UNIQUE CONTENT AND INSIGHTFUL OPINIONS ON THE SHIFTING MOVEMENTS WITHIN THE MARKET BY THE INDUSTRY’S MOST INFORMED AND INFLUENTIAL SOURCES
GLOBAL REPORT
CONSTRUCTION EQUIPMENT 2019
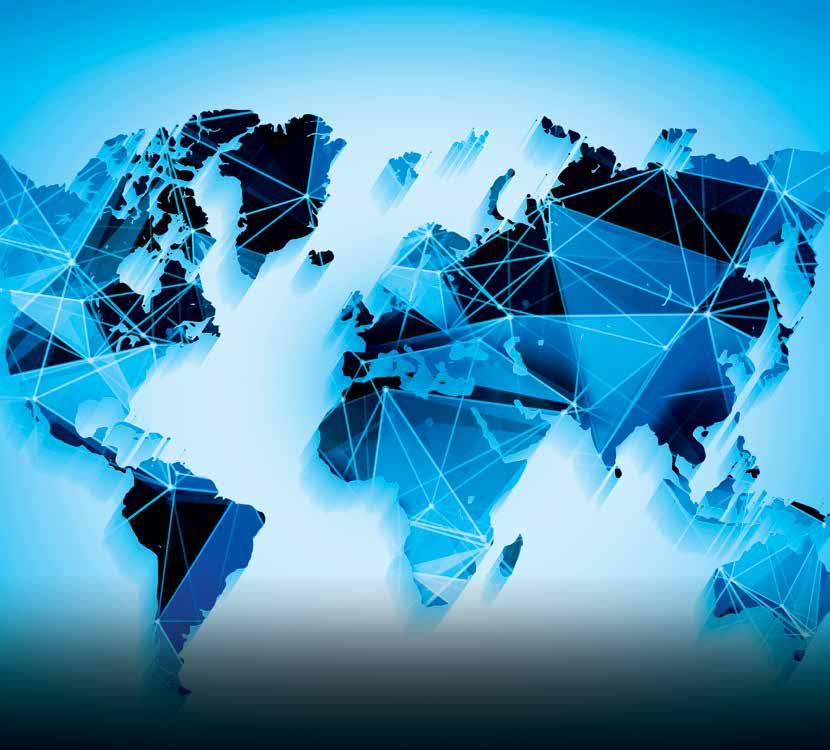
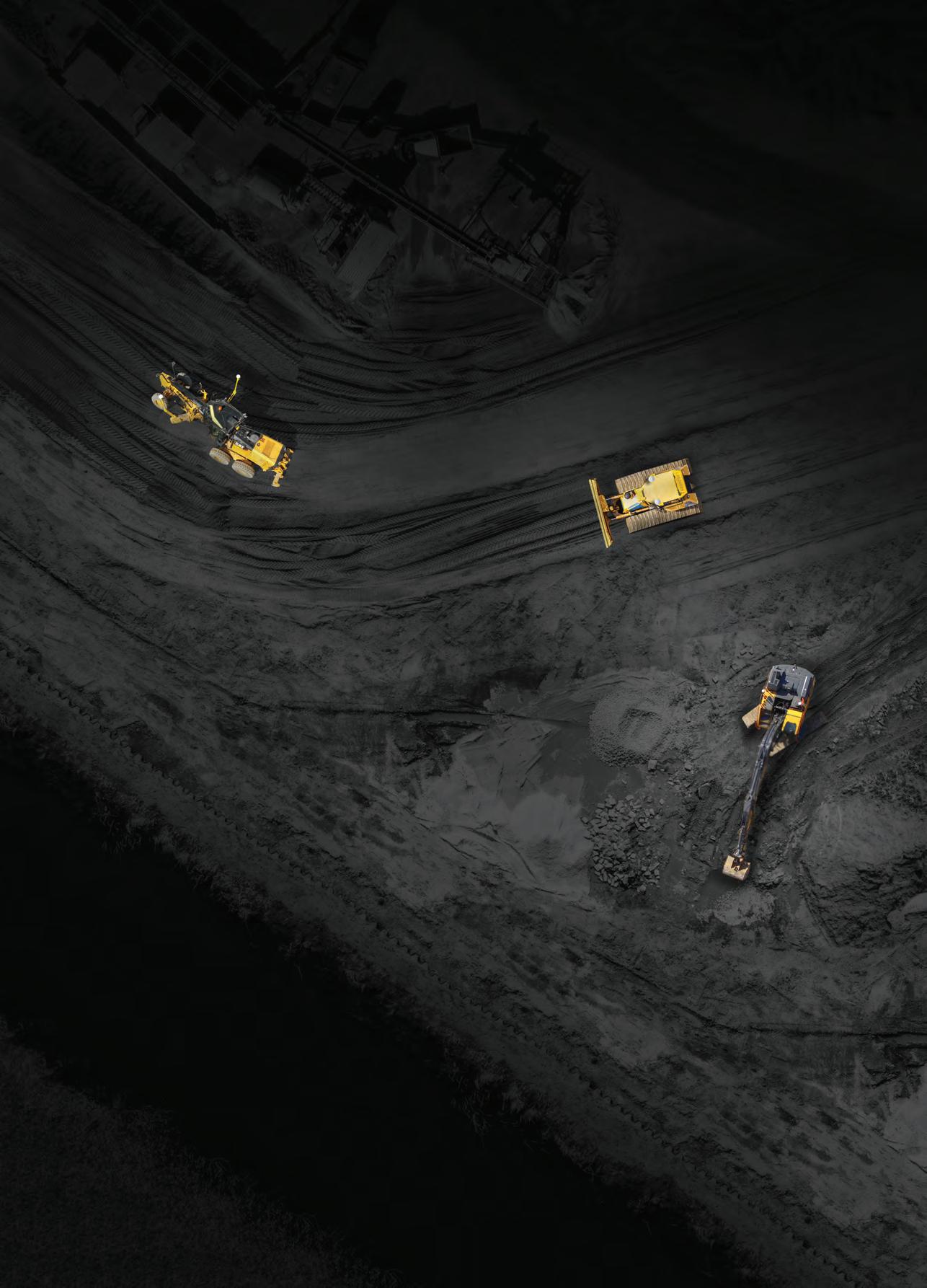
Get more from every earthmoving machine and operator on site.
The Trimble® Earthworks Grade Control Platform is a next generation machine control system that optimizes your mixed fleet for an integrated site solution. This simple, intuitive platform enables your operators to stop the guesswork and start using the friendly Android™ UI and 10-inch touch screen to drive efficiency, deliver on schedule, and do more with dirt than ever before.
Ask for the full family of next-gen machine control. From the company that invented machine control. construction.trimble.com/earthworks

For excavators, dozers, and motor graders.
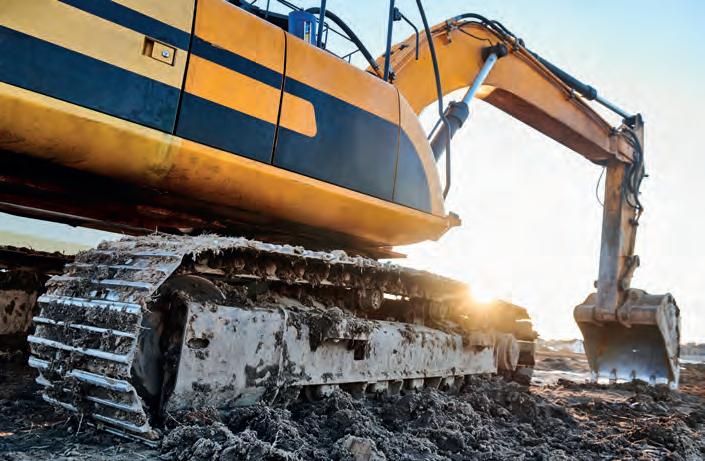

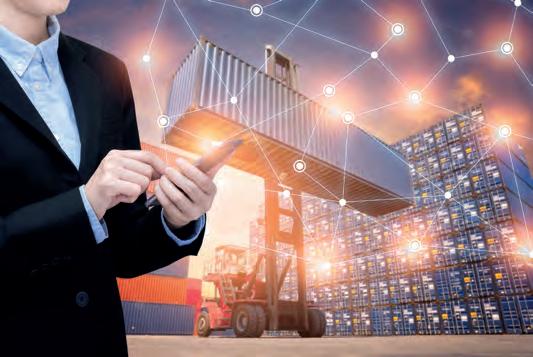
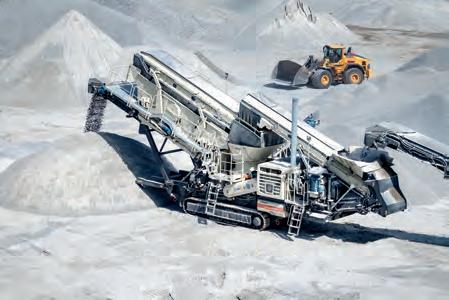
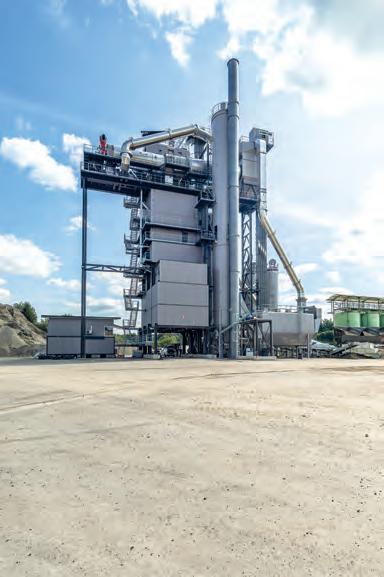
CONTENTS
06. Global markets review: Looking up
Global construction equipment demand looks much healthier as governments and private companies spend on new infrastructure megaprojects and buy the latest, state-of-the-art machines.
22. 3D printing: Additive manufacturing
3D parts printing, or additive manufacturing as it is sometimes called, is revolutionising the rapid prototyping of new equipment and making it easier to support older machinery in the field.
27. Supply chain management: Logistics 4.0
The world’s leading construction equipment OEMs are seeing a revolution on the factory floor as new, intelligent technologies are put into place to create connected and interoperable workflows.
33. Regional focus: The “Stans” It is nearly 30 years since they emerged from the old Soviet Union, but the “Stans” still require major infrastructure upgrades and many significant new opportunities still exist. Where are the hot spots?
40. Artificial intelligence: Rise of the robots
It is hard to work through the confusing, controversial and sensitive subject of machine learning in the construction equipment sector. Artificial intelligence will change everything. Is it something to fear?

44. Aggregate production: The drive to bigger machines
Quarry operators are demanding ever-bigger crushers and screeners that combine the higher capacity and lower costs per tonne of stationary equipment with the mobility and flexibility of mobile units.
48. Regional focus: Latin America revives
In a vast territory of more than 20 million square kilometres, the region’s major economies - Brazil, Mexico and Colombiahave all elected new presidents recently and Argentina has gone from hope to economic crisis. What is really going on?
52. Compaction:
New thinking and new trends
New developments in compaction technology are allowing road builders to deliver better quality road surfaces, even in difficult applications. It’s all about being as efficient and profitable as possible.
57. The world in numbers
We live in interesting times. The global economic and political landscape is in a state of flux. We have selected a mix of key facts and figures … indicators that might help you make sense of it all.
59. Diesel engines:
Stage 5 has arrived
2019 is a landmark year for off-highway engine emissions as Stage V regulations start to take effect. How are the engine makers meeting the challenges involved and clearing the air?
63. Sustainability: Being eco-friendly
The sustainability of asphalt-mixing plants has come a long way. Ammann can now foresee a future in which resources, investments, technological development and institutional change can all work together in harmony.
67. Remanufacturing:
The future looks bright
Remanufacturing gives parts and components a ‘second life.’ In the construction equipment manufacturing sector, the leading players have long championed the benefits. What is coming next?
71. Regional focus: China
- what will its OEMs do next?
China’s construction equipment manufacturers are facing a new slowdown after an explosive recovery from the depths of the dramatic slump in 20122016. We report on a country that always takes the long view.
Save minimum 15% in fuel consumption
Renewed Lokotrack® LT200HP™ crushing plant
The renewed Lokotrack® LT200HP™ mobile crushing plant can save minimum 15% in fuel consumption compared to hydraulic-driven cone crushers thanks to its direct belt drive from gearbox, and is the first Lokotrack to comply with Stage V emission regulations.
In addition to being more efficient, the renewed LT200HP also features several safety and maintenance improvements. These include elevated service platforms to ensure safe, easy access to service and maintenance points and improvements that make daily maintenance quicker and easier.
Scan QR code below to see how it looks!


Editor:
Mike Woof
Deputy Editor: David Arminas
Contributing Editors:
Guy Woodford, Enrique Saez
Designers:
Simon Ward, Andy Taylder, Stephen Poulton
Production Manager: Nick Bond
Office Manager:
Kelly Thompson
Circulation & Database Manager: Charmaine Douglas
Internet, IT and Data Services Director: James Howard
Managing Director: Andrew Barriball
Chairman: Roger Adshead
Publishing Director: Geoff Hadwick
Editorial contributors:
Liam McLoughlin, Adam Hill, Colin Sowman, Dan Gilkes, Kristina Smith, Geoff Ashcroft, Graham Anderson
COVER IMAGE: © Mirexon | Dreamstime.com
ADDRESS:
Route One Publishing Limited, Waterbridge Court, 50 Spital Street, Dartford, Kent DA1 2DT, UK
Tel: +44 (0) 1322 612055
Fax: +44 (0) 1322 788063
Email: [initialsurname]@ropl.com (e.g. radshead@ropl.com)
ADVERTISEMENT SALES
Head of Construction Sales: Graeme McQueen
Tel: +44 1322 612069
Email: gmcqueen@ropl.com
Sales Director: Philip Woodgate Tel: +44 1322 612067
Email: pwoodgate@ropl.com
Sales Director: Dan Emmerson
Tel: +44 1322 612068
Email: demmerson@ropl.com
UK / Classified, North America: Yvonne Tindall
Tel: +44 1622 844027
Email: ytindall@ropl.com
Italy: Fulvio Bonfiglietti Tel: +39 339 1010833
Email: bonfiglietti@tiscali.it
Japan: Ted Asoshina
Tel: +81 3 3263 5065
Email: aso@echo-japan.co.jp
Asia / Australasia: Roger Adshead
Tel: +44 7768 178163
Email: radshead@ropl.com
Global Report Construction Equipment
Print ISSN 2057-3510
Digital ISSN 2057-3529
WELCOME
Welcome to the Global Report: Construction Equipment 2019 provide an incisive, informative and insightful read for anyone involved in specifying the equipment that is used in the world’s highway construction and aggregates production industry.
Our team of expert writers has put together thoughtful pieces on a host of important topics, giving guidance on changing business trends as well as providing pointers to future demand. And don’t take our word for it. Global Report: Construction Equipment has twice been highlighted as one of the best business publications in the world, winning its place on the Tabbies International Editorial and Design winners’ shortlist.
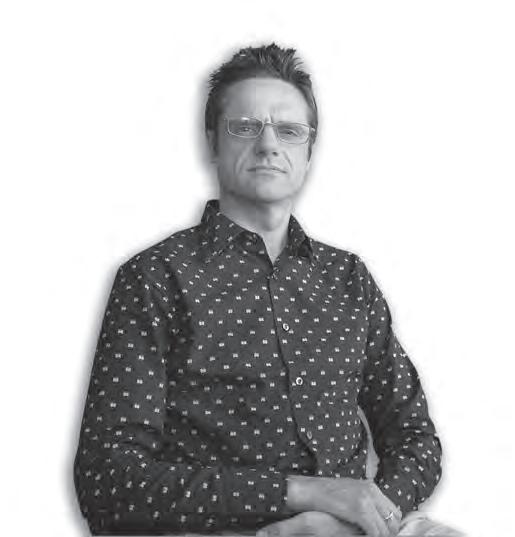
This year, the report focuses on areas such as the outlook for road building and construction equipment sales in two interesting regional markets: Latin America and the “Stans,” as well as the latest trends in logistics 4.0 and the integrated supply chain. We take a look at the fast-growing worlds of artificial intelligence, 3D printing and remanufacturing … three fascinating areas that could revolutionise everything we do and everything we use in the years ahead.
We have also lined up authoritative articles on the latest thinking in the road surface compaction market and on asphalt plant technology trends from the experts at Ammann, plus there is our usual, fact-packed review of how the global markets are shaping up around the world.
And don’t miss chapters on developments in the diesel engine market as it prepares for Stage 5, on how China’s top construction equipment manufacturers are thinking about the future, on new ideas in the recycled bitumen sector and on the drive towards ever-bigger machines in the aggregates industry.
We hope that you will find plenty of relevant facts and figures, as well as detailed thought pieces that are of interest to you and your business.
Mike Woof Editor, World Highways

A MUCH HEALTHIER OUTLOOK
Global construction equipment demand looks much healthier as we approach the end of the current decade, with governments and private companies within key regional markets spending big on new infrastructure, releasing pent-up demand for state-of-the-art machine fleets. Guy Woodford reports.
Things are definitely looking up for the global construction equipment industry. Off-Highway Research (OHR), a leading global construction equipment market research consultancy, expects worldwide construction equipment sales to increase 12% in 2018, following on from the 27% rise seen in 2017. This will take total sales to almost one million units in 2018. The total retail value of sales is tipped to approach US$99 billion.
Continued infrastructure investment in China was expected to drive up 2018 earthmoving equipment sales by 31%, following on from the 81% surge seen in 2017. This will take demand to 283,500 units, or 325,000 machines including mobile cranes and compaction equipment, making it by far the largest construction equipment market in the world in volume terms. OHR also notes that the Indian construction equipment market is set for a third consecutive year of double-digit growth. Demand is expected to rise 16% in 2018, following on from the 15% increase
in 2017, and the remarkable surge of 39% recorded in 2015. This is expected to take earthmoving equipment sales this year above the 70,000-unit mark for the first time and push the value of the Indian market to a record US$3.5 billion.
2018 was also set to be a year of strong growth in North American equipment demand. OHR states that after a hiatus in sales in 2016 due to uncertainty in the run-up to the presidential election, growth resumed in 2017, taking volumes back to their 2015 levels. Sales in 2018 are expected to rise another 13% to almost 200,000 units.
Like the North American market, demand for equipment in Europe is at a good level. Sales exceeded 160,000 units in 2017 for the first time since the global crisis, and in 2018 the market is expected to edge up to 165,000 machines. However, OHR expects this to represent the high-water mark for Europe in this cycle.
Overall, OHR forecasts that global equipment sales over the medium term will stabilise around the one million units per year mark, with a retail value of around US$100 billion.
GlobalData, another leading international business market research consultancy, expects the pace of expansion in the global construction industry to average 3.6% a year over the 2018-2022 period. In real value terms (measured at constant 2017 prices and US$ exchange rates), global construction output is forecast to rise to US$12.9 trillion in 2022, up from US$10.8 trillion in 2017.
Global construction output is forecast to rise to US$12.9 trillion in 2022
Although there are intensifying downside risks to global economic growth, notably stemming from the ongoing trade war between the U.S. and China, GlobalData tips the global economy to continue to expand in the range of 2.5% to 3% a year over the 20182022 period.
CONTINUED EUROPEAN GROWTH
On a macro-economic level, the European Union (EU) economy is entering its sixth year of uninterrupted growth, according to the Committee for European Construction Equipment (CECE).
Within the euro zone (that part of the European Union whose member countries use the euro as common currency), growth was forecast to slip back slightly in 2018 - from a 10-year high of 2.4% in 2017 to 2.1%. Growth will likely ease back even further to 1.9% this year, 2019, and 1.7% in 2020, according to the CECE’s November 2018 Economic Bulletin
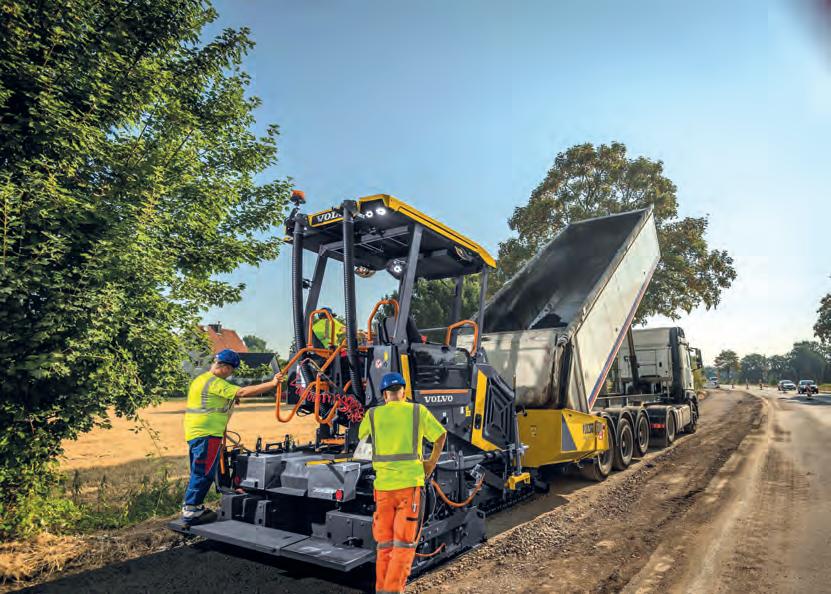
For the EU as a whole, growth is expected to follow a similar pattern, settling at around 1.9% in 2020.
The European construction equipment sector delivered another positive surprise in the third quarter of 2018. Equipment sales in Europe grew by 9.4% in the third quarter and year-to-date growth was at 9.2% after nine months.
Earthmoving equipment sales (excluding telescopic handlers) grew by 10% in the third quarter of 2018, which means that the pattern of on-going growth was confirmed again in Q3. After nine months, yearto-date growth within the earthmoving sub-sector had reached 9%. Rental demand, which had showed signs of a slowdown in the second quarter, was robust in Q3 2018. The total market volume was close to the
*note: no data for concrete equipment available at the time of writing
levels seen in 2008, but still below the peak levels of 2007.
The top three earthmoving equipment markets – which were already at very high levels – saw further growth in the third quarter: the German market grew by 4% (Q1-Q3 2018: +5%), the UK market by 17% (+4%) and France by 10% (+2%). Between them, these countries make up more than 50% of the European market. ➔
Source: CECE
Comparing product segments, growth in the third quarter showed differences, after being fairly similar in the first half of 2018. Compact equipment sales grew by 12% (Q1-Q3 2018: +9%), while heavy equipment sales only went up by 6% (+7%). Higher volume sales of compact equipment resulted in the double-digit sales increase within the overall earthmoving equipment sector.
Within the compact sector, skid-steer loaders were the best-performing product –sales grew by 20%. Mini excavators recorded a 13% increase, compact wheeled loader sales rose 6% and sales of backhoe loaders increased by 4%.
The European road equipment sector continued to show growth in the third quarter 2018. Sales were 8% above the previous year’s levels and year-to-date growth was still at 9%. As investment in road building was a part of many countries’ stimulus policies after the economic crisis, road equipment is one of the segments where recovery is most advanced.
Similar to earthmoving equipment, the three largest markets saw growth in the Q3 2018. Germany increased by 18% (Q1-Q3 2018: +6%), UK sales rose 7% (Q1-Q3 2018: -12%) and the French market saw 3% growth (ytd:+16%).
Sales were 8% above the previous year’s levels and year-to-date growth was still at 9%
In the heavy equipment sub-sector, sales of articulated dump trucks (+30%) and motor graders (+17%) showed the strongest growth. Rigid dump trucks (+8%), wheeled excavators (+8%), dozers (+7%), wheeled loaders (+4%) and crawler excavators (+3%) saw more moderate growth in Q3. With growth in sales continuing to improve over the year, the CECE’s report suggested that a double-digit increase was still a possibility for earthmoving equipment sales in Europe in 2018.
NORTH AMERICA
STRONG U.S. DEMAND
2
018 was a strong year for construction equipment demand in the United States.
Off-Highway Research (OHR) notes that after a hiatus in sales in 2016 due to uncertainty in the run-up to the presidential election, growth resumed in 2017, taking annual sales to more than 171,000 – akin to 2015 levels. In 2018, OHR expects sales to rise again to almost 200,000 units.
Construction in the US - Key Trends and Opportunities to 2022 published in October 2018 by GlobalData, a leading international business market research firm, states that the U.S. construction industry is expected to record encouraging growth over the 20182022 period, driven by president Donald
It is noteworthy that the growth in Q3 sales was attributable to growth in the light compaction segment (+9%). Heavy compaction sales were flat (-0.3%).
However, within the light compaction segment there were mixed performances for different products: sales of vibratory plates were up by 14% in Q3. Vibratory tamper sales dipped 1%. The low-volume product of pedestrian rollers saw sales rise 30%. In the heavy compaction equipment segment, tandem roller sales were up by 15% and single-drum rollers by 1%. In
contrast, trench roller sales tumbled 27% and combination rollers fell 13%.
Finally, asphalt paver sales in Q3 were 44% higher than in the previous year, but this is a low-volume product.
After a better-than-expected third quarter 2018 for the European market, the CECE report noted that sales growth in 2018 would be “almost guaranteed”. The only question is whether growth can exceed the 10% threshold, or whether it will reach only single-digit levels. Much will depend on whether the bad situation in the Turkish market will continue – a market that saw severe drops in sales.
The cyclical pattern of the sector still suggests that towards mid-2019 (after the bauma exhibition) the market peak will be reached, and the industry can expect a slight downturn. By then, recovery of the market will be very advanced, but will still fall short of the peak levels reached in 2007. Based on current economic fundamentals, and the underlying level of demand, a strong recession can be ruled out for 2019, according to the CECE report.
*CECE, based in Brussels, represents the interests of the European construction equipment industry and also works with other organisations worldwide to achieve harmonised standards and regulations.
Trump’s plans to revamp the country’s disintegrating infrastructure. In addition, GlobalData expects public and private sector investments in residential, commercial, healthcare and educational infrastructure construction projects to support growth in the industry over the forecast period.
In February 2018, the White House released its infrastructure initiative, under which the Trump administration seeks to provide US$200 billion in the next ten years to spur a projected US$1.5 trillion in state, local government and private sector investments to rebuild what Trump called America’s crumbling infrastructure.
The GlobalData report also quotes American Society of Civil Engineers estimates which suggest the country requires US$3.6 trillion to repair, upgrade and modify its aging transport infrastructure by 2020.

MAKE EVERY HOUR COUNT
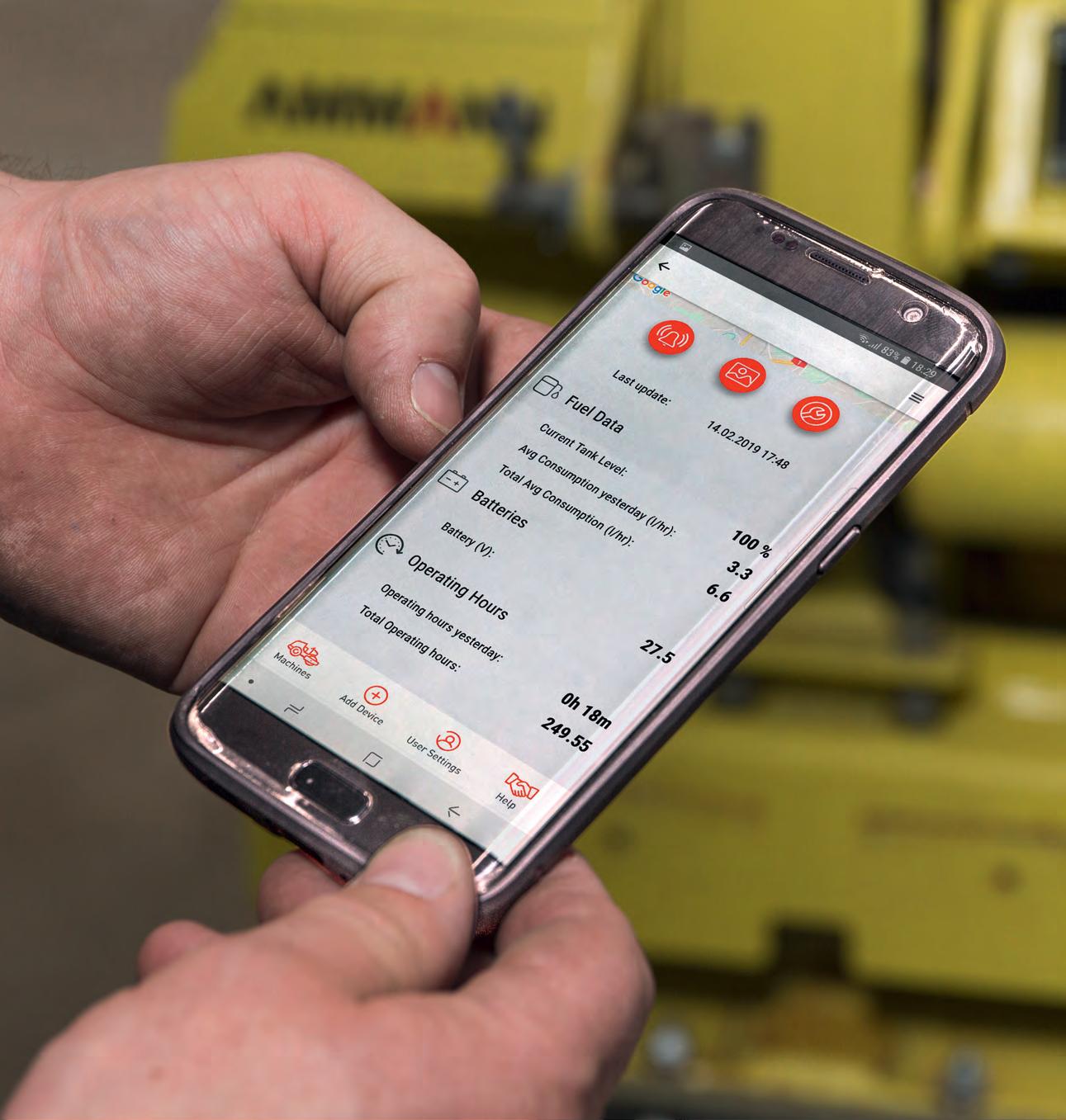
AMMANN SERVICELINK THE DIGITAL FLEET MANAGEMENT SOLUTION
Manage your equipment – anytime, anywhere – with Ammann ServiceLink. This comprehensive fleet system provides key data for light compaction equipment, heavy compaction machines and asphalt pavers. You can choose which machines to track.
• ServiceLink utilises telematics that give you the locations of the machines, hours of usage and other essential information. You’ll have access to data that will keep your machines running – and make them more productive, too.
• ServiceLink also makes it easy to plan and schedule the maintenance that protects your fleet.


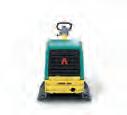

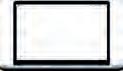
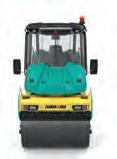
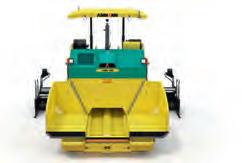
Accordingly, under the Airport Improvement Program, the U.S. government plans to invest US$3.2 billion for the development and modernisation of airports in the country.
The total construction project pipeline in the US, as tracked by GlobalData, stands at $629.3 billion. The pipeline, which includes all projects from pre-planning to execution, is skewed towards late-stage projects, with 62.1% of the pipeline value being in projects in the pre-execution and execution stages as of October 2018.
A further GlobalData report, Infrastructure Insight: The U.S. published in August 2018, notes how reduced tax rates and deregulation are expected to boost overall investment levels over the coming years, especially in the telecommunications, energy and air transportation sectors. States and local governments are pushing for higher gas tax and user fees in order to gain increased revenues for public works, while the Trump administration is seeking to harness private capital to take advantage of government spending on infrastructure at the federal, state and local levels.
The Association of Equipment Manufacturers (AEM), the North Americanbased international trade group representing off-road equipment manufacturers and suppliers, has voiced its concern about the Trump government-imposed tariffs on $250 billion worth of Chinese goods coming into the U.S. The move has led to retaliatory tariffs imposed or proposed on $110 billion-worth of U.S. goods imported to China.
BELOW: Get selling ... America requires US$3.6 trillion to repair, upgrade and modify its aging transport infrastructure by 2020.
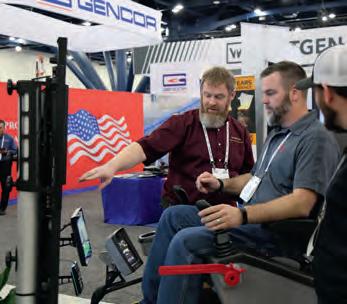
Speaking in September 2018, AEM president Dennis Slater said: “This extreme use of tariffs hurts our nation’s access to global markets and threatens many of the 1.3 million good-paying equipment manufacturing jobs our industry supports.”
Despite the continuing trade war with China, the United States economy remains red hot
On a more positive note, the AEM president welcomed the October 2018 unveiling of a new United StatesMexico-Canada Agreement (USMCA) on trade, hailing it as a “step in the right direction.” He added: “Trade agreements provide better access to customers across the globe and help us add to the 1.3 million jobs our industry supports in the United States. We urge this administration to continue working closely with the Canadian and Mexican governments to enact policies that promote continued economic growth for our industry.”
The AEM notes that nearly 30% of all equipment produced in the U.S. is intended for export, and Canada and Mexico are the
CENTRAL & SOUTH AMERICA
BIG POTENTIAL FOR CONSTRUCTION OEMS
Anew report by GlobalData highlights the enormous economic potential for infrastructure in Latin America. According to the major global business market research consultancy, the infrastructure sector in Latin America could reach a value of US$175.8 billion by 2020.
Such a huge sum creates a welcome wealth of commercial opportunities for the world’s construction equipment manufacturers.
The GlobalData report suggests that the total value of infrastructure spending in Latin America will reach $142.5 billion in 2019. The report adds that anticipated growth will
biggest and second biggest export markets respectively for both U.S. construction and agricultural equipment. The association says that since the creation of NAFTA two decades ago, the construction equipment manufacturing industry has benefited greatly from duty-free access to its two largest export markets, Canada and Mexico.
Despite the continuing trade war with China, the United States economy remains red-hot and continues to be an extremely attractive market for the global construction equipment industry.
After two years of contraction, the Canadian construction industry rebounded in 2017, and registered an annual growth of 3.1% in real terms, reported GlobalData in its May 2018 report Construction in Canada – Key Trends and Opportunities to 2022. This momentum was expected by GlobalData to continue in 2018, with annual growth of 2.6% in real terms, driven by government efforts to stimulate the economy through investment in public infrastructure and energy projects. Gradual improvements in consumer and investor confidence, as well as new policies related to the manufacturing sector, are expected by the global business market research firm to drive private sector investment in construction projects in the coming years.
Despite the possibility of new private sector investment in the construction sector, GlobalData notes that the likely persistence of high labour costs, constrained government revenue and low capital investment in the oil and natural gas sector will constrain the industry’s growth over the 2018–2022 period. Consequently, the industry is expected to register slow growth over the forecast period.
see infrastructure spending in Latin America hit $175.8 billion for 2020. GlobalData has made this analysis based on the activity for 1,711 large-scale projects in Latin America that are planned or being built at present. These have a combined value of $829.2 billion according to GlobalData.
The firm’s report: Infrastructure Insight: Latin America shows that there is a wide range of infrastructure investment opportunities for investors in Latin America due to favourable demographic trends and
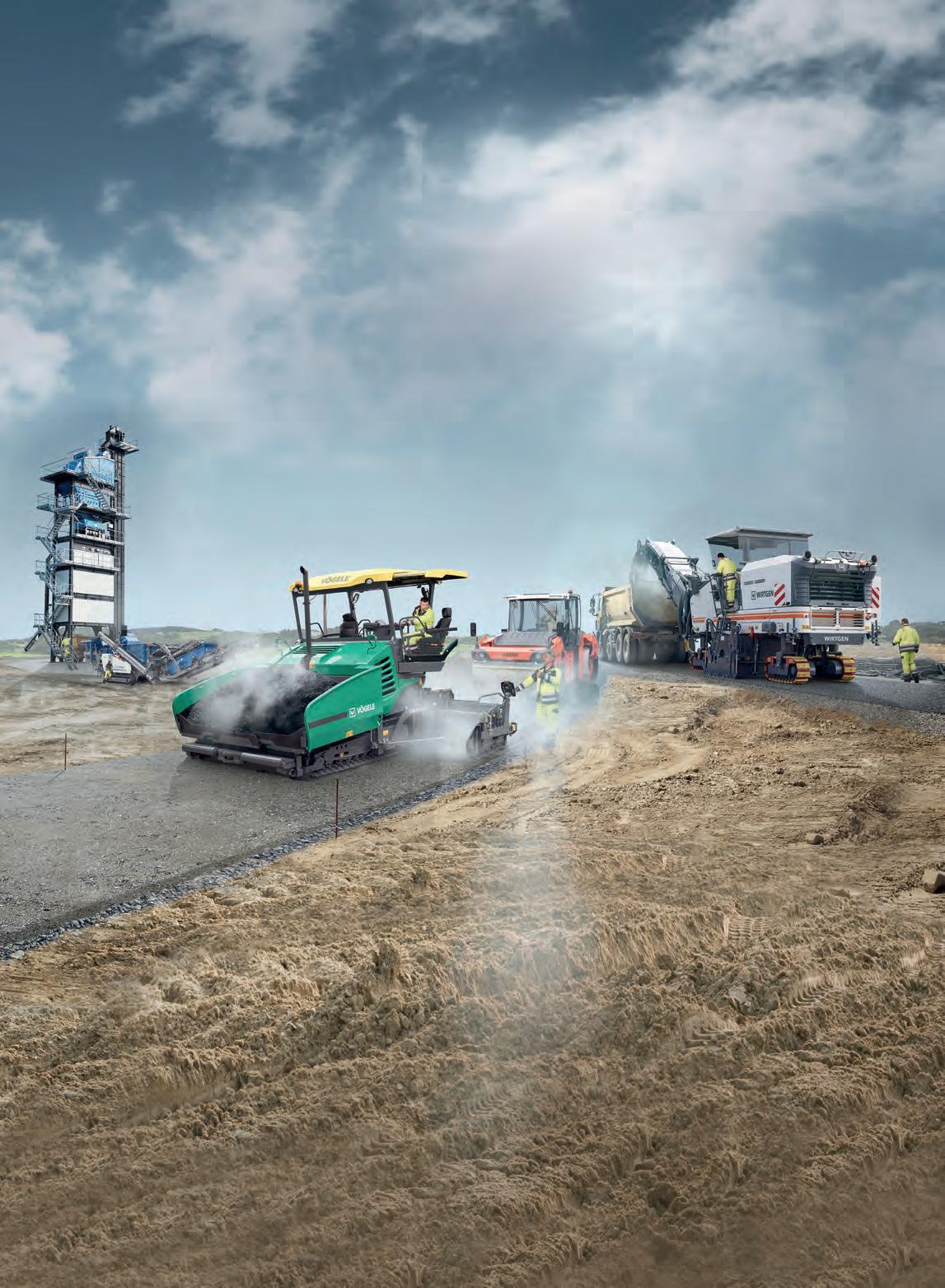

the implementation of legislative reforms.
Dariana Tani, economist at GlobalData, said, “Brazil, Chile, Mexico and Peru are set to drive overall investment between 2018 and 2022 with an expected annual average spend of $36.3 billion, $17 billion, $13 billion and $12.4 billion respectively. Projects will include the $2.7 billion SP-99 Tamoios Highway Duplication in São Paulo, as well as major metro and power projects.
Tani said that in Mexico, infrastructure project spending will be fuelled by large projects such as the construction of the $848 million Jala-Compostela-Las Varas-Puerto Vallarta Highway.
However, deteriorating external conditions such as global trade tensions, higher US interest rates and slowing global growth could slow growth in Latin America. And political uncertainty over coming elections in the region could also hinder growth. Furthermore, Tani added that there are questions over Mexico City’s $13 billion international airport project.
The GlobalData report says that with a total of 421 projects valued at $241.5 billion, Brazil has the highest number of infrastructure projects in the pipeline. This is followed by Chile with 309 projects worth $117.1 billion, Peru with 230 projects worth $83.1 billion and Mexico with 209 projects worth $98 billion. Colombia and Argentina also have a large number of projects, the former with 114 worth $66.8 billion and the latter 92, worth $58 billion. Number of infrastructure projects in the pipeline
Euromonitor International’s Construction in Brazil report published in May 2018 says the construction industry turnover of Latin America’s biggest nation is set to see an 8% increase in its CAGR (compound annual growth rate) in the 2017-2022 period, supported by an anticipated rise in private sector investment in infrastructure and initiatives such as the ‘Minha Casa, Minha Vida / My House, My Life’ programme. Although the Brazilian government failed to meet its annual target of building 610,000 new affordable housing units in 2017, plans for 2018 were set high. In spite of Brazil’s high budget deficit, authorities released a BRL45 billion (US$11.91bn) infrastructure programme.
The World Bank notes that with its GDP (Gross Domestic Product) of more than $628 billion, Argentina is one of the biggest economies in Latin America.
In its October 2018 published overview report on Argentina, the World Bank highlights how the presidential elections at the end of 2015, which saw Buenos Aires mayor Mauricio Macri narrowly defeat FPV candidate and Buenos Aires province governor Daniel Scioli, led to significant change in Argentine economic policy.
The report continues: “The new administration has moved with significant speed to implement core reforms
of the exchange rate, the agreement with international creditors, the modernisation of the import regime, reduction of inflation and the reform of the national statistics system.”
The World Bank report also notes how Argentina has taken a “very active role” on the international stage, taking the presidency of the G20 in 2018 and expressing its intention to join the OECD (Organisation for Economic Co-operation and Development) and become an observer in the Pacific Alliance.
However, the World Bank also notes that after economic growth of 2.9% in 2017, economic activity started to slow down in the second quarter of 2018, with the year set to end with a recession. The World Bank report highlights the plight of the Argentine peso, which has suffered a depreciation since April and fell close to 100% against the dollar up until October 2018. Consequently, inflation accelerated in the second half of the year.
The economic situation in Argentina led the Macri government to launch a new economic programme that includes a budget cut, an increase in revenues, and a $57 billion agreement with the IMF (International Monetary Fund).
With the country’s economic headwinds somewhat back under control, global construction equipment manufacturers may see new unit sale opportunities Argentina has taken a “very active role” on the international stage Buenos Aires, Argentina.

