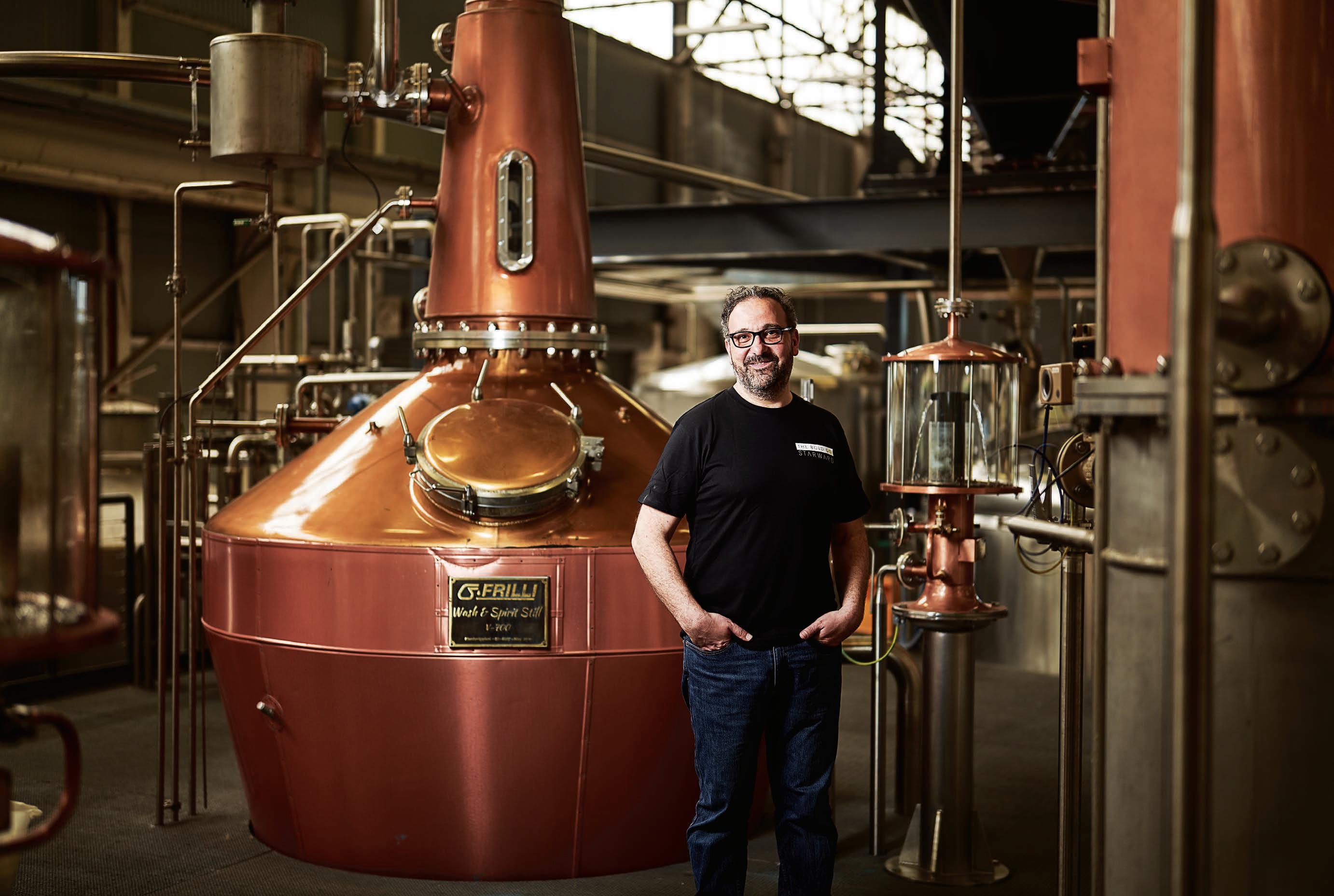
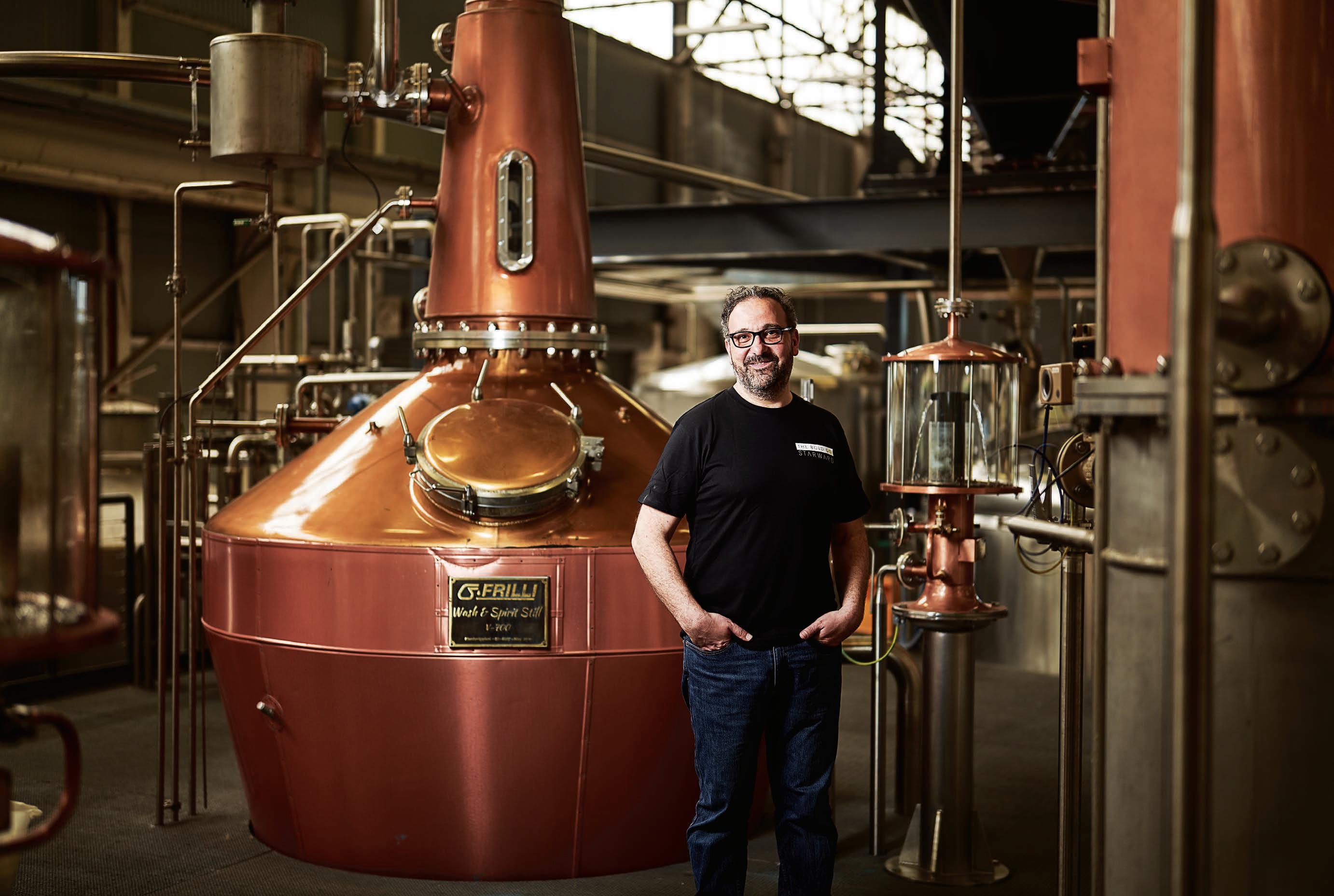
RECOGNITION Global for Australian WHISKY
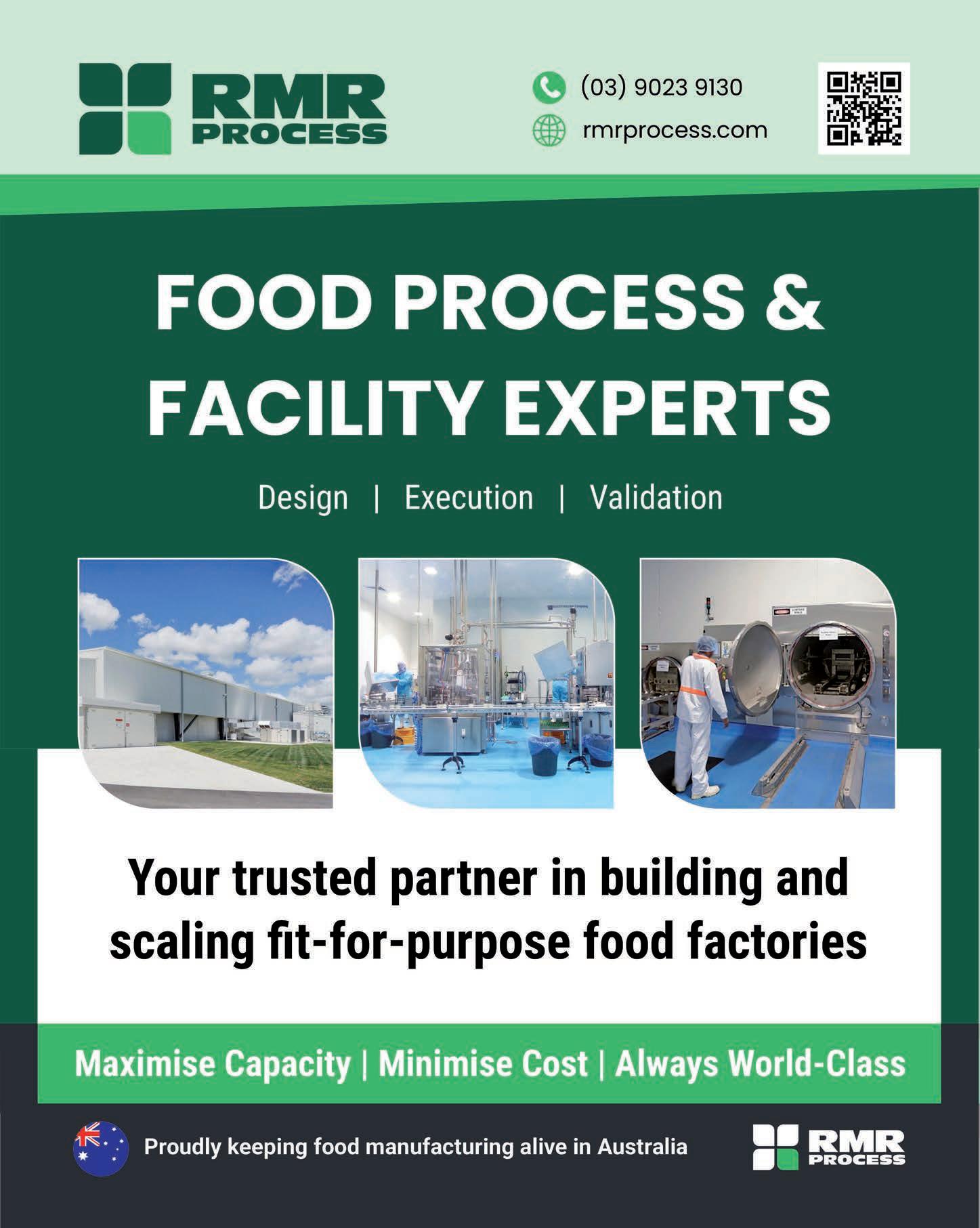
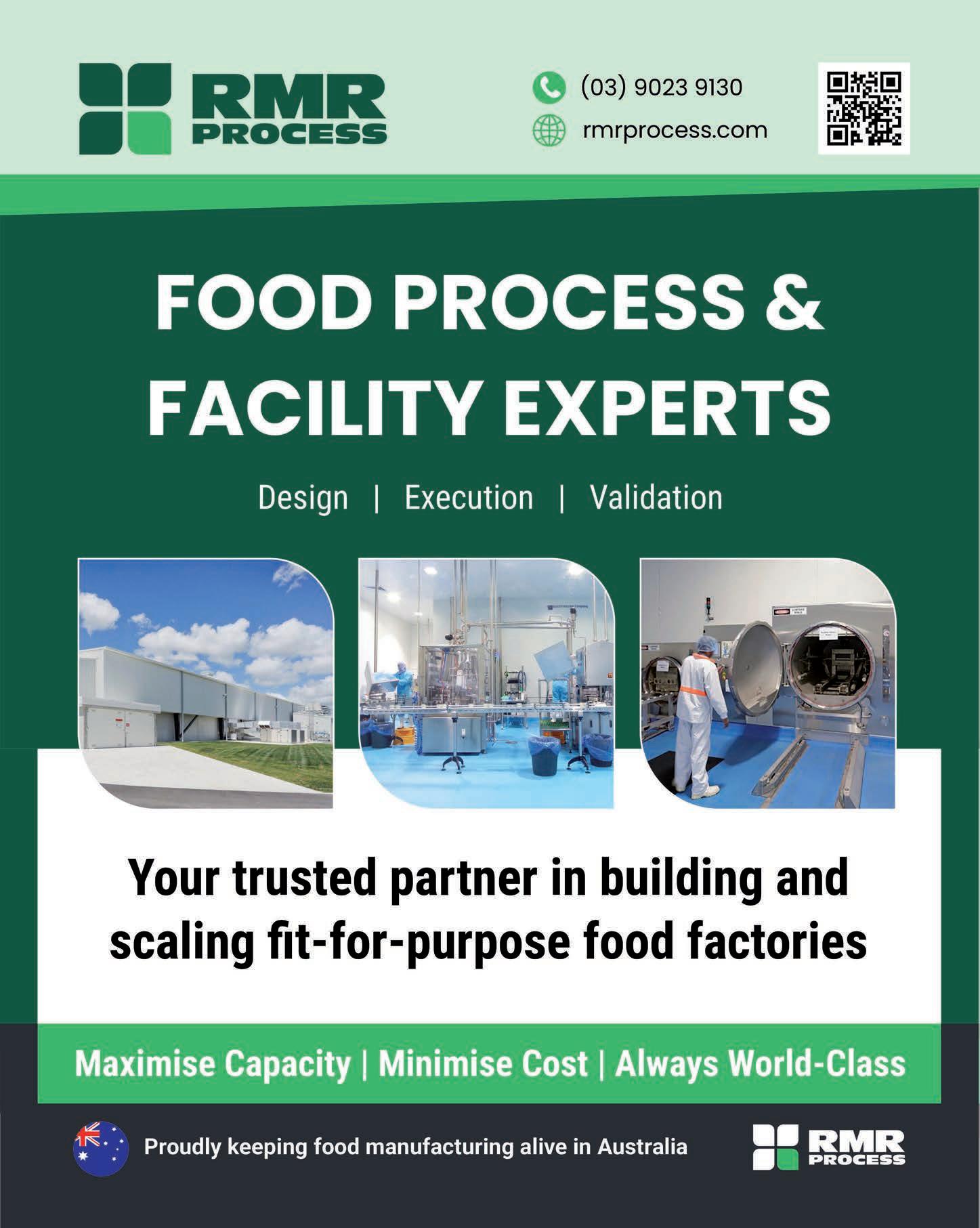
CEO: John Murphy
COO: Christine Clancy
Managing Editor: Mike Wheeler
Editor: Adam McCleery
Ph: (03) 9690 8766
adam.mccleery@primecreative.com.au
Art Director: Michelle Weston
michelle.weston@primecreative.com.au
Sales/Advertising: Joanne Davies
Ph: 0434 785 611
joanne.davies@primecreative.com.au
Production Coordinator:
Salma Kennedy
Ph: (03) 9690 8766
salma.kennedy@primecreative.com.au
Subscriptions AUS NZ O/S
1 year subscription 99 109 119
2 year subscription 189 199 209
For subscriptions enquiries please email subscriptions@primecreative.com.au
Copyright Food & Beverage Industry News is owned by Prime Creative Media and
Importance of software management

Fpublished by John Murphy. All material in Food & Beverage Industry News is copyright and no part may be reproduced or copied in any form or by any means (graphic, electronic or mechanical including information and retrieval systems) without written permission of the publisher. The Editor welcomes contributions but reserves the right to accept or reject any material. While every effort has been made to ensure the accuracy of information, Prime Creative Media will not accept responsibility for errors or omissions or for any consequences arising from reliance on information published.
The opinions expressed in Food & Beverage Industry News are not necessarily the opinions of, or endorsed by the publisher unless otherwise stated.
© Copyright Prime Creative Media, 2023
Articles
All articles submitted for publication become the property of the publisher. The Editor reserves the right to adjust any article to conform with the magazine format.
Cover Image: APS
Head Office
379 Docklands Drive
Docklands VIC 3008
Ph: +61 3 9690 8766
enquiries@primecreative.com.au
http://www.primecreative.com.au
Sydney Office
Suite 11.01,
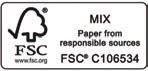
Editor: Adam McCleery
ood and beverage manufacturing stakeholders and decisionmakers are currently navigating critical changes driven by rising consumer expectations and a heightened focus on sustainability.
As the global population increases and environmental concerns become more pressing, the industry is turning to software innovation to adapt and meet these evolving demands.
Software technology has forever altered operations within the food and beverage sector.
Modern solutions such as Manufacturing Execution Systems (MES) and Enterprise Resource Planning (ERP) platforms have introduced real-time data analysis and automation, leading to improved production efficiency, reduced waste, and optimised supply chains.
These advancements help companies enhance productivity, minimise downtime, and lower maintenance costs, enabling quicker responses to market changes.
Predictive analytics, particularly those leveraging artificial intelligence (AI), are now used to anticipate equipment failures, thereby reducing production interruptions.
Additionally, software tools for process optimisation help ensure consistent product quality by refining ingredient blending and processing techniques.
In terms of food safety and regulatory compliance, software innovation plays a critical role. Advanced systems enable detailed tracking of ingredients throughout the supply chain, helping manufacturers quickly address potential contamination issues and maintain product safety.
Automated compliance systems also assist in adhering to complex regulations by generating necessary documentation and facilitating audits, thereby mitigating the risk of penalties, and saving time.
As a result, advanced automation is becoming increasingly prevalent, with robotics playing a central role in streamlining production processes. Automated systems are enhancing efficiency in packaging, sorting, and quality control, while reducing labour costs and minimising errors.
Sustainability has become a key concern in the industry, which faces pressure to reduce its environmental impact.
Software solutions are instrumental in this area by optimising energy use, reducing water consumption, and minimising waste.
Data analytics identify energy inefficiencies and support the formulation of recipes that reduce waste and utilise by-products effectively, contributing to environmental preservation and providing a competitive advantage in a sustainability-focused market.
Furthermore, as consumer preferences shift towards personalised experiences, software innovations enable manufacturers to better understand and cater to these preferences.
Data analytics and AI insights allow for product customisation and enhanced consumer engagement through digital channels, which can improve brand loyalty and customer satisfaction.
The integration of software innovation in food and beverage manufacturing is crucial for achieving operational efficiency, ensuring safety, driving sustainability, and enhancing consumer engagement.
As the industry continues to evolve, embracing these technological advancements will be essential for addressing current challenges and unlocking future growth opportunities.
By leveraging advanced software solutions, manufacturers can optimise their operations, respond to market demands, and achieve long-term success in a competitive industry.
Until next month, happy reading.
Digitize production, elevate efficiency
Evocon automates and digitises data collection from machines using sensors, PLC-s and HTTPS requests and visualises the data in an intuitive way. Evocon combines plug and play hardware and a user friendly browser-based interface
Evocon will help you achieve OEE optimization. It will help you increase equipment effectiveness, and you’ll gain real time insight on product quality, and plant and line performance. You’ll have real-time intuitive insight into production performance
Machine operators, QA , Maintenance, Operations & Production & Supply chain Managers all benefit from using Evocon. Evocon empowers everyone with information including automated reports, dashboards and checklists
CONTACT
Dan Southern CitySoft Consulting Evocon Product Champion 0480 440 989
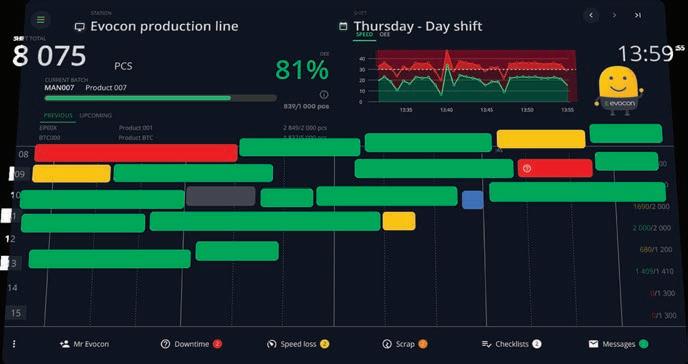
Free Evocon trial for the first ten companies to register. Register now at citysoft.net.au/freetrial
Run Smart Run Simple
CitySoft deliver food and beverage manufacturers with market-leading business solutions with an exceptional ROI.
CitySoft supply smart business solutions. We implement globally recognised products which simplify doing business. We connect equipment and software systems and use the data to create competitive advantage for our clients. Importantly, we understand the food & beverage manufacturing industry from both a business and technology basis and provide the insight and expertise to help companies run smart and run simple.
CONTACT CITYSOFT
To discover how we can help your food and beverage manufacturing business capitalize on new and existing technologies.
sale@citysoft.net.au1300 762 762
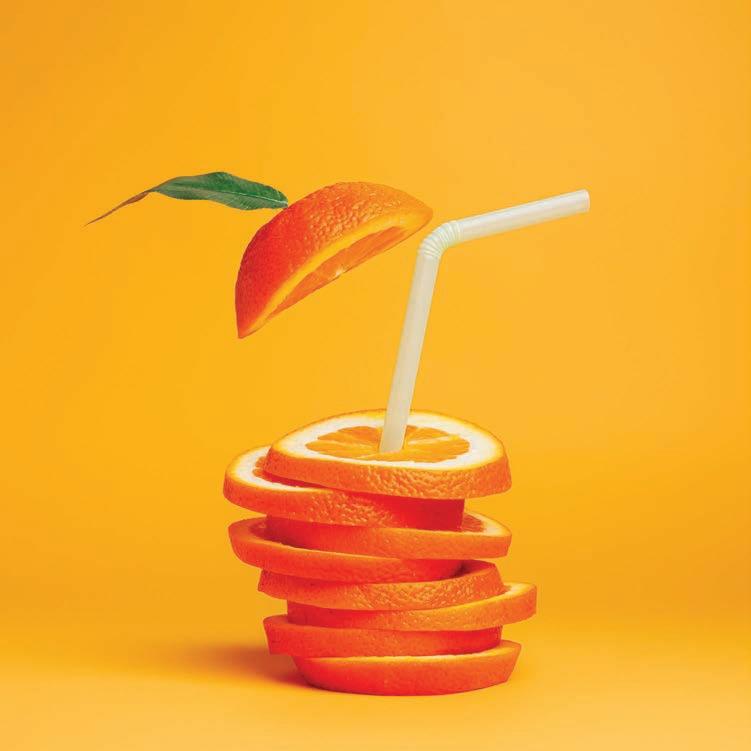
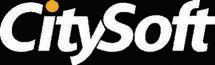
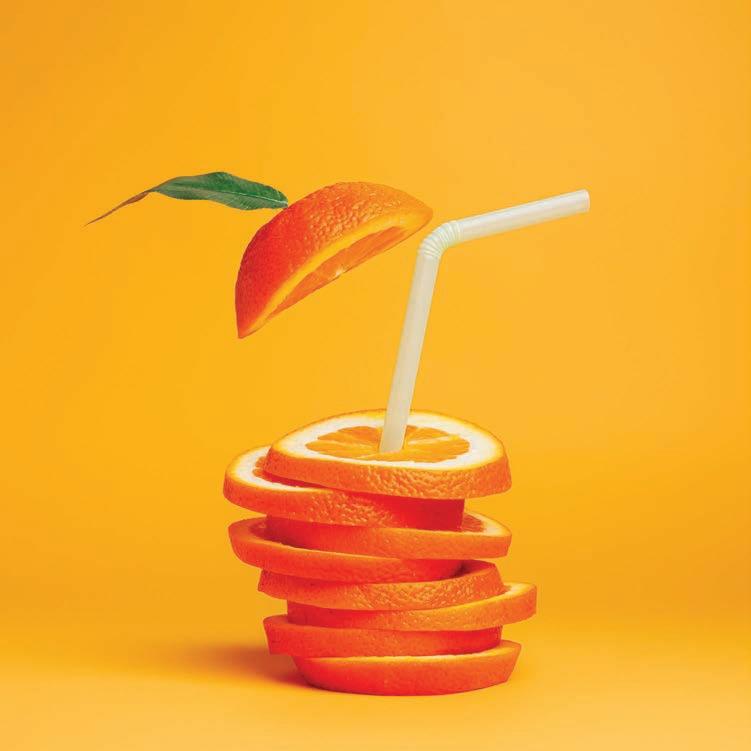
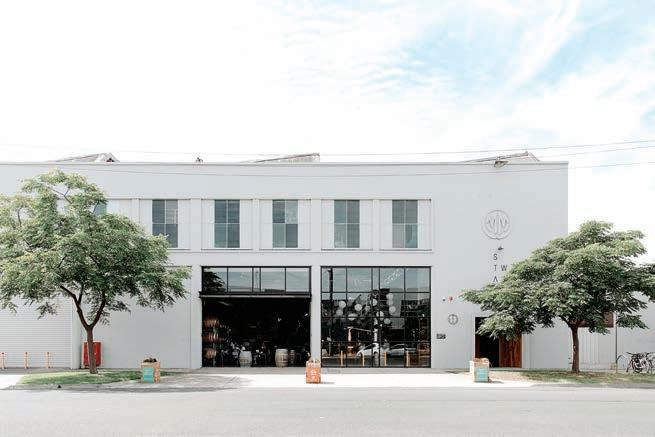

16 MEET THE MANUFACTURER
Founder of Starward Whisky, David Vitale, talks about the origins and ambitions of the acclaimed Australian distillery.
20 FEATURE INTRO
The food and beverage industry benefits greatly from the advancement and adoption of advanced software solutions
22 SOFTWARE SOLUTIONS
CitySoft are helping manufacturers make the most of real time production data.
24 SOFTWARE SOLUTIONS
Centric Software provides solutions to complement private label products
26 CONSULTATION
The team at RMR Process helps clients increase output and develop more efficient processes through expert consultation.
28 SUSTAINABLE PACKAGING
Bunzl provides various types of sustainable packaging solutions that have been developed on the back of key research.
30 INDUSTRIAL HOSES
Continental’s expertise in rubber continues to give rise to innovative industrial hose solutions.
32 PACKAGING STRATEGY
Details of APCO’s new 2030 Strategic Plan.
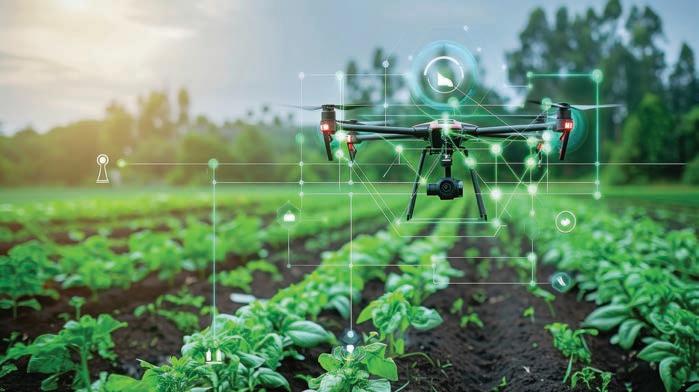
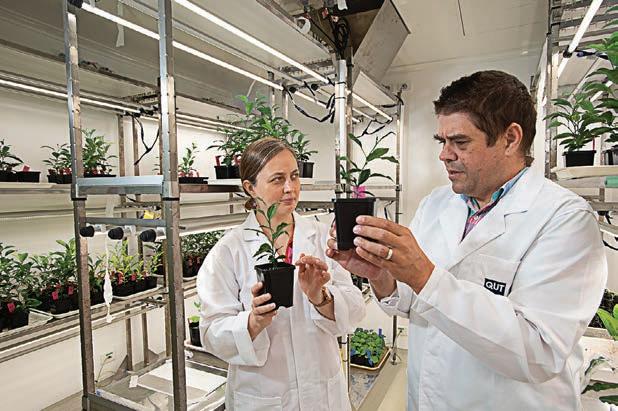
34 INFRASTRUCTURE
Stakeholders calling for a renewed focus on better infrastructure.
36 ARTIFICIAL INTELLIGENCE
Those willing to adopt AI could capitalise on its benefits.
38 GOVERNMENT
The Federal Government’s Future Made in Australia agenda has been designed to strengthen the country’s manufacturing sector.
40 FOOD SCIENCE
A collaboration between several universities is aiming to accelerate the development of new produce ranges.
42 FOOD SCIENCE
A team of researchers have introduced a new continuous manufacturing process for cultivated meat.
44 REGIONAL MANUFACTURING
The role of Australia’s regions when it comes to supporting food and beverage manufacturing can’t be understated
46 AIP
The winners of the 2024 annual Scholarship program.
48 DAIRY OUTLOOK
A look at the dairy market’s performance so far in 2024 and an outlook towards the future.
50 NEW PRODUCTS
Fonterra to expand NZ site
Fonterra is set to expand its Studholme site in the South Island to create a hub for high value proteins.
functionality and are designed to perform well in premium product applications such as medical and high-
protein sports nutrition.
Fonterra CEO Miles Hurrell said the investment of around $75 million is part of the Co-op’s strategy to
“We have valuable expertise in dairy science and innovation, making us leaders in the manufacture of dairy proteins and other advanced
ultimately grow returns to farmers.”
Fonterra president Global Markets Ingredients, Richard Allen, says the Co-op’s dairy ingredients are highly sought after by customers globally.
site will allow us to increase production
Site works at Studholme began in September with the first product due to come off the line in 2026.
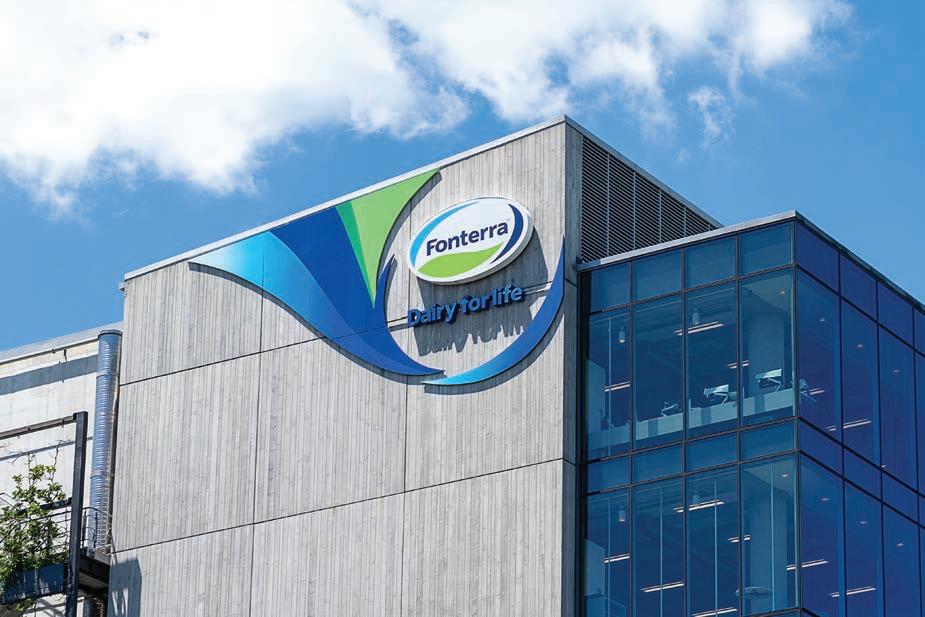
Woolworths to stop sourcing beef linked to deforestation
The Australian Conservation Foundation (ACF) has welcomed Woolworths’ announcement that it will stop selling beef linked to deforestation, in accordance with the Science-based Targets Initiative.
“No one sells more beef to Australians than Woolworths, so this commitment has enormous implications for nature and for people who want to make sustainable food choices,” said ACF’s nature and business lead Nathaniel Pelle.
“Australia is an international deforestation hotspot, but that problem is being driven by a small number of operators.
“While most graziers are not engaged in broadscale bulldozing of bushland, Australians can’t choose deforestationfree beef because supermarkets don’t differentiate.”
Pelle said the commitment–which follows in a similar path to Aldi–will change this reality.
“Australian consumers will soon be able to buy beef knowing they are supporting farmers who protect forests and woodland on their properties,” said Pelle.
“Koalas need mature trees to live in.
Threatened species like red-tailed black cockatoos need tree hollows to nest in –these only form in trees that are decades old.
“Not acting to end deforestation could have consequences for farmers, shareholders, nature and ultimately our food security.”
ACF, Greenpeace and the Wilderness Society published guidance this year that outlines what is required for Australian corporate deforestation commitments to align with global frameworks.
The Science-based Targets Initiative (SBTi), one of the world’s most influential corporate targetsetting standards, requires all food and agriculture companies to commit to zero deforestation by 2025 to retain a valid SBTi net zero target. F
“We see significant opportunities in the global high protein dairy category, which is projected to grow by close to USD$10 billion over the next four years, at an annualised growth rate of 7 per cent per annum,” said Allen.
“Increasing our manufacturing capacity for functional proteins will enable us to continue to strengthen our offerings with existing customers as well as attract new business.”
Site works at Studholme began in September with the first product due to come off the line in 2026.
In addition to producing advanced proteins, the site will continue to support the South Island’s milk processing as it has done since Fonterra acquired the site in 2012. F
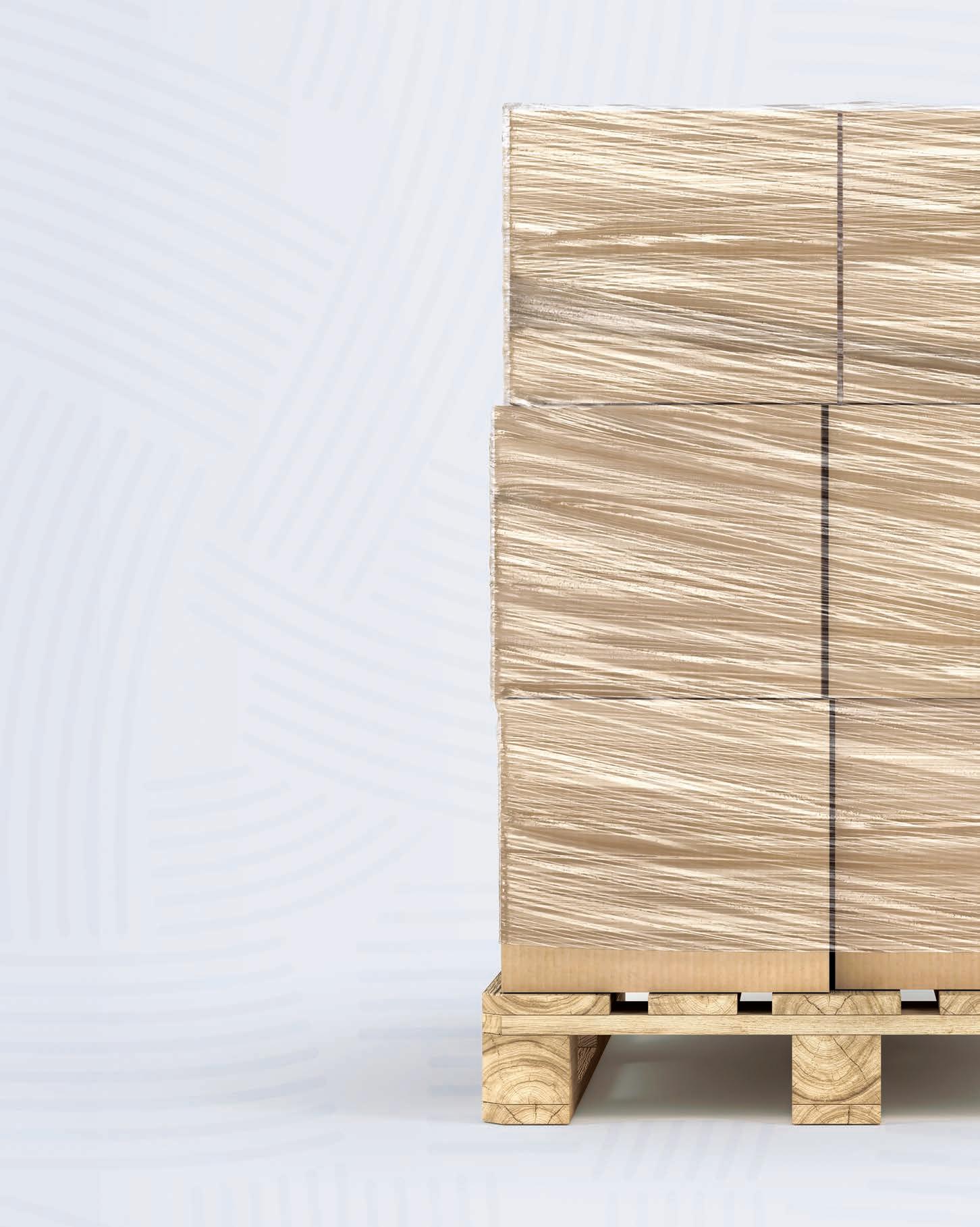
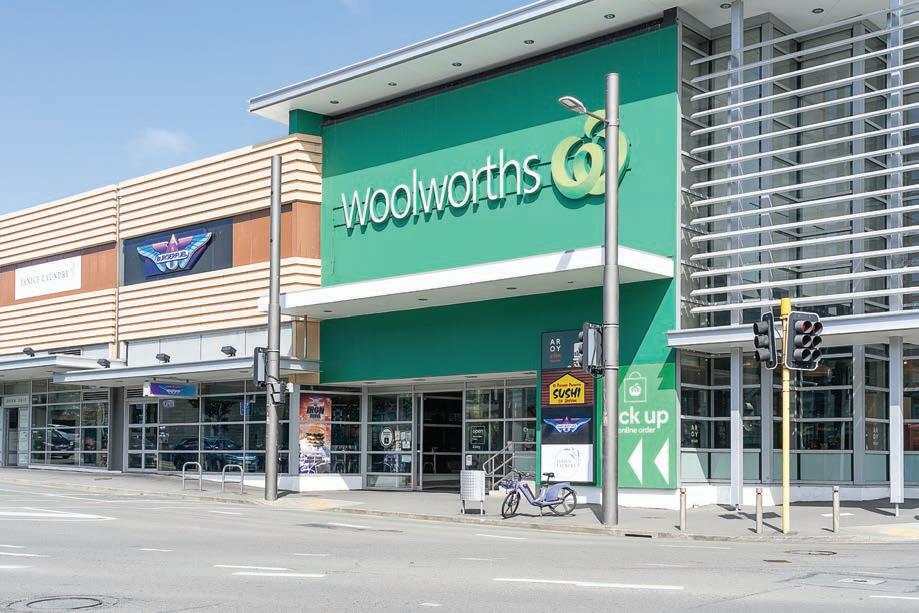
The SBTi is one of the world’s most influential corporate target-setting standards.
Our increased stretch capabilities ensure a reduction in plastic, while maintaining consistent performance.
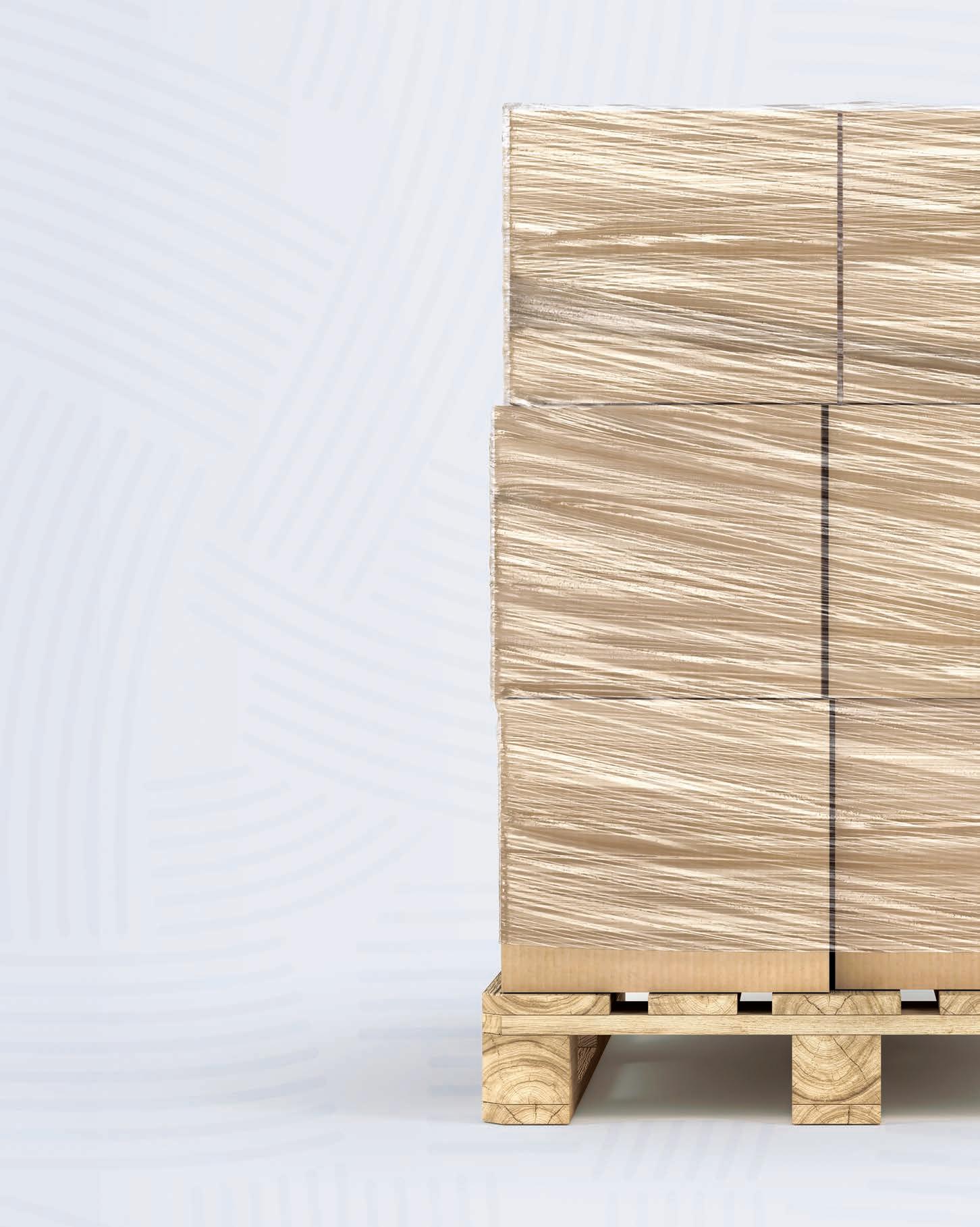
Shop our puncture resistant pallet wrap today.
www.bunzl.com.au
$15.6 million funding to re-manufacturer soft plastics
Thanks to a $15.6 million investment in advanced recycling and remanufacturing technology by the Federal Government, more than 43,000 tonnes of soft plastics are set to be recycled or remanufactured.
