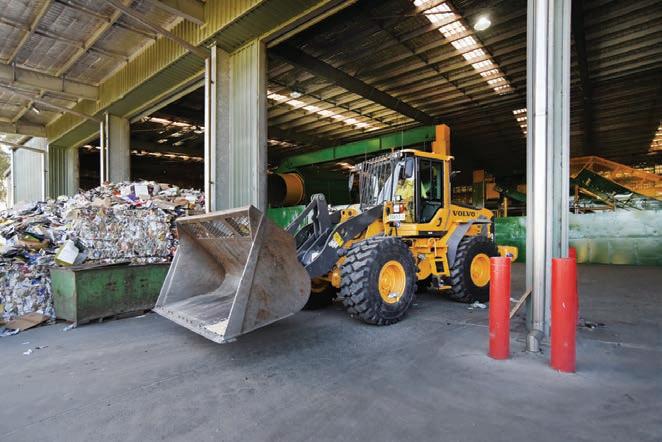
86 minute read
WIRA Awards
by Prime Group
The 2021 Waste Innovation and Recycling Awards were postponed last year due to the COVID-19 pandemic. It was great to see the resilience of the industry as it overcome lockdowns, restrictions and having to adapt to a new way of doing things. Now it is time for the industry to acknowledge it successes throughout what has been a very challenging 24 months.
These awards are all about celebrating the industry – milestones, innovation and achievements throughout 2021. The quality of nominations was high, which made the list of finalists all the more difficult to decide upon.
Judges were impressed with all of the finalists, and it was interesting to see that there was very little difference between them when it came to scoring. However, as with any competition, there can only be one winner. On behalf of Inside Waste, Waste Management Review and the Prime Creative Events Team, we offer a hearty congratulations to the 2021 Waste Innovation and Recycling Awards’ winners and look forward to seeing the latest innovations, services and projects coming to fruition over the next 12 months.
Community Engagement Success of the Year
TerraCycle School Recycling Program
TerraCycle School Recycling Program is designed to empower teachers and parents to raise the next generation with sustainable practices and values, by incorporating hands-on learning about recycling in the classroom, while driving positive outcomes for the environment.
Since 2017, TerraCycle has helped more than 5,500 Australian schools sign up to more than 40,000 recycling programs, to divert 1.8 million units of waste from landfill.
TerraCycle partners with leading brands such as Colgate, BiC, PAW Patrol and Glad to offer schools free recycling solutions. Schools that return waste earn TerraCycle points that can be redeemed to raise funds for themselves, or non-profits such as WWF and Keep Australia Beautiful.
TerraCycle first launched recycling programs in Australia for schools to sign up to in 2014. In the first four years, school sign-ups grew steadily year on year. In 2017, sign-ups increased by 111 per cent, while 2018 was the first year that sign-ups exceeded more 1,000 new schools recycling from all over the country.
TerraCycle achieved 64 per cent growth in school sign-ups from 2018 until 2019 before the onset of the COVID-19 pandemic in 2020. Despite COVID-19 and the ensuing restrictions impacting the opening of schools across the country, there was still a 50 per cent increase in school sign-ups to TerraCycle recycling programs, compared to 2017.
From 2018-20, shipment weight increased on average by 82 per cent each year.
On multiple occasions, TerraCycle created long-lasting relations with schools and their community, while driving positive outcomes for the environment by preventing hard-torecycle waste from going to landfill.
In 2014, Colgate first partnered with TerraCycle for the Oral Care Recycling Program. Through this program, collectors ship their used toothbrushes, toothpaste tubes and floss containers for recycling, instead of sending them to landfill. Since its launch, the Oral Care Recycling Program has enabled Australians to divert one million pieces of oral care waste from landfill and raise more than $100,000 in donations and prizes for schools and charities.
Ways in which the community are involved include: Hero collectors – TerraCycle puts the spotlight on top Community Collectors; TerraCycle Points Power Up – Collectors earn TerraCycle Points each time they send shipments of waste; TerraCycle Schools Newsletter; social media interaction profiling school collectors in media and blog content; various competitions; and signing up bonuses for those who join the scheme.
In addition to driving positive environmental outcomes, every time the community sends waste back to TerraCycle, they earn points, which can be redeemed and donated to a notfor-profit or an organisation such as a school. iw
Outstanding Facility of the Year
Bega Valley Shire Council
The Bega Valley Shire Council built an emergency landfill cell and resource recovery area, which was a direct response to the 2019-20 Black Summer Bushfires.
In New South Wales, about 2400 homes were lost, with the Bega Valley Local Government Area sustaining losses across 58 per cent of the shire. The fires destroyed 465 homes, damaged a further 134 homes and destroyed about 1100 outbuildings.
Although much of the damage was sustained during a day and night fire event, the fires burnt for a devastating 65 days.
During the bushfires the amount of waste the fire generated in the Bega Valley was estimated at more than 200,000 cubic metres, of which half was asbestos-contaminated. All was destined for landfill.
The landfill was under pressure after the clean-up of the March 2018 Tathra and Reedy Swamp fires. Council was proud of how it managed this clean-up but could never have expected the plans and processes it put in place then would need to be actioned again and on a bigger scale.
Bega Valley Shire Council and representatives from Department of Planning, Industry and Environment agreed to construct an emergency landfill cell and associated infrastructure at the existing Central Waste Facility (CWF).
Throughout the project, staff made every effort to ensure the community received exceptional value – designing, and constructing the facility well beyond the expectation of both the Solid Waste Guidelines and the Emergency Waste Disposal Cell Design and Siting Specifications. As such, the council now has all planning approvals, infrastructure, and capacity in place for the next disaster, which will be a matter of not if, but when.
All up, it took just 14 weeks for this facility to move from conception to becoming operational (ordinarily a project that would take up to 12 months).
The application and approval processes proved challenging, noting immense pressure to gain approval, while also ensuring due processes were followed and that all proposed activities would withstand intense public scrutiny, with much community focus around the CWF.
Most neighbouring landholders were opposed to the landfill which is subject to community scrutiny, and so staff worked to ensure that the project has been completed to best-in-class capacity. Group emails to neighbouring property owners worked well overall to keep communication lines open with the people impacted the most.
The emergency landfill cell and processing area was strategically located within the site so that the area could be used for a multitude of purposes once landfilling ceased. Staff undertook monitoring, including an increased sampling regime, with additional monitoring bores, dust jars and increased surface water monitoring – measures beyond the requirements set by the NSW EPA as part of council’s Environmental Protection Licence. iw
Workplace of the Year
Handybin Waste Services
Handybins founder Harry Wilson knows that in order for a good business to thrive, you need good staff on the ground and in the office. Having spent more than 50 years in the waste business Harry knows what makes a good enterprise tick, and at the core is the staff.
The company prioritises its staff and their contributions to waste reduction. It is excited to have seen the expansion and evolution of the company to maximise its opportunities in waste reduction. The additional training and prioritisation of safe work practices has enabled its staff to feel empowered and secure in their roles at the company.
Regular scheduled performance appraisal discussions between employees and management result in positive feedback from staff, particularly in relation to company policies such as the promotion of women in waste, subsidised waste collection services for staff, superannuation co-contributions, paid leave for performing local charity work, and free flu and tetanus vaccinations and medical check-ups through our preferred local doctor.
As well as being a pioneer in the waste arena, the company has also led the way in terms of making sure staff are looked after. Wilson just doesn’t meet the requirements under legislated labour laws, he goes out of his way to make sure his staff are looked after.
In terms of building a quality culture at Handybin, Wilson provides ongoing support to staff, in a variety of areas within the business. This includes: • An employee incentive and bonus scheme for those that are willing to go the extra mile. • Annual awards are presented to longer serving staff – for those who achieve those milestones there are anniversaries such as 5, 10, 20, and 30 years awards for being
with the business. • Super co-contributions – if a staff member makes a salary sacrifice contribution, Harry will make an extra contribution of up to $520 a year into that staff member’s super fund. • As well as the annual Christmas party for all employees, he gives out a free ham and six-pack of beer/ wine to staff members.
Wilson’s staff say he provides ongoing leadership to management to support fairness and equity amongst all staff members, including having a range of best-practice workplace bullying and discrimination policies and procedures. Consequently, employees are motivated and there is minimal staff turnover. iw
Handybins has an employee bonus scheme.
Operational Excellence Award
REMONDIS Australia
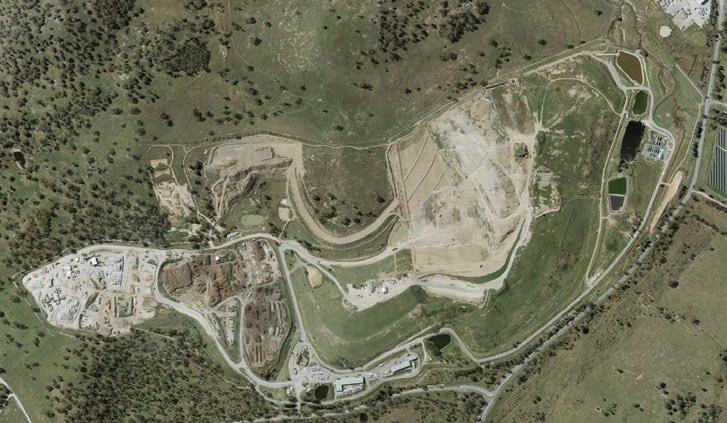
REMONDIS Australia has operated Mugga Lane Landfill, Mugga Lane Transfer Station, Mitchell Transfer Station and ACT’s Recycling Drop Off Centres since it acquired Thiess Services in 2011. REMONDIS has also operated the Mugga 2 Quarry site since 2019, which receives contaminated soils from the region. The facilities are managed on behalf of ACT NoWaste and service all of Canberra and some adjacent NSW jurisdictions. Over time, the facilities have transitioned from disposal to resource recovery operations with the REMONDIS ACT team using their operational expertise to assist the region to achieve their ambitious objectives under the ACT Waste Management Strategy 2011-2025.
REMONDIS and ACT NoWaste delivered the following initiatives and improvements: • 2016: Established the first KPI based landfill disposal contract (for MLL), delivering value for money to Government and residents with a quantifiable bonus and penalty structure; • 2017: Enhanced plant fleet, including an additional 836 compactors, to ensure operations are not impacted by maintenance activities; • 2019: Developed plans and Safe Work
Method Statements, trained staff and amended the EPA Environmental
Authorisation to receive and safely intern the remaining Mr Fluffy houses at MLL; • 2019: Replaced walking floor fleet with side-tippers, reducing turn around times from Mitchell Transfer
Station by more than 40 per cent; • 2019: Commissioned a Tarpomatic machine to reduce the amount of void space consumed by day cover; to date it is estimated the equipment has reduced the site’s
REMONDIS has delivered economic and environmental outcomes to several plants throughout the ACT.
cover requirements by 75,000 cubic metres; and • 2019: Successfully opened Mugga 2 Quarry with a unique gate fee sharing and booking arrangement that ensures staff and equipment are only present and operational when jobs are booked in with 48 hours notice.
REMONDIS has a progressive workplace safety culture that stems from great teamwork, contributions from all tiers of the workforce and a good understanding of responsibilities towards safety. Toolbox meetings, safety committee meetings, workplace inspections, audits, risk assessments and incident reports are completed to simultaneously communicate, report and consult on valuable safety aspects.
REMONDIS has delivered the social, economic and environmental outcomes that include significant operational efficiencies and cost-savings, significant reductions to greenhouse gas emissions, flexible solutions to the ACT residents and implementing measures to reduce and control air quality, which can affect nearby communities. REMONDIS has also recorded zero at-fault odour complaints for Mugga Lane Landfill during the current contract spanning more than five years of large-scale putrescible waste landfill operation.
REMONDIS has a collaborative and consultative relationship with ACT NoWaste, the owner of the facilities that REMONDIS operates on ACT Government’s behalf. REMONDIS is able to plan for, present, consult and discuss technical and operational challenges and opportunities with NoWaste on a case-by-case basis. Communication between the parties is two-way in nature, with both REMONDIS and NoWaste tabling site improvements for consideration at different times. iw
Innovation Award
Since building its MRF in 2012, and further upgrading in 2015, Handybin has successfully introduced glass, polystyrene and textile recycling to the communities it services.
The processing of these materials has led to Handybin implementing specific technology, plant and handling methods for the materials.
Glass processing
Handybin has implemented a soft material MRF with minimum breakage approach. This enables Handybin to pick whole glass and larger pieces by colour, which creates an opportunity to sell the material as a premium.
To ensure high resource efficiency for glass recovery, a new frontend system incorporating modern technology to give a cleaner primary separation of product was designed. The latest soft disc screens, bounce belts and ballistics screen softly separate whole glass containers, with minimal breakage. The disc screen is a well proven and effective way of separating containers from fibre. The latest generation of soft screen with tight collars, aids in clean separation of materials while minimising breakage of whole glass bottles.
Among other benefits of the system, the disc screens have plastic sleeves/collars to prevent further glass breakage on the steel shafts holding the discs. The intervals in the disc screen are graded differently meaning that its first few rows drop out the small broken glass and the later rows drop out whole containers. The process facilitates containers, whole bottles and larger pieces of broken glass, which fall off the bounce conveyor under the disc screen and are conveyed to the container line.
Textiles in the yellow lid recycling
Since May 2016 “Fabrics” bags have been received and processed on a permanent basis in the existing MRF. Residents are posted two “Fabrics” bags, which are used to dispose of good quality clothing that will be distributed to local charities.
The bags have been designed to ensure that clothes are collected and delivered intact. This innovation is supported by ensuring compaction rates are consistently kept low to prevent bag splitting, which helps to avoid soiling and damage to the clothing. The methodology employed at the receival plant includes extra care taken by the loader operator not to rupture bags when pushing up or depositing bucket loads of recyclables onto the main input conveyor belt. Bags proceed up the main conveyor and onward to the first receival station where they are manually removed by two sorters.
One of the two sorters picks the fabric bags from the conveyor and drops them down a chute where they are collected in 1100L bulk bins. At the end of shift, all full 1100L bins are wheeled to the Textiles Processing Area. Prior to assessment the bags are manually counted and recorded. The bags are opened by the operator and each individual item of clothing is assessed for quality. Any items deemed unusable by charities are removed as residual waste.
SPONSORED BY
TOMORROW’S SOLUTIONS. TODAY
Expanded Polystyrene
Handybin started processing Expanded Polystyrene (EPS) at its MRF in late 2013 after discussions with the NSW EPA. The company made application and received a grant towards infrastructure to process EPS. This included a polystyrene granulator, heater and extruder. In addition to promoting commercial collections and drop-off of EPS, Handybin introduced collection point trials at each councils’ waste management facilities to maximise EPS recovery.
The only way to ensure the required quality is to hand sort the product that is placed in the cages by residents. Non-EPS expanded plastics are removed, as are adhesive tapes on product and any loose material that adheres to product. Clean product is fed into the grinding section of the processor. It is heated and extruded into “sausage-shaped” lengths. The MRF Manager has devised a system where the sausage is blocked in crates. The resulting cubes are stacked on pallets and shrink wrapped to keep the product clean and allow stacking on flat top trailers for transport. iw
Outstanding WARR Project: Metro
REMONDIS Australia: Creating Change with Containers in WA
REMONDIS Australia operates the collection and processing of nonglass products for Western Australia’s Container Deposit Scheme (CDS) for the Perth, Peel and Wheatbelt regions. Containers are sorted at drop-off points by material type and then collected and processed in order to be sent to facilities for repurposing. REMONDIS currently collects and processes more than 28 million containers per month, equivalent to 500 tonnes from more than 60 locations. The company has introduced efficiencies to service this scheme, which has led to cost savings, reduced safety risks and a reduction of 1000 tonnes of CO2 emissions annually.
In many other CDS operations, containers are collected using infrastructure such as open top hook-lift bins to maintain the form of a container and therefore ease in conducting the strict audits required on CDS products in order for refunds to be processed. However, by maintaining container form, the available space within bins and trucks is not used and there is a large amount of air being transported. This increases not only the costs, but it also creates a large amount of carbon emissions due to increased truck kilometres.
As this was the first CDS in Australia that REMONDIS had tendered for, the company’s solution was to offer on-site compaction and rear-lift truck compaction to reduce the amount of air and increase the number of bottles able to be collected and transported. RFID (radio frequency identification) and trade-approved scale technology was used to ensure REMONDIS could report to the high level of auditability and accountability needed for CDS operations.
In the request for proposal provided by scheme co-ordinator WARRRL, REMONDIS was asked to give a solution based on the operations of the Queensland scheme. However, REMONDIS risked a non-conforming bid by submitting a compaction model. What was presented to WARRRL was an approach that improves industry practice to provide not only the cheapest model, but the safest, and an environmentally-friendly collection service. The company was able to reduce the number and frequency of trucks on the road, while collecting the same number of containers as seen in some east coast collection points.
The company’s target was to achieve a compaction ratio of 4:1, while providing reporting on the number of containers collected and receive no complaints from refund sites that collections were not frequent enough and therefore impacting their business – as this was one of the highest concerns from companies who operate similar producer responsibility CDS collection points on the east coast. The latest KPI reporting from WARRRL shows that REMONDIS is yet to have a complaint from refund sites and its compaction model is operating between 4:1 and 5:1.
In comparison to standard industry practice using hook-lift bins, their compaction model achieved a decrease in required truck resources. At current projection this is allowing the company to reduce more than 6,000 truck hours per annum.