BELOW: As China strives to improve the working conditions in quarries, larger customers with a focus on efficiency will want the benefits that telematics can deliver.
THE CHINESE RECOVERY
Currently home to the world’s largest population at 1.3 billion, China is the second biggest economy in the world, after the United States, and, as a September 2018 China Overview from the World Bank notes, is increasingly playing an important and influential role in development and in the global economy. Indeed, the same World Bank report highlights that China has been the largest single contributor to world growth since the global financial crisis.
China’s infrastructure spending is huge. The hugely ambitious US$4 trillion-plus ‘One Belt, One Road’ Initiative, focusing on connectivity and cooperation between China and its Eurasian neighbours via the landbased Silk Road Economic Belt (SREB) and the ocean-going Maritime Silk Road (MSR), is continuing.
Other Chinese infrastructure megaprojects include the US$20 billion Hong KongZhuhai-Macau Bridge (HZMB) – a new 55km road, bridge and tunnel link spanning the Pearl River Delta’s Lingdingyang channel via three cable-stayed bridges and one undersea tunnel. HZMB, which was due to open to traffic before the end of 2018, will connect three popular destinations in the Pearl River Delta, providing a convenient and cheap option for business travellers and tourists. It will be the world’s longest sea-crossing bridge.

125% in 2017 to just under 100,000 units. According to the global construction equipment industry market research consultancy’s analysis, sales will grow a further 40% this year to take the market to the peak of its cycle.
The sharp rise in excavator sales has been due to several factors, says OHR, including the launch of major infrastructure projects, the introduction of public-private partnership (PPP)-financing models and the clearing of old stocks and used machines from the market following the 20122016 downturn.
OHR notes that sales of hydraulic excavators alone in China rose a staggering 125% in 2017
Infrastructure megaprojects can only be completed with great volumes of construction equipment, creating exciting sales opportunities for global and leading regional original equipment manufacturers (OEMs). Sales of construction equipment in China will exceed 325,000 units this year, according to the August 2018-published Mid-Year Review from Off-Highway Research’s Chinese Service. The forecasted 30% year-onyear rise in 2018 will follow on from an 81% increase in demand seen in 2017, compared to the previous year.
OHR notes that sales of hydraulic excavators alone in China rose a staggering
Excavator sales are expected to stay reasonably high for the next four years, states OHR, although 2018 is expected to be the highwater mark in the current cycle. Slower growth in real estate projects and a reduction in PPP activity is likely to impact on sales. On the other hand, OHR notes that stricter environmental policies and the forthcoming introduction of China IV emissions laws could see an accelerated machine replacement cycle take hold.
Commenting in an interview last autumn with Aggregates Business International magazine about the Chinese construction and quarrying equipment buyer’s growing preference for excavators over wheeled loaders, David Beatenbough, LiuGong’s vicepresident of R&D, said: “Historically, wheeled loaders were used for nearly every job. They
were much lower price than excavators, more easily available, and could accomplish nearly any task required, although perhaps not as efficiently as an excavator could in many cases. Now there is much more emphasis on efficiency on jobsites. Utilisation of wheeled loaders in China is becoming more similar to usage patterns in other countries, and the ratio of wheeled loader to excavator is shifting towards the global norm.”
Beatenbough said certain groups of Chinese quarrying and construction equipment buyers are also very focused on technology. “These customers are very knowledgeable about total cost of ownership and the efficiency of their business. They are very interested in telematics and the information it can deliver. As China works to improve the working conditions in quarries, larger customers with a focus on efficiency will be favoured. These are the customers who want the benefits telematics can deliver. This type of customer is also interested in other technology advances. However, customers in China who are interested in telematics or technology are not willing to pay for it unless they can see direct economic benefits. I think this condition is stronger here than in many other markets.”
In addition to meeting rising domestic demand, OHR states that Chinese manufacturers have been exporting machines in increasing numbers over the last three years. This includes international OEMs with a footprint in China, as well as indigenous companies.
TOUGH JAPANESE MARKET
In 2018 Japan had the world’s third biggest economy - valued at $5.1 trillion - but leading economists are predicting a fall to eighth place by 2050.The forecast large drop in the country’s comparative global economic prowess will be of grave concern to the leaders of such a fiercely proud nation, as is the current weak growth in the Japanese economy, which is already affecting its national industries, including construction.
Off-Highway Research’s (OHR) August 2018 updated Global Volume & Value Service reported that Japan was one of the few key construction equipment markets not expected to grow in 2018. Although OHR predicts that demand should edge up over the coming years, it expects the Japanese market to remain relatively small at 60,00065,000 units per year.
The wider Japanese construction industry is anticipated to post only marginal growth in 2018, thanks to a decrease in building permits and generally weaker demand. GlobalData
workforce population and labour shortage is expected to continue to hamper the industry’s output growth.
Over the 2018-2022 period, GlobalData strikes a more positive note saying that the Japanese construction industry’s output value is expected to be supported by the government’s concerted efforts to promote economic growth through investment in tourism, manufacturing, energy and healthcare infrastructure projects. The Japanese government’s investment in developing expressways will also support the construction industry’s output over the forecast period. For example, GlobalData highlights Prime Minister Shinzō Abe’s January 2018 unveiled plan to invest JPY1.5 trillion (US$13.9 billion) on the development of the Metropolitan Inter-City Expressway and the Tokai Expressway.
Additionally, the works related to the upcoming 2020 Tokyo Olympic Games are expected to drive the growth of the construction industry. The total cost of construction related to the games is expected to be JPY182.2 billion (US$1.7 billion).
The Japanese construction industry’s output growth in real terms is expected to remain fairly stable
The Japanese construction industry’s output growth in real terms is expected to remain fairly stable, predicts GlobalData, recording a compound annual growth rate of
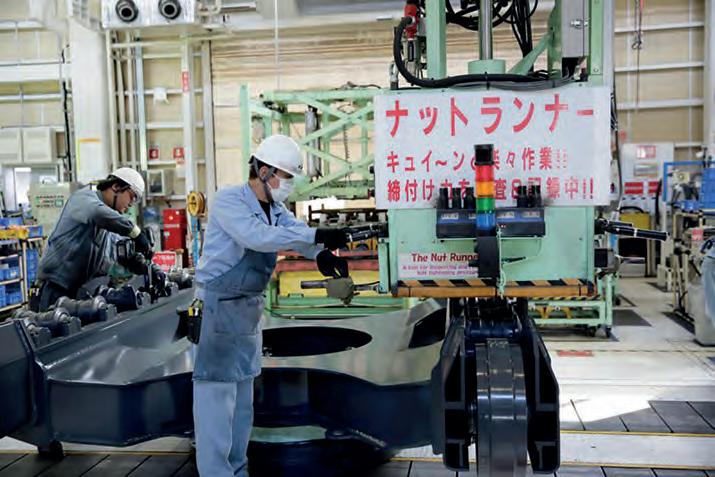
including all megaprojects with a value above US$25 million - stands at JPY28 trillion (US$249.9 billion). The pipeline, which includes all projects from pre-planning to execution, is skewed towards late-stage development projects, with 62% of the pipeline value being in projects in the pre-execution and execution stages as of 2018.
GlobalData also notes that the Japanese Ministry of Land, Infrastructure, Transport and Tourism has revealed government plans to attract 40 million foreign visitors by 2020 and 60 million by 2030. This has led the government to increase its spending on the tourism sector by 15%, going from JPY25.6 billion (US$228.2 million) in 2017 to JPY29.4 billion (US$262.1 million) in 2018.
Hitachi Construction Machinery notes that Japanese housing investment, public investment, and capital investment have increased. The Japanese-headquartered global construction, quarrying and mining equipment manufacturing giant says that Japanese demand for hydraulic excavators and wheeled loaders dipped between April and June 2018 due to the end of last-minute demands in anticipation of new emissions regulations.
In a ‘Corporate Vision’ presentation to construction and quarrying equipment trade media at Hitachi Construction Machinery (Europe) HQ in Amsterdam, The Netherlands, last autumn, the leading OEM forecast a 4% fall in hydraulic excavator unit sales in Japan in 2018, compared to the previous year.

Japan’s construction equipment manufacturers will benefit from plans to invest JPY1.5 trillion (US$13.9 billion) on the development of the Metropolitan InterCity Expressway and the Tokai Expressway ... plus works related to the upcoming 2020 Tokyo Olympic Games.
REST OF ASIA
GROWTH APLENTY
Indonesia, one of the world’s key emerging market economies, has a shopping list of impressive megaprojects that will require a huge quantity of construction equipment, building materials and personnel.
For example, the Trans-Java toll road, with a length of more than 1,100km, has an estimated cost of some US$5.5 billion. It is planned to stretch from the ports of Banyuwangi in East Java to Merak in Banten province in West Java.
Another huge project is the planned $20 billion, 40km Selat Sunda Bridge, the longest in Indonesia, to connect the western Indonesian islands of Sumatra and Java through road and railway, while the JakartaBandung super express train, which will travel the 144km between Jakarta and Bandung is estimated to cost $6.7 billion.
Suhen Agarwal, VP, sales & services, aggregates, Asia-Pacific, Metso, says that Indonesia has favourable demographics (50% of the population is under 30).
“Urbanisation, a strong labour market, and steady real-wage gains provide a solid base for 5-6%/year consumer demand growth in coming years.” And he also points to the increasing market for infrastructure.
“A flurry of major infrastructure projects in Indonesia is set to boost the construction sector. Over the next five years or so, the government aims to build 5,500km of railways; 2,600km of roads; 1,000km of toll roads; 49 dams and 24 sea ports as well as to construct power plants with a combined capacity of 35,000MW,” he says.
Off-Highway Research (OHR) reports that construction equipment sales in Indonesia are expected to exceed 17,000 units in 2018, following a third successive year of growth. This will take demand to more than twice what it was in the recent low point of 2015. This volume of equipment sales makes Indonesia by far the largest equipment market of the Association of Southeast Asian Nations (ASEAN) bloc.
Although demand is expected to be somewhat volatile over the next few years, OHR’s September 2018 report, The Construction Equipment Industry in Indonesia,
Singapore has road and tunnel contracts worth a combined $603 million
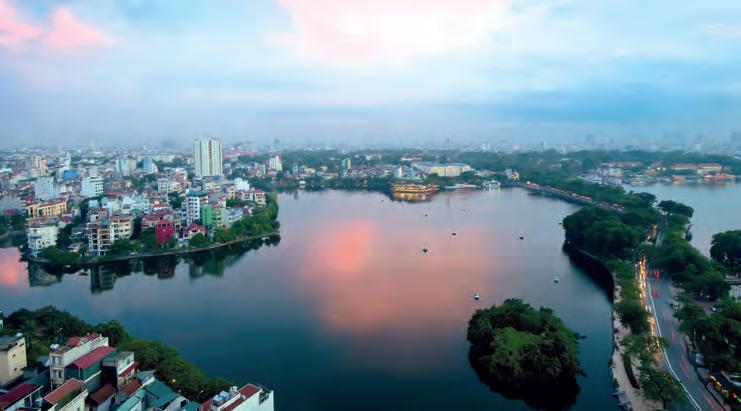
forecasts that demand will remain between 12,500 and 17,500 units up to 2022.
Investment in the mining sector has been a key driver of the recent growth in equipment sales. Construction has also played a part and is expected to continue to do so. However, OHR notes that the 2019 presidential election is expected to cause a hiatus in spending.
As well as being a large market, Indonesia is also an important manufacturing base, particularly, OHR states, for crawler excavators. In addition, compaction equipment, crawler dozers, dump trucks and motor graders are manufactured in Indonesia, making it an important country for component suppliers. The high population of equipment – OHR puts this at more than 115,000 construction machines plus a further 20,000 agricultural tractors – also makes it a significant country for global and regional companies active in the equipment aftermarket.
Other nations within South-East Asia are spending big on new transport infrastructure, generating attractive sales opportunities for global and major regional construction equipment manufacturers. Plans have been drawn up for a new highway connecting Laos’ capital Vientiane with Hanoi, the capital of neighbouring Vietnam. Expected to cost more than US$4.5 billion, the 707km route includes a border crossing between Namphao in Laos and Cau Treo in Vietnam. Sri Lanka is home to a $1 billion Central Expressway project; the $832.8 million Manila-Taguig Expressway (MTEX) is taking shape in the Philippines, and Singapore has road and tunnel contracts worth a combined $603 million.
Given its rich array of earmarked government and private company-controlled projects, South Korea’s construction GDP is forecast to grow to US$86 billion in 2018, compared to $70 billion in 2017, with construction GDP forecast to hit $91 billion in 2019. Unsurprisingly, leading global business market research consultancies believe the South Korean construction sector success story will continue beyond next year. For example, Timetric’s Construction in South Korea – Key Trends and Opportunities to 2021 report states that the South Korean construction industry’s output value is expected to rise with a compound annual growth rate of 3.99% in the 2017-2021 period.
The growth follows a 4.93% CAGR in the years 2012-2016, and will be driven, says Timetric, by the investments in public infrastructure, energy, commercial and industrial projects, and improvements in consumer and investor confidence. Moreover, a rise in building permits for the construction of residential and nonresidential buildings in the country is expected to support the industry’s growth over the forecast period.
Timetric’s study highlights that the government’s focus on developing transport infrastructure, as well as efforts to boost energy production, particularly renewables, is expected to drive funding towards the construction industry over the forecast period. The government is committed to investing KRW42 trillion (US$36.6 billion) on renewable energy infrastructure, with an aim to eliminate coal power plants in South Korea by 2020.
AFRICA
MAINLY POSITIVE SIGNS
Infrastructure spending across Africa continues at a decent pace, driven by rapid urbanisation. Indeed, the World Bank has predicted that the proportion of Africans living in urban areas is projected to grow from 36% in 2010 to 50% by 2030. This is creating eye-catching commercial opportunities for global and regional construction equipment manufacturers. The pace of construction sector growth in sub-Saharan Africa - will be particularly strong, averaging 6.6% a year in 2018-2022, according to GlobalData’s Q3 2018 Update. Meanwhile, a Deloitte study, A shift to more but less - Africa Construction Trends Report 2017, states that South Africa continues to account for the largest share of infrastructure and capital project activity in southern Africa - which includes Angola, Botswana, Lesotho, Madagascar, Malawi, Mauritius, Mozambique, Namibia, South Africa, Swaziland, Zambia and Zimbabwe – with 47.3% of projects, followed by Angola with 14% and Mozambique with 12.9% of projects. South Africa is the largest African-nation buyer of construction equipment – 5,5006,000 units/year in a 23,000-25,000 units/year continent-wide sales market.
In its South Africa Economic Update 11: jobs and inequality, published in April 2018, the World Bank argues that although its economic outlook has improved, South Africa remains constrained by its low growth potential. The Economic Update says: “Slow private investment growth and weak integration into global value chains prevent the country from reaping the new economic opportunities emerging around the globe, and from catching up with living standards in peer economies.”
West Africa – which includes Benin, Burkina Faso, Cape Verde, Côte d’Ivoire, the Gambia, Ghana, Guinea, Guinea-Bissau, Liberia, Mali, Mauritania, Niger, Nigeria, Senegal, Sierra Leone and Togo - has, according to Deloitte’s Africa Construction Trends Report 2017, 79 projects currently underway, with a committed value of US$98.3 billion. The region, highlights the Deloitte study, accounts for 26.1% of all
projects in Africa and 32% of the total project dollar value.
GlobalData notes that there will be a steady acceleration in construction activity in Nigeria over the period 2018-2022, supported by government efforts to revitalise the economy by focusing on developing the country’s infrastructure. Ethiopia will be Africa’s star performer, with its construction industry continuing to improve in line with the country’s economic expansion.
Further research by GlobalData into the East African infrastructure sector indicates that it is expected to grow steadily over the 2018-2022 period. The industry market research consultancy says there are huge infrastructure upgrades underway across the region in roads, railways and power generation. GlobalData states that the total
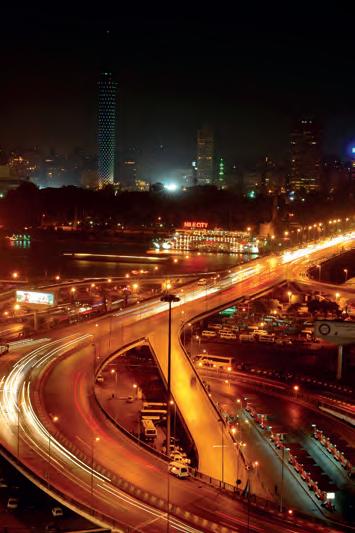
Cairo, Egypt.
“In terms of the number of $50 million-plus projects, Egypt has the most with 17”
Kenya and Tanzania) reached US$25.92 billion in 2017, a significant rise on US$6.73 billion in 2012. Output is projected by GlobalData to almost double to US$98.82 billion by 2022 (in nominal value terms).
GlobalData notes that in East Africa, the transport (rail and road) and energy sectors account for a large proportion of the infrastructure project pipeline, making up 37.1% and 45.2% respectively, with project values amounting to US$77.51 billion and US$94.55 billion respectively. Across the Eastern African economies, public-private partnerships are said by GlobalData to be funding the majority of projects in the pipeline (51.8%), while 32.8% of tracked projects are publicly funded.
A more stable political and security climate in North Africa - which includes Algeria, Egypt, Libya, Morocco, South Sudan, Sudan, Tunisia and Western Sahara - has helped pave the way in the last few years for a significant increase in the number of the region’s US$50 million-plus infrastructure projects. Deloitte’s Africa Construction Trends Report 2017 states that North Africa features 40 $50 million-plus projects, valued at a combined US$77.1bn. Deloitte highlights that the region represents 13.2% of all projects on the African continent. In terms of the number of $50 million-plus projects, Egypt has the most with 17 projects, followed by Algeria with 12 and Morocco with eight. However, the number of projects in North Africa decreased by 4.8% from 42 in 2016 to 40 in 2017, notes Deloitte, while the value of projects rose by 1.3%.
In contrast to recent years, Deloitte points out that the number of real estate projects in Northern Africa has overtaken transport projects, with the former making up 32.5% and the latter 27.5% of projects respectively. Real estate is dominated by commercial real estate (rather than industrial real estate) in terms of both US dollar value and the number of projects.
The Deloitte study emphasises the shift away from major transport works in reporting that the number of big transport projects in North Africa decreased from 18 projects in 2016 to 11 projects in 2017. This is due to the completion of seven major transport projects, with no new large-scale transport projects beginning construction between 2016 and 2017.




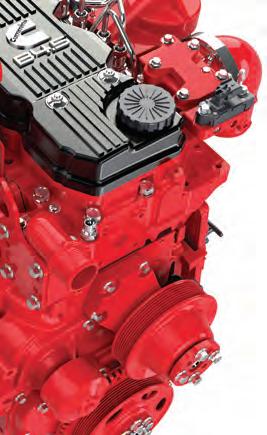
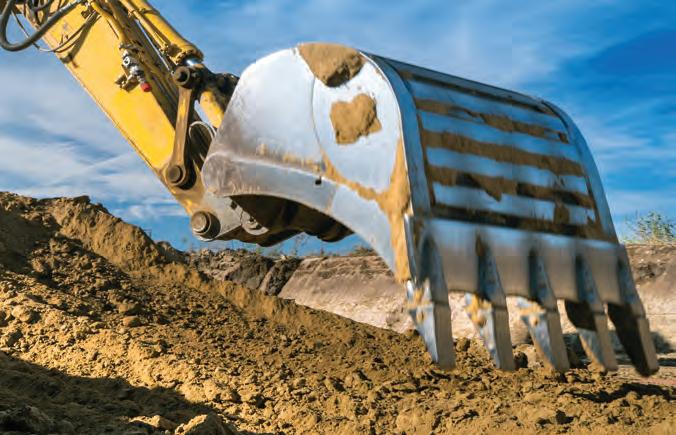
For 100 years, we have defined ourselves by our unwavering values and promise of innovation and dependability. We have led our industry by consistently turning challenges into opportunities. In the next 100 years, we will continue to defy boundaries and unleash our ingenuity in a world hungry for new power solutions.
see how we’re challenging the impossible at Bauma 2019, Hall a4.325.
BOOM-TIME INDIA
India’s prime minister, Narendra Modi, is backing a five-year national road sector investment programme worth more than $90 billion. It has increased road building in India to more than 40km a day, which has already grown from 3km a day to a staggering 27km a day. A total of 200,000km of national highways is expected to be completed by 2022. When you add in close to 10,000kms of railways under planning, and the development of port infrastructure around 10 coastal economic regions, you can understand why the world’s construction equipment manufacturers are excited about commercial opportunities in India.
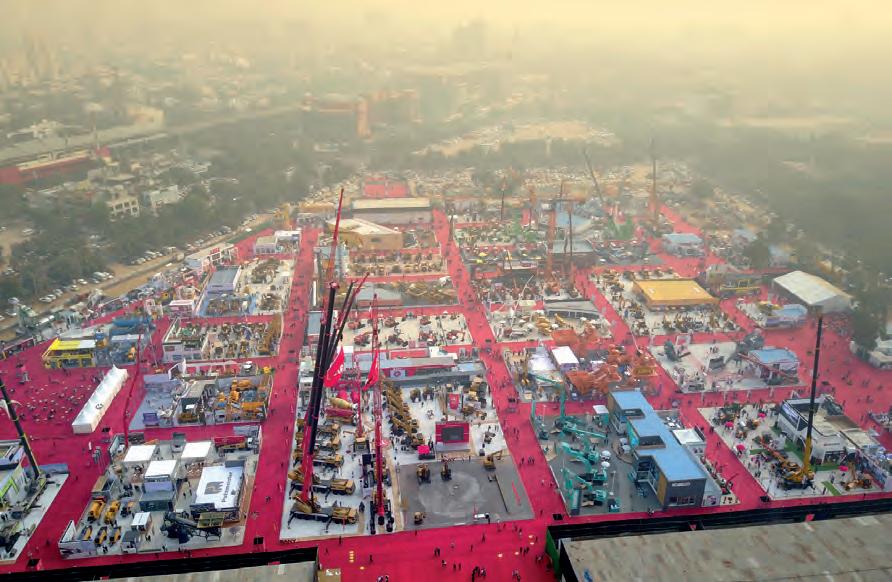
According to the 2018 Mid-Year Review from Off-Highway Research’s (OHR) Indian Service, sales of earthmoving, roadbuilding and materials handling equipment, along with portable compressors, were expected to reach 90,115 units by the end of the year. That would represent a 15% increase on the 78,109 machines sold in 2017 and a near doubling of the market since the trough of 2014 and 2015.
OHR notes that the previous peak in construction equipment sales was 72,492 units in 2011, so demand in India had already surpassed that by the end of 2017. The robust growth and recent record demand has been largely due to the Modi government’s efforts to speed up the pace of infrastructure development.
Commenting on the current market drivers, OHR’s report said: “The surge in demand in the first half of 2018 resulted from increased activity in the construction and mining sectors, and the continued momentum following the GST (national sales tax) rate reduction in November 2017. Easy availability of finance, positive sentiments and replacement demand are other factors which helped the market to grow.”
According to other industry estimates, the size of the Indian excavator market is expected to be close to 25,000 units in 2018. Demand for 3-tonne class wheeled loaders, predominantly used in quarry sites in India, is up by 30%, while 5-tonne class model demand is up 60% in 2018 compared to 2017.
Sales of rigid dump trucks (RDTs) have also been rising and manufacturers continue to launch newer hauler products, primarily
materials, processed minerals and overburden. Sales of RDTs are expected to be close to 80,000 units in 2018, compared to 65,000 units last year. The market trend indicates a transition to higher capacity trucks, from 16tonnes to 25tonnes, and to 8x4 axle trucks with 31-tonne capacities over 6x4 axle trucks offering up to 25-tonne payloads. This transition has been noticeable during the past two years.
Demand for 3-tonne class wheeled loaders, predominantly used in quarry sites in India, is up by 30%
A key reason behind rising loader and hauler demand is due to pent-up demand, as contractors and equipment rental agencies held back from updating their fleets due to the reduction in infrastructure sector projects between 2011 and 2015.
Euromonitor International (EI) tips Indian construction industry turnover to see a 4% CAGR in the period 2016-2021, as the country’s government approves new measures to expedite investment for housing construction and infrastructure development. Private sector firms are moving ahead with plans for new speciality hospital facilities as demand for high-end diagnostic and treatment services increases. EI states that the launch of new affordable homes across eight major Indian cities expanded by 22% in 2016 alone. The entire Indian construction industry grew 6% in the same year thanks to the government’s affordable housing stimulus and increased road infrastructure investment.
GlobalData’s Construction in India –Key Trends and Opportunities to 2022 report states that government investment in transport infrastructure, energy and residential projects under flagship programmes such as the 100 Smart Cities
Housing for All 2022, UDAN (Udey Deshka Aam Nagrik) scheme and the Ayushman Bharat programme is expected to drive the growth of the construction industry over the 2018-2022 forecast period.
In its April 2018 members’ newsletter, the Indian Construction Equipment Manufacturers Association (ICEMA) said that going forward, there could be some disruptions in the construction equipment industry, both from product and service perspectives. Some likely developments, says the ICEMA, are: growth in the pre-fabricated concrete business, which could lead to increased use of concrete equipment like transit mixers, concrete pump and boom; an increase in usage of specialised equipment, which could impact the backhoe loaders business in a “small way” through competition from under 14-tonne class excavators and wheeled loaders.
The ICEMA newsletter also points to rising manual labour costs, despite considerable mechanisation across key infrastructure projects, real estate, rural roads, etc. The association stresses that the need for manual labour will continue to be considerable.
Unsurprisingly, the ICEMA sees a growing digital presence within the Indian construction equipment sector. It sees that the higher penetration of e-commerce across the country is, in turn, slowly gaining traction in the construction industry.
The ICEMA believes e-commerce portals providing men and material for the construction industry, and an exclusive equipment financing institution which caters to the needs of the entire sector could materialise.
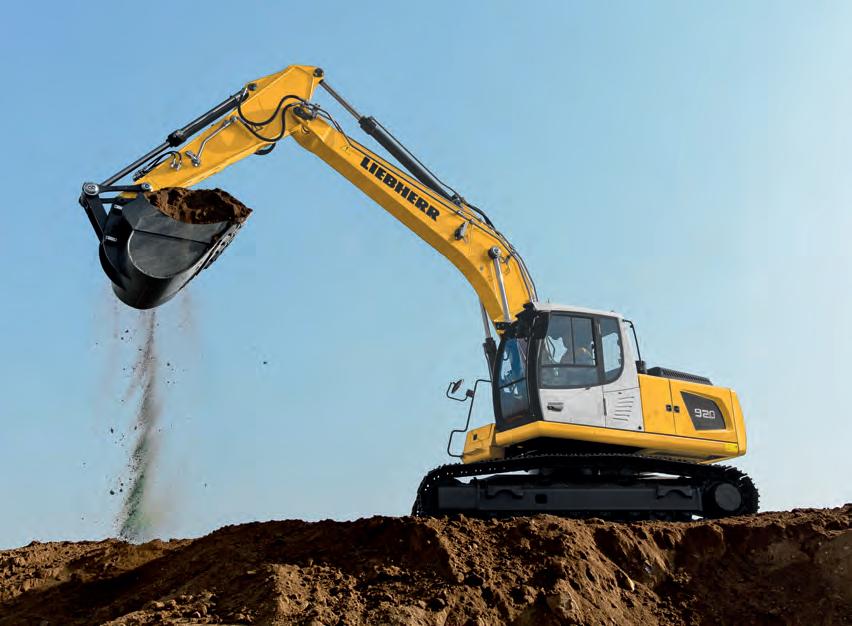
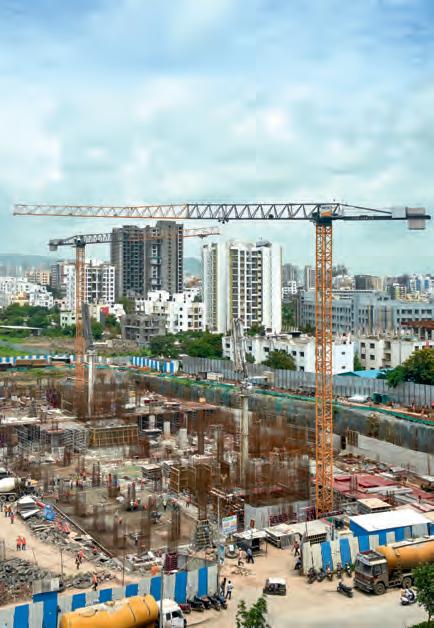
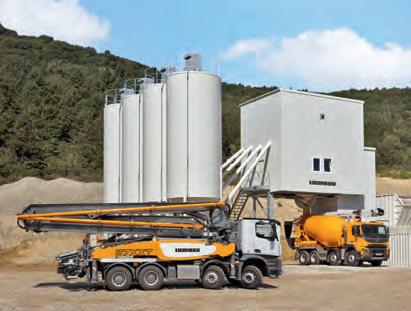
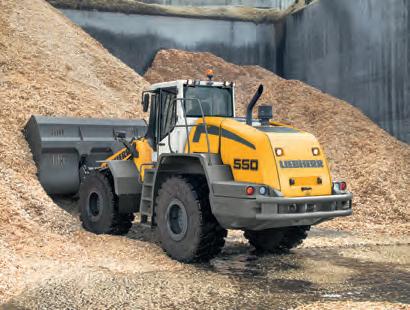
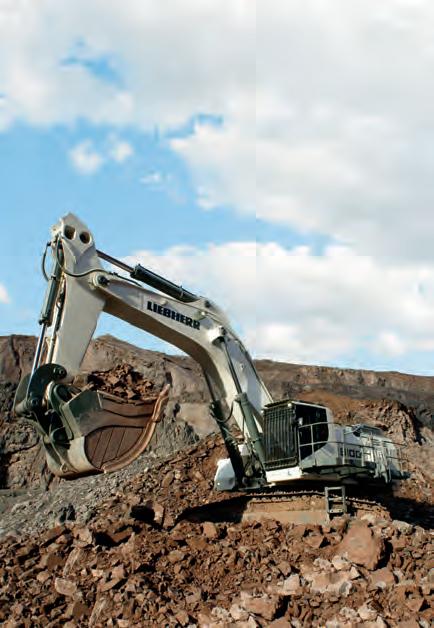
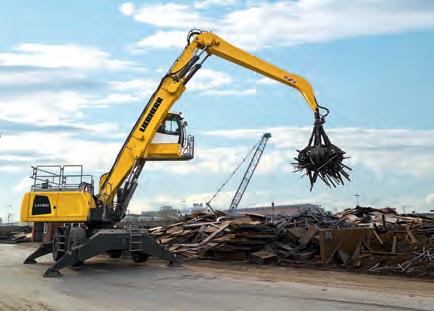
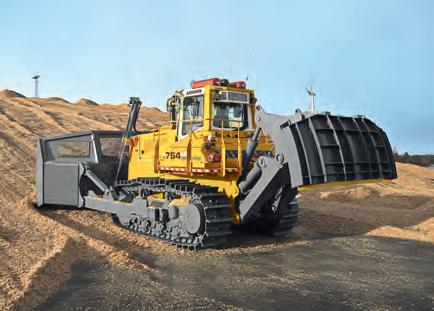
www.liebherr.com
MIDDLE EAST
MEGAPROJECTS IN FULL EFFECT
Ahuge array of construction machines and building materials suppliers are helping create the world’s biggest airport, currently taking shape in Dubai in the United Arab Emirates (UAE). The US$32 billion expansion of Al Maktoum International Airport will see 140 million passengers pass through its doors by 2025. Following its completion in 2050, the airport will have the capacity to handle 200 million passengers a year – a world away from the paltry by comparison current 7 million passenger capacity site, which is mainly used today for cargo traffic.
Al Maktoum International Airport will be a key part of a new type of city development, an aerotropolis named Dubai South. When completed, Dubai South will be home to 900,000 inhabitants, and reachable within an eight-hour flight for two-thirds of the world’s population. Dubai is hosting the next official
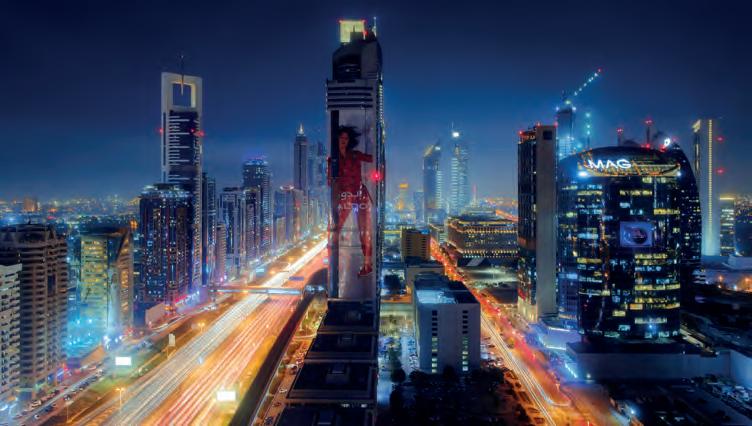
World Expo in 2020 and the Expo area is being built next to the airport. The bulk of the 25 million visitors expected to attend the Expo will travel through Al Maktoum International Airport.
Given the airport’s expansion and other large-scale infrastructure works in Dubai and other parts of the UAE, it is no surprise that the World Bank tipped the GDP of the federation of seven states to grow 2.5% in 2018. In its United Arab Emirates Economic Outlook, published in April 2018, the World Bank says that UAE oil production capacity is likely to increase, and the strength of the non-oil economy will boost economic prospects as key infrastructure projects ramp up ahead of Expo 2020.
GlobalData reports that Qatar’s economy has largely recovered from a boycott imposed in June 2017 by other Arab states, and economic growth returned to positive territory in 2018. Construction activity remains resilient, as government spending has continued on projects, despite a sharp downturn in the residential real estate market that was exacerbated by the boycott.
GlobalData expects to see strong growth in Qatar’s construction activity in 2018. Construction work related to the 2022 FIFA World Cup will help support the country’s construction industry growth over the next few years. Up to 200,000 football fans a day will attend the late November-mid-December tournament, swelling Qatar’s population by 8%.
Euromonitor International, a leading provider of global business intelligence and market analysis, reports that growth in Saudi Arabia’s construction industry is forecast to remain flat until at least 2021, as the country’s budget deficit and government austerity measures are expected to keep construction industry growth at minimal level.
In 2016, the Saudi government reduced its infrastructure and transport projects budget by 62% to SAR23.9 billion (US$6.36 billion), on the back of persisting low crude oil prices, falling exports, and the consequent soaring fiscal deficit. During the same year, Saudi Arabia’s construction industry witnessed a 1.2% decline in turnover, mostly due to re-assessment of all government capital
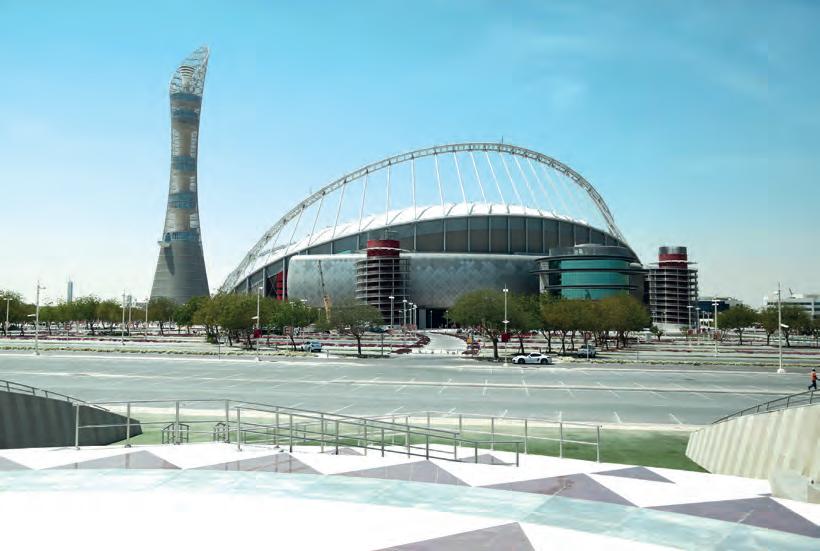
“Construction work related to the 2022 FIFA World Cup will help support the country’s construction industry growth over the next few years”
expenditure projects launched under Saudi Arabia’s Vision 2030 programme.
More positive news for global construction original equipment manufacturers (OEMs) can be found in some major developments within the industrial, commercial and hospitality construction sectors in the kingdom, supported by economic diversification strategies and greater involvement of the private sector. Despite the challenging operating environment, work has also continued apace on the Riyadh Metro and King Abdullah Economic City - two of Saudi Arabia’s most prestigious projects.
Saudi Crown Prince Mohammed bin Salman has made several impassioned calls for greater economic diversification in Saudi Arabia, including a greater role for the private sector. This could lead to new eye-catching and lucrative infrastructure
opportunities that require a wealth of new construction and quarrying machinery in their delivery, along with millions of tonnes of new building materials. Unfortunately, such projects are unlikely to be diggerready for several years.
Encouragingly, the World Bank forecasts that the Saudi Arabian economy will expand in 2018 with a 1.8% increase in GDP.
Iran’s economy is expected by the World Bank to maintain a steady growth of slightly over 4%, fuelled by a recovery in consumption and investment demand. The same source notes “some signs of pickup” in the construction sector, helping to confirm a more feel-good vibe around the country’s economy. Timetric notes that the removal of international sanctions and a rise in oil production and exports will add momentum to Iranian construction industry growth, as will an increase in the awarding of building permits
for the construction of residential and nonresidential buildings.
Kuwait is among the Gulf countries witnessing a burgeoning construction sector. The country’s ambitious Vision 2035 programme is seeing the Kuwaiti government ploughing huge sums into developing the nation’s road, rail, airport and related infrastructure, generating fertile territory for growth market-seeking construction equipment manufacturers.
Oman is another Middle East nation whose large transport and other infrastructure projects and ongoing development of its tourism industry is driving regional construction and construction equipment demand.
In the Middle East as a whole, Deloitte’s GCC Powers of Construction report 2018 predicts that transport infrastructure spending will increase from $6.847 billion in 2018 to $7.509 billion in 2019.
That level of investment is creating some exciting opportunities for global market construction equipment manufacturers.

