
17 minute read
Plastic fruit/veg labels
by Prime Group
Prioritising design in a circular economy
By Mike Ritchie
WOULD the maniac who designed the first plastic fruit sticker please stand up!
Why is it that every banana, orange, apple, kiwi fruit, and other piece of fruit you buy now comes with a plastic sticker attached to it?
I get that in some cases it improves scanning at the checkout, but why plastic?
It is ridiculous that these are not made out of wax-proof paper, or corn starch, or some other material that can be readily composted in a household compost bin or a standard industrial composting facility.
Their current fate is to contaminate household food and garden (FOGO) collection services, industrial composting and every backyard compost bin in Australia.
It astounds me that EPAs have not jumped straight onto this issue and regulated it out of existence.
If my clients pollute the environment with plastic, the EPA issues a ‘stop work’ notice and my client is prevented from continuing until the pollution is remediated and the process improved.
Why do we tolerate commercial scale pollution in the form of plastic fruit stickers (and polystyrene beads, balloons, non-compostable wet wipes, and the like) when there are clear alternative
Polystyrene beads need to be banned just like single-use plastic bags.
single options which do not cause environmental harm?
I give credit to the national waste action plan and the commitment by state governments to start banning single-use plastic, including the aforementioned polystyrene beads.
But the list needs to be expanded and the pace of reform massively accelerated.
I am not arguing that such plastics are the main cause of environmental harm to the planet, but they are a contributor to pollution and there are clear alternative options. It is the ease with which they could be substituted for compostable versions of the same thing, that frustrates me. It is so easy to fix, but only EPA’s can do it. I can’t. You can’t. Governments, and EPAs specifically, can. It should be a simple decision by the appropriate
Minister to put them on a list, giving proponents say six months to produce an alternative version, which does not cause environmental harm, or they are banned. Simple.
It amazes me that in the era of circular economy, climate change, plastic action plans and so forth, there is no state in Australia with legislation focussed on the end-oflife fate of products.
We have a plethora of regulations around things like product safety and occupational health, yet there are currently no regulations in Australia requiring consideration of the end-oflife fate of products including their recyclability or the pollution that they may cause.
Fruit stickers are just one obvious example of a failing regulatory system. So are non-degradeable wet wipes.
In the interest of free markets, we are failing to prioritise environmental protection, even where there are simple, environmentally sustainable alternatives available. That is very frustrating. iw (Postscript - the NSW EPA is preparing to ban plastic fruit stickers in the next round of regulatory reform. Minister Kean – more power to you. All states should do the same.)
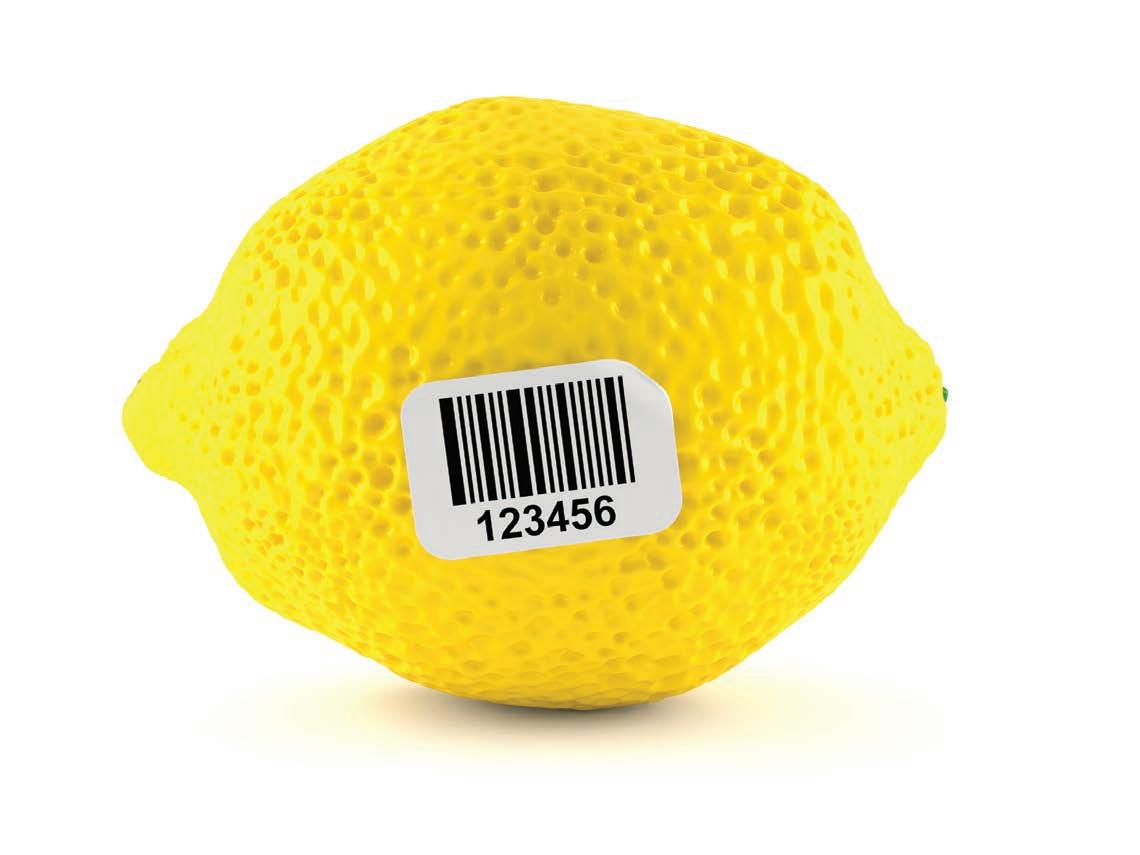
Labour shortages start to bite
By Inside Waste
“FROM a labour front, these are the most challenging times we’ve ever seen. You’re talking about wage rates going up in the order of 25-30 per cent at the moment.”
