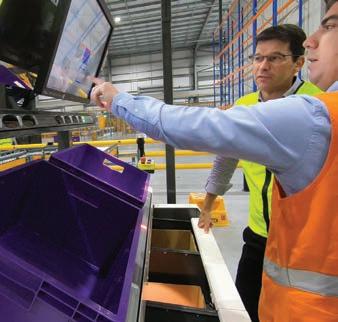
3 minute read
Challenging the supply chain talent gap
from MHD October 2021
by Prime Group
FuzzyLogX on how the continued growth of warehouse automation requires a new and improved approach to attracting and upskilling talent to drive supply chain innovation.
Fuzzy LogX is no stranger to warehouse automation, with decades of experience designing automated systems from the ground up – and always with an eye to “futureproofing” their clients’ warehouses. But with Australian businesses increasingly adopting automated solutions, new intralogistical skills and expertise are required to implement and work effectively with Industry 4.0 technologies, says Katie Walacavage, Fuzzy LogX’s Portfolio Manager.
Katie says that supply chain will remain very people-dependent, even as we enter this next phase of industrial revolution. But with the industry having suffered a talent-gap for years already, the uptake of automation means businesses will have to work even harder to bring the quality and quantity of industry talent up to speed to match the pace of technological development.
“Without a national framework that actively fosters these new technological skills, the onus is on businesses to invest in long-term training right now, because automation and robotics are changing so quickly,” she says. “Every week there’s a new AGV or AMV, new softwares and IoT devices – so upskilling must be an ongoing, longterm strategic investment. Workers and supply chain leaders must commit to lifelong training, or they’ll be left behind.”
But with great technological change comes great opportunities, too.
A McKinsey & Company report found that with the current trajectory of automation adoption, roughly $1.2 trillion could be added to the Australian economy by 2030. Deloitte Access Economics forecasts that, by 2025, there will be 156,000 more technology workers in the Australian workforce than in 2019.
“You can’t just consider single movements of the warehouse in isolation anymore – with click and collect and rapid turnaround you have to be thinking of the global supply chain as well,” Katie says. “That involves a lot of IT systems and data, and people analysing and managing that information. Businesses need people who understand how connected everything is and the larger scope of their job.”
Traditional warehouses based on manual solutions don’t require the analytical skills an automated warehouse does, but swapping excel spreadsheets for dynamic dashboards with KPIs available in real time isn’t an overnight lesson for warehouse staff.
As well as an investment in the automation infrastructure itself, businesses cannot underestimate sourcing, upskilling and retaining human capital in the new Industry 4.0 environment, warns Katie.
“Factoring in labour and skill requirements before going live with your automated warehouse is a must,” she says. “The people element needs to be front-of-mind when developing a strategic business plan.”
Upskilling also needs to occur across all levels of the warehouse, according to Katie.
“Warehouse pickers traditionally use general RF scanners, handheld or in-ear. Now they have to transition these skills to suit an automated environment, where picking is done at goods-to-person picking stations,” she says. “Health and safety managers need to be trained to work in a facility with zoning, robotics and automation.”
Warehouses are often grouped in suburbs outside of CBDs, bringing job opportunities with them. A new Amazon distribution centre in Kemps Creek is set to bring 1500 jobs to the region. Katie notes there’s tremendous opportunity for new job creation if businesses are willing to invest in upskilling workers.
“It’s a win-win because companies get more value from their workers, who in turn can command higher pay with their improved skillsets,” she says. “People worry that automation will take away jobs, but they’re forgetting the new jobs that accompany automation. And by incentivizing workers to upskill and be more adaptable, automation will help build an agile and resilient culture.
“Automation opens up myriad new and exciting job opportunities. If businesses put the resources and energy into developing their people – and advertise supply chain to the new generation of possible recruits as a dynamic and exciting industry to be in – then we might finally succeed in filling the talent gap.” ■