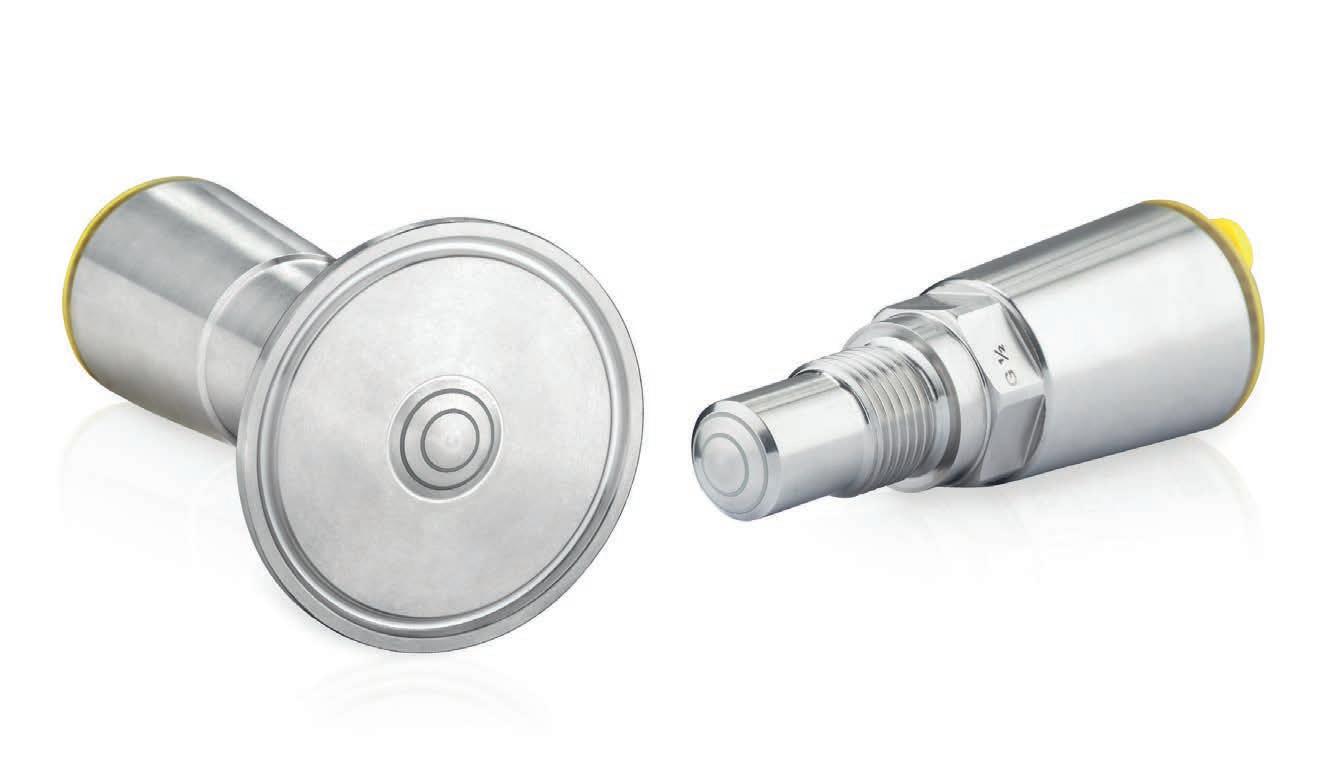
4 minute read
LUBRICATION
VEGAPOINT 24 level switches have been taken up by the industry at a rapid rate.
Easy installation, maximum efficiency
VEGAPOINT 24 level switches solve the problem of detecting sticky and viscous substances. Food and Beverage Industry News reports.
Many food and pharmaceutical products have a distinctive texture: “melt-in-your-mouth” like some processed cheeses, grainy like peeling cream or also tough, sticky, crunchy and soft. Depending on the consistency, the demands on the level measurement technology used in production increase.
After the successful launch of the VEGAPOINT range of level switches in 2020 the uptake by the industry was beyond VEGA’s original expectations but based on feedback there were still applications that required a different design and function. VEGA took this onboard and in consultation with the industry set about developing the new front-flush level switch VEGAPOINT 24 especially for use with sticky, viscous or abrasive products.
Even with the strongest buildup, it reliably detects the product level in the application and indicates it with a user-programmable, coloured illuminated ring that is highly visible. Combine this with the two transistor outputs that are independently selectable for different functions, and I/O Link industry-standard communication, and the result is a product that is designed and built to suit the applications within the industry
Runs perfectly when it lights up
Thanks to its robustness, VEGAPOINT 24 is a plug-and-play sensor. It can be installed easily in a few simple steps. Flexible production systems with frequent and fast product changes benefit from the fact that it detects all media with the help of the default setting without adjustment. And extended functions, such as interface detection or foam blanking, can be configured easily with the interface of BLUETOOTH access and a userfriendly menu.
