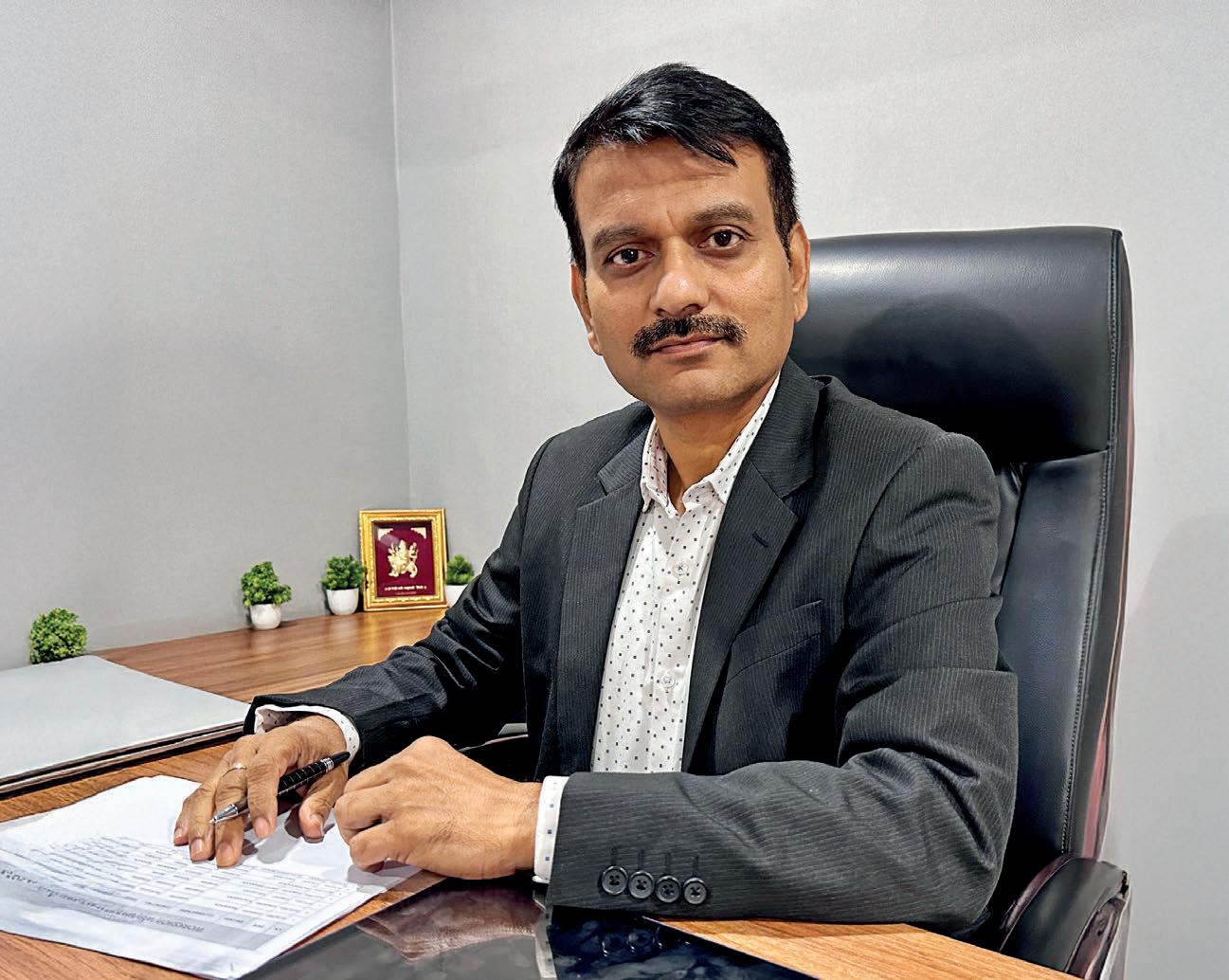

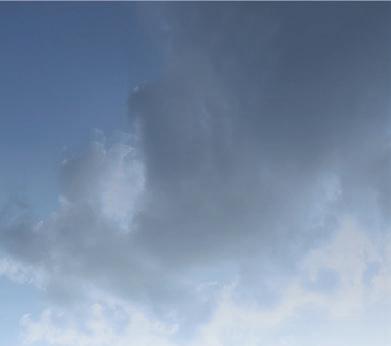
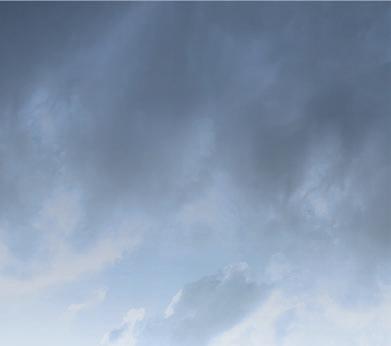
INDIVIDUAL RUNNING GEAR SOLUTIONS FOR SPECIAL TRANSPORT TASKS.
With our running gears and special axle solutions, there is nothing that can’t be transported. Your requirements motivate us to create new things. They inspire us to use our entire engineering expertise and decades of experience to develop innovative and reliable solutions together with you – customised for the type of vehicle and intended use.
The vehicle concepts for low-loaders are as varied as the transportation tasks. The use of air-sprung modules with rigid and steering axles is just one solution from our uniquely wide range of running gear systems for low-loaders. Challenge us!
What
What
DSV
A
in the US,
A market leader in the
e OEM is bringing ‘enginuity’ to its tanker
Haldex
e Chinese OEM is ramping up
BPW’s new swing axle requires minimal installation space and allows maximum design freedom.
e laminate specialist details the perfect solution for tank containers and
For modern, durable and versatile load restraint solutions, Versus-Omega presents the Scala pillar.
Since its establishment in 2019, Jagdamba Trailers has rapidly expanded, now operating in most Indian states as well as an upcoming facility in the United Arab Emirates. is growth re ects the company’s dedication to providing high quality trailer solutions, meeting the diverse needs of the market and becoming a strong international contender.
“JAGDAMBA TRAILERS HAS CONSISTENTLY RISEN TO THIS CHALLENGE BY OFFERING INNOVATIVE SOLUTIONS, SUCH AS HIGH-TENSILE STEEL TRAILERS, WHICH PROVIDE ENHANCED PAYLOAD CAPACITY WITHOUT SACRIFICING
JOST’s acquisition of Hyva consolidates the value o ering of both companies.
Automated robotic welding technology at its nest.
Tapping critical minerals and securing supply chains is essential as we move forward with the energy transition. E orts in sustainability are ramping up and so, too, is demand for the resources that OEMs and equipment specialists rely on to produce green technology.
An analysis using data from the United States Geological Survey and the International Energy Agency, with a focus on lithium, cobalt, natural graphite and rare earths, revealed which countries dominate strategic mineral supply chains. In terms of which countries hold the most critical mineral reserves, South America has nearly half of all known lithium reserves in Chile (34 per cent) and Argentina (13 per cent). Australia takes third place with 22 per cent.
As for cobalt reserves, the Democratic Republic of Congo owns 57 per cent. Australia follows with 16 per cent. Natural graphite reserves are widely spread however China (28 per cent) and Brazil (26 per cent) claim the majority of the share. Mozambique trails with 9.0 per cent.
Rare earth minerals are mainly found in Asia with China (38 per cent) and Vietnam (19 per cent) holding the biggest reserves. Brazil has 18 per cent of known global reserves.
Looking at the production and processing of critical minerals, China is the primary hub. It is responsible for processing 65 per cent of global lithium mined, 74 per cent
of cobalt and all natural graphite as well as 90 per cent of rare earths.
Mine production is concentrated, too, and does pose risks to supply chain stability. Over half of production for each mineral occurs in a single country. For instance, Australia is the top-producing country for lithium at 51 per cent. For cobalt it is the Democratic Republic of Congo (73 per cent), while China produces the highest share of natural graphite (72 per cent) and rare earths (70 per cent).
So, how do we future proof the supply of critical minerals? A likely consideration is to invest in new mining projects mainly in countries with high reserves but where production and processing rates are low. Meanwhile, there is a call for recyclers and manufacturers to nd a way to meet ever-growing demand for electric vehicles and energy storage systems. A new study found current recycling methods face signi cant challenges including high energy consumption, environmental impact and ine cient recovery of materials.
Adopting advanced techniques like direct recycling and upcycling could cut costs by up to 40 per cent while minimising secondary pollution. Emerging technologies such as bioleaching, deep eutectic solvents and robotic disassembly could transform the recycling scene.
CEO John Murphy john.murphy@primecreative.com.au
COO
Christine Clancy christine.clancy@primecreative.com.au
INTERNATIONAL SALES
Ashley Blachford ashley.blachford@primecreative.com.au
MANAGING EDITOR
Luke Applebee luke.applebee@primecreative.com.au
JOURNALIST
Sean Gustini sean.gustini@primecreative.com.au
HEAD OF DESIGN
Blake Storey
DESIGN
Laura Drinkwater
CLIENT SUCCESS MANAGER
Isabella Fulford isabella.fulford@primecreative.com.au
COVER Image: Jagdamba Trailers.
HEAD OFFICE
Prime Creative Pty Ltd
379 Docklands Drive Docklands VIC 3008 Australia +61 3 9690 8766 enquiries@primecreative.com.au www.globaltrailermag.com
SUBSCRIPTIONS +61 3 9690 8766 subscriptions@primecreative.com.au
Global Trailer is available by subscription from the publisher. e rights of refusal are reserved by the publisher.
ARTICLES
All articles submitted for publication become the property of the publisher. e Editor reserves the right to adjust any article to conform with the magazine format.
COPYRIGHT
Global Trailer is owned by Prime Creative Media and published by John Murphy. All material in Global Trailer is copyright and no part may be reproduced or copied in any form or by any means (graphic, electronic or mechanical including information and retrieval systems) without written permission of the publisher. e Editor welcomes contributions but reserves the right to accept or reject any material. While every e ort has been made to ensure the accuracy of information, Prime Creative Media will not accept responsibility for errors or omissions or for any consequences arising from reliance on information published. e opinions expressed in Global Trailer are not necessarily the opinions of, or endorsed by the publisher unless otherwise stated.
Follow us on twitter @Globaltrailer
AP Moller – Maersk has announced it will turn one of its warehouses into a female operated facility.
Located at Maersk’s Container Freight Station in Chennai, India, the move will see one complete shift operated entirely by female employees. The global logistics company says it marks a significant step forward in a commitment to diversity and inclusion, aligning firmly with India’s ambition to create equal employment opportunities for women, even in sectors that have been traditionally maledominated.
The 12,000-square-metre warehouse will now employ women across all operational functions, including loading/ unloading, picking, surveying, security, housekeeping, administration and forklift operations. This initiative will increase women’s representation at the freight station from 3 per cent to 13 per cent of the total workforce.
“This transformation isn’t just about changing our operations, it’s about challenging the status quo and setting new standards in the logistics industry,” said. Maersk South Asia Managing Director, Christopher Cook. “We are confident that this initiative will not only enhance operational excellence but also create meaningful employment opportunities for women in Chennai’s logistics sector.” The initiative builds on Maersk’s experience from its Dadri facility, which was the first of its kind, entirely operated by women facility and demonstrated improved productivity and operational efficiency.
E-commerce logistics provider, Singapore Post (SingPost), has entered a billion-dollar sale and purchase agreement.
Kuehne+Nagel will manage a Schae er logistics centre in Thailand. Image: Kuehne+Nagel.
Pacific Equity Partners (PEP), headquartered in Sydney, Australia, will reportedly acquire Australian integrated logistics operation, Freight Management Holdings (FMH), at an enterprise value of $1.02 billion AUD (approx. more than €617 million).
“The Board believes this divestment is the best option for shareholders by crystallising the unrealised value of the business and bringing forward unlocking value for shareholders,” said SingPost Chairman, Simon Israel.
Equity firm, PEP, has made more than 200 acquisitions and engaged close to $50 billon AUD (approx. €30.9 billion) in transactions including both acquisitions and exits since 1998.
“We are thrilled to welcome FMH Group to our portfolio,” said PEP Managing Director, David Brown said.
“FMH Group has a stellar track record of growth, a passionate team and a clear and compelling trajectory. We look forward to supporting them to build on their success and facilitate further opportunities.”
FMG Group is a diversified logistics holding company with divisions across 4PL, warehousing, transportation and technology. It comprises efm Logistics, Flip, Border Express, BagTrans, Spectrum Logistics, CouriersPlease and Logistics Holdings Australia (GKR Transport, Niche Logistics and Formby Logistics).
The proposed divestment is subject to regulatory approvals such as approvals from the Foreign Investment Review Board of Australia and SingPost obtaining the requisite approval from shareholders in an extraordinary general meeting of SingPost to be convened.
Schaeffler Vehicle Lifetime Solutions
Asia Pacific has selected Kuehne+Nagel to manage its Central Logistics Center in Thailand.
The 3,000 square metre assembly and packaging facility is in the Si Racha free zone district, close to the Schaeffler manufacturing plant in Chonburi. It will handle operational activities including kitting, goods receiving and shipping.
“This Central Logistics Center will serve as a key supply hub for the Asia Pacific region,” said President of Schaeffler Vehicle Lifetime Solutions Asia Pacific, Micah Shepard.
“With Kuehne+Nagel as our experienced and reliable logistics partner, our goal is to improve the accessibility and efficiency of spare parts distribution by increasing our focus on innovation, progress, and customer orientation.”
As part of its Roadmap 2026, Kuehne+Nagel identifies Asia as a key growth area, with Thailand playing an important role. A recent example is the new distribution centre in the Suvarnabhumi Airport free trade zone in Bangkok, Thailand.
