Roads Australia CEO
Boosting productivity in construction
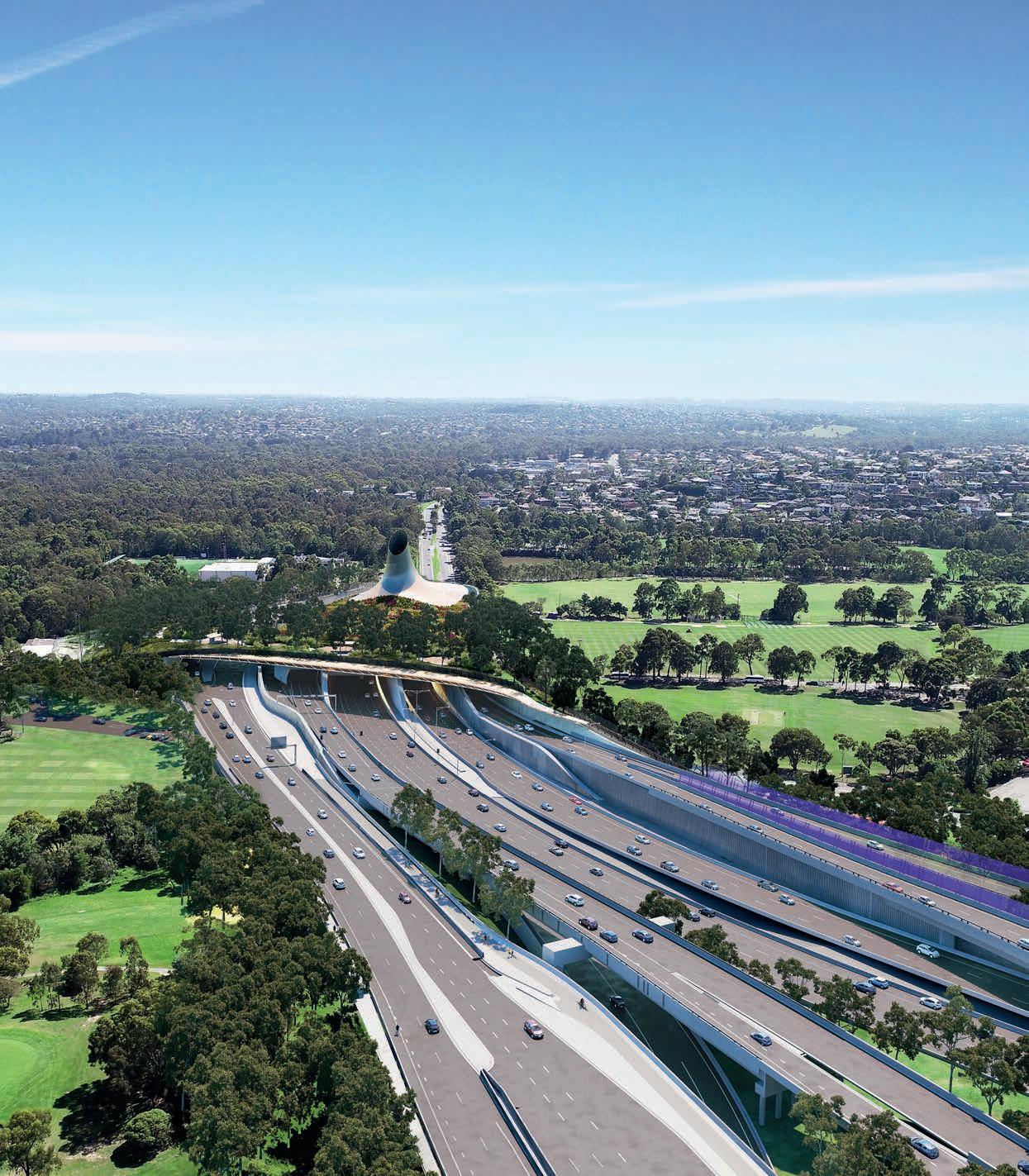
METRO TUNNELS
THE
BACKBONE OF WESTERN SYDNEY

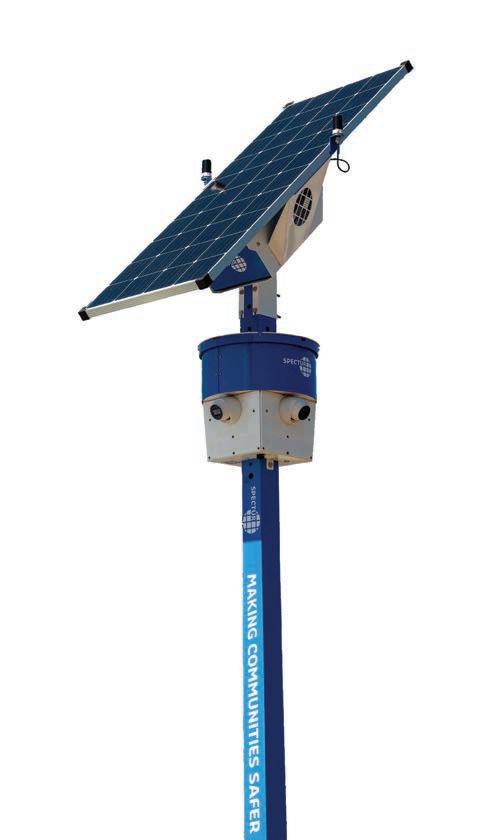
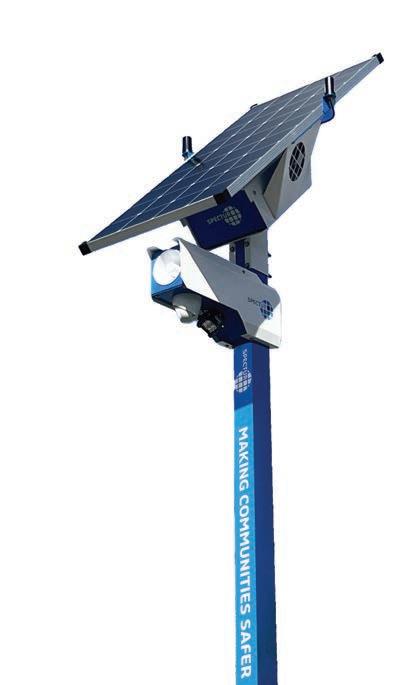
Editor
Assistant
by
Business
Marketing
Publisher
Roads Australia CEO
Boosting productivity in construction
THE
Editor
Assistant
by
Business
Marketing
Publisher
Roads and tunnels – two elements integral to modern transportation systems, and two elements we’re focusing on heavily in this issue of Infrastructure
It’s been estimated that Australia’s roads sector contributes $236 billion in value to the nation's economy each year and supports the jobs of around 1.4 million workers. In a country as large as Australia, with a widely spread population, our roads play a critical role in connecting our communities and delivering the essential supplies they rely on.
And in increasingly built-up cities, tunnels become equally necessary connectors – allowing road and rail networks to expand and create the journeys modern communities need, where pre-existing buildings and other infrastructure may not normally allow them.
In this issue, we take a closer look at Victoria’s enormous $26 billion North East Link, a new road and tunnel system that will provide a vital “missing link” in Melbourne’s road network. We’re highlighting the sustainability initiatives being incorporated into the project that will ensure the development stands the test of time.
Tunnels are also a critical part of any new rail development in metropolitan cities, and the two major projects in this space right now are Sydney Metro and Melbourne Metro. We go underground in Sydney, where tunnelling has just
up for the tunnels to commence operation in 2025.
We’re also thrilled to have contributions from some of the industry’s leading decision makers in this issue: Jon Davies, Australian Constructors Association CEO, Ehssan Veiszadeh, Roads Australia CEO, and Jonathan Cartledge, Consult Australia CEO to name just a few.
It’s a pleasure to bring you content from Australia’s biggest projects and preeminent leaders each edition –I hope you enjoy reading this issue as much as we enjoyed putting it together.
Laura Pearsall Editor, Infrastructure
PERSPECTIVES
RESTORING CONFIDENCE AND CONTINUITY
Consult Australia has undertaken a wide-ranging survey of its members to understand the critical challenges currently facing the infrastructure sector and explore ways to overcome them.
FUTURE-PROOFING PORTS: A STRATEGIC APPROACH
Modern asset management demands a strategic approach – and nowhere is that more evident than in the global supply connectors that are ports.
ASSET MANAGEMENT
ENHANCING RAIL SAFETY AND EFFICIENCY
Accurate insights from comprehensive rail data are critical to ensuring that level crossing hazards can be addressed swiftly and effectively.
DRIVING SUSTAINABLE DEVELOPMENT
With Victoria’s biggest road project, North East Link, well underway, we look at some of the sustainable outcomes it has already delivered.
INVESTING IN QUALITY INDOOR AIR
UNVEILING THE INVISIBLE
GREENER CONCRETE REPAIRS
CULTIVATING LOCAL TALENT
BOOSTING PRODUCTIVITY IN CONSTRUCTION
How can industry and government come together to make Australia’s infrastructure delivery more efficient and effective?
MEETING A TIGHT TURNAROUND
CHANGING THE SWITCHBOARD SAFETY GAME
STEERING RAIL SAFETY
THE BACKBONE OF WESTERN SYDNEY
Greater Western Sydney will be critical to Australia’s future prosperity, and with tunnelling now complete for the region’s new railway line, another vital piece of the puzzle is falling into place.
As Melbourne’s new Metro Tunnel prepares to commence operation in 2025, testing of trains through the city-shaping project is ramping up.
Modern methods of construction offer the industry a pathway for infrastructure delivery that is safe, efficient and sustainable.
New research led by government infrastructure agencies and industry leaders has found that reducing the long working hours in the construction industry could lead to a wide range of unexpected benefits.
Toby Kent has been appointed Infrastructure Sustainability Council CEO, bringing a wealth of experience and an impressive track record in sustainability, resilience and ESG delivery.
Mr Kent joins the IS Council from PwC Australia, where he served as a Partner in the Energy Transition team for the past two years.
Mr Kent’s extensive experience includes more than five years as Chief Resilience Officer for metropolitan Melbourne, as part of the Rockefeller Foundation’s groundbreaking 100 Resilient Cities program, and two years as Global Head of Sustainable Development at ANZ Bank.
He previously held senior roles in the UK and Hong Kong, driving sustainability and climate change initiatives for PwC globally.
Mr Kent co-founded and managed ResilientCo Consulting and has been an active board member of the Business Council for Sustainable Development Australia for four years. He was also Chair of the Future Business Council for three years.
Mr Kent, who commenced in August 2024, succeeds Ainsley Simpson, who departed the IS Council in February 2024 to become inaugural CEO of circular fashion association Seamless. Since Ms Simpson’s departure, Patrick Hastings, Chief Delivery and Capability Officer, had been Acting CEO until Mr Kent took the reins.
IS Council Chair, Deb Spring, expressed her enthusiasm for Mr Kent’s appointment, underscoring his deep expertise in sustainability and authentic leadership style.
“Toby has steered game-changing sustainability initiatives for both public and private organisations and has exceptional stakeholder governance and operational management skills,” Ms Spring said.
“A collaborative, values-driven leader, Toby is the ideal person to progress IS Council’s ambitious agenda.”
Mr Kent said that he is excited about his new role and the opportunity to drive sustainable infrastructure development on both sides of the Tasman.
“I am honoured to join the IS Council at this pivotal time,” Mr Kent said.
“The IS Council has had a transformational impact on the Australian and Aotearoa New Zealand infrastructure sectors. We have $300 billion in assets under rating and our members, who collectively turn over more than $50 billion annually, are championing sustainable practices that resonate globally.
“I am passionate about harnessing our collective expertise to drive meaningful change, promote strategies of shared value, and collaborate closely with industry, policymakers and the community to ensure infrastructure achieves optimal social, cultural, environmental and economic benefits.”
Ms Spring also extended her gratitude to Mr Hastings for his interim leadership.
“Patrick has been a steadfast and capable leader and has maintained our momentum during the transition period. The IS Council is now poised to scale our impact and elevate our influence.
The Hobart Airport upgrade is set to expand the capacity of the runway to better enable long-distance freight and wide-body international flights.
Once works are completed, the runway, taxis and apron will be fit for use by larger Code E aircraft such as Boeing 787s and Airbus 350s.
The upgrade will also support direct flights to Asia for the first time and increase the airport’s capability as Australia’s Antarctic gateway.
Along with works to the runway, taxiways and apron, the project includes renewal of aeronautical ground lighting and electrical systems upgrades and will extend the runway’s operational lifespan well into the future.
Construction is set to be complete by May 2025.
The Federal Government has committed $60 million towards the $130 million project, with Hobart Airport to provide the remaining $70 million.
Federal Minister for Infrastructure, Transport, Regional Development and Local Government, Catherine King, said that Hobart Airport welcomes more than 2.8 million passengers per year and that, thanks to this runway upgrade, that number is expected to climb, boosting tourism and the local economy.
“Direct Hobart to Asia routes will also allow exports to reach their destination faster, in better quality,
greatly benefiting Tasmania’s worldfamous businesses and producers –particularly the fresh produce sector.”
Hobart Airport CEO, Norris Carter, said that the runway will pave the way for non-stop international flights between Tasmania and Asia and one-stop flights to Europe.
“It’s a dream that is now fast becoming a reality, with work expected to be completed in mid-2025 and the first wide-body aircraft to touch soon after,” Mr Carter said.
“Our $70 million investment in the Runway Project and $200 million terminal redevelopment are all part of our plan to build better Hobart Airport and make tomorrow’s Tasmania possible.”
The Queensland Government has collaborated with industry to develop a roadmap to increase the state’s construction workforce.
The partnership aims to address challenges including national worker shortages and flatlining productivity that are impacting infrastructure projects across the nation.
Queensland is determined to set a new standard in the delivery of vital infrastructure such as hospitals, schools, homes and transport services that are key to building thriving communities.
A pilot in Cairns will explore ways to coordinate infrastructure procurement and delivery and grow workforce capacity with early work underway across agencies.
In recognising that new and innovative ways to deliver infrastructure are needed, the roadmap includes targets for government to work towards 50 per cent use of modern methods of construction (MMC).
The Infrastructure Productivity and Workforce Roadmap and Action Plan delivers on a commitment made in the State Infrastructure Strategy 2022–2042, with a focus on continuing and promoting the use of best practice with industry; engaging and supporting decision making around governance and frameworks; driving innovation, digital and data, including technology like digital twins; delivering training that meeting demand for growth and future skills; and becoming an industry of choice for a diverse workforce.
The State Government is investing more than $107 billion in infrastructure over the next four years delivering government priorities that support population growth and liveability.
Queensland Premier, Steven Miles, said that new hospitals, roads, rail, homes for Queenslanders and
transformational infrastructure are the building blocks of the state’s future.
“Our new roadmap sets out how we achieve that – driving productivity and workforce improvements across industry so we can do more and build more,” Mr Miles said.
“Queenslanders can trust that a government I lead has a plan for the future, and we’re going to deliver it.”
Queensland Minister for State Development and Infrastructure, Grace Grace, said that Queensland’s construction industry employs around 280,000 people and contributed $34.2 billion to Queensland’s economy in 2022–23.
“With our growing population, we need to keep building capacity in a sector that’s vital to creating the homes, schools, hospitals and roads of the future,” Ms Grace said.
“Building smarter with a highly skilled workforce is the key to boosting productivity and industry is partnering with us to achieve this.
“MMC is something that’s happening across government already, but we want to see more of it and make it more consistent.
“This work builds on the extensive support and investment the State Government has already made to support the construction sector having the pipeline of tradies it needs to thrive.
“This includes expanding our free TAFE construction apprentices to over 25s, providing $1,000 cash back on tools for first years and ensuring ten to 15 per cent of the hours on our Games Minor Venues contracts are reserved for apprentices or trainees.
“We value the support of industry and stakeholders such as the Infrastructure Association of Queensland and the Australian Constructors Association as we embark on the biggest decade of infrastructure delivery in the state’s history.”
Aten-year $1.6 billion contract has been awarded for the delivery of technology and infrastructure upgrades to Perth’s rail network.
AD Alliance, made up of Alstom Transport Australia and DT Infrastructure, has been awarded the contract, which will see it design, supply and build Perth’s High-Capacity Signalling (HCS) project.
HCS will replace and significantly upgrade the signalling and train control systems on Perth’s rail network, allowing more trains to run more often and ultimately increasing capacity by 40 per cent.
Work will include upgrades to signalling along the total length of the Transperth train network (500km); the installation of more than 7,000 transponders enabling precise train location; the introduction of new in-cab signalling equipment for 125 trains, including the Prospector and Australind regional trains; improved passenger information on more than 600 displays on 89 stations across the network; and the installation of more than 250km of electrical conduit.
The project is expected to create 230 direct jobs and support 750 jobs overall.
The HCS control technology will be housed in the new state-of-the-art Public Transport Operations Control Centre (PTOCC) in East Perth, which will be a central point to ensure smooth and safe public transport operations, including incident management.
The HCS project is funded by both the Federal and Western Australian Governments and will be delivered in stages over the next decade to minimise disruption to train operations.
The Federal Government is committing $300 million to stage one of the project.
The project has been identified by Infrastructure Australia as a priority since 2020.
Sort your entire Quest stay with the Quest App. Check-in remotely, unlock your room with a tap, manage your entire car rental bookings, and score some Airpoints DollarsTM on top of that. Enjoy!
Port of Melbourne has signed a new renewable Power Purchase Agreement (PPA) as it looks to increase its usage of renewable energy.
The agreement with Iberdrola Australia commenced on 1 July 2024, enabling Port of Melbourne to obtain more than 60 per cent of its electricity needs from renewable sources, such as Victorian-generated solar and wind. The PPA will run until the end of June 2031.
This agreement contributes to the Port’s target of achieving net zero emissions for Scope 1 and 2 port operations by 2030, in support of the Victorian Government’s commitment to net zero by 2050.
Port of Melbourne CEO, Saul Cannon, said, “With more than half our electricity soon to be sourced from renewable sources, we are
continuing work to transition the remaining 40 per cent.”
Through short-term Green Power agreements, Port of Melbourne is looking to increase its usage of renewable energy, dedicating to source 100 per cent of its business operations’ electricity needs from renewables by June 2029.
“We are also transitioning our corporate vehicle fleet and marine survey vessel to electric or zeroemissions fuel technologies,” Mr Cannon said.
The PPA signing follows a series of sustainability milestones attained by the Port, including the completion of a $475 million sustainability linked loan. Port of Melbourne has also been ranked first among Australian and international ports in the 2023 Global Real Estate Sustainability Benchmark (GRESB) Infrastructure Asset Assessment.
As Australia plans for a cleaner, healthier future, industry will have to prepare for the billions of dollars in projects that will build new roads and transport hubs.
The National Roads and Traffic Expo is a leading event in the transport industry, bringing together industry experts, government representatives, suppliers and qualified buyers to network, share knowledge and insights, and plan for a changing sector. Over two days, the event expects to see more than 5,000 attendees, 200 exhibitors, 200 speakers and 150 unique presentations.
Prior to the launch of National Roads and Traffic, Australia lacked an industrywide trade transport tradeshow. It is now a major event that provides a space for stakeholders, decision-makers and suppliers to gather from across the sector.
The expo is designed to inspire and encourage the exchange of knowledge and industry learnings, and to showcase innovative solutions providers who promise world-class excellence and infrastructure delivery.
Like all industry sectors, the push to find more efficient, more effective and less carbon intensive practices is driving big changes in transport. Digital construction tools, new electric and autonomous technologies, and cheaper, cleaner building materials all form part of the big picture of driving industry growth at National Roads and Traffic.
The event unites all stakeholders –from road operators to government agencies, leaders who are planning, developing, maintaining and managing the future of Australia’s road network.
These key decision-makers attend National Roads and Traffic to do business and get the latest information on developments in the fields of infrastructure, traffic management, smart mobility and safety.
The event has been engineered to support innovation and collaboration by combining major services and supplier
exhibition with a high-level conference of industry leaders from a wide variety of areas. In 2024, National Roads and Traffic is focusing is on the decarbonisation of infrastructure and transport sectors.
Providers of equipment, products, technology or services that further the industry’s efforts to decarbonise have been encouraged to apply to showcase their unique products and services and take advantage of the opportunity to elevate their brand, generate leads, build their pipelines and boost sales.
National Roads and Traffic is designed to be a cooperative and collaborative opportunity for the whole industry, not competing with other conferences but instead complementing them.
This free event will be held at the Melbourne Convention and Exhibition Centre from 30-31 October 2024.
For more information, visit www.terrapinn.com/exhibition/road-traffic-expo
By Jonathan Cartledge, Chief Executive Officer, Consult Australia
Consult Australia has undertaken a wide-ranging member survey to understand the critical challenges currently facing the infrastructure sector and explore ways to overcome them.
Members report a shift from too much work to pipeline uncertainty.
The confidence of businesses designing and delivering Australia’s infrastructure depends on our ability to see what’s on the horizon. But three quarters of the respondents to Consult Australia’s 2024 membership survey are operating in a higher risk environment that is harder to predict than just 12 months ago.
Australia’s infrastructure industry has spent the last four years buffeted by pandemic lockdowns and supply
chain bottlenecks, labour shortages, cost escalation and record rates of insolvencies. Local businesses have dealt with the consequences of international conflicts and global inflation.
Yet Consult Australia members tell us the most unpredictable aspects of running their businesses are the creeping or sudden uncertainties in the pipeline of projects, ‘death by a thousand cuts’ through increasing regulation and red tape, unaffordable
insurance and unfair contracts. Some of these uncertainties are outside of our control; but many of these issues sit well within our governments’ sphere of influence.
Each year we survey our members to gain insights into current business capacity, staffing impacts, market confidence and future challenges. The findings of our 2024 survey, published in the Confidence &
Continuity report, reveal a “reversal of fortunes” since 2023.
The nation’s five-year infrastructure and buildings pipeline stands at $691 billion according to Infrastructure Australia. However, the federal government’s snap strategic review of infrastructure investment slashed funding for 50 projects in 2023. State governments are now moderating their spending. This has led to uncertainty in the shorter-term, and conflicts with the clear recommendation of the review for reforms that deliver “greater transparency and certainty”.
In 12 months, we’ve witnessed a shift from most businesses saying they had “too much work” to most saying they have capacity. The sectors most likely to identify a lack of work are commercial buildings, rail and roads – no surprises there. Yet 77 per cent of respondents across almost all sectors expect to have capacity within the next 12 months.
Having some capacity gives businesses the breathing room to bid on new work; but this can become a concern when the continuity of work is not assured. Pipeline changes mean that almost half (46 per cent) of consulting businesses have made resource cuts. These cuts make it much harder for
them to ramp back up when the market does and risks inflationary pressures on labour costs.
More than half of respondents to our survey said pipeline uncertainty was their biggest challenge. Professionals who plan, design and deliver infrastructure to last 100 years or more can’t get a view of their own businesses past the next six months. This erodes confidence and creates a vicious circle where businesses can’t risk investing in a future they cannot clearly see.
Pipeline uncertainty isn’t the only crimp on confidence. Seven in ten respondents cited the escalating costs of doing business as their biggest challenge. When asked what was making business so hard, the response was conclusive. Consultants are being asked to sign contracts that pass risk unfairly down the supply chain, often to the party least able to manage that risk. There are “unreasonable T&Cs” and contracts that severely limit the coverage offered through professional indemnity insurance. Builders are becoming more “litigious” while government clients fail to acknowledge the ongoing risks for small businesses in a landscape
of “ever-changing and increasing legislation and mandatory reporting”. These issues come on top of deferred or delayed projects – often after they have passed the tender stage.
This feedback aligns with the recent Arcadis and Australian Constructors Association (ACA) Market Sentiment Survey, in which 71 per cent of respondents said current contracts did not adequately and fairly allocate risk between the contracting parties. “The apportionment of contract risk and liability is the single largest impediment to growth of our business,” one industry participant told the ACA.
Australia’s federation model can be a source of competitive strength that fuels a race to the top. But we currently risk a race to the bottom as regulatory overreach and red tape stifle business growth. In some states this means uncoordinated professional registration schemes or non-standard contract forms, in others it is in the guise of unreasonable management of liabilities or retrospective duty of care.
We know consultants are struggling to access affordable professional indemnity insurance; premiums for consulting engineers have grown by 75 per cent over the last seven years,
www.kennards.com.au/commercial
according to the Australian Prudential and Regulation Authority. Nearly half (47 per cent) of respondents to the Consult Australia 2024 survey noted insurance premium increases of up to 10 per cent, and 62 per cent said fewer insurers were offering cover. Recent new regulations, notably the NSW Government’s proposed Practice Standard for Professional Engineers, introduce new obligations that will make it very hard for smaller engineering firms to bid for work.
What’s the solution? The best way to bring the future into focus is to start at the front end of contracts. This means better planning and coordination of the pipeline of work from the outset, together with fairer risk allocation of work.
Consult Australia champions eight ‘model client’ behaviours, including avoidance of non-standard or heavily amended contracts, and ‘collaborative contracting’ principles which maintain
proportionate liability, balance rights and obligations, and fairly allocate risk. Collaborative contracting encourages industry and governments to use standardised collaborative contracts that prioritise communication and problem solving over disputation.
With the cost of poor productivity exceeding $56 billion each year, according to the ACA, collaborative contracting offers a pathway to more streamlined project delivery, as well as greater pipeline certainty.
Consult Australia’s team continues to champion greater infrastructure pipeline transparency and certainty in every roundtable, forum and committee meeting we host. It’s a message that we carry throughout the halls of power in every meeting with ministers and policymakers. We know restoring confidence and continuity in Australia’s infrastructure sector requires a concerted effort from us all. With fairer contract practices, fewer regulatory burdens and greater pipeline certainty, we can look to the future together.
Jonathan Cartledge.
On behalf of the Western Australian Transport Portfolio, the Public Transport Authority is calling for quotations for an experienced Telecommunication Infrastructure Consultant. The Consultant must possess significant understanding of the Australian telecommunications regime, work practices, business models, commercial drivers and risks associated with telecommunication systems. The Consultant will also possess audit and assurance capabilities relating to telecommunication relocation designs and construction methodologies.
The Consultant will serve as a subject matter expert, offering technical guidance to major transport infrastructure projects which includes analysing technical designs of telecommunication assets, setting engineering specifications, assuring design and supporting with stakeholder engagements.
This is an exciting opportunity to contribute to the future of transport projects in Western Australia with the potential for extension. For further information, log into www.tenders.wa.gov.au | Ref PTA240082 - Provision of Expert Technical Advice for Communications Infrastructure
By Renuka Ranaweera, Principal Asset Management Consultant,
Brightly
Modern asset management demands a strategic approach – and nowhere is that more evident than in the global supply connectors that are ports.
With an extensive coastline spanning more than 25,000 kilometres, Australia relies heavily on its ports as critical supply arteries for economic prosperity and social wellbeing. They are pivotal in shaping the nation’s economic landscape, driving growth and maintaining quality of life for all Australians.
Recent pandemic and global conflict related impacts have highlighted the critical importance of maintaining open and reliable supply chains, of which ports in Australia play a substantial and vital role. Beyond these global risks and impacts, it is important to not lose sight of the local operational risks embodied in sustainably managing port assets.
The range, complexity and interdependence of physical assets required to provide and maintain reliable port operations is extensive. These assets are also subject to dynamic operating and exposure environments in both marine and terrestrial contexts.
With many Australian ports being 30 to 70 years old, many assets will need replacement in the near future. Tightening economic conditions, environmental concerns and emphasis on minimising infrastructure and operational risks demands taking a long-term approach to managing port
assets that extends the lives of existing assets without compromising the services delivered.
For this, it is vital that reliable asset condition and performance data be collected, stored, managed and analysed to support evidence-based investment decisions. By optimising operational, maintenance and capital expenditure, costly breakdowns, operational downtime and supply chain delays can be minimised.
Adopting a strategic asset management approach is how sustainable, reliable and cost-effective port operations can be provided both now and into the future.
The ability to make optimised investment decisions in operational, maintenance and capital delivery activities is greatly enhanced when whole-of-life scenario analyses are undertaken. Combining asset data, life cycle behaviour, service strategies and investment options in powerful predictive analytical tools allows port operators to compare and contrast alternative future outcomes. Informed, evidence-based decisions can be made now that ensure ongoing future needs are sustainably met.
To achieve greater efficiencies and minimise risks in port asset management, port authorities must
adopt appropriate processes and tools throughout the asset lifecycle. Establishing a unified asset register as a single source of truth ensures the accessibility, accuracy, and currency of asset data. Technologies such as drones or remotely operated vehicles (ROVs) can significantly enhance efficiency and reduce risk during data collection, particularly for underwater asset inspections, minimising downtime and hazards to divers.
Standardising data collection methodologies using the Wharf Structures Condition Assessment Manual (WSCAM) developed by Ports Australia ensures consistency across the industry. Predictive analytics tools with 'what-if’ scenario capabilities enable decision-makers to assess the long-term impact of current decisions on the asset portfolio. Visualisation tools such as Geographic Information Systems (GIS) or Business Intelligence (BI) platforms further enhance stakeholder collaboration.
A recent pilot trial at Geelong Port successfully employed ROVs for underwater asset data capture, lifecycle analysis and GIS for data insights and stakeholder collaboration. By implementing these strategic measures, port operators can ensure sustainable delivery of critical services at the lowest lifecycle cost and minimised risk, supporting thriving communities and safeguarding Australia's economic and social future.
As port assets age and approach the end of their lifecycle, it is imperative for port asset managers to act now and make data-driven decisions. Utilise advanced analytics and predictive modeling to foresee potential risks, and implement preventive measures that avoid costly breakdowns, operational downtime, and supply chain delays.
Safeguard your port’s future with 5 data-driven strategic steps to enhance resilience, efficiency, and long-term operational stability.
Learn more at brightlysoftware.com/ports
1 Adopt a Life Cycle Approach
2 Manage Risk Proactively
3 Streamline Data Collection
4 Centralise Data
5 Enhance Communication with GIS Tools
Accurate insights from comprehensive rail data are critical to ensuring that level crossing hazards can be addressed swiftly and effectively.
Rail level crossings pose the highest safety risk on the Australian rail network, with 36 per cent of collisions resulting in injuries or fatalities, as highlighted by the National Level Crossing Safety Strategy 2023–2032. Australian Industry 4.0 enablement partner, Madison Technologies, is addressing these challenges with a solution built off the back of advanced AIoT cameras, leveraging data to enhance the safety and operational effectiveness of rail levels crossings across Australia.
Initially developed for a Queenslandbased rail operator to capture footage of vehicles crossing when the boom arm was going down, the solution excels in generating immediate, timesensitive alerts.
The real-time monitoring system swiftly identifies and alerts operators to potential hazards – such as vehicles or people entering dangerous zones. Advanced algorithms in the intelligent cameras trigger these alerts, allowing immediate action, minimising downtime, and maintaining smooth rail operations. Additional features like crowd and loitering detection help manage overcrowding and address potential risks, maintaining order and safety at crossings.
The solution provides unparalleled situational awareness through real-time footage. Equipped with night vision and weather-resistant capabilities, the intelligent cameras offer 24/7 surveillance.
The IoT Dashboard enhances this by offering comprehensive real-time
views of monitored areas, handling alarm events with ten-second video clips for quick verification and providing direct camera access for operators to view the crossing and establish if the hazard is still in place. This enables decision makers to respond swiftly and effectively to any incidents based on accurate, up-to-the-minute information.
Detailed analytics on vehicle and pedestrian activities provide critical insights. This data enables infrastructure specialists to optimise traffic flow, identify peak usage times, and allocate resources more efficiently.
By understanding traffic patterns, resources can be deployed more effectively, reducing congestion and delays, and improving overall operational efficiency. Furthermore, to ensure the solution’s seamless integration and long-term effectiveness, Madison Technologies offers comprehensive support services. This includes collaborative planning, site selection, installation, solution customisation, rigorous testing, and ongoing support.
Madison Technologies’ Rail Level Crossing Safety Solution benefits a wide range of stakeholders by enhancing safety and providing actionable insights:
Rail network operators require solutions that provide immediate alerts, real-time situational awareness, and data-driven insights to manage hazards swiftly and effectively. Madison Technologies’ solution helps operators maintain smooth operations, reduce downtime, and ensure the safety of both pedestrians and vehicles.
Infrastructure planners and decision makers need comprehensive data to inform their strategic planning and resource allocation. Detailed analytics help optimise traffic flow, identify peak usage times, and implement targeted safety measures. The insights gained support better outcomes and more efficient use of resources, ensuring projects are safe, efficient, and sustainable.
Public safety authorities benefit from high-resolution recordings of unsafe or illegal activities, greatly assisting in their investigations. This both addresses immediate safety concerns and also serves as a powerful deterrent against future unsafe behaviour, promoting a culture of safety among drivers and pedestrians. Additionally, the ability to access live views of the rail crossing supports decision-making in various situations, such as coordinating emergency responses for incidents.
The Rail Level Crossing Safety Solution is a transformative approach that leverages data to create safer and more efficiently managed rail crossings. By integrating advanced AIoT cameras and comprehensive data analytics, this solution aligns with national safety strategies and supports strategic planning and operational efficiency improvements at rail level crossings.
For a personalised demo of the solution, scan the QR code.
Industry 4.0 Enablement
Camera-as-a-Sensor
Gain insights with intelligent camera technology that provides data beyond normal camera vision, enhancing safety, efficiency and productivity.
With Victoria’s biggest road project, North East Link, well underway, Infrastructure looks at some of the sustainable outcomes it has already delivered.
North East Link has reached a critical stage, with the two tunnel boring machines (TBMs) that will connect Melbourne’s M80 Ring Road to the Eastern Freeway almost ready for launch.
Tunnelling will run well into 2026, ahead of the project’s expected completion in 2028, and the resulting 6.5km tunnels from Watsonia to Bulleen are set to take 15,000 trucks off local roads each day and slash travel times by up to 35 minutes.
An important element in this massive program of works is sustainability. North East Link provides annual reports on sustainability objectives and targets that were set in 2019 based on input from stakeholders and the community, as well as technical sustainability assessments. The project mapped those targets against the UN Sustainable Development Goals to help it achieve strong environmental, social and economic outcomes across all phases.
SUSTAINABLE INNOVATION
Implementing innovative and pioneering initiatives in sustainable design, process or advocacy that would be considered a first in Victoria
or Australia was one of North East Link’s targets, which it has achieved through the adoption of more than 220 temporary crash barriers containing recycled crumbed rubber from waste tyres. Much of the success of this initiative can be attributed to collaboration between SafeRoads, Melbourne University and Tyre Stewardship Australia.
Old tyres are a particularly problematic type of waste, as they are non-biodegradable and when discarded can leach harmful chemicals into the environment. They also create fire hazards, posing a considerable danger to surrounding communities.
By using the recycled barriers, North East Link is diverting dangerous waste from landfill while keeping its workforce safe. More than 1600 car tyres were broken down to be used in the barriers, totalling more than 10t of recycled rubber.
In addition to the crash barriers, North East Link has procured $10,000 worth of recycled plastic bollards for its work sites. The Eco T-Top Bollards are the first Australian-made 100 per cent recycled plastic bollards made from other end-of-life bollards that are collected from construction sites across Victoria.
Redirecting plastic waste into bollards is a great example of innovation on projects like the North East Link, driving the benefits of Victoria’s growing circular economy – diverting even more waste from landfill. Initiatives like this one are being driven by ecologiQ, a Victorian Government initiative to recycle content across Victoria’s transport infrastructure projects, transforming Victoria’s waste and recycling sector, creating jobs, supporting industry and innovation and building new markets for recycled materials.
By salvaging and reusing bollards, the North East Link tunnelling sites have diverted 510kg of plastic waste from landfill to date and have reduced the embodied carbon emissions on the project by approximately 840kg.
Resource efficiency is another key sustainability focus for North East Link, encompassing energy, water, material and waste reduction initiatives throughout the design, construction and operation of the program. Progress in these areas continues to be reported, with one example being the design of the Motorway Control Centre (MCC).
An essential element to the operation of North East Link, the MCC will house the technology and staff responsible for monitoring and managing the tunnel.
While there were plans to include a car park and several amenities in the basement level of the facility, the design to allow for the removal of the basement level, therefore reducing the need for 370m3 of concrete and saving more than 55t of steel.
Additionally, an estimated 730t of steel was saved with a mass timber structure, and a further 8700t were reduced from other energy efficiency measures. Solar panels and landscaping with local plants that provide habitat for the neighbouring Birrarung (Yarra River) Parklands are also a feature of the MCC building.
North East Link reported that community members were concerned about the wellbeing of the River Red Gum on the corner of Bridge Street and Manningham Road in Bulleen.
The environment surrounding the tree has prevented natural seed dispersal and germination. To preserve its legacy, seeds from the River Red Gum were harvested and used to cultivate 50 new trees. These saplings were germinated and raised at a local nursery in Eltham before being transplanted into Banksia Park, Yarra Flats Park and Westerfolds Park.
supporting the Victoria’s emissions reduction goals.
Efforts have been made to ensure the most efficient generators are being used during construction. For example, an assessment of three large generators at Bulleen found that they were only operating between 20–30 per cent of their capacity and were switched out for smaller generators, leading to savings of approximately 38t of carbon annually.
opportunities for disadvantaged and First Nations Australians.
With construction ongoing in the area, a new management plan has been established to support the survival of the original tree, estimated to be more than 300 years old.
Another target for North East Link is to mitigate the risk of urban heat islands (UHI) by replacing canopy lost during construction. The northern regions of the project were identified as an area of high-temperature and vulnerability to UHI. To combat this, the design for the North East Link includes the creation of open spaces and the planting of more than 30,000 trees.
The equivalent of five MCGs of parklands will be created along Banyule Creek at Borlase Reserve, as well as a 2km tree-lined boulevard for Greensborough Road, 2ha of green space as part of the Yarra Link green bridge over Bulleen Road and three new wetlands along the Yarra River and Koonung Creek in Bulleen and Balwyn North.
Another key priority for North East Link is making the tunnel’s ventilation and lighting systems as energy efficient as possible. To reach this goal, North East Link has looked at how jet fans can be optimised to respond to varying traffic conditions. An energy efficiency analysis found that this could reduce energy demands by approximately 15 per cent over the life of the asset, without impacting the functionality of the ventilation system or air quality inside the tunnel.
As for lighting, North East Link is looking to use photometer sensors at the tunnel portals to adjust light levels in those areas in real time, according to whether its light or dark outside. It is estimated this will reduce the energy demand of the tunnel lighting by close to 30 per cent.
Another key focus area for North East Link is to facilitate opportunities for economic development, provide a
The Willan Program is working to build engagement and career opportunities in construction for young Aboriginal people who come from backgrounds of generational unemployment. The program includes ten weeks of pre-employment training, with all successful participants obtaining a Certificate II in Construction Pathways.
The Foundations in Civil Skills pilot program aims to break down barriers for women entering the construction industry. The paid, 18-day training course was designed to equip candidates with the skills and confidence to work as a general labourer on site, and participants were guaranteed employment for one year on North East Link. Five Aboriginal jobseekers are in full-time roles with Spark subcontractors following the program.
To upskill its sustainability and social outcomes teams as construction progressed, North East Link’s central package contractor, Spark, partnered with a leadership specialist to develop the Make Your Spark program.
Recognising that positive sustainability outcomes often require organisational change, the Make Your Spark program sought to increase participants’ leadership
Road section began construction in 2024, with works on the remaining Hoddle Street–Burke Road and Tram Road–Springvale Road sections expected to commence in 2025.
Preliminary works to complete the M80 freeway kicked off in March 2024, with major construction expected to commence later in the year pending final approval of the urban design and landscape plan.
As the project continues to progress, North East Link will share its sustainability achievements, showcasing innovative approaches that mitigate the impact on Victoria’s environment will meeting the state’s infrastructure needs.
Installing advanced filtration systems in new office and apartment buildings isn’t just a matter of health and safety – it’s a strategic investment that can boost sustainability and reduce costs in the long-term.
Clean air is essential in all buildings to protect against airborne contaminants, and in the wake of COVID-19, this is more well-known than ever before.
Indoor air often contains a variety of synthetic and naturally occurring substances that can have negative health effects.
Clean air has been found to have a range of benefits, from improved health to increased productivity. It is particularly important in environments where there are high concentrations of people in condensed spaces, such as office and apartment buildings.
Prioritising high quality filtration systems at the beginning of a construction project can mitigate future costs and promote sustainable practices.
Investing in filtration technologies is integral for ensuring a healthy indoor environment, but there are other factors to consider beyond the initial cost, which is where a life cycle cost (LCC) analysis comes in.
LCC considers all the associated costs across an item’s entire lifespan, from the initial purchase and installation
to maintenance and replacement costs. When it comes to air filtration systems, it’s important that LCC also includes the costs of downtime, energy consumption and environmental impact.
For new office and apartment buildings, the holistic approach of an LCC analysis can ensure the continuous supply of clean air that boosts wellbeing and productivity, while reducing costs in the long run.
A higher upfront investment is typically rewarded by reduced ongoing operational costs such as maintenance and repair. Additionally, upfront investments often lend themselves to the incorporation of advanced technologies and efficient designs, resulting in better performance and further cost savings.
Efficient air filtration systems not only contribute to high quality indoor air, but also play a role in reducing energy consumption when the appropriate filtration system is chosen.
Environment such as office and apartment buildings do not require the same purification as hospitals, and thus, capturing larger particles is more than
To learn more, visit www.camfil.com/en-au
enough to have positive impacts on health and wellbeing. In such settings, bag filters are often used in conjunction with HVAC systems to remove dust, debris and contaminants from the air –keeping the people inside healthy while reducing energy consumption.
Camfil provides commercial and industrial air filtration and air pollution systems targeted at improving equipment productivity, minimising energy use and benefitting the environment and human health. Camfil systems feature a singular filter with greater capacity and capability than traditional air filters that require two filters to capture all particles. Camfil’s innovative single filter design reduces the replacements required, resulting in less wastage and supporting sustainability.
As a leading manufacturer of premium clean air solutions, Camfil also customers a detailed LCC report, which includes cost analysis and potential energy savings, as well as filter replacement and waste optimal filter replacement intervals, all considered at different application and environmental conditions.
Using Camfil’s Life Cycle Cost Analysis software, our experts conduct a comparative analysis of different air filters to provide you with a comprehensive report on potential cost savings.
Detailed LCC report inclu des:
Cost analysis and potential savings for energy, filter replacement and waste
Optimal filter replacement intervals
Consideration of different application and environmental conditions
Camfil offers a complimentary Life Cycle Cost analysis and supports you in selecting the right air filter sol
To send your en qu iry, please SCAN THE QR CODE
Air quality is a significant concern on construction and mine sites – where workers are exposed to harmful respirable particles like crystalline silica –making continuous monitoring critical for ensuring health and safety.
Silica dust, generated during activities using materials like concrete and stone, presents a serious health risk to those working in industries such as construction and mining. An estimated 230 people develop lung cancer each year due to past exposure to silica dust at work.1
it’s really important to continuously monitor air quality in real time.
control measures are functioning as intended.
Additionally, by feeding air quality data into Kallipr’s cloud-based platform, Captis users have a clear view of air quality levels over time.
Moreover, construction sites can also harbour other hazardous particulate matter. Knowing when silica and other contaminants exceed permissible limits can help protect workers from these hazards and ensure compliance with regulatory standards.
As leading experts in remote monitoring IoT solutions, Kallipr helps businesses to collect and store critical data in a centralised platform.
When integrated with air quality monitors supplied by Active Environmental Solutions (AES), Kallipr’s Captis data loggers can automatically capture air quality data at continuous intervals, sending that information back to a central hub, ensuring ongoing monitoring of hazard levels without the need for manual sampling.
Kallipr Technical Solutions Specialist, Armaghan Cheema, said, “When it comes to industries like construction, where dust levels can fluctuate rapidly,
“Having all the data around relevant air quality parameters can assist in making informed decisions. Users will know whether air quality levels are above or below what’s acceptable.”
Kallipr works closely with AES, a provider of air quality monitoring solutions that can measure dust and silica levels even in the harshest environments.
A spokesperson for AES said, “By continuously measuring pollutants such as dust and silica, these monitors enable site managers to swiftly identify and mitigate hazardous conditions, ensuring a safer working environment.
“This proactive approach reduces the risk of workers developing respiratory illnesses and long-term health issues caused by exposure to harmful levels of airborne contaminants.”
Through email and SMS alerts, Captis users can be notified when air quality levels exceed set thresholds, allowing them to take prompt action to protect themselves and other workers on site. Site managers can also assess whether ventilation systems, dust suppression techniques and other
1https://www.cancer.org.au/cancer-information/causes-and-prevention/workplace-cancer/silica-dust
“If you’re monitoring multiple sites, you can put that information together and see if there’s any patterns or trends,” Mr Cheema said.
This also has benefits for compliance. Australia has strict regulations regarding permissible exposure limits for silica and dust. The workplace exposure standard for respirable crystalline silica (RCS) is 0.05 mg/m3 averaged over an eight-hour period.
Through real-time monitoring and periodic regulatory air sampling, businesses have the relevant data to make sure that they're complying with those regulations to ensure worker safety.
Monitoring air quality through manual sampling alone, where someone is sent to the site, can be costly and inefficient. Especially for sites that are geographically dispersed and potentially even difficult to access.
“Having a comprehensive record of different conditions at multiple sites enhances safety programs, avoids the risk of human error and eliminates the cost and time spent travelling to the site.”
Combining the resources of our respected editorial team with the knowledge and insights of some of the best and brightest minds in the sector, Infrastructure shares thought-leading and thought-provoking content that tackles the industry’s critical questions.
www.infrastructuremagazine.com.au
With a global focus on sustainability, it’s important to look at every aspect of the infrastructure industry to find ways to get an edge.
Reducing the environmental impact of the construction industry is becoming a worldwide priority, particularly in Australia.
In New South Wales, new sustainability standards for nonresidential development came into effect from October 2023. The sustainability provisions for non-residential development include ensuring general sustainability considerations for all developments, including water and energy efficiency and waste minimisation, embodied emission measurement and reporting for all developments and more.
In response to the growing demand for more sustainable construction products and practices, Fosroc ANZ's Renderoc Plus range provides builders and engineers with a concrete repair solution that is more sustainable while also being highly durable and faster to apply.
The Renderoc Plus range boasts a significantly reduced carbon footprint, thanks to the reduced proportion of cement in its concrete mix.
According to Hamid Khan, Product Segment Specialist Concrete Repairs and Grouts, cement manufacture is a major contributor to carbon emissions.
“Each tonne of cement produced generates approximately 900kg of carbon dioxide. By replacing up to 65 per cent of the cement in our repair mortars with repurposed ground granulated blast furnace slag (a waste product from iron and steel manufacture), we reduce the amount of carbon dioxide released into the atmosphere,” Mr Khan said.
With greater strength, reduced shrinkage and greater compatibility than alternative concrete repairs mortars, Renderoc Plus products guarantee the long-term integrity of concrete repairs without the environmental cost.
The Renderoc Plus range comprises three products:
♦ Renderoc HB40 Plus – used for vertical and overhead patch repairs, with localised trowel or wet spray application, up to one square metre repair area.
♦ Renderoc HB70 Plus – used for vertical and overhead patch repairs with localised trowel or wet spray application, up to one square metre repair area. Suitable for vertical trowel builds between 5-100mm where the required strength is greater than 45MPa.
♦ Renderoc LA55 Plus – suitable for deep section patch repairs (between 50-500mm) requiring high strength (between 30-75 MPa). Applied using form pour or pump, in all orientations.
In addition to offering enhanced sustainability, durability and buildability, the Renderoc Plus range is classified RCS Hazard Free (containing <0.1 per cent respirable crystalline silica) and has options suitable for potable water.
Fosroc ANZ Area Sales Manager Mike James said he has noticed increasing interest in the Renderoc Plus range from engineers who are striving to meet sustainability targets on projects.
“Recognition of Renderoc Plus's green credentials is driving a huge amount of interest. The beauty of
the Renderoc Plus products is that they deliver sustainability benefits without comprising on durability or performance.”
All Renderoc Plus products conform to the highest European standards and deliver long-lasting repairs that extend the serviceable life of concrete structures.
The enhanced durability of Renderoc Plus repairs is due primarily to two factors: excellent product adhesion with existing substrates, and reduced permeability of the repair.
According to Mr Khan, it's the addition of the ground granulated blast furnace slag that makes repairs less permeable to moisture or chloride.
“Not only does the blast furnace slag reduce the environmental footprint, it also makes the concrete less permeable and more chemically stable," he said. "By reducing chloride diffusion, the steel reinforcement is protected from corrosion over time making the repair more durable.”
Renderoc Plus products are becoming increasingly popular with applicators, who find them faster and easier to apply.
“The consistency of the Renderoc Plus products means that in many instances, only one application is necessary, rather than multiple,”
Mr James said.
“For project managers, this means greater site efficiency. For customers, this means their projects can be completed faster.”
In an era where sustainability is not just an option, but a necessity, InfraBuild has teamed up with the University of New South Wales (UNSW) and Monash University to develop new, sustainable solutions for the construction sector.
The result is SENSE Solutions®, a new product range that provides industry with lower embodied carbon construction solutions.
These alliances are not only advancing industry innovation but are also fostering an environment where academia and industry converge to create ground-breaking solutions.
Their lead innovation, SENSE 600 reinforcement bar, is made from 100 per cent scrap steel, using up to 16.7 per cent less raw material to deliver up to 39 per cent lower embodied carbon compared to their standard 500N reinforcing steel. In addition, SENSE Solutions also offers SENSE 600 TrenchMesh™, which delivers a lower embodied carbon construction solution for the residential construction market.
The partnership between InfraBuild, UNSW and Monash has been instrumental in delivering SENSE 600. Through rigorous research and development, the teams have focused
Partnerships between industry and universities are having a positive impact in the development of new materials to suit the modern construction environment. For more information, visit www.infrabuild.com/sense-solutions
on a construction solution that optimises high strength steel and a new innovative bar design. This partnership exemplifies what can be achieved through the power of collaboration, delivering a solution to the construction industry that helps reduce resistance to change.
“By integrating academic research with industry practices, we've been able to push the boundaries of material innovation. This collaboration is a testament to what can be achieved when we combine our expertise and resources,” said Professor Stephen Foster, Emeritus Professor and Former Dean of Engineering at UNSW.
The involvement of UNSW and Monash University in the development of SENSE Solutions goes beyond research and development. InfraBuild's investment in local talent through these partnerships is a strategic move that aligns with its sustainability goals. By fostering a culture of continuous improvement, InfraBuild helps ensure that innovations such as SENSE Solutions remain at the forefront of the industry.
The ease of adoption is a critical factor in the success of these new materials, with a strong focus on SENSE 600 products being seamlessly integrated into existing construction workflows. Engineers and builders
can use the same design software and equipment, with no additional training or changes to their processes, minimising disruption and encouraging widespread adoption of these sustainable steel alternatives.
Another benefit of the SENSE Solutions range is its compliance with Australian standards. Both SENSE 600 and SENSE 600 TrenchMesh™ are CodeMarkcertified and can conform to AS/NZS 4671 and AS 2870 respectively. This precertification reduces the complexities and uncertainties associated with using imported steel, helping construction projects meet safety and quality requirements without unnecessary additional costs or delays.
This collaboration with UNSW and Monash University highlights the power of local innovation to help drive industry-wide change. By leveraging the expertise of leading academic institutions, these partnerships support the construction industry through product and process innovation.
"This collaboration is a beacon of what we can achieve when we unite for a common goal – a sustainable and innovative future for the construction industry,” Prof Foster said.
By Ehssan Veiszadeh, Chief Executive Officer, Roads Australia
How can industry and government come together to make Australia’s infrastructure delivery more efficient and effective?
Australia’s decades-long challenge with infrastructure productivity is the sleeper issue that we cannot afford to ignore.
Infrastructure investment underpins our economic growth and quality of life, however, productivity in the sector has not improved in 30 years.
Overall, Australia currently ranks 16th in the Organisation for Economic Co-operation and Development (OECD) for productivity – our lowest in 60 years. We also recently slipped from 14th to 16th in the World Digital Competitiveness Ranking.
While slowing, Australia’s infrastructure pipeline is valued at $230 billion over five years and will grow as housing, energy and defence investment increases.
The task for industry is significant, however inefficiencies in procurement and delivery persist while adoption of productivity-enhancing measures such as digital twins, artificial intelligence, machine learning and robotics, remains low.
This is driving up construction costs and impacting delivery of
the infrastructure pipeline and the sustainability of our industry.
At risk is Australia’s global competitiveness and our ability to efficiently deliver infrastructure that meets the needs of our growing communities.
Industry leaders have long called for a nationally coordinated effort to improve construction productivity and innovation.
Others have rightly argued that government can't effectively pull policy levers until there is a nationally consistent set of measures in place.
The case for change is strong but as an industry we have yet to move the dial on reforms to make Australia’s infrastructure delivery more efficient and effective.
Now that we are facing a significant shift in market conditions, can industry and government come together to fundamentally shift productivity in the infrastructure sector?
Declining public infrastructure funding, cost escalation and an increasingly difficult industrial landscape are
fundamental challenges facing the Australian infrastructure sector.
Added to that is the imperative to decarbonise, manage restrictive local content quotas and meet a complex set of standards that vary from one jurisdiction to another.
It is an undeniably challenging time to do business in Australia.
This is the clear message we hear from Roads Australia's member organisations, including transport agencies, major contractors and consultants, road owners and operators, material suppliers and technology providers.
In a financially constrained and uncertain environment, risk allocation remains a concern for industry.
Acknowledging the shared ambition for better project outcomes across the public and private sectors, there is a need for commercial approaches that are more reflective of current market conditions.
Improving public sector procurement capability also requires ongoing focus, as do improvements to bidding processes that are still characterised by unreliable
The opportunity cost for assembled project teams awaiting tender outcomes undermines the sustainability of the industry.
There is also a need to continually pursue more collaborative contracting approaches with appropriate risk allocation and mitigation between clients, contractors and subcontractors.
Project packaging, which engages all tiers of the industry, offers substantial productivity benefits and should be adopted as much as possible.
The approach taken in the Level Crossing Removal Project in Victoria is a good example, and one that has fostered a highly collaborative and innovative culture.
Last year’s necessary reprofiling of the federal infrastructure pipeline delivered hard lessons for the sector and highlighted the importance of longerterm planning.
Putting politics aside, public infrastructure is a critical catalyst for economic growth and development.
According to Infrastructure Australia, every dollar of public infrastructure investment can generate GDP increases of up to $4 over the life of an asset.
The Australian transport sector in particular is critical to our country’s success, and because it determines the physical accessibility
intrinsically linked to fairness and equity in our society as well.
With a need for ongoing investment in our transport networks, Roads Australia strongly supports a transparent and well-managed pipeline and greater rigour around investment decisions.
However, without funding commitments beyond the forward estimates, industry cannot effectively manage future workforce skills and capacity.
In the face of a huge build out in energy, defence and housing, the transport sector risks permanently losing the highly skilled and experienced talent to deliver the infrastructure and innovation our nation needs.
Already, we have seen an increasing number of redundancies in the sector.
With more certainty, industry will have confidence to build and invest in capacity and capability for the project pipeline, have greater certainty on timing, costs, and risks; and be energised to bring innovation and efficiency in project planning and delivery.
According to Infrastructure Australia, construction is one of the nation’s least innovative sectors, often lagging other economies in the uptake of modern methods of construction.
workforce productivity, however regulatory certainty is still some years away.
Transport for NSW recently launched the Gateway to Innovate initiative to create an opportunity for industry to test innovations on some of Australia’s most complex and high-profile projects.
contribute to better outcomes in terms of sustainability and safety.
As an organisation tasked with creating a place for the public and private sectors to work together towards a better transport system for more than
seize on to deliver lasting productivity benefits. We must build on what has been achieved in the past with fresh thinking, different perspectives and a willingness to eliminate hurdles and adopt innovations.
Supporting this task is a national policy priority for Roads Australia,
Fitting bulky machinery into confined utility installation sites requires additional work to remove obstructions. Employing smaller, compact equipment could help avoid unnecessary delays.
Utility installation projects often mean large, sprawling job sites, encompassing vast areas and requiring large-scale equipment, but there are instances when work will need to take place in tighter, more confined spaces.
Squeezing the bulky equipment necessary for utility installations into such compact areas could require additional works to clear land and remove obstructions. This unnecessary excavation and clearing can result in lengthy project delays and can also tarnish a job’s sustainability credentials.
Environmental, social and governance (ESG) is increasingly becoming a key focus for contractors and there are a range of ways that workers can bring more sustainable practices to job sites.
Sustainable practices on utility installation jobs can take on a variety of forms including reusing and recycling materials onsite and minimising environmental disturbance. In restricted and compact job sites it can also mean employing smaller, compact equipment to help get the job done in favour of excavating to give site access to large equipment.
The restrictions that these compact sites impose on equipment can mean the difference between accepting a job or rejecting it. Understanding the varying job sites means offering a complete range of equipment, including machinery that can be used in compact, confined job sites.
Vermeer’s Pedestrian Trenchers are the ideal solution for small-diameter utility installations, particularly when job site access is restricted. The slender profiles of the Pedestrian Trencher units mean they can comfortably access tight spaces, including passing through standard backyard gates.
The strength of Vermeer Pedestrian Trenchers does not come at the expense of their smaller size, with the three units in the range offering hightorque digging and delivering optimal power to job sites.
Difficult terrain on job sites is no hurdle for Vermeer’s Pedestrian Trenchers, with high-mount track design offering excellent traction and minimising ground disturbance. Further underscoring the adaptability of the range, the machines give operators the option to use tracks or tyres –allowing workers to unlock maximum
productivity and performance in spite of varying surface conditions.
The removal of the tail wheel on Pedestrian Trencher track units offers depth-control in uneven ground conditions and gives operators increased convenience to navigate through tight spaces. On top of this, the range’s outboard bearing support feature gives the head shaft additional protection when trenching in difficult conditions.
With Vermeer’s range of Pedestrian Trenchers, serviceability is not a problem; the engine cover design enables a quick service turnaround by offering virtually ‘no-tool’ access to all daily and weekly service points.
The hydraulic hoses and hard-line design further contribute to convenient service and maintenance, meaning less equipment downtime and mitigating project delays.
Backed by a local support network, customers can rest assured with the support of Vermeer Australia’s network of twelve branches across Queensland, New South Wales, Victoria, South Australia and Tasmania. The company’s experienced and knowledgeable service, parts and product support experts are here to help, whenever and wherever you need them.
VERMEER RIDE-ON TRENCHERS: TECHNOLOGY FOR PRODUCTIVITY, WITH DURABILITY WHERE IT MATTERS MOST.
Featuring an array of attachments like trenchers, rock saws, vibratory plough and reel carrier combos, and a telematics-ready technology package that includes TrenchSense™️, EcoIdle™️, Productivity Zone and Auto Plunge, the Vermeer RTX range is your productivity partner for open-cut installation of utilities such as gas, fibre, water and power. Ready to put the talk to the test? Contact us today for a demo.
Implementing these seven safety measures can reduce the risk of dangerous arc fault events and ultimately save lives.
According to the Australian Institute of Health & Safety, there are between six and eleven incidents involving arc faults each year in Australia that result in serious burns or death.
NHP Channel Manager – Regulatory & Standardisation, Jeff Davis – who has been on committees to design electrical standards including EL-06-08 Switchboards, EL-001 3000 Wiring Rules, EL-001-17-01 Construction and Demolition and EL-007 High Voltage Switchgear – explained how disaster could be avoided by following seven simple steps.
1. C hoose an arc fault contained switchboard
NHP’s CUBIC Modular system can protect personnel from dangerous arc fault events if all the doors and covers are in place on the switchboard.
2. Incorporate polycarbonate covers By adding polycarbonate covers to busbars and all connection joints you can come close to eliminating the risk of an arc flash.
3. O pt for a fast-acting circuit breaker
A fast-acting air circuit breaker (ACB) is a must have. NHP’s Terasaki TemPower 2 is the fastest acting ACB on the market. A single millisecond is a lifetime where highincident energy exists, so an ACB that opens and clears the fault as quickly as possible is essential. The TemPower 2 does it comfortably within 30 milliseconds.
One of the highest risk operations with any switchboard is switching the main ACB on or off, because at that point you're connected directly to the transformer. NHP’s Terasaki ACBs and TemBreak Pro moulded case circuit breakers can be operated remotely, so personnel don’t have to enter the switchroom to perform this procedure.
4. Install a photo-optic sensor
7. I nstall live line indicators
REMLIVE live line indicators
c an be installed in the CUBIC switchboard, providing a visual reminder that a circuit is live, which reduces the risk of accidents, speeds up the faultfinding process and ultimately saves lives.
Photo-optic sensors like Rockwell Automation’s ArcLogix use fibreoptic tubes – or point sensors –laid throughout the switchboard. If an arc flash occurs, extremely bright energy of approximately 10,000 lux is released and detected super quickly. It signals to the ACB to open and remove the supply to the switchboard, ultimately reducing the level of damage.
5. Install moulded case circuit breakers
This allows you to reduce the risk of arc faults even further, by segmenting the reticulation system into smaller groups, which are controlled by fast operating, current limiting moulded case circuit breakers.
6. E liminate human exposure
The other high-risk operation is to rack the main ACB in or out. NHP's TemRack iR is an automated ACB racking device, which is installed within the body of the ACB and allows for the remote racking of the ACB, thus eliminating the need for humans to enter a live switchroom and be exposed to dangerous arc fault events.
PPE is the least effective method of protection and reliability in the “hierarchy of control”, while “elimination”– which the above steps achieve – is the most effective means of protecting personnel. Given personnel don't have to enter the switchroom, they are also not required to wear heavily insulated PPE, which has been the cause of recent incidents of heat fatigue.
NHP’s Arc-Killer is a unique worldwide patented, fast-acting earthing switch system that diverts a high energy arcing fault into the low energy short circuit, which is finally cleared by an upstream circuit breaker. Arc quenching is achieved within 48 milliseconds for the DF-2+ switchgear and 25 milliseconds for the DR-6+ RMU, protecting people from significant injury.
NHP’s Services and Solutions Team is available to visit your site to assist you with implementing these measures into your switchboards, including ACB retrofits and connecting TemRack iR into your existing TemPower 2 ACB.
TemRack iR is a fully integrated, motorised ACB remote racking device. This permits safe isolation of Terasaki TemPower 2 AR ACBs, with zero physical interaction between personnel and the ACB.
TemRack iR For
nhp.com.au/TemRack
Ensuring the safety of railway systems goes beyond any one operator or network. It involves collaborating to create a positive culture that benefits passengers, workers and communities.
RSSB works to address the safety challenges rail operators face.
While catastrophic rail accidents are rare, the devastating impact they have underscores the critical importance of safety and the management of human factors in mitigating risks.
On 5 October 1999, the UK experienced one of its most deadly rail incidents in recent history, the Ladbroke Grove rail crash; two passenger trains collided almost head-on after one of them had passed a signal at danger, killing 31 people and leaving 417 injured.
Ladbroke Grove was one of a succession of bad train crashes in the UK, and following the incident, a public inquiry was held in 2000 to establish the causes of collision and look at the management and regulation of UK railway safety.
The inquiry, led by Lord Cullen, found that the industry lacked overarching safety standards and called for major change. At its core, this program of change centred on improving safety culture.
To achieve this, Lord Cullen also recommended the establishment of a new independent safety body. As such,
in 2003, the Rail Safety and Standards Board (RSSB) was formed.
For more than 20 years, RSSB has worked behind the scenes to keep the rail industry moving safely, developing standards that allow a diverse network to function as a single system.
In addition to developing and sharing standards, RSSB has led cross-industry strategies, like Leading Health and Safety on Britain’s Railways and the Sustainable Rail Blueprint, as well as cross-industry working groups and committees on subjects from mental wellbeing to driver advisory systems.
The organisation’s research has enabled existing and new vehicles to operate at different speeds on the same track, optimising journey times and maximising route capacity.
By leading and coordinating research, expertise, standards and analysis, the organisation has advanced rail safety knowledge and helped make Britain’s rail network one of the safest in the world.
Since the Ladbroke Grove rail crash in 1999, there has not been a rail incident
in the UK that has resulted in such a high number of fatalities.
RSSB’s specialists continue to work to address the complex safety challenges faced by rail operators, infrastructure partners and suppliers, not just in the UK but internationally.
In the last few years, RSSB has expanded its presence in Australia, offering organisations involved or interested in rail access to consultancy and training services, as well as affiliate membership.
The organisation offers expert support on critical technical questions, covering areas such as risk reduction, operational safety and best practice, fatigue management and optimising human performance.
A recent project saw the organisation help the Public Transport Authority of Western Australia deliver a Ballast Depth and Sleeper Spacing Review. Currently, RSSB is providing the National Transport Commission with consultancy support on rail interoperability.
Training, consultancy, insight.
The Rail Safety and Standards Board is the independent safety, standards and research body for Great Britain’s rail network. We’ve powered safer, smarter rail for more than 20 years – and now rail organisations around the world can benefit from this experience and insight. To see how we could help your organisation, download your guide to our international services.
Get your guide at rssb.co.uk/international
As transport networks become more advanced and widespread, Cooperative Intelligent Transport Systems could be the next big step in making road journeys safer and faster.
Main Roads Western Australia recently released a roadmap outlining a path to implementing Cooperative Intelligent Transportation Systems (C-ITS) across the Western Australian road network, to increase safety, improve traffic flow and enable future vehicle technology.
C-ITS is a group of technologies that allow the effective, real-time communication of data between vehicles and supporting infrastructure.
It provides information to drivers and traffic operators, keeping them informed of any changes to road conditions, including traffic, accidents, weather and roadworks. This can improve safety, traffic movement and environmental sustainability, and provide a better experience for drivers.
Infrastructure spoke to Main Roads’ Acting Intelligent Transport Systems Technology Manager, Meifang Lai, who said that the publication of the roadmap is a crucial step for Main Roads, because it sets a clear vision and strategy for the deployment of C-ITS.
“This roadmap not only outlines key components needed to implement C-ITS but also provides a coordinated plan for establishing the necessary relationships within government, industry and academia, and building our skills base here in Western Australia,” Ms Lai said.
“Detailing the short-to-medium term actions ensures that we can systematically and efficiently realise the benefits of C-ITS. Essentially, it's about moving us forward with a people, process, and technology focus and in a harmonised fashion with the rest of Australia.”
“The key benefits C-ITS will bring to Western Australians are quite exciting and impactful,” Ms Lai said.
“It will make traveling in Western Australia safer, more efficient and more enjoyable for all of us.”
One of the most obvious benefits of C-ITS is better road safety for all road users.
“Imagine driving on a rainy night, and the system alerts you to a car that has suddenly stopped ahead, giving you ample time to slow down and avoid an accident,” Ms Lai said.
“This enhanced safety feature helps protect you and your loved ones in real-time.”
The system will be able to deliver information about changes to the road environment to road users as they happen. This extends to delivering real-time network event alerts across metropolitan, regional and rural roads.
“You’ll stay better informed about road conditions, making your daily commutes smoother and less stressful.
“Whether you're driving through the Perth CBD or exploring our vast state, you'll receive up-to-date alerts to help you navigate safely.”
Ms Lai said the system will also help traffic managers to manage the competing priorities of road users.
“The roads will be more efficiently managed, ensuring everyone – from pedestrians to drivers – can get where they need to go more effectively.”
Compared to other jurisdictions in Australia and overseas, Western Australia presents unique geographical challenges to deploying C-ITS.
“Western Australia has one of the most diverse road networks in the world, from urban motorways to remote rural roads, spanning approximately 128,633km,” Ms Lai said.
“A big portion of the regional road networks have limited cellular coverage. Reaching the full coverage for C-ITS on these regional roads will be challenging.”
Ms Lai explained that one of the biggest challenges facing the delivery of the roadmap is clearly defining the ITS technology framework.
“This framework is crucial because it will guide the security, privacy, and performance requirements for C-ITS. It's like setting up the rules of the road for our digital infrastructure.
“Ensuring operational technology (hardware and software) work seamlessly together with data processing and communication systems, whilst ensuring the correct security and privacy levels are in place is no small feat, but it's essential for the success of C-ITS in Western Australia.
“Overcoming this challenge will pave the way for a safer, more efficient and better-connected transport system for all of us.”
To maximise the benefits of C-ITS across Western Australia and the rest of the country, the roadmap advocates for a nationally harmonised C-ITS ecosystem, involving collaboration between government, industry and road users.
This would enable:
♦ C-ITS safety, efficiency and sustainability benefits across Western Australia
♦ S eamless system integration between states
♦ Real-time data to optimise operations
♦ Improved and consistent data sets for network operations across Australia
♦ C-ITS features to be turned on in vehicles by original equipment manufacturers if there is C-ITS infrastructure in Western Australia
“Collaboration is essential in deploying C-ITS, and this is why we are working closely with other state agencies and the Federal Government,” Ms Lai said.
“This ensures that our C-ITS implementation is harmonised nationwide. So, when vehicles drive into Western Australia from other states, they can seamlessly enjoy the same C-ITS benefits. It's about creating a unified and efficient system that works for everyone, no matter where they are in Australia.
“Secondly, we must collaborate with the industry. Government involvement is crucial here to encourage the ongoing development and provision of C-ITS services. By working together with industry partners, we can drive innovation and ensure that the latest technologies are available to everyone in Western Australia.”
Ms Lai said that Main Roads is undertaking initiatives to ensure Australia has the required skill base to deploy C-ITS.
“One standout program is our ITS Graduate Program, now in its third year. This program offers graduates the chance to work on a wide range of innovative projects in ITS and C-ITS.
“Graduates get hands-on experience with projects like Smart Freeways, Traffic Control Systems, Real-Time Operating Platforms, and the integration of C-ITS.
“As Western Australia prepares for C-ITS deployment and operations, our program ensures that graduates are well-versed in Vehicle-toEverything communications and other critical areas.
“Our graduates are well-equipped to make significant contributions to major projects, helping to drive innovation in Western Australia’s transport network.”
Main Roads Western Australia teamed up with the Queensland Department of Transport and Main Roads for a proofof-concept (PoC) trial to understand core technologies and requirements ahead of future deployments.
The PoC trial ran from May to August 2024 and tested C-ITS awareness and warning messages at locations on Mitchell Freeway Southbound from Hester Avenue to Vincent Street.
When traveling in the trial area, the trial vehicles received messages warning them to reduce speed due to roadworks, warnings when they were above the roadworks’ speed limit, information regarding changes to speed limits on approach to and within the roadwork area, and updates on static speed limits.
Additionally, Main Roads is a participant in the iMove C-ITS National Harmonisation and Pre-Deployment Research Project, which involves implementing advanced sensor and communication technology at approximately 30 intersections across five key corridors in Melbourne. These intersections then record and transmit traffic and safety information that can be used to benefit road users.
Deploying C-ITS on a large scale in a busy urban environment allows
Limited cellular coverage of regional roads presents a challenge for C-ITS.
the participants of this trial to gain valuable data and insights that will enable the adoption of C-ITS in a nationally harmonised manner.
The roadmap consists of seven action streams which are designed to guide Main Roads through a successful implementation of an effective C-ITS network:
1. Collaboration and research –Partner with industry and research organisations to further national understanding
2. National harmonisation – Take part in national plans to deliver a harmonised C-ITS implementation, with systems that can securely manage private data to ensure a trusted transport environment
3. Future-proofing – Prepare foundational infrastructure that can be improved and expanded upon as future vehicle technologies emerge over time
4. Proofs of concept – Perform local testbed and/or test corridors to identify specific needs for Western Australia and develop readiness of C-ITS applications
5. Capability uplift – In collaboration with industry and research organisations, provide opportunities for staff to upskill, particularly in the areas of systems engineering, data engineering, cloud systems and ITS architecture
6. Systems uplift – Identify what changes must be made to the ITS environment to support C-ITS deployment and ensure they are implemented
7. Data quality, use, and management – Improve the quantity, quality and availability of road agency data to facilitate emerging C-ITS applications
Ms Lai said that Main Roads is excited about advancing the implementation of C-ITS in Western Australia through a collaborative approach at a national level.
“Our goal is to enhance safety, improve traffic flow, boost operational efficiency, promote environmental sustainability, and provide a better overall experience for all road users in Western Australia.
“We’re looking forward to ensuring these benefits come to fruition and making a positive impact on our community across the entire state.”
Greater Western Sydney will be critical to Australia’s future prosperity, and with tunnelling now complete for the region’s new railway line, another vital piece of the puzzle is falling into place.
The Sydney Metro – Western Sydney Airport line is set to become the spine of Greater Western Sydney’s transport network.
The new metro line is expected to support the growth of the region by connecting communities to each other and to the new Western Sydney International (Nancy-Bird Walton) Airport. It will link Bradfield to St Marys, connecting travellers with wider Sydney services.
This mega project – which began major works in late 2022 – is providing a major boost to the New South Wales and national economies, with an expected 14,000 jobs to be supported through the construction.
Once complete, the railway line will connect communities with major job hubs like the Bradfield City Centre and give travellers from the new Western Sydney Airport access to the rest of Sydney’s public transport system.
Jointly funded by the Federal and New South Wales Governments, the Sydney Metro-Western Sydney Airport project is intended to provide safe, reliable and integrated public transport for local communities and industries
and supports the State Government’s 30-year strategic vision for the Western Sydney Airport Precinct.
On 21 June 2024, tunnel boring machine (TBM) Marlene completed the final tunnel breakthrough for the project at the St Marys Station site, marking the end of 14 months and 9.8km of tunnelling work by four TBMs.
The 4.3km metro tunnels between Orchard Hills and St Marys were constructed by TBMs Marlene and Catherine, while Peggy and Eileen built the 5.5km twin tunnels that extend under the new Western International Airport, connecting Airport Business Precinct and Bradfield Station.
TBMs Catherine and Marlene make use of earth pressure balance (EPB) technology and are the first use of such devices on a Sydney Metro Project. EPB TBMs are better suited to tunnelling through soft earth materials like shale and clay.
TBMs Eileen and Peggy are doubleshield machines, constructed using refurbished parts from the previous excavation on the Sydney Metro City and Southwest tunnels as part of efforts
to increase sustainability. Doubleshield TBMs are more suited to harder underground conditions like sandstone. Excavation of the tunnels required the removal of 1,863,460t of stone and other materials, enough to fill 298 Olympic swimming pools. The tunnel walls are lined with 69,966 individual segments of concrete.
Western Sydney Airport Project Director, Angela Jeffery, said that the completion of major tunnelling is a significant milestone for this mega project that will completely transform how Greater Western Sydney moves – making the region better connected than ever before by creating a crucial transport link, including to the new Western Sydney International Airport.
“Four huge tunnel boring machines worked around the clock up to seven days a week to carve out the tunnels, while a team of 553 tunnellers, TBM operators and support personnel went above and beyond to ensure these tunnels were delivered,”
Ms Jeffery said.
Although the tunnels are now excavated, work inside them continues as 39 cross passages are constructed and tracks are prepared to be laid.
With major tunnelling now complete, work has begun on the next phase of construction, building the six new metro stations.
The new stations will be located at:
♦ St Marys – will connect passengers with the existing suburban railway network and the rest of Sydney’s public transport system
♦ O rchard Hills – will connect travellers with a proposed commercial and mixed-use precinct
♦ Luddenham – will service a planned education, innovation and commercial precinct
♦ Airport Business Park – will be located in the centre of the Western Sydney International airport precinct, connecting passengers to a major jobs hub
♦ Airport Terminal – will enable easy access to the new airport, connecting travellers with the rest of the world
♦ B radfield – will service the Western Sydney Aerotropolis, a major business precinct
The new underground St Marys station is already underway. The first large concrete pour at the station
Orchard Hills, Luddenham and Bradfield station sites are preparing for major station construction to begin in the coming months.
As part of Sydney Metro’s state-of-theat driverless system, the new airport line’s services will be operated from a facility at Orchard Hills.
From this facility’s operations control centre, expert train operators will be able to fully monitor and control the system, from the trains themselves down to the lifts, escalators and platform screen doors used across the railway.
Additionally, the facility will house yards for the stabling and maintenance of the fleet driverless trains.
The automatic control system includes hundreds of cameras and will be used to minimise the time trains are stopped at stations and the time between each train, getting passengers on the move faster and more frequently.
serviced by two facilities that will provide ventilation to ensure there is always fresh air in the tunnels, as well as vital exits in the case of an emergency.
These service facilities are located at Claremont Meadows near the intersection of Gipps Street and the Great Western Highway, and at Bringelly at the northern end of Derwent Road.
The Sydney Metro – Western Sydney Airport line is set to be a major travel connection between the new airport and the rest of the city, boosting tourism, business and employment opportunities.
It will also form the backbone of Western Sydney’s future, one of the fastest growing regions in the country.
“Sydney Metro-Western Sydney Airport is powering ahead, and the completion of tunnelling puts us in a great spot to open in time for when passenger services start at the new Western Sydney International Airport,” Ms Jeffery said.
As Melbourne’s new Metro Tunnel prepares to commence operation in 2025, testing of trains through the city-shaping project is ramping up.
Train testing is intensifying on the Metro Tunnel – Victoria’s biggest public transport infrastructure project in more than 40 years – as experts start ‘stress testing’ the project’s complex systems and technology.
This testing phase will involve repeated running of the new systems, trains and infrastructure ahead of opening to passengers in 2025.
Test trains have clocked over 20,000km since the inaugural journey through the twin nine-kilometre tunnels in late July 2023. They will need to travel at least another 150,000km back and forth under Melbourne’s CBD before the test team is confident the new tunnel is ready to open.
The Metro Tunnel has installed technologies never seen before on the Victorian rail network, including High-Capacity Signalling and platform screen doors at the five new underground stations.
This rigorous testing phase will include opening and closing the platform screen doors another 30,000 times to make sure they are in sync with the doors on the modern High Capacity Metro Trains (HCMTs).
Metro Tunnel Project director Ben Ryan said the relentless testing would be about “ironing out the bugs and proving reliability”.
“The Metro Tunnel is going to transform our public transport system and it’s going to transform the way people move around our city, making it easy for people to get to key connections,” Mr Ryan said.
“The trains, the tunnel and the technology all need to work together so when the project opens in 2025, passengers can have that modern, seamless experience that we are bringing to Melbourne’s train network.”
The Metro Tunnel is the most significant upgrade of Melbourne’s train network since the City Loop opened in 1981.
It will connect the key growth areas of Sunbury in the north-west and Cranbourne and Pakenham in the
south-east via a new tunnel under the city, creating an end-to-end 97km rail line, providing better connections to jobs, healthcare and education.
The project will double the size of Melbourne’s underground rail network and includes five new state-of-the-art stations, freeing up space in the City Loop and allowing the Frankston Line to return to the Loop.
Passengers will have rail access via Parkville Station to Parkville’s worldleading medical and research precinct – home to the University of Melbourne, Royal Melbourne Hospital and Peter MacCallum Cancer Centre – and the St Kilda Road employment precinct via Anzac Station for the first time. Arden Station has been built in the heart of an urban redevelopment area in North Melbourne, which will be home to about 20,000 residents and up to 34,000 job opportunities by 2051.
Passengers will have an easy transition between City Loop and Metro Tunnel services with connections between Melbourne Central and State Library stations and Flinders Street and Town Hall stations.
While construction is wellprogressed, with two stations already finished, there remains an enormous amount of testing to take place before opening.
Train testing started in late July 2023 with one train in each tunnel at low speed, and quickly ramped up to multiple trains running up to the line speed of 80km/h.
Metro Trains Principal Driver Specialist Suzy Kapteinis was one of the first to drive a train through the new tunnels.
She said it was a once-in-a-lifetime opportunity for her to work on the project.
“It’s an amazing project to be part of,” Ms Kapteinis said. “It’s one of the highlights of my career, that’s for sure.”
The project reached a major milestone earlier this year, successfully running trains at high frequency through the tunnels in a critical step of the project’s testing program.
During the testing between West Footscray and Hawksburn, a fleet of 12 trains made 18 trips every hour through the twin tunnels using the project’s High-Capacity Signalling system. This 21st century technology has been installed alongside the 20th century system in place on the existing Cranbourne/Pakenham and Sunbury lines.
It’s the first time in Australia that High-Capacity Signalling has been retrofitted to an existing network alongside a decades-old signalling system, with the two needing to be integrated seamlessly.
Major construction at Arden and Parkville stations has also finished –and Anzac will soon be next.
Work at Arden Station was accelerated for the team to start
testing the systems inside the station, allowing the project to build reliability in the technology for a smoother roll out across the other four stations.
Mr Ryan said it was a complex phase of the project.
“Everyone is excited about getting closer to opening the Metro Tunnel but we need to make sure we are thorough in testing every element of the project,” he said.
“The testing team has achieved a lot in the past 12 months since the first test trains rolled into the tunnels, but there remains a significant amount of work to do.”
The first passenger load tests were conducted mid-June, with two trains each carrying about 135 tonnes of water.
The trains were both loaded with 42 1,000-litre water tanks and almost 6,000 15-litre water bottles
to simulate how they perform with the equivalent weight of a train full of people.
In the coming months, the team will continue testing everything from lifts, escalators, security systems, communications, lighting, plumbing and power to ensure all systems are working together with Melbourne’s modern fleet of bigger, better trains.
As an example, the team will test that a train leaving Arden Station is relaying information on its location and speed to passenger information displays at all the other four stations, so passengers at every platform through the tunnels can see when the train will arrive.
Another example is testing whether train speed and location data is being relayed to the tunnel ventilation system, which uses the information to automatically operate the ventilation system as needed.
Emergency systems will also be tested, including detecting an intruder in the tunnels and fire system responses, to ensure they are communicating with other station and rail systems such as signalling.
The next stage of the project is trial operations. This is where HCMT services will run from Clayton to West Footscray through the Metro Tunnel, using all the new systems.
These trial runs are like a dress rehearsal – they will simulate timetabled services and a range of possible real-life scenarios with station staff, drivers and volunteer
Trial operations will confirm that everything is ready for a safe, reliable and efficient passenger service to begin when the Metro Tunnel and five
By Jon Davies, Chief Executive Officer, Australian Constructors Association
Modern methods of construction offer the industry a pathway for infrastructure delivery that is safe, efficient and sustainable.
Lby inefficiencies, the call to action is clear: we must find ways to become more efficient, not by reducing our workforce, but by leveraging innovation and modern methods of construction (MMC) to do more with the people we have.
The potential $56 billion windfall from improved industry productivity is not just a theoretical figure. It is a goal that can boost economic growth, support job creation and improve the living standards of Australians. However, the declining workforce in the construction industry threatens to undermine this potential. The challenge, therefore, is not just about filling the gaps left by those leaving the industry, but about transforming how we work to maximise the output from the current workforce.
Importantly, we need to correct the false idea that more productivity means people will lose their jobs. The construction industry is not facing a shortage of work but a shortage of workers. The focus must be on enhancing the efficiency of our existing workforce through innovation and MMC, ensuring that we can
of MMC. This is a pivotal moment for the industry. It offers a structured approach to overcoming existing barriers and unlocking the full potential of modern construction techniques and encouraging innovation.
MMC involves constructing more of Australia’s projects in factories than on-site. This can take the form of standard components all the way through to completed project sections and modules. This form of construction is far more productive as it is standardised, takes place in controlled environments and is not subject to sitebased risks such as inclement weather. It creates more opportunities for skilled workers in safer environments with increased opportunities for flexible work hours.
As factory-based construction creates far less waste, it therefore results in reduced overall energy consumption and can help construction’s contribution to the nation’s decarbonisation targets.
Over the coming year, the ACA will collaborate with key industry
stakeholders and state and federal governments to develop a strategy focused on increasing innovation and the adoption of MMC. This process will include a thorough review of relevant literature and a mapping of existing initiatives to identify best practices and areas for improvement. One key aspect of this strategy will be examining the barriers to innovation and the adoption of MMC. Common barriers include a lack of awareness and understanding of MMC (it’s not prefab dongas!), scale of MMC market, regulatory constraints and resistance to change within the industry. To overcome these obstacles, the strategy could recommend measures such as targeted education and training programs, increased design standardisation and incentivisation of design for manufacturing and assembly.
For instance, does every hospital in a state really have to be different? Can elements of design be standardised within states and across jurisdictions? Are there elements of a hospital that can be the same as schools, offices and other buildings, for example corridor walls?
An important component of the strategy will be establishing metrics to measure its success. The adage "what gets measured gets done" underscores the importance of having clear, quantifiable goals to track progress. By monitoring progress, all key stakeholders can ensure that the strategy remains focused on achieving tangible improvements in productivity and innovation.
While the initial focus of the strategy will be on transport infrastructure, its principles and practices can be extended to other sectors if successful. The vertical sectors such as residential construction and commercial buildings potentially stand to benefit the most from the efficiencies and innovations MMC brings. By addressing the barriers to innovation, promoting the adoption of MMC and establishing clear metrics for success, the industry will be able to do more with the people it has, ensuring that Australia can build the infrastructure it needs to thrive in the decades to come.
New research has found that reducing the long working hours in the construction industry could lead to a wide range of unexpected benefits.
