AUTOMATING WITH TMHA
Toyota continues to handle materials with its new range of autonomous solutions
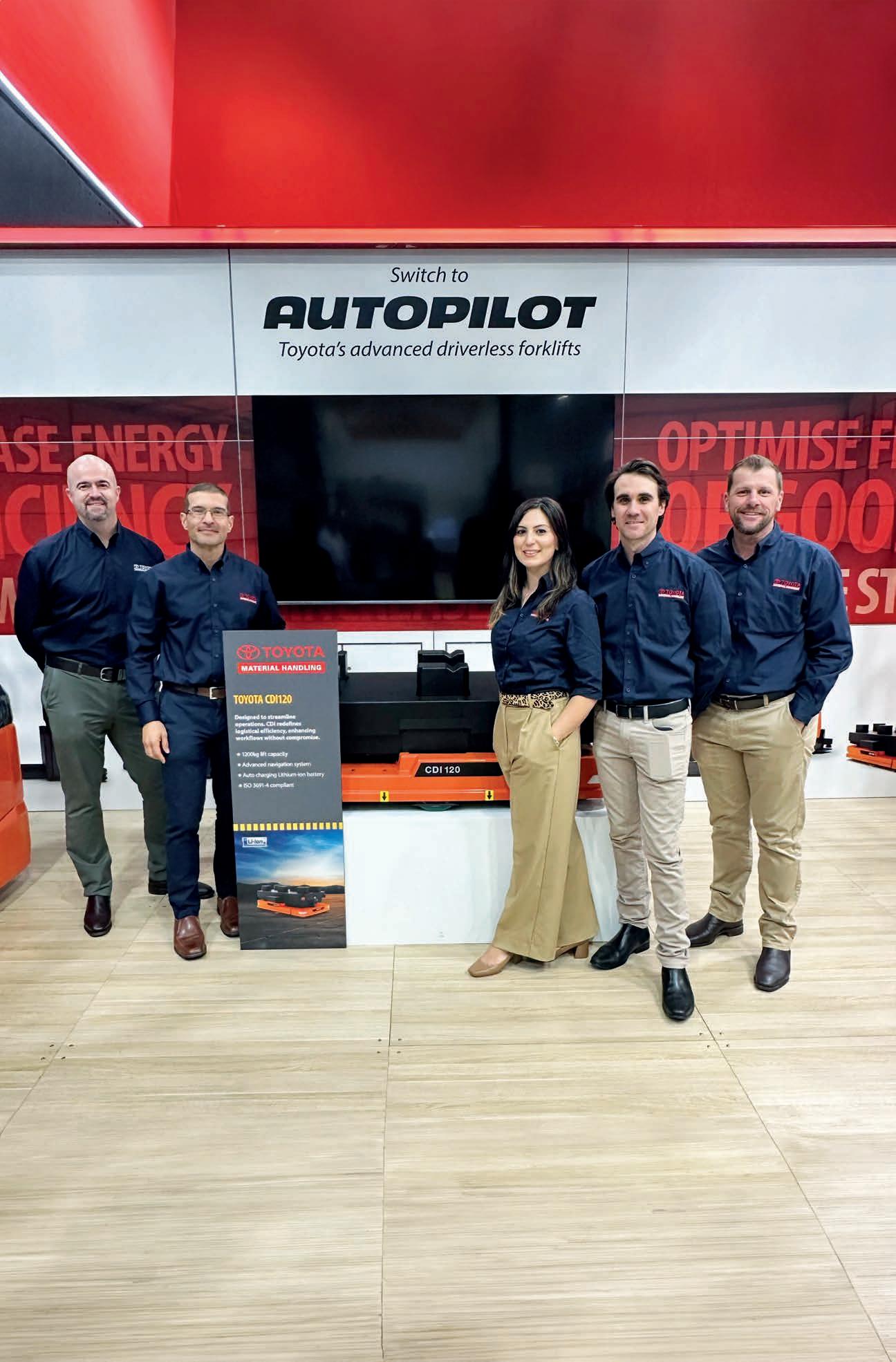
Automate X, the Kiwi company taking on the ANZ region Körber offering cloudbased solutions for warehouses UP IN THE CLOUDS DISRUPTING THE MARKET
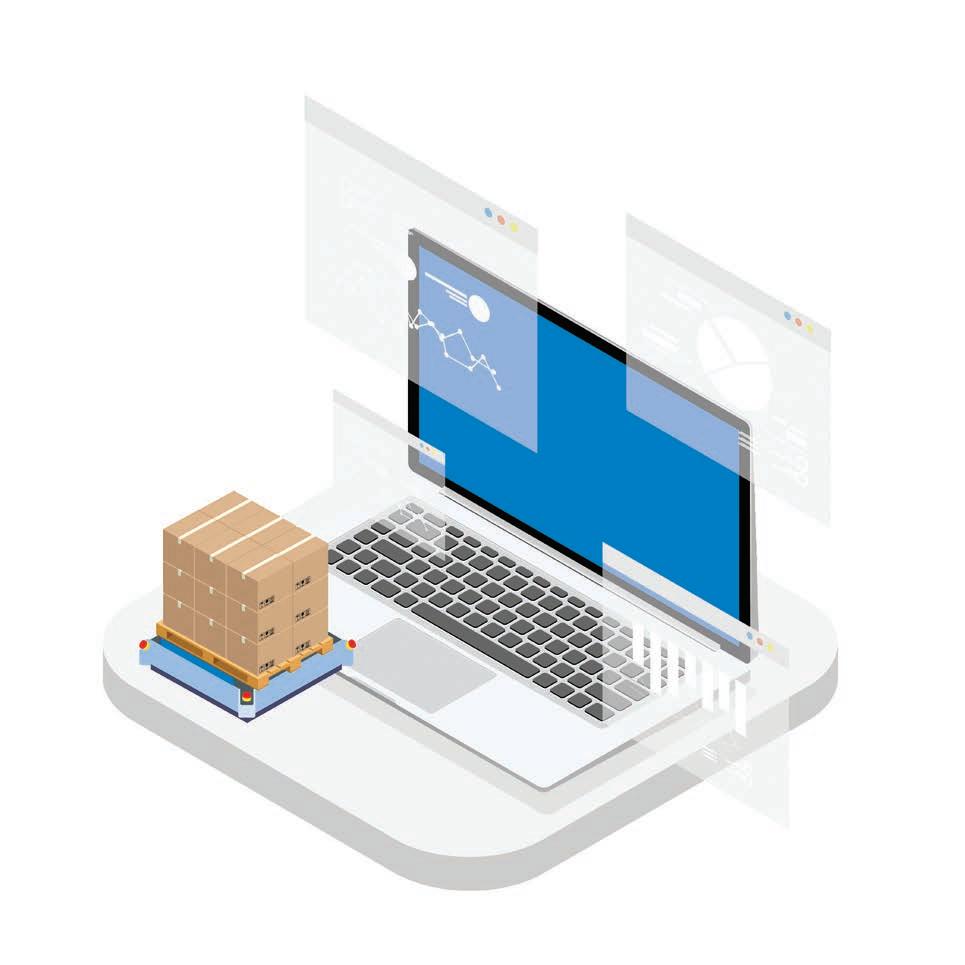
Toyota continues to handle materials with its new range of autonomous solutions
Automate X, the Kiwi company taking on the ANZ region Körber offering cloudbased solutions for warehouses UP IN THE CLOUDS DISRUPTING THE MARKET
The new 2024 Gartner® Magic Quadrant™ for Warehouse Management Systems is out and for the 6th year in a row, Körber has been named a Leader.
Scan the QR code to get your free copy of the report and discover why Körber stands out among the competition. koerber-supplychain-software.com
Scan for your free copy of the report
MHD Supply Chain Solutions is published by Prime Creative Media
379 Docklands Drive, Docklands VIC 3008
Telephone: (+61) 03 9690 8766
Website: www.primecreative.com.au
THE TEAM
CEO: John Murphy
Chief Operating Officer: Christine Clancy
Managing Editor: Mike Wheeler
Assistant Editor: Joseph Misuraca
Journalist: Mannat Chawla
Business Development Manager: William Jenkin
Design Production Manager: Michelle Weston
Art Director: Blake Storey
Graphic Designers: Danielle Harris, Jacqueline Buckmaster
Client Success Manager: Ben Griffiths
FOR ADVERTISING OPTIONS
Contact: William Jenkin william.jenkin@primecreative.com.au
SUBSCRIBE
Australian Subscription Rates (inc GST) 1yr (11 issues) for $99.00 2yrs (22 issues) for $179.00
To subscribe and to view other overseas rates visit: www.mhdsupplychain.com.au or Email: subscriptions@primecreative.com.au
ACKNOWLEDGEMENT
MHD Supply Chain Solutions magazine is recognised by the Australian Supply Chain Institute, the Chartered Institute of Logistics and Transport Australia, the Supply Chain and Logistics Association of Australia and the Singapore Logistics and Supply Chain Management Society.
ARTICLES
All articles submitted for publication become the property of the publisher. The Editor reserves the right to adjust any article to conform with the magazine format.
COPYRIGHT
MHD magazine is owned by Prime Creative Media. All material in MHD is copyright and no part may be reproduced or copied in any form or by any means (graphic, electronic or mechanical including information and retrieval systems) without written permission of the publisher. The Editor welcomes contributions but reserves the right to accept or reject any material. While every effort has been made to ensure the accuracy of information Prime Creative Media will not accept responsibility for errors or omissions or for any consequences arising from reliance on information published. The opinions expressed in MHD are not necessarily the opinions of, or endorsed by the publisher unless otherwise stated.
As September springs upon us, the largest logistics and transport exhibition in Australia, MEGATRANS, runs in Melbourne from September 18-19 with the Mercury Awards taking place in the evening of the first day. This means that the first MHD Sustainable Warehouse Award will also be handed to one lucky recipient.
In this MEGATRANS-themed edition of MHD Supply Chain Solutions, Toyota Material Handling Australia (TMHA) gives us the lowdown on its range of new autonomous solutions as it continues to sift through the exciting terrain of automation.
From across the ditch, three Kiwi companies based in Auckland: Automate X, Sandfield and vWork, dig deeper into the Australian market as they tell us why their software and hardware solutions are suited to digitising Aussie warehouses and streamlining their operations.
Then there is Toll, who talks about its new Tullamarine warehouse.
With supply chain visibility and telematics as the promo for this edition, companies like MachShip, Körber and Santova explore freight forwarding and cloud-based solutions, as well as harnessing the power of artificial intelligence for supply chains.
Material handling enterprises are always busy lifting heavy stuff. Linde, Jungheinrich and Combilift are no exceptions as they share what projects they’ve been working on and new solutions they have on offer.
We have Peter Jones from Prological sharing his wisdom in an op-ed for the Logical Outlook column.
Finally, as the new season begins and the months get warmer, keep yourself informed and up to date on this fast-changing industry by reading this special showguide edition of MHD.
Mike Wheeler
Managing Editor, MHD Supply Chain Solutions mike.wheeler@primecreative.com.au
Known for market leading Toyota forklifts and warehouse equipment, Toyota Material Handling is also proud to o er an unparalleled range of products suitable for Australian businesses. With a huge range of forklifts, elevated work platforms, scrubbers and sweepers, Taylor-Dunn electric vehicles, plus Huski skid steers, scissor lifts, and mini excavators available, chances are we’ve got the equipment that will suit. So, if you’re looking to buy hard working, fully backed equipment for your business, Toyota Material Handling has all you need to add value to your operation. That’s the Toyota Advantage.
12 TMHA displays its autonomous solutions
18 Logical Outlook on automation, people and data
24 MachShip launches new software solution
31 Körber shifting to cloud-based solutions
37 Sandfield managing complex projects
40 GS1 exploring sustainability
43 Toll opens new facility
46 Kardex partners with Douglas Pharma
58 Santova explores AI in supply chain
75 vWork on last mile delivery
82 Bonfiglioli on why cranes need drives
27 Linde improves Chemist Warehouse’s operations
34 Jungheinrich on advantages of lithium-ion batteries
49 Combilift innovating solutions
55 NORD delivering tailored solutions
21 Automate X on its offerings and innovation
61 Vanderlande automating with FASTPICK
64 Kärcher on its showcase at MEGATRANS
67 SICK improving efficiency
70 Adept Conveyor on its multifunctional conveyor systems
72 Falcon Autotech’s transformative journey
78 Nilfisk on sustainable cleaning solutions
80 Airstack Intralogistics – a one-stop shop
06 People on the Move
08 Industry Focus
52 Future of logistics at MEGATRANS
74 SCLAA on the ASCLAs
77 SCLAA on the ASCLAs
84 ASCI’s seminars, classes, and cer tificates
86 Product Showcase
Nathan Busuttil has been appointed as the head of the newly established Bulk and Warehousing Division of Visy Logistics. With more than 25 years of experience in logistics, Nathan excels in overseeing large-scale operations and maintaining high safety standards. Known for his leadership, strategic planning, and problemsolving skills, he has a track record of optimising supply chains, reducing costs, and enhancing productivity. Nathan is committed to delivering excellence and ensuring customer satisfaction in all aspects of bulk operations.
Sandfield, a provider of IT solutions, has named Matthew Keith as its new Chief Executive Officer. Matthew, a 23-year veteran of Sandfield, brings a wealth of experience in IT, logistics, and supply chain management. He has been instrumental in nurturing the company’s 35-year partnership with Mainfreight, a key client and one of New Zealand’s largest supply chain companies. In his new role, Matthew will oversee all aspects of Sandfield’s business, including its specialised supply chain division, Origin.
intralogistics and seven years in the APAC region, has joined Ferag as the APAC Service Director. He has experience in service and support roles, showcasing a passion for customer support and team development. Michael began his career as an electric and electronic engineer, progressing to site management and field service engineer roles, gaining global experience. His passion for service led him to establish a UK service organisation, growing it to 185 employees. His APAC journey includes senior roles at Daifuku, Schaefer Systems International, and Vanderlande, focusing
Jeff Triantafilo joined Argon & Co in 2022 after the merger with Fuzzy LogX and has now been made a partner of the company. He comes with an engineering background, and expertise in warehousing and logistics. Jeff has worked across various sectors such as pharmaceuticals, retail, and mining. His grasp of the latest technologies and advancements in automation and logistics reflects his dedication to emerging industry shifts and driving transformative solutions.
With 30 years of supply chain experience in automation and IT, Michelle Van Driel has held senior IT management roles in ASX 200 companies and MNCs. She has joined Ferag as Head of Intralogistics. Michelle specialises in ERP/WMS software, business transformation project management, and SAP implementation. She has led streams within major supply chain projects like Australia Post’s Future Network program and Kmart’s Automated Sorting Program. She has consulted on large automation, business transformation, and IT programs across diverse industries including retail, manufacturing, health, FMCG, resources, and NFP, bringing process expertise to complex supply chains.
Katie Budd has recently made the move from the UK to Australia and has been made ANZ Sales Manager for Vanderlande. In the UK, she began her career in the Intralogistics world eight years ago. Katie has worked in both sales and solutions design, understanding end-to-end systems.
■ Learn about the megatrends driving today’s supply chain challenges.
■ Understand how GTP solutions address these challenges whilst providing a competitive edge.
■ Discover the features and benefits of the leading solutions – AutoStore , Multishuttle GTP , and Autonomous Mobile Robots (AMRs) .
■ Read a detailed analysis and comparison of the technologies and how they align with business throughput and storage requirements.
Tennant Australia has recently unveiled its new Sydney-based Recon division, dedicated to the repair and resale of industrial and commercial cleaning machines.
This move marks a step forward in providing local businesses with sustainable and cost-effective alternatives.
The Recon Division is a step forward towards sustainability and reducing waste. This initiative supports a circular economy, where products are reused and recycled, thereby reducing the demand for new resources and lowering carbon footprints.
Tennant’s commitment to quality and durability means that every piece of equipment, whether Certified Pre-Owned or Used, meets high performance and reliability standards.
A feature of the Recon Division is the refurbishment process. Each
Cby technicians to ensure it performs like new.
The purpose of the new division is to allow businesses to maintain high hygiene standards without the high
factory direct warranty, meaning our customers can have peace of mind with purchasing from the Manufacturer,” says Jye Jones, Tennant’s National Service Manage.■
mbilift’s first multi-directional forklift is just one of dozens of patented designs where company stalwart, Mark Whyte, was instrumental in its design and development. After 26 years of service, Mark has made his mark on materials handling worldwide.
From the Combilift multi-directional C4000 in 1998, to the Pedestrian range’s tiller arm in 2012, Mark has helped Combilift reinvent forklifts so that they improve safety, maximise storage, and increase efficiency for customers.
Now working as a research and development manager, Mark remains loyal to the company ethos of continuous development.
“The company has a very good
can-do attitude, from higher management right through the entire workforce,” says Mark.
“In development, we listen to our customers and our salespeople as to what’s needed in the market.”
This has led Combilift to register roughly 140 patents worldwide.
The Pedestrian tiller arm has been one of Combilift’s most popular patents. This innovation has allowed warehouses worldwide to narrow their aisles by repositioning the operator to the side of the truck while increasing visibility.
Mark describes the moment he and Combilift’s co-founders – Robert Moffett and Martin McVicar –dreamt up the solution.
“The invention on the pedestrian model’s tiller arm was like a light bulb moment around my desk one day with Robert and Martin,” says Mark. “We said, ‘Imagine if you could just stand to the side of the forklift’. That was the beginning of a great idea.” ■
Heli Oceania marked a milestone with the opening of its new Warehouse in Australia and the launch of the G3 Series Compact Rough Terrain forklift.
The event, held on 4 July 2024, was attended by industry partners, important HELI China Staff and media representatives from across the region, showcasing Heli Oceania’s commitment to advancing material handling solutions.
The event commenced with the arrival of guests, Anguo Yang (President of the Anhui Forklift Group) and Guo Yang (General Manager of Heli Industrial Vehicle Imp. & Exp.).
“For more than 20 years, Heli’s products have crossed the ocean to Australia. Deeply cultivating this
market,” says Anguo Yang.
“Today, we bring an excellent team to take root here.
“Not only does Australia have an open business market but a gathering of outstanding talents and infinite innovative potential from all over the world.”
This year marks the 10th anniversary of the establishment of the strategic partnership between China and Australia and the 66th anniversary of Heli.
