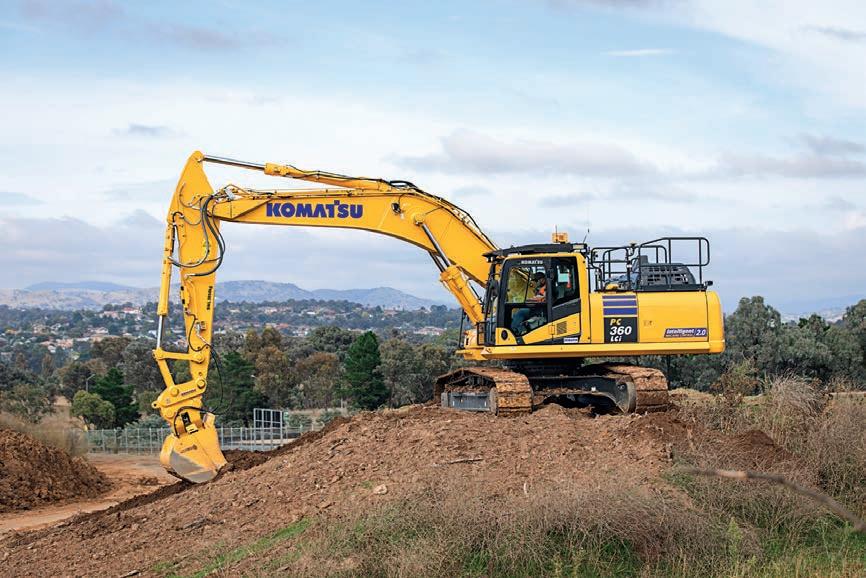
5 minute read
COVER STORY Labour productivity growth
enabling the industry to benefit from these technologies and encouraging the application of that technology in the field.
Another challenge contributing to low labour productivity is attracting and retaining people in the industry, a challenge Muir says technology can play a huge role in addressing.
“We don’t want to be putting people into construction roles that are not going to interest them and technology itself helps with that,” he says. “If a business applies new solutions and technologies across its operations, it makes employment opportunities that arise within the company more interesting to current and future generations.”
“Whereas if we’re still using antiquated methods and policies, people are just not going to be interested in joining our industry.”
Comprehensive customer support
Further to its range of technology, Komatsu’s approach to supporting the customer is paving the way for improved labour productivity across the industry.
“We believe support of the customer is paramount,” says Muir. “We have a whole series of support layers that we introduce now as part of our smart technology, because it’s not good enough to just deliver the technology to our customers – we need to be there to help them apply it or else we believe it’s not going to be applied to its full potential.”
As well as ensuring every piece of smart technology is easy-to-use, Komatsu has cultivated a dedicated support team of Smart Construction consultants available 16 hours a day to instantly assist customers. These experts can dial into the screen in the cab of a machine and show the operator in real-time what buttons to press, propose solutions using ICT and, as a result, improve productivity and safety across the workplace. This provides customers immediate guidance without them having to visit a support centre.
“As well as having that frontline support, Komatsu has technology advisors on call to visit customer sites when needed,” says Muir. “Our Smart Construction machines connect to satellites and base stations, so if the customer needs support outside of their machine, we can have a Komatsu technology advisor to their site within hours.”
But the support doesn’t stop there. Komatsu has a team of customer technology advisors that can join a business as part of the team. The difference being, a technology advisor is a troubleshooting expert who will visit a customer’s site to assist with the immediate problem or challenge at hand, whereas a customer technology advisor is an expert Komatsu customers can hire into their team. Whether they’re needed once a week or once a month, a customer technology advisor can be embedded into the team to teach and help direct the company towards technology adoption and improved productivity.
“For an earthmoving contractor for example, a Komatsu customer technology advisor can help move the business into the digital era,” says Muir. “They will help integrate Komatsu technology, assist with training, help with application and strategy, and ensure overall the business’s journey to technology adoption runs smoothly and efficiently.”
