
28 minute read
NEWS
Australian Pavilion set to expand at FHAFood & Beverage 2020
Exporting produce to Asia will be a key focus of the FHA-Food & Beverage trade event.
FHA-Food & Beverage is Asia’s largest food and beverage trade event that brings together the global food and hospitality industry and will be held from 31 March-3 April 2020.
FHA has more than 40 years’ experience in having the a selection of high-quality international products – making it the international sourcing platform for buyers in Asia. The event has expanded into two mega events – FHA-Equipment, Coffee, Bakery & Tea and FHA-Food & Beverage, to provide an enhanced experience and personalised engagement, to meet diverse demands of the food and hospitality industry.
FHA-Food & Beverage is the key business platform enabling the growth of the food and beverage industry in Asia and beyond.
Export Solutions is the Australian Representative for FHA-Food & Bev erage and has assisted Australian companies with their participation in FHA and coordinated the Australian Pavilion for the past 10 years.
“We have secured even more space for the Australian Pavilion at FHA-Food & Beverage in 2020, in the same great location in Hall 8 at the Singapore Expo close to major distributors and other key international pavilions,” said Philip Litton, director of Export Solutions. “The last edition of FHA, in 2018, was a huge success, with the participation of 164 Australian
exhibitors including nine state governments, industry bodies and government agencies
“FHA is a must-attend trade show for Australian food and beverage companie s looking to export to Asia. Whether you’re a new exporter, or one of the biggest names in the industry, the event provides the opportunity to showcase your products to real buyers from across Asia. Our aim for the upcoming edition of FHA is to redefine participants’ journey at the events to enable more targeted and robust interaction, so that they can focus on strengthening existing partnerships or explore new collaborations. At FHA-Food & Beverage, we have new profiles such as FoodTech, Natural & Organics and Meat, to name a few, and supporting these profiles with conferences and seminars. We have also developed new initiatives such as the FHA Buyers’ Programme to attract top-quality buyers from the region to the event,” said Martyn Cox, event director of hospitality, food & beverage – Singapore, Informa Markets.
“Australian food and beverage products enjoy an unburnished reputation in the Asian region for their high quality, safety and reliability. We are confident that these new initiatives and activities, coupled with the increasing interest in Australian brands, will ensure the presence of top buyers at the show,” he said.
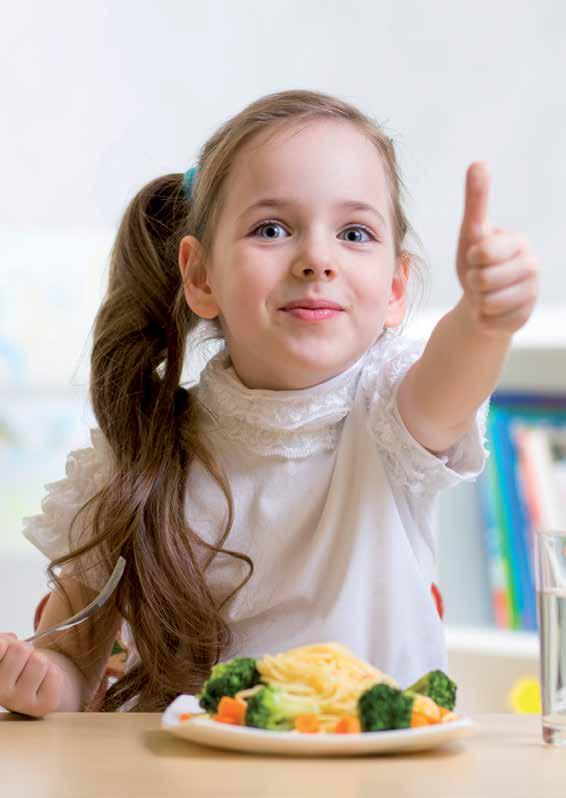
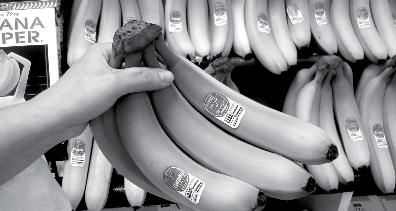
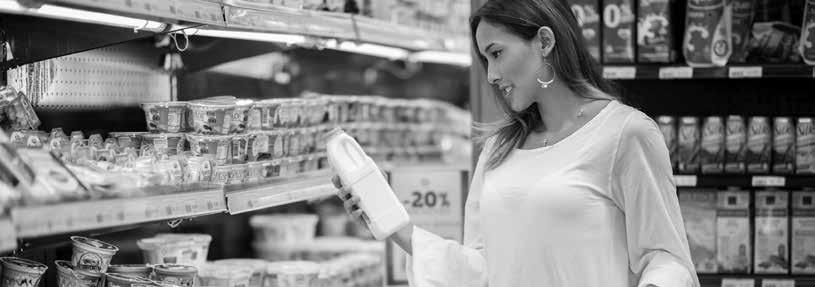
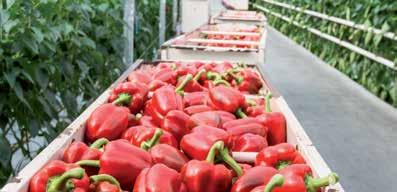
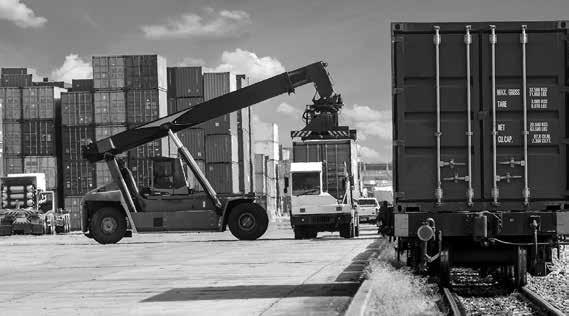
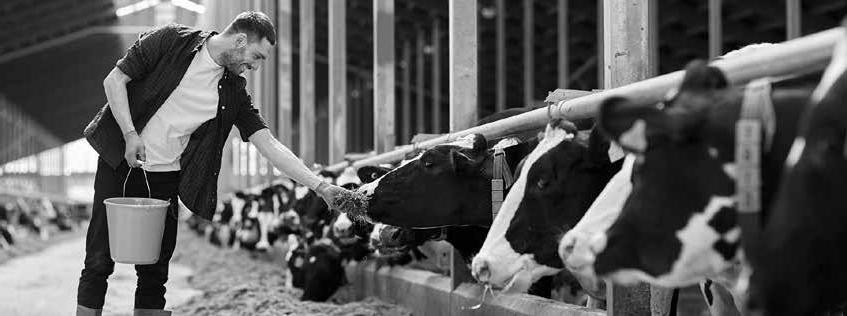
From chicken feathers to fire retardant
Researchers at the University of Auckland have developed a way to turn chicken feathers into a high-performing fire retardant
Chicken is a popular source of protein in most parts of the world and millions of chickens are produced each year to eat.