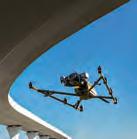
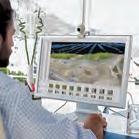
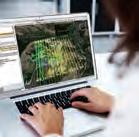
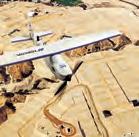
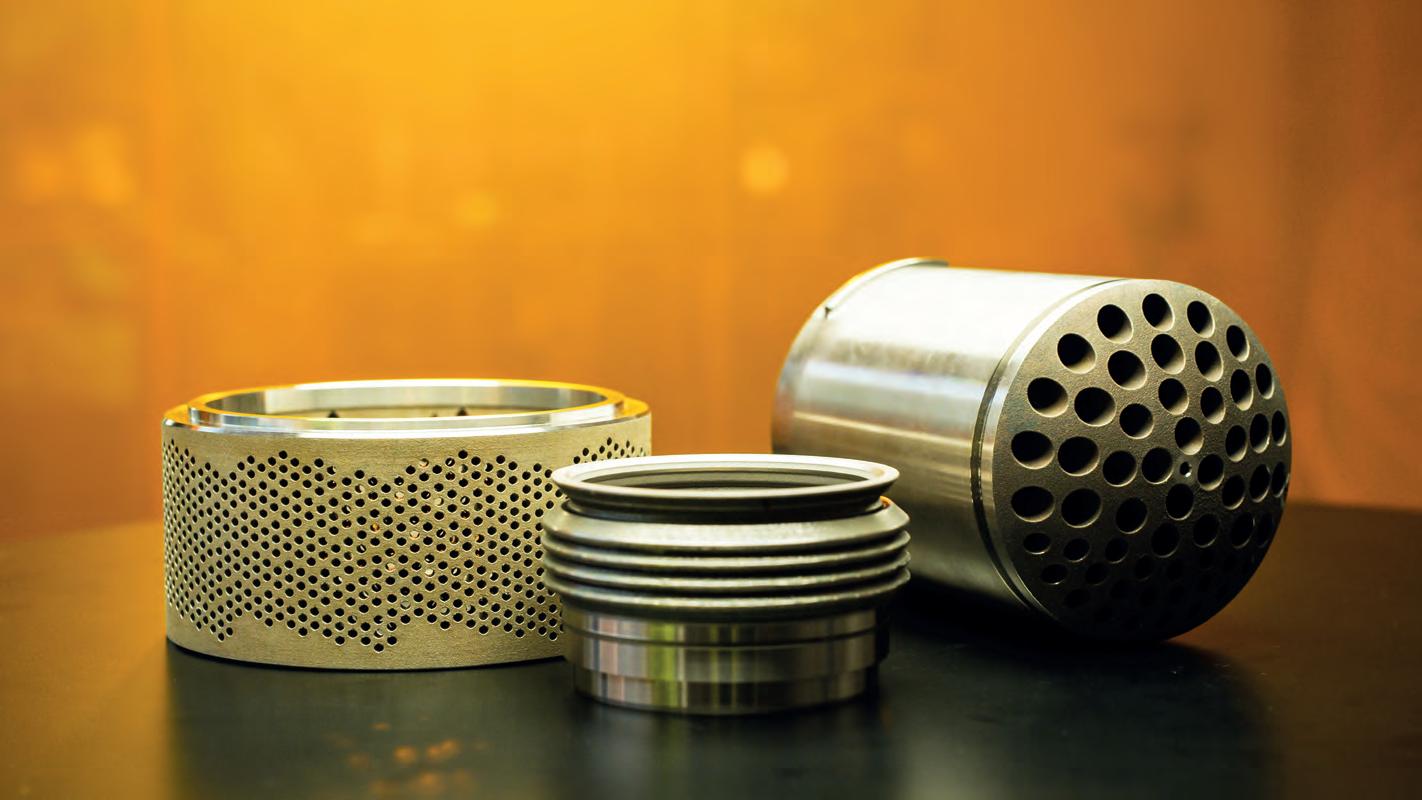
CUT YOUR COSTS AND EXTEND YOUR MACHINE’S LIFESPAN WITH 3D PARTS PRINTING
3D parts printing, or additive manufacturing as it is sometimes called, is revolutionising the rapid prototyping of new equipment and making it easier to support older machinery in the field. Downtimes can be significantly reduced if you 3D print a new part locally instead of waiting for the courier to deliver a replacement component to your site. Dan Gilkes reports.
Even the simplest piece of construction equipment is made up of hundreds of individual parts. Larger, more complex pieces of machinery can incorporate literally thousands of specific components. These can be purchased from external suppliers or developed in-house by the machine manufacturer but, either way, they require just as much research and development time as the more noticeable styling parts.
Cutting the time required to design and fabricate every component, particularly when prototyping new or improved machinery, can reduce cost as well as project duration. To achieve this, many manufacturers have been turning to 3D printing, or what is often called additive manufacturing (AM), to create evermore complex components in a fraction of the time that conventional casting, milling and welding would require.
Additive manufacturing is the opposite of subtractive manufacturing, where material is cut out or reduced using milling or drilling machinery. It is a process of making three dimensional solid objects from a digital file. The object is created by laying down successive layers of material, until the component is produced. Each of these layers can be seen as a thinly sliced horizontal cross-section of the finished object.
“Two of the biggest advantages are the cost savings and the time savings that we have achieved in prototyping,” said Lukáš Mandik, advanced technology manufacturing
engineer in Doosan Bobcat’s prototype shop in Dobris, Czech Republic.
“Cost savings largely arise with the making of parts that cannot be produced by traditional technologies such as machining and welding … parts that had to be produced by form-casting in the past: A process which required a much larger investment compared to 3D printing. The time savings using 3D printing are made as an engineer’s design can take physical shape in a matter of a few hours, ensuring that prototyping time is significantly reduced. This also allows us to reduce the number of hours needed for projects, again providing cost savings.”
Bobcat is not alone in using the technology. “We started some time ago, with plastic in-cab components,” said Marco Baffoni, CNH Industrial’s parts lifecycle manager. Indeed, CNH sister company Iveco, has used 3D printing to replace internal plastic components for its bus lines for some time.
“Up until the recent past, 3D printing was used primarily for parts prototyping,” said Don Jones, Caterpillar’s general manager of global parts strategy, speaking in an interview with Aggregates Business Europe’s editor Guy Woodford last year. Indeed, Caterpillar has been printing prototype machine parts in its R&D work since the mid-1990s.
“An engineer would do a new design and want to see what it looks like and whether it works, before taking it for production tooling. The second area it has been heavily
used in is jigs and tools for the assembly line, primarily using plastics, but we also have used 3D metal printers.”
Volvo CE will be using AM to prototype future equipment, maintaining several 3D printers for research and development purposes. However, prototyping is not the only area where AM offers a benefit.
“We are supporting customers through the life cycle of their equipment,” said Jasenko Lagumdzija, Volvo CE manager of business support.
“It’s especially good for older machines where the parts that have worn out are no longer made efficiently in traditional production methods. Producing new parts by 3D printing cuts down on time and costs, so it’s an efficient way of helping customers.”
The turnaround time for replacement parts can be as short as a week, cutting downtime for a machine in the field. This ability to replace parts for older machines also extends the equipment’s life and, because AM is designed for small-run sizes, there is no minimum order requirement, making it easier for a manufacturer to support individual customers.
TOP: 3D printing or additive manufacturing allows the creation of ever- more complex components in a fraction of the time that conventional casting, milling and welding would require.
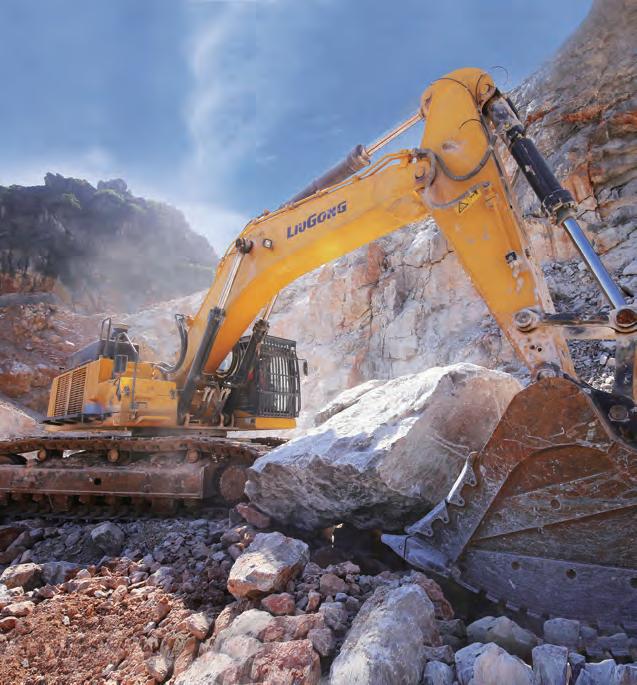
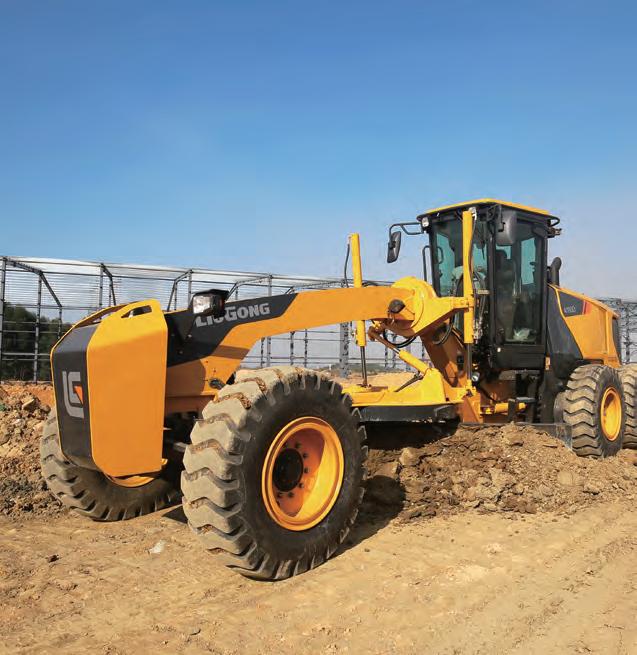
TOUGH IS WHAT WE DO
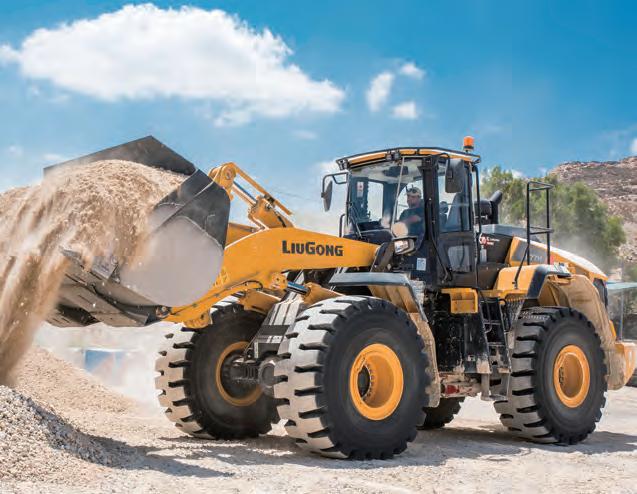
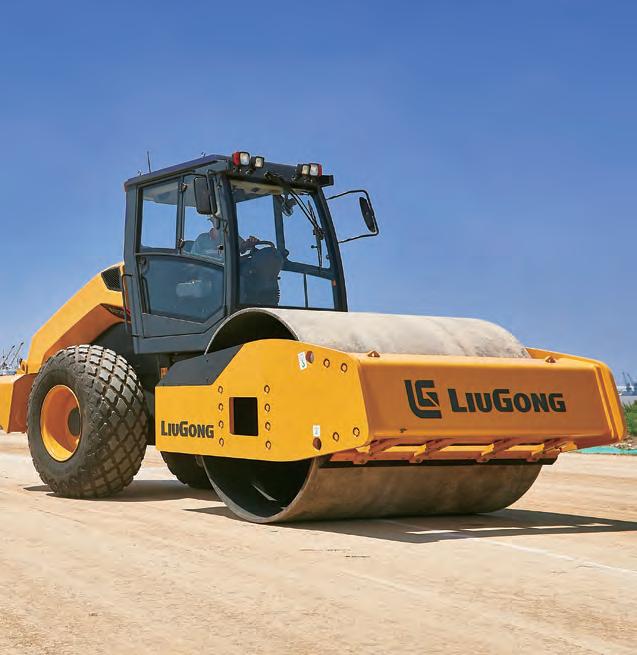
OUR LINE OF TOUGH EQUIPMENT WORKS HARD IN TOUGH ENVIRONMENTS. DURABLE AND POWERFUL, YOU CAN BE CONFIDENT YOU CAN INCREASE YOUR PRODUCTIVITY WITH LIUGONG’S POWERFUL LINE OF MACHINES. WITH A FOCUS ON THE EASY AND FLUID OPERATION AS WELL AS COMFORT, OPERATORS HAVE AN EASY TIME KEEPING UP WITH OUR MACHINES.

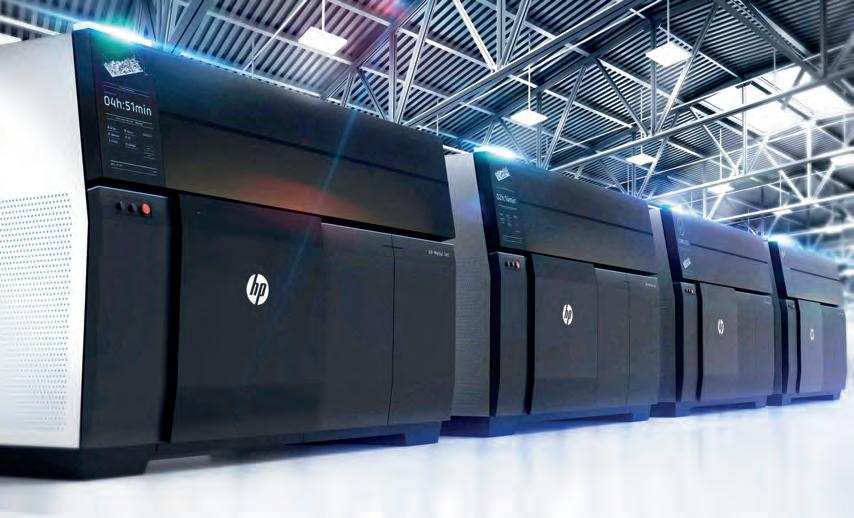
The type of parts being produced is changing, as impressive new technology like this develops and the price of AM equipment continues to fall.
CAR MAKERS LEAD THE WAY
As is so often the case, the automotive industry is ahead of the construction equipment sector, and 3D printing is no exception. Late last year, Volkswagen announced that it would be using the HP Metal Jet process to produce metal components for production vehicles.
Developed by printer manufacturer HP with component firm GKN Powder Metallurgy, parts are produced layer by layer using a powder and binder. The component is then ‘baked’ into a metallic component in what is called a sintering process. This differs from previous processes in which the powder was melted by a laser. Productivity is said to have improved by 50 times compared to traditional 3D printing methods and VW is pressing ahead with the development of the technology for mass production.
“Automotive production is facing major challenges, our customers are increasingly expecting more personalisation options,” said Dr Martin Goede, head of technology and planning at VW.
“At the same time, complexity is increasing with the number of models. That’s why we are relying on state-of-theart technologies to ensure smooth and fast production. 3D printing plays a particularly important role in manufacturing of individual parts.
“Previous 3D printing processes can only be used for the special production of individual parts or prototypes. The additive 3D Metal Jet technology from HP enables the production of a large number of parts using 3D printing for the first time. As a result, the process is now interesting for the production of large quantities in a short period of time.”
➔To produce parts for those customers, Volvo relies on its own archive of drawings and other product information, though it currently has components made by a supplier in thermoplastic. Such components include plastic coverings, portions of air conditioning units and cabin parts. However, while plastic is the primary material at present, the company is considering offering metal parts in the future.
“The customer is getting exactly the same part in replacing plastic with plastic,” said Annika Fries, Volvo CE’s aftermarket branding manager.
“We do a lot of quality assurance, the 3D parts have the same specifications and go through the same process as the original and get the same warranty, so customers can be confident they are getting a genuine Volvoapproved part.”
“We are talking about different materials too, not only plastic,” said Bobcat’s Mandik.
“First of all, it’s necessary to say we use plastic materials, like PC, ABS, ABS M30 or ULTEM 9085. Although they are plastic we are able to print some parts that can work under load. The ULTEM 9085 for example has a tensile strength of around 72MPa.
“We are investing to ensure the reliability and quality of materials is stable. The cost is coming down and the technology is developing faster, but cost is the major barrier. But we think it will be a trend that we are investing in.”
The type of parts being produced is also changing, as the technology develops and the price of AM equipment continues to fall.
“There are lots of parts for our products, especially Bobcat loaders and excavators, which could be made by 3D printing, such as fuel tanks and body parts,” said Mandik.
“Being able to produce these parts ourselves, we could be almost independent of both local suppliers and those abroad. I say ‘almost’ because 3D printing consumes lots of raw materials which still need to be supplied.
BELOW: OEMs are seeing constant advances in carbon fibre, Kevlar and 3D-printed plastics ... the latter having the same strength as metal,while also being lighter, easily 3D-printed and made of composites that don’t rust.
“Our building process runs by the FDM method - fused deposition modeling. All the parts we produce can be divided into two types – installation parts and functional parts. Under the first group, we can include body parts, some interior parts and counterweights. We use 3D printing to look at how the design works in reality, so we can assess whether or not it will work.
“In contrast, with functional parts such as a fuel tank, we are already able to print a tank, which after some small cosmetic adjustments is ready to be used in normal operations. At present, our maximum dimensions are 914 x 914 x 610cm.”
In such a rapidly developing new technology there are constant advances in carbon fibre, Kevlar and 3D-printed plastics, the latter having the same strength as metal, while also being lighter, easily 3D-printed and made of composites that don’t rust.
Crushing equipment supplier Metso has recently gone a stage further, delivering the first valves with 3D-printed parts from its Helsinki plant. The valves include 3D-printed metal components, that allow the valves to perform in a particularly demanding application, where they need to withstand numerous fast open-close cycles without maintenance.
“We are at the forefront of using 3D printing in valve applications, having started testing the suitability of 3D printing technologies for metal components already years ago,” said Jukka Borgman, director of technology development.
“We have defined and prototyped several concepts where the 3D-printed components can provide new levels of valve performance compared to components manufactured with
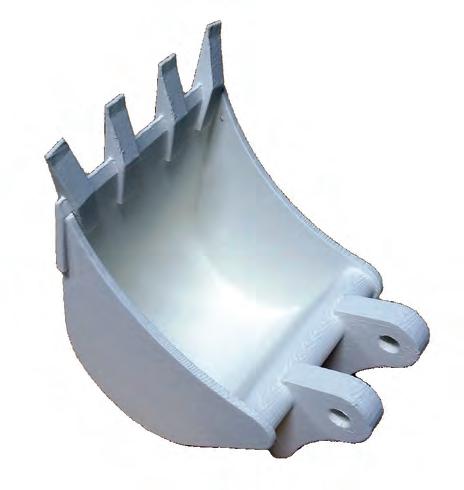
RIGHT: Spare parts distribution centres and local dealers could be equipped with 3D printers, with manufacturers sending digital files to allow localised production of components.
“The beauty of 3D printing is that it allows the customer to have devices whose new properties can only be implemented using the 3D printing method,” said Jani Puroranta, Metso’s chief digital officer.
In addition to valve component production, Metso is already using 3D printing to additively manufacture tools used to make minerals consumables parts.
“With certain products, a key benefit for the customer can be exceptionally quick delivery times,” said Puroranta.
Liebherr’s aerospace division has been producing metal components using AM for some time. In 2018, the firm installed a second 3D printer for titanium components at its Lindenberg plant, with one now used for production and the other for R&D work. However, though the construction and mining divisions are evaluating 3D manufacturing, the company has yet to produce parts for its heavy-machinery businesses using the technology. There seems little doubt though that most manufacturers will use some form of AM as the technology continues to develop.
“What’s exciting now is the recent development of new printing technology for both plastics and metals,” said Caterpillar’s Jones.
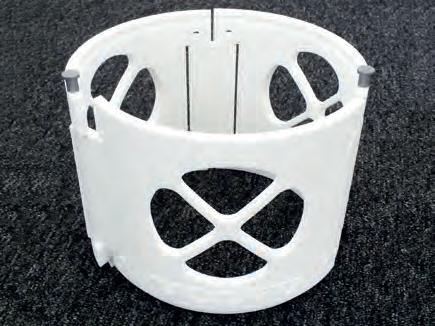
in racks. As mentioned earlier, this is particularly relevant for older equipment that may no longer be in production. While manufacturers commit to support their products long after line production has finished, this often means holding stock of slow-moving parts, or having to have individual components produced to meet a customer requirement and get a machine up and running in the field. Inventory costs should fall as a result.
“Establishing whole departments of 3D printing going forwards will take place as fast as we can get the information that supports this. Currently there is a trend to join several technologies together in one functional unit. For example, combining a five-axis milling centre with a three-axis welding head in one machine tool. In this way, we would be able to create a raw piece of steel by gradually welding in a second step … we would machine the raw steel exactly using the five-axis milling centre. This scenario would be incredibly useful for making complex shaped parts. It will allow us to be independent of external suppliers.”
Visitors to the last CONEXPO-CON/ AGG in 2017 will have seen the world’s first 3D-printed excavator at the event’s Tech Experience. The Association of Equipment Manufacturers (AEM) was part of the team that developed that 3D-printed excavator, with the Oak Ridge National Laboratory.
“3D printing is not going to change all of manufacturing overnight,” said Dr. Lonnie Love, corporate research fellow at Oak Ridge National Laboratory.
“Our solar subsidiary Solar Turbines in San Diego, makes very large gas turbine engines and they have a fuel swirler that’s 3D-printed out of metal. That fuel swirler can’t be created with traditional manufacturing. It was designed for 3D printing.
“They are producing those for full production use on their gas turbine engines. This shows that technology is moving to being able to produce very complex parts in one piece using 3D printing. If you try to make complex parts in one piece using traditional manufacturing methods, you can’t afford to, given the type of machines required. But 3D printers are faster and use less material.”
FPT intends to have some form of 3D parts printing available in some of its parts centres from as early as 2019, though only for very low-volume products.
”We are taking a basket of components that are critical but no longer easily available,” said Baffoni. “Especially for older machines that might not be in production any more.”
“At the moment, all the parts which are produced by the 3D printer in the Bobcat Innovation Centre in Dobris are fully dedicated to prototyping,” said Mandik.
The excavator was 3D-printed using a variety of machines
As the technology develops, the 3D printing process does not necessarily need to be carried out centrally by the manufacturer. Once the price allows, spare parts distribution centres and even local dealers could be equipped with 3D printers, with manufacturers sending digital files to allow localised production of components.
This would also allow dealers to carry less costly spare parts stock, with inventories stored digitally, rather than actual parts
“So, we are a long way from producing machines consisting of parts entirely produced by 3D printing. On the other hand, in industry, it’s a common thing to buy a machine tool with a part produced by 3D printing. If all standards are met, with stress testing of parts, then everything is okay in our opinion. For example, our Fortus 900MC 3D printer from the US company Stratasys, has a few parts made by 3D printing. So, it’s one 3D printer making parts for another 3D printer.
“Lots of factories around the world implemented additive manufacturing years ago. Bobcat will not be an exception in the future in my opinion, as long as the cost calculations for 3D printing give us the green light,” said Mandik.
“It’s not going to displace casting. It’s not going to displace welding. When you make these great parts at low volumes, you don’t care that it takes a week or a month, but we’ve got to go faster because it drives the productivity up and the costs down.”
Known as Project AME (Additive Manufactured Excavator), the excavator was 3D-printed using a variety of machines to create and assemble three components: a cab, a boom and a heat exchanger. The excavator’s boom was fabricated using a free-form additive manufacturing technique to print large-scale metal components.
While this was perhaps an extreme example and one that would struggle to perform on an actual construction site, it was a very graphic demonstration of what could be possible in the short- to mediumterm future. As with any new technology, developments will be driven by volume. As more equipment manufacturers invest in additive manufacturing, so the price will come down and the technology will develop at a rapid pace.
Anyone visiting a major manufacturer’s excavator factory or wheeled loader plant this year is not suddenly going to see a line of 3D printers replacing the fabrication shops that support the assembly lines. Not yet anyway … but give it a few years and additive manufacturing looks set to play an increasingly important role, both in new machine manufacturing and in supporting equipment already working in the field.

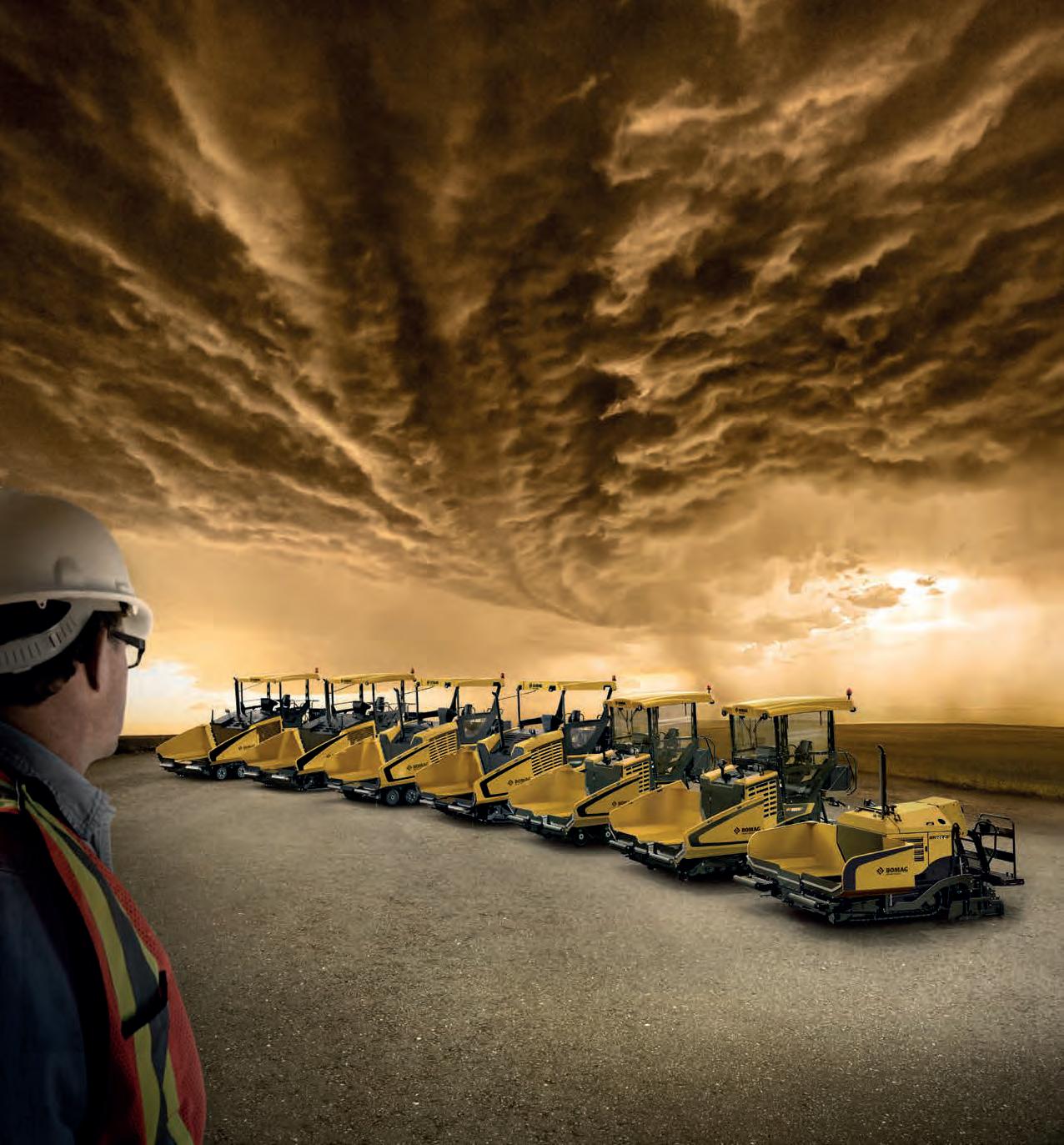
Our screed heating is ready for operation three times faster than conventional systems –cost cutting with technology.
Perfect all-round visibility of the machine edge, hopper and screed – the unique BOMAG SIDEVIEW system.
The active engine and hydraulics management system reduces fuel consumption by 20% – intelligent energy saving.
For faster screed extension set up times – the smart QUICK COUPLING attachment system.
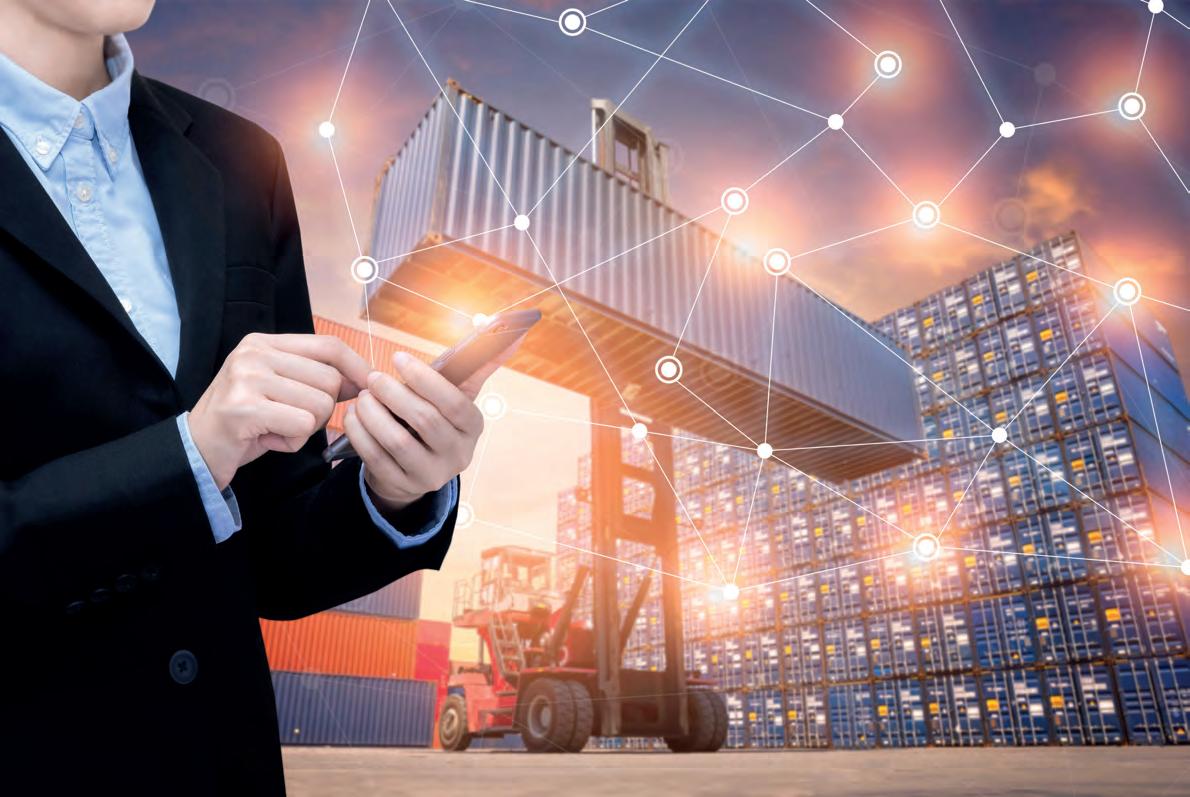
LOOK OUT FOR LOGISTICS 4.0 AS THE WORLD GETS SMARTER AND REVOLUTION TAKES HOLD
The world’s leading construction equipment manufacturers are seeing a revolution on the factory floor as new, intelligent technologies are designed to create connected and interoperable workflows. Developments such as 3D parts printing are changing age-old processes and the modern supply chain is having to become faster, smarter and more technologically integrated in order to keep pace. As we go through the fourth great industrial revolution, Logistics 4.0 has become a catchphrase for where the industry will go next. Geoff Hadwick reports.
According to flexis AG, a global leader in supply chain management software, Logistics 4.0 is about to change everything. In a recent report, the German specialist in automotive, manufacturing, and logistics software solutions said: “Industry 4.0 has been partially defined by its use of machine-to-machine communication and of internet of things (IoT) devices to create factories that operate like smart homes … (places where) an array of appliances and machines are brought into constant communication in order to create a cohesive, highly visible system.”
The objective is to create “an ideal world (in which) areas of waste and inefficiency are uncovered, certain decisions can be more thoroughly optimised, and some simple (or not so simple) processes are automated. Logistics 4.0 operates under these
same principles, but with a different set of component parts. Specifically, it makes use of ‘smart’ containers, vehicles, pallets, and transport systems in order to create a fully networked supply stream that offers supply chain managers, shippers, freight forwarders, and others the necessary visibility to perform logistics tasks in an optimal way. It becomes possible to see potential bottlenecks and breakdowns well in advance and develop counter-measures or back-up plans in time to preserve smooth operations.”
Construction logistics is a complex puzzle. End users are on the move from site to site all the time. Construction equipment is often heavy and cumbersome to store and move. The whole process can be slow and expensive when compared to an FMCG (fast-moving consumer goods) supply chain. Flexis AG believes that: “Logistics 4.0 has the potential
to pave the way for a new, more advanced conception of the value stream that involves autonomous vehicles (aka driverless cars), automated warehouse operations, and perhaps even the elimination of warehouses altogether in favour of predictive deliveries with full, zero-lead time integration into smart production processes.”
Whether or not the construction equipment sector can achieve these sorts of advances quickly, it is highly likely that our market will see the rise of ‘anticipatory logistics’ … “Supply chains in which smart technology predicts instances of demand ahead of time, enabling planners (or even autonomous machine processes) to adjust production schedules to meet future demand changes,” says flexis AG. “As anticipatory logistics becomes a reality, the global value chain will become more complex, relying on
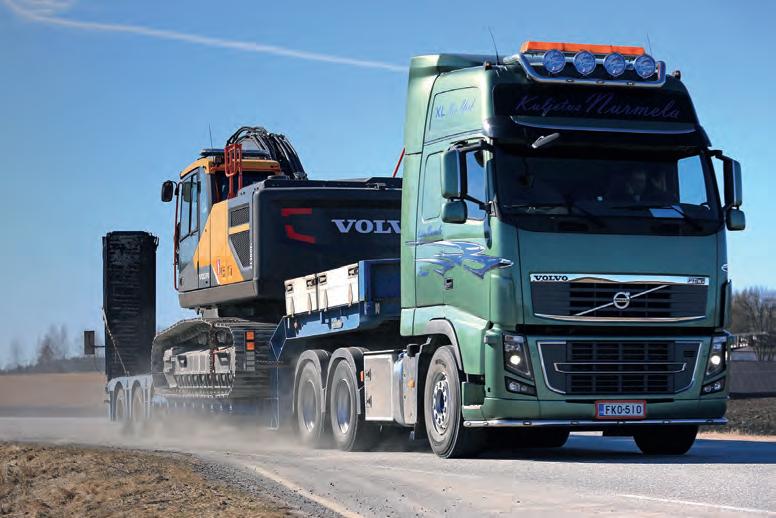
advanced predictive algorithms and the integration of more and more connected elements. It will become simultaneously much leaner, offering a more adaptive, agile environment in which lead times are shortened significantly and shortages, overages, and all manner of disruptions are made increasingly uncommon.”
Cyber security and the safe handling of data will be key
Fellow software development services provider Finoit Technologies, a company that specialises in mobile app development and internet of things (IOT) applications agrees, saying: “There has been a shift from the traditional approach to a digital supply chain making it smarter, more widely networked, and more technologically advanced … Logistics 4.0 makes use of smart technology derived containers, vehicles, pallets, and transport systems. This ensures the creation of a fully networked supply stream that offers managers, shippers, freight forwarders, and others the necessary transparency and visibility to route transport and performs other logistics tasks in an optimal way.”
Finoit points out that: “Logistics 4.0 comprises of a mix of technologies for smooth functioning, including GPS, barcodes, Data Matrix codes, radio frequency identification (RFID), sensors, electronic data interchange (EDI), the internet and telematics … as well as on-site and cloud architecture and software.”
Finoit argues that there are:
“Five elements of Logistics 4.0: 1. Visibility … One of the most important elements of technologydriven logistics is the increase in transparency and visibility from digitisation across the complete supply chain system. Visibility has encouraged the building of a smarter value stream system. Also, it has proved to be a necessary pre-requisite that has made logistics transparent and intra-operational (processes)
much more efficient and comprehensive than before. For instance: Smart ports like Abu Dhabi are already implementing solutions that make possible not just real-time tracking, but real-time viewing of documents and other mission-critical information for freight forwarders and their customers.
“2. Smart Utilities … The introduction of various ‘smart’ versions of traditional logistics components has already transformed the way shipments circulate from suppliers to end users. Smart containers and smart pallets are transforming traditional shipping workflows already and incorporating fresh ways to collect data and perform judgements based on the crucial information.
“3. IoT Adoption … With the introduction of Industry 4.0 in the market, many IoT development companies have come up with digital devices that can be deployed and embedded on factory floors and in the warehouse. Such enhancements connect them to the cloud. This not only evolves the entire supply chain management but also increases profits by producing better granular insights.
“4. Industry 4.0 Integration … The modern technology-driven logistics paradigm is closely related to Industry 4.0. The most important factor of Logistics 4.0 is its power to collaborate integration with Industry 4.0 systems and procedures.
ABOVE & BELOW: Construction equipment logistics is a complex global puzzle with clients that constantly move from site to site, requiring deliveries that are heavy and cumbersome to move.