“Our long-term partnership with Schaeffler has grown over the years thanks to our shared commitment and collaborative spirit,” said Managing Director of Kuehne+Nagel Thailand, Cambodia and Myanmar, David Roussiere. “Together, we have achieved remarkable progress and will continue to build on this solid foundation, embracing the opportunities ahead.”
A state of the art, upgraded and fully integrated global manufacturing centre of trailer systems and On/Off highway systems. Expertly designed and engineered with worldwide accessibility, offering you private label and OEM manufacturing solutions.
Drawing upon decades of expertise spanning Asia, Australia, US, and in Europe, Fuwa stands as a global manufacturing powerhouse, unrivalled as the foremost network of specialists in truck and trailer components across the globe.
Spanish logistics provider, Marcotran, has added 30 new Schmitz Cargobull semitrailers to its fleet.
The new S.CS curtainsiders with MEGA VARIOS bodies will be used for intermodal transport. The vehicles are equipped ex-works with Schmitz Cargobull’s TrailerConnect telematics system and a tyre pressure monitoring system.
With this investment, Marcotran is driving forward its growth strategy to optimise its intermodal transport offering, said Marcotran Purchasing Manager, Alberto Marco.
“With these new rail-loadable P400-coded semi-trailers in our fleet, we can optimise our routes, reduce our operating costs and improve the traceability of goods,” he said. “Technology and data play a key role in our growth strategy, and the partnership with Schmitz Cargobull allows us to access the most advanced market solutions and consolidate our position as a benchmark in intermodal transport.”
The new vehicles have a height-adjustable VARIOS body equipped with an anti-theft side tarpaulin and a reinforced anti-theft roof tarpaulin, the Schmitz Cargobull Safety Roof, which ensures the safety of the load.
In addition, the trailers are equipped with ferry equipment and TIR certification, which facilitates transport with various modes of transport and shortens handling times. The galvanised chassis with a 10year warranty ensures a long service life and increased corrosion resistance.
Krone Trailer UK announced that it now has a network of more than 400 workshops and repair vans deployed across the UK and Ireland to provide
a faster and more efficient trailer support service.
Service points on the network can be reached through a multi-lingual 24/7 breakdown hotline, the company said in a statement, adding that customers are assured of rapid response and wideranging service options.
“Whether it’s for preventive maintenance, emergency repairs or routine inspections, Krone’s service network ensures that customers are always within reach of a reliable solution, regardless of their location,” said Krone Trailer UK Aftersales Manager, James Hardie. “Time on the road is directly linked to every Krone customer’s bottom line. Our investment in a national service network of workshops and mobile repair vehicles reflects our dedication to maximising vehicle uptime.”
The mobile repair vans offer on-site assistance for a range of services, including minor repairs, diagnostics, and preventive checks. By bringing service to the customer’s location, the mobile support fleet minimises operational hold-ups and reduces travel costs, while further enhancing the value of Krone field support.
“With this network of over 400 dedicated workshops and repair vans, Krone Trailer UK reinforces its position as a trusted partner for companies across Europe,” Hardie said. “Our commitment to customer service excellence means that businesses can focus on what they do best, while Krone takes care of their trailers’ performance and reliability.”
BPW has announced it has overhauled its exclusive spare parts web shop. The new version, which is now available on the My BPW customer portal, offers
improvements that make the purchasing process more intuitive, faster and more secure. Registered spare parts dealers will find the new functions available automatically on the website.
“Our aim was to make the ordering process for commercial vehicle spare parts as efficient as possible,” said Head of OES Aftermarket at BPW, Matthias Stoof.
“We have worked closely with our trading partners to understand their specific needs and to implement them in practical solutions.”
The new shop is centred around an extended search function that makes it possible to identify BPW genuine parts quickly and accurately. Technical data is provided for each product and, in addition to availability and price, the product weight is now also displayed.
“Our customers need to be confident that the parts they order not only fit, but are also available immediately,” Stoof said. ‘Thanks to our new shop, they can see that at a glance.”
A new function also displays complementary products, such as the appropriate grease for a selected brake.
This should prevent key parts from being forgotten or ordered incorrectly. Soon regularly ordered items will be accessible directly via a watch list or the order history.
As part of its strategy to strengthen its healthcare network in Europe, Kuehne+Nagel has opened a warehouse in Budapest, Hungary.
The 2,000 square metre, GDP-compliant cross-dock facility will serve as a new hub for less-than truckload (LTL) services for healthcare customers, complementing the existing hub in Luxembourg. With two
cross-docks dedicated to healthcare goods for pan-European distribution, the logistics company can optimise routings and reduce lead times for customers, it said in a statement.
The Budapest hub provides secure, temperature-controlled environments set between 2-8°C and 15-25°C and is expected to enhance collection and distribution services across Hungary and its neighbouring countries, including Poland, the Czech Republic, Slovakia, Slovenia, Croatia, Serbia, Bosnia, Romania, Greece and Bulgaria.
“Due to the sensitive and highly regulated nature of healthcare goods, businesses were initially hesitant to shift from full-truckload (FTL) to LTL services,” said Global Head of Healthcare Road Logistics, Joerg Woyke. “We have earned their trust by demonstrating that our LTL services meet the same rigorous quality standards, while offering cost-efficiency and reduced carbon emissions. As the demand for these services grows, we are strengthening our network, enabling customers to benefit from even shorter lead times.”
The launch of the Budapest hub is part of a broader initiative aimed at optimising the road freight network in Europe to meet the demand for high-quality and efficient transportation of healthcare shipments.
CEVA Logistics is strengthening its presence in Spain with a new logistics facility in Tarragona, Catalonia.
The 18,000-square-metre warehouse, dedicated to contract logistics, is expected to improve the logistic company’s ability to serve customers across key sectors and strengthen its leadership position in the Iberian market.
Located south of Barcelona, a regional
Schmitz Cargobull were the winners of a sustainability award.
logistics hub, it will allow CEVA to partner with clients in key sectors including automotive, retail, industry and eCommerce.
“The opening of this new logistics platform in Tarragona marks a key milestone in our strategy to expand our contract logistics activities in Spain,” said Contract Logistics Product Head for Iberia, Puerto Ahedo. “It demonstrates our ongoing commitment to meeting the growing needs of our clients in the region. With more than 40 facilities and over 600,000 square meters of warehousing space, we are proud to be a leading logistics provider on the Iberian Peninsula.”
The site is built to maximise efficiency and responsiveness in warehousing and logistics, featuring 50 loading and unloading docks and ceilings over 13 metres high. The site is specially designed to handle large volumes of goods smoothly and safely, ensuring high quality storage and handling.
TIP has strengthened its Management Team Benelux with a new Country Manager.
The company announced Stefan Dhont has taken the position. Dhont started at Van Hool 17 years ago and held various positions within the family business, including Sales Director and Vice Director within the Industrial Vehicle division.
“We are delighted that Stefan has chosen TIP,” said Vice President TIP Benelux, Peter Jan Troost. “His years of experience in the trailer market, his extensive network of customers and suppliers in Belgium and his expertise will be a great addition to the daily and long-term activities of the Benelux and Belgian division, which underlines the clear ambitions of TIP in the region.”
The Antwerp branch is currently investing in a new branch office and workshop, and services are expected to be expanded to include an inspection station.
“I have worked closely with TIP since I started at Van Hool,” said Dhont. “This has ensured that the integration has gone very smoothly. In addition, I also know the majority of the suppliers, partners and customers. I see familiar customers passing by in Antwerp every day.”
Trailer builder, Schmitz Cargobull, has been recognised for its contribution to sustainable production processes.
The OEM is the recipient of the 2025 German Sustainability Award in the mobility and logistics category in the automotive industry.
A jury of experts noted Schmitz Cargobull’s product portfolio is designed for longevity and resource conservation.
Dr Otto Schulz, Member of the Board German Sustainability Award Foundation, presented the award to Schmitz Cargobull CEO, Andreas Schmitz, at MARITIM Hotel in Düsseldorf on 28 November 2024.
“As a fourth-generation family business we regard sustainability as an integral part of our company strategy and as the origin of many in-house innovations,” said Schmitz.
“The challenges of sustainable transformation encourage us to create new innovations and give us food for
thought. However, it is important for our customers and for us that the necessary sustainability measures are effective and economically viable and are not subject to overregulation.
The German Sustainability Award honours exemplary companies from 100 sectors that offer successful solutions for the challenges of sustainable transformation. The aim is to make these solutions widely available and drive forward transformation in the German economy. A total of 224 expert jurors from the fields of research, associations, consulting and civil society selected the 100 role models of change in all sectors of the German economy.
American multimodal logistics company, Schneider National, has entered into a definitive agreement to acquire Cowan Systems and affiliated entities.
Cowan is a contract carrier with a portfolio of complementary services including brokerage, drayage and warehousing. The purchase price of approximately $390 million (USD) is subject to certain adjustments. Based in Baltimore, Maryland, Cowan Systems customers include leading producers of retail and consumer goods, food and beverage products, industrials and building materials. The company operates approximately 1,800 trucks and 7,500 trailers across more than forty locations throughout the Eastern and Mid-Atlantic regions of the United States. Cowan Systems, founded in 1924, has a history of consistent growth. Upon closing, Cowan Systems will operate as a wholly owned subsidiary of Schneider, continuing a successful trajectory with its associates and trusted brand. The acquisition will further complement Schneider’s dedicated organic growth
success. Including Cowan Systems, Schneider will operate over 8,400 dedicated tractors – approximately 70 per cent of Schneider’s truckload fleet –cementing its place as one of the largest dedicated providers in the transportation industry.
“This acquisition aligns with Schneider’s long-term vision to have customer-centric dedicated solutions as the cornerstone of its Truckload segment,” said Schneider President and CEO Mark Rourke. “By complementing our organic dedicated growth success with transactions like this, we are broadening our presence to provide greater value to our customers and stakeholders.”
Canada Cartage, one of North America’s largest transportation and logistics providers, has signed an agreement to acquire Coastal Pacific Xpress (CPX).
Founded in 1986 and based out of Surrey, British Columbia, CPX is a temperaturecontrolled transport company, providing refrigerated full truckload and lessthan-truckload transportation, as well as offering cold storage cross-docks and warehouse operations in Surrey and Calgary, Alberta.
CPX also has freight brokerage service for any overflow of loads. The company has a mix of company drivers and owner operators, and almost 600 temperaturesensitive trailer units.
Like Canada Cartage, CPX provides services to customers in the grocery and food sectors. CPX’s Western Canada and Western U.S.A. services in temperaturesensitive transportation are a great fit with Canada Cartage’s food and beverage transportation services in B.C., Alberta, and the coastal states of America, the
company said in a statement. Combined with Canada Cartage’s Eastern Canadian expertise in dedicated grocery and food deliveries, the acquisition of CPX creates a convenient and efficient national solution for companies requiring temperature-sensitive transportation.
Indiana-based Wabash has announced the renewal of its strategic agreement with The Goodyear Tire & Rubber Company.
The partnership reinforces Goodyear’s position the company’s preferred supplier for its van, tank and platform trailers. “We are excited to continue our longstanding relationship with Goodyear,” said Vice President of Wabash’s global supply chain, Richard Mansilla. “This agreement strengthens our supply chain with a premium brand, enhances customer support and contributes to the continued growth of the Wabash ecosystem. We look forward to building on our shared commitment to industry innovation and exceptional service.”
Goodyear has supplied Wabash for more than 15 years, supporting its trailer product lines as Wabash has expanded its equipment offering. This renewal leverages Goodyear’s network of company-owned locations and dealerships, streamlining tyre management and service access for Wabash customers and increased uptime and operational efficiency.
“Goodyear’s collaboration with Wabash underscores our combined focus to deliver high-quality, innovative products and seamless, end-to-end services to van, tank and platform trailer customers,” said Vice President of Goodyear’s North America Commercial Business, Joe Burke.
Librelato has announced a change in its management structure with João Librelato taking over as the company’s Commercial Director.
“This change reflects our commitment to innovation and leadership in the road equipment segment,” the company said in a statement. “João Librelato brings with him a solid track record in our organisation, as well as academic training and experiences that strengthen our strategic and operational planning.”
Librelato will be responsible for expansion of market share and
consolidation in the market with his responsibilities to include managing sales for the domestic market and exports, as well as conducting product marketing, strategic marketing, market intelligence, network development and sales administration.
He will report directly to CEO, Roberto Lopes Júnior.
The transition comes at a strategic time for Librelato. Headquartered in Içara, Santa Catarina, and with operations in several countries, the company is focused on consolidating its leadership position in Brazil and expanding its presence in international markets.
info@versus-omega.com
www.facebook.com/versusomega
www.versus-omega.com
Hapag-Lloyd has opened an office in the city of Kampala, the capital of Uganda. Strategically situated, Uganda provides excellent connections to five neighbouring countries in East and Central Africa, the company said in a statement. With a population of around 50 million, the country has become an attractive market on the African continent. The Ugandan economy is on the rise with an expected GDP growth of 5.9 per cent in 2024. As a landlocked country with no direct access to the sea, it relies on neighbouring ports, such as Mombasa in Kenya and Dar-es-Salaam in Tanzania, to facilitate its international trade. The Port of Mombasa handled approximately 200,000 TEU of exports in 2023, with 22 per cent of the volume originating from Uganda, demonstrating the country’s significant role in the region’s trade flows. Most of the cargo between Uganda and the ports is transported by trucks. Apart from exporting its own
commodities, Uganda’s importance also lies in its role as a business hub for packaging and consolidating a diverse range of commodities that move throughout the region. Key exports passing through Uganda include timber and dry hides from South Sudan, cocoa, minerals, and timber from the Democratic Republic of Congo, as well as coffee from Rwanda. These flows highlight Uganda’s growing impact on East African exports and its potential for facilitating trade across borders.
The African Development Bank Group has approved a $150 million senior loan to Mauritanian state-owned iron ore firm, Société Nationale Industrielle et Minière (SNIM), to increase its logistics capacity.
