
8 minute read
KÄSSBOHRER
an additional sales office based in Durban according to Business Development Manager South Africa, Russell Vandrau.
“We have long-term goals to assemble original equipment in the next five-to-ten years in South Africa,” he said. “At present, SAF-Holland only distributes products, currently without any production capability or production facilities in South Africa.”
On trailer trends, Vandrau explained that Performance-Based Standards (PBS) or an equivalent high productivity scheme is still a new concept in the country. “PBS trailers are proving effective in reducing the number of vehicles on the road while increasing overall payload; we expect to see a positive trend in new PBS trailers over the next few years,” he said – adding that South Africa is rich in minerals and therefore the most popular freight tasks are that of transporting ore from the mines to processing facilities or to harbours for export. “The most popular trailer builds are that of tandem / tandem interlink tippers. The tandem / tandem interlink is a vehicle configuration that is native to South Africa.”
Generally, the South African trailer market has been quite volatile over the last few years, according to Vandrau, with the 2017 growth of 21 per cent levelling out to a slight negative growth in 2018.
“This is mainly due to abrupt change in political leadership and investor uncertainty,” he said. “This year looks far more positive at this stage with an 11.8 per cent increase in new trailer registrations compared to the same period in 2018. SAF-Holland South Africa is a fairly new player in the trailer market in South Africa. We are however extremely positive about our future and our market share growth in the South and Southern African regions.”
Despite SAF-Holland’s decade-long active presence in the South African market, Vandrau is seeing growth in business due to the innovative solutions that the equipment specialist is able to offer.
With a market share of more than 50 per cent, GRW is the leading trailer tank manufacturer in South Africa according to Sales Executive, Günther Heyman.
“GRW manufacture tankers for the fuel, dry bulk, animal feed and specialised tankers for chemical transport,” he says. “We also manufacture closed body trailers (both dry and refrigerated) and curtainsiders for the general freight market. The closed body trailers are SKD kits from our partner Schmitz Cargobull in Germany, which are mounted to the locally built chassis.”
GRW headquarters are in Worcester, which is approximately 120km from Cape Town in the Western Cape, and the trailer manufacturer also has a sales office in Johannesburg. There are also three service and repair branches in Johannesburg, Cape Town and Durban respectively. Heyman said that GRW is also opening a service branch in Dar es Salaam, Tanzania, soon.
Heyman confirms that the South African economy has been sluggish for the last few years.
“The manufacturing GDP has also been retracting for the last few years with a contraction of 8.8 per cent for the first quarter,” he said. “The transport GDP was also down by 4.4 per cent for the first quarter this year. Unemployment levels are also very high at 29 per cent for the second quarter of 2019 (source: www. Statssa.gove.za). These figures point to a struggling economy and to survive in such markets GRW have invested in resource and markets outside of the country’s borders. Currently GRW are exporting vehicles to Australia, Europe and other African countries.”
GRW has been a very strong player in the tanker trailer market for the past 15-20 years, according to Heyman, and it is still a core focus for the business. “We are continuing with good growth in the refrigerated market and general freight market,” he said. “The rail network has seen enormous decline over the last 20 years in South Africa and as such the freight tasks in South Africa are varied across the spectrum. Most common freight tasks are bulk material (mining and agricultural related) and containerised freight.”
Heyman said that 2018 was a busy year for GRW as it launched its tipping silo range for the European market at the IAA Commercial Vehicles Show in Hanover as well as the second generation curtainsider for local markets.
“This year GRW is focussing on the existing model range, with some minor changes for the fuel tanker range and further rollouts of variations to the second generation curtainsiders,” he said. “By the end of 2019 GRW will also install its first panel production equipment (from Schmitz Cargobull) and the first, local produced panel, vehicles should be delivered in Q1 2020.”
The South African economy is ripe with opportunity, particularly for trailer builders and other OEMs. Mining market conditions alone have the potential to significantly bolster what continues to be a volatile business portfolio. Meanwhile, government initiatives such as NEDLAC are key to driving positive social change to set the country up for future growth and industry commentators are adamant that the collection and processing of platinum group metals in the lucrative Bushveld Complex is sure to lead to a productivity revolution. www.globaltrailermag.com FAST FACT UK-based economic forecaster, Economist Intelligence Unit (EIU), asserts that South Africa is categorised by investors as one of the ‘Fragile Five’, a group of emerging markets sharing characteristics that leaves the country predisposed to external shocks. This is reported to stem from a dependency on a volatile portfolio that flows to finance current-account deficits.
TIPPI NG THE BALANCE
ADHERING TO THE MOTTO ‘ENGINUITY’, KÄSSBOHRER DEVELOPS VERSATILE AND HIGH-QUALITY VEHICLES FOR CUSTOMERS IN MORE THAN 55 COUNTRIES. THE OEM HAS SINCE EXPANDED ITS CONSTRUCTION PRODUCT RANGE TO INCLUDE STEEL HALFPIPE AND ALUMINIUM BOX STYLE TIPPERS.
