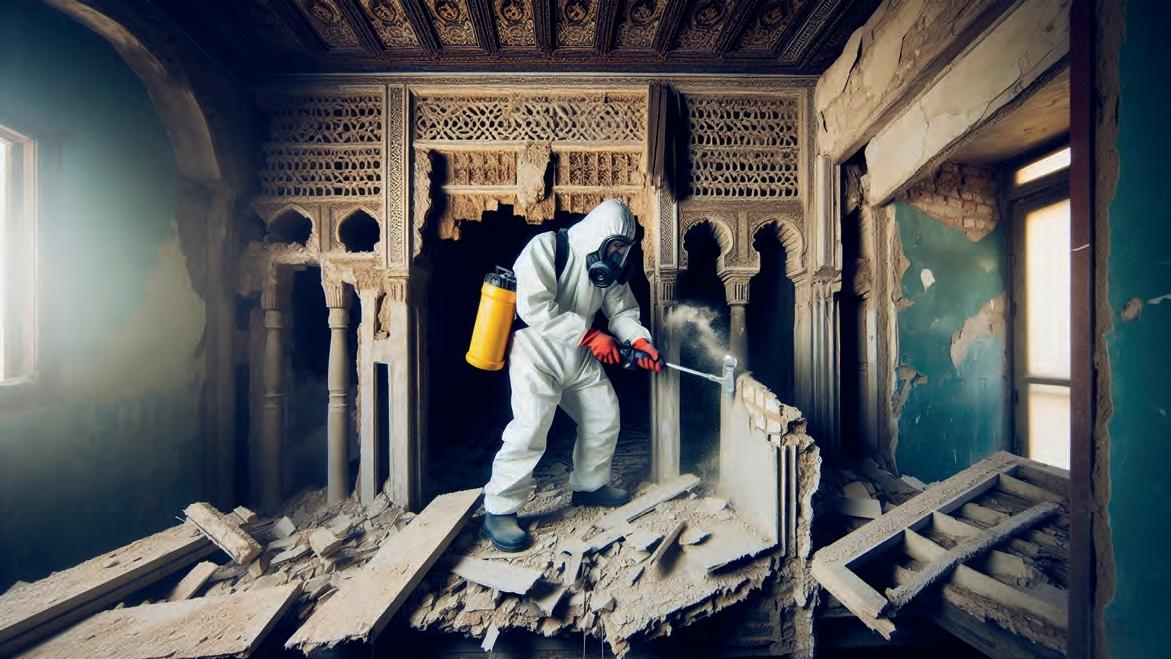
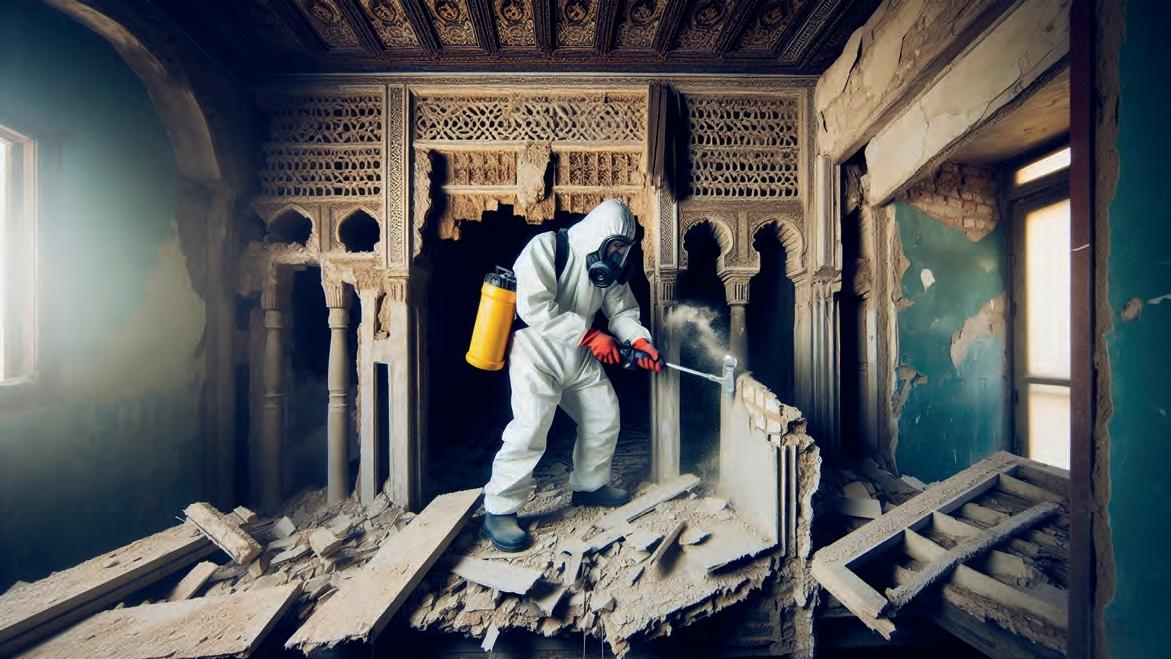
PFAS and asbestos – what are the risks?
By Inside Waste
WE ALL KNOW they are hazardous, and maybe those in power worry that complacency is the enemy, but how dangerous are PFAS or asbestos? We know that asbestos comes in various forms, and there are different risk levels. When mixed with cement, it’s not as hazardous as that which has been sprayed onto surfaces or used as insulation. The tiny fibres from spray applications are more prone to be airborne and therefore get stuck in the lungs, which could eventually cause chronic lung diseases like asbestosis.
PFAS is a different beast altogether. Also known as forever chemicals, they get that nom de guerre due to nothing other than almost being impossible to destroy under normal circumstances. Electrochemical oxidation can destroy most long-chain PFASs, but short-chain versions are a lot more challenging.
At a recent NSW Waste Collection and Recycling Association (WCRA) event
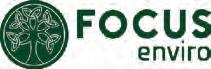
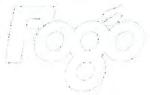
in Sydney, a couple of seminars were held that addressed these issues.
PFAS and PFOS
Andrew Mitchell from ADE Consulting spoke succinctly, and in layman’s terms, how PFAS chemicals worked.
He said that in PFAS’s simplest form, carbon atoms get stuck together w ith fluorine atoms. He said fluorine is the most electronegative element that exists.
What that means is that it holds on tightly to the carbon, and doesn’t let go, and doesn’t allow any space for microbes and bugs to get in and cut that bond,” said Mitchell. “They don’t break down naturally in the environment very well. Due to their special properties, PFAS molecules are extraordinarily useful in all sorts of industrial and chemical applications.”
He said that because they’re surfactants, they prefer to stay on edges and boundaries, it also means they don’t like water or oil, instead they like
the air/water interface, and they can travel extraordinarily long distances in water. They’re very bioaccumulative in ecosystems, and the human health and ecological guidelines are very low.”
So where do they sit on the toxicity table compared to other elements that are known to harmful to humans t he environment? Mitchell talked about lead. He said that the NSW waste C T 1 guideline for lead is 100 milligrams per kilogram.
“So that is like the thickness of four sheets of paper stacked on each other compared to my height, which is nearly two metres, or, for a time analogy, it’s about one second in three hours,” he said.
Mitchell said when looking at NSW landfill guidelines with perfluorooctane sulfonic acid (PFOS – a type of PFAS), then it was equivalent to about 1 second per week, or the thickness of 40 sheets of paper side by side along the Sydney Harbour Bridge.
(Continued on page 10)
Bigger than bottles and cans
By Neville Rawlings
RECYCLERS OF South Australia Incorporated (RSA) has represented the operators of most collection points (known as depots) in the South Australian Container Deposit Scheme for more than four decades. In doing so, it is acutely aware of how the community feels about recycling. The community are our members’ customers, the participants in the scheme and who our members are speaking with every day, as they go about their business.
Our members are leading in innovation and are regularly telling us that they want to invest further in their operations to provide more efficient services to customers, but they are being hampered by a regulatory environment that hasn’t kept up.
Following the introduction of CDS in other jurisdictions, a review of the South Australian scheme was commenced in January 2019, with the scope of the review to consider:
l Objectives of the CDS.
l Scope of containers included in the CDS.
l Scheme approvals and container markings.
l CDS container return rates, including deposit value and payment methods.
l Governance of the CDS.
The review is now well into its sixth year, and industry and the community are still awaiting any clear findings and recommendations, while the landscape of recycling and circular economy has transformed drastically. If we get the outcomes of the review wrong, everything we have built over more than 45 years is at risk.
(Continued on page 16)
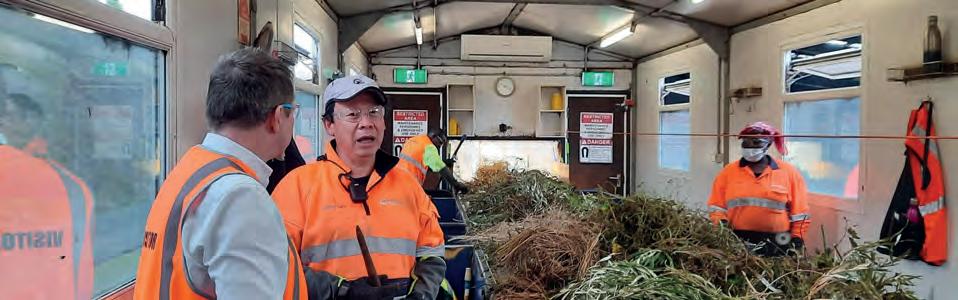
Image: Shutterstock AI Generator
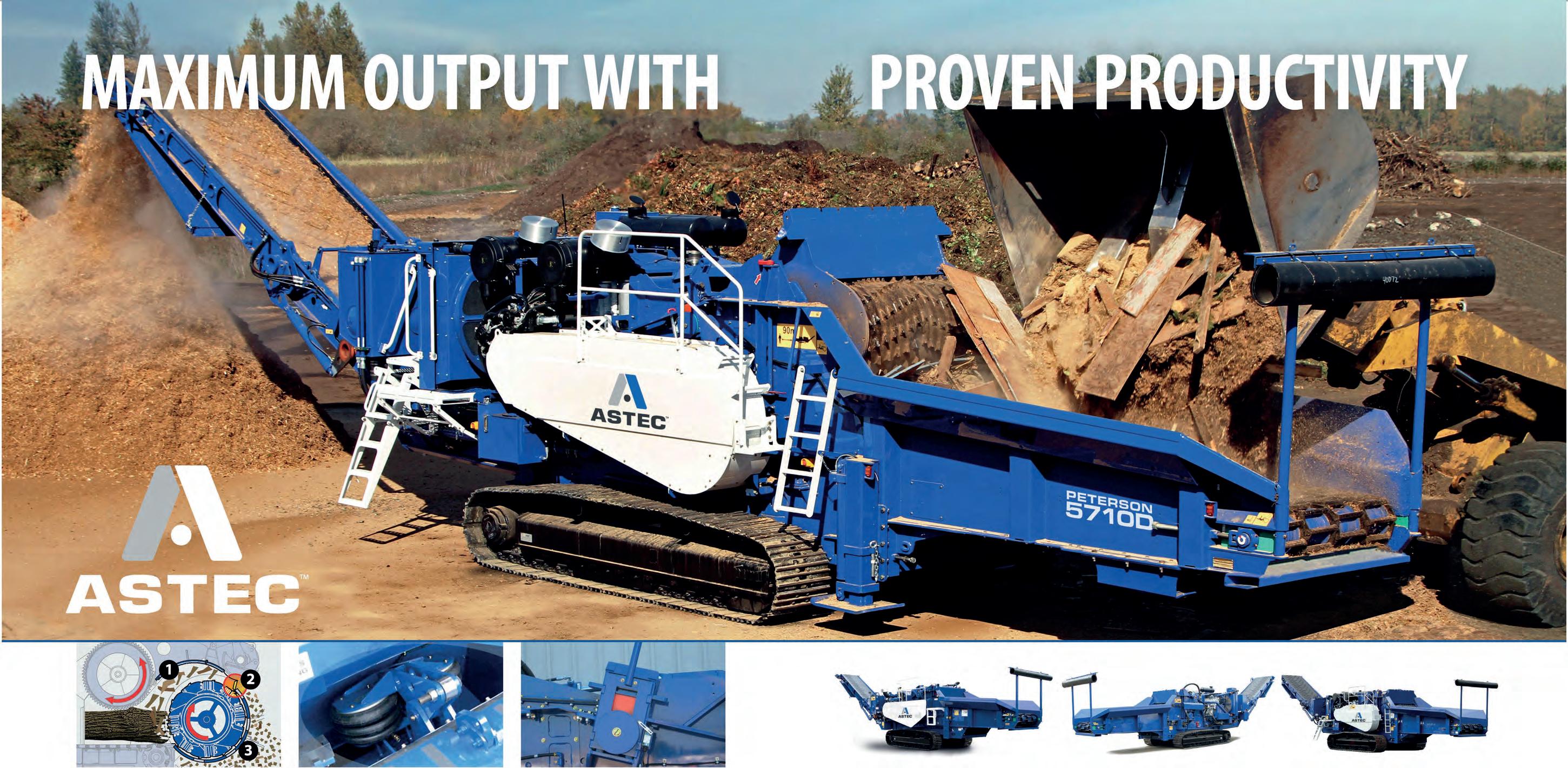
3-Stage Grinding Process
Provides Faster Reduction
Astec - Peterson's powerful up-turn 3-stage grinding process provides better fracturing of material and a more consistent product, giving you just the product your buyers are looking for.
The Impact Release System
Protects Your Investment
Astec - Peterson's patented Impact Release System's air bags provides uniform grinding and protection from contaminated feedstock, a feature unique to Astec - Peterson grinders.
Land clearing, mulch, compost, asphalt shingle tiles, scrap wood, biomass, green waste-we can handle it am
www.komatsuforest.com.au
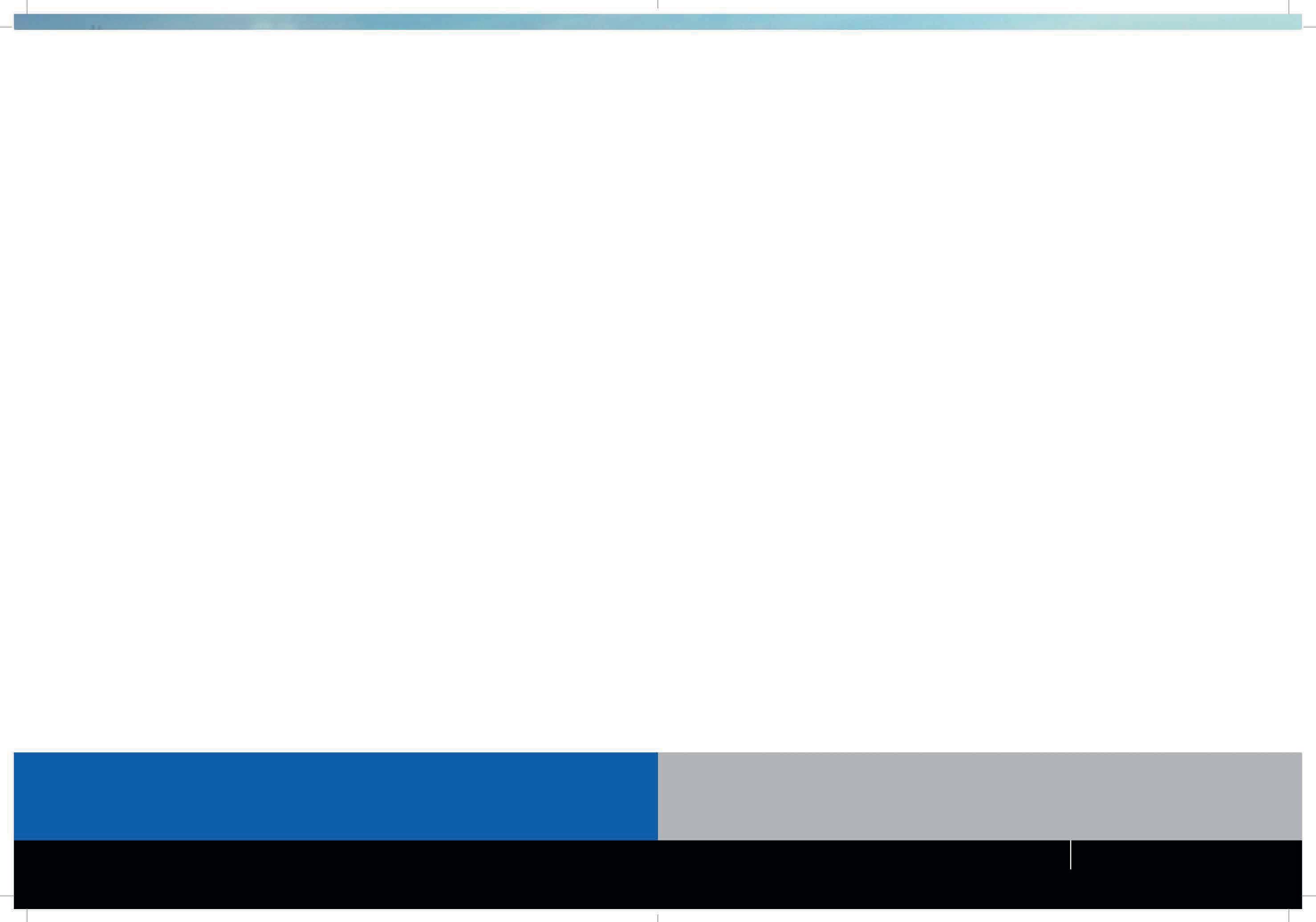
The Impact Cushion System
The Second Line of Defence
Urethane cushions and shear pins help protect the mill from catastrophic damage in the event of a severe impact from contaminants in the feedstock.
Astec - Peterson offers horizontal grinders from 433-839 kW, offering grinding solutions with output at the lowest cost per ton. Visit us at www.astecindustries.com and see why we have been leading the industry for over 35 years!
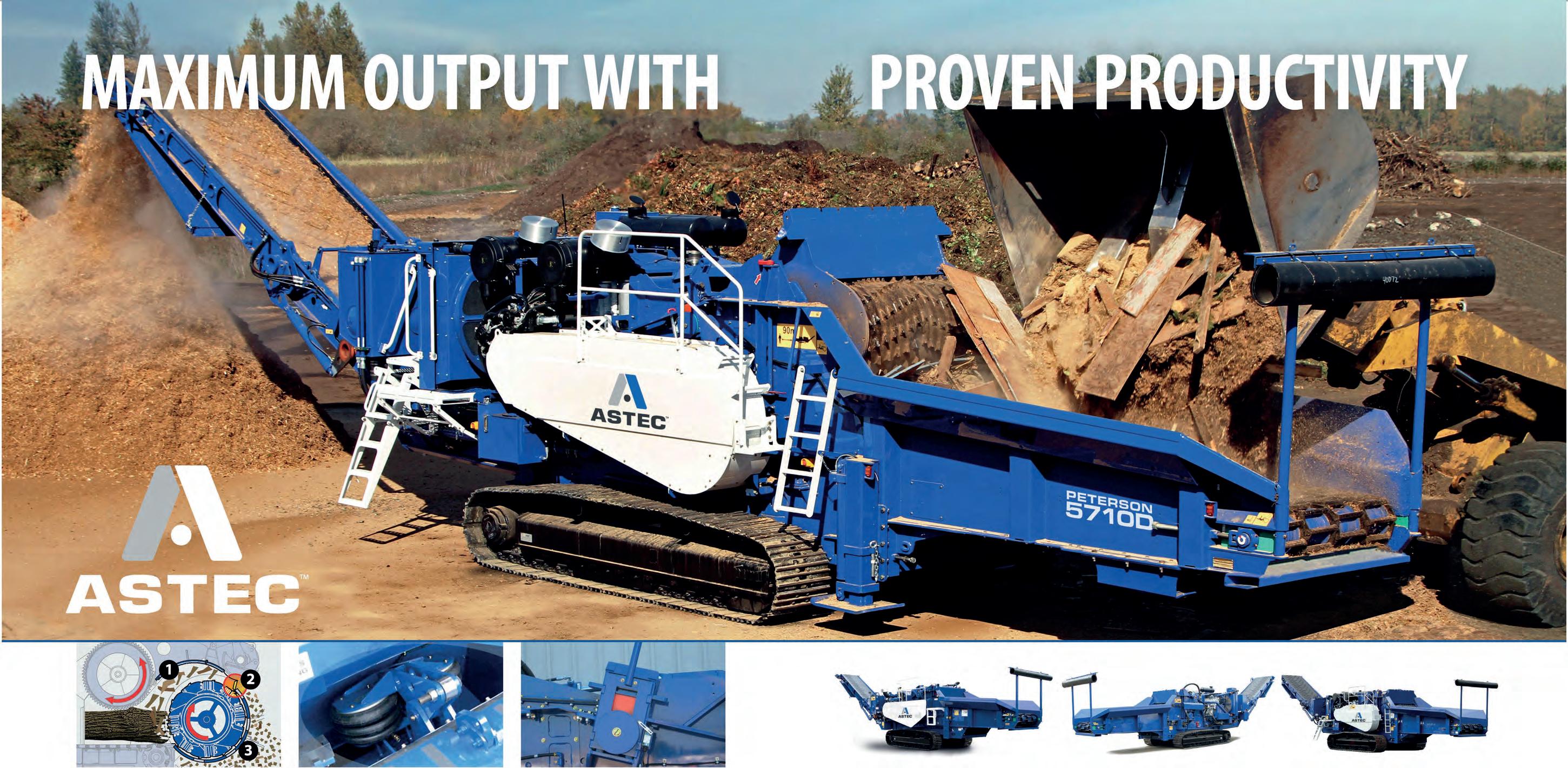
2710D Horizontal Grinder
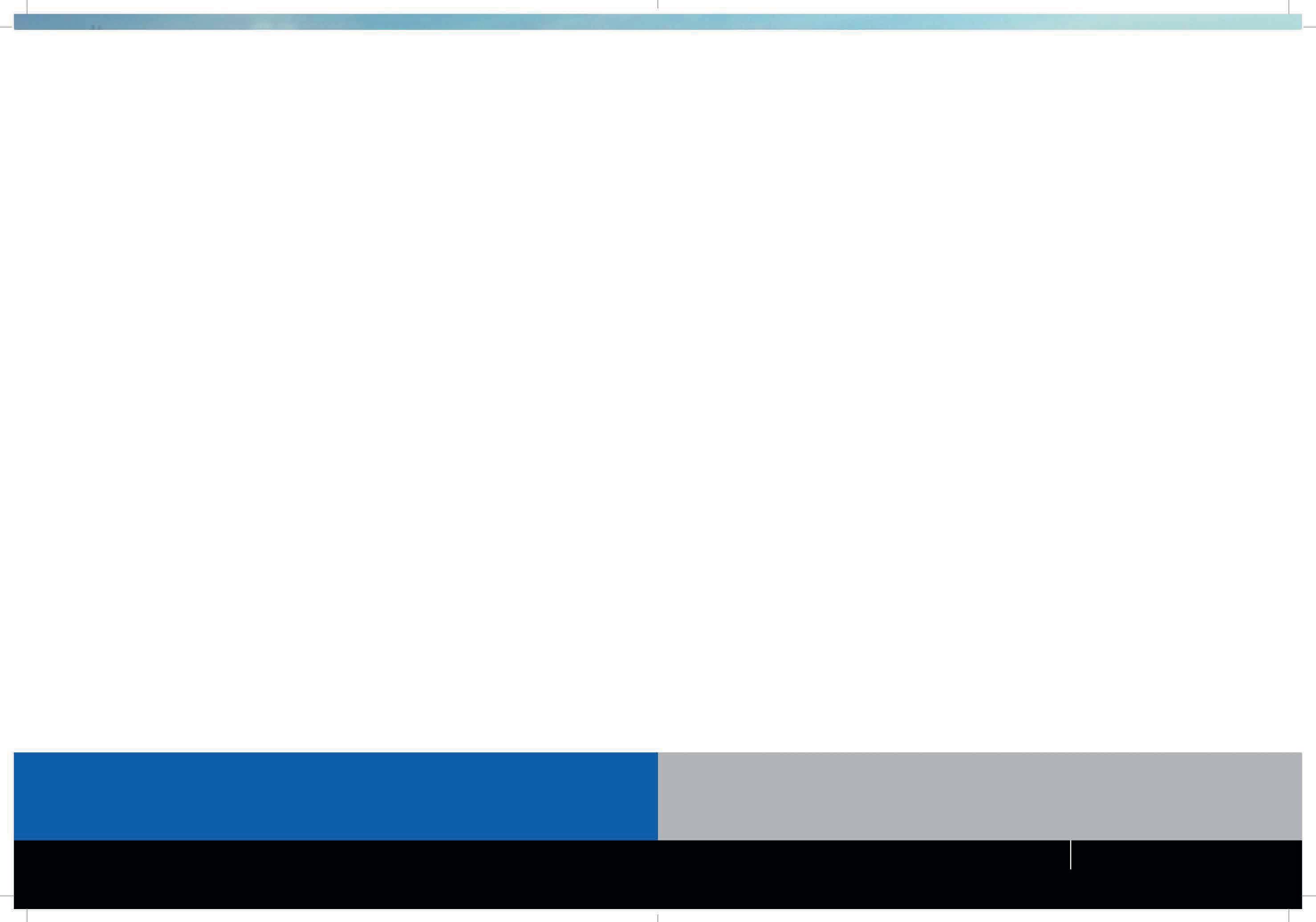
5710D Horizontal Grinder
6710D Horizontal Grinder
Largest
How bad is bad?
IN THE FIRST half of 2024, there was a hullabaloo in the inner west Sydney suburb of Rozelle over mulch that was riddled with asbestos. Everybody knows that asbestos is bad for the environment, and even worse for human health if dust finds its way into your lungs.
But how bad is bad? It depends on the form the asbestos takes. In cement form? Not too bad. In dust form? Terrible for your health.
It was with that in mind that I attended two speeches, one by CDE Consultants’ Andrew Mitchell, and Hibbs and Associates Samantha O’Callahan at an event ran by the NSW Waste Contractors and Recycling Association.
O’Callahan put some perspective on the mulch issue. While she was quick to outline the dangers of the substance, she also believes that people need to be informed of all the facts.
One such instance was an editorial in a daily newspaper where the writer advocated for mandatory asbestosfree certification for recycled products.
Chief Operating Officer
Christine Clancy christine.clancy@primecreative.com.au
Managing Editor
Mike Wheeler
mike.wheeler@primecreative.com.au
Brand Manager
Chelsea Daniel chelsea.daniel@primecreative.com.au
Ar t Director
Bea Barthelson
Client Success Manager
Louisa Stocks louisa.stocks@primecreative.com.au
Head Office
Prime Creative Pty Ltd
379 Docklands Drive
Docklands VIC 3008 Australia
p: +61 3 9690 8766
enquiries@primecreative.com.au www.insidewaste.com.au
Subscriptions
+61 3 9690 8766
subscriptions@primecreative.com.au
Inside Waste is available by subscription from the publisher.
The rights of refusal are reserved by the publisher
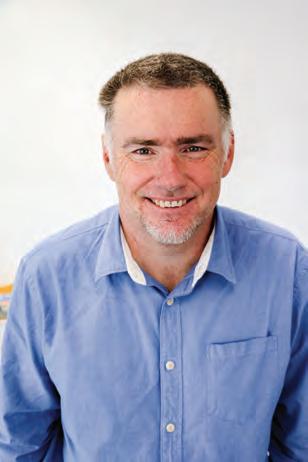
amounts – are everywhere, but the cost of doing such a thing would not only be prohibitive for a lot of businesses, but the pass-on costs to the public would not go down well.
Mitchell’s speech was about the asbestos of the 2020s – PFAS.
Again, he knows that most of these forever chemicals are not good for you – although there is nowhere near as much data on them as asbestos – and he has shown some interesting figures on just how low of a tolerance governments might be willing to accept - i.e. not much at all.
I don’t think anyone would argue how bad these substances can be for humans and the environment, but getting some insights helps put a lot of scenarios in perspective.
Have a good month.
Articles
All articles submitted for publication become the property of the publisher. The Editor reserves the right to adjust any article to conform with the magazine format.
Copyright
Inside Waste is owned by Prime Creative Media and published by John Murphy. All material in Inside Waste is copyright and no part may be reproduced or copied in any form or by any means (graphic, electronic or mechanical including information and retrieval systems) without written permission of the publisher. The Editor welcomes contributions but reserves the right to accept or reject any material. While every effort has been made to ensure the accuracy of information, Prime Creative Media will not accept responsibility for errors or omissions or for any consequences arising from reliance on information published. The opinions expressed in Inside Waste are not necessarily the opinions of, or endorsed by the publisher unless otherwise stated.
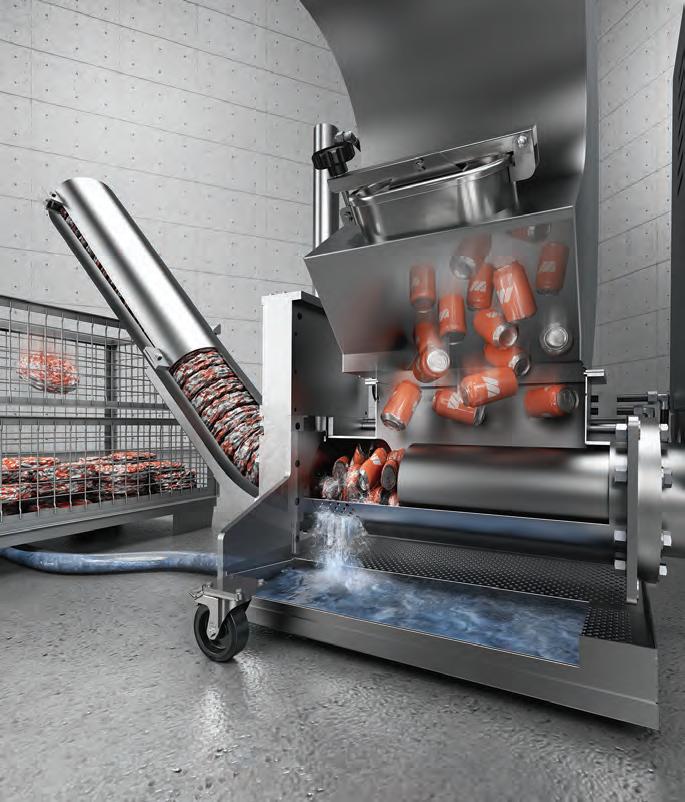
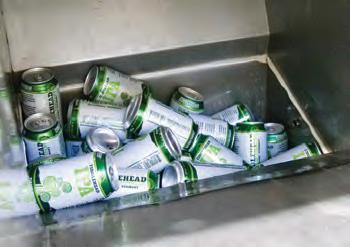
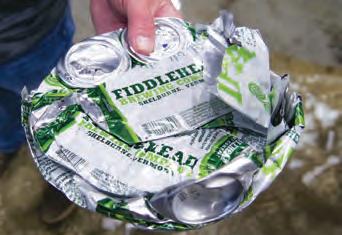





























































































Isuzu’s FVY Dual Control
We’re about to make a big splash in trash, because we’ve just launched a new range of dual control trucks. With lower tare weights than similar models from our competitors, these new trucks can carry bigger payloads. Up to 300kgs per trip! Apply that across a fleet and you’ll see huge boosts in e ciency and reduced operating costs. Visit isuzu.com.au/waste





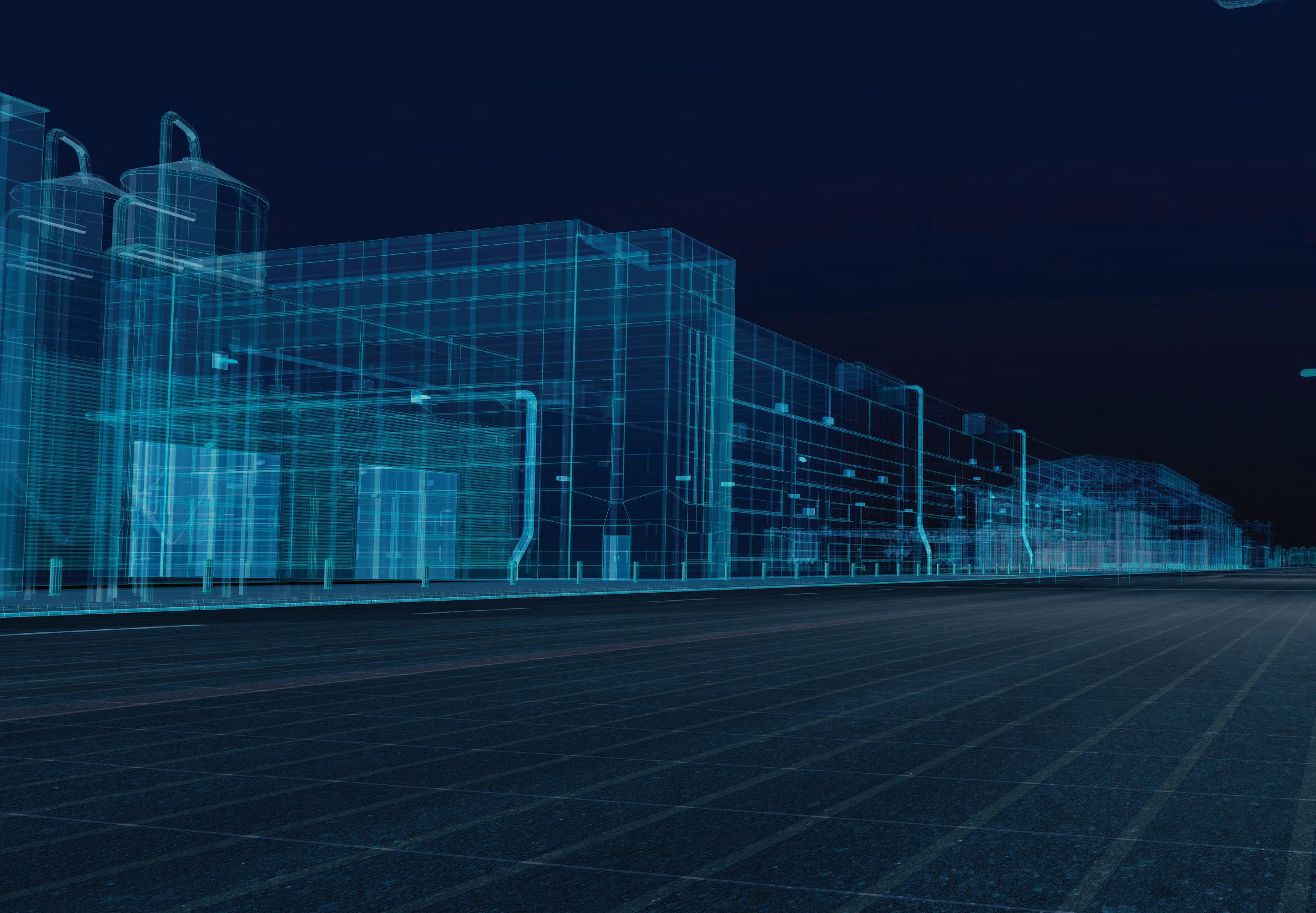
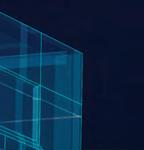
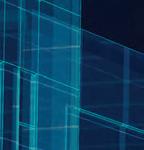
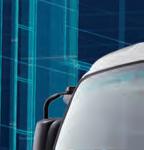
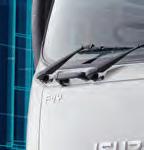
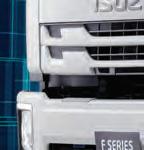
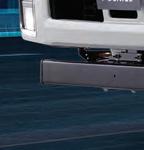
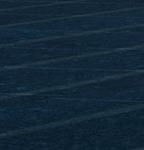
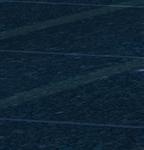
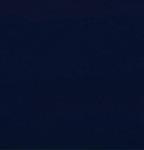
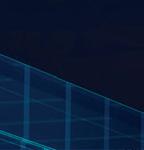
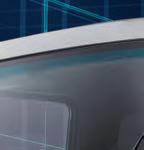
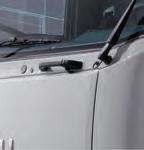
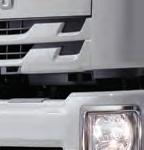
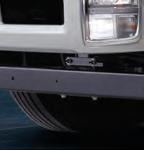
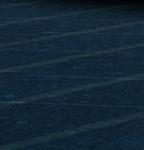

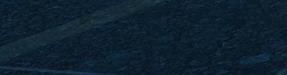
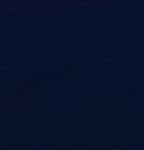
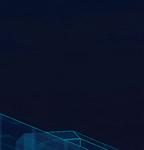
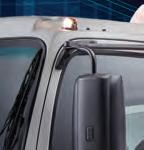
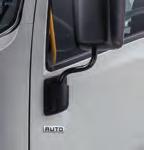
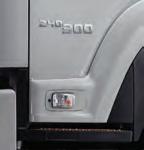
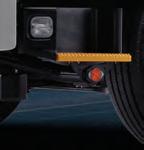
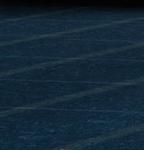
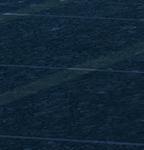
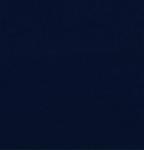

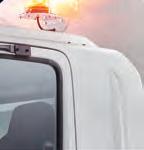
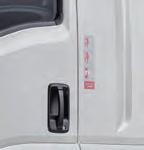


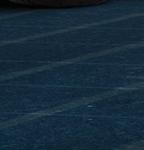
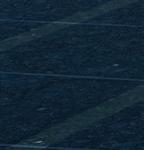
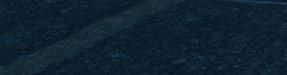
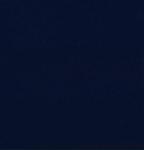
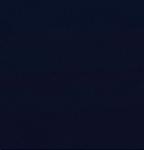
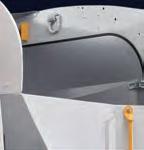
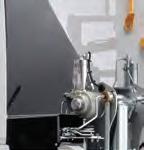
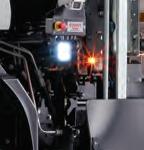

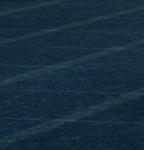
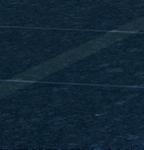
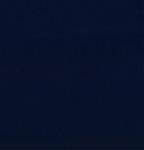
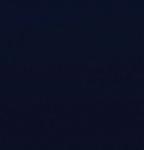
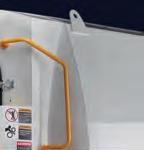


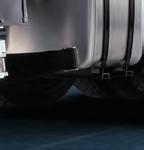

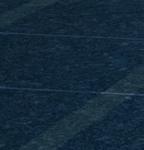
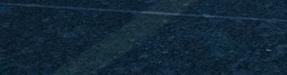


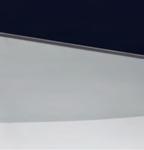

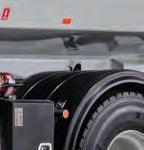
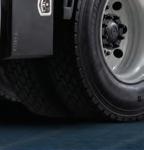
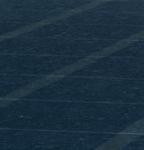
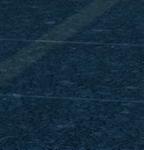
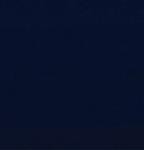
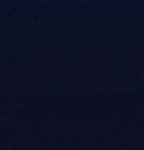
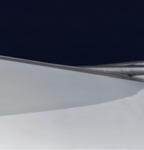



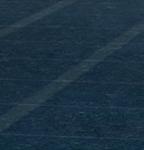
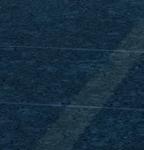
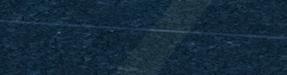
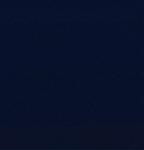
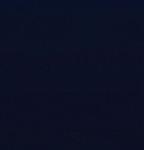
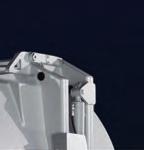
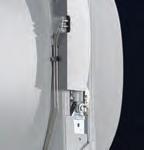
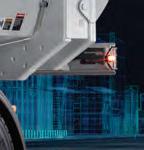
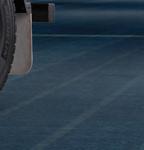
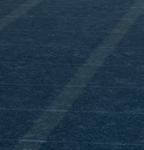
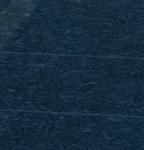
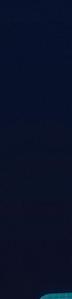

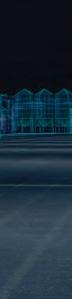
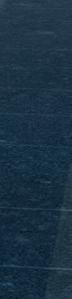
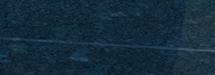
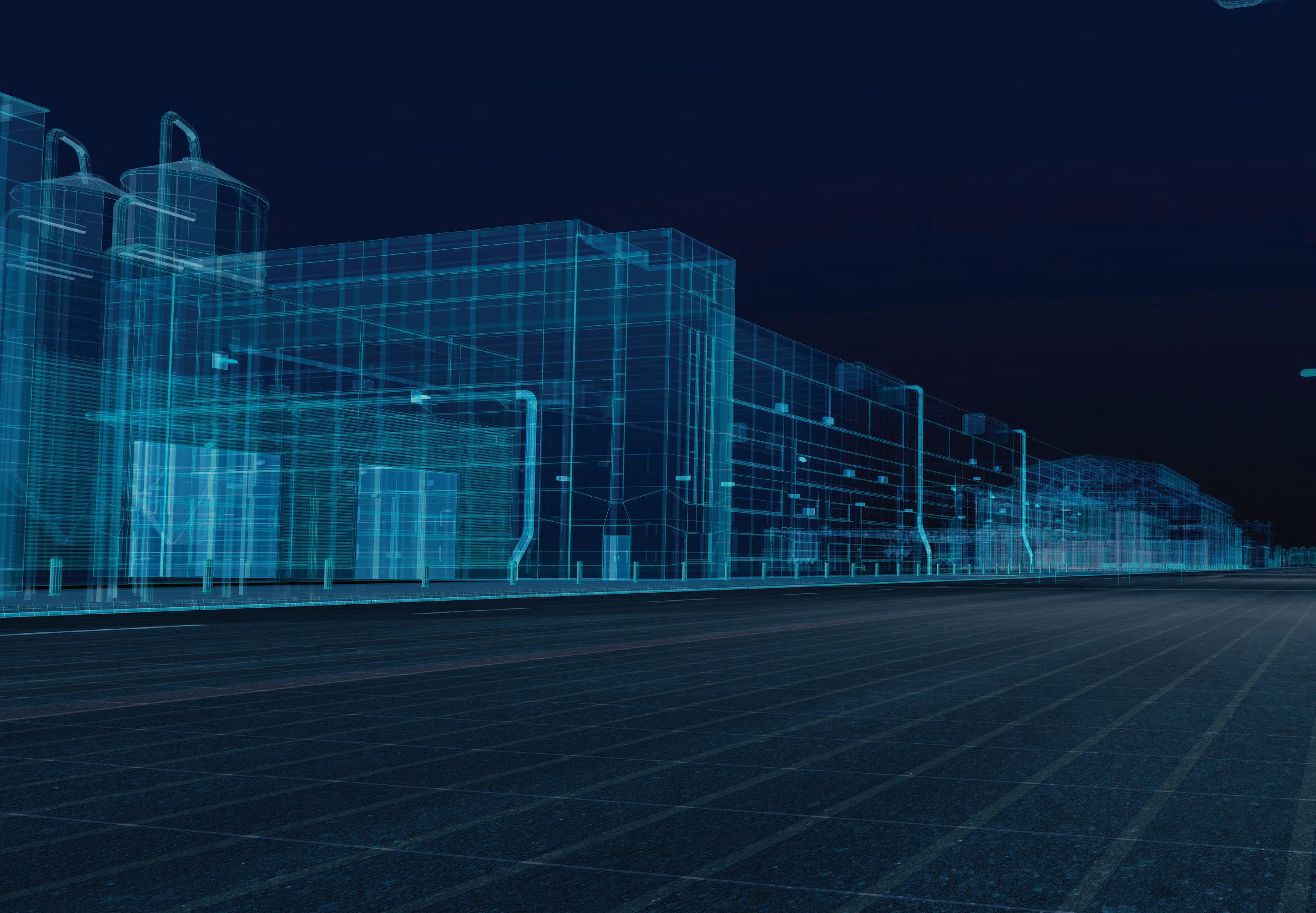
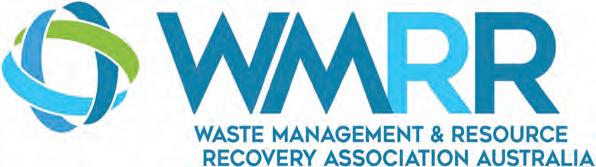
From the CEO’s desk
Waste industry needs to lead the way – government won’t
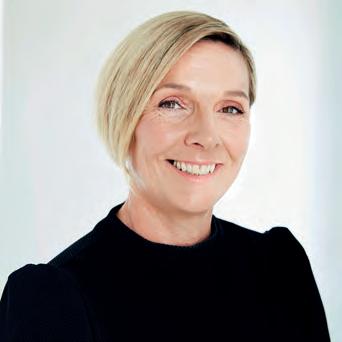
The last National Waste Report in December 2022 shows there has been an increase in recovery of about one million tonnes over the past two reporting years, whereas Australia needs over 10 million additional tonnes to be recovered to hit our 80 per cent target by 2030.
Environment Ministers will meet for the second time this year on 7 December, following the first 2018 Meeting of Environment Ministers (MEM) in April, which was in part a response to the import restrictions driven by China’s National Sword Policy and the effects this policy has had across the Australian waste and resource recovery (WARR) industry. Key decisions derived from the April MEM include:
The next report is due out by early next year. I guess it remains to be seen if there will be any material change in recovery rates, given the pace of policy implementation, facility development and real market development for our essential industry nationally.
Let’s hope though, that we do see a shift up from the current resource recovery rate of 63 per cent, given in 2024 we still need to recover more than 1.5 million tonnes a year – a jump we have not seen previously.
•Reducing waste generation, endorsing a target of 100% of Australian packaging being recyclable, compostable or reusable by 2025, and developing targets for recycled content in packaging.
• Increasing Australia’s domestic recycling capacity.
We all know what needs to be done to get to this goal – we need to use less for longer. The reality is that it is not hard, but possibly it is brave to try and shift both the consumption and production behaviours of the lucky country.
• Increasing the demand for recycled products.
• Exploring opportunities to advance waste-to-energy and waste-to-biofuels.
In 2024, we desperately need co-ordinated government action that drives regulation, investment (with certain planning support), genuine market settings that values recycled materials and local green jobs, and genuine green public procurement. Seriously, when will we get beyond viewing the use of recycled materials and repaired products as unique behaviours to realising they are mandatory habits – necessary not just for our industry but the planet. As Kamala Harris said (yep girl crush here)... “it’s (both) an environmental imperative and economic good”.
•Updating the 2009 Waste Strategy by year end, which will include circular economy principles.
It is time to take stock and examine what has been achieved since these decisions were announced. Now, seven (7) months may not seem like a long time, however in that time we have seen further markets close (Malaysia, Indonesia, Vietnam) and if you are an operator under continued financial stress, seven (7) months could make or break you.
I understand it is always a fine line for governments between showing leadership on an issue and riding roughshod over public opinion. Increasingly after two years it is looking like this Federal government is frozen by inaction either because change is seen as being too scary, too big, too risky, too expensive, too fast or a combination of all the above.
I fear this is where we are now with the Federal Government’s recent announcement of a Productivity Commission inquiry into the circular economy. It’s a topic that could arguably fall into all of the above categories (except fast), but I would argue it also falls into another – too late.
Following the April MEM, we have had three (3) states step in with varying degrees of financial assistance for industry (councils and operators). This should be expected considering almost all states (except Queensland and Tasmania) have access to significant waste levy income each year. On the eastern seaboard, Victoria has approximately $600 million in waste levy reserves in the Sustainability Fund and NSW raises more than $700 million per annum from the waste levy. There is certainly no lack of funds that can be reinvested into our essential industry.
It was with some sadness that I noted the inquiry into the circular economy. Not because of any misgivings about the PC (in fact, it will be headed by Joanne Chong, who appears eminently qualified), but because I fear the inquiry will be able to now be used as yet another excuse for government inaction.
Funding helps but as we know, the money goes a much longer way with Government support and leadership, as well as appropriate policy levers.
VICTORIA
There is a real risk that both sides of politics will argue they cannot do anything substantial on circular economy (or waste and resource recovery policy) until the Commission reports back, which is on the other side of the Federal election. The inquiry could be the fig leaf of cover the major parties will hold onto like a life buoy. Tick, tick, tick, as we head to 2030.... Not to mention that the PC report on Right to Repair, which was released on 1 December 2021, has still not been responded to by government.
Victoria has arguably been the most active and earnest in supporting the industry post-China, with two (2) relief packages announced to support the recycling industry, valued at a total of $37 million. The Victorian Government has also gone above and beyond all others states by announcing it would take a leadership role in creating market demand for recycled products.
SOUTH AUSTRALIA
Maybe there are positives to the PC inquiry. Hopefully it will, for example, expand circular economy thinking beyond just environment departments given it must be a paradigm shift that applies to whole of government – treasury, infrastructure, finance and industry just to name a few. This inquiry could provide that impetus. But the fact is we cannot tread water for another 12 months. The world is leaving us behind.
Government announced a $12.4 million support package comprising $2 million of additional expenditure, $5 million additional funding for a loan scheme, together with targeted funding from the Green Industries SA budget. The Government has also offered grants for recycling infrastructure.
NEW SOUTH WALES
At first glance, New South Wales’ eye-watering $47 million recycling support package was heralded as the spark of hope industry needed. However, on closer inspection, the bulk of this package that was funded via the Waste Less, Recycle More initiative and therefore the waste levy, was not new, making it very difficult for stakeholders, including local government, to utilise the funds as they were already committed to other activities. Some of the criteria proposed by the NSW EPA also made it challenging for industry to apply to these grants. On the plus side, efforts are being made by the NSW Government to stimulate demand for recycled content through the intergovernmental agency working groups that have been established, though no tangible increase in demand or facilities have developed… Yet.
QUEENSLAND
We can only kid ourselves for so long before the (plastic) straw breaks the camel’s back – whether it is battery fires, packaging or PFAS. Issues keep piling up and go largely unaddressed.
There are, however, plenty of actions governments could take to use less for longer that won’t fall foul of the PC report. Most of you have probably heard of the nudge theory of behavioural economics, which attempts to persuade rather than compel people to make specific decisions. And it strikes me that we could do with a little of that in the WARR space.
Given the apparent reluctance of government to take bold action to make the transition to a circular economy a reality, perhaps we need to harness other methods to elicit change?
I attended a Mood of the Nation research report presentation from SEC Newgate Australia, and it gave me some thoughts and a few key takeouts, beyond the obvious like cost-of-living issues, are top of mind for Australians.
industry however the Queensland Government has embarked on the development of a waste management strategy underpinned by a waste disposal levy to increase recycling and recovery and create new jobs. The State will re-introduce a $70/ tonne landfill levy in March 2019. There are also strong attempts to use policy levers (levy discounts and exemptions) to incentivise the use of recycled material and make it cost competitive with virgin material. However, little has been done to establish new markets and Government has not taken the lead in the procurement of recycled material. There are grants available for resource recovery operations in Queensland although no monies have been allocated to assist in 2018. This is troubling as Queensland rolled out its Container Refund Scheme on 1 November, which will likely impact the cost and revenue models of the State’s MRFs – as we have seen most recently in NSW.
WESTERN AUSTRALIA
Broadly the research found that while people do not want government to tell them how to live their lives, they are open to government showing them how to do things differently. It struck me as something we could use in WARR to highlight the importance of consuming less, making materials last longer, only getting what we truly need and shifting to circularity.
The Western Australian Government set up a Waste Taskforce in direct response to the China National Sword. As part of this announcement, the State Government urged all local councils to begin the utilisation of a three (3)-bin system - red for general waste, yellow for recyclables and green for organic waste - over the coming years to reduce contamination. While this taskforce is a step in the right direction, we are yet to see any tangible results from it or any funding for industry. In October, the WA Waste Authority released its draft Waste Strategy to 2030, which comprises a comprehensive and detailed roadmap towards the State’s shared vision of becoming a sustainable, low-waste, circular economy.
In part, this is why WMRR has been calling for years for a well-funded nationwide education campaign to drive behaviour change about consumption. We are not talking about a ‘what goes in which bin’ campaign, but one which makes people aware of the consequences of their choices on the environment – whether it relates to so-called switching from goods to services, making better use of existing products or tackling food waste, as used in the WRAP UK: Net Zero Why Resource Efficiency Holds Answers campaign.
COMMONWEALTH
One that transitions from linear to circular. And with Australia’s currently circularity rate calculated by CSIRO at 3.7 per cent compared with global average of 8.6 per cent, we really need to get moving. Australian’s value their natural environment and overwhelmingly want to leave it a better place for future generations.
The SEC Newgate report also showed strong support for the concept of the Federal Government’s Future Made in Australia plans (67 per cent) with only 11 per cent of people opposed. Our industry is key to this, as we are able to provide the input materials to ‘making in Australia’. There really is a great opportunity to embed both WARR and circularity at the heart of the plan.
We haven’t seen much to date on that, but it is not too late. Not only does it reduce the drain on the planet’s resources and help address the climate challenge, it derisks the Australian economy by making us more independent, free from overseas shocks and grows domestic green jobs. Back to Kamala – ‘when we invest in climate, we create jobs, we lower costs and we invest in families’, seriously what is not to love?
Following the MEM in April, Australia now has a new Federal Environment Minister, Melissa Price, who in October reiterated to media MEM’s commitment to explore waste to energy as part of the solution to the impacts of China’s National Sword, which is troubling (EfW is not a solution to recycling). The Commonwealth has also backed the Australian Recycling Label and endorsed the National Packaging Targets developed by the Australian Packaging Covenant Organisation (APCO), which has to date, failed to incorporate industry feedback in the development of these targets. To the Commonwealth’s credit, there has been significant coordination in reviewing the National Waste Policy, with the Department of Environment bringing together industry players and States during the review process.
So why aren’t we seeing much more action much faster in Australia (it’s not like there is a Planet B!)? Let’s hope the government grasps this opportunity with both hands.
The updated Policy will now go before Environment Ministers on 7 December. The Commonwealth can play a key role – one that goes beyond the development of the National Waste Policy. WMAA is supportive of the Federal Government maximising the levers it has, including taxation and importation powers, to maintain a strong, sustainable waste and resource recovery industry.
AHEAD OF MEM 2
On the bright side, Newgate’s research highlighted that recycling is now seen as ‘hygiene’ – simply something we must do (well done all – that message has got through), but it really is time we moved the dial so that circularity becomes hygiene too, and not just a buzz word in yet another framework.
Gayle Sloan, Chief Executive Officer, WMRR
There may be movement across Australia, with some states doing better than others, but the consensus is, progress is still taking way too long. It is evident that there are funds available in almost all States to assist with developing secondary manufacturing infrastructure, however the only way that this will really happen is if there is government leadership around mandating recycled content in Australia now, not later.

