UNIQUE CONTENT AND INSIGHT FOCUSED ON KEY TRENDS IN THE GLOBAL CONSTRUCTION EQUIPMENT AND TECHNOLOGY MARKET FROM THE INDUSTRY’S BEST-INFORMED AND MOST INFLUENTIAL SOURCES
GLOBAL REPORT

CONSTRUCTION EQUIPMENT AND TECHNOLOGY 2023
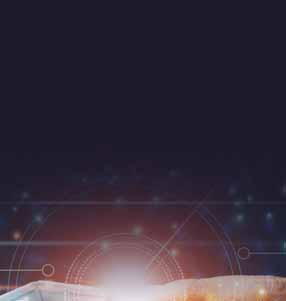

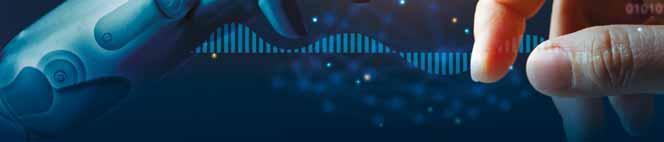

ARTIFICIAL INTELLIGENCE IS BUILDING TOMORROW’S WORLD TODAY POWERING THE FUTURE: CUMMINS ON HOW DIESEL ENGINES FIT IN AMMANN’S GREEN PLANT INITIATIVE MOVES INTO FAST-FORWARD
EUROPE IS DRIVING HEADLONG INTO AN INFRASTRUCTURE HELL-HOLE BENTLEY’S DIGITAL TRANSFORMATION IS DRIVING DIGITAL ADOPTION
ENHANCE SAFETY AWARENESS BY LEVERAGING LEICA TECHNOLOGY
BKT INVESTS IN A CONFIDENT FUTURE FOR OFF-HIGHWAY TYRES
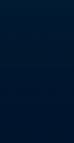
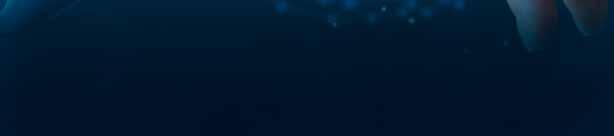
VOLVO SAYS BE HONEST ABOUT THE REAL IMPACT OF GOING ELECTRIC
www.worldhighways.com | www.aggbusiness.com

Published by
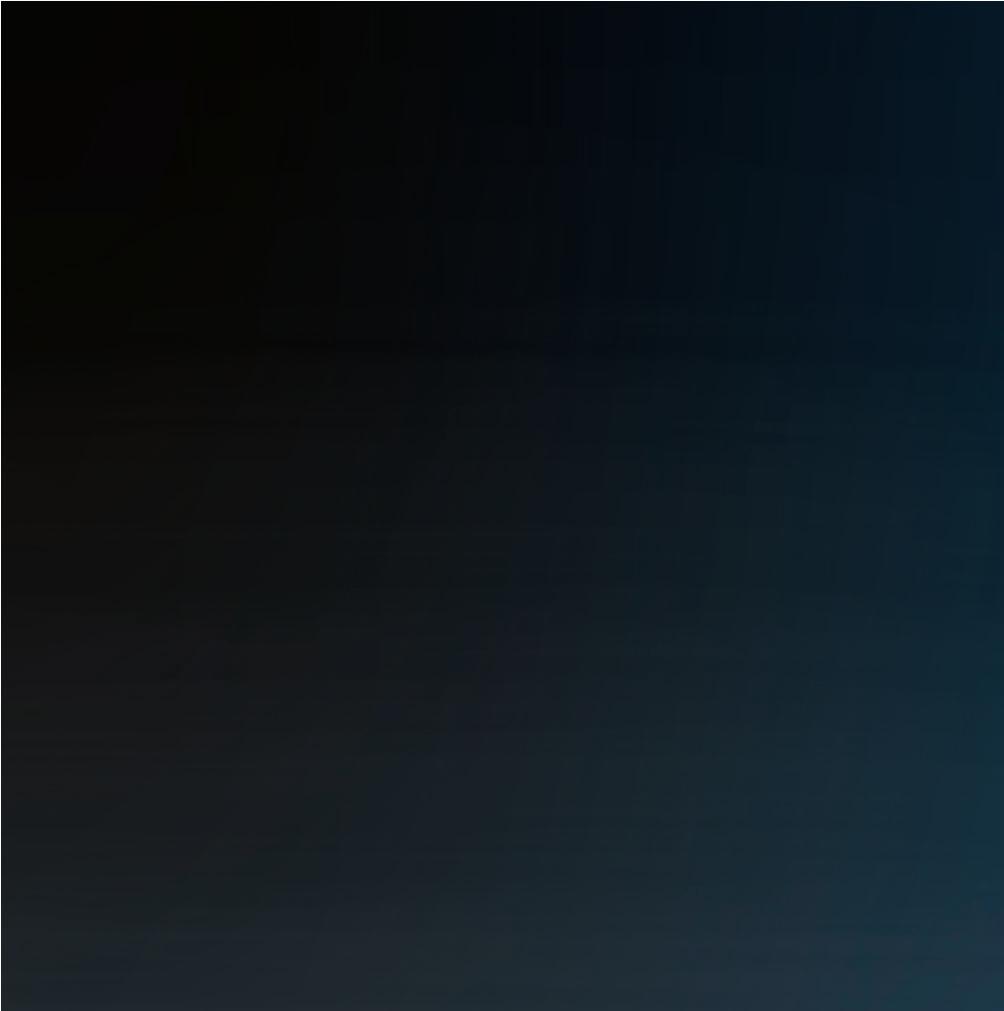
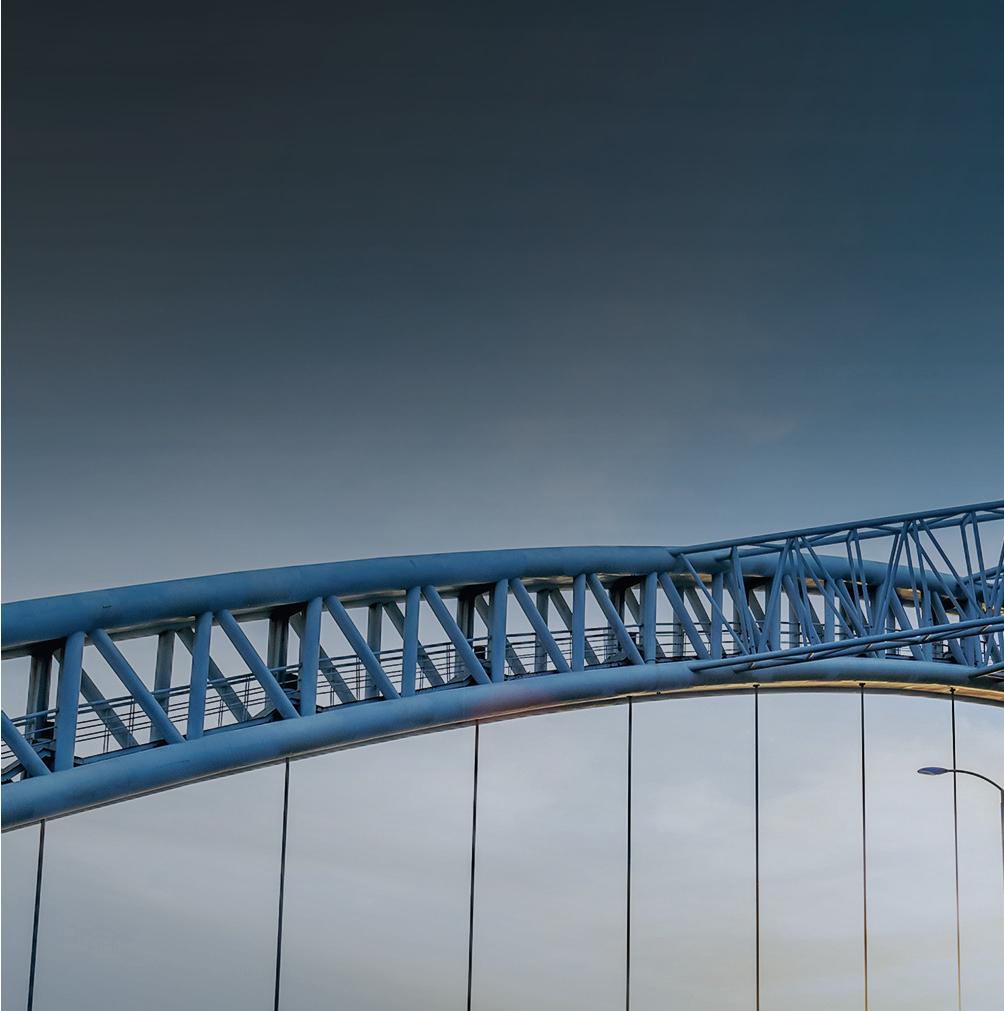
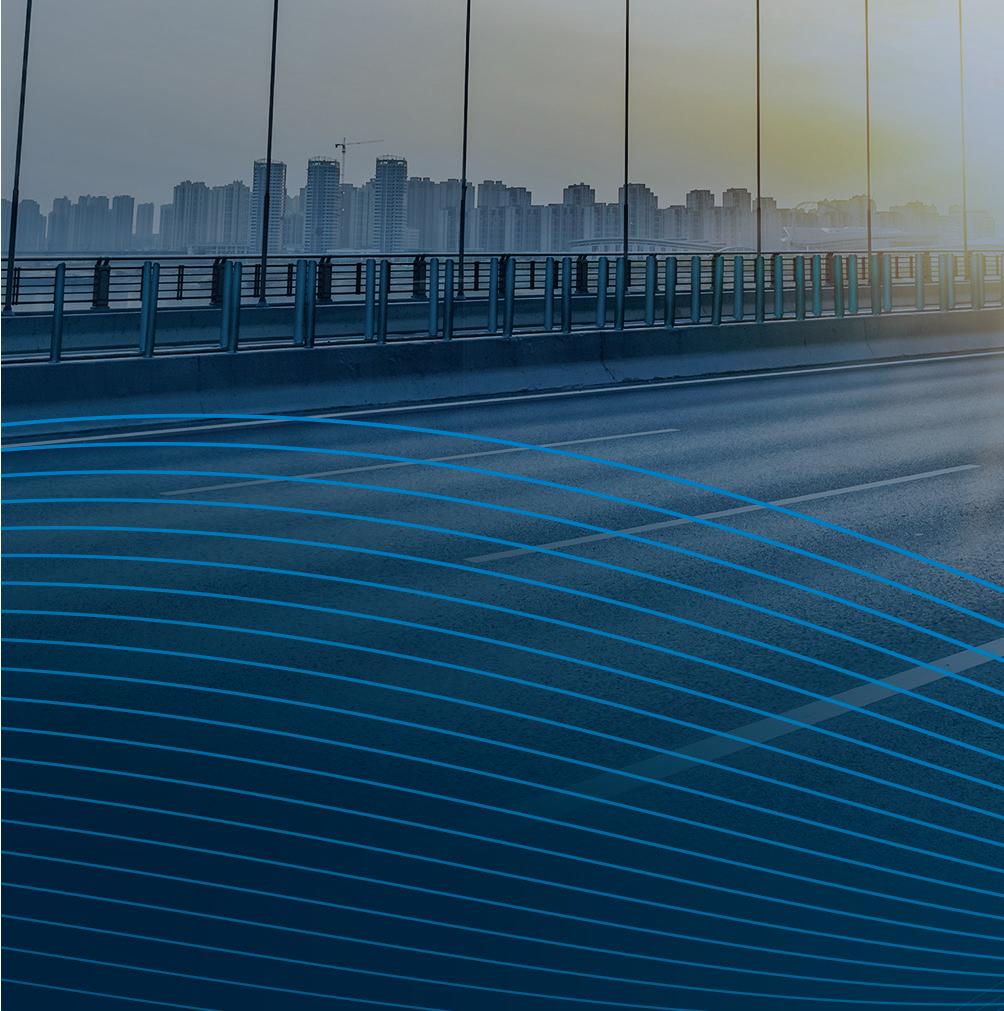
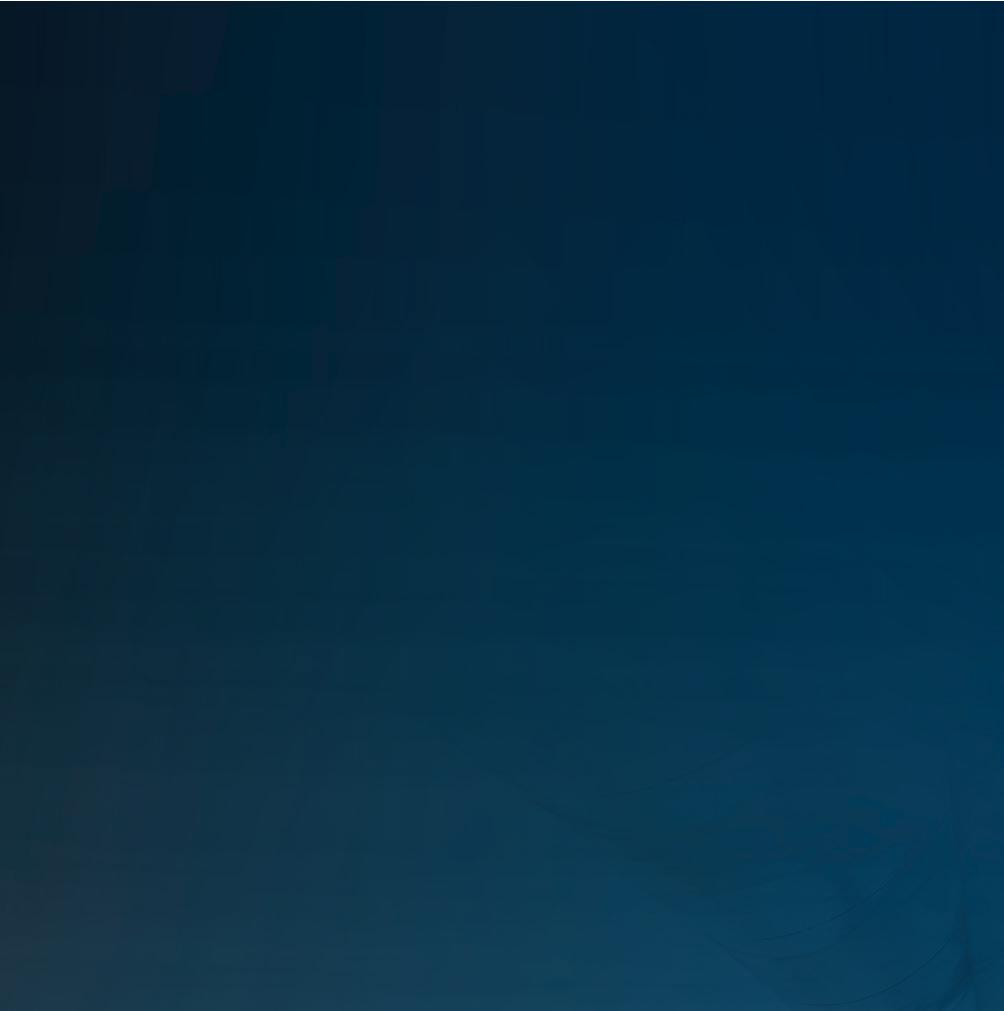
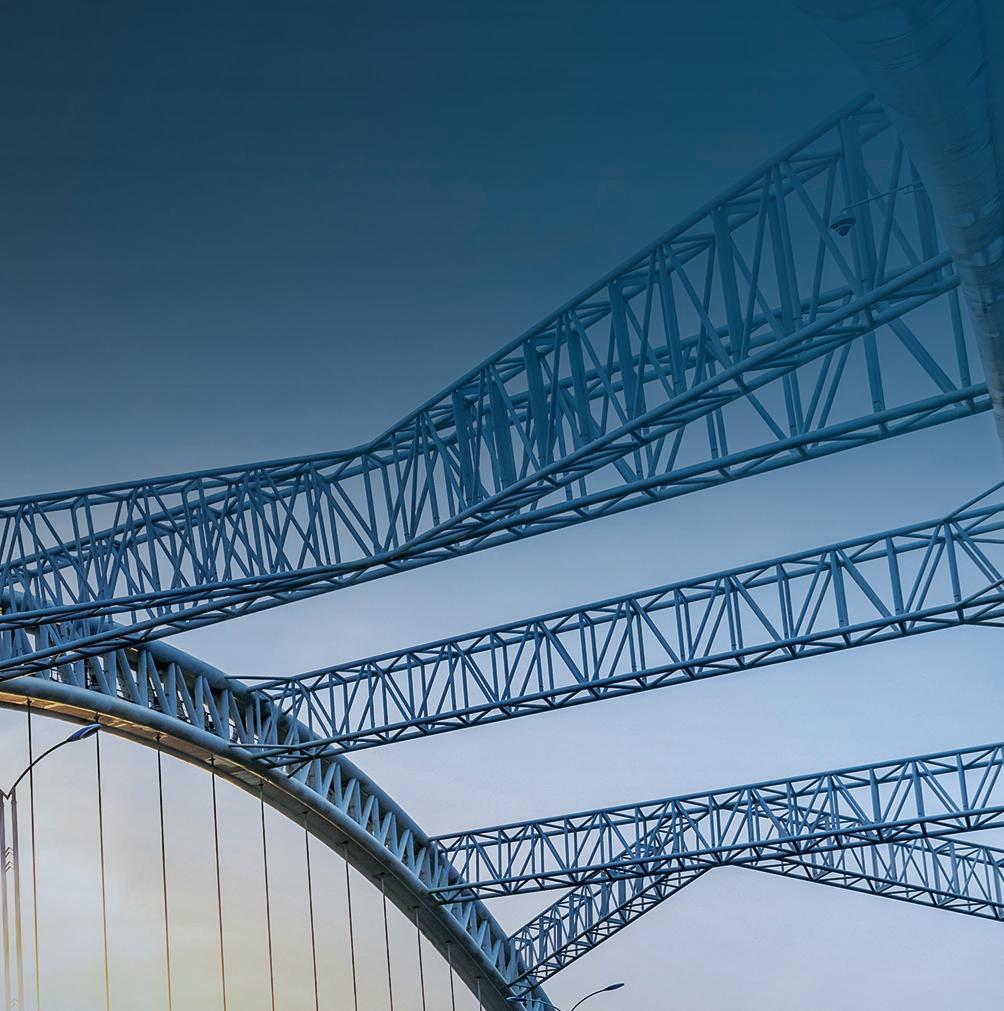
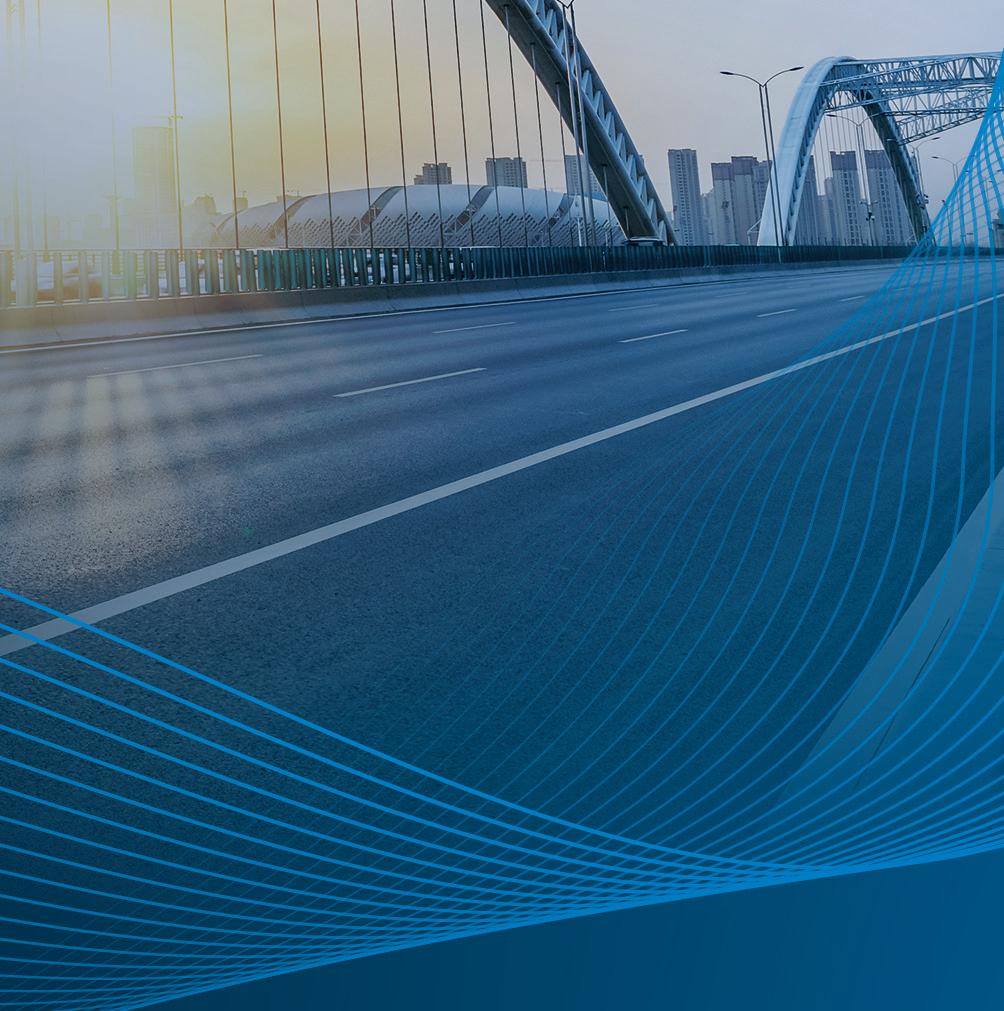
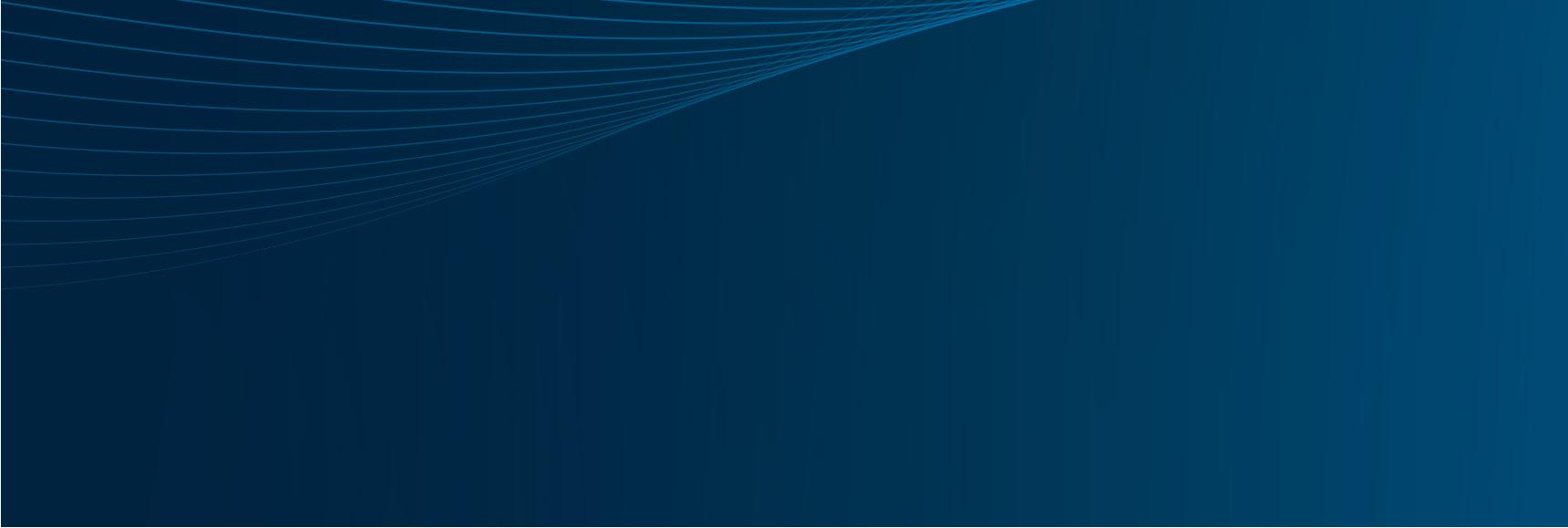
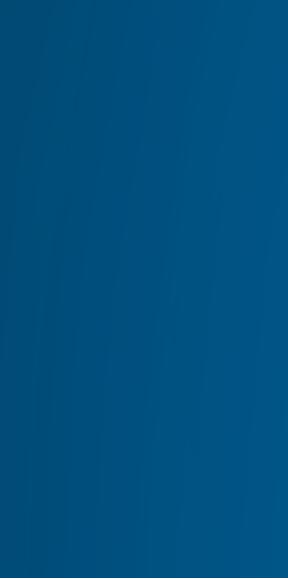
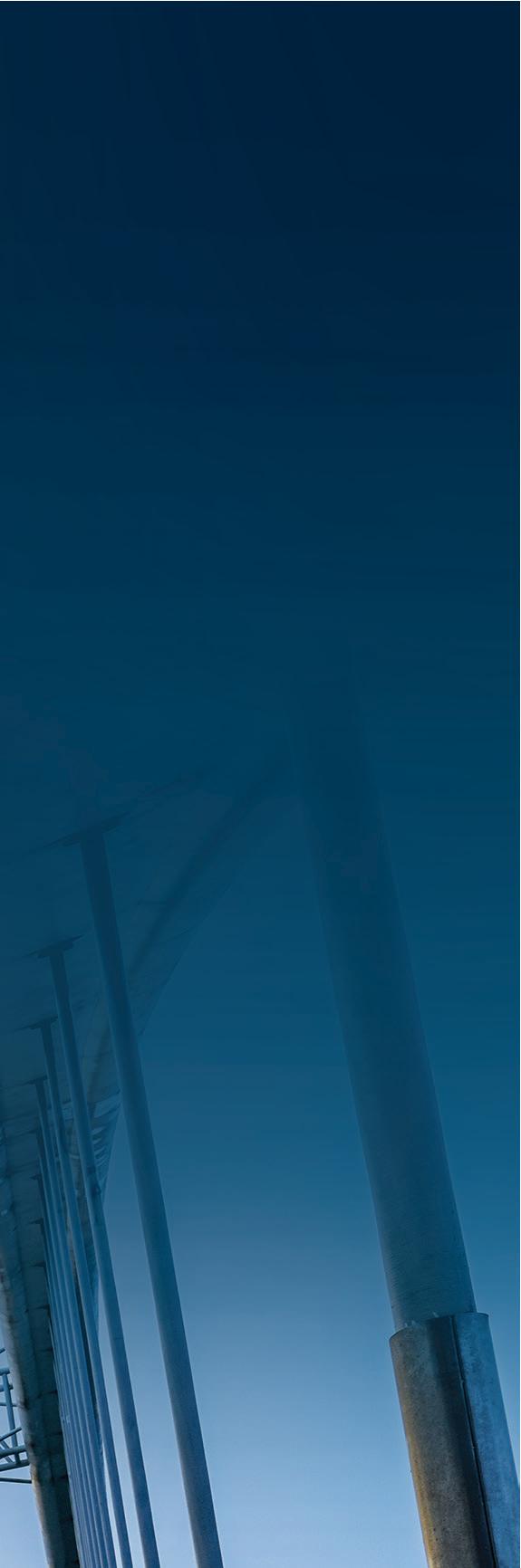
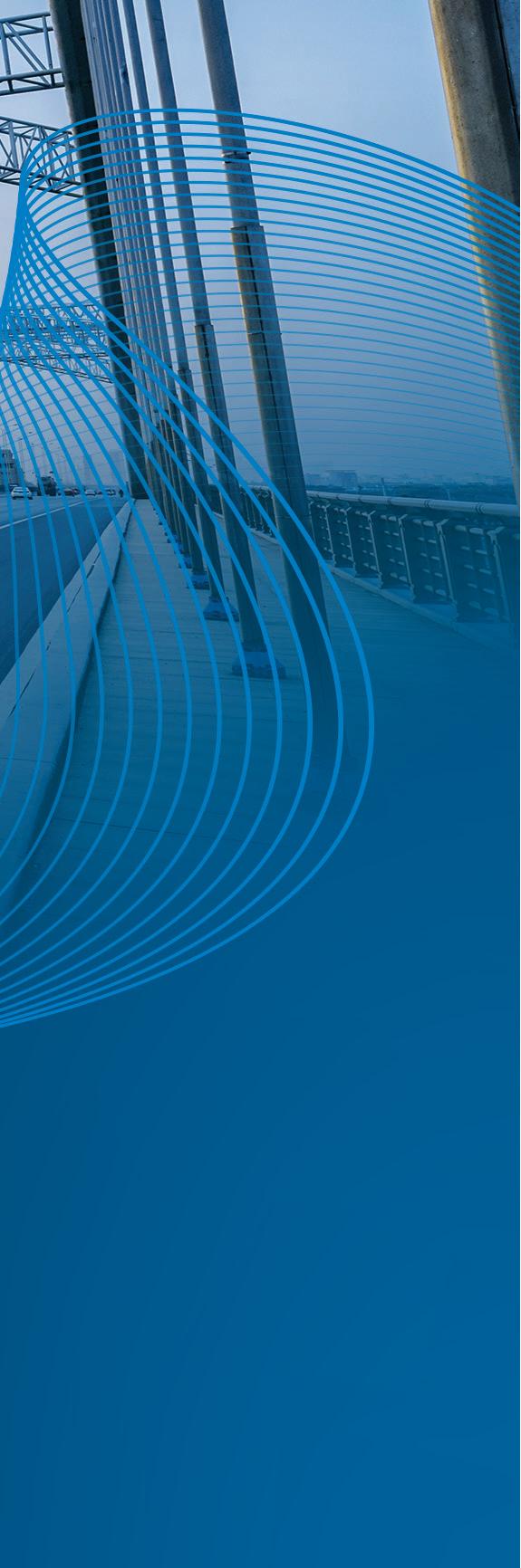
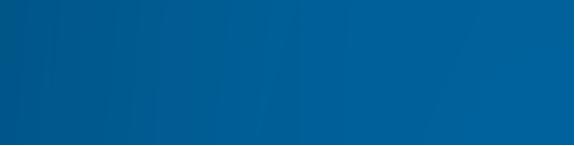
CONTENTS
05.
GLOBAL MARKETS REVIEW
A battle is raging to decide the future direction of the construction equipment market. You can easily make a case that the industry currently resembles a hotly-contested tug-of-war between growth drivers and market challenges.
19. GROUND-SCANNING
TECHNOLOGY
Ground scanning is vital to finding out what lies beneath. For any construction project, having an extensive knowledge of the ground conditions is essential before work can begin. And the technology that enables all this is getting ever more sophisticated.
24. SUSTAINABILITY: GOING ELECTRIC
Be honest: Measure the real impact of going electric. It’s vitally important to measure the ramifications of going electric, says Mats Bredborg of Volvo Construction Equipment. … But what does going electric really entail?
28. ARTIFICIAL INTELLIGENCE
AI and machine learning are constructing tomorrow’s world today. The world’s leading construction equipment firms are all jockeying for position as artificial intelligence and machine learning take root. What are the implications for the construction equipment sector?
35. ASPHALT TECHNOLOGY:
Ammann’s green plant initiative moves into fast-forward. Ammann knows that big and small steps are the best way forward on the march toward sustainable asphalt-production. The company openly says that: “At Ammann, we know it’s time to clear the air at asphalt production sites around the world. We are doing exactly that through sustainable technology and innovative solutions.”
39. THE WORLD IN NUMBERS
The world in numbers. As usual, our research team has prepared a selection of key factors affecting the global construction outlook.
44. ENGINE TECHNOLOGY: CUMMINS
Powering the future: where does the diesel engine fit in? The construction and aggregates sectors, like virtually all other industries around the world, are taking a hard look at how to decarbonise without experiencing reduced productivity and increased costs.
48. TECH SUMMIT: BENTLEY SYSTEMS
Digital transformation is key for transportation agencies and their partners to do their jobs better and faster. One way to do this is through digital delivery using digital models, data, and supporting field tools for roadway design, structures design, and construction, say the tech experts at Bentley Systems.
51. TECH SUMMIT: TOPCON APTIX
Get a hi-tech reality check with Topcon Aptix. The biggest challenge facing construction professionals and general contractors is disconnected data and/or siloed data sources. The recently launched Aptix integration platform has broken down these silos, explains Topcon’s Scott Langbein.
54.
TECH SUMMIT: LEICA GEOSYSTEMS
Enhance your safety awareness by leveraging technology. When a vital fibre-optic cable was cut during construction work in Germany, the impact was huge. Flights in and out of Frankfurt Airport were suspended, and Lufthansa’s global IT system crashed. Leica Geosystems explains the vital role digital solutions can play.
58. THE EU’S BROKEN INFRASTRUCTURE
It comes to something when contractors, manufacturers, transport firms, and even NATO are all pleading for the same thing: urgent action on heavy-transport corridors, weak bridges, crumbling road surfaces, and inept local government. Who is allowing expert engineering departments to disappear as things fall apart? And why?
63. WORKER SHORTAGE: AUTONOMY & ROBOTICS
Many studies have been completed on the global labour shortage in the construction industry. The shortage has arrived, and it’s not ending any time soon. What is going to happen next?
68. SUPPLY CHAIN
MANAGEMENT
Predictive analytics offer the global construction equipment supply chain an important new opportunity to be proactive in fostering resilience, improving efficiency, and driving growth. Exploit every bit of data you can find because, if you don’t, your business is going to fall further and further behind.
75.
TYRE TECHNOLOGY
BKT is confident about the future. Indian off-road tyre giant BKT, Balkrishna Industries, recently invited the world’s trade media to its state-of-the-art site at Bhuj in Gujarat to showcase the group’s exciting plans for the future.
78.
CARBON FOOTPRINT
Get your carbon costs right if you want to win business. It’s all very well congratulating ourselves on how developments in construction equipment and technology are reducing the industry’s carbon footprint, but are we concentrating our efforts in the right places?
83. CECE CONFERENCE
REPORT
Alternative energy: are we getting any closer? Alternative energy for construction equipment focused the minds of the 170 delegates attending this year’s CECE conference. This was the first in-person gathering postCOVID for the Brussels-based Committee for European Construction Equipment, and how best to power up the future was very much on their minds.
Editor: Geoff Hadwick
Contributing Editors:David Arminas, Guy Woodford, Mike Woof
Designers: Simon Ward, Andy Taylder
Production Manager: Nick Bond
Office Manager: Kelly Thompson
Circulation & Database Manager: Charmaine Douglas
Internet, IT and Data Services Director: James Howard
Managing Director: Andrew Barriball
Chairman: Roger Adshead
Editorial contributors: Graham Anderson, Elizabeth Kaye, Pete Kennedy, Kristina Smith
COVER IMAGE: © Pop Nukoonrat | Dreamstime.com
ADVERTISEMENT SALES
Head of Construction Sales: Graeme McQueen
Tel: +44 1322 612069
Email: gmcqueen@ropl.com
Sales Director: Philip Woodgate Tel: +44 1322 612067
Email: pwoodgate@ropl.com
Sales Director & Classified: Dan Emmerson Tel: +44 1322 612068
Email: demmerson@ropl.com
Italy: Fulvio Bonfiglietti Tel: +39 339 1010833
Email: bonfiglietti@tiscali.it
Asia / Australasia: Roger Adshead
Tel: +44 7768 178163
Email: radshead@ropl.com
ADDRESS:
Route One Publishing Ltd, Second Floor, West Hill House, West Hill, Dartford, Kent, DA1 2EU, UK
Tel: +44 (0) 1322 612055
Fax: +44 (0) 1322 788063
Email: [initialsurname]@ropl.com (e.g. radshead@ropl.com)
GLOBAL REPORT
Global Report Construction Equipment & Technology ISSN 2634-3223 (Print) ISSN 2752-8375 (Online)
POWER TO MAXIMIZE PRODUCTIVITY
Offering more power with less complexity and less weight. This engine delivers the productivity you need to keep your equipment running. Proven in a wide range of industrial applications, its power increases to 326 hp/243 kW enabling replacement of engines with higher displacement with no impact on productivity.
cummins.com/construction

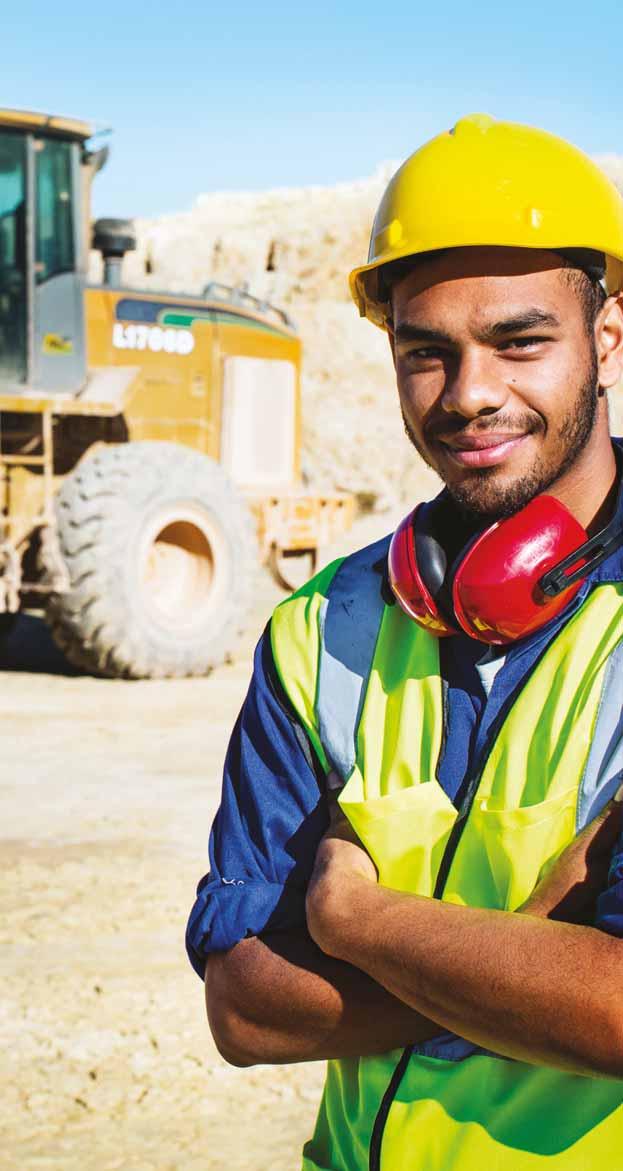

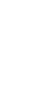
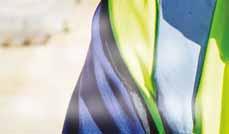



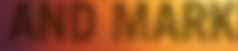
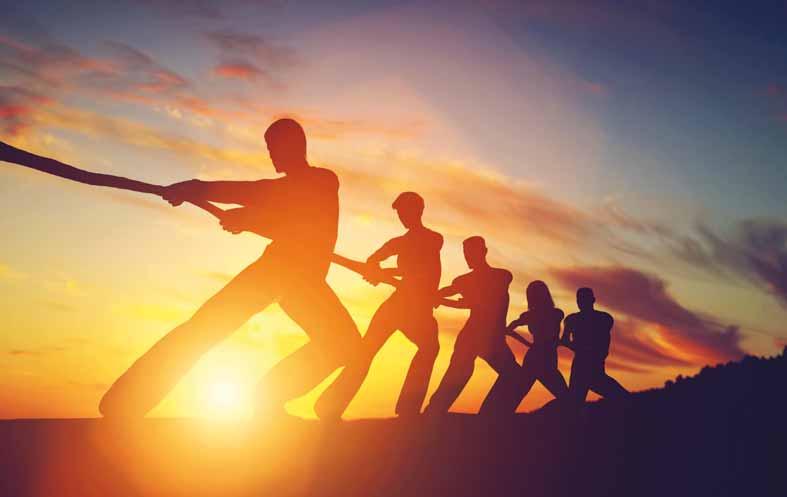



A TUG-OF-WAR IS RAGING BETWEEN GROWTH DRIVERS AND MARKET CHALLENGES
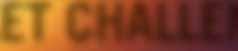


You can easily make a case that the global construction equipment market currently resembles a hotly contested tug-of-war between growth drivers and market challenges. Guy Woodford reports.
Global construction equipment sales may have fallen 7% last year to 1,201,126 units from the record high of 1,292,739 units sold in 2021 but, as Off-Highway Research (OHR), a leading business market intelligence consultancy, highlights: The downturn was all due to the collapse of demand in China. Sales in the world, excluding China, have risen by 7% in 2022. This year, OHR forecasts a 7% decline in global sales in 2023, a slightly steeper downturn than previously envisaged due to the weakness of the Chinese market. Stripping China out of the equation, the remaining world will only see a 5% downturn overall.
OHR is classifying the 2022-2025 market downturn as a “soft landing”. Only singledigit year-on-year (YOY) falls in equipment sales are expected, and the volume of machines sold should stay above one million units per year over the next four years. Before the current up-swing, OHR notes that such a volume was only achieved twice before.
The OHR forecast is based on the indication that infrastructure investment will be strong and that although interest rates are rising, they will only slow down residential construction rather than push it over a cliff
However, OHR stresses that there are risks to the forecast. Inflation was a serious
issue throughout 2022, and although improving, it remained too high in early 2023. The war in Ukraine continues to heighten inflationary pressures worldwide and exert upward pressure on interest rates.
Another leading business market intelligence firm, GlobalData, tips the
world’s construction industry output to grow modestly by 1.8% in 2023
The same source expects the global construction industry to regain some growth momentum from 2024, assuming an improvement in global economic stability.
Global sales of construction equipment by region, 2018-2022 (units)
Source: Off-Highway Research

EUROPEAN MARKET RESILIENCE
Riccardo Viaggi, secretary general of CECE (Committee for European Construction Equipment), reports that in 2022 Europe faced supply chain disruptions, high inflation, and a war in Ukraine due to Russia’s aggression, which impacted energy security and affordability in the European economy. However, Viaggi notes that the European construction equipment market remained resilient and strong, with sales in Europe, excluding the Russian market, increasing by almost 3%. And overall, Viaggi highlights that the sales in the European market were almost equal to the previous year, with only a slight decline of 0.6%.
“This shows that there is strong and sustained demand for equipment in Europe, and if the supply chain issues had not existed, the market would have experienced growth for another year,” explains Viaggi. He adds: “This underlying stability is reflected by robust industry sentiment. The climate
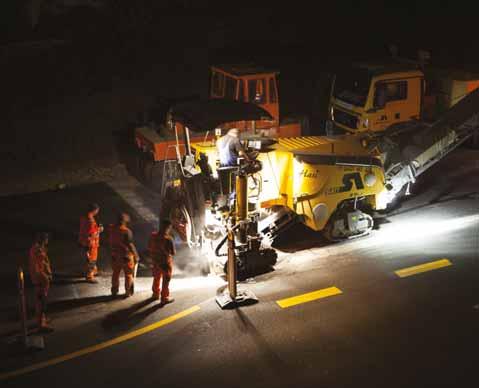
index in CECE’s Business Barometer survey went down moderately over the year as the economic fallout of the war in Ukraine unfolded. It bounced back in November after the bauma [Munich 24-30 October] exhibition.”
Viaggi continues: “If we look at the sales by country, there are only minor changes, with a few exceptions. Southern Europe was the best-performing market region in equipment sales, with a 12% growth. The exception was Turkey which experienced a growth of almost 40%, while Russia had a decline of the same magnitude.”
Analysing equipment sub-segment sales, Viaggi reports that European sales of tower cranes remained unchanged, sales of roadbuilding machinery increased by just 1%, and earthmoving and concrete machines fell by 1% and 2%, respectively. The performance of small and lightweight machinery (-0.5%) was slightly better than that of big machinery (-2%).
Additionally, machine availability increased in the second half of 2022 as supply chain problems lessened throughout the year.
Viaggi says the European building industry’s economic climate was negatively impacted by the conflict in Ukraine, tightening credit, central banks altering policies, and issues with the pricing and availability of building materials. “Among the member states of which data we have available, the highest annual increases in construction output in 2022 were in Slovenia (+44.0%), Romania (+20.4%), and Belgium (+12.9%). On the contrary, the largest decreases were in Spain (-6.9%), Slovakia (-5.8%) and Germany (-1.2%). The construction output in the EU started to grow in the last quarter of 2022, and if we compare the last quarter with the third quarter, there is an average of 0.7% growth, according to the European Commission’s latest report.”
Viaggi notes that despite all challenges, the order books of EU construction firms indicate up to nine months of workload at the beginning of 2023. Additionally, Viaggi believes that construction output in the EU should continue to increase during 2023 but at a moderate pace. The civil engineering sector looks resilient, he says. Other sectors are expected to record declines in activity.
“Supply chain issues are still impacting construction equipment sales, but investment rates in infrastructure and construction are driving the market forward,” Viaggi explains. “The market is dominated by miniexcavators, with crawler excavators, telescopic handlers, wheeled excavators, skid-steers, and backhoe loaders following closely. As sales in the European market have been steady, manufacturers report positive business conditions and near-term expectations.
“We can say that 2023 will be a year of transition for the construction industry, marked by a slowdown, but overall production growth is expected to remain in positive territory.”
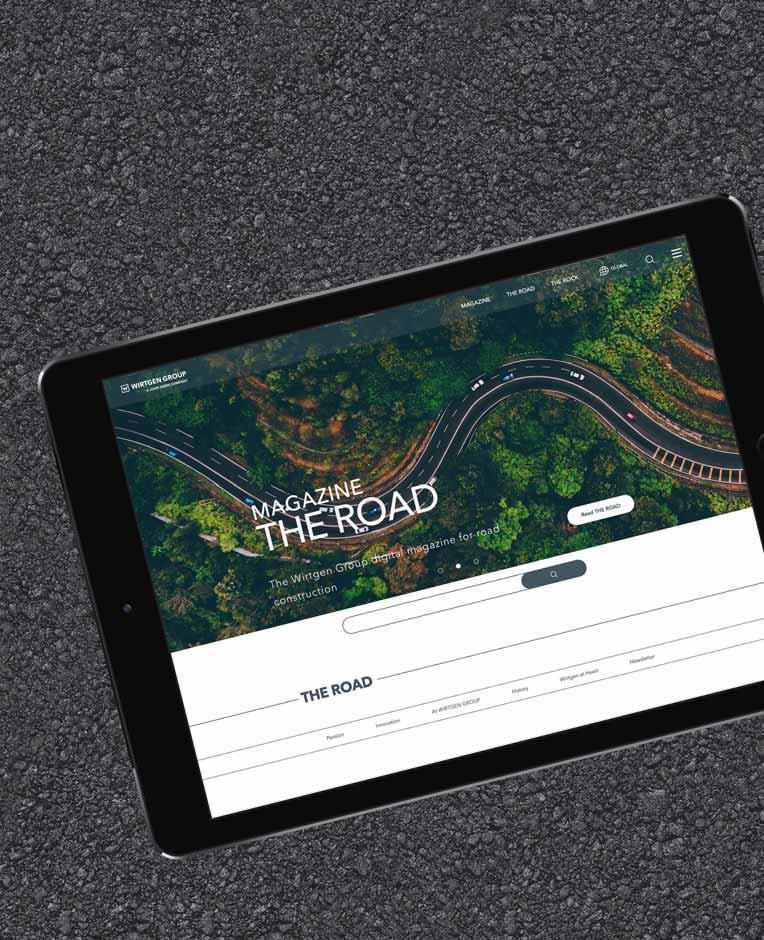
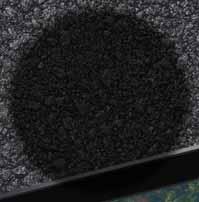
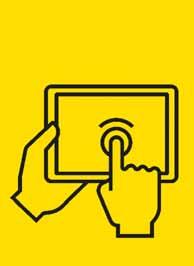
NORTH AMERICA

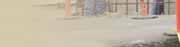
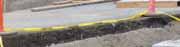

A RECORD 2022, BUT A MIXED GROWTH PICTURE
North America was the pick of the major markets last year, reports Off-Highway Research (OHR), with an 8% increase in sales to take demand to a record high of 318,855 machines sold. Compact tracked loaders are now firmly established as the most popular equipment type in the region and mini excavator sales have also grown to a significant level. Sales of these machines have largely been at the expense of skid-steer loaders and backhoe loaders.
Although a modest 1% decline in sales is expected this year, OHR says the North American market will still enjoy the secondhighest volumes ever seen. The long lead times for equipment mean that suppliers are confident of sales well into the third quarter of the year, even though rising interest rates are starting to cool off the housing market.
While this is expected to lead to a fall in sales of smaller equipment types, OHR states that infrastructure investment is on the rise in the region, thanks in part to the stimulus plans which were put in place during the pandemic years.
OHR continues: “By nature, machines used in infrastructure construction are higher value/lower volume than the compact equipment sales driven by residential building. This is therefore expected to lead to a shallow dip in sales from 2023-2026. However, North America suffers from a housing shortage, which is expected to stimulate an upturn in compact equipment sales towards the end of the forecast period.”
The American equipment manufacturing
industry is still recovering from the impacts of the Covid-19 pandemic nearly three years after its onset, according to the AEM (Association of Equipment Manufacturers).
AEM regularly surveys its members regarding their thoughts on various economic trends and how they affect their business efforts, both within the United States and abroad. In the latest survey, most respondents stated that they are still experiencing supply chain issues, with many saying that conditions continue to worsen.
“Nearly all respondents still face supply chain issues, with more than half experiencing continuously worsening supply chain conditions,” said Kip Eideberg, senior vice president Government and Industry Relations at AEM, during the association’s recently held quarterly Equipment Market Outlook Webinar. “The two driving factors we hear are the current supply chain disruptions and the workforce shortages.”
The information obtained through the association’s surveys is detailed in AEM’s Business Intelligence Dashboard and later summarised in the quarterly webinar.
The AEM says the ongoing challenges of high interest rates and energy and material prices have plagued the construction industry. However, hope is on the horizon for these issues and others to eventually be resolved.
GlobalData expects the US construction industry’s output to grow at a 4.5% annual average growth rate
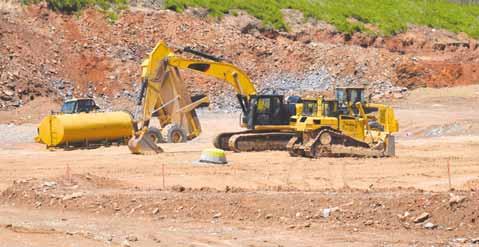
North America sales of construction equipment 2018-2022 (units)
Source: Off-Highway Research
High interest rates and energy and material prices have plagued the construction industry
(AAGR) from 2024 to 2027, supported by investment in the energy, transportation, housing, and manufacturing sectors. As part of the Inflation Reduction Act (IRA), the government allocated $369bn to energy security and climatechange mitigation programmes, intending to increase the US’s efforts to reduce emissions by 40% below 2005 levels by 2030. In line with the government’s focus on reducing carbon emissions, the Biden-Harris Administration set a goal of deploying 30GW of offshore wind capacity by 2030, enough to power 10 million homes with clean energy, and aims to advance lease areas in deep waters to deploy 15GW of floating offshore wind capacity by 2035. Furthermore, residential construction will pick up again in the latter part of the forecast period, particularly if the government goes ahead with its planned budget to invest $175bn to increase the housing supply and alleviate the affordability crisis.

