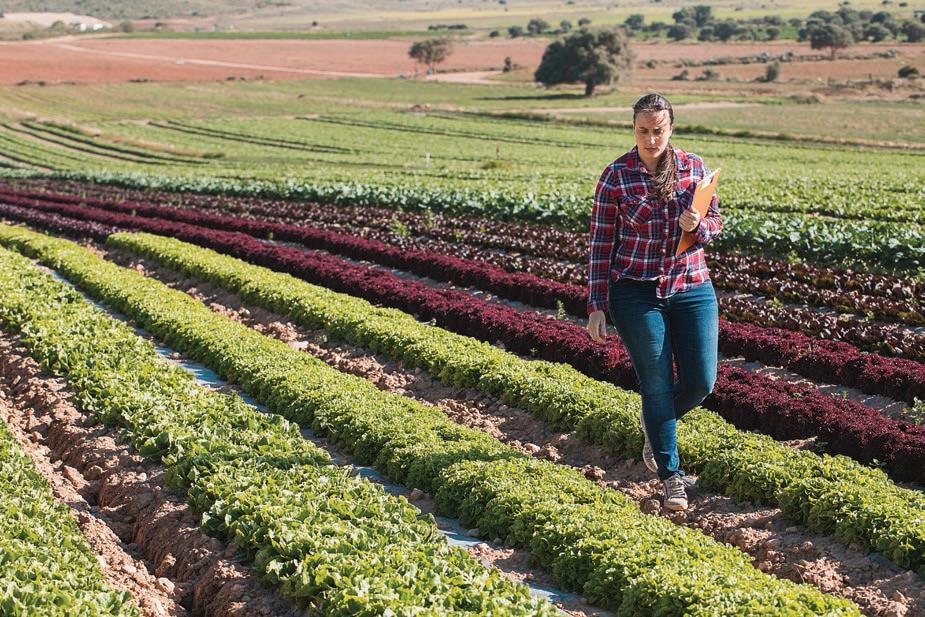
The panel of Regional Delivery Partners will also play a key role in implementing government commitments under the NHT.
Landcare funding also supports the goals of the Federal Government’s Climate-Smart Agriculture Program.
Move to strengthen manufacturing in Queensland
The Manufacturing Alliance and Manufacturing Skills Queensland (MSQ) have joined forces to leverage local intelligence to strengthen the manufacturing sector’s workforce. Adam McCleery writes.

local Queensland intelligence to inform workforce planning and training product development.
As the Jobs and Skills Council (JSC) for the manufacturing sector, the Manufacturing Alliance wants to ensure that the manufacturing industry can access workers with the skills needed to shape an innovative future made in Australia.
MSQ is also committed to future proofing the manufacturing industry in Queensland.
This partnership marks a significant step towards enhancing collaboration and knowledge exchange between the state and the manufacturing JSC, ultimately strengthening the support for the Queensland and Australian
Queensland intelligence represents a pivotal moment for the Manufacturing Alliance,” CEO, Manufacturing Industry Skills Alliance, Sharon Robertson.
“This partnership underscores our commitment to Queensland’s manufacturing industry.
“This strategic integration of local insights and expertise offered by Manufacturing Skills Queensland will enable us to develop training packages and projects that resonate with the industry’s current and future demands, ultimately contributing to a more resilient and competitive manufacturing workforce.
“We are committed to working collaboratively towards a system that supports a sustainable, prosperous future for the manufacturing industry.”
and share intelligence to accelerate key projects that strengthen the state’s manufacturing capabilities.
Manufacturing Alliance has two projects already underway; ‘Building a defence manufacturing workforce’ which is dedicated to understanding the alignment between the capacity and capabilities of the skills system and the future needs of the defence manufacturing workforce; and ‘Aviation maintenance skills pathways’ which will examine the alignment between the Civil Aviation Safety Authority’s (CASA) new licensing regulations and the training system.
MSQ is supporting these projects to ensure the Queensland’s industry is heard.
The Manufacturing Alliance and
This partnership represents a first for the Australian Government’s Jobs and Skills Councils and highlights the Manufacturing Alliance’s commitment to ensuring the solutions developed enhance workforce readiness and industry competitiveness and meet state and Australian requirements.
“Queensland’s manufacturing industry is poised for significant growth over the next decade,” said CEO, Manufacturing Skills Queensland, Rebecca Andrews.
“This partnership enables a streamlined approach for Queensland stakeholders to actively contribute to the development of products at a national level, ensuring that they accurately reflect the dynamic needs of our local
The action plan sets a path for Queensland manufacturers to respond to market changes and help drive economic growth.
“Collaborating with Manufacturing Skills Queensland to leverage local Queensland intelligence represents a pivotal moment for the Manufacturing Alliance.”
manufacturing landscape.
“Embracing the opportunity that is before us needs collaborative effort—employers, peaks, unions, training organisations and all levels of government—to future-proof the industry, build capability and secure manufacturing in Queensland.
“We are dedicated to fostering an environment where knowledge exchange and stakeholder input play a pivotal role in shaping the future of Queensland’s manufacturing workforce.”
According to figures released by Manufacturing Skills Queensland, the Queensland manufacturing industry generated $24.3 billion of value-add in 2022-23, accounting for 5.25 per cent of Gross State Product.
And the state’s share of real manufacturing value-add has grown from 16 per cent in 2003, to around 20 per cent in 2023.
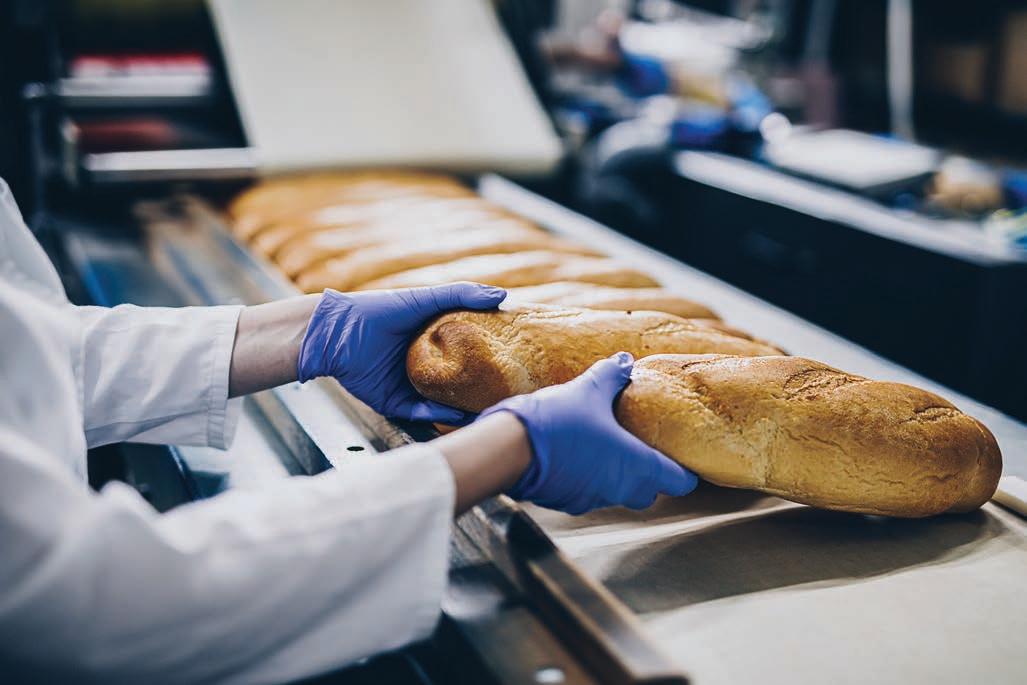
Meanwhile, with regards to employment in the Queensland sector, which the agreement aims to grow, saw 187,000 active employees in the sector as of November of 2023. Accounting for 5.6 per cent of Queensland’s total employment.
The news comes just two years after the Queensland Government announced its Advanced Manufacturing 10-Year Roadmap and Action Plan.
The action plan sets a path for Queensland manufacturers to respond to these changes, drive economic growth and create jobs.
The revised Roadmap and Action plan contains 19 actions in 5 key strategy areas to address these challenges and position manufacturers to grasp new opportunities to grow their business and create jobs.
This includes transitioning to a low carbon economy, increasing diversity
and accessing supply chain opportunities in the emerging green energy sector as part of the Queensland Energy and Jobs Plan and the Olympics and Paralympics.
The Queensland Government continues to work with local manufacturers to help them increase their international productivity and competitiveness and adopt innovative processes and technologies.
Much of this is being done through the department’s manufacturing
hubs in Townsville, Cairns, Mackay, Rockhampton, Gladstone and on the Gold Coast, to support manufacturers to become more productive and grow their businesses.
The Manufacturing Ministerial Council, comprising manufacturing industry leaders, will continue to provide expert advice to ensure the Queensland manufacturing sector remains on a strong growth trajectory to become more globally competitive. F
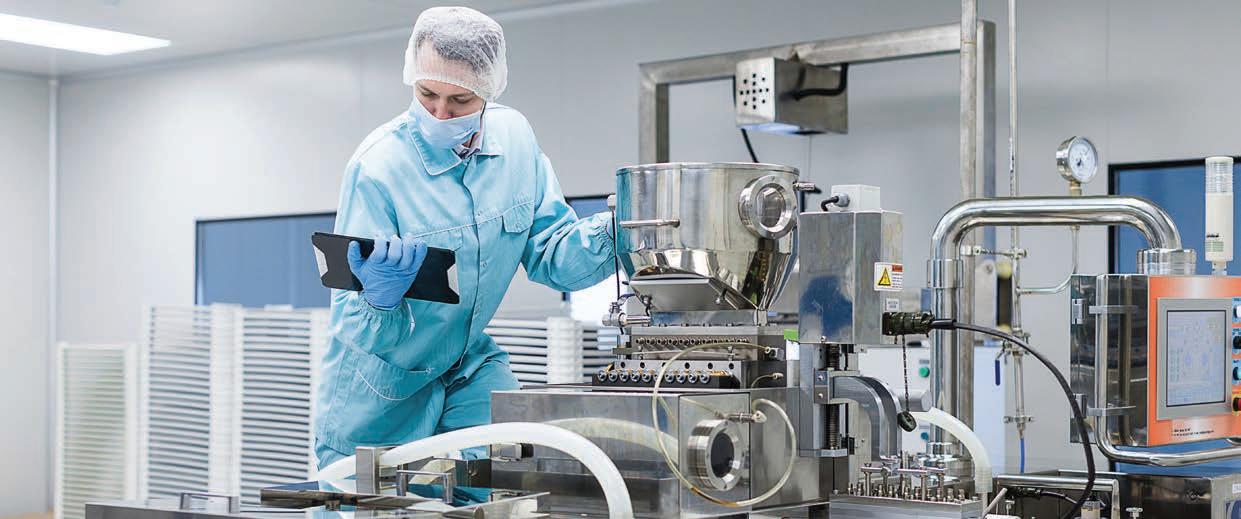
The partnership is expected to drive growth in the Queensland manufacturing sector.
The Manufacturing Alliance wants to ensure that the industry can access workers with the skills required to shape an innovative future.
Environment minsters renew focus on soft plastics
Australia’s environment ministers have renewed their focus on the National Circular Economy Framework and soft plastics schemes. Food & Beverage Industry News reports.
Australia’s environment ministers recently came together to discuss a host of key issues, including renewing focus on the National Circular Economy Framework and soft plastics schemes, due to be finalised in December.
The framework is designed to drive a faster transition to a circular economy and ensure efficient use of key resources and materials in Australia, which will have a direct impact on food and beverage manufacturing.
Ministers noted that opportunities exist in the manufacturing, food and agriculture, resources, and critical minerals sectors.
The group came to an agreement to encourage the development of stronger end markets for recycled products, as well as creating a priority list of materials or products to be identified for consideration at the next EMM.
The new national packaging regulatory scheme was also broached with advice for industry on anticipated design requirements, including recyclability, recycled content requirements, and designing out chemicals from packaging placed on the market.