Unlike its neighbours, Queensland did not provide any financial support to
Voluntary schemes like the Used Packaging NEPM, under which APCO is auspiced, are not working. We have 1.6million tonnes of packaging waste in Australia, which needs to be used as an input back into packaging. Barriers to using recycled content in civil infrastructure must be identified and removed, and Government must lead in this field and prefer and purchase recycled material. A tax on virgin material should also be imposed as it is overseas. MEM must show strong leadership on this issue. Ministers have, since April, dealt directly with operators and councils that are under stress and we have a chance to create jobs and investment in Australia at a time when manufacturing is declining. Ministers have the opportunity to be leaders of today, not procrastinators – leaders of tomorrow and we are urging
Chief Executive Officer
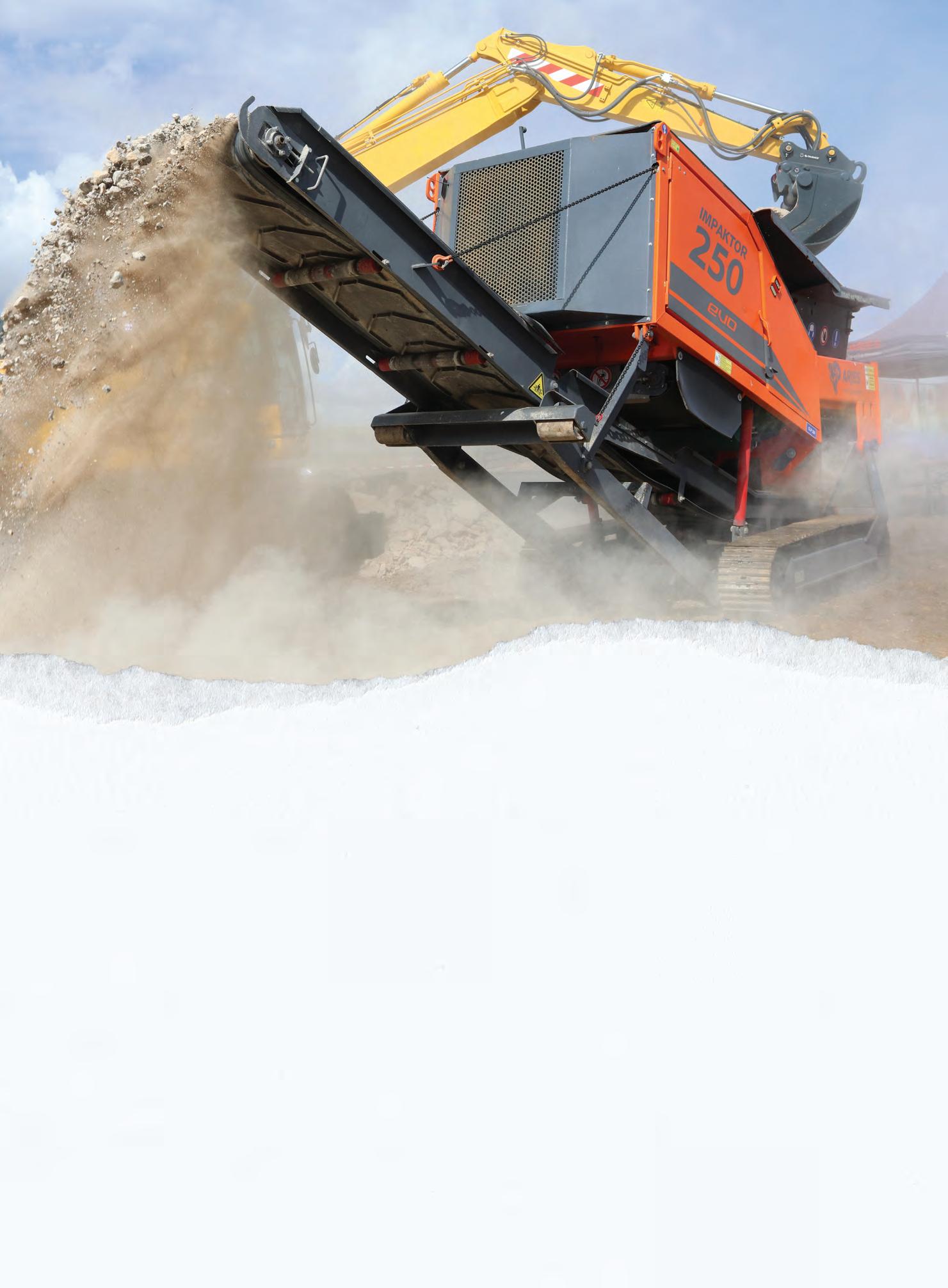
The Impaktor 250 evo is the perfect combination of shredder and crusher. Its compact dimensions, low weight, and quick setup times make it a game changer in waste processing efficiency.
For those interested in sustainable waste management, explore the possibilities with the ARJES Impaktor 250 evo.
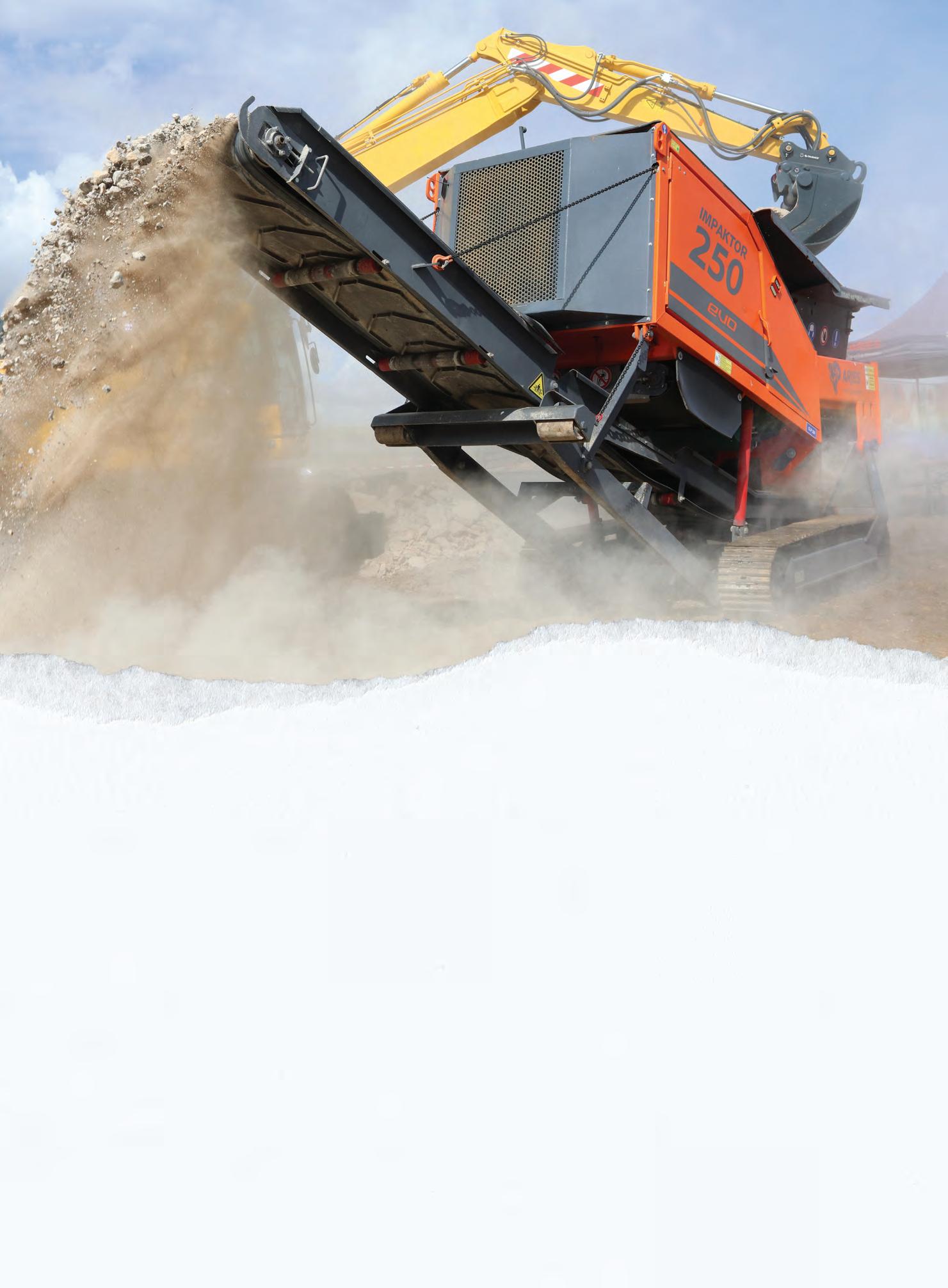
E: sales@triconequipment.com.au www.triconequipment.com.au
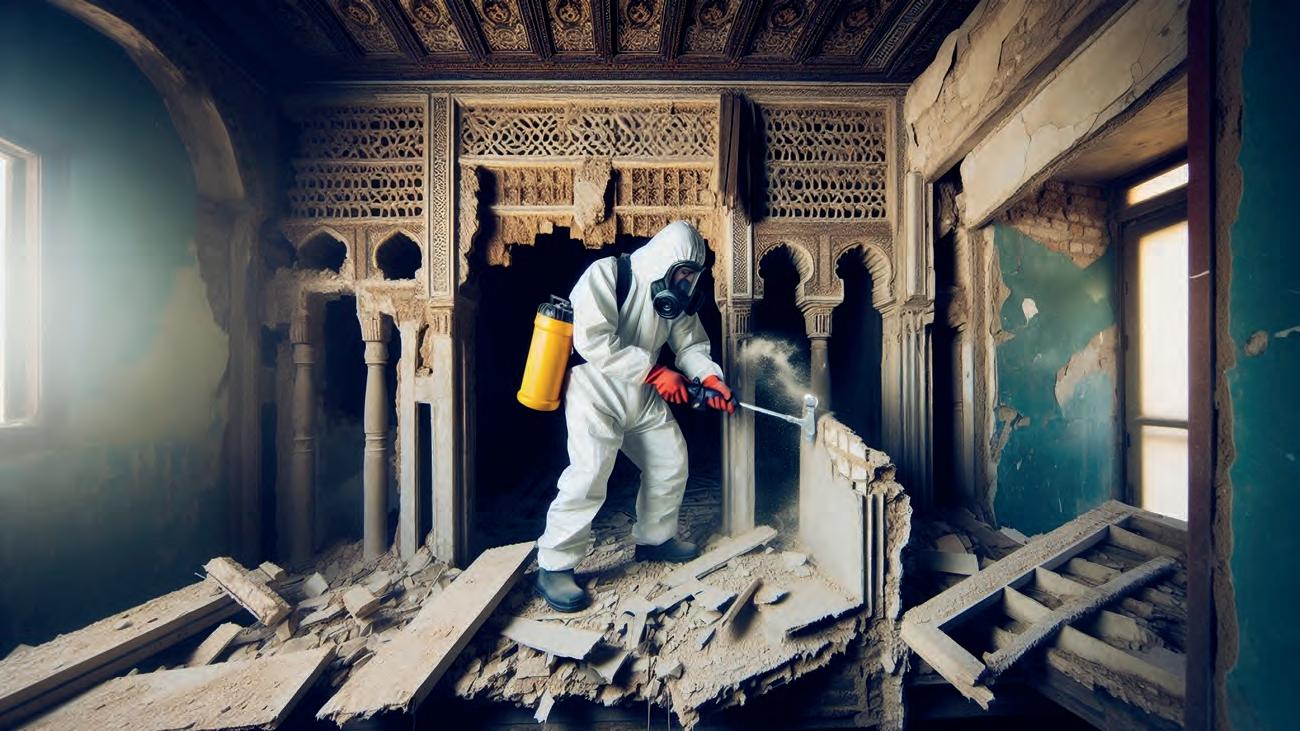
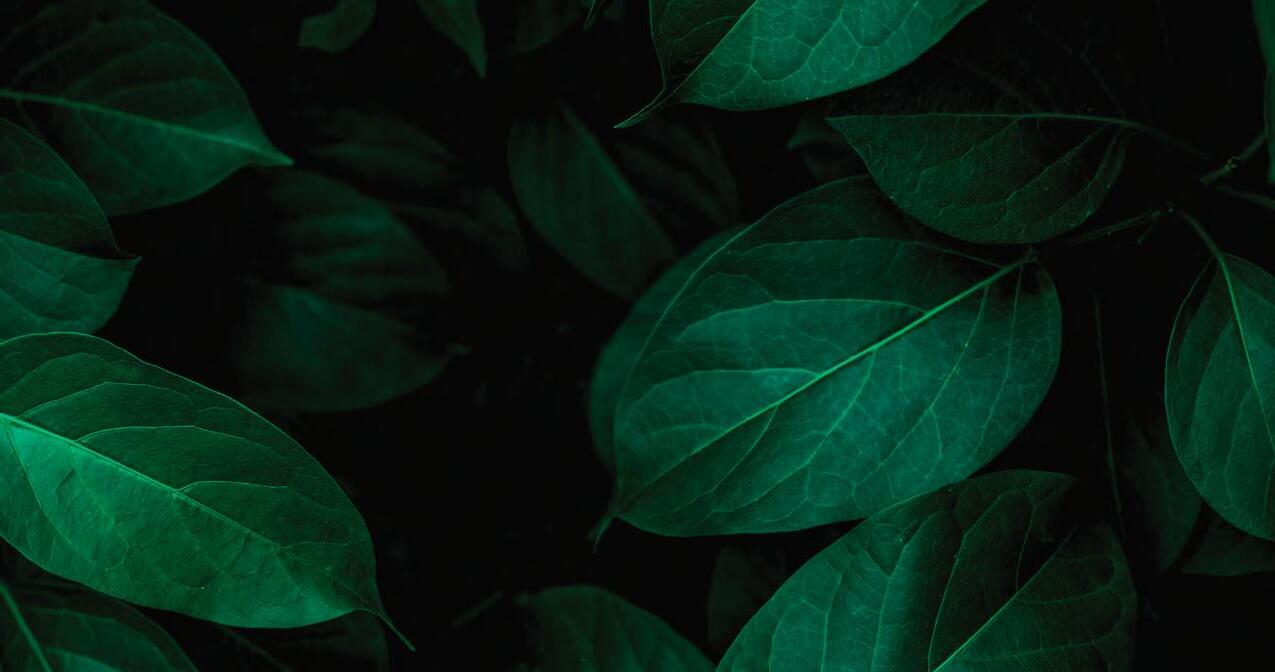


With its multi-rotor design the Genox J-series pipe shredder easily shreds HDPE pipes of all sizes.
When combined with a Genox washing plant and Genox pelletising system, you can truly close the loop on HDPE pipes. Pipe to pellets. Pellets to pipe. This is the circular economy in action.
Genox make world-class recycling solutions, for real-world recycling applications.

Call: Email:
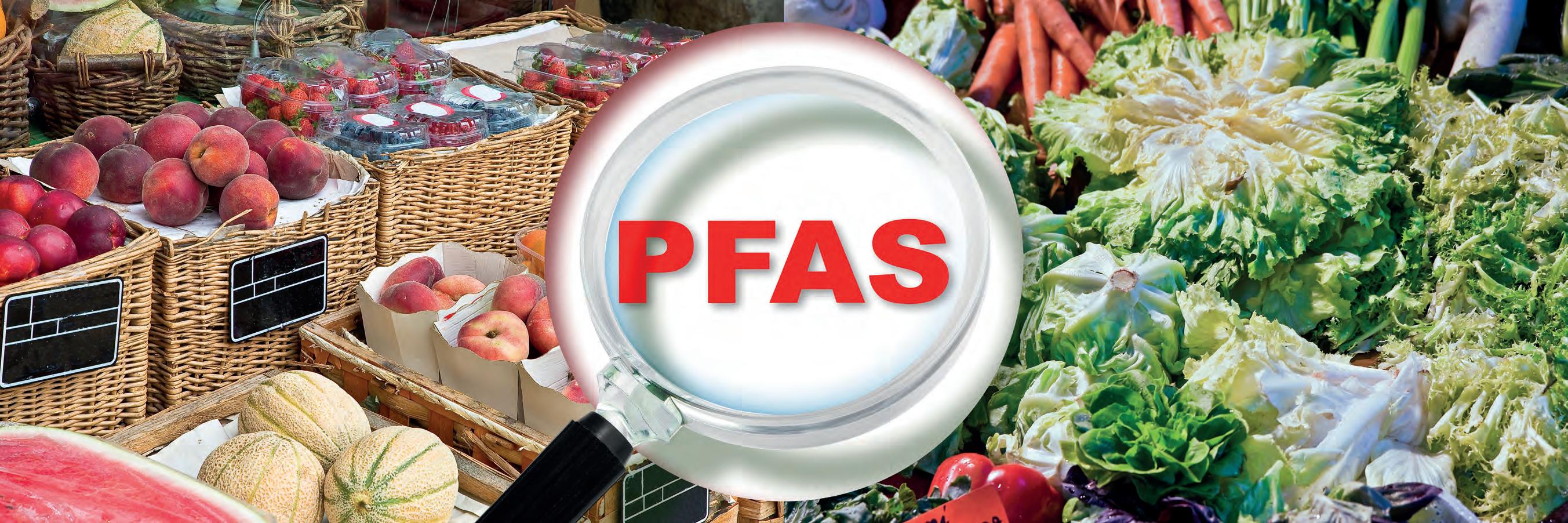
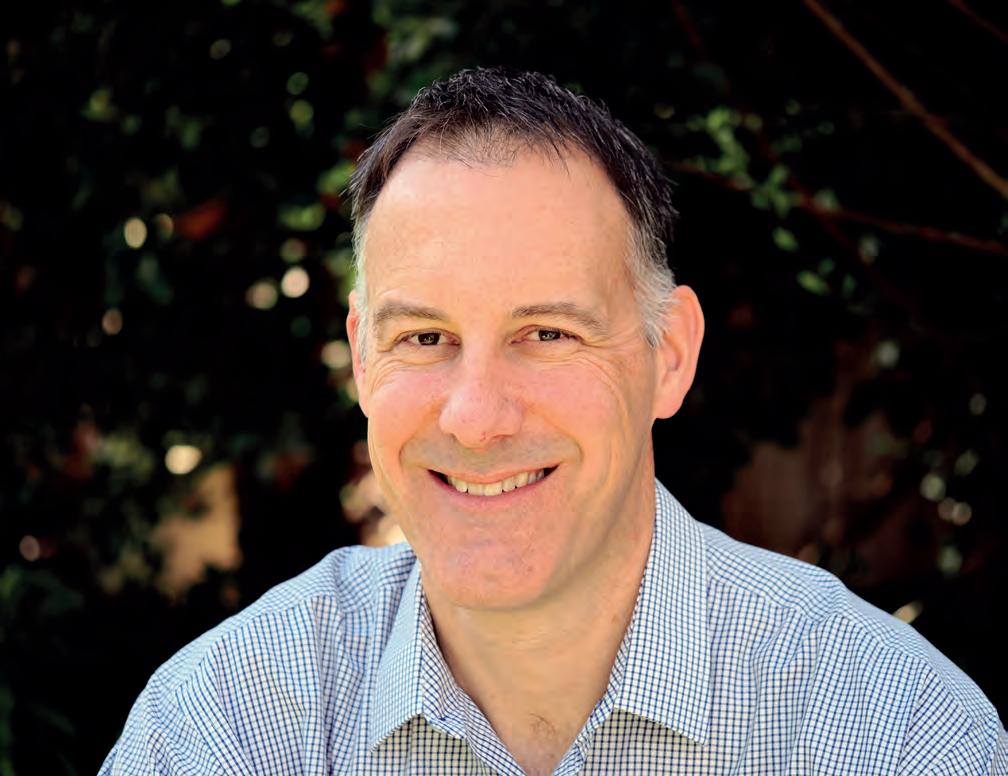
with, and that can be seen in a few resource recovery orders and exemptions. That’s equivalent to about one second in about
itchell said the Australian drinking water guidelines were 0.07 micrograms per litre, which he said is about a thickness of one sheet of paper lying across the Hume Highway between Sydney and Melbourne, or about one second
“These numbers are really low, but they are testable,” he said. “Consultants, contractors, and operators are trying to work out what to do with them.”
And how prevalent is it in the community and products? Very, according to Mitchell. It’s in firefighting foams, waste products, textiles, clothing, footwear, and carpets, which all have been treated with PFAS to make them easy to clean. It’s in an array of waterproof and grease proof packaging. It’s in the F component of FOGO. He said garden organics are pretty good, but when it comes to commercial FOGO waste, there is a lot of PFAS.
“It’s also in soils and concrete,
and asphalt is contaminated with it, so it’s everywhere,” he said.
Currently, there are not many requirements when it comes to testing for PFAS in waste, unlike asbestos, which has a myriad of rules and regulations around how it is to be handled and disposed.
“If you’re working with the site-specific resource recovery orders and exemptions, most of the recent ones require some testing for PFAS,” said Mitchell. “And that flags where the EPA is headed with the resource recovery framework in the (Dr Cathy) Wilkinson Review. Sometimes, if you have a licence to discharge from a site that’s known to have PFAS contamination, you may have to test for PFAS in that discharge. Contaminated land investigations often include testing for PFAS.”
Mitchell said there is a new standard – Industrial Chemicals Environmental Management Standard (IChEMS) – that is pointing the finger at the bad chemicals.
“This is a commonwealth government regulatory package that is about banning chemicals that are really, really bad,” he said.
Andrew Mitchell likes to put the risk of PFAS contamination in perspective. Image: Andrew Mitchell
It’s surprising the amount of products that contain PFAS – but how dangerous is it?
Image: Francesco Scatena/ Shutterstock.com
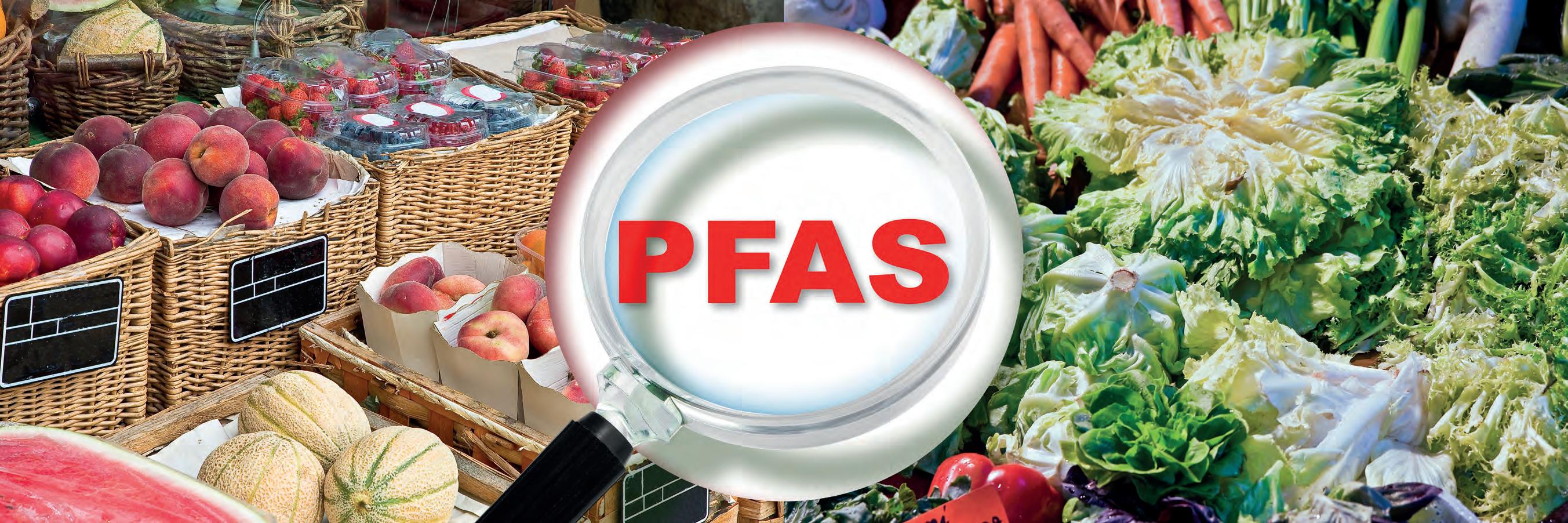
“PFAS have been listed in IChEMS. Every state has indicated that they will make it a law, but so far only New South Wales has done so via the POEO (Prevention of the Environment Operations) Act. You’re not allowed to dispose of PFOS greater than one milligram per kilogram. You’re not allowed to use it if you have more than 25 micrograms per kilogram –that’s parts per billion.”
The Queensland compost guidelines state that only one microgram per kilogram of PFAS, or one part per billion, is allowed in compost.
A recent study found that the concentration of PFAS in Queensland compost, on average, was 12 times higher than the guideline.
“This could effectively ban composting in Queensland, which, I’m sure, is not what was the
measured these parameters,” said Mitchell. “They were 7 parts per billion on average. So, some biosolids are going to comply, many are not. And where are they going to go? Who’s going to pay for that? Is that what our society wants?”
Mitchell suggested that time is needed to bring in these guidance measures. There will also need to be some expensive investment in
“Guaranteeing that materials in the recycling and waste industry are asbestos free is, quite frankly, something that can’t be achieved.”
And this might lead to some problems, according to Mitchell. This is because the concentrations outlined in the guidelines are exceeded in some of the circular economy feedstocks. He said it is possible to get an exemption under an EPL, but if a company or person doesn’t have that EPL exemption, and they use or dispose of the chemical outside those guidelines, they’re committing an offence.
He also said that Queensland could be in trouble when it comes to PFAS contamination of compost, if the results of a recent study are true.
intention,” said Mitchell. “But it’s an illustration of making policy without the connection with science and industry.”
And what about biosolids and the amount of PFAS they have? It is going to be challenging, according to Mitchell. NSW released a draft guidance on biosolids in 2023. There is a range of margins of safety that depends on the policy parameters. With unrestricted use, the PFAS limit is between 0.2 and 1 parts per billion, whereas restricted use, is between 6 and 31 parts per billion.
“Three different studies have
infrastructure and in wastewater treatment systems, and some time for the operators of those networks to find the point sources of PFAS in these systems. He thinks that endof-pipe solutions are not going to solve this problem.
Asbestos risks
When it comes to asbestos, Hibbs and Associates Samantha O’Callahan, gave the lowdown on the various types, which are the most dangerous and how they need to be handled.
F irst is the high-risk, or friable,
material. This is in materials like sprayed insulation, which can be easily reduced to powder when crushed by hand, when dry. O’Callahan said this version of asbestos is uncommon in the waste industry but does find its way into some streams on occasion.
She also pointed out that it is important to know the difference between the different types of exposure that can occur.
“We can be exposed to it every day,” she said. “For instance, during a home renovation, there is a risk because you’ve been exposed, but that risk is low. But as soon as you start seeing situations where – over your working life – you’re constantly exposed to asbestos, such as in the mining and manufacturing industries, there is a very high risk of developing asbestos-related diseases.”
O’Callahan’s biggest talking point was the recent asbestos exposure in public parks in NSW that occurred at the beginning of 2024. She pointed out that the media almost bordered on hysteria in some cases, when the facts didn’t play out in favour of what the media
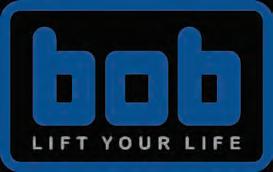
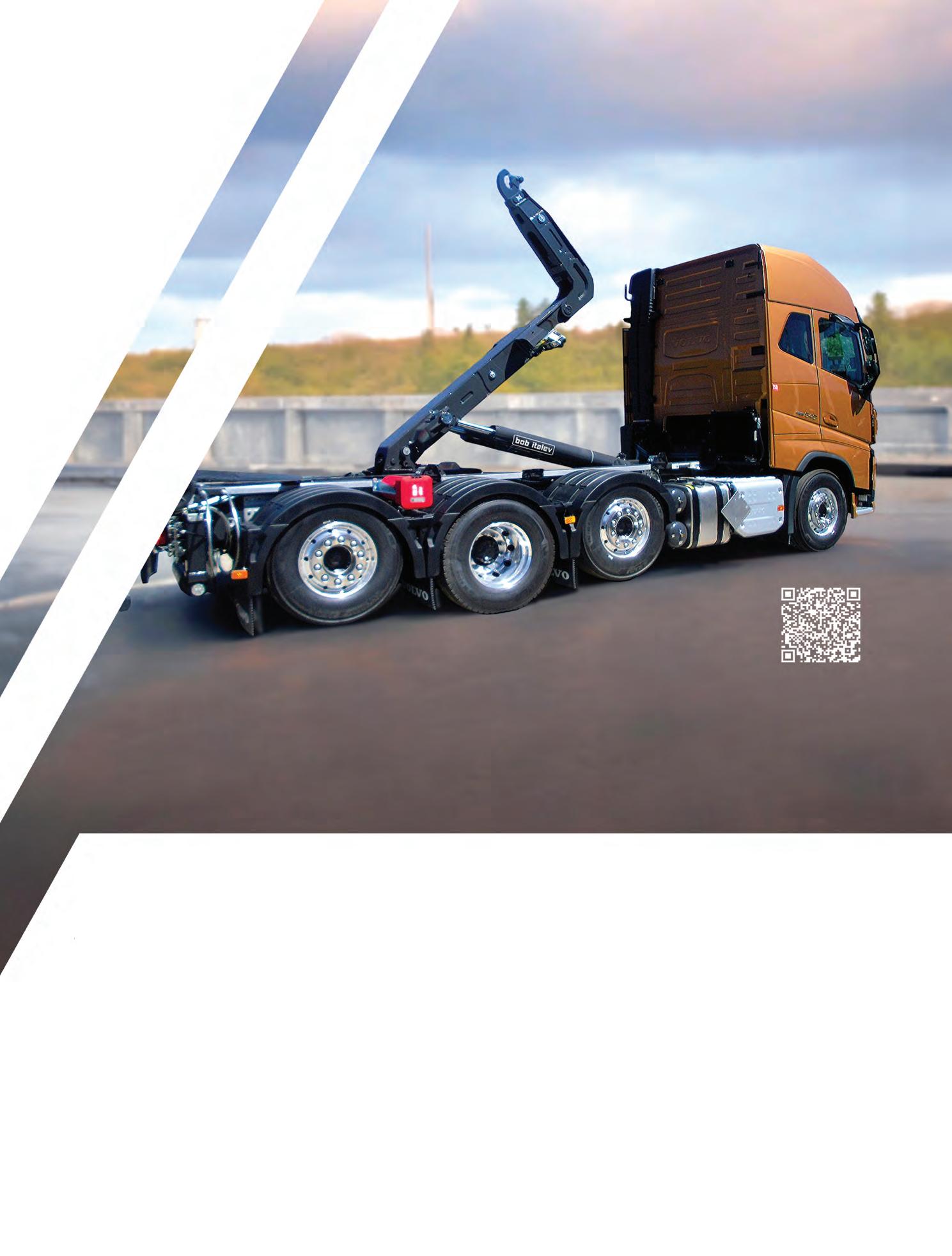
BOB HOOKLIFT SYSTEMS
Versatile, Durable, Dependable
The BOB hooklift system offers ultimate flexibility, allowing you to effortlessly switch between containers to meet a variety of waste management needs. It delivers consistent performance even in the most challenging environments. With its quick loading and unloading capabilities, the BOB hooklift maximises productivity, streamlining operations and minimising downtime. With readily available spare parts and 24/7 service support, you can ensure long-term performance.
Upgrade your fleet with BOB today!
Contact Us:


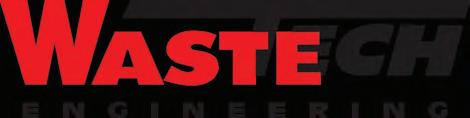
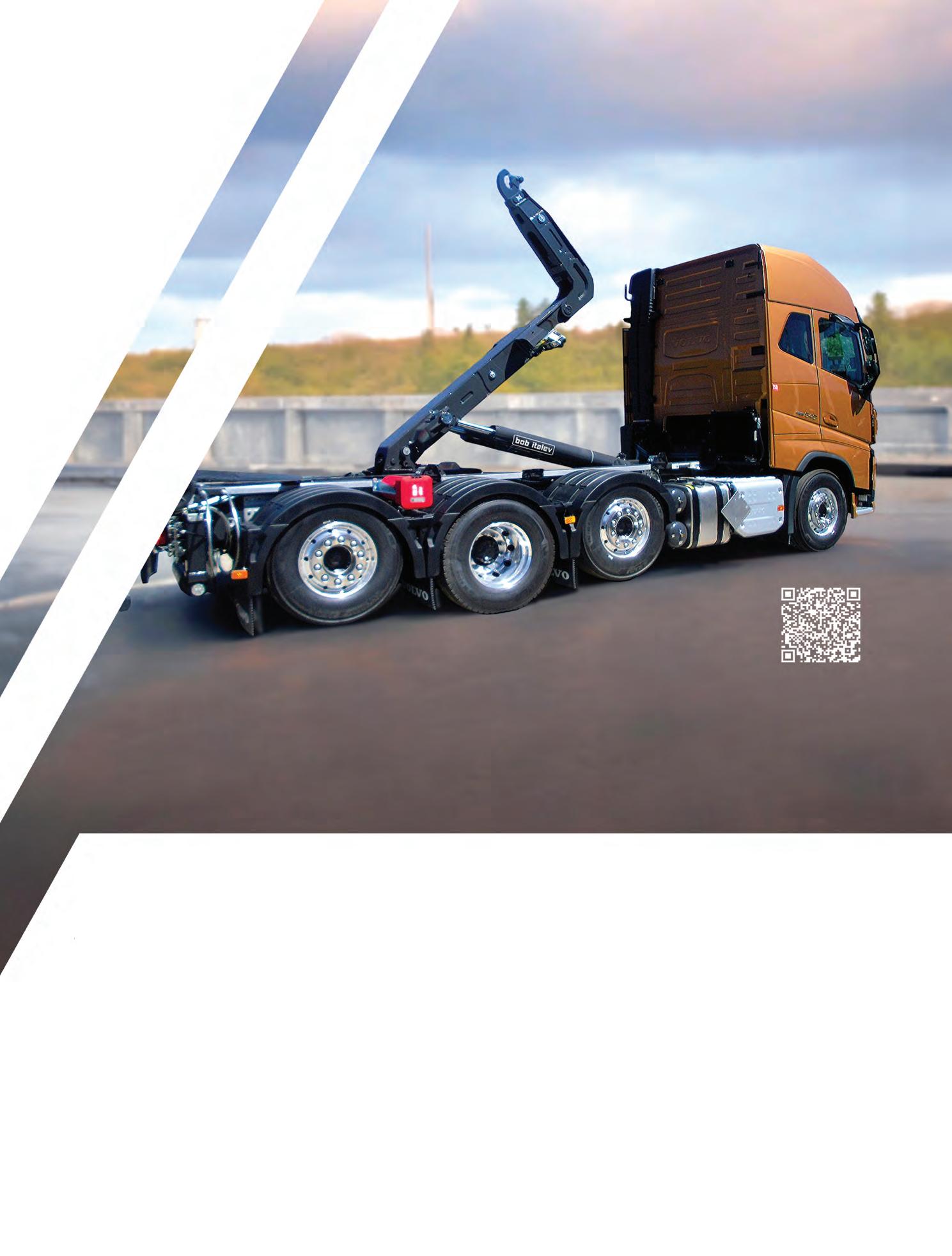
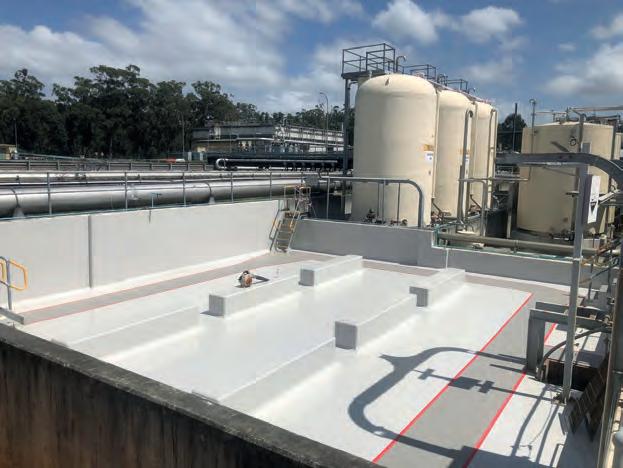
FOR CONCRETE AND STEEL

was trying to portray. One article stated that “research highlights the importance of making it mandatory to certify recycled products such as mulch to ensure their safety. These obstacles must be overcome, so we have certification of recycled products to ensure their quality performance, environmental friendliness, and safety”.
“This example article highlights a fundamental lack of understanding, or lack of reaching out to experts, with regards to the waste industry resource recovery and the perception of what certifying products actually means,” said O’Callahan. “Guaranteeing that materials in the recycling and waste industry are asbestos-free is, quite frankly, something that can’t be achieved.”
As she pointed out, it is important that everybody does their best to mitigate the exposure of asbestos in the atmosphere, but the resource recovery industry has little or
by the consultants that looked at it,” said O’Callahan. “But from an Occupational Health and Safety viewpoint, cement sheet, whether it goes through a seven mm sieve or not, is non-friable and a low risk. And the regulator did see it that way, and did allow for the cleanup to be done under the same conditions as if it were larger than seven mm.”
According to O’Callahan, occupational hygienists have stated that there needs to be significant disturbance to generate respirable fibres from asbestos cement, which is the typical contaminant the resource recovery industry has to contend with.
“It’s really important that we manage the perceived risk of asbestos as well as the actual risk,” she said.
“They are both super important and can also both shut down projects and industry. What’s the status in industry today with regards to asbestos? Essentially, you guys are in
“There were a couple of asbestos cement fragments that were smaller than seven mm, so they were classified as friable by the consultants that looked at it.”
no control of how the material is handled further upstream.
But perception matters. And although the contaminated mulch was presented as high risk for playgrounds, schools and parks, people kept going about their daily activities, said O’Callahan.
Even though the public was outraged, they didn’t seem to have an issue with the fence being the only thing that separated them from asbestos-contaminated mulch, which was really no barrier at all.



“From a health risk perspective, that most certainly was a reasonable way to isolate the contaminated mulch, because the risk actually was really quite low,” said O’Callahan. “However, the way it was hyped up in the media…it really did have a flow-on effect and got out of control.”
Once all the handwringing, investigations were completed and reports had been written, less t han five square metres of asbestos was found in the thousands of tonnes of mulch that was removed. Of that five square metres, 90 per cent of it was cement sheet, which is non-friable.
“There were a couple of asbestos cement fragments that were smaller than seven mm, so they were classified as friable
limbo with regards to how asbestos is handled. There’s still no formal process for dealing with unexpected fines.”
What happens now and into the future? There was a draft document that came out in 2014 that was designed to manage asbestos in its recovery in the construction and demolition industries. That document was then replaced by one called Standards for Managing Construction Waste in NSW, but set unrealistic expectations.
O’Callahan said that NSW is reviewing how it approaches the management of asbestos, especially about how to get greater consistency between jurisdictions.
“This is an independent scientific review, so I am hopeful that we’re going to see change in government policy, and that’s certainly the feeling that I’ve been getting at workshops and speaking to other people in the industry,” she said.
“The chief scientist’s office will deliver a report to the Minister for Environment and the New South Wales asbestos contamination committee, and we’re expecting that towards the end of this year. So hopefully we can start to see some change and some stakeholder engagement next year about moving forward.”