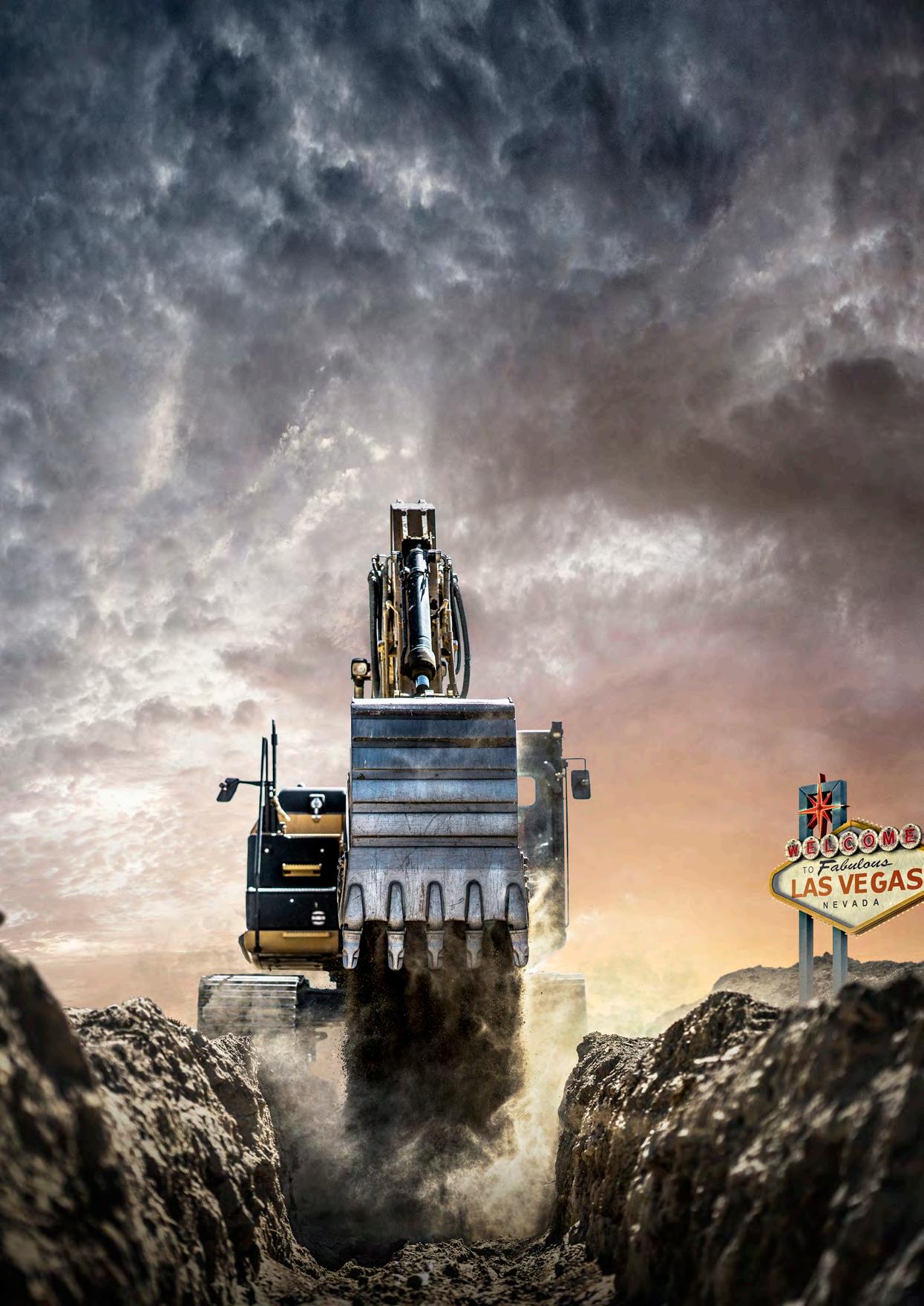
➔
This usually creates an environment that builds a synergy and communal relationship between manufacturers, shippers and end users. There is a constant security of safety from external threats, storage of important and crucial data and meeting the needs of end users. The transparency is clearer than that of any traditional approach ever followed.”
“5. Analytics ... The endgame here,” says Flexis AG, is “advances in transparency, visibility, and data collection through sensors and RFID chips. By feeding large quantities of information into predictive and prescriptive algorithms, modern logistics providers can improve their demand and shipping forecasts while uncovering potential areas of waste or possible improvement in their value streams.”
This rapidly evolving next generation of successful supply chain management solutions is going to rely on the best computing and internet of things processes possible if it is going to deliver real-time automated, sense-and-respond feedback mechanisms. Cyber security and the safe handling of data will be key. But it is the intelligent use of all this big data that will drive the biggest pay-back. For instance, US-based rail freight operator Union Pacific
THE BLOCKCHAIN
One of the key technologies spearheading Logistics 4.0 is the “blockchain.” The blockchain concept has the potential to provide new and vastly improved levels of traceability in the global construction equipment supply chain. Supply chains professionals can use it to view reliable records of where everything is, or has been, during its delivery phase.
The best way to understand the benefits and key attributes of any blockchain, or other distributed ledger technology (DLT) platform, is to think about “trust, transparency, traceability … all working together to provide distributed governance,” says Jim Beveridge, telecom and
has introduced IoT to predict failure and risk by deploying an array of acoustic and visual sensors on the tracks. These monitor train wheels by sending more than 20 million temperature readings per day back to the Union Pacific data centre for processing via data analytics. On average, three railcars per day are currently being identified for attention, inspection and/or servicing. The cost savings now run into millions of dollars per annum as delays and derailments are reduced.
To get a better handle on what companies are doing here and now, the Forbes Insight research group recently joined forces with Intel to produce a document called “IoT marches into the enterprise, transformation
follows quickly.” The survey reveals that: “As IoT efforts mature within enterprises, greater benefits are being realised. The intelligence and insights available through IoT systems are enabling businesses to expand their horizons and explore new paths not possible before. Even more noteworthy: IoT leaders identified in the survey are seven times more likely to be seeing rapid corporate growth than their less advanced counterparts.”
The report, which was based on a survey of 700 executives, shows that 63% of big company bosses say they have already introduced new or updated products or
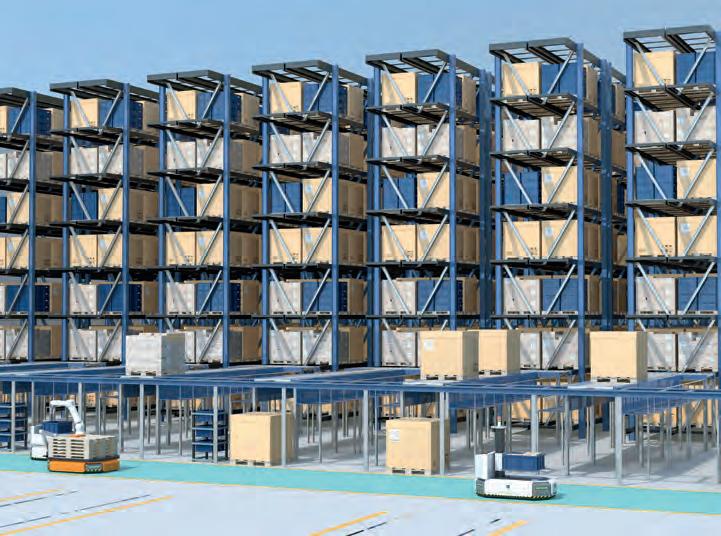
cybersecurity expert at ERTICO, an intelligent transportation system organisation in Europe that promotes research and defines industry standards.
Technically speaking, he explains that the blockchain consists of a database (or ‘blocks’) of online transactions, that are securely linked (or ‘chained’) using cryptographic functions to other blocks in a distributed meshed network, with participants in the network validating each transaction before any new block is added to the chain.
A key feature of blockchain technologies is smart, or selfexecuting, contracts. These legal
contracts are embedded in software code and stored, replicated and supervised by the network of computers that run the blockchain.
In Beveridge’s view, the disruptive aspect of the technology comes about as a result of the ease of forming a secure, trusted network of information without recourse to a central decision-making authority and the ability for the blockchain to execute legally-binding contracts.
He thinks of blockchain as analogous to a WhatsApp group: a network that is easy to form with trusted friends - the equivalent of a private blockchain. “You are invited to join the group,” he says. “In the blockchain world this is a ‘permissioned’ blockchain. WhatsApp messages are encrypted and no-one who is not part of the group can read your messages. All WhatsApp messages are organised chronologically, as are all blockchain messages.
“If messages are deleted on WhatsApp, then all the group can see that a message has been deleted. Similarly, in blockchain, any change is recorded as a new block. Data records are classified as immutable, they cannot be changed. This supports the principles of trust, transparency and traceability, enabling distributed governance.”
“Imagine electric, driverless vehicles silently breezing through the streets delivering materials to site in the dead of night”
Gerald
Morgan, Wilson James
According to Forbes and Intel: “The survey reveals that as IoT efforts mature within organisations, (they move) from laggard to leader and greater benefits are realised. The intelligence and insights available through IoT systems are enabling businesses to expand their horizons and explore new paths not possible before. IoT leaders identified in the survey are seven times more likely to be seeing rapid corporate growth than their less advanced counterparts.
“Data is the fuel of the IoT engine and as IoT progresses across partner networks (and supply chains), gaps in partners’ technology capabilities become more evident. Ultimately, IoT leaders have a much deeper appreciation and understanding about what’s required to (be) successful.”
For Jeremy Stickling, a vice president at Nussbaum Transportation, the benefits of Logistics 4.0 could not be clearer: “With the amount of data incoming from sensors on our trucks, there is a lot to manually review, aggregate, store and analyse. We need to be able to store and aggregate the data at a macro level, but still have slices of data that are granular enough to give an accurate indicator.”
The logistics (transportation) sector is not the fastest adopter of these new technologies, as the charts show, but they should be: “Almost three-quarters of IoT-leading companies, 74%, expect a profit boost of more than 25% over the coming year because of IoT, versus 10% of laggards,” says the report.
In order to help the construction equipment supply chain get there, the UKbased Chartered Institute of Logistics and Transport (CILT) recently published a series of reports on Logistics 4.0. In a piece on “The future of construction logistics,” Gerald
Figure 1: IoT maturity - by industry (reporting “selective” to “extensive” IoT implementations)
Figure 2: Organisations seeing accelerated growth in IoT networks in most recent fiscal year by industry (Exceeding 10%)
Transportation and logistics are already big players in the IoT revolution. Source: Forbes insights.
Morgan, a director at the contractor Wilson James, said: “Imagine electric, driverless vehicles silently breezing through the streets delivering materials to site in the dead of night, self-unloading, with drones delivering materials to pre-determined landing pads just in time for the next day’s work. Timings could be remotely managed, first with automatic demand forecasting, and then with an added layer of physical checks before approval of delivery is granted.
“Using 360-degree cameras within construction areas to photograph work zones, and uploading images regularly, will allow managers to monitor progress remotely, providing the advantage of up-to-date condition reports. These cameras may well be robot-programmed to scan work areas at predetermined times … or as the programme dictates.”
Morgan can also see more computer modelling being used in the planning stages of major contracts, as well as the deployment
of “smart helmets” fitted with cameras so that sites and the equipment being used there can be viewed remotely. “Technology will allow us,” he adds, “to monitor flow rates and use thermal imagery to check the operation of services. Smart, high-visibility jackets compatible with geo-fencing will alert the wearer that he or she is close to a digital exclusion zone.” Also: “Bionics will be regarded as an essential element of personal protective equipment, making people stronger.
Using exoskeletons, operatives will have no problem lifting large mechanical and electrical components into position, with one person doing the work of two.” And, as a final thought, Morgan wonders: “The question may be to what extent AI (artificial intelligence) can replace human endeavour.”
• Some elements of this article first appeared in our sister title ITS International, dated Sep/Oct 2018.
ConstructionTV.TV is dedicated to broadcasting first-class coverage of the world’s leading construction events and the latest industry trends. Combining short, high quality programmes with the latest in digital delivery, ConstructionTV.TV is optimised for mobile devices and can be accessed anywhere, anytime. Individually themed channels provide specific industry information to construction professionals needing to stay ahead in their field of expertise. With expert opinion from only the most experienced editors, ConstructionTV.TV delivers the most reliable and relevant information to the construction industry.
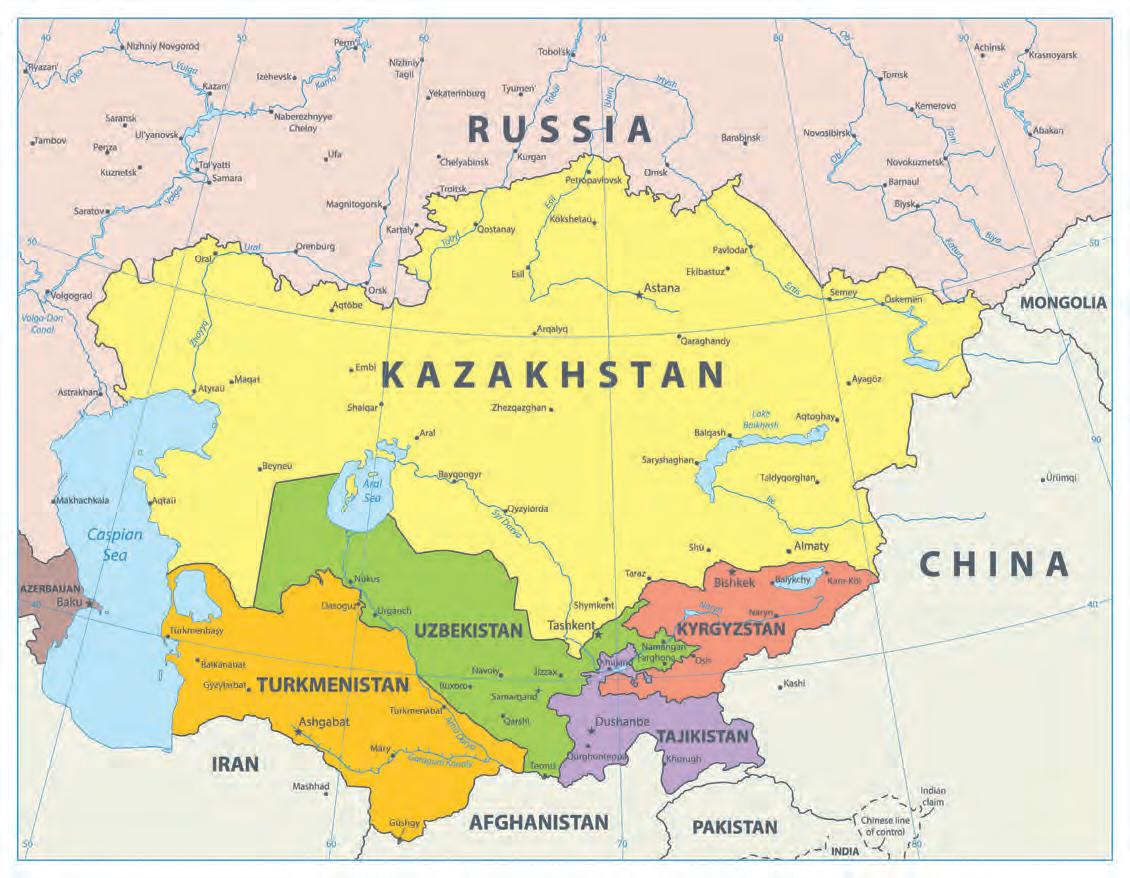
SIZING UP THE STANS
Despite nearly 30 years since emerging from the old Soviet Union, the “Stans” still require major infrastructure upgrades, and many major new opportunities still exist. David Arminas reports.
The five so-called “Stans” – Kazakhstan, Kyrgyzstan, Tajikistan, Turkmenistan and Uzbekistan - are sandwiched between the Middle East, Russia and the Caspian Sea. These Central Asian countries gained their independence in 1991 with the collapse of their overlord, the Soviet Union.
All five are Muslim by majority faith and, excluding Tajikistan, are Turkic-speaking nations – their languages being similar to Turkish. Tajikistan, though, is culturally and historically closer to Afghanistan and the old Persian empire to the south.
Importantly, the Stans are in the crosshairs of China’s ambitious transportationfocused Belt and Road Initiative announced by Chinese president Xi Jinping in 2013. Belt and Road is an international blueprint to create a global transport network centring on China. Significantly, it has also created funding – now reaching hundreds of billions of dollars – to be loaned to countries along the route designated by China as strategic. Much of the money is being spent for the
construction of not just roads but railroads and ports and comes from Chinese lending institutions.
All five Stans are keenly aware of what the improved Belt and Road transportation infrastructure can mean for their economic development. The five countries are rich in natural resources that can be exploited only with better infrastructure. For this reason alone the landlocked Stans are equally keen to attract private investment to build roads, railways and airports.
However, the Stans also suffer from occasional political upheaval, questions over human rights and continually struggle with corruption at government and business levels. Doing business in the Stans comes with a word of caution – ‘caveat emptor’.
Chinese banks are leading the way in lending to the Stans to get infrastructure projects underway. These banks include the Asian Infrastructure Investment Bank, the Silk Road Fund and the New Development Bank. Most of their US$250 billion in capital
comes from Chinese sources and lending is not only to the Stans but other nations along the old Silk Road from China to Europe. Notably, there is little capital coming from the US and Japan, mainly on political grounds with governments believing Belt and Road is a thinly disguised strategy for China to achieve global power, according to some analysts.
A recent report by Euromoney, a Londonbased analyst of global financial markets, suggested that while Chinese money is there for lending, profitable projects are not as obvious. Also, rising nationalism in many emerging nation markets such as the Stans could hamper the take-up of Chinese financing if there appears too many strings attached to the loans. Even among Chinese bankers, pessimism is rising. Andrew Collier, an independent research analyst in Hong Kong and a former president of Bank of China International in the US, is quoted by Euromoney as saying some bankers are “sceptical about One Belt, One Road” because it is difficult to find profitable projects.
Comparative Stans
➔ Guan Anping, a former legal counsel at China’s Ministry of Commerce, told Euromoney that contractual obligations are not always followed through in the Stans. “The ‘Stans’…are troublesome places to do business. Many business people there don’t honour their contracts.”
LONG-TERM APPROACH
Caterpillar has been active in Central Asia since the 1990s, working successfully with its Caterpillar dealers Zeppelin and Borusan Makina. “They have established a strong footprint with multiple branches, parts and machines repair facilities and are of a world-class standard,” explains Sergey Minko, regional industry sales manager for Caterpillar Eurasia, a division of Caterpillar.
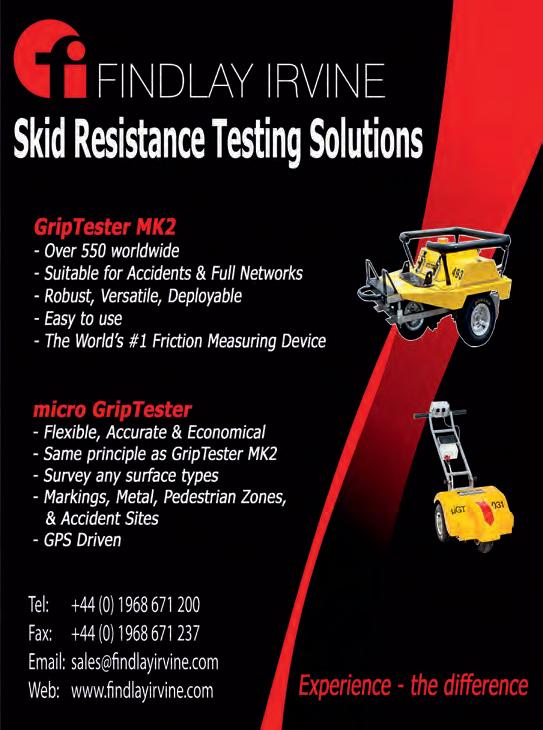
“Despite economic challenges, the region has experienced a steady growth in the past few years”
Sergey Minko, Caterpillar Eurasia
“The volume of road construction projects [in the region] has been increasing steadily since 2015. Among the main projects expected to drive equipment demand in the near future are the Nurly Zhol, a state-funded programme in Kazakhstan, a 560km six-lane express highway in Turkmenistan (see box) and a portion of the One belt, One Road project,” says Minko.
It’s a developing region so the key to successful business is being involved for the long term and focusing on sustainable business growth.
Interestingly, contractors are not looking for the least sophisticated machinery to save capital expenditure. On the contrary, says Minko. “Despite economic challenges, the region has experienced a steady growth in the past few years, driving a need for world-class modern and efficient machines,” he says.
“Growth in machines sales comes with a keen interest from private contractors for technological solutions that enable quicker contract completion and a more costeffective execution of the projects,” he says. For this reason many Caterpillar machines sold there have Cat Connect technologies, such as the automatic levelling system Accugrade.
In demand, too, is Caterpillar’s Machine Drive Power, part of the Cat Compaction Control suite of scalable technologies that improve compaction performance and efficiency. This, says Minko, is available only from Caterpillar.
Cat Payload, Assist and E-fence features on Next Generation Cat excavators are also popular. “These solutions have become the standard features for a majority of our customers.”
Specific Caterpillar equipment popular in Central Asia includes the high-production cold planer PM620, the AP655F Asphalt Paver with Mobil-Trac rubber track undercarriage system and integrated Cat Grade Control, the CS74B Soil Compactor and the RM 500B Reclaimer.
Excavators are always required, such as Caterpillar’s 320 and 330 Next Generation machines with integrated levelling systems. Given much of the region’s abundance of gravel roads – many being long, wide and flat - the 140 GC grader is a good seller. It comes with Cat GRADE digital blade slope meter to reduce the need for manual grade checking. What type of equipment will be sold most in the future? Always hard to predict for any region, but Minko sees increasing interest in machinery for cold reclamation road reconstruction. “This is now recognised as the most timesaving and cost-effective technology in most Eurasian countries.”
Meanwhile, the second-hand market remains nascent.
While there is a trend towards buying more sophisticated machinery and because contractors’ margins are tight with issues over payment by clients, contractors tend not to sell on their equipment as quickly as those in more developed countries. In other words, they are worked hard and worked often. This means that the second-hand market is not really developed, at least, not yet.
“When customers invest in assets they tend to fully utilise them and usually don’t dispose of them after a certain period of time. Second-hand machines are in competition with low priced machines from China,” says Minko. “Nevertheless, our [Caterpillar] dealers provide different solutions to support their local customers and trade-ins are gradually picking up the pace, and will create opportunities for second-hand Cat-certified used machines.”
SNAPSHOT: KAZAKHSTAN
Capital: Astana, pop. 1.05 million Roads:
84,100km paved
9,500km unpaved
500km motorway
Kazakhstan is geographically the largest Stan country – as big as Western Europe – and is the focus for many equipment makers and contractors. But with only 18 million people it has one of the world’s lowest population densities. Strategically, it links the large and fast-growing markets of China and South Asia and those of Russia and Western Europe by road, rail and a port on the Caspian Sea. The World Bank notes that Kazakhstan “has transitioned from lower-middle-income to upper-middle-income status in less than two decades”. With a total GDP of $195 billion, it outshines the other Stans (see Comparative Stans table).
BELOW: Caterpillar has been active in Central Asia since the 1990s. (photo courtesy of Caterpillar)
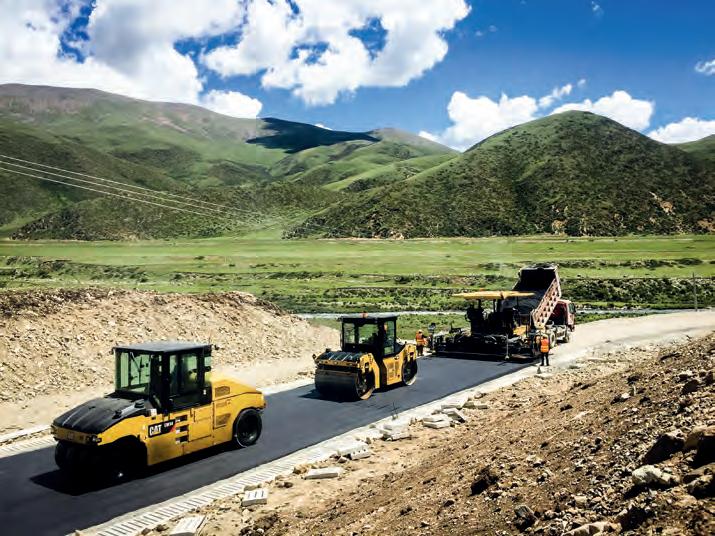
For these reasons, global equipment manufacturers often make Kazakhstan the launch pad for operations in Central Asia. One of the more recent companies to upgrade its services in the region is Hitachi Construction Machinery. The Japanese company started sending equipment to Kazakhstan in 2004 and has supplied mainly hydraulic excavators and dump trucks for the mining and construction industries in the country.
Last July, Hitachi announced an agreement with Nippon Machinery to set up Eurasian Machinery. Hitachi owns 60% of Eurasian while Nippon has a 40% stake. The company is based in the Netherlands but the opening ceremony of Eurasian Machinery was held in the Kazak capital Astana. “We traditionally continue to sell our equipment through dealerships. But this time we decided to create a new company, Eurasian Machinery, which will be headquartered in Almaty [Kazakhstan],” said Tatsuro Ishizuka, chairman of Hitachi Construction Machinery, during the opening. Hitachi noted that Kazakhstan was a key
traffic junction connecting the European economic bloc in the Belt and Road Initiative. “There are high expectations for the entire Central Asia region with respect to infrastructure and industrial developments in the future. Additionally, due to the rich natural resources that it is blessed with oil, natural gas, iron ore, copper, uranium and rare earth metals to name a few. [Hitachi] has supplied a number of hydraulic excavators for mining and dump trucks and holds a large market share in the Central Asia region,” noted the Hitachi press release.
With a total GDP of $195 billion, it outshines the other Stans
“Hitachi Construction Machinery [sic] has conventionally continued to sell machinery through dealerships in this market, but this time entered into a partnership with Nippon Machinery, which has extensive knowhow in the market, for the establishment of a sales/ service company. In the near future, HCM will pursue further business expansion in the construction machinery market of Central Asia through the new company.”
Volvo Construction Equipment, too, has been using Kazakhstan as the pivot point for its Central Asian sales, says Andrey Komov, managing director of Volvo Construction
Equipment for Russia and CIS – the Commonwealth of Independent States, an alliance of former Soviet republics that was set up in late 1991. “We started in the Stans from Kazakhstan after 2000 and later expanded into the rest of the region. We work only through independent dealers which are fully responsible for machine sales and aftermarket business,” he told Global Report. It’s been nearly 30 years since the crumbling of the Soviet Union, says Komov, but all the CIS states remain locked in step with the Russian economy.
“There is very high correlation between the economies of Kazakhstan and Russia. They are both members of Eurasian Customs Union. Under current circumstances it is difficult to forecast market development for the next couple of years due to uncertainty within the Russian economy,” he said. “If we put aside these uncertainties, we should see a minimum 20% annual growth at least for the next five or more years in all the Stans.”
Infrastructure, especially road, was significantly underinvested during the past

20 years. “So pent-up demand for new road construction is significant. All major road construction activities are one way or another connected with the Chinese Belt.”
Even so, all the Stans face similar challenges. “Availability of competent human resources in our industry is a challenge in any part of the Stan market,“ says Komov, who is based near Moscow. “The further you go to the east, the higher the corruption level. But corruption is a very broad term and implications for a business vary widely.”
At the top of the money chain, the banks have the money and are lending it to governments. But the issue is whether the money trickles down to contractor level as fast as it should to keep projects going and on schedule.
“If there is one single problem for contractors, it is the very high cost of capital. This makes them extremely dependent on timely cash payments since loans and financing are hardly affordable and very often even not available,” says Komov.

Contractors and subcontractors can live on a knife-edge waiting for payment which they will need to pay staff and to purchase material for the next part of the contract. Non-payment or slow payment force companies into cutting corners and projects can drag on, leading to legal nightmares.
As with any emerging market, explains Komov, excavators are one of the biggest selling machine groups. “Wheeled loader share is also significant but very much dominated by value - low purchase costmachines from Chinese manufacturers. Also, due to road building the demand for asphalt pavers will grow.”
CONTRACTOR VIEWPOINT
For a European company, contractual and invoicing requirements in the Stans appear extremely bureaucratic as there can be an abundance of official stamps. Regardless, many opportunities exist but local knowledge is paramount to success, explains Steve Gilpin, an associate of engineering consultancy Ove Arup & Partners International.
Arup knows about success. The global firm can boast more than 1,700 successful projects in the Commonwealth of Independent States (CIS) of which the Stans are member countries. The company, headquartered in London, has been working in the five Stans since 1993.
Projects in the Stans have been commissioned by a mix of international developers, national and local authorities and local private companies and developers. Designers need to be registered and this varies among CIS member states. For example, in Kazakhstan there are three levels of expertise for which designers can be registered, he says. Contractors also need to be registered for the specific element of construction they will be undertaking.
What CIS countries have in common is their Soviet-era planning approval and permitting process. Some countries, however, are looking to adopt either their own systems or use some of the systems and standards of other countries.
The permitting system most commonly used throughout the CIS is called the TEO - technical and economic justification system. The TEO covers design, costs for construction, operation and maintenance, as well as any correspondence with affected parties such as rail or utility providers to produce an environmental impact assessment (EIA) undertaken to local standards. The permitting system is comprised of three
permitting stages - feasibility, architectural and construction.
Whatever the issues may be with the TEO, the advantage of it is that once a company becomes acquainted with the system, employees can use their knowledge in any CIS country.
A word of caution, however. TEO is often translated into English as “feasibility study”. As such, any reference in a contract to creating or updating a ”feasibility study” needs to be carefully reviewed.
One example of this is in the conversion of a highway project, for which a TEO has been produced, assuming a traditional remeasure procurement, into a public-private partnership (PPP) procured project. If an international finance institution, such as the European Bank for Reconstruction and Development (EBRD) or the World Bank’s International Finance Corporation, is considering the project as a potential PPP, the institution’s contract may stipulate “undertake a feasibility study”.
the finance institution intended and what the consultant has priced to undertake.
The cost inputs into the TEO need to be developed as a “смета” (estimate) based on a specific procedure developed in the Soviet period that uses prevailing government construction indices. This is a very specialised task and cannot be taken lightly, warns Gilpin. In Belarus, for example, the estimate goes into the detail of defining the length of the required reinforcement tie wire.
Designers need to be registered and this varies among CIS member states
The TEO contains an environmental assessment impact study and, even though they can be very thorough, they are seldom completed to the specific requirements of the financial institution. As such, additional studies or consultations are likely to be needed.
Most consultants would assume this to mean that they should do a feasibility study of how the project would work as a PPP. But a translation of the contract for a CIS client may be “undertake a TEO”. As such, the local client may expect a full TEO to be produced or the existing TEO to be updated. All parties
The time required for these additional consultations should be factored into the procurement programme by the time the preferred bidder is announced. The ESIA (environmental and social impact assessment study), RAP (resettlement action plan), SEP (stakeholder engagement plan) should then require only contractor-specific data to be included to make them sufficiently complete for the financial institution’s required disclosure.
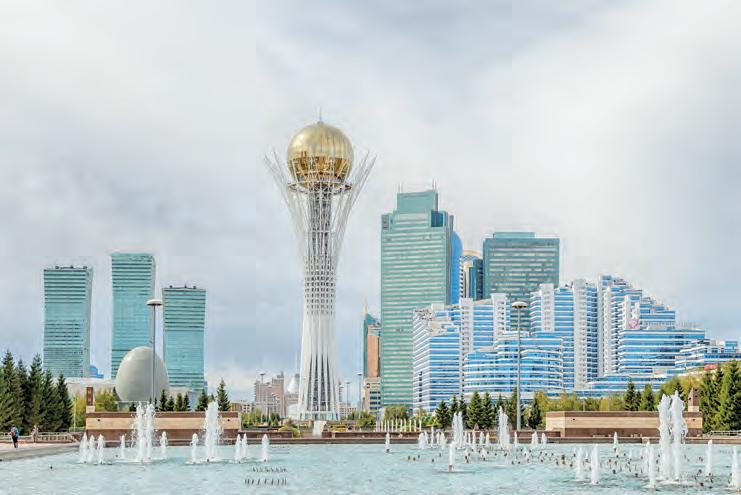
BELOW: Astana, Kazakhstan.
SNAPSHOT: TAJIKISTAN
Capital: Dushanbe, pop. 805,000
Roads: 27,767
Paved
Bitumen-treated
Gravel
Tajikistan borders Afghanistan for 1,206km, China for 414km, Kyrgyzstan for 870 km, and Uzbekistan for 1,161km, making regional cooperation a necessity to achieve sustainable economic growth. However, Tajikistan is Central Asia’s least connected and most isolated country. Also, about 80% of the roads are in poor or very poor condition, notes the Asian Development bank, mainly because of inadequate maintenance and few repairs to damage caused during the civil conflict.
According to the World Bank, the country’s limited rail network means the population of just more than 8 million people relies heavily on the few roads which are in poor condition.
In 2015, the World Bank approved $45 million to help finance the second five-year phase of the regional, multi-phase Central Asia Road Links Programme - CARs-2 - to be completed by 2020. CARs-2 focuses on the rehabilitation of around 70km of crossborder roads in the Sughd Oblast region that connect Tajikistan’s road network with that of Uzbekistan and the Kyrgyzstan Republic and accounts for 40% of the country’s overall freight turnover.
The sections being rehabilitated in Tajikistan by CARs-2 include the KuchkakKim-Isfara-Guliston border crossing (45km), the Dehmoi-Proletarsk-Madaniyat border crossing (17km) - including a link to the
SNAPSHOT: KYRGYZSTAN
Capital: Bishkek, pop. 970,000
Roads:
5,700km - Bitumen, maintained, national and international routes
5,100km - Bitumen and gravel mix, most unmaintained
23,240km - Gravel, local roads
High mountains over 3,000m with roads impassable in winter due to snow and mudslides are common in Kyrgyzstan.
Yet the southwest region is considered subtropical. While the main cities of Bishkek and Osh are well developed, many rural areas suffer from a lack of transport infrastructure
intermodal rail terminal in Proletarsk – and the Kanibadam-Patar border crossing (nearly 6km).
Existing machinery is well beyond its lifespan
Project delays are not uncommon, with the 5km Anzob Tunnel (Istiqlol Tunnel or Ushtur Tunnel) being an extreme example. The tunnel, built by the Iranian company Sabir, 80 km northwest of Dushanbe is part of the M34 highway that connects the capital to Tajikistan’s second largest city, Khujand. It was opened in 2006 although not fully completed and remained so – with no paved lanes and no ventilation system along with poor drainage – until 2014 when Iran signed an agreement to finish the tunnel and the tunnel was reopened in late 2015. It was finally competed in 2017.
According to a report in 2015 by Export.gov, part of the US Department of
that around 90% of all Belt and Road Initiative projects – in all sectors, not only highways – have gone to Chinese firms which bring in most of their own construction equipment and personnel rather than hire both locally.
The Export.gov report noted that U.S. companies may see stiff competition from Russian, Iranian, Chinese, Turkish and Italian construction companies. “There are some opportunities for construction equipment sales in Tajikistan. For example, Caterpillar, through a European partner, is active in the Tajikistan market,” the report said.
Export.gov also noted that industry representatives contacted by the US Embassy say that the sector needs almost any construction equipment, machinery, and tools that are available. “The strong demand stems from the fact that much existing
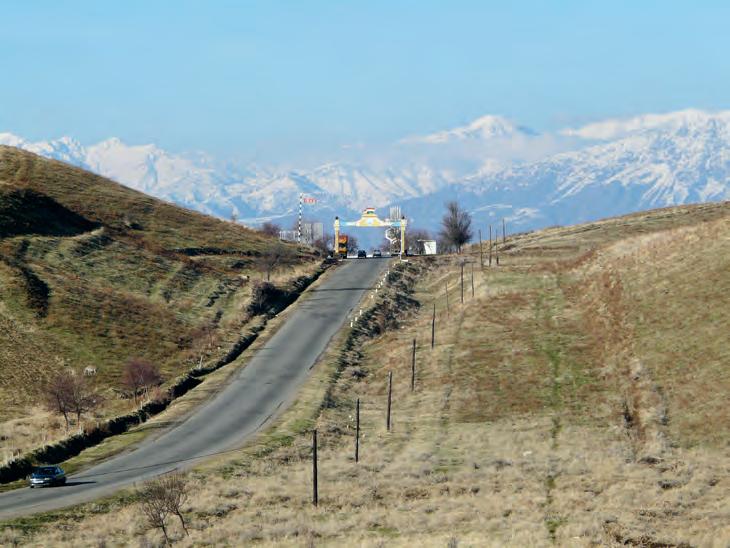
Mountain pass near Javana, in Dushanbe region, Tajikistan.
The main international routes include the 260km Osh-to-Irkeshtam on the border with China. The route is 80% or more paved but the border crossing is around 3,010m high, so weather can hamper transport.
The 550km Bishkek-to-Torugart Pass route was part of the ancient Silk Road. Around 70% is paved after a major reconstruction but heavy snow can still disrupt transport. The border crossing with China is over 3,700m high.
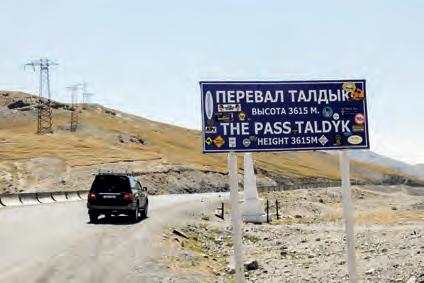
ABOVE: Near Taldyk, Kyrgyzstan: The M41, also called the Pamir Highway, traverses the Pamir Mountains through Afghanistan, Uzbekistan, Tajikistan and Kyrgyzstan,
Meanwhile, the 285km Bishkek-to-Taraz, in Kazakhstan, is reportedly now all paved.

Ashgabat and then further north-east to Türkmenabat and into Uzbekisatan.
Economic data is not readily available for Turkmenistan according to many analysts, and media reports are rife with stories about non-payment of contractors, many of whom are Turkish. Indeed, Polymeks reportedly stopped its work on the M37 into Turkmenbashi over non-payment
According to the Asian Development Bank, the government is targeting the construction or renovation of 24,000km of highways that will connect all provincial capitals and main cities by 2020.
The country’s most strategic highway, the east-west M37 which is also the Turkmenistan section of the European route E60, is about to get an upgrade. The E60 runs from the north-eastern French Atlantic coast city of Brest through to Turkmenbashi on the Caspian Sea, on through to the capital
Much of the M37 corridor is inhospitable. Turkmenistan suffers from extremes in geography as well as in economics. Most of the country is covered by the Black Sand Desert but it is rich in natural gas – believed to be the world’s fourth largest reserve.
The country is also one of the driest places in the world with an annual precipitation of around 12mm. Vicious sandstorms that bring everything, including traffic, to a standstill are not uncommon. Along with natural gas, cotton production is an economic pillar. But the country suffers from an otherwise poor economy with a resulting 60% unemployment rate. Many staple foods and utilities are heavily subsidised.
However, exploiting the vast natural gas has meant Turkmenistan has an annual GDP growth rate of 6.1%. Better highways would mean more - and more efficientexploitation of natural gas as well as better logistics for cotton.
After several years in the planning, the government finally announced in December the construction start of the 600km AshgabatTürkmenabat high-speed highway – the eastern half of the M37, according to media reports.
The 34m-wide highway is being built by Turkmenautoban OJSC under a state loan of around $2.4 billion. Connection with the Ashgabat-Turkmenbashi highway will provide an opportunity to quickly and conveniently access the Turkmenbashi International Seaport on the Caspian Sea, said Dadebay Amangeldiyev, the deputy prime minister.
The western half of the M37 from Turkmenbashi to Ashgabat is also getting an upgrade. The “express highway” also provides a necessary connection to the new international port in Turkmenbashi. Project general planner is the German architectural engineering firm Inros Lackner.
The 560km six-lane highway will run through the cities of Balkanabat and Serdar. Apart from bridges and underpasses, the project includes construction of four motorway service stations, 16 rest areas, five police stations and a police headquarters, five motorway maintenance facilities and nine toll stations.
Uzbekistan is Central Asia’s most populous country and second largest land area and economy after Kazakhstan. There is a 99% literacy rate among adults and tourism flourishes, especially in the capital Tashkent, a noted centre of Islamic art and architecture,. But as a landlocked country, Uzbekistan’s trade suffers from high transport costs. The Asian Development Bank says that “while the road network is adequate, providing access throughout the country, it suffers
from a backlog of rehabilitation work”.
The more densely trafficked international and national roads in Uzbekistan tend to suffer from backlogs in periodic maintenance and rehabilitation, with an international roughness index sometimes exceeding 7 (reflecting roads in fair to poor condition), noted the bank.
last year did Uzbekistan decide to create a ministry of transport

Only last year did Uzbekistan decide to create a ministry of transport to coordinate the development of road, rail and air, urban and river transport networks. The ministry, to come into effect this year, will take over from disparate agencies which the government noted were not putting together a coherent national strategy.
What will change? With one ministry for the oversight of all transport development it could be easier to coax loans out of international financial institutions.
announced its intention to create the ministry, Jin Liqun, president of the Chinabased Asian Infrastructure Investment Bank, visited Uzbekistan for high-level talks, including with President Shavkat Mirziyoyev, over future loans.
Uzbekistan was one of the 57 founding members of the AIIB set up by China in 2015 to fund infrastructure projects across Asia. Uzbekistan became a full member in the bank in late 2017. Around $2.7 billion could be available, according to Uzbek media reports at the time.