Heli values sustainable development and pays attention to environmental, social and corporate governance. no
A spokesperson said that the company not only pursue scommercial success but aims to make a positive contribution to local social and economic development.
Heli Material Handling Oceania will
Job scheduling and dispatch software that delivers on the bottom line •Proof of delivery, time stamped and auditable •Three-way SMS between dispatch, truck & customer •Real-time invoicing •Template driven software - works the way you do •Integrates with existing business tools
6,000+ active users
Over 400,000 jobs per month dispatched
Customers in 10 countries
vworkapp.com
create job opportunities for Sydney and its surrounding areas and actively participate in local social welfare undertakings.
The new warehouse is designed to enhance operational efficiency and provide faster local customer support to Heli Oceania’s growing customer base.
One of the highlights of the event was the unveiling of the G3 Series Compact Rough Terrain Forklift. ■
Toyota Material Handling Australia’s, Neil Beveridge, talks to autonomous solutions showcased at CeMAT 2024 in Melbourne.
Toyota Material Handling Australia (TMHA) has been a prominent player in the forklift and materials handling sectors, known for its innovative approaches and commitment to quality.
Over the past few years, TMHA has further ventured into the realm of autonomous solutions, a move that reflects the broader industry’s shift towards automation.
Neil Beveridge, Product Manager Automation at TMHA, shared insights into this transition, highlighting the reasons behind the company’s new focus and detailing the products that are set to revolutionise the logistics landscape.
TMHA also offers semi-autonomous solutions designed to streamline tasks such as order picking, while enhancing safety and costeffectiveness. As this technology becomes more sophisticated –particularly with the integration of virtual reality – its applications will continue to expand.
“We already lead the market with our manual forklift equipment,” says Neil. “Introducing autonomous solutions is a complementary extension to our existing range. The industry is rapidly moving towards automation, and not embracing it would mean falling behind.”
This strategic decision aligns with the industry’s trend towards integrating automated systems, driven by the need for efficiency, safety, and
At the forefront of Toyota’s new offerings are two Automated Guided Vehicles. Images:Toyota Material Handling Australia.
“The primary reasons businesses are automating their warehouses are labour security, safety benefits, and cost reduction,” says Neil.
“It’s increasingly challenging to secure reliable labour, and automation helps mitigate this issue while also addressing warehouse safety and the high labour costs in Australia.”
At the forefront of Toyota’s new offerings are two Automated Guided Vehicles (AGVs).
“The SAE160 is an automated stacker designed for ground transport and low-lift operations in production/ warehouse facilities,” says Neil.
“It’s an automated unit that is able to support larger higher reach units, providing a seamless transition from ground-level tasks to more complex high-reach operations.”
The CDI120, on the other hand, is tailored for facilities requiring the shuttling of goods.
“It’s a platform AGV that handles ground transport tasks without the need for forks,” explains Neil.
“Businesses appreciate it because it removes the need for forklifts in the area, enhancing safety and efficiency.
“It still requires platforms for moving goods, but it excels in basic transport tasks while allowing larger vehicles to manage the lifting tasks.”
For businesses considering the shift to automation, the question of return on investment (ROI) is crucial.
Neil outlines that, depending on the operation, a typical ROI timeframe for a three-shift, 24/7 operation is around two years.
“Achieving ROI within two years is considered a good result, especially
with continuous operation. As the number of shifts decreases, the ROI period may extend, but the benefits of automation often justify the investment.”
The move towards automation is not solely driven by cost concerns. Neil highlights labour security as a pivotal factor.
“The ability to secure skilled labour is becoming increasingly challenging, and automation helps bridge this gap,” he explains.
“Additionally, automation improves product quality by reducing the risk of damage and human error, ensuring consistent and reliable operations.”
Toyota’s commitment to sustainability extends beyond the products themselves to the manufacturing processes.
operated trucks, our autonomous Toyota also provides dedicated standard for industrial driverless
trucks,” explains Neil.
This compliance ensures that the vehicles and systems adhere to safety regulations, including speed governance and clearances. Toyota also offers maintenance packages, leveraging its network of technicians across Australia.
“We have technicians in every capital city and several remote hubs, ensuring coverage for our customers nationwide,” adds Neil.
“Our support includes both hardware maintenance and system support, with options for 24/7 assistance.”
Toyota’s participation at shows like CeMAT marks a significant moment, showcasing its commitment to innovation and customer engagement.
“CeMAT is an intralogistics show, and our combination of forklifts and AGVs fits perfectly within this space,” says Neil.
“It’s a great opportunity to connect with existing customers and showcase our offerings to potential new ones.”
The show also provided a platform to demonstrate Toyota’s dual systems – combining AGVs and forklifts –highlighting its integrated approach to intralogistics.
“Being at CeMAT allows us to reinforce our presence in the market and ensure we are at the forefront of the industry’s evolution,” adds Neil.
While leading AGVs represent one part of Toyota’s foray into autonomous solutions, these go hand in hand with intelligent automation software such as TMHA’s T-ONE.
It’s in-house software developed and installed as an integration layer communicating with the Toyota Autopilot AGVs and existing infrastructure such as warehouse management systems, goods identification and other material handling equipment.
“T-ONE offers a modern, servicebased architecture, with well-defined APIs (Application Programming Interface) for easy integration to the platform,” says Neil.
“This intelligent software offers
operational robustness and flexibility for easy scaling of your operations and quick commissioning, making it suitable for applications with a significant number of vehicles.”
The solution can be configured for a variety of flows and provides a customisable user interface for the operator supporting manual interaction with the AGV system. T-ONE also provides a set of performance metrics, with graphs presented in the user interface. What does T-ONE stand for?
Optimise your flow and efficiency.
• Optimises how your transport orders are executed and reduces order processing time due to the intelligent dynamic order allocation function.
• A llows easy scalability to expand a system as a business continues to grow.
Navigate intelligently and quickly.
• A lways chooses the most ideal path for the Autopilots by scanning the system and adapting to changes of the planned travel path.
• A llocates orders to the best-suited autopilots, taking the entire operations flow into account. Execute safely and accurately.
• Ensures that all loads are delivered when and where you need them, due to intelligent order allocation.
• Provides a robust order execution to guarantee a steady logistic flow according to the expected throughput.
How T-ONE orchestrates a company’s operation
T-ONE is at the heart of Toyota’s automated solutions: it supervises
and optimises a company’s operation. This intelligent automation software takes care of the order and traffic management of the Toyota AGVs and offers functions such as:
• order initiation;
• destination setting;
• t ransport management;
• metrics and error visualisation;
• use and security management;
• system integration; and
• battery management.
As Toyota continues to innovate in the field of automation, the company remains committed to meeting the evolving needs of the logistics industry.
With a focus on sustainability, efficiency, and safety, Toyota’s autonomous solutions are poised to play a pivotal role in shaping the future of logistics.
For businesses considering automation, Toyota offers a suite of products backed by a support network and a commitment to quality.
Toyota’s foray into autonomous solutions is not just a strategic move, but a response to the changing landscape of the logistics industry.
“Automation is about staying ahead and delivering the best solutions to our customers,” says Neil.
TMHA provides an extensive range of forklifts and warehouse equipment to its Australian customers, including AGVs (driverless forklifts), integrated pallet shuttles, elevated work platforms, scissor lifts, sweepers and scrubbers, and cutting-edge fleet management software.■
Prological’s Managing Director, Peter Jones, explains how matters of automation, people, and data were central to CeMAT 2024.
There were three take homes from CeMAT 2024: automation for small business is now real; importance of data continues to grow; and supply chain is still a people business.
With 28 years in the supply chain industry under my belt, I am excited to see how much more there is to learn. The event only confirmed the complexities amid the ever-broadening array of possibilities, not only emerging, but available today.
This year I believe I saw the largest transition in ‘intra-logistics’ capability, the most uniform communication from the event’s Knowledge Theatre and saw greater possibilities to improve supply chain capability – especially smaller businesses.
Expanding on the three key takeaways at CeMAT 2024, I’d say that:
• Automation is evolving and is becoming more accessible for smaller operations.
• People are still at the centre of supply chain. There’s an evolving awareness that with the emergence of the digital supply chain, compounded by automation, the people-related issues in supply chain have to evolve with these changes.
• Data. It’s got to be clean and accessible, ready to be turned into information in minutes – not weeks.
We have all seen the Tier-1 materials handling companies performing
incredible automated tasks with AutoGuided Vehicles (AGVs), Automated Mobile Robots (AMRs), auto-stores, pallet shuttles, Automated Storage and Retrieval Systems (ASRS), and so on.
Tier-1 companies with these tools have separated themselves from the pack previously, with smaller organisations longing for such capability in smaller, humbler facilities.
This year’s event displayed a new reality in that automation is no longer the domain of large companies, but accessible and value adding for many small companies. The world has changed.
I saw cost accessible automation that will work in 1000 sqm and 1500 sqm warehouses, with store product
at high density from floor to roof in multiple-sized totes, enabling fast and accurate picking and packing.
Also, there are modularised sortation systems that can be installed and up and running in just hours.
In 2023 I received a question from the floor after I had spoken –“what about the small businesses?” What a difference a year makes. In 2024, there is no shortage of smart automation options for smaller operations.
Today, there is a plethora of smaller, entrepreneur-led firms armed with mechatronics degrees, bravery, and the tenacity to deliver automation capability to transform smaller businesses. An expanding business inside a 1500 sqm warehouse now mightn’t need to move into the 3000 sqm warehouse to grow; automation solutions targeted at these businesses might now be the better stepping stone.
Automation for small business in small warehouses is now real, and Prological is excited to see where these improvements lead.
Because automation was such a big theme on the exhibition side of this year’s event, it was only natural that the impact on people would be a major topic from the Knowledge Theatre. I heard many speakers discussing the impact of digitisation and automation in the supply chain on people.
While re-affirming the reality that supply chain is still a people business, there’s no doubt that some of these people, moving forward, will be different to the people of the past.
Transitioning a facility and its team from traditional warehouse practices to a more automated environment will require investment in training and patience.
Some people mightn’t transition well, while others will thrive in the opportunities, finding new possibilities for themselves in the new roles required.
Mechanical and electrical engineers will become part of the supply chain team, software engineers and robot technicians will be added, while the
skillset of those ‘on the floor’ will change.
Several attendants and speakers at CeMAT discussed the importance of the transitional leadership team to prioritise the people in at least equal measure to the operational transition. It’s easy to see the new shiny toys in the warehouse – it’s much harder to see the early signs of stress and concern of those who have enabled the operation to evolve to this new state but are not sure about what their future is in this ‘brave new world.’
I live in Wollongong. Do you know how many ways there are to misspell Wollongong? If your customer data base has more than one way something is represented, that is a problem. We have all seen or heard of instances where a street has been labelled an avenue, or a package has a post code for the right suburb, but in the wrong state. When we get to our product master files, typically it is even worse.
Master data files with these errors make it more difficult to turn data into information, and in too many
Product master and order files must be complete and accurate to both specify and design any automation additions to your warehouse to enable quick and accurate decision making within the business.
Frank Bucolo, Country General Manager from Slimstock, spoke at length about the data rich, but information-poor environments he sees as his firm supports businesses and takes a fresh perspective on inventory management.
The clear message from both was the importance of quality, complete, and accurate data.
Both speakers emphasised the importance of high-quality, accurate data when undertaking changes to warehouse operations and inventory management, and how for those projects to succeed, data must be transformed into empowering information to be understood by decision makers who may not be logisticians.
Over the next five to seven years, two categories of supply chain execution will emerge. The table below by McKinsey suggests that we are at a fork in the road to the future.
Over the next five to seven years, two categories of supply chain execution will emerge.
businesses, this creates an impossible situation. This was brought home with great strength by two speakers. Michael Kemeny, Managing Director of Knapp Australia, spoke of the importance of data as it relates to progressing your operational environment, specifically your product master file and order files.
One path leads to success and will be full of businesses that get data, people and automation right. The other group will be diminishing in number and will be known as the ‘have nots’ because they didn’t get this transitional season right.
If you would like to investigate any of the above for your business, please contact Prological Consulting. ■
Ben Haughey and Jordan McFall from Automate-X, the industrial automation solutions company founded in Auckland, New Zealand, explain its offerings and projects it’s worked on.
n the midst of the COVID-19 pandemic, a new player emerged in the automation industry –Automate-X, founded in 2020 in New
As businesses faced challenges in their supply chains, the demand for automation solutions grew. Automate-X seized this opportunity to innovate across various sectors.
“We saw a significant boom in automation demand due to labour restrictions and the need for efficient Director of Operations and Co-founder
“Our solutions have been diverse, initially focusing on manufacturing machine vision, and now expanding
From the outset, Automate-X has technological advancements and offer comprehensive support systems. This collaborative approach ensures that we’re not just service providers, but also strategic partners in their growth. We offer turnkey solutions, including project management, engineering, and ongoing support,” says Jordan McFall, Business Development Manager for
“Our clients appreciate that we provide end-to-end services, from conceptualisation to implementation
and beyond. This partnership model has been crucial in our projects, especially as we expand into new markets.”
Automate-X has been active across a range of industries.
“We work with some of the largest companies in the dairy and manufacturing sectors in New Zealand,” says Ben.
“Our projects have included innovative solutions like the four-way shuttle system for a food distribution company and bespoke machine vision applications for quality control.”
““We’re proud to introduce the first mobile goods-to-person system to a client in New Zealand,” explains Ben. “This project, on the back of our first project with Geek+ in Melbourne,
Australia, marks a milestone as Automate-X expands its footprint beyond New Zealand.”
As Automate-X enters the Australian market, the focus is clear.
“In Australia, we’re concentrating on logistics automation, particularly within warehouse environments,” says Jordan. “We aim to handle everything from bulk storage to intricate logistical challenges.”
“Our team is heavily involved in every stage of the project,” explains Ben.
“Our engineers are trained in the specific technologies we use, such as Geek+. This hands-on approach makes us an extension of our client’s team, ensuring seamless integration and optimal performance.”
Automate-X’s values are partnership, nimbleness, and excellence. Images: Automate-X.
Automate-X is committed to providing robust post-implementation support.
“We offer tailored maintenance and service level agreements to meet our clients’ specific needs,” says Jordan.
“Our service team is available 24/7, providing preventive and corrective maintenance. This comprehensive support structure is crucial in ensuring our customers realise the full benefits of their automation investment.
“Our team is diverse and skilled, covering everything from machine vision and machine safety to system engineering,” adds Ben. “This versatility allows us to be nimble and responsive, adapting to any challenge that arises.
The team at Automate-X is a blend of experienced professionals from various backgrounds, united by a shared vision of robotics.
“Our team members are not just experts in their fields; they are problem solvers and doers,” says Ben. “We look for individuals who are flexible, nimble, and ready to learn new skills. This mindset is what sets us apart and enables us to deliver exceptional solutions.
“Our values – partnership, nimbleness, and excellence – are at the heart of everything we do. We aim to do things well, ensuring that our clients receive the best possible service and support.”
As Automate-X looks to the future, its plans are ambitious.
“We’re growing our team in Melbourne and plan to establish a presence in Sydney later this year,” says Ben.
“This expansion is part of our strategy to offer local support and strengthen our position in the Australian market.”
“We’re also working on several key projects, including warehouse
solutions to our clients.”
Automate-X aims to be more than just another player in the automation industry; it seeks to disrupt the market.
“We want to make a big impact and provide real value to our clients in Australia and beyond,” says Jordan.
“Our focus on long-term
“It’s not just about selling a product; it’s about educating and guiding our clients through the entire process,” adds Ben.
“We believe that automation is a journey, and we’re here to help our clients every step of the way.”
As Automate-X continues to expand and innovate, it wants to be known for its partnership-driven approach and commitment to excellence. ■
At its best when high volumes of inventory need to move in and out of storage in the right order – and at the right time.
> high performance on a small footprint
> built-in sorting and sequencing capabilities
> the fastest and most predictable lead times
> accurate item and order delivery
> less dependency on increasingly scarce labour
> adaptability to deal with new items, peaks or events
> and easy scalability to handle long-term growth
Learn more on vanderlande.com or contact our Australian experts directly at sales.au@vanderlande.com or call 1300 375 028.
MachShip’s Sam Rowse gives an insight to the company’s latest
MachShip is known for its robust logistics platform, seamlessly integrating with more than 250 Australian carriers and processing more than a million consignments monthly.
The current system automates numerous administrative tasks, providing consolidated tracking visibility across multiple carriers.
“The existing version of MachShip is well-placed to address the trend towards automation,” says Sam Rowse, Chief Revenue Officer, MachShip.
“We already deliver strongly from an automation perspective, handling routine and mundane tasks efficiently.”
The forthcoming MachShip V3 promises to elevate this foundation, introducing a sophisticated workflow engine that enhances automation capabilities.
This new feature will enable users to customise system workflows, aligning logistics operations with specific and complex business rules.
“One of the cornerstone features of MachShip V3 is our sophisticated workflow engine,” says Sam.
“It allows users to automate routine tasks even further, customising workflows based on data such as the origin warehouse, the destination address, or customer preferences.”
This engine will support intricate
logistics scenarios, such as determining the carrier mix based on the warehouse location or providing different notifications based on delivery types.
“It’s a classic ‘if this, then that’ scenario, where the workflow can be configured to handle various contingencies, provided the data is available.”
A feature of MachShip V3 is the ability to manage multi-leg and multi-carrier consignments. This feature will allow users to plan and execute shipments involving multiple stages and carriers, akin to booking multi-city flights.
“We’re introducing a feature for multi-leg consignments, similar to multi-city travel bookings,” says Sam. “This will offer more choices and visibility around freight, especially for regional or specialised areas.”
This innovation is not commonly found in competing systems, making it a good selling point for MachShip.
The increased choice and visibility are expected to be beneficial for businesses needing to manage complex logistics scenarios, including those with specialised freight profiles.
The MachShip V3 platform is designed with the current market trends in mind, where value and certainty are paramount.
“Customers today are more discretionary than ever,” says Sam.
“It’s not just about the cheapest or fastest option anymore; it’s about providing certainty around delivery times.”
The platform’s ability to offer detailed carrier analysis and reporting capabilities helps businesses understand the costbenefit balance, ensuring they can meet customer expectations reliably.
This focus on certainty is crucial, as poor shipping experiences can impact customer satisfaction.