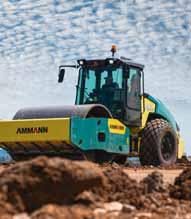
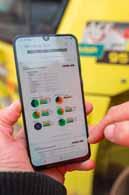
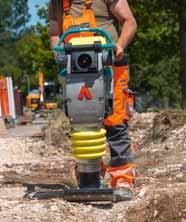
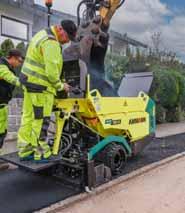
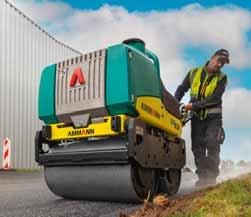
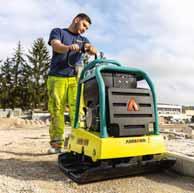
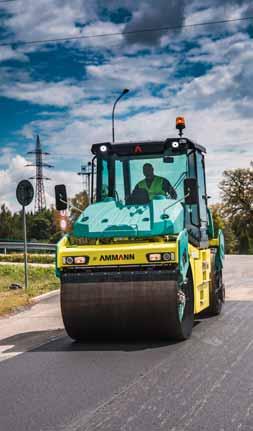
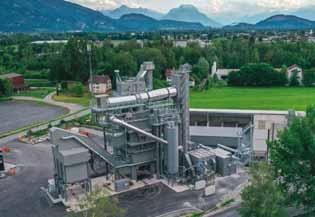
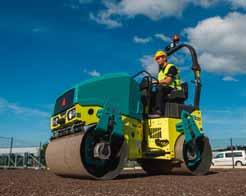
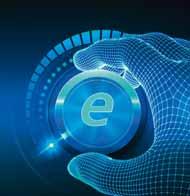
CENTRAL & SOUTH AMERICA
BIG INFRASTRUCTURE CONSTRUCTION BOOSTS REGION
The Latin America infrastructure construction market size was valued at $230.6bn in 2023 and is estimated to grow at a compound annual growth rate (CAGR) of 3.8% between 2022 and 2026, according to GlobalData. The project pipelines from countries including Brazil, Mexico, Colombia, and Argentina strongly support regional growth and offer great potential sales for off-highway equipment manufacturers.
GlobalData states that the aforementioned four countries, in terms of construction output value, accounted for more than 70% of the overall regional share in 2023. In addition, these countries are estimated to dominate the regional project pipeline with an approximate share of 69%. Brazil is anticipated to remain the front-runner with a share of more than 42% of the overall regional project pipeline.
Road infrastructure in the Latin America region is the largest segment of the infrastructure construction industry as of 2023 and is projected to continue its dominance over the forecast period, continues GlobalData. Regarding output value, Brazil is estimated to emerge as the key
country within this region, accounting for approximately 34% in 2023
The largest project in Brazil’s pipeline is the $6.2 billion Mario Covas Northern Stretch Ring Road project, which involves constructing a 44 km-long ring road. It will include the construction of road lanes, tunnels, overpasses, bridges, and highways.
GlobalData believes Mexico will follow Brazil in second place regarding construction output value and project pipelines. According to the reports released by the Ministry of Economy in November 2022, foreign direct investment (FDI) in Mexico increased by 29.5% YoY in the first nine months of 2022, reaching MXN32.2bn ($1.3 billion), with the manufacturing sector accounting for 36.3% of the total investment followed by the transport sector which accounts for 14.5%.
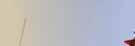
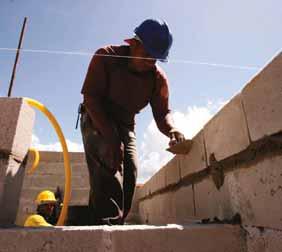
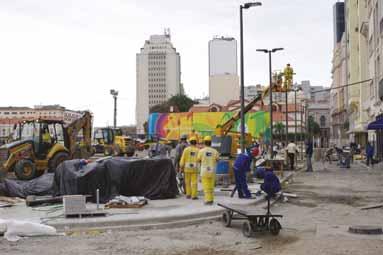
Source: GlobalData
Argentinian infrastructure construction is estimated to see an average growth rate of nearly 2.7% from 2023 to 2026, supported by transport investment. The construction of 218 roadway projects under the Ministry of Public Works is expected to be completed by 2025. GlobalData reports that the National Highway Authority of Argentina plans to rehabilitate 2,292km of roads, complete the construction of 261km of highways, and have 1,192km of highways under construction by the end of 2023.
Furthermore, as part of the Argentina Rail Modernisation Plan for 2030, the Ministry of Transport signed three memorandums of understanding (MoU) in February 2022 with Chinese companies to develop three rail projects.
GlobalData tips Colombia to register an annual average infrastructure construction growth rate of 5.9% from 2022 to 2026, primarily backed by ongoing efforts to accelerate the completion of Colombia’s 4G road infrastructure programme and push forward with plans for its 5G concessions programme. Furthermore, the new government announced the Intermodal Transportation Master Plan and National Development Plan to connect the Pacific to the Atlantic through 657km of railway lines
and 30 railway projects financed through public-private partnerships (PPPs).
According to ResearchandMarkets. com, the Brazilian construction equipment market is set to grow at a CAGR of 6.79% by 2028 against a 2022 benchmark. Prominent OEMs in Brazil include Caterpillar, Volvo Construction Equipment, Komatsu, Sany, JCB, Liebherr, John Deere, and XCMG (Xuzhou Construction Machinery Group).
The same source notes that the Argentinian construction equipment market is expected to grow significantly over the next few years due to increased funds from Inter-American Development Bank and the World Bank for new roads, rail, ports, and utilities. Foreign companies are investing in the mining sector in Argentina; for instance, ResearchandMarkets.com points to the Canadian Lundin Group investing $3,000 million in its Josemaría copper, gold, and silver mine in San Juan province.

CHANGING MARKET DYNAMICS
Off-Highway Research (OHR) notes that after two years of abnormally high sales in 2020 and 2021, thanks to stimulus spending, the Chinese market collapsed in 2022 with a 39% decline. This was not only due to the stimulus money running out, says OHR, but the impact was compounded by turbulence in the Chinese real estate sector and the country’s difficulties in getting to grips with Covid last year. Last year, the only bright spot in China was the mining segment, says OHR. Mine operators invested in dump trucks and large excavators to exploit high global commodity prices.
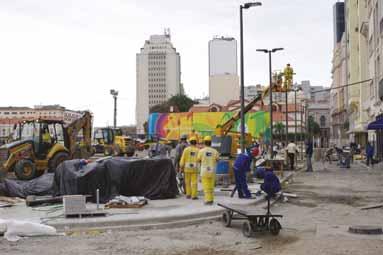
OHR forecasts the Chinese construction equipment market to continue to fall in 2023, but at a slower decline of about 18%, to settle at just below 195,000 units.
According to the industry consultancy, domestic demand may flatten out during 2024-2025, and the recovery will be very slow. OHR expects a real recovery during the period of the 15th Five Year Plan (2026-2030), primarily



as a result of increased sales of compact equipment and the recovering replacement demand; by then, the market may return to 270,000-300,000 units, but even that volume is still very much lower than what has been seen in the recent past.
OHR says a significant challenge to the future market lies in lower demand from the real estate sector, which, in line with experience, has been closely allied to the overall demand for equipment. “In the light of the saturated population and overheated supply, demand for new housing projects will decline, even though construction in the most developed areas may remain steady. Therefore, the traditional equipment demand from this sector will be significantly eroded, and other sectors will not make up this lost demand,” concludes OHR.
The China construction market size was valued at $4.6trn in 2022, according to a new GlobalData report. The market is projected to grow at an AAGR of more than 4% from 2024 to 2027.
GlobalData says investment in infrastructure will support growth in the construction industry as part of the 14th Five-Year Plan (FYP 2021-2025). The 14th FYP has 20 quantitative targets under five categories: economic development; innovation; people’s well-being; green development; and food and energy security. GlobalData reports that the residential construction sector dominated the Chinese construction market in 2022, followed by infrastructure construction.
Mordor Intelligence (MI), a global market intelligence and advisory firm, states that the Chinese construction equipment market is valued at $50bn. The same source says the market is expected to reach $68bn, registering a CAGR of 5.55% over the next five years.
According to Mordor Intelligence, excavators constitute around 60% of China’s total construction equipment sales. The China Construction Machinery Association (CCMA) says there are about 25 excavator manufacturers in the country, more than in any other country. In 2021, 274,357 excavators were sold in China. Sany Heavy Industry (Sany) was the market leader for excavators in China, with an estimated market share of around 18% in 2021, by volume.
Mordor Intelligence says that massive infrastructure projects are fuelling the Chinese popularity of excavators. In 2021, the industry research consultancy says the Chinese government spent $3.4trn on infrastructure development in China. The country’s infrastructure development focuses on constructing superhighways, high-speed railways, airports, bridges, ports, and metro systems.
Over the long term, the Chinese government’s increasing focus on infrastructure, the development of automation in the construction and manufacturing processes, and the introduction of electric construction equipment, including excavators, is expected to significantly impact construction equipment market growth, concludes Mordor Intelligence.
JAPAN
CONSTRUCTION STABILITY
Construction equipment sales in Japan fell 4% last year following a strong post-pandemic surge in 2021, reports Off-Highway Research (OHR). As such, the decline is seen as closer to a return to normal sales volumes rather than a cyclical downturn. Indeed, OHR notes that the Japanese market tends to be relatively flat and stable and generally only experiences singledigit percentage changes from year-to-year.
“Having said that, sales in Japan were constrained last year due to component shortages and long lead times for machines,” says OHR in its latest market update. “Some of that pent-up demand is expected to spill over into 2023, helping the market to a 2% rise in sales [to 66,370 units]. Thereafter, the market is expected to stabilise at more normal levels of around 63,000-65,000 unit sales per year.”
OHR highlights that the Japanese market is dominated by excavators, with 28,000 mini excavators and 24,500 crawler excavators expected to be sold this year, representing almost 80% of all equipment sales. The other high-volume machine type is the wheeled loader, which, OHR says, accounts for a further 18% of demand.
The
The Japan construction market size was valued at $552.6bn in 2022 and is expected to achieve an AAGR of 1% during 2023-2027, states a February 2023-published report by GlobalData. Investment in renewable energy infrastructure, telecommunication, and manufacturing will support the industry’s growth during the forecast period.
The key sectors in the Japanese construction market are commercial construction, industrial construction, infrastructure construction, energy & utilities construction, institutional construction, and residential construction. The residential construction sector led the Japanese construction market in 2022, says GlobalData.
An improvement in housing demand and the resulting improvement in the construction of new dwellings and residential sales will support the Japanese residential construction market’s output during 20232027.
The government plans to construct a residential building initiative comprising 560 residential units in Tokyo from Q4 2024 to Q4 2028 at a total cost of JPY70bn ($580mn).
Japan construction output by sector (% of total, 2022)
Source: GlobalData
Japan’s infrastructure construction sector’s output during the next four years will be supported by the government’s aim to develop transport and other heavy infrastructure.
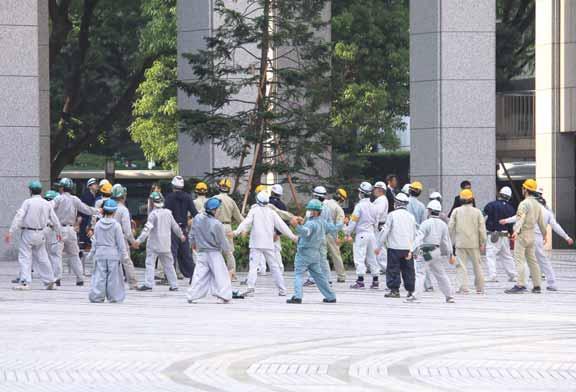
Investment in renewable energy and telecommunication projects will support Japanese energy & utilities construction -2027, continues GlobalData. Prime Minister Fumio Kishida’s government intends to generate more than 36% of the power mix from renewable energy sources before becoming carbon neutral in
Japanese commercial construction 023 will be supported by improved tourism activity and wholesale and retail trade. The country’s industrial construction sector is expected to grow over the next four years, supported by increased investment in manufacturing plant construction and an improvement in export
Due to Japan’s increasing elderly population, GlobalData tips Japan’s institutional construction market to receive continued government investment in conventional healthcare infrastructure and aged-care facilities over the next few years.

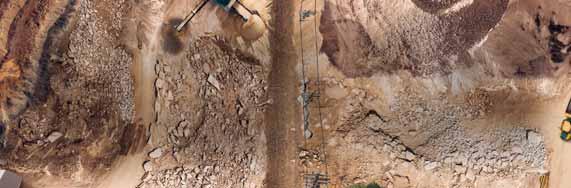
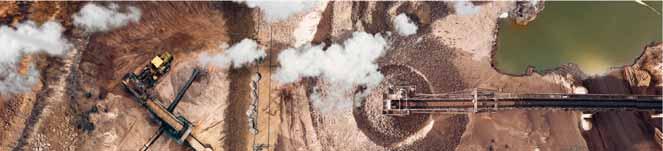
A LONG WAY TOGETHER
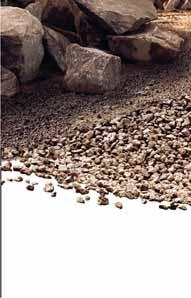
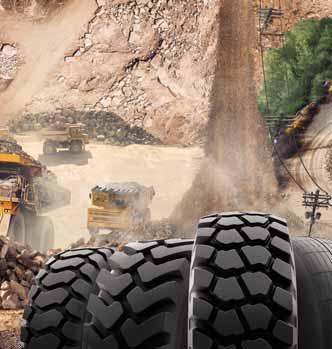
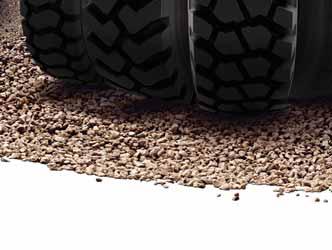

WHEREVER YOU ARE, BKT IS WITH YOU
the toughest operating conditions: from mining to construction sites.
Sturdy and resistant, reliable and safe, able to combine comfort and high performance. BKT is with you, even when work gets tough.

HEALTHY INDIAN DEMAND
Broad-based growth in Indian construction equipment sales is expected to resume this year, with the market forecast to rise 10% to 76,350 units, says Off-Highway Research (OHR). This will be driven, says OHR, by a range of infrastructure investment plans. With a general election due in 2024, this year’s budget particularly strongly emphasises investment as Prime Minister Modi seeks a third term in office.
Unfortunately, OHR says next year’s election will temporarily derail growth, and further market-specific disruption will be felt due to the introduction of CEV Stage-V emissions laws in April 2024.
However, OHR says it remains bullish about the medium- and long-term growth prospects in the Indian market, expecting equipment sales to resume their ascent from 2025 onwards.
GlobalData reports that in its latest budget, the Indian government increased its total expenditure by 7.5%, from an estimated expenditure of INR41.9trn ($522.2bn) in FY2022/2023 to INR45trn ($561.6bn) in FY2023/2024. The capital investment outlay
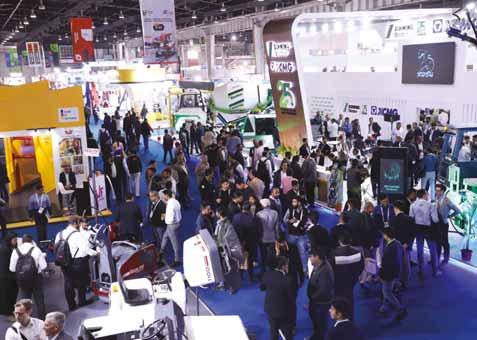
for FY2023/2024 is equivalent to 3 3% of the country’s GDP and is nearly three times the outlay made in FY2019/2020.
Pooja Dayanand, an analyst at GlobalData, said: “The sharp increase in capital investment is in line with the government’s focus on boosting economic growth and increasing job creation through investment in infrastructure development. The increase in funding will also be necessary to assist ministries in implementing projects that have been delayed by constraints such as rising interest rates, construction material prices, and labour shortages.”
The latest Indian government budget is based on seven key priorities, says GlobalData. These include inclusive development, reaching the last mile, infrastructure and investment, and green growth. As part of the latest budget, the government increased its allocation to the state-owned National Highways Authority of India (NHAI) by 14% to INR1.6trn ($20.2bn). It also announced a record-high capital outlay of INR2.4trn ($29.9bn) for the Ministry of Railways.
Dayanand continued: “The NHAI had been facing constraints in reaching its construction targets and is likely to miss its target for the second time in a row –in FY2022/2023. The increase in budget allocation could help the NHAI meet its targets in the upcoming financial year while completing its backlog targets. The significant capital expenditure allocations for highways and railways will also help improve connectivity, ease traffic congestion, and reduce travel times.”
The Indian government also increased its PM Awas Yojana (PMAY) initiative allocation by 66% to INR790bn ($9.9bn) in FY2023/2024.
Dayanand added: “The increase in allocation for the PMAY will help increase the supply of affordable housing and address the issue of housing shortages. However, increasing inflation and rising interest rates will likely affect housing demand in the short term.”
The budget includes significant allocations for supporting sectors such as renewable energy, healthcare, logistics, and irrigation. To help the country reach its net-zero emissions target by 2070, the government allocated INR350bn ($4.4bn) for priority capital investments towards energy transition and net-zero objectives and energy security.
The renewable energy sector is expected to witness an increase in investment over the coming years, given that ‘Green Growth’ is listed as one of the seven priorities in the latest budget. This will also help facilitate the economy’s transition to low-carbon intensity and reduce dependence on fossil-fuel imports.
Dayanand concluded: “The increase in capital expenditure outlay is expected to boost construction activity by fast-tracking projects that have been delayed due to rising inflation and interest rates. However, headwinds such as delay in land acquisition, inadequate manpower, delay in receiving necessary permits and rise in construction material prices could pose a downside risk to the industry’s output in 2023.”
SOUTHEAST ASIA
SOARING PRICE CONCERNS, BUT GROWTH TIPPED
Government spending on major infrastructure projects has increased across Southeast Asia, including the Philippines, Vietnam, and Thailand. But the soaring price of construction materials, lockdowns in China and the ongoing RussiaUkraine war have been significant concerns for the regional industry’s stakeholders.
In its latest report, Southeast Asia Construction Industry Report 2022: Analysis & Outlook 2018-2022 & 2023-2032, ResearchandMarkets.com forecasts that the construction industry in Southeast Asian countries, including Thailand, the Philippines and Vietnam, will continue to grow from 2023 to 2032, which is good news for offhighway equipment manufacturers and their dealer distributors.
“Relatively cheap labour and land costs have attracted many foreign investors to shift production capacity to Southeast Asia. Foreign trade has expanded, and the development of the industrial real estate, commercial real estate and infrastructure sectors has boosted the construction industry. On the other hand, with the economic growth in Southeast Asia, the real estate industry is also growing rapidly, promoting the development of the construction industry,” the report noted.
GlobalData says the Southeast Asia infrastructure construction market will be valued at $209.3bn in 2023 and is expected to grow at a compound annual growth rate (CAGR) of 6.1% over the forecast period. The rising need to provide an efficient infrastructure to the region’s growing population is expected to drive market growth between 2022 and 2026.
infrastructure represents exciting new sales opportunities for construction machine makers.
Indonesia is expected by GlobalData to remain the front-runner within Southeast Asia’s overall infrastructure construction sector, accounting for more than 62% in 2022. In the 2023 state budget, the government allocated IDR392trn ($25.8bn) for infrastructure development in 2023, a 7.8% increase from the 2022 budget allocation of IDR363.8trn ($23.8bn). The state budget will establish important facilities such as basic infrastructure. It will also be used to develop the new capital city (IKN) in East Kalimantan province in 2023
GlobalData anticipates Vietnam to occupy second place, following Indonesia’s regional market share in 2022. Regarding the project pipeline, Vietnam is expected to dominate the regional dynamics over the predicted timeline. The development and commencement of infrastructure projects in the country will likely aid the sector’s growth, the market research consultancy states. For instance, the construction of Dai Ngai Bridge is scheduled to commence in the first quarter of 2023, according to the Ministry of Transport. This is a 15.1km project that includes seven bridges and five
GlobalData tips the Philippines to register the fastest compound annual growth rate of 9.1% between 2022-2026
The significant volume of metro, tube and light-rail developments in the region is unsurprising, says GlobalData, given Southeast Asia’s rapid urbanisation and robust population growth. Insufficient urban rail-transit coverage has exacerbated traffic congestion in the region, generating high economic costs for many Southeast Asian economies. All this new transport
intersections, with the Dai Ngai Bridge being the main component. Set to cost around VND8 trillion ($342.9mn), the project is expected to be completed in 2026.
GlobalData tips the Philippines to register the fastest compound annual growth rate of 9.1% between 2022-2026. The government’s plan to improve regional connectivity through transport infrastructure development is anticipated to remain a key driver. The government’s allocation of PHP1.2trn ($22.6bn) as part of the 2023 budget will, says GlobalData, support the development of infrastructure projects in 2023
GlobalData estimated Malaysia and Thailand to occupy almost equivalent regional infrastructure construction market shares in 2022. However, Malaysia is expected by the same source to showcase 6.4% of the annual average growth rate from 2023 to 2026, and Thailand will likely record a 4.7% share over the same timeline. The Malaysian government is keenly focusing on maintaining its federal roadway network. For instance, in August 2022, the Minister of the Infrastructure Development Cluster and Works, Fadillah bin Yusof, announced an allocation of MYR1.8bn ($419mn) for maintaining federal roads throughout Malaysia during 2022.
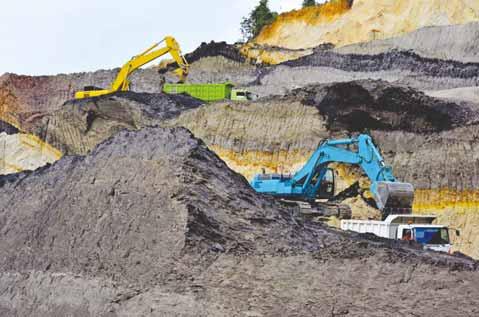
SUB-SAHARAN AFRICA
A RISING DEBT HEADACHE
Construction output in sub-Saharan Africa grew by an estimated 1.7% in 2022, compared to a growth of 3.2% registered in 2021. The industry is forecast to record a growth of 3.2% in 2023. However, significant downside risks persist, notably the rising regional debt levels, says GlobalData, a leading data and analytics company.
GlobalData’s latest report, Construction Market Size, Trends and Growth Forecasts by Key Regions and Countries, 2022-2026, is a tough read for construction equipment manufacturers seeking demand growth in sub-Saharan Africa. It states that the region’s post-pandemic economic recovery has been halted since the second half of 2022. The IMF’s Oct 2022 World Economic Outlook forecasts GDP growth in sub-Saharan Africa to remain subdued at 3.7% in 2023, following a deceleration to 3.6% in 2022. Public debt has reached about 60% of the GDP, with several countries in the region in debt distress condition or at high risk of debt-distress
Dhananjay Sharma, an analyst at GlobalData, comments: “With the gloomy economic backdrop and additional challenges specific to the construction industry, notably high construction material costs, the region’s industry will remain subdued in the short term. Both public and private sector projects will face hurdles, with the government’s revenue continuing to be directed at efforts to deal with immediate socioeconomic crises. Concurrently, high construction material prices will make projects unviable for the private sector.”
In the last two decades, GlobalData notes that Chinese funding has been a major source of growth for infrastructure projects in the region, helping Africa bridge its US$100bna-year infrastructure deficit. However, the post-pandemic Chinese economic slowdown, coupled with the substantial losses on the loans it granted to multiple countries, is resulting in a recalibration of Chinese focus on the Belt and Road Initiative (BRI) and a slowdown in Chinese investment in the region. A tightening monetary policy across developed countries also affects the region. At the same time, higher interest rates due


to high inflation weigh on both business investments and household consumption. Sharma concludes that over the longer term, growth is expected to increase from 2024 onwards, with energy and utilities outperforming other sectors. He adds: “In the short term, growth will be driven by increased activity in oil and gas projects due to higher prices. The shift towards green energy and the region’s underlying potential in renewables will drive longer-term investments.
The region’s industry will remain subdued in the short term
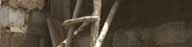
Sub-Saharan Africa construction output by sector (% of total, 2022)
Source: GlobalData
Along with energy & utilities, investments in infrastructure and the institutional sector will be driven by the continued realisation of the inadequacies of the current transport and utility systems and education & healthcare facilities.”
Deloitte’s Africa Construction Trends Report 2021 analyses a Southern Africa region comprising Angola, Botswana, Lesotho, Madagascar, Malawi, Mauritius, Mozambique, Namibia, South Africa, Swaziland, Zambia and Zimbabwe. The region recorded 106 construction infrastructure projects, an increase of 3.9% from 2020. The total value of projects increased by 18.6%, reaching $147.7bn.
South Africa recorded 37 projects (34.9%), the highest number of projects in the region. Mozambique had 16 projects (15.1%), followed by Zambia with 14 projects (13.2%) and Angola with ten projects (9.4%). South Africa also registered the highest share in value terms, accounting for 37% ($54.7bn) of the total value of projects. Mozambique followed with a share of 33.2% ($49.1bn), and Angola with 14.1% ($20.8bn).
In terms of sectoral breakdown, the transport sector recorded 44 projects (41.5%), the largest number of projects in the region. The energy & power sector came second, recording 23 projects (21.7%) under construction, followed closely by the real estate sector with 19 projects (17.9%).
MIDDLE EAST & NORTH AFRICA
MENA GROWTH IN FULL SWING
There are clear winners and losers from rising fossil-fuel prices, with the MENA (Middle East & North Africa) region firmly residing in the former camp. Additional funds generated by oil producers across the region due to the sustained fossil-fuel price hike are largely being spent on various forms of construction, which, in turn, has pushed up demand for aggregates, such as gravel, concrete, sand, and crushed stone. The GCC (Gulf Cooperation Council) countries have taken the lead in the past year, announcing building projects worth billions of dollars. This is good news for growth-hungry global construction and materials processing equipment manufacturers.
Two major events – the 2022 FIFA World Cup in Qatar and Expo 2020 in Dubai (the event was deferred by one year due to the Covid-19 pandemic) – gave a fillip to GCC construction activity.
Encouraged by the success of World Expo 2020 in the UAE, Saudi Arabia wants to hold the World Expo in 2030 as the Kingdom has already initiated infrastructure projects worth over $750bn, including NEOM city, which alone is estimated to cost around $500bn.
MENA’s construction sector growth, particularly in the oil/refinery, petrochemical/industrial, and commercial construction, is fuelled by the US$90 to $125 a barrel of crude oil. On 8 March 2023 the price of Brent crude oil stood at $80 but is expected to rise in the coming months.
More importantly, the huge spending by various regional governments in executing various infrastructure projects is expected to create thousands of direct and indirect jobs leading to more economic activity throughout the region.
For example, Morocco has approved 26 investment projects with a total budget of $2.8bn. These projects will create over 3,735 direct jobs and 23,182 indirect jobs, the country’s investment commission, chaired by Morocco’s Prime Minister Aziz Akhannouch, said on 23 January 2023
Even in Egypt, which is still recovering from the Covid-19 pandemic, the award of construction projects is set to grow by 18% to $23.5bn in 2023 from $19.9bn in 2022.
Morocco has approved 26 investment projects with a total budget of $2.8bn
While the building sector walked away with the lion’s share of $9.7bn in 2022, it was followed by the $5bn industrial and $2.7bn infrastructure sectors.
Mordor Intelligence, a
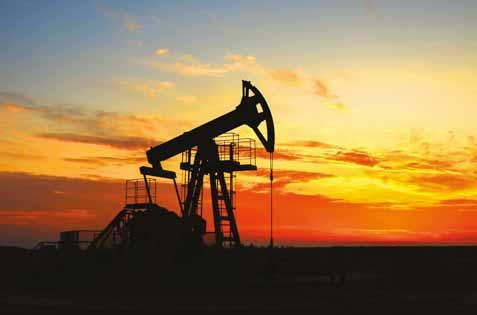
global market intelligence and advisory firm, values the MENA construction equipment market at $4.26 billion and expects it to reach $6.4 billion by 2028, registering a CAGR (compound annual growth rate) of 4% over the next five years. Saudi Arabia represents the second-largest market for the construction sector in the GCC region after the UAE, which represents more than 34% of the revenue generated, Mordor Intelligence reports. Saudi Arabia holds a revenue share of 29%, followed by Qatar and Oman with 12% and 10%, respectively. Mordor Intelligence anticipates the construction of high-rise buildings like the Jeddah Tower in Saudi Arabia to increase the demand for construction equipment in Saudi Arabia.
“The Covid-19 pandemic severely affected the [MENA] construction industry and associated equipment demand due to disruptions in the supply chain, reduced investment in new equipment procurement, [the halting] and postponement of construction projects, and unstable economic growth in many countries,” states Mordor Intelligence.
However, the same source says that since last year, the construction industry across the region has been experiencing significant growth in investment and economic development, witnessing major orders for construction equipment from GCC countries, likely to fuel market demand over the next five years.
For example, in August last year, Doosan Infracore Co., a subsidiary of Hyundai Construction Equipment, won an order to supply 62 units of construction equipment to major customers in Saudi Arabia and Bahrain.
Another major factor that is expected to push up MENA demand for construction equipment and building materials is the tragedy that struck two Middle East countries - Turkey and Syria - in the form of the massive earthquake on 6 February 2023
The Turkish government’s initial recovery plan is to build 200,000 apartments and 70,000 village houses at the cost of at least $15bn. The government anticipates that reconstructing damaged buildings, roads, and airports will take at least three to five years.

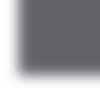
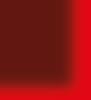
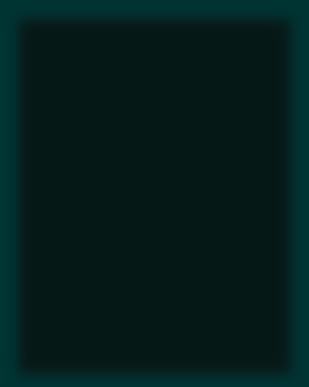


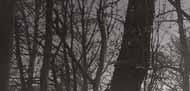
Integrating logistics data with information from on-machine technology can deliver greater efficiency for road construction
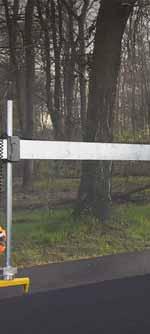
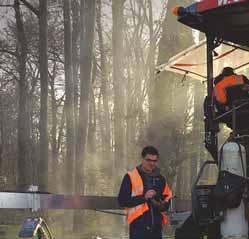
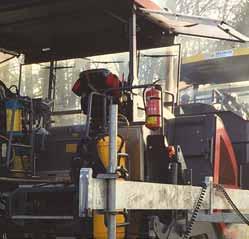
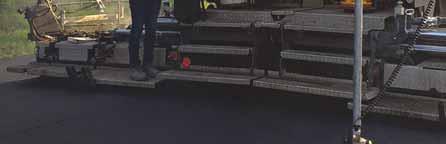
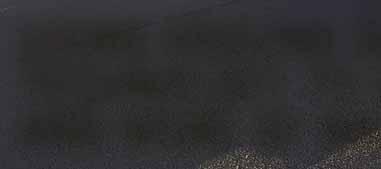
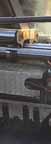
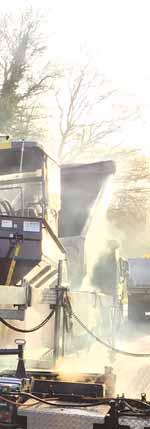
USING GROUND-SCANNING TECHNOLOGY TO REVEAL MORE AND MORE OF WHAT LIES BENEATH

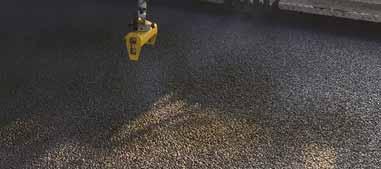
For any construction project, having an extensive knowledge of the ground conditions is an essential factor before work can begin. Geological surveys are vitally important in determining what lies underground, such as varying rock strata, buried water courses, utility pipes, and other hazards. And the technology that enables all this is getting ever more sophisticated. Mike Woof reports.
Assessing the condition of road surfaces, whether old or recently paved, can provide essential information regarding their structural strength and potential longevity. And what lies beneath can be just as important, sometimes more so.
Understanding the complex geology of any area is crucial both for structural and environmental reasons before roads or bridges or tunnels or any other structures can be built. Reinforcement may be required to provide necessary support under weightbearing columns. Meanwhile, the location of natural springs may require environmental measures to prevent contamination.
And when road works are being carried out, determining the condition of the surface is essential to know what a project will entail.
Also, knowing where utilities lie can be an issue. Councils do have maps showing the location of these but for a number of reasons,
they could be inaccurate or incomplete. Sewers or water mains can be very old in some instances, so they may not be marked accurately on local maps.
During the construction of the Crossrail project in UK capital London, for instance, the contracting team had to carry out extensive surveys before tunnel-boring machines (TBMs) could be allowed to start tunnel drives. The location of underground cables and drains had to be determined accurately. In some instances, historic structures and sites came to light during these surveys. Some were many hundreds of years old, and the authorities had absolutely no record of their existence.
HIDDEN SECRETS
The location of utilities may be unclear for other reasons too. Some years ago, a contractor was using a chain trencher to open
up a drainage channel at a roadside in East England. The trencher struck an obstruction that was not marked on the council map and the machine was then stopped as the contracting team figured out what to do.
Minutes later, several military vehicles screeched to a halt at the scene and personnel jumped out, pointing weapons at the road crew and demanding an immediate halt to the work. Unknown to the contractor, the trencher had cut through key communication cables leading to a nearby military base. These utilities were not marked on the council maps of buried utilities because they were considered secret by the military.
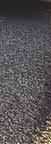
The bemused highways contractor team then faced a barrage of questions and tense moments passed until the military officer in charge realised that this was not a deliberate act of espionage by a hostile foreign power. Instead, this was an innocent mistake by a ➔
civilian contractor unaware of the location, as well as the importance, of the cables.
The incident was entirely avoidable. It is understandable that the military would not want to make public the location of key communication links to a major military base where strategic weapons were sited. It is understandable too that the civilian contractor would feel able to rely on maps of buried utilities provided by the council, especially since this was a rural area in the midst of farmland.
But simple checks using basic cabledetection equipment would have averted the incident entirely.
Using drilling rigs to take core samples is a common method of determining geology. But this can be time-consuming and is not inexpensive, requiring skilled analysis of the core samples. Seismic equipment can be used to determine geology also and is less time-consuming than using a drill rig to take core samples. But even here, analysis requires skilled professionals to carry out the work. There are, however, simple tools that can be employed for many applications instead. Cable detectors are comparatively cheap and can be bought or rented. These units are simple to operate with just basic training and can be used onsite by any construction personnel.
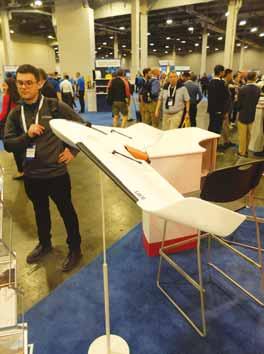
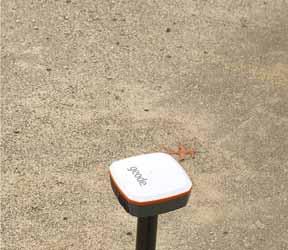
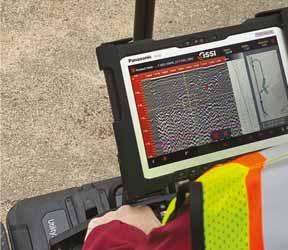

More sophisticated ground-penetrating radar (GPR) equipment is also available, although this is more costly and requires proper training to use. This can reveal the location of cables and pipes before any works are carried out.
SATELLITES AND 3D MAPPING
Data recovered using GPR tools can be geolocated using satellite positioning systems and integrated into 3D maps of project areas, highlighting to designers where underground obstructions are located. This can ensure that clash-detection measures can be employed so that construction works will not interfere with existing utilities.
Using GPR systems can also ensure that important archaeological finds in areas of historic importance are undamaged and can be excavated sensitively by experts before construction works commence.
Greek contractor Terna has used GPR systems extensively for this purpose during major highway construction contracts in the country. In a number of instances, highway alignments have been moved on Greek projects due to large and important archaeological finds initially located using GPR tools.
Meanwhile, when building a new highway in Kosovo the joint venture partners Bechtel Enka made use of GPR systems to detect unexploded munitions left over from the civil war of the 1990s, averting potential accidents onsite.
In recent years, new technology has helped
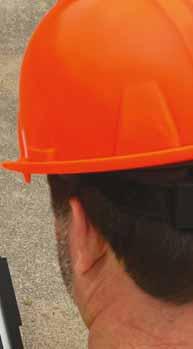
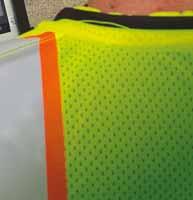
The GSSI system for GPR can accurately determine the condition of paved surfaces to set depths
take resurfacing projects in new directions in terms of the materials used, the equipment deployed, and the workflows which followed … all of them important factors in increased speed and efficiency.
For both road construction and road repair works, an assessment of the condition of existing networks is essential. Laser scanning technology can be utilised to generate point clouds of project areas, yielding important information with regard to roadside obstructions. Firms such as Bentley Systems, Leica Geosystems, Topcon and Trimble all offer an array of tools that can recover point cloud data, employing a range of equipment including automated drone systems.
DATA FROM THE CLOUD
Data from point clouds that is integrated with satellite positioning systems is vital for utilisation in 3D models of projects.
For example in Australia, recent heavy flooding has caused extensive damage to roads in Victoria State. Repair and rehabilitation works are required to ensure that road links are returned to an adequate condition. Victoria State enacted an Emergency Road Repair Blitz to deal with the issue, requiring a total of 8,400km of roads to be surveyed to determine what type of improvements will be needed.
A budget of US$115 million (A$165 million) was set for the work. The highly sophisticated intelligent Pavement Assessment Vehicle (iPAVe) will be used for the surveying process as the machine is
equipped with sophisticated laser scanning systems able to analyse a road’s structural condition. The iPAVe machine also feaures ground-penetrating radar (GPR) equipment, allowing it to assess a road’s base structure. The iPAVe machine is operated by the Australian Road Research Board (ARRB).
For road or airport runway resurfacing works, tools such as Topcon’s RD-M1 Scanner can be employed to deliver highly precise analysis of surface conditions. This system can be fitted to a van or pick-up truck, while recovering extensive data revealing the precise condition of the road surface.
The innovative RD-M1 scanner collects a constant stream of data as the user drives, delivering precise surface conditions. This allows a firm to quickly scan long stretches of road without the need for costly lane closures or rework. Normal traffic conditions continue uninterrupted,
saving time and increasing crew safety.
The sophisticated design works seamlessly with an integrated HiPer SR GNSS receiver and inertial measurement unit (IMU) to capture point data accurately while cruising at normal highway speeds. Data is automatically timestamped and stored for easy management and point cloud generation.
Once a road has been paved, it is still important to asses the quality of the work that has been carried out
The downward-facing LIDAR scanner is said to deliver optimal road surface definition, allowing speed scanning without the need for lane closures. The system can collect millions of points from a truck cab safely, while allowing scan rates of up to 100 times/second. The package allows easy installation and removal for daily use and also features graphical software for intuitive processing.
Once again, this data can be incorporated directly into 3D models, providing a highly
accurate, geolocated picture of road surface quality. Not only will this reveal cracks or potholes, it will also highlight undulations in the surface, showing how a road will have to be made more smooth to improve its ride quality. Data from this type of system can be used directly in milling machines with automatic controls governing the height of cut so that only an exact quantity of material is removed. This leaves a precise surface on which paving can be carried out.
PAVING BENEFITS
The subsequent paving operation can then be carried out in the knowledge that all surface undulations have been removed, along with failed areas such as cracks and potholes. Because only the material needing to be milled is removed, this delivers substantial savings in materials costs. Road surface materials are increasingly expensive (and asphalt-wearing courses in particular), so minimising the quantities required for a project will ensure construction-project costs are kept in check.