Billions of chicken feathers are produced by the poultry industry, most of which end up in the incinerator or landfill. They can create a range of waste issues for the chicken processing industry.
However, Distinguished Professor Debes Bhattacharyya, of the University of Auckland’s Faculty of Engineering, has found a way to use chicken feathers as a base for a fire retardant, one that is safer than many fire retardants, cheaper to produce, and solves an international waste problem at the same time.
“People pay to get rid of chicken feathers,” he said.
Chicken feathers are made of a keratinous material that is found in the hair, wool, horns and hooves of mammals. They are also naturally occurring flame inhibitors.
Fire retardants are added to industrial and consumer products such as furniture, textiles, electronics, even Christmas trees, as well as building products such as insulation.
Traditionally, halogen compounds were added to create flame-retardant material, but while they were effective, they were highly toxic. “They might have saved you from death by burning, but have exposed people to other effects that are detrimental to health.
“Furthermore, as a result of the environmental long life and bioaccumulation, traces of the compounds have been detected in everything from household dust to breast milk, causing hormone-disrupting effects,” said Bhattacharyya.
As a result, there has been a global shift away from halogenic retardants and toward other types of retardants among which ammonium polyphosphate (APP) is the most
Using feathers as a fire retardant could be the answer to chicken processors looking for ways to dispose of a potential waste problem.
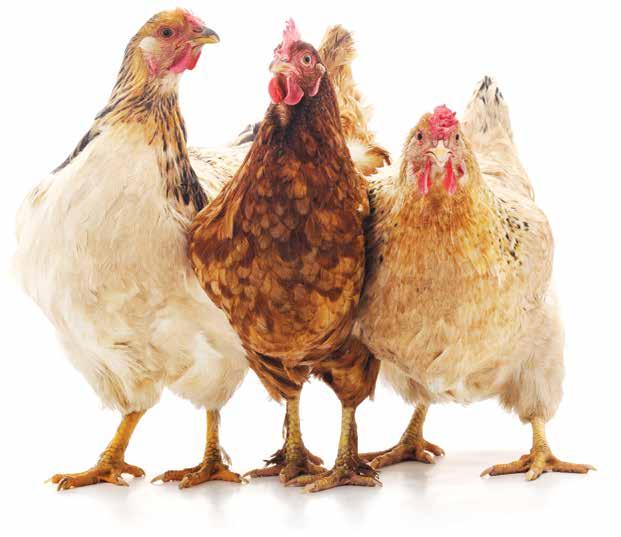
prominent. However, as they are expensive to produce, there is an increasing demand for alternatives.
Bhattacharyya and his team have previously shown that chemically modified wool fibres, also made of keratin, can also be used as an effective retardant. This could potentially provide a revenue stream for low-grade wool in an era when the price of, and demand for, wool have declined.
They more recently turned to chicken feathers as an alternative source of keratinous fibres, which are even cheaper and in many countries, more of a waste problem.
The team has developed a rapid and simple way to chemically modify the keratinous fibres of both wool and chicken feathers, and convert them into a flame retardant powder that can be added to polymeric materials.
The powder enhances the fireretardancy of the polymer by accelerating char formation – the solid material produced in the initial stages of combustion, and which inhibits combustion.
Also, standard fire retardants need to be added in high concentrations, which can reduce strength as a result. “But what we’re showing is that we can optimise the process so that this fire retardant removes this disadvantage of inferior mechanical performance compared to current fire retardants,” said Bhattacharyya.
“We also assessed this from a commercial perspective and have been able to show that the cost around this compound is up to a third lower than the existing standard compounds used as a fire retardant.
“It’s a perfect fire retardant material, passes most of the fire retardant standards, and can be used with polymeric materials.”
He acknowledges that while the method has so far been proven in the lab, producing the keratinous fibre-based product at a large scale and ensuring it is compatible with existing manufacturing processes, will need private or public investment.
