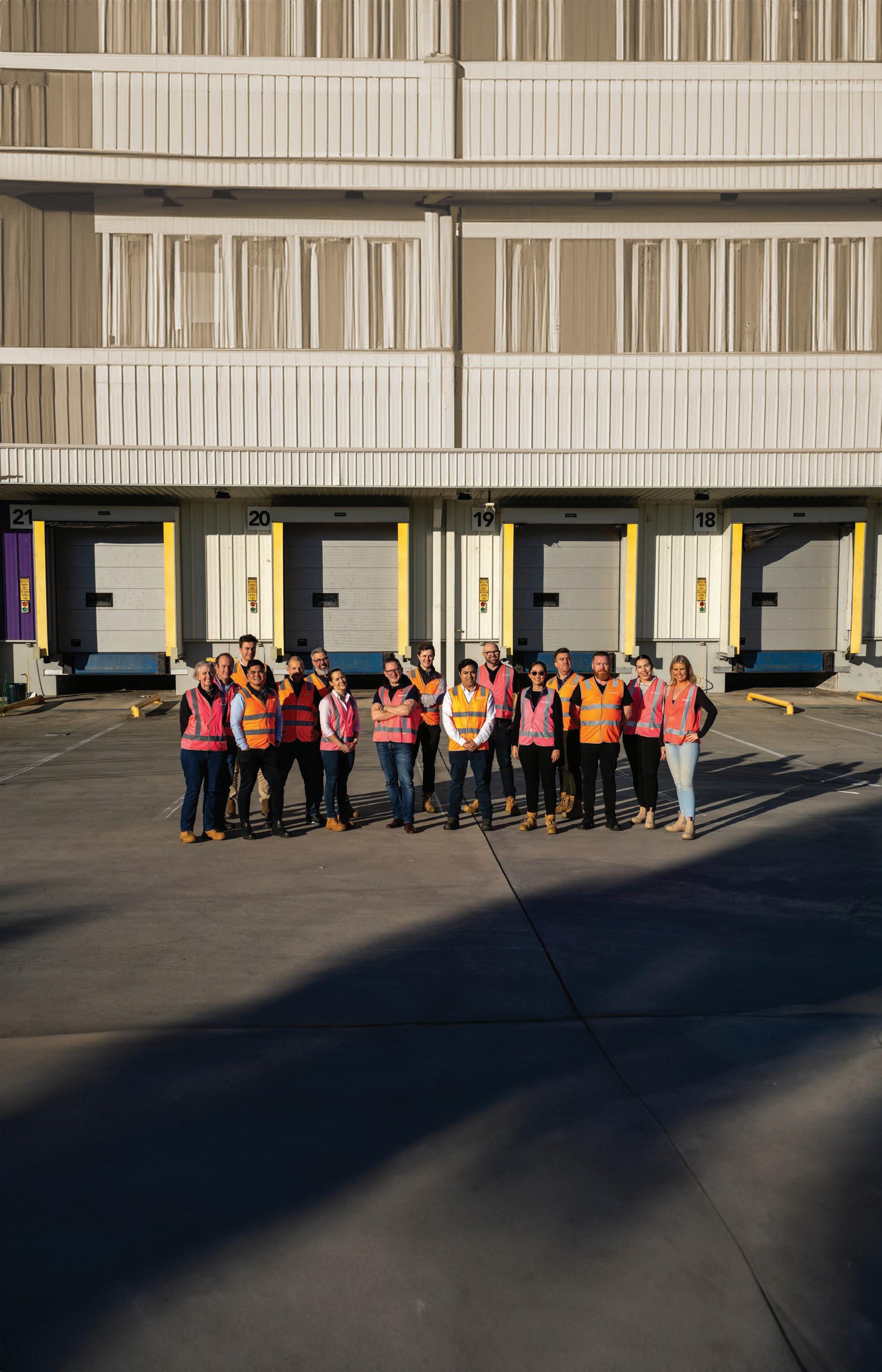
Prological on the future of a green supply chain Toyota providing sustainable forklifts to BlackLab POWERING WITH BATTERIES PIONEERING SUSTAINABLE LOGISTICS Argon & Co, the
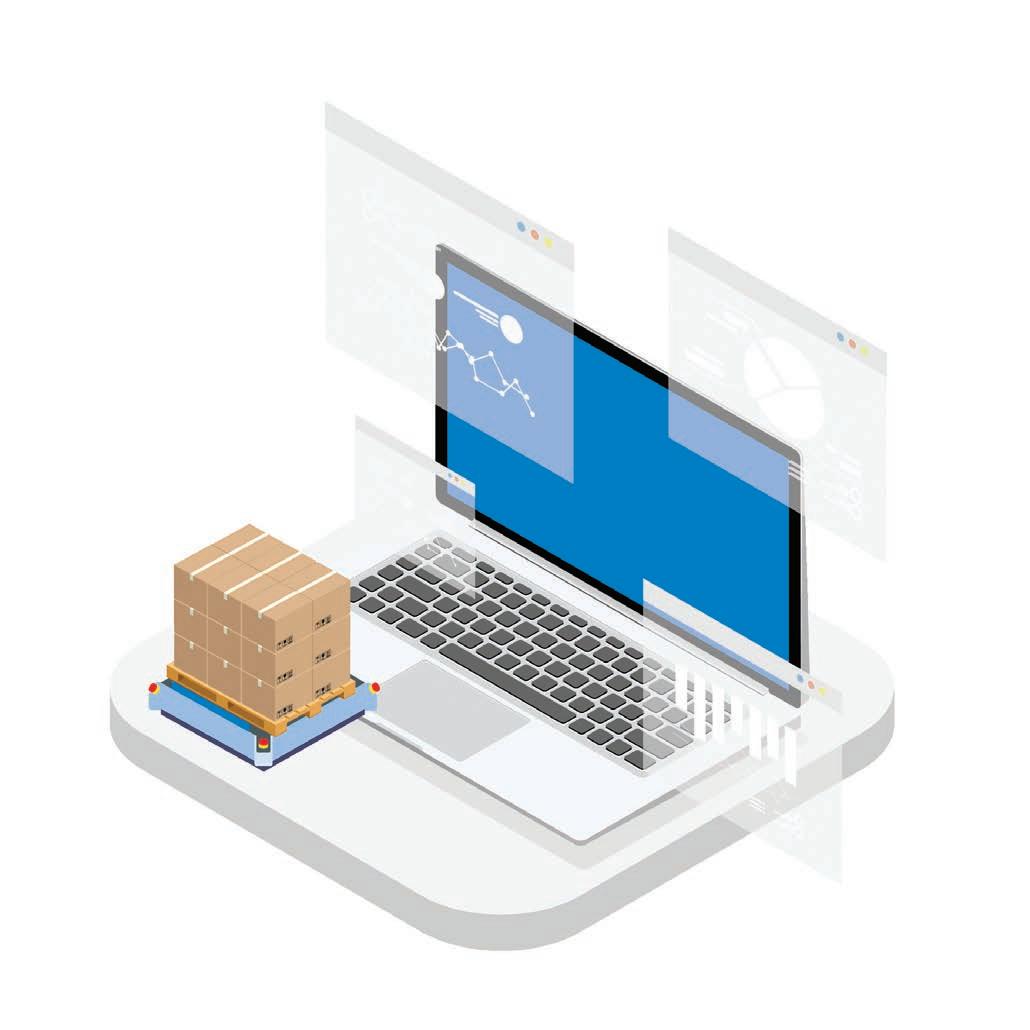
Prological on the future of a green supply chain Toyota providing sustainable forklifts to BlackLab POWERING WITH BATTERIES PIONEERING SUSTAINABLE LOGISTICS Argon & Co, the
The new 2024 Gartner® Magic Quadrant™ for Warehouse Management Systems is out and for the 6th year in a row, Körber has been named a Leader.
Scan the QR code to get your free copy of the report and discover why Körber stands out among the competition. koerber-supplychain-software.com
Scan for your free copy of the report
CONTACT
MHD Supply Chain Solutions is published by Prime Creative Media
379 Docklands Drive, Docklands VIC 3008
Telephone: (+61) 03 9690 8766
Website: www.primecreative.com.au
THE TEAM
CEO: John Murphy
Chief Operating Officer: Christine Clancy
Managing Editor: Mike Wheeler
Assistant Editor: Joseph Misuraca
Journalist: Mannat Chawla
Business Development Manager: William Jenkin
Design Production Manager: Michelle Weston
Art Director: Blake Storey
Graphic Designers: Blake Storey, Daniel Truong
Client Success Manager: Ben Griffiths
FOR ADVERTISING OPTIONS
Contact: William Jenkin william.jenkin@primecreative.com.au
SUBSCRIBE
Australian Subscription Rates (inc GST) 1yr (11 issues) for $99.00 2yrs (22 issues) for $179.00
To subscribe and to view other overseas rates visit: www.mhdsupplychain.com.au or Email: subscriptions@primecreative.com.au
ACKNOWLEDGEMENT
MHD Supply Chain Solutions magazine is recognised by the Australian Supply Chain Institute, the Chartered Institute of Logistics and Transport Australia, the Supply Chain and Logistics Association of Australia and the Singapore Logistics and Supply Chain Management Society.
ARTICLES
All articles submitted for publication become the property of the publisher. The Editor reserves the right to adjust any article to conform with the magazine format.
COPYRIGHT
MHD magazine is owned by Prime Creative Media. All material in MHD is copyright and no part may be reproduced or copied in any form or by any means (graphic, electronic or mechanical including information and retrieval systems) without written permission of the publisher. The Editor welcomes contributions but reserves the right to accept or reject any material. While every effort has been made to ensure the accuracy of information Prime Creative Media will not accept responsibility for errors or omissions or for any consequences arising from reliance on information published. The opinions expressed in MHD are not necessarily the opinions of, or endorsed by the publisher unless otherwise stated.
With CeMAT behind us and MEGATRANS in front of us, now is the time to turn our attention towards all things related to sustainability.
In this edition of MHD Supply Chain Solutions logistics and seeing what companies across the industry are doing to reduce their carbon footprint and meet the ambitious targets they’ve set up for themselves.
On the front cover, we have Argon & Co., sthe global management consultancy specialising in operations strategy and transformation, discussing strategic investments, its LEAN, Academy, and NEOS programs. We also have Prological’s Peter Jones talking about the future of sustainable-related initiatives in supply chain settings, as well as BHD Storage Solutions’ John Harrison and David Seale speaking about cantilever racking and the role of automation in warehousing.
As it is with every edition of MHD, there are usually features from new partners. Kärcher, the German-founded industrial cleaning company, introduces itself as it continues to venture into the warehousing space with its broad range of solutions.
MachShip, a specialist in 4PL solutions, celebrates its 10th anniversary this year, and it intends on being around for the next 10. During its journey of the past decade those running the company has changed its sails to a company that is not just concerned with making sure its product is competitive, but one that offers the best technologies and customer service. As company director Sam Rowse points out in the piece, evolving along with a customer’s needs is an essential ingredient in making the company a success.
Collaboration is a word that is often bandied around but can be a key ingredient in getting a project across the line. Choosing the right partner can sometimes be fraught with many red flags – be it reputation, cost, or quality of products. There were no such qualms when robotics manufacturer HAI, and supply chain solution specialists Körber, got together to help the industry find resolutions for companies wanting to fit out their DC or warehouse with the best possible gear. Both companies are confident that their solutions will not only save time and money, but also show why ACRs are the go-to solution for a lot of projects. That’s all from me. Have a great month.
Mike Wheeler
Managing
Editor,
MHD Supply Chain Solutions mike.wheeler@primecreative.com.au
14 Argon & Co on strategies and investments in the logistics space
19 Logical Outlook on the importance of supply chain sustainability
25 Dematic on tackling land scarcity and options for DCs and warehouses
30 Körber and its important collaboration with HAI to deliver AMRs
37 MachShip on how it is integrating with its carriers
22 How TMHA powering Black Solar Lab
28 Linde on its sustainable
33 Jungheinrich on how its products increase safety in the workplace
41 BHD providing cantilever racking
44 CoGri using on using robotics on warehouse floors
46 Kärcher introducing industrial cleaning
52 Addverb automating warehouses
54 Richmond Rolling Robotics on AMRs
49 Exhibitors showing their wares at MEGATRANS
56 Mercury Awards celebrating sustainable warehouses
59 SCLAA on the ASCLAs
61 ASCI’s seminars, classes, and certificates
64 Product Showcase
66 People on the Move
Michael Ignatiadis, Head of Manufacturing Strategy, Asia Pacific, JLL spoke to MHD about exploring the dynamic implications of the China +1 strategy on supply chains and manufacturing across the Asia-Pacific region. The interview delved into the strategic advantages of diversification, emerging real estate trends, operational challenges, and the economic impact of increased industrial demand in India and Southeast Asia.
MHD: How do you see the shift towards a China +1 strategy impacting the landscape of supply chains and manufacturing in the Asia-Pacific region?
JLL: The shift towards a China +1 strategy is expected to significantly impact the landscape of supply chains and manufacturing in the AsiaPacific region.
This strategy will help build a robust ecosystem of outbound industries, leading to higher localisation rates. This is beneficial for both the destination country and manufacturers as it creates growth opportunities and reduces reliance on a single source.
Moreover, by diversifying manufacturing operations across multiple countries, companies can mitigate the impact of potential future tariffs and trade disruptions. Overall, the China +1 strategy presents an opportunity to strengthen supply chains and enhance manufacturing resilience in the region.
