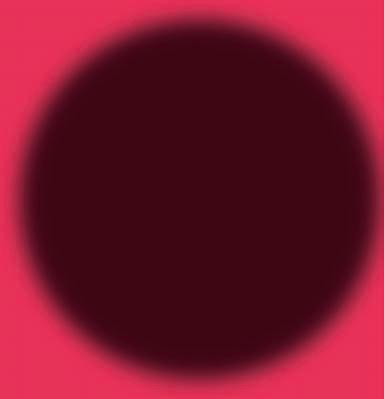
6 minute read
ASCI
WHAT IS ILS? PART C
Integrated Product Support
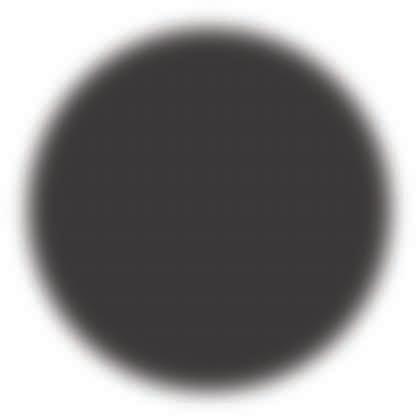
Lifecycle Sustainment Management
• Product Support Management • Supply Support • Packaging, handling, storage and information • Maintenance Planning and Management
Technical Management
• Design Interface • Sustaining Engineering • Technical Data • Computer Resources
Infrastructure Management
• Support Equipment • Training & Training Support • Manpower & Personnel (M&P) • Facilities & Infrastructure
Integrated Product Support diagram.
ASCI ACT Chapter President and ASCI ILS College Secretary, Gary Pearce, discusses Integrated Product Support, in this third instalment of a multi-part series.
The previous two issues of MHD, April and May, introduced Integrated Logistics Support (ILS). Now a change of terminology, ILS is to be replaced by Integrated Product Support (IPS), this is not to confuse or complicate the situation, just simply the changing of the guard.
Throughout the world, in particular Europe and the USA, IPS is replacing ILS, through the S-Series Specification process. In short IPS and ILS are the same, it would great if it was that simple, but in basic terms it is. The aim of the S-Series Integrated Logistics Support Specifications is to align Defence and Industry ILS/IPS requirements. Simply, current ILS standards and procedures will continue to apply to Australian Defence for the immediate future, and IPS will relate to Industry. However, IPS will eventually replace ILS across Defence.
Future Direction of ILS
There has been no real change to ILS principles and functions since introduced way back in the 1960’s, the old phrase “If it ain’t broke, don’t fix it”. Yes, over the years there has been some fine tuning, subtle changes in terminology, however nothing of significance.
The S-Series Integrated Logistics Support Specifications is a suite of specifications for product support that provides for the seamless exchange of technical data (logistics, provisioning, technical publications/IETMs, scheduled maintenance and maintenance data feedback) using contemporary webbased technologies. This results in faster, more accurate and standardised analysis and decision making that encourages the conduct of Support System analysis throughout the product’s life cycle.
S-Series ILS specifications interface with other standardised domains including Program Management, Global Supply Chain Management, Engineering, Manufacturing, Security, Safety, Configuration Management, Quality, Data Exchange & Integration, and Life Cycle Costing. The aim of S-Series is to make Defence and Industry ILS/ IPS requirements compatible. The 12 IPS Elements are shown below, are in essence an extension of the 10 ILS Elements introduced in the April Issue of MHD. In principle these IPS Elements can be mapped to the ADF ILS Elements.
In June of 2011, the SX000i Working Group was formed and SX000i development commenced. The original title of SX000i, (International guide for the use of the S-Series Integrated Logistics Support (ILS) specifications), was approved by the ILS Council in June of 2012. The current title of SX000i, (International specification for Integrated Product Support (IPS) specifications), was approved by the IPS Council in April 2019. SX000i Issue 3.0 released April 2021.
The “Traditional Ten” Integrated Logistics Support (ILS) Elements (refer to MHD April and May Issues) have generally been applied, accepted, and understood for many years and are still relevant and appropriate. The “New Twelve” Integrated Product Support (IPS) Elements (figure 1) are being used extensively now in Europe and the USA, and at some time in the future will be rolled out in Australia.
At first glance, the two ‘lists’ appear to be quite similar, but, both the elements themselves, and their definitions, are quite different. Hence the sunsetting of the ILS terminology in favor of a broader product life cycle supportfocused IPS term.
So, what is different? Most notably, the two new elements are “Product Support Management” and “Sustaining Engineering” include an extensive life cycle management focus, and both include activities and aspects that extend across the life cycle and often beyond the traditional logistics domain.
The twelve (12) elements of IPS are segregated into three (3) categories with four (4) elements in each, are outlined as follows:
CATEGORY 1 - LIFE CYCLE SUSTAINMENT MANAGEMENT
• Product Support Management - Plan, manage, and fund weapon system product support across all Integrated
Product Support (IPS) Element. • Supply Support - Identify, plan, resource, and implement management actions to acquire repair parts, spares, and all classes of supply to ensure the best equipment/capability is available to support the Warfighter or maintainer when it is needed at the lowest possible Life Cycle Cost (LCC).
• Packaging, Handling, Storage, &
Transportation - Identify, plan, resource, and acquire packaging/
preservation, handling, storage, and transportation requirements to maximize availability and usability of the material to include support items whenever they are needed for training or the mission.
• Maintenance Planning & Management
- Identity, plan, resource, and implement maintenance concepts and requirements to ensure the best possible equipment/capability is available when the Warfighter needs it at the lowest possible LCC.
CATEGORY 2 - TECHNICAL MANAGEMENT
• Design Interface - The design interface is the integration of the quantitative design characteristics of systems engineering (reliability, maintainability, etc.) with the functional IPS Elements. • Sustaining Engineering - Sustaining
Engineering spans those technical tasks (engineering and logistics investigations and analyses) to ensure continued operation and maintenance of a system with managed (i.e., known) risk. • Technical Data - Identify, plan, resource, and implement management actions to develop and acquire information; • to operate, maintain, and train on the equipment to maximize its effectiveness and availability; • effectively catalogue and acquire spare/repair parts, support equipment, and all classes of supply; and • to define the configuration baseline of the system (hardware and software) to effectively support the
Warfighter with the best capability at the time it is needed. • Computer Resources - Identify, plan, resource, and acquire facilities, hardware, software, documentation, manpower, and personnel necessary for planning and management of mission-critical computer hardware and software systems.
CATEGORY 3 - INFRASTRUCTURE MANAGEMENT
• Support Equipment - Identify, plan, resource, and implement management actions to acquire and support the equipment (mobile or fixed) required to sustain the operation and maintenance of the system to ensure that the system is available to the
Warfighter when it is needed at the lowest LCC. • Training & Training Support - Plan, resource, and implement a cohesive integrated strategy to train military and civilian personnel to maximize the effectiveness of the doctrine, manpower, and personnel to fight, operate, and maintain the equipment throughout the life cycle. • Manpower & Personnel Identify, plan, resource, and acquire personnel, civilian, and military, with the grades and skills required. • Facilities & Infrastructure - Identity, plan, resource, and acquire facilities to enable training, maintenance, and storage to maximize the effectiveness of system operation and the logistic support system at the lowest LCC. Identify and prepare plans for the acquisition of facilities to enable responsive support for the Warfighter. The aim of Integrated Logistic Support (ILS) has always been to maximise the operational availability of equipment at an optimal lifecycle cost. As a concept, all stakeholders see this aim as being sensible and completely logical. Designers should communicate with manufacturers, who should understand their supply chain capabilities, who in turn should understand the maintenance requirements etc. to achieve optimisation.
However, over the last decade there has been a noticeable decrease in the ‘Integration’ of all considerations in product development. This failing is most often characterised by less and less data exchange at every ILS cooperative boundary as items are designed, produced, used, maintained, repaired, and disposed. Less and less are we seeing the necessary ILS specialists communicating closely with one another leading to unnecessary waste throughout the entire product life cycle. Simply, the ILS engineer is not influencing the product design to make it less costly to support.
The re-framing of ILS to IPS aims to bring the focus back on the integration of all considerations which contribute to maximising the operational availability of equipment at an optimal lifecycle cost – the unwavering objective of ILS all along. ■