Three projects that were delivered in partnership with the Victorian Government have been announced under the new Recycling Modernisation Fund Plastics Technology stream.
The Recycling Modernisation Fund is a national initiative expanding Australia’s capacity to sort, process and remanufacture glass, plastic, tyres, paper and cardboard.
Naula Pty in Altona received more than $5 million for advanced sorting and processing of up to 32,000 tonnes of soft and mixed plastics products each year, to refine them to produce new plastics such as food-grade packaging.
This will help Australia to develop an advanced recycling supply chain that will turn post-consumer soft plastic waste back into food and other packaging. The project will deliver is set to deliver 61 direct jobs.
“We will fill the gap in the plastics recycling supply chain and circular economy for these plastics in Australia,” said Naula CEO and Founder, Nassib Thoumi.
“We are incredibly proud to receive this grant, it is truly a milestone in Australia’s recycling maturity.”
The first project under the $60 million Recycling Modernisation Fund Plastics Technology stream was announced in July – a $20 million investment in a recycling facility in Kilburn.
When combined with co-investment from all states and industry, the Fund has the potential to give a $1 billion
The government funding has the potential to give a $1 billion boost to Australian recycling.
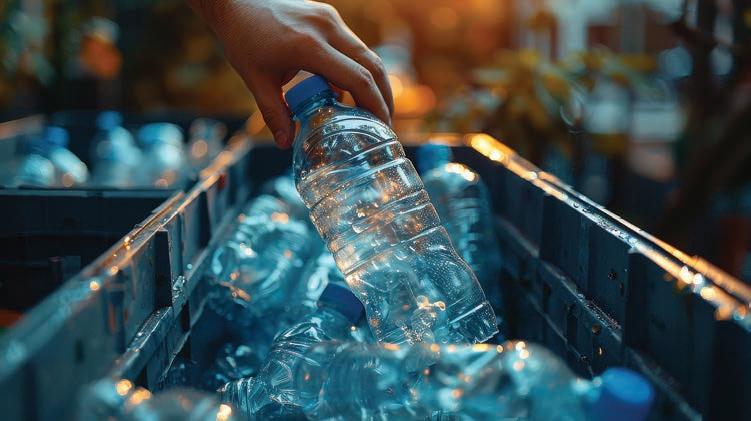
boost to Australian recycling. Nationally, the Federal Government is increasing recycling capacity in Australia by more than a million tonnes every year while creating over 3,000
jobs, including over 525 in Victoria.
The Australian Government is also supporting soft plastics recycling by improving packaging design through new national packaging laws. F
Vinehealth Australia appoint new CEO
The Board of Vinehealth Australia has announced the appointment of Dr Samantha Scarratt as CEO.
The appointment follows a national recruitment campaign to find a strong leader for the company.
Vinehealth Australia is an independent statutory authority in South Australia with a single-minded focus on grape and wine biosecurity, primarily keeping phylloxera out of the state.
Scarratt is an experienced leader and most recently was a senior consultant for Wine Network Consulting, specialising in viticulture and wine business advice.
Previously, Sam was director of Grape Supply for Accolade Wines, leading a large team to deliver grapes to winery networks across Australia and New Zealand.
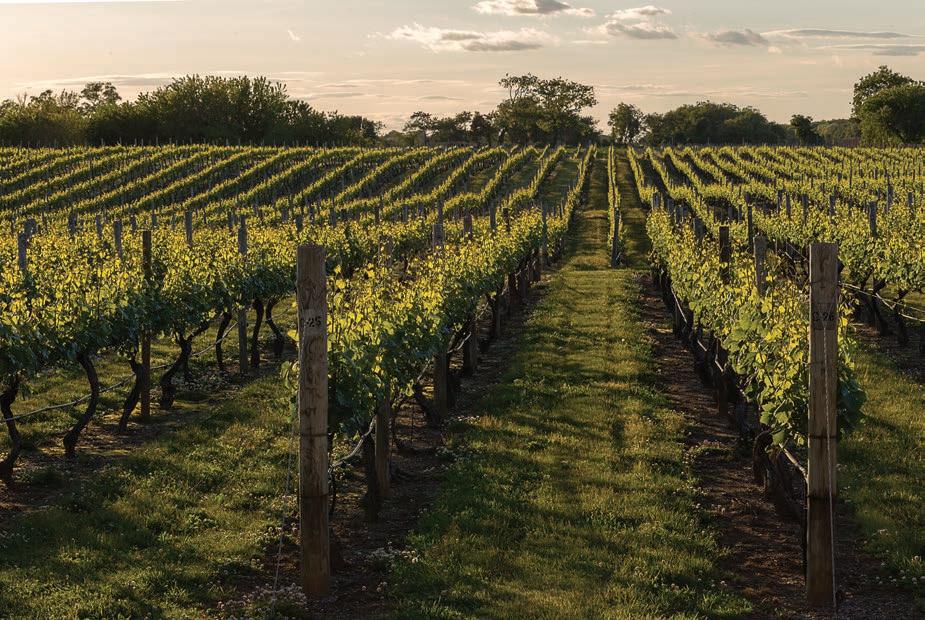
The appointment follows a national recruitment campaign.
Sam has significant experience across a variety of roles in viticulture in Australia and New Zealand and has sat on Research Advisory Committees for more than 12 years, advising on the and Oenology (ASVO) and the Australian Wine Industry Technical growers, winemakers, suppliers, and industry stakeholders to empower them Register underpins the biosecurity activities of Vinehealth Australia. F
Report aims to maximise potential of NSW aquaculture industry
The NSW Government has committed to working with industry to double the farm gate value of the NSW aquaculture sector to $300 million by 2030 with the release of the NSW Aquaculture Vision Statement.
The new statement outlines an overarching approach to the development of the State’s aquaculture industries which includes research, investment in breeding programs and a commitment to water quality improvements.
The statement came as more than 300 state, interstate and international delegates attended the national Oyster Industry Conference in Port Macquarie.
The Vision Statement is a joint industry and government initiative built on a shared approach to seafood production, developing bioproducts and climate change adaptation.
Key to delivering a doubling in the farm gate value of the NSW aquaculture industries will be industry
and government supported initiatives including:
• Managing oyster industry risk through a breeding program, plus alternate species.
• I nnovative research at DPIRD research stations and with partners.
• Opening up new areas for marine aquaculture (mussels, oysters, algae).
• Promoting the environmental benefits of aquaculture – e.g. algae, oysters and mussels all take up excess nutrients and help improve water quality.
• Streamlining aquatic biosecurity rules to facilitate access to interstate spat supply
• Protecting and enhancing water quality.
• Providing opportunities for Aboriginal people to participate in aquaculture businesses.
The Government and industry will develop a detailed roadmap that will guide implementation of the target initiatives.
Government and industry will develop a detailed road map that will guide implementation of the target initiatives.
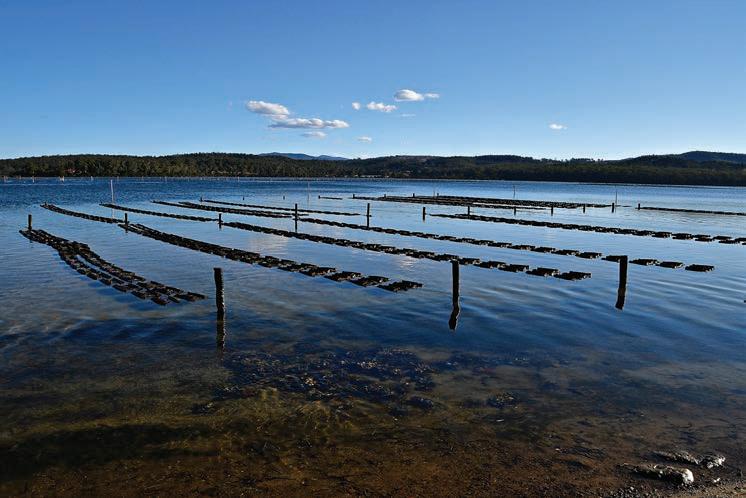
The Government has also provided financial support for aquaculture and commercial fishing businesses with fee relief as they were impacted by natural disaster and aquatic disease. F
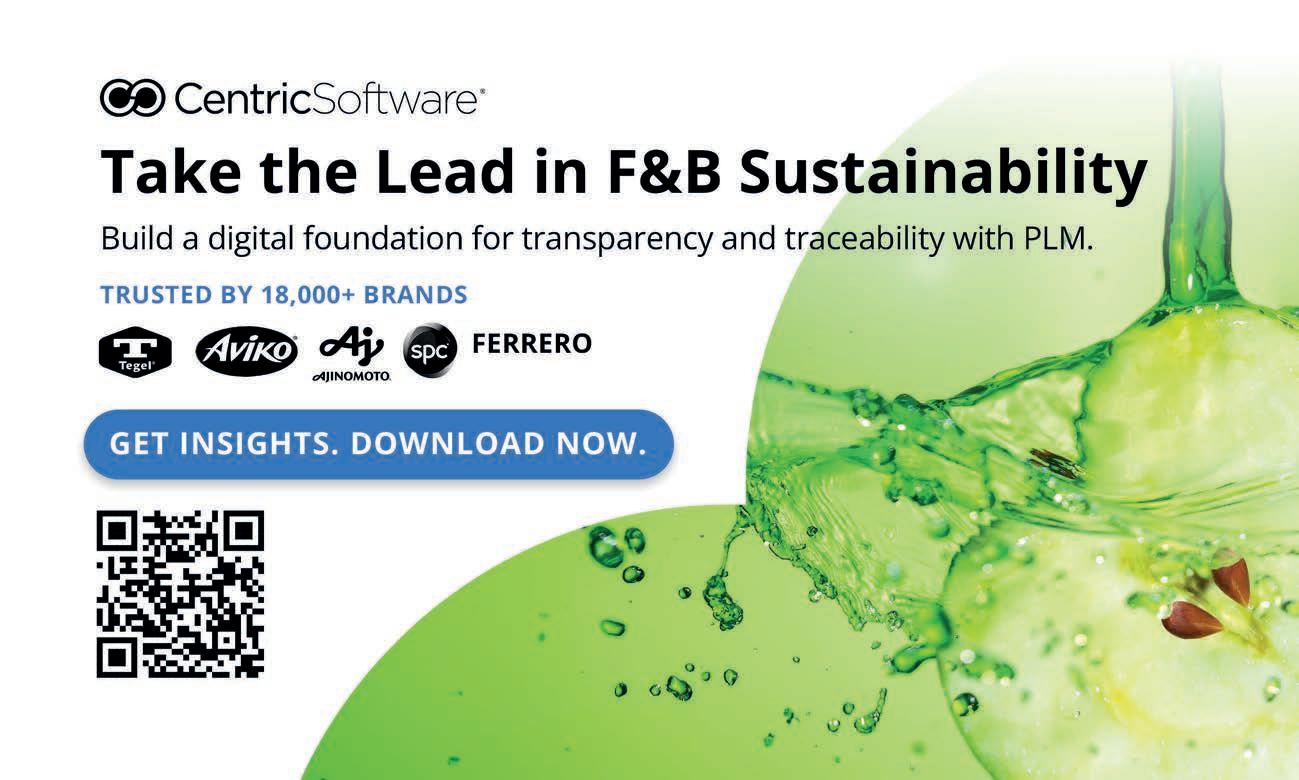
The NSW Government has recently announced it is investing more than $3 million to provide much needed upgrades at the Port Stephens Fisheries Institute.
Arange of single use plastic products have been banned in one of the most significant phases of the South Australian Government’s efforts to reduce plastic waste.
The following items are now banned in South Australia:
• Single-use plastic coffee cups and lids
• Plastic barrier bags used fresh fruit or vegetables, nuts, or confectionery
• Plastic-laminated paper shopping bags
• A ll plastic food bag tags used to close plastic bags containing food
• Plastic balloon sticks, plastic balloon ties and plastic confetti.
Next year, plastic barrier bags used for dairy products, meat, poultry, fish and seafood, plastic fruit stickers, and plastic soy sauce fish containers will join the list of banned products.
Several plastic food and beverage products banned in SA New Zealand Winegrowers launches Roadmap to Net Zero
New Zealand Winegrowers has released the New Zealand Wine Roadmap to Net Zero 2050.
The launch took place during the Research & Innovation Forum, one of the events featured in the Altogether Unique 2024 annual wine celebrations, which were held on August 30 in Wellington.
Fabian Yukich, chair of the New Zealand Winegrowers Environment Committee, emphasised that the wine industry requires a clear pathway to reach its Net Zero goal.
“Climate change is the biggest long-term challenge facing our industry. It will influence our choice of grape varieties, wine styles, viticultural techniques and regions, and importantly, the purchase decisions of our customers,” said Yukich
Community consultation shows South Australians overwhelmingly support action to ban single use plastic items.
Of more than 3,000 people surveyed, 97 per cent of respondents said they supported more single-use plastic items being banned.
“Single-use plastics are often used for seconds but they last a lifetime in our natural environment. The carbon footprint associated with making and transporting and disposing of single-use plastics is not sustainable if we are to more than halve our carbon emissions by 2030,” said deputy premier Susan Close.
Phasing out single-use plastics is an important way to reduce pollution, cut carbon emissions and protect marine life.
South Australia has taken steps to address the impacts associated with a range of single-use plastic products and
South Australia has taken steps to address the impacts associated with a range of single-use plastic products.
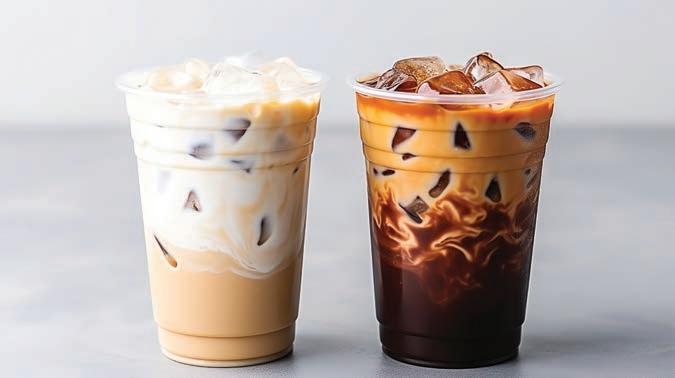
was the first jurisdiction in Australia to do so on a state-wide basis, beginning with single-use plastic shopping bags in 2009.
The Plastic Free SA program,
funded through Green Industries SA will continue to provide free advice for South Australian Businesses on the best alternatives for their products and services. F
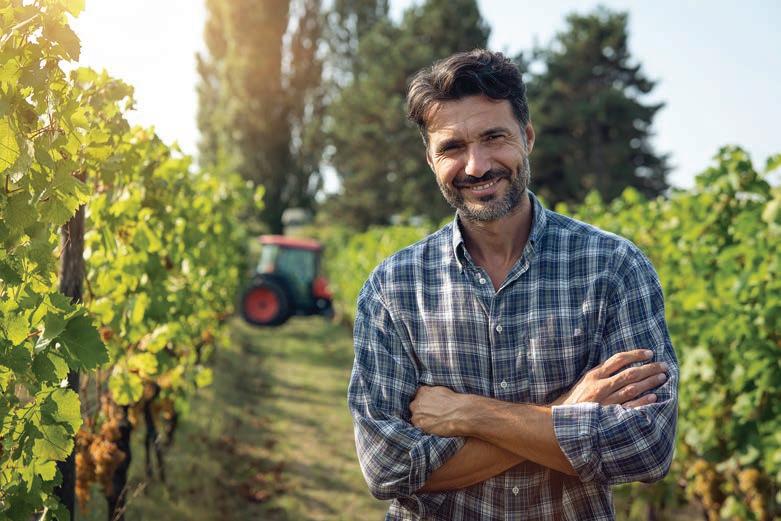
The Roadmap was made possible through the support of EECA (Energy Efficiency & Conservation Authority) and produced by thinkstep-anz.
The Roadmap outlines the wine industry’s current greenhouse gas (GHG) emissions and sets targets for
2030, 2040, and 2050.
It provides vineyards and wineries with practical strategies for innovation,
aimed at reducing emissions as quickly and effectively as possible, in alignment with the industry’s goals.
In the short term, focusing on reducing scope 1 emissions is the most practical approach. Addressing scope 2 and 3 emissions will require innovative solutions across the entire value chain, particularly in electricity generation, transportation, and packaging.
The Roadmap to Net Zero 2050 is just one component of the New Zealand wine industry’s commitment to sustainability.
ince 1995, Sustainable Winegrowing New Zealand (SWNZ) has been the wine industry’s independently audited sustainability certification programme.
As wine consumers increasingly demand greater transparency of environmental credentials, this next step by the New Zealand wine industry could give critical insight for the Australian wine industry moving forward. F
The NZ Winegrowers Roadmap to Net Zero sets targets for 2030, 2040, and 2050.
‘Too Good To Go’ aims to help fight food waste
Too Good To Go, the world’s largest marketplace for surplus food has announced its official launch in Australia beginning in Melbourne.
The Danish-born certified B-Corp aims to help households and businesses halve Australia’s annual food waste by 2030 in line with the National Food Waste Strategy.
The free to use mobile app will allow users to purchase a Surprise Bag of food, at a reduced price from a range of bakeries, cafes, restaurants, grocery stores and other businesses.
O ver 80 local businesses have joined Too Good To Go for its launch in Australia.
FoodCo’s Muffin Break and Jamaica Blue will also be joining the marketplace with select sites rolling out across Victoria throughout September.
More stores will continuously be added on the app, which worldwide already partners with more than 170,000 food businesses.
In Australia, food waste is a multibillion-dollar problem, with over 7.6 million tonnes of food wasted annually.
How the Too Good To Go App works 1. Find surplus food near you: Users search Too Good To Go’s
3. Pick up your food: Users arrive within the pick-up window that the store sets, shows their in-app receipt
at the end of the day, including prepared food, beverages and ingredients that would otherwise be thrown away.
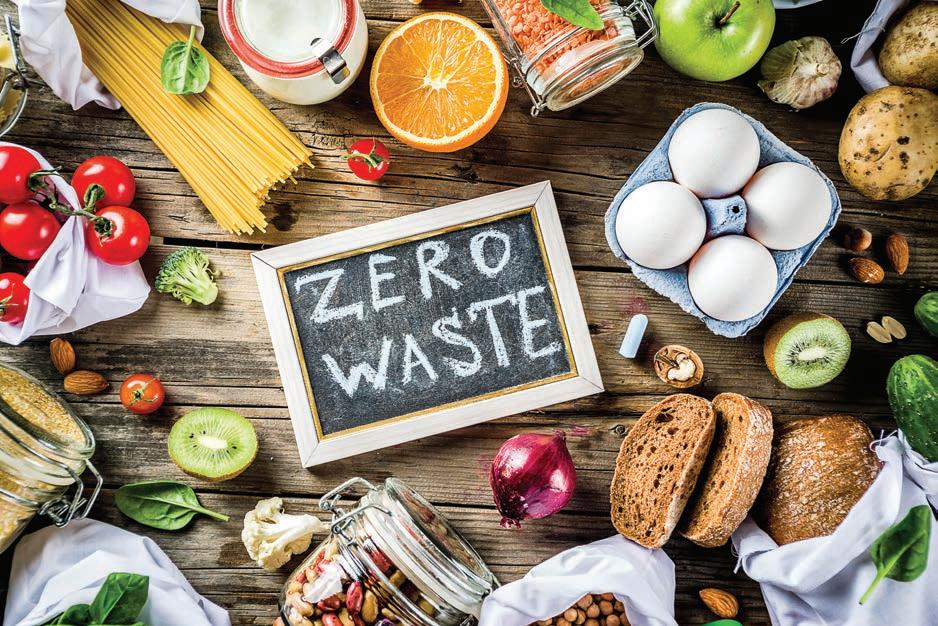
New GM of research and innovation for Wine Australia
Wine Australia has announced the promotion of Dr Paul Smith to the position of general manager, Research & Innovation.
Smith was previously Wine Australia’s Senior Research & Innovation Program Manager and replaces Dr Liz Waters who was recently promoted to COO.
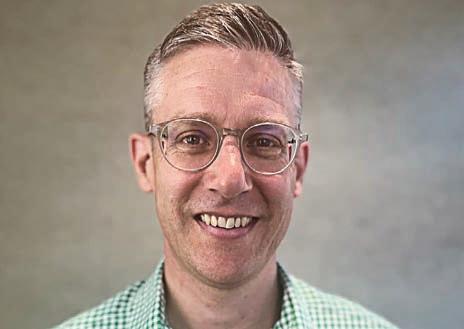
In his new role, Dr Smith will have oversight of co-investment of industry and Commonwealth funding into research, development, and adoption activities to benefit Australia’s grape growers and winemakers.
“I am excited to bring my experience in leading research projects, teams and managing a portfolio of complementary projects to this role,” Dr Smith said.
“I’m particularly passionate about maximising the innovation aspects of the investments we make by realising value from the research that forms a
foundation for practical, profitable outcomes for the Australian grape and wine community.”
Smith joined the Wine Australia team in 2017, taking a critical role in the research and innovation portfolio after a 14-year tenure with the Australian Wine Research Institute where he managed teams of grape and wine researchers.
Prior to this he completed postdoctoral research at CSIRO Molecular Science and the Department of Clinical Pharmacology at Flinders University. Dr Smith has a PhD in Organic Chemistry from Flinders University.
Wine Australia CEO Dr Martin Cole said he is delighted to announce Smith’s promotion, as over the last few he has been an instrumental part of
the organisation.
“I’m delighted to announce Paul’s promotion into this critical leadership role at Wine Australia. Paul has been instrumental in guiding continued advancement of the research and innovation responses to the critical issues identified by the sector,” said Cole.
Wine Australia is currently recruiting to backfill Dr Smith’s role which has been re-titled research impact manager and will focus on developing and executing business investment plans to drive innovation in the grape and wine sector.
Both appointments are among several that have taken place at Wine Australia in recent months to replace staff who have moved on, taken parental leave, or been internally promoted. F
Image: Wine Australia
Paul Smith is the general manager of research and innovation for Wine Australia.
The Too Good To Go App already has more than 100 million registered users in 18 countries.
Record exports for beef and sheep meat
The release of the September cattle and sheep projections updates from Tim Jackson, MLA Global Supply Analyst, show record exports of beef and sheep meat for the upcoming calendar year.
Australia’s strong market access position has improved diversification and competitiveness in the global market.
As an export-oriented, red meatproducing nation, free trade has been
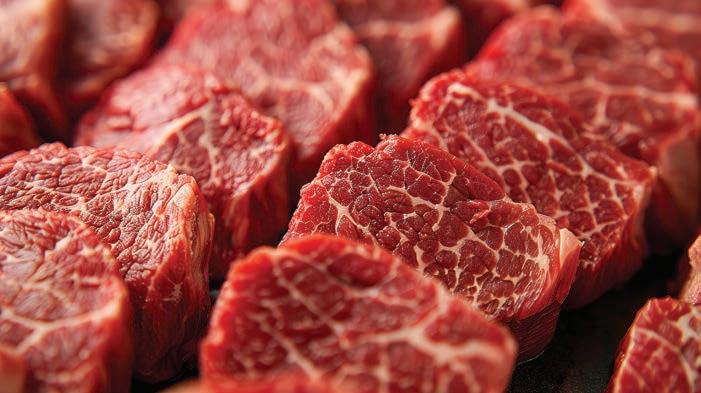
In the year to August 2024, 93 per cent of Australian beef exports were shipped to countries with which Australia has FTA.
$15 million investment into QLD aquaculture
The Queensland Government will invest $15 million into the continued growth of Queensland’s booming aquaculture industry.
The Queensland Aquaculture Strategy 2024–2034, launched last month by Agricultural Industry Development and Fisheries Minister Mark Furner, outlines the plan to put more premium Queensland seafood on plates in our state and across the globe.
“Queensland seafood is highly desired by consumers who value high-quality, great-tasting food that is sustainably produced,” said Minister for Agricultural Industry Development and Fisheries and Minister for Rural Communities Mark Furner.
“It’s important we’re continuing to invest in our aquaculture sector to give consumers choice, variety, and confidence that all Queensland seafood is sustainable and responsibly sourced.
This investment is a further boost to the $7.5 million committed to aquaculture in March 2023.
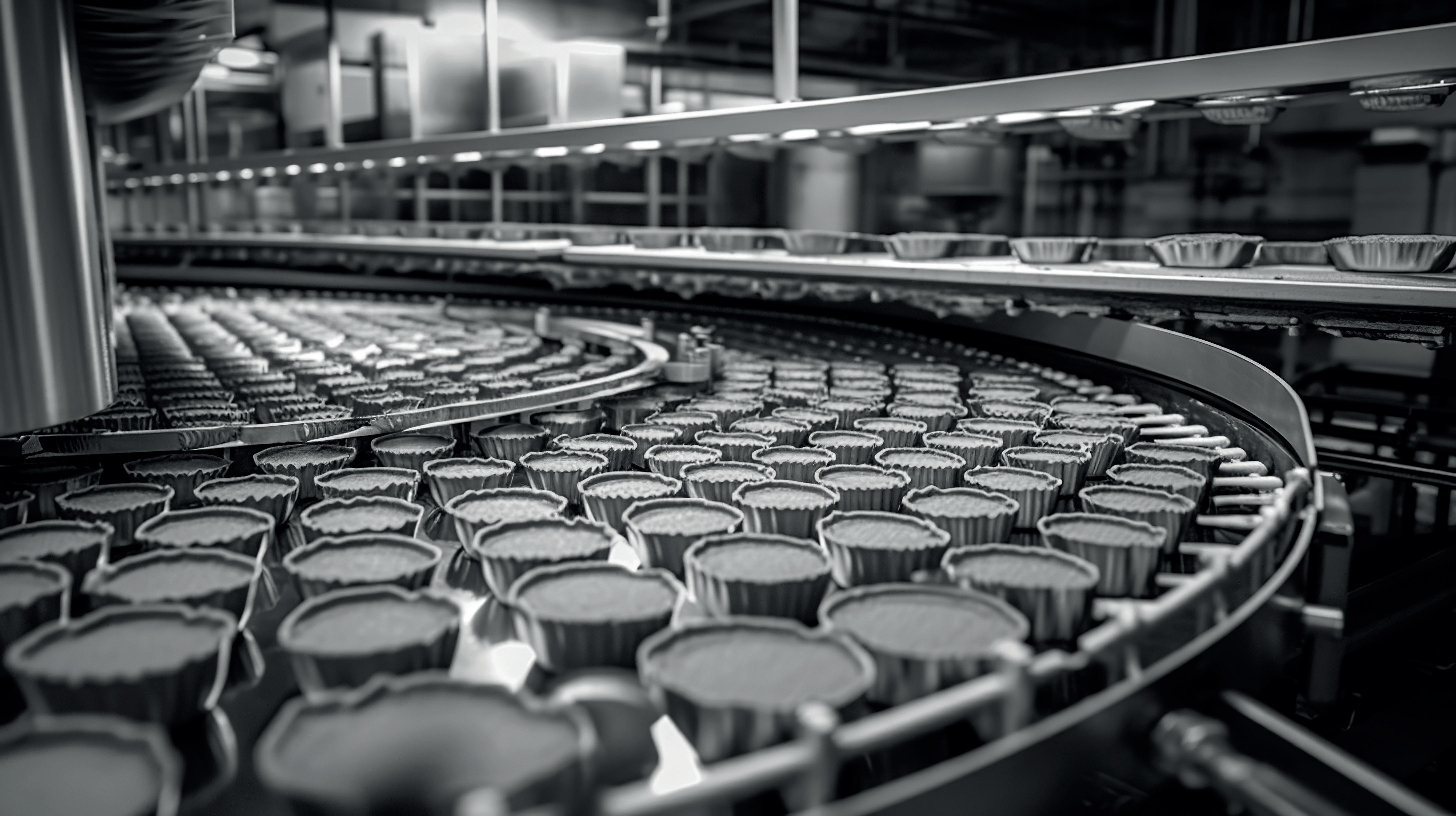
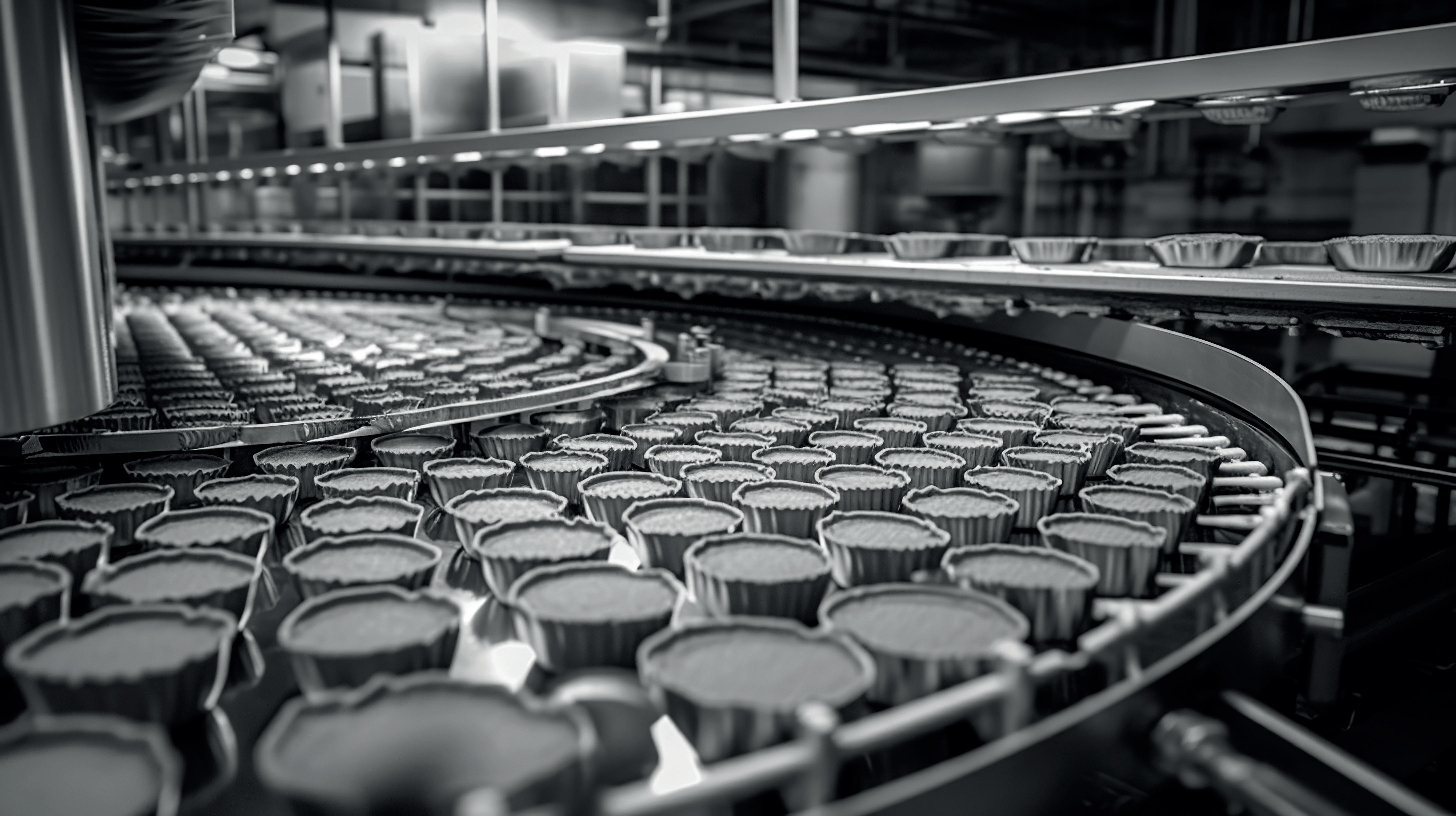
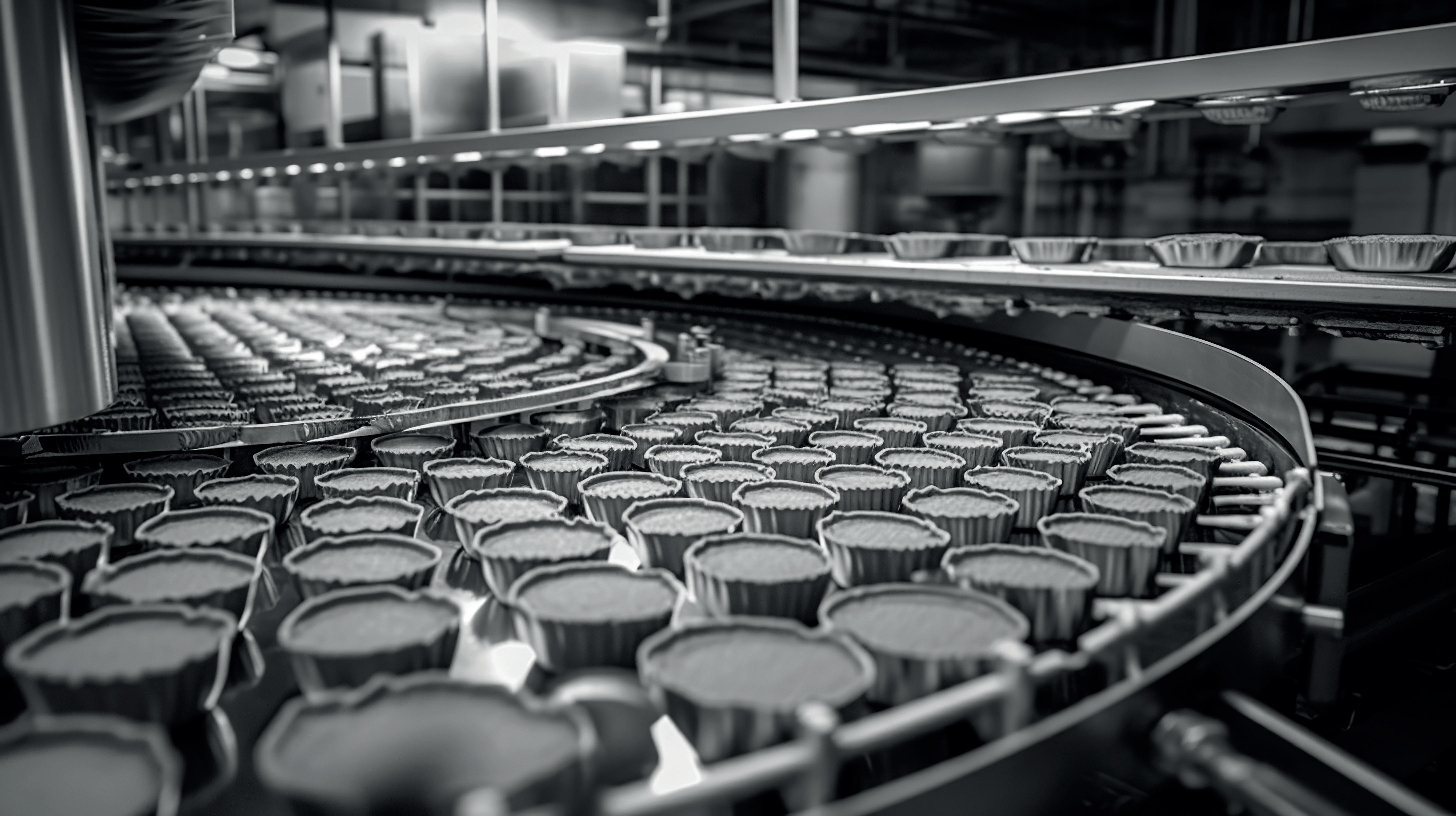
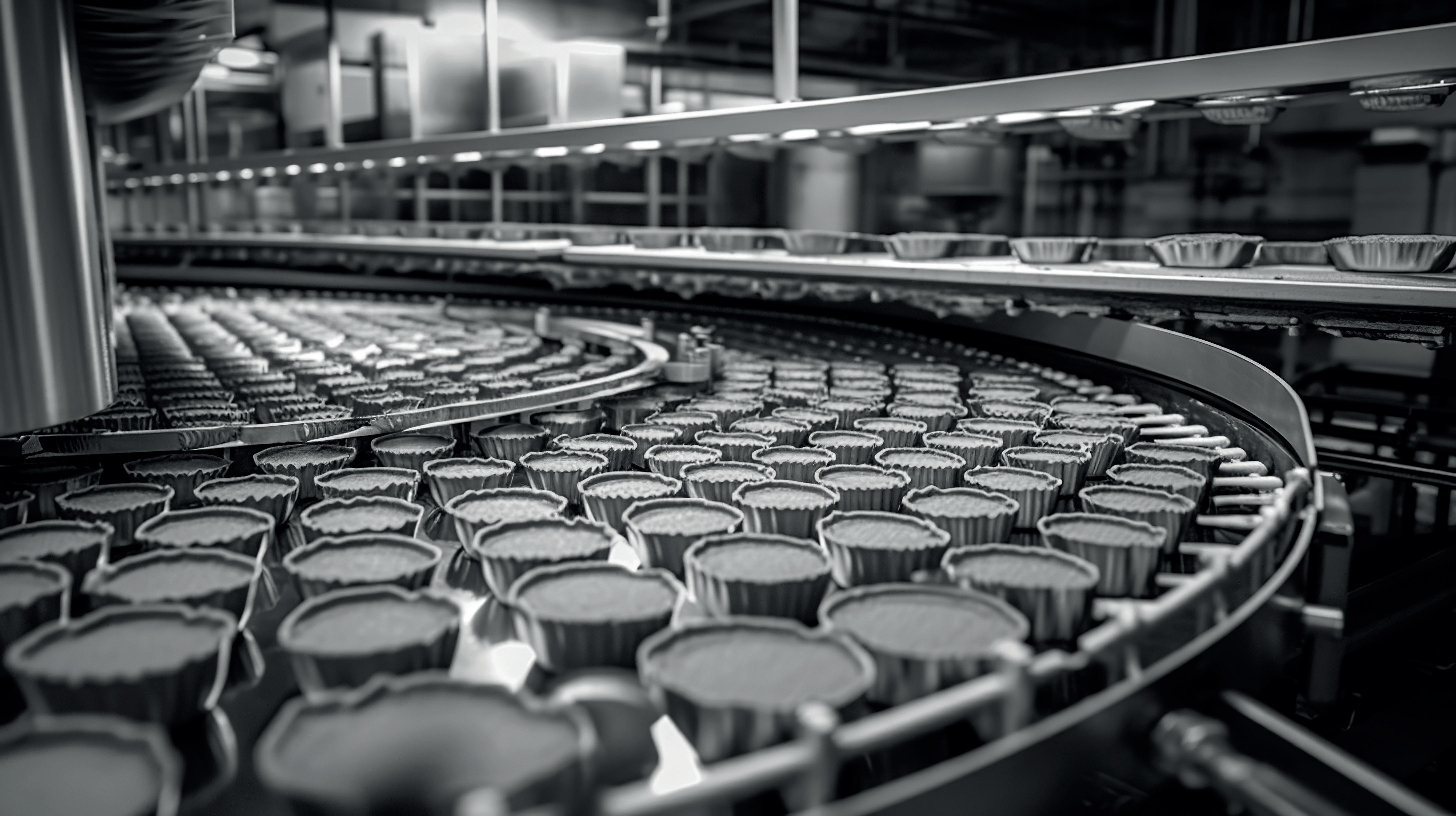
New grants for Queensland manufacturers
Queensland Manufacturing
Minister Glenn Butcher has launched a new round of Made in Queensland (MiQ) grants, with an additional $20 million available to help manufacturers grow and create more manufacturing jobs.
MiQ is a $121.5 million Queensland Government grant program
helping small and medium sized manufacturers to increase international competitiveness, productivity, and innovation, and to generate high-skilled jobs for the future.
Over six rounds, MiQ has supported 161 advanced manufacturing projects across the state, creating and supporting more than 6,500 jobs.
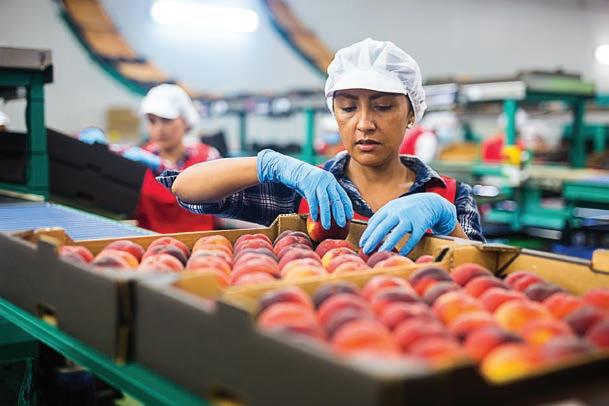
The Guidelines for
These investments have also leveraged over $261 million in private sector investment. MiQ projects are helping local manufacturers to bolster competitiveness and create more good manufacturing jobs.
“We’re helping manufacturers build supply chain resilience and grow their workforce. MiQ is a proven winner, with more than 6,500 jobs created many of those in regional Queensland,” said Butcher.
“I’m proud to help these Queensland manufacturers grow their business and I’m proud to see that Queensland is the leading state for manufacturers with more and more businesses wanting to move here because of the incredible support on offer from the Queensland ...Government.
Just like at Berg Engineering, with locations in Brisbane and Gladstone, who have received more than $975,000 in MiQ grant funding from the Miles Government.
This funding enabled Berg to buy
a multi-axis CNC machining centre and CNC horizontal boring machine. The new equipment will help this Queensland manufacturer to increase production capacity and will see six new full-time jobs created in their Brisbane facility and a further eight jobs in their Gladstone facility.
This grant program is part of the Miles Government’s more than $240 million investment in supporting manufacturers across the State, including through the Manufacturing Hub Grants and the establishment of six Manufacturing Hubs across Queensland.
The Guidelines for Made in Queensland Round 7 are available online now with applications opening from 24 September 2024 and closing on 24 January 2025.
Queensland manufacturers seeking more information about project eligibility criteria, key time frames and assessment criteria should visit the RDMW website. F
Suntory Oceania’s new $400 million Queensland facility
Production has officially started at Suntory’s +$400 million multibeverage manufacturing facility in Queensland, Australia.
This marks a significant milestone in the global drinks giant’s growth strategy, with its new $3 billion partnership, Suntory Oceania set to launch from mid-2025.
The 17-hectare site will power the partnership as the new manufacturing and distribution hub for the company’s multi-beverage portfolio of over 40 market leading brands.
The site has the capacity to hold over 50,000 pallets of product, with a highspeed glass line and two canning lines that fill at an industry-leading speed of 180,000 cans per hour.
Australia’s number one energy drink, V Energy, was the first product off the line. By mid-2025, the facility will also produce Suntory’s iconic Ready-ToDrink (RTD) alcohol brands, including – 196, Canadian Club and Dry, and Jim Beam and Cola.
The new Suntory Oceania site has the capacity to hold more than 50,000 pallets of product.
CEO, Darren Fullerton, said he was proud to see Suntory’s first Australian facility built, the largest FMCG investment into the country in the last decade.