MHD: What specific advantages do India and Southeast Asia offer that make them attractive alternatives or complements to China for supply chain diversification?
JLL: India and Southeast Asia offer specific advantages that make them attractive alternatives or complements to China for supply chain diversification. While raw materials or key components may still need to be imported from China in most sectors, these regions present unique opportunities.
First, India and Southeast Asia boast a low cost of labour and energy, making
Michael Ignatiadis, Head of Manufacturing Strategy, Asia Pacific, JLL | Image: JLL
them cost-effective manufacturing destinations. Additionally, their skilled and extensive workforce ensures access to a large pool of talent. These regions also offer significant market potential, with a rapidly expanding middle class and a large domestic market. This presents opportunities for companies to tap into consumer demand and drive business growth.
India and Southeast Asia possess abundant natural resources, which can support various industries and enhance supply chain resilience.
Last, these regions are actively investing in infrastructure development to improve connectivity within their respective countries. This focus on infrastructure drives operational efficiency and facilitates seamless movement of goods, making them even more attractive for supply chain diversification.
MHD: In terms of real estate, what trends are you observing as companies look to establish or expand their manufacturing and distribution centres in India and Southeast Asia?
JLL: As companies look to establish or expand their manufacturing and distribution centres in India and Southeast Asia, several trends are emerging in the real estate sector.
First, there is a greater supply of real estate development in these regions. While Southeast Asia is still a nascent
market, it is experiencing rapid growth, with a more institutionalised prime market. The amount of logistics prime stock has increased, with notable growth in Vietnam, Kuala Lumpur, Jakarta, and Thailand.
This trend is expected to continue, with cities like Kuala Lumpur, Jakarta, and Hanoi projected to add around 1 million sqm each between 20242026, and Bangkok and Hanoi adding approximately 600,000-700,000 square meters (sqm) over the same period.
Second, demand levels are rising as a result of strong supply. Overall net absorption, which is a measure of demand, has increased from approximately 800,000 sqm in 2019 to around 1.4 million sqm in 2023 in key cities like Jakarta, Kuala Lumpur, Bangkok, Ho Chi Minh City, and Hanoi.
Another trend is the growing preference for built-to-suit (BTS) properties where companies are increasingly seeking custom-designed facilities that meet their specific manufacturing and distribution requirements. This trend is observed prominently in Ho Chi Minh City and the smaller Manila market, where BTS developments dominate.
Last, there is greater utilisation of Special Economic Zones (SEZs). These zones offer tax incentives, streamlined regulatory processes, and infrastructure support, making
■ Learn about the megatrends driving today’s supply chain challenges.
■ Understand how GTP solutions address these challenges whilst providing a competitive edge.
■ Discover the features and benefits of the leading solutions – AutoStore , Multishuttle GTP , and Autonomous Mobile Robots (AMRs) .
■ Read a detailed analysis and comparison of the technologies and how they align with business throughput and storage requirements.
them attractive to companies. SEZs provide an ideal environment for manufacturing and distribution activities, driving their popularity in India and Southeast Asia.
MHD: What challenges do businesses face when setting up operations in India and Southeast Asia, and how can they mitigate these risks to ensure a smooth transition?
JLL: When setting up operations in India and Southeast Asia, businesses face several challenges. One common challenge is the rush to explore locations where peers have already established their presence. While this can be a consideration, it’s crucial to assess each location through an end-to-end supply chain lens. Manufacturers may have diverse suppliers and customers, and the centre of gravity should be determined based on their specific requirements. Additionally, it’s important to consider that the business landscape, including tariffs and incentives, may have
evolved since peers were initially set up in a particular location.
To ensure a smooth transition and mitigate risks, businesses should conduct thorough due diligence on the chosen site. This process should encompass commercial, technical, legal, and environmental aspects. By thoroughly assessing these factors, companies can identify and mitigate any potential risks associated with the site, ensuring a smooth and successful setup of operations.
MHD: How might the increased demand for industrial real estate in these regions affect local economies and real estate markets, particularly in terms of pricing and availability?
JLL: The increased demand for industrial real estate in these regions is expected to have an impact on local economies and real estate markets, particularly in terms of pricing and availability. The rising demand will likely exert upward pressure on rents and property values.
Logistics rents in Southeast Asia currently range from USD $55-$65 per sqm p.a, with Singapore’s average net rent at around USD $128 per sqm p.a. Rental growth is influenced by the balance between supply and demand, but the presence of larger multinational corporations that require higherquality space is likely to lead to higher rental levels. In 2023, Kuala Lumpur experienced the highest rental growth at 7 per cent, followed by Ho Chi Minh City at 4 per cent, and Hanoi and Jakarta at 2 per cent. In Bangkok, rental growth was limited due to an influx of new supply and competition from existing older assets with lower rent levels.
Values of prime logistics real estate in Southeast Asia average between USD $675-$911 per sqm. Singapore’s average capital value (across all grades) is around USD $1,900-$2,000 per sqm. Similar to rental growth, value growth in these regions follows a similar trend. Increases in demand will likely contribute to an appreciation of property values.
In a reaffirmation of its dedication to sustainability, NORD Drivesystems has again secured the silver EcoVadis award for 2024.
Following an evaluation, NORD attained a score of 68 out of 100 points, marking an improvement from last year and positioning the company above the industry average.
“In the combined assessment, we rank among the top four per cent of the manufacturer group evaluated by EcoVadis”, says Jörg Niermann, Head of Marketing at NORD.
“This positive development is also a result of our sustainable strategy.”
In the Environment category, Getriebebau NORD GmbH & Co. KG from Bargteheide reached the top one per cent; in the Sustainable procurement division, they ranked among the best 11 per cent of the assessed companies.
Since 2021, NORD has been reporting its sustainability activities according to the German Sustainability Code (DNK). The company is currently establishing
NORD has been reporting its sustainability activities according to the German Sustainability Code | Image: NORD
a sustainability network within the 10 largest subsidiaries.
“We aim to harmonise economic efficiency and sustainability and based on our company policy, we act with integrity and responsibility for the environment – locally and globally”, added Jörg.
From 2025, there will be an international sustainability report,
which will contain the key figures of all subsidiaries.
In the fields of quality and environment, the company works according to certified ISO management standards.
The company furthermore signed the UN Global Compact and follows the Sustainable Development Goals of the United Nations.
Dematic has rolled out its first end-to-end automation solution at a leading Australian meat processing facility.
The first-of-its-kind deployment combines a Dematic Multishuttle Meat Buffer system with a pallet automated storage and retrieval system that features the first installation of Dematic’s newly freezer-rated, highreach automated guided vehicles (AGVs).
“Meat processing facilities in Australia are currently faced with challenges stemming from the fact that cold storage facilities are harsh environments for workers, leading to the risk of worker injuries, difficulties in sourcing labour, and time lost in managing complex occupational health and safety issues,” says Soeren Schauki, Business Development Manager at Dematic.
“Our automation solution offers the industry an answer to overcoming these challenges, with equipment that is rated for around-the-clock operation in cold storage environments and presents minimal risk to workers.”
The Dematic Multishuttle Meat Buffer system boosts flexibility and
throughput by enabling the transfer of product cartons across aisles without the need for a conventional conveyor system, in frozen or chilled conditions. This system limits labour-intensive manual handling and offers unlimited order assembly flexibility.
The solution can pick multiple SKUs concurrently within a single aisle while providing high throughput, order flexibility, as well as accessibility to stock.
Known for its intelligent warehouse solutions, Dematic recently released its third-generation, high-reach AGVs that are all rated for deployment in freezer environments.
Designed and built in Australia, these Dematic AGV systems limit occupational health and safety risks and increase productivity by operating full-time in temperatures down to -25°C – picking and transporting products.
The advanced, self-charging AGVs feature high-precision laser guidance and the latest safety technology.
This includes a 360-degree safety scanning system with automatic slowing and stopping, emergency
-stop buttons, visual and audible warning and alarm lights.
Dematic is Australia’s only manufacturer of freezer-rated AGVs, and its fleet of AGVs was recently updated in line with Australian Standard AS 5144-4, (equivalent to international standard ISO 3691-4).
“Meat processing facilities are ideal candidates for full automation to enhance accuracy, traceability, and control of perishable food products,” says Tony Raggio, General Manager Sales – Dematic ANZ Mobile Automation.
“As a result, Dematic is experiencing increased demand for comprehensive solutions that incorporate multiple automation technologies. Our solution, which combines the Dematic Multishuttle Meat Buffer system with our freezer-rated AGV-based storage and retrieval system, has been developed to meet this demand.”
The deployment of Dematic’s cutting-edge automation solution marks a milestone in enhancing operational efficiency and safety standards within Australia’s meat processing industry.
MachShip has appointed Emily Melle to its growing team as Senior Account Manager. Emily brings 20 years of transport, logistics, and supply chain experience to MachShip. Her robust approach to customer acquisition, retention, and growth, combined with her extensive operational knowledge, will not only complement but further strengthen MachShip’s position in the FMS marketplace. Emily’s dedication to building strong relationships and delivering
Argon and Co has appointed Anthony Cappelleri as a Partner for APAC’s Procurement and Supply Chain Planning services. Anthony brings more than 15 years of global advisory and procurement leadership experience. He specialises in M&A (public and private markets), largescale IT optimisation programs, and procurement transformation, having worked across diverse sectors such as financial services, mining, telecommunications, utilities, and FMCG. Anthony will play a pivotal role in driving sustained growth and continued success across the business.
Argon & Co’s James Lee, David Ring, and Jeff Triantafilo discuss the supply chain consultancy’s focus on strategic investments, its LEAN, Academy and NEOS programs, and other ways they are helping their clients reduce operational costs and increase productivity.
Optimising warehouse and logistics operations in a competitive business environment filled with inflationary cost drivers is crucial for companies looking to improve productivity and maximise existing assets.
This is where a company like Argon & Co employs proven strategies to achieve these objectives with confidence that your business can achieve real change.
Australia faces challenges in productivity compared to global leaders.
“In the current climate, our focus is
on optimising the logistics networks and supply chains for our clients with a view of delivering sustainable cost out,” explains David Ring, Partner, Argon & Co. “We believe our independent approach enables us to deliver the right solution for our clients and deliver the best outcomes.”
“Disappointingly, when it comes to productivity, Australia sits middle of the pack versus other developed nations,” says James Lee, Partner at Argon & Co.
“Our GDP per hour worked lags behind leading nations like France, Germany and Ireland by 30 to 40 per cent. This gap underscores the need for both our government and major corporates to continue with
smart investments in infrastructure, research and development, along with accelerated skills development across our working population.”
While major infrastructure programs are vital for building future productivity, the efficiency of spending remains a concern.
“I’m not sure paying $206k to a site traffic controller is the smartest deployment of our national funds,” says James.
Currently, Australia’s R&D spend is estimated at 1.8 per cent of annual GDP compared with the OECD average of 2.4 per cent and is currently ranked 20th globally for digital technology adoption.
“The key addressing our digital savviness, will be step changing our current education and training rates for adults to rival those of Sweden and Denmark, who currently track at 60 per cent,” explains James.
Building capabilities through continuous learning and development is a core passion at Argon & Co, which has expanded its ‘Academy’ program to offer support to clients in driving operational improvement through enhanced team capabilities.
In the current economic climate, businesses are evaluating investment decisions more carefully, particularly those concerning large-scale capital investments.
“We are seeing C-suite executives challenging their teams to fully realise the potential of existing assets. The old adage ‘sweat your existing assets’ is
now a core focus for our clients and the logistics industry at large,” says James.
“Consequently, we are fielding more and more requests from our clients to conduct detailed operational analysis, with the intent of not only identifying quick win productivity opportunities, but also provide insights into enhancements required to their current state operating models, including people, process, systems and infrastructure.”
Continuous improvement capabilities are also becoming fundamental competency of logistics operations, not only to identify latent productivity opportunities, but also to ensure these losses are permanently eliminated from operations.
“Argon & Co’s LEAN-based training programs are increasingly in high demand, especially across logistics and retail operations,” adds James.
“The current trend towards ‘cost
“The
current trend towards ‘cost out consulting’ is undoubtedly playing into one of our core strengths. Here at Argon & Co, we are acutely aware to balance our client’s need for rapid realisation of productivity.
”
out consulting’ is undoubtedly playing into one of our core strengths. Here at Argon & Co, we are acutely aware of having to balance a client’s need for rapid realisation of productivity, with the need to build out robust operational capabilities that will enable them to sustain these improvements and ultimately deliver real change.”
Property costs are becoming a driver for organisations to think differently about their operations. Some companies are experiencing cost increases through managing their own facilities or increased rates passed on from thirdparty operators.
“A number of businesses coming off three-to-four-year agreements are likely to experience a significant increase in rates,” says David.
David references one client in Sydney
future-proof, opening possibilities like multi-storey warehousing.
“We take that operations-first approach,” says David. “In everything we do, we are focused on getting the best outcome for our clients and optimising their operating model –the team, the processes, and their systems.”
where a $120 per sqm increase was presented at the time of lease renewal. Although with incentives, this may come back to closer to $80 per sqm increase, it’s still a high-cost increase that will have to be absorbed.
businesses to be curious about their current property deals, including rental rates, incentives, and associated fees.
maintain the current location, then renegotiate sooner rather than later to see if you can take the incentive options to improve cashflow.
lever that a business can use to their advantage,” says David. “Streamlining operations through inventory flow both upstream and downstream – exploring
a holistic network view to determine the facility’s requirements and role. This approach ensures the selection of a site that is fit-for-purpose and
Argon & Co’s NEOS system integration practice plays a vital role in ensuring project success.
