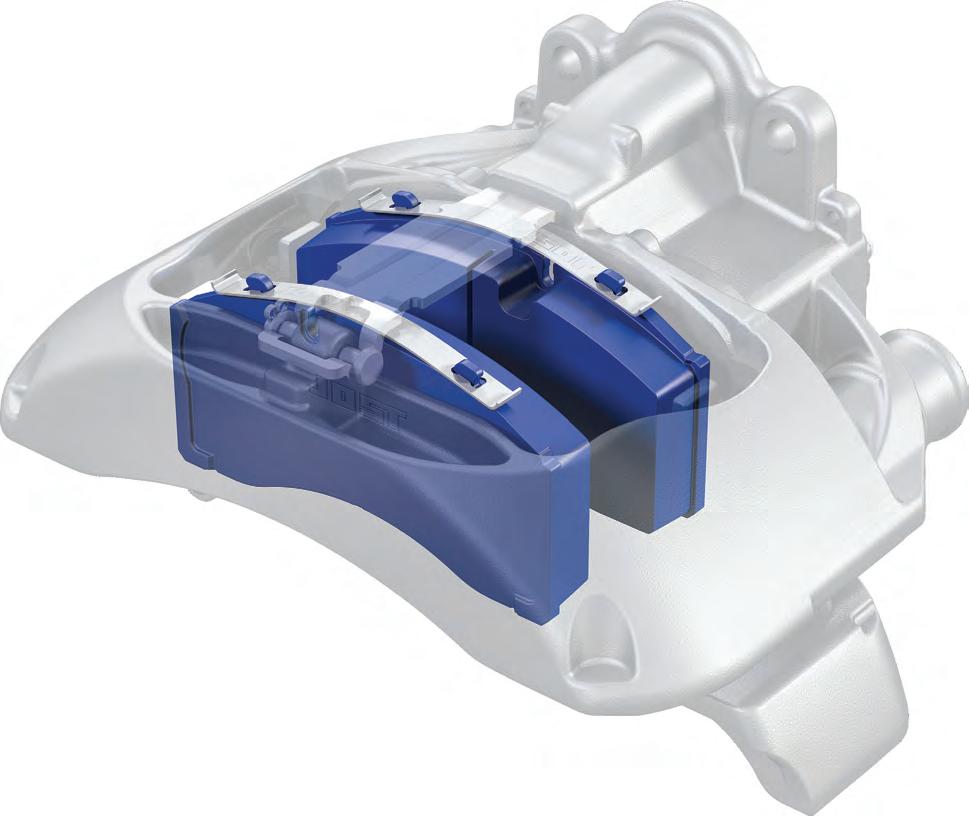
7 minute read
FLEET FOCUS
INNOVAT ION B L U E I S T H E C O L O U R O F
“Pay attention to quality when it comes to spare parts and be careful regarding cheap offers from an unknown origin,” he says.
JOST asserts that the effect of abrasion of the friction combination in brake systems is being analysed and brakes with reduced wear reduce the burden on the environment.
“Long-life brake pads support fleets in their transport operations,” JOST says. “The longer the lifetime of the pads the less downtime required in workshop. The
FAST FACT
The JOST blue pads are a result of longlasting experience of JOST: ECE R90 certified, JOST went much further. All functionalities and characteristics are ISO – and JOST laboratory tested. Additionally, a Europe-wide field test with vehicles in different transport operations has been carried out. With the JOST friction material the brake system is brought to its optimal brake performance and lowest braking distance.
vehicle’s availability improves. Proven competence of the blue JOST brake pads is also guaranteed here.”
Increased lifetime of the JOST blue pads and higher vehicle availability helps impact the economic success of each fleet, according to JOST. With all customers business success has highest priority, JOST focuses on a winwin pricing strategy.
With the enlargement of JOST pad portfolio by the blue pads for all truck and trailer applications, JOST strengthened its portfolio of original pads for JOST Truck and Trailer Axles. Made possible by the ECE R90 certification.
