
12 minute read
Feed Time Made Easy
With the hills of Te Kauwhata starting to show signs of summer dry, Farm Trader NZ’s Willie McKnight headed to a 130-hectare property with a crossbred milker herd of 300, where owner Wilbert Smolders recently added the Abbey VF2000 to his infrastructure
The investment in a new mixer wagon was well thought out, with Smolders undertaking plenty of research around the ideal wagon for his specific requirements that, due to autumn calving, requires the use of a dependable mixer wagon pretty much all-year round. Because his calves arrive at what’s often the wettest time of year, it’s essential to the successful operation of his business that he can adjust his feeding routine reliably and accurately to maintain milk production and days in milk. Feeding out is done on the covered feed pad as opposed to in-paddock because of the terrain and soil conditions. It also reduces waste and is better for animal welfare and the environment. To give the stock more space, he feeds around the outside of the pad before the central trough.
THE MACHINE
The twin auger Abbey machine of this size is aimed at farmers looking for consistency in their feed, and the VF 2000 allows bales to be added and chopped for an even quality mix. It’s also ideal for farmers wanting dependable performance with minimal maintenance. With a tub capacity of 20 cubic metres, the addition of solid rubber hungry boards allows an additional three cubic metres of space. Smolders frequently feeds out an eight-tonne load, depending on the feed mix and bulk. On the day we visited, it was a smaller three-tonne load to feed the 130-head herd still being milked, with the remainder dried off. It’s worth noting that his production levels, even at this time of year, sit at 1.6 milk solids, part of which he attributes to his accurate feed mix.
THE ELEVATOR
The 560mm slat and chain elevator comes as standard (but longer elevators are optional) offering low maintenance and longevity. Roller bearings for the elevator are easily accessible for greasing, and replacements (if required) are readily available as they are a generic bearing. Rubber gussets are placed along the hinge edge of the elevator to prevent feed spillage, and a fold-down flap offers the versatility of helping deflect dusty feed to the elevator if required. Personally, for my own preferences, I’d like to see a slightly longer elevator or a deflect chute added, just to give a bit more reach when coming up alongside feed troughs. However, as an experienced operator, Smolders doesn’t find this a problem. With a discharge height of 800mm (higher than many other models), the risk of hitting the top of feed troughs is minimised and gives added reassurance if a less experienced operator is working the unit. Operation of the feed door, chute and elevator is all controlled from in-cab and works seamlessly at the flick of switch. The same control box also allows adjustment of conveyor speed. At one metre wide, the feed out door to the elevator offers plenty of space to ensure even feeding. The machine comes with a feed door on either side, and at the time of purchase, the customer can choose their preferred side for the elevator to be set up.
CONSTRUCTION
One of the first things I noticed was the overall build quality. With my neighbour having a similar Abbey machine, but with two years’ operation under its belt, I’ve noted that the paint job is still pretty much as good as new. The distinctive orange paint is
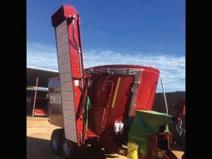
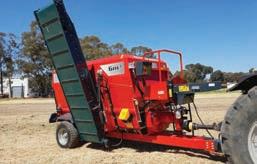
Looking for a mixer wagon?