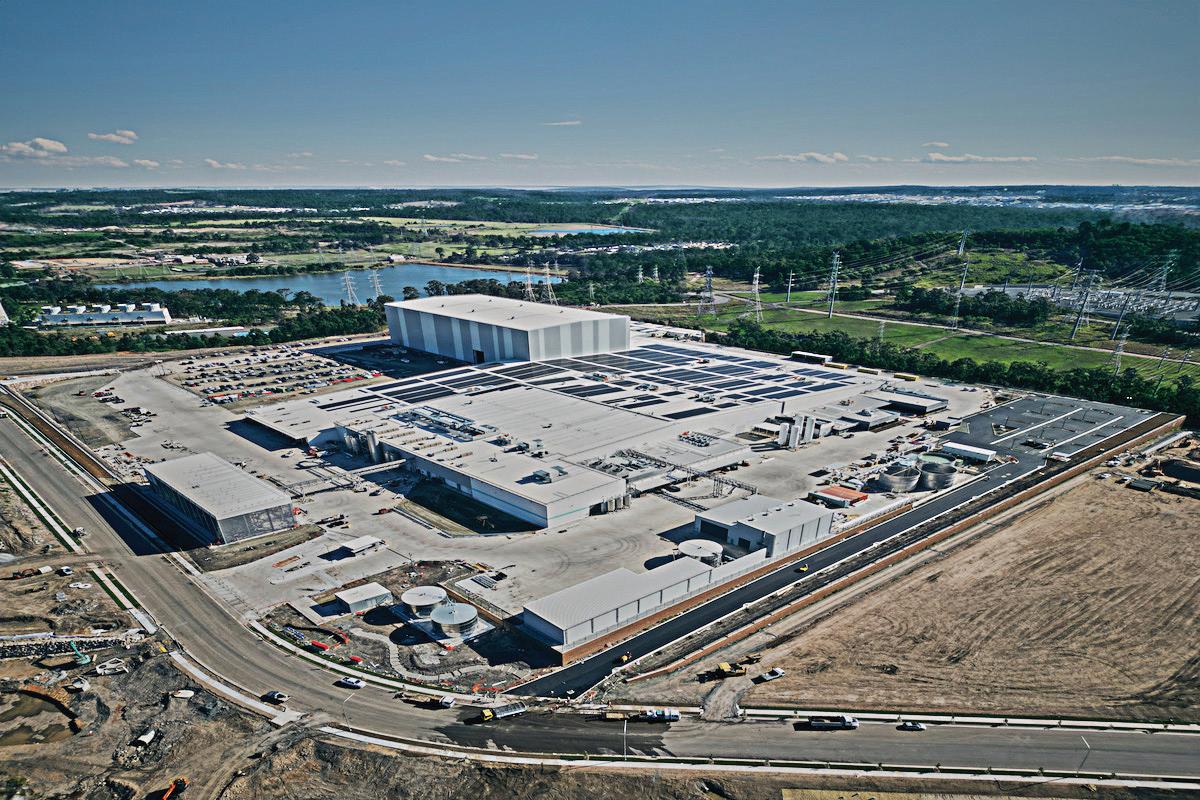
“We are excited about the growth this will unlock for Suntory in the region, and the opportunities we will be able to offer our people, our customers,
ignite the category with our full multibeverage offering.”
The facility boasts strong sustainability credentials with a
heating and cooling technology and on site waste management and water recycling facilities sets a benchmark for sustainable manufacturing. F
Made in Queensland Round 7 are available online now.
Image: Suntory
Oceania
Coca-Cola Europacific Partners (CCEP) will meet its target to use 100 per cent renewable electricity across its Australian operations by 1 January 2025, one year ahead of schedule.
The achievement will be made possible thanks to the signing of a new Virtual Power Purchase Agreement (VPPA) provided by global renewable energy player, ENGIE.
CCEP joined the global RE100 initiative in 2021 and made a commitment to power its Australian operations with 100 per cent renewable electricity by the end of 2025.
The company has since supercharged its efforts, investing in rooftop solar panels at its production sites around Australia and securing several key power purchase agreements.
This latest 10-year agreement with
CCEP Australia to achieve 100 per cent renewable electricity Investment into biosecurity for grain growers
The NSW Government has invested $13.5 million to advanced research and diagnostic technology to protect NSW grain production and food security from the threat of exotic pathogens and pests.
The $13.5 million will be a five-year co-investment through National Grains Diagnostics and
ENGIE will enable CCEP to secure the remaining energy needed to fulfil its RE100 commitment.
This will make CCEP one of the first FMCG players in the country to achieve the RE100 commitment and is an important milestone for our business,” he added.
Under the PPA with ENGIE, CCEP will purchase a percentage of renewable energy and associated Renewable Energy Credits (RECs) from the newly built Wellington North Solar Farm, owned by Lightsource bp, located in the Orana region of New South Wales.
The site spans over approximately 970 hectares, over three times the size of Sydney’s CBD, utilising more than 1.2 million solar panels and has the capacity to generate 925,000-Megawatt hours (MWh) of renewable electricity per year.
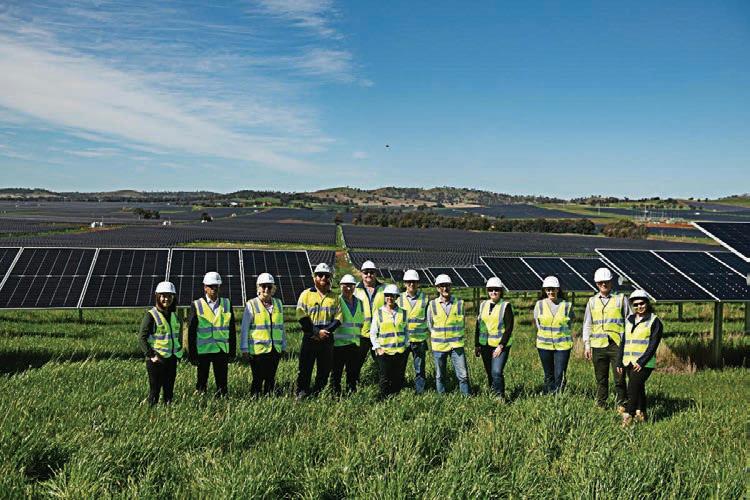
The site spans over approximately 970 hectares, more than three times the size of Sydney’s CBD.
Surveillance Initiative.
The co-investment will be led by the NSW government scientists at the Elizabeth Macarthur Agricultural Institute (EMAI), with work also underway at the Wagga Wagga, Tamworth and Orange Agricultural Institutes.
The project which aims to address critical gaps in grain biosecurity is part
It has also provided economic benefits to the local community,
including the creation of up to 400 local construction jobs. F
of the Government’s $946 million investment in protecting the State’s primary industries against biosecurity threats.
NSW Department of Primary Industries and Regional Development (DPIRD), in partnership with Grains Research and Development Corporation (GRDC), is creating new early warning
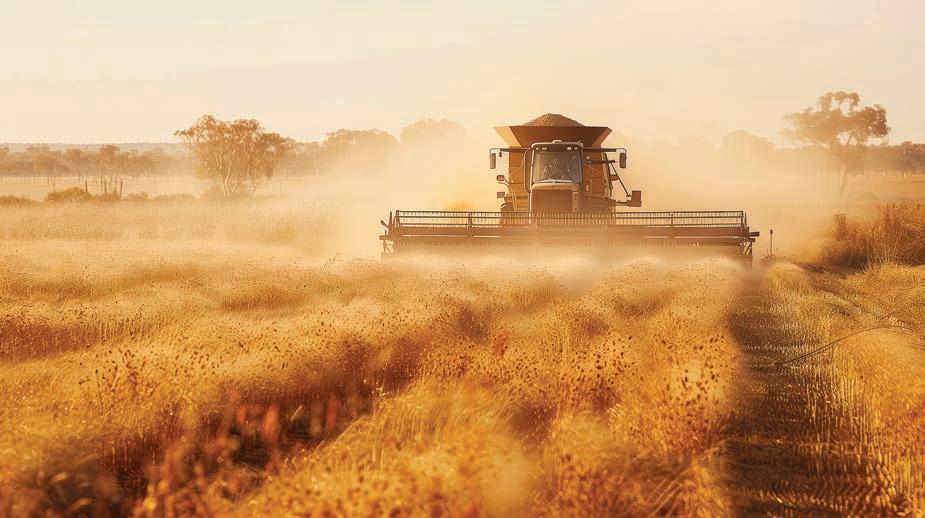
and molecular diagnostic tools.
These tools are essential to identify and reduce the impact of exotic biosecurity threats.
The work, which is targeting 16 exotic grain pathogens and 62 exotic grain pests currently not in Australia, aims to prevent billions of dollars damage to the state’s agriculture sector if there were future domestic outbreaks of these threats.
Targeted pests and pathogens, currently not present in Australia but causing significant damage internationally, include wheat blast, exotic fusarium wilt diseases and hessian fly.
Overseas, the exotic wheat blast disease, present in South America, Bangladesh and Zambia, has resulted in devastating crop losses of up to 100 per cent when the environmental conditions were conducive.
The possible spread of the wheat blast and other diseases from overseas to Australia has increased in recent years because of the international seed and grain trade, Australia sharing similar environmental conditions and global warming. F
The NSW Government’s $13.5 million investment into grain growing will be a five-year co-investment through National Grains Diagnostics and Surveillance Institute.
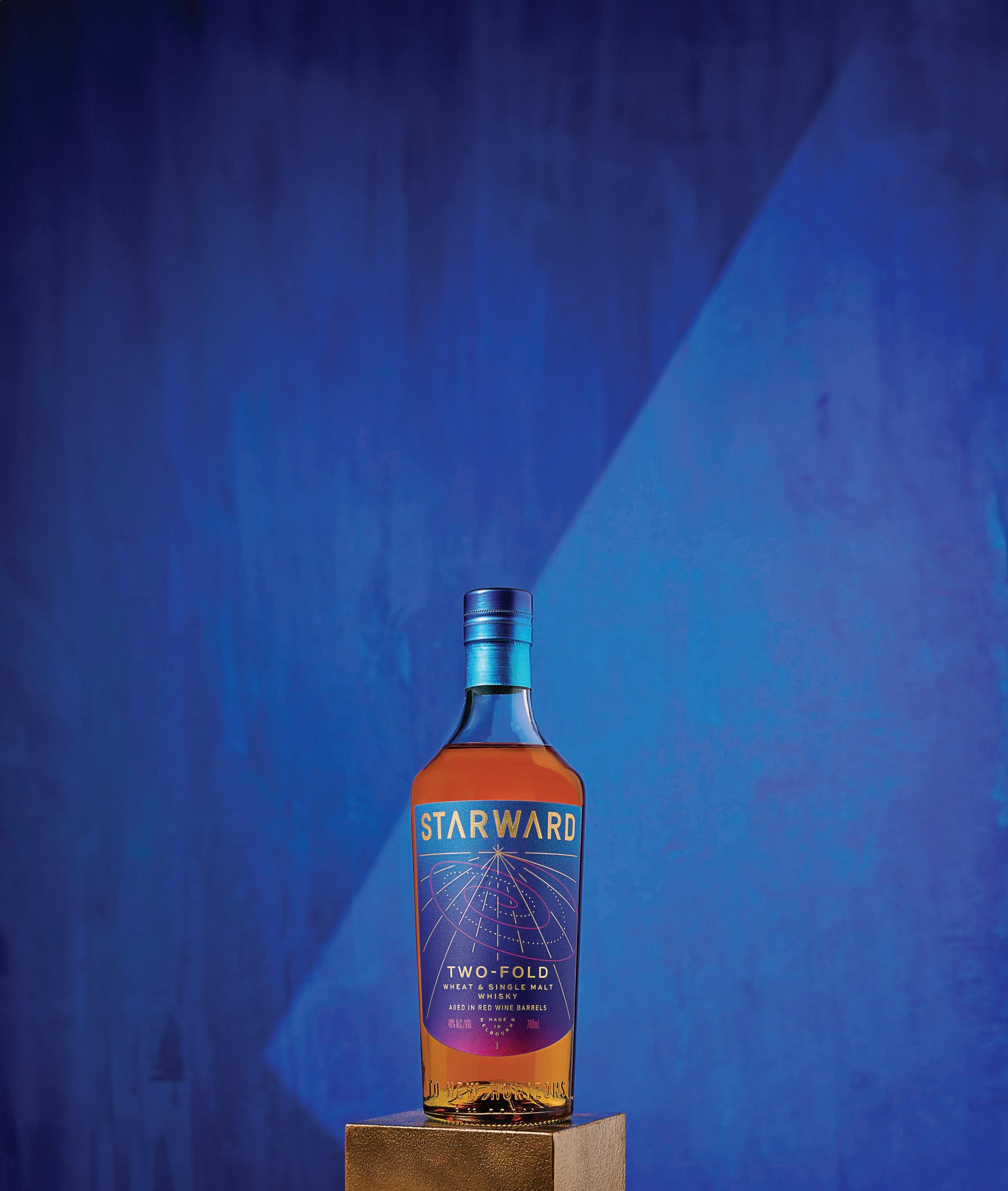
Starward Whisky: Australian flavour and global ambition
Founder of Starward Whisky, David Vitale, talked to Food and Beverage Industry News about the origins and ambitions of an acclaimed Australian distillery. Jack Lloyd writes.
Nestled within the historic Port Melbourne, Starward Whisky has evolved from an idea held together by sheer belief into a multiple award-winning distillery.
When David Vitale founded Starward, his aim was to move whisky away from the ‘special occasion’ cabinet.
“I started Starward to move whisky from something rare and scarce to something that’s readily available all around the world,” said Vitale.
Vitale’s number one priority was to make a product that was authentically Australian. Taking inspiration from the patriotic flavour profile of Scotch Whiskies, he made it his mission to make this notion a reality.
“We had to do something that was radically different to what already existed so that we had permission in the whisky world. When you open the cork, you need to know this is an Australian whisky,” he said.
Distinctively Australian whisky
This desire to create a whisky that was undeniably Australian in origin, taste and smell would lead Vitale down a path of experimentation. This is where he would stumble across a process that is now synonymous to Starward Whisky.
When traditional distilling production processes end, Starward ages its whiskies in red wine barrels that are sourced locally near Port Melbourne.
“Starward is more Australian than Scotch is Scottish. Those barrels are sourced literally from winemakers a day’s drive away,” said Vitale.
“Because we’re so close to wineries, we can empty the barrel in the afternoon and then fill it still wet with that wine character, which is a novel process that we’ve pioneered.”
Vitale described this as the moment when he and his team knew they could add to the already established
conversation of Australian whisky.
“All of a sudden, we’ve got a reason to exist,” he said.
Not only are the barrels Australian in origin, but Starward insists on sourcing local grain from farmers between the South Australian border and Geelong.
“Within a day’s drive, we’ve got all this amazing malted barley that’s sourced and then malted for us in Geelong, which is 100 kilometres down the road,” said Vitale.
“Not only are the products we source local, but they’re really distinctive and delicious.”
Local ingredients and resources aren’t the only way Starward Whisky is shaped by Australia. Vitale noted that the whisky is even affected by Melbourne’s ‘four seasons in a day’ weather conditions.
“We couldn’t make this whisky anywhere else apart from Melbourne. The reason for that is the climate,” he said.
Vitale said that as heat rises, the barrel expands and forces the spirit into the wood, which further helps the spirit extract the flavour from the barrel. When the climate turns cold, the wood contracts, leaving the whisky in a resting state.
“Instantly we’re having more of that reactive process happening all the time compared to Scotland,” said Vitale.
The lack of constant humidity in Melbourne is also a factor in the retention of alcohol during evaporation.
“Think about Scotland, it’s quite humid. That means that as the temperature rises and falls, they’re losing more alcohol than they are water from evaporation,” said Vitale.
“In Melbourne, it’s quite a unique environment where we’re losing as much alcohol as we are water, which makes for a softer maturation.”
Starward’s ‘Two-Fold’ whisky is among products to win gold at the 2024 San Francisco World Spirits Competition.
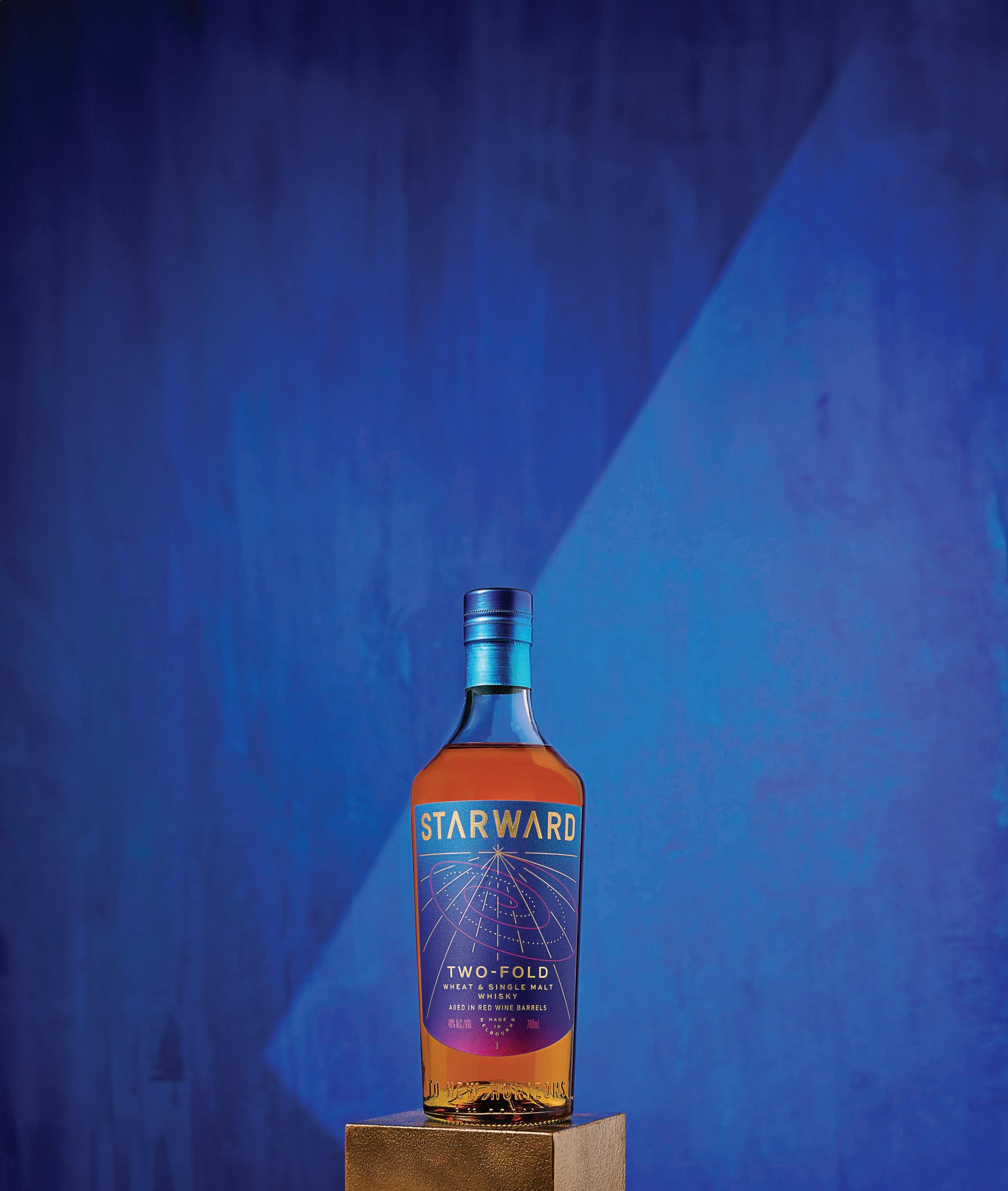

When David Vitale established Starward, his number one priority was to make a product that was authentically Australian.
Undivided focus on Whisky
Alongside its local flair, Starward’s decision to exclusively focus on whisky allows the distillery to refine its production processes.
“Focusing on the one product was critical to us,” said Vitale.
As a part of its production processes, Starward departs from traditional distilling practices by using brewing barley.
“It’s a darker malt that creates a real luscious mouth feel and texture to the whisky,” said Vitale.
Starward then ferments the barley using ale yeasts to create a more tropical flavour.
“It’s like a Belgian style yeast and a distilling yeast put together. A lot of those tropical characters you get in Starward are from the fermentation process,” said Vitale.
Vitale believes these methods mean Starward isn’t 100 per cent reliant on the barrel for its flavour profile.
“While I have a strong belief that even though 70 to 80 per cent of the flavour comes from the barrel, the other 30 per cent can make a big difference too,” he said.
Starward then distils the whisky for around six hours and can do three batch runs in a day.
Vitale said despite the quality of its processes, Starward couldn’t operate without its BRC Global Standard for Food Safety (BRCGS) certification.
Recovering and reusing energy used to heat its stills is just one of Starward’s sustainability initiatives.
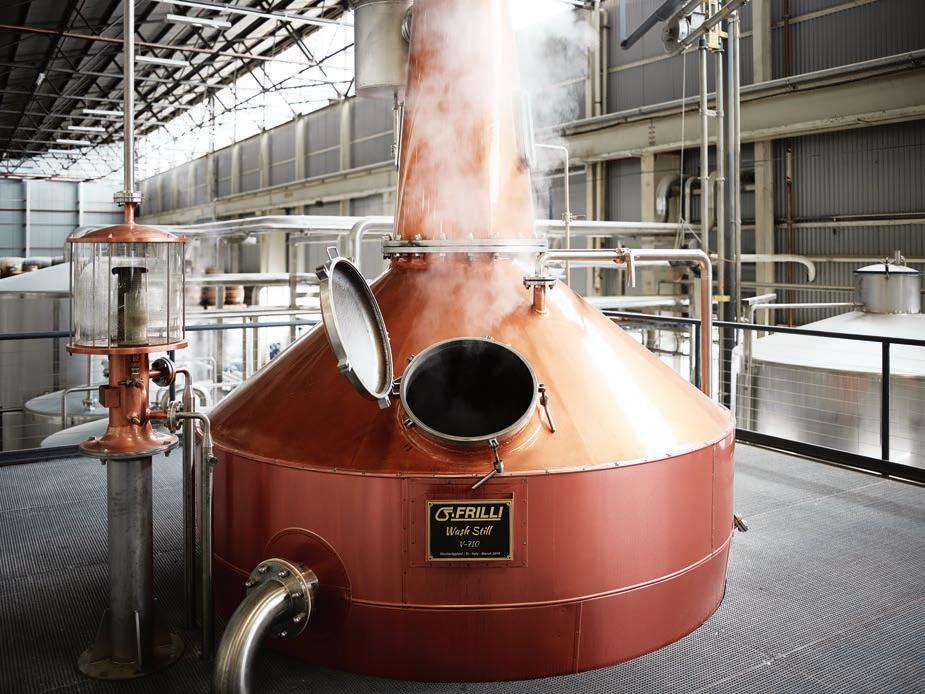
program to be certified globally under the UK initiative. That’s levelled things up quite substantially in terms of our quality assurance programs. A lot of that’s anchored in good process that we were doing anyway,” he said.
“If you just want to run a business effectively, having those programs in place sort of gets you ahead of the curve.”
In addition to its commitment to product quality, Starward Whisky is dedicated to sustainability.
“We’ve got pretty ambitious goals to have a net zero carbon footprint,” said Vitale.
A recent initiative saw the company taking 200 grams of excess glass out of each bottle they ship.
overseas, so once you start to put together the carbon footprint in terms of exports, it’s huge,” he said.
Starward also sources the glass for its core ranges domestically, allowing for a higher rate of glass to be recycled.
Energy efficiency is another priority with systems in place that aid the distillery in recovering energy that
would otherwise go to waste.
“It’s a resource-intensive business in terms of energy that we use to heat the stills up, and then cool them down again. What we try to do is recover as much of that energy as we can,” said Vitale.
Anticipating market dynamics
Aside from Starward’s focus on distilling, Vitale and production director Sam Slaney believe a large part of the process is anticipating where the market is going to be in the now and in the future.
The two have applied their previous
“I think we can get people to fall in love with our whisky 20 years before they think they’re ready for it.”
International achievements and products
Due to a blend of its processes, Starward was awarded the title of ‘Most Awarded International Distillery of the Year’ at the 2024 San Francisco World Spirits Competition.
Vitale was humbled, especially because it is the second time the distillery has been awarded the title in the event’s 22-year history.
was Starward’s fan favourite ‘Two-Fold.’ “ Two-fold is my favourite whisky that we make because it’s just so versatile, approachable and easy to drink,” said Vitale.
“It has just the right amount of complexity to it, yet it is still sessionable.”
Vitale said the product’s availability is a large factor in its popularity.
“This is what I love about these awards. It’s the ones that are most readily available that have been accoladed the most,” he said.
Aside from Starward’s award winning products, Vitale has a soft spot for a whisky that was inspired by the founder himself. ‘Vitalis’ is a single malt that was released for the distillery’s 15th anniversary.
“We don’t do 15-year-old whisky’s, because Melbourne’s climate would make them not taste that great. But we’ve got a 15th anniversary whisky called Vitalis, and that was launched December 2023,” he said.
“It’s the greatest hits of all our whisky’s
in one bottle, and that’s hard to do. If you say, just grab a little bit of everything and put it into one cask, everyone is probably thinking of Frankenstein’s monster, but it is outstanding.”
Unwavering belief through uncertain times
Despite Starward’s current success, Vitale admitted that until the distillery won hearts and minds with its modern approach, it was “touch and go for a while”.
“Those first few years of finding our feet in the Australian market when we didn’t have much of a reputation of making whisky, even though the quality of all of the whisky being made was amazing, was really hard,” said Vitale.
“I think we were like 90 days away from insolvency for two years.”
Vitale insisted the key was the belief in all the reasons why the distillery would work as opposed to all the reasons it shouldn’t.
“We started the business with a
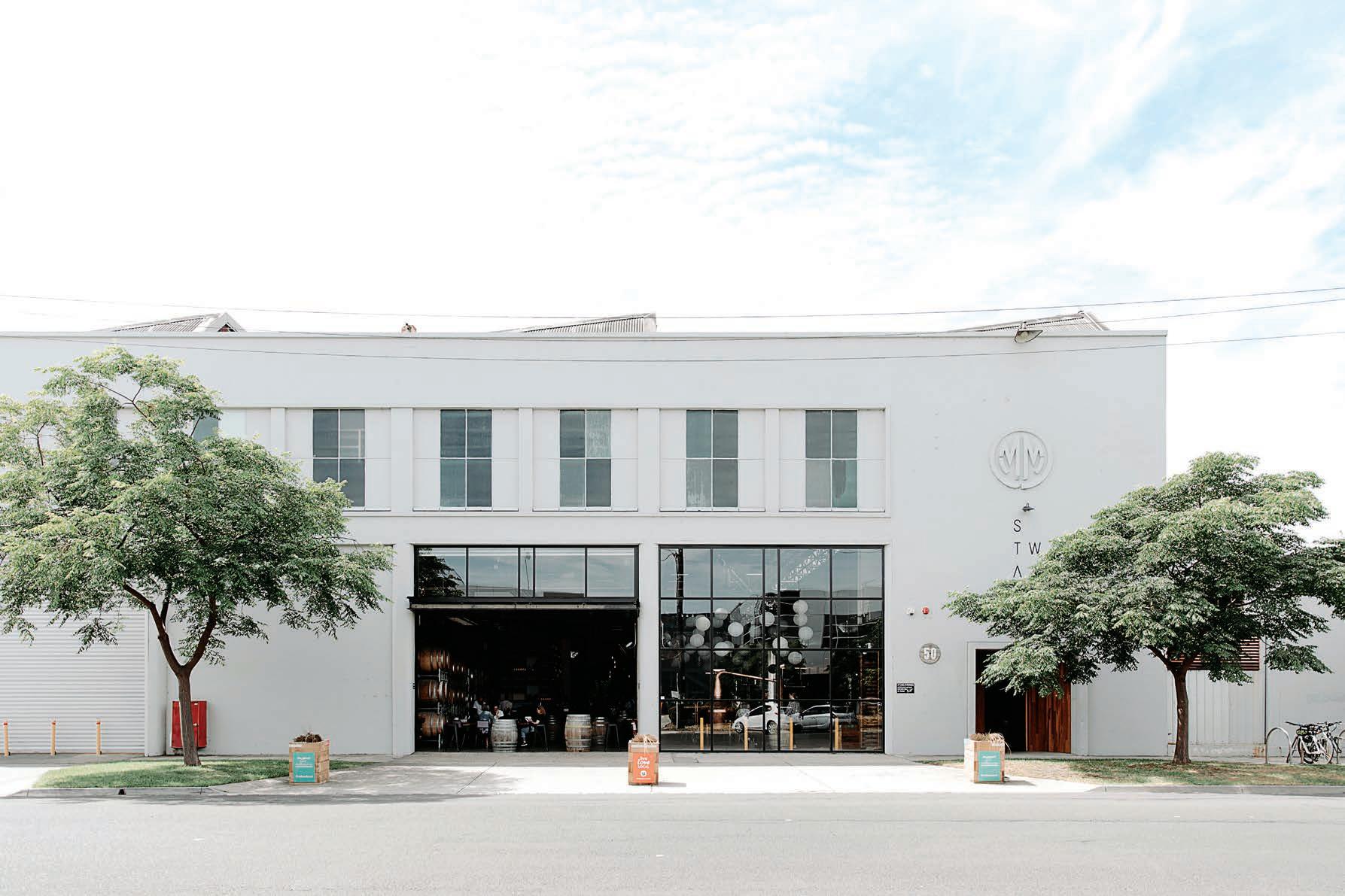
Nestled within Port Melbourne, Starward Distillery and Bar is open Thursday to Sunday.
fearless kind of belief that we could do it. It was almost irrational,” he said.
“I remember thinking no one even knows Australia makes whisky. Why are they going to choose yours instead of that product? And there were a lot of people that doubted. But equally, there were enough people that believed.”
Pioneering the future of Australian Whisky
Vitale takes this belief outside the walls of Starward in his role as vice president of the Australian Distillers Association. With knowledge gained in both roles, he believes that now is an exciting time for the Australian Whisky sector.
“It’s an exciting time for Australian whisky. We have, I think, the most innovative platform to create whisky’s that are distinctive and talk to the place they’re made,” he said.
Despite the sector’s promise, Vitale believes the industry still faces an awareness issue. For Australian whisky to take off in global export markets, he said it
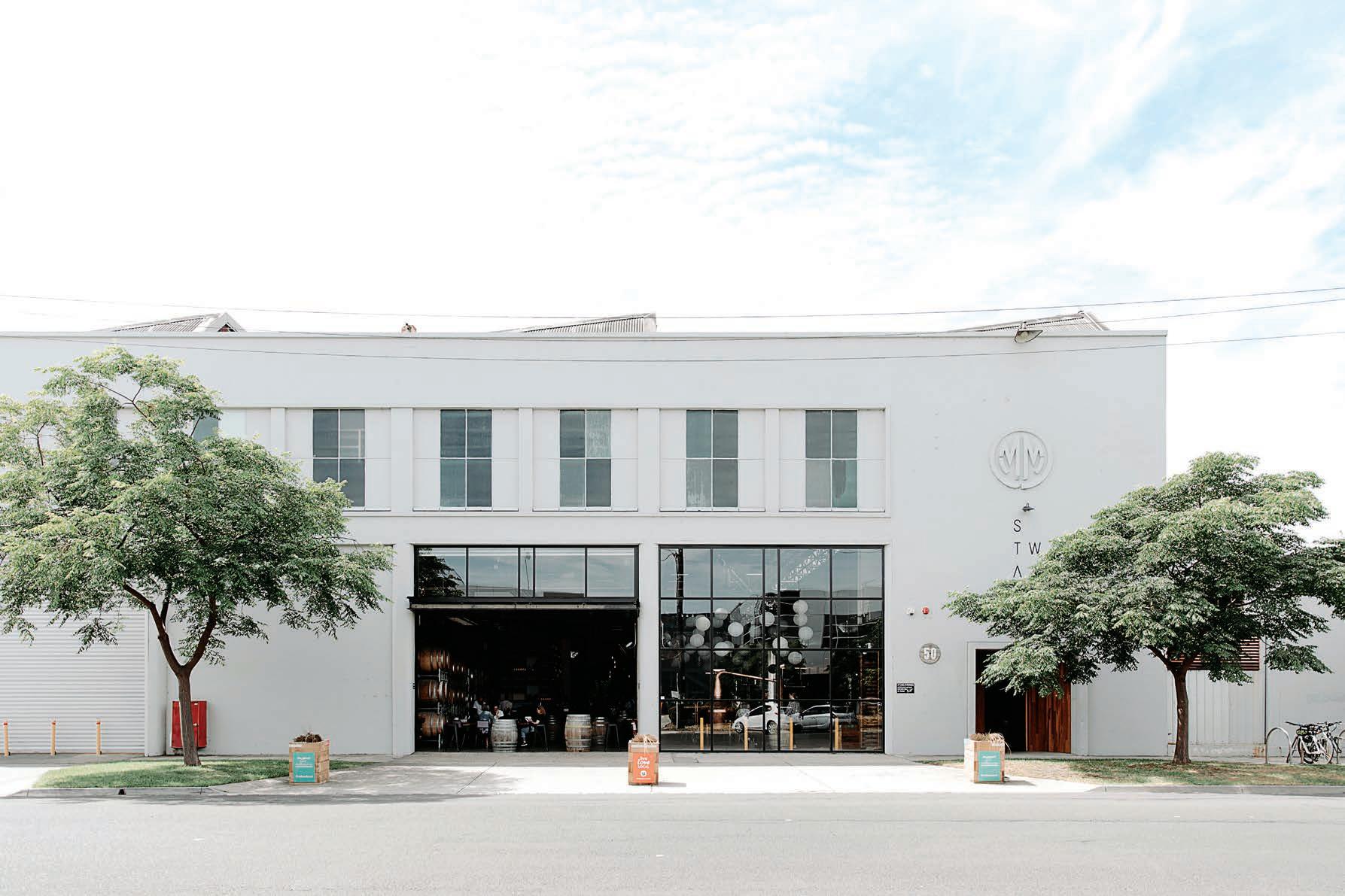
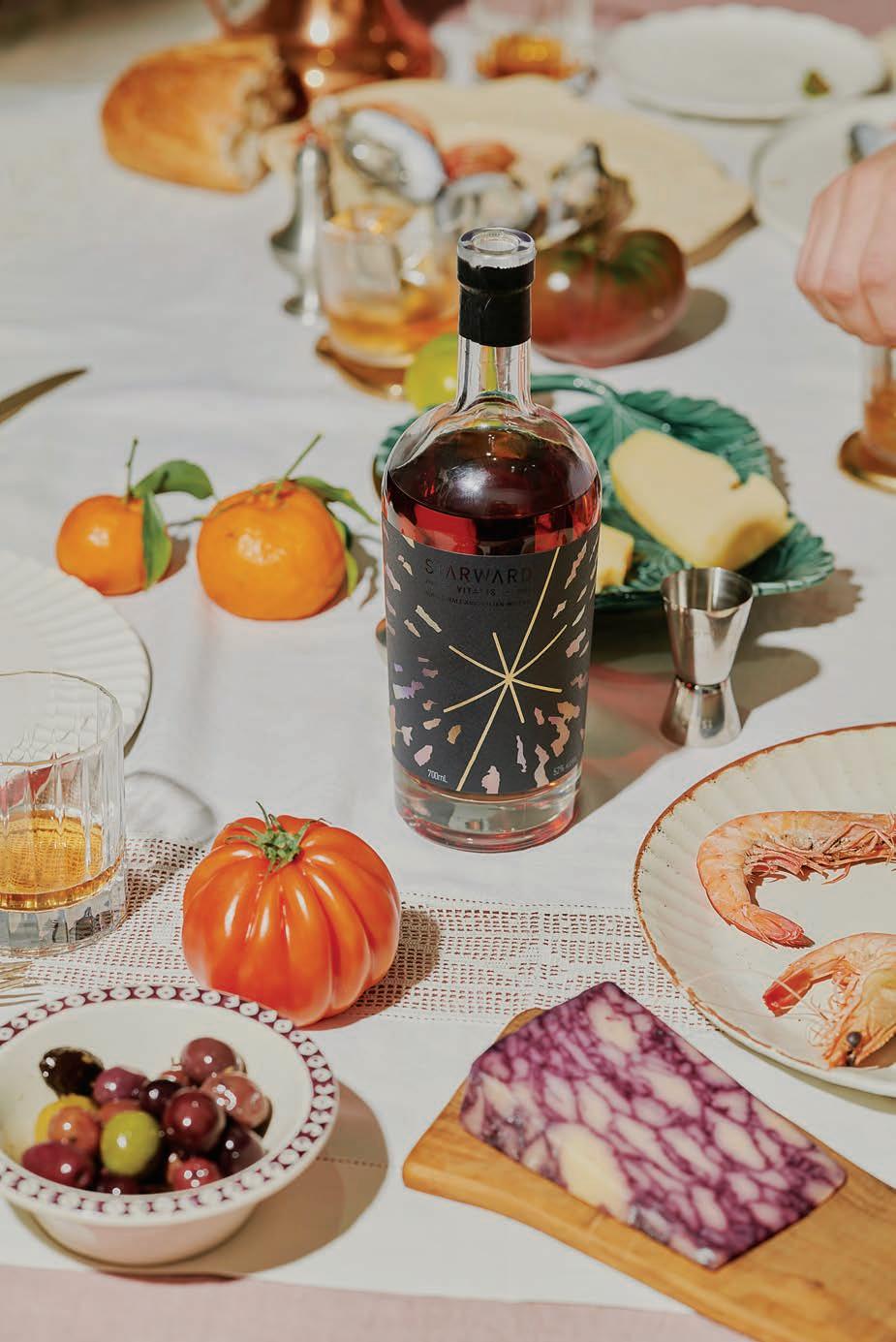
will need government funding to establish a body like that of Wine Australia.
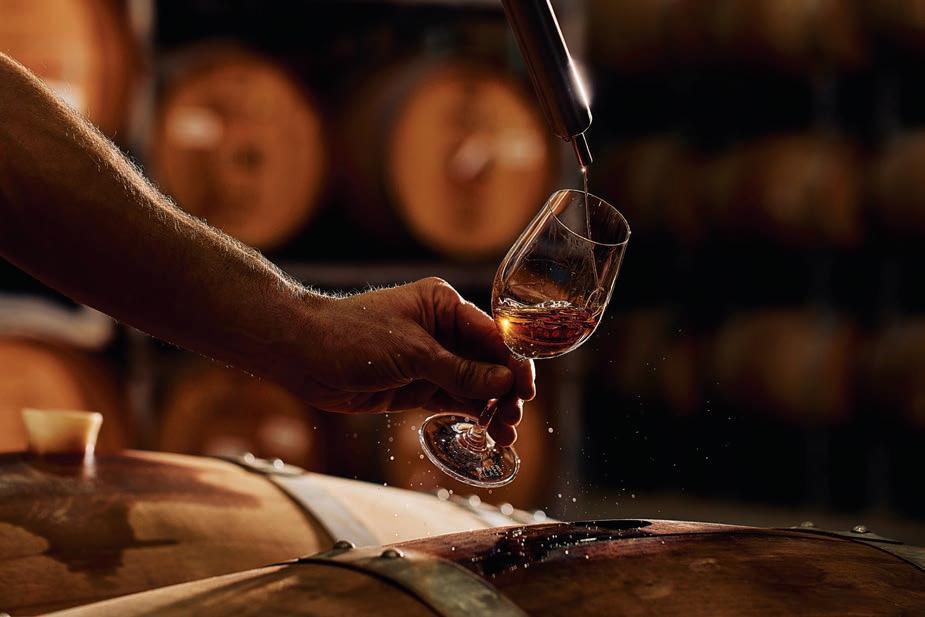
invested in Wine Australia to establish a body that can help build the credibility of Australian wines around the world. Now, four of the top ten most valuable wine labels in the world are Australian,” he said.
“We just need the government to support us the way they did wine as an export industry.”
“We’ll always be a rolling stone when it comes to innovation, flavour and quality,” he said.
“The job to be done for Starward and our other whisky-making friends in Australia is to start putting Australian whisky on the map around the world.
“There’s so much opportunity for us to take these award-winning products to
the world. That’s what gets all of us out of bed every day.”
Starward’s ambitious global goals are already underway, including the further development of its already streamlined US operations.
“The complexity in the US liquor market is the most complex in the world in terms of navigating. Now, however, the team in the U.S. is up and running and growing year on year, which is exciting,” said Vitale. F
‘Vitalis’ is a single malt whisky that was released for the distillery’s 15th anniversary.
Starward ages its whiskies in red wine barrels that are sourced from within a day’s drive of the distillery.
The impact of software solutions on the food and beverage industry can’t be understated.
The power of one’s and zero’s
The food and beverage industry is benefiting from the continued advancement and adoption of advanced software solutions in the manufacturing process.
The adoption of advanced software and product life management (PLM) solutions in food and beverage manufacturing has become integral to optimising operations and ensuring product quality.
As the industry faces increasing demands for efficiency, regulatory compliance, and innovation, these technologies offer crucial tools for managing the complexities of modern manufacturing.
Software solutions in food and beverage manufacturing encompass a range of applications designed to streamline production processes, enhance traceability, and improve overall operational efficiency.
These software and business management tools assist in the integration of various functions within a manufacturing organisation, allowing for real-time data analysis, automated reporting, and seamless communication across departments.
These systems provide a platform for managing core business processes, including inventory management, procurement, production planning, and financial reporting.
For food and beverage manufacturers, software solutions
offer specialised features such as batch production tracking, recipe management, and compliance reporting.
These capabilities are essential for maintaining consistency in product quality and meeting stringent regulatory requirements. For example, PLM solutions like those supplied by Centric Software.
PLM solutions complement other software tools by providing a framework for managing the life cycle of a product, from concept through production to end-of-life.
PLM systems enable manufacturers to track and manage product formulations, packaging designs, and ingredient sourcing, ensuring that all aspects of a product’s life cycle are optimised for efficiency and compliance.
In the food and beverage industry, PLM solutions facilitate innovation by enabling manufacturers to streamline the development of new products and variations.
By integrating PLM with other software systems, manufacturers can accelerate time-to-market for new products, reduce development costs, and enhance collaboration across teams. Additionally, PLM solutions support regulatory compliance by maintaining detailed records of product
specifications and changes, which is crucial for meeting the requirements of various food safety standards.
The integration of software and PLM solutions also supports better data management and analytics.
Advanced analytics tools embedded in these systems allow manufacturers to derive actionable insights from their data, enabling more precise forecasting, demand planning, and resource allocation.
This data-driven approach enhances operational efficiency and supports strategic decision-making, ultimately contributing to improved profitability and competitiveness.
CitySoft is one such company that provides data-based solutions, and director Ian Hill said being able to leverage data points provides businesses with a host of benefits.
“The technology introduced into the industry has caused enormous change,” he said.
“The shift from paper-based processes and manual spreadsheets to sophisticated digital solutions is no longer optional but essential for modern businesses.”
