RESHAPING FREIGHT
MachShip providing cutting-edge freight management solutions for logistics operations
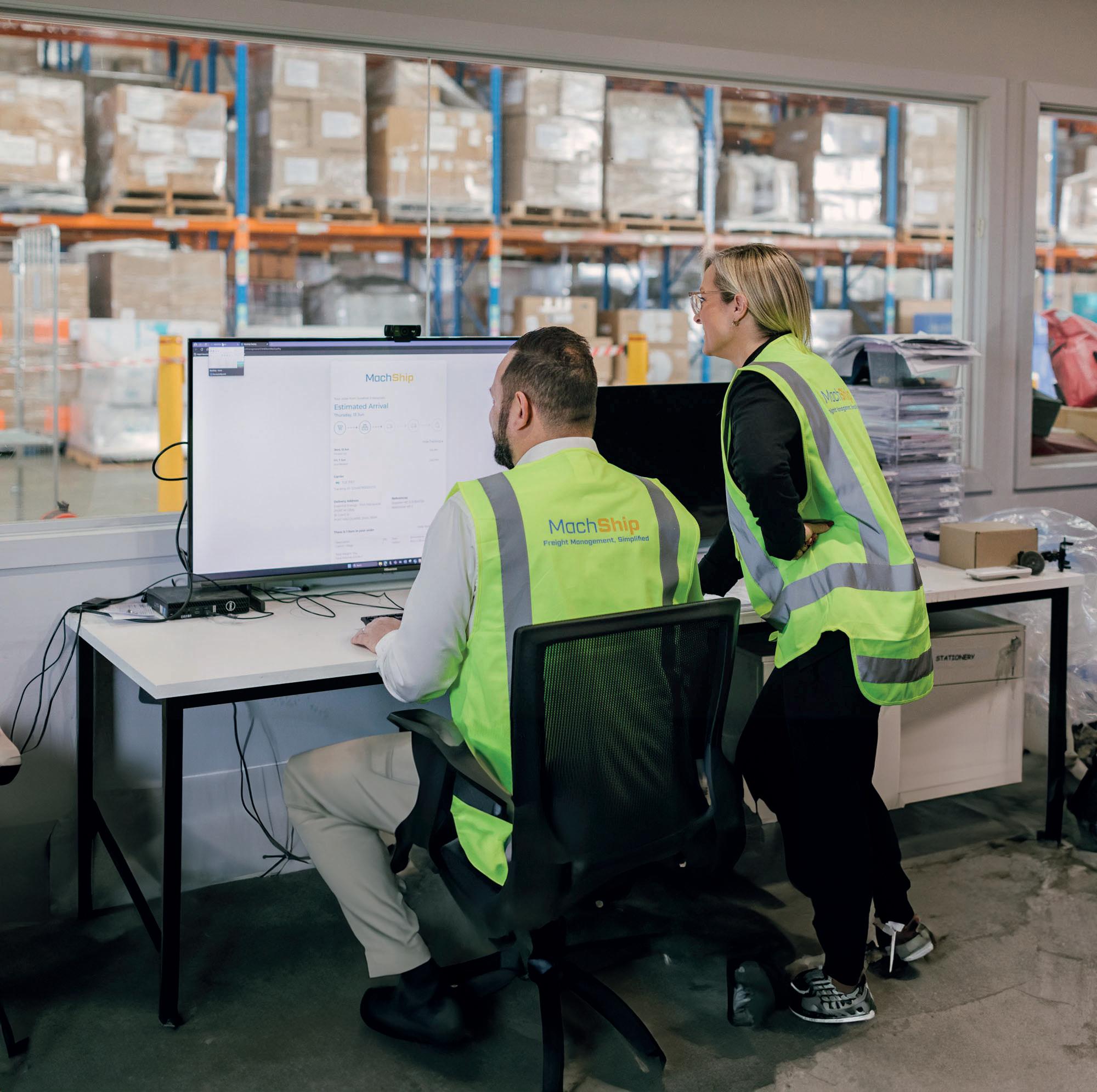
PURSUING PROGRESS
Prological on the importance of freight in supply chain
CUSTOMERS FIRST
Dematic explains how it meets operational outcomes
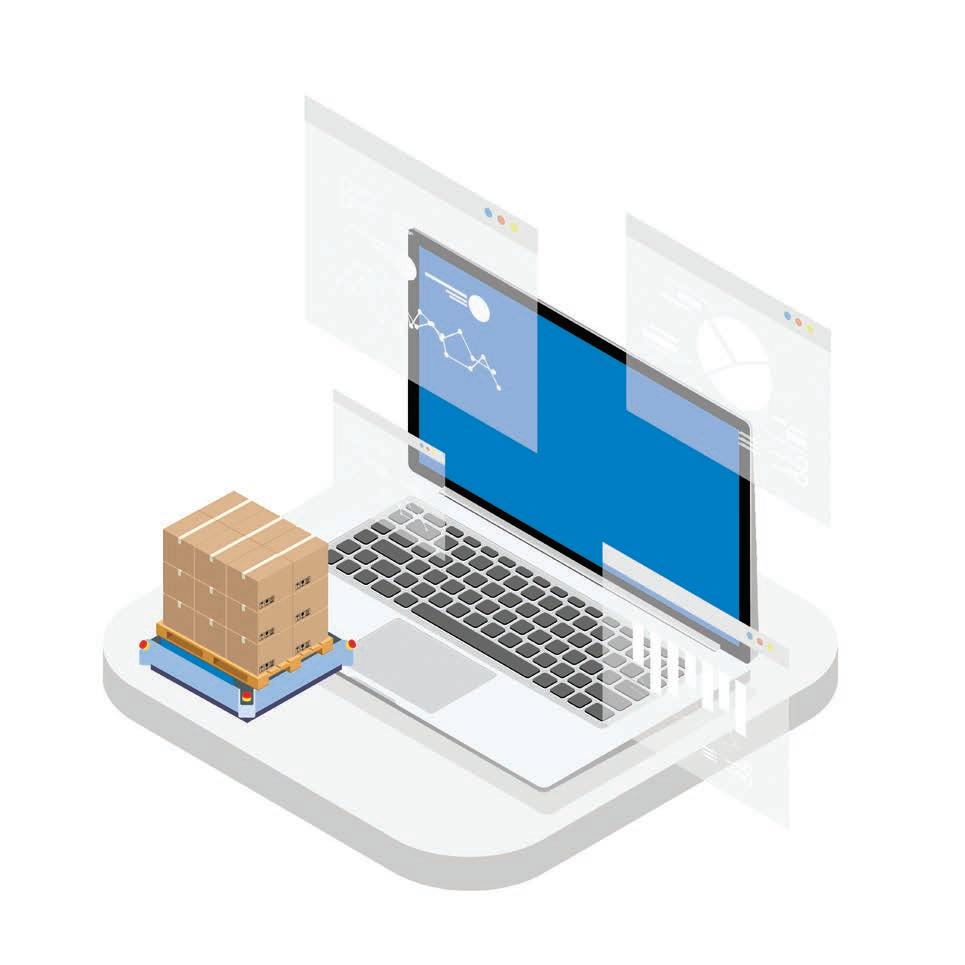
MachShip providing cutting-edge freight management solutions for logistics operations
Prological on the importance of freight in supply chain
Dematic explains how it meets operational outcomes
The new 2024 Gartner® Magic Quadrant™ for Warehouse Management Systems is out and for the 6th year in a row, Körber has been named a Leader.
Scan the QR code to get your free copy of the report and discover why Körber stands out among the competition. koerber-supplychain-software.com
Scan for your free copy of the report
CONTACT
MHD Supply Chain Solutions is published by Prime Creative Media
379 Docklands Drive, Docklands VIC 3008
Telephone: (+61) 03 9690 8766
Website: www.primecreative.com.au
THE TEAM
CEO: John Murphy
Chief Operating Officer: Christine Clancy
Managing Editor: Mike Wheeler
Assistant Editor: Joseph Misuraca
Journalist: Mannat Chawla
Business Development Manager: William Jenkin
Design Production Manager: Michelle Weston
Art Director: Blake Storey
Graphic Designers: Danielle Harris, Jacqueline Buckmaster
Client Success Manager: Janine Clements
FOR ADVERTISING OPTIONS
Contact: William Jenkin william.jenkin@primecreative.com.au
SUBSCRIBE
Australian Subscription Rates (inc GST) 1yr (11 issues) for $99.00 2yrs (22 issues) for $179.00
To subscribe and to view other overseas rates visit: www.mhdsupplychain.com.au or Email: subscriptions@primecreative.com.au
ACKNOWLEDGEMENT
MHD Supply Chain Solutions magazine is recognised by the Australian Supply Chain Institute, the Chartered Institute of Logistics and Transport Australia, the Supply Chain and Logistics Association of Australia and the Singapore Logistics and Supply Chain Management Society.
ARTICLES
All articles submitted for publication become the property of the publisher. The Editor reserves the right to adjust any article to conform with the magazine format.
COPYRIGHT
MHD magazine is owned by Prime Creative Media. All material in MHD is copyright and no part may be reproduced or copied in any form or by any means (graphic, electronic or mechanical including information and retrieval systems) without written permission of the publisher. The Editor welcomes contributions but reserves the right to accept or reject any material. While every effort has been made to ensure the accuracy of information Prime Creative Media will not accept responsibility for errors or omissions or for any consequences arising from reliance on information published. The opinions expressed in MHD are not necessarily the opinions of, or endorsed by the publisher unless otherwise stated.
Following yet another successful MEGATRANS, MHD final three months of the year when the Festive Season starts, and supply chain operations ramp up.
In this October edition of MHD Supply Chain Solutions, we look at freight forwarding and freight management solutions. A company specialising in this specific area is MachShip. The Australian-founded enterprise is changing the game for supply chain operations with its innovative freight management solutions.
Prological’s Peter Jones sheds light on the importance of freight forwarding and reveals why pursuing progress trumps the pursuit of perfection.
Paul Eastwood from Argon & Co gives reasons why businesses should rethink their supply chain strategies while Russell Pruden from Körber points out how resiliency is the key to dealing with port-related delays and disruptions.
Dematic’s Lee Koutsos outlines how the intelligent automation solutions company puts operational outcomes at the forefront and prides itself on its customer-centric approach.
Then we look at why Australian rail infrastructure manufacturer, Austrak, is over the moon with its recent purchase of a fleet for its Wagga Wagga factory from Toyota Material Handling Australia.
We also have Michael Lawrence explaining how Toll Healthcare is redefining global supply chain solutions with its expansive network, and Visy Logistics is working on its growth trajectory as it embraces automation and commits to its sustainability efforts.
Addverb transforms a 3PL provider’s omnichannel fulfilment with artificially intelligent solutions, and DLL guides Auckland-based, Cardinal Logistics, as it invests in and implements automated solutions at its new facility.
Finally, there is specialist industrial packaging company, Aurora Process Solutions, speaking about providing pallets to the Australasian market.
Enjoy reading all these features on how the supply chain is becoming more cutting edge and innovative. We’ll see you again in November.
Mike Wheeler Managing Editor, MHD Supply Chain Solutions
Known for market leading Toyota forklifts and warehouse equipment, Toyota Material Handling is also proud to o er an unparalleled range of products suitable for Australian businesses. With a huge range of forklifts, elevated work platforms, scrubbers and sweepers, Taylor-Dunn electric vehicles, plus Huski skid steers, scissor lifts, and mini excavators available, chances are we’ve got the equipment that will suit. So, if you’re looking to buy hard working, fully backed equipment for your business, Toyota Material Handling has all you need to add value to your operation. That’s the Toyota Advantage.
18 MachShip providing the competitive freight advantage
23 Logical Outlook on freight forwarding
29 Körber navigating port congestion
32 Dematic on its customer-centric approach
35 Argon & Co rethinking supply chain strategies
38 Addverb transforms 3PL provider’s omnichannel fulfilment
41 DLL guides Cardinal Logistics on automation
44 Toll Healthcare tailoring solutions
26 Toyota supplying Austrak with forklifts
46 Visy Logistics transforming logistics operations
49 Aurora Process Solutions bringing pallets to Australia
03 Ed letter
06 Industry News
52 SCLAA on its WiseTech partnership
53 RWTA on conference/exhibition and Frank Vale Award
55 ASCI’s courses and conferences
57 Product Showcase
58 People on the Move
On 9 September 2024, Australia, the United Kingdom and the United States signed a Memorandum of Understanding (MoU) establishing a new trilateral collaboration that will strengthen strategic cooperation and address risks to critical supply chains.
The MoU includes the establishment of the Australia-United KingdomUnited States Supply Chain Resilience Cooperation Group to cooperate on data sharing and joint action to build
resilience in priority supply chains, enhancing their mutual ability to identify and address risks, threats and disruption to our critical supply chains.
The Group will develop an early warning pilot focused on the telecommunications supply chain, essential for their global, digitised economies. By identifying and monitoring disruption risks to the telecommunications supply chain, this pilot will enhance all three countries’ knowledge of the vulnerabilities,
criticality and residual risks. It will develop procedures for sharing this information and responding cooperatively to disruptions.
Strengthening critical supply chains is vital for ensuring the stability and resilience needed to meet the UK’s growth mission. This agreement signifies a deepening of the important and historic relationship between the UK, US, and Australia and reinforces mutual commitment to tackling supply chain challenges. ■
To address the rapidly evolving e-commerce landscape, fashion 3PL Radial partnered with Dematic to implement an advanced Bin-to-Picker AMRs solution with intelligent software, designed to significantly reduce order processing times and operational costs. The result is enhanced supply chain efficiency, allowing Radial to meet customer demands swiftly and accurately.
With improved inventory management, increased order accuracy, and higher customer satisfaction, Radial enjoys a scalable, robust fulfilment system that adapts to market changes and seasonal peaks, setting a new standard in e-commerce fulfilment.
Learn more at dematic.com
Image: anek.soowannaphoom@shutterstock.com.
Freight & Trade Alliance (FTA) and the Australian Peak Shippers Association (APSA) have shared an update for Victoria’s freight and air cargo sectors. The Federal Government has approved Melbourne Airport’s third runway, a key development that will address the growing demands of the city’s industry. Scheduled to be operational by 2031, the runway will enhance Melbourne’s freight capacity, creating new opportunities for exporters and logistics providers.
As a critical air freight gateway, Melbourne Airport handles more than 40 per cent of the nation’s air freight exports, moving $1.8 billion in goods annually.
High-value, time-sensitive products
such as fresh produce, pharmaceuticals, and electronics rely on the airport’s efficiency.
The new north-south runway will increase capacity by allowing simultaneous take-offs and landings, reducing delays, and improving service levels. As Melbourne’s population grows, so will the demand for reliable air cargo services, and this expansion ensures the airport can meet these future needs.
Melbourne’s curfew-free operations already give freight services aroundthe-clock flexibility, valued at $6.5 billion annually and supporting over 58,000 jobs. The third runway will build on this, allowing seamless freight movement day and night.
With rising air freight demand and the growth of e-commerce, the third runway will help maintain Melbourne’s competitiveness. New direct routes to key markets like Asia, North America, and the Middle East will further boost opportunities for Victorian exporters.
Melbourne Airport moved 205 million tonnes of freight in 2022, valued at $22 billion. The new runway will help meet rising demand for imports and exports, directly benefiting industries like dairy, meat, seafood, and pharmaceuticals. This expansion positions Melbourne to better compete with other Australian airports, ensuring Victoria remains a leader in air freight logistics. ■
L’Oréal Groupe has opened its second Australian distribution centre (DC) in Redbank, Queensland.
The new purpose-built site will service L’Oréal customers across states including New South Wales, Queensland and the Northern Territory. Costing $40 million to build, it brings an extra 14,533 sqm of capacity to sit alongside the Group’s existing DC in Victoria.
“The opening of our new distribution centre in Queensland reflects a significant milestone for L’Oréal in Australia, enhancing our capabilities locally, ensuring we can continue to meet the growing demand for our products, while also cutting delivery times across key states and bringing
down transport emissions across the board,” says L’Oréal Groupe ANZ CEO Alex Davison.
“Australia and New Zealand, collectively, was one of the top growing markets for us globally last year, and there’s still untapped potential for L’Oréal. This is why we’re continuing to invest locally, and this new distribution centre is a prime example of this.
“We’re grateful to our partners TMX Transform and Goodman Group, for their support in sourcing this location, which offers an abundance of capacity and is just a mere 30 minutes outside of the Brisbane CBD.”
The new centre will lead to the creation of 60 additional jobs by the end of the year.
“This $40 million investment in our region will support new jobs that will enhance our local economy and reinforce Ipswich’s growing reputation as an attractive city for businesses and industry to thrive,” says Ipswich Mayor Teresa Harding.
“Attracting L’Oréal Groupe to Ipswich is another sign that businesses have confidence in Ipswich as we continue to boost our supply chain resilience and provide opportunities for our residents to work where they live.”
Like all L’Oréal sites across Australia and New Zealand, the DC is run using 100 per cent renewable energy as well as having a biodiversity garden and EV charging. ■
The National Heavy Vehicle Regulator (NHVR) has opened consultation for its latest Heavy Vehicle Productivity Plan (HVPP).
NHVR Chief Safety and Productivity Officer David Hourigan said the latest plan focussed on challenges affecting the trucking landscape into the next five years.
“We are open to feedback on what we see as contemporary challenges for Australia’s heavy vehicle industry,” David said.
“This includes issues like growth in the freight task, ongoing road fatalities, environmental and health impacts, the shift from asset management to optimisation, and finally, the increased frequency of unplanned supply chain disruptions.
“As the heavy vehicle sector evolves and the freight task changes, we too are evolving and changing by continually seeking new ways to refine our approach.
“Our goal is to be a modern regulator that has a deeper understanding of the issues, priorities and needs of our
industry and government customers so we can create the most effective regulatory environment.”
Since the release of the first HVPP in 2020, the NHVR – in partnership with industry and government stakeholders – has achieved many of its productivity targets, including:
• E 49 national notices and 50 state and territory notices.
• L marking Australia’s first harmonised mapping system for heavy vehicles, improving route planning and operational efficiency for the industry.
• O through assessment of more than 770 structures across 106 local councils through the Commonwealth-funded Strategic Local Government Asset Assessment Project.
• E vehicle networks in New South Wales and Victoria, with trial networks in Queensland and South Australia, supporting industry decarbonisation.
Tand logistics gathered once again at the 34th Australian Freight Industry Awards. A record crowd attended the prestigious black-tie Gala Presentation in Melbourne’s Palladium Room at Crown, celebrating excellence across the industry.
The lavish evening was once again supported by major sponsors, TWUSUPER and Viva Energy Australia, and the VTA extended its thanks to them for making this leading industry event possible.
As always – and reflecting the outstanding work being done across the industry – there was a tremendous response to the call for submissions, with judges evaluating a recordbreaking number of applications across a range of categories.
The winners of the 34th AFIAs were:
• Lindsay Fox, Personality of the Year Award – sponsored by CMV Truck & Bus
Women’s Leadership Award –sponsored by Viva Energy Australia
• Sean Draffin of Xtreme Freight, Emerging Leader Award – sponsored by Daimler Truck Australia Pacific
• Qube Bulk, Green Star Award –sponsored by National Transport Insurance
• Secon Freight Logistics, Application of Technology Award – sponsored by Transport Certification Australia
• Freight Cyber, Best Practice Safety Award – sponsored by Gallagher
• A lex Fraser Recycling, Investment in People Award – sponsored by Logical Staffing Solutions
• Australian Paper Recovery, Waste & Recycling Business of the Year Award –sponsored by RSM Group
“It was an honour to present the awards in front of so many transport industry operators and distinguished guests,” said VTA CEO, Peter Anderson.
fantastic achievements of all award winners, guests were also treated to a night of world class entertainment courtesy of Master of Ceremonies, Lizzy Hoo, and the musical stylings of the Matt Hetherington Band and the Zandra Trio.
“After what has been another challenging year, it was fantastic to take a moment to reflect on and celebrate our industry and those that keep pushing for greatness and embracing innovation to keep our country moving.
“The AFIA Committee extends its sincere congratulations to every winner and finalist and thanks those who lodged an entry and shared their stories. We look forward to building on the success of this outstanding event for many years to come.”
The Australian Freight Industry Awards will return in 2025. ■
Mobile and fixed racking AMR solutions
Goods-to-person AMR robotics
Optimises space utlilisation
Precision & safer working environment
Improved accuracy in transportation
Cost-effective scalability
Enhanced order-picking efficiency
Improved accuracy and reduced errors
Competitive advantage
High-density bulk storage- 2D shuttles
Simultaneous shuttle operations
Fast putaway and retrieval
Automated palletising & layer-picking
Reduced labour costs
High volume and consistent throughput
Data-driven insights for decision making
Enhance customer satisfaction
Increased accuracy and visibility
Jungheinrich has launched the Electric Pedestrian Pallet Truck EJE C20, which offers agility and ergonomic benefits for a variety of applications.
Designed with efficiency in mind, the EJE C20 features a 752mm lifting height, allowing operators to unload goods onto shelves without bending their backs. This capability enhances productivity in both storage and production areas. The truck’s long tiller arm ensures operators maintain a safe distance from its chassis, while its extended lever reduces the effort required for manoeuvring. For navigation in tighter spaces, the truck includes a crawl speed button and the option to operate with the
tiller in a horizontal position.
The EJE C20 incorporates a keyless access system, allowing each operator to use a personal PIN code for secure and authorised use. The onboard charger adds flexibility, enabling the truck to be charged anywhere with a standard 230V outlet. Additionally, a practical paper clip on the battery compartment cover keeps important documents easily accessible.
The EJE C20 is powered by a maintenance-free 3-phase AC motor, which, in conjunction with Jungheinrich’s in-house developed controller, delivers strong acceleration while maintaining low energy consumption. The truck’s high-quality components and construction ensure the
long life of the machine.
One of the features of the EJE C20 is ProTracLink, a solution that connects the castor wheels with a tension bar to enhance stability and protect against damage, particularly when operating on loading ramps. The truck’s design allows it to be serviced easily while minimising downtime and streamlining maintenance and repairs.
Jungheinrich’s commitment to aftersales support is reflected in its service options and access to genuine spare parts, ensuring ongoing reliability and performance. Initially designed for Euro pallets, the EJE C20’s versatility also makes it suitable for handling Australian pallets, expanding its usability for diverse transport needs. ■
MachShip’s Sam Rowse explains to MHD how the freight management solutions company provides a competitive advantage by allowing full control over logistics operations and offers unique boxing rules.
MachShip, a freight management platform, has emerged as a critical enabler for businesses seeking independence, control, and efficiency in their logistics operations.
For 4PLs (fourth-party-logistics providers) and other logistics-focused businesses, the choice of software can make or break their ability to deliver top-tier service.
With an emphasis on providing a carrier-agnostic, full-featured system, MachShip offers a solution that aligns with the needs of 4PLs, B2B, and B2C businesses.
One of the core strengths of MachShip lies in its independence from
4PLs. Unlike 4PL-owned freight management systems, MachShip is not tied to any particular set of carriers, making it a neutral player in the logistics ecosystem.
“Our platform allows 4PLs or any logistics provider to have full control over their operations without the conflicts of interest that can arise when using a competitor’s platform,” says Sam Rowse, the company’s Chief Revenue Officer.
“This autonomy is crucial for businesses that need to deliver a tailored logistics offering to their clients without external influence. This independence has been a factor in why many 4PLs choose MachShip.
“Our customers have reported rapid growth and the ability to scale their
operations significantly at their own pace.
“For instance, Benchmark Logistics, one of our clients, achieved their three-year growth target within just 12 months, largely due to the control and flexibility provided by MachShip.”
MachShip’s platform is not just about independence; it’s also about integration. With more than 500 carriers integrated into the system, and more being added each month, MachShip ensures that 4PLs and businesses have access to the full spectrum of freight profiles.
“We’ve got all freight profiles covered,” says Sam. “Whether it’s
envelopes or full truckloads, or even specialised needs like crane services, our platform supports it all. This means that 4PLs are rarely ever constrained by integration limitations, allowing them to confidently offer a range of services to their customers.”
The platform also works well in carrier invoice reconciliation, a critical feature for managing logistics costs accurately.
“Carrier invoice reconciliation allows our customers to quickly identify discrepancies between what they should have paid and what they’re being charged,” says Sam.
“This leads to accurate invoicing, whether pre-or post-reconciliation, and significantly reduces the time and errors associated with manual processes.”
In addition to its technical capabilities, MachShip places an emphasis on customer support and self-sufficiency. Sam says that 4PLs are experts in logistics and customer service.
“Our support needs to match the high level of service that 4PLs provide to their clients,” he adds. “We ensure that our support is responsive and effective, allowing 4PLs to maintain the direct relationship with their customers without us intervening.”
MachShip also empowers 4PLs to be self-sufficient, giving them the tools to onboard new customers, adjust carrier rates, and manage surcharges independently.
“We’re providing 4PLs with software that enables them to operate more efficiently and at their own pace,” explains Sam. “They’re the experts in their space, and we’re just here to support them with the best technology available.”
MachShip’s independence is not just a boon for 4PLs; it also offers advantages for B2B and B2C businesses. By allowing these companies to leverage their own carrier relationships, MachShip helps them optimise logistics costs and operational performance.
“For businesses that want to retain control over their supply chain, our platform is an enabler,” says Sam. “Wholesale and distribution businesses, in particular, benefit from the ability to manage their logistics in-house without a 4PL influencing their strategy.
“Adventure Operations, an Australian company managing multiple brands in the camping equipment sector, faced challenges in managing logistics across three different distribution centres.
“By integrating MachShip with their NetSuite ERP, they were able to streamline their freight logistics processes, “Significantly improving
MachShip’s platform is not just about independence, it’s also about self-sufficiency.
MachShip has the ability to integrate seamlessly with ERP, WMS, and other critical systems.
“
MachShip’s independence is not just a boon for 4PLs; it also offers advantages for B2B and B2C businesses.
accuracy in freight reconciliation, considerably reducing overcharges and discrepancies.”
MachShip has the ability to integrate seamlessly with ERP, WMS, and other critical systems. This is a key differentiator that sets it apart from other freight management platforms.
“We centralise freight management into one system, eliminating the need for multiple freight tools,” says Sam. “This reduces manual data entry, minimises errors, and provides timely visibility across the entire logistics operation.”
MachShip developers continually evolving the product.
An example of this integration in action is with Dobinson’s Spring and Suspension, a supplier of 4WD parts. Before using MachShip, its sales team had to manually import sales order data into multiple carrier platforms to get the best pricing and book jobs.
“By integrating MachShip with their MYOB Acumatica sales order management process, they saved over 10 hours per week, reduced human errors, and enhanced the overall productivity of the team,” says Sam.
MacShip offers up-to-date tracking information, typically updated in line with carrier systems.
“Data flows quickly and promptly, allowing businesses to track consignments, monitor carrier performance, and manage freight costs more effectively,” explains Sam.
“This centralised approach means that businesses no longer need to switch between multiple platforms; everything is managed within one system.”
The Blue Space, an online retailer,
experienced transformative results by integrating MachShip with its WMS, Unleashed.
“They eliminated clunky, manual processes, saving six hours of labour per day,” adds Sam. “The timely visibility provided by MachShip also allowed them to make data-driven decisions that improved profitability and customer satisfaction.”
For e-commerce businesses, MachShip’s ability to interpret customer-specific packing rules, often referred to as “boxing rules,” is an advantage.
“We don’t impose a one-size-fitsall solution,” says Sam. “Instead, we account for how each customer already packs their products and automate the process to match their specific logic. This approach ensures that our customers’ existing packing strategies are respected and optimised within our platform.”
By automating the interpretation of packing rules, MachShip not only saves time but also enhances freight
efficiency and customer satisfaction. Businesses can continue to pack their products in the way that works best for them, while MachShip streamlines the process and helps manage potential errors. By automating these decisions, MachShip helps customers obtain accurate freight costs and provides shipping quotes, which can be verified through the reconciliation process.
MachShip’s success in the Australian freight management sector is not just about advanced features; it’s also about the company’s approach to listening to the market and continuously improving its platform.
“We position ourselves as a leader by partnering with industry leaders – carriers, 4PLs, and consultants and listening to their needs,” explains Sam. “Our system has been developed to scratch their itch, so to speak.”
Unlike traditional dispatch platforms that offer limited functionality, MachShip provides a full-featured Freight Management System (FMS) with advanced capabilities.
“
The platform’s timely tracking feature allows businesses to monitor consignments and carrier performance.
“We’ve spent the last decade asking the market what they want and enhancing our platform based on that feedback,” adds Sam.
“Our independence allows us to engage with thousands of different operations, giving us a unique perspective and expertise that is unmatched in the industry.”
The platform’s tracking feature allows businesses to monitor consignments and carrier performance with precision, ensuring that every stage of the freight process is visible and manageable.
“Our carrier invoice reconciliation and reporting are key differentiators,” says Sam.
“These features enable businesses to generate detailed reports on freight costs, carrier performance, and operational efficiency, which are essential for making better decisions and improving profitability.”
The feedback from MachShip’s clients has been positive, particularly regarding the platform’s key features include carrier invoice reconciliation and MachShip’s independence from 4PL models.
“We’re leaders in this space because we focus on empowering our customers and ensuring they are self-sufficient with our platform,” says Sam.
He emphasises MachShip’s onboarding process and responsive
Mike McKay, CEO, MachShip.
customer support, which are designed to help businesses fully leverage their freight management system.
“We provide a reliable and feature-rich platform that adapts to the unique requirements of each business, allowing them to maintain control over their freight operations while maximising efficiency and effectiveness,” he adds.
In an industry that is constantly evolving, MachShip’s ability to adapt to market changes is a component of its success.
The platform is designed to be scalable, allowing businesses to add new carriers, integrate with additional systems, or scale up operations during peak seasons.
This future-proof approach ensures that MachShip’s clients can continue to rely on the platform as their business grows.
“Future-proofing freight operations is always on our minds,” says Sam. “Whether it’s adding new carriers, integrating with
additional systems, we’re committed to ensuring that our clients can adapt and thrive in a changing market.”
Clients have noted the ease and speed with which MachShip can be deployed, allowing them to realise the benefits without prolonged disruption to their operations.
“Integrations can take as little as hours or days, depending on the situation, and has been an advantage for our clients,” says Sam. “It allows businesses to quickly see the value of MachShip without the typical delays associated with implementing new systems.”
MachShip listens to the market, continuously improving its platform, and offering features that address the complex needs of modern businesses.
MachShip is a solution that empowers businesses to optimise their freight processes, improve customer satisfaction, and enhance profitability.
“We’re more than just a platform; we’re a partner in our clients’ success,” says Sam. ■
Addverb, a global robotics company, excels in tailored warehouse automation solutions, redefining innovation in the supply chain with intelligent robots driven by modular software and boosting a diverse product portfolio for end-to-end operational efficiency.
he efficiency of a freight forwarding process is not just a factor for consideration in an increasingly globalised market, it is a critical determinant of a supply chain’s overall effectiveness.
The recent disruptions caused by the COVID-19 pandemic have brought this issue to the forefront, highlighting the vulnerabilities in global supply chains.
These disruptions have underscored the importance of having an efficient, reliable inbound supply chain, particularly for businesses that are reliant on importing goods.
The traditional global shipping routes, established in the post-World War II era, have long provided a relatively stable pathway for international trade. However, recent geopolitical developments have introduced challenges to these routes.
“The Suez Canal, a vital artery connecting Europe with the rest of the world, is now fraught with risks due
to the ongoing conflicts in the Middle East and the threat of piracy off the coast of Somalia,” explains Peter Jones, Managing Director, Prological.
As a result, many shipping companies are opting to reroute their vessels around the southern tip of Africa, increasing both shipping costs and transit times.
Similarly, the Panama Canal, once a reliable passageway between the East Coast of North America and Australia, is facing its own set of challenges.
“Due to a lack of water in the canal, ships are now required to travel as light vessels, reducing the amount of cargo they can carry and further straining global supply chains,” says Peter.
This has led to disruptions for businesses relying on East Coast U.S. ports, including New York, New Jersey, and Savannah, among others.
In addition to these geographic and environmental challenges, global unrest is further complicating international trade.
“Eastern Europe, once a reasonably efficient supply channel, is now
severely disrupted due to the conflict in Ukraine,” adds Peter.
Ukraine, a major global supplier of numerous products, has been a critical link in many Western supply chains. Similar disruptions are occurring in Southeast Asia, with countries like Bangladesh, a major supplier to the apparel and retail industries, experiencing political unrest that adds another layer of complexity to an already challenging landscape.
The days of set-and-forget supply chain management are long gone. Today, supply chains are dynamic, with constantly shifting variables that can impact their efficiency.
“What was achievable yesterday may not be possible tomorrow, and businesses must be prepared to pivot quickly to maintain efficiency,” says Peter.
This requires a deep understanding of the various factors influencing supply chains, from geopolitical events
to environmental challenges, and the ability to design supply chains that can adapt to these changes.
One of the most effective strategies for maintaining efficiency in this dynamic environment is to have contingency plans in place.
“For large importers, we recommend keeping alternative supply chain processes alive and regularly using them to ensure they remain viable options,” adds Peter.
This means that even if 95 per cent of a business’s supply chain operates through the main channel, maintaining the other five per cent through contingency channels can provide a critical safety net when disruptions occur.
In such a complex environment, the role of advanced freight management solutions cannot be overstated. While these systems do not inherently make the freight-forwarding process more efficient, they play a crucial role in monitoring and alerting businesses when things go awry.
“Advanced systems allow you to see when things haven’t happened as expected and enable you to intervene and recover as quickly as possible,” explains Peter.
The key benefit of these systems is their ability to provide early warnings, allowing businesses to take corrective action before inefficiencies become costly disruptions.
These systems also support the broader supply chain management process by providing a control tower view of the entire supply chain.
“By setting up proactive alerts around critical timelines, businesses can ensure that any delays or issues are flagged early, giving them ample time to address the problem,” says Peter.
For example, if a supplier is unable to meet a shipment deadline, this information can be communicated to the buyer well in advance, allowing for adjustments to be made to the inventory plan.
Beyond monitoring and alerting,
advanced freight management systems also play a crucial role in decisionmaking and risk management. For larger importers, these systems offer multiple options for transporting goods, allowing businesses to weigh the cost and service implications of each option quickly.
“Whether it’s choosing between sea and air freight or selecting between faster, more expensive shipping options and slower, cheaper ones, advanced systems provide the data needed to make informed decisions,” says Peter.
These systems also serve as a repository for all supply chain data, turning raw data into valuable information that can drive continuous improvement.
“The data from advanced freight management systems is absolute gold when it comes to driving greater efficiency,” adds Peter.
For example, a business may discover that consistently choosing the cheapest sea freight option has led to increased inventory levels and a need for more warehouse space.
By analysing this data, the business can make more informed decisions about its shipping options, potentially avoiding the need for costly real estate investments.
Sustainability is another area where modern freight management solutions are making an impact.
“Some of the more advanced systems now include carbon registers, which can calculate the carbon emissions of shipping goods from one location to another,” says Peter.
This information is crucial for businesses looking to reduce their carbon footprint, as it allows them to make more sustainable choices when selecting shipping options.
The global shipping industry is also evolving to meet the demand for more sustainable practices, with newer ships using cleaner fuels and retrofitted older ships equipped with carbon scrapers.
“While the transition to a more sustainable fleet is slow due to the long-life cycle of ships, the industry is moving in the right direction,” adds Peter.
Advanced freight management systems provide the visibility needed
to make informed choices about the environmental impact of shipping, helping businesses align their operations with their sustainability goals.
Investing in integrated freight forwarding and management solutions offers businesses a range of benefits over traditional methods. First and foremost, these systems provide the operational visibility and control necessary to maintain an efficient supply chain.
“The operational side of things must be addressed first because if the supply chain doesn’t work, nothing else matters,” explains Peter.
Once the operational foundation is in place, businesses can then focus on managing their commercial outcomes more tightly.
Integrated systems also provide a platform for continuous improvement, allowing businesses to identify areas where processes can be optimised, and efficiencies can be gained.
“When things go wrong – and in international supply chains, that’s a matter of when, not if – a welldesigned system puts you in control, rather than leaving you at the mercy of external factors,” adds Peter.
The key to effective supply chain management in today’s complex and dynamic environment is to pursue progress rather than perfection.
“Understanding what best practice looks like in your environment is essential, but the goal should always be to chase progress, not perfection,” says Peter.
This approach allows businesses to continuously improve their processes, adapting to the everchanging landscape of global trade while maintaining the efficiency and reliability of their supply chains.
By leveraging advanced freight management solutions and maintaining a flexible, adaptable approach, businesses can navigate the challenges of global supply chains, ensuring that they remain competitive and resilient in an increasingly uncertain world. ■
Austrak’s Wagga Wagga factory manager, Jim Stevenson, tells MHD why the rail infrastructure manufacturer has selected Toyota Material Handling Australia as its forklift supplier.
Austrak, an Australian rail infrastructure manufacturer, has taken steps to enhance the efficiency and safety of its operations at its Wagga Wagga factory.
By choosing Toyota Material Handling Australia (TMHA) as its forklift supplier, Austrak has consolidated its entire Wagga Wagga fleet to Toyota products.
This strategic decision marks a pivotal moment for Austrak as it continues to play a crucial role in the nation’s railway infrastructure, particularly in the Inland Rail project.
Austrak is renowned for its production of pre-stressed concrete sleepers, which are essential components of railway infrastructure.
With the capacity to produce up to one million sleepers annually across its three factories in Wagga Wagga, Geelong, and Rockhampton, the company requires equipment that can handle the demands of its operations.
Recently, Austrak expanded its fleet at the Wagga Wagga facility with the acquisition of two new heavy-duty 4FD120 forklifts from TMHA.
These forklifts, with a load capacity of up to 12,000kg, are designed for the rigorous task of hauling large concrete sleepers around the warehouse.
The addition of these units is timely as Austrak ramps up production for the Inland Rail project, a 1600km freight line that will connect Melbourne to Brisbane.
The decision to standardise the Wagga Wagga factory’s forklift fleet to a single brand reflects Austrak’s commitment to efficiency and
reliability. Jim Stevenson, Austrak’s Wagga Wagga Factory Manager, explains that the choice to consolidate with Toyota was influenced by the brand’s proven track record in reliability, performance, and service.
“We’ve had a few Toyotas, and through that relationship, the decision was made to purchase two brand-new units, as well as transition our entire forklift fleet to Toyota,” says Jim.
“Previously, we had a mix of
suppliers and varying specifications, some of which were unsatisfactory. Now, with our fleet unified under Toyota, we’ve streamlined our operations and improved overall efficiency.”
The new fleet includes two leased 2.5-tonne forklifts and one 8-tonne unit, in addition to the heavy-duty 4FD120 forklifts. This move not only simplifies maintenance and service but also ensures a consistent level of quality across all of Austrak’s operations.
Austrak’s decision to partner with TMHA was not made lightly. Jim highlights several key factors that influenced the choice, including the quality of the machinery, the range of features offered, and the after-sales service provided by Toyota.
“The quality of the machine, the features that come with it, and the after-purchase service and customer support are all top-notch with Toyota,” adds Jim.
His confidence in the brand is further reinforced by his experience with Toyota products in previous roles.
Before joining Austrak, Jim managed sites where Toyota forklifts were the primary choice. This experience left a lasting impression, particularly regarding the reliability and service provided by TMHA’s technicians and sales managers.
“At my last site, we had 15 to 20 units, all of which were Toyota,” explains Jim. “We had a strong relationship with the brand, and the service was consistently excellent. I’ve tried different forklifts over the years, but in the end, Toyota has proven to be the most reliable and best-performing units in my view. Their service support is second to none.”
A crucial aspect of Austrak’s partnership with TMHA is the service provided by TMHA’s team of technicians. Jim praises the technicians for their expertise, professionalism, and dedication to ensuring that the forklifts operate at peak performance.
“I’m really happy with the service and the quality of the
technicians,” says Jim.
“The team from Toyota are experienced, know what they’re doing, and always do a good job. They clean up after themselves and bring a lot of value to the table.”
When Austrak decided to standardise its forklift fleet, it approached its three existing suppliers to determine which company would best meet its needs. TMHA emerged as the winner, not just for the performance of its machines.
“Toyota’s features, unit specifications, and pricing were all very competitive,” explains Jim.
“But what really set them apart was the fact that they sent an engineer to our site to assess our lifting activities. We wanted to optimise our operations, ensuring we didn’t end up with equipment that was either too big or too small.
“Toyota’s engineer conducted a thorough assessment, provided calculations, and recommended the ideal forklift size for our site’s specific constraints. No other supplier offered that level of support.”
The Toyota forklifts at Austrak’s Wagga Wagga factory come equipped with features designed to enhance both safety and efficiency.
One of the standout features is the PIN-code start-up system, which adds an extra layer of security by ensuring that only authorised personnel can operate the machinery.
Additionally, the forklifts are integrated with Toyota’s exclusive telematics system, I_Site. This fleet management system provides supervisors with data, including fleet utilisation, downtime, OH&S incidents, and breakdown information. By offering real-time insights into fleet performance, I_Site helps Austrak ensure that its operations run as smoothly as possible. Ergonomics have also been a consideration in the design of these forklifts, making tasks easier and safer for operators.
“One of the comments we’ve had from a safety perspective is that forward visibility is hugely improved over what we’ve had before,” says Jim. “Better visibility is crucial, especially when loading trucks and moving
materials around a busy site. Any improvement in this area is a win for us.”
The relationship between Austrak and TMHA goes beyond the supply of machinery. Jim says the strong rapport that has developed between Austrak and TMHA’s Queanbeyan-based area service manager, Nathan Charnock, and his team.
Nathan and his team have made it a point to regularly check in with Austrak, not just to ensure everything is running smoothly, but also to maintain a personal connection.
“Nathan and his team have been great,” says Jim. “They keep us informed throughout the pre-delivery and delivery process, making sure everything goes according to plan. Their approach aligns perfectly with our premobilisation process, and the delivery couldn’t have gone any smoother.”
Jim’s satisfaction with TMHA’s service and products is evident in his decision to recommend Toyota to Austrak’s other factory managers in Geelong and Rockhampton, who are also looking to standardise their fleets.
“I’ve spoken to the managers at our other sites and recommended Toyota to them,” explains Jim. “The relevant salespeople in those states have already been contacted, and conversations are underway.”
Austrak’s decision to partner with TMHA has already yielded positive results. With a more reliable and efficient fleet, the Wagga Wagga factory is well-equipped to meet the demands of its operations, including the large-scale Inland Rail project. Jim is confident that the partnership with Toyota will continue to deliver benefits well into the future.
“We’re finding reliability is great, and the service is excellent,” says Jim. “We’re more than happy with the decision to go with Toyota.”
As Austrak looks to the future, the strong foundation built with TMHA ensures that the company is wellpositioned to continue leading the way in Australia’s rail infrastructure industry. ■
In an age where port delays and disruptions are the new normal, Russell Pruden, Körber Supply Chain Software General Manager APAC, explains why resiliency is the key to a successful, profitable supply chain.
As we move through 2024, ports worldwide continue to face delays, creating ripple effects that impact Australian supply chains and businesses.
The persistent congestion at key Asian ports, and ongoing economic uncertainties worldwide, have brought supply chain resilience to the forefront of Australian business strategies.
In recent years, ports such as Shanghai, Singapore, and Hong Kong –crucial links in Australia’s trade routes – have faced unprecedented challenges.
In 2022, lingering COVID-19 lockdowns in Shanghai led to a severe backlog, with hundreds of ships waiting to dock – causing delays up and down supply chains throughout the world.
In 2024, the Port of Singapore, a vital transportation hub for Australian trade, has experienced increased vessel waiting times due to a surge in global shipping volumes.
Singapore has seen nearly 50 per cent more vessels in 2024 compared to the same timeframe last year, with delayed shipments increasing 44 per cent yearover-year.
These delays have cascading effects on supply chains, leading to inventory shortages, increased costs, and disrupted production schedules.
The situation is further complicated by the fact that Australia, being an island nation, relies heavily on maritime trade.
According to the Australian Government’s Department of Infrastructure, Transport, Regional Development and Communications, more than 98 per cent of Australia’s international trade by volume is carried by sea, which makes Australian supply chains particularly vulnerable to port congestion issues in Asia.
The trend towards larger container ships, while efficient in theory, has added strain to port infrastructure. Many Asian ports are struggling to
handle these mega-vessels efficiently, leading to longer turnaround times and exacerbating congestion issues.
For Australian businesses, these challenges translate into extended lead times, with delays at Asian ports adding weeks or even months to delivery schedules.
Unpredictable delays are also making it challenging for businesses to plan effectively, impacting everything from production schedules to customer commitments.
An additional effect involves environmental concerns, with ships idling offshore often contributing to increased emissions – a growing concern for environmentally conscious consumers and regulators.
As we navigate these turbulent waters, it’s clear that Australian businesses need strategies to overcome port congestion and build more resilient supply chains.
Here we explore key approaches and solutions to address these pressing challenges, ensuring that Australian companies can maintain their competitive edge in an increasingly complex global marketplace.
To mitigate the impact of port congestion, companies should
diversify their supplier base and consider nearshoring options, reducing dependency on specific regions and minimising the risk of disruptions.
It is naïve to suggest that organisations can easily start to move operations out of China, but are seeing more businesses start to diversify to India, Vietnam and Thailand to manage disruption.
Optimising inventory management is equally important. Maintaining higher safety stock levels for critical items and enhancing inventory visibility through technology can buffer against supply chain disruptions.
Körber Supply Chain Software’s research indicates that implementing solutions providing detailed freight information down to the SKU level can improve decision-making and response times.
Flexibility in logistics is key to bypassing congested ports. Consider using a combination of alternative transportation modes and multiple entry points, including exploring ports in nearby countries with favourable tax treatments.
Strengthening relationships with logistics providers is also vital. Negotiate flexible contractual agreements that allow for changes in shipping schedules while protecting rate structure. Data shows that strategic partnerships can ensure better service and priority during congestion periods.
Leveraging technology and data analytics is crucial for anticipating and responding to disruptions. Implementing supply chain visibility tools for real-time shipment monitoring and using predictive analytics to
forecast potential disruptions can help. IBM data shows that organisations using security AI and automation extensively save USD $1.76 million compared to those that don’t.
Preparation is key to managing disruptions effectively. Develop and regularly update risk management plans for various scenarios, including port congestion. Conduct scenario planning exercises to ensure your team can respond effectively to different levels of supply chain disruption.
Enhance demand forecasting accuracy to better align production and inventory
levels with actual demand. Collaborate closely with customers to understand their demand patterns and adjust supply chain strategies accordingly.
As we move forward, highly automated supply chains leveraging sensors, vast data, artificial intelligence, cloud platforms, and robots will become the standard. These technologies will enable smart decision automation and precise control of logistics flows.
In the context of persistent shipping congestion and port disruptions, such advancements are not just beneficial –they are essential.
While large-scale investment in traditional warehouse infrastructure may face challenges due to capital constraints, flexible automation
solutions are becoming a gamechanger.
These technologies allow businesses, regardless of size, to adopt innovative tools that mitigate the risks of supply chain disruptions, including port congestion. At Körber Supply Chain Software we understand the complexities of modern supply chain management. Its expertise in logistics technology, inventory management, and supply chain optimisation can help a company build a more resilient and efficient supply chain, ready to face challenges like port congestion head-on. The future belongs to those who adapt, innovate, and embrace the power of data-driven, flexible supply chain solutions. ■
Russell Pruden, Körber Supply Chain Software General Manager APAC
In the landscape of the Australian supply chain and logistics industry, staying ahead requires more than just keeping up with trends – it demands innovation. However, innovation doesn’t always equate to high levels of automation. It often involves the strategic implementation of technologies and software designed to optimise human processes within distribution centres. Often, by focusing on enhancing these processes, businesses of all sizes can achieve greater efficiency and adaptability in a dynamic and varied market.
One specialist in this area, Dematic, has a commitment to enhancing operational efficiency and maximising productivity in close collaboration with its customers, regardless of the size of the operation, or scale of the automation. The Dematic Real Time Logistics (RTL) division focuses on optimising manual processes and pairing improved workflows with technology enablers, specifically
warehouse WLAN, RF, Voice, Vision and Autonomous Mobile Robot (AMR) offerings. The RTL division leverages the local expertise of Dematic and its capabilities in warehouse optimisation across a range of industries – from manufacturing and wholesale to retail and third-party logistics operations, for greenfield as well as brownfield facilities. The best practice approach of Dematic reflects its dedication to understanding and responding to customer operational outcomes to deliver tailored solutions.
At the heart of this approach lies an emphasis on the customer experience and working closely with customers in partnership. Dematic RTL begins its journey not with products, but with understanding specific customer needs. By immersing themselves in the operations of customers, the Dematic consultation and design team gains
invaluable insights into workflows, pain points, and objectives – business, operational and supply chain. This customer-centric approach ensures that every solution is tailored to address specific challenges and to get the best outcomes.
Dematic RTL’s journey with its customers begins with a comprehensive walkthrough of its operations. It starts by tracing the workflow backwards, analysing each step and identifying potential pain points/areas of inefficiency or waste. By working in reverse, Dematic can analyse how each step in the process contributes to achieving the desired output or end goal of the customer’s operation. This ‘pull-through’ methodology is key to debottlenecking and determining operational constraints. By analysing operational flow and understanding the
intricacies of a customer’s operations, Dematic RTL lays the foundation for a collaborative partnership aimed at driving tangible results.
One of the features of this approach is Dematic’s ability to uncover hidden pain points, inefficiencies or opportunities for improvement that customers may not even be aware of. In many cases, pain points are only identified by a customer when a known solution exists. With broad industry knowledge and experience, the RTL team often identifies potential improvements to workflows and unidentified pain points. Dematic ensures that its solutions deliver real value and efficiency gains to its customers.
Dematic RTL has a dedicated software team that implements interfaces between any WMS and a range of manual optimisation technologies. There is no ‘one-size-fits-all’ solution and the software team is pivotal in its solution offering. The software engineers are part of the solution from the beginning, developing detailed Proof of Concepts (POCs) and then engaging in detailed operation flow workshops to scope out an optimised solution. The outcomes are customised workflows, device screens, voice tasks and vision user interfaces that provide beneficial outcomes.