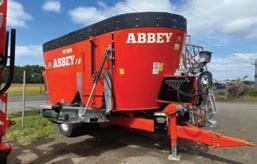
Search for ‘mixer wagon’ on
TradeFarmMachinery.com.au
or type the TA or DIY code shown here into the keyword search field
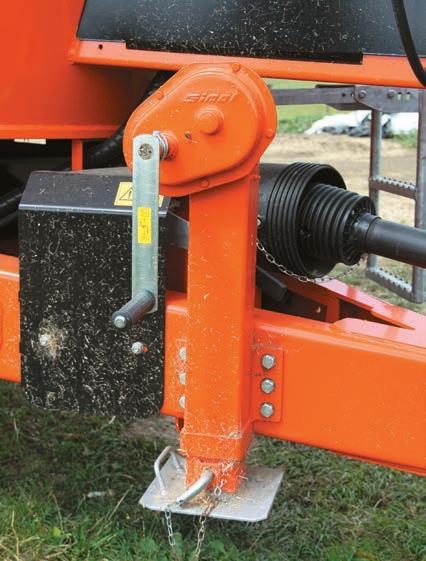
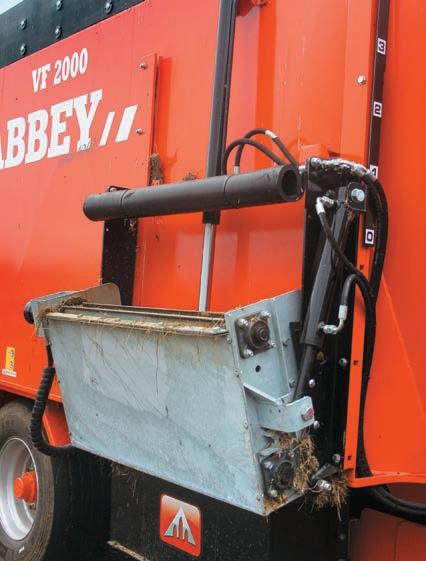
2 3
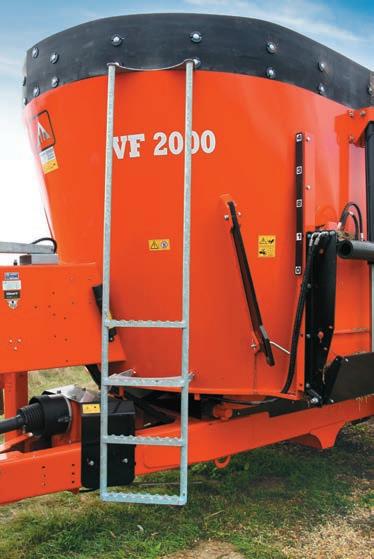
a two-pot epoxy, which seems to resist sun fade and handle the rigours of farm work well. Built on a rigid non-sprung chassis, the floor is 20mm thick for extra strength and mounting of augers, with the 8mm rolled steel tub designed to stand up to bumps and knocks. This durable build sees the empty unit weigh in at 7.5 tonnes, perhaps making it more suited to a feed pad operation rather than in the paddock, particularly taking into account Smolders’ winter-wet paddocks. For those wanting to use the machine more in paddocks, spec’ing the machine with twin axles or single axle dual wheels is an option. Rolled walls help the flow of mix into the twin augers. Equipped with seven knives per auger, each auger has a through shaft for added strength and to prevent twisting. Running through sealed bearings in an oil bath eliminates much of the need for auger maintenance.
MAINTENANCE AND SERVICE
Another drawcard for Smolders was around dependability and back-up service from Farmgard, as his former machine (a different brand) was showing signs of wear and tear, and accessing parts was proving time-consuming and costly, impacting on his ability to feed out effectively. The availability of Abbey knives was a major drawcard for Smolders. With a full stock of parts in Farmgard’s Auckland warehouse, it’s simply a quick phone call for any assistance, and there are even auger replacements on the rare occasions one is needed (usually operator error). Cost of parts also played a role in the final decision to opt for Abbey, with replacement knives less than a third of the cost of knives he faced with his old machine. The fact his property is prone to some winter flooding, coupled with the fact he’s autumn calving, means he likes the reassurance of knowing his mixer wagon can reliably work all year round.
FEED OUT ROUTINE
Being able to adjust his feed regime with ease is important for Smolders. He likes to be able to alter the feed out routine if necessary, depending on conditions, in order to keep his milk production and cow condition consistent. It’s more cost-effective to increase the amount of feed he puts through his mixer wagon for feeding out on his feed pad than upping the amount going through the in-shed feeding system. Using the mixer wagon daily also has the added benefit of the cattle being under the shelter of the covered feed pad – better for paddocks and animal welfare. The fact the machine handles large bales of lucerne and silage so well was another deciding factor in the decision to purchase this model. Counter knives at the rear of the wagon are designed to hold the bale against the augers and knives for the more consistent chop and preventing the bale from popping up as in some other brands. Smolders has chosen to up-spec his machine with hydraulically operated counter knives, meaning he can adjust them from in-cab and doesn’t need to get out to adjust with the manual pin. During peak feeding time, with two full loads a day, this could mean as many as 10 bales, so the time savings add up over a week to be worth the additional cost of hydraulic operation. At three metres high, which is a tad lower than his former wagon, the Abbey is proving the perfect size for Smolders’ existing machinery. He uses a John Deere tractor and front-end loader for lifting bales into the tub and didn’t want the additional cost of a telehandler at this stage. With the mixer wagon hooked up to a Case IH Maxxum 115, Smolders has the augers running before he starts loading feed to help minimise downtime waiting for the mix to chop and to ease pressure on the tractor, which sits at the bottom end of the horsepower required (Abbey recommends 100hp (75kW) plus for this unit).