In this edition we detail how CitySoft’s success in this niche is largely due to its adaptability to the
evolving food and beverage industry, which has been reshaped by compliance requirements, smart machines, and the integration of IoT and big data.
Hill highlights how globalisation and new competitors have impacted the industry, among other key points of note.
He said the industry has embraced software innovations and by doing so the face of the industry is changing.
Despite the advantages of adopting these technologies, food and beverage manufacturers must navigate several challenges, including the cost of implementation, the need for staff training, and the integration of new systems with existing infrastructure.
Successful adoption requires careful planning, investment in technology, and a commitment to ongoing support and maintenance.
By leveraging advanced software tools and PLM systems, food and beverage manufacturers can achieve greater efficiency, compliance, and success in their operations.
The integration of software solutions and technological innovation in food and beverage manufacturing is more than a trend; it is a necessity for staying competitive in a rapidly evolving market.
By enhancing operational efficiency, ensuring quality and compliance, driving innovation, and supporting sustainability, software solutions are transforming the industry. F
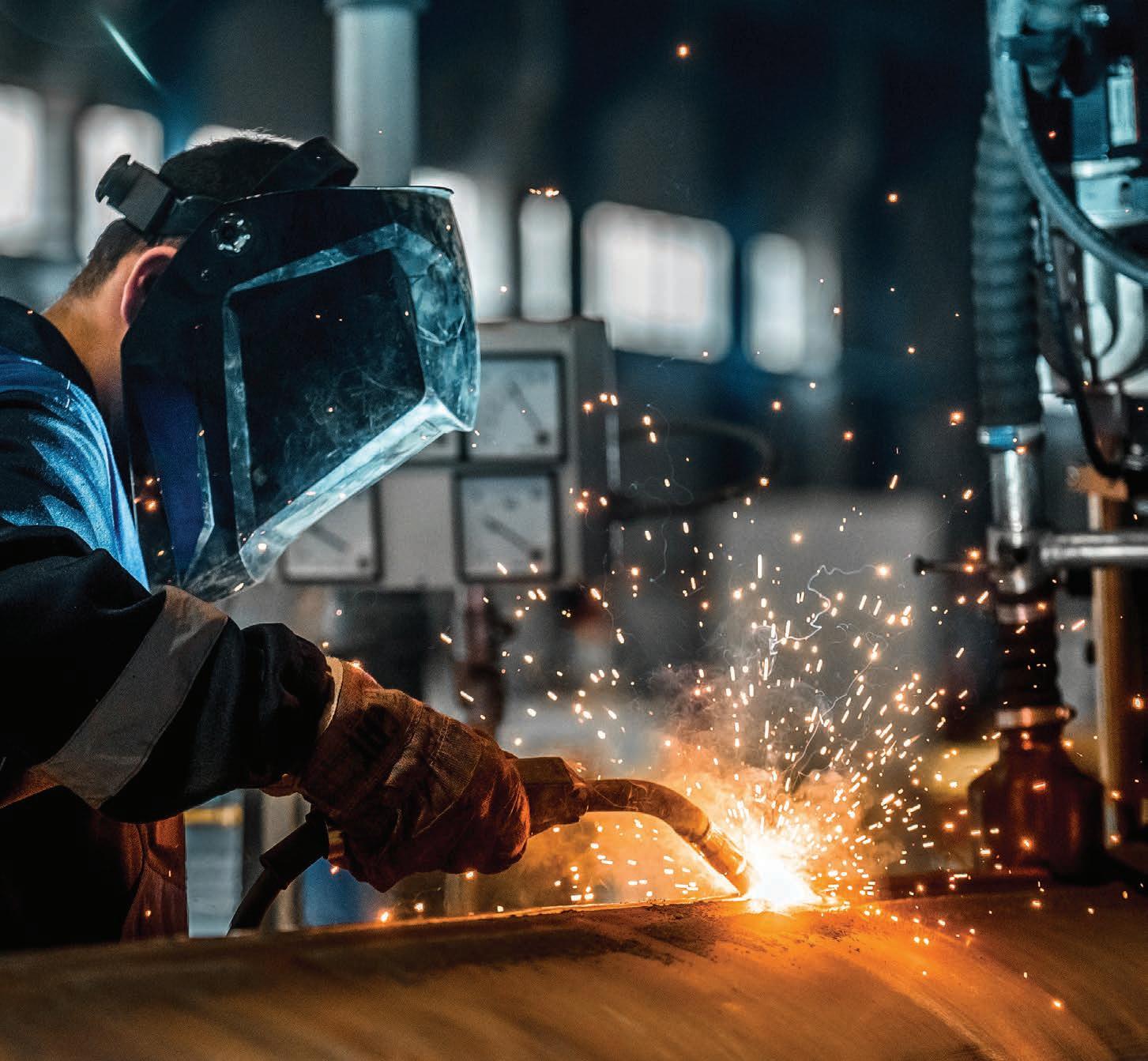
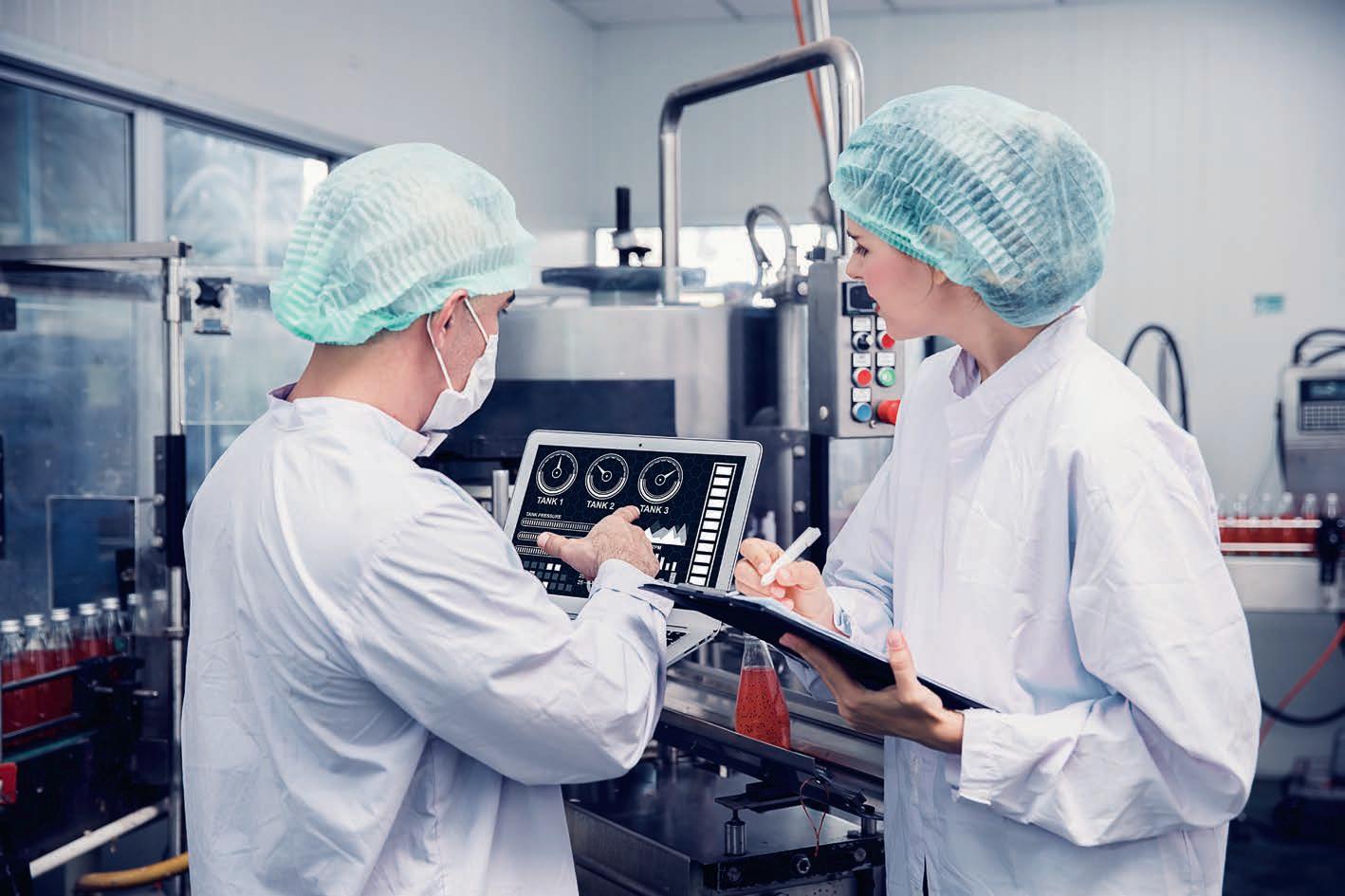
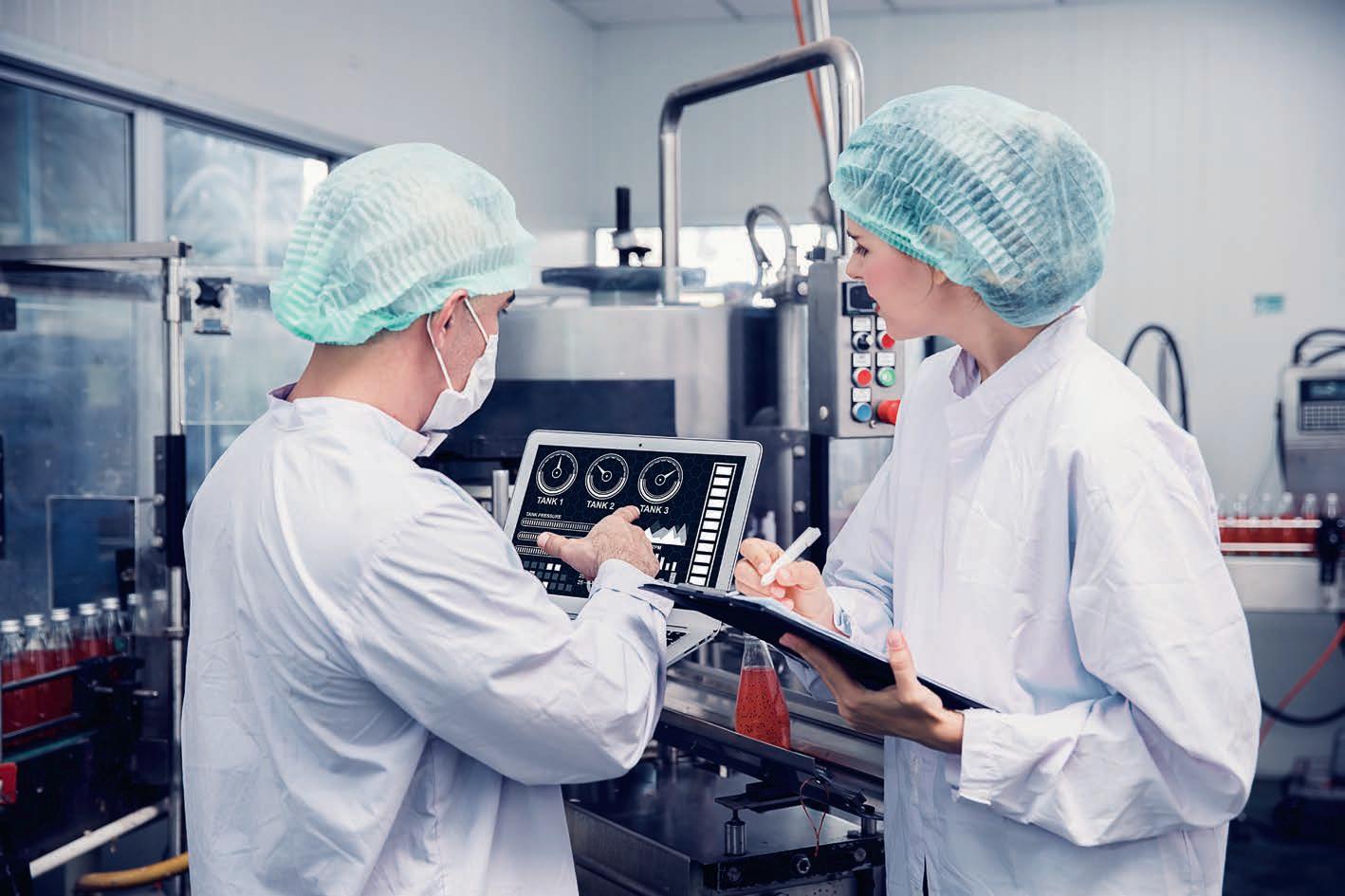
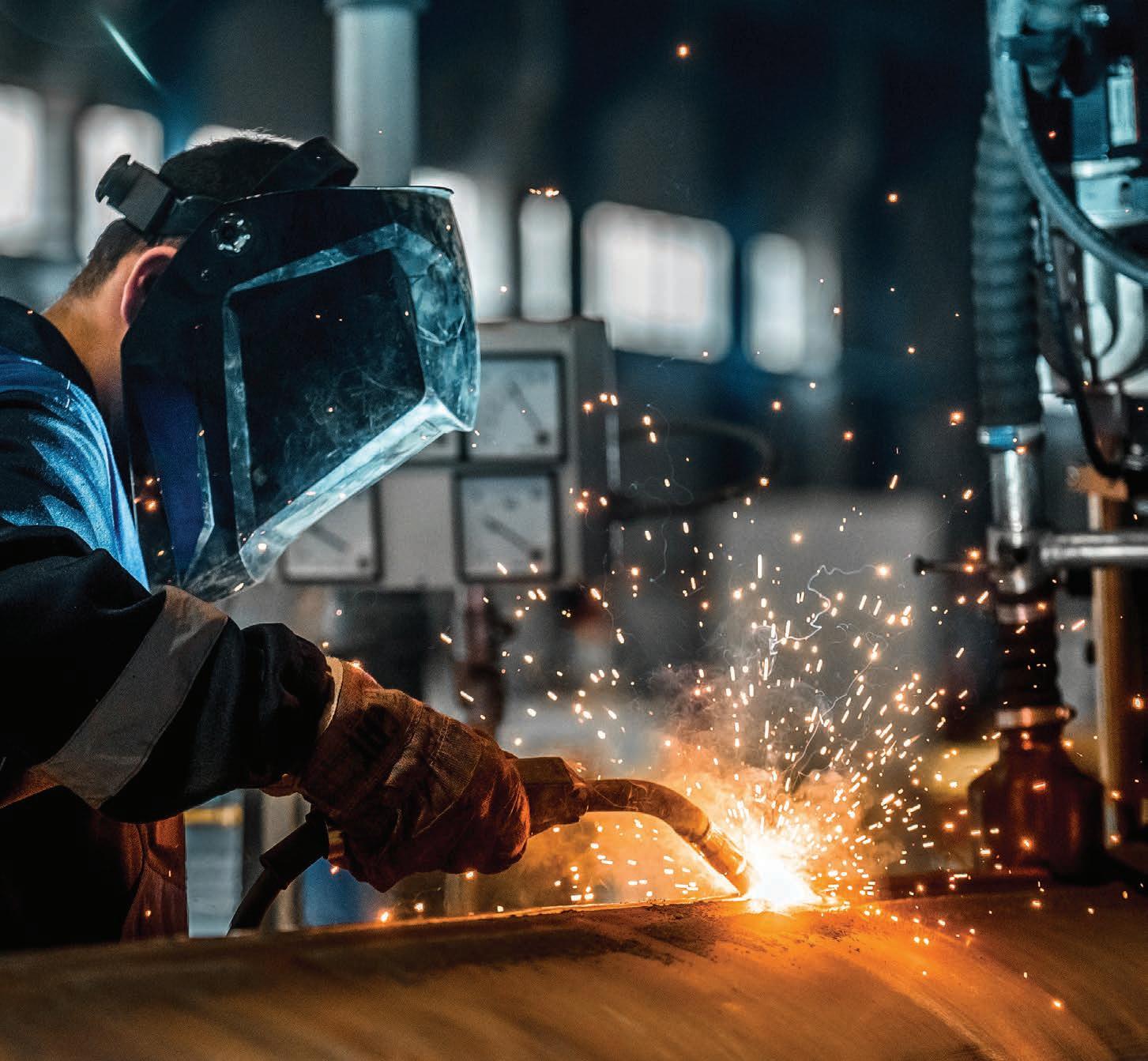
Utilising data to improve manufacturing
Software solutions are helping manufacturers make the most of real time production data to improve output, efficiency, and profitability.
CitySoft, once a traditional ERP consulting firm focused on delivering business solutions to the mid-market, has evolved into a specialised leader in the food and beverage manufacturing sector.
The company’s transformation began in earnest around 2010, when they adopted a new application called Sage X3 designed to cater specifically to this industry. By 2015, CitySoft’s expertise in food and beverage became a cornerstone of its business.
Initially, CitySoft explored various market solutions, evaluating products like BatchMaster and Beas for SAP Business One.
The company settled on representing three main products: two catering to the needs of growing and established businesses and one designed for small to medium sized enterprises.
This diversified approach allowed CitySoft to serve a broad range of businesses, including manufacturers of well-known brands, emerging brands and contract manufacturers.
Over time, CitySoft has become synonymous with food and beverage manufacturing expertise.
Its success in this niche market can be attributed to its ability to adapt to rapid changes in the industry. According to CitySoft, the landscape of food and beverage manufacturing has been reshaped by evolving compliance requirements, the rise of smart machines, and the proliferation of IoT and big data.
“There’s been a significant shift in the industry due in part to globalisation but also due to the availability of smart technologies,” said CitySoft director, Ian Hill.
The firm has focused on providing the industry with technology solutions that go well beyond the traditional domain of ERP software systems. This includes integrating smart machines, sensors, MES systems, and CMMS systems to industry specific ERP software to help clients capitalise on the new sources of digitised data.
CitySoft addresses a common
challenge in the industry: information silos. Often, dissimilar systems fail to communicate effectively, leading to inefficiencies and costly errors.
Hill spoke about a recent case where the absence of systemised storage controls and system integration resulted in a major write off of stock.
“The flow of new technologies into the industry has resulted in enormous change,” said Hill.
“The shift from paper-based processes and manual spreadsheets to sophisticated digital solutions is no longer optional but essential for businesses to compete and succeed.”
CitySoft is helping modernise businesses by introducing and integrating new industry specific software and hardware systems with existing systems; optimising business operations; and by providing businesses with actionable insights.
The company’s approach involves more than just implementing new technology.
“We help stakeholders take digitised data from many sources and turn it into effective information,” said Hill.
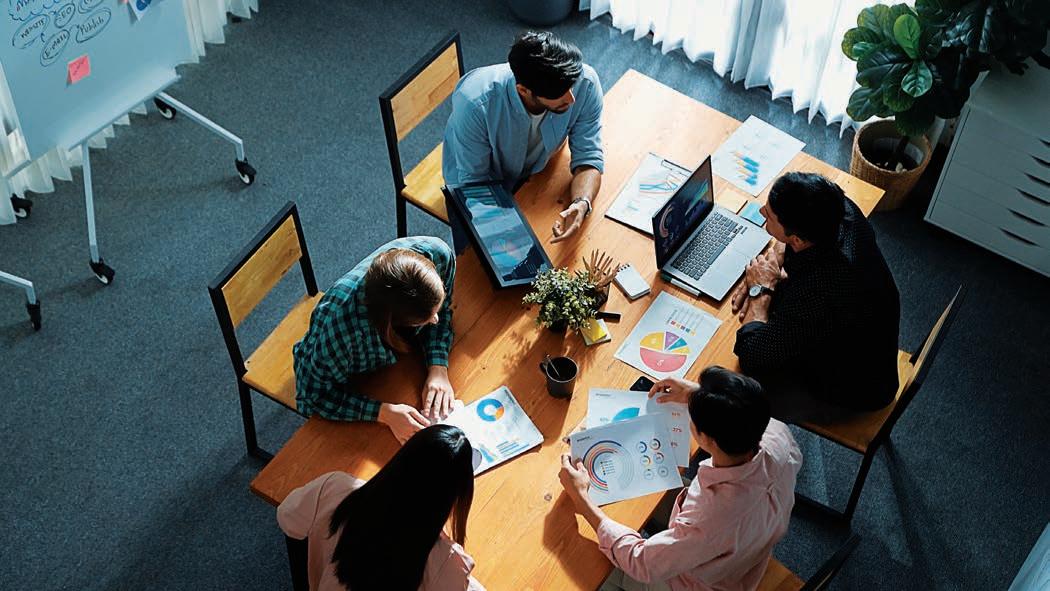
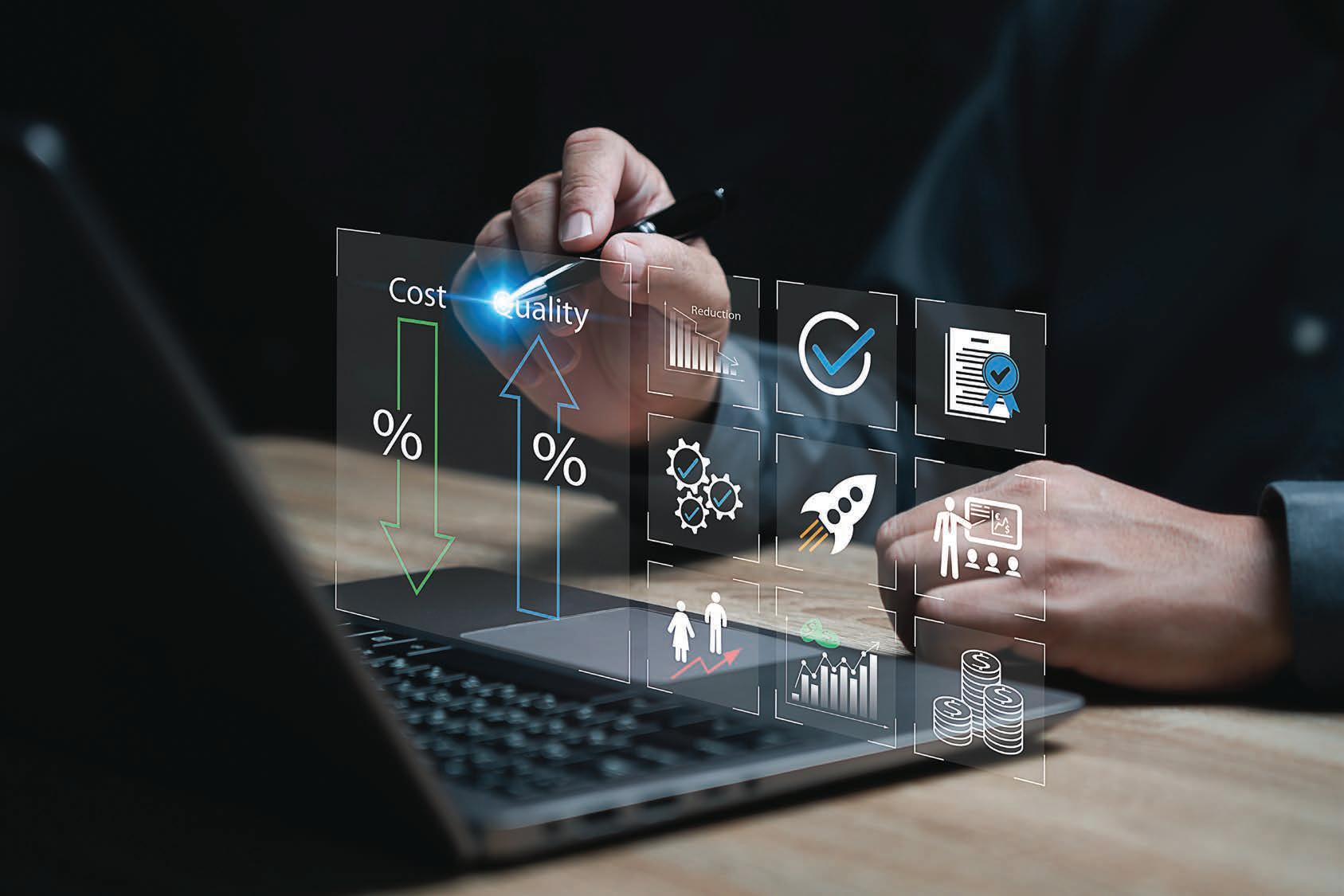
This process turns multiple sources of data into valuable insights that drive better decision-making and operational efficiencies.
In an industry where adoption of new technologies continue at pace, CitySoft stands out as a forwardthinking partner that not only understands the complexities of food and beverage manufacturing but also provides practical solutions to help businesses thrive in a data-driven world.
“In the past, the primary challenge was how do you convince businesses that they’ll be better served by spending money on modernising their business systems first, rather than investing in a brand-new machine,” said Hill.
“The thinking has changed. Now there is a growing recognition that prioritising the optimisation of existing machinery at the same time as modernising business systems is a strategy worth exploring”
CitySoft addresses a common challenge in the industry: information silos
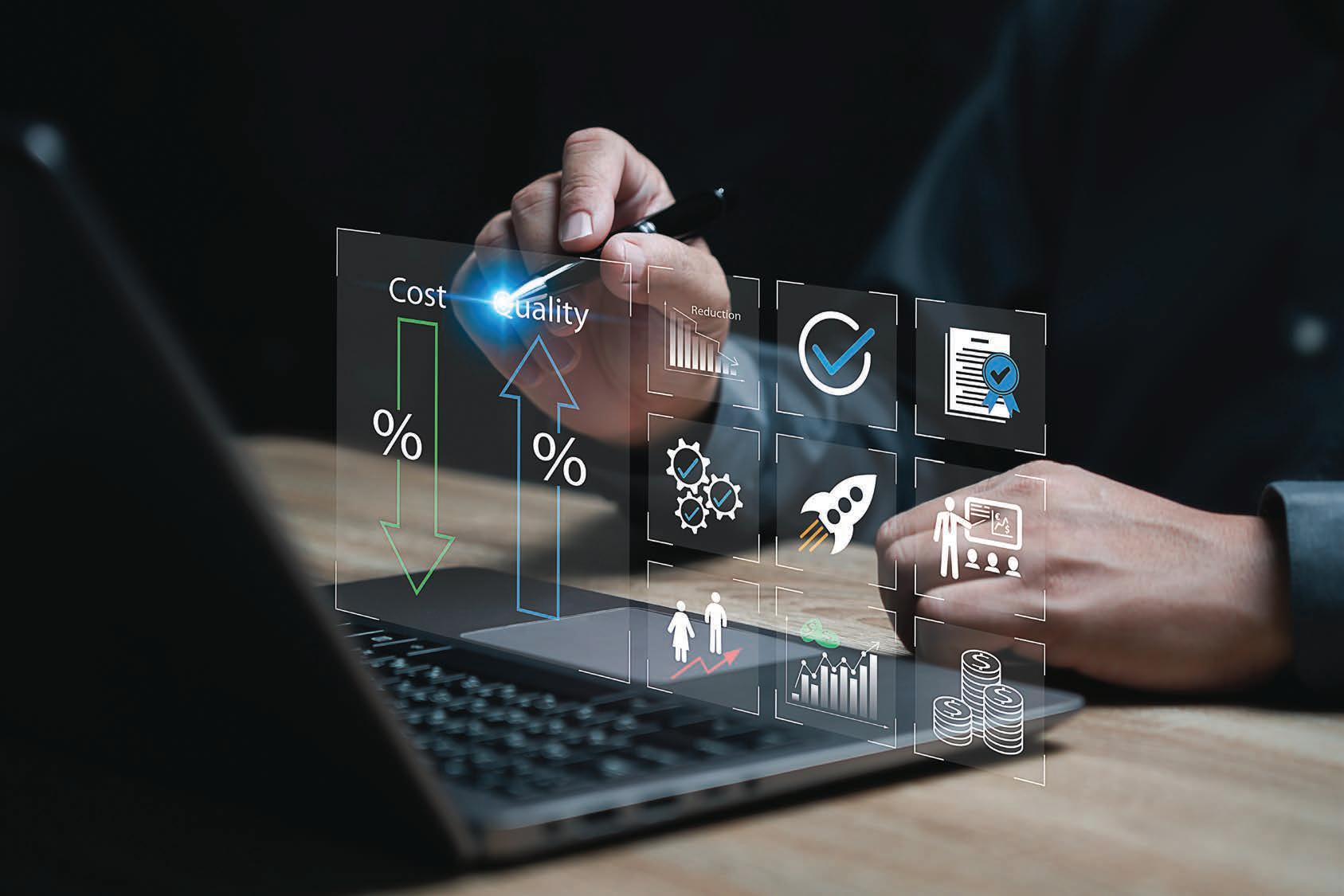
By introducing real-time monitoring of equipment businesses can optimise machinery performance, better schedule maintenance, and avoid unnecessary downtime.
“Smart sensors can extend the life and effectiveness of manufacturing equipment, from an output and a quality perspective,” said Hill.
“This real-time information makes a huge difference to the efficiency of the operation and, by extension, improves profitability by drawing down costs.”
Consider a scenario where a piece of equipment is designed to process 2,000 items per hour with 95 percent efficiency but has dropped below this benchmark.
“That information is fed back to the ERP system in real time, which may lead to the production manager scheduling a top up production order to meet production targets,” said Hill.
“Rather than discovering at the end of a run that you’re short, you can avoid that outcome altogether.”
This proactive approach is demonstrated by a recent success story with a large CitySoft customer in Victoria.
The introduction of a new Overall Equipment Effectiveness (OEE) solution led to impressive results for the client.
“We put in a trial for them and within a very short period of time they contacted us to say how thrilled they were with the results already,” said Hill.
“They’ve now introduced the product across all their machine lines.”
The simplicity of this innovative solution adds to CitySoft’s appeal.
“The great thing about the OEE solution is that it is a plug and play device,” said Hill.
“It doesn’t need any extensive technology capabilities to implement it, and the information it generates for the production manager, and others, in dashboard and report formats are easy to read and intuitive.”
The digitisation of data from multiple data sources combined with systems integration means every department involved in production has access to real-time accurate data which they can act upon with great confidence.
“It’s a well of information in real time,” said Hill.
“Our integrated solutions include information about equipment performance, linked to production schedules, work orders, the ERP system, and maintenance management software, to give operators and management the full picture of what’s happening in their business.”
Another benefit of modernising these business systems is also in being able to utilise your workforce in more efficient ways by giving them more time to work on other important tasks.
“You don’t want intelligent people wasting time on manual tasks that can be managed through automation, you want them to have more time to conduct other important tasks including
Major rewards will flow from bringing all the data and systems together in the simplest and most efficient way.
interpreting data,” said Hill.
Ultimately, Hill said, the foundation of CitySoft’s software solutions can be easily defined.
“Our industry solutions are all about turning data into information, automating and optimising business processes, connecting systems and helping companies capitalise on technologies that cut operating costs and improve profitability ,” he said.
“Whilst the industry has embraced technology, mainly in the form of smart machines, IoT and sensors, it hasn’t necessarily made the most of the streams of data the modern technologies now produce. They haven’t invested to the same extent in modernised ERP, Bi and big data analysis tools and IT infrastructure to support the growth in data volumes and their reliance on technology.
“The major rewards of IT modernisation will flow from bringing all the data and systems together in the simplest and most efficient way so a business can perform at their optimum.”
Private label gaining ground in grocery
Private label products have been steadily growing in popularity thanks to economic factors such as inflation and the changing spending habits of consumers.
Over the last few decades, private labels have continued to grow steadily in popularity.
Store brands aren’t a new idea; they’ve been around for a long time, and Centric Software can help you capitalise.
From A&P’s launch of Eight O’clock Coffee in the early 1900s to Loblaws’ famous bright yellow ‘no name’ boxes in the 1970s, and now modern retailers like Aldi and Trader Joe’s, where most products are private labels, store brands have steadily risen in popularity.
Record-breaking numbers
The 2024 PLMA Private Label Report confirms this trend with data, showing a YOY record-setting 4.7 percent increase in private label dollar sales compared to a 3.6 percent rise for national brands.
The primary force behind private labels is economic, as indicated by a PYMNTS Intelligence survey of over 1,700 US consumers where 86 per cent of grocery shoppers have altered their purchasing habits due to inflation.
Meanwhile, total store brand dollar sales during 2023 moved ahead to
$236.3 billion, an increase of $10.1 billion from the previous year and setting another record, surpassing the former high mark that was set last year Research firm Numerator also revealed that private label products are capturing a substantial share of leading retailer sales, ranging from a peak of 80 per cent at Aldi, 69 per cent at Trader Joe’s, 33 per cent at Sam’s Club and H-E-B, 29 per cent at Dollar Tree, 27 percent at Kroger, 24 per cent at 7-Eleven, to 23 per cent at Target. And the list continues beyond this.
Leaning into private label
Want to join the private label trend?
Consider a modern, flexible Product Lifecycle Management (PLM) solution to boost and refine your store-brand options for cost-conscious shoppers.
Centric PLM centralises product information and streamlines product development processes.
Retailers can quickly adapt to economic changes and the demand for affordable, high-quality products.
This streamlined approach is key to staying competitive with national brands
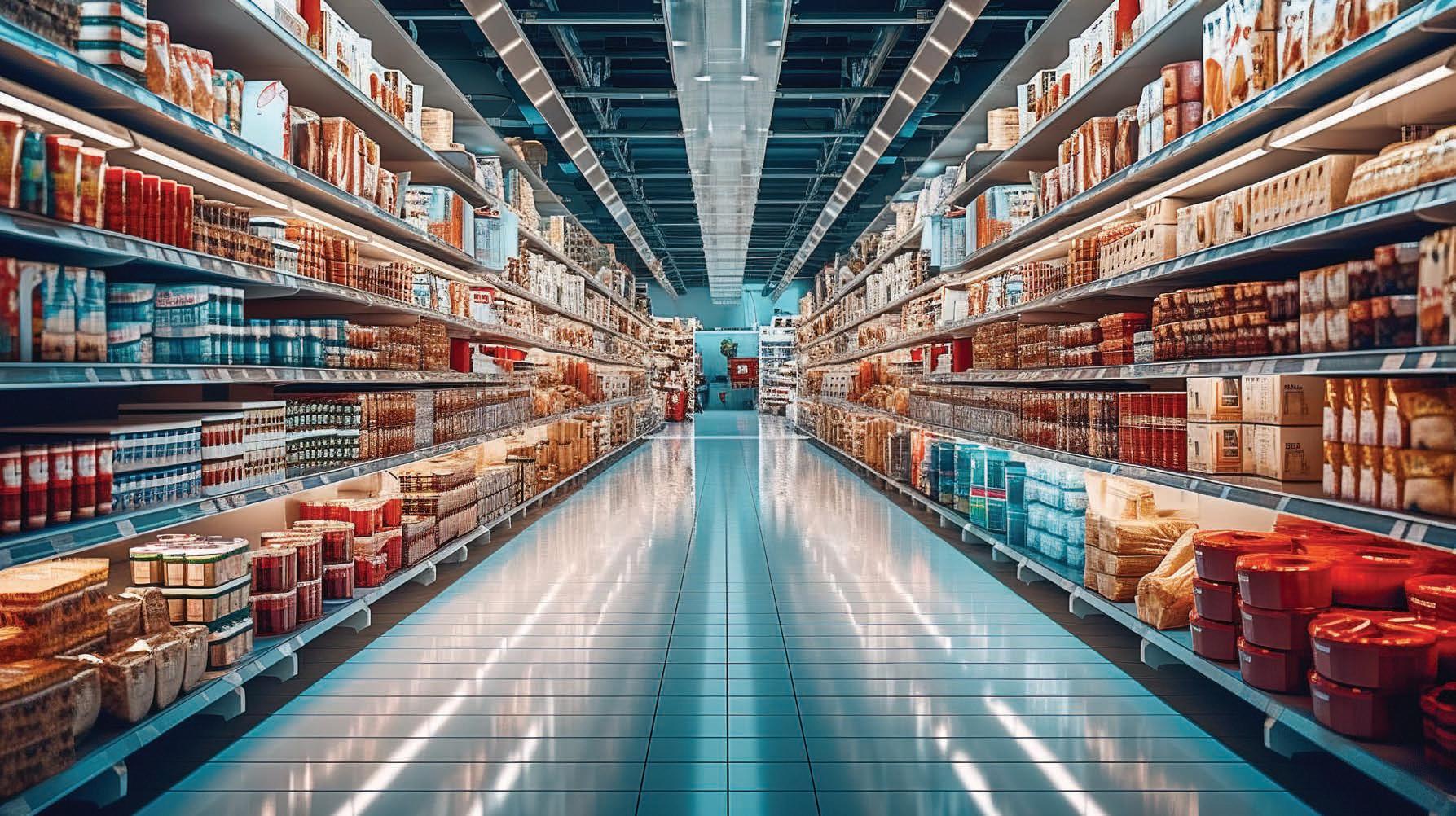
Research has shown a YOY record-setting 4.7 percent increase in private label dollar sales.
Image:
on pricing.
Meanwhile, consumer habits are shifting as well. Since the COVID-19 product shortages, people have learned to take what they can get if the national brand is unavailable.
Now that those shortages are mostly in the rear-view mirror, consumers have not reversed course to fully go back to national brands.
The quality perception of store brands is up; price is no longer the only reason for shoppers to turn to private labels.
The main draw
A 2024 FMI report reveals that more than half of consumers now choose specific stores due to private-label products. This marks a rise from 2016 when only a third of shoppers selected stores based on brand offerings.
Beyond cost, still the primary driver for buying store brands, quality and value is increasingly important.
Retailers are approaching private label lines as if they are manufacturers because that’s effectively what they’ve become.
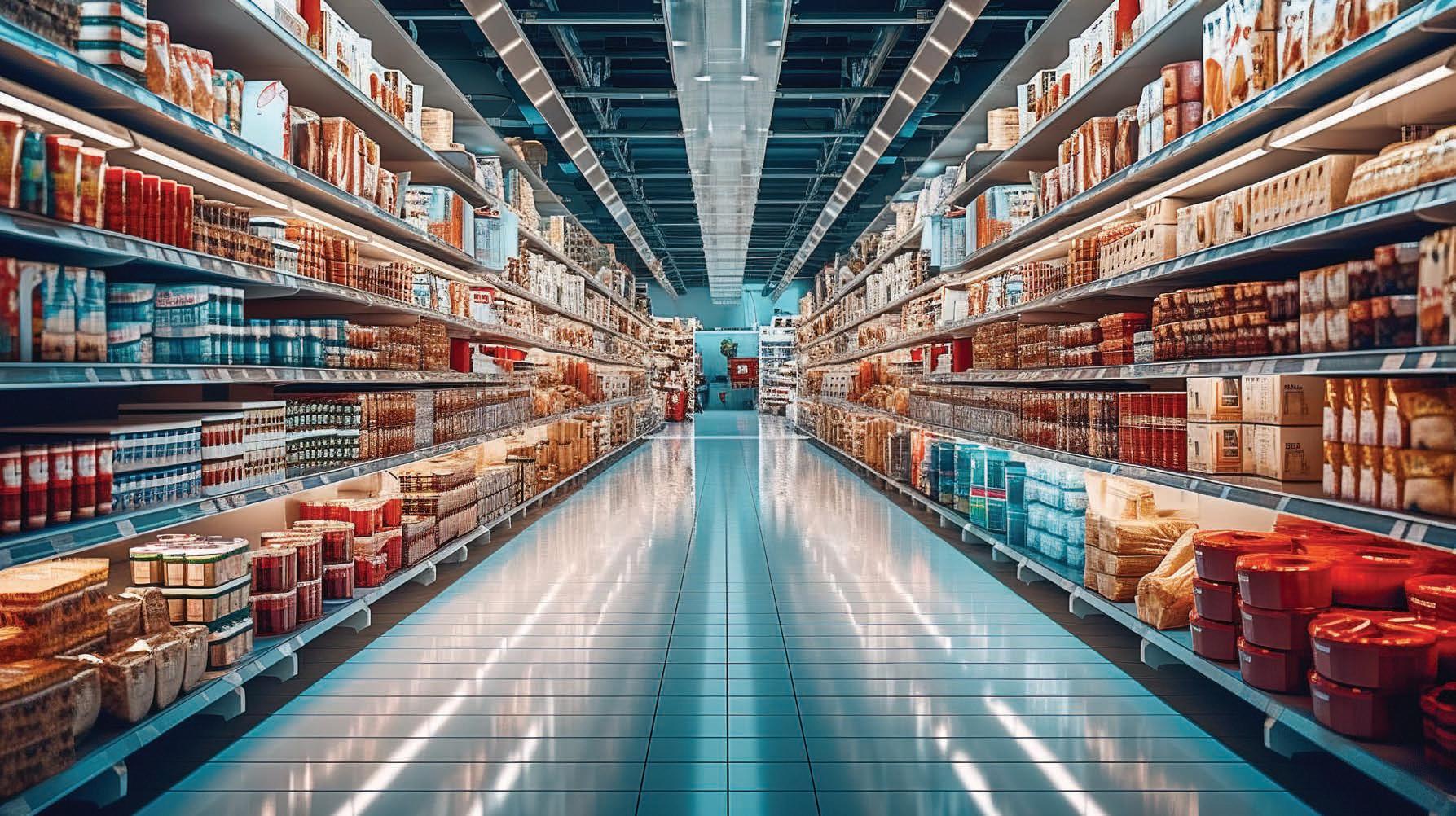
They handle all product development stages, including marketing, research and development, ingredient sourcing, regulatory compliance, labelling, and packaging, in-house.
This is where having real-time visibility into every supply chain step and tools for better supplier collaboration become crucial.