However, initial results are very promising and have attracted the interests of several multinational companies.
“Our invention, whose intellectual property rights are protected, has been tested to show that it could be a direct replacement for APP, the predominant existing product.”
ABB appoints new country managing director
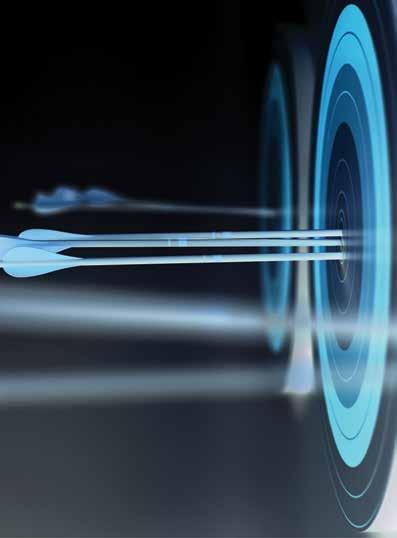
Slavko Planinic has been appointed the Australian country managing director and head of industrial automation for well-known multinational company ABB.
According to a statement, Planinic’s strong leadership and experience across all business lines will underpin ABB’s growth momentum in Australia.
He succeeds the retiring Tauno Heinola. Planinic comes to the new position with more than 30 years’ experience in ABB, having served most recently as ABB Australia’s chief financial officer.
Planinic also brings an understanding of the company’s market and therefore is well aware of the challenges facing the key industries in which the company is involved.
His oversight and involvement in key market segments and account management programs will see ABB well positioned to seize growth
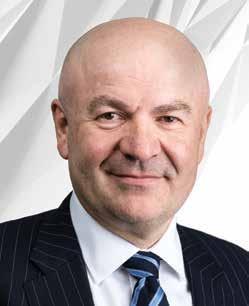
opportunities as companies look to improve their productivity and competitiveness through automation and digitalisation.
As part of his new role within the compnay, Planinic will be head of ABB Australia’s industrial automation business, which is ranked number two in the market globally. Planinic will lead a dedicated team with in-depth domain knowledge.
“ABB Australia’s commitment to supporting our customers, and ongoing engagement to grow the business in our identified segments, is stronger than ever,” stated Planinic.
“We believe industrial digitalisation and automation is a tremendous opportunity for businesses in Australia to raise their competitiveness globally and to play an important, decisive role for the future of this country.”
“For government, digitalisation offers innovative solutions for sustainable transport, infrastructure and energy challenges.
“As a technology leader, ABB is working closely with customers and industry to not only drive productivity but to do so in a way that reduces environmental impact.”
Planinic has served as a director of ABB companies in Australia for many years and has held finance leadership roles in Europe, as well as across South Asia throughout his career with the company.
He holds a Bachelor of Business Degree from the University of Technology Sydney. He also has a Master of Business Administration (MBA) from the Macquarie Graduate School of Management. Planinic will continue to be based in Sydney.
Hit all your inspection + packaging targets
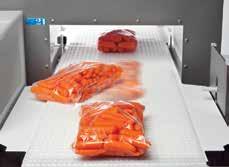
Complete packaging and inspection solutions
Ishida, CEIA and Key Technology inspection systems from Heat and Control assure precise, consistent detection and rejection of product containing foreign objects, missing or damaged pieces or packaging defects.
X-ray | Quality Control | Metal Detection | Sorting
Exclusive distributor for Ishida, CEIA + Key Technology
AUS +61 7 3877 6333 info@heatandcontrol.com www.heatandcontrol.com
Will fruit-infused water be a substitute for carbonated soft drinks?
Arecently published report on the fruit-infused water market, which includes the global industry analysis 2014-2018 and opportunity assessment 2019- 2029, projects that the fruit-infused water is expected to reach $14.7 billion by the end of 2019 in terms of value, and is forecast to reach $31 billion by the end of 2029. The report states that the flavour and the nutritional content of fruit is infused in water to increase its nutritional quotient.
The global population is becoming more health conscious, and focussing not only on healthy food, but also healthy drinks to ensure complete nutrition. Water with high nutritional quotient such as fruit-infused water, is gaining more popularity. There were several findings in the report.
Unique flavours positively influencing the intake of fruit-infused water Manufacturers of fruit-infused water offer many flavours using different fruits. Amid them, the citrus flavour is more popular among consumers. With increasing popularity of various flavours, manufacturers are experimenting and introducing new flavours. Manufacturers are coming up with innovate new combinations by infusing two or more fruits together in water. This gives new taste and colour to the water. This continuous introduction of new and innovative flavours gives choice to the consumers and is influencing them to try these n ew versions. Increasing variety and choices for consumers are expected to drive the growth of the market.
Focus on health and wellness ensures opportunities for the infused water Industry Healthy living is one of the major
Fruit-infused water is expected to be a $14-billion market by the end of 2019.