Ministers considered the growing challenge of soft plastics, and industry’s slow progress to re-establish in-store
collection since the collapse of the REDcycle scheme, while confirming their commitment to a circular economy for plastics.
States and Territories will be required to keep track of progress on a road map to staged and report back to environment ministers by the end of 2024.
This road map will address a pathway and criteria to soft plastics collection that considers national design standards currently under development, different collection approaches across metropolitan, regional, and remote locations and the wider national processing capacity.
The roadmap may incorporate different timelines in different jurisdictions.
Ministers also noted that removing PFAS in packaging is an urgent priority for all jurisdictions and will be dealt with through design standards in consultation with the Heads of EPA Australia and New Zealand (HEPA) with a report back to the next EMM.
The news of a renewed focus on the Framework and a new soft plastics scheme was welcomed by the Australian Food & Grocery Council, with AFGC CEO Tanya Barden stating this was an important step forward.
“Food and grocery manufacturers

This roadmap will address a pathway and criteria to soft plastics collection that considers national design standards currently under development.

in time and money to get an industry-led solution to soft plastic recycling on the national agenda,” said Barden.
“The announcement is an important step in driving the soft plastic circular economy and the work we have been doing on a product stewardship scheme.”
The renewal of a soft plastics scheme comes in the wake of the failed roll out of the REDcycle program.
REDcycle was an industry-led program developed and managed by RG Programs and Services Pty Ltd, and was Australia’s sole return-to-store soft plastics recovery initiative since 2011.
The program enabled the collection and processing of soft plastics, such as food packaging, plastic bags, cling wrap, and bubble wrap, into various durable recycled products.
Partnering with product manufacturers and major supermarkets, REDcycle handled initial processing before sending the materials to its recycling partners to be converted into new recycled products or otherwise utilised.
The program operated in nearly 2,000 supermarket locations across Australia, including Coles and Woolworths, and expanded to ALDI stores in July 2022.
The movement comes after REDcycle was suspended in November 2022, due to its recycling partners temporarily halting acceptance and processing of these materials.
This suspension removed the
consumers, raising concerns about existing stockpiles and future recycling options for soft plastics.
In response, both Coles and Woolworths announced they would suspend soft plastics collections from their stores until further notice.
Meanwhile, in May, the NSW Environment Protection Authority (EPA) amended Clean-up Notices issued to Coles and Woolworths, giving the supermarkets more time to manage the recovery, recycling and lawful removal of soft plastic stockpiled across the state.
identifying possible pathways to keep most of the soft plastics out of landfill.
The supermarkets have been granted an additional 10 months to comply with the notices until March 2025. This will ensure that the identified processing solution is operating at sufficient capacity to handle the stockpiled material.
The EPA required the supermarkets to submit a staged removal plan to track the progress of the supermarkets under the revised timeline.
Coles and Woolworths moved more than 5,000 tonnes of soft plastic material to safe storage last year meeting their immediate clean-up obligations to address the potential fire and pollution risk posed by 15 stockpiles found across NSW.
“Revising the time period gives the supermarkets an opportunity to secure a solution for the material so that the vast majority of the material doesn’t end up in landfill,” said NSW EPA director operations Adam Gilligan.
“We know the public, who diligently collected and dropped off their soft plastics, has been disappointed in REDcycle and the best outcome for this material is to see it recycled and reprocessed.”
“We will continue to monitor the progress of the supermarkets under the Clean-up notices including inspecting

Image: faithie/AdobeStock
Image: Coles
Ministers also noted that removing PFAS in packaging is an urgent priority.
The move comes after the failure of other soft plastics recycling schemes across Australia.
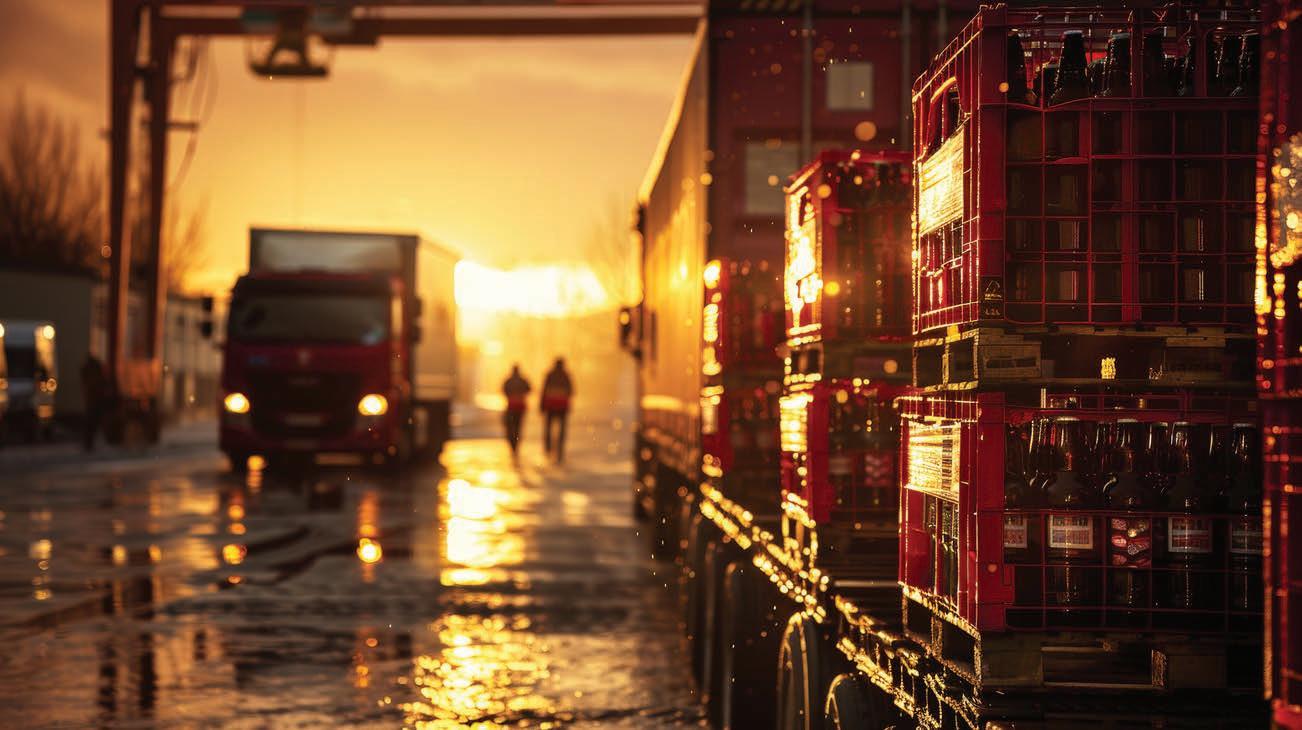
Australian wine growers re-enter China
The Australian wine industry is already reaping the benefits of China lifting trade tariffs on wine exports into the country.
Over the past two years, the Australian wine industry, especially the commercial sector in key growing regions, has faced significant challenges.
These include a multi-year tariff imposed by China that halted all bottled wine exports, ongoing impacts from COVID-19 affecting supply chains and costs, an economic environment of reduced consumer spending, declining global wine consumption, and shifting consumer preferences towards premium wines.
In November 2020, China imposed provisional tariffs, ranging from 107 per cent to 212 per cent, on Australian wine.
The impact on the Australian wine market was huge. Prior to the tariffs, China was Australia’s largest wine
export market, with exports valued at over $1 billion annually.
The Australian wine industry faced significant economic losses due to the reduced access to the Chinese market. Many producers sought alternative markets and increased efforts to promote Australian wine in other regions.
China investigated allegations of dumping and subsidisation, claiming that Australian wine producers were selling wine in China at unfairly low prices, while the Australian Government strongly denied the dumping and subsidy allegations, describing the tariffs as unjustified.
Before aiming to resolve the issue through diplomatic channels and by appealing to international trade bodies.
As a result, the March announcement
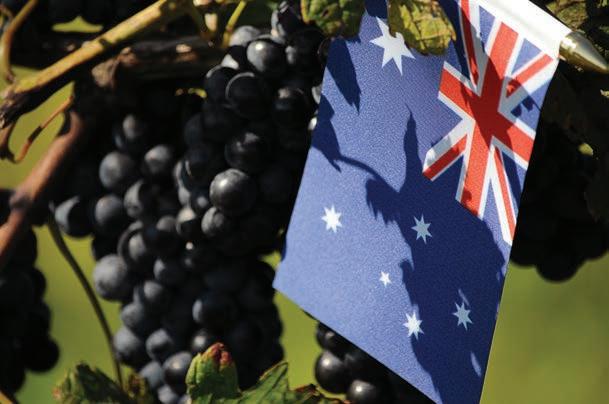
was a hugely welcome one to the Australian wine industry.
Wine Australia welcomed the announcement at the time, with CEO Dr Martin Cole highlighting the importance of continued relations between the Australian and
Chinese markets.
“Mainland China remains an important market for the Australian wine sector,” he said.
“Over many years, Australian wine companies have developed close relationships with importers, buyers
Wine Australia welcomed the move, with CEO Dr Martin Cole highlighting how important the Chinese market is to Australian wine producers.
Australian wine growers have been capitalising after China lifted tariffs earlier this year, with some brands re-entering the country in response.
and consumers of Australian wine in China and these relationships remain important to our wine community.
“Pleasingly, we know that trade and consumer sentiment for Australian wine in China remains positive.”
Some wineries, including Barossa’s Curator Wine Co, are projecting export growth of up to 60 per cent by the end of 2025 following China’s re-emergence.
The China wine export market was valued at $946.5 million per year at its peak and accounted for nearly half of the state’s wine exports before tariffs were introduced.
Meanwhile, exports to China across all categories have grown by 39 per cent over the 12 months to March.
In that same period, South Australia was the only state in the country to see its global exports grow in that time, up three per cent to $17.7 billion, compared with a national decline of 10 per cent.
Within just one month of the tariffs being lifted on bottled wine, Australia exported $86 million of quality wine to China, according to Minister for Trade and Tourism, Senator the Hon Don Farrell.
With South Australia accounting for $80 million of that.
As a sign of the advantages of the tariffs being lifted, Treasury Wine Estates (TWE) provided a market update on its Penfolds business and China strategy.
TWE CEO, Tim Ford, said it was fantastic to see local Chinese consumers reignite their passion for Penfolds’ great Australian luxury wines.
“We are delighted to be bringing more of our Australian luxury wines back to China, at a time when the luxury wine market presents significant long-term growth opportunities for Penfolds and the wine category overall,” said Ford.
“By leveraging our unique Penfolds brand status to drive ongoing demand, we remain steadfast in our clear ambition to be the number one luxury wine brand in the market.”
Penfolds MD, Tom King, added that Penfolds’ portfolio of globally sourced luxury wines continued to provide consumers from across China with access to wines from the world’s most revered wine regions such as Australia.
“The power of Penfolds to engage with consumers across four countries of origin is truly unique,” said King.
“Our most recent Penfolds China
wine releases have received excellent praise from wine critics and present an incredible opportunity to drive further connection and engagement with our consumers in China, and to become a global ambassador for Chinese luxury wine.
“Similar to the roadmap we have followed in France, we continue to explore further winemaking opportunities in China, including investing in local sourcing and production opportunities to support future portfolio growth opportunities.”
Australian Grape & Wine chief executive Lee McLean also welcomed the news that the lifting of import duties into China was already having a positive impact.
“This is a very important decision for the Australian wine industry. It reflects the positive outcome of diplomatic efforts by the Albanese government to stabilise relations with China and underscores the importance of collaboration between government and industry,” said McLean.
“We acknowledge and thank Foreign Minister Penny Wong, Trade Minister Don Farrell and Agriculture Minister Murray Watt and their respective
departments for their steadfast support of Australian grape growers and winemakers throughout the process.”
The presence of Australian wines in China will continue to complement the local wine industry, providing consumers with a broader selection of premium wine options.