“It was our goal to develop state-of-the technology pads with of convincing pricing,” JOST Axle Systems Head of Product Development, Tobias Neutze, says. “The new blue pads perform in all transport operations – this we have extensively tested.” www.jost-world.com
D F D S EXPANDS IN ROTTERDAM
DFDS is an integrated shipping and logistics solution provider.
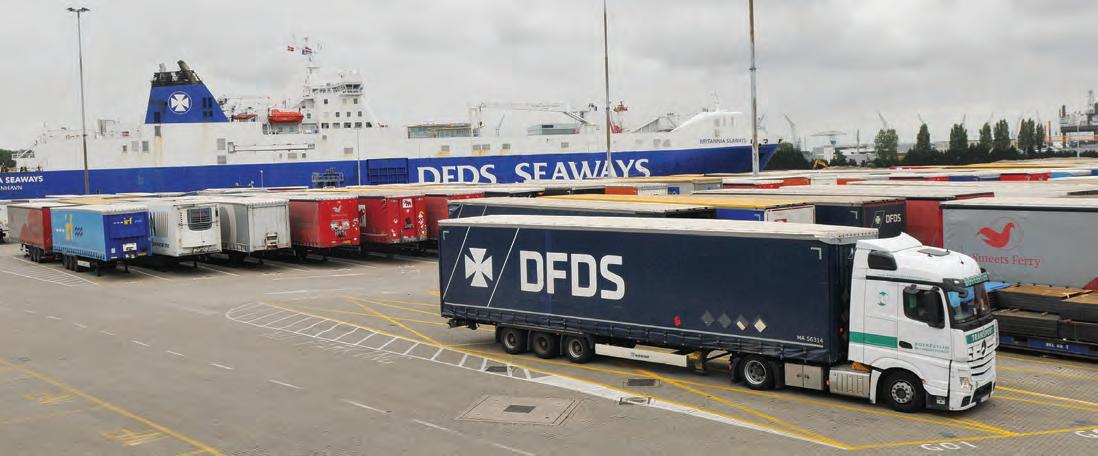
DANISH LOGISTICS SERVICE PROVIDER, DFDS, IS KNOWN FOR ITS FLEET OF VESSELS THAT CONNECT NORTH-WESTERN EUROPE. IN SOME TERMINALS, LIKE ROTTERDAM, IT OPERATES WORKSHOPS TO MAINTAIN TRAILERS AND IS SET TO BENEFIT FROM PORT-SIDE UPGRADES. [ Story by Tim de Jong ] M aintaining some 25 routes in the Eastern Sea and in the North Sea is the core business of Danish operator, DFDS. Aside from that, DFDS operates its own trailers, which customers use for complete loads or for part loads. DFDS also offers multimodal services. Since the takeover of Alphatrans, a Dutch company, DFDS also provides the transportation of exceptional loads under the new name DFDS Special Cargo. The trailer fleet is being serviced in the Rotterdam port area, among others. Trailers From the Rotterdam terminal, ferries leave loaded with hundreds of trailers to Immingham and to Felixstowe. These ships do not only carry DFDStrailers, but also many trailers of specialised trailer operators. At the large workshop in the terminal, DFDS offers a number of maintenance services. DFDS operates a fleet of 7,800 trailers.
A considerable number of this fleet have a Dutch license plate. In Europe, DFDS runs eight terminals. Those in Immingham (GB) and Gent (B) also have their own workshop, like the one in Rotterdam. But according to Leon van Campen, Manager Trucks Services and Warehouse and Assets, the reason why
DFDS Manager Trucks Services and Warehouse and Assets, Leon van Campen.
