

Melbourne councils look to EfW to solve residual waste woes
By Inside Waste
A recent application in New Zealand by South Island Resource Recovery (SIRRL), a company that is 60 per cent owned by China Tianying Incorporated, has been tasked to build an energy from waste (EfW) facility. The company’s application has been met with cynicism from some quarters. The SIRRL is calling the 365,000 tonnes of municipal and construction waste it will process as ‘sustainable’ land diversion. Some see the plant as an attempt at ‘greenwashing, and they raise concerns about air pollution, toxic waste, and greenhouse gas emissions, including from the 70-odd trucks a day delivering rubbish’, according to New Zealand’s Newsroom website.
What wasn’t mentioned in the piece is that modern EfW facilities are designed with the purpose of disposing of residual waste, because


anything that can be reused or recycled has already been separated from the waste stream.
In a paper written by Bernt Johnke titled Emissions from Waste Incineration, the author studied the amount of emissions a EfW plant produces.
The conclusion Johnke came to was:
An energy transformation efficiency equal to or greater than about 25 percent results in an allowable average substituted net energy potential that renders the emission of waste incineration plants (calculated as CO2 equivalents) climate-neutral due to the emission credits from the power plant mix.
In other words, the amount of greenhouse emissions produced by an EfW facility are neutralised because of the amount of energy it returns to the grid that doesn’t have to be produced by a power station.
The biggest obstacle EfW plant developers have is persuading councils – some backed by antiEfW driven interest groups – to sign contracts that will deliver waste to the plant. This is because of the impression that these plants are nothing more than giant incinerators with little to no technology to stop millions of tonnes of CO2 being pumped into the air.
Which brings us to Mick Cummins. Cummins is the CEO of Bayside City Council in Victoria and he led a process with eight other Councils to sign contracts to supply non-recyclable household waste to the new Maryvale Energy from Waste facility.
Cummins said that the consortium initially had 16 councils onboard, but by the time it came to signing the contract, nine were left. Why did the others drop out?
(Continued on page 14)
27 Circular economy 30 BSC needs legislating
38 2025 WIRA awards
Commercial food waste collections coming to NSW
By Mike Ritchie and Virginia Brunton, MRA Consulting Group
THE NSW Government is going to mandate commercial food waste collection (COFO). This is excellent for NSW, and the Minister Penny Sharpe and Premier Chris Minns are to be congratulated for this reform. For those of you who don’t know what we’re talking about, from July 1, 2025 large food waste generators will need to have a dedicated food waste collection system. Food waste will no longer be able to go to landfill. Food waste in landfill is a massive greenhouse gas generator, contributing most of the 11 million tonnes of greenhouse gases released from landfill each year. That is equivalent to the annual emissions of about 3 million cars. The key businesses that are proposed to be covered by the food collection requirement will likely include:
1. S upermarkets (with a floor area > 1,000m2)
2. Institutions including:
• h ospitals
correctional facilities
e ducation facilities
c hildcare facilities
s eniors’ housing
3. H ospitality including:
h otels and motels
r egistered clubs
f ood and drink premises including food courts
The scheme is proposed to capture the biggest food waste generators in the NSW economy.
(Continued on page 20)

Energy from Waste facilities get a bad rap because sometimes people don’t understand the technology. Image: Industryandtravel/shutterstock
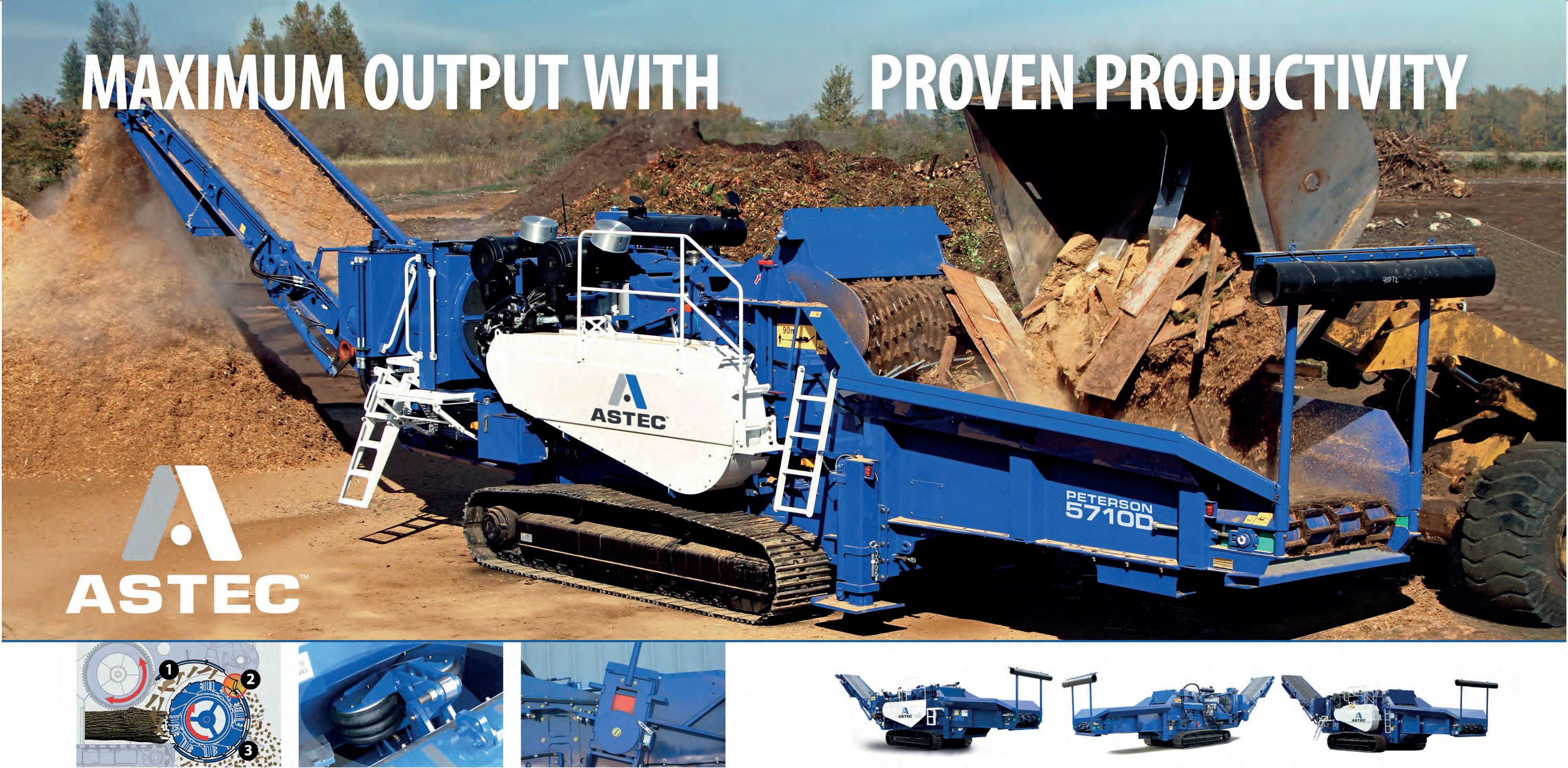
3-Stage Grinding Process
Provides Faster Reduction
Astec - Peterson's powerful up-turn 3-stage grinding process provides better fracturing of material and a more consistent product, giving you just the product your buyers are looking for.
The Impact Release System
Protects Your Investment
Astec - Peterson's patented Impact Release System's air bags provides uniform grinding and protection from contaminated feedstock, a feature unique to Astec - Peterson grinders.
Land clearing, mulch, compost, asphalt shingle tiles, scrap wood, biomass, green waste-we can handle it am
www.komatsuforest.com.au

The Impact Cushion System
The Second Line of Defence
Urethane cushions and shear pins help protect the mill from catastrophic damage in the event of a severe impact from contaminants in the feedstock.
Astec - Peterson offers horizontal grinders from 433-839 kW, offering grinding solutions with output at the lowest cost per ton. Visit us at www.astecindustries.com and see why we have been leading the industry for over 35 years!
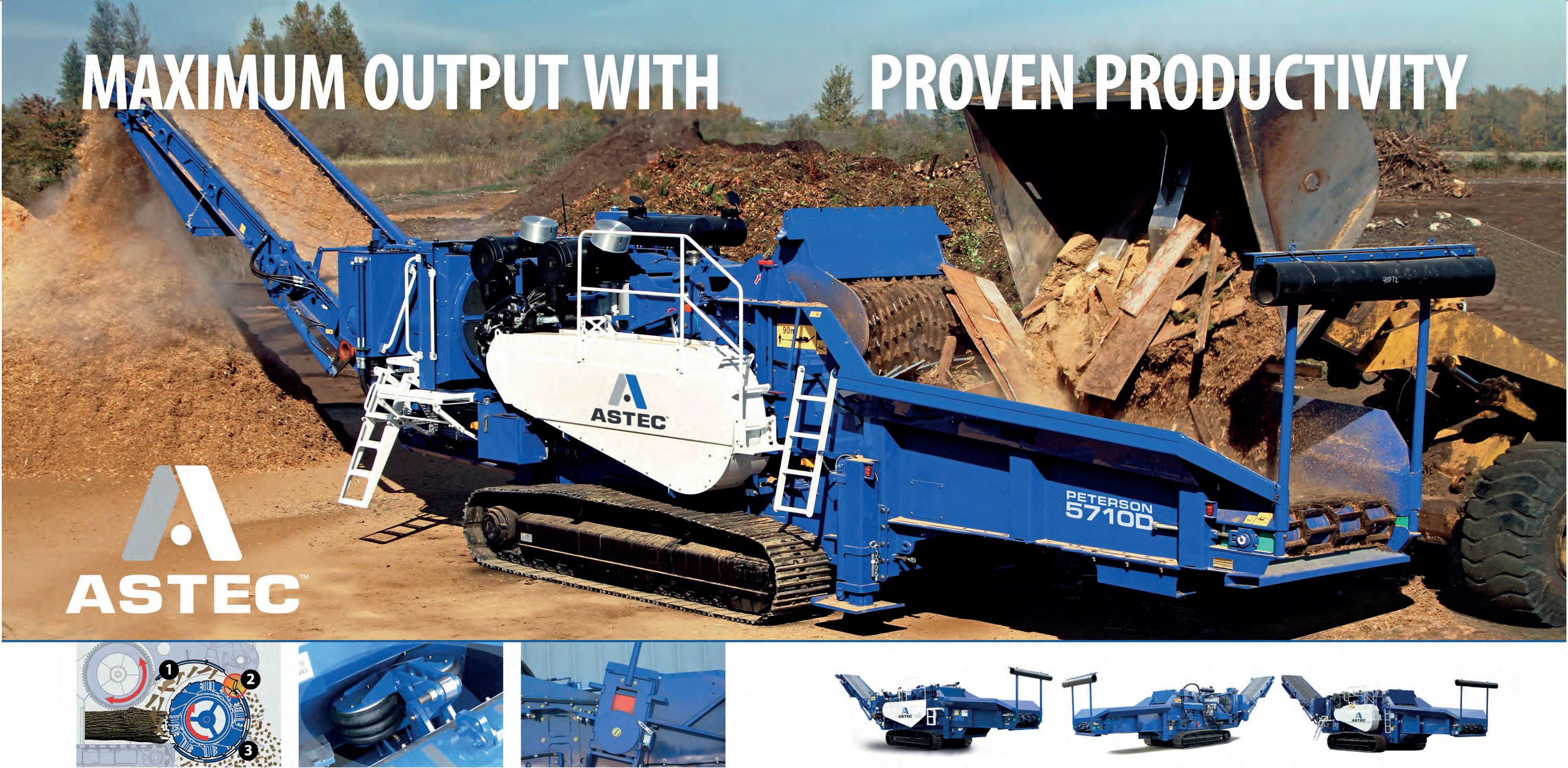
2710D Horizontal Grinder

5710D Horizontal Grinder
6710D Horizontal Grinder
Largest
Chief Operating Officer
Christine Clancy christine.clancy@primecreative.com.au
Managing Editor
Mike Wheeler
mike.wheeler@primecreative.com.au
Brand Manager
Chelsea Daniel chelsea.daniel@primecreative.com.au
Ar t Director
Bea Barthelson
Client Success Manager
Louisa Stocks louisa.stocks@primecreative.com.au
Head Office
Prime Creative Pty Ltd
379 Docklands Drive
Docklands VIC 3008 Australia
p: +61 3 9690 8766 enquiries@primecreative.com.au www.insidewaste.com.au
Subscriptions
+61 3 9690 8766 subscriptions@primecreative.com.au
Inside Waste is available by subscription from the publisher. The rights of refusal are reserved by the publisher
Articles
All articles submitted for publication become the property of the publisher. The Editor reserves the right to adjust any article to conform with the magazine format.
Copyright
Inside Waste is owned by Prime Creative Media and published by John Murphy.
All material in Inside Waste is copyright and no part may be reproduced or copied in any form or by any means (graphic, electronic or mechanical including information and retrieval systems) without written permission of the publisher. The Editor welcomes contributions but reserves the right to accept or reject any material. While every effort has been made to ensure the accuracy of information, Prime Creative Media will not accept responsibility for errors or omissions or for any consequences arising from reliance on information published. The opinions expressed in Inside Waste are not necessarily the opinions of, or endorsed by the publisher unless otherwise stated.
It’s about attitude
IN our industry, it seems every six months there’s déjà vu. Same issues, same problems, few outcomes. Like everybody, I have an opinion. And that is all it is. What are the main issues surrounding waste and its lack of progress on many fronts? What are the bottlenecks? Is it the companies within the industry? The big players and the little guys? Not from what I can see – they all seem innovative, trying to find solutions, and hellbent on taking the ‘waste’ industry to what it truly should be – a resource recovery industry. Waste should make up less than five per cent of what we do. Everything else should be being reused or recycled. Whether you talk to execs at Remondis, Bingo or Veolia, or the smaller guys starting to make it big such as Repurpose It or Ecocycle, they are all on the same page – they want to make a difference.
To me the biggest bottleneck is government. Whether it be federal, state or local, most agendas appear to have little to do with the state of industry, and to be more about scoring political points. The worst thing to happen at a political level was the former Assistant Minister for Waste Reduction and Environmental Management, Trevor Evans, losing his seat at the last election. I’m apolitical. My point

about Evans isn’t about the party he was
Waste, he rang me (unsolicited) to have a chat and give his point of view on industry issues.
When the current minister entered office, I rang her press secretary for an interview about her thoughts on where the industry was heading. “Give her a couple a months to get settled in the job,” I was told. “Sure,” I said. Here we are two years later. Crickets chirping. I’m not that important that she needs to talk to me, I’m pointing out a difference in attitude.
Without government being engaged, rooting for the industry, listening to the industry’s needs and wants (instead of thinking about the next election cycle and having knee-jerk reactions to the –sometimes – ill-informed public opinion), I could write this column word for word three years from now and it would still be relevant. And that’s the pity.
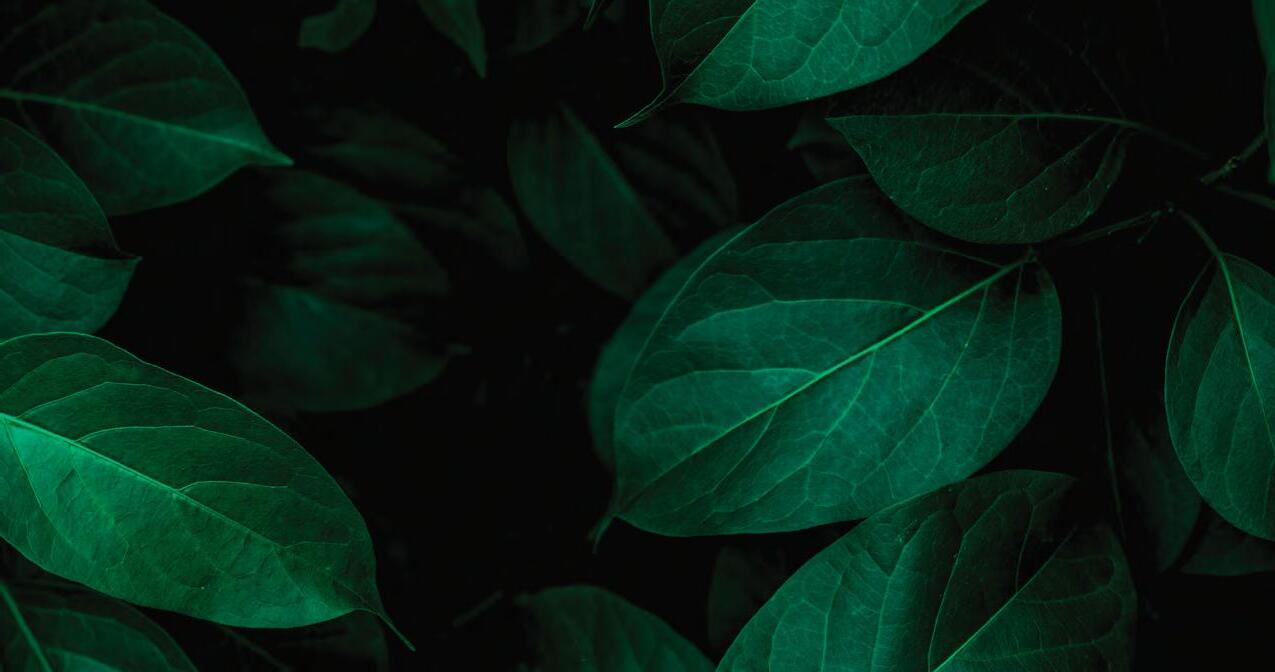

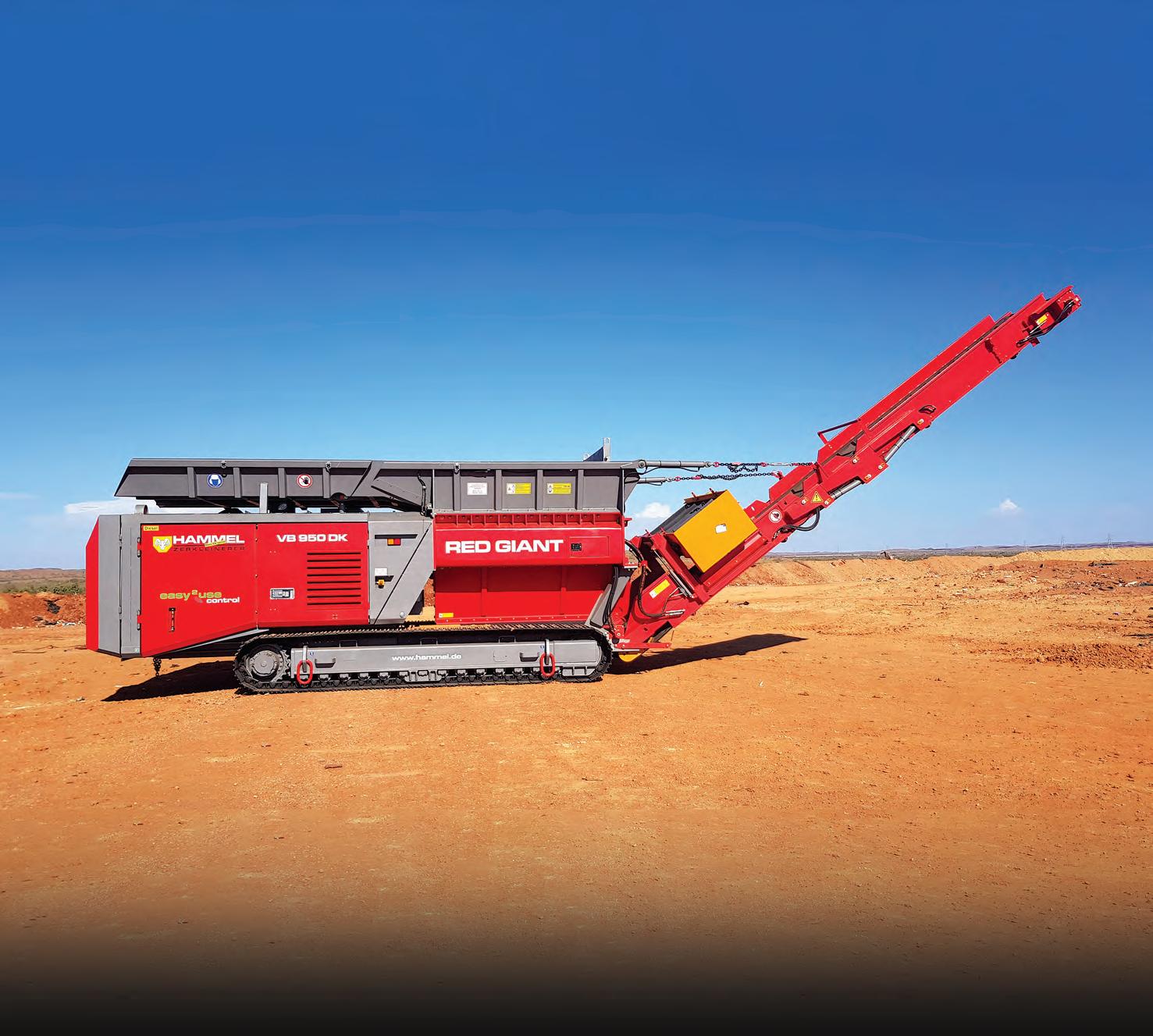
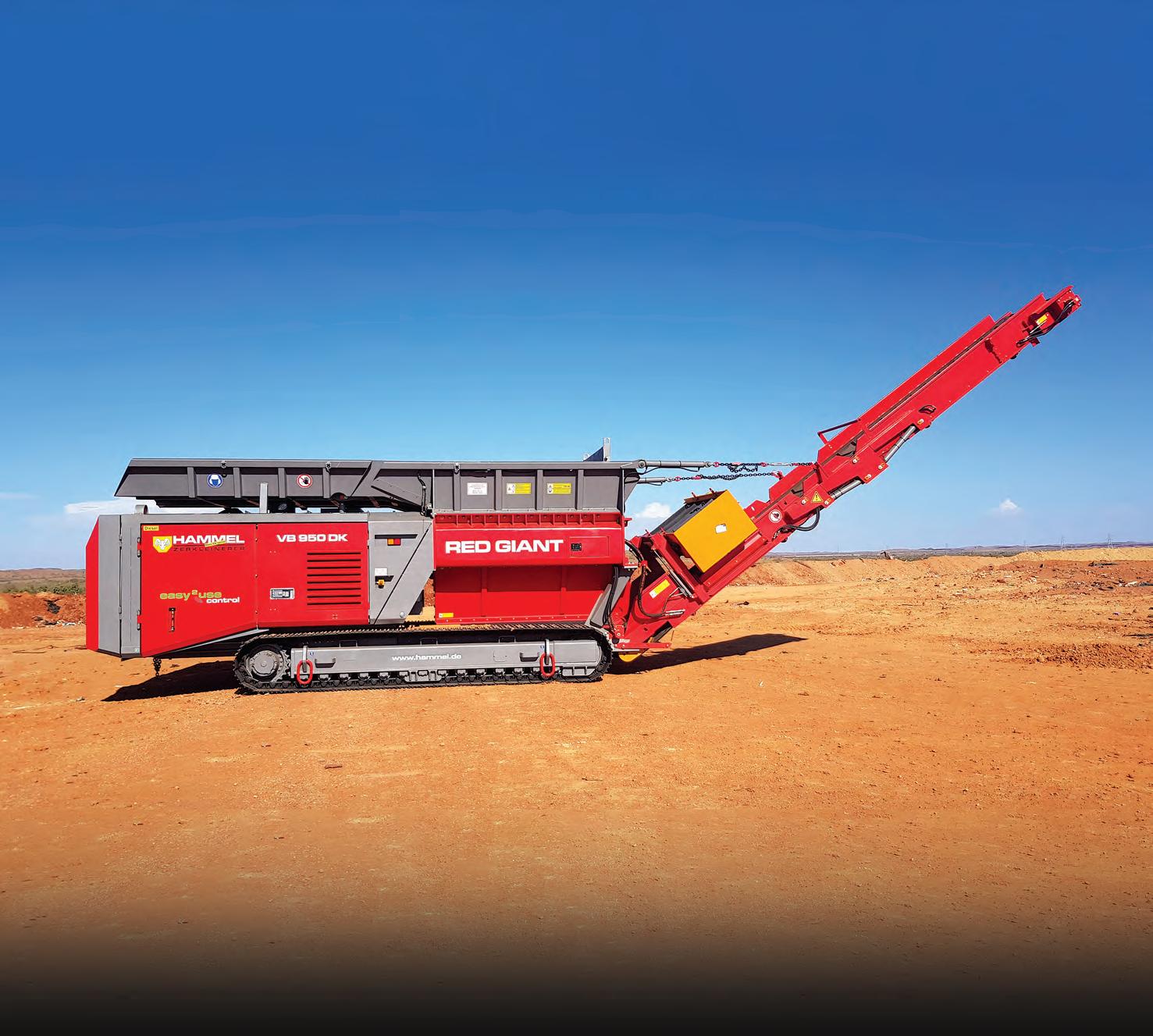

Recyclable sensor materials unveiled
PROFESSOR Chiyoung Park of the Department of Energy Science and Engineering at DGIST (President Kunwoo Lee) in South Korea, has developed a new material poised to advance highsensitivity recyclable sensor technology.
Working in collaboration with Professor U-hyeok Choi of Inha University (President Cho Myeongwoo), Park’s team created a recyclable highsensitivity sensor based on the dynamic polymer network. This next-generation material is garnering attention for its ability to combine environmental sustainability with high performance.
Existing high-sensitivity sensors have been limited by performance degradation due to fatigue and repeated use. However, the dynamic polymer network developed by the research team maintains excellent sensitivity and durability by using vinylogous urethane bonding. This bonding structure selfheals in response to external stimuli such as temperature, light, and pressure, preventing performance degradation even after repeated use.
The dynamic polymer network is also sensitive to various mechanical movements, heat, and light, and sensors based on the network excel at detecting human body movements. Researchers have demonstrated that the sensors can accurately detect finger bends, changes in facial expressions, and even swallowing movements in the throat. One of the biggest strengths of the
technology is that it can maintain the same sensitivity after recycling without any degradation.
Addressing the growing issue of e-waste, the team designed the technology to combine recyclability with high performance. They believe the dynamic polymer network’s versatility supports repeated use and recycling, potentially leading to significant reductions in e-waste. Their work promises to have farreaching implications not only in sensor technology but also in next-generation electronics, wearable devices, and medical equipment. The team continues to work on commercialising the technology for widespread industrial applications.
“Our material offers excellent processability and can be recycled mechanically or chemically,” said Park. “The polymer network undergoes a simple recycling process, which we expect will extend the lifespan of electronic devices and wearable sensors, significantly reducing electronic waste.”
The research received support from the Industrial Technology Alchemist Project, funded by the Ministry of Trade, Industry and Energy, and the Basic Research Center Project of the Ministry of Science and ICT.
The findings (first author: Gyeonghyeon Choi, integrated MS/PhD student) were published in the Chemical Engineering Journal.
Bald Hill Quarry Pty Ltd Convicted of Five Environment Protection Offences in the Land and Environment Court
Bald Hill Quarry Pty Ltd (“BHQ”) has been prosecuted by the Environment Protection Authority (“EPA”), pleaded guilty and was convicted in the Land and Environment Court of NSW (“the LEC”) of five offences against the Protection of the Environment Operations Act 1997 (“POEOA”). The offences arose from BHQ’s use of shredded waste tyres as daily cover for its landfill at Bald Hill instead of virgin excavated natural material (“VENM”) between 14 October 2021 and 9 May 2022, without the EPA’s approval and contrary to its environment protection licence.
On 9 May 2022 there was a fire at the landfill involving the shredded waste tyres which caused air pollution. BHQ failed to notify the EPA and other relevant authorities immediately of a pollution incident which caused or threatened material harm to the environment.
BHQ was convicted of offences against:
1. s 115(1) of the POEOA, for negligently disposing of waste in a manner that was likely to harm the environment;
2. s 126(1) of the POEOA, for dealing with materials in a manner that caused air pollution;
3. s 64(1) of the POEOA, for breaching condition O1.1 of its environment protection licence for failing to carry out landfilling activities in a competent manner;
4. s 64(1) of the POEOA, for breaching condition O5.3 of its environment protection licence for failing to use VENM as daily cover at the landfill; and
5. s 152 of the POEOA, for failing to immediately notify all relevant authorities of a pollution incident causing or threatening material harm to the environment.
On 31 October 2024 the LEC convicted and fined BHQ the amount of $341,000, ordered it to pay the EPA’s costs agreed in the sum of $236,250, and to publish this notice. The LEC’s judgment may be accessed at https://www.caselaw.nsw.gov.au/decision/192df7c0e3dd4bb16ba18189#_ Toc181285784.
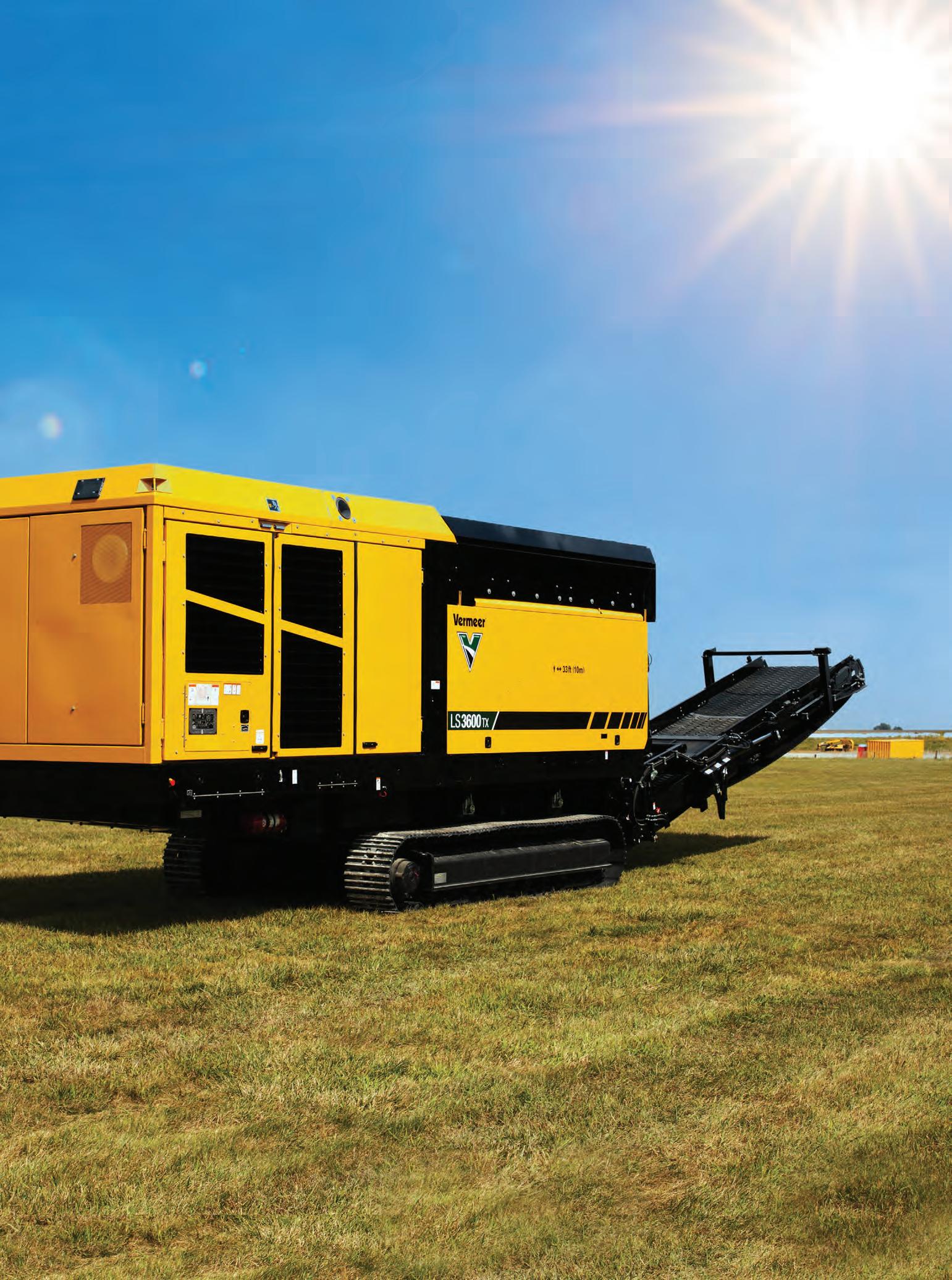
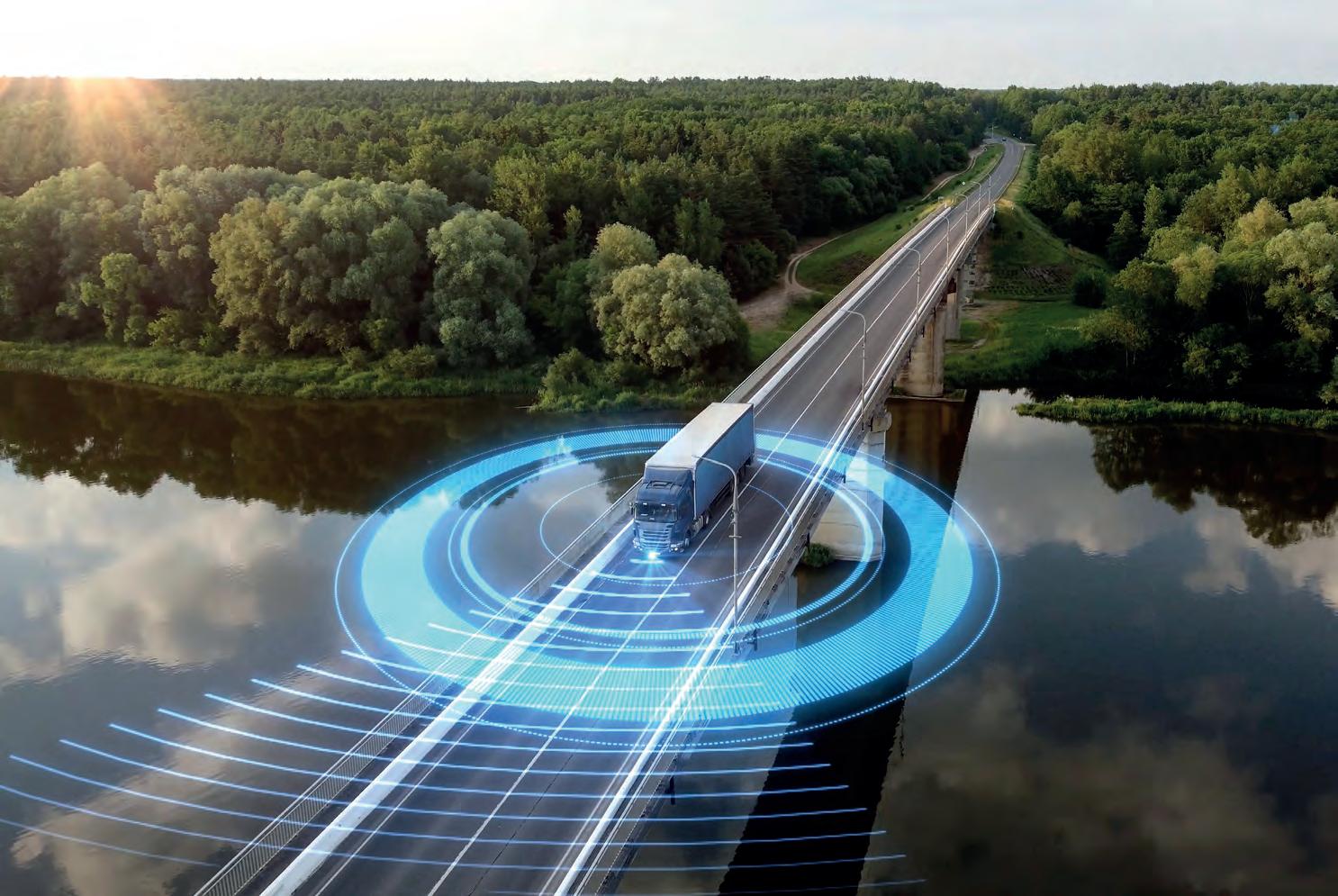
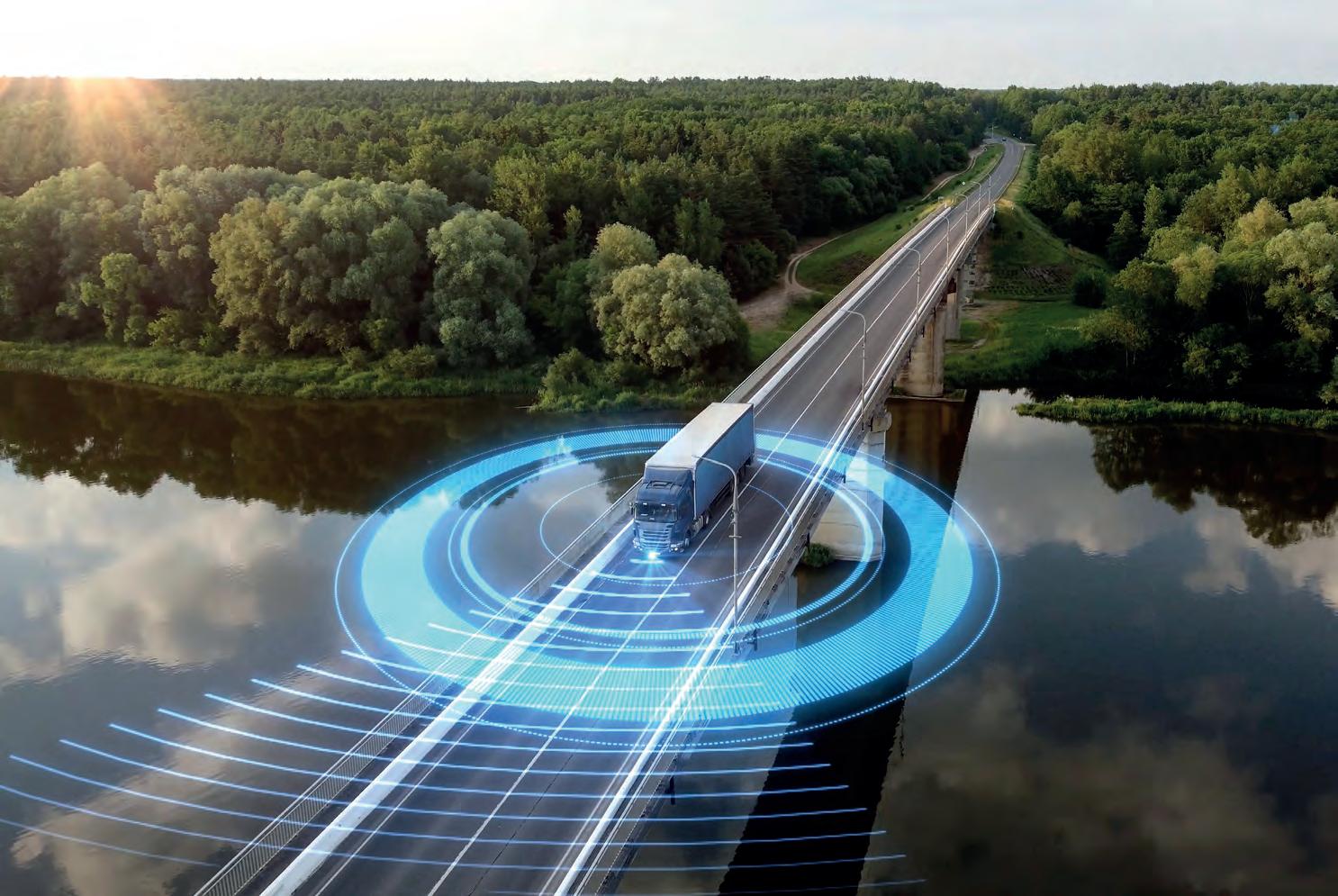
THE LOW SPEED SHREDDER CHANGING THE GAME
INTRODUCING MORE VERSATILITY TO VERMEER’S ORGANIC RECYCLING RANGE.
The single-shaft LS3600TX is the first low speed shredder from Vermeer, delivering high torque and featuring exclusive innovations that efficiently process contaminated waste streams and help protect critical machine components. Plus, unparalleled access to the rotor, comb and engine compartment addresses longtime industry maintenance issues. It’s time to step into the future of low speed shredding equipment. Contact your local Vermeer Australia team today.
VERMEERAUSTRALIA.COM.AU | 1300 VERMEER Vermeer and the Vermeer logo are trademarks of Vermeer Manufacturing Company in the United States and /or other countries. Product specifications are subject to change by OEM. © 2024 RDO Equipment Pty Ltd (trading as Vermeer Australia). All Rights Reserved.