Bigger than bottles and cans
(Continued from the Cover)
It is important to recognise that while the South Australian CDS is the oldest in the country, and is un ique in its quasi-market-based system and limited regulation, it remains the best performing scheme in the country.
A review of the comparative performance of schemes undertaken by Total Environment Centre in 2023 (using a mix of FY21 and FY22 data) shows that South Australia remains at the top of the leader board, with return rates more than 10 per cent above NSW, Queensland and WA. One reason for this success is it being almost exclusively depot based. In addition to CDS containers, many of our members depots also accept
a range of out-of-scope products including wine bottles, cardboard and plastic, gas bottles, fluorescent tubes and even paint cans. Our customers love the fact that they can come and talk to us, and that even if our members don’t accept a product, they can generally tell them who does. It’s this human interaction and feedback that you can’t get from a website, an app or a reverse vending machine.
It’s continued success does not mean that the South Australian CDS is not without its issues.
As an example, advanced sorting machines, including those developed and built in South Australia and used extensively in Queensland, the ACT, WA and Victoria, cannot yet be implemented effectively as they would see customers presenting
materials to be automatically counted, only for aluminium cans to then be manually hand-sorted and separated by brand. This is an utterly ridiculous and archaic requirement. Some depots are also restricted from baling collected products before transport, resulting in trucks transporting loads that are largely air, leading to higher transport movements and carbon emissions than necessary.
Changes to the scheme in South Australia must not introduce barriers such as machines that can’t read crushed containers, which are a prime example of how ineffective decisions hamper success and impede progress. Continuing to accept crushed containers is non-negotiable, as it offers volume efficiencies
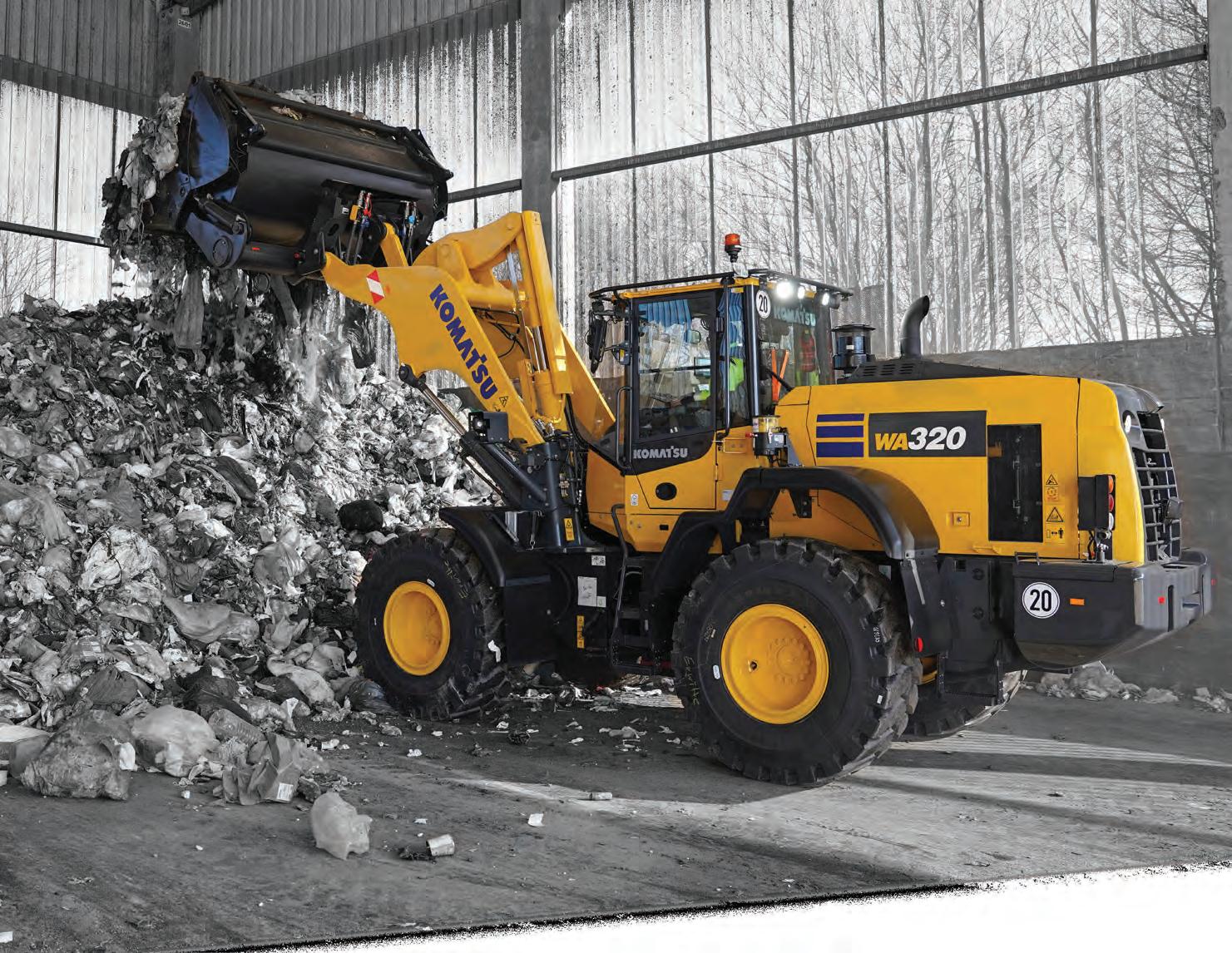
for both transport and collection, while simultaneously maintaining incentives for reducing litter – a primary objective of the original CDS in SA. Similarly, harmonisation of scope must not exclude currently accepted containers, such as those with a volume less than 150 ml.
These inefficiencies are simple to solve, with the solutions already developed by experienced recyclers who understand what works, what the community wants, and what the system needs.
As part of the CDS review, a discussion paper in 2021 highlighted that a revised governance model could be closer to the models employed in Queensland and Western Australia, where a single network operator is responsible for the operation of the scheme. Such a model may have worked for the establishment of greenfield schemes, including a network of collection points and logistic
Unlike most other states, South Australia already collects wine and spirit bottles at its collection points. Image: Gemenacom/shutterstock
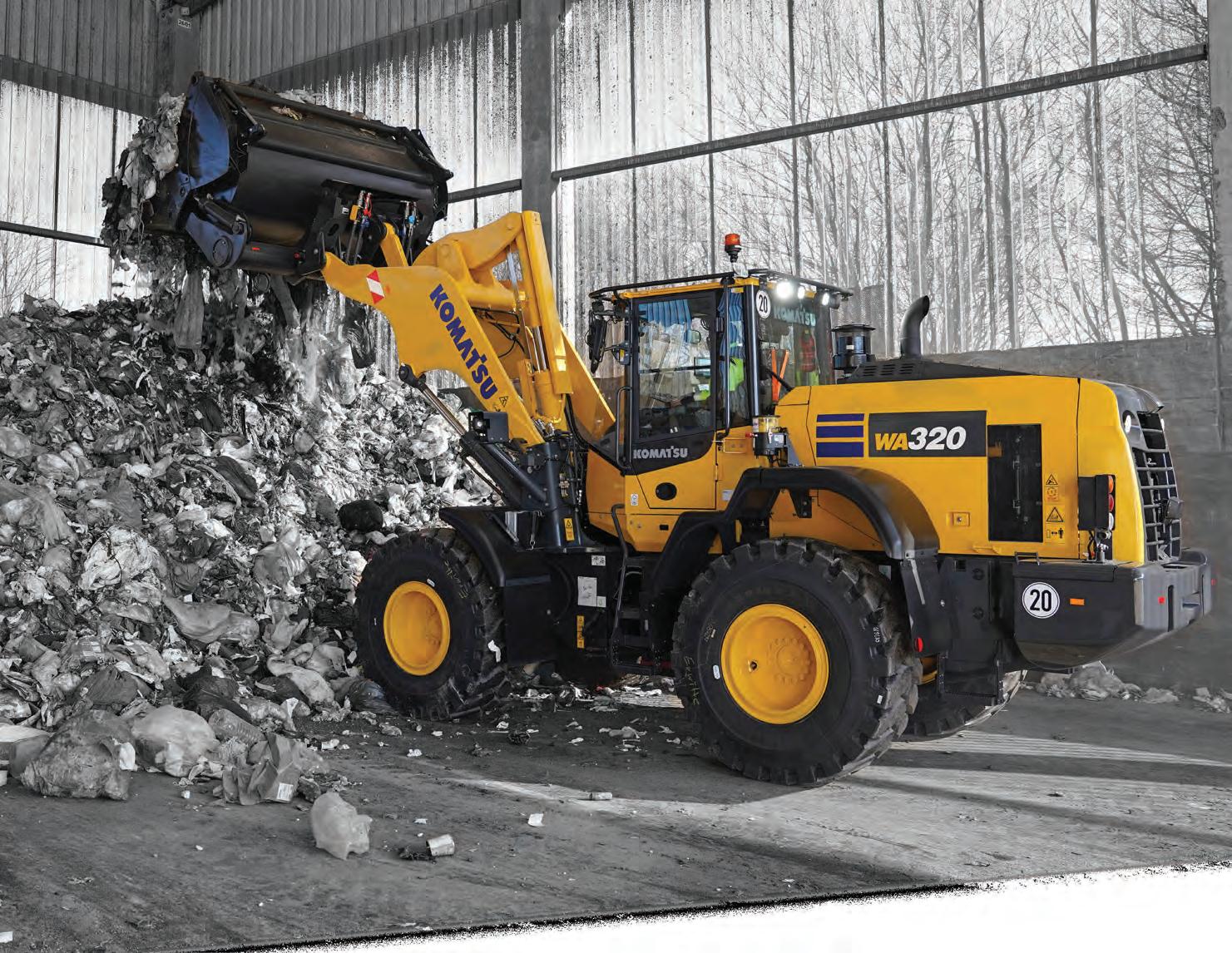
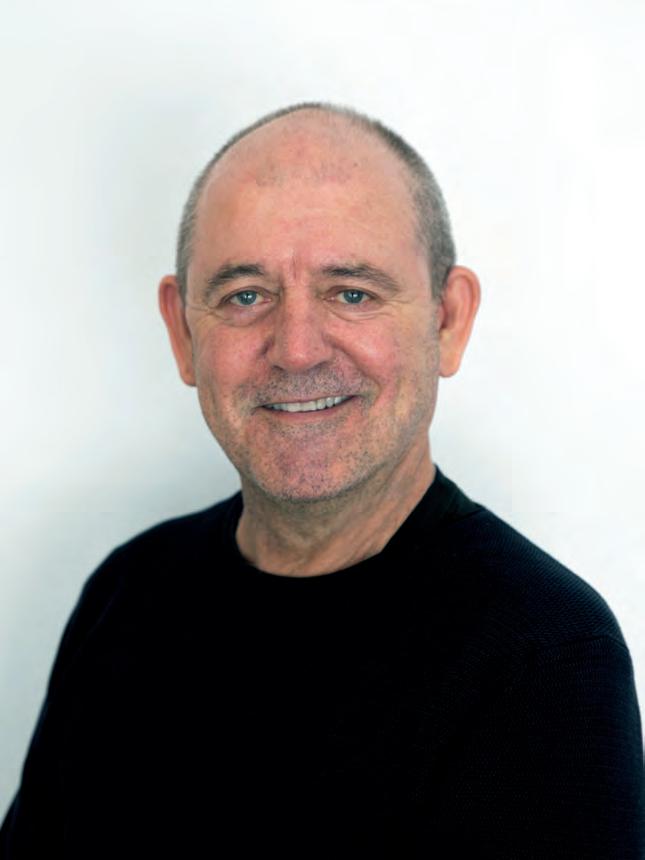
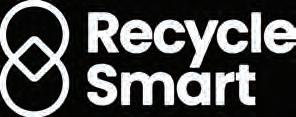
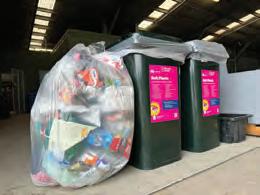
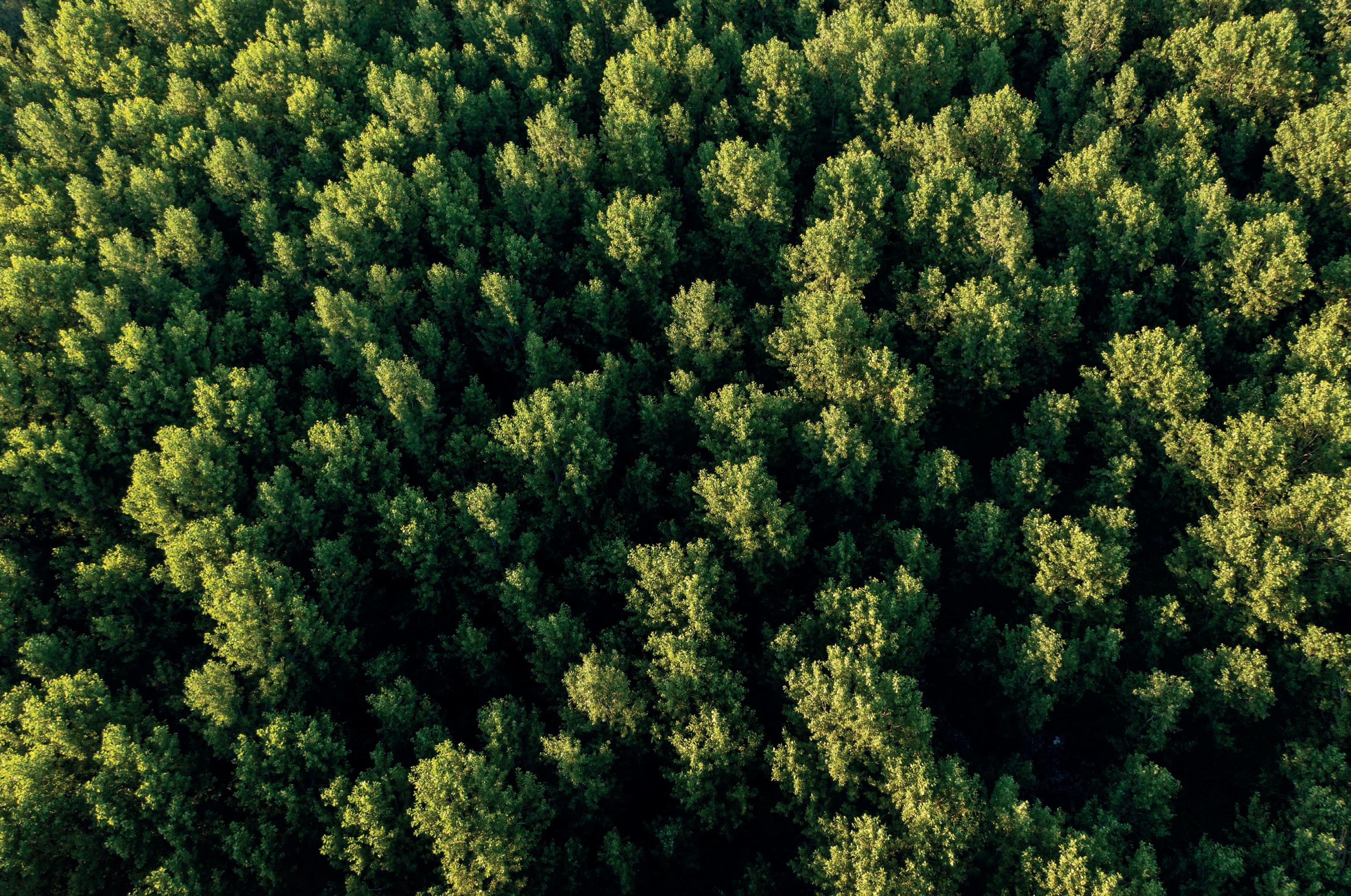
operations where none previously existed. The situation in South Australia is totally different with an existing network of well-established collection point operators served by competing network operators, which is delivering the best return rates in the country.
While not without its issues and anachronisms, it cannot be denied that the South Australian CDS is still delivering the best return rates in a now national set of schemes and doing so in possibly the most cost and environmentally efficient way.
As an example, in South Australia, the ownership of the returned glass containers is by the collection points; those containers are aggregated through a company and on-sold to one of South Australia’s glass container manufacturers, where the cullet is processed through a new beneficiation plant and goes directly into new glass containers. This mechanism reduces the input costs and carbon emissions from the glass plant and provides a per tonne value for the glass back to the scheme that would make our friends in other states weep. This high value product ultimately reduces the cost of the
scheme for all participants.
The risk for South Australia is that we now have a review in its sixth year, which needs to be urgently concluded, but without destroying the best performing scheme in the country.
A dopting a scheme model from other states for the sake of expediency would be a grossly retrograde step that risks 45 years of hard work by existing scheme participants.
Rather than focussing on destroying a working governance model, which requires only minor tweaks, the conclusion of a review should focus on the issues on which the community is demanding action.
The Queensland Government’s recent inclusion of wine and spirit bottles in their CDS shows they have ‘read the room’ understanding public frustration and responding accordingly. In the eyes of the community, excuses for not increasing scope have lost all relevance, and have the appearance of pandering to lobbying by parties with vested interests.
The recent behavioural report prepared by the Heads of EPA group
Recyclers Association of South Australia’s president Neville Rawlings. Image: Neville Rawlings
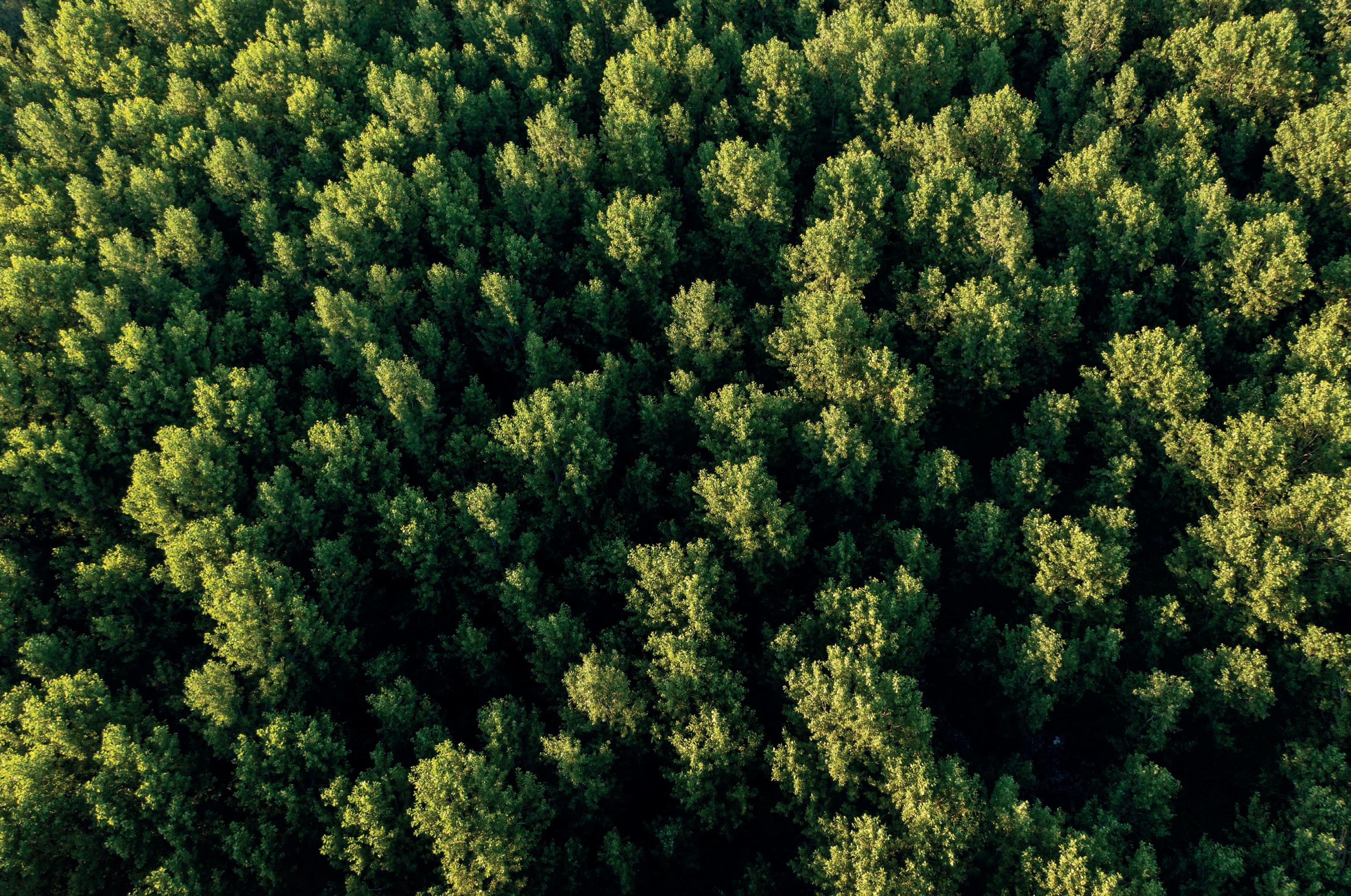
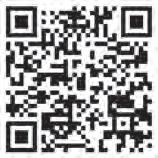
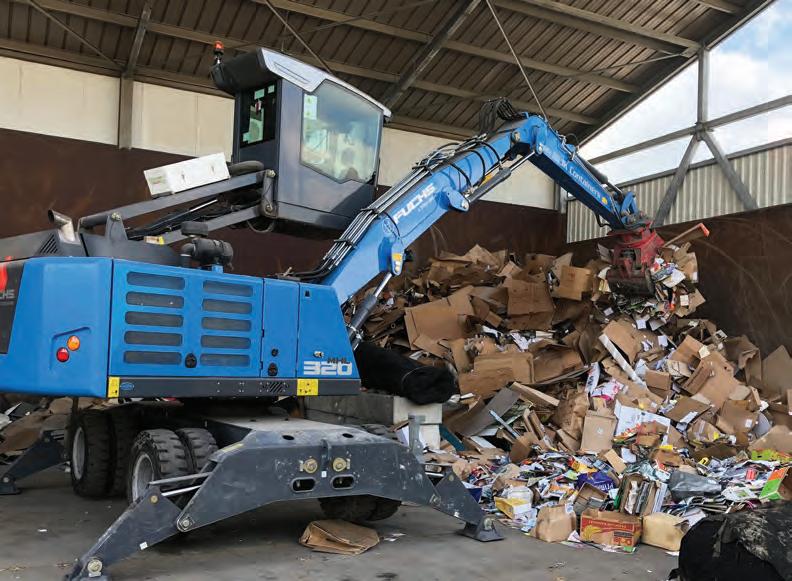
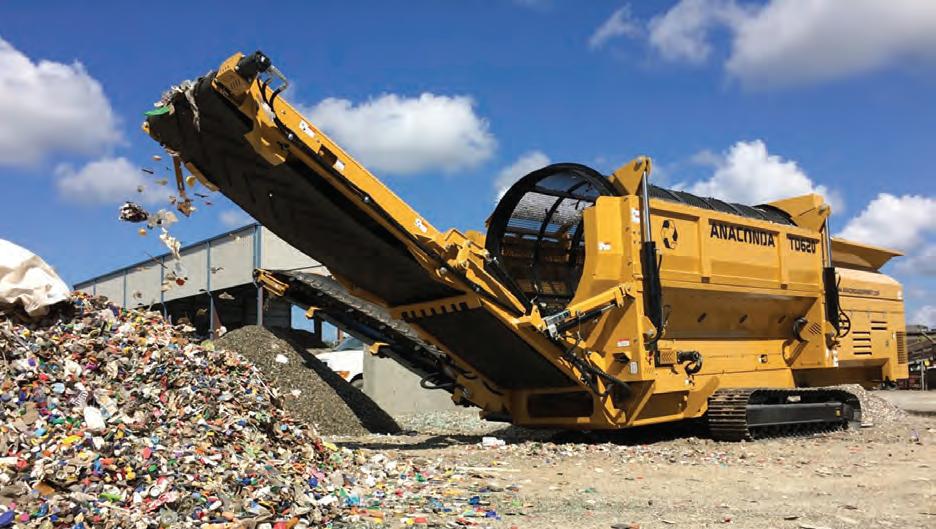
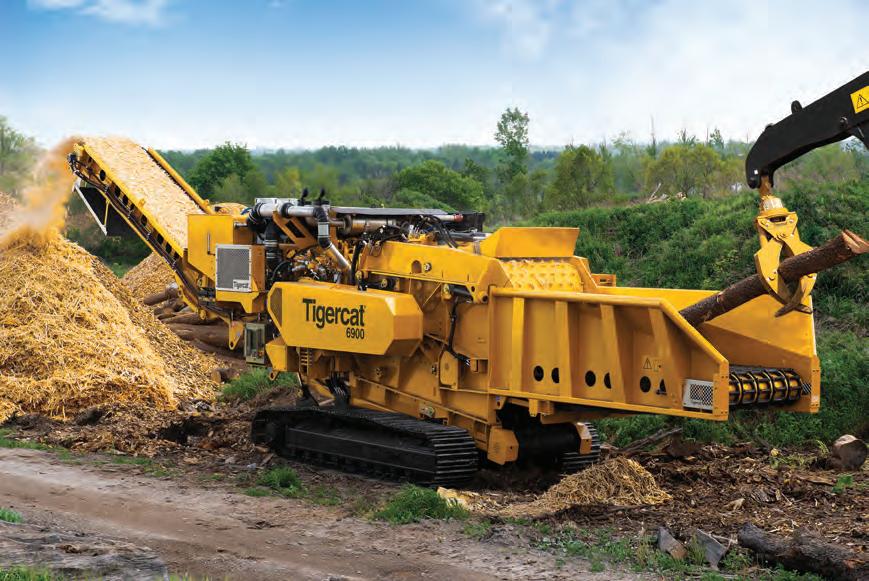
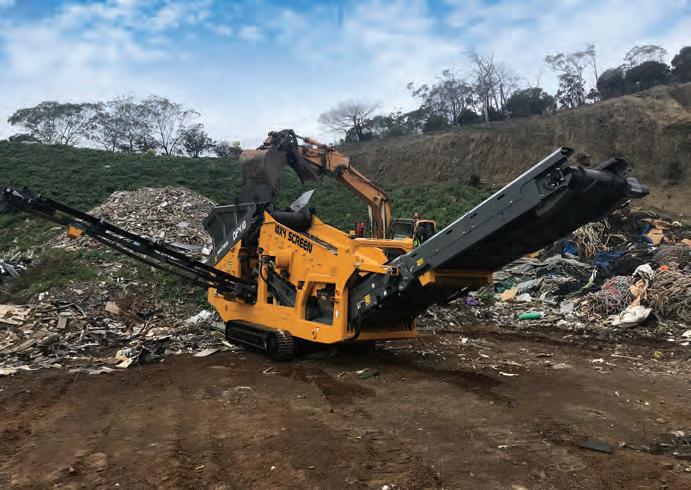
Invest in quality machines that are backed by a national parts and service footprint for the ultimate
From material handlers, to trommels, stackers, grinders, screens, dozers and more. Our industry specialists will create a personalised solution for your business. Onetrak, the exclusive national distributor for Fuchs, Tigercat, Anaconda, Dressta, Hidromek and Striker.
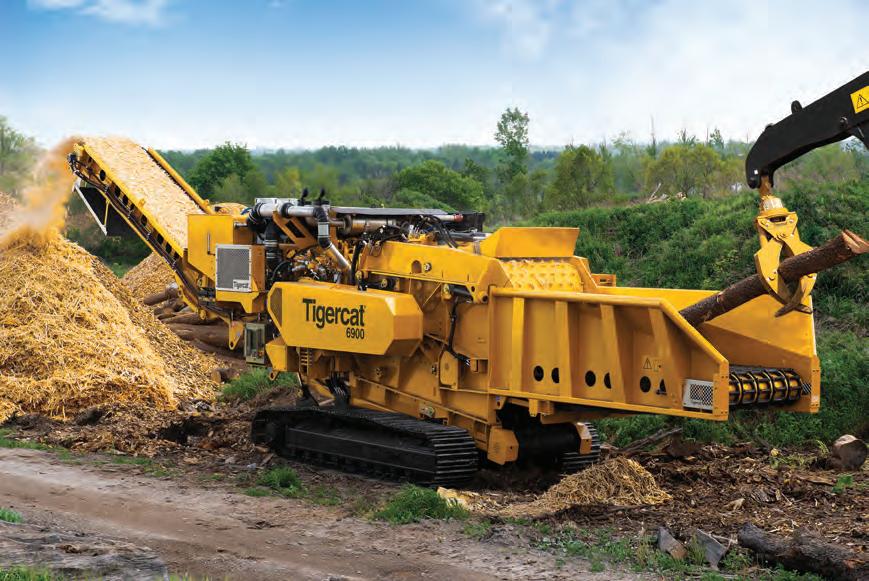
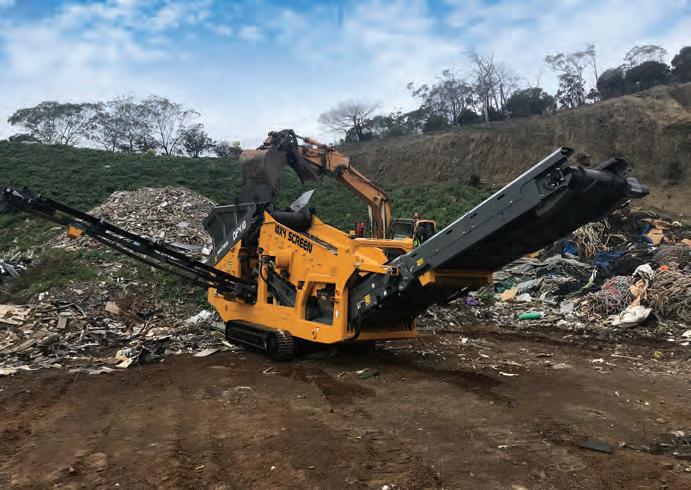
has provided further insight. The HEPA report indicated that for consistent users and irregular users, increasing the refund amount was the biggest insight to maintain and encourage participation at 43 per cent and 42 per cent respectively. RSA has long advocated for review of deposits to ensure that they remain set at a level that encourages participation.
In an Inside Waste article several years ago, RSA highlighted that the 5 cent deposit applied to containers in South Australia in 1977 would today be worth more than 35 cents., With the current 10 cent deposit, consumers have seen the real value of their deposit eroded by more than 70 per cent since the introduction of the South Australian scheme. With 10 cents in 2008 now worth 15 cents, the real value of the deposit has eroded by over 30 per cent since South Australia increased the deposit from 5 cents to 10 cents.
While achieving a deposit value equivalent to that at the introduction of the South Australian CDS may not be achievable in the immediate term, the increase in scope demanded by the community would go some way to offsetting the erosion of the
deposit through inflation. Moving forward, there should be a clear and defined pathway to review of the deposit amount, such as a review every decade being enshrined in the scheme legislation taking inflation into account.
With the medium-term potential for scope to move beyond just beverage containers, reform must ensure that the scheme
containers and litter reduction.
This is bigger than just bottles and cans. Ultimately it is about the amount of material that moves through the scheme to true circular outcomes, and the governance of a modernised scheme must reflect this.
RSA advocates a model that builds on the established depot network in South Australia, retains competitive tension in the ‘back-of-house’ of the
community that the CDS operates transparently and prioritises environmental and social outcomes over commercial gains.
RSA’s vision for a modern CDS integrates more than 40 years of innovation and experience. This approach is about enhancing an already successful system by addressing its flaws and adapting to new challenges. It’s about leveraging
“The community’s demand for change is clear, and the benefits of a modernised CDS are undeniable. By embracing these proposed changes, South Australia can once again lead the way in recycling and circular practices, setting a standard for others to follow.”
facilitates such ongoing growth and improvement of the scheme. The governance model adopted now will control what happens in the future. That governance model needs to be independent and free of conflicts. The governance outcome can’t entrench the beverage industry as the custodian of the scheme, as has occurred in several jurisdictions. To do so would be a huge step backwards for South Australia as the scheme needs to truly move beyond beverage
scheme, and provides for oversight by an independent governance board who has the powers required to ensure the scheme meets objectives.
In addition to raising refund values, RSA emphasises the importance of independent governance. The current system’s entanglement with vested interests has led to compromised decisions. An independent governing body would act as the ‘people’s representative’ and ensure on behalf of the
past successes to create a more robust and efficient future.
The community’s demand for change is clear, and the benefits of a modernised CDS are undeniable. By embracing these proposed changes, South Australia can once again lead the way in recycling and circular practices, setting a standard for others to follow. The time to act is now, and the opportunity for positive change is within our grasp. Let’s seize it.
Maximise Recovery... Reduce Landfill Costs
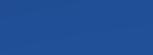
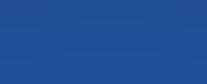
through…

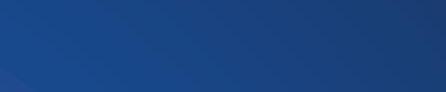


Superior Equipment
equipment


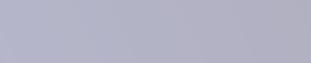
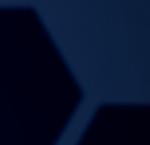
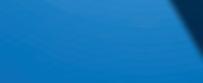
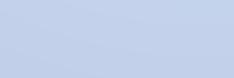
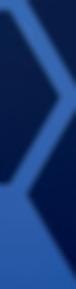

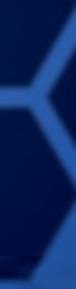
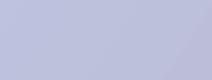

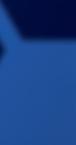
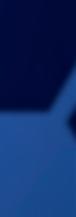
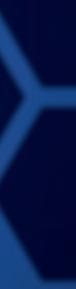

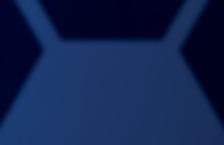

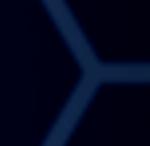
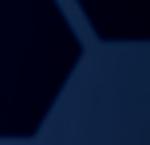
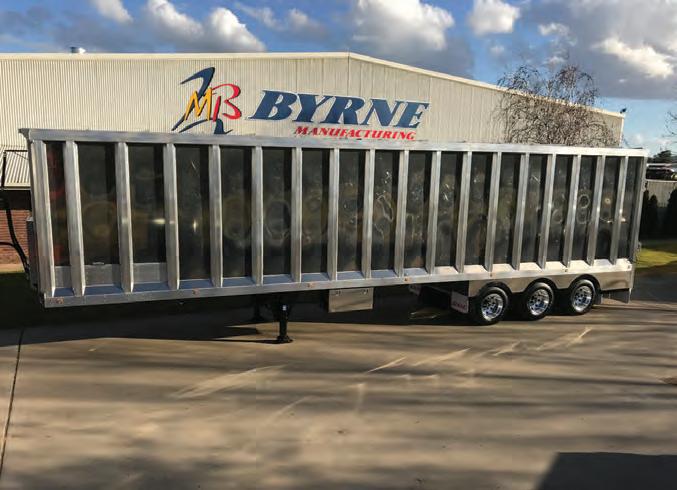

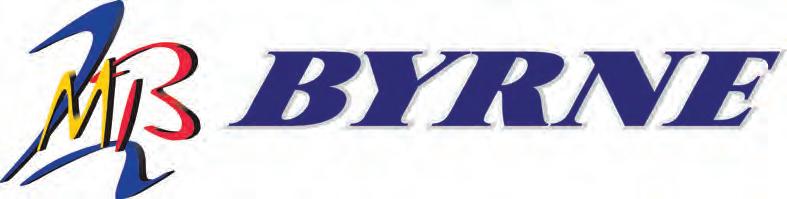
MobileMuster looks to up the recovery rate
By Inside Waste
MANAGED BY THE
Australian Mobile Telecommunications Association (AMTA), MobileMuster is ramping up its presence in the mobile phone reuse/recycling and refurbishment market. While it has seen an increase in collection of mobile phones, there is still a long way to go, according to its marketing and public relation manager, Joel Murray.
In 2022/23 the association collected 96 tonnes via its MobileMuster initiative, while for 2023/24 that has gone up to 109 tonnes. Murray said that while it is a good start, there are still millions of broken phones sitting in homes and businesses around the country.
T he association is aware that there is a lot of work to do, and has initiated a lot of engagement with the community, with plans to do much more in the near future.
“We’ve done a lot of work, and we are working hard to increase awareness and change behaviours through marketing campaigns,” he said. “We’re getting better traction and we’ve also increased efficiency on the back end, focussing on working with more business partners for larger collections, rather than the consumer just dropping one phone off at a time.”
He said that it’s those efficiencies that are leading to larger gains, as the numbers indicate. A recent IPSOS
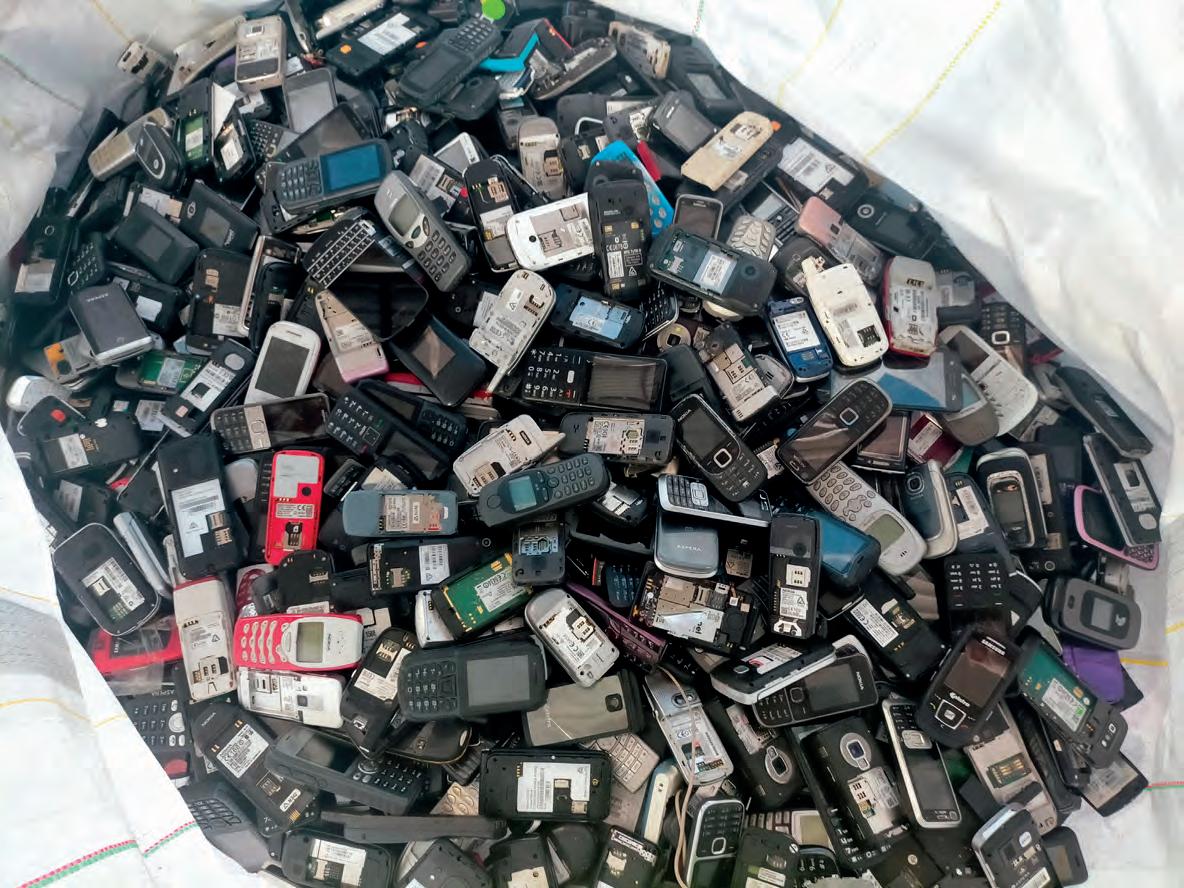
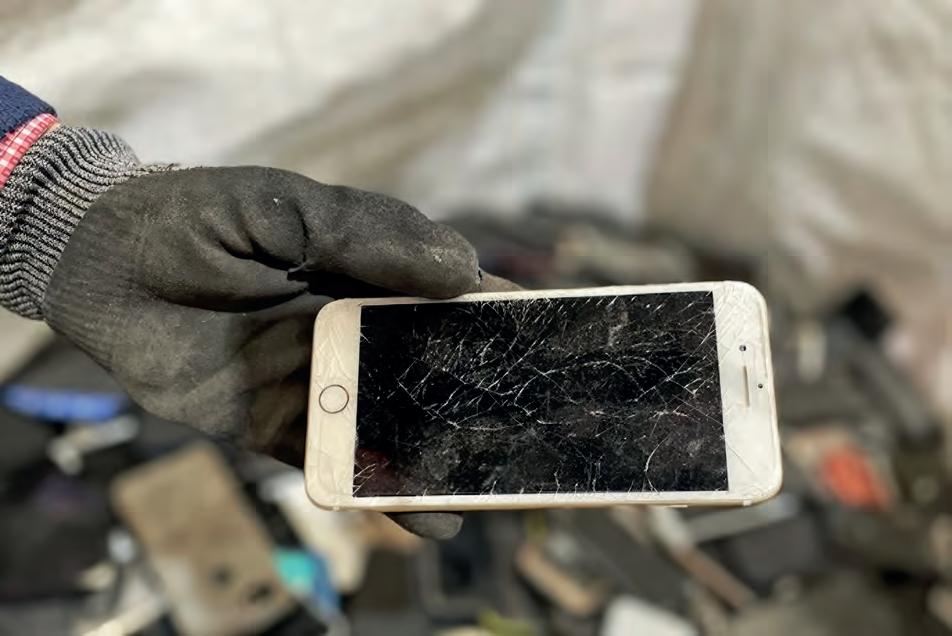
“It’s the aluminium, plastic, the glass that’s valuable, and that’s the stuff that can be reassembled over and over.”
year they have gone from 13.8 million down to 13.3 million – a decrease of 500,000.
From an environmental perspective, refurbishment or reuse are the best outcomes for a second-hand phone, but if these options are no longer viable, recycling is the only way to go. And while the status quo might suggest the importance of the rare earth and other metals being reused, Murray said there is more value in the aluminium, plastic and glass because those materials make up the greatest volume of ingredients when it comes to the construction of a phone.
“There is a bit of a misconception that the gold is what recyclers are after in phones,” he said. “People don’t realise that the cost to post a
MobileMuster collected 109 tonnes of used mobile phones in the past year. Images: AMTA
Recycling is the last resort for mobile phones – reuse and refurbishment are preferred.
phone back or send it to a recycling facility costs more than the amount of gold that’s in a phone. It’s the aluminium, plastic, the glass that’s valuable, and that’s the stuff that can be reassembled over and over. There’s also cobalt, nickel, iron, lithium, that kind of thing, but only in small quantities.”
Murray also says there are more altruistic reason for making sure mobile phones are disposed of correctly. He said the more materials that are recycled, “the less we need to dig up habitats of various animals and dig into the Earth in order to get those materials to make new mobile phones”.
MobileMuster has worked hard to get the message across. Murray said that current statistics show that one in three people have claimed to have recycled a phone, with one in two intending to do the same. It is converting that other two thirds that is the tricky issue. And it’s not like the organisation hasn’t offered a myriad of options for people to recycle their mobile handsets. Vodafone, Optus and Telstra stores – and their partners –have drop off points. Australia Post has also come to the party whereby you can post your old phone back to
MobileMuster at no cost to the consumer.
The hardest part is the motivation for people to go to their drawer or shed or wherever, and actually pick it up and put it in a bag,” he said. “Some people think ‘there’s no tangible outcome for me,’ but they should do it because it’s the right thing for the environment.”
MobileMuster has also learned that they key to scale is with other businesses, with a view to work with more organisations and find opportunities that benefit both parties. Whether that be working with existing waste management organisations, or otherwise.
pack them up in a box and send them to us,” said Murray. “You just jump on our website and all that information is there. We can also provide a certificate to show how your business is improving its sustainability measures through mobile phone recycling.”
One aspect that worries a lot of people – across the spectrum – is what happens to their stored data. Murray said he can assure the public and businesses that MobileMuster does not access phone data.
for their recycling efforts.
In the case of zoos, the monies go to initiatives that help protect habitats of animals that are affected by mining of materials that go into making mobile phones.
Murray also said the organisation is looking at ways to incentivise consumers to return the phones, to keep up with trade-in services.
“Some people think ‘there’s no tangible outcome for me,’ but they should do it because it’s the right thing for the environment.”
Companies are always changing providers, updating phones, and making sure they have the most upto-date communication features. This means there is a lot of churn in that space and therefore plenty of phones that need to be refurbished or recycled.
“If you own a business and have a backlog of outdated, unused devices floating around, it’s absolutely free to
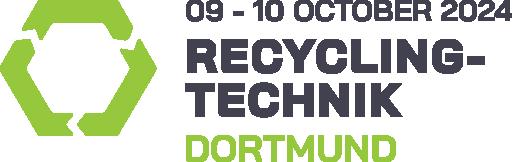
“Once it goes into a MobileMuster Box and is picked up, it’s never turned on,” he said. “It’s never accessed. It’s literally dismantled and chucked into a shredder, and there’s no way to access that data once it’s been processed. Your data is safe through the process. And if people do want to be extra safe, we have instructions on how to wipe it off before you drop it off.”
MobileMuster also partners with charities such as the Salvation Army, DV Safe Phone, and several zoos. It gives a rebate to these organisations
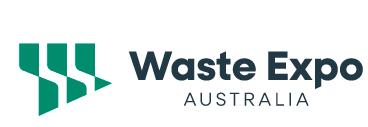
Melbourne, 23-24 Oct 2024
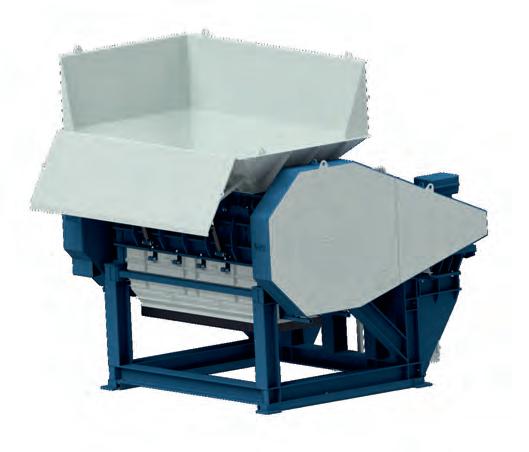

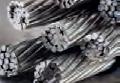

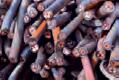
www.eldan-recycling.com • info@eldan-recycling.com
“Those trading and resale services typically will refurbish the phone and then resell it, and they will give consumers some cash back,” he said. “When it reaches a point where it no longer has value, that’s when you send it to MobileMuster for recycling.”
Murray also said that at the end of the day the MobileMuster service is easy to use and it’s free. Users or businesses don’t have to pay to ship to anyone and they don’t have to sign up to anything.
“Send them our way and it’s all sorted,” he said. “Get in touch with us, and we’ll discuss your needs and what we can do.”
A3:502
Rimini, Nov 5-8 2024
• Modified for recycling of tough material, e.g. ASCR cables Cu scrap & Al cables and low-grade cables.
• The rotor is manufactured with hard-face welding.
• Screens with different hole sizes are available .
• Exchangeable wear parts makes it a virtually indestructible machine.
• Large fly wheel to minimize current spikes.
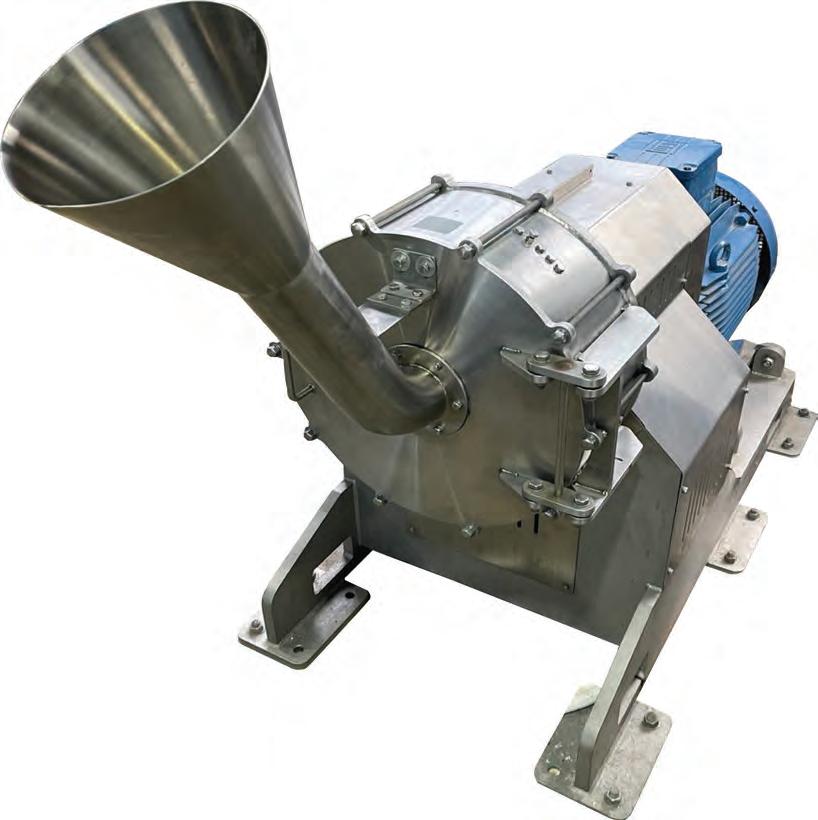
The State of packaging recycling
By Mike Ritchie
IN 2018 THE AUSTRALIAN Government established the 2025 National Packaging Targets. The four targets to be achieved by 2025 were:
1. 100 per cent of (all) packaging being “reusable, recyclable or compostable”.
2. 70 per cent of plastic packaging being recycled or composted.
3. 50 per cent average recycled content (RC) included in packaging (not to be confused with the recycling rate (RR) –the amount that is actually recycled).
4. The phase out of problematic and unnecessary single-use plastic packaging.
A few observations:
1. Being “reusable, recyclable or compostable” does not mean that it actually is reused, recycled or composted. Just that it is capable of being so. Whether it is or not is a matter of economics and systems –see below.
2. The current rate of plastic packaging recycling is a paltry 18 per cent (target 70 per cent; APCO).
3. The weighted average RC is 42 per cent with most of it in cardboard (54 per cent) and glass (41 per cent). The laggard is plastic of course (average 9 per cent). Steel cans are also surprisingly low (8 per cent). (Refer Table 1).
4. Phasing out problematic single-use plastic packaging is a no-brainer and needs to go faster.
But there is some good news –the total packaging RR is 61 per cent. Cardboard (71 per cent) and Glass (63 per cent) do all the heavy lifting.
New RC targets were applied per packaging stream in 2019 (Table 1):
l Cardboard/paper (60 per cent).
l Glass (50 per cent).
l Metal (35 per cent).
l Plastic packaging (20 per cent).
- PET (Polyethylene; 30 per cent).
- HDPE (High density polyethylene; 20 per cent).
- PP (Polypropylene; 20 per cent).
- Flexibles (20 per cent).
None are achieving their RC targets, but cardboard (54 per cent) and glass (41 per cent) are close.
Fast forward to 2023 to a new Environment Minister in Tanya Plibersek and a crop of new State Environment Ministers. In June 2023 they put out a release saying:
“In an Australian first, packaging will soon be subject to strict new government rules aimed at cutting waste and boosting recycling … These new rules will help make sure packaging
is minimised in the
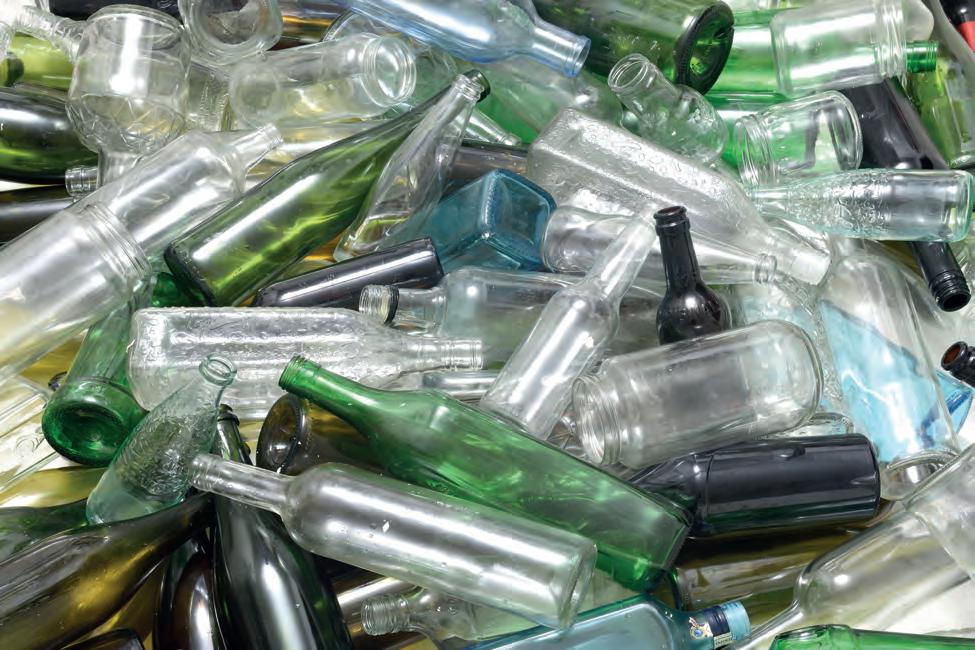
first place, and where packaging is used it is designed to be recovered, reused, recycled, or reprocessed.
The rules will include mandatory packaging design standards and targets – including for recycled content (RC) and to address the use of harmful chemicals in food packaging.”
Good stuff. There has been an almost unanimous round of applause for such action. But five years on from the National Packaging Targets and a year on from Minister Plibersek’s announcement, not much has happened. Two-and-half million tonnes of packaging is still sent to landfill each year. More than one million tonnes of cardboard, 800,000 tonnes of plastic packaging and 500,000 tonnes of glass are still landfilled each year.
Surely if we want to create a circular economy, we need to start with the obvious right in front of us. We need to create the market incentives or policy proscriptions to get this recyclable packaging out of landfill. It is not difficult. But it requires political will and political support.
It requires investment in infrastructure and systems to lift RR and RC. The 2.5 million tonnes of packaging that goes to landfill does so because it is cheaper or easier to landfill it compared to recycling. Rational for many generators.
Similarly, if we want to improve recycled content then it needs to be mandatory and applied to all packaging both imported and locally manufactured (otherwise only responsible companies
will do it and others will free ride).
Table 1 shows the increase in recycling rates and recycled content required to achieve the targets, based on the latest (2021/22) APCO data on RC and RR.
Some key points from Table 1:
Overall:
l Achieving the current RC targets will drive an uplift in recycling of more than 382kt over all streams (761kt required).
l Aluminium is the only stream already achieving (and exceeding) the RC target.
l But we still need to recycle another 13kt to achieve the RR target. For two streams a mandatory RC rule
Glass is one of the waste streams doing well when it comes to recycling rates, but it could do better. Image: Josep Curto/Shutterstock.com
would also see RR grow substantially:
l Paper and cardboard – by 203kt and by default it also achieves the RR target.
l Glass – by 103kt and by default it also achieves the RR target.
l For these materials lifting RC lifts RR in a material way.
l Bit of a no-brainer.
However, plastic and steel require stronger interventions than just an RC mandate. Key plastic streams:
l Achieving the current RC will drive an uplift in recycling of only 78kt.
l 353kt is required to hit the RR target. Steel:
l Achieving the current RC will drive an uplift in recycling of only 23kt.
l 4 4kt is required to hit the RR target.
- To hit the plastic/steel RR targets other additional interventions will be required. RC alone will not go far enough.
We must do mandatory RC reform. Good on Ministers for pushing it. But we will need to do much more to get a handle on plastic recycling. The gap is more than half a million tonnes. We must fix it. We need to walk and chew gum.’ Ministers must put in place a mandatory packaging system with targets for RC and RR. Mandatory means there
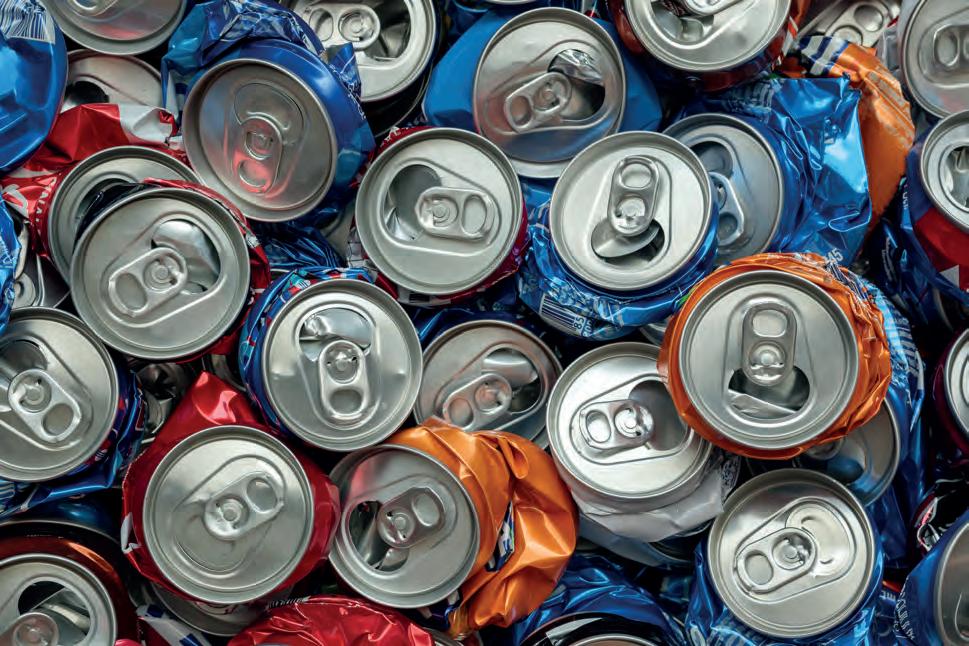
are no free riders. Costs should be met via an “eco-modulated” levy on packaging placed on market. That levy should be lower for products with high RC and RR, and vice versa. It is what Europe has been doing for a decade.
As an aside – for RC rules to actually help lift RR for plastic in Australia, they will probably need to be accompanied by some sort of incentive to use Australian recycled plastic pellets. Why? Because it will almost always be cheaper to import
PROVEN RELIABLE AND PRODUCTIVE
recycled content plastic pellets than make our own here in Australia, due to scale and the costs of labour.
Summary:
l Reform is taking too long. There are green shoots of investment in RC and RR, but it is far too slow and patchy.
l Minister Plibersek has made the right noises and has been strongly supported by industry and communities (including the
manufacturing and retailing sectors via APCO).
l We need to create the political space for her and colleagues to introduce legislation to create a mandatory packaging scheme with real targets and real teeth. ASAP.
l Please let the Ministers know you support such action.
Mike Ritchie is the managing director of MRA Consulting Group.