“The Australian wine sector has made a long-term commitment to building the market for Australian wine in China, with many wine companies having developed close relationships with importers, buyers and consumers of Australian wine over many years,” said McLean.
“We are working closely with the Australian Government and Wine Australia to ensure a coordinated approach is taken to re-entry and that the sector is well positioned to re-establish trade relationships.
“We look forward to seeing Australian wines back on Chinese dining tables and rejuvenating our relationship with customers and business partners in that market.
“We will also, however, be maintaining our focus on diversifying our export footprint and growing demand here in Australia as well.”
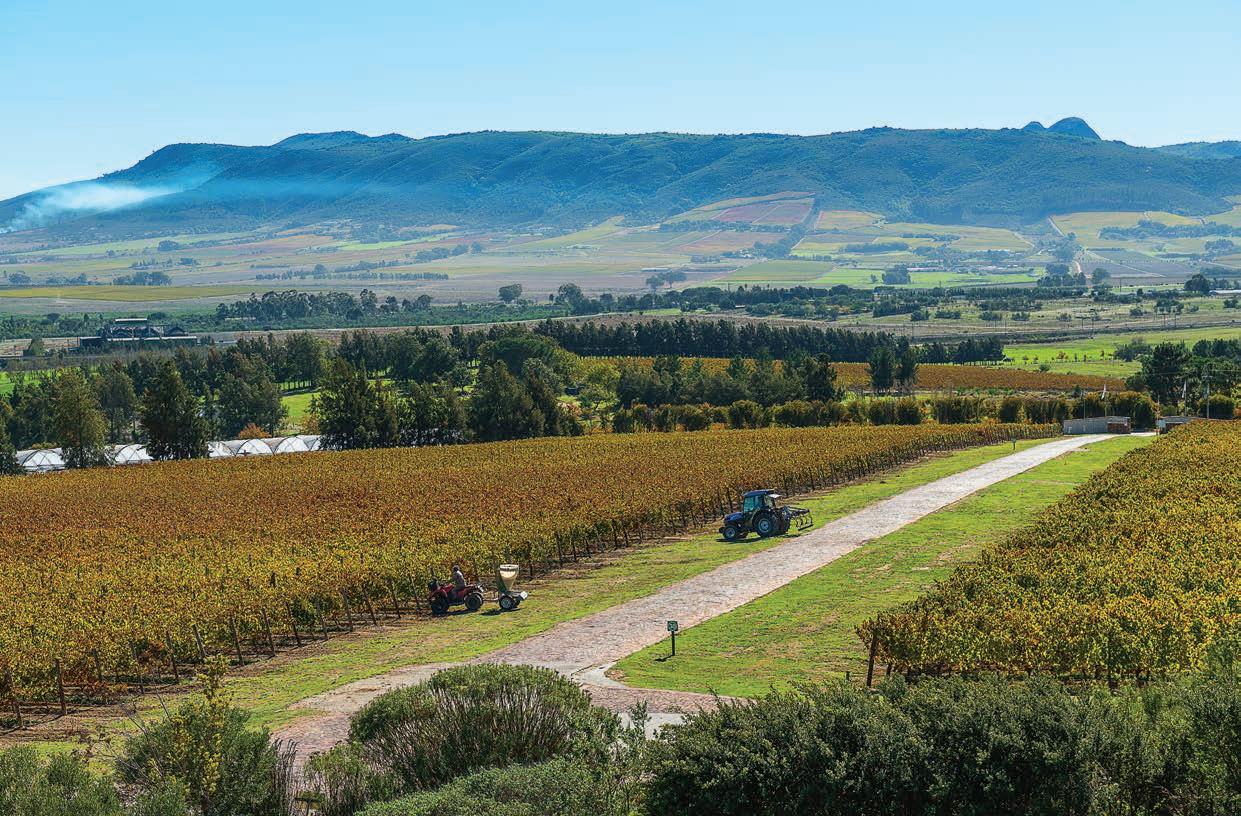
Some wineries are already projecting export growth of up to 60 per cent by the end of 2025.
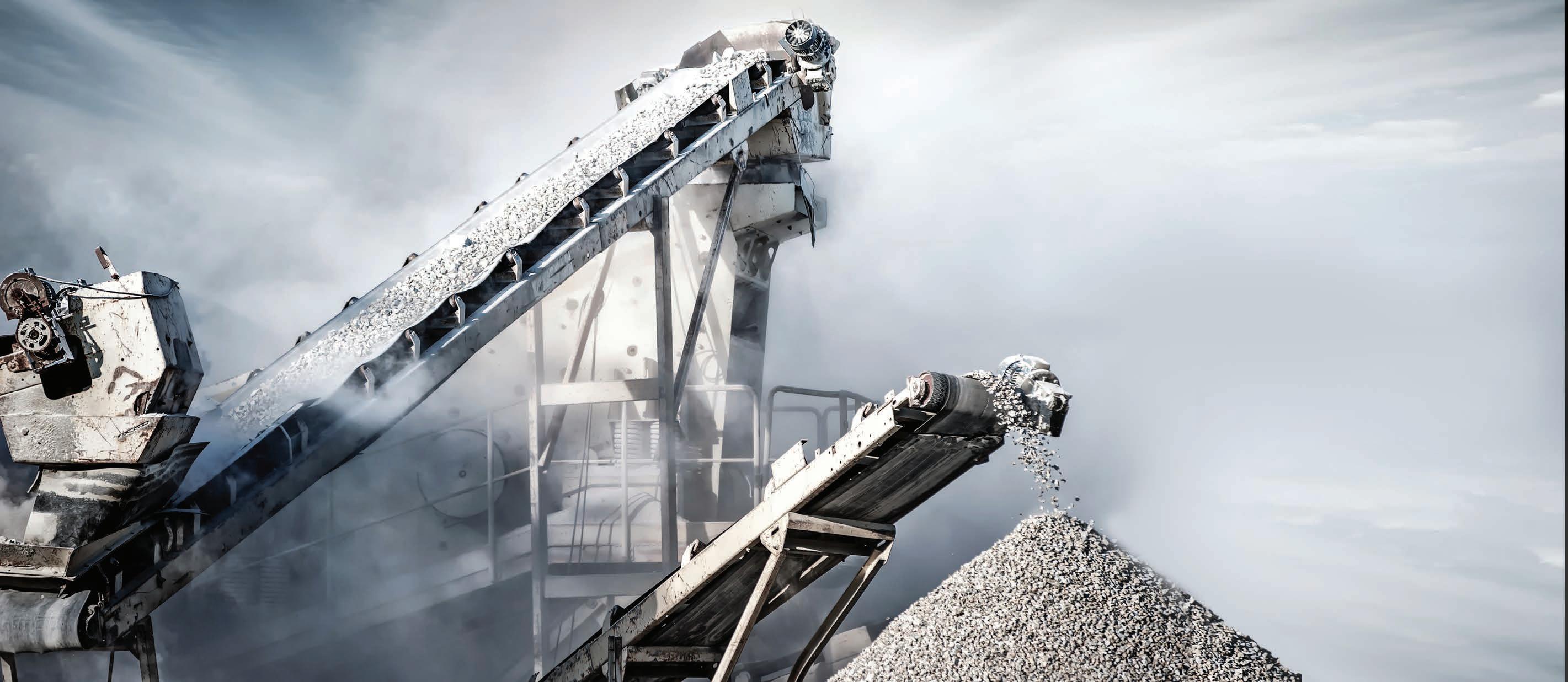
STRALIAN LK NDLING
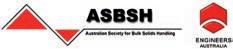
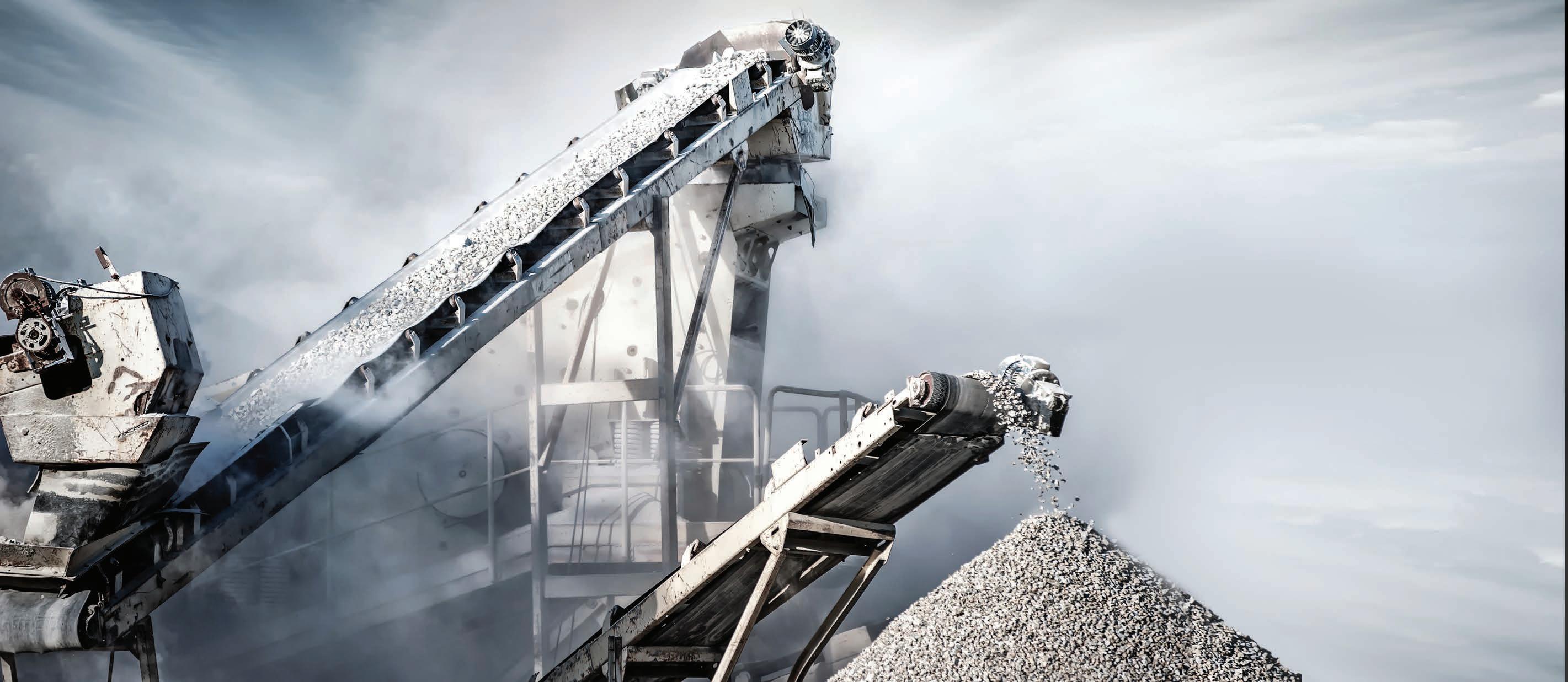
Fight against food waste continues
State Governments, along with the Federal Government and food waste advocacy groups, continue to work hard to combat food waste and insecurity.
Australia is facing an alarming food waste crisis, with new data revealing that the country discards more food than ever before, despite governmental and association programs being designed to reduce it.
According to a recent report by the Department of Agriculture, Fisheries, and Forestry, Australians are throwing away approximately 8 million tonnes of food annually, amounting to $36 billion in waste.
This increase represents a significant rise from previous years, highlighting a growing issue that has both environmental and economic implications.
Food waste also contributes to approximately three per cent of Australia’s greenhouse gas emissions, primarily due to the organic matter in landfills, which releases methane, a potent greenhouse gas.
The report identifies several key factors that are contributing to the surge in food waste.
These include:
• O verproduction and supply chain inefficiencies: Farmers and producers often grow more food than can be sold, leading to excess that is eventually discarded. Inefficiencies in the supply chain, such as poor storage and transportation conditions can also result in significant losses.
• Consumer behaviour: A considerable portion of food waste occurs in the household. Australian consumers often buy more food than needed, influenced by marketing strategies and bulk discounts, leading to spoilage and disposal of unused items.