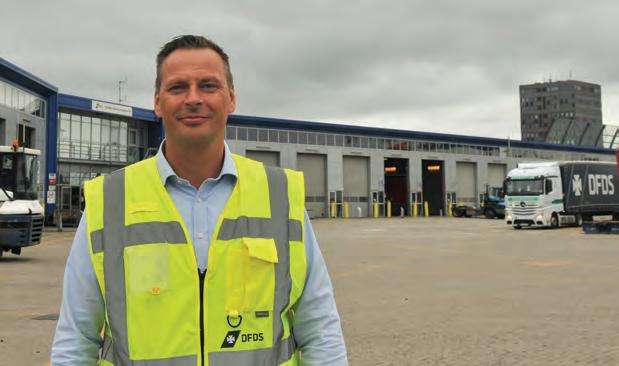
the Rotterdam workshop is the biggest, is that very many clients request DFDS to do a lot of maintenance work on their trailers.
“The idea is that waiting times for our customers to board the ship, can be used to execute common maintenance, as well as MOT, tyre checks , or any other kind of technical service.” Van Campen explains that they work closely together with a local tyre specialist and with fridge supplier, Thermo King. “DFDS even provides services on the Rotterdam terminal to temporarily store goods waiting to be transferred again. Recently, two brake benches were installed to be able to do more annual examinations on trailers. Sometimes we manage to execute eighteen examinations in a day, which requires some expertise as well as knowing where to look underneath a trailer.”
He says that at any moment, up to 1,100 trailers can be parked at the terminal premises, waiting for the moment to board ship for the UK. DFDS also purchased lifting columns to provide mechanics with more space while they work on a lifted trailer.
“Investments were mainly made for the part of our workshop which deals with axles and braking systems,” Van Campen says. “We also have a workshop taking care of the bodywork of the trailer.”
Van Campen demonstrated a trailer which nearly seems to collapse when the mechanic manages to open one of the rear doors. This doesn’t happen, but mechanics hurry themselves to reinforce the bodywork before the revisions on the bodywork start.
“It’s not possible to exactly tell how many trailers we service here on an annual basis,” he says. “The work varies a lot. But I can assure you it is always busy.”
He explains that trailers being operated in ferrywork are the trailers that suffer most.
“They spend hours on deck of a ship suffering from salt water blown over deck by fierce winds,” he says. “The result is that sometimes you already see the damage after only two years in service.”
Wooden planks In this bodywork-part of the workshop there are many wooden planks stacked for use. ”Planks and stanchions are loose parts which for some reason get lost every now and then,” Van Campen says. “Of course, we see developments towards trailers without planks or with planks stacked in vertical folders inside the tarpaulin. Those planks are made out of aluminium, but they tend to get lost sometimes as well. It would be a good thing if a definitive solution would be found.”
Van Campen explains that the trailers DFDS buys for its own fleet, are coming from Krone, Schmitz Cargobull and Kögel. Not all of them are yet equipped with telematics, but Van Campen says that he works closely with some DFDS customers who are bringing their fleet online.
“I expect that it is a question of time
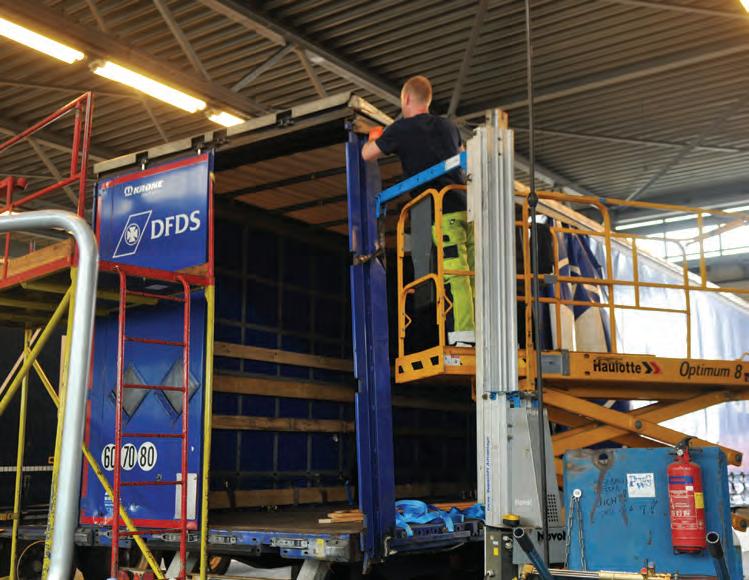
DFDS has its own workshop in Rotterdam.
before we will see more of this,” he says. “You always know where your trailers are, you have insight in the numbers, the distances, the maintenance, uptime, you name it.”