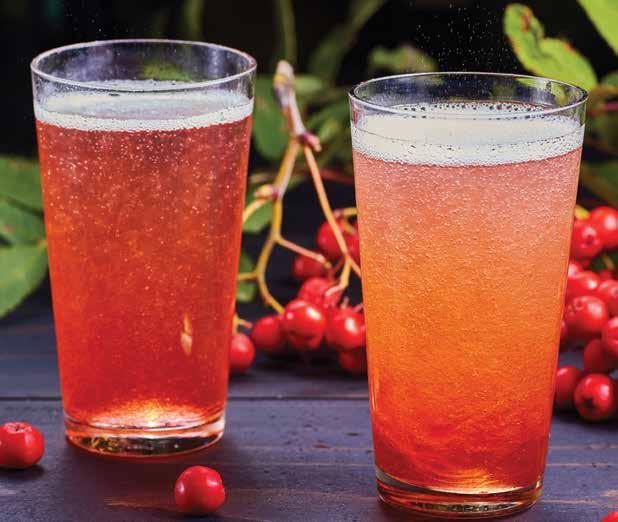
objectives of consumers worldwide. The urban population is more conscious about fitness. When infused water is paired with a health regime, manufacturers of fruit-infused water get the benefit of positioning their product in the health segment. This provides great opportunities for manufacturers to introduce more flavours in the wellness market.
Fruit-infused water as a healthy substitute for soft drinks Fruit-infused water is a hydration product that has a taste and nutritional ingredients that can complement a healthy diet. Fruit-infused water can be considered as a substitute for normal drinking water and other soft drinks. Fruit-infused water is consumed along with a healthy diet by health-conscious consumers, and this trend is expected to boost the market demand in the nutritional segment.
Increasing consumption of bottled water fueling the market growth The consumption of supplied water is decreasing as the consumption of bottled water is increasing day by day. Consumers prefer bottled water in the hotel/restaurant/catering sector, and also while travelling.
Carrying bottled water is a much better choice for consumers rather than opting for supplied water when on a tour.
This leads to an increase in demand and consumption of bottled water and thus, also increases the demand for bottled water in fruit flavours. The demand driven by the consumption of bottled water is fuelling the market growth of fruitinfused water.
Impact of plastic packaging bottles on the environment Manufacturers of fruit-infused water commonly use plastic bottles for packaging. The usage of plastic has a hazardous effect on the environment as well as human health. Any type of water, which is stored in plastic may cause ill effects on human health after consumption.
Carbon footprint also increases when plastic is used as a packaging material. Therefore, the use of plastic bottles for packaging could be restricting the growth of the fruitinfused water market.
Science can detect gluten in any food S cientists from Australia’s national science agency, CSIRO, can now detect gluten in any food and show which grain it comes from, making it easier for food companies to correctly label their products.
At the National Science Week, it announced it has discovered a way to detect gluten in the less well-studied grain, rye, completing the “Grand Slam” of gluten-containing grains. CSIRO was the first to be able to detect specific glutens in the other three gluten grains – wheat in 2015, barley in 2016, and oats in 2018.
Current commercial tests can only tell that gluten is present in a food but not the grain it’s from. The various detection kits currently available also give variable results of how much gluten is present.
Protein analytics expert with CSIRO, Professor Michelle Colgrave, explains how completing the picture
The CSIRO has discovered a way to detect gluten in rye.
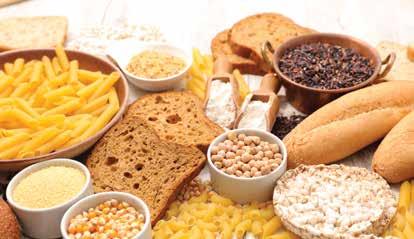
with rye can help consumers and food manufacturers.
“Being able to detect any protein in diverse foods and beverages will help food companies ensure that what’s in the pack is what’s on the pack, and help consumers trust pack labelling around gluten-free claims,” Colgrave said.
This technology offers many applications for the food industry –from helping track contamination in their raw ingredient supply chain, to improving product quality, food safety and meeting regulations.”
The researchers analysed 20 cultivars of rye from 12 countries, which they milled into flour, extracted the gluten proteins and used high
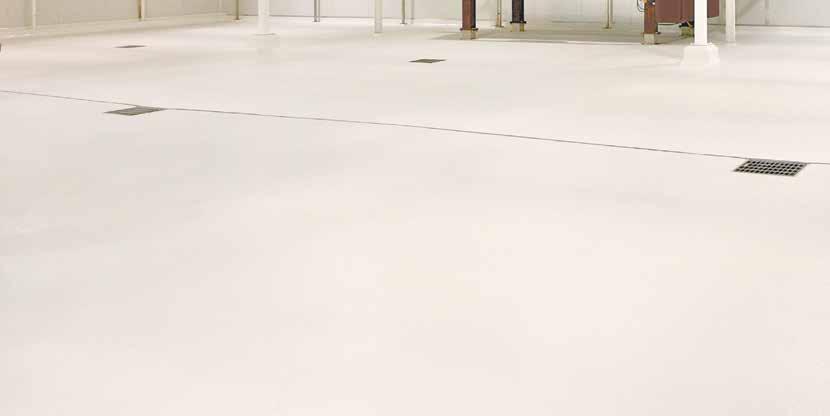
resolution mass spectrometry to identify and quantify the proteins. The analysis revealed six proteins specific to all rye varieties but that don’t appear in other grains.
“Detecting gluten proteins in their original grain is relatively simple, but when they’re in food products consumers buy at the supermarket and have been baked, extruded or processed in other ways with other ingredients such as salt and sugar, it is a lot more complex.
The team tested a range of commercial flours, breakfast cereals and snack foods and detected the six rye proteins in all the foods that contained rye as a labeled ingredient. They found one “gluten-free” breakfast cereal that contained trace amounts of rye, which did not appear on the ingredients list, and one sample of flour from the wheat-related grain, spelt, which was contaminated with about two per cent of the product.
