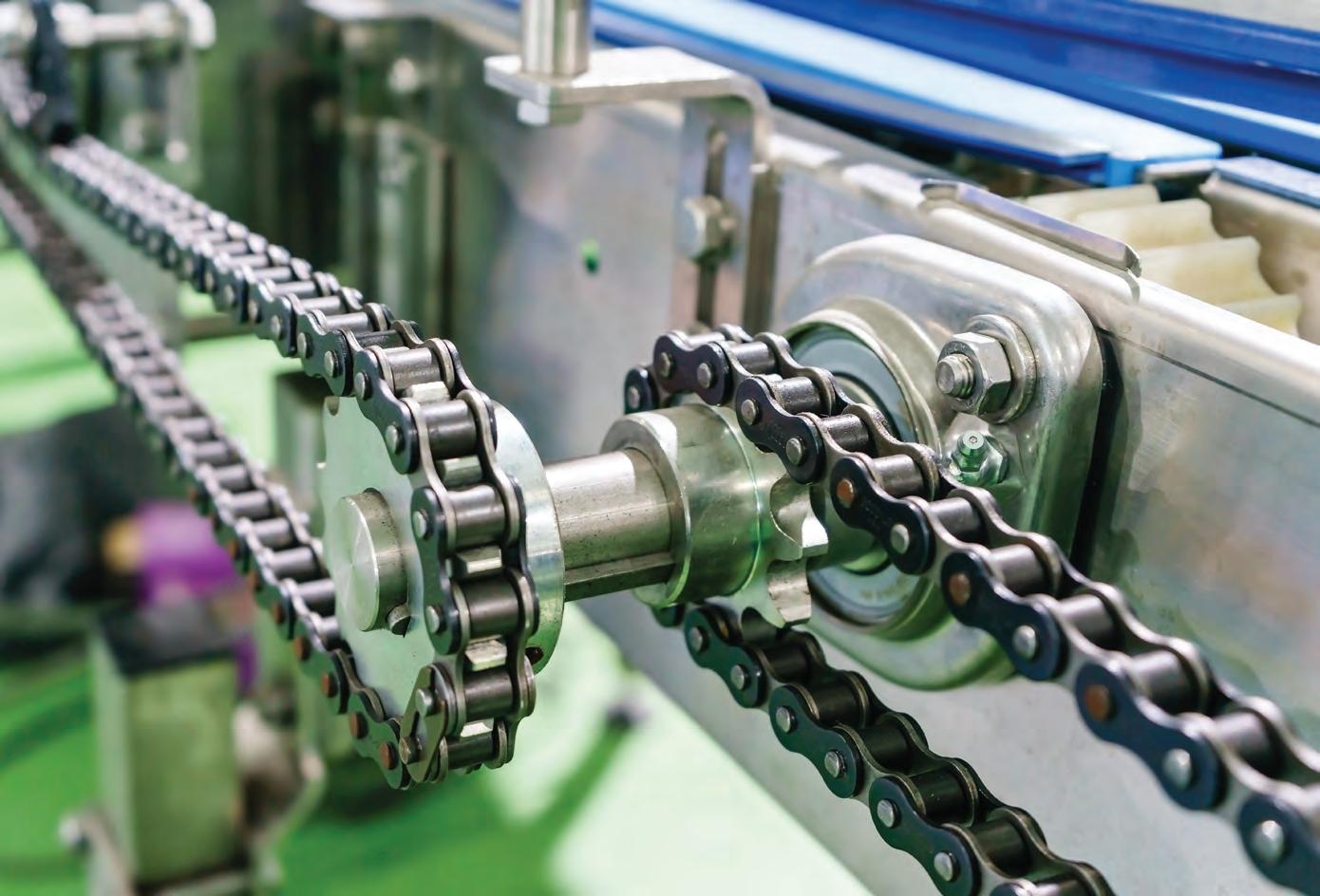
4 minute read
LUBRICATION
Improving chain lubrication in the food and beverage industry
Supplied by JSG Industrial Systems, the SKF Lincoln ORSCO Series 170 is a lubrication system that is increasing machine maintenance efficiency. Food and Beverage Industry News reports.
Roller chains are used across the food and beverage sector but are critical in meat production.
The beef industry is a pillar within Australia’s economy and the equipment used to produce the meat is no less important than the final product. Roller chains are a key component of this industry, functioning in many abattoirs across Australia and New Zealand.
To be able to function to the best of its ability, these chains need to be consistently maintained; the pins, bushings, sliding surfaces and any rolling element that are exposed to consistent wear, need to be regularly lubricated to continue functioning with high volumes, at an efficient rate.