The approval, granted on 29 November 2024, is part of SNIM’s $467 million logistics expansion program, which aims to double the transport capacity of its iron ore railway by 2030.
The investment will enable the
company to produce higher value-added products, such as iron ore pellets, and includes plans to construct a 12 MW photovoltaic solar power plant as part of decarbonising efforts.
The initiative also underscores the African Development Bank Group’s commitment to fostering sustainable economic growth and promoting inclusive development in Mauritania.
“This program is a crucial forerunner of SNIM’s future growth as a producer of high-quality iron ore and will facilitate its downstream integration,” said Solomon Quaynor, the Bank Group’s Vice President for Private Sector, Infrastructure and Industrialisation.
“It also represents a significant step forward for Mauritania’s mining sector and will help establish a true regional industrial hub in the medium term.”
Quaynor highlighted the project’s broader social and economic benefits, including community empowerment, job creation, particularly for youth and women and the development of new regional partnerships.
DP World has deployed a fully electric Internal Transfer Vehicle (ITV) at the Port of Brisbane’s Fisherman Island in Australia.
The electric ITV is expected to eliminate more than 120,00 litres of diesel fuel consumption annually, reinforcing the operator’s leadership toward sustainable, efficient port operations.
As a key trade hub for agricultural exports, motor vehicle imports, and containerised trade, Fisherman Island, according to DP World, plays a vital role in Queensland’s economy.
The electric ITV is designed to carry
containers which can weigh as much as 88 tonnes within the port, replacing diesel-powered ITVs, reducing carbon emissions and supporting Queensland’s environmental and economic goals.
This initiative is part of DP World’s sustainability strategy to build an efficient and sustainable supply chain for the future, which includes targets to achieve net-zero emissions by 2050, with a near-term target of 42 per cent reduction of carbon footprint by 2030.
DP World collaborated closely with the Port of Brisbane and the National Heavy Vehicle Regulator (NHVR) to integrate the electric ITV seamlessly
into the port precinct.
The joint effort demonstrates how private and public sectors can work together to drive meaningful progress in reducing emissions across the supply chain.
SINCE ITS ESTABLISHMENT IN 2019, JAGDAMBA TRAILERS HAS RAPIDLY EXPANDED, NOW OPERATING IN MOST INDIAN STATES AS WELL AS AN UPCOMING FACILITY IN THE UNITED ARAB EMIRATES. THIS GROWTH REFLECTS THE COMPANY’S DEDICATION TO PROVIDING HIGH QUALITY TRAILER SOLUTIONS, MEETING THE DIVERSE NEEDS OF THE MARKET AND BECOMING A STRONG INTERNATIONAL CONTENDER.
Amajor milestone in Jagdamba Trailers’ journey is the launch of a new trailer manufacturing plant in the United Arab Emirates (UAE), marking the start of its international operations. is plant is set to begin production in August 2025. is strategic initiative aims to serve the Middle East, African, and European markets, positioning the company as a global supplier of trailers and utility carriers.
Jagdamba Trailers aspires to become a globally recognised brand, driven by innovation, strategic expansion and a customer-centric approach. Additionally, the company is focusing on diversifying its product portfolio to include utility carriers such as fuel tankers, garbage compactors, concrete mixers, train trailers and modular trailers.
Gyan Singh Kshatriya, the visionary Director and CEO of Jagdamba Trailers, brings more than two decades of unparalleled expertise in the trailer industry. His strategic acumen and ability to forge robust relationships with key stakeholders have been pivotal in driving the company’s remarkable growth trajectory.
Since its inception, Kshatriya has been the driving force behind Jagdamba Trailers’ rise as a leading manufacturer of diverse trailer solutions. Under his dynamic leadership, the company has earned widespread acclaim for its innovation, quality, and reliability. Looking ahead, Kshatriya envisions transforming Jagdamba Trailers into a globally recognised brand. He possesses an in-depth understanding of the technical aspects of various types of trailers and their applications. is expertise facilitates new product development, product improvements, and value analysis, ensuring that Jagdamba Trailers remains at the forefront of innovation. His profound knowledge of product life cycles and assembly line optimization has been highly bene cial in achieving optimum production e ciency while keeping costs at a minimum.
Currently, Kshatriya is spearheading the development of a state-of-the-art manufacturing
Ultra-light weight trailers made of Hardox.
plant in the UAE, a signi cant milestone in Jagdamba Trailers’ global expansion. His handson involvement in cra ing international business strategies underscores his commitment to positioning the company as a formidable player on the world stage.
With a keen understanding of market dynamics and a relentless focus on innovation, Kshatriya continues to chart a bold path for Jagdamba Trailers, ensuring its place as an industry leader both in India and beyond
“ e Jagdamba Group’s journey began in 1991 with small ventures in textiles, limestone and dolomite mining, stone crushing, and rolling mills,” said Kshatriya.
“In 2019, the company expanded its horizons by establishing a trailer manufacturing plant in Raigarh, located in Chhattisgarh, central India. Initially, the plant had a capacity to manufacture 100 trailers per month, which has since increased to a monthly production of 300 trailers. e product range initially included tippers, atbeds and sidewall trailers, and has now expanded to include semi-low bed trailers, low beds, curtainsiders, bulker trailers and tankers.”
Jagdamba Trailers boasts a state-of-the-art manufacturing facility equipped with advanced machinery such as CNC press brakes, CNC shearing machines, CNC plasma cutting machines, CNC laser cutting machines, semi-automatic shotblasting, primer booths, paint booths and a highly sophisticated Welding Machines. Additionally, the company has developed a comprehensive line of jigs and xtures to ensure product accuracy. e factory shed spans 15,000 square meters, with an additional 120,000 square meters of open area for plant operations and vehicle storage. e company is ISO 9001:2015, 45001:2018 and 14001:2015 certi ed.
Jagdamba Trailers employs a workforce of 550, including both permanent and contractual workers. e company has invested approximately $3.0 million USD in technological advancements only and has provisions for an additional $2.0 million USD in the coming years.
“ e company’s commitment to quality and innovation drives its continuous growth and success in the trailer manufacturing industry,” said Kshatriya.
In terms of its achievements, Jagdamba Trailers has achieved several signi cant milestones
that underscore its innovation, expertise, and industry leadership.
“One of the most notable accomplishments is securing a prestigious bulk order for missile-carrying trailers for the Defence Research Development Organisation (DRDO), a subsidiary of the Ministry of Defence, Government of India,” said Kshatriya.
“This achievement reflects the company’s capability to meet the stringent requirements of defense applications.
“In addition, Jagdamba Trailers has become an approved supplier to leading OEMS such as Ashok Leyland, Tata Motors and Volvo Eicher.
e company supplies a variety of trailers for their fully built trucks, which are distributed through their dealer networks across India. is partnership
Jagdamba Trailers became approved suppliers to Ashok Leyland and Tata Motors and is the proud recipient of the ‘Emerging Brand in the Indian Trailer Industry’ award from India Iconic Brands and Leaders. These are the testament to the company’s rapid growth and impact in the industry. This recognition re ects the trailer builder’s commitment to excellence, innovation and leadership in the sector.
with renowned OEMs highlights Jagdamba Trailers’ reputation for quality and reliability.”
On the innovation front, Jagdamba Trailers has successfully developed lightweight trailers that are 2.0 metric tonnes lighter than conventional models.
“This breakthrough allows customers to bene t from increased payload capacity, setting a new trend in the industry,” said Kshatriya. “ e company is at the forefront of design development, driving advancements that enhance efficiency and performance.”
Another innovative achievement is the development of an automatic top covering mechanism, specifically designed to perform effectively in harsh mining conditions. With increasing government regulations focused on environmental protection, this product is expected to see high demand in the near future.
“ ese milestones demonstrate Jagdamba Trailers’ commitment to innovation, quality, and customer satisfaction, solidifying its position as a trailblazer in the trailer manufacturing industry,” said Kshatriya.
Jagdamba Trailers recently delivered a eet of Hardox-made trailers to riveni Earthmovers, a
renowned mining company. ese trailers were speci cally designed to address the company’s operational challenges and sustainability goals.
“ e trailers delivered to riveni Earthmovers are 2.0 metric tonnes lighter than the ones currently in use at their iron ore mines,” said Kshatriya. “ is weight reduction was a critical requirement, as it allows the company to carry an additional payload of 1,500–2,000kg, signi cantly improving their operating economics. Additionally, these trailers are designed to be towed by LNG-powered prime movers instead of traditional diesel engines, aligning with riveni Earthmovers’ commitment to reducing carbon emissions and promoting sustainable energy practices.”
Designing these trailers posed a unique challenge for Jagdamba Trailers. e goal was to create a lightweight yet durable solution that could handle the demanding conditions of iron ore mining while meeting stringent weight and environmental targets. By leveraging advanced materials like Hardox steel and innovative engineering, Jagdamba Trailers successfully developed a solution that not only met but exceeded the client’s expectations.
“In India, Central Motor Vehicle Rules (CMVR) govern trailer operations, typically allowing triple-axle trailers coupled with 4x2 prime movers to have a Gross Vehicle Weight (GVW) of up to 54 metric tonnes. For tip trailers, the tare weight usually ranges between 15–16 metric tonnes, leaving a payload capacity of 38–39 metric tonnes. However, if pneumatic suspension is used instead of mechanical suspension, an additional 1.0 metric tonne per axle is permitted, with the cumulative GVW capped at 55 metric tonnes.
“Given these regulations, the demand for lighter trailers with higher payload capacity is growing. However, achieving this without compromising on strength and performance remains a signi cant challenge in the Indian trailer industry.
“Jagdamba Trailers has consistently risen to this challenge by o ering innovative solutions, such as high-tensile steel trailers, which provide enhanced payload capacity without sacri cing durability. For customers requiring even greater e ciency, the company has developed Hardox trailers, which are signi cantly lighter than traditional models while maintaining exceptional strength and performance.”
e delivery of these Hardox trailers to riveni Earthmovers exempli es Jagdamba Trailers’ commitment to delivering tailored solutions that address speci c client needs. By enabling higher payload capacity and supporting LNG-powered operations, these trailers not only improve operational e ciency but also contribute to the client’s sustainability goals. is case study highlights Jagdamba Trailers’ ability to innovate and adapt, ensuring that its equipment helps eets overcome their most pressing challenges while adhering to regulatory requirements and industry standards.
One of Jagdamba Trailers’ most popular products is the 34-cubic-metre tip trailer which is designed to transport materials such as coal, y ash, iron ore, and blue stone. is trailer is constructed using high-tensile steel, speci cally grade 450 (BSK46), with thicknesses of 4mm and 5mm for optimal durability and strength.
A distinctive feature of our trailers is that all longitudinal components – such as sideboards, top rails, underbody runners, and oor members – are jointless, enhancing structural integrity. e chassis members are also jointless and made from 400 and 450mm rolled beam sections, contributing to the overall robustness of the design.
“To ensure reliability and performance, our trailers are tted with triple axles rated for 15 tonnes each,” said Kshatriya. “ ey employ a combination of tandem mechanical suspension with an 18-tonne capacity and one pneumatic suspension rated at 13 tonnes, allowing us to
achieve a GVW of 54 tonnes, in compliance with regulations.
“For traction and stability, each trailer is equipped with 12 radial 1000:20 tyres. e hydraulic systems we use are sourced from reputable brands such as Hyva, Hidromas, or Wipro, ensuring high-quality performance. Our hydraulic kits typically feature a stroke length of 4850 mm and consist of four stages of telescopic cylinders, providing a tipping angle of 37-38 degrees, which is su cient for e ciently unloading the speci ed materials.”
e 34-cubic-metre tip trailer is a testament to Jagdamba Trailers’ commitment to innovation, quality, and customer satisfaction. Its robust construction, advanced features, and compliance with industry regulations make it a reliable and e cient solution for heavy-duty freight applications. By combining high-tensile materials, jointless design, and precision engineering, Jagdamba Trailers ensures that this product meets the highest standards of performance and durability, catering to the diverse needs of its clients. As for the state of the road transportation industry and trailer design, Kshatriya has observed notable trends
particularly when it comes to increasingly pushing the limits of payload capacities, o en operating with weights exceeding 60-70 MT.
“ is shi presents unique challenges that require us to enhance the strength and performance of our trailers to ensure they can handle such demanding loads e ectively,” said Kshatriya. “To meet these requirements, we focus on several key design enhancements. First, we use higher-rated axles that can better withstand the increased stress associated with heavy loads. We also incorporate reinforced wheel rims to provide additional support and stability. Hydraulic systems are another critical component, and we ensure they are robust enough to manage the operational demands of these heavier trailers.
“In terms of structural integrity, we utilise thicker steel plates for the box structure of the trailers. is not only increases strength but also adds durability. We pay particular attention to reinforcing areas that are more vulnerable to wear and stress, ensuring that the trailer remains reliable over time.
“Safety is paramount in our design philosophy, which is why we leverage advanced braking technologies, such as Electronic Braking System (EBS). is system enhances braking e ciency, helping to prevent skidding and reducing the likelihood of accidents—a crucial factor when handling such heavy loads.
“Additionally, we employ state-of-the-art CAD and CAE so ware for dynamic analysis during the design process. is allows us to simulate real-world conditions and optimize our trailers for performance and safety. By integrating these advanced technologies and design practices, we are well-equipped to meet the evolving needs of the transportation industry, delivering trailers that not only meet regulatory standards but also excel in performance and reliability.”
The OEM has an ambitious target for the 2025-26 scal year to produce 5,000 trailers from the Indian facility and an additional 1,000 trailers from the new UAE site. The UAE plant is speci cally designed to cater to the Gulf, African and European markets, with a goal of achieving an annual output of 3,000 trailers by 2027. As part of Jagdamba’s global expansion strategy, it is also exploring opportunities to establish a trailer and utility carrier manufacturing plant in Africa.