Huddle appointed new head of commercial at Deliveroo Australia O nline food platform Deliveroo has appointed Laura Huddle as head of commercial in Australia.
Huddle joins Deliveroo after more than nine years at event technology platform, Eventbrite, where she joined as employee Number 20 and held multiple roles including head of sales and business development for Asia Pacific and head of marketing – Australia and New Zealand.
Huddle will oversee Deliveroo’s relationship with the more than 11,000 restaurants on the platform in Australia, as well as focus on growing the number of restaurants with whom Deliveroo partners. The appointment comes as Deliveroo continues to expand the restaurants on its platform, having more than doubled the number of partner restaurants in the past 12 months.
“This is an incredibly exciting time to be joining Deliveroo, a company that is focussed on transforming the way people think about and experience their favourite foods. Partnering with, and enabling the success of Australia’s best and mostloved restaurants ,is key to this,” said Huddle.
“There’s no doubt that the traditional restaurant sector is changing as consumers are looking for both the convenience of on-demand food delivery and an amazing dine-in experience. I’ll be focusing on ensuring that Deliveroo can best position our partner restaurants to succeed across both.”
During her time at Eventbrite, Huddle opened the Australia, New Zealand, Singapore, and Hong Kong markets, drove experimentation
within the small and medium business segment, and led APAC sales to achieve increased performance.
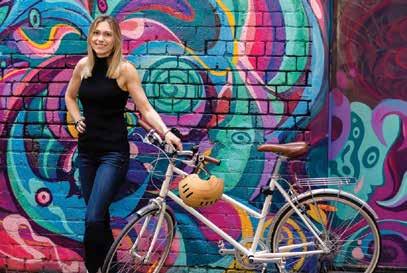
Laura Huddle will focus on growing the number of restaurants with whom Deliveroo partners.
One Chain, Multiple Behaviors.
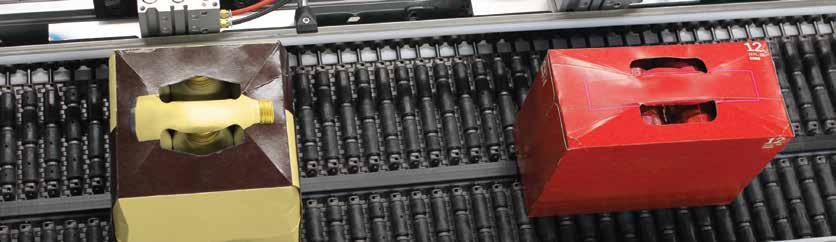
Food & Beverage manufacturing companies need to handle packages, boxes, cases, pouches, and bags efficiently — with minimal to zero damage. Rexnord ® is proud to introduce its new ART™ Dynamic Chain that provides the ability to create MULTIPLE behaviors — zero back line pressure, rotation, acceleration, deceleration, low pressure accumulation, metering, and sequencing — in ONE single conveyor design, unlike others that require multiple conveyors to perform those behaviors.
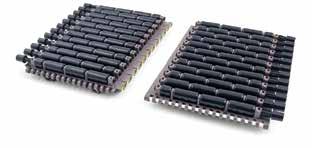
Contact Rexnord today to learn more about ART Dynamic Chain. sales.australia@rexnord.com or Tel 02 4677 6000
AIP education director appointed Professor at Sichuan University P ierre Pienaar, education director for the Australian Institute of Packaging (AIP) and President of the World Packaging Organisation (WPO), recently received an appointment as Professor to the Sichuan University in Chengdu, China.
Chengdu is the fourth largest city in China with a population of 17 million and is the capital of Sichuan Province.
Sichuan University was founded in 1896 and is one of the three oldest universities in China. It is one of the most prestigious national key universities in education, research and social impact in China. It is engaged with 248 global academic universities and research institutes in 42 countries. The University has 34 faculties, 354 Doctoral programs, 438 Master Programs, 142 undergraduate programs and is ranked #13 out of 2914 universities in China. Sichuan University has some 60,000 full time students and 3,000 international students living on campus and attending classes each year. Including Postgraduates, Master and PhD level students, teaching and administration staff the number increases to 100,000 across three campuses located in Chengdu.
Pierre Pienaar will focus on sustainability in packaging among other subjects he will teach at Sichuan University.
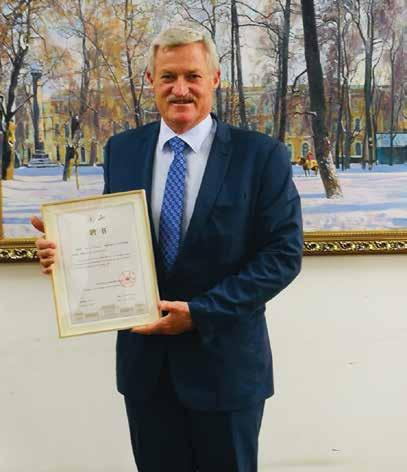
Pienaar has been lecturing industrial design students as part of the Sichuan University Immersion Program for three years now.
According to Pienaar, his focus within the Immersion Program is material science, packaging management, sustainability in packaging and packaging design subjects. All of the units have assessment pieces at the end where they need to attain a minimum of 60 percent.
“While my teaching focuses on Industrial Design students, people from other courses and faculties, such as design, graphics, engineering, arts, sciences, often attend my classes,” Pienaar said.