The compaction methodology can easily be adapted and used by other CDS providers nationally. The technology used to both compact bottles and cans, as well as RFID and trade approved scales used to track the movement and weight of bottles, while expensive, is adaptable to multiple vehicle types. iw
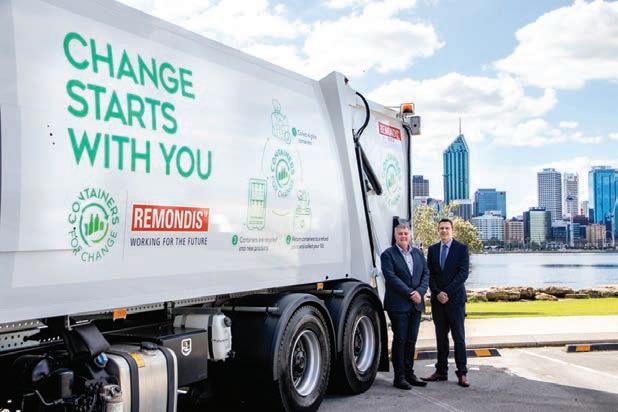
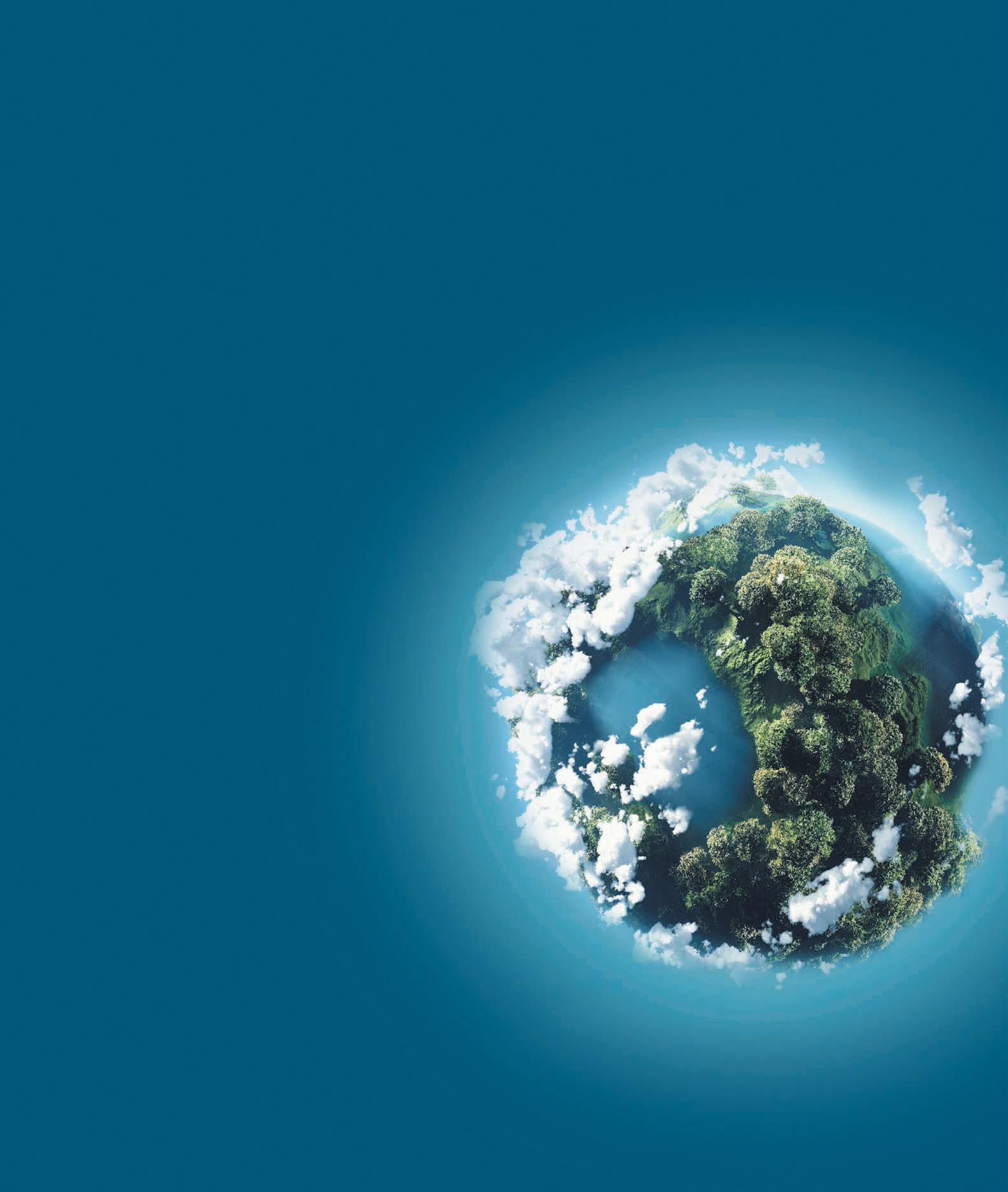
Woman of Waste
Susie McBurney: REMONDIS
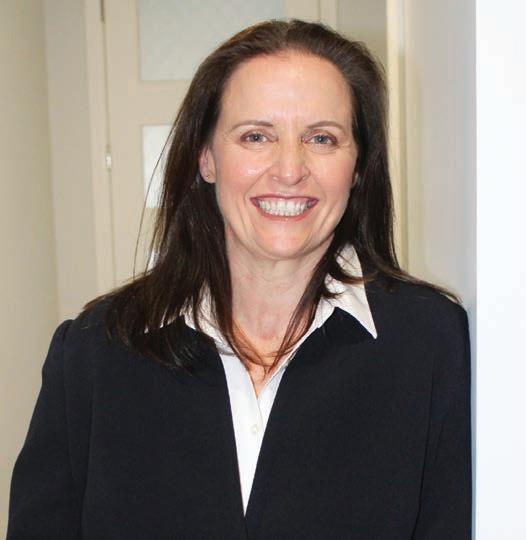
Susie McBurney has more than 20 years’ professional experience in the waste industry, spanning a number of senior management positions at both REMONDIS and Cleanaway. McBurney grew up involved in a waste and recycling business that was started by her family. McBurney’s journey in the industry, coupled with her background in Chartered Accounting, has given her practical and data-driven experience managing complex operations across all solid and liquid waste streams. As REMONDIS’ general manager for NSW and ACT, she oversees the management of more than 15 sites, including landfill operations, composting and material recovery facilities, and domestic and commercial collection depots. McBurney has been a participant in the waste industry her entire life – from a child interested in her family’s waste business, to becoming general manager of the company at age 24.
During her tenure as general manager, she increased turnover by 500 per cent and then sold the business to the publicly listed Cleanaway in 2005. Since then, McBurney has shown impeccable leadership and driven organisational change in every role she has been involved in. She was the first female Operational State Manager at Cleanaway in 2012 and first female State General Manager at REMONDIS Australia in 2014. Throughout her career, she has navigated complex projects in collections, processing and infrastructure including: • Managing the Sydney Olympics waste contract for the Darling Harbour
Precinct. • Managing site upgrades to
Cleanaway’s Kooragang Island facility for Liquid Waste. • Managing the emergency removal of asbestos and waste of 44,000 pallets resulting from a building roof collapse due to a record hail storm in 2007. • Led the construction and development of REMONDIS’ awardwinning Organics Resource Recovery
Facility in Awaba, NSW. • Currently leading the development of REMONDIS’ 50,000sqm Tomago
Recycling Precinct in NSW.
McBurney is the NSW/ACT general manager for REMONDIS, representing the company’s largest operational footprint in Australia. She is responsible for 11 operational sites and an additional four depots across NSW and ACT and has grown the business considerably since she started in 2014.
She led from concept to completion, the construction and operation of REMONDIS’ Lake Macquarie Organics Resource Recovery Facility.
McBurney has always championed diversity and inclusion where possible. While at Cleanaway, she was asked to take part in the pilot program of Cleanaway’s My Mentor – Courageous Woman, a 10-week program with key females within the organisation and designed to help their career development and to understand and work on their strengths and weaknesses for career progression.
McBurney has continued to influence and mentor other women. She has engaged in numerous speaking opportunities including WARR’s Women of Waste industry breakfast, the Coffs Waste Conference and as a speaker for Cleanaway’s My Mentor – Courageous Women Program. She is a believer in REMONDIS’ graduate program, which ensures graduates are given the chance to participate across all of the business and continues to mentor graduates who enter the waste industry, this year mentoring business graduate Paige Milligan.
She believes in always supporting her employees and is very much a hands-on manager, being out in the yard or onsite as she understands that there is a need to break down the barrier that waste management is often perceived as male oriented. iw
REMONDIS general manager for NSW and ACT, Susie McBurney. SPONSORED BY
Outstanding WARR Project: Regional
McMullin Building Demolition – Drumderg
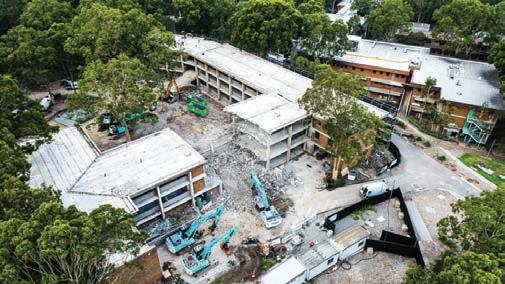
The demolition of the McMullin Building proved to be a benchmark project for the University of Newcastle, Drumderg and TSA Management in establishing complementary protocols for planning, achieving and exceeding best practice environmental, recycling, HAZMAT removal and safety across all phases of the demolition project.
In total the project included: • 99.83 per cent of materials diverted from landfill – above six-star Green
Star standard for the project • 97 per cent World-leading safety score (independent auditor) • 35 Significant trees retained • 15,000+ tons of concrete crushed and processed on site.
Detailed planning and investment into specialised equipment were all contributing factors to the project’s success.
The University of Newcastle engaged Drumderg Services as the head contractor for the demolition of the McMullin Building and Theatre buildings located at the University’s Callaghan Campus in Newcastle, following a tender process that focused on experience, innovation, as well as sustainable practice.
The project was managed by TSA Management, and overseen by the Infrastructure Facilities Services department of the University.
The demolition works were monitored and recycling initiatives reported monthly.
Through identification of the waste streams and recovery options the project exceeded the requirements to achieve a diversion of 99.8 per cent of the building fabric from landfill.
Through Drumderg’s full-time operation of one of the largest C&D and C&I plants in Australia, this project benefitted from the intimate knowledge of the nuances of demolition waste and how to maximise recovery on site.
This was evidenced by managing offtakes directly into industry, such as waste wood produced from the demolition being mulched and transformed into chipboard, to separating vermiculite and friable insulation from the building mass so that 15,000t+ of concrete and brick were decontaminated and crushed on site into a road base ready for reuse.
Effective recycling strategies were conceived in the development of the demolition methodology and demonstrated in 3D modelling, which articulated: • materials separation on site; • loading out zones; and • identifying waste streams.
Several other sustainability opportunities were taken up including: 1. The retention of an additional 35 trees during the works, originally nominated for removal. 2. Recovery of resources for reclamation and donation. This included liaising with charities that could repurpose retained items to give back to local communities, using identified waste repurposing streams. 3. The project allowed for reclaimed material to remain on campus for reuse by the University, 4. Engagement with University Research
Teams. The project presented a unique opportunity for University researchers given the building’s age, structural composition, coastal location, and its endurance through the 1989
Newcastle earthquake. Researchers from the College of Engineering,
Science and Environment were able to capture data throughout demolition to calculate the carbon footprint and laboratory assessment. 5. Safety & Innovation. Safety was an integral part of the planning and implementation of the project.
There were no incidents recorded throughout the project’s duration, a testament to the safety culture embedded by Drumderg and the
University. iw
The building’s demolition had more than 99 per cent of its materials diverted from landfill.
Since we began in 2014, we have led major initiatives to minimise waste and maximise resource recovery in Melbourne. While we are focused on the future transformation of the recycling and resource recovery sector, we are also looking back proudly on the significant contribution we have made to the community. Later this year, we will move to a new business unit, Recycling Victoria, where we will continue to work with you to transition to a circular economy. You can read about our impact here: mwrrg.vic.gov.au/impact.
Best wishes, Metropolitan Waste and Resource Recovery Group

Leader of the Year
Harry Wilson: Handybin Waste Services
Harry Wilson is an industry icon, with a career spanning 50 years in the waste and resource recovery sector. His working career has included both small private companies and large Australian blue-chip corporations and developing his own business. He has lead innovation, conducted research and shared results leading to best practice. He has given back to the sector his time and expertise as an active executive member of WCRA, NSW for more than 20 years and served as President for 11 years.
Wilson is synonymous with resource recovery, championing for the betterment of the sector.
In 1987 Wilson left his corporate position with Brambles to start a waste collection business for Sulo Australia MGB, introducing the efficiency of the mobile garbage bin and increased productivity of single driver side-loading collection vehicles to councils across Australia and South East Asia.
In 1992, he acquired that business and named it SMS Municipal Services. In partnership with councils and the communities they serve, it went on to introduce trials to identify best practice outcomes to maximise recycling while minimising contamination. He piloted projects aiming to optimise bin sizes and service frequency for both recyclables and residual waste.
He designed and built some of Australia’s most sophisticated MRFs of the 90s to process materials to the highest quality to ensure end markets. He also pioneered garden waste collections in Willoughby Council from 1993. In so doing, he diversified collections from just general waste to include recycling and garden organics. He did this using mobile garbage bins and sideloading trucks instead of bags, crates SPONSORED BY
Handybin’s Harry Wilson.
and bundled green waste services.
His years of pioneering collection trials and processing garden organics and recyclables came to the fore in 2005. Combining his logistics background with his deep understanding of resident behaviour, Wilson created a new company called Handybin Waste Services and won the kerbside collection and MRF processing contracts for Coffs Coast – three mid-NSW north coast councils of Coffs Harbour, Bellingen and Nambucca.
At the same time, in partnership with Paul Coffey a leading organics expert, they started Biomass Solutions, winning a 20-year processing contract of organics and mixed waste for Coffs Coast.
Being at the start of the introduction of the mobile garbage bin in Australia, better known as the “wheelie bin”, Wilson has been heavily involved in the evolving landscape of municipal collections.
With a career spanning more than 50 years in the industry, he has witnessed, and been a part of, enormous changes.
He has brought innovation to the industry as an employee, as a business owner, but also as an association director and president. iw
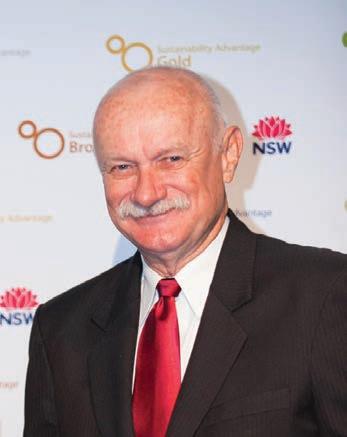
Young Professional of the Year
Tara Osborne, General Manager – BINGO
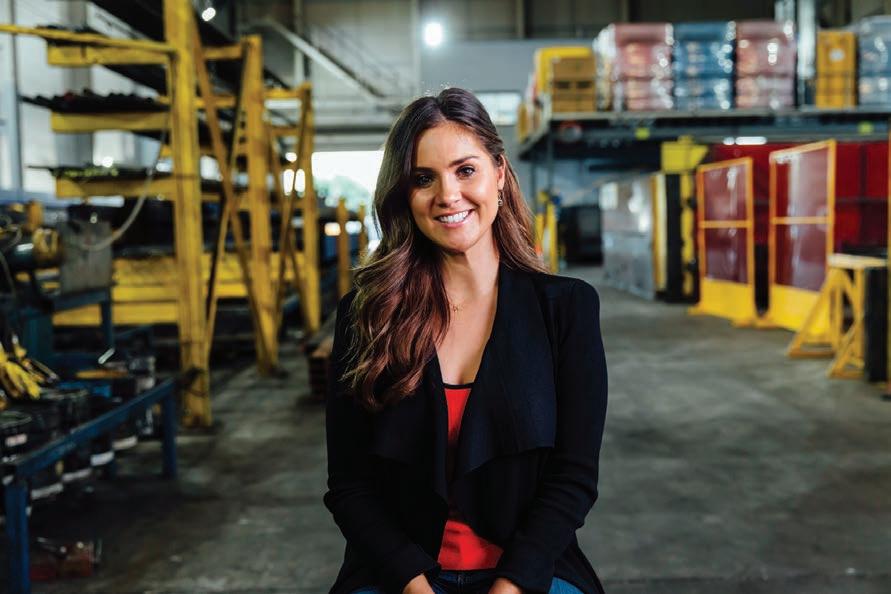
Tara Osborne has been at BINGO for more than four years and has seen the company through its Initial Public Offering (IPO) and several large acquisitions. She has been an important part of the leadership team and BINGO’s recent success.
Osborne started her career working at Credit Suisse in is Equity Capital Markets team in 2012. Not long after, she began work for IntraAsia, which was focused on emerging markets. Her next job was with industrial engineering business BroadSpectrum, which in turn was bought out by Spanish conglomerate Ferrovial, which among other things, has waste assets. This was Osborne’s first foray into the waste business.
“The opportunity at Bingo came up when [Bingo CFO] Chris Jeffrey was heading up the development team as the chief development officer,” she said. “I was approached to help corporate development function. I set up investor relations for the company once they listed on the ASX in May 2017.”
Being made a general manager at 28 hasn’t curbed Osborne’s ambition, although she does love her current roles and sees potential in many aspects of the business.
“I do a bit of everything when there are challenges in the organisation,” she said. “For example, the floods at the moment. We are having challenges with certain assets around water issues. I can jump into the team and pull different people together and have a discussion about what is the strategy.
“Then there are issues like changes in the regulations, such as the recent ones covering recovered fines. I’ve been leading that internally and making sure we are looking at our response with industry to the EPA and also preparing the business operationally for that massive change and shift,” she said. “I work on the innovation side of the business internally to try and solve some of their issues. Like looking at offtakes for certain products that might be problematic such as engineered timber or PVC.”
And as for her future, she has plenty of areas she would like to cover off before moving up the corporate ladder.
“I would like to get a bit more
Osborne became a general manager at BINGO at the age of 28. operations experience and move horizontally to widen my experience beyond the corporate skill set that I have,” she said. “Eventually, I would like to take a C-suite position helping grow the business. I’m not in a hurry to move up.
“I would rather move across and expand my skill set so that I am in the best position possible to make that step up.”
And the issues she would like to work on?
“I’d like to work on things like turning waste into fuel, or waste into methanol,” she said. “There are so many opportunities out there to collaborate with other industries – high carbon industries – we need to almost partner with them because they are important.
“With green activism and where it is heading, I am of the view that waste – such as biomass – is a coal replacement. We need to move away from coal.
“You have cement kilns, and you have steel manufacturers who have to look at RDF or biomass. It’s constantly moving and evolving.