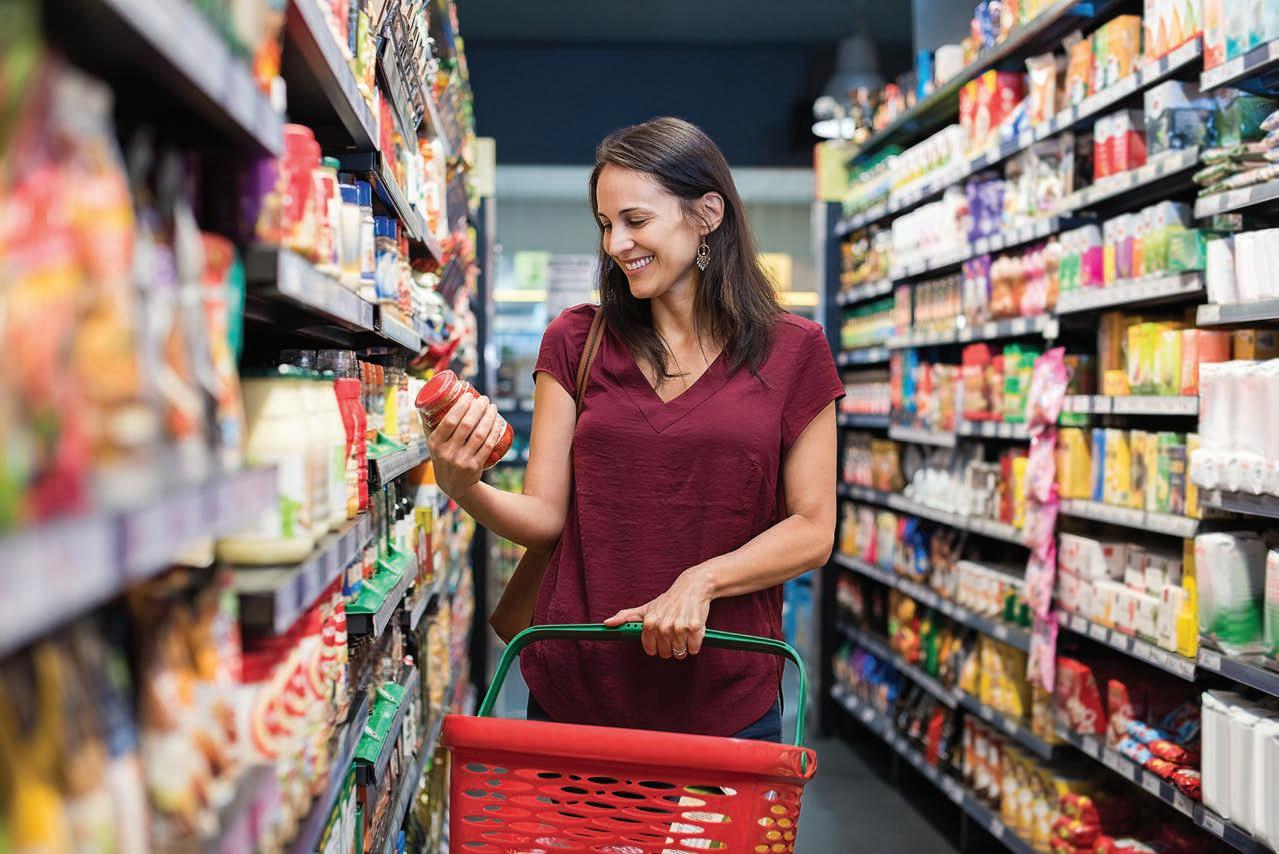
With PLM, retailers can now ensure consistent quality, which is essential for building customer loyalty and attracting new shoppers.
Modern PLM enables quick response
Grocery retailers’ advantage over national brands is that they have consumer databases and can react quickly to create products people want.
Food trends like organic, gluten-free, and plant-based items can be developed and slotted into a company’s private label lines while controlling exact product characteristics, introductiontiming and coordination with shelving and marketing strategies for the product launch.
Meanwhile ‘healthy’ product attributes within a unified store-brand line address consumer needs effectively.
Centric PLM manages complex product portfolios effortlessly, providing retailers with tools to innovate and adjust its private label offerings to align with consumer preferences.
Centric PLM centralises product information and streamlines product development processes.
The company also simplifies tracking of government regulations (FDA, USDA, EU, FSANZ) and ingredient certifications such as kosher, halal, and vegan when all are housed in one digital repository.
Sustainability
Consumers are increasingly aware of sustainability and make choices based on it. According to an NIQ report, 69 per cent of consumers feel that sustainability matters more now than two years ago.
They seek assurance that the ingredients in their food are sourced without harmful environmental practices.
Meanwhile, legislation also plays a role: in the EU, Environmental Social Governance (ESG) reporting is mandated for companies that meet certain criteria, such as size and being listed on EU-regulated markets.
In terms of consumer perception, packaging is the most visible factor—less
plastic is preferred, and recyclability is important if plastic must be used.
With Centric PLM, grocery retailers can incorporate sustainable practices into product design, manage ingredient sourcing, ingredient certifications as well as sustainability metrics.
Centric is set up to track the percentage of recycled materials in a package to make sure it meets eco-requirements.
The future of private labels is bright
Recently released figures from Circana (the merged IRI and NPD firm) indicate that private label sales could surpass $250 billion in 2024.
Currently, private label accounts for about 22 cents on the dollar of grocery spend.
It is not disappearing. As companies advance into higher-end private label products and expand current storebrand lines, the private label market
share is set to grow.
With Centric Software solutions, flexibility and configurability support adapting to future retail trends, such as the demand for more personalised customer experiences, for instance.
The software’s scalability guarantees that retailers can consistently innovate and remain ahead of the competition as consumer demands change.
Centric Software solutions enable grocery retailers to adeptly manage their private label products, tackling economic pressures, evolving consumer preferences, and the demand for highquality, sustainable items.
This positions Centric as a crucial partner in advancing the success of private labels in today’s competitive grocery market.
To learn more, down the F&B Rise to the Sustainability Challenge eBook on the Centric Software website F
A 2024 FMI report reveals that more than half of consumers now choose specific stores due to private-label products.
A new factory is not always the best approach
The team at RMR Process helps clients increase output and develop more efficient processes through expert consultation that ultimately saves on costs.
RMR Process has established itself as a key player in Australia’s food and beverage manufacturing industry through expert insights on how to best enhance the entire production process.
Based in Melbourne, RMR Process employs a team of expert engineers with a proven track record in designing and constructing top-tier food processing facilities, alongside providing strategic growth support to clients.
RMR Process takes pride in helping customers form strategies to achieve their growth objectives, partnering with manufacturers aiming to enhance their process capabilities and facility design, as well as with multinational corporations seeking expert consulting for expansion and optimisation projects.
Leveraging over 25 years of industry experience, RMR Process has developed a scaling model that supports growth while adapting to the dynamic market landscape.
This model helps manufacturers make cost-effective decisions about expanding their capabilities while managing associated risks.
Before the onset of COVID-19, manufacturing industries primarily focused on streamlining or optimising their process lines.
Today, however, the landscape
As businesses navigate the complexities of the post-pandemic world, they are expanding and enhancing existing process lines to boost throughput capacity, aiming to meet heightened demand while managing operational costs.
Peter Taitoko, director of RMR Process, is seeing first-hand this ongoing transformation of the food and beverage manufacturing industry.
The pressure on food manufacturers today comes from all directions, including high supply chain costs, margin pressures from retailers, high energy costs and compliance costs.
For those needing to expand operations the challenges extend to high construction costs, onerous town planning conditions and lengthy planning processes.
The post-pandemic era has driven a transformation towards local manufacturing, driven by both necessity and cost-saving measures.
Many manufacturers are experiencing unprecedented activity due to the demand for locally produced food and beverages as well as emerging growth channels such as direct-to-consumer products.
Companies that are well-positioned with high-demand products, like readyto-eat meals and convenience foods, are facing soaring demand and struggling to

Conversely, those not adapted to the current market conditions are struggling. This development reflects a “two-speed economy” in the food sector.
Both ends of the spectrum are increasingly looking to increase output and reduce costs. Optimising the balance between operational staff and automation remains critical.
This development arises from a dual challenge: while governments push for job creation, manufacturers grapple with high labour costs and a shortage of suitable workers.
For example, most grant funding options target job creation rather than how Australia’s high-quality products for local and overseas markets can be lever-aged, creating a stronger food and beverage industry and supply chain through non-traditional channels.
This has created tension between the desire for more employment opportunities and the necessity of using automation to control costs.
As a result, manufacturers are striving to find an ideal balance between operational staff and automation.
“More and more we’re looking for opportunities to speed factories up and increase process throughput and reliability before we consider capital intensive facility up-grades or new builds,” said Taitoko.
Every factory has unique needs, which is why the initial step in RMR’s model is to encourage the manufacturer to consider a pivotal question, if they maintain the same number of operational staff but increase productivity, would that be appealing? The typical response is ‘yes’.
“Although our core business is designing and building food factories, we always start by minimising or eliminating the need for construction simply because of cost and the fact that the food industry tends to move at a much faster pace than the construction industry and local councils” said Taitoko.
While full automation is feasible for large high-end companies, most local
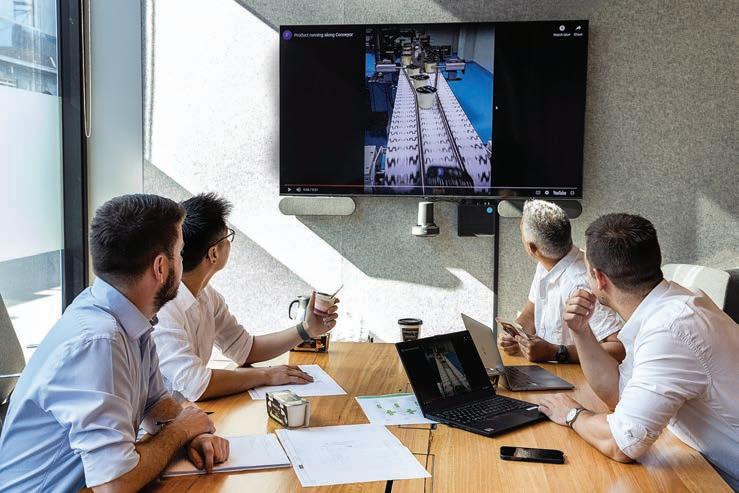
businesses lack access to such advanced technology.
Therefore, the focus is on enhancing process efficiency and accelerating operations while retaining essential human roles in a staged approach.
“We start by reducing or removing labour-intensive repetitive tasks and providing automated solutions where it is practical and affordable” said Taitoko.
“Our intention is not necessarily to remove labour from factories, rather to increase productivity and increase outputs with existing staff numbers.”
Upskilling is a crucial aspect of this transition.
Workers are trained to move from manual roles to more technical positions, such as line technicians.
Staff may be redeployed to roles in raw materials handling, packaging, or distribution.
Alternatively, they are upskilled for quality control positions. The approach aims to make the most of the existing workforce while adapting to evolving demands.
The focus then changes to enhancing facility performance with the current workforce and infrastructure.
For instance, by incrementally increasing the instantaneous throughput of key capital equipment throughout the entire process and adding automation capability to help smooth out the line performance, you can gain significant upside in production volumes, in some cases many times existing capability.
Taitoko said RMR Process has a string of examples of working with clients where throughput was significantly increased without adding extra operational staff or expanding the facility.
These cases underscore the potential of optimising existing operations rather than constructing new facilities allowing
RMR Process employs a team of expert engineers with a proven track record in designing and constructing top-tier food processing facilities.
RMR Process takes pride in helping customers form strategies to achieve their growth objectives.
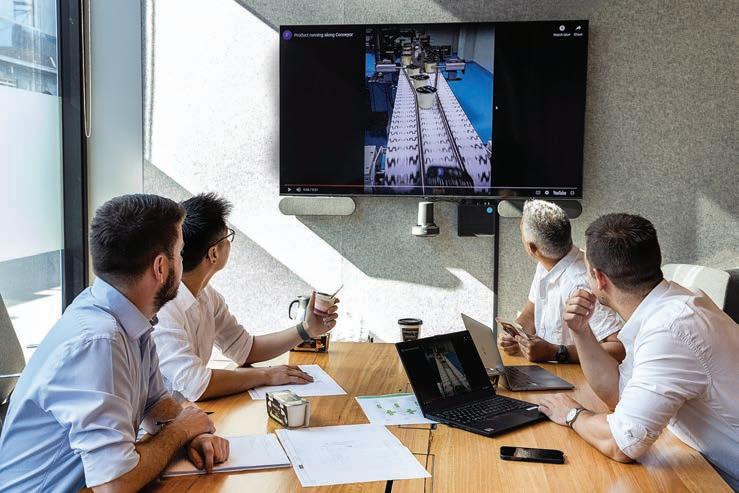
companies to scale in control.
If new products are desired, a modest investment to modify the existing line might be proposed.
This strategy emphasises leveraging existing facilities, equipment, and workforce effectively, rather than relying solely on facility expansion.
COVID-19 has also exacerbated global supply chain issues, complicating the ongoing procurement of imported ingredients.
In response, manufacturers are exploring ways to add value to these ingredients domestically and this should have a positive long-term impact on
the industry.
For example, efforts are being made to source and mill dried ingredients locally, leading manufacturers to explore local value-adding processes, whether through co-manufacturers or by maximising their own facility through in-house development.
The challenge extends beyond local production.
The Australian food industry struggles with the underutilisation of its potential, particularly regarding exports.
“We need to do better at leveraging off our high-quality products and increase our own value-adding opportunities from ingredient supply to finished goods,” said Taitoko.
The prevailing mindset of exporting primary produce with minimal value addition persists, despite the government’s focus on manufacturing jobs rather than strengthening existing industries.
“It’s rather like watching iron ore get shipped off only to import it back as ball bearings a year later. In food we need a total mindset shift towards a local supply chain that keeps up with rapidly changing local and overseas consumer demands,” said Taitoko.
However, funding remains an obstacle, exacerbated by the withdrawal of manufacturing grants during the last
election cycle.
Meanwhile, Taitoko said, relying solely on government support is not always a viable strategy but thankfully there are alternative funding options available that are more accessible today than ever before, however it is still critical to remove unnecessary costs from expansion projects.
The introduction of the RMR process is a unique advantage that helps offset the challenges posed by lower labour costs and cheaper manufacturing overseas.
“We believe the primary reason manufacturing has traditionally moved offshore is due to the high capital cost to establish a site and we’ve seen many projects abandoned because of this,” said Taitoko.
“Companies need to demonstrate that they will get a return on their investment.”
Over the past two decades, RMR’s model has resulted in numerous projects being salvaged by managing to remove traditional roadblocks and find alternative scaling options.
“For instance, a project initially quoted at $24 million was reduced to $13 million,” said Taitoko.
“It must be said that this is not necessarily by finding cheaper builders for example, but rather by finding
smarter ways to expand such as staging the project over a number of phases to facilitate a controlled expansion over a longer time frame and still allowing the manufacturer to scale their operations.
“We have many of these examples. Such cost reductions are achieved by designing fit-for-purpose processes without inflating costs or enriching construction companies or equipment manufacturers.”
The model has also enabled some food manufacturing to be repatriated back to Australia once a positive return on investment was achievable.
“Our model suits all size companies and off the back of industry challenges and the need to increase local supply, we’ve not experienced this much activity in the industry despite a lot of companies struggling at the moment,” said Taitoko.
As companies increasingly seek more efficient ways to manage projects, the role of specialist consultants becomes crucial.
The post-pandemic era has seen an increase in workload for manufacturing consultants as the reputation of consulting firms extends beyond local borders. This recognition underscores the importance of specialised consulting in navigating the complex landscape of modern manufacturing. F

NEED TO REDUCE
BOD BILL?
Bunzl’s innovative approach to sustainable industrial packaging
Bunzl provides various types of sustainable industrial packaging solutions that have been developed on the back of market and scientific research.
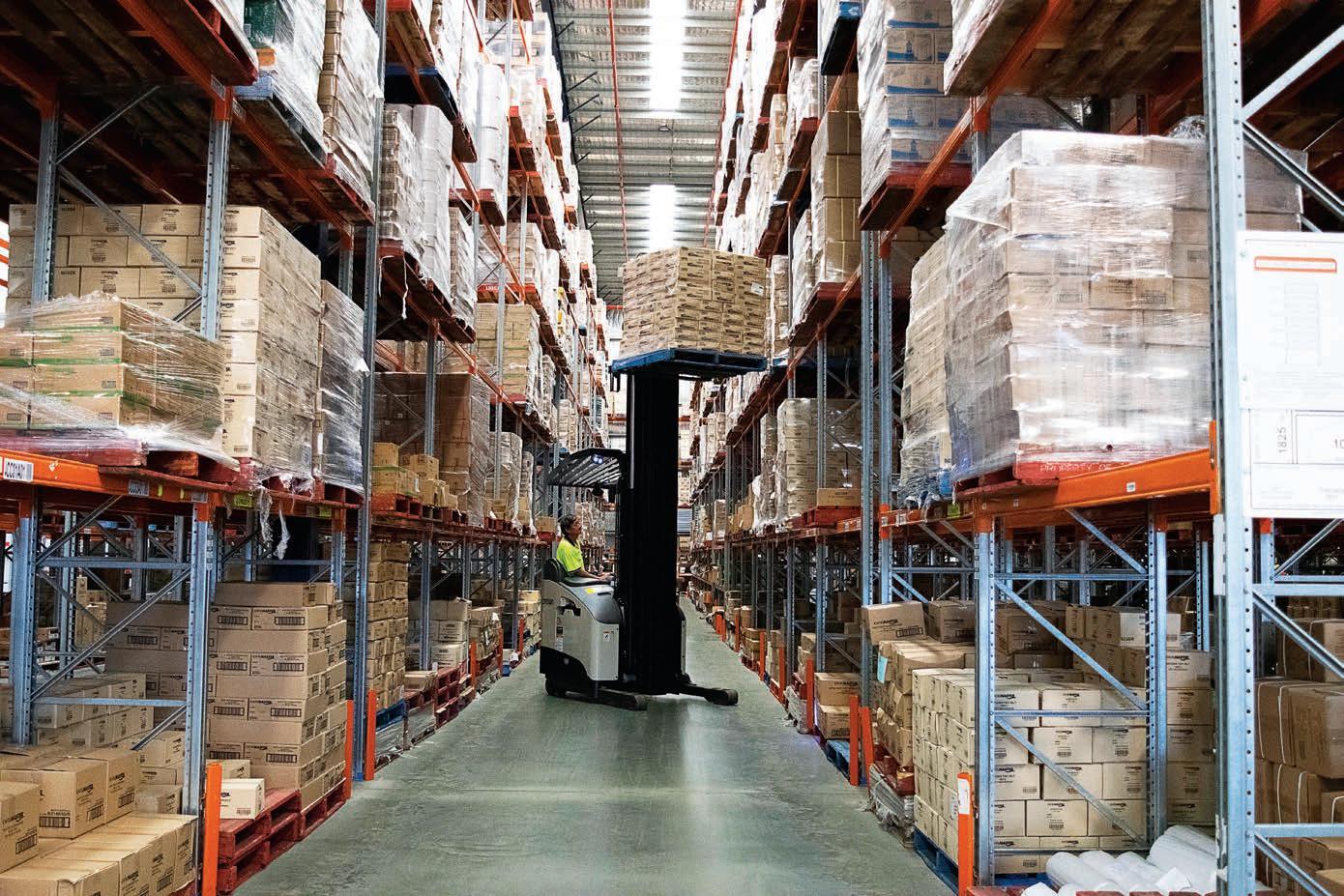
Wand efficiency
ith a focus on innovation and meeting customer demands around industrial solutions, Bunzl Australia and New Zealand’s dedication to sustainability is evident across its product range, including with its Advantage pallet wrap.
“Pallet Wrap is a high focus area for us because it’s something that is always going to be used in the market,” said Bunzl ANZ national business development manager for Industrial Packaging & Machinery, James Beleno. “And it’s an often-ignored area of plastic reduction for a lot of businesses.”
One key innovation of the wrap is its high stretch capability, allowing for more pallets to be wrapped with a single roll.
This not only reduces the amount of plastic used but also minimises the amount of wrap that needs to be disposed of.
In an effort for further innovation in industrial packaging, Bunzl ANZ explored the use of recycled, biodegradable, and compostable pallet wraps.
However, trials quickly showed that recycled pallet wrap can lead to increased plastic usage due to inconsistent quality and variability in the recycled materials.
“It’s incredibly difficult to pursue because of the inconsistency. You can’t control the quality of plastic that’s getting recycled and it often doesn’t hold up to the standards required,” said Beleno.
Despite the challenges, Bunzl remains dedicated to finding effective solutions that balance environmental benefits with practical performance, continuing to push the boundaries of sustainable industrial packaging.
“We use 100 per cent virgin material with about 8.9 per cent recycled resin in the actual formulation,” said Beleno.
“Our Innovation is the high grade resin and formulation used to develop Advantage pallet wrap, which gives our customers better efficiency improvements and load containment.”
An example of the benefits customers can expect from the wrap comes from a new 3PL Logistics Client here in Australia.
“For the last 10 years, this customer had used the same two suppliers, so they were somewhat apprehensive when it came to trying something new,” said Beleno. “Using the latest Advantage pallet wrap and machinery innovation, we were able to reduce their plastic usage by 100 tonnes per years.”
Beleno explained that although it
may seem counter intuitive, Advantage pallet wrap gives you better results with less material used.
“The resin formulation being part of our wrap also helps to create high clarity, along with its high strength, meaning you use a lot less plastic, and you get a better load containment.”
This is the reason Beleno says it’s important to meet clients in a face-toface scenario as much as possible.
That way, he can best explain the benefits of the wrap and run physical trials so that customers can see the actual efficiency improvements, sustainability improvements and improved load containment.
“When we take this product out into the market, we make sure to put a big focus on the sustainability side and the impact on their environmental
Images: Bunzl
As sustainability
requirements grow, innovative solutions like Bunzl’s Advantage pallet wrap help manufacturers reduce plastic use.
footprint and how it also impacts their own customers,” he said. “Because at the end of the day, they’re the ones disposing of the plastic.”
Being able to demonstrate the advantages in person also helps clarify results for clients.
“Sometimes it’s hard for them to believe that we can take 100 tonnes of plastic out of the equation,” said Beleno. “The 3PL client that I mentioned earlier were sceptical to begin with. But once we put the film in and set up the machines, we ran it and were able to demonstrate the numbers and show them what the significant sustainability and cost savings are. They immediately signed off and partnered with Bunzl for their pallet wrap and pallet wrappers.”
The importance of sustainability in the food and beverage manufacturing sector continues to only get more important, for both manufacturers and consumers.
“Sustainability is a massive talking point with any customer and any customer’s customers. The major supermarkets in particular are very big on sustainability,” said Beleno.
And with the number of pallets arriving at supermarkets across Australia, it means any reduction in pallet wrap use can have a beneficial flow-on effect.
“Our work with logistics companies’ adoption of our pallet wrap has had a huge impact, meaning a reduction of anywhere from 80 to 100 tonnes less plastic use per annum,” said Beleno.
Part of the close relationships between Bunzl and its clients is an emphasis on customer feedback and reviews to help inform development going forward.
For a long time, many companies relied on the same sources for their materials, resulting in products that were essentially the same but merely differed in branding.
“We were supplying what everybody else supplied and we all bought it from the same manufacturer,” said Beleno.
Recognising the need for change, the experts at Bunzl took steps to address the market’s stagnation.
“For us, we wanted something very different in the market,” said Beleno.
“We focused on what could be improved upon in the sector and what the customer really wants.”
This approach involves directly engaging with customers to uncover gaps and unmet needs.
“It was about speaking to customers
and understanding what they’re not getting in the market and what we can do differently,” said Beleno.
By aligning with a new supplier and emphasising innovation, the company aimed to bring a fresh perspective to the industry.
“From my experience, when we went to market with thinner films of higher quality, with higher grade resins that we use to go down in thicknesses, I feel that we started leading the way,” said Beleno.
The company’s commitment to high quality products has helped it establish a strong reputation in the industry.
Looking forward, the drive for innovation is expected to continue shaping the sector and Bunzl continued research and development.
“With that said, I think the sector will always be driving forward and innovating,” said Beleno.
“As the industry progresses, it will undoubtedly see more companies challenging conventions and setting new standards for excellence.” F
Scan this QR code to contact James Beleno and receive specialist advise for your business.
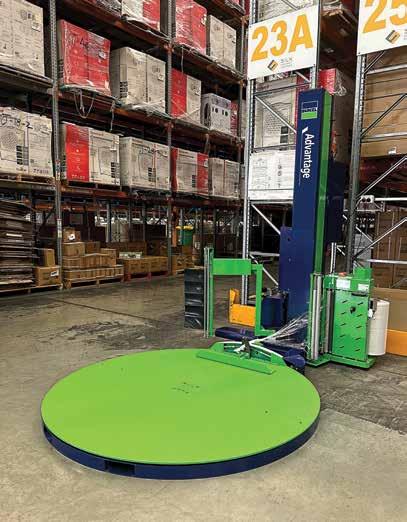
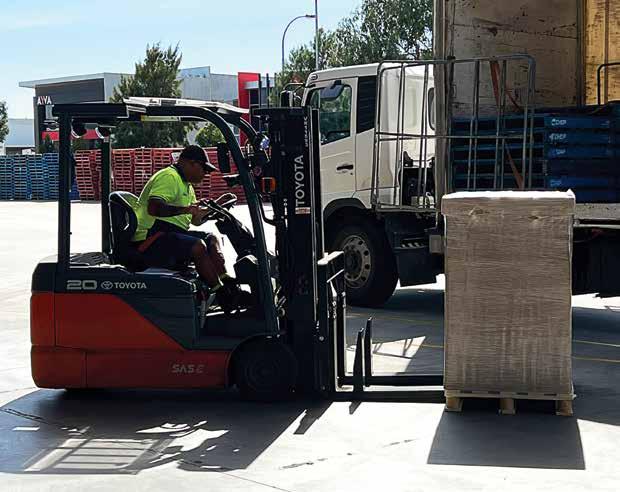
Bunzl’s dedication to sustainability is evident across its product range.
By using Bunzl’s Advantage pallet wrap, one client was able to reduce plastic use by 100 tonnes per year.
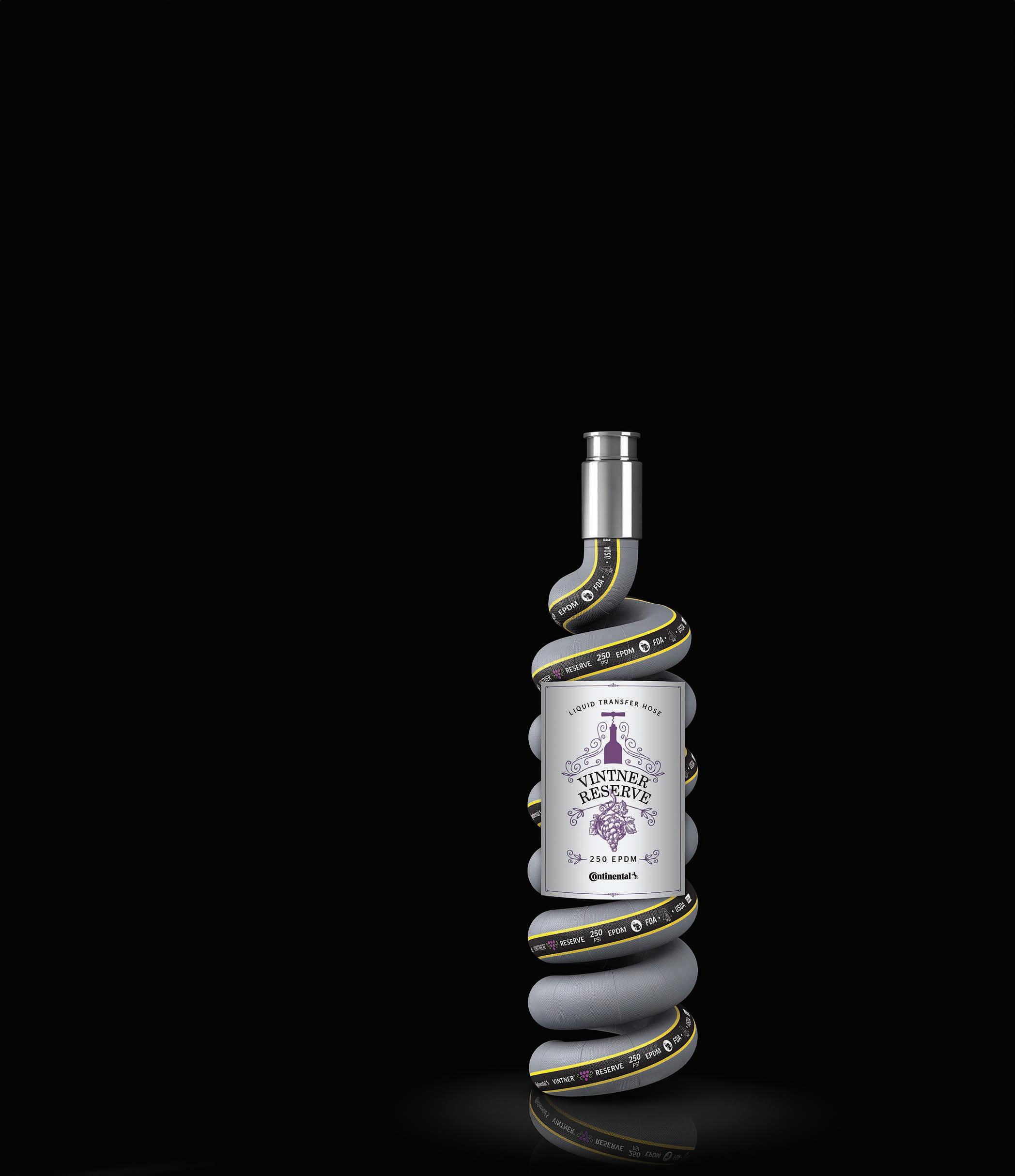
Navigating market challenges
Continental’s expertise in rubber continues to give rise to innovative industrial hose solutions for the food and beverage manufacturing industry.
Finding the right industrial hose can be a daunting task in the face of regulatory compliance requirements and the glut of options on offer. But making the right selection will ultimately benefit a company in the long run.
Something that the experts at Continental are keenly aware.
Continental has been a key player in the Australian industrial hose market, renowned for its high-quality products and dedication to innovation.
It’s range of specialised hoses, such as the Vintner and Extreme Flex Beverage and Milk hoses, ensures compliance with food safety standards and supports efficient, hygienic processing.
The company’s reputation, particularly within the food and beverage manufacturing industry, is a testament to its commitment to excellence.
“We’ve been a major player in the industrial hose market here in Australia and have built a strong reputation within the food and beverage industry for the quality of our products,” said Lee Cranswick, head of Sales Distribution –AUS/NZ, Industrial Solutions APAC, ContiTech.
ContiTech is a division of Continental that specialises in the development and production of highperformance industrial products and solutions.
At the forefront of hose technology, Continental continues to set high standards with products like the Extreme Flex Petrol & Oil and Extremeflex Versiflo hoses.
These hoses, designed for petroleum and water suction and discharge, have remained in high demand.
Both Continental’s Extreme Flex Petrol & Oil and Extremeflex Versiflo industrial hoses are engineered for top-tier performance in challenging environments where flexibility and durability are essential, along with versatility and reliable fluid handling in a variety of industrial applications.
“We still lead the world in quality and performance,” said Cranswick.
However, the industrial hose sector is currently facing challenges.
Economic downturns in various
countries and a softening market have impacted the industry.
Amid these challenges, Continental’s focus remains on the quality and innovation of its products rather than competing on price.
Continental’s sales team prides itself on explaining not just the features of its products, but how these features translate into practical benefits for customers.
For example, the Vintner hose, with its monofilament helix, is highlighted for its durability and resistance to crushing in tight spaces.
“In tight spaces, like those found in many start-up breweries, the monofilament helix allows the hose to bounce back into shape if it’s run over by a forklift,” said Cranswick.
Similarly, the Easy Clean beverage hose is designed for environments where frequent cleaning is necessary.
Its cover facilitates easy cleaning, making it suitable for settings where hygiene is crucial.
“Our hoses can be wiped down or washed off and used in different areas without worry,” said Cranswick.
less suitable for high-temperature applications or wash downs.
“PVC hoses have a lower temperature range compared to rubber hoses,” said Cranswick.
A good example of Continental’s
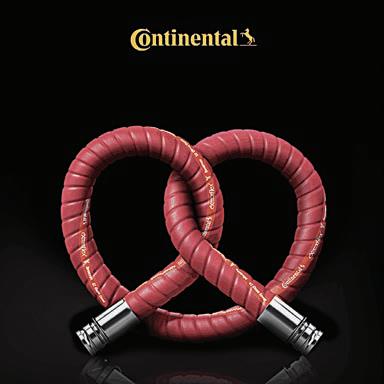
Continental continues to set high standards with its products.
Continental’s commitment to advanced technology is also evident in products like the washdown, and some of their food and beverage transfer hoses, featuring Microban cover technology.
Microban cover technology is an advanced antimicrobial treatment integrated into the outer cover of its hoses.
The technology is designed to inhibit the growth of bacteria, mould, and mildew on the hose’s surface.
This can be beneficial in maintaining cleanliness and extending the hose’s lifespan.
“A 30-metre assembly can be moved from one section to another without any risk of contamination, thanks to the Microban cover,” said Cranswick.
Despite a higher up front cost, Continental’s hoses offer long-term savings through durability and versatility.
While cheaper alternatives like PVC hoses exist, they come with trade-offs, particularly in temperature tolerance, as the PVC’s lower range makes it
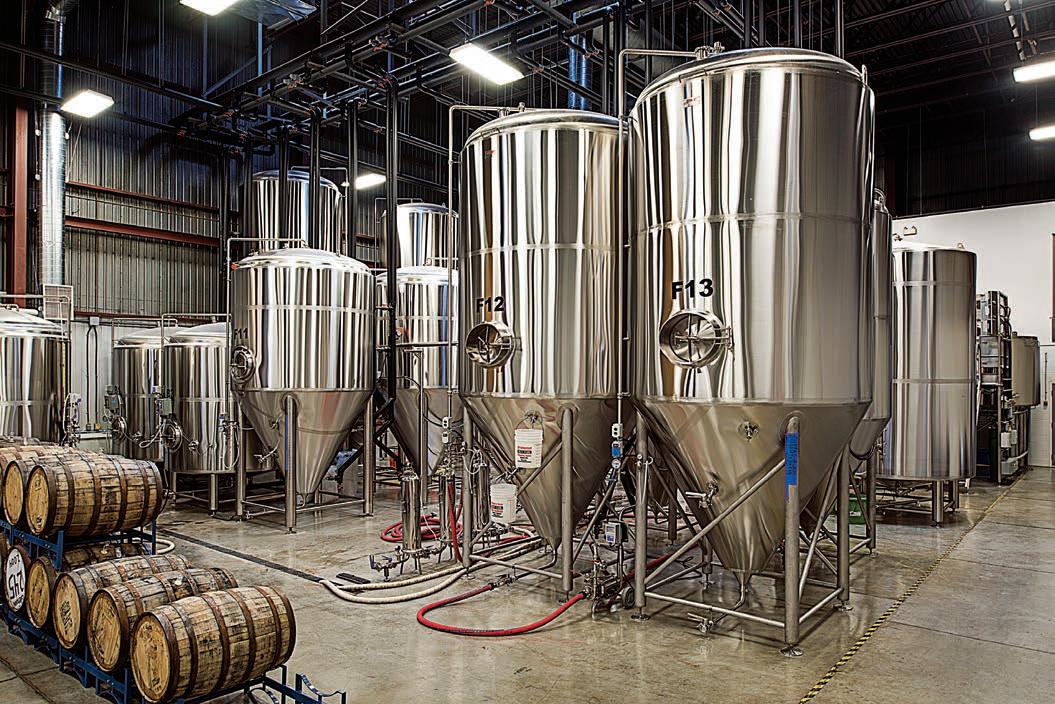
The Vintner hose is highlighted for its durability and resistance to crushing.
product value is a case study with an international airport terminal
When complaints about water taste were traced back to a low-quality PVC hose, Continental provided a highquality alternative and immediately received positive feedback.
“When customers come to us with specific needs and ask for our brand, it’s a testament to our product quality,” said Cranswick.
The long-standing reputation of Continental’s range of products is an ongoing demonstration of the company’s commitment to excellence and meeting the unique needs of the industry.
“In tight spaces, like those found in many start-up breweries, the polyfilament helix allows the hose to bounce back into shape if it’s run over by a forklift.”
“We up sold the client to a fit for purpose hose, which had quite a significant cost difference but eliminated the issue” said Cranswick.
“This investment not only solved the taste issue but also highlighted the importance of choosing the right product for long-term satisfaction.”
Cranswick also underscored the significance of maintaining a good reputation.
“Issues like these can impact not just the product, but also the business’s reputation,” he said.
With heightened awareness of hygiene, especially in the food and beverage industry, the emphasis on quality and reliability becomes even more critical.
Continental’s dedication to premium quality is reflected in customer requests for specific products.
Despite occasional challenges, Continental remains focused on delivering high-quality solutions.
“We’ve consistently had excellent products,” said Cranswick.
The company’s ongoing efforts to educate customers about its full range of offerings are also crucial in maintaining and enhancing its reputation while learning their exact needs.
Continental’s products are always designed to offer flexibility, durability, and ease of use, to help manufacturers maintain the quality and safety of their products while optimising their operations.
To learn more, visit www. continental-industry.com. F
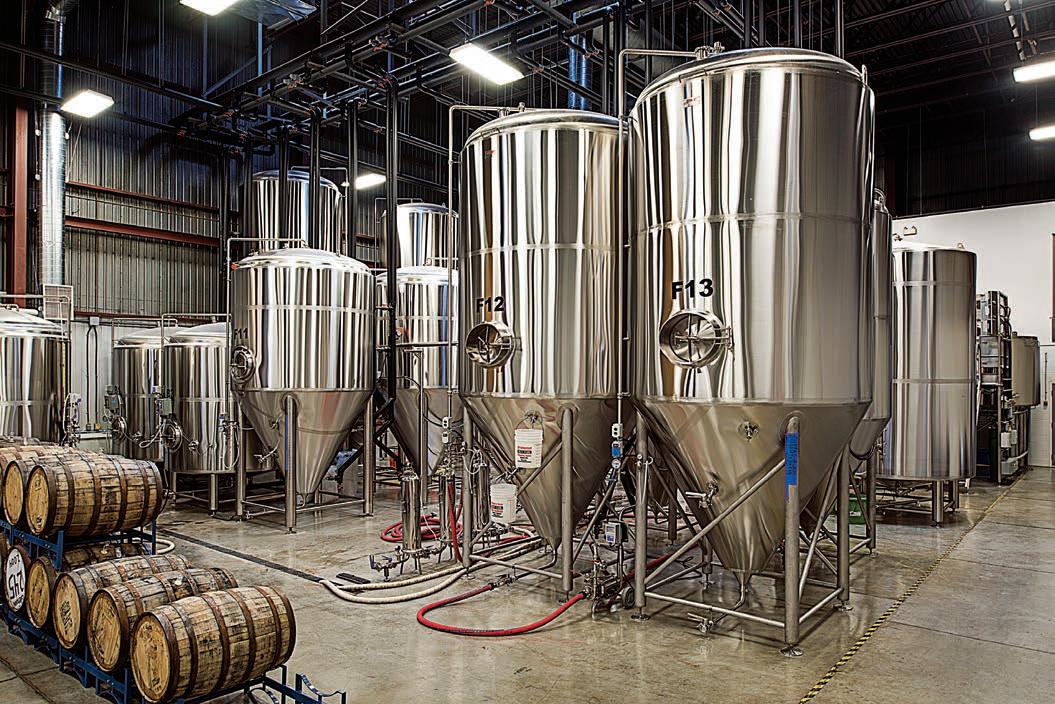
FEEDING MADE EASIER!
The VSS EziPack gives highly accurate, repeatable feed for fine dosing of product or filling small containers.

The precision pneumatic drive ensures instant start/instant stop with no feed over-run to be allowed for.
With a standard electronic scale and electropneumatic controller you’ll get exactly the right quantity every time!
New APCO strategy maps ambitious plan for packaging
APCO’s new 2030 Strategic Plan provides economic incentives for material circularity and to establish mechanisms for achieving national packaging targets.
The Australian Packaging Covenant Organisation (APCO) has unveiled its 2030 Strategic Plan, challenging the status quo to achieve ambitious national packaging goals.
For the first time in Australia, the strategy outlines a path for the industry to take on increased responsibility for enhancing recycling efforts to meet national targets.
“We know that our members have made great strides in improving the recyclability of packaging and genuinely want to see our recycling rates improve,” said APCO’s CEO, Chris Foley.
“But the analysis is clear: we need to take a more hands-on approach to recycling if we’re going to see the results that the community expects.”
The plan proposes a membership fee structure designed to promote packaging material circularity and grant brands the
social license to operate in Australia.
After analysis and member consultations, APCO’s fees will be adjusted from FY27 to reflect the types and quantities of packaging brands introduce to the market, with higher fees for materials that are more challenging to recover, recycle, or need to be disposed.
It’s hoped this approach will encourage brand owners to eliminate and reduce packaging, adopt reuse models, and switch to materials and formats that are easier to recycle.
Crucially, revenue from the new fee structure will be invested in the downstream system to address economic barriers impeding progress toward national packaging targets.
These funds will support end markets, enhance reprocessing infrastructure, and strengthen collection networks.
Highlights of the plan include:
• I ncreased recycling: direct support for high-quality collection, recycling, and packaging stewardship activities that, additional to business-as-usual, will enable the achievement of recycling targets and the production of high-quality Australian recycled content.
• New membership fee model: following modelling and targeted consultation, APCO member fees will be calculated using eco-modulation (ecological modulation). This will be based on each member’s packaging profile and incentivises the design of packaging for reduction, reuse, and recovery. The aim is for these to be in place in the financial year 2026-27.
• New indicators: The goals of the Covenant will be tracked using new indicators in addition to the NPTs,
including the reduction of materials sent to landfill. By 2030, this reduction target is set at 1 million tonnes.
• Social license: the plan ensures that brand owners will have a supportive system that allows community expectations on packaging design and disposal to be met.
Though this method is new to Australia, it has been successful in countries like the Netherlands, Belgium, and France.
The strategy follows a thorough review of Australia’s packaging targets by APCO in 2022, which identified technical and economic barriers hindering higher recycling rates.
Foley added that the new strategy will add to, rather than replace, Australia’s existing recycling system and activity.
“We’re aiming to support and grow the existing system”, he said.
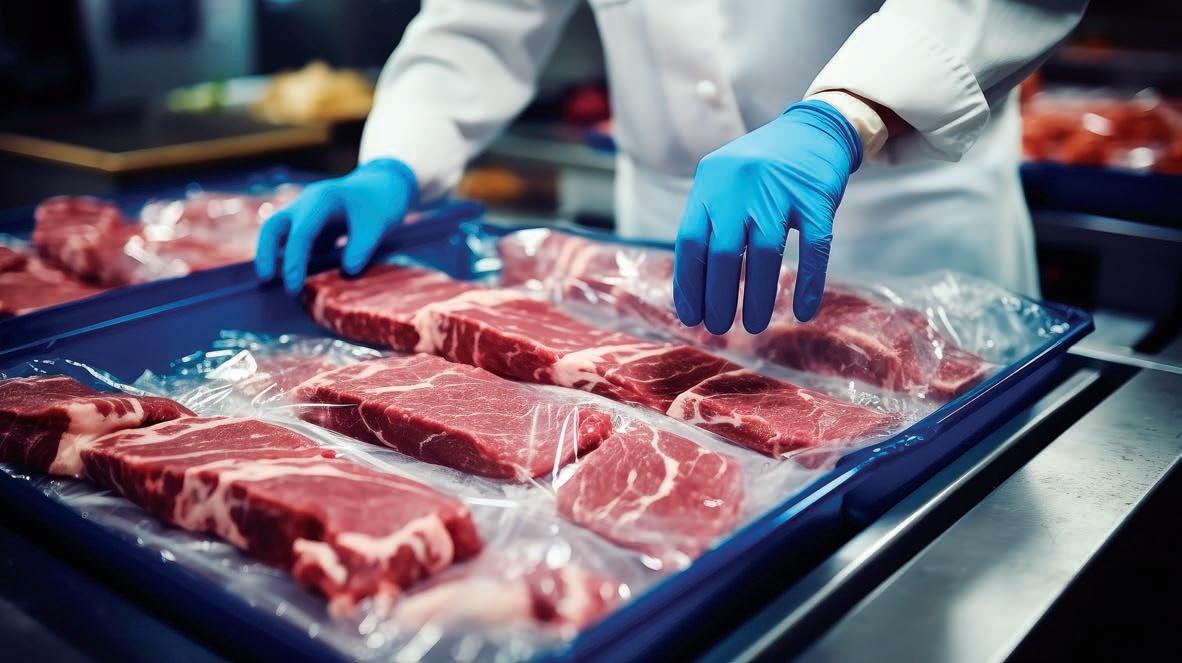
“Local governments and the waste and recycling sectors are key. Together, we need to collect and work out where funds can be most effectively applied to
“That could be collection systems for problematic materials such as expanded polystyrene or a national consumer
APCO is responsible to Australia’s Environment Ministers for achieving the national packaging targets. The Covenant’s goals stay the same with the new strategy, aiming to enhance packaging and material recovery and
The Covenant’s progress will be monitored with new indicators, such as
collaboration with APCO’s more than 2400 industry members and key stakeholders, including waste and recycling sectors, industry associations,
“At Unilever, we believe EPR schemes where companies pay to support the
The APCO plan proposes a membership fee structure designed to promote packaging material circularity.
collection and processing of packaging can help to improve recycling systems,” said Brooke Sprott, head of Sustainable Business and Communications –Unilever ANZ.