“The number of students vary from year to year in the Immersion Program, but on average there would be 55 to 75 attending classes; which run from 8am to 5pm, Monday to Friday,”
“I am certainly honoured to have this conferred on me from a prestigious university like Sichuan University. I am even more thrilled that leading universities, such as Sichuan University, acknowledges packaging and all that it is and means to society,” he said.
“Sichuan University acknowledges the principles of good academic practice and high ethical standards and they want to see innovative teaching that aims to educate students as critical and responsible members of society and provide them with advanced knowledge.” Prof Pienaar said.
Pienaar has been lecturing at a number of other Universities in China since 2014 including Beijing University and Jiangnan University in Wuxi.
ifm raises $7,000 for Starlight Children’s Foundation
ifm recently held a fundraiser for the Starlight Children’s
Foundation with a Christmas in July theme, with ifm’s staff and their partners attending along with some of the company’s customers.
The night was very entertaining, with people bidding on holidays and various household goods – from refrigerators to weekends away and everything in between.
The Starlight Children’s Foundation is a charity that grants seriously ill children a “once in a lifetime wish”. ifm raised more than $7,000, which will go towards giving a seriously ill children a wish, an experience for the child and their family, which is aimed at increasing a child’s happiness and wellbeing.
These wishes include going on holidays, meeting a celebrity or sport star, experience wishes (e.g. swimming with dolphins) gift wishes (e.g. cubby house, pets) and more.
“ifm is proud to be a responsible corporate citizen and give back to the community,” said ifm director Dave Delany. “We really are very proud of our efforts for the Starlight Children’s Foundation. It was a great event and everyone had a lovely time.”
Getting milk from farm to fridge quickly
Swinburne University will lead a research project valued at over $2 million to develop new technology that will get milk from farm to fridge more quickly, enhancing the productivity and competitiveness of Australia’s $13.7 billion dairy industry.
The ‘Live Inbound Milk Supply Chain Monitoring and Logistics for Swinburne’s Milk Supply Chain project will be conducted in collaboration with Bega Cheese.
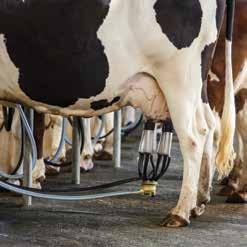
Productivity and Competitiveness’ project (Milk Supply Chain Project) has just received $600,000 under round 7 of the federal government’s Cooperative Research Centres Projects (CRC-P).
CRC-Ps are designed to improve the effectiveness of Australian research by bringing researchers and industry together to solve real-world problems and deliver tangible outcomes.
Swinburne’s two-and-a-half-year project will develop an Internet of Things (IOT)-based system that links dairy farms, milk carriers and a milk processor, and allows live monitoring of milk supply chains. The data collected will enable highly accurate milk supply forecasting.
Swinburne’s Milk Supply Chain Project will be conducted in collaboration with Bega Cheese, Telstra and three Australian milk suppliers.
Director of Swinburne’s Internet of Things (IoT) and project researcher, Professor Dimitrios Georgakopoulos, says the project will improve operational efficiencies and create opportunities to generate revenue.
“We will be using cutting-edge technology, including over 700 sensors, to measure specific aspects of the supply chain. We will also use Telstra’s newly-deployed Narrowband Internet of Things (NB-IoT) network, which is Australia’s largest IoT network and one of the largest in the world,” Professor Georgakopoulos says.
“The data collected by the IoT sensors will find trends to make production schedules more efficient and enable highly accurate milk supply forecasting. These collectively enhance the chain’s productivity and competitiveness,” Professor Georgakopoulos says.
Swinburne continues to celebrate industry research success
This Milk Supply Chain Project is the fourth Swinburne project to receive funding under the CRC-P grant scheme since it was introduced in 2016.
Separate rounds have allocated funding to: • develop a new and unique biodegradable and renewable bio-based oil • introduce an Australian graphene characterisation and certification capability, and • investigate high-performance energy storage alternatives to lithium-ion batteries. Swinburne 4.0
This project is part ogF Swinburne’s Industry 4.0 Initiative, which helps global industry solve challenges and create opportunities from the profound changes wrought by the industrial revolution.
Swinburne is the only university in Australia with a holistic Industry 4.0 strategy and recently won the Australian Business Award for business innovation.
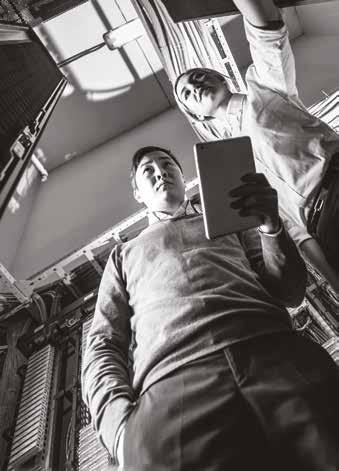
Destocking of beef reaches record levels – MLA
The first half of 2019 saw beef exports increase by six per cent.