“An overwhelming number of one-star reviews are due to shipping issues, not product quality,” adds Sam. “Meeting shipping expectations is crucial to avoid negative reviews and ensure customer satisfaction.”
MachShip V3 will also introduce an enhanced reporting engine, moving beyond the current Excelbased reports to offer more visually engaging and meaningful presentations of data.
This upgrade will support retailers and other businesses in making data-driven decisions.
“V3 will bring our data to bear in a far more meaningful, useful way,”
This flexibility ensures that businesses can access and analyse their data in the most suitable format for their needs, whether for internal assessment or regulatory reporting.
The visibility provided by MachShip V3 will help users track key performance indicators, monitor supply chain efficiency, and identify areas for improvement.
As the trend towards omni-channel retail continues to grow, MachShip’s integration capabilities become increasingly vital.
The platform’s ability to integrate seamlessly with various retail systems, including shopping carts, marketplaces, warehouse management systems, and ERPs, ensures a unified and efficient operation across all channels.
“We fit into existing processes, whether through file-based integrations, APIs, or even simple email-based setups for smaller operations,” says Sam.
This flexibility allows businesses to operate efficiently from their preferred systems, ensuring a smooth logistics operation from order placement to delivery.
MachShip’s integration capabilities provide a seamless customer experience, essential for retailers looking to excel in an omni-channel environment.
In response to growing concerns about sustainability, MachShip V3 will introduce a carbon calculator.
“The carbon calculator will enable
make more sustainable choices, such as optimising delivery routes and selecting eco-friendly transport options.”
The introduction of the carbon calculator aligns with the increasing demand for sustainability in logistics, offering users the tools to make actionable steps towards reducing their environmental impact.
Beyond the immediate enhancements in V3, MachShip aims to evolve into a comprehensive logistics-focused ERP platform.
“We currently focus on freight management, but we’re looking to expand into areas like inventory management and order management,” explains Sam.
“We’re also exploring tools for international shipping, customs clearance, and more.”
This ambitious roadmap reflects MachShip’s commitment to continuously improving and expanding its offerings, ensuring that the platform remains at the forefront of logistics technology.
MachShip V3 represents an advancement in logistics technology, building on an already strong foundation to offer enhanced automation, sophisticated reporting, and integration capabilities.
With features like the sophisticated workflow engine, multi-leg consignments, and a carbon calculator, MachShip V3 is poised to set new standards in the industry.
As businesses navigate the complexities of modern logistics, MachShip V3 offers the tools and flexibility needed to stay ahead of the curve, delivering value and certainty in a rapidly changing market. ■
Chemist Warehouse’s David Brennan and Jude Thomas talk about why the pharmaceutical wholesaler is using Linde Material Handling Australia’s lithium-ION solution.
Chemist Warehouse has partnered with Linde Material Handling Australia since 2008, and over the years, both companies have worked together on multiple projects that have continuously improved Chemist Warehouse’s operations.
David Brennan, GM of Supply Chain at Chemist Warehouse stated, “Chemist Warehouse’s journey with Linde started as a short-term rental
only. Over the years, that expanded based on the excellent customer service we received, the reliability of their trucks, the technology advancements they could provide, and their ability to quickly and efficiently service our needs which in turn allowed us to service our customers.”
The partnership has adapted to suit the changing needs of the business. The most recent upgrades include the introduction of FleetFOCUS, Linde’s
Telematics system, and the rollout of a Lithium-ION battery technology solution across their national fleet.
UPGRADING FROM LEAD-ACID TO LITHIUMION BATTERIES
Chemist Warehouse made the decision to upgrade its entire fleet from lead-acid batteries to LithiumION battery technology based on the recommendation of trusted advisers at
Linde who knew the intimate details of Chemist Warehouse’s application needs. This upgrade resulted in:
• P roviding more uptime: As Li-ION batteries have a longer run time than lead-acid and can be fast-charged at any time; and
• L ess maintenance: In that it removed the requirement of weekly watering of the lead-acid batteries, as well as needing to expose the batteries during charging.
A huge benefit that Chemist Warehouse has experienced from this upgraded solution is increased utilisation of their fleet. This was a key driver behind the decision to change, particularly the fact that operators could fast-charge the trucks via opportunity charging — where operators can put the truck on charge at any time for any amount of time.
Brennan stated, “On any given week, Chemist Warehouse will be delivering anywhere within the vicinity of 70,000 boxes to our stores across Australia. What we’ve been able to do has been incredible. Linde’s system and their fleet work when we need them to work, and we’ve been able to push out incredible volumes as a result.”
Another recommendation from Linde to Chemist Warehouse was the introduction of their FleetFOCUS telematics software. Once FleetFOCUS had been rolled out across their national fleet, Chemist Warehouse was able to immediately identify operational issues that needed to be addressed.
Brennan stated, “What we noticed immediately upon implementation is that everybody has their favourite truck. Some trucks were being utilised for 30-40 hours a week and others 0-10 hours per week. FleetFOCUS gave us the visibility to better manage the trucks to ensure they were all being utilised equally.”
Another benefit from the introduction of FleetFOCUS was that it removed the need for a paper-based pre-start checklist. With the removal of all paperwork, all faults, reports and accidents were immediately inputted into the system and were easily managed across the country.
Jude Thomas, National Safety & Facilities Coordinator at Chemist
Warehouse commented, “It’s been very important to have FleetFOCUS in place because of our large fleet and the number of operators we have.” When it comes to the visibility FleetFOCUS provides, as well as the usefulness of the reporting function, Jude commented, “FleetFOCUS has improved our reporting immensely given the fact we can generate any report in real-time. It gives our managers a better understanding of where their fleet is, which trucks are operational, and which are out of action and why. It empowers our team to make more informed decisions on how to better utilise the staff and set operations up as best as possible at the beginning of each shift.
“Safety-wise, FleetFOCUS has massively improved our ability to manage our fleet.” Brennan added, “As incidents have happened, we’ve been able to alert users and key decision-makers in real-time.”
FleetFOCUS empowers businesses to address all accidents as they happen and organise servicing as quickly as possible so trucks can get back into operation as fast as possible. ■
Falcon Autotech is a global intralogistics automation solutions company. With over 10 years of experience, Falcon has worked with some of the most innovative brands in E-Commerce, CEP, Fashion, Food/FMCG, Auto and Pharmaceutical Industries.
CONTACT US:
Email: salesenquiry@falconautoonline.com Website: www.falconautotech.com
Körber’s Darren O’Connor and Jamie Sterling speak to MHD about managing warehouse operations with cloud-based solutions.
Cloud-based solutions, particularly SaaS, have revolutionised the way businesses manage their operations. Images: Körber.
The shift to cloud-based solutions represents a leap forward in the supply chain and logistics industry. The cloud offers businesses scalability, flexibility, and efficiency, while alleviating the burdens of technical administration and infrastructure management.
As more companies turn to Software as a Service (SaaS) for their logistics needs, it’s worth exploring how these innovations are shaping the industry.
“The SaaS offering takes away the technical administration of the solution,” says Darren O’Connor, Director of Solution Delivery, Körber. “You no longer need to be worried about the technical resources to maintain it.”
The ability to adjust resources based on demand without substantial upfront investments in hardware is a game-changer for many businesses.
This relief from technical upkeep allows companies to focus on their core competencies instead of the complexities of IT infrastructure.
“With SaaS, we can scale that out to suit all the users on all the systems that we look after,” adds Darren.
“This scalability is a significant benefit that you wouldn’t typically have if you managed everything on-premise.”
One of the features of cloud solutions is their integration capabilities.
“None of our warehouse management solutions operate as islands,” says Jamie Sterling, Head of APAC Sales Software, Körber.
“They are all integrated into something, whether that’s a source of orders, an output, or integration with a transport provider.”
This seamless integration
ensures that the systems can work harmoniously within the broader IT landscape, enhancing efficiency and coordination while being designed to be adaptable.
“We go to market with an adaptability capability,” adds Jamie.
“You can take our solution, create your own or adapt existing processes, feature enrichment.”
This means businesses aren’t limited by the out-of-the-box functionalities of the software; they can customise and bolster features to meet their specific needs.
Another aspect of cloud software is the empowerment they provide to businesses.
“We enable our customers to hold their own destiny, enrich their own solution, and manage their own changes,” says Darren.
This autonomy allows businesses
to innovate and adapt without being tied down by the original software provider’s roadmap.
Körber also offers training through its academy, ensuring that clients are equipped to make these changes independently. This approach not only enhances customer satisfaction but also reduces reliance on external support for routine adjustments.
“We encourage customers to take ownership because we are a software company that wants to sell solutions, not just services,” says Jamie.
In addition to operational benefits, cloud-based solutions also offer environmental advantages.
“The cloud-based model does lower your environmental footprint,” says Jamie.
“Cooling large data centres is more efficient than cooling smaller, scattered facilities.”
This efficiency translates to lower energy consumption and reduced costs, which is particularly beneficial for businesses looking to improve their sustainability profile.
“With scale comes economics and reduction in costs, including those associated with air conditioning and electricity,” adds Jamie.
These savings can be significant, especially for companies with large warehouse operations.
A well-managed disaster recovery plan is crucial for any business, and cloud solutions offer a reliable option.
“For customers who have done on-prem implementations without a disaster recovery plan, moving to the cloud ensures they have a genuine disaster recovery solution,” explains Darren. Regular testing and verification of these plans provide peace of mind that, in the event of a disaster, the business can quickly recover. The return on investment (ROI) from these solutions is also noteworthy.
“Our SaaS solution can accommodate businesses from 15 to 500 users,” says Jamie.
“As they grow, they acquire more subscription licences, enabling scalability without significant additional investments. Flexible scaling ensures that businesses can grow at their own pace without being constrained by their IT infrastructure.”
The versatility of these solutions is evident in their widespread adoption across various industries. This diversity showcases the adaptability of the systems to different operational needs, whether it’s managing cold storage for perishable goods or handling complex logistics for spare parts.
“Our client base ranges from large retail brands to mining and healthcare sectors,” says Darren.
“If you’re operating a distribution centre and moving goods, our solutions can be adapted to manage those activities,” adds Jamie.
The trend towards increased automation in warehouse management is expected to continue.
“The entry point for automation is now lower, and the physical modifications needed are being
reduced,” says Jamie.
This shift means that more businesses can access automation technologies, enhancing productivity and efficiency.
Furthermore, voice technology is improving in warehouse management systems, which makes it easier for businesses to integrate voice commands into their operations, improving workflow, and reducing errors.
“Voice is now available in multiple ways and runs on standard industry devices rather than specialised ones,” adds Jamie.
As the logistics industry continues to evolve, the shift towards cloudbased solutions represents an opportunity for businesses to enhance their operations.
The benefits are clear: scalability, integration, adaptability, environmental efficiency, and robust disaster recovery.
For businesses considering this transition, the message is clear: embrace the future of warehouse management and reap the rewards of a well-managed, scalable, and environmentally conscious operation.
“The breadth of our offerings ensures that businesses can find a solution tailored to their needs, whether they’re a small enterprise or a large corporation,” says Darren. ■
MHD speaks to Anthony Zhao from Jungheinrich Australia about the advantages of lithium-ion batteries, their lifecycle, opportunity charging, and better efficiencies, benefits, safety, stability, sustainability, and cost effectiveness.
As the material handling industry continues to evolve, advancements in battery technology have become a crucial factor in enhancing efficiency and sustainability.
Jungheinrich’s lithium-ion batteries represent a major leap forward compared to traditional lead-acid batteries, offering numerous benefits for businesses looking to optimise their operations.
Anthony Zhao, National Sales Technical Support – Energy Solutions at Jungheinrich Australia, shares insights into the advantages of Jungheinrich’s lithium-ion batteries and the innovations driving its customers’ success.
Lead acid technology is more than 100 years old and hasn’t advanced much in the past decade, while lithiumion technology has seen a greater investment that leads to faster development and wider applications.
“Lithium-ion batteries have experienced rapid development and diverse applications, from electric vehicles to power tools,” says Anthony.
The familiarity with lithiumion batteries in everyday devices has made the technology more accessible and desirable for industrial applications.
They possess greater efficiency during both charging and discharging compared to lead-acid batteries. With the recuperation brake energy, they can achieve energy savings of 20 per cent or more.1
Lithium-ion batteries save time by
charging faster. They can recharge up to 50 per cent within 30 minutes of opportunity charging.2
There’s also no need for battery exchanges for multi-shift applications. Furthermore, battery bays aren’t required for charging additional shift batteries and neither is operator maintenance for cleaning the batteries.
One of the most notable advantages of lithium-ion batteries is their extended lifecycle.
“A standard lead-acid battery typically offers around 1200 life cycles,” adds Anthony. “In comparison, our lithium-ion batteries can reach up to 3000 cycles or more, translating to significant cost savings.”3
This longevity not only reduces the frequency of replacements but also minimises maintenance needs.
No flammable gas emissions are emitted during charging, meaning they’re safer to use. They’re sustainable and eco-friendly because
they’re 90 per cent recyclable and release 20 per cent less CO2 overall.4
Jungheinrich can provide a full energy solution package to its customers thanks to its ability to combine efficient lithium-ion batteries with chargers and forklifts.
Lithium-ion batteries offer superior efficiency compared to their lead-acid counterparts.
“The efficiency of lithium-ion batteries ranges from 93 per cent to 97 per cent, which means more of the energy you pay for is actually used,” explains Anthony.
This high efficiency, coupled with the ability to opportunity charge, significantly boosts productivity.
“With opportunity charging, you can quickly recharge the batteries during short breaks, keeping the equipment ready to go and reducing downtime,” adds Anthony.
Lithium Iron Phosphate (LFP)
Jungheinrich offers a wide lithium-ion battery range.
safety rating. The solution not only has cost saving benefits, but also ensures higher Electric Materials Handling Equipment (eMHE) availability, which maximises utilisation to increase productivity.
Safety is another critical aspect where lithium-ion batteries excel. Unlike lead-acid batteries, which can emit flammable gases during charging, lithium-ion batteries are sealed and free from such risks.
Traditional lead-acid batteries require regular maintenance, including checking water levels and cleaning terminals to prevent corrosion.
In contrast, lithium-ion batteries are virtually maintenance-free.
“The fully enclosed design of our lithium-ion batteries eliminates the need for regular upkeep,” explains Anthony.
This feature not only reduces labour costs but also enhances the overall reliability of the equipment.
Environmental sustainability is a growing concern across industries, and the material handling sector is no exception.
“Our lithium-ion batteries are 90 per cent recyclable and require less water to produce than lead-acid batteries,” adds Anthony.
Additionally, the energy efficiency of lithium-ion technology contributes to lower carbon emissions, aligning
Jungheinrich’s approach to integrating lithium-ion technology into its forklift models focuses on customisation and adaptability.
“We work closely with our customers to tailor energy solutions that meet their specific operational needs,” says Anthony.
This includes assessing the appropriate battery capacity and charging infrastructure, ensuring that the transition to lithium-ion technology is seamless and costeffective.
“We introduced the first production-ready lithium-ion forklift truck over a decade ago, and we’ve continued to refine our technology since then,” adds Anthony.
The latest iteration of Jungheinrich’s BMS offers enhanced data analytics capabilities, providing valuable insights into battery performance and usage patterns.
The new charger has up to 97 per cent efficiency and optional capability for Load Management.
Lithium-ion serviceability is assessed at the truck’s end of life for potential reuse in a new truck and/or the cells can be repurposed for use in energy storage systems.
Anthony sees a bright future for lithium-ion technology in the material handling industry.
Data logging is accessible for
Expertise in providing customdesigned packages best suited to individual customer applications including Total Cost of Ownership (TCO) assessment demonstrating cost and CO2 reduction forecast.
Jungheinrich’s new POWERLiNE range with integrated lithiumion batteries reduces physical dimensions by up to 30 cm, with an ergonomic operator compartment and CO2 neutral footprint up to the time of delivery.
“As battery technologies evolve, we’re seeing greater focus on sustainability and efficiency,” explains Anthony.
“Our new chargers, with up to 97 per cent efficiency, are a testament to our commitment to reducing energy consumption and carbon footprints.
“By embracing lithium-ion technology, we’re not just improving operational efficiency; we’re also making a positive impact on the environment,” adds Anthony.
“Our focus on customisation and innovation ensures that our customers can fully realise the benefits of this technology in their unique settings.”
In an industry where efficiency and sustainability are paramount, Jungheinrich’s lithium-ion batteries stand out as a forward-thinking solution that meets the needs of modern material handling operations.■
1.https://www.jungheinrich.co.uk/your-solutions/lithium-ion-technology/lithium-ion-products/li-ion-battery-life-cycle-1291296#:~:text=Lithium%2Dion%20 batteries%20reducethe%20carbon,trucks%20with%20lead%2Dacid%20batteries.
2.https://www.jungheinrich.com.au/products/batteries-charging-technology/forklift-batteries/lithium-ion-batteries-534690
3.Lead acid 1200 cycles in general industry excepted standard. Li-ion cycles: https://www.jungheinrich.com.au/products/batteries-charging-technology/forkliftbatteries/lithium-ion-batteries-534690
4.https://www.jungheinrich.co.uk/your-solutions/lithium-ion-technology/lithium-ion-products/li-ion-battery-life-cycle-1291296#:~:text=Lithium%2Dion%20 batteries%20reducethe%20carbon,trucks%20with%20lead%2Dacid%20batteries.
TGA licenced, custom-built 10,000m2 facility dedicated to Life Sciences and Healthcare Logistics. Strategically located in the Melbourne Airport Business Park with prime access to the airport, seaport, rail terminals and key road-freight arterials.
Key features include:
• Controlled ambient, cold chain and ultra-low frozen product storage
• Cold chain storage +2°C - +8° capacity for 1173 Pallets
• Controlled ambient storage (+15°C to +25°C) capacity for 7,796 pallets
• Schedule drug storage
• Value added services
• Validated active and passive cold chain solutions
• Tier 1 WMS system backed by quality assured processes
• ISO 27001 (Cyber Security accreditation)
• 5 star green star rating compliant*
*Certification is in process
Sandfield’s Alan Dowsett, who is head of its specialist supply chain division, Origin, tells MHD what software solutions are available for businesses managing complex logistics-related projects.
Logistics Service Providers (LSP) across the supply chain industry have historically struggled to incorporate technology solutions that help them meet their current and longrange objectives.