Rock body Hardox tipper.
Looking at the company’s growth, Jagdamba Trailers operates a manufacturing plant in the strategic location of Chhattisgarh, central India. A region, Kshatriya said, is rich in natural resources and industrial activity.
“ e area is surrounded by numerous coal mines, stone mines, power plants and steel plants, all of which generate signi cant demand for various types of trailers, particularly tipping trailers and atbed trailers,” said Kshatriya. “Additionally, the high density of cement plants in the region drives demand for sidewall trailers and cement bulkers.
“ e region is poised for substantial growth due to ongoing and planned infrastructure development projects, including highway construction, urbanisation, railway expansion and airport development. ese initiatives are expected to fuel the growth of the manufacturing and logistics sectors over the next 8–10 years, creating a robust demand for trailers and transportation solutions.
“Given these factors, we are optimistic about the region’s potential. We anticipate a consistent 10–12 per cent annual growth in both the manufacturing and logistics sectors over the coming decade. is growth will not only bene t industries directly but also strengthen the overall economic ecosystem, creating opportunities for innovation and expansion in the trailer manufacturing industry.”
As a key player in this region, Jagdamba Trailers is well-positioned to support and capitalise on this growth, delivering high-quality, customized solutions to meet the evolving needs of its customers.
Jagamba Trailers also provides a ermarket support for its clients across India.
“To ensure prompt assistance, we have established partnerships with local motor garages that can quickly address any issues or complaints that may arise,” said Kshatriya. “ is network enables us to deliver timely solutions, minimising downtime for our customers.
“In addition, we maintain close relationships with our key vendors, who supply critical components such as axle suspensions, hydraulics, and tyres. We verify that these vendors have a robust service network in all regions where our trailers operate, ensuring accessibility and reliability.
“Our commitment to customer satisfaction is re ected in our goal to keep trailers o the road for no longer than eight hours due to any issues. We are proud to report that we have consistently achieved this target, reinforcing our reputation for excellent a ermarket support and responsiveness in the industry.”
www.jagdambatrailers.com
MANY BUSINESSES AROUND THE WORLD ARE ADAPTING TO GEOPOLITICAL AND ECONOMIC PRESSURES BY REINFORCING THEIR SUPPLY CHAINS TO REMAIN AGILE AND COMPETITIVE. IN MANY INSTANCES, MANUFACTURERS AND SERVICE PROVIDERS ARE MAINTAINING DUAL SUPPLY CHAIN ARRANGEMENTS TO SATISFY CONSUMER DEMAND AND MITIGATE RISK.
Tari s, sanctions, embargoes, political instability, among other disruptors including natural disasters and cyberthreats, greatly impact the global economy. It also a ects how OEMs manufacture and distribute their products. So how does big business maintain supply chain continuity and guarantee a reasonable level of service in this complex operating environment? Out of necessity, it commits to a strategy, a contingency plan.
As trade tensions between China and the US grow, businesses in the Asia Paci c region – according to research released from Economist Impact and DP World – are adopting diversi cation strategies and digital innovation to maintain supply chain resilience. About 33 per cent of these Asia Paci c (APAC) businesses are creating parallel supply chains to avoid disruptions caused by geopolitical risks, while 29 per cent are creating dual supply chains to cater for Chinese and US markets as companies navigate the complexities of increasingly fragmented trade environments.
e h annual TradeinTransitionstudy surveyed more than 3,500 supply chain executives around the world. e global ndings, which were launched at the World Economic Forum, reveal that rms are being forced to adapt at speed to rising protectionism and shi ing geopolitical alliances, with business continuity and cost management as chief concerns.
e research has outlined three main trends in APAC trade.
1. Strategic diversi cation to manage risks and regional pressures
Adoption of ‘China Plus One’ strategies and the creation of parallel supply chains have become more prevalent among APAC businesses, spurring the growth of alternative production hubs in other Asian countries such as ailand and Vietnam. Firms in APAC are also increasing regional integration and establishing dual supply chains to better mitigate geopolitical risks, reduce costs and strengthen oversight.
2. Leveraging government intervention and recon guration
Supply chain regionalisation is further incentivised by the negotiation and implementation of regional preferential trade agreements which result in enhanced cost control, operational e ciency and support for local economies. About 38 per cent of APAC business leaders saw increased opportunities in the region with the likes of the Comprehensive and Progressive Agreement for Trans-Paci c Partnership (CPTPP) and the Regional Comprehensive Economic Partnership (RCEP) in e ect, while 30 per cent enjoyed cost savings given reduced tari s on exports in member countries. Almost a quarter (23 per cent) of respondents also reported enhanced sourcing within the region, strengthening local supply chains and reducing dependence on markets outside the region.
3. Technology adoption to counter labour shortages and enhance e ciency
Businesses continue to invest in emerging technologies such as automation and arti cial intelligence to address workforce shortages and sustain productivity. ese investments are paying o , with 36 per cent of APAC business leaders reporting signi cant reductions in trade operation costs, and 28 per cent seeing improvements in resource planning and supply chain e ciency. Governments in the region are also supporting technological transformation, with initiatives such as Japan’s Society 5.0 empowering businesses through digital innovation.
Glen Hilton, CEO & Managing Director, Asia Paci c, DP World, said: “ e Asia Paci c region is in an era of signi cant transformation. As businesses in the region implement bold strategies – diversifying supply chains, capitalising on regional trade deals and adopting frontier technologies – to drive expansion, they must also balance ambition with caution to sustain momentum in the face of global geopolitical instability. Our customers can count on DP World to help them strike this balance. With our suite of end-to-end supply chain solutions anchored by our strong network of ports and terminals, we stand ready to help businesses design agile supply chains for them to tap on Asia Paci c’s unparalleled growth potential.”
John Ferguson, Global Lead, New Globalisation, Economist Impact, added: “In 2025 and the foreseeable future, global trade will be shaped by three forces: shi ing geopolitics, climate change, and a new wave of AI and automation. Yet, businesses are not retreating from international trade but are stepping up to the challenge. Firms that stay agile and cost-e cient will have the edge. Firms that also combine risk management with AI experimentation and openness will be best placed to win in this new chapter of globalisation.”
With more than 30 years of experience in logistics as well as port and terminal operations, Glen Hilton has been delivering e ective and innovative solutions that make
trade ow and unlock greater opportunities for people and businesses.
As the CEO and Managing Director for DP World in the Asia Paci c region, Glen oversees the company’s operations across several markets including Australia, China, Hong Kong SAR, the Philippines, South Korea, ailand, and Vietnam. Based in Singapore, Glen leads a team of more than 10,000 employees in developing and implementing DP World’s commercial and operations strategies to accelerate growth across the region and deliver unrivalled value to customers and partners. He has also worked to build strong partnerships with Chinabased suppliers and maximise port-side investments in Türkiye, Europe, and Southeast Asia.
Hilton started his career with DP World in 2005 and within a year, was tasked to lead port operations in the Dominican Republic, which grew by 80 percent under his stewardship. He was subsequently named regional Head of Southeast Asian operations, a role he held for four years prior to his current appointment.
Hilton also previously served as the CEO of Malaysia’s largest container terminal at the Port of Tanjung Pelepas and was General Manager of international cargo handling for an airline in his native Australia.
Q: Do you have any important messages you would like to share in regards to supply chain diversi cation?
A: Companies should view supply chain diversi cation as an investment towards long-term resilience rather than a reactive measure to immediate disruptions. Diversi cation is a multi-step endeavour that requires deliberate strategic planning and weighing options among di erent con gurations of supplier networks and manufacturing bases.
According to this year’s Trade in Transition research led by Economic Impact and supported by DP World, 46 per cent of businesses globally are diversifying geographically to access new markets and mitigate disruptions. However, this strategy is most e ective when considered alongside other supply chain management approaches such as developing dual supply chains, reshoring, or regionalising. Businesses must build approaches tailored to their speci c circumstances.
Q: Have you observed any recent logistics trends that you would like to elaborate on?
A: Technology is transforming the logistics sector within the APAC region and around the world. We anticipate continued adoption of frontier technologies such as AI, IoT and blockchain to optimise manufacturing and distribution work ows. ese technologies enhance demand forecasting, inventory management and route optimisation, resulting in more efficient and cost-effective operations. IoT and blockchain, in particular, are enabling real-time tracking and monitoring of goods, signi cantly improving transparency and traceability. According to the 2025 TradeinTransitionreport, technology adoption in supply chain management is already delivering tangible results in the APAC region, with 36 per cent of business leaders reporting signi cant reductions in trade operation costs with the help of technology. As digital integration deepens, these technologies will be pivotal in addressing challenges such as labour shortages and improving e ciency, while enhancing visibility and responsiveness.
Q: The report touches on trade tensions between the US and China. Would you like to weigh in on this in light of the recent Trump inauguration?
A: Global trade today is more complex than ever, demanding agility, resilience, and innovation. At DP World, we empower businesses with the
global infrastructure, local expertise, and advanced technology needed to thrive in this evolving landscape across fragmented markets.
For businesses targeting both Chinese and US markets, dual supply chains o er a critical solution to navigate the complexities of increasingly fragmented trade environments. ese supply-chain models enable rms to adapt to divergent regulatory requirements and trade policies in each market, ensuring continuity and reducing the risk of operational delays. In fact, within APAC, 29 per cent are creating dual supply chains to cater for the Chinese and US markets.
Q: What are your thoughts on the latest report? Does anything surprise you? Did you expect to see these results?
A: e latest Trade in Transition report reinforces the trends we have been observing over the past few years, as businesses focus on cultivating supply chain resilience in the face of an increasingly complex global trade environment, driven by geopolitical tensions, shi ing consumer demands, and the need for greater resilience.
We see growing adoption of the ‘China + 1’ strategy among businesses. Companies are not abandoning China but are instead supplementing their operations by building manufacturing and supply chain hubs in alternative markets such as Vietnam, Malaysia and ailand. is approach allows businesses to maintain presence in the world’s second largest economy while reducing overdependence on any single market.
e growing acceptance and adoption of technology is also a positive signal that the industry is looking at di erent ways to improve e ciency and productivity.
Q: Are businesses around the world doing enough to reinforce their respective supply chains?
A: Businesses worldwide have made signi cant strides in reinforcing their supply chains, but the dynamic nature of today’s trade environment means that there is always more to be done. e growing adoption of strategies like supply chain diversi cation, regionalisation, and dual supply chains demonstrates a heightened need for supply chain resilience in the face of geopolitical tensions, economic uncertainty, and climate-related disruptions.
Another area where businesses need to do more is in addressing ESG requirements. With global regulations like the EU’s Carbon Border Adjustment Mechanism (CBAM) and Corporate Sustainability Due Diligence Directive (CSDDD) setting the bar higher, companies must focus on reducing Scope 3 emissions and ensuring ethical practices throughout their supply chains.
Ultimately, reinforcing supply chains is a continuous process. As trade policies evolve and risks emerge, businesses must remain agile – leveraging technology, fostering partnerships, and reevaluating their strategies to ensure e ciency, sustainability and resilience.
Q: Should businesses internationally generally seek to establish dual supply chains amid geopolitical risk?
A: Establishing dual supply chains can be an e ective risk management strategy for navigating geopolitical uncertainties. According to the 2025 Trade in Transition report, 32 per cent of global businesses are using dual supply chains to retain to key markets like the US and China while mitigating geopolitical risk.
However, dual supply chains are just one approach within a broader range of supply chain strategies that businesses can adopt, such as diversi cation, regionalisation, nearshoring or localisation. e right approach depends on speci c operational needs, industry requirements, and risk pro les. For instance, diversi cation spreads risk but demands precise execution to control costs, whereas localisation enhances control but limits the supplier pool. Success lies in striking the right balance between these approaches.
Q: What are the consequences of potentially over investing supply chains? Or, what are the consequences of not investing in contingencies for moving freight?
A: Supply chain management has become an essential focus for businesses worldwide.
A 2023 survey by Accenture saw executives claiming to miss revenue growth opportunities of between 7.4 per cent to 11.0 per cent due to disruption in their engineering, supply, production and operations, highlighting the need for businesses to invest in supply chain and operational resilience to remain competitive.
However, no two businesses are the same. Companies must tailor their supply chain investments to align with their unique circumstances, ensuring they take calculated risks balancing growth potential and stability of operations.
Q: Can you link any developments in the commercial road transport industry to the topics discussed in the report?
A: Technology is changing the game for the commercial road transport industry and more broadly for the logistics industry.
Road freight is seeing increased integration of advanced technologies to optimise operations and address existing ine ciencies. Telematics and IoTenabled systems enable real-time vehicle tracking, route optimisation, and predictive maintenance, while AI-powered tools are enhancing freight planning and reducing downtime.
Government intervention through trade agreements like the Comprehensive and Progressive Agreement for Trans-Pacific Partnership (CPTPP) and the Regional Comprehensive Economic Partnership (RCEP) continue to encourage the regionalisation of supply chains, which have a direct impact on the road freight industry.
By reducing trade barriers and harmonising customs procedures, these agreements facilitate cross-border trade, increasing the demand for e cient road freight services to connect manufacturing hubs, distribution centres, and regional markets.
Moreover, the integration promoted by these agreements incentivises the development of regional transport corridors and cross-border infrastructure projects. For example, the Greater Mekong Subregion corridors are being enhanced to support the increased movement of goods within RCEP countries, creating signi cant opportunities for road transport operators to scale their operations and improve e ciency.
On a broader level, governments across the Asia-Paci c and Oceania region are increasingly prioritising domestic manufacturing and economic growth policies. Comprehensive Economic Partnerships, such as the Australia-UAE and New Zealand-UAE agreements, are establishing bilateral free trade frameworks that strengthen economic ties. As economic growth takes center stage for policymakers, governments will look to streamline operations, reduce expenditure, and invest in sectors that drive economic expansion – helping to curb in ation and ease cost-of-living pressures on households.
www.globaltrailermag.com
www.flatlaminates.com Close to you since 1962 HIGH QUALITY GRP FOR TANK CONTAINERS.