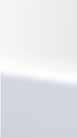

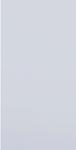
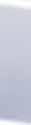
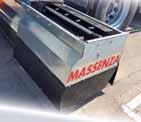




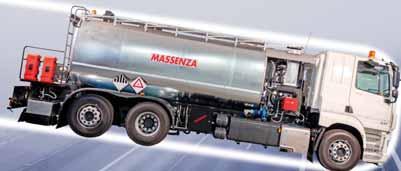

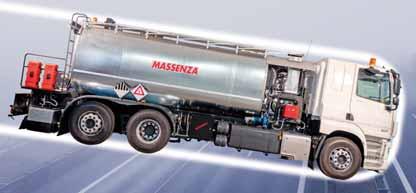

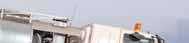
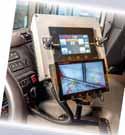
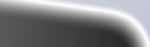
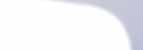

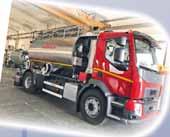







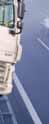

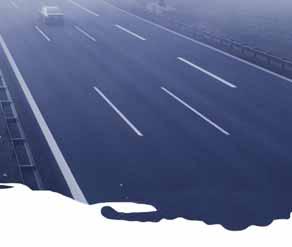


The Topcon RD-M1 system can be fitted to a pick-up truck and used to carry out accurate, high-speed checks of road surface condition

During asphalt paving, sophisticated tools can now be employed to ensure quality is optimised. Heat-scanning equipment mounted on the asphalt paver will monitor temperature gradient of the mat behind the screed. This highlights inconsistencies and areas of temperature segregation, as well as showing sections that are cooling and which will require a priority for compaction to be carried out. Paver manufacturers such as VÖgele offer their own proprietary heat-
Sophisticated tools can now be employed to ensure quality is optimised
Using scanning systems can ensure milling operations are carried out accurately to deliver smooth surfaces that can be paved on directly
scanning systems, alongside equipment from specialist suppliers such as Moba or Leica Geosystems, Topcon or Trimble.
Similarly, heat-detection equipment fitted to asphalt compactors can be combined with technology that determines the degree of compaction carried out. Major compactor manufacturers such as BOMAG, Caterpillar, Dynapac, Hamm and Volvo CE offer their own proprietary systems, in addition to the technologies from
specialist suppliers like Leica Geosystems, Topcon and Trimble.
These systems can also be integrated with tools such as the BPO package from Volz Consulting that track the logistics of materials supplies, to ensure more efficient working. Meanwhile, the Wirtgen Group offers its own proprietary system with similar performance. These packages can be used for the value chain, from operation and resource management to merchandise management such as purchasing, sales, invoicing, freight accounting, production data collection, production and logistics. Users of such packages can employ them for material production, as well as road-milling and paving applications.
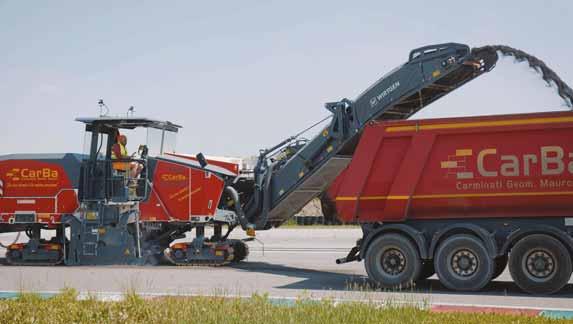
Due to real-time networking, data such as delivery notes, invoices, material orders or offers can be exchanged. Deliveries of minerals from an asphalt mixing plant can be monitored automatically and only need to be confirmed. Raw material orders can be transmitted electronically, reducing order costs.
Once a road has been paved, it is still important to asses the quality of the work that has been carried out. The PaveScan RDM 2.0 is a second-generation asphalt density-assessment tool ideal for nondestructive asphalt compaction testing, quality assurance/quality control of new pavements and determining pavement nonconformity.
By uncovering inconsistencies that occur during the paving process, including
During road construction work in Greece, contractor Terna used GPR technology to ensure the road alignment did no damage to archaeological sites

poor uniformity and significant variations in density, PaveScan RDM 2.0 helps to avoid premature failures like road ravelling, cracking, and deterioration along joints.
SEAMLESS INTEGRATION
The seamless GPS integration, realtime onscreen data output and export options mean that this system is ideal for government transportation agencies and paving contractors alike. The pavement density-measurement technology used in PaveScan RDM 2.0 is an accepted American Association of State and Highway
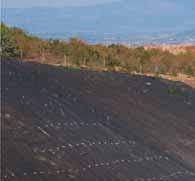
When the Bechtel Enka joint venture partners built a new highway in Kosovo, GPR systems were used to ensure there were no unexploded munitions in the way of the excavation works
Transportation Officials (AASHTO) specification, PP 98-19.
The complete PaveScan RDM 2.0 system includes a rugged deployment cart and an integrated concentrator box that accommodates up to three sensors. It includes housing for cable management and hot-swappable, dual batteries.
The new sensor design was built specifically for the extremes of the asphalt paving environment and features a green laser to aid location accuracy. Also available is a system upgrade kit to expand to three sensors for better pavement coverage.

Additional GPS options and mounting pole provide high-precision location information and work seamlessly with the PaveScan interface.
Using laser scanning and GPR tools in combination with geolocation systems to augment 3D renderings of projects has become essential for construction works both before and after any work is carried out.
Analysing conditions can deliver major cuts in construction time, reducing the need for reworking and delivering higher quality while also lowering overall projects costs.
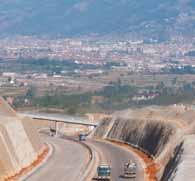
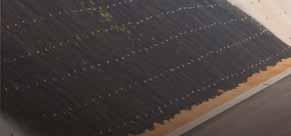
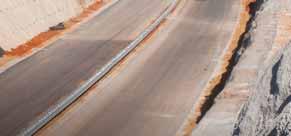

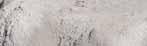
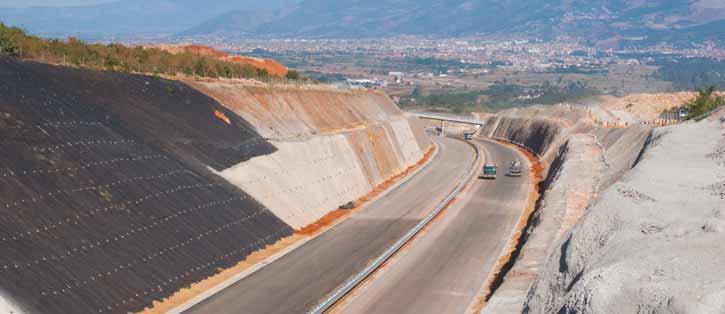


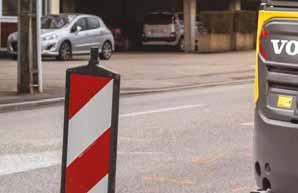
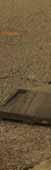
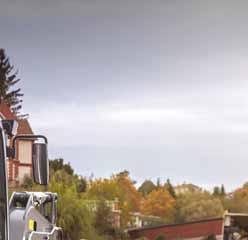
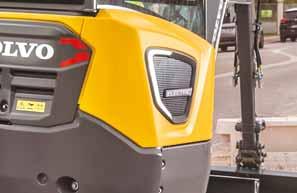
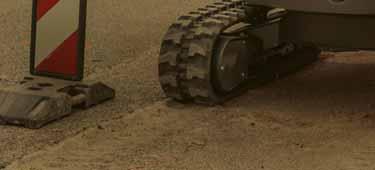
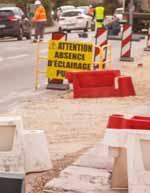
BE REALISTIC AND MAKE SURE THAT YOU MEASURE THE REAL IMPACT OF GOING ELECTRIC

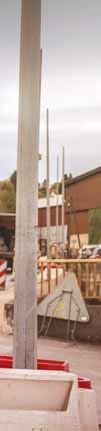

It’s vitally important to measure the real impact of going electric says Mats Bredborg, Head of Customer Cluster Utility at Volvo Construction Equipment. In 2021, the construction industry accounted for around 35% of energy and process-related CO2 emissions according to a report by the UN Environment Programme. Our industry plays a vital role in healthy economies, but it must play its part in cutting emissions and pushing for a more sustainable way of working of course. What does going electric really entail?
It’s clear that sweeping change is needed if we are to collectively transform the highway construction, maintenance and utility works industries and we understand the complex challenges that lie ahead for customers ... from materials choice and production technology, to supply chains and transport.
As we all know, steps are being taken already, and there are solutions available today that can significantly reduce emissions. Electric machines are one of these solutions and they are growing in popularity. No longer just a vision for the future, they are in operation today on sites across the world in a wide variety of different applications including highway maintenance and utility work. Aside from being zero emission, they
are also quieter, helping meet ever-stricter air pollution and noise disturbance regulations.
Whilst many customers understand the benefits offered by electric machines, concerns about cost and performance can be a stumbling block towards adoption. Changing the way we measure their impact is one solution to help pave the way for wider uptake.
We need to look beyond the initial purchase or rental cost for an electric machine, which in many cases may well be higher than for a conventional machine equivalent and dig a little deeper to uncover equally important benefits that we can and should be measuring. Cost to operate, the reduction in CO2, health and safety benefits for operators and passers-by, their ease of use,
operator feedback and of course, their ability to get the job done.
Measuring their impact is something that Volvo Construction Equipment (Volvo CE) has been doing in its own assessment projects … and the following results may come as something of a surprise:
COST
INCREASE IS MARGINAL
Electric machines are often considered prohibitively expensive from an upfront capital cost point of view. It’s important however, to look at the full picture.
Fuel costs and servicing are traditionally significant contributors to the operating costs of construction machines. With no engine to service and no need for diesel – the cost of which is at an all-time high – electric

Source: Volvo CE
machines can be cheaper to run. We found a less than 1% increase in project costs to use electric machines over diesel. Whilst the initial rental price was higher, the cost of electricity to power the machines was much lower than the price of diesel.
Add in reduced maintenance and the cost savings from machine idling time – which is eliminated with electric machines - and suddenly the cost for electric machines becomes more favourable.
KINDER ON THE POCKET AND THE PLANET
Arguably the strongest and most widely understood argument for electric machines is the reduction in CO2 emissions they deliver. If the road construction industry is to get to grips with its CO2 contributions, electric machines offer a ready-made solution, especially when they are powered by renewable energy.
On an 11-week project to install electric charging stations, electric machines used in
Source:
place of their diesel counterparts saved an impressive 3,000kg in CO2 emissions. That’s equivalent to taking 17 cars off the road for a month.
QUIET PLEASE
Noise pollution still constitutes a major environmental health concern in Europe, being a problem for 1 in 5 EU citizens. Directives to reduce environmental noise are becoming increasingly stringent, ➔
➔ necessitating construction sites to implement preventative measures like acoustic barriers and providing workers with personal protective equipment (PPE). Eliminating noisy processes is the best way to deal with noise on a construction site.
Using electric equipment in place of traditional diesel engines delivers a noticeable reduction in ambient noise and pollution. The noise levels from electric machines are around 20% lower than for diesel machines, making them ideal for use in busy inner city and urban environments, outside schools, shops, offices and hospitals for example, where noise regulations may be toughest. They also allow work to continue later into the night or begin earlier in the morning, helping to get the job done faster and delivering cost savings. Operators, too, benefit from the lower noise levels making work more comfortable and allowing them to communicate more easily with site managers and other site staff without the need to shout or shut down the machines. Better communication also has a positive impact on health and safety on site.
COMPARABLE – OR IN SOME CASES BETTER – PERFORMANCE
Electric machines are based on conventional construction design, with just the electric components replacing the diesel engine. This means comparable performance to the diesel versions. In fact, the controls themselves are identical to a diesel-powered machine.
Once operators adapt to the charging
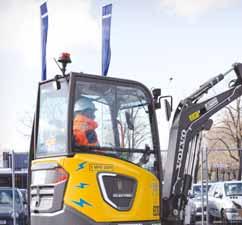
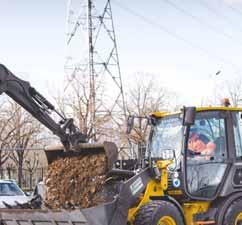
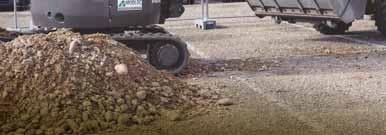
requirements, any reluctance is overcome, and they quickly realize electric machines can get the job done in just the same way as their traditional diesel counterparts but with zero emissions.
And with less noise they can communicate more effectively without having to halt operations to discuss the job at hand, meaning it can be completed more efficiently, with less room for confusion or errors and creating a safer work environment for everyone. In fact, feedback is usually so positive electric machines become the operator’s choice.
PAVING THE WAY FOR MORE SUSTAINABLE WAYS OF WORKING
Being more sustainable is achievable without compromising on performance or profitability. For what can be marginal cost increases on a project, it is possible to radically transform highway construction operations.
The world is changing and we need to adapt and find more sustainable ways of
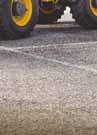
working. With their zero-emission operation, electric machines offer a transformative solution for the highway construction sector to significantly reduce its carbon emissions. Climate-saving choices exist already today. Adopting these now will pave the way for new innovations and initiatives in the future. Together we can play our part to deliver a more sustainable construction future.

Mats Bredborg
Having spent more than 30 years with the Volvo Group, based in Europe, Asia and the Americas, Mats Bredborg has been at the centre of the great technical transformation that construction equipment has undergone. In his latest role with the company, Mats has become a global influencer, championing the many benefits (and undoubted challenges) of what is without doubt the industry’s biggest and most ambitious challenge yet: the transition toward electromobility.
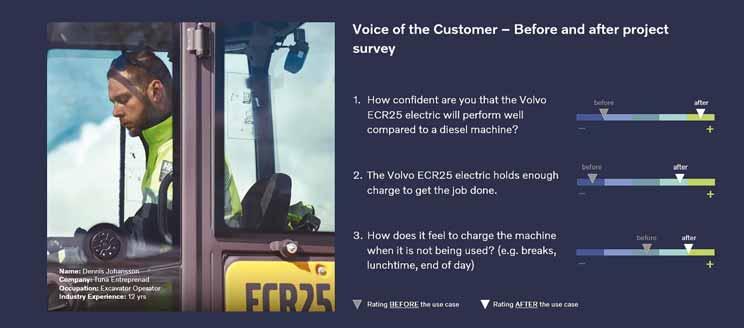

TAKE A LOOK AT THE FULL POWER OF AN ELECTRIC ECOSYSTEM WITH VOLVO’S E-WORKSITE
Last year, Volvo CE set up a fully-electric worksite (E-Worksite) in Gothenburg, Sweden, not only to benchmark an electric jobsite, but also to test how a set of electric construction and utility machines could work successfully across different tasks within a demanding urban environment.
The company saw this assessment project as “a vital next step in the electrification journey.”
According to Carolina Diez Ferrer, Head of Advanced Engineering Programs, at Volvo CE: “We are already delivering electric solutions that offer zero- exhaust emissions, reduced noise, and a much more comfortable work environment, but that is only half the challenge.
“We are also committed to helping our customers reach their own climate goals through complete site solutions with a holistic sustainable approach. This exciting partnership allows for a comprehensive investigation into the varied infrastructure and support system needs for electric machines to really perform to their best, no matter the task at hand.”
On-the-ground testing like this is essential in helping to move the transition to e-power forwards
And for Peter Lindgren, Business Developer Electrified Transports at the City of Gothenburg Urban Transport Administration, the aim is a real-life test: “To achieve the City of Gothenburg’s climate goals we need to reduce greenhouse gases and we see that electric construction machines will help us in this environmental work by reducing local emissions of both nitrogen oxides and particles, as well as noise. The partnership as part of the Electric Worksite is of great value and we see that this research project has the capacity required to speed up our green transformation”.
As Mats Bredborg explains, on-the-ground testing like this is essential in helping to move the transition to e-power forwards. As Volvo CE says: “Project planners are answering questions such as how to ensure best value for money for customers and what are the most energy-efficient methods of supplying
electricity to power the machines. Beyond the technology itself, business models, infrastructure and support systems, regulatory frameworks and a mindset change are all required on the road to full acceptance.
“It is a complex puzzle to solve as there will
be no one size fits all. The findings will prove important not only for municipalities in deciding how to develop the appropriate legislation, but also for industry partners in bringing technical solutions to market – both in the immediate future and over the next two decades.”
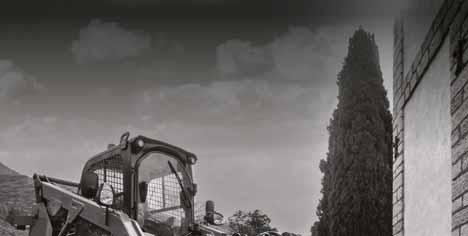


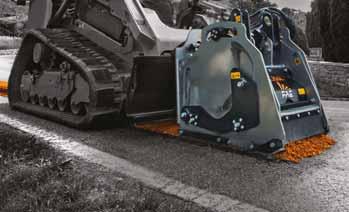

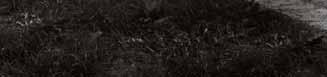

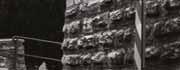

info@fae-group.com fae-group.com A new era has begun for skid steer road planers. The FAE RPL/SSL and RPM/SSL are dedicated to resurfacing roads in preparation for laying a new layer of asphalt or concrete. The FAE RWM/SSL , with disc rotor is ideal for
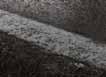


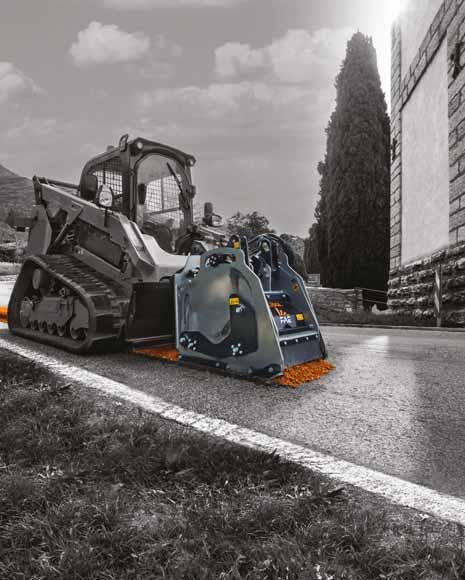
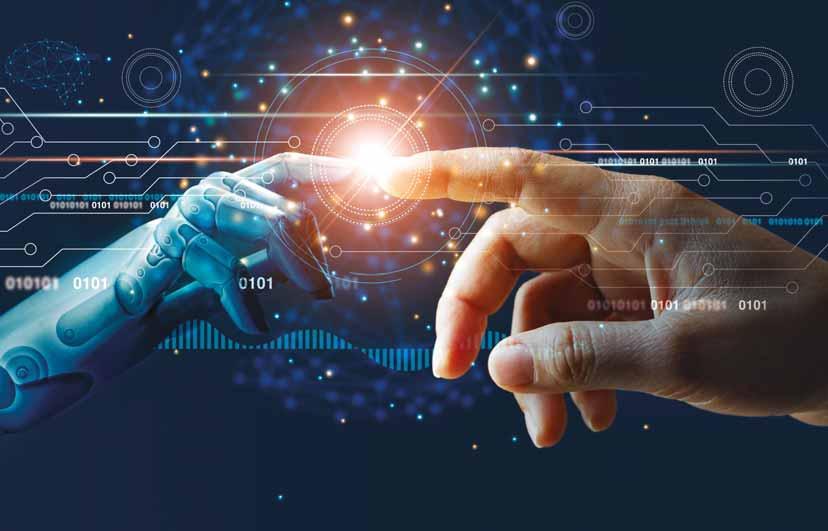
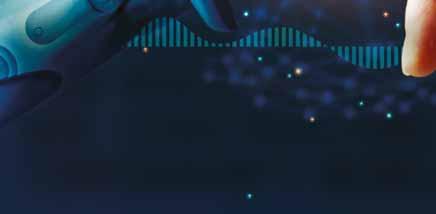
ARTIFICIAL INTELLIGENCE AND MACHINE LEARNING ARE CONSTRUCTING TOMORROW’S WORLD TODAY
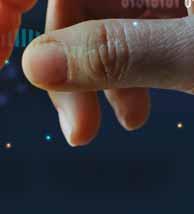
The world’s leading construction equipment firms are jockeying for position as AI takes root. Companies based in China, USA, Europe and India are all battling for control as another new industrial revolution transforms the world. Graham Anderson reports.
Back in the 1970s, the gravel-voiced American singer-songwriter Tom Waits wrote “Step Right Up”, a sort of musical monologue about a super product that would do everything its owner wanted.
It would mow the lawn, deliver the pizza, pick up the kids, walk your dog, double up on sax, and get rid of your gambling debts. He sang: “It’s a friend, it’s a companion, it’s the only product you will ever need.”
Tom Waits was satirising what he saw as out-of-control consumerism. But he might as well have been welcoming his listeners to the coming world of artificial intelligence.
Political leaders of all stripes are certainly beginning to take note of the social and economic changes that are heading our way, and their impact on geopolitics and individual industries.
Last September, US National Security Advisor Jake Sullivan, made a speech at a Global Emerging Technologies summit in which he stressed the huge significance of AI to the US and the West’s economic ambitions.
He said that the US has been complacent
in the past and allowed its competitors and adversaries to take advantage of its openness - something that would not happen in future.
According to Sullivan: “Advancements in science and technology are poised to define the geopolitical landscape of the 21st century. They will generate game-changers in health and medicine, food security, and clean energy.”
TAKING THE LEAD
He added that a select few technologies are set to play an outsized importance over the coming decade, including microelectronics, quantum information systems, and artificial intelligence, and leadership in these would be both a national security and economic imperative.
On one level, he and the US government are responding to the challenge posed by China. In July 2017, China’s State Council announced that the country aimed to become a leader in AI by 2030
By some metrics China seemed until recently to be already ahead of its
competitors. Earlier this year Japanese media conglomerate Nikkei Asia reported that the number of published Chinese AI research papers had risen five-fold in little more than a year.
But the recent and rapid emergence of generative AI technologies such as ChatGPT in the West has significantly altered the competitive landscape, challenging China’s perceived position.
An added complication in these times of polarised political stress is that many Chinese companies work successfully in the West and vice versa. Away from geopolitical rivalries, industrialists of all stripes are trying to understand the real-world implications for their companies and markets.
The major-projects end of the construction industry has been grappling with the rise of BIM - building information management- for some years along with its impact on design, planning and project management.
Now, the industry is beginning to see the development of increasingly sophisticated AIinspired autonomous equipment, with major
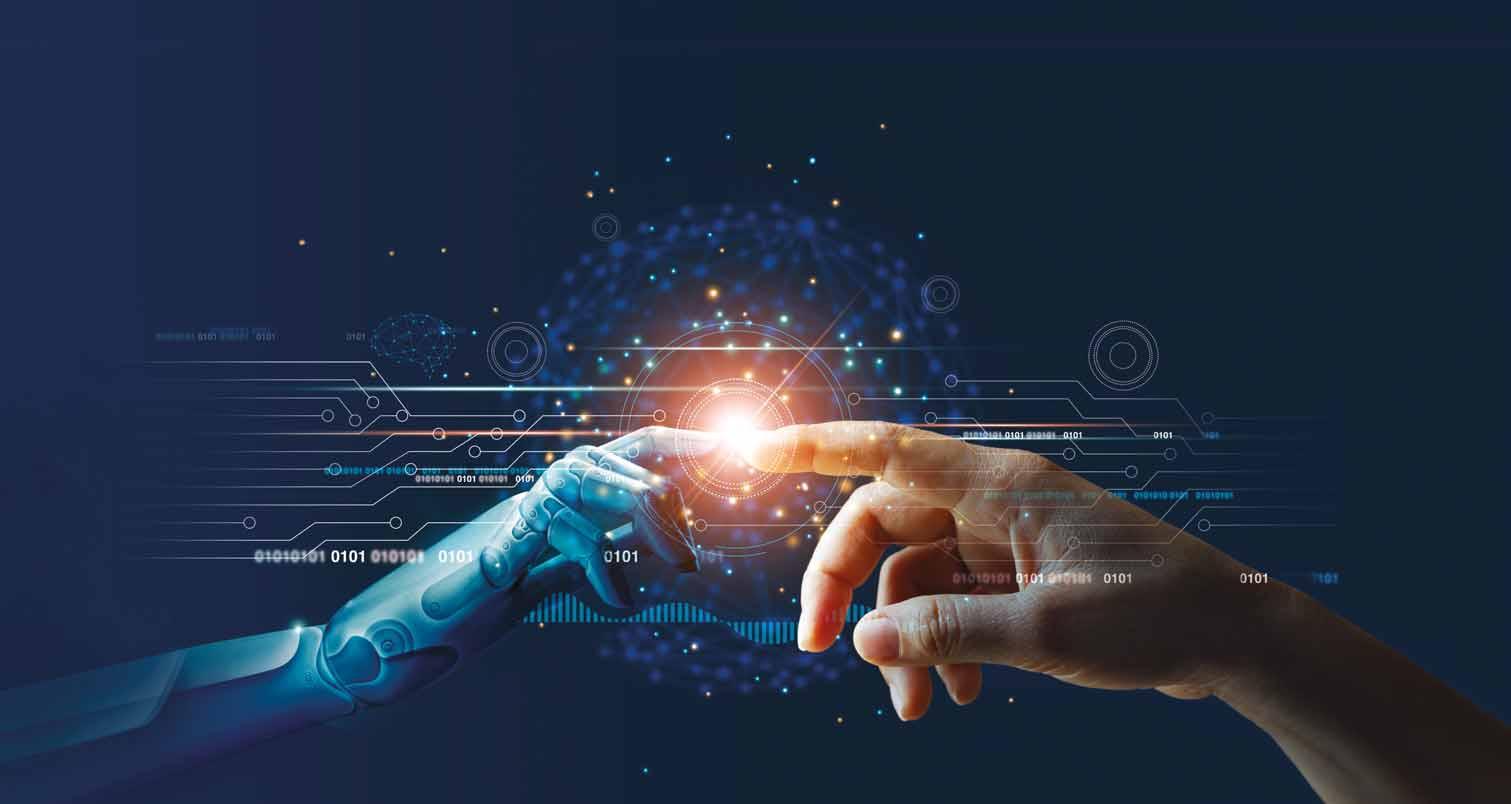
intelligence.
TRIMBLE’S 5-STAGE PROCESS
One company at the cutting edge of such trends is Trimble, the US-based industrial technology specialist. Construction is one of Trimble’s core markets and it works with a range of companies across the supply chain from architects and project managers to utilities and OEMs.
A particular focus has been on the rise of autonomous equipment. Cameron Clarke, earthmoving industry director for Trimble Civil Construction, says that the company

sees autonomy as a five-stage process, starting from Level 1 where the operator performs most tasks, but AI provides guidance assistance that optimizes human decisionmaking, through to the total autonomy of Level 5 with the vehicle replacing human operator tasks at an experienced operator level.
Clarke explains that this has huge implications for the wider industry well beyond the operation of a specific piece of equipment.
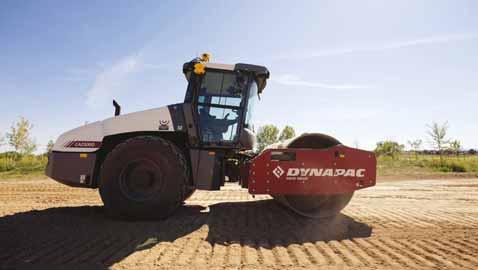
“Each level has different requirements for an autonomous piece of equipment to be safe, for it to know what to do, to be able to receive a task, to report what it is doing etc. These requirements can be broken into valueadd items that can be added to a portfolio of solutions to make sites more productive and safer along the way to a future state of autonomy.”
He continues: “But for any level of autonomy to be safely deployed to a job site, site data has to be captured and fed back into a repository where analytics can be applied and decisions be made to have the intelligence to optimize and coordinate the site.
“Autonomous equipment can only be successfully applied in an ecosystem that is set up for sophisticated use of site data. To support the making of plans and optimizing the work of the autonomous equipment on the ‘whole’, a complete picture is required, not an incomplete or outdated data set. Only then autonomous machines can work in harmony together with other autonomous machines and manned machines.”
He adds that connected site technology is part of a whole system of autonomy in construction. “It enables the management of multiple types of machines from multiple
brands to be orchestrated from an integrated environment.
“Construction sites are very dynamic environments: adding a machine has a massive impact on all the other machines on the job.”
XCMG IS TRYING OUT AUTONOMOUS ROAD CONSTRUCTION
In China, leading equipment manufacturer XCMG has been running a series of projects trialling autonomous road construction and maintenance.
To date, what the company calls its “unmanned cluster construction equipment” has participated in 15 highway construction projects that cover 12 provinces across China, including the Pan-Dalian Expressway, the Jingxiong Expressway, reconstruction and expansion of the BeijingTaipei Expressway and the Shanghai-Nanjing Expressway maintenance contract.
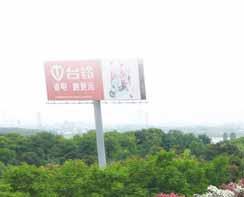
XCMG - which signed a strategic cooperation agreement with Trimble in March this year - concluded that the unmanned equipment was between 15-20 per cent more efficient than traditional construction operations.
Cui Jisheng, general manager of XCMG’s road machinery division, said: “Our
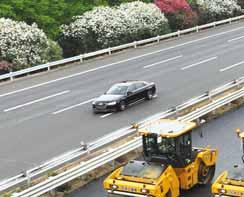
autonomous road construction technology efforts focus on three core points: efficiency, quality, and cost.
“Just like automated production lines in the manufacturing industry, automated construction technology can improve standardization and achieve high-quality, high-efficiency construction solutions.”
Fellow Chinese OEM Sany - known for its cranes and heavy construction equipment - has teamed up with Californian autonomous vehicle specialist Pony.ai to develop, produce and sell fully autonomous self-driving heavy-goods vehicles and build a highend autonomous driving heavy-truck brand. And in India, both big and small firms in its fast-growing technology sector are also moving rapidly into the space offered by AI-related opportunities, like their Chinese counterparts.
Company CEO Vikshut Mundkur says that Constra helps construction leaders and project managers to streamline their project management processes by allowing them to oversee their project remotely, resulting in faster, more accurate, cost-effective, and more efficient design, construction and postconstruction management.
He believes that the application of AI in construction is scaling rapidly and says that real estate and construction companies are steadily adopting visual-intelligence platforms for remote management of their projects - with many solutions built on AI technologies by Indian companies.
The unmanned equipment was between 15-20 per cent more efficient than traditional construction operations
DATA SECURITY IS A HOT TOPIC
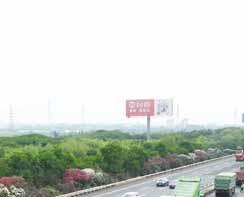
Just one of many examples is HUVIAiR, based in Bengaluru, formerly Bangalore and the centre of India’s burgeoning technology sector.
HUVIAiR has launched a project management software called Constra.
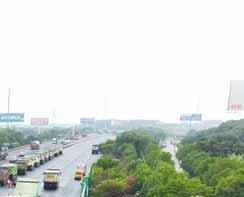
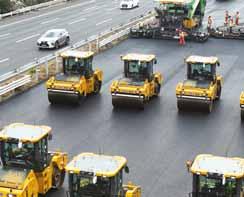

In Europe, regulators and industry are engaged in increasingly heated debates about data security and ownership. Despite this, activity is at a similar pitch. The EU-funded InfraROB project will focus on automating, robotising and modularising road construction and maintenance work. More specifically, it will develop, among others, autonomous
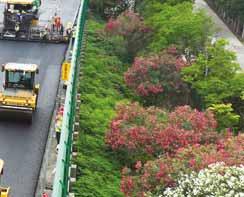
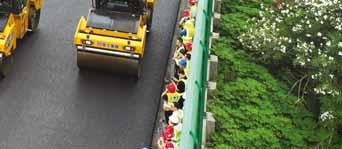

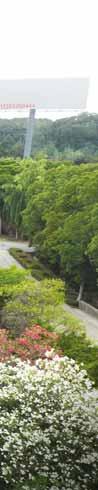

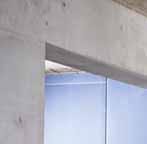
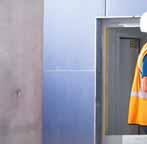
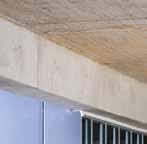
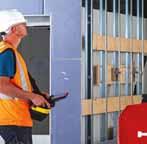
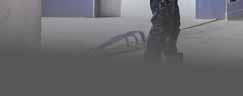
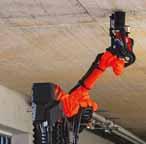

WE ASKED CHATGPT TO ANSWER, IN ITS OWN WORDS: HOW WILL AI AFFECT THE CONSTRUCTION EQUIPMENT INDUSTRY?
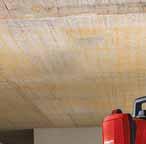
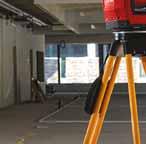

Q: What impact will AI and machine learning have on the global construction equipment industry?
A: AI and machine learning are expected to have a significant impact on the global construction equipment industry. Here are a few ways in which this technology could change the industry:
1. Predictive maintenance: AI and machine learning can be used to predict maintenance issues in construction equipment before they occur. By analysing data from sensors and other sources, AI algorithms can identify patterns that indicate when a component is likely to fail. This allows for preventive maintenance to be scheduled, reducing downtime and improving productivity.
2. Autonomous operation: AI and machine learning can also enable construction equipment to operate autonomously, without the need for human intervention. This could include self-driving bulldozers, excavators, and other equipment, which could work around the clock without the need for breaks or rest.
robotised systems and machinery to carry out line marking, repaving, and the repair of cracks and potholes.
Road maintenance is also the focus of a project in the city of Herne in western Germany for contractor Hochtief and its technology subsidiary Edgital.
They have developed a digital solution incorporating artificial intelligence to analyse the town’s 380km road network, to allow them to deliver a maintenance programme at the right time and as efficiently as possible. Initially, a database is being developed and integrated into a digital twin BIM model with road condition information which will be used to create an efficient road condition maintenance programme.
The mayor of Herne, Frank Dudda, said, “The basis for efficient planning is to identify weak points in good time and to record precisely when maintenance measures make sense. To do this, we need continuous data
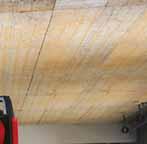
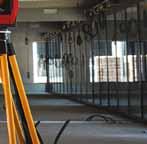
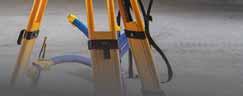
3. Optimization of equipment usage: AI and machine learning can help construction companies optimize the usage of their equipment. By analyzing data on equipment usage, AI algorithms can identify ways to improve efficiency and reduce downtime. For example, algorithms could help determine the best times to use equipment, or which equipment is best suited for specific tasks.
4. Improved safety: AI and machine learning can also improve safety in the construction industry. For example, sensors and cameras could be used to detect hazards on construction sites, and algorithms could be used to alert workers to potential dangers. Similarly, autonomous equipment could reduce the risk of accidents caused by operator error.
Overall, AI and machine learning have the potential to transform the construction equipment industry by improving efficiency, reducing downtime, improving safety, and enabling new capabilities such as autonomous operation. However, the adoption of these technologies is likely to be gradual, as the industry faces challenges such as the high cost of equipment and the need for specialized training for operators.
collection on the condition of roads.”
In March, Liechtenstein-headquartered international power-tool manufacturer Hilti announced a strategic partnership with San Francisco-based construction robotics firm Canvas. This followed in from its acquisition of software specialist Fieldwire for an approximate US$300 million in 2021.
Founded in 2017, Canvas is the manufacturer of a drywall finishing robot that utilises artificial intelligence, machine learning, robotics and 3D technology to apply both drywall finishes in a fraction of the time of conventional methods.
It also reduces injuries and captures almost all the dust, and demand was outstripping the company’s ability to supply.
Hilti launched its own semi-autonomous ceiling drilling robot Jaibot in 2020, and Thomas Hillbrand, a member of Hilti’s executive board, said: “We’re excited to support Canvas in reimagining better ways of
working through the power of robotics and AI.”
OHR BOSS URGES CAUTION
Despite the noise around AI and the plethora of products vying for attention, Chris Sleight, managing director of respected market analysts Off-Highway Research, urges caution.
He says: “AI - and its relations - is not really impacting the industry in a major way yet. Autonomous equipment is really being used in circumstances like big mines, and to a certain extent on major road building projects, where the layout is fixed and there are fairly well-established routes and processes. This is where it is having the greatest impact.
“But most construction sites are very complex things, and for them autonomy is problematic.”
As a result, Sleight argues that construction
will be a late adopter of technological change. “AI, in its early construction guises, is going to be about how projects are run and planned in a smart way, before it impacts work on complicated sites.
“Construction is not going to be the first industry that is going to be revolutionised by AI, although the accelerating development of BIM means it is likely to have an increasing role on complex, high value projects.”
As for the construction equipment sector, it won’t be leading the pack. “It does not do anything like that first - it does not have the size and research scale of, say, the automobile sector.
“To be honest, autonomous equipmentand its AI parent - is not what the industry is talking about. Fuels are dominating conversations at the moment, and the relative roles of electrification and hydrogen in the markets of the future - although electrification might create software platforms that help provide a foundation for the next steps towards machine learning and autonomy.”
ASK CHATGPT. IN ITS OWN WORDS … WHO IS THE RACE LEADER?
Q: Who is ahead in the use of AI in construction - China, India or the West?
A: The use of AI in construction is a rapidly evolving field, and it is difficult to make a direct comparison of the adoption of AI in construction between countries like China, India, and the West. However, I can provide some general information on the use of AI in construction in these regions.
China is known for being at the forefront of AI technology and is investing heavily in the development and implementation of AI in construction. In recent years,
China has used AI for a range of construction applications, including intelligent monitoring of construction sites, optimizing project scheduling, and improving safety management.
India is also investing in AI technology and has been using AI for construction monitoring, predictive maintenance, and quality control. Indian construction companies are also leveraging AI for generating construction schedules and improving supply chain management.
In the West, AI adoption in construction is also growing, and many companies are developing and implementing
Sleight does acknowledge that technological change is impacting the skills that companies need, both now and in the future, a point taken up by Trimble’s Cameron Clarke.
AI tools and systems to improve construction productivity and safety. For example, AI can be used to automate and optimize construction scheduling, monitor worker safety, and analyze construction site data to improve decision-making.
In conclusion, while there is no clear winner in the use of AI in construction, China and the West are at the forefront of AI adoption, and India is catching up quickly. However, it’s important to note that the development and implementation of AI in construction are constantly evolving, and there is still much room for growth and innovation in this field.
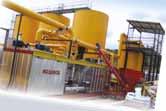
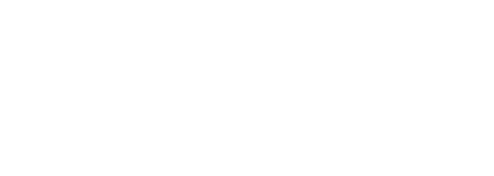


“Construction industry workers’ skills
need to progress in a way that they can both manage high-level technical activities as well as understand the limitations of technology, identifying any discrepancies in the process. Gone are the days when you can be trained once and be set for 25 years.
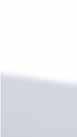

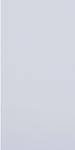

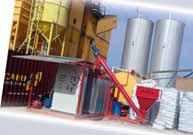


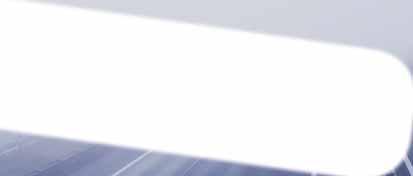

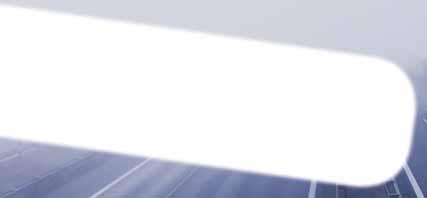

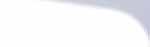
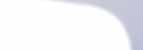

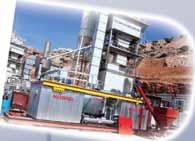






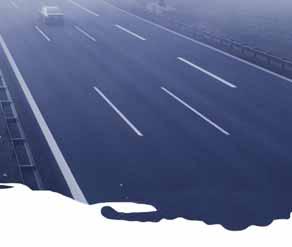


“Skills increasingly required by construction workers will include the operation and maintenance of autonomous equipment and robots, as well as the ability to optimize work processes to match the systems’ capabilities and limitations.
“Some workers will also need to be familiar with BIM solutions and datasets being used to guide the machines and provide situational intelligence.”
He adds: “Perhaps the most important skill of all will be flexibility and the ability to adapt their roles to new technologies. Upskilling can start from teaching the basic capabilities such as operating the machine or robot...to more complex capabilities like programming machines and operating and coordinating an autonomous fleet.”
He said that people must not be afraid of the technology but embrace it. “Yes, some will need higher IT skills, but solutions still need to be usable and easy.”
BE MORE PRODUCTIVE
AI, machine learning and its extended family will also provide an opportunity for construction to improve its historically poor productivity record.
Trimble has done research into the effects of adding horizontal steering control to a compactor on compaction overlap and found that the use of assisted steering functionality cut the time taken to complete a task by almost 30 per cent and reduced labour costs by 40 per cent - as well as slashing fuel consumption and CO2 emissions. But perhaps the biggest upheaval will not be felt by the equipment itself, but in how businesses are run. Back in 2020, the management consultants McKinsey published a report called “The next normal in construction” which said that the industry - huge and essential but with a poor record on innovation and productivity - should anticipate a wave of AI-inspired disruption.
The report said: “A combination of sustainability requirements, cost pressure, skills scarcity, new materials, industrial approaches, digitalization and a new breed of player looks set to transform the value chain.”
And as AI takes root, that disruption might impact not just machine operators but a wide range of jobs from HR and marketing to law, sales and general administration.
For the moment, there are far more questions than answers.
- Will global political strains force a separation of Western and Chinese technologies and companies, or will they continue to work together
- Will AI create as many jobs as it will lose?
- How will the use of AI develop and be regulated?
- What about data security? Can we stop ‘bad actors’ taking control of machinery?
- Who will own the data that autonomous equipment will produce?
- If an autonomous machine has an accident, who is at fault?
One thing is certain. Artificial intelligence - and its offspring - is coming to a company and a construction site near you. As for the rest of the questions, watch this space
Doosan Construction Equipment is now
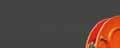







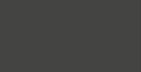






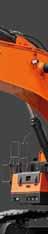

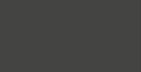

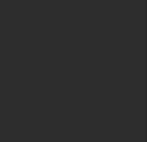



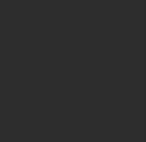




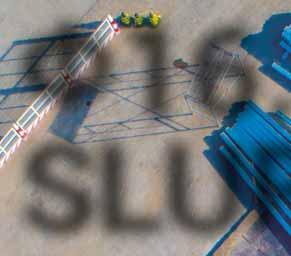
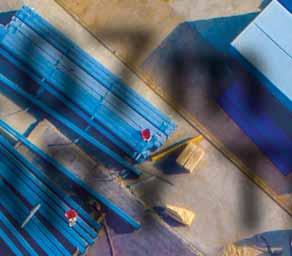
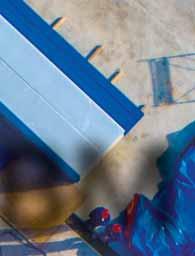