• Date label confusion: Misunderstanding and misinterpretation of ‘best before’ and ‘use by’ dates cause consumers to throw away still edible food.
• R estaurant and hospitality industry: High levels of waste are generated by the food service industry, where portion sizes and buffet-style dining contribute to the disposal of large
amounts of uneaten food.
The consequences of this waste are far-reaching. Environmentally, it continues to add to climate change while depleting natural resources used in food production. Economically, it represents a massive loss of potential income and increased costs for waste management.
In response to this growing crisis, the Australian Government has launched several initiatives aimed at reducing food waste. The National Food Waste Strategy, which aims to halve food waste by 2030, has been bolstered with additional funding and resources.
It also helps give effect to Australia’s obligations under the United Nations Framework Convention on Climate Change in helping reduce greenhouse gas emissions, primarily through the diversion of food waste from landfill.
Key measures in the strategy include:
• E ducational programs aimed at changing consumer behaviour and encouraging more sustainable practices.
• Collaborations with retailers, restaurants, and manufacturers to improve supply chain efficiency and promote the donation of surplus food to charities.
• I nvestment in technologies that extend the shelf life of food and improve storage and transportation conditions.
Community organisations and non-profits are also playing a crucial role. Food rescue programs such as OzHarvest and SecondBite are working tirelessly to redirect surplus food to those in need, reducing waste and addressing food insecurity.
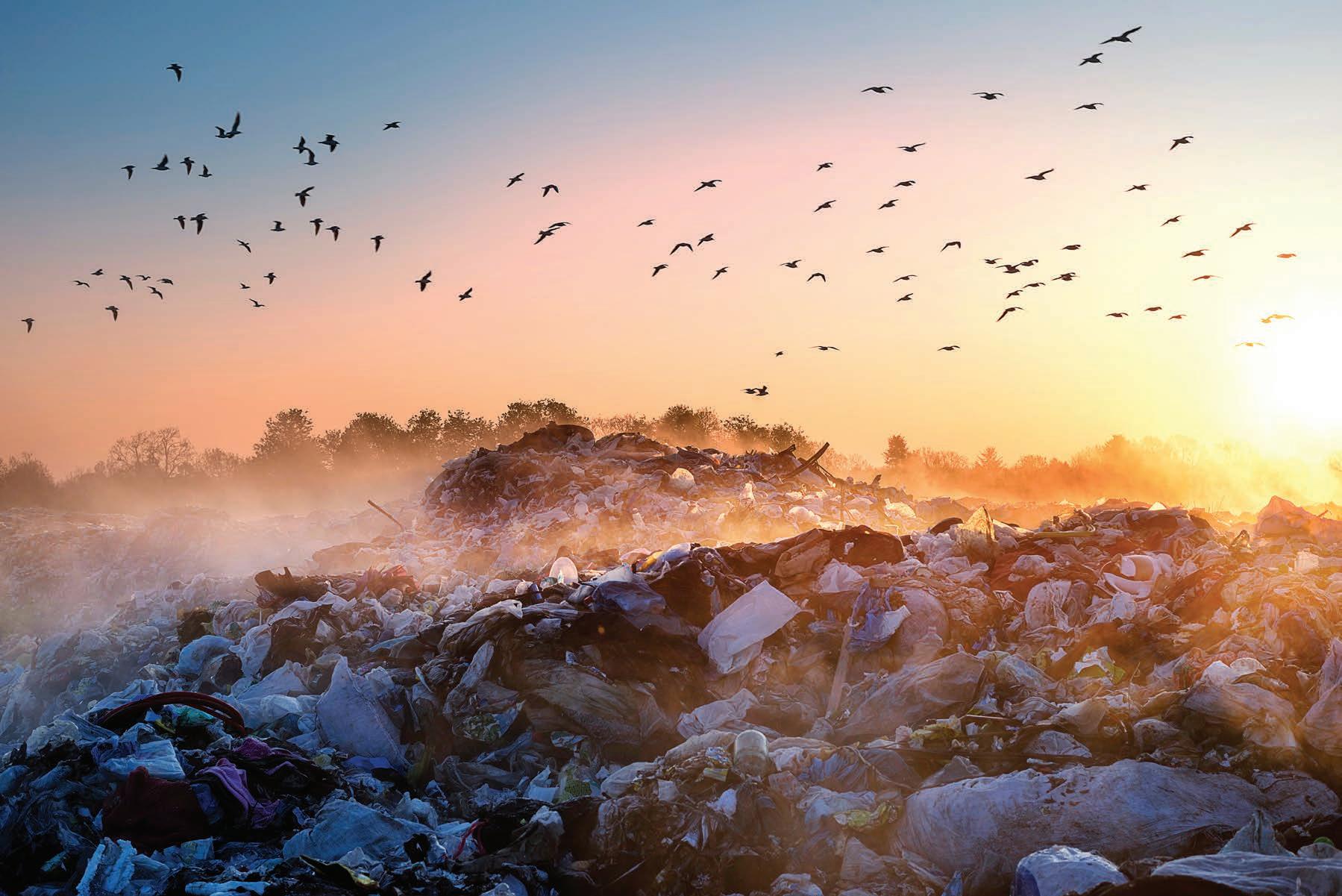
While these efforts are steps in the right direction, experts stress that a comprehensive approach involving all stakeholders is essential.
“We need a cultural shift in how we value food,” said Dr. Emily Harris, a leading researcher in sustainable food systems.
“From farm to fork, everyone has a role to play in reducing waste and
protecting our environment.”
The food waste crisis in Australia serves as a stark reminder of the need for sustainable practices and conscious consumerism. As the nation grapples with this challenge, the collective efforts of government, businesses, and individuals will be crucial in turning the tide and ensuring a more sustainable future for all.
Meanwhile, to combat food waste, the Queensland Government announced a new food waste diversion project in May.
The Department of Agriculture and Fisheries (DAF) has partnered with Brisbane-based not-for-profit FareShare and End Food Waste Cooperative Research Centre to develop nutritionally balanced, long shelf-life meals using rescued food.
“DAF is working towards creating as much value as we can from what we produce here in Queensland,” said DAF Food Technologist Patricia Lindeman.
“A key mission of the Queensland Government is nutrition delivery and ensuring every community in Queensland has access to good quality produce and nutritious foods.”
The meals will be made from at least 95 per cent rescued food, including fresh produce from surplus farm crops.
FareShare currently converts rescued food into delicious, nutritious frozen meals, providing much-needed support
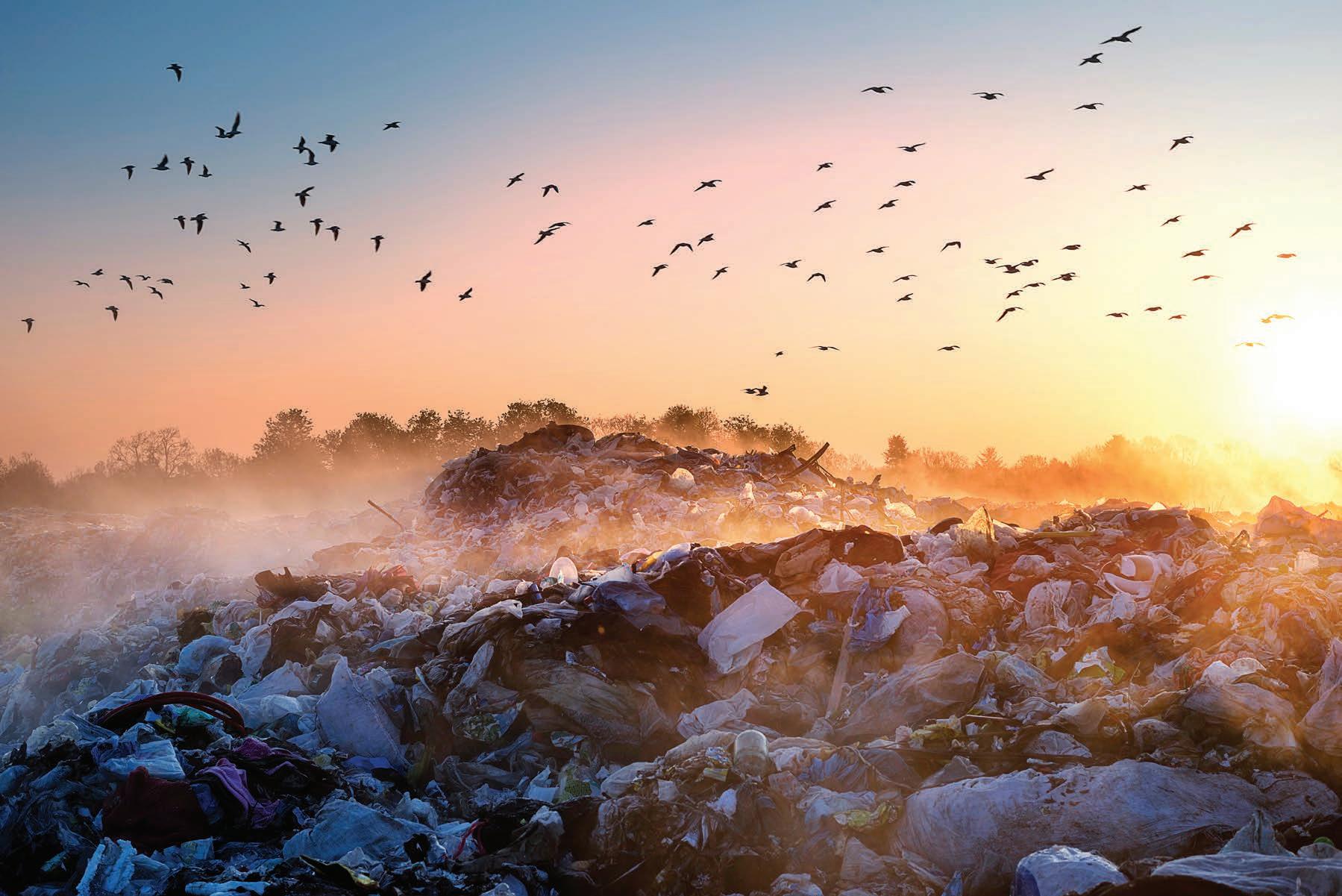
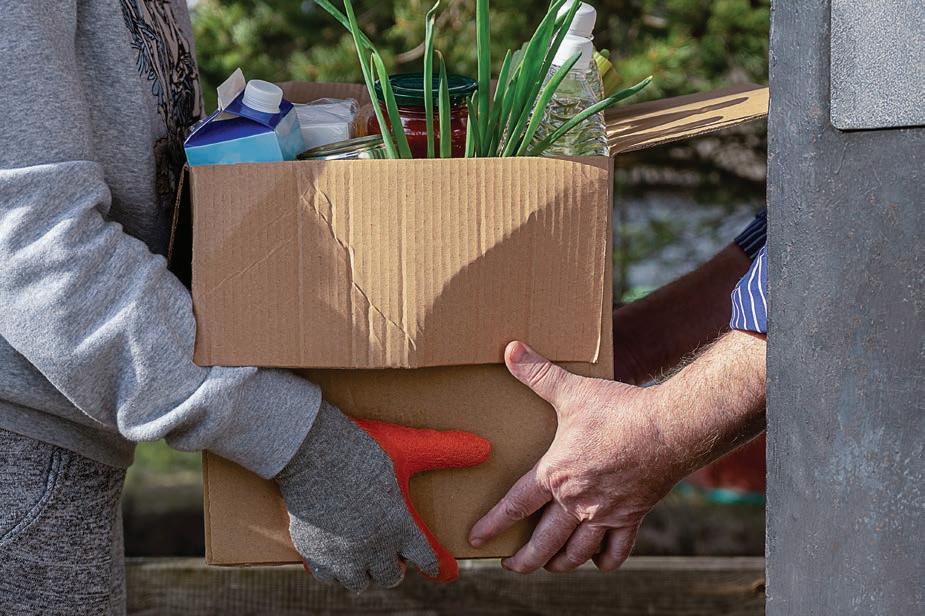
to Australians experiencing food insecurity.