4
OPERATION
With large single-axle flotation tyres, the Abbey rides
1. A consistent and finely chopped mix being evenly delivered into fed troughs 2. Strong galvanised ladder for viewing access 3. The 560mm slat and chain elevator tucked away for transport 4. Heav-duty three stage jack
Abbey VF 2000
Height
3,000mm Weight 7,500kg Wheel width 2,250mm Tub size 23 cubic metres
Capacity Augers Knives
Gearbox Drive Min power
20 cubic metres Twin vertical Seven manganese boron knives per auger Two-speed PTO (540/1000) 100hp

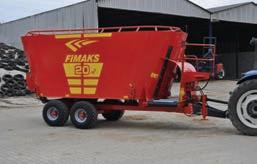
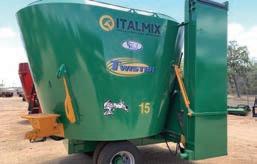
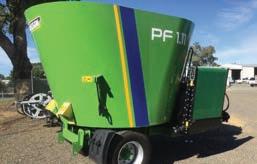
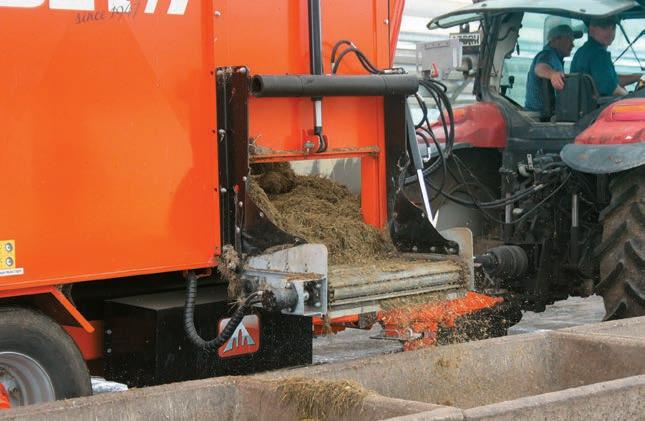
7

8
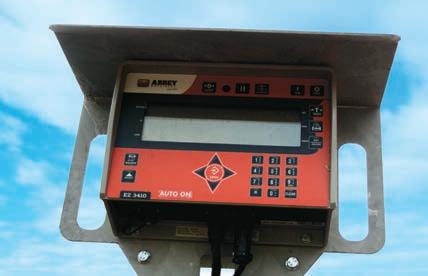
9
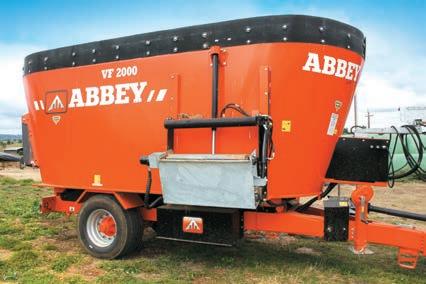
5. One of four individually suspended weigh cells 6. The feed elevator is controlled from in-cab 7. Easily manoevered DigiStar scales 8. A standard tractor reaches with ease into the 3m-high Abbey tub 9. The 20 cubic metre tub is robustly designed to last

Pluses
Simple to operate 800mm elevator height 3m loading height Robust durable build Versatile for all feed types Twin augers for consistent feed chop Easy access to parts Individual rotor lift options: electric, hydraulic, neither
Minuses
Lack of elevator side protection Heavy weight for off-road use
smoothly to and from the feed pad, even fully loaded. The rigid chassis provides ample base strength for the augers to pivot off, keeping the mix constant at all times. A large three-stage jack with wide footing is secure enough to carry the weight of the wagon. It’s also equipped with a handbrake, which can be used rather than chocking the machine. Hydraulics brakes come as standard along with LED lights. In terms of maintenance, like any machine, oil levels need to be checked and greasing (of the elevator bearings) should be done regularly. It also pays to visually check the sharpness of knives a couple of times a season.