“We are a management consultancy made up of specialists, but we can only lead horses to water,” says Jeff Triantafilo, Partner at Argon & Co.
“That’s where NEOS comes in, taking our clients the whole way through delivery by managing software delivery and increasing the likelihood of success.”
NEOS focuses on deploying software applications, particularly in warehousing, including Warehouse Management Systems (WMS) and Transportation Management Systems (TMS).
“We already increase the likelihood of success of our projects, through a high level of detail around engineering and design data science to create best practice operations, whether they be greenfield or brownfield. This leads to a high level of confidence in design,” said Jeff.
This added capability allows Argon & Co to maintain stewardship over the delivery phase ensuring minimal failures during transitions. NEOS is a response to the increasing demand for new or upgraded enterprise application systems, positioning Argon & Co as a preferred partner in this area.
“You cannot have a cookie cutter approach, but rather a system integrator that must understand your business case to deploy the change, and that’s consulting,” says Jeff.
Argon & Co’s operations-first consultancy approach is designed to address the unique challenges faced by businesses today.
By focusing on optimising people,
processes, and systems, Argon & Co helps clients achieve vertical startup, a concept from manufacturing that aims to realise benefits as soon as possible.
“Vertical startup is a concept that is very well used in manufacturing, and it’s about realising benefits as soon as possible. We’re just applying it to warehousing and logistics projects,” explains Jeff.
This involves meticulous planning and training to ensure that operations can meet the changes and deliver the expected results.
Securing capital for projects is challenging, particularly in a tight economic environment. Argon & Co’s approach involves a strong baseline understanding of operations, coupled with funding strategies and operational excellence.
This methodology ensures that clients not only secure the necessary funding but also achieve operational readiness to meet the changes effectively.
“We are able to cherry pick the best of practices that have been born out of other service offerings and integrate them into our own services,” explains James.
Argon & Co’s independence is also a significant advantage.
“We are quite proud of our independence,” adds David.
“We are not linked to a property transaction, a system vendor, or have a history of working with big thirdparty logistics providers. For us, it’s about finding the right solution
“You
cannot have a cookie cutter approach, but rather a system integrator must understand your business case to deploy the change, and that’s consulting. This allows us to have a market leading offering.
”
for our clients and leveraging our network and capabilities to deliver the best outcomes.”
Argon & Co’s strategies for optimising warehouse operations are rooted in an understanding of the challenges and opportunities in today’s business environment.
By focusing on strategic investments, rapid realisation, continuous improvement, and property optimisation, it offers comprehensive solutions tailored to clients’ unique needs.
“At the front end, we talk about cost out projects, helping you to fund a client’s transformation,” says Jeff.
“At the back end, we can use our operational excellence and our knowledge across the supply chain to provide assurance to the delivery too. It’s not just about funding your project and using existing savings.
“But also, once you’ve gotten the approval to go and spend, sometimes hundreds of millions of dollars to get that assurance, we can also deploy the capability that we have in manufacturing, around operational excellence to get your operation ready to meet the change.
“Often, people focus on the design and business case, but it’s the people in the operations who need to change. That’s where we focus.”
As Australia strives to improve its productivity and competitiveness, Argon & Co stands ready to support businesses in achieving their operational goals and unlocking future potential. ■
Peter Jones, Managing Director at Prological, talks to MHD about the future of sustainable logistics in Australia, including the challenges of securing government grants for EVs and the importance of independent analysis.
ith Prological as a supply chain consultancy firm having a strong foothold in the area of sustainability, its founder and Managing Director, Peter Jones, knows what steps both industry and government might consider to ensure the future is greener than ever.
The urgency for sustainable solutions in logistics has never been more pressing. The Australian government’s recent initiatives underscore a pivotal movement towards greener logistics, marked by grants and projects that could reshape
Peter offers insights into the challenges and opportunities these developments present.
Team Global’s $190 million federal grant is a testament to this evolution, a significant step towards establishing a battery-electric or hybrid-electric fleet at an industrial scale.
million worth of trucks and the global battery supply constraints.
“Battery electric cars are prioritised in both allocation of resources (manufacturing and materials) and in receiving transitional economic assistance from governments globally,” he explains.
In particular, Team Global and Australian National Courier (ANC) have emerged as frontrunners in this transformative journey, securing funding to implement ‘industrial
Historically, electric vehicle (EV) initiatives have been limited to small ‘prototype’ environments, but this funding catalyses a paradigm shift, enabling Team Global to navigate the complexities of operating EVs at scale within the Australian context.
Peter refers to two primary challenges Team Global faces: acquiring $190
“This prioritisation for cars over trucks has been in part driven by political gravitas and domestic recharging conveniences, further complicating the supply chain for industrial vehicles.”
Australia’s right-hand drive vehicle requirements have added another layer of complexity, necessitating additional research, development, and safety approvals by European, Asian and North American EV truck manufacturers
Peter remains optimistic about Team Global’s prospects, acknowledging the grant as a “fantastic” opportunity for an Australian company to conduct an industrial-scale trial of electric vehicles.
his sentiment extends to ANC, which has received $45 million from a similar grant pool for Project Spark, aimed at their last-mile livery fleets.
Electric vehicles, with their inherent advantages in short-range distribution, align well with this initiative, promising a cost-effective and sustainable solution to urban
If successful, these initiatives could see metropolitan rigid vehicle fleets transitioning to sustainable options over the next decade, contingent on vehicle availability.
However, as Peter points out, Australia’s logistics landscape is dominated by long-distance travel, a domain where battery-electric vehicles currently fall short.
“We’re waiting for other technologies to catch up,” he says, emphasising the potential of hydrogen as an alternative fuel and potentially better suited to high-mass and long-range vehicles.
New South Wales has already embarked on initiatives aimed at hydrogen trucks, due to grants aimed at developing a supporting network and creating a test fleet at diesel operating parity.
These trials are set to commence operations in 2026.
The broader logistics ecosystem also presents opportunities for sustainability, particularly within warehouse environments, according to Peter.
“If every warehouse in Australia was covered in solar panels, we would produce up to seven times Australia’s daily electricity requirement,” he says.
However, retrofitting existing buildings poses challenges due to structural limitations and dynamic loading changes.
The solution lies in forwardthinking design, ensuring new facilities are equipped to maximise sustainable energy production and storage, not just for today, but also into the future.
Warehouse stock has an average life cycle in Australia of approximately 45 years.
Therefore, whatever is designed into a new building in 2024, is close to as good as that building will get until 2069, when it is knocked down and rebuilt.
Prological, a company at the forefront of this movement, has collaborated with the University of Wollongong’s Sustainable Building Research Centre (SBRC) to pioneer sustainable industrial real estate models.
Its research indicates that solar and battery systems can power industrial
operations and vehicle fleets with a return on investment of less than five years in some cases.
This time frame is also compressing as battery technology improves in capability and becomes more cost effective as well.
“Our research picked up what was the global benchmark, our research outcomes... have now become the global benchmark,” says Peter.
This model provides a roadmap for businesses to design facilities that accommodate future energy requirements from the outset, mitigating the need for costly retrofits, if engineering requirements can even be met.
Despite these advancements, Australian businesses face several challenges in implementing sustainable logistics solutions.
“The first thing is that they’re primarily being sold systems by systems providers, rather than having systems designed for them,” explains Peter.
Independent analysis and tailored solutions are crucial for optimising sustainability initiatives.
Furthermore, he says, the need for consistent government policy is paramount.
“We’ve got to get bipartisan agreement on both the targets, medium and long term, and the macro processes to get there,” says Peter.
Government initiatives play a pivotal role in fostering sustainable logistics. Beyond grants and funding for industrial trials, policies promoting road-to-rail conversions could reduce carbon emissions.
The Inland Rail project, aimed at improving connectivity between major cities, exemplifies such initiatives.
Additionally, establishing standards for sustainability in industrial real estate would help to drive the adoption of green practices across the sector.
Measuring and reporting carbon footprints is another critical aspect for logistics companies.
“Carbon is like litter in the air,” Peter says.
This highlights the imperative to reduce emissions (air borne litter) irrespective of political beliefs.
Businesses increasingly recognise the commercial importance of sustainability, driven by the expectations of global partners and customers.
Transparent carbon reporting not only meets these expectations, but also positions companies as leaders in the transition to a greener economy.
The landscape of logistics in Australia is undergoing a profound transformation, driven by a confluence of technological advancements, government initiatives, and industry leadership.
As Peter’s insights illustrate, the journey towards sustainable logistics is fraught with challenges but also brimming with opportunities.
With concerted efforts from businesses, government, and research institutions, Australia can pioneer a future where logistics not only fuels economic growth but also champions environmental stewardship.
The road ahead is long, but the destination promises a greener, more sustainable world for future generations. ■
If you would like to discuss any area of this article, please reach out to Peter Jones at Prological (www.prologicalconsulting.com)
Measuring and reporting carbon footprints is one of several critical aspects for logistics companies.
Paul Deegan, BlackLab Solar electrician and Toyota 8FBE20 owner.
BlackLab Solar’s Paul Deegan talks about why he’s invested in Toyota Material Handling Australia’s energy-efficient, battery-powered 8FBE20 forklift.
In the heart of Rylstone, New South Wales, BlackLab Solar, a solar energy specialist, has harnessed the power of Toyota Material Handling Australia (TMHA) forklifts to boost efficiency and safety.
Run by licensed electrician Paul Deegan, the business specialises in high-quality solar installation and maintenance, setting a standard for excellence in the industry.
Paul, who manages all aspects of BlackLab Solar, found the demands of installation, maintenance, and ordering
increasingly challenging without the right equipment.
After years of using an old diesel forklift purchased from a neighbouring farmer, Paul decided it was time for an upgrade.
A former pilot, Paul utilised his hangar at Rylstone to store solar equipment. Following a period of heavy rain, he needed a forklift suitable for indoor operation.
After evaluating several options, Paul chose the Toyota 8FBE20 electric forklift, influenced by Toyota’s reputation for high-quality materials.
“This new one’s been an absolute delight, it’s fantastic,” says Paul. “I
wasn’t price-driven; I just wanted the best. Compared to the old one, it’s a precision machine. You move a lever, and it moves exactly.”
The transition to an electric forklift marked a shift for Paul, who values precision and reliability.
“Every time I get on it, I think, ‘how good is this,’” he says.
The forklift’s precision and ease of use were an improvement over the old diesel model.
“In the old days, starting the business, I was in Sydney hand-
loading solar panels with my kids,” he says. “Now, I’ll lift six pallets off a truck in 15 minutes. It’s just great.”
Paul’s expertise in battery and energy storage technology made him appreciative of the Toyota forklift’s batteries.
Operating in his off-grid, solarpowered hangar, the forklift runs with zero carbon footprint, charging entirely through solar power.
This alignment with BlackLab Solar’s commitment to sustainability underscores the harmony between solar energy and electric machinery.
Since acquiring the Toyota forklift a year ago, Paul has been impressed by its performance and reliability. He also values his relationship with TMHA and area sales manager Richard Bopping, who have ensured a seamless ownership experience.
“It’s made a huge difference – I’m 43 years old, and I’m almost singlehandedly running a million-dollar business,” explains Paul. “Having that machine, knowing I can jump on it, get the panels in the back of a truck in 10 minutes and I know it’s going to start – it appeals to someone like me.”
Paul highlights the minimal maintenance required for the forklift, praising the support from TMHA.
“When servicing needs to be done, I just make a call, and they send out a van with all the necessary gear. I can stay on the job, and they look after everything for me,” he says.
With more than 20 years as a qualified electrician, Paul founded BlackLab Solar after a decade of flying with the Royal Flying Doctor’s Service.
Returning to the electrical industry with a focus on solar installations, Paul emphasises quality in every project.
The Toyota 8FBE battery electric forklift features cutting-edge control technology and an ergonomically designed operator compartment.
It has 20 per cent improved operating time over previous models, due to its enhanced motors and drivers.
Key safety features, such as the System of Active Stability and Active Mast Function Controller, minimise risks of tip-overs and adjust mast
angle and forklift speed according to load height and weight.
Paul’s commitment to high standards and quality equipment is evident in his choice of forklift.
“Everything here is sensitive and expensive. Having a precise forklift means less damage to costly items,” he explains. “I chose Toyota because I did a bit of research and felt they were the best.
“My old Toyota lasted about 6000 hours. I wanted something tried and tested and quickly decided on an electric forklift from Toyota.”
TMHA’s customer service also played a role in Paul’s decision.
“They handled the paperwork, helped out with finance, and even provided a loaner forklift while we waited for the new one. It was all seamless,” he says.
Paul has no plans to expand BlackLab Solar, but he knows where to turn if new equipment is needed.
“If I needed any new equipment, TMHA would be my first port of call,” he says.
The Toyota forklift has not only met but exceeded his expectations, making it a valuable asset for his business.
BlackLab Solar’s story is a testament to the importance of quality and reliability in equipment for small businesses.
By choosing Toyota forklifts, BlackLab Soar has enhanced the efficiency and safety of its operations, aligning with the business’s high standards.
As BlackLab Solar continues to thrive, it stands as a shining example of the positive impact of investing in the right tools and technology.
Paul’s journey from hand-loading operations to a streamlined, efficient business powered by solar energy and Toyota forklifts is inspiring. It underscores the critical role of choosing the right equipment in achieving business success and sustainability. ■
Falcon Autotech is a global intralogistics automation solutions company. With over 10 years of experience, Falcon has worked with some of the most innovative brands in E-Commerce, CEP, Fashion, Food/FMCG, Auto and Pharmaceutical Industries.