Improved workflows, however, are only one part of the solution. Dematic RTL has a range of operational analytic reporting platforms to help track, in real time, the performance of the manual tasks and pivot when needed. Live streams on customised dashboards mean the operation team are presented with the data they need in the format they want it.
Dedicated project managers and engineers are assigned to each project to oversee its execution and ensure smooth communication. These project managers act as a central point of contact for the customer and coordinate all aspects of the project, from planning to implementation.
Dematic RTL offers expertise in various technical areas relevant to
warehouse and logistics operations, such as WLAN, RF devices, voice solutions, vision-guided tasks, and AMRs.
It leverages this expertise to design and implement optimised solutions that meet the requirements of each customer.
Dematic RTL remains impartial when recommending solutions, focusing solely on what is best for the customer’s specific needs. This includes an evaluation of a range of technologies and products to identify the most suitable options for each customer, of the provider.
Armed with an understanding of customer requirements, Dematic RTL leverages an array of technologies, products, and solutions to craft tailored offerings to meet the specific needs of each customer. Dematic considers factors such as the size of the operation, industry requirements, and budget constraints when recommending solutions. Whether it’s streamlining processes, enhancing connectivity, or optimising workflows, these solutions are designed to deliver tangible benefits and drive operational excellence.
Dematic RTL takes a holistic approach to warehouse optimisation, considering all aspects of the operation, from rack systems to automation. The approach also recognises that human performance is a crucial element of supply chain efficiency and as such the solutions are designed to optimise human workflows, productivity, accuracy, asset management, and more. This philosophy has resulted in the development of performanceenhancing layering such as gamification, which focuses on the underlying psychological needs of staff and provides for a more engaging workplace, increased performance, and higher job satisfaction.
Throughout the project lifecycle, the company provides support. Dematic ensures that customers have access to the resources and assistance they need to implement and maintain their solutions.
Essential to Dematic RTL’s approach is the POC, where proposed solutions are validated and tested before implementation. This reallife experience allows the operators to touch, feel and interact with the proposed solution and ensures alignment and transparency throughout the implementation process. With dedicated project managers overseeing every stage of the project, from conception to execution, Dematic ensures seamless implementation and timely delivery.
Beyond implementation, Dematic RTL remains committed to supporting its customers through every stage of their journey. With dedicated technicians and a robust service infrastructure, Dematic RTL’s dedicated Customer Service team offers round-the-clock support and maintenance, ensuring that its range of solutions continues to deliver optimal performance. By offering after-sales service and support, as well as a local repair centre, Dematic reinforces its commitment to customer satisfaction and success.
Dematic RTL’s approach is scalable, meaning it can accommodate the needs of both small startups and large multinationals’ distribution centres. Solutions are tailored to the size and scale of each customer’s operation, ensuring flexibility and adaptability. Futureproofing is also built into solutions, to ensure they can be easily and quickly scaled up in line with customer business growth.
In a rapidly changing supply chain industry, Dematic RTL’s customercentric approach stands as a testament to its commitment to excellence. By prioritising customer outcomes, uncovering hidden pain points and opportunities for optimisation, and delivering tailored solutions, Dematic redefines the boundaries of operational efficiency and productivity.
As the Australian supply chain industry continues to evolve, Dematic remains at the forefront, driving innovation and empowering its customers to thrive in an increasingly competitive market. ■
The shift from “Just-in-Time” to “Justin-Case” has highlighted the need for a more responsive supply chain model Image: Anastasiia@Adobe Stock.
Argon & Co’s Paul Eastwood delves into key concepts such as Just-in-Time versus Just-in-Case strategies, self-healing supply chains, and the approaches to adopting a responsive supply chain.
Argon & Co, a global consultancy specialising in supply chain and manufacturing operations, has solidified its presence in Australia through significant growth over the last three years. Originally founded in 2001, Argon & Co has expanded its influence, now operating with more than 700 experts across 17 offices worldwide, where almost 200 Argonauts are in the local market.
The last three years have established Argon & Co. as a key player in the Australian market, where the firm leverages its industry expertise to drive transformative solutions for a spectrum of clients by empowering them through strategy, ideas, and action to change how they operate at every level.
In the aftermath of the COVID-19 pandemic, the discourse around supply chains has evolved from efficiency-driven models to resilience-focused strategies. The prevailing notion of transitioning from “Just-in-Time” to “Just-in-Case” has seen an adoption among businesses aiming to safeguard against disruptions.
However, this shift has not been without its pitfalls. Many companies have overemphasised buffering against potential crises, resulting in inflated costs and inefficiencies that were initially justified but now warrant reassessment.
The crux of the issue lies in the misapplication of the “Just-in-Case” strategy, which means some companies have changed their entire supply chain, end to end, to build contingency.
“Rather than completely redesigning
your supply chain to handle every possible contingency, it’s more effective to create a flexible and responsive system,” says Paul Eastwood, Managing Partner, APAC, Argon and Co.
“By doing this, you maintain efficiency and agility, allowing your supply chain to adapt quickly to unexpected events without increasing costs.”
A smart supply chain design balances efficiency with the ability to respond swiftly to disruptions without incurring high costs. The goal should be to engineer a supply chain that performs optimally during normal conditions and can flexibly adapt to extraordinary circumstances.
Clients encounter various opportunities and challenges in their supply chains, influenced by goals such as cost reduction, service enhancement, complexity management, or growth.
“It’s essential to integrate logistics, manufacturing, procurement, and other components rather than viewing them in isolation,” says Paul.
“For optimal results, these elements must work together harmoniously, recognising necessary trade-offs. As supply chains evolve, leveraging new technologies like AI and advanced analytics can enhance visibility and responsiveness, turning supply chains into a competitive advantage.”
Argon and Co. specialises in crafting adaptive supply chain solutions, helping businesses streamline their processes and reduce costs while ensuring they stay agile and competitive.
A self-healing supply chain relies on minimal human intervention, using AI, data analytics, and machine learning to process information and make decisions autonomously. It adjusts and optimises the supply chain by rebalancing, prioritising, or resequencing events for better outcomes.
While human oversight may be needed for approvals, the system predominantly operates on datadriven automation. For maximum effectiveness, the supply chain must be well-integrated across suppliers and customers, functioning cohesively like a single organism to harness its potential.
Achieving a ‘self-healing’ supply chain requires a nuanced approach to supply chain management. This involves evaluating physical elements such as the length of supply chains, flow paths, and critical stock points. At the same time, the “mental muscles” of supply chain management – such as team capabilities – are augmented by generative AI and machine learning.
The concept of a “self-healing” supply chain, which operates with true connectivity and intelligent decisionmaking, is crucial. Such a system can adapt dynamically, prioritising needs and optimising responses to maintain customer satisfaction and operational efficiency.
“Businesses need to consider their operations, suppliers, and customers, ensuring data connectivity and understanding across all points,” adds Paul.
Paul Eastwood, Managing Partner, APAC, Argon and Co. Image: Argon and Co.
informed decisions, adjust needs, and rebalance resources, enabling the entire supply chain to adapt and self-heal. This requires a collaborative approach where the entire value chain, from raw materials to end customers, can interact and respond effectively.”
Automation and AI are transforming supply chains, but their adoption rates and strategic applications vary. Many businesses are investing in basic automation for processes like invoice recognition and delivery scheduling.
However, true AI integration – such as multi-variable forecasting – is still in the early stages, with limited adoption beyond planning and less so in manufacturing. Automation is often seen as a long-term strategy to counteract wage inflation and labour shortages, particularly in light of disruptions like COVID-19.
“When considering automation investments, it’s crucial to understand what you’re replacing. Automation often upgrades technology, but if it’s replacing people, you should evaluate the business case with a longer-term perspective,” explains Paul.
“Automation not only mitigates longterm risks and offsets potential future inflation but also needs to align with your long-term business strategy. It should offer flexibility for evolving models and products, ensure future labour availability, and deliver a worthwhile return on investment.”
The long-term considerations of return on investment (ROI) and risk management are paramount. Businesses
must evaluate whether their stock levels and supply chain strategies are aligned with the probability of catastrophic events. While maintaining excess inventory might seem prudent, the true question is whether such investments yield a favourable balance between cost and benefit.
As labour shortages and inflation drive up operational costs, investing in automation to reduce reliance on human resources becomes increasingly relevant. Automation can enhance the robustness of supply chains, making them less susceptible to the vagaries of human and economic factors.
“Business leaders must focus on designing supply chains that are lean yet adaptable, leveraging technological advancements to build resilience,” says
advanced digital technologies, from procurement to distribution. By leveraging AI and automation, businesses can enhance resilience and efficiency, creating a system that not only manages costs but also adapts quickly to changing demands.