“The circular economy and innovations space. I have the best job in the organisation.” iw
Big beverage has little say in WA CDS
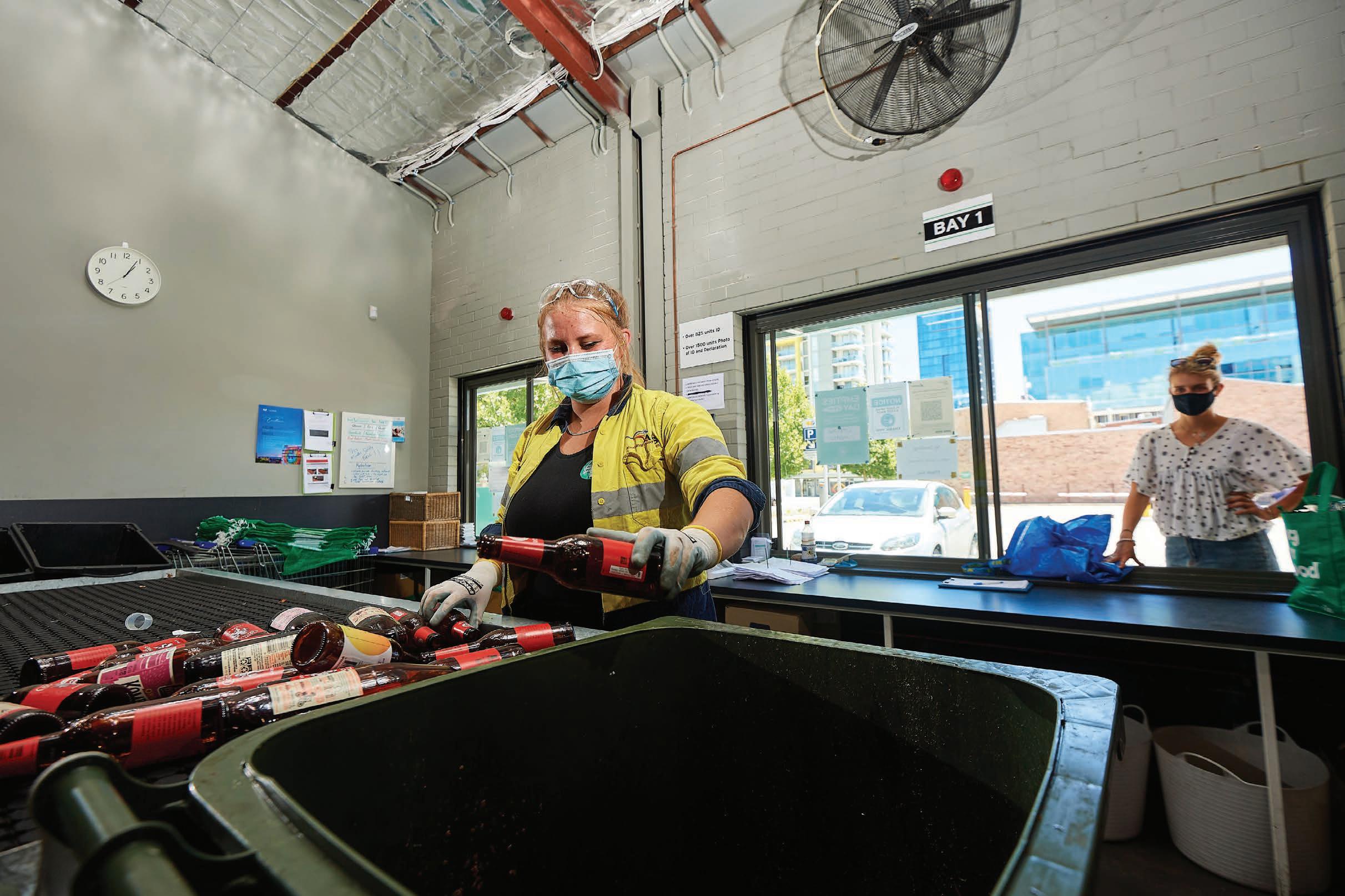
By Inside Waste
“WHEN we look at commentary about Western Australia generated out of the east coast we get frustrated because there is this myth about the scheme being run by ‘big beverage’, which is simply not true.”
So says Tim Cusack, the CEO of WA Return Recycle Renew (WARRRL), the entity responsible for the Containers for Change container deposit scheme (CDS) for Western Australia. Cusack is passionate about the state’s CDS but is perturbed about misinformation that has stated WARRRL is nothing but a mouthpiece for the big beverage manufacturers who fund the scheme.
“Big beverage has three of nine seats on our board [those three seats don’t have higher voting rights than the other six seats], and they have provided seed capital for the scheme to be established, getting it ready to operate on October 1, 2020,” he said. “It operates like any board. It has an independent chair and five independent directors who very much protect their independence. Look at the results. I ask those who critique our scheme to look at the results, which speak for themselves.”
Cusack said the scheme has been successful and has so far returned just over $108 million to communities throughout the state. It has 77 refund point operators that provide 258 refund points. One achievement that he is especially proud of is that any person who lives in the Perth metro area only has to travel a maximum of four kilometres to find a place to dispose of their containers.
“We have an internal objective to get it to 290 refund points before the end of the year,” he said. “We have an incredible array of refund points across regional WA, which is amazing when you think the size of WA is the size of continental Europe. And let’s not forget the isolation of some very remote communities, so to have a presence in those areas is fantastic and speaks to how much the community has embraced the scheme.”
The beneficiaries of the scheme include local government organisations, aboriginal corporations, sporting organisations and community organisations such as Lions Club and Men’s Shed. Cusack said there are diverse not-for-profit groups in the mix, including the disability sector. Two of the biggest disability employers in Western Australia – Good Sammy Enterprises and Ability Centre – are both operators within the scheme. As for big beverage companies, Cusack said they have limited influence. Being on the board they do have a say, but not a majority opinion, he said. People need to be less cynical about them as entities and look at what they are doing. In other words, look at the reality, not the perception.
“I will give you two examples. Gage Roads Brewing is an independent WA brewing company,” he said. “It has agreed to promote the container deposit scheme on its packaging. The first beverage company in Australia to do so. Why? Because they actually have a genuine commitment to resource recovery. They have a corporate commitment to that. To manifest that commitment, they put it on the packaging to encourage their consumer to get the material, once finished, back to a refund.
“Then you look at Coca-Cola. There are critics of Coke, but you look at what they commit to publicly in all of their corporate statements and look at what is on their packaging. They have a real commitment to it. They are about to build a PET site, part of a joint venture with PACT and Asahi, that is going to build massive investment on the east coast. This is multi-million dollar investment in recycling. I don’t hold a candle for Coke, but I just want to make the point; if you look at the beverage sector generally, you can see incredible commitment to resource recovery and recycling.”
The scheme has been ongoing for the past 16 months and so far has a redemption rate of just over 76 per cent. While Cusack wants that number to increase, he is happy with the way the scheme is running, albeit
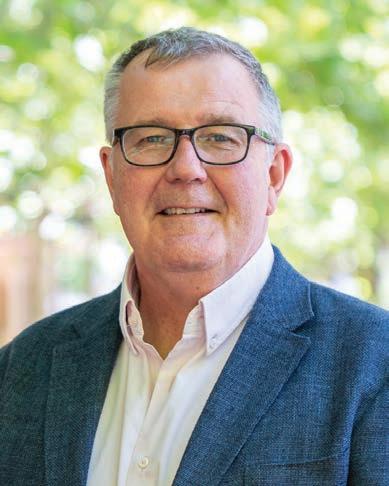
The WA CDS has returned more than $108 million to communities in WA. with a minor hiccup.
“The only issue we’ve had has been our IT point of sale system,” he said. “Only really in the sense of functionality gaps, if that makes sense. There are things our refund centres wanted the operating system to do that it couldn’t do. We are now on the latest version, and we have done a lot of enhancements to that software environment. As we roll out we fix those bugs, we provide functionality enhancements. That is being really well received and is very popular and the community have embraced it.”
He said they also use what is called the Member Number scheme. It is a facility that allows organisations and individuals to send their refund to a bank account rather than receiving cash.
“It can be their own account, or even a charity or community group they support,” said Cusack. “So far, we have transferred more than $3.7 million to community groups in donations alone. We have transferred many more millions – somewhere along the lines of $12-13 million – to the community groups that actually run refund points because they get 100 per cent of the handling fee where they are providing the refund point service, which is another unique feature to our scheme.”
As the CEO, Cusack is looking ahead and sees two key opportunities that he would like to take advantage of over the next 12 to 18 months. One is to continue to extend the reach of the scheme – to make it more localised than it is today.
“We have 4500 community groups and charities with a member ID number,” he said. “That tells you the amount of interest right across one end of the state to the other, and those organisations can provide access to the scheme though donation points.
“We are actively pursuing that at the moment. We do expect to see a much wider presence in the community through an informal donation structure than simply relying on the refund points themselves.”
He said that they also need a stronger partnership with the waste management sector. The WARRRL already has a strategic partner in the form of Cleanaway, who provides the majority of logistics and processing services outside of Perth. In Perth, they have a relationship with REMONDIS, who is the provider of logistics and processing for nonglass items.
“We have good partnerships with those two companies, but we are working hard to extend those partnerships to the other major players in the waste sector in WA because they are all involved in capturing eligible containers,” said Cusack. “And not all of that material is getting back to the scheme. It is about making sure we have opportunities for separation of source in all settings – not just residential settings. To pursue that, we are attempting to build stronger partnerships, closer relationships with the waste sector in the state.” iw
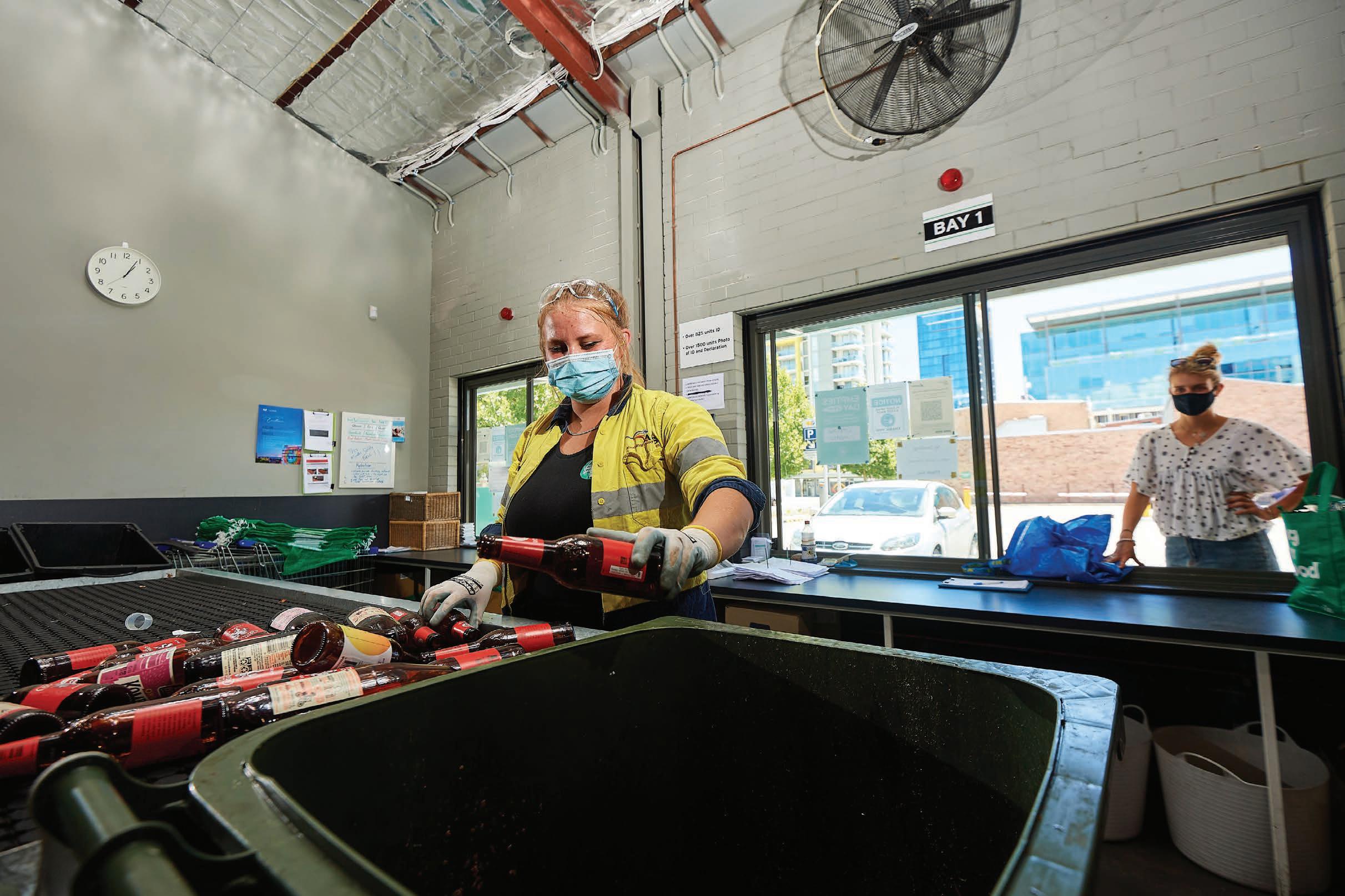
WARRRL’s Tim Cusack.
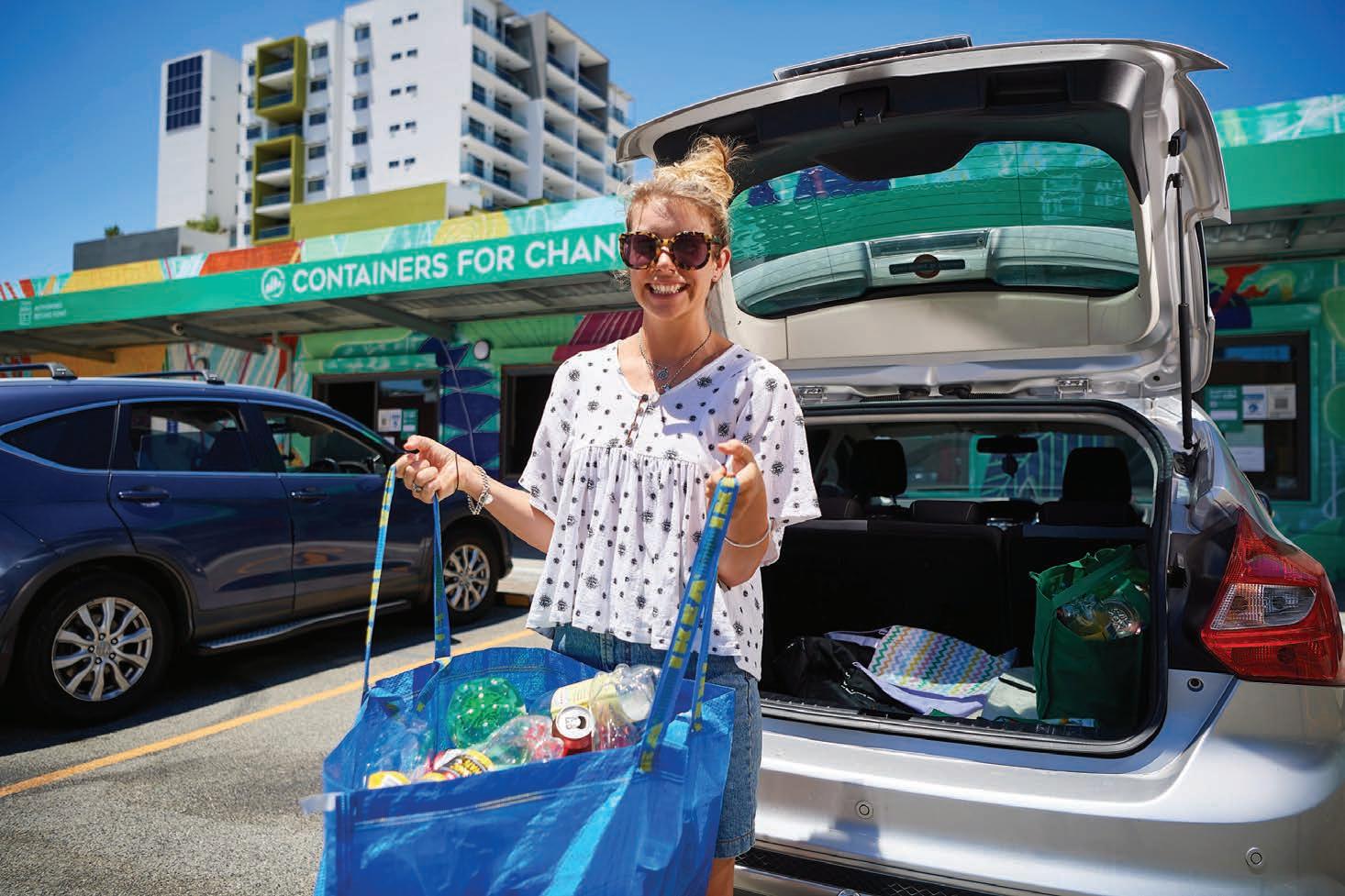
AI helps sort batteries
EcoBatt has pooled best practices from around the world to build an automated battery sorting system.
By Inside Waste
WHEN building its Melbourne facility, the EcoBatt team visited battery recycling sites around the globe, learning from their success, failures and experiences.
Director of EcoBatt and Recycal, Doug Rowe, said the lessons learned by colleagues overseas proved invaluable when sitting down with the engineering team at COVA design to come up with a patented automated battery sorting system that separates battery chemistries.
“Taking the best bits from each of their operations and being able to start with a clean sheet enabled us to build a plant that incorporates all their observations and suggestions,” Rowe said.
“We felt privileged that they were so willing to share their experiences and they continue to follow the progress and development of our battery sorting plant.”
Rowe said many and varied batteries are collected from EcoBatt’s recycling drop-off points. The battery sorting plant can sort them down to the smallest cell battery to the larger alkaline or lead acid batteries. It can also remove batteries that may contain sand or vermiculite, which is a group of hydrated laminar minerals such as aluminium-iron magnesium silicates.
“It is not just a couple of sorting conveyors in a row with people trying to pick chemistries by eye,” Rowe said. “It’s a sophisticated automated system with Artificial Intelligence reading the batteries and placing them in their correct category by chemistry. We can sort about 10 tonne per day during one shift.
“Accurately sorting of these batteries is so important as the chemistries differ greatly from battery to battery. Each reacts differently and contains different metals.
“We continue to see so many different batteries coming through from industry and we continue to learn more about them every day. Sorting them and keeping the chemistries together allows for much safer and controlled recycling and processing.”
Rowe said safety is one of the main concerns when sorting batteries. He said that EcoBatt’s sorting facility has all the safety systems in play including thermal cameras inside the sorting shed, sprinkler systems, sand boxes, and specialised metal fire extinguishers in case of any emergency. Separate outdoor storage containers also have sprinkler control, suppression systems and heat detection. He says anything of concern can safely be put in these containers, which are further protected by a Fire Rover fire detection and suppression system.