Maintenance Trailers in the DFDS fleet stay in operation for some ten years. So, on an annual basis, some 750 need to be replaced.
“Ideally, I’d like to see the trailers to be replaced some time earlier, for instance after seven or eight years. Nowhere in road transport does a trailer wear quicker than in ferrywork,” Van Campen says. “In the final three years we see more expensive repair work and parts replaced. I suspect that maintenance costs would come down when we would maintain a somewhat shorter lifespan.”
On an annual basis, trailers are maintained twice a year, for the annual examination and a second time in between.
Mechanics In Europe, there’s a severe shortage of drivers and mechanics. Van Campen now has 28 people working in shifts at the workshop in the terminal.
“The level of education at high schools these days falls way apart from the skills we need here,” Van Campen says. “So, we started to educate people for our jobs by ourselves. Recently, we hired a young guy with another background in education. We see that he’s a big talent who feels at home at our workshop. That is actually comforting. We hope that he will stay with us.”
Van Campen says that his current workforce is stable with sufficient experience in various skills – and these go as far as revising the terminal trucks needed to move trailers to and from the ferries as well.
Brexit Less of a comforting thought is the upcoming Brexit.
“All we see is that DFDS is ready for any scenario,” Van Campen says. “However, we fear that across the pond, this is not yet the case. This worries us actually. Nothing seems to be prepared and the attitude of the British is that ’we’ll see, let’s just get out of the EU in the first place.’ Nobody knows where this will lead to.”
Extension In spite of Brexit, DFDS in Rotterdam eyes to extend their terminal significantly. Terminal management waits for an approval to make use of the area that they have bought to make the terminal much bigger.
“We’re looking to ready the area for construction work,” Van Campen says. “When ready, we can accommodate 500 more trailers.” www.dfds.com
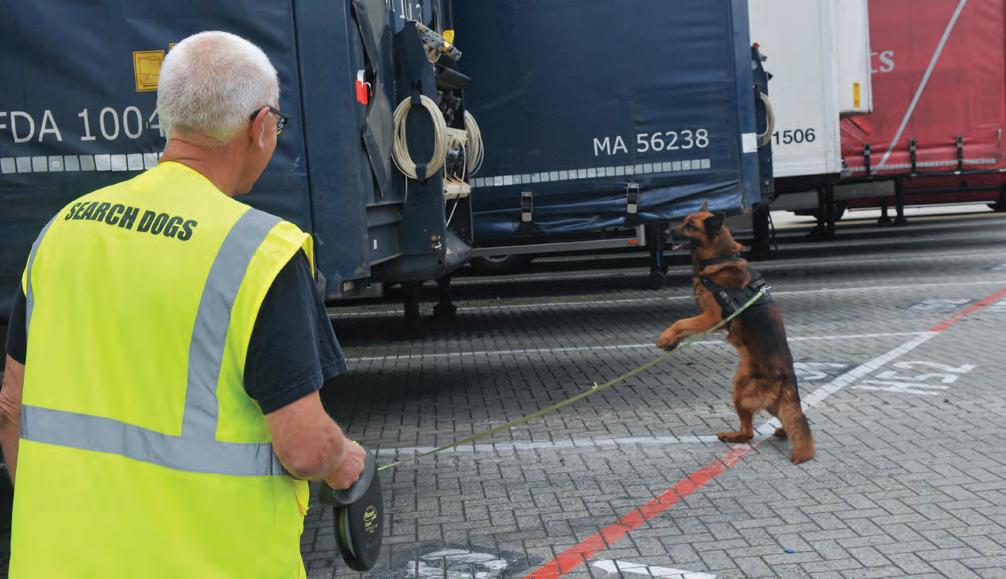