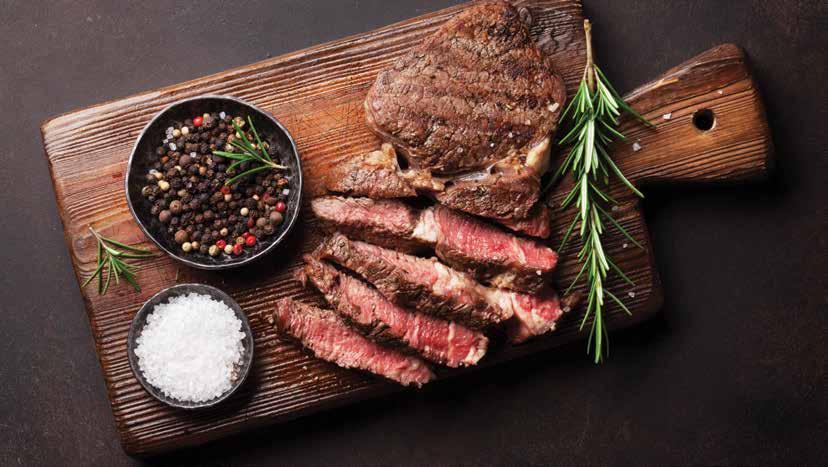
Cow turnoff has reached record levels as severe water shortages across many key beef production regions have accelerated the pace of droughtinduced destocking, according to Meat & Livestock Australia’s (MLA) Cattle Industry Projections August Update.
Cow and heifer slaughter reached 58 per cent of total adult cattle slaughter for three consecutive months from March to May, as many beef producers continue to destock or manage depleted breeding herds.
MLA senior market analyst, Adam Cheetham, said total Australian adult cattle slaughter for 2019 is now forecast to increase three per cent year-on-year to 8.1 million head.
“Elevated female slaughter and poor conditions have combined to drive average carcase weights lower so far this year to 282.5kg/ head,” Cheetham said.
“Despite national slaughter being revised higher, the lower carcase weights have underpinned unchanged production levels at an estimated 2.3 million tonnes carcase weight (cwt), two per cent below the five-year average.
“The lot feeding sector continues to support national beef production and has been a critical link in the supply chain during the prolonged dry period.
“The number of cattle on feed reached a new record in the March 2019 quarter and has remained above the 1.1 million head mark for the fourth consecutive quarter.
“This number is expected to remain high, given the challenges of finishing cattle on limited pasture reserves.”
Cheetham said the national herd is estimated to have declined 7.3 per cent, to 26 million head for the year ending June 2019, while estimated branding rates have also fallen, reducing the number of calves on the ground this season.
“On the upside, prices for finished cattle have improved this year and are likely to find continued support given an expected tightening of supply during the remainder of the year,” Cheetham said.
“This year has seen the largest premium between the heavy steer indicator and the Eastern Young Cattle Indicator (EYCI) in the last decade.
“Young cattle prices have been reasonably subdued and, until seasonal conditions allow restockers to re-enter the market with confidence, the store market is unlikely to see any significant price corrections.
“However, if a solid break in conditions were to materialise, there is the potential for young cattle and productive female prices to experience significant increases.”
Cheetham said demand for Australian beef has remained robust this year, supported by a depreciating Australian dollar and rising demand from China.
“In the first half of the year, Australia’s total beef exports increased six per cent and grainfed shipments reached record levels. However, coming up against some supply constraints in the second half of the year, 2019 exports are expected to finish the year steady at 1.13 million tonnes shipped weight (swt),” said Cheetham.
“Dry conditions have also supported cattle exports, with total shipments up 19 per cent in the first half of 2019. Cattle shipments are forecast to finish 2019 at 1.15 million head, up six per cent year-on-year.
“Beyond the weather, factors such as exchange rates, production in the United States and cattle price movements, trade developments and demand from China will remain important price drivers for Australian beef.”
Conagen, a US-based biotechnology company focusing on research and development, announced its breakthrough development in the commercial production of natural aromatic compound, y-Decalactone from natural substrates using its proprietary technology. Found in many ripe fruits and particularly peaches, y-Decalactone is a versatile compound used commercially in formulations with distinctive fruit flavours of peach, apricot and strawberry in food, beverage, fragrance, nutrition, renewable materials, and pharmaceutical markets.
The technology created for the y-Decalactone product provides for more than 20 different lactones, many of which have not been available commercially because of a lack of reliable sources.
“The strengthening and expansion of Conagen’s lactone production platform will better meet consumers’ demand for nature-based, clean ingredients,” said Oliver Yu, Ph.D., co-founder, and CEO of Conagen.
The compound is a member of a much larger family of lactones. Variations in the structures of lactones define their unique sensory properties with mainly fruity and buttery characteristics. These diverse characteristics create a wider spectrum of application options for manufacturers that use lactone flavours in their products.
“Conagen’s lactone products are natural and non-GMO, making them ideal for use in a variety of consumer products,” said vice president of research and development, Casey Lippmeier, Ph.D.
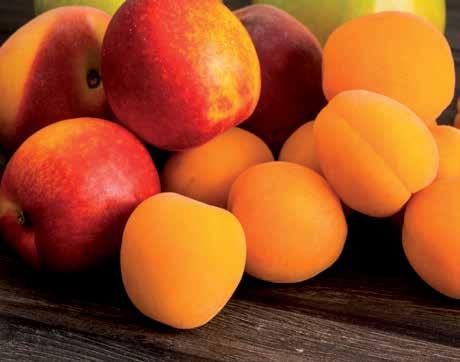
y-Decalactone is used commercially in formulations with distinctive fruit flavours such as peach and apricot.
APS Industrial strengthens commitment to Queensland with branch relocation A PS Industrial has announced that it will be relocating its Brisbane office to 49 Borthwick Avenue, Murarrie, effective from August 19, 2019.
