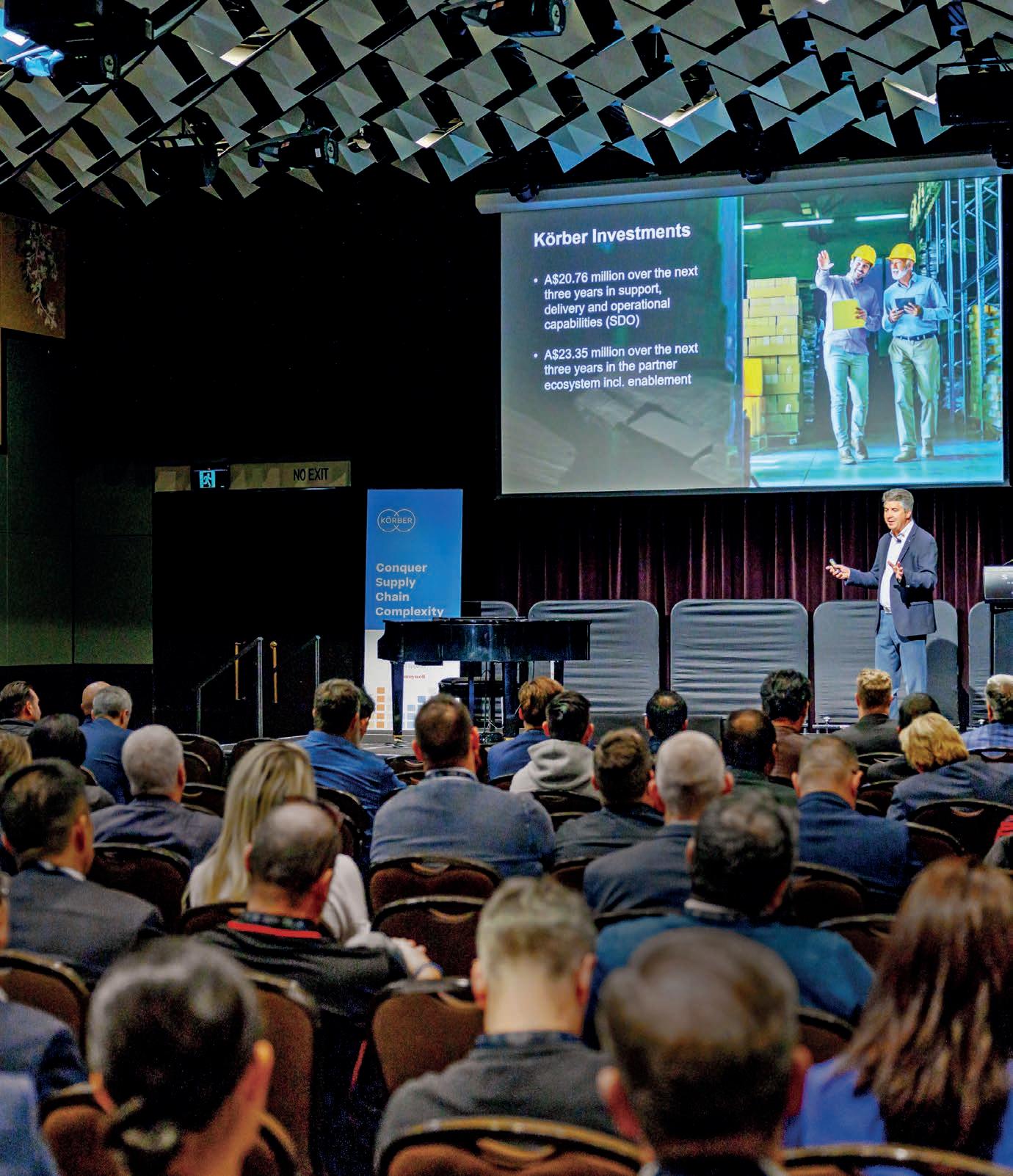

Building on the success of our first in-person Elevate last year, this year’s event will help you chart your course toward operational excellence and supply chain resilience. Featuring keynotes from industry leaders, insights into the latest technology, and networking opportunities, you won’t want to miss our Elevate event and early bird offer.
CONTACT
MHD Supply Chain Solutions is published by Prime Creative Media
379 Docklands Drive, Docklands VIC 3008
Telephone: (+61) 03 9690 8766
Website: www.primecreative.com.au
CEO: John Murphy
Chief Operating Officer: Christine Clancy
Managing Editor: Syed Shah
Editor: Edward Cranswick
Journalist: Joseph Misuraca
Business Development Manager: William Jenkin
Design Production Manager: Michelle Weston
Art Director: Blake Storey
Graphic Designers: Louis Romero, Kerry Pert
Client Success Manager: Janine Clements
Contact: William Jenkin
william.jenkin@primecreative.com.au
Australian Subscription Rates (inc GST)
1yr (6 issues) for $78.00
2yrs (12 issues) for $120.00 – Saving 20%
3yrs (18 issues) for $157.50 – Saving 30%
To subscribe and to view other overseas rates visit: www.mhdsupplychain.com.au or Email: subscriptions@primecreative.com.au
MHD Supply Chain Solutions magazine is recognised by the Australian Supply Chain Institute, the Chartered Institute of Logistics and Transport Australia, the Supply Chain and Logistics Association of Australia and the Singapore Logistics and Supply Chain Management Society.
As the calendar turns to March 2024, the landscape of supply chain and logistics continues to evolve, guided by innovation, sustainability, and strategic foresight. This edition of MHD Supply Chain Solutions magazine is imbued with stories that reflect these guiding principles, showcasing how industry leaders and companies are navigating the complexities of today’s market with agility and vision.
Our cover story this month brings you an inside look at Körber’s Elevate APAC conference, an event that has quickly become a cornerstone for discussing future trends, challenges, and opportunities within the supply chain and logistics sector. This year’s conference in Sydney will be no exception, offering a platform for thought leaders and innovators to converge, share insights, and explore the technologies shaping our industry’s future. From groundbreaking software solutions to the latest in automation and robotics, Elevate APAC is a beacon for those committed to driving the industry forward.
Also this month, Prological’s Peter Jones delves into the intricate world of cold chain warehousing, unpacking the critical design considerations that underpin efficiency, sustainability, and product integrity. From temperature management to energy-efficient building materials, Peter’s insights provide a comprehensive overview of what it takes to operate successfully in this vital sector of our industry.
Highlighting our commitment to showcasing innovative logistics solutions, we take a closer look at the GPT Group’s Apex Business Park. Situated in the dynamic Western corridor between Brisbane and Ipswich, Apex Business Park epitomises the integration of strategic location, cutting-edge facilities, and environmental sustainability. Spread over 15.5 hectares, this estate is set to redefine the logistics and supply chain landscape, offering unparalleled access and services while maintaining a steadfast commitment to sustainable development practices.
While these stories stand out in our March issue, they are but a glimpse of the wealth of content in store.
We invite you to dive into these pages, where the themes of innovation, resilience, and sustainability continue to form the bedrock of our discussions. Here’s to a month filled with learning, growth, and sustainable advancement in our industry.
Happy reading. See you next month.
Edward Cranswick Editoredward.cranswick@primecreative.com.au
There are three new leadership appointments in APAC for DHL Supply Chain. Image: DHL Supply Chain
DHL Supply Chain has announced three new key leadership appointments in Asia Pacific –two in Indonesia and one in Taiwan with all roles becoming effective as of January 01, 2024.
The global leader in contract logistics appointed Sivananthan Sukumaran (Siva) as Head of Operations for DHL Supply Chain Southeast Asia. Siva was most recently the Managing Director of DHL Supply Chain Indonesia.
Matthias Gehrsitz takes over from Siva as the Managing Director of DHL Supply Chain Indonesia while Louis Liao has been appointed as the new Managing Director of DHL Supply Chain Taiwan.
“We are excited to announce these key leadership appointments, marking a significant stride in fortifying our management team in Asia Pacific,”
says Javier Bilbao, CEO DHL Supply Chain Asia Pacific.
“Each of these leaders brings their own set of unique expertise and proven track record in enhancing customer service and innovation. Their roles will be instrumental in navigating our teams through the ever-evolving logistics landscape and reinforcing our position as the global leader in contract logistics.”
In his new role, Siva will be responsible for enhancing overall operational efficiency and performance, ensuring the successful implementation of new business wins across the organisation’s Southeast Asian cluster.
Matthew succeeds Siva as the Managing Director of DHL Supply Chain Indonesia. He comes to DHL after an 11-year tenure at DB Schenker Malaysia where he held various roles in Project
Management, Tender Management, Solution Design, and Operations before taking on a leadership role as the National Head of Business Development and Commercial Management.
“Siva and Matthias are leaders with extensive experience and market insights,” adds Andries Retief, CEO, DHL Supply Chain Southeast Asia, to whom both Matthew and Siva report.
“Their leadership will be crucial to the business as we continue to expand and tailor our solutions to the diverse demands of our customers in one of the fastest growing regions in the world.”
Louis is a familiar face to DHL Supply Chain, having begun his career as an Assistant Operations Manager in DHL Supply Chain Taiwan’s Service Logistics Operations Manager in DHL Supply Chain Taiwan’s Service Logistics operations team in 2008.
When consolidating its multiple Brisbane sites into the new Heathwood DC, Asahi made the decision to upgrade from previously very labour-intensive operations to a fully automated warehouse solution, eliminating manual handling of pallets.
With the introduction of a satellite ASRS solution, Dematic helped Asahi maximise storage capacity, reduce operating costs, and improve efficiency and productivity to better meet the needs of its customers.
Read more and watch the video at Dematic.com
Dematic.com
02 9486 5555
info.anz@dematic.com
Vanderlande says it automated Irish food retail and wholesale company, Musgrave’s, west Dublin facility with one of its integrated warehouse solutions, which became operational at the end of 2023.
It notes that it is supporting the company’s future growth ambitions and its need to manage labour scarcity issues with the ADAPTO shuttlebased automated storage and retrieval system (AS/RS).
“We believe this is the most advanced food distribution site in Ireland,” says Steve Young, Musgrave’s Head of Supply Chain Development.
“Vanderlande’s integrated solutions shows that it’s possible to invest in an automated warehouse system, even
on lower throughputs. We can look forward to expanding our operations with confidence.”
With its flexibility and lean infrastructure, Vanderlande’s ADAPTO is central to the operation. Sixty-four shuttles can access 67,200 product locations across 15 aisles that provide double-deep storage.
In addition, Radioshuttle – a palletbased picking system designed by Toyota Material Handling UK – deals with the fastest 200 stock-keeping units (SKUs) in the warehouse. The combined operations now account for approximately 400,000 cases per week of ambient grocery volume.
“We’re delighted that this successful collaboration will help Musgrave to realise its growth ambitions,”
adds Robert Viegers, Vanderlande’s Executive Vice President for Warehouse Solutions.
“We have a portfolio of solutions than can cater for the requirements of all food retailers – both large and small. And the scalability of our systems also means that our customers can effectively future proof their businesses.”
Four goods-to-person and three decanting workstations have also been installed. Designed by Vanderlande with ergonomics in mind, they are all height adjustable to minimise lifting duties for operators and each can handle around 500 cases per hour. The scalability and flexibility of the new system also provides scope for further extension at the centre.
TMX Transform says generative AI and simulation are making more noise in supply chain, given the compounding global impact of geopolitical, technological, and environmental disruption.
It notes the mandate has never been clearer for organisations to transform their supply chains, and simulation, which replicates realworld environments in a digital environment, is one way they are doing it.
“Simulation is an incredible technology, but it is not an ‘off-theshelf’ product or a ‘slap-on’ service,” Glen Borg, Head of Simulation at TMX. “The value and impact of simulation always depends on the client and what business problems they need to solve. We always start with the problem –not the solution.”
Companies can visualise, validate,
and test designs for DCs, warehouses, and supply chain optimisation prior to any implementation, according to TMX Transform, a pioneer in the simulation space.
“Like most advanced technology, simulation is valuable when it is created and operated by subject matter experts, who know the technology in and out, but can also contextualise and interpret the outputs and scenarios to clients, because they have been on the warehouse floor themselves,” adds Glen.
The complexity of supply chains has been increasing for years, but the solutions and ways clients can tackle that complexity may not necessarily get the same attention. Nonetheless, businesses need a data-informed approach to DC design that reflects real operations, rather than using averages to predict requirements.
Simulation, along with augmented reality (AR) and virtual reality (VR), equip clients with insights into DC operations and greenfield facilities. Simulation can be used for:
• Network performance optimisation – identifying efficient network configurations that minimise costs and maximise service levels through simulation modelling and synthesising demand.
• DC optimisation and operations validation – creates virtual representations of manual and automation DCs to assess performance and to identify gaps, potential issues, and effectiveness of operations.
• Automation feasibility validation – creates models of real-world processes through simulation to evaluate the impact of automation on productivity, efficiency, and cost.
Through multidirectional movement and sequencing, Vanderlande’s shuttle-based automated storage and retrieval system (AS/RS), ADAPTO, delivers goods fast and accurate in the appropriate order, enabling same-day deliveries.
Learn how Vanderlande customers benefit from FASTPICK to efficiently handle both their e-commerce and store orders.
>
As part of its focus on sustainability, MEGATRANS2024 will examine cold chain solutions and how they can impact the whole chain function.
To increase the focus on making the cold chain more sustainable, including reducing carbon emissions, minimising waste, and adopting eco-friendly
technologies, MEGATRANS2024 will feature exhibitors working in this space as well as conference sessions covering the latest technologies, innovations and regulations.
“The challenge for MEGATRANS2024 is to unite the logistics industry in building a sustainable future,”
Show Director, Lauren Chartres
said. “By providing a forum for like-minded suppliers and industry leaders to connect to connect, across the exhibition, conference and jobs pavilion, we hope to play pivotal role in that process.”
Take advantage of the important opportunity MEGATRANS2024 presents.
Businesses can display their cold chain solutions at MEGATRANS2024.
Image: FOTOGRIN/Shutterstock.com
Dematic has announced that global wholesaler, retailer, designer, manufacturer and distributor of premium apparel, AS Colour, will transform its Melbourne DC with automation featuring a Dematic Multishuttle® goods-toperson (GTP) solution.
As a compact, high-throughput automated storage and picking system, Dematic notes its solution features high-density tote storage and sequenced order picking for better productivity.
The system is capable of processing varied order types, including small e-commerce orders, medium and large B2B orders, as well as retail store fulfilment.
“Dematic has been a really strong technology partner, helping us from a global perspective, and we see this as a long-term partnership as we continue to expand as a business in the future,” explains Lawrence Railton, Managing Director, AS Colour.
“We’re excited to again partner with Dematic on the Melbourne chapter of our automation.”
The modular, scalable Dematic Multishuttle at the Melbourne DC will be 18 levels high and four aisles storing over 55,000 totes, with additional capacity built in for projected future growth.
Product and order totes will be retrieved and delivered in the required sequence to GTP picking workstations for efficient, ergonomic, and accurate order picking.
“Due to our growth over the last 5–10 years, we have outgrown many distribution facilities. Rising demand led us to building a brand-new facility with the focus on automation,” adds Lawrence.
The system will be capable of sustainably delivering up to 1,500 product totes per hour across the five GTP picking workstations (an average of 300 product totes per hour to each independent picking workstation).
After orders are fulfilled at GTP workstations, order totes will be temporarily buffered within the Dematic Multishuttle before being released and conveyed to the packing sorter in precise order sequence to support efficient packing processes.
“AS Colour was the first company to choose the Dematic Multishuttle GTP solution in the New Zealand market,” says Seth van Dijk, Business Development Manager, Dematic.
“The Auckland system has 18 levels and features two aisles storing just under 20,000 totes with four ergonomic GTP workstations.”