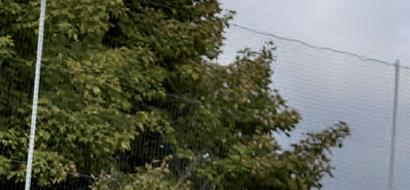
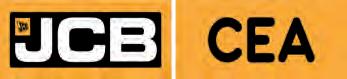
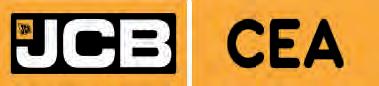

Standard designed for those doing the right thing
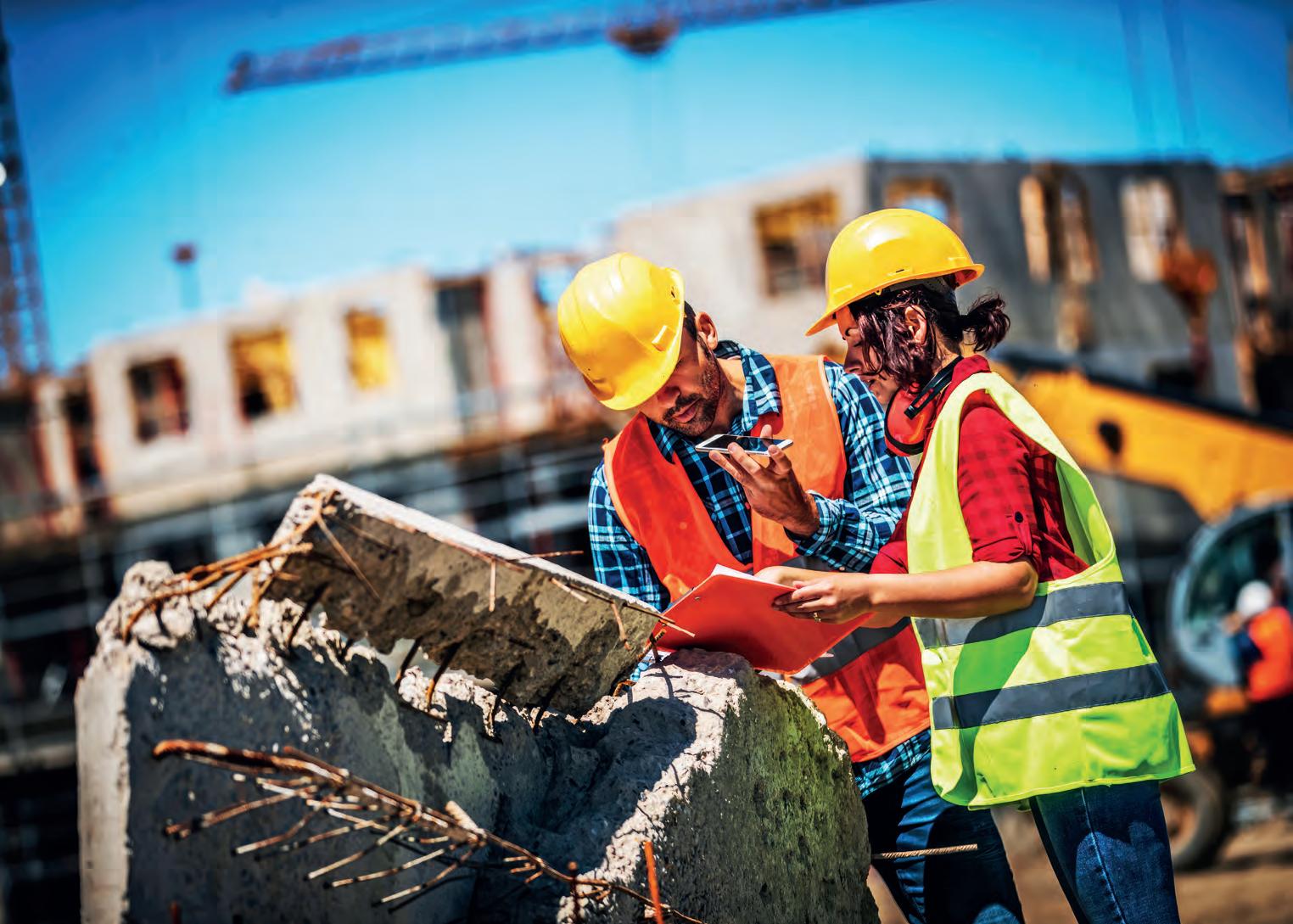
By Inside Waste
LIKE MANY INDUSTRIES, the resource recovery/waste sector has a lot of rules and regulations. Rightly so, most would say, due to the nature of the business. And the nature of the business also means that there are certain expectations around how activities are conducted. Not only from within the industry, regulators, and government entities, but the public at large. Yet, how can such activities and their impact on the wider world be measured? More importantly, how can businesses offer a reliable indicator to those with limited knowledge of how the resource recovery is run that they are crossing their t’s and dotting their i’s?
Standards. Every industry has them. Qualified, bona fide, measurable standards. With that in mind, GECA, an independent, not-for-profit organisation, has developed the Construction & Demolition Waste Services ecolabel standard aimed explicitly at the C&D waste market. A critical aspect of becoming certified against this standard is that “... applicants must show that they follow the waste priority hierarchy, starting with waste avoidance. These measures divert waste from landfills and reduce the burden on raw materials”
Josh Begbie is the CEO of GECA and has been with the company for just
over 16 months. While he concedes that the diversion from landfill rate for C&D, at about 70 per cent, is good, getting to those 80 and 90 per cent targets is not easy.
“It starts getting much harder, and it requires effort, thought, innovation, collaboration, and communication to get past that 70 per cent,” he said.
“I think there can be a tendency for some people to feel, ‘Ah, you know, we’re doing alright. We’re good. We’ll just stay there’. At GECA, we want to encourage people to keep minimising their impact and grow their circular outcomes.”
This is why he believes having a standard that pushes beyond current thinking and expectations is vital. GECA wants to help drive improving behaviours and find the right balance between being aspirational and being achievable. He realises that there are a lot of dodgy players out in the market who will get rid of their construction waste by not doing the right thing. This is why it is essential to have a standard because it provides a rigorous thirdparty framework for accountability and transparency.
“The certification helps with that because with the standard, these things get checked, and they get checked regularly,” said Begbie.
And where did the standard come from? Who decided what would go into the standard, and what type of things
does it encompass? GECA’s strategic communications manager, Kendall Benton-Collins, explains.
“We adopted and modified a standard initially developed by our fellow Global Ecolabelling Network (GEN) member, Eco Choice Aotearoa in New Zealand,” she said. “They developed the recipe for best practice in C&D waste services following ISO 14024 principles. We then adapted that standard to the Australian landscape, which has its own nuances and needs.”
As is the case for all 27 of GECA’s product and service ecolabel standards, Benton-Collins said it involved a lot of research internally with GECA’s standards and technical team, and then a large amount of consultation. This process included a voluntary technical advisory group of critical players
along the construction and demolition value chain. Once feedback had been received, it was incorporated into the draft standard to balance best practices and industry capabilities.
“Our standards aim to deliver substantial environmental benefits, but if we set the bar so high that it’s out of reach, we’re not able to affect positive change,” she explained.
Finally, the draft standard was open for feedback from the public and industry professionals during a 90day consultation period before being finalised by a Standards Committee.
In other words, GECA wanted to open it up to as many interested parties as possible to get the best results for the standard itself.
Begbie also pointed out that the standard can be malleable – not as a
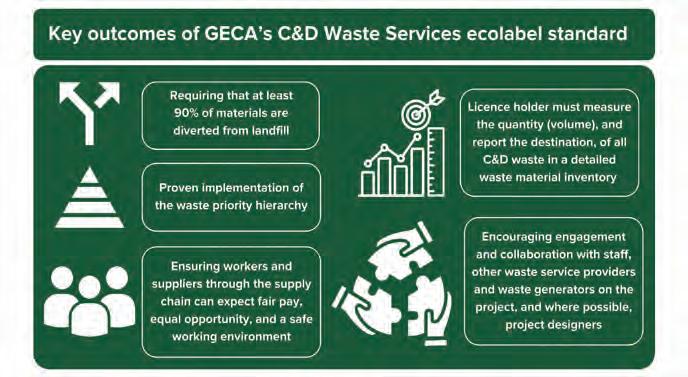
Standards increases expectations that C&D specialists will do the right thing when it comes to disposal of the waste stream. Image Credit: GECA
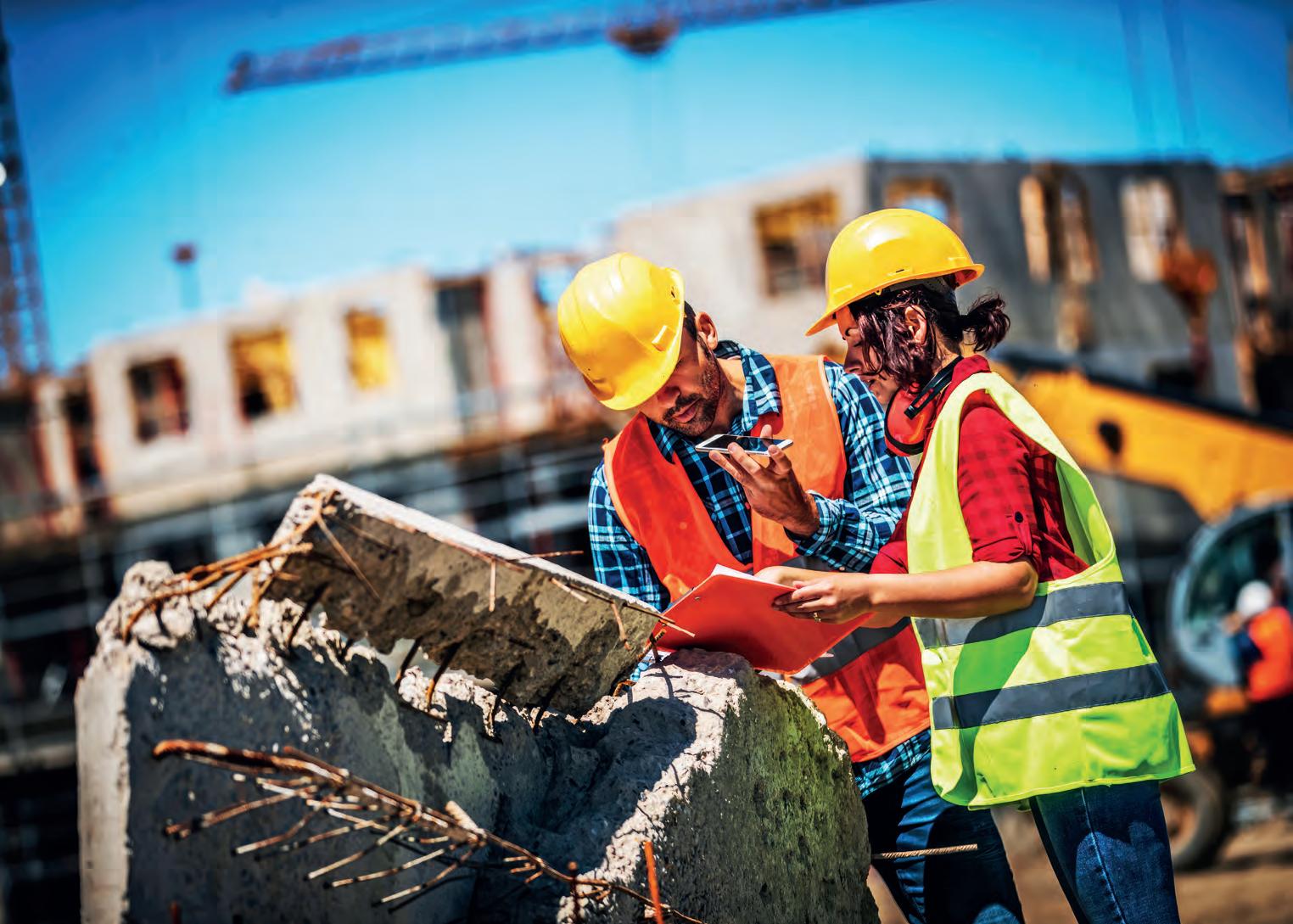
matter of course, but more about if there are changes within the industry that might need to be considered when companies go through the process.
“We have a continuous improvement mindset,” he said. “This doesn’t mean we do a full update every year. It often can be quite a few years between a formal update, but we’re always seeking feedback from the market, such as, has anything significant changed? Has there been a technological shift that means we can be more aspirational than we could have been?”
And does the state or federal government have a say in how the standard is put together? The government’s part in the process is somewhat different, but it does have a role.
“Their part is not to judge whether or not our standard is okay; they judge whether or not GECA is a reputable organisation with a clear process for developing a good standard,” said Begbie. “They don’t assess each standard; they assess the process that we use to create standards, which is our ecolabelling scheme. They have to give their tick of approval whenever we change that process. That’s what
the ACCC (Australian Competition and Consumer Commission) does for us.”
In addition, GECA is the only Australian member of GEN, a network of the world’s credible and robust lifecycle ecolabels, with 39 members across nearly 60 countries. GECA’s membership includes a formal peer review process for mutual trust and confidence. Begbie said not all ecolabels on the market have this level of assessment. Some of them use the fact a government has okayed
the bar in a way that drives positive change for people and planet.”
Grasshopper Environmental was the first organisation to certify against GECA’s C&D Waste Services standard. It was doing work with Laing O’Rourke, and the construction company wanted an entity that had the best practices and was a leader in its field while working on Sydney’s Central Station Metro project.
According to the team at Grasshopper Environmental, “many of
demolition waste that is being created correctly.
“Everyone knows that this is a problem, right?” said Begbie. “The building and construction industry knows there’s underreporting of construction demolition. This standard helps prove that those doing the right thing are doing so.”
Finally, Benton-Collins also points out that it’s not just about monitoring what is happening to construction and demolition waste. The standard
“The building and construction industry knows there’s underreporting of construction demolition. This standard helps prove that those doing the right thing are doing so.”
their processes as a green light, whereas GECA welcomes the additional oversight of GEN. The GECA team also monitors what other reputable ecolabel organisations are doing worldwide, especially in North America and Europe.
“When they start to signal a change with something that we haven’t seen yet, we can say, ‘Is that coming? What does that look like? How can we encourage that in the Australian context?’” said Begbie. “And we try and keep that balance right, but also raise
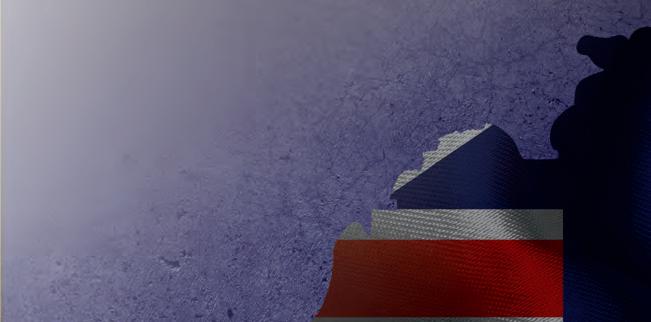
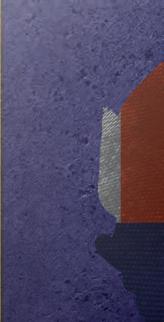
our customers require their own GECA certification for their projects, so it made sense for us to get ours too. This has made it easier for our customers to know their waste contractor is reliable and committed to helping them achieve their waste diversion targets. It’s a win-win”.
One aspect where the standard will win favour, will be among the companies that are doing the right thing already – making sure they are reporting the right amount of
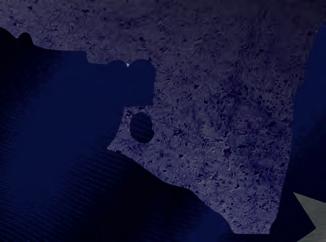

A proud Australian-owned family business, Garwood International has been at the forefront of specialised waste collection & compaction equipment design and manufacture for over 45 years, providing high quality, innovation equipment solutions to meet the needs of even the most challenging operating environments.
• Rear, Side & Front Loading compaction units
• Single and split-body collection vehicles from 4m2 to 33.5m2

encompasses peripheral subjects that must be considered in the C&D space.
“Yes, you’re going to get those hot spot criteria around diversion from landfill, but we also need to make sure that all human health is looked after in the construction process,” she said. “Even issues like modern slavery, or if there are any chemicals of concern, need to be covered. It’s a start-to-finish standard that looks beyond what you would expect in areas of recycling and waste.”












• VWS Enviroweigh bin weighing equipment for refuse vehicles
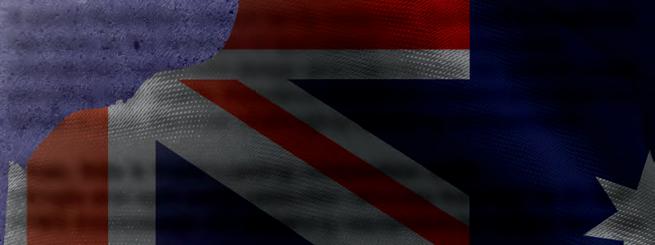
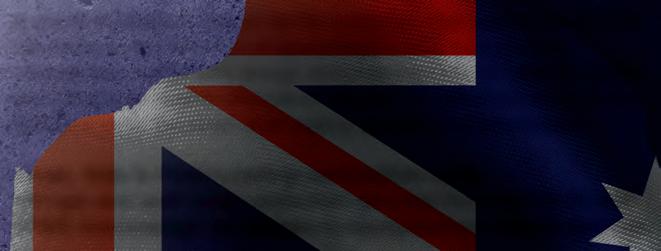
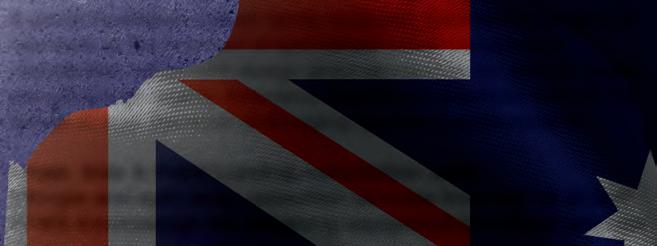



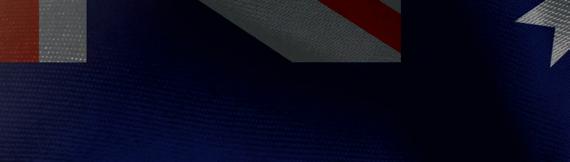




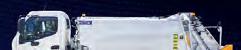
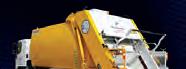





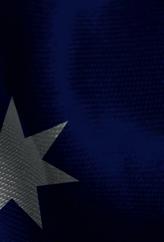

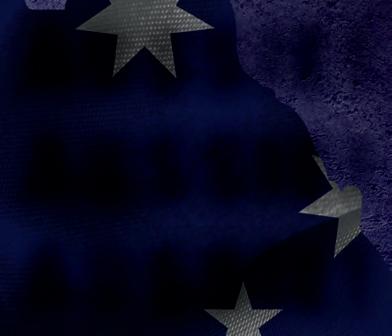
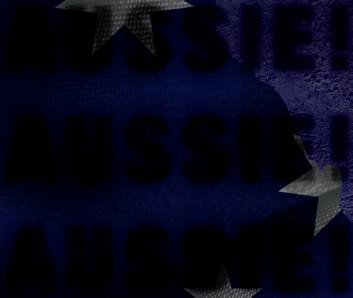



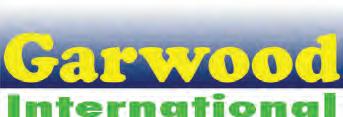
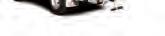



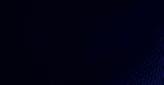


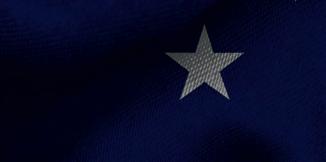

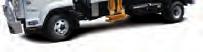


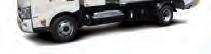


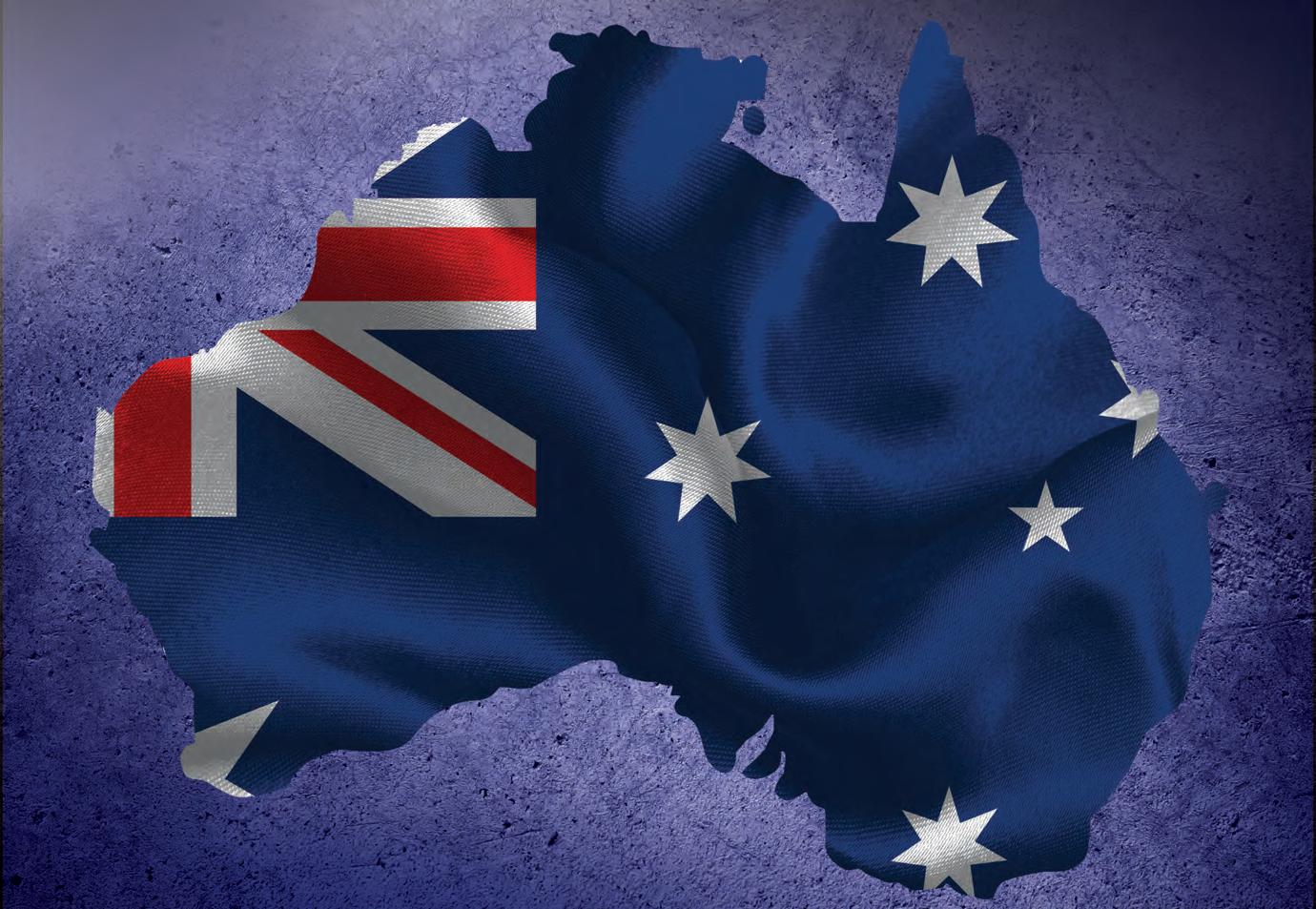
Training needs to take front seat to industry needs
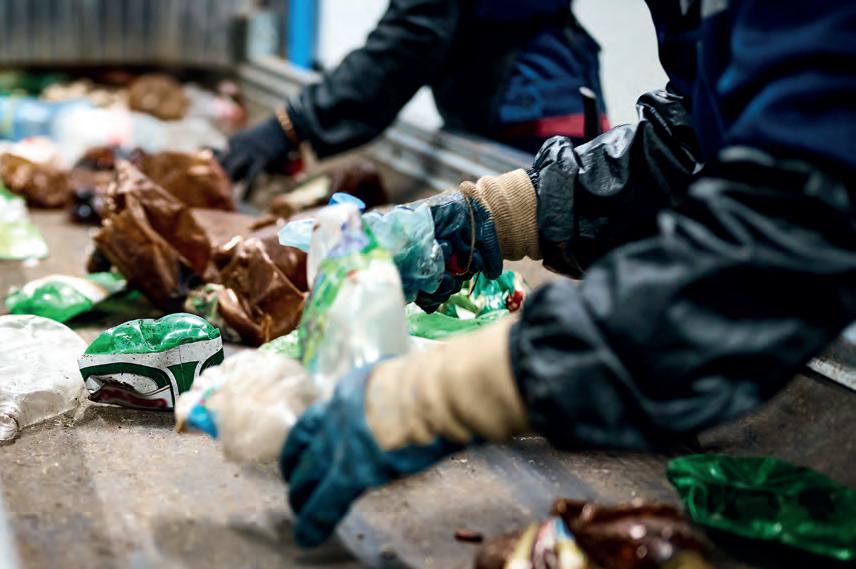
AUSTRALIA’S WASTE management sector has traditionally focused on conventional methods of waste collection, transport, and disposal. However, the sector is gradually evolving with the incorporation of technologies such as automated sorting systems, advanced recycling processes, and data analytics for waste tracking and reduction. Despite these advancements, existing t raining programs often lag, failing to equip workers with the necessary skills to operate and maintain new technologies effectively.
According to IBIS world the Waste Treatment and Disposal Services in Australia are worth about $4.5bn annually via 802 businesses and employing 7,079 people.
The shift to a circular economy and alternate disposal models such as councils’ introducing FOGO services has dampened the industry’s revenue growth. Smart operators are meeting these challenges by changing business models and introducing novel waste treatment and disposal methods, like energy generation and composting soil conditioners and road bases.
Regulatory fees and charges are forcing up the costs of handling treatment and disposal services for hazardous materials like asbestos, chemicals and biomedical waste. The key Industry sectors include the treatment and disposal of:
approximately.
2. L iquid waste – (sewerage) – 21 per cent approximately.
3. H azardous materials (Asbestos, medical waste) – 20 per cent approximately.
4. Organics (food and garden waste) –15 per cent approximately.
5. Heavy materials (masonry, concrete and steel) – 10 per cent approximately.
6. O ther waste – 1 to 2 per cent approximately.
In the latest Australian Government Labour Market Insights this industry sector is lumped together under, electricity, gas, water and waste services occupations. Occupations related to electricity, gas, water and waste services industry, by skill, indicate environmental specialists’ occupations make up 39 per cent of this industry sector, with 31 per cent being professional-level engineers, scientists, and consultants and only 8 per cent listed as environment managers.
According to the Australian Bureau of Statistics, the waste management industry employed more than 30,000 people in 2021, yet a large portion of these workers lack formal training in the latest technologies and sustainable practices. Current training programs primarily cover basic operational skills, with limited emphasis on advanced technological competencies and the principles of a circular economy.
It’s the environmental managers that develop and implement
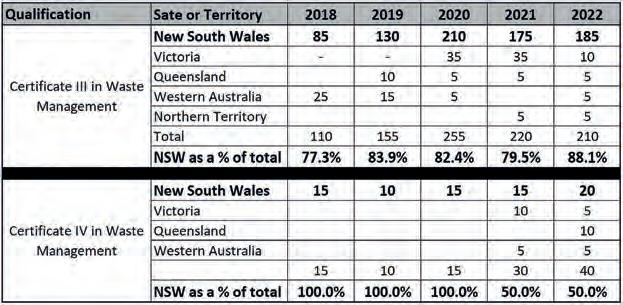
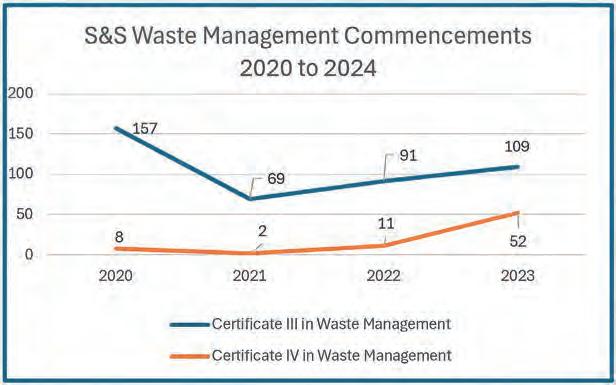
environmental (including waste) management systems. Their roles may vary from organisation to organisation. The job role will likely include identifying, solving, and alleviating environmental issues including waste streams.
To support these job roles waste management qualifications were created and have been used for several years now.
The current qualifications are the Certificate III in Waste Management (CPP30719) and the Certificate IV in Waste Management (CPP40919).
These qualifications are contained in the Property Services
Training Package (CPP).
The Certificate III in Waste Management (CPP30719) aligns to job roles including waste collection (and transfer) and processing (including resource recovery) in municipal, solid, commercial, industrial, construction and demolition (C&D) waste management. The elective categories are:
1. Waste operations with a focus on safe operations withing waste transfer stations and landfill sites including static waste processing plant.
2. Waste collection, utilising imported transport and logistics units of
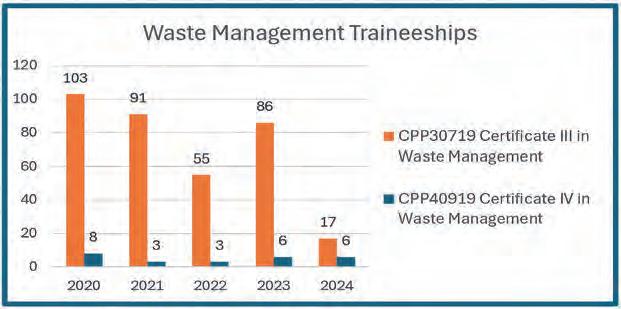
CHART 2. NSW Traineeship Commencements 2020 to 2024
CHART 1. NSW S&S Commencements in Waste Management
Some resource recovery/waste workers lack training in the latest technologies and sustainable practices. Image: Nordroden/ Shutterstock.com
TABLE 1. Waste Management qualification national up take 2018 to 2022