The construction industry has the capability and capacity to step up to the productivity challenge, but even more so with a high level of support from construction technology providers. Komatsu’s customer-centric approach proves that with the right support, improved labour productivity is more achievable than most realise. Rather than simply introducing Smart Construction technology to the market, Komatsu is making the path to new productivity gains seamless and inviting by not only providing the latest in intelligent technology and products, but also supporting its customers into the digital era.
“Unlike some companies that will look to outsource support, we find that providing multiple layers of support and services in house is vital to helping our customers throughout the entire process of technology adoption,” says Muir.
Environmental, Social and Governance
Adding to the labour productivity challenge, Environmental, Social and Governance (ESG) standards play a huge role in the success of a construction business. The impact a business has on the environment and society is becoming ever more important. Owners, investors and project owners are placing an increasing importance on ESG factors and it is something that business operators need to keep top of mind in order to be competitive.
With a vision of reducing the carbon footprint of the construction industry worldwide, Komatsu is looking at multiple different power generation opportunities and methods, from electric to hydrogen cell, to keep its equipment on the move.
“There are many ways in which technology coming into the industry can improve overall ESG,” says Muir. “On the environmental side, our Smart Construction machines reduce rework, they reduce the amount of fuel you’re burning and therefore the amount of carbon you’re emitting, and they get the job done in two thirds of the time.”
“The ESG benefits of our smart machines are tremendous, especially in the environmental space.
“Helping with ESG is the ability to measure it – our Dashboard can measure litres per tonne, emission clouds and can show you, depending on the number of machines which we track by satellite, what the emissions balloon would look like all the way down to the type of engine that it’s running.”
On the social side, Komatsu’s Smart Construction machines improve workplace conditions by strengthening employee health and safety. By improving efficiency, the technology enables the operator to get the job done quickly and reduces the need for manual labour. Machine surround cameras can alert operators if someone is standing too close to a machine and eliminate oversights that may have resulted in an incident. Further, new generation electric excavators emit next to no external noise emissions ensuring minimal impact to society.
“Our Smart Construction machines get the job done in less time,” says Muir. “We’ve seen instances where a project has gone on for more than five years when our technology could have helped the contractor complete it in three.”
Moving into the digital era
Though the future of the Australian construction industry is uncertain, Muir says he is confident that over the next five years we’re going to see an uplift in overall labour productivity.
“We’re already seeing an increasing adoption of machine control and machine guidance as well as design tools and digital twin future we’ll see an upturn in technology application.”
In the next 10 years, Muir says the productivity benefits of technology could be exponential. “Technology adoption needs to become the norm across the construction industry if we want to tackle the labour productivity challenge,” he adds.
“We believe there’s a market here for the technology, and innovation investment in the construction industry is climbing rapidly – it’s a key indicator that we’re moving in the right direction.”
Looking again at McKinsey & Company’s Reinventing Construction: A Route to Higher Productivity report, it names seven levers to drive improved labour productivity across the construction industry. Komatsu’s smart technology and approach to customer support bolsters two of the most important levers: the improvement of on site execution; and the infusion of digital technology, new materials and advanced automation.
The report names four key methods of improving on site execution – the introduction of rigorous integrated planning, implementation of collaborative performance management, the effective mobilisation of projects, and collaboration to reduce waste and variability. From a customer support perspective, Komatsu readily enables these four courses of action.
In terms of infusing digital technology, new materials and advanced automation –Komatsu goes above and beyond to ensure its consistently innovating its technology offering to provide forward-thinking solutions to the construction industry. The company’s ever-evolving Smart Construction range is a testament to Komatsu’s goal of improving productivity, efficiency and safety for its customers.
