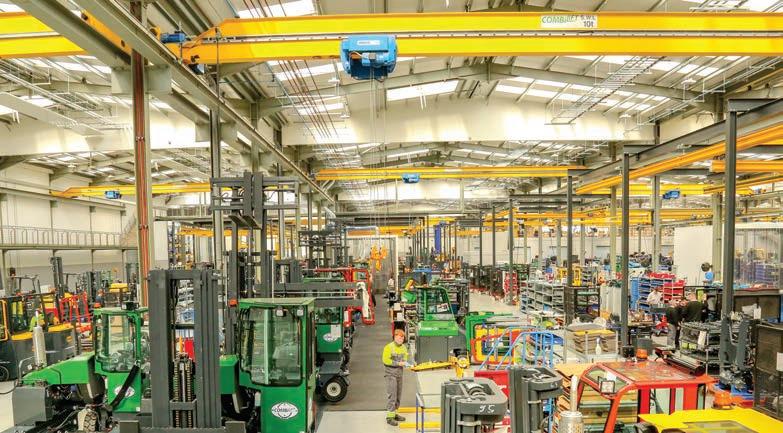
5 minute read
Sustainability built into materials
from MHD October 2021
by Prime Group
SUSTAINABILITY BUILT INTO MATERIALS HANDLING
Combilift has been ramping up its sustainability objectives over the past several years – from increasing its range of electric equipment to its own sustainable manufacturing facility. Chris Littlewood, Country Manager Australia for Combilift, explains how.
Chris Littlewood, Country Manager Australia for Combilift, says that implementation of sustainability into the company’s operations is not simply a matter of corporate social responsibility.
“Yes, we do take very seriously our obligations to the environment and broader society,” Chris says. “But it’s more than that. Sustainability is actually fundamental to our value proposition as a business.”
He notes the powerful follow-on benefits that materials handling equipment can have for sustainability.
“When you think about what Combilift do, we provide materials handling solutions that can increase your storage by up to 50 per cent or more,” Chris says. “This of itself can reduce an organisation’s footprint massively. When you reduce your physical footprint, you are reducing your carbon footprint – by reducing your energy cost as well as other associated costs such as heating, lighting, and maintenance. It all adds up and makes a big impact.”
Combilift’s focus on sustainability starts at the core of its operations – as evidenced by its new factory in Ireland, officially opened in 2018. Chris says that sustainability was a paramount consideration during the design and build of the facility.
“Everything from biomass fuel in our paint lines to minimise gas usage and take 473 tonnes CO2 out of our production in doing so; to generating 10 per cent of our total daily energy requirements from solar panels which – by the way – in Ireland is saying a lot.”
Chris adds that the facility also engages in rainwater harvesting and that 30 per cent of its roof space is covered in skylights to minimise electricity usage. “Sustainability is also literally built into our machines,” he says. “You could, if you wanted, recycle 95 per cent of a standard Combilift machine.”
Sustainability features were built in to Combilift’s new production facility, built in 2018.
BY POPULAR DEMAND
Chris says that Australia is unlike most of the other 85 markets in which Combilift operates in that it demands relatively little on a regulatory level to push businesses to adopt more environmentally friendly machines. The demand for more sustainable equipment is spearheaded by the customers themselves, rather than by the Australian government, and is testament to the growing culture of eco-awareness among many businesses.
Further benefits of electric power are reduced maintenance costs and longer service intervals, as there is no longer need to check and top up fluids, lubricants, coolants or oils. Noise pollution is also no longer an issue – and drivers, the workforce and visitors on site also appreciate the quiet operation, as do neighbouring residents and businesses, particularly in urban areas.
“Around 50 per cent of the machines we manufacture for Australia are now electric,” he says. “We now offer our multidirectional forklifts in electric up to 12-tonne lift capacity, combining emission free operation with powerful performance; we manufacture electric straddle carriers which have the capacity of lifting 35 tonnes; and nearly 100 per cent of our warehouse equipment range – including the Aisle Master articulated reach trucks and our pedestrian reach and counterbalance stacker – are electric.”
The uptake of lithium-ion battery electric units has gathered pace this year, Chris says.
“Our new Aisle Master OP or Aisle Master Order Picker comes lithiumready as standard, and customer demand
Combilift offers a range of battery powered electric straddle carriers.
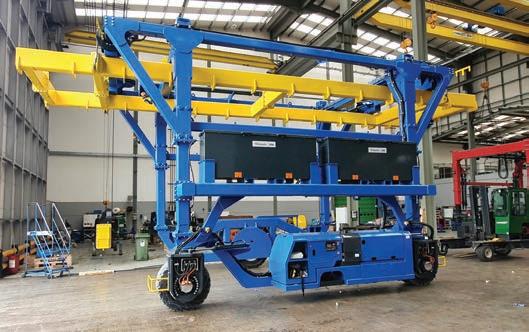
has pushed us to build our articulated range that can work in even narrower aisles. With Australian pallets that means in aisles 1.8m or narrower. I really cannot see us going backwards with electric from here on in.”