Origin, Sandfield’s supply chain division, not only caters to the core requirements that are universal across the logistics sector, but also thrives when supply chain operations invariably get “creative.”
With more than 30 years of experience delivering supply chain software, Origin uses its suite of products and development expertise to help its customers differentiate themselves from the competition.
Origin partners with organisations across the entire market but has often found it aligns best with businesses whose supply chain needs are both unique and complex. This includes specialised freight types used in the transport of containerised goods, break bulk, bulk goods, and general freight.
“These businesses are not just looking for software; they’re looking for a unique way of working that the software can showcase,” says Alan Dowsett, Head of Origin, Sandfield.
Some of Origin’s customers include Qube, Tasman Logistics, PrixCar, Mainfreight, and HW Richardson to name a few.
Many LSPs (like those involved in mining contracts or operations at ports) need specialised logistics solutions to secure contracts and provide services to their customers in the way they demand.
In some cases, the physical requirements dictate that entirely new types of equipment need to be built to properly service the contracts. Lateral thinking is the key to helping these companies succeed.
“Typically, customers come to us because they are trying to do something complicated, something different from their competitors,” says Alan.
“They’re responding to unique customer requirements or new contract demands.”
Generally speaking, these businesses are utilising processes that involve a level of specificity (both in terms of equipment and infrastructure) that is unable to be adequately served by off-the-shelf software systems. As an example, one Origin customer manages the transport of industrial steel coils and beams using rail.
In recent years, there has been a shift in how logistics companies view their technology stack.
Many of these companies have not historically viewed technology as a way to differentiate themselves; rather, they saw software technology as a tool to meet basic operational needs.
“In the logistics sector, if you’re not approaching things with a unique mindset, you’re going to struggle to win new contracts,” says Alan.
Previously, the industry relied on large ERP systems that attempted to cover all aspects of the business without really standing out in any particular area. Over time, the market has evolved and now there’s a growing
preference for the flexible and scalable capabilities that SaaS (Software as a Service) options provide.
The rise of SaaS solutions has further complicated the landscape. While these solutions often excel in their niche areas, they can be challenging to modify and integrate.
“Many large logistics companies still look for solutions they can alter to fit their business needs, but SaaS solutions don’t always play nicely with that requirement,” says Alan.
This situation creates a dilemma: companies want the flexibility to adapt software to their unique processes, but they also want the efficiency and scalability that SaaS offers.
Origin’s journey from a custom software developer to offering a suite of productised solutions reflects its growth and expertise in the logistics sector.
“We built a platform to support our custom solutions, which over time, has evolved into productised offerings in transport management systems, container freight station solutions, and customer portals,” says Alan.
This evolution allows Origin to offer robust solutions that not only supply the core capabilities needed to cover the bulk of industry-standard operations, but also provide the flexibility to pivot to additional capabilities, as needed.
Due to the varied and specific requirements of most logistics operators, companies will always lean towards software solutions that not
only integrate seamlessly across various platforms, but also offer the flexibility to adapt to unique business needs.
Through various projects Origin has been able to work with supply chain partners to create solutions that did not exist. This focus on customisation, integration, and direct client collaboration positions Origin as a leader in providing innovative logistics solutions.
“For us, it’s about ensuring our clients have the tools they need to differentiate themselves in a competitive market,” explains Alan.
LSPs’ customer expectations around the digital experience have also changed over time.
“Digital experience used to just mean you could email the customer,” says Alan.
Now, customers expect real-time, accurate information, accessible through portals and integrated directly into their systems.
They also want to receive timely, accurate data in a format they can work with. Without this functionality, it’s nearly impossible to productively interact with the data so that basic tasks can be completed, such as updating order statuses or disputing charges.
This shift towards customer visibility and self-service is a critical factor in the logistics sector’s digital transformation.
Origin’s collaborative approach extends beyond software development to implementation and support.
Rather than outsource these functions, Origin’s dedicated teams work directly with clients throughout the process.
“Our developers, who are also experts in the software and supply chain, help implement and support it,” says Alan.
This direct involvement ensures that clients receive tailored solutions and timely support, a key distinction in the market.
One of the biggest technology challenges in logistics today is managing and integrating a variety of systems across the supply chain that may have been built by multiple providers and were never specifically designed to work together.
This often results in applications that don’t communicate effectively with each other, leading to siloed data and labour inefficiencies.
“If you’re moving goods around your supply chain and those goods touch each of your different systems, which one do you look at to find out where the goods are right now?” asks Alan.
Origin addresses this challenge by utilising Sandfield’s integration solution, Crossfire, to connect both the internal and partner systems creating a single source of truth across the supply chain.
“We collect and organise all the necessary data together to provide visibility and orchestration across these solutions,” adds Alan.
Crossfire has been designed specifically for the high-performance requirements of supply chains, processing more than 1.4 billion messages annually.
Alan emphasises two key aspects: internal integration within a company’s systems and external integration with
customers’ systems.
“It’s not just about logging into a portal to see where something is; it’s about having that data integrated directly into the customers’ systems,” says Alan.
The single source of truth provided by Origin is crucial for companies that need to coordinate activities across multiple systems and provide real-time visibility to their customers.
“Crossfire connects these different systems together and then Origin makes sure they can work together in a meaningful way,” says Alan.
One example of Origin’s unique approach is its work with a prominent LSP in the vehicle transport sector, a niche market with few available solutions.
Origin provided a middle ground between a custom option and a productised solution, helping its client meet the conditions unique to its business without having to build a solution from scratch.
Another example is Origin’s technology managing the complexities associated with the loading, unloading, and tracking of specialised bulk container transport used to move ore from mines to destination ports. Due to the complex nature of the operation, Origin’s client was looking for a partner who could examine the problem creatively.
In the end, Origin was able to accommodate the nuanced processes of this large logistics provider and allowed it to streamline its operations and improve performance.
What sets Origin apart from other logistics software providers is its ability to efficiently adapt its product suite to meet specific business needs.
Origin’s core range of technology products have a long history of streamlining operational processes across the supply chain. Origin works closely with its customers to adapt its software to fit its customers’ unique requirements.
“We never say no to a challenge,” says Alan. ■
SICK at CeMAT 2024: INNOVATE. AUTOMATE. ELE VATE.
Experience our latest Ident Gate System for seamless, automated goods identification at the loading dock, and our advanced DWS track and trace system for large pallets with 4-sided image-based label reading, dynamic weighing, and dimensioning. Tailor your logistics with our modular solutions, and leverage our digital tools to visualise and analyse all collected data. Connect with our team to transform your warehousing operations now. https://s.sick.com/CeMAT-Australia-2024-DWS
GS1 Australia’s Dharshi Hasthanayake reveals how the company’s traceability standards enhance the end-user experience of rail freight services to promote its role as a more sustainable method of transporting goods.
With the Federal Government’s legislated commitment to achieve net zero by 2050, several industries, including transport and logistics, are beginning to focus on reducing emissions
Commitment to rail freight is one of the ways the industry has looked to diversify, as it can reduce carbon emissions, air pollution, congestion and road crashes.
According to an Australasian
Railway Association (ARA) submission into NSW Governments Freight Policy Reform, rail freight accounted for just 4 per cent of total transport emissions, despite handling 56 per cent of Australia’s total freight. An ARA commissioned report in 2020 from Deloitte Access Economics even outlined that rail freight produces 16 times less carbon pollution than road freight.
But more can be done. The
transport and logistics industries are now beginning to explore ways to make rail freight even more sustainable.
Manager of Sustainability and Circularity at GS1 Australia, Dharshi Hasthanayake, aid the sector is now actively, for example, investigating ways to reduce the reliance on diesel for rail freight operations by considering alternative fuel types.
“This includes moving away
from reliance on diesel for rail freight operations using alternative fuel types including batteries, electrification, hydrogen and ammonia,” she said.
Hasthanayake said that the ARA are core to driving this shift, and are engaged in multiple initiatives to promote rail freight. The ARA has collaborated with other key industry players on the Future of Freight campaign, and the Rail Freight Productivity Review: Establishing an Efficient Freight Transport Network.
The ARA’s most recent key report on supporting the sector to net zero, the Rollingstock Decarbonisation Critical Path, identified a potential road map transitioning rail to low and zero emissions, which includes opportunities for further decarbonising the rail freight sector.
One company that is embracing the potential of rail freight to lower emissions is GS1 Australia, a leading provider of standards for over 25 industry sectors.
GS1 Australia is a not-for-profit organisation focused on providing supply chain solutions for its over 22,000 member companies.
With road freight expected to increase significantly over the next decade, Hasthanayake said the company is playing its part in enhancing the experience of rail freight services to attract more end-users.
“GS1 Standards can assist rail freight in improving the end user experience, providing the confidence and reliability that customers seek from their supply chain services,” she said.
“Growth in this area will reduce the reliance on road transport and support achieving our national net zero targets.”
GS1’s global supply chains standards streamlines experience of rail freight services by implementing a standardised barcode system that tracks goods and enhances operation visibility.
Hasthanayake said a flagship for GS1 Australia is ‘Scan4Transport,’ a global standard for encoding transport data. This initiative captures key information from a freight transport label and
GS1’s global supply chains standards streamlines experience of rail freight services by implementing a standardised barcode system. Image: GS1 Australia.
accurately processes and integrates its data into the relevant systems.
“The standard supports companies across the transport process including first mile, sortation and last mile activities and enables them to keep pace with the growing needs of their customers,” said Hasthanayake.
‘Scan4Transport’ then sends vital details regarding the shipment, such as its recipient and destination, to be managed through the supply chain network.
“Scan4Transport standards enable interoperability across networks and supply chains which will allow Customers agility to utilise rail freight services and maintain traceability that is standardised within the Road freight networks,” said Hasthanayake.
Hasthanayake mentioned that Global GS1 standard barcodes – a part of this standardised system – offer several advantages that enable businesses to move away from manual paper-based systems. She said the use of these barcodes allows for the storage of a large amount of digitally embedded data that couldn’t otherwise be handled by traditional systems.
“2D barcodes are particularly useful for storing information relevant to the transport process – for example ship to address, dangerous goods information, weight – as it enables the information to be available in both on-line and off-line environments by simply scanning the barcode,” said Hasthanayake.
Hasthanayake continued by saying that GS1 barcodes, such as the GS1-128,
offer quick and highly accurate data capture.
“Barcodes such as the GS1-128 are used to encode data like the serial shipping container code. They allow for quick and accurate data capture, which is essential for managing logistics on rail, ensuring that goods are efficiently loaded, transported, and unloaded,” she said.
Hasthanayake also detailed GS1s adoption of Application Identifiers (AI) that are now a part of the company’s standardised barcoding system.
“The new Application Identifiers released are part of this standard. They unambiguously indicate the meaning of the data element following it. Enabling the data to be encoded in a globally standard manner that all stakeholders can understand,” she said.
To underscore the effectiveness of the company’s standards and barcode services in the logistics industry, Hasthanayake recalled a recent case study involving an Australian steel manufacturer.
“An iconic Australian steel manufacturer implemented barcode scanning for the picking and loading function of reinforced steel bundles. With the implementation of SSCC barcode labelling, warehouse staff were able to load trucks 2.5 times faster,” she said.
By utilising the standards developed for transport labels, Hasthanayake said that customers will begin to experience smoother processes.
Specifically, she noted that GS1 Australia customers often see improvements in first and last mile processes, sortation, visibility of task requirements, efficiency and interoperability.
Not to mention, GS1 standards will also enable businesses to comply with environmental regulations.
“With the additional of the benefits of Project i-Trace, the GS1 Standards will enable businesses to comply with environmental regulations, providing the framework for reporting and verification,” said Hasthanayake.
Going forward, GS1 Australia will continue to support rail freight by enhancing its end-user experience, in turn encouraging more in the industry to adopt this sustainable mode of transporting goods. ■
The ceremonial ribbon has been cut and operations are now in full swing at Toll’s largest specialised healthcare warehouse facility in Victoria, which is now open for business.
A$20 million TGA-licensed healthcare facility at Melbourne’s Tullamarine Airport Business Park has been custom designed to support the requirements of its growing customer base. It will support the warehousing and distribution of medical supplies, including pharmaceuticals, vaccines, antivenoms, medical devices, and overthe-counter medicines.
Constructed by CMW Design & Construct (VIC) the facility’s development also has a focus on sustainability, targeting a 5-Star Green Star building certification. This building is set to be the first within the Melbourne Airport Business Park to achieve such an accreditation.
Mel-Air, CMW and Toll recently held a ribbon-cutting ceremony with several dignitaries to mark the official opening of the site and the precinct in which it resides.
“None of this would have been possible without the support, attention to detail and collaboration from our key partners at TMX Transform, CMW Design and Construct as well as the team at Melbourne Airport Property,” says Michael Lawrence, General Manager of Toll’s Healthcare business in Australia.
The facility has received one of the highest ratings from customer auditors in the region and is well on track to receive an A1 compliance rating from the Therapeutic Goods Administration. Its advanced specifications on security, mechanical systems and electrical redundancy are critical for the nature of its operations.
The 10,000 sqm temperature-
controlled facility is a significant addition to Toll’s network servicing the health care industry. This state-of-the-art asset has been custom built to support CSL Seqirus’ operations situated on the adjoining site, which produces influenza vaccines for Australia and the rest of the world, antivenoms, and blood plasma.
This strategic decision and collaboration will bolster Toll’s tailored support by handling both finished goods distribution and supplying raw materials and packaging to the CSL Seqirus manufacturing facility – which is nearby.
“We are proud to strengthen our partnership with Seqirus
and expand our footprint in the healthcare logistics sector,” says Michael.
“This new facility exemplifies our commitment to delivering high-quality, tailored supply chain solutions to meet the evolving needs of our customers.”
Toll Healthcare ensures the safe warehousing and reliable transportation of temperaturesensitive pharmaceuticals and medical supplies across the whole of Australia.
It’s committed to ensuring the highest standards of quality and assurance for its customers, through effective processes, preparation and execution to deliver safe and reliable services across Australia.
Michael is equally as proud of the service his team and broader business provide.
“This new facility in Tullamarine is another example of our commitment to excellence and customer satisfaction within the Healthcare sector,” he says.
Energy efficiency has been a focus in the planning and construction of this facility, with the certification underway targeting a 5-Star Green Star building rating (certification in process).
The warehouse has energy-saving LED lighting with motion sensors which turn on/off automatically.
The site also has a 60kw solar panel installation, and supplementary power is 100 per cent accredited GreenPower, supported by supply from the Melbourne Airport Solar farm.
There’s also the capacity for rainwater harvesting via the 20,000L rainwater on-site storage and there are EV charging systems available on site for cars and trucks.
From a sustainable practices’ perspective, as the facility is adjacent to the CSL Seqirus manufacturing facility, this will reduce the number of trucks on the road between the current or previous Toll and CSL facilities.
Toll Healthcare also provides
a reverse logistics services and solutions that remove one-timeuse-packaging and other waste from the supply chain, favouring reusable and sustainable packaging and distribution methods.
Effort and consideration also went into the landscape design to ensure it has native Australian flora and that the plants are compliant with existing Melbourne Airport regulations so as not to attract birds or other wildlife to a busy and congested traffic area.
Space optimisation has been a critical aspect of the planning with the warehouse floor being designed and
prepared for “Very Narrow Aisle” (VNA) racking and manual handling equipment (MHE) usage should this be required in the future due to growth. All MHE and forklifts are fitted with Lithium-Ion batteries, which store a lot of energy in a small space which in turn translates into longer battery life and faster charging times – this delivers operational benefits and efficiencies.
Being able to monitor and control the temperature across different zones is critical and the facility is 100 per cent temperature controlled throughout. There are three temperature-controlled zones that have been fully validated and approved: Controlled Ambient, 15-25˚C (9935.2 sqm)
• Cool Room, 2-8˚C (1428.3 sqm)
• Freezer, -21˚C (64.7 sqm)
There is a Building Management System (BMS) and a Temperature Monitoring System (TMS) to ensure there are not any temperature exclusions in the facility.
The facility is equipped with secure and monitored loading zones with temperature-controlled docks and trailers as well as a state-of-theart warehouse management system (WMS) that provides real-time traceability of inventory, as well as orders.
The focus on monitoring and controlling temperature throughout its supply chain continues from the warehouse environment through to transportation by using a fleet of modern vehicles equipped with GPS tracking, temperature monitoring and data logging devices.
Temperature-controlled packaging is also provided, through using validated and qualified materials and methods that ensure the integrity and stability of the products during transit.
Toll Healthcare’s quality management system (QMS) at the new Tullamarine facility provides the foundation for everything it does to assure that it meets or exceed the customers’ quality requirements.
Its QMS is a governance framework that controls and monitors all aspects of warehousing and distribution operations, ensuring that Toll meets or exceeds the requirements of relevant industry standards, such as Good Distribution Practice (GDP), Good Manufacturing Practice (GMP), ISO 9001 and ISO 13485.
The QMS ensures the facility follows the best practices and guidelines of regulatory bodies, such as the Therapeutic Goods Administration (this facility has a TGA A1 rating), the Poisons licence requirements of each of the states, the Medicines and Medical Devices Safety Authority (Medsafe), as well as the Environmental Protection Authority (EPA).
This facility also benefits from being within a prime location. The Tullamarine Airport Business Park setting provides convenience not only to the new CSL manufacturing facility and its operations, but more broadly provides access to key roadways and distribution hubs across Melbourne, allowing more convenience, speed and access by being within:
l 4km of Melbourne Airport.
l 2.2km of the Tullamarine Freeway .
l 2.5km of the Metropolitan Western Ring Road.
l 4.4km of Essendon Airport.
l 15km of the Melbourne CBD.
l 16km of the Melbourne Port and Docklands areas.
“This is a first-class facility, supported by a committed and professional team,” says Michael.
“Our relationship with CSL has also been of vital importance in allowing us to deeply understand their needs and then customise a plan and a facility that will enable us to support them – and others – with an unprecedented level of service and consideration.”
Michael is emphatic when signalling Toll’s growth plans and future commitment within the Healthcare sector.
“This facility is another signal of our intent and commitment to grow our Healthcare business and provide greater service and support to the sector,” he adds.