CONTACT US:
Email: salesenquiry@falconautoonline.com Website: www.falconautotech.com
In this op-ed for MHD, Dematic’s Consulting Manager, David Lamb, explains how land scarcity in Australia is affecting the overall production of various industries, and how Dematic is mitigating these challenges to maximise efficiency and streamline supply chain operations.
number of Australia’s industries, spanning – from food and beverage to retail, wholesalers, and spare parts – today face a common dual challenge: land scarcity due to urbanisation and the resulting surge in land costs.
These issues result in large barriers for these industries to overcome, yet also create opportunities for innovation, enhanced efficiency, and ongoing sustainable practices.
Against this backdrop, there is a need to explore strategic responses and new approaches to navigate both current challenges and future uncertainties.
The phenomenon of urban sprawl, particularly along Australia’s eastern seaboard, has significantly impacted food and beverage, retail, wholesaler and spare parts supply chains.
With more than half of Australia’s population residing in just three cities on the eastern coast along with a spike in e-commerce, the demand for land in these urban centres has soared, creating severe land scarcity.
As a comparison, in the UK or US this proportion of the population would instead be spread across approximately nine and 27 cities respectively.
The situation is most acute in Sydney, where a CBRE report found that there was only a 0.2 per cent vacancy rate for buildings of 5000 square metres or more during the first six months of last year. This is the lowest rate recorded globally.
CBRE says rents in Sydney are
highest at $215 per square metres, compared to $119 per square metre in Melbourne, where the vacancy rate was also higher.
The congestion in Australia has not only inflated the cost of available land but has also necessitated a rethink in how suppliers manage their logistics and distribution networks to service increasing demands of their customers.
When considering their logistics footprint, food and beverage suppliers must implement optimised solutions that not only enhance economies of scale but also maintain agility in response to fluctuating market demands, without sacrificing performance.
It’s imperative they leverage their
existing land footprints to achieve increased storage capacity, heightened throughput, improved facility velocity and greater overall value, ensuring every square inch contributes to operational efficiency and effectiveness. By co-locating and integrating warehouses with existing manufacturing sites, the food and beverage industry aims to streamline operations, reduce transportation needs, and ultimately mitigate the impacts of urban congestion.
One leading solution used for these logistics requirements is an Automated Storage and Retrieval Systems (AS/RS), which offer a way to enhance storage efficiency within the limited available space.
An AS/RS provides the high-density, high-capacity storage for pallets in an automated solution and at a high speed, which also helps to reduce reliance on
labour during a time of low worker availability.
Combined with the capability of automatically loading and unloading trucks, this solution provides a fast, accurate and cost-efficient storage and delivery solution.
Because automated warehouses do not need to accommodate manual access, they can be a high bay configuration that takes up less cubic space for the same amount of storage — typically 25 per cent to 35 per cent more storage density over traditional warehouses, and with heights typically 30 to 35 m (and up to 45 m) they can deliver more than 200 per cent increased storage in the same land footprint.
With an AS/RS solution, stock cannot be lost or forgotten, as the system provides complete and real-time visibility of overall inventory.
The Diageo AS/RS System in Huntingwood exemplifies this approach, integrating high-density warehousing next to its Sydney manufacturing centre.
This strategic move not only improves storage efficiency but also reduces the logistics footprint by eliminating the need for multiple storage locations, minimising truck movements and manual operational touches between facilities.
With the rise of e-commerce, consumers have grown accustomed to expedited shipping options, and many expect their orders to arrive rapidly. As a result, retailers are increasingly using speed as a competitive differentiator.
In markets like South Korea, companies such as Coupang have set the bar high by offering lightning-fast two-hour deliveries. This trend not only reflects the surging expectations of consumers but also serves as a glimpse into the future of retail logistics.
As competition intensifies and consumer expectations continue to soar, the ability to deliver orders quickly, accurately and reliably is vital for retailers seeking to stay ahead in the ever-evolving retail landscape.
In today’s fast-paced retail landscape, the strategic positioning of distribution centres close to stores and consumers has become a critical factor for success.
This facilitates faster order fulfilment, streamlines transport and logistics, and reduces the need for extensive backroom store operations.
For wholesalers and spare parts operations, proximity to their businessto-business (B2B) customers is necessary to meet the demands of a quick turnaround market.
Whether it’s mechanics repairing vehicles, mining operations maintaining heavy machinery, or builders overseeing construction projects, the ability to access parts quickly is essential for ensuring uninterrupted operations.
By locating distribution centres near their B2B customers, wholesalers can streamline their supply chains, reduce delivery times, and provide the level of service necessary to support their clients in meeting their own deadlines and commitments.
Retailers, as well as wholesalers and spare parts operations, are also further optimising their supply chain footprint, overcoming current labour availability
challenges and ensuring that products reach their intended destinations quickly and efficiently, through automation.
Solutions such as the Dematic Goodsto-Person (GTP) Multishuttle system, AutoStore systems, and Autonomous Mobile Robot (AMR) picking systems are capable of enabling high capacity reaches picking, which is ideal for retail, wholesale and spare parts distribution centres.
The choice between Dematic GTPMultishuttle, AutoStore or AMR picking solutions depends on various factors, such as a company’s business model, supply chain structure order profiles, products handled and constraints such as building footprint and height.
For instance, businesses with high order volumes may benefit from the fast throughput capabilities of GTPMultishuttle solutions.
Companies operating with limited warehouse space may find AutoStore’s high storage density more suitable for their needs.
While companies with limited headroom and high order volumes may benefit most from an AMR Binto-Picker, and those with lower order volumes most suited to an AMR Shelfto-Person solution.
As the food and beverage, retail, wholesaler and spare parts industries look to the future, they face a landscape marked by rapid change and increasing complexity.
The challenges of land shortages and rising energy costs necessitate a strategic approach that balances immediate needs with long-term sustainability.
The pivot of these industries towards innovative storage solutions and energy-efficient practices highlights a commitment to overcoming these challenges through adaptability and foresight.
By optimising the logistics footprint and embracing sustainable operations, the sector is not just responding to current challenges but is also preparing for the future. ■
David Lamb, Consulting Manager, Dematic
MHD sits down with Linde Material Handling Australia’s Greg Wood to explore everything related to its sustainable lithium-ion forklifts.
In recent years, the sales of electric forklifts have outpaced those of internal combustion (IC) machines, marking a shift towards more sustainable practices in the materials handling industry.
This trend mirrors the broader automotive sector, where traditional counterbalance forklifts are increasingly being replaced by electrically powered machines.
These electric forklifts offer numerous advantages: they are more energy-efficient, cheaper to operate, cleaner, safer, and easier to maintain – valued contributions to a greener environment.
Historically, battery-powered forklifts were confined to lighter indoor applications.
Advancements in battery technology have expanded their use to outdoor environments and rough terrains, where they handle increasingly heavy and bulky loads.
Greg Wood, Technical Solutions Manager at Linde Material Handling (Australia), highlights this shift.
“We can see a very definite move to Li-ion machines,” he said.
Lead-acid batteries have long dominated the market, powering around 60 per cent of electric forklifts.
However, the demand for lithiumion (Li-ion) powered machines is accelerating rapidly.
Since the first Li-ion patent was granted in 1989, the technology has evolved, becoming more economical and finding its way into fleets worldwide.
“We have shipped a plethora of trucks with Li-ion batteries at Linde Australia, and we can only see demand increasing as the options unfold in our product portfolio,” Greg says.
Linde offers a range of Li-ion models, from the compact three-wheeled E12–E20 EVO series to the E100-E180 series of heavy trucks capable of lifting loads of up to 18 tonnes to heights of up to 10 metres.
“Across our truck portfolio, we have nearly 100 per cent of our trucks available with Li-ion,” explains Greg.
“We can offer up to three different battery capacities in each truck series –and always at least two charger powers per voltage class. This gives customers a huge variety of different options when deciding on a Li-ion powered truck.”
Even before the recent fuel price hikes, battery-electric forklifts were a popular option in warehouses and distribution centres.
Rising energy costs and inflation have further heightened the focus on increased energy efficiency, an area where Li-ion technology excels.
Li-ion systems demonstrate higher energy system efficiencies: up to 30 per
Linde executives emphasise that their Li-ion batteries and vehicles represent cuttingedge energy systems that prioritise efficiency.
higher than fuel cells, and 58 per cent higher than IC trucks.
According to Greg, Li-ion battery systems generally deliver savings for companies drawing their electrical energy from the grid.
“In most test cases, a lead-acid battery with a 50Hz charger, only 56 per cent of the energy ends up powering the truck,” he says.
“If the company uses an HF charger for the battery, the system efficiency is much better – up to 73 per cent.
“The combination of Li-ion batteries and matched chargers can offer the highest system efficiency – at least 85 per cent.
With smart use of energy recuperation (regenerative systems), the efficiency values can be even higher.”
Energy costs aren’t the only factor driving interest in new battery technologies. Li-ion batteries improve the productivity of electric forklifts due to their high energy density.
“A Li-ion battery has a higher power
delivery because the voltage discharge curve is flatter than lead-acid as the battery charge level drops,” Greg explains.
“When comparing lead-acid and Li-ion batteries with an equal kWh rating, lithium will do more work for you.
“Their higher power delivery and useable capacity means that a truck will run for longer and perform better over the discharge cycle.”
Li-ion batteries also need to be charged less frequently and are much quicker to charge than their lead-acid counterparts.
Many of Linde’s batteries can achieve a full charge cycle within as little as one hour.
“What’s more, these batteries are also suitable for intermediate charging as often as required, eliminating the need for a battery change/swap,” says Greg.
“Depending on the intensity of the operation, all that’s needed is a quick recharge during the lunch break and the vehicles are ready to go for several more hours.”
The unique characteristics of Li-ion batteries offer fast charging and opportunity charging, increasing truck availability and overall flexibility.
“Overall, the Li-ion battery, with at least 2,500 complete charging cycles, can be charged almost twice as often as a lead-acid battery,” says Greg.
Li-ion batteries require no maintenance, such as water topping, and their closed system of cells and modules means they don’t release emissions, which is beneficial for employee health.
Due to their chemistry, Li-ion batteries have a longer service life than lead-acid batteries, offering an improved return on investment (ROI) for customers.
“The customer benefits also create additional opportunities for savings across the entire service life of the battery,” adds Greg.
Switching to Li-ion also enhances workplace health and safety.
“When we eliminate the need for battery changing, we minimise operator handling of batteries and the need for battery rooms,” Greg says.
“And since the Li-ion cells are virtually maintenance-free, the
operators cannot come into contact with dangerous acids.”
Hydrogen produced by lead-acid batteries can turn into dangerous oxyhydrogen gas, but Li-ion batteries pose no such risk.
In accidents involving forklifts, enormous forces are exerted due to the weight.
To ensure that the Li-ion batteries in the vehicles are protected even in extreme situations, Linde’s bigger batteries (48 V and 90 V) have been subjected to a crash test of the maximum load.
The multi-level safety system in place with Linde Li-ion batteries applies at the cell, module, and battery level.
Li-ion systems demonstrate higher energy system efficiencies.
“The configurations for the batteries are also extremely varied, which means greater value is placed on highquality craftsmanship than on largescale automated processes.
“ When comparing lead-acid and Li-ion batteries with an equal kWh rating, lithium will do more work for you. Their higher power delivery and useable capacity means that a truck will run for longer and perform better over the discharge cycle.
Linde’s parent company, the KION Group, produces most of its own Li-ion batteries at the KION Battery Systems plant in Karlstein am Main, Germany.
This in-house production means that Linde Performance Plus batteries are designed alongside the machines into which they will ultimately be installed.
“Batteries are manufactured here for an extremely broad range of trucks,” says Greg.
At present, no fewer than 80 employees work in production, and in research and development, at the KION battery plant.”
Environmental considerations are now integral to significant purchases, with Linde executives emphasising that their Li-ion batteries and vehicles represent cutting-edge energy systems that prioritise efficiency while safeguarding both people and the environment.
“Linde’s Li-ion powered trucks meet all sustainability requirements, with zero-emission operation and the highest system efficiencies for charging,” explains Greg.
“The use of Li-ion powered forklifts and warehouse equipment makes any application significantly more energy efficient, resulting in the same overall output being achieved using less energy.”
Certified life cycle assessments show that the use phase of trucks is the main driver of pollution, and switching to highly efficient Li-ion technology can reduce your carbon footprint.
Linde is also conscious of its endof-life responsibilities, employing various recycling strategies. After their first life, Linde Li-ion batteries can be refurbished and re-used in another truck application. ■
Scan the QR code for more on Linde Material Handling’s sustainability practices.
Körber has partnered with HAI Robotics to deliver industry leading automation and robotics projects across the country. MHD recently sat down with the two organisations to learn more about their successful partnership.
Körber and robotics specialist, HAI, have partnered to bring their collective expertise together.
robotic solutions.
intralogistics solutions, Körber continually seeks new and innovative partners to provide the best solutions for customers.
In response to increasing costs and labour shortages, Körber joined forces with HAI Robotics to offer comprehensive automation solutions.
From increasing costs to labour shortages, logistic operators in Australia are constantly under pressure to meet stakeholder demands.
As a result, Körber and robotics specialist, HAI, have partnered to bring their collective expertise together and provide clients with all-in-one
“Partnering with Körber, with their expertise in software and integration solutions, allows us to provide competitive solutions to clients.”
Körber’s Andrew Leslie, the head of the company’s AMR division for APAC, agrees.
“Körber has completed some of the biggest and most complicated automation projects in Australia, and to succeed at this level requires real dedication from all parties,” says Andrew.
businesses to strategically schedule orders so that they meet delivery deadlines.
“We boost overall efficiency by minimising the number of handling steps for each order while reducing the power requirements compared with traditional fixed automation solutions.”
And why is the collaboration between HAI and Körber important?
“HAI Robotics are leaders in Autonomous Case-handling Robot (ACR) technology and multiple types of
totes-to-person robots,” says Andrew.
“At Körber we offer an end-to-end solution, and we can now leverage HAI’s extensive options for customers in different areas such as the totes-toperson space.”
Will agrees that both companies are a good fit for a variety of reasons and envisions both companies being able to provide a variety of competitive solutions to many sectors soon.
Körber and HAI are targeting various markets as their combined solutions will tick a lot of boxes for those seeking cost-effective solutions to their supply chain needs.
“Most [companies in this space are] in the field of goods-to-person,” Will says.
“Compared with other AMR solutions, HAI Robotics focuses on a more refined aspect – totes-toperson. This provides us a competitive advantage in B2C and loose picking for industries such as e-commerce, apparel, small spare parts, and healthcare.”
Both organisations emphasise data-driven solutions tailored to each client’s needs. Andrew Leslie enjoys analysing customer data to create superior solutions.
“We work to analyse data from customers that shows their current operations, and then the problems they have,” he says. “Then it is on us to create a solution that is better than all of our competition – which we continue to do.”
Andrew has spent his career building conveyors and production lines and
has a background in automotive manufacturing.
He believes that many organisations need to start exploring scalable, agile automation solutions sooner rather than later if they want to keep pace with the competition.
This is one of the reasons he believes there is good synergy between Körber and HAI Robotics.
The partnership allows Körber to mix and match robots for optimal project outcomes. For instance, in a current project, they are using multiple robot types to complement each other’s strengths.
Their nearly completed project for Myer’s NDC showcases the use of three different robots addressing different picking processes.
What are some of the key features of HAI robots that make them such a suitable fit for the type of projects Körber is involved in?
“First is density,” Will notes. “The
latest ACR can achieve a storage height of 12 metres, allowing it to compete with most multi-shuttle systems in the industry in terms of storage density.
“Then there is accuracy. Our HAIQ software manages robot movements and integrates with clients’ WMS, ensuring the right tote is delivered to the correct position in the most efficient way.
“Finally, we have efficiency. HAI has conducted more than 1,500 projects globally, resulting in an average productivity increase of 2.4 times compared to traditional warehouses.”
The combination of skillsets and technology expertise within both companies is paramount to helping customers.
“Körber provides WMS and Commerce solutions, which complement our AMR integration – this contributes to us being one, trusted supply chain partner,” adds Will.
“Furthermore, our APAC support team ensures customers’ cybersecurity, compliance and efficiency challenges are constantly also addressed.”
Looking ahead, Andrew is excited about the potential of autonomous mobile robots.
“With consumers demanding faster deliveries, efficient processes in distribution centres are imperative. Agile automation solutions can prioritise orders based on customer needs,” says Andrew. “This is where the magic really happens.”
The partnership between Körber and HAI Robotics is a great example of how collaboration can help meet the evolving demands of the logistics industry. ■
Jungheinrich’s Product Manager, Robert Skalba, talks about what the company is doing to guarantee safety in the warehouse utilising its advanced safety features.
Forklifts are essential in numerous industries, providing support for lifting and transporting heavy loads. However, their operation comes with inherent risks, and accidents involving forklifts are frequent. These incidents often lead to severe injuries or even fatalities, making it imperative to adopt advanced safety measures.
In 2022, WorkSafe Victoria accepted 142 claims for injuries caused by forklift incidents.
The nature of these incidents varied, with pedestrians being struck
by forklifts constituting a significant portion. Additionally, poorly secured loads led to 9 injuries when they fell on workers, and 5 incidents involved forklifts tipping over.
These accidents not only lead to people tragedy, but also effect business reputation and come at a cost. In 2022 alone, the highest fine reached AUD$475,000, while many other companies were also fined.
Jungheinrich is a leading global intralogistics provider and has been driving the development of innovative, sustainable products and solutions for all aspects of material flow for more than 70 years. For more than 20 years, Jungheinrich’s products have been
enabling Australian customers for their business success. With innovation as one of the key values, Jungheinrich has been at the forefront of this endeavour, developing cutting-edge solutions to ensure safer forklift operations.
One of the primary causes of forkliftrelated accidents is the lack of awareness among pedestrians about forklifts operating in their vicinity. To address this issue, all Jungheinrich trucks available in stock are equipped with spotlights that project light on the floor both in front of and behind the forklift.
“This way, pedestrians know that a forklift is approaching and can take the necessary precautions,” says Robert Skalba, Product Manager from Jungheinrich Australia.
Depending on the forklift truck type, other visual warning systems can be used to reduce the number of accidents. For instance, in case of vertical order pickers, warning zone lights extend the area accordingly to picking height. By doing this, even if the operator drops the load from the high altitude, warning zone lights cover the whole dangerous area and inform pedestrians about the risk.
Additionally, each counterbalance forklift is fitted with a sound buzzer, providing an audible alert to anyone nearby.
“The combination of visual and auditory signals ensures that pedestrians are not only able to see but also hear the forklift approaching, significantly reducing the risk of accidents,” explains Robert.
Nowadays, there is a lot of noise pollution. This is why Jungheinrich offers not only the standard warning buzzer, but also the self-adjusting one, providing noise level between 5 and 10 above ambient dB(A). Thanks to this
to further improve forklift safety.
“One reason accidents happen is related to overloading the truck,” says Robert.
OperationCONTROL is designed to prevent such incidents.
“OperationCONTROL weighs the load and compares it with the capacity plate data to ensure the forklift can lift it safely at the desired height,” says Robert.
“If the load exceeds the forklift’s
load into consideration and adjusts the speed of the truck accordingly. These systems work together to ensure forklifts operate within safe parameters, thereby minimising the likelihood of accidents.
“Even a slow-moving forklift can injure or kill, yet too many employers
using reversing cameras, adhering to load capacities, and ensuring that only licensed workers operate forklifts can mitigate risks.
To enhance forklift safety, employers should implement several key measures:
1. Comprehensive training and induction. Ensure workers receive appropriate training including the operation of each truck and any attachments, induction and maintaining a register of such training.
2. Traffic management plans. Develop and regularly update traffic management plans to separate pedestrians and forklifts.
3. Effective communication systems. Establish robust communication systems between operators, transport contractors, and ground staff.
4. Signage and barriers. Erect clear signage and physical barriers where necessary to guide pedestrian and forklift traffic.
5. Pre-operating checks, regular inspections and maintenance. Conduct regular inspections and maintenance of machinery and vehicles by qualified personnel.
6. In the event of a fault or the forklift becomes unsafe, report and tag ‘out of service’ and isolate.
“
Jungheinrich has developed sophisticated systems such as OperationCONTROL and CurveCONTROL to further improve forklift safety.
Advancements in technology offer additional layers of safety for forklift operations. Jungheinrich’s several key innovations include:
• Spotlights and audible alarms. Forklifts equipped with spotlights project light on the floor, alerting pedestrians of the forklift’s presence. Audible alarms further enhance awareness.
• OperationCONTROL Systems. These systems weigh loads and check capacity plates to prevent overloading. For example, if a forklift rated to lift two tonnes up to three metres attempts to lift the same weight above this height, the system issues a warning and, depending on the model, an audible alert.
• CurveCONTROL Systems. These systems automatically adjust the forklift’s speed when navigating curves, reducing the risk of tipping over.
• Pedestrian Detection Systems. AI-supported cameras detect pedestrians and can slow down or even stop the forklift if someone is too close, preventing accidents. ■
1. More than 140 workers injured in forklift incidents last year –January 31 2023.
Our cutting-edge material handling products are engineered to enhance efficiency, safety, and productivity. From robust forklifts to versatile pallet trucks, our equipment is designed to meet the rigorous demands of your business.
As MachShip celebrates its 10th anniversary, Chief Revenue Officer, Sam Rowse, speaks to MHD about how the platform has integrated itself into more than 250 Australian carriers’ logistics operations.
Adaptability and responsiveness are crucial to logistics, especially when meeting market demands for sustained success. MachShip, founded in July 2014, epitomises this adaptability.
Initially targeting the 4PL (fourthparty logistics) market, MachShip has grown into a platform that caters to enterprise-level B2B and e-commerce sectors.
This evolution has been shaped by the dynamic and demanding nature of the 4PL industry, driving MachShip to continually expand and enhance its capabilities.
When MachShip first entered the logistics technology market, it targeted 4PL providers.
“We found ourselves working with two pioneering 4PLs who were our initial customers,” says Sam Rowse, Chief Revenue Officer, MachShip.
“At that point in time we had multi-carrier connectivity and a good breadth of features.
But their demands were really high, pushing us to grow our capability suite.”
These initial customers were market leaders with high expectations, setting the bar for MachShip’s capabilities.
“Their demands pushed us to connect with more carriers and grow that carrier network,” explains Sam. “They needed Dangerous Goods capabilities, robust invoice reconciliation, and parent-child company structures.
“Over time, they helped define our roadmap.”
This demand-driven growth transformed MachShip from a promising platform into a comprehensive logistics management solution.
Over the past decade, MachShip has witnessed an evolution in the 4PL industry. Initially, the focus was on competitive rates.
“What we’ve seen in the last 10 years is this expansion of a 4PL’s capabilities beyond just competitive rates,” says Sam. “It’s grown from competitive rates to customer service and technology.”
This shift in focus drove MachShip to enhance its platform continually.
“Our 4PL customers needed us to provide excellent customer service
and cutting-edge technology,” adds Sam. “They pushed us to be a great product, integrating more carriers and improving our features. We’ve evolved alongside them.”
This evolution has cemented MachShip’s reputation as a purposebuilt solution for 4PLs, with its capabilities now extending to enterprise-level B2B and e-commerce sectors.
One of MachShip’s standout features is its carrier invoice reconciliation. This capability has delivered savings for customers.
A recent example is Global Truck Imports, a 4PL and carrier. Its general manager reported saving more than $4,000 per month through MachShip’s carrier invoice reconciliation.
“MachShip identified cost
discrepancies, saving this business $50,000 in their first year,” says Sam. “This is significantly more than their subscription, providing a multiple times return on investment.”
Before using MachShip, businesses often relied on spreadsheets or spotchecking to identify discrepancies. MachShip automates this process, reducing it from many hours or even days to mere seconds.
“It becomes a regular part of the finance operations of a business,” adds Sam.
This automation and efficiency are crucial for 4PLs and other businesses managing complex logistics operations.
MachShip’s integration with more than 250 Australian carriers ensures seamless connectivity and performance, even for businesses managing complex logistics across multiple sites.
MachShip accommodates each carrier’s integration requirements, whether API-based, file-based, or even email-based. This flexibility ensures that MachShip can connect with any carrier, regardless of their technological sophistication.
“We fit in without intruding. Carriers love us for that,” says Sam. “We always ensure that their labels are compliant and tracking information is pulled
back into our system for consolidated visibility.”
Sustainability is becoming increasingly important in the logistics industry, and MachShip is poised to contribute with its upcoming freight carbon calculator.
“Sustainability is a frequent agenda item in board meetings now, and it’s taken seriously,” adds Sam. “The carbon calculator will provide businesses with visibility into their carbon footprint, empowering them to make informed decisions.
MachShip’s extensive data collection from freight movements gives us the confidence to create a robust, data driven carbon calculator. It will be meaningful and deliver actionable insights. This tool aligns with MachShip’s commitment to supporting businesses in their sustainability efforts.”
MachShip’s independence in freight management is a core part of its DNA.
“We’re not a broker, and we don’t have relationships at a rate level with carriers,” explains Sam. “This independence is crucial because a large part of our customer base consists
of 4PLs.”
This independence allows MachShip to connect with a range of carriers, providing greater market reach and value to its customers. The same principle applies to ERP, WMS, and e-commerce platform integrations.
“We partner with businesses but never on an exclusive basis,” adds Sam. “Logistics is integral to the economy and limiting ourselves to a few brands would reduce the value we provide to the Australian logistics market.”
This brand-agnostic approach ensures that MachShip can serve a broad array of customers and industries.
As MachShip celebrated its 10th anniversary in July 2024, it stands as a testament to how listening to market demands and evolving accordingly can lead to sustained success.
Over the past financial year, MachShip has processed more than one million consignments monthly and managed more than one billion dollars in freight spend annually. Its platform is used by more than 3500 businesses, including major Australian brands.
“We’ve come a long way in the past 10 years, driven by the demands of our customers and our commitment to providing a comprehensive logistics management solution,” says Sam.
MachShip’s journey from a promising start-up to an industry leader underscores the importance of adaptability, customer service, and technological innovation in the logistics sector.
MachShip’s story is one of evolution driven by customer demands and market needs.
From its beginnings in the 4PL market to its current role as a comprehensive solution for enterprise-level B2B and e-commerce logistics, MachShip has consistently adapted and grown. Its commitment to independence, sustainability, and seamless connectivity positions it as a pioneering force in the logistics industry.
As it celebrates its 10th anniversary, MachShip looks forward to continuing its journey of innovation and excellence in logistics management. ■
360° Multi-Line Lidar
5x Lidar Cameras
3000mm Max Fork Height
1500kg Max Load Capacity
8hrs Battery endurance with smart opportunity charging
Ultimate smart safety solution including Anti-collision and auxiliary pallet navigation and detection
Exceeds AS5144, ISO 3691-4, ISO 12100, ISO 1175 Standards and CE certification
Ask our team about how our AMRs can revolutionise your business!
BBHD’s John Harrison and David Seale explain to MHD the storage solutions company’s cantilever racking and the role of automation in shaping warehousing’s future. Specialising
HD Storage Solutions has been manufacturing and supplying cantilever racking to its clients since 1999.
During this time, it has seen many changes, including the recent impact of automation on the warehouse distribution industry.
BHD offers adaptable and creative racking systems that suit most integrators’ needs, ensuring seamless integration with various automation solutions.
“Cantilever racking has always been our specialty,” says John Harrison, General Manager of the company.
“The business was founded on it, and we continue to promote and sell significant quantities to the Australian market.”
This focus has kept it ahead in the market dynamics, especially as
the demand for pallet racking and warehouse automation increases.
The introduction of various styles of pallet racking, combined with automation, has spurred BHD’s expansion into new market segments.
Efficiency and control over the supply chain are critical to BHD’s operations.
“We are the manufacturer,” says David Seale, Queensland State Manager, BHD Storage Solutions.
“We have over 100,000 square metres of manufacturing plants under our roof.
“This allows us to supply the chain from the beginning – from design to quoting – to manufacturing and shipping.”
This level of control ensures that it can maintain efficiency and keep clients informed about their orders. Their manufacturing facilities are ISO
9000 certified, ensuring consistent product quality across all operations.
BHD has adapted its designs to maximise space and efficiency for clients in various industries, particularly steel and timber.
“Our cantilever systems have evolved significantly,” explains John.
“We now go up to nine metres high, with narrow aisles to maximise floor space. This design allows for quick retrieval of specific items without having to move others, increasing efficiency.”
The ability to retrieve products quickly is essential for industries where space and time are critical.
Serving industry clients like Komatsu comes with unique challenges.
“Komatsu’s equipment varies greatly in size and weight,” says David.
“We’ve had to design multipurpose racking that can handle everything from four-tonne motors for large excavators to smaller components for mini excavators.”
The solution involves implementing mobile racks, which reduce floor space requirements and improve retrieval times.
These mobile racks can handle up to 16 tonnes per bay, allowing for efficient storage and retrieval of heavy equipment.
BHD is committed to continuous improvement and meeting the evolving needs of its customers.
“Our cantilever systems have seen numerous upgrades over the years,” says John.
“We’ve increased steel thicknesses and grades to handle higher loads. All our racking complies with the highest certification standards, ensuring safety and reliability.”
The company’s modular design allows for flexibility and adaptability, catering to clients’ specific storage needs.
The consultation process is integral to BHD’s approach.
“We start by understanding what the client wants to achieve,” explains John.
“From there, we design and custom manufacture racks to suit their specific needs.
BHD products allow for flexibility and adaptability.
“It’s a collaborative process, with multiple drafts and client feedback to ensure the final product meets their requirements.”
This customer-centric approach has enabled the company to develop tailored solutions that fit within existing buildings or new constructions.
BHD is investing in research and development, particularly in warehouse automation.
“We’ve built a new factory in China
with a large R&D centre dedicated to automation racking,” says David.
“We’re testing and developing solutions to meet the stringent requirements of warehouse automation.”
This investment aims to futureproof the business and keep pace with industry trends, ensuring they remain at the forefront of racking solutions.
BHD has a strong focus on cantilever and pallet racking solutions tailored for automation.
Its manufacturing capabilities, commitment to quality, and customercentric approach, have enabled it to meet the diverse needs of clients across various industries.
As BHD continues to invest in R&D and adapt to the changing landscape of warehouse automation, it’s poised to remain a key player in the industry for some time.
“We’re looking forward to the changes that the warehouse automation space is bringing,” says David.
“Our product offerings are evolving in line with market requirements, and we’re excited about the future opportunities and challenges.”
For businesses seeking innovative and efficient racking solutions, BHD remains a reliable and forwardthinking partner. ■
MHD speaks to Glenn Powell, General Manager of Face Consultants on how his company can help make a warehouse run efficiently.
Tfuture made in Australia’.
The strategy is based on four themes:
• National Capacity – to support the domestic market and global exportation of Australian robotics and automation.
• Increased Adoption – raising awareness and incentivising businesses to adopt and integrate the new technology into their operations.
• Trust, inclusion and responsible development and use – ensuring safe, secure, and inclusive technologies are used to benefit workers.
• Skills and diversity – support for all Australians from all backgrounds so they can contribute to and benefit from new
and using responsible robotics and automation technologies,” says Glenn Powell, General Manager of Face Consultants, a company specialising in the design, testing, and surveying of concrete floors for industrial and commercial warehouse facilities. Robotics, and how they are distributed throughout a warehouse, and their impact on a warehouse floor, are key issues that need to be considered when automating a DC, according to Glenn.
“There are many robotics currently being used in warehouses,” says Glenn. “With the most common being Automated Guided Vehicles, also known as AGVs, which follow
Robots or AMRs, which use sensors and cameras to navigate rather than following a set path. They are frequently used to move inventory, replenish stock, and pick orders.
Another useful tool is stationary, or mobile, robotic arms that are equipped with suction cups or grippers to pick stock from shelves and pack boxes or pallets.
Finally, there are Collaborative Robots, or Cobots, which are robotics designed to work alongside humans to help them when tasks are dangerous, repetitious, or strenuous.
Using robotics for packing, sorting, picking, transportation, and inventory management is now commonplace, but the first practical AGV prototype was
developed in the 1950s by the Barrett Electronics Corporation in Illinois, USA.
They used a tow truck to move materials in a warehouse, with the position guided by a wire placed in the floor.
AGVs were first introduced in Australia in the late 1970s and early 1980s, typically used in manufacturing or logistics sectors.
AMRs appeared in the early 2000s, with companies such as Amazon Robotics (formerly Kiva Systems) playing a significant role.
Early adopters in Australia at this time included retailers, e-commerce, and logistics
“There are multiple benefits to using robotics within warehouses, such as automating repetitive tasks, reducing labour costs and human error, and streamlining order fulfilment [in conjunction with inventory management],” says Glenn.
“AGVs and AMRs increase materials handling and logistics productivity, while robotics such as Cobots work alongside humans to boost flexibility and reduce injury risks.”
New warehouse robotics in 2024 include BionicHive’s Squid Robot. Although developed in 2016, the Squid Robot is just being introduced to the market, offering an automated, autonomous solution for picking and replenishing boxes.
The robots can deliver anywhere within the warehouse, moving across the floor and vertically and horizontally up racks.
LG’s CLOi CarryBot delivers small to medium packages across almost any distance. Designed to deliver items end-to-end using autonomous driving and obstacle avoidance, operators can stay within their assigned zones.
The beauty of the CarryBots is they can integrate with a WMS to create efficient order distribution and scheduling. They can also be programmed to navigate most floor plans, with virtually unlimited pick-up and delivery points.
Agility Robot’s Digit is ‘the most advanced Mobile Manipulation Robot (MMR) on the market’.
A bipedal robot, Digit is designed to grasp and handle items while moving. It can circumnavigate tight spaces and
corners and is now being trialled by Amazon to pick up and move empty totes once inventory has been depleted.
Retro-fitting lift trucks with automated systems have been available for some time. However, new dualmode robotics integrated into existing lift trucks mean they can operate autonomously or manually at the touch of a button. This allows peak performance during busy periods and the ability to revert to manual operations when the warehouse is quieter.
Technologies such as telematics and advanced infrastructure-free navigation systems help to minimise human error and optimise workflows.
“Apart from the obvious financial considerations, one of the first, but frequently overlooked areas needing investigation, is the floor of your warehouse or facility,” says Glenn.
suitable for an efficient and successful automated warehouse, including the working parameters of the robotic equipment.
A predictable surface means precise movements with no interruptions, and a flat and level floor optimises robotics efficiency, speed, safety, and stability.
With robotics, different characterises are also required. These can include gloss, friction and light reflectivity.
“We are also seeing floors wear differently within defined movement areas and where the robotics turn,” says Glenn.
Floors are literally wearing out, so abrasion resistance is also a key requirement for the long-term performance of an automated solution.
“Flat floors also affect maintenance as they reduce wear and tear and increase the robotics’ lifespan,” says Glenn.
“Floors are easier to maintain and keep clean, creating less dust and, therefore, less impact on cameras and sensors.”
The first step is to contact a company like Face Consultants, who will deliver unbiased results with no vested interest in the outcome.
Using the latest digital floor flatness testing technology is essential, as is agreeing on a clear method of compliance checking.
All stakeholders then understand
Surface regularity, flatness, levelness, curvature, step transitions, and abrasion resistance must be considered. So too should surface characteristics such as specified gloss, friction, and micro-roughness requirements.
Once floor testing has been completed and any deviations from specifications identified, then any required floor remediation is carried out.
CoGri Australia is a specialist in upgrading floors for robotic systems, whether it’s grinding a floor into tolerance or repairing joints or cracks. If it’s a new project, the floor design is a critical stage. The floors must be designed and constructed in a way that allows robotics to operate at their optimum performance.
After the floor is constructed, or remediation is carried out, a final testing of the completed floor surface must be completed to ensure compliance.
“The world of robotics for warehouses is so exciting right now,” says Glenn.
“But introducing them carries its share of hard decisions, from which type of equipment will benefit your operations, to how best to finance them. The quality of the floor your robotics operate on shouldn’t be one of them. A little due diligence at the start can prevent a world of problems and delays later.” ■
Kärcher, the leading brand in cleaning technology, has been operating for almost 90 years.
During this time, the company has continued to innovate and lead the industry, providing a wide range that caters to various industrial and commercial needs, ensuring cleaning solutions for a variety of sectors.
The German-founded company has been present in Australia for 40 years and is now in its third decade in New Zealand.
Kärcher’s product range includes everything from robotic sweepers and scrubbers to manual, human-operated industrial equipment. Products as small as battery operated stick vacuums to supersize vehicle wash systems.
“We offer solutions in truck wash, bus wash, and car wash,” says Mick Askew, Sales Director, Professional, Kärcher.
“We’re a solution-based selling business. “It’s important for us to have a diverse range of industrial sweeping and scrubbing equipment, but also hot and cold-water pressure washers and wash systems. We supply solutions for the market, a one-stop shop.
“We can provide everything from
MHD talks to Kärcher Sales Director, Mick Askew, about the cleaning equipment company’s continued foray into the industrial and warehousing space.
cleaning the trucks to cleaning the floors, offering site-specific transport and logistics solutions.”
This array of products is a testament to Kärcher’s commitment to meeting the diverse cleaning needs of its customers.
Among the flagship products are the KM 170/600 sweeper and the B 260 scrubber.
The KM 170/600 – as Mick describes as the biggest of the range – is notable for its 170-centimetre width and 600litre capacity. The B 260, on the other hand, has 260 litres of clean and dirty water capacity, making it suitable for environments that require stringent cleanliness, such as food manufacturing and pharmaceutical facilities.
In an era where sustainability is paramount, Kärcher is at the forefront with its green initiatives.
“We understand the importance of sustainability to our customers, so we now offer more products with lithiumion batteries,” explains Mick.
“They will have a seven-year life, reducing the need for frequent replacements and thereby minimising landfill and battery waste.”
This commitment to sustainability is evident in Kärcher’s recent win of the
Bunnings contract, where every store in Australia will be cleaned using lithiumpowered equipment.
Understanding the diverse financial needs of its customers, Kärcher offers various purchasing and leasing options.
“We strive to offer our customers not only choice in product solutions, but choice in financing too,” says Mick “Through Kärcher Financial Services we have OPX options, as well as direct lease and rental options on top of outright purchase.”
This flexibility allows businesses to choose the most cost-effective solution, whether it’s a capital expenditure or an operating expense. One of the advantages of working with Kärcher is the focus on maximising uptime and minimising downtime.
“The ROI is really key because time is money,” explains Mick. “With a rental contract, you’ve got the reassurance of always having that machine up and running.”
Kärcher ensures this through stringent Service Level Agreements (SLAs), offering immediate repairs or replacement solutions to keep businesses operational. Preventative maintenance is a cornerstone of Kärcher’s approach. “
We always encourage a service
contract with any outright purchase,” adds Mick.
“Preventative maintenance helps avoid reactive maintenance, which can often be more costly and disruptive.”
Kärcher’s standard warranty on industrial equipment is one year, but Kärcher Full Service Programs are available, which provide cover for four years.
The Kärcher group has 19 factories and logistics centers worldwide, with the latest addition being Vietnam opened in July 2024. Kärcher has two key industrial manufacturing plants, one located in Italy and one in Germany.
This global manufacturing network ensures high-quality products and efficient distribution. Across Oceania, Kärcher has a presence with hubs in all key cities.
“Our Kärcher Centres offer customers a unique experience,” says Mick. “We have the widest range of products on display and highly knowledgeable staff to offer guidance and support.”
With head offices in Melbourne, Australia, and Auckland, New Zealand, Kärcher is well-positioned to serve the region effectively.
Kärcher’s service network is extensive, with 40 Kärcher technicians across Australia and New Zealand servicing key clients like Coles, Aldi, and Bunnings.
Kärcher also has a strong dealer network across ANZ with more than 60 locations across the region. This coverage ensures Kärcher can meet the service and maintenance needs of customers across ANZ.
Cleanliness in industrial settings is crucial, not just for aesthetics but also for operational efficiency.
“A clean environment will help maintain machinery and reduce wear,” explains Mick.
Kärcher’s industrial machines feature advanced filtration systems to keep dust and debris at bay, ensuring cleanliness and efficiency. Safety is another critical aspect.
“Businesses must ensure that the cleaning equipment used by their
employees is safe and easy to use,” says Mick.
Kärcher’s machines are equipped with various safety features, including overhead protection, seatbelts, and lighting kits, to ensure safe operation in busy industrial environments.
Kärcher Fleet is the comprehensive fleet management solution that gives customers a clear view of their assets and a wealth of information.
This information helps customers optimise their cleaning operations and ensures timely maintenance and repairs, reducing downtime.
Kärcher’s presence in Australia dates back 40 years, a milestone recently celebrated.
“Globally, we celebrate our 90th year next year, which is testament to the strength of the brand” says Mick.
Over the past five years, the business has nearly doubled its growth, highlighting Kärcher’s strong market presence and innovative approach. Kärcher’s has ambitious growth plans.
“We’ve worked on our 2030 plan and are looking to grow this business significantly in the next five years,” adds Mick.
This growth will be driven by continued investment in key business verticals.
“We want to increase market share in commercial sectors and showcase our capabilities as a comprehensive cleaning solution provider outside of the consumer market where we are most commonly known,” explains Mick.
Kärcher’s track record and support network make it a reliable partner for businesses looking to enhance their cleaning operations.
With a diverse product range, flexible financial options, and a robust service network, Kärcher is well-equipped to meet the evolving needs of its customers. ■
Mercury awards help push the boundaries of what is possible in logistics and supply chain management.
The MHD Mercury Awards stand as a testament to the achievement within the logistics, supply chain, and materials handling industries.
These prestigious developments to ensure sustainable practices and celebrate the dedication, innovation, and exceptional accomplishments of companies that drive the sectors forward each year.
From warehousing through to sea
freight and everything in between, the awards acknowledge not only the major players in these industries but also the rising stars of tomorrow.
It is a platform where organisations can showcase their contributions and highlight their transformative impact within their respective fields.
Proudly sponsored by SEW Euro Drive, the Mercury Awards have served not only as a benchmark for excellence but also as a catalyst for
continuous improvement and industry advancement.
By honouring outstanding achievements across various categories, from operational excellence to sustainability initiatives, these awards inspire others to raise their standards and push the boundaries of what is possible in logistics and supply chain management.
In 2024, the Mercury Awards will join hands with the Australian Bulk
Whatever automation you adopt, the first question you need to ask is, will my floor meet the demands of the equipment using it?
Don’t overlook the importance of your warehouse floor. Whether a brand-new facility or an existing warehouse, your floor is critical to a successful implementation.
Unsure? Call us today - we
Specialists in robotics
Design
Design peer reviews
Concrete mix designs
Consultancy & testing
Surveying
On-Site Q&A
Dilapidation inspections
Slab loading capability studies
Grinding for AMRs, AGVs, VNA
Concrete floor repairs
Floor upgrades
Coatings and screeds
Slab replacements
Joint resealing
Wire guidance installation
Defect audits
Bespoke repairs
Decentralised drive technology reduces wiring efforts
Variant reduction optimises stocks
Low weight and compact installation spaces thanks to high power density
Handling Awards, forming a collaborative gala evening that promises to be a highlight on the industry’s calendar.
This combined event will bring together leaders and innovators from both the logistics and bulk solids handling sectors under one roof and offers a unique opportunity for networking, knowledge sharing, and celebrating the collective successes of these industries.
By integrating two distinct awards programs into a single gala event, the organisers aim to enhance brand visibility, expand industry connections, and create a larger platform for recognition.
This synergy not only amplifies the prestige of each individual but also fosters a deeper sense of community and collaboration among professionals who are shaping the future of logistics and materials handling.
Participants in the 2024 Mercury Awards can anticipate a grand celebration of achievement, marked by keynote speeches, industry insights, and, of course, the presentation of coveted awards.
The nominations for the awards are free and must be completed using an online form by 11:59 pm Friday 9 August 2024. The seven award categories are below -
1. Supply Chain Innovator of the Year
2. Best Technology Application
3. Sustainability Initiative Award
4. Freight Transport Solution of the Year
5. Best Storage Solution
6. Contribution to Industry Award (This Award recognises an outstanding contribution to the field of logistics and materials handling. This category is not open for nomination)
7. One standout category at the 2024 awards is the MHD Sustainable Warehouse Award Warehouses play a crucial role in the supply chain, and their adoption of sustainable practices can impact emissions reduction and environmental stewardship.
This category underscores a pivotal shift towards sustainability within logistics operations and aims to celebrate and promote the ground-breaking efforts of warehouses across the nation that are reducing their emissions and implementing sustainable practices.
“The MHD Sustainable Warehouse Award was introduced to recognise outstanding projects that celebrate sustainable initiatives,” says Lauren Chartres, Show Director.
“So many companies are either building or retrofitting facilities and we wanted to celebrate the innovations and commitment to ensuring your business is sustainable.”
The competition welcomes nominations from warehouses that are leading the charge in sustainability, using advanced technologies, renewable energy sources, and innovative carbon offset strategies.
Whether it’s through the deployment of electric industrial equipment or the adoption of cutting-edge renewable energy solutions, this competition is a platform for showcasing how warehouses are evolving to meet the demands of a more sustainable future. ■
TGA licenced, custom-built 10,000m2 facility dedicated to Life Sciences and Healthcare Logistics. Strategically located in the Melbourne Airport Business Park with prime access to the airport, seaport, rail terminals and key road-freight arterials.
Key features include:
• Controlled ambient, cold chain and ultralow frozen product storage
• Cold chain storage +2°C - +8° capacity for 1173 Pallets
• Controlled ambient storage (+15°C to +25°C) capacity for 7,796 pallets
• Schedule drug storage
• Value added services
• Validated active and passive cold chain solutions
• Tier 1 WMS system backed by quality assured processes
• ISO 27001 (Cyber Security accreditation)
• 5 star green star rating compliant*
*Certification is in process
Ranmeet Singh, Head of Solutions, Addverb Australia, talks about warehouse automation, robotics solutions, and Addverb in Australia.
Founded in 2016, Addverb has risen to prominence as a global robotics and automation powerhouse, with a presence spanning India, Australia, North and South America, South-East Asia, Europe, and the Middle East.
The company’s industrial robot technology and automated warehousing systems are transforming material flow management, boosting throughputs, optimising storage, enhancing productivity, and refining inventory management, while reducing operational costs.
Through a unique four-dimensional approach – discover, design, deploy, and dedicated support – Addverb has delivered automation solutions to highprofile clients like Maersk, DHL, Myer, Hindustan Unilever Limited, PepsiCo, the Coca-Cola Company, Marico, Johnson & Johnson, and many more.
product portfolio of fixed and flexible automation systems such as autonomous mobile robots (AMRs), sorting robots, automatic storage
and retrieval systems, and picking technologies, fuelled by enterprise software, which helps it to provide different and customisable solutions to customers.
One of the key aspects that sets Addverb apart from its competitors is its in-house manufacturing facility. The Bot-Verse, located in Noida, India, is a testament to this commitment.
Spanning more than 600,000 square feet, this state-of-the-art facility is dedicated to advancing the robotics ecosystem.
“With only steel sheets coming in as raw materials, the entire process from design conceptualisation, R&D, to manufacturing is conducted in-house,”
The facility’s capacity to manufacture 100,000 robots annually positions Addverb as a key player in the global market.
This venture promises to drive technological advancements, foster creativity, and shape a brighter future for both the industry and the world. Addverb differentiates itself through a focus on innovation and a customercentric approach. Its solutions encompass both fixed automation (conveyors, shuttles, cranes) and flexible automation (AMRs, sorting robots).
It competes with established players in fixed automation and product-focused companies in flexible automation. Its ability to offer complete solutions across both domains –managed by its proprietary software
Leveraging AMRs and robotic sortation ensures smoother material flow and enhanced productivity. Images: Addverb.
quickly tailor solutions to meet specific operational requirements, ensuring automation solutions effectively address unique customer needs.
The proprietary software and hardware integrate with existing systems, minimising disruption and maximising efficiency gains from automation initiatives.
Addverb’s dual expertise in hardware and software is a game-changer for warehouse operations.
timelines effectively.
By retaining control over scalability and expansion capabilities, Addverb can scale to accommodate growth or changing demands without compromising performance or reliability.
This approach fosters rapid innovation cycles, incorporating customer feedback and industry trends into updates, enhancing functionality, and boosting customer satisfaction.
Advances in safety systems have opened numerous doors to automating many manual tasks without compromising safety. Addverb leverages its expertise in machinery safety to provide solutions that benefit customers by adhering to accepted ISO norms for human-machine interaction, ensuring machines are safe for operators in the warehouse.
“One of our notable implementations is a sortation solution for a leading 3PL player, where robots can be safely stopped wirelessly, meeting international ISO standards,” explains Ranmeet.
Another emerging trend is the four-way shuttle ASRS, revolutionising warehouse automation with its high operational efficiency.
This system maximises storage density by utilising vertical space, accommodating up to 10 pallets per square metre.
Its versatility and flexibility allow seamless movement in both x and y axes, adapting to evolving warehouse needs.
The global supply chain faces numerous challenges, from geopolitical uncertainties to natural disasters and global health crises.
Traditional, manual-driven supply chain models are proving insufficient to cope with today’s business complexities.
Companies now recognise the urgency and important of adopting advanced technologies that enhance efficiency, accuracy, as well as adaptability, says Ranmeet.
“Warehouse automation is emerging as a transformative force in the quest for resilient supply chains.
“The integration of robotics and automation in the supply chain is proving to be a game-changer,” he says.
By leveraging cutting-edge technologies such as robotics, artificial intelligence, and the Internet of Things (IoT), companies can streamline their operations, reduce human errors, improve overall efficiency, and introduce agility and scalability – key elements in building resilience.
Despite the transformative impact of robots and industrial automation, Addverb’s adoption presents both challenges and opportunities. This includes managing vast inventories amidst diverse customer preferences and meeting evolving demands for faster delivery strains on traditional warehouse models.
Addverb addresses these challenges by integrating advanced picking and sorting systems like Pick-toLight technology to enhance agility and meet accelerated delivery
“Additionally, cutting-edge tracking solutions such as RFID and IoT-enabled sensors offer real-time visibility into perishable inventory, mitigating losses,” says Ranmeet.
Maximising storage capacity in space-constrained warehouses remains a priority.
Addverb achieves this through utilising automated storage and retrieval systems like carton shuttles and pallet shuttles, optimising efficiency without compromising space utilisation.
In addressing the prevalent issue of labour shortages, Addverb strategically implements automation solutions, particularly in established facilities.
The deployment of AMRs and robotic sortation offers immediate relief, especially in brownfield sites where labour scarcity is acute.
Leveraging AMRs and robotic sortation ensures smoother material flow and enhanced productivity in warehouses facing labour constraints.
Addverb’s journey from its inception in 2016 to becoming a leader in robotics and automation is a testament to its pursuit of innovation and customer-centric approach.
By leveraging its in-house manufacturing capabilities, dual expertise in hardware and software, and staying ahead of industry trends, Addverb continues to revolutionise warehouse operations and supply chain management.
As the industry evolves, Addverb remains committed to providing cutting-edge solutions that not only meet but exceed the demands of its diverse clientele.
It is shaping a brighter and more efficient future for global logistics and automation. ■
MHD finds out from Richmond Rolling Robotics how its Autonomous Mobile Robots are energy
efficient, sustainable, safe, and can collect real-time data.
Australia’s supply chain and logistics industry is undergoing a transformation, propelled by advances in technology and the everevolving demands of e-commerce consumers, making innovative lastmile solutions a necessity.
In the realm of ‘smart warehouses’, Richmond Rolling Robotics’ Autonomous Mobile Robots (AMRs) have emerged as a critical technology for automating picking and packing, improving productivity, streamlining workflows and reducing human errors.
Importantly, these next-generation robots also contribute to sustainability goals, benefiting both the environment and the bottom line.
ENERGY EFFICIENCY AND REDUCED CARBON FOOTPRINT
AMRs such as Richmond Rolling Robotics Flex, Max and Apex Series
are designed to operate with optimal energy consumption, utilising the latest in lithium battery technology.
Unlike traditional forklifts and other warehouse vehicles that rely on fossil fuels such as diesel, AMRs like the Apex Forklift Series are powered by electricity and can be recharged using renewable energy sources including warehouse solar panels.
This transition leads to a reduction in the carbon footprint and overall emissions.
With large-scale warehouse operations in manufacturing, retail, health and dispatch centres looking to lower emissions ahead of 2030 targets, AMRs are becoming a key component of overall environment initiatives being made by industry.
Additionally, their advanced navigation systems ensure minimal energy wastage by optimising travel routes and reducing idle times.
Richmond’s AMRs are flexible and can navigate tight spaces and complex layouts more effectively than traditional warehouse equipment such as forklifts and order pickers.
This capability enables better utilisation of available warehouse space, reducing the need for additional storage facilities, overhead lighting, heating and cooling and the environmental impact associated with constructing new buildings. These AMRs also offer scalability. As warehouses grow or undergo layout changes, they units can be easily reprogrammed and redeployed with minimal disruption.
This adaptability means that warehouses can expand operations without the need for significant new investments in infrastructure,
leading to lower resource consumption and waste.
By maximising existing space, warehouses can minimise their physical footprint and the associated energy costs.
Human errors in picking and sorting lead to waste, both in terms of materials and energy. Richmond’s AMRs are equipped with advanced sensors and real-time inventory software, reducing the error rates across warehouse operations.
Accurate inventory management ensures that products are not lost or damaged, reducing overall waste. This contributes to more sustainable logistics by ensuring less energyintensive product manufacturing and the more efficient use of resources.
Safety is also a critical aspect of warehouse logistics, and Richmond’s AMRs play a role in enhancing it. By taking over potentially dangerous tasks – such as lifting heavy loads or operating in hazardous environments – AMRs reduce the risk of workplace injuries.
Fewer accidents mean fewer
disruptions and less need for medical interventions, contributing to a more sustainable work environment. It will make the lives of workers easier by minimising the manual strain and risk of injury throughout each shift.
AMRs are equipped with sensors and connectivity features that allow for real-time data collection and analysis. The data can be used to continuously monitor the performance and condition of warehouse operations. By harnessing this data, predictive maintenance ensures equipment is serviced before any failures occur, reducing downtime and the resource costs associated with emergency repairs.
and eco-friendly packaging, the integration of Richmond’s AMRs in warehouse logistics is a step toward achieving sustainability in the industry.
This proactive approach not only contributes to a leaner, more efficient warehouse operation but also helps to meet sustainability objectives.
With many businesses already adopting initiatives such as renewable energy, green building
The best part of Richmond Rolling Robotics AMRs is they can operate in almost any warehouse space without the need for pre-installed guiding systems that are necessary with Automated Guided Vehicles (AGV).
As more Australian warehouse operations deploy these intelligent AMRs to power their day-to-day workflows, the sustainability and cost-saving benefits will only grow with time, making it a win-win for businesses and the environment. ■
MEGATRANS, Australia’s largest logistics transport, supply chain, and materials handling exhibition event, returns to Melbourne this year.
In a fast-evolving logistics and supply chain landscape, MEGATRANS stands as Australia’s foremost integrated logistics and supply chain exhibition and conference.
The event is set for 18-19 September 2024 at the Melbourne Convention and Exhibition Centre.
Biennially hosted by Prime Creative Media, MEGATRANS will spotlight the industry’s pivot towards key priorities – future fleets, zero-carbon warehouses, traceable supply chains, and cold chain solutions.
“Before launching MEGATRANS2024, we asked the industry, ‘What is important to you?’ The resounding response was ‘Sustainability’, hence this year, our focus was on the sustainable supply chain – from zerocarbon warehouses to electric fleets and beyond,” says Lauren Chartres, Show Director for MEGATRANS2024.
The event is supported by sponsors, including the Networking Lounge Sponsor, Loscam, and Prime Creative’s Association Partners, SCLAA, and VTA.
An integral part of the event is to offer a platform for industry leaders to connect and deliberate on the role of sustainability in the future of the supply chain, and how they will be a part of the solution.
It will also showcase sessions led by industry leaders steering sustainable supply chain advancements, delivering insights and strategic perspectives.
Lauren also mentioned the steps Prime Creative Media is taking as hosts in line with the theme of the event.
“At PCM, sustainability isn’t just a goal; it’s a commitment,” says Lauren.
“For our events, including the upcoming one, we’ve reduced singleuse products, prioritised reusable
Speakers will discuss developments to ensure sustainable practices. Images: Prime Creative Media.
Partnering with suppliers who share our strong sustainability ethos is key – like the Melbourne Convention and Exhibition Centre, which diligently sorts waste to minimise landfill impact.”
The exhibition floor will feature diverse exhibitors presenting stateof-the-art warehousing solutions and transportation technologies.
“MEGATRANS is the leading supply chain event on the calendar,” says Sam Rowse, Director of MachShip, a key exhibitor at the event this year.
“We’ve exhibited once before and attended several times. Our
experiences there.
“In terms of new interactions and leads, the outcomes have been extremely positive and have translated into significant gains for our business. This event is where our market gathers, and we aim to make a significant impact.
“We have two specific goals: first, to continue growing our knowledge and experience in the sustainability space. MEGATRANS is crucial for achieving that and staying current. Secondly, we see an opportunity to communicate our sustainability initiatives to the market.”
The attendees will be able to hear from speakers representing companies such as ANL, Toll Group, Prological, Deloitte, Jones Lang LaSalle, Mosaic Brands, OneStop, and the Victorian Government.
“An event like MEGATRANS is a great way to expose the technology we’ve developed to the market and gives us a unique opportunity to speak to hundreds of people who are within this industry to get their feedback and use that to drive our product development journey as well,” says Dominic Lindsay, CEO and Co-founder at Nexabot, an exhibitor at the event.
Based in Melbourne and founded in 2023, Nexobot is an automation startup that has been working for the last couple of years to build, design manufacture, and parcel item sorting robots locally.
Furthermore, MEGATRANS will play host to the MHD Supply Chain Solutions Mercury Awards. This prestigious event seeks to honour businesses and individuals epitomising innovation, excellence, and leadership within the industry with a special focus on a new category – The MHD Sustainable Warehouse Award.
The MHD Sustainable Warehouse Competition aims to celebrate and promote the ground-breaking efforts of warehouses across Australia that are reducing their emissions and implementing sustainable practices.
“We contribute to sustainability by significantly reducing shipping emissions through local manufacturing here in Australia. We employ extensive 3D printing capabilities locally, minimising our reliance on imports. This approach allows us to reduce our carbon footprint from shipping to about one-fifth that of our competitors,” explains Dominic.
“Our use of 3D printing also affords us access to a diverse array of materials. Our primary material, bioplastic derived from corn instead of oil, exemplifies our commitment to environmentally friendly practices.”
A new feature of MEGATRANS –Fleets of the Future will offer fleet
next decade. From electric vehicles to charging stations, telematics solutions and fleet management software, companies offering these cuttingedge technologies will come together, for the very first time.
“With the decarbonisation of transportation coming fast, our vehicles are undertaking a oncein-a-century transformation”, says Lauren.
Technology that was previously unattainable is now a reality, and progressive fleets are locking in their solutions promptly. Companies who want to be included in future fleets must take advantage of every chance to showcase their technologies, Lauren added.
In partnership with the Refrigerated Warehouse & Transport Association of Australia (RWTA), MEGATRANS2024 is set to emphasise enhancing the sustainability of the cold chain, with efforts directed towards lowering carbon emissions, cutting waste, and integrating eco-friendly technologies.
Cold chain solutions are critical for preserving the integrity of perishable goods. From food to pharmaceuticals, advanced cold chain solutions will play a pivotal role in the sustainable supply chain of the future.
The event will showcase exhibitors engaged in this space and will host conference sessions discussing the newest technologies, innovations, and regulatory developments to ensure sustainable practices in the whole chain function.
logistics industry by incorporating advanced energy-efficient technologies, renewable energy sources, and strategic carbon offsetting to minimise carbon footprints.
MEGATRANS2024 will highlight the pioneering concept of zerocarbon warehouses and showcase a diverse array of solutions that enable environmentally friendly warehouse operations like never before.
Traceability in supply chains is increasingly vital in today’s global economy, ensuring transparency and accountability at every stage of the supply chain process.
These standards not only bolster commercial efficiency by streamlining operations and reducing risks but also promote ethical sourcing practices. By enabling companies to trace the origins and journey of products, traceability measures help combat the proliferation of counterfeit and substandard goods, safeguarding consumer trust and brand reputation. It is also important to remember that robust traceability frameworks are instrumental in ensuring adherence to the highest sustainability standards, facilitating the identification of environmentally responsible practices supporting efforts towards reducing carbon footprints and promoting circular economy principles. ■
Go on the website to register for MEGATRANS 2024 - https://megatrans. com.au/register/
NOMINATIONS ARE NOW OPEN FOR THE AUSTRALIAN SUPPLY CHAIN & LOGISTICS AWARDS
The annual ASCL Awards recognise the outstanding achievements of Supply Chain & Logistics professionals and organisations across Australia, celebrating industry excellence and championing collaboration, innovation, and success.
The ASCLA are the industry’s longest running and most prestigious awards. The SCLAA is proud to host this year’s 63rd Awards, recognising individuals and companies who have contributed to the advancement of the Australian Supply Chain and Logistics industry.
HAVE YOUR ACHIEVEMENTS RECOGNISED
We are inviting companies and organisations to become part of these prestigious 2024 National Awards night. Showcase your organisation, strengthen brand awareness to industry leaders and be the Ambassador of Excellence by recognising its highest achievers. LEARN MORE
The Forecasting and Demand Management course will take place from 20 to 21 August 2024 and will be conducted via Zoom.
Join the Australasian Supply Chain Institute’s (ASCI) upcoming Forecasting and Demand Management 2-Day Course to improve your forecast accuracy with less forecasting effort, which will take place from 20 to 21 August 2024.
This workshop will provide you with a step-by-step approach to achieving improvements in your forecasting process, the mistakes to avoid and surefire approaches that will reduce your forecasting effort.
Accountabilities and cross-functional links will be discussed to enable you
to assess the quality of your current processes against world-class checklists.
Options on “where to meet the customer” will also be addressed, including the strategies associated with setting safety stocks, your product offering and a simple approach to simulating stock levels.
Classes are conducted daily, from 9 am to 5 pm Sydney Time, totalling 16 training hours. Participants will join via Zoom.
ASCI members can register for $1,950, while non-members can register for $2,350. ■
Uncover sustainability trends, insights and impacts on supply chains with Nick Gothard
We’re thrilled to announce Nick Gothard, Senior Leader of Defence and Aerospace Sector, as our Keynote Speaker at the ASCI Supply Chain Sustainability Series, on the topic “Procurement as an Enabler of Sustainability”.
Register now to secure our early bird offer of $500. Don’t miss out on this opportunity to uncover sustainability trends, insights and impacts on supply chains. ■
The Australasian Supply Chain Institute (ASCI) is happy to announce the launch of the new ASCM Supplier Relationship Management Certificate, designed to empower you with the skills and knowledge to drive innovation, enhance quality, and increase efficiency in your supplier relationships.
This premier continuing education program offers comprehensive insights and best practices for transforming supplier relationships into competitive advantages. Enrolling in this program will give you an in-depth knowledge of supplier relationship management concepts, tools, and industry trends.
The ASCM Supplier Relationship Management Certificate program will equip you to:
• Identify, evaluate, and strengthen supplier and vendor relationships
• Negotiate supplier contracts and agreements effectively
• Evaluate and monitor the benefits and risks associated with suppliers
• Enhance organisational efficiency and drive value across your supply chain
This self-paced online program comprises 20 hours of comprehensive education and concludes with a final exam. Throughout the program, you will have access to various resources, including flashcards, video clips, and practice questions, all of which aim to
enhance your understanding of each topic.
Upon successfully passing the exam, you will earn a certificate and a digital badge that can be displayed on your LinkedIn profile and within your email signature. Furthermore, you will also earn 20 certification maintenance points upon program completion. Don't miss this opportunity to elevate your skills and significantly impact your supplier relationships. Enrol in the Supplier Relationship Management Certificate program today and take the first step toward unlocking the full potential of your supply chain. ■
Contact ASCI for more information.
Swisslog automated warehouse solutions’ scalable, flexible Vectura stacker crane for high bay warehouse automation reduces energy consumption of pallet warehouse operations by up to 25 per cent, thanks to features including regenerative energy design for optimal use of cycles. With an outstanding 99.7 per cent availability, and providing a solution reliability with over 50 years of continuous improvement behind it, Swedish-designed Vectura performs equally well in temperatures as low as -30°C in a frozen food warehouse, or in ambient environments as high as +50°C. Proven in more than 600 customer installations, and operating at heights up to 50m, Vectura’s single-mast design reduces cost and uses less space, setting the standard for innovative design for pallet cranes in high-bay warehouses. It achieves very high storage density, with single to multi deep reach, in high buildings and, where land space is limited.
For more information visit www.swisslog.com/en-au
Global cube storage company AutoStore introduces its latest capability, the Grid and Vending Machine solution, designed to simplify warehousing automation. The ConveyorPort is a workstation in its simplest form, where bins are dropped on a conveyor and transferred to an opening outside of the grid. Smart covering and sensors ensure operator safety. The CarouselPort is designed to work with the operator, in harmony with robots to ensure the next bin is always ready. The workstation operates with three rotating arms, each holding one bin tray. The vending machine solution includes various robots and chargers, as well as a dummy display unit, and a grid structure with 60 Bins.
For more information visit www.autostoresystem.com
The ECE series truck stands out among low-level order pickers due to its innovative features tailored for accessibility, efficiency, and operator comfort. Its height-adjustable steering wheel, known as the “jetPILOT,” ensures accessibility for operators of various heights, making it inclusive for everyone. The operator-oriented working space ensures all necessary equipment, such as scanners, shrink wrap, and documents, are conveniently within reach. Furthermore, the truck can be customised with cutting-edge technology to enable semi-automation in warehouse operations, with the possibility of integrating with Warehouse Management Systems (WMS) based on customer requirements. Experience the difference with the ECE series truck today and elevate your warehouse operations to new heights. To learn more about how our innovative features and customisable options can streamline your workflow and enhance operator satisfaction, visit our website.
For more information visit: www.jungheinrich.com.au
ifm Track and Trace Gate is the complete solution for your automated and transparent logistics in your incoming and outgoing goods processes. By directly transferring all goods flows to the IT level, you can organise the inter-locking of production, inventory, and suppliers more efficiently than ever before.
For more information visit www.ifm.com/au/en