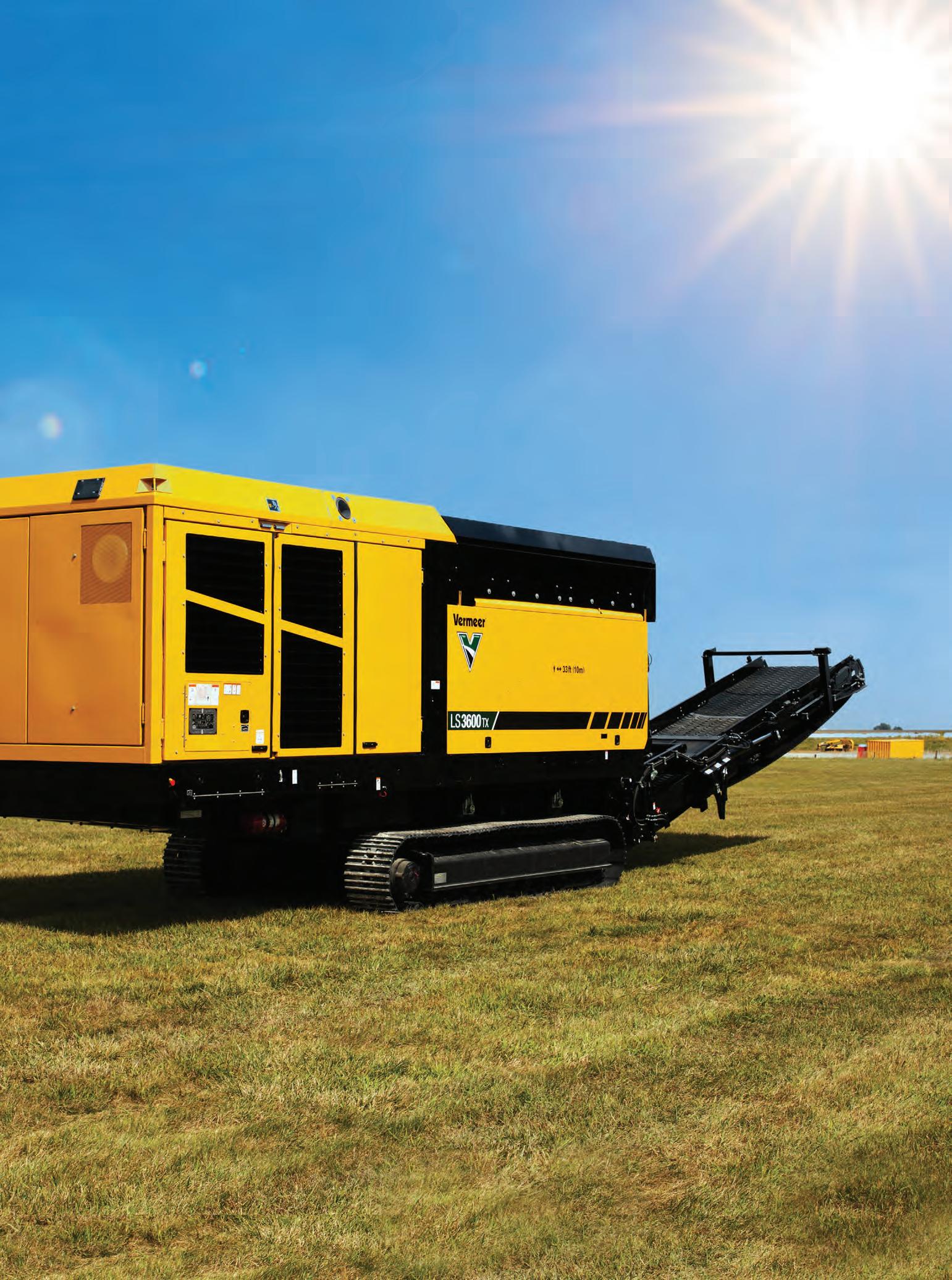
Recycling mistrust unfounded
NEW research from Planet Ark has uncovered a widespread misunderstanding among Australians about what happens to their recycling, with about one in three (31 per cent) mistakenly believing that most items in their recycling bins end up in landfill.
This misconception stands in contrast to reality, with most correct items placed in recycling bins successfully processed and recycled. Approximately 80 per cent of all items placed in household recycling bins are recycled, with about 14 per cent not recycled due to contamination (items that shouldn’t be placed there in the first place). Only the remaining six per cent is not recycled due to breakage or process inefficiencies.
Participants in the research also identified knowledge that most of their recycling was being processed and recycled appropriately as the primary reason people would be more motivated to increase
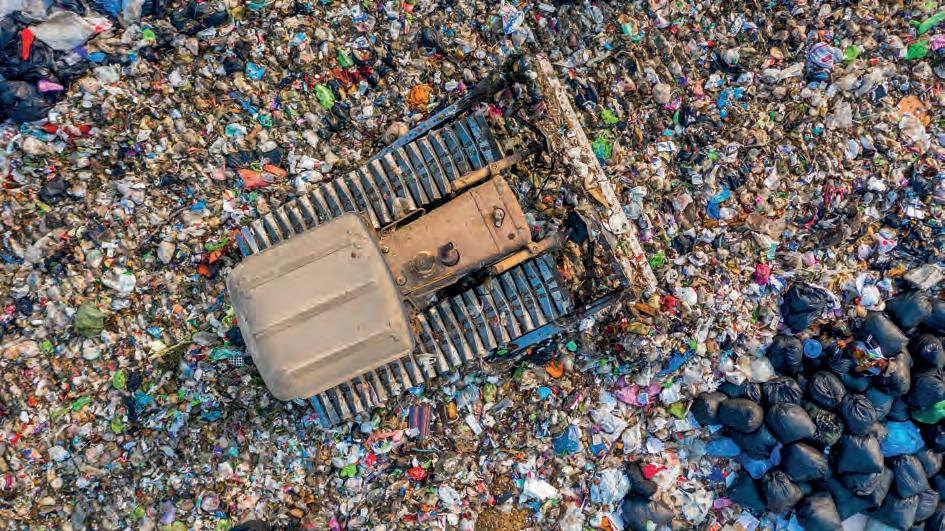
in landfill is a detractor from people’s recycling efforts and continues to undermine public confidence in the recycling system.
Rebecca Gilling, Planet Ark CEO, expressed concern about how the persistence of these myths and the mistrust they cause hinders progress
their efforts to recycle do make a difference. The majority of correctly recycled items do not go to landfill, and the system in place is effective at recovering valuable resources, reducing greenhouse gas emissions and cutting down on the need for raw

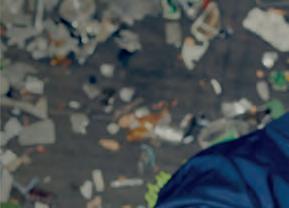
Planet Ark is redoubling efforts to provide educational resources to clarify what can and cannot be recycled at home, information on items that can be recycled through product stewardship schemes, and how to reduce waste through reuse and repair initiatives.
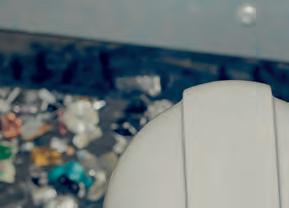
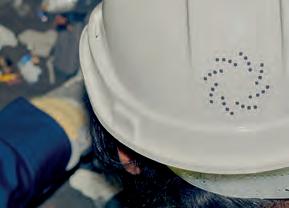

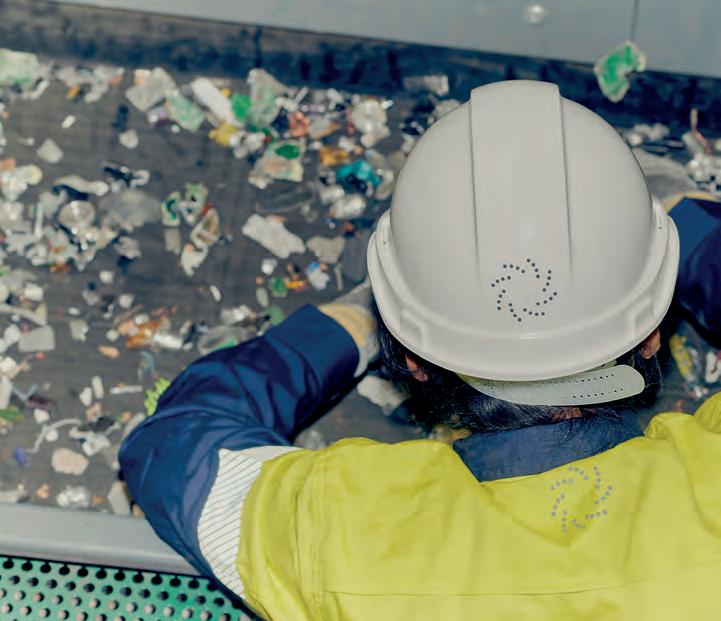


About six per cent of household waste is not recycled. Image: Kalyakan/ stock.adobe.com

The COMPAKTOR 300 is a mobile two-shaft shredder for processing construction & demolition waste, natural and waste wood, commercial waste and more.
The COMPAKTOR 300 has a new name, but when it comes to its structure, it is not a blank sheet on the global recycling market. The disposal companies of the construction and demolition sector value the ARJES brand for their extremely flexible and strong shredder that comes along with the best price-performance ratio of the industry.
T: 1300 859 885
E: sales@triconequipment.com.au www.triconequipment.com.au
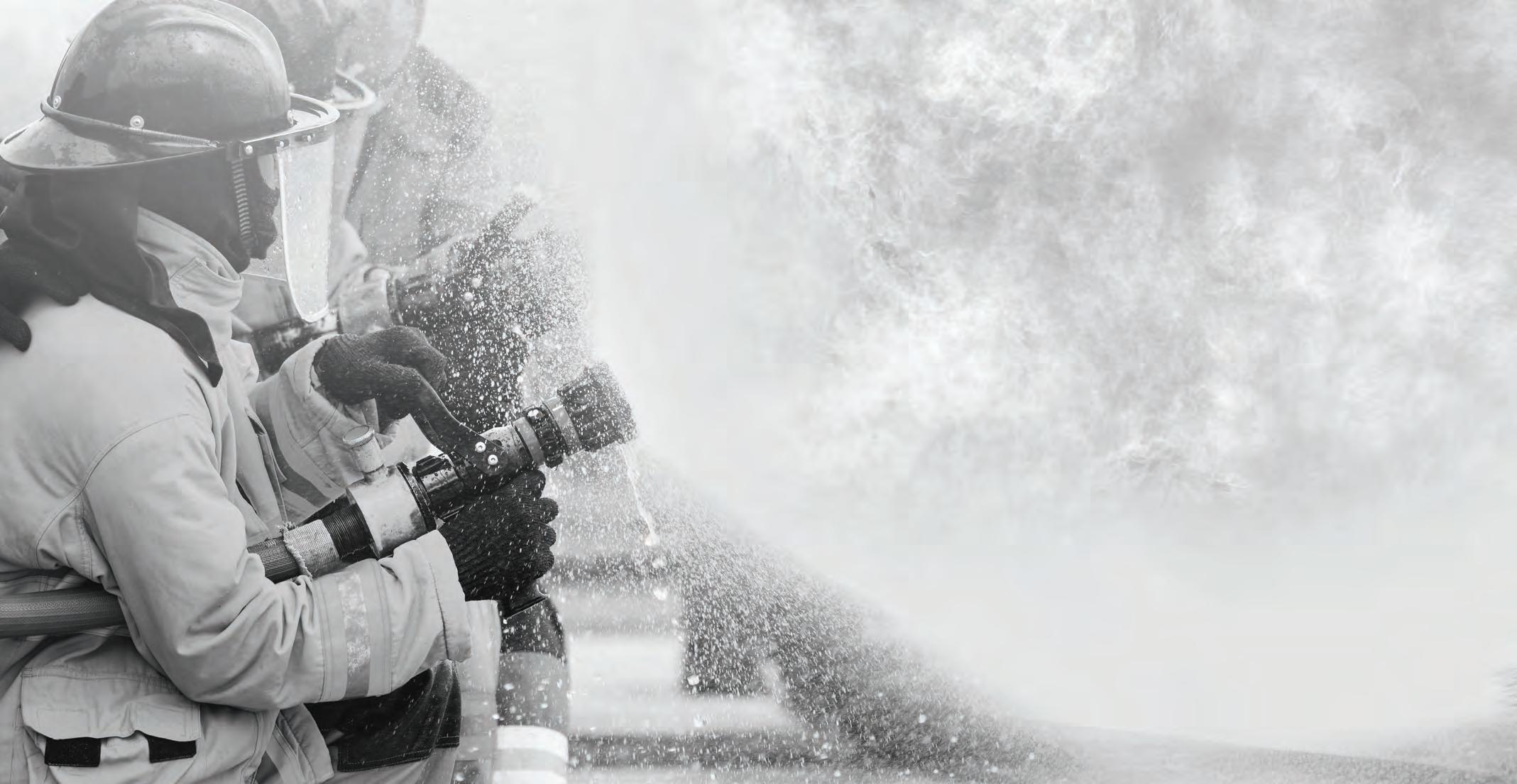
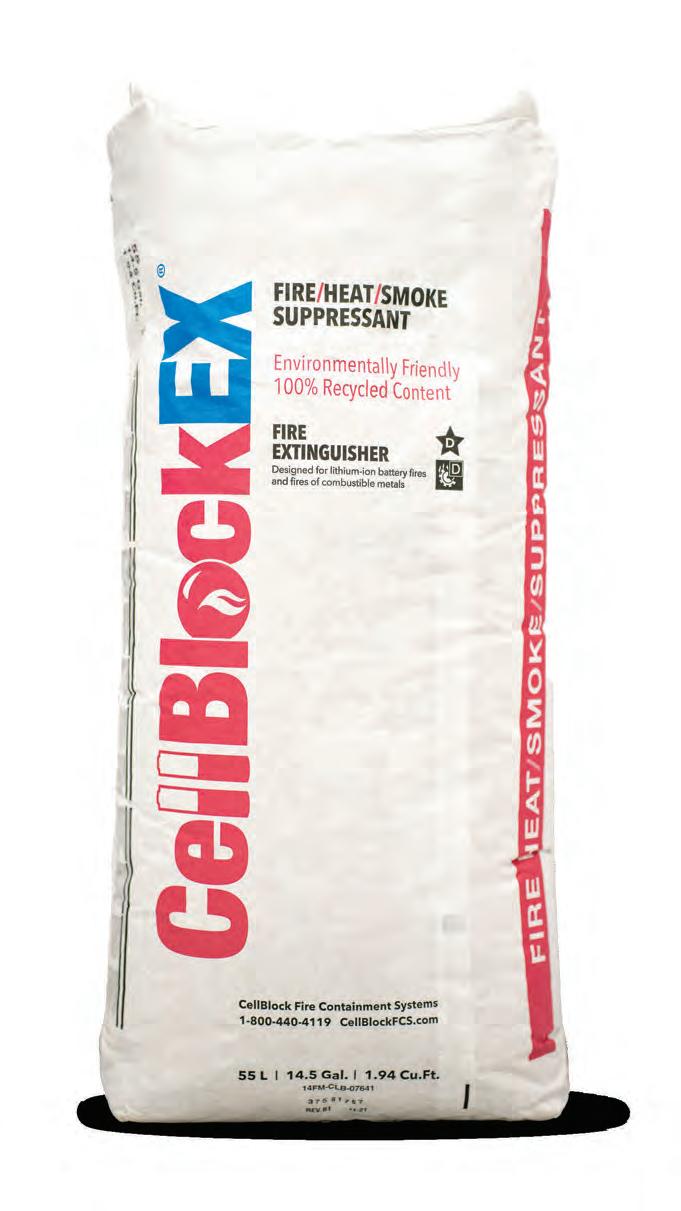
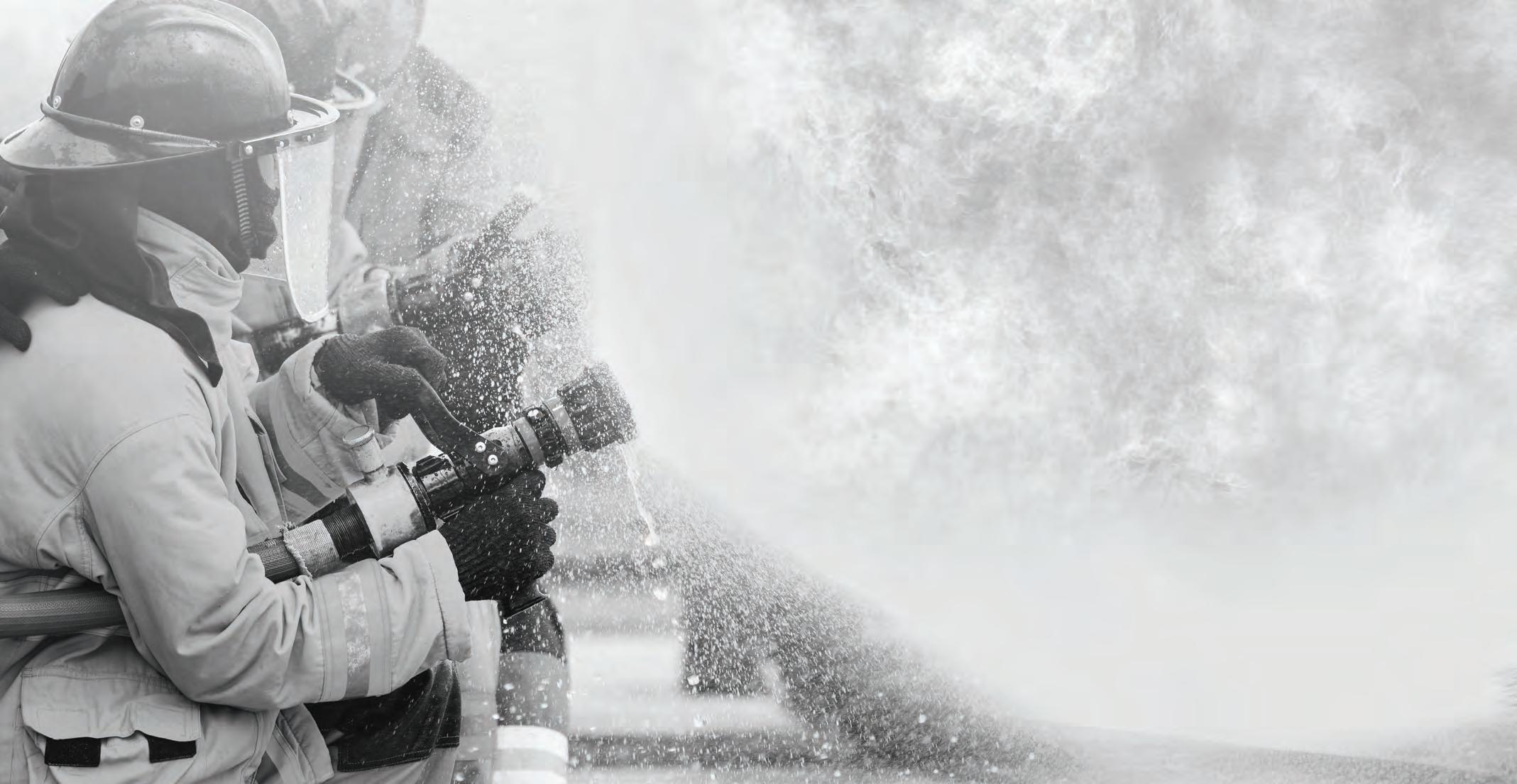
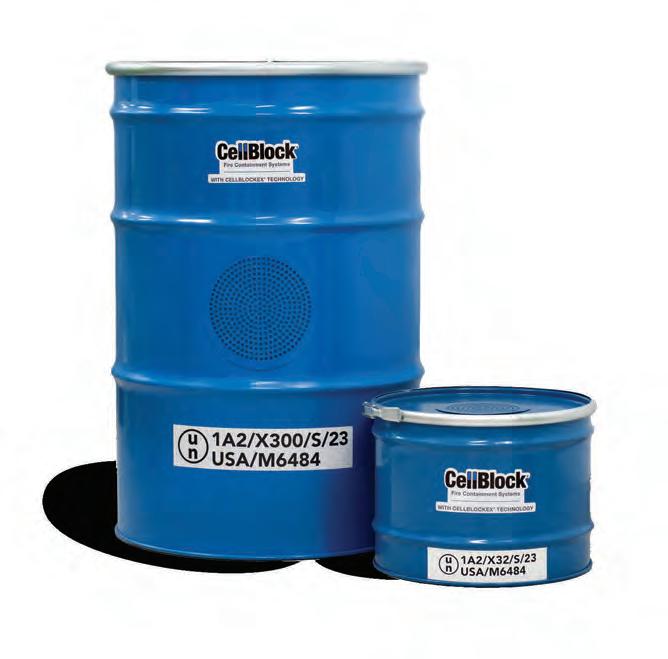
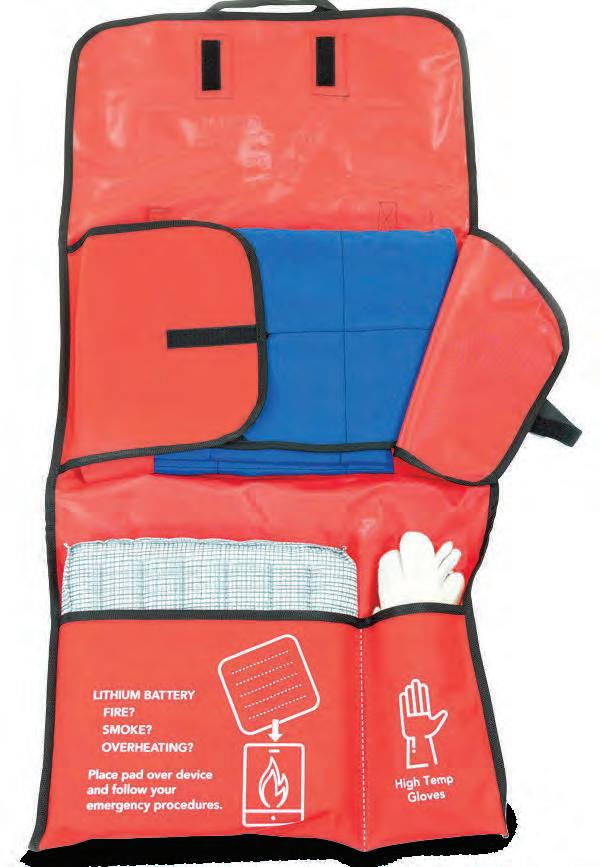
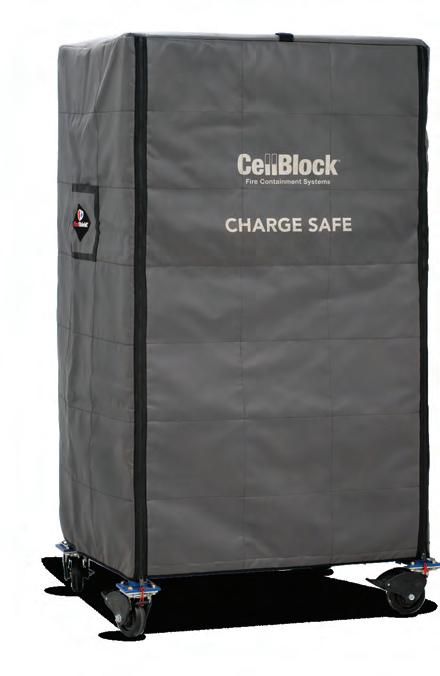

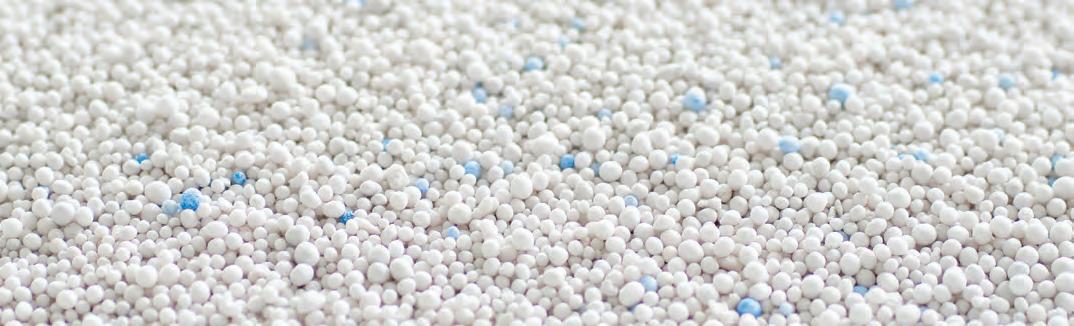
development increase $70/ policy material to procurement operations is November, we to Government for coming direction, October, comprises of Minister, explore Sword, has Packaging (APCO), development significant of review The the maximising strong, than that secondary is Australia auspiced, which content lead material this that Australia be urging
National packaging laws
Again, see previous – why can’t we adopt and accept the approaches taken in the EU? With the successful adoption of a national framework, like what we have recently seen in the EU with the adoption of the Packaging and Packaging Waste Directive 94/62/EC, this would again provide a consistent framework under which everything flows. Better still, many of the multinationals that import to Australia already operate under this regime.
In theory, it was a bit of a relief to finally see a document on regulating packaging. After 15 months of handwringing since there was national agreement to introduce design rules and regulate packaging, and over two decades of failed and ineffective policy – this is probably the best we can say.
WMRR’s full response to the packaging proposal can be found in our submission, but in short, it is disappointing there was little consideration of the systems thinking required across all three waste streams. In all honesty haven’t we moved beyond ‘recyclable’ as the measure? Instead, it must be ‘actually recycled’, and in Australia given the export restrictions, this means creating
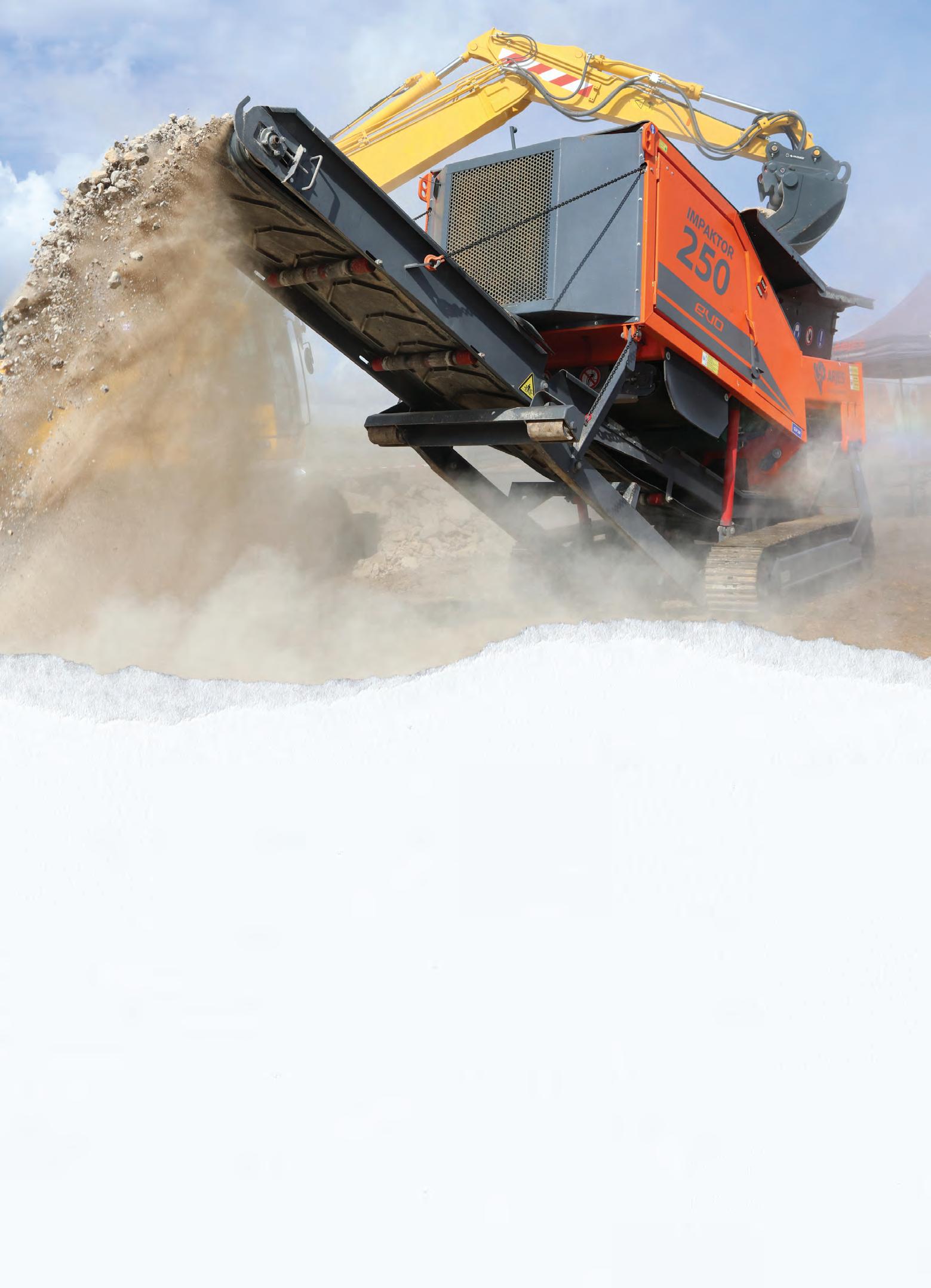
infrastructure and ensuring market demand for recycled materials.
Regrettably none of the options proposed provided for a funded scheme –including market development and packaging recovery at scale – to address the capacity shortfall the paper highlights. Packaging reform needs to drive the necessary shifts to achieve a regulated scheme that meets the targets set, as well as building a safe circular system for all packaging at scale (not just what goes through the household). The current consultation paper fails to do this. It also failed to consider other current legislation such as export restrictions and container deposit systems – both of which are part of the packaging ecosystem. One can only hope the consultation is genuine and the government listens.
Conclusion
There remains a lot to be done, and a lot could be done with strong considered regulation from the Minister who arrived prepared to ‘regulate’. I have every digit crossed that we will see the brave and clever regulation soon, so that we can create a circular economy in Australia and stop going around in circles.
There was a lot of hope riding on the new minister who promised to act and regulate. Image: Sue Martin/Shutterstock.com.au
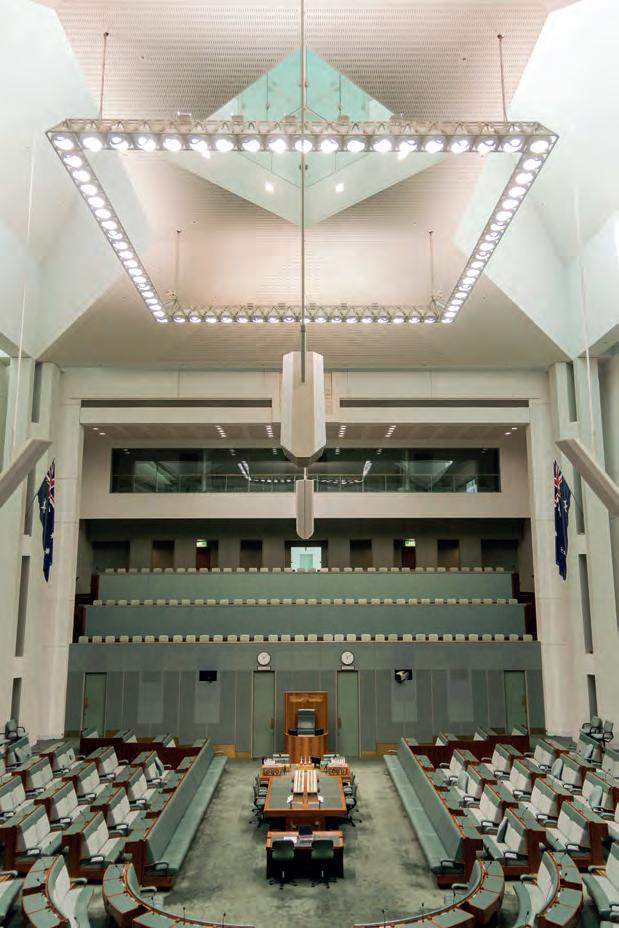
The
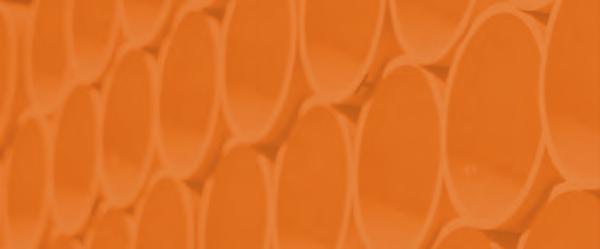
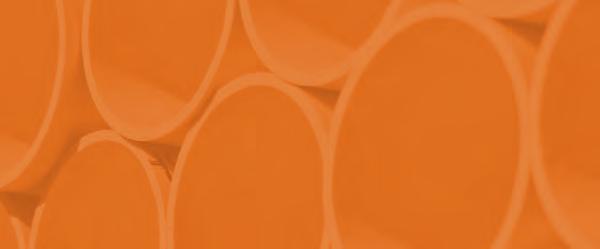
CONSTRUCTION PLASTICS
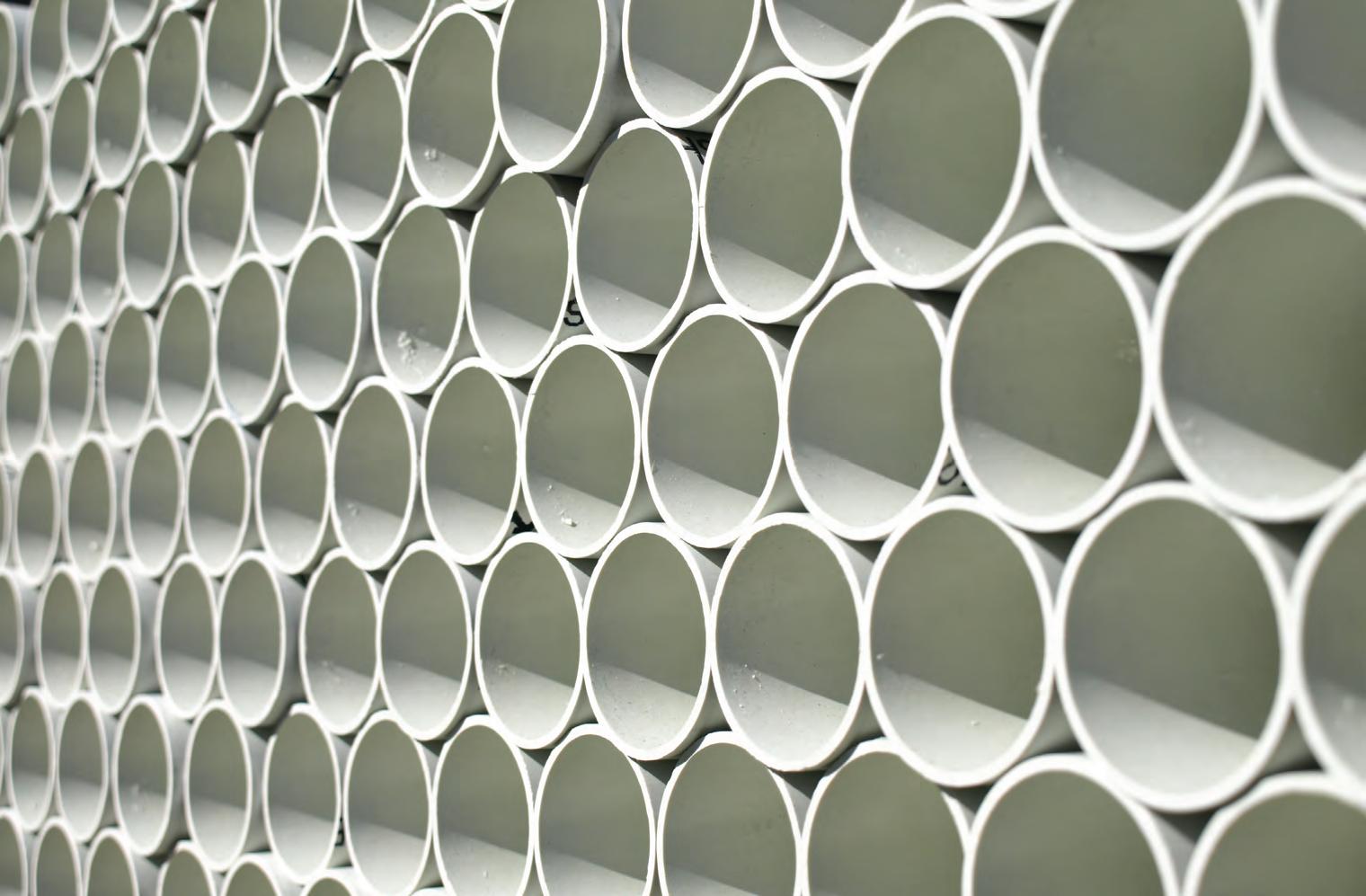
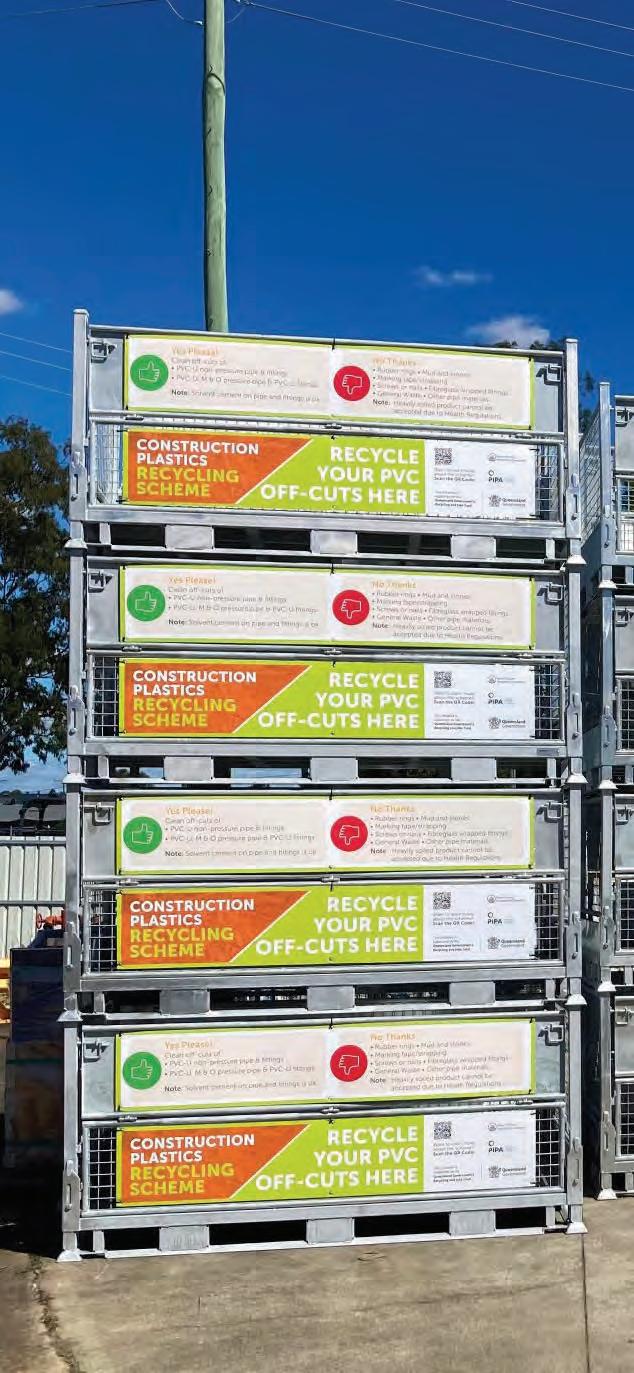
PVC PIPE AND FITTINGS CAN BE MANUFACTURED INTO NEW PIPES THAT CAN LAST OVER 100 YEARS!
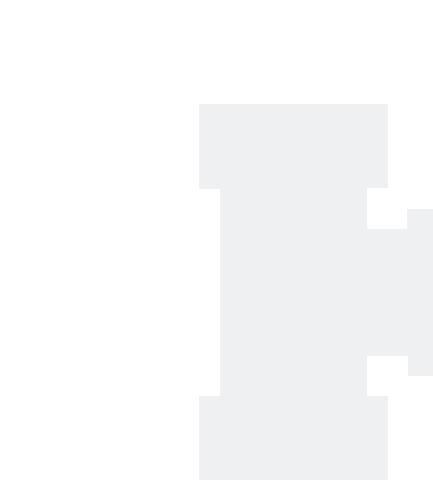
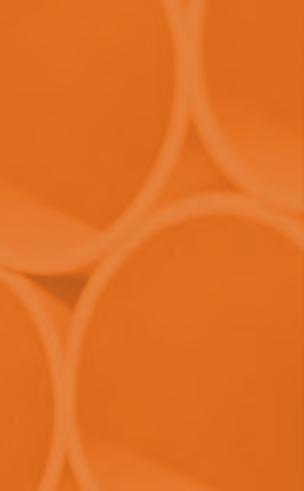

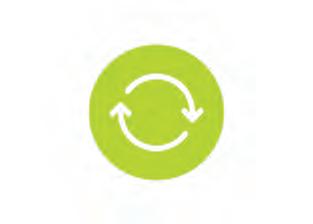
WHILE ON-SITE, COLLECT PVC OFF-CUTS & DROP THEM OFF AT ONE OF OUR BIN LOCATIONS. TOGETHER WE CAN BUILD A MORE RESPONSIBLE, SUSTAINABLE FUTURE.
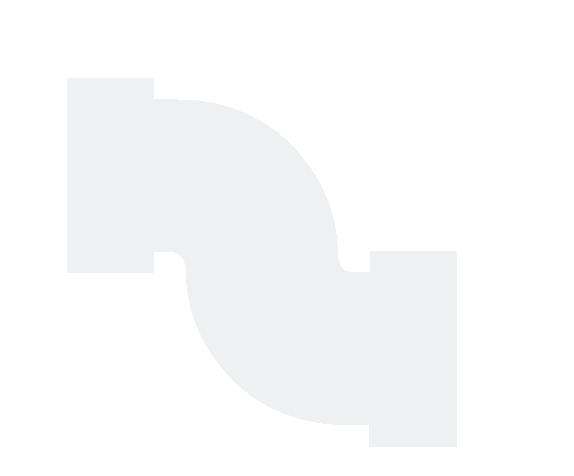
DID YOU KNOW?
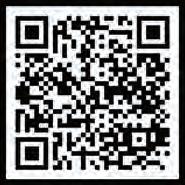

We now have 40 bin locations across Queensland. Find out more.

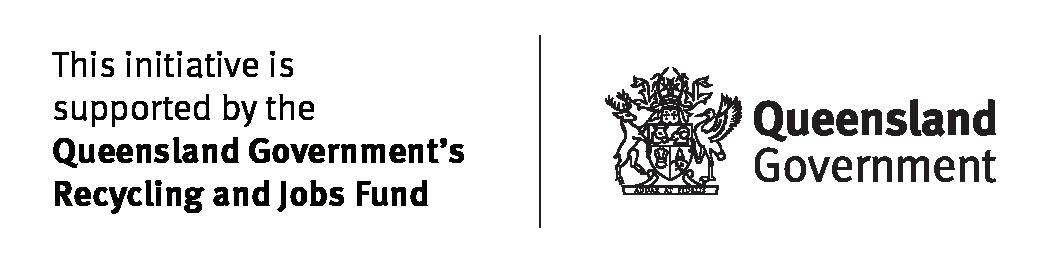
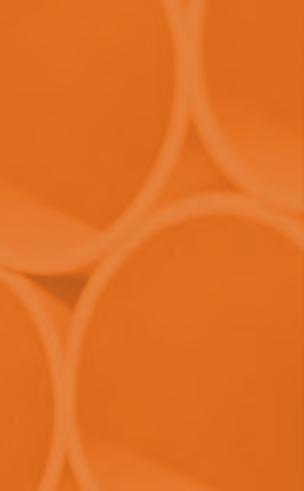

Melbourne councils looks to EfW to solve residual waste woes
(Continued from the Cover)
“They did so because I think they had a sense of risk greater than their appetite to take those risks,” he said.
And the influence it took to get the other nine onboard? Cummins said there were several conversations with the other councils, and with people within his own community, and a familiar theme emerged.
“The easiest way I’ve found into these conversations with people in the community is the contrast with what we currently do with waste, which is essentially sticking it in a hole and burying it, recovering nothing and producing significant amounts of methane gas,” he said.
“Once people get an understanding that we’re not talking about a 44-gallon drum with a few holes poked in and rubbish being incinerated –
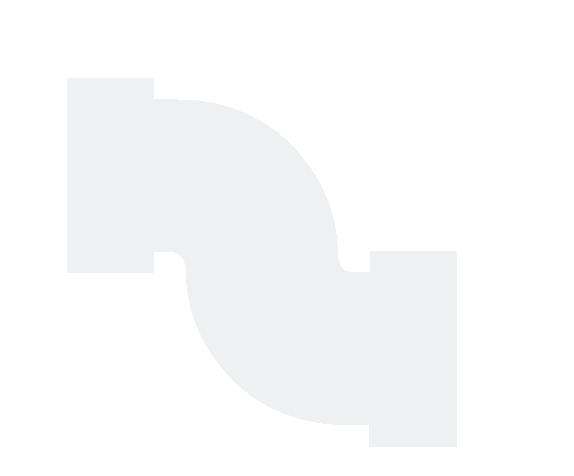

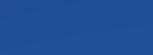
we’re talking about a very advanced piece of technology that has been used extensively around the world. Once we tell them it is a proven technology and is heavily regulated – I think people start to feel a bit better about the process. Also, once you talk about the comparative greenhouse gas emissions compared to landfill, people start to feel more comfortable.”
Cummins has also engaged with a climate change action group based in Bayside, who are agitated at the facility being given the go ahead.
“I sat down with them, went through how we’re approaching this and the alternatives available,” he said. “And whilst they still had some reservations, they went away feeling more relaxed about this as a solution and getting ourselves off landfill. I think everyone agrees that landfill is a primitive way of dealing with waste.”