“New customers are welcome, as the growth and opportunities this facility provides Toll healthcare, and our customers – both current and emerging – is exciting for all of us.”■
Kardex’s Grant Smith and Douglas Pharmaceuticals’ Andrew Mackintosh explain how their partnership has enabled them to automate and expand the New Zealandbased company’s operations while maintaining staff levels.
Founded in 1967 in New Zealand, Douglas Pharmaceuticals is now one of the country’s largest privately-owned pharmaceutical companies and a respected name in the global pharmaceutical industry.
As well as producing prescription drugs, Douglas develops, manufactures and distributes a wide range of consumer health and wellness products.
As a growing company with both domestic and international customers, it faced the common issue of its manual, highly utilised warehousing operations becoming a bottleneck, particularly for its fast-moving consumer healthcare range.
This dilemma spurred a collaboration with Kardex, an automated storage solutions specialist, which has global partnerships
with AutoStore, Rocket Solution, Robomotive, and Sumobox.
The partnership allowed Kardex to enhance Douglas’s operations by increasing warehousing efficiency and storage capacity without expanding the physical footprint.
Douglas has always prioritised customer service. However, the manual nature of its warehousing operations was starting to hinder productivity and employee satisfaction.
“Douglas is incredibly focused on delivering exceptional customer service,” says Andrew Mackintosh, General Manager of Supply Chain at Douglas.
“However, our traditional manual warehousing methods were becoming
a bottleneck, impacting the operating environment for our team and challenging our ability to maintain the high service levels we’re known for.
Additionally, the increased pressure on our warehouse team was affecting morale.”
Recognising the need for change, Douglas sought a solution that would not only solve its immediate storage capacity issues, but also enhance overall operational efficiency. This is where Kardex’s expertise came into play.
“What Kardex did really well was they invested a lot of time upfront, getting to know the context of our business, our products, and our goals,” adds Andrew.
“They went beyond just understanding our current state and asked for a lot of our operational data
to run simulations and come back with various scenarios for different automation solutions, ensuring the best fit for Douglas both now and in the future.”
The collaboration between Kardex and Douglas led to the selection of the AutoStore system, an automated storage and retrieval solution.
“The major benefit for us is the increase in storage capacity,” explains Andrew. “The AutoStore solution will expand our storage capacity by 30 percent while using only 10 percent of our warehouse footprint. We also anticipate significant improvements in inventory control and replenishment processes through the automation tool.”
The decision to implement Kardex AutoStore was not taken lightly. Douglas considered multiple options, including expanding its existing warehouse, purchasing a new facility, or utilising a third-party logistics provider. However, these options didn’t offer the benefits of automation.
“We were answering our storage capacity issue, but we weren’t getting the other benefits that come with automation,” says Andrew.
“With AutoStore, we saw a 68 per cent improvement in operational throughput from order receipt to dispatch, without any other related changes to our operational workflow.”
Grant Smith, Director of Business Development AutoStore, ANZ Kardex, highlights the importance of understanding the unique needs of each business.
“When we talk to customers, we make sure to understand all aspects of their business, not just the immediate pain points,” says Grant.
“This helps us tailor solutions that address both current problems and future opportunities.
“For Douglas, we facilitated a process that involved detailed simulations and scenario planning, which were crucial for validating and fine-tuning their assumptions. This support was instrumental in building a solid business case for automation.”
Grant further emphasises the role of
Kardex as a partner rather than just a solution provider.
“Our approach is to work closely with our customers, helping them understand their business better and challenging them with questions around data and operations. This collaborative process is essential for developing a roadmap that aligns with their growth projections and operational goals.”
The implementation of AutoStore is set to revolutionise Douglas’s warehousing operations.
The increased storage capacity and improved inventory control are just the beginning.
“The automation solution will not only address our current storage capacity issue but also significantly enhance our overall operational efficiency,” says Andrew.
“We anticipate improvements in inventory control, replenishment processes, and a substantial reduction in operational bottlenecks.”
The automation system allows the company to maintain its workforce while scaling operations.
“One of our key drivers was to grow our business without the need to double our workforce or cut it in half to pay for the automation,” explains Andrew.
“This approach aligns with our community-based values and heritage, showing that automation can support growth without compromising on employee retention.”
For small and medium enterprises (SMEs) contemplating automation for the first time, both Andrew and Grant offer valuable insights.
initially focused on solving our immediate problem of limited storage capacity,” says Andrew.
“However, with Kardex’s facilitation, we also considered our long-term business goals and how automation could help us achieve them. My advice is to invest time in understanding both your current challenges and future opportunities.”
“The first step for SMEs is to ascertain their pain points and what’s holding them back from growth,” adds Grant.
“It’s important to understand your problems before looking for solutions. Partnering with the right integrator or consultancy is crucial for navigating this process. At Kardex, we pride ourselves on being a partner who helps SMEs understand their business better and develop tailored automation solutions.”
The partnership between Kardex and Douglas exemplifies how thoughtful planning and collaboration can lead to operational improvements.
By investing time in understanding the business context and leveraging advanced automation solutions, Douglas is well positioned to achieve its growth ambitions without compromising on customer service or employee satisfaction.
As SMEs continue to navigate the challenges of a changing market, the lessons from this collaboration serve as a valuable guide.
Automation is not just about technology; it’s about understanding your business, setting long-term goals, and choosing the right partners to help you achieve them.
For Douglas, the journey with Kardex has been transformative, paving the way for a more efficient, productive, and scalable future. ■
Combilift’s Martin McVicar and Chris Littlewood explain how the company is helping Australian businesses optimise their operations with innovative material handling solutions.
Record-low vacancy, postpandemic economics, and demand for sustainable technological development have sent Australian warehouse real estate into a period of flux.
All these factors have created an environment for manufacturers to optimise their operations and set themselves for long periods of growth.
To support these endeavours, materials handling specialist, Combilift, has developed its own capabilities in warehouse design and forklift technology.
With an Australian presence borne from decades of Irish manufacturing, Combilift is well placed to understand and complement the needs of Australian warehouse operators.
In 2024, those needs lie in increasingly modern facilities that enable sustainable, automated, and efficient production.
However, as vacancy levels around the country return from record-lows of around one per cent i – some of the lowest globally – there is little room for burgeoning manufacturers to move.
This is leading many to consider a demolition and rebuild of their facilities, according to JLL Australiaii Head of Supply Chain, Richard Phillips.
“You can’t even put some of the simplest automation into older warehouses because the infrastructure doesn’t enable their deployment,” he says.
“So, you’ve got buildings that
are 35-plus years old coming up for refurbishment anyway, plus the appeal of automation and increased cubic capacity are driving owners and developers to look at the viability of knock down and rebuild.”
This is where Combilift comes into play.
On top of delivering innovative, multi-directional forklift technology, Combilift has put its decades of experience to good use, offering a free warehouse planning serviceiii to maximise floorplan efficiency.
Clients of this service have been known to double their storage capacity using Combilift’s warehouse design, coupled with its forklifts for narrow and very narrow aisles.
By reducing the aisle widths, warehouse owners can fit more aisles into the same space – all while incorporating their chosen tech.
Combilift CEO, Martin McVicar, often emphasises his belief that the floorplan should always come first.
“We have a saying we’ve been using for the last number of years – ‘it’s more important that the customers should optimise what they’re doing before they invest in automation’,” he says.
“That’s why we have a team of engineers that offer free warehouse design, and that really has enabled a lot of our customers to maximise their cubic footprint.”
As consumer demand and online shopping soared during the pandemic, manufacturers struggled with a severe lack of warehouse space to cope with the influx. This inspired a raft of investment in new construction and demand for warehousing, much of which is due to be complete in 2024.
JLL reportediv that Sydney’s Outer Central West has 278,000 sqm of warehousing under construction, while Melbourne’s west has 432,000 sqm and Brisbane’s south is expecting 309,000
Combilift is well placed to understand and complement the needs of Australian warehouse operators.
sqm of industrial warehousing.
Much of this demand has come from the Transport, Postal and Warehousing (TP&W) sector (51 per cent), followed by manufacturing (20 per cent).
And that demand is strong financially. A Savills report v from April 2024, titled ‘Is Manufacturing Making a Comeback?’ found that AU$33.3 billion had been invested in warehouse properties since 2019.
The report suggested that such interest had been fuelled by suggestions of greater onshore manufacturing and the security of Australian supply chains – far removed from the geopolitical turmoil of Europe and Asia. This has led industrial and logistics sectors to overtake residential real estate as the preferred area for investment in Australia.
All this talk of investment, new warehouses, and onshore manufacturing implies the need for the machinery and equipment to keep it all running.
Having navigated Ireland’s economic booms and busts in the 1990s and 2000s, Combilift has the experience to capitalise on Australia’s own era of homegrown manufacturing.
This led to innovations like the Aisle Master vi, a versatile articulated forklift
i Property Council of Australia, ‘Industrial property’s $1.2 trillion economic impact revealed in new report,’ 2024
ii JLL, ‘Why knocking down warehouses is on the rise,’ 2023
iii Combilift, ‘FREE Warehouse Planning with Combilift,’
iv JLL, ‘Demand dynamics have shifted for Australian industrial,’ 2024
that changed the game for forklift drivers globally.
The product’s clever design complements a well-designed warehouse and allows operators to navigate increasingly narrow aisles of just 1.6 metres wide.
Similarly, Combilift’s Pedestrian stacker range enables significant improvements to warehouse capacity, while improving safety for even beginner operators.
Combilift Australia country manager, Chris Littlewood, says the range achieves Combilift’s main goals of boosting efficiency, safety, and productivity.
“The forward visibility of the Pedestrian reach vehicles greatly reduces the risk of incident in tight confines and ensures the vehicle is stress-free to operate,” he says.
“The operator’s position allows a greater level of control over the products when moving them around, with up to four-way reach in even the narrowest aisles.”
So, no matter how old, new, wide or narrow a warehouse is, Combilift has the solutions to uplift the changing landscape of industrial real estate.
As a manufacturer, Combilift can’t claim to have all the latest warehousing forecasts, just that it has the solutions for customer pain points as their needs arise. ■
v Savills, ‘Warehousing Sees $33.3 Billion Investment As Green Transition Drives Industrial Values, Says Savills Report,’ 2024
vi Combilift, ‘The Versatile Articulated Forklift’ Combilift, Pedestrian Stackers
Client-centric services meeting time, budget and resource constraints
4PL SOLUTIONS
Comprehensive supply chain management solutions, including transportation, warehousing, distribution and last mile delivery.
OCEAN FREIGHT SERVICES
Reliable, agile and competitively priced FCL, LCL and consol services with varying routings and transit times.
AIR FREIGHT SERVICES
Partnering with global carriers to provide time sensitive and quality services globally.
MARINE INSURANCE SOLUTIONS
Comprehensive marine insurance solutions for complete peace of mind.
SANTOVA LOGISTICS AUSTRALIA
Santova is an international, technology-based trade solutions specialist, delivering innovative end-to-end supply chain solutions. With offices across 11 countries, our team in Sydney and Melbourne provides unrivaled expertise and experience when managing the import and export of cargo globally.
Our constant innovation and technological development keep our customers ahead of the game. TradeNav, Santova’s inhouse shipment management system, enables visibility, transparency and accurate realtime tracking functionality required to proactively manage your supply chain.
santova.com | santova.com.au
MEGATRANS 2024 is your chance to explore the future of logistics. Featuring top industry experts, groundbreaking technologies, and invaluable networking opportunities, this event is a must-attend.
MEGATRANS, Australia’s largest exhibition and conference for supply chain and logistics is set to take place in Melbourne on 18-19 September 2024 at the Melbourne Convention and Exhibition Centre.
“We noticed that while many events focused on individual stages of the supply chain, there was no comprehensive event covering the entire logistics process from manufacturing to end consumer,” says Lauren Chartres, Show Director.
“Our goal was to create a forum for discussing improvements across the whole supply chain.”
Attendees can expect a showcase of cutting-edge technologies, insightful conferences, ample networking opportunities and discussions with many industry leaders.
Issues covered include workplace diversity, focusing on the importance of creating a workforce that reflects broader societal demographics. Ethical Supply Chain, addressing how traceability can ensure sustainability by promoting ethical practices and transparent supplier relationships and Real Estate Planning, which will be explored as essential for supporting the logistics industry’s growth.
Attendees can expect a showcase of cutting-edge technologies | Images: Prime Creative Media.
While speaking with MHD, JLL’s Richard Phillips mentioned key factors behind the company’s decision to participate in the event.
“JLL decided to get the senior executives into customerfacing forums more aggressively this year from a corporate marketing perspective,” says Richard.
“This will be the third or fourth forum I will have been invited to and lead discussions on, which varies across property ESG decisions, vacancy decisions, changing phases of the property marketplace, and a disparate number of things that I will talk about.”
“In terms of the conference, we aim to provide insights into how companies can enhance their operations, supported by case studies showcasing proven success. This is designed to be educational, not a sales pitch,” says Lauren.
The event is supported by sponsors, including the Platinum Sponsor – Loscam; Event Sponsors – Transvirtual and Geotab; and Prime Creative’s Association Partners - ICHCA, RWTA, SCLAA, TCA and VTA.
“Our decision to exhibit at Megatrans 2024 reflects Geotab’s commitment to leading telematics innovation and fleet management solutions,” says David Brown, Geotab’s Associate Vice President, APAC.
“The event offers a prime platform to showcase our cuttingedge technologies, engage with industry leaders, and highlight how our solutions enhance fleet efficiency, safety, and sustainability.”
This event will address the industry’s key priorities such as future fleets, promoting zero-carbon warehouse solutions, enhancing traceability in supply chains, and advancing cold chain logistics.
Luke Olsen – Managing Director - APAC, Microlise, talked about his company’s previous experience in the event.
“We exhibited at Megatrans in 2018 and 2022, achieving great success by connecting with supply chain professionals eager to innovate,” he said. “This year’s theme, “sustainability,” aligns perfectly with the priorities of many of our 400+ customers across Australia, New Zealand, the United Kingdom, and France.”
He says the company contributes to a sustainable future by providing fleet operators with advanced tools to monitor, manage, and maintain their operations efficiently. Its integrated ecosystem improves fuel efficiency, reduces emissions, and optimises resource utilisation through better route planning, digitisation, and driver behaviour improvements.
Register for MEGATRANS now. The event is free to attend. https://megatrans.com.au/
Decentralised drive technology reduces wiring efforts
Variant reduction optimises stocks
Low weight and compact installation spaces thanks to high power density
Max Jarmatz, Managing Director, NORD DRIVESYSTEMS, discusses the company’s growing global operations and cutting-edge technology, delivering sustainable solutions tailored to industrial needs.
AGerman family-owned business – NORD DRIVESYSTEMS, a stalwart in the industrial sector with more than 60 years of legacy – has achieved remarkable growth over the past decade, solidifying its position as a €1 billion enterprise spanning operations across 35 countries.
The company’s commitment to innovation is underscored by its investments in Australia, where it has been engaged since the early 2000s, establishing its own factory in 2008 and expanding its footprint ever since.
“We are currently one of the top gearbox and drive systems brands in Australia, serving a diverse range of industries like intralogistics and material handling,” says Max Jarmatz, Managing Director, NORD DRIVESYSTEMS, ANZ.
“Our expertise in material handling, particularly in warehouse automation and baggage handling systems highlights our capability to cater to the evolving needs of this crucial sector. Beyond smart gearmotors for conveyors, our solutions extend to those for food and beverage applications, reflecting our comprehensive industry coverage.”
Headquartered in Melbourne, the company operates a manufacturing facility and maintains sales and service presence across all states in Australia. The company continues to invest in enhancing its local infrastructure and expanding
A municipal works, civil and commercial construction event.
17-18 September 2025,
In September 2025, a new event will be landing at the Melbourne Convention and Exhibition Centre. Converge will bring together leading decision makers in the Municipal Works, Civil and Commercial Construction space, to share the tools, ideas and technologies that are shaping these sectors.
production capacity while leveraging its German R&D prowess to introduce cutting-edge products tailored for the Australian market.
Sustainability has become a cornerstone of responsible corporate practice. Logistics company,DHL, has embraced this ethos with its new air freight hub at Cologne Bonn Airport, powered by cutting-edge technologies from NORD DRIVESYSTEMS.
Since its launch in August 2019, the hub has set new benchmarks in efficiency and environmental responsibility. Spanning 12,000 sqm with a sorting capacity of 10,000 parcels per hour, it operates tirelessly, 24-hours a-day, six-days-a-week. At the heart of its operations is NORD DRIVESYSTEMS gear, engineered to ensure peak performance with minimal environmental impact.
Central to DHL’s commitment to sustainability is the reduction of energy consumption and CO2 emissions. The hub’s conveyor systems, extending over 2.5 km, rely on 800 LogiDrive drive systems from NORD. These units are not only efficient, but also tailored to meet DHL’s operational needs, emphasising energy savings and operational reliability.
The LogiDrive systems feature IE5 permanent magnet synchronous
motors, known for their energy efficiency across varying speeds and loads. This technology not only enhances operational performance but also reduces lifecycle costs, thereby ensuring a rapid Return on Investment (ROI) critical in today’s competitive logistics landscape.
“LogiDrive represents a versatile solution not limited to airports but crucial for material handling across sectors such as post, parcel, and warehouses,” says Max.
“It offers a seamless integration with existing conveyors, incorporating gearboxes, frequency inverters, and necessary cable sets. This comprehensive package simplifies installation for customers, requiring minimal setup effort. It includes interfaces for sensors and bus systems communication onboard, eliminating the need for additional components or complex wiring.
LogiDrive enhances energy efficiency by combining advanced frequency inverters with state-of-theart IE5 motor technology, delivering energy savings compared to outdated systems from previous decades.
“In simpler terms, our technology introduces a new motor series that significantly reduces energy consumption both during start-up and while running,” explains Max.
“Instead of generating a magnetic field using current, our motors integrate magnets, thereby saving energy typically used for motor induction.
“This innovation enables motors to achieve energy savings of about 40 to 50 per cent compared to traditional asynchronous models. Furthermore, our inverters can adjust power consumption based on demand, meaning the motor draws only as much power as necessary, not the full rated capacity. This capability has persuaded many of our major customers to adopt and invest in our technology.”
NORD’s drive solutions have servicefriendly attributes, such as plugand-play technology and integrated frequency inverters. These innovations simplify maintenance, enhance safety, and minimise downtime, crucial for uninterrupted operations at scale.