“Batteries need to be respected and handled correctly and we go out of our way to ensure we do all we can to make that happen,” he said.
There is some hand sorting at the beginning of the process to remove batteries in plastic bags and other mixed items.
EcoBatt also accepts mobile phones in its battery collection bins located around Australia. The phones are separated along the processing line and stored in bins for further recycling. The phone batteries are removed to recover specialised battery materials and metals inside them, while the phones themselves are processed separately. Mobile phone charges and accessories and wearables including smart watches can also be recycled in the collection bins
Rowe said it ensures clients have easy access to recycling. “Batteries now play such an important part in our lives with many finding their way embedded into all kinds of toys, tools, mobile equipment and indeed all around the household,” he said.
“Even in the workplace batteries are found and needed in so many devices. Without a way to recycle them, people would store them in drawers, leave them around the house or workplace and in many cases, they would be placed in the rubbish bins.
“Now there is an answer to recycle the batteries and more importantly, collection points all around the country for them.” iw
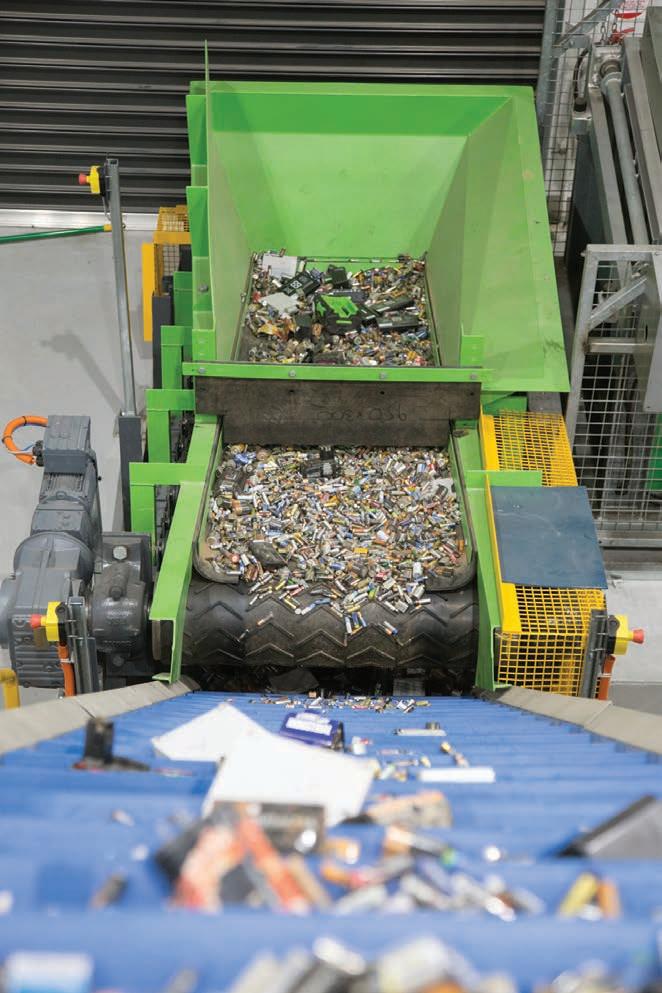

The chemistries vary from battery to battery.
HiAce Steel supports local waste management sector
Beach Bin engineered for the Australian coastline
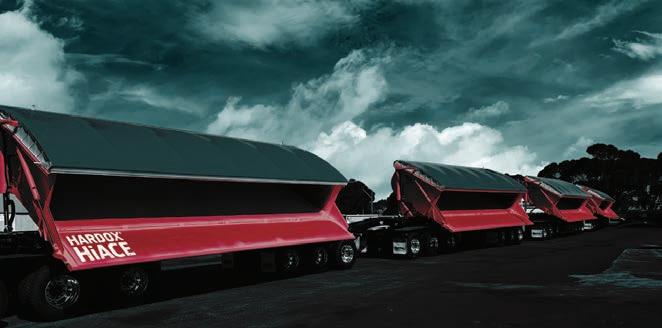
By Inside Waste
GLOBAL steel manufacturer and supplier, SSAB, is helping Australian businesses withstand wear challenges in severe conditions with the Hardox HiAce range. Engineered for applications in acidic and corrosive environments, Hardox HiAce abrasion-resistant steel is an structural material for garbage trucks, recycling containers, tipper/ dump bodies, and other heavy-duty equipment.
A 2019 report found that Australia produced 7.5 million tonnes of hazardous waste in a two-year period, which was a 34 per cent uptick on the previous generation and represented 11 per cent of all waste generated nationwide. This number is only rising: • 290,000 tonnes of e-waste material have been diverted to landfills to date; and • an additional 100,000 tonnes of solar panel waste are forecast to enter the waste stream by 2035. In these environments, the steel in truck and tipper bodies, and other equipment can come under attack from different types of acids. This acidity oxidises the steel’s surface, making it more prone to wear. Therefore, Australian businesses require tougher equipment to protect profitability, equipment condition, service life, and the environment.
“Australia’s harsh climate and growing volumes of hazardous waste have created the perfect storm for corrosive wear. Hardox HiAce is a true wear fighter for organisations looking to protect their equipment, especially in the acidic or corrosive environments that threaten waste management,” said Matthew Spiteri, country manager for Australia and New Zealand.
Hardox HiAce’s corrosion-resistant steel plate slows down the oxidation process, allowing the full hardness of the material to counteract wear. It performs the same as 450 HBW steel in pH-neutral environments. In low pH levels, it can extend equipment service life up to three times longer compared to 400 HBW steel.
Its increased wear resistance also allows for the use of thinner plates without jeopardising service life – translating to more payload when fully loaded and, when traveling empty, more fuel savings and fewer CO2 emissions. This steel has been embraced by businesses across the country. One example is Bruce Rock Engineering (BRE), which implemented it into its new Super Quad mining trailer combination for iron ore transport.
BRE used Hardox HiAce in the Super Quad’s floor plate and the trailer sides, which has effectively extended the life of trailer bodies – even in tough climates like Western Australia’s Pilbara Region. Hardox HiAce has also lightened the load – the 60m Super Quad road trains have a payload up to 141t in order to maximise capacity.
“We never hesitated for a minute before introducing Hardox HiAce into a Super Quad mining trailer combination for iron ore transport. Changing from Hardox 450 to Hardox HiAce hasn’t caused any challenges in the workshop. All that has changed is the higher resistance towards corrosive material,” said Brenton Verhoogt, operations manager at BRE. iw
The Hardox HiAce range of steel is designed for harsh environments like the waste industry.
HOT sand between your toes, wild salty hair, sunburnt noses…the Australian beach can be a uniquely fun, but hostile, environment. That’s why, between way too many trips to the beach for “site assessments”, the team at Source Separation Systems has leveraged its unique expertise in waste diversion, to design a new public place bin designed specifically for the Australian coastline.
The Beach Bin builds upon the National Park Range, with several new features.
While still manufactured in their factory in Newcastle NSW by the Source Separation team, this unit is built from aluminium, making it a robust solution for coastal environments.
Housing standard 240 Litre Wheelie Bins, the wall panels of the enclosure are fixed to the ground, with the longer panels bolted and reinforced with silicone during installation. This feature minimises litter in coastal areas, which are typically associated with high winds, as smaller waste items are unable to escape from the base. It also reduces the build-up of sand from within the unit, ensuring the internal bins remain easily accessible.
The limited air flow created by the sealed base also minimises the risk of fire, by reducing the amount of oxygen feeding any potential flames from the base.
The Beach Bin is available in a standard Landfill and Recycling design, with other streams including Organics available on order.
The Landfill unit is available with an optional ashtray, which allows cigarette butts to be extinguished and then deposited into a separate compartment within the frame. Butts are then transferred to the Landfill MGB on collection.
Source Separation Systems is known for its high-quality outdoor units, which are uniquely engineered and manufactured for durability. The panels are constructed with a dual sheet design for strength, with the powder-coated outer panel individually replaceable if damage does occur, which adds to the longevity of the solution. These interchangeable panels can also be vinyl wrapped, transforming the bins into information hubs for the promotion of community events and messages.
An effective and durable solution, the Beach Bin is sure to be another popular option in the Source Separation Systems’ range of waste diversion products. iw
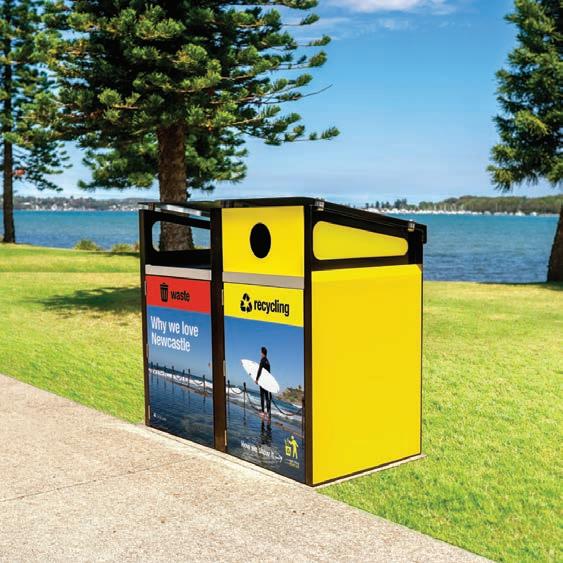
Sticker price not only reason to buy truck range
By Inside Waste
ISUZU’S recently compiled Future of Trucking Report (FoT) surveyed over 1,000 truck owners and fleets across Australia. It revealed that highest on the list of priorities for Australian fleet owners was the issue of profitability.
An increasingly competitive market environment in combination with the global pandemic and escalating operational costs, is working to drive down margins.
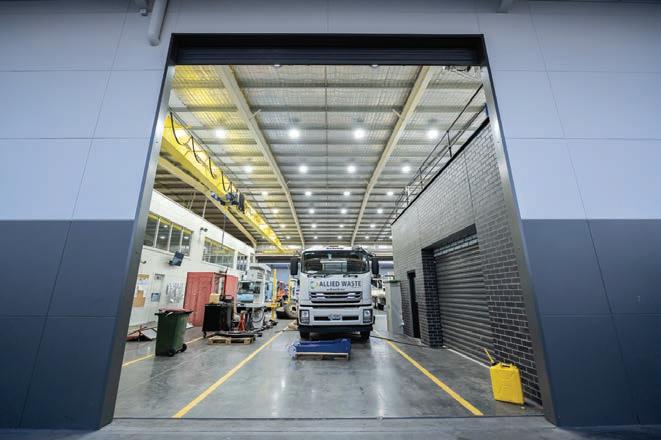
In for life
In tackling the issue of profitability, fleets are increasingly looking at the ‘lifetime’ costs of capital equipment, alongside many other operating costs.
Isuzu’s FoT report found that 64 per cent of businesses believe the total lifetime cost of ownership was far more important than the sticker price.
In the less populated states, this figure was higher, such as in Western Australia (71 per cent) and the Northern Territory, where 79 per cent of truck businesses held this view.
Warranty
A key aspect of the lifetime cost of a piece of capital equipment is its warranty, and despite appearances, not all warranties are created equal.
Isuzu Australia national service manager, Brett Stewart, said warranty was an area often overlooked at the time of sale, and mis-managed, can carry huge implications for owners and have a long-term effect on the overall operations of a company that relies on trucks in their day-to-day working environment.
“Some warranty products may match the manufactures’ warranty provisions, although the product itself may be handled by a third party outside of the OEM, especially in regard to extended warranties,” he said.
“You need to ensure that your warranty (factory or extended) is ‘like for like’ with your expectations. They are sometimes hard to identify, but there can be tricks and traps. A common complaint is that there are sometimes limits applied dependent on the cost of the repairs over a given time frame.
“Another hurdle customers face with their warranty is rejected claims. This often occurs when a claim is adjudicated by parties outside of the OEM, where substandard product understanding can lead to frustrations and challenges.”
It is important to check out the warranty conditions when investing in a new truck.
Best in field
With this in mind, and following the recent release of the N Series, Isuzu trucks has delivered a robust factory warranty offering that includes: • All N Series 4x2 cab chassis trucks
are now backed by a factory warranty of six years (or 250,000 kilometres) and six years of Isuzu’s 24-hour roadside assist. • Regarding Isuzu’s pre-built Ready-to-
Work range, all 4x2 models also come covered with a six-year (or 250,000 km) factory warranty for the cabchassis, six years roadside assist and a comprehensive three-year warranty on pre-built bodies.
“What we’re signalling with this offering is the confidence we have in the N Series product. iw
Shredding? Think Diamond Z
By Inside Waste
THE Diamond Z is a high-speed grinder that processes green and timber waste, reducing the particle size of material.
Diamond Z offers a range of tub, horizontal, and solid waste grinder models designed to suit any application from composting to construction and demolition, land clearing to tyre disposal, municipal solid waste to asphalt shingle grinding.
The unit comes standard with a fluid coupling drive system, eliminating friction elements prone to wear, tear and failure.
In addition, the coupling unit eliminates any shock that may be caused to the engine in the event of contaminants entering the grinding chamber, the coupler is electronically monitored for more interface management.
The Diamond Z range feature the ‘down cut’ combined with the heavyduty pin and plate style hammer mill designed to reduce down time.
All cutting and wear edges are bolt on replaceable.
The breakaway mill bearing mount features an impact reduction system to allow for the processing of contaminated waste
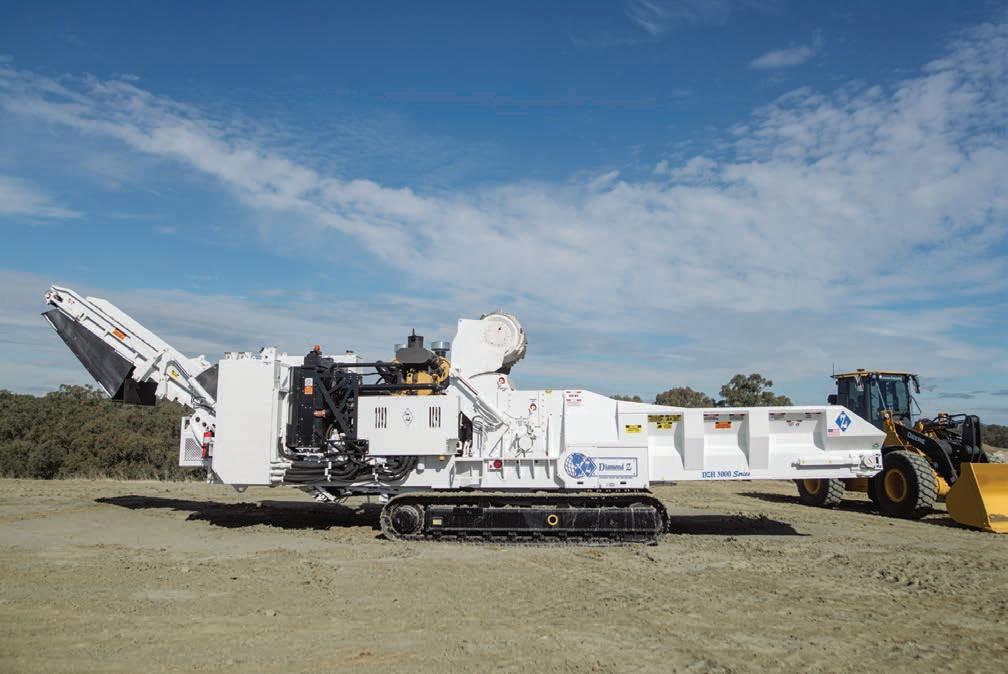
The Diamond Z allows for the processing of contaminated waste.
Diamond Z set the bench mark when it comes to high-speed designs, including the patented hydraulic rod puller and break away mill bearing mounts.
The Diamond Z 3000 unit is designed for the Australian market, has a smaller frame for easier freight, as well as 800 horse power engine.
The DZH3000 is ready to make an impact in the industrial grinding segment. The smaller, lighter, more cost-efficient model is infused with all of Diamond Z’s proven performance. It has 580 horsepower and comes in at 28 tonnes. iw
Circular economy not gaining as much traction as needed The environmental issues shaping voter concerns A survey conducted by C|T Group on behalf of Veolia
3/4
Three out of four voters say waste management issues concern them (75%). We’re concerned about the environment.
Outside of the economy and cost of living, voters are most concerned about the environment. We support environmental investment.
Less supportive voters view the economy, job creation and support of new industries as more important than environmental issues.
Two in three
voters (67%) support the state government diverting funds from key areas to waste management initiatives.
While 79% agree, 35% of voters strongly want waste recycling companies to have a greater advisory role in Government.
79%
agree
35%
strongly agree
60%
When told about the transition to the Circular Economy, most voters support it.
Almost all voters agree
NSW should invest in waste to energy technology to reduce landfill (82%).
We support Waste to Energy technology.
Low awareness
High concern
There’s high concern about waste management despite low awareness of the issues. 27%
27%
26%
aware of waste export bans
aware of contribution of landfill to climate change
aware of lack of recycling and recovery infrastructure
We’re unaware of waste policy.
NearlyHalf
of NSW voters (45%) are unaware of State Government’s waste policies.
Very few are familiar with NSW climate change policies and the circular economy transition.
3%
aware of climate policy
4%
aware of circular economy transition
Methodology
Results are based on By Inside Waste an online survey conducted on 7 17 October 2021 in NSW
RESEARCH commissioned by Veolia reveals that outside of the economy and cost of living, NSW voters are most concerned about the environment. In a post-pandemic world, voters say environmental sustainability is a priority, and that they support investment in recycling and waste initiatives to help prevent climate change – even if it means diverting funds from elsewhere.
Research shows: • 75 percent of people say waste management issues – such as reducing waste, increasing recycling and minimising emissions – are of concern • 67 per cent of people support diverting funds away from other key areas to increase investment in waste management initiatives and infrastructure.
The NSW Government has set the roadmap for a sustainable future, with commitments to halve emissions, drive greater recycling and adopt technology, such as Energy from Waste (EfW), to reduce the reliance on landfills, all by 2030. This aligns with the Federal Government’s targets to recover 80 per cent of materials and reach net zero by 2050.
Despite this, Veolia’s research reveals that voters are not aware of the Government’s environmental agenda.
Only 3 per cent of people say they are ‘definitely aware’ of NSW climate policies and only 4 per cent say they are aware of the transition to a circular economy.