Kässbohrer tippers are making a difference with their weight advantage and robustness. Due to considerable investments in continuous innovation, backed by a strong R&D team, Kässbohrer offers a customisable product range that takes freight requirements and route geography into consideration.
The first tipper that Kässbohrer produced was in 1938, and the modern development cycle commenced with the launch of a 2011 tipper semi-trailer specified for
construction-related applications.
Through experiences in select markets, Kässbohrer continued to develop its vehicles with rigorous concept development, design validation, parts and vehicle prototyping to test the most advanced technologies.
This approach to tipper design emphasises the company’ engineering excellence. The K.SKA, for example, features a unique patented modular structure as well as a lower centre of gravity.
Kässbohrer’s aluminium box style tipper, K.SKA, is light in design, with an unladen weight of 5,040kg, and does not compromise on durability. This build is also optimised for payload and fuel saving gains.
“Designed at our R&D centre, K.SKA features a patented unique modular upper structure design,” says Head of Product Management, Cetin Sarvan. “The aluminum side panels feature 4mm inner thickness and 2mm outer thickness, while the floor panels are 6mm in thickness and are made from 6000-series aluminum and can be reinforced with extra aluminum wear plates.”
The modular design of the K.SKA also enables easier repair and maintenance.
“The K.SKA chassis is made of S700MC and coated with KTL as standard to prevent rust perforation,” Sarvan says. “Also, the K.SKA is fitted with a five-step high pressure H type hydraulic cylinder that enables robust, stable and safe product discharge.”
K.SKA also offers prolonged product life with body fix and assistant frame structure, according to Sarvan.
“Through these features, K.SKA achieves upper
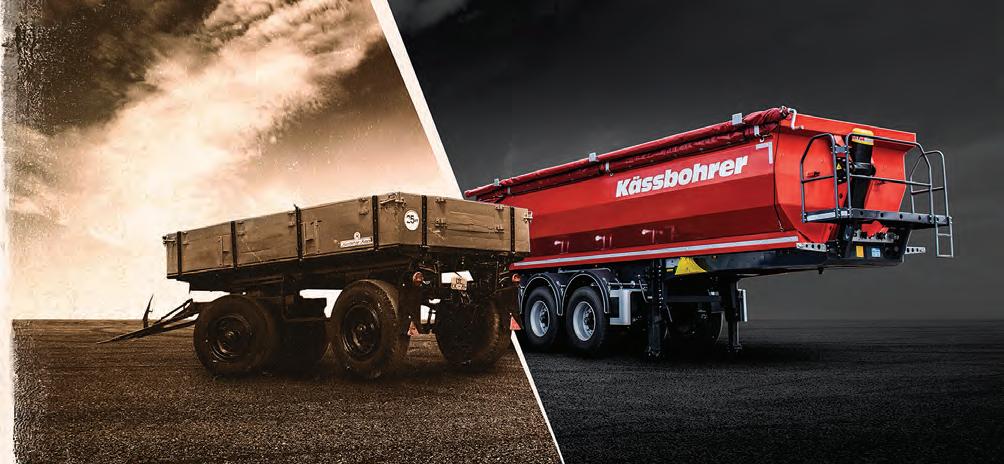
TIPPI NG
Kässbohrer’s very first tipper and its latest iteration.
structure and chassis integration prevents vibration and noise and increases vehicle stability,” Sarvan says. “This integrated structure reduces reverse movements on tipping shaft and hydraulic cylinder connections, as well as lateral forces on welding zones which may arise during a cruise and ensures prolonged product life.”
Kässbohrer’s steel halfpipe tipper, K.SKS, has a tare weight of 5,800kg. The upper structure is made of high abrasion resistant HB450 quality steel and the chassis are made of KTL coated S700MC steel. K.SKS can also be fitted with the five-step high pressure H type hydraulic cylinder.
To ensure safer and more efficient operations on the roughest of roads, Kässbohrer tippers typically feature a well-designed upper structure and chassis positioning with a lower centre of gravity to achieve optimal load distribution.
“On the other hand, the steel halfpipe tipper, K.SKS, prevents bulk adhesion on the body and ensures fast unloading through unique ‘V’ form on the floor,” Sarvan says. “Body floor durability is enhanced with internal box profiles under the V shape. A wide tipping shaft ensures operational safety and stable tipping operation by distributing the load to a wider area. This innovation also allows for a faster and more efficient unload.”
Options for remote-controlled hydraulic rear doors, hydraulic bumpers and tipping, along with weight saving features and inner coating solutions ensure that the Kässbohrer tipper range can be tailored for fleet versatility.
“Moreover, operational features such as tilt alert, traction help, automatic lift axle, safety brake function, automatic unloading/cruise suspension levels, finisher brake, and smartboard are standard for Kässbohrer tippers,” Sarvan says.
As one of Europe’s fastest growing semi-trailer manufacturers, Kässbohrer aims to maintain its position as one of the top tipper manufacturers on the continent.