“With our solution, even during a night shift breakdown, you don’t need a specialist or certified electrician on site,” says Max. “For instance, to replace an inverter, you simply open four screws – no rewiring necessary.”
“It’s a mechanical change that anyone with basic tool skills can handle, allowing parameters to be adjusted just like transferring data via a USB stick, or connecting a computer or phone. This ensures applications are up and running again within minutes, much like fixing a 4G router at an airport. The same ease applies to gearboxes due to our optional plugand-play system instead of messy wires. Mains and VFD can be plugged in, typically resolving issues in just minutes. It’s truly remarkable.”
Configurable interfaces are available for encoder feedback, STO, photo eyes and others. In addition, the frequency inverters can be equipped with a maintenance switch and a key switch for safe maintenance. An integrated Ethernet-based bus system was also implemented. To complete the drive solution, NORD also can supply the cable sets. Potential sources of error were thus eliminated, facilitating fast commissioning.
NORD DRIVESYSTEMS continues to deliver tailored solutions that redefine industry standards. With a steadfast commitment to technological excellence and environmental responsibility, NORD DRIVESYSTEMS remains at the forefront of driving global industrial progress. ■
AI adoption in supply chains has not yet reached its full potential. Santova’s Arne Walter talks about how collaborative efforts and organisational changes are essential for unlocking AI’s transformative potential.
It’s hard to read any news without encountering discussions about Artificial Intelligence (AI), especially in supply chain management.
While there’s a perception that AI is omnipresent in supply chains, the reality differs, as highlighted by recent industry surveys. According to a Deloitte and MHI survey, 85 per cent of respondents believe AI will reshape supply chains in the coming years, yet only 27 per cent are currently using AI tools, revealing a substantial 58-point adoption gap. While adoption levels have increased over recent years, the gap
has widened from a 48-point base in 2020 (MHI 2020 report: 60 per cent expected AI to reshape supply chains in the coming years/12 per cent actual usage). It seems AI adoption levels in the industry cannot keep up with the expectations of the technology by managers and supply chain leaders.
Why is it then that there is such a large gap between perceived utility and the implementation of AI solutions in supply chains to date?
“We have been involved in research on AI adoption in automotive supply chains in Germany, in cooperation with the Royal Melbourne Institute of Technology (RMIT) with Professor
Kamrul Ahsan and Professor Shams Rahman”, says Arne Walter, Director, Santova Logistics.
“Part of this research tries to answer exactly this question by asking how companies’ structure organisational and technology resources should adopt AI. The study has analysed 11 automotive suppliers to investigate how these companies have implemented AI projects in their supply chains. The results of the study also offer interesting insights into the barriers to AI adoption that persist in the industry.”
These barriers help to explain the AI adoption gap that we continue
to observe in surveys of supply chain leaders resulting in supply chains being unable to fully leverage AI technology and its associated productivity gains, according to Arne.
“We need to start by fencing in the terminology, as part of the problem certainly lies in what we refer to as AI,” he said. “This is partly also due to the recent hype around the technology.”
AI applications can be distinguished into four general groups: descriptive, predictive, prescriptive, and cognitive.
Descriptive AI applications include diagnostics; for example image recognition to spot quality issues in manufacturing. Predictive AI makes use of large datasets to learn and make predictions for the future. Typical applications for predictive AI can be found in supply chain demand planning and predicting future demand.
Prescriptive AI goes one step further by analysing large datasets to find an optimum between different scenarios. These applications can be used to plan advertising spent between different media platforms to maximise the impact of dollars spent or plan product-store allocations to maximise revenue by placing products in stores or within the store to maximise sales. These applications often also include demand planning at the distribution centre or store level.
Predictive and prescriptive AI are often implemented in conjunction with other technologies in supply chains, like advanced robotics in automated warehousing for example.
Cognitive AI is best known as generative AI, machines that seem truly intelligent. Most cognitive AI applications utilise the same technology as predictive AI as they are based on pattern recognition also used by the large language models that power generative AI. Generative AI applications are ubiquitous but using them in supply chain management is still limited. What inhibits organisations from implementing AI tools? The reasons
could be varied. Recent research done by Santova along with RMIT identifies some factors.
1. Technology often seems somewhat experimental making it difficult to establish a return on investment at the outset of the project. Despite all the hype, once it comes down to putting money on AI, many company boards hesitate as they fail to quantify their value. Use cases or small pilots can help to demonstrate the value of AI technology on a small scale.
2. Hand-in-hand with these issues goes management’s understanding of the technology. Often driven by technology hype, decision-makers are unclear about the tangible benefits of AI in the context of their company.
3. A lack of affordable AI talent and data availability in the right context, quality and quantity. These points can be summarised in the key findings seen in this research, confirming findings from other studies. Technology adoption like AI is not a technology issue. It is foremost an organisational issue and requires organisational change. This includes leadership understanding of the technology to make the appropriate decisions and steer the business through the technology adoption process.
All these issues compound in an ongoing lack of AI adoption in supply chains, which seems out of sync with the sky-high expectations and possibilities the technology offers.
Many companies are turning to external parties to support them. Specialised companies can provide AI expertise and access to cloud-based computing power that is required to run AI models. Santova Logistics, as a technology-based international trade solutions provider, is doing exactly this for its clients.
Santova is empowering its clients by providing them with access to
AI technology that allows them to manage their supply chains smarter and more cost-efficiently without the need to invest in AI technology directly.
Its predictive ETA AI tool uses deep learning technology to provide realtime predictions of vessel ETAs. On a transactional level, this allows clients to anticipate ETA changes in advance and implement mitigation strategies that result in real cost savings.
On a strategic level, Santova provides predictive analytics tools to customers that allow them to create a digital twin of their supply chain that can be analysed to identify efficiencies on various levels.
The tools are instrumental in exposing inefficiencies and opportunities for cost savings. The differentiator is in the implementation – it is relatively easy to analyse a dataset and identify improvement opportunities within a client’s supply chain. This is where most advisory service providers stop.
Santova adds a layer of understanding, working with the customer to implement change. Santova recently identified considerable potential cost savings by consolidating LCL cargo from various suppliers using predictive data analytics for a large client – that was the easy part.
Implementation of these initiatives required a close working relationship with the client, suppliers and service providers through the process of Inco term changes, procurement negotiations and workflow setup resulting in quantifiable cost and lead time savings.
The gap between AI’s potential use and current adoption in supply chains persists. Challenges like AI’s perceived experimental nature, ROI ambiguity, and leadership understanding hinder widespread implementation. Santova Logistics follows a solution-oriented approach, offering AI tools for realtime decision-making and cost savings without extensive internal investments by their clients. ■
Expand Storage capacity 4 times. Increase throughput 10 times
Why partner with Kardex?
The right partner can help you navigate the automation journey to meet and exceed your goals. Kardex has a dedicated team with many years of experience in planning and implementing tailor-made AutoStore solutions within a wide range of industries. Our aim is to take everything into account – combining different technologies and providing complete, integrated, and cuttingedge intralogistics solutions from a single source.
We have dedicated project managers committed to working side by side with you through system concept, design, and installation. Our team will also be onsite during the installation and ramp up phase to ensure a smooth transition for you and your team. Using our extensive nationwide service and support network, you will be fully supported throughout the lifecycle of your AutoStore system, even in the most remote location. We are always close to you – worldwide.
Vanderlande is finalising new deals for automating warehouses with its FASTPICK goods-to-person and ADAPTO solutions, as detailed by Sales Director Roald de Groot and Sales Manager Katie Budd.
Since arriving in Australia in 2012, Vanderlande has brought its specialist knowledge in logistics process automation across warehousing, airports, and parcel sectors to the fore.
The Netherlands-based company’s portfolio including innovative systems, intelligent software, and life-cycle services ensures fast, reliable, and efficient automation technology for numerous Australian customers.
Its warehousing solutions are used by many top global e-commerce and retail brands in food, fashion, and general merchandise, supporting same-day delivery for billions of orders, with nine of the 15 largest global food retailers depending on its solutions.
When a business grows above a certain threshold, there are various benefits to introducing automation and moving away from a wholly manual operation – increasing efficiency being among the most notable.
“It’s a big step to introduce complex automation into a warehouse for the first time. This is particularly true when you operate in a segment that is not familiar with automated solutions,” says Roald de Groot, Sales Director of Vanderlande Australia.
“From the cost of the investment through to selecting and installing the right solution, there are many factors to consider. By forging solid relationships, we provide support throughout the
Kärcher’s newly appointed national Business Development Manager, Richard Boothey, speaks to MHD about the KIRA B50 and KM 170/600, which will be
From its humble beginnings focused primarily on pressure washing equipment, Kärcher has grown over the past 90 years to become the leader of cleaning solutions.
This evolution highlights Kärcher’s commitment to providing cleaning equipment for a range of materials handling and logistics facilities.
At Prime Creative Media’s upcoming MEGATRANS event, Kärcher will showcase its total cleaning equipment range, demonstrating its innovative solutions for both facilities and fleet vehicles.
“The concept of total cleaning is, particularly in transport logistics, a total inside out clean of not only facilities but fleet vehicles as well,” says Richard Boothey, National Business Development Manager, Kärcher.
This includes automated truck wash systems for external cleaning and battery-powered backpack vacuums, and carpet extractors for the interiors.
For logistics facilities, Kärcher offers large area sweepers and floor scrubbers to ensure comprehensive cleaning.
One of the key innovations Kärcher will showcase is the KIRA B 50 autonomous floor scrubber.
“That’s one of the key products that we’ll be showcasing at MEGATRANS, which gives facility owners a highly efficient cleaning solution,” explains Richard. By automating cleaning tasks that do not generate income, businesses can reallocate labour to more productive activities such as picking, packing, and distributing.
This not only saves money but
“Kärcher’s equipment is designed to meet the varying demands of different sectors.
also enhances overall operational efficiency.
Kärcher’s solutions reduce downtime all while increasing productivity. For example, an automatic truck wash system can clean a truck in two minutes compared to half an hour with a manual pressure washer. Over time, these savings accumulate substantially.
Kärcher prides itself on its network of trained service technicians across Australia, ensuring that all equipment is maintained efficiently.
“In terms of an ROI, we very often sit down with clients and show them what that return on investment will look like,” says Richard.
Kärcher also offers financial solutions that include maintenance programs, providing customers with a single monthly invoice that covers both equipment and maintenance.
This approach helps businesses avoid large capital expenditures on cleaning equipment.
The KIRA B 50 is a revolutionary addition to Kärcher’s product portfolio.
“It has its own automatic docking station,” explains Richard. “The machine will go back to the dock, empty itself out of all the dirty water, clean out the dirty water tank, automatically refill itself, recharge if it needs to, and then fire itself back out and go and do some more cleaning.”
This autonomous operation minimises operator intervention, making it efficient.
The unit is equipped with advanced sensors and LiDAR technology, allowing it to run all night on its lithium-ion battery.
KM 170/600 features a two-metre sweep path with dual front brushes and a 600-litre hopper capacity.
For large area sweeping, Kärcher offers the KM 170/600, described by Richard as “the biggest machinery in the fleet”.
This industrial sweeper features a two-metre sweep path with dual front brushes and a 600-litre hopper capacity.
It’s designed to quickly and efficiently clean large, hard-stand areas, preventing debris from being tracked into warehouses.
Optional features like an enclosed cab with heating and air conditioning make it easier to encourage staff to perform cleaning tasks, even in challenging conditions.
Kärcher’s equipment is designed to meet the varying demands of different sectors, from healthcare and education to retail and manufacturing.
“In terms of the transport logistics sector, what we’re talking about is larger equipment, industrially designed and manufactured to last and withstand those tougher operating environments and long operating times,” says Richard.
This durability ensures that Kärcher’s machines can handle the rigours of large-scale operations and last for extended periods.
“Our measures are aimed at reducing emissions in production, recycling of raw materials and a reduction in plastic
into its manufacturing processes. The company also incorporates water and detergent-saving technologies in its floor scrubbers, reducing environmental impact.
Additionally, Kärcher is transitioning much of its battery fleet to lithium-ion, further enhancing sustainability.
Kärcher sees MEGATRANS as an ideal platform to showcase its innovative products and reach a broader audience.
“MEGATRANS is the biggest transport and logistics exhibition in Australia,” says Richard.
“We see MEGATRANS as a great opportunity to showcase our product and bring it to a wider audience that we traditionally haven’t reached before.”
This event will help Kärcher highlight its range of solutions tailored for the transport and logistics sector.
Kärcher’s participation in MEGATRANS underscores its leadership in providing total cleaning solutions for various industries.
“With this technology and our extensive range, we have solutions for each specific sector, making transport logistics more efficient and sustainable,” adds Richard.
MEGATRANS attendees can look forward to seeing these cuttingedge innovations firsthand and understanding how Kärcher’s solutions can benefit their operations. ■
SICK Australia focuses on providing high-quality products, technical support, and customised solutions to enhance operational efficiency and safety.
With a reputation for highquality sensor technology, SICK Australia continues to innovate cutting-edge solutions that benefit food and beverage manufacturers.
Recently, SICK showcased two of its latest solutions at CeMAT Australia – the Logistics Lector Array and the Ident Gate System.
The Logistics Lector Array is part of SICK’s product line aimed at improving efficiency in warehouse and distribution environments.
The Lector Array is used for reading and interpreting barcodes and other types of codes. It’s often employed in automated sorting systems, conveyor systems, and other settings where quick and accurate data capture is crucial.
This sensor array features multiple scanning units that work together to read codes from various angles and distances, ensuring reliable and fast identification of items.
“The Logistics Electric Array electric System is made up of what we call a matrix camera device,” says John Butera, Sales Manager, SICK Australia.
“Inside, the system features a high-resolution matrix camera with its own illuminating LED lighting and the camera technology comes with AI-Based decoding to provide quick, precise identification of the relevant code region. Using super-
The Lector Array is used for reading and interpreting barcodes. Images: SICK Pty Ltd.
resolution, the system read poor quality barcodes better than a traditional laser scanner.
LECTOR ARRAY
The array helps streamline operations by enabling accurate tracking of inventory, enhancing sorting accuracy, and reducing manual handling. It’s useful in highthroughput environments where speed and precision are critical.
“It’s a segmentation process, which is to say it’s able to differentiate the difference between the barcode itself and other noise such as other writing on the label,” explains John.
“If you’ve got a label that’s got a lot of text information and it has a barcode, it just hones straight onto the barcode. It’s able to filter out a lot of noise that’s generally caused by text information around the barcode.”
The Lector Array has onboard AI segmentation processes that can highlight a barcode from other text information.
The camera’s wider field of view also presents added advantages for users, particularly around cost throughput.
“In other words, when you’re looking at a complete camera tunnel, it reduces the number of scanners that you need to cover a large area, which saves on costs,” adds John.
Whereas older versions may not have had the same field of view, the updated system allows for fewer scanners and speeds up the process, maintaining high throughput levels.
“On top of this, a particular matrix camera can handle speeds of three and a half meters per second,” says John.
“Back in the day, typical camera technology in this space was always around that two metre per second mark. If you’ve got high-speed requirements, this solution can meet those demands.”
In older versions, this process had the potential to slow down the decoder, but with the improved decoder, it quickly and reliably differentiates between a barcode and text information.
“Hence, the decoding process is much higher, much quicker, and so the efficiencies come from reading those barcodes fairly quickly,” adds John.
“It’s an important part of the Logistics Lector Array, to have improved decoding capabilities through those methods.”
Overcoming challenges with advanced technology
Several factors can impact the readability of a barcode, from light contrast to rubbing on the label itself. This new technology mitigates the issues this creates.
“The Lector Array’s imaging processor is an improved one, with the ability to see the differences between the poor-quality barcodes versus the good ones,” says John.
“That’s probably the main thing to highlight out of the camera, being an image device, and it’s dependent on what it sees.”
The Lector Array also has onboard processes that can highlight a barcode
from other text information in that area, on top of being relatively easy to use.
“The set-up process, or AI Integration, is very easy to do. You don’t have to be a scientist to set it up successfully because it’s got a lot of intuitive self-teaching capabilities and functionality involved,” adds John.
Meanwhile, the Ident Gate System was also a hit at CeMAT. The Ident Gate System from SICK is designed for automated identification and tracking in logistics and industrial applications.
It’s specifically tailored for managing and optimising processes related to the sorting and tracking of items, such as parcels or pallets, within distribution centres or production lines.
“Basically, the Ident Gate System has two columns and is able to read RFID tags, along with reading barcodes,” says John.
“The system has multiple technologies on board, and in the one that we had at CeMAT we were demonstrating that it’s a device that allows you to validate what’s going out of the warehouse into the truck is accurate.”
The Ident Gate System also has the capability to simultaneously read multiple RFID tags.
“And it completes those tags all at once as you traverse this device through the warehouse to the truck loading area. If there’s an incorrect item in there, it picks that up as well,” explains John.
“In other words, if you’ve got products that aren’t supposed to go out, it’s able to capture that as well. It has the best of both worlds. It has the
RFID reader, and it also has the electric cameras as well.”
The system also has smart sensor technology on board, which can detect the direction of travel.
“That way it knows that the object is going through one area, through to the other area, and it can see that detection, validating it as it does,” says John.
“Essentially it acts as an identification gate that detects the objects that are running through. It gives you an added layer of product security, along with savings because it’s able to track and validate the product quickly and reliably.”
Both the Ident Gate System and the Logistics Lector Array came about like all of SICK’s solutions, through research and development based on learnings from supporting customers.
“A lot of our products are along those sorts of lines. We aim to be innovative, and our customers support that innovative approach,” explains John.
The scalability and flexibility of the Ident Gate System was another key selling point for the solution at CeMAT.
“When you think about the scalability, obviously it’s to deal with higher throughputs. It gives you the ability to adapt accordingly,” says John. “We made sure the solution was easily scalable to meet the diverse needs of different customers.”
Its role in inventory management is another important aspect of the solution.
“Because when you’re bringing products into your environment, you want to embed that into your inventory as well,” says John. “In other words, we can interface this to most ERP systems that are out there.”
To learn more about the Logistics Lector Array and Ident Gate System, visit www.sick.com.au. ■
System Design Engineer at Adept Conveyors, Philip Chan, spoke with MHD about how the company’s multifunctional conveyor systems meet the evolving needs of the materials handling industry.
Adept Conveyors is renowned for designing, manufacturing and installing quality conveyor systems that are low in cost and high in versatility.
Adept’s systems can handle a diverse range of tasks, offering both automated and manual conveyor systems.
Philip Chan, System Design Engineer at Adept Conveyors, says the systems’ adaptability to various factory layouts and operational needs is a strength of the company.
“Every customer is different,” he explains. “They might have a different layout to their neighbours next door. To cater to this, we offer tailored solutions to support their requirements.”
Not only does Adept offer flexibility, but Philip says the company also prides itself in delivering a fast turnaround of system orders.
“Sometimes we can even turn around orders within a week, depending on the size of the order,” he adds.
While the company offers conveyor systems for various industries, it particularly excels in the material handling industry sector.
“We offer a system designed for a broad range of customers in the logistics industry but mainly focus on the material handling industry,” says Philip.
Aside from adaptability and timeliness, Philip says a reason why customers
return to Adept is its commitment to simplicity. While many rely on innovation and technology for a competitive edge, Adept Conveyors prioritises reliability and simplicity.
“Our previous owners between them have more than 80 years of experience,” explains Philip.
“These systems are tried and true. If they’ve been proven in the past they work effectively, why reinvent the wheel?”
Despite this, the company doesn’t turn its back on innovation, instead it continually assesses new technologies if they improve workflow.
“We recently came across a wireless control card that could connect to powered rollers,” adds Philip. “All you need is just an application on a mobile phone or an iPad, and you can connect to it.”
It’s no secret that when purchasing conveyors, customers see reliability as a major priority. To consistently meet these standards, Adept employs tight measures that ensure components used in systems have an unmatched level of reliability.
The company sources all its components from Marx-Rollentechnik GmbH, a German based conveyor component exporter with who it has a lengthy relationship with.
“We have used the same suppliers, basically, ever since we started operating as a business,” says Philip.
“All our products are Australian made, but the components are from a German company and have that European quality.”
Beyond this, Adept offers an extra layer of quality assurance to ensure systems are never returned.
“We test the conveyors, make sure they run, and then disassemble it, get all the little components painted or powder coated, then put it together and test it again,” adds Philip.
“We also have a quality assurance process where every job that goes out, we do a random check of the rollers and the componentry.”
Not only is reliability a key concern, but sustainability has been a recent focus area of the company. The company is currently fine-tuning suitability processes that help reduce overheads and material waste.
“In the engineering and the design phase, we always look at ways to reduce overheads and material waste. We always try to reutilise it,” explains Philip.
The strengths of Adept Conveyors have led to some high-in-demand offerings, including the Gravity Roller, Powered Roller, and Belt Conveyor systems.
“The Gravity Roller conveyor systems are very economical because they use gravity, which is free. There’s no electrical component,” says Philip.
The proposed capabilities of Adept conveyor systems would mean little
layout issues for a material handling environment.
The first project involved a supplier of pet equipment who needed a conveyor system to bring goods from a mezzanine level down to the ground floor.
“When we visited the site, they were doing everything manually, they were pushing everything around the whole
finished packing the boxes.
“They were happy with that system because I’m sure it would have minimised downtime and the labour component.”
Philip also recounted a situation where he and his team successfully tackled a severe bottleneck for a customer who didn’t know how to streamline a flow of materials.
“Instead of someone running
After what has been a quiet period for Adept, Phil emphasises that reaching the new financial year has seen production rapidly pick up.
For the foreseeable future, Adept Conveyors is focusing on new and exciting orders from both existing and new customers in the smallgoods and parts distribution sectors. ■
www.bonfiglioli.com/australia/en www.bonfiglioli.com/new-zealand/en
Falcon Autotech is reshaping global warehouse automation with innovative technology and a robust international footprint. Sandeep Bansal, Chief Business Officer and Chris Josey, Regional Head ANZ share insights into the company’s transformative journey.
Since its inception in 2012, Falcon Autotech has established itself as a trailblazer in the realm of warehouse automation solutions. Initially focusing on solving specialised automation challenges for clients, the India-based company designs, manufactures, supplies, implements, and maintains cuttingedge warehouse automation systems.
“Falcon Autotech initially focused on specialised machinery. By 2012, recognising a gap in India’s warehouse automation market, Falcon developed a local technology stack to replace costly imports from Europe and Japan. Today, Falcon is a leading player in India’s intralogistics sector, commanding over 75 per cent of the sortation market,” says Sandeep.
With operations spanning 15 countries, Falcon Autotech has advanced in the sector, specialising in cutting-edge technologies including sortation, robotics, conveying, vision systems, and IoT.
“Since our launch, we have expanded our product line to include static and dynamic weighing systems, sortation and conveyor systems, and our latest innovation, the fully 3D ASRS system, NEO,” says Sandeep.
“About three years ago, we began our international expansion by establishing sales offices in Australia, the Middle East, and Europe, with plans for the US,” says Chris Josey,
“Since launching in Australia in March 2023, we’ve achieved
remarkable success, including recent system awards for the New Zealand market. We’ve installed systems across Europe, the Middle East, India, and Australia, and we’re excited to continue our growth with a planned launch in the US market by March 2025.”
These installations include partnerships with major players in industries such as E-Commerce, CEP (Courier, Express, Parcel), fashion, food/FMCG (Fast Moving Consumer Goods), automotive, and pharmaceuticals.
AI is turning traditional operations into agile, data-driven marvels. With real-time data analysis, AI enhances inventory management, optimises sorting, and predicts maintenance
needs, all the while accelerating speed and accuracy.
The AI works at multiple stages in the warehouse automation system.
“One basic use of AI is analysing data from sorters to improve the accuracy of labels, reducing the chances of missorts and efficiently reading unreadable labels before sending the information back to the sortation system”, says Sandeep.
“However, the most significant application we’ve seen is in the automated storage and retrieval systems. Today’s ASRS systems, including our newly launched Neo, can analyse historical data, predict future demands, perform ABC categorisation, and auto-map inventory to specific stations. There are numerous use cases for AI in enhancing ASRS functionality.”
Falcon recently has also enhanced one of its oldest product lines –Dimension Weight Scanning (DWS) Systems. Companies often need DWS for storage space planning, optimising packaging size for outbound products, correcting freight costs and vehicle space utilisation.
“By integrating high-end vision cameras and AI technology, we’ve advanced DWS to accurately capture the volumetric weight of irregularly shaped items. For instance, it can now determine the cubic volume of a water bottle or a polybag of tomatoes, showcasing another example of how AI and vision technology are transforming our products,” adds Sandeep.
Warehouse automation offers the potential for enhancing operations, cutting costs, and boosting customer satisfaction. Yet, the transition to automated systems is fraught with challenges.
According to Falcon Autotech, there is an uptick in the trend of adoption of warehouse automation technologies, especially since COVID-19, which highlighted the reliance on human labour.
“The acceptance level has increased with a higher inquiry level,” said Chris. “Organisations are more motivated to invest as they see the importance of focussing on improved efficiencies, productivity increases and accuracy. Accompany this with a strong ROI and the business case with our solutions is very strong.
The biggest challenge in this market is securing skilled labour. To address this, we’ve partnered with specialised organisations in Australia, allowing us to sustainably grow our footprint while ensuring we can support our products throughout their entire lifecycle.”
Falcon Autotech’s NEO is set to transform how businesses approach efficiency, productivity, and inventory management. Unlike traditional ASR systems limited to X and Y axis, NEO can move in three axis, climb racks without the need for lifts or conveyor systems, reaching heights up to 12 metres.
This innovation allows businesses to utilise vertical space, access any SKU with any robot, and seamlessly interact with any ‘goods to person’ station.
The NEO system, powered by cutting-edge robotics, AI, and advanced sensors, features five groundbreaking components: NEObots, NEOgrid, NEObins, NEOit, and NEOstations.
“Two key trends we’re seeing are the increasing unavailability of skilled labour and the rising cost of land, which is continually escalating, says Sandeep.
“As quality land becomes more expensive, businesses must focus on utilising vertical space effectively. We’re observing warehouses expanding from eight metres to sizes of 12, 16, and even 24 metres in height. Companies must leverage vertical height and find systems that can boost productivity levels by three to four times, which is exactly what our ASRS achieves.
Our system delivers a productivity boost of around four to five times by minimising the need for operators to walk the warehouse, allowing them to remain static while products are delivered to them. This goods-toperson technology is highly efficient, reduces fatigue and workplace incidents and adds another level of security to our clients’ products.
Additionally, our system utilises vertical height effectively, currently supporting storage up to 12 metres and potentially up to 16 metres in the future. This capability meets approximately 80 to 90 per cent of market needs.”
NEO offers an ROI of around three to three and a half years. In Australia, however, it typically sees an ROI of about one and a half years – two years, though this can vary based on the size and scale of operations. On average, Neo delivers a return on investment in about 18 months in the Australian market.
Falcon Autotech maintains a paperless policy and focuses on using recyclable materials and renewable energy in its manufacturing processes. Its technology is designed with energy efficiency featuring power-saving
modes that deactivate unused components to conserve energy.
“We are incorporating recyclable plastics in our NEO bins and exploring models to collect and recycle these bins from customers for reuse. These initiatives are part of our broader commitment to sustainability,” adds Sandeep.
Initially focusing on developing automation solutions tailored to the Indian market, Falcon has distinguished itself from multinational competitors by emphasising homegrown innovation.
This commitment aligns with the Make in India initiative, showcasing its ability to produce high-quality, competitively-priced products. As demand grows, Falcon has penetrated international markets, including Europe and the USA, while continuing to invest in R&D to stay ahead of industry trends.
“Our approach to international markets is straightforward”, says Sandeep. “First, having a proof of concept in that market is crucial, as demonstrated by our success in Australia. Second, robust sales and support networks are essential; we ensure peace of mind for our customers by maintaining a 100 per cent success rate over the past 12 years with all projects still operational. Lastly, building a strong partner ecosystem is key, which is why we’re establishing our dealer and agent program in Australia to enhance accessibility and support for our technology.”
Falcon Autotech’s advancement in warehouse automation reflects its leadership in integrating innovative technologies and global expansion. By leveraging AI and robotics, the company continues to address complex supply chain challenges while maintaining a focus on sustainability and efficiency. ■
MHD sat down with dispatch and delivery management company, vWork and its CEO Roy Moody, to discuss first-time delivery and last-mile delivery logistics.
Achieving sustainability isn’t just a buzzword – it’s a crucial goal for businesses aiming to meet both environmental and customer expectations.
One key area that holds potential for reducing carbon footprints is the optimisation of last mile delivery.
Roy Moody, CEO of vWork, shares insights into how companies can leverage advanced job scheduling and dispatch software to not only boost profitability, but also contribute to a more sustainable future.
“Improving your first-time delivery rate can make a huge difference in how efficiently you use resources like fuel and vehicles,” says Roy.
This efficiency translates into reduced fuel consumption and less wear and tear on delivery vehicles, which are critical factors in achieving sustainability.
Achieving high first-time delivery rates is not straightforward. It requires a robust system that can adapt to real-time changes and unforeseen circumstances.
Roy emphasises that last mile job scheduling and dispatch software is instrumental in this regard, offering a clear and identifiable return on investment both in financial terms and in reducing carbon footprints.
A pivotal aspect of enhancing first-time delivery success is maintaining clear and consistent communication with customers.
“Once real-time scheduling is implemented, you can send reminders to customers about upcoming deliveries and allow them to track the vehicle,” explains Roy.
increases the likelihood of successful deliveries but also reduces the need for repeat trips, thereby conserving fuel and resources.
Real-time visibility into delivery schedules enables companies to make informed decisions about the most appropriate vehicle for each delivery route.
“You can determine whether a small van or a larger truck is better suited for a specific run, and even assess the feasibility of using electric vehicles for shorter routes,” adds Roy.
This data-driven, decision-making process is a stepping stone towards more sustainable fleet management.
Route optimisation is another tool in the quest for sustainability.
“Route optimisation aims to reduce the overall distance travelled by the fleet, thus saving fuel and reducing vehicle wear and tear,” says Roy.
Effective route optimisation considers various factors, including customer
By optimising routes, companies can reduce the number of vehicles on the road, which not only cuts down on emissions but also lowers operational costs.
“Manual route planning is timeconsuming and prone to errors,” adds Roy.
“If something changes, all that work can be wasted. With vWork’s route optimisation, any changes can be quickly incorporated, and the updated schedule is instantly communicated to drivers.”
This automation not only enhances efficiency, but also reduces the administrative burden, allowing companies to focus on other critical areas of their operations.
Three-way communication between the dispatcher, driver, and customer is one feature that makes vWork proud.
“It’s amazing how much it has
inaccessible due to weather conditions, customers can communicate this to the dispatcher and driver, who can then adjust the route accordingly.
“This feature significantly reduces waiting times and idling, which are not only costly but also environmentally damaging,” adds Roy.
The ability to reschedule deliveries on the fly ensures that goods are delivered efficiently, further enhancing customer satisfaction.
Roy explains that some new clients have adopted vWork specifically because their customers demanded it, highlighting the importance of reliable delivery services in today’s market.
Another key feature of vWork’s software is the use of automated templates. These templates capture essential customer requirements and job details, reducing the risk of errors and ensuring that all necessary information is readily available.
“In the past, companies relied heavily on driver knowledge and experience,” explains Roy.
“But with automated templates, even new or contract drivers have all the information they need to complete the job successfully.”
This standardisation helps companies maintain a consistent level of service, regardless of who is
“In
Australia, vWork’s clients include companies involved in grocery delivery, in-home care product delivery, and even civic asset maintenance.
”
carrying out the delivery.
“Details like access protocols, dock locations, and any special requirements are all captured in the template, ensuring that no critical information is overlooked,” adds Roy.
This approach helps businesses achieve high first-time delivery rates, reducing unnecessary trips and lowering the overall carbon footprint.
While electric vehicles (EVs) and hydrogen-powered vehicles are often touted as the future of sustainable transport, Roy says there are strides to be made even without these technologies.
“Getting the right last mile job scheduling and dispatch software in place is the first step. It has to be software that works with your existing business processes,” he explains.
Roy shares that even companies that consider themselves efficient often find room for improvement once they implement vWork’s software.
“
Another key feature of vWork’s software is the use of automated templates.”
“We’ve seen businesses improve their fleet utilisation by up to 20 per cent, simply by optimising their operations,” he adds.
This efficiency gain translates into reduced fuel consumption and lower emissions, demonstrating that sustainability is achievable even with conventional vehicles.
vWork’s solutions are not limited to Australia. The company serves customers in 10 countries, including a diverse range of industries.
“Our clients range from medical distributors in San Francisco to supermarkets and industrial building supply companies,” explains Roy.
This global presence underscores the versatility and adaptability of vWork’s software, making it a valuable tool for businesses worldwide.
In Australia, vWork’s clients include companies involved in grocery delivery, in-home care product delivery, and even civic asset maintenance.
This range of applications demonstrates the software’s ability to meet the needs of various sectors, from healthcare to construction.
Optimising last mile delivery is a critical component of any sustainability strategy. vWork’s job scheduling and dispatch software offers a solution that improves efficiency and profitability and also contributes to reducing the environmental impact of delivery operations.
“It’s not just about checking a box; it’s about genuinely making a difference,” says Roy.
With the right tools and strategies in place, businesses can achieve sustainability gains, even before transitioning to electric or hydrogenpowered fleets. ■
ASCL INDUSTRY EXCELLENCE AWARD
Dedicated to Mike Munns, FAIMM Award Inaugurated 1987.
ASCL SUPPLY CHAIN MANAGEMENT AWARD
ASCL FUTURE LEADERS AWARD
Dedicated to Vince Aisthorpe Award inaugurated 2009.
ASCL AUTOMATION, ROBOTICS OR EMERGING TECHNOLOGY AWARD
Dedicated to Doug Beattie Award Inaugurated 1984. Award Inaugurated 2021.
ASCL TRAINING, EDUCATION & DEVELOPMENT AWARD
Dedicated to the late Professor Peter Gilmour Award Inaugurated 2002.
ASCL INTERNATIONAL SUPPLY CHAIN AWARD
Award inaugurated 2016.
ASCL ENVIRONMENTAL EXCELLENCE AWARD
Dedicated to Mr Ken Pike, Award Inaugurated 1966.
ASCL BIG DATA, IT & BUSINESS INTELLIGENCE (BI) AWARD
Award inaugurated 2021.
PRE DINNER DRINKS + CANAPES | 3 COURSE ALTERNATE DROP DINNER + DRINKS | MC SAM MCCOOL
Grand Ballroom, Sheraton Hyde Park Sydney
ASCL START-UP AWARD
Award inaugurated 2021.
SECURE YOUR TABLE
WORKPLACE HEALTH AND SAFETY AWARD
Award inaugurated 2024.
TRANSPORT LOGISTICS EXCELLENCE AWARD
Award inaugurated 2024.
VIEW AWARD CRITERIA SUBMISSIONS
15 SEPTEMBER 2024
1 OCTOBER 2024 FINALISTS ANNOUNCED SUBMISSIONS CLOSE
WINNERS ANNOUNCED AT THE ASCL AWARDS GALA
15 NOV 2024, Grand Ballroom, Sheraton Grand Hyde Park Sydney
NNilfisk keeps sustainability and efficiency at the forefront of its product development, as demonstrated by the CS7020 Combination Sweeper/Scrubber dryer cleaning solution.
ilfisk’s CS7020 is helping transform industrial cleaning with its string of innovative features designed for efficiency, productivity, sustainability, and safety.
Sustainability is at the forefront of every Nilfisk solution, and the CS7020 is no different.
“The common aspect of cleaning with a combination machine, scrubber, drier, sweeper – any machine like that – is the use of water or chemicals to assist the cleaning process at the floor,” adds John.
“Anything that can be done to reduce water consumption and chemical consumption is important and many people within the warehouse and distribution areas are conscious of that.”
A feature of the CS7020 is its optional Ecoflex™ System, which can be
built into the machine to promote sustainability. This system allows users to adjust water flow and chemical usage based on cleaning needs and the nature of the site, reducing both water and detergent consumption.
“Clean with detergent or green with just water? We say both,” says John. “It enables users to select different cleaning intensities and conserve resources effectively.”
Additionally, the CS7020 is designed with user convenience in mind.
“Different facilities require different cleaning in different areas. By applying the right blend of brush pressure, water or detergent, the Ecoflex™ system is the professional and green solution to any cleaning challenge” says John.
As a result, the machine solution enhances productivity by allowing for faster, more efficient single pass
cleaning without compromising quality of clean.
“With the customisable CS7020, you can make adjustments to water levels and detergent usage on the go, making it a highly versatile and adaptable solution,” says John. “It’s also a very easy to use solution with a simple control panel. It’s mostly a one touch button operation, which means it’s very easy for any user to get on and to use those features as well.”
Its Smart Flow technology further optimises cleaning efficiency by adjusting water and chemical flow based on the machine’s speed. This ensures that water or chemicals are not wasted, even during complex manoeuvres such as aisle end turns and busy site areas.
“Smart Flow controls the flow of water and chemicals needed for the
scrub brushes, preventing issues like excess water down the end of an aisle,” says John. “It helps reduce water usage, costs and improve overall efficiency.”
The CS7020’s capabilities extend to its performance metrics as well. The machine can clean up to 12,000 sqm per hour and even reach up to 50,000 sqm from a full battery charge, depending on settings and usage. It combines sweeping, scrubbing, and drying functions all in a single pass.
“The CS7020 is not only highly effective in sweeping but also excels in scrubbing and drying, making it a popular global choice among users,” adds John.
In the realm of energy efficiency, lithium-ion batteries are becoming increasingly prevalent, which is what also drives the CS7020.
“We’re seeing a significant shift towards lithium-ion batteries due to their consistent performance, zero emissions and fast and opportune charging capabilities,” says John. “Previously, long-hour usage sites and operations required hybrid models with diesel or LPG, but now, lithium batteries are proving to be productive,
convenient and an affordable solution.”
John says Nilfisk has three main sources of energy for its solutions.
“In our case, our main three energy sources are batteries, and our lithium-ion batteries. The other two sources we have in some of our larger machines are what we call a hybrid model, a combination of battery/diesel or a battery/LPG,” says John.
“Demand for hybrid machines are shifting more and more to Lith-Ion battery powered solutions. It’s changing quickly, and machine pricing is becoming more affordable.”
As logistics businesses continue to face competitive pressures and tighter margins, the CS7020 offers a sustainable, efficient, and costeffective cleaning solution. Its advanced features and user-friendly design make it a valuable asset for modern industrial cleaning needs.
Nilfisk’s new Industrial battery powered vacuum cleaner – the VHB436 is adding to the suite of innovative cleaning solutions Nilfisk offers. This state-of-the-art vacuum
cleaner, powered by lithium-ion batteries, addresses several key challenges in large facilities such as warehouses and distribution centres.
One of the primary advantages of the VHB43 is its ability to eliminate the need for long power cords out in the site aisles.
“In facilities like warehouses, you don’t want long mains powered cords laying all over the place,” says John Mahar, Commercial Product Manager-Pacific for Nilfisk.
“The VHB436 offers a cordless vacuum cleaning solution that allows for thorough cleaning even in hardto-reach areas, like the back of aisles or underneath racks, where traditional power outlets are not available.”
The global demand for such solutions is on the rise rapidly, particularly in North America and Europe. The focus is not just on tidying up, but on ensuring that every corner of the facility is addressed and cleaned easily and effectively.
“Our smart customers won’t just leave that spill or dust and dirt in the corner or down the end of the aisle,” says John. “They want to get it cleaned up fast, especially in critical areas like 3PL logistics sites where all visible areas should be spotless” ■
When it comes to finding materials handling solutions for any size of warehouse, Airstack and CIMC have an array of solutions. Here’s why.
As the name suggests, Airstack Intralogistics is a company that specialises in logistics warehouse management systems and software.
Founded by Henry Hui in 2022, the company has already started its first project in Yennora NSW and is looking to spread its wings in Australia as it offers a suite of solutions. One of the keys to its success is its collaboration with one of the big players in the Southeast Asian space, China-based CIMC Pteris Global. Such relationships help both companies offer best-inclass solutions to clients. How big is CIMC in the scheme of things?
“Big,” says Henry.
The company recently supplied an array of products to the newly built Foshan IKEA Home Furnishings Logistics Centre based in Guangdong Province in southern China. It will serve as the procurement centre for the South China region and will cover 15 stores in the South China market, including Hong Kong and Macau.
The IKEA Foshan project is the most automated ASRS in IKEA’s portfolio.
It is the only one that requires the simultaneous operation, storage, scheduling and transportation of three types of pallets. South China has higher requirements for cargo turnover capabilities and greater storage capacity compared to the rest of the country. Additionally, IKEA’s range of products requires operations 14 hours a day, 297 days a year, which imposes high demands on system stability. Some of the statistics surrounding the IKEA build are mindboggling. For a start, there is the size of the warehouse.
“This project has a total area of about 40,000 sqm and a warehouse area of about 24,000 sqm,” says CIMC marketing manager Jimmy Chang. “And the warehouse has a total of 101,928 storage locations. CIMC provided a total of 14 stacker cranes, each over 35 metres tall.”
“Our WMS and WCS systems must ensure seamless integration with IKEA systems –the ability to manage, operate, and schedule the three types of pallets – half pallets, IKEA pallets, and European pallets.”
Another component is the ability to offer bespoke solutions to clients, says Henry. And that was a key to the success of the IKEA project.
“We can integrate just about anything,” says Ken Seto, Business Development Manager for Airstack Intralogistics.
“It’s not like IKEA sells standard equipment. Their packs are longer than usual pallet sizes, as well as being heavier and lighter depending on the circumstances. We’ve been able to accommodate them because our gear is flexible and customisable and can give the customer what they require. Also, CIMC is an end-to-end company, so you don’t have three or four different companies doing different parts of the project; they design and develop, manufacture, install and commission, and they do the software.”
“That’s the beauty of CIMC – they can provide all requirements, whether it be stacking cranes or shuttles, or robots. They’ve got the in-house technology, so it’s like a one-stop shop, and this shop is really big and
can provide everything that customers need.”
And what about TUV certification?
“At CIMC, we are certified with TUV and the European standard,” says Henry. “Getting to the Australian and New Zealand standards is not hard for us, because it is very similar to the European standard. All plant and equipment supplied into Australia and New Zealand will comply to AS/NZ standards.”
It is with this background that Airstack and CIMC have joined forces to help create materials handling solutions for the Australian market. As well as AS/RS warehouse systems, conveyor and sortation equipment, and AGV/RGV/AMR vehicles, Airstack offers warehouse management software solutions.
“The top firms in China work on massive warehouses,” says Henry. “We feel Australian warehouses will need to go higher, to best utilise the costly per square metre rate for land. We see
range. CIMC can go up to 50 metres. This combined with automation will provide the most cost effective and efficient warehouse solution.”
Henry can’t emphasise enough how important it is that the Australian market should know that Airstack, along with CIMC, are here for the next stage of Australia’s evolution in the warehousing and logistics space. He remembers a time when Australia was the big kid on the block in terms of how big DCs and warehouses could become. In the past 20 years, China has superseded Australia and then some. However, Henry believes, due to how much smaller the world has become in terms of transportation and the speed at which cargo and products are moved around the globe, Australia
“In Australia, I think that in the past, there have been few companies able to provide full large scale automation solutions,” he says. “I believe CIMC can complete these projects, no matter how large or small, because we’ve done more than 700 of them in China already.”
The final piece in the puzzle is the WMS. How good is it, and does it do a thorough job?
“The system we provide is very strong in its capabilities,” says Henry. “It helps the customer to minimise all the issues.”
“CIMC created their own WMS system,” says Ken. “It was developed in house, so it’s not off the shelf and modified it’s actually created by CIMC.”
Henry points out that being China based, doesn’t mean there are no boots on the ground in Australia when it comes to back-up service.
“What we did with our Australian projects is that we have two engineers who will stay on site for a year to make sure the equipment is running every day,” he says. “We also have 24 hours software support available should the need arise and a store of spare parts.”
Henry emphasises the importance of after-sales service for both Airstack and CIMC’s success in Australia: “A stable and reliable warehouse system running without interruption is vital to our clients in their daily operation and it is our mission to make sure we deliver it.” ■
Cranes need drives. And drive specialist Bonfiglioli has a unit to suit most crane applications. Here’s why.
Cranes are a key piece of infrastructure in DCs and warehouses. They are responsible for making sure SKUs are handled correctly and dispatched to their destination with minimal fuss. For a crane to work at its maximum, it needs many moving parts, none of which are as important as a drive. A drive is the workhorse and helps make sure a crane works at its maximum effectiveness.
The National Sales Manager for Bonfiglioli Australia is Harry Singh. He knows how crucial drives are in making sure warehouse and DC operations are running smoothly. While drives are an integral part of
a crane’s make up, there are other issues that are at the forefront of Harry’s mind when discussing drives.
“The first and the most important point comes to my mind always is safety,” he says. “That’s because with a crane you’re lifting something. The first thing we ask ourselves with a crane is, ‘what is the client going to do with this crane? Which environment is going to be using inside or outdoor? And then most important question is; what is the FEM (The European Materials Handling Federation) class of the crane?’ These all have a relation to safety in terms of the operator being able to do their job properly without coming to harm.”
Harry said that it is important when choosing a drive to make sure the user knows the parameters that are required to make it work effectively and efficiently.
“If any of these parameters change, the product category can change,” he said. “Based on our past 25 years’ experience in Australia, our HDP series of drives are popular, especially in overhead versions, such as gantry cranes and bridge cranes. They are reliable and safe because the service factor on these gearboxes is high and so far, we haven’t had a single failure in the past 25 years with this product.”
Having the capacity to handle high loads is also an important ingredient for a drive. DC and warehouse work can be intense, so clients expect a lot out of their plant and machinery.
HDP series offers output torque range up to 210,000 Nm. Some of the crane drives we supply can be as big as 4.5 tonne. These machines are designed to work hard and work long hours.
As well as warehousing, other materials handling capabilities where Bonfiglioli drives are used include boring machines for tunnelling, which have been in uses in projects in both New South Wales and Victoria. The drives need to be big for such developments because the cranes are also huge. One latest application was on the WestConnex project near the ANZAC bridge in Sydney.
“When the boring machine digs inside, it also adds panels/frames around the shaft, so the structure doesn’t collapse,” says Harry. “These cranes have two functions. One is that they can move those frames and other heavy machinery to go in the tunnel. Secondly, They are also used to remove excavated material out of the tunnel and load on trucks. They will design a crane of 100 tonnes for fast speeds, and a 550-tonne unit for slow speeds.”
While the HDP range is an integral part of Bonfiglioli’s offerings, it also services the needs of smaller cranes, with the new HF range of gearboxes.
series was designed in Bonfiglioli’s factory in India. HF series was developed for cranes with 500kg- 7 tonne capacities.
“The benefit of this new product is that it has a motor with a brake inside, but you also have the option to add a secondary brake at the back of this drive,” said Harry. “It’s a double safety feature. We’ve been selling this product in Australia for the past two years, and the response to it has been very good. This year we doubled the turnover on this product in Australia and APAC. It’s ideal for small warehouses and factories where you need to move a smaller weight –between half a tonne and five tonne max.”
While quality is a key part of Bonfiglioli’s range, availability is also something that needs to be taken into consideration for clients. The local company has that covered, too, says Harry.
“We have $10 million worth of stock on the shelf in Australia,” he said. “The bigger HDP series gearboxes we can build within one to two working days.”
These pieces of kit can be expensive, so having a maintenance plan in place is paramount.
Harry said that every three months the maintenance people from the crane company generally do a visual
They check critical things such as signs of unusual wear & tare, vibrations, noise and oil leakage around the drum area.
“Most customers normally ask for a gearbox lifespan between two to three years for a tunnel project with maybe a maximum of five years,” Harry said. “However, we design everything around a minimum of five years lifespan, and it can go up to 10 years if you maintain it properly. Some places have been running gearboxes in the crane for more than 25-30 years without a problem. They just do regular maintenance and oil changes.”
He said the quarterly maintenance is done in situ, while every five years they will remove the drive from the crane for an inspection & overhaul by a certified repair centre to make sure it meets Bonfiglioli’s strict quality specifications.
“With the 12-month check they take an oil sample from the gearbox and get an external third party to see if there is any impurity or abnormalities in the oil,” said Harry. “They report the results to us, and we will have a further look if necessary. After five years they send the gearbox back to Bonfiglioli for a major overhaul. We strip down the gearbox fully – down to even a single bolt – and check everything in detail. We change all of the bearings and seals, inspect each gear stage internally, rebuild it, repair it sent back to the client and it will be good for another five to 10 years.”
In Australia, Bonfiglioli has it head office in Sydney, while there are branches in Melbourne, Brisbane and Perth. It also has more than 90 distributors and resellers facilities throughout Australia so it can support clients in regional parts of the country too. ■
The Supply Chain Sustainability series offers an excellent opportunity to network, learn, and collaborate.
The ASCI Supply Chain Sustainability Series 2024 provides a platform for professionals and industry experts to share the latest developments in their field. The series offers an opportunity to network, learn, and collaborate with people interested in a specific subject, including procurement, operations management, and logistics management.
The national theme for the series is Supply Chain Sustainability. event will focus on the relevance of the national theme to a particular aspect of the supply chain. The events will be held across cities in Australia, including Sydney, Brisbane, and Melbourne, between September and November 2024.
As a participant, you will have the opportunity to:
• learn from the best in the industry; and
• network with other professionals
build valuable connections and enhance your career.
Registration for the ASCI Supply Chain Sustainability Series 2024 is now open. Take advantage of the early
Contact ASCI if you have any questions or need more information.
ASCI looks forward to seeing you at the ASCI Supply Chain Sustainability Series 2024. ■
The new assessment tool is structured into five levels and seven assessment areas, focusing on end-to-end supply chain operations.
The Australasian Supply Chain Institute (ASCI) has announced its latest partnership with VCARE Academy – introducing the Supply Chain Knowledge Evaluation Assessment (SCKEA) for professionals.
The SCKEA is an evaluation that goes beyond the traditional method by identifying areas for improvement and ensuring that supply chain teams have the most up-to-date knowledge and skills to manage cost-effective operations and supply chain complexities, and overcome disruptions.
The SCKEA is structured into five levels and seven assessment areas, focusing on end-to-end supply
chain operations. For organisations, this provides a clear snapshot of employees’ existing skills, allowing an organisation to develop a capacity roadmap for its team, ensuring they have the skills needed to succeed.
The Human Resources Department can leverage the tool to evaluate candidates for better skill assessment. Using SCKEA, companies can be confident in the skills and abilities of their teams.
Individuals can assess their skills, address weaknesses, and improve their skills through professional development in areas including supply chain strategy, inventory management, sourcing and procurement,
and transportation, and supply chain resilience.
Don’t miss out on this opportunity – contact ASCI today to learn more about SCKEA.
The MRP course will take place from 29-30 October 2024 via Zoom.
Join the Master Planning & Material Requirements Planning (MRP) two-day course to improve the key processes that enable effective inventory management and higher levels of customer service. It will take place on 29-30 October 2024. By attending this workshop, attendees will learn how to improve individual processes and link them effectively to the relevant internal or external process, develop an effective five-step IBP process supported by the MPS and key IBP performance measures to ensure accountability throughout the organisation, identify the purpose of MPS & DRP, and
using simple Pareto, complex Pareto, and statistically derived safety stocks for improved customer service.
This course is suitable for managing directors of small firms and their direct reports, S&OP/ERP project team
members, personnel from demand management, order entry, customer service, IT staff, master schedulers, production planners, inventory controllers, distributions planners, capacity planners, purchasing personnel and key middle managers involved in the pre-S&OP meetings, i.e., demand, supply and partnership/integrated reconciliation/pre-S&OP steps. Classes are conducted daily, from 9 am to 5 pm Sydney Time, totalling 16 training hours. Participants will join via Zoom.
ASCI members can register for $1950, while non-members can register for $2350.
Swisslog automated warehouse solutions ‘scalable, flexible Vectura stacker crane for high bay warehouse automation reduces energy consumption of pallet warehouse operations by up to 25 per cent, thanks to features including regenerative energy design for optimal use of cycles. With an outstanding 99.7 per cent availability, and providing a solution reliability with over 50 years of continuous improvement behind it, Swedish-designed Vectura performs equally well in temperatures as low as -30°C in a frozen food warehouse, or in ambient environments as high as +50°C. Proven in more than 600 customer installations, and operating at heights up to 50m, Vectura’s single-mast design reduces cost and uses less space, setting the standard for innovative design for pallet cranes in high-bay warehouses. It achieves very high storage density, with single to multi deep reach, in high buildings and, where land space is limited.
For more information visit www.swisslog.com/en-au
Global cube storage company AutoStore introduces its latest capability, the Grid and Vending Machine solution, designed to simplify warehousing automation. The ConveyorPort is a workstation in its simplest form, where Bins are dropped on a conveyor and transferred to an opening outside of the Grid. Smart covering and sensors ensure operator safety. The CarouselPort is designed to work with the operator, in harmony with Robots to ensure the next Bin is always ready. The workstation operates with three rotating arms, each holding one bin tray. The Vending Machine solution includes various Robots and chargers, as well as a dummy display unit, and a grid structure with 60 Bins.
For more information visit www.autostoresystem.com
The ECE series truck stands out among low-level order pickers due to its innovative features tailored for accessibility, efficiency, and operator comfort. Its height-adjustable steering wheel, known as the “jetPILOT,” ensures accessibility for operators of various heights, making it inclusive for everyone. The operator-oriented working space ensures all necessary equipment, such as scanners, shrink wrap, and documents, are conveniently within reach. Furthermore, the truck can be customised with cutting-edge technology to enable semi-automation in warehouse operations, with the possibility of integrating with Warehouse Management Systems (WMS) based on customer requirements. Experience the difference with the ECE series truck today and elevate your warehouse operations to new heights. To learn more about how our innovative features and customisable options can streamline your workflow and enhance operator satisfaction, visit our website.
For more information visit: www.jungheinrich.com.au
ifm Track and Trace Gate is the complete solution for your automated and transparent logistics in your incoming and outgoing goods processes. By directly transferring all goods flows to the IT level, you can organise the inter-locking of production, inventory, and suppliers more efficiently than ever before.
For more information visit www.ifm.com/au/en