This is where the SKF Lincoln ORSCO series 170 lubrication systems come in; with particular success being found in roller chains used in abattoirs across Australasia, the demand for this product is forecasted to increase.
The system was created by SKF Lincoln, whose distribution rights are held by JSG Industrial Systems in Australia, Indonesia, New Zealand, and Southeast Asia. SKF assists equipment manufacturers and production facilities worldwide with an aim to improve equipment, such as roller chains, reliability and total cost of ownership and energy.
How it works
What differentiates the SKF Lincoln ORSCO series 170 system from others is the use of air to propel the lubricant at a low pressure yet high-velocity rate. This increases the system’s accuracy - despite the small amount released, it penetrates to a

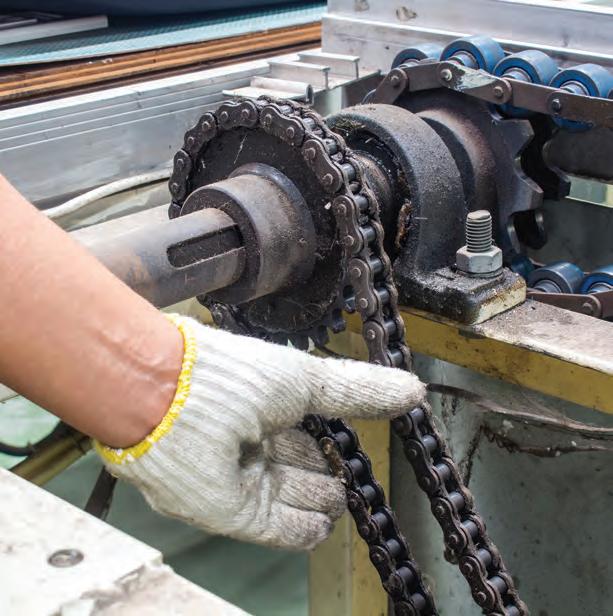
The SKF Lincoln ORSCO series 170 lubrication systems are ideal for keeping roller chains performing at a high standard.
high degree.
Through using this compressed air to deliver the lubricant, the roller chains are greased faster than previous method’s such as the drip and brush techniques. The system works through producing a continuous thin stream of lubricant onto the chain, specifically the pin and bushing, which is the primary wear point of a chain.
It is able to do so with pinpoint accuracy due to the use of air. This allows the lubricant to move between these two points while also coating the roller and bushing surface as well. This amount of lubricant is released on a continuous and controlled basis that helps coat every chain link.
Once the stream of lubrication is co-ordinated with the specific chain requirements, the application will be equal with the rate of consumption. Factors such as the chain length, speed and consistent temperature will affect how the system will be set up.
According to SKF Lincoln Industrial, application of lubrication through the ORSCO system reduces the consumption rate of lubrication by 60 to 80 per cent.
The lubricant not only greases and moisturises the primary wear points, but also provides a cleaning effect through the spray nozzle. This nozzle is also patented by SKF and works to remove contaminants and debris left over from production. Looking at the nozzle specifications, SKF provides three tip lengths and spray patterns that can change the lubrication stream from continuous to pulses. The benefit of this is the ability to custom design the nozzles bespoke to the application or machinery.
Benefits
Utilising ORSCO is important in increasing the overall life of the chain. Through consistent lubrication, overall downtime including the frequency of general maintenance is reduced. This means, in abattoirs, more meat can be produced and exported.
The 170 series also reduces machinery oil consumption producing cleaner conditions.
SKF Lincoln previously installed an ORSCO Model 170 series for a large soft drink bottler. This company found that there was a decrease in oil usage and spillage on the factory floor and within six months the company reported that it was able to pay back its initial investments.
Design
The ORSCO series 170 comes as an easy-to-install system that is made up of combining controls, valves stack and a reservoir. The series is also available as a modular packaging including a Valve Stack series (VS) or a Valve Stack-Reservoir (VSR) series. At maximum capacity, the Series 170 system can lubricate up to 16 points with an ability to vary the lubrications patterns.
It features a compact, modular design with low amounts of external piping designed for OEM use; in addition to these benefits, specific parts can be removed and serviced if needed. The fixed volume system increases control of the amount of lubricant released, decreasing oil waste and overhead costs. The injector rate functions at 1 Hz meaning that it can also be applied to systems that require large amounts of consistent lubricant. On larger doses, the system can deliver up to four drops per second.
In addition to the ORSCO series 170 system recent success in abattoirs, it is also used effectively across a range of industries including beverages, food processing and baking, as well as materials handling. F
Increasing machine maintenance and efficiency creates better end results.
New brands
Designed by ennioEARTH Condensed Natural Smoke & Compostable Netting