But the transportation and storage of frozen food has limitations where power supply is challenging in remote communities or during disaster relief.
“This collaborative project will enable FareShare to develop a new range of tasty, nutritious, shelf stable meals, as they require no chilled transport or storage,” said Fiona Maxwell, executive director, FareShare.
“These meals are especially suited to disaster relief and can be delivered into remote communities ahead of seasonal weather events, when supply chains can be disrupted for weeks at a time.”
in package) fresh foods can significantly extend shelf life and alleviates the
requirement for refrigerated or frozen storage.
The meals will help vulnerable members of the community, including those experiencing food insecurity and homelessness, people in remote communities, and can be utilised during natural disasters.
DAF consumer sensory and product development scientists will ensure the meals are nutritionally balanced, retain their quality during processing, look good, taste good and can be easily prepared.
It is estimated the project will rescue between 80,000 and 100,000 kilograms of food waste in the first year of
and up to 375,000 complete meals by the second year.
At full capacity, there is potential for 500,000 kilograms of food to be processed per annum.
By the project’s end, it is anticipated FareShare will be manufacturing at least 500 extended shelf-life meals daily.
“Australia produces enough food to feed 75 million people a year. Yet, millions of Australians go hungry regularly. Fighting food waste can help fight food insecurity,” said End Food Waste Cooperative Research Centre CEO Dr Steven Lapidge.
“We’re proud to support this important project that will enable increased volumes of food to reach people in need instead of going to waste.” F

New data has revealed Australia is discarding more food than ever before into landfil.
From farm to fork, industry stakeholders said everyone can play a part in combating food waste.
The food waste crisis in Australia serves as a stark reminder of the need for sustainable practices and conscious consumerism.
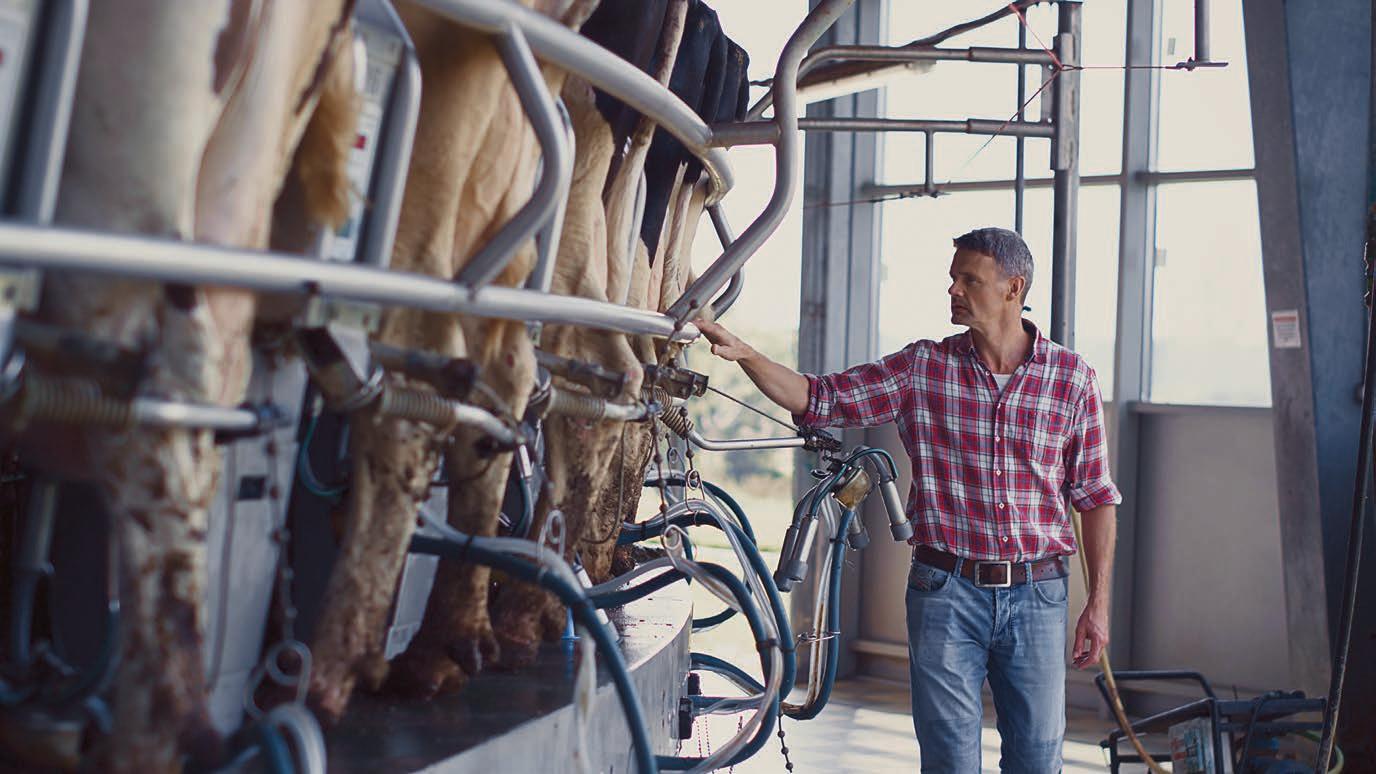
Global trade declined 1.5 per cent year-on-year in Milk Solids Equivalents.
Mixed results and forecasts for dairy sector
Supply chain developments and consumer demand continue to have a heavy impact on the global dairy market, but forecasts look positive for Australia
Global fundamentals remain mixed across products and major producing regions, but there are developments in supply and demand that have altered the outlook.
Global trade declined 1.5 per cent year-on-year in Milk Solids Equivalents (MSE) terms in April but was 3.2 per cent higher in the last quarter. The April decline was mostly due to weaker trade for major milk powders and fats, while cheese and dry whey trade expanded significantly.
The seasonal firming in the EU fat market will likely come in Q3-2024, but the supply side is uncertain. Milk output will gradually improve across the region as warm weather sets in, but rainfall in the short-term remains widespread and the ongoing effect of excess moisture on forage quality and milk solids output is uncertain.
Tighter cream supplies due to both demand and supply effects will stabilize the butter market. Elevated prices may burn off some demand but the larger threat in Q4 from seasonally higher NZ availability lingers.
The durability of global fat demand (already weaker at higher prices) as NZ output builds will have a critical influence on the EU market.
Sluggish demand and sustained higher NZ supply will continue to limit the upside for SMP, despite low EU and US stocks.
While trade in developing market regions outside China increased as buyers restocked, increasing ingredient prices will test viability of trade (especially in MENA) in coming months.
The US cheese market remains important due to the contest between the big three producers. Tighter stocks,
lower cheddar output, and improving demand should be supportive.
The US production outlook is uncertain despite cheese capacity additions. While central region milk solids output is growing, supply faces headwinds due to limited heifers and poor margins.
This comes on the back of a mid-year forecast from Rural Bank, stating Australian dairy farmers will produce around 4.6 billion litres in the second half of the year.
This is on pace with the previous year which say Australian dairy farmers produce 4.62 billion litres of milk from July to December of last year. However, this will still be around four per cent below the yearly averages. But combating this drop, are figures showing the rate of dairy farmers leaving the sector slowing down.
“Dairy farmers will have to contend
with tighter margins in the upcoming season. While input costs have stabilised, lower farm gate prices will reduce profitability,” Mik Harford, Agribusiness relationship manager, Leongatha.
“Seasonal conditions vary significantly in the dairy regions with some facing very tough conditions that will challenge milk production in those areas, but the national milk pool should remain reasonably stable if slightly down on last year.
“With recent seasons delivering favourable economic conditions, milk producers have had the opportunity to invest in their businesses which will help them cope with lower prices this season.
“For most dairy farmers a profitable season in the 24/25 season remains on the cards, but dry conditions will see some facing a tough year ahead.”
Case being made for spirits industry reform
Key industry stakeholders have urged the government to look at key reforms to improve the spirits sector going forward.
Australia will miss out on the economic opportunity presented by its promising spirits manufacturing sector without urgent intervention by the Federal Government, the Inquiry Into Food and Beverage Manufacturing heard.
Peak industry bodies Spirits & Cocktails Australia and the Australian Distillers Association today appeared before the House of Representatives Standing Committee on Industry, Science and Resources at Parliament House.
Australian Distillers Association chief executive Paul McLeay said the Australian distilling industry should be integral to the government’s Future Made in Australia policy.
“However, the Government’s outdated policy settings and inaction has placed Australian-made spirits at a significant competitive disadvantage in
our home market and abroad,” he said.
“Just as previous governments recognised the potential of Australian wine, with the right policy settings and infrastructure, Australian spirits can realise a $1 billion export opportunity by 2035.
“If we do not act now, Australian distillers will be outpaced by other emerging spirits markets in meeting growing consumer demand for premium products – and Australia will miss out on the economic windfall that could be ours.”
Spirits & Cocktails Australia director Nicole Lestal said the Government must release the hand brake that is the current excise regime.
“While Australian spirits account for 20 per cent of alcohol consumption, it accounts for 50 per cent of alcohol taxes,” she told the Committee.
“This structural disadvantage impedes innovation and opportunities to re-invest in Australian spirits manufacturing.
“Our global spirits industry experience tells us that when governments act decisively and across multiple fronts to provide coordinated support, it incentivises investment to achieve scale and unlock further opportunities for economic value-add
and innovation.”
Meanwhile, Mark Hill, treasurer, Spirits & Cocktails Australia and managing director, Suntory Global Spirits Oceania, said Suntory’s new $400 million carbon neutral facility in Ipswich, Queensland, provides the Committee with a real time example of the positive impact that direct foreign investment can have on the Australian food and beverage manufacturing sector.
“However, there is little or no incentive for global spirit companies to invest in the expansion of the Australian spirits industry while our excise rates are so overwhelmingly uncompetitive with other countries like Japan, the United States, Ireland, Scotland and Mexico,” he said.
Satya Sharma – director, Spirits & Cocktails Australia and chief executive officer, Lark Distilling Co, said whiskey from the ‘new world’ was continuing to gain in popularity, and Australian distillers needed to take advantage.
“Australia has an opportunity to grow our category into something of global significance synonymous with quality and innovation, following in the footsteps of Japanese and Scotch whisky, while contributing substantially to domestic employment and economic
growth,” said Sharma.
Holly Klintworth, president, Australian Distillers Association and managing director, Bass & Flinders Distillery, echoed Sharma’s sentiments.
“We know that nothing tastes like Australia. Australian spirits celebrate flavour and unique native ingredients that are not found anywhere else in the world,” she said.
“This provides Australia with a point of difference from other spiritsproducing nations. That’s why our industry needs coordinated, targeted support to both succeed at home and take distinctive Australian spirits to the world.”
According to figures from Global Data, the Australia spirits market was valued at $15.2 billion in 2021. The market is projected to grow at a CAGR of more than 9 per cent during the forecast period.