When asked about globally proven technologies that allow for the shift away from landfilling, voters strongly supported it. Up to 82 per cent of voters say that NSW should invest in Energy from Waste technology to reduce landfilling. Voters also want recycling and waste companies to play a greater advisory role on waste management initiatives (79 per cent agree).
“The NSW public have a sophisticated understanding of climate issues. Numbers show that people want change and they support the investment needed to make it happen,” said Richard Kirkman, CEO and managing director for Veolia Australia and New Zealand. “This is fantastic news because their priorities already align with policies that preserve resources and protect biodiversity.
“Interestingly, those voters who were less supportive of the green agenda were motivated by economic matters. These voters overwhelmingly support initiatives that focus on creating jobs, driving new industries, and stimulating growth. This means that investments that deliver financial gain and employment – like the development of Energy from Waste facilities – also align with public motivation.
“Australia is one of the highest producers of waste in the world, and landfills all of its non-recyclable waste, which emits greenhouse gas emissions, and remains in the ground for generations. We need to move away from this – the voters want it, the government wants it, and we are ready to deliver it.”
Veolia says there has never been
• n=1,251 random sample online (inclusive of a n=326 marginal seat boost); effective sample size after weighting is n = 971 (78%). • At a 95% confidence level, there is a maximum margin of error of approximately +/ 3%. • Take caution when interpreting subsamples, as they will be subject to a higher margin of error than the overall sample. • The data is weighted by Age Sex interlocking and Education. better time for the NSW Government • Figures may not sum to 100% due to rounding. Statistically significant differences are represented using arrows. to drive forward their climate policies for voters by: • Investing in infrastructure – through more recycling facilities, and the quick adoption of energy recovery technologies to extract value from food organics in the form of biogas, and energy from non-recyclable waste, which helps to decarbonise. • Work closer with the waste management industry – recycling and waste management. • Companies welcome continued engagement with the NSW Government on the steps required to generate a more sustainable state. • Re-engaging the public – closing the knowledge gap on existing policies will help everyone to play their part in moving up the waste hierarchy toward recycling and away from landfilling. Kirkman said voters can also do their bit by ensuring they avoid waste where possible, reuse where they can and recycle everything that can be recycled. iw
Marginal Seat Boost Sample Lib/LNP Marginals East Hills (0.5%) Penrith (1.3%) Dubbo (2%) Upper Hunter (2.5%) Holsworthy (3.2%) Goulburn (3.7%) Heathcote (4.9%) Tweed (4.9%) Wollondilly (5.5%) Lab Marginals Lismore (1.3%) Coogee (1.6%) Kogarah (1.7%) Strathfield (5%) The Entrance (5.2%) Port Stephens (5.8%) The Entrance (5.2%) Port Stephens (5.8%)
Results makes job worth doing, and doing well
AFTER graduating with a Bachelor of Economics from Western Sydney University, it didn’t take Maria Juchkov long to realise that maybe finance and its peripheral line of work wasn’t for her. Instead, she dipped her toe in the world of retail, then decided to head to Macquarie University and complete a degree in sustainable development.
“It tied up my loose ends of my first degree because the first degree was the economy and how it is based around profits,” said Juchkov. “With the sustainability degree, I learned how it focusses on equalising people, the planet and profit. It really stuck with me. And I really enjoyed it.”
After graduating two years ago, Juchkov landed a role as a resource recovery officer – solid waste services, for Cleanaway. It is a busy job that although it has 5am starts, is diverse enough to make it an attractive career option for Juchkov. A typical day starts with municipal bin audits whereby she enables behaviour changes in recycled by using educational tags on bins based on contamination levels.
“I check bins for two to three hours – on average about 200 bins per day,” she said. “Each day it is a different suburb, a different area. Once the bins are checked and tagged, I return to the office to analyse the data, write reports for council and research impactful communication styles to drive better recycling in residents.
Maria has developed her experience across two council contracts in Sydney. Her work on the first contract saw strong improvements in recycling with contamination being reduced by 50-70 per cent. This was achieved through social incentives, immediate rewards and progress monitoring – all important factors supported by behaviour change science.
“For one contract, if any residents repeat contamination we send out letters reminding them that certain items must be kept out,” she said.
This is one example of progressive monitoring. When there is gross contamination present in recycling bins, Cleanaway can refuse a service.
“If you’re going to treat the recycling bin as a garbage bin, then you might as well use a garbage bin,” she said. “If you say you are not going to collect the bin once, that is usually enough of a motivation for residents to get their act together. It generally tends to fix the problem.”
The biggest issue out there in recycling bins is plastic bags and soft plastics. Over the past two years of bin audits, these materials were contributed to about 50 per cent of the contamination found.
Juchkov is upbeat about her job and what it entails. She likes the early morning starts and that she gets to go to different areas every day as it allows her to see greater Sydney. She also likes seeing the results that they collect from the bin tagging program because usually by the end of the checking period, contamination has been noticeably reduced. And how does she see the future? What are some of the issues she sees in the industry and what would she like to see actioned?
“It would be great to see similar programs roll out across various councils and even more collaboration between the councils and the private sector,” she said. “I know what I am doing is also occurring internally at some councils. Having more opportunities to collaborate and to share our results and practices would be great. A lot of what I do does tie into behavioural science, so to be able to connect the practicality with the science and the research that goes on there would be ideal.”
Having worked in the industry for more than two years, Juchkov was surprised at how much she didn’t know when she first joined the company because what she thought she knew, and the reality, were not the same thing.
“The industry is definitely not what I expected,” she said. I thought I was good at recycling and knew what was recyclable and what wasn’t. But six months into the job I learnt not all plastics are accepted in the kerbside recycling, such as buckets, and plastic cutlery because they don’t get picked up by the MRFs. There are also sizing and material issues, which means it gets complicated.
And although Juchkov’s time in the industry has been brief, she sees the bigger picture and starts talking about aspects that makes it seem like she’s a veteran.
“We need to make the industry more streamlined,” she said. “It’s not just the responsibility of consumers, or waste companies or manufacturers. Good, sustainable product and packaging design make it easier for households to understand and recycle correctly, which makes it easier for waste companies to collect and sort without contamination, which means more can be reused in remanufacturing. There is a great opportunity there.”
Working for Cleanaway has been a good experience so far. Juchkov said everyone is motivated with the work that they do, and it helps that her team is really into sustainability.
They also devour all into the latest information about what is going on in the industry – trends, what councils are doing, the latest innovations and where the government is headed with its policies.
They do a lot of troubleshooting, and also look externally for answers. She said it is a really supportive environment – from management to those on the ground doing the physical work.
“The drivers are really easy to work with, and they understand why I do it,” she said. “When I first started, because the role is relatively new, the drivers didn’t understand what I was doing. They were like ‘why should I leave the bins for you? All I want to do is pick up the bins and go home.’ Once I explained my role, and they were able to see a reduction in contamination during their shifts, they were ready to get onboard. They are really good to work with. The drivers for one of the contracts are really proactive about getting the feedback to the residents as well.
Overall, Juchkov loves what she does and can see a future in such a career.
“Seeing the results is really rewarding. It is telling us what is really working and that is a nice part of the job and a great change to witness,” she said. iw
Some audits and feedback to residents resulted in up to 70 per cent less contamination.
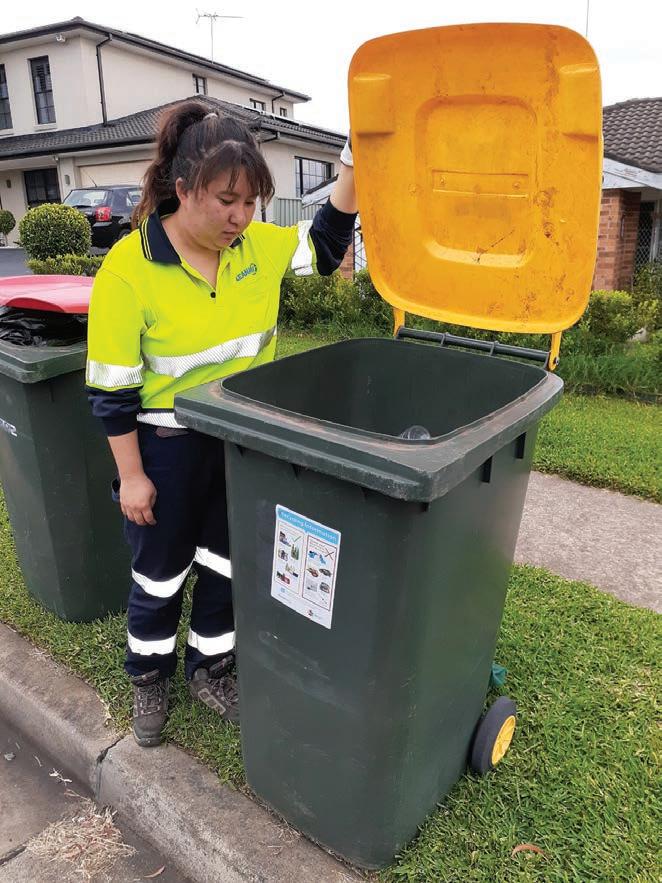
CAPS Australia
Company Overview:
CAPS Australia is a privately owned and proud Australian company intent on remaining at the forefront of compressed air, critical power generation solutions. CAPS offers capital sales, rental equipment, engineering & manufacturing, service and parts.
CAPS has over 40 years of experience in the Australian market with nine branches across Australia and over 170 employees, including 60 service technicians covering the full national footprint with a 24/7 service offering. CAPS is an independent company with the flexibility to search globally for the best products and technologies that best serve the Australian market’s needs and unique conditions.
CAPS has world-renowned partner brands such as Ingersoll-Rand, KOHLER/ SDMO, AIRMAN, Sauer, Pedro Gil and many more.
CAPS has in-house engineering capabilities, able to customer engineer any equipment to your needs and specifications. Back this with our Australian ISO 9001 accredited manufacturing facilities, CAPS can provide the complete end-to-end solution.
Products & Services:
• Power Generators • Air Compressors • Dryers • Blowers • Spare Parts • 24/7 Servicing • Engineering services • Rental / Hire
Products & Services:
• KOHLER/SDMO • AIRMAN • INGERSOLL-RAND • TEKSAN • SAUER • BEKO • DEEPSEA
Core Capabilities:
CAPS Diesel Generators; together with KOHLER are tailored designed to meet onsite limited real estate; featuring superior transient performance; maximum reliability; low specific fuel consumption & market leader with high power density for various segments.
Our portfolio covers high speed diesel generators up to 4600kVA (50 Hz); available with different voltage configurations; packaged either in a purpose-built acoustic enclosure or plant room install.
Standby Diesel Generators guarantee energy security for waste to energy facilities; to prevent critical process sudden shutdowns; which are termed detrimental to both equipment & revenue generation.
The CAPS Diesel Generators are engineered; tailored built to deliver superior performance but also meet stringent requirements related to real estate; load acceptance & noise performance; together with in-house engineering & local partners.
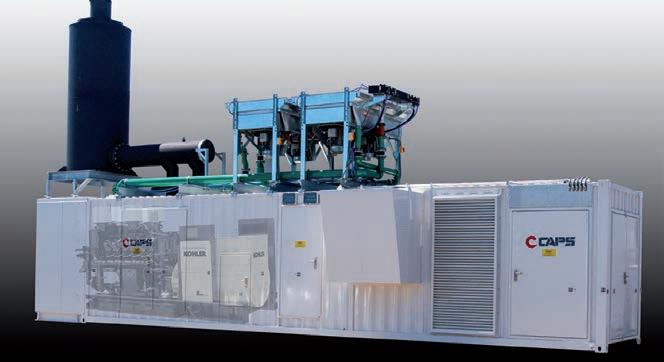
Contact Details:
CAPS Australia
185 Planet Street Welshpool WA 6106 Phone: 1800 800 878 Email: info@caps.com.au Website: www.caps.com.au
Key Contacts:
Nestor DeNiese
National Sales Manager – Power Generation Number: +61 8 6250 9871 Email: nestor.deniese@caps.com.au
Ecocycle
Company Overview:
Ecocycle Industries has built a reputation of renown for the handling and processing of Mercury based waste in Australia. With some 20 years of experience, we have the National network with facilities in each State to support and look after our valued clients. We deal with most of the larger waste company’s, councils, and industry direct.
Mercury is seen in lighting waste, dental amalgam, button cell batteries, TV’s – computer monitors, and lap tops, and other waste catalyst, soils etc and we are able to handle and recycle all these various types of waste.
We have a range of specialised stillages, smaller bins, Hook Bins, cabinets, boxes and DG approved containers, with DG registered trucks and DG licenced drivers.
This unique processing ability with the National footprint has allowed us to move into Battery Recycling “EcoBatt” and E Waste recycling “Eco E Waste” and links nicely into what we do with metal recycling at Recycal. We have our foundries “Castings Tasmania” melting down our steel and making quality castings for industry in Australia and “ACL Metal Powders” using scrap copper, lead and tin to make Copper based powders for our export markets. This vertical integration allows to use most of the recover metals in house and have the highest recycling rates while making green products from recycled metals and solar power. You can be confident when using our group you will have your materials recycled safely and efficiently, with a first class service back up with quality equipment and containers that will give you the confidence and comfort needed.
Contact Details:
Ecocycle Industries
5-11 Reo Crescent Campbellfield Melbourne Victoria 3061 Phone 613 93089415
Key Contacts:

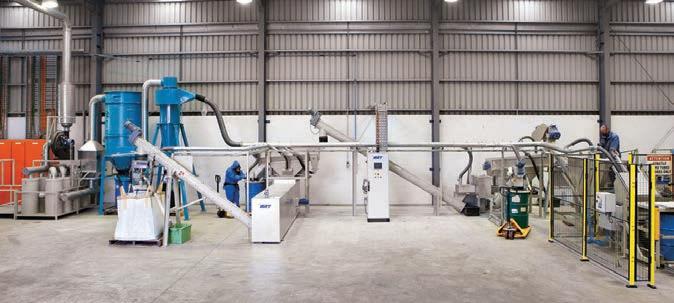
E Waste/Mercury
Tyson Ord
0433205840 tyson.ord@ecocycle.com.au Batteries
Peter Cage
0428722144 peter.cage@ecobatt.net
Metals
Jarrod Munday
0431319087 jarrod.munday@recycal.net
Davis Earthmoving & Quarrying Pty Ltd
Company Overview:
Davis is an industry leader in mobile waste processing in NSW. The company has a range of over 100 pieces of Plant & Equipment on offer for hire or contract in our privately owned fleet. All equipment is modern, portable and efficient. We offer services in Green Waste Recycling, Glass & Concrete Recycling, C&D Shredding, Crushing, Screening, Land Clearing, Mulching, Haulage, Recycled Products & Landscape Supplies. Established in 1975, we are proudly Australian, family-owned and operated, contracting state-wide in NSW. Davis has a reliable reputation and extensive experience gained over 45 years. We are regular contractors for Councils in NSW and have completed tens of thousands of government, civil and commercial projects. For decades we have been delivering high rates of resource recovery. We process, supply and deliver quality materials using innovative and environmentally responsible solutions. We process over a quarter of a million tonnes of material per annum. CEO Eric Davis has in-depth knowledge and experience in sustainable recycling. The company’s focus is recycling and repurposing materials that would otherwise end up in landfill using our high-powered equipment. Our aim is to transform the way the world views and values waste, striving forward towards a circular economy.
Products and Services:
• Green Waste Recycling • Low Speed, High Speed, C&D Shredding • Crushing & Concrete Recycling • Glass Recycling • Screening • Forest Mulching, Timber & Stump
Grinding • Land Clearing, Road Widening &
Forestry • Quality Recycled Landscaping Supplies • Plant & Equipment Hire • Bulk & Heavy Haulage
Brands:
For hire • Low Speed Shredders; Komptech,
Pronar • Horizontal Grinders; Diamond Z,
Peterson • Mobile Crushers; Rubblemaster,
Metso, Kleemann • Soil & Trommel Screens; Pronar, Metso • Picking Stations; Kiverco • Forestry Mulchers; FAE • Excavators 1.8 to 46 tonne; CAT,
Komatsu • Dozers • Rollers, Compactors & Drotts • Wheel & Track Loaders; CAT Posi-Track
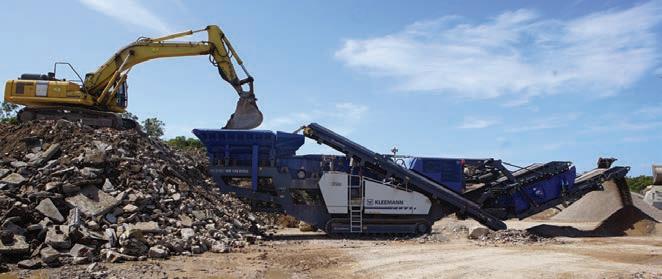
Core Capabilities:
Davis offers high-powered, mobile waste processing equipment for hire or contract in NSW. Our Low Speed Shredders process bulky C&D, logs, palms, carpet, tyres & mattresses with ease. Our Horizontal Grinders process green waste, C&D, timber, stumps & logs. Our mobile Crushers recycle concrete, brick, rock and glass. Mobile and Trommel Screens process soil, timber & green waste. We have equipment available for forestry mulching, subdivisions, road constructions, grubbing, firebreaks. We operate our own service centre for scheduled maintenance and field repairs, this guarantees safety, quality and maximum efficiency for our machinery with minimum down time for our customers. We are dedicated to maximizing productivity and efficiently recovering environmentally sustainable and quality recycled products for beneficial reuse.
Contact Details:
Davis Earthmoving & Quarrying Pty Ltd
PO BOX 19 TERREY HILLS NSW 2084 Phone: (02) 9450 2288 Email: davisem@davisem.com.au Web: davisem.com.au
Eriez Magnetics
Company Overview:
Leading specialists in metal separation, resource recovery technologies, and developing new recycling strategies and processes.
