
3 minute read
COMPRESSOR TECHNOLOGY
Using oil-free compressed air in production has a host of benefits.
Australia urges the industry to look at oil-free air compression
William Chan, from Caps Australia, speaks with Food and Beverage Industry News about the benefits of oil-free compressed air and why companies should make the change now.
Caps Australia product manager for gas and special projects, William Chan, said CAPS is your complete solution provider for all types of oil-free air equipment depending on your budget. There are many ways you can achieve oil-free air, which is critical to comply with relevant standards but food and beverage manufacturers can reduce the risk of contaminating their product through lubricated compressed air by simply going oil-free at the point of compressing the air rather than treating the air through a number of processes downstream.
“The reason why so many manufacturers are using lubricated compressors is mainly the cost factor, it costs less in terms of capital investment,” said Chan.
“Second to that is the higher efficiency of the compressor, also in terms of cooling. However, the main issue is the lubricated compressors run the risk of leaking lubricant into the compressed air stream which in turn contaminates the process downstream.”
Chan said contamination was something industries, especially food and beverage, can’t afford to endure because of the potential ramifications on a product designed to be consumed.
However, there are solutions available.
“One of the ways is using a true oil-free compressor, the longterm benefits associated with less ancillary equipment and servicing combined with the significant reduction of risk, could be a smart
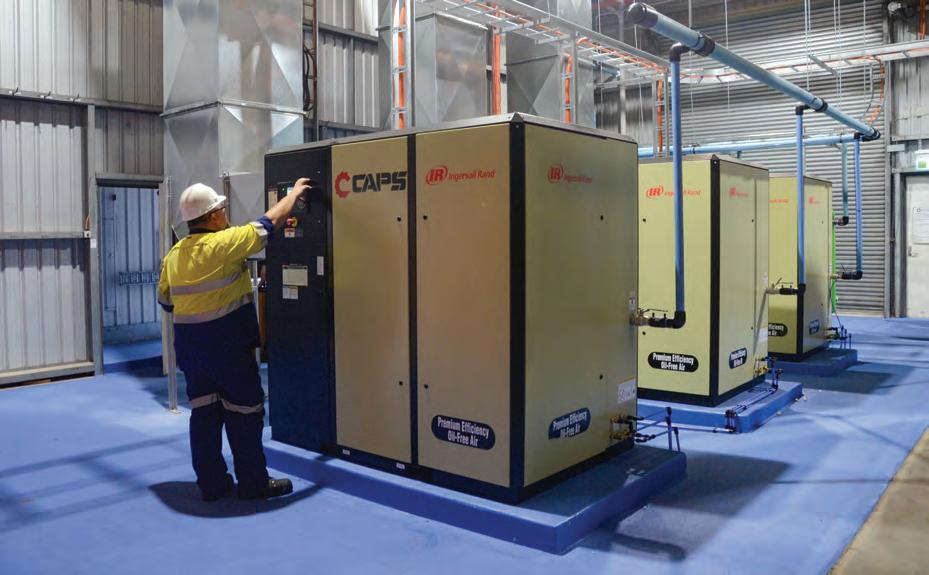
investment” said Chan.
When a lubricated compressor is used in the manufacturing process a range of requirements must be met to make sure the lubricant doesn’t contaminate the food, which requires a several machine pieces.
“A compressor is only one part of the whole jigsaw puzzle so after the compressor you need to include filtration and drying of compressed air to achieve the quality required,” said Chan.
“For example, if the compressed air will be in direct contact of the food product, then you must have dry and clean compressed air. That means the moisture level in the compressed air must be minus 40 degrees dew point.
Caps Australia is well equipped to achieve this. “Clients don’t just require a compressor, they need a whole train of equipment to produce oil free air and every piece of equipment will contribute to efficiency,” he said.
Another selling point from Caps Australia is the ability to develop a tailored approach for each client’s individual needs.
“We want to offer the industry options to exceed the industry standards and requirements, so they are better prepared for future growth,” said Chan,
“That is why we customise, through specialist in house engineering. All the installations for our clients to make sure we provide the equipment to not only meet their needs but exceed them.”