WILL AI REPLACE OR INFORM PLANT OPERATORS?
It is hard to work through the confusing, multi-faceted and sensitive subject of machine learning in the construction sector. Artificial intelligence is coming, though, and it will change everything. Is it something to fear? Colin Sowman has been talking to the leading players in the sector and has found that the likely reality may be more down-to-earth than many expect.
The potential use of artificial intelligence (AI), also known as machine learning, has been a topic of conversation in the construction sector for some time. Many jump straight to the ‘end game’ of fully autonomous machines turning construction sites into new roads and railway lines, bridges and tunnels, without a human in sight – and what will that mean for jobs?
So sensitive has this topic become that some in the construction machinery sector declined our invitation to participate, although while you can never say ‘never’, such prospects appear still to be a distant dream given the mountain of difficulties to overcome.
To start to get a grip on the implications of AI, it is first necessary to understand the capabilities and limitations of the technology. In a recent radio interview for the BBC’s Today programme, AI expert Dr Vivienne Ming of the Silicon Valley-based Singularity University, said: “We are afraid of AI because we are afraid of ourselves. The AI that is smarter than us hasn’t been invented and it isn’t just around the corner either.
ABOVE: Volvo dig assist helps operators achieve right-first-time results. BELOW: 3D schematic on the Dig Assist readout.
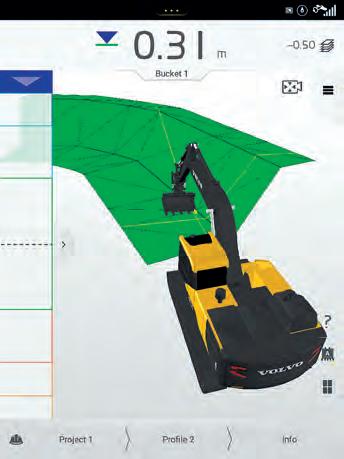
“What exists today is an enormously complicated and powerful tool – it is a hammer and it is what you build with it that actually matters.
“The biggest problem is that we have turned over some of the most difficult decisions in society to a bunch of young people that have spent their career learning how to construct hammers – but they’ve never actually built a house. They have never actually solved a problem in the real world.”
She continued: “The definition of AI is ‘any autonomous judgement made under uncertainty’.” Although she prefers to define AI as “any brief expert human judgement made cheaper, faster and increasingly better than a human can make it.”
Dr Ming cites a competition staged by Columbia University between a group of human lawyers and an AI system developed by a start-up company to analyse complicated contracts. The competition was to find loopholes in a number of contracts. “The humans found 88% of the loopholes, and the AI identified 95% - but that’s not the big difference. The big difference is that
the humans took 90 minutes to read each contract, the AI took 22 seconds.
“So, if you are the CFO [chief financial officer] of a major organisation and you are looking at your financial analysts, lawyers and computer programmers, you are starting to think ‘why am I paying for all these extra people’?”
Such examples exemplify the power of AI operating within a limited, pre-defined and repetitive process, but Dr Ming emphasises that “these machines do not think – at least not as of today. We can teach a machine to recognise a giraffe in every photograph – but it understands absolutely nothing about giraffes even as it outperforms us in our ability to identify them.
“These are simply algorithms to turn enormous amounts of numbers into a decision but it does so without core understanding,” she says, adding that we should stop talking about artificial intelligence and start talking about augmented intelligence.
How does, or will, AI play out in the construction sector? Well, as could be expected, it will vary enormously from ‘will have little impact’ to ‘completely revolutionise and reduce jobs’.
In the construction equipment sector, mention AI and many people do indeed jump straight to the idea of automated machines – operating without the need for a human operator - but that is too big a jump for most in the industry. And while it is clear that AI is widely misunderstood, some of the calls for new regulations indicate some legislators share that misunderstanding.
For his part Dale Camsell, senior technical consultant with the UK’s Construction Equipment Association, says: “All those in the industry are keen to talk about AI and to be seen to embrace it, because nobody wants to be left behind. But many don’t fully understand what AI is, or the implication of its implementation. There is not necessarily a link between AI and automation.”
Volvo CE’s electromobility strategy and business development manager Dr Fares Beainy, picks up this theme saying: “Automation and machine learning are closely intertwined. However, automation could be attempted without machine learning, and machine learning is much broader than automation. That being said, accomplishing automation at high levels of autonomy without using machine learning is a cumbersome task, and would be limited to specific applications/tasks, where the machine/vehicle would lack intelligence to adapt, and might be less robust.”
“If you want to make machines run more efficiently, then digitisation could prove an enormous benefit – but that doesn’t necessarily mean AI”
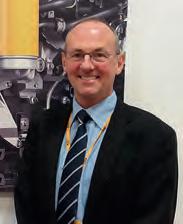
senior technical consultant
BELOW: In-cab monitor showing where the compaction target has been reached.
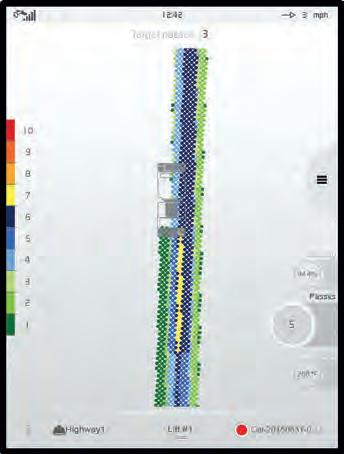
In the construction equipment sector, he highlights automating a single or multiple functions as a good example of automation without machine learning. This could be an autograding function on an excavator, which could be accomplished without machine learning by using sensors and analytical models.
“On the other hand,” he adds, “an operator assistant function such as Density Direct, uses neural networks, a type of machine learning.” This system directly measures and plots the degree of compaction achieved during the operation of a vibrating roller. Having input the required level of compaction, the operator covers the ground and the read-out indicates when the target has been achieved, thereby guaranteeing the required compaction with the minimum number of passes. Those results are also logged along with GPS coordinates to create a record of conformity to specifications.
This problem of defining AI, machine learning or automation is one that divides legislators too. For instance, should legislation define and regulate AI and machine learning or simply legislate for the outcome? As the European Union’s Machinery Directive, the legislation designed to ensure machines are safe before they can be sold within the EU, is currently being revised, we will find the answer in the next year or so.
Camsell points to the current directive, saying it is intentionally not specific because it has to cover a range of machines doing a number of jobs and ensure that the operator and others in the vicinity of the working machine are not in danger. “Therefore, if it is the machine itself making the decisions or a human, it doesn’t really make any difference, the machine has to be safe regardless of the decision-making process.
“From a regulatory point of view, the first step will have to be developing a set of terms and definitions in order that everybody uses the same words to describe the same function(s). With AI and machine learning being such new technology, currently such definitions do not exist.”
Any lack of regulatory framework has not prevented the development of functions like Density Direct or Dig Assist and AutoDig which help new operators achieve the efficiency of the experienced ones. In the mining sector there are already fully autonomous trucks running on pre-set routes within (or just outside) the mine, so what are the barriers to having construction machines operating autonomously?
➔ Camsell says, “If you want to make machines run more efficiently, then digitisation could prove an enormous benefit – but that doesn’t necessarily mean AI.”
Beainy agrees: “To my knowledge, none of the commercialised operator-assist functions (besides Density Direct) utilises machine learning at their core, which limits the scope and application of these functions. The autonomous mining trucks, for instance, only run over pre-set routes, making them location and application specific.”
Safety will always remain an overriding aspect and a limitation to deploying autonomous machines, and the examples that do exist, like the mining trucks, run only in confined and remote locations with limited human presence. To be able to operate on a construction site, object and human detection methods would be necessary.
This is technically possible and Camsell points to the construction sector’s tendency to adopt technology from elsewhere –often from the automotive sector where pedestrian and obstacle detectors already exist. Autonomous emergency braking (AEB), as required on road-going trucks (and soon to be mandatory on new cars too) is a good example. However, he points out that the volume of units produced in the on-road sector is many times that of construction machinery, thereby spreading the development costs over a greater number of units.

BELOW: Illustration of how Density Direct measures and plots the compaction process.
“Think about the machine like a human baby that explores the environment and learns from experience”
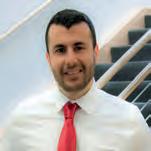
Dr Fares Beainy, electromobility strategy and business development manager, Volvo
Even if such technology does exist in different sectors, Camsell says the construction environment creates additional challenges which extend far beyond simply mud and dust. While cars and trucks do one job, drive on roads that are more or less uniform and are segregated from pedestrians, many pieces of construction machine carry out a variety of duties on sites where they mix with unsegregated workers. Furthermore, buildings spring up on previously empty areas of the site, holes are created and then filled, new pipes and cables are laid, all requiring route changes for site machines, creating nodig areas and so on.
It would be possible to reprogramme every machine with the changes but they often occur with such regularity it would not be cost effective, while the consequence of failing to do an update could be massively expensive or even fatal. The algorithms required for the machine to react automatically to ever-changing site conditions would need self-teaching capabilities to enable it to evolve and self-tune once deployed. This would also require a large amount of data to train machines to accomplish specific tasks before they could be deployed. Volvo’s Beainy puts it like this: “Think about the machine like a human baby that explores the environment and learns from experience. Autonomous construction equipment would use machine learning methods to train through examples [the training data] to learn how to perform specific tasks.
This would add many layers of difficulty, effectively requiring ruggedised super computers, thus making the hardware very expensive. In reality many potential hazards on construction sites are hidden, often buried. Would it be possible to equip an autonomous excavator to detect unmapped underground cables or pipes?
Not according to Beainy: “No such technology exists in a form that could be integrated into a mobile construction equipment. This issue already exists with humans operating the machines, but could be improved with autonomous machines which could use maps of such utility lines to avoid accidents.”
This is very much in line with Dr Ming’s statement about augmented intelligence.
In other areas Camsell sees opportunities to deploy some existing technology to prevent all too common accidents. He cites fitting currently available sensors to the counterweight of an excavator to prevent it striking a site worker, or using ‘geofencing’ to ensure the boom or tailswing never encroaches areas such as live traffic lanes.
Likewise, the problems of poor visibility from the cab, or the operator checking the available visibility aids, could be addressed. “AI systems could be taught to recognise a human, to understand that the non-moving object behind is a wall that creates a trap zone, to realise the vehicle parked in front of the dump truck is not visible to the operator.”
The option then is whether the systems simply alert the operator of the danger or prevent the machine from moving off, slewing, lowering a load etc.
To allow for such developments, new standards are unlikely to define direct visibility and specify mirrors or cameras but will leave the door open for other intelligent systems.
Does that mean an ever-changing construction site will be too difficult an environment in which to cost-effectively use fully autonomous machines and instead, expanded and improved operator-assist functions or remote operation in dangerous applications will be used?
Camsell says he is hearing very little about automation from any of the manufacturers to whom he has spoken.
However, Beainy points out that today’s machine operators do not have full autonomy - they rely on their supervisor or the superintendent to give them a specific task. In turn, the supervisor gets that task from the project manager, who gets the task from the project engineering team, that gets the job from the client.
best humans can do and augment it with what machines can do,” Beainy says.
Away from the site, automation is starting with construction site management systems and there have been examples of using AI to improve estimating and work scheduling. The data for such processes is available to enable AI systems to ‘learn’ from earlier jobs and factor in variables such as soil/rock types and even weather forecasts.
The question is, how much will these systems improve planning accuracy and will they avoid the unexpected problems that so often make a mockery of schedules?
Beainy starts by outlining the limitations: “AI can learn to avoid the problems experienced on previous projects but, as of today, AI algorithms cannot predict something that has not been seen before.
Laser scanning for site surveying can produce accurate 3D maps in a day rather than weeks
“Do we expect a wheeled loader to somehow know that a pile of rocks needs to move from location A to location B, all on its own? Of course not. No matter what, these tasks will need to trickle down, until they get to the machine level.
“Once the machine gets a task to accomplish, if it can accomplish task after task, that are different, without human interference then it is considered fully autonomous.”
Such automation may be possible but it would be challenging given today’s constraints such as computing processing power, sensor capabilities, object- and people-detection algorithms’ maturity, and the level of investments required.
Another consideration in the process of automation is functional safety and certification as defined by Safety Integrity Level (SIL) certification. It is far more challenging to have SIL-level certification on machine learning algorithms than on ‘dumb’ machines which only do what the operators instruct them to do.
Fully autonomous construction equipment is possible and apparently some prototypes are being demonstrated but as part of a larger system. “What we need to do is to take the
“That said, AI can help avoid the unexpected because it can have a larger scope of experience than a single human. Imagine if contractors could take their most experienced and capable employees and have them on the job twenty-four hours, seven days a week, they would have a higher chance of avoiding the unexpected.”
Progress checking using drones or laser surveying equipment has moved on from a simple pixel to pixel comparison from one week to the next. According to Beainy, AI can provide an experienced eye to look for specific anomalies or characteristics to help predict or observe things at a larger scale and in a shorter time period.
As mentioned above, the use of laser scanning for site surveying can produce accurate 3D maps in a day rather than the weeks that it would take a team of surveyors using traditional methods. Such speed also means it is viable to amend maps as the site progresses to check the correct profiles and structures are being created in the right places.
AI is already helping engineers optimise designs, to specify how projects should be constructed and achieve the best balance between the number and size of machines needed to meet the schedule. These databases of previous jobs can be thought of as a library of projects completed over the past few decades which can be automatically called up as reference for the new design. Citing the example of building a new bridge, Beainy says that once the parameters (length, width, carrying capacity, ground conditions…) are entered, the system can provide an optimised
design and a plan of how it should be efficiently constructed.
As an intermediate step, AI systems can be used to check traditionally drafted designs and construction methods before they are actioned. In both cases the use of AI can provide the bedrock for compiling and storing the building information modelling (BIM) records.
Once construction is under way, AI is being used in the management of the project and to control tasks. For example, if work is falling behind schedule in one area (workers may have called in sick or left, inclement weather etc.) the AI system will adapt the project accordingly and identify where to best deploy the available staff to minimise any delay. If empowered to do so, the system can automatically amend and issue the work orders to the site manager and, potentially, in future years directly to the autonomous machines.
So where do our experts expect to see applications of machine learning in the construction equipment sector?
From his viewpoint, Beainy expects repetitive loading tasks on construction sites and quarries to be automated as well as load carrying on predefined routes, similar to remote mining applications, but on construction sites with humans. Road paving, especially soil or asphalt rollers using neural network technology such as Density Direct will also become more widespread. However, beyond that he is very tight-lipped.
Camsell believes AI and machine learning will be used to counter particular problems rather than full automation being implemented. But his prediction comes with a very large caveat: “The only way much of this technology will be adopted is if it becomes a legislative requirement – either by statute, included in the project specification, or incorporated into local authorities’ planning approval system.”
He says the predominance of plant hire in the construction sector means that unless required to do otherwise, contractors hiring a machine will usually go with the lowest priceand that means a basic specification.
“Unless they can immediately benefit from these automated functions - and that looks unlikely on most sites - then contractors would not willingly pay the additional hire charges for such high-spec machines. And if there is no demand, plant hire companies won’t invest in these machines and the technology will go nowhere.”
Now that is something everybody can recognise.
DEMAND FOR BIGGER AND BETTER UNITS AT AN ALL-TIME HIGH
Mobile machines dominate a buoyant global market for crushers and screeners, but quarry operators are seeking the best of both worlds. They want crushers and screeners that combine the higher capacity and lower costs per tonne of stationary equipment, with the mobility and flexibility of mobile units. Liam McLoughlin reports.
Over the last 30 years the market for aggregates equipment such as crushers and screeners has undergone a transformation. Until the late 1980s mobile crushers and screeners were just small wheel-based units and not a major part of the overall crushing and screening business. Since then mobile units have become increasingly important in the processing of material at quarries.
Mobile crushing and screening equipment is mainly used by the construction and mining industries. In the construction sector it is prominently used for the processing and manufacturing of aggregates. According to a recent report published by Persistence Market Research (PMR), the growth of the construction industry coupled with the mining industries in various emerging countries across the globe will create significant further demand for mobile units in the future.
PMR predicts the global mobile crushers and screeners market will see a compound annual growth rate (CAGR) of 7.4% from 2018 to 2026. In 2017, the market was valued at US$2,168.6mn and is expected to reach US$4,073.4mn by the end of 2026.
The report adds that the general reduction in transportation costs due to the introduction of mobile crushers and screeners has been the key driver of growth in the overall market across the globe. Mobile units can be taken to any desired location to be used for processing at the construction or mining site, reducing time and money
involved in the transportation of raw materials for further processing.
The major applications of mobile equipment include primary on-site crushing and screening at stone quarries, mineral mining sites, construction sites, in addition to recycling of waste-demolished concrete and other material.
Most of the growth in the mobile crushing and screening market in the near future will come in the Asia-Pacific region, according to an analysis by IndustryArc. It adds that growing urbanisation and increasing focus on productivity is driving demand for mobile crushing and screening equipment.
Out of a global CAGR of around 5.57%
crushers and screeners can be prominently seen in most geographical regions, with Asia-Pacific regions adapting very quickly to mobile technology due to high transport costs.
Industry players are currently focusing on designing electric mobile jaw crushers that deliver maximum productivity with low transportation costs, according to a report by Allied Market Research. It forecasts that the global market is expected to be valued at US$2,550mn by 2022. Mobile crushers dominate the market (with a 73.8% share in 2015) and are projected to maintain this through to 2022. Asia-Pacific was the leading region in 2014 accounting for around

A report by Mordor Intelligence says that Asia is a major developing region and therefore the construction and mining industries are expected to grow rapidly there. The enhanced manufacturing units and rising industrialisation, coupled with higher transportation costs in countries such as China, India and Japan, promote the growth of the mobile crushers and screeners market.
“The construction industry in China is growing at an insatiable rate and is expected to add US$2.1 trillion to the global construction output by 2030,” the report states. “The country’s ‘one belt, one road’ policy is driving co-operation and trade with its neighbouring countries, thus driving massive investments in construction. Moreover, China is dealing with an ageing population, which could drive the construction of healthcare facilities.”
With planned investment of US$68 billion by 2019, Indonesia is one of the fastest growing construction markets in Asia. A recent reduction in interest rates has made funding more affordable and this has positively affected the construction industry in the country.
The Mordor Intelligence report states that India is also one of the fastest growing construction markets and is expected to spend US$13 trillion in the construction industry by 2030. The country’s rapidly expanding population is generating significant housing demand, owing to an increase in disposable income and urbanisation.
A GLOBAL OUTLOOK
Key global players in the crushing and screening equipment sector include Metso, Sandvik, Terex, SBM Mineral Processing, Kleemann, Keestrack, McCloskey, Anaconda, Astec, DUO, Maximus, QMS and Lipmann. Kieran Hegarty, president of Terex Materials Processing, says that global demand for crushing and screening products is at an all-time high with all of his company’s traditional markets – North America, Europe and Australia – being very strong.
“We’re also making good headway in countries which are more difficult to penetrate – Russia, South America, the majority of Asia and Africa,” says Hegarty. “Our businesses continue to focus on introducing new products, and improvements to existing products, designed to address specific customer needs in the crushing and screening industries globally.”
Despite the preference for mobile units, aggregates equipment customers are seeking the best of both worlds, according to Marcel
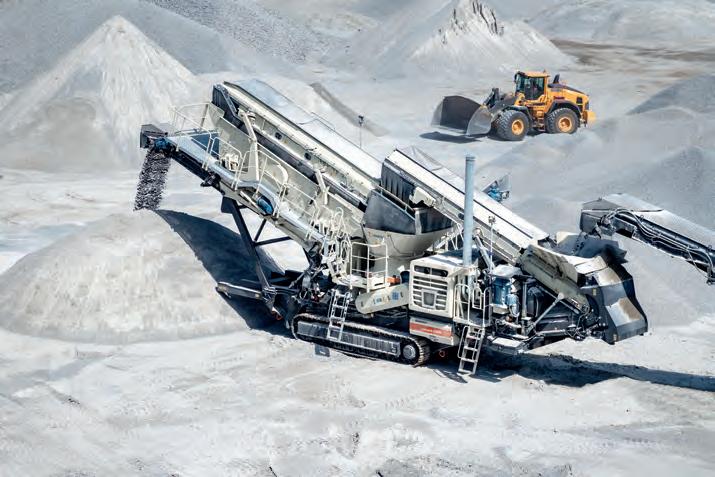
Kerkhofs, marketing manager at Belgiumbased manufacturer Keestrack. “They want the advantages of stationary plant: higher capacity and performance, high-quality material, lower costs per tonne, with the mobility and flexibility of mobile equipment. Bigger mobile equipment is playing a critical success factor in this. Higher and bigger conveyors reduce logistics costs and cost per produced tonne. Mobile stackers combined with mobile plant facilitate the attraction towards bigger mobile equipment.”
He adds that users are also looking into electric drives to lower the costs per tonne even further and not to be dependent on a diesel engine. “Besides this, the electric drives have less downtime and repairs, servicing and breakdowns than on engines with hydraulic drives,” Kerkhofs says.
Hegarty says that, due to the thriving aggregates industry, many quarry operators and contractors are looking to produce greater volumes of final aggregate product while lowering production cost per tonne.
ABOVE: The Metso Lokotrack 330D mobile crushing and screening plant.
operation, as the loader can be employed elsewhere,” says Hegarty. “It also improves site safety, through the reduction of loader and haulage truck movements.”
While acknowledging the trend for quarry operators and contractors moving to greater output volumes, Hegarty says his company is also seeing huge potential for compact crushers and screeners to meet end users who are working on smaller residential construction projects as well as plant and tool hire. “There are more and more contractors crushing and screening,” he adds. Terex produces the EvoQuip range of compact crushers and screeners to cater for this market.
The major challenge for mobile is making it transport-compliant
“This is not necessarily achieved by making larger machines,” adds Hegarty. “What Terex MP are focusing on is making our crushers and screeners work more efficiently with better performance figures.”
To help quarry owners better cope with bigger production levels, Hegarty says that Terex MP has also developed its conveyor range because the expense of using wheeled loaders – such as the cost of diesel and operators to control them – has become “extortionate”. The new Terex MP tracked conveyor is designed to facilitate a higher stockpile, reducing the use of a loader and the attendant costs for the customer.
“It equates to less downtime and more efficiency throughout the processing
Asked whether quarry operators and contractors are looking to lower production costs by producing greater volumes of final aggregates with fewer machines, Finnish original equipment manufacturer (OEM) Metso responds that this depends on the market.
“Not all markets are moving in the same direction,” says Renaud Lapointe, Metso senior VP, business and product management. “In China, for example, there is a trend towards environmentally-friendly, large-scale ‘super quarries.’ Small quarries are being closed. In India, on the other hand, we don’t see our customers going for bigger capacities.”
He adds that the trend in Western and Eastern Europe is also different and, due to the terrain, aggregates transport costs are high, and operators need to have enough quarries to cover the market. Even within Europe needs differ. In Finland, Lapointe notes the trend is towards smaller ➔
➔ equipment, as project sizes for contractors are getting smaller. In Sweden, operations tend to concentrate on bigger quarries, and there is more demand for large-capacity crushers.
To go for large-capacity plants, quarries also need to have deposits with a long lifetime. “Big deposits are not so easy to find anymore,” says Lapointe. “Government policies also impact the decisions. For example, in Europe, it is hard to get a permit for large-capacity quarries. Emission levels also need to be taken into consideration.”
The technology is in place to produce large crushing machines, according to Hegarty, who says that the engines to drive them are readily available and already used in other areas of the Terex business. “However, the major challenge for mobile is making it transport-compliant, with machines of this size requiring being split into pieces – making it more expensive to make and set up,” Hegarty says. ”As a result, the majority of our development has been in single-piece loads and lower production capacity.”
Terex’s MPS (Minerals Processing Systems) brand has traditionally headed up the company’s large-plant projects, with one currently in its portable range, the wheeled CRJ3750 crusher, that can produce up to 1,180 tonnes per hour.
BELOW: The Kleemann Mobicat MC 162 RRP crushing and screening unit at the Prasville limestone quarry in France. The giant machine can process up to 1,000 tonnes of material per hour.
While noting that large plant is a niche market – mostly for mines and very large quarries – Hegarty says Terex is working to fill this space and have a couple of larger plant models, capable of processing 800 to 900 tonnes an hour of material depending on the feed, in the development phase for its Powerscreen and Terex Finlay businesses.
Metso has had large mobile crushers and screeners in its range for a long time, both for the aggregates industry and for mining applications. One of the largest Metso mobile crushing plants, the Lokotrack LT160, is located in Australia. Weighing 285 tonnes and measuring 12 metres high by 25 metres in length, it can crush up to 1,150 tonnes of rock per hour.
In 2018, Metso complemented its portfolio of mobile, large-capacity crushing and screening plants with the acquisition of the Swedish company Jonsson. The Jonsson plant can process up to 1,150 tonnes of rock per hour, and one model can even be equipped with primary and secondary crushers on one track. This primary-secondary combination is typically used in heavy-duty aggregates processes.
says the new crushing unit can be delivered in standard containers from the factory as well as easily moved from one site to another using standard prime movers. It claims the flexibility of the concept allows producers to profitably offer their customers contracts of various sizes.
The Keestrack range of mobile crushers and screeners can go up to 500 tonnes per hour on the crushing side and to 8001,000 tonnes on some of the scalping units. Marketing manager Marcel Kerkhofs said the company is looking at developing larger mobile crushing plants for the future of up to 750 tonnes per hour. For this reason, Keestrack is building a new factory in Italy to offer a new product range that will come to market around 2020-2021.
The aggregates equipment engine market is in a transition period
“The larger and more professional quarries are looking for much higher tonnage and also with the advantages of the mobile units, plus the capability of shifting from one type of aggregate to another without making many changes to the plant,” Kerkhofs adds.
Metso is now introducing new higher capacity models to its wheel-mounted NW Rapid crushing unit series. In addition to the bigger jaw crusher model, the NW Rapid units are now also available with a variety of robust cone crushers, including the first model with the MX crusher. The company
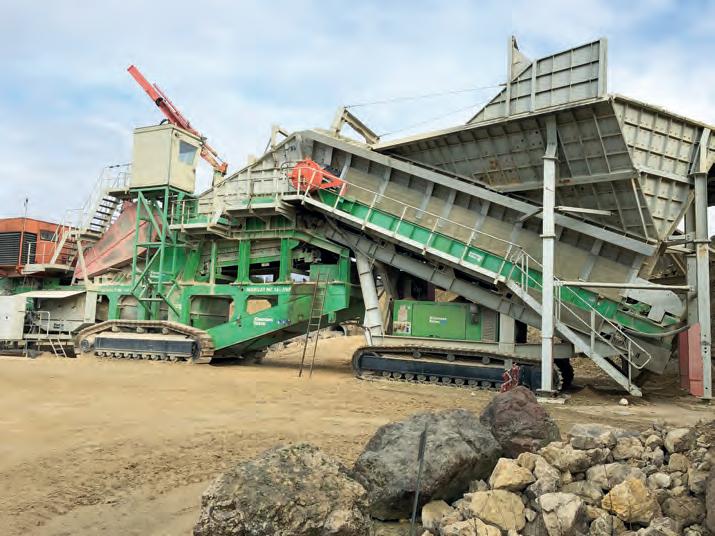
He does not think that dealers will need incentivising to push larger mobile machines to customers. “The market place and the end customer will be asking for this and, if we can design the units to do the job as requested, a mobile unit will offer the same advantages as a stationary unit without the disadvantages,” he says.
“It is the job of the manufacturers and the distributors to inform the market and the end customer of the new R&D concepts and to prove we are capable of doing this by showing examples to customers where the new equipment is running.”
Metso says that, rather than developing products that it would push the market to buy, its target is to serve customers and adapt its portfolio to match their needs. “We listen to the market carefully and draw conclusions for our R&D roadmap,” the company says. Vincent Levesque, area sales manager Kleemann for the Paris area at Wirtgen France (subsidiary of the parent company WIRTGEN GROUP, crushing and screening equipment manufacturer brand of Kleemann), says that the market for large mobile crushers and screeners that can process huge amounts of material is likely to remain a niche one. “You need a very big quarry to operate these machines,” Levesque says.
Kleemann produces the giant Mobicat MC 162 RRP crushing and screening machine that can process 1,000 tonnes per hour. Only two such machines have been deployed, one in Chile and the other in France at the Prasville limestone quarry operated by SMBP at Berchères-les-Pierres, near Chartres.
Larger machines will have potential ramifications for engine design, fuel consumption and the supply of spares. Kimmo Vesamäki, VP technology at Metso, says: “Bigger machines are typically electric-driven – either from an external power source or on-board genset – and fuel consumption is somewhat smaller than with hydraulic units. Spares and wears are bigger but still available.”
His colleague at Metso, Renaud Lapointe, adds that globally, the aggregates equipment engine market is in a transition period with fossil fuel, and the trend is towards electric units. “Metso can already offer hybrid units, and we want to increase the share of these in our portfolio,” he adds. “However, we have to keep in mind that some of our customers are working on remote sites where diesel is the only option.”
RESEARCH AND DEVELOPMENT

says. “Regular reports on machine and fuel consumption, output production tonnages, GPS machine tracking, operating hours – all help customers manage their fleet, which is particularly useful for contractors and plant rental companies.
Manufactured sand is becoming an essential product for global economic growth
Several of the aggregates equipment suppliers interviewed for this article said they are investing heavily in research & development. Kerkhofs says that Keestrack is focusing its R&D on areas such as the mobility of the units, in particular developing lightweight units that use higher grade ST70 steel to reduce the weight of the equipment, ensuring that they remain mobile and within road transport limitations.
On the economics side of the business, Keestrack is researching high-capacity plants to reduce the costs per tonne of materials produced. In terms of the environment, it is developing hybrid electric drive units that produce far less emissions, or no emissions at all if they run connected to the electrical grid.
Terex MP is focused on widening its portfolio into areas the company hasn’t previously been able to accommodate, according to Hegarty. He adds that there is also development in new technologies such as telemetry.
“We’re very aware that our machines are huge investments for our customers, so telemetry – technology that pulls data from their machines in the field – helps them make informed decisions about their fleet,” he
“In addition, our telematics is tied into predictive maintenance, where customers can know when their machine is due a service or when parts need replacing. With telematics, we work with our customers to maximise uptime and longevity of their machines and can make sure that we can have the right parts, at the right place, at the right time.”
Lapointe says that standardisation and modularisation of the equipment guides Metso’s R&D work and design. “Normally, it’s easier to standardise medium- and small-capacity equipment,” he adds. “Good modularisation and standardisation produce cost savings that will benefit both the manufacturer and the customer.”
Manufactured sand is becoming an essential product for global economic growth, according to Lapointe, as most countries want to preserve their natural sand deposits. He says that there is a need for premium manufactured sand production equipment so that the sand quality has the same – or even better – properties as natural sand.
“Recycling is also becoming more and more common,” he adds. “At Metso, about 40% of our compact mobile equipment is used for recycling applications, and the focus is towards high-quality end products. Currently, the biggest demand is for trackmounted units with impact crushers below 50 tonnes.”
An indicator of where the aggregates and quarrying industry may be heading is provided by the Electric Site quarry project
in Sweden operated by Volvo Construction Equipment and its customer Skanska.
The pair have recorded claimed groundbreaking results from the research project at the Vikan Kross quarry near Gothenburg.
The duo tested the viability of the Electric Site research project in a 10-week trial from September to November last year. The tests are said to have shown a 98% reduction in carbon emissions, a 70% reduction in energy cost and a 40% reduction in operator cost.
GOING ELECTRIC
The Electric Site project aims to electrify each transport stage in a quarry – from excavation to primary crushing, and transport to secondary crushing. It incorporates electric and autonomous prototype Volvo CE machines, new work methods, and site management systems, which together form a complete site solution. New technology encompasses machine and fleet control systems and logistic solutions for electric machines in quarries.
At an open day held at the Vikan Kross quarry in November 2018, Melker Jernberg, president of Volvo CE, was asked when the technology could actually become available to quarry operators as an ‘off-the-shelf’ solution.
“This is the big challenge,” Jernberg responded. “I think the confidence now in our organisation is to do it much quicker than we thought ten weeks ago. You won’t be able to buy it tomorrow, but it will be quite soon.”
In January 2019, Volvo Trucks supplied its first commercial autonomous transport solution for real day-to-day operation to Norwegian mining company Brønnøy Kalk AS. Six autonomous Volvo FH trucks are being used to transport limestone over a five-kilometre stretch from an open-pit mine to a nearby port. The solution is said to offer companies working in many industries such as aggregates production and mining greater flexibility and efficiency, as well as increased productivity.
Buenos Aires, Argentina.
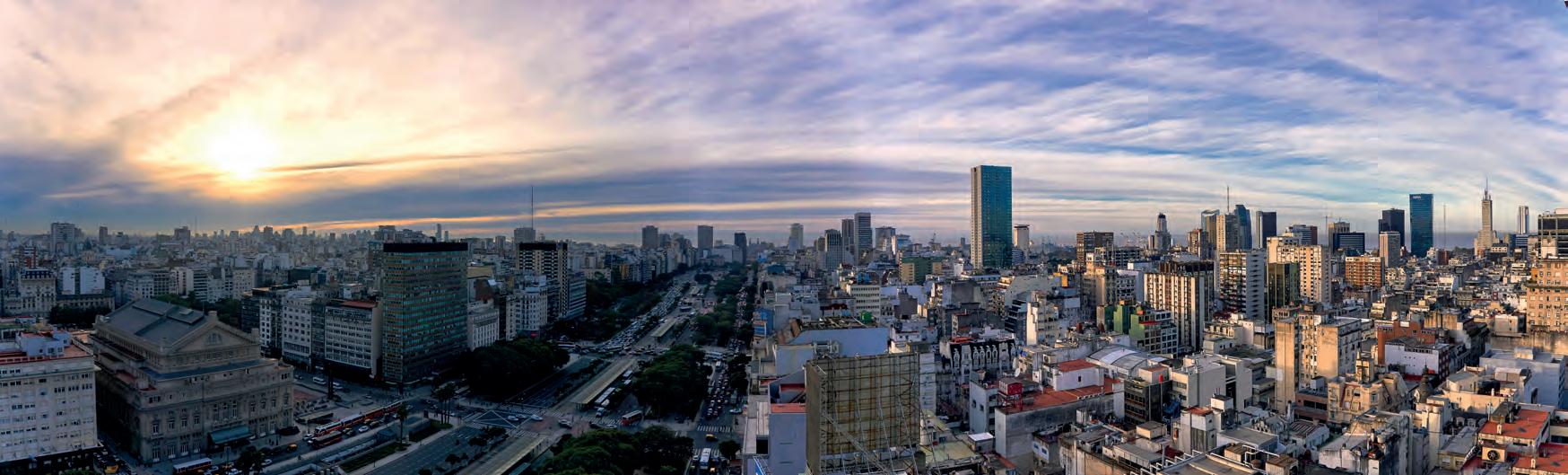
BRIGHT SPOTS EMERGE AS THE LATIN AMERICAN MARKET CONTINUES TO EVOLVE
Reporting on a vast territory that encompasses more than 20 million square kilometres is not an easy task. Add to Latin America’s size the fact that the region’s major economies - Brazil, Mexico and Colombia - have all elected new presidents recently and that Argentina, the country most notably influenced by Europe, has gone from hope to economic crisis … an overall assessment of the continent’s economy starts to become very mixed. However, Enrique Saez, editor of Construccion Pan-Americana, is equal to the challenge. Here is his expert view on what is happening and how to spot the good news in this vast and evolving market.
There is a liberating tango in the air in Argentina. The Argentine government has awarded contracts for the first public-private partnerships (PPP) in the country. The National Roadway Assessment Commission recently signed contracts to award the first six tenders … all of which will be delivered via PPP. The plan is to develop more than 7,200 kilometres of new national highways. The companies carrying out the work on these road corridors will all be Argentinian, with the exception of Portobased Mota-Engil from Portugal.
It is worth bearing in mind certain factors when assessing these decisions. For well over a decade this vast country was governed by either Nestor Kirchner (2003-2007) or his wife, Cristina Fernandez de Kirchner (20072015), both of whom led Peronist (populist) governments that aligned themselves with Venezuela’s Hugo Chavez, Brazil’s Lula da Silva and Cuba’s Fidel Castro. And these were arrangements that suited their political interests.
For the last three years, moderate rightwinger Mauricio Macri has been modernising the Argentinian economy and opening it
up to the international community. He has been busy paying off the national debt (Kirchner had threatened to default), as well as streamlining ministries and privatising public companies. The management and construction of roadways was converted into a pseudo-private entity over a year ago, with the expected opposition from Kirchner loyalists.
The first stage of the PPP implementation was scheduled to start last October and attracted 32 offers from 10 consortiums, made up of 19 national and seven international companies. Each company can be awarded a maximum of two contracts.
will be built or upgraded through the construction of 1,610 kilometres of national highways, 3,310 kilometres of safe routes, 324 kilometres of special works and 26 kilometres of connecting roads. This makes 5,270 kilometres of roadworks in total. The remaining 2,007 kilometres will relate to improving and maintaining the existing road network.
Without question, the PPP is an exciting development in the country
The plan for the new Network of Highways and Safe Routes is divided into three bidding stages, with a total investment of around US$ 12,500 million for the first 5 years and over US$ 4,200 million for the next 10 years.
During the three stages approximately 7,277 kilometres of national routes
The first stage of the development of the network includes the concessions for the new road corridors, totalling 3,300 km of roads in Buenos Aires, Cordoba, La Pampa, Mendoza and Santa Fe. The construction of new highways (813 km), safe routes (1,494 km) and special works (252 km) is planned, in addition to 17 connecting roads to various locations. The total investment estimated in the first stage will be more than US$ 8,000 million, US$ 6,000 million during the first four years and more than US$ 2,000 million during the subsequent six to 15 years in complementary and maintenance works.
Diesel taxes are expected to finance the works and the toll revenue will pay for the maintenance and operation of the corridor. The payment for Stage I works will begin in 2021 using existing resources, without the need to create new taxes.
There are two other factors to bear in mind that might complicate Macri’s intentions. Firstly, the commodities boom that boosted imports (construction equipment was a winner) developed into a steep monetary crisis almost overnight: a sudden change of fortune not without precedence in Argentina. The government had to seek help from international lenders in order to control the situation.
Secondly, there are some major infrastructure projects yet to be finished in the country. The so-called Represas de Patagonia (Patagonia’s dams) is a project to develop two massive hydroelectric plants in the south of the country. The project was initially awarded to a Kirchner-linked construction company with Chinese financing that came with demanding conditions attached. It is undoubtedly a delicate matter in the country because of the hint of corruption surrounding it. However, once the Macri administration makes a decision, it might well revitalise the infrastructure industry in the country, with other roadbuilding and public transportation
projects (bus rapid transit (BRT) and trains in the Buenos Aires area, airport remodelling, etc.) to follow. Without question, the PPP is an exciting development in the country. As it takes two to tango, it will be interesting to see if Macri’s partners (the provincial governments still loyal to the Kirchner regime) are willing to grab their dancing shoes.
STOP THE PRESSES! BOLSONARO IS HERE
In 2012 Brazil prided itself on a growing economy that had just surpassed the United Kingdom’s as the fifth largest in the world. The downward spiral that followed in the ensuing years has culminated in the election of a new right-wing president. In recent years, the country has witnessed the Lava Jato megascandal in which construction companies (Odebrecht being the main culprit) bribed the entire political system. Revered former president, Inacio Lula Da Silva, and former Odebrecht CEO, Marcelo Odebrecht, have ended up behind bars. The economy collapsed, investment stopped, and the entire country slipped into a siesta-like state - until things started to change in 2018. Jair Bolsonaro emerged as a key political
player. The newly labelled ‘Brazilian Trump’ waited less than three days after taking office to announce his privatisation plan that aims to attract US$ 1,859 million through railway concessions, as well as concessions for a dozen airports and four port terminals in the country.
How is Bolsonaro going to incorporate the Brazilian army into the privatisation scheme?
Brazil may well be able to offer ample opportunities in both the PPP and privatisation arenas. A pioneer in the management of roadways in Latin America, the country badly needs new highways and fresh money to fund its ambitious hydroelectric plans (over a dozen new dams are still unfinished). Public transportation is also in need of investment. Some of Brazil’s states have taken care of that matter themselves while others have been suffering. The Sao Paulo Metro system has seen the withdrawal of investment while some BRT lines in the south-east continue to grow. However, the only major subway project to be announced during the crisis was the Belo Horizonte Metro. This situation could change if private money is secured, especially from foreign companies in a country where local contractors have long been the kings. Another Brazilian sector which could see growth is airport infrastructure. Government agency Infraero owns and controls 60 airports in the country. However, the two most important airports (Guarulhos in São Paulo and Galeao in Rio de Janeiro) are controlled and managed by private entities. At the time of going to press, Bolsonaro had announced his intention to privatise some of those 60 airports, with some of them subject to major remodelling plans.