That is the conundrum that Tyrecycle CEO Jim Fairweather finds himself in – pay high wages or don’t have a workforce. Such is the current situation in many parts in the waste industry as labour shortages hit and wages start to rise.
The culprit? As with many cases over the past two years, COVID-19. Like a lot of labour-intensive industries, the waste arena relies on overseas workers to fill in the myriad of gaps that appear in the work force when there is low unemployment. However, due to strict immigration legislation due to the COVID outbreak, a lot of the blue collar, overseas-based labour that would walk into a job in the waste industry are now stranded in their home countries unable to get back into Australia. Add to that people who are close contacts, have COVID, along with a general lack of labour due to low unemployment, then you “have the perfect storm”, according to Fairweather.
The answer? Simple – open the borders, said Fairweather. And he doesn’t mean let everybody in with no restrictions. But he does believe the government needs to be more malleable in allowing people into the country that have been double vaccinated, had a booster and are willing to adhere to local rules around spreading COVID – i.e. wear masks, sign into premises and keep social distancing.
“We need to get international labour back in the market because we are running at four per cent unemployment, and we cannot find the people to fill the slots,” he said. “And the people we can find are extremely expensive for the roles that they do, and it is putting huge cost pressure on operators likes us in terms of delivering a value for money service to our customers.”
Fairweather said the costs of shipping are adding to margins being squeezed, which means they have had to pass some of those costs onto customers. This in turn has meant they can’t pass the labour costs to the consumer because Tyrecycle has already asked them to shoulder some of the burden with shipping.
“And when you’re talking about the shipping costs, you’re talking about that now being far greater than what our collection costs are,” he said. “Just the cost of moving the TDF (tyre derived fuel) offshore is now far greater than what we were originally charging our customers for the whole service.”
Fairweather said that his companies are currently running at 60 per cent labour capacity. In days gone by, labour hire agencies would have filled in the missing gaps but the market is so tight they can’t even do that.
“We were running at about 50 per cent no shows for interviews at one stage as people stayed home with job keeper,” he said. “That has fallen away now, but it is incredibility hard to get people.”
While he is not too worried about the immediate future, in six months’ time is could be a different story. Then there are the issues of the current force being over stretched, which leads to tiredness, and then safety issues start to kick in.
“We can sustain it for now and into the medium term we are okay,” he said. “We are hoping in the next six months the borders open up and this labour issue goes away or at least starts to improve. The danger will be whether it starts to impact the capacity of the market to collect all the tyres. Our workforce is very tired. They are working long hours and lots of overtime just to get through the sheer volume of work we have on the go at the moment.
“Our primary concern is the health and safety of our workers. You need to
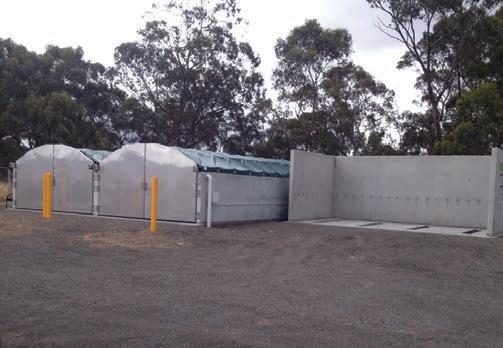

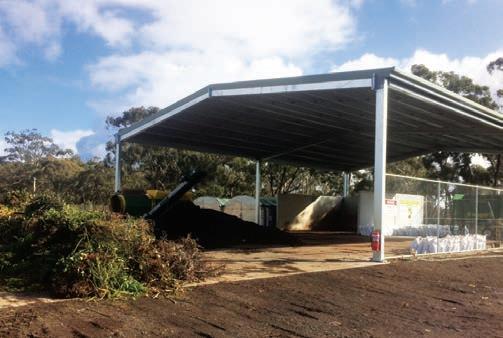
FOR ALL YOUR FOGO PROCESSING REQUIREMENTS
35 years international experience, call us to discuss your project
FABCOM® In Vessel FOGO Tunnels FABCOM® MAF Compost System Quality Assurance Compost Quality Odour Control Contaminant Management Organic Certification R&D for your Plant/Process Wireless Process Control Australian owned technology Wireless Temperature, O2, Humidity probes
FABCOM® Organics Under Control©
www.FAB-COM.com.au
Email: info@spartel.com.au Web: www.FAB-COM.com.au Mobile: Harrie - 0414 37 66 99 John - 0421 43 97 44
make sure you are managing fatigue and all those sorts of things. It is always important, but especially so in this environment. We are managing that very carefully. Lately, the top two items in my board report every month is managing our labour force and safety.”
The final aspect that worries Fairweather in the immediate future is the ramping up of blue collar labour needed in other, better paying industries.
“The tricky part at the moment, is that for this type of work, the mines are getting busy again,” he said. “And when the mines get busy they can pay whatever they want to pay, and you just lose workers.
He said in the waste industry, drivers have gone from $30 an hour to $40 an hour. Fitters have gone from $35 an hour to $50 an hour. Plant operators have gone from $26 an hour to $34 an hour. If a worker does a 10 hour day and some overtime and double time and other penalty rates, they are probably earning $550 a day, which equates to $130K.
While Fairweather is concerned at the moment, he is a not a gloom merchant. He does see an end to the issue but would like the government to step up and shorten the amount of time it will take the overseas workforce to start entering the country again.
“We are okay at the moment,” he said. “It has been a complicating factor that the COAG waste bans just come in as well. There is lots of movement in the market. There are smaller operators dropping out of the market, which is increasing the demand for our services.
“Our outlook is we remain very positive, and we think the borders will open and we are confident we can continue to run the business cost effectively, efficiently and maintaining our service levels for our customers. As we go forward, and as the borders start to open up, that should ease pressure in the labour market , which will continue to grow on the trajectory we were on.” iw
Collecting used tyres from clients has become an issue as the labour force shrinks.