Dematic Warehouse Control Software (WCS) will be an optimisation layer between the AS Colour’s Warehouse Management Software (WMS) and the automated equipment that provides the most efficient picking tasks and transportation of goods throughout the system.
The Victorian Transport Association (VTA) says its March 17 to 19 State Conference line-up is quickly taking shape with cybersecurity set to be high on its agenda.
It notes it is looking forward to sharing the provisional conference program with members, and other transport industry stakeholders within the coming fortnight.
“In the interim I am pleased to confirm additional details and a keynote speaker to address conference delegates on the fastemerging commercial threat of cyber security, which over the past 12 months has impacted dozens of public and private organisations, and government departments and agencies,” says VTA CEO Peter Anderson.
“Dr Derek Bopping is the Australian Signals Directorate (ASD) First Assistant Director-General Cyber Engagement and Head of the Melbourne State Office, with a focus on establishing the ASD’s national presence under its Redspice Program, and we’re thrilled to have him
Instances of data breaches have grown massively in Australia in recent years.
Image: Song_about_summer/Shutterstock.com
present at the conference.”
Instances of data breaches have grown massively in Australia in recent years in both frequency and cost. The average cost of a data breach in Australia has grown 32 per cent in the last five years, reaching $4.03 million according to the 2023 Cost of a Data Breach Report.
“The transport industry forms an integral part of Australia’s national security infrastructure and is not immune from cyber threats and foreign ‘actors’ disrupting our systems and processes,” adds Peter.
“It is incumbent on every operator to take appropriate steps to ensure their business is suitably protected, and we are fortunate to have someone with Dr Bopping’s credentials and reputation to inform us on the latest cyber intelligence, best practice, and mitigation strategies and tactics.”
ASD is an Australian Government intelligence agency responsible for cyber security. Its operatives gather foreign signals intelligence through covert information acquisition, which includes intercepting and analysing communications related to national interest issues such as terrorism, weapons proliferation, and cyber threats.
A range of conference packages and price-points are available, and these can be viewed at www.vta.com.au.
State Conference 2024 is proudly sponsored by industry super fund TWUSUPER, who are very generous and long-standing supporters of this and other VTA events.
Quarantine
Biosecurity Import/ Export Accredited
Quarantine Inspections/Unpack
Quarantine Rural
Tailgate Inspections
LCL/FCL Fumigation
Quarantine
Approved Wash Bay
Steam Clean
Warehouse & Distribution
20,000 sqm ambient temperature
3PL Capabilities
15,000+ sqm of heavy rated hard stand
Bulka bags / palletised / loose cargo
Transport Connecting transport links to international trade
General Freight
Bulk/Heavy Haulage
Intra/Inter – rail and road
Specialised Equipment Supply Chain Solutions
Specialised lifting attachments, slip sheets and slings
Weighbridge
Reach stackers (45 Tonne)
Forklifts (16T, 8T, 3.5FT)
Direct Connectivity to Flinders Adelaide
Container Terminal
Reefer plugs to accommodate chilled containers
Independent Road
Access to both sites
FAK Consolidation/ Deconsolidation
Figures released by Port of Newcastle (PoN) reveal a shift in weather and demand has had a significant impact on its diversified trade results for 2023.
CEO Craig Carmody says the overall trade figure, which contributed $48 billion to the economy, is not representative of a reduction in import and export volumes across our diversified trade.
“Overall, Port of Newcastle had an increase of almost five per cent on total trade volume, which can be attributed to the return of China to the Australian coal market, representing a quarter of all coal exports,” adds Craig.
“The Port’s exposure to carrying volume risk is evident, put simply, if China did not lift their restrictions, the Port’s volumes would have been the lowest experienced in several years.
“For Port of Newcastle and our region, we need to ensure we continue down our path of diversification.
Last year’s results highlight how we cannot continue to rely on a single commodity, we cannot wait and relive what occurred when the steel industry left Newcastle.”
Executive Manager of Business Development Matthew Swan says a reduction in diversified trade export volumes reflected the current challenges facing the market.
“After three years of ideal harvest conditions for agribusiness, the shift to El Niño has had a direct impact on our farmers, with wheat exports down 34 per cent to 1.7 million tonnes, with volumes subdued for CY2024,” explains Matthew.
“It’s the first-time wheat has been under two million tonnes since 2021. Meals and grain exports continued to perform well, with a 31 per cent increase in volumes (629,006 tonnes), and mineral concentrates experienced modest growth, with a total 397,000 tonnes exported.”
The 2023 trade figures come at a time when Port of Newcastle has been
vocal in the need for the Port and region to accelerate diversification.
“2024 will be a year of consolidation and focus, one that focuses on expanding our existing container trade relationships, supporting wind and solar energy projects, along with development of the Clean Energy Precinct,” says Craig.
ASD is an Australian Government intelligence agency responsible for cyber security. Its operatives gather foreign signals intelligence through covert information acquisition, which includes intercepting and analysing communications related to national interest issues such as terrorism, weapons proliferation, and cyber threats.
A range of conference packages and price-points are available, and these can be viewed at www.vta.com.au.
State Conference 2024 is proudly sponsored by industry super fund TWUSUPER, who are very generous and long-standing supporters of this and other VTA events.
From March 19 till March 21, Vanderlande’s experts will be at LogiMAT 2024 to discuss the challenges faced by warehouse operators and give advice based on the company’s extensive portfolio.
This advice will be related to the Netherlands-based company’s innovative systems, intelligent software, and life-cycle services.
“We are looking forward to meet with customers at this year’s LogiMAT exhibition,” says Robert Viegers, Vanderlande’s Executive Vice-President for Warehouse Solutions.
“We pride ourselves on listening carefully to what each customer requires for their operations. And our team is ready to explain how we can help to bring innovative, efficient automated warehousing solutions, whilst dealing with pressing issues such as sustainability and labour scarcity.”
Visitors to the Vanderlande stand (J31 in hall 1 in the Stuttgart Trade
Fair Centre) can enjoy an in-depth look at FASTPICK, the company’s goods-to-person order fulfilment system. An interactive 3D model reveals how this market-leading solution works, helping warehouses all over the world to improve throughput and order accuracy.
Exciting new technologies, such as robot pickers and autonomous vehicles, are currently making the news, and Vanderlande’s team of experts will be able to explain how they can be smoothly incorporated into the company’s future-proof warehouse solutions.
During an exclusive session for LogiMAT’s Exhibitor Insights on Tuesday 19 March (14:30 in Forum North, hall 7), Vanderlande will be joined by Digitec Galaxus –Switzerland’s top e-commerce retailer. Together, they will shed light on the behind-the-scenes challenges faced by e-commerce logistics operators.
Vanderlande will also have a
presence on stand H48 (in hall 10) hosted by Toyota Material Handling.
Vanderlande is a market-leading, global partner for future-proof logistic process automation in the warehousing, airports, and parcel sectors. Its extensive portfolio of integrated solutions – innovative systems, intelligent software, and life-cycle services – results in the realisation of fast, reliable, and efficient automation technology.
The company focuses on the optimisation of its customers’ business processes and competitive positions. Through close cooperation, it strives for the improvement of their operational activities and the expansion of their logistical achievements.
Vanderlande’s warehousing solutions are the first choice for many of the largest global e- commerce players and retailers in food, fashion, and general merchandise across the globe. The company helps them to fulfil their promise of same-day delivery for billions of orders, with nine of the 15 largest global food retailers relying on its efficient and reliable solutions.
As a global partner for future-proof airport automation, Vanderlande’s market-leading baggage handling systems and related passenger solutions can move over four billion pieces of baggage around the world per year. These are active in more than 600 airports, including 12 of the world’s top 20. In addition, over 380 of Vanderlande’s security lanes are installed at checkpoints worldwide.
Vanderlande is also a leading supplier of process automation solutions that address the challenges in the parcel market. More than 52 million parcels are sorted by its systems every day, which have been installed for the world’s leading parcel handling companies.
In
Anthony Beavis, Körber Managing Director APAC, explains in this op-ed the importance of having the right data, diversifying supply networks, harnessing automation, using omnichannel fulfilment, and the supply chain’s future.
Geopolitical tensions, extreme weather events and ongoing economic frailties in 2023 put supply chains to the test, underscoring the importance of handling adversary.
As we head into 2024, leaders’ confidence in supply chains is starting to gain momentum again, however, embracing data-driven decisions and contingency plans is crucial.
As consumer dynamics evolve alongside socioeconomic volatility, businesses are being asked to sense demand shifts and orchestrate responsive fulfilment quickly.
This is and will remain a huge
challenge, but technologies enabling greater agility, transparency and predictivity are easing the burden and leading to many success stories.
Warehouse automation is accelerating dramatically as facilities embrace robotics and smart systems to unlock new efficiency frontiers.
Autonomous mobile robots (AMRs) can dynamically shuttle inventory for optimised workflows, and automated storage and retrieval liberates floor space while enabling rapid order processing via optimised SKU locations.
Cognitive automation through robotic process automation (RPA) and conversational AI is taking on repetitive administrative tasks for businesses as well.
According to McKinsey, automated warehouses can reduce operating costs by up to 30 per cent with throughput velocity gains over 25 per cent, while research by MIT finds
every dollar spent on control towers yields three dollars to $10 in cost savings.
On top of this, data from IBM shows that organisations that use security AI and automation extensively save USD $1.76 million compared to those that don’t. The global average cost of a data breach in 2023 was USD $4.45 million, a figure which is on the rise every year.
To leverage advanced technologies like cloud computing, predictive analytics and artificial intelligence, companies should first establish integrated digital foundations spanning their end-to-end supply chains.
Collating the right type of customer, sales and product data is the key to driving enhanced datadriven decision making, real-time visibility, and streamlined flows.
Amazon Australia has announced the launch of its Prime FREE One-Day Delivery service in more Australian cities, saying this service is now available to Prime members on eligible orders.
This service has become available in Brisbane, Geelong, Gosford, Newcastle, and Wollongong, and requires no minimum spend with more than a million items available.
“When customers shop online, they want to know they are getting a great price and that their order will be delivered to them fast, with no additional costs,” says General Manager of Amazon Australia, Matthew Benham.
“We are committed to growing the value of Prime in Australia, so we are
excited to announce the expansion of Prime FREE One-Day delivery on a huge selection of products to even more cities.”
Amazon Australia notes its customers can order as late as midnight for next-day delivery, making it even more convenient to shop on Amazon.com. au. Prime is Amazon’s membership program providing savings, convenience, and entertainment in one single membership.
Amazon Australia now has six fulfilment centres, including a facility in Lytton, Brisbane, which is the same size as two Rugby League fields, and can house more than one-and-a-half million items from Amazon.com.au.
“We are able to offer customers
fast delivery speed as a result of our continuing investment and expansion into our operations in Australia,” adds Matthew.
“By building fulfilment centres and delivery stations close to where our customers live and work, packages travel shorter distances, which enables us to speed up delivery.”
Amazon notes its delivery capacity increased by almost 50 per cent in 2023, and it added 600 permanent roles to its operations network, with even more Amazon customers around Australia now able to access an enhanced delivery experience, including faster delivery, delivery on evenings and weekends, and reattempted deliveries for customers when they are not home.
With State Conference 2024 only six weeks away, the Victorian Transport Association (VTA) is pleased to confirm the attendance of the Australian freight and logistics industry’s key national regulatory bodies.
Between March 17 and March 19, these regulatory bodies will deliver important updates to delegates.
“The National Heavy Vehicle Regulator (NHVR) has been a strong supporter of the VTA, and I’m delighted that CEO Sal Petroccitto and members of his team will be joining us to provide important operational and safety information,” says VTA CEO Peter Anderson.
“Access, safety, and enforcement
are always critical issues for freight operators, and it’s terrific to have Sal on the agenda to outline the NHVR’s priorities for
the year ahead.” The NHVR is Australia’s regulator for heavy vehicles and is tasked with the administration of the Heavy Vehicle.
SICK tells MHD about its new advanced track and trace system designed to enhance data accuracy and elevate customer experience and the five main benefits of using this solution.
Accuracy in package identification is crucial in modern logistics. When each package reaches its correct destination on time, trust is built, and customer satisfaction is bolstered.
Missteps, however, can erode this trust and become destructive for businesses. Enter SICK’s RFMS Pro, an advanced track and trace system designed to enhance data accuracy and, in turn, elevate customer experience. Here’s how this system can boost logistics operations.
SICK’s Radio Frequency Modular System1 is a top-tier, high throughput system in which businesses can invest in for process optimisation and transparency in the delivery chain. It combines the best of RFID technology, a smart control system, and sensors that pinpoint a package’s location on a conveyor. What makes it even more unique? It’s flexible. You can easily adjust it to fit different logistical needs.
But what truly makes the RFMS Pro indispensable is its promise of complete transparency in the supply chain. It does this by ensuring accurate identification of packages, leading to fewer mistakes, reduced misplaced items, and ultimately, happier customers.
Benefits of Using the RFMS Pro for Enhanced Package Identification
• Design Versatility: The system’s range of tunnel design options, stemming from two standard modules, minimises the planning and design work. This adaptability ensures the system fits seamlessly into different logistical environments.
• Quick Commissioning and Integration: Minimal installation time is required, thanks to the easy commissioning of the modules. Furthermore, integration with
SICK’s 4Dpro means adding barcode scanners to an application has never been simpler.
• High Throughput: The RFMS Pro’s design enables minimal space between objects, ensuring faster processing and higher throughput.
• Cost-Effective and Reliable: A maintenance-free design combined with high-quality components from a single source ensures not only reliability but also savings in time and money.
• Complete Transparency: The integrated service, monitoring, and diagnostic tools, coupled with data output on interfaces like Ethernet, ensure a seamless flow of accurate information.
The RFMS Pro finds its applications in a myriad of industries, including retail, logistics, storage, automotive, and airports. It serves pivotal functions such as:
• Master data acquisition of items, popularly known as “item level tagging”.
• Verification of goods received against payment advice, ensuring no discrepancies in transactions.
• Control over goods receipt and issue, offering an extra layer of oversight.
• Identification of closely positioned objects on conveyor belts, ensuring no mix-ups in delivery.
In essence, whether it’s group or single tag detection, or ensuring accurate package identification for those closely placed on conveyor belts, the RFMS Pro promises efficiency.
In an era where customer satisfaction hinges on the accuracy and timeliness of deliveries, solutions like the RFMS Pro emerge as invaluable. For logistics companies, embracing such advanced track and trace systems is not just a pathway to operational efficiency but a sure-fire strategy to win customers’ trust.
By ensuring that the right package reaches the right customer at the right time, companies can cultivate loyalty and foster long-term relationships. After all, in the world of logistics, accuracy is not just about getting the job done – it’s about making every customer feel valued and satisfied.
The National Heavy Vehicle Regulator (NHVR) has announced the successful conclusion of Operation Forager, a four-week initiative dedicated to combating heavy vehicle driver fatigue during the holiday season.
The NHVR partnered with police across the country to conduct Operation Forager, which commenced 20 November 2023, to heighten awareness about the critical nature of managing fatigue while driving heavy vehicles.
The national operation represents another step forward in the NHVR’s ongoing commitment to enhancing road safety and ensuring the wellbeing of both heavy vehicle drivers and the wider community.
“Work diary and fatigue-related education was provided in 623 of these intercepts, accounting for
approximately 156 hours of roadside education with drivers, highlighting the NHVR’s commitment to safety within the heavy vehicle industry,” says Paul Salvati, NHVR Chief Operations Officer.
“Operation Forager shows the effectiveness of our holistic approach to safety, that combines education with enforcement, ensuring that heavy vehicle operators are not only aware of the regulations but also equipped with the knowledge to make informed decisions on the road about their safety
“I would like to commend the heavy vehicle industry for their safety efforts over the busy holiday period, particularly during the severe weather events we experienced across the country.”