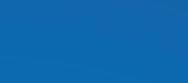

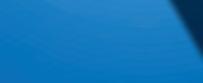
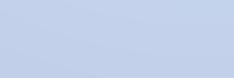


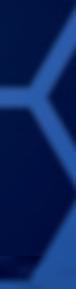
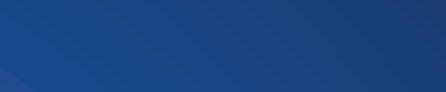
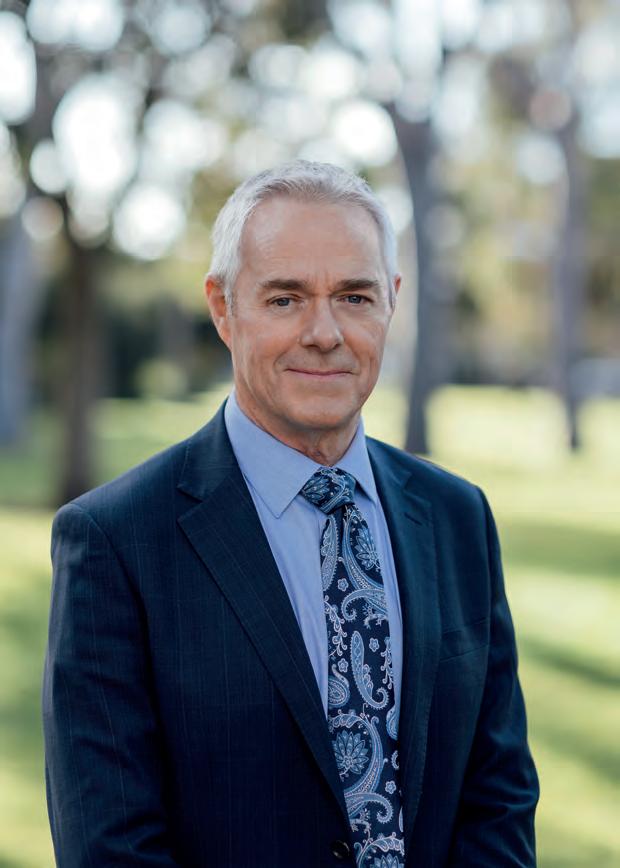

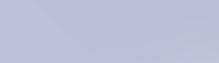

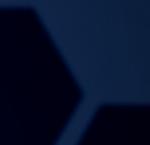
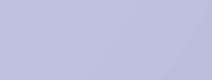
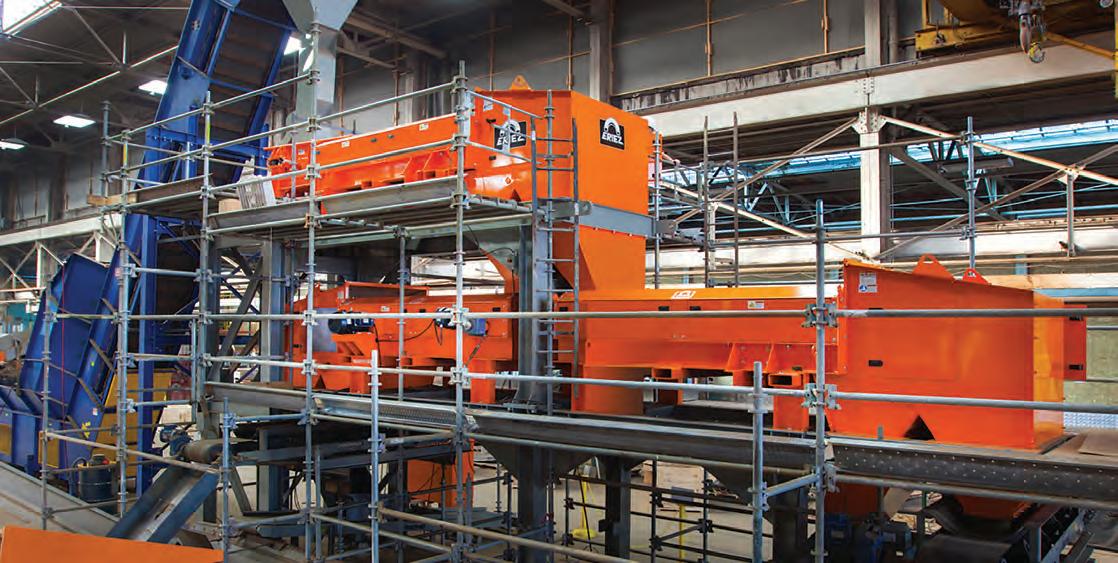
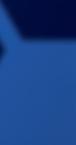
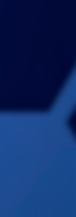




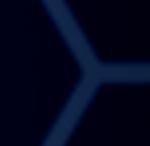
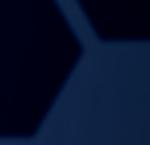
Bayside City CEO Mick Cummins. Image: Bayside City Council
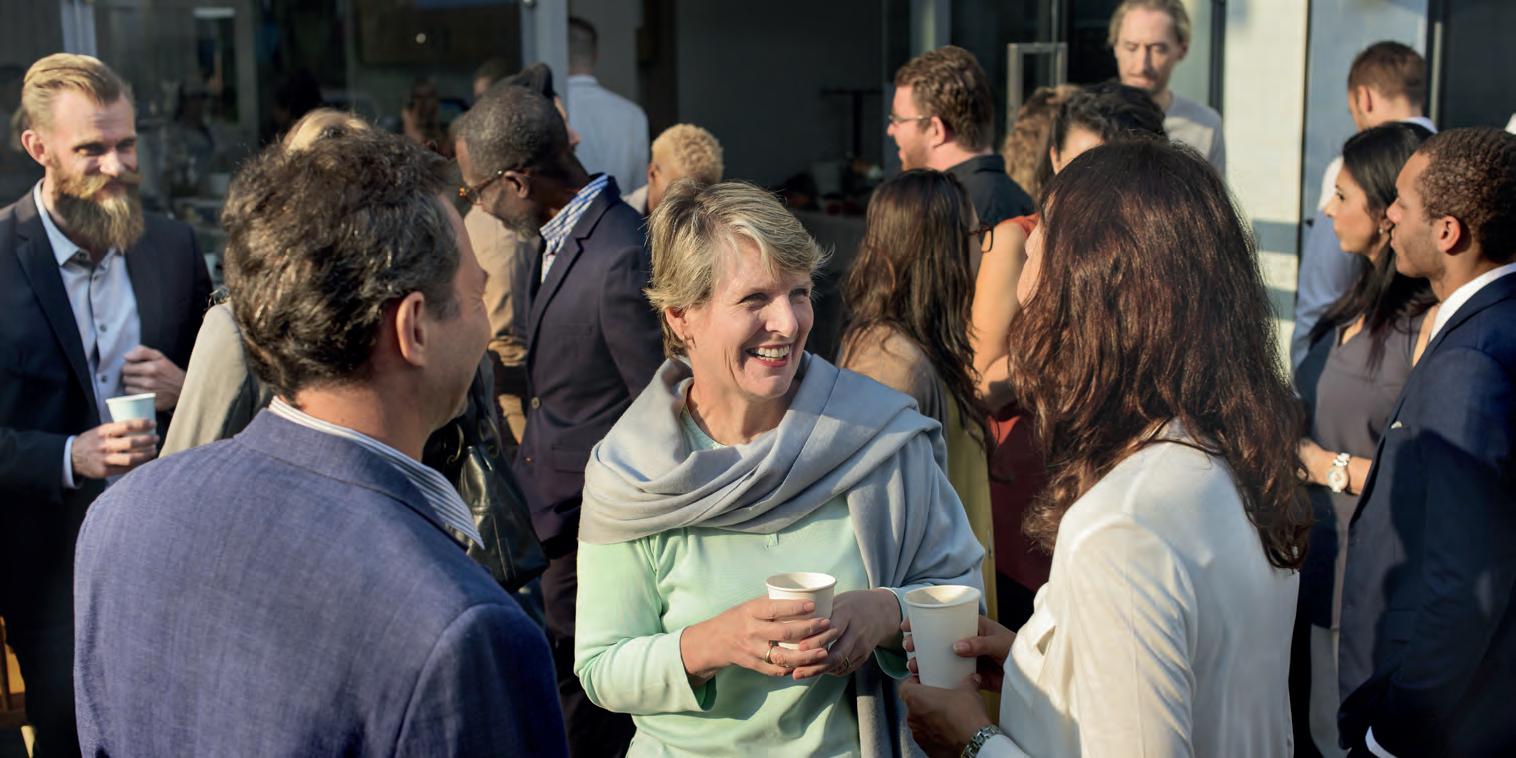
“It is a cost that will escalate over the period of the contract, but in a way that it will be substantially less than the rate of increase in landfill costs.”
Cummins is at pains to point out that the council’s decision to send their residual waste to landfill wasn’t something that happened off the cuff over a cup of coffee at the local café. It has been more than six years in the making after they realised that the last landfill in southeast Melbourne has a life of about another five years before it is full. The councils wondered aloud what the future would look like without a viable landfill, and so they started looking around for alternatives.
“My infrastructure director at the time had been involved in an ongoing series of meetings and was of the view that if this project was to gain traction, it needed the CEOs of the 16 councils in the southeastern Melbourne to be on board,” he said. “We convened a meeting of 16 CEOs, which has pretty much kick started this process, with the assistance of the state government who funded the procurement.”
The Council’s formed a separate company, South Eastern Metropolitan Advanced Waste Processing, to undertake the procurement and each Council provided a Board member and these nine people have guided the way forward.
That was four years ago, and as
Cummins tells it, they have “been all over the place in terms of trying to find effective solutions” – ideas that were commercially viable and would produce the right sort of outcomes. He said one of the complications –which everybody knew was going to be an issue from the get-go – was trying to get 16 councils to agree on the same outcome, which is why the number dropped to nine. However, he points out that at the end of the day something needed to be done, and they came together to find a workable solution.
Finding a common ground with the consortium who are building the facility did have its ups and downs as the negotiations were carried out, but Cummins said that they were about to “land a deal that we felt was commercially viable for councils”. The outcome was a quid pro quo deal that suits both entities.
“We provided a minimum waste guarantee, which is less than the waste that we’re likely to be generating,” he said. “That allows them to get the appropriate financial backing on board for the project, because these are very expensive pieces of equipment to build. They needed to have guaranteed access to a minimum volume of waste. In return
for that, we got long-term access to the facility at a competitive rate.”
It is a rate that will escalate over the period of the contract, but in a way that will be substantially less than the rate of increase in landfill costs. Cummins said that once all the resources/waste have been reused or recycled, there will be about one per cent left over that will be taken to the facility.
I t will be a close call as to whether all the pieces would fall into place because the facility is due to come online in 2029, about the same time the landfill is due to close. The councils did look briefly at other alternatives but another solution they looked into would mean a lot of the waste would be transported through built-up areas of Melbourne, which was not feasible.
What has the feedback from the various councils’ communities been like? Overall, Cummins said, the support was at about 77 per cent in favour from ratepayers and those in the Maryvale area where the facility is being built.
“I think it genuinely does have community support down in LaTrobe Valley,” he said. “It will bring employment, and it also provides some certainty to access to energy
for the paper mill, which is also an important employer in the local community.
“I’ve got no doubt that there are people out there who think that burning waste is not the way to go, but none of them have demonstrated an alternative other than some sort of magic wand strategy. They will wave something at it and the waste will disappear. That’s not the world we’re living in.”
Cummins realises there is sensitivity around EfW facilities, but if anti-EfW advocates dig a little deeper, they will realise the alternative is worse. He said he could understand the sensitivity around EfW facilities, but believes the focus should be on the negative implications of landfills and their impact on the environment. Councils across Australia have got historical landfills that they’re still trying to clean up from a greenhouse gas emissions point of view, but also there are other ongoing issues such as groundwater contamination and migration of methane.
“There wouldn’t be a council in Australia that’s not battling with these problems from historical landfill use,” he said. “People don’t understand just how appalling landfill is as an option.”
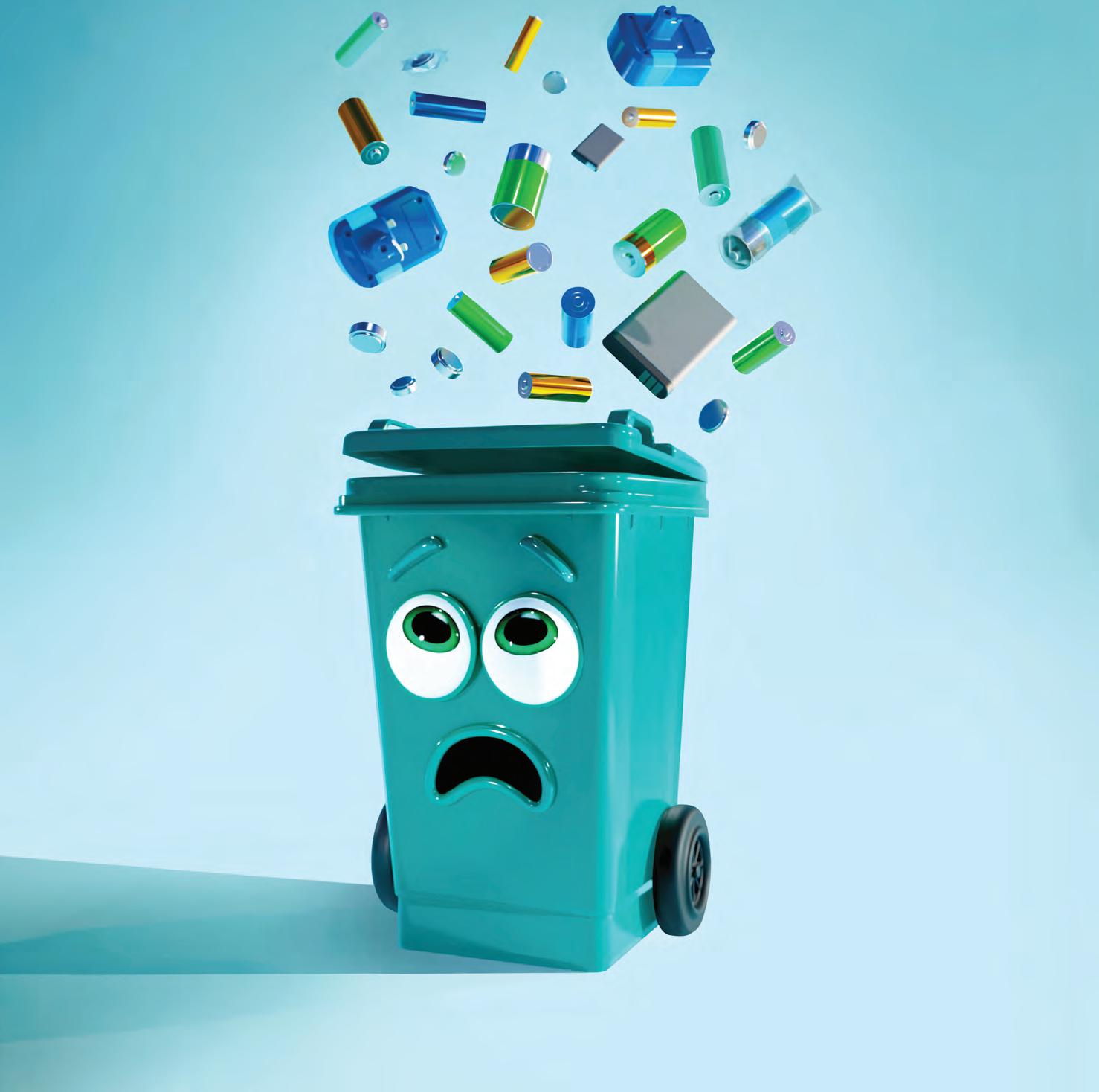
Community collaboration was a key factor getting councils onboard, according to Cummins.
Image: Rawpixel.com/shutterstock
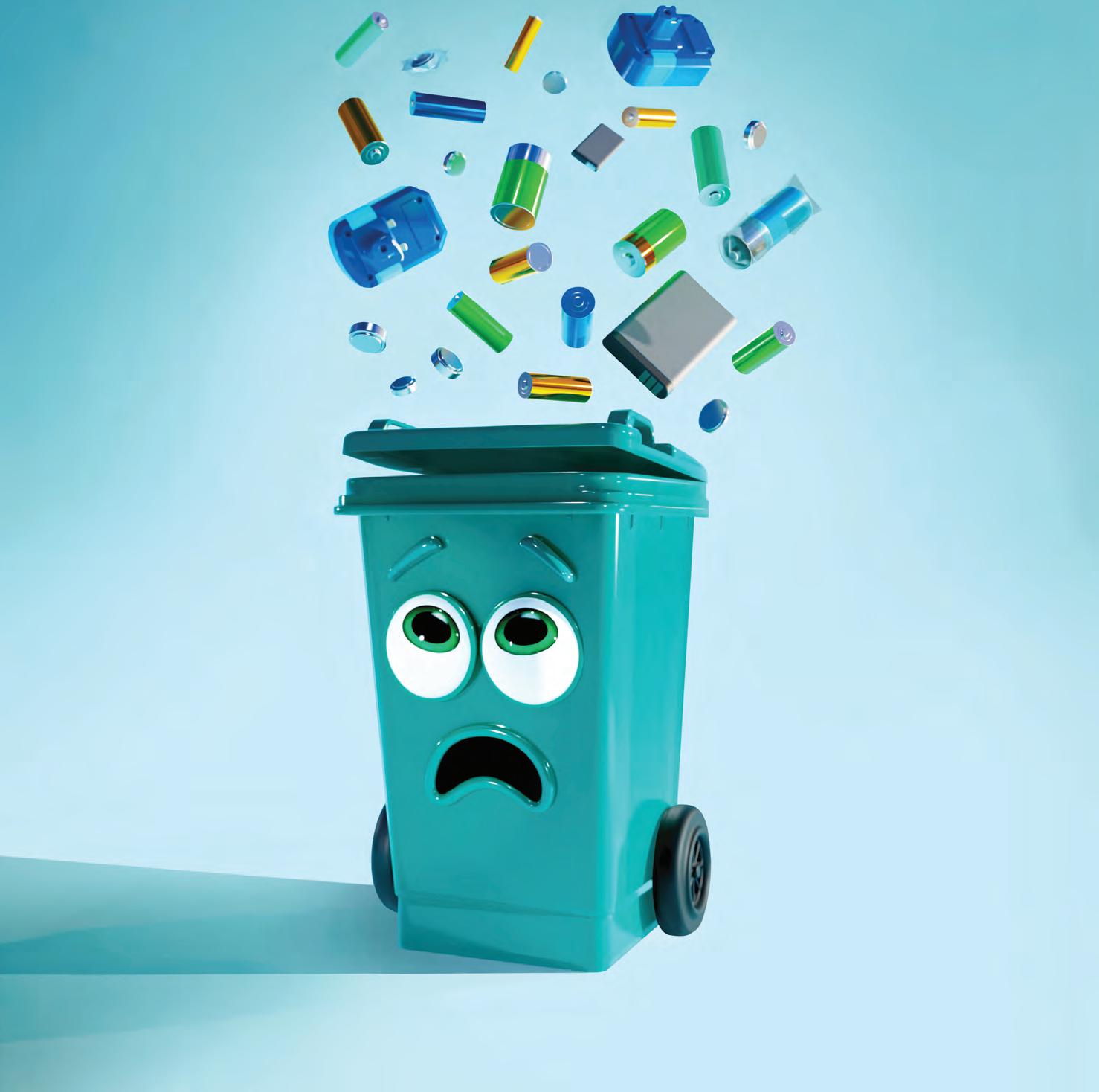
Higher fees good incentive
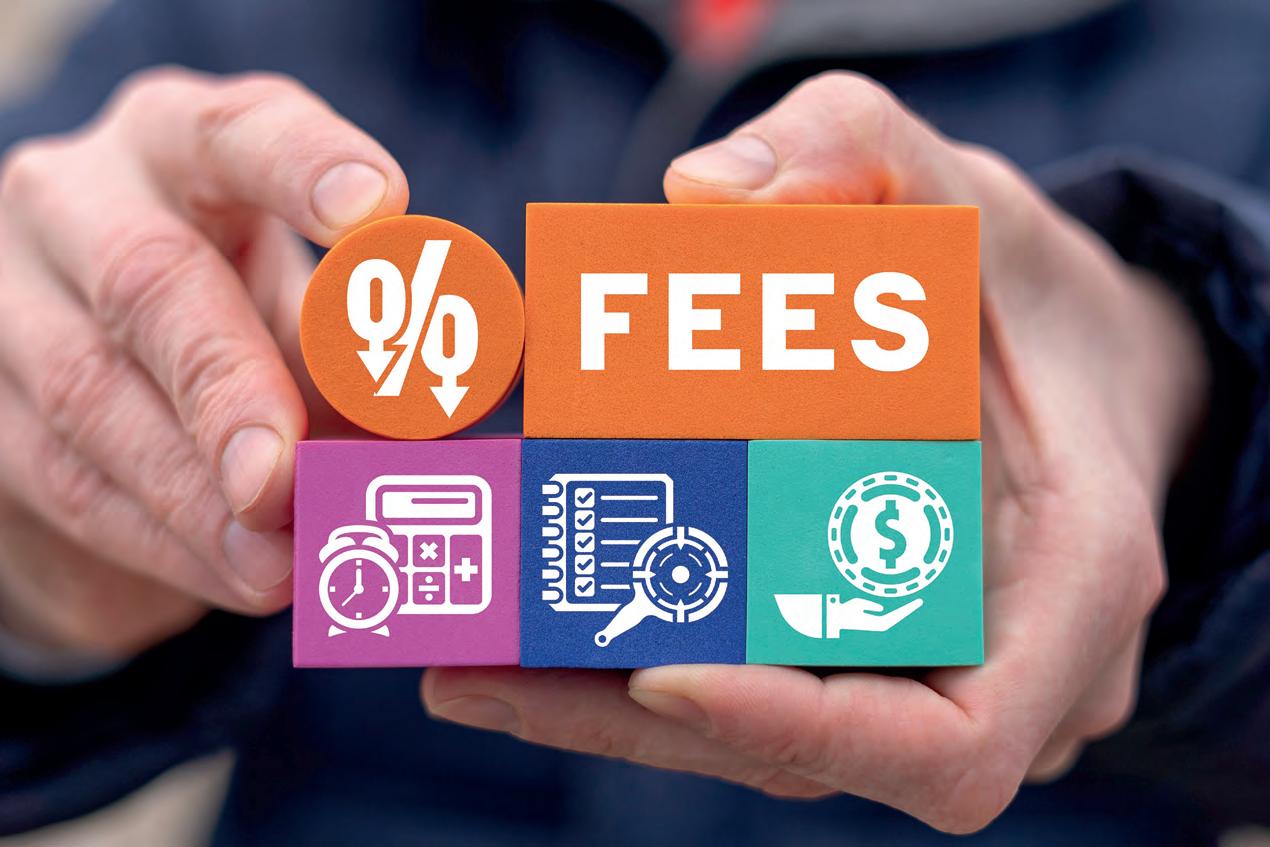
By Rob Kelman
AS Mike Ritchie recently detailed (Oct/Nov issue of Inside Waste ) and as industry also agrees, Australia will go nowhere near meeting its packaging recovery and associated targets. So, the Commonwealth Government has outlined a plan to adopt some form of Extended Producer Responsibility (EPR) scheme for packaging.
But as I outlined earlier this year, packaging manufacturers and users will do everything they can to avoid paying the ‘full net costs of recycling’, which is the basis for the best performing European packaging EPR schemes.
The key to an effective packaging recovery scheme in Australia will be the scheme fees. If these are too low, as the Australian Packaging Covenant Organisation (APCO) is outlining, it will simply fall over as the Redcycle scheme did. Scheme fees run right through successful European EPR schemes that Australia should be emulating, from collection, processing and end markets.
These fees will of course differ for packaging formats based on ecomodulation. Fees would be offset for
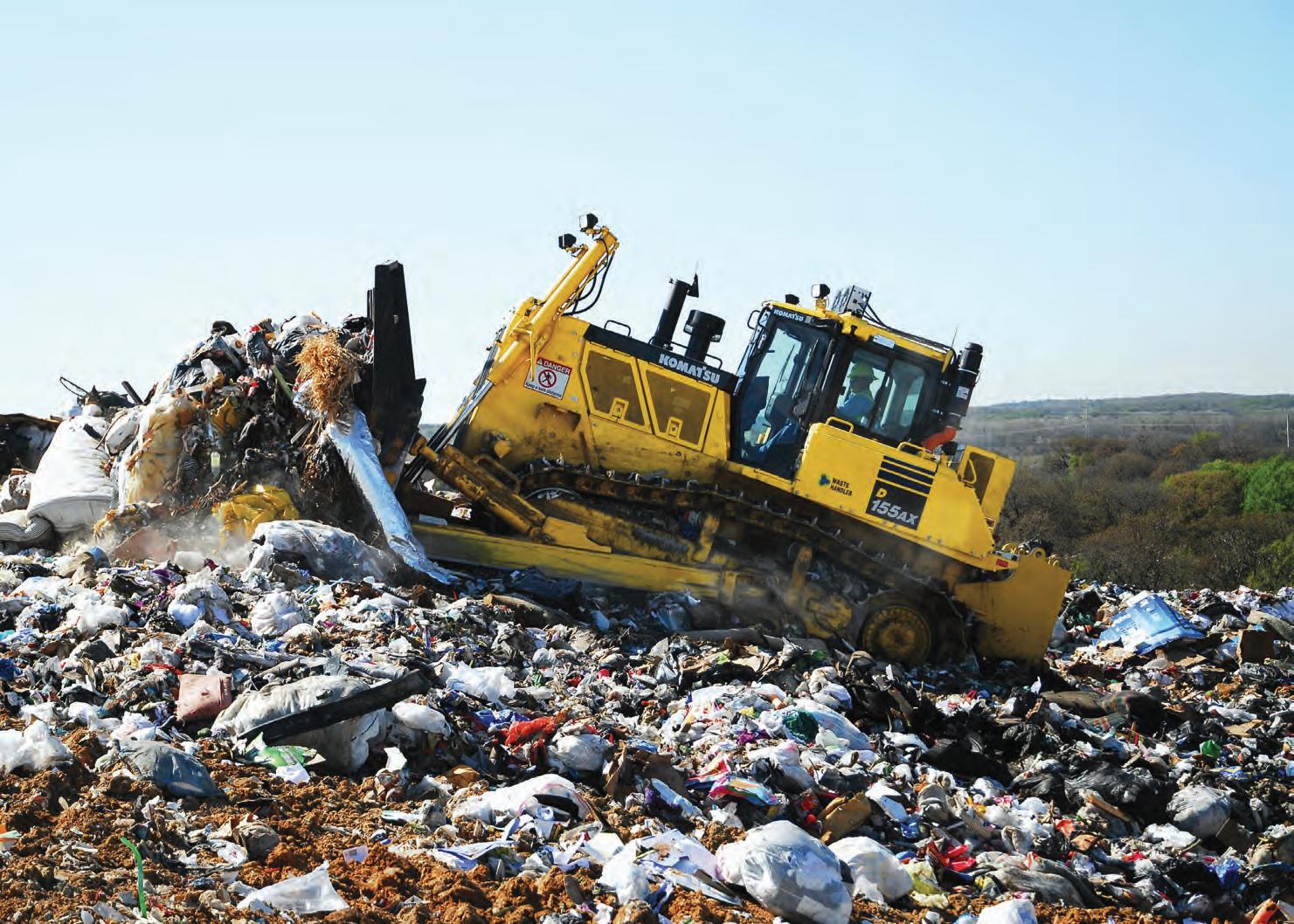
instance by the sale of the material; but importantly, fees will in effect ‘force’ the outcomes we want including much greater domestic processing (and some exports will also remain and could be useful as we transition to more domestic demand).
If for instance a producer packages in cardboard (e.g. a Weetbix box) the fees will be relatively low. The cardboard is easy to collect, fully recyclable and there are viable existing processing facilities and end markets.
A composite plastic package on the other hand that is difficult to recycle, has few existing processing facilities, a narrow range of end markets and to which the recovered materials will compete against cheaper virgin materials fees will be higher.
Fees in this case will of course cover scheme admin and collection costs but also end market outcomes. This could include subsidies for recovered processed materials against its virgin competitors in order to guarantee off-take contracts necessary for Australian industry to invest in new processing facilities.
Best performing European packaging EPR schemes embody this notion of ‘full net costs of recycling’.
Fees across Europe (Austria, Belgium, Germany) for multi-layer plastic for instance are in the order of $1000+ per tonne ‘put on market’. These fees cover:
Collection including financial distributions to councils for their existing kerbside recovery programs. This rightly shifts the cost burden for packaging recovery from councils and rate payers to producers and users of packaging.
T here may be additional collection programs such as retail or public place also funded by the scheme, but in reality, kerbside across Europe as it does in Australia forms the back-bone of the collection system
M aterial Recovery Facility (MRF) upgrades and new builds. The Belgium scheme itself invests in the construction of new MRFs, and additional sorting technologies for effective recovery will be required across Australia.
P rocessing and subsidies for end markets in order to ensure private sector investment in such facilities.
APCO is leading industry efforts to inform the Commonwealth on their preferred approach and are proposing
a scheme that does not cover the full net costs of recycling. Some in industry are perversely suggesting Australia should limit its targets and ambitions on the basis of ‘why collect more packaging if we can only process a small portion of that which is currently generated’!
Additional regulations will be required for packaging in Australia including bans on certain impossibleto-recycle packaging formats, reuse requirements and bans on singleuse items and recycled content mandates, which can additionally drive demand for recovered materials.
But, the whole point of an EPR scheme is to drive up collection, processing and end markets. The scheme should be designed to achieve ambitious outcomes including ensuring new processing facilities can be invested in by industry with certainty. If we don’t embed this principle, and the appropriate scheme costs, it will simply show we have learnt nothing from the Redcycle collapse.
Robert Kelman is a director of Asia Pacific Reloop
Fees could lead to more domestic processing. Image: Panchenko Vladimir/shutterstock.com
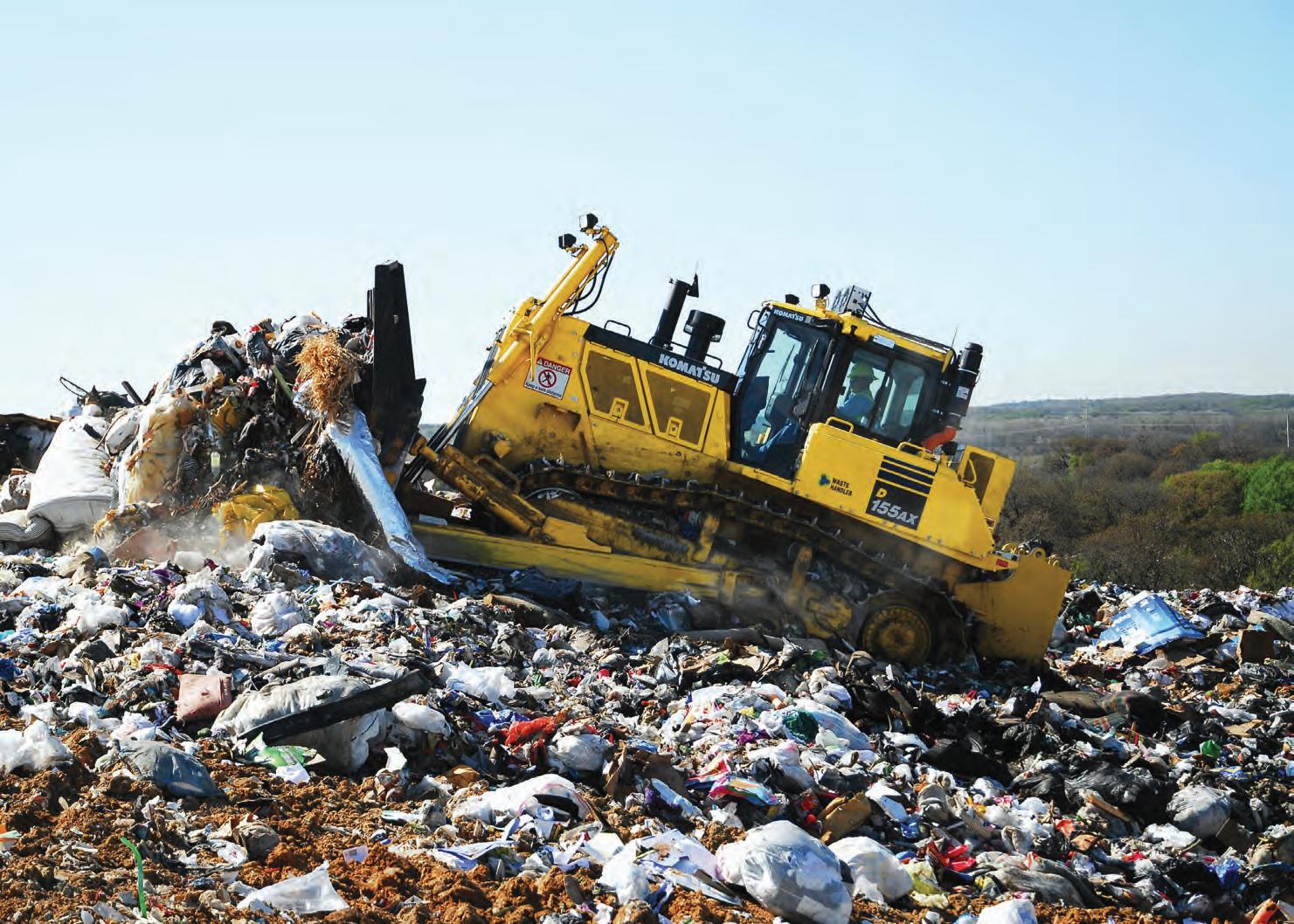
Clearing the way: Komatsu Waste Spec Dozers
Built for productivity and efficiency
The waste processing industry requires purpose-built equipment for moving highly variable materials. Komatsu creates machines and solutions designed specifically for the difficult terrain and materials involved with handling waste. Our advanced Dozers equipped with smart technology, are engineered for productivity to support your goals of a zero-harm environment.
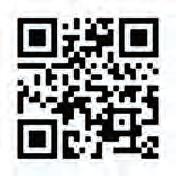
Commercial food waste collections coming to NSW
(Continued from the Cover)
Interestingly, the EPA has decided to use the size of the red (residual) bin out the back of the business as the threshold test for whether they are included in the mandate or not.
This is with the exception of supermarkets, which are tested based on floor area.
Why use the size of the red bin as the threshold test? I assume it is because it is easy to see and to test. So, how will it work?
From 2025 to 2029 the threshold will slowly reduce to capture more food waste generators. Excellent plan. Here is the test for premises:
• ≥ 3,800L of residual waste bin capacity to start on 1 July 2025;
≥1,900L of residual waste bin capacity to start on 1 July 2027, and
≥ 660L of residual waste bin capacity to start on 1 July 2029.
As a result, by 2029 most large businesses in NSW that generate food waste will have dedicated food
collection system. Small businesses, e.g. those with a single 240 litre garbage bin, will not be included in the mandate.
The EPA is proposing part or full exemptions for some businesses in special circumstances (which makes sense). We don’t know the colour and flavour of that but having discretion is sensible.
For building complexes (think Westfields), the requirement will be on the property manager, not the individual tenants. How that is then translated to tenants is not spelled out, but I assume there will be an obligation for Westfields to get its tenants to follow suit.
Each business will need to provide enough organics bins to meet the food waste generation rate for that business and they cannot mix the food waste with general waste thereafter.
The Government hasn’t drafted the regulations yet, but they are talking about all the normal enforcement procedures and penalties for noncompliance.
Interestingly, they are asking local councils to take on most of the normal monitoring and enforcement. That aligns with council business, but I suspect local government will be asking for some funding support at least while the system is being rolled out.
What does it mean for NSW businesses?
In MRA’s view it will not have much impact on large supermarkets. Most of them have been running food waste collection systems for years. MRA has worked with all the major supermarkets to set up farmers’ food waste collection systems, food donation and composting systems. Doing so is good for the planet and generates ACCUs (carbon offset credits). It will however stimulate action by a few smaller supermarkets and those in the inner city for whom farmers programs etc have proven difficult or costly. These will be in the scheme and must introduce new food collection. That is a good thing.
For the rest of business in NSW it will mean tendering or seeking quotes for a new FO (Food Organics) collection service. Easily done and there are now plenty of waste and recycling companies offering that service.
T here are also plenty of composters and green energy generators (such as anaerobic digestion) willing to take the organics.
There is no lack of interest and investment to grow these markets.
On the downside, MRA is a bit concerned that some food waste generators might try to “game” the bin threshold test by simply replacing large bins with smaller bins collected more frequently. However, they will be captured in later years as the threshold reduces so it should not be a big problem. Time will tell.
Probably the biggest risk we see is that a business owner might decide that the inconvenience of separating food waste is too

great. They could simply rent a food collection bin, put it out the back, but never use it. It would be up to a council officer to discover the rort. Currently, food waste collection and processing is generally more expensive than landfill for most businesses – this is a potential outcome at least for a small number of business owners.
Hence, we would expect the EPA using some of the landfill levy funds to support local government enforcement and training.
As smaller businesses implement commercial organics, contamination in COFO is likely to rise, therefore collectors need to work with their clients to minimise this issue. The EPA should be proactively involved by delivering relevant education programs, another worthwhile use of levy funds.
With those minor caveats, we congratulate the NSW EPA and the Minister Penny Sharpe for delivering on this reform.
It will improve resource recovery, create hundreds of jobs, reduce landfill consumption and reduce greenhouse gas emissions.
It will generate almost 500,000 t/ year of additional organics for use in green energy generation and compost manufacture.
This will be great for NSW, and we hope that other States follow.
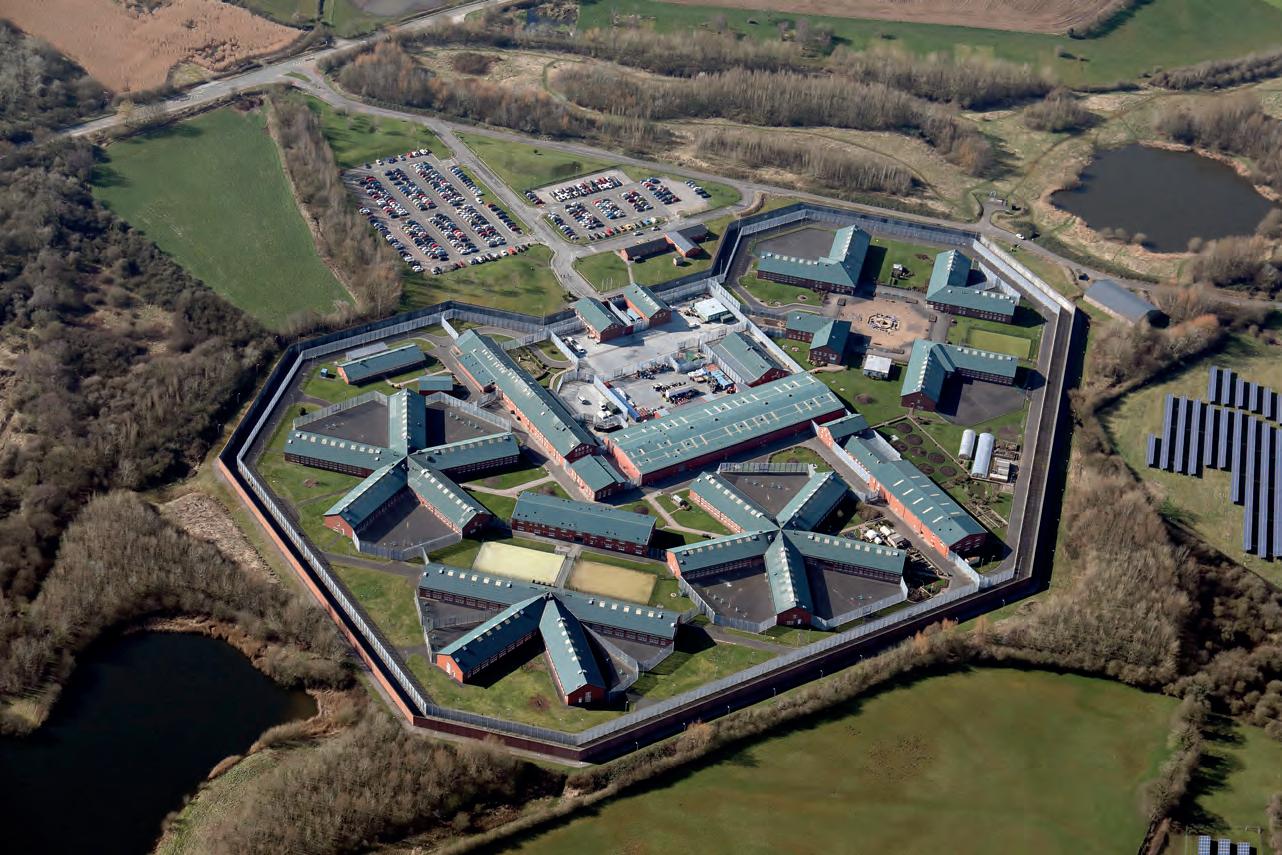

Correctional facilities are also a target of the new food waste legislation. Image: Neil Mitchell/shutterstock.com
Supermarkets are a key area targeted by the NSW government in its manadated collection of food waste. Image: ArieStudio/ shutterstock.com



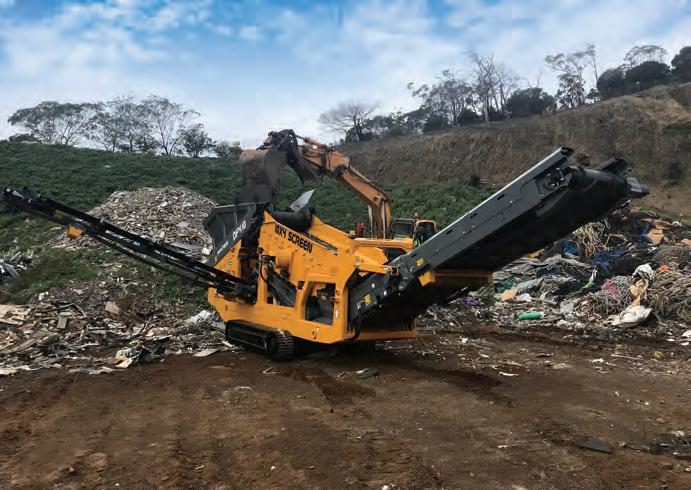
Invest in quality machines that are backed by a national parts and service footprint for the ultimate
From material handlers, to trommels, stackers, grinders, screens, dozers and more. Our industry specialists will create a personalised solution for your business. Onetrak, the exclusive national distributor for Fuchs, Tigercat, Anaconda, Dressta, Hidromek and Striker.