“The eco-modulated fee structure being developed by APCO is a significant step towards enhancing packaging material circularity in Australia.
“This initiative aligns with Unilever’s plastic reduction goals and reinforces our commitment to lead by example for systems change on a global scale.”
Suzanne Toumbourou, CEO, Australian Council of Recycling, called the strategy a ‘game-changer’.
“This collaborative and forwardthinking approach is a game-changer, aiming to enhance packaging material circularity and drive improvements across the entire supply chain,” she said.
“We welcome the focus on creating investment certainty and markets for the recycling system, supporting community confidence and delivering environmental benefits.”
The Covenant and NEPM are designed to ensure brand owners help mitigate the environmental impacts of packaging.
By fulfilling their collective obligations as Covenant signatories, brand owners gain access to APCO’s support and resources. In exchange, they
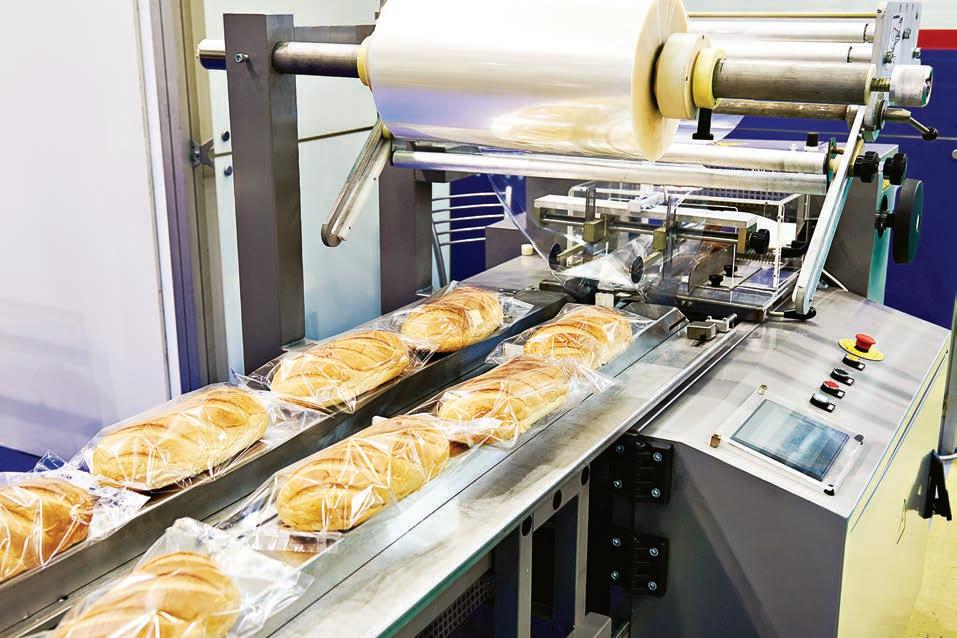
provide funding to enable APCO to drive progress toward the targets and goals.
APCO, in turn, is accountable to the Environment Ministers for its efforts.
The strategy will be updated
as required in response to the packaging reform process currently underway under the leadership of the Commonwealth Department of Climate Change, Energy, the Environment and Waste (DCCEEW).
According to the time line, the next step will see State and Federal Governments undertake any necessary legislative processes to establish the new regulatory scheme ahead of establishing them by the end of 2025. F
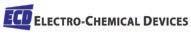
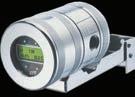

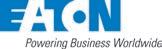


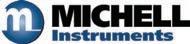

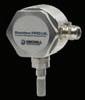

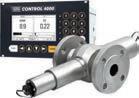
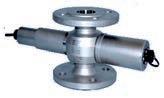
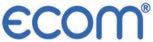

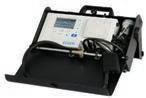

APCO’s new 2030 Strategic Plan follows a thorough review of Australia’s packaging targets in 2022.
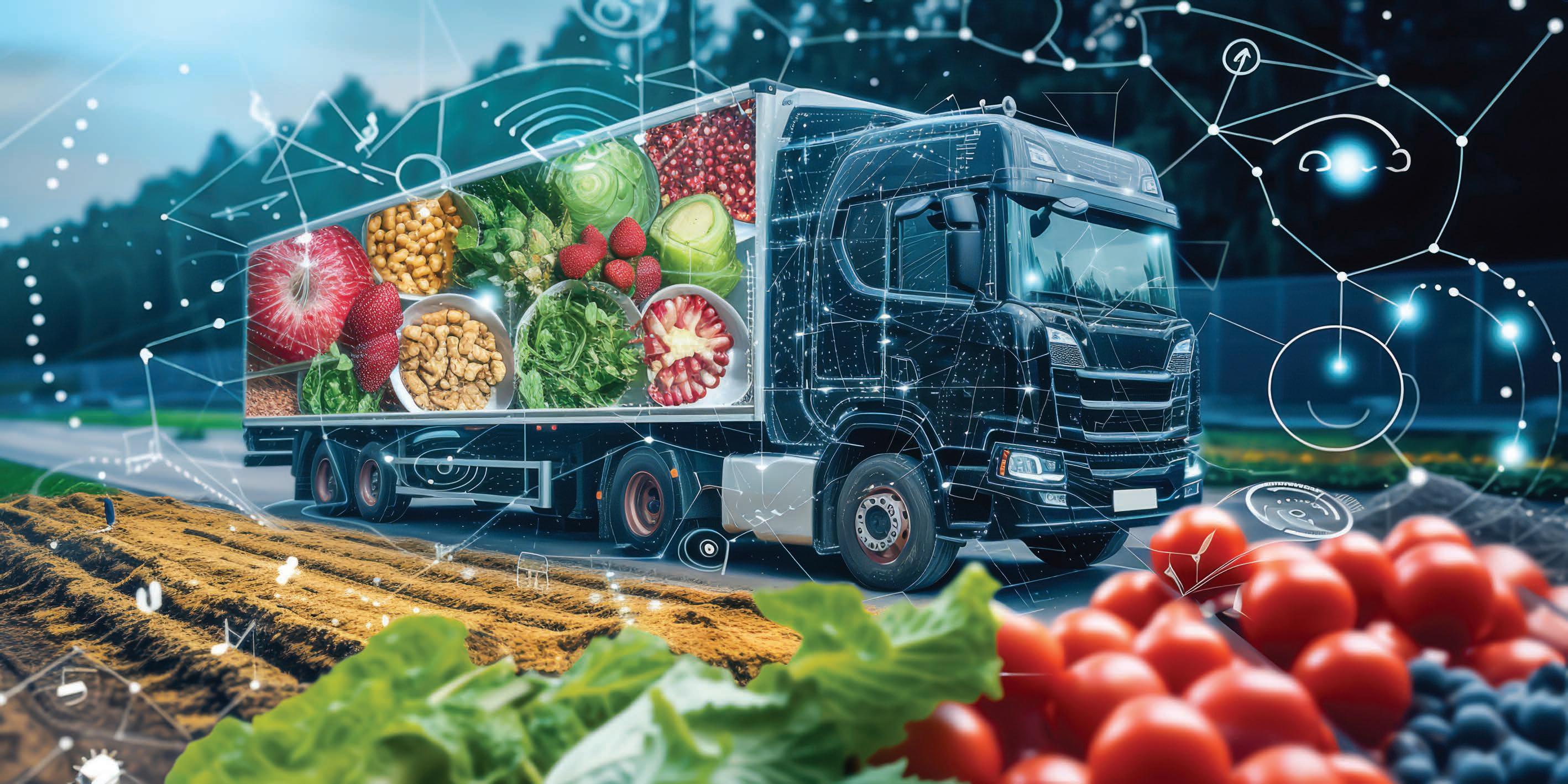
Strengthening infrastructure is a supply chain priority
Key
stakeholders are calling for a renewed focus on better infrastructure and strategic investment to create more efficient supply chains.
Strengthening the resilience of Australian transport infrastructure and addressing high freight costs remains a top supply chain priority for food and grocery manufacturers, according to a survey at the Australian Food and Grocery Council’s (AFGC) Supply Chain Summit.
Frequent failures of transport infrastructure, due to natural disasters and other factors, have hindered industry productivity through congestion and delays.
In addition, rising energy, freight, and input costs are putting pressure on food and beverage manufacturers, impacting profitability, and future national capability.
AFGC stakeholders have called on the government to implement recommendations from its recent National
Freight and Supply Chain Strategy.
The National Freight and Supply Chain Strategy was designed to enhance the safety, productivity, and resilience of freight and supply chains as demand continues to grow.
The strategy outlines a national plan for government and industry to follow across all freight modes until 2040 and beyond, with a review scheduled every five years.
Some key points included:
• A new goal on ‘decarbonising the freight and supply chain sector’.
• A n updated goal of ‘safe, secure and resilient supply chains’ and for resilience to be strengthened in the body of the refreshed strategy.
• A n updated goal of ‘a skilled, portable and adaptable workforce’ and for skills and workforce to be
strengthened in the body of the refreshed strategy.
• A n updated goal of ‘improved efficiency, productivity and international competitiveness’. Another recommendation was to reflect the National Urban Freight Planning Principles in the new strategy, and interoperability to be expanded and strengthened in the refreshed strategy. The seven principles are:
1. Understand the value, needs and characteristics of freight movement and incorporate in strategic and statutory transport and land use planning.
2. Safeguard the resilience of all major freight handling facilities and freight corridors within and between neighbouring jurisdictions, including local government areas.
3. Identify and plan areas for new freight facilities and freight-intensive land uses.
4. Plan for efficient freight movements and complementary land uses around
freight facilities and precincts, including intermodal terminals.
5. Promote building and precinct design and usage that considers freight needs.
6. R ealise the importance of rest and refuelling facilities.
7. R espond to changes in freight movements, including smaller scale freight movement and emerging technologies.
It also urges government investment to fortify the East-West freight rail line and East Coast freight rail network, critical arteries for delivering food and groceries to consumers nationwide.
“The vitality of the food and grocery industry hinges on efficient supply chains to ensure uninterrupted access to food for Australian households,” said AFGC CEO Tanya Barden said.
“Yet the industry is constantly dealing with disruptions and preparing for future threats.”
When the strategy was released in 2019, it marked the first time that
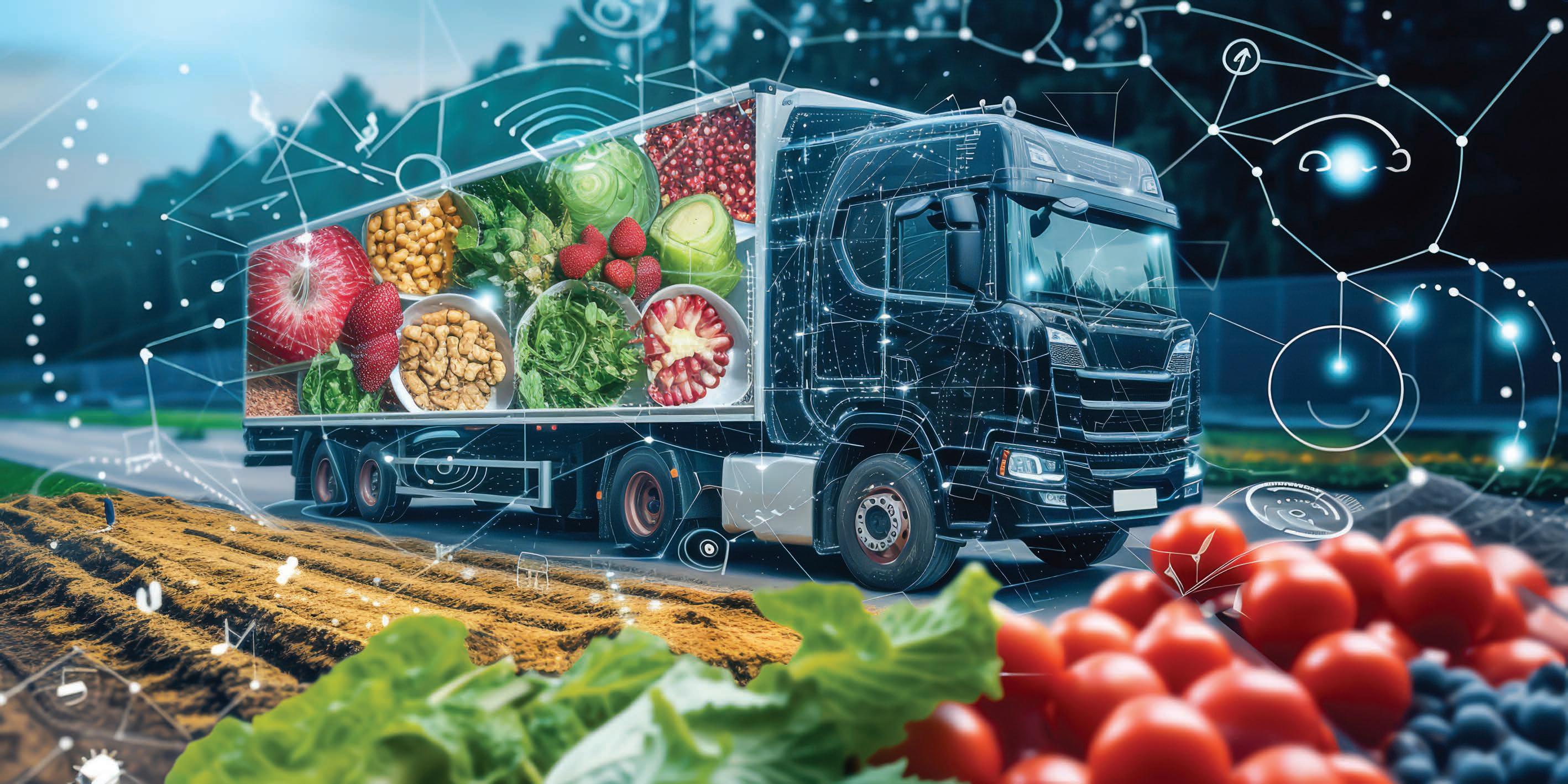
government and industry had come together to create a national plan aimed at boosting the efficiency, effectiveness, and reliability of Australian supply chains.
Australia’s economy relies heavily on efficient freight transportation across long distances and international borders.
The country’s supply chains are essential to handling the increasing freight demand, which is expected to rise by 26 per cent from 2020 to 2050.
This means freight movement will grow from 756 billion tonne-kilometres in 2020 to 964 billion tonne-kilometres by 2050.
Meanwhile, domestic supply chains are necessary for supporting international trade by connecting trade gateways like ports and airports with the wider economy.
Without resilient infrastructure, the industry has been forced to divert resources away from activities that increase innovations and productivity to cope with infrastructure issues.
A separate survey of AFGC members
conducted in February revealed an average increase of 49 per cent in freight costs due to infrastructure-related challenges.
The industry is adapting where it can, with all survey respondents leveraging technology to navigate persistent supply chain disruptions.
The survey results also confirmed that COVID-19 pandemic-related disruptions were still impacting the flow of goods.
Government initiatives, like 2023’s National Disaster Preparedness Summit, have also enabled successful collaboration across the supply chain, using past experiences with floods, bushfires, and the COVID pandemic for future planning.
Despite some uncertainty, there has been positive changes in the sector since the pandemic, such as a renewed focus on decarbonisation and emerging technologies.
These changes have also played a key role in bringing forward the 2024 strategy review by a year, to 2023.
And now, a year on, the
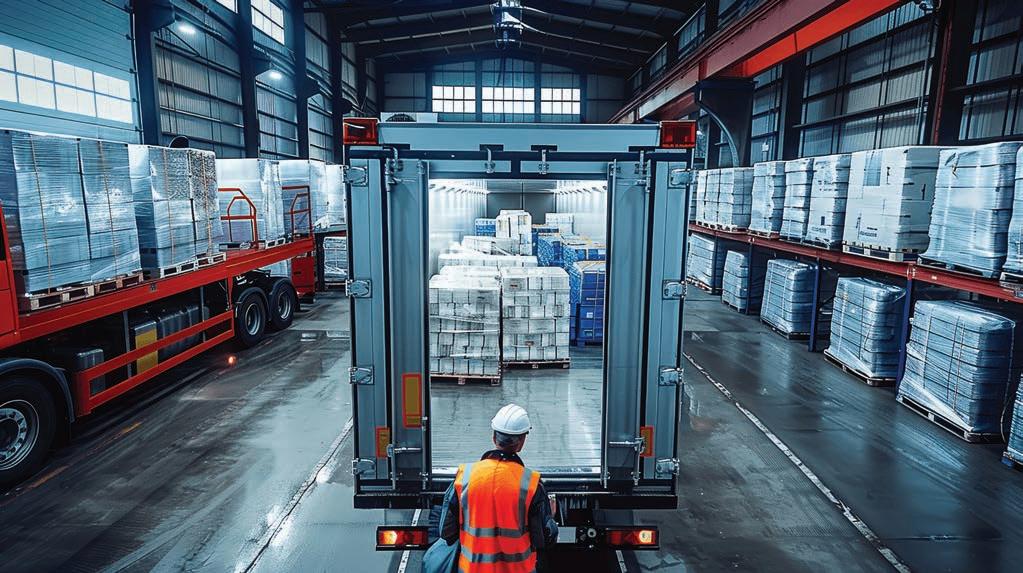
AFGC is calling for the strategy recommendations to be implemented.
to include the largest manufacturing sector in its Future Made in Australia
Frequent failures of transport infrastructure have hindered industry productivity through congestion and delays.
Australia’s economy relies on efficient freight transportation across long distances and international borders.
Artificial Intelligence’s recipe for success
Artificial Intelligence is here to stay, and those willing to adapt to the emerging technology could be well placed to capitalise on its benefits.
Technologies such as computer vision and machine learning are used to inspect and sort fruits and vegetables.
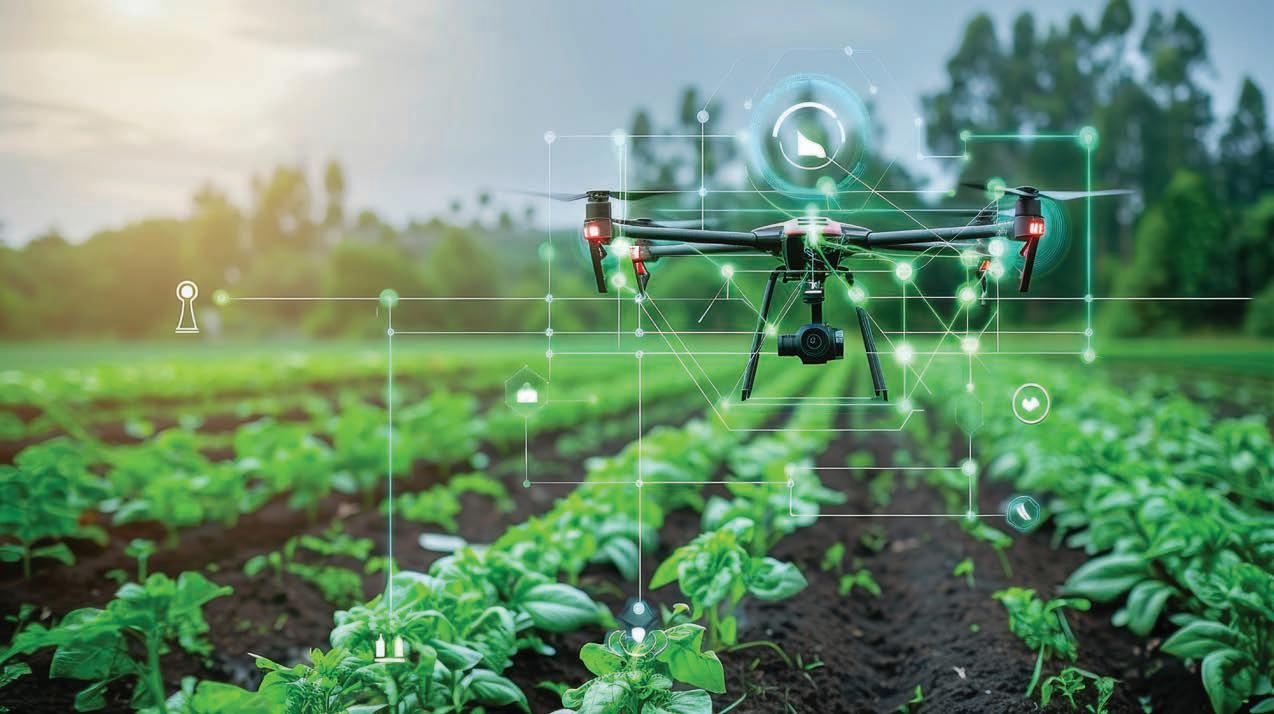
Ar tificial Intelligence (AI) is making strides in the food industry, reshaping processes from farm to table.
A recent study, “Application of Artificial Intelligence in Food Industry—a Guideline,” outlined how AI is enhancing various aspects of food production and distribution.
AI is now integral to the food supply chain, bringing advanced technology to every stage. With AI systems also performing roles like being a digital sous chef, as well as improving the quality of produce that is being picked during processing.
AI is already being adopted for a string of functions within the food and beverage manufacturing industry, including in quality control and assurance, supply chain optimisation,
and process automation.
Technologies such as computer vision and machine learning are used to inspect and sort fruits and vegetables, identifying imperfections and contaminants with greater accuracy than human inspectors.
Meanwhile, in quality control, AI algorithms analyse food product images to detect defects that may not be visible to the naked eye. Ensuring that products like apples, bakery items, and meats undergo rigorous checks to maintain high safety and freshness standards.
Supply chain management, a complex challenge in the food industry, also benefits from AI’s capabilities.
AI helps streamline the supply chain by forecasting demand, optimising inventory levels, and managing logistics. Predictive analytics can anticipate
changes in demand, ensuring that manufacturers have the right number of raw materials and finished products on hand.
Predictive analytics assist companies in forecasting demand more accurately, which minimises waste and optimises inventory levels.
AI is used to predict when equipment is likely to fail or require maintenance. By analysing data from sensors on machinery, AI models can forecast potential issues before they occur, minimising downtime and reducing maintenance costs.
AI-driven logistics also enhance delivery efficiency, ensuring timely arrival of fresh produce while reducing environmental impact.
AI’s influence extends to food processing and manufacturing, where
robotics and AI systems perform tasks such as ingredient mixing and packaging. These technologies increase production efficiency, precision, and customisation.
One such area that has been a point of importance for the industry since its inception is food safety.
AI systems are already being employed to enhance food safety by monitoring factors such as temperature, humidity, and contamination levels.
For example, AI can analyse data from sensors to ensure that food is stored and processed under optimal conditions to prevent spoilage and contamination.
Personalisation is another area where AI is making a difference.
By analysing health data and dietary preferences, AI provides tailored
nutrition recommendations.
This capability allows for personalised meal plans and product suggestions based on individual health goals and activity levels.
Customer engagement is also improved through AI-powered tools. Chatbots and recommendation engines on websites and food delivery apps offer personalised interactions and suggestions, enhancing the overall consumer experience.
Despite its benefits, the integration of AI in the food industry also presents challenges, including concerns around data privacy, cyber security, and potential job displacement.
The study emphasises the need for careful implementation of AI technologies, balancing innovation with ethical considerations.
AI is also impacting the food industry by enhancing quality control, supply chain management, processing efficiency, personalisation, and customer engagement.
And as AI continues to evolve, it will play a crucial role in shaping the future of food production and consumption.
The paper provides an overview of how automation and advanced sensing technologies are transforming red meat processing, offering solutions to enhance quality, efficiency, and economic viability in the industry.
In the report, Foodservice Update Q1 2024, Rabobank outlined how AI is becoming more accessible to global foodservice operators of all sizes, facilitated by the offerings of software-
Report co-author, RaboResearch senior analyst Thomas Bailey, said today’s AI applications in food service are primarily focused on increasing efficiency, reducing staff workload, optimising marketing strategies, and improving customer experience.
“The use of AI in food service ranges from streamlining human resources processes to incorporating advanced technology into kitchen equipment,” he said.
“Customer interactions are also being transformed through AI, with highly performing chatbots and telephone assistance software improving the customer experience and operational efficiency.
“AI software can be used to improve text and images, personalise customer interaction, understand brand perception, and implement more focused pricing strategies.”
However, the report says, implementing AI is not without its challenges.
“AI is a work in progress, it is far from perfect, and its implementation comes at a cost,” said Bailey.
“The adoption of AI also carries potential risks, including customer alienation and technology-related issues.”
Despite these obstacles, Bailey said, the integration of AI into food service is not just a trend but a competitive necessity.
“And we encourage food service operators and industry partners to stay informed and adapt to the evolving
One Australian wine producer, Treasury Wine Estates, has adopted AI technology, such as autonomous vehicles, and AI sensors, all to improve grape yield.
According to TWE’s 2022-23 sustainability report, the winemaker was able to conserve water and reduced the effects of unpredictable weather and extreme events through investments in automated irrigation, predictive analytics, and sensors, giving a glimpse into the positive impact AI is already having on key stakeholders within the industry.
In May 2024, The Australian Academy of Technological Sciences and Engineering submitted a list of recommendations on how the continued implementation of AI technology can be capitalised on by industry.
The ATSE made the following recommendations:
1. Engage and support the food and beverage manufacturing sector in establishing a decarbonisation strategy.
2. Support uptake of AI-driven and automation technologies to drive innovation and productivity in the Australian food and beverage manufacturing industry.
3. I mplement policies and incentives that encourage the food and beverage manufacturing industry to accelerate adoption of circular economy practices across the supply chain.
4. Uplift research and development investment to 3 per cent of GDP.
between industry stakeholders and research institutions.
6. Promote government-backed training and industry-academia partnerships to align vocational programs with technological advancements.
“These technologies can streamline processes, reduce waste, provide valuable insights into consumer preferences, and improve availability and affordability of healthy foods,” the submission read.
“Government support, initiatives promoting a circular economy, and strengthened collaboration are key drivers for the industry’s resilience and sustainability.”
AI will continue to revolutionise the food and beverage manufacturing industry by enhancing efficiency, quality, and innovation.
The integration of AI technologies has already demonstrated an ability to streamline production processes, from predictive maintenance that anticipates equipment failures to automated quality control systems that ensure product consistency.
By leveraging machine learning algorithms and real-time data analytics, manufacturers can optimise supply chains, forecast demand with greater accuracy, and reduce waste.
As consumer expectations evolve, AI provides valuable insights into market trends and behaviour, allowing companies to adapt swiftly and effectively.
AI is not just a tool, but a transformative force that helps improves product quality, and
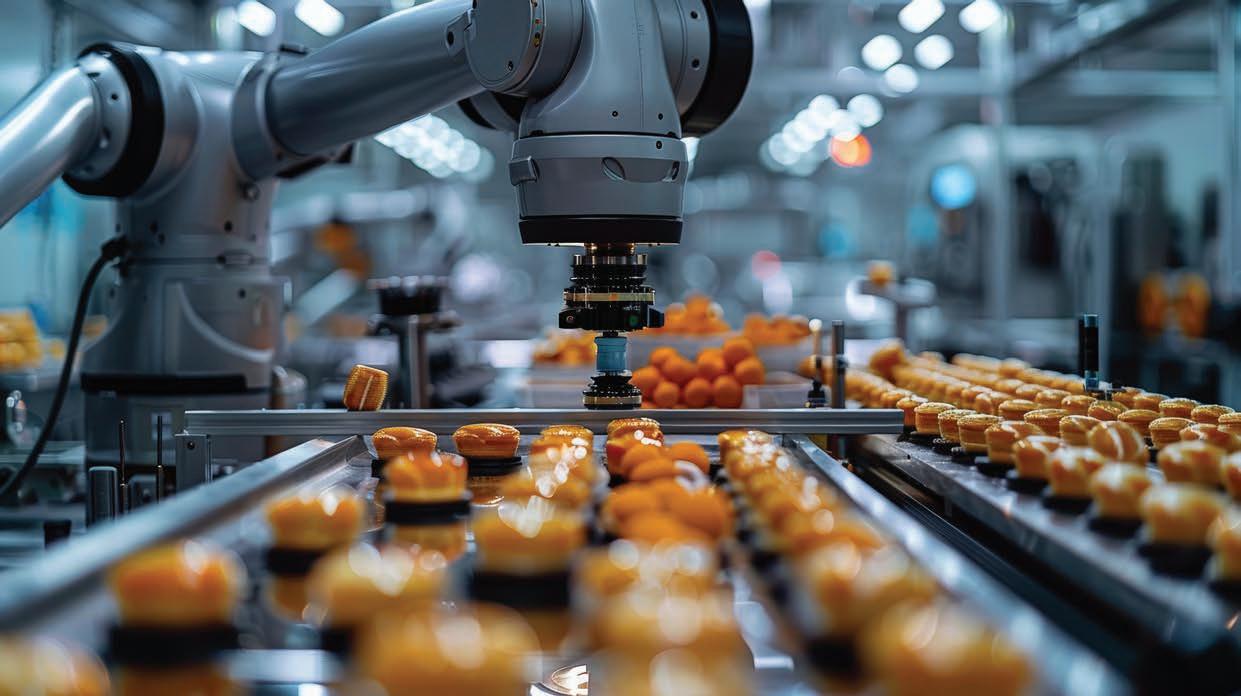
AI is already being adopted for a string of functions within the food and beverage manufacturing industry.
Bolstering Australian manufacturing capabilities
The Federal Government’s Future Made in Australia agenda has been designed to strengthen the country’s manufacturing sector while driving growth.
Australia’s economic landscape is undergoing a transformation, driven by the global shift towards net zero emissions and intensified geopolitical competition.
These developments are reshaping the value of natural resources, disrupting trade patterns, and spawning new market opportunities.
In this evolving environment, Australia’s inherent strengths, its natural assets, trade partnerships, and commitment to open markets, are all set to play a key role in maintaining and enhancing its competitive edge.
The Australian Government has introduced the “Future Made in Australia” agenda to harness these opportunities and secure the nation’s economic future.
“This legislation is all about unlocking private sector investment to build a stronger, more diversified and more resilient economy powered by renewable energy that creates secure, well-paid jobs around the country,” said Prime Minister Anthony Albanese.
“It embeds into law a disciplined and rigorous approach that will govern Future Made in Australia investments, to make the most of our net zero potential and ensure the benefits of these investments are widely shared and flow to local communities.
“This package does three main things. It will legislate our new National Interest Framework, introduce a robust sector assessment process, and outline the Community Benefit Principles that will apply to investment decisions.”
At its core, the initiative aims to drive private sector investment into key industries while strategically using public funds to address gaps and stimulate growth.
The newly established National Interest Framework is central to this strategy, providing a structured approach to evaluate and guide significant public investments.
The framework is divided into two main streams.
• T he Net Zero Transformation Stream focuses on industries crucial for achieving emissions reduction and maintaining long-term competitive advantage.
• T he Economic Resilience and Security Stream addresses sectors vital for national security and economic stability where private investment alone may not suffice.
Additionally, the government’s investment approach includes community benefit principles, emphasising support for local communities, skills development, and job security.
This comprehensive strategy is outlined in the framework, which will inform decisions on major public investments, including those related to Australia’s ambition to become a Renewable Energy Superpower.
The 2024–25 Budget reflects this vision, with targeted incentives designed to foster private sector growth in renewable energy and related technologies.
Beyond this, the Future Made in Australia package encompasses broader
The newly established National Interest Framework is central to the strategy.
investments aimed at advancing critical technologies and creating a more competitive business environment.
Treasury will oversee the implementation of the National Interest Framework, with more details to be disclosed as part of the legislative package.
In navigating these global shifts, Australia is positioned well to leverage its strengths to drive economic growth and resilience.
Modernising and diversifying Australia’s industrial base is central to the government’s plan to benefit from global economic changes.
Meanwhile, the 2023 Employment White Paper emphasises how coordinated industry and regional policies, along with a supportive environment, can create a dynamic and inclusive labour market.
The Future Made in Australia package in the 2024–25 Budget supports this goal by attracting investment, promoting renewable energy, enhancing resource value, and
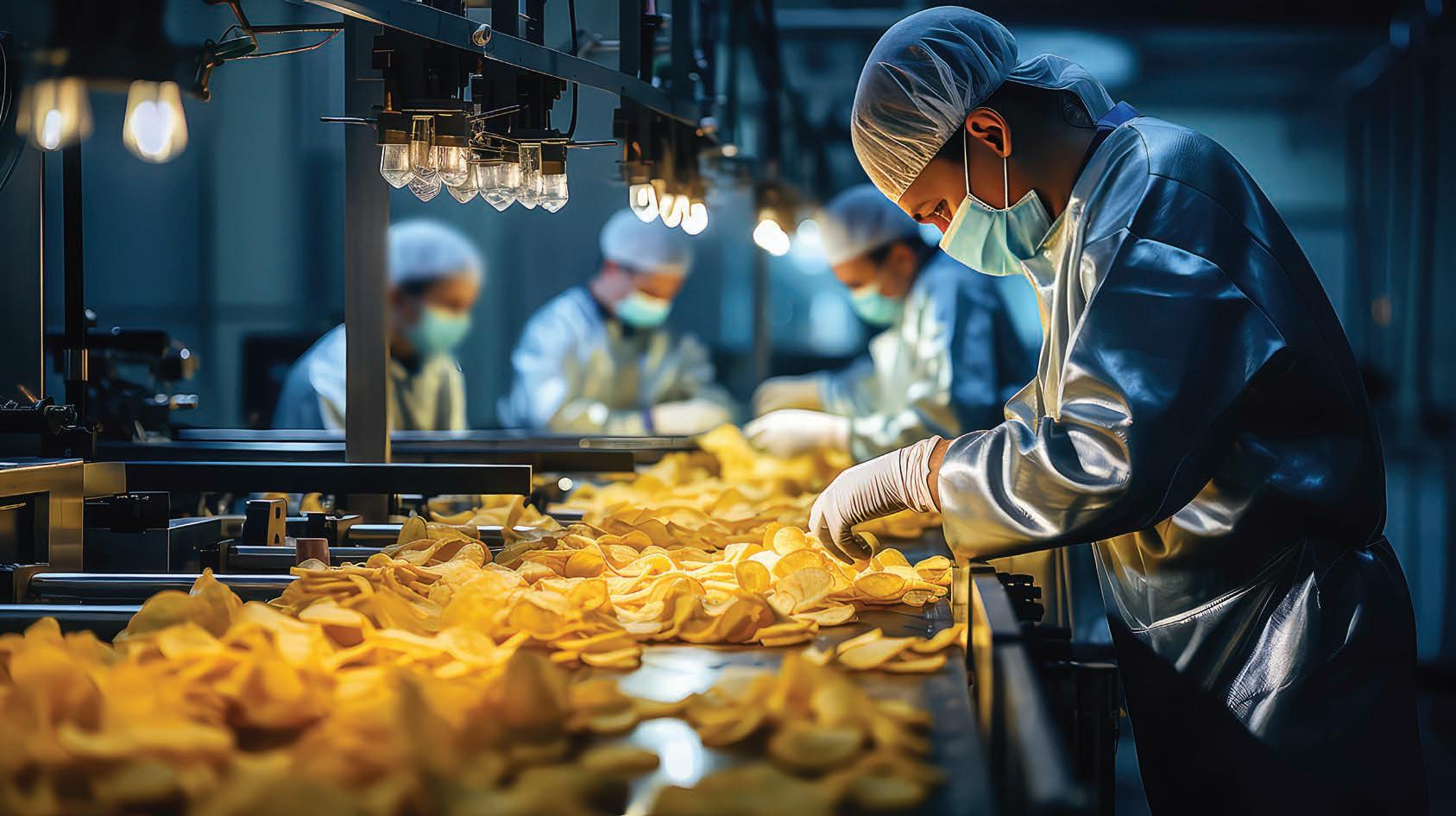
investment to align economic incentives with national interests and encourage private investment in priority industries such as food and beverage
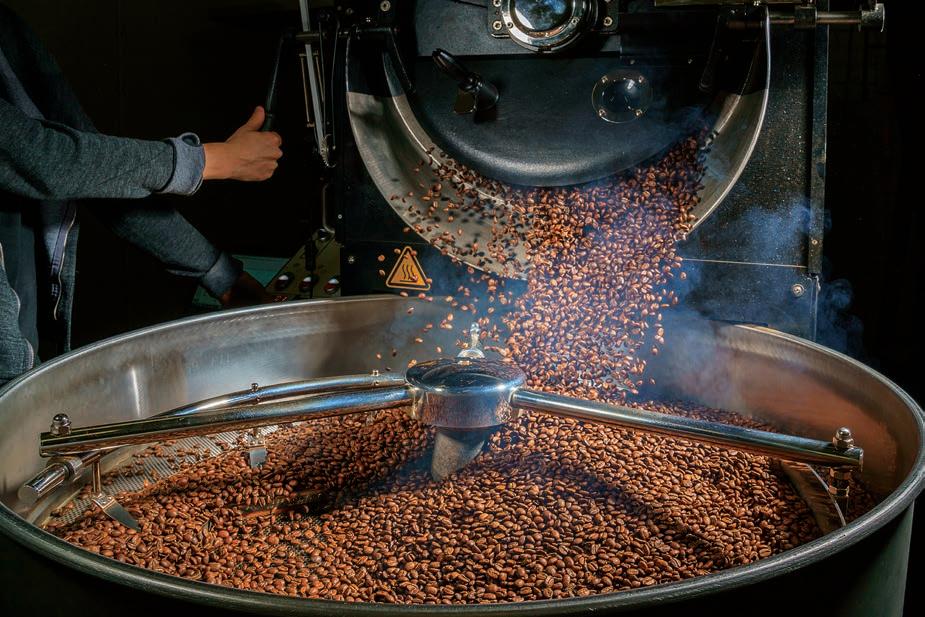
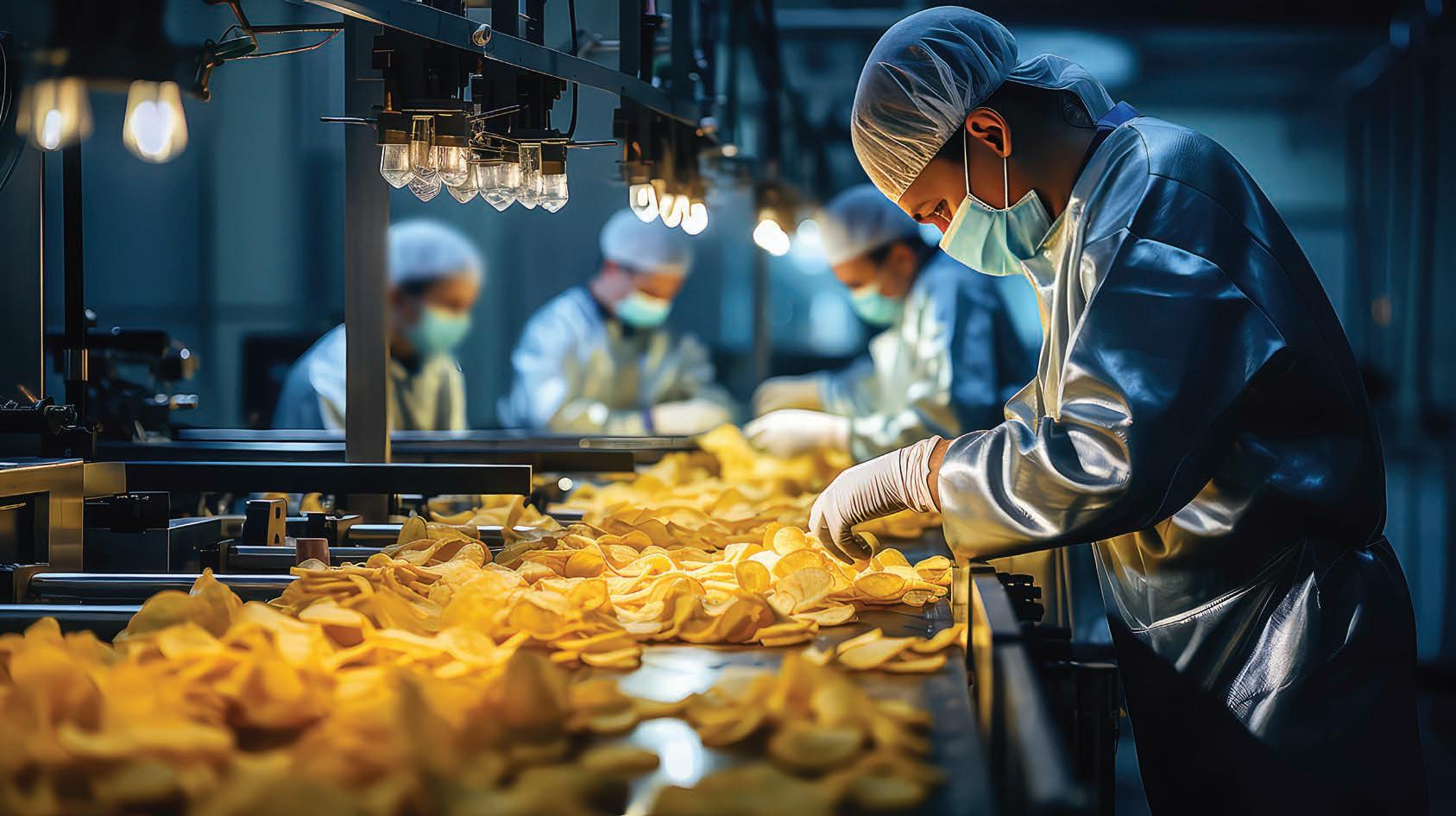
agree that effective policies are needed to address emissions, drive decarbonisation, encourage long-term investment in clean technologies, and to capitalise on economic opportunities.
This environmental challenge also presents an opportunity for private investment and improved productivity.
Increasing geopolitical risks and recent global events, such as the COVID-19 pandemic, have heightened the focus on economic resilience with many major economies now renewing industrial policies.