Only metal in the tank
“This device is specifically designed and manufactured for the beverage, food and pharmaceutical sectors. Here, mixing and conveying are all about efficiency and safety, even with demanding liquids and bulk solids like molasses or nut-nougat cream,” said Volker Allgaier, product manager at VEGA.
The front-flush design of VEGAPOINT 24 ensures universal application possibilities and no interference with agitators or mixing mechanisms.
“Even cleaning procedures will work safely and efficiently alongside the flat measuring tip,” Allgaier said. “And the measuring face of the sensor also copes with sandblasting. This is because there is only metal in the tank.”
Compared to plastic, he concludes, extensive tests have shown an extended service life by a factor of four.
Fits like a glove
Users achieve visibility of their processes with the new VEGAPOINT 24. The relationship between durability and low life cycle costs is groundbreaking. The decisive factor, however, is flexibility of use: with its versatile process fittings and adaptors, the level switch fits like a glove - even in already existing systems.
Benefits
The VEGAPOINT 24 has a long list of features from its use, including a flush process connection. This can be used with mechanical flushing and cleaning systems, and it casts no spray shadow.
Other benefits include bypassing build up with factory settings because no customer setup is required. It works on low dielectric liquid processes with factory settings, and it has individually settable outputs.
The VEGAPOINT 24 can also detect different liquids in a process. For example, it can tell the differences between food product and cleaning liquids, which in turn mitigates contamination risks.
The sensor is also resistant to abrasion, has hygienic process connections available along with various process connections and all of this within a compact form.
All those features come with the low-cost VEGAPOINT 24 Level switch.
Unique selling points
The complete flush process connection is one of the many unique selling points for the VEGAPOINT 24.
As a result, it can be used with pigging systems while casting no spray shadow. The ease of use for the VEGAPOINT 24, which ignores build up with factory settings and requires no customer setup, helps the piece work on low dielectric liquid processes with factory settings. A critical component for the food and beverage industry is the VEGAPOINT 24’s ability to detect different liquids during a process. For example, differences between food products and cleaning liquids.
All surfaces of the VEGAPOINT sensors that come into contact with the medium are made of PEEK and stainless steel and have optimal roughness values.
All materials are also approved and tested according to Food and Drug Administration (FDA) and EG 1935/2004. This has been confirmed by independent laboratories and institutes. The design of the devices is certified according to the European EHEDG Directive and the North American 3-A SanitaryStandards Inc. VEGA sensors also ensure that all required media are available with sufficient reserve in every process step and reliably withstand the complex CIP and SIP processes.
The selling points of VEGA’s sensors make them a quality choice for the food and beverage industry, solving historical issues with the manufacturing process while also being flexible, suited to adaptation with quick interchange. F
One of the available hygienic adaptor accessories for the VEGAPOINT 24.
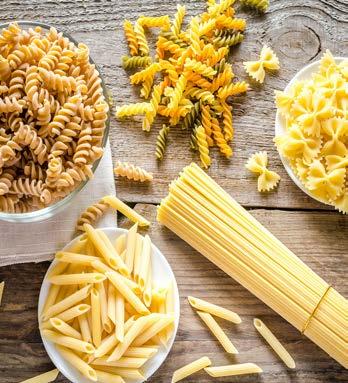
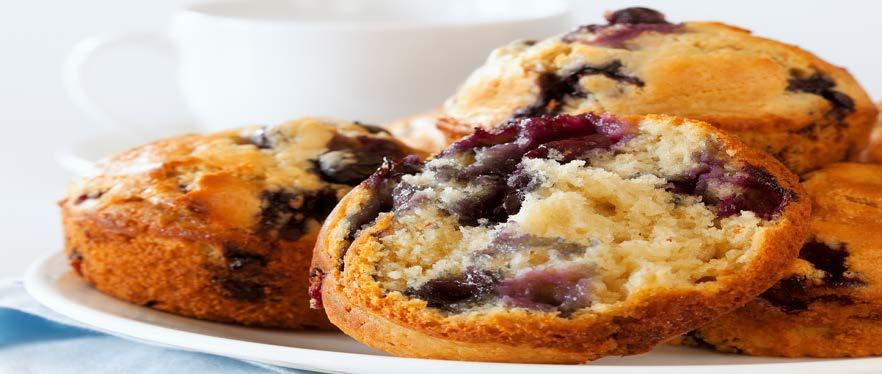
The accurate detection of egg protein in heat processed foods, such as bakery products or pasta has previously been challenging.
To overcome these issues ELISA Systems has developed a new Processed Egg Residue Detection Kit that incorporates a novel, straight-forward sample extraction to allow high efficiency detection of egg protein in both heat processed and non-processed foods.
Our new innovative Processed Egg Residue Detection kit is now in stock and is ready to go!