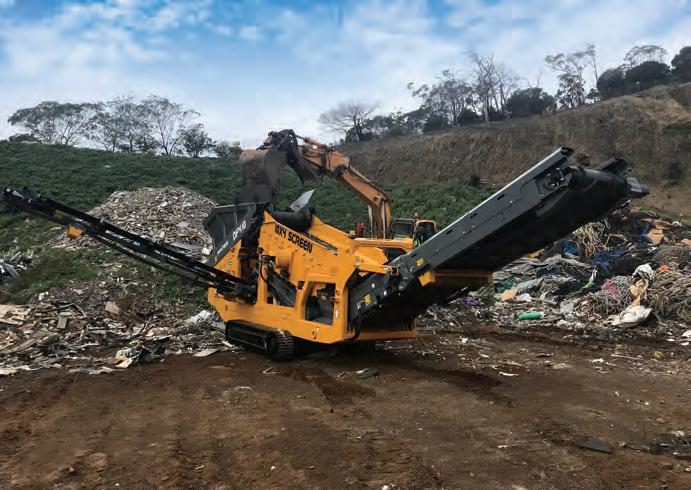
A transition to certified compostable produce stickers
By John McKew
AN agreement has been reached between the fresh produce industry and composting organisations to accelerate the transition to certified compostable Price Look Up (PLU) stickers. This intent was reached at a meeting in Niagara Falls, Canada, on October, 1 with the discussions leading to the agreement to develop a multi-phase framework to support this transition through the development and adoption of a global standard for compostable PLUs.
The planned transition to certified compostable PLUs in the European Union (EU) by 2028 provides the added momentum to accelerate a worldwide adoption to this collective goal. Additional meetings within the fresh produce and composting sectors are planned in the coming months to expand engagement and finalise the action plan by the end of 2024.
“Moving to a certified compostable format for PLUs is a priority for organics recycling facilities,” said John McKew, National Executive Officer, Australian Organics Recycling Association, and member of the International Compost Alliance (ICA). “The current plasticised format is not compatible with producing quality compost, nor can the stickers be easily removed during the organics recycling process. This can result in the collected organics being sent to landfill or incineration, contributing to climate change, and diminishing a crucial resource to build soil health. Because of the global sourcing network for produce, the members of the International Compost Alliance applaud the produce industry in recognising the importance of this transition and its timeliness to ensure both our industries can positively contribute to food production and supply as well as take care of the health and well-being of our soils.”
“CPMA is delighted to see the fresh produce and composting industries work together towards a global standard for compostable PLU stickers. Given PLUs are an integral part of global fresh produce supply chains, this global dialogue is a must,” said CPMA President Ron Lemaire. “Accelerating the adoption of compostable PLUs is a global priority given the risk that
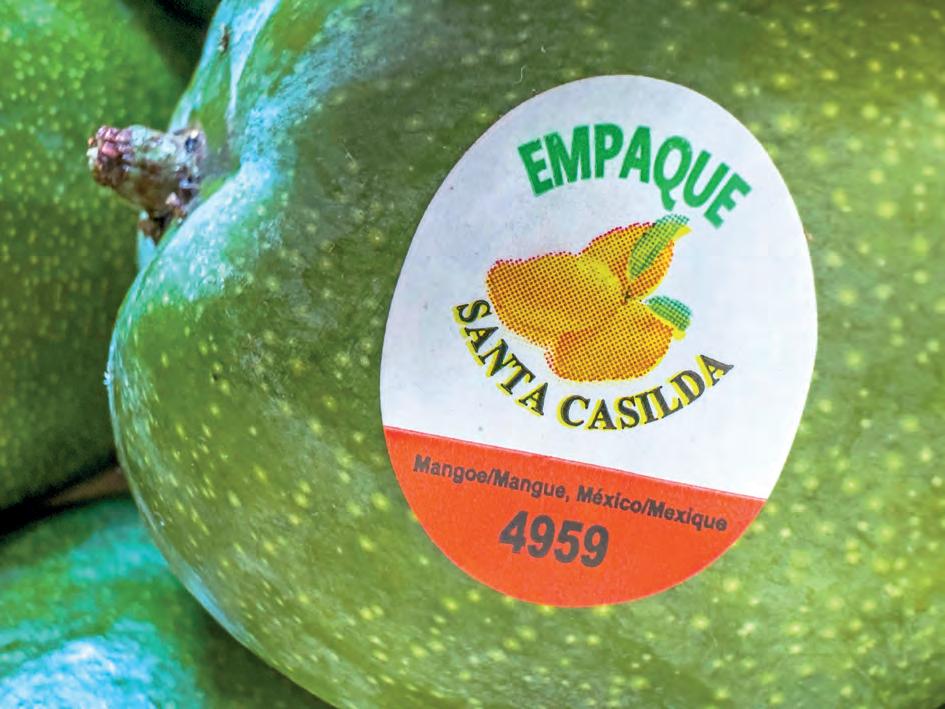
fresh produce supply chains, while also ensuring that food waste is increasingly recycled into value-added products.”
The meeting was jointly organised by the Canadian Produce Marketing Association (CPMA) and the Compost Council of Canada, with the support of the Government of Canada. In-person and virtual attendance included representatives of the fresh produce industry, including members of the International Federation of Produce Standards – IFPS (the International Fresh Produce Association, United Fresh New Zealand, CPMA, Fruit and Vegetable Growers of Canada), Ontario Fruit and Vegetable Growers Association (OFVGA), as well as technical experts from global PLU manufacturers. The global compost industry was represented through the International Compost Alliance (ICA) with in-person representation from Australia, the United States, Ireland, the United Kingdom, Italy, the European Union, and Canada. Government representatives from the United States Department of Agriculture (USDA) and Environment and Climate Change Canada (ECCC) were also in attendance.
included the fresh produce industry outlining the critical role PLUs play in helping accurately and effectively identify fresh produce for enhanced traceability, inventory control and pricing at retail. The composting industry outlined the impacts of discarded PLU stickers accompanying fresh produce waste sent to organics recycling, including consumer-sourced, commercial, and business organic waste sources. Given most PLU stickers are currently non-compostable and difficult to remove, physically contaminating the organics recycling process and adversely impacting the finished compost quality and value, the meeting provided a strategic opportunity to identify a way forward, which recognises each industry’s respective priorities.
Through open and collaborative dialogue, industry representatives acknowledged the need to accelerate the development and adoption of certified compostable PLUs. Given the global nature of fresh produce supply chains, and the potential regional variability of industrial composting processing requirements, industry representatives acknowledged the benefit of working together to develop
these efforts could help promote the increased recycling of organic materials, helping contribute to the reduction of food loss and waste.
Outcomes of the meeting included identifying a draft framework to move forward, including the draft elements of a global compostable PLU standard, comprised of compositional as well as in-field testing requirements. A draft multi-phased roadmap towards timely and global adoption of a standard that reflects the evolving global regulatory landscape was also identified.
Next steps include broader engagement of industry representatives with their respective regional and global counterparts to disseminate the meeting’s key findings. This will include broader engagement with fresh produce stakeholders in the EU and other key markets where PLU requirements are rapidly evolving. A Compostable PLU Standard Action Plan will be developed and launched by industry stakeholders before the end of 2024, leading to actions to promote and accelerate the development and adoption of certified compostable PLUs starting in 2025.
The adoption by most OECD countries of a universal compostable Price Look Up sticker is now in the planning stage. Image: Oasisamuel/ shutterstock.com
Plumbing industry leads way with recycling scheme
IN November 2021, the Master Plumbers’ Association of Queensland (MPAQ) and the Plastics Industry Pipe Association of Australia (PIPA) launched the Construction Plastics Recycling Scheme pilot program with key industry partners to educate and divert PVC offcuts from landfill.
The scheme works with collection bins placed in locations where PVC offcuts are generated. This includes TAFE and training colleges, construction and housing sites, and merchant stores, providing facilities for plumbers and drainers at locations they frequently visit. These bins are collected by PVC pipe manufacturers, sorted, audited and then the usable material is recycled back into non-pressure PVC pipes. The data from the audit is recorded and reported to the State Government and is also used by the plastic pipes industry to advocate the environmental and sustainability benefits of PVC pipes and fittings.
Th e Construction Plastics Recycling Scheme officially began with collection

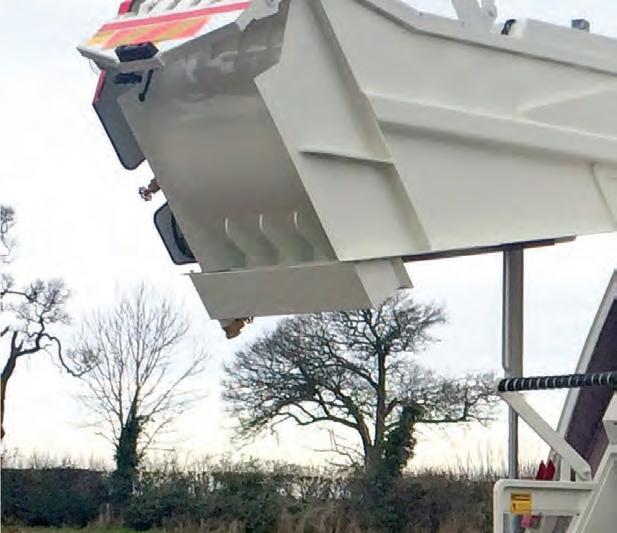
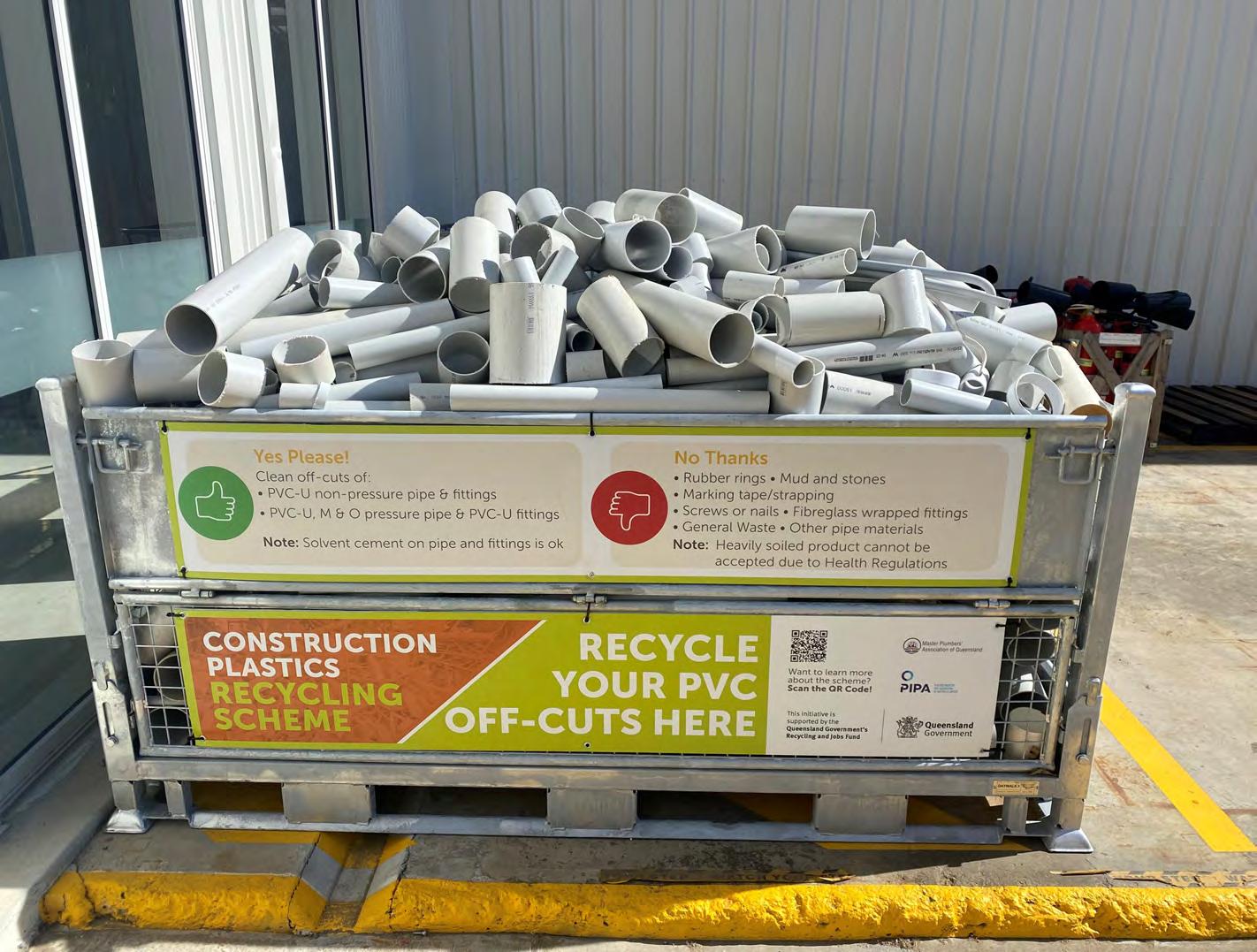
bins delivered to seven participating locations across South East Queensland (SEQ). In 2022, the Scheme extended into phase 2, celebrating National Recycling Week and growing its locations to 16 across SEQ.
Throughout the duration of the scheme – with phases one and two successfully completed – there have been learnings and insights into the operation and collection, including the importance of behavioural change and education.
“It can’t be underestimated the important of education when it comes to these types of schemes and behaviour change takes time,” said Penny Cornah, executive director of MPAQ. “The growth of participation into p hase 3 shows the change plumbers and other stakeholders want to take when it comes to recycling. This year we have seen the scheme expand to 40 locations across a broader region of Queensland, including regional and the addition of recyclers to the locations. One of the objectives of the scheme is to have this
across all of Queensland and replicated across other states – becoming our industry norm”.
To date, the scheme has collected 14 tonnes of off-cuts, which is a relatively low number compared to the amount of PVC pipe used each year and this is thanks to the durability and long service life. However, it has been identified within the installation of PVC pipes in plumbing applications off-cuts are generated and this resource needs to be diverted from landfill.
The off-cuts are 100 per cent recyclable and can be recycled up to 8-10 times. It’s critical to understand the volume to enable the plastic pipes industry to educate its position, especially when it comes to policy recycling targets and to look to economically viable solutions to capture this resource and re-use and recycle.
PIPA Executive General Manager, Cindy Bray, said the key to a circular economy is designing products to last.
“One of the common plastics used for pipe production is PVC; thanks to its
durability and long service life, typically more than 100 years. This m aterial is found on all building sites today,” she said.
Although most of the PVC goes into the buildings, there can be off cuts that can be reused and reprocessed into new PVC pipes. Overall, the process of producing, recycling, and reusing pipes have minimal environmental effects highlighting the never-ending benefits to implementing the Scheme. Plastic pipes are smart, efficient, and sustainable, providing long-lasting and reliable infrastructure both now and into the future.
So, how can you help and get involved? It’s easy. Jump on board and participate in the Construction Plastics Recycling Scheme, check out the collection locations, continue the conversation on the recyclability of PVC off-cuts and begin separating your off-cuts on site. It doesn’t matter how small the volume is collectively; it’s a valuable resource that can be diverted from landfill and recycled.
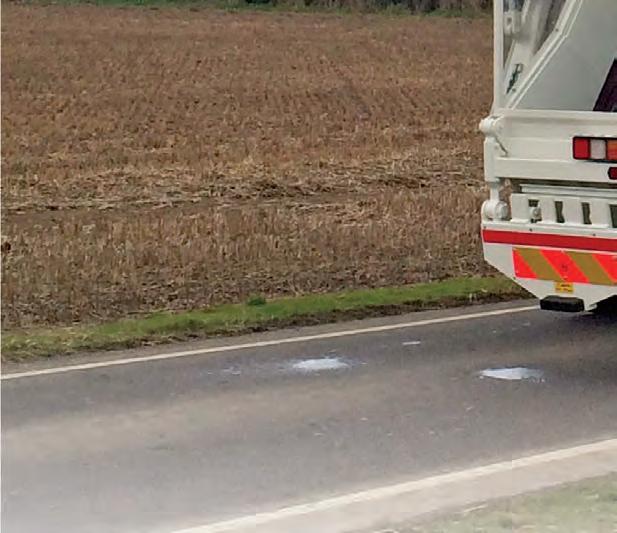
The Construction Plastics Recycling Scheme has so far collected 14 tonnes of off-cuts. Image: PIPA

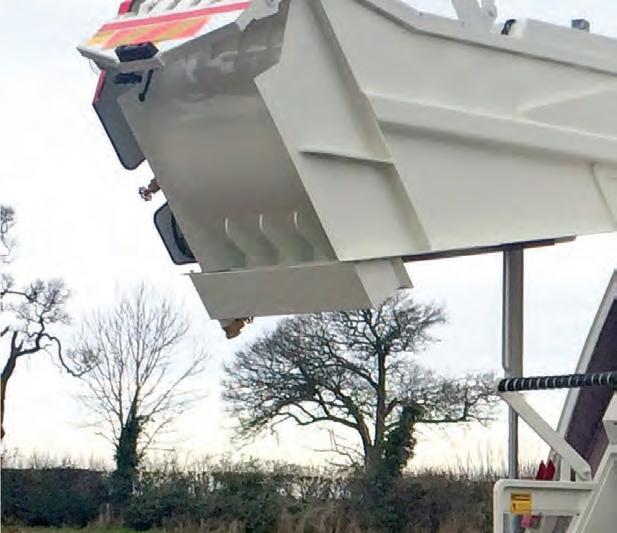
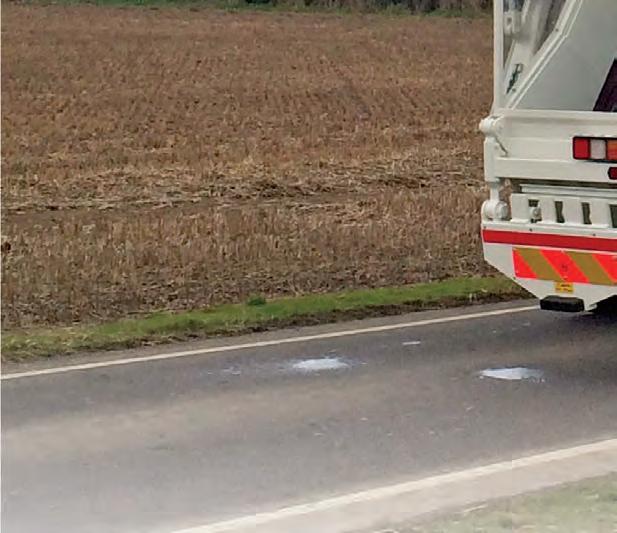
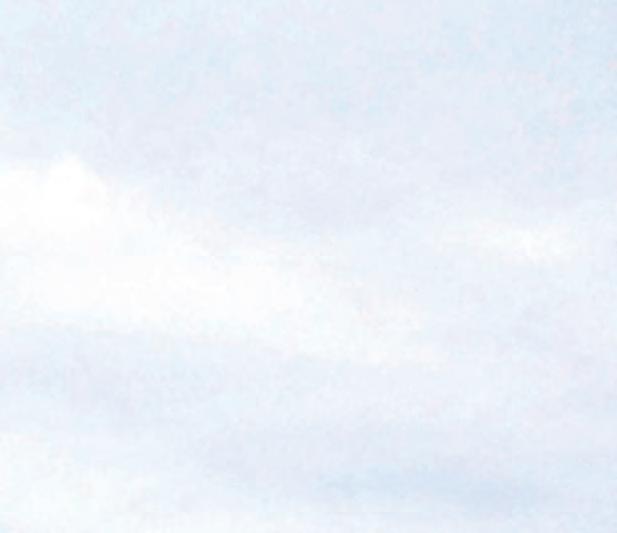
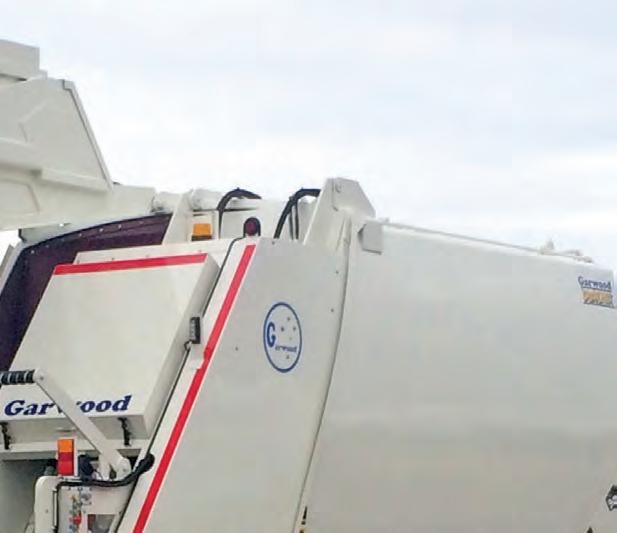
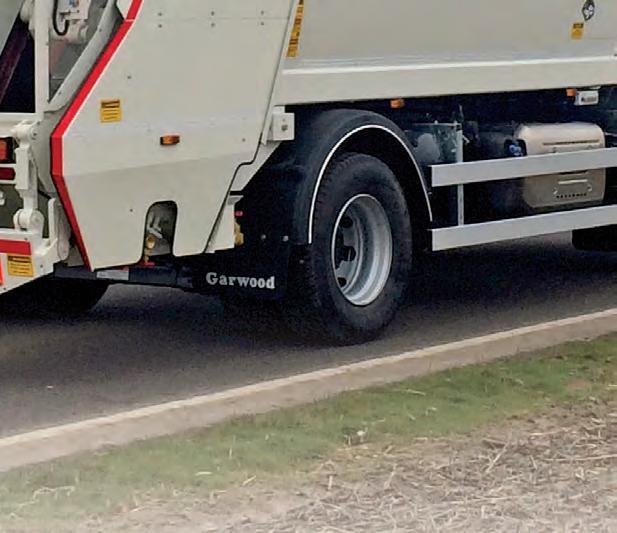
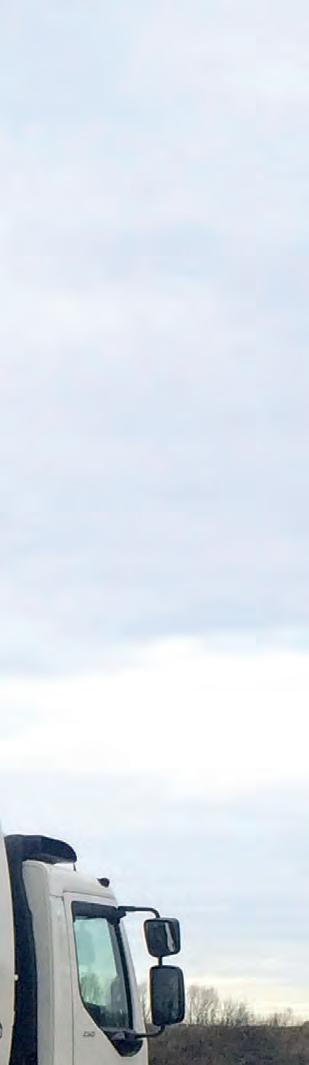

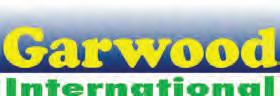


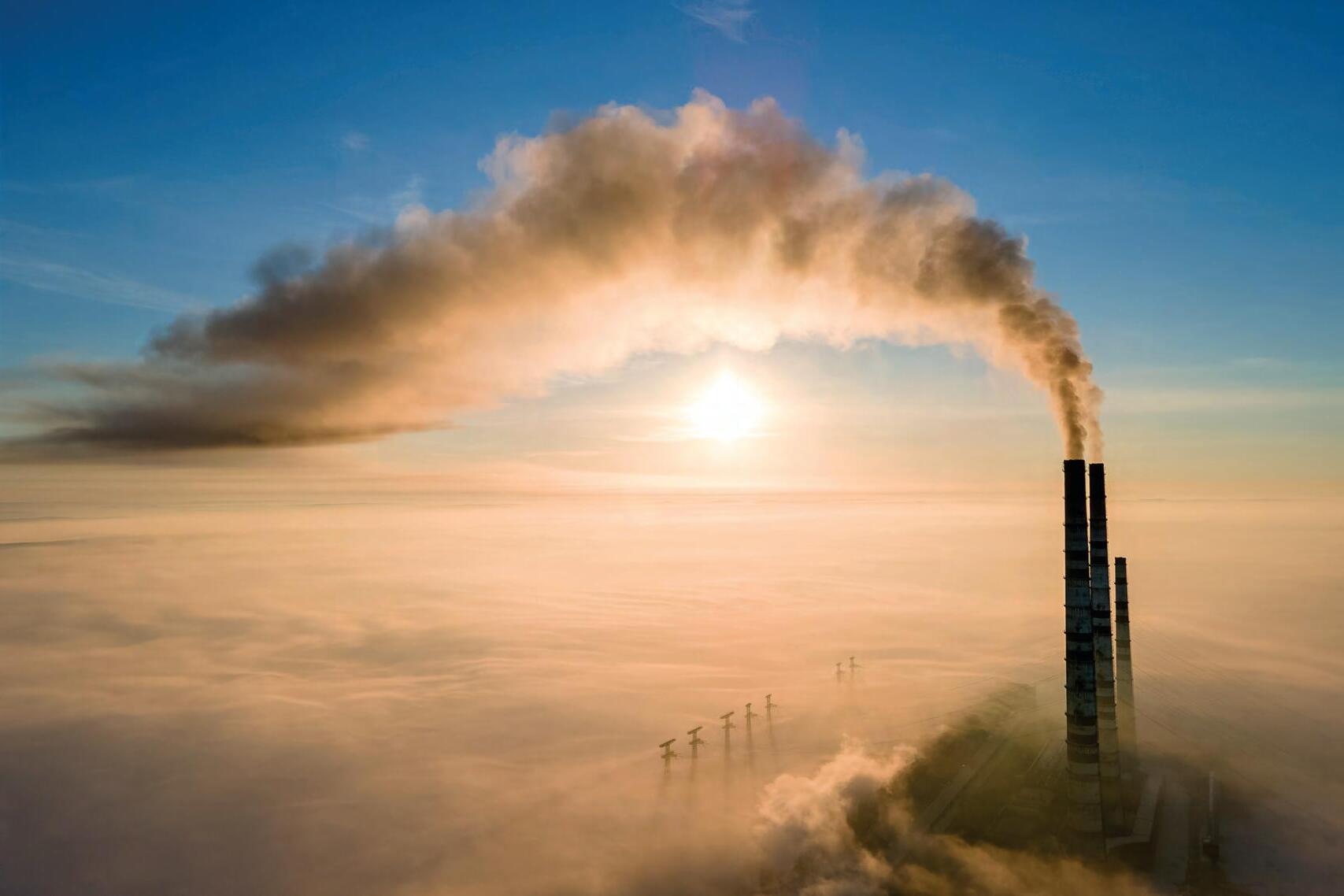
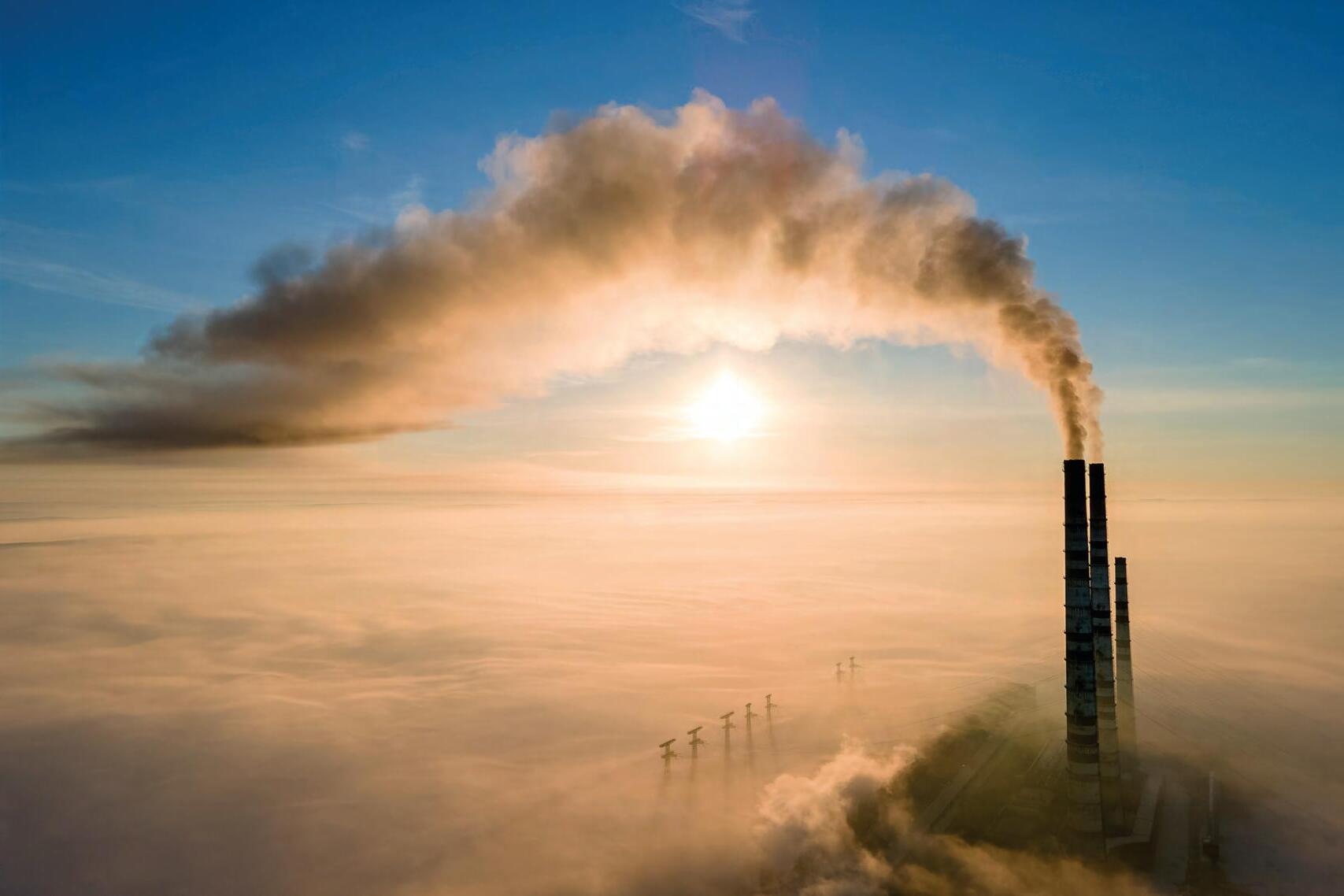
How to become truly circular
THE concept of a circular economy (CE) is increasingly seen as a gamechanger for tackling the global challenges of resource recovery, waste management, and sustainable development. However, achieving true circularity is a complex and multifaceted endeavour, far from being a universal remedy. Despite growing interest in CE, the gap between current practices and the ideal remains significant.
At the recent Waste Expo Australia in Melbourne, Dr. Heinz Schandl, CSIRO Environment’s CE lead, delivered a seminar titled Advancing Australia’s Circular Economy Transition –Economic and Policy Implications . In his presentation, Schandl laid bare Australia’s position in its CE journey and the ambitious steps needed to realise meaningful progress. His message was clear: while gains have been made, much more needs to be done to integrate circularity into Australia’s economy effectively.
“Under current policies, the indicators suggest that while the resource recovery industry will continue to grow, the circularity rate will not,” Schandl said. “With targeted circular economy policies, we could reduce domestic material consumption slightly, stabilise the material footprint, and even lower it per capita.”
The circularity gap: where we are and where we need to be
The circularity rate measures the proportion of materials re-entering the economy after use. In Australia, this rate is a mere 4 per cent, highlighting the enormous scope for improvement. Schandl emphasised that improving resource productivity could enhance this rate, with benefits extending beyond waste reduction to include economic gains and climate action.
“Improving resource productivity and material efficiency is critical,” Schandl explained. “For example, in Australia, better management of materials could contribute to at least a fifth of our greenhouse gas abatement targets. Beyond emissions reductions, this also has substantial economic benefits.”
Schandl pointed to global studies by organisations such as the OECD and UNEP, which show that investing in CE practices yields short-term economic gains and better long-term outcomes. These studies underscore the importance of linking circular economy strategies with broader sustainability goals, such as reducing greenhouse gas emissions and conserving resources.
Challenges for high-income economies
For high-income nations like Australia, reducing the material footprint is particularly challenging. Economic growth and population increase often drive higher consumption, complicating efforts to decouple resource use from development. Schandl noted that countries such as Japan and the Netherlands face similar challenges but have made more progress in transitioning to circularity.
“High-income economies have deeply ingrained consumption patterns that are hard to break,” he said. “However, countries like Japan and the Netherlands provide valuable lessons on how to integrate circular practices into the economy without compromising development.”
Learning from global leaders
Japan, a pioneer of the “reduce, reuse, recycle” policy, has embraced CE principles for decades. Similarly, the Netherlands leads in green initiatives, with its circularity rate reaching an impressive 30 per cent. These nations have implemented systemic changes, including national policies, infrastructure investments, and societal shifts, to embed circular practices across industries.
Schandl compared waste flows and material streams in Australia, Japan, and the Netherlands, identifying key similarities and differences. For example, Australia generates slightly more waste from fossil fuel streams, while Japan produces more biomass waste. The Netherlands, due to its unique geography, generates significant waste from dredging activities.
“Despite these differences, the overall waste streams are not drastically different,” he said. “However, when it comes to circularity rates, the numbers tell a different story. Japan achieves 20 per cent circularity, and the Netherlands leads at 30 per cent, while Australia lags at just 4 per cent.”
Bridging the circularity gap
To address this gap, Schandl explored hypothetical scenarios to illustrate the potential and limitations of various strategies. For instance, shifting entirely to renewable energy might reduce Australia’s reliance on fossil fuels but would have minimal impact on the circularity rate.
“This is because coal ash, a byproduct of coal burning, is currently recycled in cement production,” he explained. “Eliminating coal ash removes this contribution to
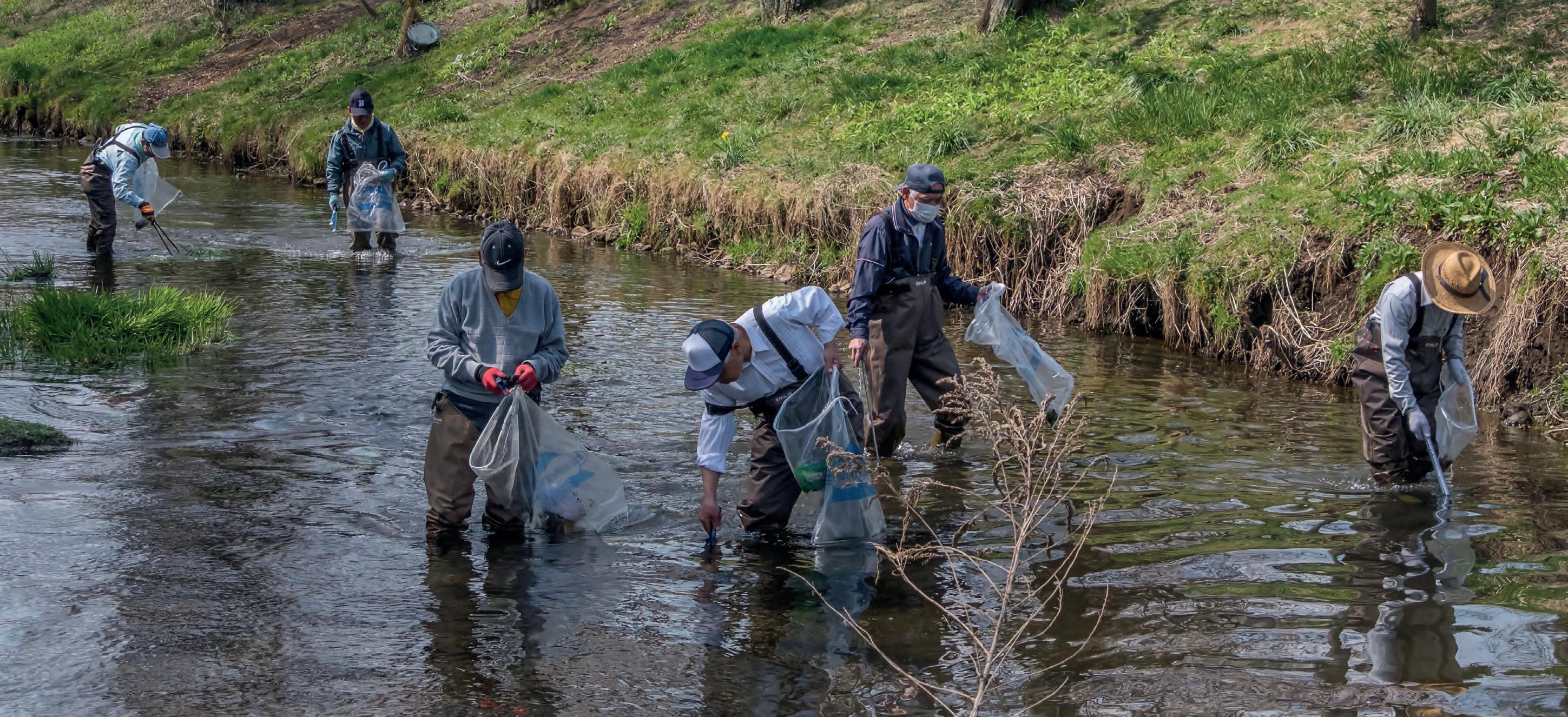
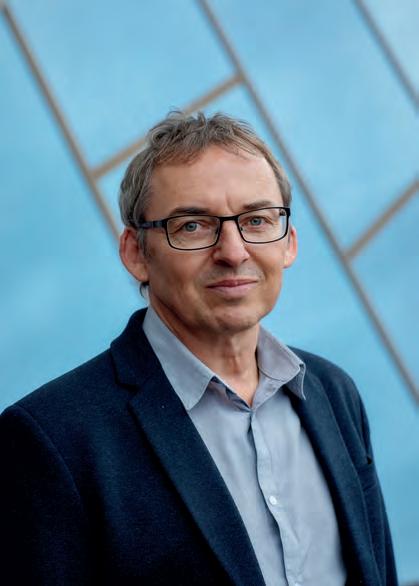
circularity, demonstrating how complex the relationship between energy systems and material flows can be.”
Schandl also considered the impact of recycling all landfill waste, a radical but illustrative scenario. Even under this assumption, the circularity rate would rise only to 5.3 per cent. Incorporating modest recycling of mining waste could increase it further to around 6.3 per cent. Taken together these strategies would raise Australia’s circularity rate to 8 per cent.
“Achieving an 8 per cent circularity rate would represent significant progress, doubling our current rate,” he said. “However, it still leaves us far behind global leaders like Japan and the Netherlands.”
Rethinking circularity: material footprint vs. managed materials
Schandl highlighted the importance of rethinking how circularity is measured. Traditional metrics often focus on the proportion of recycled materials relative
to the overall amount of materials that are managed in the economy. However, shifting the focus to the material footprint, the total resources required for consumption independent from where they are sources from, offers a more comprehensive perspective.
“When we consider the material footprint as a denominator for calculating the circularity rate, Australia’s circularity rate changes profoundly,” Schandl said. “Under this approach, Australia achieves a 13 per cent circularity rate, surpassing Japan’s 12 per cent but still trailing the Netherlands’ 15 per cent.”
This broader perspective underscores the global nature of CE challenges. While individual countries can improve their practices, global collaboration is essential to address systemic issues, such as the production of agricultural and mining materials that underpin global consumption.
Toward a circular economy transition pathway
Schandl called for a clear and actionable CE transition pathway to guide Australia’s efforts. He expressed optimism about the federal government’s forthcoming national CE framework, which aims to consolidate national efforts and accelerate CE initiatives across sectors.
“Having a national framework is an important step,” he said. “But true progress requires international alignment.
“We need global agreements on CE goals, similar to the climate and netzero targets already in place.”
He emphasised the importance of high-level indicators to measure progress, linking CE targets with planetary boundaries, human wellbeing, and socio-economic outcomes.
“Circular economy is, after all, about the economy,” Schandl said. “Its purpose is to avoid prematurely
Dr Heinz Schandl circular economy lead at CSIRO Environment.
Image: Heinz Schandl
Japan was the first country to adopt the reuse and recycle mantra. Image: Mahathir Mohd Yasin/shutterstock.com
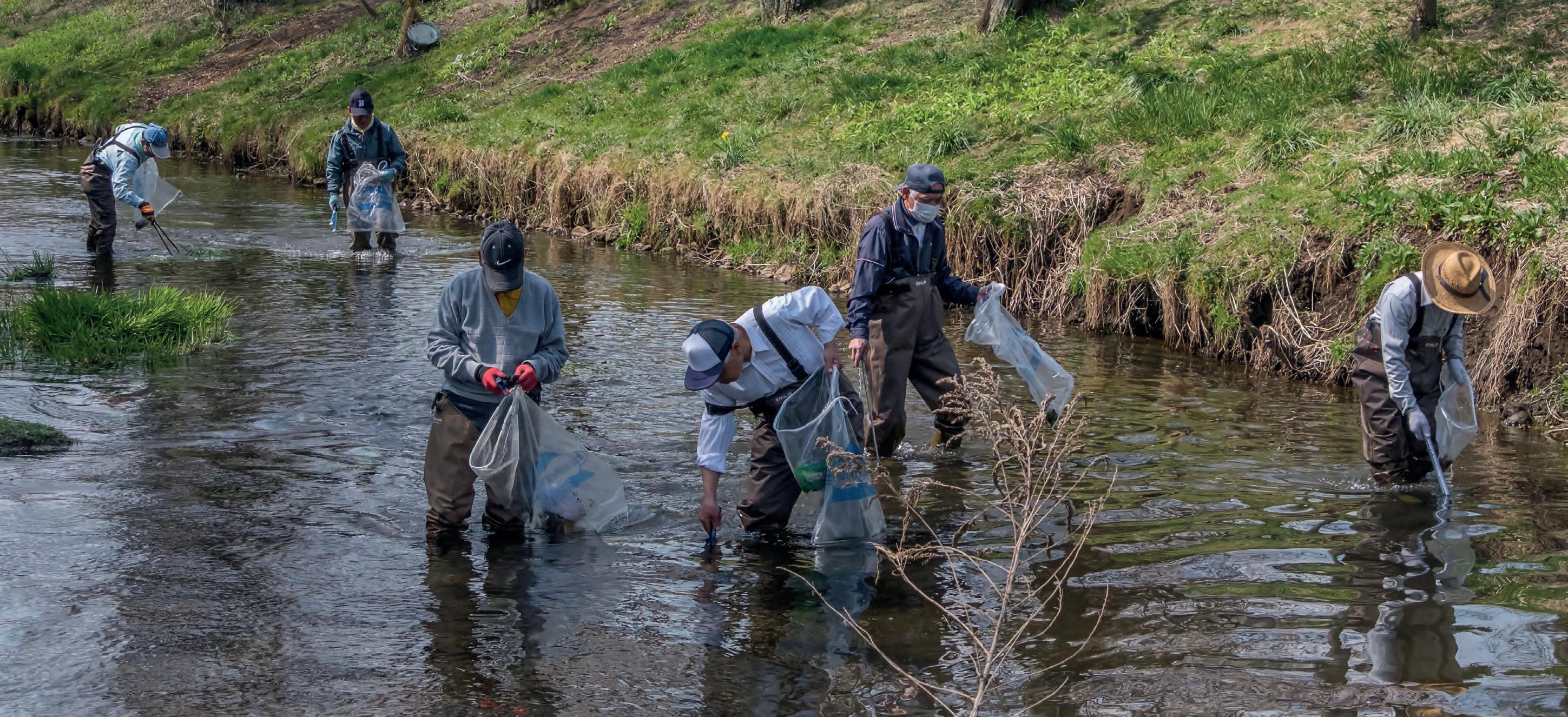
losing the economic value of materials. Achieving this requires a systemic approach, addressing all material flows – energy, technical, and biological – and rethinking provision systems, including housing, mobility, energy, and food.”
The role of innovation and systems thinking
Schandl also cautioned against pursuing CE innovations without considering the broader system. While digital technologies, artificial intelligence, and other advancements are essential, they must be integrated into a holistic strategy that addresses key provision systems.
“For example, domestic manufacturing capabilities are crucial for circularity,” he said. “If we cannot produce the components and materials needed for housing, mobility, energy, and food systems locally, we will struggle to achieve true circularity.”
The way forward: a coordinated approach
Schandl concluded with a call for thoughtful and coordinated action.
While the vision of a circular economy inspires many, he urged stakeholders to think critically about how such an economy would function in practice.
“To be champions of a circular economy, we must first understand its complexities,” he said. “Innovations are important, but they must be underpinned by systemic changes in how we consume, produce, and manage resources.”
The path to a truly circular economy is challenging, but with strategic policies, global cooperation, and a commitment to systemic transformation, it is achievable. As Schandl reminded the audience, the goal is not just to recycle more but to fundamentally rethink how resources are used, ensuring a sustainable future for both the planet and its people.