Paul notes Operation Forager placed a strong emphasis on the importance
“By investing significant time and effort in educating heavy vehicle drivers on work diaries and fatigue, especially new drivers, we aim to create a lasting extends beyond the operation,” he adds.
“Education is an investment in safety. By ensuring drivers understand the importance of accurate work diaries, we are arming them with the knowledge to actively manage their work and rest hours.”
Paul explains while education is a powerful tool in preventing fatiguerelated incidents, the NHVR doesn’t hesitate to enforce the Heavy Vehicle National Law where required.
DHL’s Terberg tractors will work 24 hours per day. Image: DHL Supply Chain
DHL Supply Chain (DHL) is continuing the decarbonisation of its Australian transport fleet by introducing additional new electric vehicles (EVs).
The company has added two Terberg YT200EV electric yard tractors to its truck fleet and is supporting Australian electric vehicle manufacturing with the introduction of its first SEA Electric light duty truck to its last-mile fleet.
“Guided by the division’s Green Transport Policy, we are modernising our fleet within our supply chain and aiming for a better and cleaner way to do things,” says DHL Supply Chain Senior Vice President of Transport, Bill Rolfe.
“While we are committed to providing reliable services for our
customers, we are monitoring the industry for sustainability breakthroughs and communicating with our global counterparts to identify and roll out the latest in proven green technologies.”
DHL’s Terberg tractors will work 24 hours per day, manoeuvring consumer product trailers into position at a customer site. The units replace two diesel-engine tractors, reducing C02 emissions from trailer towing at this site.
The Terberg YT200EV is equipped with a Next Generation, cobalt-free lithium iron phosphate (LFP) battery and a 240kW traction motor capable of towing up to 88 tonnes. They also cost significantly less to run than the units they replaced.
The SEA Electric 300-85 EV light
duty truck uses a proven Japanesebuilt chassis and cabin, assembled in Australia with an Australian-designed electric driveline.
For simple maintenance, SEA Electric’s simple inboard mounted battery design requires no thermal cooling. It produces no tailpipe emissions while providing a 200-kilometre range.
These fleet updates have come soon after DHL announced its first Australian EV, the Volvo FL truck.
The ongoing deployment of these vehicles in Australia aligns with DHL’s global Environmental and Energy Policy, a strategic step towards decarbonising transport solutions and achieving significant reductions in GHG emissions, in accordance with the Group’s Sustainability Roadmap.
We are happy to announce the launch of our new 0.2t A series lithium storage assist vehicle. This is a compact and flexible vehicle that is perfect for picking small goods in warehouses, hardware stores, supermarkets etc. The unit has a 100kg hydraulic powered picking table, and also 115kg capacity lower storage tray.
The 24v/125ah lithium has fast and opportunity charging which greatly improves working efficiency.
Even at great heights, the operator feels confident thanks to the all-around safety protection, such as automatic closing doors, right and left hand sensing, front and rear flashing lights, tilt switch sensor etc. All these will help ensure operators are in the correct position as they operate the equipment, resulting in fewer injury risks and less potential downtime.
The AC motor significantly reduces the maintenance costs and downtime. Maintenance free lithium batteries reduce downtime and provide greater life span than traditional wet cell or gel batteries.
sales@hcforkliftau.com
www.hcforkliftaustralia.com
Conquest National Sales Manager, Chester Larsen, speaks to MHD about the dangers of silica and how the industrial cleaning equipment company can combat it with its wet sweeping solutions.
As attention on the perils posed by airborne dust intensifies, warehouse, manufacturing, construction and industrial facilities managers are grappling with how to mitigate the risks within their workplace, keep their workforce safe, and avoid penalties for non-compliance.
Adopting effective dust control measures not only ensures regulatory compliance, but also safeguards operational continuity.
Silica dust: the silent killer in industrial and construction work environments
Silica dust, composed of microscopic crystalline silicon dioxide particles, is found in many common building materials. One hundred times smaller than a grain of sand, silica dust easily becomes airborne through standard material handling and processing processes, including cutting, grinding, drilling, and handling diverse materials.
When inhaled, the small silica dust particles pose serious health risks to anyone exposed to the contaminated air. Under national WHS (workplace Health & Safety) laws, workers and management have obligations that relate to silica dust exposure. Failing to manage silica dust risks heavy fines and enforceable warnings, potentially leading to site closures. The most recent measure is the prohibition of engineered stone.
“It’s important to stay close to state-based workplace safety regulators,” says Conquest National Sales Manager, Chester Larsen. “These regulations are evolving as we collectively better understand the risks of silica dust, and they want to work with manufacturers, businesses, and construction companies to improve dust control practices.”
Using water is the most effective way to dampen the threat of dust. Water weighs down dust particles, preventing them from becoming airborne, and more easily captured by dust control measures. This includes floor cleaning.
The true solution to combating industrial dust is wet sweeping, which state regulatory and SafeWork Australia, recommend. Unlike dry sweeping, wet sweeping does not rely on filtering airborne particles. Instead, through the application of water, it prevents particles from becoming airborne in the first place during both the sweeping and disposal process.
“The industry is shifting towards integrating water into processes to counteract dust,” says Chester.
“Conquest, with its innovative technology, strategic methodologies
and unwavering commitment to health, safety and environment sustainability, is proud to work with our clients and the industry to provide the solutions to this need.”
Conquest heavy duty wet sweeping solutions
Conquest’s CC1200 combination sweeper scrubber uses water to minimise airborne dust during cleaning. Offering dual functionality, the CC1200 also translates to a 50 per cent labour saving and reduces operational costs, too.
The Conquest XR is a dedicated large capacity, ride-on scrubber that incorporates a light sweep functionality. Heavy duty and corrosion resistant, the XR is ideal for use in industrial work environments.
For more information about wet sweeping for dust control in your facility, call conquest on 1800 826 789 or download its Comprehensive Guide to Dust Control in Industrial Facilities.
Swisslog has announced that Walmart will install a Swisslog automation solution within its Valdosta, GA, facility to enable seamless material flow and increase uptime.
Walmart is planning to break ground on the milk processing facility and the project is scheduled to be completed in 2025.
The intralogistics warehouse automation and software company’s facility follows a series of successful installations globally, including in Australia and New Zealand for leading supermarket chains.
“Swisslog has a long history with pallet technology, so our expertise in this area can help supermarkets, grocery stores and e-grocery companies achieve optimal space utilisation and throughput,” says Charles John, Senior
Sales Consultant – Food and Beverage, Swisslog Australia and New Zealand.
“When demand for a product, like milk, is increasing, but land is becoming increasingly expensive, an automated warehousing solution that makes better use of the same space, or footprint, can help companies like Walmart, or local players, to gain a competitive edge.”
According to Walmart, the automated storage and retrieval solution (ASRS) will bolster the company’s capacity to meet consumer demand for milk. It continues the company’s commitment to building a more resilient and transparent supply chain to deliver high-quality products. This is Walmart’s second milk processing facility. The company worked with Swisslog to open its first milk
processing facility in Fort Wayne, IN, in 2018.
Designed by Swisslog’s automation experts, the ASRS brings together five Vectura pallet stacker cranes with KUKA palletising and de-palletising robots, a ProMove pallet conveyor system, as well as a conveyor system for small loads.
The automation solution operates on synchronised intelligence from Swisslog’s SynQ software, which provides warehouse management, material flow and automation control system functionality in a single, modular platform.
“We are excited to partner with Walmart once again to open its second milk processing facility,” says Sean Wallingford, President and CEO of Swisslog Americas.
The Victorian Transport Association (VTA) is delighted to announce Victorian minister for roads and road safety, and ports and freight, Melissa Horne, will formally open State Conference 2024.
The event will be held from Sunday March 17 till Tuesday March 19 at Silverwater Resort, Phillip Island.
“Minister Horne headlines a rapidly growing list of speakers from industry, government, regulators, and other transport industry stakeholders the VTA is arranging to address delegates over the two days of the conference, under our theme this year of Future Freight Landscapes,” says VTA CEO Peter Anderson.
“With so many critical issues on the radar that fall under Minister Horne’s portfolio responsibilities, including road and rail freight infrastructure, productivity at our ports and waterfronts, and training and skilling logistics workers of the future, it will be timely to hear from the Minister
about the Victorian Government’s priorities for the year ahead.
“Minister Horne has been diligent, consultative, and highly professional in carrying out her portfolio commitments and we appreciate her taking time to join us this year.”
VTA state conferences have a proud history of being content-rich and this year’s program will carry on that tradition, with a focus on emerging issues like cyber-security, artificial intelligence, the gig economy and related legislation, and other topics.
“We look forward to sharing our provisional program over the coming weeks, which will outline a strong line-up of presenters and social and networking opportunities,” adds Peter.
“A trade exhibition will feature product and service innovations from a range of industry suppliers, and we anticipate showcasing presentations and associated equipment from many domestic and international manufacturers.”
A range of packages and price-points are available, and these can be viewed at www.vta.com.au.
The Victorian Transport Association (VTA) tells MHD about the Fair Work Legislation Amendment passing in the senate and what it means for the transport, freight, and logistics industry.
After its passage in the Senate with amendments last Friday, the Fair Work Legislation Amendment (Closing the Loopholes) Bill 2023 has now passed the House of Representatives and will become law after receiving the assent of the Governor General.
The VTA wishes to congratulate the Australian Road Transport Industrial Organisation, along with NatRoads, TEACHO, the TWU, and the National Road Freighters’ Association for their work over many, many months on this legislation. In my capacity as National Secretary of ARTIO, it has been a
pleasure to work with such incredibly passionate people on legislation that is good for the industry, along with the VTA and our broader membership.
For those unaware, the Fair Work Legislation Amendment (Closing the Loopholes) Bill 2023, under Part 16
directly refers to the establishment of a Road Transport Advisory Group (RTAG) within the Fair Work Commission. This will be the initial body of reference in raising specific issues that currently degrades the equality and fairness within the workplace and contractual chains.
Through our ARTIO membership, the VTA supported advocacy that will deliver the road transport industry a more effective framework to address the many industrial relations gaps within the industry. This has been achieved with the passage of the legislation.
The beneficiaries of the ongoing improvements will be those business operators, drivers and logistics workers that will come into the road freight industry in the decades to come.”
Since developing world’s first engine-powered multidirectional forklift – the C4000 – Irish manufacturer Combilift has not taken its foot off the innovation pedal. And having recently celebrated its quartercentury anniversary in 2023, the company marked the occasion with the debut of several exciting new products.
The Combi-CB70E, is the latest addition to Combilift’s range of electric machines. Launched alongside a handful of new products, including the Combi-CUBE, as part of the manufacturer’s 25-year celebrations, the bright green multi-directional forklift is a testament to Combilift’s commitment to innovation.
Colin Gray, Combilift’s Regional Manager for Norway and Finland, says the CB70E combines both wellestablished and newly developed features to set a new bar for lifting efficiency – even in tough conditions.
“We see a lot of applications such as sawmills where the yards aren’t paved,
so operators are often dealing with rough surfaces and potholes,” he says.
“With the CB70E’s extra-large wheels, we see applications like these as a huge potential market for us. That’s a big reason we launched the machine at the Ligna international timber and woodworking show in May 2023 – and we’ve had a lot of interest in it since then.
Combining a 7000kg lift capacity with a small footprint and excellent manoeuvrability, the CB70E has been designed to enable operators to move bulky loads more easily in tighter areas.
“Typically, counterbalanced forklifts will measure 3.5m from the face of the fork the back of the machine,” Colin says. “So, operators will need a certain amount of clearance if they’re turning into an aisle with a load of timber. With the CB70E, that measurement is 2.68m – almost a metre smaller.”
Combined with the CB70E’s
multi-directional design, Colin says, the manoeuvrability benefits are essentially doubled.
“We see this as a huge benefit in both timber and steel applications,” he says. “For anybody handling awkward loads of seven tonnes or more, manoeuvrability is key.”
Another feature of the CB70E is its independent traction system, which eliminates the need for differential lock on slippery surfaces and reduces long load momentum twisting when travelling laterally.
The global management consultancy specialising in operations strategy and transformation, Argon & Co, has announced the appointment of its new Partner South East Asia.
Former SAP Ariba, PwC, KPMG and Johnson Controls leader, Nelson Chow, will lead Argon & Co’s Singapore office with a remit across the APAC region.
Argon & Co says he has earned his deep business and digital transformation knowledge throughout his 20-plus years of consulting experience focusing on operational excellence, margin improvement, and technology transformation.
“This appointment comes at a time of continued growth within the APAC region,” says Paul Eastwood, Managing Partner of
Argon & Co APAC.
“We recognise an incredible opportunity to expand our presence and capabilities whilst upholding our robust relationships and esteemed reputation in core sectors.
“Nelson will no doubt play an important role in shaping the APAC business, introducing fresh perspectives and innovative approaches to how we operate.”
In addition to his professional achievements, Nelson is deeply committed to nurturing the next generation of business and digital talents. He serves as a Visiting Lecturer for the Global Supply Chain Master Program at the Hong Kong Polytechnic University and as an Advisor for the Global Supply Chain Master Program at the Hang Seng
University of Hong Kong.
“I am thrilled to join Argon & Co as we embark on this journey together, particularly amidst the vast opportunities for growth in Asia’s dynamic market,” says Nelson Chow, newly appointed Partner.
“The region’s burgeoning economy, marked by a rising GDP and expanding middle class, presents significant potential in the consumer and manufacturing sectors, especially in luxury, retail and FMCG.
“I am confident that our hands-on approach and commitment to tangible results will drive success for both global and local companies in Asia. Together we will redefine industry standards and shape a resilient and sustainable future for our clients across the region.”
Following on from the success of the first in-person Elevate APAC conference in Melbourne last year, Körber is moving its premium supply chain event to Sydney in 2024. MHD gives an overview of what to expect from Elevate APAC 2024, and why it’s a must-attend for businesses to stay ahead of the technology curve and improve their own levels of customer service.
On May 7-8 2024, Körber’s Elevate APAC will give an opportunity for attendees to come together with like-minded businesses in Sydney to gain news and insights about supply chain technologies – helping leaders identify their strategic direction, accelerate decision-making, and drive their organisation’s future success.
This year’s Elevate APAC theme is ‘Chart Your Course,’ where keynote speakers, site visits and breakout sessions will focus on navigating the seas of supply chain disruption and complexity with the latest technology and innovation. Customer experience is at the core of this concept and will be a major focus when industry-leading experts provide actionable insights for supply chain’s current and most important trends.
This year’s agenda will be packed with Körber customer stories, product information and demos, opportunities to network with peers, and meet with the Körber APAC and Global team and its partners. There’ll be a deep dive into Körber’s suite of supply chain products and solutions, the opportunity for attendees to see Körber products in action and learn about real-life business transformation stories.
On top of this, the conference focuses on shared pain points being felt by businesses in the APAC region. By taking a collaborative approach to problem solving and leaning on the industry’s brightest minds for solutions, Elevate is a platform to gain valuable insights to achieve new levels of success today –and into the future.
The event builds on the resounding success of Elevate 2023 in Melbourne, which attendants hailed as “a great opportunity to meet top vendors for future pursuits” and “the best pace of conference I’ve attended in years.”
In 2023, more than a third of the 180 attendees were executive leaders, while 18 per cent were in operations. Nearly half were either the Owner, Director or Senior VP of their company, while 37 per cent were in either middle-
level or senior management. For 2024, Elevate has built on this attendant base, pivoted the theme and introduced new sessions hosted by Körber’s vast network of supply chain technology partners and customers.
As well as the overarching theme of ‘Chart Your Course’, the event can be broken down to into three key themes which all help drive a better customer experience for Körber’s customers and end users.
1) Digitisation and automation: How key technologies such as Autonomous Mobile Robots, Warehouse Management Systems, Order Management Systems and Transportation Spend Optimisation help to achieve business goals and gain competitive advantages.
