
47 minute read
NEWS
from Global Trailer 63
by Prime Group
NEWS INTERNATIONAL
ASIA
CHINA
Chinese media has reported the founding of a state-owned logistics group which aims to strengthen supply chains amid pandemic disruption. The new company, China Logistics Group, was formed through a merger with China Railway Materials, China National Materials Storage and Transportation Group, Huamao International Freight Limited Company Shenzhen Branch, China Logistics and China National Packaging Corporation. The merger follows global supply chain disruption which has constrained operations particularly at Chinese ports where just one Covid-19 case can result in business suspension. Strategic investors and parent firms of China Eastern Airlines, COSCO Shipping and China Merchants Group will respectively hold share percentages of 10 per cent, 7.3 per cent and 4.9 per cent in the newly-formed group. China’s State-owned Assets Supervision and Administration Commission (SASAC) and China Chengtong Holdings Group will evenly split the remaining shares. Chengtong Holding is centrally-managed by SASAC, giving the state asset regulator control over all the remaining shares. China Logistics Group is reported to cover 30 Chinese provinces, has a presence in five continents and operates three million vehicles.
HONG KONG
Danish shipping company, Maersk, has reached an agreement to acquire a Hong Kong-based contract logistics company which specialises in omnichannel fulfilment services, e-commerce and inland transport. Maersk is set to acquire LF Logistics. The transaction will add 223 warehouses to the existing portfolio, bringing the total number of facilities to 549 globally, spread across a total of 9.5 million square metres. “The acquisition of LF Logistics is an important and truly strategic milestone on our journey to become the global integrator of container logistics; a global logistics company that provide digitally enabled end-to-end logistics solutions based on control of critical assets,” said Maersk CEO, Soren Skou. “With the acquisition of LF Logistics, we add critical capabilities in Asia Pacific to support our customers long term growth in Asia Pacific as well as capabilities and technology we can scale in our contract logistics business globally.” As part of the agreement to acquire LF Logistics, Maersk will enter a strategic partnership with Li & Fung to develop logistics solutions. LF Logistics operates an extensive Pan-Asian network for B2B and B2C customers within retail, wholesale and e-commerce. “We recognise that for LF Logistics to be a global leader in the industry, achieving scale is of paramount importance,” said the CEO of Li & Fung and LF Logistics, Joseph Phi. “Maersk provides the ideal fit for our people and our customers. It has a substantial presence around the world and will utilise LF Logistics’ talent base and operational platform across Asia to build out its logistics and fulfilment offering globally. “This is testament to the strength of our team, our unique operations-centric culture, and superb growth potential. Together we will deliver a compelling value proposition that allows our people to attain their full potential and our customers to achieve sustainable competitive advantage.” LF Logistics is a privately owned company by Li & Fung (78.3 per cent) and Temasek Holdings (21.7 per cent). LF Logistics is organised through two business units: In-Country Logistics (ICL) and Global Freight Management (GFM). Founded in 1999, LF Logistics is primarily focused on providing contract logistics solutions to customers in Asia-Pacific. LF Logistics is run as a standalone company separate from Li & Fung. Over the last 22 years, LF Logistics has significantly expanded its geographic presence, with an intention of providing integrated logistics solutions to customers across Asia-Pacific. LF Logistics employs 10,000 people and has 223 warehouses and fulfilment centres in 14 countries totalling 2.7 million square meters. In the full-year 2020, LF Logistics reported a revenue of around 1.3 billion USD and a post-IFRS 16 adjusted EBITDA of USD around 235 million USD, with the ICL business generating a revenue of around 850 million USD and a post-IFRS 16 adjusted EBITDA of around 230 million USD. For the fullyear 2021 the ICL business is expected to report a revenue around $1 billion USD with an adjusted post-IFRS 16 EBITDA around $250 million USD.
RUSSIA
Logistics firm, Tablogix, has acquired the warehouse and transport operations of Finnish company, Itella Logistics. Tablogix has taken the Moscow facilities of Itella LLC (part of Itella Logistics) which includes warehouses in Krekshin (60,000 square metres), Odintsovo (40,000 square metres) and Khimki (80,000 square metres). In 2020, Tablogix’s warehouse operations reportedly accounted for more than 200,000 square metres of rented and client space in the Moscow
NEWS INTERNATIONAL
ASIA/ AFRICA
region. Following the acquisition of Itella assets the total warehouse space of the merged company will exceed 400,000 square metres. “The acquisition of Itella Logistics’ warehousing and transport business will enable Tablogix to achieve significant synergies by diversifying client portfolio, increasing operational efficiency and increasing the scale of business,” said Tablogix CEO, David Lane. “We have literally surrounded Moscow with high-quality warehouse space, which means that customers no longer need to compromise on the optimal location.” Valery Sinyaev, Chief Financial Officer of Tablogix, has forecast growth of about 8-12 per cent per year in transport and logistics services following this acquisition. “If earlier warehouse facilities were needed to store and send goods to stores, now the systems are being rebuilt, and we can talk about an increase in the volume of deliveries from the manufacturer directly to the consumer,” said Sinyaev. Since 1994, Tablogix has been among the largest logistics service providers in Russia. With a staff of more than 1,000 people, the business’ services include storage, professional handling of products in warehouses, distribution and delivery of goods.
SINGAPORE
Transport and logistics company, GEODIS, has improved its road transport connections in Singapore, Malaysia, Thailand and Vietnam. The company’s fleet of vehicles and expanded network of partners enables full and partial loads to be carried by road along the Singapore, Malaysia, Thailand axis, and now Vietnam. The addition of the service to Vietnam will serve businesses driving the manufacturing boom in that country over recent years, helping the region become a vital supply chain node for many hightech, retail, and FMCG businesses. Launched in November 2019, the Road Transport service of GEODIS in Southeast Asia was created to meet the needs of companies looking for a daydefinite road transportation solution for their cargo, in the range of 30 to 1000 kilos per shipment. The expanded road network for Full Truck Load (FTL) and Less than Truck Load (LTL) service provide freight management from first to last mile and offers additional options for existing GEODIS customers, in addition to air and ocean transport modes. The door-to-door road option has the advantage of loading space flexibility, with benefits of lower rates than air freight, shorter transit times than ocean freight, and on-the-ground expertise for customs clearance. Since March 2021, GEODIS has expanded its road network capabilities by offering both standard and personalised solutions including its RoadDirect, RoadFast, and RoadSave services. With these differing levels of service, GEODIS balances transit time and costs to ensure customers can tailor the solution that best fits their needs to include door-to-door service, customs brokerage and onward distribution. Accompanying the new expansion of the Road Transport service of GEODIS is a dedicated access to a rate calculator and automated quotation system, which will be available towards the end of 2021. “Our expanded service aims to give our customers greater flexibility and reliability of service in the context of current supply chain disruptions affecting air and sea cargo flows,” said GEODIS SubRegional Managing Director – South East Asia, Lakshmanan Venkateswaran. “The service refinements come at a pivotal time as ASEAN’s manufacturing productivity and market expansion are gaining momentum due to the confluence of events that is motivating global companies to diversify their supply chain options.”
AFRICA
Logistics provider, Kuehne + Nagel, has expanded its network of offices in Africa to support a rise in demand for its services. These offices are managed and supported by a control tower in Durban, South Africa – a single point of customer contact responsible for a compliant, high quality and easy-to-access network across Africa. It allows for complete visibility across the network, including remote locations, while ensuring Kuehne + Nagel’s global service standards; supervising data quality, enabling shipment visibility and managing cargo flow. With this expansion, Kuehne + Nagel provides its customers better access to African markets and while offering African manufacturers specialised and industry-specific solutions to meet soaring demand in markets such as pharma & healthcare, perishables, emergency & relief and project logistics. Sub-Saharan Africa plays an increasingly significant role in worldwide trade as it is home to more than one billion people, half of whom will be under the age of 25 by 2050. Kuehne + Nagel has been actively present in Africa for almost seven decades after opening its first office in Johannesburg in 1954. The company provides its customers with full visibility across a strong and compliant supply chain by combining the strengths of a local presence with Kuehne + Nagel’s global operating
NEWS INTERNATIONAL
ASIA/ EUROPE
ZF successfully launches new Commercial Vehicle Solutions Division.
systems and processes. The expanded Africa network is fully vetted and audited by an external global auditing company to ensure ongoing adherence to the highest level of compliance and ethical standards. It provides the full range of international services including Air, Sea, Road and Contract logistics to address the demands of the African continent. “Africa is blessed with natural resources and a young entrepreneurial population,” said Kuehne + Nagel President Middle East and Africa, Lee I’Ons. “Now is the time to unlock this potential and create growing, thriving economies. There are many elements to this, one being the logistical ability to connect global markets for end consumers and suppliers. With the new control tower in Durban, we are ready to address this great African opportunity.” With this expansion, Kuehne + Nagel will be represented in 18 African countries: South Africa, Kenya, Uganda, Tanzania, Egypt, Angola, Namibia, Madagascar, Zimbabwe, Swaziland, Mozambique, Mauritius, Botswana, Nigeria, Ghana, Ivory Coast, Senegal and Rwanda. Until the end of the first quarter 2022, Kuehne + Nagel plans to increase its footprint with a second expansion on the continent.