In a statement from the Australian Council of Trade Unions, Michele O’Neil, ACTU president, said the organisation supported the Future Made in Australia plan.
“We can’t leave Australian workers behind; we need to grab the opportunity that our amazing natural resources give us,” said O’Neil.
“Where we put workers and communities at the heart of the transition by embracing a strong role for government with conditions on how public money is spent.
2050, we are projected to create between one and two million new direct jobs over the next 25 years.
“By fulfilling our potential as a world leader Australia can not only support local jobs and the reduction of Australia’s climate pollution, but also contribute to cutting the world’s climate pollution.
“Future Made in Australia leverages our unrivalled sun and wind power to create the jobs and build the industries that will form the backbone of the clean energy economy and the key to our national security.”
The Future Made in Australia agenda aims to tackle the key structural and strategic challenges facing the Australian economy.
The State of the Industry report details the importance of food and grocery manufacturing to Australia’s economy.
Key highlights:
• I ncrease in value: Turnover, or the value of the sector, increased by 11.6 per cent to $163 billion, reflecting strong demand from a year of record
prices. Many wholesale prices rose for the first time in a decade.
• Profitability Challenges: Despite higher top line growth, operating profit fell by 7 per cent to $7.2 billion due to persistent cost pressures from commodities, energy, and shipping rising faster than wholesale prices.
• Employment Impact: Employment rose by 4.1 per cent to 281,269 workers, with 37 per cent of jobs based in regional areas, emphasising the sector’s growing importance as a major employer across Australia.
• I ncentives boost investment: Government’s temporary full expensing tax measure helped stimulate capital, investment which rose by 24.5 per cent to $4.2 billion, largely directed towards plant and equipment upgrades, particularly in automation to counter labour shortages and enhance efficiency.
Australian Food & Grocery Council Tanya Barden CEO said the importance of the food and beverage manufacturing sector could not be underplayed.
“Our industry is a cornerstone of the Australian economy, providing essential
Australians. Recent and ongoing global supply chain disruptions have made our industry even more critical from a national resilience perspective,” said Barden.
Barden said investment in the industry needed to increase in coming years to prepare for the continued clean energy and circular economy transition and the continued adoption of digital technologies.
However, according to industry figures, suppliers are still struggling with lower profitability and rising living costs.
This makes it harder for the industry to cover the increasing expenses for energy, labour, transport, warehousing, and insurance.
Barden said the Future Made in Australia policy is a critical step to keep jobs and production in Australia’s largest manufacturing sector.
“We urge the government to back this key industry by implementing tax incentives for food and grocery manufacturing to be globally competitive, contributing to Australia’s economic prosperity, as well as net zero transition,” she said. F
At its core, the initiative aims to drive private sector investment into key industries.
Genetic advancements for next-generation orchards
A collaboration between growers and several university plant scientists is aiming to accelerate the development of new produce ranges.
Growers and plant scientists from several universities have joined forces on a new tree crop program designed to speed up the development of several produce ranges.
The $41 million tree crop program aims to develop new almond, apple, citrus, macadamia, and mango varieties, to be sold to consumers both nationally and abroad.
The project aims to develop smaller, high-density orchards for higher yield, supported by automation to reduce the pressures caused by labour shortages.
The new varieties will also feature desirable traits such as better storage and quality, higher nutritional content, and climate resilience for sustainably produced Australian-grown fruit and nuts.
Delivered through Hort Innovation’s Frontiers investment program, the fiveyear initiative is led by a collaboration between the Queensland University of Technology (QUT), Murdoch University, University of Queensland (UQ) and Western Sydney University (WSU).
Hort Innovation CEO Brett Fifield said this investment would prepare tree crop industries for a more productive and profitable future.
“Equipping plant breeders with the
tools they need to develop genetics for the next generation of orchards will support the horticulture industry to enhance resilience to climate change and diseases, find efficiencies through the adoption of automation technologies, and increase productivity,” said Fifield.
“In the long-term, this program will enable the development of new varieties of almond, apple, citrus, macadamia and mango to ensure their long-term viability and global competitiveness.”
The program draws on over five years of research in tree genomics and crop physiology to improve orchard production systems and develop new tree crop varieties.
The program is also in collaboration with national levy and publicly funded breeding programs, with research providing breeders with advanced genetic knowledge and tools to create new varieties with desirable traits.
QUT program director, evolutionary geneticist Professor Peter Prentis, from QUT’s School of Biology and Environmental Science, said the goal was to grow smaller trees with greater disease resistance, productivity, storage time and enhanced climate resilience.
“To fast-forward the process of breeding new varieties suitable for the next-gen orchard, we will use traditional
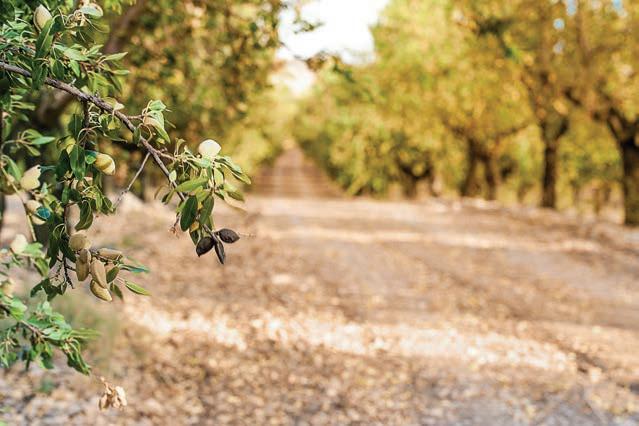
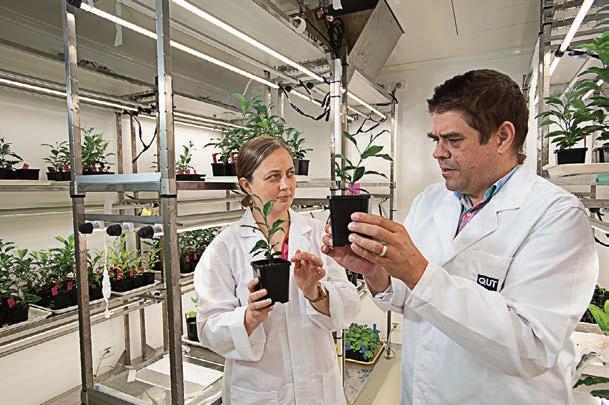
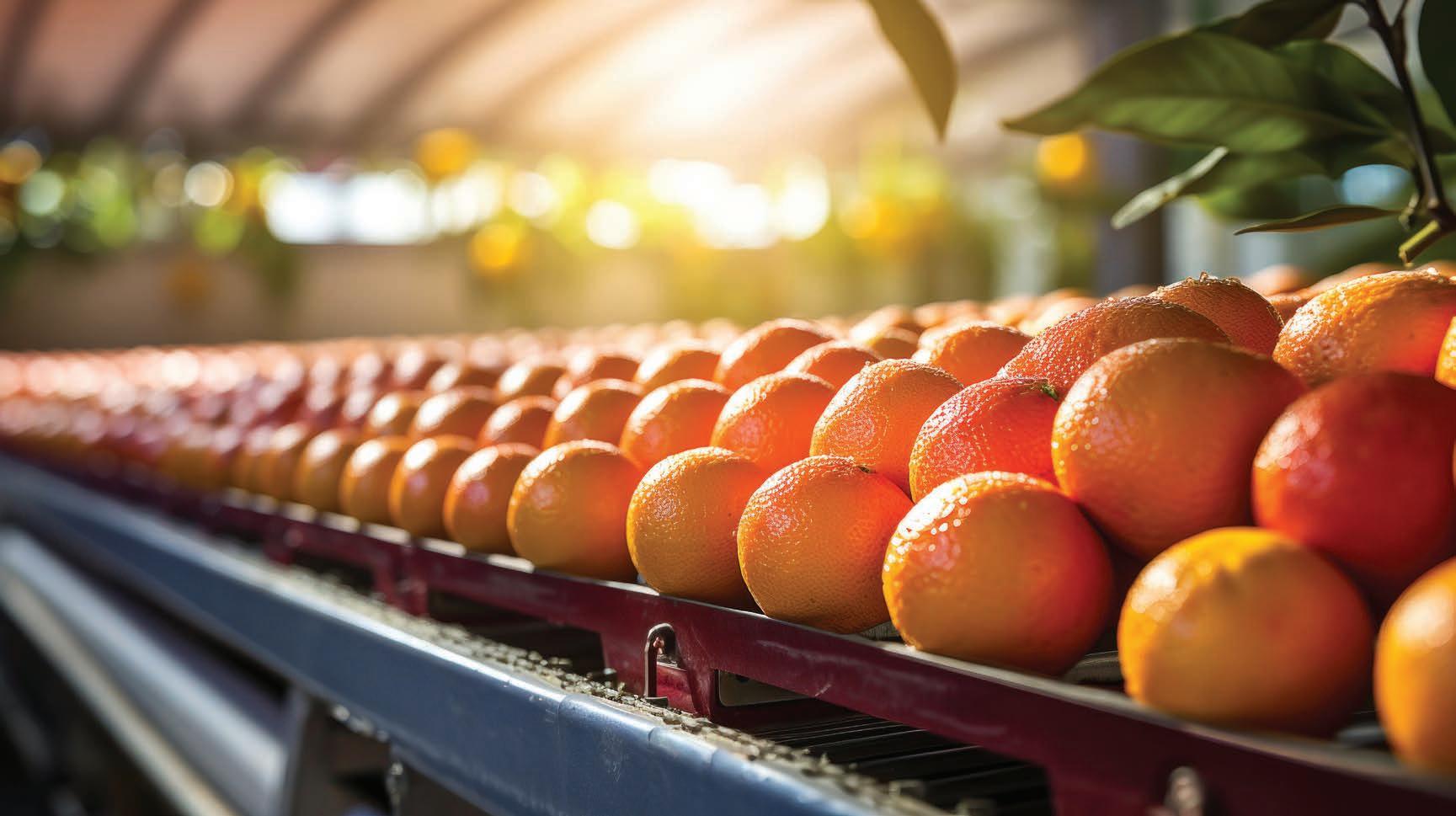
The $41 million tree crop program aims to develop new almond, apple, citrus, macadamia, and mango varieties.
Plant scientists are working on ways to speed up the development of several crops.
Image: AK Media/AdobeStock
Almonds are Australia’s seventh largest crop with sizeable production facilities in Victoria and South Australia.
Image: Wararat/AdobeStock
already operate that produce large yields.”
Prentis added that this development would also enable robots to move up and down planted rows for easier automated picking.
Meanwhile, Western’s node leader and plant molecular biologist associate professor Christopher Cazzonelli, from the Hawkesbury Institute for the Environment, said the goal is to grow smaller trees with greater productivity.
“This transformative endeavour promises to accelerate the development of new cultivars and sustainable growing practices, ushering in a new era of efficiency and innovation for Australian tree crop orchard systems,” said Cazzonelli.
“To fast-forward the process of breeding new varieties suitable for the next gen orchards we intend to develop and integrate molecular markers into genomic selection models and
access to varieties that are productive and profitable.
“As we move into the next generation of orchards, we need access to varieties that are designed for the latest production techniques and automation options, including having a small tree structure and high yields with sound commercial production and improved pest resistance,” said Bryen.
“Growers are focused on delivering consumers with what they are looking for in the most efficient way we can, maximising productivity and reducing costs.”
Lindsay Bryen, chair of the Macadamia Industry Variety Improvement Committee, emphasised that it’s crucial for the industry to access productive and profitable varieties.
Meanwhile, QUT program director Professor Peter Prentis said the program has a focus on maximising resources.
“To maximise space and resources in
area and support the implementation of automated management tools that will help growers improve their productivity at reduced costs.
“The research will then flow directly to active breeding programs that can use this knowledge and these tools to assist them in accelerating the development of new fruit and nut varieties for Australian producers.”
Professor Prentis said QUT’s leadership in robotic vision and drone technology would be used in the first phase of the project to obtain data on the tree’s characteristics including key flowering and growing style traits.
“Our first step is to provide breeders with the genomic tools to deliver new varieties and to do this our robots will take images of existing trees to enable breeders to study and understand their traits and help generate trees with desirable trait combinations.
“Climate change is another challenge
management tools to help these orchard crops flower more consistently.”
According to the Australian Bureau of Agricultural and Resource Economics and Sciences, in Australia, almonds are the seventh highest grossing crop, oranges are eighth, and macadamia nuts sit in 10th position.
Demonstrating the importance of this research, a new Rabobank report detailed how Australia’s almond exports continue to grow faster than the global average, while only accounting for 9.5 per cent of global almond exports.
For macadamias, Australia represents 25 per cent of global trade, reaching 17,2000 metric tons KWE in 2023.
“And as China and India, another major tree nut market, have limited domestic production, we expect further growth in imports will be required to meet demand, which Australia’s growing production is well placed to provide,” said report author, RaboResearch analyst Pia Piggott.
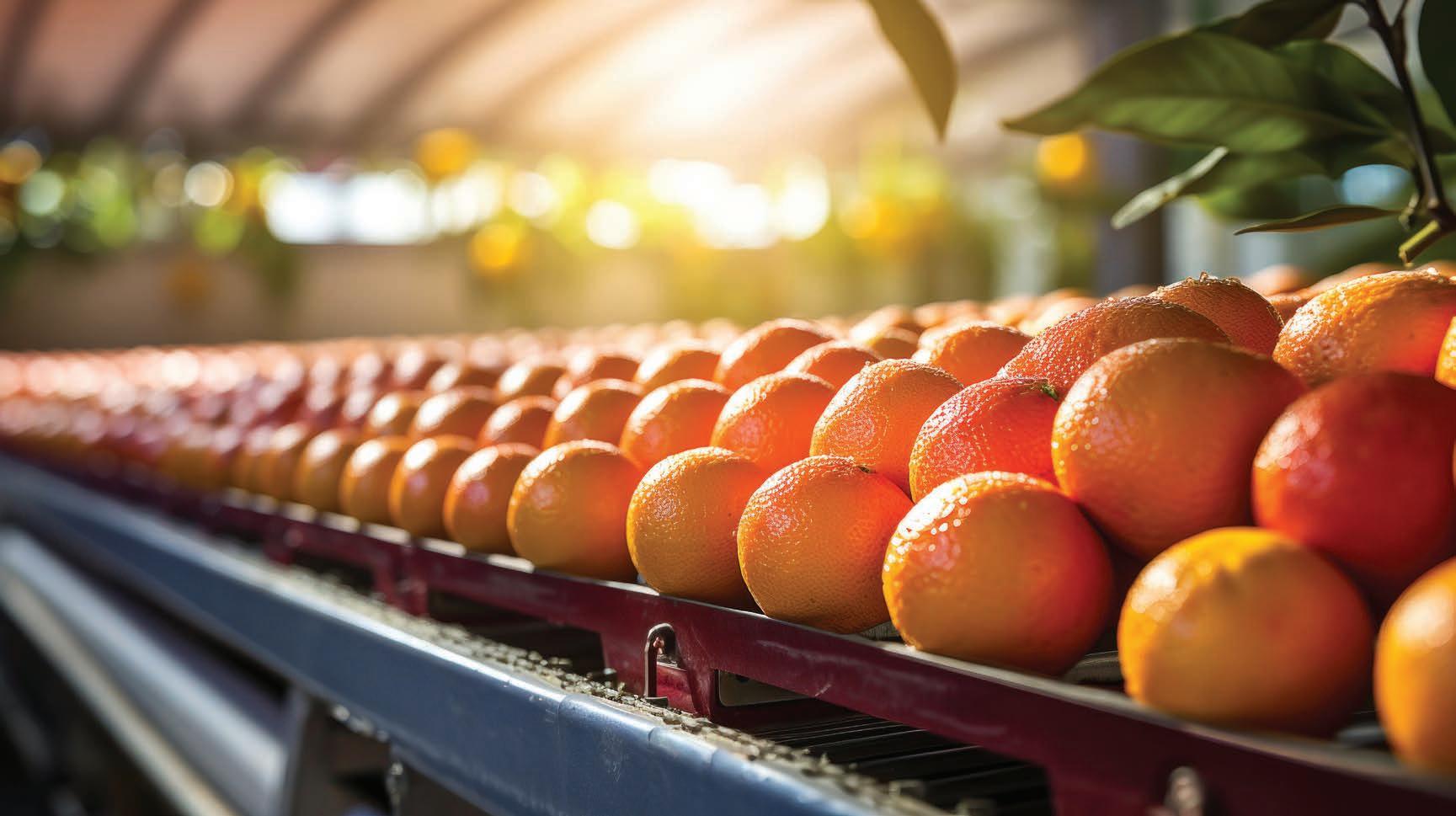
This research project could help provide a better outcome for producers by helping increase the output of three out of 10 of the country’s most lucrative crops. F
1.
2.
3.
4.
5.
8.
Australia’s Top 10 Crops:
Sugarcane - Major crops in Queensland and northern New South Wales,
Wheat - Major production areas in Western Australia, New South Wales, and Victoria.
Barley - Widely grown in Western Australia and South Australia, barley is a key export crop.
Cotton - Predominantly grown in New South Wales and Queensland.
Canola - Mainly produced in Victoria, New South Wales, and Western Australia.
6. Wine Grapes - Key regions including South Australia, Victoria, and New South Wales.
7. Almonds - A growing sector with significant production in South Australia and Victoria.
Oranges - Major production areas in Queensland and New South Wales.
9. Avocados - Major production in Queensland and New South Wales.
10. Macadamia Nuts - Grown primarily in Queensland and New South Wales.
Breakthrough in cultivated meat research
The innovation is designed to address growing concerns around the scalability and cost-effectiveness of cultivated meat and its future role in helping mitigate food insecurity.
In a major advancement for cellular agriculture, Professor Yaakov Nahmias, founder of Believer Meats, and a team from the Hebrew University of Jerusalem have introduced a new continuous manufacturing process for cultivated meat.
Cultivated meat is made by harvesting cells from an animal and growing them in a bioreactor.
These cells replicate and develop into muscle and fat tissues, which are then
This research represents a step forward for the economic feasibility of cultivated meat.
shaped into familiar products like steaks or chicken nuggets. Plant proteins are often used to give these products a final texture.
This innovation tackles the industry’s critical challenges around the scalability and cost-effectiveness of cultivated meat.
The study, “Continuous Manufacturing of Cultivated Meat: Empirical Economic Analysis,” published in Nature Food,
demonstrates the use of tangential flow filtration (TFF) for the continuous manufacturing of cultivated meat.
The new bioreactor system allows biomass to expand to 130 billion cells per litre, with a yield of 43 per cent by weight, and runs continuously for 20 days, enabling daily harvests of the biomass.
The research also presents a culture medium that contains no animal components with a cost of $0.63 per
litre. As a result, this medium would support the long-term, high-density growth of chicken cells.
In other words, this continuous manufacturing method could reduce the cost and complexity of cultivated meat production, potentially bringing it closer to everyday consumers.
“We were inspired by how Ford’s automated assembly line revolutionised the car industry 110 years ago,” said Nahmias.
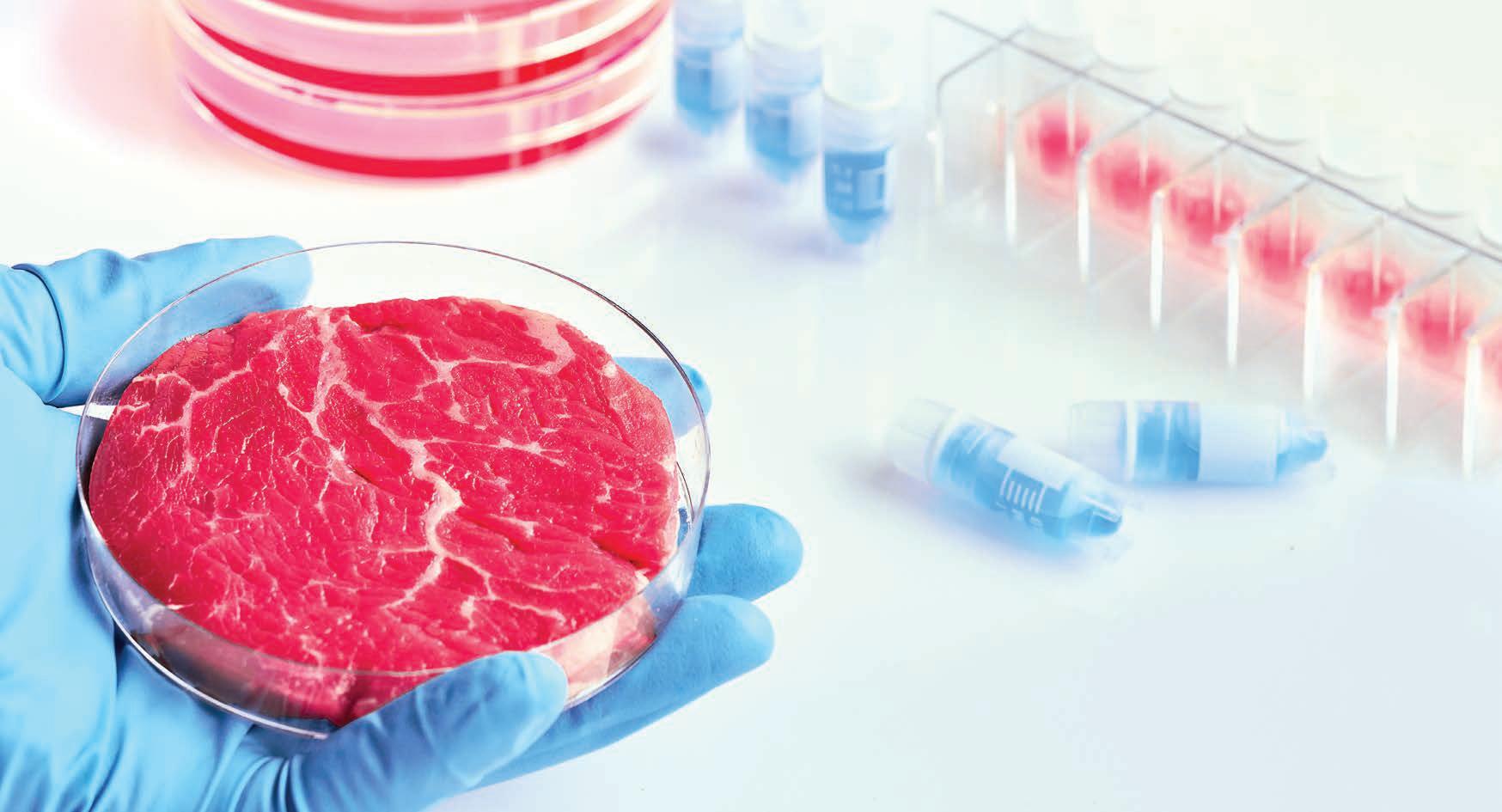
“Our findings show that continuous manufacturing enables cultivated meat production at a fraction of current costs, without resorting to genetic modification or mega-factories.
“This technology brings us closer to making cultivated meat a viable and sustainable alternative to traditional animal farming.”
Bruce Friedrich, president of The Good Food Institute, also expressed his support for the research.
“GFI applauds the spirit of openness that continues to characterise cultivated meat researchers like Dr. Nahmias and his colleagues, who understand that showing the scientific potential of cultivated meat will benefit all scientists working in the field,” he said.
This research represents a step forward for the economic feasibility of cultivated meat, addressing previous concerns about high costs and low yields.
Utilising this empirical data, the team conducted a techno-economic
analysis of a hypothetical 50,000-litre production facility.
The analysis suggests that the cost to produce cultivated chicken could potentially drop to $6.20 per pound, making it comparable to the price of organic chicken.
Dr. Elliot Swartz, principal scientist at Cultivated Meat, The Good Food Institute emphasised the significance of the study’s findings.
“This important study provides numerous data points that demonstrate the economic feasibility of cultivated meat,” he said.
“The study confirms early theoretical calculations that serum-free media can be produced at costs well below $1 a litre without forfeiting productivity, which is a key factor for cultivated meat achieving cost-competitiveness.”
Swartz added that empirical data remains the bedrock for any cost model of scaled cultivated meat production.
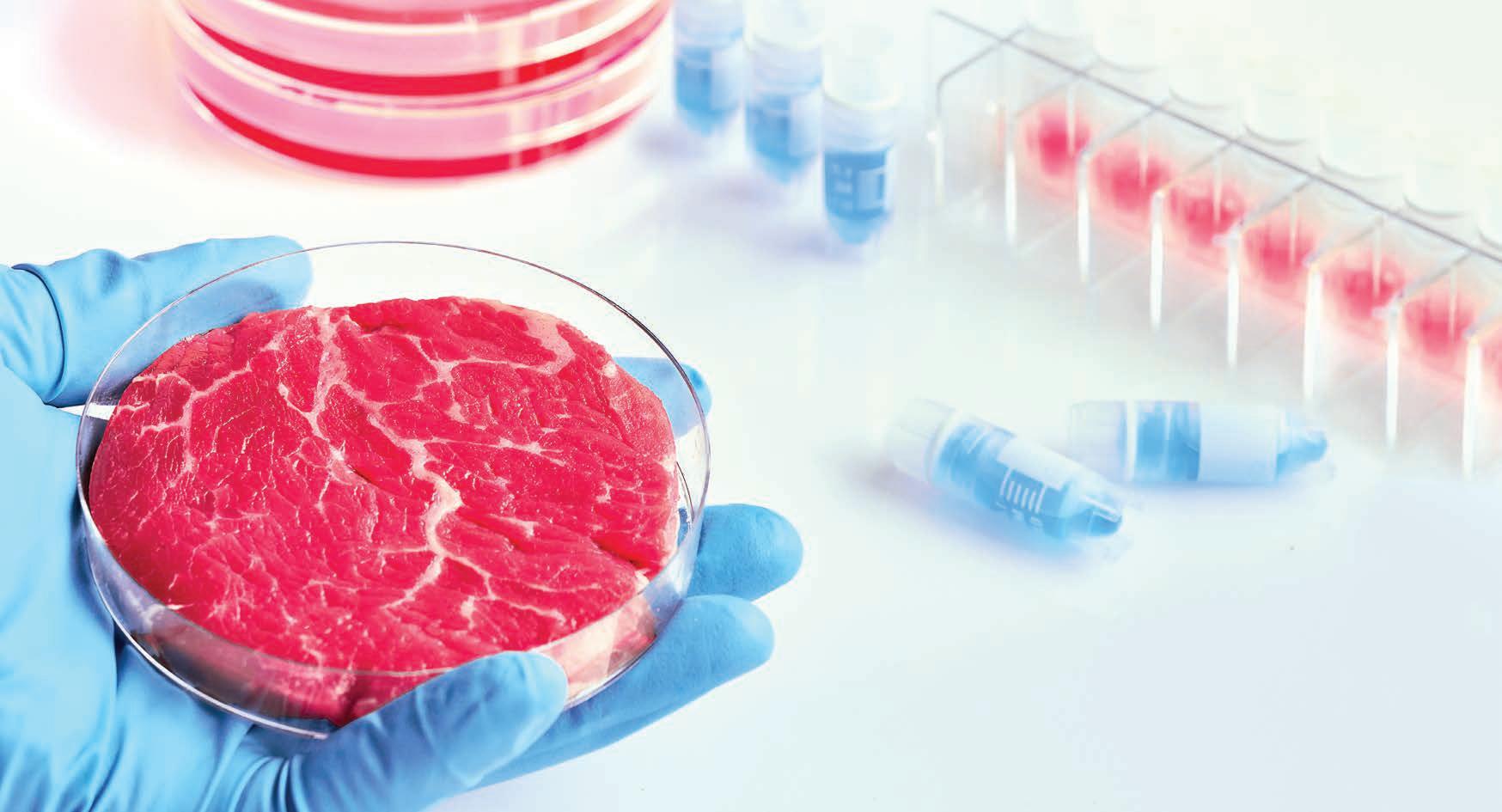
“And this study is the first to provide real-world empirical evidence for key factors that influence the cost of production, such as media cost, metabolic efficiency, and achievable yields in a scalable bioprocess design,” he said.
The authors noted that other factors would also impact the final market price of cultivated meat.
However, this research highlights how continuous manufacturing could greatly reduce production costs, making cultivated meat more affordable for consumers and more competitive with conventional meat products.
Results also showed how cellular agriculture can help meet global demand for animal products while also supporting environmental and ethical goals by reducing the need for traditional livestock farming.
This research is the first to demonstrate a cost-effective way to produce cultivated meat and provides the first solid economic analysis based on real data.
In practical support of the technology, Believer Meats is building the world’s first large-scale facility for producing cultivated chicken.
With global demand for animal protein set to double by 2050, cellular agriculture could help meet this need, especially as traditional livestock farming reaches its limits.
Despite recent FDA approvals for cultivated meat production, large-scale production of cultivated meat has yet to become a reality.
Earlier analyses raised concerns about the costs of factories and raw materials, questioning the economic viability of producing cultivated meat.
This research introduces innovative solutions, such as a new filter stack perfusion that lowers factory costs, an animal-free medium that cuts raw material expenses, and continuous manufacturing that boosts factory capacity.
These advancements could allow a small 50,000-litre facility to produce 2.14 million kg of cultivated chicken annually at a cost comparable to USDA organic chicken.
It’s hoped this technological breakthrough could greatly improve animal welfare, food safety, and food security, helping to meet the needs of a global population facing the effects of climate change.
The study is likely to attract widespread interest from various fields and gain media attention because of its important implications for the future of humanity.
This latest development comes just one year after a study by the University of Californian concluded the production of cultivated meat would ‘not work’ on a large scale.
Monash University professor Paul Wood, AO, has studied cultivate meat extensively and said multiple studies concluded that producing cell-based protein in a lab ‘will be far more energy intensive when it’s produced at scale’. F
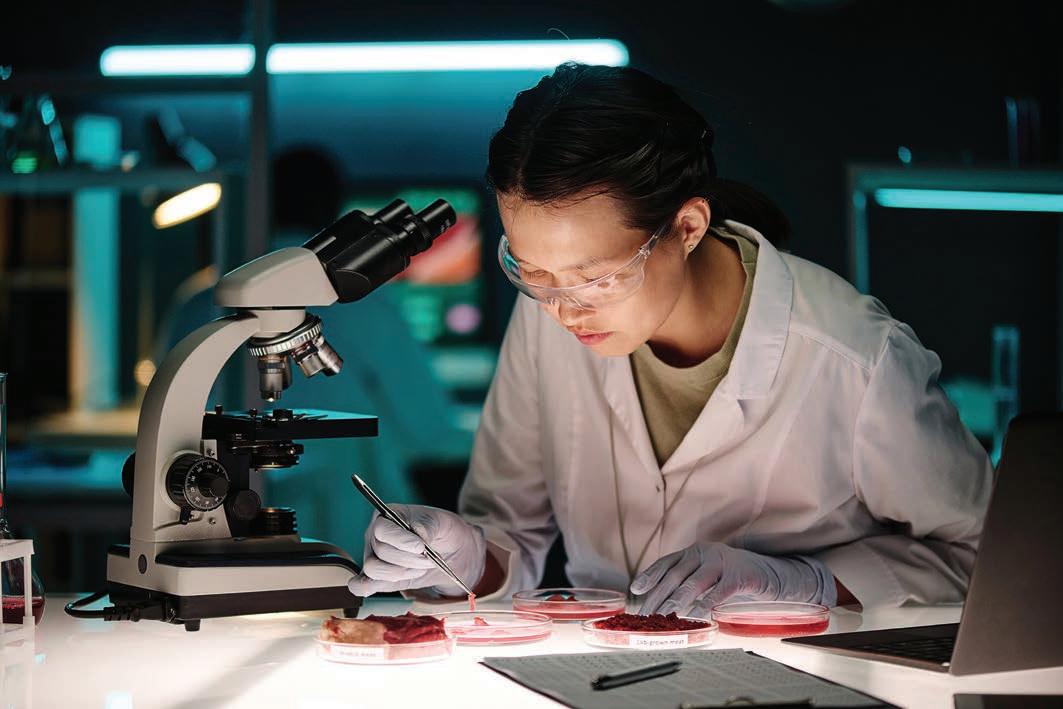
A continuous manufacturing method could reduce the cost and complexity of cultivated meat production.
The Future Made in Australia policy represents a key opportunity for the government to leverage regional manufacturing.
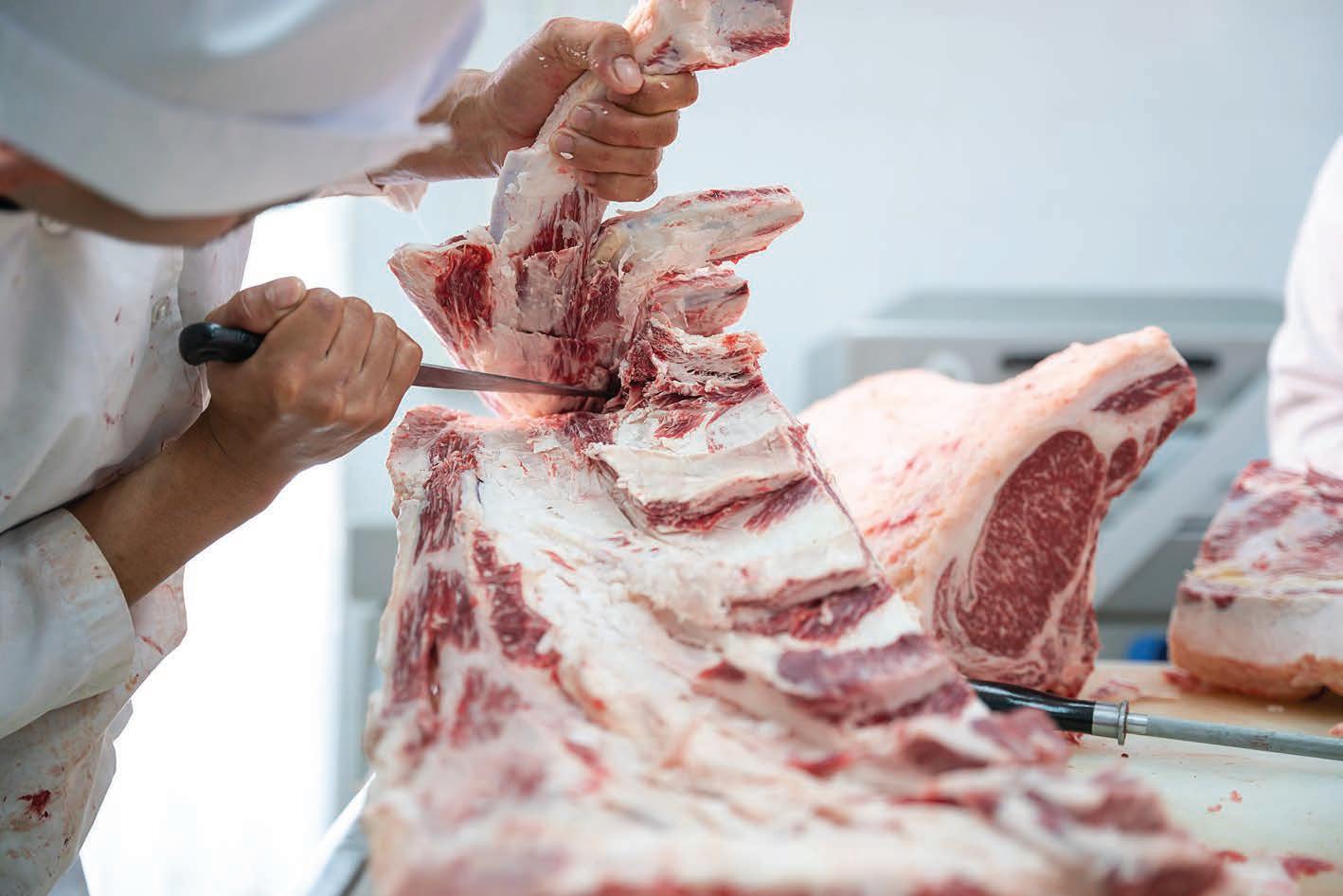
Regional manufacturing a key pillar
The role of Australia’s regions when it comes to supporting food and beverage manufacturing can’t be understated, as government aims to grow the sector.
Food and grocery manufacturing is crucial for regional Australia, providing jobs for nearly 40 percent of the sector’s 280,000 workers. In this context, Greater Shepparton stands out as a key player, transforming local agricultural products into wellknown Australian brands.
Last month’s joint event by Community for Greater Shepparton and AFGC underscores the sector’s strength in the region, often referred to as the “Food Bowl of Australia.”
The area’s diverse production— ranging from dairy and canned fruits to instant soups and liquid fabric softeners—demonstrates its robust manufacturing foundation.
Among some of the key crops
produced in the Greater Shepparton area includes fruits like peaches, plums, apples, and nectarines.
Data reveals:
• Largest manufacturing sector: Food and grocery is the largest manufacturing sector of the Greater Shepparton region, which includes Moira, Shepparton, and Campaspe
• Economic contribution: The sector generates over $3 billion annually
• Employment impact: It accounts for 66.5 per cent of total manufacturing jobs in the region
• Product dominance: Dairy manufacturing represents 52 per cent of the sector while fruit and vegetable processing accounts for 22 per cent. Greater Shepparton, contributing
around 25 per cent of Victoria’s agricultural output, excels in converting local produce into a variety of products, supporting both employment and the regional economy.
However, the sector faces national challenges, including the need for a skilled workforce, energy security, and resilient supply chains.
As the global economy shifts toward lower carbon practices, significant investment is essential to advance clean energy, circular economy transitions, and digital technology adoption to remain globally competitive.
The AFGC urges the government to support regions like Greater Shepparton through investment tax incentives to strengthen the future capabilities of this
crucial industry, ensuring continued job creation and economic contribution.
The Future Made in Australia policy represents a key opportunity for the government to leverage regional manufacturing potential.
“Manufacturing is important, but we can’t take it for granted,” said AFGC CEO Tanya Barden.
“Today’s data highlights the significant size and importance of the food and beverage industry, but it also underscores the need for future investment to keep this sector competitive and robust.
“The government has a golden opportunity to leverage Australia’s natural agricultural endowments by supporting regions that process them into products.”
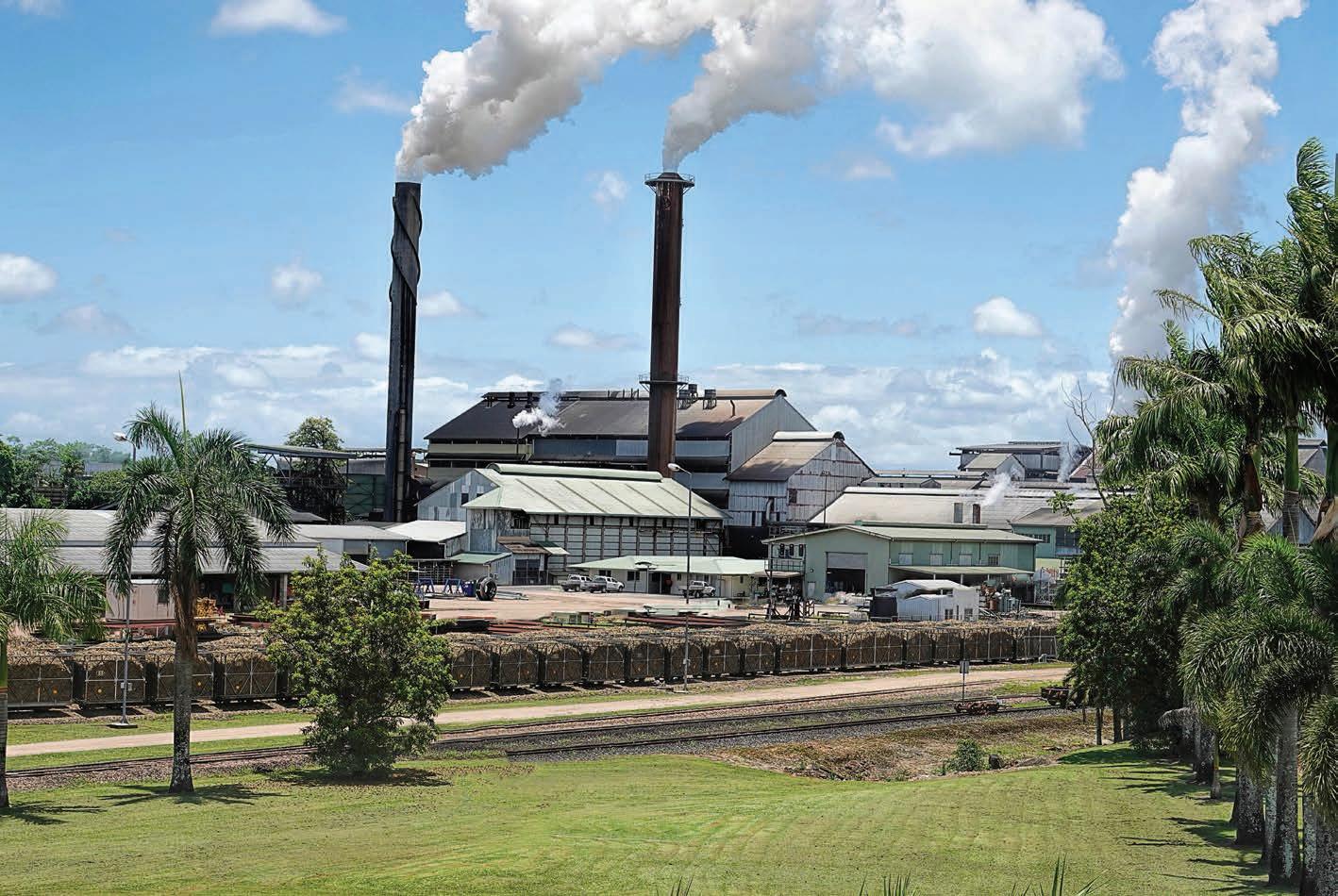
“Greater Shepparton’s impact goes beyond producing fresh local produce. It’s about transforming products from farm to supermarket shelf through manufacturing,” she said.
“This is now the lifeblood of the region’s economy and employment. We’re excited about our partnership with AFGC to showcase how essential food and grocery manufacturing is to our region, Victoria, and the nation.”
Victoria’s entire food and beverage manufacturing sector accounts for nearly a third of the state’s manufacturing income, exporting over $10.8 billion in manufactured food and beverage products annually, and employing more than 79,000 people.
Key food manufacturing regions include areas in Victoria, such as Shepparton and the Goulburn Valley, the Hunter Valley, and the Riverina in New South Wales), and Queensland’s Wide Bay region.
Some notable food manufacturers and producers located in regional Australia include Saputo Dairy Australia, Bickford’s Australia, Harrington’s Foods, and the Manildra Group.
fastest growing markets in Asia, the Pacific Rim and Europe.
Global powerhouse, Nestle, is a great example of the benefits food companies can obtain by using manufacturing facilities in the country’s regions.
Nestle has operated in regional NSW for more than 100 years and has manufacturing sites at Smithtown in the Macleay Valley, and Blayney in the central west.