2) Labour management: Labour shortages and skills gaps are a challenge for the majority of Australian businesses. Gamification and strategically deployed automation provide an opportunity to turn this challenge into more efficient work processes.
3) Sustainability and agility: ESG initiatives are now a priority in board rooms across the country. Körber technologies can build in flexibility and agility to supply chain disruptions, decrease carbon footprints and better staff wellbeing.
New information technology and tools for capturing and manipulating data are emerging all the time. For most Australian businesses, it is no longer a question of whether to digitise. To maintain a relevant, profitable business it is now a question of how much digitisation is needed, and how soon.
At this year’s Elevate, Körber will explore how businesses can prepare for digitisation, and which strategies are working for a particular profile of business. Software is fundamental to
success in the digital supply chain. At the centre of any automation project should be the right Warehouse Management System (WMS). The WMS is a hub to synchronise the flow of goods and resources throughout warehouses and distribution centres and the adjacent stages of the supply chain.
At Elevate, software experts from Körber will not only explain the key functionalities of WMS but be a sounding board for businesses who are unsure how to safely improve their warehouse efficiency. WMS talks will cover:
• Inventory visibility and management – especially important in today’s
New information technology and tools for capturing manipulating data are emerging all the time. Image: Körber
complex inventories with thousands of SKUs.
• Planning and managing inbound tasks, including goods receiving, slotting, put-away, and outbound tasks like picking, staging, carrier selection, and shipping.
• How to leverage system data, KPIs and analytics.
Körber’s Transport Spend Optimisation (TSO) is another vital cog in well-run supply chains. Tracking and controlling transportation spend is a challenge and a tangled mix of vendor relationships, financial processes and data sources creates complexity.
A continued pressure to reduce costs, streamline payments and simplify the supply chain remains high on the agenda for Australian businesses this year. TSO enables companies to leverage advanced analytics and real-time data to gain better visibility into supply chain operations, which empowers businesses to make informed choices, identify inefficiencies and streamline transportation routes, resulting in reduced carbon output and cost savings.
Körber’s cloud-based TSO is designed to help shippers reduce their total transportation spend across all types of freight, as well as drive operational improvements throughout supply chain planning and merchandising processes.
Additionally, Autonomous Mobile Robots (AMRs) are being heavily adopted in distribution centres around the country, and Körber’s team of experts are excited to delve into why. Commonly used in warehouses to sort, pick and drop products, AMRs offer supply chain operations the ability to scale up and down when volume increases or decreases and can easily
be redeployed to improve efficiencies wherever demand is set at a particular time. Compared to more traditional fixed automation, AMRs offer a new level of flexibility to cater for different warehouse layouts and sizes.
At the core of the supply chain industry are the people who drive its operations. The marriage of technology with the right people can help businesses grapple with the pressures of meeting escalating customer expectations for faster delivery and greater product variety.
At Elevate 2024, Körber will assess and confront the increasing demand on supply chains to cope with labour shortages and skills gaps. Technology emerges as a pivotal solution to this people problem, promising to unlock operational savings while enhancing safety and productivity for the workforce. Warehouse managers find themselves under mounting pressure to recruit, train, and engage staff amidst growing customer demands and unforeseen peaks in activity.
Voice-directed work, a technology that provides structured verbal instructions to workers via connected headsets, offers streamlined direction and feedback mechanisms. This industrial voice technology is tailored for high-volume, time-critical warehouse operations, improving accuracy and safety across various functions.
The integration of gamification into warehouse operations is also proving to be a powerful tool for engaging and motivating the workforce. By leveraging game mechanics to incentivise positive behaviours and achieve performance goals, gamification fosters increased employee engagement, safety
awareness, and productivity.
Incorporating these technological solutions into labour management practices is crucial for building resilient and adaptive supply chains of the future. Elevate conference attendees can expect to delve deeper into these strategies, gaining insights into their practical implementation and how their own business can overcome one of industry’s biggest challenges.
Supply chain agility takes centre stage at this year’s Elevate conference, where industry leaders will converge to address the evolving landscape shaped by consumer demands and global disruptions. With SKU proliferation and shifting delivery norms, Elevate will explore how supply chain operators can leverage strategic partnerships – treating technology providers as integral partners – and embrace innovative technologies like cloud-based simulation tools to increase agility and adaptability. Real-time analytics and unified control systems can optimise workflows, while Generative AI promises smarter, data-driven decision making.
In conjunction with supply chain agility, sustainability is and has been a hot topic for industry for a number of years. In 2024, the urgency of solving the climate crisis has never been higher, and people’s awareness of their impact on the planet is growing. Global forces are imposing more and more regulations on businesses to become more sustainable. But as the supply
chain makes efforts to cut their CO2 emissions and carbon footprint, it also needs to keep demanding customers be satisfied.
Talks at this year’s Elevate conference will centre around changes in consumer habits and loyalty, and how the “conscious consumer” is creating a new, highly competitive market for businesses. With sustainability at the forefront of Körber’s focus for years, the supply chain leaders are intensifying efforts to address climate change challenges. As larger corporations demand ecofriendly practices, the importance of understanding processes and supplier practices has never been more critical.
Sustainability experts will explain practical solutions to reduce waste and carbon footprints while enhancing profitability. From rethinking plastic usage to embracing electric vehicles and warehouse automation, Körber’s portfolio of solutions strive for increased visibility, energy efficiency and waste minimisation across the entire supply chain operation. Elevate participants will learn how cuttingedge technologies such as AMRs and artificial intelligence overlap with Körber’s WMS and TSO to empower businesses to make informed choices, identify inefficiencies and streamline transportation routes, resulting in reduced carbon output and cost savings. ■
What does the theme “Chart Your Course” mean for Körber and for the conference?
Nikki Jones, Körber APAC Marketing
Director: Chart your Course is about navigating through supply chain complexity and setting the direction for your organisation. Elevate amalgamates industry trends, insights, technology news and best practices to help businesses consider their course ahead via enhancing operational efficiency, mitigating risks and improving customer experience to drive sustainable growth.
Reflecting on the successful in-person return of Elevate in 2023, what new or enhanced networking opportunities can attendees expect at the 2024 conference to help them navigate the challenges and opportunities in the supply chain industry?
Nikki Jones: Attendees will have access to customer site visits, breakout sessions focusing on different challenges in the industries, and an exciting Appreciation Networking event in line with theme of Chart your Course. As with all Elevate events, key components are the opportunity to connect industry peers and share knowledge and learnings through conversations during the catered breaks, discovering new ways of working with our technology partners and engaging different experts and SMEs.
How will the 2024 conference showcase the latest innovations and technologies that have solidified Körber’s leadership position?
Nikki Jones: As well as sharing Körber’s product roadmap and its new technology enhancements, Elevate will highlight the level of expertise involved in project delivery and support infrastructure required to best serve our customers. It’s this level of dedication which earns Körber industry recognition such as our recent 4.6/5 rating in Gartner’s Customer’s Choice in 2023.
Considering the attendee testimony from the 2023 event regarding the quality of interactions and the calibre of decision-makers present, how is the 2024 conference planning to enhance the attendee experience and facilitate meaningful connections?
Nikki Jones: As a technology partner in the industry, this conference is about sharing knowledge. It brings together industry peers from different professional backgrounds, whether you’re in front of house or back of house, academic or industry, the power of making connections is what each attendee makes of it. We believe that the more we give, the more we get back. It’s exciting to provide an environment of varying opinions with different perspectives, at Elevate people are open to sharing their own challenges and getting help from experts who can change and transform their business.
Nikki Jones, Director of Marketing at Körber APAC answers burning questions for Elevate APAC 2024With sustainability on everyone’s minds, warehouse design has come under particular scrutiny for opportunities to economise on energy usage and make operations more environmentally friendly. But with their intense energy usage, cold chain warehouses are of even greater concern than other kinds of facility, says Peter Jones, Managing Director of Prological.
Peter emphasises the enormous energy demands required to power HVAC systems in these vast buildings, pinpointing this as the primary challenge facing the sector today. “In our current world environment of carbon reduction, the cold chain is a huge consumer of energy,” Peter says. This concern has propelled Prological to explore technologies aimed at significantly reducing reliance on grid electricity through on-site power generation and storage, with preliminary modelling indicating a robust return on investment for such initiatives.
But before we get to those – what are the primary elements that go into designing a cold chain warehouse, and what challenges do they present?
Peter elaborates on three pivotal design elements crucial to cold chain facilities: the imperative for airtight buildings, the logistical intricacies of managing inbound and outbound interfaces, and the sophistication of HVAC systems.
“The integrity of the building’s seal is paramount; any leakage, while not compromising temperature control, markedly increases electricity consumption,” Peter says. “The second element addresses the challenge of maintaining this seal while facilitating the movement of goods into and out of the warehouse, often leading to expensive solutions such as integrating vehicle parking
inside the facility or employing sealed aprons for external loading areas. Designing these elements into a cold chain facility at an efficient level is critical.”
The most expensive part of a freezer warehouse, says Peter, is the defrost system in the floor. “In a freezer, if you don’t have a defrost system in the floor, you end up with a situation similar to the old manual defrost freezers at home. In a 20,000 square metre freezer warehouse, the solution has been to install heating (defrost) systems in the floors of the freezer sections, which operate periodically to prevent moisture on the floor from freezing. There are significant peak loads to turn on, with a very high energy consumption while running.”
According to Peter, Australia finds itself somewhat behind the curve in cold chain warehouse design, particularly when juxtaposed with global counterparts in the United States and Europe. “The largest cold chain company in Australia now is Americold,” pointing out that while American firms are significantly engaged in carbon reduction efforts, European companies are even more advanced in integrating sustainability into their operations.
This disparity in technological adoption and efficiency improvements, Peter suggests, is not due to a lack of available technologies in Australia but rather a combination of infrequent construction of cold chain facilities and a hesitancy to embrace new solutions. Cold chain warehouses, as specialised structures designed to maintain specific temperature ranges, are built less frequently than their ambient warehouse counterparts. This, coupled with the significant capital expenditure required, means that opportunities to incorporate the latest advancements and designs are
rare and often overlooked in favour of cost-saving measures during the construction phase.
He recalls the last significant wave of cold chain warehouse constructions approximately five years ago in locations like Truganina in Melbourne, and Arndale Park in Sydney, suggesting that the pace of technological advancement has since outstripped these facilities’ capabilities.
The crux of Peter’s concern lies in the reluctance to invest in the latest technology during the design and construction of new facilities. This hesitancy, driven by the high initial costs associated with cold chain warehouses, risks perpetuating a cycle of long-term energy inefficiency. “The inclination to reduce upfront costs can lead to increased operational expenses over time due to suboptimal energy performance,” he says. “This scenario underscores a broader issue within the Australian cold chain sector—a need for a paradigm shift towards valuing long-term sustainability and efficiency over short-term capex savings.” Through Peter’s lens, embracing the latest in cold chain technology and design principles is not just an opportunity for Australian companies to align with international best practices but a necessity to ensure the future viability and environmental responsibility of the cold chain industry.
With industrial property a scarce commodity in Australia today, what opportunities are there for retrofitting cold chain warehouses?
Given the complexities involved in designing a cold chain warehouse, opportunities to retrofit are relatively limited, Peter says.
“The interface between the interior
and exterior of the warehouse presents a relatively straightforward area for retrofitting,” he says. “Components such as doors and loading docks, which are prone to wear and tear, offer tangible opportunities for improvement by incorporating more efficient, modern materials and mechanisms.”
HVAC systems, integral to maintaining the cold chain’s temperature requirements, also represent a key area for upgrades. As these systems reach the end of their lifecycle, replacing them with the latest technology can markedly improve energy efficiency. Peter underscores the importance of seizing these moments of equipment redundancy to introduce advancements that could reduce the overall energy consumption of the facility.
However, the prospect of integrating on-site power generation and storage, such as solar panels, into older warehouses is considerably more complex. The challenge lies in the structural limitations of these buildings, which were not originally designed to bear the additional load of solar arrays. “The roof is not designed to carry that static load, let alone the dynamic load,” Peter explains, pointing out the engineering hurdles of retrofitting such systems onto existing structures. The dynamic load introduced by solar panels,
in particular, can significantly increase the wind load on the roof, complicating – even prohibiting – the retrofitting option.
Despite these obstacles, Peter advocates for a forward-thinking approach to warehouse design and retrofitting, emphasising the importance of aiming to surpass current best practices. This philosophy not only ensures that new facilities are built to the highest standards of efficiency and sustainability but also encourages a continuous improvement cycle within the global cold chain infrastructure. By prioritising the adoption of cutting-edge technologies and designs, the industry can make strides towards reducing its environmental impact while enhancing operational efficiency.
A fundamental challenge confronting the sector is the separation between those who bear the cost of energy consumption and those who design and construct the buildings, Peter says. “Often, the operational realities of energy efficiency are not a priority for those who lease these facilities. This disconnect underscores the need for a more integrated approach to warehouse design, where operational efficiency and sustainability are core considerations from the outset.”
Moving forward, Peter identifies several key areas for development. The adoption of the most efficient
HVAC systems, such as heat pumps for refrigeration and in-floor heating for defrosting, is crucial. Additionally, innovative design solutions for the interface between the warehouse interior and exterior can significantly reduce energy loss.
Take floor defrosting, for example:
“The opportunity exists to turn this around, such as using solar arrays on the roof, where the ambient temperature under the solar array is about double whatever the ambient temperature of the day is. Systems are now available to capture that heat and store it in a thermal change product, or via several other new technologies, which in turn, is then used for the floor’s defrost system. This transitions one of the most expensive inputs of a cold chain warehouse to operate into an almost free process, as the energy now employed would otherwise have been wasted.”
A particularly exciting opportunity lies in the realm of energy generation and storage. For cold chain facilities, which have high electricity demands, the investment in on-site power generation and storage systems, even with today’s battery costs, is justified and beneficial. As battery technology advances and costs decrease, Peter anticipates a future where energy storage becomes viable for a wider range of facilities by the end of the decade. ■
Figuring out the nuts and bolts of Shiperoo, a leading-edge 3PL disruptor through the lens of retail industry veteran and Shiperoo’s trusted advisor, Glenn Keast.
Shiperoo, the new brain child of supply chain techpreneurs Nishan Wijemanne and Rizan Mawzoon, recently paved way for a new era in third party logistics services by launching a tech-first retail fulfilment and returns management service redefining the traditional 3PL approach experienced by retailers. With a generous injection of more than AUD $30m in strategically located high-tech fulfilment centres built with dynamic first-generation robotic automation solutions and advanced returns management software, the founders have added another crucial layer to their growth strategy – a robust advisory team.
MHD sat down with Glenn Keast, Shiperoo’s trusted advisor and retail operations legend to learn about how Shiperoo is switching up the gear.
Glenn, what led you to take on advisory commitments at Shiperoo?
I have known Nish and Riz for more than 15 years, a connection that has built significant trust which is a pivotal element for me. Over the years they have proven that trustworthy relationships are built on the basis of exemplary solutions and an equally exemplary team, along with an inherent ability to back yourself with the results. Being able to trust someone that has got great intent is very critical for me.
Anyone in the industry who knows these two individuals well also knows about their uncanny ability to not take themselves too seriously, and that they have a bit of fun and they are never fazed during times of strong challenges. Their purpose of being and drive to achieve success for retailers was articulated very clearly to me right from the start when they conceptualised Shiperoo and I knew they were on to something good for our industry.
I also loved that Shiperoo’s innovative solution design would solve two critical retail challenges - fast, efficient, dynamic fulfilment and returns
management, both with high visibility. Many 3PLs have knocked on my door over the years and I have not yet seen service that aids retailers to operate as efficient omni warehouse the way Shiperoo has proposed. The COVID pandemic as well as the advancement of eCommerce over the last 10-15 years has driven strong requirement around returns and e-fulfilment, and these are two challenges that have left retailers with too little to choose from when it comes to picking a 3PL or do it yourself. Both options come with more cons than pros due to the underwhelming nature of how 3PL service offerings are designed and how risky DIY can be. For returns in particular, there has been limited service offering for an end-to-end returns management provider, leaving little retailers to procure multiple service providers when what they actually need is an allencompassing service.
How has your experience at Cotton
On Group managing growth and operations helped with your advisory commitments at Shiperoo?
I think one of the attractions at Shiperoo were their goals and aspirations for growth, which was also what originally attracted me to Cotton On, which has grown exponentially during my times as COO. At Shiperoo, I can feel the adrenaline in their approach. The Shiperoo team does a tremendous job of understanding and researching individual retailers and the market dynamics through their robust relationships which helps them design next-level service offerings. It will be exciting to watch the Shiperoo team as they set out to become one of the fastest growing fulfilment and returns management providers in the market.
Based on your extensive exposure to technology in the retail industry, what input have you had in Shiperoo’s tech decisions? The advent of omni warehousing has
been on the rise over the past decade, and COVID pandemic has made it a necessity rather than a need for retailers. There are too many retailers and 3PL providers who are not quite knowledgeable in use of modern tech to facilitate omni warehousing. Since I was acutely aware of this limitation amongst retailers, the advanced technology that Shiperoo team had conceptualised instantly piqued my interest. The reliability to drive dynamic outcomes as well as facilitate growth for retailers is a perfect fit for just about any type of retailer. Retailers that partner with Shiperoo for their fulfilment and returns management will now be able evolve and make better decisions across their entire business from better in-store and online operations, favourable return policy and same-day shipping, through to revaluating product choices thanks to the visibility offered by Shiperoo. Deciding whether to work with a 3PL or manage fulfilment themselves is easy as Shiperoo facilitates and offers both scenarios in the form a creative, neverseen-before service. There is now truly an opportunity for retailers to invest in a fulfilment player with the right tech and supply chain experience rather than just box shifting and getting products from A to B.
What are your aspirations and hopes for the retailers when it comes to a positive fulfilment experience?
Retailers should not have to worry about fulfilment if it is done well. Too often if supply chains fail, teams and suppliers try and change things without a holistic outcome. To me the Shiperoo service offerings across the board will allow retailers to just operate and sell product, with the confidence that fulfilment will just happen. Ultimately my biggest aspiration for fellow retailers is to work with a service provider that is committed to go above and beyond, and one that designs a solution for them rather than just
invite all retailers into facilities that are simply a generic template for retail fulfilment.
It is easy to recommend tech when you have been in the frontline of tech and tech creators. I have been fortunate enough to watch Shiperoo’s tech get designed and unfold in what they call their “dream facilities”. To me, this solution exposes retailers to a better way of doing things and helps retailers transition or transform their fulfilment strategy whilst mitigating risks associated with moving. It allows retailers to act now and get on with growth rather than solve things that they are not internally geared up to solve themselves. I am not here to be a brochure for Shiperoo. Instead, I am here to advocate what is best for retailers after having been an integral part of why the Shiperoo service has been designed the way it is.
Over the years, Nish and Riz talked about seamlessly connecting the consumer-facing end of retail with the supply chain end. How do they incorporate this connection at Shiperoo?
Firstly, ‘operational visibility’ and ‘access to information’ are paramount for retailers. Having too many systems procured to have access to various types of analytics that are not necessarily connected to the supply chain end can cause more damage and hamper growth by encouraging skewed business decisions.
Secondly, the timeliness of returns can help retailers drive a much higher value for product that has been returned. Currently the ‘returns’ area has experienced a rather underwhelming level of atention when it comes to the financial impact of returns.
The Shiperoo service offers actionable reporting as a core offering. It has been designed to solve visibility challenges for all levels of retail teams including merchandising, product as well as operational teams to bring about a connected experience and make holistic decisions.
Why do you think that there has been a lack of players who have tackled the visibility and returns challenge head on under one 3PL provision?
A lot comes back to the ever changing
world of retail. It is not a surprise that the consumer has been driving behaviours in the retail industry with their complex expectations on how they choose to get their products e.g. in store, or go online, or reserve them to collect in store and how they return them. So, the last thing that the retailers are often trying to solve is their supply chain, and that is the catch-up component that has been overlooked for many years. Eventually everybody will get there and there will be new challenges to solve along the way. However, Shiperoo’s take on resolving this overlooked component is in the form of an overall experience consisting of high-speed fulfilment, a complete returns management solution, reporting and visibility, with the goal of improving the landscape of 3PL service. To me this is a huge step forward.
What challenges do retailers face in the areas if fulfilment, returns, aged inventory and excess stock?
Returns can come from everywhere and they take a lot of time to get back to the retailer. The timeliness to get returns back from store or customer, the timeliness to process the credit and process it back to a shelf to be able to be picked from again is a true challenge that ties back to a retailer’s operational systems and efficiencies. Whilst there are numerous players offering what is termed as ‘returns processing’, there is far more to returns than just processing. It ultimately ties back to having a robust supply chain so the product’s value can be recovered and not lost to time, resources and processing mechanisms. With a full returns management experience at Shiperoo, all of a sudden we are talking
about retailers being able to get their returns’ value out of the sunken cost basket and also add value to a customer’s returns experience where they are able to see their credit faster and build further retail brand loyalty.
Shiperoo is soon going to take their returns management service to the next level by adding a consumer-facing returns facility for retailers to offer their customers. This advancement is currently in the “stay tuned” lane and I am excited about it being launched soon.
Q How do you feel about the responsibility you have within the retail community?
I have had opportunities over the years to be involved in many advisory roles. My journey as COO at Cotton On Group has offered me significant opportunity and experience in managing and being part of “growth and expansion”, which is a primary motivating factor for me when it comes to aligning my energies. So naturally, having an opportunity to be a trusted advisor and teach some of my repertoire to the Shiperoo team is exciting, as I know it is geared for significant growth.
The other part of me strives to encourage emerging leaders, change makers and entrepreneurs in whichever way I can. Ultimately a great idea and a successful business have one thing in common and that is ‘good people’. I see my strong advisory alignment with the founders of Shiperoo as a pathway to ensuring that good people will ultimately create a good business and lift up the standards of service providers in our business community. ■
BHD Storage Solutions explains to MHD how it’s completed a full-scale cantilever racking project for partner and family-owned timber wholesaler, Woodhouse Timber.
Woodhouse Timber, a leading family-owned timber wholesaler, embarked on a strategic initiative to expand its operations and enhance storage capacity. In partnership with BHD Storage Solutions, they explore the successful completion of a fullscale cantilever racking project at Woodhouse Timber’s newly constructed 7200 sqm warehouse in Darra, Brisbane.
Established in 1983 by Chris Woodhouse, Woodhouse Timber has evolved into a national powerhouse in the timber industry. Known for its commitment to quality products and exceptional customer service, the company’s growth led to the need for an efficient storage solution to accommodate its expanding inventory.
The collaboration between Woodhouse Timber and BHD Storage
Solutions commenced in 2020 when David Seale, the Business Development Manager at BHD, forged a strong relationship with Drew Woodhouse, the Director of Operations at Woodhouse Timber. Together, they set out to address Woodhouse Timber’s unique racking requirements.
BHD Storage Solutions was engaged from the early planning stages, tasked with designing a racking
system that would optimise available space, allowing for the storage of a higher volume of timber packs per square metre. The primary goal was to achieve increased storage capacity and operational efficiency through the implementation of innovative racking and warehouse management systems.
BHD proposed a solution centred around 9000 mm high double-sided cantilever columns. This design, exceeding the standard 5800 mm column height, resulted in a 37 per cent reduction in floor space
requirements. The use of narrow aisle forklifts further contributed to a 35 per cent decrease in unproductive floor space compared to standard aisle configurations. This innovative approach saved a substantial 1500 sqm of floor space, equating to an estimated cost saving of $1.5 million in land and building expenses.
Due to the storage efficiencies achieved by the initial racking system, BHD Storage Solutions continued its collaboration with Woodhouse Timber. In 2024, the installation of an
additional 196 9000 x 410 cantilever columns was completed, covering 90 per cent of the warehouse floor space. This expansion further maximised storage capacity, significantly reducing storage costs per annum per metre.
The collaboration between Woodhouse Timber and BHD Storage Solutions exemplifies the power of tailored storage solutions in boosting operational efficiency.
The focus on maximising warehouse floor usage, reducing aisle widths, and increasing vertical storage capabilities resulted in substantial cost savings for Woodhouse Timber. The project underscores the significance of strategic storage solutions in driving down operational costs and enhancing overall supply chain efficiencies.
BHD Storage Solutions takes pride in its ongoing partnership with Woodhouse Timber, contributing to the company’s journey of success. This project serves as a testament to the impact of innovative and customised storage solutions in optimising warehouse operations and achieving significant cost savings. Looking ahead, both companies anticipate continued shared successes through their collaborative efforts. ■
In 2024, the installation of an additional 196 9000 x 410 cantilever columns was completed. Image: BHD.Flinders Warehousing & Distribution Operations Manager, Todd Clarke, tells MHD about the company expanding its operations in South Australia, improving security and safety in its warehouses, and implementing a new WMS.
Growth is on the horizon at Flinders Port Holdings (FPH), with an increase in cargo tonnage, grain tonnage and total containers in the 2022-23 financial year, with further growth anticipated in 2024.
South Australia’s ports are the gateway to trade for the state, with more than 2000 ships calling during the past financial year including cargo ships transporting grain and other agricultural products, mining equipment, aquaculture, wine and other food and beverages.
More than 90 per cent of South Australia’s exports and imports pass through the state’s ports.
In the year ending June 30, total cargo tonnage increased by 7.7 per cent from 23.9 million tonnes to 25.7 million tonnes, reflecting an increase in two-way trade.
Total container numbers increased
by 2.9 per cent, from 328,537 TEU (twenty-foot equivalent units) to 337,959 TEU.
Thanks to significant year-onyear volume growth at Flinders Warehousing & Distribution (FWD) since its inception four years ago, there has been an ever-growing need for storage and services capabilities, with improved systems and an optimisation strategy is underway.
FWD is perfectly placed to offer customers additional benefits given its proximity to the Flinders Adelaide Container Terminal (FACT) which runs 24/7. Rail and road connectivity provides seamless access to the port; easy transfers of containers between the terminal, Empty Container Park and both FWD sites; and quick turnaround of containers from vessel discharge
From ship to warehouse, no trucks are involved – just cranes and straddle carriers within the internal port network. The new straddle carriers used to move cargo are also hybrid –
the first of their kind in the southern hemisphere. This also allows FPH to meet sustainability targets and produce lower emissions.
To cater for the increasing usage of South Australia’s ports and in particular Outer Harbor, FWD’s largest warehouse – with a floorspace of 20,000 sqm – has just doubled its capacity by investing in and introducing racking.
The racking allows the warehouse to hold double the number of pallets vertically – now catering for more than 3000 pallets and duplicating the warehouse footprint. The installation of the new racking system was finished in January (2024).
Doubling the storage capacity at FWD provides significant benefits for FWD customers, both importers and exporters alike.
From a production perspective, doubling the storage capacity means fewer movements from rack to truck and rack to container and easier access to customers’ stock.
It provides visibility of cargo and ease in identifying where the cargo is stored through the sophisticated warehouse tracking and management system FWD now has in place.
The system makes it easier to identify specific pallets and identify which ones need to be moved faster than others.
Along with its increased capacity, the warehouse is fully insulated and maintains an ambient temperature, allowing for the storage of temperature-sensitive products.
With the growth predicted in the Outer Harbor precinct over the next 25 years, having more warehousing space
will become increasingly important for importers and exporters.
FPH has recently installed a higher level of security in its warehouse, in readiness to become Customs bonded. Once this licence has been granted, it will enable FWD to hold high-risk materials and equipment related to various industries’ demands.
The additional security includes extensive CCTV, automatic swipe access gates with face recognition and enhanced traceability processes and procedures to ensure every item, which passes through the facility is controlled in accordance with Australian Border Force’s (ABF) strict requirements.
FWD will apply to the federal government for both the 77G Depot Licence and 79G Warehouse Licence, which allow for the movement and storage of under-bond containers, still being held for ABF verification or control, however it will allow the FWD team to unpack and store cargo on behalf of the ABF.
Having 77G and 79G accreditation
offers customers significant flexibilities by allowing FWD to commence the inspection of cargo without having to call in customs officers, and peace of mind that security regulations are being complied with.
FPH is also going through the Defence Industries Security Program (DISP), which allows FWD to store and transfer defence machinery and componentry through its facilities. With ASC an Outer Harbor neighbour, and with FPH being strategically aligned, gaining this approval by the Department of Defence is an important step for FWD.
Over the next 12 to 24 months, a new warehousing management system is being developed and implemented, which will save FWD operators time. Along with its electric forklifts, FWD’s environmental footprint is being further reduced. The warehousing system is part of the FWD optimisation project,
which ensures better usage of the warehouse’s footprint, and more seamless movement of inbound and outbound cargo.
The 20,000 sqm warehouse has been built to the highest industry standards, with an undercover awning the entire length of the facility, which ensures trucks, and their cargo is protected from the weather when loading or unloading.
The eight unique container bays provide not only an awning but side coverage, which closes around all sides of the container and offers complete weather protection to ensure the integrity of customers goods at all times.
With the increasing capacity to store cargo and shipping numbers growing, FWD has employed another eight team members over the last 12 months and is looking for continued growth. ■
Todd Clarke, Operations Manager, Flinders Warehousing and DistributionMHD spoke to Scott Coy, Director – Rental & Sales Management, Jungheinrich, about its integrated lithium-ion solutions and how the German-based material handling company is leading the way in producing sustainable products.
Jungheinrich, the Germanfounded material handling company, started selling its solutions in Australia during the 1970s and the 1980s in New Zealand through dealership arrangements. In 2015, via an acquisition, Jungheinrich Australia formally entered the Australian market. Similarly, in 2022, it also entered the New Zealand market.
The pioneer of alternative power solutions began researching and developing lithium-ion technology in 2007 and unveiled its first concept lithium-ion pallet truck in 2008. In 2011, the first Jungheinrich lithiumion pallet truck entered the market.
Between 2011 and the present day, Jungheinrich moved its lithium-ion battery up the Ingress Protection (IP) ratings – which grades the resistance of an enclosure against the intrusion of dust or liquids – to a rating of IP54.
Additionally, it has managed to reduce the energy required by the forklift truck to operate, increasing run time and significantly increasing the volume of lithium-ion trucks across the market globally.
While lead acid batteries have been used for many decades, lithium-ion batteries have only been available for the past 15-odd years. These greener, safer and more efficient solutions are proving to be more sustainable than their non-electric predecessors.
“We like to say Jungheinrich was born electric,” says Scott Coy, Director – Rental & Sales Management, Jungheinrich. “Dr. Friedrich Jungheinrich pioneered electric forklift trucks in the 1950s in Hamburg, Germany. We don’t outsource the
Scott Coy, Director — Rental & Sales
Jungheinrich. Image: Jungheinrich.
manufacturing of our trucks; we manufacture our own integrated lithium-ion solutions. Lithium-ion
solutions from Jungheinrich have been tested for a long time, we have the longest experience with these technologies, they are 100 per cent safe, and we continue to improve on them.”
Jungheinrich Lithium-ion products are cleaner and more reliable than their lead-acid counterparts. Not all lithium-ion products are the same – as an example – the batteries in smartphones differ greatly from the ones made for electric vehicles and the ones made for material handling equipment such as forklifts.
“Different materials than those in smartphones and vehicles are used to create the lithium-ion technologies we manufacture with our products,” explains Scott. “Further to this, not all lithium-ion batteries in forklifts in the market have the same quality as Jungheinrich’s.”