GERMANY
Technology company, ZF, has announced the successful start of its new Commercial Vehicle Solutions (CVS) division, effective 1 January 2022. The new division combines ZF’s expertise in the commercial vehicle industry and will significantly advance solutions for safe, sustainable and digitised transport. The new division unites ZF’s former Commercial Vehicle Technology and Commercial Vehicle Control Systems divisions, the latter of which was formed from ZF’s May 2020 acquisition of WABCO. “With the new CVS division, ZF is now positioning itself as the world’s largest component and system supplier for the commercial vehicle industry,” said Wilhelm Rehm, member of the ZF Board of Management with responsibility for the new division. “Thanks to our broad technological positioning and global market presence, we can offer our customers the key solutions they need to transform their product portfolio from a single source. Leveraging our regional structure, we offer significant advantages and close customer proximity for truck, bus and trailer manufacturers as well as fleet operators, wherever they are in the world. “In line with our ‘Next Generation Mobility’ corporate strategy, CVS will accelerate ZF’s global growth strategy.” ZF’s Commercial Vehicle Solutions division is supported by around 25,000 employees based across 61 locations in 28 countries. The CVS division, according to ZF, is helping shape the future of commercial transportation ecosystems. “Our mission is to be the preferred global technology partner to the commercial vehicle industry,” said ZF. “Powerfully combining ZF’s commercial vehicle systems expertise, extensive technology portfolio and global operations, the division serves the full commercial vehicle industry value chain. As the automotive industry progresses towards an increasingly autonomous, connected, and electrified (ACE) future, ZF’s CVS division innovates, integrates and supplies components and advanced control systems that help make commercial vehicles and fleets operate more safely and sustainably. CVS unites ZF’s former Commercial Vehicle Technology and Commercial Vehicle Control Systems divisions, the latter being formed following ZF’s acquisition of WABCO in Spring 2020.”
GERMANY
Logistics company, Deutsche Post DHL Group, is set to welcome a new CEO in 2023. The Supervisory Board of Deutsche Post AG has extended Frank Appel’s contract as DPDHL Group CEO until 4 May 2023. His previous contract runs until 31 October 2022. Appel will continue to serve as DPDHL Group CEO until the Annual General Meeting in 2023. Thereafter, Tobias Meyer, will take over as DPDHL Group CEO. Meyer joined the company in 2013 and has held a wide variety of
NEWS INTERNATIONAL
EUROPE
positions including Head of Corporate Development, Chief Operations Officer at DHL Global Forwarding, and Head of Operations and IT at Post & Parcel Germany. He has been CEO of Post & Parcel Germany and a member of the DPDHL Management Board since March 2019. “In Tobias Meyer we have a recognised expert of the company taking over as DPDHL Group CEO,” Dr Nikolaus von Bomhard, Chairman of the Supervisory Board of Deutsche Post AG. “He is the ideal choice to continue the very successful path the company has charted. With Strategy 2025, the Management Board successfully executes along the major megatrends of digitalisation, sustainability, Globalisation, and e-commerce.” Von Bomhard added: “We thank Frank Appel for his support to assure this seamless transition. Frank Appel’s performance during his more than 13 years at the top of DPDHL Group has been outstanding. He made the company into a leading global logistics powerhouse that connects people and markets, thereby enabling global trade. Under Appel’s leadership, the company has posted one record after the next. Deutsche Post DHL Group has much to thank him for.” Appel: “After careful consideration, I have decided not to remain for another full term in office. I do this totally convinced that Deutsche Post DHL Group is led by an exceptional management team and supported by highly engaged employees. In Tobias Meyer, we have a top class manager and great colleague to follow as the next DPDHL Group CEO. Under his leadership, Post & Parcel Germany successfully managed the turnaround. I couldn’t have hoped for a better successor.” As part of a smooth transition, Meyer will take over the Corporate Function Global Business Services from Appel in July 2022, and hand over his role as CEO Post & Parcel Germany to Nikola Hagleitner, currently Chief Sales Officer at Post & Parcel Germany. Hagleitner has been with the company since 2005 and has worked in three of the five divisions at Deutsche Post DHL Group. With experience across operations, sales and business development, Nikola brings a wealth of expertise to her new position. In addition, the Supervisory Board has also extended the contract with Oscar de Bok, CEO DHL Supply Chain, for another five years to 30 September 2027.
GERMANY
The Supervisory Board, the Management Board and the staff of Schmitz Cargobull mourn the loss of Bernd Hoffmann, who passed away on 8 December 2021, aged 78. Bernd joined the former Schmitz Anhänger GmbH & Co KG as a marketing manager in 1974. He advanced to managing partner and was a member of one of the three owning families. He became a member of the Board of Management in 1988 and guided the fortunes of Schmitz Cargobull AG from 2003–2008 as Chairman of the Board. In 2008, he then transferred to the Supervisory Board. Bernd played a decisive role in expanding and restructuring Schmitz Cargobull AG, and in successfully developing the European company into the market leader in the trailer industry. With the sales of trailers from Schmitz Cargobull throughout Europe and beyond, Bernd initiated the union of Europe’s east and west, north and south from early on. In addition to sales, global communication and understanding were always among Bernd’s key focal points, and he made a major contribution to advancing the company’s internationalisation. Bernd was awarded the Cross of Merit (Verdienstkreuz am Bande) from the Order of Merit of the Federal Republic of Germany by the Federal President, Christian Wulff in 2011. Members of both the business community and wider society have expressed their appreciation of his outstanding achievements, such as his dedication to institutions focused on supporting young people, as well as his passion for football. “His entrepreneurial vision and business courage were valuable cornerstones for our company,” Schmitz Cargobull said in a statement. “We will honour Bernd’s memory.”
GERMANY
In 2021, Kässbohrer achieved market success, experienced growth following the appointment of new country managers, expanded its product portfolio and aftersales network and rolled out K-Finance leasing partnerships. The OEM is reported to be in the top three in Netherlands in all groups of Europe’s widest product range and tops the list in Germany and Poland with its tanker and silo vehicles. As the business welcomes new European climate law, which is committed to at least 55 per cent in carbon emission reduction, Kässbohrer anticipates an ambitious transition period for industry. This is why the OEM is working closely with customers, stakeholders, associations and universities to innovate. The OEM is developing award-winning vehicles for multimodal transport – the next generation of longer vehicles for more
NEWS INTERNATIONAL
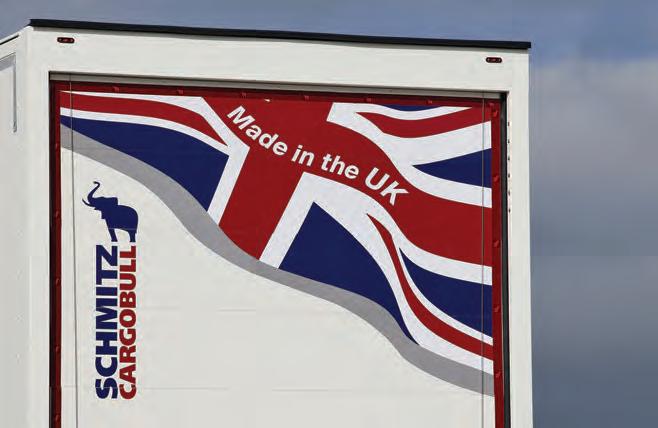
EUROPE
Kässbohrer Board Member, İffet Türken.
load along with investment in smart tech for future digital integration. “In 2021 we have concluded European Union backed Aeroflex project which has been ongoing since 2017,” said Kässbohrer Board Member, İffet Türken. “We actively worked with other OEMs and manufacturers to create the future of road transport with efficiency, safety, and sustainability in mind but especially worked to finalise the book of recommendations for future implications collaborating with industry stakeholders and representatives both at European and regional levels. As the challenge we face is urgent, we all need to work together.” To improve customer satisfaction, Kässbohrer continued to expand its sales and aftersales teams worldwide In 2021, Marco Contoli was appointed Italy Country Manager and Piotr Kowalski was named After Sales Manager in Poland. Jordi Llecha, in 2020, became Spain Country Manager. “Kässbohrer is also constantly expanding aftersales network by almost 100 per cent over the last four years starting with Germany, Poland, Netherlands, France, Italy and Spain reaching 653 locations,” said Türken. “Our service network is carefully chosen to have the necessary competencies to address all the needs of our customers operating with the widest product range in Europe; 95 per cent of our service network is also competent to serve body work of our tank silos, tippers, box and reefers along with advanced maintenance of our low bed range. Complementing our ever growing competent service network, our spare parts operations operate out of five locations with 90 per cent availability and 24-hour dispatch service.” In addition to these services, the OEM has also established partnerships with leading leasing companies. “Our K-Finance program provides competitive financing options to our customers,” said Türken. “In 2021, we established a new partnership with BNP Paribas Leasing Solutions in Spain and France and EFL in Poland. “Kässbohrer will continue to innovate and grow with its stakeholders for operational safety, efficiency and meet the urgent challenges for carbon emission towards the next 125 years.”