The Smithtown factory, originally a milk processing plant, was acquired by Nestlé in 1921. By 1934, it had become the birthplace of Milo, which has since become Australia’s beloved choc-malt drink.
Today, around 200 people work at the factory, where they produce Milo, Nesquik, Nestlé Malted Milk, and a wide variety of Nescafé coffee mixes for both the Australian market and international customers.
Over the past decade, Nestlé has invested more than $50 million in the Smithtown facility, with another $77 million planned to boost future production capabilities.
The Nestlé Purina Blayney
The facility employs over 280 people and supports more than 60 local businesses and contractors in western NSW, prioritising the use of locally sourced ingredients.
Over the past ten years, more than $200 million has been invested in the Blayney site. A significant $101 million upgrade in 2022 was aimed at boosting production capacity and expanding export opportunities.
“Regional NSW offers us reach into key eastern states markets, access to the agricultural ingredients we need and a stable workforce,” said Michael Kane, director Technical and Production, Nestlé Oceania.
“Regional NSW also offers our employees access to a great lifestyle, where they can be part of strong local communities and have an impact in the communities in which they work and live.”
The CSIRO recently completed its Inquiry into Food and Beverage Manufacturing in Australia report and found that increased investment from State and Federal Governments was key to strengthening Australia’s food and
foster knowledge sharing, research collaboration, and resource pooling,” the report stated.
“Such a platform, supported by technology and science-backed approaches, would nurture innovation, stimulate new commercial ideas, ensure the industry’s competitive advantage and sovereign food infrastructure capability, and secure the future workforce of the food and beverage manufacturing industry.”
Among the CSIRO’s other recommendations was continuing to progress training and infrastructure development strategies for regional manufacturing.
“This will overcome logistic challenges and enable value addition to agricultural products. Emerging technologies, such as precision fermentation, can be used to produce any kind of food ingredient,” the report stated.
The future of regional food and beverage manufacturing appears to be bright off the back of both private and public funding continuing to increase for the sector. F
Regional food and beverage manufacturing accounts for 40 per cent of the industry’s workforce.
Winners announced for 2024 ABA Packaging Scholarships
The Australasian Bioplastics Association (ABA), in partnership with the Australian Institute of Packaging (AIP), is pleased to announce the winners of the 2024 annual Scholarship program for Australia and New Zealand.
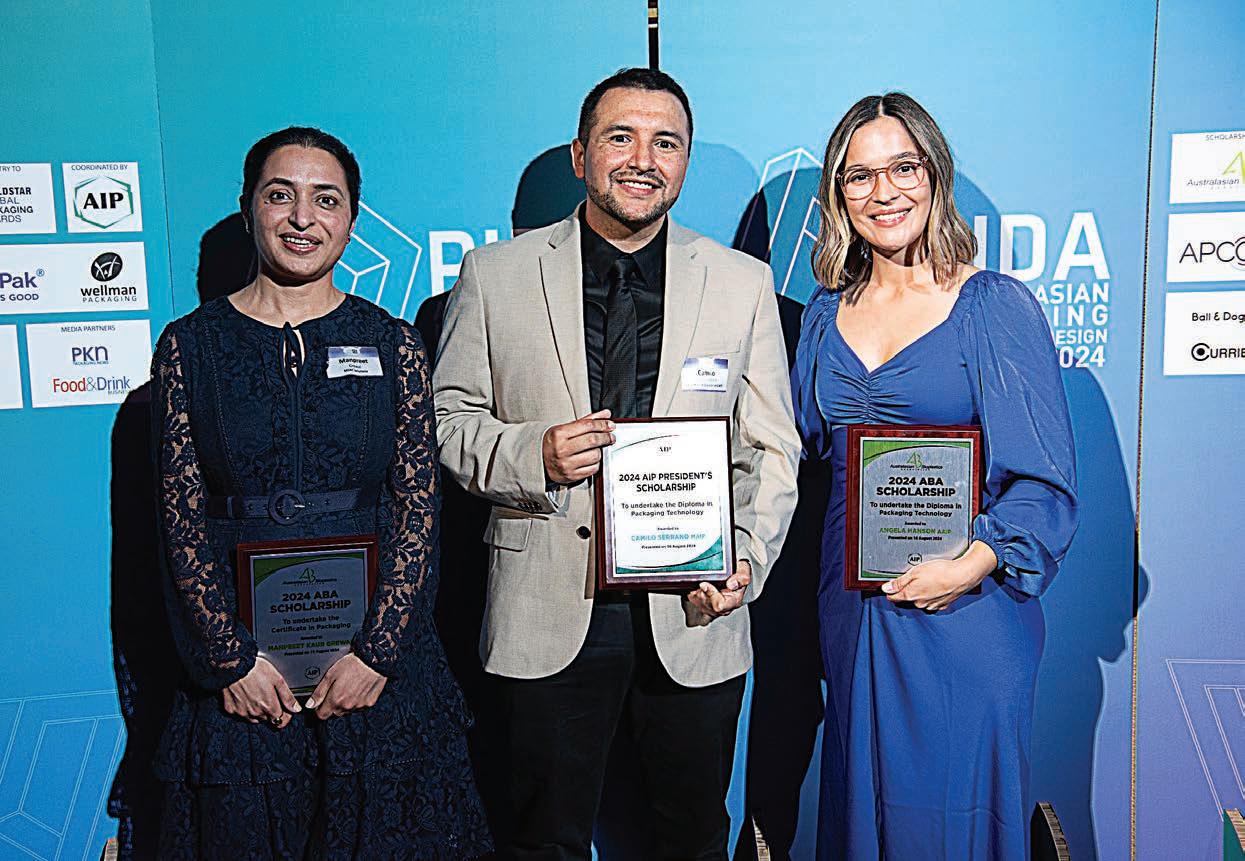
The Certificate in Packaging is the ideal first qualification for those working in the packaging industry.
The Scholarship program enables one eligible candidate the opportunity to undertake a Diploma in Packaging Technology and a second person the opportunity to undertake a Certificate in Packaging.
The Certificate in Packaging
The Certificate in Packaging is the ideal first qualification for those working in the packaging industry and is an introduction to the industry for those starting out on an exciting career in packaging.
The Certificate in Packaging provides a level of insight and understanding of the packaging industry that adds real and measurable value to
careers and businesses.
This qualification provides the student with the detailed overview of packaging materials and processes that broadens their knowledge and equips them for progression within the packaging industry.
The 2024 ABA Scholarship Certificate in Packaging scholarship winner is Manpreet Kaur Grewal, Product Technologist, MSAC Solutions.
Since joining MSAC Solutions in 2021, Manpreet has had the opportunity of being involved in the critical task of collecting and validating packaging data for major Australian retailers such as Coles, Woolworths and 7 Eleven.
As a qualified food technologist,
Manpreet is particularly intrigued by the complexities of food packaging, where sustainability, food safety, and cost considerations intersect.
While her experience in managing packaging projects has sharpened her ability to collect and validate quality data, Manpreet recognises the need to deepen her knowledge of packaging materials, formats, development, and sustainability to truly excel in this domain.
The Certificate in Packaging will provide her with a solid understanding of packaging materials and their functionalities, allowing her to make better informed decisions and contribute more effectively to projects.
In the next five years, Manpreet envisions herself thriving as a packaging technologist specialising in food packaging. Equipped with a deeper understanding of packaging materials and their implications for sustainability, product integrity, and food waste reduction, she aims to become a trusted advisor capable of recommending optimal packaging solutions.
The Diploma in Packaging Technology:
The diploma is internationally recognised as the premier qualification in the packaging industry and prepares students to take responsibility for packaging operations at any level
Images: AIP
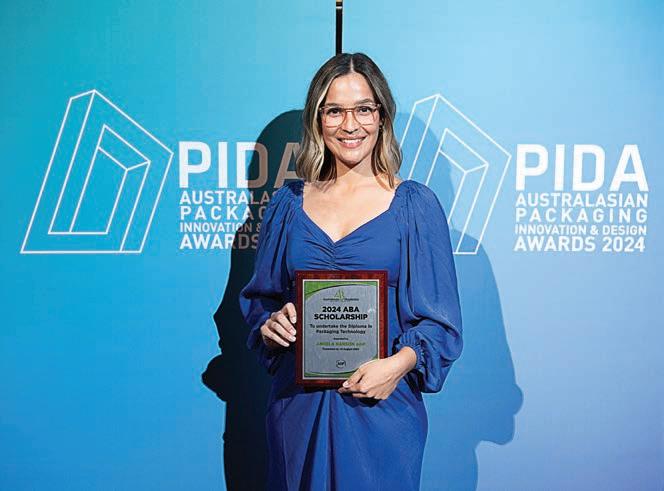
through the supply chain and can also lead to higher level study. Students who successfully complete the Diploma in Packaging Technology are equipping themselves for progression within the packaging industry to a position where they can assume responsibility for packaging in a company at any point in the supply chain.
The 2024 ABA Scholarship Diploma in Packaging Technology scholarship winner is Angela Hanson AAIP, Packaging Technologist, Tip Top.
After completing a Bachelor of Applied Science (Food Science and Nutrition) at the University of Queensland Angela worked as a Food Microbiologist 12 months before moving on to a Product Development Technologist role at Tip Top Bakeries –George Weston Foods (GWF).
As an industry professional, but also as a consumer and a parent, Angela could clearly see the opportunity to do better for our planet – especially through packaging.
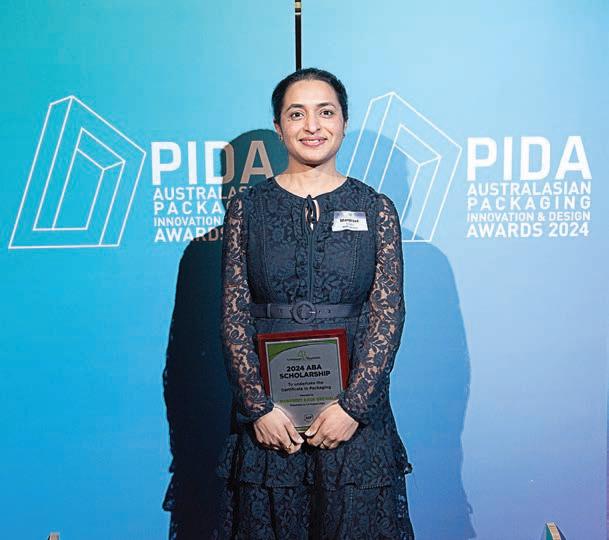
So, to drive change and improvement and to follow her passion 12 months ago Angela applied for, and was successful, in moving to the role of Packaging Technologist.
As a technically minded person Angela sees an opportunity to become a more well-rounded packaging professional by completing the Diploma in Packaging Technology.
Angela has recognised that she has numerous areas where her knowledge can be improved and believes that the
scholarship will assist her in developing professionally and grow within her role.
She wants to add more value to GWF in reaching their goals and being a champion of sustainability.
In her future she hopes to be a packaging expert driving innovation for a sustainable future for food, packaging and beyond.
The AIP would like to take this opportunity to commend the ABA for providing such invaluable professional development to the industry. F
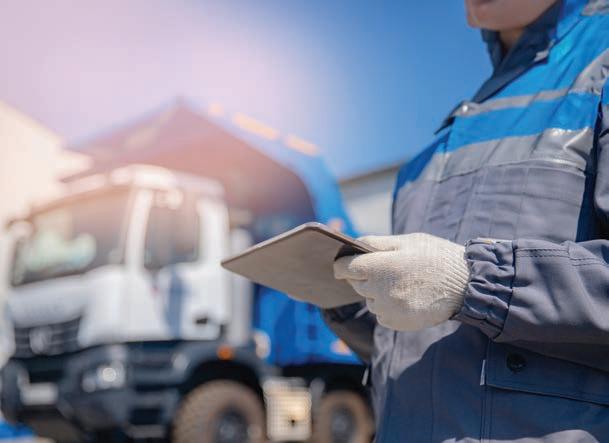
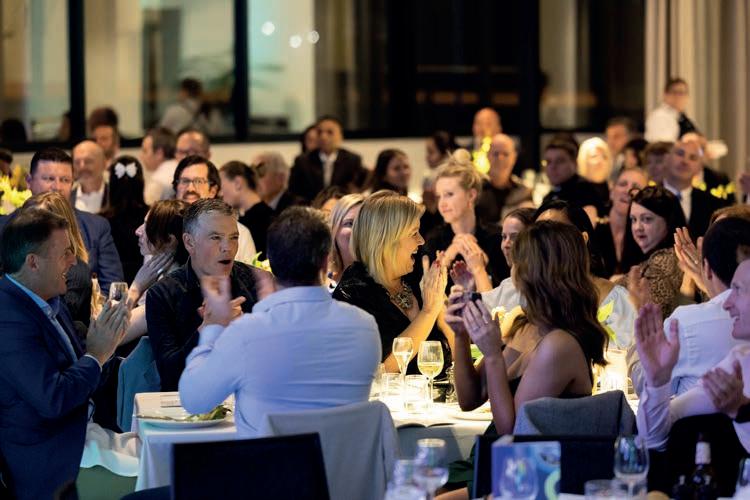
The 2024 ABA Scholarship Diploma in Packaging Technology scholarship winner was Angela Hanson.
The 2024 ABA Scholarship Certificate in Packaging scholarship winner was Manpreet Kaur Grewal.
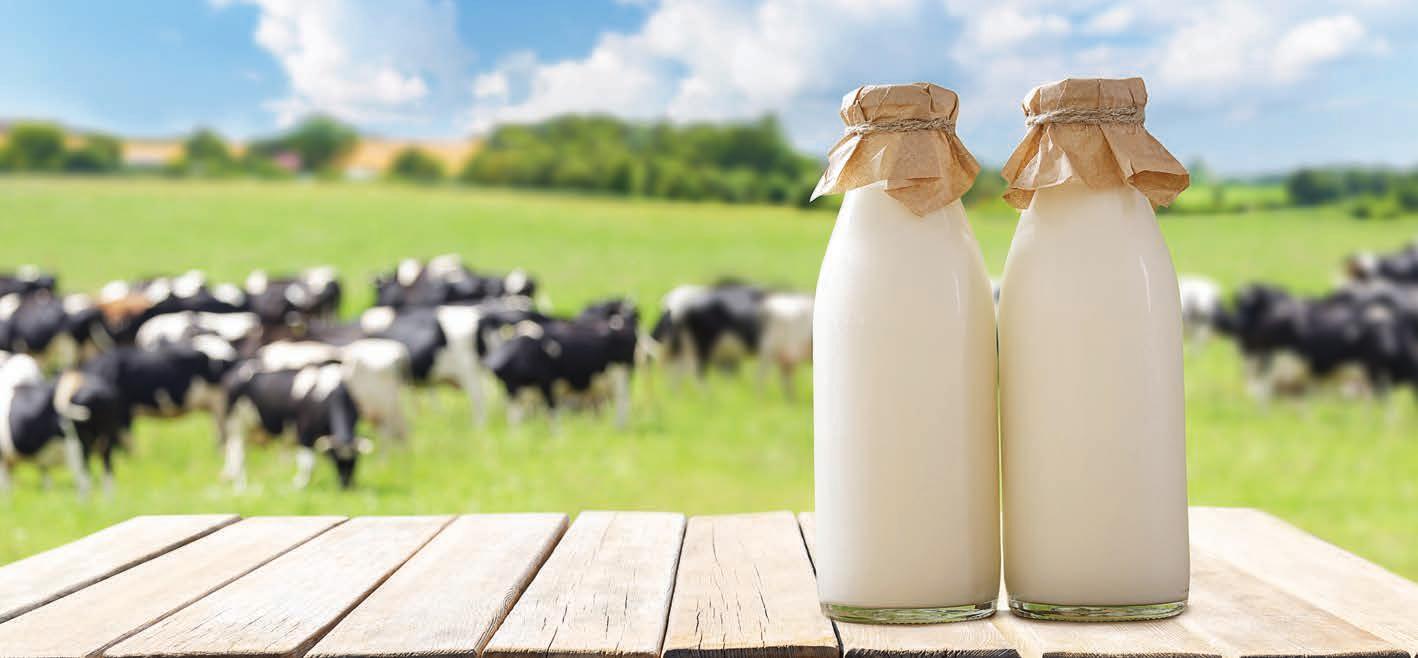
Key drivers of dairy industry in third quarter 2024
Australia’s milk production for the 2023/24 season is expected to surpass Dairy Australia’s earlier predictions despite weak demand for dairy products.
Despite a slight recovery at the beginning of 2024, global dairy markets continue to face challenges in balancing supply and demand, according to the latest Dairy Outlook Report from Dairy Australia.
Weak demand for dairy products is limiting price increases, as inventories in importing countries stay high and economic challenges continue to suppress consumer spending.
Although global inflation is slowly decreasing, it is expected to stay above target levels for the remainder of 2024.
This season, Australian dairy farmers have been protected from global market pressures due to favourable milk prices, improved weather, and stable input costs, all of which contribute to a positive profitability outlook.
According to the 2024 National Dairy Farmer Survey, the Australian dairy industry is experiencing its most stable period in a decade.
Despite the increased climate and market volatility of the past four years, the proportion of farmers feeling optimistic about the industry’s future has remained consistent at 68 per cent in 2024.
Meanwhile, 83 per cent of farmers are confident about their own businesses and expect to achieve operating profits this season. The trend of consecutive profitable seasons has led more farmers to report being in a “stable and content” position.
The easing of weather challenges
in most Australian dairy regions has set the stage for a profitable season and bolstered farmer confidence.
As prices for the new season are announced, connections to international market trends will become more apparent, potentially tightening margins on farms and affecting both farmer confidence and milk production.
Nevertheless, many dairy farms have capitalised on the strong performance of the 2023/24 season, positioning themselves well to navigate the upcoming changes and make informed decisions about their next steps.
Global supply Situation Outlook
A flat peak season is expected for Northern Hemisphere milk production, as wet weather impacts linger in parts of Europe and the US milk herd continues to decrease.
New Zealand recorded strong comparable production figures in the final months of last season, which are expected to continue tracking below last year. Global supply is likely to remain stagnant over the rest of 2024.
Australian market Situation Outlook
Cost-saving shopping behaviour has become a long-term shift for Australian consumers. Many households continue to gravitate towards private label products or increasing in-home consumption as an alternative to out-ofhome occasions.
The volumes sold across most key dairy categories continue to grow, supporting value retention in retail. Additionally, Australia’s imports of dairy have slowed (July to February), but competitive pressure remains. High inflation over 2024 will continue to drive cost sensitive purchasing.
Global demand
Importing activity remains dampened by low consumer demand in China and high inflation across other key export markets. With recovery expected over the longer-term, this dynamic is likely to define the remainder of 2024.
Nonetheless, there have been some reports of increased demand for Oceania product, amid the array of ocean freight disruptions currently at play.
Inputs
While drier conditions have persisted in some dairying regions, timely rainfall has bolstered winter feed production and crop prospects in others.
On balance, this is expected to support feed availability into the 2024/25 season, keeping prices relatively steady. Additionally, indicative fertiliser prices are also expected to remain under pressure, and temporary water prices remain historically low.
Global economy
Inflation remains above target for many economies. However, global inflation is forecast to decline steadily through to
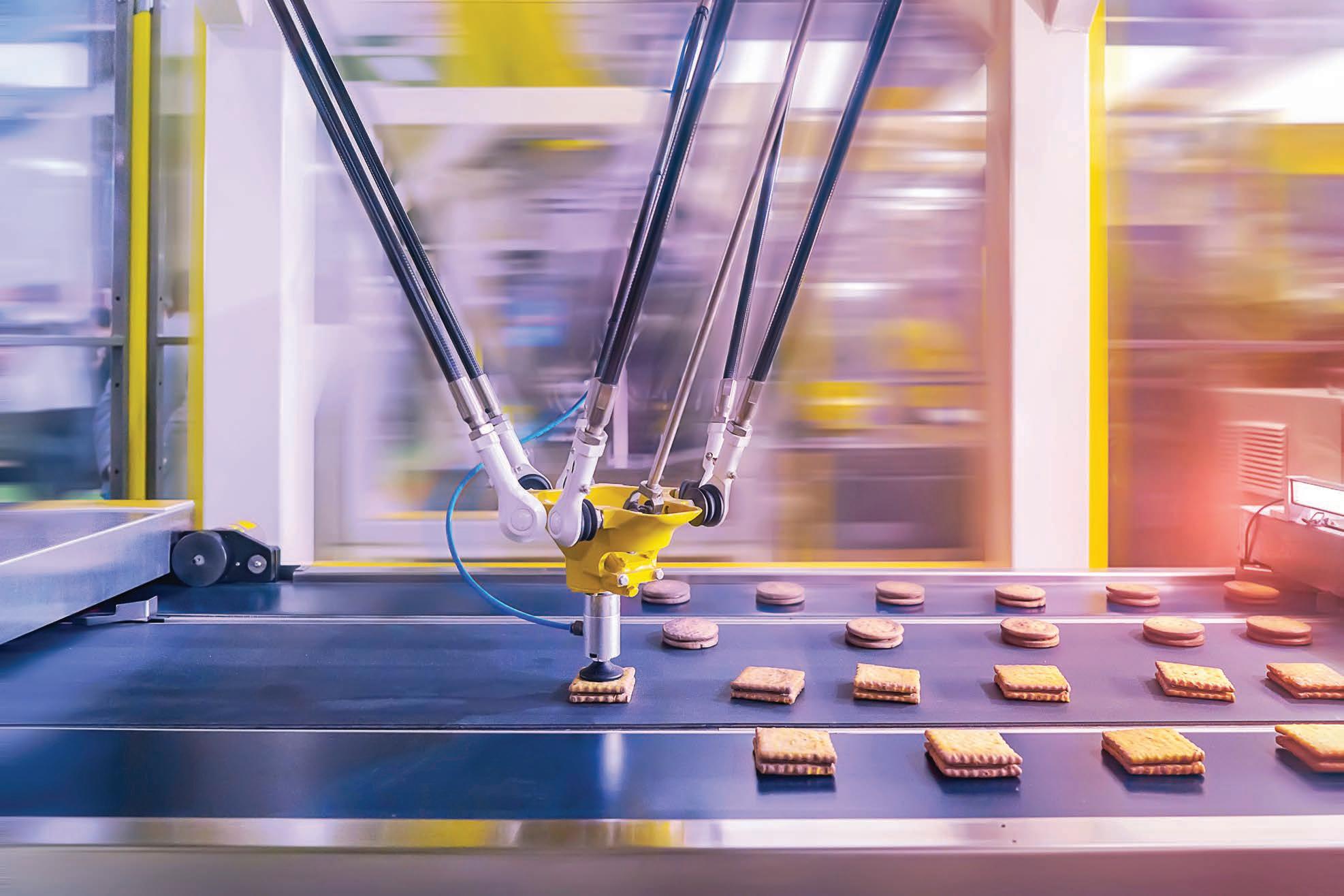
2025, while global economic growth is expected to remain steady (relative to 3.2 per cent) over the same period.
Despite the strict monetary policies of the last two years, steady recovery is on the cards over the long-term, with advanced economies leading the way
Australian production
Because of more moderate seasonal conditions, Australian milk production has bounced back from the lows of 2022/23, likely ending the 2023/24 season between 2 to 3 per cent above 8.13 billion litres.
While this growth has been further supported by robust milk prices and easing input costs, expectations for 2024/25 are weighted towards a small decrease in national milk production.
Exchange rates
The Australian dollar continues to track below last year and the absence of interest rate movement in the United States continues to delay appreciation of the Australian dollar.
The Australian dairy industry appears to be demonstrating resilience and optimism as it navigates a complex global landscape.
With production surpassing earlier forecasts and a stable period of confidence among farmers, the sector is well-positioned to handle emerging challenges.
Dairy Australia’s full market outlook report can be found on its website. F
Many dairy farmers have capitalised on the strong perfroamnce of the 2023/24 season.
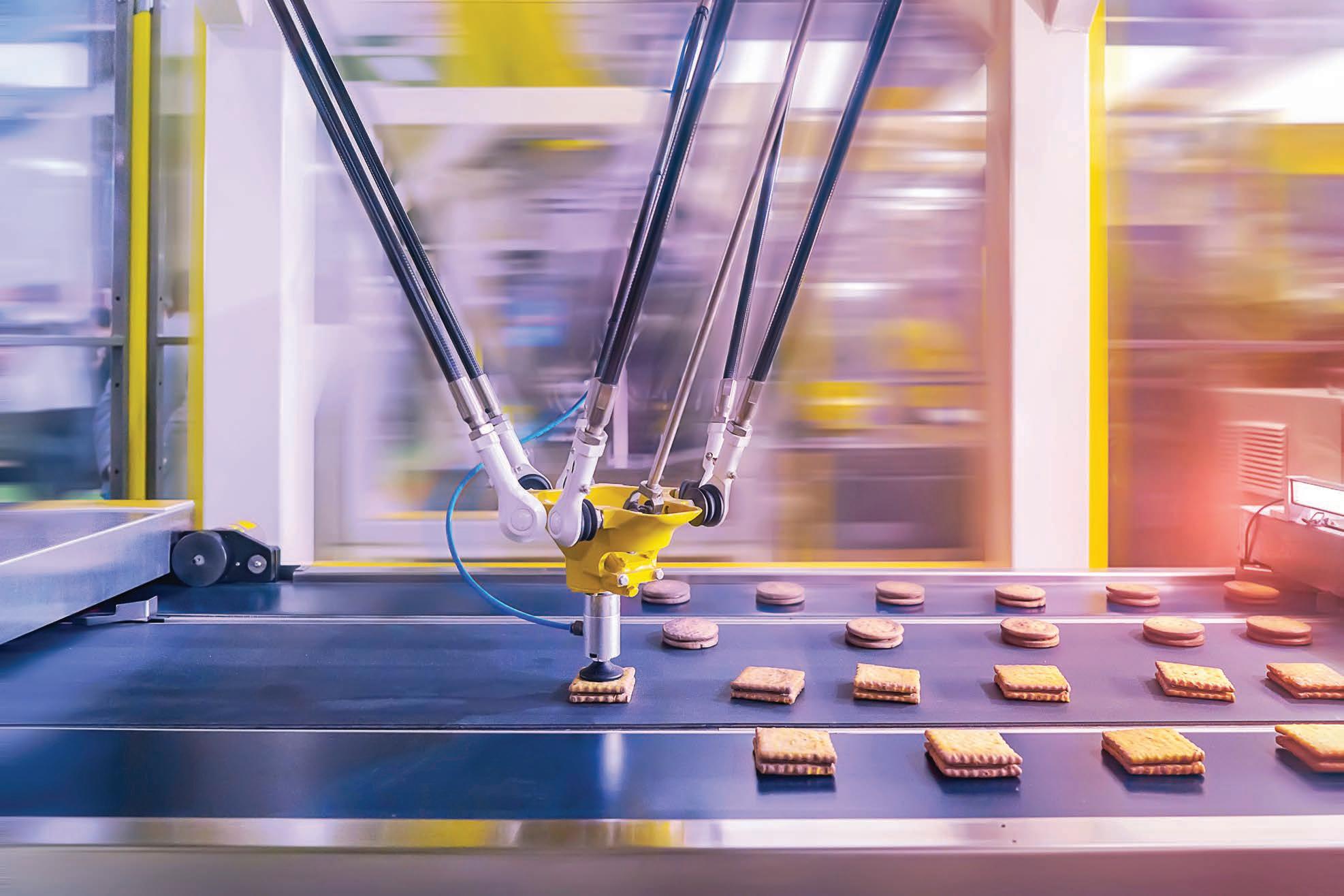
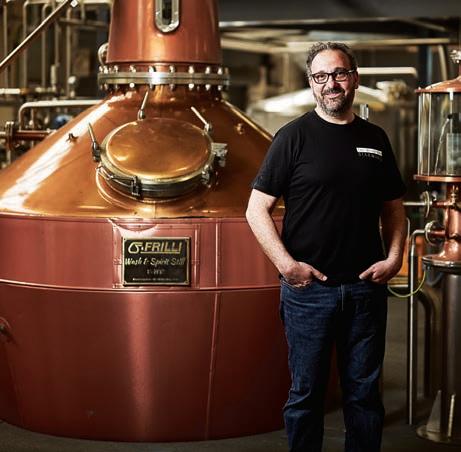
Innovative valve helps optimise processes
The Bürkert Type 2000 Classic is designed to efficiently handle steam, liquids, and gases under high pressures and temperatures. Its pneumatic actuation allows for swift, precise operation, minimizing downtime and ensuring consistent flow rates. The compact angle seat design facilitates high flow rates, making it ideal for space-sensitive applications.
Versatile in use, the Type 2000 manages CIP/rinse water in breweries and steam or hot water lines in dairy plants. With FDA-approved options and features to prevent contamination, it supports product purity essential for high-quality consumables.
Constructed from corrosion-resistant stainless steel, the valve meets stringent hygiene standards in the food and beverage industry, making it suitable for dairy processing, beverage production, and brewing. Its design supports sterilization and pasteurization processes.
The externally piloted angle seat valve operates efficiently with single or double-acting piston actuators, tailored for various temperatures. The nearly straight flow path enhances flow rates, while the self-adjusting packing gland ensures excellent sealing. These maintenance-free valves can be easily upgraded with accessories like position indicators and manual overrides, enhancing their versatility for various applications.
Features:
• Stainless steel or gun metal housing with threaded, clamped, or welded connections
• Long service life
• High flow rate
• Durable actuators with a modular accessory program
Bürkert
1300 888 868 www.burkert.com.au
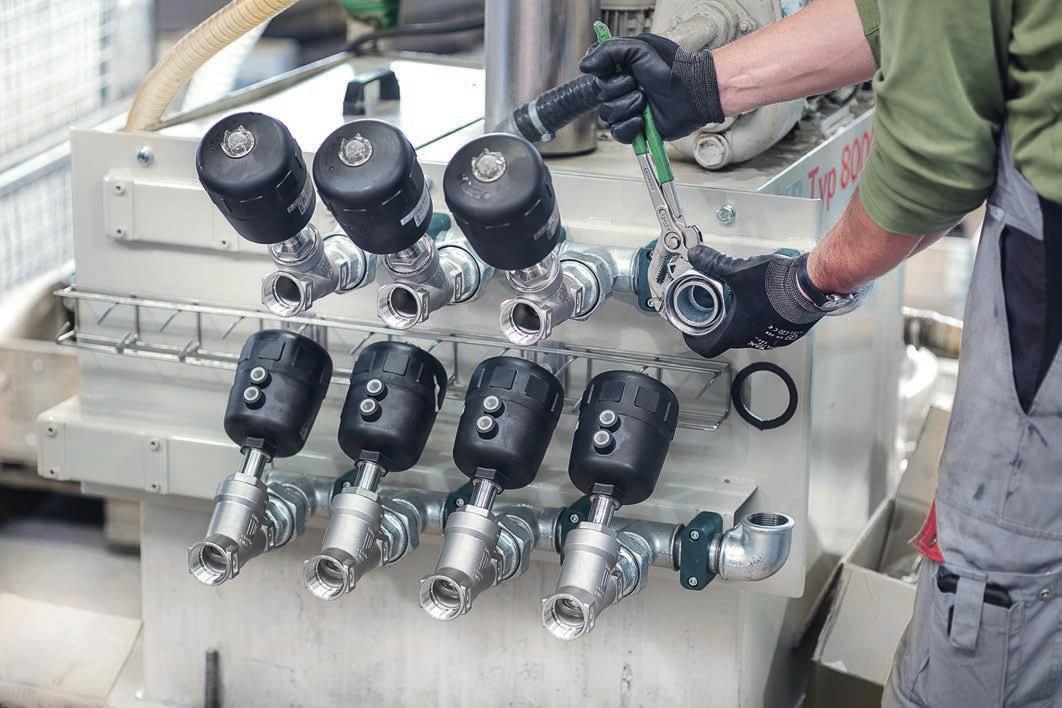
New food grade cylinder ticks all the boxes
SMC Corporation has now added a rod-type electric actuator to its range –specifically designed for the food manufacturing industry.
Complete with a IP69K protection from dust and water jets, stainless steel external parts and an NSF-H1 food grade rating, the HF2A-LEY series answers to the rigorous requirements of one of the largest manufacturing sectors in both Australia and New Zealand.
It is also capable of handling high temperatures up to 85°C and highpressure water jets of up to 10 Mpa.
The HF2A-LEY series is made from US FDA compliant materials, coupled with the smooth clean design for less residual liquid accumulation.
The new HF2A-LEY series ticks all the boxes when it comes to equipment requirements in the food processing and manufacturing industries.
Features::
• Enclosure: IP69K equivalent
• Smooth design for less residual liquid accumulation
– External parts: Stainless steel 304
– Scraper, Static seal: US FDA compliant material (Blue)
– Grease: NSF-H1 grade
• HF2A- series lubricants or rust proof agents are not used for external parts. Otherwise, lubricants or rust proof agents for the food machinery are used.
• US FDA compliant materials are used.
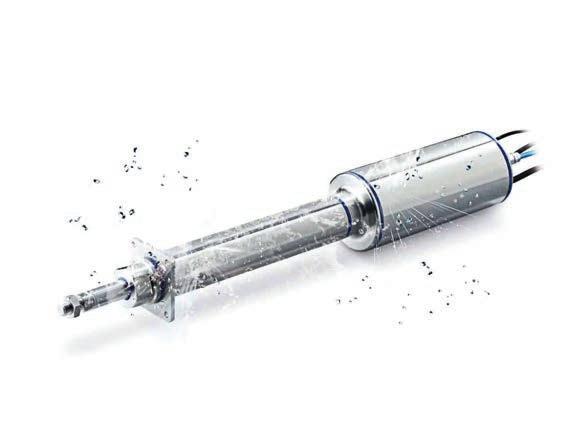
• Work load: Max. 80 k* * Size 63, Lead
•
Backplane Systems Technology presents the VECOW’s IVX-1000
Backplane Systems Technology is pleased to present VECOW’s IVX-1000. The VECOW IVX-1000 is a cutting-edge in-vehicle computing workstation designed to meet the demanding needs of the mining industry.
The IVX-1000 features a fanless design, ensuring dust resistance and compliance with EN50155:2017 standards. Its robust 16V to 160V DC power input, with 4kV DC isolation and up to 500V surge protection, ensures stable operation even in fluctuating power conditions. The workstation also includes software ignition power control and optional UPS support for uninterrupted performance.
The IVX-1000 excels in connectivity, essential for mining operations. It boasts 8 independent 2.5GigE LAN ports, including 4 with IEEE 802.3at PoE+, along with an additional GigE LAN port. This ensures reliable communication and data transfer, crucial for real-time monitoring and control in mining operations. Multiple wireless configurations, including 5G, WiFi, 4G, and LTE, provide versatile communication options for remote mining sites.
Security and network reliability are paramount in mining applications. The IVX-1000 supports Intel vPro, TCC, Time-Sensitive Networking (TSN), and TPM 2.0, addressing these critical requirements. For AI-driven tasks, the workstation features Intel Deep Learning Boost and the Intel Distribution of OpenVINO toolkit. The optional VHub AIoT Solution Service further augments its AI capabilities, facilitating advanced edge AI applications.
Features:
• Workstation-grade Platform : Intel Core i9/i7/i5/i3 Processor (14th gen, codename : RPL-S Refresh/RPL-S/ADL-S) running with Intel R680E PCH supports max 65W TDP CPU
• Optional supports outstanding AI computing productivity by advanced
Hygienic
flow meter with IO-Link
The SM Foodmag magnetic-inductive flow sensor is changing the measurement of liquid and creamy foods.
Featuring IO-Link technology, it is the first sensor to offer digital data transmission from the process, effectively removing the final blind spot in fully digitalized and transparent production. The sensor’s display and omnipresent status LED deliver real-time information about its current status directly on site.
The sensor measures the current flow rate, total volume, and flow direction, and also detects the presence of the medium (often called empty pipe detection). Additionally, it transmits conductivity and temperature data to both the control system and IT level, potentially reducing the need for extra measurement points in the system.
When paired with ifm’s patented cables, the standard M12 connection provides a quick, waterproof, and error-free link to your data infrastructure. Its standard installation dimensions, along with a variety of seals and process adapters, simplify integration into existing systems.
The app-based menu and guided installation streamline parameter setting, while the SM Foodmag delivers enhanced visibility both locally and digitally inside the pipe, ensuring greater process reliability.
The game changer Hygienic flow meter with IO-Link
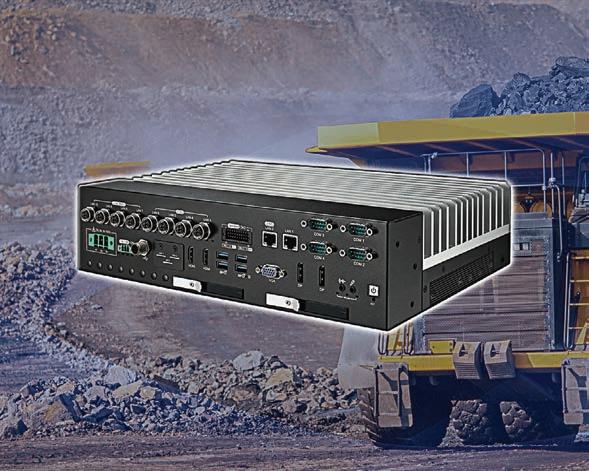
• Fanless design for railway in-vehicle applications, fully compliant with EN50155 : 2017
• 8 Independent 2.5GigE LAN M12 X-coded with 4 IEEE 802.3at PoE+, 1 2.5GigE LAN, 1 GigE LAN, 4 Isolated COM
• 2 Front-access 2.5”SSD/HDD Tray, multiple 5G/WiFi/4G/3G/LTE/GPRS/ UMTS
• Supports Intel vPro, TCC, Time-Sensitive Networking (TSN), and TPM 2.0
• Optional VHub AIoT Solution Service supports OpenVINO based AI accelerator and advanced Edge AI applications
Backplane Systems Technology (02) 94576400 www.backplane.com.au
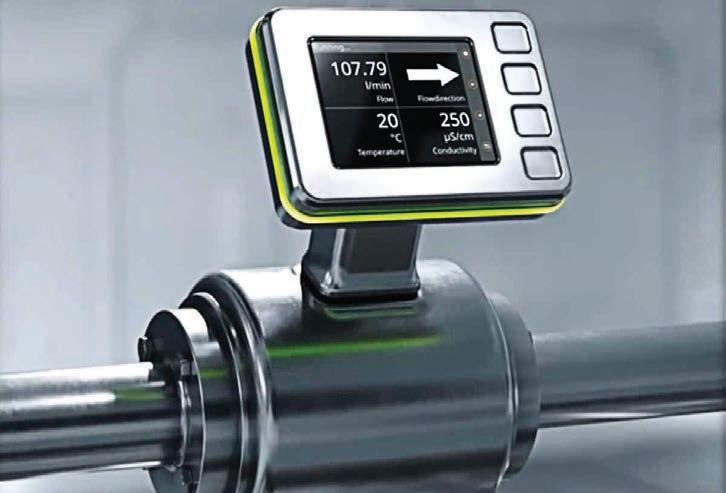
• Magnetic-inductive flow meter completes the portfolio for the food industry
• Reduces the need for measuring points by providing flow rate, total volume, temperature and conductivity
• Easy to set up thanks to app-based menu and guided installation
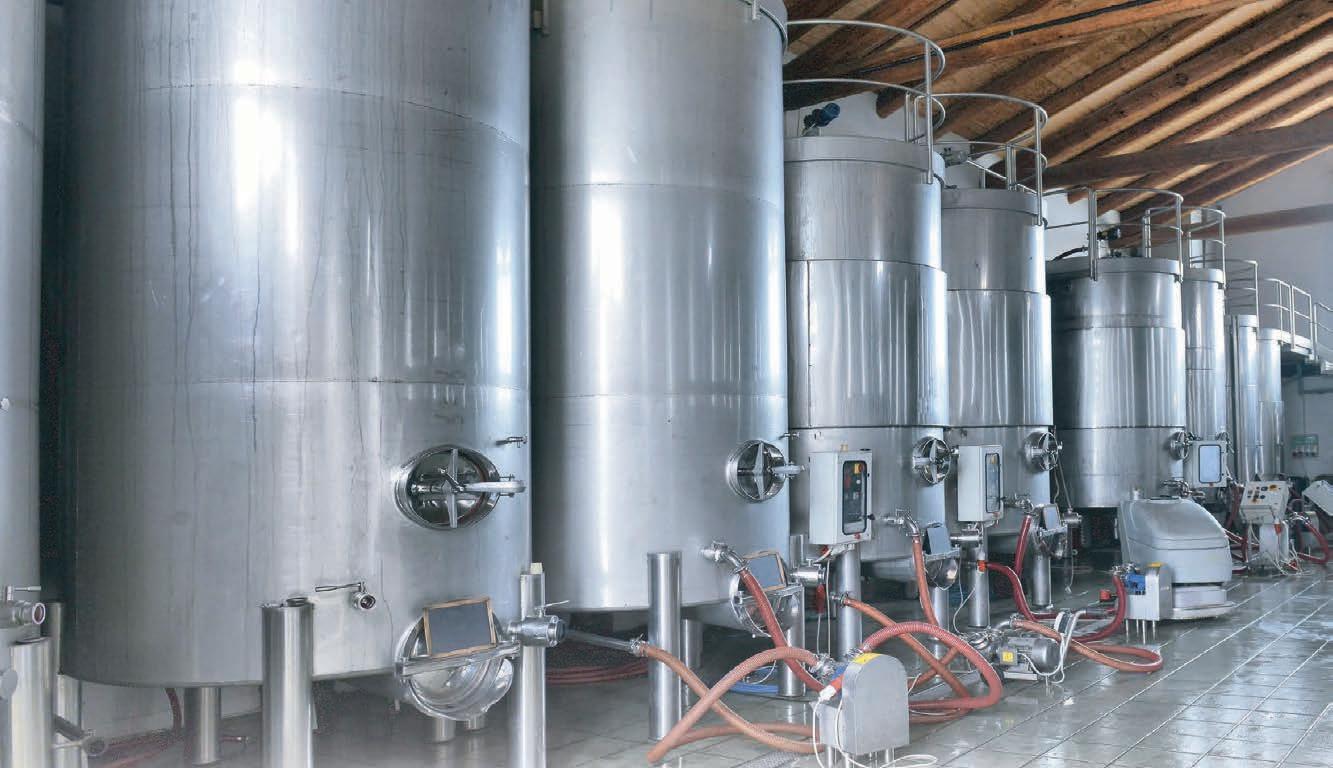
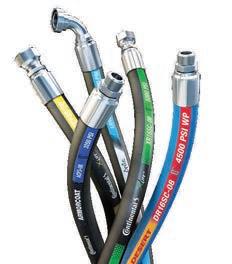
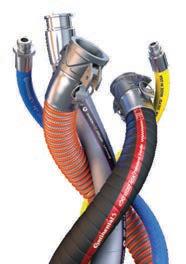
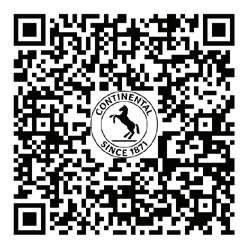