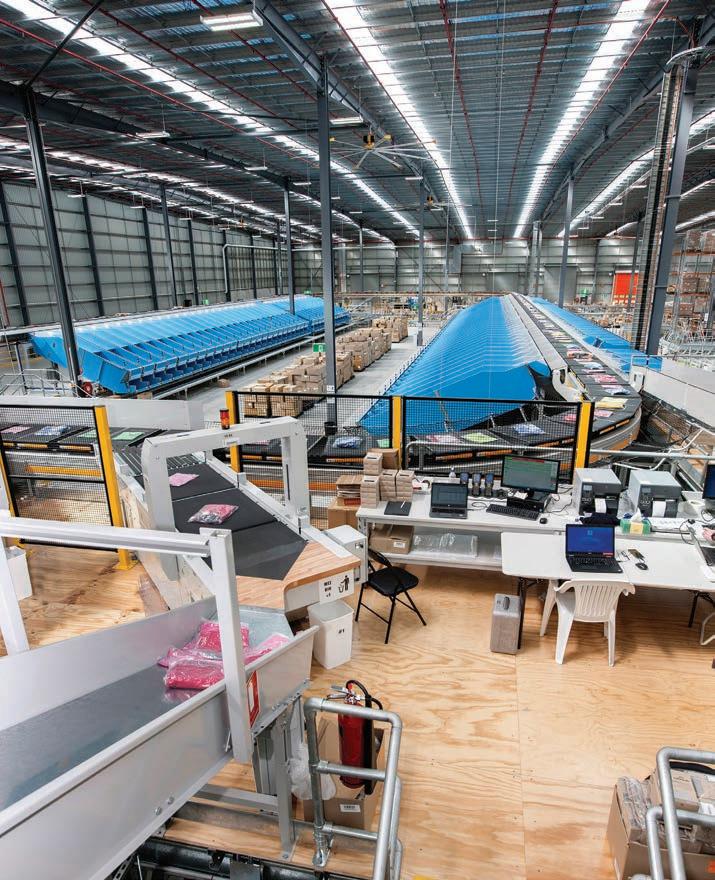
5 minute read
No two warehouses are the same
from MHD October 2021
by Prime Group
MHD talks to Philip Artlett, Solutions Development Manager at Dematic, about the value of its consultative approach in working collaboratively with customers before, during, and after the implementation of specific warehouse solutions.
Solving warehouse problems involves assessing multiple strategies to compare and contrast how they would apply to a particular warehouse, according to Philip Artlett, Solutions Development Manager at Dematic. Dematic’s broad portfolio of products and technologies allows for this exploration, which is underpinned by a consultative and commercial approach.
“The consulting process begins with working with the customer to establish the solution requirements, what we call the ‘design level’,” Phil says. “This helps to identify potential growth parameters for the future, and is backed by extensive data analysis.”
“From there, the process works a little like a funnel, because we initially take three or four concepts that make the most sense. We then talk to the customer and provide them with a return on investment model for each of these concepts to determine how much money can be invested in different levels of automation inside the distribution centre.”
By zooming in on different concepts, Dematic can further refine the design level.
“We can analyse order line data from a company’s sales history to identify what system would be best suited for now, and for ten years down the track,” Phil says. “This information, paired with product characteristics from product master data, forms the basis of our next decision.”
Before solutions are designed, manufactured and installed in the warehouse, Phil asks the customer, and himself, ‘What is the biggest pain point?’
“It’s amazing the varied answers we get – and sometimes the biggest problem is something really simple that can easily be missed,” he says. “We’ve seen businesses over the years spend huge amounts of money completely redesigning their supply chains, or at least their warehouses, and then they still have those pain points – because they weren’t addressed at the outset.”
As every stone is unturned, Dematic gets to know its customers’ operations meticulously. Consultative selling is part and parcel of the solution provider’s sales and go-to-market strategy, communicating with its customers’ senior management as well as with warehouse managers and operators on the ground to establish a rounded understanding of operations.
“We don’t just want data and spreadsheets,” Phil says. “As well
Dematic’s batch pick and sort system processes both retail and online orders together.
Dematic Goods-to-Person solutions handle wholesale, retail, and e-fulfilment – all in the one system.
as very sophisticated quantitative analysis, we want to talk to the people on the floor. We want to go to the site to talk to the workers driving forklifts and running the warehouses to see what specific sort of problems our customers are facing.”
Phil says one of the most common pain points comes from failing to adjust to smaller, more frequent orders in the e-commerce era.
“Often a warehouse or a system’s design is for a certain number of orders per day,” he says. “When those orders become half as big and twice as many – that’s a real problem.”
Despite a rapid rise in online order fulfilment during the lingering pandemic, there are very few pure e-commerce companies operating in Australia. Bricks and mortar remain essential and – in some cases – the backbone of many Australian businesses.
Dematic’s Goods-to-Person picking solution takes this into account by integrating wholesale B2B picking fulfilment and retail replenishment with e-fulfilment – all in the one system.
“Developing an omnichannel system allows us to get the balance right between retail and e-commerce channels for our customers,” he says.
“As one goes up and the other goes down, which can happen day by day, the system can still cope with the varying mix of those channels.”