competency, with a focus on transport of both solid and liquid waste and hazardous materials.
3. Waste processing with a focus on green waste processing for compost.
(Note: wastewater and sewerage treatment is not included).
The Certificate IV in Waste Management (CPP40919) facilitates job roles in supervising waste collection, processing, waste minimisation and resource recovery operations across commercial, residential, industrial and C&D waste management.
These people will be leading teams, identifying and solving common collections and processing problems.
Key focus areas include:
1. Work health and safety and environmental regulations.
2. Facility management including environmental controls, site
operations and stakeholder engagement.
The national data seen in Table 1 shows NSW leads the country in the uptake of the national waste management qualifications, with the Certificate III in Waste Management
“Smart
Commencements in the Certificate III have waned from 157 in 2020 to 109 in 2023 , but inversely, commencements in the Certificate IV in Waste Management have grown from just 8 in 2020 to 52 in 2023.
Traineeships
Since 2020 the number of people taking up traineeships in NSW has been declining. The Federal Governments “Boosting the Apprenticeships Commencements (BAC)” funding did not appear to have a major impact on the traineeship commencements as can be seen in Chart 2.
pattern recognition in recycling plants, and even robot street sweepers and autonomous garbage trucks are being employed. If they are not in Australia yet, they will be in the future.
Waste management and logistics companies will need to take advantage of these new technologies to remain competitive. The Transport and Logistics Training Package has qualifications that underpin waste collection services. The Certificate III in Waste Driving Operations (TLI30419) was the original qualification, but it was superseded by the Certificate III in Driving Operations (TLI31222). This
operators are meeting these challenges by changing business models and introducing novel waste treatment and disposal methods, like energy generation and composting soil conditioners and road bases.”
being the predominant qualification.
Interestingly, there has been an increase in First Nations people commencing the Certificate III in Waste Management from just five in 2019 to 15 in 2022. In NSW Smart and Skilled (S&S) supported training in waste management commencements have had their ups and downs as seen in Chart 1.
Transport and Logistics in Waste Management
Technology is having a major impact on all industries now, not least in waste management. Artificial Intelligence, robotics and machine learning are already part of the waste management infrastructure in various roles. In advanced economies things like smart bins, machine learning through
qualification is designed for those engaged in driving-related job roles such as a waste vehicle driver.
The Certificate III in Waste Driving Operations, which was superseded in 2021, was used only across Queensland, South Australia, Western Australia, and Tasmania. Table 1 shows 2019 was the peak year for this qualification.
Waste driver training is critical to
Stand out from the crowd and give clients confidence your C&D waste service is a better choice for people and planet!
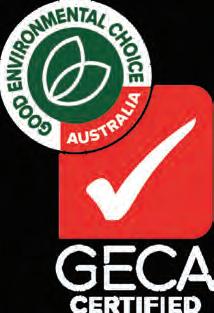
TABLE 2. First Nations people commencement in the CIII Waste Management
TABLE 3. Certificate III in Waste Driver Operations enrolments in Australia 2018 to 2021.
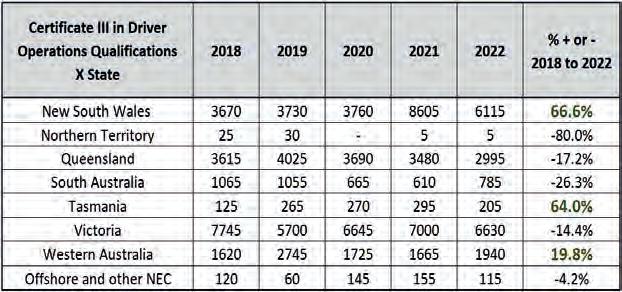
the waste management Industry. The various sectors use specialised vehicles to collect and process waste materials. The training needs to reflect this. Given the loss of the specialised Waste Driving Operations course there only remains the Driver Operations course. A breakdown of the data demonstrates training in this area has increased in some states, notably NSW (up 66 per cent) but not in the other populous states of Victoria (down 14.4 per cent)and Queensland (down 17.2 per cent), see Table 5. If we compare the enrolments across the two qualifications we see that waste Driving Operations accounts for around 0.54 per cent (on average) of the total
number of drivers being enrolled over the years observed. See Table 6. If we apply 0.54 per cent to the total number of enrolments in driving operations you might consider the number of waste drivers being trained in each state to be similar to those in table 7.
The future for waste management training In Australia
The future for the industry will be technology driven with automated sorting systems utilising: l R obotics and artificial intelligence to sort waste more efficiently and accurately than manual processes.
l A dvanced recycling technologies such as chemical recycling and bio-based recycling are emerging.
l Digital skills and data analytics and devices to assist in monitoring waste streams, optimising collection routes, and predict maintenance needs.
l Waste-to-Energy technologies used to convert putrescible waste into energy, offering an alternative to landfill disposal. Training programs should cover the operation, safety, and environmental implications of waste-to-energy facilities. Modern vocational training programs must incorporate training that reflects these emerging skills and be flexible enough cater to the different needs of industry sectors and skills levels required and provide a pathway to higher education operations.
ACFIPS Industry Training Advisory Body is a not-for-profit organisation funded by the NSW Government to be a conduit to and from industry to
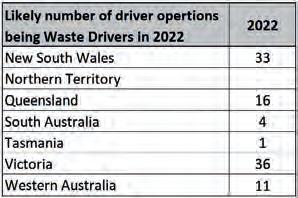
government on vocational education and training matters relevant to the waste Industry. The body wants to hear from the industry on what it s ees as the critical training issues for the sector. BuildSkills Australia is the new Jobs and Skills Council initiative started by the federal government that is responsible for the development of the Property Services Training package under which the Waste Management qualifications.
Greg Cheetham is the senior project officer - ACFIPS Industry Training Advisory Board.
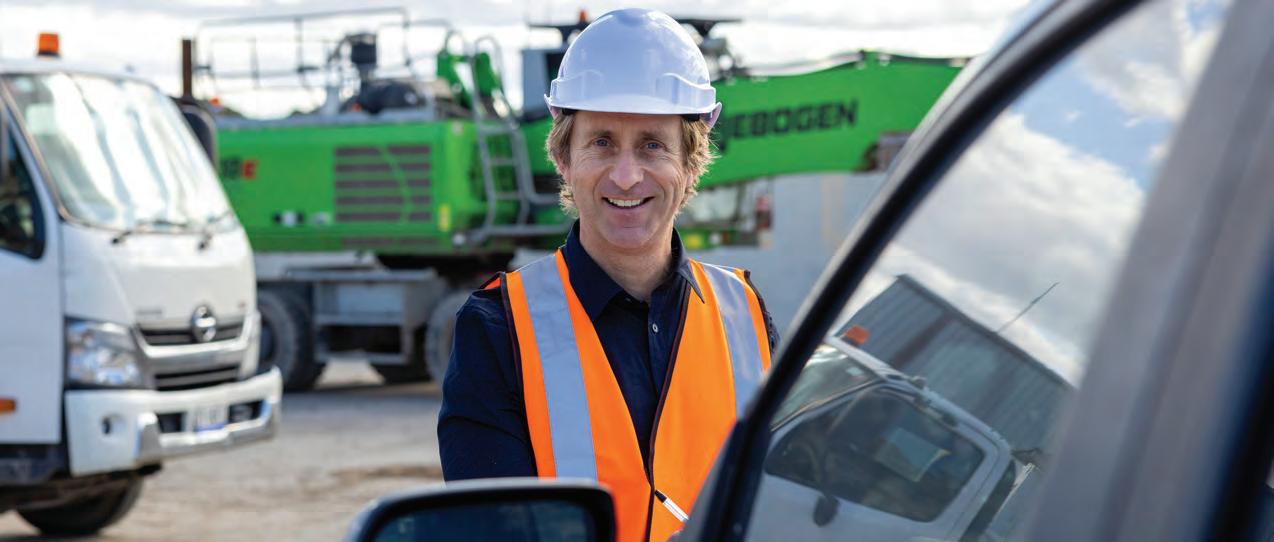
TABLE 6.
TABLE 4. Certificate III Driver Operations enrolments X State
TABLE 5. Comparison between Waste Driving Operations and Diving Operations enrolments
AORA assesses paper for improved state harmonisation
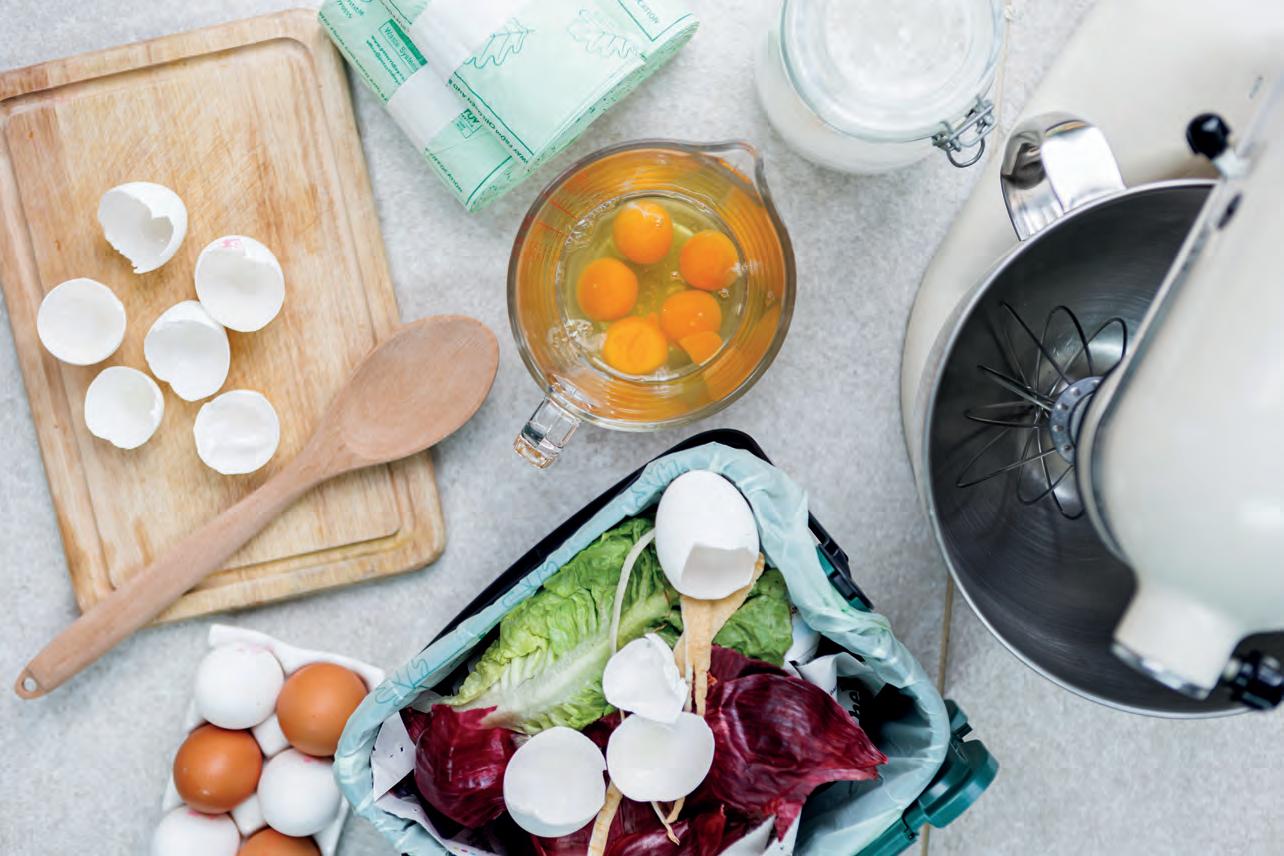
By John McKew
THE AUSTRALIAN Organics Recycling Industry (AORA) is currently reviewing its position paper on Food Organics and Garden Organics (FOGO). This review has been undertaken to ensure the Australian organics recycling industry has a clear guidance framework for the key issues and considerations for recycled organics throughout the transition from household Garden Organics (GO) collections to the mandated FOGO collections, and the delivery of Food Organics (FO) and FOGO collections for businesses by 2030 (as per the National Waste Policy Action Plan 2019 – updated 2022 – Action 6.04).
The AORA FOGO Position Paper works in concert with AORA’s national strategy roadmap, Vision 2031: The 10 Year Roadmap for Australia’s World Leading Organics Recycling Industry, which states: Amongst those ambitious objectives is a national target of less than 5 per cent of organic waste to landfill by 2031. This document also addresses the greatest industry challenge, which is
contamination of the feedstock. AORA supports a greater state and national focus on systemic and behavioural improvements to achieve better source separation. We support national bans on all non-compostable, single-use plastics and persistent chemicals –the sooner the better. Above all, this industry vision calls for genuinely integrated decision making by all governments, reflecting the needs of a production cycle in a circular economy, and with greater long-term certainty around supply, operations, and demand.
The current state government consultations on FOGO, especially in NSW and VIC, have also provided impetus for this review and offers the opportunity to pursue improved harmonisation across states as the transition to FOGO accelerates, something for which AORA consistently advocates.
Of recent concern to AORA has been the Recycling Victoria Household Waste and Recycling Draft Service Standard 2024, which states compostable plastic caddy liners, including caddy liners
certified to AS 4736 and AS 5810, will not be acceptable in the household standard contents list for a FOGO service (unlike the NSW position that allows for certified compostable caddy liners within a FOGO service).
AORA supports the use of certified compostable caddy liners as part of the transition to food organics (FO) within a FOGO stream. Certified compostable bin liners offer an effective solution for households and commercial entities to manage food waste efficiently. These liners make it easier for consumers to collect and transport food scraps, increasing participation rates in organics recycling programs. Furthermore, they help maintain cleanliness and hygiene, reducing barriers to participation in these programs.
AORA advocates for the inclusion of these type of liners in all FOGO introductions (as applicable). Additionally, AORA believes that making the liners available free-of-charge to households via their local council as part of their transition to FOGO further enhances participation within the FOGO service.
It also works to reduce the use of non-certified caddy liners, which if not certified compostable, are another source of unwanted contamination within the FOGO stream. It is generally accepted that the cost to councils of providing certified compostable caddy liners free-of-charge to households is offset by the reduction in landfill charges through the diversion of FOGO.
The recycled organics industry is committed to generating high-quality compost outputs that promote the protection of the environment and human health, specifically through the diversion of organic material from landfill. The success of household and business FOGO mandates and the circular economy relies on materials being accepted in the dedicated FO or FOGO stream, being not only theoretically compostable, but responsibly compostable within existing operations.
The revised AORA FOGO Position Paper will be available is available on the AORA website (www.aora.org.au).
John McKew is the National EO for AORA
AORA supports the use of certified compostable caddy liners as part of the transition to food organics. Image: Peter Ridley Waste System/shutterstock.com
Succession planning –start early to avoid pain
By Inside Waste
MORE THAN 50 per cent of business in the waste industry are a family concern. Starting a business, working hard and taking a few risks, and making sure the business is left in the right hands –usually the next generation of the family – can be fraught with issues.
Christian Buxton from Buxton Consulting Group has some practical experience when it comes to succession planning. He spent two decades with his father building up an integrated waste management business – the Sunshine Groupe – before he left to form his own enterprise. When it came time for his father to sell Sunshine Groupe, he brought Buxton in as a consultant to help
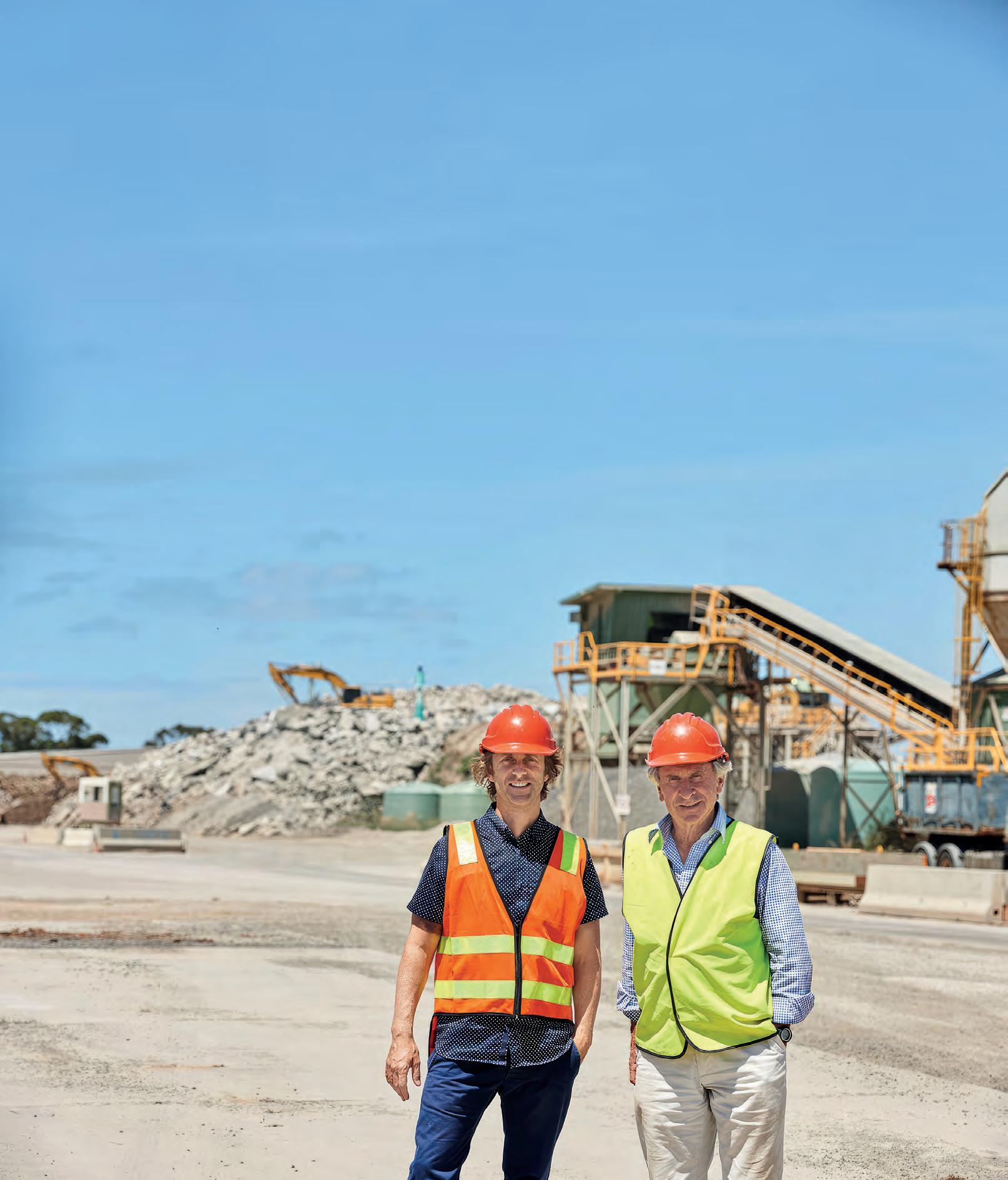
unload the business. It was then, Buxton realised that having a succession plan was important.
“We’re really at a tipping point at the moment because the late baby boomers, who founded a lot of these businesses, are now reaching this transitional age where they’re either seeking to get out of the business for health reasons or other concerns,” he said. “There’s a whole family discussion that needs to happen. There’s also family dynamics like politics – all those things get brought into that situation.”
Buxton said that his transition was easy. His brother, who was in the business for a while, left to become a yoga teacher, and none of the third generation were old enough to take over
the Sunshine Groupe being aged 15 and 12 respectively. It was a matter of onselling. However, he is aware that there is a plethora of businesses in the waste industry where it won’t be as simple.
He believes most family business work well when everybody has a similar vision, and the values align. One of the reasons he started his own business was because he and his father were a little out of sync in some areas of the enterprise. ‘
“We agreed on the vision, but disagreed on the timeline and how we were going to get there,” he said. “This meant that some of our values started to move away from each other. We were of a different generation.”
A couple of years after Buxton
left the company his father had some health issues, which is when Buxton was brought back to help get the business ready for sale.
“It’s quite a rigorous process that you go through. Dad asked me to come back and help negotiate that sale,” he said. “I agreed to come back as a consultant, which I did for 12 months. We successfully negotiated a sale that suited both parties.
“Looking back, I think if you are going to choose to sell the business, you really want to have at least three years to plan for that, because of the process of evaluation and all the different things that need to be done.”
While the selling of the Sunshine Groupe ended well, Buxton believes on
Christian Buxton (right) with his father Tom. All images: Christian Buxton
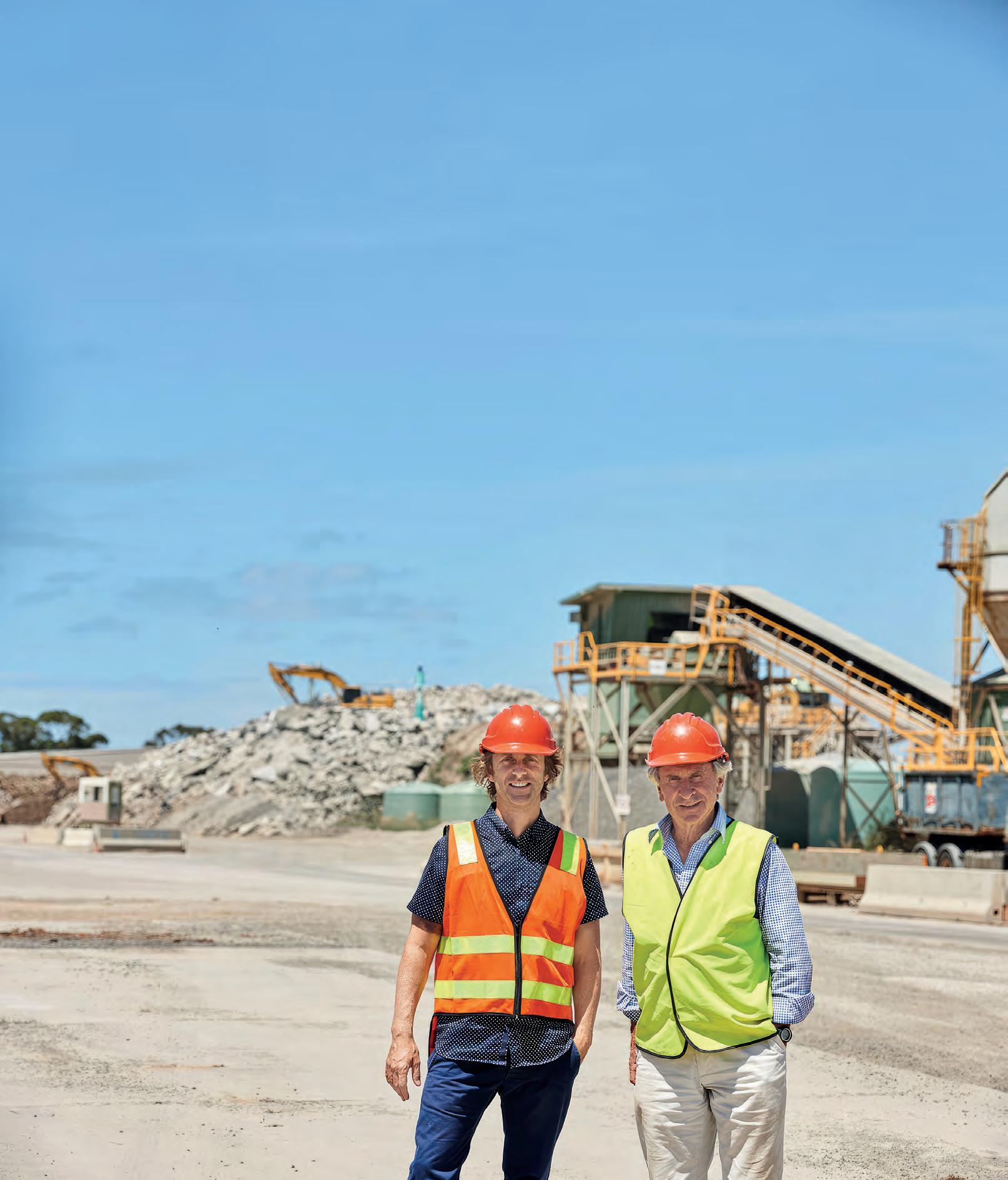
reflection and hindsight a lot of pain and distress could have been avoided had there been a succession plan.
“I strongly urge founders and the next generation of the family business to have the courage to start to have these conversations earlier on to develop a plan to avoid unnecessary pain and conflict,” he said. “You need to maximise the opportunity in succession whether that be a sale, or preparing the business for the next leadership group – whether that be from the within the family or from outside.”
He sees the benefits of planning as:
l Helping resolve family ownership and family business leadership issues, or at least bringing them to the fore.
l Keeping the family and business integrated and synchronised.
l Making sure the family wealth is protected and managed well.
l Allowing family and the business to be able to create legacies.
Talking to the industry, Buxton believes there is a need for succession planning, and because he’s been through it, he knows the pitfalls and issues that might arise.
“Because sometimes there’s family issues that can get in the way compared to a normal business without family dynamics,” he said. “There’s always challenges with any business but in a family business you have family dynamics and family history and family communication – or in some cases lack of communication. Sometimes you need help from outside to create clear communication pathways, or get a career collective vision for where you want to go.”
There are other factors that also need to be assessed with the family business,
especially in the waste industry. There is a lot of specialised knowledge that the older generation have – not only in terms of how to run plant and machinery, but also when it comes to dealing with local and state legislation and dealing with regulators.
“These businesses, unlike other businesses, are highly regulated,” he said. “It’s a barrier of entry. These regulations can often be a disruption to doing business, and you’ve got to know how to navigate them and take advantage of the opportunities that that presents.”
Buxton also warns not to be myopic when looking at options. He finds in most cases family members think there are only two options when it comes to succession plans – they either have to sell the business or hand business on the next generation.
“There’s multiple choices that can be made in that transition,” he said. “And if you sell the business, what do you do with that money? Put it into residential property? There’s a yield of about 2.5-3 per cent if it’s residential property, while commercial/industrial is about 8 per cent. What about the stock market? It can be about six per cent with the average about 4.5 per cent.”
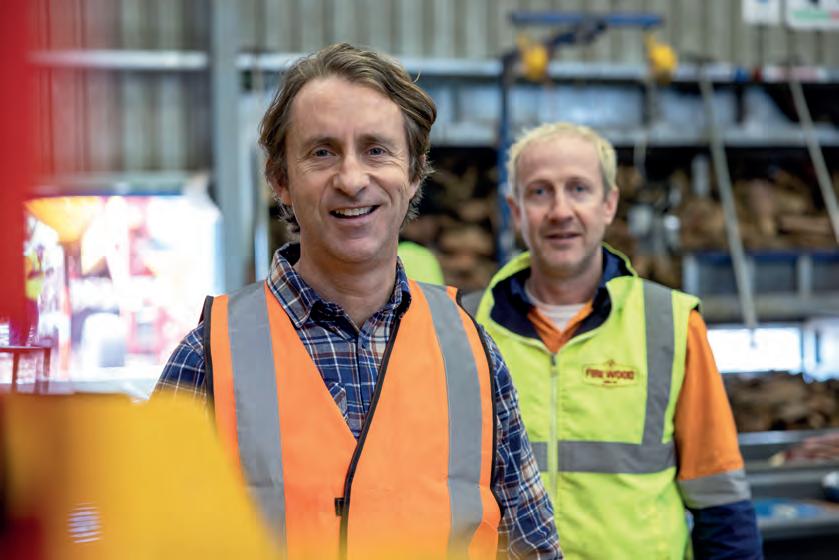
manager, until the next generation come up to speed,” said Buxton. “They might want someone else to run the business for them and continue to get a return for the family into the long-term future.”
goes – will only enrich lawyers and other third parties.
Then there’s the chance that the seller might want to work in another arena, or even retire. Maybe the next generation doesn’t want to be involved in the business, or they do, but don’t understand it.
“You might see it on to the next generation, but maybe they’ll have to put a CEO in charge, or an operations
Buxton reiterates that the biggest issues are caused by that family dynamic and all that encapsulates. This can be anything from one member have a substance abuse problem, through to siblings not getting on or have different values. Buxton believes preplanning can address all these issues, because the legal mess that can result from not having hashed these issues out before deciding to take the plunge – whichever way that
“No doubt there can be difficult things that need to be addressed, but it’s far better for everyone if they’re addressed before any important decisions are made.”
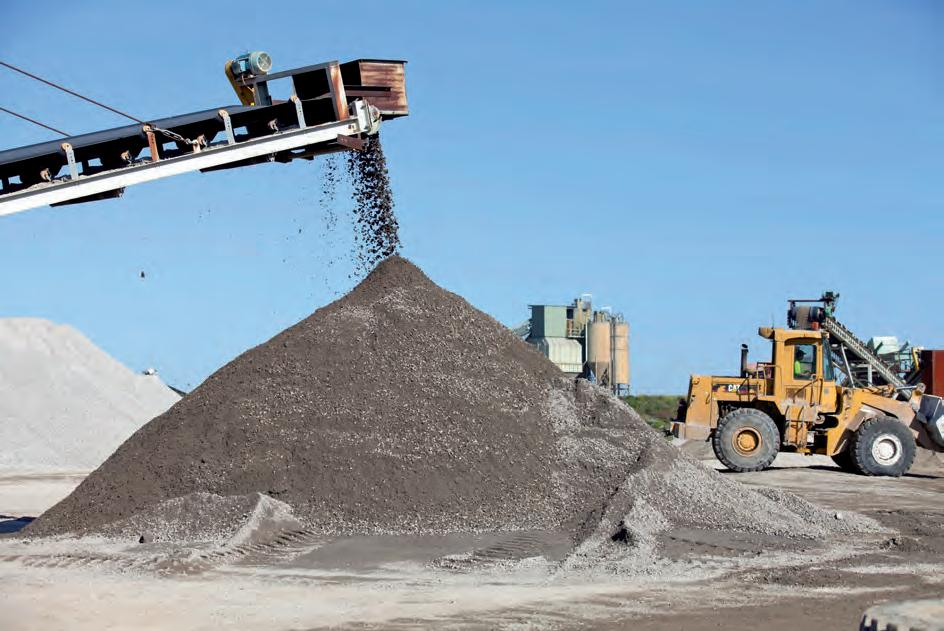
“No doubt there can be difficult things that need to be addressed, but it’s far better for everyone if they’re addressed before any important decisions are made,” said Buxton. “Succession planning is a hot topic. Lawyers are good if you want to have a fight with each other. But who’s experienced or knows how to address the conversation with the family, so they can start a process about what needs to be done? You’re far better off to work the plans out yourselves internally, and then instruct the professionals with what you want to do, rather than pay them to help you work it out. Lawyers, by nature, are either two things: combative or risk averse. You end up in these loops.”
Finally, Buxton said, don’t forget about the peripheral players. They’ll want their say and are prone to bend the ears of the principal players in the merrygo-round.
“Partners will be having these secondary conversations with the main players, and they’ve got their wishes and desires, too” he said. “It can get quite tricky. But the thing is, if you bring it out of the table, and it’s all clear, then you can negotiate an outcome. Nobody is going to be 100 per cent happy, but if we can get most people to 70 per cent satisfied, then that can be a better outcome if matters are left as they are.”
Overall, there are a lot of benefits for planning the future of a company in terms of succession plan. Having a conversation is a good start, and will help make life easier for everybody once the nuts and bolts of an agreement have been decided upon.
Christian Buxton said that a lot of pain and stress can be avoided if there is a clear succession plan.
The Sunshine Groupe has been sold to the satisfaction of those doing the selling.
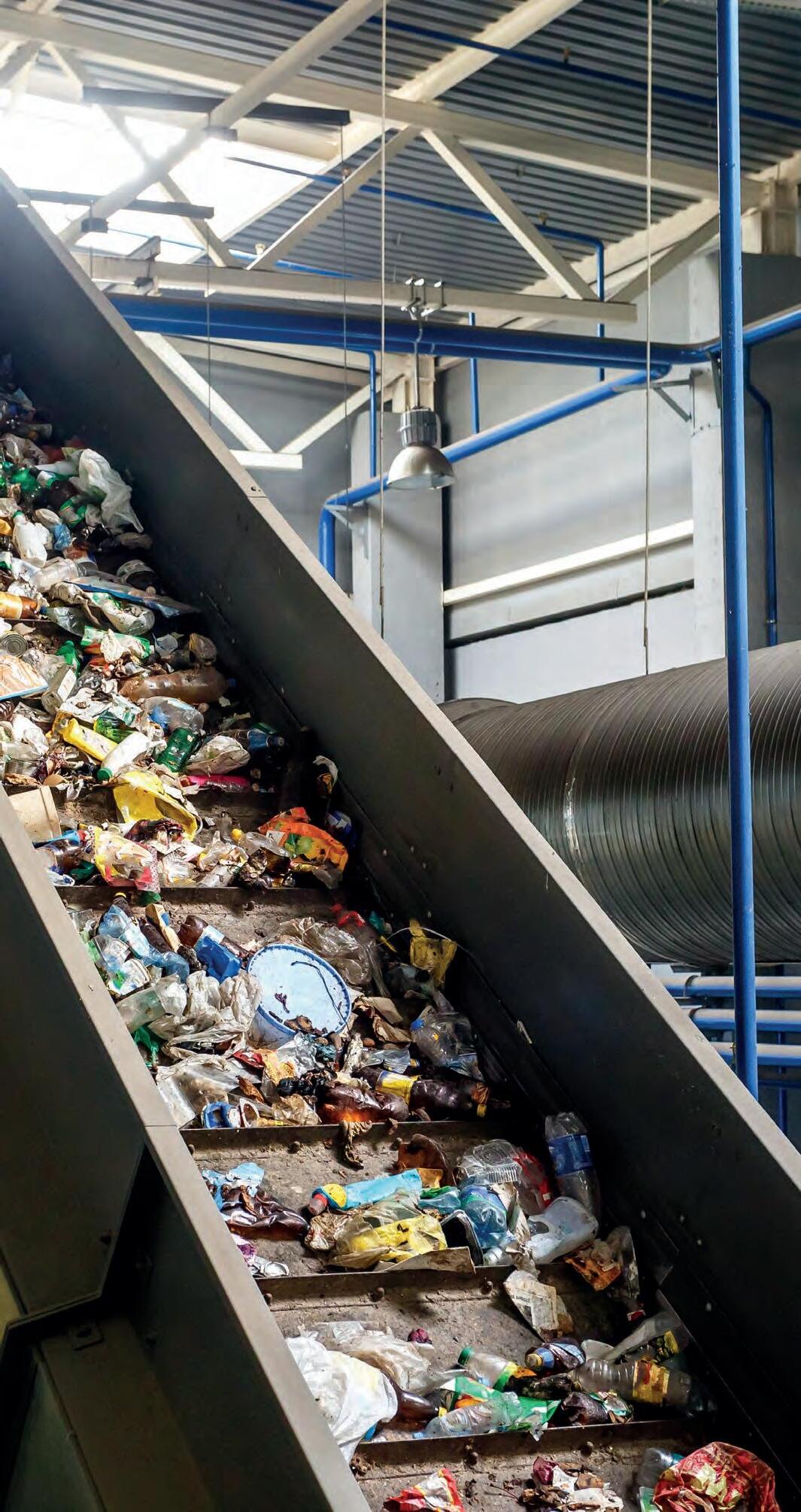
The problem with PFAS
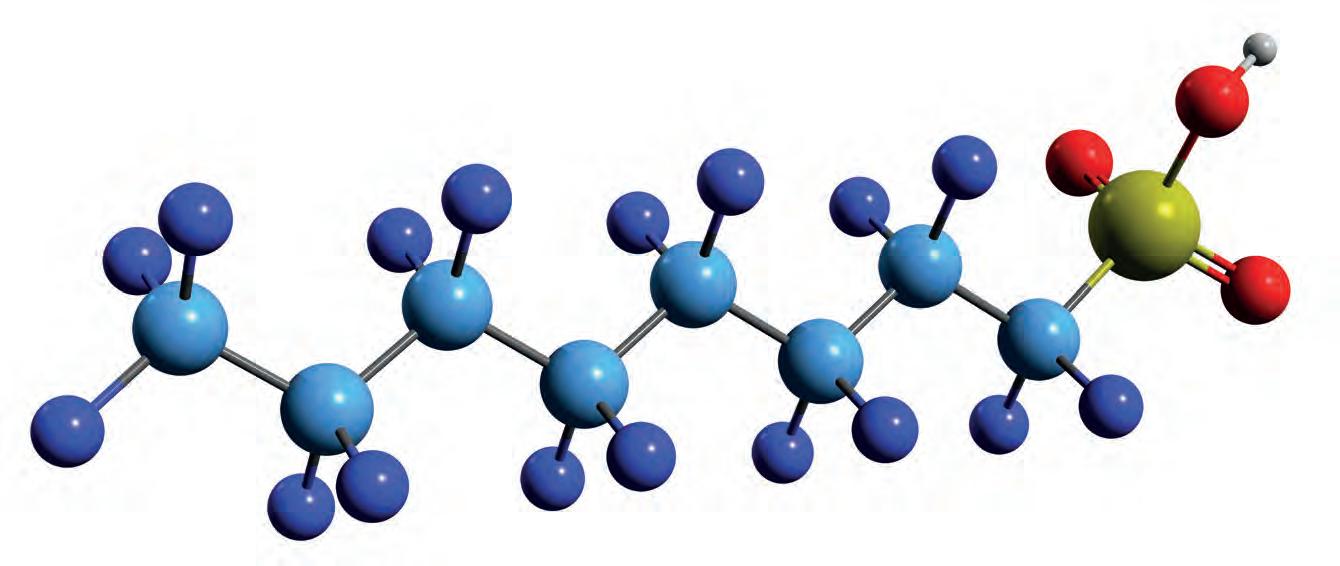
By Pradeep Shukla
DUBBED FOREVER chemicals, Per (or poly) fluoro alkyl substances (PFAS) have infiltrated environments far and wide, from farmland to drinking water supplies to oceans. In the realm of environmental contaminants, few other chemicals have garnered as much scientific attention and concern as PFAS. However, the contaminants still elude many in the water industry. For followers of global environmental issues, this contamination is a stark reminder of the lead pollution scare of the early 19th century. Just as the proliferation of leaded gasoline, driven by the use of tetraethyl lead in fuel, resulted in the widespread permeation of lead in water, soils, and biota, the use of PFAS group of synthetic chemicals has similarly infiltrated ecosystems worldwide. These resilient pollutants refuse to degrade, accumulating in the tissues of living organisms, however the detailed information on the effects of public health is sparce. Despite these risks, regulatory frameworks around the world are only beginning to catch up, with varying standards and enforcement levels. In this article, I have embarked on a comprehensive exploration of PFAS, examining their nature, origins, impacts, regulatory landscape, available technologies for management, and the path forward in addressing this emerging challenge.
What are PFAS and where do they come from?
Unlike conventional pollutants, PFAS pollution is not caused by a single
chemical. It encompasses several hundred compounds characterised by a shared chemical feature: a chain of carbon-fluorine links, giving them the term Per Fluoro, the initial two letters of the PFAS abbreviation. Typically, environmental testing of water and soils focuses on around 30 to 74 PFAS species within this expansive chemical family.
The fact that these chemicals contain strong carbon-fluorine bonds renders them resistant to biological and chemical degradation, giving them the nickname “forever chemicals.” The chemistry of forming such unique carbon-fluorine bonds has its origins in the Manhattan Project, which aimed to develop a new material inert enough to withstand the corrosive effects of uranium hexafluoride, required for use in factory parts such as pipes, gaskets, and sealants. After the war, the 3M company identified the commercial potential of these properties, leveraging them for a range of industrial and consumer applications, including non-stick coatings, water-repellent textiles, and firefighting foams.
Among the PFAS family, those with eight carbon-fluorine links, (Per Fluoro Octanoic Acid) PFOA and (Per Fluoro Octane Sulphonic Acids) PFOS, are notable for their human health impacts, attracting attention in research and regulatory contexts.
Discovery and current usage
The commercial application of PFOS began in the 1950s when 3M first used it as a key component in its anti-staining spray Scotchgard and anti-stick food wrapping paper,
known as “scotchban.” Gradually, it found its way into a plethora of other products, ranging from firefighting foam to cosmetics. 3M’s discovery of PFOA led to its sale to Dupont for use in Teflon and other coating materials.
Aqueous Film Forming Foam (AFFF), a fire suppressant containing high levels of PFOS, became crucial in firefighting due to its high surfaceactive properties, producing thick foam capable of swiftly suffocating chemical fires. Since the 1950s, defence forces and firefighters have used large volumes of AFFF for training exercises and combating fire hazards. 3M’s Light Water and other manufacturing brands were supplied in thousands of tonnes over several decades. Runoff from fire training exercises has been polluting water and land bodies in their vicinity. As environmental health concerns escalated, 3M and other companies opted to replace PFOS and PFOA with new PFAS chemicals.
For instance,3M substituted PFOS with PFBS in 2002, while Dupont switched from PFOA to GenX in 2009. Although these newer replacements are considered less toxic, they are equally persistent, accumulating in the environment. Recently, efforts have focused on phasing out PFAScontaining AFFF and transitioning to non-fluorinated fire suppressants. However, the legacy of 50 years of use has left a mark on the planet that will take time and effort to remediate.
Several socially and environmentally conscious businesses are gradually eliminating PFAS from their ingredient lists, but this task is challenging. PFAS continues to be employed
PFAS encompasses several hundred compounds characterised by a shared chemical feature. Image: kseniyaomega/stock.adobe.com
in industrial processes such as metal plating, semiconductor manufacturing, and oil recovery due to their ability to form stable coatings and reduce surface tension. Trace levels of PFAS can also be found in products ranging from nonstick cookware and guitar strings to dental floss, makeup, hand sanitiser, brake fluid, ski wax, fishing lines, and numerous other items. The widespread use of these chemicals means it may take years, if not decades, to fully replace them.
The problematic nature of PFAS
Known for their resistance to bio-degradation processes, these substances tend to accumulate rather than break down in the body of any organism that is exposed to them. This characteristic leads to their distribution in the blood and tissues, resulting in “biomagnification” in organisms higher up the food chain.
The potential for PFOS accumulation in human blood was recognised decades ago, primarily among workers at 3M’s manufacturing facilities, as reported by Kris Hansen (an ex 3M scientist) in an interview with a New Yorker reporter. Over time, scientists began detecting these chemicals in blood samples from non-worker populations and animals with no direct exposure to PFAS manufacturing processes. The pervasiveness of PFAS in the environment has been so significant that researchers have had to analyse historically archived blood samples stored in deep freezers to find samples without detectable levels of PFAS, as contemporary samples
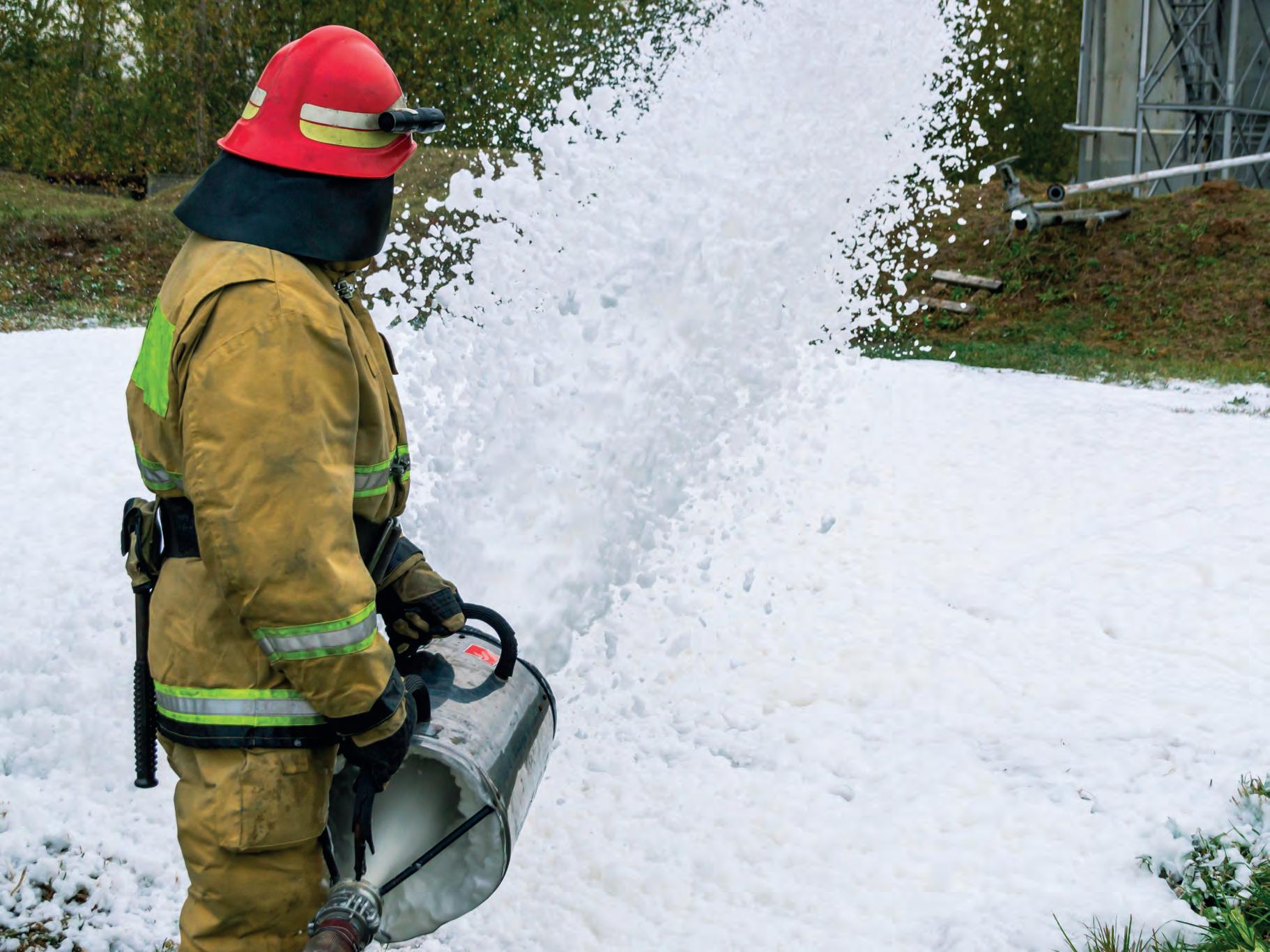
consistently show their presence. These findings underscore the consensus that PFAS proliferation in ecosystems and organisms occurred after the widespread production and use of these chemicals.
In the Australian context, recent studies from both contemporary blood sampling, and archival sample analysis, have noted that blood concentrations of PFOS tend to be higher than those of PFOA in the general population. A study on PFAS levels in the blood serum of firefighters in Australia revealed concentrations up to ten times higher than those found in the general population, although these levels decreased after exposure to AFFF was suspended. On a positive note, the Expert Health Panel for PFAS, commissioned by the Australian
Government Dept of Health and Aged Care to assess potential health impacts associated with PFAS has suggested that the presence of PFAS in blood serum does not necessarily indicate adverse health effects but has recommended additional investigation.
In contrast, the National Toxicology Program (of US Dept of Health and Human Services), reports that both PFOS and PFOA pose immune hazards with some evidence suggesting hypersensitivity and related outcomes. It is noteworthy that many of the reported health effects of PFAS are based on animal studies using relatively higher doses than those typically encountered by humans. Some studies, both in animals and humans, have found associations between PFAS exposure
and health effects, but due to physiological differences between species, these results are not always consistent and several research in on-going.
Pathways into the environment
The natural environment operates as a complex and interconnected matrix where chemicals (good or bad) migrate between various compartments, facilitating the rapid spread of PFAS within a relatively short timeframe. Currently, the PFAS group of chemicals is ubiquitous in natural water reservoirs, sewer water, and treated wastewater discharged from treatment plants. They are also found in landfill leachates, surface runoffs from waste processing facilities, biosolids,
and soils historically contaminated by biosolids. Additionally, certain areas, known as PFAS hotspots, show contamination due to the use of AFFFs at locations such as defence training areas, airports, seaports, and firefighting training sites. The Australian PFAS Map is an interactive tool that allows users to view these hotspots across the country (https:// pfas.australianmap.net/).
PFAS can be released into the environment through both primary and secondary sources. Primary sources include direct releases, such as surface runoff from AFFF use at fire training sites, or from industrial facilities that manufacture or use PFAS. These runoff waters enter surface-water reservoirs, which then recharge groundwater, thereby spreading PFAS contamination
Since the 1950s firefighters have used AFFF for training exercises and combating fire hazards. Image: EdBelkin/ shutterstock.com
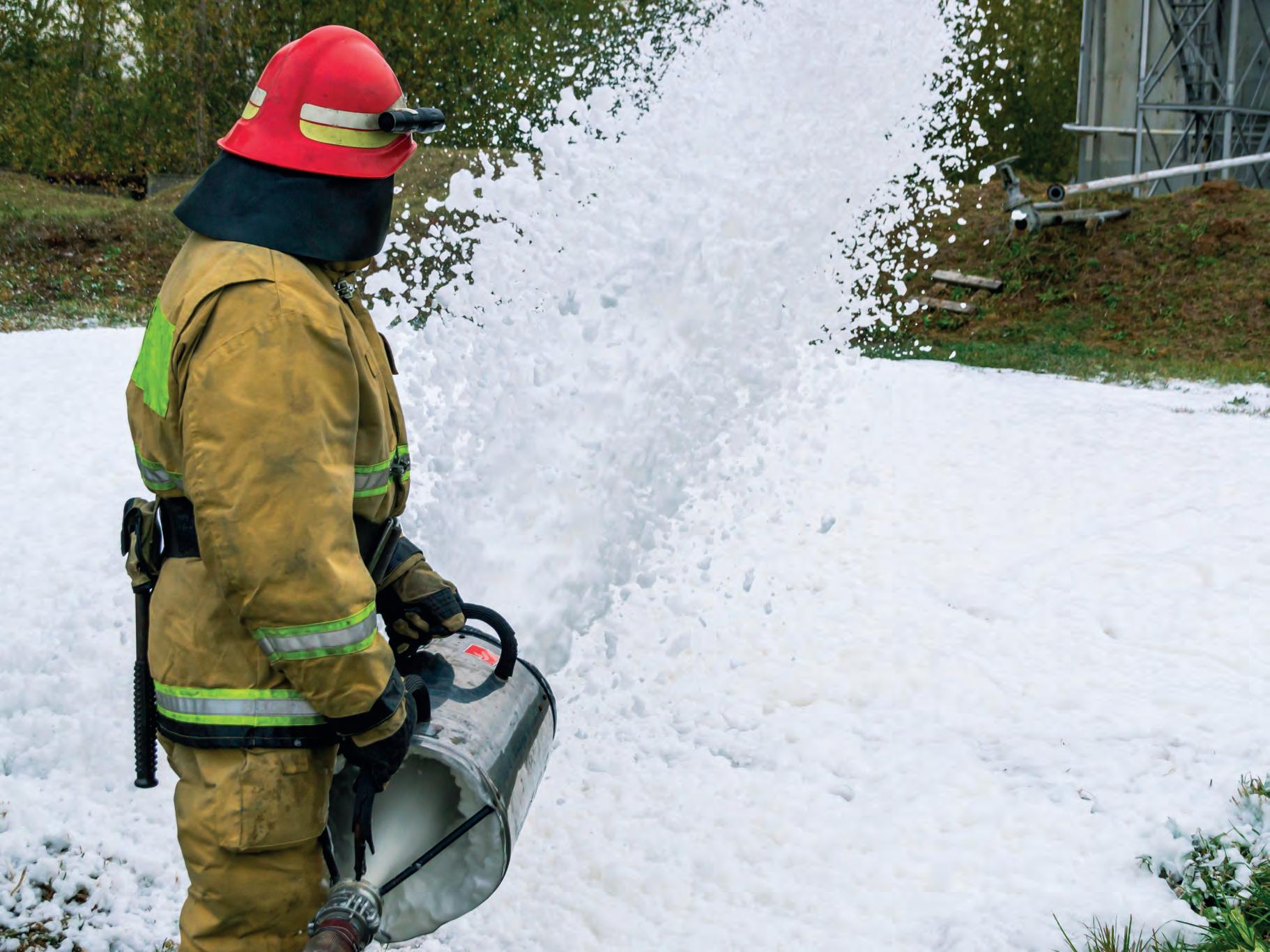
through water bodies.
Secondary sources include landfill leachates and treated wastewater, as conventional treatment systems struggle to remove PFAS. The treated wastewater often ends up in rivers, streams, or the sea, further dispersing PFAS into the environment. Biosolids and compost also contribute to the spread of PFAS when applied to land area, where plants absorb these chemicals, ultimately entering the food chain.
A simple discharge of PFAScontaining solid waste, such as from a general waste collection system, can spread PFAS throughout the environment, ultimately re-entering the food chain.
Technologies for PFAS management
The urgency to manage PFAS pollution has spurred the development of various treatment technologies. Traditional methods involve immobilising pollutants into solid adsorbents like activated carbon, followed by disposing of the adsorbent in secure landfills. However, this approach faces challenges and push back from landfill operators, who restrict disposal of PFAS-laden materials due to environmental concerns.
Given PFAS’s widespread dispersion in the environment, treatment methods for contaminated water broadly fall into technologies that separate (remove/extract) PFAS from water and those that destroy the separated/extracted PFAS. A third category, although not popular, involves immobilising the contaminants at the source by constructing a barrier wall and/or capping the affected area.
The infograph (pictured below)
provides an overview of emerging treatment techniques categorised by their developmental stage for water and wastewater treatment. Technologies on the left side of the graph are in early stages of development, while those on the top right are commercially mature and widely adopted.
The leading technologies for separating PFAS from water include foam fractionation, ion-exchange, and membrane processes. Drinking water can be effectively treated using membrane processes such as Reverse Osmosis (RO) or lowpressure Nanofiltration (NF). Most RO systems can achieve more than 99.9 per cent removal of all PFAS species. NF, on the other hand, is particularly effective for long-chain PFAS (i.e. PFAS with carbon-fluorine links greater than six) but offers limited removal of short-chain species.
However, treating large water reservoirs with high-pressure membrane processes like RO can quickly become cost prohibitive. Additionally, the presence of co-contaminants in natural water b odies can reduce the effectiveness of membrane processes from an operational and maintenance s tandpoint.
Ion-exchange is primarily used for treating surface and groundwater through pump-and-treat methods. While foam fractionation has gained popularity in treating leachates and wastewater due to its effectiveness in environments with high salinity and organic loads.
Some Australian companies are at the forefront of foam fractionation technology, offering large-scale installations globally, including in the US and Europe. Contaminants separated during these processes

are collected as rejects and then subjected to high-energy thermal treatments such as plasma destruction or incineration for complete destruction. Many nextgeneration technologies feature autonomous operations, making them suitable for remote locations and reducing the need for permanent onsite staffing.
Sludge and biosolids are secondary materials contaminated with PFAS that result from conventional water treatment processes. Since most wastewater treatment plants lack the capability to effectively remove PFAS, these contaminants accumulate in biosolids. Managing these materials involves solidification and stabilisation techniques, using binders and Portland cement to convert organic waste into hard impermeable solids with limited leachability of PFAS, which can then be disposed in landfill.
Dried biosolids with a high calorific value can also undergo thermal processes such as incineration or smouldering to destroy the parent material including PFAS. Additionally, biochar can be produced from biosolids, offering commercial value. However, it’s important to note that gas emissions are a concern with these thermal processes, necessitating regular monitoring to ensure environmental compliance.
What is the future in PFAS management?
Looking ahead, the future of PFAS management relies on advancing technologies and processes that can effectively remove and destroy these persistent chemicals from our environment and water supplies.
Innovations in treatment methods, coupled with stricter regulatory frameworks, will be crucial for mitigating further contamination and protecting public health. Effective treatment of secondary sources such as wastewater and leachate are necessary to prevent PFAS from reentering the environment.
Additionally, increasing public awareness and corporate responsibility are essential for driving sustainable practices and reducing the global footprint of PFAS.
As research continues to uncover new insights into PFAS behaviour and impacts, proactive measures and public-private partnerships will be key in shaping a cleaner, safer future for all.
Pradeep Shukla is a process engineer who specialises in PFAS treatment research.
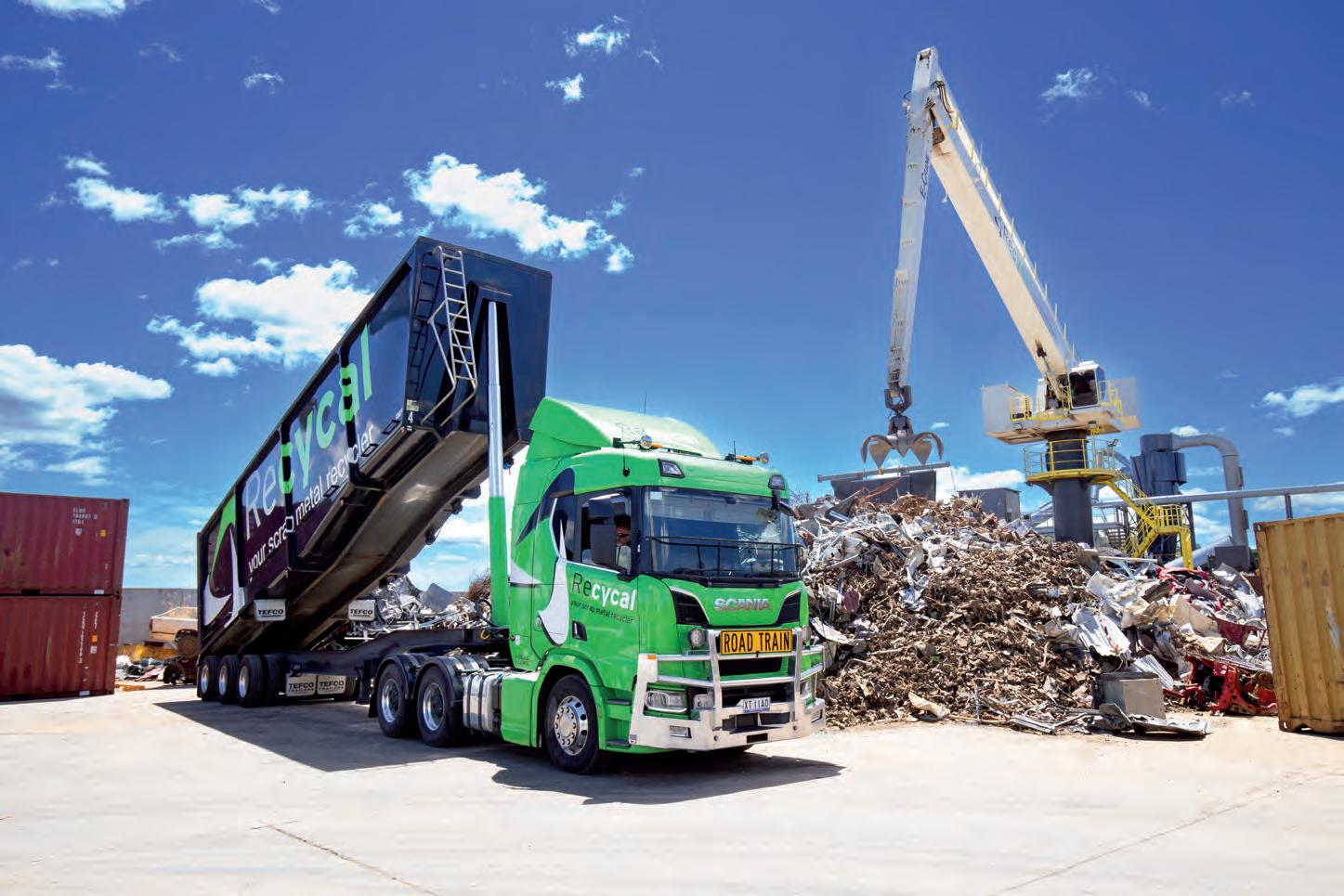
Recycal is future proofing recycling in the Apple Isle
By Inside Waste
IN A WORLD increasingly conscious of environmental sustainability, Recycal is a family-owned enterprise that is rooted in the metals recycling industry. It offers services that not only address environmental concerns but also contributes to the local community. Through its recycling programs, advanced facilities, and commitment to corporate social responsibility, Recycal is making an impact on both the environment and society.
Recycal has invested $29 million in its Rocherlea plant, including approximately $2 million in federal government funding, to ensure Tasmanians are not disadvantaged and have a heavy-duty shredder to meet the critical needs of the island state.
This investment allows Recycal to process all unprocessed scrap metals generated in Tasmania and all types of e-waste.
Recycal’s investment in advanced processing capabilities ensures that even challenging materials can be efficiently recycled. The company’s forthcoming $23 million floc processing plant will recover metals as small as 1mm. This facility not only boosts Tasmania’s environmental
sustainability but also reduces the quantity of valuable metals that end up in landfills.
A legacy of excellence
The Rowe family’s involvement in the recycling industry dates back to 1990 with the establishment of Southern Rocycling. This business laid the foundation for what would become Recycal, a company reborn in 2012 with a mission to revive the legacy of superior service. Drawing on decades of experience and knowledge, Recycal rekindled relationships with past clients and expanded its customer base.
Recycal has an array of processing equipment, including state-of-the-art shredders and non-ferrous sorting and separation plants. This capability enables Recycal to handle most scrap metals with precision and expertise, ensuring maximum recovery rates and high-quality end products. This focus on precision and efficiency not only maximises client returns but also minimises the amount of waste that ends up in landfills.
Cutting-edge facilities
Recycal’s infrastructure includes concreted yards with stormwater pits that have removable grates, triple inceptor pits, and with cyclonic
HumeCeptor units filtering the storm water before it finally leaves site. At Recycal, muddy, disorganised sites are not acceptable. State-of-the-art concreted facilities not only attract top-tier employees but also enhance equipment longevity, ensure safer operations, and maintain cleanliness by preventing dirt and mud trails when trucks depart the site. Its sites are equipped with AI camera technology that detect any rise in temperature, enhancing the management of security, fire prevention, and overall safety.
Its yards are also equipped with fire hose reels, and the Rocherlea site has more than 20 hydrant outlets strategically positioned around the premises. These features not only enhance operational efficiency but also ensure that Recycal’s processes are environmentally friendly and safe.
The company’s commitment to maintaining a professional presentation is evident in the upkeep of their sites.
Large landscaped areas, water features, and clean yards and vehicles reflect Recycal’s dedication to excellence. This attention to detail sets a benchmark in an industry where a “she’ll be right” attitude often prevails. At Recycal, its professional image is paramount, reflecting its
commitment to both its clients and the environment.
New shredder
Over the past 50 years, commodity prices have declined to such an extent that, for approximately seven of those years, recycling unprocessed scrap was uneconomical, leading to its disposal in landfills. However, with the shredder now in place at Recycal’s Rocherlea yard, this need never happen again.
The shredder produces a clean, dense, suitably sized “green recycled steel” for its sister company, Castings Tasmania, which melts it down to create various castings for both Tasmanian and mainland industries. This closed-loop system ensures that valuable materials are continually repurposed, reducing the environmental footprint, and allows Recycal to help its clients achieve their decarbonisation goals.
Environmental stewardship
At the heart of Recycal’s operations is a commitment to environmental sustainability. By reusing and remelting recycled scrap metal and diverting metalrich unprocessed waste from landfills, Recycal contributes to reducing the need for mining, conserving energy, and
Recycal aligns with the principles of a circular economy, where materials are continually reused and recycled. Images: Recycal
minimising landfill usage. Its efforts align with the principles of a circular economy, where materials are continually reused and recycled, minimising waste and environmental impact.
Recycal also processes copper PVC cable offcuts to recover the pure copper, which is transformed into copper granules. These granules are used by another sister company, ACL Metal Powders, in Tasmania where they are melted down to make a fine sintered powder that is exported globally. This intricate, vertically integrated network of recycling and repurposing, ensures that metals are efficiently reused, highlighting Recycal’s role in reducing waste and promoting sustainability.
Recycal also offers demolition services tailored to meet the demands of large-scale projects rich in metal content. Backed by a team of experienced professionals, Recycal Tasmania has refined and expanded its recycling services to align with evolving industry requirements. Its good safety record and commitment to returning sites to clients in pristine condition have been instrumental in driving its success.
The company’s array of equipment – ranging from mobile shears to large material handlers, complemented by a fully equipped fleet of heavy vehicles and bins – enables it to efficiently handle virtually any metal-rich demolition project. This infrastructure ensures that Recycal can meet the needs of diverse projects with precision and proficiency.
It also specialises in the recycling of transformers, managing the removal process both on-site and off-site. Its eco-friendly processes ensure that all contaminants are safely contained, meeting the highest environmental standards. Safety is a top priority, and Recycal adheres to Australian standards, ensuring their clients undertake testing
Ecocycle, specialises in recycling mercury, working closely with Recycal to tackle challenging recycling tasks.
Ecocycle
Recycal’s sister company, Ecocycle, is a mercury and silver recovery and recycling enterprise. With operations spanning every state, Ecocycle is fully licensed by Environmental Protection Agencies for the handling and recycling of mercurycontaining waste. Silver from X-rays, silver and mercury from oil and gas industries, dental amalgam, and button cell batteries are all recycled and the metals recovered. Mercury is required to be retired from early 2025 and Ecocycle is putting a new plant into its Kwinana Beach facility to turn elementary mercury into mercury sulphide.
Castings Tasmania, another sister company, has a history dating back to its establishment in 1834, an icon of the Tasmania landscape. In 2019, Recycal assumed full operational control of the foundry, and with a $10 million investment is revitalising it into a modern, efficient, and sustainable enterprise. Currently employing approximately 100 staff, Castings Tasmania is leading investments aimed at modernising the foundry ensuring it can compete, but more importantly stand out, with quality on-time, Australianmade green castings.