SCALES AND GEARS
The tub sits on four load cells, two at the front and two rear, which ensures even weight recording through the DigiStar scales. The scales rotate for easy viewing from both the loading tractor and the mixer tractor. The large screen is protected with a cover, against both rain and sun for improved viewing. Optional Bluetooth technology is available for those wanting to sync the scales to their phone or print out mixes. Keeping with his long-held tradition, Smolders still operates off his trusty piece of paper on the tractor window – common for many mixer wagon operators. A galvanised ladder is mounted on the left side for observation and access. A streamlined dual gearbox system sees each auger with its own gearbox, running in sync to draw the feed into the centre of the augers. This contributes to the consistent fine chop and mix these machines are known for. The Comer SOM planetary gearboxes come with a three-year warranty. These gearboxes are connected with a Bondioli driveshaft, with shear bolt protection. Conveniently, Farmgard is also the importer and agents for Bondioli and Pavesi power take-off driveshafts. Auger speed can be changed manually from 540 to 1,000 rpm by means of a lever on the front of the wagon. As an optional extra, a cable can be added to allow changing the gearbox speed from the cab. This assists with faster tub emptying at the end of the feed. Farmgard recommends that tub mixing starts at 540 rpm, increasing to the higher speed when the tub is almost empty.
FEED REGIME
Throughout the year and depending on conditions, Smolders feeds approximately 200 silage bales and lucerne silage, all harvested on-farm, as well as 20 hectares of maize and palm kernel, straw, and soy hull and various minerals. Quantities vary depending on seasonal pasture growth. Milk production figures sit at around 150,000kg of milk solids for the 300-cow herd (approximately 500kg per cow). This is steadily rising, which is why the Abbey VF2000 plays such a vital role in allowing him to accurately know what he’s feeding his stock and adjust accordingly. It also gives tight cost control, important when considering the fluctuating payout figures.
SUMMARY
For me, the logic behind investing in a quality machine is money well spent. Price-wise, the Abbey sits in around the middle of the market but comes with all the features needed and punches well above its weight. Build quality is top-notch, all elements of the design have been thoughtfully considered for maximising function and performance, and it can be spec’d for individual requirements. Adding to this is the convenience of having a readily accessible range of parts and back-up service available nationwide through Farmgard’s dealer network in Australia. For more information, contact Farmgard business development manager Luke Rowney at 0438 793 794.
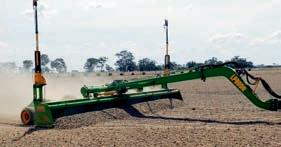
LP Series
Introducing the LP8000, 8 meter or 6 meter width Land Plane, twin mast independent for lift precision, dragging capabilities of approximately 5 cubic meters.