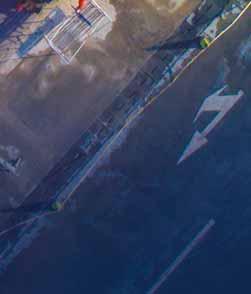
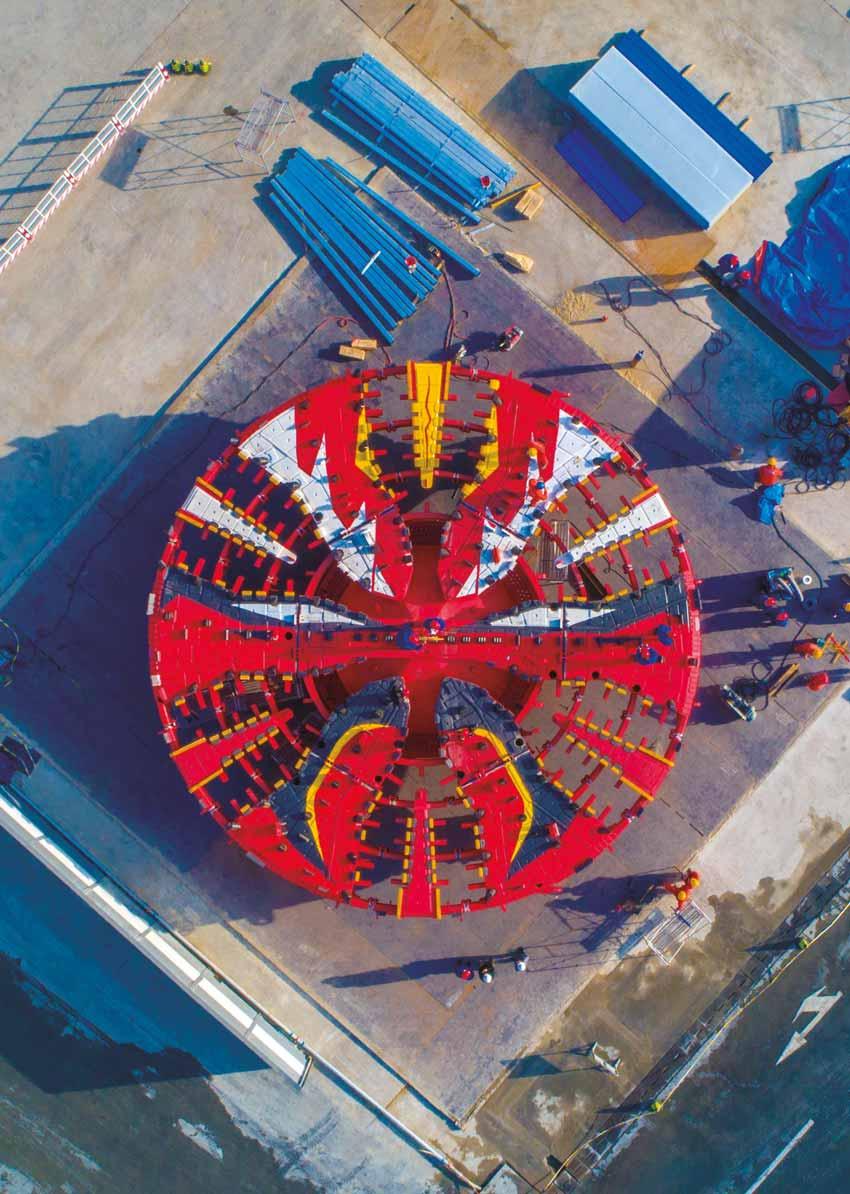
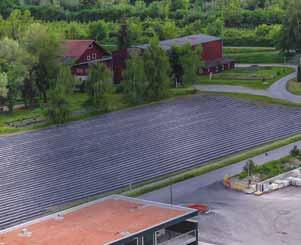
AMMANN’S GREEN PLANT INITIATIVE MOVES INTO FAST FORWARD
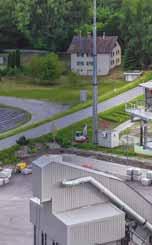
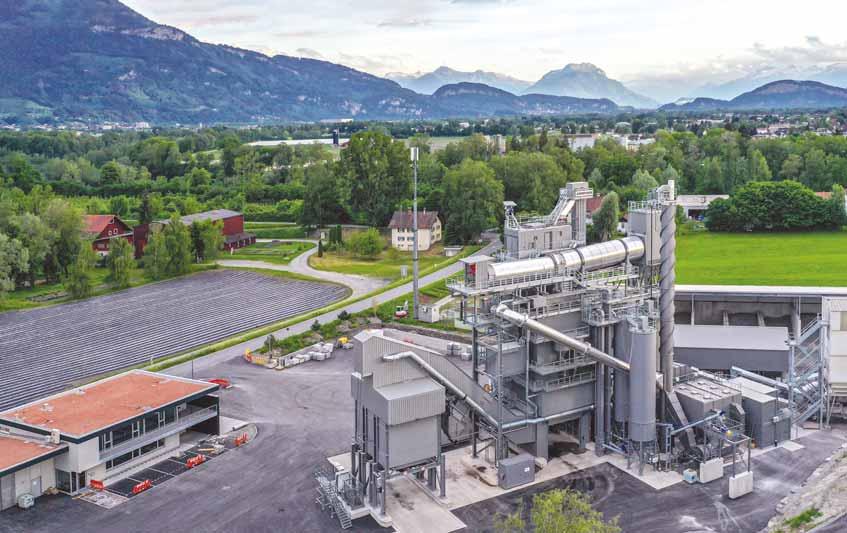
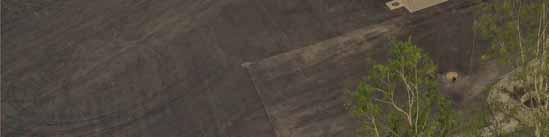
Ammann knows that big and small steps are the best way forward on the march toward sustainable asphalt production. The company openly says that: “At Ammann, we know it’s time to clear the air at asphalt production sites around the world. We are doing exactly that through sustainable technology and innovative solutions.”
Ammann is hard at work developing asphalt plants that advance recycling and minimise emissions. Yet new plants are only part of Ammann’s Green Plant initiative, which can be summarised by the company’s commitment to:
• Reduce emissions
• Utilise non-traditional fuels
• Minimise material usage, in part through the use of RAP
• Improve existing plants through sustainable retrofits
THE ‘BRAINS’ BEHIND IT ALL
Before going into a deeper analysis, Ammann says that when it hears about plant technology, it immediately brings to mind the Ammann as1 Control System. The proprietary system is the “brains” behind Ammann’s sustainability. It runs in the background of all the group’s green efforts.
The as1 offers efficiencies that reduce emissions and material usage – and enable all the built-in recycling technology to perform. The system also gathers and processes key data to uncover even more improvement opportunities.
REDUCING EMISSIONS
The main focus is on trimming CO2, VOCs and NOx in the combustion process and on reducing the residual dust content after the baghouse. The removal of blue smoke is another initiative.
Reduction of CO2 emissions is accomplished by actively cooling the drum, increasing drying efficiency and utilising energy sources such as biofuels and wood dust, says Ammann. “Our technology can diminish CO2 by 10% or even considerably more, depending on the age of the plant and the technology chosen.
Sustainability initiatives are often bound together, and emissions are one example. The biggest reductions in indirect CO2 emissions result from the implementation of RAP – and Ammann plants are industry leaders in RAP utilisation.”
BLUE SMOKE TREATMENT (BST)
Blue smoke is a challenge the industry has faced for years – and Ammann has found an answer.
Blue smoke emissions have been around since the advent of asphalt-mixing plants. The smoke released during loading resulted from
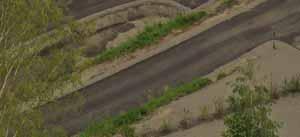
the extremely high temperatures required in the production process.
The temperatures were a necessity. Therefore, little could be done to stop the smoke.
Now, new regulations are requiring steps be taken to mitigate the fumes. It’s a challenge for those in the industry, but Ammann has found an answer.
Ammann Blue Smoke Treatment (BST) captures vapours that previously escaped during loading. With BST, the trapped fumes undergo a filtration process where oily particles are removed, and the remaining gas streams sent to the burners.
BST is a cost-effective solution. It does not require the use of complex and costly confinement methods, and the filtration system is highly efficient and inexpensive to operate.
WARM MIX ASPHALT (WMA)
While conventional asphalt is produced at around 160°C, the low-temperature processes of today allow production temperatures of around 120°C. Lowering the manufacturing temperature eases energy needs, and therefore emissions, too.
WMA impacts the entire production process – including drying, mixing sequences and recycling. Ammann has focused its research and development on the complete manufacturing process for WMA.
HEATED BITUMEN TANKS
There are other somewhat hidden opportunities to trim CO2 emissions, including the bitumen tank farm.
A traditional farm consists of horizontal tanks heated with thermal oil. “Changing to an electrically heated, vertical tank farm results in considerable advantages,” says Ammann. “There is no oil consumption and therefore no emissions.”
DUST MITIGATION
Ammann plants remove dust through a highly efficient baghouse fi exhaust dust to less than 10 mg/m3, an exemplary benchmark. (Ammann is in the process of reducing this value significantly again, to less than 5mg/m3.)
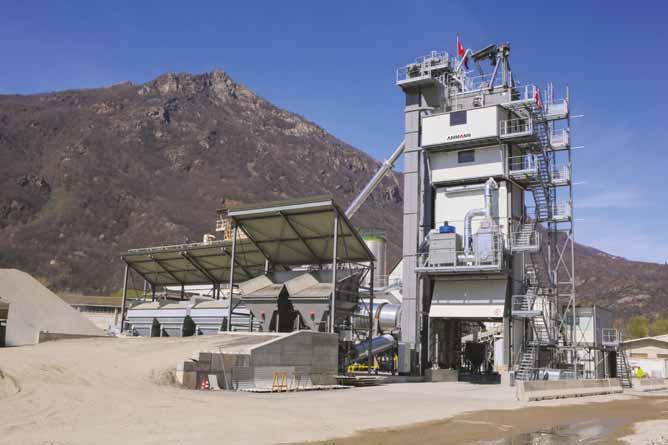
Dust reduction points are an opportunity for further improvement. Taking preventive measures at the cold feeder, load-out, skip hood, overflow silo, filler loading area, screen, belts and transfer points makes a big difference – in addition to the efforts provided through the baghouse.
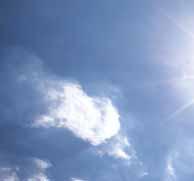
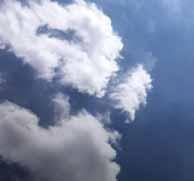
New plants are only part of Ammann’s Green Plant initiative. There is also a commitment to reducing emissions, using non-traditional fuels, and minimising material usage
SOUND SUPPRESSION
Sound-suppression efforts start with equipping burners with variable-speed motor drives, which are much quieter, and stack silencers, which control exhaust noise. There are many sound-suppression options, including cladding the entire plant.
USING NON-TRADITIONAL FUELS
Alternative fuels are continually evaluated. Here are a few to mull over:

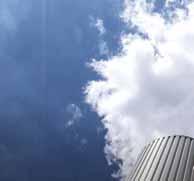
Biofuels
They support climate protection and reduce dependency on mineral oil. Examples of these fuels are rapeseed and sugar cane.
Ammann biofuel burners can also utilise more traditional fuels such as natural gas, LPG, light and heavy oil and kerosene. This alleviates the concerns of customers who are hesitant to rely solely on newer fuels.
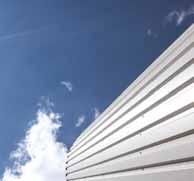
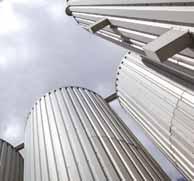
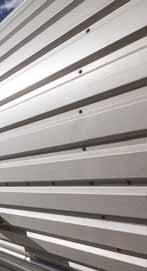
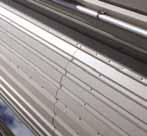
Waste fuels
The benefits of waste fuels are two-fold: preserving natural resources and reducing pressure on landfills. Tall oil, which is a waste product of cellulose sulphate production, can be used to power plants. Wood dust is another material that can be transformed into fuel. It also is locally sourced, reducing the emissions that occur during transport of the fuel.
Hydrogen
In the near future other fuel types, such as hydrogen, will significantly reduce gas emission values. The use of hydrogen is under development at Ammann.
RAP AND MINIMISED MATERIAL USAGE
Ammann does not consider RAP as waste, but rather a perfectly fine substitute for virgin materials. The aggregates in reclaimed asphalt typically show little ageing and are mechanically and geometrically within the quality ranges of new material.
The bitumen in RAP has extra life as well. Its ageing is limited and can be compensated for by using small amounts of new bitumen. Utilising RAP enables savings on both aggregate and bitumen costs – while reducing emissions, initially and over the lifetime of a road.
100% RAP
On the high end of RAP utilisation is the Ammann ABP HRT (High Recycling Technology) Asphalt-Mixing Plant. It can
Ammann’s customers have gone on the record to say that the recycled mixes produced by the manufacturer’s latest plants surpass all expectations and are often better than others made with 100% virgin aggregate.











produce mix with up to 100% RAP. No virgin aggregate is required.
There is considerable technology and innovation involved in the HRT concept, in particular the RAH100 counterflow drying process. Essential to the RAH100 is its gentle heating process.
The heating is usually where the complications with RAP material arise. RAP must reach its target temperature, but the valuable bitumen will be damaged if the
material is heated too quickly.
The RAH100 eliminates that concern. It consists of two connected sections. One is a hot gas generator that contains a burner and forces air toward the second section, which is a counterflow dryer.
The RAP enters at the far end of the counterflow dryer section and moves toward the heat chamber. At the end of the counterflow dryer, RAP is transported to an accompanying silo. The heated RAP mix leaves the dryer before the temperature becomes excessive, so it never reaches that critical temperature where the bitumen is
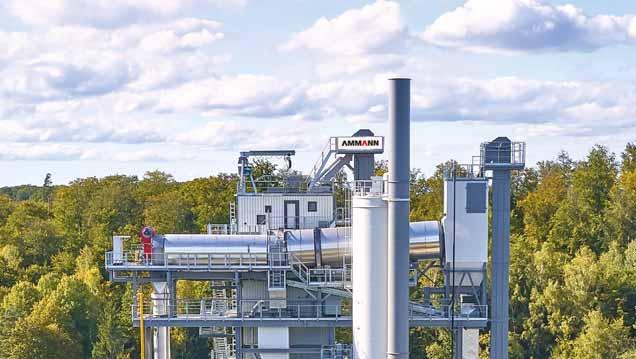
THE ULTIMATE RECYCLER
e ABP HRT plant equipped with RAH100 dryer can produce mix with 100% recycled at includes, but is not limited
With certain configurations, the plant can utilise recycled materials, such as tyres and printer cartridge toners, to supplement the existing bitumen.
PRACTICAL ALTERNATIVES
e percentage of RAP utilised is usually much less because of the amount of RAP that is available, and the recipes defined by the authorities. Ammann has options for lower percentages of RAP usage.
0 is a parallel flow dryer where % hot recycled materials can be e RAH50 is a middle-ring dryer that
incorporates up to 50% recycled materials. Recycling can also occur at Ammann asphalt-mixing plants that do not employ these specific dryers. Up to 40% cold recycled material can go directly into the mixer, meaning any plant from Ammann is capable of utilising that percentage of RAP.
ELIMINATING WASTE
With most continuous asphalt-mixing plants, the first and last few tons of every shift are waste. Ammann experts developed a patented solution that ensures all mix has
RETROFITS
the proper percentage of larger aggregates and fines from the very start to the very end. The creative approach prevents up to 5 tons of mix per plant per shift from going into the scrap pile – every day.
MAKING MIXES LAST
What can minimise usage better than not having to rebuild a road?
Ammann recycled mixes have been monitored by governmental agencies around the world. Their testing shows that these mixes last longer than those developed
New, greener plants with advanced systems can certainly take a bite out of emissions. But we live in a world where a new purchase isn’t always an option.
Some of the best sustainability opportunities lie in improving what is already on the market. We need to have a nod toward reality and understand that not every business can or will purchase a new plant. Therefore, we improve what is already on the market. Enter retrofits.
A retrofit costs a small fraction of the price of a new plant and is available for asphalt-mixing products made by Ammann and other manufacturers.
TWO QUICK WINS

Asphalt producers might be surprised by how much they can accomplish with their existing plant. A very easy first step is to upgrade the control system. A modern control system can have a significant impact on efficiency, and that cuts across many parts of the process. Improved efficiency will lessen fuel usage, emissions and material waste.
Another easy improvement: new burners that reduce emissions through added efficiencies. Modern burners also enable the use of alternative fuels.
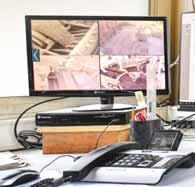
by other plants that utilize purely virgin aggregate.
According to Ammann, its customers are on the record as saying the recycled mixes produced by Ammann surpass their expectations – and the expectations of their customers, too. These end users say Ammann recycled mixes are better than others made with 100% virgin aggregate.
It’s a classic win-win outcome.
This article was produced in association with Ammann.
COMPREHENSIVE RETROFITS
A more thorough retrofit still costs a fraction of the price of a new plant and is compatible with products made by Ammann and other manufacturers. There are a host of benefits, including recycling solutions. A retrofit enables the use of foam bitumen, waxes and other additives. Special bitumen and alternative mixing cycles can be utilised as well.
The plant owner can determine the level of the commitment. Many retrofit customers incorporate a new dryer, which optimizes heat transfer – and of course reduces emissions – and enables the employment of an expanded range of materials, including RAP.
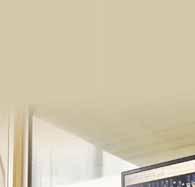
A retrofit can include environmental upgrades to the bitumen tank and baghouse. It can incorporate noise reduction solutions, too. A host of technological improvements can be made – including revamped burners, mixers and the control system. Ammann plants also are engineered for easy integration of future options and technologies such as enhanced use of additives, fibers and more recyclable materials.
Asphalt producers won’t just be up to date today – but tomorrow, too.
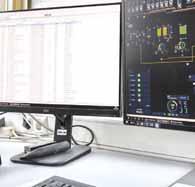

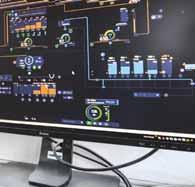
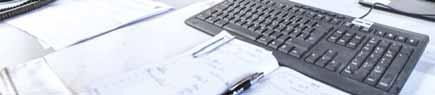


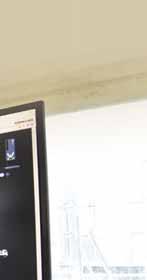
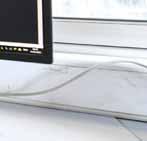
A modern control system can have a significant impact on efficiency, and that cuts across many parts of the process.
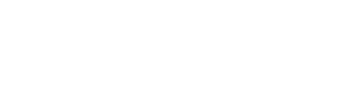

THE WORLD IN NUMBERS
As usual, our research team has prepared a selection of the key factors affecting the global construction outlook. To make the information easier to digest, we have split the infographics into eight different sections: Global Economy; Global Risks; Labour and Employment Trends; Equipment Trends; Technology Trends; Supply Chain Trends; Corruption; and Energy Trends. We hope you find the data interesting and useful.
GLOBAL ECONOMY
Energy crisis: Looking ahead to 2023, do you agree/disagree with the following statement? Source:
Economic growth: What is your expectation for economic growth in the following geographies in 2023?
Source: Chief Economists Survey, World Economic Forum, December 2022
ENVIRONMENT
65%
Expect more extreme weather events next year than this year
57% Think 2023 will be the hottest year on record in their country
45%
Expect a natural disaster to hit a major city in their country
SOCIETY
Think it is likely that there will be no further COVID-19 lockdowns in their country
This ranges from 82% in Indonesia. To 43% in China 60%
WORLD SECURITY
Think it is likely that nuclear weapons will be used in a conflict somewhere in the world in 2023 (up from 34% last year). This feeling has increased by more than 10pp in 25 of 31 countries 48%
Key findings: Where we have been and where we are headed, at a glance
Source: Ipsos Global Advisor Predictions 2023, December 2022 (left and below)
TECHNOLOGY
47%
Expect a space rocket to be launched en route to Mars in 2023
39%
Expect space tourism service moon trips to launch in 2023
27%
Expect a brain implant to restore lost memories in 2023
OUTLOOK FOR 2023
Not surprisingly given all of this... Optimism that next year will be a better year than this year has fallen from 77% to 65% And is at a 10 year low
Optimism that the global economy will be stronger next year than it was this year has fallen from 61% to 46% And is at a 10 year low
GLOBAL RISKS
Global risks ranked by severity over the short and long term
“Please estimate the likely impact (severity) of the following risks over a 2-year and 10-year period”
World Economic Forum Global Risks Perception Survey 2022-2023
Cost-of-living crisis
Natural
Failure
LABOUR AND EMPLOYMENT TRENDS
Regional shares of the global labour force (in percent), 2022
Source: ILO Modelled Estimates and Projections (ILOEST) Database, International Labour Organisation, November 2022
Anticipated decline in labour force participation rates 2015-2030 (percentage points)
Source: International Labour Organisation website, 21 Feb 2023
CORRUPTION
The perceived levels of public sector corruption in 180 countries/territories around the world
Source: Corruption Perception Index, Transparency International, 2023
ENERGY TRENDS
Global share of buildings and construction operational and process C02 emissions, 2021
Global share of buildings and construction final energy demand, 2021
Source: 2022 Global Status Report for Buildings and Construction, UN Environment Programme, 2022
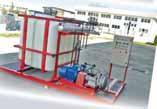
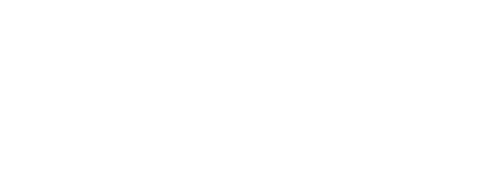


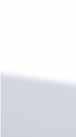

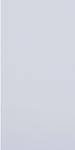




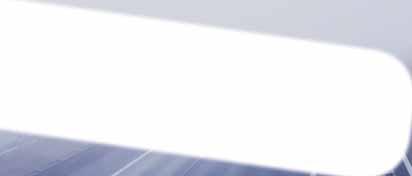
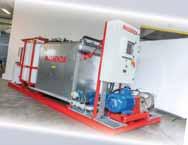
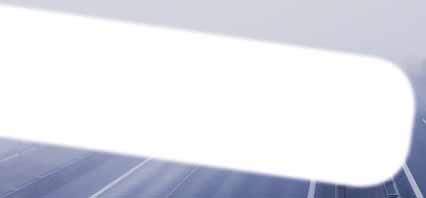

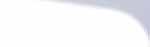
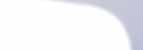

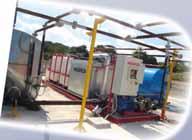





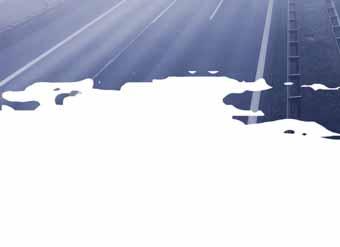



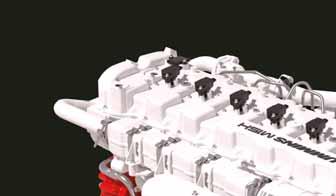







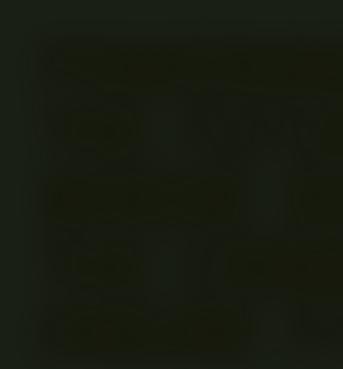
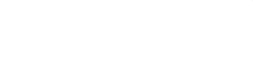

POWERING THE FUTURE: WHERE DOES THE COMBUSTION ENGINE FIT IN
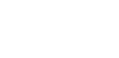
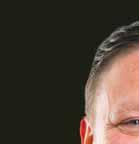

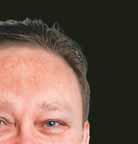

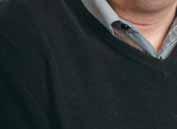
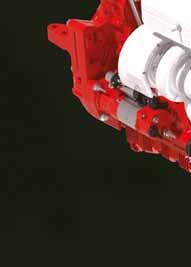

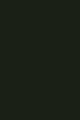
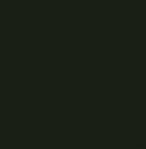
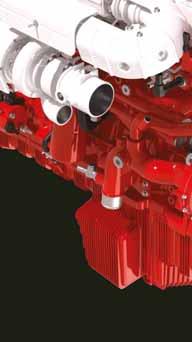
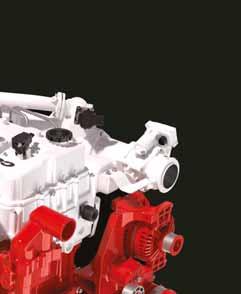
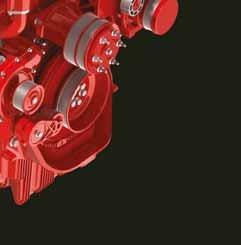

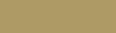
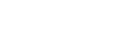
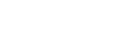
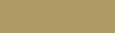
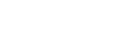
Ce construction and aggregates sectors, like virtually all other industries around the world, are taking a hard look at how to decarbonise without experiencing reduced productivity and increased costs. At the centre of this question is the role of the diesel-powered internal combustion engine, traditionally the beating heart of machinery, and what, if anything, can replace it. Steve Nendick, marketing communications director for Global Off-Highway at Cummins, reports.



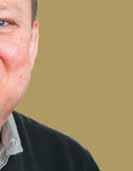


ummins’ answer to this almost existential question is that there will continue to be a very strong case for the use of the diesel engine, albeit in its advanced form, to meet the varying power demands of construction machinery in the short and medium terms.
However, technology is advancing rapidly. Recently, we’ve seen the emergence of a new fuel-agnostic breed of internal combustion engines, the logical next step in the evolution of engines, which opens up the use of hydrogen as fuel in a ‘traditional’ power solution. In the longer term, new innovative technologies, such as hydrogen fuel cells and battery-electric, may very well assume the mantle as the go-to power solution for certain applications, despite challenges.

THE DEMAND FOR ADVANCED DIESEL POWER
For construction and aggregates OEMs and operators, the diesel engine will remain the go-to choice for most machinery for the immediate future, as only it can practically meet the demands of their intense duty cycles. For example, the energy consumption of a 20T excavator over a working day amounts to around 480kWh. Whilst current battery or hydrogen fuel cell technology wouldn’t be the optimal power solution for this application, advanced diesel engine technology provides the performance and machine capability required.
Today’s latest generation of diesel engines can also meet the power demands of these machines with reduced emissions. European
emissions legislation for off-highway applications has driven a 96% NOx and 97% particulate matter reduction since 1999 when first introduced. The latest phase, Stage V, mandates ultra-clean diesel technology and introduces a particulate matter number count only achievable using a diesel particulate filter (DPF) for the first time.
Fuel efficiency, and by extension CO2 emissions, has also improved. This is demonstrated by Cummins’ own range of Stage V diesel engines, the Performance Series. They deliver on average 10% more power and 20% more torque than their predecessors. Their greater power-density capabilities mean that they can be used in place of other similar engines of higher displacement, using less fuel without


impacting productivity and emitting less CO2 emissions.
These engines also present a lower cost installation for the manufacturer –another added benefit alongside a reduced environmental impact.





Following the adoption of advanced diesels, operators can maximise their potential by adopting several measures that will further reduce the overall environmental impact of their operations, as well as maximising performance and cutting running costs.
DEPLOY “STOP-START”

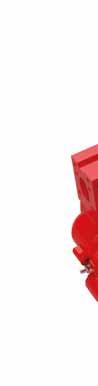
Most construction and aggregates machines idle for fairly long periods during their working day. Idle shut-off, or stop-start capabilities, can be deployed to reduce idle time, which cuts fuel consumption, emissions and onsite noise. Recently, we’ve seen fuel savings of 10% when Stop-Start is deployed on our B6.7 Performance Series engine.

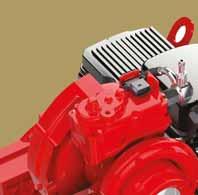
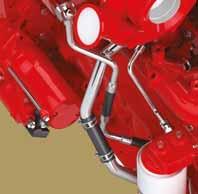
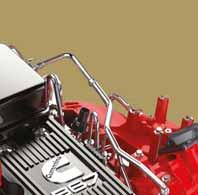
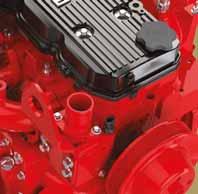








To dispel an industry myth, stop-start systems don’t compromise engine life. To integrate stop-start technology eff Cummins engineers work jointly with customers to tailor engine control software to the OEM’s machine controller software. The OEM controller observes the machine operations and relays them to the engine control module when it is appropriate and safe for the machine to shut off. Due to this tailoring per application, with a limited number of stop-starts allowed per hour, this technology provides on-site emissions and sociability benefits whilst maintaining the lifespan of the engine and associated components.
DROP-IN DIESEL SUBSTITUTES



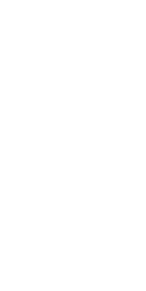
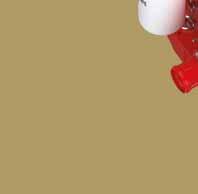
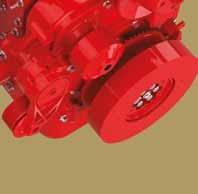
chemical and physical properties are similar to those of diesel fuel. HVO also has around 7% less fuel density, minimal aromatic and sulphur content and a higher cetane value compared to diesel. Regardless of these differences, HVO can be combined with diesel in any ratio, if needed. This allows for a smooth transition for operators when making the move away from traditional diesel to biofuel.
CONNECTIVITY
To dramatically reduce total CO2 emissions from machinery, operators of many advanced engines can adopt diesel substitute fuels, such as B20 biodiesel or hydrotreated vegetable oil (HVO100). These biodiesels are drop-in substitutes for traditional diesel fuel, which can be used by many modern diesel engines. Indeed, Cummins Performance Series engine range, from 3.8 to 15 litres, runs on these substitute fuels without modifications or an impact on servicing.
B20 means a mix of 80% diesel with 20% renewable biofuel. HVO on the other hand, is collected by processing lipids such as vegetable oil, tallow, or used cooking oil. It delivers up to a 90% reduction in greenhouse gas emissions compared to diesel ‘from wellto-wheel’.
Another benefit of HVO is that its
Connectivity and telematics are additional tools to improve site and machine efficiency, reducing costs and environmental impact with current products. This technology helps off-road equipment OEMs and fleet managers to gather and analyse data to identify usage trends and field-based issues, such as excessive idling and the inefficient tasking of machines. Service response is much quicker with technicians able to arrive at remote sites with the correct parts and tooling, improving availability and productivity.
As engines are a key part of the machinery, their integration is essential to the efficacy of telematics systems. Cummins Performance Series engines can work through OEM telematic systems or independently with a number of leading telematic service providers such as Trimble, Topcon, TeliQ, Saucon, Elevat and others.
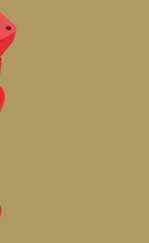
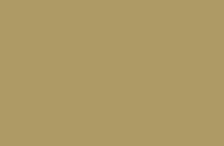
TAKING INTERNAL COMBUSTION TO A NEW LEVEL
One of the most exciting engine technology developments in recent years is the creation of fuel-agnostic engines, which are designed to accelerate the decarbonisation of a variety of sectors and applications.
Fuel-agnostic engines are single platforms, with a shared base engine, that can support various low-to-zero fuels, including ‘traditional’ diesel, natural gas, low-carbon biodiesel/HVO and hydrogen, which is zerocarbon if produced with renewable energy.
The opportunity to use these low-tozero-carbon fuels in an internal combustion engine, a power solution that is more aligned with current vehicle designs, reduces complexity for OEMs and their customers. The reuse of appropriate components also drives economies of scale while providing reliability and durability equal to diesel. This all contributes to putting construction and quarrying sites on a quicker, less risky and lower cost path to decarbonisation.
Speaking from experience, Cummins’ own fuel-agnostic engine, our 15-litre platform (rated 400 – 675hp, depending on fuel), is designed for heavy-duty performance in key off-road applications including excavators, wheeled loaders, road planning and haul trucks. The hydrogen-powered version will be available for this heavy-duty work, with
➔ it rated from 400-to-530 hp (298-395 kW), with a peak torque of 2600 Nm Significantly for those looking to decarbonise, it produces no CO2 emissions running on zero-carbon green hydrogen.
The 15-litre platform’s development was a complete clean-sheet design for Cummins. This really encouraged us to push the internal combustion engine onto the next rung of its evolutionary ladder, with design innovations to maximise power and torque capability while reducing weight and size, but without impacting durability.
Interestingly, rather than simply facilitating a move away from diesel, the development of the engine platform has enabled us to squeeze even more performance from diesel fuel – with less environmental impact. In its diesel-fuelled form, it will offer a broad power range of 450-to-675 hp (335-503 kW) with an impressive 3000 Nm peak torque. Using B100 biodiesel enables up to a 70 percent reduction in carbon and using HVO renewable fuel achieves up to a 90 percent reduction.
Although in their infancy, these fuelagnostic engine platforms will start to become more mainstream in the coming years as OEMs and operators seek to utilise new fuels, in particular green hydrogen, to decarbonise. However, there is an argument
that these are power solutions to aid the transition to net zero, with more radically different zero-emission technologies ready to take over in the long term
FUTURE SOLUTIONS: BENEFITS AND CHALLENGES
There are currently two alternative powertrain technologies that could offer decarbonised solutions to power offhighway machines of the future: the fuel cell and battery-electric.
Fuel cells aren’t a new technolog y - they were first referenced in 1838. Like batteries, fuel cells are energ y converters – they use an electrochemical reaction to take the chemical energ y stored in a fuel source and convert it to electricity. Unlike batteries, which contain a fixed supply of energ y, fuel cells do not require recharging If fuel, typically hydrogen, is continuously supplied to the fuel cell, only electricity, water and heat will be produced
The biggest advantages of hydrogen fuel cells are that they can offer an efficient power solution for heavy-duty vehicles and hydrogen fuel can be produced onsite in a quarry or construction site via an electrolyser.
It is expected that introducing hydrogen engines in the market will also accelerate the growth of hydrogen production and storage
infrastructure to support the widespread adoption of fuel cell powertrains.
Fuel cells used in off-highway machines will be challenged by the need for clean, vibration-free installations. This is difficult in quarries or construction sites, and Cummins will learn with our customers the best ways to manage this. However, as the technolog y advances, these issues are being addressed. Battery-electric technolog y is another point-of-use zero-emission power solution being introduced into the construction industry. The technolog y has been implemented in more compact machines designed for urban operations, for example mini excavators, where quietness and no tailpipe emissions are desired
However, due to the practicalities of the construction industry, battery-electric solutions will most likely be suitable only for smaller machines with less intense duty cycles. There is also the issue of charging. For site managers running battery-electric machines, there is the need for access to adequate charging facilities, which is currently difficult to do due to lack of infrastructure. Again, these challenges will likely be overcome as the technolog y evolves with increased power-density capacity and supporting infrastructure, especially in urban environments to support EV car charging.
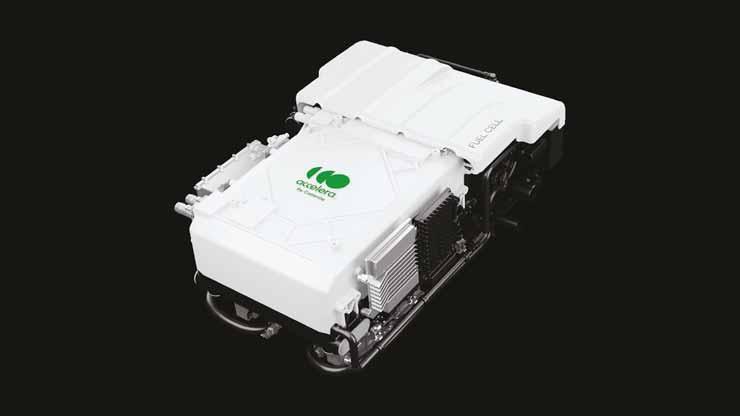
Fuel cells aren’t a new, they were first referenced in 1838. Like batteries, fuel cells are energy converters – they use an electrochemical reaction to take the chemical energy stored in a fuel source and convert it to electricity, but they don’t require recharging. If fuel, typically hydrogen, is continuously supplied to the fuel cell, only electricity, water and heat will be produced.
It’s an interesting time to be a powersolutions provider. Cummins may have name in diesel engines, but it’s a the times that we’re investing billions developing low-to-zero emission solutions. We understand the need e-ranging and evolving portfolio of to equip operators with the tools to ecarbonise.
internal combustion engine will to play a significant role in this even those fuelled with diesel. now, operators can switch their fleets latest ultra-clean, ultra-efficient ines and take full advantage of ies such as telematics and diesel substitutes to reduce their emissions. In diate future, the newly developed en-fuelled agnostic engines will offer and equipment manufacturers a uty, zero-carbon solution, based on d easy-to-integrate technolog y. further ahead, we can expect new ies such as fuel cells and batterymature.
gh it’s been more than a hundred since the first Cummins engine was , there’s still plenty of time for the y’s evolution.
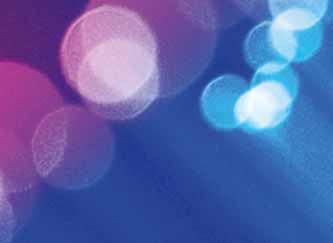

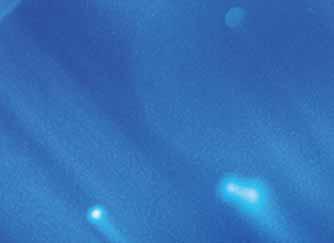
Trimble Dimensions 2023 User Conference provides more opportunities to unleash the power of your Trimble technology than ever before.
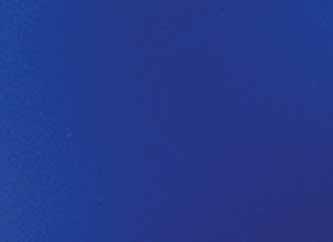
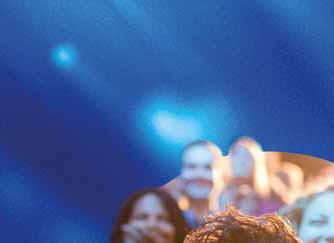
With hands-on workshops and in-depth learning, you’ll discover new ways to get more value from the products you use.
While you’re at it, you’ll realize the network effect of connecting with the Trimble community, sharing knowledge and working together move your business forward.
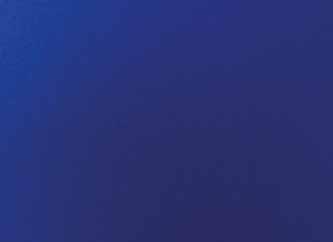
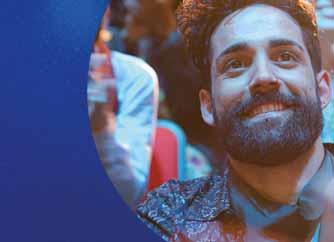
With so much to learn, you don ’t want to miss this.

NOVEMBER 6–8, 2023 THE VENETIAN RESORT, LAS VEGAS
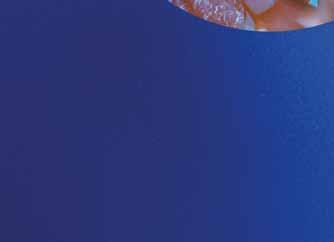

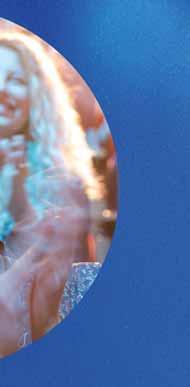
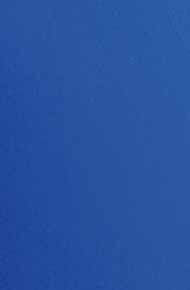
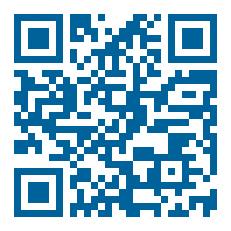
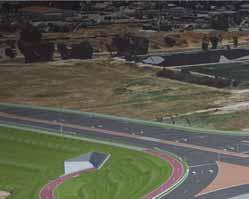
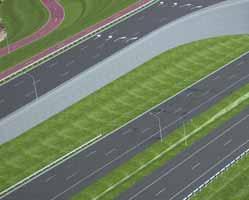
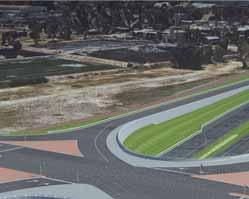
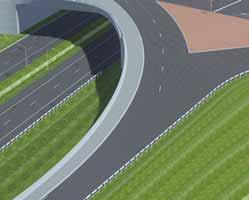
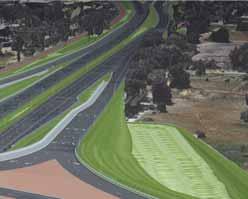
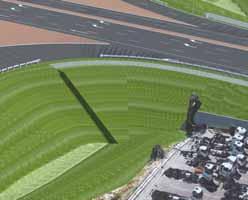
DIGITAL TRANSFORMATION IS DELIVERING DIGITAL ADOPTION
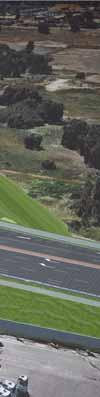

Digital transformation is key for transportation agencies and their partners to do their jobs better and faster. One way to do this is through digital delivery using digital models, data, and supporting field tools for roadway design, structures design, and construction, say the tech experts at Bentley Systems.
Digital delivery incorporates streamlined processes to manage asset information as it changes through a project’s development lifecycle. The whole process chain will contain all of the project’s different elements within a digital model … a model that can include 2D and 3D elements with attached attributes and references.
Contractors and construction inspectors can use digital models on the project site and the as built deliverables are an accurate representation of the constructed project. Digital delivery makes it easier to review the design intent and develop high resolution 3D visuals, providing improved design quality. It can make a significant impact on reducing project cost overruns, and the 3D design enables designers to test whatif scenarios to refine constructability and optimize project cost.
The process improves design efficiency and enables contractors to benefit from a more complete representation of the design intent, which is delivered in a more directly usable format. It enhances construction planning and designers spend less time extracting information.
And last, but by no means least, digital delivery improves as-built records, saving valuable time that contractors don’t need to spend on marking up PDF plans.
GREAT EASTERN HIGHWAY BYPASS
An example of digital delivery used in action is the Great Eastern Highway Bypass, which will reduce congestion by serving as a critical connector between two major highways in Perth, Australia. One part of the project involves replacing the current signalized intersections with new grade-separated interchanges to better accommodate more than 60,000 motorists daily.
Main Roads WA contracted Greater Connect Alliance, a consortium comprised of Arcadis, AECOM, and Laing O’Rourke, to develop, design, construct, and deliver the new interchanges and upgraded highway.
The Greater Connect Alliance team embraced innovative digital strategies to determine that a holistic digital execution plan, based on Bentley applications, would enable them to better visualize and more efficiently complete the project.
Adopting collaborative digital engineering
ABOVE: The Great Eastern Highway Bypass will reduce congestion by serving as a critical connector between two major highways in Perth, Australia. The project involves replacing the current signalized intersections with new grade-separated interchanges to better accommodate more than 60,000 motorists daily.
strategies allowed the Greater Connect Alliance to visually review and compare design alternatives and determine an optimal design that resulted in fewer than 10 on-site clashes while saving 18 months in time.
And working in an integrated digital platform using Bentley applications facilitated value engineering and sustainability, reducing material quantities and land acquisition. The team reduced the project footprint by 50%, offsetting the project’s impact on the surrounding environment. In this case, digital delivery and digital twins provided the engineers with the ability to visualize assets across the entire lifecycle to track change and
to perform analysis that optimizes asset performance.
Overall, digital delivery allows contractors, construction firms, and road and bridge owner-operators to leverage digital twins so that project teams can gain more visibility into the design. Digital twins also allow managers and owners to understand the implications of design decisions early in the process and help them achieve improved performance across the asset lifecycle.
ARTIFICIAL INTELLIGENCE AND MACHINE LEARNING
Artificial intelligence (AI) and machine learning (ML) technology provides numerous benefits to transportation agencies including allowing them to optimize operations, shed manual processes, and move faster. Use cases of AI and ML in the transportation industry illustrate why the technology is seeing an upward surge and why organizations should adopt the technology.
For example, we see this technology being used for bridge monitoring and inspection to augment traditional physical inspection processes. Transportation agencies and their supply chains can create a 3D digital twin of any bridge using drone or handheld photography and gather real-time data and insights structures with field sensors to improve decision-making.
Agencies can also utilize a reality mesh to augment inspection process, tag condition notes directly in the 3D environment, and remotely review the condition of the structure. Artificial intelligence and machine learning defect detection enables automatic identification and classification of defects in the field. This allows inspectors to tag condition notes directly in the 3D environment, and remotely review the condition of the structure. Inspection data required to correct issues can be seamlessly handed over to maintenance, design, and construction workflows to create substantial savings.
Another user of digital twin technology is Collins Engineers, which has been using them on projects in the United States for the past several years. Combining Internet of Things and sensor data with a digital twin gives Collins Engineers the ability to make data readily available to everyone in context so that they can use that data to make decisions about the bridges.
Using Bentley’s reality modeling and digital twin applications, they performed virtual inspections and established a mixed reality environment for the team and public to view
3D digital twins allow teams to inspect bridges remotely, record their findings, and accurately pinpoint the areas that are in need of repair.

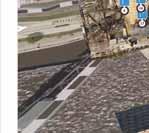
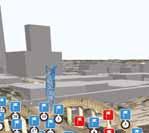
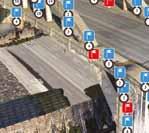
a digital twin. This process also helps provide stakeholders with a better understanding of the restorative design works. Traditionally, inspection notes were recorded and communicated using pencil and paper accompanied by photos.
While necessary to augment on-site inspections, teams couldn’t solely rely on this approach because it lacked the detail needed to make definitive decisions and safely complete the project. However, the 3D digital twin enables the field team to inspect the bridge remotely, record their findings directly on it, and accurately pinpoint the areas that are in need of repair.
By adopting a digital strategy and a datacentric approach, data is made available to
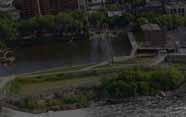

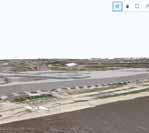

the right person at the right time to quickly analyze large amounts of data to produce actionable insights, make better-informed decisions, and provide better outcomes.
MODERNISING IN AN INCLUSIVE AND EQUITABLE WAY
Transportation agencies need to balance equity and innovation, keeping mobility ecosystems functioning and accessible while encouraging modernization. Transportation planning and roadway design have traditionally focused on the needs of drivers rather than those of all users of the street.
Over time, this approach contributed to the development of an environment where other modes of transportation including walking,
Collins Engineers has been combining the Internet of Things and sensor data with a digital twin to make data readily available to everyone in context. Using Bentley’s reality modeling and digital twin applications, they performed virtual inspections and established a mixed reality environment for the team and public to view a digital twin, replacing pencil and paper notes and printed photos.
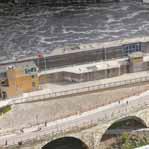
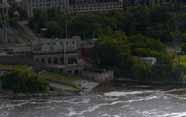


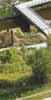
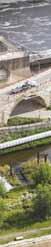
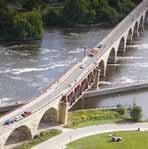


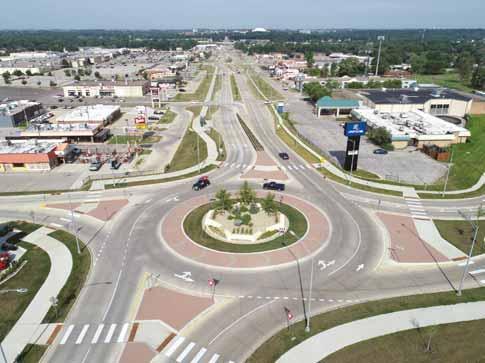
bicycling, or transit did not see the same level of investment. To ensure that everyone is intentionally included in the design process, leading jurisdictions are spearheading more inclusive and collaborative approaches.
Complete Streets methodologies also known as Living Streets, Home Streets, or Woonerf are streets designed and operated to enable safe use and support mobility with all users in mind to make the transportation network safer and more efficient.
Dutch, Danish, and German cities have incorporated living-streets-design concepts and policies and have seen improvements in overall street safety, as well as for the more vulnerable modes of transport such as walking and cycling. Complete Streets can address a wide range of elements, such as sidewalks, bicycle lanes, bus lanes, crossing opportunities, median islands, roundabouts, accessible pedestrian signals, curb extensions, streetscapes, and landscape treatments.
This approach can reduce motor vehiclerelated crashes, pedestrian risk, and bicyclist risk. It also promotes walking and bicycling by providing safer places to achieve physical activity and can increase business traffic in local communities.
SIX LANES CARRYING 20,000 VEHICLES A DAY
A project example is University Avenue. Located in the busy community of Cedar Falls, Iowa, it was a critical 2-mile, six-lane divided highway supporting more than 20,000 vehicles per day. The corridor lacked pedestrian and bicycle accommodations and at over 60 years old, had exceeded its expected lifespan.
With increasing public pressure to improve roadway conditions, as well as to provide nonvehicular access and spur economic growth, Cedar Falls initiated a USD 38.9 million modernization initiative to transform and revitalize the corridor.
The project criteria included improving traffic flow and safety, ensuring bicycle and pedestrian access and mobility, providing a “living street” compatible with existing networks, facilitating commercial access, and minimizing capital investment and operational costs. To best address the city’s priorities, Foth, a Green Bay, Wisconsin company that delivers innovative design solutions, introduced specific design elements including roundabouts, a lane reduction, and a Complete Streets approach to accommodate multimodal travelers.
Faced with intense public involvement and aggressive timelines, compounded by technical and engineering challenges that required coordinating multiple phases and teams, the organization required
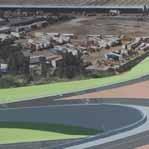
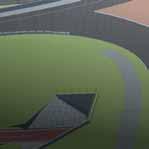
LEFT: University Avenue is a 2-mile long 60-year-old highway in Cedar Falls, Iowa, that supports more than 20,000 vehicles per day. Prior to the University Avenue modernization project, it was a six-lane divided highway without pedestrian accommodation or bicycle lanes.
integrated digital applications to meet city and stakeholder demands. To gain public buy-in, Foth delivered a digital model and information-rich 3D visuals, providing a successful solution to present the design concept from the community’s point of view, accelerating approvals for the new roundabouts, and producing benefits and cost savings to the city and the public.
The new design improved safety and reduced injury accidents by 89%, resulting in USD 1.9 million in savings and a decrease in travel time equivalent to more than USD 1 million in savings annually.
Digital technologies are helping to drive innovation for initiatives such as Complete Streets. Reality modeling and 3D technologies allow community members to see details about the project in a format they can comprehend and provide their feedback.
This enables a better project in the long run as the community can be engaged ahead of time and changes can be made earlier in the process before the design is finalized. Because 3D reality models can be easily understood, they can accelerate the decision-making process and improve project team collaboration from design through construction.
Once again, it is all about using the best digital transformation technology out there to work harder, faster, and smarter.
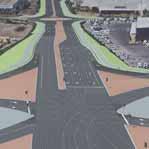
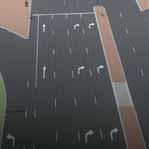
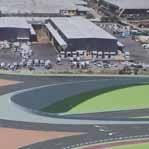
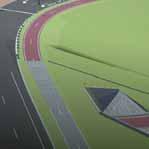
A reality mesh can augment the inspection process, tag condition notes directly in the 3D environment, and remotely review the condition of the structure. Artificial intelligence and machine learning defect detection enables automatic identification and classification of defects in the field.
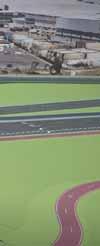


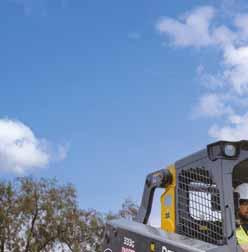
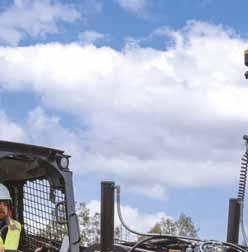
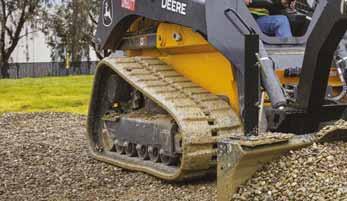
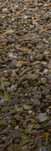

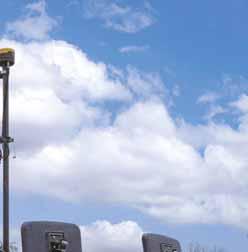
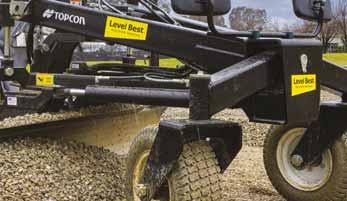
GET A HI-TECH REALITY CHECK WITH TOPCON’S APTIX

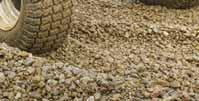



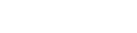
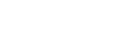
Every now and then, a really, really useful tool arrives on the market, one that will make a big difference to a company’s bottom line because it solves a problem that has been plaguing business for years. One such tool is Aptix, an integration platform that connects various Topcon and third-party software applications (see box).
“There is a challenge in the construction business of mixed fleets on site,” explains Scott Langbein, global director of Business Development and Marketing for the Integration Services team at Topcon Positioning Systems. “Each OEM manufacturer is very good at what they do with their own telematics.
“Aptix allows the telematics from different machines to be visualised and compared together. No longer does a scheduler or project manager have to log into the different


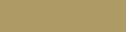
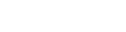
The biggest challenge facing construction professionals general contractors is disconnected data and/or siloe sources. The recently launched Aptix integration broken down these silos, explains Topcon’s Scott Langbein

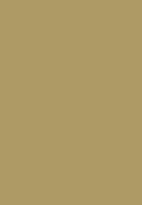
manufacturers’ websites to see that particular brand of machinery on site. This is the goal of an inte platform,” he says.