We stand right in the middle of every project realization.
GORICA GROUP DISTINGUISHES ITSELF AS AN INDUSTRY LEADER IN THE SILOS AND TANKERS SEGMENT BY OFFERING VARIOUS SPECIALISED PRODUCTS, METICULOUSLY DESIGNED FROM VARIOUS MATERIALS LIKE CARBON STEEL, ALUMINIUM AND STAINLESS-STEEL TO SUIT SPECIFIC FREIGHT NEEDS.
As part of his insight into GORICA’s operational philosophy, Domen Bockor, General Manager of Sales & Marketing, said: “Being a market leader in the Middle East, we constantly innovate and adapt our products to meet client and market requirements. Our focus is on increasing productivity, reducing total cost of ownership, and providing exceptional local a ersales support.”
GORICA is committed to innovation and customer satisfaction. Bockor emphasised the company’s approach to maintaining its market leadership by focusing on key aspects like productivity, design and support.
is strategic choice of materials ensures each tanker or silo is perfectly suited to the demands of the industries it serves, from oil and gas to waste management. For instance, GORICA acid tankers are designed for the safe transport of corrosive substances like hydrochloric acid, demonstrating GORICA’s commitment to safety and e ciency.
GORICA’s local and international market
In a discussion about GORICA market in uence and strategy, Bockor provided an insightful overview of the trailer builder’s primary operational focus within the Gulf Cooperation Council (GCC).
“Our core local market spans the United Arab Emirates, but our reach extends broadly across the
GCC, where there is a signi cant demand for our specialised transportation solutions,” he said.
According to Bockor, the leading markets within the GCC that have shown robust growth and demand for GORICA’s services include the Kingdom of Saudi Arabia, the UAE, and Oman. is strategic positioning allows GORICA to e ectively serve these critical sectors, reinforcing its status as a leader in industrial transportation solutions across the region.
Further broadening its horizon, GORICA has recently tapped into the Commonwealth of Independent States (CIS), targeting markets in Azerbaijan, Armenia, and Kazakhstan. is expansion not only diversi es GORICA’s market base but also showcases its ability to adapt and respond to the unique logistical and infrastructural challenges presented by diverse geopolitical landscapes.
GORICA’s extensive portfolio in the tanker and silo industry is meticulously designed to cater to a wide array of industrial needs, emphasising versatility and specialised functionality. eir o erings are strategically divided by target industry, ensuring that each vehicle is optimised for its speci c use.
For the oil and gas sector, GORICA supplies acid tankers and cement and barite bulker tankers, including the innovative Tripod (3x700 c ) Cement silo semi-trailer, designed for complex logistical operations. In the realm of dry bulk transportation for the construction industry, their cement bulk tankers stand out for their e ciency and durability.
The perishable goods sector benefits from their stainless-steel milk and water tankers, along with aluminium bulk tankers for animal feed and our, demonstrating GORICA’s commitment to maintaining the integrity of sensitive products.
Additionally, the waste management industry has seen signi cant enhancements with the introduction
GORICA Group is focused on the development of lighter-weight trailers as well as Total Cost of Ownership (TCO) analysis so that operators and heavy equipment owners bene t from the solutions that yield optimal performance and productivity gains.
of specialised equipment like vacuum, jetting, combination tankers, and super suckers, catering to the growing demands of urban sanitation and environmental management. e surge in fracking activities has also increased the demand for their acid tankers, particularly from major international companies in the oil and gas industry, showcasing GORICA’s capability to respond to industry trends and customer needs with precision-engineered solutions.
Competitive edge and market leadership
GORICA’s tankers and silos stand apart in the market due to their stringent adherence to international safety standards. GORICA leverages European design principles, expertly adapted to meet the unique demands and challenges of the Middle East and Africa (MEA). is commitment ensures that all products meet or exceed the rigorous requirements of global regulatory bodies. As Bockor said: “We strictly follow international safety standards, European design adapted to Middle East and Africa markets.”
Recognising the unique needs of di erent markets, GORICA customises its products to align with the speci c road regulations and climatic conditions of the Middle East and Africa.
“Being a market leader in all these segments in the Middle East, we constantly innovate and adapt our products to meet client and market requirements,” said Bockor. is localised approach not only enhances functionality but also ensures longevity and reliability in harsh environments.
GORICA has recently expanded its tanker and silo o erings with the launch of the 3x80 BBL chemical blender/mixing tanks, speci cally designed for the demanding and ever-changing needs of the oil and gas industry. is latest innovation highlights the company’s commitment to providing solutions that meet the precise needs of their clients in various sectors.
In response to GORICA’s clients need for more sustainable and cost-e ective solutions to grow and support their businesses, Bockor said the company is focused on creating. “Our focus is on more lighter weight products and total cost of ownership analysis where clients do not look only at price, but performance, productivity and total cost of ownership.”
www.goricagroup.com
KÄSSBOHRER, EXCELS IN LIQUID AND BULK GOODS TRANSPORTATION WITH ITS 10 PRODUCT GROUPS AND MORE THAN 100 DIFFERENT VEHICLES.
With its competent R&D, Kässbohrer constantly develops Europe’s lightest tipping and non-tipping silo range and silo containers with respect to volume and compartment options, lling and discharge e ciency, high maneuverability, and safe operations Proudly presenting the lightest ADR tipping silo in Europe as well as the only manufacture to o er 90m3 tipping silo as standard, Kässbohrer recently launched Europe’s lightest non-tipping 54m3 food silo.
Manufactured to the highest quality with automated processes as well as TUV-DEKRA certi ed welders from Kässbohrer Academy for welding technologies, Kässbohrer silos undergoes rigorous testing in its R&D facilities for durability and top performance in though road and climate conditions as well as most e cient and user friendly lling and discharge operations.
With Enginuity, Kässbohrer continues to take its customers in bulk goods including dangerous and food bulk goods transportation business to the next level.
Europe’s lightest tipping and non-tipping silo vehicles
Presenting Europe’s lightest silo range, Kässbohrer successfully meets its customers’ operational needs with its high-quality tipping K.SSK silos including the lightest ADR tipping silo vehicles suitable for transporting powder, or granular materials such as sugar, co ee, plastics, ash, and much more with 40m3 to 90m3 loading capacities and non-tipping
K.SSL silo vehicles suitable for low-density powder transport such as cement, food transportation with 31 m3 to 54m3 volume options according to the density of the material that needs to be transported.
Fast operating and e cient tipping silo range
Kässbohrer’s lightest tipping silo series in Europe, K.SSK tipping silo’s with their tare weight starting from 5,050kg provide operational e ciency with their loading capacity and fuel savings.
Expertly designed with enhanced ow angles, and smooth aluminium surfaces the K.SSK series feature high quality OEM hydraulic tipping systems with tilt angle of up to 45 degrees, electrohydraulic pump alongside its high-quality stainless steel electro-polished discharge cone. e result is fast discharge times, no material residue and e ciency in operations.
Kässbohrer’s proven robustness chassis is manufactured in one seamless piece, presents high quality, high durability thus a long and e cient life. In addition, Kässbohrer’s K.SSK tipping
ADR silo is the lightest ADR silos in the market. Kässbohrer ADR series can be o ered in volumes of 40m³ to 60m³ depending on your versatile dangerous powder and granular materials need such as carbide, coal, ashes, and metal chips. K.SSK ADR series, are designed, analysed, and tested in compliance with ECTA/DOW recommendations and ADR regulations.
Maximum e ciency, highest variety lling and discharge non-tipping silos
Kässbohrer non-tipping silo series, K.SSL are Europe’s lightest non-tipping silo series starting from 4.500 kg tare weight, for higher load capacity in chosen volume as well as maximum fuel e ciency.
With its design and manufacturing expertise, Kässbohrer non-tipping silo series presents tank construction, lling and discharge options to meet the exact operational need of its customers.
Exactly designed with optimum cone angles, Kässbohrer non-tipping silos are manufactured to highest quality seamlessly accommodating options such as separation wall in the tanker, di erent amount of lling domes, pneumatic lling necks, various aeration cone types, freefall butter y valve, ringduse, air compressor, standpipe strings that are positioned under or within the chassis for discharge from the rear as well as lateral discharge via funnel is possible on the le or right side.
Kässbohrer non-tipping silos are expertly manufactured with box frame aluminum chassis featuring safe lateral inclination, and lower center of gravity which results in high maneuverability even in the toughest working conditions.
Kässbohrer continues to meet the industry’s demand for high-quality silo containers, o ers silo containers for e cient and reliable intermodal transportation. K.CON series combining an ultralightweight structure of just 2,540kg with a 60.4 m³ capacity in 40’ length. Available in 20’, 30’, and 40’ options, to meet the exact need of its customers for bulk transportation across road, rail, and sea. With proven stackability up to 170,000kg, a light yet durable frame, and 4+1 storage capability, the K.CON silo container o ers an optimised balance of weight, capacity, and operational exibility.
www.kaessbohrer.com
The new Haldex system.
CREATED TO COMPLY WITH LAST YEAR’S UPDATE EUROPEAN REGULATIONS FOR TRAILER SYSTEMS, THE HALDEX TPMS 2.0 HAS A LONG LIST OF ATTRIBUTES WITH A FURTHER EVOLUTION EXPECTED TO LAUNCH THIS YEAR.
Haldex has launched an updated tyre pressure monitoring system that is compliant with new R141 European regulations, which will come into force for all trailer systems in May 2024.
e Haldex TPMS 2.0 system consists of rim-mounted wheel sensors, wireless receiver and control unit, optional handheld digital tool, plus a smartphone app. It is designed to continuously monitor tyre pressures and temperatures and alert operators of problems with low tyre pressures, in a simple and easy-to-use interface. It is compatible with the Haldex EB+ 4.0 EBS electronic braking system.
Tyres running at low pressure require more fuel to move and heat up because of internal friction. ese conditions could, in an extreme case, lead to a blow-out.
Since tyre pressures decrease in proportion with falling temperatures, an unsophisticated TPMS could ag a false positive tyre pressure alert on very cold days. at is the reason why EU legislation, which came into force for new types of trucks and trailers in July 2022, requires that TPMS pressure readings are temperature-compensated. ere are other technical requirements in terms of data communication, incuding a new
standardised data transmission format between a TPMS receiver unit and the trailer EBS system (which is via a wired CAN-Bus sensor). For that same reason, the Haldex TPMS 2.0 features a data gateway that will read signals from other brands of TPMS receivers.
Between the RCU and the wheels, individual wheel sensors send data over a wireless radio spectrum signal using a proprietary protocol. e RCU determines system status and receives the analogue signals, digitises them, and forwards them on.
As a minimum, the system must submit a warning if a tyre pressure drops below a certain threshold –by default 20 per cent, although it could be set at a lower fraction. If the truck is equipped accordingly, tyre pressures, warnings, alerts and system status can be displayed in the cab. Pressures measured are up to 10 bar.
TPMS 2.0 exceeds regulatory requirements by assigning each wheel a unique identi er. is niceto-have feature helps make it easier to identify the problem tyre, which isn’t an easy task in case of a single slow puncture on an eight-axle, twin-wheel low-loader, for example.
To support the TPMS 2.0 functionality, Haldex
provides three supplemental devices. First is a new handheld TPMS trigger tool, which wirelessly connects to wheel sensors to read tyre pressure, temperature, ID and battery status. Second, a small diagnostic box works with Haldex’s own smartphone app to con gure the system. ird, Haldex’s permanent, trailer-mounted display, EB+ Info Centre, which presents axle, suspension and brake diagnostic data, can display tyre information including pinpointing problems (which axle, which side).
e Haldex TPMS 2.0 system works for up to ve axles, 20 tyres and up to four spares. Although the regulation only requires wheels touching the ground to be measured, Haldex is going the extra mile to allow a spare tyre to be ready and waiting pre-con gured, so that a service technician need not demount the tyre to t the sensor.
Wheel sensors are powered by a non-replaceable battery rated for seven years’ operation. To conserve power, sensors transmit less frequently when the vehicle is stationary, only waking at wheel speeds in excess of 20km per hour. On twin wheels, the 143g sensors should be mounted 180deg apart. RCUs should be no more than 3m from wheel sensors, which means that on full trailers, two RCUs might be required. e system is set up and diagnosed using Haldex’s DIAG++ maintenance so ware.
In a further evolution of the system expected to launch early next year, the TPMS 2.0 RCU will be able to automatically identify new wheel sensors and their location, a er new wheels have been installed, and the trailer is driven for a few metres. at plug-and-play system, pre-con gured for a speci c trailer type, will remove the need for a technician to manually enter the wheel sensor IDs into the system.
Haldex does not just comply with regulatory requirements, it exceeds them, improving the performance and road safety of its products for customers now and in the future.
www.safholland.com
SCHMITZ CARGBOBULL HAS TYRE PRESSURE MONITORING SYSTEMS WITH AUTO-LOCATION FUNCTIONALITY ON ITS TRAILERS AND SHARES MORE DETAILS ON AN UPCOMING FULL SERVICE RETREAD TYRES CONTRACT OPTION.
The right tyre pressure plays a vital role when it comes to increasing economic e ciency and safety. e Tyre Pressre Monitoring System (TPMS) automatic monitoring function makes it easier to maintain the correct tyre pressure. is signi cantly improves both driving behaviour and driving safety. e right tyre pressure also plays a decisive role in extending tyre service life, reducing fuel consumption and carbon emissions, and increasing economic e ciency. A er all, vehicles stuck with a at tyre cost time and money.