UK
Salford Van Hire has acquired the first 40 S.KO PACE SMART semi-trailers from Schmitz Cargobull for nationwide contracts with major supermarkets, retailers and parcel delivery companies. The new assets, which are the first to have been constructed in Schmitz Cargobull’s Manchester factory, join Salford Van Hire’s existing fleet of 1,800 dry freight curtainsiders and reefers, half of which were also supplied by Schmitz Cargobull. “We are very proud to be the first logistics business in the UK to acquire these new S.KO PACE SMART semitrailers which are perfectly suited to our needs,” said Salford Van Hire Contract & Fleet Engineering Director, Steve McNally. “The fact they are manufactured in the UK is hugely beneficial both for lead times and cost, as well as reducing our environmental impact – which they will continue to do on a daily basis because of their lightweight construction.” Featuring a galvanised MODULOS chassis, innovative STRUKTOPLAST panels and options for three different
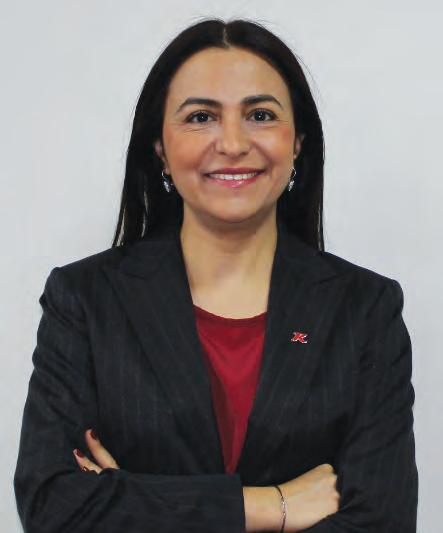
Salford Van Hire acquires 40 new Schmitz Cargobull dry freight semi-trailers.
NEWS INTERNATIONAL
EUROPE
floor strengths, the fully modular S.KO PACE SMART is EN 12642 code XL certified and comes with Schmitz Cargobull’s telematics system TrailerConnect fitted as standard. Innovative lightweight panels mean each semi-trailer weighs around 600kg less than competitor models, and its payload potential on day one will be maintained for the life of the asset – qualities which will translate into reduced emissions and lower fuel bills. Salford Van Hire has worked with Schmitz Cargobull for more than 10 years and the team’s confidence in the manufacturer meant they placed their order without the need to trial a demonstrator vehicle. “We have always been impressed by the quality, design and build of Schmitz Cargobull trailers so we were completely confident in our choice to be the first to run S.KO PACE SMART trailers,” said McNally. “Now we have them, they are already exceeding our expectations.” Expected to be in operation seven days a week, the new trailers will be used to support Salford Van Hire’s largest customers who transport a variety of dry freight and parcels. Independent and privately-owned, Salford Van Hire is one of the largest and most well-respected car and commercial vehicle rental and contract hire organisations in the UK, with bases in Leeds and Manchester.
UK
Transport business, DWP & Sons, has extended its fleet with seven refrigerated trailers from Schmitz Cargobull which are also fitted with TrailerConnect for optimal cold chain visibility. The new assets join a 27-strong exclusively Schmitz Cargobull trailer fleet comprising 20 reefers, four Euroliners and three box trailers, which transport fresh and frozen produce across the UK, Europe and Asia, from DWP & Sons’ base in Stoke-on-Trent. TrailerConnect telematics enables DWP & Sons to monitor all variables on each trailer from a single dashboard, including the internal temperature, tyre condition and door security, and the system sends SMS or email alerts in case of security concerns. “We have worked with the Schmitz Cargobull team for many years and they always deliver what we want,” said
Association honours Lecitrailer leader. DWP & Sons Operations Director, Phil Houlton. “Their telematics package gives total transparency for us and for our customers. We can see everything from weight, temperature and distance a trailer has covered all in one neat package. “The trailers we currently have on the fleet are doing a fabulous job and the new ones will be working just as hard. They are brilliant trailers to pull, which is part of the reason we keep returning to Schmitz Cargobull.” Currently, two of DWP & Sons’ trailers are being used to advertise Stoke-onTrent’s cultural and heritage attractions with eye-catching liveries designed by the local council. There are plans for Stoke City Football Club to wrap a third trailer in its colours. Houlton, who was born and bred in Stoke and works alongside Managing Director Danny Poole, said: “Danny and I have always been keen to support the community, so we try to put something back into the local area where we can, particularly after such a difficult period. We’re proud to promote Stoke-on-Trent.”

EUROPE
Expected to remain in operation for four years, the new assets will be used seven days a week, 365 days a year, and will predominately be pulled by DAF XF tractor units.
SPAIN
Fernando Leciñena Lafuente, founder and President of Lecitrailer and founding partner of Asfares, has received recognition for a lifetime of service to the semi-trailer industry. The event, held in the new Lecitrailer offices, was attended by more than 30 representatives of the sector, all members of Asfares as well as former members of the association.
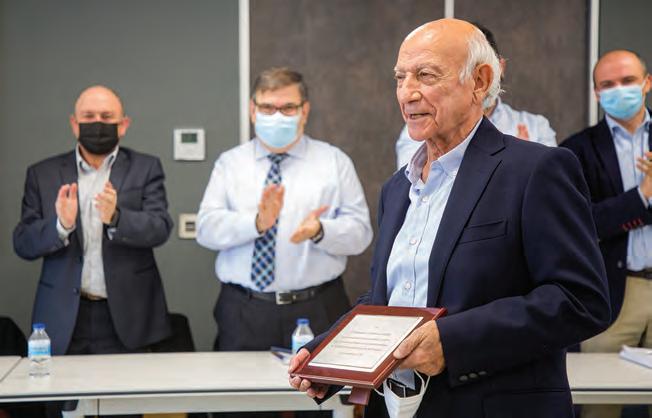
Fernando Leciñena Lafuente.
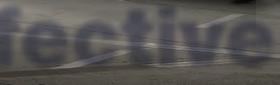

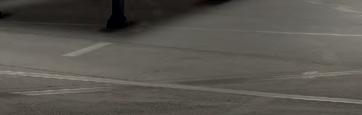
Uniquely e ective
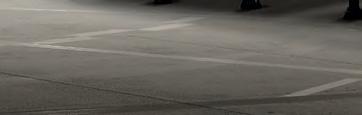

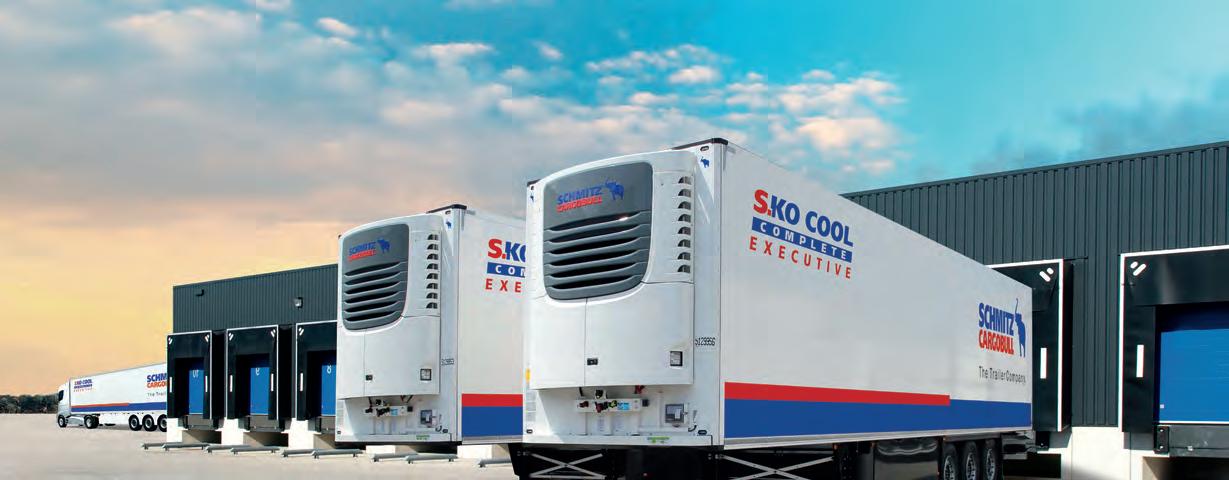

The S.KO COOL SMART EXECUTIVE is our top of the range reefer semitrailer, and includes our exclusive S.CU transport refrigeration unit. Refrigerate more coste ectively with our outstanding insulation system. Our services and TrailerConnect® telematics system are included to ensure lower maintenance costs and an impressive resale value. More Information: +44 (0) 1925 732886, www.cargobull.com


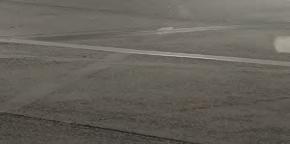
NEWS INTERNATIONAL
EUROPE/ MIDDLE EAST
Asfares Director, Julio Viartola, opened the tribute by showing the constitutive act of Asfares, of which Fernando Leciñena had been a signatory in 1982. Then Miguel Vidal, President of Asfares, thanked Fernando Leciñena for his dedication to the sector, stating that “in the history of the semi-trailer of this country, he had undoubtedly written many chapters” and stressed “the recognition, gratitude and admiration” for Leciñena. Asfares, is the association formed by the Spanish manufacturers of trailers, semi-trailers, tanks and all kinds of bodies such as tarpaulins, tippers, vans, refrigerators and containers. It also includes manufacturers of equipment and components for these vehicles. It was created and registered in 1982 to represent the common interests of the sector, to interact with the Spanish administration, ministries, CCAA, ITVs, OCAs, other associations, carriers, shippers. Furthermore, it is a founding member of the European Federation CLCCR, which represents manufacturers in international organisations. The association’s objective is to work for the advancement of the sector at the national and European level, with the commitment to contribute with better, safer and more efficient vehicles.