Products and Services:
• Magnetic Pulleys & Scrap Drums • Ballistic Metal Separators • Suspended Electromagnets • Eddy Current Separators • Stainless Steel Separators • Fines Metal Recovery Systems • Airless Metal Recovery Systems • Technical Service, Repairs and
On-site Inspections
Brands:
• P-Rex® Scrap Drum • Shred1™ Ballistic Separator • FinesSort® Metal Recovery System • RevX-E Eddy Current Separator
Core Capabilities:
Eriez designs and manufactures equipment to successfully recover and beneficiate ferrous and nonferrous metals. Identify and remove unwanted metal contaminates to minimise product rejection and maximise product purity. We can help you achieve greater recovery at a higher-grade product delivered at a lower cost per ton. Recover valuable resources from: • MRF, MSW, C & I and C & D, • E-waste, • Tyre recycling and Scrap metal yards, • Energy from waste feed and bottom & fly ash, • Green waste processing, composting and road sweepings
Contact Details:
Eriez-Australia
21 Shirley Way, Epping, Victoria 3076 Phone: 61-3-8401-7400 Email: sales.au@eriez.com Web: www.eriez.com.au
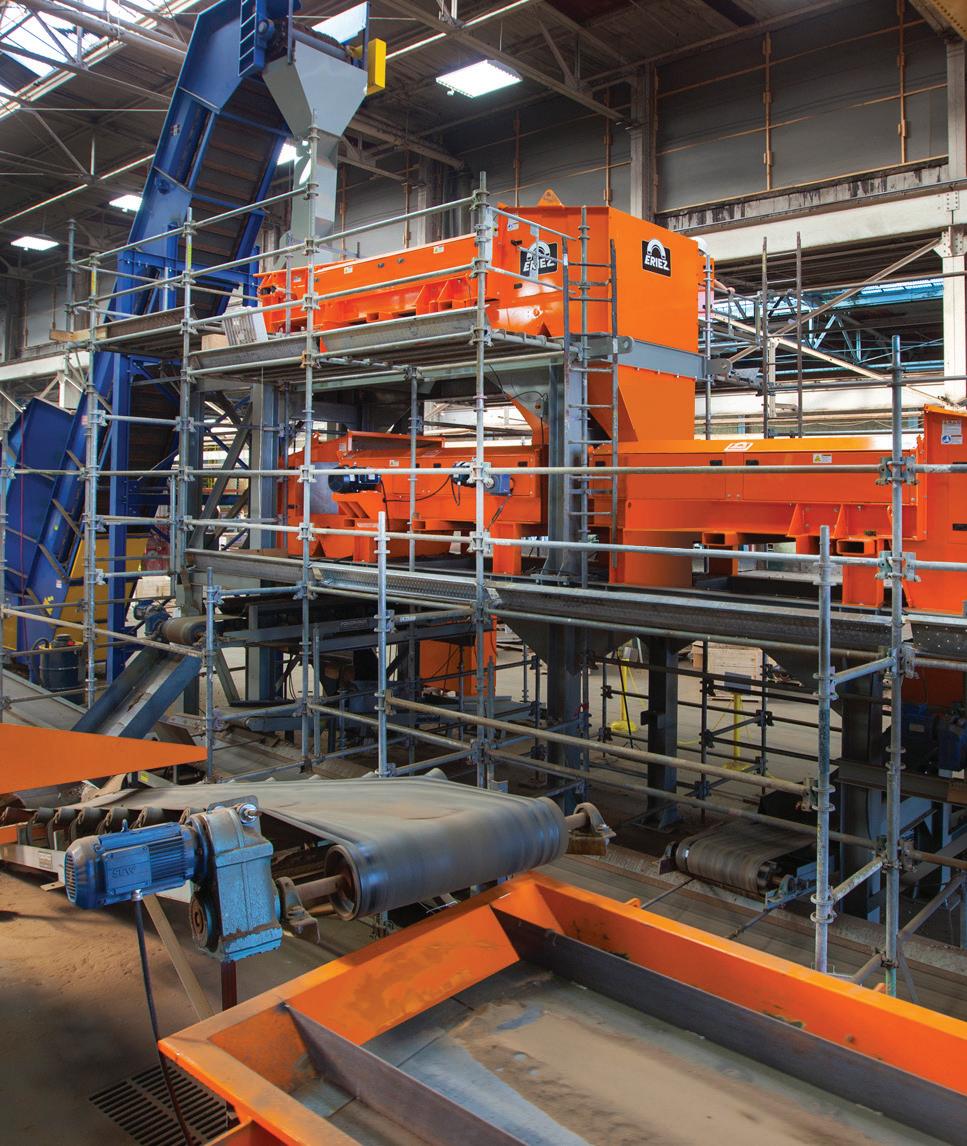
ResourceCo
Contact Details: Recent Projects/Installations:
ResourceCo Head Office
Level 1, 162 Fullarton Road Rose Park, SA 5067 Phone: (08) 8406 0300 Email: enquiries@resourceco.com.au Web: www.resourceco.com.au
Company Overview:
ResourceCo (RC) is a global leader in the recovery and re-manufacture of primary resources, extracting maximum value from materials otherwise destined for landfill.
ERSKINE PARK PLANT
Operations commenced at Tyrecycle’s (RC’s tyre recycling division) new multi-million-dollar plant at Erskine Park in Sydney, producing in excess of 10,000 tonnes of rubber crumb for the construction industry, generating 40,000 tonnes of TDF, and providing a local circular economy solution to rubber waste.
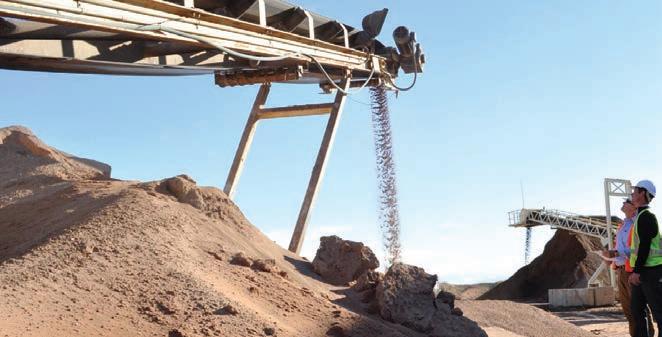
Tricon Mining
Company Overview:
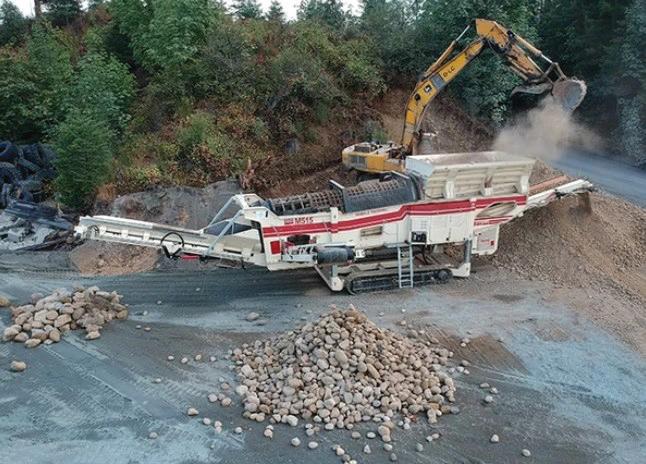
Tricon Mining Equipment Pty Ltd was founded in 2001. Years later; now recognised as one of Australia’s leading materials handling solutions suppliers within Australasia. Continually meeting client expectation and demand for supply, maintenance, servicing, inspection, training, and repair services has made Tricon Equipment what it is today, 20 years on.
Tricon Equipment is one of Australia’s leading suppliers of mobile crushing, screening, recycling, conveyor and associated equipment components since operations began. Tricon has a well-established customer base and have dedicated ourselves to deliver on customer service, support and satisfaction.
In understanding the importance of the productivity and reliability of our products to your business, we appreciate the value of minimising downtime and place great emphasis on after sales support.
Our attention to the details that help your business on a practical level flows into individualised after-sales programmes, and a commitment to customer care.
With Tricon, you get our knowhow and insider information over the long-term. Our trained service engineers have experience with a wide range of crushing, conveyor and screening equipment - and have access to a huge range of OEM & aftermarket spares.
Tricon is here to ensure our customers receive the right equipment, at the right price - and delivered on time to meet project schedules.
Our products and services meet, and in most instances exceed Australian quality, safety, and environmental standards. Tricon works in alignment to AS/NZS ISO 9001-2016 and management systems comply with Commonwealth and State Legislation.
Our suppliers, fabricators, and designers work safely and efficiently all using industry best practices and Australia OHS & Workplace Practices. • Recycling Trommel’s • TeleStackers • Mobile Conveyors
Products and Services: Brands:
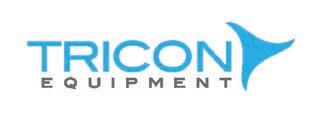
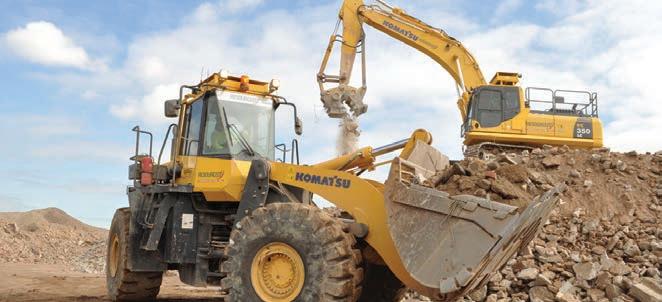

• C&D & C&I Recycling • Disposal, Treatment & Management of Contaminated Soils • Renewable Energy &
Alternative Fuels • Tyre & Waste Rubber Recycling • Recycled Construction Material • ResourceCo Pty Ltd • Southern Waste ResourceCo • Cleanaway-ResourceCo • SUEZ-ResourceCo • Tyrecycle Pty Ltd

• Impact Crushers • Cone Crushers • Conveyor Pulleys • Dewatering Plants • Blending Plants • Conveyor Components • Spare Parts
Contact Details:
Tricon Mining Equipment
11 Lucca Road, Wyong NSW2259 1300 859 885 sales@ticoneequipment.com.au triconeequipment.com.au
Komatsu Forest
Company Overview:
Komatsu Forest is one of the world’s largest manufacturers of forest machines. We are represented on six world continents by a network of dealers and our own sales companies.
Komatsu Forest’s head office is in Umeå, Sweden, and we have two manufacturing units, in Sweden and the USA. Our own sales companies are located in Sweden, Norway, Finland, Germany, Austria, France, United Kingdom, Russia, USA, Australia and Brazil, and our network of dealers represent us on all other important forestry markets.
Our extensive service organisation takes care of the machines, ensuring that they perform their best throughout their service lives. We have workshops throughout the world, service vehicles for quick assistance, in-house machine and methodology instructors to help maximise productivity, and support functions for everything related to our machines and services.
Products and Services:
We offer products and services that increase productivity while simplifying the working day for you as a machine owner.
We combine all our services under our Customer Care concept. This is our promise that you will enjoy the benefits of Komatsu Forest’s investments in research, development, servicing, support, logistics and innovative services. These combined resources are at the very heart of Komatsu Forest’s offer.
Our goal is to make your working day as safe, problem-free and profitable as possible, no matter where in the world you operate. Let us show you that by choosing Komatsu, peace of mind and accessibility can become a natural part of your working day.
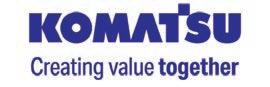
Brands
• Komatsu • Peterson • TimberPro
Core Capabilities:
Our world-wide network of highly trained service professionals is ready for you.
We know how important it is to be close to service and maintenance when help is needed. Therefore, we have a market-wide network of highly trained service professionals that knows your Komatsu, Peterson & Timberpro machine in every detail. They are, in turn, in constant contact with the Komatsu Forest head office so your voice or needs are never more than a call away from our collective expertise. Furthermore, we are constantly developing new services that will help you in your everyday work.

We offer:
• Workshops and field services throughout Australia & New Zealand • Well qualified personnel with expert knowledge of Komatsu & affiliated machines • Field Service that enables us to remain close to you and your
machine • Support and maintenance throughout your machine’s service life • Maintenance agreements with fixed maintenance prices and other benefits
Contact Details:
AUSTRALIA
Komatsu Forest Pty Ltd 4/11 Ave of Americas Newington, NSW 2127 T : +61 2 9647 3600 E : info.au@komatsuforest.com
NEW ZEALAND
Komatsu Forest Pty Ltd 15C Hyland Cres Rotorua, New Zealand M: John Kosar + 64 274 865 844 M: Paul Roche + 64 21 350 747
Komptech CEA
Company Overview:
Komptech CEA is the Australasian distributor of Komptech machinery and systems for the treatment and processing of solid waste and organics waste materials for recovery and recycling. Our product range includes over 30 different types of both mobile and stationary machines that cover all key processes in modern waste processing including: • Single-shaft and dual-shaft industrial shredders • Compost windrow turners for commercial operations • Star screen and trommel screen machines • Material separation equipment including windsifters, ballistic separators and stone contaminant separators • Stationary recycling system solutions including shredders, separators and screening machines
Brands:
• Rowan • Komptech
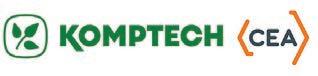
Core Capabilities:
With a specialized product portfolio that includes over thirty different types of machines covering all key processes in modern waste handling, a consultative guiding approach to solution development for customers, and full service aftersales support and parts, Komptech CEA has become a leading supplier to the recycling and waste processing industry.
Providing customer value is our focus as we strive to be the industry’s technological leader through continual innovation. Komptech CEA is dedicated to working with you to help you solve your waste problems and identify opportunities with comprehensive, detailed solutions driven by world-class technology.
Contact Details:
Sydney
50 Skyline Crescent Horningsea Park, NSW 2171 1300 788 757 www.komptechcea.com.au
Melbourne
109 Merola Way Campbellfield, VIC 3061 1300 788 757 www.komptechcea.com.au
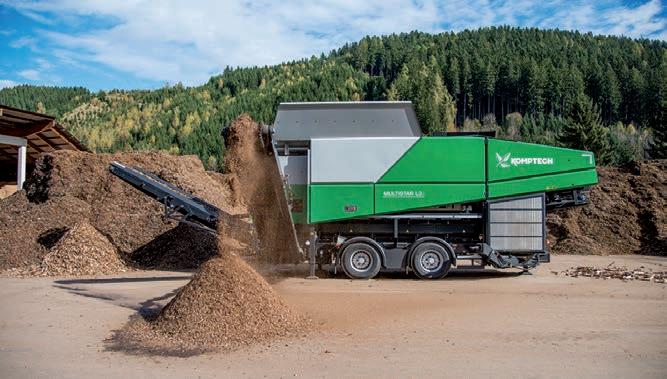
Brisbane
11 Kiln St, Darra 4076 1300 788 757 www.komptechcea.com.au
Adelaide
Perth
Auckland
96 Gavin Street Mt Wellington 1060 0800 435 269 www.komptechcea.com.au
Key Contacts:
Craig Cosgrove
Hitachi Zosen Inova
Company Overview:
Hitachi Zosen Inova (HZI) is a global leader in energy from waste (EfW), anaerobic digestion (AD) and Powerto-Gas, acting as an engineering, procurement and construction (EPC) contractor delivering complete turnkey plants and system solutions for energy recovery from waste.
Since 2015, HZI Australia, a 100% subsidiary of HZI, is developing new projects in Australia, New Zealand, and the South Pacific. Its first project, the 300,000 tpy East Rockingham WtE is now in construction and will start commercial operation in Dec 2022.
Products/Services:
• Thermal treatment of residual waste, energy recovery, flue gas treatment, and residue recycling • Dry anaerobic digestion of food & green resources, renewable power production, biogas upgrading to biomethane and bio-CNG • Power-to-Gas for volatile electricity into renewable synthetic gas for
a carbon-neutral economy • Development, Design, Build, Finance,
Own, Operation & Maintenance
Brands:
• Hitachi Zosen • Aquaroll, DYNOR, Kompogas, • HZI Etogas, HZI DryMining
Core Capabilities:
Energy from Waste, Renewable Gas, Project Development, EPC, O&M, Asset Management
Recent Projects/Installations:
NORTH LONDON ENERGY RECOVERY FACILITY (ERF) – START OF OPERATIONS IN 2026 London, UK
On the 24 January 2022, the UK’s second largest waste authority signed a landmark Engineering Procurement and Construction (EPC) contract. HZI will deliver the newest and most advanced technology in the ERF on behalf of North London Waste Authority.
The project’s scope incorporates building a two-line ‘chute to stack’ ERF facility, which will use proven technology to treat up to 700,000 tonnes of non-recyclable residual waste each year. The plant will generate reliable baseload electricity to power up to 127,000 homes, including heat and hot water for up to 50,000 local homes.
HZI will provide core ‘chute to stack’ technologies, advice on plant erection and commissioning support services, with the role starting on the 1 February 2022.
The new ERF facility will prevent residual waste from ending up in landfill, where it generates methane, a greenhouse gas which has a warming impact 80 times greater than CO2. The new ERF will also save the equivalent of 215,000 tonnes of CO2 each year – the equivalent of taking 110,000 cars off the roads.
Visit: https://www.hz-inova.com/ hitachi-zosen-inova-to-delivertechnology-for-north-london-energyrecovery-facility/
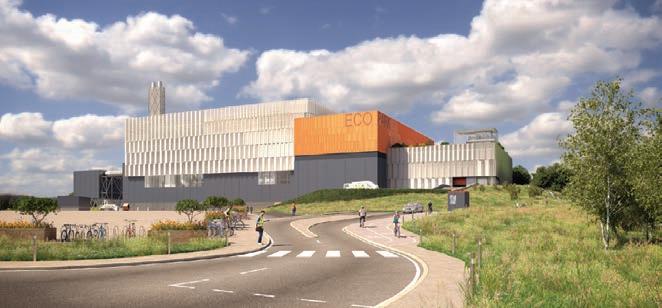
Contact Details:
Hitachi Zosen Inova Australia Pty Ltd
Level 17, 40 Mount Street North Sydney, NSW 2060 Phone: 02-8003 4110 Email: info@hz-inova.com Web site: www.inova.com
Key Contacts:
Dr Marc Stammbach
02 – 8003 4110 info@hz-inova.com
Applied Machinery
Contact Details:
55-61 Nissan Drive Dandenong VIC 3175 Phone: 03 9706 8066 Email: sales@appliedmachinery.com.au Web: www.appliedmachinery.com.au
Company Overview:
Applied Machinery is one of Australia’s largest suppliers of quality recycling machinery. Over 30 years industry experience enables us to deliver turnkey solutions for all manner of recycling applications across Australia.
Products and Services:
• Shredders and granulators • Plastic washing, tyre, and e-waste recycling plants • Repelletising systems/screen changers • Polystyrene recycling machines
Brands:
• Genox • Polystar • Fimic • Greenmax
Core Capabilities:
Applied Machinery has the capability to service the smallest single machine requirement, through to the largest of multi-site, staged installations and complete recycling line, turn-key projects. We supply some of Australia’s largest recycling organisations. A wide range of shredders and granulators are always in stock for quick delivery.
Recent Projects/Installations:
PORT PLASTICS Port Macquarie
Polystar Repelletising system and Genox large format shredder to drive recycling operations in the Port Macquarie region and reduce the need for transport of recyclables to metropolitan centres.
Diverseco
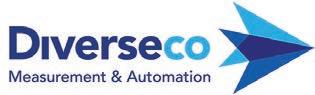
Company Overview:
• Truck wheel washes for EPA and road safety compliance. • Automated waste sortation systems: comprehensive and completely automated robotic sortation systems for MRFs.
As one of Australia’s leading measurement and automation solutions providers, we at Diverseco pride ourselves on the sheer scope of our problem-solving expertise and supply of industry leading innovative technologies. We are heavily involved across a wide range of industries, with a comprehensive solutions portfolio specific for the waste management industry that includes both driver-specific solutions and robotic automation solutions for material recovery facilities.
Products and Services: Brands:
• Waste Robotics • BinWeigh
Core Capabilities:
At Diverseco, our core capabilities reside in our ongoing ability to meet and exceed customer requirements through our extensive problem-solving resources: we are ideal partners for any organisation looking to turn their operational problems into new, profitable capabilities.
• Waste vehicle on-board payload optimisation and overload monitoring (Chain of Responsibility and legal-fortrade operations). • Weighbridges and portable truck scales for accurate vehicle weighing and accountability.
Contact Details:
3309 Logan Road Underwood, QLD, 4119 M: 1300 069 970 E: onboardsolutions@diverseco.com.au W: diverseco.com.au
Australasian Specialty Coatings
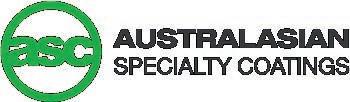
Company Overview:
Australasian Specialty Coatings – ASC – is an experienced coatings company located in Blacktown. We work in Construction and Maintenance and provide a range of Protective Coatings and Treatments for Concrete & Steel.
We have been established since 2003 and we have a strong track record in achieving outstanding results for our customers. ASC successfully works with a wide variety of customers including Sydney Water, Ericsson, Veolia Environmental and Water Services, Suez Water and Waste Services, Unilever, Coca Cola Australia, General Mills, Bega Foodservice, George Weston Foods, Diageo, etc.
ASC is an experienced organisation with ISO 9001, 14001 and 45001 Certified Management Systems as well as the NSW Government 5th Edition. We are also members of the Master Builders Association.
Products and Services:
Flooring (Epoxy and polyurethane) – Commercial & Industrial
Floor Resurfacing, Concrete Remediation, Concrete Repair, Anti-Slip Flooring, Anti-Static Flooring, AGV Flooring, Self-Levellers, Demarcation & Line marking
Coatings for Concrete
Densifiers, Waterproofing Membranes, Sealers, Concrete Resurfacing, Epoxy and Polyurethane Flooring, Chemical Bund Linings, Acid-Resistant Coatings
Protective Painting Services
Abrasive Blasting, Vapour Blasting, Shot-Blasting, Corrosion Control Coatings, Chemical Resistant Coatings
Contact Details:
ASC Head Office
1/14 Chicago Avenue Blacktown, NSW 2148 Phone: 02 8840 8888 Email: enquiries@acoatings.com.au Web: ascoatings.com.au
Spartel Pty Ltd
FABCOM® Organics Under Control©
www.FAB-COM.com.au
Contact Details:
aspects organic waste processing from waste generation to soil beneficiation products, technology, process data processing and control, odour prevention and control
Harrie - 0414 37 66 99 E: info@spartel.com.au W: www.FAB-COM.com.au
Company Overview:
Spartel Pty Ltd was founded in 1995 by Dr Harrie Hofstede, specialist waste management scientist in waste composting and pollution control. The company has a consulting arm, Hofstede & Associates, and waste technology R&D programme under the umbrella. The R&D has resulted in six patents in international markets. We have designed and developed two main large-scale composting systems under the FABCOM® Brand. FABCOM® Tunnels and the FABCOM® MAF system.
Core Capabilities:
The overall core capability is all
Products and Services:
• FABCOM® Tunnel compost plants • FABCOM® MAF composting system • Wireless data transmission and processing over a 2 km radius • Aeration controlled by process data • Remote access process control • Design and construct of compost plants • Development and optimisation of compost process and products • ODOROV™ effective odour control agent for organic waste • High nitrogen composts (4% N)
Recent Projects/Installations: :
FABCOM® MAF SUEZ Newcastle
Raymond Terrace NSW Dedicated FABCOM® MAF aeration system for post Bedminster compost maturation & drying; Capacity 10,000 tpa
Garwood International
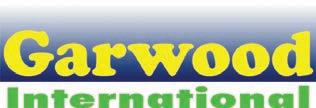
Company Overview:
Garwood International a 100% Australian owned & family operated business. All equipment purchased from Garwood International is supported via our comprehensive aftermarket services. With our head office located in Sydney, we also have Service and Sales in Melbourne and Brisbane. We can partner with any of your existing service providers Australia wide.
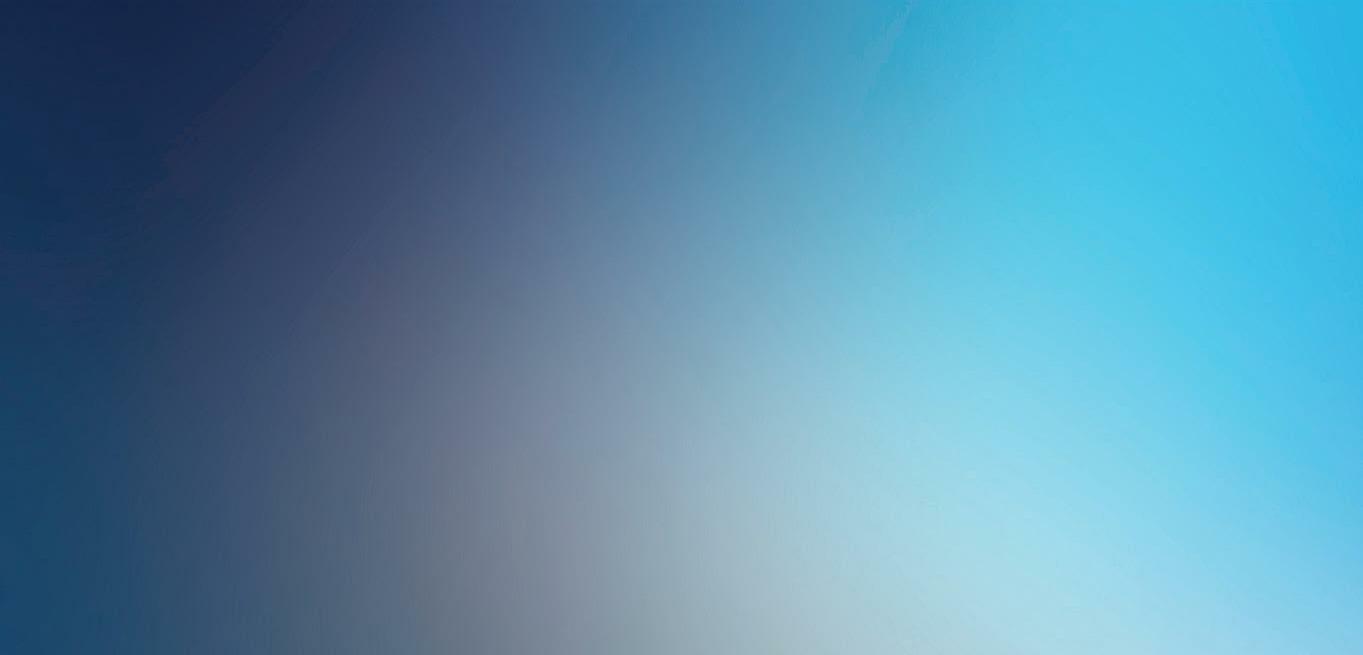
Products and Services:
GARWOOD Garbage COMPACTORS
Rear, Side, Dualpact & Front Loaders. • Footpath Sweepers • Tow Behind Trailer Brooms • Bin Weighing Systems • Enviroweigh, LoadWeigh and VOPS™ 2 bin weighing equipment
Core Capabilities:
Garwood International has grown to become a leading designer, manufacturer and distributor of specialised waste and recycling collection and compaction equipment. The company’s reputation for high quality, innovative products, together with its enviable record of outstanding customer service and after-sales support, has delivered strong and consistent growth over the past three decades both in Australia and Internationally.
Clients:
Our Clients range from City Councils, National and International Airports, Department of Defence to Local Government Sectors and Private Contractors.
Contact Details:
Garwood International
Ph: 02 9756 3756 3 Hexham Place, Wetherill Park, NSW, 2164, Australia Website: www.garwoodinternational.com.au
GET YOUR CAPABILITY STATEMENT IN NOW!
Capability statements are a popular medium in Inside Waste that give the industry an insight into your business – how it can help potential clients, the services you offer, and products you sell.
If you want access to all the major stakeholders in the waste industry then a Capability Statement is a great introduction to those decisionmakers, allowing your business to get a crucial foothold in a competitive market.
If you want to know more about Capability Statements and how they can help your business Contact Chelsea Daniel-Young: Email: Chelsea.daniel@primecreative.com.au | Ph: 0425 699 878
Davis Earthmoving & Quarrying Pty Ltd FOR HIRE RUBBLEMASTER IMPACT CRUSHER RM120GO! FOR HIRE
Application: Mobile Concrete Crushing, Rock Crushing, Glass Recycling, Landfill Management Suitable material: For processing glass, concrete, brick, tile, asphalt and rock. Features: Track mounted, remote control, closed material circuit, mesh screen with integrated refeeding belt, 3 rotor speeds Unit Dimensions: Screen Area 5,5 m² Weight: 35 tonne Motor: John Deere Throughput: Up to 350 tonnes per hour Finished product size: Graded high quality final aggregate in a single pass Price: FOR HIRE OR CONTRACT. Rates available. Contact for more information: Davis Earthmoving & Quarrying Pty Ltd Phone: 02 9450 2288 Email: davisem@davisem.com.au Web: www.davisem.com.au
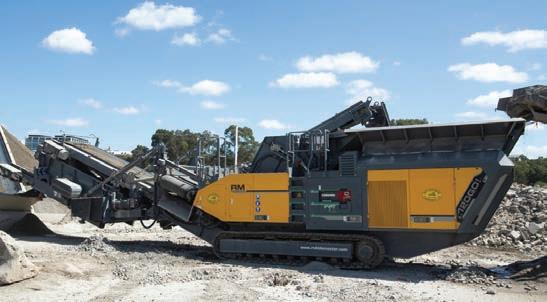
Davis Earthmoving & Quarrying Pty Ltd FOR HIRE PETERSON 5710C HORIZONTAL GRINDER FOR HIRE
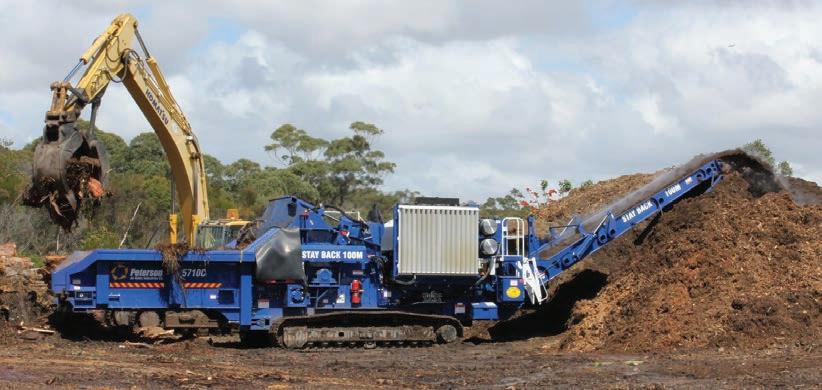
Application: Timber Grinding, Land Clearing, Green Waste Mulching, Landfill Management Suitable material: For processing trees, palms, logs, stumps, vegetation, green waste, brush, land clearing debris, mixed woody feedstocks Features: Track mounted, remote control, high lift feed roll, magnetic head pulley Unit Dimensions: Feed opening 152 x 102 cm Weight: 43 tonne Drive Type: PT Clutch Motor: CAT C27 Speed: High speed 1,050 HP Finished product size: Superior particle size control, fine products, mulch Price: FOR HIRE OR CONTRACT. Rates available. Contact for more information: Davis Earthmoving & Quarrying Pty Ltd Phone: 02 9450 2288 Email: davisem@davisem.com.au Web: www.davisem.com.au
Davis Earthmoving & Quarrying Pty Ltd FOR HIRE
Davis Earthmoving & Quarrying Pty Ltd FOR HIRE DIAMOND Z DZH 4000TK HORIZONTAL GRINDER FOR HIRE
Application: Mobile Timber Grinding, Land Clearing, Green Waste Mulching, Landfill Management Suitable material: For processing trees, palms, logs, stumps, vegetation, green waste, brush, land clearing debris, mixed woody feedstocks Features: Track mounted, remote control, quick screen change, reversing fan Screen Area: 3,800 square metres Weight: 38.5 tonne Drive Type: Fluid Coupling Drive Motor: CAT C18 Speed: High speed Throughput: Up to 120 tonnes per hour Finished product size: superior particle size control, fine products, mulch Price: FOR HIRE OR CONTRACT. Rates available. Contact for more information: Davis Earthmoving & Quarrying Pty Ltd Phone: 02 9450 2288 Email: davisem@davisem.com.au Web: www.davisem.com.au
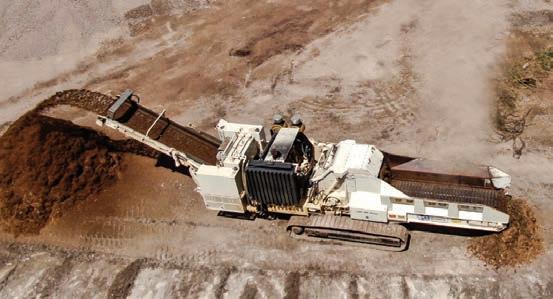
PRONAR MRW 2.85G TWIN SHAFT LOW SPEED SHREDDER FOR HIRE
Application: C&D Shredding, Timber Grinding, Land Clearing, Green Waste Mulching, Landfill Management Suitable material: Mattresses, C&D, tyres, carpet, green waste, municipal industrial waste, bulky materials, pallets, tree stumps, light scrap Features: Track mounted, remote control Weight: 26 tonne Drive Type: Hydraulic Motor: CAT C9.3B Price: FOR HIRE OR CONTRACT. Rates available Contact for more information: Davis Earthmoving & Quarrying Pty Ltd Phone: 02 9450 2288 Email: davisem@davisem.com.au Web: www.davisem.com.au
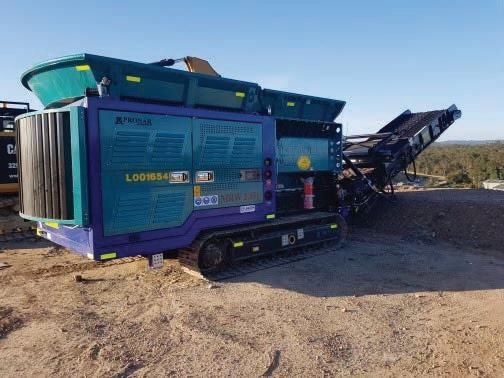
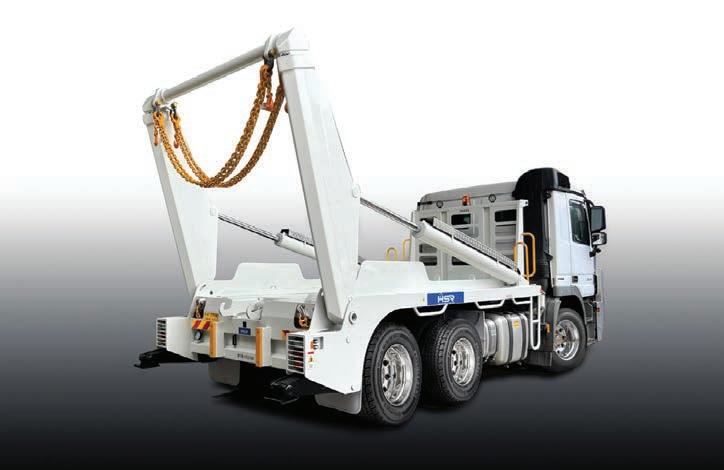
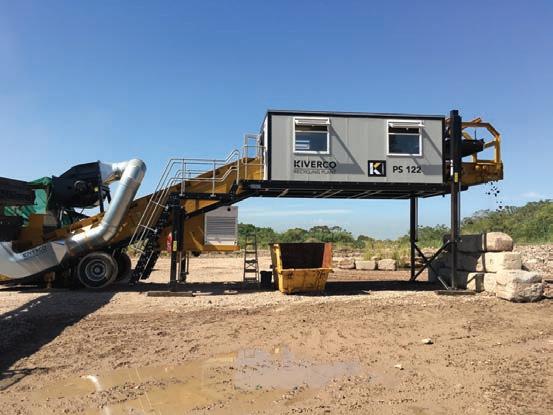
HSR-RC Range of Rear Load Refuge Compactors
Unit Dimensions: from 2080mm high – 3450mm high, 2095mm – 2490mm wide Weight: 2,000kg – 5960kg Capacity (in weight): 5m³ -32m³ No. of units in range: 26 Finished product size: 5m³ -32m³ Options/Extras: bin lifter, auto greasing systems, tool boxes, hand wash, lighting and customised control systems, pressure washers and bin cleaning systems, hard waste and green waste specifications, automatic bin capture and more Price: contact Nick on 0499 944 969 More: certified Australian Made and Owned Name: Nick Phone Number: 0499 944 969 Webpage: www.hsrsx.com.au Email: admin@hsrsx.com.au
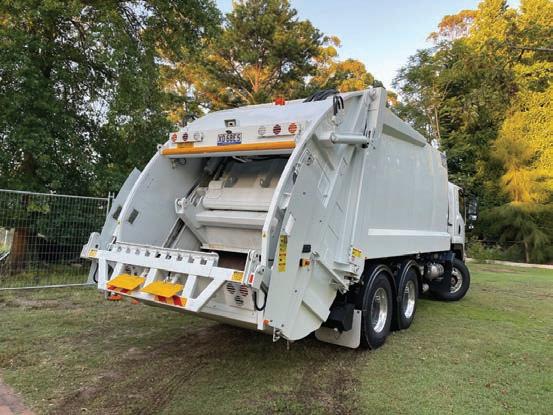
Applications: Mobile shredding for C&D, mattresses, tyres, carpet, bulky goods, greenwaste Features: On tracks, remote control, over-band magnet Unit Dimensions: 11371 x 3327 x 3635 working unit position Weight: 26.50 tonne Drive Type: Hydraulic Motor: CAT C18 Rotor diameter/lengths/speed: 3m Speed (slow/high): 38 rpm max Throughput: Up to 100 tonne per hour Price: FOR HIRE OR CONTRACT. Rates available More: Contact Davis Earthmoving & Quarrying Pty Ltd for further information: Phone: 02-9450 2288 Email: davisem@davisem.com.au Web: www.davisem.com.au
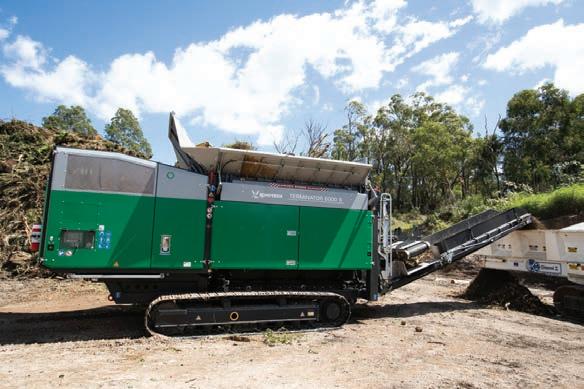
HSR, SX Range of Skip Loaders
Unit Dimensions: 3600mm to 5800mm deck length Weight: 1200kg to 3750kg Capacity (in weight): 4,000kg to 16,000kg payload No. of units in range: 5x plus multiple combinations
Finished product size:
Options/Extras: remote controls, hydraulic tower tarp, auto greasing systems, lighting, hand wash, toolboxes, tarp and mesh storage, shovel and broom holders. Price: please call 0488 333 260 or contact HSRSX.COM.AU for more information. More: Certified Australian Made and Owned Name: Jake Henderson Phone Number: 02 9725 3347 or 0488 333 260 Webpage: www.hsrsx.com.au Email: admin@hsrsx.com.au
HSR Southern Cross
PS122 Picking Station
Unit Dimensions:
Weight: 19,000kg
Capacity (in weight): No. of units in range: Finished product size: Options/Extras:
• Dual Power/Mains Changeover • Fan Blower Module • Overband Magnet Module • Clean Fix Fan • Site Axle • Trap Door Bins • Cabin Air Conditioning • Feeder With Impact Protection Price: TBA More: The Modular PS Picking Station offers unrivalled set-up simplicity (no cranes are required), operator comfort, safety, and environmental protection. It combines air separation, magnetic separation and manual sorting - all in one compact unit.
Name:
Phone Number: 1800 182 888 Webpage: www.lincom.com.au Email: sales@lincom.com.au
PS122 OPERATING LENGTH 16.1m 52.9ft OPERATING WIDTH 3.4m 11.2ft OPERATING HEIGHT 5.6m 18.2ft WEIGHT 19,000kg 41,888lbs
Kiverco
FOGO / Organic Tunnel System
Unit Dimensions: Varies depending on volume requirements Capacity (in weight): 10,000 + Tonne pa Options/Extras: Expandable Systems - increased demand Price: POA More: Spartel has specialised in compost system engineering for 30 years and invented the patented aerated composting systems. This system utilises a VSD aeration system with temperature and oxygen feedback to control the process and a purposely designed Biofilter to treat captured process air. This leading technology meets all requirements in the area of organic waste recovery and composting standards. Name: Dr Harrie Hofstede Phone Number: 0414 376 699 Webpage: www.fab-com.com.au Email: Harrie@spartel.com.au
FSR 140/120-260 Dual Control
Unit Dimensions: 6,555/ 2,240/ 2,665 Weight: 14,000 kg (GCM) No. of units in range: 1
Options/Extras:
• Roof mounted amber warning beacon with light bar • Fire extinguisher • Airbag compatible bullbar • Air deflector Price: See your local Isuzu dealer More: The FVY 240-300 Dual Control features identical twin steering for maximum operator ease; the left-hand steering input is transferred through a gear driven cross shaft mounted inside the cab, meaning the steering columns adjust in unison for the optimum position. Name: Isuzu Trucks Phone Number: 1800 035 640 Webpage: www.isuzu.com.au Email: www.isuzu.com.au/contact-us/
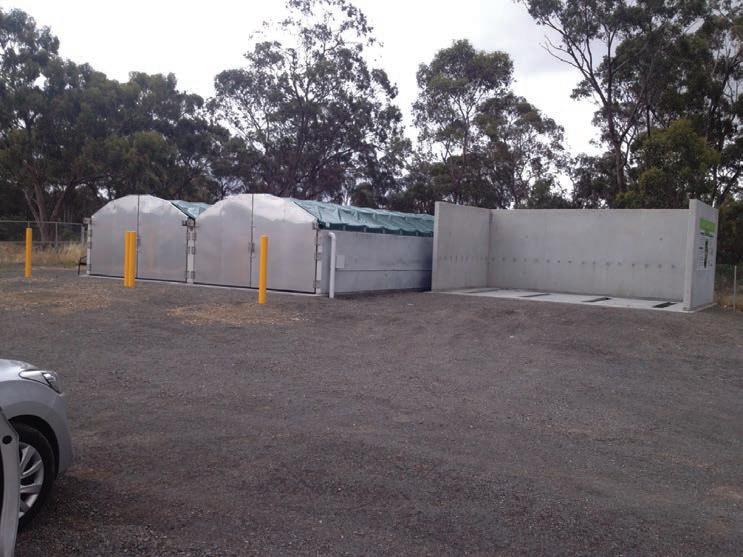
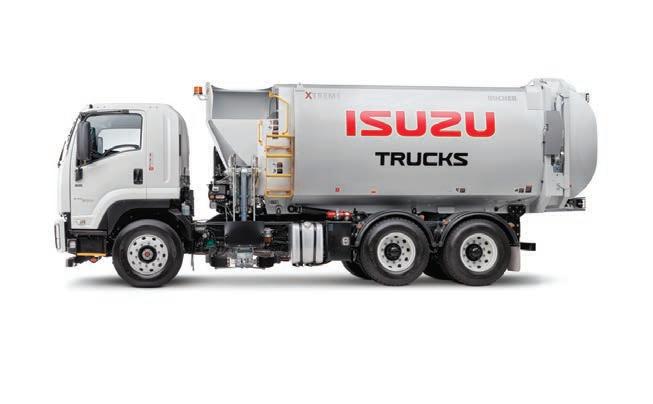
Garwood Dualpact
Model types: 50/50, 60/40 and 70/30 splits Configuration: Fitted to any 4x2, 6x4 and 8x4 cab chassis Capacity: 6, 8, 10, 12, 15, 20, 22, 24m3 Payload: From 2.5t to 10t Length: 2800mm to 8200mm Construction material: High tensile steels Weight: 3000kg-7800kg Max load on arms: 300kg single lift and 800kg WCL Lift cycle time: Variable – single lift 6-12 secs, WCL 8-14 secs Compaction system: Rear loading with individual hoppers sweep and pack action More: www.garwoodinternational.com.au or (02) 9756 3756
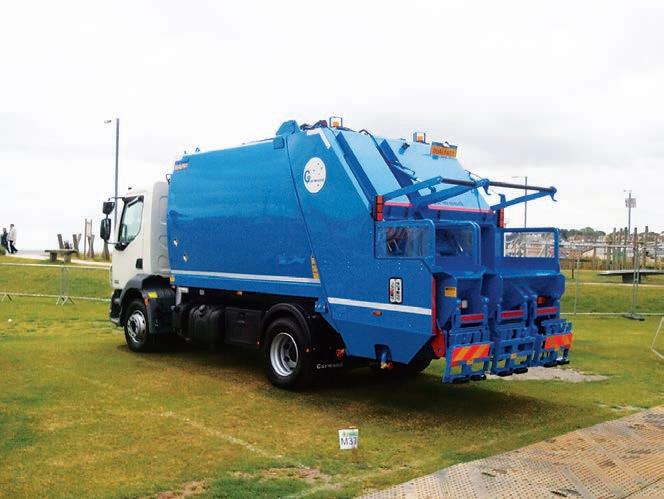
Isuzu Trucks
Garwood International Boschung Urban-Sweeper S2.0
The Boschung Urban-Sweeper S2.0. A Compact Sweeper that is fully electric powered and re¬leases ZERO emissions. Company: Garwood International Product/model name: Boschung Urban Sweeper S2.0 Unit Dimensions: Length 4300 mm (With standard broom) Width: 1150 mm Height: 1990 mm Gross Vehicle Weight: 3500 kg Hopper Capacity: 2.0 m3 with 1200 kgs payload Water Tank: Clean water tank 190L with 400 litres recycling water tank Sweeping Width: 2300 mm (standard broom) Features: Ability to deliver entire 8-hour shift at a charging rate of two hours with the supercharger, or eight hours with standard charger, LED Lights Two 20kw electric motors for a maximum speed of 45km/h Options/Extras: Automatic central lubrication system, Spray gun with high pressure water pump, 3rd front broom, Articulated hand suction hose More: info@garwoodinternational.com.au or (02) 9756 3756
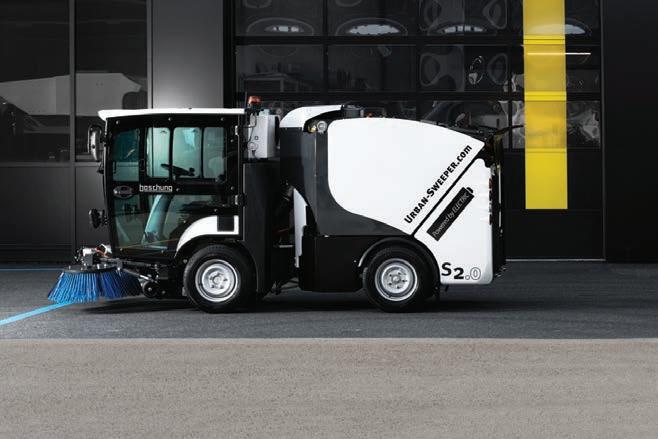
Garwood Sideloader
Model types: Litterpact GII and GIII Configuration: Fitted to any 4x2 and 6x4 cab chassis Capacity: From six through to 29m3 Payload: From 2t to 10t Length: 2400mm-7400mm Construction material: High tensile steels Weight: 1800kg-6200kg Maximum load on arms: 180kg Lift cycle time: Variable – about 6 sec Compaction system: Paddle and push panel type More: www.garwoodinternational.com.au or (02) 9756 3756
Garwood Rearloader
Model types: Miner, Bantam, Compact, Powapact, Maxipact Configuration: Fitted to any 4x2, 6x4 and 8x4 cab chassis Capacity: 4,5,6,8,10,12,15,20,22,24,28m3 Payload: From 2.5t-10t Length: 2600mm to 8200mm Construction material: High-tensile steels Weight: 2200kg-7800kg Maximum load on arms: WCL 800kg Lift cycle time: Variable – single lift 6-12 sec, WCL 8-14 sec Compaction system: Rear loading with sweep and pack action More: www.garwoodinternational.com.au or (02) 9756 3756

Garwood Frontloader
Model types: EV026, EV031 and EV033.5 Configuration: Fitted to any 6x4 & 8x4 cab chassis Capacity: 26-31-33.5 Payload: dependent on chassis selection Construction material: Bisalloy and Hardox Maximum load on arms: 2800kg Lift cycle time: 18 secs Compaction system: Twin telescopic pack cylinders. Half and full pack ejector. Base price: P.O.A More: Daniel McHugh - (02) 9756 3756, www.garwoodinternational.com.au or info@garwoodinternational.com.au
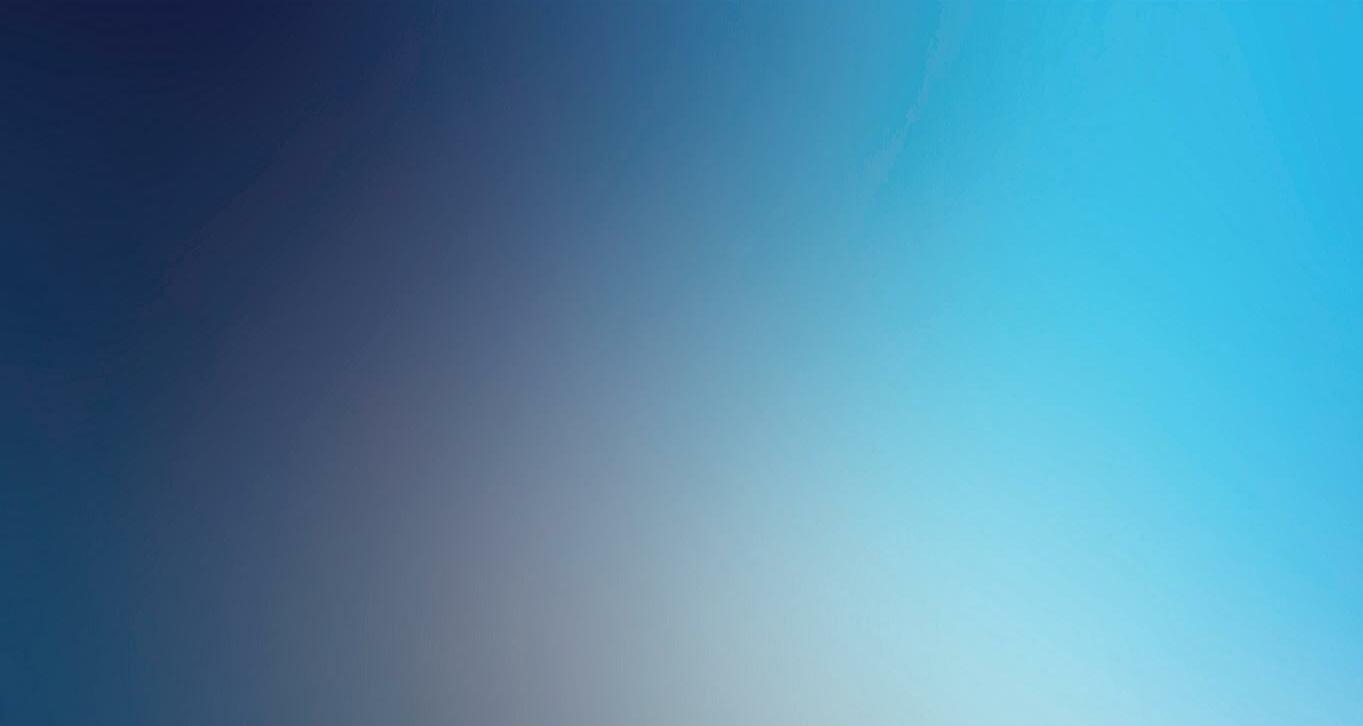
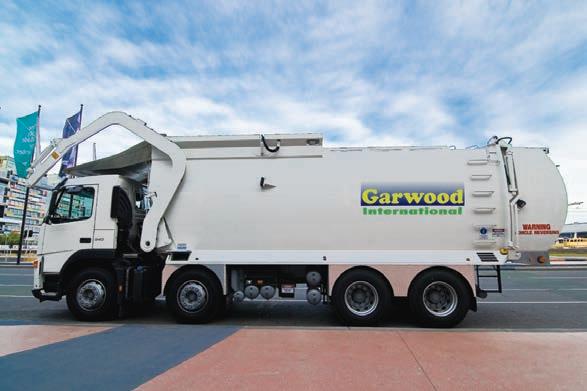
Garwood International

GET YOUR PRODUCT PROFILE IN NOW!
If you wish to let our readers know your latest machinery and its capabilities, then you should be in Inside Waste’s Product Profile section.
For more information on how to make the most of this opportunity contact Chelsea Daniel-Young:
How hard is it to sing Kumbaya?
EVENING SIR,
This land offers dichotomies for the ages. It doesn’t know what it’s doing – fire, flood, hot, cold, plagues of locusts, infestations of mice. It’s enough to test the mettle of even the most hardened Double-0 – I’d rather have Scaramanga, Blofeld or Drax to deal with any day of the week than the topsy turvy spell of weather we’ve had over the past two years, and its associated disruptions.
As any good member of our service knows, a good foundation is to be had spending our formative years in the boy Scouts. The merit badges, jamborees, obstacle courses, and helping others to help themselves. And let’s not forget sitting around the campfire singing Kumbaya. Great moments indeed.
So where is this verbal outpouring of reminiscing about inclement weather patterns and rodent invasions and the halcyon days of rubbing two sticks together to garner campfire joviality, leading you may ask? The former acknowledges how the ravages of inconsistency can lead to an unbalance in nature, while the latter seeks to bring stability to those around you.
I know it is a long-winded metaphor, but my point is this; the former is what I am seeing in the waste industry at the moment, through no fault of those at the coalface. Almost anybody who has anything to do with the sector would love it to have the consistency of a good spotted dick at the Elephant and Castle at Kensington – outer crunch with some smooth custard.
Harmonisation, sir, that is what they want. And they’re not getting it. Whether it be with landfill levies, FOGO bins, or kerbside collections, the cities, towns and states are all over the place. ‘Each jurisdiction to its own’, I hear you say. Well, sure. But how hard is it to get on the same page with something as simple as, say, landfill levies? If you speak to the various councils, state agencies, state governments and even the blessed Federal lawmakers, they all want to be at one – like Akela strumming the guitar around the bonfire. But the devil is in the details. Or maybe it’s egos? I’m unsure. All I know is industry is hitting its collective head against a brick wall.
What to do, what to do, eh? That Evans man is a good chap – well-liked by the industry, as is his counterpart in the opposition, Wilson. They keep each other honest. However, there is only a certain amount they can do – bit like trying to get Q to explain all those gadgets in precise, clear English.
And if the governments don’t come to the party, then what? Looks like industry might just have to do it on its own. Anyway, here’s hoping El Nina, El Nino – why not throw in the Pinta and Santa Maria for good measure – or whatever quirk of nature is bearing down on Terra Australis, heads off into the sunset so things around here can return to normal – hot summers, mid-afternoon thunder storms, mosquitoes, flies the size of a Harrier Jump Jet, and Prime Ministers lasting longer than two years in the job. Not much to ask for, eh, Sir?
Regards JB