Schmitz Cargobull has been successively installing the TrailerConnect® telematics system in all trailers as a standard feature ex works since 2018. Since the beginning of 2024, all trailers have been equipped with tyre pressure monitoring sensors as standard and comply with UN ECE R 141 regulation, which has been in force since July 2024. is regulation makes a TPMS mandatory for all newly registered trailers. Schmitz Cargobull’s TPMS monitors the tyre pressure in real time and warns of
sudden or gradual loss of pressure or of overpressure. With the help of the auto-location function, Schmitz Cargobull TPMS sensors can be automatically detected and assigned to the corresponding wheel position. e time-consuming and error-prone training and assignment process is no longer necessary. is saves time and money for both customers and workshops. In addition, auto-location o ers maximum security and transparency immediately a er a spontaneous tyre change or workshop visit. e beSmart app enables drivers to view and monitor the status of the tyre pressures and temperature on their trailer at any time. Alarm messages in the event of deviations enable the driver to react at an early stage, thus minimising downtime. In addition, the tyre pressure information is also transmitted to the tractor unit via the CAN bus interface. Depending on the trailer type, the corresponding information is also shown on the tractor unit’s display. is enables constant monitoring and rapid intervention by the driver.
In the future, Schmitz Cargobull customers will have the option of choosing retreaded tyres as a replacement, as part of a Full Service Retread Tyres service contract. To date, Schmitz Cargobull vehicles have been tted almost exclusively with new tyres as replacements. Depending on their quality and condition, tyres in the truck sector can be retreaded up to two times, achieving a useful life of up to 660,000 kilometres. e retreading is carried out in compliance with strict quality regulations and is certi ed in accordance with ECE regulation 109. e treads are tailored to the speci c vehicle types and use, with the aim of continuing to optimise rolling resistance, fuel consumption and mileage even a er retreading.
e Full Service Retread Tyres contract won the European Transport Award for Sustainability 2024 from HUSS-Verlag, in the Rental, Leasing, Financing, Service Contracts category.
www.cargobull.com
The TrailerConnect® portal can be used to monitor the status of the trailer and tyres easily and conveniently in real time, while e-mail or app noti cations can be issued in the event of deviations.
SAFETY FOR BOTH DRIVERS AND VEHICLES IS THE FOCUS OF ALL DEVELOPMENTS AT ASPÖCK SYSTEMS. THE NEXT GENERATION OF TYRE PRESSURE MONITORING SYSTEMS – ASPÖCK TPMS – NOT ONLY REDUCES THE RISK OF ACCIDENTS, IT ALSO EXTENDS THE SERVICE LIFE OF THE TYRE AND SIGNIFICANTLY MINIMISES FUEL COSTS AND CO2 EMISSIONS.
ABOUT ASPÖCK SYSTEMS
Key gures for scal year 2023/2024:
• €169 million sales of the Austrian HQ | 420 employees
• €235 million sales of the Aspöck Group | 1500 employees
• Export quota 94 per cent
• 8 sales subsidiaries | 4 production locations
Low air pressure is the cause of around 90 per cent of all at tyres and that accounts for as much as 30 per cent of the fuel consumption of a vehicle. With these gures in mind, you quickly see that huge amounts of resources are currently being wasted. By monitoring the tyre pressure, you can get the most out of your eet – a communicative group of sensors takes care of this check for you.
e Aspöck TPMS monitoring system is compatible with the EBS systems of all wellknown manufacturers. With its know-how, Aspöck Systems manufactures the appropriate cabling solution for this, specially tailored to customer requirements. e individual initial programming is then easily implemented: e associated hand tool records the sensors of all the wheels on the vehicle and transfers the programming to the main receiver, which takes over communication with the towing vehicle during operation. is is where the USP of the tyre monitoring system – the Auto Locate – comes into play. is function signi cantly reduces the service e ort and minimises downtime. How does it do that? Regardless of whether a sensor or wheel is being replaced or the position of all the wheels is being changed, Auto Locate takes over the teaching of each individual sensor at this point, without the need for any subsequent programming.
Let’s move on to the mounting: the sensors are attached to the rim – either to internal valves or to a belt – and enable precise monitoring of tyre pressure and temperature. e Aspöck TPMS is in constant communication with the towing vehicle and warns the driver if a tyre is running at a pressure below its normal pressure or at a temperature above its normal temperature. A warning signal is then triggered in real time and displayed on the towing vehicle’s display. e robust safety system complies with UN ECE-R 141 and meets the European General Safety Regulation (GSR).
In the future, the company’s own information platform, Aspöck Connect, will improve the continuous ow of information. It supports the service network and keeps it up to date. e programme provides the users with a clear overview of the TPMS product information from the Aspöck specialist departments. Instructions including technical data, product-speci c tools and so ware are available for all registered users to download with ease.
Aspöck TPMS is compatible with all well-known EBS brands. With the automatic sensor recognition, Auto Locate, and the customer-speci c Aspöck cable solutions, the tyre pressure monitoring system is the preferred solution for eets and trailer OEMs.
e new video provides a detailed overview of all the functions of the Aspöck TPMS: https://www.aspoeck.com/en/news/aspoeck_TPMS_ lm_30747
www.aspoeck.com
FUWA-VALX IS REVOLUTIONISING TRAILER SAFETY WITH ITS CUTTING-EDGE TYRE PRESSURE REFILL SYSTEMS.
Eective January 2024, the ECE R 141 regulation mandates the use of Tyre Pressure Monitoring Systems (TPMS) on trailers. For Fuwa-Valx, this is more than just a new rule, it is an opportunity to lead the way in innovative trailer technology. As a result, the company has expanded its portfolio to include Tyre Pressure Re ll Systems (TPRS), going beyond basic monitoring to deliver comprehensive tyre management solutions.
While TPMS focuses on real-time tyre pressure monitoring, TPRS takes things a step further by ensuring optimal tyre performance through automatic re lls. e system adjusts tyre pressure on the go, reducing wear, improving fuel e ciency, and enhancing overall safety. is proactive approach saves operators time and money, minimising the risks associated with underin ated or overin ated tyres.
e push for TPMS underlines the importance of tyre management in the commercial
vehicle sector. Poorly maintained tyres can lead to higher fuel consumption, increased wear and tear, and potential safety hazards. TPRS not only addresses these concerns but also provides peace of mind by keeping tyre pressure consistently within the optimal range.
Together with some partners Fuwa-Valx has developed a TPRS system that is both e cient and easy to integrate into existing trailer setups. Along with the standard parts the system features a specially designed VALX hubcap,
along with durable hoses and adapters. Once installed, it monitors tyre pressure continuously and automatically adjusts it when necessary. is ensures that tyres remain at their ideal pressure, even during long hauls or in challenging conditions. By maintaining proper in ation, the system extends tyre lifespan and contributes to a smoother, more e cient ride.
Fuwa-Valx TPRS solutions are designed with practicality and performance in mind. e company understands the challenges faced by eet operators
and o er systems that are reliable, straightforward to maintain, and compliant with the latest regulations. By adopting VALX’s TPRS, operators can reduce operational costs, enhance road safety, and stay ahead of regulatory requirements.
Fuwa-Valx is committed to driving innovation in the trailer industry. e introduction of TPRS is just one example of how we aim to provide practical solutions that bene t operators and the environment alike. As the industry evolves, we’ll continue to adapt and deliver products that meet the highest standards of e ciency and sustainability.
For more information on Fuwa-Valx TPRS solutions, visit the VALX website or contact the team.
www.valx.eu
Li Guiping, Chairman and CEO of CIMC Vehicles recently shared the company’s practical experience in three aspects: the use of ‘Star-Chained Plan’ to deal with intensive domestic competition, the prologue to the third venture, the new development pattern of the third venture.
1. The Star-Chained Plan to deal with intense domestic competition
e Star-Chained Plan reshapes the hard and o strengths in the product domain, restructures the marketing organisation, and builds productive services to break through homogenised competition and form di erentiated competitiveness.
Hard strength is o en related to technology and is tangible, while so strength is intangible but equally important for a company’s development. A good CEO should value both hard and so strengths equally. According to Guiping, hard strength includes equipment installation, order production, product delivery, while so strength includes organisational readiness, excellent marketing readiness.
2. The prologue to the Third Venture – the Star-Chained Plan
Star-Chained Plan integrates the resources of seven domestic semi-trailer manufacturing plants, aiming to enhance market share, sales volume, and operating pro t, and ultimately improve pro tability through high production e ciency, short delivery cycles, and strong brand marketing.
e vision of Star-Chained Plan is to reshape the business model and organisational structure of semi-trailer production and sales in line with the standards to new quality productive forces. e core evolution is re ected in shi ing from customised trailers to modular-design; transitioning from internal competition to internal collaboration; and moving from order-based production to productdriven sales.
is evolution involves procurement, production, logistics, local manufacturing in the market and sales.
e Star-Chained Plan is the primary initiative under CIMC Vehicles’ third venture journey over the next eight to 10 years. It will have a profound impact on the company’s core competitiveness, including its customers, employees, society and the environment. More importantly, it will a ect performance and capabilities. Within CIMC Vehicles’ sales team of 500 people, we have maintained a stable headcount, yet the average sales performance per person has
increased by 30 per cent. Amid the widespread trend of pay cuts, the income of sales personnel has risen by 30 per cent proportionally.
3. The new development pattern of the Third Venture
e Star-Chained Plan marks CIMC Vehicles’ ird Venture. e rst venture began in 2002, and within just seven years, CIMC Vehicles achieved explosive growth, with revenue increasing from 50 million in the rst year to 9.0 billion in the seventh year, mainly from the domestic market.
e second venture started in 2010, shi ing the core business focus from domestic to intercontinental operation, utilising a dual-production model to manufacture semi-trailers and refrigerated trailers in North America.
During this phase, the output value in overseas market signi cantly increased, with two acquisitions completed. We also conducted two IPOs within three years, and since 2012, we have been distributing dividends to our shareholders every year.
A er more than two decades of development, CIMC Vehicles has established advantages in market resources and the governance structure of a publicly listed company. However, like all other Chinese manufacturing companies, it is currently facing a
severe situation where the high growth rate of the domestic market has rapidly declined. In addition, the management team that participated in the rst two ventures has aged, and their thinking is facing signi cant bottlenecks.
Looking ahead, CIMC Vehicles will, on the basis of stabilising the ‘intercontinental operation, local manufacturing’ foundation, fully implement the Star-Chained Plan, create new quality productivity, promote structural changes in production organisation, and establish competitive advantages in markets, brands, capabilities, resources, talents, and organisations, leading the Chinese semi-trailer industry into a new development pattern and actively exploring new overseas growth spaces in the global south market.
www.cimcvehiclesgroup.com
BPW HAS UNVEILED A NEW 7-TONNE SWING AXLE SYSTEM FOR LOW LOADERS WHICH TAKES ECONOMIC EFFICIENCY TO A NEW LEVEL.
Whether wind turbine blades, concrete bridges, or even entire drilling platforms: Making the impossible transportable is part of the daily routine for the engineers of axle and running gear specialist BPW. In order to meet these future challenges.
The significantly more compact swing axle generation, which is suitable for many applications, will be presented for the rst time at Bauma in Munich this year.
As the world’s leading trade fair for construction machinery, Bauma in Munich is a festival of fascinating engineering achievements that captivate not only industry professionals. Challenges such as the energy transition, the backlog in bridge and highway renovations, cost pressures in the construction industry, and the globally rising demand for raw materials call for the innovative spirit of the commercial vehicle industry.
As a system partner of leading special vehicle manufacturers, BPW Bergische Achsen KG ensures that special transport goods are transported reliably and economically. Swing axles are o en used for such transports. ey are integrated into pendle axle units (swing suspensions), which enable the transport of heavy goods in di cult terrain due to their high li ing capacity in combination with axle load compensation. However, not all vehicles are built for extreme applications: To transport excavators, cranes and other construction machinery to the site, low-loaders with swing axles are required that are as reliable as they are economical - the cost pressure in the construction industry is also becoming increasingly noticeable in commercial vehicles.
In order to meet these market requirements, BPW has further developed its 7-tonne swing axle. e new universal swing axle, which will be presented to industry professionals for the rst time at Bauma (Stand FN 821/9), combines maximum exibility, maximum load capacity and compact design at an attractive market price. State-of-the-art manufacturing technologies, smart design principles and the targeted use of proven large-scale production technology make this possible.
anks to its variable application options, the new swing axle can be used with 17.5-inch or 19.5-inch single tires. Depending on country and approval regulations, the universal swing axle can be used either as a 6- or 7-tonne axle, which corresponds to an axle line of 12 or 14 tonnes. e compact design fully meets the current design requirements for low-loader vehicles and ensures optimum utilisation of installation space. e proven BPW ECO Drum drum brake is used, featuring a large lining volume for long service life and the well-known C-clamp technology for excellent maintenance.
Adapted to the requirements of the swing axle market, the brake is combined with the drum in front of the hub principle. e wheel bearings are maintenance-free. e use of the latest high-volume technology results in a weight saving of up to 15 kilos per axle body, which leads to a higher payload and thus contributes to increased economic e ciency.
“With the new 7-tonne swing axle, BPW once again sets benchmarks in terms of load capacity, maintenance-friendliness, and e ciency – all at an extremely competitive price,” said BPW Product Manager, Ziya Albayrak. “Customers bene t from a very compact design, higher payload, lower maintenance costs, and long service life. e market launch of the new 7-tonne swing axle is planned for the end of November 2025.” www.bpw.de
FIRE
Brianza Plastica is an Italian family business company founded in 1962. It is a leader in the production of breglass laminates and stands out in the market for its quality, breadth of range, state-of-the-art technology, reliability and widespread logistics. e company, thanks to its ve production plants in Italy, supplies Glass bre Reinforced Plastics (GRP) – produced both in continuous and in discontinuous – to satisfy all market requirements. Over the years, this composite material has replaced aluminium, providing manufacturers of commercial and tank container vehicles with an excellent long-term solution. It is lighter, more exible, and resistant to corrosion. e reduced weight translates into improved fuel e ciency and increased payload capacity. Its exibility allows it to absorb shocks and vibrations, reducing the risk of damage. GRP is highly resistant to corrosion, making it ideal for harsh environments. is makes it more durable and less prone to degradation compared to aluminium, which can corrode over time.
Elycold is a high-quality fibreglass laminate, produced discontinuously with a polymerisation process at ambient temperature that ensures excellent atness and an extraordinary seamless nish. It is available in widths up to 3,400mm and thickness from 1.0 to 3.6mm.
Elycold Lite represents the ideal solution for those seeking thicker laminates with good rigidity and low speci c weight, while retaining all aesthetic details and values. e use of resins and speci c microspheres allows increased thickness, without adding weight, decreasing the density of the laminate and providing greater rigidity, contributing to the atness of the panel and concealing the underlying structures. All these features make it ideal for constructing walls of commercial and temperature-controlled vehicles.
Elyplan is a high-quality GRP laminate available in rolls and sheets, with or without gelcoat, produced by continuous lamination, which ensures the highest possible polymerisation of the composite material. e result is a perfectly at product, with very tight dimensional tolerance, o ering excellent quality at a competitive price. e use of the nest raw materials and a gelcoat made from highly elastic isophthalic resins ensures high resistance to yellowing, impermeability to water vapour and condensation. It is available in widths up to 3,200mm and thickness from 0.8 to 3mm.
Elyplan Extra-Glass is designed for high resistance and light weight with a tensile strength up to 230 Mpa. It combines important features, such as lightness, due to the low speci c weight, and high mechanical strength, resulting from the high percentage of glass content. It also makes it a perfect combination suitable for vehicles that require high impact resistance and weight saving.
e extreme exibility, lightness, resistance to chemicals and yellowing, easy washability of the Elycold and Elyplan breglass laminates range make them an excellent choice for covering tank containers and walls of commercial and temperaturecontrolled vehicles.
Elyplan Fire Perf: a complete range with improved re behaviour
Brianza Plastica has developed a complete family of breglass laminates which responds to the growing market demand for products with improved re performance, in compliance with various European and global standards.
Top of the range is Elyplan FP 220, a 2.0mm GRP laminate in class B-s1, d0, according to the UNI EN 13501-1 standard, the maximum re performance for breglass laminates. is product is pre-treated on the surface to allow the customer to apply their
Brianza Plastica is a leader in the supply of high quality GRP laminates.
favourite top coating such as, for example, PU-based paints or decorative wall sheets, with maximum freedom of choice.
According to the UNI EN 13501-1 standard, the letter S (Smoke) indicates the production of smoke in combustion, in a range from 1 to 3: the higher the value, the more smoke is produced. e letter D (Dripping), in a range from 0 to 2, stays for dripping during combustion: a GRP laminate as Elyplan FP 220, class B-s1, d0, does not produce dripping during combustion.
Other products of the range are Elyplan FP 230, 2 mm thick, available in class C-s2, d0 and FP 230, 1.5 mm thick, in class D-s2, d0.
Brianza Plastica designed Elycold and Elyplan breglass laminates range as an excellent choice for panels widely used in the commercial vehicle sector and for covering tanks of any size. Both are extremely durable due to their waterproofness and UV-light resistance, longterm surface durability, a low level of yellowing – recorded by aging tests performed with UV-CON and Xenotest – and total impermeability of the panel. e washable and scratchresistant surfaces promise easy maintenance and always good quality and nal appearance. ey are available in a wide range of colors to meet all needs. Furthermore, Brianza Plastica GRP laminates o er bene ts not only to the end consumers, but also to manufacturers, by providing a unique solution that drastically reduces installation time.
www. atlaminates.com
When it comes to transporting goods, safety and e ciency are key according to Versus-Omega. Traditional sliding pillars, used for securing cargo, have been around for a long time, but they o en come with limitations. Scala, a new and innovative solution, is changing the game with its versatile and durable approach to load security.
One of the most impressive features of Scala is its exibility. Scala’s sliding pillars can be combined in many di erent ways, but the best part is that it uses just a few key parts. is means companies don’t need to keep a large inventory of spare parts, which simpli es logistics and saves money. Whether you need xed, extendable, or li able pillars, Scala has a solution to t your needs.
e interchangeable parts also mean less storage space is required, and it’s easier to nd the right component when needed. If a part is damaged, it can be replaced individually, so you don’t have to replace the entire pillar.
Durability is crucial in the world of cargo security. Scala pillars are designed to last longer and withstand the wear and tear that comes with everyday use. e pillars have a smooth, protrusion-free design, which helps prevent damage to trailer components like tarpaulins. e riveted construction makes the
pillars stronger and more resilient than traditional welded versions, while the cast and forged hookand-pin mechanisms ensure long-term reliability.
e best part? If a Scala pillar is damaged, only the broken part needs to be replaced. is saves both time and money while keeping the system running smoothly.
Safety is a top priority for any cargo system, and Scala takes this seriously. Traditional sliding pillars can sometimes fall unexpectedly, which is a major safety risk. Scala’s double interlock system keeps the pillar securely in place when it’s opened, preventing accidents and ensuring both the driver and the vehicle are safe.
Additionally, Scala has a lever-operated handle for locking and unlocking the pillar. is makes it easier and safer to handle, compared to older systems that o en require awkward or di cult movements.
Scala’s exibility goes beyond just parts. Whether you need a xed pillar, an extendable pillar, or a li able pillar, Scala has a solution. It also includes freely movable and lockable pillars for added convenience. e system can easily be adapted to t any cargo or vehicle, making Scala a great choice for a wide range of transportation needs.
One of the biggest advantages of Scala is how easy it is to put together. e system uses the same monobolt across all parts, eliminating the need for di erent types of fasteners. is simpli es assembly and reduces the chance of mistakes. With only two pillar body options available in S355 and S700 steel grades, Scala is adaptable to create a wide range of pillar variations, making it e cient for any type of load.
Scala o ers several useful accessories to enhance the cargo securing system. ese include plank holders, vertical and horizontal sideboard locks, and even OXO holders for expandable goods. No matter what you’re transporting, Scala has the right accessories to make the process easier and more secure.
Scala is more than a new product – it is a better way to secure cargo. With its combination of exibility, durability, and safety, Scala is setting a new standard in the industry. It helps businesses save money, reduce complexity and keep drivers safe.
www.versus-omega.com
JOST’S JUST-FINALISED ACQUISITION OF HYVA SEEKS TO CONSOLIDATE THE VALUE OFFERING OF BOTH COMPANIES, COMBINING THEIR MARKETS TO SATISFY COMMERCIAL VEHICLE COMPONENT MANUFACTURING CUSTOMERS ON A GLOBAL SCALE.
JOST and Hyva have coexisted as titans in the world of commercial vehicle solutions manufacturing for decades. Both companies were established as humble production operations out of Germany and the Netherlands, respectively, and have since grown tremendously to service a multitude of markets across Europe and the rest of the world.
Now, looking to expand this outreach even further, JOST has moved to acquire Hyva. is acquisition, announced at last year’s IAA Transportation and nalised at the end of January 2025, has been an integral aspect of JOST’s newly developed e orts to service more markets with greater technology.
According to JOST CEO, Joachim Duerr, the production scale that the acquisition of Hyva will bring to JOST’s operations is key to this recently de ned global strategy.
“JOST has a strategic process for deciding how we want to develop,” he said.
“A little more than a year ago, we started reviewing our global strategy – seeing how the commercial vehicle industry was developing, what the demand from our customers looked like, and how we needed to position ourselves as a company. We found that product scale will be more important for the business in the future, as well as global relevance for our customers.”
Achieving this larger product scale is essential for JOST to capitalise on the commercial vehicle industry’s recent growth trends and adapt to its increasingly stringent and complex technology requirements. By supplying newly up-and-coming Original Equipment
JOST CEO, Joachim Duerr.
Manufacturers (OEMs), body builders, dealers and end users with commercial vehicle equipment, JOST will expand its presence to more markets around the world and increase its global in uence as a result.
Hyva was decided as the company for JOST to acquire due to the plethora of similarities between them; Joachim expressed that Hyva’s product o ering greatly complements JOST’s own.
“Hyva’s product o ering works well with our existing product portfolio,” he said.
“When you think of couplings worldwide, you think of JOST. And if you think of tipping cylinders and hydraulics, you think of Hyva. It is a global brand, recognised in all relevant commercial vehicle markets. To that end, it is an extremely good t for us.
“When the opportunity came up to enter discussions, I was quite excited, and we were able to achieve a good deal. It allows us to carry out the next strategic steps of building a home for Hyva, which in turn allows them to develop better under the roof of JOST.”
JOST’s acquisition of Hyva – which marks the former’s largest acquisition in its history –will consolidate both companies’ manufacturing capabilities and international market shares, expecting to spark a signi cant synergy between them. e combination of Hyva’s strong presence in Asian markets with JOST’s presence in North America and Australia stand to benefit both companies.
From this acquisition, JOST’s sales and regional coverage will increase substantially, along with the brand’s market penetration, through the very precise and deliberate integration of JOST products and services into previously competitive areas, to create real value opportunities for customers.
Another priority of this acquisition is to bring production costs down for product manufacturing across the board, ensuring the company’s competitiveness – an outcome Joachim plans to achieve with many mechanisms while presiding over an increase in product o ering and coverage globally.
“We want to focus on bringing costs down by combining purchasing volumes, engineering work, electronic systems and more,” he said.
In addition to the consolidation of both companies’ international markets and product lines, JOST’s acquisition of Hyva will also stand to a ect each company’s internal administration and approach to business.
JOST and Hyva are like-minded organisations that share corporate ambitions, product o erings and complimenting business values – as evidenced by the acquisition itself. Given this alignment, Joachim is con dent that any administrative di erences between the companies can be absorbed into operational strengths.
“ ere are a lot of similarities, and there are also some di erences,” he said. “ ose di erences serve as opportunities to select better operation methods for JOST.”
ese opportunities for re nement are present in various forms. While Joachim has acknowledged a potential obstacle in combining the day-to-day administrative duties of both JOST and Hyva, he is certain that a strong line of communication will smooth the transition for employees and customers alike.
“ is is a typical challenge that you have when you integrate two companies,” he said.
“It’s just important that we have good and open communication so that our employees, and customers, understand the way we run and build trust with our brands. e right communication will allow us to focus on opportunities and gure out the steps we need to take to approach them.”
Another opportunity for business re nement comes in the form of both companies’ approaches to the culture and conventions of the speci c markets they operate in.
Because of JOST and Hyva’s mix of market penetration in di erent regions, both companies will need to learn how to e ectively operate in each other’s market space –another dynamic that Joachim believes will also fuel synergy for both organisations.
“Culturally, when it comes to competence in certain markets, a business needs to understand the certain history of these markets as well as the relationship with customers, suppliers and dealers,” he said. “We will use the stronger part of this understanding from both companies and create an even stronger cultural basis for business operations. e local-to-local approach, meaning specialised knowledge tailored to the diverse regional needs, has always been part of JOST’s DNA.”
JOST’s acquisition of Hyva stands to make waves in the commercial vehicle solutions manufacturing industry, uniting two of its behemoth presences into one international powerhouse of production. Armed with plentiful industry and acquisition experience, Joachim Duerr and JOST are ready for more.
www.jost-world.com
Images: JOST.
TRAILER REFURBISHMENT OFFERS VARIOUS BENEFITS FOR FLEETS FROM MAXIMISED UPTIME TO SIGNIFICANT EMISSION REDUCTION TO EXTENDED OPERATIONAL LIFESPAN. DSV CONTINUES TO PROMOTE THE CIRCULAR ECONOMY WITH ITS LATEST COLLABORATIVE EFFORT.
To cut emissions and improve eet e ciency across Europe, TIP Group and DSV will refurbish 500 Schmitz Huckeback trailers.
e initiative follows the successful refurbishment of 1,100 trailers in 2023 and 991 trailers in 2024 which were part of previous collaboration e orts between TIP and DSV.
TIP said the di erence in emissions from a new and refurbished trailer shows considerable savings of an estimated 8,000 tonnes of carbon dioxide savings for the 500 trailers over the extended use period. Also, the company calculated the refurbishment of a used curtainsider emits an estimated 2.7 tonnes of carbon dioxide. is includes materials, energy and heating used for refurbishment.
DSV has doubled the operational lifespan of each trailer. A er ve years of active use, the trailers are expected to run for six more years in the DSV eet.
DSV and TIP will further strengthen their workshop cooperation across Europe.
TIP Group and DSV continue their trailer refurbishment program. Image: TIP Group.
The enhanced maintenance programs aim to minimise downtime and guarantee peak trailer performance, maximising eet productivity.
“We are proud to add a new chapter to our longstanding collaboration with DSV,” said TIP Group Deputy CEO, Arjen Kraaij.
“Both companies advocate for circular economy initiatives that contribute to the reduction of carbon emissions. Refurbishment is a great example, both supporting DSV’s sustainability ambitions and optimising their eet performance, a true win-win.”
Flemming Steiness, Managing Director, DSV Global Equipment Services, said: “At DSV, we work hard to reduce our environmental impact with both innovative and practical solutions. Refurbishing trailers instead of replacing them is a simple yet powerful way to cut emissions while maintaining the high-quality service our customers expect. Circular economy initiatives like this are essential to lowering our overall carbon footprint, and we’re excited to partner with TIP Group to drive real change.”
is unique collaboration is o cially sealed during the TIP leadership strategy kicko , for both companies to celebrate their long-term partnership founded on shared values, innovation and a common goal to drive positive change in the logistics sector.
“TIP and DSV have a long-term relationship,” said TIP Group Vice President Sales & Marketing, Rogier Laan.
“We are very pleased to further enhance our collaboration, o ering exibility to DSV and making use of each other’s workshops across Europe.
“Our partnership is built on trust, innovation and making a positive impact.”
www.tip-group.com www.dsv.com
TO MAINTAIN PACE WITH INNOVATIVE AND LIGHTER-WEIGHT MATERIALS USED TO FABRICATE TRAILERS, VALK WELDING IS PUSHING THE BOUNDARIES OF WELDING TECHNOLOGY.
The pursuit for lighter, more e cient heavy vehicles and trailing equipment is relentless in the commercial road transport industry. is drive for weight reduction brings signi cant welding challenges, as the materials used become thinner and more complex. Ensuring perfect weld quality is paramount to maintaining the structural integrity and safety of these vehicles. Valk Welding’s ARC-EYE CSS Adaptive solution o ers a reliable way to consistently achieve high weld quality.
Welding is crucial in the production of transport vehicles, from cars and trucks to trains and aeroplanes. e quality of the welds directly a ects the durability, safety, and performance of these vehicles. Manufacturers strive for weight savings and therefore use advanced materials and constructions that require precise and high-quality welding techniques. Examples are advanced aluminium and stainless-steel tanks and high strength steel trailer chassis. Any compromise on weld quality can lead to structural
deficiencies with potentially catastrophic consequences.
e use of these lighter and thinner materials increases the risk of warping, cracking, or incomplete fusion during welding. Moreover, the complexity of the various trailer models demands more advanced welding techniques and equipment. To achieve high weld quality, innovative solutions are needed that can adapt to changing conditions and ensure consistent quality.
Valk Welding’s ARC-EYE CSS Adaptive solution addresses all these challenges. is system uses real-time monitoring and adaptive control to maintain optimal welding conditions. By continuously adjusting parameters such as speed, voltage, and current, the ARC-EYE CSS Adaptive ensures that each weld is performed under the best possible conditions, regardless of variations in, for example, the material or other environmental factors.
e system’s ability to adapt to changing conditions is crucial for achieving perfect welds. It minimises the risk of defects and ensures that the welds meet the stringent quality standards required in the transport industry. is not only enhances the safety and reliability of the vehicles but also reduces the need for costly rework and repairs.
In addition to the ARC-EYE CSS Adaptive solution, Valk Welding’s Welding Wire Service Centre plays a vital role in achieving perfect weld quality. e Welding Wire Service Centre specialises in selecting the ideal welding wire for each speci c application. e choice of welding wire is crucial as it a ects the strength, durability, and overall quality of the weld.
As the transport industry continues to push the boundaries of design and e ciency, the importance of perfect weld quality cannot be overstated. Valk Welding’s innovative solutions, such as the ARC-EYE CSS Adaptive system and the Welding Wire Service Centre, provide the tools and expertise needed to meet these challenges. By ensuring consistently high weld quality, they help manufacturers create lighter, safer, and more e cient vehicles, paving the way for the future of transport.
Visit the Valk Welding website for more information about the ARC-EYE CSS Adaptive solutions and the Welding Wire Service Centre.
www.valkwelding.com
NEW COMMERCIAL VEHICLE BODIES, PROPULSION SYSTEMS AND EQUIPMENT ARE AMONG THE DOZENS OF PRODUCTS, TECHNOLOGY AND SERVICES LAUNCHING AT WORK TRUCK WEEK 2025.
Attendees can explore the latest innovations in the Work Truck Show exhibit hall, experience high-tech vehicles during Ride & Drive, and hear from the industry’s leading chassis manufacturers about products under development.
Work Truck Week 2025 runs 4-7 March at Indiana Convention Center in Indianapolis. More an A Trade Show, it encompasses Green Truck Summit, e Work Truck Show, NTEA Annual Meeting, Ride & Drive, educational program and more. Green Truck Summit is 4 March 4, educational sessions run 4–6 March, Work Truck Show exhibits are open 5-7 March and Ride & Drive runs 5-6 March.
“ e number one reason industry professionals attend Work Truck Week is to nd new products,” said NTEA President and CEO, Steve Carey.
“There’s nowhere better to discover the latest commercial vehicles, truck equipment and technology, and to meet face-to-face with manufacturer engineers, technical specialists, up tters, industry experts and peers.”
While many exhibitors keep their new products under wraps until Work Truck Week opens, others are already sharing information about what they’ll showcase in Indianapolis. To learn more, check out the Product Gallery at wtw25.mapyourshow.com. Filter by ‘new’ to see the latest products, including commercial vehicle seats, bodies, cameras, power systems, lights, controls, chemicals and more.
It’s not just the products that are new, there are more than 40 companies exhibiting at Work Truck Week for the rst time this year, including 25 in the New Exhibitor Pavilion. e Pavilion is in Rooms 137–139 across from the Hall I Work Truck Show exhibit hall entrance. It opens an hour before the main exhibit hall on 5-6 March.
Work Truck Week also gives attendees the unique opportunity to take the wheel of commercial vehicles featuring the latest advanced technology, propulsion systems and other sustainability o erings during Ride & Drive. It is open on a rst-come, rst-served basis to all attendees.
In addition to what’s new, Work Truck Week attendees also can see what’s next by participating in the educational program. Green Truck Summit on 4 March kicks o with a keynote address from Jennifer Brace, Chief Futurist at Ford Motor Company. Other forward-looking Special Sessions include Navigating the Future: Selling and Servicing the Tech-Driven Truck and the inaugural Commercial Vehicle Data Exchange & Reception, both held 6 March.
Finally, only at Work Truck Week do leading commercial vehicle manufacturers share their latest chassis speci cations and designs, review body and equipment installations and provide insight into future vehicle and technology plans during exclusive annual Chassis Updates. is year, 15 manufacturers
are holding these insightful sessions: Bollinger Motors, Daimler Truck North America, Ford Pro, Freightliner Custom Chassis, GM Envolve, Hino Trucks, International, Isuzu Commercial Truck of America, Kenworth Truck Company, Mack Trucks, Mercedes-Benz USA, Mullen Automotive, Peterbilt Motors Company, RAM Professional and Ree Automotive.
Explore current trends, delve into technical details and learn new strategies for success through the Work Truck Week 2025 educational program. Learning opportunities include new Special Sessions on talent development, commercial vehicle data, and selling and servicing the tech-driven truck, as well as a full slate of shorter Breakout Sessions.
e 2025 educational program provides insights and strategies to help commercial vehicle industry professionals plan for the future and enhance operational growth. Key topics include market data and industry trends, vehicle engineering and compliance, government regulations, chassis OEM updates, workforce development, eet management, vehicle propulsion and sustainability solutions and more.
“Education is one of the core pillars of Work Truck Week,” said Jennifer Mitchell, NTEA Senior Director of Content Development. “We have sessions for eet managers, vehicle up tters, truck dealers and other industry professionals with a wide range of experience, from those just starting out to seasoned veterans.”
Navigating Today’s Workplace is the topic of this year’s Generation Next Leadership Workshop & Networking Reception on 5 March. Led by Amy Hirsh Robinson, Chief People O cer for Kings Hawaiian, it will provide actionable tools and strategies to thrive in a competitive work environment. Robinson also leads the session Future-Proo ng Your Workforce: Strategies for Talent Development earlier the same day. is session will reveal how to develop talent from within an organization and explore new methods for sourcing diverse, skilled candidates from outside.
Truck dealers will learn from NADA/ATD experts how automation, arti cial intelligence and connected technologies are transforming the commercial vehicle industry and how these changes impact selling and repairing vehicles during Navigating the Future: Selling and Servicing the Tech-Driven Truck on 6 March.
Commercial Vehicle Data Exchange & Reception showcases new possibilities for obtaining, analysing and using data, understanding market trends and improving business processes. Led by representatives from NTEA, S&P Global Mobility, GEOTAB and ClearKinetic, this new half-day Special Session is held 6 March.
e popular Getting Started with Fleet Management all-day workshop returns on 5 March, as does the follow-up course, Advanced Principles of Fleet Management on 6 March. Both are led by experts from RTA Fleet.
Breakout Sessions between 4-6 March run the gamut from a basic introduction to the commercial vehicle industry to preparing for the future. Registration for a GTS or WTW Conference Package includes access to all Breakout Sessions.
www.worktruckweek.com
Image: Aaron/stock.adobe.com
Indianapolis, Indiana
North America’s largest work truck event is aimed at the people who design, build, use and maintain commercial vehicles and equipment. www.worktruckweek.com
Image: Travel Faery/stock.adobe.com
Munich, Germany
Leading Trade Fair for construction machinery, building material machines, mining machines and construction vehicles.
www.bauma.de
Image: SeanPavonePhoto/stock.adobe.com
New Orleans, Louisiana
The Technology & Maintenance Council Annual Meeting includes North America’s premier transportation technology exhibition. https://tmcannual.trucking.org/
Image: See Less/stock.adobe.com
13-15 MAY
Rotterdam, Netherlands
Bringing together more than 11,000 attendees, Breakbulk Europe provides a networking platform to grow connections and strengthen key relationships.
https://europe.breakbulk.com
Image: TheaScheuerGregersen/stock. adobe.com
Herning, Denmark
Transport is Scandinavia’s leading transport fair for everyone working in or with the transport industry. www.transportscandinavia.com
Image: John Nicklin/stock.adobe.com
26-29 MAY
Quebec City, Canada
Promoting and supporting road freight transport technology, safety and policy through information exchanges between researchers, policy makers, regulators and the transport industry. www.hvttforum.org
Transport Logistic 2025 2-5 June Munich, Germany www.transportlogistic.de/en/trade-fair
Intermodal Expo 2025 15-17 September
Long Beach, California www.intermodal.org/intermodalexpo
NUFAM 2025
25-28 September Karlsruhe, Germany www.nufam.de
Transport and Logistics 2025 14-16 October Antwerp, Belgium www.transport-logistics.be/nl/
SOLUTRANS 2025 18-22 November Lyon, France www.solutrans.fr
IAA Transportation 2026 15-20 September Hanover, Germany www.iaa-transportation.com
HAMMARSDALE-BASED RADIAL TRUCK TYRE RECYCLER, MATHE GROUP, HAS PROCESSED ITS MILLIONTH RADIAL TRUCK TYRE, BRINGING THE TOTAL AMOUNT OF RUBBER CRUMB PRODUCED FOR RE-USE IN KEY INDUSTRIAL AND CONSTRUCTION APPLICATIONS TO AROUND 38,500 TONNES ACCORDING TO CEO DR MEHRAN ZARREBINI.
Based on an in ll of 100 tonnes of rubber crumb per full size arti cial football eld, this equates to 385 full size football elds or 700 full size hockey elds (assuming 55 tonnes is needed to create the elastic layer underneath arti cial grass).
e amount of rubber crumb produced would have provided the asphalt and seal needed to pave at least 8,000 kilometres of roads.
Dr Zarrebini, a British investor who initially acquired iconic KwaZulu-Natal based carpet manufacturer, Van Dyck, discovered Mathe Group as a small operation with just 20 employees operating in New Germany in 2016. He was looking for rubber crumb to manufacture acoustic underlays and acoustic cradles for ooring in high rise buildings – products that he has since improved and continues to export.
Having acquired a 49 per cent shareholding in Mathe Group, he relocated the company to its present site in Hammarsdale, signi cantly boosting production through ongoing reinvestment in plant over the past eight years. Mathe Group currently recycles approximately 700 radial truck tyres per day to produce 30 tonnes of rubber crumb – 70 per cent of each 55kg truck tyre becomes rubber crumb and 30 per cent is waste steel which is exported via the port of Durban.
rough its own research and development or through working with key partners, Mathe Group’s portfolio of products has grown to include non-slip paving and ooring for agricultural use, ballistics products and gym mats, rubber pavers and the in ll for sports elds. Various sizes of rubber crumb are also key ingredients in bitumen for road resurfacing, non-slip paints, moulding of parts for the automotive industry, the retreading of tyres and the production of brake linings.
Dr Zarrebini said that a number of challenges have stood in the way of Mathe Group not achieving its important millionth tyre milestone far sooner. ese include the Covd-19 pandemic which shut down the plant for 18 months, loadshedding, water shortages and ongoing legal battles and delayed implementation of the Industry Waste Tyre Management Plan (IWTMP).
Mathe Group is currently awaiting the renewal and expansion of its tyre quota from the
Waste Bureau. is will enable this highly successful business to signi cantly expand output and continue to develop new products.
At present, 50 per cent of a tranche of new equipment needed to replace existing plant will arrive in South Africa at the beginning of the New Year with the remainder ready to be shipped during the second quarter of 2025. Dr Zarrebini said ongoing replacement of equipment that comes into contact with abrasive hard rubber and steel is essential.
He added that Mathe Group is nalising external funding for additional upgrades to the existing line which enable the company to diversify. “For the phase two investment, we designed the equipment to have the exibility to process radial steel truck tyres as well as a variety of other tyres. Although nylon truck tyres are few and far between now because trucking companies prefer to use radial steel tyres that are of a higher quality and retreadable, this gives us the security of more variant tyre supply.”
Waiting in the wings – and dependant on the delivery of more tyres for recycling – is a phase three investment. Mathe Group has already been granted a waste management license for the installation of a completely new line to complement its existing one.
www.globaltrailermag.com
With over 45 years of experience, Valk Welding provides customized solutions, including welding wire, consumables, software, training, and support. We assist with production automation for both large series and single pieces, and for small to large products. Valk Welding is driving change in Europe and beyond!
Heavy transportation traffic becomes electric, green and quiet with the recuperation axle SAF TRAKr
Every great E-Mobility concept begins with a first step: the new e-axle system from SAF-HOLLAND – the innovative technology for the electric transformation. safholland. com