SPAIN
In a year of widespread growth in the semi-trailer market in Spain, Lecitrailer has once again gained the trust of its customers, to continue, for 22 consecutive years, as the leader in the national market. In 2021, Lecitrailer reached a market share of 25.64 per cent, with 3,560 registered vehicles and a growth of 38.2 per cent compared to 2020, according to official figures from Asfares, the Spanish Association of manufacturers of trailers, semi-trailers, tankers and trailers. By product families, the figures for tarpaulins stand out, in which Lecitrailer has finished as the first brand in the market with a 38.34 per cent market share and 1,810 units registered. These good results have undoubtedly contributed to the good market acceptance of Elite, the new generation of Lecitrailer tarps, the most complete, profitable and exclusive, launched on the market at the beginning of the second half of the year. The figures for reefers also stand out, a family in which, for the second consecutive year, Lecitrailer has ended the year as the leading national manufacturer, with Lecitrailer’s Evolution refrigerators occupying second position in the market with a share of 21.29 per cent, 922 units, and a growth of 40.33 per cent. Of the rest of the families, we Lecitrailer also highlights the first position achieved in the van family with a share of 42.86 per cent and the second position in the market in container ships with a 19 per cent share. One more year, the good results of the national market have also been produced in the foreign markets in which Lecitrailer is present. In France, Lecitrailer is already the third brand in the market with a share of 9.81 per cent and 2,279 registered semi-trailers. Third place in the ranking of registrations also in the Portuguese market with an 8.45 per cent market share. In the same way, it has established itself as a reference manufacturer in other markets such as Italy, Russia, Belgium, Holland, Denmark and the United Kingdom. Lecitrailer’s export figure reaches 57 per cent of production. “Since Lecitrailer was founded 32 years ago, the customer has always been at the centre of all our activity,” said Lecitrailer General Manager, Carlos Leciñena. “I want to take advantage of this occasion, and I speak on behalf of each and every one of the members of Lecitrailer, to thank our customers for the trust they have placed in our brand, since they are the true protagonists of these good results and help us to continue to evolve and improve day by day.”
SPAIN
TIP Trailer Services has agreed to acquire Nextrailer Rent (NEXT-rent). NEXT-rent is a business from Guillén Group, a Spanish equipment service provider and trailer manufacturer. The Wielton Group will take over the trailer manufacturing business of Guillén Group. TIP will integrate NEXT-rent assets, around 900 trailers, in its existing Spanish business. This puts TIP in a strong position for long-term growth as it further strengthens its position in the Spanish market. The completion of the transaction is expected to take place in January 2022. “This acquisition is another key milestone in the growth path of TIP,” said TIP President and CEO, Bob Fast. “It will support our asset growth strategy, whilst complementing our existing offering. “In addition to being a well-established business within the trailer manufacturing sector and rental sector, the acquisition will enable TIP and the Wielton Group to work with new customers, support them with additional trailers and provide the best flexible commercial trailer fleet solutions,” he said. “With TIP and Wielton we found great partners to guarantee a successful future of our business,” said Jose Luis Guillén, current owner of the Guillén company.
MIDDLE EAST
“With these two partners we are able to bring our operations to the next level and profit from synergies – in the production of trailers with Wielton and for the rental and lease business together with TIP,” he said. “Through this acquisition, NEXT-rent customers will be able to access the range of services offered by TIP across Europe,” said Gonzalo Elosegui, Director of TIP in Spain. “Over the next months, both companies will work on the fleet integration to manage a smooth transition with customers and suppliers. “Also we are glad to welcome the staff of NEXT-rent in the TIP family and are convinced that they will play a pivotal role the successful integration of the company in TIP.” NEXT-rent is based in Valencia close to the largest harbour in the country and provides customers across Spain with leasing and rental services. TIP’s Spanish division will have a combined fleet of over 2200 trailers, curtainsiders, vans, reefers and chassis configurations.
DUBAI
Transport and logistics company, Aramex, has welcomed a new Chief Financial Officer (CFO) to its team. Nicolas Sibuet has accepted the role and brings more than 26 years of experience across shipping, oil & gas and aviation. Most recently, he served as CFO and Acting Senior Vice President for Strategy, Marketing and Communications at Abu Dhabi Airports. Sibuet also has extensive experience as an expert advisor to Boston Consulting Group where he worked on transforming and restructuring companies. Additionally, he was the Vice President for Marketing and Business Development at Weatherford, where he participated in the restructuring and disbursement of Weatherford drilling contracting arm, WDI. Prior to that, he held multiple roles in the oil & gas and shipping
YOUR PARTNER FOR SUSTAINABLE LAST NEW! MILE
DELIVERY
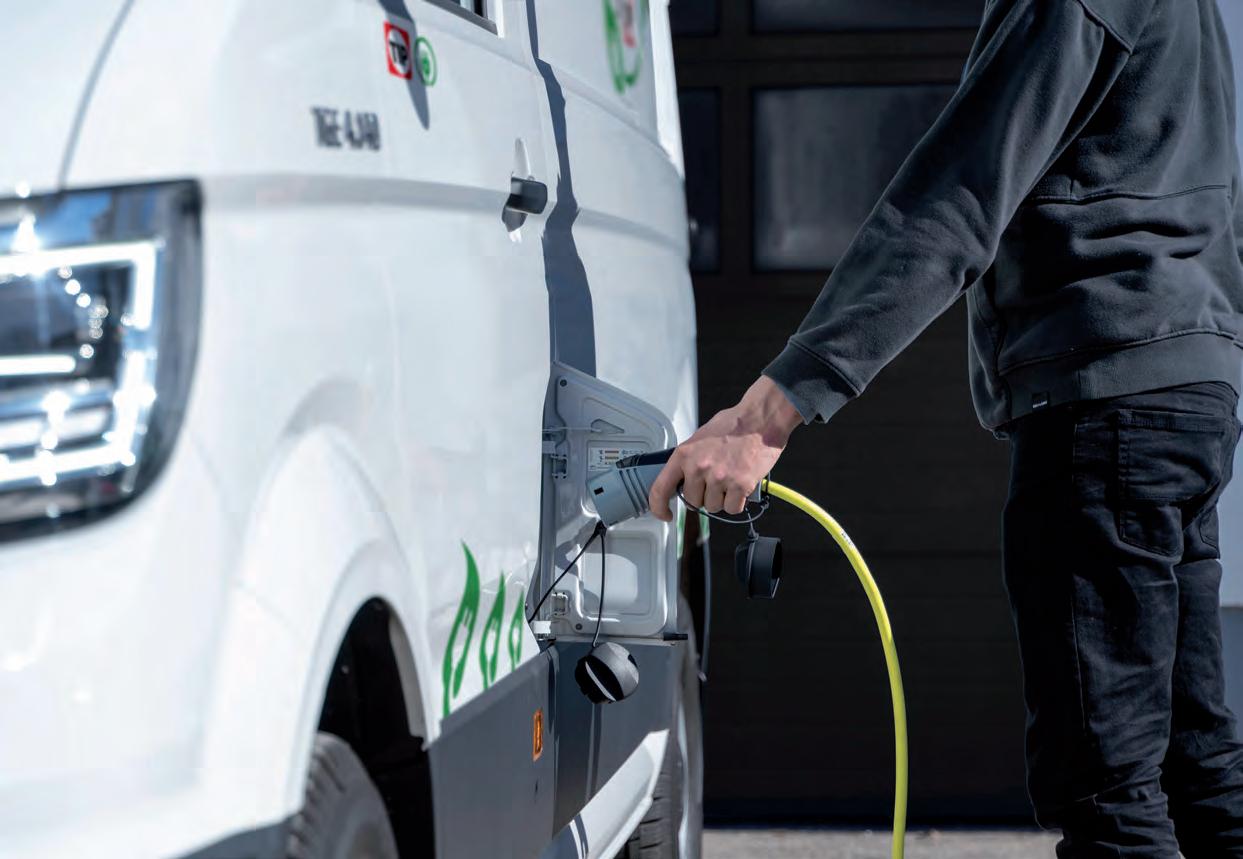
NEWS INTERNATIONAL
MIDDLE EAST/ NORTH AMERICA
industries, delivering successful funding requirements to support business growth as well as leading and structuring finance departments. “I am pleased to welcome Nicolas as Aramex’s CFO,” said Aramex CEO, Othman Aljeda. “He is a seasoned executive with a proven track record of leading companies towards transformational growth and has deep knowledge in various industry trends. “His extensive experience will play a key role in the execution of our strategic priorities and will enable us to further optimise our recently redesigned operating model, as we seek to grow our global market share. The management team and I are looking forward to working closely with Nicolas to enable the company achieve sustainable growth for our key stakeholder groups.” Sibuet holds a Master’s Degree in Economics and Accounting from the University of Western Brittany in France and a Postgraduate Degree in Finance from the Strasbourg University in France.
US
Equipment specialist, SAF-Holland, wishes Rob Nissen a happy retirement after 29 years of service. He is well known as the industry’s fifth wheel coupling expert and sets a great example for others to follow with his eager and willing spirit. The National Senior Service Manager is retiring in February. He joined the company in 1993 as General Service Manager and has since held various roles in the business including 22 years as Directing Field Service, three years as Technical Service & Training Manager and a four-year stint as National Senior Service Manager. Prior to joining SAF-Holland, Nissen worked for more than two decades in truck and trailer maintenance and service. SAF-Holland fifth wheel service training video shoot featuring award winning Rob Nissen. “An active participant in the Technology & Maintenance Council, in 2015 he was awarded the prestigious Silver Spark Plug Award – the highest honour from the ATA recognising outstanding contributions to the improvement of equipment, maintenance and management practices,” SAF-Holland said in a statement. SAF-Holland President – Americas, Kent Jones, said Nissen’s loyalty and commitment to the organisation as well as his knowledge and experience will be greatly missed. “We thank Rob for his outstanding contributions and leadership during his career at SAF-Holland,” said Jones. “We wish him well in his retirement.” Frank Sonzala, Vice Chairman of CIE Manufacturing, congratulated Nissen on his well deserved retirement. “May you have a long, happy and healthy one filled with love family and no crazy deadlines or multiple paged reports,” he said. “The industry and all your friends will miss you. I know I will.”