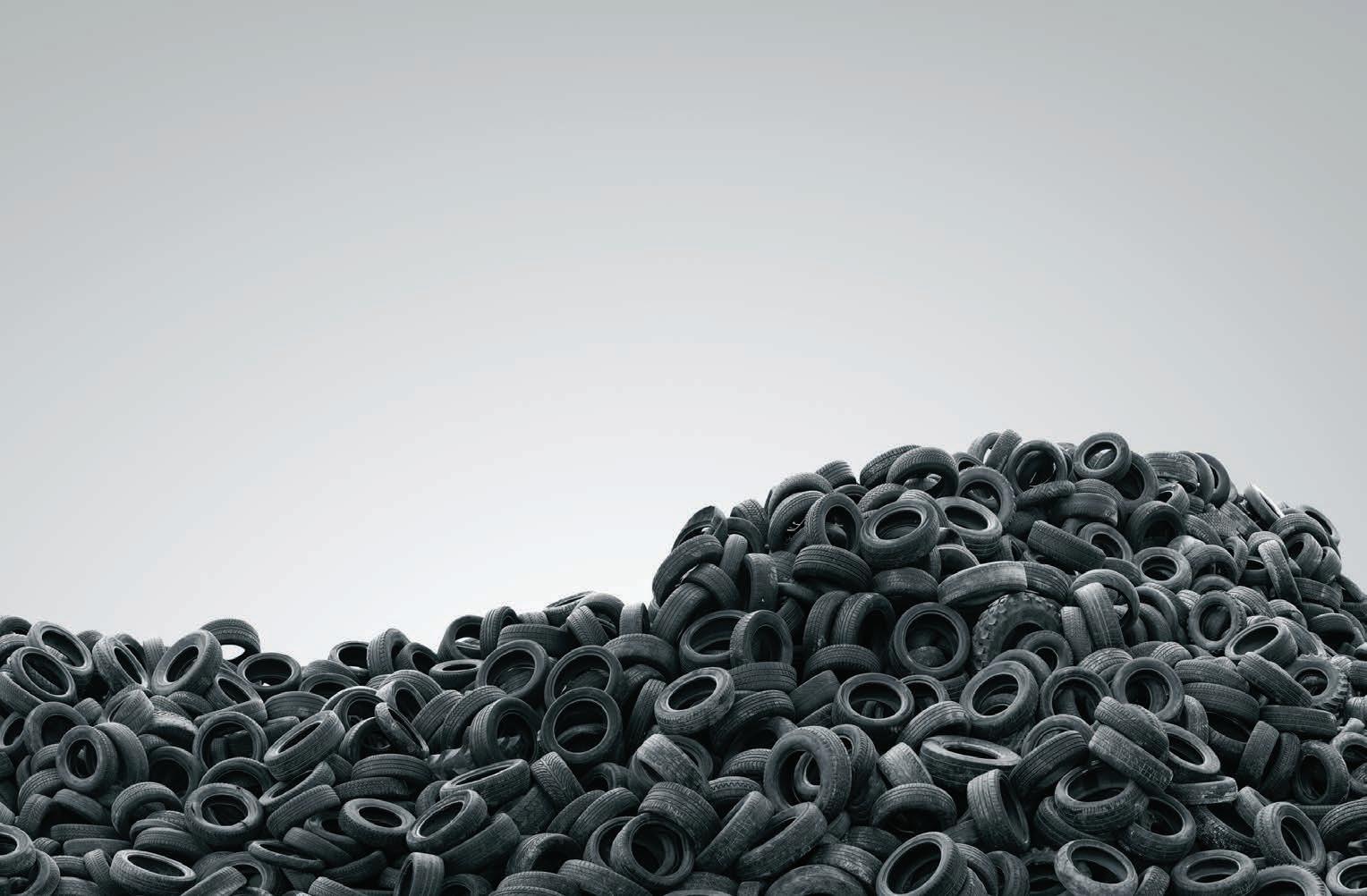
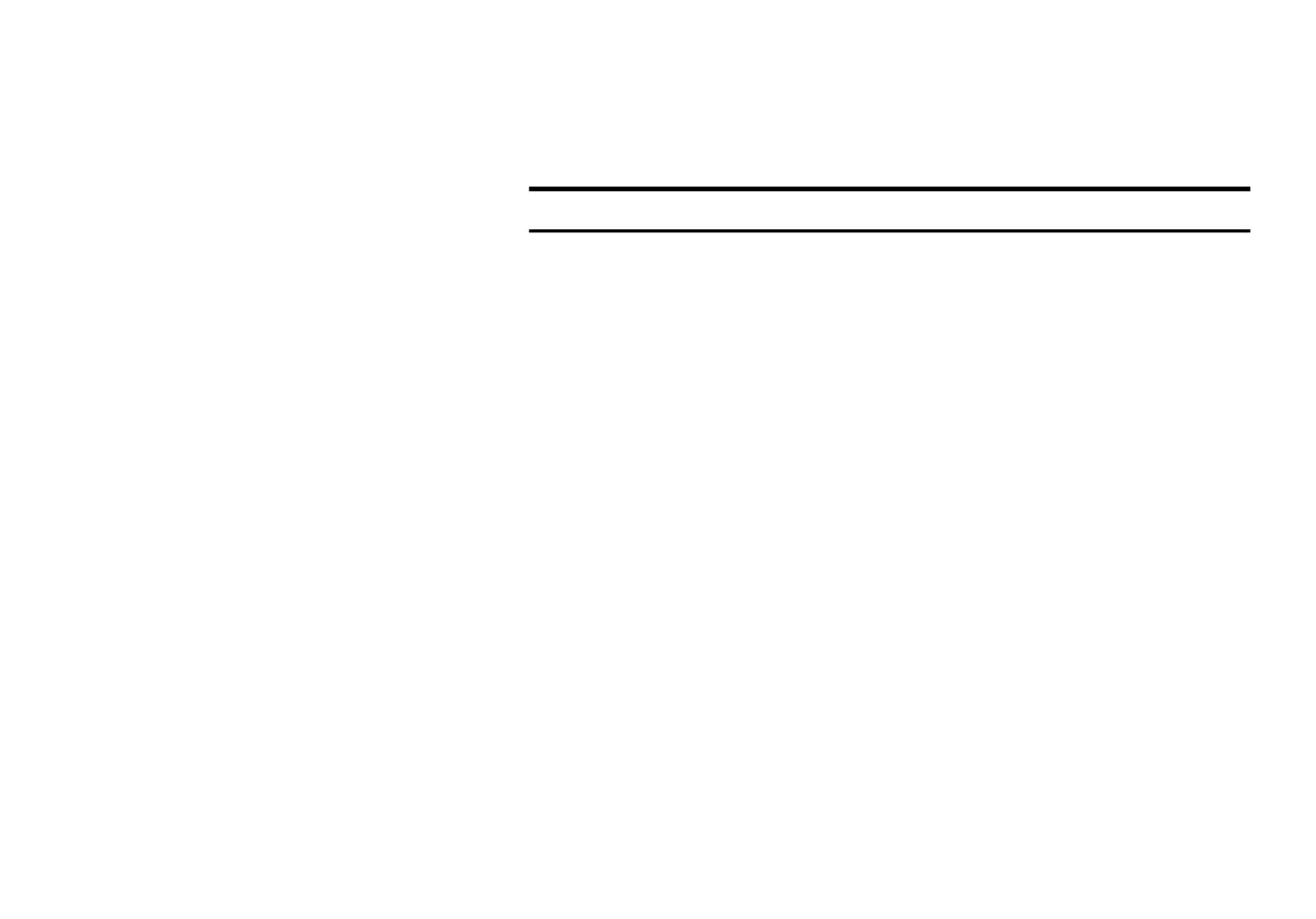
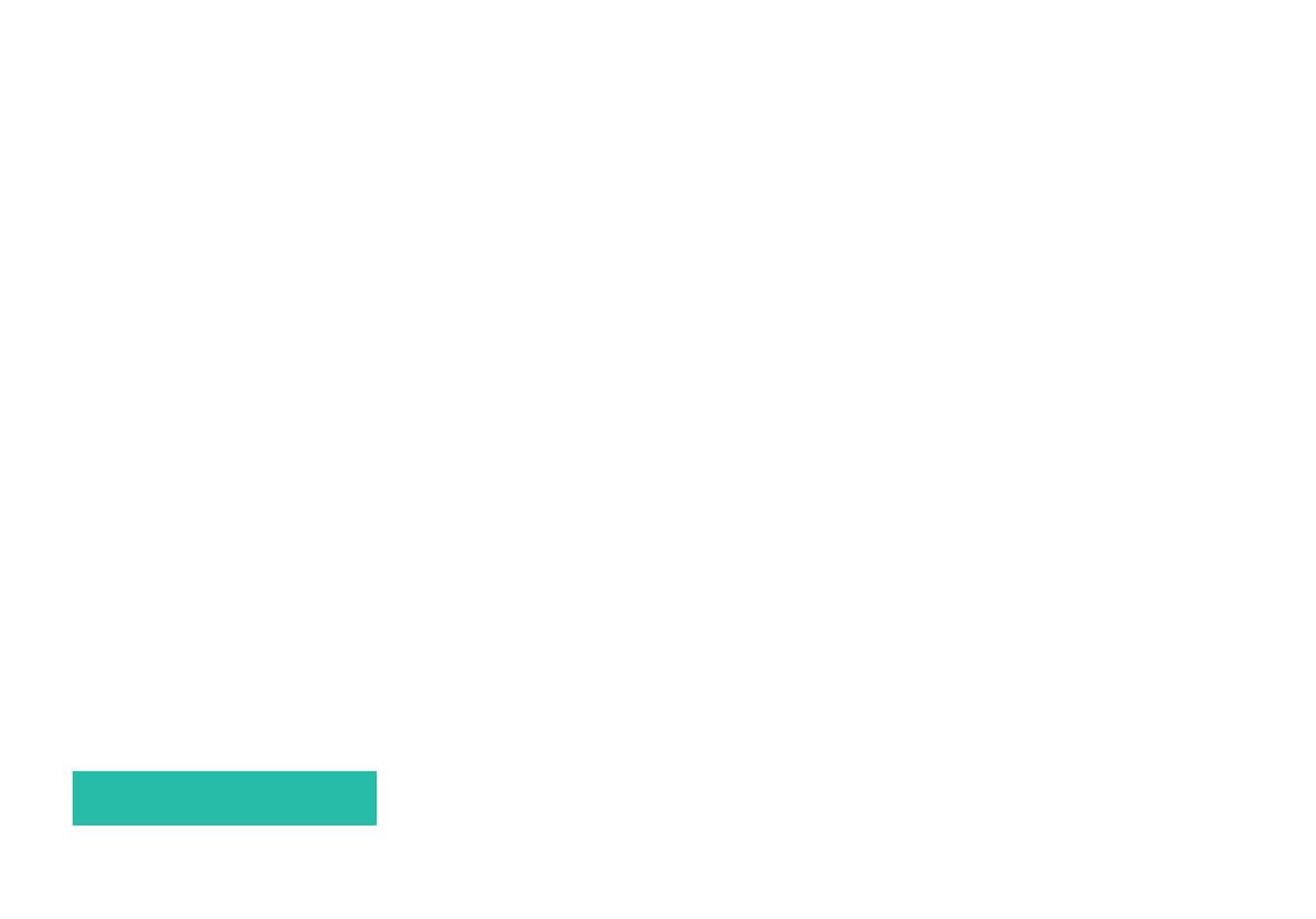
Join the recycling revolution: sales@recyclesmart.com
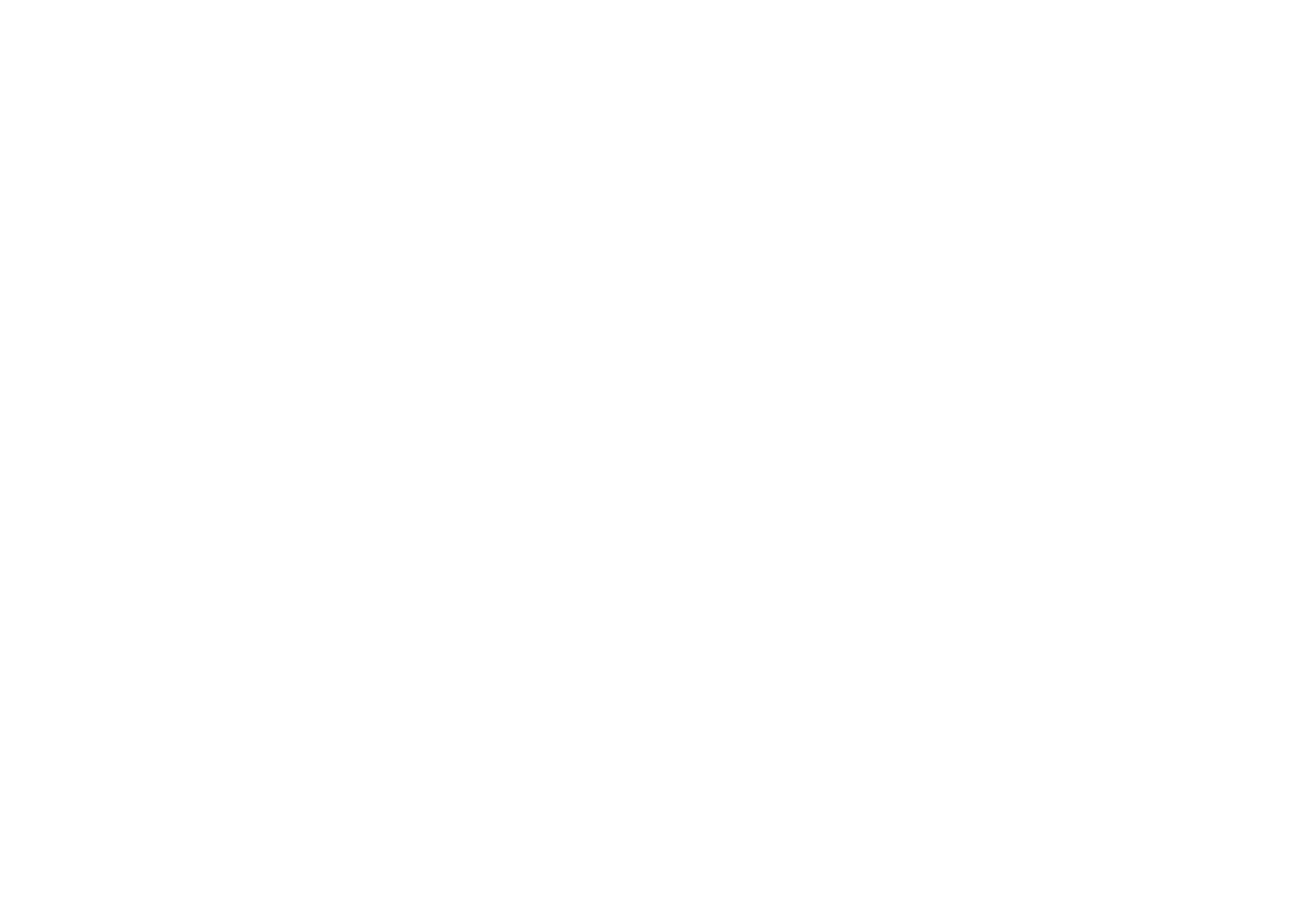
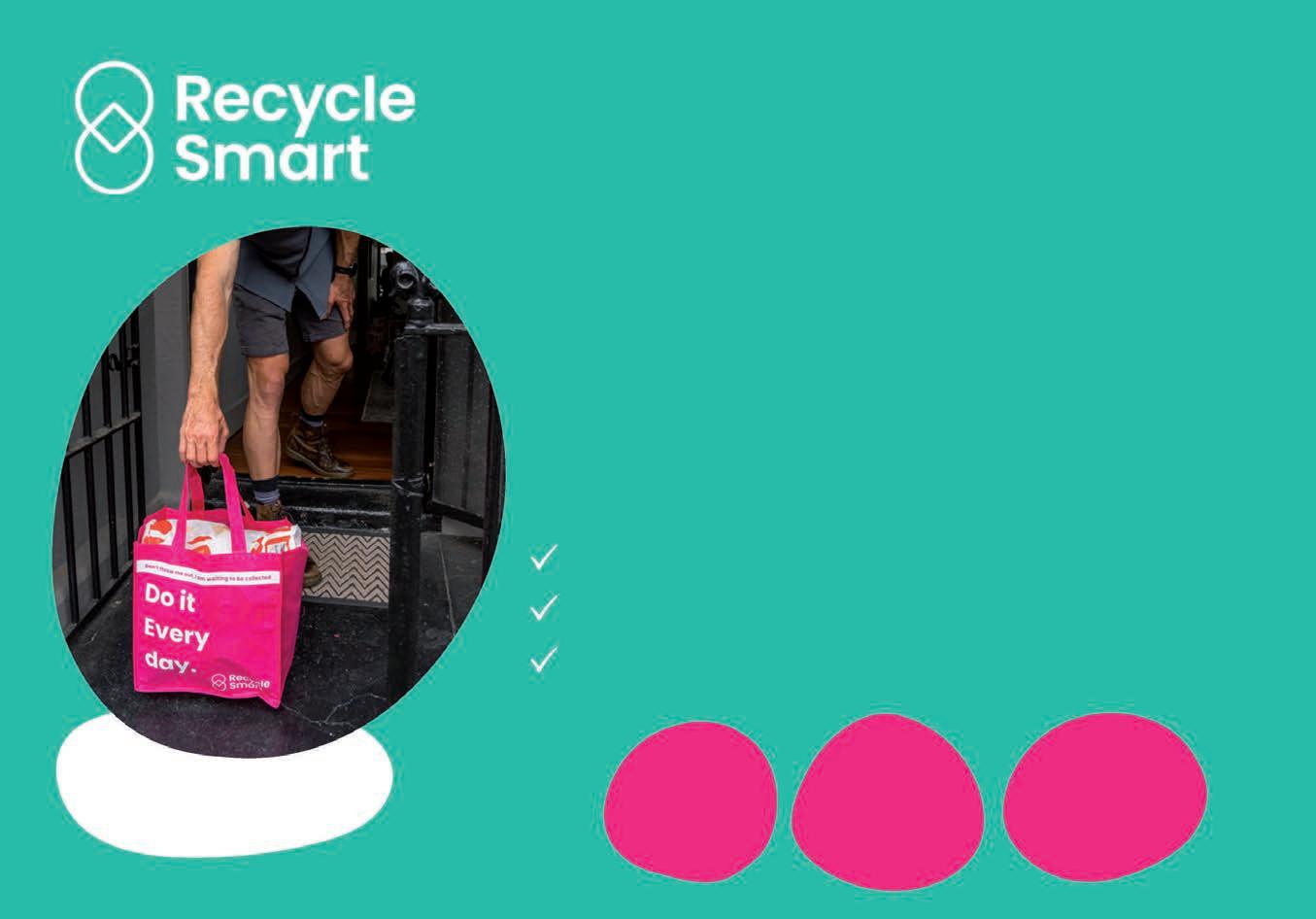
THE FUTURE OF RECYCLING IS HERE
Meet RecycleSmart, an on-demand collection service for tricky-to-recycle items. With