fostering community engagement, and championing environmental sustainability, Recycal exemplifies what it means to be a responsible and forwardthinking enterprise in the modern age.
Safety and Innovation
Championing the circular economy
Recycal is an advocate of the circular economy, where materials are continually reused and recycled, minimising waste and environmental impact. Metal recycling plays a pivotal role in closing the loop within the production cycle, curbing landfill waste, and minimising the demand for primary raw materials and critical minerals.
Recycal adheres to the highest safety standards, with rigorous training for all employees and the use of protective gear to ensure safe operations. Since 2016, the group has adhered to the ISO management system and holds ISO 9001, 14001, and 45001 accreditations, and is currently working on obtaining its R2 accreditation. These certifications underscore its dedication to excellence in safety and environmental management.
Innovation is a cornerstone of Recycal’s operations. The company
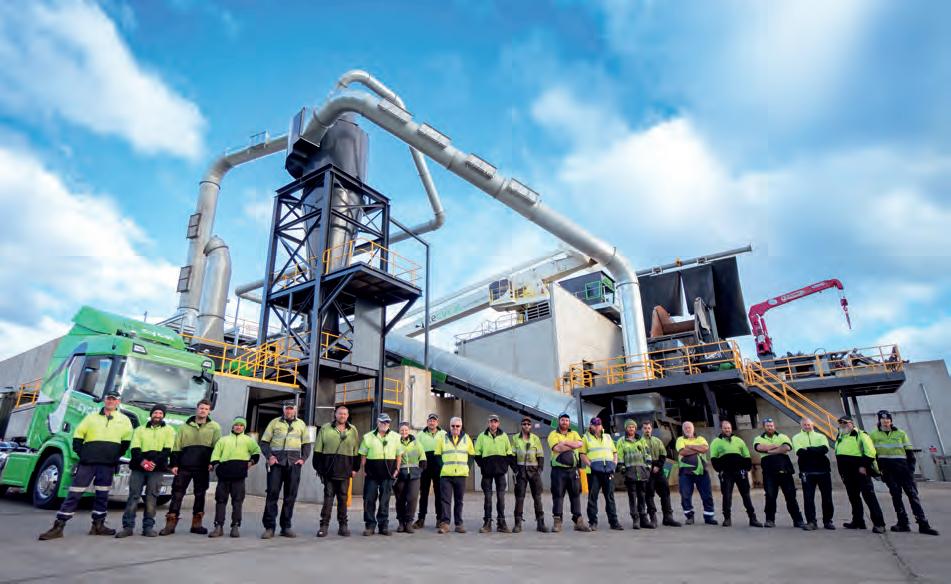
research and development since 2012, leading to groundbreaking projects that divert thousands of tonnes of waste from landfills. Recycal’s management team is steadfast in its pursuit of pioneering recycling methodologies, striving to enhance its corporate clients experience while giving them the comfort they need in environmental excellence.
This ethos of continuous improvement and forward-thinking has earned Recycal recognition from their clients. This pursuit of excellence ensures that it remains at the cutting edge of the recycling industry.
A vision for the future
Recycal’s vision for the future is one of continued growth and innovation. The company is committed to expanding its reach and impact not only in Tasmania but across Australia. By investing in recycling technologies and facilities, Recycal aims to set new standards for sustainability and efficiency in the recycling industry nationwide.
The Honourable Pam Allan, Chair of the Tasmanian Waste and Resource Board, envisions Tasmania as “a place where nothing is wasted”. Recycal is at the forefront of making this vision a reality, dedicating itself to creating a cleaner, greener Tasmania. However, its ambition extends beyond the borders of Tasmania. Recycal is equally committed to fostering a sustainable future for all Australians, ensuring that valuable resources are recovered and repurposed efficiently throughout the country.
Recycal’s nationwide efforts in recycling and resource recovery are crucial in reducing landfill waste, conserving natural resources, and mitigating environmental impact.
Recycal’s processing equipment includes state-ofthe-art shredders.
The shredder at the Recycal’s Tasmanian site produces a clean, dense, suitably sized “green recycled steel”.
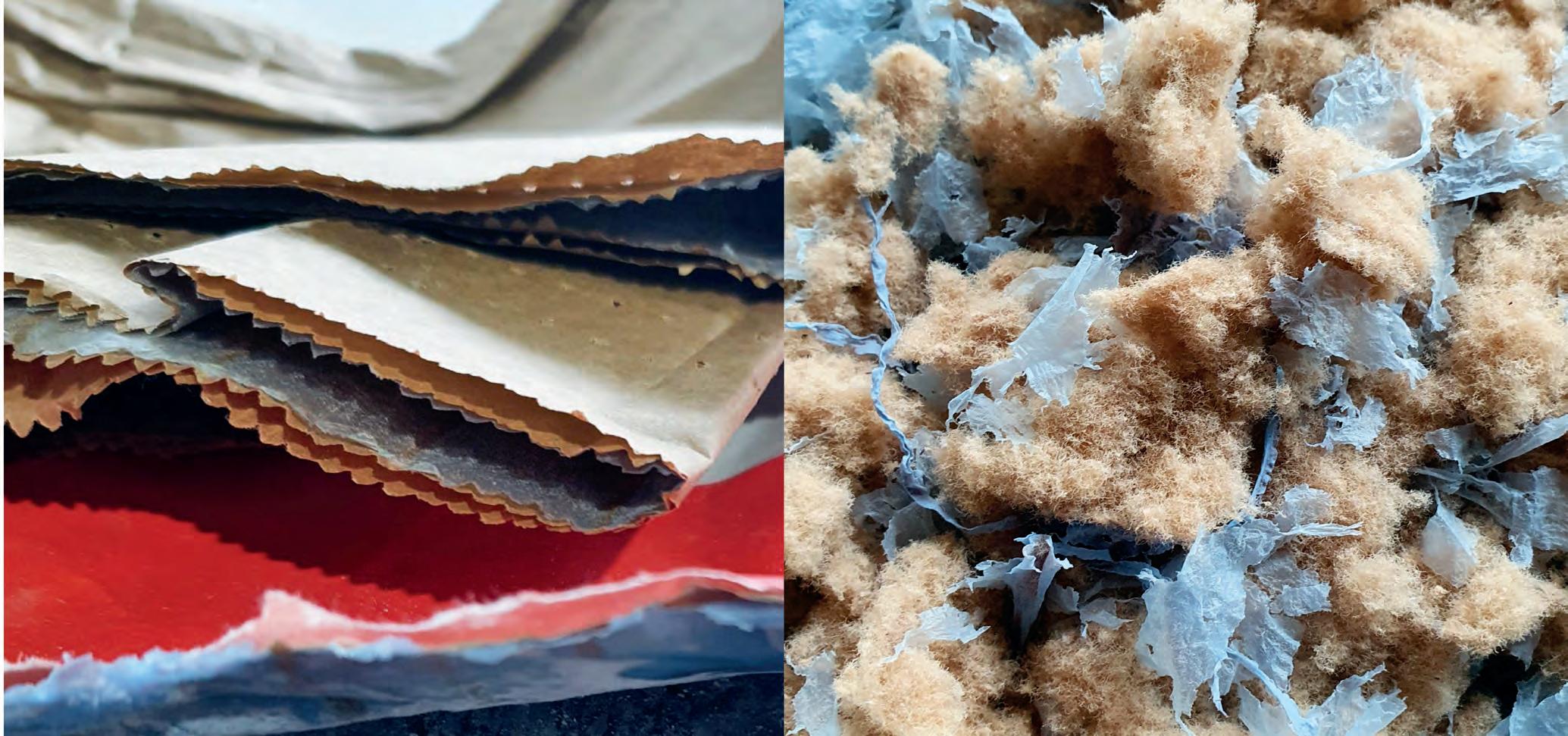
Vortair helps battle waste issue
By Inside Waste
FOOD TECHNOLOGIST and business development manager Tom Debney believes the team at Vortair has unlocked technology that could not only change the way people deal with waste, but also convert it to added value products.
The Vortair technology has caught the eye of many and was recently awarded the AIFST (Australian Institute of Food Science and Technology) Peter Seale Innovation Award for 2024 in recognition of its potential.
“The technology, and the potential of what can be done with something you would normally throw out, brought me to Vortair,” Debney said. “The ability to convert waste into something useful is fantastic and Vortair gives the opportunity to put a waste product back into circulation.”
The machine is a new technology for particle size reduction. It uses vortexes to disrupt materials, so they mill upon themselves, resulting in a more rounded particle.
One of the advantages of the technology is the ability to control the micron size of materials and maintain temperatures at a level where there’s no nutritional losses. This is important when dealing with organics or food products. And it’s here that the Vortair shows promise to help combat a critical waste problem.
Food waste
Australians waste about 7.6 million tonnes of food annually, according to the Department of Climate Change, Energy, the Environment and Water (DCCEEW). There are losses at every point along the food supply and consumption chain, including on farms during processing and transport, hospitality operators, supermarkets, and households.
The Vortair system has been trialled on many horticultural inputs, converting them to a paste, dry flour, or powder suitable as an ingredient in soups, sauces, stocks, and other products.
Debney said work has been
completed on apple and pear pomace (the pulpy residue remaining after juice has been extracted from the fruit) as well as grapemarc (the skins, pulp, seeds, and stems of grapes that remain after pressing).
Apple pomace milled into a powder can be used in alternative protein products, with the fibre acting as a binder. Grapemarc has a high polyphenol content, which makes it good to use in therapeutic products. And milling rejected allium such as onion and garlic could open opportunities to use waste garlic and onion as a replacement for imported powders.
Muscle and oyster shells are also on the milling menu. Milling would not only reduce the shell waste, which would normally be landfilled, but it would also produce a product with high calcium content.
“There are so many things we could do with this technology. It’s offering a solution for a whole range of problem wastes,” Debney said. “But there’s no point in doing something unless there’s
an end market that’s worth chasing.
“In the case of fruits and vegetables, it has the potential to open new markets for manufacturers. Once you take the juice off the product, you’ve still got high value material. But there are also significant advantages if this technology reduces the waste that farmers would normally throw back onto their paddocks.”
Debney has experience in developing strategy, management, and process control in businesses across Australia and overseas.
He is involved in mentoring several startups within the CSIRO On program, which is designed to accelerate Australia’s most promising research breakthroughs from mind to market. He also has a passion for developing processes that have an impact on improving the use of resources.
With an understanding of chemistry, physics, micro-biology and cost analysis, Debney was asked to look at the Vortair several years ago. He said he instantly recognised its capabilities.
The unit is offering a solution for a whole range of problem wastes streams. Images: Vortair
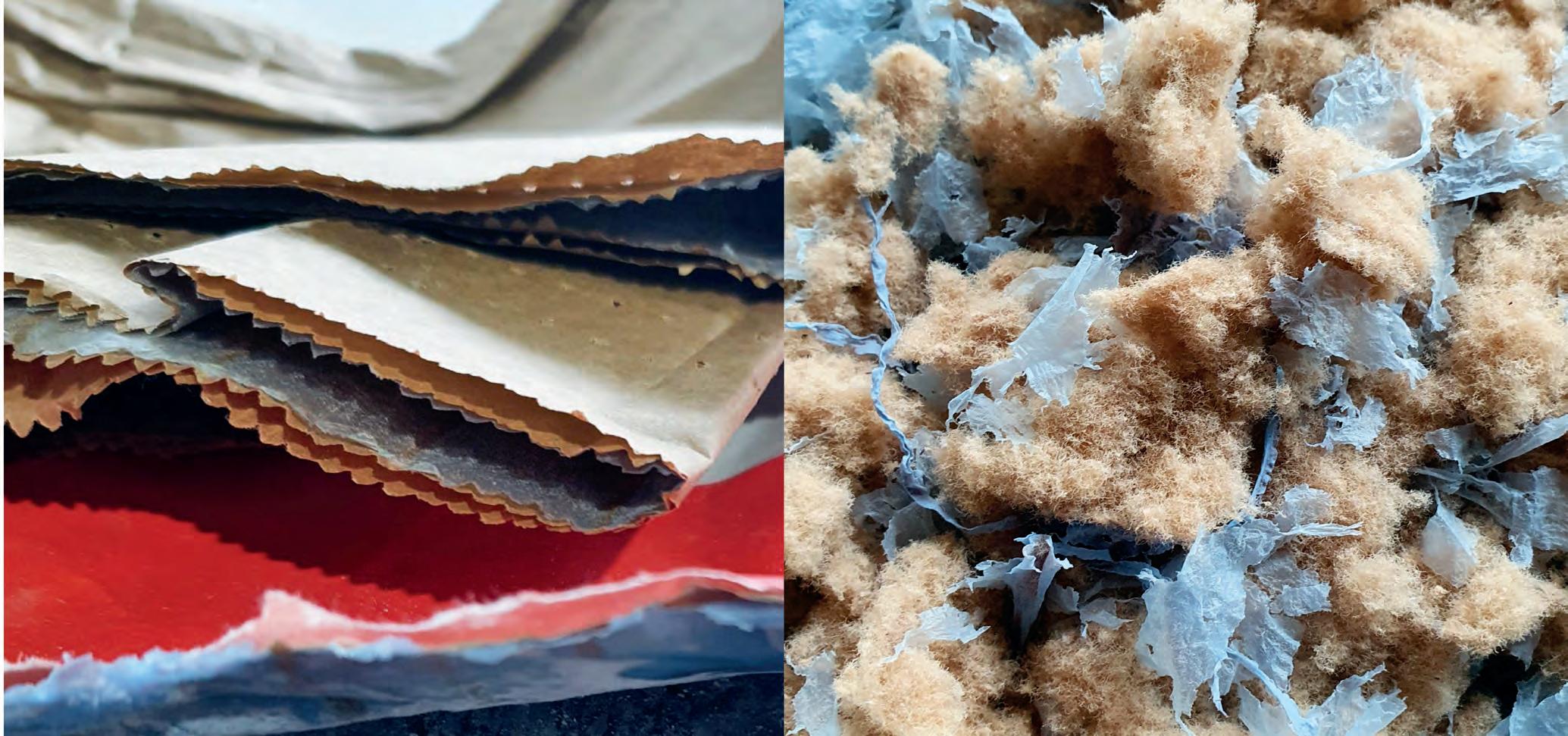
“This technology is going to solve a lot of people’s problems,” he said. “Reducing waste is critically important but if we can convert what was once waste into something y ou get a return on, it’s well worthwhile doing.
“There’s a whole lot of material that doesn’t get off farm because it’s the wrong size, or colour, which can now be upscaled and put into other products rapidly. In theory, that brings more farm return, but also reduces a dependance on a lot of imported dried powders. We’d be able to make them here and keep it economic. I think it will make some business in Australia more viable on a global scale.”
The Vortair machines are manufactured in Australia and assembled in Bayswater, Victoria, with fabrication taking place in Shepparton, Melbourne, and Dandenong.
The Food Grade Vortair 500 uses stainless-steel 316 with a single piece titanium rotor for milling food-grade materials. The standard Vortair 500 machine is made from high-tensile steel with tungsten carbide blades for increased wear resistance milling hard and tough materials.
Now at a commercial stage, the first machine has been sold for processing
pomace waste into a powder. Having a machine in action has sparked a rush of new inquiries from global and local fast moving consumer goods companies.
Vortair aims to establish a food safe facility with several machines operational to assist with further trials. It is also considering manufacturing a smaller, mobile machine to mill in situ for farmers or producers.
Until then, Debney continues to liaise with potential customers, working through how to feed the mills, food safety concerns and nutritional content for a variety of feedstocks.
While Vortair is not aiming to provide all those services, he said it’s important to understand the potential challenges and limitations to help
companies move forward.
And it’s not just food waste solutions being sought. The Vortair can mill plastic wrap or poly-lined bag waste back to a flake or finer powder that has potential to be reused in the manufacture of Low-density polyethylene (LDPE) and High-density polyethylene (HDPE) products.
“I’m constantly surprised by the amazing results we’re getting with the things we can mill,” Debney said.
“It’s left me scratching my head and wondering about the possibilities. I continue to get ‘wows’ when we’re doing trials.
“I think this machine has incredible possibilities to change what and how people deal with waste.”
“There’s a whole lot of material that doesn’t get off farm because it’s the wrong size, or colour, which can now be upscaled and put into other products rapidly. In theory, that brings more farm return, but also reduces a dependance on a lot of imported dried powders. We’d be able to make them here and keep it economic.”
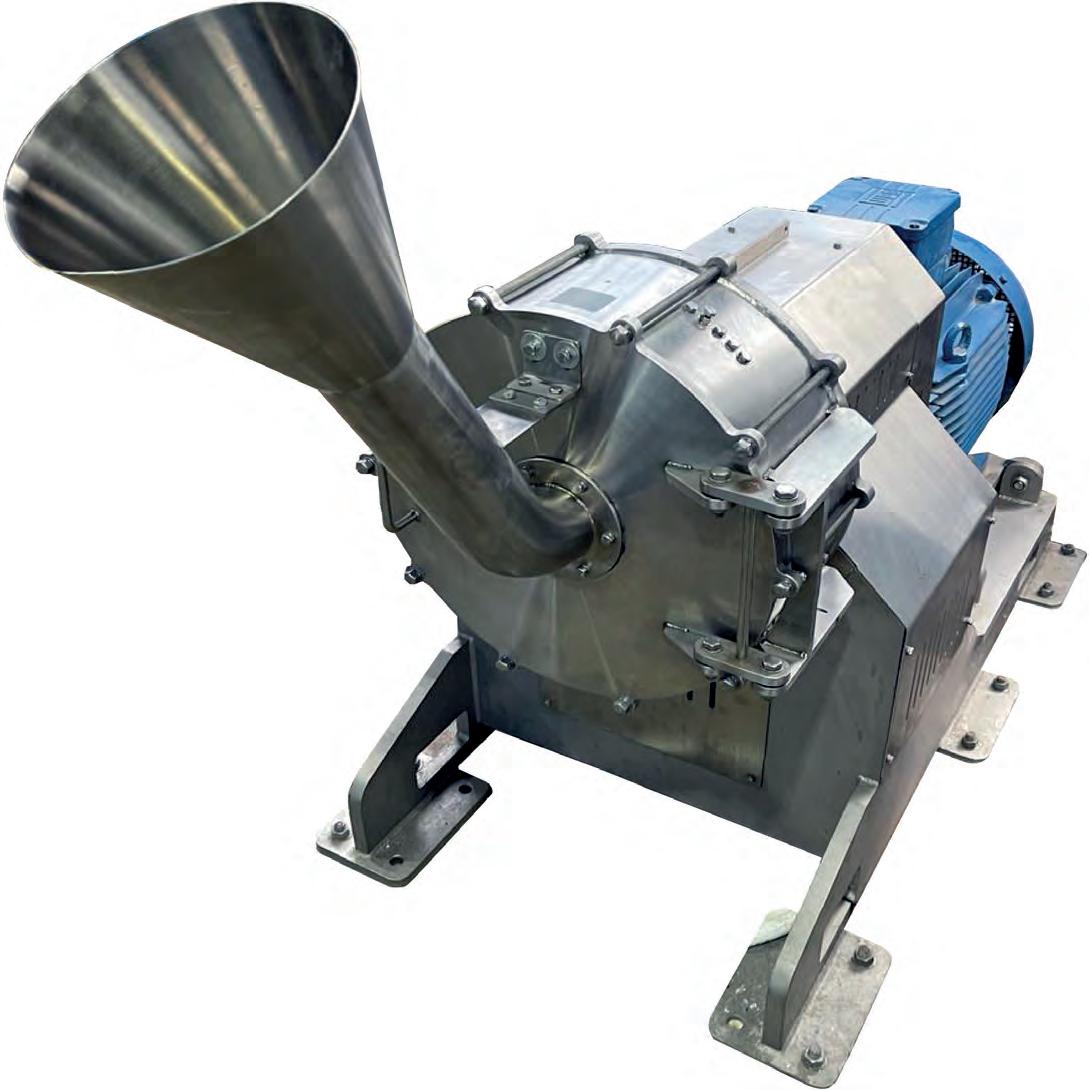
The Vortair 500 can help with making sure food waste is turned into a useful product.
needed.
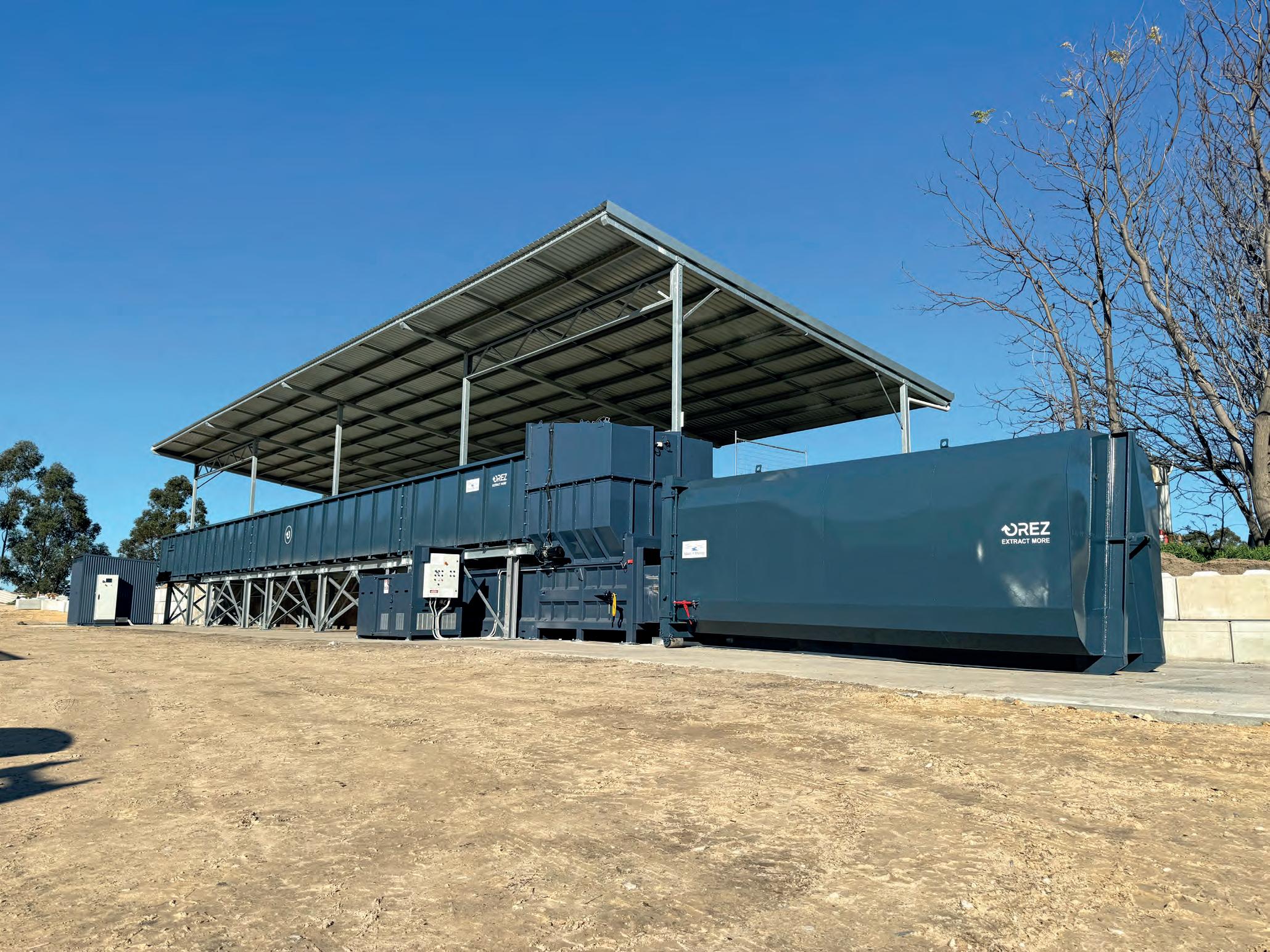
Walking tall with new resource machinery
By Inside Waste
WHEN THE SHIRE of Murray in Western Australia was future proofing an expected increase in population over the next few decades, its resource recovery/ waste disposal requirements were one of the key issues that needed to be addressed.
The Shire’s director of infrastructure services, Alan Smith, has been with the council for 20-plus years and knew that resource recovery infrastructure would need to be tackled sooner rather than later, as the outer Perth suburb started to grow.
“When I first started at the council there were probably about 8,000-9,000 people in the area,” he said. “We’re just edging on 20,000 now, and our future population is going to be up to 70,00080,000 people.”
When he started looking after the transfer station in 2010 it was nothing more than a 4m x 3.5m shed with a toilet next to it. As the population has
grown, so has some of the amenities. Recently, it has gotten to the point where new efficiencies needed to be incorporated.
Smith said the Council knew it would eventually want a moving floor, which would allow customers to dump their waste on a moving platform that puts the unwanted refuse into compact bins. Once a bin is full, it is then taken away.
Before the moving floor, the amenities had been built to include a high safety barrier to manage any fall risk when community were unloading at the tipping wall, but there were still safety concerns.
“When we constructed a new shelter at the tipping wall, we also installed gate barriers between the community and the bins,” he said. “We told the public at that time that the gates were a short-term solution, and that we were moving towards a moving floor.”
Another reason for the Council to embrace moving floor technology was cost savings. Smith and his team
calculated that a moving floor and its accessories could save them anywhere between $100,000-$150,000 a year in transport costs alone primary due to increased compacted of waste.
“The selling points of the moving floor and the compactor were not only; ‘do we get rid of these barriers and enable people to interact with a moving floor,’ but also within six to eight years the floor will be self-funded due to the savings in transport costs and be a longterm cost benefit for us,” he said.
A tender went out and was awarded to OREZ, a company that specialises in turn-key solutions for the waste and recycling industry.
Darren Quin is one of OREZ’s business development/project managers, who is based out of the Victoria office. Quin believes one of the reasons OREZ won the tender was because it took the time to work through the design and invited the Shire to visit similar installations used in other council transfer stations so they
could see how easy the moving floors were to operate for both the rate payers and operational staff.
It also gives Council an opportunity for resource recovery because the material is spread across the floor, according to Quin.
“You get a look at cardboard, you get a look at plastics, you get a look at steel and other items of value,” he said. “Then there’s the likes of batteries and other contaminants that can get dumped in with other materials in one hit by residents. You can now get a look at those items and either pull them off the floor or not put them in there to start with making it easier for staff to advise and educate residents, who unintentionally or otherwise dump stuff that they shouldn’t be.”
Smith points out that the Council is continually being proactive in providing organised areas within the facility that separate items that can be recycled. But he knows it requires ongoing community engagement and
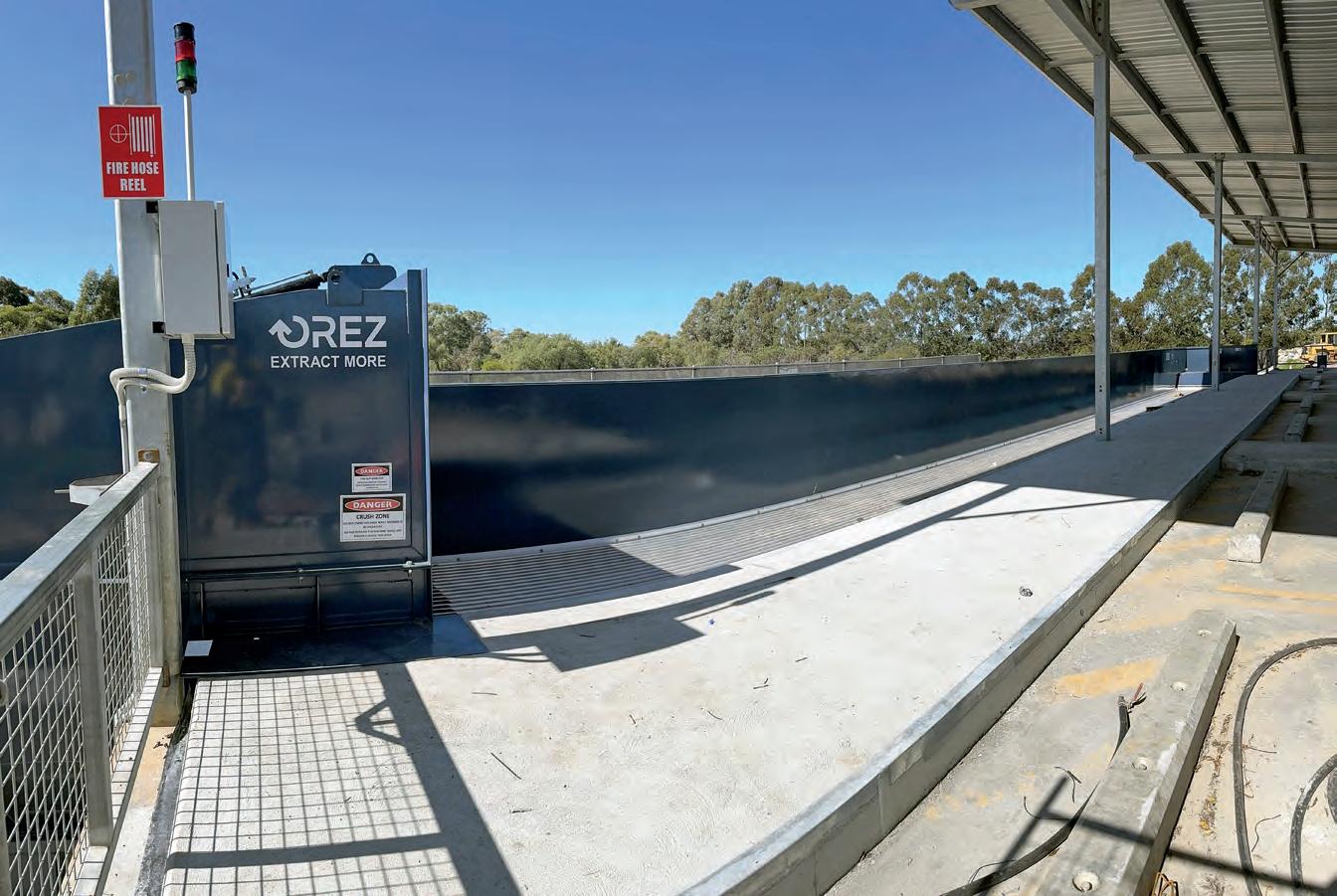
The system currently has six bins set up, but it is expected that a maximum of four will be
Images: Orez
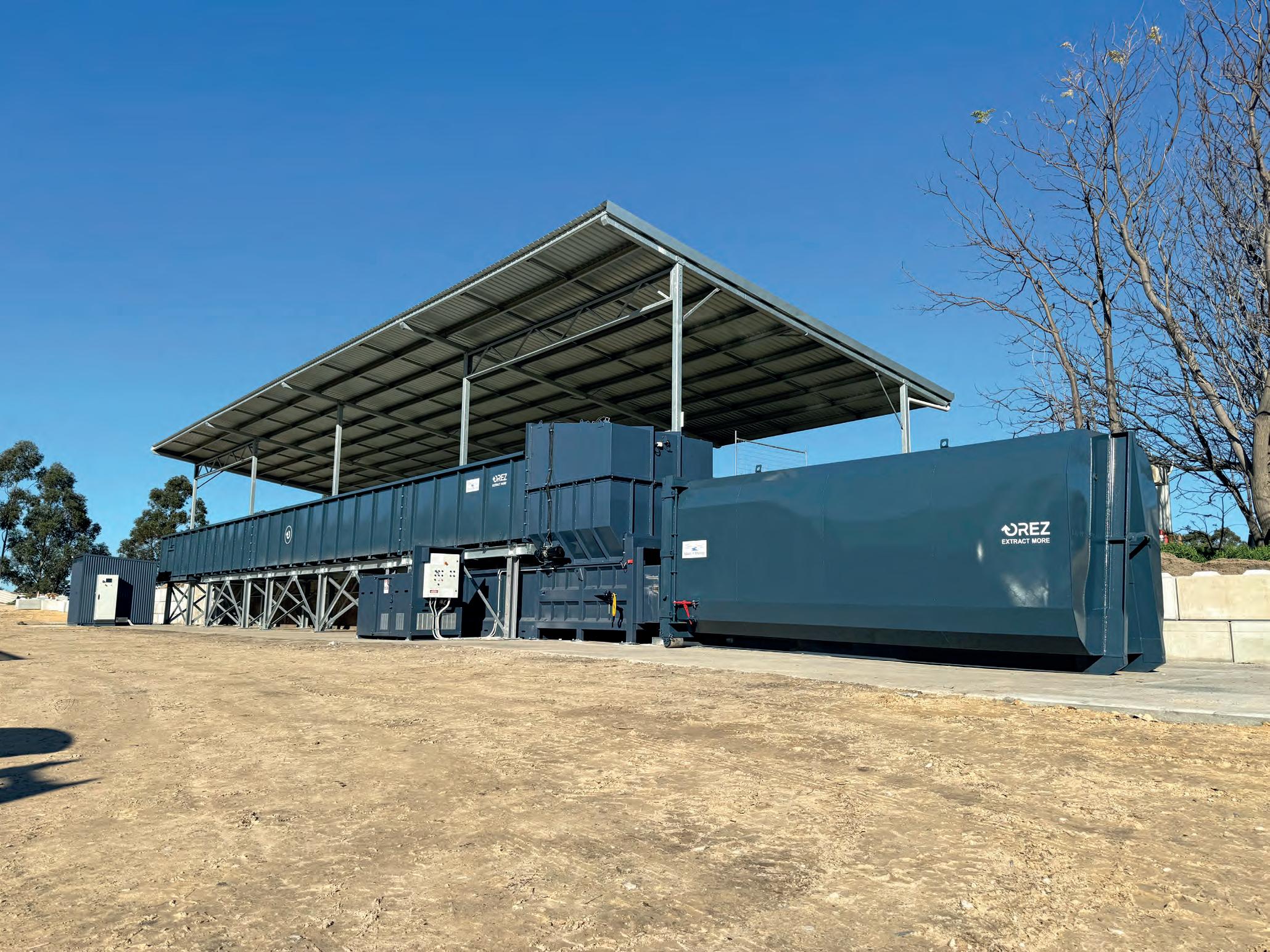
will take time for the community to embrace increased recycling and source separation.
“We’re also enabling community to access the transfer station more often with unlimited tip passes and this has allowed increased interaction and education, so they have started to load their trailers to suit the source separation,” he said. “When they first come in, they can see the individual stations – whether it’s tyres, batteries, recyclables, cardboard or others – and get those things out of the downstream system.’
Does it need to be modular, and can more pieces of infrastructure be added later, especially if the council expects the area to grow by another 50-60,000 residents? Not necessarily, according to Smith. As part of the project, OREZ provided six compactor bins as part of the set up, but even at its busiest, Smith expects to use a maximum of four. And even if there is an increase there are other ways to manage the waste load.
“It just means that our current waste contractor will service those bins
more often,” he said. “It’s not that you need three or four moving floors, you need the rotation of those bins to be changed over more frequently to allow for increased material. A worst-case scenario is you might have additional bins and rotations come into play.”
The moving floor itself was easy to install, said Quin. It was made off site and due to its modular design, took less than a week to set up. He said that OREZ installed the solution in about four to five days, and then there was a day of commissioning and operator training. Once everything arrived it went up very quickly and smoothly. Most of the sections were preassembled and were craned into place. The transfer station was only out of action for a week.
The floor itself is 25 metres long by 2.3 metres wide and 60cm deep. When it comes to ongoing maintenance Quin recommends giving the floor a full clean before the weekend so the plant can operate in tip-top condition during the busiest time of the week. There is also the quarterly service, but that depends on how much use the plant has
“When they first come in, they can see the individual stations – whether it’s tyres, batteries, recyclables, cardboard or whatever – and get those things out of the system.”
had over that period.
Smith and the Council are happy with the piece of plant and OREZ’s work on it.
“We’ve known Darren for a long time, and he’s just a great guy to deal with,” said Smith. “When we commissioned it, we allowed a few residents up on the floor, and they started tipping on the new moving floor. They were amazed with the ease of the set up compared to the gates that were previously in place. It’s a marked improvement.”
“It’s been a great journey, for the past 12 to 14 years. We’ve got a facility that’s got potential to move forward and create an environment that the community can enjoy and learn from rather than just being somewhere to just dispose of waste.”
“Efficiency, convenience, and sustainability are at the heart of this initiative,” said Ollie Brunt, sales and partnership manager for OREZ. “The Shire of Murray, with this project, aims to not only streamline waste disposal processes but also minimise environmental impact and reduce costs. The installation of a moving floor and waste compactor represents a significant leap in operational efficiency for waste delivery and disposal in the region. OREZ is proud to have played a key role in making this improvement possible.”
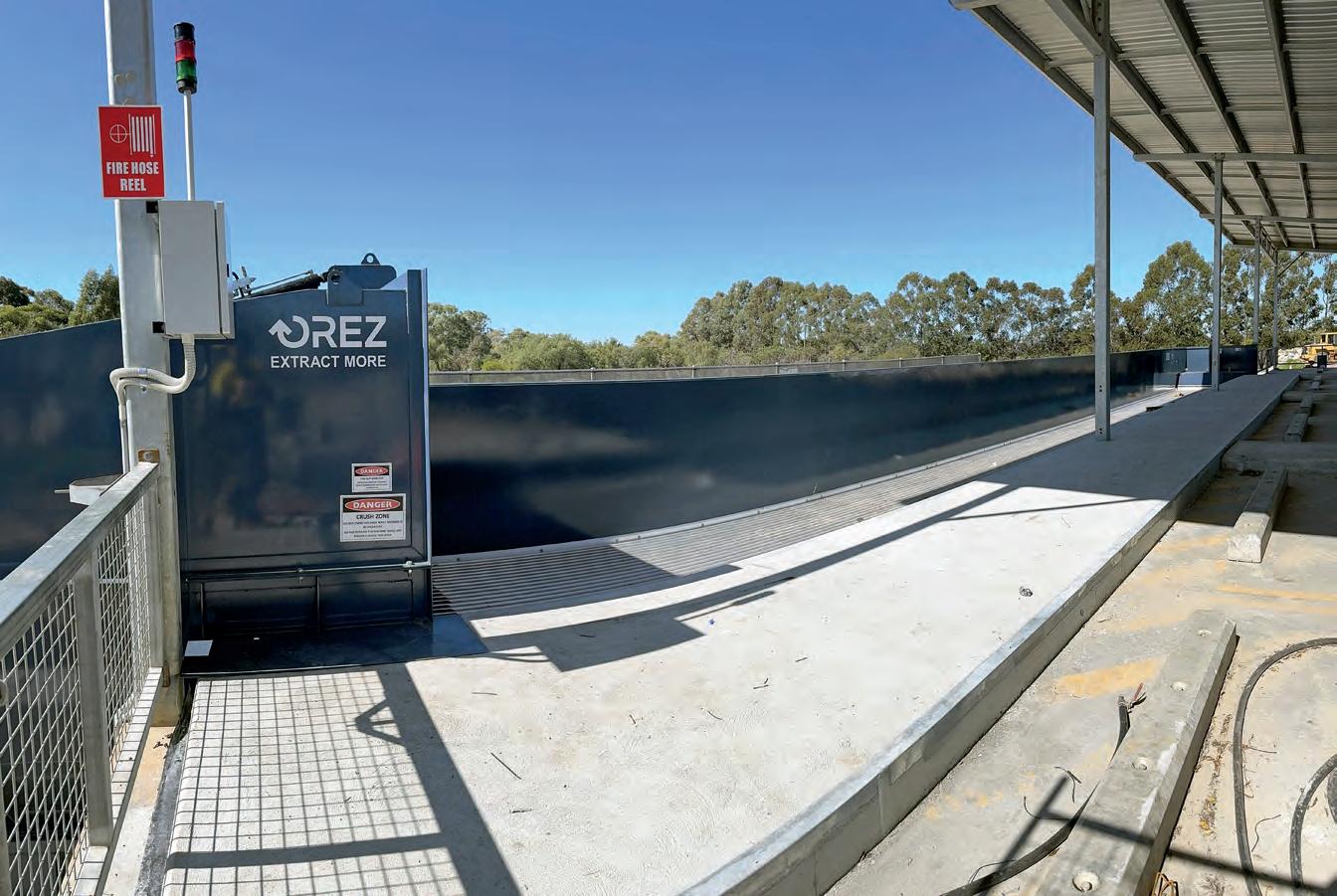
Byrne Trailers perfect fit for resource recovery sector
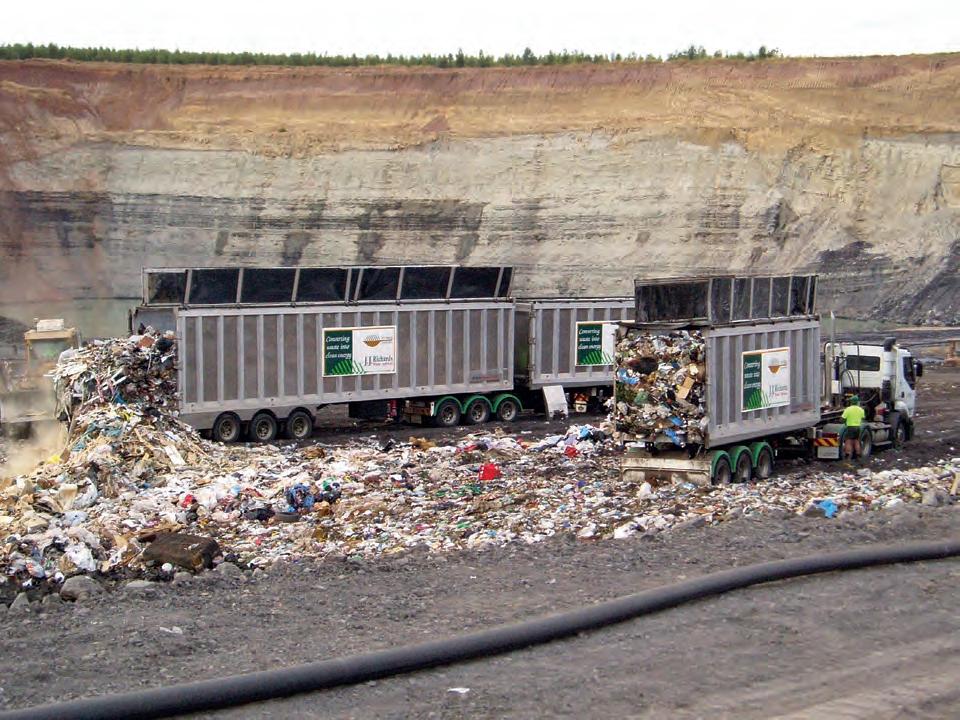
keep industries on the move. One of its specialities are walking floor trailers, which are equipped to make the moving of recycled and waste products easy.
Sam Gwynne is the sales representative at Byrne Trailers and provides insight into what makes walking floor trailers so good.
One of the features of these trailers is that their bins are made from aluminium, which means they are
sturdy, can handle big loads, and do not rust.
“They are a fully welded aluminium construction,” he said. “The only thing that’s steel is the chassis. The other thing about aluminium is that it offers strength and less tare weight.”
The company’s first build of its redesigned walking floor trailers was in 2018 and has been making inroads into the market ever since. Now it’s going for a big push to be one of the big players in the market. There are two main types of trailers it produces. The sheet and post trailer is for heavy materials, like
mulch, and other such products,” said Gwynne. “Our heavy-duty sheet and post trailer is designed for construction and demolition, compaction, and municipal waste. It can also be designed to be fully leak-proof or leak resistant.”
Both trailers can vary in size and capacity. They can range anywhere from 40-48ft with 4.3 or 4.6m in height. The company’s standard 45-foot trailer can take on 94 cubic metres, while the 48-
HDG handles tough materials
The ELDAN Heavy-Duty Granulator (HDG) is modified for recycling tough material, including electrical waste such as ASCR cables, low-grade cables with some impurities, as well as non-ferrous metals, refrigerators, industrial waste and more. The product’s new knife system with integrated rotary knives/ knife holders with a rotor, provides a solid foundation for the resistance required when processing heavy objects. The knives are straight and can be used on all four sides, and grind materials easily. Friction clutches protect the machine from material overload and the belt drive ensures a simple transmission. The HDG also processes RDF well and can produce
20mm material size.
The HDG is designed and manufactured to process tougher, hard material such e-waste with high Fe content. The HDG also performs well as a pre-chopper for these materials and other copper or aluminium cables and can include various screen hole sizes down to 12mm and upwards, according to customer requirements.
A summary of HDG features includes:
• an adjustable knife clearance, which optimises the cutting function;
• the product knives can be reground multiple times on a “flat-bed” grinder ensuring long life and low operation costs;
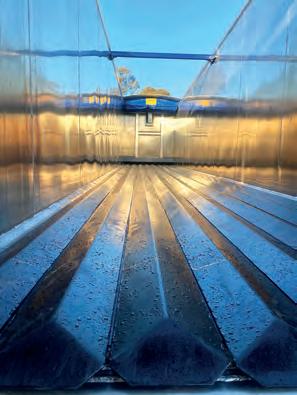
foot trailer can take up to 104 cubic metres.
Byrne trailers can also offer custom PBS designs to suit all needs
Another key feature is that the trailers are built to last. Gwynne talks of some customers that have had trailers for more than two decades and haven’t had to have any structural repairs done on them.
“And with something like one of our V-floor products, you’d get longer than 20 years out of them,” said Gwynne.
Many of Byrne Trailer clients have a specific flooring in their trailer to suit their needs and products. The floors range from different thicknesses of aluminium to heavy-duty steel.
As for the flooring system in the trailer, Byrne Trailers partner with the Keith Walking Floor brand, which is manufactured in the USA.
“We believe Keith are the superior brand,” said Gwynne. “Keith has a representative based in Melbourne to help with any issues or questions that we come across.”
As for back-up service, Byrne Trailers has representation in Wagga Wagga, NSW and Toowoomba Queensland.

Friction clutches protect the HDG from material overload.
Image: Eldan
Walking floor trailers handle large capacities, making them ideal for the resource recovery sector.
Byrne Trailer’s walking floor units are made of fully welded aluminium. Images: Byrne Trailers
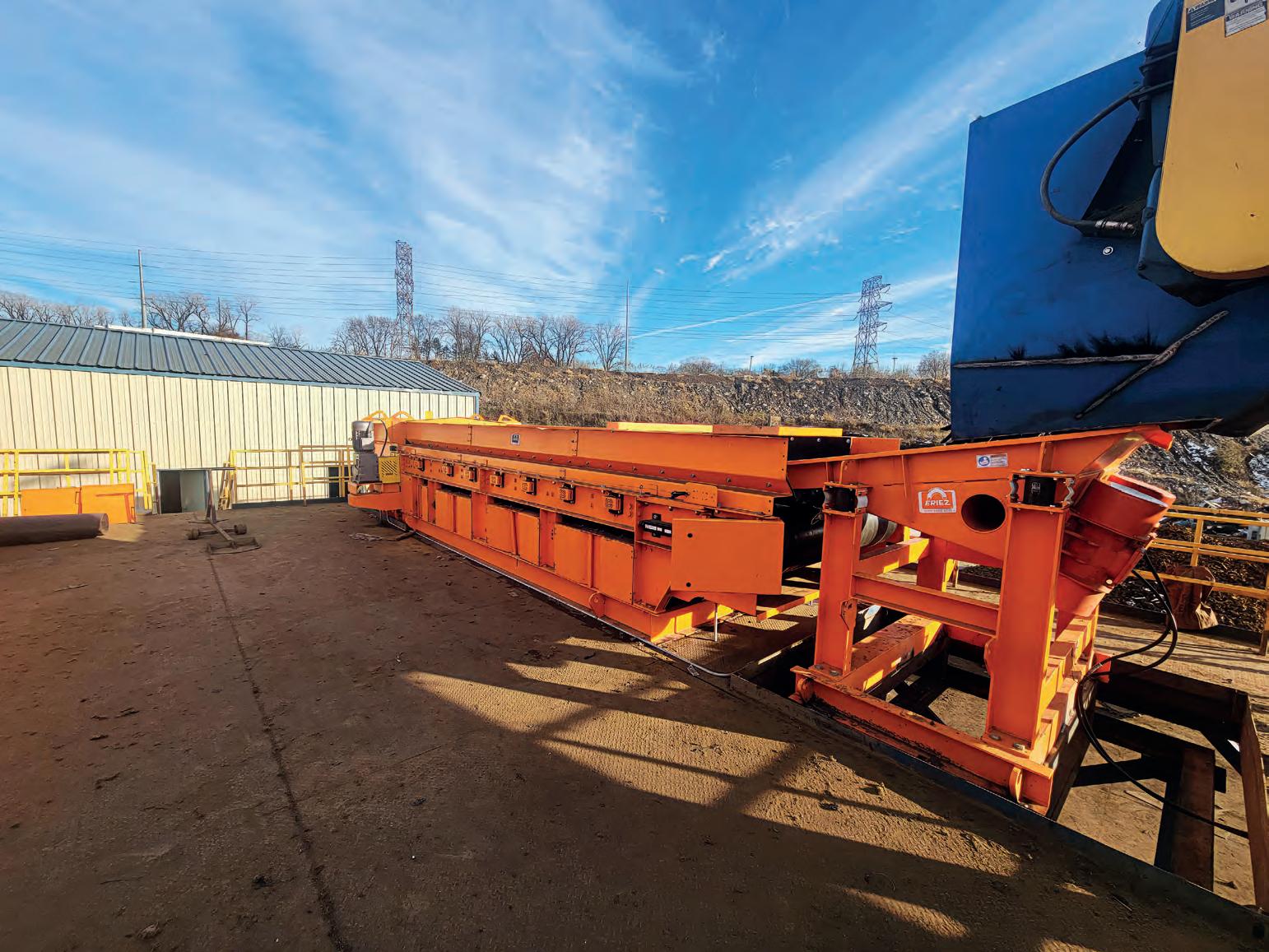
Separator and shredder offer premium recovery options
ERIEZ IS EXPANDING its line of recycling equipment with the introduction of dynamic pulley separators, which are designed to liberate entrapped steel and magnetic fines from recycled materials.
This equipment improves downstream separation and the grade of non-ferrous metals.
The separator is suited for recovering ferrous fines from ASR and Waste-ToEnergy bottom ash.
Positioned upstream from an eddy current separator, the high-strength unit uses a Rare Earth permanent magnet pulley rotating at an off-set speed from the belt, creating an agitating magnetic field. This improves ferrous recovery or removal and allows non-ferrous material to continue to downstream equipment.
For ASR applications, the separator can be used with weaker magnetic drums to recover ferrous nuggets from the ASR stream. Discarded fines material that has passed through the initial screening process goes to the unit for removal of ferrous materials. The non-ferrous fraction can then be further processed on an eddy current separator.
“The agitating action generated the dynamic pulley separator allows for fine ferrous to be recovered while freeing up valuable non-ferrous metals to be recovered downstream,” said Jonathan Schulberg, Business Development Manager for Heavy Industry, Australia and New Zealand. “The Eriez DPS helps to debulk and reduce material burden upstream of eddy current separators and other downstream non-ferrous separation equipment providing for improved Zorba grade and recovery.”
The unit is also effective for ferrous
removal from plastics, rubber and similar materials. These separators provide a high-powered agitating magnetic field to pull metal contaminants out of the product flow, improving purity and protecting downstream equipment from damage.
The dynamic pulley separator is available in 40-inch and 60-inch widths and can be accommodated for base or suspended mounting ahead of an eddy current separator.
Shred1 ballistic separator
After more than a decade on the market, the Eriez Shred 1 ballistic separator is still delivering premium, low-copper shred. It enables scrap processors to secure higher pricing per tonne, resulting in a swift return on investment (ROI).
With global steel demand surging, scrap processors face increasing pressure to supply high-grade ferrous products to steel mills. This ballistic separator meets this challenge by producing premium, low-copper shred from automobiles and other mixed consumer waste containing complex steel components.
It efficiently separates iron-rich ferrous materials from mixed metals and waste streams post-drum magnet flow, producing two distinct fractions – No. 1 Shred, a premium, low-copper (0.16-0.2 per cent Cu) product, and No. 2 Shred, a traditional ferrous product.
Positioned strategically after primary scrap drums and before the picking station, the Shred1 employs a unique magnetic element for maximum ferrous recovery. Schulberg points out that
many customers opt to install the Eriez PokerSort to complement the Shred1 by removing long, troublesome components, commonly known as pokers, from the process.
Over the years, Eriez has tested the Shred1 ballistic separator, processing more than 1,000 tonnes of shred using an X-ray analyser. Results consistently show an average copper content below 0.2 per cent, lower than that of the control group from multiple shredder yards.
Schulberg said that scrap processors worldwide are achieving impressive returns with the Shred1.
“By recovering low-copper shred that commands top prices per tonne and reducing the need for hand-picking, the Shred1 is proving its value in the field and earning customers’ loyalty,” he said.