US
ACT Research’s preliminary reports show trailer net orders closed on a softer spot with OEMs booking 26.6k in units in December. That was 17 per cent lower than November and 40 per cent below the previous year’s volume. “After a very conservative path from April through August, OEMs cautiously began to accept additional orders in September,” said ACT Research Director CV Transportation Analysis and Research, Frank Maly. “That careful posture continued through the remainder of the year. “OEMs continue to balance staffing and supply-chain challenges as they seek to ramp production volumes to better fulfil fleet equipment demands. “Even with the lower December order volume, preliminary results point to month-over-month growth in industry backlog as the year closed, and it appears that 2022 production slots are now committed through August, at current build rates. “This preliminary report puts the fullyear 2021 net orders at almost 248k trailers, down about 17 per cent from 2020. The decline is entirely the result of supply-chain and staffing issues, as OEM output continues to trail actual fleet demand.”
US
Troy Cooper stepped down from his role as President of XPO Logistics, effective 27 December 2021. Cooper will continue working with the company as senior advisor through to 30 June 2022. “With the spin-off of GXO [in 2021], and in light of the progress we’ve made transforming XPO into a pure-play transportation company, Troy and I agreed this was a natural time for him to step down,” said XPO Logistics Chairman and CEO, Brad Jacobs. “Troy’s contributions over the past decade have been invaluable, particularly his efforts driving the growth of our best-in-class truck brokerage business from its earliest days and his leadership of our European operations from 2015 to 2017. “We’re very well positioned with strong leaders in each of our business lines, with Mario Harik as acting president of
NORTH AMERICA
less-than-truckload, Drew Wilkerson leading North America transportation, and Luis Gomez leading Europe transport. “I’m grateful Troy will continue to provide counsel to me and our leadership team over the next six months, and we wish him all the very best going forward,” he said. “It’s been an honour to work with the team as we’ve built XPO into a leading freight transportation services provider,” said Cooper. “The leadership team we’ve assembled is the best in the industry, and it’s gratifying knowing that the business is in excellent hands and our prospects are so bright.”
US
Stoughton Trailers will begin manufacturing chassis products in Waco, Texas. The new Waco facility will add additional chassis capacity to Stoughton’s already expanding capacity in Wisconsin. In December 2021, Stoughton installed a new chassis production line at its Stoughton, Wisconsin, facility. As part of its future chassis production plan, Stoughton purchased a parcel of land in Waco and is building a new manufacturing facility to further expand chassis production capacity and tap into alternative labour markets. The construction of the Waco facility is underway and is expected to be completed quickly. Stoughton aims to move equipment into the facility by March and beginning chassis manufacturing by early Q2 2022. This site is expected to employ up to 125 people. The company has also added a new chassis production line in Stoughton, Wisconsin. Once ramped up to full production, the company expects to employ an additional 150 people in the Stoughton plant assembling chassis and manufacturing components to feed the other chassis production lines.
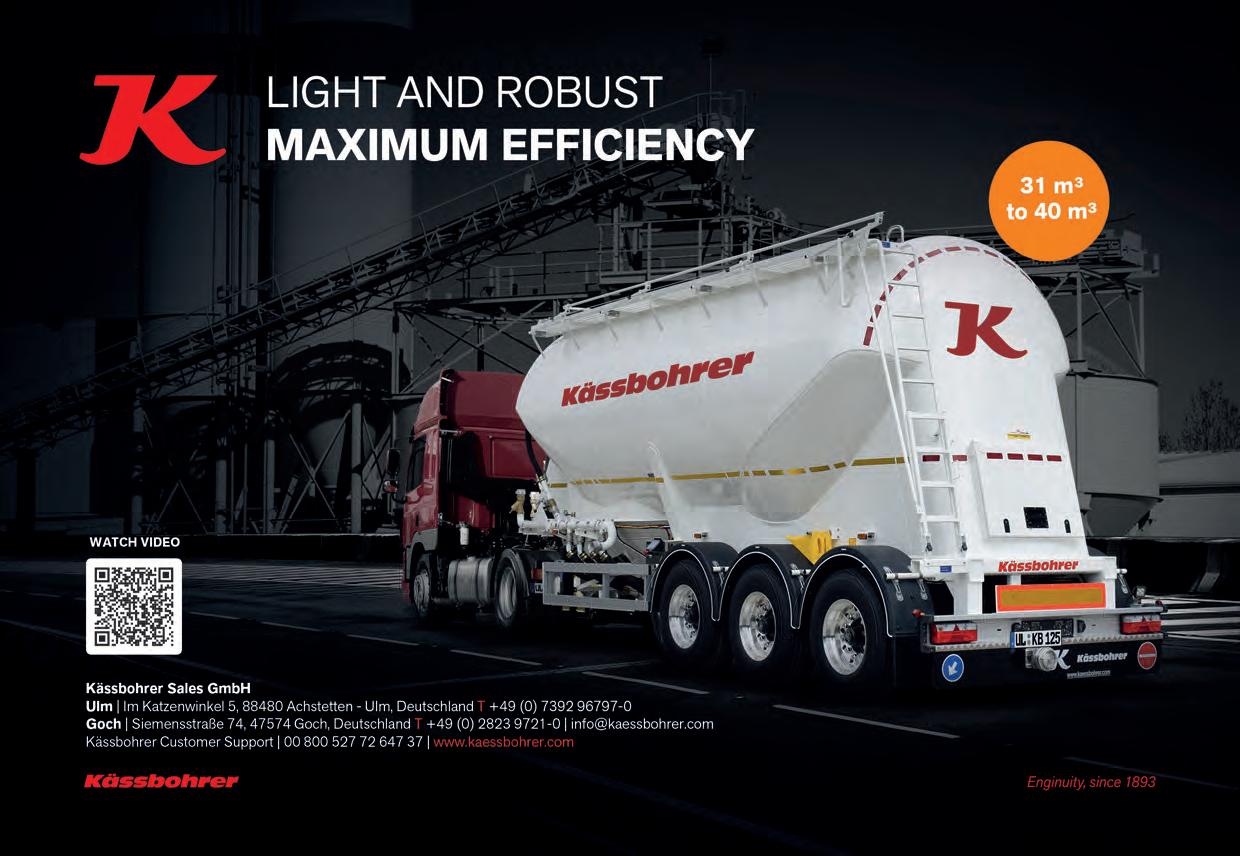
SOUTH AMERICA
When the Waco, Stoughton, and Evansville facilities are operating at capacity, the collective output of all three sites will increase the run rate to approx. 20,000 to 25,000 chassis per year, hitting that rate by September 2022. “The new Waco facility and Stoughton production line will help fulfill our customer production commitments for 2022 and beyond,” said Stoughton President and CEO, Bob Wahlin. “By the end of 2022, the company will have invested $25 million dollars expanding our chassis production capacity. “These investments would not have been possible without the remedial relief provided by the antidumping and countervailing duty orders on chassis from China. “I would like to thank our facilities, operations and chassis team members for their hard work to date on these important projects.” The new Waco location provides Stoughton Trailers with convenient access to the many seaports, railyards and chassis customer locations in the southern tier of the US.
BRAZIL
Randon Companies has outlined a new leadership structure. Randon Companies has separated the position of President and CEO, currently held by Daniel Randon. As President-Director, Daniel Randon will focus on the business’ internationalisation plan and innovation agendas considered central to the group’s strategy. The current Executive Vice President and COO, Sérgio L. Carvalho, will take over as CEO of Randon Companies, effective 1 January 2022. In the position of CEO, Carvalho now leads the Executive Committee of Randon Companies and will be at the head of the group’s four business divisions, including the Financial and Digital Services, which was not under his responsibility in the previous position. With this, Carvalho leads: Trailers Division, which includes all Randon Implementos operations; Fras-le Division, which includes the company and its controlled units. At Fras-le, Sérgio maintains the position of President and CEO; Auto Parts Division, which includes Castertech, Suspensys, Master and Jost Brasil units; Financial and Digital Services Division, which includes Randon Consórcios, Banco Randon, Banco Randon and R4 Digital, fintech created with 4all. The corporate areas of Randon Companies also report to the new CEO, recognised for his deep knowledge of the sector and for his successful trajectory in management positions, many of them in the United States. The same applies to the units dedicated to innovation and technology: Randon Technology Center (CTR), Nione, Randon Tech Solutions – RTS Industry, Randon Ventures and Conexo.
BRAZIL
Librelato, is preparing to open a new 20,000-square-metre site in Içara, SC, along the BR 101 highway. The dealership, owned by brand representative, Compac, will sell new and used products and offer technical support as well as a Libreparts unit for original parts. “This is a strategic location and we will be closer to customers traveling on the BR 101, gaining greater visibility and offering more facilities for truck drivers,” said José Carlos Sprícigo, CEO of Librelato. According to the executive, this will be the second Libreparts under the responsibility of the Compac commercial representative. In February, the same representative also foresees the opening of another Libreparts box in Imbituba, SC. According to one of the project’s owner, Adriano Pacheco de Souza, the idea for the new construction came from Compac’s strategic planning to be closer and closer to the customer. “One of our pillars is to serve everyone with excellence,” said de Souza. “Therefore, we see this need to offer customers this new service point, with a privileged location and adding other services that they can do in the same place.” Box Libreparts – The Liberparts boxes are units built in containers, installed in places of great movement of trucks such as gas stations, fairs, industrial parks and close to ports. These outposts will reportedly offer higher-turn parts such as lighting systems, tarpaulins, quick-change valves, safety items such as reflective strips and lashing straps. Librelato aims to establish 20 of these boxes by the end of 2022. The OEM is also hoping to grow its network to a total of 30 Libreparts stores in this time.