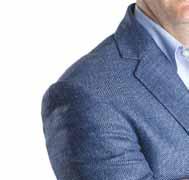


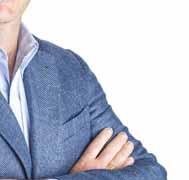

The basis for the recently launche Aptix came from within Digital Construction Works (DCW), a venture started between Topcon Bentley Systems in late 2019. Earlier this year, Topcon took full control DCW and reorganised it as a Topcon business unit, now focused on and integration services. Langbein, more than 25 years in the positionin construction industry, has been involved in developing the global network and distribution of Aptix. Langbein says that up to now, finding out if site work is on track the billing gets done.










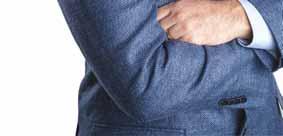
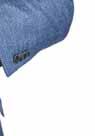
A
tim If a for coul planne happen Th of the consu can CO2 dem and What to see now for 15as site
“For mana outperfor machine tasks.” It might be that one operator works much better with a particular manufacturer’s machine as against similar machines from other manufacturers.
The advantage of Aptix is the visual representation of comparative data – automatically updated in near-real time – of how a contractor’s machinery is working on site

IN THE DRIVING SEAT
“In this way, Aptix is about risk management,” he says. The risk has been reduced of having to re-grade a road or push more earth to another area on site.
“It lets the contractor be more competitive because they can fine-tune their normal mode of operation, meaning they bid more accurately.” In the mid- to longer term Aptix can give a contractor a good track record, meaning that for a potential client, they are low risk when it comes to possible cost overruns for a planned project.
The companies most likely to be interested in Aptix are specialty subcontractors or a general contractor who is managing several subcontractors. “Ideally, it is the person responsible for the schedule, the planned work versus actual - someone who is concerned about keeping to schedule or a general contractor who is organising subs doing utility work or road grading work with a lot of heavy excavation. Aptix can empower such people who are responsible for this.
“Everyone knows machine telematics, it’s been around for years. Telematics data
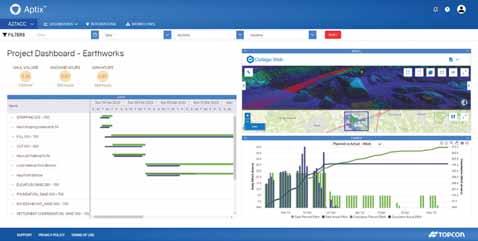
Aptix solves the major issues that have bedevilled contractors which have mixed fleets and loads of disconnected operational data
is not pretty to look at,” he says. It comes on a large Excel sheet, bunches of columns and so-called “Excel jockeys” sift through the numbers, sorting them and finding relationships.
As an integration platform, Aptix sorts the telematics data, the model data and the scheduling, bringing three ingredients into one visualisation. “I can look at all three separately, but it’s only when you combine all three into a single vision that you see relationships. And this allows vision of things that you can’t see when viewing separately. The biggest benefit is near-real time of on-site work on your project.”
CO2 VISIBILITY
Langbein readily admits that Aptix as a sustainability tool was not high up on the list of priority goals for the platform However, after demonstrating Aptix to contractors –especially in Europe - he quickly became aware of how increasingly high up on their priority list it was to measure CO2 and emissions from the machines. Aptix, even in its present form, can be a major enabler for achieving a contractor’s sustainability goals. At the moment within Aptix, carbon emissions are based on the time that the machine has been running But that is not as accurate a measurement as Langbein would like. After all, how much of that time running was spent idling for some reason and not actually pushing dirt around? Or the machine
could be really working hard, pushing out much more emissions.
“The next step for Aptix will be to have the CO2 emissions based on the telematics data of fuel used,” he says. “In the Netherlands, for example, if the contractor can come in under his CO2 limits as defined in the contract, the company can look forward to performance bonuses. We would like Aptix to be the document of record for the contractor getting a performance bonus. Now I’ m excited!”
THE FUTURE
When a customer sees a demonstration of Aptix, says Langbein, they often ask if Topcon can integrate an ERP (enterprise resource planning) system, can it connect to a billing system, or can it connect to a company’s safety data.
“There are a number of construction companies that have amassed data on their own bespoke in-house systems, for things like inspections or safety that are not the products of boxed off-the-shelf software. If these companies want [their own data] to be integrated, we can do this under integration services and it will be a bespoke solution.”
In the longer term, as autonomous on-site vehicles are developed and proven, there could be a connection. “Aptix pulls in the ingredients that an autonomous vehicle needs to know, like design model and the work schedule. It’s the schedule that has to be broken down into tasks for autonomy to work, far more detailed than for humanlevel tasks. But it’s going in that direction.”
Aptix will follow along the development of AEMP 2.0* , he says, for semi-autonomous and fully autonomous off-road equipment.
Even before the official launch of Aptix, Langbein and his colleagues had been thinking of future refinements. In other words, Aptix is only the beginning Topcon is looking at using it in a vertical environment, meaning construction projects that rise up from the ground – buildings, arenas, factories – and integrating it into Building Information Modelling, BIM. Data about electrical work, steel material supply, fire suppression, ventilation and other functions will need to be collected and integrated - a huge task, he notes.
*The US-based AEMP (Association of Equipment Management Professionals) has created a telematics standard to provide structure and benchmarking for the sector. It says: “The AEMP Telematics Standard, was first published as ISO 15143-3, in
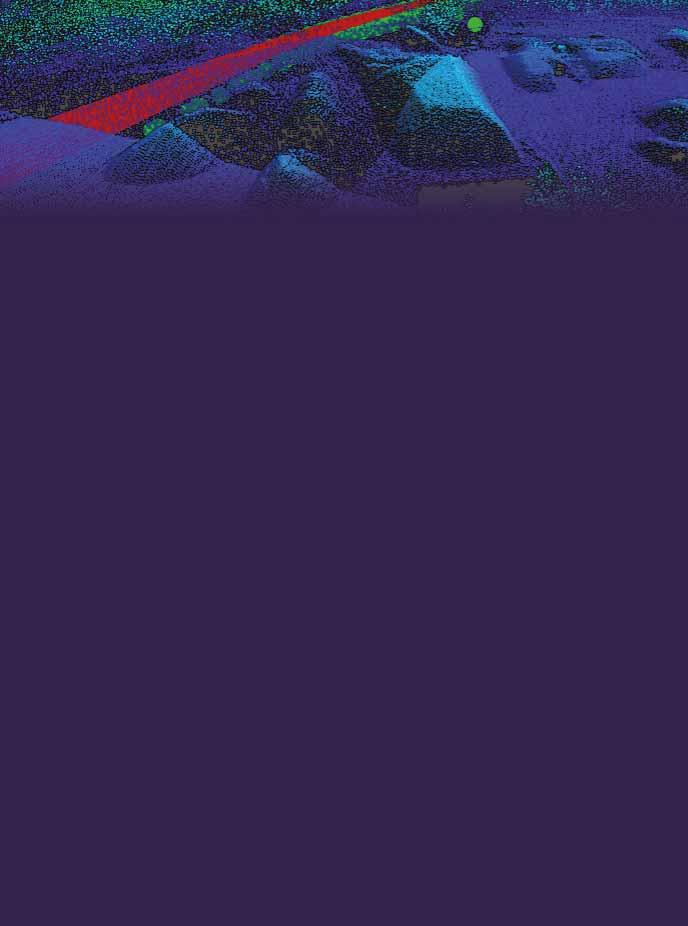
INNER WORKINGS OF APTIX
Today, GPS, sensor technology, guidance, in-cab visual control panels and telematics all help machine operators do the best job and get the best out of their equipment. Now comes Aptix, an agnostic integration platform launched globally this month as a subscription service.
Aptix raises the bar for improving project and risk management. It allows clear near-real time visualisation of machine and operator performance for project managers and project schedulers in a site office and the machine operators in the field – no matter what machines are used and from which manufacturer.
Importantly, it does this automatically by connecting various data sources on the machines to back-office analytics.
Aptix does three things. It automates distribution of schedule changes, automates distribution of model changes
and automates reporting (feedback from the field) on planned versus actual work – the most challenging and most important aspect.
It is a drag-and-drop solution, via an Autodesk Construction Cloud, meaning messages are sent out to machines via the cloud. Autodesk alerts Aptix that a new schedule exists. Aptix consumes the new schedule and puts it into machine control format for distribution into the field.
With a design model change, somebody has to send out a work plan change to machines operating on site. Manually, somebody must tweak the model change data into machine change format and then physically go out into the field, with a USB stick to each machine.
Aptix automates this in a similar drag-and-drop process by dragging the design model change data into Autodesk construction cloud. Aptix engages an
2016 by the International Organization for Standardization (ISO). The standard specifies the communication schema designed to provide mobile machinery status data from a telematics provider’s server to third-party client applications via the Internet. AEMP provides this Telematics Standard Support website as a resource to help its members integrate and utilise the ISO standard for their business.”
• For additional information, please go to: https://www.aemp.org/news/321367/Anothertechnology-step-for-AEMP-Telematics-withnewly-published-ISO-Standard.htm
automatic workflow engine and automatically distributes information. The machine driver is sent an alert on their in-cab screen that the task has been updated. This process also eliminates the possibility of the operator choosing the wrong work plan or an incorrect surface model to follow due to driver distractions or even machine operation during the moment of choosing.
Aptix, as an agnostic environment, will work with all machines, thanks to Topcon’s Tierra Blend+, a tool for gathering remote machine locations, operating hours and machine information. It also allows Aptix to work with the leading construction equipment manufacturers. Visually, Aptix allows the site office to see which machine is working according to a new schedule and design and which is not. This is a quick way to alert those operators not on schedule to check their schedule.
Key terms/definitions
• API: An application programming interface is a computing interface which defines interactions between multiple software intermediaries. It defines the kinds of calls or requests that can be made, how to make them, the data formats that should be used, the conventions to follow, etc.
• OAuth2: OAuth is an open standard for access delegation, commonly used as a way for Internet users to grant websites or applications access to their information on other websites but without giving them the passwords.
• OEM: Original equipment manufacturer
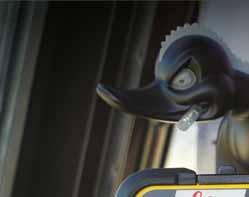
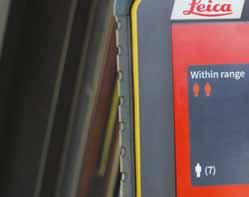

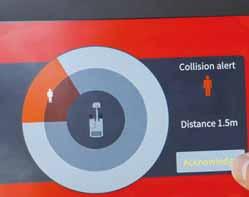
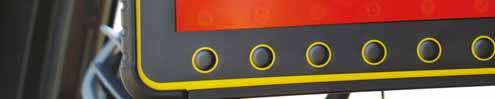
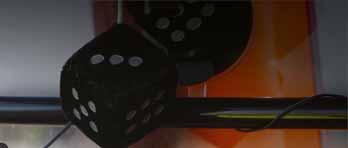
Leica iCON PA80: Integrates the Personal Alert functionality into the Leica MC1 machine control solution.
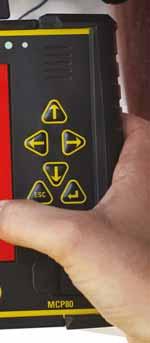
CULTIVATE BETTER ON-SITE SAFETY AWARENESS BY LEVERAGING TECHNOLOGY

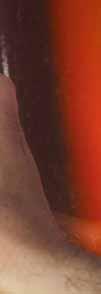
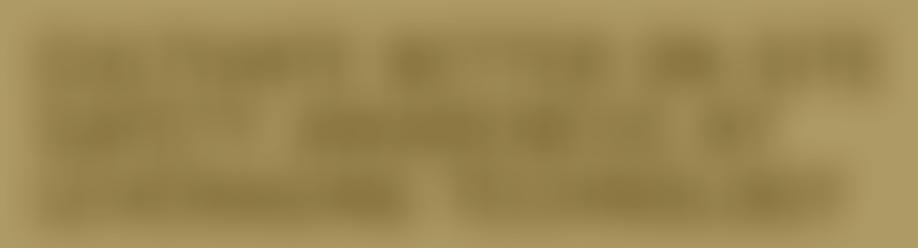

When a vital fiber-optic cable was cut during construction work in Germany, the impact was huge. There were telecom disruptions affecting the greater Frankfurt area, all departures and landings at Frankfurt Airport were suspended, and Lufthansa’s global IT system crashed. Leica Geosystems says it is vital to put in place “strategies to protect people, equipment, and assets… and to emphasise the crucial role digital solutions play in ensuring safety.”
In the USA alone, utility strikes are estimated to cost more than $40 billion a year. And that only applies to what happens beneath the ground.
Every business wants to avoid unnecessary expenses to stay financially healthy. In the world of construction, keeping costs in check is especially vital.
But when it comes to safety, it is not just about money. It is about people, not least because the construction industry remains one of the riskiest sectors globally, with high rates of fatalities and injuries.
Construction workers are three times more likely to be killed and twice as likely to be injured compared to workers in other
occupations. That means during a 45-year career, a construction worker has more than a 50% risk of experiencing a disabling injury and a 1-in-2000 chance of being fatally injured on the job. These sobering statistics remind us that safety must be the top priority. Both from a humanitarian and economic point of view, as construction injuries cost nearly twice as much as in other industries.
TECHNOLOGY IS THE KEY TO SITE SAFETY CULTURE
By understanding the importance of safety, we can accelerate a culture that prioritises it. Therefore, regular safety training sessions, hazard identification programs,
and tool-specific training are mandatory for all personnel on a construction site. Furthermore, it is vital to adapt to the changing world. Over the past decade, digital solutions such as machine control technologies have made operations more accurate, efficient, and sustainable. They also, increasingly, have become a platform for safety awareness solutions directly in the cab. The displayed information gives machine operators a better understanding of their surroundings and can prevent machine-topeople, machine-to-machine, and machineto-object collisions.
With accurate positioning and measurement of sites, capturing relevant

data starts early and continues throughout the project life cycle. The right distances and volumes are essential for construction safety as the information will define later operations through the design model. Reality-capture technologies provide fast access to accurate and holistic digital replications of the actual site conditions. Capturing the data with autonomous laser scanners such as the Leica BLK2FLY additionally minimises risks for construction surveyors as climbing on stockpiles or into excavation pits becomes obsolete. To avoid cutting fiber cables or pipelines, the site conditions must be determined for future above-ground and inground operations. Modern utility detection radar systems uncover hidden safety hazards and help avoid major incidents.
As part of Hexagon, Leica Geosystems is a global leader in sensors, software, and autonomous solutions and has more than 200 years of experience in measurement and survey. Based on this expertise, we have developed a whole-solutions portfolio to increase safety awareness on construction sites. Focusing on heavy equipment and moving vehicles, we tackle one of the industry’s most significant hazards, as struck-
3D Avoidance Zone system: Automatic height, depth and slew hydraulic control for excavators to protect both concealed and visible heavy construction assets and infrastructure.
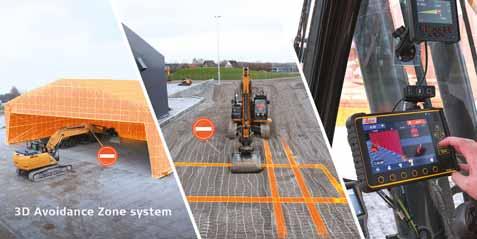
PROTECTING PEOPLE, EQUIPMENT, AND ASSETS WITH TECHNOLOGY
To increase safety awareness, Leica Geosystems and Xwatch Safety Solutions joined forces to enable safer operation of construction equipment. Xwatch’s XW Series of safety systems includes dual-height sensor limitation and height and rated capacity indication (RCI), also called safe load indication (SLI). Integrated with Leica Geosystems 2D and 3D machine control and
is allowed per health and safety requirements or local legislation.
The latest combined solution allows users to create or import 3D avoidance zones above and below the surface area directly within the Leica MC1 machine control software. From overhead obstructions to busy areas, existing infrastructure, and underground utilities – approaching these zones triggers the hydraulic functions of the excavator to slow down or even entirely stop.


The PA10 combines a tag worn by ground personnel which communicates with anchors on the machines and vehicles to alert all parties if a person is getting too close. The solution provides three configurable alert distances and gives audio, visual, and vibratory feedback to the pedestrian as well as visual and audible feedback to the machine operator or driver.
To enhance this functionality, PA80 integrates the personal alert solution with the Leica MC1 machine control. The machine operator receives visual and audible warnings
directly on the in-cabin display. Pedestrians with a PA tag can trigger a panic alert that will notify the machine operator. When a tagged person or object is within a preconfigured zone around the machine, the Xwatch technology allows to proportionately slow down and safely stop the machine. Adding collision avoidance technology (CAS) to the personal alert solutions brings in machine-to-machine communication, calculating potential collisions within a range of up to 800 meters.
Extending the on-site visibility enhances
safety even more. The VA80 (Visual Aid) is a plug-and-play IP camera with a 120 degree field of view. The solution allows operators to capture images and geographic locations of single logged points to increase the as-built documentation. Incidents or hazardous situations can be recorded and exported via USB and Leica ConX. The connection to the cloud-based collaboration platform also improves remote support, as the actual situation can be shared via a live camera feed.
DATA-BASED INSIGHTS INCREASE SAFETY AWARENESS
Adopting the technology and frequent training helps pedestrians, machine operators, and office personnel to increase safety awareness on-site and minimize incidents. The Leica ConX Safety Awareness Module uses the existing Leica ConX cloud infrastructure to collect data and alerts generated from the Leica iCON PA10, iCON PA80, and CAS solutions. Site managers have a complete overview of incidents and potential incidents. Measuring and analyzing the data will further improve the level of safety over time as it helps to avoid similar situations in the future.
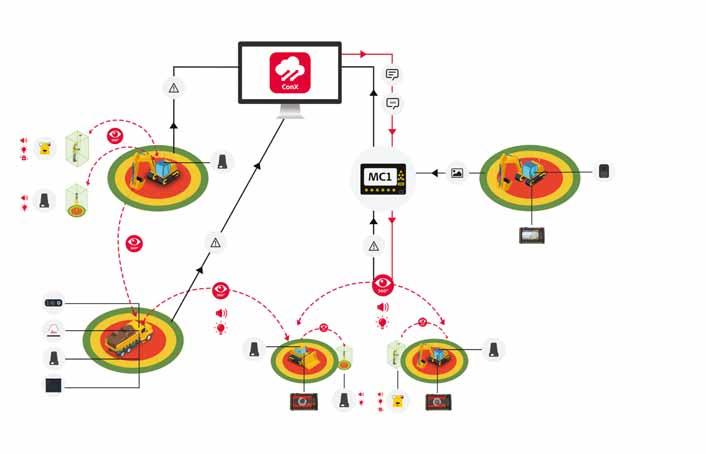

Data can be filtered and exported by event, equipment type, specific machine, and event danger level. Additionally, the module visualizes the selected data on a heatmap, making it easy for safety managers to identify elevated risk areas – or even specific machines at substantial risk.
To enhance office-to-field communications, office personnel can send SOS alerts to all MC1 software users, selected users, or specific machine operators. This way, field crews can be informed about anticipated events that might affect their work or on-site emergencies, like fires, chemical spills, and severe weather. The recipients must acknowledge the notification, which helps identify units that might still be in danger and make quick decisions concerning further actions.
PREVENTION IS BETTER THAN CURE
In this dynamic environment, prevention is certainly better than cure. One of the biggest challenges in overseeing health and safety on a jobsite is the lack of awareness of what

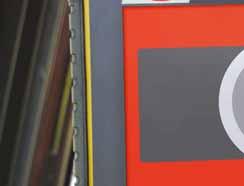
is happening on site. While near misses and potential incidents are unlikely to be reported, preventative action can only be taken by knowing about them.
Industry leads and authorities are responsible for cultivating safety awareness and taking appropriate actions. Technology can help mitigate risks and protect human lives, equipment, and assets. It even goes beyond physical safety. Providing peace of mind addresses the psychological aspect of workers’ well-being, fostering a positive work environment and promoting a sense of security and confidence in their daily tasks.
While construction workers benefit from a better perception of their surroundings, office staff are enabled to further improve conditions based on data from real-life situations. It is all about enhancing safety and job satisfaction, improving productivity, and promoting sustainability.

Brad Mullis is product manager at Hexagon’s Machine Control division, responsible for driving product development Leica Geosystems’ Safety Awareness portfolio. He joined Leica Hexagon, in 2018 as a progressed to Product Management in 2020. Prior to that, he worked as a contracts manager and site agent for contractors specialising in urban civils, roadbuilding, bulk earthworks & services. Mullis studied at the Durban University of Technology in South Africa.
This article was produced in association with Leica Geosystems.
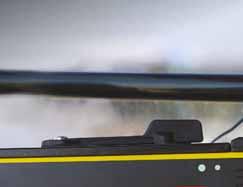

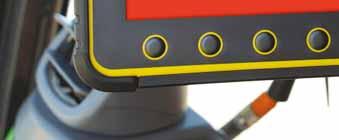
Industry leads and authorities are responsible for cultivating safety awareness and taking appropriate actions
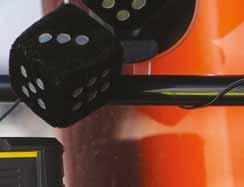
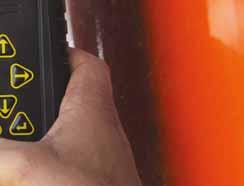
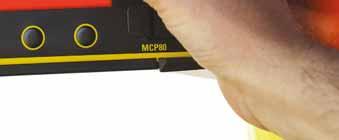
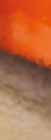
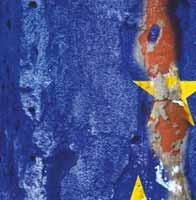

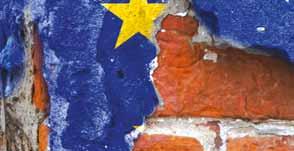
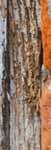
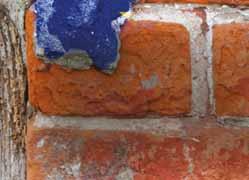
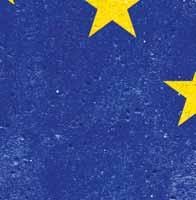
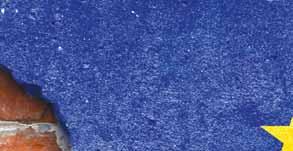

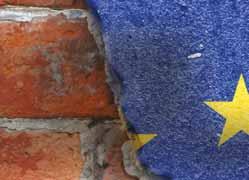
EUROPE IS DRIVING HEADLONG INTO AN INFRASTRUCTURE CRISIS
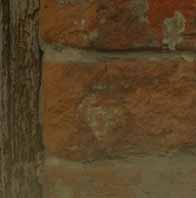

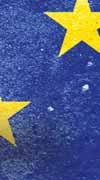

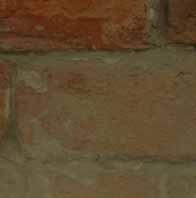
Atorrential rainstorm hit Genoa in North-west Italy on the morning of August 14, 2018. Local eyewitnesses reported a lightning strike hitting the Ponte Morandi bridge, a viaduct carrying the A10 motorway over a deep gorge in the Polcevera River.
At 11.36am, a 210-metre-long section of the bridge collapsed, killing 43 people. Around 35 cars and three trucks fell into the river and onto the industrial estate below.
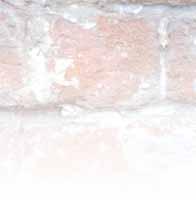
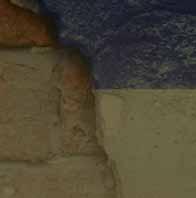
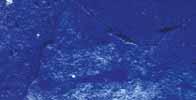
It comes to something when contractors, manufacturers, transport firms, and NATO are all pleading for action. They are saying the same thing: The EU’s broken infrastructure is destroying the continent’s industrial and defensive base. They want urgent action on heavy transport corridors, weak bridges, crumbling road surfaces, and inept local government. Who is allowing expert engineering departments to be destroyed as things fall apart? And why? Graham Anderson reports.
This is not a new problem, but it is beginning to have a very negative impact on Europe’s global competitiveness. Things have been getting steadily worse since the financial crisis of 2008.
In the wake of the crash, money was tight and successive national governments prioritised tax cuts as a mechanism to try and stimulate economic growth at the expense of public investments that might support industrial productivity and efficiency.
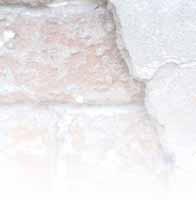
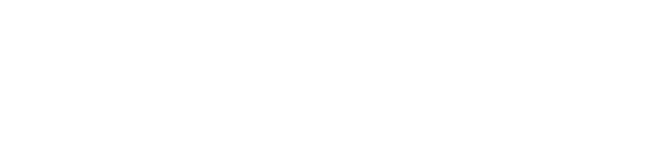
The Genoa tragedy caused a major political controversy about the poor state of infrastructure in Italy. According to the respected Milan-based daily newspaper, Corriere della Sera, this was at the time the 11th bridge collapse in Italy alone since 2013. It also raised wider questions about the condition of bridges across Europe.
Whatever the precise engineering causes of the collapse, which led to a year-long state of emergency being declared in the Liguria region, it has become symbolic of Europe’s growing problem with its crumbling infrastructure. The EU is suffering from a lack of coherent planning and long-term investment strategies.
The worries go beyond business and the economy and have security implications too.
NATO has long been concerned that it would be unable to move heavy equipment (such as tanks) quickly enough to respond to an incident on Europe’s borders … A theoretical worry that has now turned into a real-life crisis following Russia’s invasion of Ukraine.
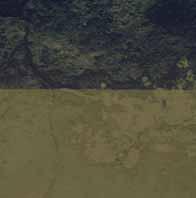
investigative journalists based in the Netherlands.
Their work revealed that poor roads and weak bridges were still hindering the supply of military equipment from ports across Europe to the east, according to military experts. Europe’s political leaders have simply not given the issue a high-enough priority.
RUSSIA MOVES FASTER


Various senior military figures went public with their worries back in 2017.
In response, the European Commission started investigating supporting a network of upgraded routes that could be used by both military and commercial operations.
The issue recently attracted the attention of The Investigative Desk, a group of
They quoted former NATO officers who said that after the Russian invasion of Crimea in 2014, it was clear that Russia could move large units within 72 hours, far faster than NATO could respond.
But despite fine words, not a lot has happened.
What is more, the increasingly obvious impact of climate change is focusing attention on the need for both appropriate investments - in rail and energy, for example - to reduce CO2 emissions and also to improve resilience in cases of extreme weather.
For years, the complaints from companies in the construction sector across Europe - from major contractors and equipment manufacturers and materials suppliers - have
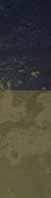

been dismissed as ‘special pleading’ simply intended to boost turnover and profi In recent months, the debate has centred on Germany, Europe’s biggest economy and the main centre of heavy manufacturing and engineering.
According to Germany’s Federal Statistical Office only about 13% of the 40,000 bridges in the federal road network are in good or very good condition and more than one in ten bridges has serious defects.
The economic and practical impact is huge. In Hamburg, for instance, local freight businesses are reporting that some of their traditional client companies are now using alternative ports such as Rotterdam and Antwerp because of the delays in Germany.
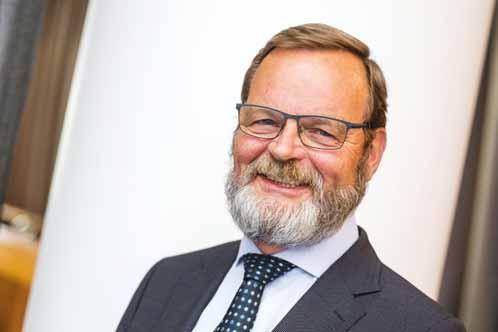
“In a way, heavy transport is the ‘canary in the coal mine’ telling us that something is seriously wrong.”
Shippers are finding other ways to get things moving. And, due to the high number of dilapidated bridges in Germany, Autobahn GmbH is often reluctant to issue permits for heavy transport, or to issue long-term permits for regular journeys at all.
Autobahn GmbH (the authority responsible for Germany’s main road network) says that the load reduction on bridges is a precautionary measure, but that brings little comfort to the companies affected.
Ton
Klijn,
director of
ESTA
And then, at the end of last year, the Bavarian construction association Bayerische Bauindustrieverband launched a scathing attack on the current state of affairs.
One of the many examples it gave concerned the transport of large construction machinery. It said that the restrictive rules governing the award of permits demand that the cargo is precisely identified, including the exact type, manufacturer and model. But this is often not possible, as the type of machine required on site and its availability is often not known far in advance.

Its concerns were backed up by one of Germany’s leading construction equipment manufacturers, Liebherr.
ects of the infrastructure problems, especially the dilapidated bridge structures, are manifold. Many bridge structures may not be used by our heavy transports, so there is virtually no route for our equipment that we can take directly without detours,” said Tobias Ilg, head of marketing at LiebherrWerk Ehingen, the company’s mobile and crawler crane division which is based near the city of Ulm, roughly halfway between Stuttgart and Munich.
“Here is an example,” he says. “We ship a large part of our export equipment via the seaport of Bremerhaven. The direct route from Ehingen to Bremerhaven via the A7 is about 765 km.
“But the actual authorised route is via eastern Germany on the A9, partly via Magdeburg and, depending on the type of crane, this is a journey of up to 1,190 km. So, sometimes we have to drive more than 50% additional kilometres.
“Because more and more bridges are being closed for large and heavy transports, it is becoming increasingly difficult for us to find suitable routes for our equipment.”
Also, he adds: “If we do find a route, it may usually only be used under certain conditions. These include, for example, driving time restrictions and mandatory escorts by civilian escort vehicles or the police. Here, too, we notice that the conditions imposed are increasing.
“Many bridge structures may not be used by our heavy transports, so there is virtually no route for our equipment that we can take directly without detours.”
Tobias Ilg, Liebherr-Werk Ehingen
“In some regions in Germany since the start of this year we are only allowed to drive with all equipment of more than 4 axles between 10 p.m. and 6 a.m. In addition, the processing times for transport permits at the authorities have been increasing for some time and can sometimes take up to 8 weeks.”
Ilg recognised that although Liebherr’s situation is difficult, many of its customers are exposed to this problem on a daily basis.
GERMANY IS A FIASCO
Germany’s heavy transport and crane association BSK - Bundenfachgruppe Schwertransporte und Kranarbeiten - recently added their voice to the debate through a joint statement with

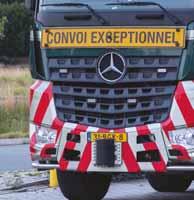
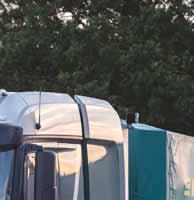

fellow organisations in the engineering, construction, transport, logistics and wind energy sectors.
They said: “This is in danger of becoming a real fiasco, especially for large-capacity and heavy-duty transports and the affected sectors of the capital goods industry, due to a total failure of the transport infrastructure across the board. For example, there are no new wind turbines without corresponding transport routes.”
Erik Maassen, commercial manager for Netherland-based Bolk Transport, is equally scathing.
“We are facing more and problems with weak infrastructure. In the Netherlands, Germany, Belgium, France, Italy, and many more countries, a lot of infrastructure is old and badly maintained.
“For exceptional transport this problem is much bigger than regular transport as we cannot easily take a bypass route.”
He added that one of his biggest concerns is the notice period they are given before a route is closed or downgraded: “So we might have a permit on a specific route and out of the blue a downgrade comes, then our permit is no longer valid, we don’t get a substitute and the transport is blocked or postponed for several weeks or months.”
The situation is often exacerbated by the lack of specialist expertise in the offices of the permit-issuing authorities.
Since the Genoa tragedy, authorities across Europe have understandably erred on the side of caution and have been increasingly reluctant to issue permits unless they are absolutely certain the proposed route is safe.
In addition, in the wake of the financial crash in 2008, local authorities lost many of their more experienced engineering staff and many are unable to carry out the necessary route assessments.
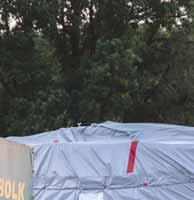
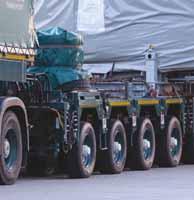
COMPANIES FORCED TO DO IT THEMSELVES
“So we might have a permit on a specific route and out of the blue a downgrade comes, then our permit is no longer valid, we don’t get a substitute and the transport is blocked or postponed for several weeks or months.”
Erik Maassen van den Brink, commercial manager, Bolk Transport
As a result, transport companies and their clients are reduced to carrying out engineering studies themselves - adding further delays and costs.
Infrastructure resilience was top of the agenda at April’s Eurobridges conference organised by FIEC, the European Construction Industry Federation which represents contractors and industry bodies in 27 countries.
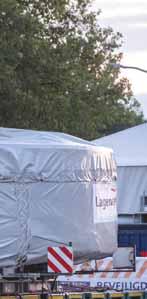

It is calling for the guidelines for the EU’s Trans-European Transport Network (TEN-T) to be revised to oblige members states to make appropriate infrastructure investments with a particular focus on the state of roads and bridges.
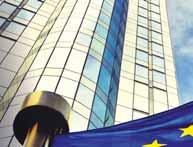
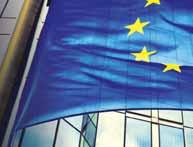
FIEC added that it is essential to guarantee finance for maintenance through tax revenues, grants and road pricing, and by adding maintenance requirements into project contracts.
José-Michael Chenu, FIEC vice president and strategic marketing director for Vinci, the French international construction company, stressed the economic damage and the difficulty the EU will face in achieving its environmental targets without action.
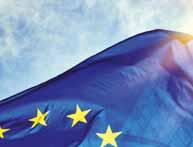
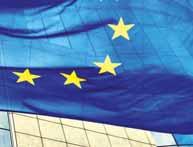
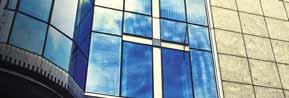

“FIEC has repeatedly advocated for the importance of regular maintenance of the existing infrastructure, the uptake of innovative infrastructure, and the swift implementation of these projects. All this is vital to meeting the EU Green Deal goals.”
José-Michael Chenu, FIEC vice president and strategic marketing director for Vinci


“Politicians must understand that if there is a transport, there is a manufacturing company behind it and not all the companies can be moved to more accessible locations...if this topic is not correctly and urgently addressed many European industries will risk closure.”
Fabio Belli, CEO Fagioli
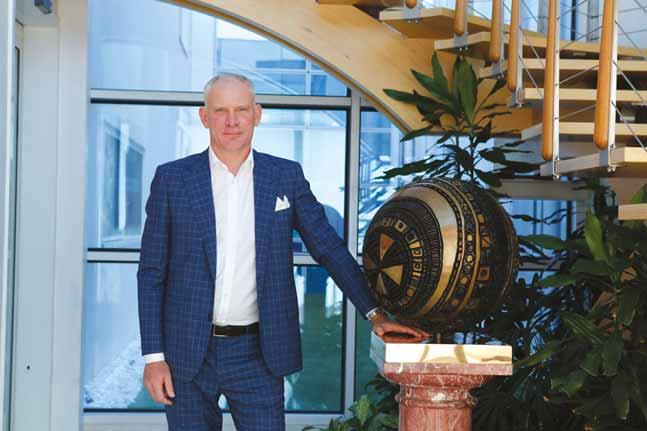
“FIEC has repeatedly advocated on the importance of a regular maintenance of the existing infrastructure, the uptake of innovative infrastructure, and the swift implementation of these projects. All this is vital to meeting the EU Green Deal goals.”
Ton Klijn, director of ESTA, the European Association for abnormal road transport and mobile cranes, said the warnings from the industry have been ignored for far too long.
“In a way, heavy transport is the ‘canary in the coal mine’ telling us that something is seriously wrong.

“The extreme difficulties being faced by heavy transport is a clear and urgent warning that our failure to plan and deliver longterm investment in infrastructure is already having real and very negative economic consequences, and that the situation is getting worse by the day.”
ESTA has members in 23 countries and is well placed to gather information from right across Europe.
Klijn continued: “Two major trends are the growth of the wind industry and the increase in off-site construction. But both rely on being able to deliver heavy loads to site for our clients.
AN ILL WIND IS BLOWING
“The development of the wind industry is crucial if Europe is to meet its climate targets, but that is being hampered by the increasing difficulties experienced by companies needing to deliver the increasingly big wind turbines from factory to site or port.”
Klijn also raised the issue of the growing pressure in Germany for heavy transport to make greater use of the rivers, canals and railway networks.
“This is fine in principle - but the devil as they say is in the details, such as crane and quayside capacity. Transporting heavy loads
by canal, river or rail necessitates developing loading and unloading facilities, for example.
“Our response is quite simple - where are the plans? Because without the plans, these are just words.”
He added: “We need our politicians both in Brussels and at national level to get a better grip on this situation urgently. This is not an issue just for the heavy transport companies - it is an issue that is impacting the competitiveness and efficiency of European industry as a whole.”
Klijn is just one of a growing number of like-minded and increasingly vocal business people warning of the consequences of inaction.
Fabio Belli is CEO of Fagioli, one of the Italian companies responsible for completing the replacement GenoaSaint George Bridge, designed by Italian Genoese-born architect Renzo Piano and inaugurated in August 2020.
He argues that our political leaders must be made to realise the economic consequences of failing to invest. “Politicians must understand that if there is a transport, there is a manufacturing company behind it and not all the companies can be moved to more accessible locations.
“If this topic is not correctly and urgently addressed many European industries will risk closure and their production transferred elsewhere.”
Liebherr’s Tobias Ilg summarised the frustrations: “Without heavy transport, we will neither succeed in the energy transition, nor in housing construction, nor in the expansion of the infrastructure itself. Therefore, it is imperative that there be a rapid and unbureaucratic expansion of the transport infrastructure all over Europe.”
Graham Anderson is a business journalist specialising in international construction, transport and energy markets.
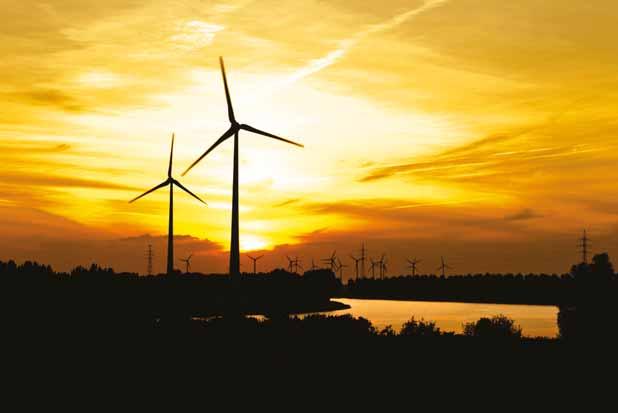
“The development of the wind industry is crucial if Europe is to meet its climate targets, but that is being hampered by the increasing difficulties experienced by companies needing to deliver the increasingly big wind turbines from factory to site or port.”
Ton Klijn, director of ESTA
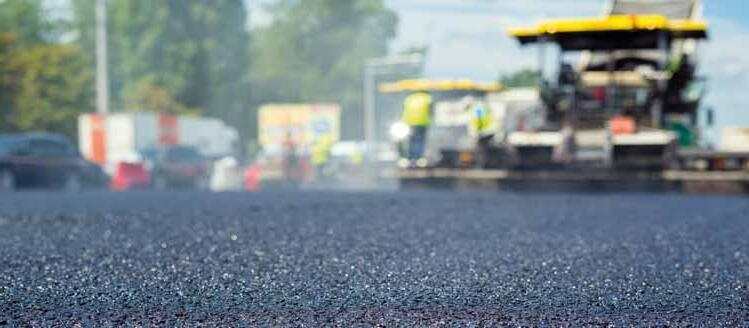


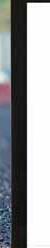

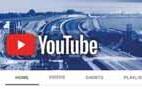
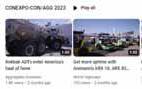

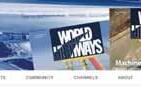
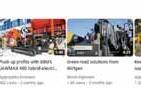
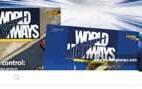



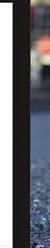

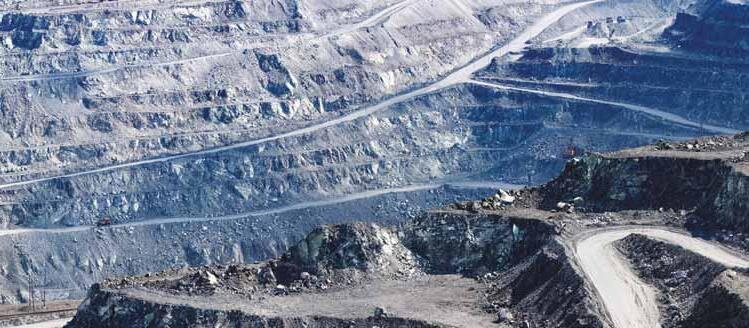
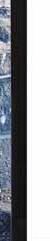



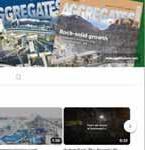

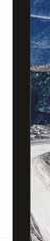
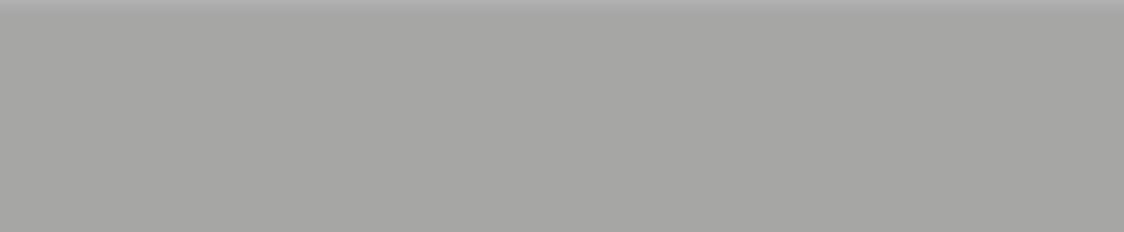
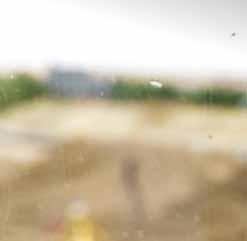
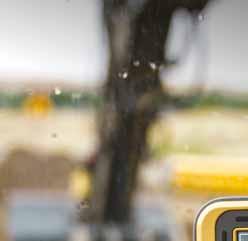
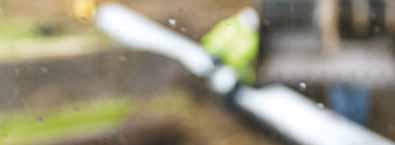
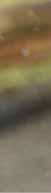
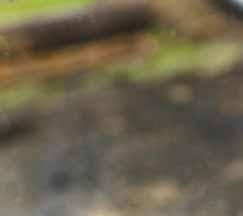
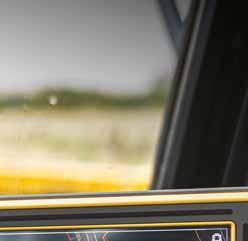
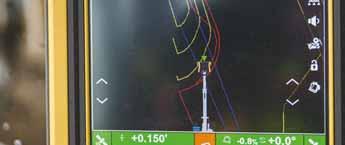
WHO’S OPERATING THE SHOVEL?
THE WORK IS THERE, BUT WHO’S GOING TO DO IT?