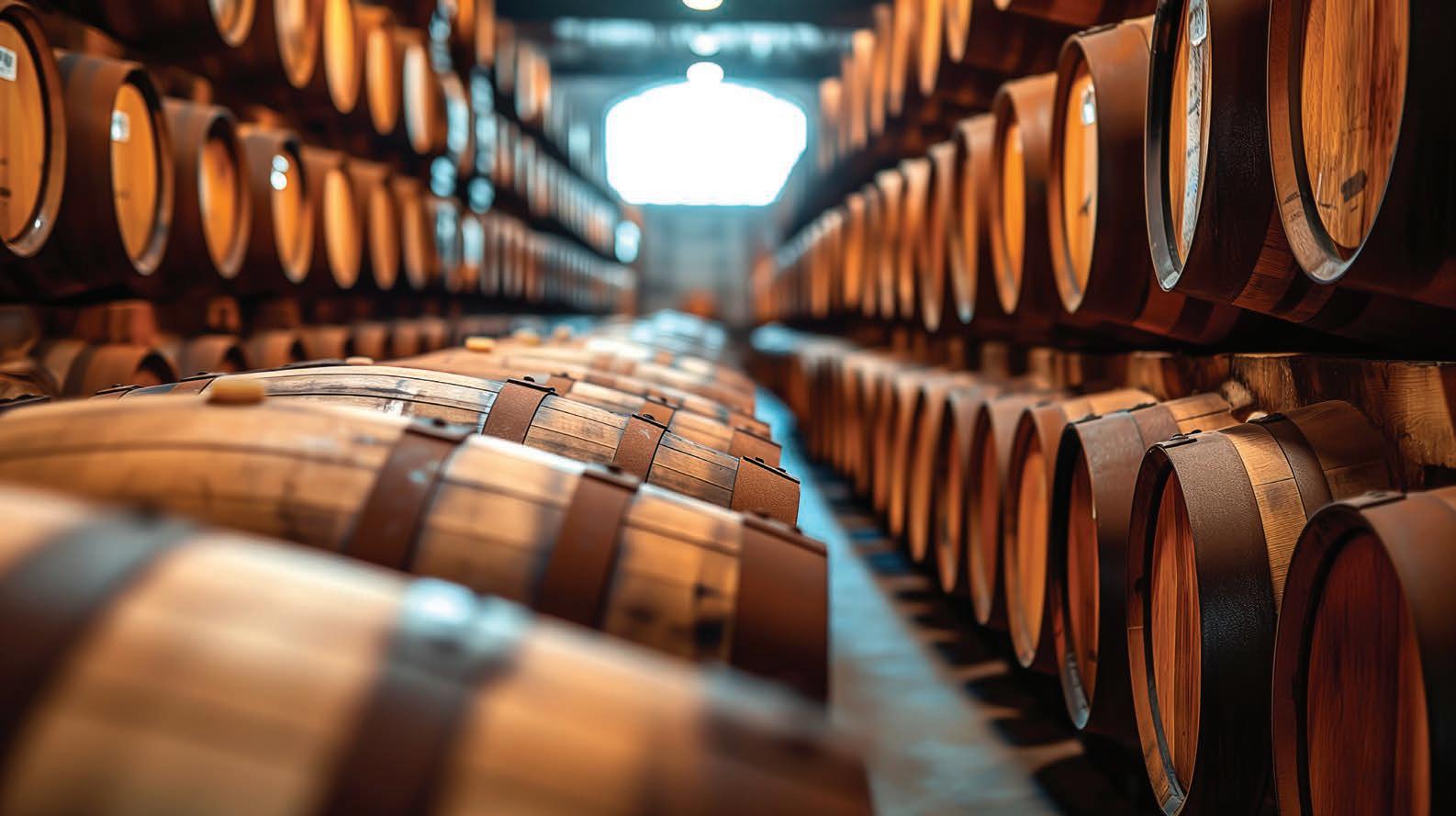
The Australian spirits market was led by the flavoured alcoholic beverages category in both value and volume terms. Vodka is forecast to register fastest value and volume growth in 20212026, during the same period.
It’s hoped reforms will only increase the profitability of the sector going forward. F
Food manufacturers call for collaboration on health outcomes
The AFGC has used the Diabetes Inquiry Report as a chance to strengthen collaboration with Australian food manufacturers and key stakeholders.
One of the leading organisations for food and grocery manufacturers has acknowledged the Diabetes Inquiry report and recognises it as a chance to strengthen collaboration with stakeholders and better produce for consumers.
“The AFGC’s interest in this inquiry stems from the crucial role played by food and beverage manufacturers in promoting healthier diets by offering nutritious options and clearer information on pack,” said CEO of the Australian Food and Grocery Council Tanya Barden.
AFGC and its members are already engaged in government’s flagship voluntary initiatives such as the Healthy Food Partnership and the Health Star Rating System.
“We welcome the report’s focus on multi-pronged interventions to improve health outcomes, including education and better urban planning to enable physical activity. An evidence-based approach where all players have a role in supporting a consistent strategy, based not only on products, but also diets, education and activity, is the way forward,” said Barden.
While AFGC understands concerns about marketing certain foods, particularly to children, it emphasises

that the impact of such restrictions on health outcomes remains unproven and knows restrictions on food advertising will not serve as a silver bullet for addressing diabetes, nor obesity due to its complex, multi-factorial causes.
The food and beverage manufacturing industry has long supported self-regulatory codes managed by the Australian Association of National Advertisers (AANA), and the industry advertising code specifically influencing this sector has also recently been reviewed and strengthened.
Similarly, AFGC advises caution regarding the proposed tax on sugarsweetened beverages due to lack of
evidence of its efficacy and the potential disproportionate impact on family budgets amid a cost-of-living crisis. The proposed tax ignores the economic realities of time-poor, budget conscious Australians.
AFGC stated it stands ready to work with government on the multifaceted issue of obesity effectively, with the industry set to play its part too.
The comments from the AFGC come less than a month after the association also highlighted its stance on ‘ultra-processed’ food.
“As makers of packaged food, we play an active role in keeping consumers informed. That is why the AFGC and its
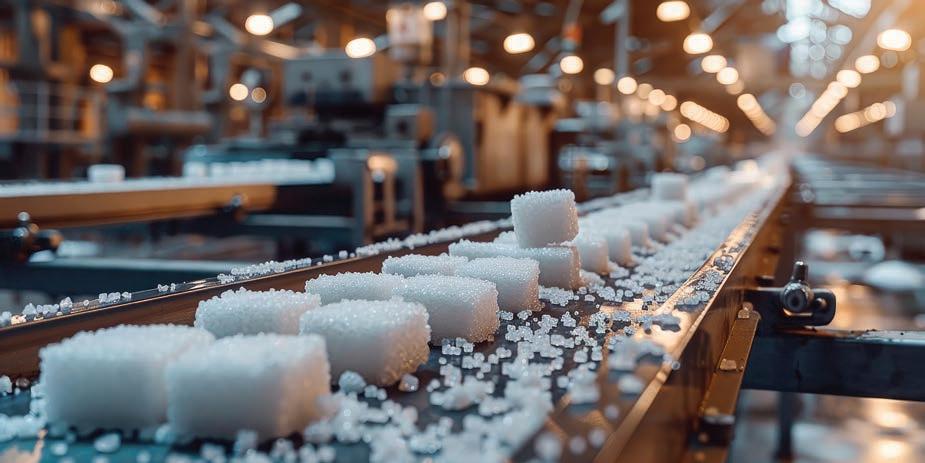
members are allies with the Government in flagship voluntary initiatives such as the Healthy Food Partnership and the Health Star Rating System,” an AFGC spokesperson said.
“We support an evidence-based approach to regulatory change in this sector with a focus on achieving specific outcomes including a healthier society. We advocate for holistic approach that emphasizes portion control, education and physical activity.”
The AFGC is concerned that the labelling of ultra-processed foods is not based on current nutrition principles and does not consider dietary patterns. Some of the foods described as ultraprocessed are core foods, such as flavoured yoghurt, whole grain bread, and soy milk, which may cause consumer confusion.
“Broad and sweeping regulation would likely increase costs for manufacturers and consumers alike with minimal impact on the health of the Australian community,” the spokesperson said.
“Through food and beverage product development and reformulation, portion control measures, food labelling and collaborations with government, food and beverage manufacturers have demonstrated their readiness and ability to act and look forward to continuing this engagement.”
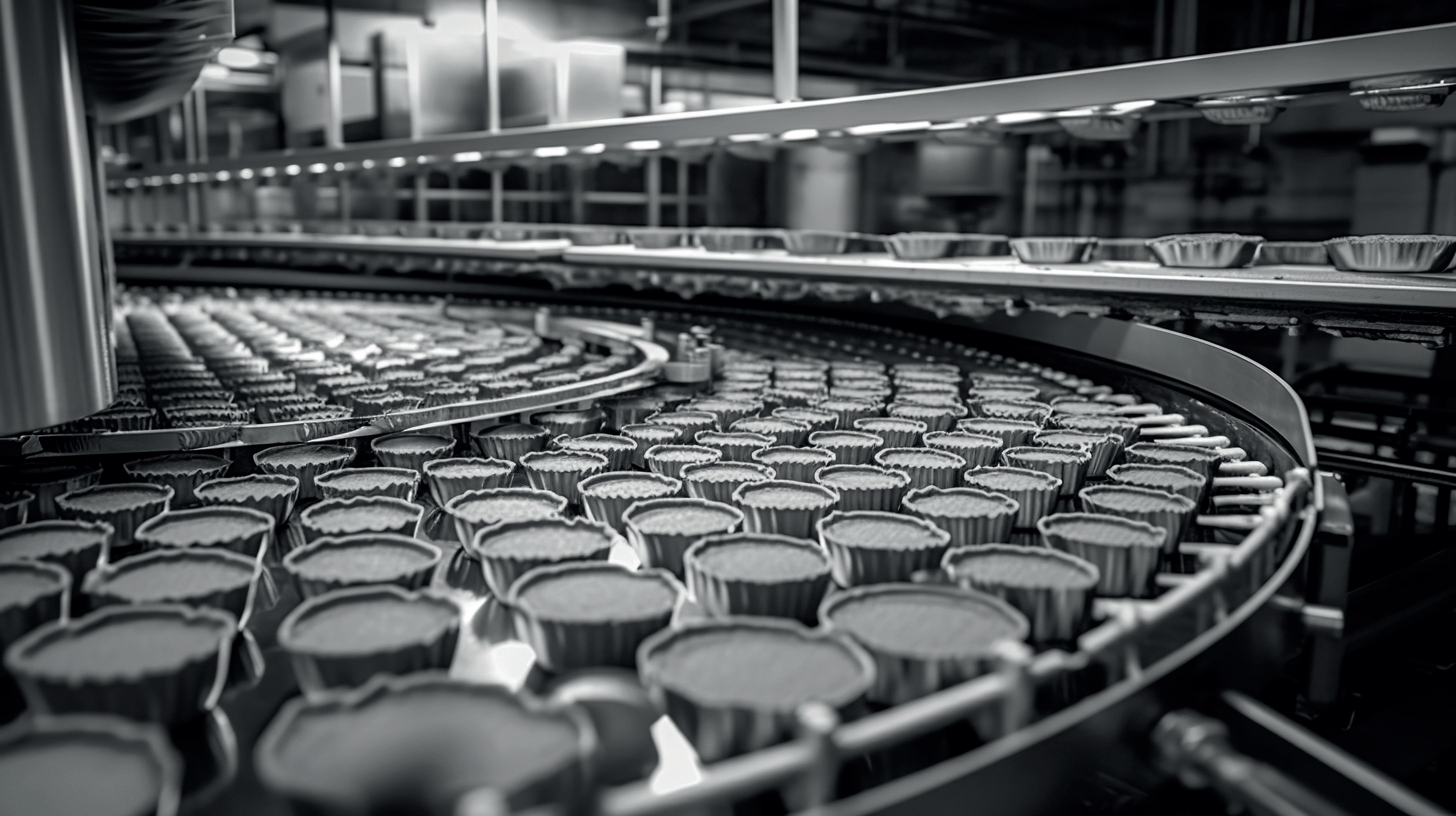
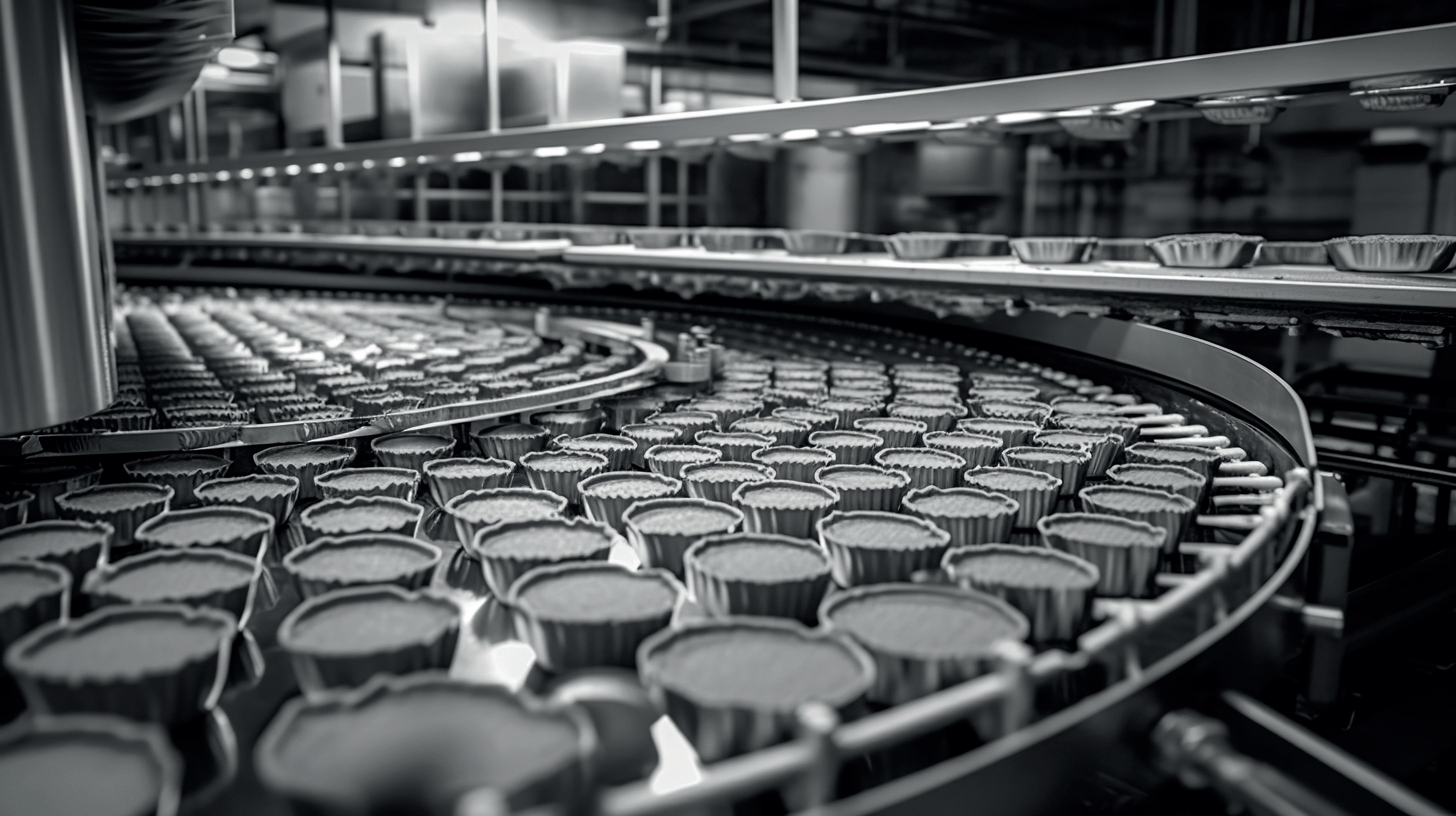
The AFGC is already engaged in the government’s flagship voluntary initiatives such as the Healthy Food Partnership.