Dematic’s recent work with an established apparel company illustrates the transition many businesses are facing. The brand’s retail sales form the majority of its business, but its e-commerce sales have been rapidly increasing in the past twelve months.
Keeping flexibility in mind for a changing business profile, Dematic proposed a batch pick and sort system to pick both retail and online items in one wave.
“The Crossbelt Sorter distributes items either to large chutes for packing to cartons for the store, or to smaller chutes where individual orders can be sorted,” Phil says. “Using the one piece of equipment at the heart of a system means it is flexible, with any mix of online and retail replenishment.”
Dematic’s Crossbelt Sorter can handle a range of items including plastic totes, cardboard cartons, trays, stuffed envelopes and poly bags with throughputs as high as 80,000 items per hour.
“In order to address the potential problem of the company’s changing profile, we reserved a portion of the sorter for future expansion,” Phil adds. “Depending on how the business is moving, more units can be picked and sorted for retail or online.”
Once a solution is chosen, Dematic’s software, systems, mechanical, and electrical engineers help the customer ramp up to go live with the product.
“We’re in a unique situation where we have so many Australia and New Zealand-based engineers available to support our projects right through from start to finish, and later with ongoing support and maintenance,” he says. “We can help onsite with more than 100 staff across software, project management, mechanical, controls, structural, and systems – on top of more than 270 local customer service employees.”
The consultative strategy works most effectively when a customer chooses Dematic as a partner early, according to Phil.
“We respect the tender process, but inevitably, the most successful projects have been those where the customer has made an early call as to who they want to work with and embarked on a partnership and collaborative phase with us early on,” he says.
“The customer then has all of the critical information at the source, supported by decades of consulting experience, a deep understanding of industry drivers, and the broadest range of solutions and technologies on the market.” ■
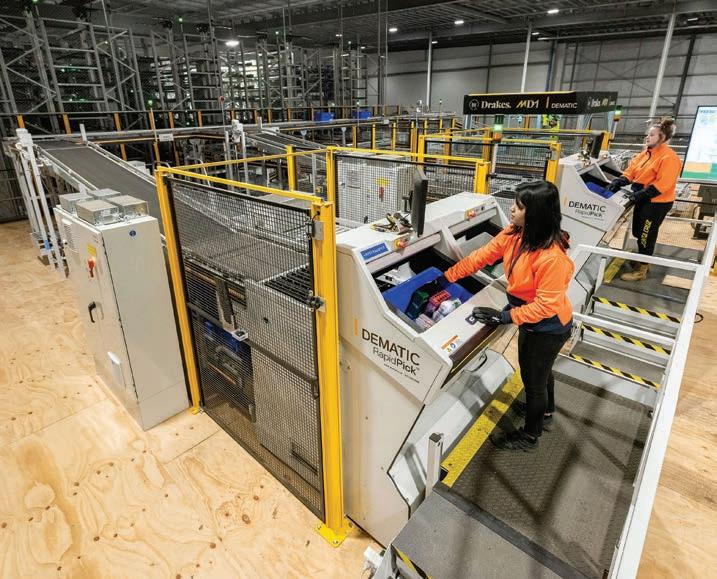
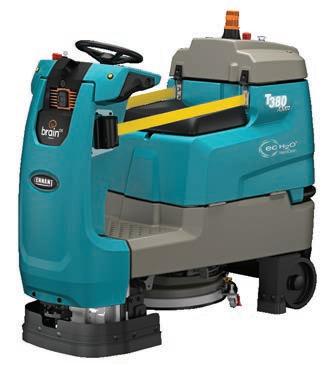
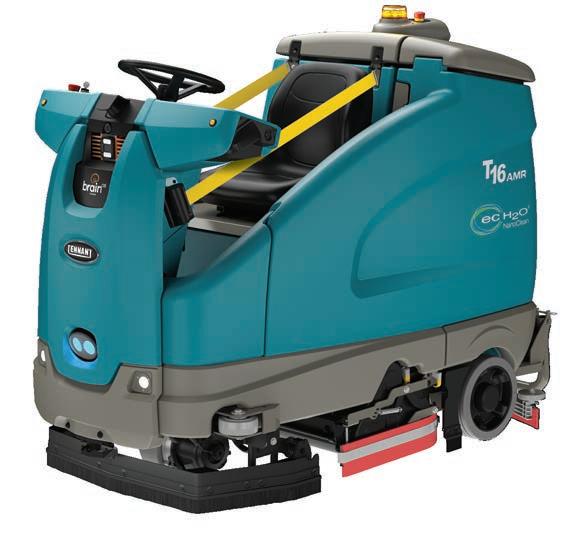
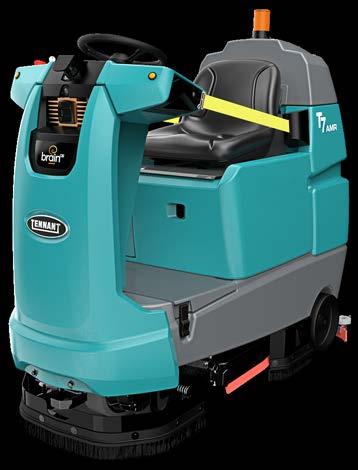