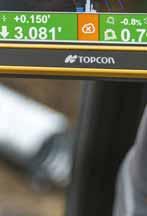


Many studies have been completed on the global labour shortage in the construction industry. All sorts of questions have been asked and lots of numbers have been crunched, but they all seem to come to the same conclusion: The shortage has arrived, and it’s not ending any time soon. What is going to happen next? Pete Kennedy reports.
These are frustrating times for the construction industry. The work is there, and too often it can’t be done. “We are creating shovel-ready projects, but with no one to operate the shovel,” says Ed Brady, president and CEO of the Home Builders Institute (HBI), a U.S.-based organisation. Time and money are being wasted.
How to address this issue? The consensus among many is to utilise more technology to cover the gap between the workers ... and the work. Specifically, there is a great deal of talk about autonomy, automation and robotics.
How can this technology help the construction industry overcome its labour shortage?
MAKE OPERATING THE TECHNOLOGY LESS COMPLICATED
Demonstrations of autonomy capture audiences at trade shows, but automation is making a difference today. Automation can make a novice operator good – and a good operator great.
“We know experienced operators are retiring, and there isn’t a huge influx of
talent,” said Kevin Garcia, general manager of Civil Specialty Solutions at Trimble. “The people we do get (as replacements) need to be upskilled quickly.”
Garcia said automation is designed to improve productivity, not necessarily replace workers. It could, however, change the roles those workers play.
“We still have a large labour shortage,” he said. “Some of this automation isn’t meant to take people out of the seat. It’s to find enough workers. We have to accomplish more with fewer people.”
Making the complicated simple is one way of doing more with a smaller workforce. Garcia pointed to pavers as an example.
It can take years to master paving machines. The operator must manage trucks (or the material transfer vehicle), monitor the feed belts and the auger box, and keep watch over a host of other developments. On top of all that, operators have to steer the machines.
“That’s easier said than done,” Garcia said. “If we’re doing the steering automatically, and we’re managing the speed, operators can fully focus on material feed.”
MAKE THE JOBSITE LESS COMPLICATED
Making machines less complex is a great start. How about using automation to simplify the entire jobsite?
Garcia said resources should be allocated to the most expensive, most complicated projects. Every complexity removed makes the entire site more efficient – and therefore gets the best ROI in terms of labour.
Consider the asphalt placement process: There is a paver with a machine operator and two screed operators; between two and four compactors with operators; and often a material transfer vehicle that is fed by a team of trucks.
An autonomous soil compactor could replace one operator while working on a simple jobsite. Automating the paving could create efficiencies that impact every step of the process and ultimately deliver more value.
“It’s optimising where your expenses are,” Garcia said. “It comes down to cost, complexity, workflow and mitigation.”
“The goal is not autonomy,” Garcia said. “The goal is to get the work done.” ➔
ADD EFFICIENCIES TO ALL PARTS OF THE PROCESS – IN ALL PARTS OF THE WORLD
Ivan Di Federico of Topcon takes a macro look at the issue. He said an exponential increase in the world population is a key factor in the labour shortage. In the early 1960s, there were three billion people on the planet. “All the available resources had to take care of those three billion people,” he said. That includes materials for housing, roads and other capital projects.
“Fifty years later, we are at eight billion plus,” he said. Yet the resources haven’t grown at that pace.
The construction industry is directly impacted by the increased demand for housing and infrastructure, leading to a shortage in available workers. As demand for new construction projects increases, it can be difficult to find enough skilled workers to meet the needs of the industry.
Therefore, the machines, labour and resources need to be stretched. “If we don’t have the product of machine control, we couldn’t support the infrastructure needs of all these people coming into the world,” Di Federico said.
The use of this automation is common in some regions of the world – and now needs to become prevalent everywhere.
“With automation, we are making sure
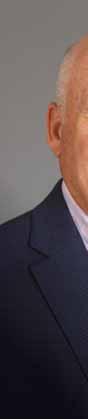

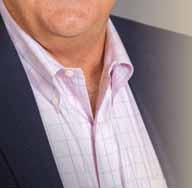
Ed Brady president and CEO, Home Builders Institute
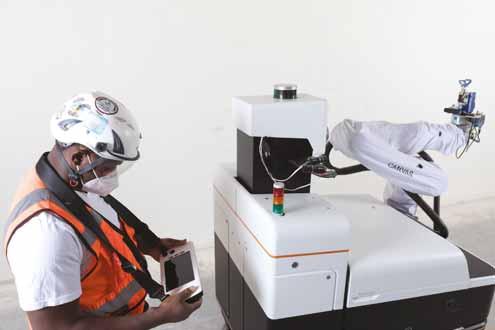
that anyone who works in construction has enough tools to build houses and highways for the eight billion who need it,” he said.
Significant efficiencies can be uncovered by utilising automation across all parts of the construction process. For example, houses can be prefabricated off-site, making them accessible to additional types of technology at newly established stages of the process.
A recent World Economic Forum report bolsters Di Federico’s claim. “Automation not only speeds up the manufacturing process; it also stretches scarce talent,” the report states.
“Going forward across industries, automation, the industrial internet of things, virtual and augmented reality, and machines equipped with artificial intelligence effectively give workers superpowers. These advancements help create more efficient processes, improve safety, shorten training time and relieve workforce pressures,” the report concludes.
CONSTRUCTION TECHNOLOGY AND LABOUR
KEY DEFINITIONS
• Autonomy refers to equipment that works independently and adapts to changing conditions without input from an operator.
• Automation refers to the use of technology to help the operator run the machine. Automation can increase efficiency and accuracy, but still relies on human input and oversight.
• Robots are typically designed to perform tasks – either autonomously or with human guidance – that are too difficult, dangerous or repetitive for humans to do manually.
HELP WORKERS ENJOY THEIR JOB
Making work interesting is a great recruiting and retention tool. Technology can do the “boring” work, leaving humans to the more enjoyable tasks.
One example: Canvas, a San Franciscobased startup, is using robots to tape and finish drywall. During a recent test, the robot applied tape, sprayed mud and sanded.
The results were impressive. A seven-day job was completed in two. The finish was Level 5+, a very high grade, according to e-newsletter Construction Dive.
An operator supervised the robot, but the labour was dramatically reduced. In addition, commanding the robot was no doubt more enjoyable than mudding and sanding.
Canvas makes a strong case that this robotic technology is a “breakthrough.” The fact the construction industry is behind much of the rest of the world in adoption is part of the reason for the worker shortage,
maybe as many as 10 years, before operator-less machines begin working on jobsites. (And perhaps very isolated jobsites at that.)
HOW SUBSTANTIAL IS THE CONSTRUCTION LABOUR SHORTAGE?
• A report by the Associated General Contractors of America (AGC) stated 80% of construction firms in the U.S. are having difficulty finding workers – and the shortage is expected to get worse.
expected to face a shortage of 56 million workers by 2030. It is predicted to be especially harsh in Asia and Africa, where rapid urbanisation is straining existing infrastructure and housing.
WHY IS THERE A LABOUR SHORTAGE?
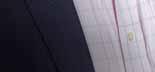
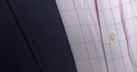

HOW CLOSE ARE WE TO HAVING AUTONOMOUS MACHINES ON CONSTRUCTION SITES?
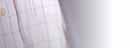
Experts say it’s likely to be a minimum of five years, and
• The Home Builders Institute (HBI) estimated there are 300,000 to 400,000 unfilled jobs in home construction in the U.S.
• The World Economic Forum reported that the global construction industry is
“Many factors have contributed to the labour shortage crisis, including the lack of educational opportunities in secondary schools. Technical education has taken a backseat to the college-bound track in our schools. Outdated perceptions of the industry have also persisted for several decades. Immigration policy has cut off supply. Lastly, the industry has not recruited enough women and minorities to the trades.”
said Chelsea Allison, company spokesman for Canvas.
“Construction has lagged peer industries like manufacturing and logistics when it comes to better tools, making meeting these challenges difficult,” Allison said. “In fact, this situation has exacerbated the poor working conditions that have led to early retirements and poor recruitment of young people, women, and minorities into the trade.”
HELP YOUR WORKERS TO STAY WORKING
Robots can prevent unnecessary injuries by taking on the more dangerous jobs required on site, according to Raffi Holzer, an automation expert who founded Avvir.
“Flying drones, for example, can scale heights to perform site inspections,” Holzer wrote in Construction Drive. “Prefabrication systems allow for building on the ground in controlled environments, increasing both quality and safety.”
Using automation or robots can dramatically reduce injuries that result from the four most common causes of construction accidents: falls, electrocution, getting caught between objects and getting struck by objects.
It can’t solve the shortage, so start scrambling Brady, of HBI, said the shortage will continue to be a chronic problem in the home construction industry. He sees a hole much deeper than automation alone can overcome.
“We are at a crisis level of labour that is affecting housing affordability,” he said. “If we don’t invest in more training now, we will not be able to provide U.S. citizens with affordable and accessible housing.”
Training, he says, is the main path forward. Even with the help of technology and automation, we must invest in training the future generations of skilled labour if we want to overcome the shortage “crisis” anytime soon, he said.
“We need to provide more training and raise awareness of the industry and the lucrative opportunities within the industry,” he said. “This means exposing individuals to the trades at a younger age.”
He advocates accelerated credentialing that will increase productivity in the workforce, as well as changing the narrative around construction careers.
“We need to convey that this is an honourable occupation where you can make six figures and have your own business,” Brady said.
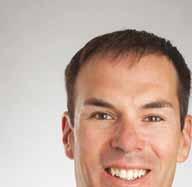
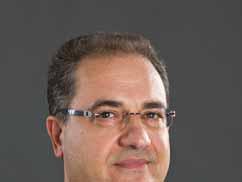
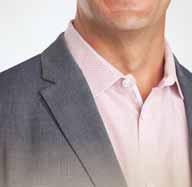


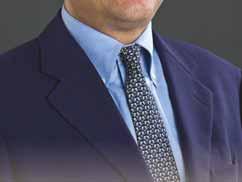
THE PURSUIT OF AUTONOMY MIGHT BE MORE IMPORTANT THAN ACHIEVING IT
Some experts in the industry believe there is too much importance placed on autonomy as a benchmark. Kevin Garcia of Trimble is among them.
The march toward autonomy is really a series of small steps. “You don’t completely go from manual to autonomous in a single bound,” said Garcia, general manager of Civil Specialty Solutions at Trimble. Each of those steps has its own value.
Consider the technology in a car today vs. a passenger vehicle from 20 years ago, Garcia said.
Passenger vehicles added blind spot detectors, GPS and other technologies on their way to developing driverless vehicles. Those advances make cars much safer and more pleasant to drive – yet a driver is still needed today.
It’s the same with construction equipment, Garcia said. The machines still need operators, but some elements – in the case of certain machines, the speed and the steering – can be automated. Those are big gains, even if the machines still require an operator.
We won’t see fully autonomous machines on construction sites for another five to 10 years, said Ivan Di Federico, executive vice president and chief strategy officer for Topcon

Positioning Systems. Still, we are already seeing many beneficial by-products from its pursuit.
Autonomy requires solutions that can be immediately utilised, he said. For example, sensors developed in the quest for autonomy are improving productivity. Safety is improved, too. “By adding the sensors to increase productivity, you already have a first step to a very smart safety warning system,” he said. “That is at no additional costs.”
Given some of the expert comments, why bother with autonomy? Why not just automate?
Di Federico believes a “hype” is needed to sustain market interest. It’s easier to put resources toward a concept with a clear end goal that everyone understands than toward a vaguer “autonomy” target.
The idea reminds Di Federico of NASA’s Apollo missions. The goal was to land on the moon, but small steps made toward achieving it brought a plethora of new products to the world – including watches with new quartz and digital display technology.
The goal of autonomy has also spurred other breakthroughs that have immediate value, including sensors that track other machines and even people on the jobsite and send data in real time.
Get real: some hard numbers on automation and productivity
What is the specific impact of automation on productivity? A recent Trimble test provides some answers.
The study examined horizontal steering control on compaction overlap and, in the process, provided a great deal of insight into the impact of automation on productivity –and ultimately profitability.
The bottom line: Using automatic steering leads to significant savings in time and fuel burn.
THE TEST
The study team established the following control variables:
• Area to be compacted: 836.127 m2 (300 ft x 30 ft)
• Operators: skilled and novice
• Machine: Dynapac CA2500D compactor with a Cummins QSF3.8 Tier 4 Final engine
• A common soil composition
Two randomly selected operators performed the manual and assisted steering operation 20 times. They used the same machine and covered the same area for both manual and assisted steering. The auto-assist drive mode path planner was preset to a 15% overlap.
PASS COUNTS AND PERCENTAGES
As expected, automatic steering has a significant positive impact on the relative overlap, reducing expected value and variance.
Overlap in the assisted steering mode stayed very close to the preset 15%, while the manual overlap varied from 30-50% between operators. The consistency of overlap in assisted steering mode results in a more predictable outcome and helps to avoid the issues of over- or under-compaction.
Trimble computed the length of the compactor drum path to provide a more complete picture of overlap consistency.
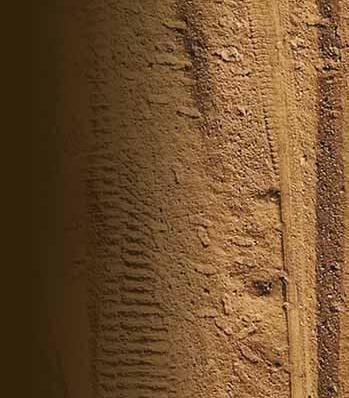
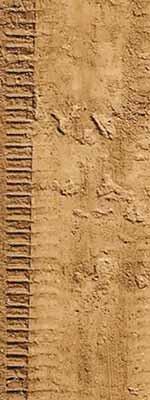
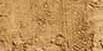
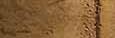


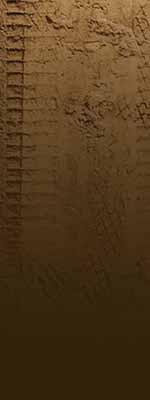



Manual drive mode led to significantly longer paths and, consequently, significantly longer engine run times – which resulted in lower productivity and sustainability.
Further, operating in assisted mode dramatically reduced the time to complete the compaction operation (by about 25% and 40% for operators 1 and 2, respectively). See Table 1.
From a sustainability (and fuel-burn) perspective, the numbers were equally impressive. The team tabulated CO2 emission and fuel burned. See Table 2
The cumulative results of all trials (20 automated/20 manual) found that the use of assisted steering led to an average time reduction of 43.8 minutes (29.4%) and an average reduction of fuel consumption of 1.65 gallons (26.46%) compared to manual steering.
Applying these savings to a typical historical compaction job results in significant financial savings.
The potential carbon savings using the average (26.46%), equates to an average saving of 680 gallons (26.46% x 2,569) across the testing scenario, which is equivalent to a carbon savings of over 15,262 pounds. See Table 3.
Similarly, when the time savings are applied against a historical project, an impressive reduction in labour cost is also realised. See Table 4
1Source: https://gasprices.aaa.com/ 10-18-202
2Source: https://www.eia.gov/environment/emissions/co2_vol_mass.php
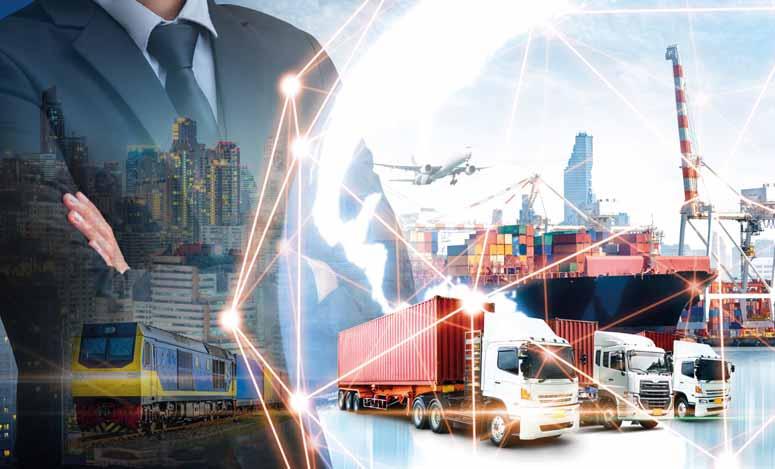
USE
IT OR
LOSE
IT: THE BRAVE NEW WORLD OF SUPPLY CHAIN DATA
Predictive analytics offer the global construction equipment supply chain an important new opportunity to be proactive in fostering resilience, improving efficiency, and driving growth. Exploit every bit of data you can find. If you don’t, you’re going to fall behind. Eliz abeth Kaye reports.
Disruptions to the global supply chain are nothing new but the Covid-19 pandemic and the impact of subsequent lockdowns on global manufacturing, purchasing and transportation forced a sea change in views about supply chain resilience. In addition, the upsurge in climate-related disasters and volatile geo-political situations is adding to trading-environment difficulties which need speedy responses and flexibility. Business leaders can no longer hunker down and hope for the best. Disruption is the new norm and the costs of multiple disruptive episodes, plus the potential damage to a company’s reputation, are too high to ignore. Increasingly, company survival and future competitiveness will rely on the optimal management of data which is set to increase exponentially in the coming years. Global supply chain consultancy State of Flux warns that companies are failing to exploit the information already available to them. It found that one in five companies still relies on Excel spreadsheets to manage supplier data and 13% admit to having no system at
all in this area. S&P’s Supply Chain Survey Report 2022 identifies a lack of highfunctioning platforms and technology, and limited visibility across the supply chain as key problems. Cost optimisation and a deficit of expertise are also significant issues.
While no company could ever be fully prepared for every possibility, it’s essential to plan for the most business-critical risks in the current environment. So, how can companies harness this wealth of information?
DATA ANALYSIS
Analytics are nothing new but organisations are adopting technology now because of growing data volume, easier-to-use software, tougher economic conditions and a heightened awareness of the need for competitive differentiation.
Analytics summarise relevant, trusted data and enable data-driven decisions to be made by uncovering previously unseen patterns and generating insights to drive future planning. Supply chains, in particular, produce huge amounts of data. Analytics can
help make sense of it all.
Supply chain analytics can be divided into three types: descriptive analytics; predictive analytics; prescriptive analytics. They can help an organisation identify likely future scenarios and subsequent business implications via a series of steps which then mitigate disruption and risk. It’s time to be proactive rather than reactive.
THE DIGITAL ROADMAP
Companies need to identify a roadmap for the digital transformation process and need to fully understand their current practices before moving to a digital platform. They must identify exactly what they want out of the process. Are they focusing on business optimisation or transformation? What do they want to know about the future based on the past, what do they need to understand and predict, and what decisions and actions will be taken as a result? What stage is the company at already in terms of digital business maturity? Is the organisation ready for change itself, the impact of the
transformation and the new cultural environment required?
Due to the potentially far-reaching impact of any such transformation, the strategy needs to be communicated across the organisation. Everyone needs to be on board. As supply chain expert and president of LMA Consulting Group Inc., Lisa Anderson, said in a 2023 press release: “It is critical that operations, sales, finance, IT and others understand the customer and their needs so that the company is in a position to react and respond.”
Once systems are in place, they must be tested to evaluate the impact on the organisation and its customers. Flexibility and agility should be embedded in the system so that it can respond to change which now becomes a constant.
Leading manufacturer Komatsu says it has transformed the way it does business in recent years by working with software giant SAP to create a tailored automated portal called K-View. In a 2020 interview with Supply Chain Digital, Daphyne Woodard, manager Order & Distribution Continued Improvement, Komatsu America Corp, said: “The K-View portal has increased our supply chain efficiency in multiple ways. The automated portal streamlines our processes and also provides real-time visibility into our inventory and order status. Most importantly, K-View has cut the amount of time it takes to create orders from hours to 30 seconds, improving productivity and customer service. The current deployment of K-View is our first step in an extended transformation. We initially wanted to develop a portal that supported our distributors and end customers. After its launch, we realised how beneficial the portal was for our business, so we expanded it to our departments and entire supply chain.”
A DATA-DRIVEN RESPONSE TO DISRUPTION
Accessing the right data helps companies work their way out of a potential crisis. Technological research and consulting firm Gartner identifies six steps in the process of responding to a disruptive event (sense, visualise, respond, predict, model, design). Initially, the unfolding event is monitored using real-time data. The event’s impact on the supply chain is then contextualised using visualisation analytics to identify critical fail points. This is especially pertinent for companies with complex supply chains made up of multiple global suppliers providing numerous parts and components. Using machine learning and artificial
PREDICTIVE ANALYTICS PROCESS
Source: Predictive Analytics Market, MarketandMarkets, October 2021
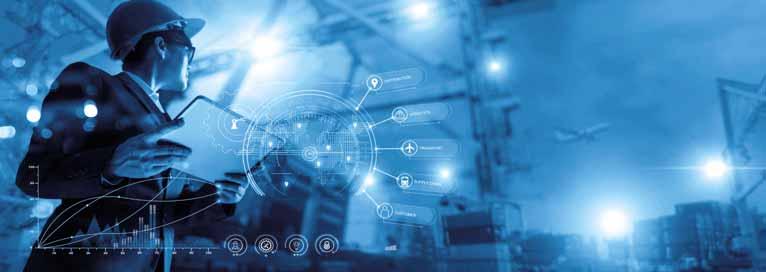
➔ intelligence, the unfolding event can be tracked and immediate action identified to minimise the impact on the supply chain. Machine-learning algorithms, unlike traditional statistical modelling that relies on past representative data, can forecast and interpret the near-real-time data generated by a dynamically evolving event. Immediate action mitigates the short-term disruption, giving supply chain managers time to work on longer term scenarios. Optimisation and scenario modelling can be used to evaluate different policies, focusing on a short-term, lean supply chain while working towards the quickest recovery possible.
Using long-range forecasting, simulations and other analytics techniques, companies are well placed to weigh up the issues. The supply chain can then be repositioned to maximise new opportunities and increase resiliency by, for example, increasing inventory or near-shoring a manufacturing process. Businesses can then determine optimal inventory levels, maintain a real-time sense of demand and the ability to respond to it. Other benefits include improvements in procurement, warehouse efficiency and logistics, to name but a few.
CLEAN DATA IS GOOD DATA
From the outset, ‘clean’ data is required. Bad data can be worse than no data so current information must be checked for accuracy. Failure to do so could lead to poor choices based on incorrect details – a potentially costly mistake.
Clean data identifies the system’s pain points and highlights where investment is
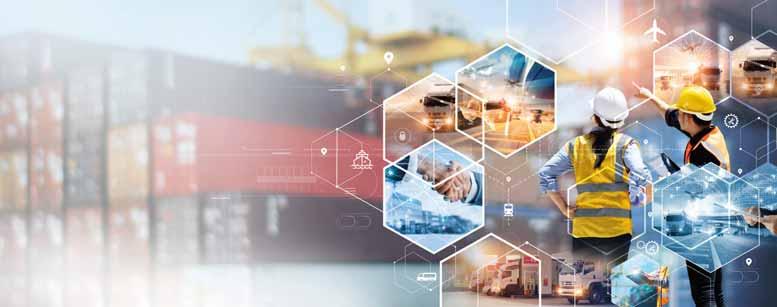
Serialisation, whereby a unique barcode is assigned to every individual product in the supply chain, means each component can be tracked and traced from raw-material production and processing right through to manufacture and distribution. As well as improving visibility it is a useful tool against counterfeiting.
As consumers’ service expectations rise, so data needs to be exploited to enhance the customer experience. Consumers themselves can be a source of a significant amount of the necessary data required to improve those processes directly affecting them. Surveys, customer feedback and activity monitoring can square the clean-data circle.
However, with information coming from an ever-broader range of supply chain sources as data points multiply, true 360-degree visibility remains elusive. While numbers of supply-chain-centric software providers in the market are growing, there is as yet no real market leader.
A BRAVE NEW WORLD
According to Gartner, the next ten years will see technology transforming the decision-making process. In the next two to five years robotic process automation (RPA) will increasingly be implemented to streamline processes such as procure to pay, order management and customer claim management. By 2030, more complex tasks typically requiring human judgement will be automated using machine learning, digital supply chain twins and artificial intelligence. Thereafter, hyperautomation will lead to supply chain autonomy. None of this signifies the end of human involvement. Far from it in fact, because companies will need to embrace the evolution of their workforce as members of Gen Z (those born between 1997-2012) enter the business world. Known as ‘zoomers’ because they are the first generation to encounter digital technology from childhood, they will view hyperautomation as the natural way to free up time for those value-added tasks still requiring human input.
In the post-Covid world, companies failing to invest in digital technology will be left behind. A recent PwC study found that data-driven companies are three times more likely to achieve significant decision-making improvements than those relying less on data.
Market research company Global Market Insights estimated the value of the supply chain analytics market at more than 6bn in 2022, growing to a predicted $30bn in 2032. How can companies maximise their investment and avoid potential pitfalls?
Biggest data-related challenges for supply chains (survey respondents across 36 industries)
Source: Supply Chain Survey Report, S&P Global Market Intelligence, 2022
Integration of data across users, technologies, and the broader supply chain
Timely and easy access to data
Manual processes and errors in managing data
Checking data quality and correcting bad data
Ability to handle growing data requirements (volumes, types, analytics, reporting needs etc.)
Data and technology siloes/fragmentation Cyber risk/digital security
Understanding data lineage (from what source did it come from, when, who is using the data etc.)
Most pressing challenges (survey respondents across 35 industries)
Source: Supply Chain Survey Report, S&P Global Market Intelligence, 2022
Supply chain resilience
Economic fragility
Global security
US-China trade policy
Climate agenda
Organisations’ perception of procurement and supply chain resilience over the past five years
Source: A survey by Deloitte in partnership with the Chartered Institute of Procurement & Supply, 2022
73% of respondents in a recent BSI survey of more than 150 clients acknowledged significant concerns about supply chain digitisation amongst their chief risk officers (CROs) and chief operations officers (COOs). Responsibility for the digitisation process, however, is no longer just a technology issue. Those CROs and COOs need to be involved too. Digitisation marks a significant shift in the concept of control but the technology allows companies to move from annual safety checks to a state of continuous assurance via constant data analysis.
Supply chain leaders must keep abreast of key advances in disruptive supply chain technology. These include 3D printing, fog computing, autonomous vehicles, drones, wearable tech, robotics and automation, blockchain and the Internet of Things, all of which have revolutionary potential. Blockchain guarantees the provenance of goods and transaction security while the potential for data exchange via the IoT is phenomenal. In 2022 there were one trillion smart sensors in use in the supply chain, all feeding live data to those in charge of supply levers. Professional services company Deloittes predicts that by 2030 this number will increase to something like 10 trillion sensors. The ability to exploit and manage data will be transformed. With supply chain visibility enhanced and the automation and streamlining of administrative processes in place, companies are much better placed to focus on strategic initiatives.
LEGAL TRANSPARENCY
Recent legislation such as the UK’s Modern Slavery Act (2015) and the German Supply Chain Due Diligence Act (enacted January 2023) is forcing companies to get to grips with their second- and third-tier suppliers so that they can identify potential legal breaches of international law within the chain. Failure to do so and to react accordingly can lead to accusations of unaccountability, consumer backlashes and even financial penalties. Environmental, social and governance (ESG) initiatives are now key performance indicators. Shareholders and customers are increasingly demanding accountability here. Businesses need to have full supply chain visibility to ensure legal compliance and to devise corporate responses to areas like sustainability. JCB has already identified its supply chain as its second-largest impact area in terms of climate change. It is using data from suppliers via its Supplier Code of Conduct to look at ways of reducing carbon emissions and packaging waste.
SUPPLY CHAIN TECHNOLOGY PREDICTIONS
By 2026, 75% of large enterprises will have adopted some form of intralogistics smart robots in their warehouse operations
By 2026, more than 75% of commercial supply chain management application vendors will deliver embedded advanced analytics, artificial intelligence and data science
By 2026, 25% of supply chain execution vendors will have rewritten their core application to a microservice architecture but only 5% of supply chain organisations will have adapted to true composability.
Through 2025, 25% of supply chain decisions will be made across intelligent edge systems
TOP BUSINESS PRIORITIES FOR TECHNOLOGY IN 2023
Optimising resilience, operations and trust
Scaling vertical solutions, product delivery or everywhere
Pioneering customer engagement, accelerated response or opportunity
Pursuing sustainable technology solutions
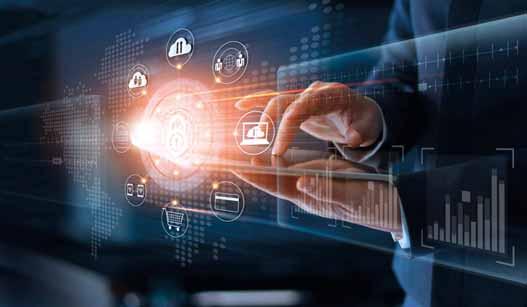
Unavoidably, digitisation brings with it the risk of cyberattacks. Software supply chain management company Sonatype has reported a 742% increase in software supply chain attacks in the last three years. Other reports have indicated particular problems with hackers targeting open-source code. Critical to organisations’ infrastructure, 80% of the code in modern applications comes from existing operating systems which can be outdated and therefore more vulnerable to attack. There is also a 32% chance that the latest version of a software code package will have known security vulnerabilities, according to software development company Endor Labs.
Companies need to be particularly vigilant regarding back-door attacks whereby cyber criminals target vendor companies as an easy entry point for malware, ransomware or denial service attacks. These can then move upstream or downstream along the supply
aimed at small to medium-sized enterprises (SMEs), larger companies need to be assured their suppliers are employing appropriate security measures, according to a report by Accenture, the information technology consultants. The report indicates that in the US just 14% of SMEs are protected, while the UK government estimates almost a third of UK firms with digital supply chains are vulnerable to cyberattacks.
Using supply chain mapping (SCM) companies can record, store and use information on who their suppliers are, what they provide and how they provide it. With this level of information to hand companies are more able to manage cybersecurity issues, as well as being in a better position to comply with legal, regulatory and contractual issues.
With so many headwinds, now is the time for companies to invest in supply chain technology to optimise resilience, improve customer service and reduce costs.
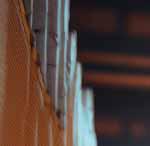

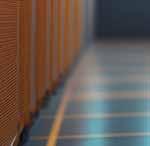
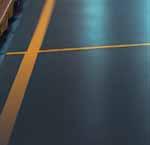
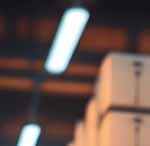

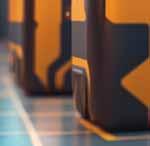
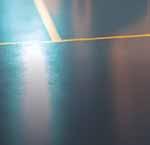
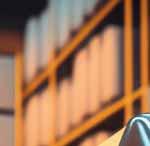

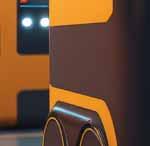
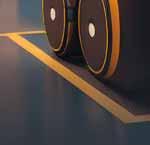

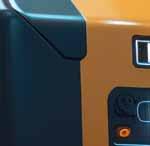
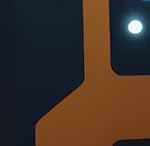
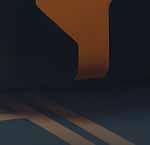
The digital warehouse: steps to success
Warehouse automation involves significant upfront and maintenance costs, and considerable planning. It involves anything from implementing basic systems to reduce repetitive tasks to advanced systems using artificial intelligence and robots. The longterm advantages, including improved data management efficiency, greater security, lower costs, improved delivery times and reduced operational and legal risks, are transformational.
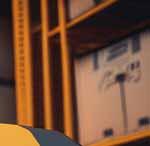
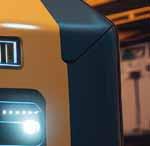
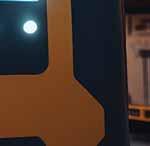
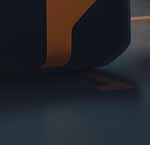
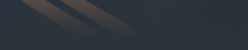
Labour shortages and logistics pressures have spurred a 15% increase in warehouse automation investment, according to Accenture’s 2020 Supply Chain Survey Increasing work volume and changing business requirements are also motivating factors.
The transformation process is not easy and requires considerable groundwork. Too many companies seek quick-fix solutions and fail to choose appropriate technologies for
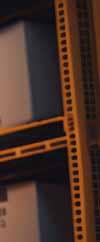


their specific needs. Planning based solely on traditional key performance indicators will fail to accommodate the bigger picture or realise the long-term investment value. While the automation process is essentially directed at eliminating labour-intensive duties, machines alone are not the full answer. Human-machine collaboration needs to be built in from the start.
According to Accenture, four elements are key to the successful transformation of the
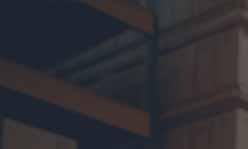
To generate desired returns from warehouse automation investment, companies must design the right digital architecture for their warehouses
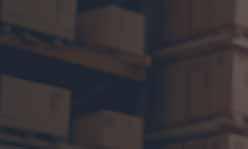
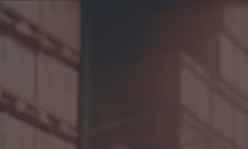
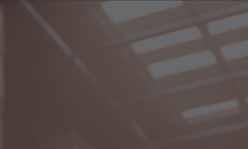
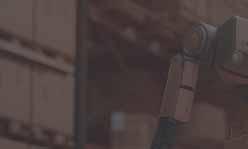
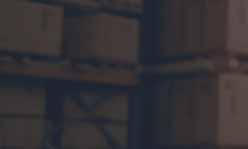
Generate intelligence with data on the cloud
Deploy intelligent technologies to generate insights for decision making in real time
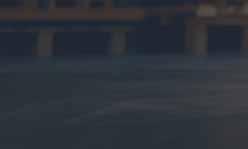
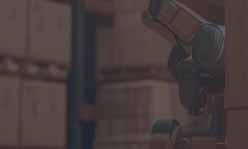
Enable autonomy in processes and systems
Build a smart core capable of autonomous response capabilities
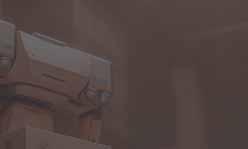
Source: Value-driven warehouse automation: A new approach to warehouse operations that maximises return from digital investments, Accenture, 2021
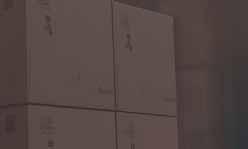
Create collaborative harmony between humans and machines
Design warehouse solutions to maximise human and machine collaboration
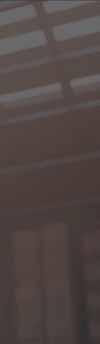
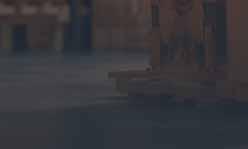
Build the foundations with data on the cloud
Data availability is the prerequisite to realising value with any type of warehouse
warehouse into a driver of both new value and growth: -
• Identifying the role of the warehouse in the overall supply chain strategy
• Avoiding one-size-fits-all solutions
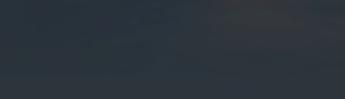
• Identifying and including the less obvious but still vital returns when calculating return on investment
• Building digital architecture for end-to-end connectivity, ensuring technologies are both integrated and combined
Data is often held in siloes, visible only to a few. To be truly beneficial, data needs to
be visible across the entire value chain by storing it in the cloud. Using data analytics, machine learning and/or artificial intelligence means the millions of data points collected daily in a warehouse can be leveraged into continuous real-time intelligence, leading to more accurate predictions of demand, better resources planning and improved service levels.
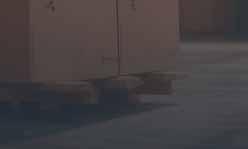
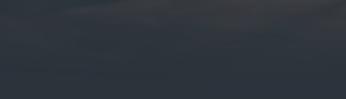
An integrated platform managing the activity and process flow is required. The platform type depends on the autonomy and automation levels required by each business but most require one of three systems: a
Source: 2020 Supply Chain Survey, Accenture
warehouse management system dealing with operations and processes; a warehouse control system directing the flow of automated technology activity; a warehouse execution system which is a mix of the first two.

In a 2023 interview with McKinsey, as part of its Logistics Disruptors series, Deborah Surrette, chief commercial officer of GreyOrange, comments on the customer demand for education in the warehouse automation process.

“A huge part of our job that our go-tomarket teams and industry experts have is to educate clients on how they can solve their problems. If we looked at a pie chart of our hours spent, at least 60% is on education about opportunities and alternatives.”
A final word of warning – run the old and new system alongside each other until everyone is happy. A gradual migration to a new system highlights issues which can then be ironed out along the way – a much better option than risking the loss of key data and upending the smooth running of the whole operation by banking on the success of an untried new system.
Elizabeth Kaye is a widely-experienced freelance writer and editor. She writes regularly on the supply chain, warehousing and distribution industries and has edited websites, newsletters, and magazines in many other sectors including healthcare and military history.
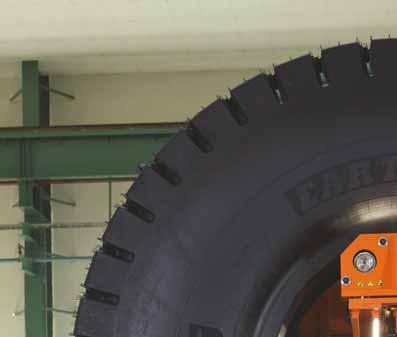
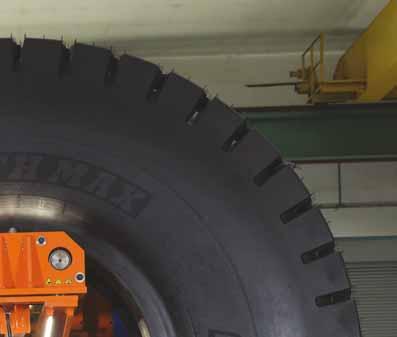





BKT INVESTS IN ITS CONFIDENT GROWTH VISION
Indian off-road tyre giant BKT, Balkrishna Industries, recently invited the world’s trade media to its state-of-the-art site at Bhuj in Gujarat to showcase the group’s exciting plans for the future. These include a doubling of the company’s turnover to US$2bn by 2026 and an increase in annual tyre production to 600,000 tonnes. Guy Woodford reports.
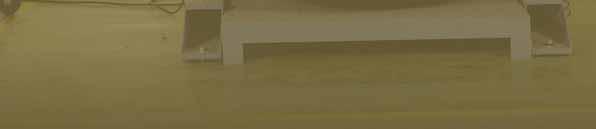
Speaking at BKT’s newly acquired 65-acre site, just a short distance from the company’s main site at Bhuj, marketing and communication manager Gabriella Usiello outlined the company’s plan of action.
This will include a second carbon-black production facility dedicated to external sales, a second power plant to supply the significantly enlarged operation and an assembly line making rubber tracks for agricultural machinery.
“We are incredibly proud of this new acquisition and the growth opportunities it offers BKT. We are constantly looking for ways to improve and grow. This additional
land is going to be another game-changer for us, giving us more room to expand our production capabilities and take our operation to the next level,” she said, adding: “We are confident that with this new site, we will continue to produce the highest quality products and meet the demands of our customers.”
Usiello’s speech followed an extensive tour for the assembled media of the facility which will employ more than 4,770 workers. The vast site is more like a village, complete with growing onsite accommodation for employees and their families. There are shops, a school, medical services, and sports and other recreational facilities. By the end

of next year, 1,240 employee families and 400 single men will be living at BKT Bhuj. Work on the site is expected to be completed in 18 months to two years.
Day two included a press conference at The Trident Hotel in Mumbai focusing on the trip’s theme, Enter the Future. The media party heard from a number of top BKT executives, including chairman and managing director Arvind Poddar and joint managing director Rajiv Poddar.
“In our future, BKT will double its turnover. In our future, the combination of production, distribution and brand promotion will allow us to achieve new standards,” said Arvind Poddar.
Gabriella Usiello spoke to global trade media on BKT’s planned Bhuj facility expansion site. The current cutting-edge Bhuj site is behind her
“People have asked me if all this was really necessary … so much in such a short time. The goals we set ourselves when we decided to open the Bhuj site were proportional to the financial solidity of the time but above all to a vision which is as great as it is concrete,” said Rajiv Poddar.
“Growth has always been in step with demand. Global tyre demand is growing, and we see no signs of it slowing down over the next five years. This demand started to rise during the 2020 pandemic, which today is above pre-Covid levels.
“The journey we started out on at Bhuj in 2012 was never a return journey, but one to prepare ourselves to discover the future.”
BKT’s 25” to 57” off-the-road (OTR) tyre range supplies many industries, including construction, quarrying, mining, industrial, earthmoving, ports and agriculture. The company has more than 10,000 employees and offers a staggering 3,200 products in 160 countries across five continents. With its global headquarters in Mumbai, the company has three subsidiaries: BKT Europe in Seregno, near Milan, Italy – which has a 10% share of the continent’s OTR tyre market; BKT USA in Copley, Ohio; and BKT Tires in Toronto (Canada). There are six production sites in India, one in Bhiwadi, Chopanki, Dombivli and Bhuj, and, since autumn 2021, two in Waluj, a large village located to the west of the city of Aurangabad in the central part of Maharashtra state.
BKT’s consistent investment in digitalisation and automation at its current Bhuj site has increased production speed, volume and final-product quality. The amount of product discarded has been
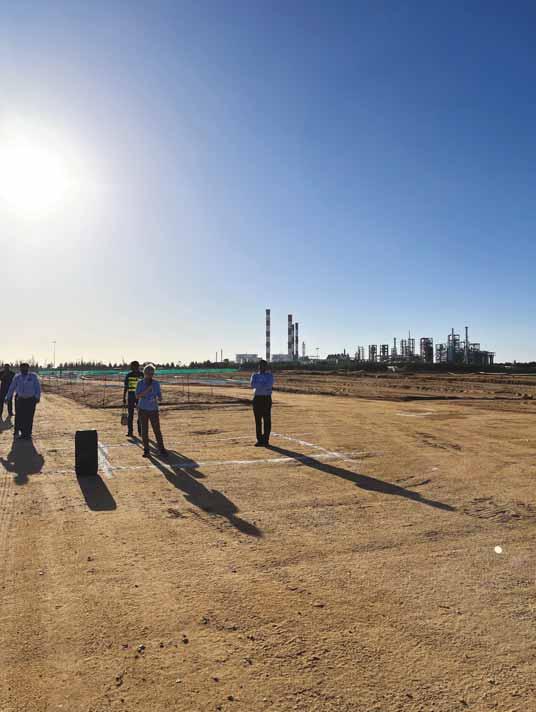
BKT Bhuj’s power plant became operational in 2013, giving the site a reliable and controlled source of electricity
have been drastically reduced, and worker comfort improved.
The extended facility, including the new fully digitalised carbon-black plant dedicated to external sales and the state-of-the-art rubber-tracks assembly line, will meet significantly increased market demand for these products. It is anticipated that 5% ($100mn) of BKT’s targeted $2bn annual turnover by 2026 will be generated by carbon-black sales with the 198,600 tonnes earmarked for tyre tread production in 2023 predicted to rise to 500,000 tonnes per year by 2026.
Moving the rubber-tracks assembly to a new purpose-built site will free up space to allow BKT to increase its off-the-road tyre
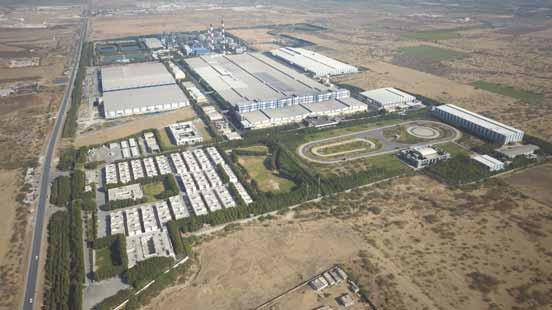
an extremely fine, fluffy, black particle, 10 to 500 nanometres (nm) in diameter, and this ‘carbon black’ is used to strengthen the tyre rubber compound.
BKT Bhuj’s carbon-black plant began operating in 2017 with 65,000 tonnes of hard-grade carbon black for tyre treads produced in that year. In the following year, production increased to 110,000 tonnes. The production of soft-grade carbon black started in 2018. This is used in the casing compound to improve strength and durability, generating less heat. In 2021, the total production of the two types of carbon black reached 138,000 tonnes per annum, while last year, it rose to 165,600 tonnes. The goal for 2023 is 198,600 tonnes. BKT Bhuj’s
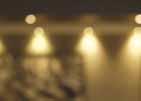
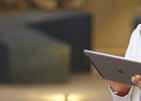
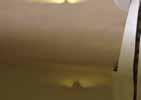
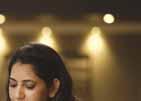
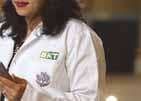
spends 3.5% of its $1bn annual turnover on research and development
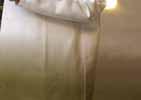
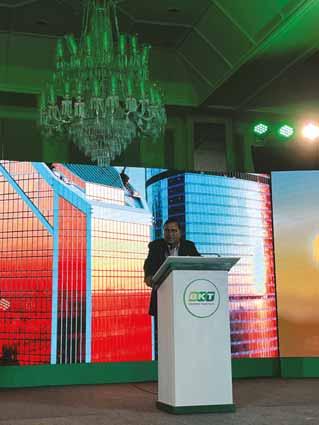
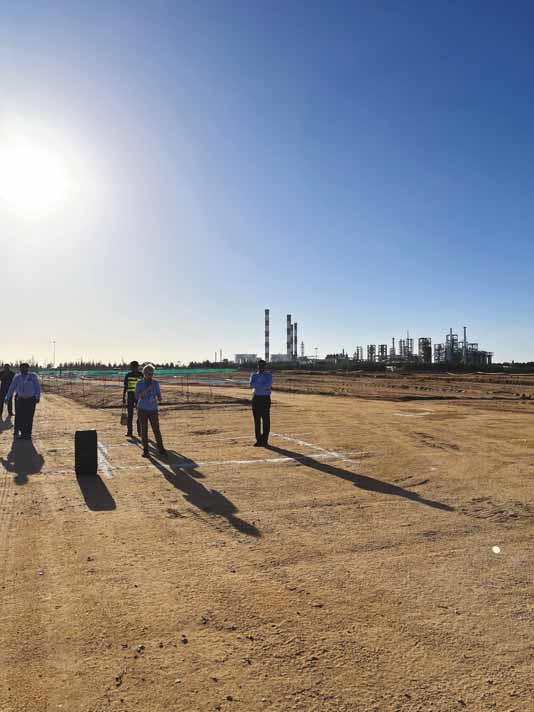


research and development centre plans to add a third ‘speciality’ type of carbon black, which has different properties to the carbon black used in rubber compounds. These properties offer high resistance to colouring, a high purity level, a low ash level and a very low level of PAHs. This makes speciality carbon black suitable for specific applications such as paints, plastics and inks.
BKT has also introduced a new approach to carbon-black production, making the whole process more sustainable. For carbonblack transportation, BKT substituted bulk bag containers with mobile silos. This means that the tyre-production plant receives the carbon plant using mobile silos transported pneumatically to the storage. This will eliminate the need for BKT to use 100,000 bulk bags over the next few years. Furthermore, the whole transport system is designed to reduce energy usage and consumption. Every transfer system is controlled by weight and energy used – with BKT aiming to reduce energy consumption by up to 70%. This will save more than two million kilograms of CO2 emissions annually, comparable to the emissions rate of 5,000 100m2 apartments.
At the same time the gas used to manufacture carbon black is now ending up in a co-generation plant able to reuse 75,000m3 of gas per year. This saves 215,000 tonnes of coal per year.
BKT Bhuj’s power plant became operational in 2013, giving the site a reliable and controlled source of electricity. Today, solar panels and the cogeneration plant allow the facility to produce its own energy. Last year, the cogeneration plant was expanded from 20MW to 40MW per year, and work is underway to increase the power generated by self-produced renewable resources.
Water is also at the heart of BKT Bhuj’s power-plant sustainability. Since 2019, a zeroliquid discharge (ZLD) principle has been adopted, meaning no liquid waste is released
outside the plant. All water used in the plant is treated, purified and reused. The objective of the ZLD principle is to conserve water resources, reduce the environmental impact of wastewater discharge and improve the plant’s overall efficiency and sustainability.
When the first tyre rolled off the Bhuj production line in 2012 following a $500mn investment, the plant was located across 123 hectares. Before starting the works, the landscape was completely arid with neither water nor electricity. After laying many kilometres of drinking-water pipes and power lines the site grew exponentially : 126 hectares in 2016, 131 in 2019, 137 in 2021, and 258 in 2022. By the end of 2023, it is forecast to reach a total surface area of 323 hectares, of which 283 acres have already been acquired.
More space provides the possibility to install new machines, accommodate more test areas, and increase volumes and all that goes with it. From 92 tonnes of daily production in 2015, BKT Bhuj ended 2022 with its best result ever - 436 tonnes daily. This is timely as BKT’s business has,
as Rajiv Poddar noted in the Mumbai press conference, increased by 49% compared to the pre-pandemic period. This remarkable achievement reflects the Indian multinational’s readiness to embrace new opportunities and challenges.
BKT spends 3.5% a year of the company’s turnover on research and development (R&D). Its R&D Centre is said by the company to be the “cradle which allowed the Bhuj site to grow into what it is today”. Established in 2017, this hub develops products and processes to ensure BKT can maintain its leadership in the international off-the-road tyre market. Led by a specialist team of researchers and analysts, it remains one of the world’s most important and up-todate tyre research centres.
Finding the right solutions requires testing. For this reason, a special test track was inaugurated in the R&D centre’s first year. With six different tracks, this circuit includes tracks for tyre-performance tests in both dry and wet conditions, an asphalt track and a sloping concrete track. Thanks to a wide variety of tests, many important characteristics such as traction, handling, comfort, soil compaction, and much more, can be measured here, thanks to highprecision devices and instruments.
Having seen the vast BKT Bhuj site firsthand and after listening to BKT’s senior management team lay out the company’s hugely ambitious plans for growth, few would bet against such a vision becoming a reality in 2026.
This report was produced in association with BKT.
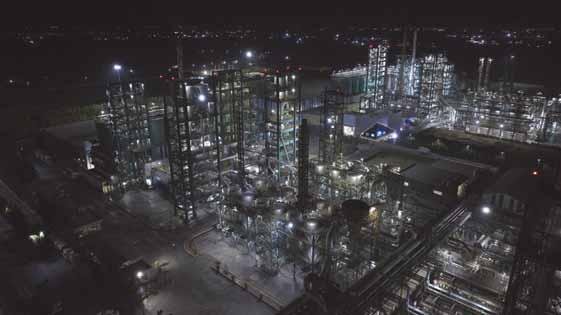
BKT’s carbon-black plant at its soon-to-be-expanded