Finally, there is a particular question worth looking at closely: how is Bolsonaro going to incorporate the Brazilian army into the privatisation scheme? This requires some explanation. Jair Bolsonaro is a career soldier who served during the middle of the dictatorship (1964-1985). During those two decades the Brazilian Army was a key player in the construction industry for which it earned respect. The legacy of the Brazilian army in infrastructure is enormous. Brazilian army engineers have been responsible for the development of construction and infrastructure projects that nobody else dared to undertake at that time. It will be interesting to see how a former soldier of that era will combine that legacy with his proprivatisation, free-enterprise agenda. ➔
Brazilian states might also have a say in Bolsonaro’s plans. São Paulo is responsible for one third of the Brazilian economy. The four southern and the three south-eastern states control the bulk of the national economy. It will also be interesting to see how the new government develops a privatisation scheme in the heavily subsidised north-east and Amazonian regions, and to monitor the response from the influential regional governments in the south. The key, it seems, is to open up the country to the world, something that Brazil has been needing to do for decades.
A CHINESE SITUATION IN ECUADOR
One of the main trends in South America in recent years is the decline in populism. This might affect the relationship between the continent and its main money lender - China. For the last decade, the Asian tiger has been financing major infrastructure projects in the region, in exchange for minerals or other natural resources, mainly petroleum. Other planned projects, such as the so-called Nicaraguan Canal, have been mysteriously shelved.
Cuba, Venezuela, Bolivia, Argentina and Ecuador have all received Chinese funds for their infrastructure projects. These deals always include Chinese labour and machinery managed by a Chinese contractor (sometimes with a local partner).
It seems that fissures are appearing in the relationship between Ecuador and the eastern giant, not only literally (in the dams built and financed with Chinese capital) but between the Ecuadorian leaders and their financiers.
Certain
According to some, the Coca Codo Sinclair dam (a mega-project and a significant symbol of progress in the Andean country) should never have been built in such a tremendously vulnerable location. In addition, the key Ecuadorian officials involved in the construction of the dam - a former vice president, a former electricity minister, and even the former anti-corruption official who oversaw the project and was heard discussing bribes in a recording since made public - are either already behind bars or are currently accused of bribery.
Route One Publishing has reported several times on the construction of the mega dam. It looked like a great step forward in improving the well-being and collective life
“In terms of infrastructure, the six-year term of former president Enrique Peña Nieto was considered a moderately productive period”
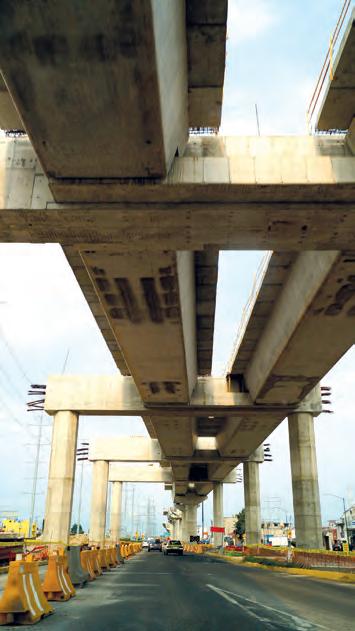
of the Ecuadorians, but now cracks have appeared everywhere, not least in the dam itself, and the country has a huge debt of US$ 19,000 million.
The socialist government of president Correa did not want the dollarized economy of his country to depend so much on oil. The decision was made to pay via oil, sold at a discount to his Chinese financiers who, in turn, resell it and make a profit. At the moment, certain indications point to 80% of Ecuadorian oil being in Chinese hands.
This situation is interesting since Ecuador was one of the first countries in the region to expel Odebrecht (twice) for corrupt practices.
This state of affairs may well be mirrored in other countries such as Bolivia and Venezuela.
A NEW PRESIDENT IN MEXICO
The year ended in Mexico with the inauguration of the first left-wing president in its history, Andres Manuel López Obrador, who won 53% of the vote in a landslide victory. In terms of infrastructure, the six-year term of former president Enrique Peña Nieto was considered a moderately productive period. Despite the weakness of the Mexican peso against the US dollar and the decrease in oil production (the main source of income for the country), a
series of road projects was completed in the country. The Ministry of Communications and Transportation (SCT) announced an investment of around US$ 850 million to improve the Mexico-Querétaro highway and connect the capital with the mega airport that was being built in the country.
Among the projects expected to be completed in 2018 was the 74-kilometre Atizapán-Atlacomulco highway, with investment of around US$ 450 million.
According to a final statement the ministry said it expected to complete three highway projects, with two more in progress, which will improve connections between central Mexico and the rest of the country.
The Peñón-Texcoco highway is to be the main direct link between the new international airport and Mexico City. At 10km in length, an investment of around US $100 million has been allocated.
The SCT also included in its plans the resurfacing of the 185km Mexico-Querétaro highway, again improving commercial connections in the country. 140 kilometres will be replaced by hydraulic concrete and 45 kilometres with high-quality asphalt.
The Mexico-Toluca train line and major subway and elevated trains in both Guadalajara and Monterrey, two other key industrial hubs in the country, were under construction or nearing completion. On a regional level, the states of Veracruz and Baja California Sur were among the most
productive regarding infrastructure. These are just small projects by Mexican standards, a country with a population of over 125 million covering nearly two million square kilometres. This was the situation the day before the general election.
The first major headline generated by Andres Manuel López Obrador (AMLO), Mexico’s new president, was the cancellation of the Sir Norman Fosterdesigned New International Airport of Mexico (NAIM), a megaproject with a price tag of US$ 8 billion which is already 20% completed (the former government declared it was 31.8% completed). The decision was the result of a referendum held among one million inhabitants one month before the new president took office. The new airport occupies 4,400 hectares, 15 kilometres from the centre of Mexico City, in an area of significant geological complexity. Nobody has clarified what will happen with the partly built terminal building and control tower, or with the foundations for the terminals.
DÉJÀ VU IN COLOMBIA
Ports dredging and airport investments are also some of the major goals
Colombia was the third country in Latin America to see the election of a new president in 2018. In fact, it was not such a big change. Alvaro Uribe, a previous president of the country and political enemy of Juan Manuel Santos (the outgoing president), saw his ally and former protégé Ivan Duque elected as the new president. In terms of infrastructure spending and development Colombia is the most promising country in the region. Its 4G roadbuilding scheme which has been underfunded and delayed during recent years due to political uncertainty, would make Colombia a modern and well-connected country when completed.
areas in the country. As a result, the Barranquilla Canal is going to be dredged. Another major project is the Circunvalar de la Prosperidad which connects Barranquilla to Cartagena.
In his first meeting with representatives of the infrastructure industry, the president of the National Agency of Infrastructure (ANI), Louis Kleyn, explained that only six 4G concessions are ahead of the 35% completion threshold. The projects Girardot-HondaPuerto Salgar and Cartagena-Barranquilla and Circunvalar de la Prosperidad are more than 90% complete while the Pacific 2 and 3 projects are 57% and 49% complete respectively.
According to López Obrador, the cancellation of the NAIM and the construction of the airport in Santa Lucía (a former army airport) will represent a saving of US$ 5,000 million. Despite compensation announced by the incoming government, the Mexican stock market suffered a downturn as a result of the news and the already weak peso lost some value. In order to mitigate the impact of the decision, the government announced that the new airport would be finished in record time. It also stated that Toluca airport, some 50 kilometres away from the capital, would also receive investments from the government.
“The city of Bogotá has already secured the funds to enable it to start planning the construction of the Bogotá Metro”
However, after almost six months in office, the Duque administration is yet to provide the 4G scheme with funds. One of its first measures was to find financing for emergency projects that needed completing, mainly in the area of road maintenance. Ports dredging and airport investments are also some of the major goals. Previous Colombian governments have had two main goals regarding infrastructure: the development of the Magdalena River (the principal river in the country) as a corridor for goods transportation, and the development of the
Two other major projects are 36% and 39% completed. In 2019, the ANI is expected to finish the construction of two projects, and to readjust the schedule of a further 13. By 2020, the government expects to conclude two more projects.
The city of Bogotá has already secured the funds to enable it to start planning the construction of the Bogotá Metro, a project the city has dreamed about for almost five decades. In the meantime, other megaprojects are moving forward in Latin America: the Quito, Lima, Santiago, Panama City and Belo Horizonte Metro systems, airports in Colombia, hydroelectric projects in Honduras and the Dominican Republic, to name but a few.
Hopefully, stable trading and a strong US
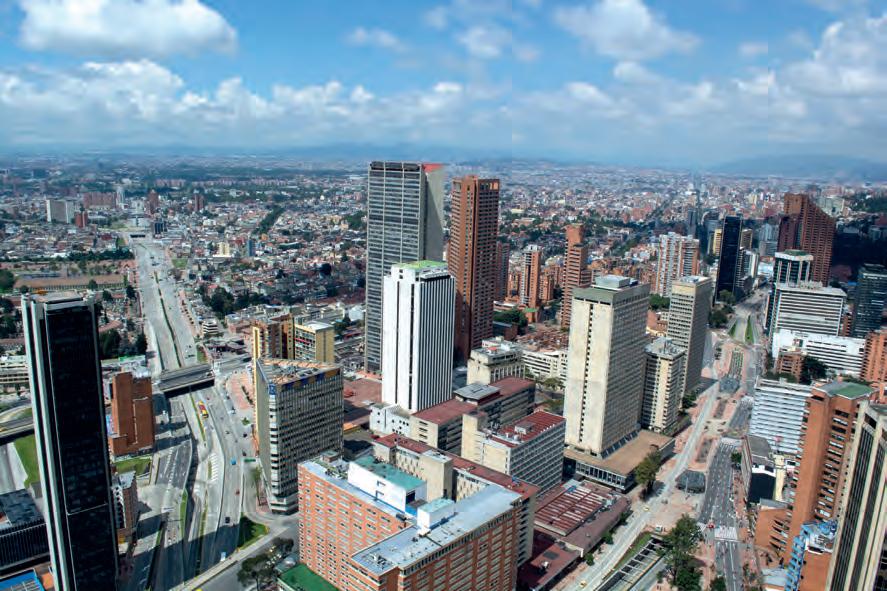
Colombia.
INNOVATIONS IN COMPACTION EFFICIENCY
New
developments in compaction technology are allowing road builders to deliver better quality road surfaces even in difficult applications - Mike Woof writes
The latest asphalt compactors are helping deliver higher quality in road construction applications than previous generation machines. Firms now offer machines available with lowemission engines and aftertreatment systems for use in regulated markets, which also deliver major gains in fuel efficiency.
Advances are being seen in terms of performance and output, with the latest equipment also able to benefit from sophisticated machine control technology. Most of the key compactor manufacturers allow their machines to operate using machine control systems, which deliver huge benefits for productivity and finish quality.
Using machine controls allows asphaltcompactor operators to schedule working more efficiently. Machine control systems mean that compactors can achieve more homogenous results by ensuring that surfaces are brought to the correct specification. The control systems feature displays inside the cab showing operators how many passes each area has already received, and how many more are required. This makes sure that necessary compaction grades are achieved while the systems also allow operators to work more productively, wasting less time for each portion of the job.
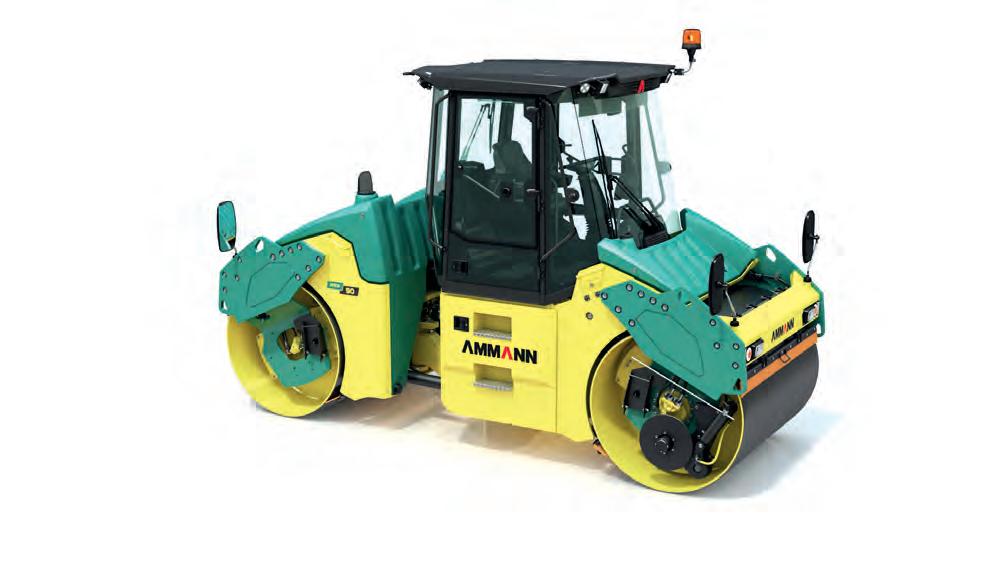
ABOVE: Ammann introduced its ARX 90 oscillatory compactor in 2016.
BELOW: Caterpillar’s CB15 model is available with an oscillation drum.
Intelligent compaction systems on asphalt compactors rely on heat sensing tools (such as infra-red scanners), in addition to the systems measuring the degree of compaction. This adds another dimension in that the operator is able to schedule work to be carried out based on the temperature gradient. Areas of the mat that are cooling can be prioritised for compaction first, before the temperature drops too low.
Measurement of compaction effect is achieved either by estimating the compaction density or the material stiffness. Various manufacturers use one or the other system, though at present there has not been an empirical and independent study to say which is more effective.
Further advances in machine control systems for compactors have allowed improved efficiencies for entire fleets of machines that are working together. The control systems between each working compactor are interlinked, so all the operators see the progress of all the machines on a site. And for example, an operator in one compactor can see on the screen the work other units have already carried out.
For asphalt surfaces, intelligent compaction plays an important role in delivering quality road construction. One of the key factors is by helping to eliminate the risk of over-compaction, which can otherwise lead to damaged surfaces, as the aggregates (bound in the bitumen to make up the asphalt) can fracture and crumble.
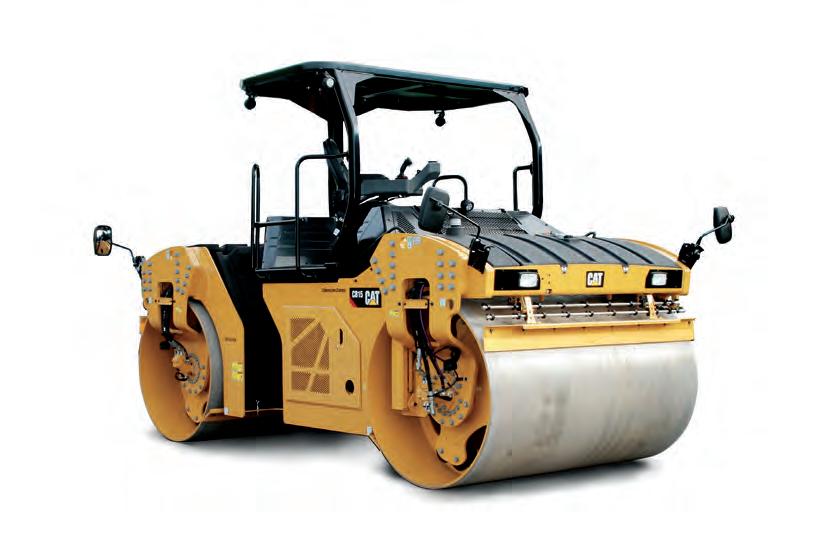
So-called intelligent compaction technologies can make major gains in road construction productivity, as well as allowing the recorded data to be used later on for further investigations, should early wear issues occur for example. Linked to paving construction and logistics software, the machine control systems on compactors can assist in monitoring asphalt quality from the plant to the paving quality site. This helps to optimise overall
working efficiency while also providing a wealth of as-built construction data that can be analysed for quality assurance, and also stored as part of the project model for future reference.
By utilising compaction control systems in the machines, a contractor is able to monitor performance and use GPS information to log the data accurately onto a grid. The collated data can then be checked at a laboratory as well as being evaluated separately by a consultant. By documenting operations at the site, data is then embedded into the construction model for the project.
Should any problems appear in the surface subsequently, the contractor can have full access to accurate information showing exactly what paving and compaction work was carried out, to which specification and when.
Compactors
And the prospect for intelligent compaction technology also looks to be taking a radical step ahead in the not too distant future. At the Trimble Dimensions event held in Las Vegas in November 2018, the firm demonstrated its prototype autonomous compaction system, currently under development. The machine being demonstrated was a soil compactor and the firm emphasised that when the first autonomous compactors do come to market in coming years, they will likely be used on large construction projects where the machines can operate safely in defined areas, away from personnel.
featuring oscillation drums were first introduced in the 1980s
A number of trials using the latest intelligent compaction systems have been carried out for asphalt road construction. In 2017, the Missouri Department of Transportation carried out a year-long test to prove the technology (World Highways July/ August 2018), highlighting the major benefits it can deliver both for contractors and clients alike.
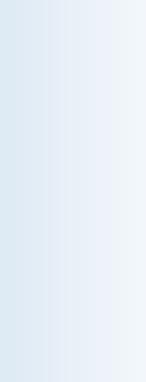
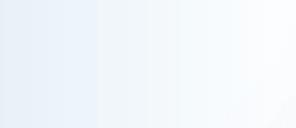
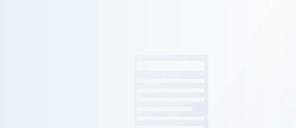
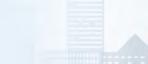
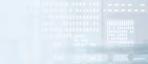
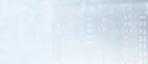
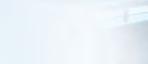
However, as the technology develops further, it seems likely asphalt compactors using Trimble’s autonomous controls will also become available. These will most likely suit duties on large highway or airport runway jobs, away from the general public and where machines can operate in a closed environment. In theory, the compaction machines would be able to operate autonomously right up to the paving machines, using software to prioritise the workflow and recording as-built data, as with current generation equipment. This will go some way to address the increasing problems many contractors face in finding
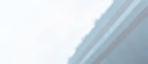
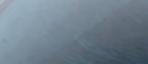


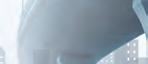
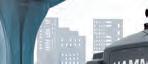
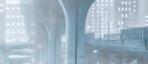
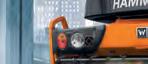
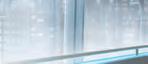
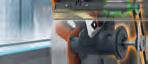
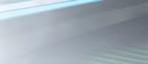
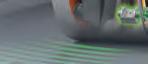

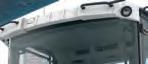

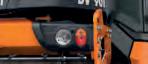

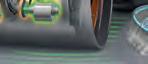
construction personnel, as well as potentially boosting site safety in the longer term.
Meanwhile, another development in asphalt compaction that is seeing a raised profile in recent times is for machines featuring oscillation drums.
The concept can hardly be described as new. Compactors featuring oscillation drums were first introduced in the 1980s, with German firm Hamm pioneering the technology. However, the concept remained a comparatively niche system for many years, with contractors proving reluctant to switch to this new system, despite the claims for its effectiveness made by Hamm. Instead, contractors proved content to stick with the tried-and-tested vibration compaction systems, first developed in the 1930s.
However, in recent times the mood in the road construction sector has changed, recognising many of the benefits offered by oscillation.
A key issue is in understanding how the system works. With a conventional vibrationtype drum, the compaction forces are directed vertically downwards. This does indeed generate the necessary forces for compaction, ensuring that voids within the asphalt mat are eliminated and allowing the required material density to be reached.
Even so, this type of compaction also has its shortcomings. A key issue is that because the compaction forces are directed vertically
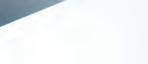
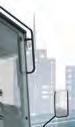
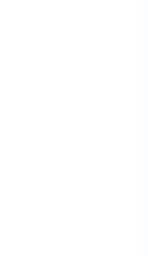
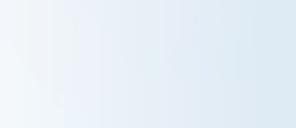
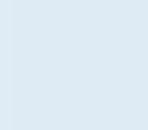
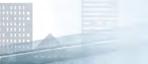
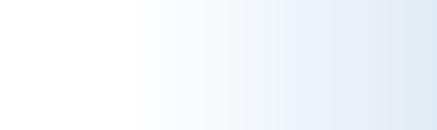
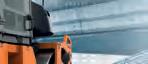
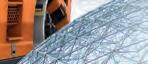
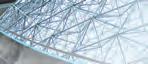
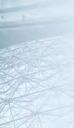


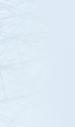
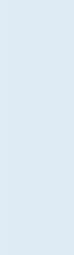
www.hamm.eu CLOSE TO OUR CUSTOMERS. One drum, twice the oscillation: HAMM’s patented solution combines the advantages of a split roller drum with the benefits of HAMM oscillation. It provides for top quality and a rapid increase in compaction on all asphalt construction sites. This ensures optimum results, even in tight curves and when compacting asphalts which are prone to displacement, when dealing with thin layers or working on bridges and in close proximity to historic buildings.
“The prospect for intelligent compaction technology also looks to be taking a radical step ahead in the not too distant future”
downwards, they can bounce off base layers and be reflected back in all directions. As a result, compaction with vibration cannot be used in certain road construction applications.
For obvious reasons, the resonances emanating from vibration-type compaction cannot be tolerated for bridge paving purposes. Firstly, the vibration forces could cause structural damage to the bridge itself, particularly if the vibration frequency matched with a hitherto unknown tertiary harmonic frequency of the bridge deck. Secondly, the impact forces of the vibration would be lessened due to the behaviour of the bridge deck, most particularly with structures with more flexible deck designs such as suspension bridges. In this latter instance, the actual compaction effect would be lessened considerably, resulting in ineffective operation of the machine.
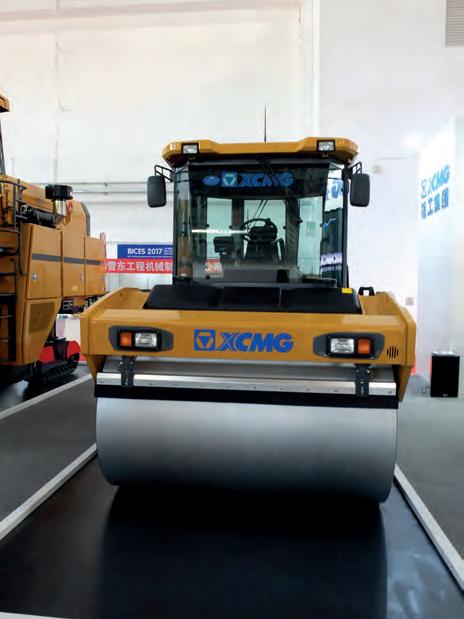
in urban areas that are close to homes or businesses.
However, all of these issues can be addressed by using compaction by oscillation instead. Again, understanding how the oscillation drums work is crucial to appreciating why the technology can be more
a kneading effect on the mat. The compaction forces are directed to the asphalt surface only and are not transmitted to the surrounding area. As a result, the forces are not reflected and do not travel the same distance as with conventional vibration systems.
This allows the quieter oscillation-type compaction to be utilised in urban areas or industrial zones, without fear of causing problems to surrounding buildings or sensitive computing equipment.
Moreover, oscillation compaction can be used effectively for bridge construction. In fact, the use of oscillation-type compactors has helped boost paving quality for bridge deck construction applications. Contractors would otherwise have to use deadweight-type rollers for asphalt compaction. And deadweight-type machines would require far more passes to achieve specified density values, reducing overall productivity.
Oscillatory compaction offers a method for achieving required pavement density efficiently and productively for bridge deck construction purposes.
This is of particular importance for bridges with steel decks, where asphalt pavements may typically face rapid wear rates due in part to insufficient material densities having been achieved during compaction carried out using deadweight-type machines.
There are other benefits too. With an oscillation-type drum, the risk of over-
Compaction with vibration can also be noisy, making it unsuitable for us in urban applications where housing may be located close to the site. The forces generated by vibration compaction can also be transmitted some distance from the working area, resulting in additional disturbance. For areas where sensitive computing equipment is being used, this is not acceptable. Similarly, concerns over the potential damage to historic (or modern) buildings caused by vibration compaction mean that it may face further restrictions with regard to use

RIGHT: Sakai’s novel oscillation compactor has this feature on both drums, as well as conventional vibration.
than actually required to reach density. By comparison, with a vibration-type drum, the risk of cracking or crushing the aggregates within the asphalt are all too real should too many passes be made.
This ability to compact without risking aggregate crushing also means that oscillation drums are well suited to use with thin lifts, now commonly used in many modern and advanced highway applications, such as when dual-layer asphalt paving is applied.
The technology has improved too with recent generation oscillation compactors. The newest machines feature split drums, allowing them to compact efficiently even when turning, without risking damage to the surface. Some of the newer machines also have gear drives to the compaction exciters, which are said to require less maintenance than the belts used on some of the earlier generation units.
The benefits of the technology have prompted many construction machine manufacturers to offer equipment featuring oscillation drums.

Hamm certainly pioneered this market and now has the widest range of oscillationtype machines in its product line-up, but other manufacturers have since followed suit.
The firm’s close German rival BOMAG has done more than most to develop a range of oscillation compaction solutions. BOMAG’s oscillation system has been developed over the years and the current generation package is said to be highly efficient.
However, Ammann, Caterpillar, Dynapac, Sakai, Volvo CE and Chinese firm XCMG also number amongst those that have ‘dipped a toe in the water’ so to speak, with regard to the market for oscillation compaction. These three firms now all offer at least one oscillatory compactor model, in addition to their conventional vibration-type machines. For XCMG in particular, this is a key step, given China’s massive programme of bridge
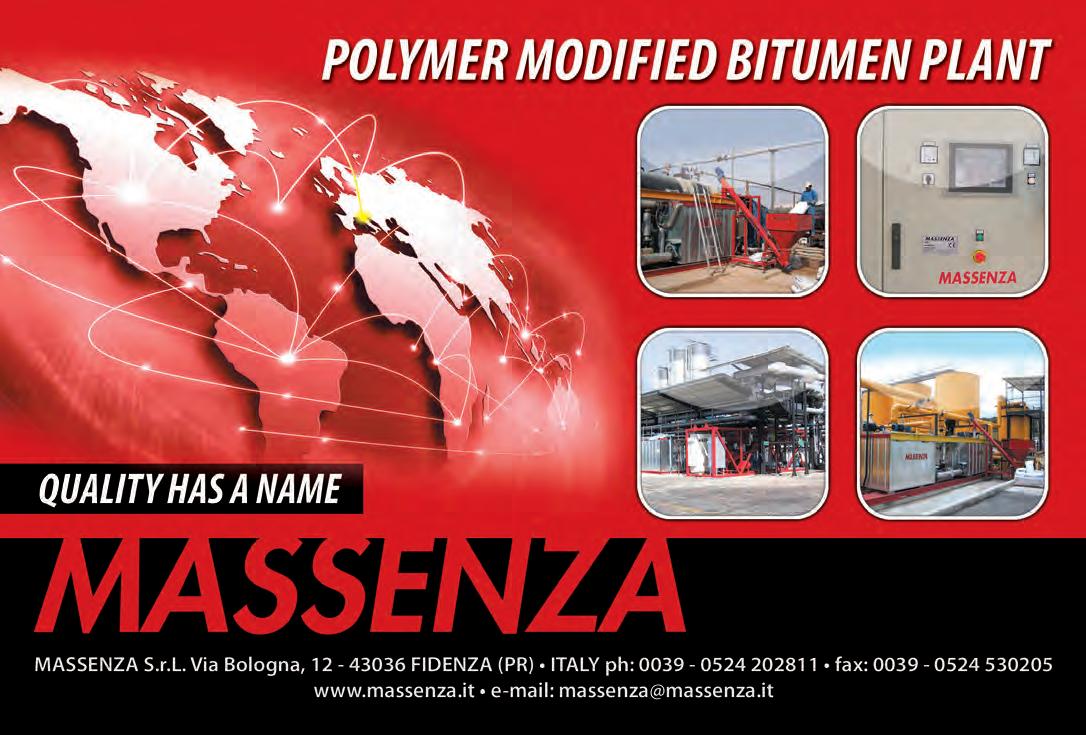
construction, and could well deliver lucrative sales. Chinese contractors are also winning a number of bridge construction contracts in overseas markets such as Africa, with these firms typically buying fleets of Chinese machines to carry out the work. Again, XCMG could well capitalise on this, something for which other Chinese construction machine firms may well take note in the future for their own product range developments.
Of the oscillation compactors on the market to rival those from Hamm (and BOMAG), Sakai’s offering stands out from the rest. Firstly, the SW888ND-1 differs radically from other compactors on the market as this novel design offers both oscillation and vibration options on both drums. By comparison, its rivals all feature oscillation on one drum, with conventional vibration on the other. The Sakai design allows the user a wide degree of compaction modes, with the options of either oscillation or vibration on both drums or just one drum. This is a key point as it means the machine can deliver increased productivity over competing units. Sakai’s roller can achieve compaction density in half the number of passes as both drums can deliver the correct form of compaction, whichever the requirement for the specification. And overall, oscillation is regarded as a
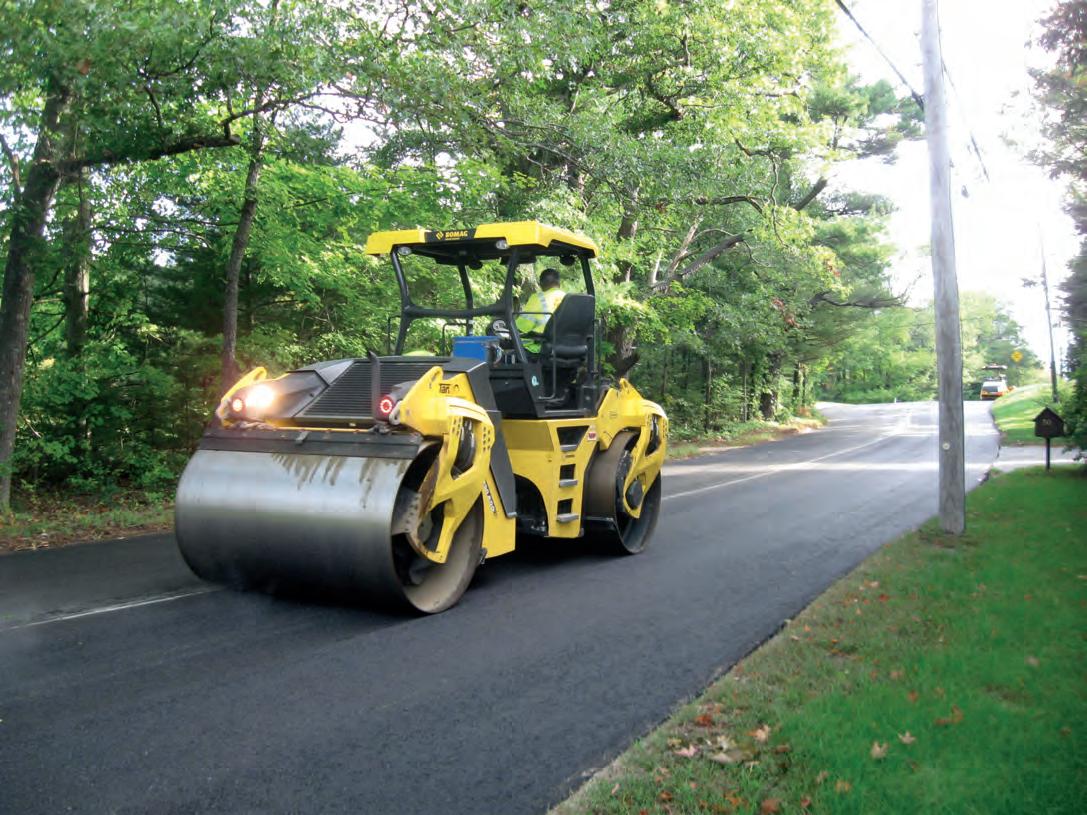
originally in prototype format.
Hybrid operation is particularly suited to
The system utilises a hydraulic hybrid system with a hydraulic reservoir that stores power during normal operation.
This then operates when
ABOVE: BOMAG’s latest generation oscillation system is said to be more efficient than before. BELOW: Hamm has developed a compactor with hybrid drive, as well as oscillation.
important step ahead as it allows the firm to power the machine with a much smaller engine than would normally be required.
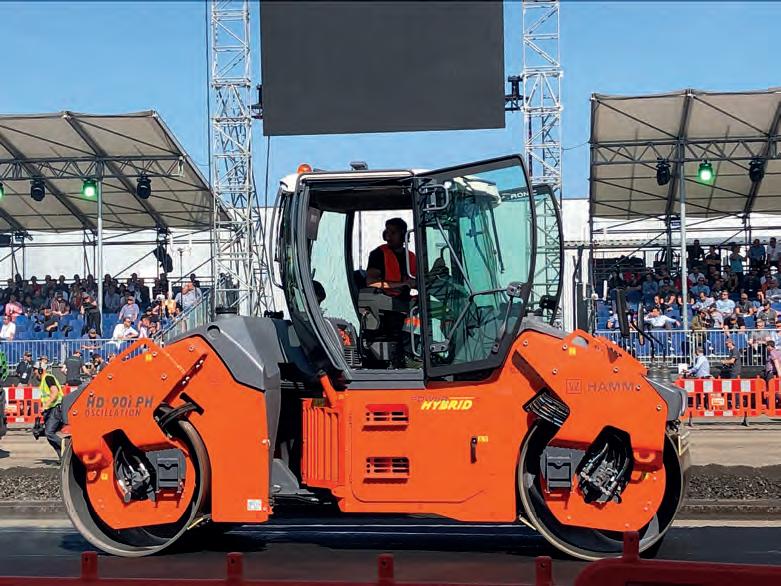
This lowers overall fuel consumption and as the engine has a less complex exhaust emission control system, it also lowers maintenance needs (and costs) considerably.
While the hybrid machine does indeed attract a premium purchase price, its lower running costs will prove attractive to contractors looking to the medium-long term.
It is worth bearing in mind that hybrid operation is particularly suited to compaction work due to the nature of these machines. Moving forward and backward repeatedly for each compaction pass energy would otherwise be wasted. Instead, some of this energy can be recirculated using the hydraulic reservoir, boosting overall efficiency and cutting fuel consumption.
Hamm’s machine is not the first hybrid compactor to have been unveiled (BOMAG exhibited a prototype diesel-electric hybrid compactor some years ago), but it is the first to be commercially available. And it is highly likely that rival firms will offer similar hybrid asphalt compactors on the market in due course.
THE WORLD IN NUMBERS
We live in interesting times. The global economic and political landscape is in a state of flux. In a brave new world of protectionism and populism, of Donald Trump, of riots on the streets of Paris, and of Brexit … things are very hard to predict and the global outlook feels very wobbly. Will the UK end up sacrificing
prosperity and security to ideological obsession? Will President Macron really be able to streamline the French economy, or will he fail to take the people with him? Will the Democrats start blocking President Trump’s every move in the House of Representatives? Will the US trade war with China escalate out of control? Will the EU change course as its
The world’s biggest economies for 2019 and 2020 by GDP
Source: FocusEconomics
The world’s leading emerging economies by GDP growth in 2019 (Annual variation in %)
Source: FocusEconomics Consensus Forecast August 2018
election cycle looms? Will Russia intensify military action against Ukraine? Will there be a new global financial crisis? Will Brazil’s new president Jair Bolsonaro boost growth? Will Germany falter as Chancellor Merkel moves on? Who knows? All we can offer in the Global Report is a series of key indicators. Here are a few facts and figures to ponder:
The world is going digital
Source: we are social TOTAL POPULATION 7.593 BILLION URBANISATION: 55%
INTERNET USERS 4.021 BILLION PENETRATION: 53% UNIQUE MOBILE USERS
3.196 BILLION
PENETRATION: 42%
2.958 BILLION PENETRATION: 39% ACTIVE SOCIAL MEDIA USERS
5.135 BILLION PENETRATION: 68% ACTIVE MOBILE SOCIAL USERS
ONE TO WATCH: INDIA
Key logistics indicators
Source: www.ciltuk.org.uk
$1.9 BILLION WAS THE GLOBAL MARKET REVENUE OF THE LOGISTICS ROBOT MARKET IN 2016 90% OF EXPERTS IN THE SECTOR BELIEVE INCREASED DATA COLLECTION WILL CHANGE THE WAY DECISIONS ARE MADE OVER THE NEXT FIVE YEARS
20 MILES IS THE DISTANCE AMAZON DRONES CAN TRAVEL BEFORE REQUIRING RECHARGE
70% OF WAREHOUSE, IT AND OPERATIONS PROFESSIONALS PLAN TO HAVE MORE AUTOMATION
30 MINUTES IS HOW LONG IT WOULD TAKE TO TRAVEL FROM AMSTERDAM TO PARIS ON A HYPERLOOP SYSTEM
63% OF GLOBAL CUSTOMERS HAVE NO IDEA THAT THEY ARE USING AI ON A DAILY BASIS
STAGE V DRIVES EUROPE’S DIESEL ENGINES TOWARDS A MUCH CLEANER FUTURE
2019 is a landmark year for off-highway engine emissions, as Stage V regulations start to take effect. Geoff Ashcroft talks to engine makers about how they are meeting the challenges, and looking to exceed these requirements for clean air quality.
Compared to Stage I, the latest requirements for Stage V emissions regulations represent a 96% reduction in oxides of nitrogen (NOx) and a 97% reduction in particulate matter (PM). And with the intention of almost eliminating PM from diesel engines, to improve air quality, Stage V also introduces a particulate count. This criteria replaces the previous measurement of particulate mass, and is a requirement for all off-highway, mobile diesel engines, spanning from 19-560kW. As it looks, around 99.9% of particulate matter is expected to be eliminated.
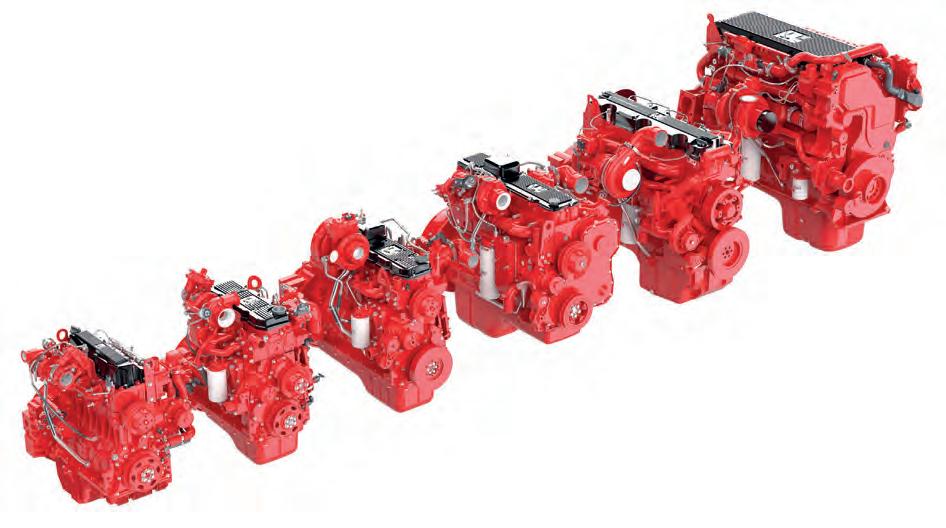
production since April 2018, some eight months ahead of schedule. It said that over 200 customer installations are complete or in progress, for original equipment manufacturers (OEMs) currently taking Cummins Stage V power units.
ABOVE: Stage V legislation takes effect this year for engines with 0-55kW and over 130kW power ratings. Engines with outputs from 56-129kW fall under Stage V in 2020.
Smaller F3.8 and B4.5 engines meeting the need of the 75-150kW sector are about to go into production, with the heavy-duty X12 and X15 engines – 250-503kW – already being manufactured.
For the first time, these regulations also bring in engines above 560kW ratings. And crucially, this ultra-low PM level is deemed only achievable with the integration of a diesel particulate filter (DPF) system.
It is a move that puts Europe ahead of the US EPA for the first time, and applies to all non-road mobile machinery. It is a catch-all that includes variable speed and fixed speed engines as found in rental and temporary power units.
Stationary engines – those permanently installed in one location and never intended to be moved – fall outside these regulations. Stage V legislation takes effect in 2019 for engines in the 0-55kW and over 130kW power ratings. Engines with outputs from 56129kW fall under Stage V in 2020. Cummins B6.7 and L9 engines offer power outputs from 116-321kW and have been in
“Cummins has combined DPF, diesel oxidation catalyst (DOC) and selective catalytic reduction (SCR) systems with advanced combustion technology,” explains Cummins marketing communications director, Steve Nendick. “This solution has enabled an increase in power and torque, in a smaller, lighter, easier to install package, with reduced servicing requirements.”
“Our latest after-treatment system is 20% lighter and 40% smaller than the equivalent Stage IV products.”
Typically, we are delivering 10% more power and 20% more torquE
The firm reckons to have met the stricter emissions as a result of removing exhaust gas recirculation (EGR), and switching to a single module after-treatment technology – and is all part of the company’s $1bn investment for R&D across all markets, to develop appropriate engine solutions.
Cummins engines over 560kW use an SCR-only strategy, with the after-treatment device slotting into the space of the engine’s original exhaust silencer, simplifying installation. With common architecture used globally, the firm said there was no change to installation on this size of power unit from Tier 2 to Stage V. When it comes to PM count, Nendick says the firm has learnt a lot from its automotive business, which introduced this technology to satisfy Euro 6 on-road emissions in 2014. And while engine complexity has increased with every step of emissions, Cummins’ objective has been to add value for OEMs and end users, and this is something that Stage V installations will continue to deliver.
“With a single module for after-treatment and without EGR, our 75-321kW engines are simpler, but they also bring significant
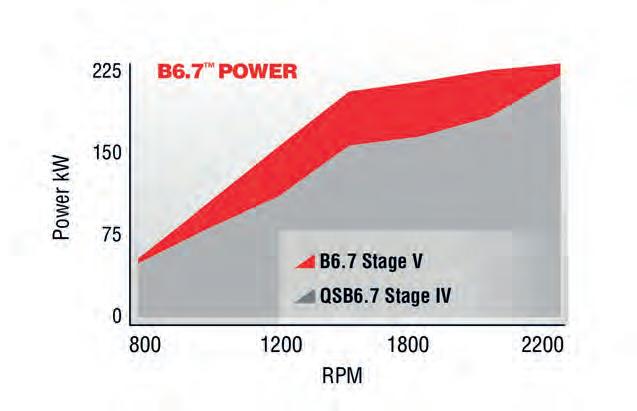
➔
performance benefits too,” he says. “Typically, we are delivering 10% more power and 20% more torque.”
While the power units are more efficient on fuel use, there is a marginal increase in diesel exhaust fluid (DEF) consumption. But this is offset by a lower total fluid cost compared to Stage IV.
For Volvo Penta, Stage V regulations mark the introduction of the Swedish maker’s first diesel particulate filter (DPF) system for offhighway applications.
“It would have been easier and cheaper to just take existing technology from our on-highway division and push it onto our offhighway OEMs,” explains Andreas Viktorsson, Volvo Penta’s chief project manager for Stage V. “But we could see drawbacks of taking this type of approach for off-highway applications. So we focused on using our proven technology, but in a different way.”
He says that a tailor-made Stage V solution has meant better integration for
“Our system is totally passive, and every drop of fuel we burn contributes to making heat or power”
Andreas Viktorsson, Volvo Penta