our Power Pickup service, we collect soft plastics, e-waste, clothes and other problem waste from your resident’s doors and ensure they are recycled properly.
Recycling has never been easier
Introduce your council to a recycling service that integrates seamlessly, collects critical data and delivers an impressive user experience.
Plug-and-play:
Works with available local recycling options
Quick-to-market:
Only 2 weeks set up from the signature of the contract
Affordable
From just $5,000 per month.
13
Councils
31,000
Pickups
146,700kgs
of waste diverted from landfill
Environmental licences and authorities – a timely reminder
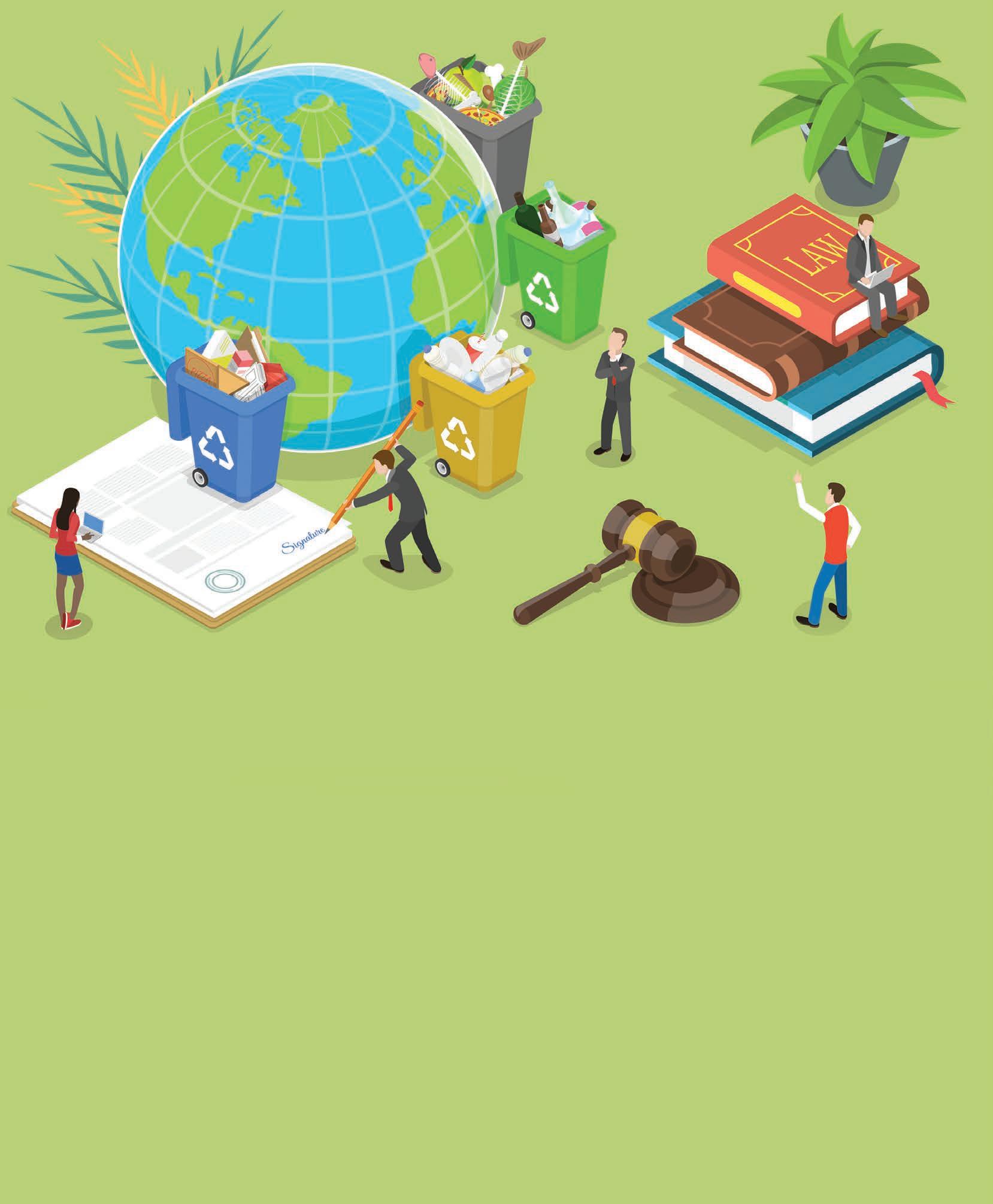
By Gavin Shapiro
NOT a week goes by without a prosecution of an operator in the waste industry in one of our environmental courts, either for unlawfully carrying out activities without a licence, or breaching licence conditions. State environmental regulators are vigilant in enforcing licences and breaches against the waste industry, with some recent prosecutions serving as a timely reminder to pay close attention to your licence and licensing requirements.