The AFGC has also advised caution regarding the proposed tax on sugar-sweetened beverages.
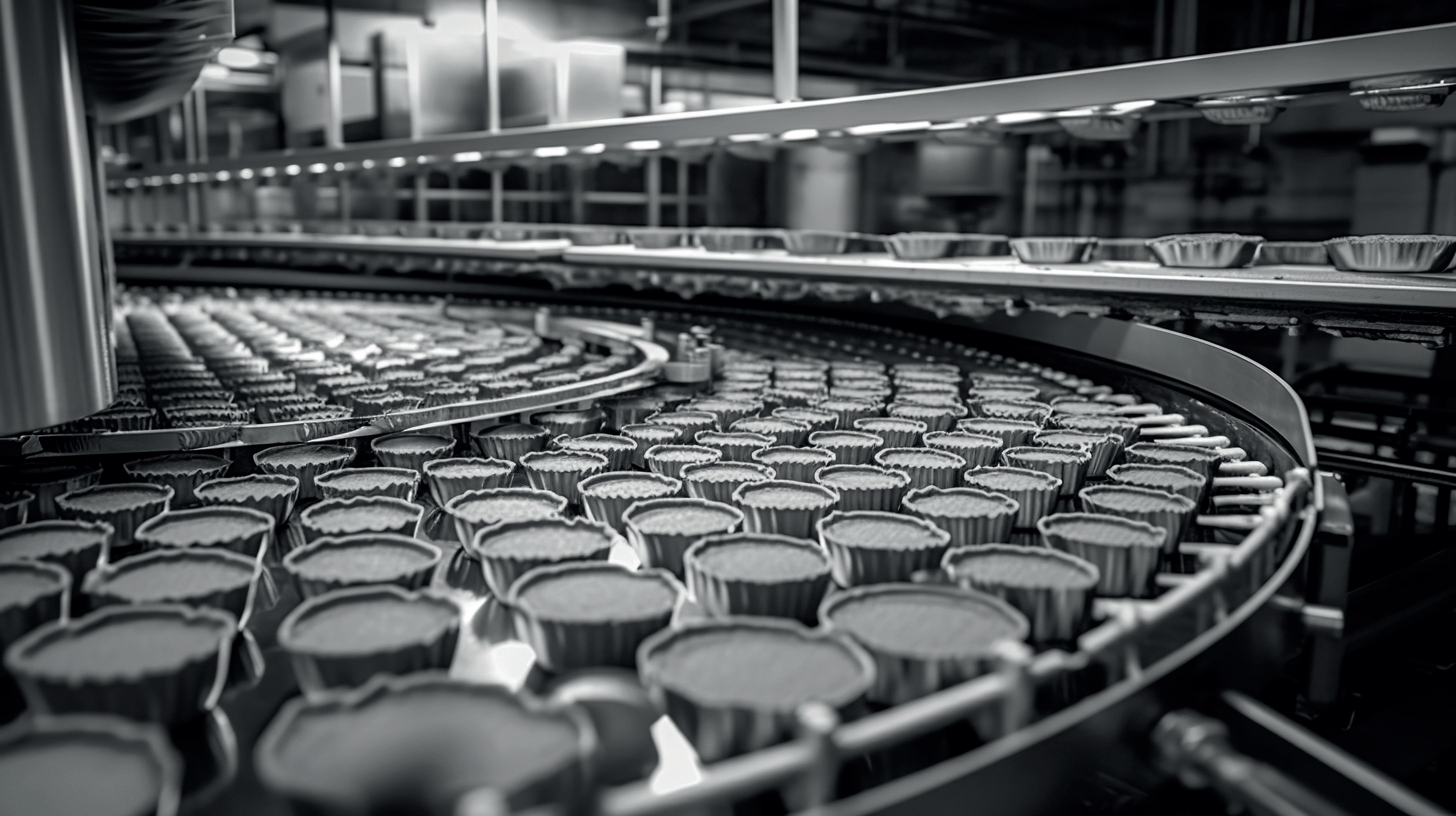
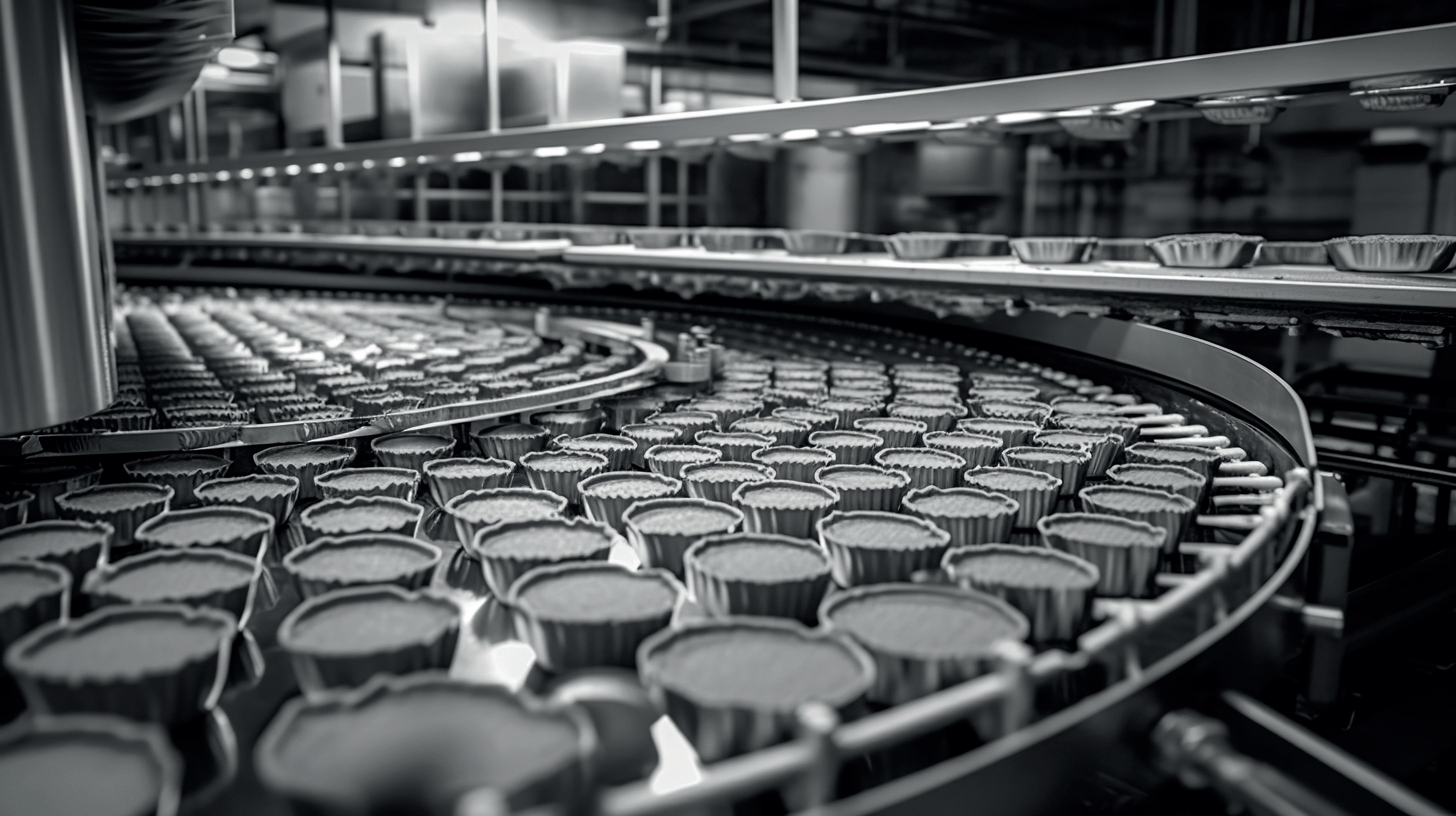
Vortab VIP Flow Conditioner tames turbulent flows
The Vortab Insertion Panel (VIP) Flow Conditioner features a unique design that maximises flow meter performance with minimal pressure drop in a simple to install, lightweight thin panel design that overcomes turbulent pipe flow profiles.
The Model VIP blends the proven performance and superior low pressure drop of Vortab tab-type flow conditioning technology with the low cost and ease-of-installation of an insertion panel type flow conditioner solution.
Multiple flow meter technologies, and particularly centre-point types, require several diameters of straight pipe run to meet their meter’s accuracy specifications.
The Vortab VIP Insertion Panel Flow Conditioner solves the pipe straight-run dilemma. A VIP installed in just 3 pipe diameters downstream from the flow disturbance and with the flow meter installed at just 3 pipe diameters downstream of the VIP neutralises the flow disturbance and produces the symmetrical and swirl-free repeatable flow profile that ensures a flow meter installation meets its accuracy and repeatability specifications. The thin, lightweight panel design of VIP is easily installed between flanges or can be welded in place.