OEM customers, without compromising on installation, cooling packages and operation. But it hasn’t been an easy journey.
“We have had to include a DPF – and many of our OEM customers came to us for a Stage IV solution simply because we didn’t have a DPF,” he says. “During that time, our customer base has grown from around 100 to over 300 customers, so we had to make sure that we got Stage V right.”
He adds that meeting Stage V emissions is impossible without a DPF, but to make its integration as seamless as possible, the engineering process involved creating a fully integrated power unit, that maintained Volvo Penta’s existing SCR after-treatment unit, but with the addition of a separate DPF.
“We chose to produce a DPF that was identical in size to the SCR unit, so it could be dropped in to the space formerly occupied by the SCR package, very close to the engine’s exhaust outlet,” he explains. “We could then
much less critical than the DPF.”
Viktorsson says that the inclusion of a DPF could not compromise either the installation or performance of the engine – it had to be complementary.
To avoid injecting fuel into a DPF to provoke a regeneration, Volvo Penta worked closely on heat management, to mildly increase the engine’s temperature to maintain combustion temperature. This has led to improved after-treatment efficiency, and avoids the need for stationary DPF regeneration.
“Our system is totally passive, and every drop of fuel we burn contributes to making heat or power, which improves overall efficiency,” he says. “So we’re seeing power gains of up to 10% across D5, D8 and D11 engine platforms.”
Perhaps more importantly, Volvo Penta says it has seen a positive reduction in fuel use of up to 5%, which is said to be enough to offset the cost of the engine, over its lifetime.
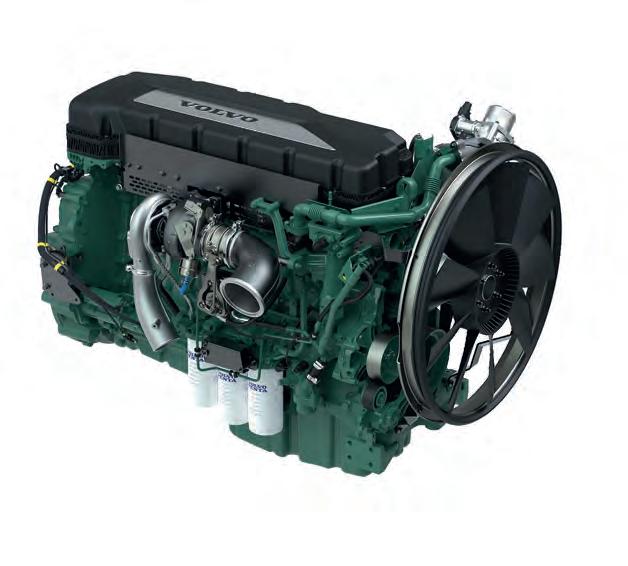
RIGHT: Caterpillar is determined, its says, to “developing engines that deliver improved performance, simplified installation and reduced operating costs.”
“We also expected to see an increase in DEF consumption, but we’ve improved the mixing and dosing too, keeping urea consumption at the same level experienced at Stage IV – again, another useful benefit for customers.”
Volvo Penta’s entire Stage V engine platform will be rolled out during 2019. The D13 engine has just started to go on sale to customers, and will be followed by D8, D11 and D5 variants. The flagship 16-litre D16 will follow later in 2019 for extreme power applications, and will be rated up to 585kW.
Such development represents a substantial investment over the last four years, in pursuit of clean air quality and the achievement of near elimination of particulate matter from diesel engines.
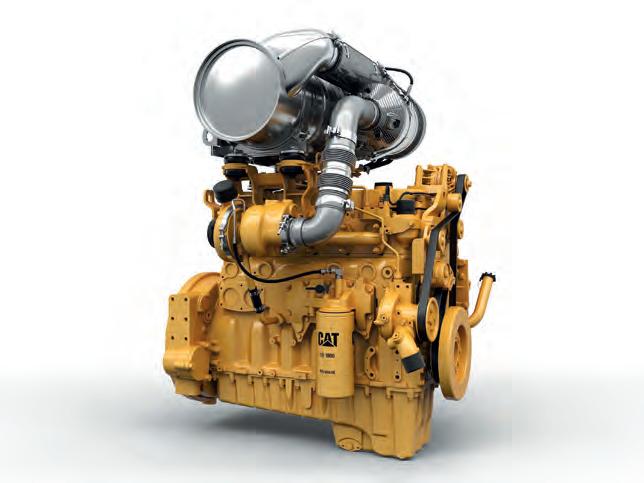
“Our two-can solution can be easily expanded, but we’re anticipating a focus on electrification and hybridisation as we move forward,” says Viktorsson.
Perkins has been working with over 800 OEM customers around the world, using technical integration workshops and a modular engine range, to collaborate with customers and deliver a tailor-made solution for each application.
Over the last three years, Perkins has launched its full range of EU Stage V engines from 0.5 to 18.1 litres. The Stage V range delivers powers from 8.8 to 470kW and includes the introduction of the Perkins Syncro 2.8 and 3.6 litre engines - a new family of products designed to meet the needs of original equipment manufacturers.
At the top end of the range, Perkins also took the opportunity to introduce four powerful platforms, with displacements of 9.3
technologies including common rail fuel systems, selective catalytic reduction, diesel oxidation catalysts and diesel particulate filters, as Oliver Lythgoe, product concept marketing manager at Perkins, explains.
“For over a decade, machine developers and end users around the world have taken advantage of our transparent DPF regeneration capabilities,” he says. “At Stage V we’ve made DPF integration easier, and our engines continue to use a regeneration process that runs automatically without machine or operator interruption.”
“Importantly for the machine operator or owner, this means duty cycles and workload are never affected and productivity is always maintained.”
BELOW: A key consideration for many OEMs is utilising installation space within machines ... an area where a compact aftertreatment package has become a priority.

“We have delivered significant improvements to our engines, all of which match customer demand for value, innovation and performance,” he adds. “On the fourcylinder 1200 Series for example, customers will benefit from a 15% increase in power, 10% more torque and 5-10% reduction in fuel consumption.”
As part of Perkins commitment to Stage V, the Peterborough, UK-based site is also building a dedicated facility for the manufacture and integration of engine aftertreatment packages.
Sister firm Caterpillar has increased power density on its 13-litre engine in the move to Stage V emissions compliance. Renamed the C13B, this revised power unit is available with power outputs from 340-430kW, and the enhanced power density is said to provide the equivalent power of a 15-litre engine, but with 32% less weight than the larger engine.
“The C13B represents a continuation of our commitment to develop engines that deliver improved performance, simplify installation and reduce operating costs,” says Jeff Moore, product director, research and development for 7.2- to 18-litre engines.
A revised after-treatment system, like so many others achieving Stage V compliance, incorporates DOC, DPF and high-efficiency SCR technologies, while eliminating the need for exhaust gas recirculation.
Cat’s after-treatment package version is 63% lighter and 65% smaller than its current equivalent, and the improved combination of technologies is said to deliver transparent regeneration, and does not impact on performance. While DEF consumption remains unchanged, fuel use is reduced by 6%, while oil service intervals are 600 hours. A 5,000-hour DPF ash service is required.
MTU, part of the Rolls-Royce Group, has chosen a one-can solution for exhaust aftertreatment, as it sets out its stall for Stage V emissions compliance. A key consideration for many of the company’s OEM customers is that of utilising installation space within machines – and it’s an area where a compact aftertreatment package has become a priority.
Much of that development has been achieved through a development project between MTU and Daimler, which has been operating over several years with more than 100 test vehicles providing a depth of knowledge for refinement and installation.
Meeting the stringent emissions standards has also required MTU to carry out a series of engine design enhancements to improve the combustion process, in addition to using an SCR system in combination with a DPF. ➔
BELOW: Stage V hopes to almost eliminate all particulate mass from diesel engine emissions with the introduction of a particulate count for all off-highway, mobile diesel engines from 19-560kW.

drive systems that communicate with the power unit. These changes are productivityboosting, while reducing the lifecycle cost, said the company, which has taken a long-life focus of typically, up to 18,000 hours.
In addition, improvements in power delivery, torque spread and increased efficiency have also been noted while meeting Stage V legislation. And this is reflected in fuel savings of up to 3% compared to its Stage IV predecessors.
To get ahead of the supplychain process, the firm has been producing its Series 1000, 1100, 1300 and 1500 engines for customers since June 2018 - some seven months before the new directive enters into force.
flexible layout options, to simplify installation on machines.
Hinting at future developments, FPT has lifted the lid on a modular concept power source, called Cursor X. Proposing a multipower, multi-application, modular power source that could be used in tractors, trucks, wheeled loaders and other machine types, Cursor X points a possible way forward for equipment manufacturers to offer customers power source choice with minimal re-engineering.
There will be no one-size-fits-all solution as there has been for diesel for several years
It said these latest power units have been specifically designed for industrial applications in the construction sector, and are based on Mercedes-Benz commercial vehicle engines from German maker Daimler. They also cover the 115 to 480kW power range.
MTU said its engine characteristics include higher torque at low rpm to promote a further reduction in fuel consumption, while offering an extended power range compared to the firm’s Stage IV derivatives.
FPT Industrial’s second-generation Hi-eSCR 2 – applicable for engines from 56-560kW – integrates a maintenance-free filtering device on its SCR catalyst to achieve Stage V status. This addition enables the device to comply with new emissions limits without incurring a penalty on its physical size – FPT said the unit occupies the same
The encapsulated driveline has been designed to be the same size as a six-cylinder diesel engine, but with a modular assembly that would be easy to integrate into existing machinery or scale up into heavier equipment.
The power source could be fuelled by a natural gas internal combustion engine, by batteries for full EV use, or by a hydrogen fuel cell. With a range of power inputs, the Cursor X package would be paired with a choice of power transmission solutions to suit the machine requirements. In each case the external appearance would remain the same, making it easy for machinery makers to offer a choice of power to meet individual customer needs.
As a powertrain integrator, FPT recognises that its mission has changed. The firm has to develop the best powertrains to efficiently convert energy for a vehicle, using any available source, suggesting that in future, there will be no one-size-fits-all solution as there has been for diesel for several years.
for its sub-19kW air-cooled diesel engines, in a category that was previously not targeted by existing standards.
It has also gained over six years’ experience with a diesel particulate filter installed on its common rail TNV engines over 19kW. This reflects experience gained from over 400,000 units in the market, and this scaleable technology has been applied to meet the new regulations on sub-19kW engines.
An advanced level of technology is being used on Yanmar’s latest high output 4TN101 and 4TN107 engines, which feature singleand twin-stage turbocharging respectively, to achieve outputs of up to 105kW and 155kW.
Yanmar’s after-treatment system integrates DOC, DPF and SCR technology, in a module design said to be compact enough to mirror the width of these 3.8 litre and 4.6 litre engines.
This provides a wide range of flexible installation solutions for OEMs said the firm, to simplify customers’ design requirements while improving external accessibility.
Small-engine efficiency has not been overlooked by Hatz – the firm has developed an electronic control system for single cylinder diesel engines, to manage fuel injection efficiency.
Called E1 technology, Hatz has met Stage V emissions with its air-cooled B and D-series up to 12kW, offering the platform to integrate machines with small-capacity, low-power engines into the advancing world of digitisation.
Its water-cooled H-series and mechanically controlled models in B, D, G, L and M-series are also compliant with Stage V regulations.
SUSTAINABILITY IS OPENING UP A NEW FUTURE FOR ASPHALT-MIXING PLANTS
The sustainability of asphalt-mixing plants has come a long way in a relatively short time. If you operate asphalt plants, you need to commit now to innovation if you want to make the most of plants already in operation. We have asked the experts at Ammann to give you a guide to all the latest thinking. The future starts here and it is all about maintaining change in a balanced environment … a future in which “the exploitation of resources, the direction of investments, the orientation of technological development and institutional change can all work together in harmony.”
Sustainability efforts continue to be at the forefront of the asphalt manufacturing industry. Significant gains have already been made, yet more must – and will – be done to preserve precious natural resources and protect the world around us.
Most, if not all, asphalt-mixing plant manufacturers are pursuing some degree of sustainability. That certainly includes companies like Ammann, which says that: “We are steadfast in our commitment to continue to offer technologies that provide the giant leaps the industry requires. And we do this with the knowledge that the less visible gains – in areas such as retrofits – present perhaps the best opportunities to meet the needs of our customers while protecting the world around us.”
According to the Swiss-based giant: “Asphalt-mixing plant sustainability efforts fall into three broad categories:
1. Creating technology that makes new plants more environmentally friendly.
2. Developing products and processes that drastically reduce the environmental impact of plants already at work in the field.
3. Providing products with built-in financial incentives that encourage businesses to take advantage of the available green initiatives. This last point will be explored in detail later, but it deserves some explanation up front. Manufacturers must be aware that the world’s cleanest plant is useless if it does not
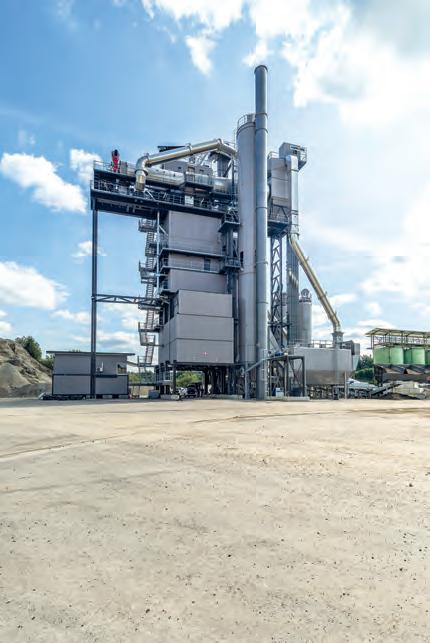
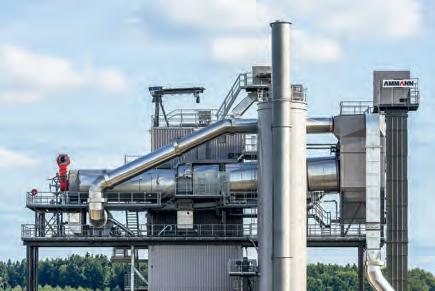
add value for the customer. Businesses don’t have the luxury of investing in plants that are green but don’t provide the necessary productivity or quality.
That’s where manufacturers such as Ammann enter the picture. It is a responsible and industry-leading manufacturer that must create solutions that improve both sustainability and profitability. Fortunately, the two can go hand in hand.With that as a backdrop, let us explore how manufacturers can deliver products that meet the financial requirements of our customers and the sustainability requirements that safeguard our planet.
Challenge 1: Create technology that makes new plants more environmentally friendly.
The process starts with innovation. Incremental improvements are essential to product development and sustainability efforts. But sometimes, a giant leap forward is needed. Such breakthroughs require innovation – the development of new ideas and methods.
A common trait shared by true innovators is the love of a challenge. These are the men and women who ponder a problem while driving to and from work. It’s their last thought many nights, and their first thought many mornings. Our industry will need these innovators as the marketplace demands even more sustainability. Fortunately, history has shown we are equal to the task.
The narrative behind the launch of the Ammann RAH60 drying drum shows the levels of commitment and creativity that were needed to develop this product – and that will be required to make future advances. The short version of this product development story, for our discussion, is that reclaimed asphalt pavement (RAP) must be heated for inclusion in mix – though the recycled materials cannot become too hot or the bitumen will be damaged.
Ammann developed a unique approach to this challenge. Fresh aggregate was heated in a separate dryer and – because it lacks a bitumen coating – could be heated at a much higher temperature. The RAP was then mixed with that hot aggregate to provide the necessary heat without damaging the RAP’s bitumen coating.
This was a completely original solution. It was a true innovation and is indicative of the type of creative problem solving we pursue to this day. Even with this accomplishment, the experts at Ammann wanted to achieve more. Their goal was a utilisation rate of 100%, and they were determined to reach it.
Heat again was the challenge. Reaching the 100 per cent goal would mean the innovative process used by the RAH60 was not an option because no fresh aggregate, which acted as a secondary heat source, could be used. Eventually, the team was inspired to create a counterflow process that allowed the RAP to make an ‘early exit.’ The process was incorporated into the RAH100. The RAP enters at the far end of the counterflow dryer section and moves toward the heat chamber. It drops out of the dryer before it enters that chamber – and therefore never becomes so hot that the bitumen is damaged.
This advancement was the result of the re-evaluation of the RAH60; it was a
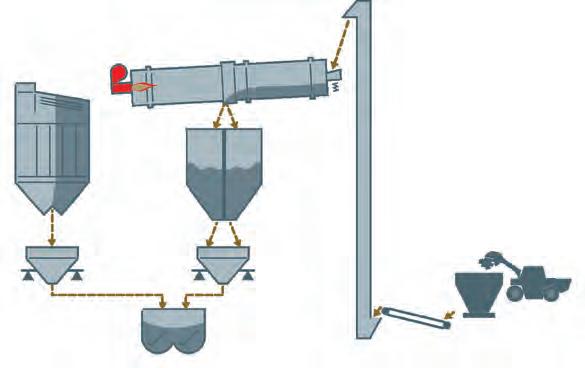
ABOVE: Recycling addition up to 100% directly into the mixer.
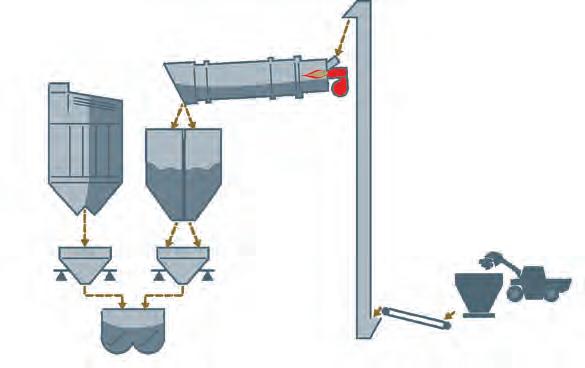
ABOVE: Recycling addition up to 60% directly into the mixer.
continuation of the previous effort … not a completely new start. Without the innovation of the RAH60, the RAH100 might never have been developed.
In that same vein, future innovations will include improvements on existing technology. Ideas here include:
Leveraging the control system ... Quality control systems impact sustainability in several ways. A good system makes the green technology accessible by quietly working behind the scenes and limiting the knowledge required of the operator. The technology is complex; there is no doubt about that. But if a well-designed control system is used, the technology will be easily accessed through intuitive interfaces. The control system must also be comprehensive, helping the plant achieve efficiencies throughout the process, and ensuring all components are working together to maximise productivity.
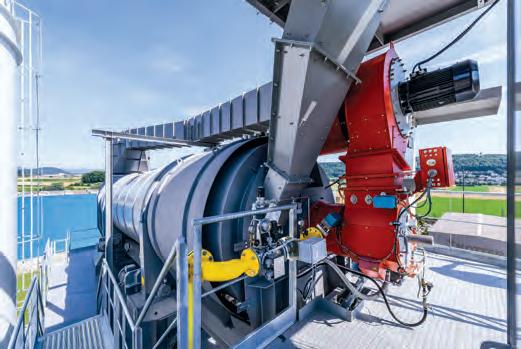
Improve existing components and processes ... Giant leaps are needed to transform the asphalt-mixing plant industry. But significant sustainability strides can be made by some lower-profile enhancements – specifically, from re-examining existing components and procedures.
A need for these advancements has emerged more recently as asphalt-mixing plants must increasingly be located closer to residential
“Electrically heated bitumen tanks are key tools in the fight against odour”

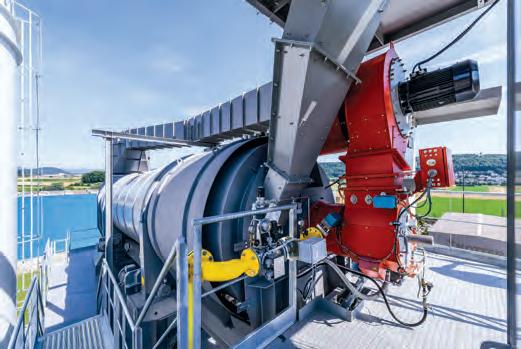
areas. That makes it essential that components minimise noise and odour. Noise suppressors that are placed on flues are one solution. They are quite effective and easy to install whether the plant is new or as a retrofit.
In addition, various levels of plant cladding are available. Some are relatively basic, such as applying additional insulation to certain components. From there, noise suppression efforts can be expanded, all the way to complete cladding. In these cases, the entire plant – including dryer, filter, ventilator, compressor and other components – is located inside a building clad with sound-reducing panels. Residential areas also require odourreduction initiatives. Electrically heated bitumen tanks are key tools in the fight against odour. Casings for the tanks have been upgraded in recent years – a trend that no doubt will continue. The tanks are extremely energy efficient, which minimises emissions. Load-out areas can also be clad to reduce odours. Misting units are available for the loading area, or in the stack.
These improvements can be achieved at new or existing plants.
Challenge 2: Develop products and processes that vastly enhance the sustainability of plants already in the field.
The world would be greener if all asphalt manufacturers purchased new, advanced recycling plants that were quiet and efficiently burned clean fuel. Unfortunately, the reality is that won’t happen; the economics just won’t allow it. That doesn’t mean considerable adjustments can’t be made … the key is upgrading the plants already in operation.
Retrofits might not garner the same attention that technologically advanced new products do, but the plant overhauls are every bit as crucial to environmental protection.
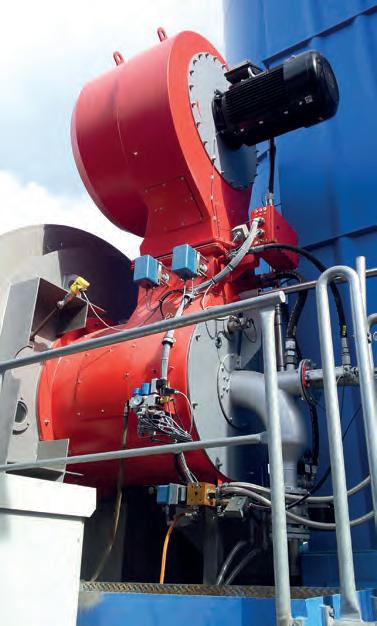
ABOVE: Woodchip emissions can be offset by the oxygen provided during the tree’s life.
BELOW: Complete cladded plant. In these cases, the entire plant – including dryer, filter, ventilator, compressor and other components – is located inside a building clad with sound-reducing panels.

The great news is that new plants and retrofits can work in tandem to quickly upgrade the overall sustainability of the asphalt industry. Think of this scenario in terms of the automobile market. A car with breakthrough emissions technology would be the choice of many buyers. But it would take years for the new models to replace the old and deliver the improved emissions across the marketplace.
Now, think of the environmental impact of the new car and reducing the emissions of all vehicles already on the market. This is the scenario with asphalt-mixing plants. Thousands are operating around the world, yet only a few hundred new plants are installed each year.
Upgrading those plants already in operation is the biggest opportunity to strengthen global sustainability. The environmental benefits can be enormous when an existing plant is retrofitted. Here is a look at some of the key components that can be improved – and the potential impact on sustainability.
Environmental upgrades...Among the potential enhancements are a revamped bitumen tank system and baghouse, noise reduction and an ability to manufacture lowtemperature mixes.
Technological enhancements...The burners, the mixer, the control system and the recycling system are updated to utilise the latest technology.
A rejuvenated plant....Retrofit options include replacement of the dryer and mixer and the addition of a wear-protection system.
Extended plant life...A retrofit can add another 10 years onto the life of a plant –which is typically between 10 and 20 years. Life is extended primarily by protecting key components with wear-resistant materials.
Access to alternative fuels...Retrofits can also enable the use of additional fuels, including those that can be sourced locally. Fuels that are available locally require less energy consumption for transport.
Fuels can also be renewable and carbon neutral. For example, woodchip emissions can be offset by the oxygen provided during the tree’s life.
Challenge 3: Make the sustainable process financially feasible.
Many sustainable practices inherently lead to cost savings. In some ways, the asphalt- ➔
mixing plant industry doesn’t have to develop financially feasible products – it simply needs to more actively promote the existing opportunities. Here are some sustainability efforts and the associated cost savings:
The use of RAP ... A plant that utilises 60% RAP is capable of cutting its production costs by 30 to 40 per cent. This is true with new plants and those that are retrofitted to add recycling capability.
Low temperature asphalt ... The use of LTA delivers production cost savings of around 35%. Again, this can be with a new or retrofitted plant. The savings result because a lower temperature mix requires less fuel to bring the materials to the desired temperature. Of course, emissions are also reduced when less fuel is burned.
Alternative fuels ... Some of the biofuels burn cleaner and cost less to purchase. They are often available locally, which means a reduction in transport costs as well. A plant
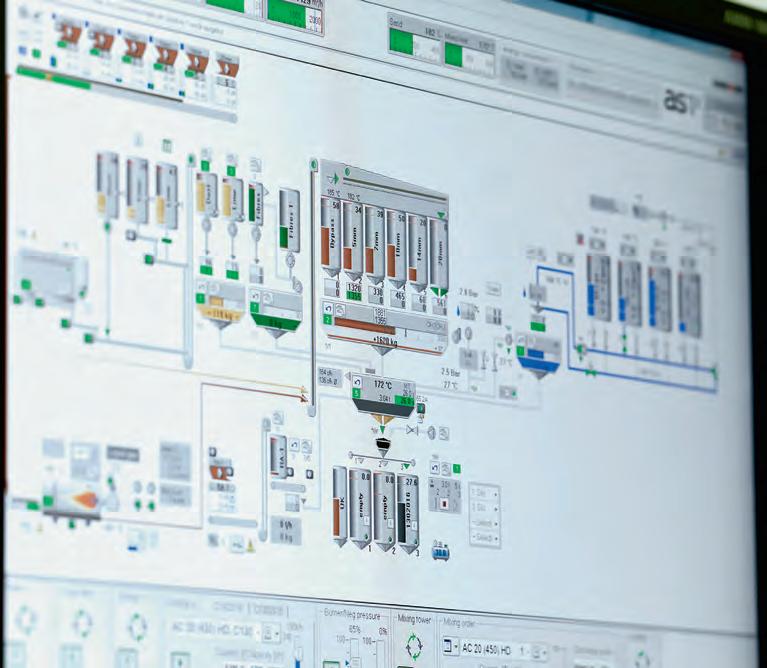
fuel jumps. In addition, many plants can combine fuel sources to help offset the use of less green energy.
Extended plant life ... A great deal of raw materials is required to manufacture an asphalt-mixing plant. Therefore, making that plant last longer maximises the potential of these resources. A plant’s life can be extended by utilising wear-resistant materials –including new products that protect parts and
delaying an investment in a new plant is an enormous cost-saver for a business.
Future fit ... The best manufacturers build plants with the knowledge they won’t be ‘new’ forever. Plants can be ‘future fit,’ meaning they are designed for easy modification as new technologies and processes become available. Adding such technological upgrades in an unobtrusive manner is extremely cost effective.”
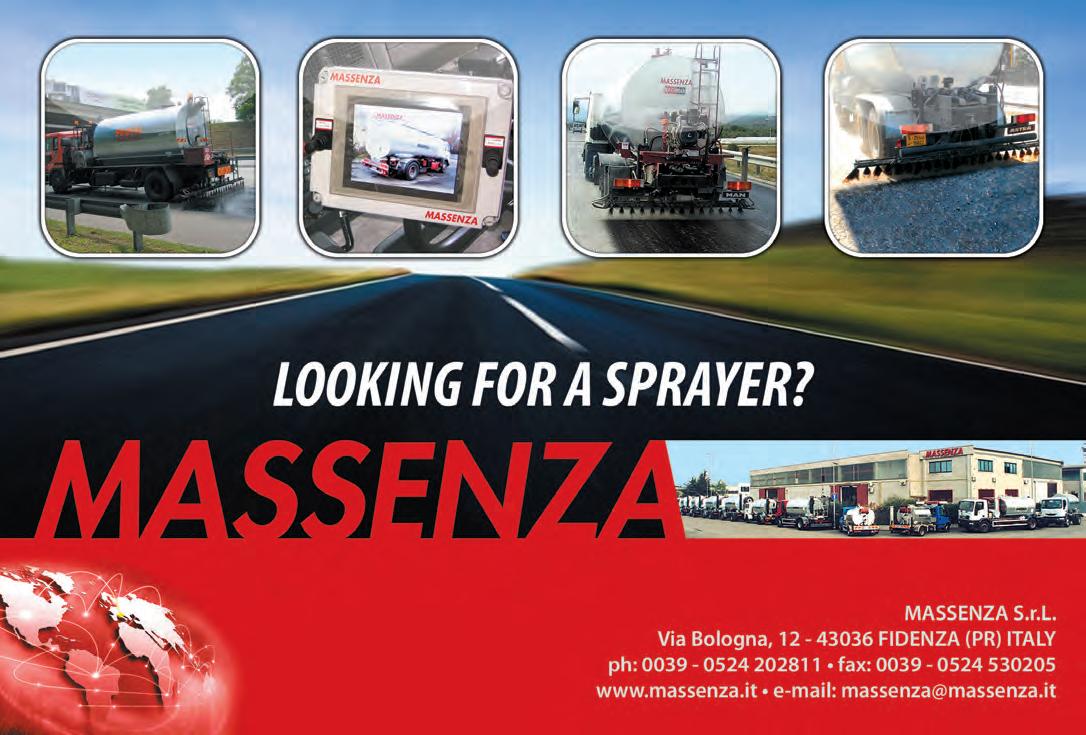
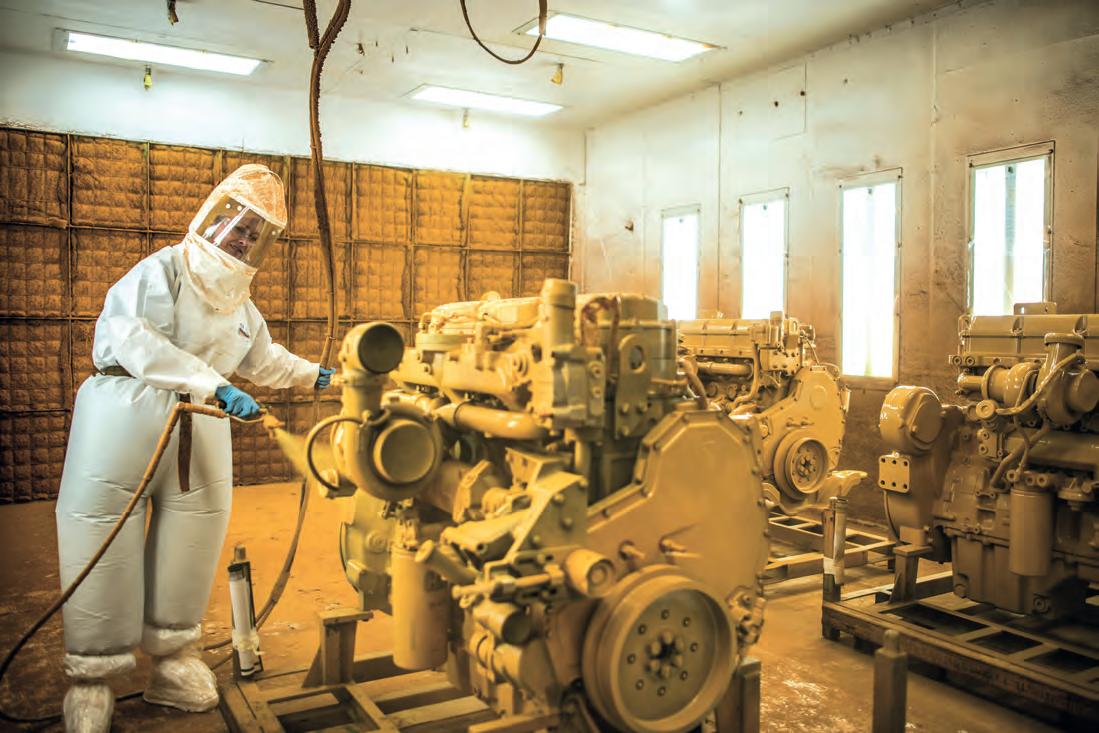
SQUARING THE CIRCLE
The concept of remanufacturing – of giving parts and components a ‘second life’ - is now gaining traction worldwide as part of a wider environmental and economic movement. In the construction equipment manufacturing sector, the leading players have long championed the benefits. What do they think is coming next? Adam Hill reports.
With margins sometimes vanishingly small, price makes a difference.
The construction industry thrives on maximum uptime and fleet performance. With that in mind, wouldn’t it be advantageous to have access to parts and equipment which offer the same warranty as new products, but which cost less?
This sounds like a fantasy, but in fact it already exists.
Remanufacturing – or ‘reman’ – is a certified industrial process which takes an existing component at the end of its working life and re-makes it so that it is as good as new. This is done by taking the old product (called a ‘core’), sorting it, cleaning it, machining it, inspecting it, re-assembling it and testing it to the same standards as a new part. Any product – an engine, a wind turbine blade, a brake caliper, a laptop, a scalpel, an iPhone, whatever – can be a ‘core’. It’s just the generic name for ‘the thing that you are going to remanufacture’.
Customers who think there is something intrinsically problematic about putting a remanufactured part in their vehicle should think again. The aviation industry has been doing this for years – it’s just that airlines don’t tend to shout about the fact that your
flight is being kept in the sky by using parts which have already had one life.
An ‘as new’ remanufactured product is sold with its own warranty. The advantage to the customer is that it will be cheaper –often around 75-80% of the price of a ‘new’ one – but will have the same, or better, performance. The estimated value of the worldwide reman market is €175 billion.
REMAN POWERHOUSES
Europe and North America are the current reman powerhouses, with China increasingly heavily involved. Governments and organisations in each of those countries or regions have given political support to the concept of remanufacturing over the last few years.
Reman is a pillar of the ‘circular economy’ (as opposed to the current ‘linear’ economy which is characterised by the phrase ‘make, use, dispose’) and its significance has been highlighted with high-profile policy positions and legislation. These include the United Nations’ 2030 Agenda for Sustainable Development (2015), the European Commission’s 2016 Circular Economy Package and China’s 13th Five-Year Plan in 2017.
ABOVE: Big yellow remanufactured machines: Caterpillar is reputedly the largest reman operation in the world.
(photo courtesy of Caterpillar)
Construction equipment companies are very much on board with all this – in fact, several of the best-known are way ahead of the curve. The attraction of remanufacturing parts and machinery is clear: customers are on a continuum, from those who want – and can afford - new parts and equipment; to those who want to extend the life of their existing products and are prepared to buy cheaper (but equally reliable) parts to do so.
In turn this enables companies to provide high-quality, best-cost solutions for external and internal customers alike. One worry for original equipment manufacturers (OEMs) is that, by creating a market in their own remanufactured parts, they will be cannibalising new business. On the face of it, this seems obvious; it is interesting, then, that the argument does not wash for hard-nosed multinationals like Caterpillar.
Its Cat Reman brand is well established – in fact, it is reputedly the biggest reman operation in the world, suggests a US
International Trade Commission surveyand boasts 7,000-8,000 unique part numbers. It employs 4,000 people, has facilities in the US, South America, Europe and Asia, and positions itself as a high-technology, low-cost, global brand focused on salvage capabilities. The reasons Caterpillar – and many other OEMs – seemingly take a counter-intuitive stance on reman are two-fold.
The first is that a market for non-new parts already exists: back-street garages and ‘spray and pray’ merchants will already be churning out versions of your components, often with little regard to the process and the quality of the end result. At least doing your own reman helps exercise some control. And let’s face it, if someone’s going to make money out of doing it, it might as well be you (plus there is also a reputational aspect to think of).
The second point is that you will be actively helping all kinds of customers to prolong the life of your products. OEMs are able to retain – or recapture - aftermarket business for older vehicles that might otherwise have gone to cut-price parts manufacturers.
BUSINESS SENSE
There is in fact a third reason, which we shall come on to: reman has a positive effect on the environment. But, as John Disharoon, Caterpillar’s director of market access, pointed out in a recent interview: “You can talk about the environmental attributes [to customers] but it has to make business sense for them – and for Caterpillar. When Cat started remanufacturing 45 years ago we were satisfying a customer need.” Companies could not wait a week for a rebuild so it made sense to have a cheaper stock of parts available straightaway. “Some customers are always going to buy new,” he continues. “We’re more
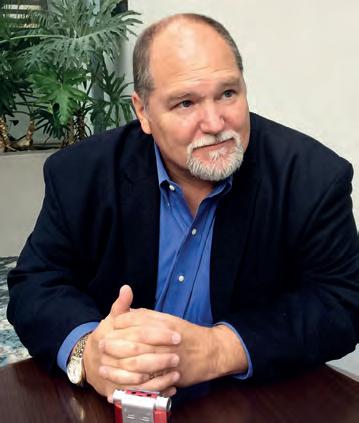
“Reman is the best way to provide the lowest lifecycle operating cost to our customers. Cat equipment is designed so durably, and is designed up front for multiple rebuild cycles. If we can breathe new life into the equipment then we can help the customer.”
Cummins diesel engines are used in construction equipment from bulldozers to excavators, and its reman operation was started for similar reasons. Typically, Cummins Diesel ReCon’s remanufactured products retail for 15-20% less than new ones. But they might fill an urgent gap for customers which have a vehicle out of action. A new engine – especially if it is not the latest model – might take 12 weeks to arrive; but a reman one can often be with the customer at 8am the next day.
Colin Pettigrew, product engineering leader at the company’s reman plant in Cumbernauld, Scotland, says: “The reman business allows us to support customers for a long period.”
BLUE CHIP BRANDS
than willing to sell a new part. You also have a whole bunch who don’t want to pay for new but want to be sure of quality. What reman does is give us a price point between a new part and an aftermarket part, which can be 40-50-60% less than new.”
Tana Utley, who is in charge of Caterpillar’s Large Power Systems Division and has responsibility for the group’s remanufacturing business, told trade magazine ReMaTecNews:

Other blue chip brands such as Hitachi Construction Machinery Europe also recognise these advantages and openly push their reman options. In much the same way as Cat Reman, Hitachi Remanufactured Components are promoted as cost effective and reliable, whether for preventative maintenance or to get operators back up and running as quickly as possible.
The group’s reman centre in Oosterhout, Netherlands, specialises in main pumps, travel and swing motors, and cylinders for most medium and large excavators, and ultra-large mining machines, as well as transmissions on ZW180 and ZW310 wheeled loaders. It offers a 12-month warranty. While it only works on Hitachimanufactured components at Oosterhout, it uses a network of original equipment suppliers for other components, including axles and transmissions for wheeled excavators, wheeled loader engines and dump truck transmissions.
Getting hold of cores is crucial for the remanufacturing industry – without them, there is nothing to remanufacture – and therein lies a problem. In this regard, Hitachi’s reman programme is quite typical, offering in effect an exchange system. Customers who buy a reman component from stock are asked to send their used component, via a local dealer, back to the centre. It is then assessed and evaluated for repair.
Reverse logistics – the process of getting
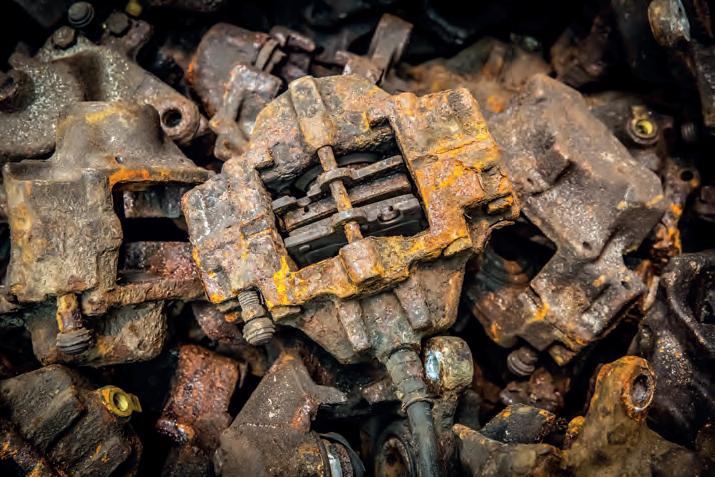
WHAT CAN YOU REMANUFACTURE?
In theory, pretty much anything can be remanufactured – assuming there is a market for it. For example, APRA (the US reman trade association) began life in 1941. That was the year the Japanese attacked Pearl Harbour and damaged eight US Navy battleships, sinking four. A little-known aspect of the aftermath is that all but
one of these were raised, with six returning to service before the end of World War Two. For good reason, this is therefore seen as the time when the benefits of remanufacturing became obvious on a grand scale. While one of the most obvious areas for reman is the automotive industry, aviation remanufacturing is also big business. As if to
cores back into circulation so that they can be used again – is crucial to the remanufacturing process. As Pettigrew says: “Some OEMs struggle to get into reman; the biggest struggle is getting the core back.”
At Caterpillar, dealers are credited for core return and are encouraged to buy into the ‘lowest lifecycle operating cost’ message. “Dealers understand the value proposition for customers,” Utley said. “Our machines run thousands of hours per year and parts consumption and parts costs count in the equation for the customer. That also gives dealers the opportunity to earn income by delivering product support services to the customers. I would hope we are viewed as large and connected to our customers through our dealer organisation. The dealer organisation is so critical in getting the cores back to us, and this is something ingrained with our business.”
Volvo Construction Equipment (CE) allows users to order a factoryremanufactured exchange component from their dealer, allowing them to resume operations with minimal downtime. The original defective component is sent to Volvo CE for reman.
While OEMs such as Hitachi, Volvo,
prove the point about the reman sector’s problem with confusing terminology, the airlines tend to refer to their remanufacturing activities as MRO (maintenance, repair & overhaul).
Consumer electronics (e.g. remanufactured iPads), medical devices and industrial machinery are other major areas of activity.
Cummins and Caterpillar often have their own in-house reman operations, thirdparty remanufacturers fall into two broad categories - either independent or approved. In fact, in a fragmented industry which is largely made up of small to medium-size companies, large groups such as these construction equipment manufacturers are the anomalies in remanufacturing terms.
OEM DRIVERS
A recent report, Accelerating Growth of the US Remanufacturing Industry: A Stakeholder Guide, sees significant potential in OEMs driving remanufacturing. Its author, the founder of the Circular Futures thinktank Tessa Vlaanderen, says they can scale up quickly and aggregate volumes that drive economies of scale. “They can play a leading role in unlocking foreign markets building on their international experience and networks,” she says. They can also leverage their experience of supply chain integration, production technology R&D and “most importantly in designing for remanufacturing, building on increasing volumes of customer data”. The idea of design for reman is important: OEMs know in detail how something has been designed
LEFT: Cores are the lifeblood of the remanufacturing industry.
(photo courtesy of Tom Lee)
and built, thus giving them a tremendous advantage when it comes to taking it apart, making everything as good as new, and putting it back together.
In fact, access to their own intellectual property is the OEMs’ greatest competitive advantage, giving them design access that third-party reman companies can only dream of.
But that doesn’t stop OEMs trying their hand at reman with other brands. Cat Reman, for instance, also remanufactures products for Perkins, Alcoa and Ford.
However difficult it can be, the rewards are there. Jenae Johnson-Carr, plant manager at Cummins’ Cumbernauld site, points out another reason why remanufacturing is attractive for OEMs: “When the market goes down, reman is very stable. That’s a huge benefit to us, even when you see cyclical changes.”
Remanufacturing is also a broad church and organisations are likely to have more than one string to their bow: US-based Detroit Reman, for example, is primarily an engine remanufacturer but also remanufactures other parts such as electronics, transmissions, fuel systems, aftertreatment, axles/carriers, turbochargers, and fuel systems. Its products are used in heavy-duty trucks and mining equipment, among many others – and it also does contract reman for other manufacturers, leveraging the experience and facilities that it has built up over decades.
In the construction sector, reman is not confined to heavy vehicles either. German tunnel boring machine (TBM) manufacturer Herrenknecht has had a remanufacturing capability for 20 years; and now, outside of China, two-thirds of its TBMs are using remanufactured components.

The company also reports that remanufactured TBM parts have an additional value in some regions of the world: in European countries such as Norway and Sweden, environmental value is starting to move up the priority list for customers.
ENVIRONMENTAL IMPACT
This is because you would need to have been living under a rock to miss the memo in which it was made clear the earth has finite resources and we need to use them more responsibly. Well, reman allows companies to do just that: the process preserves much of the material in original product, so less raw material is used than for manufacturing new products. This means reman typically uses less energy, which in turn means CO2 emissions are reduced. Increasingly scarce and valuable raw material is kept in use for longer. Volvo CE, for instance, says it reuses on average 85% of materials and lowers energy consumption by 80% compared to producing a new component. And, as we have seen, customers get cheaper products which work just as well – and have their own warranty. Caterpillar says that over 500,000 tonnes of material has been returned to it and repurposed since 2010.
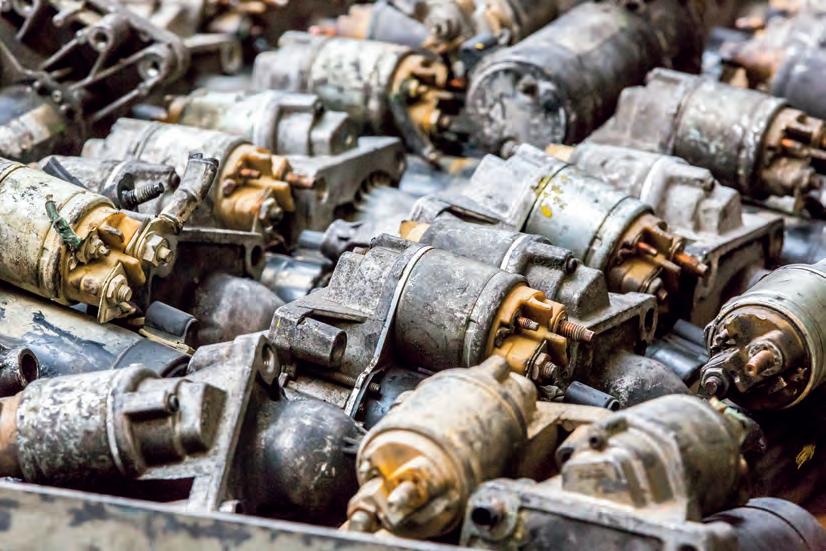
REMANUFACTURING IS NOT RECYCLING
Remanufacturing is one of the cornerstones of a broader movement called the ‘circular economy’.
This is a challenge to the ‘linear economy’ (the dominant economy at present) where you make a product, sell it, and then it is disposed of. The circular economy
focuses on the maximum recovery of material and involves making the product, selling it, using it – and then re-using it, perhaps several times.
Hence recycling is part of the circular economy, but is different to remanufacturing. Reman purists quibble over
terms such as rebuilding, repair or refurbishment – and it is true that some practitioners are engaged in remanufacturing without calling it that. It probably doesn’t help that there is no single, agreed, global certification for remanufacturing.
A report late last year by the UN’s International Resource Panel - Redefining Value: The Manufacturing Revolution. Remanufacturing, Refurbishment, Repair and Direct Reuse in the Circular Economy – is perhaps the most comprehensive ever on the subject. Lead author Nabil Nasr is a veteran researcher in the remanufacturing sector and his work belies the perception that the pursuit of sustainability must come at an economic cost. He writes that the circular economy “can offer an opportunity to achieve significant value-retention and environmental impact reduction, while also creating economic and growth opportunities for industry members”.
Komatsu Group cites resource conservation and waste reduction as one of the key draws of remanufacturing, and promotes its reman business at 12 centres round the world under the umbrella of ‘Reman-Net’. These include: Komatsu Indonesia, which supplies parts such as engines and transmissions for large construction machinery and hydraulic cylinders; while Komatsu Reman Center Chile supplies components for electric dump trucks; and Komatsu Remanufacturing Asia operates exclusively in the Indonesian market. For countries
such as China, Russia, India and Brazil – which are not part of Komatsu’s global supply chain – the company has set up individual reman centres, most recently in Magadan, eastern Russia. The company uses IC (integrated circuit) tags and twodimensional bar codes to manage each item’s remanufacturing history, and to track quality
will ultimately lead sceptical customers to trust parts which have had at least one ‘life’.
But it must be said that a process of customer education is well underway and remanufacturing will be an increasingly important part of the industrial mix in many sectors over the coming years. But that won’t surprise the construction equipment

Beijing, China.
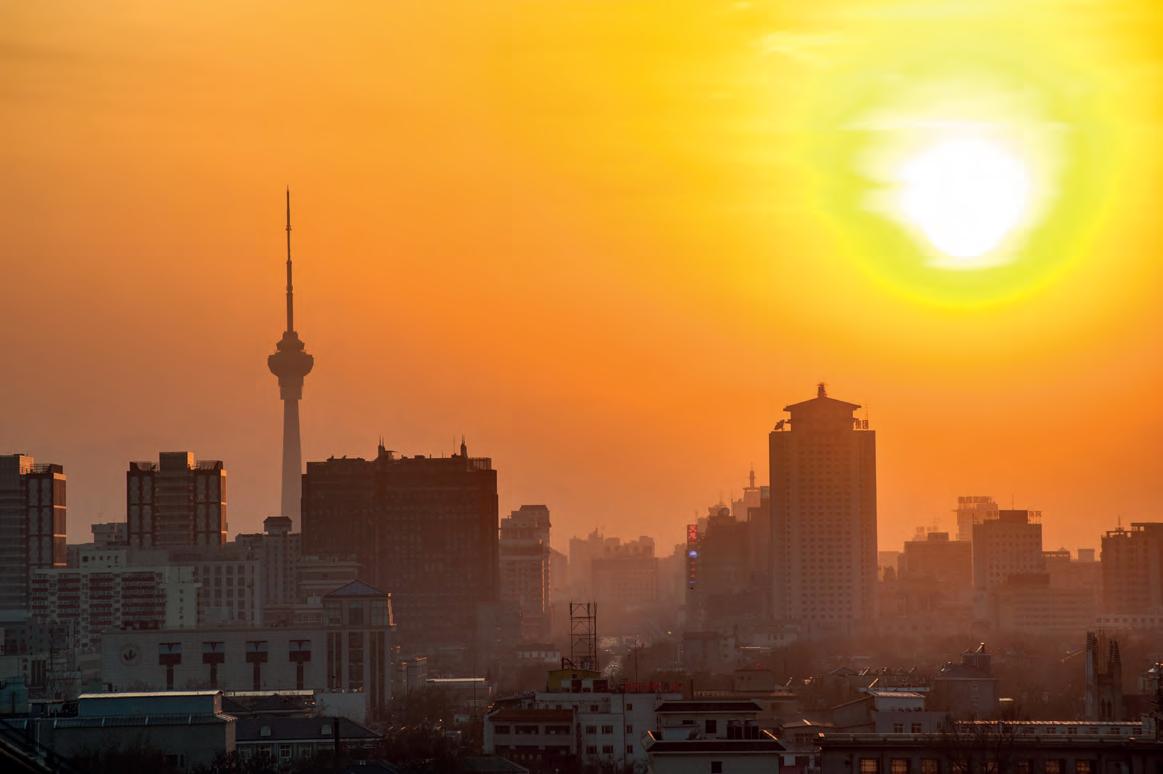
EXPECT MORE GROWTH AND TURBULENCE
China’s construction equipment manufacturers are facing a new slowdown in the next two years after an explosive recovery from the depths of the dramatic slump in 2012-2016. Graham Anderson reports on a country that always takes the long view.
Global uncertainties – notably Brexit in Europe and the ongoing trade dispute with the Trump administration in the USA – combined with an uncertain domestic market are creating strong headwinds.
Admittedly, these negatives are being offset by the Chinese government’s huge Belt and Road Initiative (BRI), recently described by one leading commentator as the largest coordinated infrastructure programme in human history.
Indeed, such is the scale of the BRI that some senior executives were privately wondering if they would have to scale back their current international development strategies to deal with the huge number of Eurasian projects coming on stream.
However, it now appears that such thinking has been quietly shelved and while there are no signs of the market returning to the extreme turbulence of recent years, there seems to be little doubt that the recent and rapid levels of growth will not continue.
And most manufacturers insist that despite the impact of market volatility, global uncertainties and the scale of the BRI projects, their long-term strategies remain fundamentally in place, even if tweaked around the edges. One such voice is that of David Beatenbough, vice president, Research and Development, for one of China’s leading manufacturers, LiuGong.
He said: “After a strong recovery during 2017 and 2018 we expect 2019 to level off, or even decrease a bit. The past two years were fleet replacement years with customers updating machines they had held through the downturn. Now the machine park in China is quite young so there is much less urgency to replace machines.
“The new China IV regulations on engine emission standards will be implemented in 2020, so there will be some pull-ahead sales into 2019, but because the fleet is so young we don’t expect a tremendously large number of pull-ahead sales.
“Overall, the China market remains strong. There are some shifts in core applications and real estate continues to be weaker than other segments, but infrastructure development and environmental applications continue to thrive.”
But as for the impact of market volatility on the company’s strategy he – like many of his rivals - emphasised their long-term thinking.
“There are some short-term concerns, but market disruptions occur all around the world at various times.
“As each situation comes up we develop plans to manage through the disruption; the same approach applies to both Brexit and the current trade situation in the USA.
“I think the key point for LiuGong is that
we have a long-term focus, and our strategic planning is based on this long-term vision. Disruptions impact our short-term actions as needed, but we generally keep our long-term visions intact.”
He said that LiuGong has a strong and well-embedded global strategy and that the BRI is supporting that strategy, not changing it.
“We have 10 sales & service subsidiaries located in all key markets around the world allowing us to provide local support to international customers.
“LiuGong was one of the first Chinese companies to export from China. We have long recognized the importance of strong distribution and we have invested heavily in dealer development throughout the world.”
He added: “Belt and Road has not really changed our company focus, but it has accelerated and made our progress in those areas more cohesive.”
The international strategy of XCMG, another of China’s leading equipment manufacturers, also remains undimmed, despite the changing external picture.
XCMG describes itself as the fifth largest construction machinery company in the world and the second largest in China, and through its “Going Global” strategy the company has set up more than 300 distributors in overseas markets.
Speaking at the end of last year, Lu Chuan, president of Machinery for XCMG, said that the company would be making more “aggressive forays” into overseas markets, especially but not exclusively in the BRI regions, and would be looking to “quicken the pace” of its international strategy.
He said the company’s aim was to reshape itself into a totally global entity based on what he called truly “internationalized thinking” and at the same time turning the countries and regions along the BRI routes into major markets for XCMG’s products and technologies.
But any thought that the BRI workload would lead to a weaker focus on more developed markets appears misplaced.
Bin Zhen, director of XCMG Europe, told the Global Report: “We are working hard on developing our operations in Europe - and especially in the UK, Germany and France. To that end, we are looking to expand our dealer network and also to deepen our relationship with rental companies in those markets.
“Today, we believe our products, for example our excavators and our earthmoving equipment, are of the very highest quality, so we are looking for professional partners to promote that message throughout the European Union.”
Of course, as head of XCMG’s European operations, one would not expect Bin Zhen to say anything different. But even allowing for a good dose of hyperbole, there is no doubt that the quality of equipment produced by the top Chinese manufacturers can these days compete with the best. However, for any new company looking to establish itself in a mature
Units sales of construction equipment (000s) *Forecast
Europe 125128142161165164155152
North America 172172159173196220243259
Global total sales 823691702893997989953994
% Market change -5-1622712-1-44
China mkt share % 2617172429262121
Source: Off-Highway Research
market, finding those partners is far from easy.
It is a point stressed by Chris Sleight, managing director of respected specialist consultancy Off-Highway Research.
“I don’t think the Belt and Road means that Chinese firms are less interested in Western markets, but there has been something of a reality check, a bit of a reckoning, if you like,” he said.
“Some years ago, it seemed that almost
THIRST FOR INTERNATIONAL ACQUISITIONS REMAINS UNQUENCHED
Experts believe that the Chinese equipment manufacturers’ interest in overseas acquisitions will continue as they strive to boost their influence and expertise.
In one of the latest deals, Chinese crane manufacturer Zoomlion confirmed the acquisition of German tower crane company Wilbert at the end of last year.
Wilbert will be added to Zoomlion’s stable of international players that includes CIFA, the world’s
third-largest concrete machinery manufacturer, and UK trenchless technology firm Pow-R Mole.
“I am sure that the top Chinese companies’ strategy of overseas acquisitions will continue,” said Off-Highway Reseach managing director Chris Sleight.
“The top Chinese companies want to be global players, but to do it organically will take a long time and the obvious short cut to achieve their strategic aim is through
acquisition.So I do not doubt that there will be more acquisitions, but perhaps not in the companies’ existing sectors.
“Instead, I think they will be in contiguous sectors, such as agricultural machinery or forklifts, sectors that will broaden their market exposure and expertise and perhaps give them new dealership and distribution networks that they can use to develop the market position of their core products.”
every Chinese equipment manufacturer was saying “we are going to be in the top three in the world”.
“The PR spin at the time was clearly unrealistic – but it remains the case that the top Chinese firms still harbour that ambition to be major global players.
“But for a Chinese firm trying to break into mature markets in Europe and North America distribution and establishing a professional and high-quality dealer network remains a major obstacle.”
Sleight continued: “The simple truth is that many of the top dealers have well-established franchises and are in long-term relationships with existing manufacturers.
“They would need a good reason to switch to a Chinese firm, which means that the Chinese are left either dealing with weaker dealerships or establishing new networks which takes a lot of time and investment.”
Sleight also agrees with Beatenbough’s view of current market dynamics.
“There was a major change in the market that really started in 2016 and one of the factors in that has been the development of the belt and road policy.
“Two years ago the first contracts were released and had a huge impact. The Chinese equipment market had been through a huge boom and bust and the four years between 2012-2016 were very tough – the market crashed.
“By our measure of the market, in 2017 sales were roughly 80 per cent higher than in 2016. At the time of speaking, we have not seen the final numbers for 2018 yet, but expect them to show a further 30 per cent rise.
“The Belt and Road has had a profound effect, especially on excavator sales – indeed, a lot of equipment of all sorts is being sold as a result.”
But going forward, he argues that the picture is somewhat less rosy. On the BRI, he argues that many of the current projects have passed the earthmoving stage where equipment usage is at its peak. And in addition, despite the BRI, overcapacity remains an issue in the Chinese equipment market.

Sleight adds: “In the depths of the 2012-2016 slump, some factory utilisation rates were as low as nine or ten per cent. Things are better today, but overall there is still more capacity than the market needs and some smaller players – none of the majors, I should stress – have pulled out.”
CCMA is predicting that China’s construction equipment sector will grow by 10% in 2019
Despite unit sales growth of 136% in two years – an extraordinary feat – OffHighway Research is now predicting a fall of nine per cent this year and a further 21 per cent drop in 2020 before a slight upturn of just over four per cent in 2021 – although even after this slowdown, unit sales are still almost 80 percent above 2015 and 2016 levels.
OHR says that there appears to be a shift
within China’s construction market towards more repair and maintenance work –which may reduce future volatility.
And they point out that the Chinese government’s close management of the economy means future major construction stimuli such as those that spurred the development of the high-speed rail system just over a decade ago cannot be ruled out.
Perhaps with such thoughts in mind, Qi Jun, chairman of the China Construction Machinery Association was more optimistic than either Sleight or Beatenbough.
In January, the International Monetary Fund’s ‘Global Economic Prospects’ report
forecast that China’s economic growth would be 6.2 per cent, the same as its previous prediction last October.
The report surprised many more pessimistic observers who expected that the IMF would downgrade its forecast, but the organisation said that growth in China remains robust, in part reflecting resilient consumption, and prices of newly constructed residential buildings have rebounded, including in firsttier cities after a period of correction.
Qi Jun said the CCMA is predicting that China’s construction equipment sector will grow by 10 per cent in 2019, well ahead of GDP growth, and that growth will be driven by the government’s investment strategy along with continuing equipment replacement further stimulated by the new stage four emissions regulations.
THE BELT AND ROAD INITIATIVE (BRI) – BIG, CONTROVERSIAL AND HERE TO STAY
When early in his period in office, the then US president Barack Obama spoke about wanting his country’s foreign policy to pivot towards Asia, he probably did not have China’s Belt and Road Initiative in mind as a factor to consider.
Yet a further “pivot to Asia” for the global economy is just what China’s hugely ambitious project is aiming to achieve – though not, of course, for the benefit of the USA.
While both international and Chinese construction companies, equipment manufacturers and suppliers of all sorts
understandably welcome the huge number and scale of the infrastructure projects involved, the BRI’s long-term value lies in the strategic shift that they represent and the markets that they open and energise for future development, especially for China and its manufacturers.
The BRI has six economic corridors:
– a Eurasia land bridge from China to Rotterdam in the Netherlands – China-Mongolia-Russia corridor – China-central Asia-west Asia to the Mediterranean in Turkey – China-Indochina Peninsula
– China-Pakistan – Bangladesh-China-IndiaMyanmar
The scale is huge, with consultancy PwC estimating that the BRI will require infrastructure investment alone of US$5 trillion.
It has not been plain sailing, and several projects are facing increasingly vocal local opposition.
But with many Asian governments struggling to fund their infrastructure needs, Chinese government support offered through the country’s export-import banks is often welcome.
And in a recent report, consultancy Oxford Business Group said the BRI is “boosting Beijing’s drive to internationalise its currency and find new markets to maintain growth, as well as using up excess capacity at home”.
For China’s top equipment manufacturers, and their international rivals, the BRI will be a key driver of growth for years to come, not just through the initial infrastructure investment but the secondary economic development that will flow from those initial projects.
“The country’s sustained and stable investment in fixed assets is the basic guarantee for the overall demand for construction machinery,” he said, adding that while the Belt and Road projects are helping to drive exports, the demand for better environmental performance in domestic markets is also boosting new machine sales by restricting the use of older equipment. What is more, he argues that the development and uptake of the latest technologies will further boost demand for new equipment, a point also stressed by LiuGong’s David Beatenbough.
Beatenbough said: “Very definitely we will see changes in the near future. If we look back at the development of hybrid machines 10 years ago we can see that initiative was driven by high oil prices, and as the fear of escalation of oil price faded away, the hybrid initiatives also faded – the benefits and paybacks just weren’t there.
“Information and data is everywhere and we need to interpret and apply it wisely”
David Beatenbough, LiuGong
“Now it is different. Technology has changed, and continues to change faster and faster. Information and data is everywhere and we need to interpret and apply it wisely, and environmental pressures continue to build around the world. As an industry we must respond.
He added: “Advances in battery technology, driven by the automotive industry are changing the potential for electrification very quickly. There are also many important advances in autonomous technology.”
Whatever changes are coming down the line, the industry is building on a hugely successful period.
Qi Jun said the CCMA’s analysis showed that in 2018 sales of nine core products increased by 25.5% year-on-year. Among them, the sales of excavators exceeded 200,000 units, a new record.
And while the domestic market remains dominant, exports are becoming ever more important, and are being boosted significantly by the BRI. Qi Jun said that total exports of the nine major products increased by 34.4% year-on-year – a number that included 19,100 excavators, almost double the 2017 total.
Nonetheless, in some commentators’ eyes, the scale of the BRI and its long-term importance for the Beijing government raises questions about international and exporting strategies across the Chinese construction sector.
Some observers have asked whether the increasing practical focus on Eurasia that underpins the BRI strategy will make some companies rethink their existing global
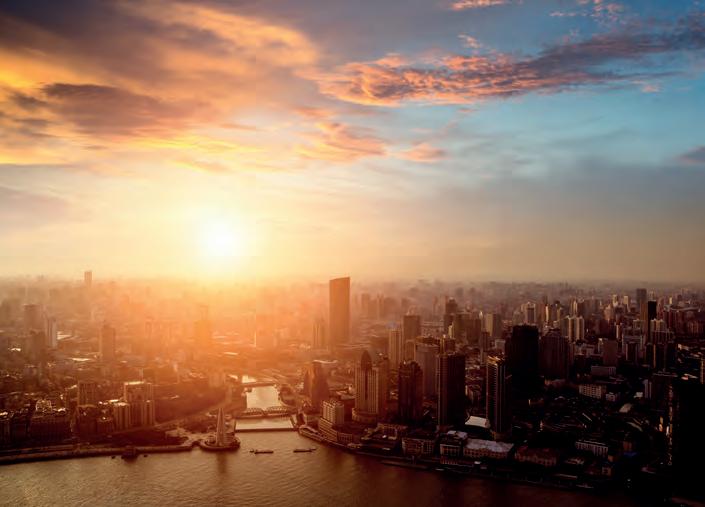
Shanghai, China.
expansion plans in Europe and the Americas. The importance placed by the Chinese government on the BRI is, of course, not in doubt, and senior members of government are well aware of the significant role of the equipment manufacturers in helping to deliver it.
At last year’s National People’s Congress (NPC) in Beijing, Chinese Premier Li Keqiang pointed out that the Guangxi region – where manufacturer LiuGong is based – has what he described as “obvious advantages” when trying to exploit the opportunities presented by the BRI. Guangxi is the only coastal province in western China and an “important pivot” on the Maritime Silk Road. Premier Li’s remarks underlined just how closely the Chinese government is watching the sector to ensure it is in a position to deliver BRI projects.
LiuGong Chairman Zeng Guang’an attended the same congress as NPC deputy for the Guangxi Zhuang Autonomous Region.
In such a fast-changing and sometimes tempestuous market, one thing is clear.
The excitement – if that is the right word – faced by China’s construction equipment manufacturers is not over yet, despite the rapid recovery in the past two years. Trump, Brexit, fears of a slowing domestic economy and the huge strategic and project stimulus of the BRI will see to that.
As one manager put it: “Any business executive with an appetite for managing turbulence and rapidly changing fortunes should come and work in our sector. One thing is certain – they won’t be bored!”
EXHIBITIONS REFLECT RECENT BUOYANT GROWTH
The sharp pick-up in the Chinese construction markets looks like delivering a boom for the country’s exhibition organisers.
The 2019 BICES exhibition in Beijing later this year will celebrate both its own 30th anniversary and will also coincide with the 70th anniversary of the founding of the People’s Republic of China.
Organisers CCMA are optimistic that the celebrations coupled with a strong domestic market and the opportunities presented by the Belt and Road projects will deliver the biggest and busiest exhibition for many years.
The upbeat mood was set by a successful Bauma China held in Shanghai at the end of November.
The event saw exhibitors up 13 per cent over the previous show at 3,350 and visitors up 25 per cent at 212,500.
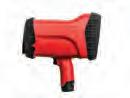

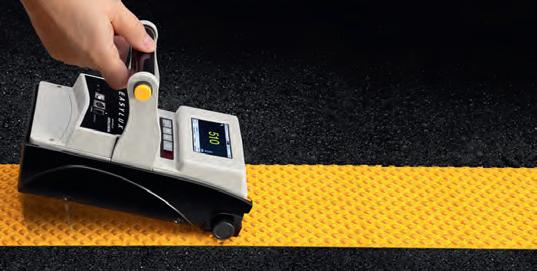
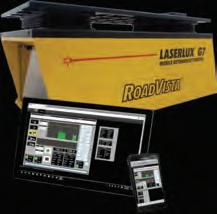
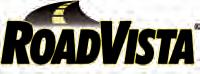


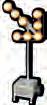
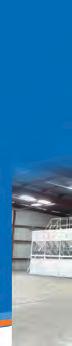
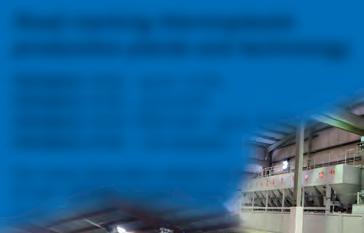
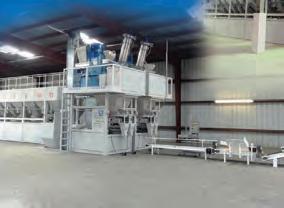

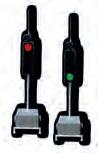
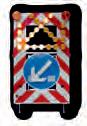
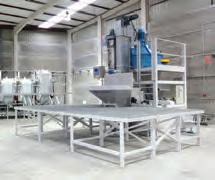
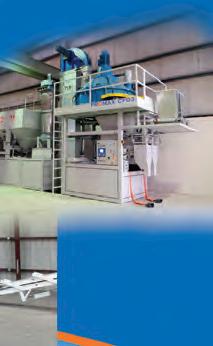

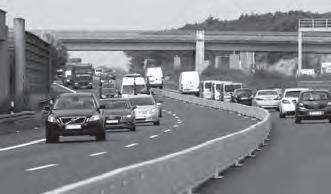
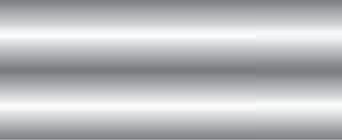
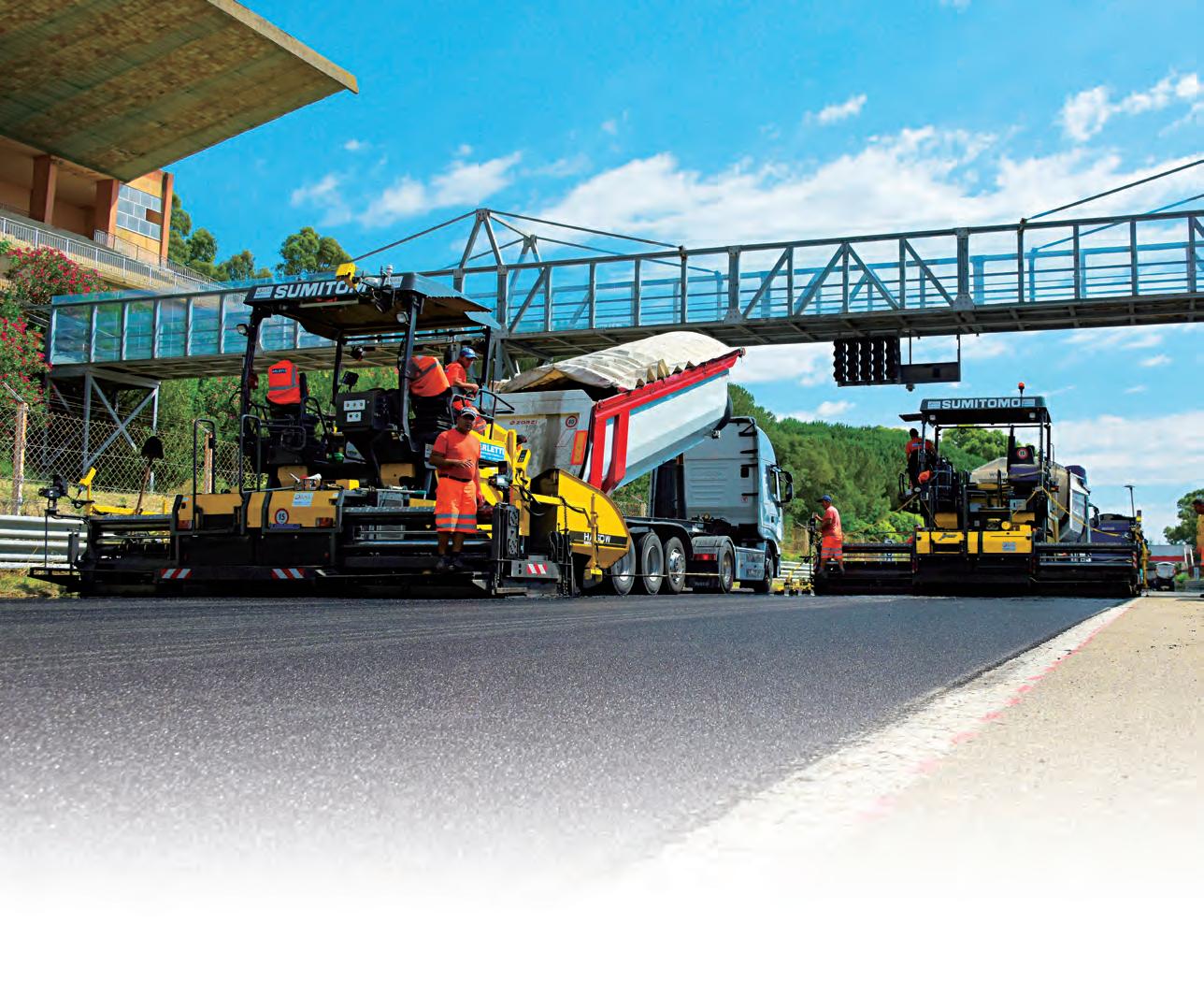

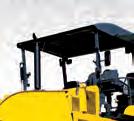
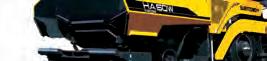



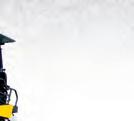
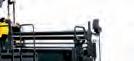

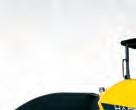
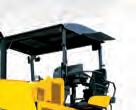
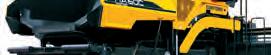

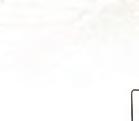
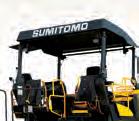
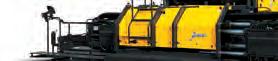
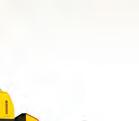
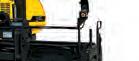