When do I need a licence?
The specific requirements vary in each state, as do the names and types of licences. But broadly, each state’s environmental legislation sets out categories of ‘scheduled’ or ‘classified’ activities – activities (carried out at a facility or in transportation/vehicles) that require a licence. Scheduled activities for waste include either a facility that receives/stores/disposes/processes waste over certain thresholds (such as landfills, MRFs, EfW facilities, FOGO and composting, etc), and transportation of waste – typically, with lower thresholds for more hazardous waste types, or liquid waste in the case of transport.
Sometimes, there can be complexity in determining if a licence is required. For example, some types of waste may need to be tested or chemically analysed for proper classification. More often, facilities don’t hold licences if they expect to be under thresholds, but then realise far too late that the volumes of waste they are accepting put them over the threshold – something that has led to many prosecutions. Accurate forecasting of volumes and careful systems, including appropriate documentation and testing/sampling to ensure that only authorised waste types are received, are part and parcel of ensuring that you either stay under licence thresholds, or hold the appropriate licence for the appropriate materials.
Offences
Each state’s environmental legislation establishes numerous offences related to waste. These are typically: transporting waste to a place that does not hold the requisite licence to receive it; receiving waste at a place that does not hold the requisite licence to receive it; treating a place as a waste facility without the requisite licence; or breaching the conditions of a licence.
By far the most common prosecutions relate to transporting waste to land that does not hold the requisite licence, or treating a place as a waste facility without the requisite licence. Often this is because these are waste dumping cases – i.e. ordinary land without a licence obviously cannot be used as a landfill. However, many prosecutions also occur because the wrong waste type has been accepted, meaning the land does not hold the necessary licence for that waste type, for example, asbestos-contaminated waste, the wrong categories of C&D waste, hazardous waste, etcetera.
The other most common reason for prosecutions is the breach of licence conditions. While many operators would consider themselves law-abiding, compliant operators, it can be surprisingly easy to commit a breach.
Perhaps the most common licence breach prosecuted by regulators is for accepting waste above annual licence limits. This leads to the next issue to remember regarding prosecutions. Not only can regulators seek a criminal conviction and fine, in many states they can seek a ‘monetary benefit order’ – that is, whatever profit waste made as a result of the breach (e.g. exceeding authorised volumes) can also be recouped by the regulator, over and above the fine
and conviction. It’s also worth noting how severe the penalties can be. For serious offences, there are potential prison sentences of up to seven years for individuals, and fines of up to $5 million for companies.
What if the regulator won’t grant the licence, or grants it with onerous conditions?
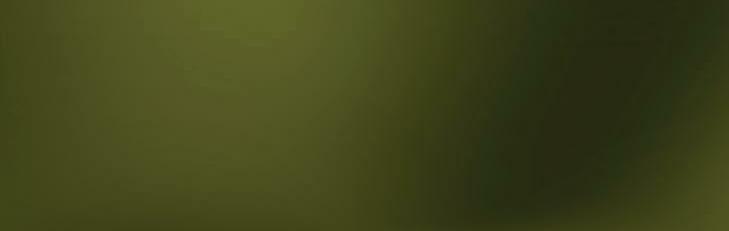
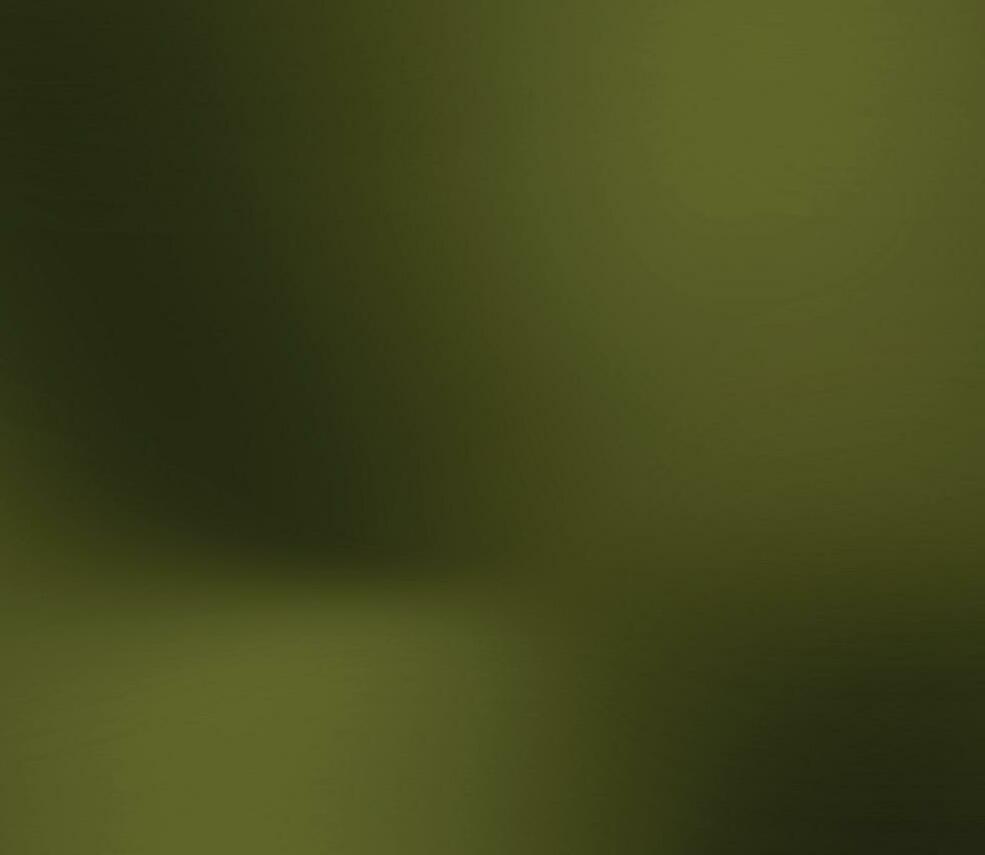
Most jurisdictions allow an applicant to appeal against a refusal of a licence application, or any licence conditions that they are unsatisfied with. These are ‘merit’ appeals, meaning that the Court or Tribunal decides the case on what it considers most appropriate – not necessarily on strict legal principles. This means that matters of scientific and technical evidence, likely impacts, and financial and economic factors, can all play a part in the Court’s decision – having the Court act as an independent umpire is a powerful tool for applicants if they consider the regulator’s decision was unreasonable.