“Kässbohrer manages all design validation and production processes allowing it to test the robustness durability and safety of the upper structure, the chassis and their integration as a whole hence producing well balanced and safe tipper products,” Sarvan says.
Currently, Kässbohrer has 413 service points in Europe to support its customers during their operations, whereas the service network has 336 service points that are dedicated to repairs and maintenance.
“Kässbohrer’s after sales network are trained to provide the best repair and maintenance services while Kässbohrer Hotline is available 24/7 in 23 countries and 27 languages,” Sarvan says – adding that the Kässbohrer website is available in seven languages, featuring an easy-to-use map showing all service locations. “Kässbohrer’s customer service is accessible by phone or through the website and can solve even the most complicated issues in under 24 hours.”
Kässbohrer will be exhibiting its K.SKS in Germany, Karlsruhe Messe, at the NUFAM fair in September and at Solutrans in Lyon, France, in November. www.kaessbohrer.com
EXHIBITION SPACE NOW ON SALE
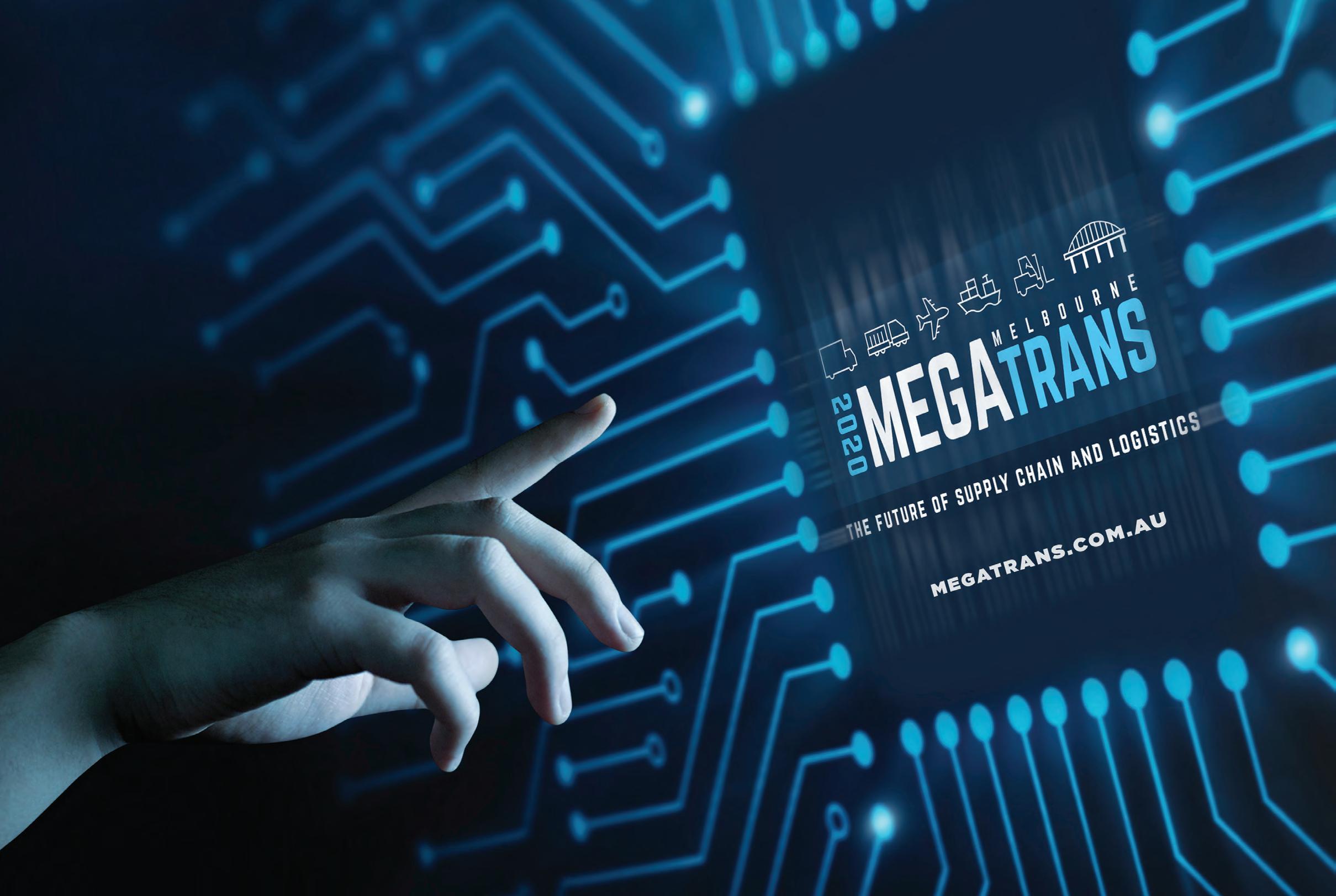
1ST - 3RD APRIL 2020 MELBOURNE CONVENTION & EXHIBITION CENTRE