While consumers may be concerned about the safety of lithiumion batteries, Scott reassures Jungheinrich’s products are 100 per cent safe and says education is key to understanding this.
Lead acid batteries need to be charged in cycles and levels checked
while lithium-ion batteries can be charged any time. They charge quicker than lead acid batteries and require zero maintenance – meaning reduced downtime.
Jungheinrich trucks have fully integrated lithium-ion solutions, which means its offering is superior to many of its competitors who have bolt-on lithium-ion solutions.
Lithium-ion is a cheaper investment overall because it requires fewer service, less maintenance and incurs lower downtime costs over the duration of the truck’s operation.
The use of a lithium-ion battery reduces the CO2 emissions up to 52 per cent when compared with an internal combustion truck. Green electricity can further improve the balance of electric vehicles.
“By being a pioneer in this space, we’re ahead of the game,” says Scott. “We can improve what it looks like and increase its power storage. We don’t bolt on a lithium-ion battery to our solutions because our products
are fully integrated.”
Jungheinrich prides itself on its after-sales support. It often says that its sales team sells the first truck, yet the after-sales team sells every truck thereafter. It firmly believes that if it doesn’t properly support and service its customers following that first sale or rental, it won’t have any business.
“Seventeen years ago, the concept of lithium-ion batteries was futuristic,” adds Scott. “They’ve now been a reality for the past 13 years. Our goal is to educate customers on the benefits of a lithium-ion solution and make the product even more energy efficient.
“Our product portfolio includes electric counterbalanced trucks, hand pallet trucks, high-rack stackers, reach trucks, low level order pickers, pedestrian trucks, stackers, order pickers, tugger trucks and trailers, and mobile robots. Quite simply, all trucks in our range are available in lithium-ion, without any additional lead time as it is purely a standard option for Jungheinrich trucks with the share of lithium-ion to lead acid very high. Feel free to speak to us to find out more.” ■
Vanderlande’s Director of Warehouse Solutions, Roald de Groot, speaks to MHD about how the automation technology company’s FASTPICK solution has been helping Dutch haberdashery and yarn wholesaler, De Bondt.
Vanderlande’s FASTPICK solution helps De Bondt in the Netherlands to manage growth.
De Bondt is the largest combined haberdashery and yarn wholesaler in Europe. It is a completely onestop, online shop for retailers in the handicraft sector and ships goods to more than 70 countries across the world.
The company selected Vanderlande’s highly automated goods-to-person (GtP) warehouse
solution – FASTPICK – to help it manage strong growth and maintain high levels of customer service.
De Bondt offers an extensive range of around 60,000. Delivering a highquality service to its customers is essential to this “business with a family”, which was established 50 years ago by the current Managing Director’s parents. Fast delivery is a firm promise, as orders received
before 6pm are guaranteed to be shipped on the same day.
When COVID-19 struck, the need to invest became urgent as orders rose dramatically. “The amount we had to process compared to before the pandemic was up by around 150 per cent,” explains Dora Kasper, De Bondt’s Logistical Manager.
“At first we thought the situation would only last up to three months, but it kept going and we started to worry that we would not be able to keep up using our existing infrastructure.”
The buoyant order book and increase in revenue meant the time was right to take the first step in automation, and the company began its search for a partner. “We chose Vanderlande because they were remarkably quick to understand what we needed,” says De Bondt’s Managing Director, Job de Bondt.
“I particularly liked the allinclusive nature of their solution, which covered our entire process – they are a complete system integrator.”
Central to Vanderlande’s solution is its shuttle-based automated storage and retrieval system (AS/ RS), ADAPTO. Order lines are supplied to GtP workstations in compartmentalised totes by shuttles with a high capacity and in a strict sequence.
Operators pick orders straight into cartons in an error-free, singletouch process. They are guided by clear on-screen instructions and
intuitive lights that indicate the exact compartment to pick from.
In terms of housekeeping, FASTPICK gives De Bondt tremendous flexibility, because totes can be split into a
maximum of eight compartments. This means quantities of popular items can be spread over multiple totes, which helps to smooth the order flow.
There’s no waiting for a busy tote to become free. In addition, the system gives the business clarity
about how much stock it is holding and where it can be found.
“We can offer an even more professional service to our customers because of the new system,” says Dora. “We’re sending out orders in a more reliable way and making fewer picking mistakes.”
Job agrees, adding that the business has been provided with a high degree of functionality on a small footprint.
“The system is hugely adaptable and can easily handle peak times during different parts of the day,” he says.
“Some competitors may have a bigger range than us, but they don’t have our operational excellence.”
Roald de Groot from Vanderlande Australia adds that they are working on some FASTPICK projects in Australia at the moment as well. The flexibility and adaptability combined with the proven ADAPTO technology makes this a very interesting solution for our customers. ■
Intermodal Terminal Company is striving to change the terminal game in Australia and has begun so by constructing a new facility at its site in Somerton, Melbourne.
Wholly owned and backed by Aware Super, one of Australia’s leading superannuation funds managing $170 billion on behalf of its 1.1 million members, the Intermodal Terminal Company (ITC) aims to assemble a national portfolio of terminals with its first being the $400 million development of Somerton Intermodal Terminal (SIT).
Austrak Business Park founder and owner, Mark Assetta, said he was delighted the vision of establishing a major intermodal terminal at Somerton to service not only Melbourne and Victoria but also the national supply chain was fast coming to fruition under the stewardship of ITC.
“I’ve always said Somerton is perfectly positioned and sized to act as a key intermodal terminal in the supply chain – it sits within the major rail corridors of the ARTC north-south standard gauge and the VicTrack broad gauge networks. It enjoys direct access to the Hume Highway and other freight feeder roads, and services an existing large catchment of containerised freight movements and consolidation,” he said.
“I congratulate both ITC and Aware Super for supporting the future development and growth of Australia’s freight and logistics sector – this significant investment at Somerton will help make the national supply chain more productive for decades to come.”
With a background in investment management and transport infrastructure development, ITC founder and CEO Mishkel Maharaj was immediately impressed with Somerton’s unique location, the scale of the site, and the many benefits it would bring to both the national supply chain and broader community.
Maharaj said the SIT’s capacity
will allow the rail freight market to flourish while also benefiting the wider community, enabling more freight to move on rail, thereby helping to reduce traffic congestion, road accidents and damage, and transport emissions.
“The benefits of the future SIT are compelling: it’s where a lot of freight movements and volumes are currently concentrated and it’s close to existing large-scale distribution centres and warehouses, Melbourne CBD, port, and airport,” he said.
“For example, Coles’ national distribution centre is located within the existing 135-hectare Austrak Somerton Business Park.”
Maharaj said it was rare to find large parcels of industrial zoned land with direct access to major rail and road freight corridors, while also being positioned within an existing business and logistics precinct close to a CBD and port.
“Significantly, with existing intermodal capacity set to be constrained within the next decade, SIT offers a privately funded solution to both the Victorian and Australian governments in coming years to secure future growth for freight movements
in both state and national rail supply chains,” he said.
Maharaj said its vital rail freight has sufficient terminal capacity to grow and that future facilities are independently owned and operated so the whole supply chain can benefit from a competitive transport landscape.
“The SIT will be just that, and best of all, it’s funded by the private sector providing federal and state governments more scope to allocate limited taxpayers’ funds to continue to improve the resilience and capacity of existing interstate and regional rail freight networks,” he said.
Maharaj said once construction is completed in 2025, the SIT will be the largest intermodal terminal ever built in Australia. It will have an overall footprint of 45 hectares, including more than 30 hectares of concrete hardstands.
“The sheer size of the SIT allows an array of operational advantages and options for future customers, notably the ability to efficiently decouple, load and unload 600-metre port shuttle services and 1,500- and 1,800-metre interstate freight trains,” he said.
Maharaj said the future SIT provides
customers with the ‘best of both worlds’ when it comes to accessing ARTC’s 7,500 kilometre standard-gauge interstate network and VicTrack’s intercity and regional broadgauge network.
“Having direct access to VicTrack’s broad gauge network allows the future SIT to also service bulk steel and paper products originating from Victorian mills, with the intermodal terminal providing dual-gauge rail sidings to facilitate transfer of product between broad and standard gauge networks,” he said.
“Similarly, containerised products and commodities originating from regional Victoria and southern New South Wales can also be transferred between broad and standard gauge networks at a future SIT.”
• Strategically located within the existing 135-hectare Austrak Somerton Business Park, which has already attracted a host of customers, including supermarket chains, big box retailers, and freight forwarders.
• Direct access to the ARTC standardgauge interstate network and VicTrack broad-gauge network.
• Direct access to the Hume Highway, Somerton Road, and Craigieburn Bypass. The latter is the major heavy vehicle feeder from north-eastern Australian capital cities, Murray and Goulburn Valley’s agricultural and manufacturing areas, and links into the M80 Ring Road, Princes Hwy (M1/A1), Citylink (M1/M2), Western Highway (A8/M8), Monash Freeway (M1) and East Link (M3).
• Future customers of ITC will have the option to shuttle containers seamlessly between Somerton and stevedoring terminals at Port of Melbourne via 600 metre services. By rail, Somerton is only 22.5 kilometres north of Australia’s largest containerised port.
• Initially, 11 rail sidings will be available for above-rail freight operators to access, including 750and 900-metre sidings to facilitate decoupling and loading/unloading of 1,500- and 1,800-metre interstate freight trains, respectively.
• Laying of post-tensioned concrete slab (i.e. concrete slab instead of
rock ballast) in terminal hardstands resulting in longer-life, hence less interrupted, operations (i.e. less maintenance required).
• Several empty container parks totalling approximately 10 hectares in size.
• ITC has already placed orders for the following electric powered machinery and equipment: (i) seven remote railmounted gantry cranes to be supplied by Konecranes (ii) seven Kalmar reach stackers, and (iii) two Kalmar empty container dual handlers.
• Deployment of such state-of-theart electric powered machinery and equipment will reduce operational emissions at the future SIT.
• Direct connections to both the future Melbourne-Brisbane Inland Rail and northern endpoint of the Victorian Government’s Port Rail Shuttle Network.
• Future SIT will involve an open access regime, with ITC being the owner and operator of the terminal.
• Export/import customers, including regional shippers, will enjoy the added benefit of the SIT being a customs bonded facility.
• Full suite of services on site, including container repairs, washing and fumigation.
ITC Chief Development Officer Leigh Cook said the size of the future SIT and deployment of many and varied beneficial operational features and technologies will enable the first phase of the facility to process one million 20-foot equivalent units (TEU) each year.
“The ITC team has a proven track record in both developing and operating freight terminals, so we were incredibly excited to be able to conduct detailed design work on a superb site to make it truly customer-centric,” he said.
Cook said with the advent in the future of additional rail sidings, gantry cranes, and slip lanes for trucks, the SIT has potential to process up to two million TEUs each year.
“I’ve been involved in the freight and logistics sector for decades, but I’ve never seen a site like Somerton – it ticks all the boxes in terms of size and capacity, location and configuration, direct rail and road network access, and close proximity to port and large distribution centres and warehouses,” he said.
Maharaj said ITC was fortunate to be chaired by industry leader and former ARTC CEO John Fullerton, who brings a wealth of knowledge, experience, and connections in the freight sector.
“What John doesn’t know about rail freight is really not worth knowing. He has more than 40-years’ experience in the freight and supply chain sector, was inaugural chair of Freight on Rail Group (FORG) Australia and the Cooperative Research Centre for Rail Innovation, and a director of the Rail Industry Safety and Standards Board,” he said.
Fullerton said he was excited to chair the ITC and be involved in the development and construction of a major intermodal terminal in Australia’s supply chain.
“The ITC will help to inject greater competition into the rail freight sector, and the SIT will help to shift more containerised and bulk freight from road to rail, thereby reducing emissions in the hard-to-abate national supply chain,” he said.
ITC Chief Operating Officer, Brendon Gibson, said the company estimates the future SIT will help remove the equivalent of 500,000 truck trips each year off already heavily congested Melbourne streets, roads and motorways, including the Hume Highway and M80 Ring Road.
“ITC estimates removing this number of truck trips will help reduce emissions in the national supply chain to the tune of 189,000 tonnes each year,” he said.
Gibson said the future SIT will play a vital role in helping federal and state governments achieve mandated emissions reduction targets, not to mention assisting future SIT customers reduce their emissions in supply chain operations.
“For instance, in a 2020 report commissioned by the Australasian Railway Association, it was estimated rail freight produces up to 16 times less carbon pollution than road freight per tonne kilometre travelled,” he said.
The same report estimated road accident costs are 20 times higher than rail for every tonne kilometre of freight moved. A single container of freight switched from road to rail, between Sydney and Melbourne, would reduce accident costs by around $109. ■
With a focus on sustainability spanning over 30 years, Toyota continues to be at the forefront of ecological innovation. MHD delves into Toyota’s enduring dedication to environmental conservation and highlights its most recent strides in sustainable materials handling.
n 1992, Toyota Motor Corporation unveiled its visionary approach titled, ‘A Comprehensive Strategy for Global Environmental Concerns: Earth Charter.’ This pivotal declaration laid the foundation for Toyota’s progressive approach to their environmental goals.
While Toyota had always been recognised as a pioneer in maximising efficiency while economising on resources, the 1992 “Comprehensive Strategy for Global Environmental Concerns: Earth Charter” marked a significant shift. Reflecting on the past 30 years, it was a commendably early recognition of the need for sustainability, particularly highlighting climate change.
“The foremost challenge facing humanity is ensuring that we bequeath a rich natural environment to the generations to come. Everyone needs to pay heed to this concern,” the Earth Charter of 1992 states. “This challenge doesn’t recognize borders – global issues like climate change require a united, global effort.”
The Charter’s “Comprehensive Strategy” focused on innovating technology to decrease the ecological impact of cars and their manufacturing plants. Additionally, it aimed at expanding environmental initiatives through Toyota’s worldwide production, marketing operations, and even extending to its suppliers, distributors, and dealers.
Since 1992, Toyota’s commitment to the Earth Charter has been consistently fortified. In the recent past, Toyota Industries Corporation emphasised its “Environmental Outlook,” making “climate change mitigation” their paramount environmental concern. Furthermore, in 2015, Toyota Motor Corporation launched the ‘Toyota Environmental Milestone 2050,’ presenting a series of challenges for its global subsidiaries, including:
1. A 90 per cent reduction in CO2 emissions from new vehicles (using 2010 as a reference);
2. Complete eradication of CO2 emissions in operations;
3. Zero CO2 emissions from dealers and suppliers;
For
4. Emphasis on water conservation and safeguarding water resources;
5. Advocacy for a recycle-centric society; and
6. Focusing on biodiversity conservation, species protection, and habitat rejuvenation.
Toyota Material Handling Australia (TMHA) has commendably achieved, and in some cases surpassed, these lofty goals. For instance, the Toyota Industries Corporation had set a goal to cut emissions by 26 per cent (from the 2012 fiscal year) by 2021. Yet, Toyota’s European plants, some of which produce equipment for TMHA, achieved an impressive 31 per cent reduction.
Glen Ryan, Product Manager at TMHA, highlighted that traditionally, forklifts exceeding 3.5 tonnes mostly relied on internal combustion (IC) engines over electric power.
“But in early 2019, we introduced to Australia our innovative 8 FBMT and 9 FBMT series,” Glen says. “These represent our battery electric forklifts in the 3.5 to 8.0 tonne range. Previously, such weight ranges would require IC forklifts, leading to not only environmental concerns but also health issues for operators exposed to exhaust. Our new range eradicates these concerns, prioritizing the operator, surrounding workers, and the environment.”
Michael Marks, in charge of Warehouse MHE products at TMHA, pointed out that Toyota’s R&D has predominantly been dedicated to optimising its battery-electric range, aligning with Toyota’s principle of perpetual enhancement.
“The evolution we see today is not just in machinery efficiency but also in the batteries that power them,” Michael observes.
Michael elaborates on the advantages of lithium-ion batteries over traditional lead-acid ones. “Unlike lead acid batteries, which need about eight hours to charge from 20 per cent, lithium-ion batteries can be charged anytime, without affecting their longevity.”
The practical benefits of this are immense, especially for large enterprises operating round-theclock. With faster charging cycles and
consistent energy delivery, companies can achieve significant cost savings and flexibility.
“By collaborating with a top OEM for our lithium-ion cells, who aligns with Toyota’s environmental values, we’re dedicated to aiding our clients in realizing their own green goals,” Michael adds. “Adopting lithium-ion could potentially reduce a company’s CO2 footprint by up to 20 per cent.”
Glen emphasises the growing preference for electric battery machines. He states that currently, these products command approximately 60 per cent of the market share.
Toyota’s relentless pursuit of innovation will inevitably continue to shift the industry toward batteryoperated equipment.
Three decades since the unveiling of the 1992 Earth Charter, Toyota’s unwavering dedication to both its customers and the planet has only intensified, as evidenced by TMHA’s new facility in Dandenong South, Victoria.
“Incorporating eco-friendly measures was non-negotiable for us,” says TMHA COO Cameron Paxton. “From rainwater harvesting systems to energy-efficient LED lighting, we’ve made every effort to reduce our carbon footprint. Our ambition is to set a benchmark for environmentally conscious operations in the material handling industry.”
From the products it makes to the facilities it works in, Toyota and TMHA continue to work around the clock for a greener future. ■
Increasing costs and higher customer expectations are cutting into profits, so companies often put heavy pressure on manufacturing and warehousing operations to improve productivity while controlling costs. This often means achieving increased throughput levels with the same or fewer resources.
But even a state-of-the-art forklift driven by the most skilled operator may still be costing the operation too much money if it’s powered by liquid propane (LPG) or lead acid batteries that require changing-out during work hours.
Historically, traditional lead acid forklift batteries in single-shift or lighter-duty applications could be charged between shifts or off-hours, so change-out was not necessarily needed. However, in applications that run more than 1500 hours per year, this recharging pattern will generally not meet performance needs, so these same traditional lead acid batteries will need to be changed out during active operating periods.
Changing-out traditional lead acid
forklift batteries and LPG tanks has hidden costs that are often overlooked when choosing a forklift power source. Wasted time, worker safety risks, and wasted floor space associated with change-out all add up to hurt your bottom line.
Forklift batteries can weigh 500 to 2000kg - requiring dedicated changing equipment and space inside the facility. Hoisting batteries in and out of forklifts opens the risk of exposure to accidents.
In combustion-powered forklift equipment, the average LPG tank weighs approximately 18kg and needs to be routinely lifted up to about one metre onto its back deck. With a single tank change per shift, an operator will lift more than 5000kg in one year - the weight of an entire forklift - opening up the potential for back injuries, severe muscle strains and other injuries. How risky is routinely picking up that much weight to that height for your shorter operators, or those with pre-existing back injuries?
Traditional lead acid batteries and LPG tanks require time daily to change-out as well as time to perform routine maintenance, costing you throughput. LPG-powered forklifts have internal combustion engines and powertrains that are more costly to maintain and must be taken out of operation for longer periods to perform maintenance. Traditional lead-acid forklift batteries require a weekly watering programme which occupies the time of assigned employees or hard cost of a third-party service provider.
A typical three-shift operation could require a battery change or LPG tank change once per shift. If the changeout process takes an average of 15-20 minutes, a single forklift may be down and non-productive for 45-60 minutes every day - just for battery or LPG tank changes. For facilities with large fleets of equipment, those hours can equal hundreds of thousands of pounds every year in labour and lost throughput. Additionally, with traditional lead acid- powered forklifts, performance drops as the
battery discharges and its state of charge diminishes the equipment’s speed during the latter portions of a shift - making it less productive and the operator is finally forced to go and swap batteries again.
Industrial floor space is expensive, so building additions are often financially unfeasible. This leaves growing operations to seek new ways to increase their throughput within the same facility footprint.
Most often, LPG tanks are stored in racks outside, taking up space where additional inbound or outbound trucks, yard spotters and other productive logistics equipment could be staged. A traditional battery room and equipment to accommodate changing traditional lead acid batteries occupies indoor space that can account for thousands of square feet that don’t generate revenue.
If you could get rid of your battery room, how would you use that freed-up space? In many cases, a facility may be able to increase revenue-generating SKUs or even rent out extra space for profit by eliminating a battery room.
“
More robust forklift battery technologies such as lithium-ion, thing plate pure lead, and flooded lead acid designed to ‘fast charge’ can eliminate changingrelated costs by using opportunity charging instead of changing out LPG tanks and traditional lead acid batteries.
More robust forklift battery technologies such as lithium-ion (Liion), thin plate pure lead (TPPL) and flooded lead acid designed to “fast charge” can eliminate changingrelated costs by using opportunity charging instead of changing-out LPG tanks and traditional lead acid batteries. With these more advanced options, equipment operators can simply plug into chargers during brief non-operating periods, such as work breaks, lunch times and between shifts, so there’s no unnecessary downtime. In many cases, it is recommended that chargers be placed conveniently throughout the facility for quick and easy use by operators. The constant recharging also helps to keep these solutions at a higher state of charge to help ensure consistent performance throughout a shift with no required watering.
Tired of paying the price for changing batteries and LPG tanks that drag on your productivity and throughput?
EnerSys says it can conduct an application study and use simulation to help a business pick its optimum power solution. ■
In a world where the logistics and supply chain industry is predominantly male-dominated, Kenter International Logistics emerges not only as a beacon of innovation and excellence but also as a staunch supporter of gender diversity and empowerment. Founder Emily Jackman’s personal journey and her company’s sponsorship of the Women in Industry Awards underscore the growing recognition of women’s contributions and the ongoing challenges they face in the sector.
Kenter International Logistics, a freight forwarding company with a global reach, has been making waves under the leadership of its founder, Emily Jackman. With a rich history of 13 years in the business, Emily’s path to success was anything but conventional. “My journey through the logistics landscape was diverse and challenging. I’ve managed ships, worked on the port, and delved into freight forwarding. Each role was a building block towards creating Kenter,” she reflects.
This diverse background has been instrumental in shaping Kenter into a company that prides itself on offering bespoke logistics solutions to its clients.
Despite its small size, with a team of four in Australia and ten offshore, Kenter’s impact on the logistics industry is profound. The company’s success is attributed to its innovative approach, breaking away from traditional siloed operations to foster a team capable of handling comprehensive logistics tasks from start to finish. Emily highlights the importance of this approach: “We’ve built a team that thrives on versatility and dedication. This strategy, while unconventional, has been key to our ability to deliver exceptional service to our clients.”
The foundation of Kenter and Emily’s personal growth within the industry was not without its trials, particularly during the Global Financial Crisis (GFC). Emily candidly shares her experiences, noting, “The GFC was a reality check. It taught me resilience
and the importance of adaptability. Despite the challenges, it was a period of tremendous learning and growth for both myself and the company.” These experiences have not only fortified Kenter’s operational strategies but have also prepared it to navigate the uncertainties of the market, including the recent challenges posed by the COVID-19 pandemic.
A significant aspect of Emily’s narrative is her advocacy for gender diversity and empowerment in logistics, a sector traditionally dominated by men. Her early career experiences, supported by male mentors who offered flexibility and understanding, allowed her to balance motherhood with her professional ambitions. “It’s crucial
for women to know that it’s possible to have a fulfilling career and family life simultaneously. The support I received early on made a significant difference, and it’s a message I’m passionate about sharing with other women,” Emily states.
This passion is evident in Kenter’s sponsorship of the Women in Industry Awards (WII), which recognises the achievements of women across various industrial sectors. For Emily, the WII is more than just an event; it’s a platform for showcasing the resilience, talent, and innovation that women bring to industries where they have historically been underrepresented. “Supporting the WII is not just about celebrating the accomplishments of women in heavy
industry. It’s about acknowledging their struggles, supporting their growth, and paving the way for a more inclusive future,” she explains.
Emily’s experiences have also shed light on the persistent challenges and biases women face in male-dominated fields. From being overlooked in favour of male counterparts to encountering outdated attitudes, these challenges have fuelled her determination to advocate for change.
“I’ve faced numerous obstacles, from subtle biases to overt discrimination. These experiences have not deterred me; instead, they’ve strengthened my resolve to fight for gender equality in the logistics industry,” she asserts.
Despite these hurdles, Emily is optimistic about the progress being made towards gender equality in the workplace. She observes a shift towards more inclusive practices within companies, leading to a more balanced and diverse workforce. “The inclusion of women in leadership roles and decision-making processes is becoming increasingly valued. This shift is not just beneficial for women; it enhances the creativity, efficiency, and overall success of businesses,” Emily notes.
As the conversation about gender equality in the industry continues to evolve, Emily envisions a future where initiatives like the WII are
no longer necessary because gender parity has been achieved. Until then, she remains committed to supporting and celebrating the achievements of women in the industry, fostering a culture of inclusivity and empowerment.
In closing, Emily reflects on the broader implications of her work and the importance of continuing to advocate for gender diversity and equality. “My dream is for the logistics industry to become a place
where gender is no longer a barrier to success. By supporting each other, sharing our stories, and challenging the status quo, we can create a more equitable and prosperous future for everyone in the industry,” she concludes.
Her leadership at Kenter and her advocacy for women in industry not only challenge existing norms but also inspire a new generation of women to pursue their ambitions in logistics and beyond. ■
This September, Australia’s largest logistics event, MEGATRANS, is returning to Melbourne, bringing together industry experts to explore the many ways the supply chain can be made more robust and sustainable.
In a rapidly evolving logistics and supply chain world, MEGATRANS is rebranding itself to reflect the industry’s shift towards sustainability. Held every two years, MEGATRANS has built a formidable reputation as the leading supply chain and logistics event, and will run across 18-19 September 2024.
The year 2024 will see the logistics industry make its most significant
shift to date towards sustainability, with investments in this space set to skyrocket, according to MEGATRANS Show Director Lauren Chartres.
“The sustainable supply chain is going to be the top focus in the new year,” says Lauren, who oversees MEGATRANS, Australia’s largest logistics event taking place in Melbourne in September 2024.
“The past few years have been
about securing supply chains at any cost, after they were disrupted by the pandemic. Now that supply chains have settled, and stock levels risen, major logistics companies are telling us that they are looking to invest in sustainability.”
It’s an investment, Lauren says, that is being supported by the federal government’s most recent budget that provided more than $4.5 billion
in climate-related spending. This includes $20.9 million over five years to decarbonise transport and infrastructure.
The freight transport sector currently contributes to 46 per cent of emissions nationally, and transporting people and goods around Australia is predicted to be the country’s largest source of emissions by 2030.
Challenges of sustainability, Lauren points out are not just around environmental factors. She notes that the logistics industry is still struggling to secure and diversify its workforce
“We need to start building up the next generation of the logistics industry now,” says Lauren. “And it needs to be reflective of this generation so the industry can mirror its values and set itself up for the future.”
The show will similarly offer solutions for companies investing in traceability, as well as cold chain solutions, areas that are so vital for a sustainable supply chain at every level.
Lauren and the team at MEGATRANS are supporting the industry’s sustainable priorities by focusing the entire conference and expo on the long-term sustainable supply chain.
Integral to MEGATRANS2024 is its standout conference, promising a rich experience for attendees with its diverse range of expert presenters. More than 150 industry leaders will grace the multiple, free-to-attend conference stages on the trade floor, offering insights and perspectives from various supply chain sectors.
An exciting addition to the 2024 event is its collaboration with the Australian Bulk Handling Expo (BULK2024). This partnership provides attendees with a dual registration benefit, granting access
to both game-changing shows. MEGATRANS will play host to the esteemed MHD Supply Chain Solutions Mercury Awards. This prestigious event seeks to honour businesses and individuals epitomising innovation, excellence, and leadership within the industry.
The confluence of the exhibition, the conference, and the awards Gala dinner, scheduled for September 18, creates a synergistic platform. It’s a unique opportunity for logistics and supply chain professionals to converge,
network, learn, and celebrate — all under one roof, at one defining moment.
Additionally, there will be the inaugural MHD Sustainable Warehouse Awards. This event will feature the most sustainable warehouses from across Australia and include the announcement of 2024’s MHD Most Sustainable Warehouse in Australia.
MEGATRANS is held every two years, and this year it will run over two days – 18 and 19 September 2024 – at the Melbourne Convention and Exhibition Centre. It’s supported by distinguished sponsors, including the Networking Lounge Sponsor, Loscam, and Association Partners, SCLAA, and VTA.
To be part of this transformative experience and align your brand with the future of logistics, explore exhibiting opportunities at MEGATRANS2024. ■
Learn more at www.megatrans.com.au
The GPT Group’s Apex Business Park is a prime industrial estate ideally situated to offer prospective tenants a well-connected base for East coast operations in Australia.
In the competitive Australian industrial real estate landscape, new developments are expected to meet the evolving commercial and lifestyle needs of the customer.
The ideal business park offers proximity and rapid access to transportation networks, enhancing logistics and supply chain efficiency – a critical factor for businesses in sectors ranging from manufacturing to e-commerce.
Additionally, sustainability and employee wellbeing have become key considerations, with green certifications and amenities that promote a healthier, more productive workplace increasingly required by customers. These modern industrial facilities not only accommodate the location, environmental and technology needs of contemporary occupiers, but also provide flexibility in size to cater to a wide range of businesses.
Apex Business Park in Brisbane is being developed progressively by The GPT Group (GPT) with facilities that have been designed to address these varying needs. Upon completion, the
estate will offer 70,158 square metres of prime logistics space across five facilities, located in the growing western corridor between Brisbane and Ipswich and addressing the low levels of market supply.
It features excellent connectivity to arterial roads and highways, superior sustainability credentials and amenities designed to enhance operational efficiency and staff wellbeing. The estate provides flexibility for prospective tenants, with spaces ranging from 3,703sqm to 21,814sqm, catering to diverse customer needs.
Apex Business Park is also positioned well above the adopted flood regulation line, with flood-free access.
With the second stage of the estate recently completed, MHD caught up with the GPT team to find out what positions Apex Business Park at the forefront of high quality logistics developments.
GPT is Australia’s oldest property trust, launched in 1971. Since its establishment, the business has worked
closely with its customers and the industries they serve to develop a comprehensive understanding of their needs and requirements.
“GPT has a long track record as a developer and owner of high quality properties, which provides customers with peace of mind knowing they can grow their business with an experienced and trusted partner,” says Amy Ng, Development Manager in Logistics at GPT.
“GPT has assets under management of over $32 billion across a portfolio of high quality Australian real estate, which includes approximately $4.7 billion in logistics assets. We continue to progress our development pipeline, which is approximately $2 billion.”
“The first warehouse at Apex Business Park was completed in May 2022,” Amy says. “It’s a 12,450 square metre warehouse, fully leased to Saab.
“We recently completed construction of the estate’s second stage, comprising a standalone 11,712 square metre space that’s ready to lease and occupy now. Of the remaining three stages, two have received development
approval, with the third on the way.”
“Location is an important benefit,” Amy says. “Apex is surrounded by the Cunningham and Warrego highways to the north, and Brisbane Road from the south, delivering fast connectivity to the Brisbane CBD, Ipswich, Brisbane Airport, and the Port of Brisbane. There is also B-double access throughout the estate.”
“The precinct is well established,” adds Melissa Gardner, National Director of Leasing, Logistics at GPT. “There are gyms, cafés, pharmacies and food retailers nearby. The estate has more than 840,000 households within a 60-minute transit, and 225,000 households within a 30-minute drive, offering great access for both the captive workforce and last-mile distribution customers.”
Ms Gardner says tenants of Apex Business Park are well-supported by the Brisbane-based management team.
“We have a dynamic and personalised service available on a day-to-day basis, with team members regularly on-site,” she says. “Our occupiers benefit from having that resource available to service their needs.”
“Sustainability is front of mind at GPT,” says Amy. “All of our warehouses target a minimum FiveStar Green Star Design and As-Built rating. Key initiatives include a rooftop solar array and on-site batteries, solar hot water, LED lighting, low-carbon concrete, and rainwater harvesting for use in toilets and landscaping.”
Where possible, the estate has been developed with Australianmade building materials and products
designed to endure Australian conditions, and GPT has also used low volatile materials, paints, and adhesives.
Apex Business Park not only provides modern, high quality warehousing; it’s in the process of creating a vibrant environment where businesses thrive. “The proximity to major retailers and distribution hubs like Costco, Australia Post, Australian Pharmaceutical Industries, and The Reject Shop, all within a five to ten-minute drive, underscores Apex’s appeal as a prime location for businesses looking to capitalise on Bundamba’s growing economic activity,” says Melissa.
Bundamba’s reputation as an area benefitting from ongoing growth is key to understanding the allure of Apex Business Park. “Bundamba is a really expanding corridor in Brisbane and it’s a great time for occupiers to secure modern space in a growing market,” Melissa adds. Amy agrees, noting the corridor’s potential for high population growth, further driving the demand for well-located industrial and logistics space.
GPT’s approach to tenant relationships goes beyond the transaction; it’s about fostering genuine long-term partnerships. “GPT focus on truly partnering with our customers to provide them with the best possible experience,” says Melissa.
“We are able to draw upon our knowledge and expertise to deliver spaces that meet our customers’
needs, while they can benefit from our networks and the opportunity to grow as we build out our development pipeline.”
These partnerships extend to wellbeing initiatives, such as GPT’s collaboration with Healthy Heads in Trucks & Sheds. “We are a Premier Partner of Healthy Heads in Trucks & Sheds, and we encourage our occupiers to sign up for the Healthy Heads resources. We host roadshow events for our customers, and we promote key strategic initiatives that Healthy Heads address, including awareness and advocacy with the goal of building literacy and reducing stigma around mental health challenges,” explains Melissa.
The initiative is part of GPT’s commitment to supporting the mental and physical health of the workforce within Apex Business Park and across its logistics portfolio, ensuring a holistic approach to business success.
Apex Business Park is delivering prime quality industrial space through sustainable developments, and is ready to accommodate the evolving needs of tenants. Its location, amenities, and GPT’s proactive partnership approach provide a solid foundation for businesses looking to expand and thrive in the dynamic Queensland market. As the area continues to develop, Apex Business Park is poised to remain a key offering in the low-vacancy industrial and logistics sector, offering unparalleled opportunities for growth, innovation, and success. ■
Visit: www.apexbusinesspark.com.au for more information and to explore leasing opportunities.
The Supply Chain and Logistics Association’s Independent Director SCLAA Chair, Mentoring Program, Stephen Lakey, talks to MHD about the national organisation’s mentoring program, which will run again during 2024.
Back in 2011 I participated in my first mentoring program. I wasn’t seeking a mentor at the point; in fact, I knew very little about the benefits of having a mentor, but it was a requirement of the organisation that I was in at the time.
Over the years I moved from being a mentee to a mentor, yes – the tables were turned – and I was now on the other side of the table, responsible for the onboarding, guidance, and personal development of a new chum.
While the organisation I was in had a short mentoring time frame, I found that many of the relationships formed through the program lasted long after the official program had finished, and some of the mentees are still among my closest friends today well over a decade after the official program had finished.
Over the years I have seen many of my mentees achieve their goals, get their dream job, start a business, and achieve personal success.
“Yes, this is possibly the most satisfying program I have ever been involved in,” I thought to myself one warm summer evening sipping a latte in my hammock.
But what is it that makes mentoring work, fills a place that formal training at school, universities, parents, friends, and work programs don’t seem to fill? I believe it is – like many things in life –about relationships and a genuine care of one to another.
A mentor freely giving his or her time to another person in a purely selfless way opens the door for open and honest conversations about where the mentee is, and
“ My experience of mentoring has been one of fanning the ember of potential deep inside until it becomes a flame. ”
where they would like to be.
Discussions about the path to their goals and career planning. The road bumps along the way and strategies to overcome them. Someone to be accountable to, someone to encourage you, and on occasion provide some tough love when needed.
My experience of mentoring has been one of fanning the ember of potential deep inside until it becomes a flame, then a raging fire, and sometimes a rocketship bound for the stars. Seems over dramatic? I have seen it happen many times. Encouragement and belief in someone are one of the most underrated drivers of success.
I am so pleased to be chair of this year’s SCLAA mentoring program and look forward to running the program with such a potential to change lives.
Registrations for mentors and mentees will open late March with the program running from July to
December 2024.
Mentees will meet with their mentors at least monthly either face to face or virtually, and the program will have a launch event, mid-program workshop, and closing ceremony.
The program is open to students and anyone in the supply chain industry, and yes – you can be both a mentee and a mentor. Matching will be conducted at a state level and based on your profile indicated on your registration form.
You can get more information and register your interest in the 2024 mentoring program via https://www. sclaa.com.au/mentoring-program/.
Congratulations on investing in yourself, and I wish you the best experience in this year’s SCLAA mentoring program. ■
Wolters Kluwer’s Vice President, Global New Client Engagements, Alessio Lolli, outlines the five supply chain performance drivers for fostering efficiency and responsiveness in a business’s operations.
For supply chain planners, striking a balance between responsiveness and efficiency is tricky. Let’s explore how supply chain drivers can be optimised for responsiveness or efficiency so you can determine the priority for your business.
While supply chain efficiency has long been the primary goal of many organisations, as a priority, efficiency now competes directly with the need for responsiveness. We’re operating in a time where instability, supply chain disruption, and rising costs reign supreme.
The increased productivity and lowered costs efficiency offers have – in many cases – been pushed down the agenda in favour of a supply chain that can accommodate unexpected fluctuations in the market and changes in customer preferences.
The tricky thing is, that this reprioritisation might not be forever. In today’s climate, your priority could be responsiveness. But, in calmer times, you’d optimise for efficiency.
For companies battling between responsiveness and efficiency, this article will explore how performance drivers can be optimised in favour of supply chain efficiency or responsiveness.
#1: PRODUCTION
Production optimised for responsiveness: The key to responsiveness in production is to ensure production lines have the capacity to pivot to meet fluctuations in consumer demand quickly. A few ways to do this:
• Ensure your factories have excess capacity;
• Use flexible manufacturing techniques to produce a wide range of items;
• Have multiple, smaller production facilities close to distribution centres and customer hubs to decrease delivery time.
Production optimised for efficiency: Conversely, if you need to foster efficiency, you’ll want to take the opposite approach. To prioritise efficiency:
• Schedule your production facilities to have little excess capacity;
• Focus on producing a limited range of items;
• Centralise production in large central plants for better economies of scale (even though delivery times may be longer for some customers).
Inventory management optimised for responsiveness: Optimising responsiveness can dictate stocking higher product levels and at more warehouse locations. Efficient inventory allows for unexpected fluctuations in demand that can be met promptly. However, this approach incurs higher storage costs, which must be weighed against the benefit of widespread availability.
Inventory management optimised for efficiency: To foster efficiency in inventory management requires reducing inventory levels of all items, especially those that do not sell frequently.
Careful analysis is required to pay
back successfully, as lowering inventory levels can result in stock-outs, unmet demand, and missed revenue opportunities. You can also limit stock to select central distribution centres to limit economies of scale and attain cost savings.
Location optimised for responsiveness: Location, location, location. To prioritise responsiveness means maximising convenience. You’ll want to establish operations within a close range of customer groups.
For example, fast-food chains use location to respond to their customers by opening many stores in high-volume markets. Having many locations allows chains to respond quickly to consumer demand — but this approach also increases operating costs because now they have to staff and run many stores.
Location optimised for efficiency: Efficiency is achieved by operating from a select few locations and centralising activities.
For example, e-commerce retailers serve global markets from a few central locations performing various activities. While this centralised approach allows e-commerce retailers to run efficiently, it also makes them susceptible to disruption.
Transportation optimised for responsiveness: Faster modes of transportation, such as air freight, offer faster and more flexible delivery. The
downside? They’re expensive, which can limit the quantity of goods you can ship.
FedEx and UPS are two companies that provide high levels of responsiveness in the last mile of delivery, using expedited transportation methods to deliver products often within 48 hours.
Transportation optimised for efficiency: Transportation efficiency can be achieved by moving products in larger batches by bulk carriers, such as ships or railroads, less often. While bulk carriers are a great option when your goal is volume and cost reduction, you sacrifice speed and flexibility by using this approach.
Using a centralised distribution centre instead of multiple separate locations is another way to improve efficiency and save on costs, but, again, it will sacrifice delivery speed and responsiveness.
#5: INFORMATION
Information optimised for responsiveness: Knowledge is power. The technology for collecting and sharing information has become more widespread, easier to use, and more affordable. Supply chain solutions can now use internal performance and external market data to re-plan supply chain plans based on real-world events and scenarios.
For example, if a TikTok video causes a sudden surge in demand, supply chain planning software can illuminate the supply chain effects. It can tell you how much supply you’ll need to produce and how much inventory to send to which distributors.
Information optimised for efficiency: With all internal supply chain data centralised in one location, supply chain planning software that uses advanced AI-based analysis can also illuminate inefficacies and optimise efficiency.
For example, AI-based software can recommend assembly line schedules to optimise the production of a certain product.
The good news is you can have responsiveness and efficiency too. AI-based supply chain planning has evolved to give you the best of both worlds. CCH® Tagetik Supply Chain Planning is our finance-forward, predictive planning solution. It connects demand, inventory, supply, production, sales, and operations planning with financials, giving you a 360° view of your supply chain.
With CCH Tagetik, your supply chain plans dynamically update as situations unfold and plans are executed, showing you the ripple effect of any customer, product, or supplier change across all supply chain, operational, and financial plans.
With real-time data, scenario analysis, and AI to create accurate predictive forecasts, you’re armed with the knowledge to be responsive while optimising operations for efficiency. ■
The Australian Supply Chain Institute started its instructor-led courses for 2024 in February. It explains why
it’s important to upskill in what is an ever-changing and unpredictable industry.
Offer faster and more flexible delivery. The downside? They’re expensive, which can limit the quantity of goods you can ship.
Happy New Year! We hope this email finds you in good spirits and health. As we enter the new year, it’s a great time to reflect on our personal and professional goals. If you resolve to keep learning and upskill yourself, we have the perfect opportunity for you.
Our instructor-led courses on supply chain management will be starting this February. As you’re aware, the
supply chain management industry is becoming increasingly digital, which means professionals in this field must have technology and human communication skills.
Digital tools have grown rapidly in response to global disruptions, but this has also made it even more important to keep up to date with the latest developments in the industry.
Our courses are designed to help you improve your knowledge and skills in supply chain management. Our expert instructors will guide you through the
latest developments in the industry, and we’ll provide you with hands-on training to help you apply what you’ve learned in your daily work.
This is an excellent opportunity for you and your team to upskill and reskill yourselves. Don’t miss out! Please register for our courses today and take the first step towards achieving your New Year resolution.
If you have any questions or need course recommendations, please don’t hesitate to contact us. We’re here to help. ■
WOMEN IN INDUSTRY NOMINATIONS ARE NOW OPEN.
Now is your chance to nominate an industry leader who you believe is advocating for positive change and deserves to be recognised.
PROUDLY PRESENTED BY
MHD
Thurs 20 June, 2024
The Women in Industry Awards recognise outstanding women leaders from across Australia’s industrials sector.
Todd Clarke was recently appointed Operations Manager at Flinders Warehousing and Distribution (FWD). Todd manages the daily operations and through strategic planning, business development and improvement processes is leading future growth for FWD, which is part of the Flinders Port Holdings Group of companies. Todd started his notable career within SA’s freight, logistics and supply chain sector at Cube over 14 years ago.
Daniel brings over 20 years of extensive experience in the material handling industry, having made significant contributions across two major brands prior to joining Jungheinrich. Throughout his career, Daniel has been instrumental in driving major/key account sales, working closely with some of the world’s most renowned blue-chip brands. Currently serving in a pivotal role within the New South Wales branch of Jungheinrich, Daniel plays a vital part in expanding the brand’s presence in Australia.
Stuart Warren joined Hangcha as Sales Manager, NSW, effective 15 January 2024, based in Sydney. He brings with him extensive experience in the forklift industry, having worked at Toyota Material Handling Australia for almost 20 years. Prior to his move to Hangcha, he was the National Sales Manager at Hyundai Forklift Australia for almost five years. Stuart is very excited about joining Hangcha. and is keen to contribute to its team’s success.
Congratulations to Julian Brancaccio for securing a move to Autostore from HAI Robotics as the new BDM in ANZ. Julian now adds Cube Storage to his robotics assembly CV having been key in implementing rack-to-person AMRs, table top sortation robots and automated case handling robots. He has comprehensive knowledge of robotics and how to standardise any system for proper evaluation and comparisons for organisations looking to automate their facilities.
Do you have career news to share? Email Edward Cranswick at Edward.Cranswick@primecreative.com.au to be featured.
HUBTEX’s FluX Electric Multidirectional Counterbalance Forklift Truck has had some significant and innovative updates. The latest generation has load capacities of up to three tonnes. It has a new central driver’s position, which provides a higher-up all-round visibility compared to its predecessor. Additionally, the patented 360° HX steering has been added to the compact three-wheel running gear for the first time, ensuring smooth changes in direction from longitudinal to transverse travel. It handles both pallet and long-load transport in a single vehicle. This hybrid used as a front and sideloader makes the new 3T FluX 30, suitable for a wide range of sectors, from the timber and metalworking industries, through to the building materials trade.
For more information visit www.hubtex.com.au
Global cube storage company AutoStore introduces its latest capability, the Grid and Vending Machine solution, designed to simplify warehousing automation. The ConveyorPort is a workstation in its simplest form, where Bins are dropped on a conveyor and transferred to an opening outside of the Grid. Smart covering and sensors ensure operator safety. The CarouselPort is designed to work with the operator, in harmony with Robots to ensure the next Bin is always ready. The workstation operates with three rotating arms, each holding one Bin tray. The Vending Machine solution includes various Robots and chargers, as well as a dummy display unit, and a grid structure with 60 Bins.
For more information visit www.autostoresystem.com
Poor ocean visibility puts a strain on global supply chains, logistics costs, and customer service. At the root of the issue is low-quality data that hinders personnel productivity, streamlined operations, and proactive exception management. Today, more than ever, shippers and 3PLs need global ocean visibility with the data quality, intelligence, ETAs, and proactive exception management that ensures efficient, costeffective, reliable, and sustainable global transportation. Project44’s Ocean Visibility solutions is here to help, with a suite of solutions that uses first-in-class data and analytics to improve personnel productivity, allow for proactive exception management, reduce logistics costs, improve customer service, and empower users for agile transport planning and procurement.
For more information visit www.project44.com
ifm Track and Trace Gate is the complete solution for your automated and transparent logistics in your incoming and outgoing goods processes. By directly transferring all goods flows to the IT level, you can organise the inter-locking of production, inventory, and suppliers more efficiently than ever before.
For more information visit www.ifm.com/au/en
Argon & Co is a global management consultancy that specialises in operations strategy and transformation. With expertise spanning the supply chain, procurement, finance and shared services, we work together with clients to transform their businesses and generate real change. Our people are engaging to work with and trusted by clients to get the job done.
Start your transformation journey today and download our credentials pack:
argonandco.com