In practice, a lot of cases end up settling early on in the process, as even the threat of having the regulator’s decision overruled can prompt a rethink. It’s also for this reason that typically, the regulator will give a licensee an opportunity to comment on draft conditions before they’re imposed.
It’s important to bear in mind that many states allow an appeal against a ‘deemed refusal’ – that is, failure to make a decision within a certain period of time. In NSW, this is either 60 or 90 days. Applicants often needlessly wait more than 6-12 months without a decision, when they could have appealed the ‘deemed refusal’ – and potentially settled the case or received a decision from the Court by then.
Importantly, appeals can only be commenced within a very short time after the decision (refusal or imposition of conditions), or ‘deemed refusal’ – just 21 days in NSW. It is crucial to watch the clock closely.
As licensees know, regulators also regularly review licences, and can amend or impose new conditions. Again, such decisions can be appealed.
Finally, in systems such as NSW where the environmental regulator also has input to the development application process, it is worth bearing in mind that when you appeal against a failure to grant the development application, the Court has the power to also overrule the environmental regulator’s opposition to the proposal.
Common licence conditions and breaches – pay close attention to your conditions
In each state, there are a range of standard-form conditions. These relate to factors such as the types of materials that can be received/processed/stored, volume and capacity limits, monitoring requirements, control and limits on emissions of substances, control of fire hazards and stockpiles, record keeping and reporting, requirements to maintain plant and equipment properly, and to operate plant and equipment completely. In addition, there are specific conditions developed for each site and operation, and conditions imposed for pollution reduction studies and programs if the regulator is seeking to improve performance at the site.
Given how serious the consequences can be for breaching licence conditions, licensees need to be confident that they understand all of their obligations clearly and have systems to ensure compliance.
It can be surprising how often we think we know what licence conditions mean, only to realise on re-reading them that they are ambiguous and can have multiple meanings. The Courts used to read ambiguities against the regulator so that licenses weren’t unfairly penalised for misunderstanding an ambiguous conditions. These days the Courts are more typically reading conditions whichever way they consider makes most sense, regardless of the outcome for the licensee – so resolving ambiguities and understanding conditions clearly is critical.
An example of why it is so important to understand the requirements of conditions comes from a case where I defended a construction client – although involving a development consent condition, the principle was equally applicable. The condition required the client to submit a traffic management plan (TMP) to the Council. They did so. The TMP stated that only certain trucks should be used. However, there was no condition that required the TMP to be followed. The Council issued multiple fines as different trucks were used, arguing the condition had been breached. When the client appealed, we successfully argued that the requirements of the condition – to submit the TMP – were complied with, so there was no breach.
On the other side of the ledger, there are countless cases where operators have been convicted and fined for breaching conditions relating to quantities of material received, waste types received, noise, odour and pollution control requirements, and not maintaining plant and equipment properly.
Who’s liable for a breach?
The laws in each state make licensees responsible for all breaches related to the licence. It is not usually sufficient to argue that it was an employee or contractor who committed the breach – the licensee in most cases is still automatically liable for their actions. It’s therefore critical that licensees have robust, well-documented systems in place to ensure that anyone coming onsite complies with relevant licence conditions. I have been involved in multiple EPA investigations where those systems – including contractor induction records, training records, and the like – have proven critical in defending the client.
Most state environmental laws also make directors and managers of companies personally liable for the offences committed by the company. While this is more typically used against smaller companies where it is easier to demonstrate who was in control and gave directions, it can be applied to larger companies.
In a number of states, corporate and executive liability can even pierce the corporate veil, to pursue parent and related companies and directors of related entities (with NSW’s POEO Act being amended imminently).
Conclusion
The saying goes “you’ve got to spend money to make money”. For waste operators, it’s far better to spend time and money upfront obtaining favourable licence conditions and developing systems to comply with them, than it is to spend time and money in Court, and on lawyers down the line. Equally, it’s worth remembering your rights to appeal where necessary, to keep the regulators honest. iw
Gavin Shapiro is a partner at Hones Lawyers. He specialises in the waste industry, including waste contracts, waste legislation, EPA investigations and prosecutions, and operational issues.

SUSTAINABLE SOLUTIONS FOR AN EVOLVING INDUSTRY
OPAL COVE RESORT Coffs Harbour | 3-5 May 2022
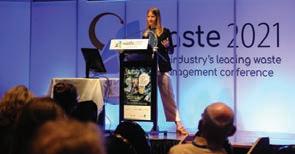
Conference registration and accommodation bookings now open! Sponsorship and exhibition opportunities still available!
Can’t attend in person?Register for the live broadcasts and participate from the comfort of your own office, or watch later at a time convenient to you.
Maybe you just want to see the equipment and technology on display and hear from the suppliers?Register for the Equipment & Technology Expo as a standalone.
There is an option to suit everyone, so don’t miss your opportunity to be a part of the industry’s leading waste management conference.
0474 629 908 www.coffswasteconference.com.au
Supported by: