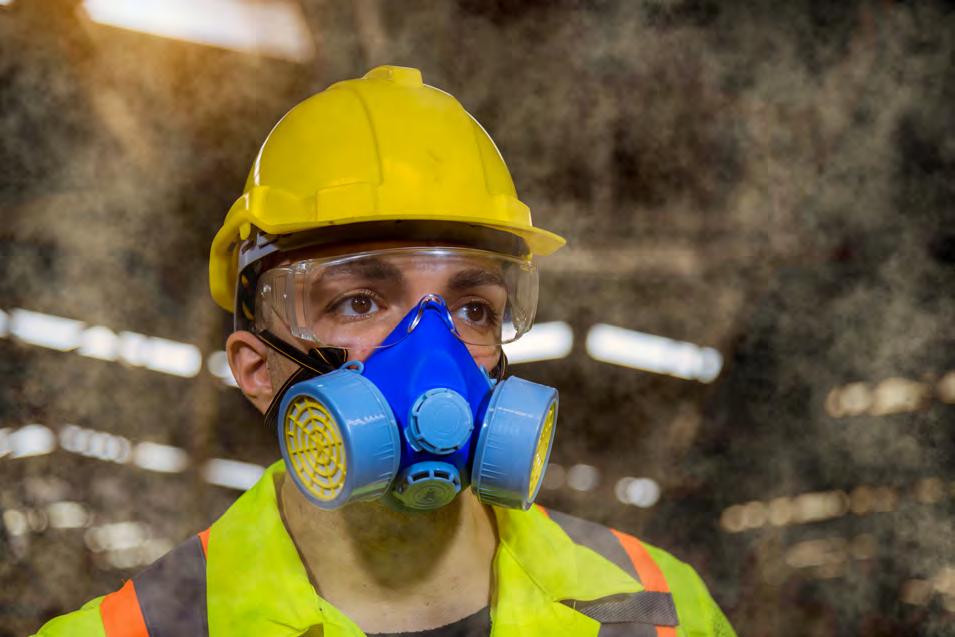
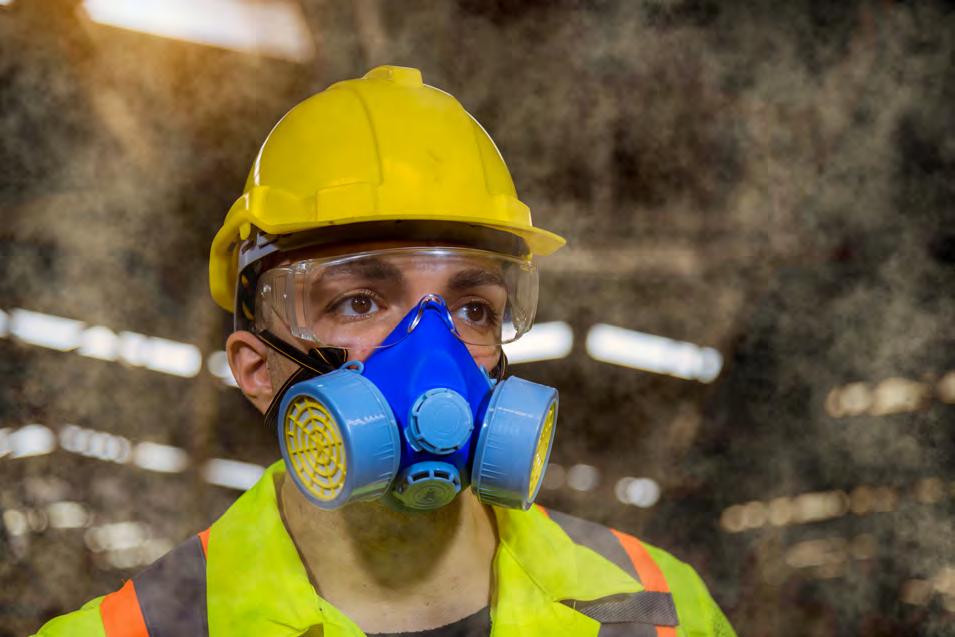
PFOS – a case study
By Ruth Jarman, Dr Jackie Wright, Therese Manning, Dr Kate Langdon, and Dr Belinda Goldsworthy
The world is made up of chemicals. When assessing risks from any chemical, it is important to acknowledge that the fundamental building blocks for the entire planet are chemicals. Whether it is the water we drink, the air we breathe, the food we eat, the ground we walk on, the houses we live in, the things we have in our houses or workplaces or what we ourselves are made of –everything is made from chemicals.
Some chemicals are essential to keeping us alive or to let plants or other animals live. A range of chemicals are used in everyday items like food, clothes, computers, kitchen appliances, cars, houses, r oads, trains, planes, hair dyes,

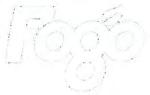
beauty products, toothpaste, shampoo and flea rinse for our pets etc. Other chemicals are naturally occurring, like spider and snake venoms or well-known poisons like arsenic or mercury.
Given that everything in the world is made from chemicals, the presence or detection of a chemical in the environment does not equal an unacceptable risk to people or the environment. Rather it is the amount of a chemical that we are exposed to, how we are exposed to the chemical and sometimes when we are exposed to the chemical. This applies to the chemicals we manufacture as well as naturally occurring chemicals – some substances are quite benign, and some may be considered more toxic. For all chemicals, the potential to cause harm depends on the dose or amount that can get into our bodies.
We use the human health and
ecological risk assessment process to determine if the amount of a chemical present in our environment could pose a risk to us or the environment around us. In Australia, we have established Government guidance on how to undertake a human health and ecological risk assessment. This guidance is not chemical specific, hence, is valid for all chemicals, including per- and polyfluoroalkyl substances (PFAS). There is no reason for PFAS to be treated any differently to other chemicals. It is our experience that treating PFAS differently to other chemicals can create practical, logistical, financial, health-based and communication issues. These issues can outweigh any positive effects and benefits that may be gained from applying an overly cautious approach to PFAS management.
(Continued on page 18)
28 The case for infrastructure
30 Missed opportunity
38 New tyre recycling facility
Brokering collaboration between industry and government
By Inside Waste
During a couple of days in November last year, a dedicated group of resource recovery delegates attended Circularity 2024, an event devoted to all things circular economy.
The organisers brought together an array of experts from a variety of arenas within the industry to give their insights and opinions on a myriad of subject matters. One of the key features of the program was a round table featuring members of the Circular Economy Ministerial Advisory Group (CEMAG).
Led by Professor John Thwaites, chair of the board for Climateworks Centre, the other members of the panel were Fortescue Innovation’s Dr Larry Marshall, Dr Dominique Hes from Greenfleet, and Planet Ark’s Paul Klymenko.
Initiated by the Federal Minister for the Environment and Water, Tania Plibersek, the point of CEMAG is to “advise the Australian Government on the opportunities and challenges for Australia’s transition to a more circular economy”.
There are 12 people on the advisory group, and they look into all aspects of the circular economy and its different sectors, such as mining, construction, infrastructure, roads and bridges, manufacturing, plastics, agriculture and food waste, resource recovery in waste streams, as well as water and wastewater.
(Continued on page 23)
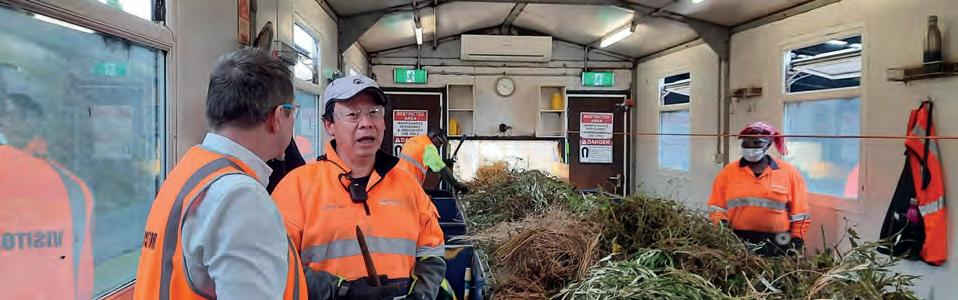
Image: APChanel/shutterstock.com
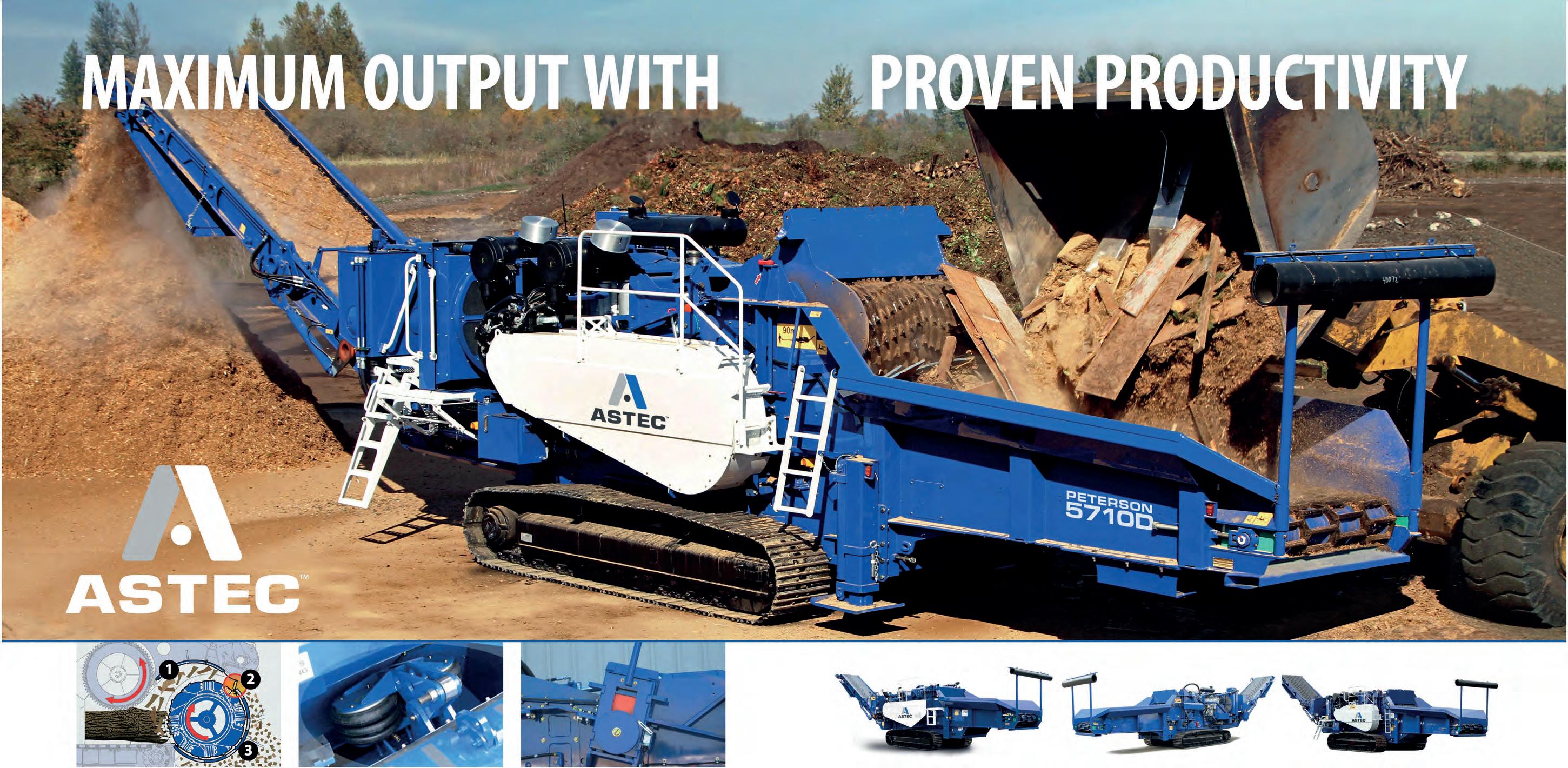
3-Stage Grinding Process
Provides Faster Reduction
Astec - Peterson's powerful up-turn 3-stage grinding process provides better fracturing of material and a more consistent product, giving you just the product your buyers are looking for.
The Impact Release System
Protects Your Investment
Astec - Peterson's patented Impact Release System's air bags provides uniform grinding and protection from contaminated feedstock, a feature unique to Astec - Peterson grinders.
Land clearing, mulch, compost, asphalt shingle tiles, scrap wood, biomass, green waste-we can handle it am
www.komatsuforest.com.au
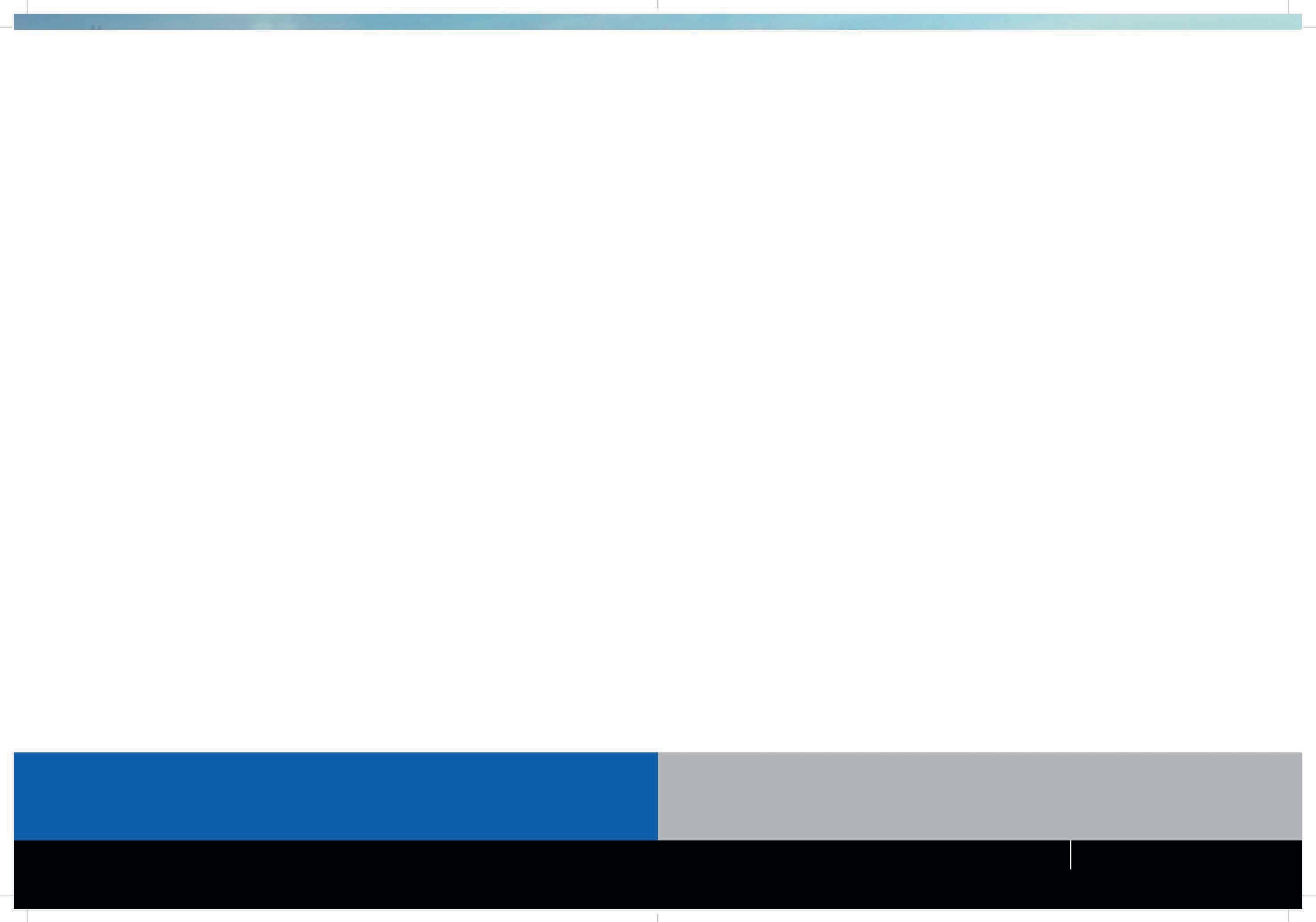
The Impact Cushion System
The Second Line of Defence
Urethane cushions and shear pins help protect the mill from catastrophic damage in the event of a severe impact from contaminants in the feedstock.
Astec - Peterson offers horizontal grinders from 433-839 kW, offering grinding solutions with output at the lowest cost per ton. Visit us at www.astecindustries.com and see why we have been leading the industry for over 35 years!
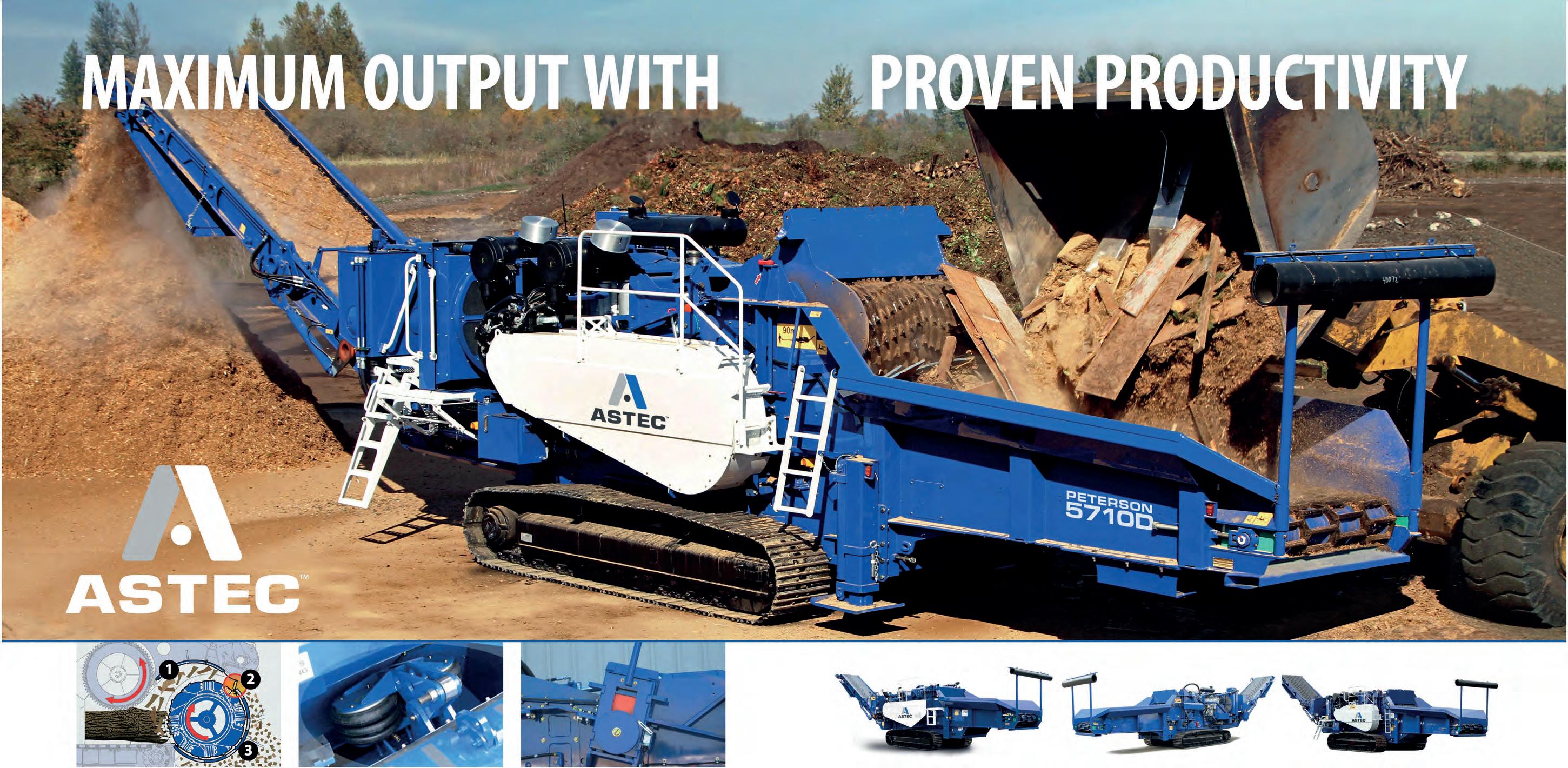
2710D Horizontal Grinder
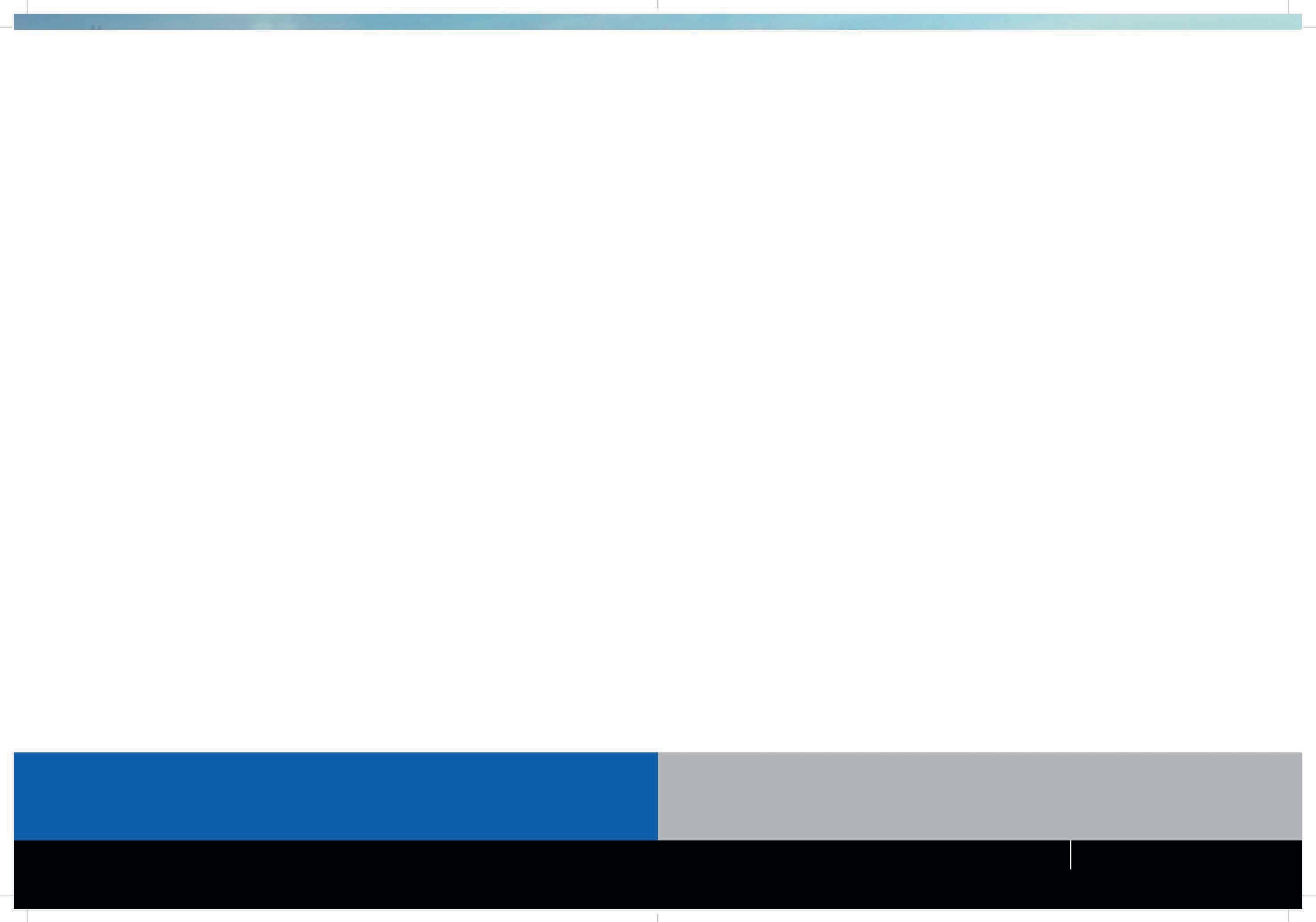
5710D Horizontal Grinder
6710D Horizontal Grinder
Largest
Chief Operating Officer
Christine Clancy
christine.clancy@primecreative.com.au
Managing Editor
Mike Wheeler
mike.wheeler@primecreative.com.au
Brand Manager
Chelsea Daniel chelsea.daniel@primecreative.com.au
Ar t Director
Bea Barthelson
Client Success Manager
Louisa Stocks louisa.stocks@primecreative.com.au
Head Office
Prime Creative Pty Ltd
379 Docklands Drive
Docklands VIC 3008 Australia
p: +61 3 9690 8766 enquiries@primecreative.com.au www.insidewaste.com.au
Subscriptions
+61 3 9690 8766 subscriptions@primecreative.com.au
Inside Waste is available by subscription from the publisher. The rights of refusal are reserved by the publisher
Articles
All articles submitted for publication become the property of the publisher. The Editor reserves the right to adjust any article to conform with the magazine format.
Copyright
Inside Waste is owned by Prime Creative Media and published by John Murphy.
All material in Inside Waste is copyright and no part may be reproduced or copied in any form or by any means (graphic, electronic or mechanical including information and retrieval systems) without written permission of the publisher. The Editor welcomes contributions but reserves the right to accept or reject any material. While every effort has been made to ensure the accuracy of information, Prime Creative Media will not accept responsibility for errors or omissions or for any consequences arising from reliance on information published. The opinions expressed in Inside Waste are not necessarily the opinions of, or endorsed by the publisher unless otherwise stated.
Growing up
A 21st birthday is a significant milestone in the Australian cultural landscape. It is the transition from adolescence to adulthood. It’s not lost on me that the 21st anniversary of this publication also sees a trend where the industry is becoming more mature than it was 20plus years ago.
Over that time, there have been many initiatives, none maybe more important than the government appointing an advisory group for the circular economy - CEMAG. Made up of a cross-section of people both involved directly and indirectly with the resource recovery industry, this eclectic gathering of individuals has put forward some recommendations that the government is taking onboard vis-à-vis the circular economy.
While it released an interim report last year, chair John Thwaites says a comprehensive report with more recommendations will be forthcoming. And while the group waxed lyrical about the Environment Minister and her colleagues being super engaged with the advisory group, I stand by my editorial in the last issue of the mag where I believe that engagement needs to cross over into the wider

covered this subject a lot over the past 12 months as the wider community starts to take an interest in what they are and how they affect the environment. We have a piece from toxicology expert Ruth Jarman and her colleagues who while not saying that these chemicals are not harmful to humans, as scientists they’d like more data. In the piece they discuss the importance of making sure any studies of PFAS and other such chemicals are robust and can withstand the scrutiny of peer reviews. While they do not draw any conclusions of how harmful or not forever chemicals are to the human body, she does believe in the scrutiny of data sets. Currently, she’s not convinced about how a government body is going about setting up guidelines for how to handle such chemicals and what the safe limits are for humans.

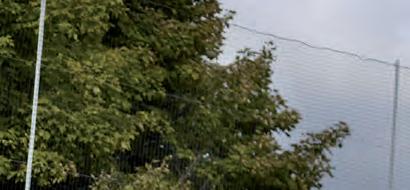
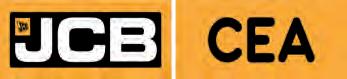
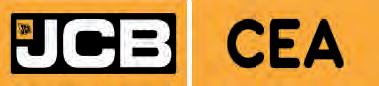
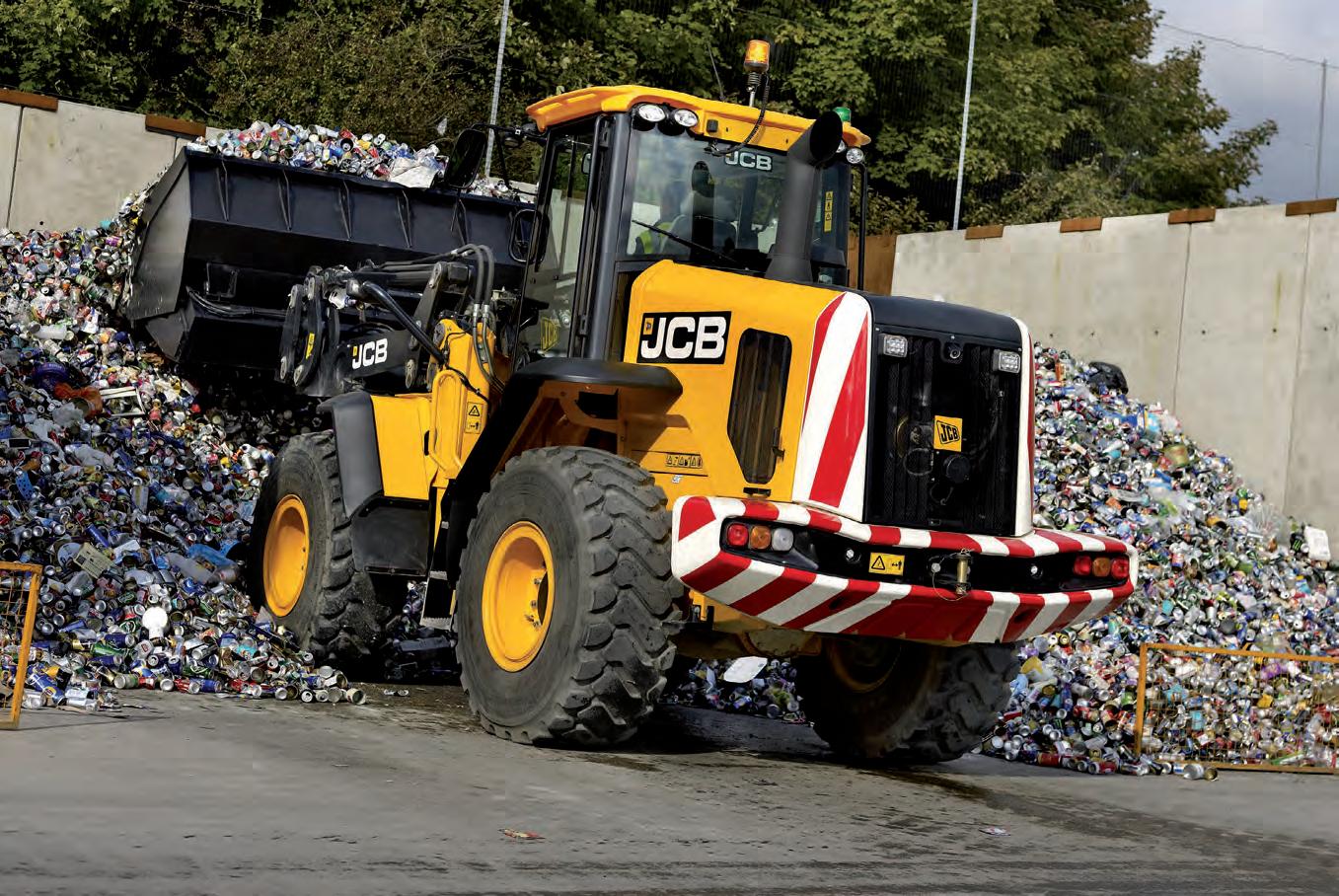
AUSTRALIA’S WASTE & RECYCLING POWERHOUSE.
Onetrak is thrilled to announce the acquisition of CSS Recycling, a leading provider of waste & recycling solutions. This partnership marks a significant milestone for Onetrak, further solidifying our position as the specialists in material processing equipment.
This partnership reflects our shared commitment to innovation, quality, and excellence, enabling us to deliver a broader range of solutions, greater value, and exceptional specialised service to our customers.
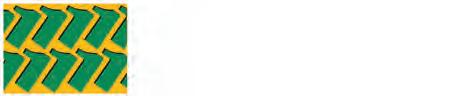



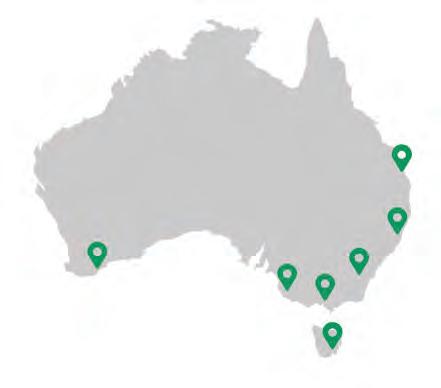
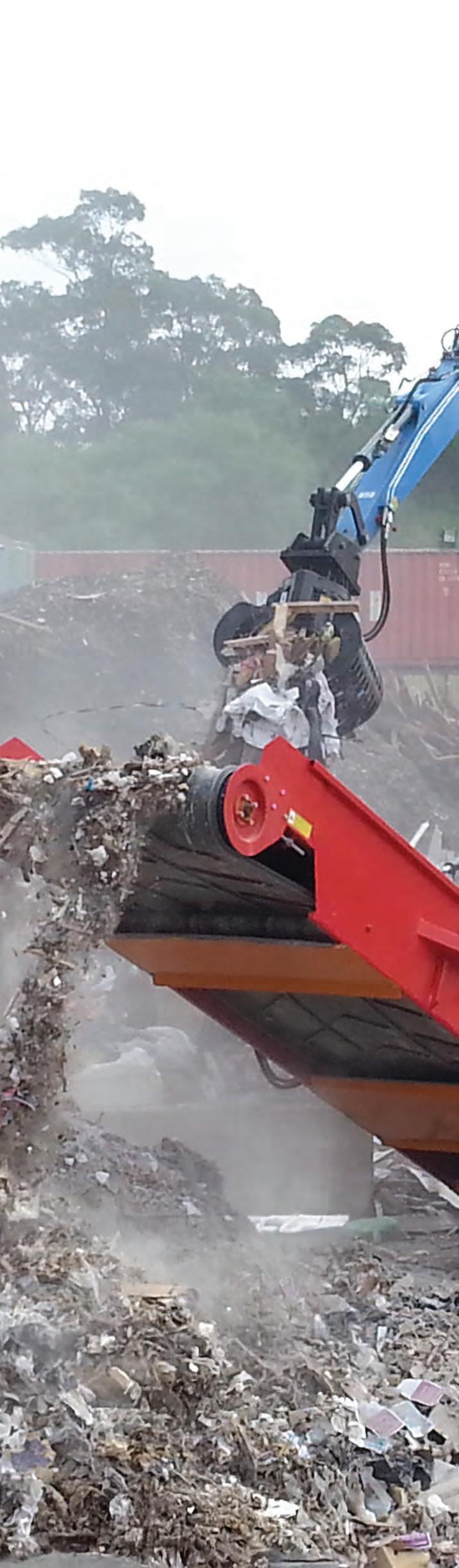
Monetising landfill gas at Lucas Heights
CLEANAWAY has announced a joint venture with Australian bioenergy and methane abatement company LMS Energy to process and monetise landfill gas (LFG) at Cleanaway’s Lucas Heights landfill.
Under the terms of the joint venture, LMS Energy will invest approximately $46 million in the construction of new bio-electricity assets, including a 22MW generation facility, which will replace the existing electricity generation infrastructure owned and operated by a third party.
Cleanaway will contribute exclusive rights to the landfill gas at Lucas Heights for 20 years. Both parties will hold equal ownership in the venture, leveraging their combined capabilities to maximise returns while minimising the capital outlay for Cleanaway. The formation of the venture is subject to third-party approvals, which are customary for such a transaction .
“Optimising our landfill gas
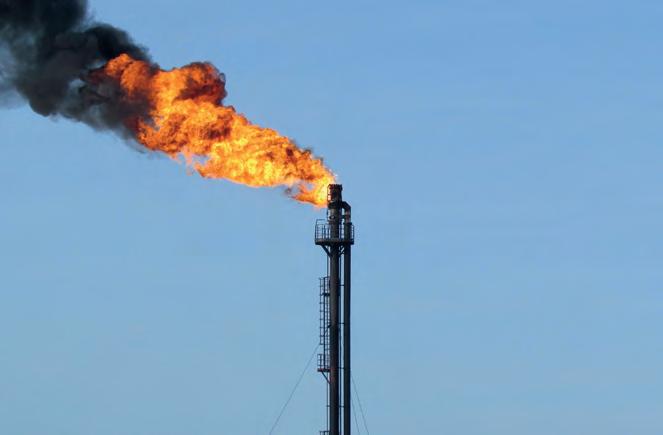
opportunity is a key focus area of our Blueprint 2030 strategy and is part of our Operational Excellence program of work,” said chief executive officer and managing director of Cleanaway, Mark Schubert. “[This] announcement is particularly rewarding, as it
represents a meaningful step towards achieving our target of more than $50 million of EBIT in FY26 from the Operational Excellence program.
“The JV aligns with our commitment to disciplined capital management, and utilising capital-
lite approaches to grow earnings and drive improved returns for shareholders while also supporting our commitment to reduce greenhouse gas emissions.”
Through the sale of landfill gas, provision of services, and from the JV itself, Cleanaway expects the partnership to contribute incremental EBIT of approximately $5 million in FY25 and approximately $10 million in FY26. Beyond FY26, post full commissioning of the assets, assuming current operating and regulatory conditions, the partnership is expected to deliver incremental EBIT of approximately $15 million per annum.
Consistent with LFG capture and monetisation being an initiative pursued as part of Cleanaway’s Operational Excellence focus, the EBIT accretion from the JV is factored into its FY25 EBIT guidance. Cleanaway continues to expect FY25 EBIT to be between $395 and $425 million.
Engineering positive change
We regard waste as a valuable resource, and strive to achieve sustainable development through its avoidance, recovery, and reuse.
By aligning projects with Circular Economy principles, we are working with governments, industries, and communities to help close the loop on waste and build a resilient future. Together, we are engineering positive change.
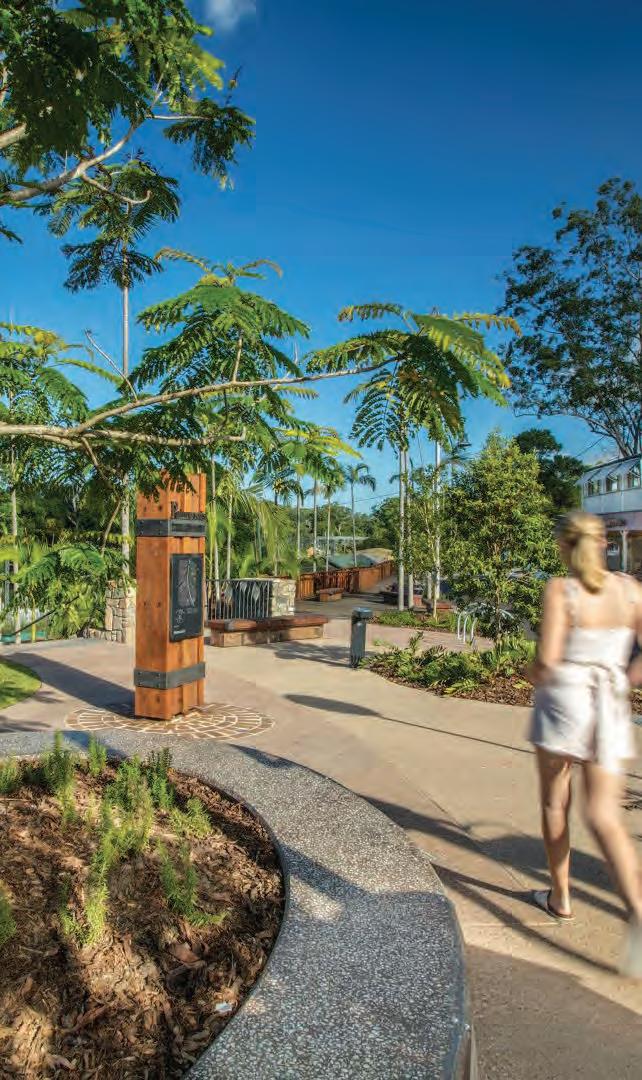
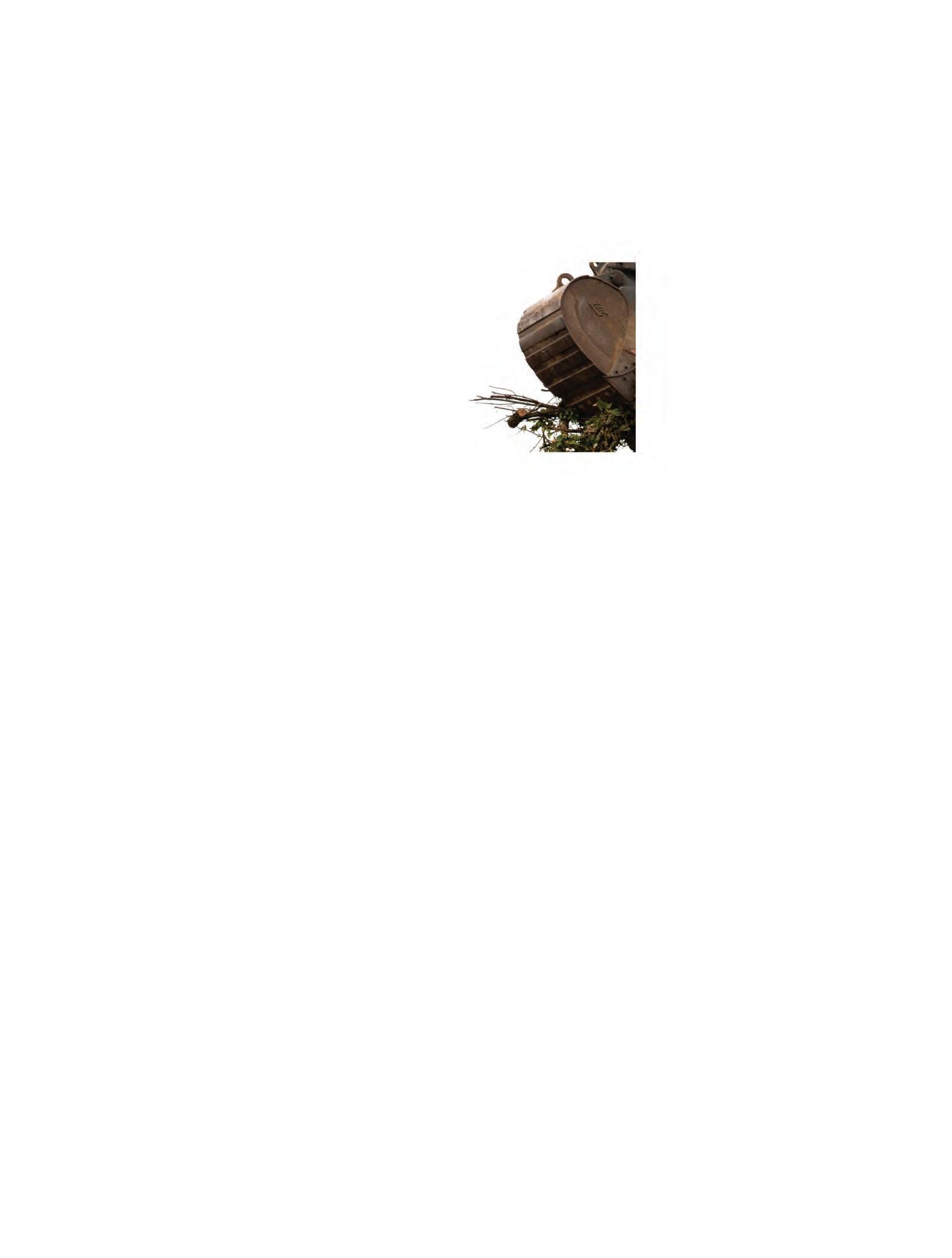
Optimising landfill gas opportunities is a key focus area for Cleanaway. Image: eleonimages/stock. adobe.com
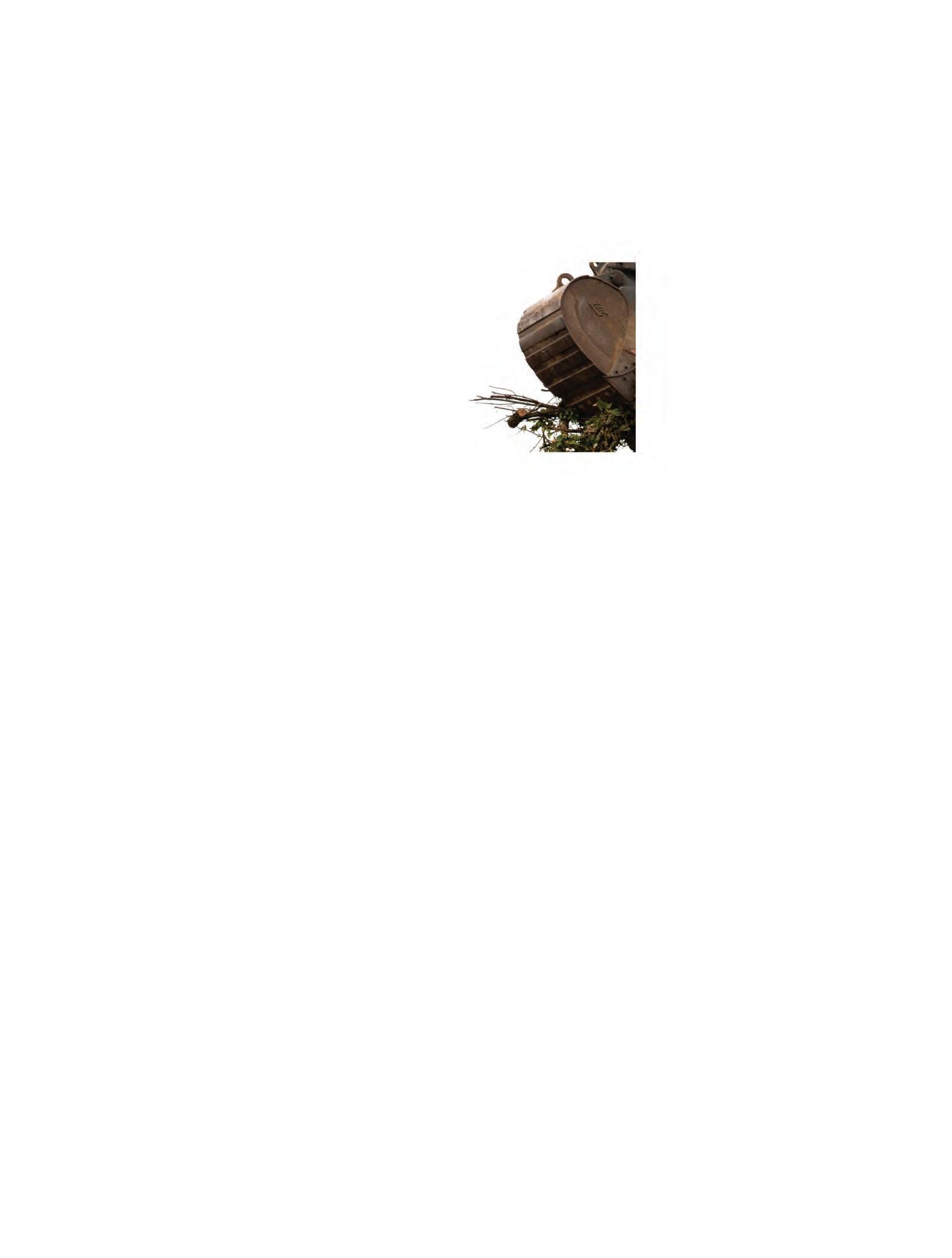
VIC CDS gets CountAIner AI to boost processing times
FOR the first time in the Southern Hemisphere, AI is being used to reduce waste and boost recycling capacity in Victoria’s container deposit scheme.
CountAIner uses advanced AI machine learning to count, identify and process eligible returns in bulk at speeds of up to 1,500 containers per minute.
Minister for Environment, Steve Dimopoulos, has announced the new AI-powered recycling machine is in operation at the CDS Vic Depot in Dandenong South, to process more containers more quickly and efficiently.
Over the past three years, ReturnIt has worked together with Canadian engineering company Machinex to develop and refine the CountAIner technology for use in Australia –with the CDS Vic depot Dandenong South being the only unit to deploy this high-speed counting equipment
outside of North America.
Victoria’s CDS has seen more than 1 billion containers returned in its first year alone, putting $100 million back in the pockets of Victorians and reducing litter to landfill by half since CDS Vic was launched on 1 November 2023.
More than $950,000 has been donated by Victorians through the scheme to over 4,200 charities, community groups and local sports clubs – supporting great causes across the state.
With more than 650 refund collection points and growing, CDS Vic makes it easy for Victorians to cash in their containers, recycle waste and divert more litter from landfill.
The CDS is part of the state government’s $515 million investment to transform the state’s waste and recycling systems, driving progress towards diverting 80 per cent of waste from landfill by 2030.
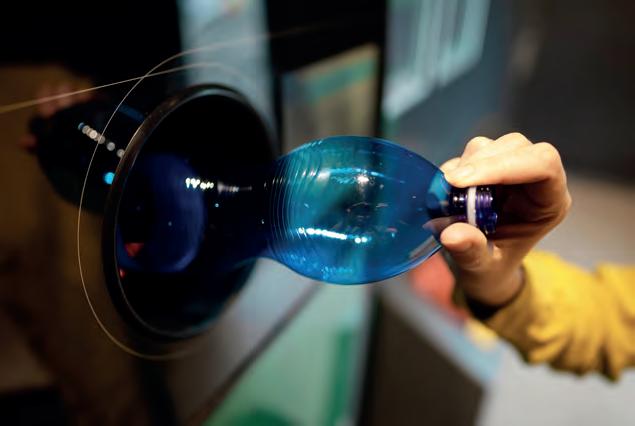
“This advanced AI technology brings speed and precision that will transform how we recycle in Victoria –driving smarter, more efficient waste management across the state and country,” said Dimopoulos.
“The Dandenong South
manufacturing precinct is the heart of innovation in Victoria – it’s wonderful to see AI technology like the CountAiner being deployed for both environment and economic benefit for all Victorians,” said Member for Dandenong Gabrielle Williams.

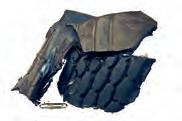
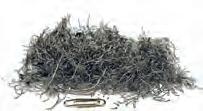
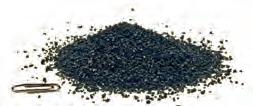



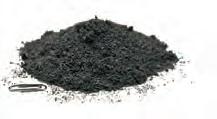
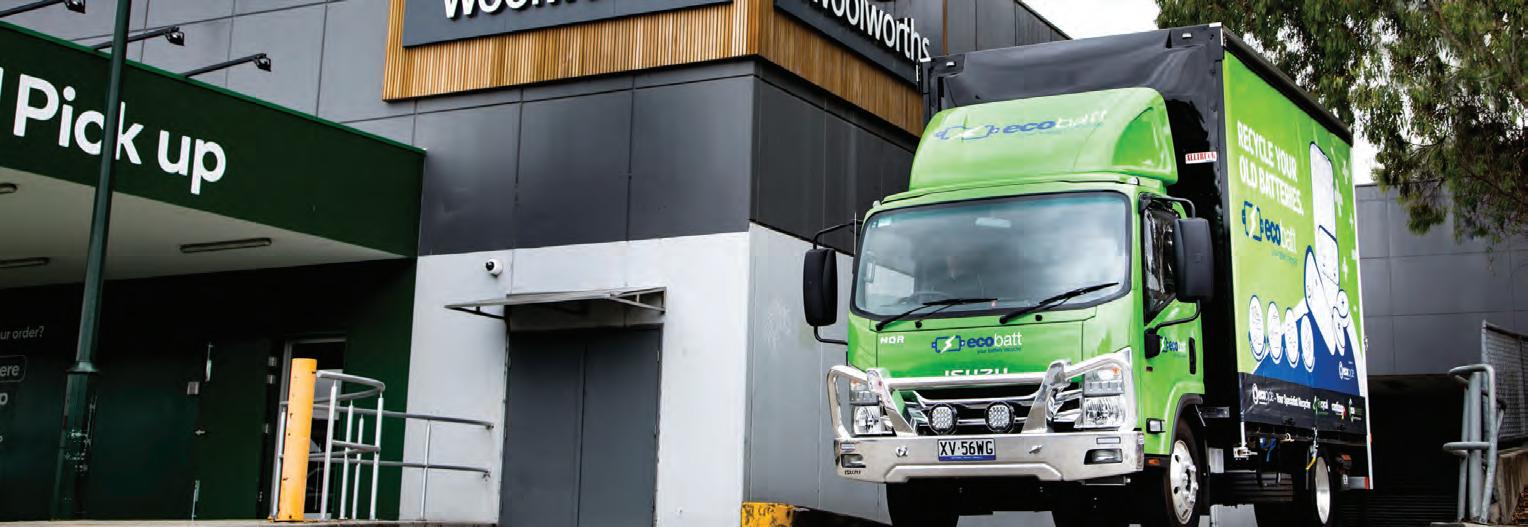
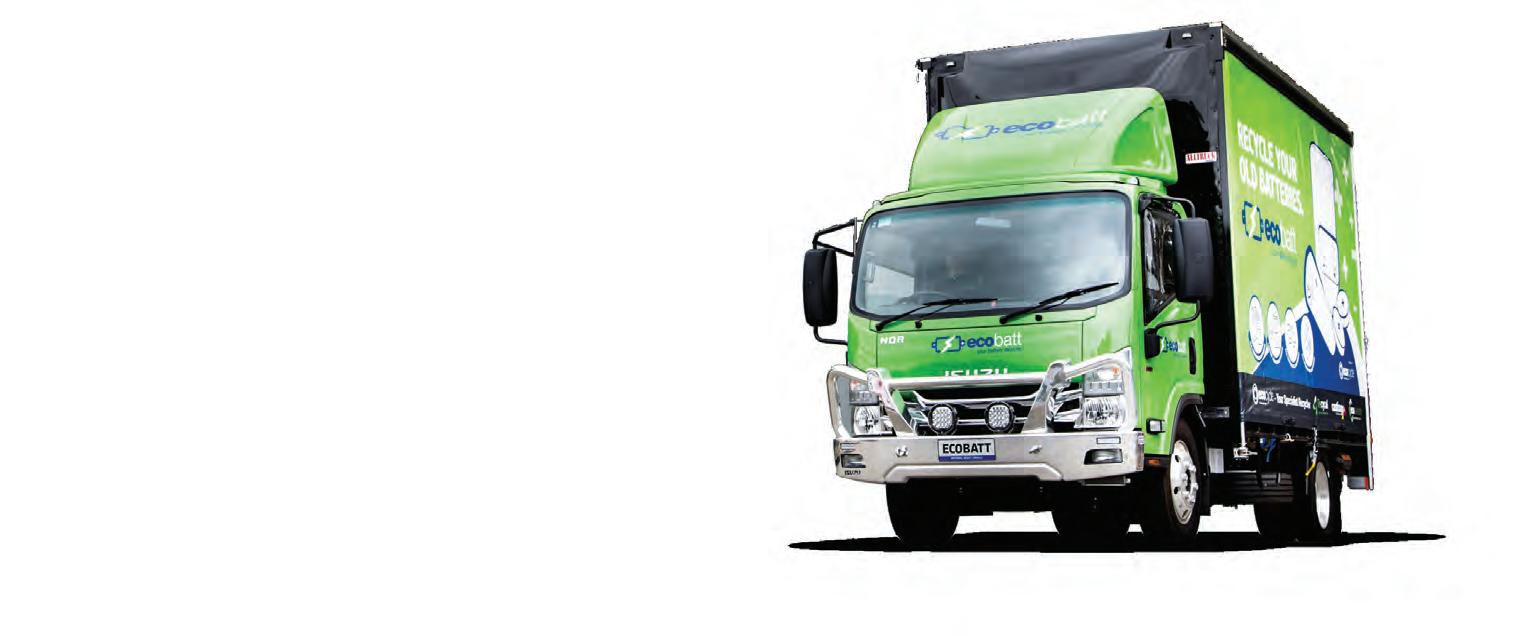
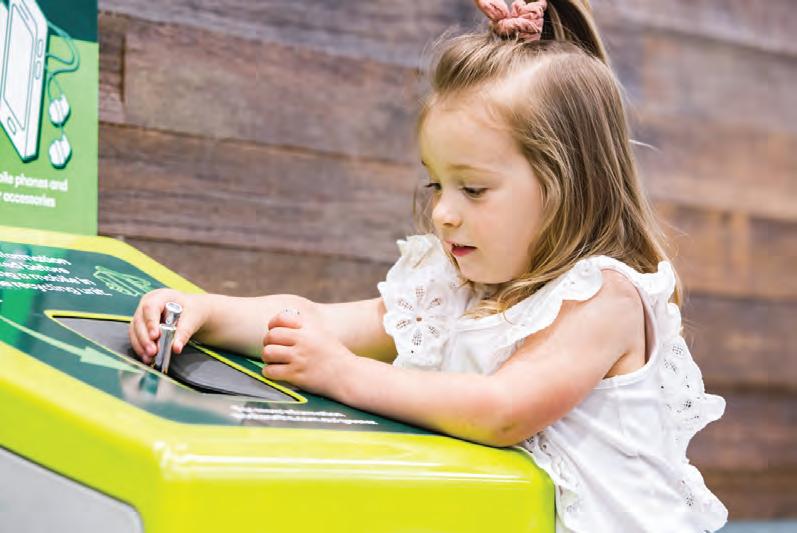
Victoria’s CDS has seen more than 1 billion containers returned in its first year. Image: M-Production/Shutterstock.com.
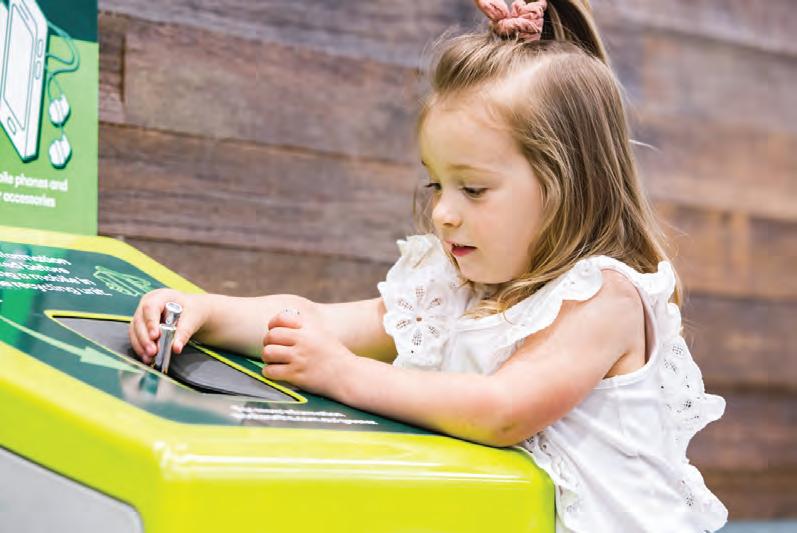
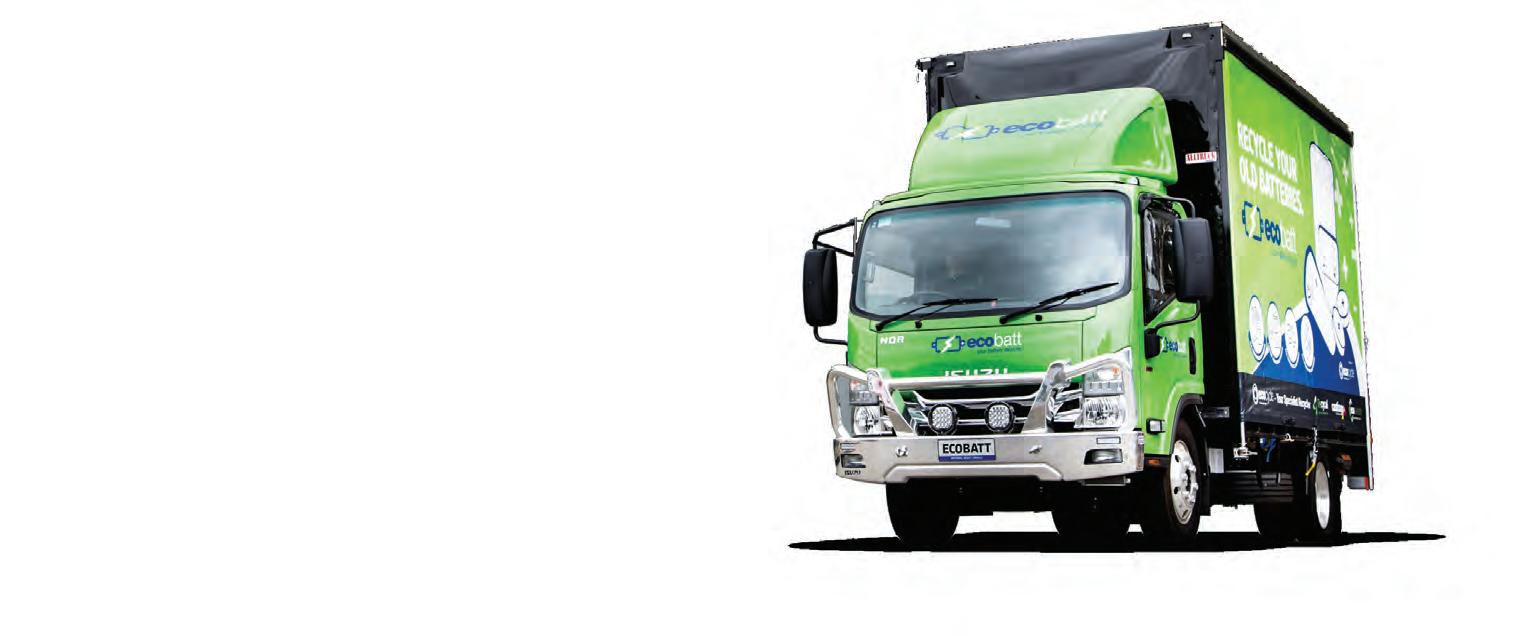
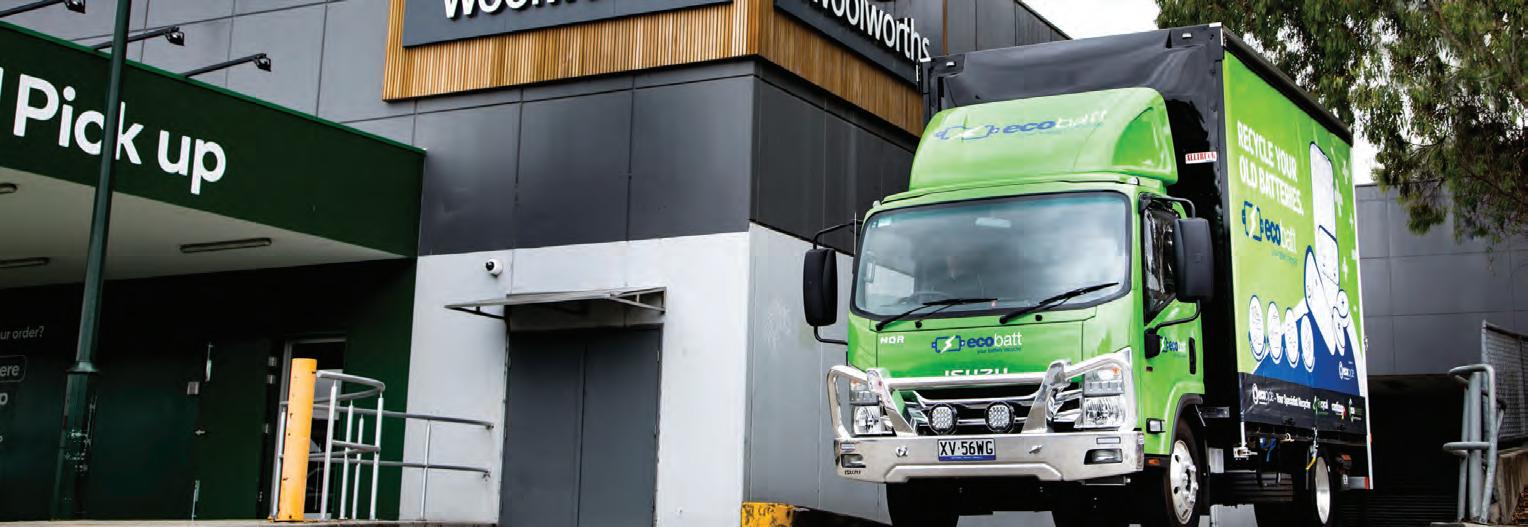
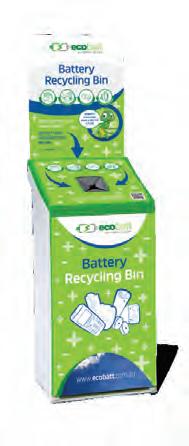
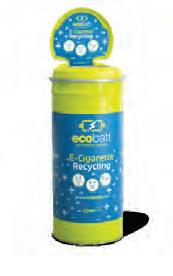
EPA commences prosecutions over asbestos mulch
THE NSW Environment Protection Authority (EPA) has commenced a suite of prosecutions against three companies and one individual i n response to its asbestos in mulch investigation that started in 2024.
The prosecutions follow the largest investigation in the EPA’s history, which was launched a fter bonded asbestos was discovered in mulch at Rozelle Parklands. During the investigation more than 300 sites were inspected, with 79 sites identified as having used contaminated mulch. All 79 sites have now been cleaned up by owners.
A t otal of 102 alleged offences have been charged against VE Resource Recovery Pty Ltd (1 charge), the sole director of VE Resource Recovery Pty Ltd, Arnold Vitocco (1 charge) and two entities
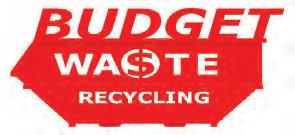
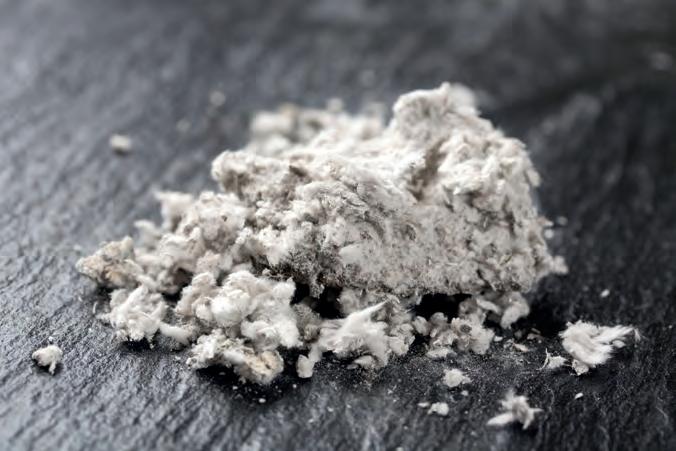
More than 300 sites were inspected for suspected asbestos-contaminated mulch. Image credit: Tsuboya/stock. adobe.com
trading as Greenlife Resource Recovery Facility, namely Freescale Trading Pty Ltd (50 charges) and Runkorp Pty Ltd (50 charges).
The offences relate to 26 sites, i ncluding Rozelle Parklands. The charges, which will be heard in
Budget Waste Recycling Pty Limited and Mr Michael Calleija convicted and fined for contravening prevention notices
Budget Waste Recycling Pty Limited (Budget Waste) and its sole director Michael Calleija were prosecuted by the NSW Environment Protection Authority (EPA) and pleaded guilty to offences related to contraventions of prevention notices.
Budget Waste operates a resource recovery and waste storage facility at 311 Doonside Road, Arndell Park NSW 2148. Budget Waste is the holder of Environment Protection Licence No. 20645 for that premises.
As the EPA was concerned that Budget Waste was carrying out its licenced activities in an environmentally unsatisfactory manner, the EPA issued a prevention notice to Budget Waste on 25 May 2022. The prevention notice required Budget Waste to cease receiving waste and carry out a volumetric and topographical survey of waste on its premises. The EPA issued a supplementary prevention notice to Mr Michael Calleija on 25 November 2022, directing him to undertake these same directions referred to in the prevention notice issued to Budget Waste.
Between about 26 May 2022 and about 23 December 2022, Budget Waste continued to receive waste at their licensed premises and failed to carry out a volumetric survey between about 1 June 2022 and about 24 January 2023.
On [date], the Land and Environment Court of New South Wales convicted Budget Waste and Michael Calleija for contravening the prevention notices and made the following orders:
In proceedings 164057 of 2023:
1. The defendant, Budget Waste Recycling Pty Limited, is convicted of the continuing offence against section 97 of the Protection of the Environment Operations Act 1997 (NSW) as charged.
2. Budget Waste Recycling Pty Limited is to pay a fine in the amount of $234,000.
In proceedings 164049 of 2023:
3. The defendant, Mr Michael Calleija, is convicted of the continuing offence
t he Land and Environment Court, cover five categories:
1. E nvironment Protection Licence breach offence against VE Resource Recovery Pty Ltd in relation to an alleged failure to carry out resource recovery
activities competently.
2. E xecutive liability offence alleged against Arnold Vitocco as director of VE Resource Recovery Pty Ltd in relation to the company’s alleged licence breach offence.
3. C arrying out scheduled activities without a licence offences against both Freescale Trading Pty Ltd and Runkorp Pty Ltd for allegedly carrying out scheduled activities, namely resource recovery and waste storage, without a licence issued by the EPA.
4. Mulch order”offences against both Greenlife companies, for allegedly breaching a Resource Recovery Order, the Mulch Order 2016.
5 R euse of asbestos waste offences against the two Greenlife companies, for allegedly reusing asbestos waste.
against section 169A of the Protection of the Environment Operations Act 1997 (NSW) as charged.
4. Mr Michael Calleija is to pay a fine in the amount of $25,000.
In proceedings 324738 of 2023:
5. defendant, Mr Michael Calleija, is convicted of the continuing offence against section 97 of the Protection of the Environment Operations Act 1997 (NSW) as charged.
6. Mr Michael Calleija is to pay a fine in the amount of $75,000.
In proceedings 164049 of 2023, 164057 of 2023 and 324738 of 2023:
7. Pursuant to s 122 of the Fines Act 1996 (NSW), a moiety of 50 percent of any fine determined by the Court be paid to the prosecutor.
8. Pursuant to s 248 of the Protection of the Environment Operations Act 1997 (NSW), the defendants to pay $3,100.00 to the Environment Protection Authority for its costs and expenses reasonably incurred during its investigation of the offences.
9. Pursuant to s 257B of the Criminal Procedure Act 1986 (NSW), the defendants to pay the legal costs of the Environment Protection Authority as agreed or as may be determined under s 257G of the Criminal Procedure Act 1986 (NSW).
10. Pursuant to s 250(1)(b) of the Protection of the Environment Operations Act 1997 (NSW), the defendants, at their expense:
1. within 60 days of the date of these orders, cause a notice at a minimum size of 139mm x 129mm to be published within the first 12 pages of the Sydney Morning Herald with the text of such notice and the Budget Waste Recycling Pty Limited (ACN 112 980 293) logo (of reasonable size) as set out in Annexure A to these orders; and
2. within 60 days of the date of these orders, cause a notice at a minimum size of a quarter of a page to be published within the first 12 pages of Inside Waste with the text of such notice and the Budget Waste Recycling Pty Limited (ACN 112 980 293) logo (of reasonable size) as set out in Annexure A to these orders.
11. Within seven days of the date of publication of the notices referred to in order 10, the defendants to provide the prosecutor with a complete copy of the notices published pursuant to that order.
The Court’s judgment may be accessed at https://www.caselaw.nsw.gov.au/ decision/193197d50069efb8a9b571af
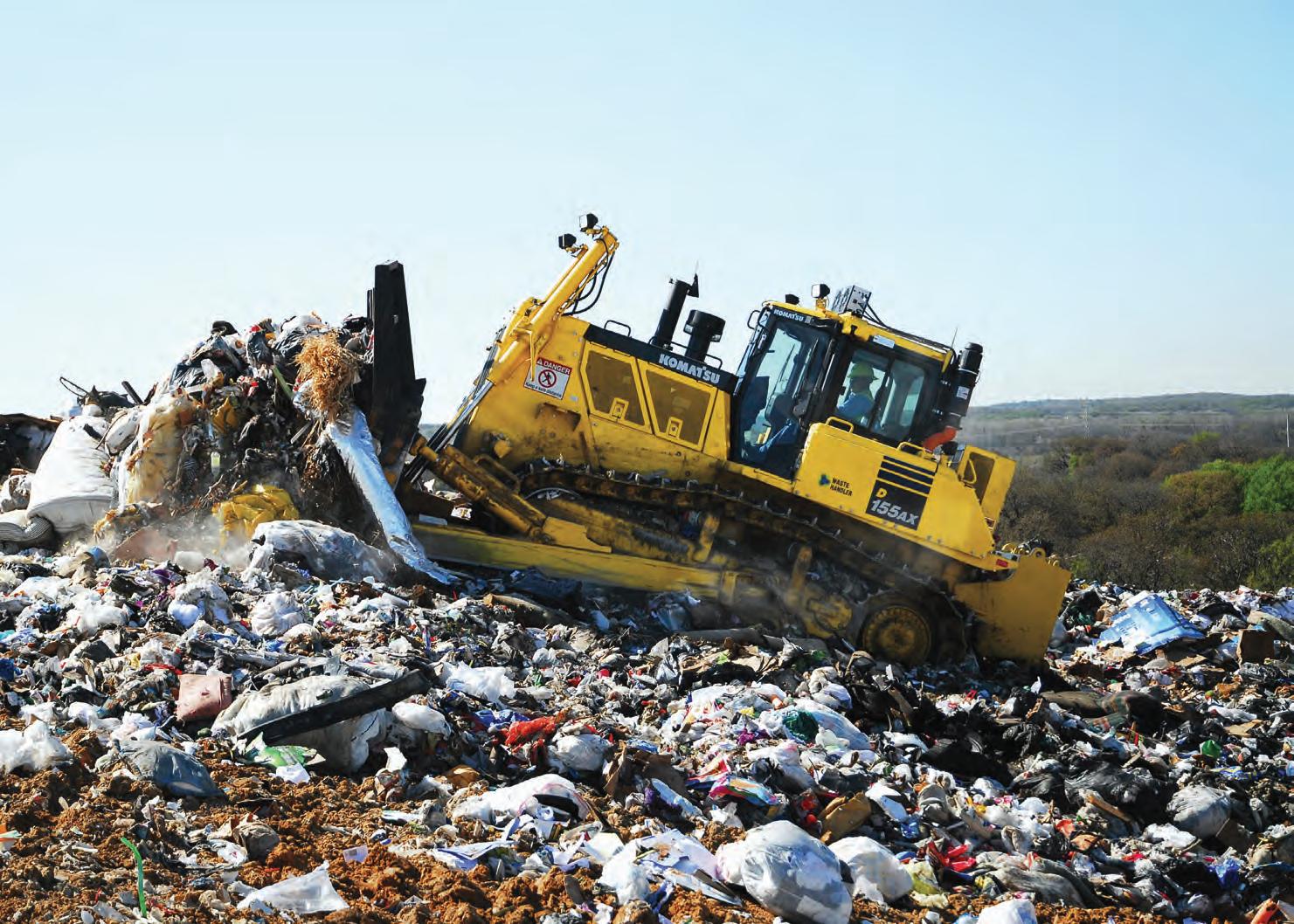
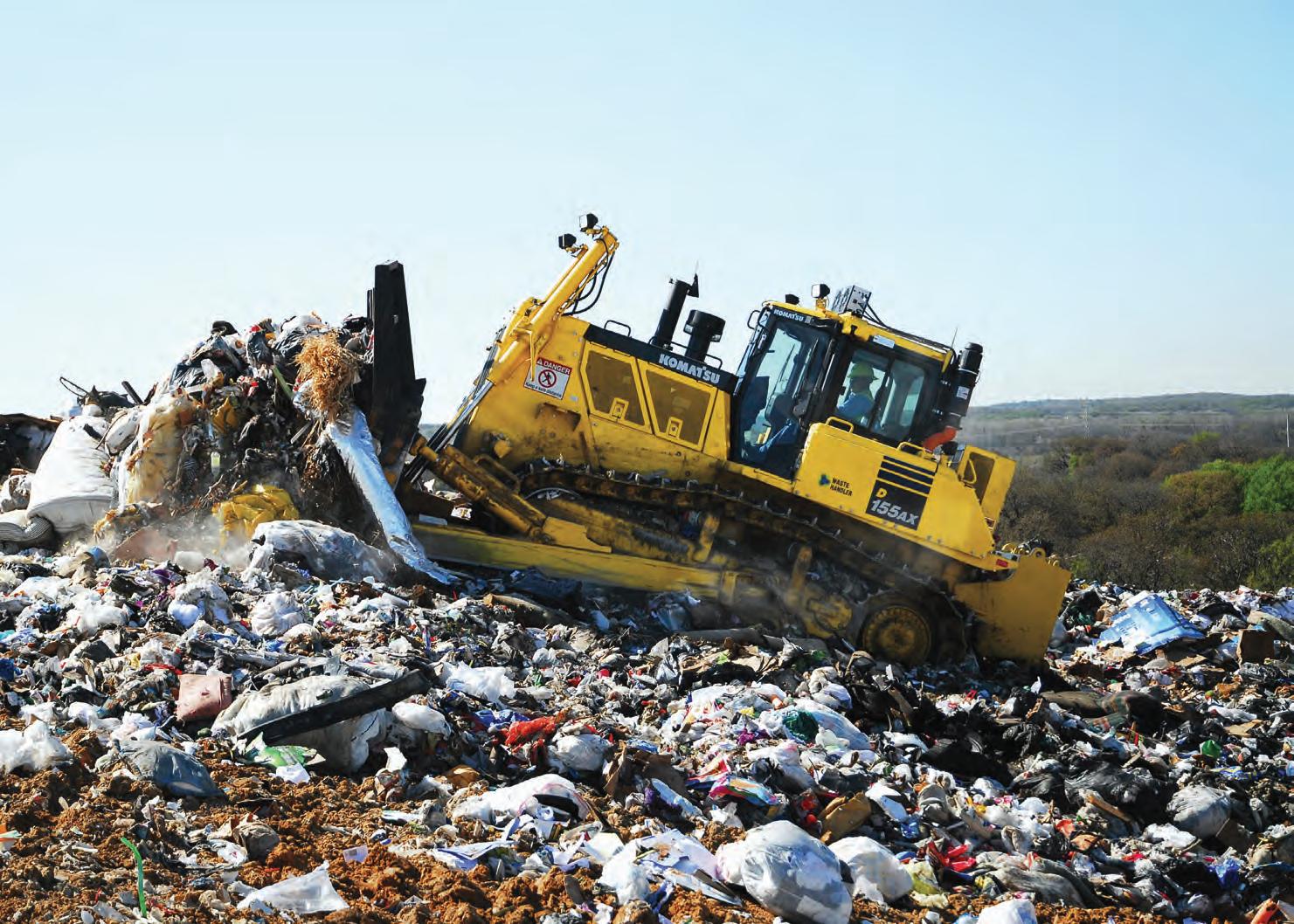
Clearing the way: Komatsu Waste Spec Dozers
Built for productivity and efficiency
The waste processing industry requires purpose-built equipment for moving highly variable materials. Komatsu creates machines and solutions designed specifically for the difficult terrain and materials involved with handling waste. Our advanced Dozers equipped with smart technology, are engineered for productivity to support your goals of a zero-harm environment.
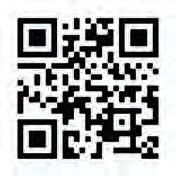
Veolia and Cleanaway sign deals with defence
CLEANAWAY has been announced as the new Resource Recovery and Waste Management contractor for Defence in Queensland (QLD) and Western Australia (WA) in a six-year partnership that has the potential to extend to 2035.
Operational from 31 March 2025, the contract includes scheduled work and Survey & Quote projects, supporting Defence events and exercises and is aligned to the Federal Government’s 80 per cent waste diversion target by 2030.
“We’re proud to bring our sustainability expertise and extensive service capability to Defence’s Base Services program. The contract will drive growth in our QLD and WA regions and create opportunities to increase our
positive social and economic impact for local communities,” said Cleanaway CEO and managing director, Mark Schubert.
“We’re excited to welcome Cleanaway as part of our Base Services team of industry partners. Cleanaway has demonstrated their commitment to working collaboratively in the delivery of Base Services and to our shared vision for increased resource recovery and social impact,” said Defence spokesperson, Luke McLeod.
Cleanaway’s network maps closely to Defence locations, ensuring high levels of directly delivered service, which creates jobs and provides economic benefit to local business, keeping procurement and investment
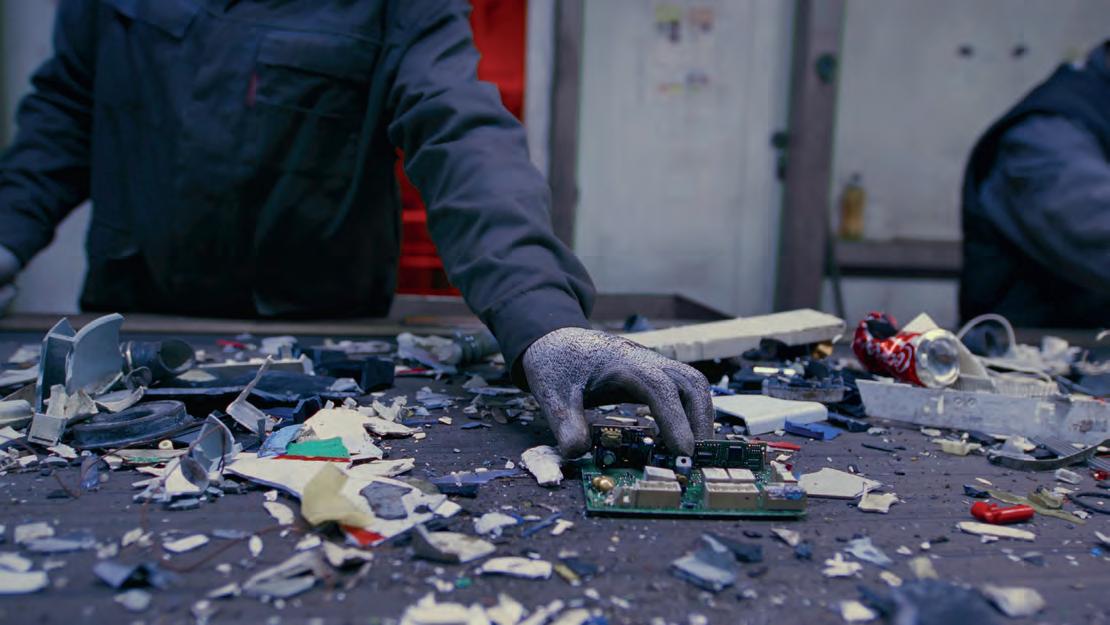
within the Australian economy. Cleanaway will provide an account team structured to respond to demand-driven, surge and emergency requirements.
In addition, Cleanaway will provide a resource recovery and waste management roadmap that prioritises engagement, education and innovation. Aligned with the Australian Waste Policy 2030, its approach brings together service data with an understanding of what drives
landfill diversion to ensure every site can individually achieve their goals.
Veolia has also signed a new sixyear contract with The Department of Defence., which will see a data-driven approach brought to bear on its waste management processes.
Using its reporting platform, ecoLogic, Veolia will help Defence deliver on its target to divert 80 per cent of its waste from landfill by 2030 as part of a contract that has some of Australia’s
‘Maggot robots’ devour food waste in processing facility
CIRCULAR Economy scaleup Goterra has opened its doors to a new facility harnessing technology to tackle the mounting issue of food waste. The system uses insects called Black Soldier Fly larvae to break down food waste onsite rapidly, at a large scale. Housed in deep-tech, shipping container-sized units dubbed ‘Maggot Robots,’ the larvae can devour vast amounts of food waste.
The process saves up to 97 per cent of C02 emissions compared to food organics being disposed of in landfill.
This process yields high-value products for agriculture, including an organic fertiliser and nutrient-packed insect protein that supports a circular economy. Further Scope 3 emissions are saved by handling waste onsite at Wetherill Park, avoiding additional vehicle miles to landfills that are fast filling up and running out of space.
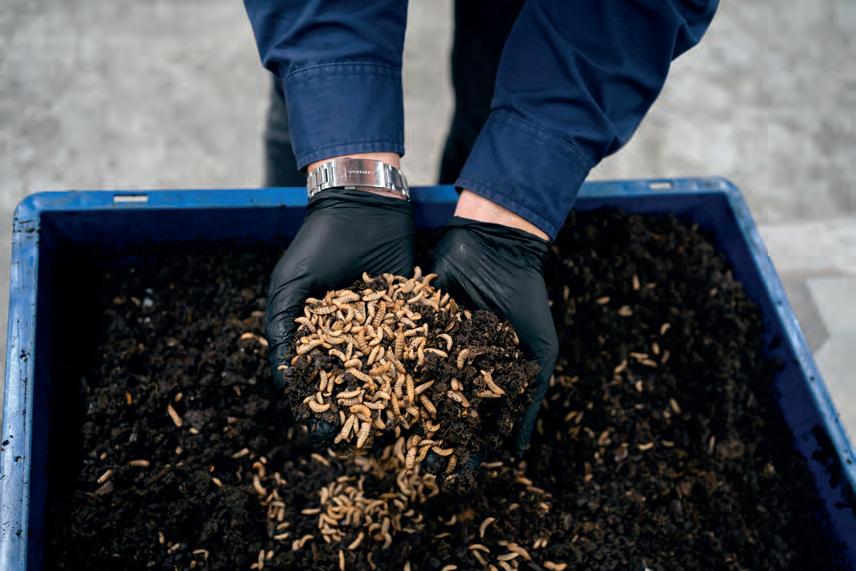
Black Soldier Fly larvae breaks down food waste onsite rapidly.
isn’t suitable for hunger relief charities.
Woolworths is the site’s founding customer, sending food waste from its stores across the Sydney region, which
Woolworths has been partnering with Goterra to process its food waste since 2020.
Waste management company, Cleanaway, will be collaborating with
Woolworths and Goterra to transport the food waste from Woolworths, along with other aggregated loads from its customers around the city to the facility.
Goterra CEO, Olympia Yarger, said this decentralised model is transformative
for Sydney, which produces more than 500,000 tonnes of food waste annually, mostly trucked to landfills outside the metro area.
“For too long, food waste has decomposed in landfills creating methane, a GHG with a global warming effect 25 times more potent than CO2. Our partnership with forward-thinking partners like Woolworths and Cleanaway will help change that,” said Yarger.
The site processes more than 100 tonnes every week, and will create 10 new jobs for locals to Fairfield City Council and provide a blueprint for a system with the highest order of food waste recovery.
The larvae inside Goterra’s units work around the clock, enabling 24/7 waste processing. Sensors track temperature, humidity and waste levels, automatically adjusting conditions to optimise digestion.
Goterra is expanding its fleet of modular waste units across Australia, providing scalable, decentralised and emissions-reducing waste solutions.
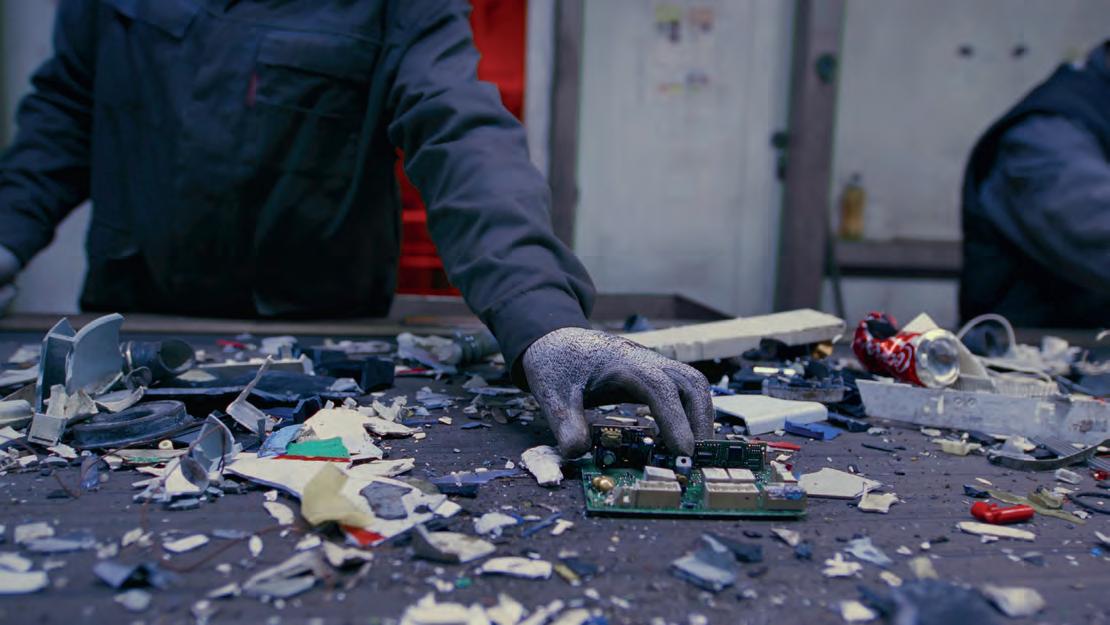
highest standards in quality assurance, risk management, and ambitious waste management goals.
This new contract builds on a 10-year
working relationship between Veolia and Defence, which delivered waste management around the country, including advances in FOGO processing, innovative treatment for complex waste types and a reduction in waste going to landfill.
Data has become a key part of recycling and waste management across every part of the Australian economy, with the effectiveness of recycling and waste management becoming more reliant on the quality of intelligence through all points of a materials lifecycle. Defence will be taking that to the next level with the Defence Base Services Transformation Program. This program will see new resource recovery hubs added to Defence sites.
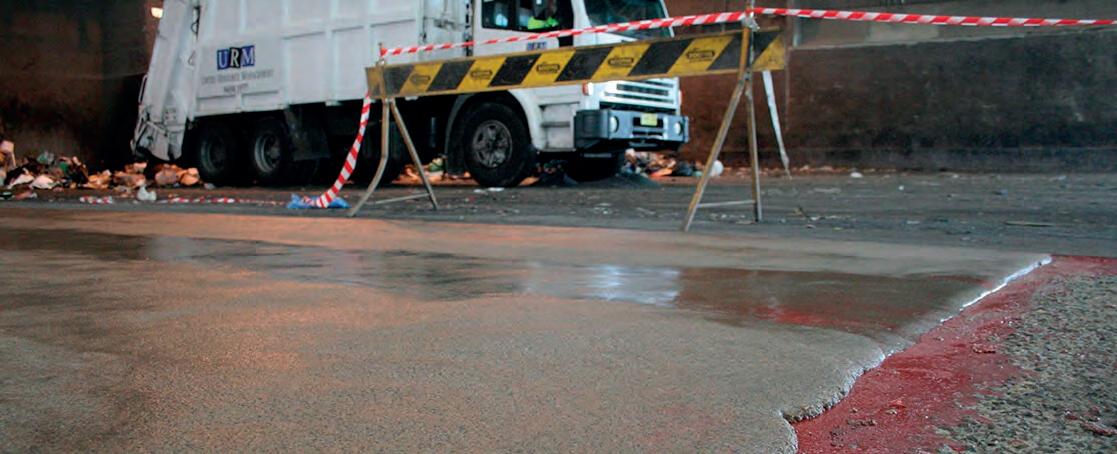
The creation of new resource recovery hubs on the bases, will also see increased job opportunities for local communities, small- to medium-sized businesses, and Aboriginal and Torres Strait Islanders. Just as importantly, it will open doors to employment pathways for veterans transitioning back into civilian life.
Central Coast Council fined $418k over wastewater spill
CENTRAL Coast Council has been ordered to pay a total of $418,562 by the Land and Environment Court for failing to maintain a sewage pipeline, which caused a water pollution event in Narara Creek near Gosford in April 2023.
The incident occurred when the West Gosford Major Sewage rising main, or pipeline, failed and around 1.83 million litres of untreated sewage was released into the creek, which is a tributary of the Brisbane Water estuary.
The Court found that the Council did not properly maintain the rising main at its South Sewage Treatment System in Kincumber and failed to undertake preventative maintenance work following a similar failure of the rising main in 2020.
EPA executive director operations, David Gathercole, said the 2023 incident resulted in pollution of Narara Creek, Fagan’s Bay and Brisbane Water.
“Apart from the obvious odour and visual pollution impacts that would
have been observed by the community, the release of untreated sewage into the environment resulted in increased ammonia levels as far as Brisbane Water and reduced dissolved oxygen levels in surface water,” Gathercole said.
“These changes in water quality can severely impact aquatic plants and animals.
“Following the earlier incident in 2020, the Council failed to implement a suitable preventative maintenance plan that may have prevented this latest event. It is crucial that the Central Coast Council ensures it has effective maintenance and repair schedules in place to protect the community and the environment.”
In addition to a fine of $105,600 the court agreed to a Council proposal to complete a restoration project of the Narara Creek Wetlands, valued at $151,900. The Council has also been ordered to pay the EPA’s costs of investigating and prosecuting the matter bringing the total penalty to $418,562.
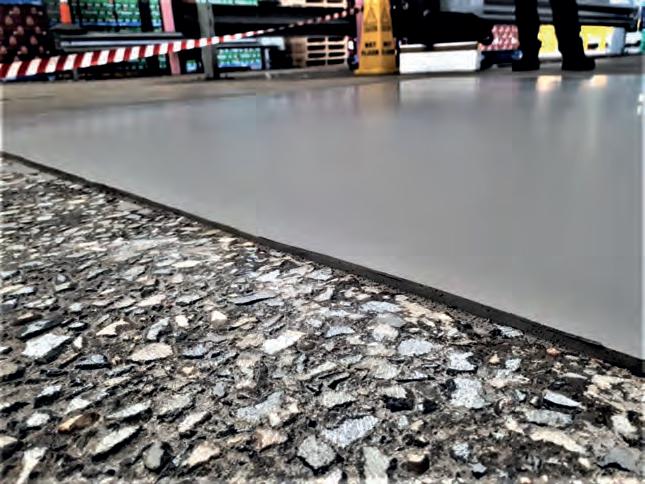



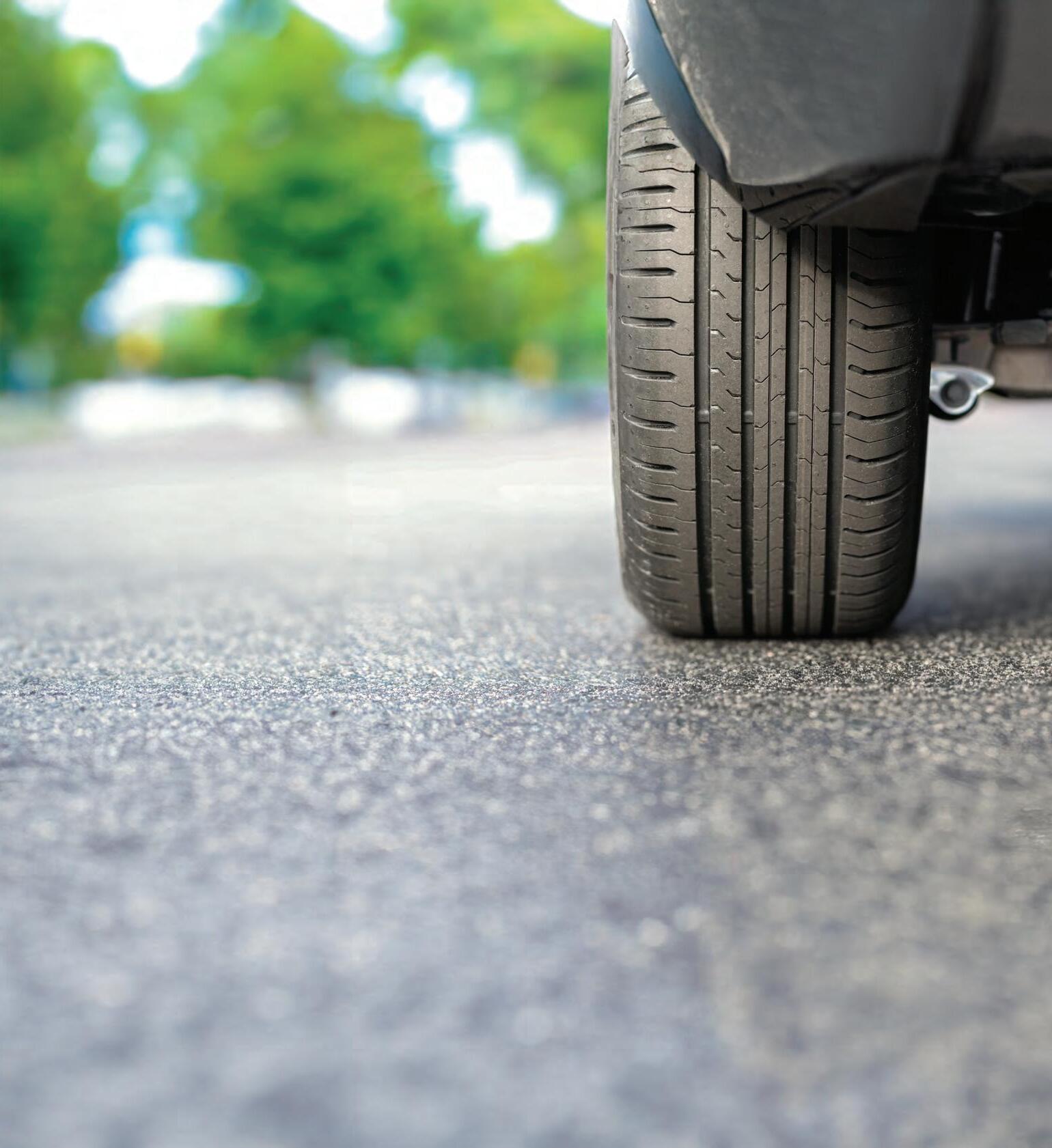
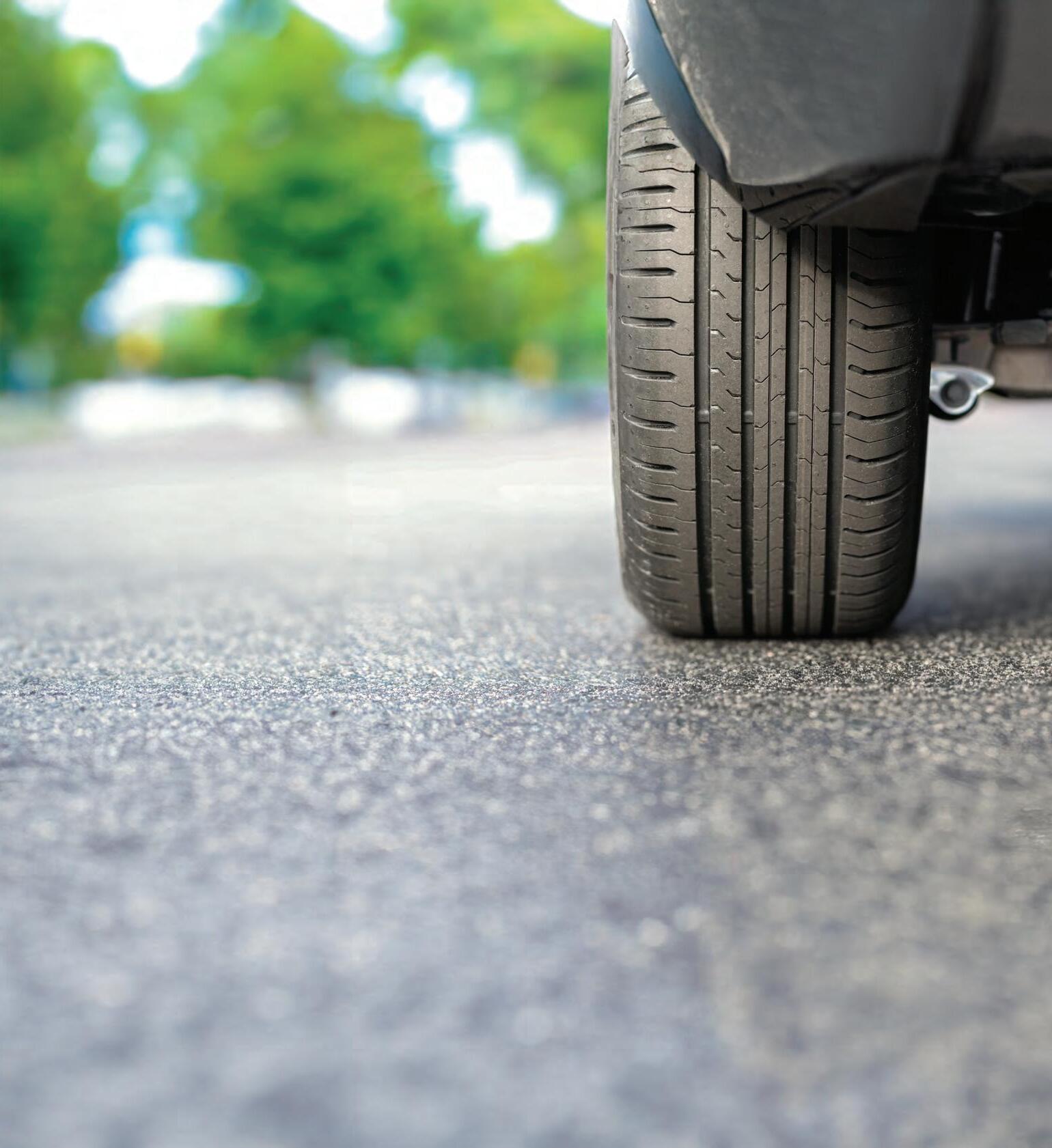
Muswellbrook Shire Council fined over waste water leak
A council has been fined and issued with an official caution after a leak of ferric sulphate at its water treatment plant earlier this year in March. The incident occurred at Muswellbrook Shire Council’s water treatment plant.
the corrosive liquid, which is used as a coagulant, leaked from a hole in the ferric sulphate storage tank and spilled into a contained (bunded) area.
The NSW Environment Protection
A that a temporary pump was left on, following a regular floor cleaning of the bund. This resulted in ferric sulphate inadvertently pumping into an onsite evaporative pond that stores waste lime, a by-product of the drinking water process.
Gathercole said the incident was
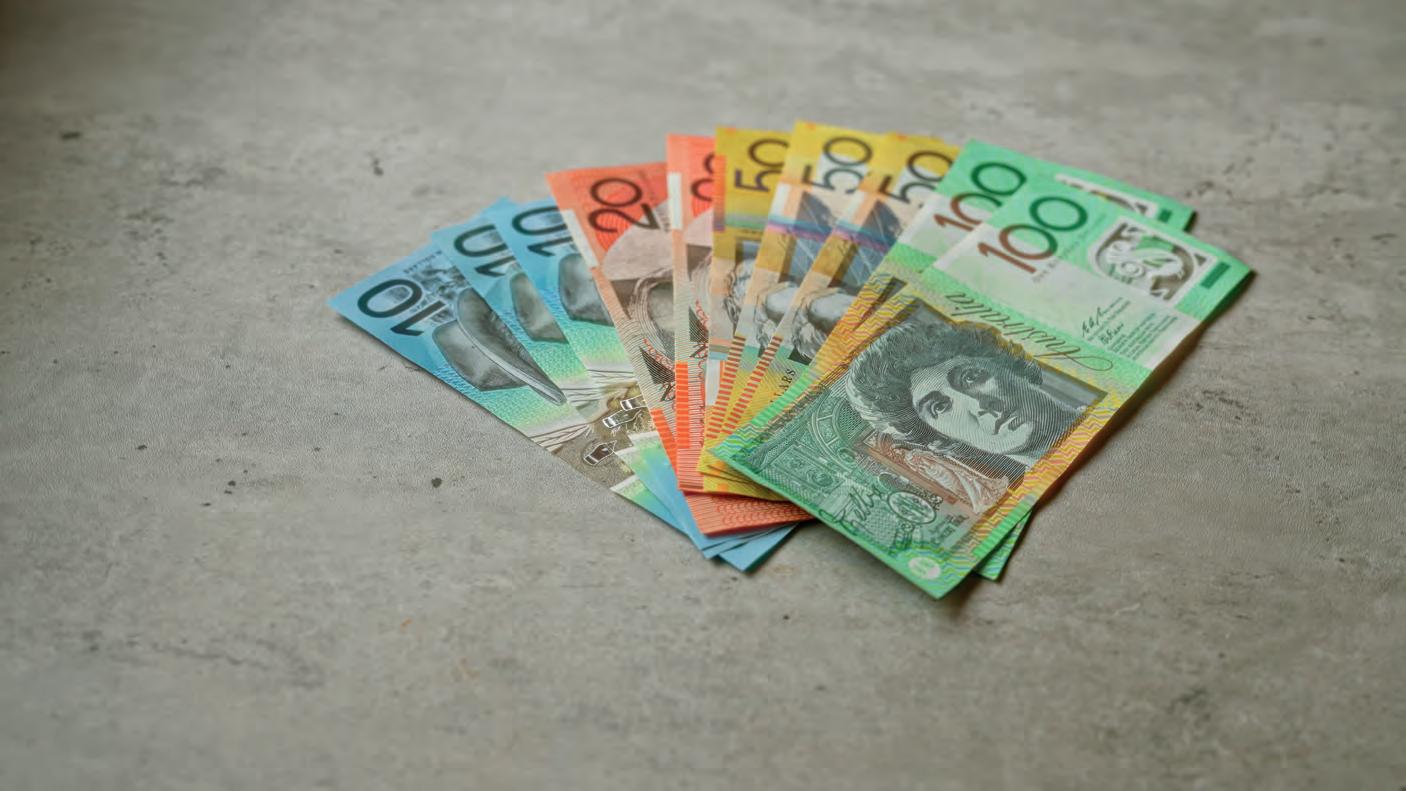
efficient manner.
“Fortunately, this was contained onsite and did not result in any actual harm to the environment or human health,” Gathercole said. “Any situation where equipment is not
operated properly runs the risk of potentially serious environmental impacts. It is also particularly important when working with chemicals to ensure that all processes and safety precautions are followed
Struggling to recycle your plastics?
to prevent any potential harm or pollution of waters, as has occurred in this incident.”
Muswellbrook Shire Council has now implemented onsite measures to prevent future incidents.
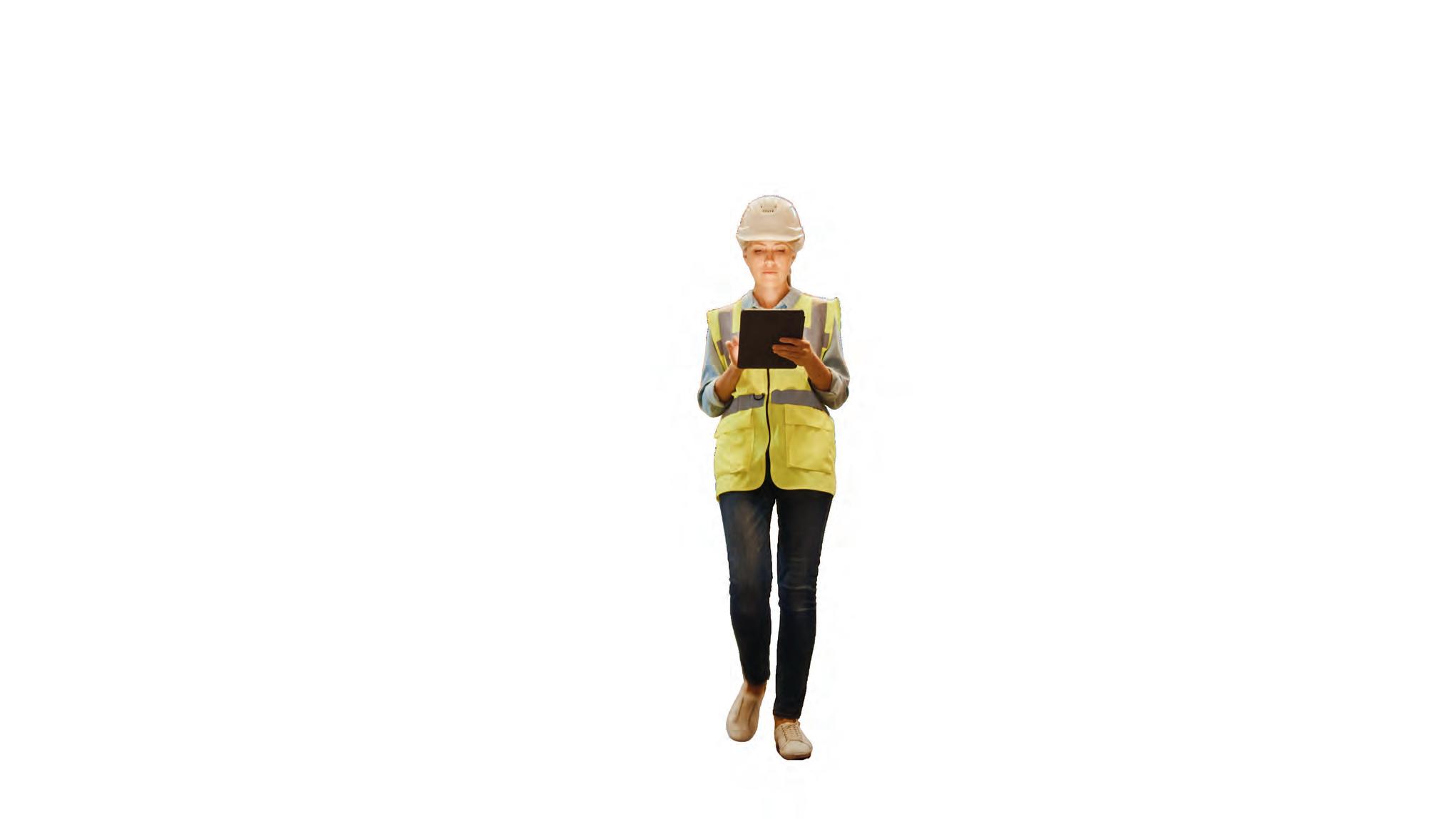
Our products complement the circular economy by being recyclable with mainstream soft plastics where programs exist and if not they will biodegrade in modern landfill 90% faster than conventional plastic with no microplastics. They have the same strength, flexibility, versatility and shelf-life as conventional plastic.
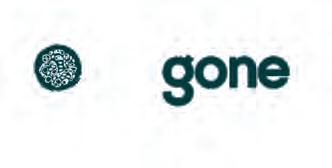
VWMA wants action over battery fires
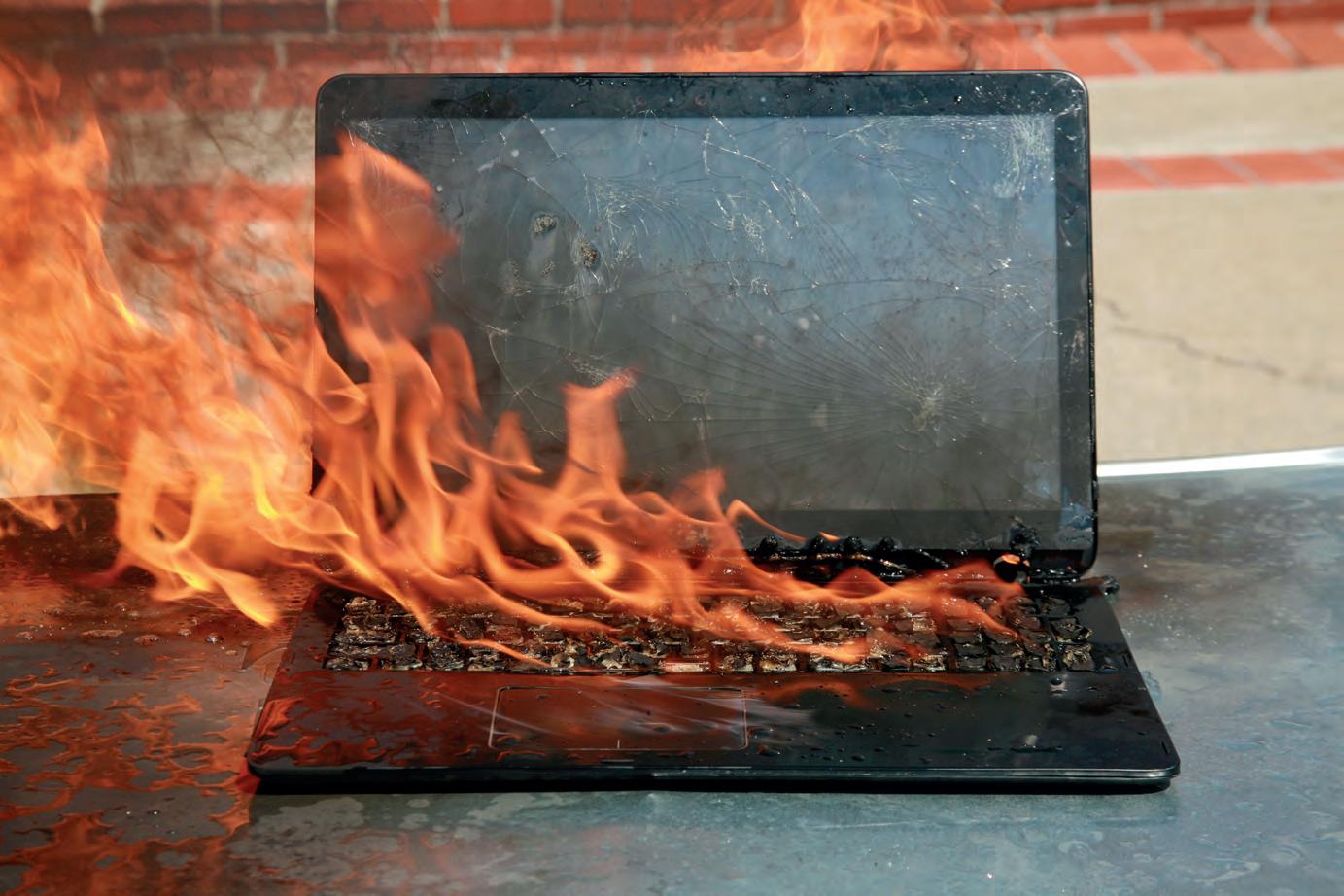
THE Victorian Waste Management Association (VWMA) is urging the Victorian Government to take immediate steps to address the growing threat of lithium-ion battery (LiB) fires, particularly as the state braces for peak bushfire season.
A growing safety challenge
Improper disposal of lithium-ion batteries poses fire risks, impacting every level of Victoria’s waste and recycling sector. While awareness is growing, current efforts remain fragmented, with inadequate transparency among stakeholders.
Despite the VWMA’s ongoing advocacy for better solutions, a lack of government investment continues to heighten risks for the sector and the broader community. The OECD has identified lithium-ion batteries as a critical safety challenge for developed nations. Catastrophic fires, such as those seen overseas in high-rise apartments and waste facilities, could become a reality here without decisive action.
State-led programs promoting battery use, including in vehicles and renewable energy systems, have amplified these risks without adequate planning for safe end-of-life management.
Industry leading the way
The waste and recycling sector has already invested millions in people, infrastructure, and innovative practices to mitigate fire risks. In 2024, the VWMA demonstrated its ideas through actions by:
Delivering engagement and professional development initiatives for councils and industry stakeholders.
• Driving innovations and fostering collaboration across the sector. Developing industry standards for emergency response to “hot-load” incidents. However, these efforts remain unsupported by direct state government funding, leaving industry and community assets – rather than
government assets – most vulnerable to fire threats.
Time for innovative solutions
Addressing lithium-ion battery fires demands fresh thinking and updated resource allocation strategies. The VWMA is calling on the Victorian Government to:
1. Lead national – champion lithiumion battery safety at the next
strategies, and emergency responses across government to tackle this challenge effectively.
“The rules governing the Sustainability Fund must be modernised to reflect the realities of 2025 and beyond,” said VWMA Executive Officer Mark Smith.
“The rules governing the Sustainability Fund must be modernised to reflect the realities of 2025 and beyond.”
Meeting of Environment Ministers (MEM) and push for national prioritisation of this issue.
2. Invest and collaborate – partner with the VWMA to expand its work programs and deliver solutions that improve battery disposal and reduce fire risks.
3. Adopt a comprehensive approach – align policies, resource recovery
“Victoria has an opportunity to lead the nation in tackling lithium-ion battery safety. By acting now, the State Government can protect lives, safeguard infrastructure, and set a benchmark for national collaboration and innovation in waste and resource recovery.”
The VWMA remains committed to working with the government and industry stakeholders to develop meaningful solutions that protect communities, infrastructure, and the environment from the dangers of lithium-ion battery fires.
The OECD has identified lithium-ion batteries as a critical safety challenge for developed nations.
Image: mikeledray/ shutterstock.com
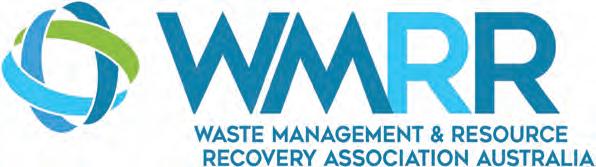
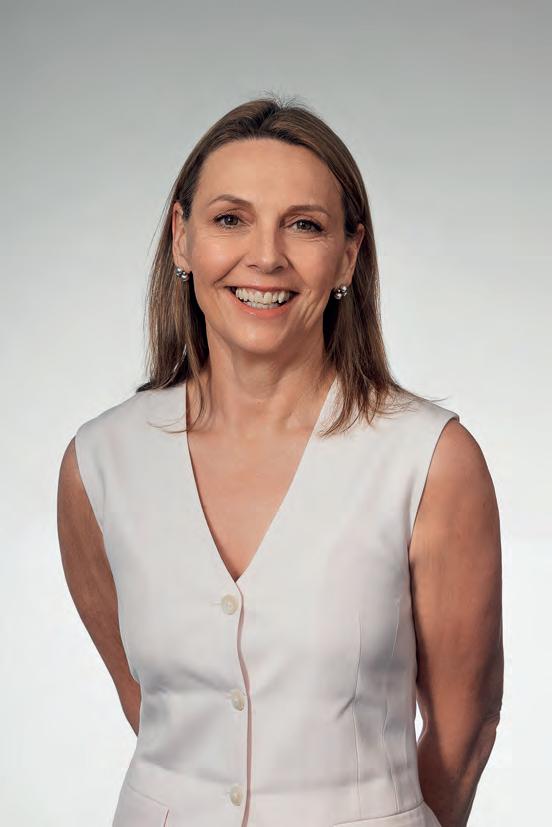
Finally some good news, but still plenty to do
After what seems like months of false starts and a general lack of action to move towards our often-cited Net Zero and Resource Recovery targets, it was pleasing to end 2024 with a little bit of good news; the increase in the national recovery rate of 3 per cent (about 2 million tonnes) in National Waste and Resource
Environment Ministers will meet for the second time this year on 7 December, following the first 2018 Meeting of Environment Ministers (MEM) in April, which was in part a response to the import restrictions driven by China’s National Sword Policy and the effects this policy has had across the Australian waste and resource recovery (WARR) industry. Key decisions derived from the April MEM include:
In December 2024 we watched the Environment Minister’s Meeting pass us by without even a whimper. If not for the NSW Environment Minister’s commitment to act on batteries, we would wonder what the meeting discussed. While I appreciate that an updated National Waste Action Plan (note the word ‘action’ but the lack of actions within) and a Circular Economy Framework were adopted (Framework but no action in this one either), their lack of enforceable actions (let alone penalties) to achieve the 2030 targets or apparent desire to achieve these was bitterly disappointing.
•Reducing waste generation, endorsing a target of 100% of Australian packaging being recyclable, compostable or reusable by 2025, and developing targets for recycled content in packaging.
• Increasing Australia’s domestic recycling capacity.
• Increasing the demand for recycled products.
• Exploring opportunities to advance waste-to-energy and waste-to-biofuels.
It acknowledged that the hard work of so many in our industry is paying off, with target areas such as organics increasing by 1.4 per cent. This demonstrates that with policy, markets and targeted funding, there can be change. And while the total amount of waste generated increased by about 1 million tonnes, there was a slight decrease per capita – another (small) positive.
•Updating the 2009 Waste Strategy by year end, which will include circular economy principles.
However, I think we all know that despite this good news, it is nowhere near enough of a shift to put Australia on the necessary sustainable path required to hit the national 2030 targets.
It is time to take stock and examine what has been achieved since these decisions were announced. Now, seven (7) months may not seem like a long time, however in that time we have seen further markets close (Malaysia, Indonesia, Vietnam) and if you are an operator under continued financial stress, seven (7) months could make or break you.
As we kick off 2025, you might be forgiven for wondering how we got here. Since China’s National Sword thrust us into the national spotlight (and we saw for the first time since Peter Garrett was Environment Minister real discourse about our essential industry at the Federal level), we appeared to be on a strong trajectory for continued action to create both the economic and environmental settings required for the planet
I think we would all agree that the current Federal government started with a positive energy – a clear stated commitment to legislative action to reduce Green House Gas (GhG) Emissions to 43 per cent below 2005 levels by 2030 and action on the Safeguard Mechanism to assist. Coupled with this we saw commitments to protect 30 per cent of Australia’s land and seas by 2030, create a nature repair market and establish an independent EPA.
Following the April MEM, we have had three (3) states step in with varying degrees of financial assistance for industry (councils and operators). This should be expected considering almost all states (except Queensland and Tasmania) have access to significant waste levy income each year. On the eastern seaboard, Victoria has approximately $600 million in waste levy reserves in the Sustainability Fund and NSW raises more than $700 million per annum from the waste levy. There is certainly no lack of funds that can be reinvested into our essential industry.
We even had a new Environment Minister saying all the right things – that she was “prepared to regulate” and understood the importance of focusing on the system. For a moment there we had a commitment to create mandatory packaging design standards by 2025 and regulate packaging as well as solar panels and electrical equipment – all of which create significant problematic waste streams for our industry and the community at large.
Funding helps but as we know, the money goes a much longer way with Government support and leadership, as well as appropriate policy levers.
VICTORIA
The stage was literally set for our industry to succeed: reduce emissions, reduce reliance on virgin materials and finally, it appeared the need for regulation was understood. And this wasn’t for the sake of it, but to create the necessary level playing field and rules of engagement that all in the supply chain require to thrive.
Victoria has arguably been the most active and earnest in supporting the industry post-China, with two (2) relief packages announced to support the recycling industry, valued at a total of $37 million. The Victorian Government has also gone above and beyond all others states by announcing it would take a leadership role in creating market demand for recycled products.
SOUTH AUSTRALIA
I vividly remember attending a speech by Minister Chris Bowen when he was appointed Minister for Energy and Climate Change, where he lamented the lack of action of the previous government and reminded us that there were only 90 months until 2030. Well, here we are with only 60 remaining and what do we have and what’s happened? Not much I am afraid.
Government announced a $12.4 million support package comprising $2 million of additional expenditure, $5 million additional funding for a loan scheme, together with targeted funding from the Green Industries SA budget. The Government has also offered grants for recycling infrastructure.
NEW SOUTH WALES
At first glance, New South Wales’ eye-watering $47 million recycling support package was heralded as the spark of hope industry needed. However, on closer inspection, the bulk of this package that was funded via the Waste Less, Recycle More initiative and therefore the waste levy, was not new, making it very difficult for stakeholders, including local government, to utilise the funds as they were already committed to other activities. Some of the criteria proposed by the NSW EPA also made it challenging for industry to apply to these grants. On the plus side, efforts are being made by the NSW Government to stimulate demand for recycled content through the intergovernmental agency working groups that have been established, though no tangible increase in demand or facilities have developed… Yet.
QUEENSLAND
Unlike
industry however the Queensland Government has embarked on the development of a waste management strategy underpinned by a waste disposal levy to increase recycling and recovery and create new jobs. The State will re-introduce a $70/ tonne landfill levy in March 2019. There are also strong attempts to use policy levers (levy discounts and exemptions) to incentivise the use of recycled material and make it cost competitive with virgin material. However, little has been done to establish new markets and Government has not taken the lead in the procurement of recycled material. There are grants available for resource recovery operations in Queensland although no monies have been allocated to assist in 2018. This is troubling as Queensland rolled out its Container Refund Scheme on 1 November, which will likely impact the cost and revenue models of the State’s MRFs – as we have seen most recently in NSW.
These documents did however quietly move some of these targets. For example, we lost the target date for eliminating problematic plastics and moved out the target for ‘creating a circular economy’. When you look at the data in the National Waste and Resource Recovery Report and see that the recovery rate of plastics is now at 12.5 per cent (a decrease of 0.4 per cent) yet the amount of plastic waste generated has increased by 14.5 per cent (11.6 per cent per capita) – you can possibly understand politically why these changes occurred. But given the desire for a high ambition for plastics globally, why can’t we have the same ambition at home?
WESTERN
AUSTRALIA
The Western Australian Government set up a Waste Taskforce in direct response to the China National Sword. As part of this announcement, the State Government urged all local councils to begin the utilisation of a three (3)-bin system - red for general waste, yellow for recyclables and green for organic waste - over the coming years to reduce contamination. While this taskforce is a step in the right direction, we are yet to see any tangible results from it or any funding for industry. In October, the WA Waste Authority released its draft Waste Strategy to 2030, which comprises a comprehensive and detailed roadmap towards the State’s shared vision of becoming a sustainable, low-waste, circular economy.
COMMONWEALTH
In 30 months, what have we seen at a Federal level? In essence, not a lot. We have seen a continuation of the previous government’s agenda, with the continued application of the export restrictions, and the rollout of the Recycling Modernisation Fund (RMF). Yes, we are grateful that this funding was not halted. However, the promise of creating local Australian demand and onshore markets to date has been avoided. And while we would much rather remanufacture in Australia, the lack of sufficient market demand for recycled products and the lack of both policy and regulatory action in this space means that we do need to continue to tap into the global market and export materials (in particular plastics) that can be recycled. The systems thinking does not appear to have arrived in practice as yet, I’m afraid.
It was one area that desperately required attention, given it is at the forefront of every household’s thinking and behaviour and the material most impacted by the export restrictions is packaging. This is one area wholly (in theory) in the Federal government’s area of responsibility with the Used Packaging NEPM, and the independent review of the scheme in 2021 makes it clear that it requires reform. However, we enter 2025 with APCO publicly stating that yet again it will be missing its targets (no problems as no consequences for that). There is no proposed reformed scheme, or even worse, no adopted mandatory design guidelines that will stimulate demand for local recycled materials on shore. Albeit it remains a ‘priority’ (but unlikely to be addressed before the Federal election I suspect).
Following the MEM in April, Australia now has a new Federal Environment Minister, Melissa Price, who in October reiterated to media MEM’s commitment to explore waste to energy as part of the solution to the impacts of China’s National Sword, which is troubling (EfW is not a solution to recycling). The Commonwealth has also backed the Australian Recycling Label and endorsed the National Packaging Targets developed by the Australian Packaging Covenant Organisation (APCO), which has to date, failed to incorporate industry feedback in the development of these targets. To the Commonwealth’s credit, there has been significant coordination in reviewing the National Waste Policy, with the Department of Environment bringing together industry players and States during the review process.
After all the talk of being ‘prepared to regulate’, we are heading towards the end of this term of government with none in sight, and very unlikely to have any prepared by the time a federal election is called. The one bright spot to possibly bookend the year with is the proposed review of the Recycling and Waste Reduction Act 2020, which is slated to occur in early 2025. This, if used well, must assist Australia in transitioning to a legislated future circular economy regulating the environmental performance of materials and products including imports, implementing clear design rules and labelling. It was also great to see the report of the Circular Economy Ministerial Advisory Group recommend this legislative approach and lay out what that could look like in their ‘Circular Advantage’ report released in December 2024, highlighting that we can have the tools to do this – we just need the political will.
The updated Policy will now go before Environment Ministers on 7 December. The Commonwealth can play a key role – one that goes beyond the development of the National Waste Policy. WMAA is supportive of the Federal Government maximising the levers it has, including taxation and importation powers, to maintain a strong, sustainable waste and resource recovery industry.
AHEAD OF MEM
2
Let’s hope 2025 is finally then the year of action that we all know we need.
There may be movement across Australia, with some states doing better than others, but the consensus is, progress is still taking way too long. It is evident that there are funds available in almost all States to assist with developing secondary manufacturing infrastructure, however the only way that this will really happen is if there is government leadership around mandating recycled content in Australia now, not later.
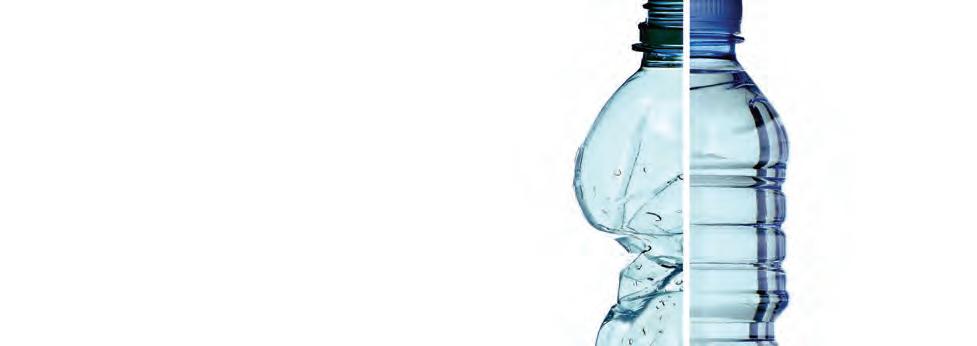
Voluntary schemes like the Used Packaging NEPM, under which APCO is auspiced, are not working. We have 1.6million tonnes of packaging waste in Australia, which needs to be used as an input back into packaging. Barriers to using recycled content in civil infrastructure must be identified and removed, and Government must lead in this field and prefer and purchase recycled material. A tax on virgin material should also be imposed as it is overseas. MEM must show strong leadership on this issue. Ministers have, since April, dealt directly with operators and councils that are under stress and we have a chance to create jobs and investment in Australia at a time when manufacturing is declining. Ministers have the opportunity to be leaders of today, not procrastinators – leaders of tomorrow and we are urging them to act and not just talk in December.
Gayle Sloan Chief Executive Officer
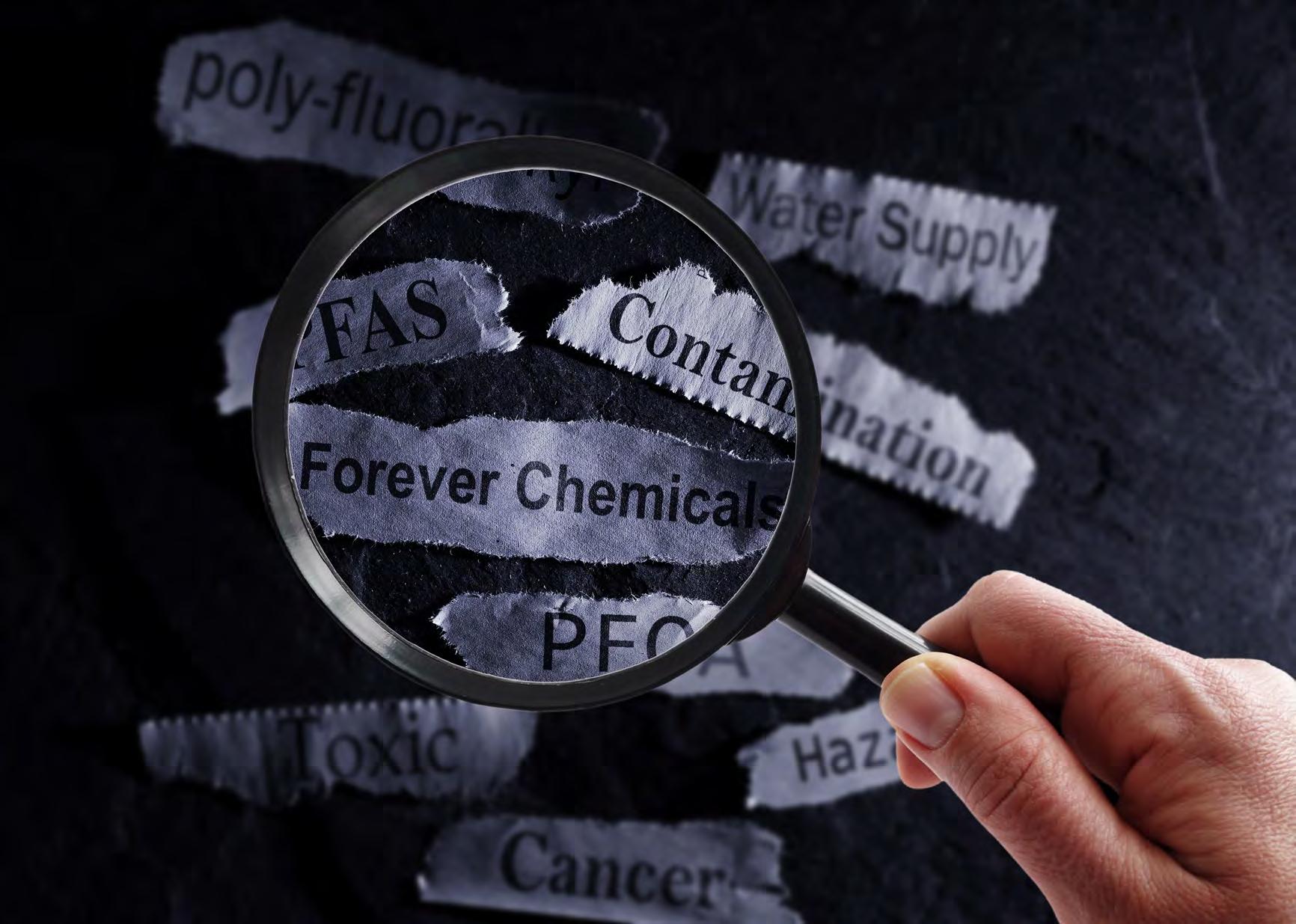
PFOS –a case study
By Ruth Jarman, Dr Jackie Wright, Therese Manning, Dr Belinda Goldsworthy and Dr Kate Langdon
The draft guideline
PFAS is an umbrella term that describes a group of many chemicals with carbon-fluorine bonds. Perfluorooctane sulfonate (PFOS) is arguably the key PFAS in Australia. Hence, this discussion focuses on PFOS. Australia has a current drinking water guideline for PFOS that was established in 2016/2017. In October 2024, the National Health and Medical Research Council (NHMRC) published a draft drinking water guideline for PFOS (the “draft guideline”) that is around 20fold lower than the current guideline: • the current guideline for PFOS (+PFHxS) is 0.07 µg/L (70 ng/L) the draft guideline for PFOS is 0.004 µg/L (4 ng/L).
A decrease in the drinking water guideline for PFOS would be considered appropriate where this decision was supported by new and scientifically robust information that changed our understanding of how this chemical might cause adverse health effects. However, a detailed review of the draft documents released by NHMRC indicates there were many issues in the approach adopted for this chemical.
First, the NHMRC ignored the recommendation of the independent
expert toxicologist they engaged to review and update the PFOS guideline.
The approach adopted by NHMRC to determine the draft guideline included engaging an independent expert toxicologist from a consulting firm to undertake a detailed review of the toxicity of PFOS to humans. Independent peer-review of this independent expert report was then completed by Professor Brian Priestley. The NHMRC ignored the recommendations of the consulting firm, as well as the independent peerreviewer, when they determined the draft guideline. An explanation of why NHMRC ignored the advice from the selected and suitably qualified experts has not been provided.
Second, the toxicity study adopted by NHMRC is not robust or appropriate for setting guidelines. The derivation of a draft guideline for PFOS relies on the selection of a key toxicity study (or studies) from a detailed review of the scientific literature. Usually the key study(s) are ones that show an adverse effect at the lowest dose (i.e. most sensitive). Where toxicity can be assessed based on a threshold approach (as is the case for PFOS), the toxicity reference value describes the amount of a chemical that a person can be exposed to daily over a lifetime via all potential exposure pathways without any adverse health effects – i.e. the “acceptable” or “tolerable” daily intake.
In line with normal practice for such reviews, the consulting firm determined which of the published toxicity studies were robust and appropriate for use in determining a toxicity reference value for PFOS. The review by the consulting firm resulted
possible to choose only one key study because even the most robust studies had issues. This means that there were multiple results describing the toxicity of PFOS and that those results could not be separated – they were all equally suitable for determining a
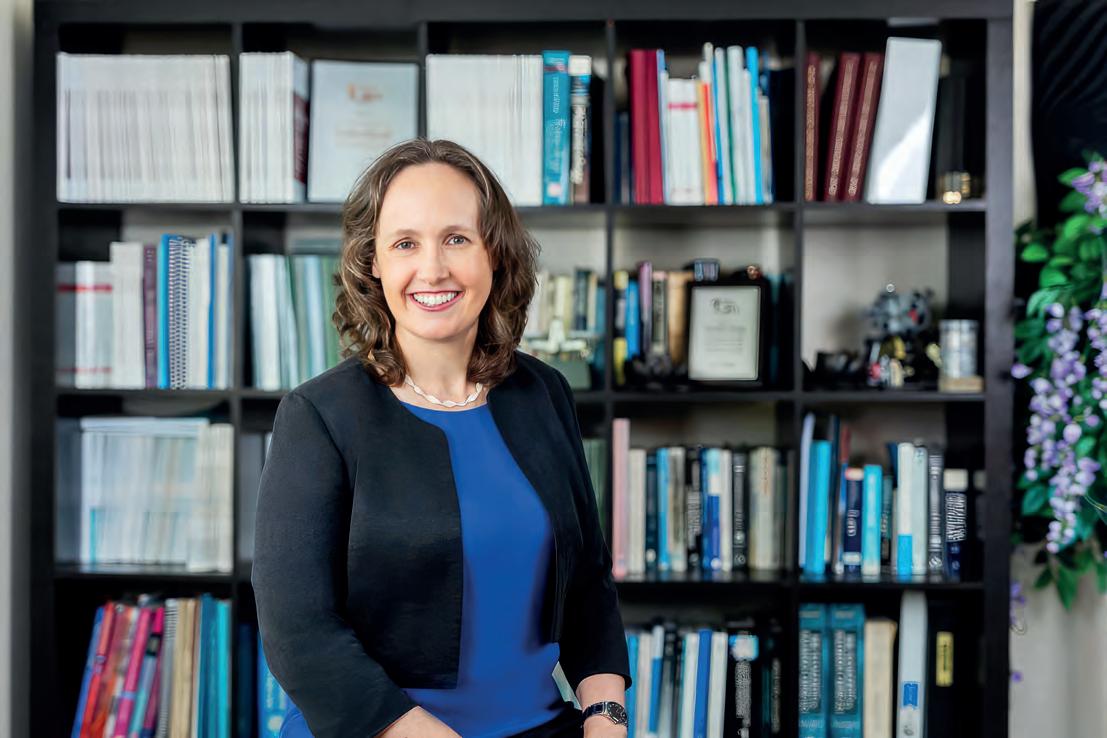
enRiskS’ senior consultant Ruth Jarman. Image: enRiskS
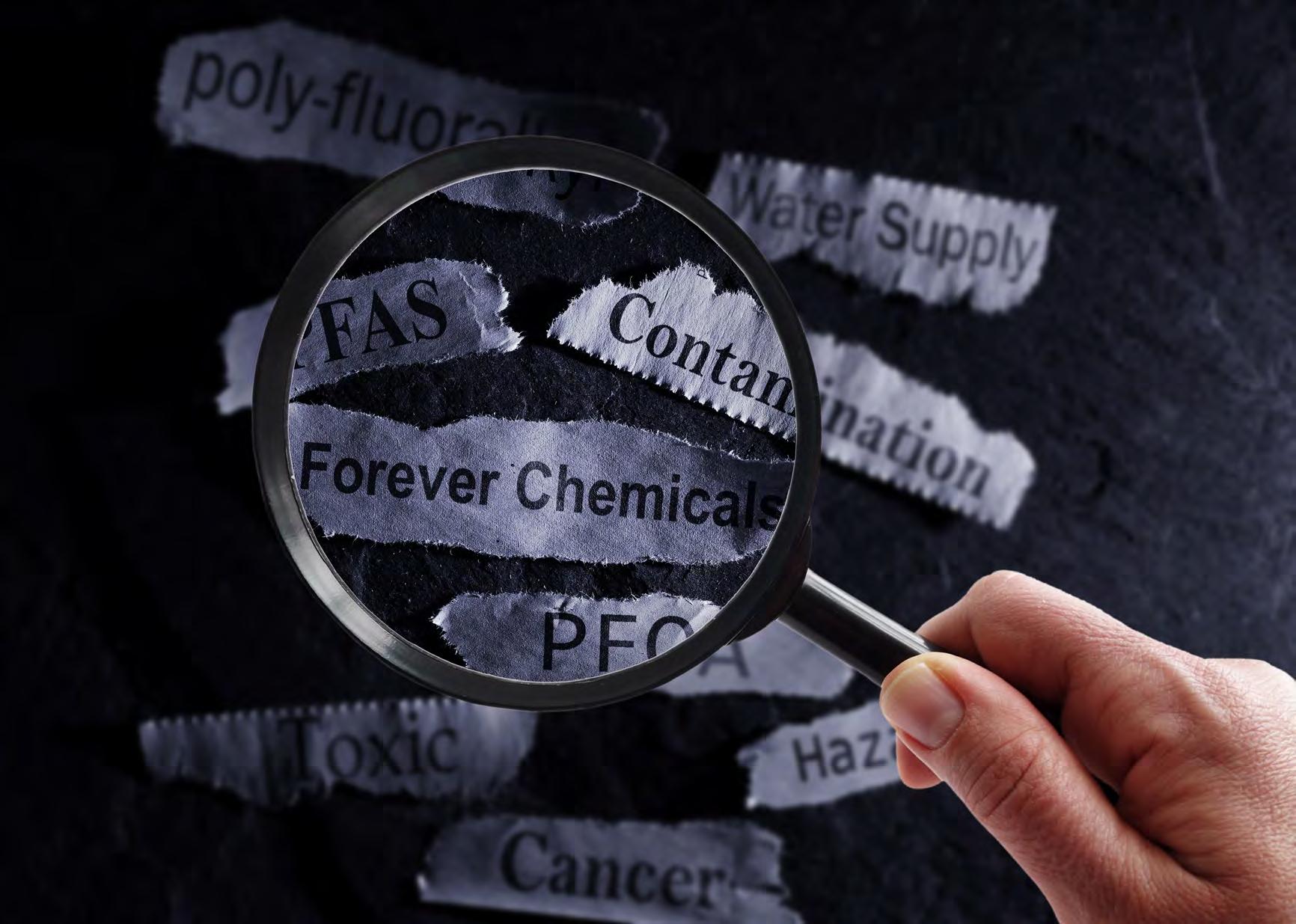
the studies and endpoints that they considered relevant and robust and then they calculated the following four drinking water guidelines for PFOS using those toxicity reference values:
0.0034 µg/L (3.4 ng/L).
0.027 µg/L (27 ng/L).
• 0.077 µg/L (77 ng/L; equal to the current guideline).
0.095 µg/L (95 ng/L).
The consulting firm then recommended that the guideline for PFOS should remain at 0.07 µg/L (i.e. 70 ng/L; retain current guideline for PFOS + PFHxS) based on its understanding of the details, limitations and uncertainties of each toxicity study.
As noted, the NHMRC ignored the recommendations of the consulting firm, recommending instead a draft guideline for PFOS of 0.004 µg/L (4 ng/L). This was based on a toxicity reference value of 0.98 ng/kg bw/ day, which is 20-times lower than the current value endorsed in Australian guidance of 20 ng/kg bw/day.
A detailed review of the toxicity study selected by NHMRC by enRiskS has identified a range of issues with this study including:
• the shor t duration of the study
– this was not appropriate for a
chemical such as PFOS that is this persistent within the body; effects were only identified at very high doses that are not consistent with potential exposures by people; equipment used in the study included Teflon – i.e. a known source of PFAS; analysis of study data with potentially non-validated laboratory analysis methods; and
• selection of a study endpoint that may not actually be adverse.
by the consulting firm was chosen. As a result, the draft guideline for PFOS is 0.004 µg/L (4 ng/L), which is the same as the value adopted by the United States Environmental Protection Agency (USEPA) earlier in 2024. The USEPA drinking water guideline was determined using a completely different approach than that adopted by the NHMRC. It is not normal practice for Australia to directly adopt US guidelines. In fact, for drinking water guidelines, the guidance written by the
gave a value of 0.1 µg/L (100 ng/L). Third, other PFOS guidelines for PFAS will decrease by 20 times, too. Currently, Australia uses a toxicity reference value of 20 ng/kg bw/day for calculating guidelines for drinking water, recreational water, soil, biosolids and food. If the toxicity reference value proposed by NHMRC as the basis for this drinking water guideline for PFOS (i.e. 0.98 ng/kg bw/day) is formally adopted, then the other risk-based guidelines for PFOS would need to
“In Queensland, regulators have long held the view that ‘any PFAS is bad PFAS’ and the only PFAS concentration allowable in the environment is ‘zero’; which, as an aside, is not scientifically possible.”
Review of the draft guidelines for the various key PFAS published by NHMRC also demonstrates an inconsistent approach, where the following was selected: PFOS and PFBS: the lowest/most conservative guideline calculated by the consulting firm was chosen.
• PFHxS: the highest/least conservative guideline calculated by the consulting firm was chosen.
• PFOA: the guideline recommended
SAVE ON EMISSIONS ... AND YOUR BOTTOM LINE
NHMRC indicates that the Australian guidelines take the World Health Organisation (WHO) Guidelines for Drinking Water Quality as their point of reference. The hierarchy of sources listed by NHMRC places USEPA guidance as the 5th or 6th choice. Guidelines from the WHO, New Zealand and Canada are all preferred above USEPA values. It is noted that WHO do not have a current guideline for PFOS but a draft value they issued a year or so ago
be revised. Such revisions would be significant as they would result in guidelines that would mean: many waterways may no longer be suitable for recreational use; soil in many areas would not be suitable for residential purposes (residential land would then be considered contaminated with associated property blight);
• organic resource recovery products (such as biosolids, compost, FOGO
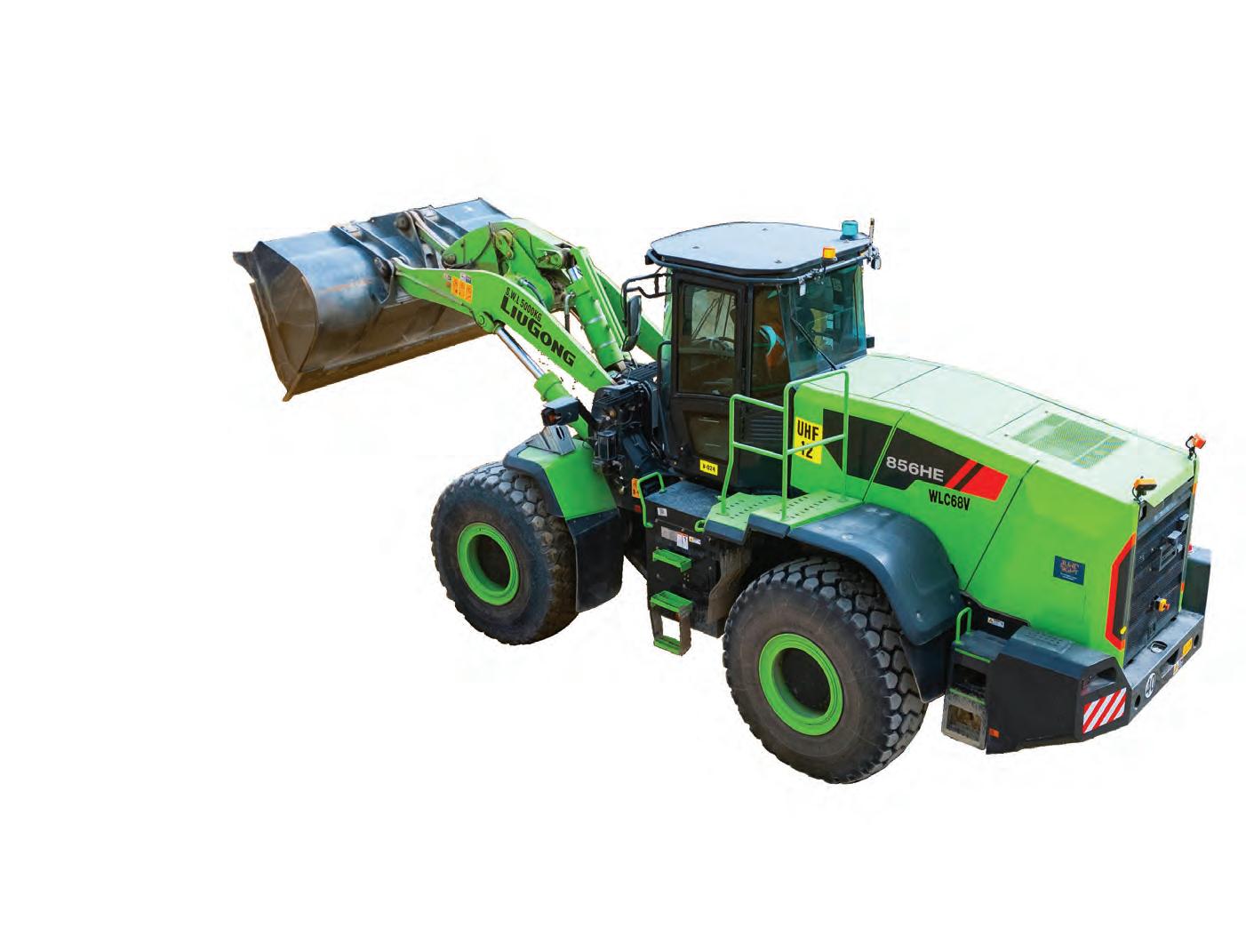
There is a range of forever chemicals, but what does the data say about them?
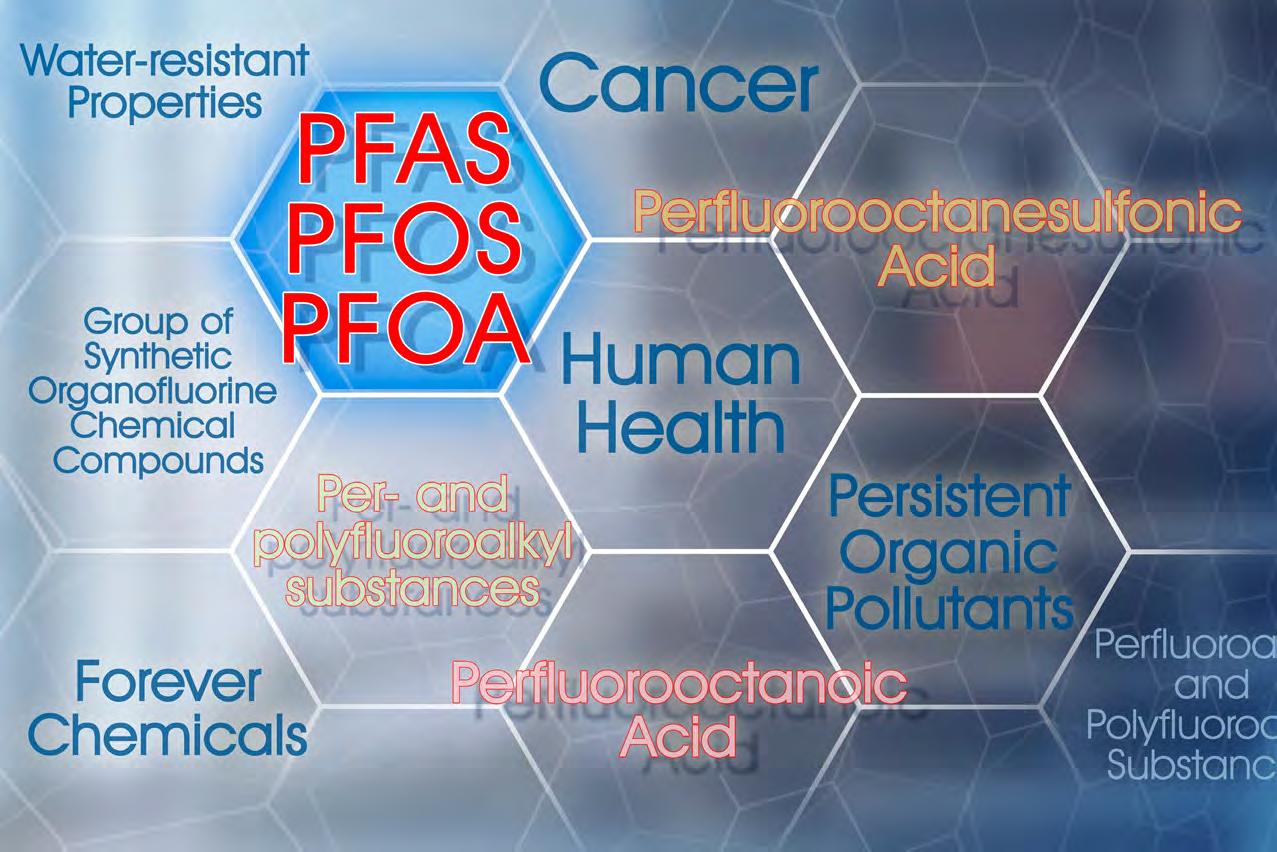
Financial Management of Your Landfill
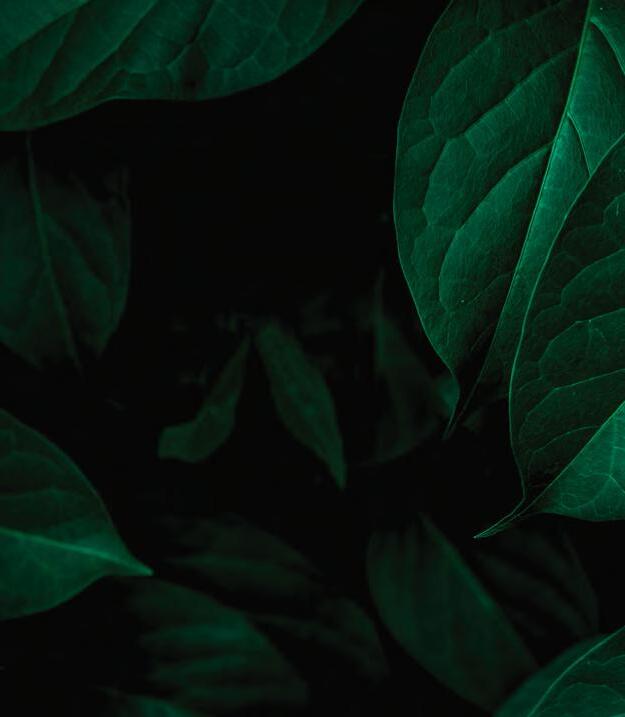
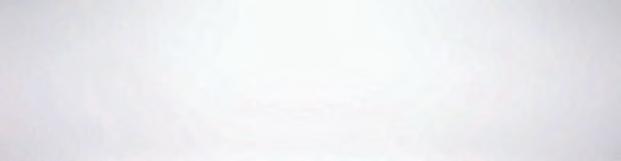
any purpose (impacting on a circular economy and reducing nutrient cycling back into our soil);
• guidelines would be similar to, or below existing, ambient levels in the environment; water authorities would not be able to comply with requirements for reuse of biosolids or treated wastewater meaning these materials would need to be disposed of, impacting on the potential for appropriate management of sewage in Australia; and
• existing food products, including seafood, eggs and beef may no longer be considered safe for consumption and/or export mostly due to lack of ability to measure the relevant concentrations to demonstrate compliance with the guidelines.
PFAS risk issues, or perceived PFAS risk issues, are already impacting on Australia’s ability to move towards a circular economy, particularly in relation to the use of compost, FOGO and biosolids. For example, in Queensland, regulators have long held the view that “any PFAS is bad PFAS” and the only PFAS concentration allowable in the environment is “zero”; which, as an aside, is not scientifically possible. This is why it is so important that the toxicity reference value used to derive the draft guideline is supported by sound and robust
difficult to report against and comply with PFOS guidelines.
Many of the revised guidelines for soil, food, biosolids etc. would not be able to be measured by commercial laboratories in Australia and costs for contaminated site investigations, remediation and management would increase.
Guidelines close to (or less than) the commercially achievable laboratory limits of reporting also create issues in regard to the ability to demonstrate compliance. It is well-known that measurements have uncertainty and variability. This is due to how and where the samples are taken as well as the method used in the laboratory. These uncertainties increase as the measurement targets lower and lower concentrations especially close to the lowest level the laboratory can measure (i.e. limit of reporting).
Given that PFOS measurements need to target parts per trillion levels, the uncertainty in the measurement can be plus or minus 100 per cent. That means doing repeat measurements on the same sample might give a range of concentrations such as 1 to 8 ng/L. These values all indicate what is present in the sample and are all equivalent. If you only do one measurement you might get 8 ng/L (i.e. above the guideline and requiring action) or you might get 1 ng/L (i.e. below the guideline and not requiring
Image: Francesco Scatena/ shutterstock.com
action). This is a fundamental characteristic of measurement and cannot be avoided. Those using measurements need to understand how to deal with such uncertainty.
In addition to measurement uncertainty, it is also important that the limit of reporting provided by a laboratory is sufficiently below the relevant guideline value so that it can be demonstrated with confidence that a sample complies with a guideline value or not. Often guidance indicates a limit of reporting around 10 times lower than the relevant guideline value is needed. Pushing limits of reporting lower may not be achievable with the available equipment and, if possible, drives up costs of analysis as the effort to achieve lower limits of reporting increases.
Cross contamination also becomes an issue with extremely low limits of reporting. If the chemical of interest could be present in the equipment used to take the sample or on people taking the sample, then the chemical could end up in the sample from these sources. In this case, the concentration measured in the sample would then be higher than it actually is. Given how widespread PFOS are in everyday items, it is difficult to control their presence at a site where samples are being taken. Current guidance suggests people shouldn’t wear sunscreen when taking samples for PFAS analysis – clearly a bad idea when people are outdoors in the field for long hours. Then there is the issue of current ambient exposures not being readily adequately addressed.
The draft guideline does not consider or address peoples’ current exposure to background sources of PFOS. Unlike many chemicals, biomonitoring information is available
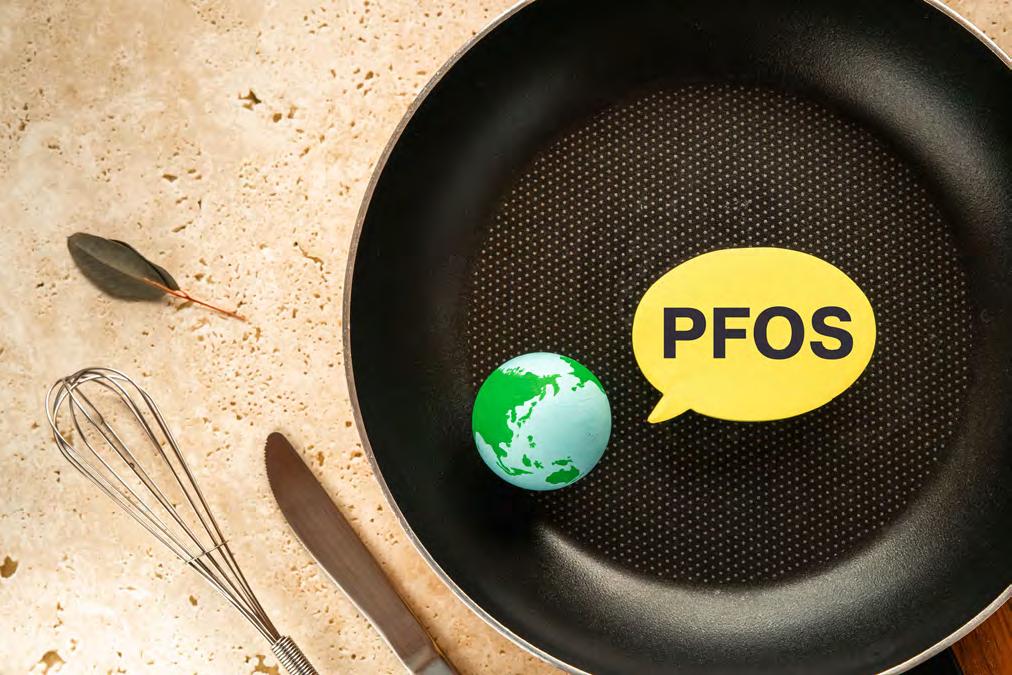
“Many of the revised guidelines for soil, food, biosolids etc. would not be able to be measured by commercial laboratories in Australia and costs for contaminated site investigations, remediation and management would increase.”
on ambient concentrations of PFOS in serum in the Australian population. This information shows PFOS serum concentrations in Australians has decreased since 2000 (Figure 1).
These measurements indicate that people in Australia have a background daily intake of PFOS around 0.8 ng/kg bw/day. Comparing this background intake to the toxicity reference value chosen by the NHMRC for the draft guideline means that about 80 per
cent of the proposed toxicity reference value is already taken up by these existing exposures. This aspect was not discussed by the NHMRC and will have an impact on the calculation of the draft guideline.
Finally, there are the issues of fear, stress and anxiety, which can cause adverse health effects. Parts of the media, and some state regulators, have targeted stories and guidance on the “forever” nature of PFAS and the potential for health effects of these chemicals without explaining the science correctly or in detail. This increases the levels of fear and anxiety in people who may be living in areas where investigations are occurring or where PFAS chemicals are detected in drinking water supplies. Stress and anxiety are known to cause adverse health effects, so these media stories and guidelines are generating adverse health effects that are unrelated to the presence (or not) of PFAS.
Journalists and state regulators need to take their responsibilities seriously. For journalists, this includes checking out all sides of a story especially when they do not have sufficient training or qualifications to properly evaluate what they are being told by the experts they choose to interview. For regulators, this includes providing guidance that is science based and communicating
these guidelines appropriately to other stakeholders. A draft drinking water guideline for PFOS of 0.004 µg/L (4 ng/L) feeds increased levels of fear, stress and anxiety. The NHMRC needs to be certain that the proposed drinking water guideline is supported by robust science and toxicity studies to justify such increased levels of concern with associated fear, stress and anxiety in the community.
Déjà vu?
Significant costs for cleanup have already occurred in Australia in relation to PFOS concentrations in water, based on complying with low guideline values for the protection of aquatic organisms. It has been demonstrated that this low guideline value was based on flaws in the dataset and the statistics used to calculate the guideline. We should not repeat this problem and cause even more costs for cleanup unless we are confident in the scientific basis. We do not yet have that confidence.
Ruth Jarman, Dr Belinda Goldsworthy, Dr Kate Langdon, Therese Manning and Dr Jackie Wright are consultants at enRiskS
Figure 1: Changing serum concentrations in Australian population for PFOS 1
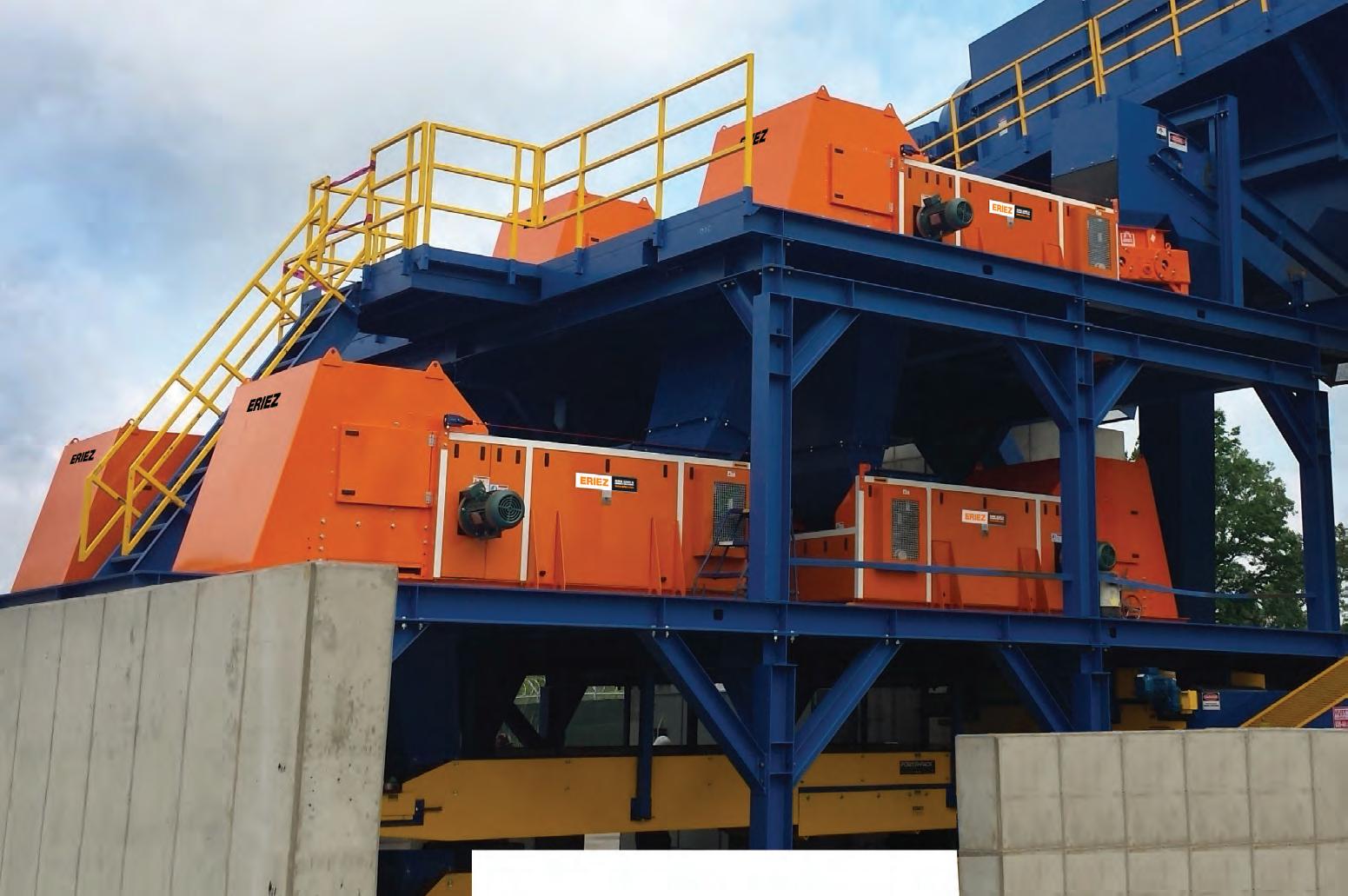
Invest in the Best to Maximize Revenue
Eriez patented the world’s first Eddy Current Separator in 1969. Today, our full range of recycling equipment can be found all over the globe, increasing recoveries and maximizing revenues. Eriez. Always the Right Choice. Eddy Current Separators from Eriez effectively remove non-ferrous metallics from automobile shredder residue (ASR), municipal solid waste (MSW), plastics, glass cullet, electronic scrap, and more.
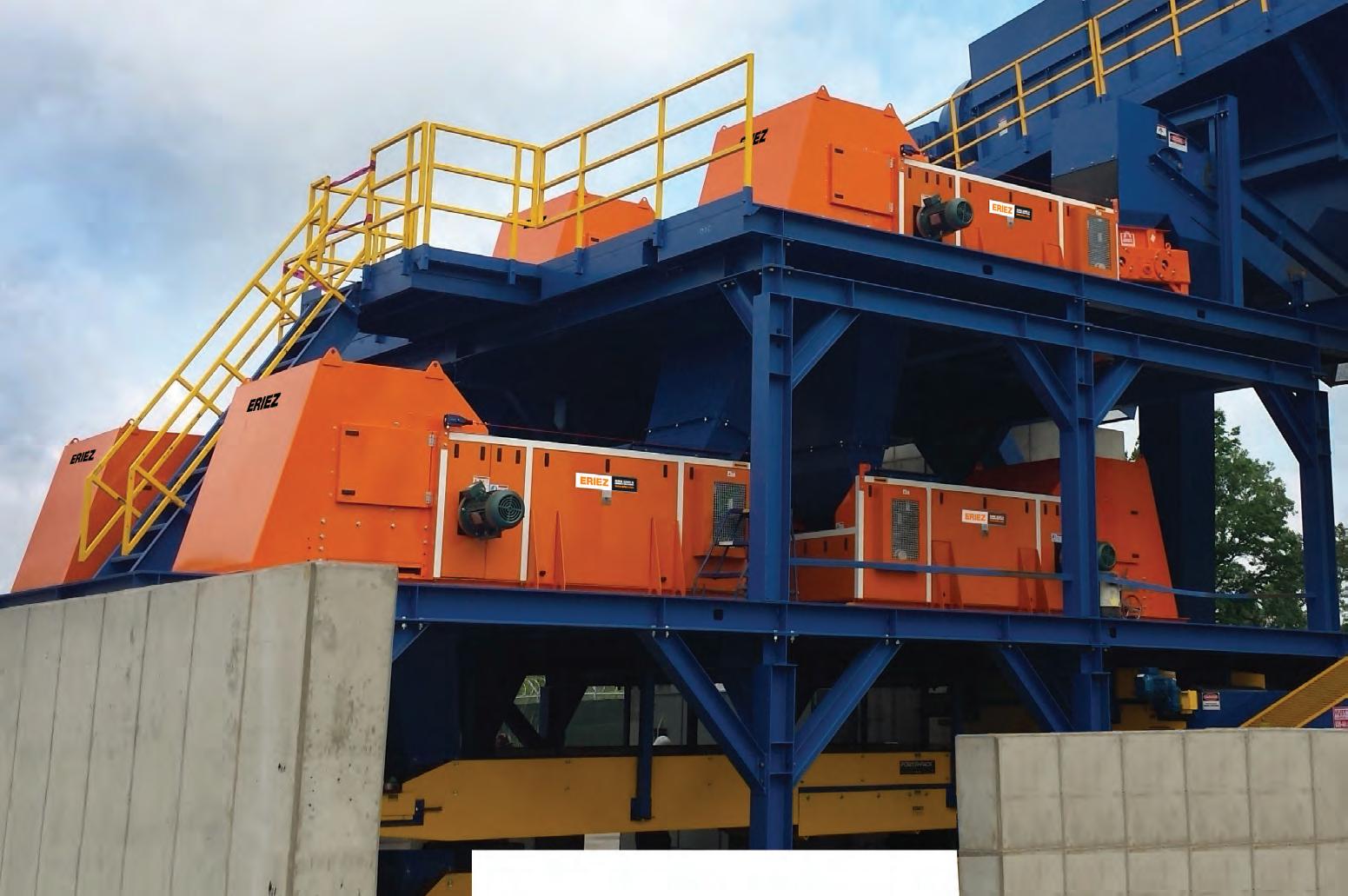
Brokering collaboration between industry and government
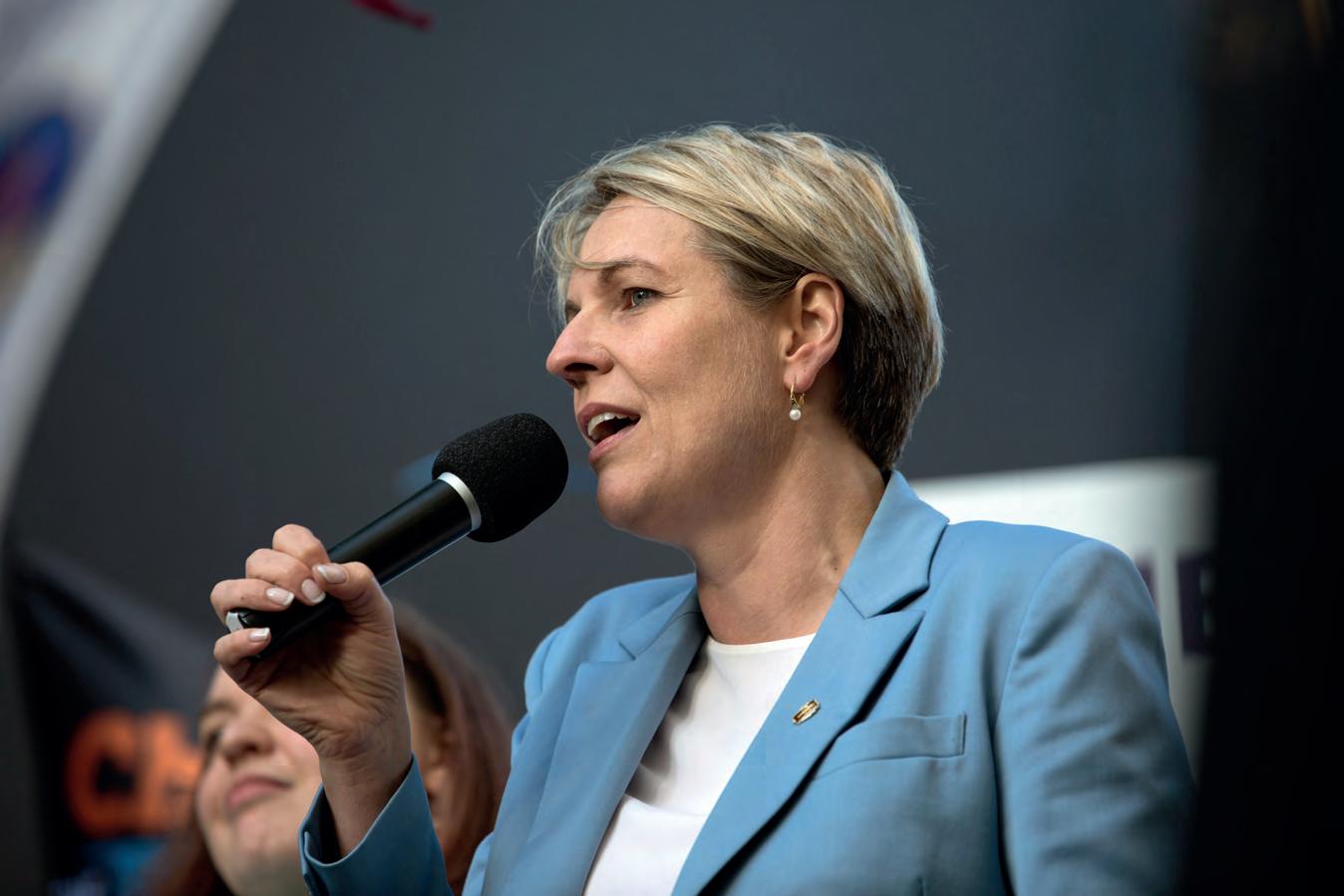
By Inside Waste
CEMAG released an interim report in 2024 giving an update on what it has managed to accomplish over the past couple of years. Thwaites was bullish about how well they have done so far.
“The good news is that a number of our recommendations have already been adopted,” he said. “The first recommendation was that there should be a Productivity Commission inquiry into the opportunities of a circular economy. And Jim Chalmers, the Treasurer, has agreed to that. And that is important, because if you’re going to convince treasury… and business about a circular economy, the best way to do that is to have a Productivity Commission report to identify the opportunities and barriers.”
The second core recommendation, which has been adopted, is around government procurement. The
Australian Government purchases about $75 billion worth of goods annually, and that is a lever t hat can help create a market for circular economy products, according to Thwaites.
He said that following the report, the federal government announced that it would be implementing an environmentally sustainable procurement policy. Thwaites said that it was already in place with construction contracts.
The third recommendation being implemented is that the circular economy should be embedded in all core government policies. An example of that is the national reconstruction fund. It’s worth $18 billion and now has circularity as one of its criteria when companies are bidding for contracts.
“But this also is applying across government activities like critical minerals,” said Thwaites.
Moving forward
The group is still working on the full report and there will be other recommendations to come out of it. One of the core proposals is for Australia to have a National Circular Economy policy.
“We don’t have a policy, but 72 countries around the world do,” said Thwaites. “And that policy needs to set ambitious targets. I know from my experience in g overnment, it’s often targets that drive change, and we believe that that framework should have some ambitious targets. We also need to set out what are the priorities and who’s going to do what.”
He said there are two levers that are essential – the market lever and the regulatory lever. In Australia, we need both, he said, with the regulatory lever underpinning the market lever to a large degree. He said Australia should look to the
European Union’s Ecodesign for Sustainable Products Regulation (ESPR) as a blueprint.
“That not only allows for product stewardship, it also enables the setting of standards that are going to drive the circular economy,” he said. “Standards for products in things like repairability, reusability, and the presence of dangerous chemicals.”
He believes that currently, Australia has a hodgepodge of state regulations, as well as bits and pieces of Commonwealth legislation. He said what the country needs is a comprehensive national approach –a harmonised methodology between t he Commonwealth and the States because industry has stated many times that it is a barrier mo ving forward.
Another recommendation will be around innovation and research. Instead of funding businesses and individual projects, Thwaites and
The federal minister for the Environment and Water, Tanya Plibersek, was instrumental in bringing CEMAG together.
Image: Sebastian Reategui/ shutterstock.com
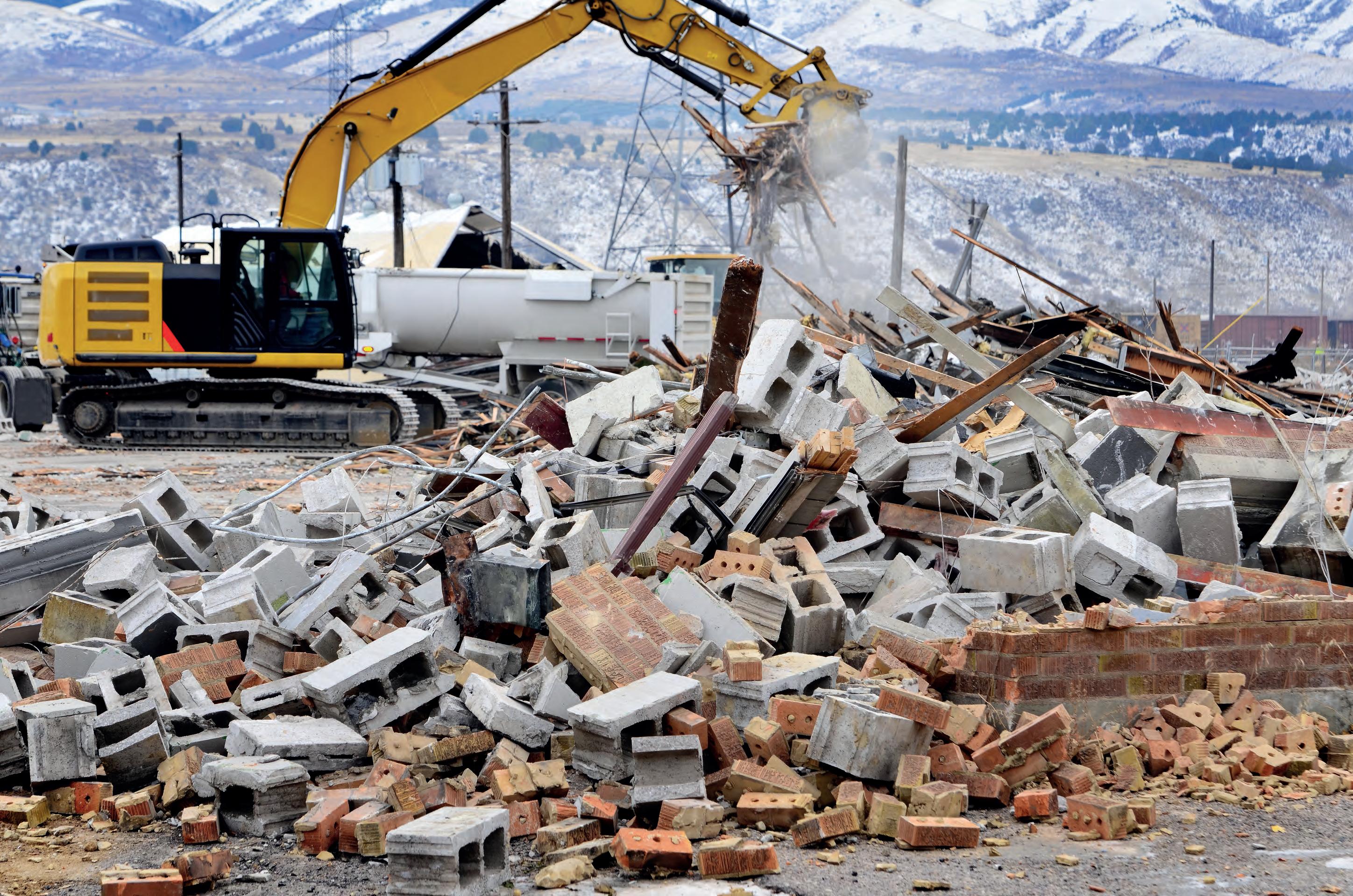
the team are looking towards a challenge-based funding approach.
Marshall said it’s not just about creating a circular economy, although that is an important aspect, but about where Australia stands in the world when it comes to having a plan for the future.
“Australia is in the top 10 for our ability to invent and do research, but we’re in the bottom for our ability to turn that into something that drives the economy or that solves a national challenge,” he said.
“Australia invented the solar cell design, which is made in China today. We didn’t back it. We didn’t innovate it. We didn’t turn it into what the Chinese did. We also invented a third
of the world’s polymers because we invented the design platform called RAFT, which enables polymers to be made. But again, we didn’t commercialise them.”
He said the key ingredient that has been missing in the past has been funding to enable Australia to be the first to commercialise innovations developed on these shores. However, an entity called Main Sequence Ventures (MSV) was created, which has funded sciencebased startups like Uluu and Samsara Eco. These companies have created polymers that are 100 per cent recyclable and made from nature, not petrochemicals.
“For me, this is part of our second
chance to do the things that we should have done 20 or 30 years ago, but do them better,” he said. “We created MSV to try and plug this gap. [This means] big institutional investors, like the superannuation funds and others, are starting to step in with impact investing – a desire to have social good/public good coming out of financial returns.”
Harmonisation
When the advisory group got together, one of the first things Hes noticed was that everybody was on the same page. She felt there were no hidden agendas, which meant the group could hit the ground running. They could concentrate on the bigger
picture, such as the pain points of the industry and how they could b e solved.
Hes agreed with Thwaites that harmonisation is needed, especially in the building sector. She pointed out that most buildings the country will need over the next 30 years have already been built, but there still needs to be a plan for those that will be demolished, thus the need for a common specification to do so.
“When we knock the buildings down, how do we reuse the materials?” she said. “Having the standardisation and specification so that it’s not harder to reuse a product like concrete than it is to buy it new is critical for enabling that
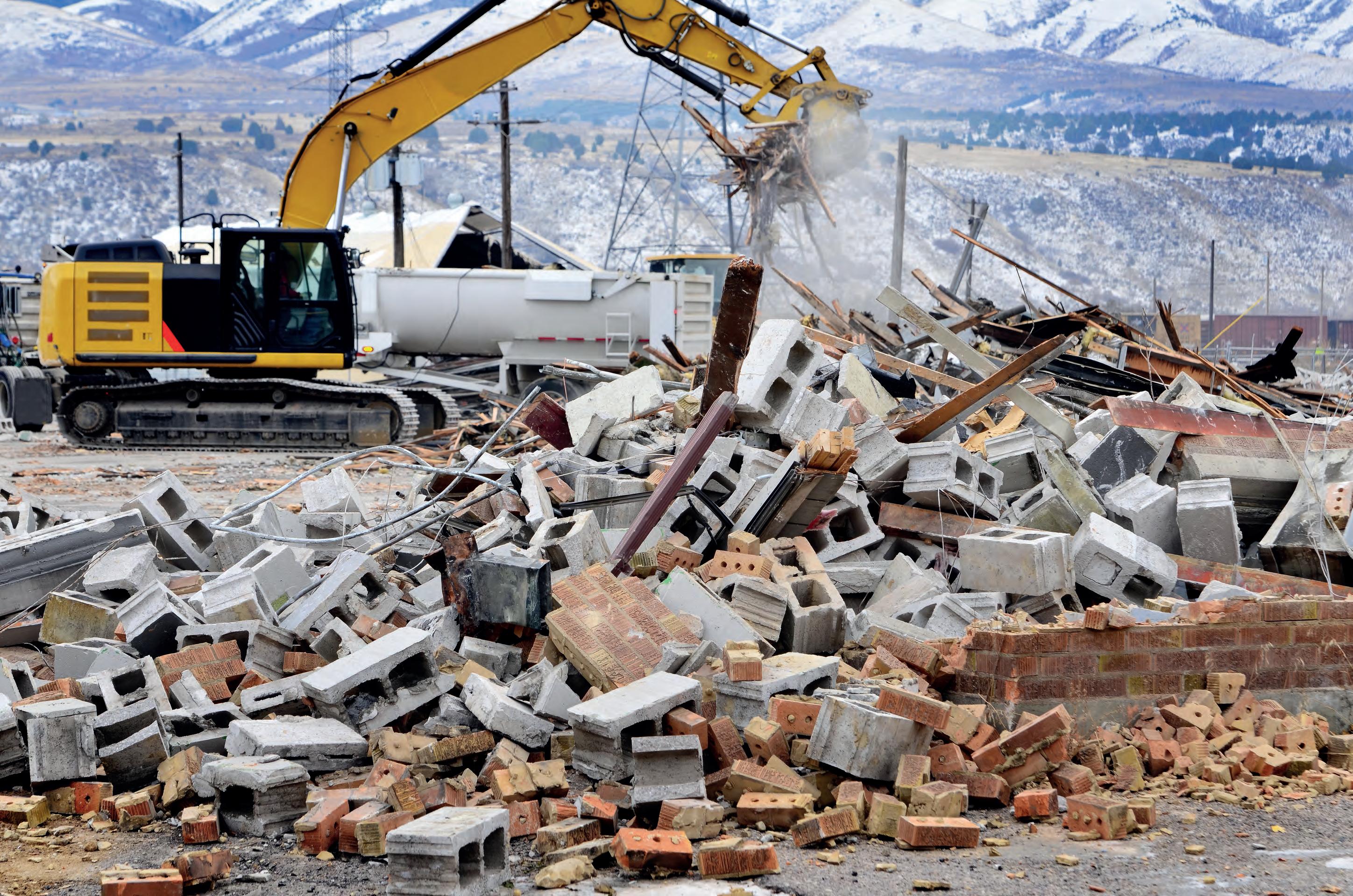
pain point to be solved for industry.”
For Klymenko, one of the key elements that has made the circular economy an easier sell to industry is what he calls the ‘literacy level’ among government ministers. He said he had worked with government ministers in the past on many initiatives in the resource recovery sector and always felt he was part of a silo as opposed to a group.
“This time they came prepared to talk about the circular economy – they weren’t just there to get a pitch from us,” he said. “They were telling us what they were planning to do in their portfolios…we had this incredible engagement, which is the reason why we’ve managed
to get some of these interim report recommendations through. If we don’t think in systems and we just think in boxes or silos, we will often make mistakes”
An issue that both Klymenko and Hes touched on was the role of brokers in the harmonisation of the CE. Collaboration between the different parties sometimes needs a third party to make sure people were on the same page.
“There’s a capital C in circular economy, and there’s a capital C in collaboration,” said Klymenko. “You cannot achieve one without the other. And that recognition among government and us that we’re going to need not just transition people,
but good transition brokers. Because the quality of the transition broker will determine the speed of the transformation.”
Challenge-based funding to research and development
Utilising a challenge-based funding model can have its drawbacks, but how can it be enacted when it comes to research and development?
Marshall said that UK-based economist Mariana Mazzucato came to Australia to explain how they did it. It turns out Australia did the opposite of what they do in Europe.
“We invented our own Australian version of missions,” said Marshall.
“We spend $1.4 billion to throw away $26 billion of materials, which are very usable.” Image: Lane V Erickson/shutterstock.com
“The difference between us and Europe is the European Union puts about €3 billion into a national missions program, and that’s taxpayer money.
“The national missions that we have in Australia are the opposite, in that about 90 per cent of that money comes from Australian or US industry. The reason it was so important to do it that way was to convince industry that sustainability could be financially beneficial. It could be profitable, not a tax. Whereas, if we’d done it the European way, it would have just been government money, and we wouldn’t have moved industry.
“There’s definitely been a change
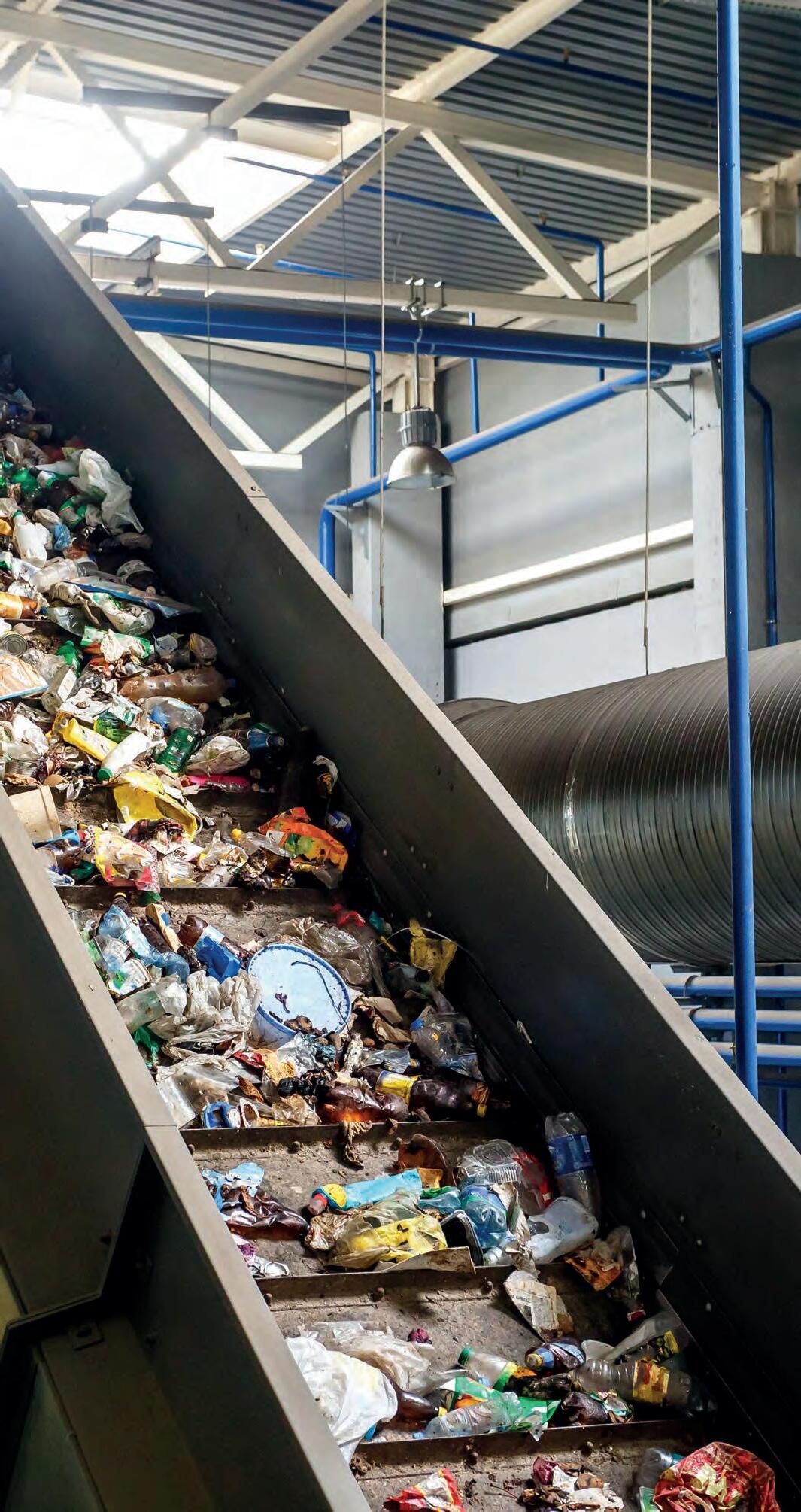
in the financial institutions in Australia to actually see this as an opportunity, not a threat. And that’s huge.”
How does the advisory group see mandatory climate-related financial reporting affecting the circular economy in Australia?
Thwaites said that from this year, large companies will be subject to the regime of mandatory climaterelated financial reporting.
“I understand it does not specifically cover circular economy or circular economy issues, although they are closely related,” he said. “In analysing your climate risks and your credible transition plan towards net zero or your climate targets, the circular economy could well be a key component of that. And I would expect that some companies will be looking at circular economy measures as part of their transition.
“Having said that, under the International Sustainable Finance rules, the circular economy is a specific consideration, and in the first iteration of reporting, as I understand, it’s voluntary for companies in Australia, and they will be able to report on that. Our Ministerial Advisory Group has recommended that over time, that we move to a situation where the
circular economy measures material use, waste, etc, would become part of the reporting system. I do think this is going to drive a lot of focus within businesses on circular economy opportunities. I’d say to all of you, if you’re in a business that’s going to be reporting, you need to be looking at the circular economy.”
Key learnings
What were some of the takeaways from their time with the advisory group? For Hes, it was gaining more clarity about the wastage in the C&D space.
One of the figures that shocked me…is that we spend $1.4 billion to throw away $26 billion of materials, which are very usable,” she said. “If you’re building a new house, that’s $10,000 worth of materials that are coming to your house sitting there –maybe half a pallet of bricks – which then goes to landfill. There is great potential to do more with those materials.”
For Klymenko, it was when he was at a meeting with treasurer Ji m Chalmers and was talking to AustralianSuper CEO Paul Schroder, who stated that the superannuation industry doesn’t get approached about investing in the circular economy.
“That was a real shocker,”
he said. “That was one of the reasons why we started talking to [financial firm] Boston Global [about investing in the circular economy], because I thought there’s a significant opportunity there. Obviously, we’re hoping to mobilise our funds from people like AustralianSuper.”
Klymenko also reiterated how important talking through issues is to the circular economy. He gave the example of people no longer wanting to use plastic packaging in their food. Some innovators have come up with fibre-based alternatives, which are okay for some foods, but not others – like takeaway items. It can lead to unintended consequences if not thought through properly.
“Fibre is not really designed to be water and grease resistant,” he said. “What do we do? We add PFAS, which takes care of the water-resistant issue, but when we go to compost it or recycle it, we’ve got a chemical concern, which is very hard to ever get rid of.”
Conclusion
All members of the panel seemed upbeat about the future, especially with the current engagement of the federal government. Whether that translates to other parts of
the industry feeling the same way is yet to be seen. Klymenko summed it up best when he spoke about how much progress had been made over the past five years.
“Just to give a sense of context, I was on the National Waste Policy Committee back in 2018/19, and I tried to get it turned into a circular economy policy. It was received with resounding negativity is probably the best way to describe it,” he said. “I had one person out of 12 s upporting me.”
Since then, he said, the currency of the circular economy has grown globally due to the work of the EU and other countries that have adopted circular economy policies.
“What that’s really left us is that feeling that we’re the odd person out,” he said. “If 75 per cent of the OECD have got a policy, and we haven’t, what’s going on? Because that’s our club.
“Now I’m having conversations with people in the investment community, not because of net zero etc, but because they see there’s an opportunity for a much more resource-efficient system. Everyone loves efficiency. I think that at their core, even if they can be wasteful at times, they love the fact that the circular economy is an efficient system.”

Hitting the NSW waste targets is good politics
By Mike Ritchie
ON 1 November 2024, during the NSW Circular Economy Summit in Sydney, the Minister for environment Penny Sharpe and the CEO of the NSW EPA Tony Chappel in separate landmark speeches said “NSW has a waste crisis and we are here to fix it”… or words to that effect (my emphasis)
Most in the audience breathed a sigh of relief that finally someone was listening and going to act upon repeated warnings that NSW is in trouble.
Waste disposal options in Sydney are nearing critical shortage while the State has fallen behind in delivering on the National Waste Targets set in 2019. For clarity the Targets for 2030 are: 80 per cent diversion from landfill; 5 0 per cent reduction in organics to landfill; and a 1 0 per cent reduction in per capita waste generation.
We are stuck at 60 per cent recycling, have no chance of achieving a 50 per cent reduction in organics to landfill (a massive greenhouse gas generator) and per capita waste generation has grown by 2 per cent since 2019, rather than fallen.
Achieving the targets on the other hand will lead to transformational job creation in the NSW recycling industry, greenhouse gas reductions and economic investment.
“Why the hold-up?” you might ask.
To achieve these targets, we need infrastructure for source segregation (bins and trucks), and to build sorting and processing facilities for mixed waste.
The Minister and CEO announced:
“As a State, we’re at a critical juncture. We must act now to ensure our infrastructure keeps pace with growing waste volumes, and to maximise recycling and recovery efforts.
Through a mix of innovative projects, strategic investments, and collaboration, we can turn this challenge into an opportunity.”
Action on the infrastructure front has been a long time coming. At long last, there is movement after years of advocacy. It seems so obvious and politically popular.
But, why is building waste infrastructure in NSW so hard? It isn’t because of a lack of willingness by industry, or action by community groups, or advocates or financiers or the public.
Everyone thinks building infrastructure to improve recycling rates and to reduce landfilling is a good idea. The only downside is that you need to build it next door to someone. There is the rub. That is why it takes five years minimum to get a planning approval for any waste infrastructure of any scale – if you get one at all.
NSW has long adopted a laisse faire (proponent led) planning system, which works fine for shopping centres and home renovations, but is an abject failure for waste.
We centrally plan power stations, water treatment facilities, schools, parks, roads, electricity networks, hospitals etc but not waste infrastructure.
When it comes to waste infrastructure, we leave to proponents (industry or councils) to propose and defend against the whims of local ‘oppositionism’.
Worse still, in NSW we require a ‘social licence’ as one of the preconditions for planning approval.
When is a local community ever going to agree to a ‘social licence’ for an incinerator or a landfill or even for that matter, a 200,000t/yr resource recovery facility?
It is a laudable objective to obtain community support or ‘social licence’, but as a concept when applied to large (and therefore strategically important) waste infrastructure, it is a bit silly.
No-one in their right mind wants a landfill next door to them. Next door to someone else, no problem. Just not where it is proposed to go.
I cannot believe the number of times WMRR, ACOR, AORA and other associations, along with private companies, have made this point to Government Ministers, EPA leadership and to independent Government inquiries. It is a particularly unique problem to NSW.
It got so farcical that at one point I was told by a senior planner in the Dept of Planning that “we are not communist China Mike. We don’t centrally plan infrastructure”. What?
With the Minister’s announcement of the impending release of a NSW Infrastructure Plan, it seems we might finally see some measure of common sense and some strategic planning for waste.
It is worth pointing out that most other States have such plans and it is
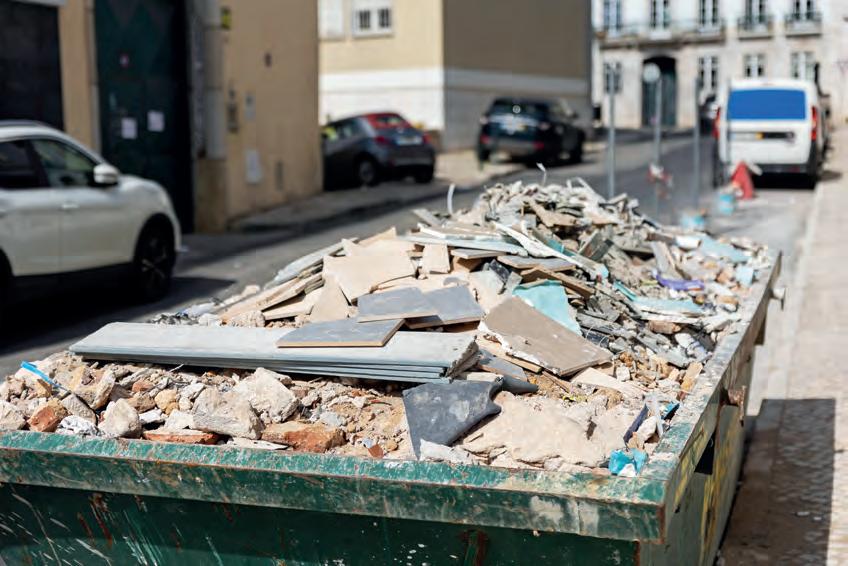
To reach landfill diversion targets an additional 4MT of C&D/C&I waste needs to be diverted. Image credit: Konstatin— Shishkin/Shutterstock.com
no surprise that lots of investment goes there instead of NSW. Capital is mobile. Jobs are created where facilities are built and operated.
SA has Green Industries to promote waste infrastructure. Victoria has Resource Victoria and a waste infrastructure investment prospectus to encourage investment. QLD has its EfW and investment programs.
In NSW, up to now, we have been leaving it to proponents to fight it out with residents, oppositional local governments and ultimately and often, the arbitration of the Land and Environment Court.
Importantly, those proposing and defending facilities are afforded almost no guidance from the State Government on whether such infrastructure is needed, wanted or necessary.
How much more productive would it be if the State Government just told us what the State needs and then industry and councils got on with building it.
It doesn’t mean that locals can’t object to a particular proposal but at least it will mean that project proposals are set within a broader strategic
framework of need. Dumb proposals will still be rejected but proponents with good proposals will at least have the backing of the State’s needs assessment. So, the announcement of an impending State Waste Infrastructure Plan by the Minister came like fresh air. Finally. The Government engaged Arcadis to help prepare the plan, but we have not seen it yet.
The sooner we release it to the public, to investors, proponents and operators the sooner NSW can get on with it.
To provide clarity on scale and to give a benchmark to review the Arcadis Plan, the MRA team pulled together our own version of a State Infrastructure Plan (see graphic on page 39).
I have provided an overview here to give readers some idea of the magnitude of the task and the absence of time.
To achieve the State targets, we need to divert an additional 5.7 MT per year in NSW by 2030. That equates to the a range of tonnages per waste stream (see below).
We even added in a new landfill for Sydney (which has nothing to do
REQUIRED BY 2030 TO HIT THE TARGETS (WITH GROWTH)
with hitting the targets but is seen as an urgent priority).
Those 2,751 bits of different kit will mainly be built by the private sector and councils.
The three critical things the private sector and councils need from the State government are the plan, a financial incentive, and regulatory certainty that the rules will not change sometime in the future.
We turned to the existing s.88 landfill levy for the financial incentive. It raises $0.9B per year. The contribution required to facilitate the above investment is $1.3B once. A bit over a year’s worth of levy, once.
All up this would employ thousands of people and release an investment boon of at least $6B in private sector money. That is 5:1 investment. Driven by grants based on those levy funds. (I hear you say – that sounds like a very good deal. Let’s get on with it).
But of course, life is never that simple. We cannot just take $1.3B from Treasury (even if the s.88 levy was introduced for recycling purposes). Most of it is spent on schools, roads and hospitals etc.
So, we came up with an answer as to how to use the levy to fund this infrastructure without having to ask Treasury to reallocate existing levy funds, which we acknowledge is a historical sore point for many in our sector.
A $18/t real increase in the landfill levy over three years with those funds 100 per cent hypothecated to the infrastructure plan gets the funding moving.
That is three cappuccinos per house per year.
If Government wants to accelerate the program faster to achieve the 2030 targets, then it can borrow from the future known levy increases to fund grants now. That is what we suggested.
Of course, others make the valid case that we should just keep lifting the levy until the investment happens – that is, we should not depend on grants. Or governments could ban materials from landfill or require EPR, which would stimulate investment irrespective of the levy settings.
Or we could do all of them at that same time. And we should.
We handed the plan and funding model to the EPA. We hope that they take it seriously.
The EPA recently announced they will release the infrastructure plan over “the next period”, “in chapters”.
As long as it covers what investors and councils need, we shouldn’t care how they release it.
But Minister, please make it soon. It is good for recycling, for jobs, for the regions and for the planet.
Mike Ritchie is the Managing Director, MRA Consulting Group
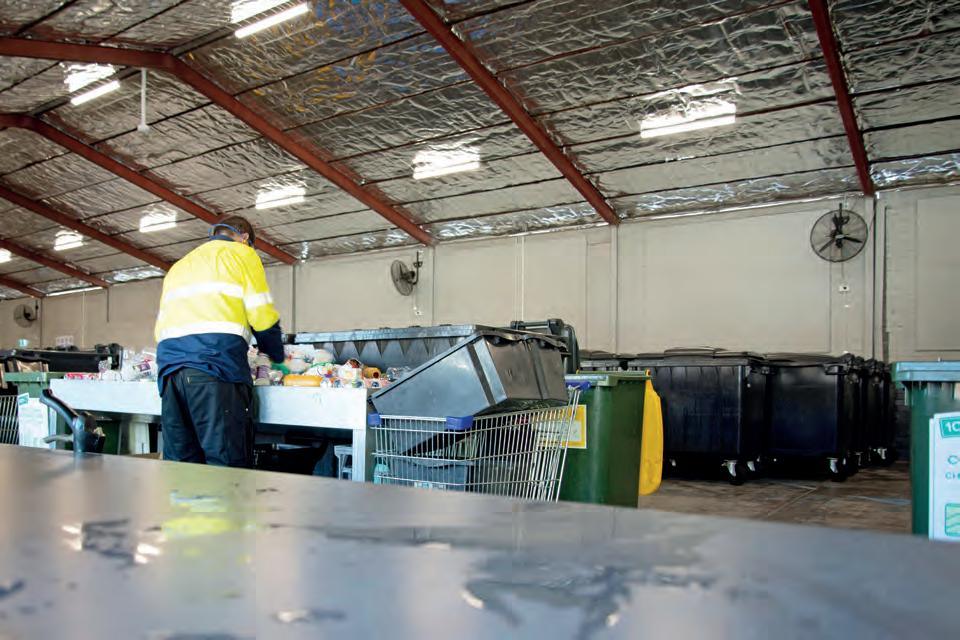
NSW takes the lead on vape disposal as national progress stalls
By Shannon Mead
A clear path toward the safe disposal of embedded batteries appears no closer after the December Environment Ministers Meeting concluded without any notable national action. Within a
day of the meeting, EPA NSW confirmed the introduction of legislation in the new year to address the issue. While a welcome step, it is far from the anticipated national solution required to deal with embedded batteries, including those found in disposable vapes, a
solution desperately needed by the industry and public alike.
Let’s rewind one year. The Communique from the November 2023 Environment Ministers Meeting highlighted a common concern among the Ministers around the safety risks
posed by lithium battery disposal. It was noted that Queensland would lead work to inform regulatory actions.
Seven months later, in June 2024, the public were further updated that managing batteries was a matter of priority, and that acting quickly was
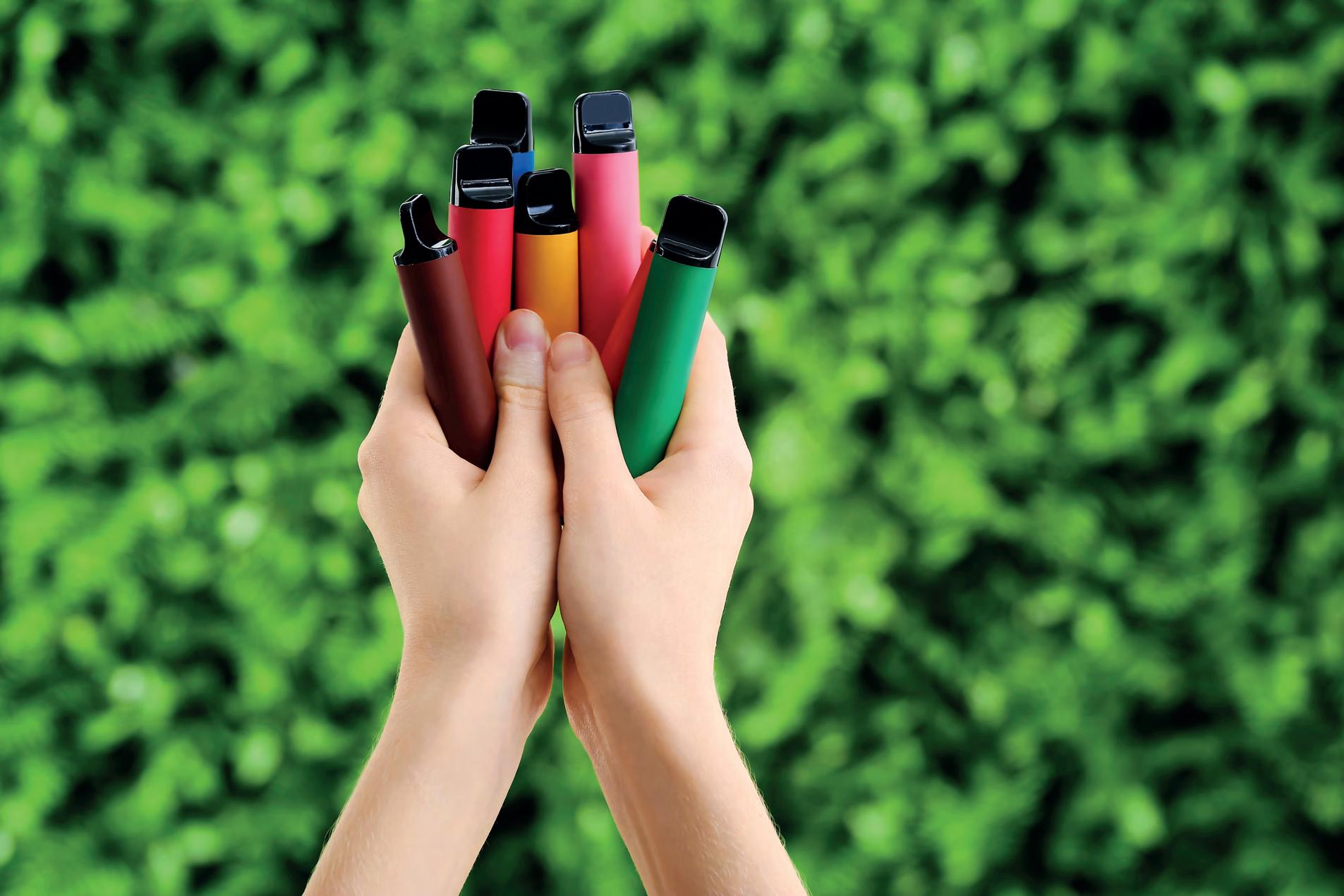
Because vapes are imported and sold illegally, there is no company or brand to levy.
Image: Pixel-Shot/shutterstock.com
of critical importance to protect both lives and property. With this in mind, it was somewhat disappointing for stakeholders to learn on December 10th that, although an urgent need to address the problem was still identified, the only progress was a draft Regulatory Impact Statement by NSW and Victoria, along with the disclosure that NSW would announce their own measures.
It appears that some decision makers may have hoped that the various actions from the Commonwealth around vapes would also eliminate issues around their disposal. While it is evident that the importation ban on disposable vapes and restrictions on retail sales has reduced their availability, there is no conclusion that it has reduced the amount of people still discarding vapes in domestic and public bins, nor the impact caused by these devices once they are incorrectly disposed.
Despite various marketing campaigns and partnerships around the risks associated with binning batteries, it is clear that not everyone understands that their vape – or toothbrush, or IOT device – may contain a lithium-ion battery because they can’t see the battery that is embedded in the vape device. Images and videos of trucks emptying their contents onto suburban roads to manage fires have become too common.
Various sources, including waste industry publications and fire departments, note that there are hundreds of fires caused each week by incorrect disposal of batteries, including devices with embedded batteries such as vapes. Often containing lithium-ion batteries with poor quality chemistry, vapes are an ignition source and can create a dangerous thermal runway – a phenomenon in which the lithium-ion cell can enter an uncontrollable, selfheating state.
Product stewardship
Though there have been several calls for a product stewardship scheme to be mandated to strengthen the current voluntary B-Cycle scheme, a way to cover the costs associated with vapes has always been overlooked. As these are products that have been imported and sold illegally, there is no company or brand to levy. However, while there are still differing views on what type of product stewardship model would be best, and no clear answer as to who would pick up the tab, the unanimous opinion seems to be that something must be done to protect the lives of workers in the waste industry.
NSW currently offers 21 sites where devices with embedded batteries (including vapes) can be dropped off. RecycleSmart offers curbside vape
collections for residents who are subscribed to their program, either directly or via participating councils. There are also commercial solutions for large scale disposal, managed by companies such as EnviroStream.
No More Butts’ budget presubmission for 2022-23 requested funds be allocated in the budget to deal with this issue, yet three years after it was raised, and more than one year after the government highlighted it as a critical issue to resolve, there is still no national program in place. Although it is encouraging to see the leadership from NSW emerge from the ashes, it is nonetheless disappointing that, after a year, a national response to address this critical issue is yet to be delivered. Fragmentation of solutions across states does not remedy the situation. The lack of consistency in e-waste to
landfill strategies confuses the issue even further, with some states prohibiting the disposal of vapes into landfill yet not offering any practical method of alternate disposal.
Moving on to solutions: the lowest hanging fruit is pharmacy drop-offs. Pharmacies are now theoretically the only place to purchase vapes, so a return scheme should be an easy and important step to introduce. The Return Unwanted Medicines scheme, or Pharmacycle, are opportunities to consider here. The expansion of NTCRS and/or B-Cycle to include vapes in their scope at their drop-off centres would address the issue.
As for funding, there are different means that can be considered, including redirection of penalties from illegal imports and retail raids. Every truck that is forced off the road to deal with
a battery fire creates a cost to council that will undoubtedly be passed on to ratepayers in some format. Every facility fire can drive up insurance premiums and cause issues in lost productivity. Luckily, there has not been any documented loss of human life to date, but we should consider whether the cost of ongoing inaction has indeed put more strain on the economy than it would have if the funding had been put toward finding a solution a year ago.
We look forward to seeing the NSW legislation proposal and ensuring the swift implementation of a fit-for-purpose model that can be replicated across other states, or indeed on a national level. We cannot waste any more time.
Shannon Mead is the executive director of No More Butts
“Three years after it was raised, and more than one year after the government highlighted it as a critical issue to resolve, there is still no national [vape] program in place.”
While vape availability has been stalled, there is no evidence the amount being disposed of in public bins has been reduced. Image: Iryna Budanova/shutterstock.com
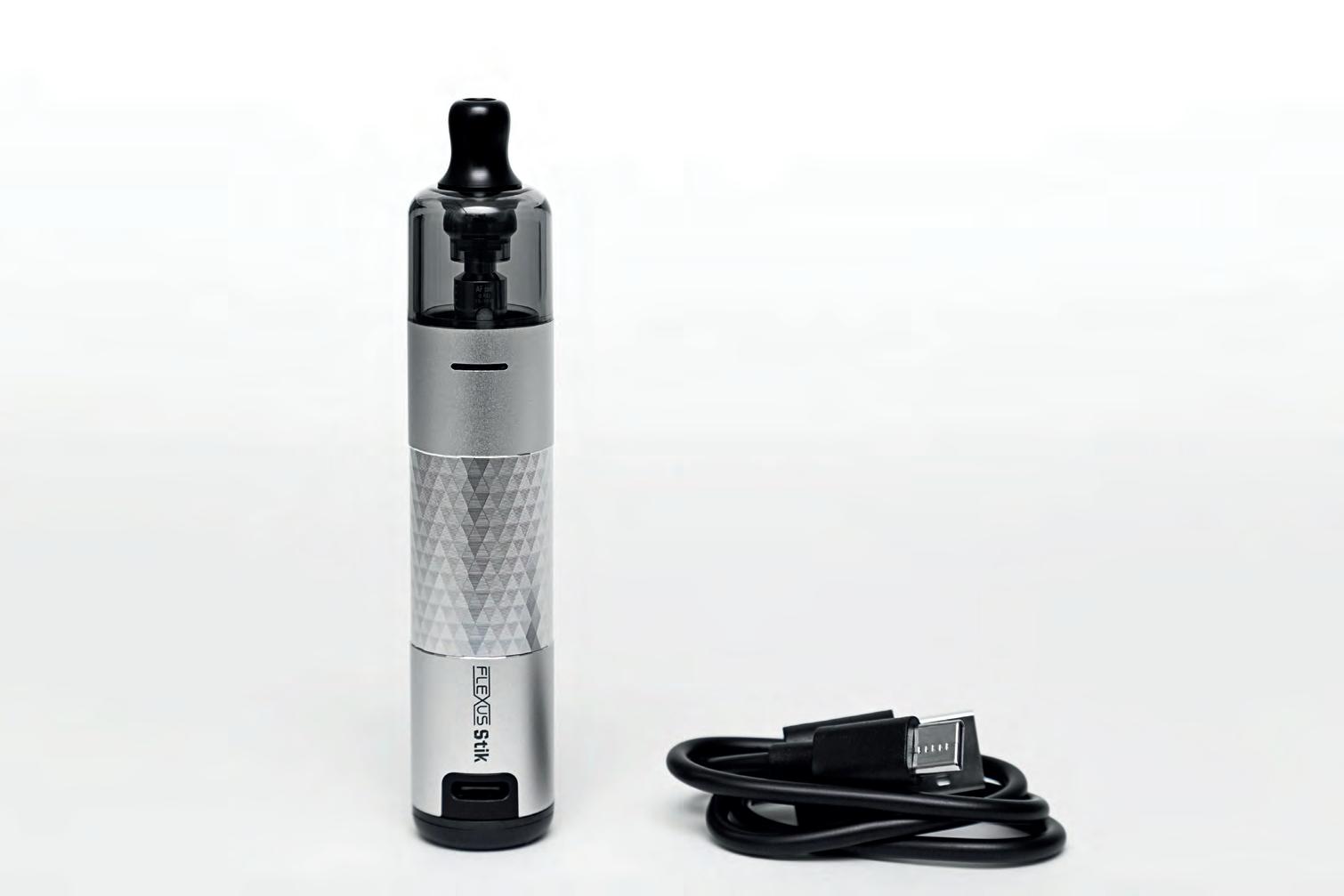
Advancing circular economy goals in a growing Australia
By Linda Nordin and Dr Wade Mosse
AS Australia’s population accelerates toward an estimated 39 million by 2050, the challenges of waste generation and resource management grow more complex. To address this, the Australian Government has launched a Circular Economy Framework, a roadmap to double the nation’s circularity by 2035. Released by the Department of Climate Change, Energy, the Environment and Water (DCCEEW) in December 2024, this framework is much needed and will provide guidance, a clear vision, and real-world examples to cut emissions and waste. The framework outlines three supporting targets to: shrink our per capita material footprint by 10 per cent; lift our material productivity by 30 per cent; and safely recover 80 per cent of our resources. These goals demand not just technological advancements but systemic changes that span
policy, business, and community engagement.
When we apply the IPAT model (Impact = Population x Affluence x Technology), commonly used in sustainability, to show how human activity impacts the environment, we can quantify the interplay of key factors driving waste and inefficiency. They are: • I mpact – the amount of waste generated by our society/ economy.
P opulation– as usually understood.
A ffluence – level of consumption of goods/materials.
Technology – (1- circularity percentage), a factor allowing for how much of a material is reused/ recovered rather than wasted; a circular economy would have a technology score of zero and thus no ‘impact’ by this model.
Australia’s population is forecast to grow by an estimated 9 million by
2050, meaning waste generation would be projected to increase by 18 million tonnes annually on current trends. This presents a significant headwind to our ambitions to be more sustainable and reduce our levels of waste generation. Similarly, current business models often prioritise economic growth (affluence) over sustainability, and while consumerism supports economic growth it is seldom the environmentally friendly option. Short product lifespans, non-repairable designs, and rapid redevelopment of infrastructure all tend to come with waste as a by-product, while trends like fast fashion, frequent tech upgrades, and online shopping further exacerbate waste generation through increased packaging and disposability.
So, with embedded upward trends in the P and A factors in the model, it becomes clear that a sustainable outcome for our planet requires support from technology, in the form of the Circular Economy (CE). Australia is
currently far from achieving the 2035 targets. For example, the national average resource recovery rate is only 62 per cent based on the 2024 National Waste and Resource Recovery Report. This average is also underpinned by the large Construction & Demolition category (C&D) which achieves a recovery rate of 80 per cent, mainly due to the heavier material (e.g. concrete, rocks and soils) that is fairly easy to recycle today; as a result the Municipal Solid Waste (MSW) and Commercial and Industrial (C&I) categories are under addressed and will be a priority for future efforts in building a circular economy.
This article explores practical strategies Australia can adopt from global leaders like the EU, which has successfully implemented circular systems. Australia can implement scalable, tailored solutions to address challenges such as long distances, diverse demographics, and limited source separation practices. To achieve Net Zero and Circular Framework targets, Australia must shift toward systemic change by integrating CE strategies that balance economic growth with sustainability, reduce consumerism-driven waste, and foster

Are we on track to achieve our circular economy goals? Not yet. But with focused efforts on systemic change, enhanced infrastructure, and innovative recovery strategies, the pathway to a sustainable future is
Circular economy principles
While initiatives in Australia aim to reduce waste to landfill, current waste generation rates, future growth projections, and recycling performance make it clear that these efforts alone are insufficient. Achieving Australia’s CE targets requires a shift from the familiar linear mindset – focused on “take, make, waste” – to a circular mindset that emphasises resource regeneration, reuse, and efficiency. This transition offers not just environmental benefits but also opportunities to gain a competitive advantage in the market. At SMEC, we view best practice in efficient and circular waste management to be when our projects enable the transformation of solid material, energy and water waste into
SMEC worked with the Queensland Department of Transport and Main Roads (QTMR) to achieve the first ISC ‘Leading’ rating for a QTMR project by integrating sustainable design and construction methodologies on the M1 Upgrade: Varsity Lakes to Burleigh project.
resources that circulate over and over. By aligning with Ellen McArthur’s three core principles of CE together with the 10R Principles of CE Framework (e.g., Refuse, Redesign/Rethink, Reduce, Reuse, Repair, Repurpose, Refurbish, Remanufacture, Recycle, Recover), we aim to design out waste at its source and contribute to a more sustainable future. Taking a circular approach when designing infrastructure and future urban communities makes for a seamless and integrated resource system ensuring that resources are continuously circulated back
to regenerate our nature and to create a climate positive and healthy environment.
Lessons from global leaders
Australia currently falls short of its 80 per cent resource recovery target. Drawing on more than two decades of CE experience in Sweden and the UK, SMEC’s Circular Economy lead, Linda Nordin, highlights key practices from global leaders that Australia can adopt to accelerate its progress. They are:
Tailored Collection Services
– custom-designed systems based on household types and demographics to ensure participation, reduce contamination, and maximise recovery.
S upportive Policy and Legislation – introduce mandatory targets, such as food waste separation, single-use plastic bans, and landfill bans, as seen in the EU, to encourage compliance and drive innovation. For example, the EU’s Corporate Sustainability Reporting Directive (CSRD) has been a key step toward reducing greenhouse gas emissions, improving sustainability, and advancing the circular economy. Australia’s new mandatory sustainability reporting requirements, effective from January 2025, are currently only designed to cover climaterelated financial disclosures but have the opportunity to be expanded to cover a broader sustainability scope including CE, aligning corporate practices with national goals and accelerating the adoption of CE principles.
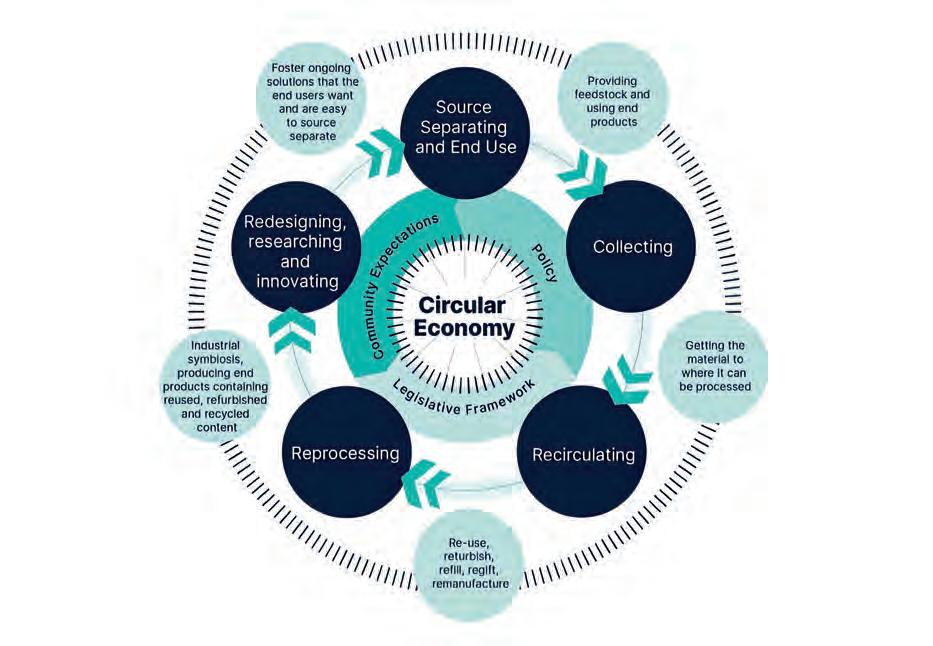
onsumer Education – carbon footprint and recycling labels on products empower informed choices, increasing accountability across the supply chain.
usiness Commitment –companies embracing CE principles view sustainability as a competitive advantage, with models emphasising reuse, repair, and resource efficiency.
ircular Infrastructure – circular precincts, recycling malls, and battery recycling hubs streamline resource recovery and promote industrial symbiosis.
Every community and business faces unique challenges. By thinking outside the box and implementing tailored, cost-effective solutions, organisations and municipalities can play a pivotal role in advancing Australia’s CE goals.
Applying a 5-step approach to CE
To achieve a modern operational waste management system that aligns with the principles of CE, we have developed a 5-step (Figure 2) approach to embed CE principles across infrastructure projects, businesses, local government areas (LGAs), and communities.
The framework focuses on delivering measurable outcomes and practical solutions to reduce waste, emissions, and costs and help projects align with Circular Framework targets, ISO and ISC standards.
Through feasibility studies, costbenefit analyses, and tailored strategies, we can empower stakeholders to
transition towards a more resilient and sustainable circular economy.
We highlight three practical examples of how to introduce Circular Systems to reduce emissions and increase diversion rate.
Tailored collection systems: overcoming Australia’s unique challenges
Australia’s geography and diverse communities pose challenges to waste collection and reprocessing.
Examining the supply chain is crucial, and closing the loop starts with designing affordable collection systems for councils that provide sufficient, uncontaminated quantities of feedstock for reprocessing. Without this, closedloop systems cannot function. However, Australia’s supply chain often struggles with insufficient or contaminated feedstock for reprocessing facilities.
Food waste, a key target for combating climate change, presents an opportunity. It contributes onethird of human-caused greenhouse gas emissions, generating 8 per cent of global emissions annually. Yet, food waste collection and reprocessing remain limited across Australia, with some local governments finding systems like FOGO (Food Organics and Garden Organics) cost prohibitive. Tailored solutions are essential, considering demographic factors such as urban density, suburban layouts, and remote communities.
Drawing from international case studies can guide the development of cost-effective systems suited to Australia’s unique needs. In Europe, food waste is often co-digested with other organic materials at anaerobic digestion (AD) facilities, including sewage treatment plants, to produce biogas and compost. This approach reduces emissions and closes resource loops. SMEC advocates for integrating scalable solutions in Australia by combining residential, industrial, and commercial collection streams. Proven technologies such as in-vessel composting, and AD can reduce emissions – preventing up to 616 kg CO₂-e per tonne of food waste compared to landfill – while creating valuable renewable resources.
SMEC has collaborated with local governments to develop innovative, source-separated services for comingled, food, and green waste. These solutions, inspired by global best practices, help lower collection costs, improve feedstock quality, and reduce greenhouse gas emissions, ultimately closing the loop.
To advance circular systems, Australia must expand its collection infrastructure, implement financial
FIGURE 1
FIGURE 2
1. Define a baseline, Set SMART targets to measure progress
2. Embed CE in your vision and strategy
3. Align business model with CE ISO, ISC standard etc
4. Undertake feasibility studies, priorities and Implement
5. Keep going! Evaluate and improve
incentives, and mandate commercial recycling. International examples from Sweden, the UK, Germany, and beyond demonstrate how technologies like multi-compartment bins, underground vacuum systems, and mobile recycling vans can achieve high participation and low contamination rates. By adopting such approaches, Australia can increase recycling rates, cut emissions, and move closer to 80 per cent circularity.
Circular hubs and precincts: catalysts for industrial symbiosis
SMEC leverages national and international expertise to develop circular hubs that drive sustainable practices and foster industrial symbiosis. Globally, initiatives like the Renew Hub in Manchester and Sweden’s ReTuna Återbruksgalleria –the world’s first recycling mall – offer insights and inspiration for similar projects in Australia.
Circular hubs come in various forms, ranging from small-scale reuse centres for household goods, tools, and textiles to advanced reprocessing facilities and recycling malls. Closer to home, local
initiatives such as the Circular Economy Club on the Gold Coast play a critical role in promoting knowledge sharing, collaboration, and circular practices across cities.
These hubs are instrumental in managing bulky residential and commercial waste, as well as construction and demolition materials. By fostering reuse, they reduce emissions – for instance, reusing one pair of jeans saves 20kg of CO₂, large furniture 80kg, and electrical equipment 160kg. Such efforts align with Australia’s Net Zero targets and Circular Economy Framework goals.
Every city has the potential to develop a Circular Hub tailored to its unique needs and demographics.
Brisbane and the Gold Coast represent exciting opportunities as they prepare for the 2032 Olympic Games with a commitment to climate neutrality. By collaborating with local governments, industries, and communities, Australian cities can overcome challenges like high initial investments and create sustainable reuse and sharing infrastructure that benefits both the environment and local economies.
Integrating Circular Economy principles into the built environment
As a multi-disciplinary engineering firm, SMEC has a history of delivering major infrastructure projects around the globe. The Waste and Resource Recovery team within SMEC collaborates closely across disciplines to assist engineers in embedding CE principles into infrastructure projects for the built environment. By applying the four foundational principles –adaptability, deconstruction, circular
material selection, and resource efficiency – SMEC can work with clients to make the shift from linear to circular design thinking.
This shift can be implemented across infrastructure sectors, including rail, roads, hydropower, energy, reprocessing facilities, and urban communities. For example, in Queensland, SMEC worked with the Department of Transport and Main Roads (QTMR) to achieve the first ISC ‘Leading’ IS Rating for a QTMR project by integrating sustainable design and
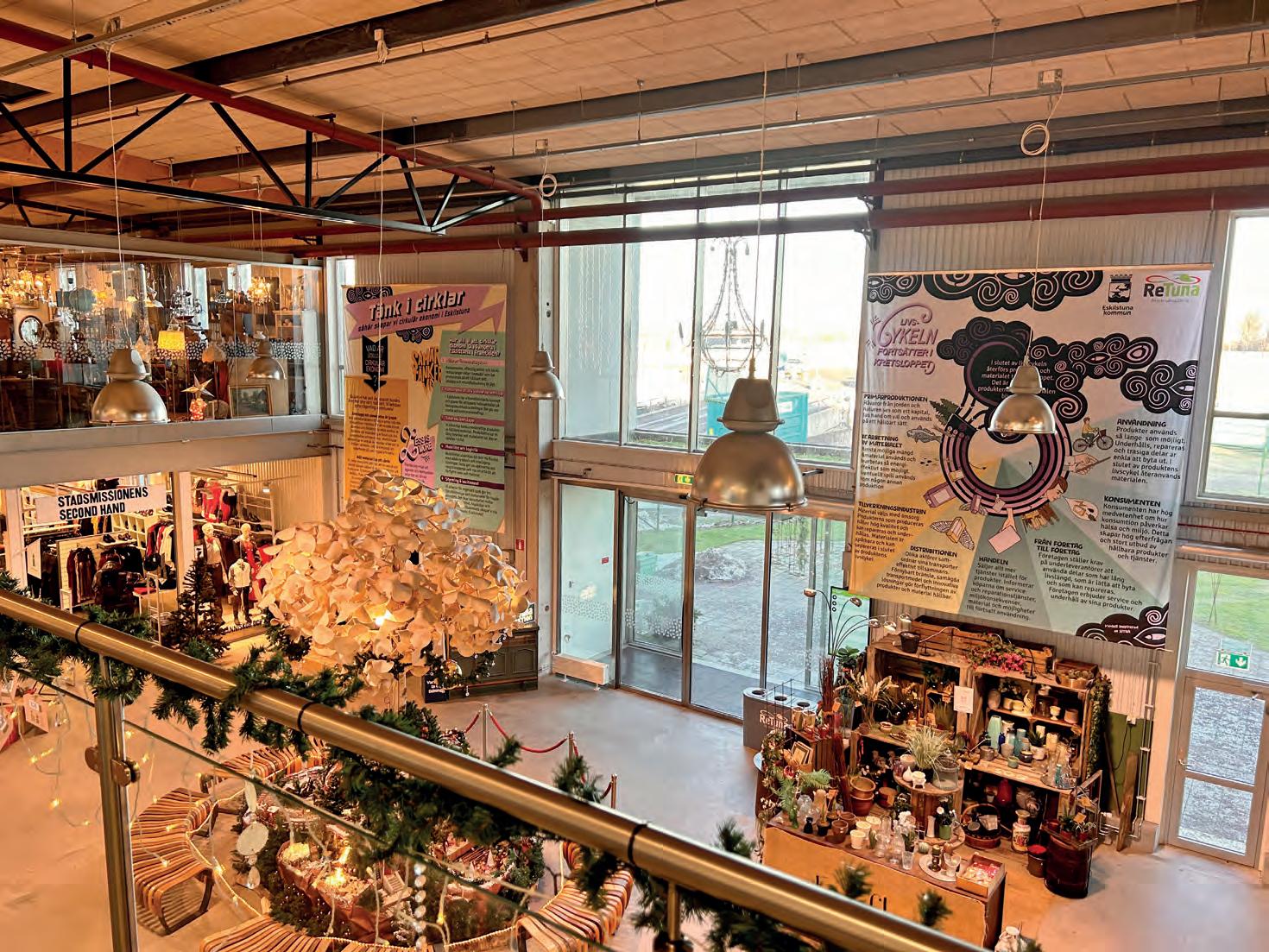
ReTuna Återbruksgalleria –the world’s first recycling mall.
Source: A circular economy engagement tool for the assessment of new and existing buildings (Jan 2023, Chalmers University of Technology, Sweden)
The four high-level principles for circular building Design and Adaptability Design for deconstruction
Resource Efficiency Circular Material Selection
construction methodologies on the M1 Upgrade: Varsity Lakes to Burleigh project. The team were able to integrate Australian-first innovations including concrete fracturing, invertebrate sensitive road design, and also retain significant infrastructure to reduce material use and waste.
We can also look to examples from ecologiQ, an initiative developed as part of Victoria’s Big Build, for inspiration to provide a framework for reuse and integrating recycled content across Victoria’s infrastructure projects.
The process begins with measuring current performance to establish baselines for achieving higher standards and ratings. Key considerations include:
1. Refuse – integrate existing infrastructure and natural features into designs using regenerative approaches, such as on-site production of green concrete/steel.
2. Design for End-of-Life – ensure designs are repairable, lowmaintenance, and durable while allowing easy deconstruction, cost efficiency, and material recovery.
3. Modular Design – incorporate modularity to enhance maintenance, extend longevity, and adapt to evolving needs.
4. Replace Virgin Materials – utilise reused or recycled materials wherever possible, such as green steel and circular building products, to maximise resource efficiency.
5. Design for Adaptability –anticipate future technological advancements by allowing for reuse, material recycling, and digital tracking systems to manage end-of-life processes. Ultimately, these initiatives aim to reduce embodied carbon in our built environment, which currently accounts for up to 40 per cent of the world’s total embodied carbon.
Transforming waste into opportunity
Australia stands at a pivotal moment to embrace the Circular Economy and achieve its Net Zero and Circular Framework targets. By implementing practical, scalable solutions, Australia can reduce waste, lower emissions, and foster economic growth through circular innovation. Together, by daring to be innovative, mitigate risk and take small incremental actions every day, we can close the loop on waste, achieve an 80 per cent recovery rate, and build a sustainable, Net Zero future for generations to come.
Linda Nordin is a senior associate engineer and Dr Wade Mosse is a regional manager ANZ - Waste & Resource Recovery for SMEC
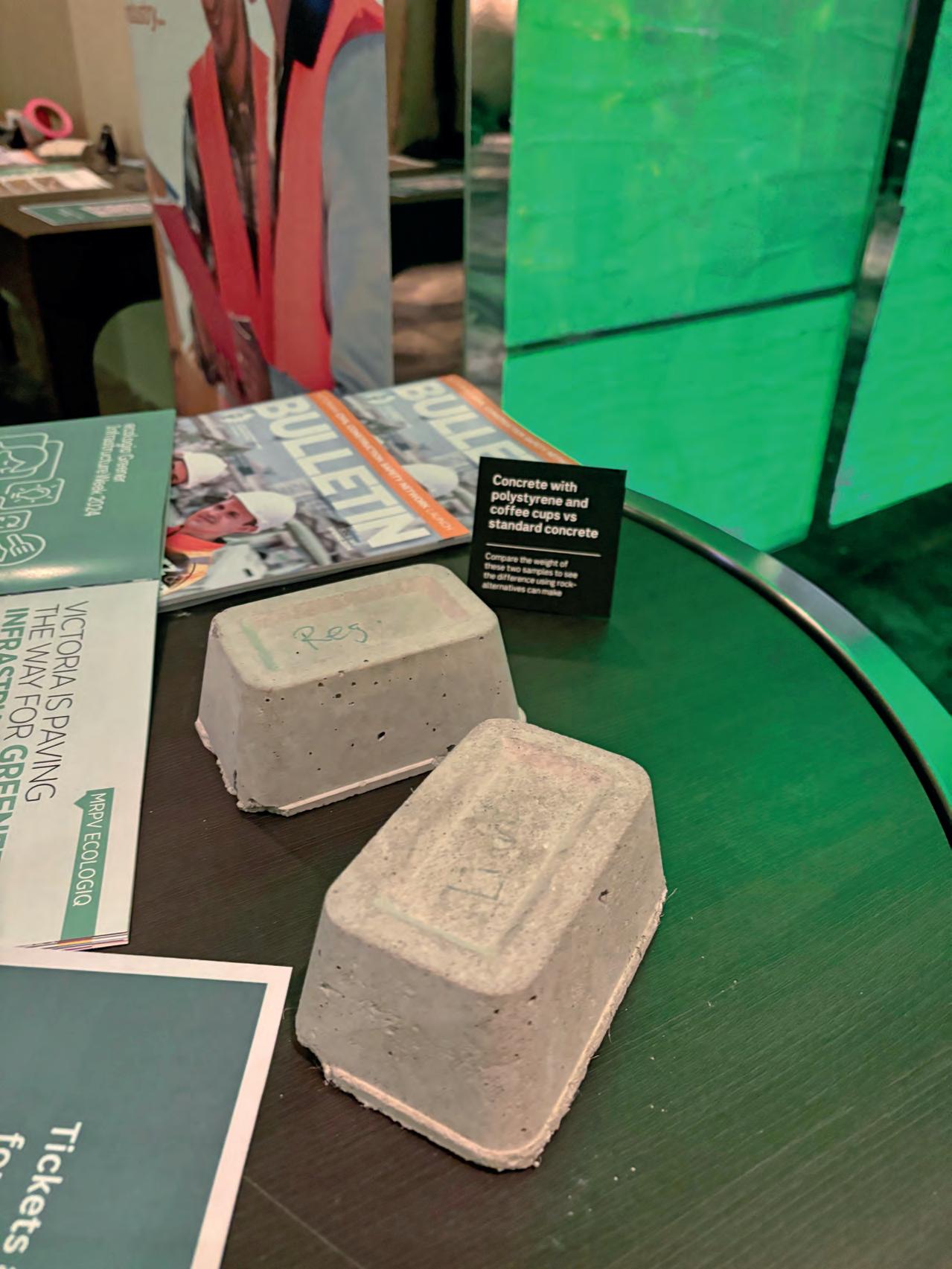
The ecologiQ launch in Melbourne.
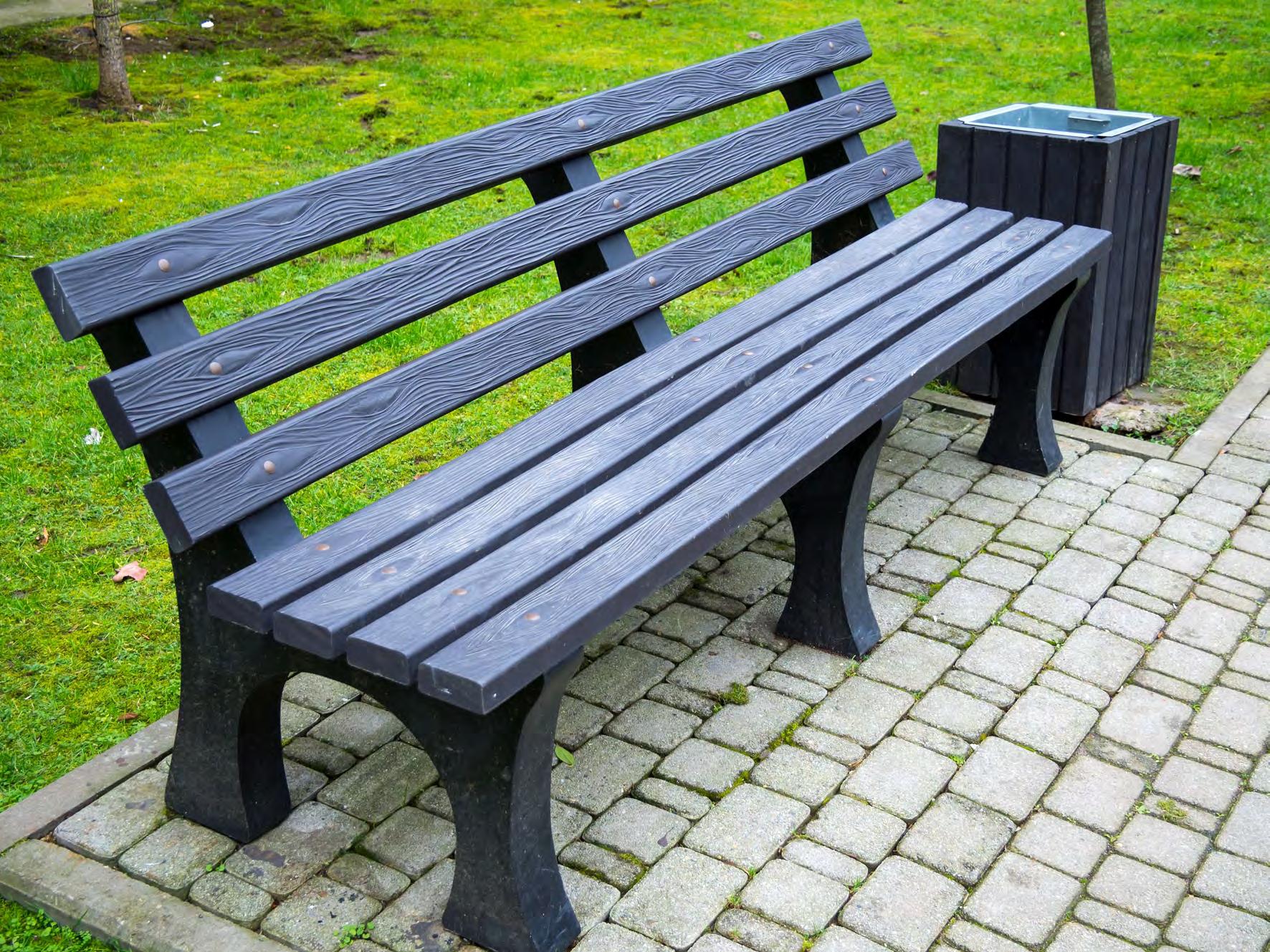
Transparency needed with recycled plastic content claims
By Dr Ross Headifen, Biogone
TRANSPARENCY needs to be at the forefront of any conversation when it comes to claims about recycled plastic content in products – especially as we start along the journey of moving to a circular economy. With the emphasis on incorporating recycled materials into plastic products intensifying, it is essential to avoid confusing or misleading claims that could affect end users.
Governments are establishing recycling targets, and the concept of the circular economy is gaining traction. This creates an incentive to prominently feature ‘contains recycled content’ on labels. Not only does this appeal to consumers who wish to make environmentally responsible choices, it also places increasing pressure on manufacturers to demonstrate compliance with established sustainability goals.
The term recycling is becoming increasingly complex as more emphasis is
put on incorporating less virgin material and more reclaimed materials from post use. Across the gamut of manufacturers and users there are claims on packaging like ‘recyclable’, or on company websites terms such as ‘we recycle our waste’. They are all vying for the green benefit of appearing to be doing the right thing with respect to avoiding making waste. All good actions, but those are the easy actions. None of these claims deal with using previously used material to make new similar materials, which is the definition of recycling.
We also want to shift the paradigm from the idea that plastic recycling is taking plastic waste, and instead of sending to back to original manufacturers, is being repurposed into other down cycled applications such as garden furniture or road base. This is repurposing the plastic waste not recycling it in the circular economy.
When evaluating claims regarding recycled content on labels, transparency
regarding the source of that material is crucial. This openness enables consumers to understand what they are purchasing and to assess how products labelled as ‘contains recycled content’ compare against one another.
Recycled material can be separated into two categories:
1. Post Consumer material (PCR). This is really what most general consumers think of when they hear contains recycled content. They think their plastic bags and wrappers they have taken the time and effort to put into a recycling bin, have been sent to a place where new products are made from them. This is the form of recycling that has the best benefits to the environment. It is plastic waste being reclaimed and not sent to landfills or let loose as litter. It helps with the reduction in use of virgin plastic material.
2. Post Industrial material (PIR). This is where factories collect the off cuts and scrap they make within when manufacturing a product line and re-process it so it can be fed back into the production machines again to produce more product. It is recycling within the factory. Unlike PCR, this recycled material has never seen any consumer use but is still a valid use of the factory’s plastic scrap. But it is not spurring the consumer to recycle or manufacturers to seek out PCR material as their inputs. What is needed are standardised icons
that everyone will recognise immediately as to what the source of the recycled material is. Two such symbols are proposed. They both show the circularity of the process but clearly indicate the different sources of the recycled material. Having such readily visible symbols will promote increased usage of PCR material and thereby drive the circular economy even stronger.
We are at the cusp of the circular economy, making it imperative to establish clear and transparent claims regarding circular economy plastic materials. Now is the time to proactively address potential greenwashing associated with ‘contains recycled content’ claims aimed at increasing sales.
The circular economy offers a promising solution to many of our plastic waste challenges while safeguarding our environment and oceans. Greater awareness among consumers and governments will enhance consumer’s purchasing decisions and exert pressure on manufacturers to accurately label recycled content in their products. Implementing PCR content requirements will be essential to advancing the circular economy.
This will necessitate that manufacturers display a PCR logo on their labels, thereby requiring them to source certified PCR materials.
Dr
Ross Headifen is a co-owner of Biogone
Icons for Post Consumer Recycled Plastic (PCR) and Post Industrial Recycled Content (PIR) are needed to help consumers know the difference. Image: Biogone
Christmas decorations like these are made from recycled plastics. Image: VPales/shutterstock.com
Grinder does the dirty work
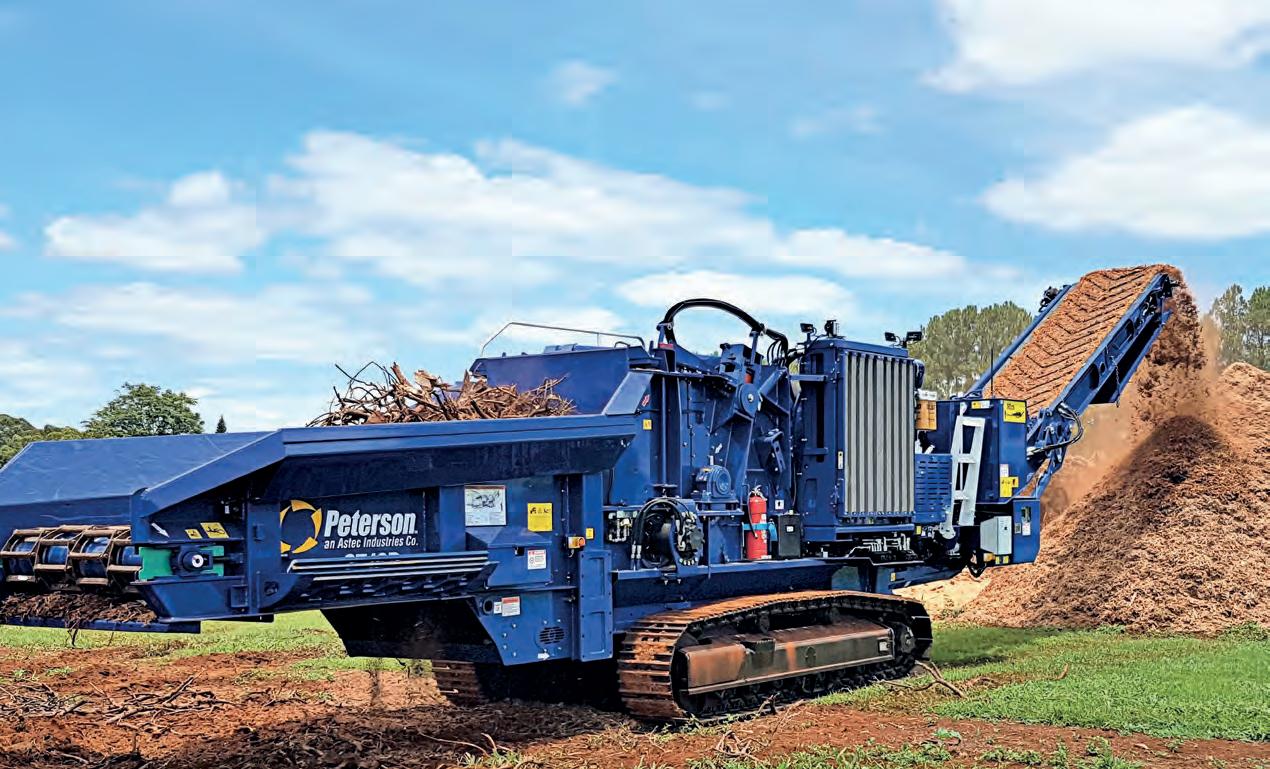
KOMATSU Forest has enjoyed a growing market with the Astec/Peterson horizontal grinder range since acquiring the Australian Dealership in 2010. Initially the range was focused on the chipper products, which complimented the company’s forest machine business. Known for its performance and reliability in North America, this range, when added to the expansion of recycling green waste in Australia, has been a further bonus for Komatsu Forest.
While the horizontal grinder industry is relatively small in Australia, Komatsu Forest has sold 36 units in recent years. The standout in the range has been the Peterson 2710D, accounting for more than 70 per cent of units sold throughout Australia. Its history includes:
T he first 2710 being sold to Tripodi Transport for recycling waste in Sydney.
S nell Contracting in Northern Territory bought several units that have helped rehabilitate Rio Tinto’s Grove Mining site.
J efferies Group in Adelaide utilising a unit that helps manufacture composite from councils’ waste material.
S mallmon Bros in Wagga using a unit for recycling waste throughout the Riverina region NSW.
Eco Veg Land Management based in west Sydney has a grinder that
assists in recycling waste material.
J ones Forest Management in northern Queensland uses its unit for land clearing and mulching.
“We’re extremely pleased with the Peterson’s success and have been somewhat surprised by the growth of the Peterson grinder sales,” says Brett Jones, managing director Komatsu Forest.
The Peterson 2710D is designed for operations requiring high production and frequent moves between jobs. It is powerful, with a Caterpillar Tier II C18 765 hp (570 kW) engine for export. Heavyduty and mobile, the 2710D has high production throughput for a machine of its size.
The unit’s large feed opening is suitable for processing odd-sized feed stock. Measuring 153 cm x 81 cm, when boosted by Peterson’s high lift feed roll, the feed opening’s maximum lift of 112 cm, is among the largest in its class.
It also features a large grate area that enables it to produce materials to exact specifications. The quick-change multiple grate system makes it easy to customise grate configurations to produce a variety of finished materials. Grates are removed through an easyaccess door on the side wall.
Triple grouser 50cm-wide tracks enables better handling on hilly or rocky terrain, which helps maximise productivity.
“We’re extremely pleased with the Peterson’s success and have been somewhat surprised by the growth of the Peterson grinder sales”
Other features include:
T hree-stage grinding process provides faster reduction.
Peterson’s powerful up-turn threestage grinding process provides better fracturing of material and a more consistent product, giving users just the product buyers need.
T he impact release system protects the investment. The grinder’s patented impact release system’s air bags provide uniform grinding and protection from contaminated feedstock, a feature unique to these grinders.
T he second line of defence –the impact cushion system urethane cushions and shear pins – help protect the mill from catastrophic damage in the event of an impact from contaminants in the feed stock.
Peterson horizontal grinders are known for their robust design, versatility, and efficiency in processing a range of materials. These machines come equipped with a variety of features that make them indispensable in waste management, forestry, and recycling
applications. There are four horizontal grinder models; 2710D/4710D/5710D/ 6710D, which are available as either wheeled trailer or self-propelled track.
In Australia, these grinders are typically powered by high-capacity Caterpillar Tier III engines, which provide the necessary power to drive the grinding mechanism and handle tough materials with ease. They feature adjustable screens or grates, allowing operators to control the size of the output material. This flexibility is crucial for meeting specific requirements in various industries, such as producing biomass fuel or creating mulch for landscaping. They are equipped with advanced remote control systems allowing operators to adjust settings, monitor performance, and troubleshoot from a distance, improving safety and operational efficiency.
Since its founding in 1981, Peterson has specialised in turning low-grade materials into high-value products. Its commitment to research and development has pushed the boundaries of what horizontal grinders can achieve.
Heavy-duty and mobile, the 2710D Peterson grinder has high production throughput for a machine of its size.
Image: Komatsu Forest
Smooth sailing for new Port Hedland OTR processing facility
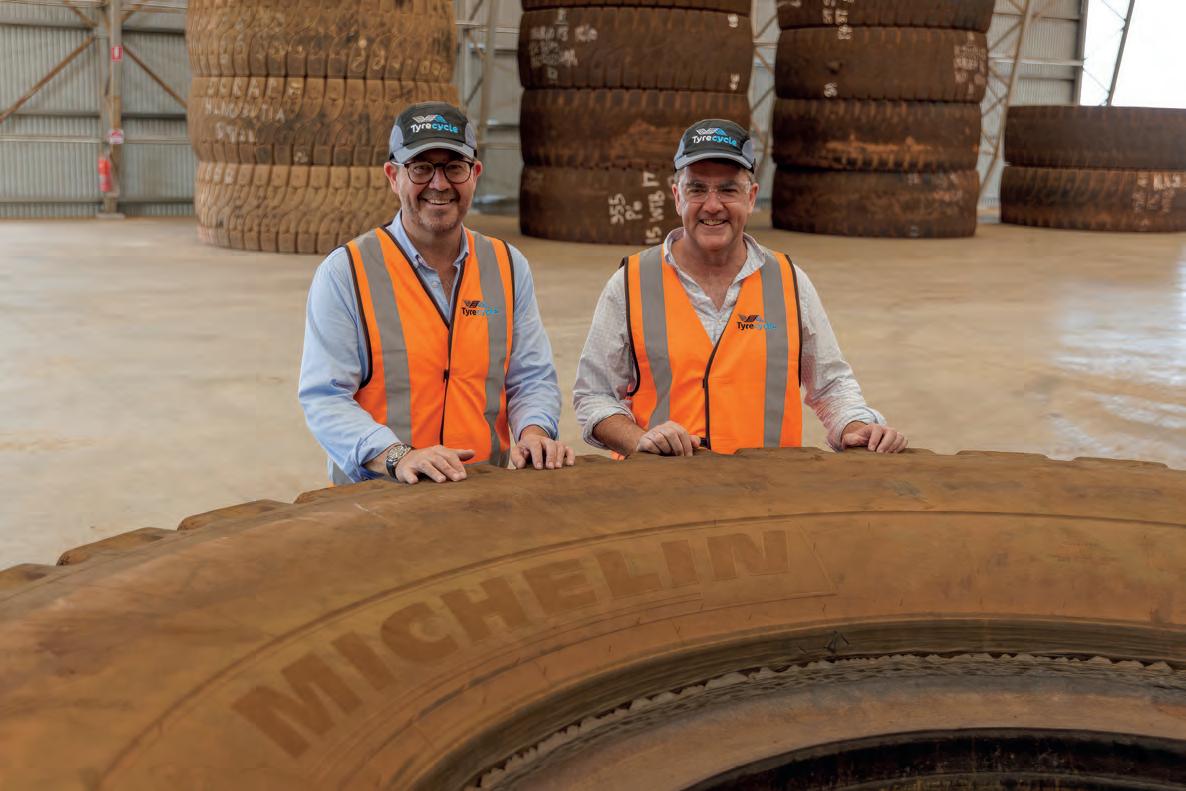
OFF-THE-ROAD tyres, or OTRs, are a troublesome waste stream that, over the years, have been hard to reuse or recycle. One of the more robust users of these tyres is the mining industry, who usually bury them once they have reached their end of life.
Tyrecycle CEO Jim Fairweather and his national team knew that something needed to be done, which led the company to build a tyre recycling facility in Port Hedland, WA.
Tyrecycle, part of the ResourceCo Group, started planning the facility just over five years ago and broke ground almost a year ago. Like a lot of projects, it was the planning – and getting planning permission – that took the most time getting the enterprise off the ground.
“The preparation is important; you’ve got to get all of that right,” said Fairweather. “Overall, in terms of sending people overseas to look at equipment, troubleshooting ideas, and then working through to getting board approval and presenting a sound business plan – it all takes time. Then there was engaging
with mining customers, which was also a very important part of the process.”
Any successful processing facility is only as good as the people who run it, and the equipment installed. The Port Hedland piece of kit is no exception. And it has to be, because to say that the vast majority of mining tyres are huge is an understatement. Some come in at up to 4m in height and can weigh as much as 4-5 tonnes.
To start processing these tyres, you need a special piece of equipment. Enter the T-Rex. Like its long-extinct dinosaur counterpart, this piece of kit has a set of jaws designed to chomp these gigantic tyres into more manageable pieces. This OTR cutter comes from Italian machine specialist Salvadori Recycling and is the first piece of equipment of its kind in Australia.
Fairweather said the installation of the ‘T-Rex’ – and the facility itself – marks an important milestone for the company and Australia’s ability to create sustainable outcomes for Australia’s resource industry
by recycling material from a waste stream that was previously buried in disused mines.
Tyrecycle’s new facility, which is currently the only one of its type in the country, will have an initial 30,000-tonne per annum processing capacity, pre-processing the OTRs for further refinement at the company’s East Rockingham site in Perth. One key ingredient during commissioning was the speed at which the team managed to familiarise themselves with the new equipment.
“In terms of how to use the equipment, we’ve significantly reduced our cycle times of processing the OTRs,” Fairweather said. “With this being an Australian-first, we’ve never used the equipment before, so studying and operating and learning how to use it that quickly and safely has been wonderful for us.”
Once the material has been cut down to size, the pieces are transported down to the company’s East Rockingham recycling facility, where they are turned
into tyre derived fuel (TDF) or crumb rubber. The crumb rubber is destined to be used in the roading industry.
Fairweather said it is satisfying to see such a potentially destructive environmental hazard reduced – in some cases – to a speck of black dust, 0.7millimetres in size, which can be
According to Tyre Stewardship Australia (TSA) figures, currently about one per cent of OTRs are recycled from the
“There’s been a huge market failure when it comes to the collection of OTR mining tyres,” said Fairweather.
“Having said that, our mining customers have been waiting for a solution. They’ve certainly been working really closely with us to try and make
As mentioned, the current facility has the capability to process 30,000 tonnes a year, but what about the potential to process the current annual output of Pilbara OTRs, which is 50,000 tonnes a year? Not a problem, said Fairweather.
“The shed is big enough for us to put another one of these plants in,” he said. “This would bring our capacity up to 60,000 tonnes a year. We’re also looking at building other facilities in other mining centres like the Southern Goldfields in WA, the Curragh-Bowen Basin in Queensland, and the Hunter Valley in NSW.”
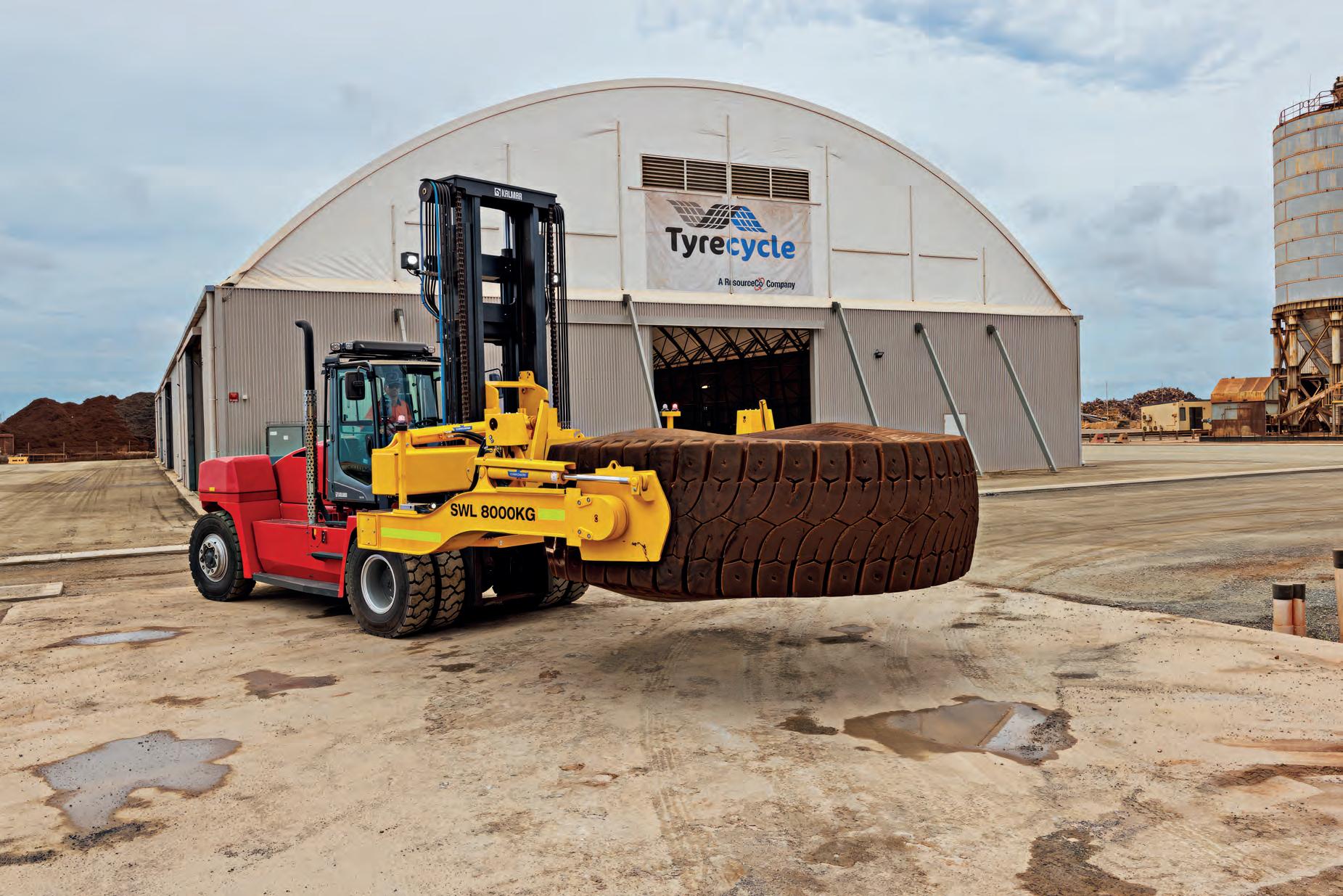
As well as making TDF and crumbed rubber, Fairweather said they are looking further afield when it comes to finding markets for the processed product.
“Some of the processing we do is domestic market dependent,” he said. “We also have a strategic alliance with a company in India who also take our processed material. They produce four times the amount of crumb rubber that we do, and one of the products they produce is micronised rubber particles (MRP). This can be used as a replacement for virgin rubber in the manufacturing of new tyres. We don’t have that in Australia yet. We are already sending a lot of material to them each month because they use our output as feedstock for their processing.”
As for processing the tyres in what is a relatively isolated part of not only the state but also the country, Fairweather
Tyrecycle CEO Jim Fairweather (left), and ResourceCo managing director Simon Brown (right).
Images: Tyrecycle
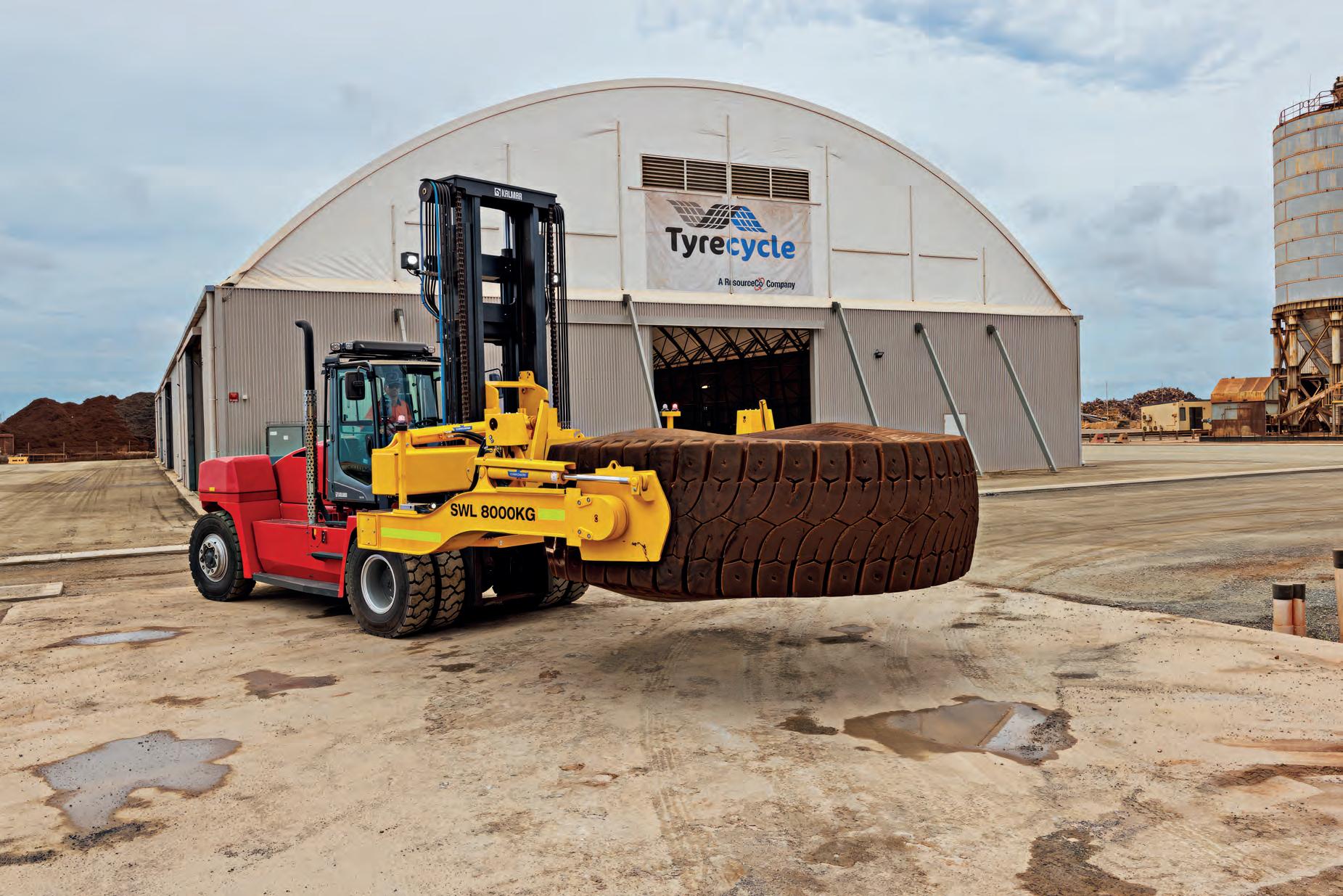
“To start processing these tyres, you need a special piece of equipment. Enter the T-Rex. Like its long-extinct dinosaur counterpart, this piece of kit has a set of jaws designed to chomp these gigantic tyres into more manageable pieces.”
said that was one of the most important aspects of the whole project.
“I cannot reiterate enough how important it is to have the facility near to the mine sites,” he said. “From a transport efficiency point of view – not just for us, but for the mining companies too – and from a cost perspective, and almost as importantly, from a carbon emissions perspective, we’re minimising a lot of issues.”
Overall, the process has left Fairweather and his team pleased with how it has come together.
“I think it’s gone incredibly smoothly,” he said. “We haven’t had any hiccups with the build at all. We also haven’t had any hiccups with the commissioning
of the machines or the equipment.”
As mentioned, once the tyres have been cut, they are on a two-day truck drive to Tyrecycle’s processing plant in Perth, where they are further processed. As for the future, and making sure there will be enough feedstock, Fairweather said it is an ongoing process and one that he is confident will be fruitful for Tyrecycle.
“We’re in discussions with all the major mining companies in the Pilbara,” he said. “They’re all coming to the party. The fact that the plant and everything’s gone so smoothly means that we did our due diligence correctly – it was well planned, well executed – means we’re very happy.”

OTRs are a problematic waste stream that can now be recycled and reused in other industries.
Tyrecycle Trading, Mining and Strategic development manager Ashley Battilana (left), and Tyrecycle Port Hedland operations manager Kane Goldsmith.
A new way of doing business
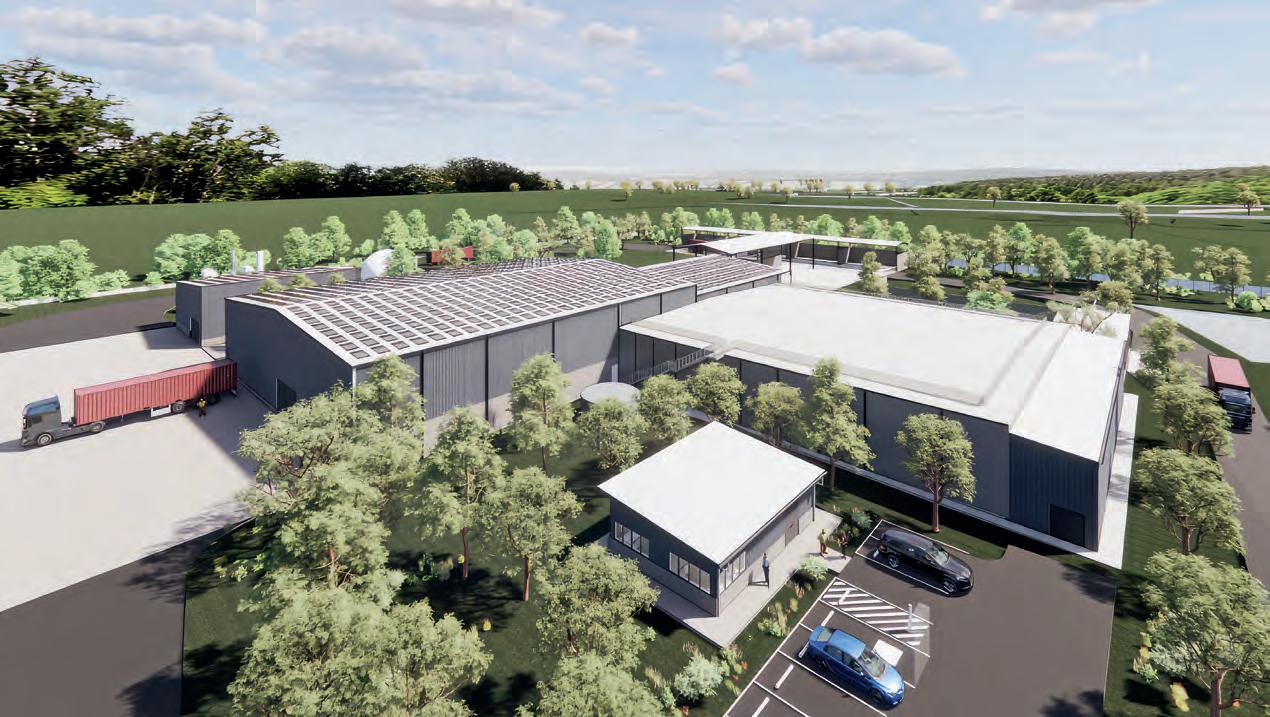
LACK of infrastructure in the resource recovery sector is a bugbear for many, whether it is councils, associations or the public at large – trying to make sure Australia’s needs are met is becoming a challenge. Especially when it comes to trying to meet government-mandated recovery targets. Regional Australia has long relied on landfills to meet their waste disposal needs. However, the public attitude towards dumping waste in landfills has changed for the worse, so councils are learning that recovery of these items can lead to better outcomes in many ways. It means less waste landfilled, and therefore less greenhouse gases created, as well as finding a revenue stream for the reprocessed products.
Enter OREZ. OREZ is a company that is starting to make a name for itself in the resource recovery sector as a one-stop shop for designing and constructing advanced organic processing and bio energy facilities. It can design and build facilities to meet the needs of most councils, especially those in regional Australia.
Sean Galdermans is the general manager of OREZ. The company has recently won a contract to design and build an advanced organics recycling facility for the Tamworth Regional Council, which is based in northern New South Wales.
All going to plan, the build will start in Q3 of 2025 and is set to be completed by Q1 2027. The council had already put
the facility up for tender twice but failed to find a solution in the market that met its stakeholder requirements. Then along came OREZ.
“I feel we were successful in winning the tender because we proved to Council very early on that our team has all the relevant technical knowledge in-house,” said Galdermans. “This limited the need for a number of consulting firms, combined with an excellent and flexible understanding of commercial strategies to deliver these types of projects. The process started early on with a couple of concepts – developed into a preliminary design – where we were setting the boundaries of the project. We worked hand-in-hand with the council to make sure we meet all the interim milestones. While the concept was being developed, the commercial teams very quickly combed through the contract, and mutual ground was found within a couple of months. We then moved into that next phase of the design.”
Lance Jeffrey is OREZ’s delivery manager. He came onboard about 12 months ago to add gravitas to the pitch due to his background as a senior project manager that has helped build a variety of facilities in different industries. He said OREZ has shifted its business model to be more all-encompassing.
“Up until recently, industrial composting facilities and anaerobic digesters have typically been delivered through design processes – typically bid-build type processes – where a
contractor builds a facility that’s been designed by someone else,” said Jeffrey. “In other words, the guts of the facility just forms part of the bigger picture, and it just becomes another commodity of build.
“OREZ’s evolution naturally positions us to take on the head contract role, either as EPC (Engineering/Procurement/ Construction) or EPCm (Engineering/ Procurement/Construction management), by leveraging our engineering and process expertise.”
Galdermans technical sales background merged with Jeffrey’s experience building such facilities – and their joint abilities complemented by new CEO Max Bergomi’s expertise in bringing it all together with his commercial acumen – means OREZ is taking the company to the next level. All three are excited about the future for the company as it increases its offering to the market. And what will the Tamworth facility offer in term of capacity?
Currently, most of the industrial feedstock streams go to landfill. This new facility will not only be capable of processing around 35,000 tonnes of organics a year but will have the capacity to do more if need-be. Galdermans said the Council’s intention is to have future growth capacity of up to 50,000 tonnes per annum. The facility’s modular design means there is enough room to leave space after the original facility is commissioned to retrofit any expansion. And the facility itself? What is
some of the key features? Galdermans said it is the first facility of its type for Australian councils that will incorporate wet anaerobic digestion with in-vessel composting. There’s also going to be two distinct receival areas in the facility, he said.
“One for the more industrial liquid/ sludgy types of feedstocks that go through a digestion process,” he said. “This will help generate clean electricity on site, which will provide the power we need for the composting facility. The surplus will then be fed into the grid.” He said that the anaerobic digestion and the composting tunnels go handin-hand from a process perspective. This is because one generates a lot of water while the other one needs a lot of water. Also, the digestate, a by-product of the anaerobic digestion process, is a feedstock that is mixed in with the kerbside collected organics and is composted through the In-Vessel Composting system and turned into compost.
“In Tamworth, being regional, they do struggle with water. It’s quite dry up there,” he said. “To have that kind of process that is balanced and compliments one and another, while producing energy from an organic feed stock – that is now diverted out of landfill – means there’s many wins.”
The plant is also designed to process some of the difficult feedstocks that will be coming through the facility.
“There are different types of
An artist’s impression of how the new facility will look once completed. Images: OREZ
feedstocks that are not as easily composted in the traditional way and will now be running through the renewable energy plant,” said Jeffrey. “Council is happy about providing that for its ratepayers. There are businesses in the region that need to get rid of difficult wastes – the category three waste –that are currently going straight to landfill.”
And while sustainability was a key ingredient, Galdermans said it wasn’t the only consideration that council looked at when the site was being designed. It also had to fit the bill commercially.
“What was always very clear is that it has to make sense for their residents whilst Council is trying to transition to FOGO and meet the state targets,” he said.
Once the facility is built, it will be owned and operated entirely by the
council. However, Galdermans highlights there is an intent from both parties for OREZ to stay involved in supporting Council’s ongoing operations.
“As the experts, we can make sure the process keeps running in the most optimal way, while they handle daily operations themselves,” he said. “It’s a process support package where we make sure that the asset is running as efficiently as possible.
“Many times, we’ve delivered a piece of infrastructure to find that within two to five years the asset is running at 60 per cent of its original design and commissioning capacities due to deteriorating maintenance and process knowledge. We are one of the few in the industry that have that knowledge to make sure that the project keeps running at its best. We’re not just an infrastructure provider.”
There will be some residual waste due to the nature of the FOGO coming in having some contamination, which means there will still be some marginal landfill. However, nowhere near as much that will have been the case before the facility has been built.
“The aim of the game is trying to keep your feed stock as clean as you can, so your end products are clean too,” said Galdermans. “Most of the product will be turned into compost and mulch to be reused or resold by the council.”
CEO Bergomi said that this project is a great showcase and case study for what OREZ can bring to the market.
“One of the exciting things for us is this project represents one of the best end-to-end examples of organic recycling and how it can be made feasible,” he said. “It involves In-Vessel Composting, anaerobic digestion,
and reusing power generated from biogas, reducing operating costs, with excess energy available for sale on the grid. I think there’s probably no other project in Australia that has every single component as a part of it.
“We are keen to make this project a showcase for other councils to follow. We believe this project can show other regional councils that recycling is feasible by investing in advanced organic processing facilities.
“These commercially viable facilities do not necessarily require subsidies and produce valuable resources, significantly reducing landfill waste. The renewable electricity generated, and the high-quality organic matter produced, can be used for soil enrichment, can benefit communities and the environment across Australia.”
“I feel we were successful in winning the tender because we proved to Council very early on that our team has all the relevant technical knowledge in house, limiting the need for a number of consulting firms, combined with an excellent and flexible understanding of commercial strategies to deliver these types of projects. The process started early on with a couple of concepts – developed into a preliminary design – where we were setting the boundaries of the project.”
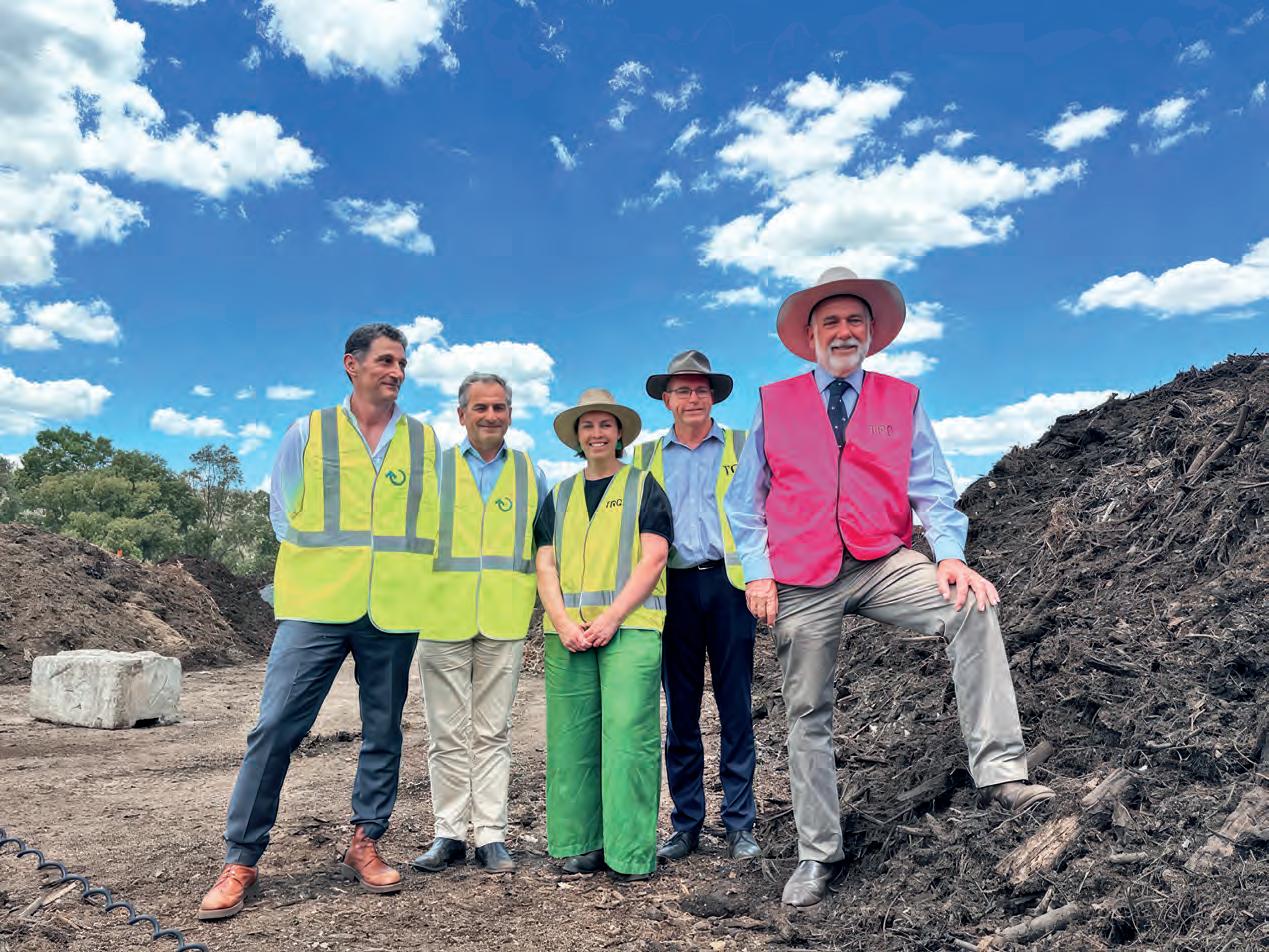
From left: OREZ CEO Max Bergomi; CFC Group Executive Chairman Philip Cardaci; Tamworth Regional Councillors Naomi Schipanski and Bruce Logan; and Tamworth Mayor Russell Webb.
LiuGong electric range sparking interest
LIUGONG’S RANGE of electric-powered equipment and machines are already rolling in the Australian market.
LiuGong was one of the first equipment companies to identify the potential of the battery electric vehicle (BEV) for the construction and civil industry and has invested more than $100 million in research, development and machine testing over the past eight years.
There are nine product areas in total, from aerial access equipment to heavy-weight excavators and wheel loaders. A sign of LiuGong’s confidence in the range is the company’s offering of five-year/10,000-hour warranties with the machines, covering batteries, motors and controllers.
James Lipman, from the LiuGong distributor in Australia, said features such as significantly reduced energy and maintenance costs compared with operating diesel machines, as well as reduced carbon emissions, were attracting the interest of numerous companies around the country.
“Companies can now buy a machine to help hit their corporate responsibility and sustainability targets, as well as their cost of ownership targets,” Lipman said.
“They recognise they can pay significantly less in cost over five years while still taking advantage of all
A mid-size wheel loader comparison indicated fuel and maintenance savings of $210,000 over five years, as well as emission savings of more than 330 tonnes, which was more than the emissions produced by the diesel machine and, hence, would be available for offsetting other emissions.
A range of LiuGong electric machines already are operating in Australia, from mine sites in WA’s Pilbara region through to manufacturing plants in Victoria, including the 922FE excavator, as well as wheel loaders at either end of the size spectrum, the 6.4t 820TE and the 20.6t 856HE.
The 24.1t excavator’s large-capacity lithium iron phosphate battery can store 423 kilowatt-hours (kWh) and the machine provides digging breakout force of 105 kilonewtons (kN). Its permanent magnet synchronous motor offers 165 kilowatt (kW) of power, equivalent to more than 220 horsepower, and the excavator comes with a 1m3 bucket.
The electronically controlled hydraulic system with the 922FE also provides pure electric drive for easy control.
Around the world – including Australia – there are more than 6000 electric wheel loaders operating in the field.
The small, 60kW 820TE offers a quiet, energy-saving and environmentally friendly solution. It can store 70.5kWh
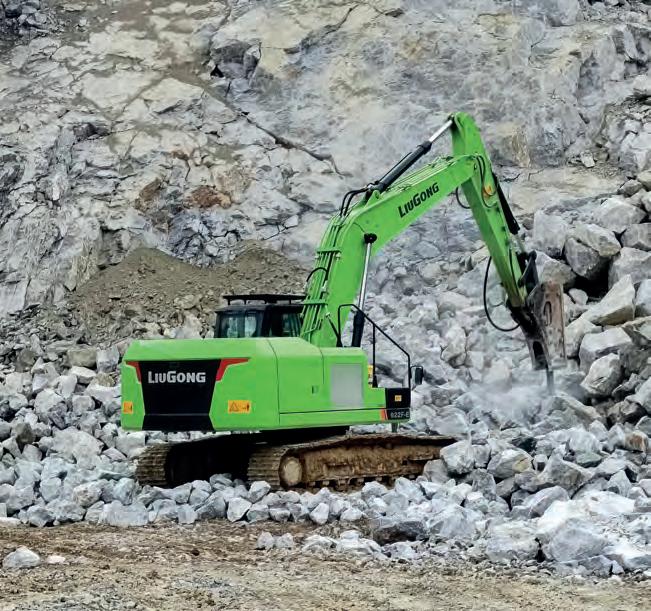
Worldwide testing with the 856HE demonstrated it was able to work up to 14 hours a shift before requiring recharge, proving more than adequate for customer needs,
Lipman said the electric transmissions improve transmission efficiency and reduce noise for smooth shifting, while operators also enjoy a higher comfort level in the machines compared with a constantly running diesel engine.
Electric power delivers a quieter operating environment with reduced vibrations, creating a less stressful working atmosphere for operators. The elimination of exhaust fumes also improves overall air quality, enhancing operator health and well-being.
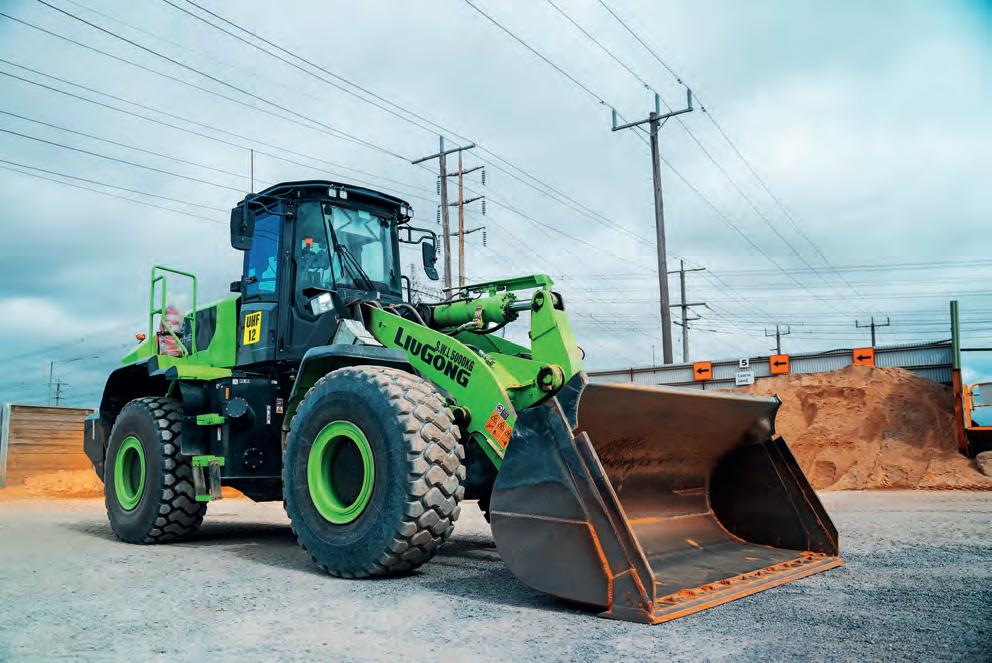
include quarries, batching plants, manufacturing and corporate offices.
Holcim operations manager for Gippsland East, Michael (Mick) Radford, said the company was committed to decarbonising its operations on the journey towards net-zero emissions.
“The use of zero-emission vehicles like the LiuGong wheel loader aligns with our roadmap, bringing us closer to achieving our goals,” he said.
And there were other features of the 856HE which impressed.
“It performed better than we all expected,” Radford said. “The loader could work long hours between charges and could keep up with the production, which meant it didn’t have to stop in the middle of the day to charge up. That means the charging time is less, so the cost is less.
“Electric machines, unlike diesel ones, also only need to be serviced every thousand hours, so the maintenance cost is much lower. And you haven’t got things like oil filter changes and labour time to worry about.”
Radford was also pleased with the design that enables hydraulics to be programmed via software to make them harsher or softer.
“So we can make adjustments like the speed of the machine,” he said.
Radford was also pleased with the service aspect of LiuGong.
“When we first bought the LiuGong equipment, the team spent a lot of time with us checking that all was good and coping with any problems that arose,” he said. “After a couple of months, you’d think that this level of service would fade away, but not so … I’d still be getting phone calls every couple of weeks checking on any issues. The level of support is outstanding.”
LiuGong’s 24.1t electric 922FE excavator can store 423 kilowatt-hours and the machine provides digging breakout force of 105 kilonewtons.
Holcim, a specialist in building materials, has trialled a wheel loader and acknowledged it has performed better than expected.
Partnership drives success for Jumbo Bins and Onetrak
JUMBO is a family-owned local waste management business that offers a diverse selection of skip bins, hook bins, site bins, portable toilets and similar equipment for hire throughout the Greater Brisbane area and the Sunshine Coast. Its close-knit team is dedicated to delivering a friendly and competitive service to both individuals and businesses. Jumbo’s bins are available in various sizes and are suitable for a range of applications.
Moreton Bay Recycling is also part of the Jumbo Group, a concrete disposal and recycling facility located in Narangba, north of Brisbane.
It accepts clean concrete waste generated from construction and demolition projects and processes it on-site to produce high-quality recycled concrete products available for pickup or delivery.
To enhance the recycling capabilities at Jumbo, the company is in the process of establishing a resource recovery facility that will sort waste materials for further recycling.
This facility will feature the new Anaconda scalping screen, which will be used to screen construction and demolition waste.
The Anaconda DF410 has been paired with two Onetrak rental machines: the Hidromek HMK640 wheel loader and the HMK145 excavator.
Jumbo is already familiar with Anaconda through its partnership with Moreton Bay Recycling, as the recycling company currently owns an Anaconda stacker. This familiarity extends to the Onetrak team, who provide service and support. The territory manager frequently visits to check on any additional business needs.
When asked how they first connected with Onetrak, a spokesperson said, “We have previously requested quotes from various staff, including for the Fuchs Material Handlers, known as one of the top brands in the market, which we will certainly consider in the future, when ready.”
The decision to collaborate with Onetrak and Anaconda was straightforward due to their established relationships. When Jumbo chose to incorporate a scalping screen into its fleet, it explored several options. It was operating on a tight budget and needed a compact machine to fit onsite posed challenges.
Ultimately, the company found
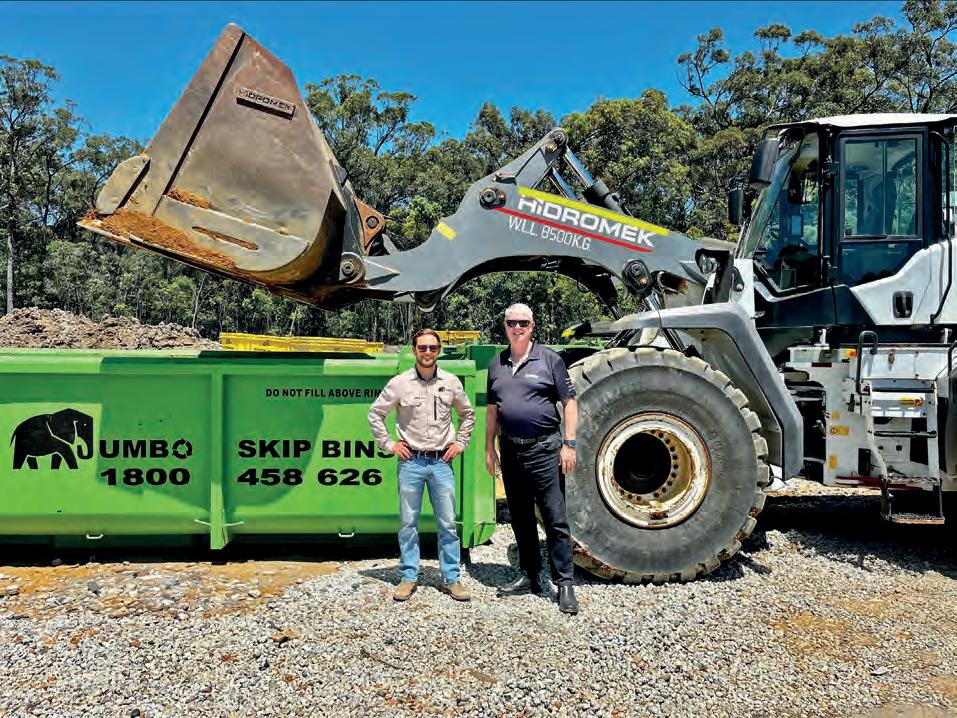
no competitor that could meet its specifications, which included needing an overband magnet as part of the unit. The team at Jumbo has provided positive feedback about the Anaconda machine.
Chad Burnham, Jumbo’s recycling supervisor, noted that the machine runs well, and it is easy to maintain with routine maintenance such as greasing and lubricating. Initially, the magnet required repositioning on the belt, due to the size of the product. Since this issue has been resolved the machine has been running smoothly.
He also suggested adding more platforms for staff to monitor the belts, which Onetrak will relay back to the factory.
Ian Brooks, Jumbo’s fleet manager,
reports that this machine is doing the job it was built to do.
He hasn’t had much time to have a thorough look over the machine as yet, but it appears to be well built.
He also mentioned that Trent Gaiero, the field service technician at Onetrak, has been helpful with responding to technical questions, and he has been training them on the machines’ functionality.
The team are also impressed with Hidromek. They have experience with various brands and appreciate how the Hidromek provides the fine motor control needed when using the grab attachment for picking up debris, which allows for precise handling like an extension of their own hand. As for maintenance,
since everything is still relatively new, it has been straightforward with no issues. The equipment is robust and requires minimal upkeep, following a simple maintenance schedule.
Shane Gatehouse, the recycling operator at Jumbo, brings more than 20 years of expertise in operating this machine for sorting construction and demolition (C&D) waste. He states, “It’s the best machine I’ve ever used.”
“This machine is very well built, with solid construction,” said Brooks “The machine allows you to easily change parameters and it is very user friendly.”
Onetrak is eager to maintain its partnership with Jumbo and Moreton Bay Recycling, and they will keep delivering effective solutions.
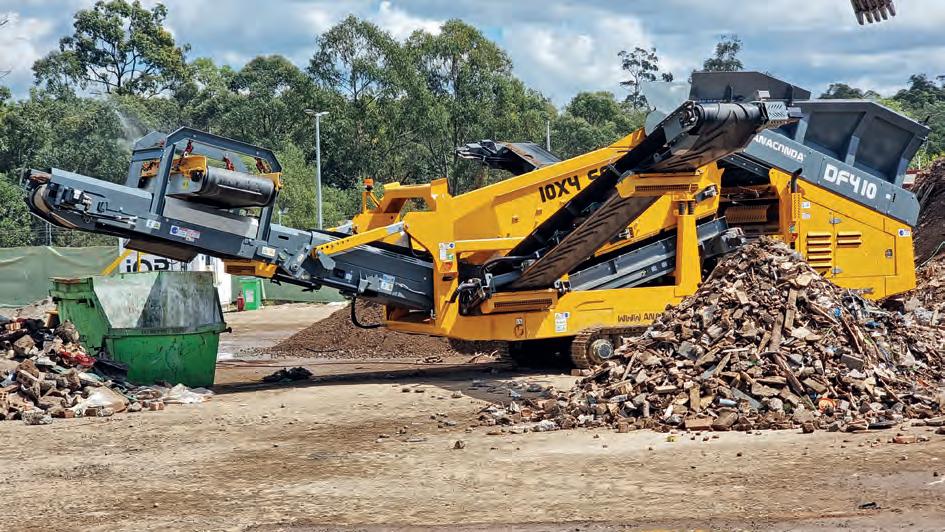
Anaconda machines are easy to maintain.
The Anaconda work well with Onetrak’s rental machines. Images: Onetrak
Specialised equipment makes light work of OTR tyres

are troublesome. However, some are more difficult than others. There’s an organic focus to streams like FOGO and the (non-treated) wood content of C&D waste, whereby environmentally friendly solutions can be found. Yet, there are other streams, there are just plain ugly. Soft plastics – well, most plastics –immediately spring to mind. Another is tyres. And it is the latter that has caused many issues when it comes to disposal.
One of the key prerequisites to making sure tyres are recycled, reused or disposed of correctly, is making sure they can be broken down properly. This is especially true for off-road tyres (OTR), even more so with those involved in industries like mining. Some of the tyres are huge – they can weigh hundreds of kgs and be anywhere from 1.5 metres to 4 metres high.
Eldan Recycling is a Danish-based company that offers specialised equipment that can help break down tyres so they can be processed properly. Carsten Nielsen is the company’s Pacific area sales manager, who has been part of a recent process to help an Australian-based customer meet its needs when it comes to breaking down these huge tyres.
are talking about 100- to 150-kilo pieces. After the Italian company has done the pre-cutting, our equipment does the chopping down into even smaller pieces.”
Nielsen said that Eldan Recycling equipment is currently being used as several lines running in New South Wales, another in WA, and two-and-ahalf lines running in Melbourne. The key, he said, is to make sure that the tyre waste is small enough to be used and resold, and in some cases, exported as TDF (tyre derived fuel).
“It can only be 150 mm or less because you can’t export bigger than 150 mm. That is illegal,” he said.
As wells as the rubber being used as TDF, there is another product in a tyre that can have high value depending on how it is extracted – the steel.
“Steel is a quite valuable product, because you can get anywhere between $200 to $300 a tonne if it’s cleaned correctly,” said Nielsen. “With our system the purity of the steel is up about 98 per cent. With other systems you might get 90 to 92 per cent purity, maybe even
How does the system work in practical terms? When a tyre is initially processed, the steel isn’t extracted separately; the pre chopping part of the system cuts it up with the rest of the tyre. Then a device called a rasper cuts it down to a certain size. When the tyres are cut, it has the effect of liberating the steel from the rubber.
“The steel might have a little bit of rubber attached to it when it comes out of the raspers,” said Nielsen.
“For example, let’s assume we have a 20 mm screen in the rasper –the material falls through; some of the rubber comes out with the steel attached, and some comes out clean and will be picked up by a magnet next to a screener where you are bouncing the rubber and the steel.”
He said that any steel that is free of rubber will fall through a screen and will go out on a vibratory outlet, and there is also have an air stream going up to remove the textile, which is another component of the tyre. The rest is a mixture of rubber and steel.
the magnet and the steel. So, you go to a secondary drum magnet where the steel is airborne because of the magnetic field. The rubber will fall down in between those two magnets.”
It is a combination of the screening, the blower for the textiles, and the double drum magnet for the steel that makes it so clean. However, once the initial action is completed, on the top layer of the screener there will still be some rubber and steel, which means it is still not clean enough. The product is then put back into the rasper to have one more rerun.
“You’re not throwing away any rubber, and you have a clean steel,” said Carsten.
Fit for purpose
Nielsen also points out that Eldan Recycling is hands on in all aspects of building a line that fits the purpose of its clients.
“We build everything,” he said. “Almost all of it is being designed and built in-house. With that being said, we are not producing the conveyors and
Eldan Recycling’s equipment is currently being used as several lines running throughout Australia. Images: Eldan Recycling
“Eldan
Recycling offers a lot of quality stuff on the line. We have machines I installed in Australia almost 20 years ago that are still running strong, even after the line had to be relocated to another factory when the company moved”
the small stuff. We buy that from a sub supplier, who has been supplying us with belt conveyors for the past 20 years.”
The new WA facility was commissioned in November, and it has since produced its first 600 kgs of rubber granules. Eldan Recycling worked with the client to make sure everything was in place. Collaboration was the key, as there were several issues that needed to be taken into consideration.
“What is going to be the best building to get for the equipment?” said Nielsen. “It wasn’t a large footprint, so we had to ask ourselves, ‘Can we squeeze it all in? Can we reduce the footprint for the Eldan Recycling machines?’ Also, ‘Where was the best area for storing the tyres before they are processed?’”
This last part was important because all state EPAs have strict requirements about how many tyres can be stored, where, and for how long.
Nielsen said that the decision also had to be made as to how far down the tyres were shredded.
“Do we produce granules, TDF, or do we produce powder?” said Nielsen. “And luckily for Elden, they wanted to do it all including going all the way down to powder. The powder is used for mainly for road, construction. We’re doing everything.”
Some of the tyres can weight up to four tonnes. They are initially cut up by a MT-Rex cutter, which chops the tyres into manageable sizes. They are then feed into the line that Eldan Recycling
has set up. The line can throughput about eight tonnes an hour with ODT tyres, and about 10-15 tonnes an hour with car tyres.
When it comes to back up service, Eldan Recycling monitors its gear online and the company is only a phone call away to help troubleshoot any issues. Nielsen says its service should never be underestimated.
“One of the reasons why we convinced our tyre client to buy from us is that we answer all their queries straight away,” he said. “They are working with salespeople who know their stuff. My background is up in supervisor for installs when I was way younger. Also, I’ve been working with the technical part all my life.
“Eldan Recycling offers a lot of quality stuff on the line. We have machines I installed in Australia almost 20 years ago that are still running strong, even after the line had to be relocated to another factory when the company moved.”
Finally, Nielsen said that Eldan Recycling always backs its products. This is outlined in the company’s contracts when it signs up new companies to install a line.
“When we make a contract for a line install – like we’ve done for this Australian client – we state that we can do a certain amount of tonnage,” he said. “With this purity, and a certain amount downtown for maintenance, our products get the job done.”
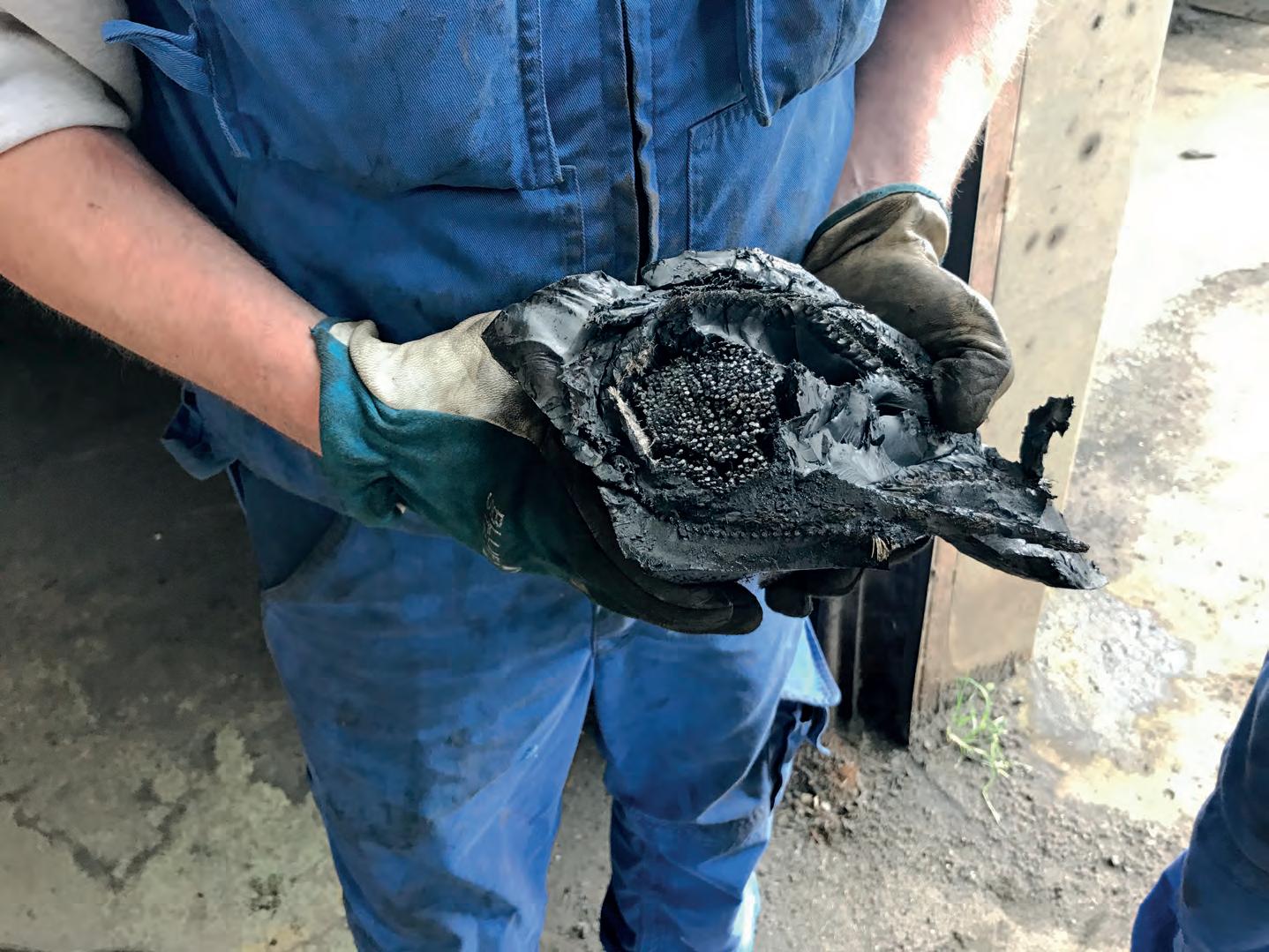
Sometimes less is more
WHEN it comes to equipment designed to cut through the rubbish, Eggersmann offers up a series of shredders, star and trommel screens, and windrow turners that can meet the needs of those processing organics, tyres, mattresses, and an array of other troublesome waste streams.
Represented in Australia by Skala Environmental, the company’s sales director, Craig Cosgrove, said that the quality of the equipment has shone through this year with good sales volume across all models, with the company gearing up for a busy 2025.
“Skala Environmental has been very successful with the new S60 Star Screen this year, with all units selling before they land in Australia,” he said. “They’ve done extremely well. Eggersmann has done a great job of
simplifying and optimising the machine design, while retaining high throughput and fuel efficiency.”
The Eggersmann mobile product line encompasses well-known brands such as Teuton, Forus, Terra Select and Backhus
Shredders
Cosgrove said the FORUS shredders are ideal for councils because they are compact and get the job done. There are many types of streams the units are capable of processing, including green waste, waste wood, solar panels, commercial and electronic waste, as well as glass and household waste.
There are two units in the series – the F25 and F38 – which have a throughput of 40 tonnes per hour, and 80 tonnes per hour respectively. They
come in track, hook lift, and mobile versions.
There are a myriad of features, but some of the highlights include easy maintenance due to large doors that give access to the engine; an over-band magnet that can be raised and lowered hydraulically; multifunctional rotor tools; individually adjustable shafts; and intuitive control. These features allow users to customise a machine to their individual needs. They also have an array of optional features, such as a hopper extension, as well as being able to adjust the grain size of the throughput.
The TEUTON shredder range is for those looking for higher throughputs. The Z50 and Z60 have throughputs of 95 tonnes and 120 tonnes, respectively. They can process the same types of
materials as the FORUS series, but in larger quantities. They have an array of features, including a screen basket for precise particle sizing; a reversing rotor in case of foreign objects; the ability to adjust the cutting gap without having to use tools; and various rotor and counter tooth arrangements for different applications.
Screeners
And if you operate a good shredder, you’ll also need a good screener. Eggersmann has two screener ranges – TERRA SELECT and STAR SELECT. The TERRA range has two versions – the T 50 and T 60. The T 50 has a throughput of up to 150m³ an hour, while the T 60 can process up to 200m³ an hour.
Cosgrove said the T 50 is up to 200mm larger in diameter than the
Both machines are capable of processing shredded C&I and C&D waste, compost, soil, green household waste, plastic, and glass products.
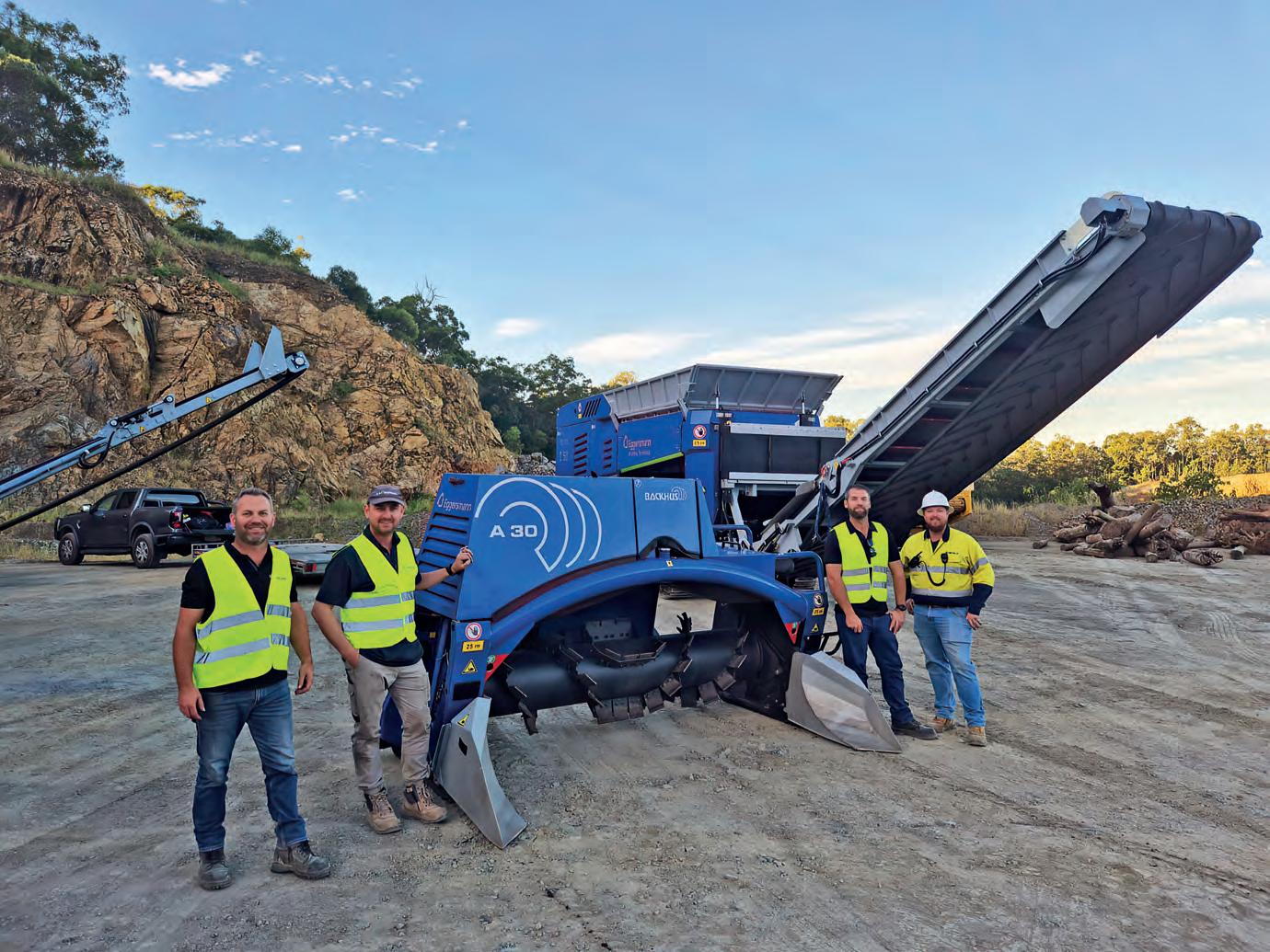
The Skala team with an A30 windrow turner. Images: Skala
market average in the five-metre class, which increases the screening capacity by 20 per cent. This is suitable for companies that have a lot of products that needs processing in a short amount of time.
One of the key features of the T 60 is that it offers precise separation efficiency. Cosgrove also points out that the machine’s design means changing out the trommel screen is quick and easy.
Both machines are capable of processing shredded C&I and C&D waste, compost, soil, green household waste, plastic, and glass products.
The STAR SELECT mobile unit is the elite unit of the screener family.
It has a throughput of 300m³ an hour, separating into 3 fractions, offering precise separation.
The newly developed star screen system means it can operate with difficult substances including claybased soils and grate ash.
Turners
Finally, there is the BACKHUS range of windrow turners. These machines come in various configurations, from the BACKHUS A 30 through to the A 75 machine. And if users need more oomph, there is the BACKHUS CON range that goes up to a 10m-wide machine. The number designation of each unit indicates the size of the windrow widths the machine can apply. For example, the A 30 can operate in windrow widths of 3m, while the A 75 can operate in widths of 7.5m.
Depending on y machines vary in the amount of turning capacity and height they can work to when out in the field. For small work areas, the BACKHUS A30 can turn out 700m³ an hour at heights of up to 1.3m. Meanwhile, the BACKHUS CON 100 has a capacity to turn 7200m³ at heights of up to 3.2m.
Additionally, if you are in an enclosed building, Eggersmann has designed the LANE TURNER LT, which has a turning capacity of up to 2,000m³. It can process MSW, biowaste, digestate, EFB and sewage sludge to name a few.
Cosgrove said the simplicity of operation with these machines cannot be underestimated. As well as being rugged, they are a work horse when it comes to processing.
“With some of the current equipment available, it gets to the point where there’s so many smarts going on in the machine, that when it breaks down it can be expensive and cause complications,” he said. “With Eggersmann kit, they’ve got the smarts, but it’s in a simplistic package – you don’t need 10 sensors when one will do.”
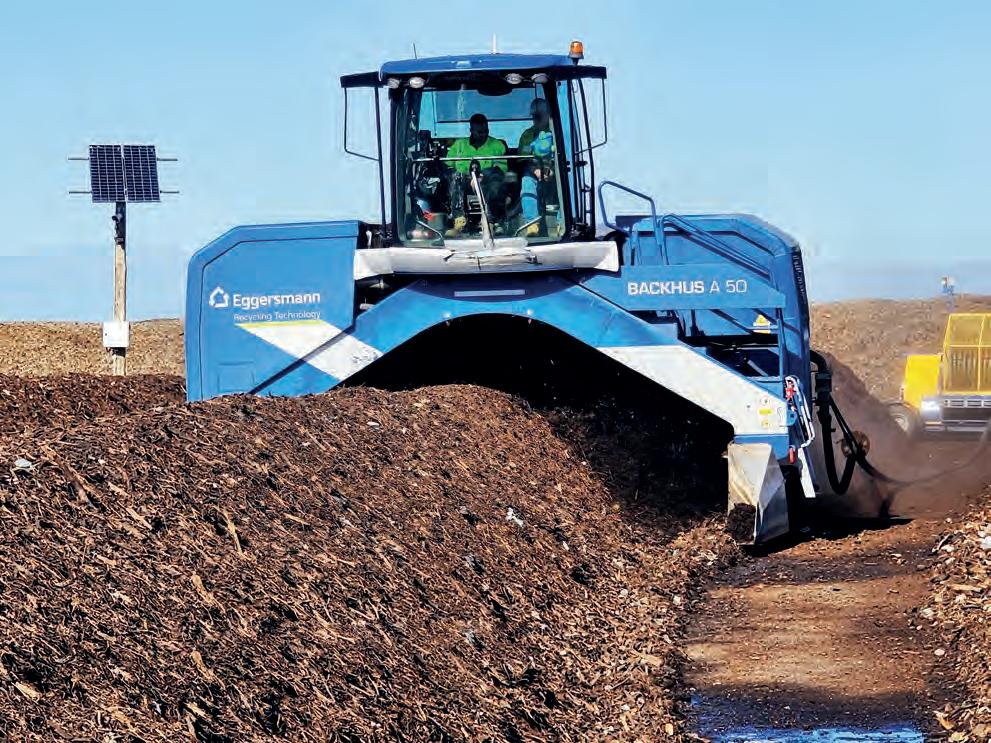
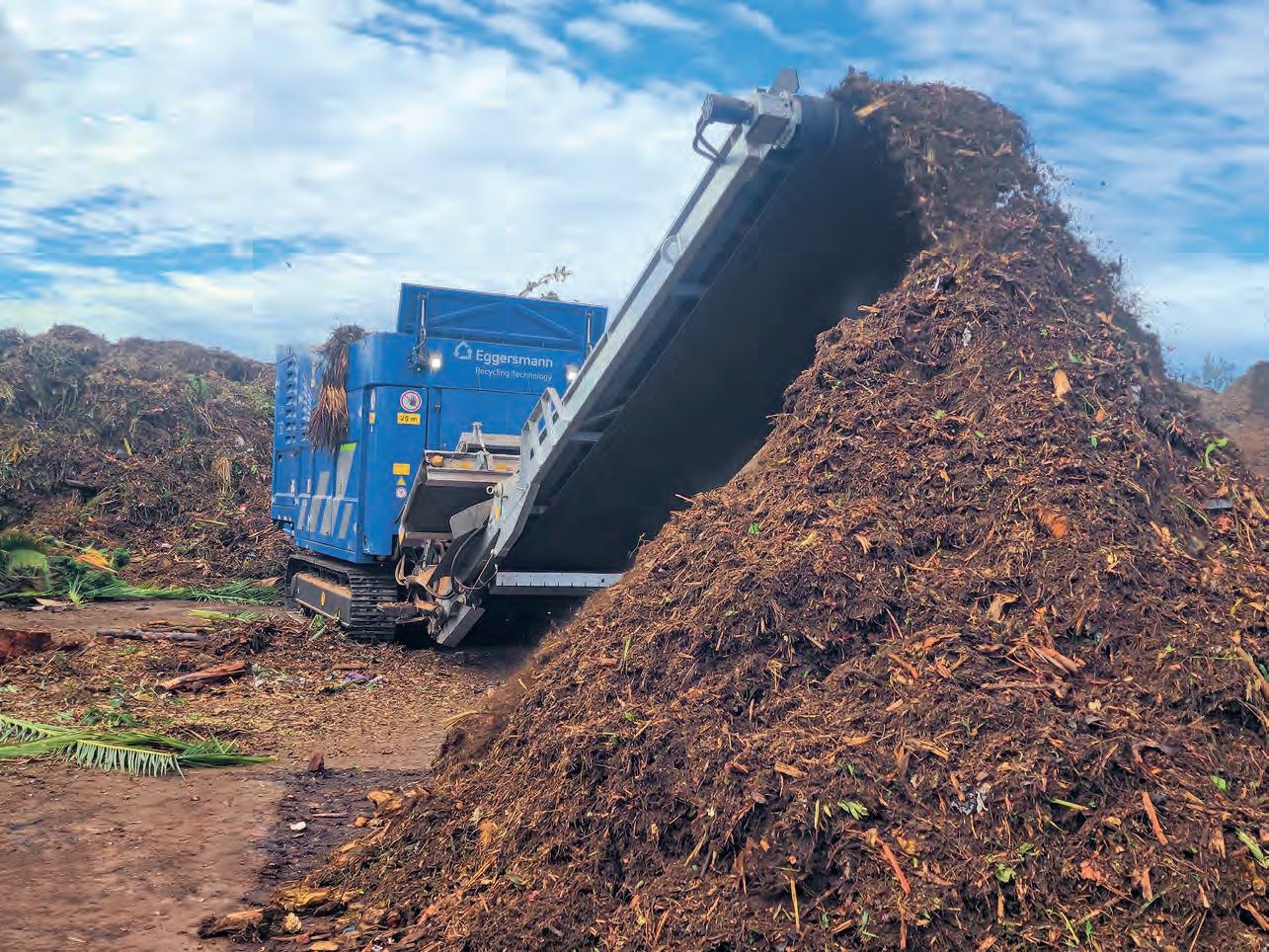
The range of Eggersmann shredders have high throughput with a range of waste streams.
Eggersmann machines like this windrow turner are the workhorses of the waste and resource recovery industry.
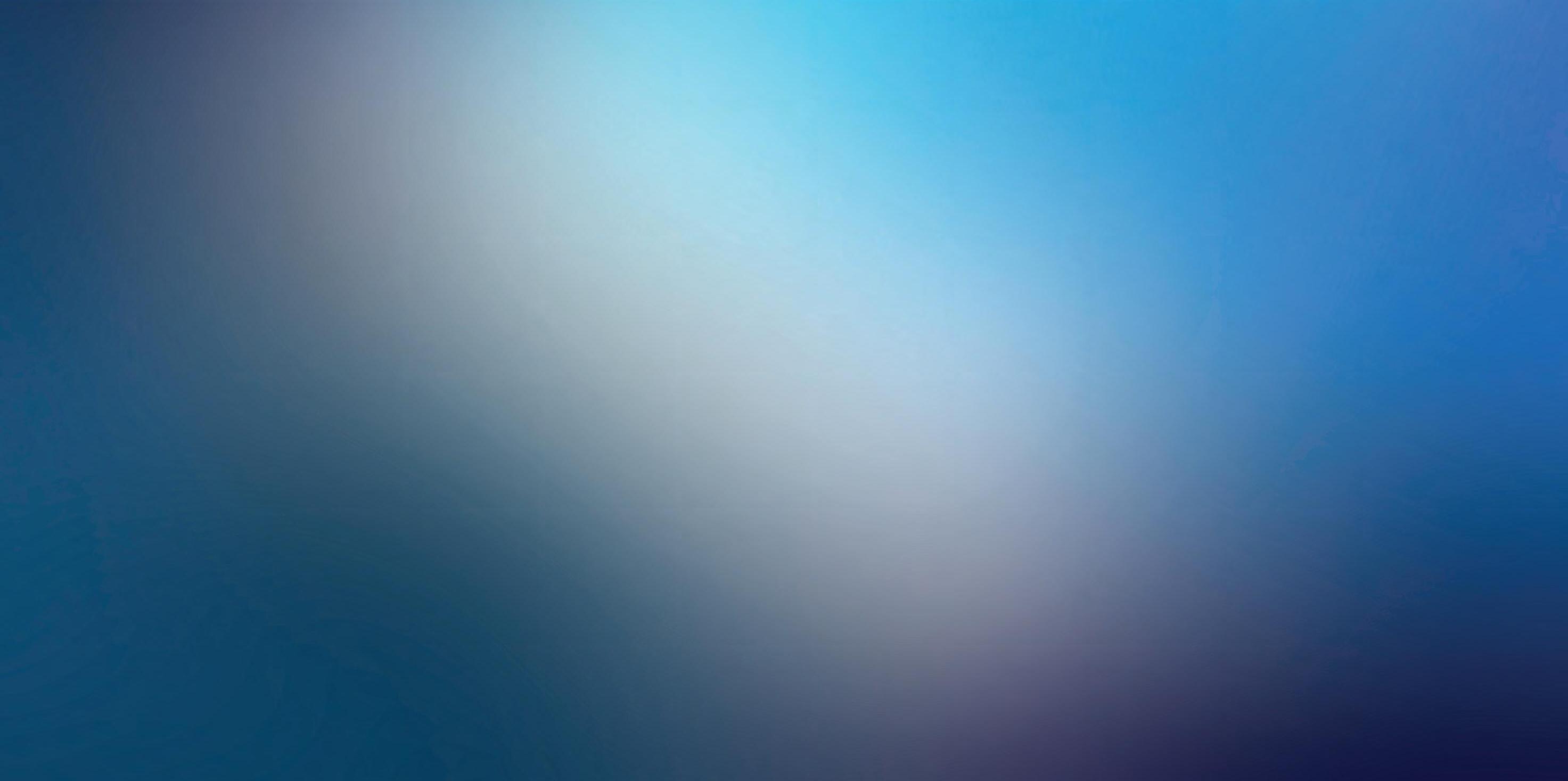
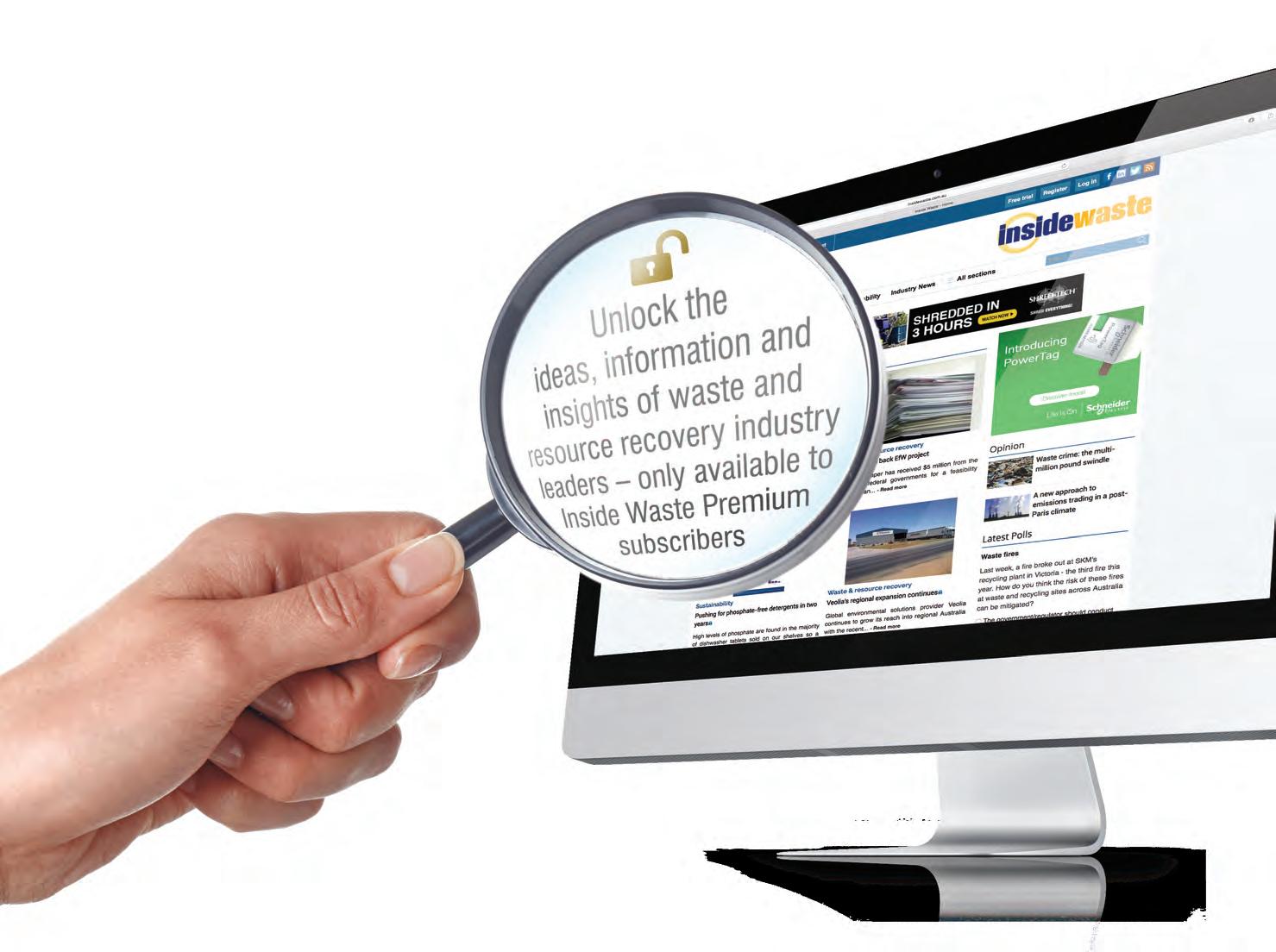
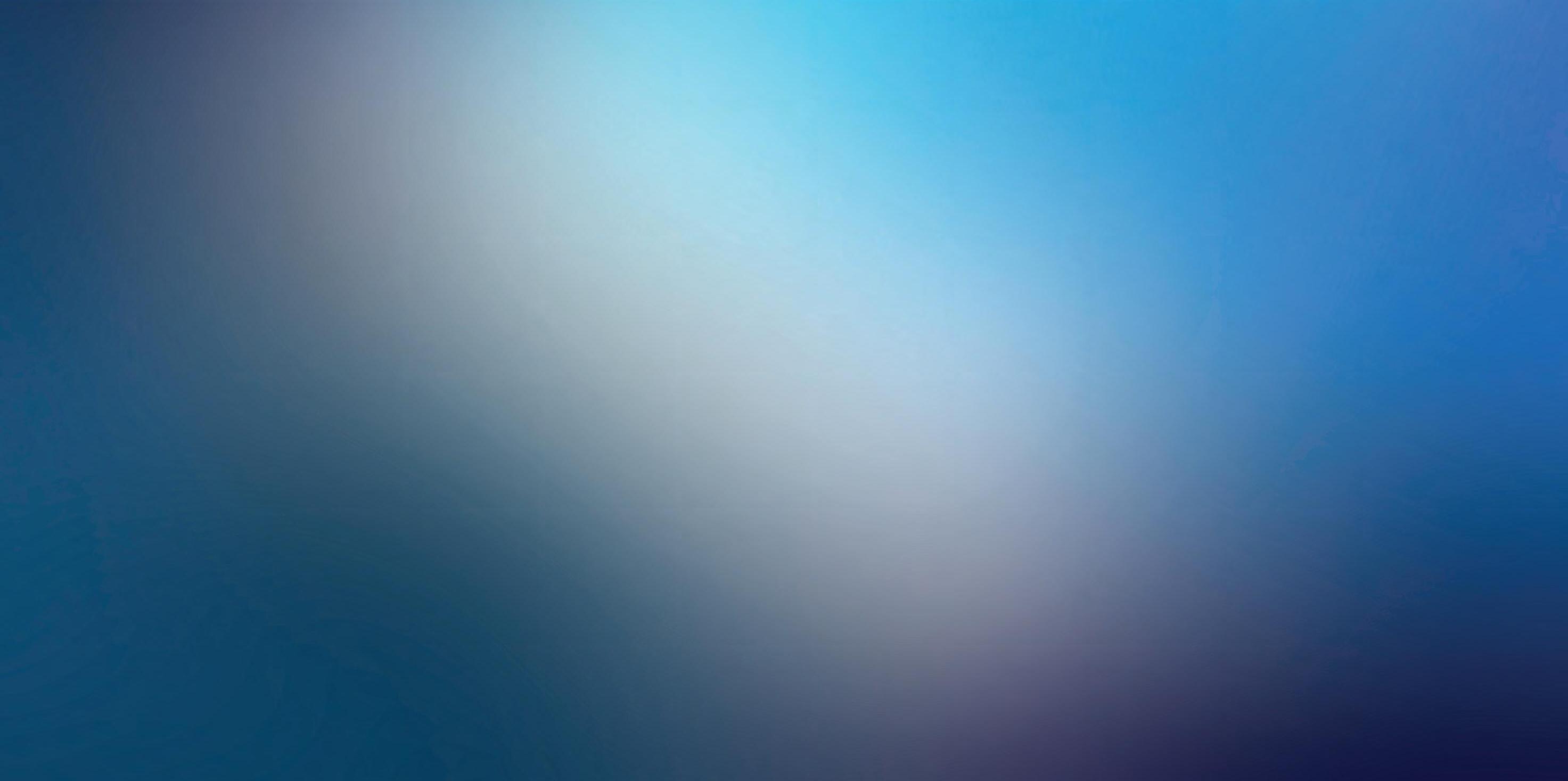
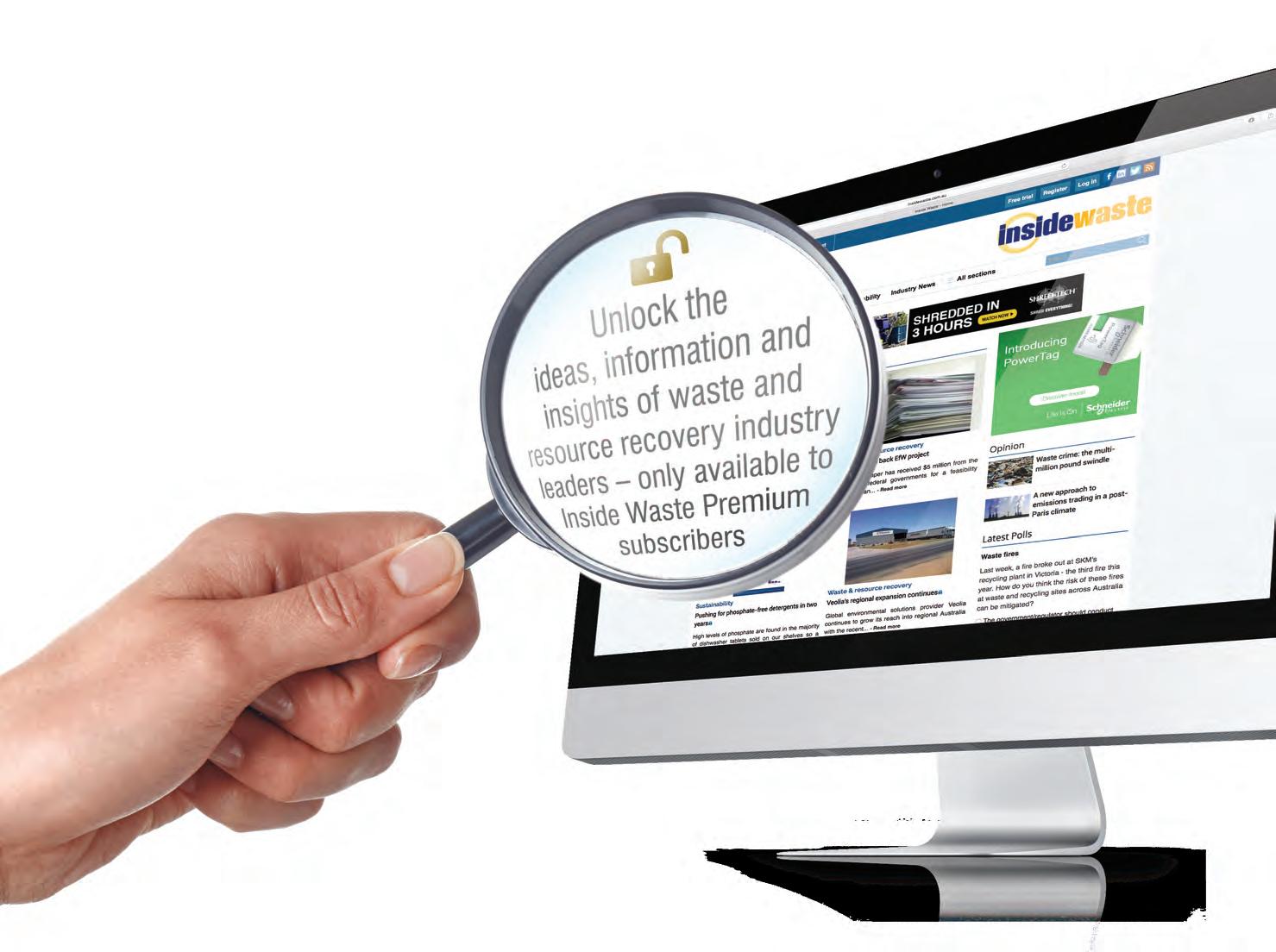
The right shredder for your waste stream
SIZING and recycling waste materials requires unique equipment depending on the type of waste stream, meaning processing facility managers must carefully choose the right machine for the job.
Correctly sizing a waste stream means analysing the type and quantity of waste, as well as the rate of processing required.
When it comes to sizing wood waste, construction and demolition (C&D) material, and municipal solid waste (MSW), the two most common equipment types are low-speed shredders and high-speed grinders.
It’s important for waste facilities to know which materials work best with each machine so they can process waste more efficiently, enabling effective waste management.
One-stop-shop
As a provider of industry equipment, Vermeer supplies both shredders and grinders for waste processing.
Vermeer has been in the recycling and forestry equipment spaces for 30 years. While it was initially known for its highspeed tub and horizontal grinders, the waste processing market has changed and today Vermeer offers low-speed tools as well, providing a comprehensive product offerings for the waste industry.
Several factors influence whether a low-speed shredder or high-speed grinder is best suited to a particular operation, such as the type, size and shape of the material to be processed and the desired end product.
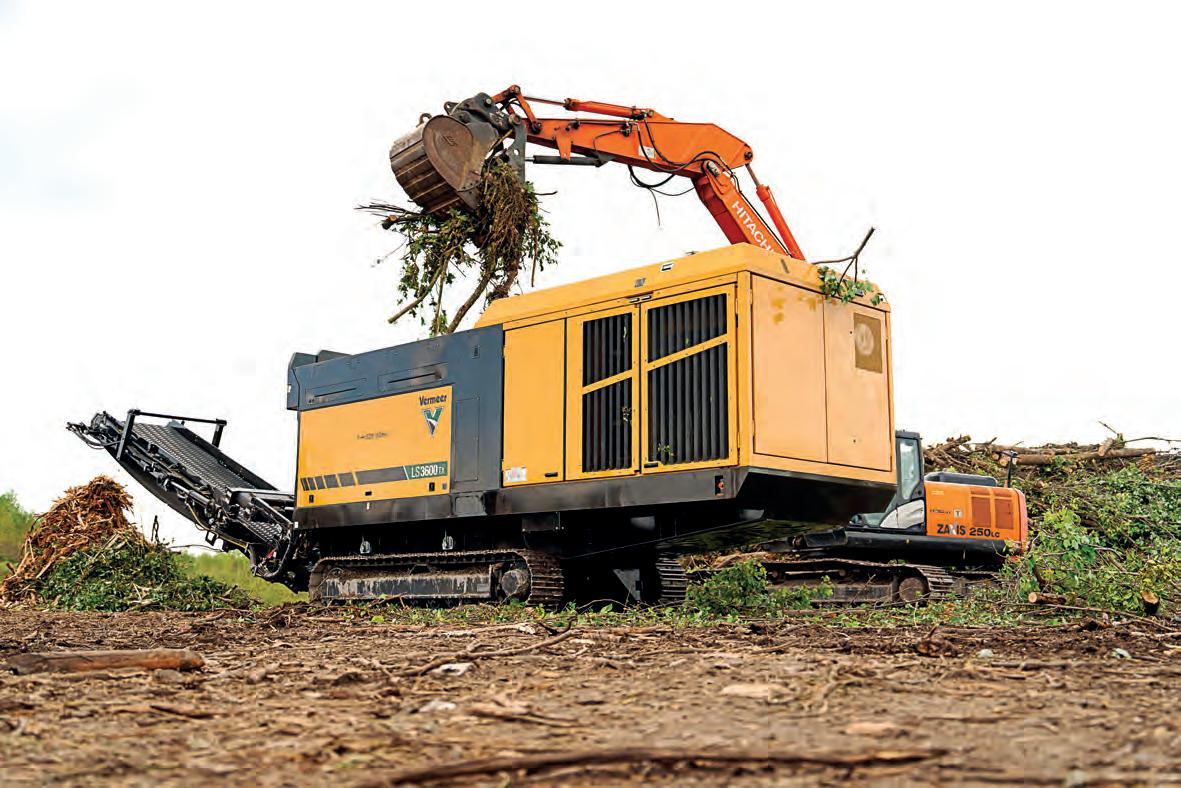
High-speed grinder
High-speed grinders typically use fastspinning hammer mills, from 800rpm to 1,300rpm, for quicker material processing compared to their low-speed counterparts.
This makes them suitable for facilities where contamination isn’t a factor and throughput is a high priority. These grinders provide consistency and control
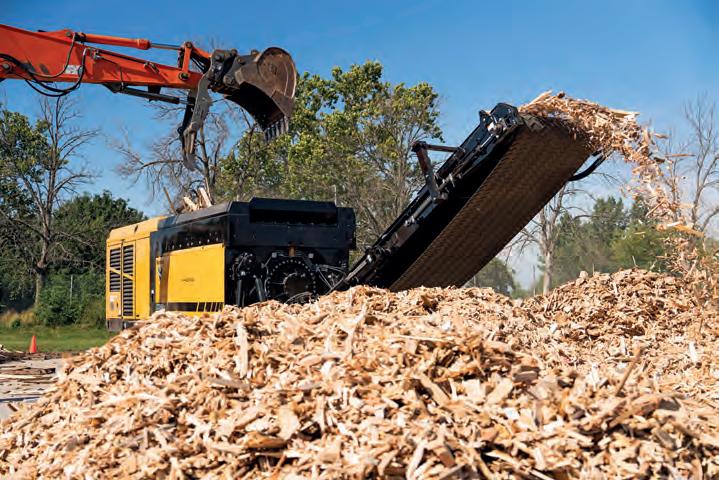
over the final product’s size, thanks to adjustable cutter tips and screen sizes.
Grinders are best for turning organic waste like trees, plants and yard materials into products such as compost, mulch and biofuel.
Low-speed shredder
Low-speed shredders are versatile and are often used to process contaminated waste that may cause damage to a highspeed grinder.
Thanks to their low rotor speed and high torque, shredders can manage a range of difficult waste streams including C&D waste, contaminated green waste, MSW, as well as storm and land clearing debris.
Shredders can be equipped with crossband magnets to better process waste streams contaminated with ferrous metals. Not only does this allow for managing a wider range of materials, but it can also potentially unlock additional revenue streams.
Low speed, high power
The LS3600TX low-speed shredder is the most recent addition to Vermeer’s line-up of waste processing equipment. This machine is designed to be a
productive, feature-rich and versatile option, incorporating cutting-edge technology that efficiently processes contaminated waste streams and helps safeguard critical machine components.
Featuring a single-shaft welded rotor and adjustable comb, the LS3600TX shredder is powered by a 456hp (340kW) CAT Tier 4 Final/Stage V engine.
It also comes with a full-function remote control mode, allowing operators to adjust the machine and access data from a distance. The shredder also has a tracked undercarriage, which enables operators to reposition and manoeuvre it around a jobsite.
The LS3600TX is equipped with a 3m-long rotor and a mechanical driveline designed to optimise horsepower transfer. To protect the driveline system against unshreddable objects, the shredder includes a reversible mechanical transmission with an external torque limiter that will automatically disengage the drive when maximum torque is reached.
The LS3600TX is the culmination of Vermeer’s 30 years of experience and innovation in the recycling and forestry sector.
The LS3600TX low-speed shredder efficiently processes contaminated waste streams.
The LS3600TX shredder is powered by a 456hp (340kW) CAT Tier 4 Final/Stage V engine. Images: RDO
Building Australia’s Future – together.
Over the next 10 years, the Australian Government is investing more than $120 billion in infrastructure development. Will you be a part of it?
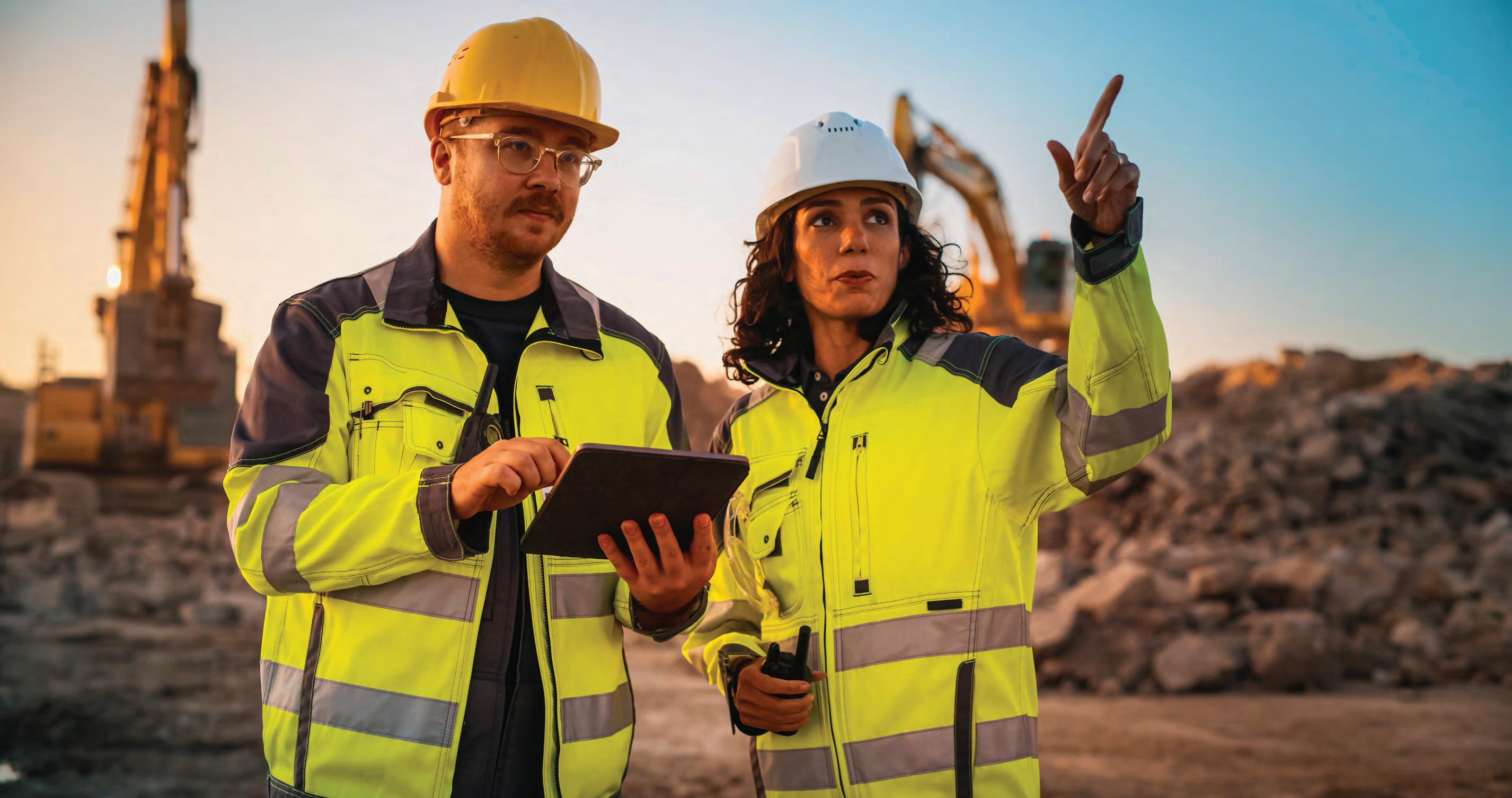


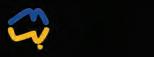


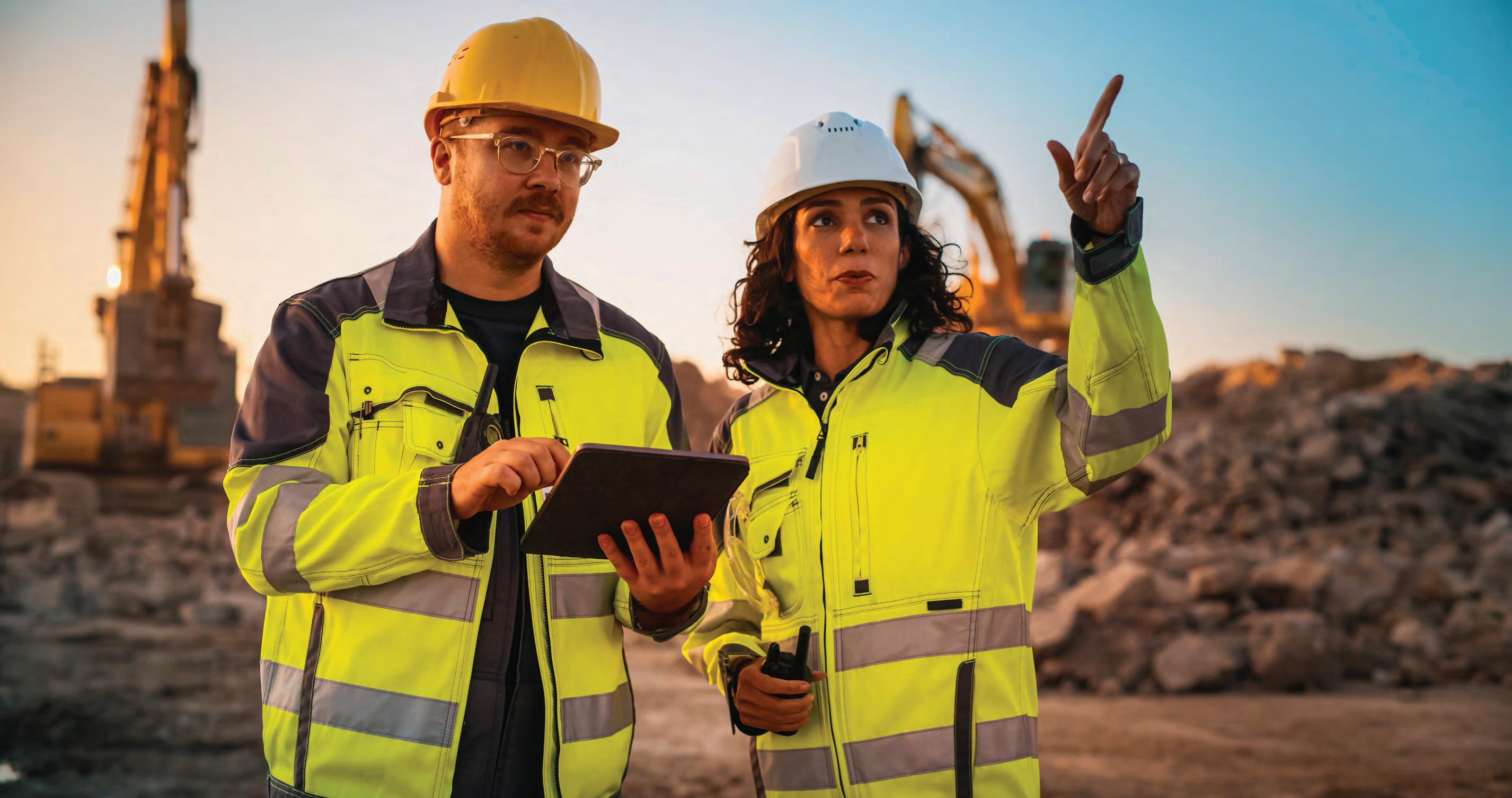
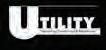
The role of floor topping in waste disposal sites
THROUGHOUT Australia, waste disposal sites are critical infrastructure for managing the byproducts of human activity. These facilities must endure harsh conditions, including heavy machinery traffic and exposure to various chemicals and leachate. One of the key elements in maintaining the safety, functionality and integrity of the concrete substrate on these sites is the
use of purpose-designed floor toppings. Floor toppings provide a protective layer that enhances durability, reduces maintenance costs, and extends the lifespan of the asset.
It is essential to understand the specific requirements and uses of each facility to choose the appropriate floor topping. Factors such as the type of waste, traffic load, and chemical
exposure must be considered. Australasian Specialty Coatings (ASC) is a flooring and protective coatings company that specialises in servicing the waste and water industry. It is often asked to assess the condition of the tipping floor sheds whereby the reinforced steel has started to pertrude from years of wear and tear. As is common with putrescible waste tipping
floors, the top layer of the concrete floor is often eroded from a mixture of heavy machinery movements and the corrosive effect from leachate reacting with the concrete slab.
ASC’s clients range from large multinational waste companies to municipal councils and private businesses and often have 24-hour, seven-day-aweek collections and tipping.
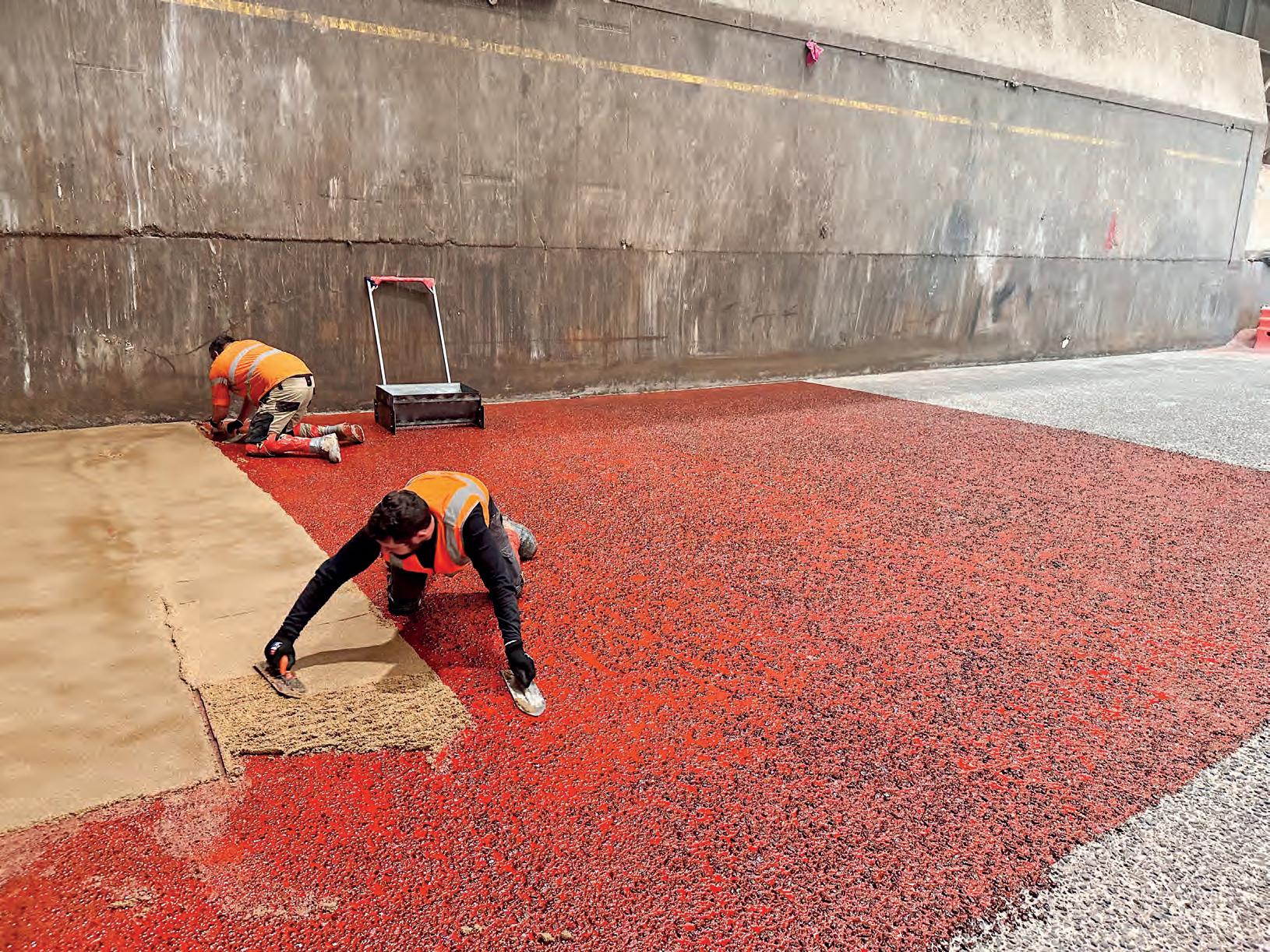
Once the surface has been correctly prepared, the next step is to treat cracks and spalling in the floor with resin injections.
The company understands there needs to be a fast turnaround solution that will have minimal impact on the daily operation to these critical sites in handling Australia’s constant waste stream.
Traditionally, sites have had to be closed while concrete rectification (pouring a new slab) was undertaken. The problem with that was that the new concrete had to cure up to 28 days and was still not chemically resistant to leachate.
ASC has designed a chemicalresistant wear coat that can be installed over a weekend (up to 500 sqm), which means a site does not have to close down. With planning between ASC and the client, normal operations can continue while rectification work is completed.
After the relevant paperwork and safety briefings, the job usually starts with the worksite being excluded with bollards and the slab being washed down then dried overnight with fans. Early the next morning ASC starts the preparation and installation process by first abrasive blasting the slab to remove any trapped waste, and provide the correct key for the upcoming surface installation.
Once the surface has been correctly prepared, the next step is to treat cracks and spalling in the floor with resin injections to seal and bridge the weakest points.
The next stage is to coat the area with an acid-resistant primer, which can be coloured so in the future wear patterns are clearly visible and repaired accordingly. Once the primer has started its chemical reaction, ASC then starts to place the TUFF COAT screed over the surface. This can be varied in thickness but typical floors with 200,000 tonnes per year require approximately 20mm. The screed coat is left to cure for more than eight hours over night. The next day a skim coat is placed over the surface and aggregates laid in the skim coat to assist the wheels of the machinery.
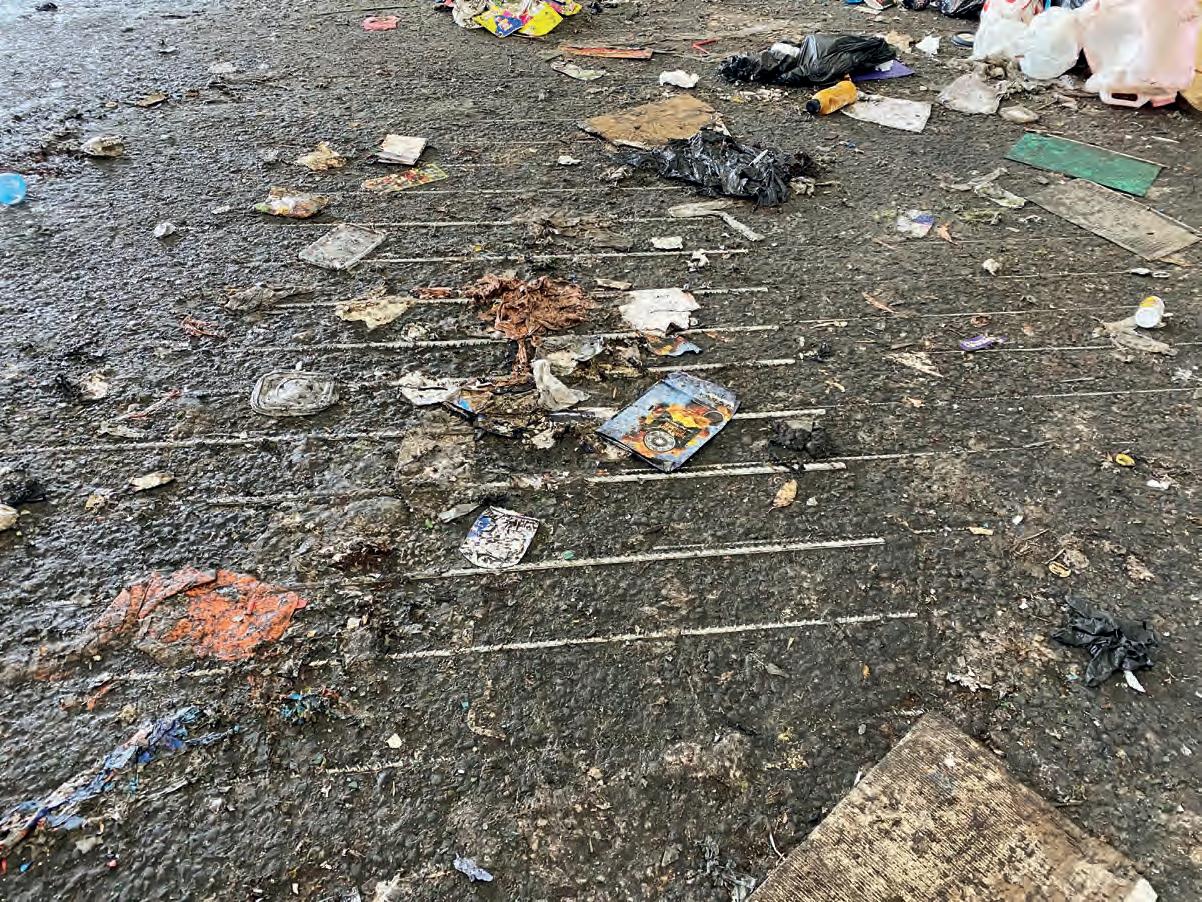
The area is completely chemically cured and is ready to go back into action. The process has minimal down time and delivers a brand-new leachate-resistant floor that allows client to carry on with their operations with minimal fuss.
ASC’s managing director Louis Longhi explains that floor toppings are an essential component in the maintenance and longevity of waste disposal sites by providing a barrier between the concrete substrate and protecting against abrasion and chemical attacks.
“We build long term relationships with our clients to understand their individual sites and operations ensuring once the initial floor is laid,” he said. “We monitor the condition for ongoing wear and tear.”
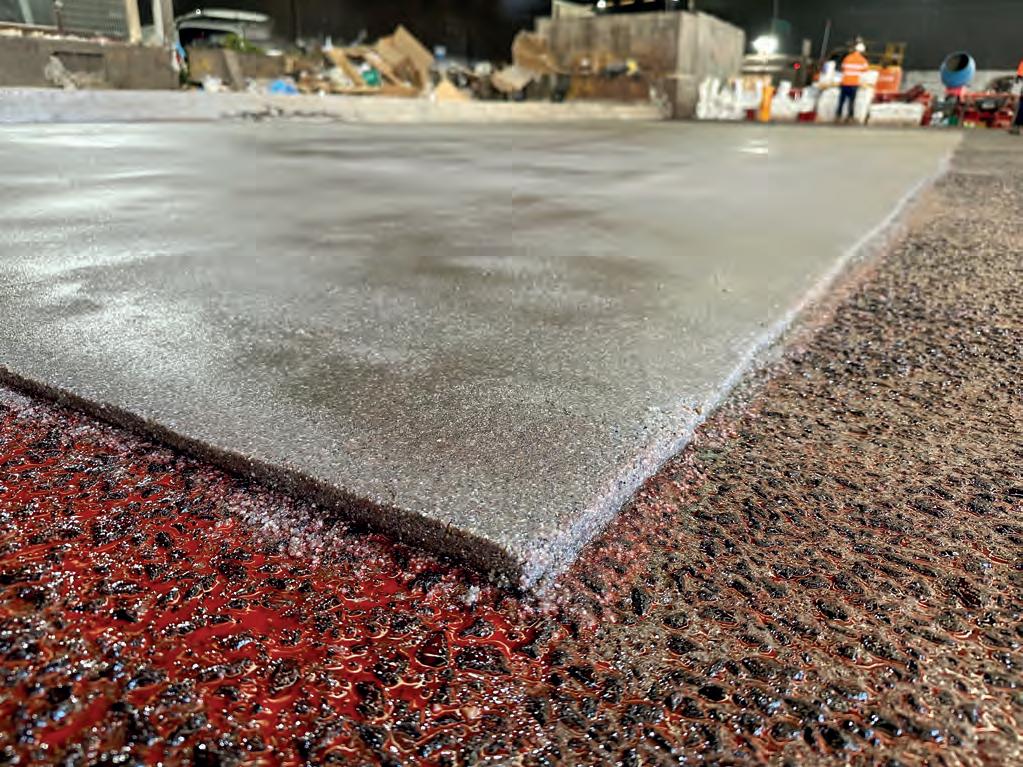
The new leachate-resistant floor allows clients to carry on with their operations with minimal fuss.
Images: Australasian Specialty Coatings
The top layer of concrete on putrescible waste tipping floors is often eroded from the corrosive effect of leachate reacting with the concrete slab.
Clothing Reuse Export Accreditation scheme update
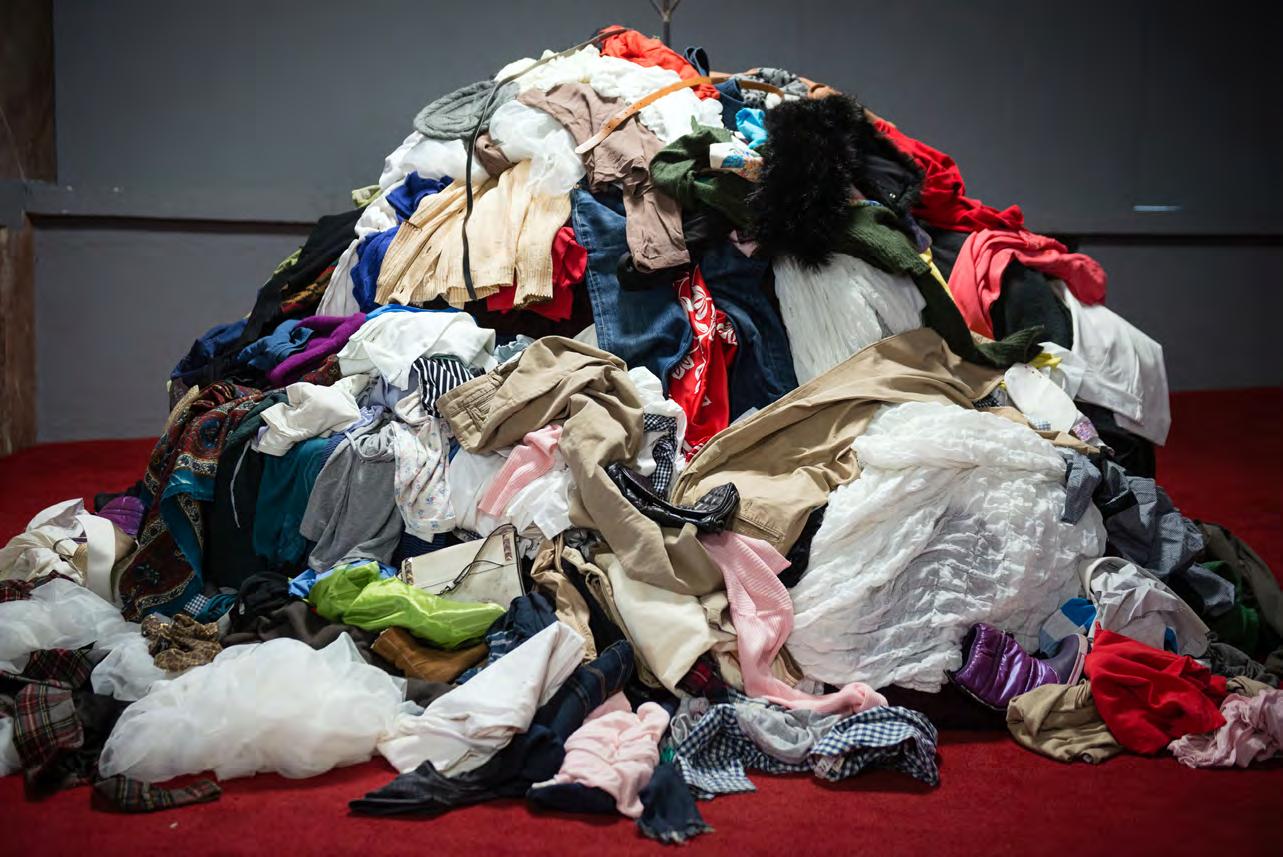
Accreditation Scheme, Australia now has data on the quality of clothing reuse exports from accredited organisations in the Charitable Reuse Australia network. This includes that 94 per cent of all clothing items exported are either reused in their original form overseas, or used as rags, cleaning cloths and/or upcycled, as well as:
• 7 2 per cent is wearable used clothing exported for resale/reuse in original form. Sorting is done either domestically onshore by op shops and/or is sorted overseas by commercial exporters on stock collected independently.
• 22 per cent is non-wearable used clothing exported for conversion into cleaning cloths, rags or upcycling. Most rags/cleaning cloths are reimported back into Australia for retail sale domestically, including at big box retailers.
• 6 per cent is gross contamination and waste that is removed and sent to disposal in Australia before export. Australian governments and consumers can be confident in the
ustralian op shops are renowned for the quality and efficacy of their domestic sorting of clothing donations, conducted by 5,200+ staff and 33,000+ FTE volunteers who catch any clothing waste domestically, to ensure it is not inadvertently exported overseas. Australia is unique, together with the UK in having a strong local charity sector to sort onshore before export. Australian op shop sorting is second to none globally with its large and effective charity sector that has been operating successfully in reuse for over 140 years, and now with 3,000+ shops.
• Of the 310,000 tonnes of clothing items donated to op shops every year, 86 per cent is used and 14 per cent is waste. That’s a total of 43,400 tonnes of clothing waste that is unusable and not able to be commercially recycled domestically, going to Australian landfill every year.
• This onshore sorting ensures Australian charitable clothing reuse exports are of the highest quality, with waste caught before
similarities with overseas exports markets, with our lighter fabrics and prints proving suitable for markets like Kenya and the Pacific, where an excess of winter garments might otherwise be wasted.
• This higher spring/summer percentage from Australian fashion ensures more exported garments are fit for purpose, and waste is reduced.
Quality clothing reuse exports continue to find active reuse markets overseas, providing affordable clothing to those with lower incomes and prioritising reuse to extend the wearable life of garments. At the same time, the trade generates environmental and social benefits both domestically and overseas.
Domestically, the trade generates around $50 million for social welfare at home with charities getting paid about 50 cents per kilo on export prices.
The trade also diverts 100,000 tonnes of wearable/usable clothing for reuse that would otherwise go to landfill in Australia.
The only reason these wearable garments can’t be sold domestically is
Overseas, it creates millions of jobs and helps alleviate poverty and encourage gender equality with many of these jobs going to women involved in resale markets and repair.
The Clothing Reuse Export Accreditation Scheme is now entering its third phase, with overseas audits and foreign end market verification planned for next year.
Extending the supply chain visibility, Tier 2 buyers will also be verified at this stage, providing an audit assessment of the material usage figures identified in the second phase.
The third phase will also include a robust Modern Slavery element including a key Worker Voice outreach, where the program will seek to engage workers directly, through its collaboration with other non-profit organisations both domestically and overseas.
Beyond that, the program is working on a rolling three-year development plan that will ensure that the Clothing Reuse Export Accreditation Scheme is the most ambitious, robust and effective one of its kind globally.
Eddy Current Separator
Eriez Ultra High-Frequency Eddy Current Separator recovers ultra-fine aluminium, copper and other nonferrous fines materials typically missed on traditional eddy current separators from ASR. The UHF Eddy’s combination of a rotor designed to produce exceptionally high gauss at the belt’s surface, with magnetic poles operating at higher rpms creates ultra-high frequency changes resulting superior separation of fine nonferrous and even bare copper wire.
Company: Eriez
Name: Jonathan Schulberg – Business Development Manager – Heavy Industry Eriez Australia
Phone Number: +61-3-8401-7400
Webpage: www.eriez.com/APAC.htm
Email: jschulberg@eriez.com

Permanent Deep Field and Electromagnetic Scrap Drums
Using our sophisticated design software and unique magnetic circuits, Eriez provides permanent and electromagnetic scrap drums with deeper magnetic fields to reclaim ferrous materials in automotive shredder residue (ASR), materials recovery facilities (MRF), municipal solid waste (MSW), scrap metal yards, wood waste, slag, incinerator bottom ash, foundry sand and minerals processing applications.
Permanent Deep Field Magnetic Drums
This design uses permanent magnets and bucking poles to project a deep magnetic field capable of removing ferrous from distances of up to 15 inches (380 mm). The permanent scrap drums are ideal for applications with limited or unstable electrical power.
Electromagnetic Scrap Drums
The All Electro Agitator type utilizes a deep field rectangular core pickup magnet to reach out and grasp the ferrous, and a second rectangular-core agitator magnet to flip or agitate the ferrous, cleaning it of contaminants such as loose mud, paper, fluff and trash. Eriez also builds a non-agitating transfer design that uses a deep field radial pickup magnet and pole shoes to convey or transfer the ferrous around the drum shell to the discharge area.
Eriez Suspended Electromagnets
Company: Eriez
Name: Jonathan Schulberg, Business Development Manager – Heavy Industry, Eriez-Australia
Phone Number: +61-3-8401-7400
Webpage: www.eriez.com/APAC.htm
Email : jschulberg@eriez.com
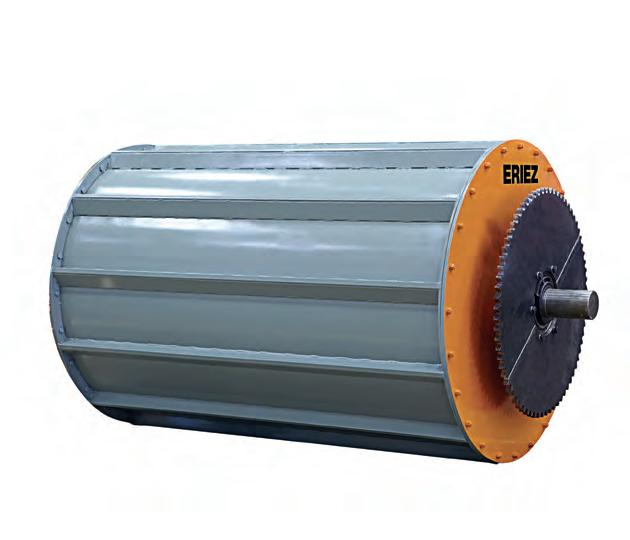
The Suspended Electromagnet provides tramp metal collection from conveyed materials. The electromagnet is typically mounted or suspended over a conveyor belt to remove large pieces of tramp metal that represent a hazard to downstream crushers, mills, pulverizers and grinders. Suspended electromagnets also remove sharp metal that can damage or tear expensive conveyor belts, especially at transfer points. Product purity is enhanced with the separation power of the suspended electromagnet.
Features & Benefits:
• Exclusive oil expansion tank prevents condensation and protects against hot spots to extend coil life
• Aluminum or copper coils use Nomex insulation and fiberglass spacers to prevent shorts
• Five-year warranty on coil assembly
• Adjustable oil expansion tank design for any installation angle is mounted with slotted brackets, allowing the user to rotate the tank so the moisture drain is always on the low side
• Lift lugs now include two side-by-side holes to allow for simultaneous hoisting and installation of the suspension gear
• 23 magnet sizes, 69 standard models and hundreds of special designs available for unique applications
• Special options, including:
- CSA approved designs for both
- Upgraded coil design for elevations greater than 3,000 feet above sea level
- High fire point coolants
- Zero speed switches
- Dust covers
- Pulley guards and controls
- Permanent extensions and monitoring devices
- Force-cooled units available for high temperature applications
Company: Eriez
Name: Jonathan Schulberg, Business Development Manager – Heavy Industry, Eriez-Australia
Phone Number: +61-3-8401-7400
Webpage: www.eriez.com/APAC.htm
Email : jschulberg@eriez.com
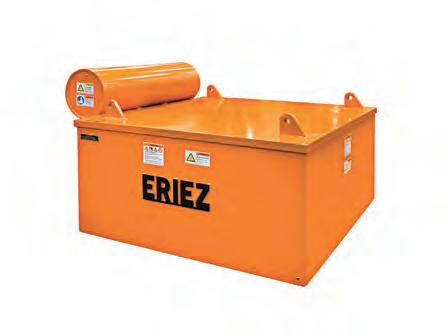
ERIEZ
Always something new to learn in the resource recovery industry
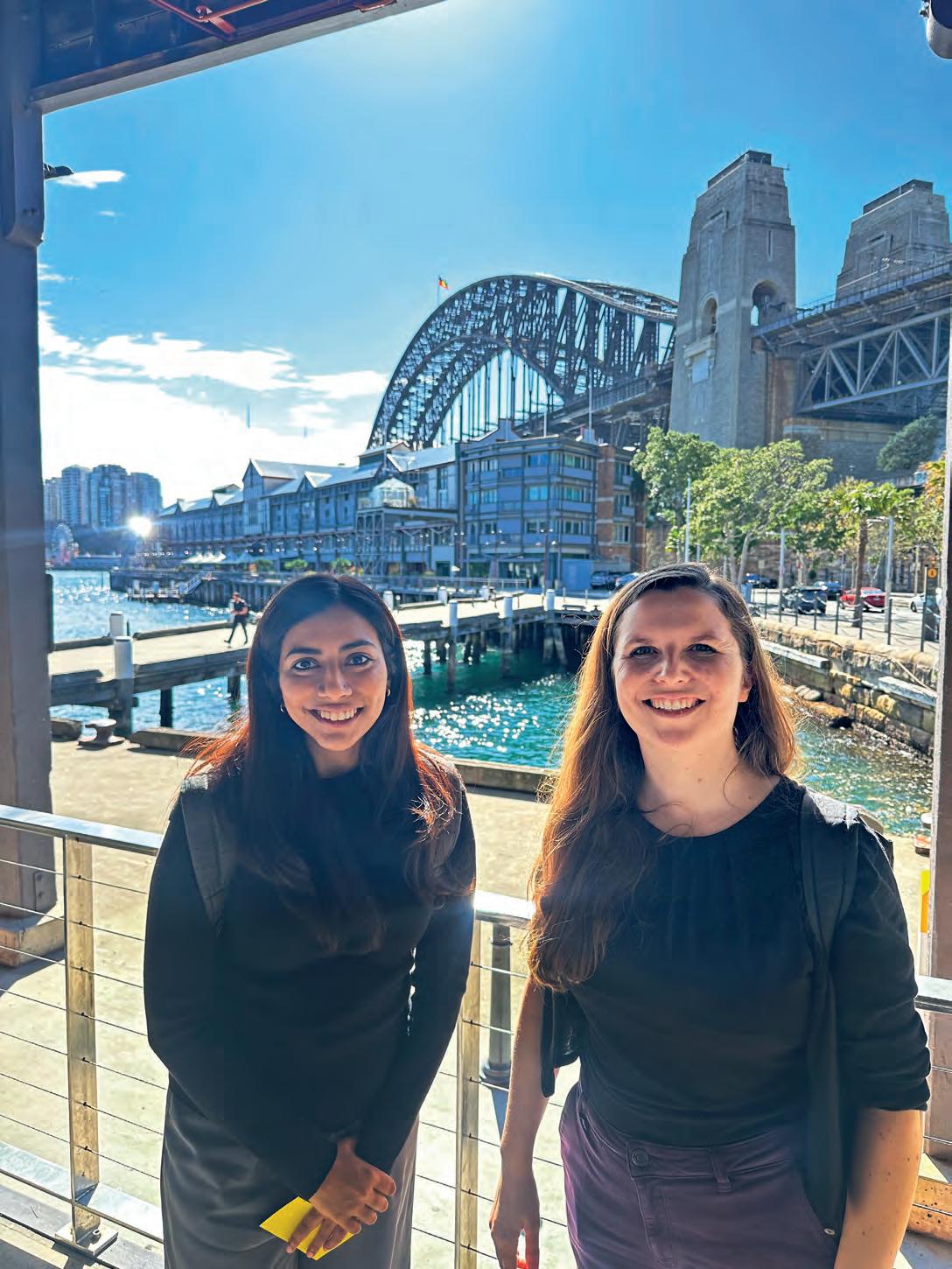
DRISYA Pavithran, a Graduate Environmental Consultant at Arcadis, has found herself immersed in a field that constantly challenges and educates her. With a background in chemical engineering and a master’s degree in environmental engineering, Pavithran has built a career in the resource recovery sector – an industry she describes as both dynamic and continually evolving.
“I feel like I’m always learning something new in this industry. And if I stay in it, I know that learning will never stop,” Pavithran said.
Pavithran’s journey to the waste and resource recovery industry began far from Australia. Originally from India and growing up in Oman on the Arabic Peninsula, she was struck by the stark contrast between waste management practices in rural India and Oman. During the COVID-19 pandemic, Pavithran travelled to her grandmother’s village in rural India, where waste was often burned due to the lack of proper disposal systems.
“When I was living at my grandmother’s, there were no rubbish trucks. Everything, including plastics and textiles, was burned. I never really thought about the implications of waste management until then,” she said.
This experience, combined with her studies and an internship at a waste management consultancy in India, sparked Pavithran’s interest in the resource recovery space. Despite initially considering a career in wastewater management, her fascination with the environmental challenges posed by waste led her to focus on the broader sector.
Upon completing her Master’s degree at the University of Wollongong in 2022, Pavithran was eager to begin her professional career. Following an unsatisfactory stint in the hospitality industry, she sought a role that would enable her to make a meaningful impact on society. She found the perfect fit at Arcadis, a design and consultancy organisation specialising in natural and built assets, with a team focused on circular economy and waste advisory.
“From the moment I spoke to them, I knew Arcadis was the right place for me. I started working there at the beginning of 2023, and it’s been an incredible learning experience ever since,” she says.
At Arcadis, Pavithran’s role
Drisya Pavithran (left) at the WMRR NSW Women in Waste leadership breakfast. Image: Drisya Pavithran
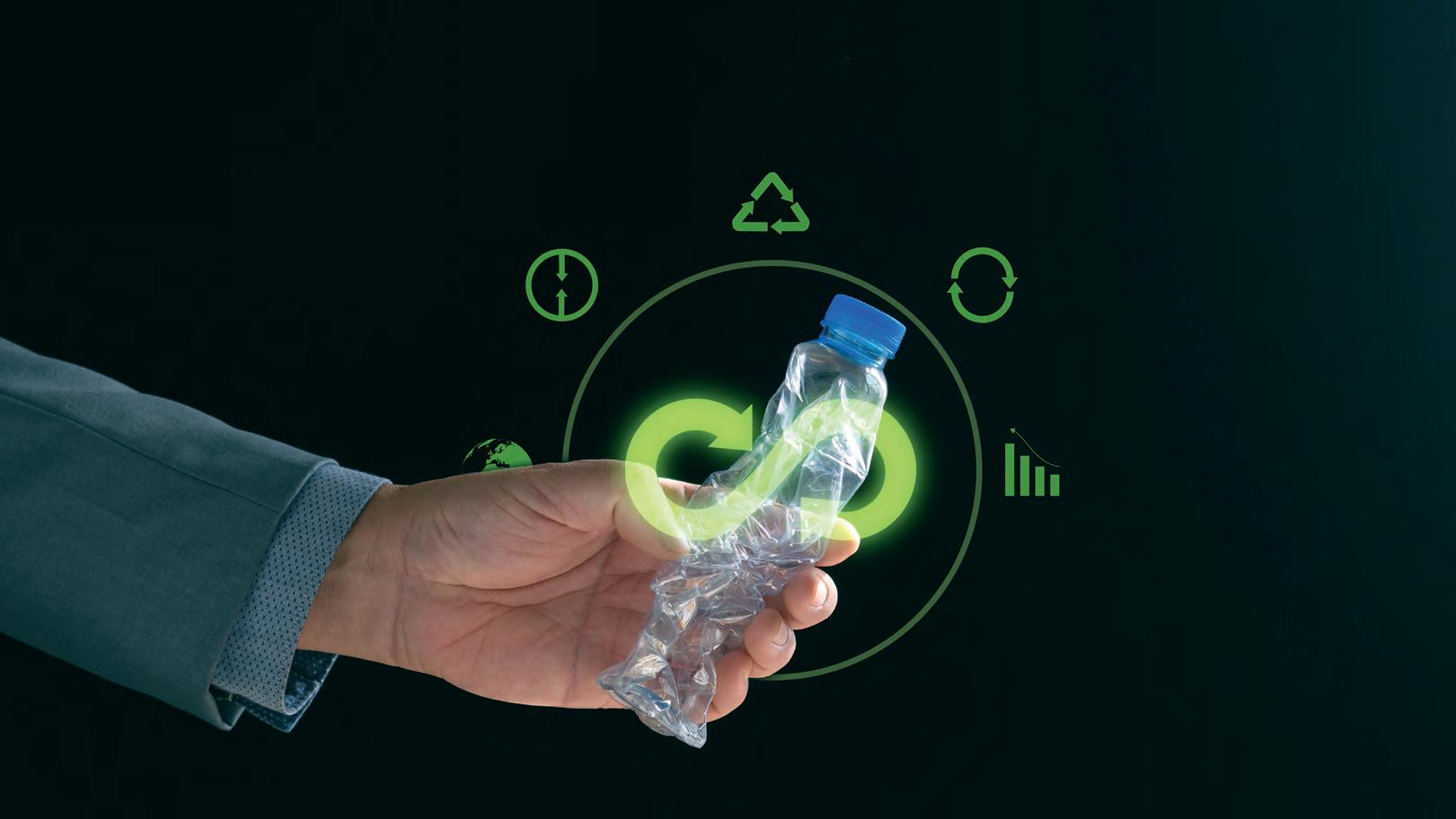
“From the moment I spoke to them, I knew Arcadis was the right place for me. I started working there at the beginning of 2023, and it’s been an incredible learning experience ever since”
encompasses a range of projects, each offering learning opportunities. She enjoys the variety of tasks, from waste generation and material flow assessments to stakeholder engagement and infrastructure options assessment. One of her first projects at Arcadis involved feedstock assessment for an organisation in southeast Queensland, a niche area she had never encountered during her studies.
“I was working with data, researching into council bin systems, and engaging with stakeholders. It was very hands-on, and I loved the diversity of the work,” she said. “The projects I’ve worked on have been diverse and that’s what I love about my job. For example, my team at Arcadis was involved in delivering the residual waste infrastructure assessment in New South Wales, which was a huge learning platform. I’ve learnt a lot about how to engage with a multitude of stakeholders at once.”
Pavithran works a lot with state and federal government entities and does due diligence work for organisations that want to invest in resource recovery/ waste infrastructure.
Does Pavithran enjoy working in
the waste industry, and are we doing a good job? “Yes,” she does, and “yes, we are,” she said. Having witnessed waste management practices in rural India, Oman and Australia, Pavithran has a unique perspective on the industry’s challenges and achievements. Despite some criticism of Australia’s waste practices, she believes the country is doing a commendable job.
“The waste industry in Australia is doing a fair job, especially compared to places like India, where the challenges and the real-life implications are much more severe. There is a real passion here for improving the system and meeting targets for resource recovery,” she said.
Pavithran points to the strong push from industry professionals who are determined to meet governmentset recovery targets and ensure that waste materials are properly sorted. This commitment to sustainability is one of the things that excites her about the sector.
For Pavithran, every day in the resource recovery industry brings new lessons, not just about the physical aspects of the job, but about the technologies and trends shaping the
future. A self-described academic, Pavithran thrives on learning about emerging technologies and innovations in the waste sector.
“We’re all educators at heart, especially when it comes to guiding the younger generation,” she said. “If you’re someone who enjoys learning and making a tangible difference in the world, the waste industry is a great place to be.”
While Pavithran is optimistic about the industry’s progress, she is also aware of its challenges. One of the biggest issues she sees is the mounting pressure on landfill capacity, especially as the Greater Sydney region grapples with increasing amounts of both putrescible and non-putrescible waste.
“I do know that people believe that landfill gate fees should be higher and that we shouldn’t dispose of anything in landfills and there should be resource recovery targets for every waste stream,” she said. “I think the pinch point is going to be the landfill capacity for putrescible and nonputrescible waste. It’s not just an issue for people in the industry, it’s going to be an issue for ratepayers and taxpayers. The future of waste management lies in improving infrastructure including energy from waste facilities and investing in new technologies, not in opening up more landfills.”
Looking ahead, Pavithran is particularly interested in two areas:
is interested in two areas: the circular economy and product stewardship. Image: HappyBall3692/shutterstock.com
the circular economy and product stewardship. She believes that transitioning to a circular economy, where materials are reused and recycled, is essential for the future. In particular, she is drawn to the concept of producer responsibility, where manufacturers are accountable for the lifecycle of their products.
Pavithran shares a recent project in which she helped Australian Resilient Flooring Association explore the reuse of resilient flooring materials. Through recycling trials, the team successfully facilitated the repurposing of PVC flooring waste, ultimately leading to a product now sold as garden edging material at Bunnings.
“This kind of reuse is the future,” she said. “We can’t keep relying on virgin products. The more we reuse and recycle, the better it will be for the environment.”
As Pavithran continues her journey in the resource recovery industry, she remains motivated by the opportunity to make a real-world impact. With a focus on circular economy practices and a passion for product stewardship, she is eager to learn more and contribute to shaping a more sustainable future.
“I want to work more in the space of product stewardship because I believe that’s where the future lies. If we can get it right, we’ll be doing more than just managing waste - we’ll be transforming the way we think about resources,” she concludes.
Pavithran
Wasted Space: How bad is bad?
Hi Sir,
Hope you had a good holiday! Off to the country to spread some good cheer among the landed gentry, no doubt. And why wouldn’t you. Lovely time of the year to be in Old Blighty. Sometimes I miss the wind, snow and rain, especially around this time of the year.
Which brings me to one of my little bugbears that has been keeping me awake at night: forever chemicals. At first, I thought it might be a case of them being ‘the next asbestos’. This range of undesirable chemicals seems to be everywhere at the moment – in the water, on the ground, in clothing, furniture –just everywhere. And they might be the next asbestos – i.e. something
“A
that is repellent to our species. But how dangerous is it? The thing is, we don’t really know. It could be really dangerous. It might be slightly dangerous. It might not be dangerous at all. A recent draft drinking water guideline from the National Health and Medical Research Council (NHMRC) located here in this Great Southern Land has now decided the amount of PFOS (a particularly prevalent and concerning forever chemical) allowed in such water should be 20 times lower than current guidelines.
“By jove, why not,” I hear you mutter. Fair enough. After all, better safe than sorry, right? However, a concise dissertation (I know, an oxymoron) by experts in toxicology is
questioning this new guideline and its limits. The issues? Well, there are a few, such as the analysis of study data with potentially non-validated laboratory analysis methods; the short duration of the study; and the use of a known source of PFAS – Teflon – being on some of the equipment used.
And to add to all this, the NHMRC hired a consulting firm to independently review and upgrade the guidelines. They also engaged a prominent specialist to peer-review the consultancy company’s findings. What did the NHMRC do with the findings and peer-reviewed work? It ignored them and set its own baselines anyway. You might say, “Well, so
what? Maybe the NHMRC had its own set of data”. Not quite. This is why they hired the consultancy in the first place.
I’m all for making sure guidelines are solid, especially when more studies are needed. Yet one wonders why a government entity spent money on a report and peer review it didn’t want.
This is an entity that got an extra $9 million from the government in 2023–24 for increased ‘operational costs’. Hhhmmmm. Let’s hope in the future it makes decisions and sticks with the outcomes.
The last thing we would want is unnecessary fear-mongering. Let’s get the data to back up the claims!
JB
recent draft drinking water guideline from the National Health and Medical Research Council located here in this Great Southern Land has now decided the amount of PFOS (a particularly prevalent and concerning forever chemical) allowed in such water should be 20 times lower than current guidelines.”


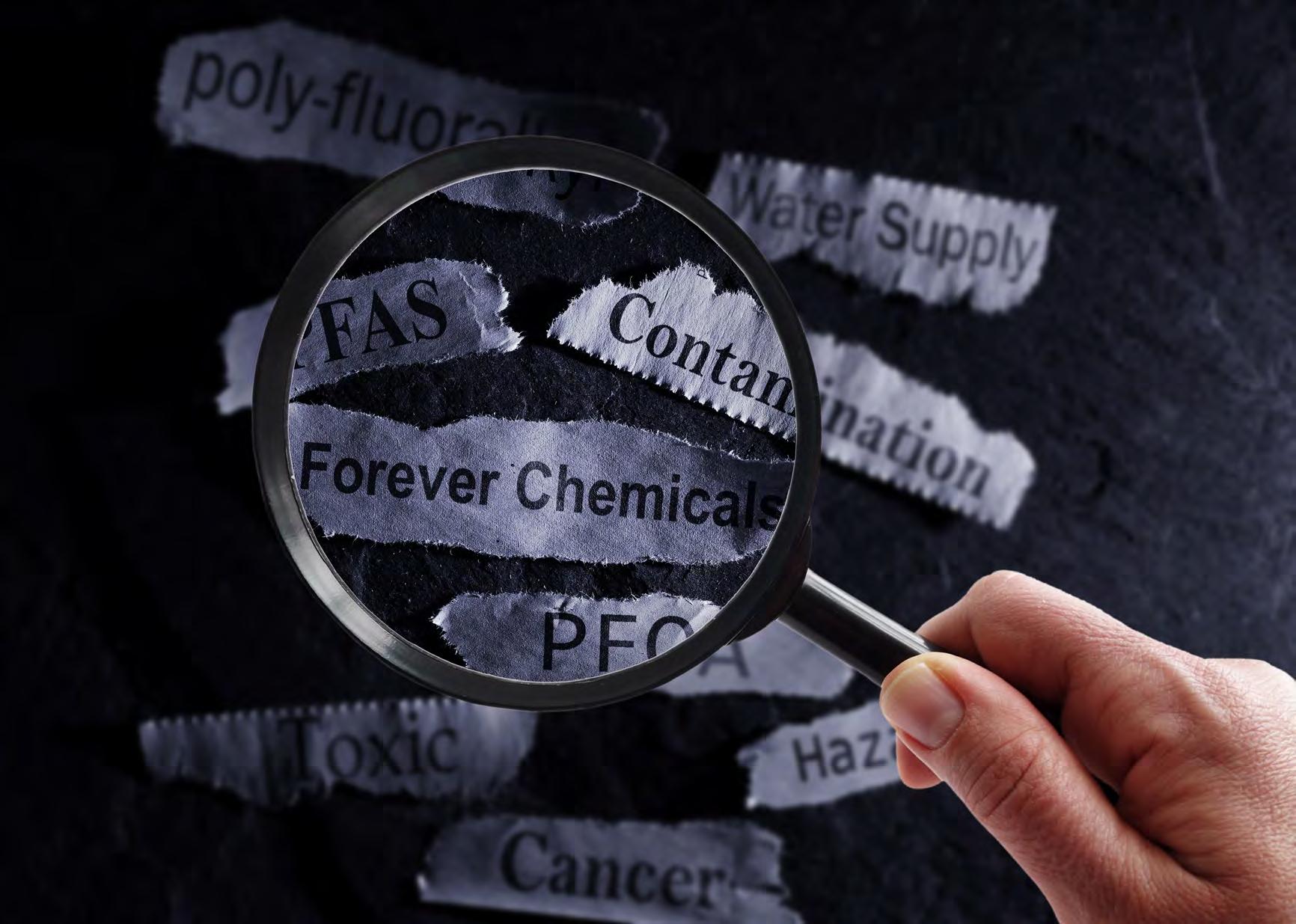

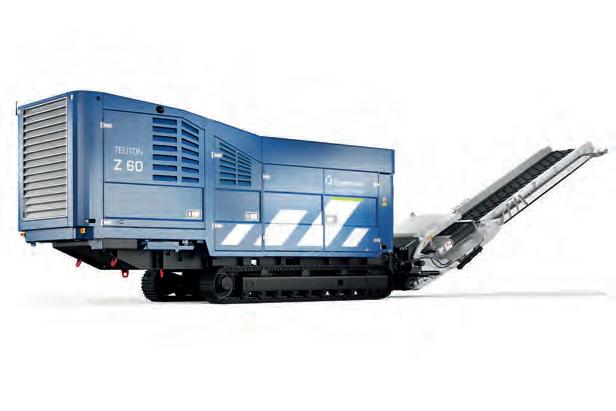
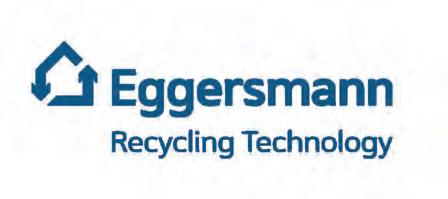
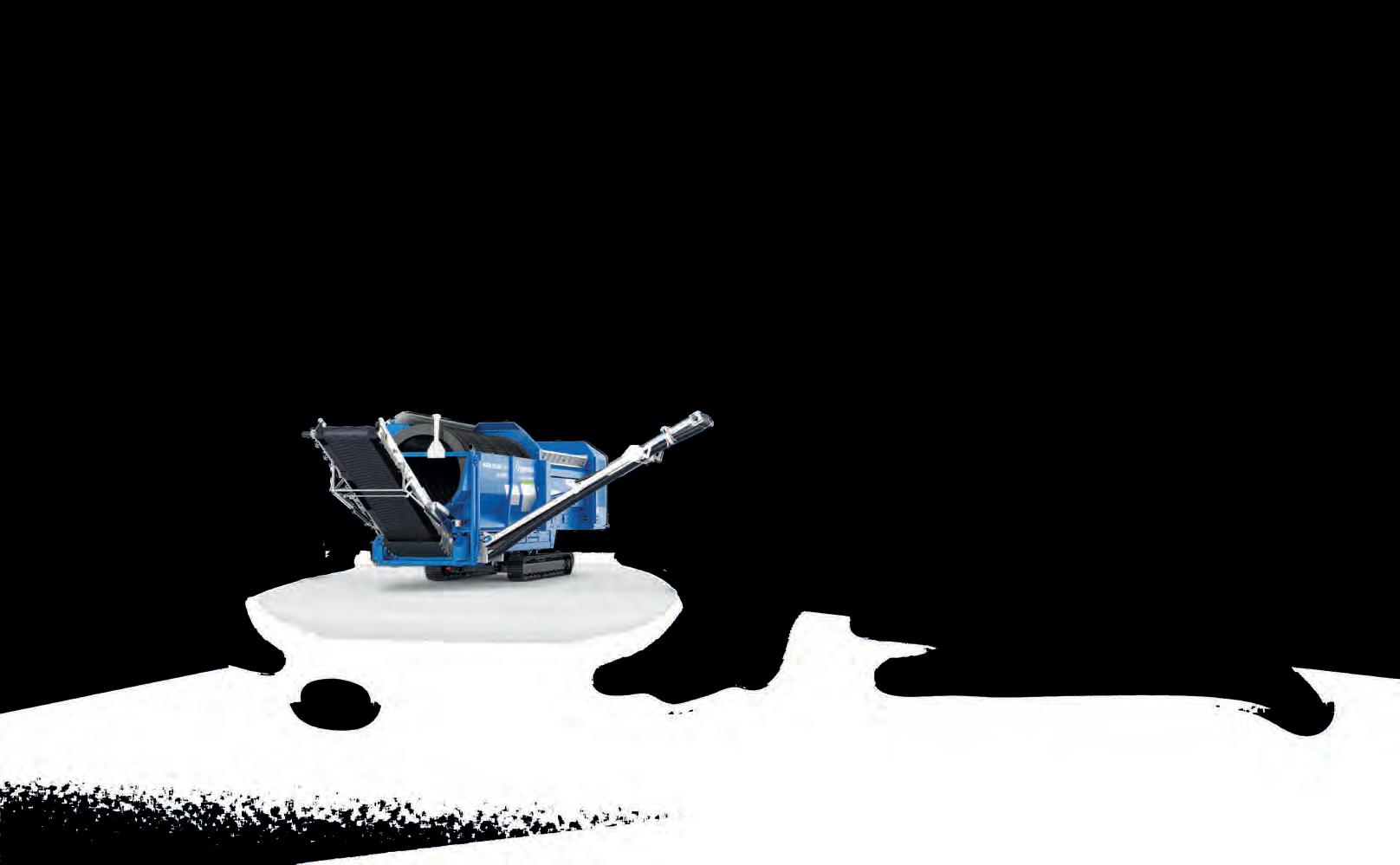
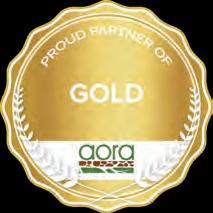
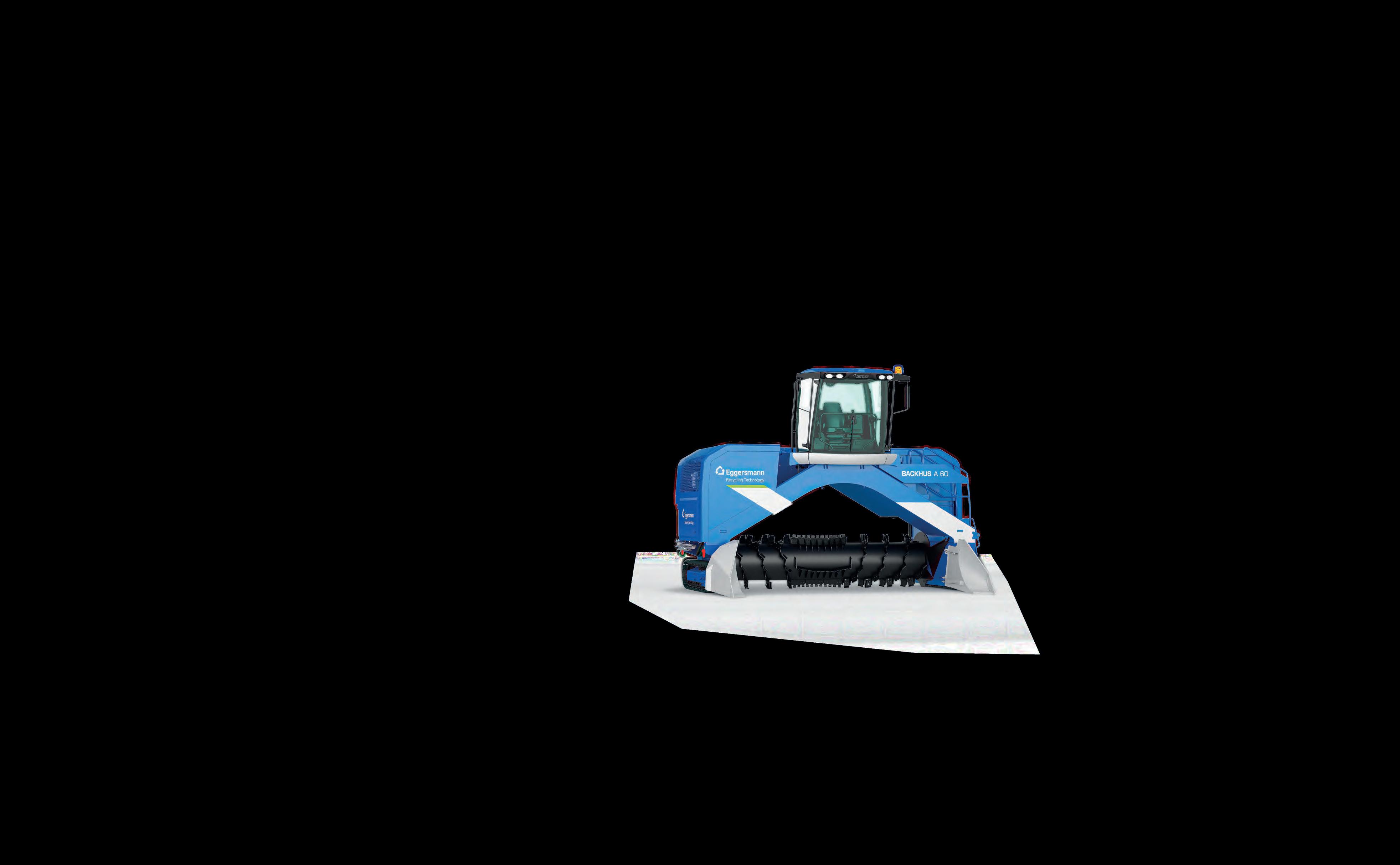