Schandl said there is a reason it is called the Circular Economy –it’s because we want to keep the economic value of a product. Image: Miha Creative/shutterstock.com

B-cycle scheme moving toward greater regulation
By Inside Waste
THE Battery Stewardship Council
(BSC) is leading the charge on battery recycling in Australia, with its B-cycle Scheme undergoing a review. This review aims to assess the scheme’s current progress while laying the groundwork for future improvements. Libby Chaplin, CEO of BSC, emphasises the importance of this review.
“We’re at a critical point where action must be taken to address the exponential increase in used batteries, their changing risk profile and recycling costs,” she said. “The review of the B-cycle Scheme will help us stay ahead of this challenge, but we also need to push for stronger regulations to ensure batteries are recycled safely and sustainably.”
Key challenges facing battery recycling
The scheme has made notable strides, including the collection of over 2.9
million kilograms of batteries in 2023-24, with more than 5,200 dropoff points established nationwide. With 90 per cent of the loose battery market and 60 per cent of the power tool battery market participating, B-cycle’s together with its recycling partners, have helped recover 73 per cent of the materials processed from batteries. However, several key challenges persist:
M anaging cost fluctuations – fluctuating imports and escalating costs for recyclers make it difficult to sustain operations due to inconsistent income and rising expenses.
Free riding – some businesses still “free-ride,” benefiting from the scheme without contributing financially, which limits the scheme’s overall impact.
B attery-related fires – the increasing incidence of fires in waste and recycling facilities, especially from lithium-ion
batteries, poses financial and safety risks.
S tatic financial model – the current model does not fully support the needs of the expanding battery recycling sector.
A ustralia’s small battery recycling sector – the limited infrastructure makes it difficult to scale operations to meet the growing demand for recycling.
Variable risks of different battery types – handling different types of batteries, such as button batteries and cadmium-based chemistries, adds complexity to recycling efforts.
“We’ve made significant progress, but we need stronger regulations to address free riding and enable the scheme to manage the diverse range of battery chemistries, particularly problematic ones like lithium and cadmium,” said Chaplin.
Scheme review consultations and expected changes
BSC has consulted widely during the Scheme review, engaging more than 350 stakeholders through forums in Brisbane, Melbourne, and Sydney, alongside industry meetings and online surveys. The feedback has been invaluable in refining policy settings to future-proof the scheme.
Key changes include a shift towards eco-modulated levies, designed to improve circularity in the battery lifecycle. Importers are being asked to prepare their systems for reporting on different battery chemistries by July 2025, with full implementation expected in 2026.
The expanded scope of the scheme is also being explored, with a proposal to include vapes due to environmental concerns over their disposal.
“These consultations are shaping a stronger scheme,” said Chaplin.
“We’re addressing stakeholder

concerns, from managing new battery types to setting up a cost recovery model to ensure the longterm viability of the system. As a result of feedback, we are refining the approach including a move to performance-based recycling rebates, building on the approach used by the Used Oil Scheme.”
B-cycle’s push for regulatory reform
BSC is also pushing for regulatory reform to compel greater participation in voluntary schemes and curb free riding. A draft Regulatory Impact Statement is expected by the end of 2024, outlining how regulation can enhance the effectiveness of the Scheme.
“ The success of B-cycle 2.0 hinges on regulatory frameworks that support sustainability. We’ve submitted draft rules to demonstrate how free riders can be brought into the fold, including online sales. We are working closely with Federal, State and Territory governments to integrate stronger rules for responsible battery management,” Chaplin said.
Safety remains a key focus, particularly given the rising number of battery-related fires. BSC’s Never Bin Your Batteries and This
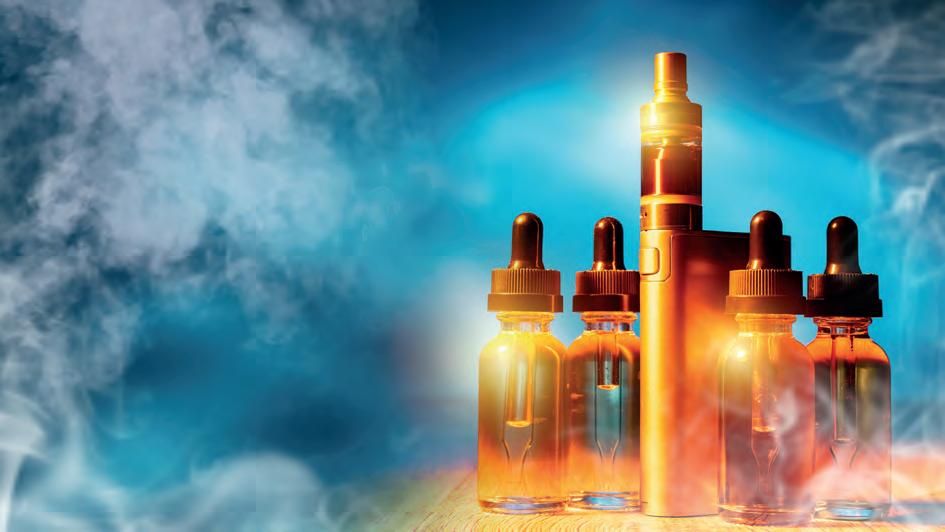
public to take preventive measures.
“The increasing number of lithiumion battery fires is a wake-up call. We need consumers to understand how simple actions, like taping battery terminals, can prevent fires and protect both the environment and public health,” said Chaplin.
The Scheme’s campaign and growth
Looking ahead, BSC has several new initiatives planned for 202425, including a household battery recycling awareness campaign to run
lithium-ion batteries. Additionally, State-based awareness campaigns will continue to be rolled out across the country, aiming to encourage behaviour change through targeted messaging. Chaplin outlined the organisation’s proactive approach.
“We’re not only tackling the current challenges but preparing for what’s to come,” she said. “Whether it’s expanding the scheme to cover vapes or adjusting our financial models to stay competitive with landfill costs, we’re ensuring that B-cycle is future-proofed.”
including seeking re-authorisation from the Australian Competition and Consumer Commission (ACCC). The changes will require free rider regulation and include increased public awareness and improved financial support for recyclers and collectors.
“We encourage all stakeholders to engage with this process,” said Chaplin. “Now is the time to have your voice heard, to contribute ideas and ensure we build a scheme that meets the needs of all participants while continuing to protect our environment.”
One of the BSC’s main focusses is to get free-riders included in the B-Cycle scheme. Image: Shutterstock/wk1003Mike
The Battery Stewardship Council is looking to include vapes as part of the scheme.
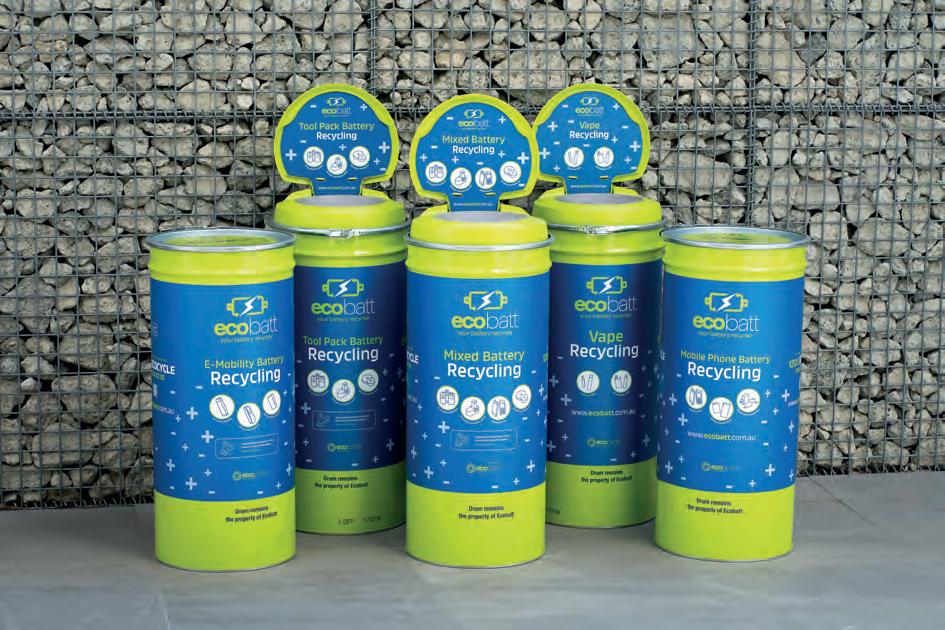
The Risks of improper battery disposal
AS consumers increasingly rely on electronic devices to power their everyday lives, the use of batteries has grown exponentially. From mobile phones and laptops to electric vehicles and household tools, batteries power devices that are integral to modern living. Yet, as convenient as batteries are, their end-of-life disposal is a growing concern. Batteries contain hazardous chemicals that can leak into the environment, pose fire risks, and harm public health if not disposed of correctly. With the rising prevalence of batteries, it’s essential to understand the risks they present and the solutions available to ensure safe disposal. One company making inroads in this area is Ecobatt, whose Lithium Safety Drums offer an effective and reliable solution for battery storage and recycling.
The dangers of improper battery disposal
The environmental and health risks associated with batteries stem from the chemicals and heavy metals they contain, such as lithium, nickel, cadmium, and lead. When batteries end up in landfills or are otherwise improperly disposed of, these chemicals can leak into the soil and water systems, contaminating ecosystems and potentially entering the food chain. Beyond environmental concerns, the metals in batteries can have health implications for humans, causing respiratory problems, skin irritation, and even cancer if exposure occurs over extended periods.
However, one of the immediate dangers with batteries, particularly lithium-ion batteries, is their propensity to catch fire or explode if damaged or improperly handled. Lithium-ion batteries are highly efficient, providing more energy
in a compact form. However, this efficiency also makes them volatile under certain conditions. A battery that has been punctured, exposed to high heat, or crushed can enter a state known as “thermal runaway,” where it generates extreme heat, potentially leading to combustion. In worst-case scenarios, battery fires can lead to explosions, putting lives and property at risk. As more of these batteries enter the waste stream, the risk of such incidents increases, highlighting the urgent need for safe disposal methods.
The role of Ecobatt’s lithium safety drums
In response to these challenges, Ecobatt, a specialist in battery recycling, has launched the Ecobatt Lithium Safety Drum – a product designed to address the risks associated with battery disposal. These drums provide a safe and secure method for
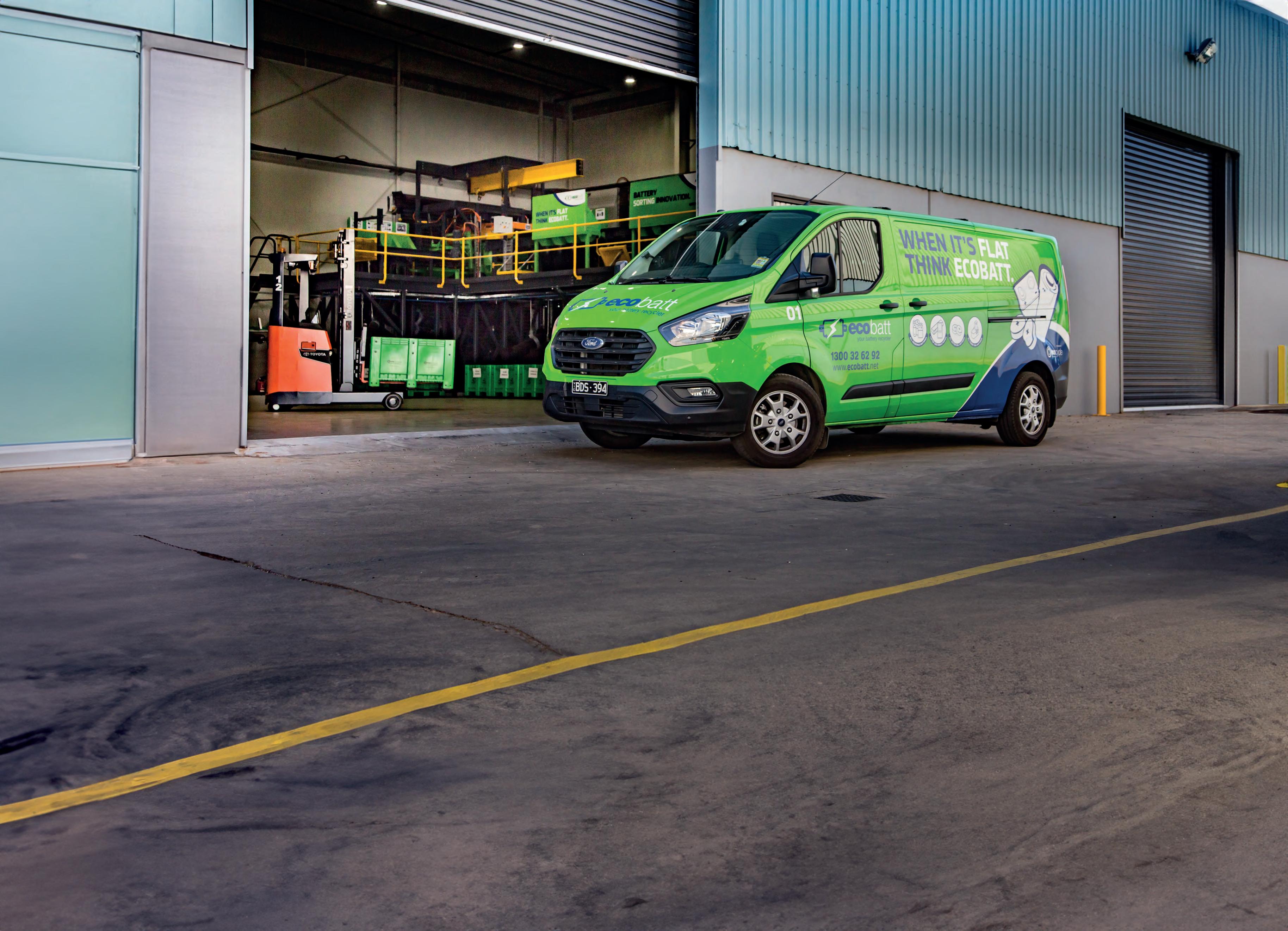
storing and transporting lithium batteries so they can be recycled safely. They come in two capacities, 53 litres and 62 litres, making them suitable for a range of settings, from small businesses to large commercial sites, schools, and collection points. What sets these drums apart is their robust design, specifically engineered to contain the potential hazards associated with lithiumion batteries. Made of durable steel, they are equipped with a patented overpressure lid that includes a flame-arresting filter. This feature is important because it allows the drum to contain thermal runaway events, should they occur. The flame-arresting filter prevents flames from escaping, and the overpressure system is designed to manage the gases generated in such an event, ensuring that pressure is released safely.
Lithium Safety Drums provide a secure method for storing and transporting batteries.
Images: Ecobatt
Why safe storage matters
The safe storage and transport of batteries are crucial steps in the recycling process. Once batteries are safely contained, they can be collected and transported to recycling facilities, where materials are recovered, and hazardous elements are safely managed. By ensuring that batteries are securely stored in these drums, businesses and individuals are taking the first step towards responsible recycling, helping to reduce the environmental impact of batteries and support a more sustainable future.
The drums cater to different battery types with a selection of specialised lids. The three-hole lids feature a triangular design, suitable for safely disposing of smaller format batteries, such as vapes and mixed household batteries. This design is particularly suited to environments like schools, where it’s essential to prevent children from accessing the contents inside.
For larger batteries, such as tool
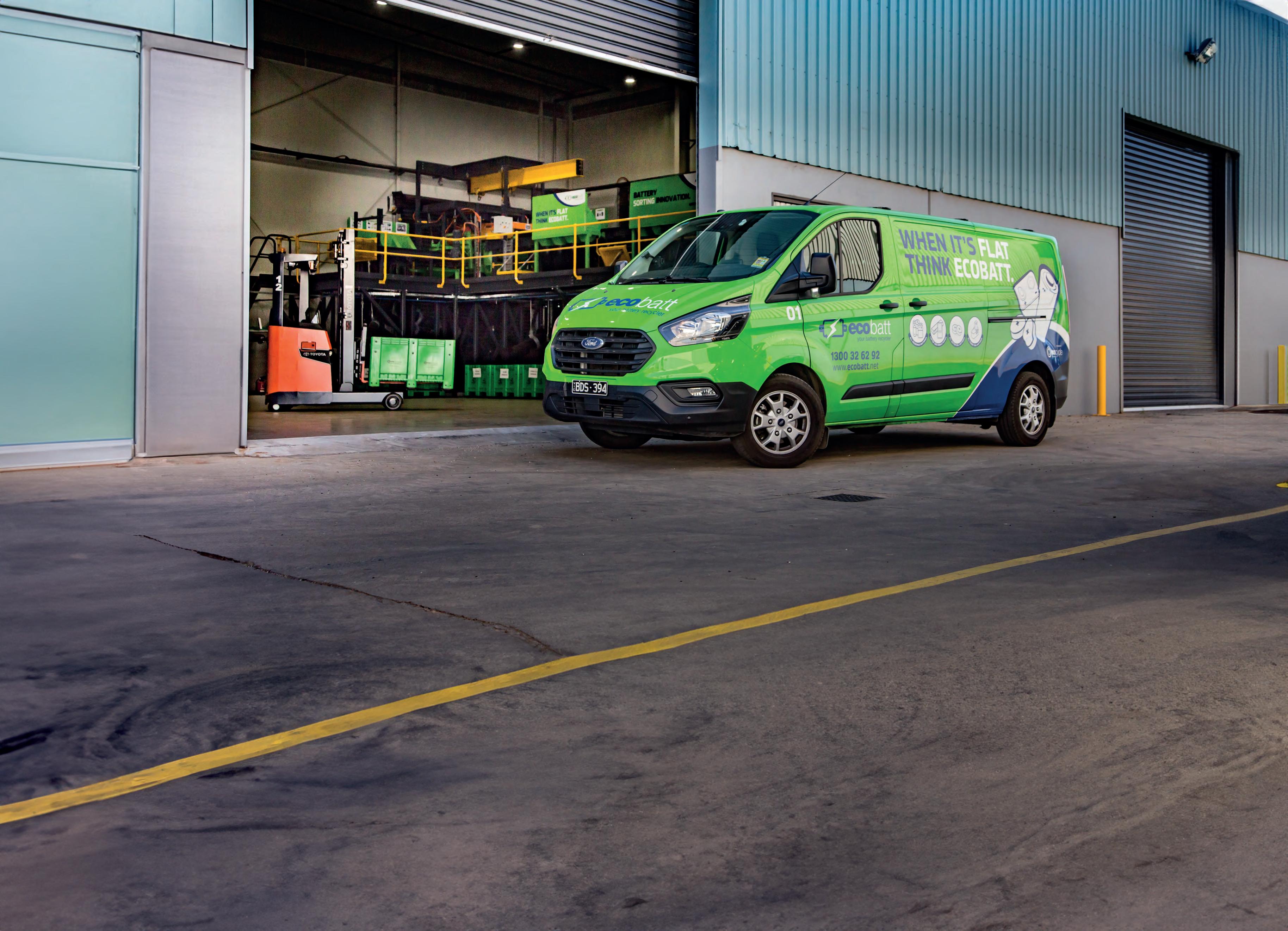
pack batteries and mobile phones, the single-hole lids provide a secure entry point that minimises risk. Finally, transport lids serve as multifunctional solutions, not only enabling safe collection and transport of batteries like e-mobility batteries and mobile phones, but also acting as secure storage solutions at private sites.
Customised to enhance branding
Ecobatt offers businesses the ability to personalise their Lithium Safety Drums, blending safety with brand identity. Companies can incorporate their logos and unique design elements, seamlessly integrating the drums into their operational or retail environments.
The customisation option makes Ecobatt’s drums adaptable and professional, whether used in retail spaces, schools, or corporate facilities, providing both functionality and brand visibility.
Meeting the demand for battery disposal
With the demand for batteries only projected to rise as more devices and vehicles rely on battery power, the need for safe disposal methods becomes more pressing. The growth in lithium battery usage brings an increase in potentially hazardous waste. Without safe and secure storage options, these batteries pose risks to public safety and the environment.
By offering specialised solutions like the Lithium Safety Drum, Ecobatt is not only addressing the immediate safety concerns, but also supporting a circular economy where valuable materials are reclaimed, reducing the need for new raw materials.
In a world where environmental responsibility is increasingly crucial, the role of companies like Ecobatt cannot be understated. Its products manage battery waste safely and sustainably. By facilitating secure storage and disposal, Ecobatt enables businesses,
schools, and public organisations to contribute positively to environmental efforts while ensuring the safety of people and property.
Batteries are an indispensable part of modern life, but their disposal requires careful consideration. The risks associated with lithium-ion batteries highlight the importance of safe handling and storage. These drums provide an effective solution to these challenges.
By investing in these safety drums, organisations can play their part in reducing the risks associated with battery disposal, protecting the environment, and promoting a sustainable approach to battery recycling. In a time when safety and sustainability are paramount, these drums provide a dependable, professional solution that helps protect people, property, and the planet.
Ecobatt solutions help make sure batteries are disposed of correctly so there is no adverse effect on the environment.
Job in resource recovery ‘eye opener’ for recent grad
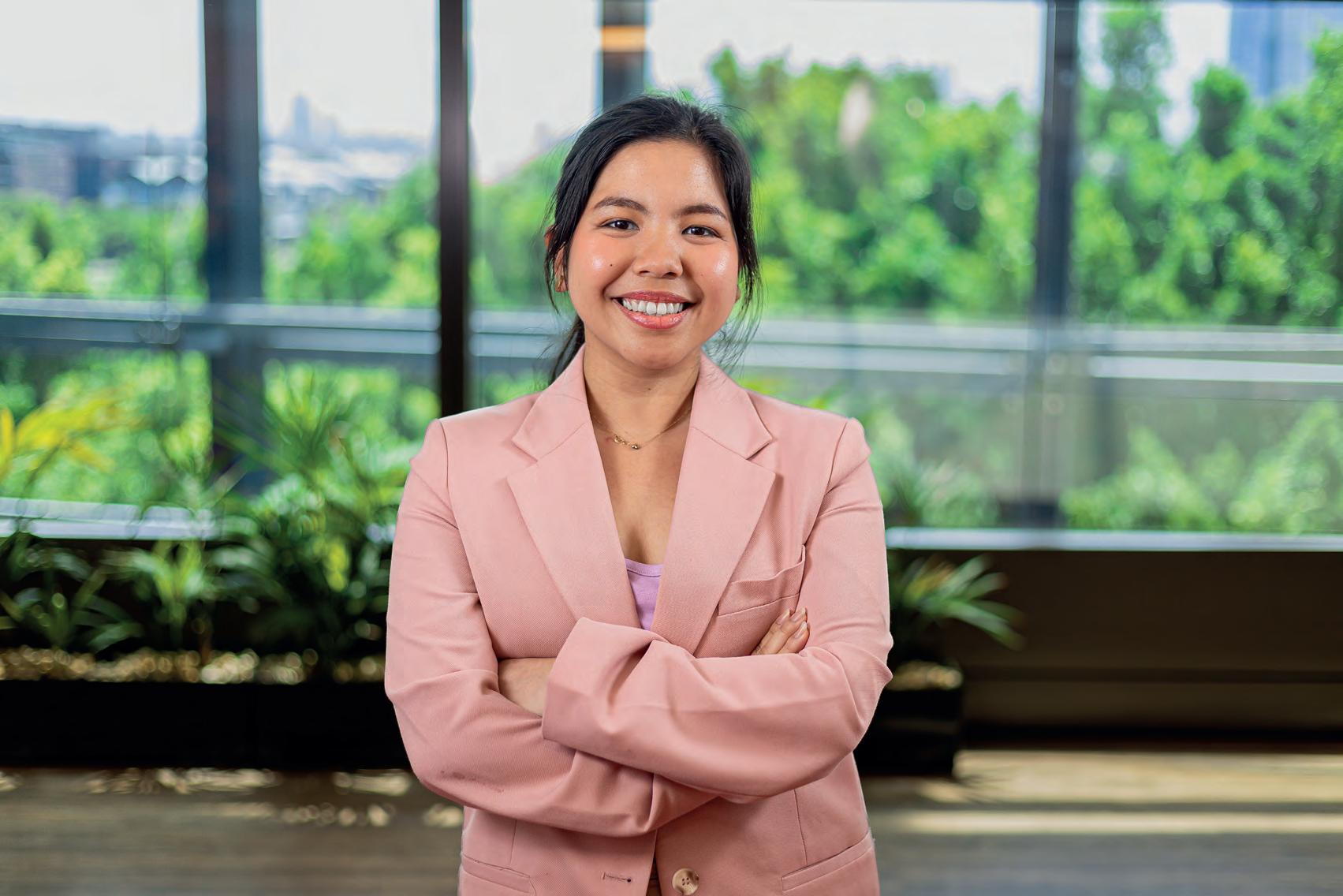
GROWING up in the Philippines, Tabitha Tatoy initially had designs on working in the STEM field when thinking of a career path. When it came to tertiary education, Tatoy was adamant that the sciences were her calling, specifically geology.
She applied for a place at Macquarie University for a science degree, but before she arrived in Sydney, the university had changed the major from a Bachelor of Science majoring in Geological Science to one that majored in Earth and Environmental Science. The geology
part was still part of the qualification, but the emphasis had changed.
“I think that they did this because they had more of a need for environmental students,” she said. “It was very last minute for me to do the environmental part, but I am very thankful that they changed it because it opened up more options.”
Once she finished her degree, Tatoy was going to start a master’s because she originally wanted to do research but had a change of heart when thinking about the direction that would take her career.
“The more I got into my degree, the more I realised that the only people that read research papers are going to be other researchers, especially when it comes to environmental sciences and soil types,” she said.
It was after that epiphany that Tatoy decided to look for a full-time job and put her master’s degree on hold. She applied for jobs in the mining and environmental consulting industries, and also for one job in the waste/resource recovery sector with Veolia. It was here that she got the
position of business development graduate.
“I applied for the job at Veolia because I wanted to get hands-on experience,” said Tatoy. “I wanted to do something with my degree like soil sampling or researching.”
She has found the job to be a welcome learning curve and is pleased with how she is going so far. What do her day-to-day activities consist of? It has a lot of variety, said Tatoy. She sees the business development position akin to project development/ delivery. The biggest project that
Hands on experience is one of the reasons Tatoy took the role at Veolia.
Image: Tabitha Tatoy
she is currently working on is Veolia’s Woodlawn energy from waste (EfW) endeavour, which is currently at the planning stage. She said one of the most important parts of this project for her is stakeholder engagement, which means she has gained some great experience working with the local community and government regulators. What are some of the specifics of the role?
“Every day is different, but last week I had a community engagement event,” she said. “I wrote some of the event collateral such as the FAQs, as well as the event planning and run sheets to make sure it all went smoothly.”
Rewarding
Like a lot of young people who start their career in the waste/resource recovery industry, Tatoy finds the environment a lot different on the inside from what she thought it was
like on the outside. There are many aspects that she was unaware of before she started in the role.
For example? She didn’t realise that it was private contractors that generally picked up the waste. She thought all councils did it themselves.
“I also didn’t realise how technical the recycling process was – I was lucky enough to visit a recycling facility and the amount of machinery and handling that goes into sorting recyclable waste was impressive,” she said.
Tatoy finds the business development aspect has been rewarding for her because she now sees the effect her work can have on the wider community and how it can make a difference.
“I know that what I’m doing is an essential service,” she said. “I never really looked at it that way before. If your bins don’t get picked up, or if we didn’t ensure people’s waste was
recycled properly, it affects everyone, especially our planet. It’s been very rewarding for me on that aspect.”
The future
Tatoy said she is too early into her career to make any decision on whether the resource recovery industry will be something she will be part of for the rest of her life.
However, what she has been involved with so far, she said, makes for an interesting career moving forward.
“As part of my role with Veolia I’ll participate in three rotations across the business,” she said. “I’m currently in business development, but I’m looking at a rotation for environmental reporting next. I’m keen to get my hands on the operational side of the business. I’ll then try to do something in the environmental advisory space.”
Tatoy feels that because she’s so new to the business, it’s all about
trying to learn and soaking up as much information as she can.
“When I first applied and got hired, I didn’t really know what business development was, or what the industry was about,” she said. “It’s so much more than just collection from your household.”
As for her own future, Tatoy feels she might be in the industry for the long haul. She finds it interesting, lots to do, and plenty of challenges ahead.
“Hopefully I can get more experience within business development and get multiple other projects under my belt,” she said. “ I know the business has so many opportunities, even within other states, too. I want to get some operational experience that I feel would help me to grow and align with my studies , and to help make a positive difference to the environment.”
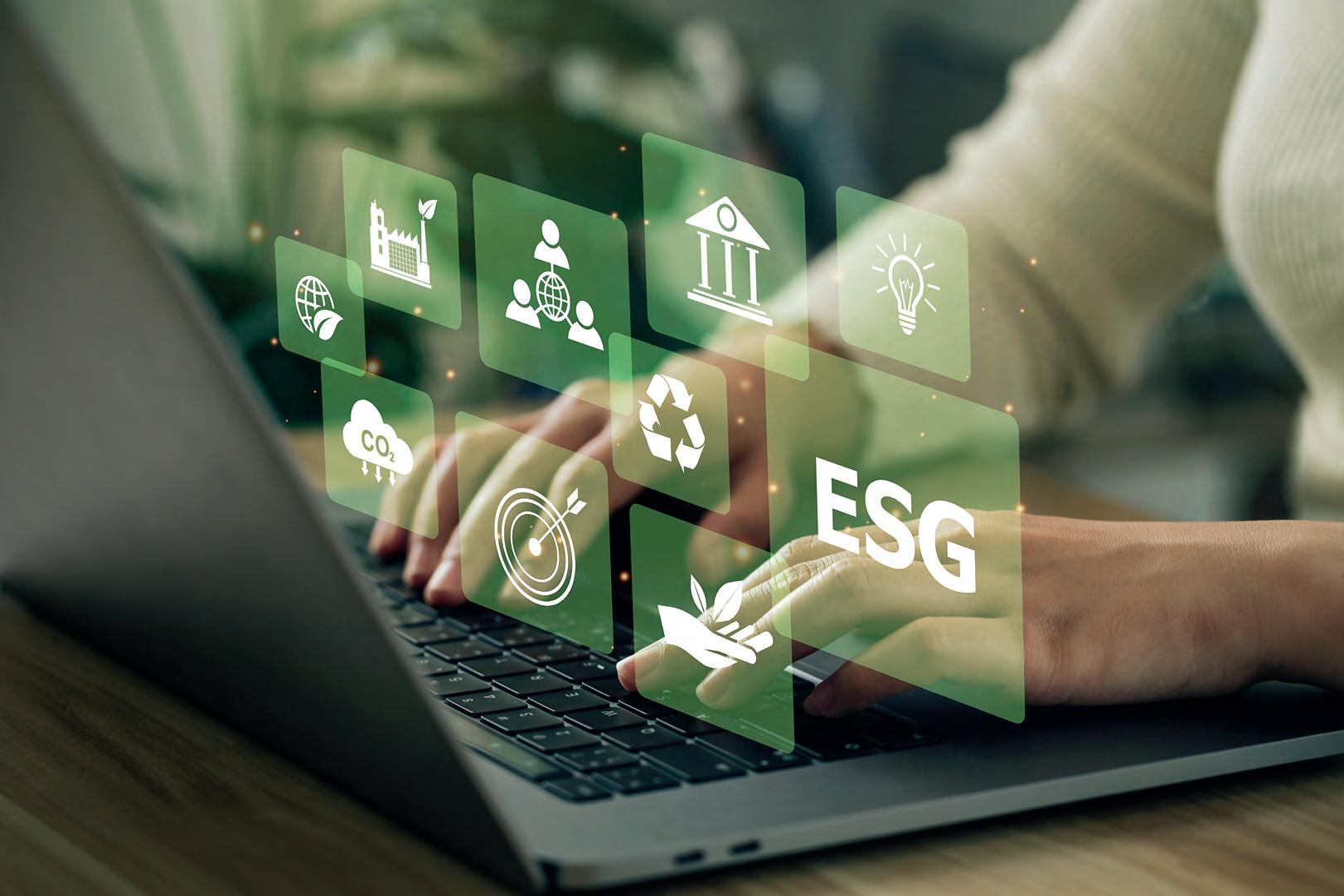
One of the rotations Tatoy will be involved with at Veolia will be environmental reporting.
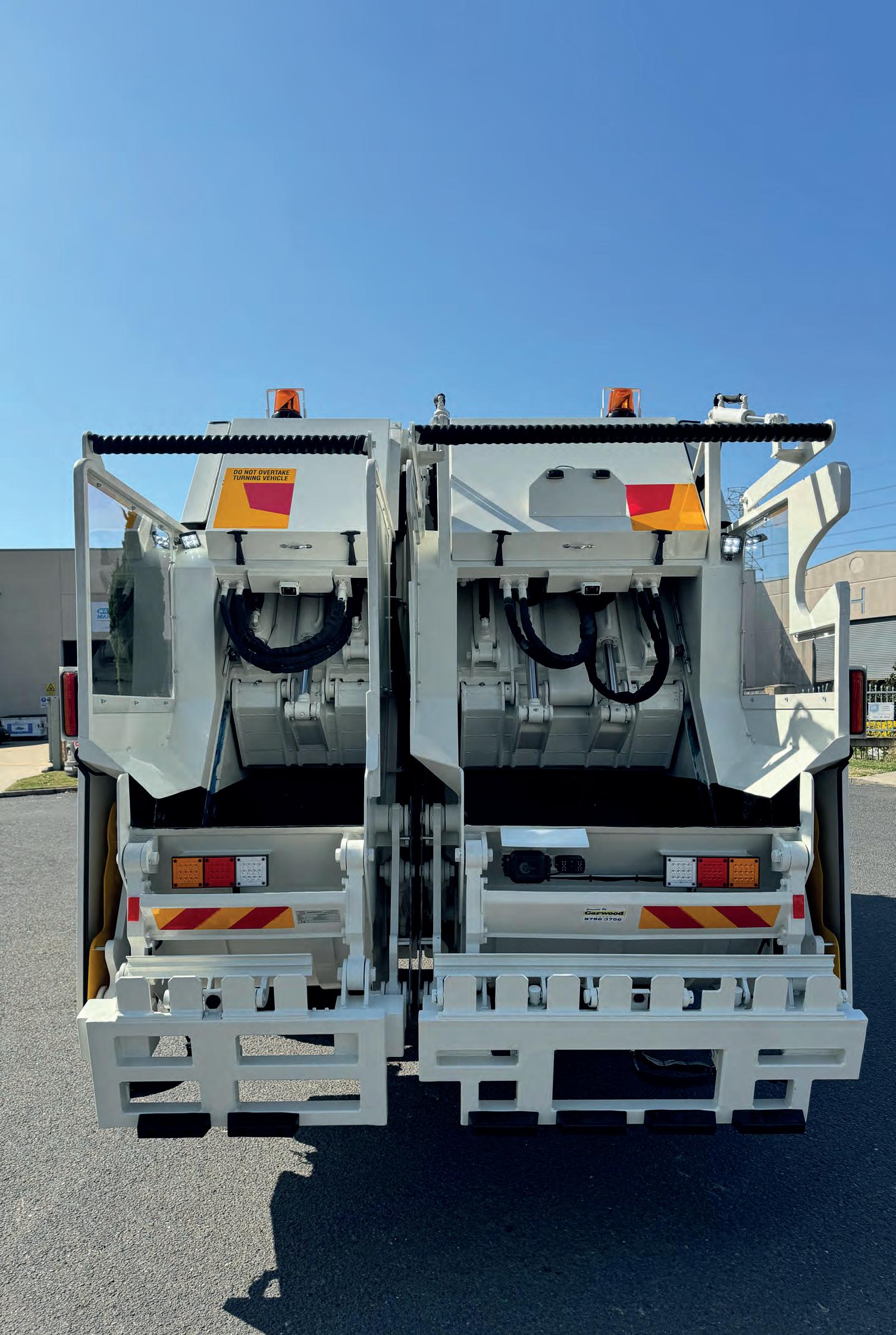
No one-size fits all with
Garwood compactor range
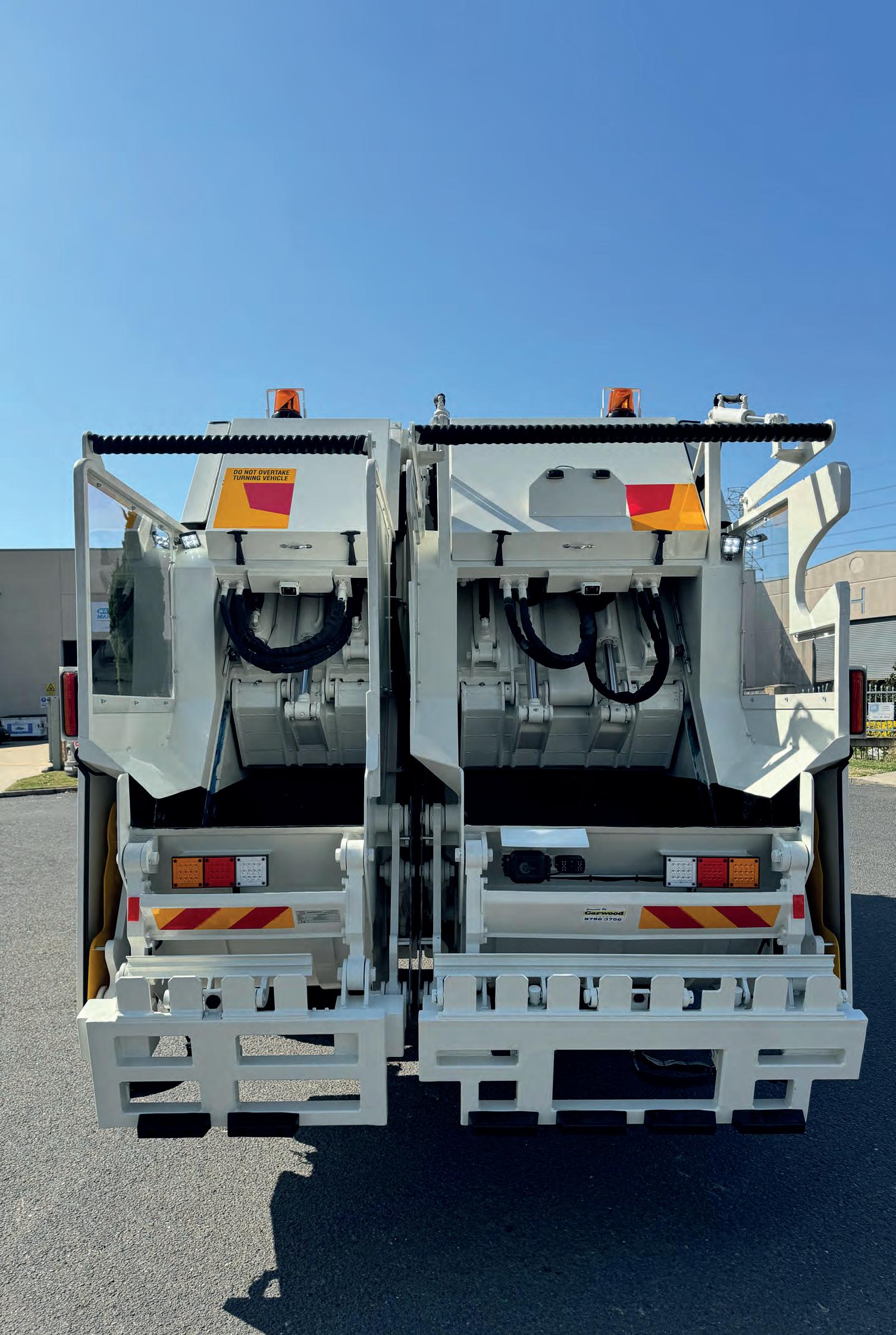
DUALPACT is the aptly named rearloading compactor range from OEM Garwood, a company that specialises in equipment for the waste and resource recovery industry.
The compactor can be fitted onto a chassis and comes with split tailgates that have a wall down the middle of the body that allows users to split different waste streams/ resources being collected.
Daniel McHugh is the managing director of Garwood, and he has seen an uptick in interest for the product over the past 12 months. It was showcased at the Coffs Harbour Waste Conference, AWRE and the recent Waste Expo Australia event held in Melbourne. In all three instances, interest was high at the capabilities of the machines.
“The tailgates are completely separate, and with a wall in the middle of the body there’s zero chance of getting cross contamination,” he said. “You can pick up any type of waste, or two types of waste – one side can have paper while the other side might be glass. It’s up to you.”
They come in three split configurations – 50/50, 60/40 and 70/30, which allows for more storage for more prolific waste. McHugh said the DualPact is beneficial in places like regional or rural settings where councils and/or contractors drive out to farms or acreage, or other remote places where different waste streams need to be picked up and it’s also very efficient in city & town centres where you have litter bins with General waste and recyclable bins side by side.
“They can do that in one run with one truck, where normally they’d have to send two trucks,” said McHugh. “Or the truck would have to do one pick up and then go round again to pick up the second waste stream.”
One of the key points about these compactors is that they are made locally by Garwood. Being an OEM means the company can configure each unit to a customer’s needs. The make-up of these bespoke models can be discussed before they are built.
“We rely on information from the customer as to the percentage rates they might require for the compactor,” said McHugh. “They’re basically getting two trucks in one body. You’ve got the two tailgates that are split, and two lifter mechanisms fitted to the tailgates at the back end of the unit. We also separate the control systems from one side to the other, which means they are truly independent. It means that if the unfortunate circumstance arises where there is something that is causing one side to break down, the other side will run because of those
independent control systems.”
McHugh said that Garwood has garnered a lot of interest via its UKbased subsidiary Garwood Europe. Garwood has been in Europe since 2002 and exports some of its compactors and other products to the region.
“There’s a high demand for these products in the European market. We’ve been selling the DualPact there for 20 years,” he said. “We’ve seen an
increase in sales of this product in the Australian market, too, because there’s a lot of areas that can be used. It seems the more we promote this, the more people are putting in orders.”
McHugh says that Garwood has developed this product over the past 20 years, and it is now starting to pay dividends as it is now getting a good reputation. Also, a lot of councils and contractors can see the benefits
of having a two-in-one compactor designed for collecting roadside waste.
“People are getting more confident with the product and its ability to do what we say it can,” said McHugh. “We can do body sizes from six cubic metres right up to 24 cubic metres and sizes in between.
“They can be custom-fit onto most truck chassis, too.”
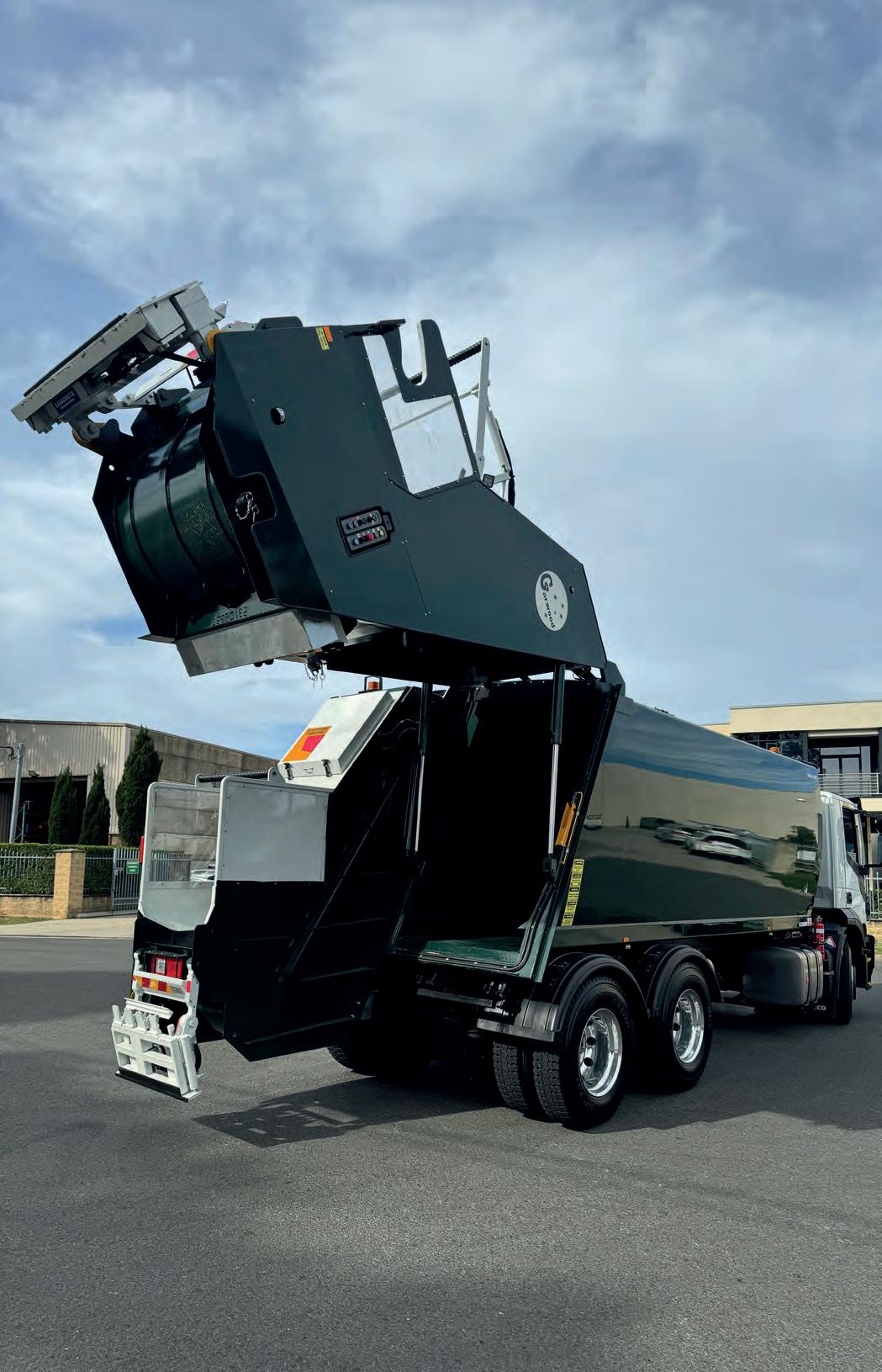
The tailgates are separate with a wall in the middle of the body to stop cross contamination.
Waste Innovation and Recycling Award winners announced
A packed gala dinner held at The Trust in Melbourne’s CBD saw a range of categories being decided in the 2024 Waste Innovation and Recycling Awards (WIRA). Sponsored by Veolia, REMONDIS, Re.Group and Visy, the awards saw an array of finalists go head-to-head as the winners were announced. Congratulations to all the finalists, and well done to the winners.
OUTSTANDING WARR PROJECT – REGIONAL
Awarded to Queensland Corrective Services for its Environmental Management Recycling Program
Lotus Glen is the northern most
correctional facility in Queensland. In 2022 it commenced the Environmental Management Recycling Program.
Utilising prisoner labour it diverted about 50 per cent of its waste from landfill. It is the largest recycling program in a correctional facility in Queensland.
Seventy-four per cent of its population at Lotus Glen are First Nations. The facility is not only looking to protect the environment, but also provide training and opportunity for people on release. The end goal is to utilise all resources available to reduce waste to the lowest possible level, offset carbon, increase sustainability and provide opportunity to reduce recidivism.
INNOVATION AWARD
Awarded to ReSource For ReSource: Pioneering Ethical and Innovative Recycling – Proudly Sponsored by Veolia Australia and New Zealand
ReSource is an Australian specialist in e-waste processing. Recognising that the old way of recycling e-waste isn’t enough to not only tackle the volume of e-waste but to process it as efficiently and sustainably as possible, the company has invested in technology to raise the standards of what’s possible. ReSource has introduced new advancements, including AI-driven battery sorting, proper recycling of alkaline and zinc carbon batteries and
high-efficiency recycling for low-value items. It has implemented dual-stage activated carbon filters to ensure it doesn’t have heavy metal or VOC emissions from its processing entering the atmosphere. Its also implemented AI-powered thermally activated fire cannons to stop any fires that might come from e-waste. It is also the first company in Australia to be energy negative in its processing, due to its 860-kilowatt solar system.
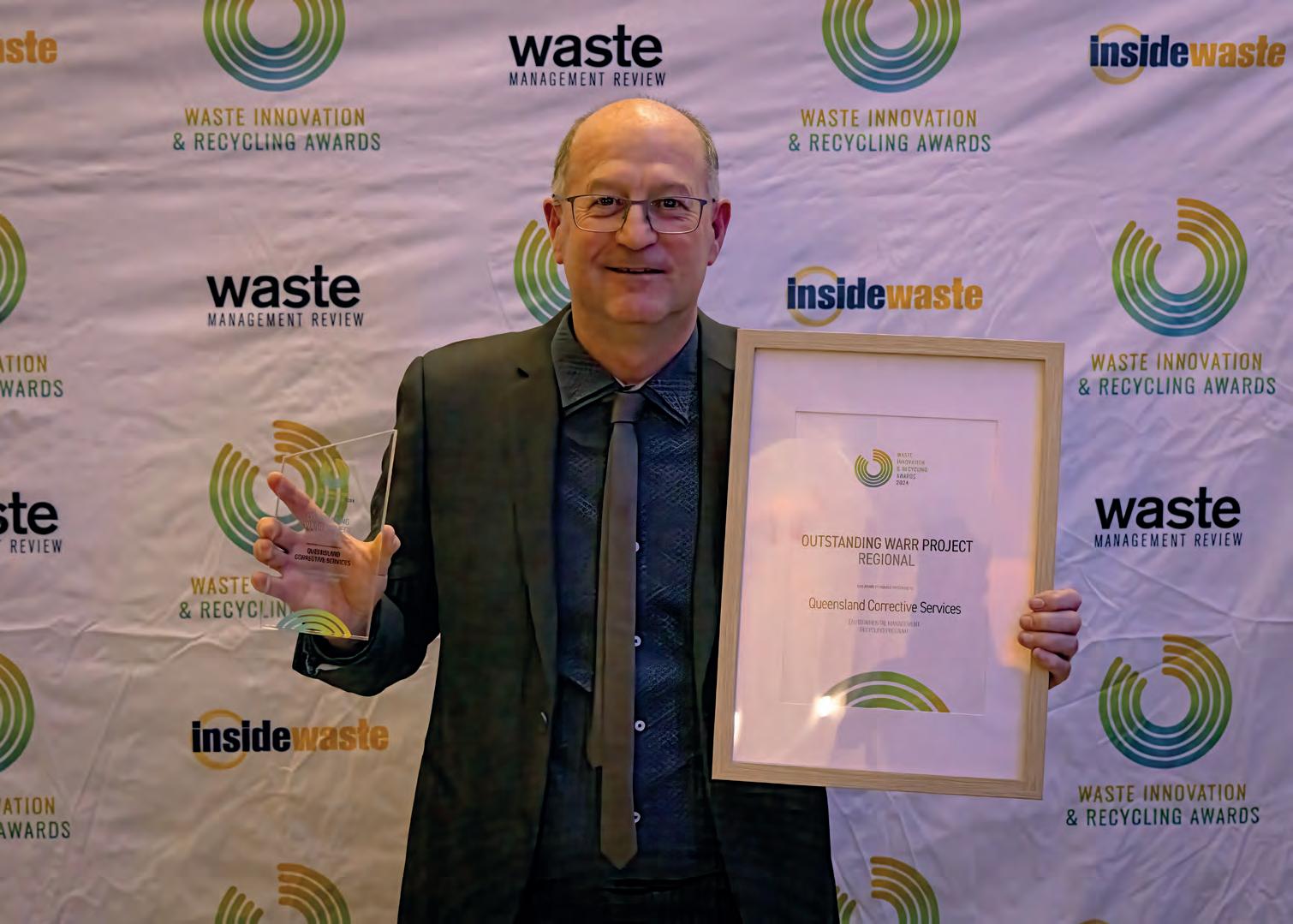
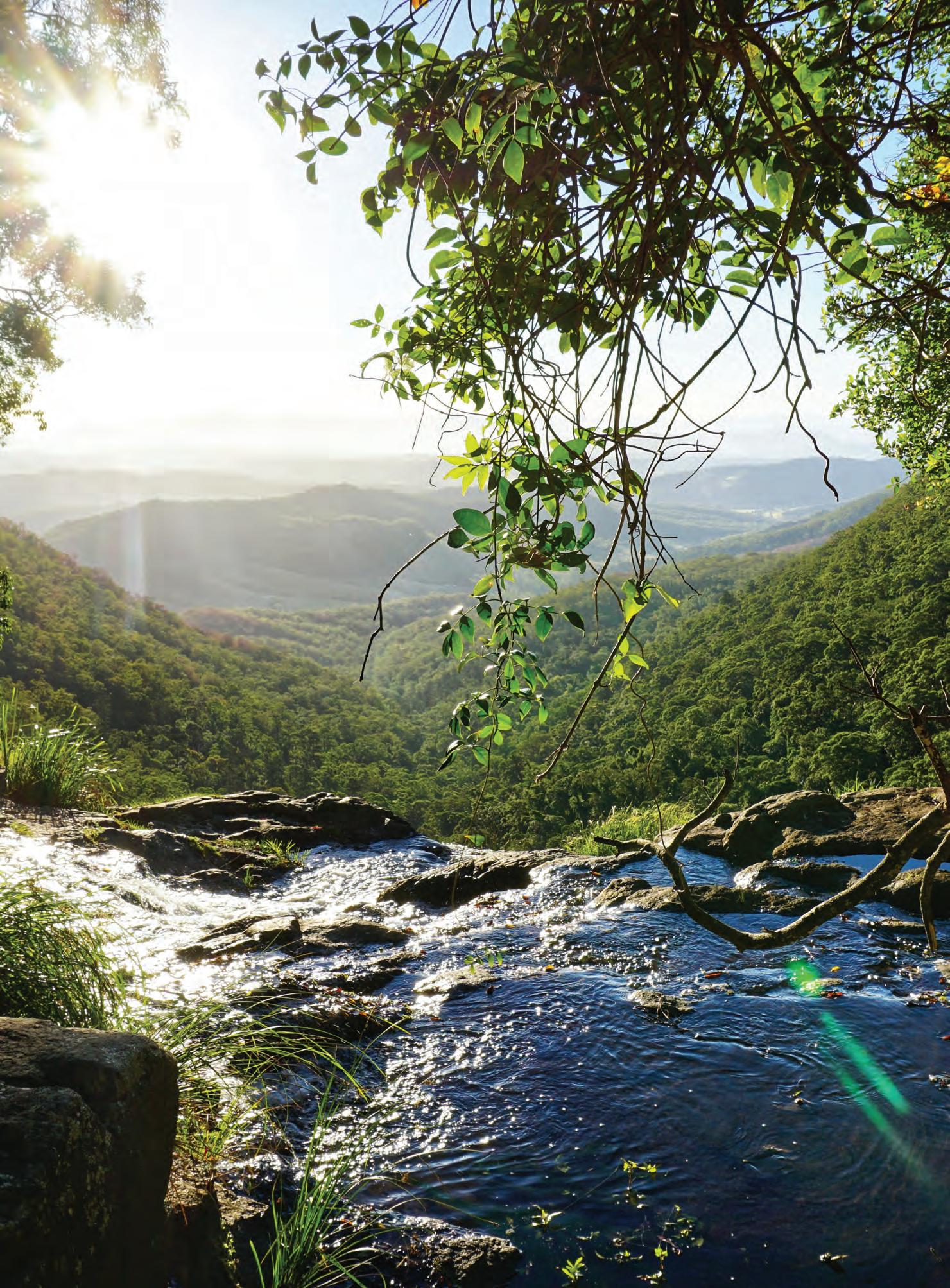
The Outstanding WARR Project Regional Winner was the Queensland Correction Services. Images: Dorman Creative
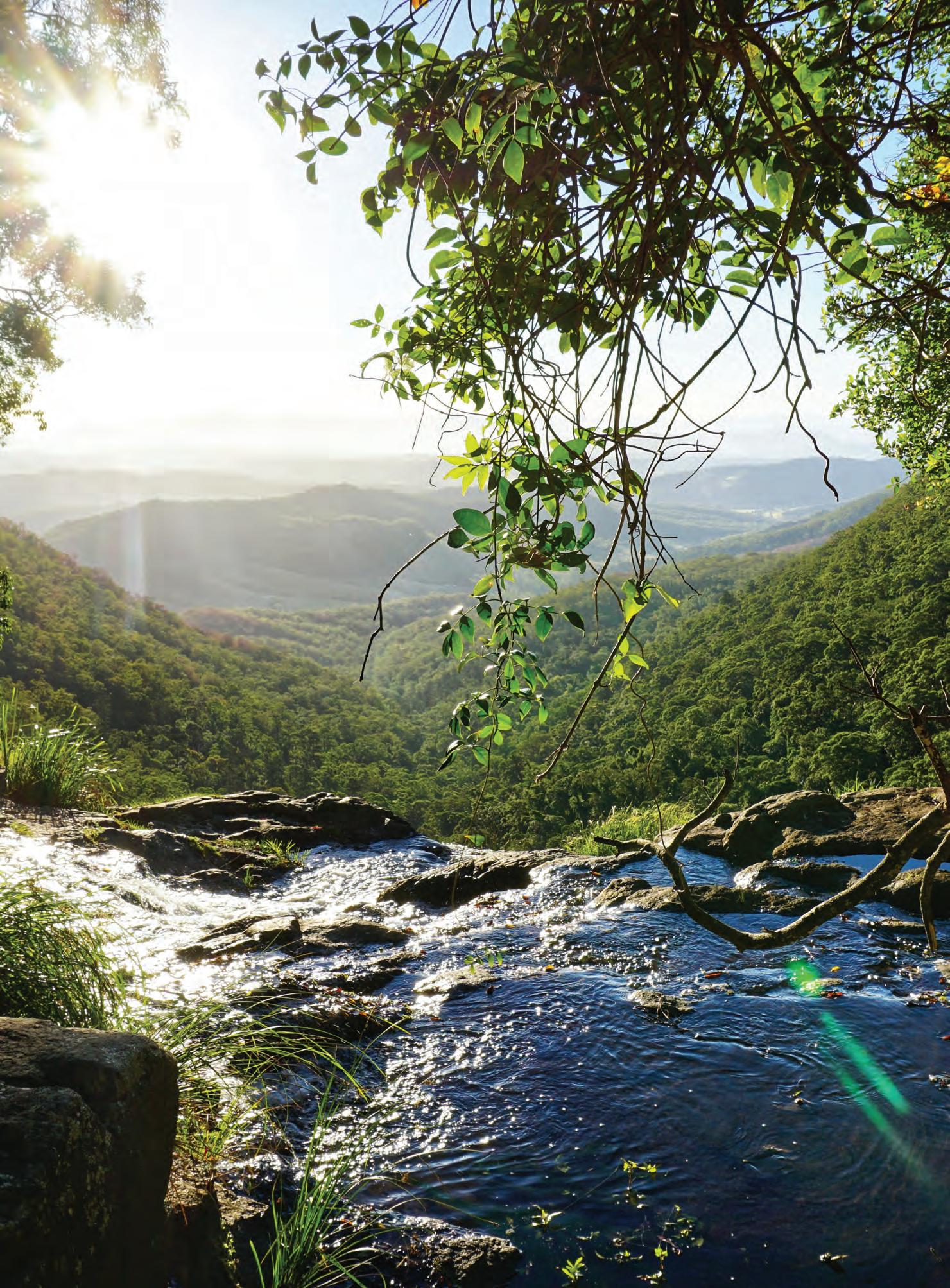

YOUNG PROFESSIONAL OF THE YEAR
Awarded to Thomas Anton from Repurpose It – Proudly Sponsored by REMONDIS Australia
Anton is the Head of Customer Experience at Repurpose It. He is driven by his passion for providing circular outcomes for customers and has been promoted to his current role due to his exceptional work and innovative mindset. He manages the entire customer experience, including the front line of communication with clients, ensuring a positive customer experience, and fostering long-lasting relationships with customers. With a team of 15 staff members in customerfacing roles across the business, setting expectations and building leadership and autonomy in the team has been paramount to his team’s success. Anton’s team works across multiple sites – Epping, Montrose, and Hallam. He ensures he actively participates in the day-to-day activities of all sites ensuring they are engaged and supported.
OUTSTANDING WARR PROJECT – METRO
Awarded to Waste Circularity Team – Frankston City Council for the implementation of its separate glass service Frankston City Council implemented a separate glass service to all residential households in October 2023 including the introduction of shared bins for the first
time within the municipality. The rollout was seamless due to planning and communication with the community.
Frankston City Council was able to implement the new separate glass service simultaneously with a reduction to the annual waste charge. The communication plan for the
implementation of the new glass service was enhanced by completing Councils initial Gender Impact Assessment, allowing for an intersectional approach to all communications. A portion of the planning process was allocated to ensuring accurate data was collated and provided to delivery contractors in the most effective format.
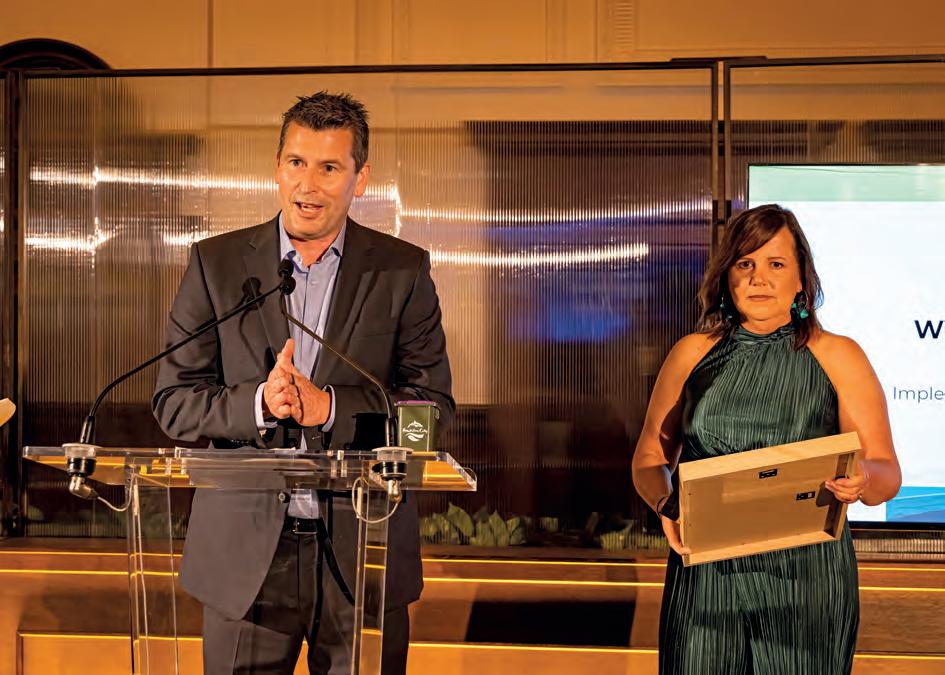

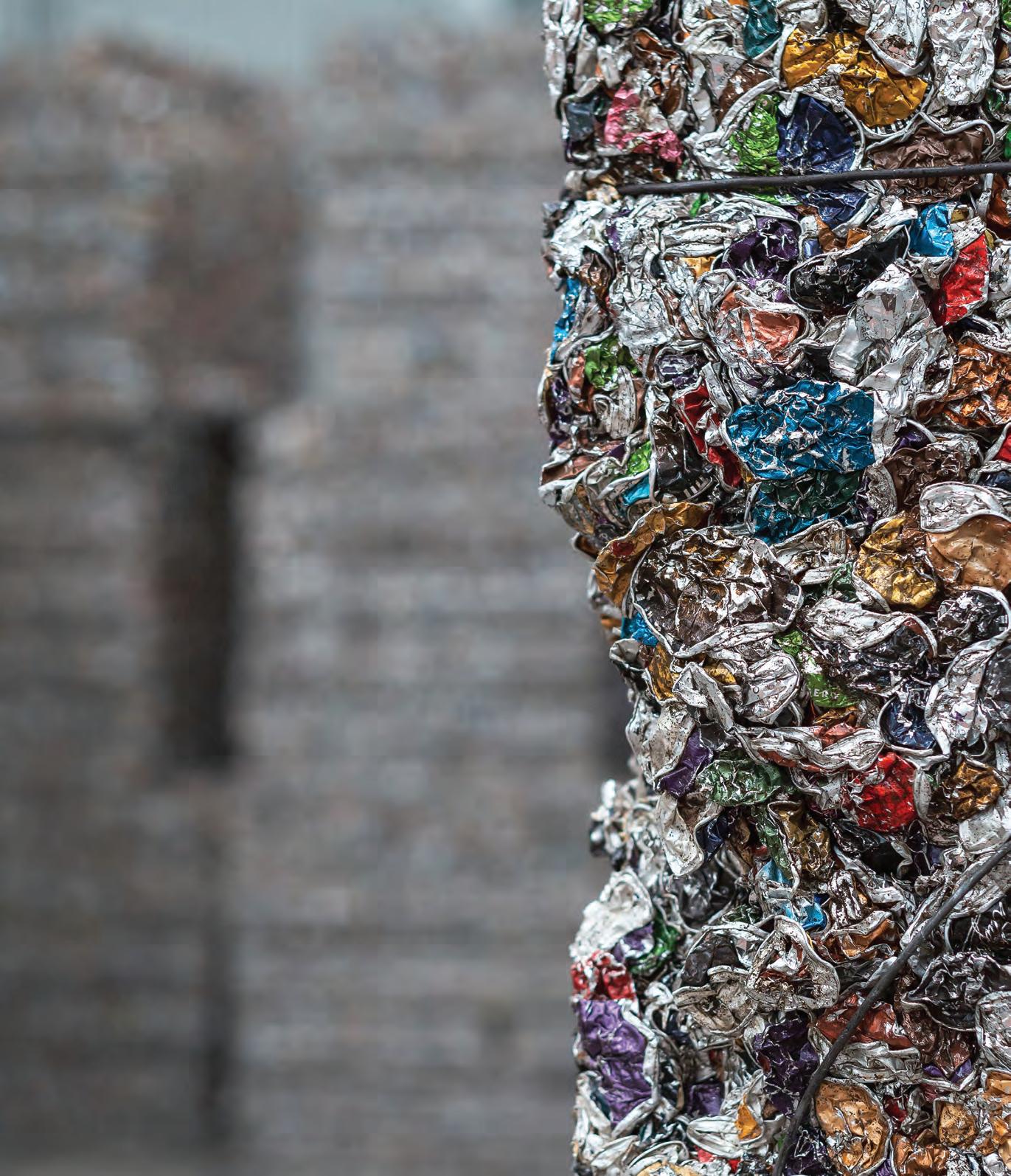
The Outstanding WARR Project Metro Winner was Frankston City Council and its glass bin initiative.
Melbourne-based Thomas Anton from Repurpose It landed the Young Professional of the Year.
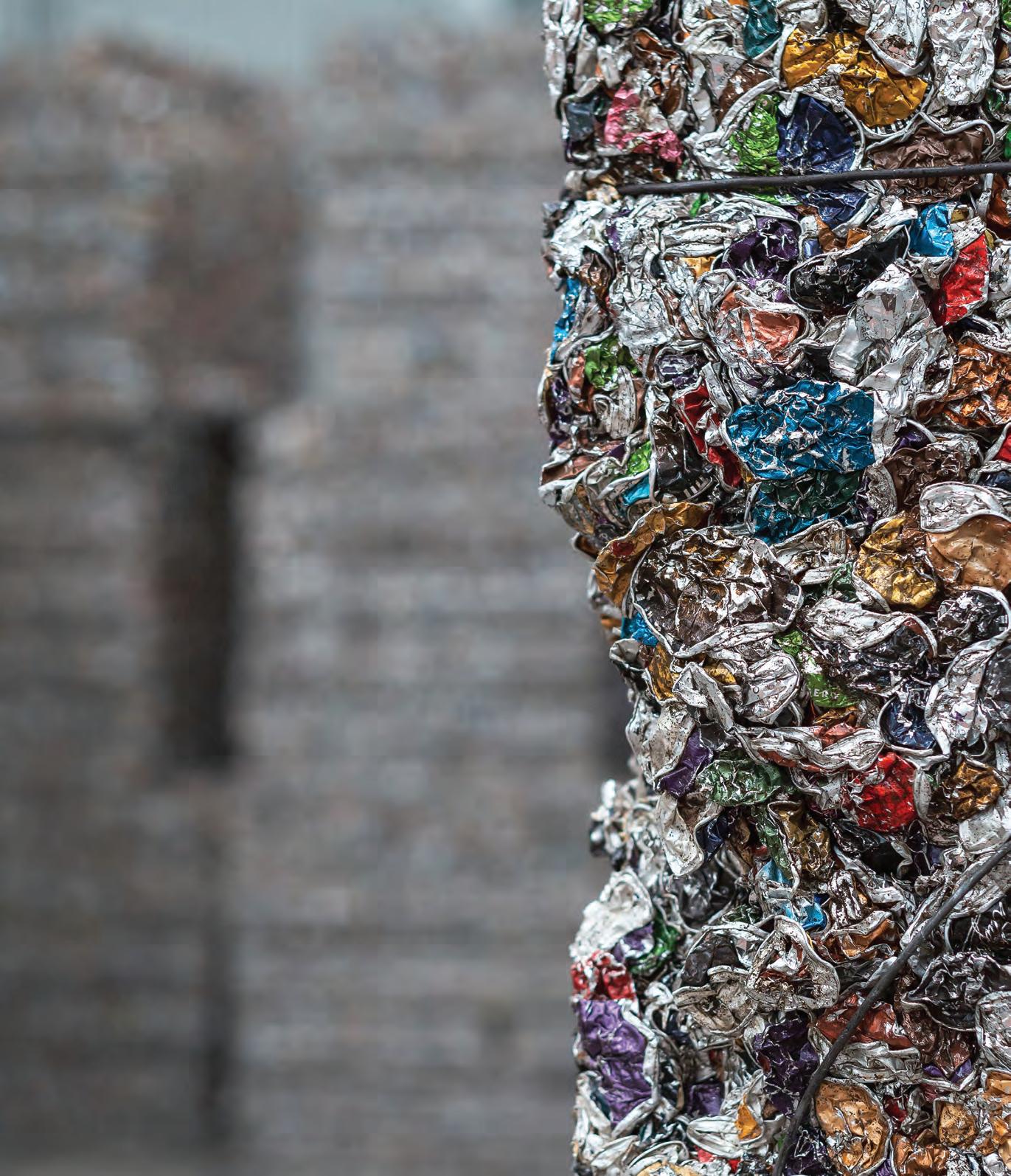
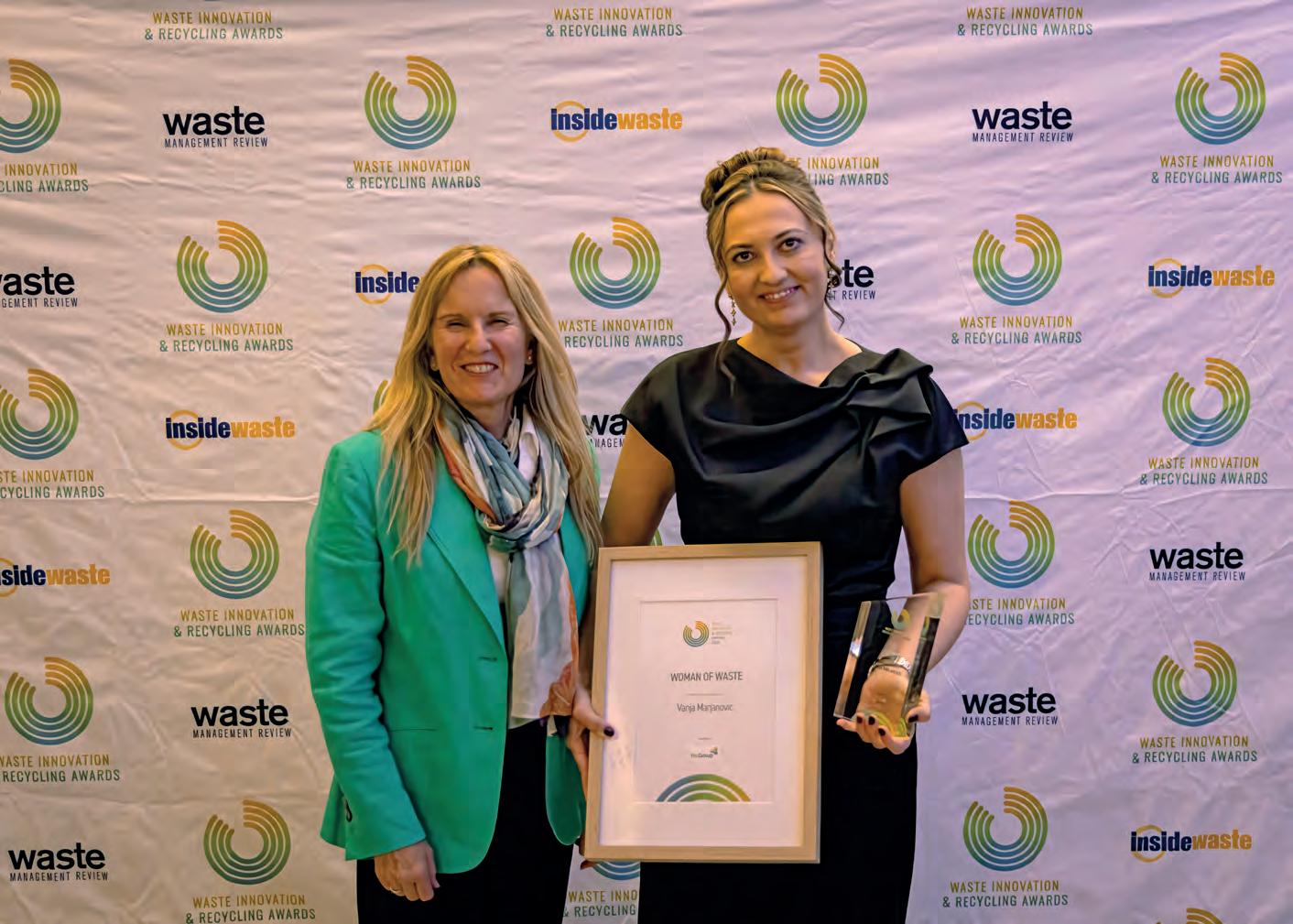
WOMAN OF WASTE
Awarded to Vanja Marjanovic from the City of Melville – Proudly Sponsored by Re.Group
Marjanovic is the Waste Coordinator at the City of Melville. Since moving from Croatia to Perth in 2000 to escape conflict, she’s learned English, completed her studies and quickly risen the ranks of the waste industry. Industry peers know her for her ability to improve operations, align strategy and respect and support her staff. Marjanovic is responsible for overseeing a team of 30 staff members, more than $10 million in fleet, a further $5 million in assets and plays a key role in behaviour change, best practice innovative waste management practises. She also provides expert guidance on waste management plans to both internal and external stakeholders, which includes high rise and high-density MUDs. She also ensures efficient contract management and contributes to the development of annual operational and capital budgets for the department.
OUTSTANDING FACILITY AWARD
Awarded to Rino Recycling for its new recycling facility
Rino Recycling is a state-of-the-art construction and demolition waste recycling facility in Pinkenba, Brisbane, transforming 1.5 million tonnes per year
of co-mingled waste into high-quality recycled construction materials, including aggregates, road base, fill, and sands.
The facility is the world’s largest under one roof by volume and the
wet and dry processing technologies and automated processing, sorting, and separating technologies to process diverse waste streams, enhancing waste recovery rates and efficiency. It represents a ground breaking step towards a circular economy by reducing





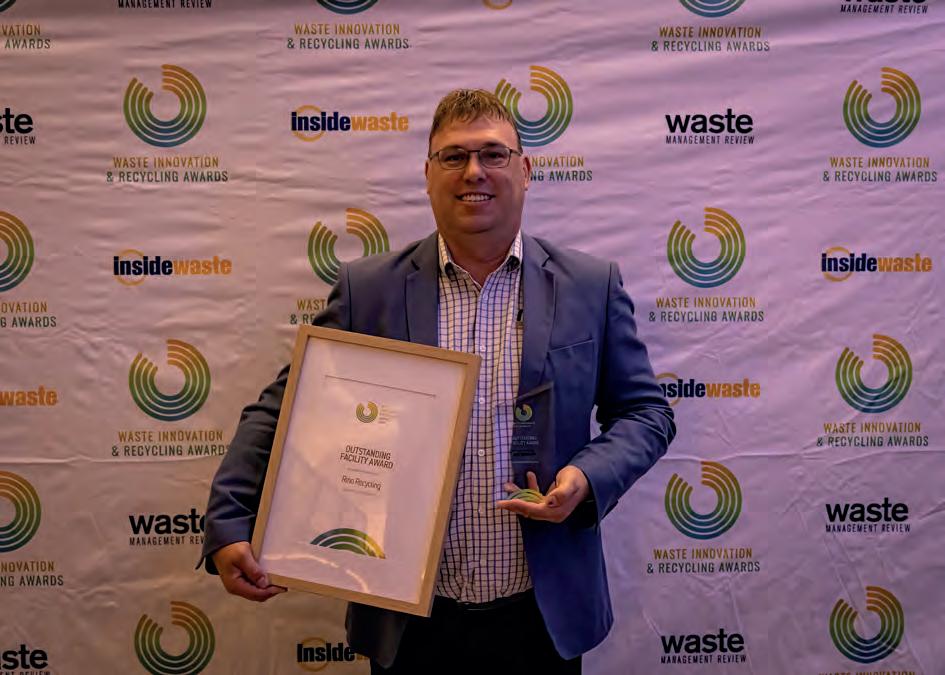
This Woman of Waste award went to Vanja Marjanovic from the City of Melville.
Rino Recycling from Queensland won the Outstanding Facility gong for its C&D waste recycling facility.
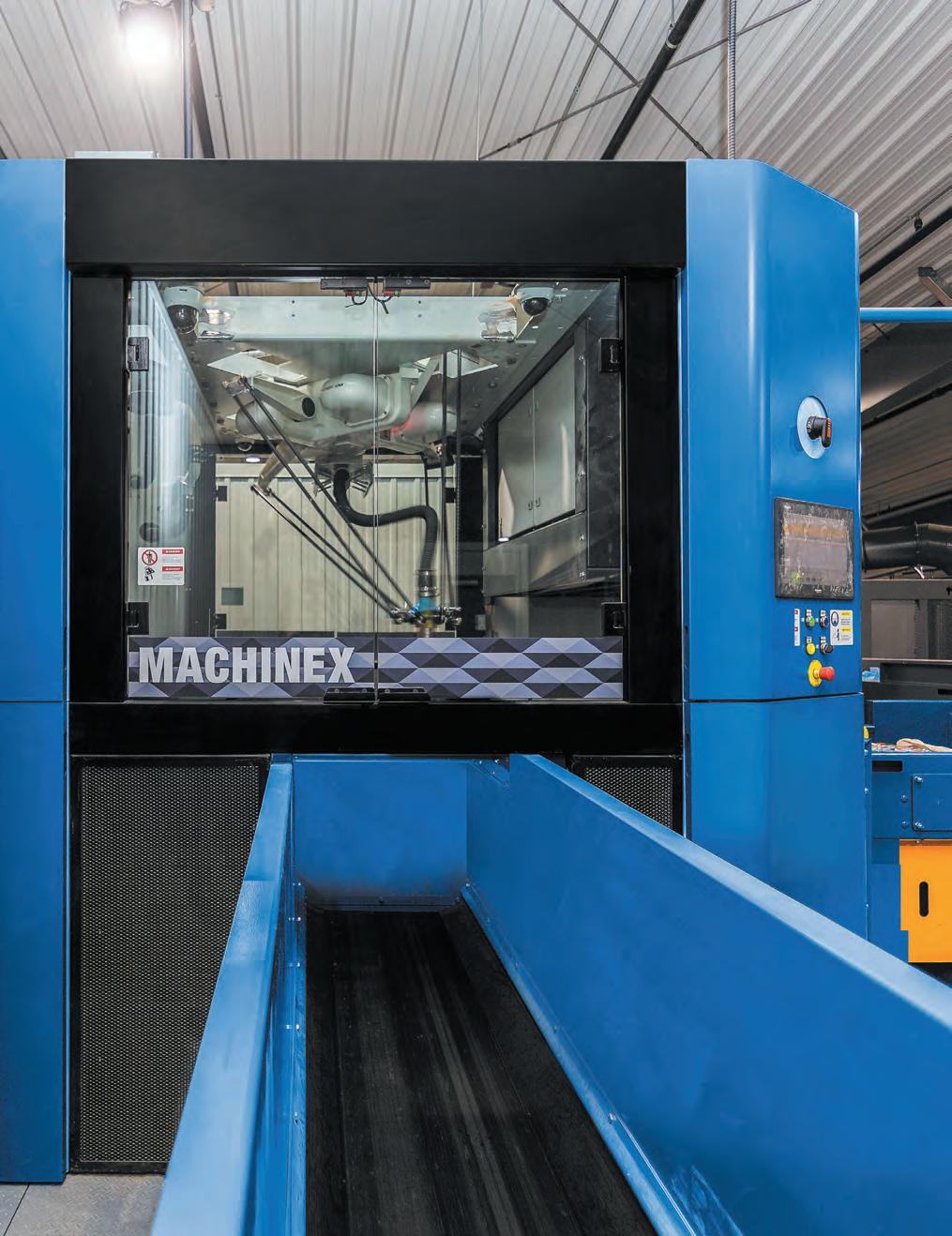
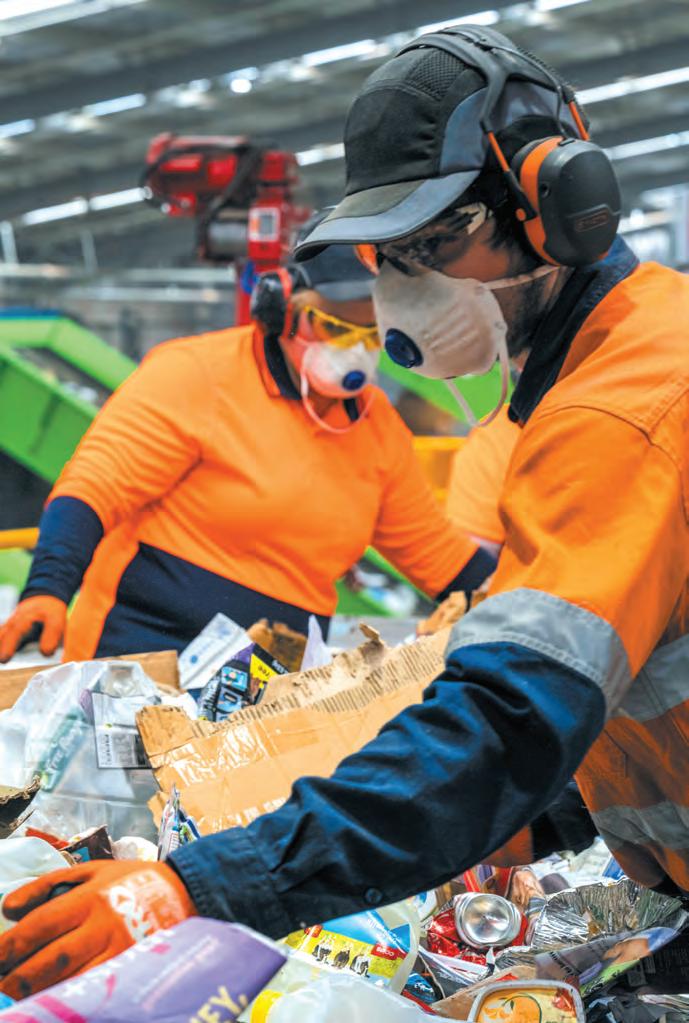
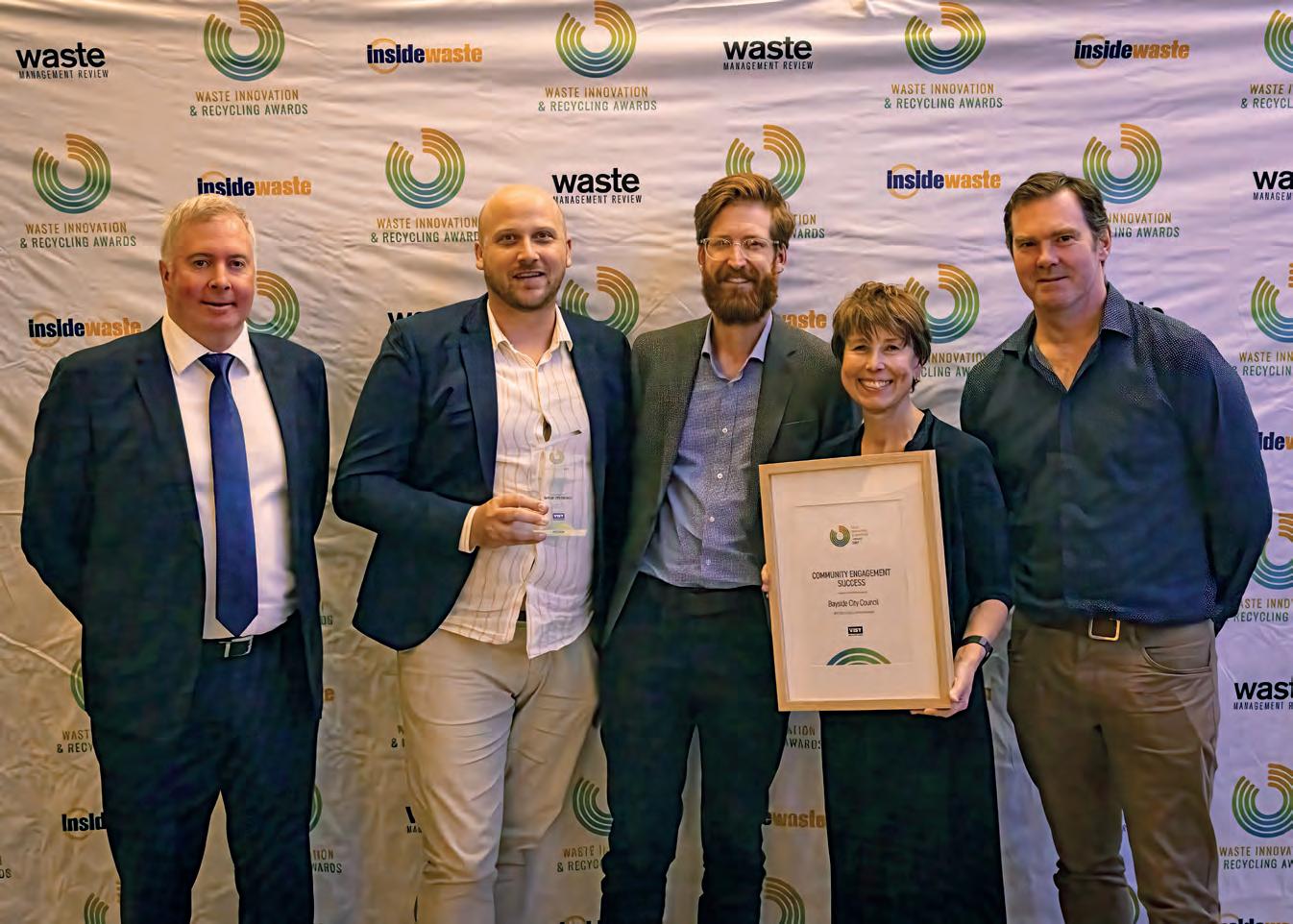
COMMUNITY ENGAGEMENT SUCCESS
Awarded to Bayside City Council for its Bayside Roving Repair Program – Proudly Sponsored by Visy
Bayside launched an initiative focused on reducing waste by encouraging repair and reuse rather than throwing items away. The program started a repair culture across Bayside giving the community opportunities to repair items destined for landfill, while building knowledge and social connections through events. Workshops had different themes – from repairing textiles, books, electronics, furniture and bicycles. The workshops didn’t just offer repair services; they were also spaces where the community could learn new skills, exchange knowledge, and form connections. The roving nature of events meant they were held in a range of locations, making them accessible to a wider audience.

LEADER OF THE YEAR
culture of sustainability.
Awarded to Narelle Anderson from Envirobank
Narelle Anderson is the founder and managing director of Envirobank. With a visionary approach, she has championed innovative solutions to combat waste, fostering a
Narelle’s leadership has positioned Envirobank as a leader in environmental stewardship, implementing cutting-edge technology and consumer-friendly initiatives to enhance recycling efficiency.
Her commitment to environmental
responsibility has garnered widespread recognition, making her a prominent advocate for sustainable practices.
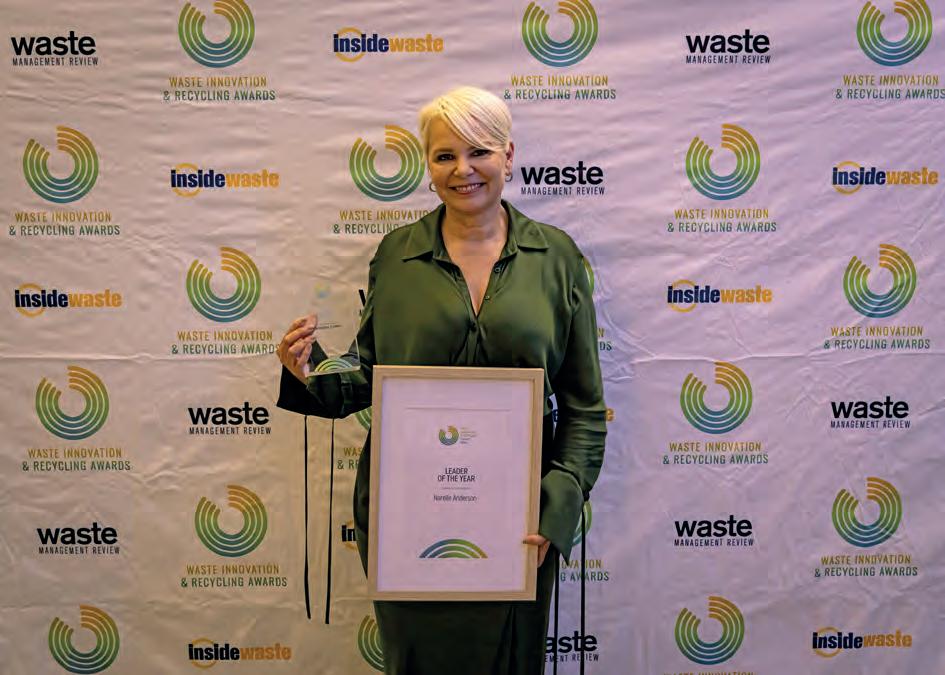
Through her inspiring leadership, Narelle continues to drive impactful change, promoting a cleaner, greener future for Australia and for future generations.
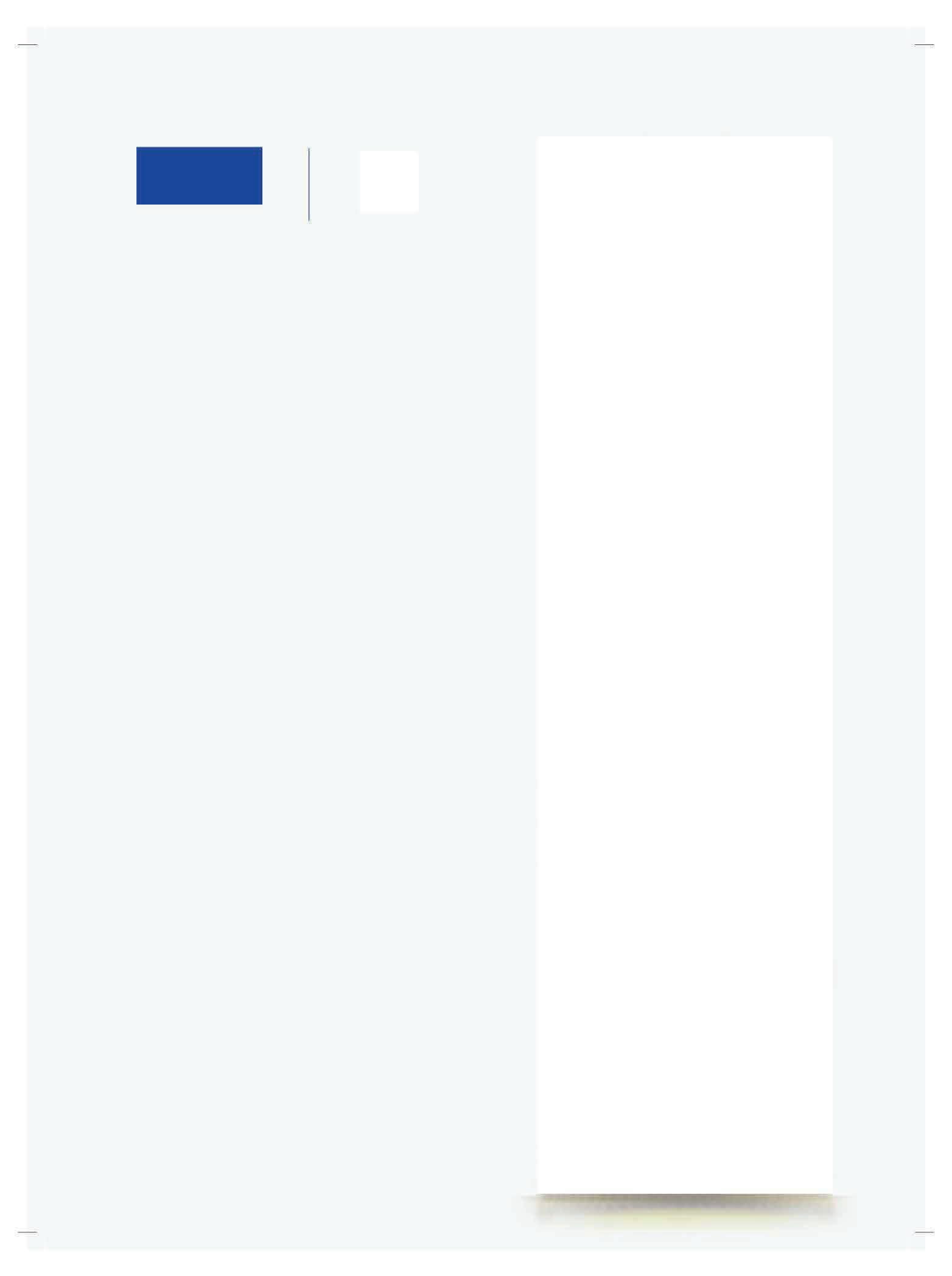
Bayside City Council’s Roving Repair program was the winner of the Community Engagement Award.
Envirobank’s Narelle Anderson was given the Leader of the Year award for, among other things, her championing of sustainability initiatives.
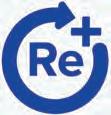
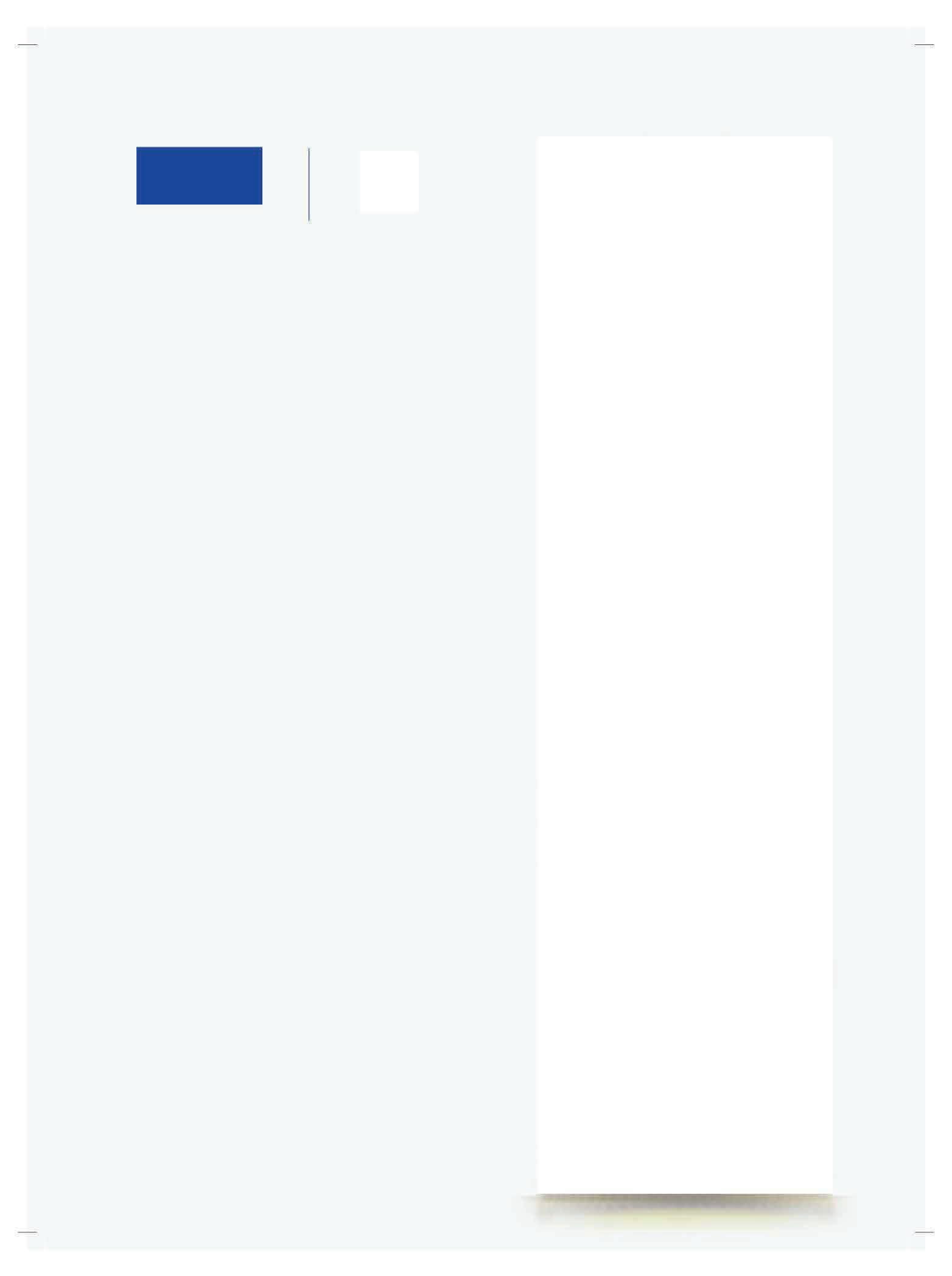
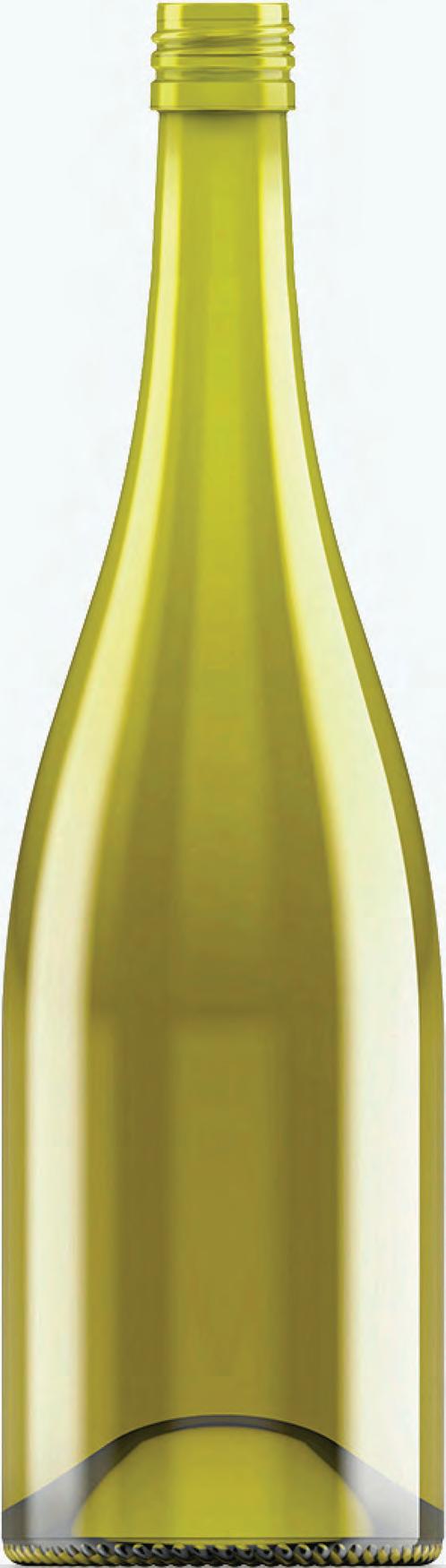
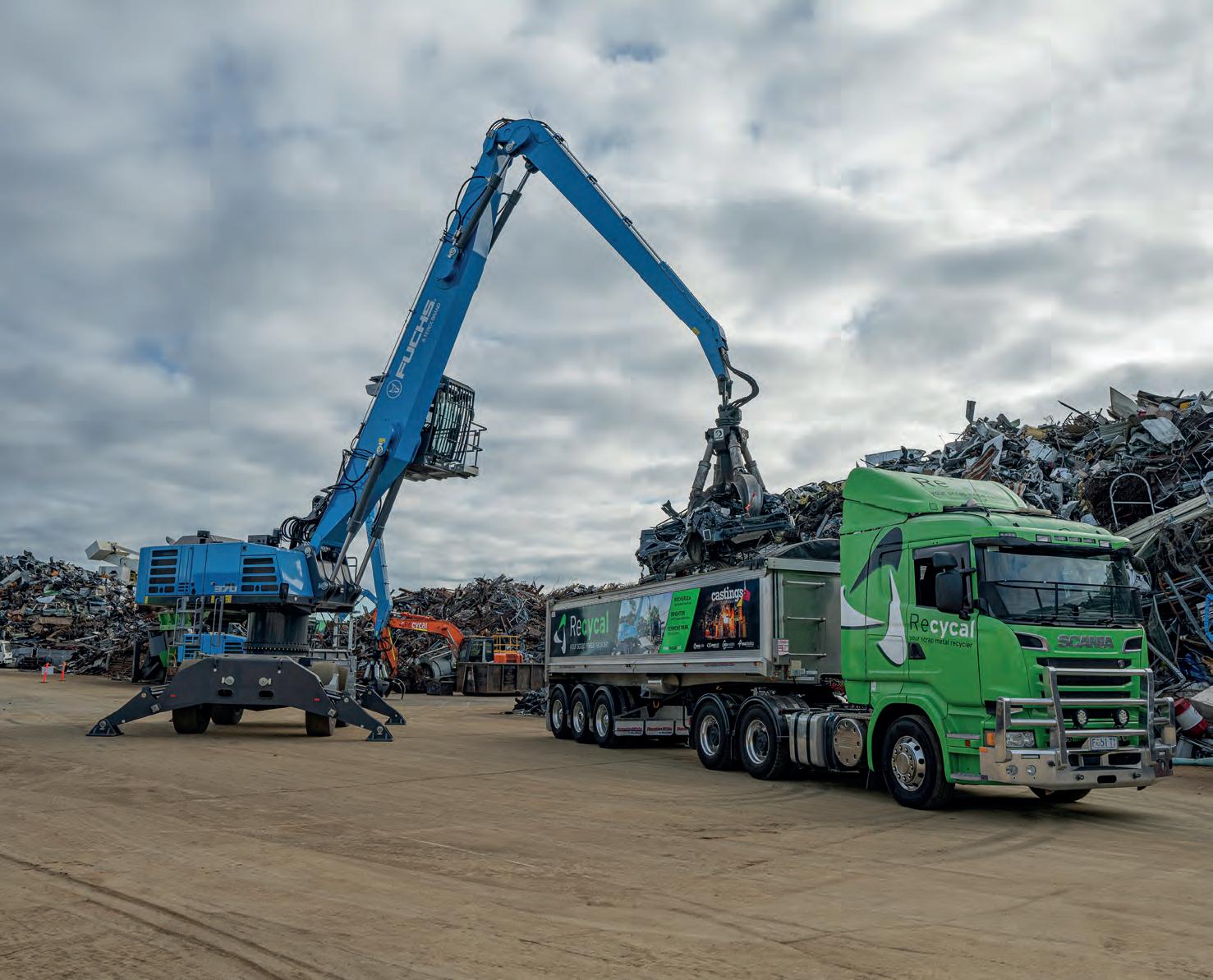
Materials handlers smooth and reliable
TOM Barrett is the operations manager at Recycal Rocherlea in Tasmania. Recycal is a family-owned metal recycling business that operates several locations throughout the country.
Its facility in Rocherlea covers 14 acres and employs a dedicated team of 40 staff members. Recycal takes pride in its knowledge of the recycling process. With multiple sites, a fleet of trucks, technical expertise, and a partnership with a local foundry casting in Tasmania, Recycal offers a recycling solution from start to finish.
At present, it utilises five Terex Fuchs material handlers, all provided and maintained by the Onetrak team. Recycal was already familiar with the Terex brand, known for its reliability and support, making the company’s decision to expand its fleet with Terex Fuchs machines a natural fit.
“Our journey began six years ago with the purchase of an MHL 355, which continues to perform exceptionally,” said Barrett.
“Since then, we have added two MHL 350 machines, along with a MHL320 and a MHL370 to our fleet. Fuchs machines are user-friendly, have
long service intervals that minimise downtime, and are smooth and reliable to operate.”
A spokesperson from Onetrak said the MHL320, one of Recycal’s latest machines, excels in recycling, consistently delivering a reliable performance.
Its versatility offers a spectrum of possibilities from precision sorting to heavy-duty loading tasks.
With various boom versions, undercarriages, and special equipment options, the MHL320 can be customised to align with a customer’s requirements, providing a tailored solution for individual needs.
Along with its mechanical features the MHL320 also considers operators with its operator-centric design. The cab is a reinforced steel structure with soundproofed, heat-insulated panoramic windows for best allround visibility. Inside, heating and air conditioning, with separate heat exchangers and fresh and recirculated air filters, make for a comfortable environment.
The operator’s seat is an aircushioned comfort seat with swinging armrests/joysticks, safety belt, lumbar
support and headrest. It is designed to enable fatigue-free work due to universal adjustment options for the seat position and the arrangement of the seat cushion in relation to the armrests and joysticks.
In an era where sustainable waste management is paramount, the Fuchs MHL320 material handler emerges as a beacon of visibility, reliability, and innovation. It represents a
commitment to a productive and more efficient future.
“I have had nothing but positive experiences with the Onetrak team,” said Barrett.
“Jake is always available, and Rodney has been a pleasure to work with.
“ I highly recommend Onetrak for their outstanding product knowledge, service, and support.”
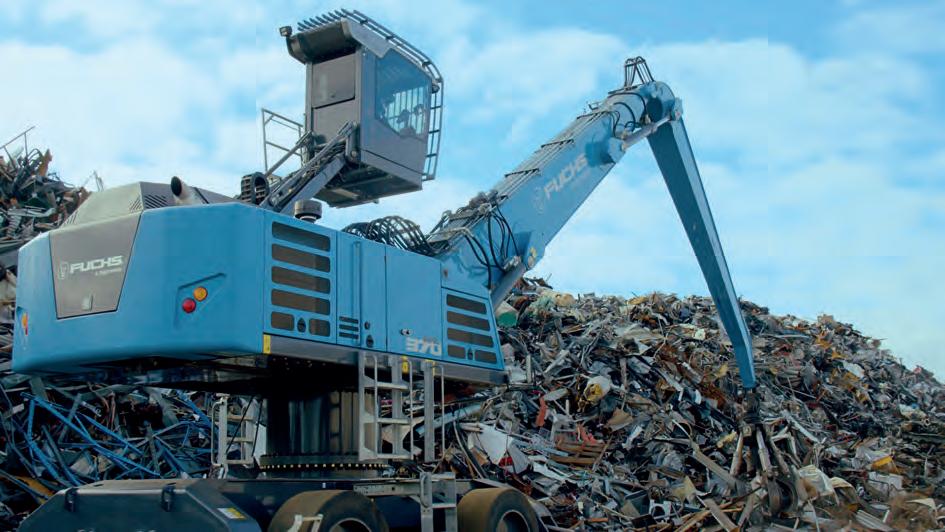
Recycal operators find the Terex machines smooth and reliable to operate. Images: Onetrak
The Telex machines make life easy for operators at the Recycal facility in Rocherlea.
Locally made means local support from Eriez
JONATHAN Schulberg may not have been in the resource recovery industry as long as some, but he does remember the days when separating out the different waste streams was not only unimportant, but nobody even thought about getting a monetary return. How the industry has changed.
Schulberg is the business development manager for Eriez, a USbased company based – unsurprisingly –out of Erie, Pennsylvania, in the US.
Machinery designed for source separation is just one of the various products the company specialises in, and Schulberg is aware how important a good piece of kit can help with a company’s bottom line, especially if they can extract valuable metals.
“The machinery we have today has shown massive improvements in recovery efficiencies,” he said. “In the past, you were relying on people manually sifting through material. Our range makes that a lot easier.
“For example, our eddy current separator does effectively the reverse of what a magnet does. A magnet attracts ferrous material, while the eddy current repels only conductive nonferrous materials – aluminium, copper, brass, and the like. Over time, these materials have been able to garner a sell price per tonne higher than what is scrapped steel.
Once collected, said Schulberg, aluminium can go on the market for as low as $1,100 a tonne or up to $2,000 a tonne. He said there is another bonus in that you also end up with a relatively
clean waste stream once the separators have done their job.
“If they can recover a high proportion of their metals in their stream, that essentially means more dollars for them,” said Schulberg. “Imagine if you have one or two tonnes recovered per day to three or four tonnes recovered per day? If aluminium is going at $1,300 a tonne, and you can recover four tonnes of it, that’s a reasonable amount of additional revenue that you’re making daily. And most plants would operate at a minimum eight hours a day.”
But one of the key features of Eriez’s offering that Schulberg wants to highlight is its locale. While the company has its origins in the Northern Hemisphere, it has had a presence in Australia for over 50 years. It manufactures its own product, and it doesn’t buy in non-Eriez products.
“One of our key benefits from a customer’s point of view is that because we’re local, we offer local service and support,” he said.
“And that became very important during the times of COVID. A lot of companies that we were dealing with had equipment from other companies that was supplied from overseas, and they were struggling to have that equipment supported locally. We were in a very advantageous position because everything was based in Australia, so it was easier for us to get equipment and help our local customers.”
Also, customers have to look out for hidden costs – unintentional or otherwise. Because a lot of Eriez product
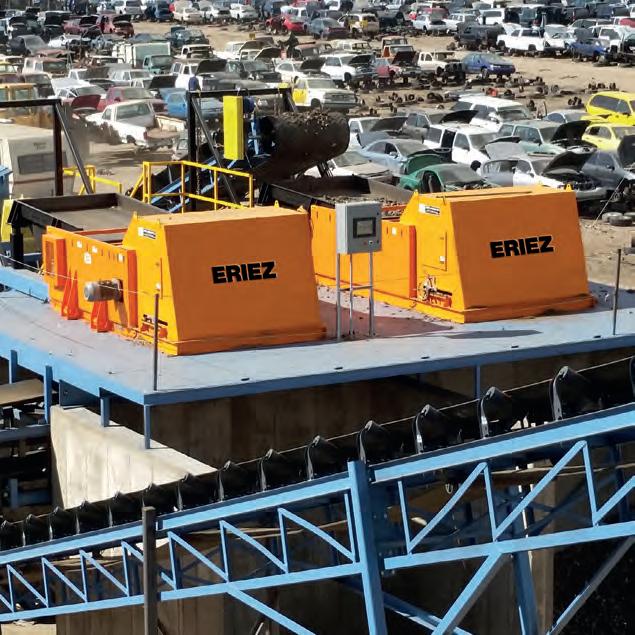
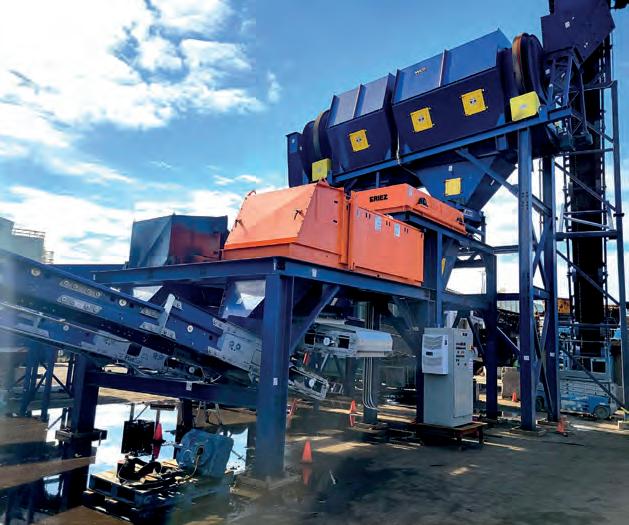
is manufactured locally, it already complies with the standards required by Australia’s regulatory authorities. With some equipment, these standards are strict and must be adhered to for safety reasons. There have been cases where cheap imports have had to be amended to make sure they meet local standards, which has meant any cost savings that a client may have made in the initial price is eaten up, or sometimes exceeded, by them having to upgrade the piece of equipment so it can be legally operated in Australia. This is not the case for Eriez plants or machinery.
This is why when clients buy from Eriez, the equipment is ready to go. And what are some of its hero pieces of machinery? Schulberg says it’s hard to go past its aforementioned eddy separators that recover nonferrous metals.
“We utilise high gradient magnetic elements, which operate at a high rotational RPM that produces the eddy current field,” said Schulberg.
“With a few different designs in the rotor makeup itself, we can recover very fine, non-ferrous metals – we’re talking one millimetre plus – through to very coarse material streams that are 25 millimetres plus.”
He said that the area of application is wide with eddy current separators, which means they can also work low volumes in industries like PET plastics, as well as fine materials such as sands, through to industrial applications like C&D and C&I plants, where the material loads are heavy.
There is a range of eddy current separator widths available from one metre wide up to two metres wide that can cater to most resource recovery applications. As far as process loads themselves, Eriez engineers can modulate to increase the quantity of them to meet a customer’s processing requirements and capacities.
“That’s something that’s very simply and easily done, whether it’s via an EPC engineering company or with the customer directly,” said Schulberg. “The eddy currents themselves are very low on maintenance costs. We’ve designed these units over time to get them to a point where they can operate for years on end, with very little customer involvement to keep them up and running.”
Over the next 18 months to two years, Schulberg can only see Eriez – and the industry has a whole – growing. He sees many factors for this, such as local and state governments knowing their constituents want more recycling, companies wanting social licenses, as well as a growing population creating more waste that need recycling.
“As we generate more waste, we need to process more volume,” he said. “It’s a constant cat and mouse game for the waste processing industry – staying ahead of the curve and understanding where the growth centres are situated. We have to get the infrastructure and everything in place. Once that population hits a certain point, we’re well prepared to handle the waste generated from those places.”
Extracting valuable materials can help increase a processing plant’s bottom line. Images: ERIEZ
Having maintenance staff available to maintain plant and machinery is just one advantage of Eriez having an Australian footprint.

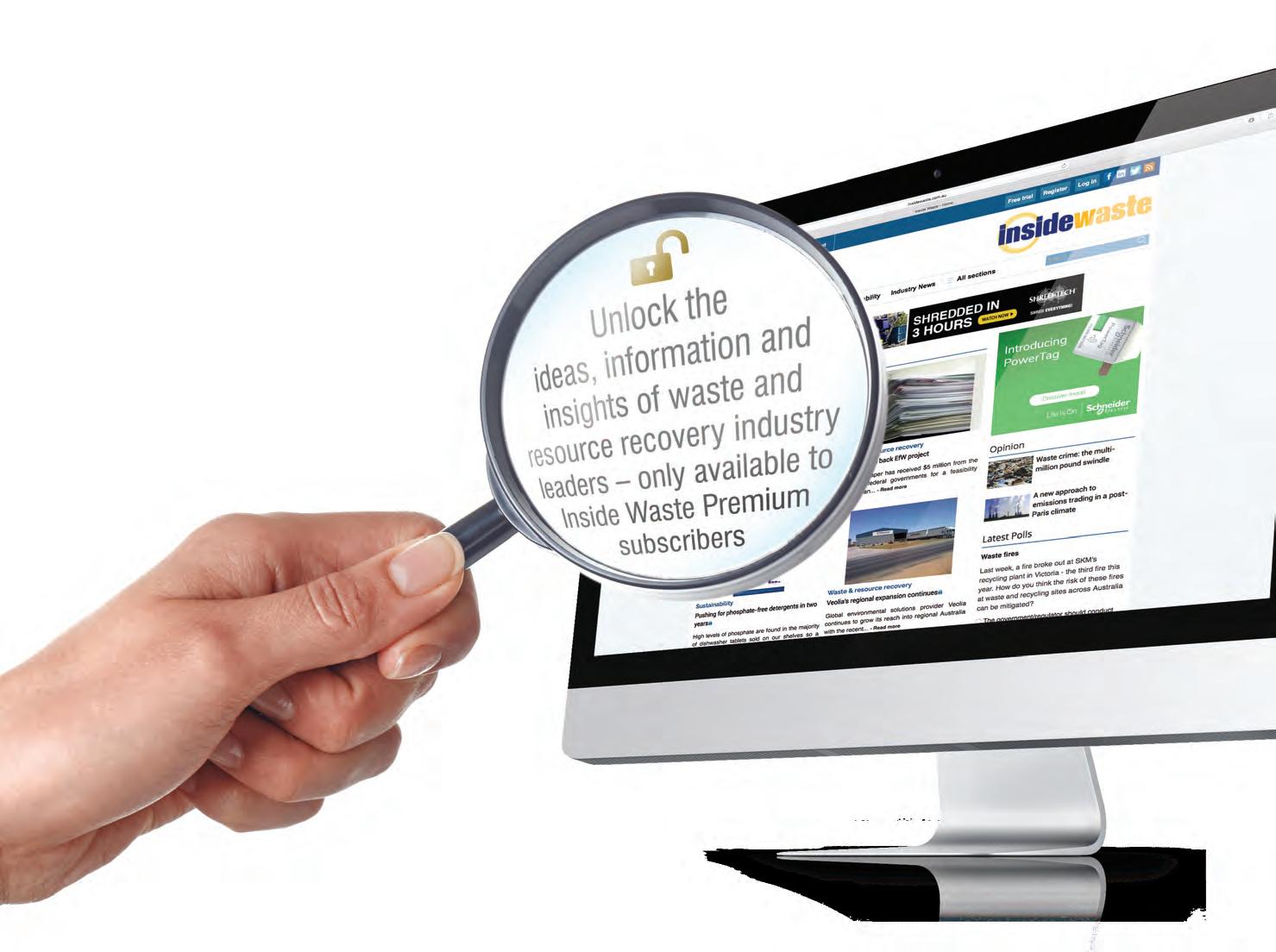

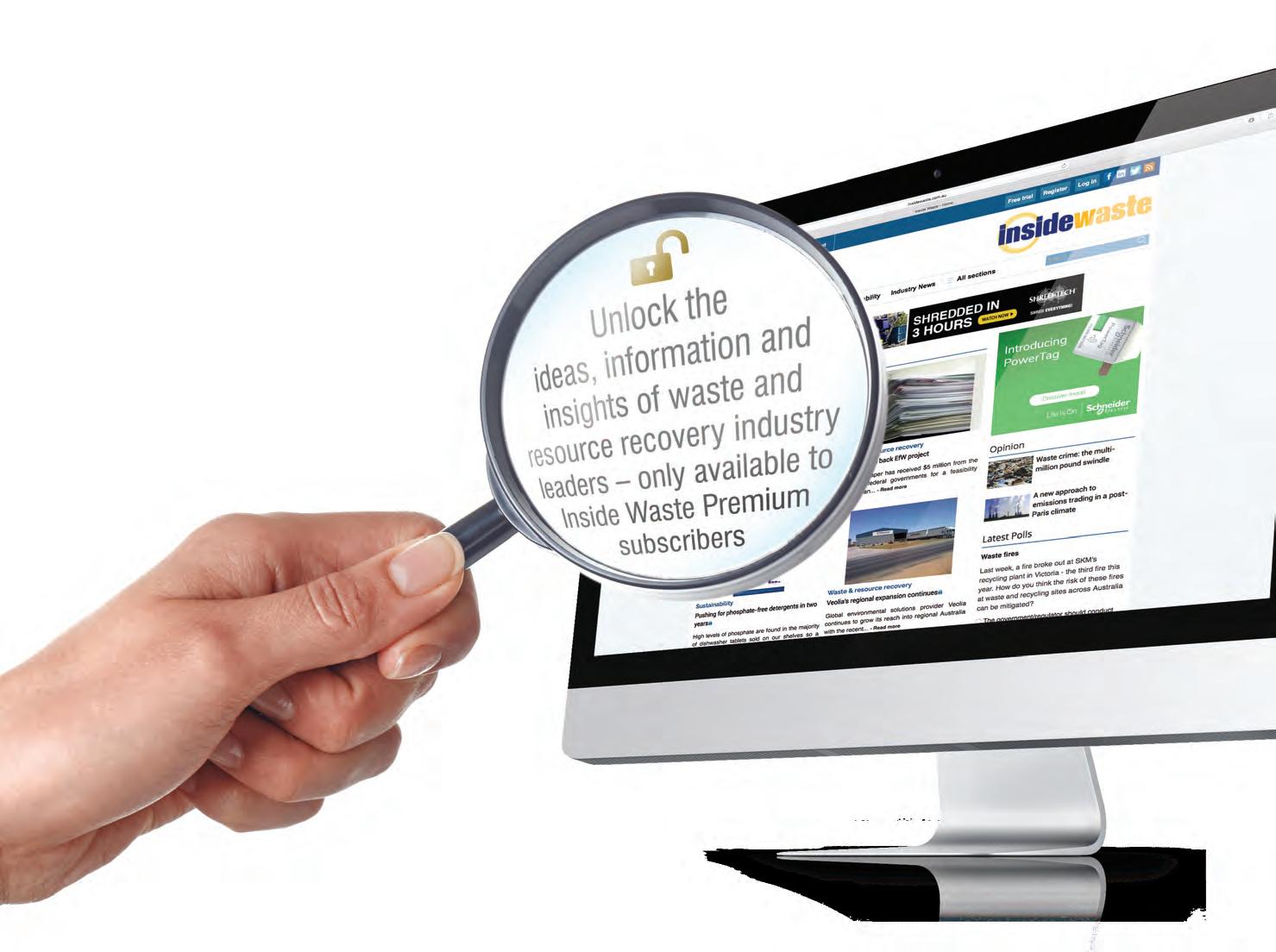
Re.Group’s commitment to building a sustainable tomorrow
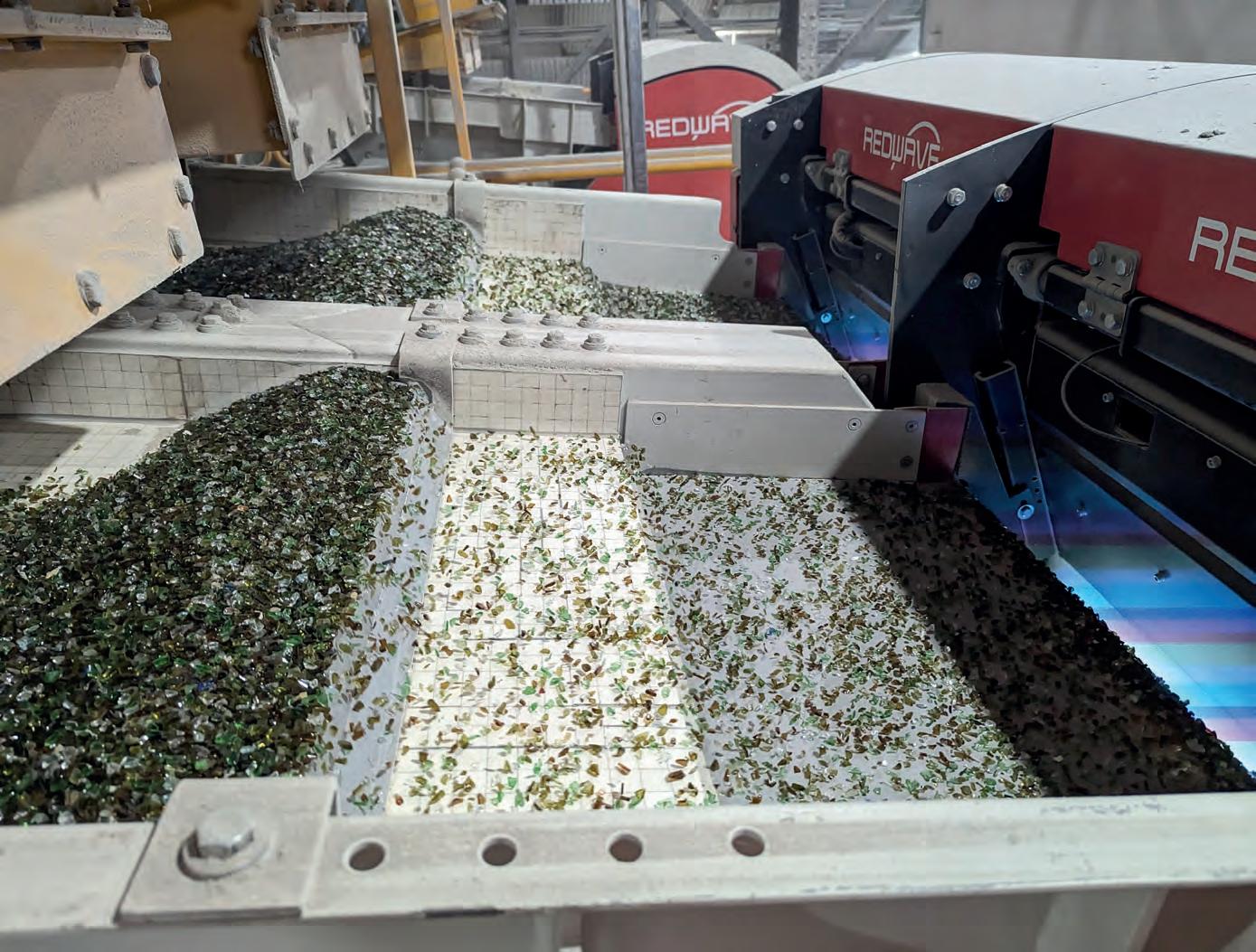
By David Singh, Managing Director, Re.Group
VICTORIA celebrated the one-year anniversary of its Container Deposit Scheme (CDS) in November, and the state marked an impressive milestone: one billion containers returned in just 12 months. Re.Group is thrilled to have contributed to this outcome, with five of our Return-It depots ranking in the top 10 metro refund points. This achievement underscores the positive impact our network is having in Victoria and across Australia.
Re.Group has grown over the past decade. This organisational growth is not just of the bricks and mortar kind, but also industry knowledge
and experience through the carefully selected acquisition of employees who are our greatest assets, and through formation of true partnerships with our clients and other stakeholders. We have demonstrated time and a gain the great outcomes we can deliver by working collaboratively together with local governments, community groups, and our industry partners; we always strive to work well with others and remain focused on the ‘big picture’.
We set out with a vision to deepen our impact on recycling and drive our mission for a wasteless society, with our values at the heart of all that we do. Today, our MRF and CDS networks reach millions of Australians across NSW, VIC, QLD, SA, WA, the ACT, and
New Zealand, although this growth has not come without its challenges. If you’re reading this magazine, you’d know that waste management and resource recovery is a tough gig for a multitude of reasons – batteries, need we say more? But it is these very challenges that drive our commitment to developing high-quality facilities and solutions.
This is why we are incredibly proud of the many new, award-winning facilities that we have built in the last decade, including our Adelaide SMRF and more recently, the Sunshine Coast MRF. You may have read about these facilities in the media – we’re not shy of our accomplishments, and nor should anyone in the sector be. What we do is hard, and meaningful; when
we do it well, we make a difference for the communities we serve, and we should celebrate those outcomes proudly when we can.
New and shiny kit is often exciting to rave about, but one of the things that perhaps we do not do as well is talk about our deep commitment to –and the accompanying grunt work in – bringing our older facilities acquired in 2022 into the Re.Group fold, or the Re.Group way. Back in 2022, against the backdrop of infrastructure gaps in NSW and Victoria, the urgent need for increased local processing due to the export bans, and our vision to improve resource recovery outcomes through our tried and tested management principles and plant design, we acquired Polytrade which
Re.Group’s optical sorters at the Enfield Glass Beneficiation Plant that colour sort glass into green and amber, and flint cullet. Images: Re.Group
AGRICULTURE FARMING EDUCATION WASTE
MANAGEMENT RESOURCE MANAGEMENT
CONSERVATION MANUFACTURING RESOURCES
ENERGY HEALTH & SAFETY INFRASTRUCTURE
ENGINEERING MINING CONSTRUCTION
QUARRYING AGRICULTURE FARMING EDUCATION
WASTE MANAGEMENT RESOURCE MANAGEMENT
CONSERVATION MANUFACTURING RESOURCES
ENERGY HEALTH & SAFETY INFRASTRUCTURE
ENGINEERING MINING CONSTRUCTION
QUARRYING AGRICULTURE FARMING EDUCATION
WASTE MANAGEMENT RESOURCE MANAGEMENT
CONSERVATION MANUFACTURING RESOURCES
ENERGY HEALTH & SAFETY INFRASTRUCTURE
ENGINEERING MINING CONSTRUCTION
QUARRYING AGRICULTURE FARMING EDUCATION
WASTE MANAGEMENT RESOURCE MANAGEMENT
SEARCH FOR TOP INDUSTRY TALENT THROUGH OUR JOBS BOARD.
CONNECT WITH ALIGNED CANDIDATES.
BOOST YOUR CHANCES OF FINDING SKILLED APPLICANTS.
SCAN TO CREATE AN ACCOUNT TODAY AND DISCOVER YOUR PERFECT MATCH!
POWERED BY CAREERONE
had a number of MRFs across these states. Since then, we have made, and continue to make, significant investments in these MRFs to not just provide much needed capacity, but to also support better outcomes in resource recovery of both commingled recycling and CDS.
We pointed to Victoria’s impressive CDS record early in the piece, and the success our Return-It team has had in the world’s newest container refund scheme. A pillar of support for the scheme has been our Hallam Container and Plastics Sorting Facility, and this is a prime example of our ongoing investment. In 2023, Re.Group embarked on a journey to transform the Hallam recycling facility into a dual-purpose operation that could optically sort both containers from our CDS collections (except glass –but more on that to come) and mixed plastics received from our network of MRFs.
O ver the course of eight months (and millions of dollars later), our talented RDT engineering team had equipped the facility with a host of advanced equipment, from new trommels, magnets, windsifters and eddy currents, to high-tech optical sorters that sort plastics into six separate polymers, including clear PET, coloured PET, natural HDPE, and Polypropylene. The outcomes for mixed plastic sent to this facility are the same as we achieve in those shiny new sites. While there’s different pathways for getting there, we ensure the same great outcomes for the materials that the community trust us to process.
In Sydney, our Enfield Glass Beneficiation Plant (GBP) has added another layer of capability to our network (on top of our existing GBP in Dandenong Victoria – where that CDS glass goes). Commissioned in August 2022, the new GBP is designed with the latest glass processing technology to handle and colour-sort glass into cullet for bottle-to-bottle recycling. It is state-of-the-art, with specialised equipment installed to colour sort glass into 8-50mm and 3-8mm glass fractions. It is built with an advanced glass cleaning system featuring different types of vibrating screen systems, magnets, and eddy currents, as well as x-ray sorting and 16 optical machines that sort glass into amber, flint, and green cullet.
With a built capacity of 100,000t/a, there is an exciting opportunity to grow glass processing in Sydney, so watch this space.
These are but two of our acquired assets that we have made myriad improvements to. Investment continues in these MRFs and we
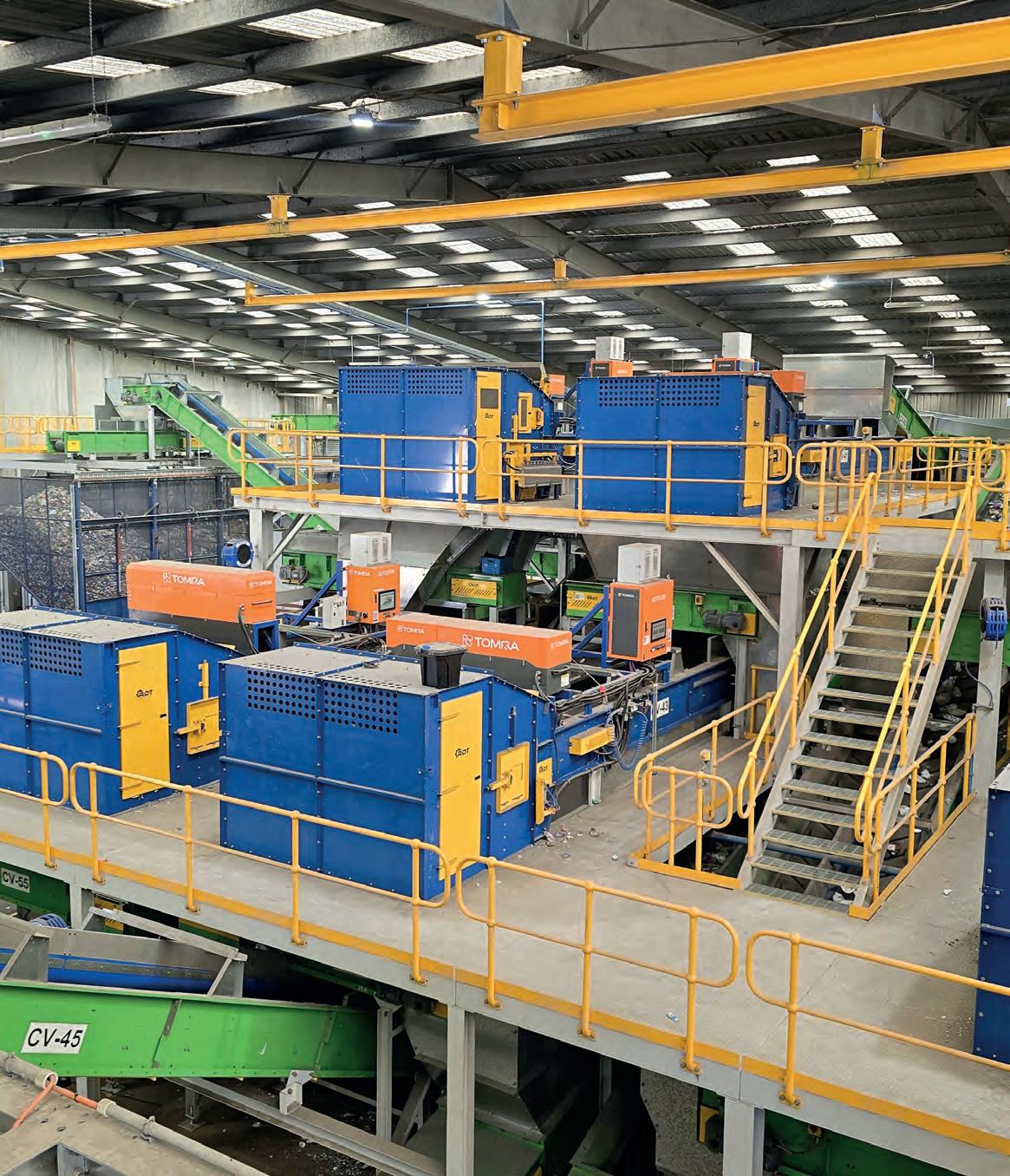
“We set out with a vision to deepen our impact on recycling and drive our mission for a wasteless society, with our values at the heart of all that we do.”
have a pipeline of upgrades slated for our other facilities, including our Dandenong MRF and GBP, and Chinderah MRF, alongside other exciting new projects that we’ll soon unveil.
We’re not content with mediocre. What we aspire to achieve is a network of Re.Group facilities – old,
new and everything in between –that consistently meet the highest standards that we set for ourselves. At the end of the day, we may not be able to fully control the materials we receive (though we will continue to educate and advocate), but we can certainly continue on a path of improvement to provide certainty to
our customers and the community that partnering with Re.Group means choosing a future-focused, resilient approach to recycling. Our mission is to make sure every material we handle has the best chance at a second, third, or even continuous life, contributing to a truly circular economy for Australia.
Re.Group has transformed its Hallam recycling facility into a dual-purpose operation that can optically sort containers.

Closing the loop on solar
AUSTRALIA’S unprecedented adoption of solar energy presents both an environmental triumph and an impending waste management challenge. With more than 3.19 million PV installations generating over 27.2 gigawatts of power, the nation leads the world in per-capita solar energy generation. This clean energy infrastructure, weighing approximately 1.3 million tonnes, represents both a remarkable achievement in renewable energy adoption and a looming recycling challenge.
W hile solar power reduces carbon emissions, the industry faces a critical sustainability challenge. Forecasts indicate an 18-fold increase in solar panel e-waste between 2019 and 2030. With the average lifespan of solar panels being approximately 20 years, Australia’s early adoption of solar technology means we’re now approaching a critical juncture where the first wave of installations will reach end-of-life.
“The ‘stuff’ in e-waste – in particular, solar panels – isn’t trash. It’s valuable material that can be reused,” says Sircel CEO, Anthony Karam. “We should be doing whatever we can to support scalable and commercially robust solutions to allow that material to be liberated and re-introduced back into the circular economy. We can’t continue to be a single-use society.”
Breaking new ground in solar recycling
In response to this challenge, Sircel is launching an initiative: a solar panel recycling facility based in Parkes, Australia. This state-of-the-art facility represents a step forward in addressing Australia’s mounting e-waste crisis by tackling the incoming “avalanche” of endof-life solar panels.
The environmental implications are substantial. Historically, most defunct solar panels – up to 85 per cent in Australia – end up in landfill. Valuable materials are lost, and potentially
harmful components can leach into soil and groundwater. Sircel’s facility achieves recovery rates of up to 100 per cent of materials from each panel, reducing landfill waste while returning resources to the circular economy.
The facility employs cutting-edge technology, enabling the systematic breakdown of solar panels into their constituent materials.
“Solar panels are 100 percent recyclable,” explains Karam. “The aluminium is generally high grade so when it comes out clean it can be reused easily. It has high-quality glass as well, and there’s plenty of downstream industrial uses for it. As for the wafer itself, there’s a little bit of copper, but predominantly silver and silicon, which are also sought-after elements.”
Scale and impact
The processing line methodically removes the junction box, aluminium frame, and separates the glass from the laminate in just one minute per panel. At full capacity,
the facility can process at the rate of one panel per minute. That’s more than 420 panels a day and more than 100 tonnes per year.
To put this in perspective, a single 100MW solar farm typically contains around 10,000 panels. With Australia’s rapid solar adoption, particularly in the commercial and industrial sectors, the volume of panels to soon be recycled is substantial. Large commercial installations can range up to 2MW in size, while residential installations – which account for over 20GW of Australia’s solar capacity across 3.3 million households – typically comprise 16-18 panels per system.
Market development and innovation
Sircel has well established markets for recovered aluminium and copper, and is actively developing outlets for other materials recovered, including glass cullet and plastics components.
While global solutions for silicon
Solar panels are 100 per cent recyclable – nothing should be going to landfill.

“We should be doing whatever we can to support scalable and commercially robust solutions to allow that material to be liberated and re-introduced back into the circular economy. We can’t continue to be a single-use society”
recovery at scale remain elusive, Sircel continues to invest in research and development.
“We’ve got a whole wave of panels that are coming to their end of life soon, and we need a better solution for them,” says Karam.
The company works with partners to process cell laminates using conventional technologies, maximising precious metal recovery while minimising landfill waste.
Industry challenges
Despite the environmental imperative, there are challenges within solar recycling that might lead some operators to compromise standards and cut corners.
Sircel charges a sustainable gate fee for panel processing, but some operators offer to pay for panels, raising questions about the viability of their recycling practices.
“The minimum gate fee for the panel should be less than it would cost to go
to landfill so it’s a win for the customer,” said Karam. “I know the numbers intimately. My question is, ‘How can you make money if you’re paying someone $5 a panel?’”
Corner-cutting and driving prices down leaves little incentive for anyone to build the infrastructure required to properly tackle this problem.
The e-waste recycling industry can be equally opaque, and some operators still employ unethical practices, including shipping waste overseas.
“You have to invest in plant and machinery,” he said. “Some people are saying they are processing 20,000 tonnes a year manually. How can you manually dismantle 20,000 tonnes of e-waste a year?
What’s really happening is that the waste is taken to a facility where they cut a cord then ship it overseas. They can tell their clients that they’ve recycled e-waste and even give them a certificate saying so.”
The need for cohesive policy
The solar recycling industry currently lacks comprehensive regulatory frameworks for managing end-of-life solar panels. The Smart Energy Council has proposed product stewardship schemes and developed ideas that will have great impact, but Karam advocates for better support for specialised recyclers.
“We’re actually a green technology company in resource regeneration. We don’t consider ourselves to be in the waste industry,” Karam emphasises.
“Government and large industry players understand there’s a huge difference between these two things: we’re a critical cog in the circular economy machine, which should be building the fabric of our communities.”
As Australia’s solar capacity continues to grow, the need for responsible end-of-life management becomes increasingly critical. For most companies, institutions, and
households who invest in solar, the environmental and decarbonisation benefits are paramount. End-of-life management is crucial to ensure that system upgrades don’t negate the environmental benefits delivered through their lifetime. Sircel works with national waste channel partners focused on increasing landfill diversion rates and improving ESG outcomes. However, Karam said there’s a need for industry-wide cooperation.
“We just need more cohesive framing around the consumption and management of e-waste,” he said.
With its Parkes facility, Sircel is setting new standards for solar panel recycling in Australia, proving that environmental responsibility and resource recovery can go hand in hand. The challenge now lies in ensuring that the entire industry adopts similarly high standards to create a truly sustainable circular economy for solar energy infrastructure.
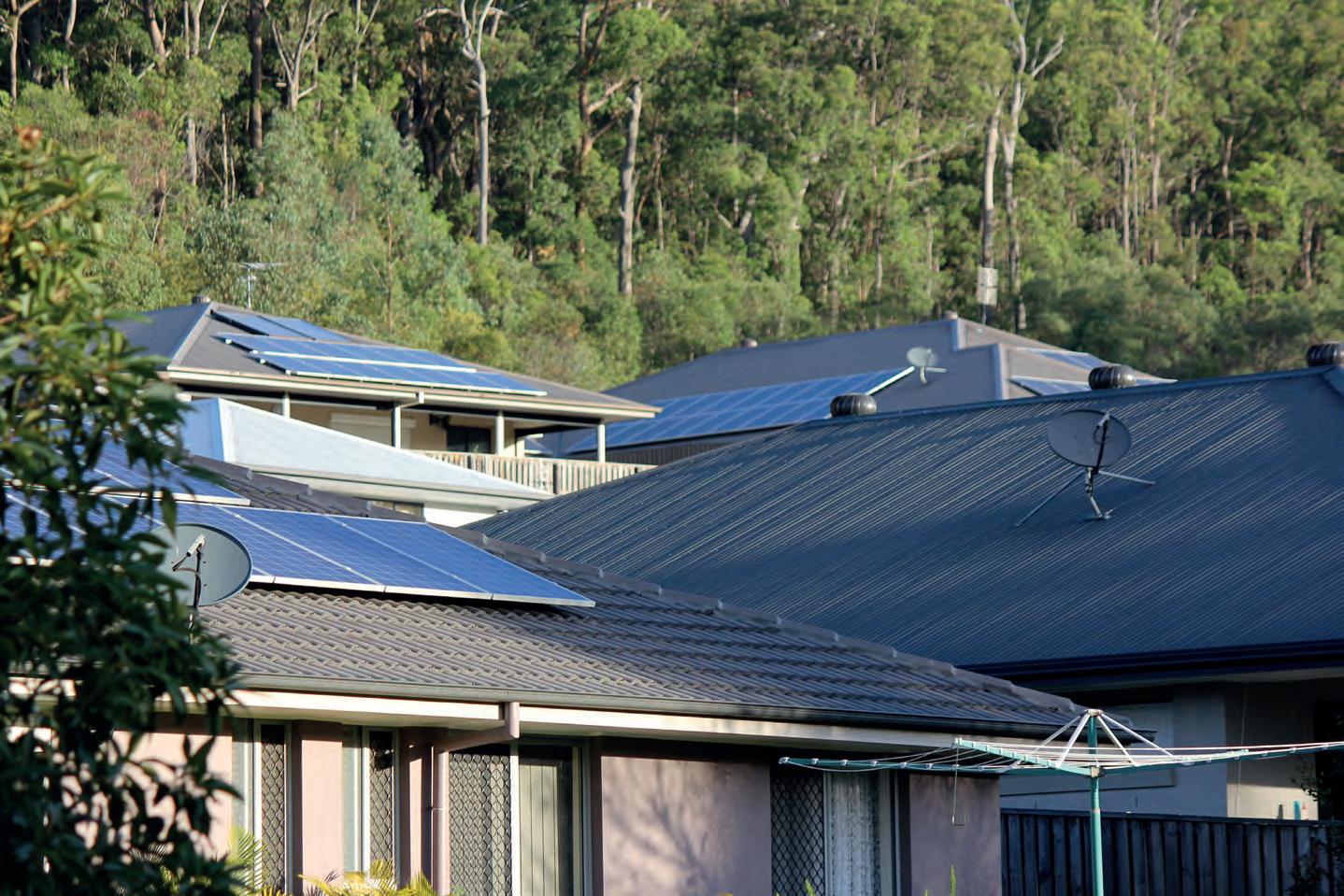
Efficient waste solution for
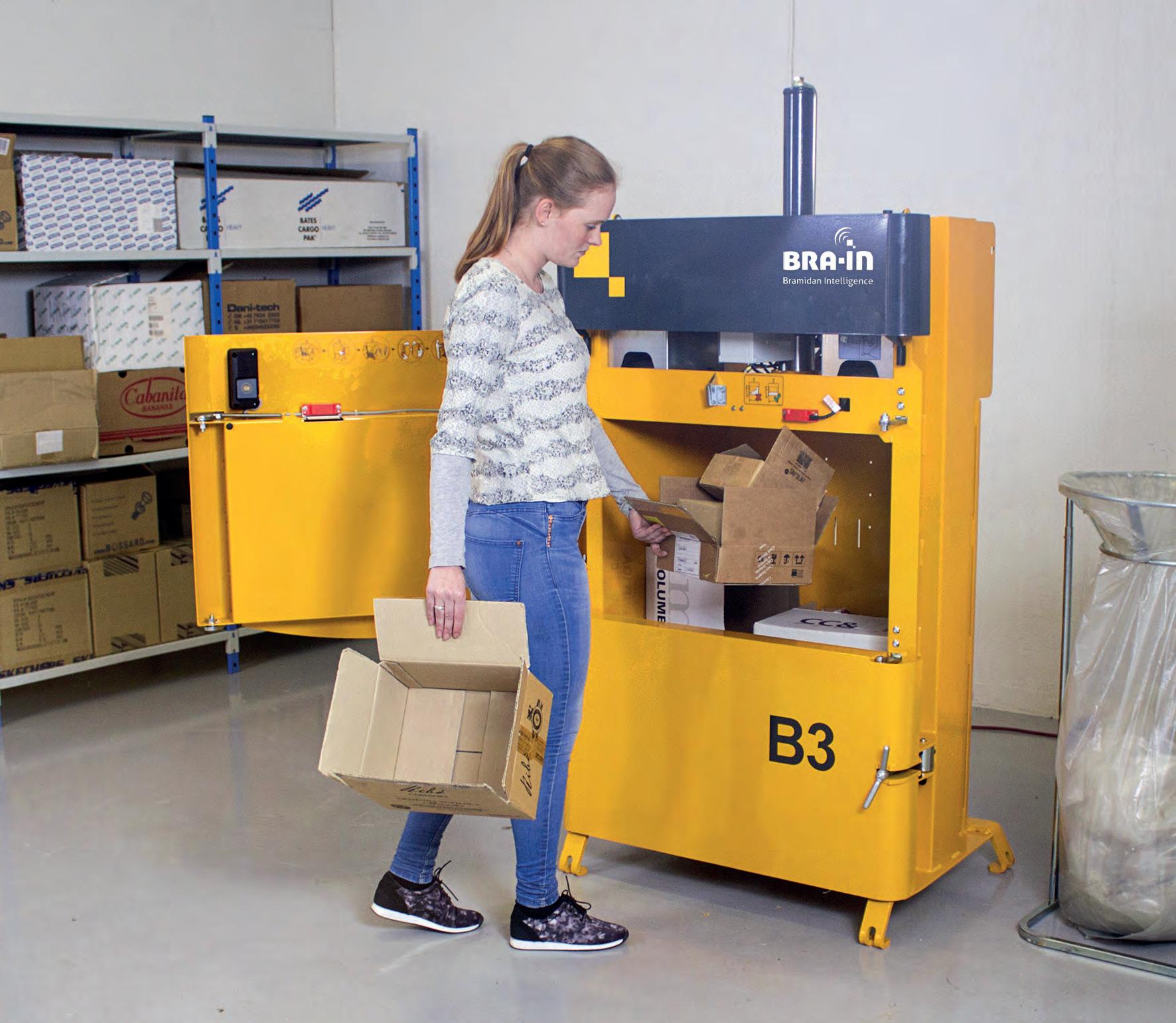
method for consolidating on-site packaging waste.
Wastech is the exclusive distributor of the Bramidan range of balers, which includes several models tailored to specific needs.
The vertical balers are suited for businesses where space is limited, offering a compact design that doesn’t compromise on performance.
On the other hand, the heavyduty balers are engineered for high throughput, allowing businesses to process larger volumes of waste quickly and effectively.
According to Brianna Armstrong, key account manager at Wastech Engineering, the benefits of using these balers are clear.
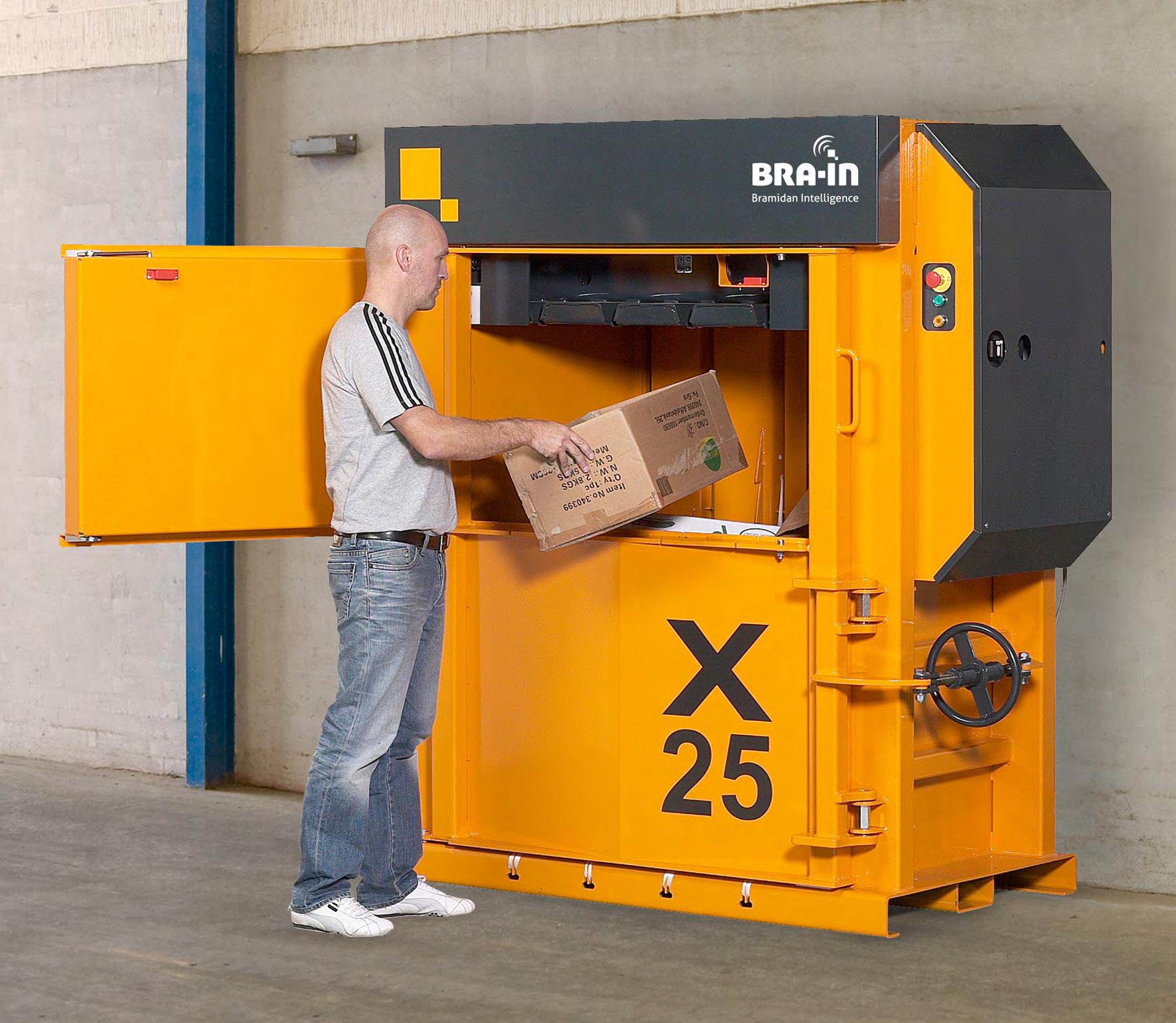
Balers can save time and money for businesses that take advantage of their features. Images: Wastech
Some balers are suitable for places that have limited design.
For businesses that rely on collection trucks for waste removal, baling offers an advantage. Without compaction, waste takes up more space in the collection truck due to air pockets within the uncompressed materials. This results in multiple trips to dispose of waste. However, using a baler maximises truck capacity, allowing for more materials to be collected in a single trip, reducing both collection frequency and costs.
Enhanced safety features
In addition to their efficiency, these balers are equipped with advanced safety features.
“The operation is designed to require two-hand activation,”
Armstrong added. “Both buttons must be pressed simultaneously to initiate the compaction process, ensuring the operator’s hands are kept clear of the machine during operation.”
Depending on the model, balers offer two modes of ejecting compacted material – automatic or manual.
Hi gh-capacity models like the B50 XL SD baler feature a 50-tonne compaction force, with the capability to bale up to 750 kilograms of material at a time. Notably, the balers eliminate the need to break down cardboard boxes, as the force crushes them into a much smaller size for easy disposal.
Space-saving solutions for high-traffic areas
The X Series balers are ideal for businesses operating in areas with limited space, such as loading docks or other high-traffic zones.
“The B series balers are too tall for spaces with height restrictions,” explained Armstrong. “That’s where the X series comes in. These units are specifically designed for places like visitor centres, shopping malls, and busy docking areas where floor space is at a premium.”
Specialist baler series for specialised waste
The Specialist Baler Series is designed for businesses that need to manage unique types of waste. These balers can drain
liquids, crush materials like aluminium cans, and handle drum waste. Compact yet powerful, these units are capable of reducing waste volume by up to 90 per cent, which leads to savings in both space and disposal costs.
Exclusive
distribution and
support
An advantage of choosing Wastech Engineering is that they are the exclusive distributor of the Bramidan balers in Australia. This means customers have a single point of contact for both purchasing and after-sales support. Wastech offers maintenance and service, with technicians available nationwide to assist with any technical issues or servicing requirements.

The B series has excellent safety features.
Auger Compactor
Unit Dimensions: Between 4200 to 7200 x 2480 x 2400 mm
Weight: 3500kg
Price: Contact Wastech Engineering for more information
More: Ability to handle specific waste type and handling/loading method.Designed to handle wet waste with no cavities behind the chamber area for waste to gather.
Name: Wastech Engineering
Phone Number:
Webpage:
Email:
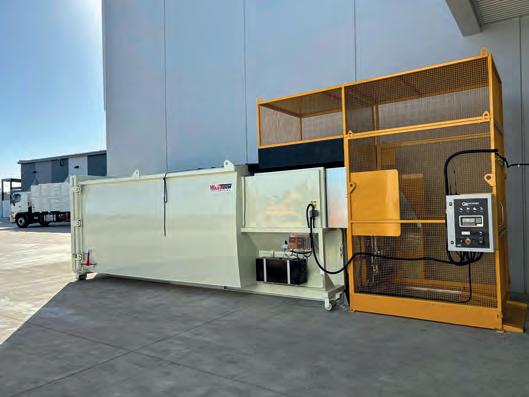
Unit Dimensions: 2495 x 1660 x 3590 / 2540 (mm)
Weight: 3750kg
Capacity (in weight): 650-800kg
Price: Contact Wastech Engineering for more information
More:
• Comes with BRA-IN (Bramidan Intelligence) Monitoring System
• Extra-large chamber
• 8 wire tying for a more stable bale
• Standard with a sliding door that opens automatically
• Bales are optimised for transport
• Stack bales 2 and 2 instead of 3 to optimise a truck load
Name: Wastech Engineering
Phone Number: 1800 465 465
Webpage: wastech.com.au
Email: sales@wastech.com.au
Bramidan B5W Baler
Unit Dimensions: 1355 x 895 x 2370 (mm)
Weight: 600kg
Capacity (in weight): 80-110kg
Price: Contact Wastech Engineering for more information
More:
• Comes with BRA-IN (Bramidan Intelligence) Monitoring System
• Perfect for handling large boxes
• Comes with a wide filling opening
• Ef ficient retainers hold compressed materials down
• Bale is tipped out automatically
• Front-placed strap rolls for easy strap change
• Operates on single phase power supply
Name: Wastech Engineering
Phone Number: 1800 465 465
Webpage: wastech.com.au
Email: sales@wastech.com.au
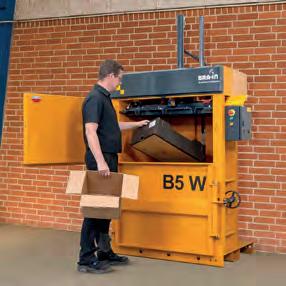
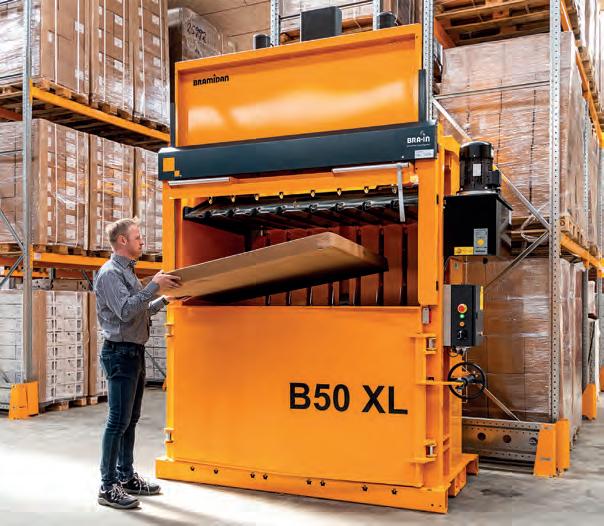
Fire Rover Fire Suppression System
Unit Dimensions: 6096mm (L) x 2438mm (W) x 2591mm (H)
Weight: 6000kg
Capacity (in weight): Water Tank: 3785 litres
Price: Contact Wastech Engineering for more information
More:
• Advanced fire detection analytics with human verification
• Remote-controlled suppression
• On Guard — 24/7
Name: Wastech Engineering
Phone Number: 1800 465 465
Webpage: wastech.com.au
Email: sales@wastech.com.au

Bramidan Baler B50 XL SD
WASTECH ENGINEERING
S4000 Stationary Compactor
Unit Dimensions: 6448 x 1900 x 1720 mm
Weight: 5800kg
Price: Contact Wastech Engineering for more information
More:
• Comes with a clear top opening and chamber volume of 4m³ that can accept large product loads.
• Compatible with 31-60m³ containers and transfer trailers.
• Comes with its own stand-alone hydraulic power pack and oil cooler.
Name: Wastech Engineering
Phone Number: 1800 465 465
Webpage: wastech.com.au
Email: sales@wastech.com.au
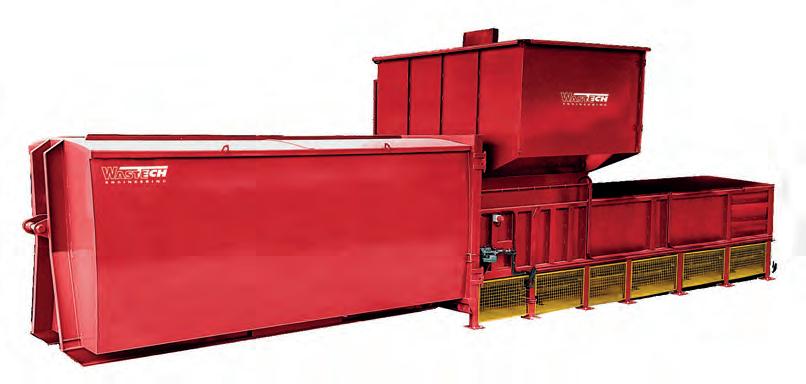
S8000 Stationary Compactor
Unit Dimensions: 8950 x 2200 x 2000 mm
Weight: Approx. 11000kg
Price: Contact Wastech Engineering for more information
More:
• Designed to cater for a high throughput of up to 120 tonnes per hour.
• Compatible with all feed types including moving floor, push pit, conveyor and front-end loader.
• Constructed from high tensile steel built to withstand high compaction force.
• Can accept large product loads and increased penetration into the Trailer for less spring back and improved seperation with less spillage.
• Compatible with 60m³ transfer trailers and comes with its own stand-alone hydraulic power pack and oil cooler.
Name: Phone Number:
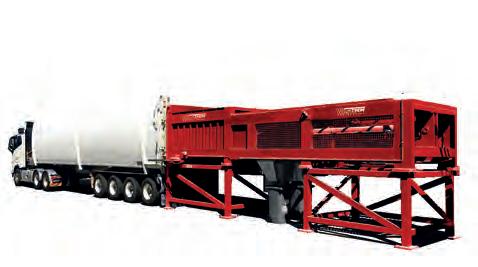
Bramidan X25 Baler
Webpage: wastech.com.au
Email: sales@wastech.com.au
Transfer Trailer
Weight: From 11100kg
Price: Contact Wastech Engineering for more information
More: -
• 53 – 65m3 Triaxle
• 65 – 75m3 Quad Axle
• 114 – 120m3 A -Double
• 106m3 Pocket Road Train
• 130m3 Road Train
• 70m3 Top Load Moving Floor Trailer
• Material: High Tensile Steel (5mm floor, 4mm walls and roof)
• Rear Door Cycle Time: 15 Secs. (Hydraulic Operation)
• Preferred Hydraulic Pump Size: 80l
/ min
• Working Pressure: 2,100 PSI
• C ylinder Type: 5 & 6 Stage Telescopic Cylinder with Centre Support
• Eject Blade Cycle Time- Eject: 140 secs. | Retract 150 secs. (5 Stage Cylinder - Single Trailer)
• Doors: Top or Side Hinged Rear Doors (Hydraulic or Manual)
Name: Wastech Engineering
Phone Number: 1800 465 465
Webpage: wastech.com.au
Email: sales@wastech.com.au

Unit Dimensions: 1745 x 1260 x 1995 (mm)
Weight: 1410kg
Capacity (in weight): 200-300kg
Price: Contact Wastech Engineering for more information
More:
• Comes with BRA-IN (Bramidan Intelligence) Monitoring System
• Provides a stable compaction, a powerful pressforce and a low overall height.
• For various types of material – even expandable
• Large and wide chamber
• Retainers prevent in-chamber material expansion
• Short cycle time for fast clean up
• Moving parts are protected inside the machine
• Low overall height
Name: Wastech Engineering
Phone Number: 1800 465 465
Webpage: wastech.com.au
Email: sales@wastech.com.au
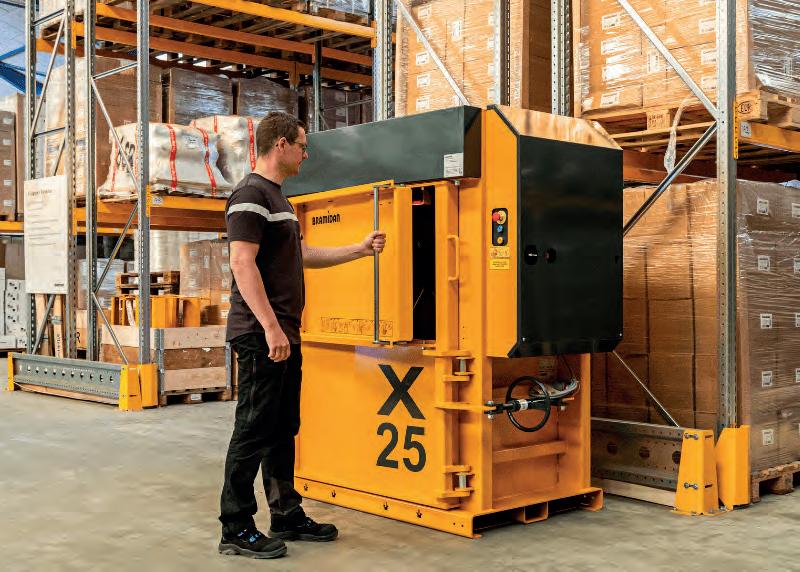
WASTECH
Biting the hand
Dear Sir,
The government! Ah, yes, our overlords – those in the know. Those that hold the purse strings. They who are above us mere mortals. Those who are an easy target.
The Westminster System that we adhere to in the Motherland has its quirks – both positive and negative. The first past the post system is one that lends itself to a two-party state (although the masses are onto them aren’t they, with a plethora of parties now appearing on the backbenches having their say).
Then you have the preferential system down here in this Great
Southern Land. To me, it’s a mess. But our cousins in the Antipodes love it. Spreads the love and allows many voices to be heard in the echo chamber of Parliament House in Canberra.
Me? I’m pretty agnostic about any political system. It is there to do a job. What catches my eye are the parliamentarians. Are they doing their job? What is their agenda (outside of their obvious political affiliation)? Are they there to serve themselves or their people?
I talk of this because of a couple of recent pieces I read online from the local mouthpiece of the waste industry. One was titled Industry needs to lead
the way – government won’t. To be fair the author did point out that governments do have to take in the wider public opinion, but that doesn’t mean they stay static. And that was one of the key planks of the piece. Government(s) are doing plenty of surveys, reports and papers – but very little action.
The other piece was titled NSW Government Taking Action on Landfills Really? They are? Talk about being a pound short and a day late, Old Boy. The piece waxed lyrical how NSW would run out of landfills in the next 10 years and that everybody – the government, public and environmental
groups – needed to get together to find solutions or the costs would be dear for households and businesses. Really? The industry has only been saying this, for, oh, forever!
I don’t think governments realise how engaged the industry is. This isn’t a bunch of ne’er-do-wellers sitting around doing nothing. They are a passionate rabble attempting to make a huge difference in a trying industry. Governments need to start being part of the solution. Not the problem. PS: please don’t show this to the PM.
Yours JB
I don’t think governments realise how engaged the industry is. This isn’t a bunch of ne’er-do-wellers sitting around doing nothing. They are a passionate rabble attempting to make a huge difference in a trying industry.

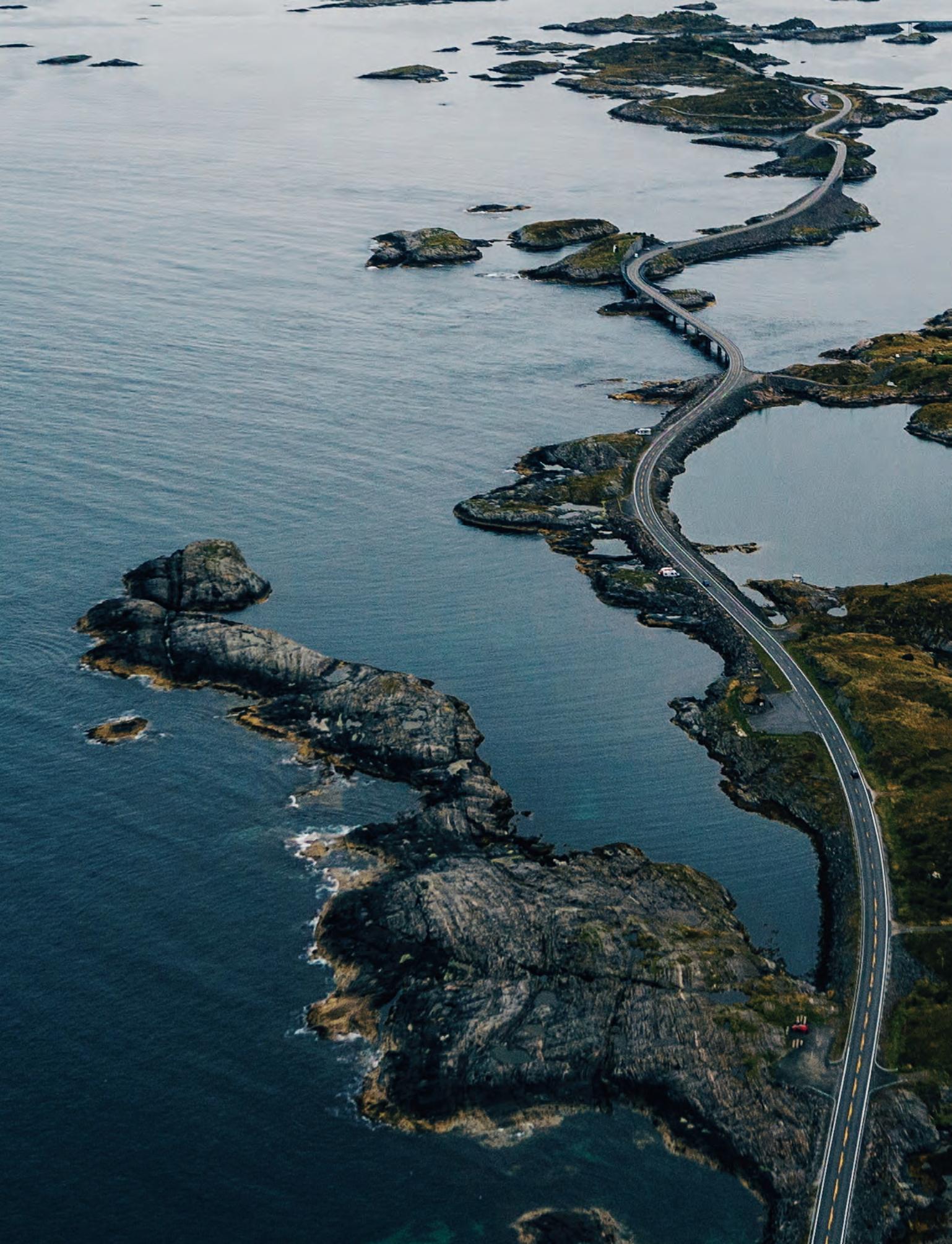
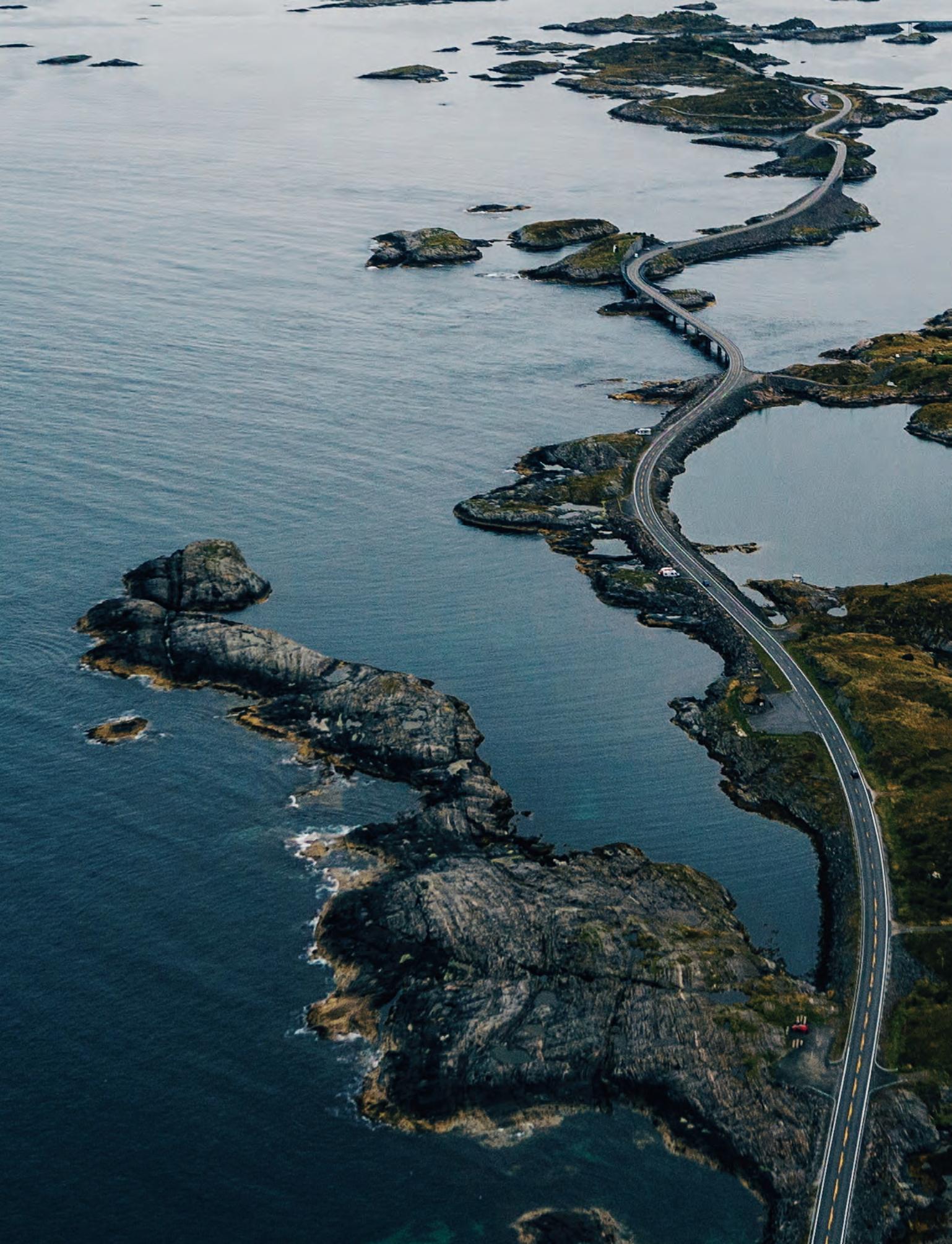
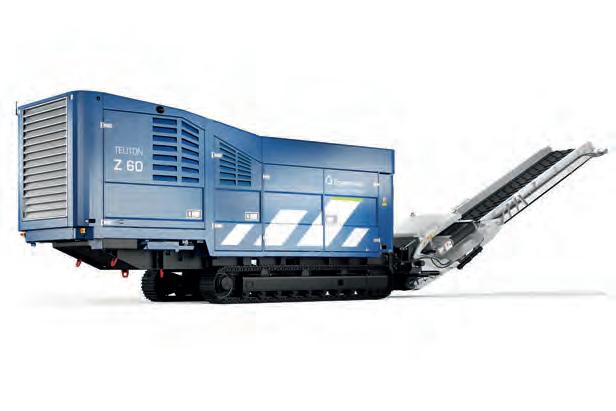
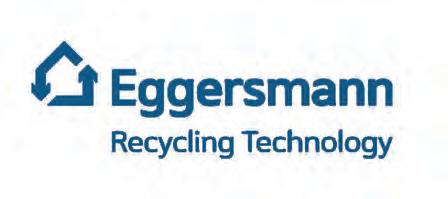
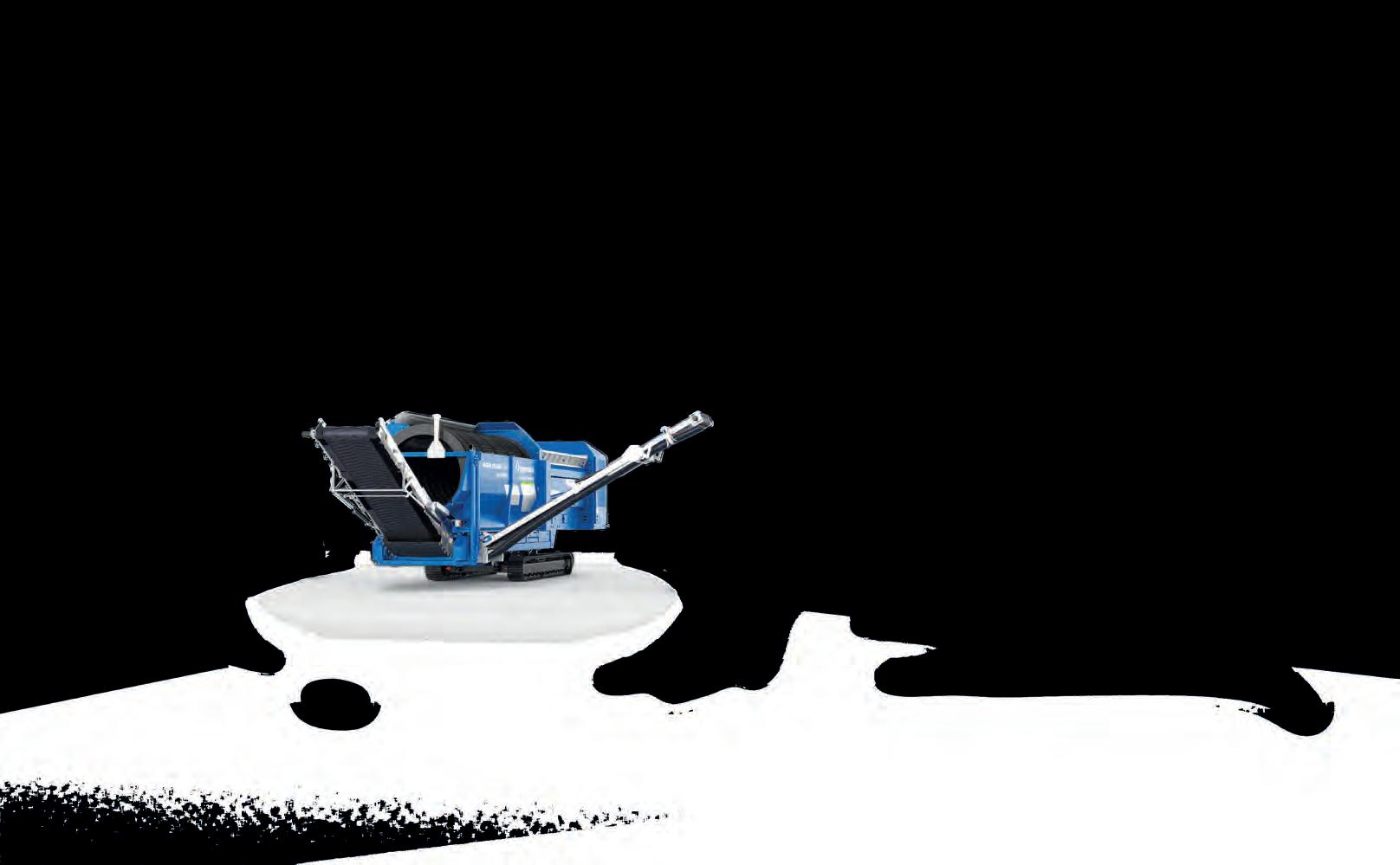
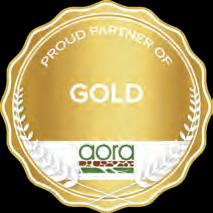
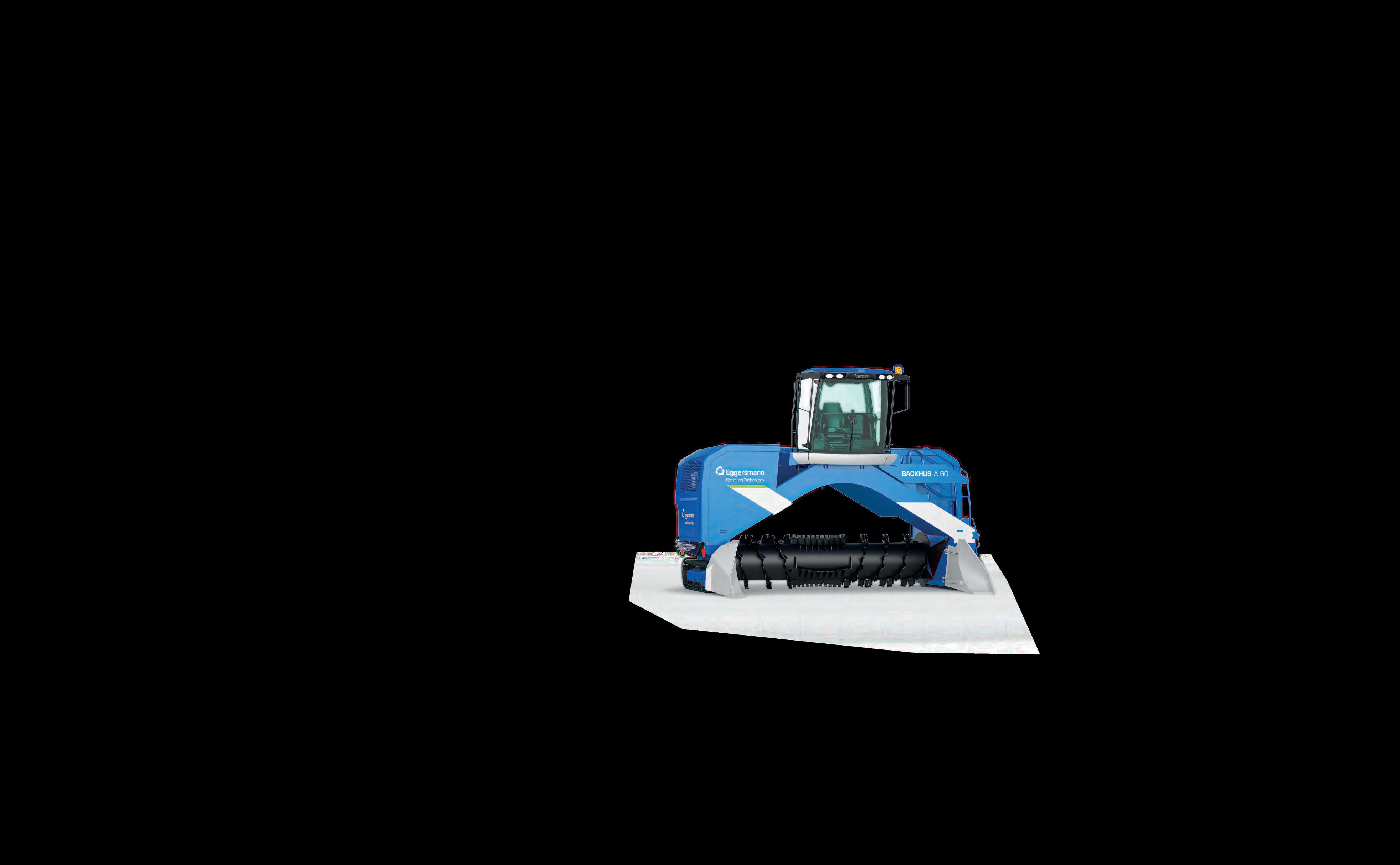