Melbourne’s leading construction and major infrastructure event
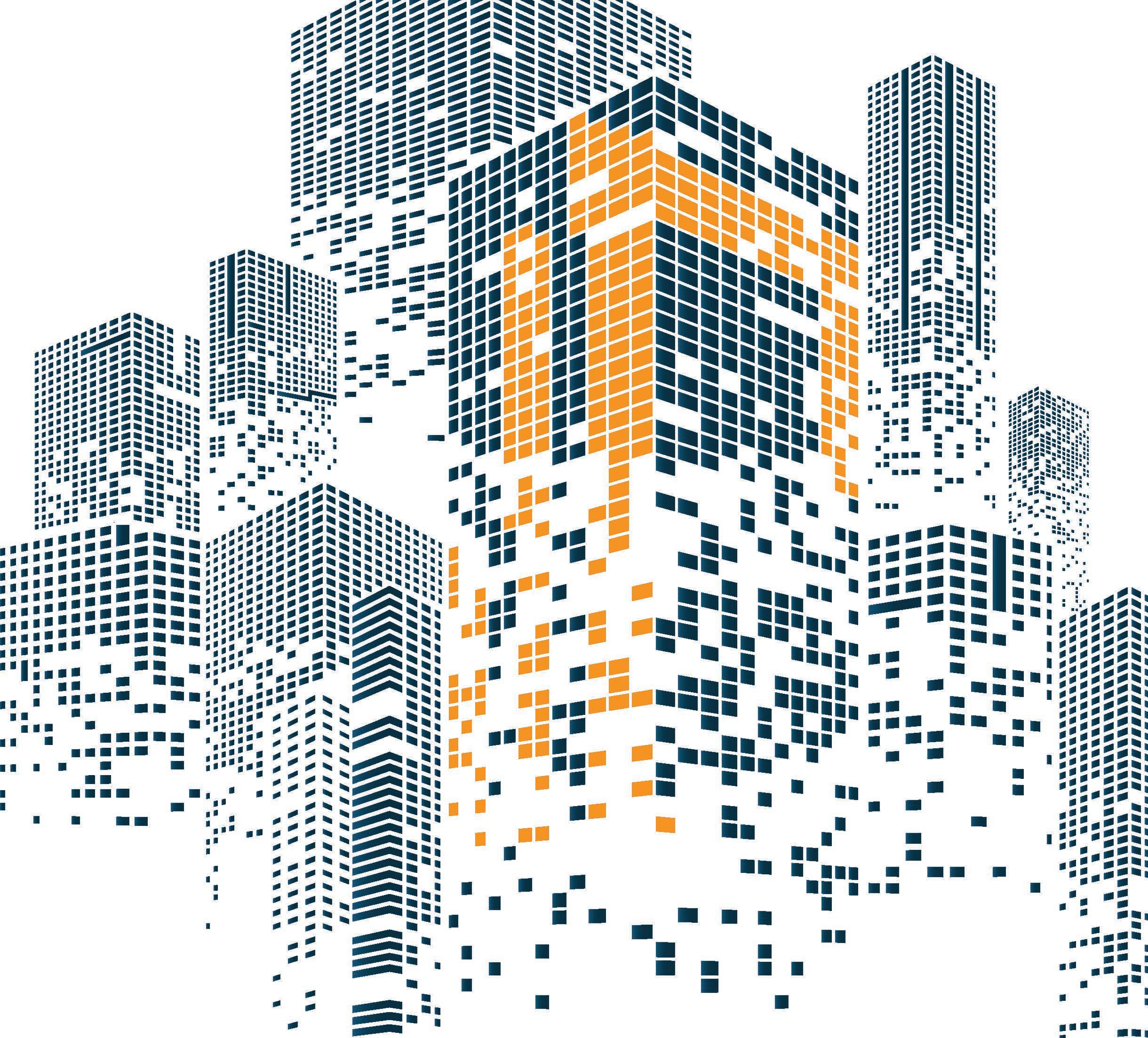
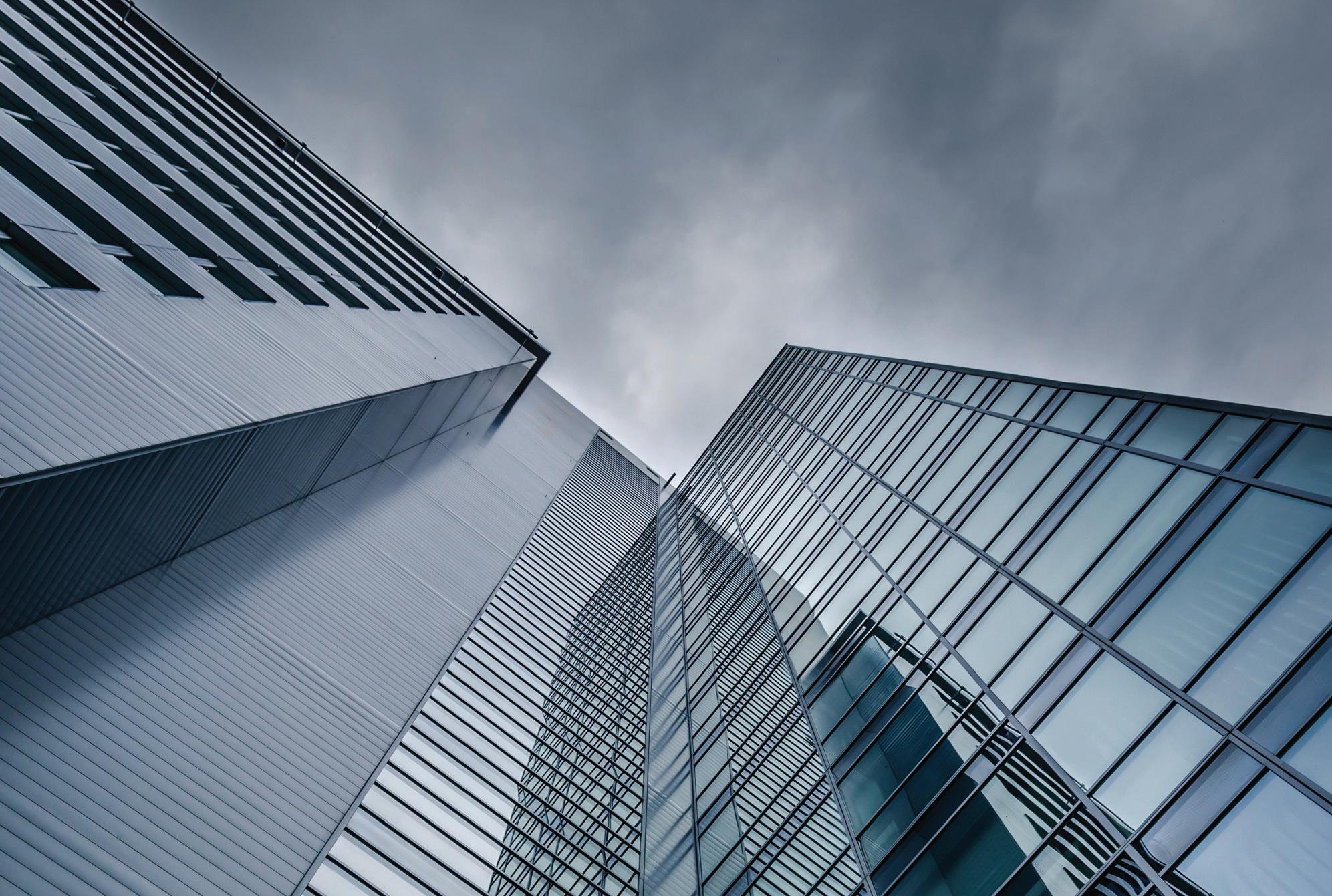
Inside Construction Expo will deliver
Targeted messaging in over 19 industry-leading publications that reach more than 80,000 decision makers across multiple sectors
Digital communications to 28,000+ engaged readers
Premium networking opportunity with industry leaders at the Foundation Awards gala dinner
Supporting Sponsor
Conference Sponsor Association Partners
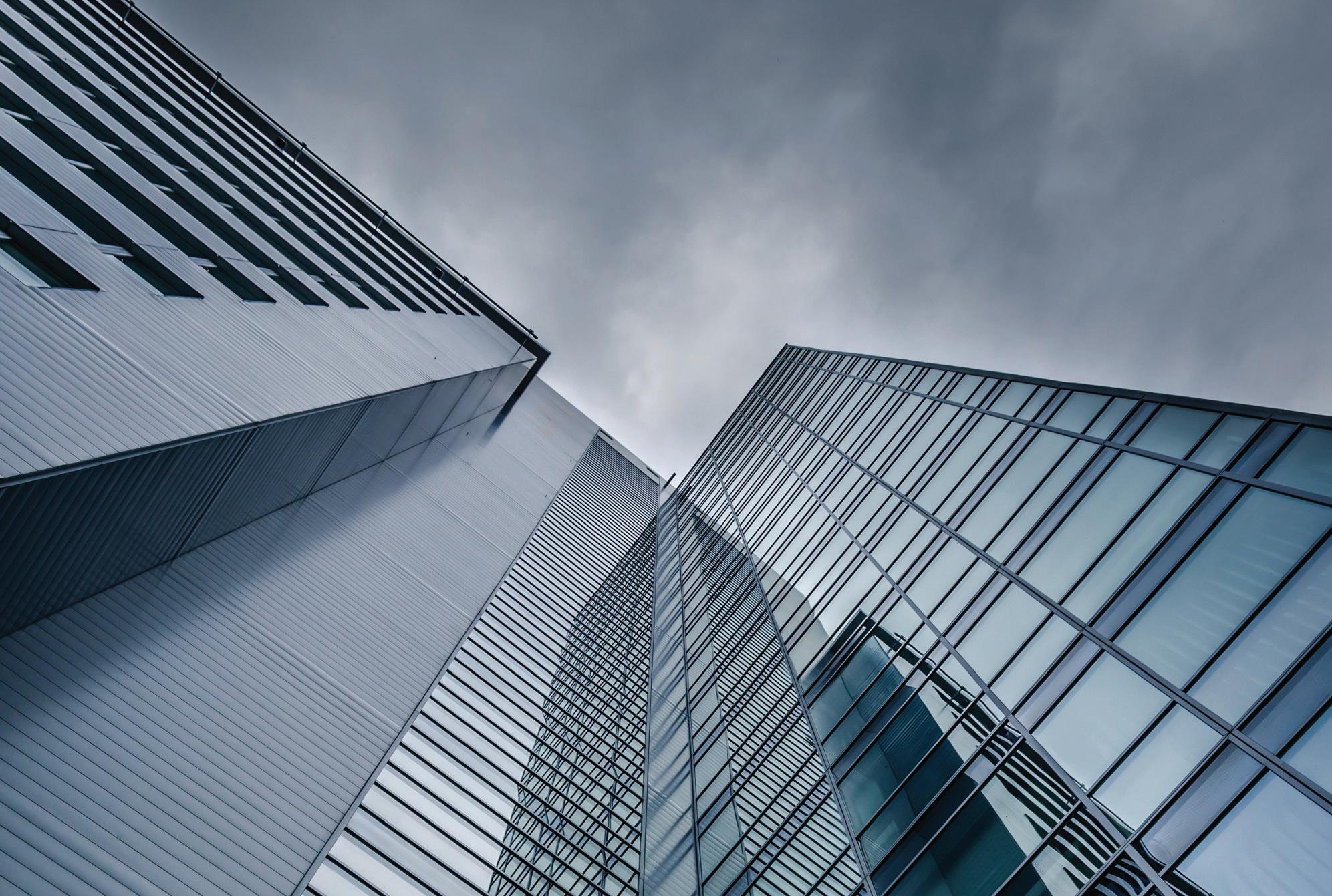
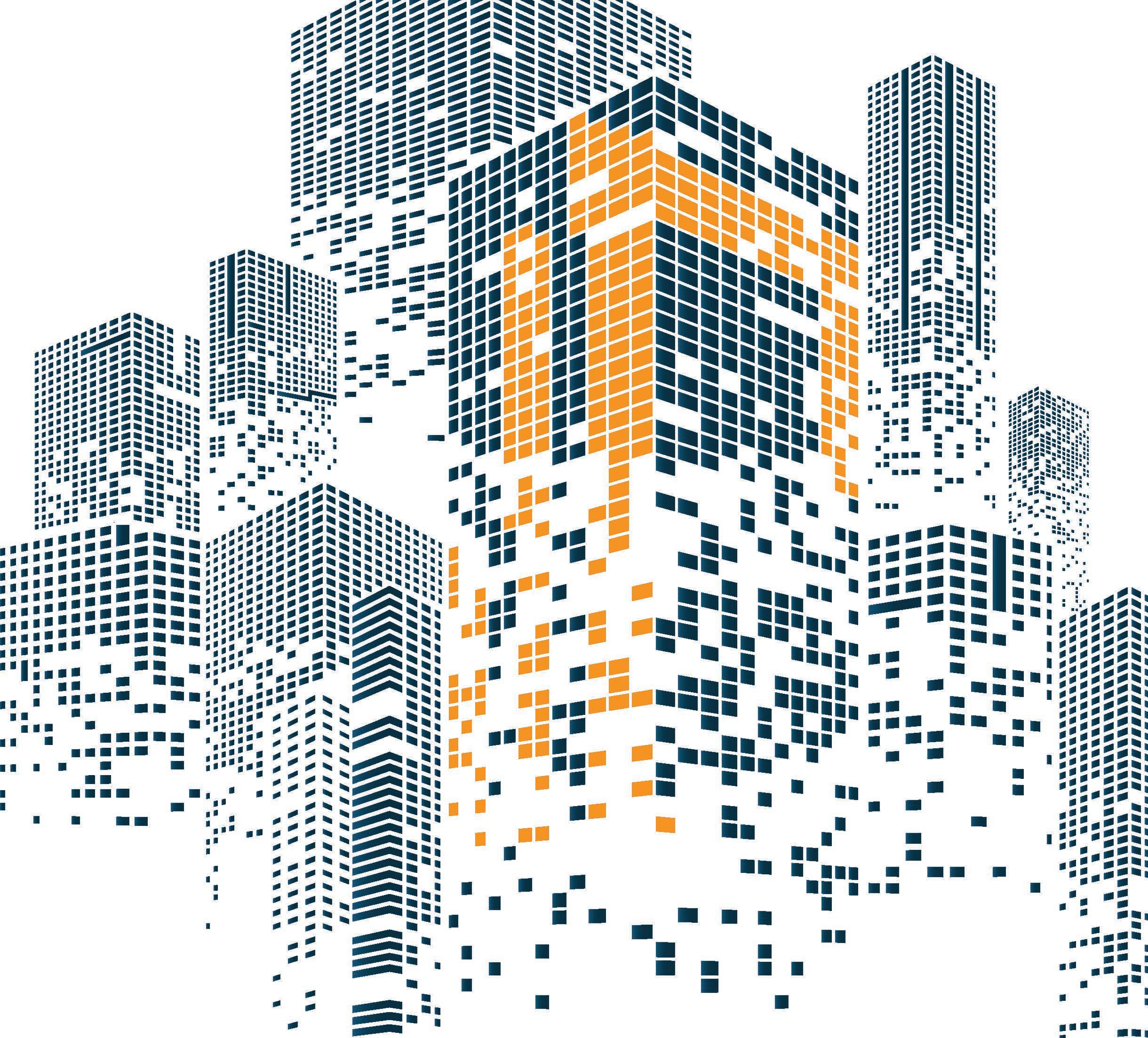