The Shred1 employs a unique magnetic element for maximum ferrous recovery. Images: Eriez
The dynamic pulley separators provide an agitating magnetic field to pull metal contaminants out of the product flow.
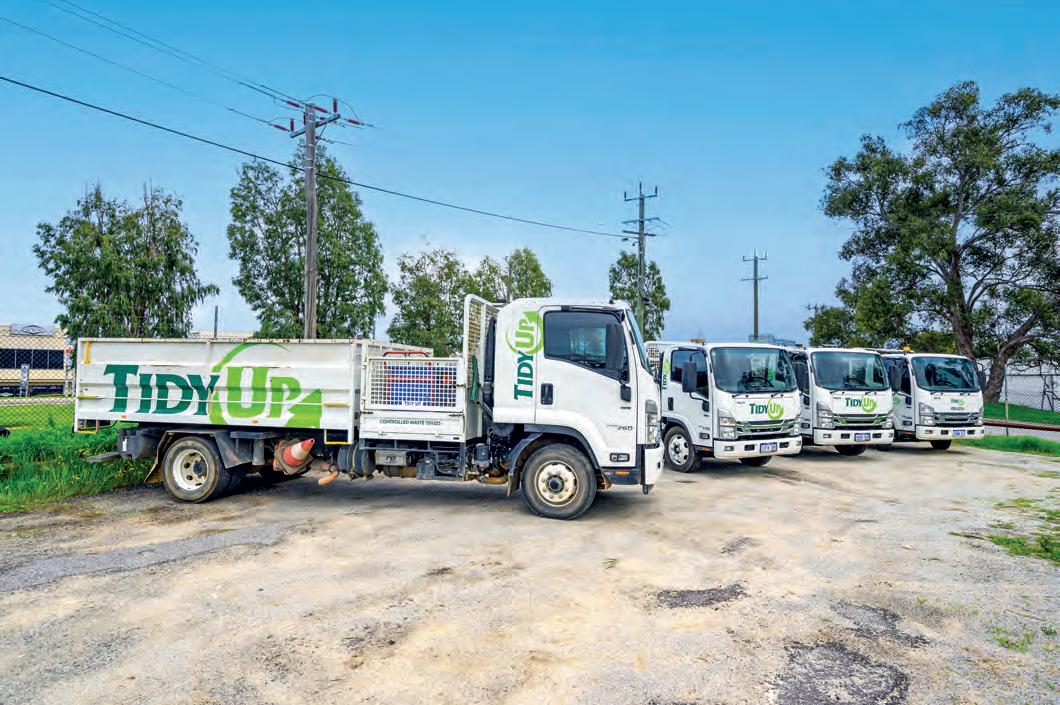
“I don’t want our vehicles being held up on the road or my drivers feeling frustrated if the trucks aren’t in peak condition. Operational efficiency keeps our business model strong.”
Assurance that the new trucks will perform reliably comes in the form of an Isuzu Essentials service agreement, which is factored in as an upfront cost with purchase of new vehicles from the Major Motors dealership.
Tidy Up plans a fleet for greener days
By Inside Waste
HOMEGROWN PERTH RECYCLING company, Tidy Up, has a vision of ‘life without landfill’.
The business, and its aptly named ‘Tidy Team’ handles a gamut of waste services: from e-waste, green waste, metal, cardboard and paper through to construction materials, furniture and unwanted items from customers houses or businesses.
The operation was first established in 1975 by local entrepreneur Des Berry, who carted away green waste in garden bags under the name Berry’s Jumbo Bags from his family home in Mount Pleasant, Western Australia.
Now known as the successful Tidy Up operation, it services the Perth metro region from a warehouse, store, and yard based in Cockburn Central.
Roots in the region
It was the 1990s that saw a big shift in the original concept, as Tidy Up diversified to meet client demand, explains business development manager, Tony Berry – the second generation of Berry recyclers.
“In the late 90s, we could see that recycling was going to be massive… as we came to pick up the garden bags for people each day, they would ask us to load other material,” Berry said.
“Recycling just took off from there. Our services were so in demand by 2012 that we sold the original garden bag business to focus purely on recycling.”
Now a B Corp Certified company, Tidy Up is committed to moving, disposing and recycling rubbish in a socially and environmentally friendly manner, with the ‘life without landfill’ motto permeating their actions.
“That’s what our team lives by every day, and we are always moving towards it,” Berry said.
“I’m not sure that we’ll ever fully achieve a life without landfill, but that is our overarching goal, whether it’s getting furniture and homewares back into the community or collecting e-waste to be delivered to our sorting partners.
“Our teams are strategically loading their trucks in such a way that they can either get the material back here or get it directly to one of our suppliers, communicating with our office so that everything is coordinated for the best possible results.”
Fleet expansion
Supporting the collection side of Tidy Up’s operation is a carefully constructed fleet of medium-duty truck models, specified with custom tipper bodies.
Trucks are either loaded by hand or by a team member using Tidy Up’s telescopic handler forklift, affectionately referred to as ‘the Green Goblin’.
The choice of truck model comes down to vehicle versatility and the ability to handle the company’s large range of waste types and sizes.
Tidy Up currently run an Isuzu NPR 75190 with Automated Manual Transmission (AMT), an NQR 87-190 AMT, and an FSR 140-260 with 6-speed Allison automatic transmission.
The newest truck to join the ranks is an additional NQR 87-190 AMT with a customised tipper tray and storage unit built onto the cab chassis, which arrived in April this year.
Berry notes that the business made the strategic move to a more efficient fleet in 2007, approaching sales manager Peter Dewar at Major Motors Isuzu in Perth for
a better solution than using a passenger vehicle and trailer.
“I went into the Major Motors dealership with a 4WD that was towing a trailer and said to Peter, ‘Hey, can you help me solve this problem?’” Berry recalls.
“He had the vision for the kind of truck I needed and together we were able to make it happen. I have never looked back.”
Steadfast approach
Tidy Up has implemented plans for a conscientious replacement schedule on its trucks, turning them over every four to five years or around the 200,000 km mark.
This, and a pre-planned maintenance schedule, which keeps them operating in peak condition and at maximum efficiency, play into the business’ steadfast approach to sustainable operations.
“We have very important clients that
The Essentials service package covers the first six services (up to 72 months), including the use of genuine OEM filters and lubricants, washer fluids, wheel bearing repacking and a range of other inclusions, plus the guarantee that work is conducted by factory-trained technicians familiar with the product.
This makes Tidy Up’s fleet maintenance schedule – and its various compliance obligations such as Chain of Responsibility laws – a more streamlined process.
“We look after the trucks because they’re the backbone of the entire business.”
Looking to the future
Accountability across all facets of the business is important for Tidy Up, which goes the extra mile to show clients it’s serious about its promises, such as releasing data on the amount of landfill waste processed on their own website.
Berry says this level of scrutiny helps to keep staff motivated and the business on its toes providing the best possible service – which includes utilising their Isuzu truck fleet to its full potential.
“Isuzu Trucks are a massive part of our development and our public image, offering us reliability and comfort, and boosting morale for our team,” he said.
“We have expansion plans in place to grow the rubbish removal side of the business, but we’re also introducing a new service which we are very excited about. Our Isuzu trucks are going to help
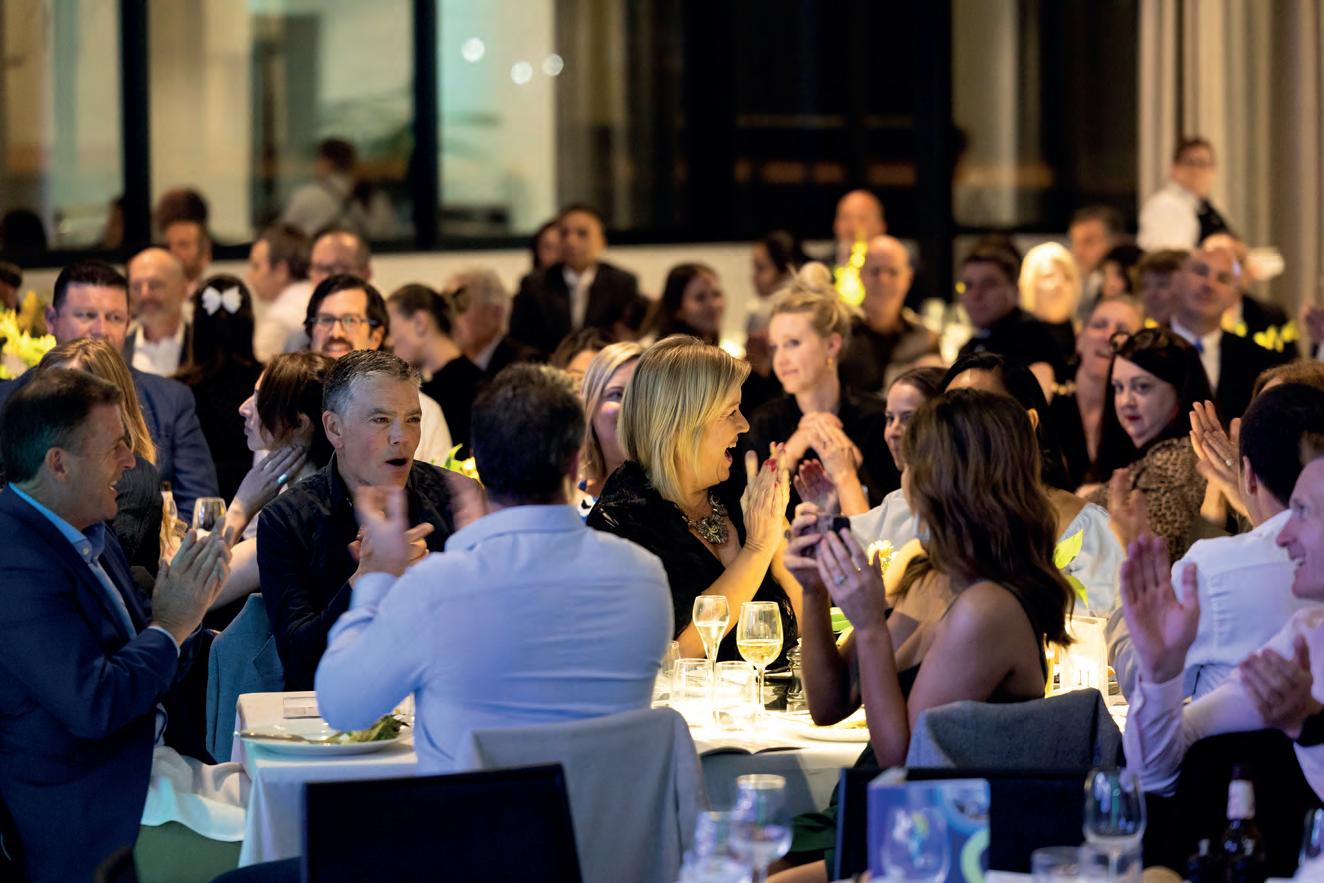
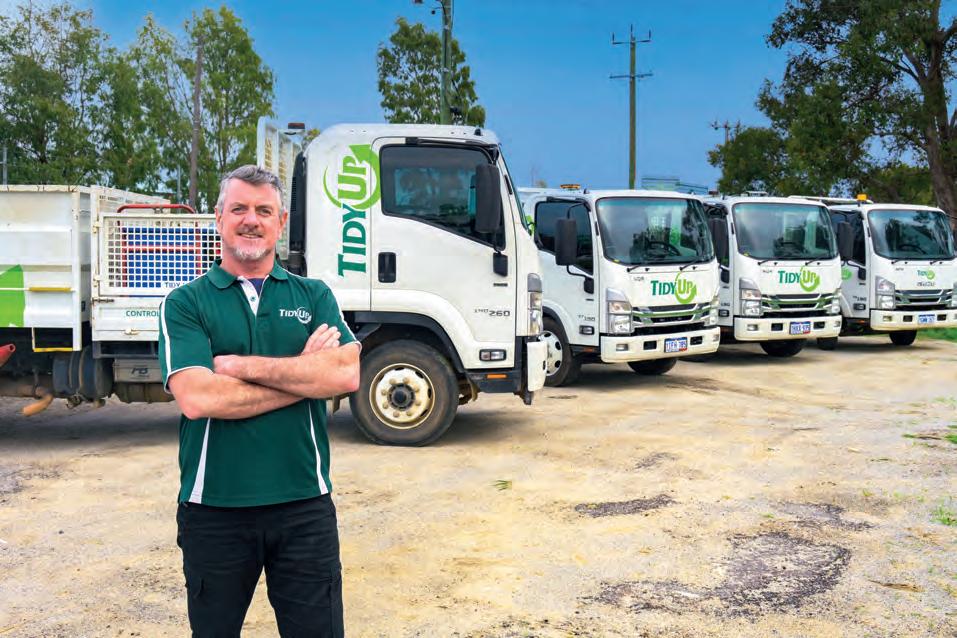
The choice of truck comes down to the ability to handle the company’s range of waste types and sizes. Images: Tidy-Up
Tony Berry in front of his fleet of Isuzu trucks.
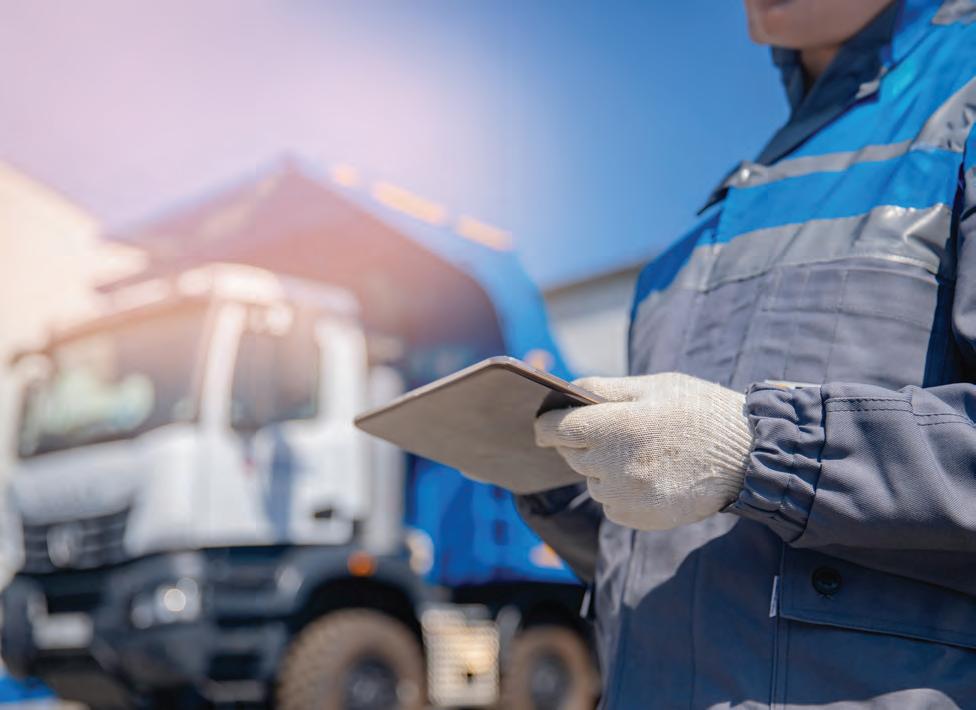
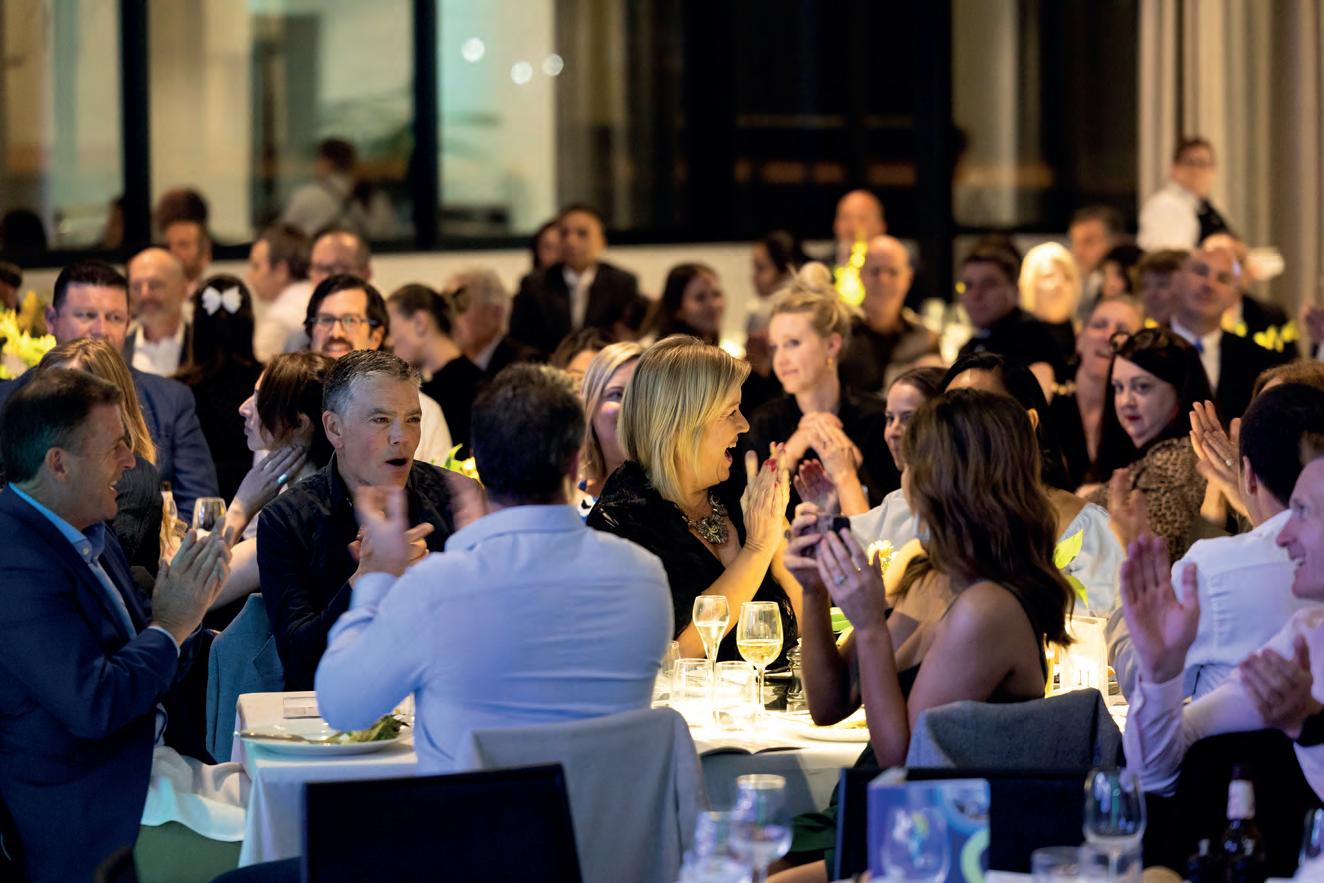

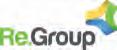

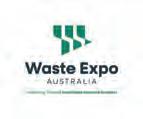
Top tips for waste and recycling
By Inside Waste
AS AUSTRALIA HEADS TOWARDS a sustainable circular economy, waste management operations need to stay ahead of the curve to remain efficient and profitable. Improving efficiencies onsite by choosing the right equipment and fine tuning the processes, ensures investments can be made in innovation and technology in order to keep their business in line with this fast-paced industry. Achieving these goals can be challenging. To help enhance waste management practices, machinery specialist Onetrak has compiled its top tips. These strategies can aid in creating a thorough practical plan for an operation.
Determine the categories of waste materials
To begin, pinpoint the specific types of waste materials you plan to manage. Whether it’s plastic, paper, metal, or electronic waste, each type demands specialised machinery and tools. For example, a plastic recycling plant might need shredders and crushers, whereas a paper recycling facility might require balers and pulpers.
Examine the scope and size of your operations
Take into account the amount of waste materials that need handling daily or monthly. This assessment will dictate the necessary capacity and size of machinery and equipment. Avoid investing in machines that are either too small or too large for operations. Evaluate the space within the facility to determine the suitability for installing machinery and equipment. Take precise measurements to confirm compatibility with the selected machines. Also, take into account aspects like ventilation, safety regulations, stockpiling and the ease of movement within the facility.
Set a realistic budget
Recognise the constraints and establish a practical budget for acquiring machinery and equipment. It’s crucial to find a middle ground between affordability and quality. Keep in mind that opting for dependable, long-lasting machines will result in cost savings in the long run. Partner with a supplier that provides a variety of flexible purchasing options tailored to a person’s needs.
Efficiency and productivity
When selecting machinery, prioritise high processing efficiency and productivity. Efficiency plays a vital role in the profitability of your waste management operations. Choose equipment capable of managing substantial waste volumes, while reducing energy consumption and maximising production output.
Support and maintenance
When looking into recycling machinery, it’s crucial to assess the maintenance needs and the level of support offered by the manufacturer. Regular maintenance is key for the machines to perform at their best and last longer. Check for spare parts availability, service agreements, and technical support options.
Safety features
Ensure the safety of employees and the environment by choosing machinery equipped with strong safety features. Seek out features such as emergency stop buttons, safety guards, automatic shut-off systems, good visibility and user-friendly interfaces to reduce the chances of accidents. Having a clear vision is essential for feeding and loading operations.
This might involve using raised cabs or platforms.
Ensure effective dust control measures are in place. Regular maintenance and monitoring, high-quality filtration systems, wet/foam suppression techniques, staff training on PPE, and vigilance help minimise airborne particles, ensuring worker and environmental protection from dust exposure risks.
Practice efficient materials handling
Sorting materials correctly is a crucial element of efficient recycling to enable smooth processing. Operational efficiency is vital in the recycling sector, ensuring waste materials are processed and recycled in the most resourceful and costeffective way. This includes streamlining processes like collection, sorting, storage and processing to maximise recycling volumes and reduce waste. Consider conveyors, magnets and optical scanners to separate the recyclables and minimise manual handling.
Look into the design layout to reduce re-handling as well as integrate safety measures and environmental factors to prevent accidents and reduce
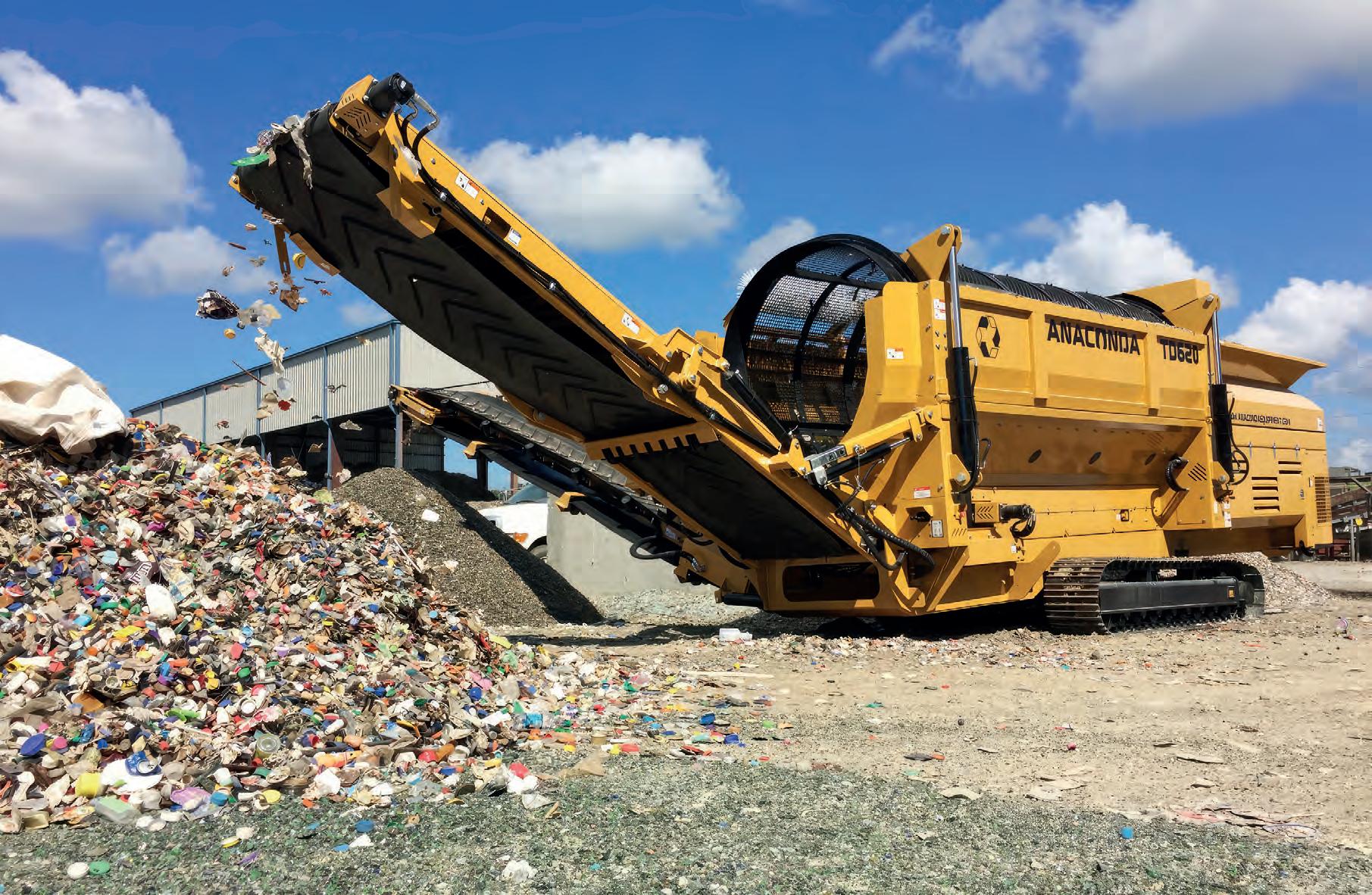
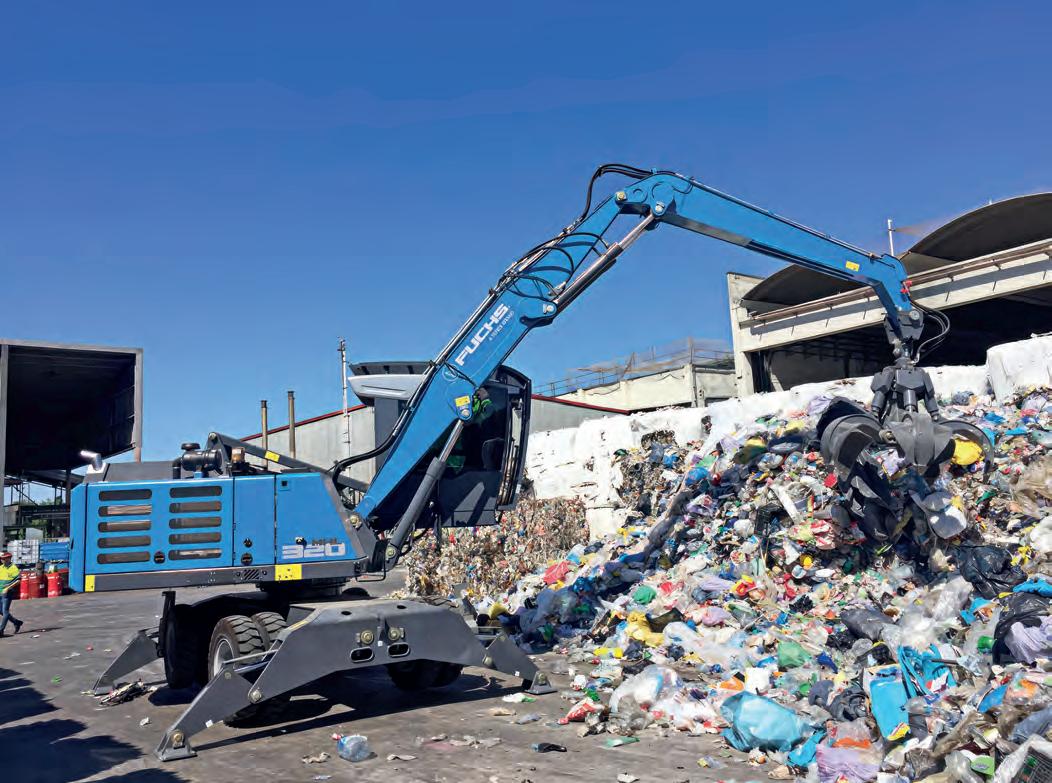
Dependable, long-lasting machines are a must for resource recovery facilities.
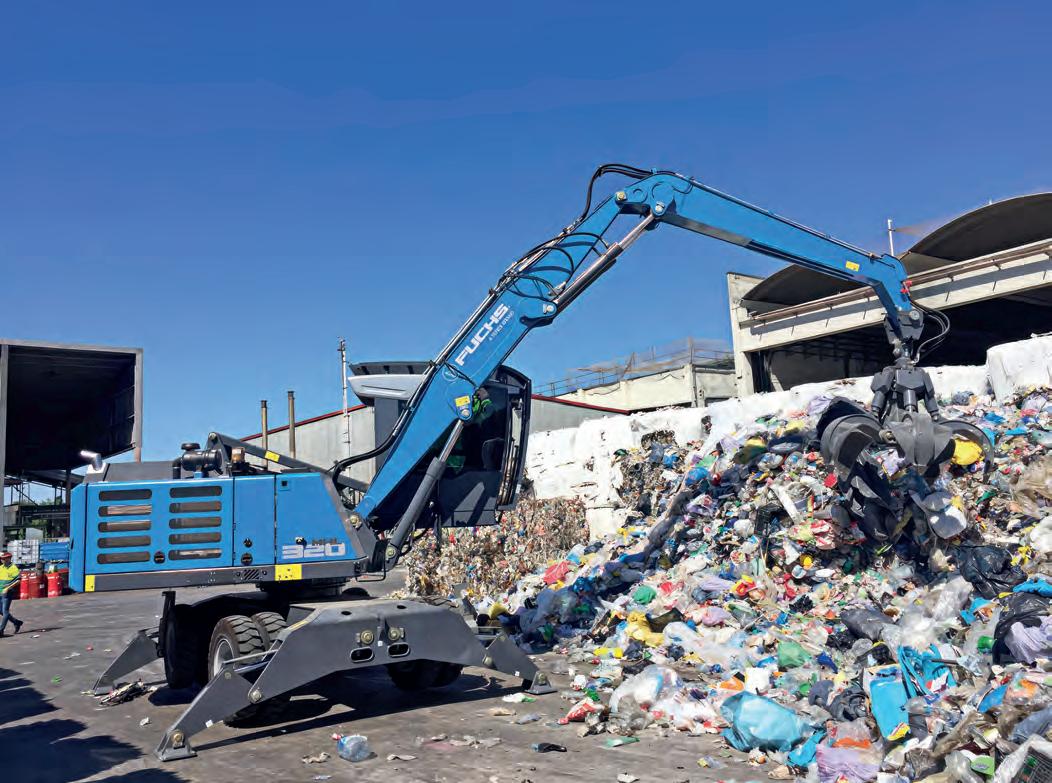
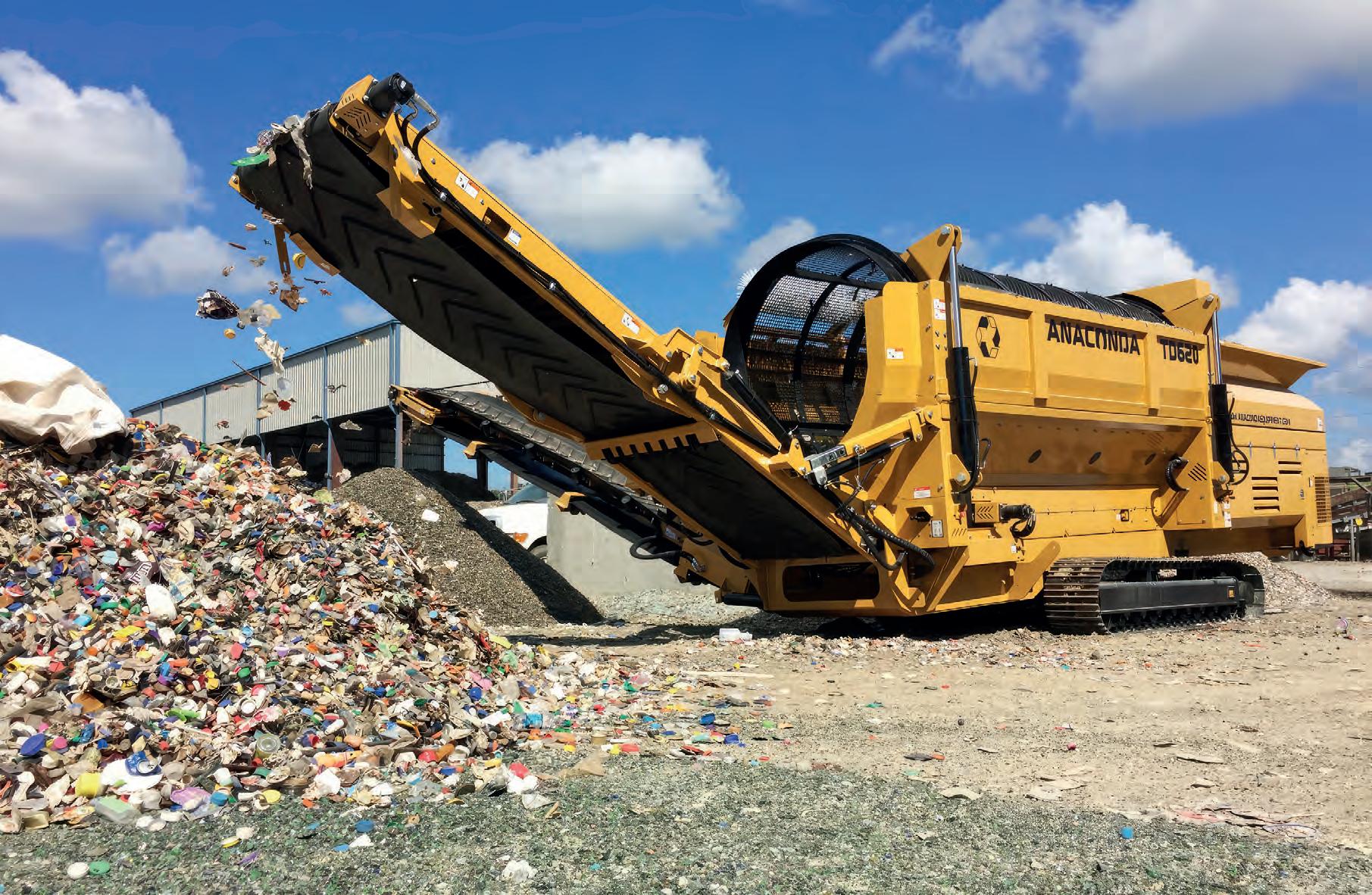
the operations impact on the nearby ecosystem.
Loading and feeding techniques
CONSIDER:
• Proper positioning to maximise the reach, stability and capabilities of the machine.
• Smooth control and steady movements can make faster work as this avoids inaccuracies and damaging equipment.
• Minimise movement by planning ahead to reduce cycle times.
• Implementing GPS and telematics –these technologies provide instant feedback on the machine’s performance, the accuracy of tasks, and even predictive maintenance notifications. Additionally, they offer valuable data to assist operators in enhancing their skills.
• Provide regular training.
Finding value in other products onsite
The delivery of waste materials, especially C&D waste, can include bricks, concrete, soil, timber, metals with limited plastics, plasterboard, ceramics and paper. For bricks and concrete consider crushing and recycling these for another income stream. This not only diverts waste from landfills
but also provides a sustainable source of materials for future construction projects. Soil and timber can be repurposed as well; soil may be enriched and used in landscaping or gardening, while timber can be processed into mulch or reclaimed for building purposes.
Metals, being highly recyclable, can be sorted and sold to recycling facilities, ensuring they are reused in manufacturing new products. Limited plastics should be carefully segregated and sent to appropriate recycling centres to minimise environmental impact. Plasterboard can be broken down and its gypsum content recycled for use in new plasterboard or as a soil conditioner.
Ceramics, although more challenging to recycle, can be crushed and used as aggregate in road construction or as a base material for new ceramic products. Paper, one of the more straightforward materials to recycle, should be collected and sent to recycling plants where it can be pulped and transformed into new paper products. Additionally, the plant may incorporate composting facilities for organic waste and advanced waste-to-energy systems to maximise resource recovery.
With minimal control over feed material, always be prepared for the
worst-case scenario. This includes implementing robust sorting and preprocessing systems to handle unexpected contaminants and varying material compositions. By investing in versatile and adaptable technologies, the plant can ensure operational efficiency and maintain high standards of safety and environmental compliance.
Engage in continuous staff training and development programs to equip your team with the latest industry knowledge and best practices. This not only enhances productivity but also fosters a culture of innovation and responsibility among employees. Regularly review and optimise processes. Conduct audits and seek feedback to identify areas for improvement and implement changes that increase efficiency and reduce waste.
By taking these proactive steps, you can create a resilient and sustainable operation that not only meets but exceeds industry standards.
Waste streams are always changing
Pay attention to the seasons and local events, as they can greatly influence the types of waste generated. For example, during the summer months, there
might be an increase in plastic waste from outdoor activities and barbecues. After Easter there is more aluminium while after Christmas there is an influx of paper. Similarly, during back-to-school season, you may notice a surge in discarded packaging from school supplies and electronics.
Understanding these patterns allows for better planning and resource allocation. It helps in optimising recycling processes, ensuring that the right machinery and manpower are available when needed most.
Ultimately, being vigilant and adaptable in the face of changing waste streams is key to creating a more sustainable business. By recognising patterns and preparing accordingly, you can turn challenges into opportunities.
“Finding the right partner to manage your machinery requirements for waste and recycling needs is not as hard as you think. A supplier that prioritises your success by adding value over and above your initial purchase is key. Industry knowledge is priceless, especially when it is backed up with servicing Australia wide,” said Onetrak’s national sales manager for industrial material handling, Sam Powell.
In
Images: Onetrak
How New Belgium Brewery manages waste with WEIMA
EVEN WITH MODERN manufacturing equipment, production waste in the food and beverage industries are inevitable. Despite all best endeavours to avoid wastage, often filled product must be destroyed to avoid product and bin scavenging for CDS refunding.
This results in high disposal costs and poor environmental outcomes. A solution is to depackage, dewater and compress waste on-site to reduce volumes and increase recovered recyclables and get paid for the recycled packaging.
The WEIMA PUEHLER series presents technology developed for the food and beverage industry. The E.200 and G.200 recycling presses are built for hygienic, in-house waste processing.
Brewing for efficiency
Founded in 1991 in Fort Collins, Colorado, New Belgium Brewing emerged as a craft beer brewer, with a commitment to inspire social and environmental change embedded in its core values from the beginning. New Belgium consistently seeks out partners that prioritise good stewardship of the planet and found WEIMA, a manufacturer of shredding and compressing machinery, as one of those partners.
Recognising the need for a solution that could efficiently manage its increasing production waste, New Belgium invested in the WEIMA G.200 drainage press. This machine, equipped with stainless-steel components, offered a improvement over its previous equipment.
The WEIMA G.200 Drainage Press
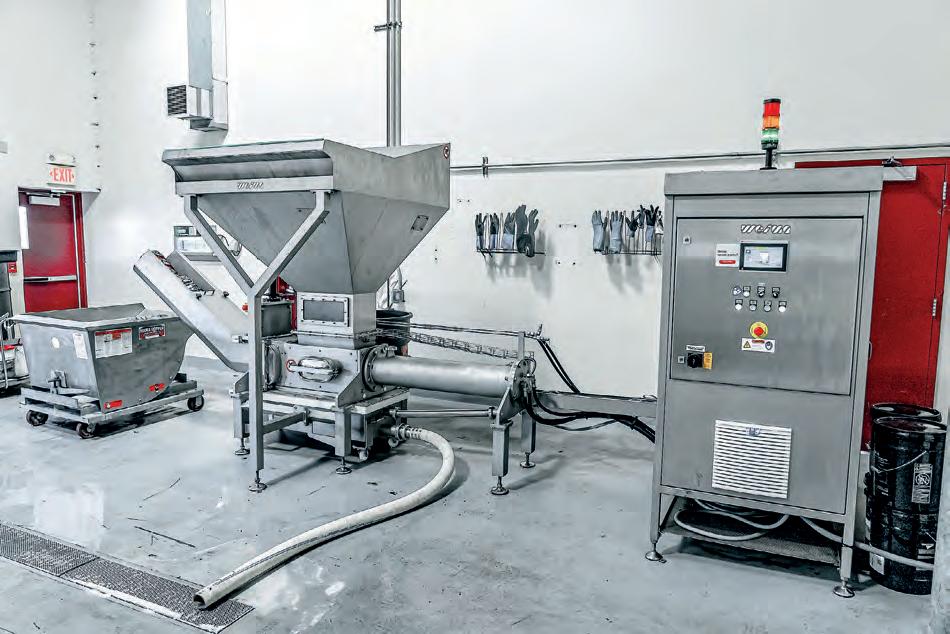
ability to produce 200 mm diameter discs, this machine excels in size reduction, facilitating transportation efficiency and streamlining waste management processes.
It is equipped to handle liquids and messes with ease, ensuring hassle-free cleanup and maintenance. Additionally, the WEIMA drainage presses can be customised with a liquid discharge drain pan, providing an extra layer of convenience and cleanliness to production operations.
The Beginning of New Belgium Brewing
New Belgium was founded by Jeff Lebesch and Kim Jordan. A bike trip through Belgium originally gave Lebesch the inspiration to bring Belgian brewing traditions to his hometown of Fort
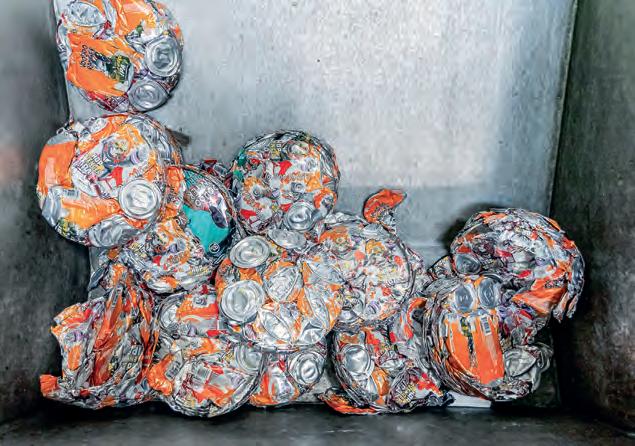
a human-powered philosophy into all that it does, which has contributed to its success in becoming the largest craft brewer in the nation and expanded across the country from its original site in Fort Collins, Colorado, to Asheville, North Carolina and most recently, Daleville, Virginia.
Prioritising sustainability
As the company grew, so did its commitment to social and environmental responsibility. In 2003, it became a B-certified corporation, harnessing the power of business to address pressing global challenges. This milestone marked a new chapter in its journey, solidifying its position as a company with sustainable brewing practices.
“Since our earliest days, New Belgium has been committed to minimising the environmental impact of our operations. Effective recycling systems are the foundation of this commitment and the WEIMA drainage press has become a valuable and efficient addition to our recycling program” says Caitlyn Wouters, Sustainability Specialist
The WEIMA Way: efficiency
New Belgium experienced a surge in productivity after adding a second canning line to its packaging facility. This necessitated a more effective waste management solution to keep up with its increased production. In response to that demand, the brewery installed the WEIMA G.200 drainage press in June 2023. The unit, equipped with a 5.5 kW motor and a 200 mm disc size, has
seamlessly integrated into the company’s operations, offering enhanced efficiency and waste diversion. New Belgium recycles approximately two tonnes of alumnus per month from its Fort Collins location.
“Our previous press was not made for liquid and beer spills. With the G.200, we have a stainless-steel system that we can hit with caustic foam and water, without worrying about rust or paint issues,” said Soren Daugaard, manufacturing excellence site lead.
Danny Banister, packaging manager, highlighted the ergonomic and efficiency gains facilitated by the WEIMA machine.
“Operators can now use equipment instead of hand-loading into our crusher, resulting in significant time savings and improved efficiency,” he said.
“Additionally, the increased capacity of the WEIMA G.200 allowed the brewery to crush anywhere from 5 to 15 hoppers of cans per day, driving operational efficiency.”
“So really the key takeaways for WEIMA are – it’s faster, it’s safer, and it’s cleaner,” said Daugaard.
With the support of WEIMA, New Belgium continues to lead the charge towards a more sustainable and efficient future, embodying its commitment to inspire social and environmental change, one can at a time.
CEMAC technologies distributes WEIMA depackaging technology in Australia and provides ongoing servicing and spare parts. Offering machinery ex stock from the Melbourne warehouse, customers are welcome to visit and view available solutions.
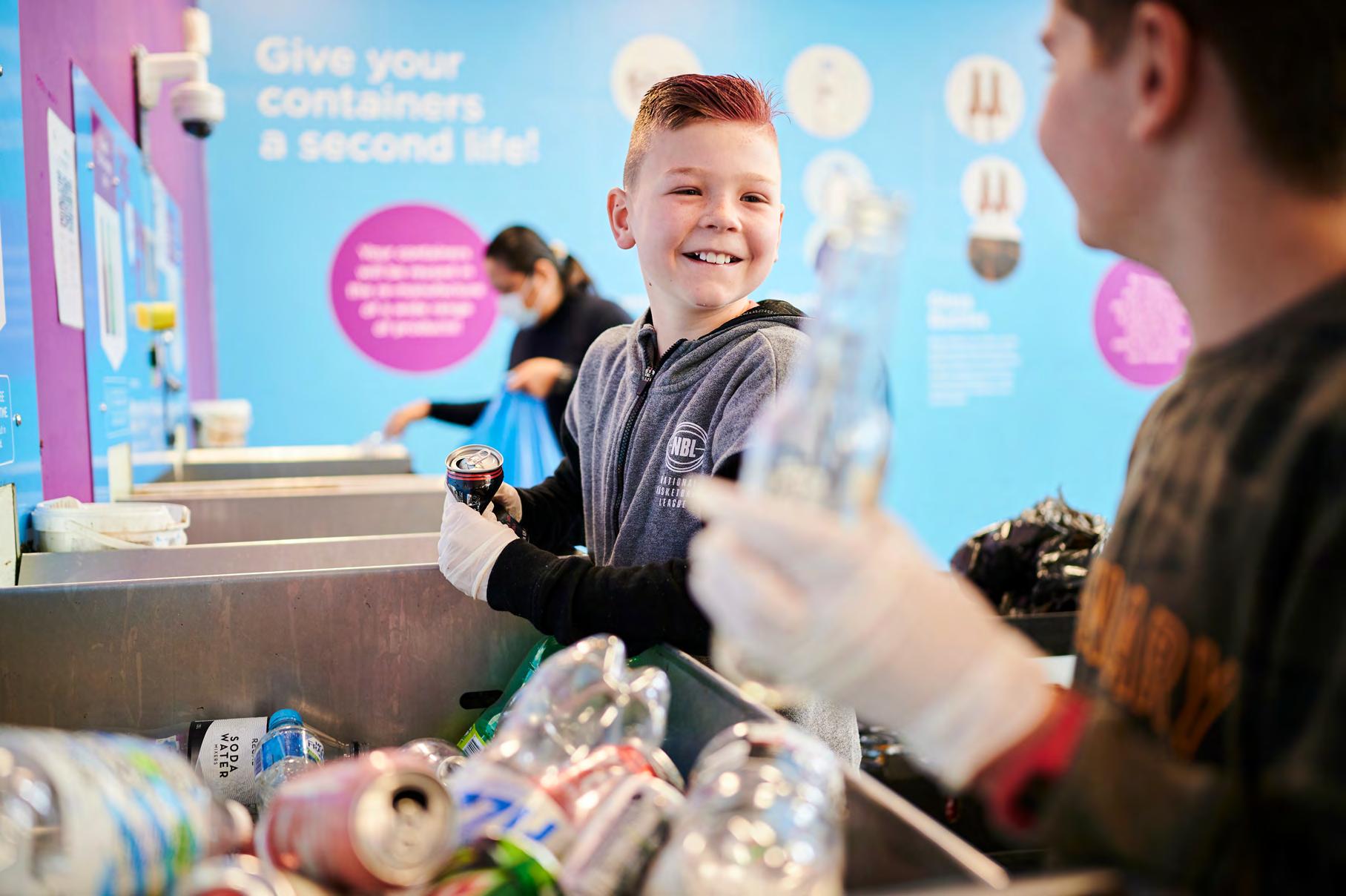
The WEIMA G.200 drainage press is a
Drained and compressed beer cans from the drainage press.
The G.200 drainage press at New Belgium Brewery. Images: CEMAC