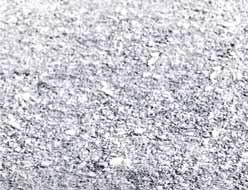
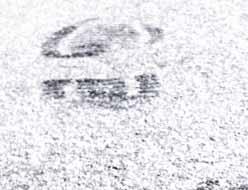





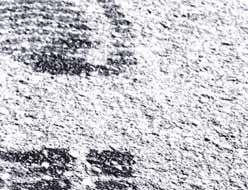
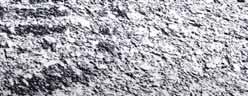
GET YOUR CARBON COSTS RIGHT IF YOU WANT TO WIN BUSINESS

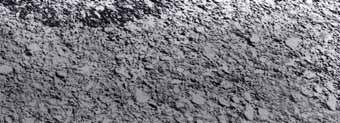
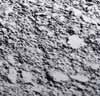
It’s all very well congratulating ourselves on how developments in construction equipment and technology are reducing the carbon footprint generated by building and maintaining the world’s highways, but are we concentrating our efforts in the right places? Are we on the right track, or have we got it completely wrong? There is a lot of new thinking out there, especially when you are bidding for new contracts. Kristina Smith reports.
With countries around the world committing to achieving net-zero carbon emissions by 2050 – and some of them even earlier than that – the race is on to reduce the embodied carbon in our roads due to their construction and maintenance. That means unpicking every stage of a road’s lifecycle from extraction of materials through to recycling and reuse.
There have already been some claims of net-zero or carbon-neutral roads. But these often depend on carbon offsetting to get them down to the zero mark, and the celebratory press releases that announce them rarely spell out how much carbon from a scheme has been offset.
Beyond the PR claims, however, some road authorities are introducing new regulations and contracts aimed to drive their roadbuilding industries to do things differently. Among the leaders are Norway and the Netherlands. The results are innovations
among contractors and their supply chains: new types of asphalt plant, use of biobinders, battery-electric equipment and – crucially –measures to increase the longevity of roads.
Norway’s national road authority Statens vegvesen now adjusts tenders based on carbon cost as well as capital cost. The lowest bidder in carbon terms does not have its price adjusted but all its competitors have five NOK (€0.5) added on to their tender prices for every kilogram of carbon emissions they come in above the lowest carbon bidder. The result is that the authority has seen its carbon emissions fall from 60kg per tonne of asphalt in 2019 to 47.5kg in 2022.
Now Statens vegvesen is trialling a further incentive to reward contractors for offering longer-life roads. “Our contractors are investing in climate-friendly equipment, they are doing a lot of research and development, and we see that their knowledge is getting better and better,” says Thor Asbjørn Lunaas,
chief engineer at Statens vegvesen. “For our part, as an authority, it is very important that we are predictable and give them a long-term view.”
THE CARBON PIE
Perhaps the biggest challenge facing road owners, and the wider industry, is a lack of data related to carbon emissions and roads. To make informed decisions about where to concentrate effort and spending in developing and trialling new solutions, authorities first need to understand where most of the carbon is concentrated.
This is something that DecarboN8, a network of eight UK universities dedicated to decarbonising transport, addressed in a 2022 study and report, Measuring Road Infrastructure Carbon. The researchers looked at three-lane, two-lane and single-lane roads over a 40-year lifecycle, calculating the carbon during the material production,
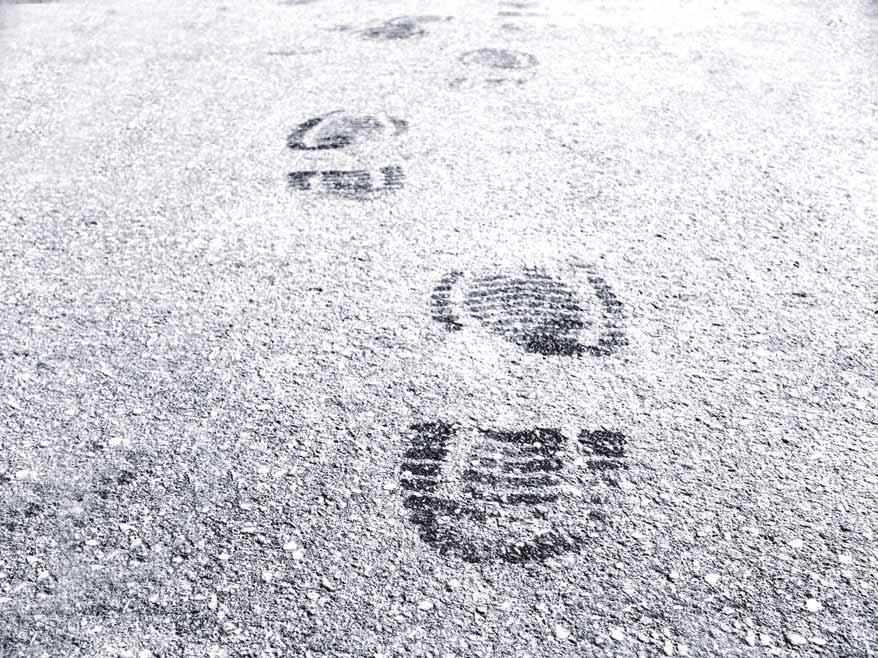
material transport, construction, lighting during road operation and maintenance phases.
The study found that, on average over the three widths of road, material production accounted for 70% of embodied carbon over the lifetime of the road, material transport contributed 10% on average, construction 2%, lighting 13% and maintenance 4%. The study considered roads with a 40-year life, with resurfacing every five to 10 years.
These findings show that initial efforts to lower the carbon footprint of highways should be concentrated in the materialproduction phase of the cycle. This is also the conclusion drawn by contractors in Norway.
Geir Lange, major asphalt project lead for Viedekke, speaking at the specialist asphalt conference E&E Event in Vienna in November 2022, shared its ranking of which investments gave the biggest return in terms of carbon savings. Top of the list was fuel type and consumption at the asphalt plant; second came alternative binders, such as biobased materials; third came aggregates and additives.
Alternative fuels for transport and construction machinery could offer smaller carbon reductions, said Lange.
DECARBON8 STUDY
The DecarboN8 study went on to look at how the different layers of road construction contributed to embodied carbon. In the UK, the build-up of a main road is generally subgrade, sub-base, base course, binder course and surface course. The study found that
around 60% of the embodied carbon is tied up in the binder and surface courses.
In trying to map out the best routes for decarbonisation of UK roads, DecarboN8 looked at various options including replacing virgin aggregate with recycled aggregate in various layers of the road, substituting up to 20% of the bitumen with a bio-binder and using recycled asphalt planings (RAP). Including RAP in the surface layer could lead to carbon savings of 10 to 16 % initially, the researchers said, although some of those savings would be lost due to the need for
more frequent resurfacing, lowering savings to between two and 9%.
This last point illustrates the complexity of decision making around road materials and carbon-saving. There is little point in announcing huge carbon savings up to the point a road is laid, only for it to need resurfacing three or four years later.
Predicting how long a road will actually last is challenging, says Berwich Sluer, director at   Partners in Solutions, a Netherlands consultancy which advises road authorities on how to optimise pavement
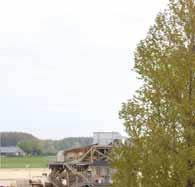
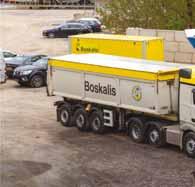
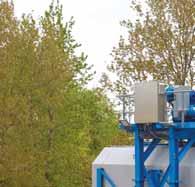
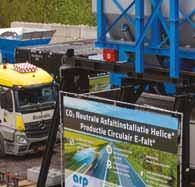


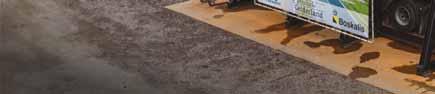

➔ quality and life. For instance, porous asphalt has an expected lifetime of 13 years in the Netherlands but recent changes such as the falling quality of bitumen, the use of RAP and warm-mix technologies mean that the actual life could be anywhere between three and 15 years, says Sluer.
“If you want a clearer picture of the real surface life today, you have to focus on getting reliable information about the process of laying the road and about the mechanical properties of the materials you use,” he says.
Sluer and fellow director Natascha Poeran were alerted to the challenges related to materials while working on a large roadmaintenance project. “It was a long stretch of road, miles and miles, and we were finding that the asphalt that we had laid the night before was ravelling and potholes formed almost immediately,” recalls Poeran. “We found out that the composition of that batch of bitumen was so very different that, combined with other suboptimal conditions, the result was poor quality asphalt.”
The Netherlands has been using a fundamental, or performance-based approach, to specification for around 15 years. However, tests done on a proposed contractor mix in the laboratory are not necessarily replicated in the field, as the above example demonstrates.
Sluer and Poeran are creating a framework for road authorities in the Netherlands which will combine new testing regimes for the constituent materials in an asphalt mix, control and recording of the laying process
and testing of the road as soon as they are laid. Sluer calls this combined information a ‘process quality footprint’ which, over time, will help in decision-making about the design of future roads.
ENERGY TRANSITION
Given that the biggest bang for your buck when looking for embodied carbon savings comes from improving the production phase, it’s not surprising that most contractors are starting with changes to asphalt plants. The burners used to dry and heat up the aggregate use the biggest proportion of the energy at a plant.
Nordic contractor Peab is replacing fossil-fuel oil with biofuels for the firing and heating of the aggregate which it says halves the energy needed during the manufacturing process. Of its 90 plants in the Nordic area, Peab Asfalt has converted 20 plants in Sweden – where it received funding from the government – four plants in Denmark, three in Finland and two in Norway. There are multiple measures that can reduce energy consumption, and hence carbon emissions, at asphalt plants (see Ammann article page 35). Simple ones include improved insulation or erecting covers over stockpiles of aggregates in wet climates. Lowering the heat of production to produce warm-mix asphalt, rather than hot-mix, is another way to save energy and carbon. This doesn’t require modifications when done by using warm-mix additives. Although plants don’t need modifications
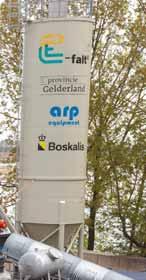
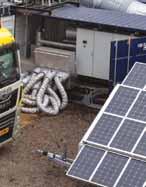
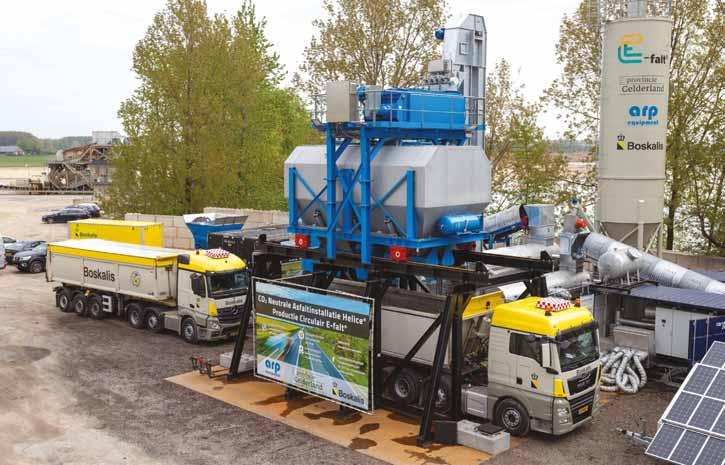
to use small proportions of RAP, specialist plants are needed for higher percentages. Technologies such as parallel drum where the RAP is preheated, can allow up to 70% RAP to be used, and have been available for some time.
More advanced plants are under development.   is working with ARP Engineering to produce an electric asphalt plant which is more energy-efficient than a standard plant and which can activate RAP more effectively. The goal is to achieve 95% RAP in surface-layer asphalt. Currently 95% RAP is only used in the lower road layers in the Netherlands with up to 65% used in the top layers.
The process relies on using processed and graded RAP. Getting the right proportion of the various sizes of re-used aggregate in a mix – expressed by the gradation curve – is vital, explains Poeran
“The new plant had a built-in facility to dose all the different gradations separately,” she says. This also requires a more disciplined approach to the production of RAP, either milling the layers of the road one at a time or sorting the milled material later to separate out the different sizes.
RAP is delivered to the mixing drum via a helical screw which gradually raises its temperature, with the movement of the screw helping to activate the bitumen in the RAP. By using foaming technology, the mixes can be made at a lower temperature than for standard mixes. Any virgin aggregate need only be heated to 120 to 130 degrees C rather
than the traditional 185 degrees C. A small amount of fresh binder, with a foaming additive, is heated to around 160 degrees C with the mixing temperature between 110 and 120 degrees C.
The first prototype of the new electric plant, named Helice due to its helical screw, has been built and tested. After some design improvements, the second one will start production in a few months, says Sluer. “If that is successful, the next one will be built to full scale.”
In the Netherlands, contractors are spurred on by a system that takes environmental factors into account when awarding tenders. Introduced in 2015 for public procurement contracts, this involves the calculation of an Environmental Cost Indicator which is translated into a cost in Euros, which is then subtracted from the tender price.
tandem rollers, and Kleemann’s all-electric MOBIREX MR 130(i) PRO impact crusher.
“Decarbonisation is a standard component of our product development,” says Martin Hilken, team lead, product marketing, Vögele. “For electrified products, we strive for standard rechargeable batteries, charging systems and service concepts which all need to be available from the outset.”
Some contractors are reducing carbon emissions by switching from diesel to hydrotreated vegetable oil
Wirtgen plans to increase the number of batteryelectric and hybrid-electric machines it offers across its product brands. The biggest demand for these, says Hilken, is coming from the Nordic countries and the Netherlands.
to concerns over it containing unsustainably farmed palm oil. Biodiesel, or fuel that is a blend of petroleum diesel and biodiesel are also options.
Recognising that a longer pavement life means lower lifetime carbon emissions, Statens vegvesen is now working out how it can incentivise contractors to build longerlasting roads. Under this pilot form of contract, contractors can choose their own mix design which must fulfil functional requirements related to resisting permanent deformation, resistance to rutting from studded tyres, durability and friction.
This means that the Netherlands is perhaps the most advanced with the energy transition of paving plant. For instance, Bam Infra Nederland announced last year that it had commissioned New Electric to convert a Wirtgen paver to run on a 270kWh battery and two electric motors. Then in September it said that it had converted a diesel paving machine to hydrogen, with the help of energy system supplier Koninklijke van Twist.
The Wirtgen group is already producing electric models of its smaller paving equipment, such as Vögele’s new MINI road pavers, which include two batteryelectric models, Hamm’s battery-electric
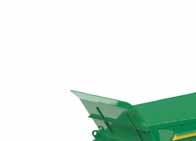
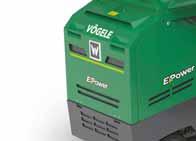
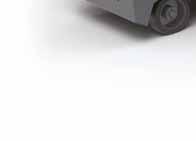
As contractors reduce more carbon from the production of asphalt, so carbon savings from plant will become more important, says Lunaas of the Norwegian market: “We aren’t seeing much electric equipment like rollers or pavers at the moment,” he says. “The contractors look at where the biggest chance to reduce carbon emissions is, and they see that it’s not in the laying of the pavement, it’s in the heating and the bio binder. In a few years, it will be more interesting to invest in electric equipment.”
HYDROTREATED VEGETABLE OIL
Some contractors are reducing carbon emissions by switching from diesel to hydrotreated vegetable oil (HVO) as an initial step on the energy-transition journey. HVO has some challenges, however. It is more expensive than regular diesel and, in the UK, some clients have banned its use due
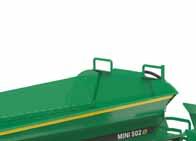
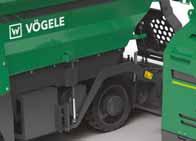

When comparing tenders, the adjustment for carbon savings is made first and then an adjustment for lifetime is made with improvements to Wheel Track and Prall test performance converted to a percentage increase in pavement life (see Figure 4). The cost of the road per year is then calculated by dividing the adjusted cost by the adjusted life and the lowest wins.
“It will be some years before we know how well this approach works, but initial tests on the roads after they have been paved show that they have achieved much better results than were required by the specification,” says Lunaas. “They are over-fulfilling our requirements.”
With four pilot projects last year, three this year and four or five planned for 2024, the authority hopes to get a better understanding of how the embodied carbon and longer life weightings work.
One issue that has yet to be ironed out, says Lunaas, is finding a parameter that can be consistently tested at laboratories. Currently, different laboratories are giving different results when testing the same specimen
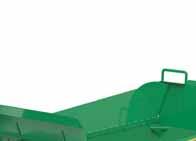
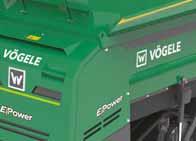


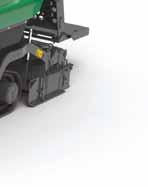

Damage mechanism/Test method
Prall (change in pavement life in % for each unit change in Prall-value for AADTM > 10,000)
Prall (change in pavement life in % for each unit change in Prall-value for AADT 5,000 -10,000)
Wheel Track (increased pavement life in % for each unit decrease in WT - value (PRDAIR))
Norway is now incentivising contractors to produce longer-lasting roads. Better performance in Wheel Tracking and Prall tests boosts predicted lifetime.
➔ using wheel-track testing for resistance to deformation and Prall testing for resistance to rutting from studded tyres.
Ensuring the right compaction and hence density of an asphalt pavement has long been recognised as an important factor which directly influences the longevity of a road. In the US, some states offer incentives, or penalties linked to achieving the required density.
Up until recently, it has been difficult to measure density on the fly. “People have been trying to determine compaction in real time since the 1960s,” says Sesh Commuri, a professor of electrical and biomedical engineering at the University of Nevada in Reno, who himself has been working towards this goal for the past 20 years.
“Intelligent compaction took root in the early 2000s when the Federal Highway Administration funded several studies. The idea was to set a target density that the machine would then achieve by automatically adjusting the frequency and amplitude of vibration of the roller drum,” says Commuri. “But the only feedback during compaction is the vibratory response of the roller. Trying to find the correlation between density and roller vibrations is not straightforward. The vibrations of the roller are affected by the stiffness of the material being compacted and the underlying foundation of the road, which are usually unknown. Further, the stiffness of the material is a function of temperature that changes during the compaction process.”
than density. An intelligent compaction system records the number of roller passes and provides a compaction value, based on the vibration of the roller drum.
Today’s systems consist of GPS, accelerometers, infrared thermometers for the hot-mix asphalt and an onboard computer so that the roller driver can see what is happening with compaction and adjust accordingly. Some systems can combine paver-mounted infrared thermal sensors to measure the asphalt surface temperature. Modern developments include moves to automation and the use of AI.
There are two ways in which accurate real-time density measurements can reduce carbon emissions
Bomag launched its Asphalt Management IC system back in 2001, developing it over the years with its latest version, unveiled at ConExpo this year, being an autonomous roller. The Robomag 2 is a concept roller based on Bomag’s BW 177 D singledrum compactor, equipped with GPS, Lidar and position sensors so that it can operate autonomously. AI-based advances see machine learning deployed to allow real-time readings of the density of the asphalt – rather than the compaction value. In 2021, Volvo launched its Compact Assist with Density Direct which expresses real time density as an air-void ratio. It uses machine learning in the form of artificial neural networks, requiring a calibration strip to set it up.
to existing rollers. “The installation takes less than 30 minutes,” says Commuri. “The calibration process is simple to perform and is easily accessed through buttons on the RTDensity user interface. The entire calibration process takes no more than an hour.”
There are two ways in which accurate real-time density measurements can reduce carbon emissions. First, it reduces the tendency of the contactor to over-compact the asphalt mix, just to be on the safe side, which means that less fuel is required for the roller. And second, it reduces the likelihood of waste, since any quality issues can be identified and addressed during construction while the material is still hot and pliable –rather than later in the day when the road has cooled and the material is unalterable.
Currently, the only reliable way of measuring density during construction is by using nuclear density gauges but these provide measurements at specific locations rather than over the entirety of the pavement. “That is the only feedback the site supervisor has,” says Commuri. “With the RT Density system, the supervisor can use a handheld device to see quality of the entire pavement in real-time during construction.”
MEASURING SUCCESS
The last important piece in the carbonreduction jigsaw is data and data management. In the Netherlands, a group of major contractors – Ballast Nedam, BAM, Boskalis, Dura Vermeer, Heijmans, KWS, Strukton and Van Gelder – have joined forces to create a Pavement Information Modelling (PIM) system. The contractors can use this to access, analyse and manage their own data with the data also shared anonymously for the greater good.
“This requires us to completely renew our information structure and network,” says Sluer. “Ontologies are being developed so that we can really make data interoperable and, by doing that, we can analyse it with a lot less effort and cost.” Ontologies set out how data is stored and ordered in a standardised format, regardless of the variety of data formats used by manufacturers to supply data from their machines and systems.
So, instead, equipment manufacturers developed intelligent compactors that provide a measurement of compaction, rather
Launching commercially this summer is RT Density, a system which also uses machine learning to estimate the density of the road during construction. However, the unique aspect of RT Density, developed by Commuri, is that it can be retrofitted
The goal is to collect and analyse enough data to help create accurate models that will predict a pavement’s life. Armed with this information, road authorities and their supply chains will be much better positioned to understand the longevity and carbon implications of different material and technology combinations.
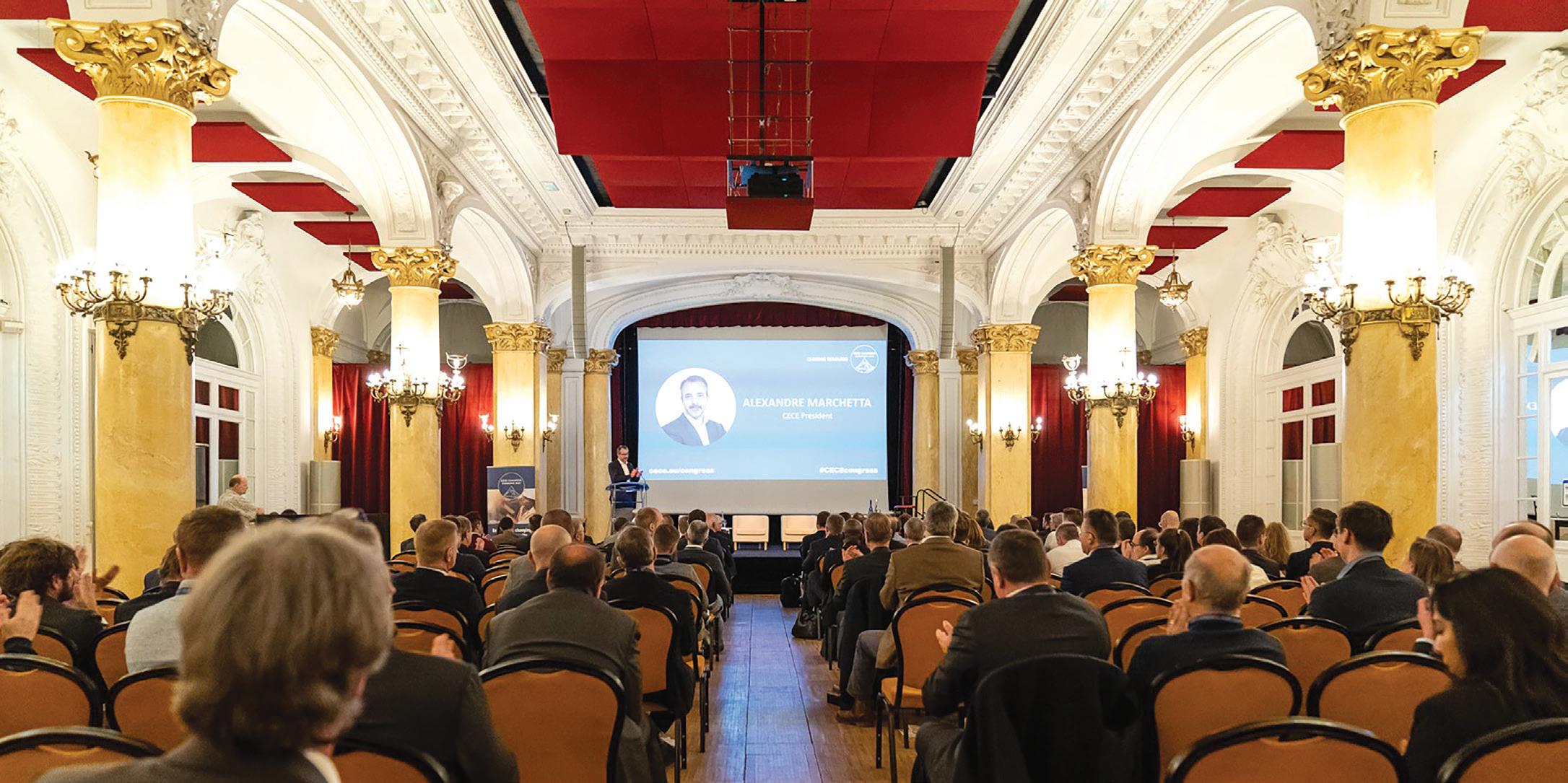

ALTERNATIVE ENERGY: ARE WE GETTING ANY CLOSER?

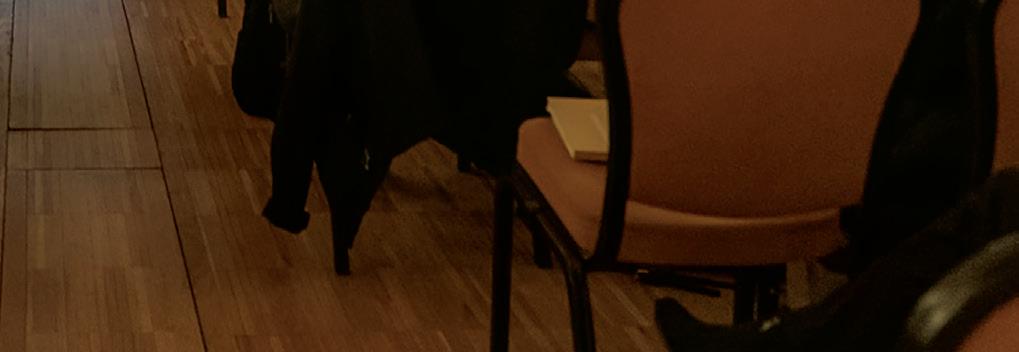
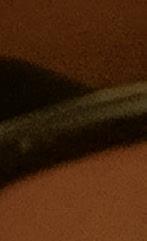
Alternative energy for construction equipment focussed the minds of the 170 delegates attending this year’s CECE conference. is was the rst in-person gathering post-Covid for the Brussels-based Committee for European Construction Equipment, and how best to power up the future was very much on their minds. David Arminas reports from Chamonix, France.
This year’s CECE event was being held amid a growing sense of optimism for the €40 billion European construction equipment sector. A er an economic meltdown caused by the Covid pandemic, there has been a slow rise in sales back to something resembling normal.
e Brussels-based trade association and lobbying group was clearly pleased to give some good news for a change. e 2022 European sales gures “de ed the odds”, according to the CECE Annual Economic Report. Despite in ation, ongoing supply chain disruption, the war in the Ukraine, and global economic uncertainty, the stable market performance surpassed expectations. Sales in Europe – excluding Russia –increased by almost 3% in 2022.
Most of the regions saw minor rates of growth and some saw small declines. However, southern Europe was notable for an almost 12% growth in sales. Incredibly, Turkey had an almost 40% increase in sales while Russia reported an equal decline.
Road machinery saw a minimum increase in sales of 1% while sales of tower cranes remained steady. e concrete machinery market declined 1% and earthmoving equipment sales slipped back 2%. Light and compact machine sales fell back only 0.5% while heavy machinery dipped by 2%.
Despite supply chain disruptions, machine availability generally increased and 2023 is expected to have a strong start because of a high order backlog. Nonetheless, with high in ation and low GDP growth of around 0.3% expected for the coming year, the outlook is uncertain.
NET-ZERO COMMITMENT
While the economic outlook is good, the health of the industry as it moves towards mid-century depends on how well it can accommodate the net-zero carbon-emissions reduction that the European Union requires by 2050. Even though the construction equipment sector in the EU’s 27 member countries produces only about 0.5% of
Europe’s total greenhouse gas emissions, the sector has committed to net-zero carbon emissions. To achieve this there are four “interdependent pillars”, as the CECE calls them, to reduce carbon emission from construction equipment.
One is the integration of optimised machine components, or simply machine e ciency. Another is optimisation of the work ow on site, including best machine choice for the job. Digital technologies and better operator training to maximise machine e ciency are also essential. Finally, the possibility of selecting alternative energy sources: battery, electric, hydrogen or a hybrid solution will be required.
Energy choice depends on several factors. Will the machine be used continuously and thus a ect energy consumption per hour, per shi or throughout the day? How remote is the site and what access is there to any alternative energy source?
Bringing machines that use these alternative energy solutions to market is slow ➔



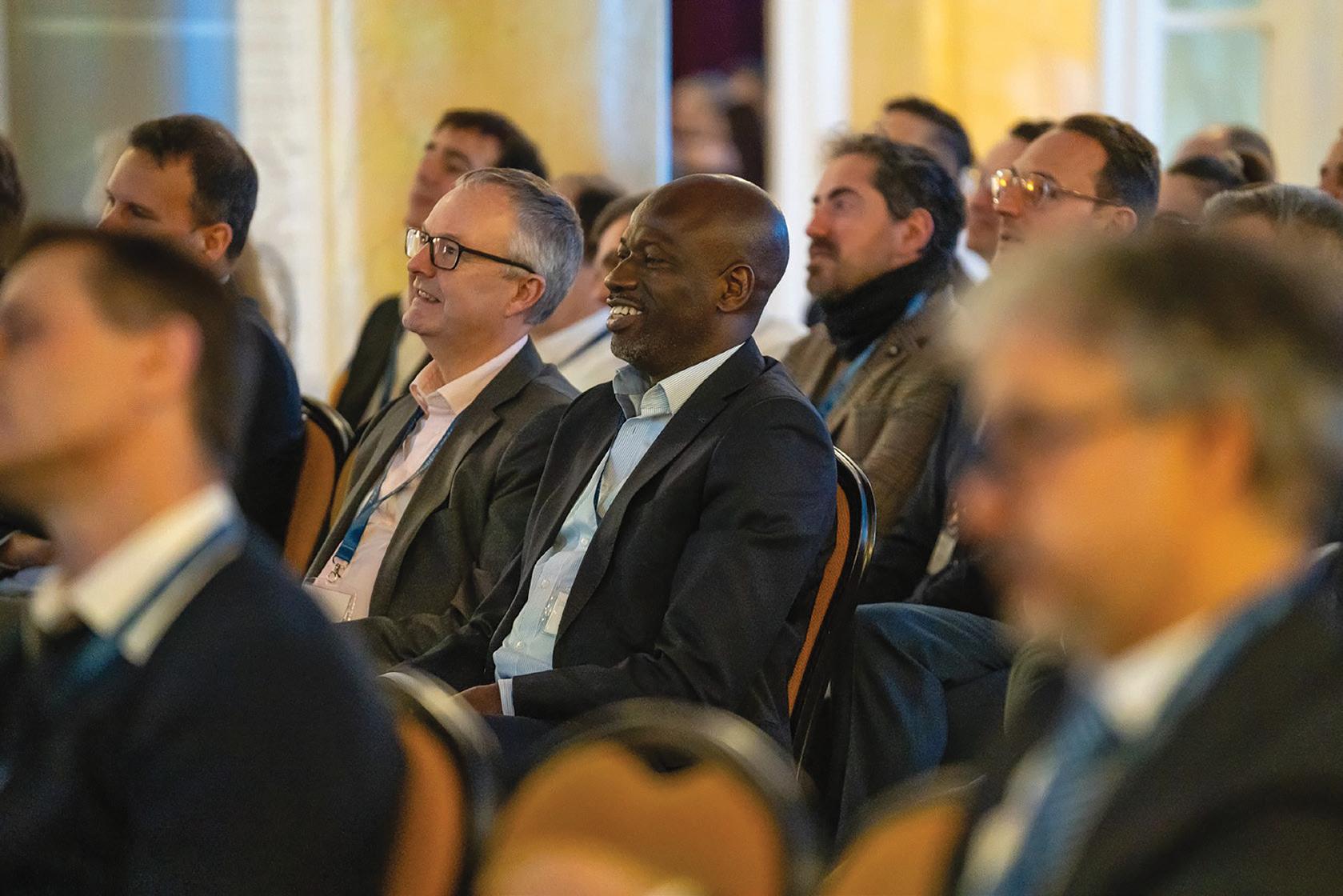
Volume battery cell manufacture for NRMMs – non-road mobile machinery - will be based on automotive cells, for volume reasons, as well as investment. e summary above shows the automotive cell price and a range of the pack price for non-road. Smaller 48V batteries, as found in mini excavators or compact construction equipment, are being sourced from automotive or materials handling (usually forkli ) vendors. Larger cells may be custom-made for NRMM and also used in energy storage in other sectors such as rail and marine. Automotive demand is, however, increasing prices in the short term and there may be a period of levelling out before prices fall a er 2025
Source: KGP Commercial Powertrain Intelligence
and will remain so for even up to a decade. Prototyping is essential in the rst instance and then moving to production and in su cient numbers to satisfy demand is next.
But attaining volume production to o er customers lower unit costs and access to and lower cost of alternative sources will be the game changers.
Achieving decarbonisation and net zero needs supportive European Union policies. To help with all this governments must incentivise eet owners to take on so-called green machines when their old machinery needs replacing.
But the CECE warns that legislation towards attaining net zero must target the goal of achieving net zero and speci cally not the choice of machinery and alternative energy for the sake of it.
While all this is playing out in Europe, there must be similar e orts within other countries and regional groupings to ensure a level playing eld for exports and sales of European-made machinery.
REGULAR FUEL SUPPLY
So where does that leave the contractor who nds himself increasingly having to show potential clients that his CO2 footprint is getting smaller and smaller? One way is moving towards alternative fuel for his machinery. Even with new machinery coming onto the market that uses electricity – either from on-site power generators or on-board batteries - or have engines recon gured in some way to burn hydrogen or
have engines designed speci cally to burn hydrogen - the most pressing challenge, for the moment, at least, is the regular supply of reasonably-priced alternative energies. is is particularly the case for hydrogenburning equipment, explained Jean-Baptiste Martin, from Total Energies. He is head of hydrogen development for France, focussing on mobility and industrial applications. His company aims to be in the forefront of creating the “hydrogen value chain”, as he calls it.

One of the themes of the CECE Congress 2023 was diversity in the construction and construction machinery sector (image courtesy CECE)

e rst stage is to design an onsite or nearsite supply depot and fuelling station. is is a project management approach that requires engineering and design consultancies where the installation must comply with whatever regulations. It all must be constructed and then commissioned. Regular servicing will be required as well as experienced operators of the systems. Last but not least, a regular supply of hydrogen with a low CO2 footprint must be available. As well, the site might need its own on-site renewable electricity generation.
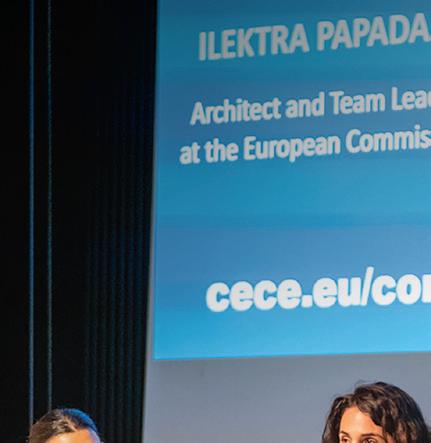
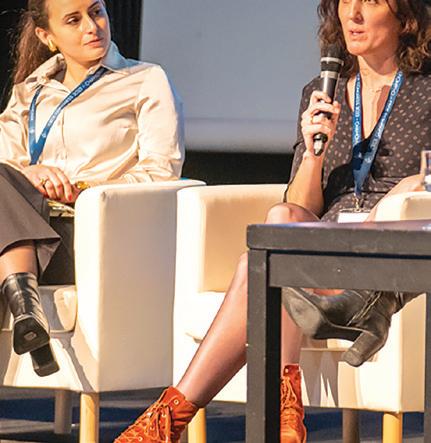
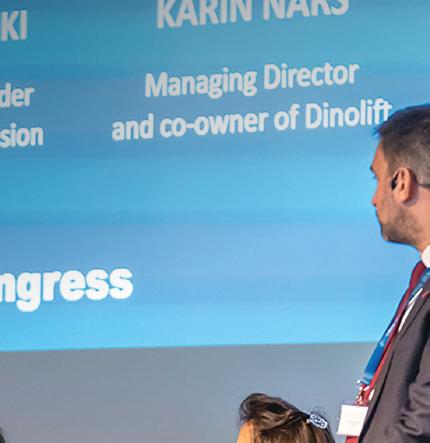
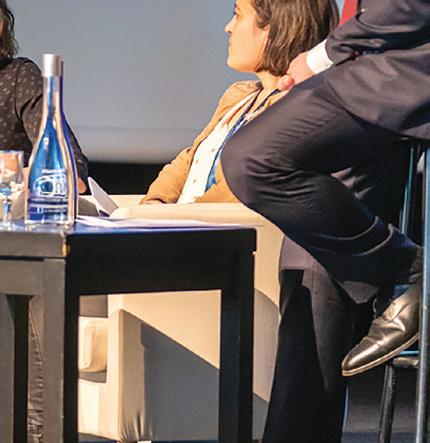

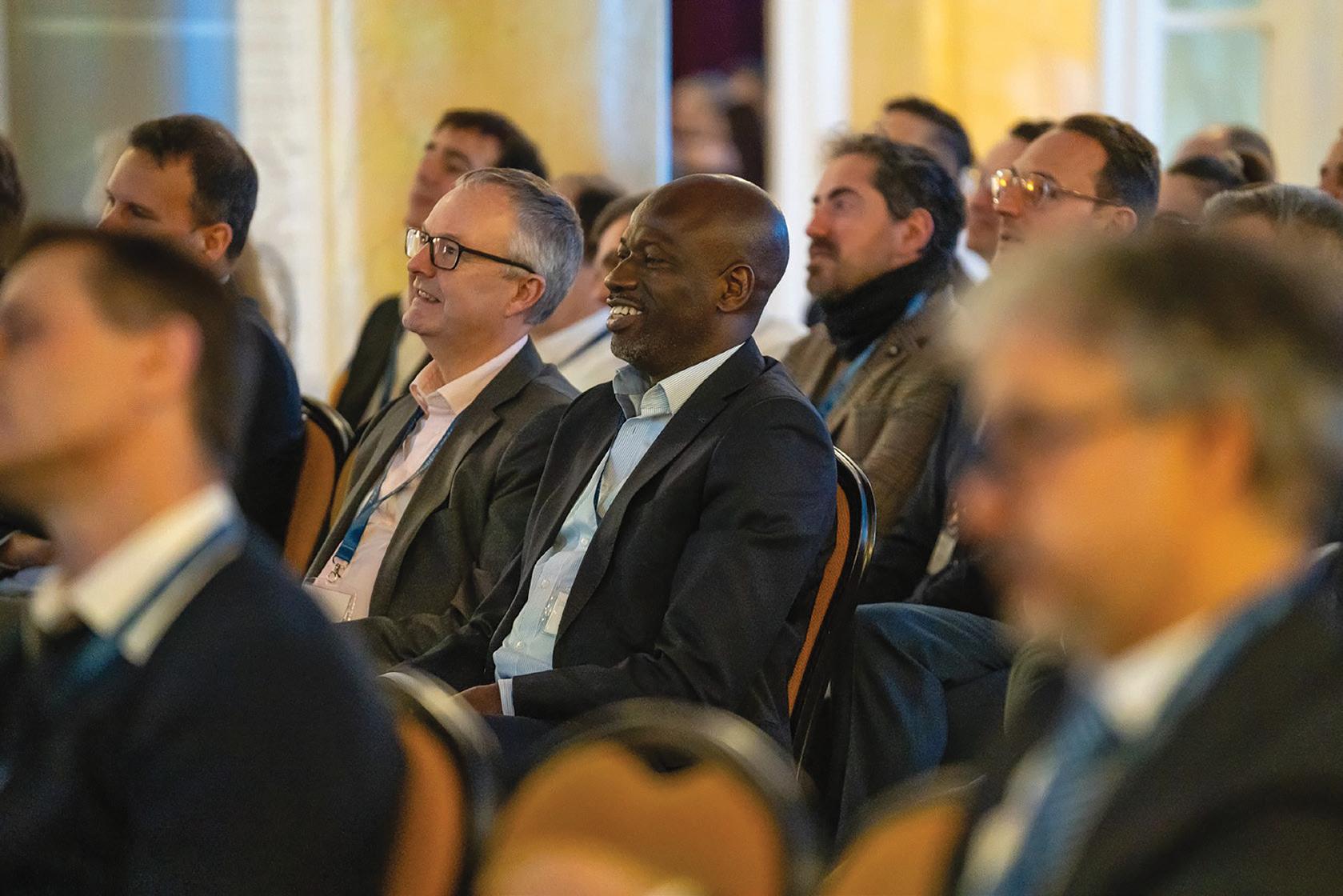
He believes that such off-road hydrogen supply sites will rely on compressed hydrogen for a long time before liquid hydrogen can be used and altered on site. Meanwhile, for worksites such as those for highways, the refuelling station likely needs to operate fleets of suitable delivery vehicles to bring the hydrogen directly to machinery in the field.
Excavators are not likely to travel a mile back to refill and then return to their job station.
One such solution being tested is the deliverable-to-site HyCARE project, turning delivered liquid hydrogen into a gaseous state for use in machinery. This hydrogen-as-aservice project aims at developing a hydrogen production and storage system.
The tank will link hydrogen and heat storage to improve energy efficiency and to reduce the footprint of the whole system. It will be connected to a 55kW Proton Exchange Membrane (PEM) electrolyser as hydrogen provider and a 20kW PEM fuel cell as hydrogen user. The tank will be installed on the site of ENGIE Lab CRIGEN, a research and operational expertise centre dedicated to gas, new energy sources and emerging technologies.
The research institutes – including University of Turin as project coordinator - provide expertise in the development and characterisation for metal hydrides for H2 storage, structural, chemical and thermo-dynamical characterisation, system modelling, design, construction and testing.
Three SMEs (small-to-medium-size enterprises) are in charge of providing the key components of the HyCARE system: the metal-hydride (MH) pellets for hydrogen storage; the heat-recovery system with phase changing materials; and the container. ENGIE Lab CRIGEN (France) is in charge
Non-road mobile equipment and suitable battery applications: AG = agricultural equipment, CE = construction equipment and MH = materials handling equipment. Source: KGP Commercial Powertrain Intelligence
Equipment
Mid-Size Equipment
Equipment
Extra-Large Equipment
Exc, Compact WHL, Site Dumpers, Small Ag, Rollers, Asphalt Finishers, Telehandlers, Compaction
Crawler, Wheeled Exc, STL/CTL, WHL, Telehandlers Materials Handling Loaders, Forklifts, Graders, Compaction
Crawler Exc, WHL, Mobile Cranes, Drilling/Piling Rigs, Processing Equipment, Large Tractors/Combines, Forestry, Port Handling, Large Materials Handling
Mining Equipment, Marine, Rail
: Mild Hybrid/Battery Electric/H2
AG: M.Hybrid/ F.Hybrid/H2
CE: M.Hybrid/ Umbilical/H2
: Umbilical/H2 Battery Electric
: Umbilical/H2
: H2/Umbilical
of installing and testing the HyCARE system on site.
is “hydrogen-as-a-service” must have fuelling stations with dual pressure of 350 and 700 bar, be a high-capacity and highly exible system transportable and deployable within four to six weeks.
HYBRID DEVELOPMENT
Bárbara Gregorio, divisional product marketing manager of innovative energies and digital solutions at Atlas Copco, outlined to delegates what a future power grid at a construction site might look like. Hybrid solutions on construction sites are becoming a crucial aspect of the industry as it looks to reduce emissions and improve energy e ciency.
Atlas Copco provides power solutions to its customers, including diesel generators, alternative fuels and hybrid solutions.
e integration of battery systems and energy storage with renewable energy sources such as solar panels is playing a vital role in making energy consumption more e cient.
one of Atlas Copco’s hybrid energy storage systems to the generator. is resulted in a signi cant reduction in fuel consumption, cost savings, and CO2 emissions, she said. e hybrid system reduced the local consumption by around 75%, improved the average load of the engine from 10% to 85% and reduced the running hours of the generator by 90%. Even when the generator was not running, the batteries were still in operation, making this application perfect for hybrid systems.
In battery technology, the term “cycle” refers to a full discharge and recharge of a battery; the typical expectation for lithiumphosphate batteries is 5,000 to 6,000 cycles, equating to a lifespan of 20 years for a machine that undergoes one cycle per day. A hybrid system that includes a large battery pack can signi cantly reduce the size of the generator and its energy consumption by more than 50%.
By considering a hybrid system, machines can last for 20 years or more
She presented a case study of a customer in the UK who was operating a 20-year-old diesel generator with a daily fuel consumption of 3,540 litres. e low load of the generator led to frequent maintenance and black lm leakages, making the engine more prone to failure.
To address this issue, the customer added
HYDROGEN UNIT FROM HYUNDAI
Other advantages of using alternative energy solutions include increased generator lifetime as well as reduced fuel and oil consumption. In her conclusions, Gregorio stressed that when considering the load pro le and energy consumption of a machine, it is important to consider alternative energy solutions such as hybrid systems. ese systems can help prolong the lifetime of machines and bring other bene ts, such as lower investment costs and increased
utilisation and resale value. By considering a hybrid system, machines can last for 20 years or more, ultimately bringing cost and environmental bene ts to the customer.
VOLVO E-WORKSITE
ere will never be a silver bullet for what people call the “green transition”, said Carolina Diez Ferrer, head of advanced engineering programmes at Volvo Construction Equipment. Instead, it will be a gradual change, undoubtedly supported by technologies such as electri cation, hydrogen fuel cells and alternative fuels.
However, new and improved technologies are only part of the path to a green transition. To achieve the goal of becoming carbon neutral as a society and ful lling the Paris Agreement, industries will need to change mindsets, business models, infrastructure, regulation and support systems.
Most importantly, it is crucial to ensure e ective collaboration with various stakeholders, including governments, society, and other parts of the industry. Volvo CE itself has set an ambitious goal to become 100% fossil-free by 2040. is includes not only their products but also their entire value chain, said Diez Ferrer.
To this end, Volvo CE initiated its E-Worksite project in 2021 in Göteborg, Sweden, which was recognised six years ago as the most sustainable city in the world, an element that made it the ideal location.

ese systems can help prolong the
element that made it the ideal location. e project aim was twofold: to demonstrate the e ectiveness of electric construction equipment and how it can be
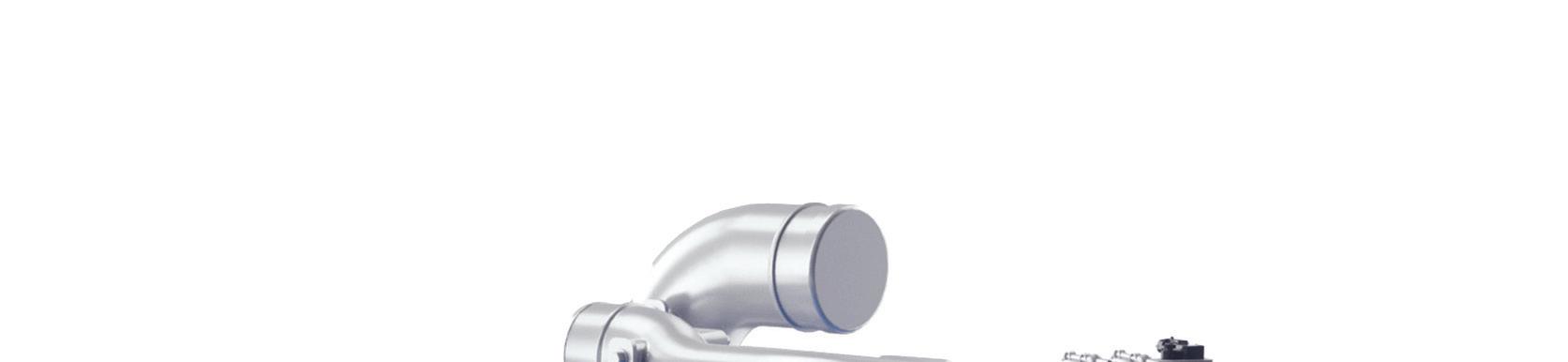

HD Hyundai Infracore is aiming to mass produce hydrogen-burning internal combustion engines (ICE) in 2025. The rm unveiled a prototype earlier this year, an 11-litre engine that produces 300kW of power and 1,700Nm of torque at 2,000rpm.