The Model VIP Flow Conditioner is particularly effective with wide turndown and/or low flow sensitive flow meter technologies, such as thermal dispersion, that measure in transitional flows. The VIP provides a highly repeatable flow profile during laminar, transitional, and turbulent flow conditions. VIP has been extensively tested in Vortab’s NIST traceable flow stands under actual installation conditions with elbows, valves, headers and other flow disturbers.
VIP is easy to order and specify. The standard Model VIP Flow Conditioner is manufactured of 316L stainless steel in sizes for installation
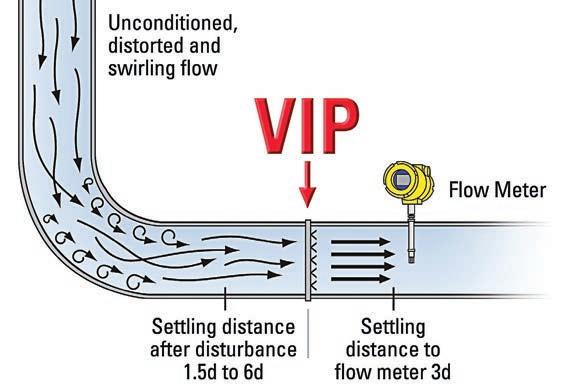
in pipes from 50 to 999.9 mm. Other materials and larger line sizes are available upon request.
AMS Instrumentation & Calibration Pty Ltd (03) 9017 8225 www.ams-ic.com.au
Expansion of FLEXI-FLOW Compact Series
The latest iteration of the FLEXI-FLOW Compact series introduces a range of innovative models and features, including instruments tailored for lower flow ranges starting at 0-5 mln/min. Additionally, the series now includes down ported instruments for applications where top-mount installation is required, and flow controllers equipped with integrated shut-off valves to provide a higher degree of leak tightness or enable emergency shutoff. One of the key enhancements in the FLEXI-FLOW Compact series is the incorporation of EtherNet communication, providing seamless connectivity and integration capabilities for modern industrial environments. The new models, like the original FLEXI-FLOW Compact instruments, leverage a unique through-chip sensor combined with proven by-pass technology. These thermal mass flow meters and controllers deliver exceptional performance, boasting a reduction in size by 35 per cent compared to traditional instruments, making them the smallest on the market for flow ranges up to 20 ln/min.
The advanced sensor technology ensures not only stable flow control but also rapid response times, with settling times smaller than 150 ms, facilitating precise control even in dynamic process conditions. Integrated temperature and pressure sensors, along with an onboard gas database, ensure unparalleled accuracy across varying process parameters, making the FLEXI-FLOW Compact instruments adaptable to a wide range of applications. Moreover, the instruments offer comprehensive monitoring and control features, including integrated temperature and pressure sensors, USB-C port for easy setup, optional Bluetooth communication for
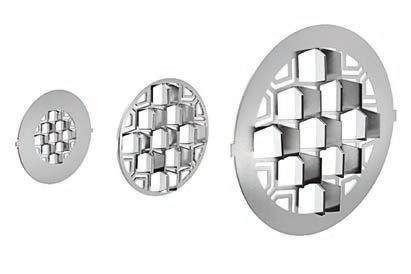
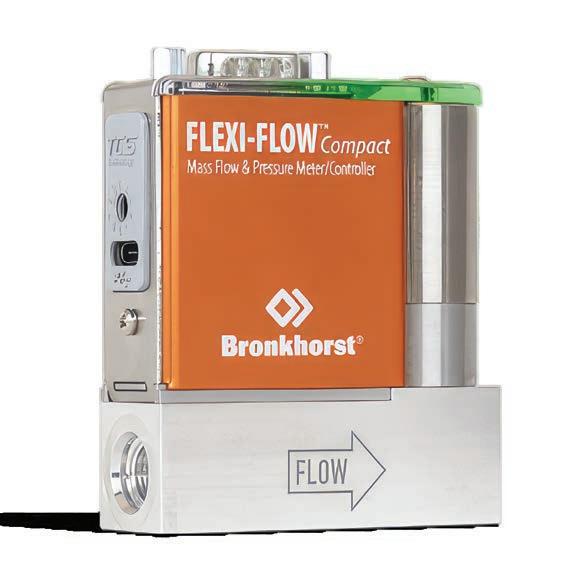
enhanced accessibility, and NAMUR status indication through coloured LEDs and digital output parameters.
Bronkhorst www.bronkhorst.com
+31 (0)573 458 800
The FS10A is a fast responding, highly repeatable sensor, which installs easily into a standard tube tee fitting or the SP76 (NeSSI) modular manifold.
Utilizing FCI’s long proven thermal dispersion flow measurement technology, the FS10A Analyzer Flow/Switch Monitor is designed with proprietary equal mass sensing to achieve outstanding sensitivity and repeatability. The instrument’s wetted parts are superior corrosionresistant 316L stainless steel with Hastelloy C-22 sensor tips. The sensor element has no moving parts to foul, clog or maintain, which ensures continuous reliability and virtually no maintenance. There are no cavities, orifices or dead-legs to trap or contaminate samples, which preserves sample integrity and faster sampling times.
The instrument’s remote configuration is Div 1/Zone 1 FM approved for hazardous environments. The remote configuration is useful when the sensor’s installation area is subjected to high temperatures or for mounting directly to the front panel of the analyser placing its display in a more convenient location for technician viewing.
The FS10A Analyzer Flow Switch/Monitor is designed with an easy-toread top-mounted, flow rate monitoring LED array for at-a-glance visual indication of operational status of proper flow rate to the analyser or sampling system, or that an alarm/trip point has occurred.
The Model FS10A is ideal for use with nearly all types of process and emissions sampling systems, including gas chromatographs (GCs), mass
Analyser flow verification relies on SIL-2 rated Flow Switch/Monitor in hazardous environments Energy savings with SMC Air Management System
The SMC Air Management System (AMS) is designed to optimise the use of compressed air in various industrial applications, ensuring efficiency, cost savings, and improved system performance.
The Air Management System is available in two basic configurations that vary by the standby regulator used. The A type utilizes the electropneumatic regulator while the B type uses the manual type standby regulator. Simple combination of standby regulation, hub and isolation valve
• OPC UA and fieldbus communication at base units
• EtherNet/IP and PROFINET protocols available (EtherCAT in development)
• Electro-pneumatic or manual standby regulator types
• Modular connection to SMC FRL components
• Four sizes available in port sizes from 1/8” to 1”
Key Features:
• Energy Savings: The AMS helps in reducing energy consumption by monitoring and controlling the flow and pressure of compressed air, thus minimizing waste and ensuring efficient use.
• Pressure Control It provides precise control over air pressure, maintaining optimal levels for various processes and preventing overpressurization which can lead to energy loss and equipment wear.
• Flow Monitoring: The system can monitor the flow rate of compressed air, helping to identify leaks and inefficiencies in the air distribution network.
• Integrated Components: SMC’s AMS often integrates various components such as regulators, flow sensors, pressure sensors, and controllers, providing a comprehensive solution for air management.

Fluid Components International (03) 9017 8225 www.fluidcomponents.com
• Remote Monitoring and Control: Advanced models offer capabilities for remote monitoring and control, allowing users to adjust settings and monitor performance from a distance, enhancing convenience and operational flexibility.
• Data logging and analysis: The system can log data over time, providing valuable insights into air usage patterns, helping in predictive maintenance, and further optimising system performance.
• Modularity: SMC’s AMS is typically modular, allowing for easy expansion and customisation according to specific application needs.
Benefits:
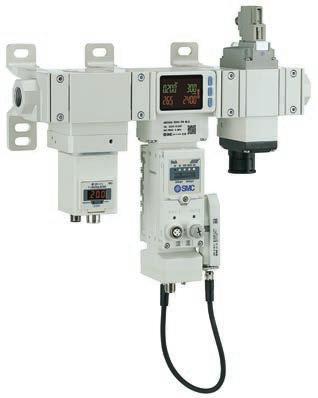
• Cost Efficiency: By optimising air usage, the system helps in reducing operational costs associated with energy consumption and maintenance.
• Enhanced Performance: Improved air pressure and flow control contribute to better performance.
• Sustainability: Reducing energy consumption and waste supports environmental sustainability goals.
SMC (02) 9354 8222
www.smcworld.com
spectrometers, optical spectrometers, photometers, and others.
WASTE INNOVATION & RECYCLING AWARDS
Recognising excellence across the waste and resource recovery sector. Sponsorship opportunities are now available for 2024.
www.wasteawards.com.au
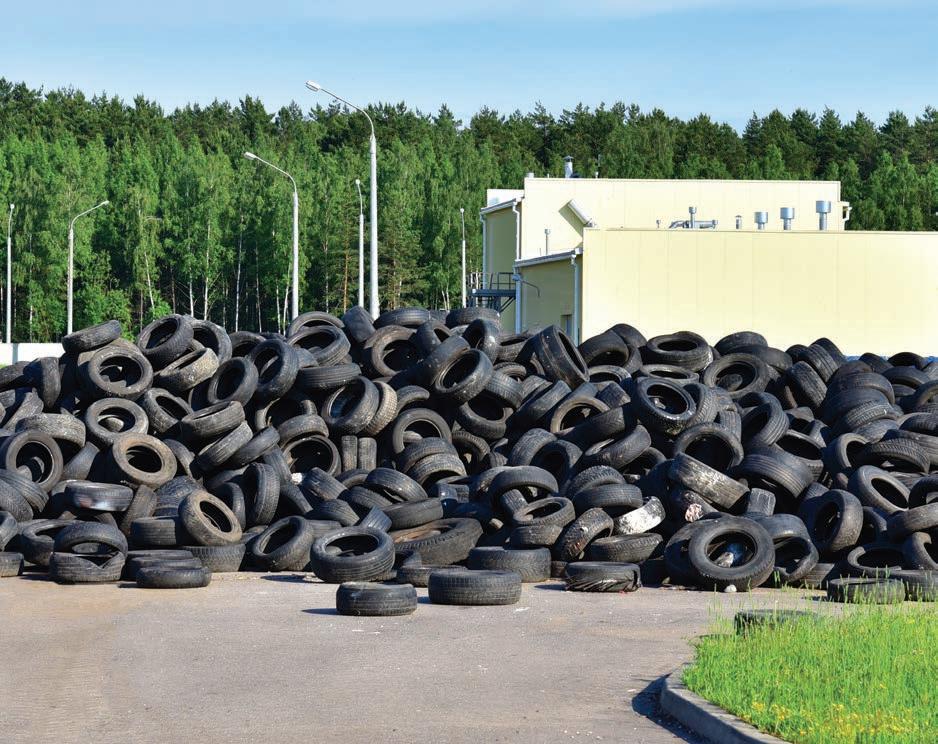

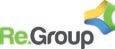
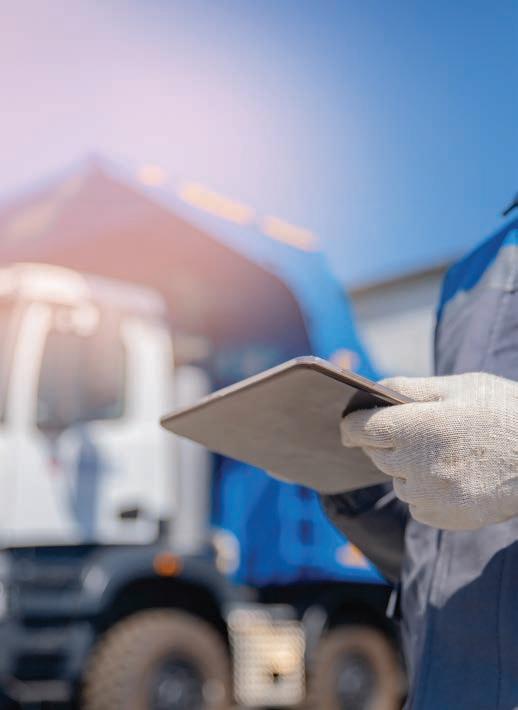