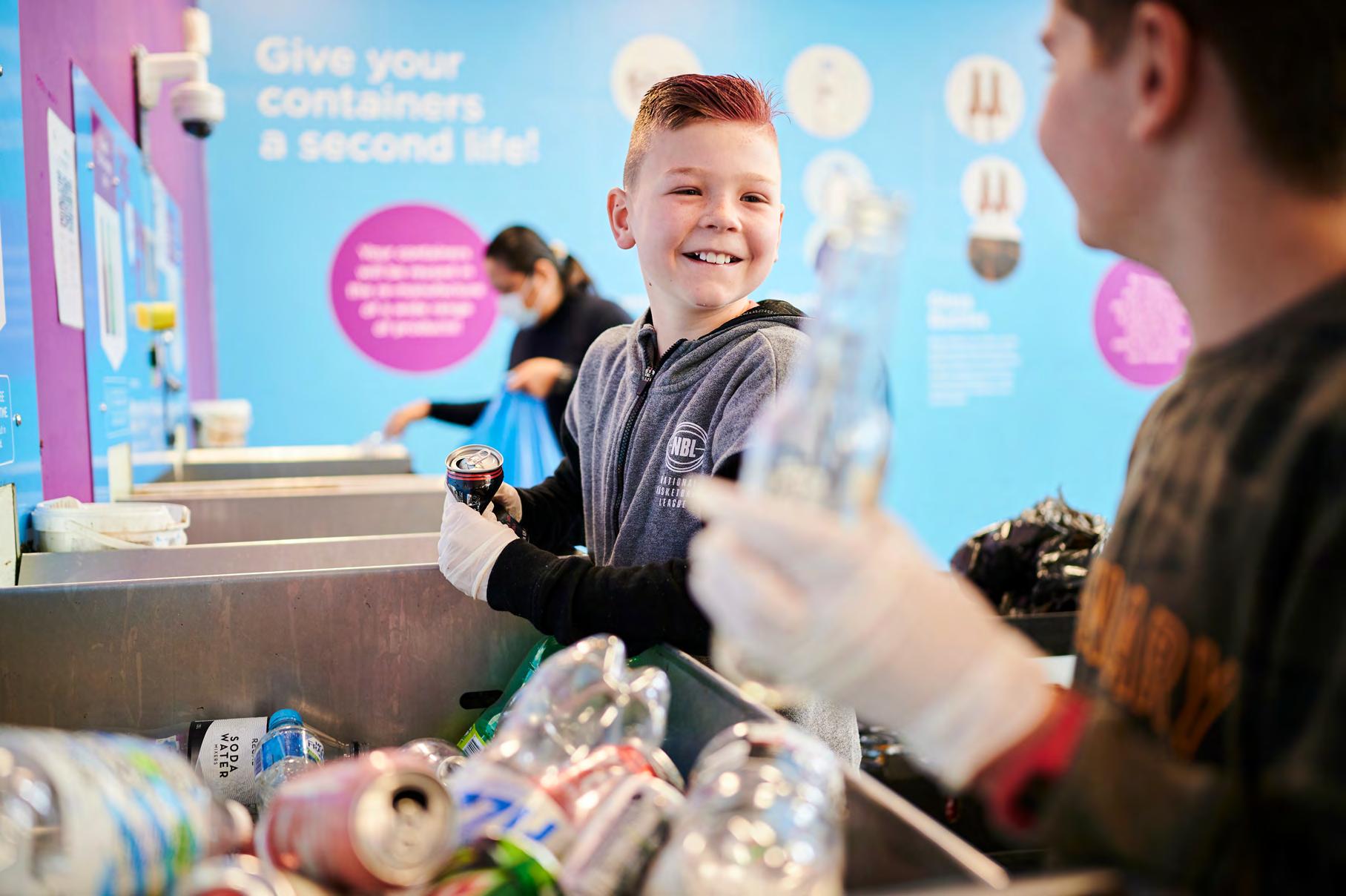
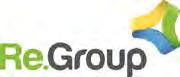
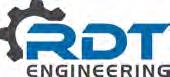
Shredder punches above weight
IF YOU’RE IN THE recycling, construction or waste disposal industry and need a reliable, hard-working shredder, then take a look at the ARJES Impaktor 250.
Designed for a variety of waste streams, the Impaktor 250 is a 14-tonne machine that can shred anything from C&D waste and organics, through to metal and concrete.
Cailean Woods is a sales manager at resource recovery/waste machine specialist and distributor of Impaktor products, Tricon. He said that the machine is proving to be popular due to an array of features.
“There’s not too many machines in that size that can shred scrap metal and cars and the like,” he said. “And being only 14-tonne, it’s very easy to move around small sites, which also means it’s a low transport cost to get at the site.”
He said it’s good for contractors because they can do most of their shredding on site instead of transporting the material offsite.
It comes with three different types of shafts depending on what material is being processed. There is one designed
for green waste, another for concrete, while the third is for everything else.
Wood said that each shaft is easy to interchange as there are only four bolts that need to be removed to replace one of the shafts.
“You pull out the four bolts and kick off the back hopper wall plate,” he said. “Then you just lift the shafts out and put the new ones in. It takes about 15-20 minutes at most.”
As for throughput, Woods said that the shredder’s output is measured in tonnes per hour, but how many tonnes each hour depends on the product being processed.
Back-up service is always something that clients are interested in and Woods said that Tricon have that covered, too. Based out of Warnervale on the NSW Central Coast, Woods said there is plenty of parts in stock.
“One of the great things about this machine is that there is not a lot of moving parts to it, so we don’t have to stock thousands of spare parts,” he said. “It’s a simple, user-friendly machine.”
Woods said he sometimes sells a
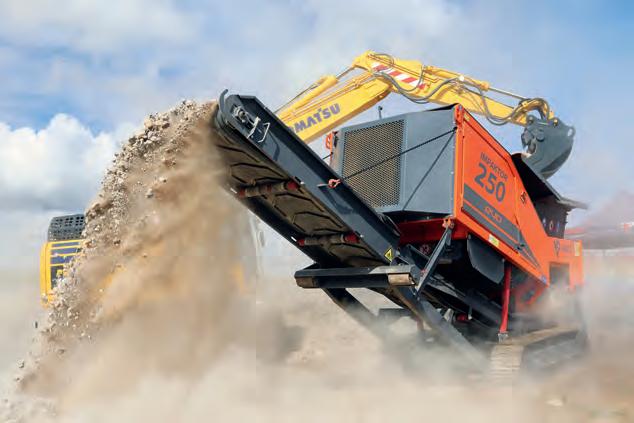
critical spare part with the machine because the it won’t take up much room on a shelf.
Also, most of the spare parts are cost-effective so if something did happen to the machine, having that spare part around means the contractor can carry on without having to worry about excessive costs of replacing the piece.
Finally, Woods points out that another
Peterson stops company getting stumped
GRINDING OUT STUMPS is not a great way to spend an afternoon, but it’s a great business when done right. Just ask Mike Lloyd from Stridem who specialises in
So why Peterson gear?
“For a start, grinding can be quite hard on machinery, so you need gear that can last,” said Lloyd. “However, you also need a good
he said that in the past they have gone the extra distance for him when it has mattered most.
“We’ve had a few catastrophic
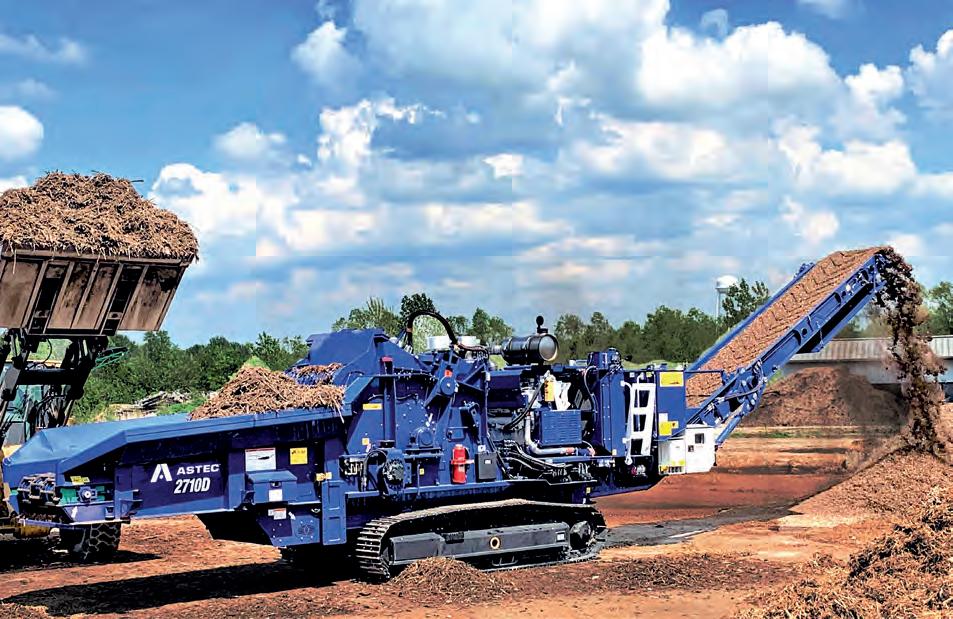
of its features is the ease of access to the machine when it needs maintenance .
“What you find with a lot of these machines is there’s not much access for your service guys to get in and maintain the shredder,” he said. “With the 250 there’s loads of room and we’ve had great feedback from customers about how easy it is to maintain, and the room they’ve got to work in.”
to be in tip-top shape due to the harsh nature of the work. He used to do a lot of work on gum trees, but now pine is what his team concentrate on the most. There’s no doubt tree stumps are the hardest part of the job.
“Stumps are a nasty sort of material,” he said. “We’ve got a pretty serious team behind me, boilermakers and the like, so we can do it all in house. And for that we need some pretty serious equipment.”
As for the throughput, this also impresses Lloyd.
The amount of work a machine can get through is important due to Stridem wanting to resell the product it shreds/ chips – whether that be as mulch, biomass, or potting mix.
“We used to have old bits of gear we’d get at auctions and put it all together and work with it,” he said. “Then we got the Peterson machines, which have given us the ability to shred large volumes quickly. I’ve come from a pulp company to now where we process anything from massive trees to stumps, which is why the type of equipment we use is so important .”
The 2710D comes in an array of engine configurations including the Caterpillar Tier IV C15 580 hp (433 kW), C18 755 hp (563 kW), or optional Tier II C18 765 hp (570 kW) for export. Its feed opening can take a range of materials and measures 153 cm x 81 cm. When boosted by Peterson’s highlift feed roll, the feed opening’s maximum lift is 112 cm, which is among the largest in its class.
The Peterson 2710D grinder is a hard-working machine that gets the job done for people like Mike Lloyd. Image: Komatsu Forest
The ARJES Impaktor 250 allows contractors to do most of their shredding onsite. Image: Tricon
Hooklifts make life easier for waste collection services
ONE OF THE UNSUNG work horses in the resource recovery sector are hooklift collection systems.
These systems are designed to improve productivity and reduce the number of truck movements, particularly on construction sites and at the back end of shopping malls where much of the waste collection takes place.
One brand known for its reliability and performance is B.o.B hooklifts, which are manufactured to high European standards in Italy.
The Australian exclusive distributor of B.o.B hooklifts is Wastech Engineering. The company has a presence nationally and is proud to be part of a team that helps fit up, service, and distribute the equipment.
Wastech’s business development manager, Greg Scott, realises he’s on to a winner, not just because of the quality of the product but its work rate and reliability across all B.o.B models.
And what makes this range so special?
“There are several factors,” said Scott, “but one of the main ones is the articulated hook, which allows for smoother and more flexible loading and unloading, especially in confined or uneven spaces. The twin locking capabilities, with both front and rear locks, provide an additional layer of security, ensuring the load is tightly secured. This double-lock system enhances safety by significantly reducing the risk of bin movement during transport.
“The articulated hooklift is especially advantageous in scenarios where clearance is a challenge. We see it in places like shopping centres, hospital basements, and commercial buildings. That’s when the articulated hook becomes the X factor for haulage companies, delivering superior manoeuvrability in tight spaces.”
The quality of the product is another highlight, according to Scott. He said the units are designed to last well past 10 years, crafted with attention to detail and good craftsmanship.
“B.o.B gear is tough and durable; they’re aimed at all types of users who want multiple uses and multiple lifts every day of the year for in excess of 10 years,” he said. “On the occasion the owner or fleet controller does need a spare or replacement part, Wastech
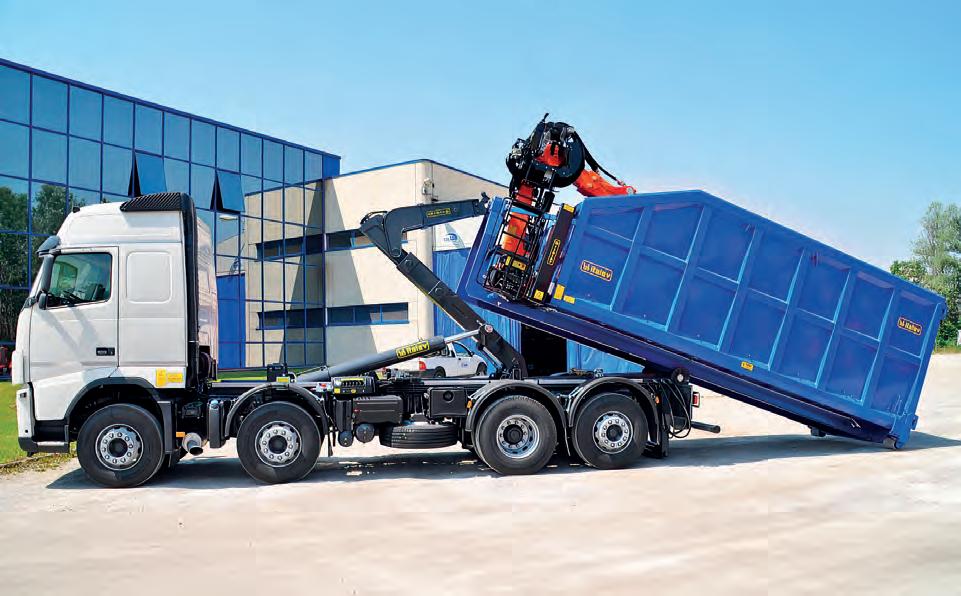
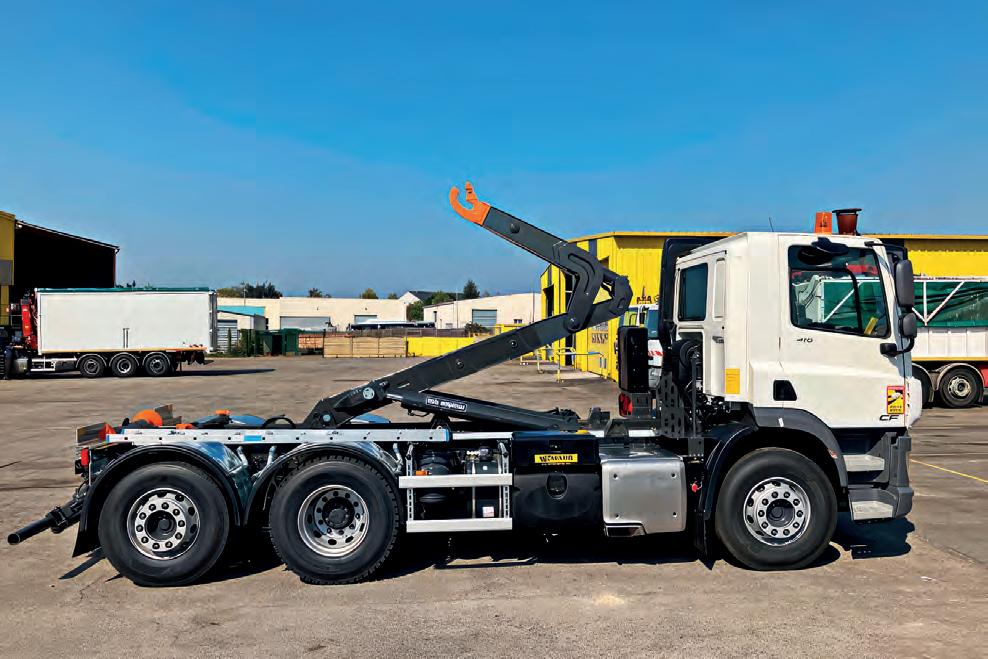
“B.o.B
gear is tough and durable; they’re aimed at all types of users who want multiple uses and multiple lifts every day of the year for in excess of 10 years.”
is well equipped, as we have plenty of spares in stock for different types and models. Our ability to facilitate spare parts being distributed nationally stems from a well-organised and experienced team who are available to help deliver at a reliable and trusted price.
It is also important that the right unit is used for the right job. Wastech experts can help make sure everything goes to plan from the outset.
“We work very closely with our supplier and are continuously looking at new innovations; one of B.o.B’s greatest assets is having the ability to be flexible to the buyer’s needs,” said Scott. “We can fit and supply a very large range
of articulated and telescopic-rated hooks varying from 10-, 16-, 20-, and 32-tonne units. The 20-tonne units are mostly used for C&D, C&I, light, and heavy commercial applications, but we can also offer smaller units for tighter access sites and specialised services.”
Scott also said that, operationally, the B.o.B hooklifts are one of the easiest units to operate, and an operator can be trained on them in a short amount of time.
“If we are supplying and fitting the units, then training is also a part of the purchase package; we take real pride in our ability to offer this to our customers.”
Wastech is also looking to grow its presence not just in the waste sector but also in the farming and water cartage industries. Like its product range, the company isn’t limited to one type of hook; it wants to be in as many industries as possible.
“We want to build a connection with truck and heavy equipment haulage companies and start having conversations with them about why B.o.B,” said Scott. “We know the B.o.B. hooklifts are reliable (over 600 in use currently in Australia), and anyone who has owned a B.o.B will tell you they are very affordable, and well within the market range.”
Articulated hooklifts are a great tool to have in scenarios where clearances is a challenge.
B.o.B. hooklifts are suitable for unloading in confined or uneven spaces. Images: Wastech Engineering
AutoLoadBaler Cardboard Press
Product/model name: AutoLoadBaler by Strautmann
Unit Dimensions: (WxDxH) 2110 x 2150 x 3050 mm
Weight: 3100kg
Capacity (in weight): 2 bales/up to 900kgs per hour
Price: Contact us for a custom quote
More: In the bustling environments of supermarkets and distribution centres, efficient waste management is crucial for optimising operations and reducing costs. Strautmann’s AutoLoadBaler offers a game-changing solution tailored specifically for these settings, delivering substantial labour and time savings while enhancing OH&S measures.
Features & benefits:
• No pre-crushing or compacting required
• Easy to use, high capacity cart for loading/exchange
• Automatic machine filling and baling process
• Compact design – less than 5m² footprint
• 1 hour time saving per 100 kg carton compared to conventional vertical presses
• Installation close to the point of origin thanks to small footprint
• Easy and safe handling during operation and bale tying
• Produce profitable bales
• Quiet operation
Ecohog EQS 1200-SM2
Unit Dimensions: Transport Dimensions (10.7m x 3.2m x 3.3m)
Weight: 10t
Capacity (in weight): Dependant on Materials being processed
Price: From $320,000.00 + GST (Plus Options)
Name: CEMAC technologies
Phone Number: (03) 8400 6066
Webpage: www.cemactech.com/strautmann
Email: info@cemactech.com
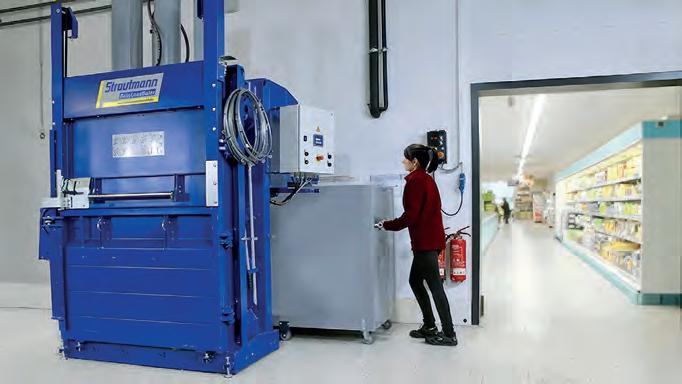
Ecohog EQS 1200-SM3
Unit Dimensions: Transport Dimensions (16.6m x 3m x 3.7m)
Weight: 17t
Capacity (in weight): Dependant on Materials being processed
Price: From $425,000.00 + GST (Plus Options)
More: The Ecohog EQS 1200-SM2 Picking Station is the most versatile “mobile” picking station in the range. Utilizing smart spacing for ejection chutes and CAT Diesel Gensets for Stand alone power (units can run from Mains Power also), with Ecohog Airhog Vacuum system and Eriez Over-Belt Magnets, these are the picking stations for your site.
Name: Sales – CSS Recycling Solutions
Phone Number: 1800 644 978
Webpage: www.cssequipment.com.au
Email: info@cssequipment.com.au

Unit Dimensions: From 2 Metres in length, Up to 10+ Metres, depending on Production requirements.
Weight: From 2.5t
Capacity (in weight): Up to 200+ tonnes per hour (Depending on Materials and Screen Length)
Price: Depending on Sizes and Options (Contact CSS for more information)
More: The Ecostar HEXACT DDS Screen is a static dynamic disc screen with anti-wrapping system, able to operate in most waste materials and recycled materials with problematic contamination, due to the patented anti-wrap system. High speed & High Production on Organics and perfect for FOGO. The machines are custom sized to customers specification.
Name: Sales – CSS Recycling Solutions
Phone Number: 1800 644 978
Webpage: www.cssequipment.com.au
Email: info@cssequipment.com.au
More: The Ecohog EQS 1200-SM3 Picking Station is the large versatile “mobile” picking station in the range. Using CAT Diesel Gensets for Stand alone power (units can run from Mains Power also), with Ecohog Airhog Vacuum system and Eriez Over-Belt Magnets, these are the picking stations for your site, if you need a large picking station, but still mobile to move around site or from site to site.
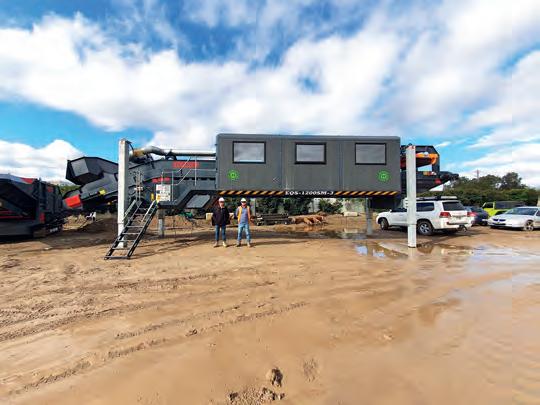

Ecostar HEXACT DDS Screen
Ecostar HEXTRA DDS Screen
Unit Dimensions: 15.5m x 9.4m x 4.6m
(Operating Dimensions)
8.7m x 2.5m x 3.1m (Transport Dimensions)
Weight: 21t
Capacity (in weight): Up to 150tph (Depending on Materials)
Price: $700,000.00 + GST (Plus, Depending on Options)
More: The Ecostar HEXTRA DDS Screen is a fully mobile dynamic disc screen with antiwrapping system, able to operate in most waste materials and recycled materials with problematic contamination, due to the patented anti-wrap system. High speed & High Production on Organics and perfect for FOGO.
Name: Sales – CSS Recycling Solutions
Phone Number: 1800 644 978
Webpage: www.cssequipment.com.au
Email: info@cssequipment.com.au
Hammel VB 850 DK
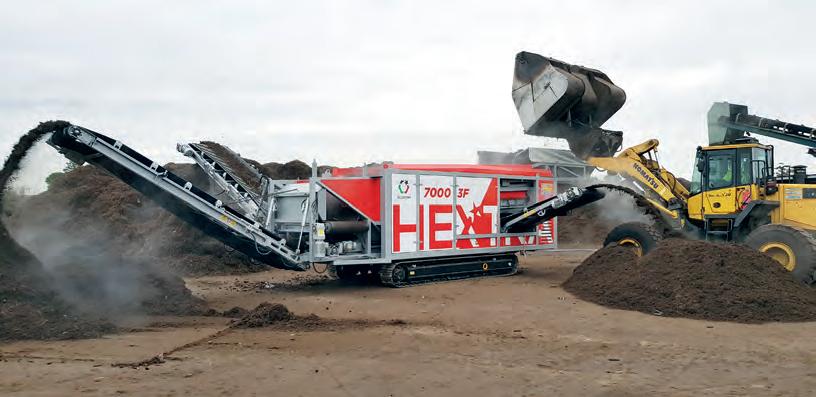
Hammel VB 950 DK (RED GIANT)
Unit Dimensions: Transport Dimensions (8.7m x 2.5m x 3.1m)
Operating Dimensions: (12.9m x 2.5m x 3.1m)
Weight: 31t
Capacity (in weight): Production up to 100tph om General Waste
Price: From $950,000.00 + GST
More: The “Original Twin Shaft” Primary Shredder from Hammel Recyclingtechnik. Powerful and Mobile, for most Waste Types.
Name: Sales – CSS Recycling Solutions
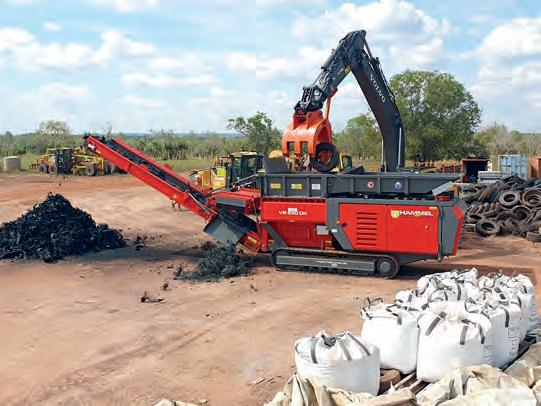
Unit Dimensions: 8m x 3.4m x 5.7m
Weight: TBC
Capacity (in weight): Production up to 20tph (on Light Guage Scrap Metal)
Price: TBC
More: The Wendt Corporation Offers Hammer Mill Shredders for the Scrap Metal Shredding Industry, from 1,000Hp and up to 10,000Hp. The M6060 is available in Diesel or Electric and is the starter model.
Name: Sales – CSS Recycling Solutions
Phone Number: 1800 644 978
Webpage: www.cssequipment.com.au
Email: info@cssequipment.com.au
Unit Dimensions: Transport Dimensions (11.4m x 3m x 3.3m)
Operating Dimensions: (15.5m x 3m x 3.3m)
Weight: 46t
Capacity (in weight): Production up to 200tph (on General Waste)
Price: From $1.2m + GST
More: The “Original Twin Shaft” Primary Shredder from Hammel Recyclingtechnik. The first large scale mobile Primary Shredder for most waste types.
Name: Sales – CSS Recycling Solutions
Phone Number: 1800 644 978
Webpage: www.cssequipment.com.au
Email: info@cssequipment.com.au
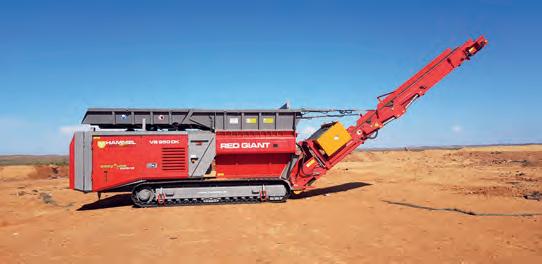
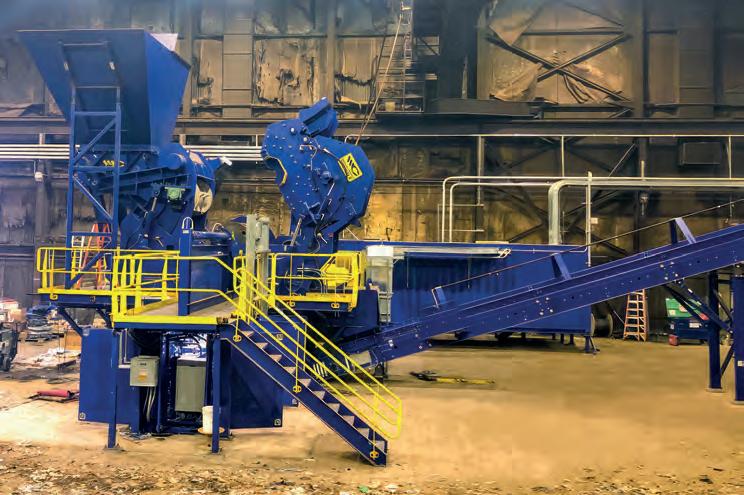
Standards under the spotlight
Evening Sir.
Standards. We all have them. Whether it’s your own personal mores, morals and principles, or the mission statement by which your company is run, there is a line in the sand where you set the rules.
Of course, there are those that have little or none, but dress them up to be what they are not. A bit like the People’s Democratic Republic of Korea or the Democratic Republic of East Germany. Not too sure if those who formed those monikers were having a little ironic chuckle to themselves, or that they really meant it. They believed their ‘standard’ of democracy was a totalitarian dictatorship.
Which brings me to our erstwhile friends in the resource recovery industry down here in this Great Southern Land. To ask if there are
some dodgy operators in the waste space is like asking; does a one-legged duck swim in circles?
Which is why it is interesting that a company has gone to the lengths to create a standard whereby companies follow a set of processes to make sure certain criteria are being met – i.e., they are doing the right thing.
Right now, all over the country waste contractors are either sighing with relief or cussing like drunken cowboys on a bender in some Wild West bar. Why? Well, there are some pretty good operators out there doing their best to make sure they leave the planet in a better condition from which they found it. Unfortunately, they are usually up against unscrupulous operators whose moral compass has been left
where their bank balance begins.
“So what?” I hear you ask. “What does a standard mean?” Two things. It puts an operator under the spotlight on how it manages its business, and it means they can’t fudge the numbers.
I realise there are cynics out there, and the doubters. All I have to say is ESG. “What’s that?” you say. Get used to it. It is an acronym for Environmental, Social and Governance – that is, companies are now adopting these principles when it comes to sustainability. Some call it woke, some common sense – I call it something that has to be taken seriously. This is because some of the bigger players in the market, who have deep pockets and money to spend, are demanding it from their suppliers. Price will always have its place,
but it is now part of a whole new set of criteria.
Suppliers are a canny lot, and they can see the winds of change happening. The new generation of customers coming through are looking for companies that care about the environment and are taking those criteria into consideration when making purchases.
Which means if contractors tend to dump C&D waste on the side of the road, or they don’t recycle it or reuse when these are options, this standard will find you out. And if you want to work with some of the big companies on the block, some are demanding standards like this one as a minimum for doing business with them.
Yours truly, JB
“It is an acronym for Environmental, Social and Governance – that is, companies are now adopting these principles when it comes to sustainability. Some call it woke, some common sense – I call it something that has to be taken seriously.”
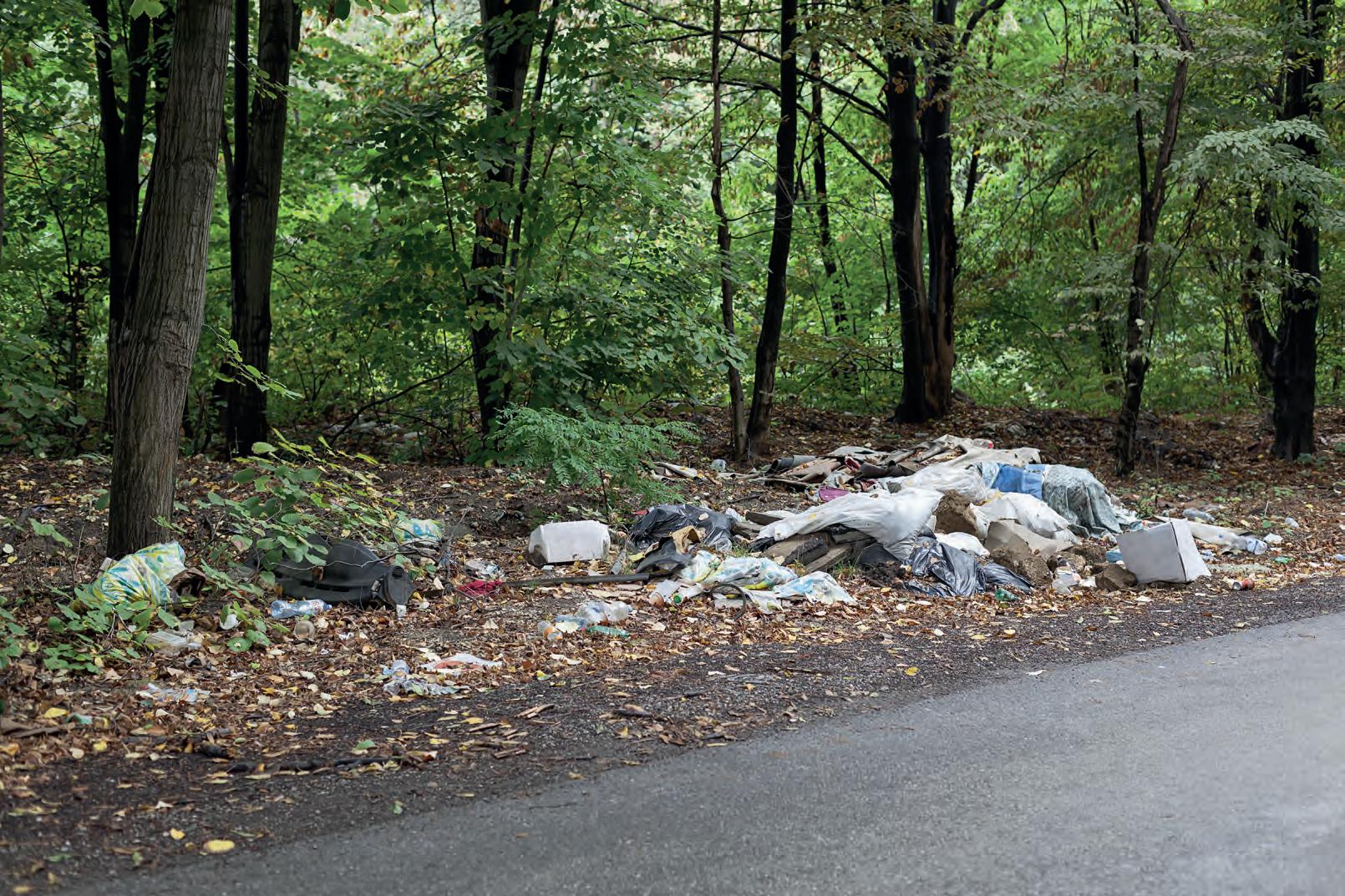
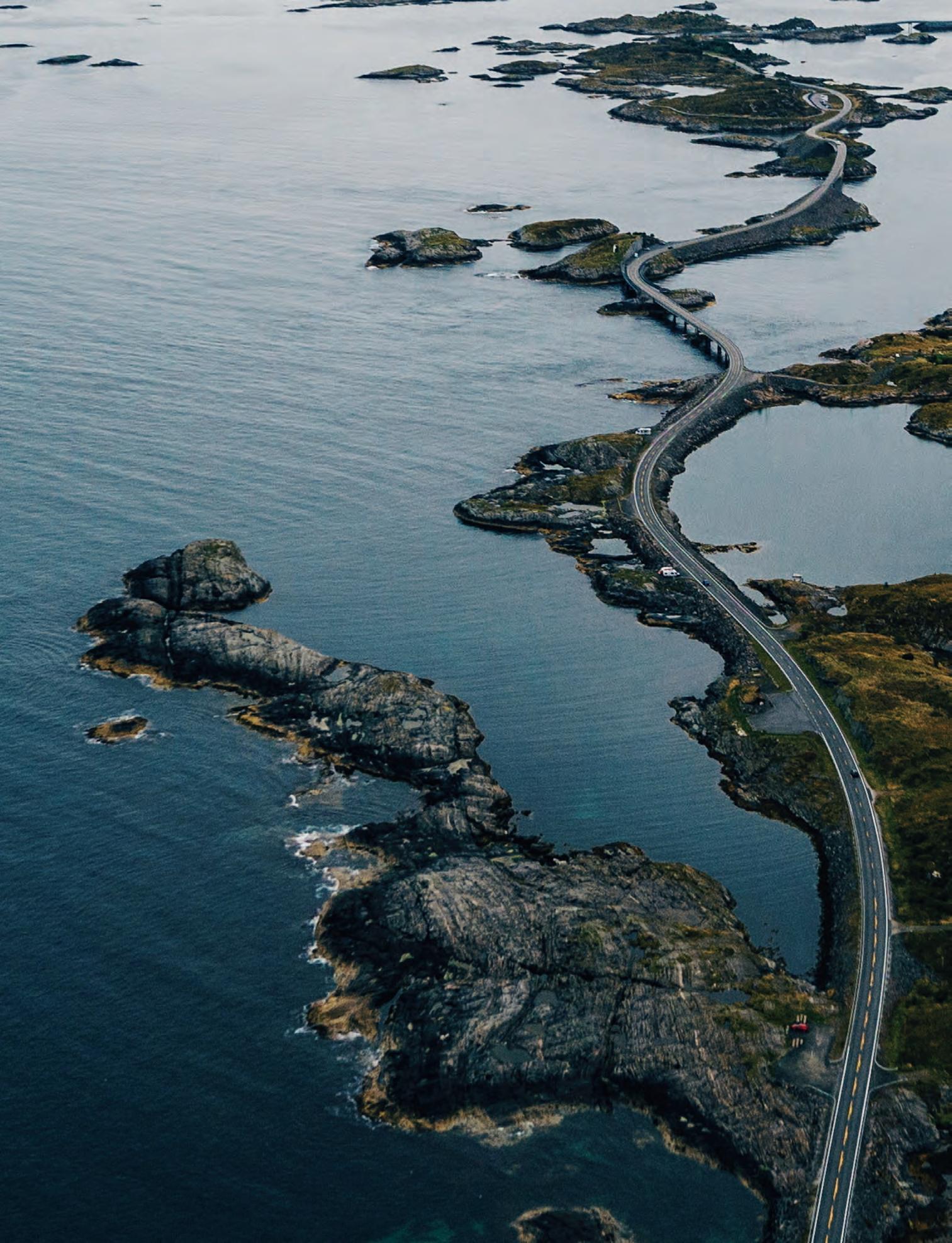
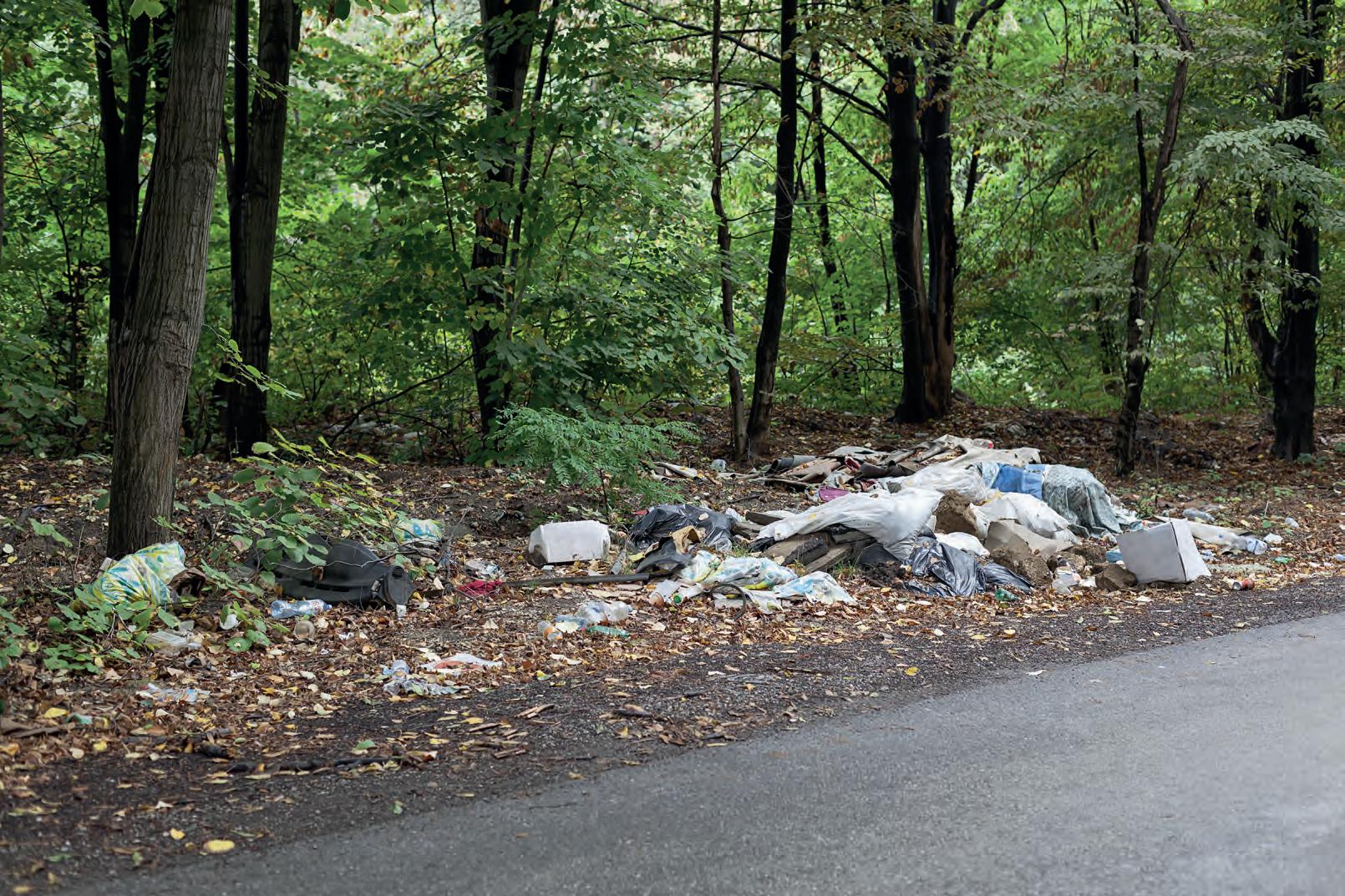
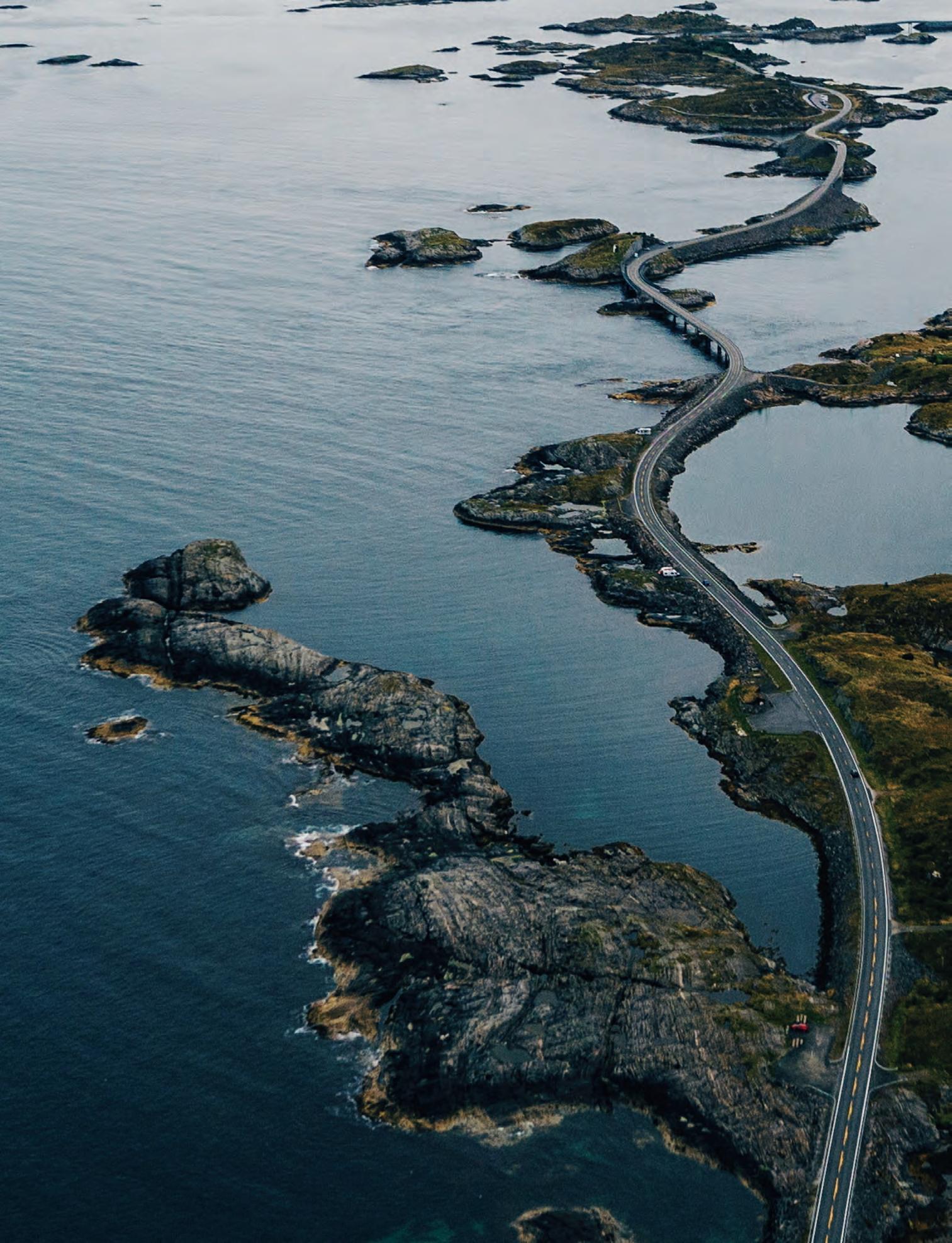
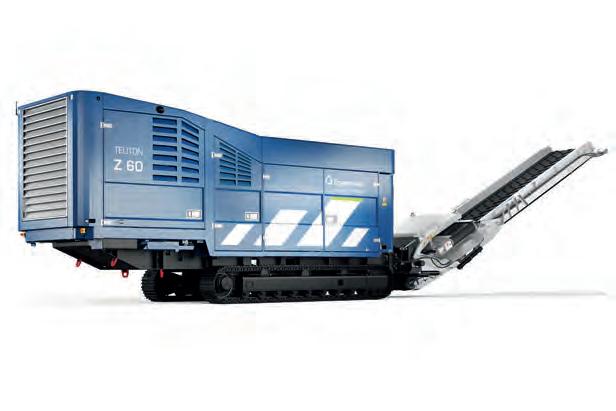
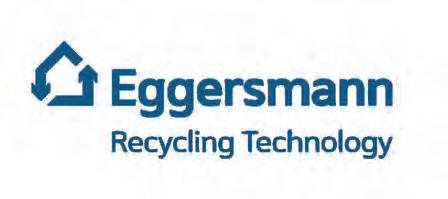
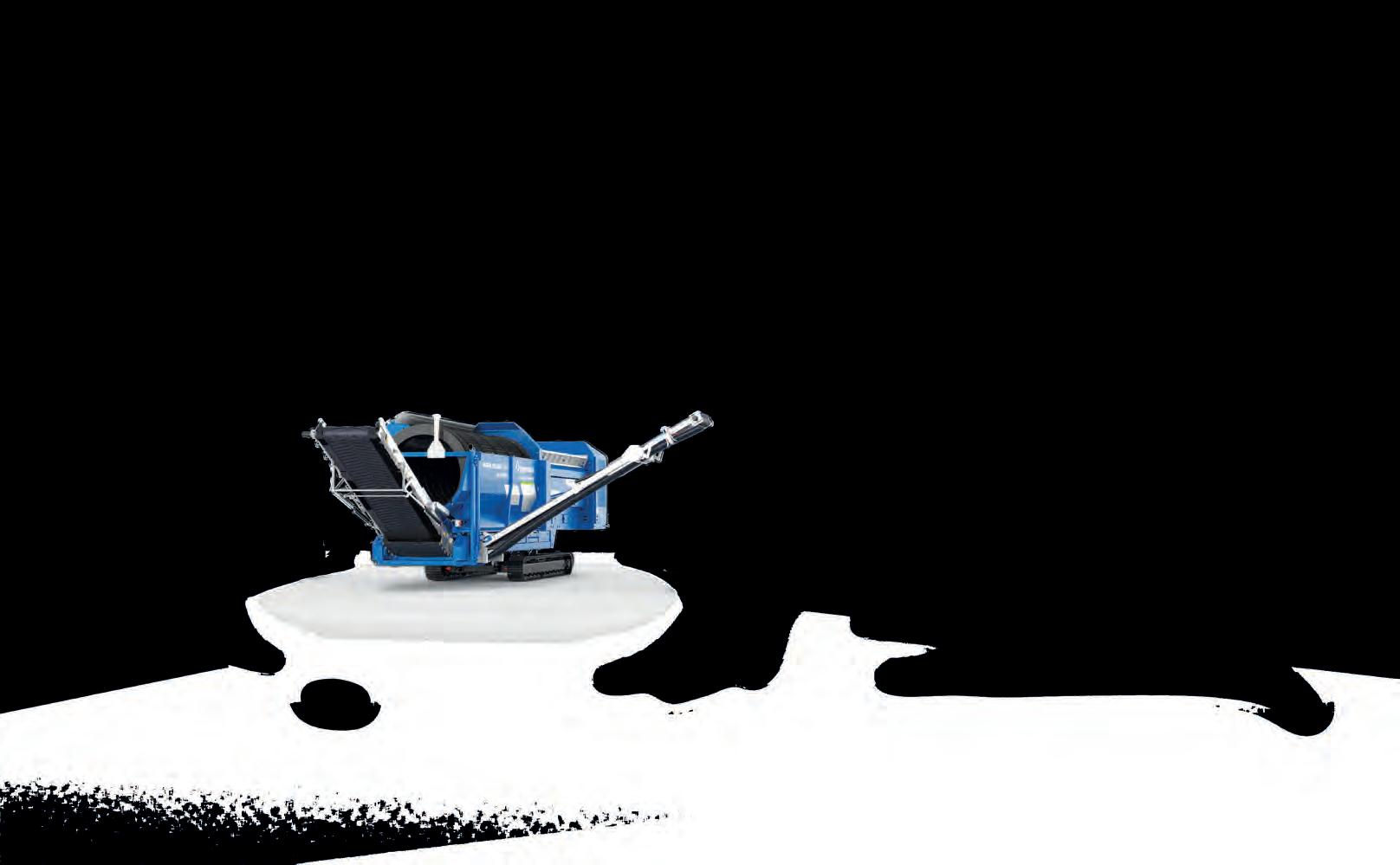
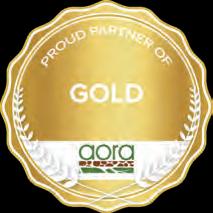
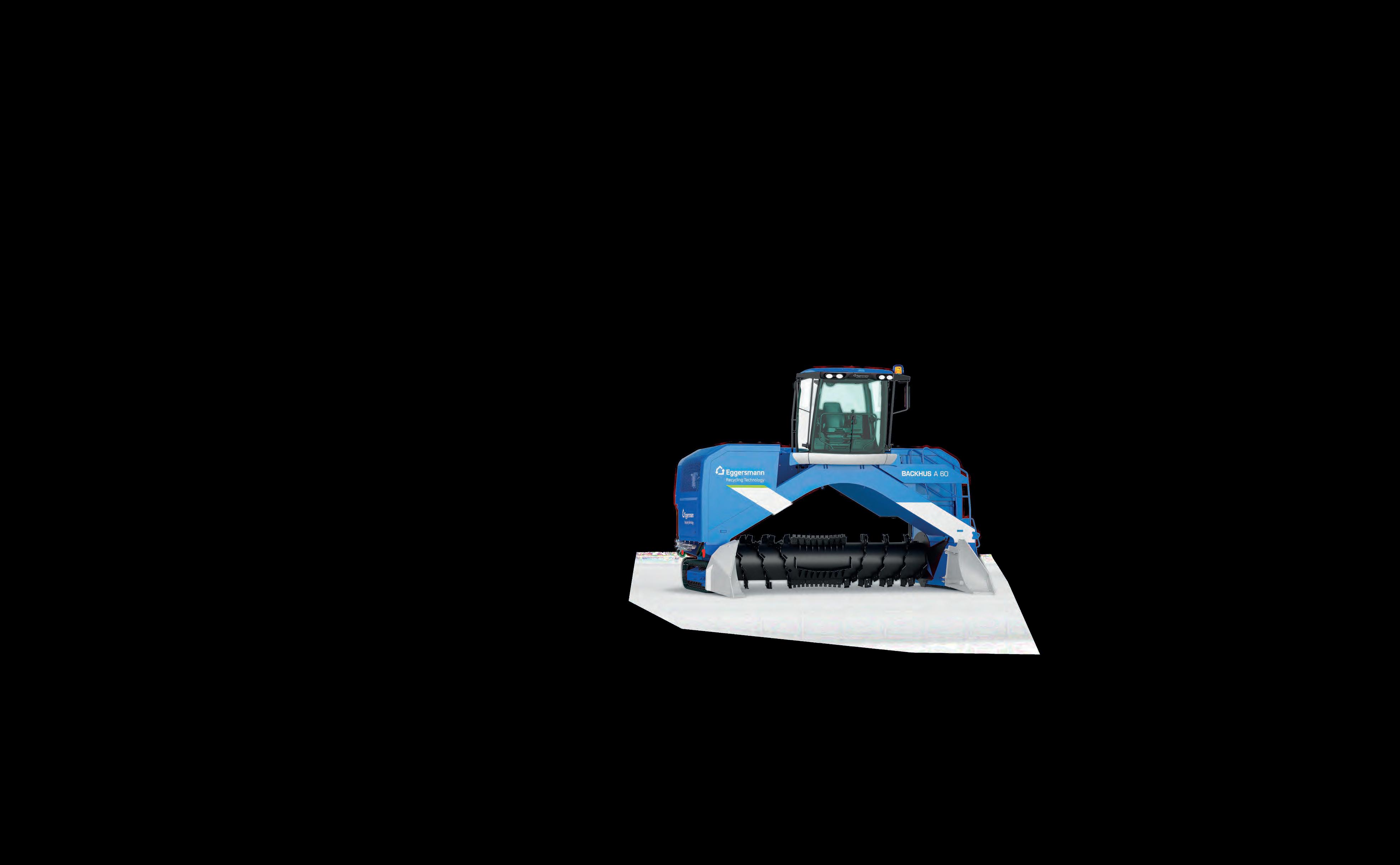