Sustainability improvements are not limited only to Combilift’s electric range, however.
“In our non-electric trucks, we have changed most of the engines in our C-Series and CB multidirectional range to Tier 4 or above,” Chris says. “This is going to have a major impact on indoor air quality as well as sustainability. This is a global, customer-led change. Our customers are demanding a lower environmental and health impact, and Combilift – and, in turn, our suppliers – are listening.” M
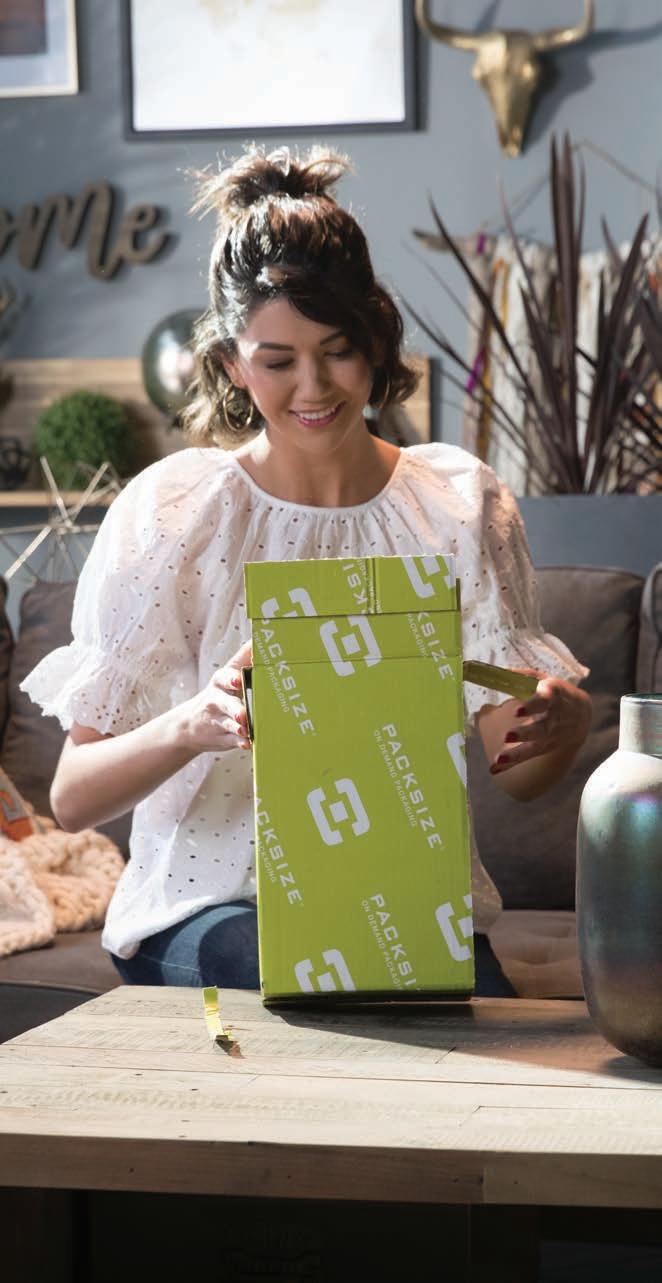
C
Y
COMBILIFT’S GLOBAL SUSTAINABILITY PUSH

CM
Chris notes that Ireland, where all Combilift products are manufactured, is a signatory to the United Nations 2030 Agenda for Sustainable Development, which identified 17 sustainable development goals.
“Combilift are not going to change the world on our own,” K Chris says. “But we did choose five of those goals where we thought we might be able to have a small impact. These included Health, Education, Innovation, Responsible Consumption and Production, and Partnerships.”
He says that the company is constantly working to improve and make more robust its supplier qualification process to improve the sustainability of its manufacturing.
“A good example of this is from our paint line, where we only use water-based paints which have no petroleum content,” Chris says. “By doing so we have cut our VOC [volatile organic compounds] emissions by 73 per cent. This is a win for both the environment and for our employees’ health.”
For its environmental management initiatives, Combilift has been awarded with ISO 14001 recognition – an internationally agreed standard setting out the requirements to improve an organisation’s environmental management system.
“This means we are recognised for complying with the most stringent rules governing industrial waste and environmental damage,” Chris says.
“I can say with confidence that sustainability concepts are really in our DNA,” Chris says. “Our machines are 95 per cent recyclable, the water utilised in our facility is harvested rainwater, the energy we use is drawn from the sun, our drying rooms are powered by biomass, and our machines are fundamentally designed to reduce warehouse space – thereby reducing energy usage and building materials. It all adds up to an impressive sustainability commitment.” ■
MY CY CMY
Consumers prefer right-sized packaging
Have you ever paused to think about the impact of plastic mailers, oversized boxes, and void filler on the environment and your bottom line? Packsize machines and integrated software deliver on the customization, support and uptime your packaging workflow requires, helping you to place the priority on your customers’ experience.