The Construction Industry Culture Taskforce (CICT) recently released two major reports that highlight key cultural issues in the industry, which include long hours, high turnover, lack of diversity and poor mental health.
The CICT developed its draft Culture Standard to address these cultural challenges and create transformative cultural change in the industry across three key pillars – time for life, wellbeing and diversity and inclusion.
The Taskforce, established in 2018, is a strong partnership between industry and government, led by the Australian Constructors Association and the governments of NSW and Victoria. Infrastructure agencies across both governments are playing a crucial leadership role in the Taskforce partnership by participating in piloting the draft Culture Standard to drive these important cultural shifts.
Chair of the CICT and interim Chief Commissioner of Infrastructure Australia, Gabrielle Trainor AO, said cultural change was at heart transforming the construction industry.
“Cultural change in the industry is one of the key ways to address the acute skills shortage that has led to escalating labour costs and stagnant productivity in an industry which has so many other reasons to be a place to have a great career,” Ms Trainor said.
The Taskforce’s Culture in Construction Pilot Projects: Interim Report, led by RMIT University and released in May 2024, explores workers’ experience and preferences in relation to work hours and the benefits of a 50-hour cap over a five-day work week. Data was collected from five public infrastructure projects, three in NSW and two in Victoria, where the draft Culture Standard was implemented. Integrated strategies were used by the pilot projects to improve time for life flexibility, diversity and inclusion, and the mental health and wellbeing of workers.
Overall, the report shows clear links between the three pillars, with mental health and wellbeing and work engagement significantly and positively linked to gender diversity, respect and organisational fairness, as well as time for life.
Despite the focus on creating inclusive workplaces, the report highlights that some women experienced banter and behaviour that they viewed as either sexist or inappropriate. However, it also shows that, when reported, these issues were dealt with quickly and effectively with the appropriate support from the management team.
Results were overall positive on wellbeing, though findings demonstrate the need to address work hour pressure holistically. Indeed, an interesting finding in the report is the impact of the compression of the work into a 5-day week on worker stress levels.
The report found that an average of 50-hour work weeks, arranged over five days, had strong support amongst site workers and did not appear to adversely affect site productivity. 84 per cent of salaried respondents and 61 per cent of waged respondents preferred this schedule over the current industry norm of longer working hours where workers typically exceed 50 hours per week and Saturday work is routine.
Ms Trainor said the lack of work-life balance faced by many construction workers can cause significant stress, relationship issues, reduced productivity and was a leading reason people left the industry.
“The five-day work schedule preferred by the workers in the study allowed them to spend more time with their kids, play sport, see friends or relax, and a two-day weekend also ensured they were better rested and recovered from the work week,” Ms Trainor said.
“Monday to Friday is clearly shown in this study to be the ideal. But the Culture Standard provides for the reality that not every project can work five days. These findings also demonstrate the positive benefits of a deliberate and accountable focus on ensuring no-one works excessive hours and flexibility is built in, and where measures on diversity and wellbeing are also in place to support the other key aspects of cultural change women and young men are looking for.”
Before the implementation of the draft Culture Standard on the pilot projects, some waged workers were concerned about the effect on their pay. However, once the Culture Standard was in place, many of these same workers commented that the effects on
their pay had been minimal and, even though they may have experienced a small reduction in their earnings, the benefits of spending more time with their family and friends far outweighed the costs.
Another significant finding of the Taskforce’s research has been that young people are deterred from joining the construction industry because they don’t believe the working hours can deliver them a work-life balance. The Taskforce’s report Intention to Pursue a Career in Construction/Infrastructure was released in April 2024 and surveyed male and female trainees aged between 17 and 23 who spent two years working in the infrastructure industry via the NSW Government Infrastructure Traineeship Program (NSWITP).
The NSWITP was established by the NSW Department of Education and the other NSW Construction Leadership Group members. Now in its fourth year, this unique whole-of-government pathway program introduces Year 12 school leavers to the construction sector through two years of work-based placements and the completion of a Certificate IV in a universal high-demand qualification to bolster entry into the
construction sector. It also has a focus on bringing diversity into the sector to expand workforce growth by actively targeting female students, and young people who identifying as Aboriginal or Torres Strait Islander, have a disability or live in rural and regional areas.
The results of the RMIT led research indicate that workers are significantly more likely to decide to pursue a career in construction when they perceive a good fit between their priorities and what a construction career can offer. Trainees identified job characteristics associated with having a healthy and balanced life as being important in their career decision making. Only 31 per cent of surveyed trainees felt they could achieve the balance between career and outside work commitments within the sector.
These findings provide evidence that suggests the construction industry must adopt new ways of working, that enable time for life, improved health and wellbeing and increased diversity to attract and retain young workers.
The construction sector currently employs 1.32 million people yet is facing a shortfall of at least 229,000 skilled public infrastructure workers to build future projects. Failure to attract and retain a diverse range of new workers
is narrowing the construction industry’s talent pool and reducing its capacity to deliver the nation’s $237 billion infrastructure pipeline by 2027.
Ms Trainor said the findings were concerning as construction skills shortages have already contributed to escalating labour costs and stagnant productivity.
“This has serious implications for the industry’s productivity. Skills shortages translate to higher costs. We believe working hours, the dreadful statistics on health and wellbeing and on diversity in construction are interrelated and must be tackled together,” Ms Trainor said.
“Construction is in so many ways an exciting and immensely satisfying industry, and if it offered better worklife balance, including more flexible hours, and wherever possible a five-day Monday to Friday week, we would be significantly more likely to attract young people, notably young women.”
Both the NSW and Victorian governments are supporters of the Culture Standard.
NSW Government agency Health Infrastructure pioneered early research into the benefits of a five-day work week for construction workers with partners UNSW and Roberts Co in 2021. Health Infrastructure has since implemented a five-day work week on 25 project contracts totalling approximately $2.2 billion.
“The five-day week is one of a range of initiatives that are working together to improve the experience and appeal of working on our project sites,” Acting Chief Executive Health Infrastructure Emma Skulander said.
“We consistently find that providing flexible working arrangements for construction workers improves their work-life balance – and importantly, makes no material difference to the economic viability of our projects.”
The agency’s Sydney Children’s Hospital Stage 1 and the Minderoo Children’s Comprehensive Cancer Centre participated as a Pilot Project. It continues to apply the Culture Standard across its portfolio, refining it over time in line with feedback from the project team and supply chain.
Health Infrastructure is also partnering with the NSW Government’s Women in Construction program to place project officers with head contractors to attract, upskill and retain female employees on key sites. The agency now has Officers in place on most of its major hospital redevelopments including Liverpool Hospital, Westmead Hospital, Children’s Hospital Westmead, Sydney Children’s Hospital Randwick, St George Hospital, Shoalhaven Hospital and John Hunter Hospital.
“Our project teams are benefiting from the skills and capabilities of women who see construction as a compelling career choice. The Culture Standard aligns with Health Infrastructure’s values and directly supports our delivery agenda. We are proud to be improving the working experience of all the valuable individuals involved in our projects and are committed to continuing to innovate in this area,” Ms Skulander said.
To learn more, visit www.constructionindustryculturetaskforce.com.au
By David Hawkes, Interim Associate Director of Policy, Institution of Civil Engineers
Effective and efficient construction processes could be the key to improving productivity.
It’s likely not news to anyone reading this that stagnant productivity has been a longstanding issue in Australia. Nor is it likely to be news that in the last year the Federal Government has made construction productivity and market capacity national cabinet priorities.
It’s a problem that has received analysis from organisations such as Infrastructure Australia, the Australian Constructors Association, Engineers Australia and the Productivity Commission.
With this being said, you might be asking why a UK-based institution is diving in.
The answer is that the challenges the country is facing are by no means unique to Australia.
As a global membership organisation with 97,000 members spread across more than 160 countries, (including 2,300 members in Australia), the Institution of Civil Engineers (ICE) harnesses the experience and insight of its membership to advise policy and decision makers on infrastructure delivery all over the world.
In other words, by delving into Australia’s challenges, we may find insights that are universally relevant.
With that said, if there’s any consensus in the wide-ranging, international discussion on infrastructure productivity, it is that there is no single route to fixing it. Nor does the ICE expect to be able to come up with a set of recommendations that will be a magic fix.
What we do hope to be able to do is offer fresh insight into some of the challenges, and how they can be overcome, by examining improving infrastructure delivery through the lens of process.
For solutions to be successful, you must identify, and agree on, the problem you’re trying to solve.
You must also be sure you’re speaking the same language. It’s no use introducing productivity measures and tools to collaborate better if you don’t agree on a definition of productivity or what successful collaboration looks like.
This is something that’s often overlooked by infrastructure professionals and policy makers alike.
So, before proceeding, let’s examine what the ICE means by productivity.
At a high level, productivity refers to the rate at which goods and services are produced (output) per unit of labour, capital, raw materials, etc. (input). Thus, productivity can be understood as a ratio of the quantity of output against the quantity of input used.
Most reports reference research by the Productivity Commission, which typically refers to either labour productivity – the ratio of output to hours worked – or Multifactor productivity (MFP) – the ratio of output to the combined input of labour and capital.
However, these are incomplete measures for communicating the state of infrastructure delivery. They do not capture any improvements in the quality of outputs or an expansion in the range of outputs.
These definitions also ignore the fact that infrastructure is not created solely for infrastructure’s sake, but rather to serve the needs of the public by delivering better social, economic and environmental outcomes – not outputs.
So, the question is, do we need to change how we measure productivity?
This brings us back to examining infrastructure delivery through the lens of process.
More specifically, at the ICE, our view is that processes should be examined for effectiveness and efficiency.
Effectiveness is about making sure that the solution delivers the outcome required or, put simply, to do the right thing.
A more effective process produces outputs of a greater quality or at a greater scale. Effectiveness means selecting the right projects, making the right design choices and choosing the right delivery models.
Efficiency focuses on improving how that outcome is achieved or, in simpler terms, to do things right.
Efficiency involves a considered approach to the consumption of materials, effort, talent, data, energy, carbon emissions, land and ecosystems. A more efficient process is one which has a greater ratio of outputs to inputs. This will also reduce costs and provide better value for money.
In this context, efficiency includes the increased outputs that economic productivity measures capture, but also effectiveness measures like driving positive social impact, carbon and climate outcomes, and includes a greater range of inputs than solely labour hours or labour and capital.
In a nutshell, to improve productivity, you must increase both effectiveness and efficiency.
That means government departments and companies involved in infrastructure delivery need to analyse their processes for effectiveness and efficiency to identify the problems they need to solve.
Otherwise, we’re all just guessing at what could make it better.
When that happens, solutions applied with the best will in the world may do little good and could end up hindering progress.
To jumpstart this analysis, the ICE has published a paper with some themes for discussion.
I’ve already touched on one: a shared and comprehensive definition
of what productivity is in the context of infrastructure delivery should be established.
The second is to achieve an infrastructure pipeline that is stable, sustainable, and that supports Australia’s vision for the future a robust project assessment process should be created. This should align with longterm infrastructure goals.
Lastly, tools like standardised collaborative contracts to better mitigate and more fairly distribute project risks should be considered, as these could help improve the conditions for productivity.
Our aim now is to gather further insight into the challenges that need to be overcome.
Our team is particularly interested in insights that will help shape the policy environment, but thoughts from practitioners are also very welcome.
In particular we’re interested in responses to the following questions: 1. Are there more effective outcome measures for the infrastructure delivery sector than labour
productivity or Multifactor productivity (MFP)?
2. How can social, economic and environmental outcomes be considered alongside economic measures for a more holistic understanding of infrastructure delivery?
3. How can infrastructure projects be consistently subject to robust, transparent, independent assessment against long-term infrastructure goals?
4. Is Australia’s national vision for infrastructure clearly articulated? Is its vision reflected in its infrastructure pipeline?
5. Are government decision-makers adequately held to account for infrastructure project selection? If not, can this reasonably be achieved?
6. D o government and industry have the capacity to correctly deliver and administer collaborative contracts? If not, how should this be achieved?
You can share your views with the ICE policy team by emailing policy@ice.org.uk
30 & 31 OCTOBER 2024 | MCEC MELBOURNE
AUSTRALIA'S BIG TRADE SHOW FOR THE ENTIRE ROADS TRANSPORT ECOSYSTEM
YOUR CHANCE TO BE PART OF AUSTRALIA’S BIGGEST INFRASTRUCTURE PROJECTS
5,000