BRAZIL
Randon, in partnership with Volvo Trucks Brazil and other partners, has unveiled a dump truck innovation. The ‘Concept Trailer’ will be tested during South America’s grain harvest on routes connecting the farming
SOUTH AMERICA
regions to main ports. The trailer design is weight optimised and also features automated components and sensors. It has fewer welded seams, uses high-strength aluminium and steel, resulting in a product that is a tonne lighter than similar models and is said to be manufactured using processes that are unprecedented in the sector. Aerodynamic drag is also reported to be reduced due to a lack of vertical struts on the body and the inclusion of deflectors. The vehicle also has an anti-tip system to help correct it in hazardous conditions. In addition, the Concept Trailer has a set of electronics that improves operational efficiency and safety, such as a rear sensor and camera that is interlinked to the braking system, which trigger it automatically if there are obstacles in the way. Coupling and decoupling has also been optimised. Sensors on the fifth wheel and an electric lifting device make this procedure safer and ergonomically easier. The cargo can be covered by a fully automated tarp, activated by remote control, which saves time and means that the driver does not need climb onto the trailer. In addition, the system identifies when the trailer is not loaded and automatically raises the axles, reducing tire wear and fuel consumption. “This new product has a special design, is a tonne lighter and is fully connected to the tractor and the driver – it brings the future to the present, as a new concept in transporting cargo,” said Randon Companies Superintendent Director – Assembly Division, Sandro Trentin. “The company’s next step is to apply the technology from this concept we are launching now, to the next generation of products that are already part of the company’s portfolio.”
Intelligent Trailer Program
Boost your trailer’s IQ to benefit from…
Load Optimization
Operational Efficiency
The ZF Intelligent Trailer Program. Intelligent connections of braking system, sensor technology and chassis control enable more than 40 advanced trailer functions. To optimize daily operations and to provide greater safety, efficiency, and sustainability. Everywhere and anytime: at the yard - on the road - at the dock. Learn more at www.intelligenttrailer.com Driver Comfort & Effectiveness
Advanced Safety
Fuel & CO₂ Reduction
MAKING
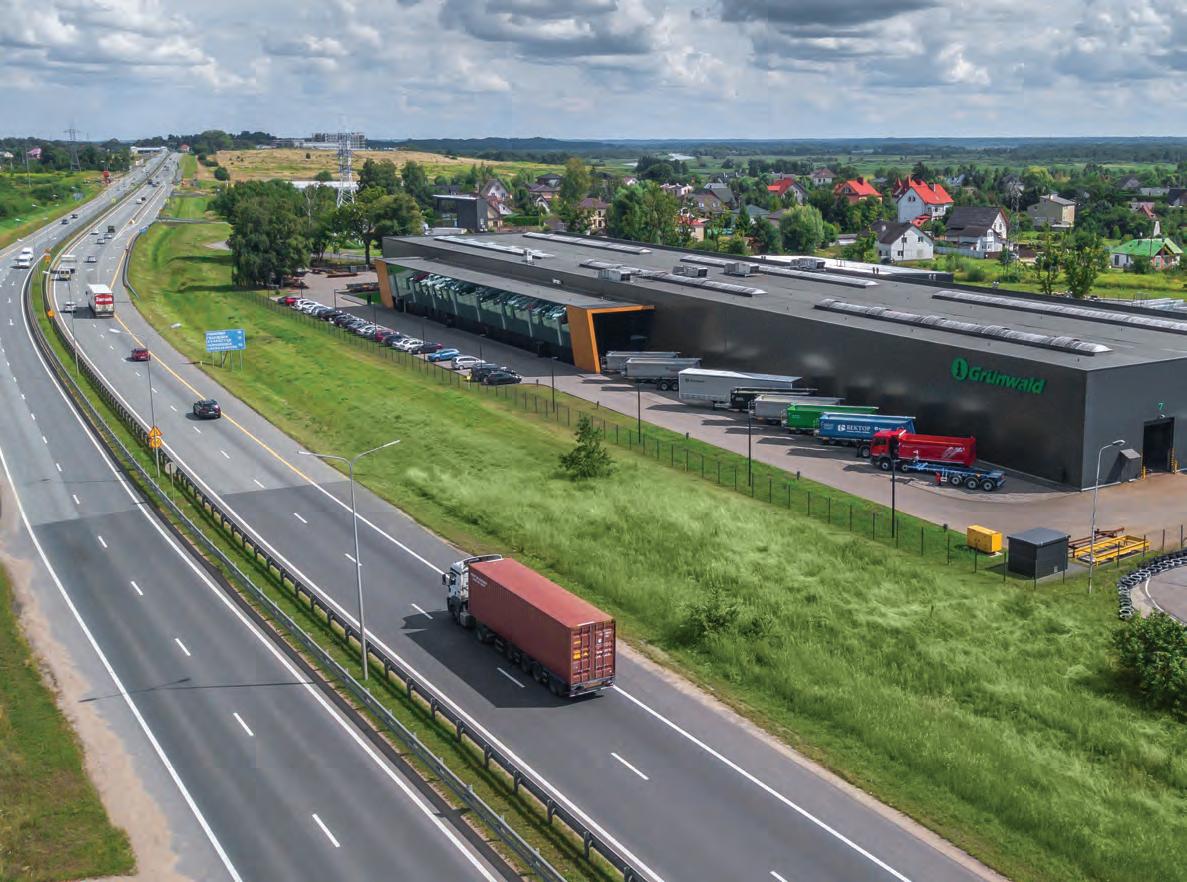
CONNECTIONS
GRUNWALD IS A BUILDER OF ADVANCED COMMERCIAL VEHICLES FROM THE SOUTH BALTIC REGION AND IS CONTINUOUSLY IMPROVING ITS PRODUCTS WITH NEW TECHNICAL SOLUTIONS. EVERY PASSING DAY THE RUSSIAN OEM IS BECOMING MORE OF AN INTERNATIONAL ENTERPRISE AS IT DELIVERS SEMI-TRAILERS AND SUPERSTRUCTURES TO MORE AND MORE LOCATIONS AROUND THE WORLD.
Founded in 2007 and based in the westernmost region of Russia – in the city of Kaliningrad near Poland – Grunwald is gaining momentum in the trailer manufacturing scene. By 2008, the business participated in transport exhibitions across its home country and the following year it collaborated with a large design bureau from Germany, adopting their experience and technology.
In 2010, Grunwald became an official supplier and partner of Volvo Trucks. Two years later, in 2012, the OEM produced its 1,000th semi-trailer under the Grunwald brand.
Since 2013, a project has been launched to create and manufacture Grunwald cargo superstructures for the chassis of European trucks. In 2014-2015, the first export deliveries of Grunwald equipment to the countries of the European Union started. Since 2016, the company developed at a rapid pace. Over the years, production facilities have been built and reconstructed, the range of models has been expanded, and the volume of deliveries is growing, including to foreign markets.
Grunwald HQ.
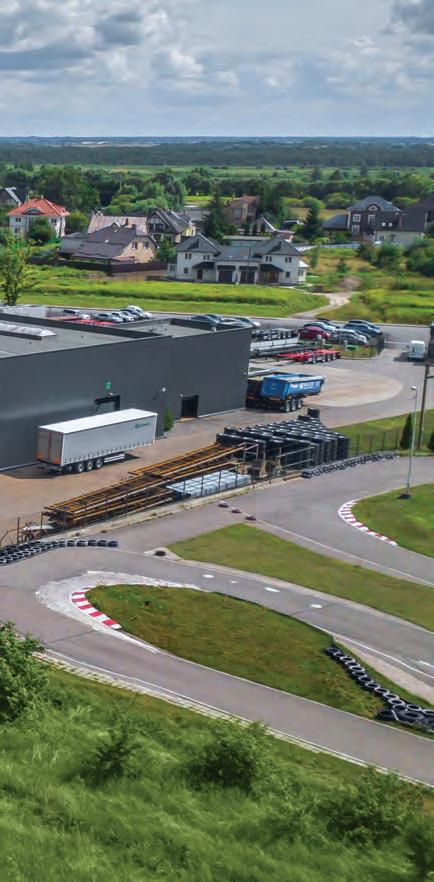
Aleksey Drach Grunwald, CEO
The Grunwald brand has been certified under the Hardox in my Body program of the Swedish steel specialist, SSAB. Another Swedish concern – Scania CV AB – included Grunwald in its list of certified partners. In 2018, Grunwald passed the European homologation and received the right to supply its products to all countries of the European Union.
In 2019, a joint product of Grunwald and the German concern MAN, an 8x4 dump truck, received the ‘Dump Truck of the Year’ award.
15 years of Grunwald
Throughout the history of Grunwald, the position of CEO has been occupied by the inspirer and founder of the company, Aleksey Drach. In general, he has 25 years of experience in the field of transport and the successful management of several manufacturing and trading companies in this field.
Drach said the direction of the company’s most recent activity is the production of modern commercial vehicles including semi-trailers, trailers and superstructures on truck chassis.
“The company carries out a full cycle of industrial production, including
Steel tipper semi-trailer with tarp.
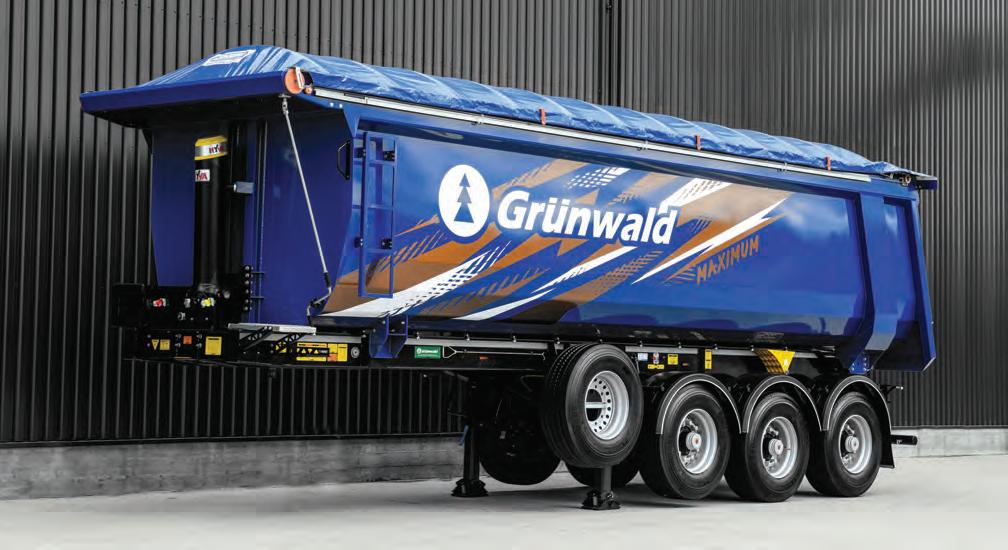
metal processing, assembly and welding operations, painting cycle and final equipment,” he said. “Currently, the company includes three modern production sites and its own service station. The total area of production complexes is over 22,500 square metres. The company employs 550 qualified specialists.”
Industrially, Russia is a country with a welldeveloped industrial economy according to Drach.
“Due to our geographical position in the South Baltic region, surrounded by the countries of the European Union, Grunwald has equally close relationships with suppliers of materials and components from both Europe and Russia. Therefore, we can always offer our customers the best options and delivery times.”
Of the heavy vehicles it produces, Grunwald specialises in tippers, including semi-trailers, trailers and superstructures.
“By industry, these are construction, mining, manufacturing and the agricultural sector,” said Drach. “The growth in sales of Grunwald dump trucks, among other things, is due to a harmonious model range, high customer focus and excellent performance. In addition, we are actively developing our main line. The line of container semi-trailers has withstood an almost complete renewal of the model range with a new generation which is more efficient, lighter and modern. Grunwald curtain and flatbed semitrailers are gradually increasing their share in production, too. In the near future, we plan to significantly strengthen in this segment including plans to build a separate conveyor to expand the production of those models.”
The OEM’s main goal for 2022 and beyond is the forward movement and sustainable development of the business.
“The growth of financial results allows us to gradually implement our investment program – to expand production, invest in equipment, and train new specialists,” said Drach. “Of course, we have clear commercial goals – to increase the number of loyal customers. Since customer support
“SINCE CUSTOMER SUPPORT IS ALWAYS THE NUMBER ONE GOAL, WE HOPE THAT THE NUMBER OF GRUNWALD FANS IN OTHER COUNTRIES WILL CONTINUE TO GROW.” Aleksey Drach Grunwald, CEO is always the number one goal, we hope that the number of Grunwald fans in other countries will continue to grow. We have been able to set ourselves a development vector for a long time, in which every subsequent year becomes more successful than the previous one, and we intend to maintain this trend. A good example of expanding interaction with new customers is the case of clients from the African continent. Initially, customers needed a specific solution - equipment that was ready to work in the most extreme conditions. We have provided such a solution. After the clients were convinced in practice of our competence, the qualities of the created transport, its reliability and unpretentiousness, they were imbued with great confidence in the brand and paid attention to our other products, including products from the second direction – dump superstructures on chassis.”
Reinforced skel for container handling applications.
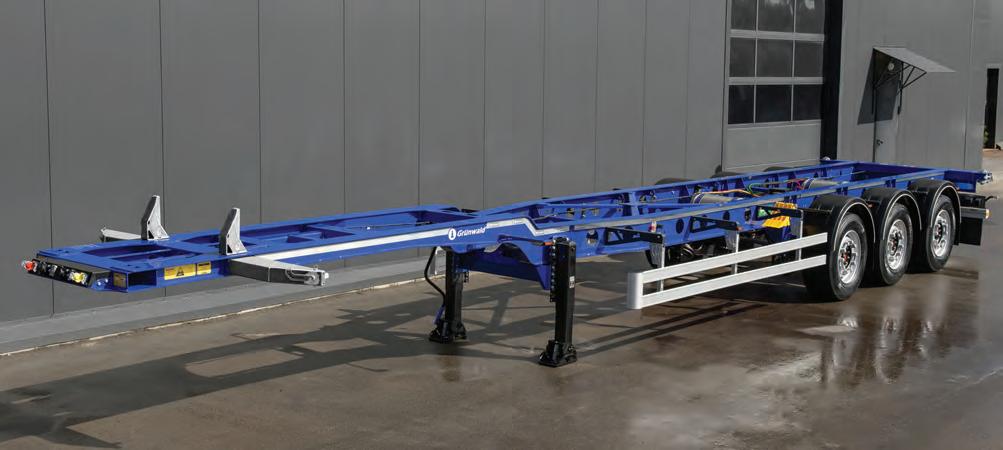
Heavy duty tippers are especially popular among Grunwald’s export markets.
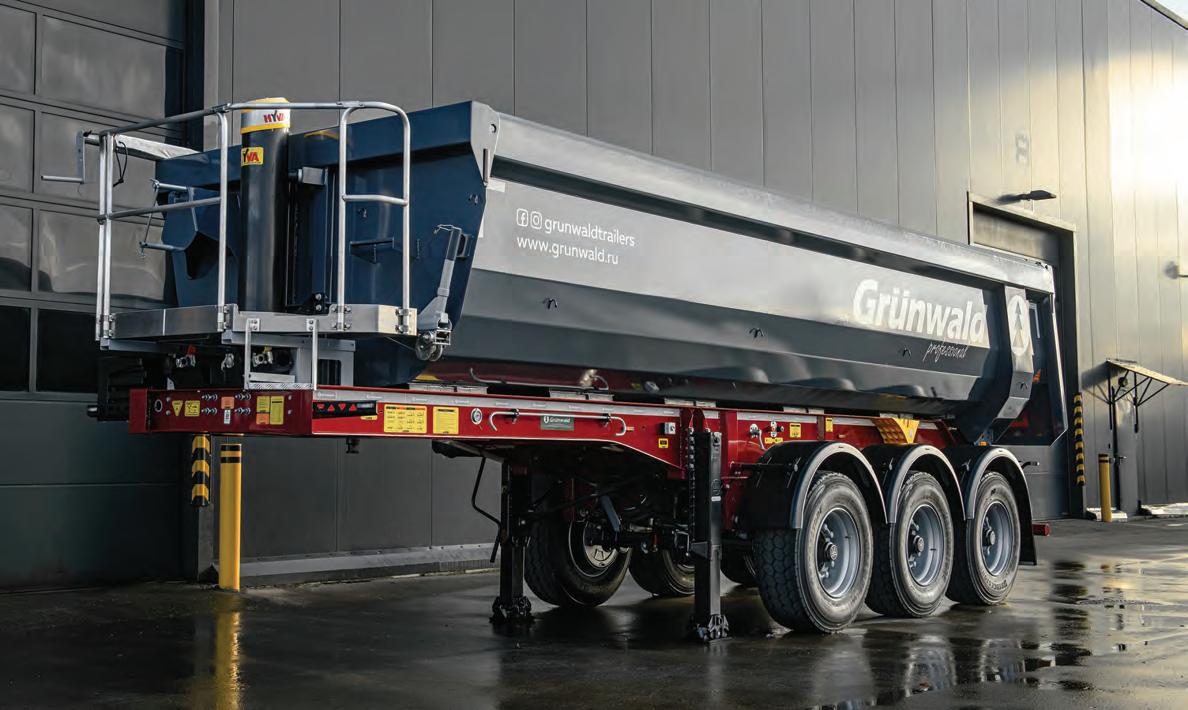
Improving tippers for mining applications in Africa
Grunwald is finetuning its tipper product for use in foreign markets.
The product line, according to Grunwald, is constantly evolving, adapting for regional tasks.
“The useful volume of the new superstructures Gr.M25-SB-SI is 25-metrescubed,” said Grunwald.
“Grunwald engineers are careful to ensure that the quality of the components matches the nature of future transport tasks and the site of use. Therefore, the body is made of wear-resistant and impact-resistant Hardox 450 steel. The use of the original material is confirmed by the certification marks ‘Hardox In My Body’ on the sides of the body.
“In accordance with the transport task for working with highly abrasive materials, the base of the body is reinforced. A removable canopy covers the cab space to provide the required level of safety. Reliable hydraulic equipment from leading European manufacturers is used. The superstructure also combines a low centre of gravity and class-leading interior width. The new Gr.M25-SB-SI superstructures are mounted on a pilot batch of truck chassis and are awaiting shipment to the site of future use.”
Facing freight challenges head-on
Grunwald produces road transport equipment and in turn offers its customers transport solutions. Drach eloquently points out how the OEM stands out from others in the market: “What distinguishes our solutions from others is our attention to the true needs, involvement in the business processes of our customers and, of course, the quality of execution. For the convenience of our clients, we provide related useful tools, such as trade-in or financing with the support of our partner – Siemens Finance.”
Drach is confident the key transport trends from the customers’ point of view will remain unchanged – high efficiency and achieving the lowest possible cost of ownership.
“At the same time, the ways to achieve this goal will be determined primarily by the working conditions, the place of operation, and regional characteristics,” he said. “Technological, modern solutions are in demand on the European market. Transport is created from advanced materials. The priority is to reduce its own weight with a high load capacity. Therefore, we are looking for modern engineering solutions, using the best materials, such as high-strength and wear-resistant steels, and new generation components. In other regions, with difficult working conditions, often in the absence of asphalt roads, powerful and heavy equipment is in demand that can withstand maximum loads. Our competence in creating reliable and enduring transport is in demand here.”
Another key point of difference for Grunwald is its philosophy and unique experience.
“From the very moment of foundation, we adopted advanced technologies,
Grunwald offers industry modern transport solutions for a variety of applications.
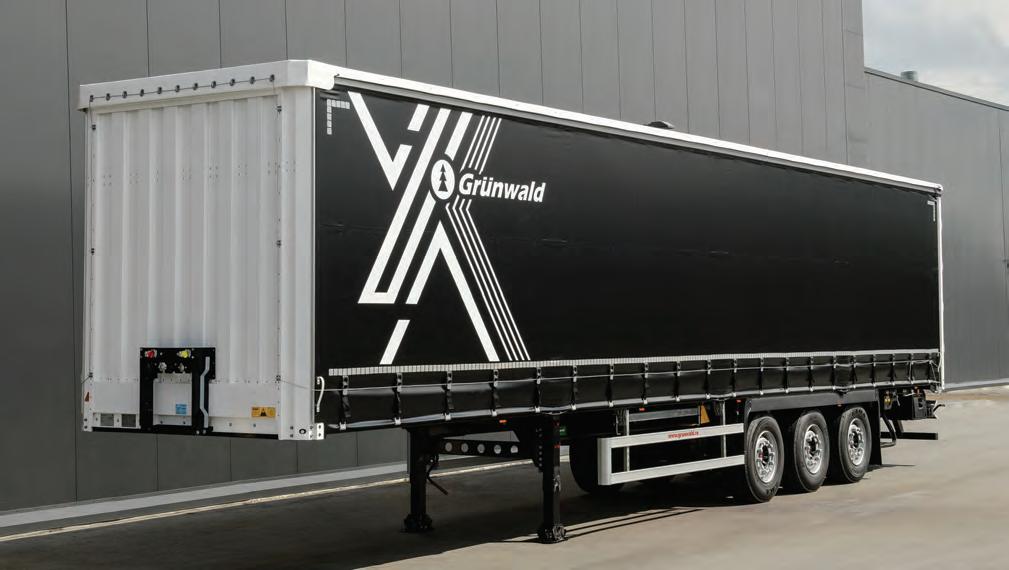
Aleksey Drach Grunwald, CEO
sought to rethink the world experience, cooperated with leading design bureaus in Europe,” said Drach. “Today, the high level of competence of Grunwald engineers is recognised by leading vehicle manufacturers. We supply bodywork solutions directly to the Volvo factory; we are also part of the Scania licensed suppliers system. At the same time, we remain a very flexible company, developing in close cooperation with customers. Therefore, we can create an offer that will meet the expectations of each individual client and regional specifics to a high degree. In addition, we provide good delivery times.
Manufacturing and distribution
Current production capacities allow Grunwald to produce up to 4,000 vehicles per year.
“Our goal is to expand our capabilities through the commissioning of new production facilities,” said Drach. “Now a new modern production complex is being launched, which will be able to reach its planned capacity within a year. According to our forecasts, in 2023, we will reach a new significant milestone of 5,000 units per year. In addition, our investment program provides, starting from 2024, to begin construction of a specialised complex to produce curtainside semi-trailers.”
In terms of the geography of sales, it is quite extensive and covers a vast area from Finland and Sweden in the north to Armenia in the south, from the countries of Central Europe to customers from the Far East.
“At the end of 2021, the Grunwald brand is represented in the markets of more than 10 countries,” said Drach. “Special mention goes to deliveries to the European countries and the African continent. For several years, we have managed not only to increase the volume of these deliveries, but also to expand our product offer. In general, we pay a lot of attention to development in new markets. Every year we take significant steps towards the global nature of deliveries, the brand has new regional representatives and points of presence. Also, we are looking to develop our dealer
network in new markets, therefore we invite professionals from the world of freight transport to cooperate extensively and, possibly, represent the interests of the Grunwald brand at regional levels. It should be noted separately that we invite logistics, transport and construction companies from any corner of the world, any region to get acquainted with our products.”
Grunwald container chassis reach Germany
The first Grunwald container chassis, comprising a batch of 15 units, will become part of the fleet of a large German operator and will start working on intermodal routes in Germany.
A completely new model Gr.C-L3-40-45 has become an expression of all the main trends of our time in the development and creation of vehicles of this class, the OEM said in a statement.
“The semi-trailer is designed for rapid shipment of 40′ high cube and 45′ high cube containers and has high practicality and excellent performance characteristics,” said Grunwald.
“The design, thought out to the smallest detail, allows you to perform a larger amount of work with containers in less time.
“The technical load capacity of the semi-trailer retains a high value of 34,000kg.
“The frame of the semi-trailer is entirely made of high-strength steel, taking into account the most modern design principles and solutions.
“The fitting system, both simple and functional, includes a pair of adjustable clamps in the front of the frame and a pair of stationary fittings together with a retractable bumper in the rear. The new retractable bumper has passed comprehensive tests in the European Certification Organization and has confirmed its reliability and safety. The semitrailer is equipped with an SAF axial unit or JOST axial unit at the customer’s choice. The basic version includes the WABCO Optilink monitoring system.
“First, the global container market shows steady growth in 2021. At the same time, the largest growth in demand is accounted for by the segment of containers with a larger capacity. The growth of cargo turnover pushes carriers to purposefully switch to more efficient container road trains. The first delivery of Grunwald container semitrailers to Germany confirms the brand’s entry into a high level of competitiveness and the desire for stable relationships with customers in foreign markets.”
www.grunwald.ru
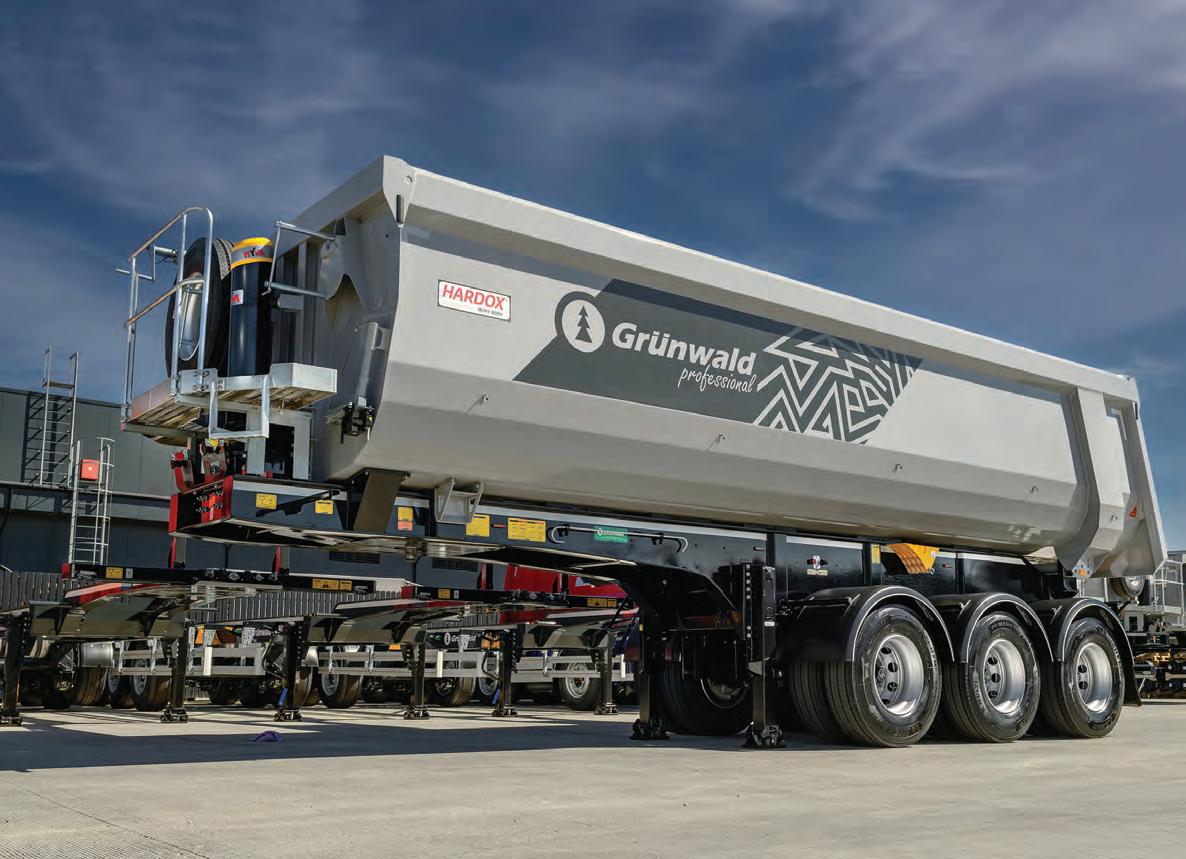