The 1,500sqm facility provides a boost to APS Industrial’s ability to service the local Queensland market with increased local stockholdings and office space. Together, these two factors enable greater local access to its product portfolio as well as the necessary capacity to support the ongoing recruitment of technical support, product management and customer service roles.
“APS Industrial is now over 12 months old and in this time we’ve seen a significant uptake of our products and services in Queensland, which is very pleasing. To cater for this growing customer base and product demand – both now and into the future – we have invested in a new branch location,” said David Hegarty, managing director of APS Industrial.
“This significant increase in local stock-holdings paired with our new national distribution centre in Melbourne ensures we are well placed to get the products to our customers quicker than ever before and that’s incredibly important to us,” Hegarty continued.
The move follows the launch of APS Industrial on March 1, 2018 where its master distribution partnership with Siemens in Australia was announced, as well as other core national distribution agreements with Weidmüller, Rittal and EPCOS (a TDK Group Company). Since those initial launch agreements, APS Industrial has also announced national distribution agreements with KATKO and
Grace Engineered Products.
“From the outset of APS Industrial, our focus was clear – partner with the world’s leading industrial manufacturers to bring the broadest portfolio in the industry to Australia and match that with exceptional customer service,” said Hegarty. “There’s no question our Queensland team have lived up to those core promises and this new move enables us to continue and build on this moving forward,” said Ernest Van Niekerk, state manager – Queensland, APS Industrial.”
Coles agreement secures power from three solar power plants S olar power plants capable of generating sufficient electricity for 39,000 homes will be built in regional New South Wales following a landmark 10- year agreement between Coles and global renewable power generation company Metka EGN.
In the first deal of its kind to be made by a major Australian retailer, Coles will purchase more than 70 per cent of the electricity generated by three solar power plants to be built and operated by Metka EGN outside the regional centres of Wagga Wagga, Corowa and Junee – the equivalent of 10 per cent of Coles’ national electricity usage.
The photovoltaic solar plants will supply more than 220 gigawatt hours of electricity into the national electricity grid. Producing the same amount of power from non-renewable sources would result in more than 180,000 tonnes of greenhouse gas emissions every year, or the equivalent of the annual emissions of 83,000 cars.
Coles group CEO, Steven Cain, said the increased use of renewable energy was a major part of the company’s commitment to be the most sustainable supermarket in Australia.
“Coles has been a cornerstone of Australian retail for more than 100 years, and ensuring the sustainability of our business is essential to success in our second century,” he said.
“We are thrilled that with this agreement, Coles can make a significant contribution to the growth of renewable energy supply in Australia, as well as to the communities we serve.
“We have already made changes throughout our business to use energy more efficiently, which has enabled us to reduce our greenhouse gas emissions by four per cent over the past financial year and more than 30 per cent since 2009, despite growing our store network.
“Over the past two financial years alone, we have invested more than $40 million in energy-efficiency measures, including upgrading all store lighting to LED by the end of 2019 and the installation of solar panels on 30 stores.”
Coles chief property and export officer, Thinus Keeve, said Coles was the first major Australian retailer to commit to buying renewable energy through a Power Purchase Agreement.
“Agreements like this are crucial to growing renewable generation capacity in Australia because they give the developers the certainty they need to invest,” he said.
As well as supporting large-scale generation projects, Coles is working with property partners to increase on-site generation of renewable power at stores and distribution centres.
“We plan to install solar panels on another 38 stores this financial year and we will be working with our landlords and property developers to identify further locations suitable
for on-site solar power generation,” Keeve said.
The projects announced recently were developed by Australian renewable energy developer Terrain Solar, with the support of advisory firm PwC, as part of a portfolio of renewable generation plants. Metka EGN acquired the portfolio earlier this year and will build, operate and own the plants.
“Terrain Solar is incredibly proud of this landmark agreement that will underpin the construction of three new renewable energy plants in regional New South Wales,” said Terrain chairman David Griffin.
The new solar plants are expected to support more than 250 jobs in regional NSW, including over 240 during construction and 10 ongoing roles.
Construction is scheduled to begin in September and the plants are expected to commence supplying power to the grid in July 2020.
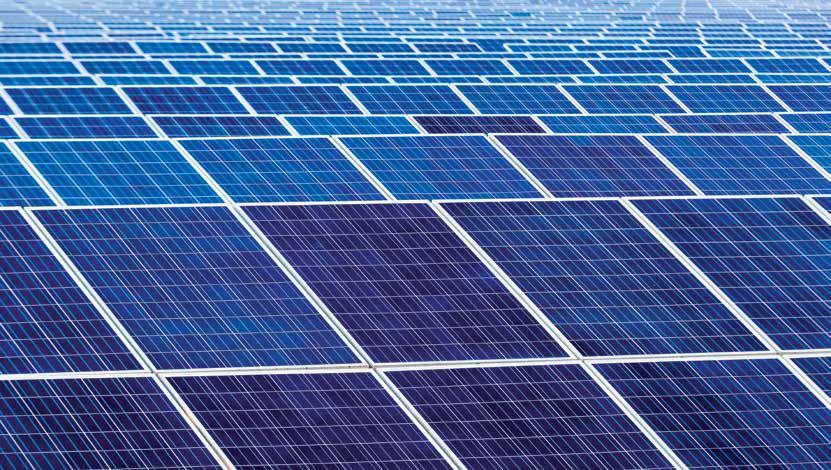