With a push towards mitigating contamination risks Caps Australia is well positioned to help any food and beverage manufacturer to achieve that goal. F
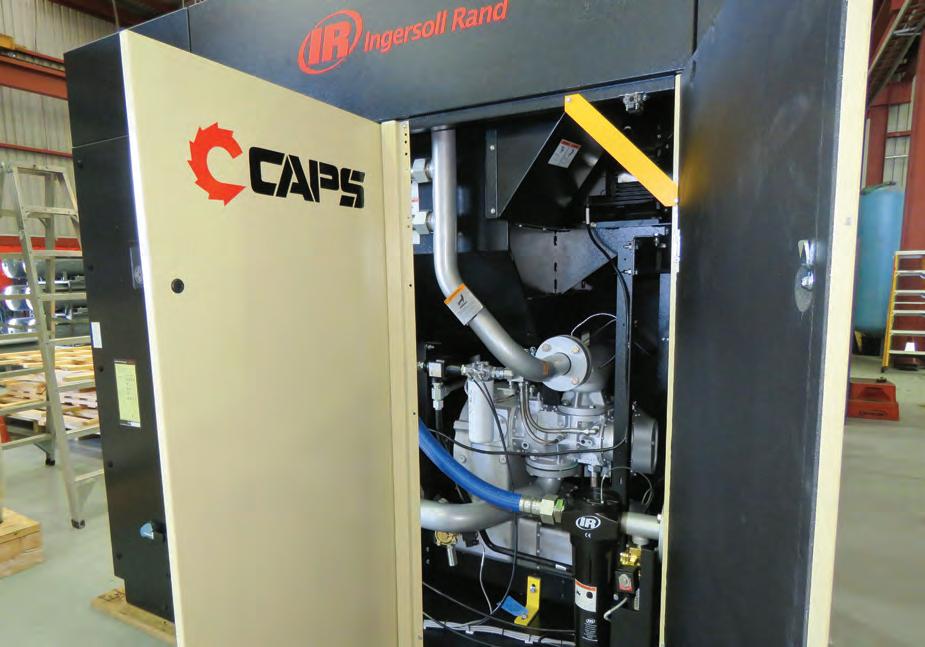
Dry compressed air is critical to keeping moisture levels low.
The intelligent choice for compact automation
The family of Siemens SIMATIC S7-1200 controllers are the ideal choice when it comes to flexibly & efficiently performing automation tasks in the lower to medium performance range.
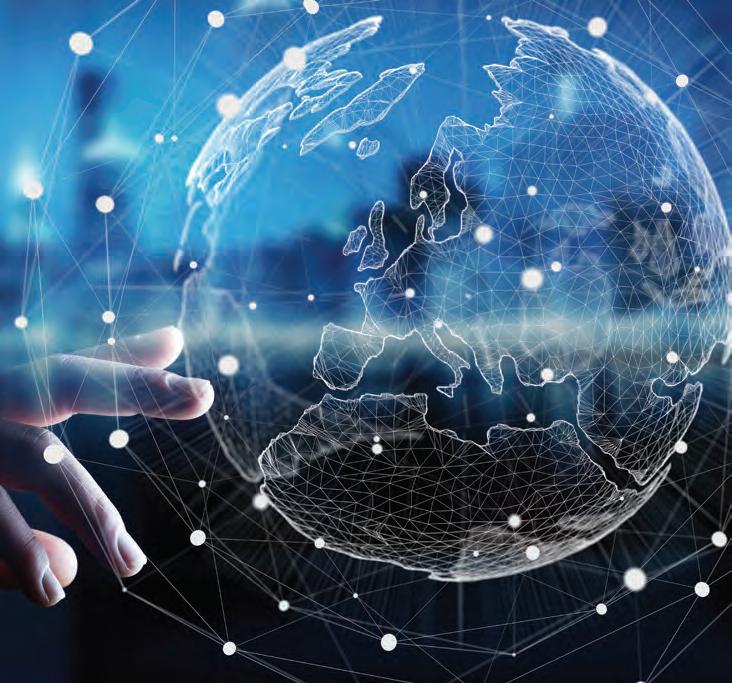
Scan the QR code for more exclusive content!
Efficient Engineering Innovative Design Technology Integrated Security Integrated

NATIONAL DISTRIBUTORS OF