DG Series
The DG Series is currently being manufactured in 3.6m or 4.2m width Drag Grader has independent lift for laser precision. Dragging capabilities of approximately 3.5-4.5 cubic meters
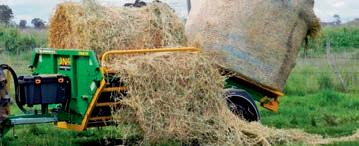
Bale Bull Round
The BBR maintains a strong robust design capable of handling the heaviest bales. This machine is capable of carrying two bales and feeds on both sides. It is one of the only machines in the market that is able to feed the toughest of silage bales
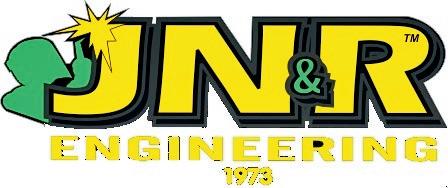
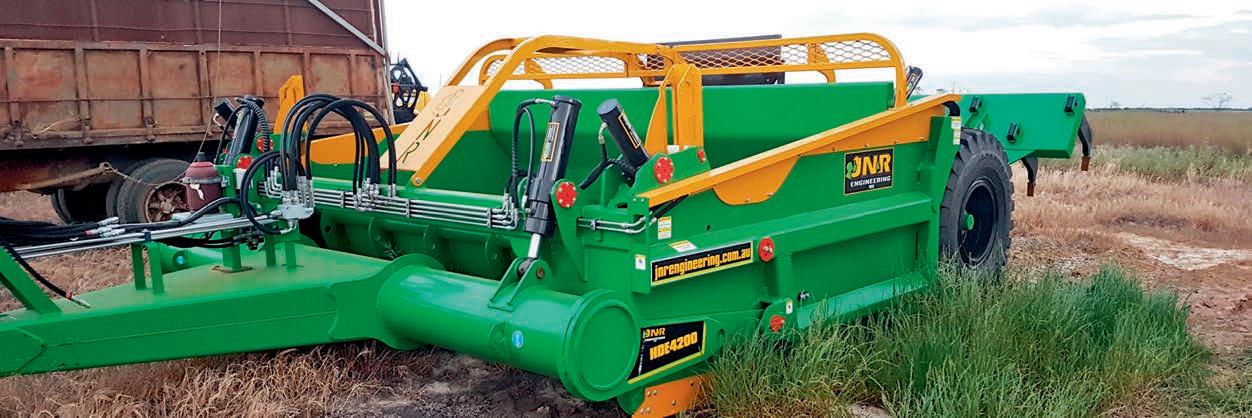
HDE Ejector
www.jnrengineering.com.au
Leopard Ejector
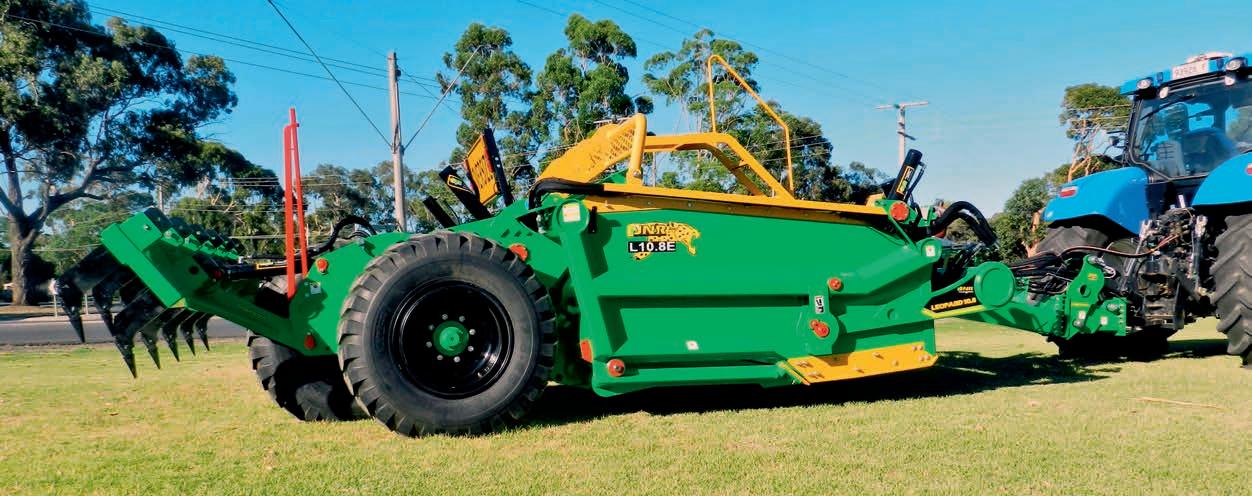
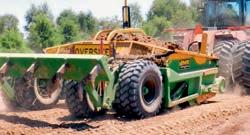
HDB Bucket
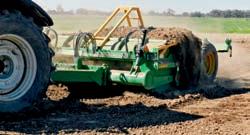
LB Bucket

Bale Bull Square
Features an adjustable moving arm for feed out control and on road transport, capable of carring two bales.