The company said that the unit meets the Tier 5/Stage 5/Euro 7 regulations which require its emissions to be reduced by 90% from the current level to meet Zero CO2 (below 1g/kWh) and Zero Impact Emission (Zero Emission in EU). Hydrogen engines are powered by low-purity hydrogen, making them durable, economical and energy-dense - suitable for mid-to-large-sized vehicles and vehicles for long distances. A single charge of 10 minutes enables a distance of up to 500km. HDI says that the units are 25-30% more economical than fuel cells or battery packs when vehicle price and maintenance costs are considered.
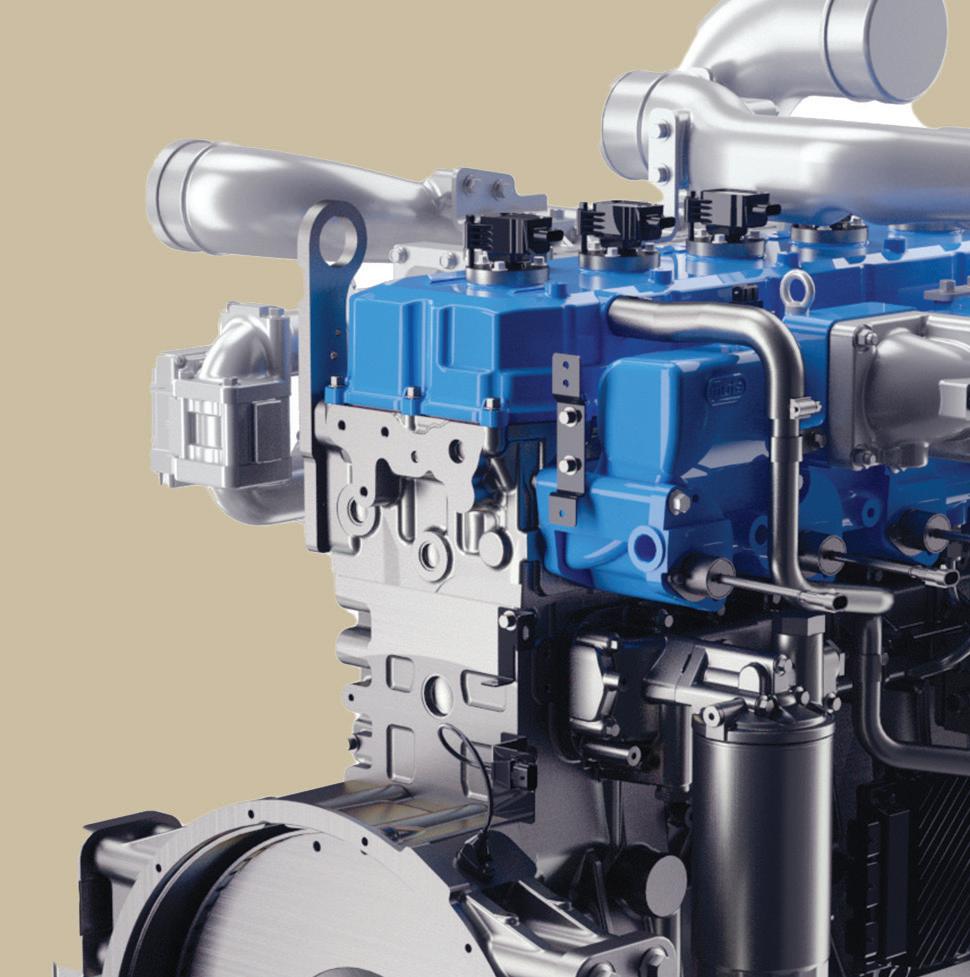


“Hydrogen internal combustion engines will be used in mid-to-large-sized commercial vehicles such as construction equipment, trucks and buses and mid-to-large-sized power generators,” said Kim Joong-soo, head of HDI’s engine division. Production will start in 2024 and ramp up to full-scale mass production in 2025.

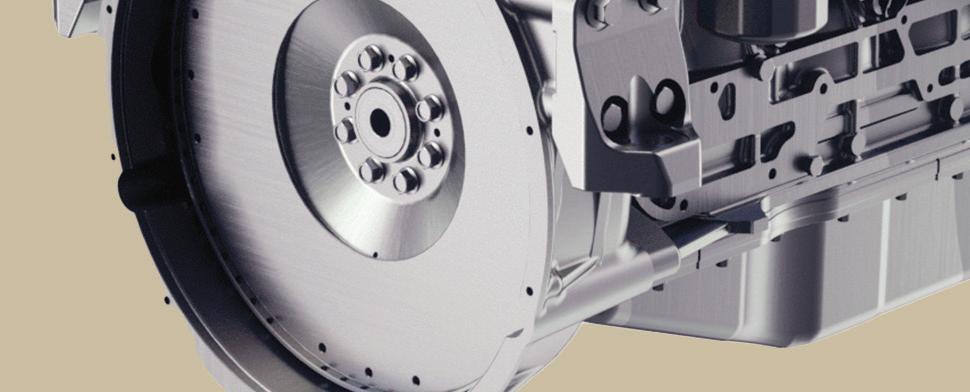

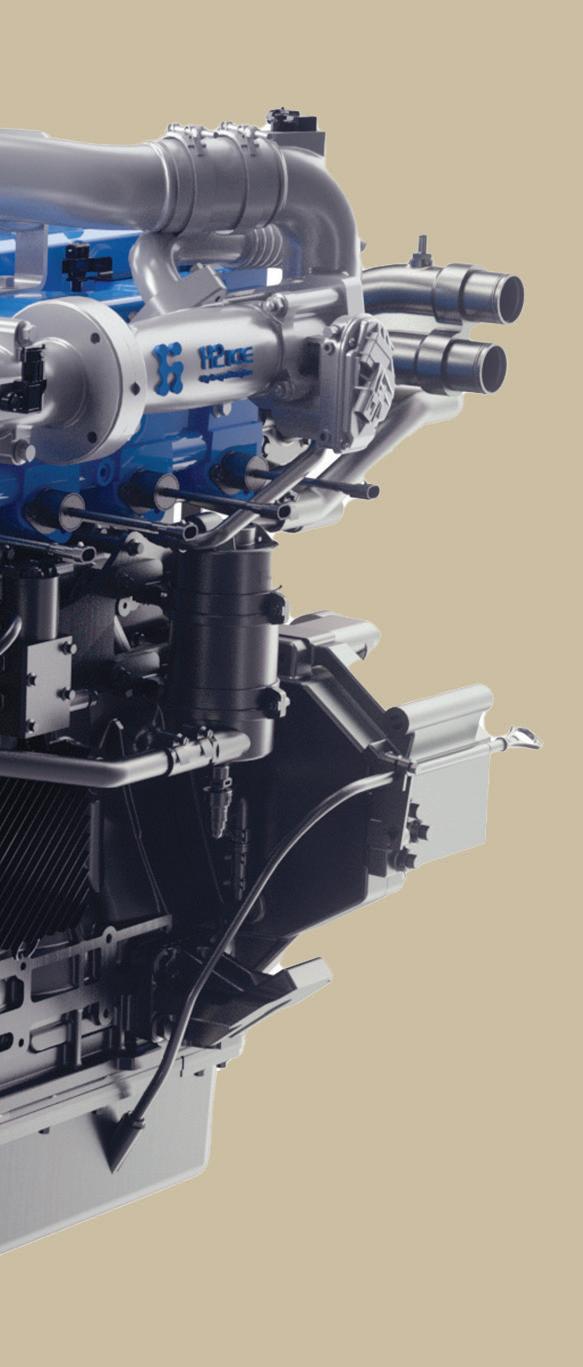

A ground-breaking research project with Volvo Construction Equipment (Volvo CE) and partners in Göteborg, Sweden, to explore every aspect of the electric ecosystem is helping to deliver a complete site solution for real urban applications (image courtesy Volvo CE)
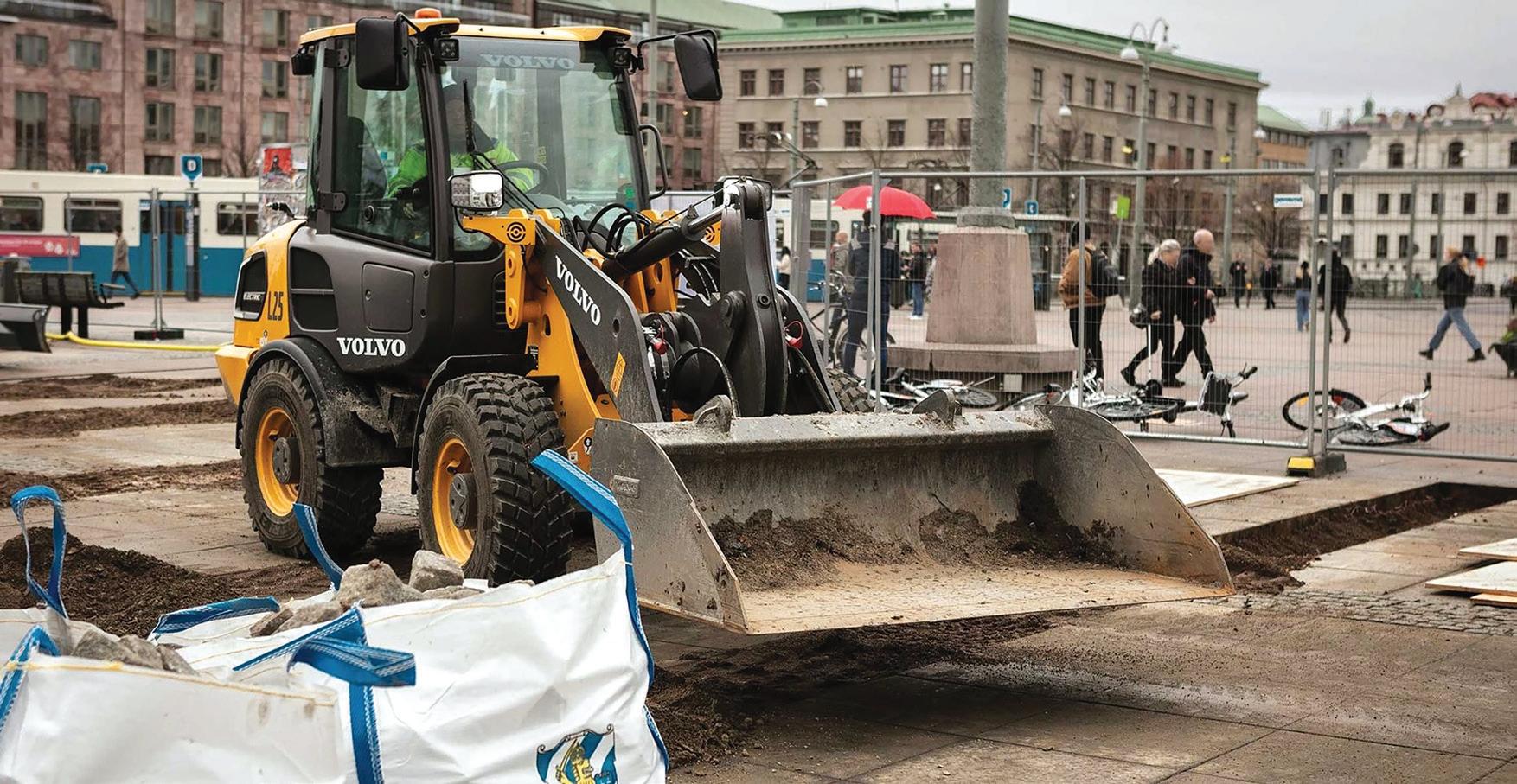
used on a worksite and to train the operators on how to use the machines in the most e cient way. e project has also achieved cooperation of the government, universities, research institutes and construction companies.
e rst step of the project was to test the machines that were already on the market while also testing medium- and large-scale machines. In another on-site project, Volvo’s own L25 Electric compact 40kW wheeled loader and the ECR25 20kW mini excavator worked on di erent types of jobsites doing di erent work. e work ranged from moving dirt, excavating, rebuilding and grading tasks.
Evidence concluded that a level 2 charging was su cient for most work. e L25 Electric loader could work for eight hours before needing to be charged and the ECR25 excavator needed to be charged only during the operators’ break time. Volvo CE also conducted its own analysis and found that infrastructure issues can be solved with proper site management and power control.
In conclusion, the machines were found to improve the work environment, there was a quick learning curve for the operators and customers trust the company to help with the transition to electric machines. e project is ongoing and further activities will be conducted, she said.
BATTERY OPTION
On a positive note, KGP Commercial Powertrain Intelligence estimates that the sector could achieve zero-emissions targets within ve to 10 years.
e obvious bene ts of lowering the carbon footprint are many: air quality, lower noise, lower fuel costs, reduced maintenance cost and improved productivity. Holding all this back is reaching signi cant investment
in getting batteries to be more powerful and with longer charging cycles. But thankfully, investment opportunities will be found in infrastructure and charging systems to help contractors to charge and reach the same level of productivity with their electric machines.
Availability of alternative fuel is, of course, one of the big issues a ecting the green transition, said Alex Woodrow, managing director at KGP. “O -road will need dedicated infrastructure. In a lot of cases that will be expensive and o en take signi cant time to set up, leading to possible project delays. So, there will be niche and targeted applications of alternative fuel use that can achieve zero emissions early. But these will remain limited through 2030.”
ere are ve times the number of electric machines available today compared to even 2019. By 2032 globally, around 17% of o road machinery will be zero-emissions such as hydrogen or electric.
What is hindering the rise being even higher is the di culty in converting the larger machinery to use hydrogen. Given that, notes Woodrow, there will be a continued demand for fuels such as renewable diesel HVO100 and synthetic diesel that can be produced using green hydrogen.
All will be more expensive than fossil diesel but will have a much lower carbon footprint and ultra-low NOx (nitrogen oxide) and PM (particulate matter).
CECE, Committee for European Construction Equipment, represents and promotes the interests of European construction equipment manufacturers and companies in related industries. It also co-ordinates the views of national associations and their members by in uencing other national and pan-European institutions and organisations.
DEFINITIONS:
HVO100 DIESEL
HVO100 (hydrotreated vegetable oil) fuel is made from 100% renewable material and is free from any fossil fuels. It is produced by using sustainably sourced vegetable and animal matter to ensure its production does not have any negative impact on the environment.
SYNTHETIC DIESEL
Synthetic diesel fuels can be made from carbon-containing feedstocks, such as natural gas or coal, in a process developed by Fischer and Tropsch in the 1920s. That process has been further developed by oil companies.
GREY HYDROGEN
Grey hydrogen is produced from fossil fuels, resulting in carbon dioxide emissions released into the atmosphere.
GREEN HYDROGEN
Basically, green hydrogen is produced by using renewable energy – wind, water, solar or from low-carbon power - to power the electrolysis of water. Green hydrogen (GH2 or GH2) has signi cantly lower carbon emissions than grey hydrogen, which is produced by steam reforming of natural gas, which makes up the bulk of the hydrogen market. Green hydrogen produced by the electrolysis of water is less than 0.1% of total hydrogen production.
BLUE HYDROGEN
Blue hydrogen is hydrogen is produced from natural gas and supported by carbon capture and storage. The CO2 generated during the manufacturing process is captured and stored permanently underground. The result is low-carbon hydrogen that produces no CO2. However, Blue hydrogen does not reduce energy dependence on gas and perpetuates a development model based on fossil fuels.
LEVEL 2 CHARGING
A level 2 charger requires a 240-volt electrical source. Compared to a level 1 charger (120-volt). It allows the charging of a fully electric vehicle ve to seven times faster or up to three times faster for a plugin hybrid.
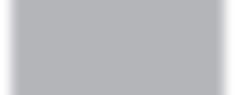
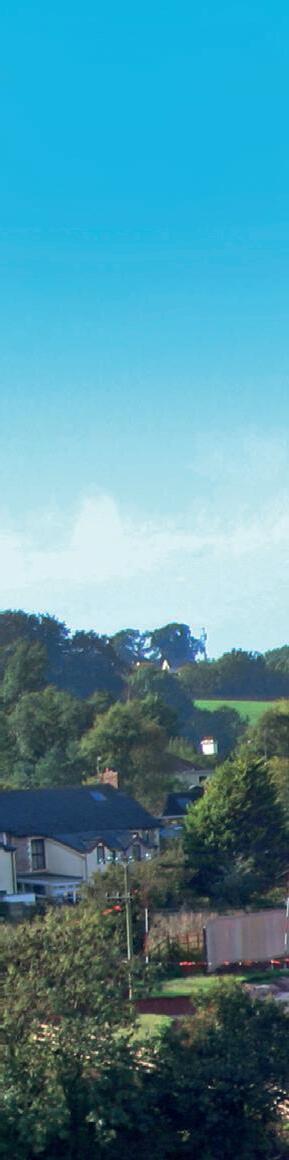
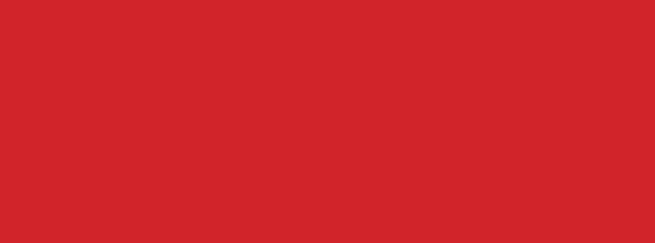
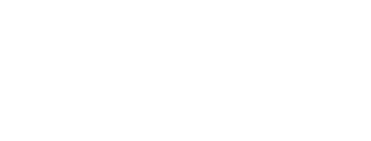
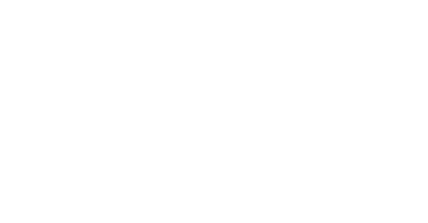
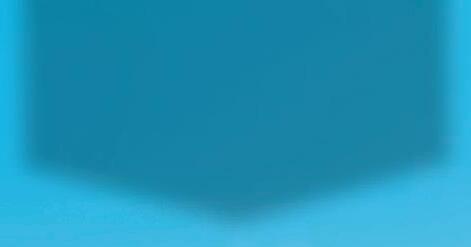
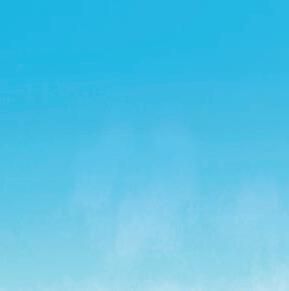


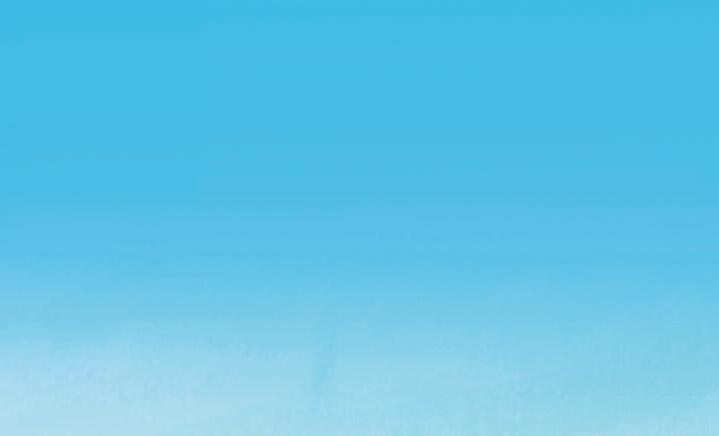
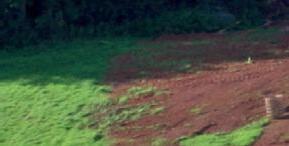


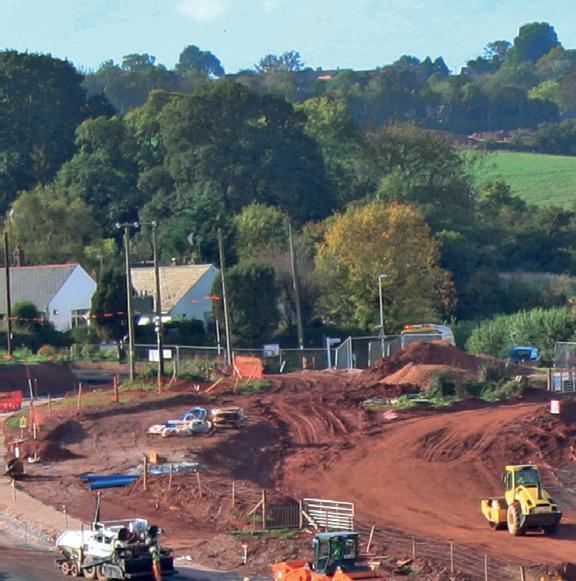
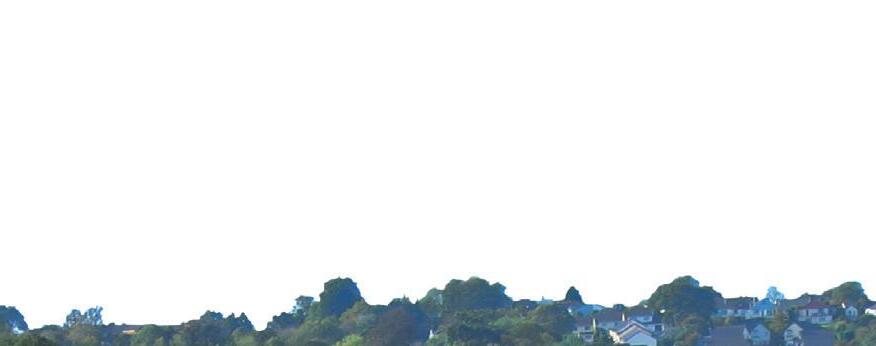

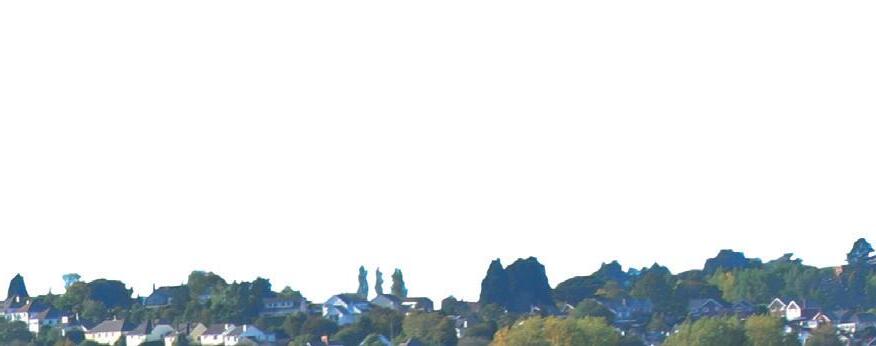
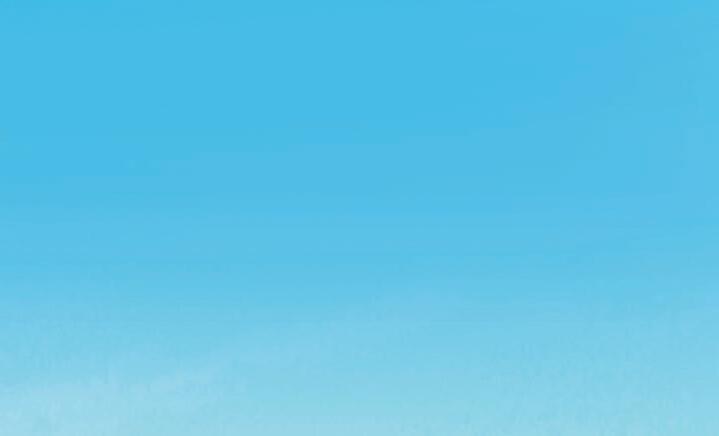

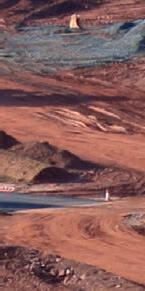
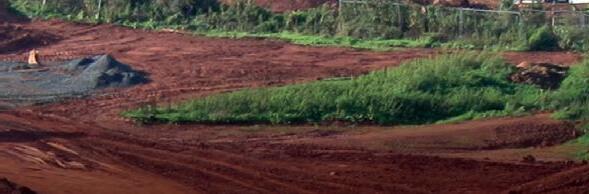
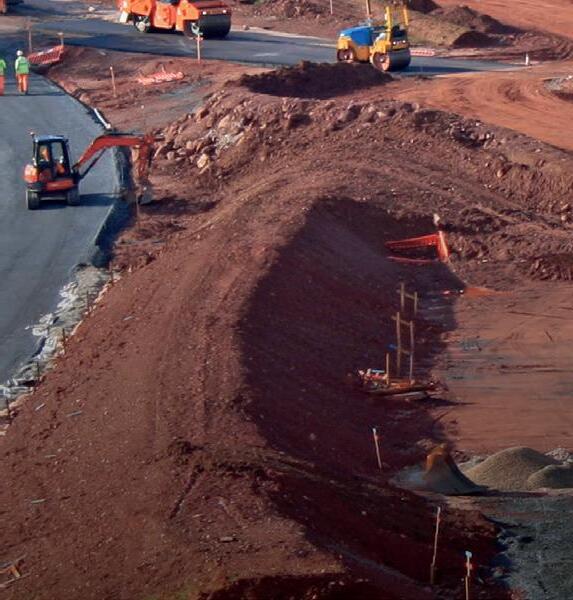


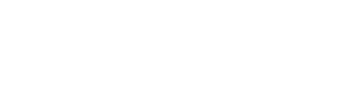

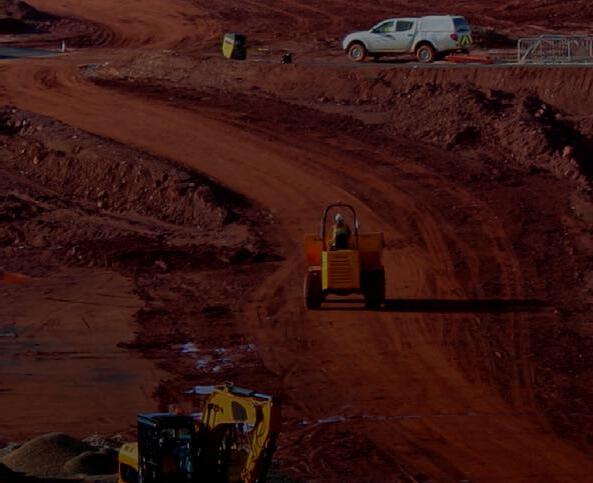
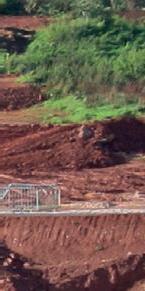



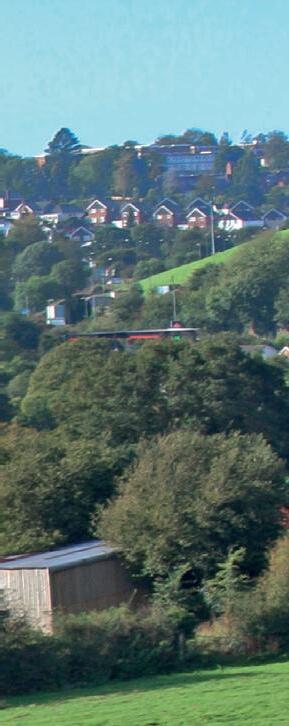


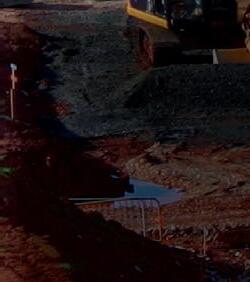

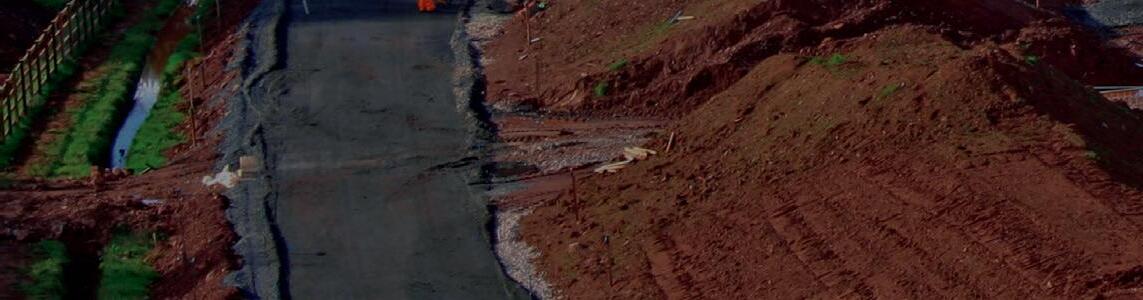
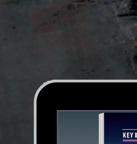
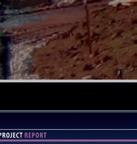
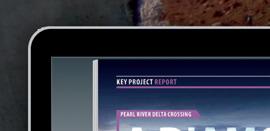
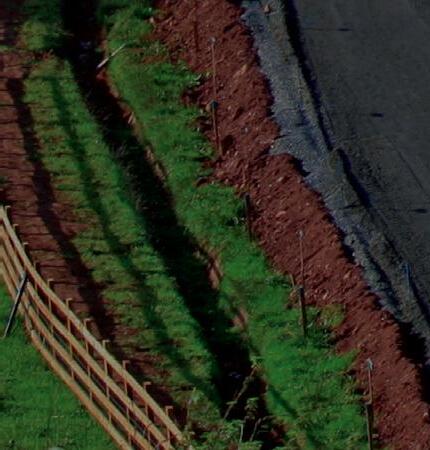

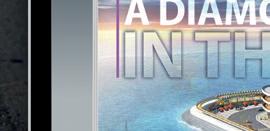


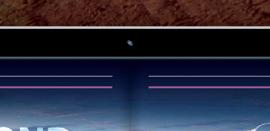
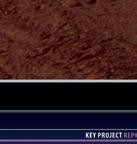


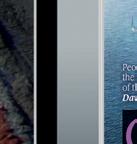
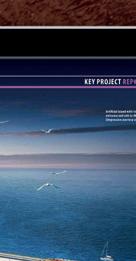
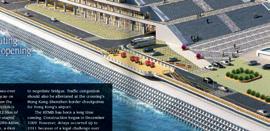
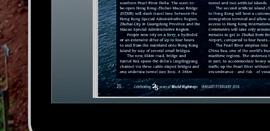
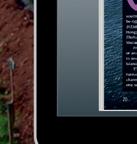
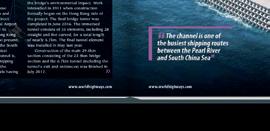
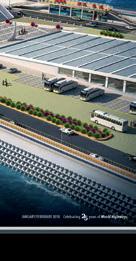
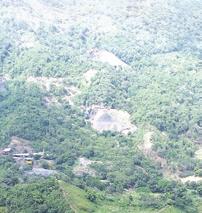

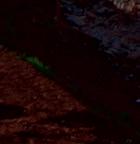
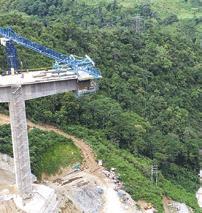

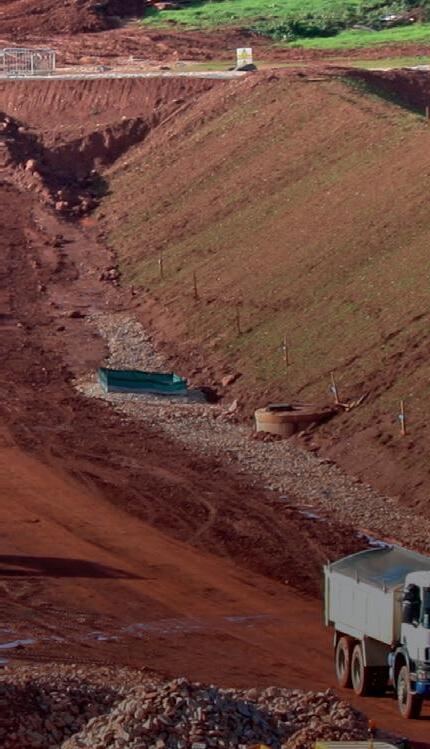
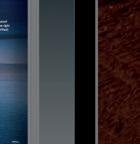

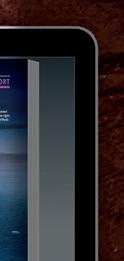
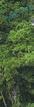
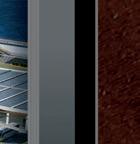

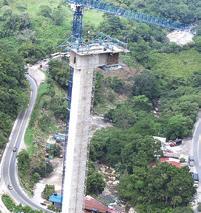

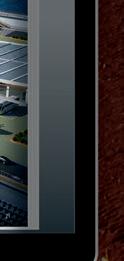
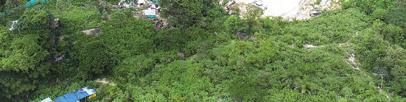
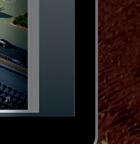
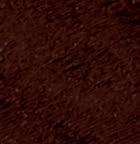
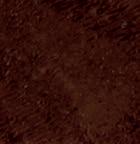
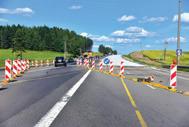
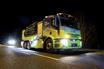
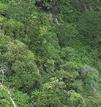
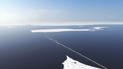

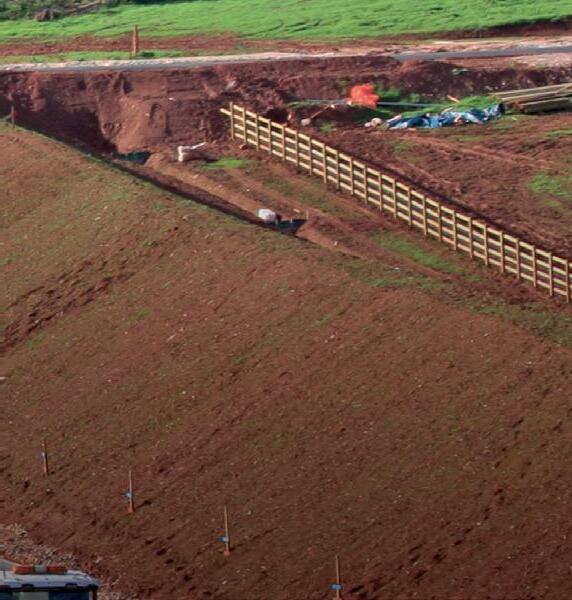




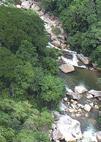
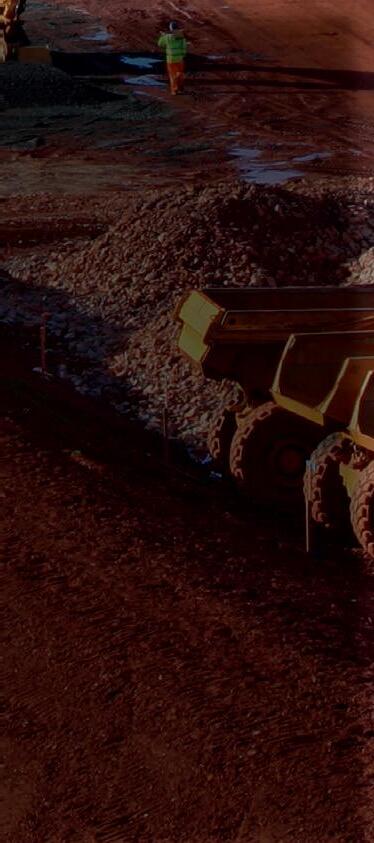
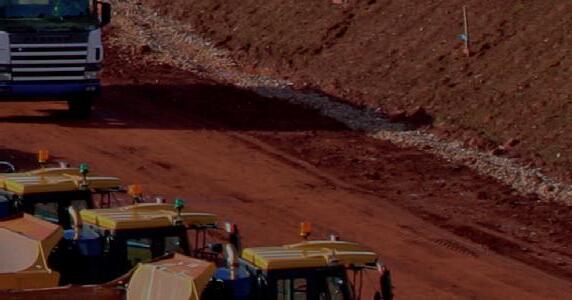
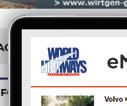
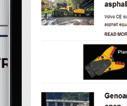
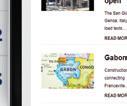
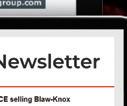
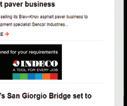
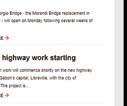
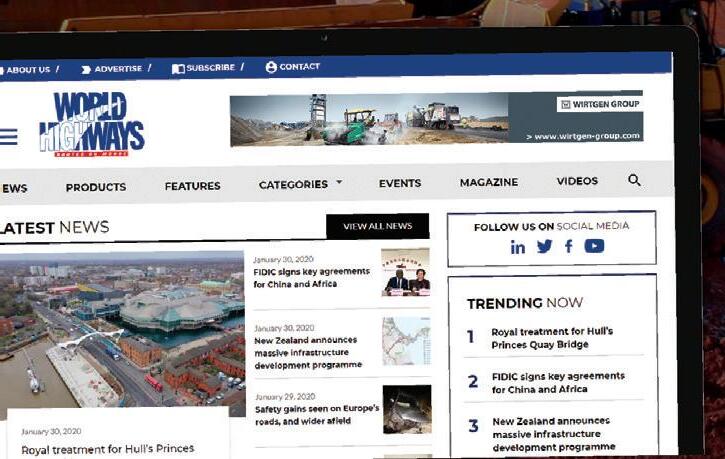
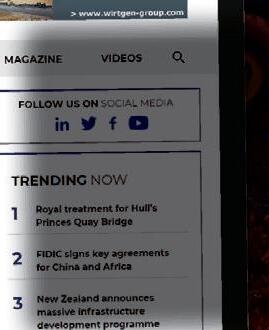
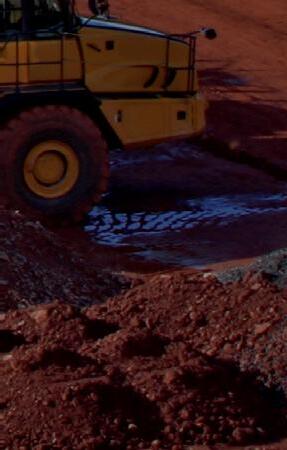


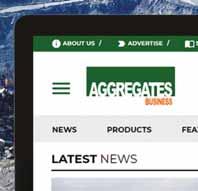
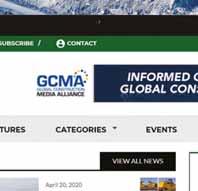



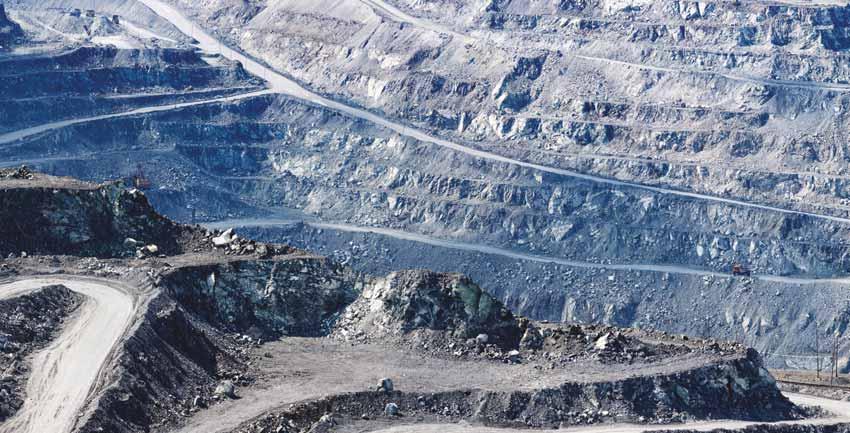
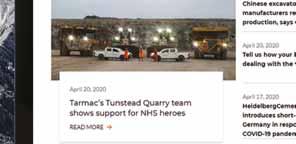

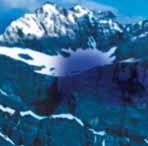
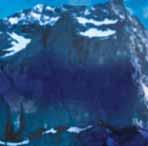
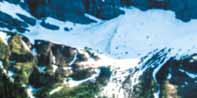
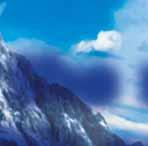
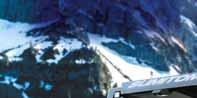

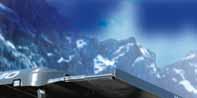

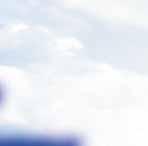


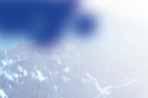
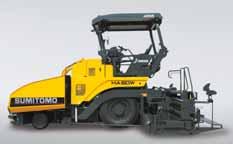



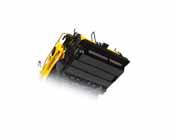
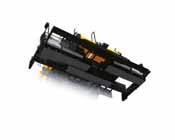

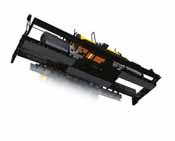

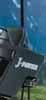


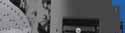
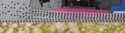
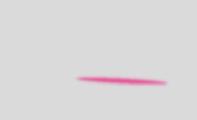


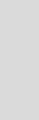


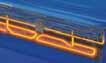

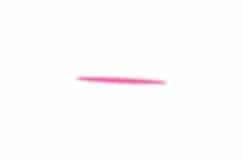



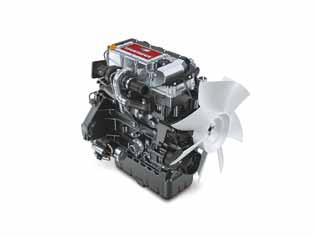

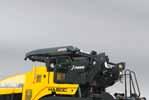