“At Argon and Co, our expertise in analysing interdependencies and implementing strategic investments allows companies to build robust, selfhealing supply chains that can thrive in the modern landscape.”
The post-pandemic era demands a revaluation or rethinking of supply chain strategies. The shift from “Just-in-Time” to “Just-inCase” has highlighted the need for more responsive and cost-effective models. The challenge lies not just
TGA licenced, custom-built 10,000m2 facility dedicated to Life Sciences and Healthcare Logistics. Strategically located in the Melbourne Airport Business Park with prime access to the airport, seaport, rail terminals and key road-freight arterials.
Key features include:
• Controlled ambient, cold chain and ultra-low frozen product storage
• Cold chain storage +2°C - +8° capacity for 1173 Pallets
• Controlled ambient storage (+15°C to +25°C) capacity for 7,796 pallets
• Schedule drug storage
• Value added services
• Validated active and passive cold chain solutions
• Tier 1 WMS system backed by quality assured processes
• ISO 27001 (Cyber Security accreditation)
• 5 star green star rating compliant*
*Certification is in process
Addverb explains how it transformed warehouse operations for an omnichannel fulfilment centre with its innovative automation solutions.
In the dynamic world, where staying ahead of the curve is crucial and innovation drives success, a 3PL provider in sports and fashion faced a formidable challenge.
Its expansive omnichannel fulfilment operation, covering the territories of Australia and New Zealand, required an advanced warehouse automation solution capable of seamlessly managing the ebb and flow of seasonal peak demands.
It needed to streamline an array of 68,307 SKUs, handle high dispatch volumes, and process returns with pinpoint accuracy. It was a tall order that demanded a revolutionary approach.
Stepping up to the plate with a blend of expertise and cutting-edge technology was Addverb, a company that specialises in robotics and warehouse automation.
Known for its solutions that have transformed warehouse operations across diverse industries, Addverb was the perfect partner to tackle this task.
The company’s suite of automation technologies, including Autonomous Mobile Robots (AMRs), Automated Storage and Retrieval Systems (AS/ RS), picking robots, and intelligent software solutions such as Warehouse Management Systems (WMS), Warehouse Execution Systems (WES), Warehouse Control Systems (WCS), and Fleet Management Systems, is designed to optimise efficiency, accuracy, and space utilisation.
OBJECTIVE: UNLEASHING OPERATIONAL EXCELLENCE
The facility, brimming with an inventory of 60 per cent footwear, 30 per cent apparel, and 10 per cent
Addverb’s innovative solution not only met but exceeded the expectations of one of the 3PL provider. Images:
accessories, required a versatile system adept at processing both B2B and B2C orders.
The primary goals were clear: reduce fulfilment time and costs, enhance accuracy, and optimise the returns process. Effective storage and order flow management were essential for quick and accurate material movement in the warehouse.
To enhance operational efficiency, Addverb designed a solution that seamlessly combines the strengths of both fixed and flexible automation.
The solution comprises Autonomous Mobile Robots (AMRs) for agile material movement throughout the warehouse, and Automated Storage and Retrieval Systems (ASRS), including pallet shuttles and carton shuttles, to maximise space utilisation and manage order prioritisation.
To streamline returns, a Multi-Carton Robot System was implemented, allowing for swift and cost-effective processing. Additionally, a combination of carton shuttles and sorting robots facilitated rapid order consolidation and dispatch, especially for B2C orders.
Mixed-Case Palletisers and Box-It Workstations, ergonomically designed, supported the integration of various automation systems, while
strategically planned conveyor lines ensured smooth and efficient material flow.
At the core of this solution is Addverb’s Warehouse Execution System, Concinity, which orchestrates the operations within the expansive 330,000 sq. ft. facility.
This AI-enabled system optimises order fulfilment through efficient picking and routing strategies, offering real-time visibility into inventory status. The result? A seamlessly coordinated flow of materials, ensuring faster and reliable fulfilment.
The impact of this state-of-the-art automation solution brings a host of advantages, including:
• Dispatches 100,000 pieces daily to 2500 distribution nodes.
• Sorts 3600 items per hour with a double-layer sortation system and 300 bin locations.
• Achieves the throughput of 125 tasks/hr as single and double cycles through AMRs.
• Achieves throughput of 150 pallets in/hr and 150 pallets out/hr through pallet ASRS.
• Achieves throughput of 1600 totes in/hr and 1600 totes out/hr through tote ASRS.
• Total of 14 GTP stations achieves picking throughput 110 totes per station/ hr.
Key features include mixed case palletisers, ergonomic workstations, and conveyor lines seamlessly managed by Concinity.
This AI-driven optimises picking and routing, offering real-time inventory visibility and control.
The facility dispatches 100,000 items daily to 2500 distribution points, boasting 16,500 pallet positions and 86,400 tote positions.
Addverb’s innovative solution not only met but exceeded the expectations of the 3PL provider.
The integration of advanced technologies marks a new era in warehouse management. This collaboration not only enhances operational efficiency but showcases the immense potential that arises when industry leaders join forces.
By combining cutting-edge robotics and intelligent software, Addverb has created a paradigm shift in warehouse automation, setting a new standard for efficiency, reliability, and accuracy in omnichannel fulfilment operations.
With a vision firmly rooted in continuous innovation and a commitment to redefining the future of warehouse operations, Addverb is poised to lead the charge towards a smarter, more efficient, and more sustainable future. ■
• Provide smooth transitions at transfer points
• Reduce pinch points for improved worker safety
• Quick and easy installation
Brendon Furness, CEO of Auckland-based Cardinal Logistics, sat down with MHD to explain how finance partner, DLL, has supported its investment in complex automation-related projects.
he landscape of logistics is undergoing a rapid transformation, driven by advancements in automation and the need for more efficient supply chains.
Cardinal Logistics, a third-party logistics (3PL) provider specialising in fast-moving consumer goods (FMCG) has been working with its global financial solutions provider, DLL, as it implements automation solutions across its national network.
The partnership has not only accelerated the integration of advanced automation equipment but is also laying the foundation for a more sustainable and scalable business model.
Cardinal Logistics has established itself as a key player in New Zealand’s logistics market. Brendon Furness, CEO of the company, shares insights into its journey, noting that the company’s operations span freightforwarder integration, container
transportation across road, rail, and sea.
“We’re privately held and focused almost exclusively on the FMCG industry in New Zealand,” he says. “Automation will enable us to expand into other industries and regions”.
Cardinal manages a combination of its own nine warehousing sites as well as two third-party managed locations, delivering essential goods nationwide through the robust transport network.
The decision to invest in automation came from a clear strategic need to enhance operational efficiency and meet the high demands of FMCG.
“Our environment is fast-paced and continuous, and automation provides a circuit breaker that benefits both our customers and staff, particularly in terms of volume smoothing, workload balance, and health and safety,” adds Brendon.
Cardinal’s investment in automation was driven by the desire to keep pace with global trends and maintain strong
customers who already employ automation in their overseas operations.
Brendon notes that although Cardinal began its journey towards automation shortly before COVID-19, the pandemic highlighted the need for supply chain resilience. Since then, the company has focused on sourcing land, building infrastructure, and executing its automation fit-out. Cardinal’s first automated site went live earlier this year, with a larger phase two rollout scheduled to begin in February 2025.
The equipment chosen for this transformation includes an Automated Storage and Retrieval System (ASRS) and goods-to-person carton buffering, which are key for optimising the handling of FMCG products.
“We’ll implement 120,000 pallets of ASRS racking in Auckland, but the real game-changer is the 62,000 carton goods-to-person buffering system,” says Brendon.
He adds that carton picking is a component of FMCG logistics in New Zealand due to the geographic diversity of retail distribution.
The adoption of automation enables Cardinal to streamline its operations and deliver products more efficiently.
“Our goal was to optimise the sustainable delivery of our customers’ products to retail shelves in the most cost-and-time-effective way possible,” explains Brendon.
“We also wanted to improve health and safety across all our sites, ensuring a sustainable service level.”
To support its long-term automation program, Cardinal sought a specialised finance partner capable of handling the
complexities of automation assets.
“We needed a partner with both scale and international expertise in supply chain and automation,” says Brendon.
Cardinal’s choice to work with DLL was driven by the latter’s understanding of both automation technology and the Australasian market.
Steven Davey, DLL’s Intralogistics Lead for Australia and New Zealand, reflects on the importance of this relationship.
“We don’t see ourselves as just a finance partner – we’re a strategic partner embedded in Cardinal’s longterm goals,” he says. “Our role is to understand not just the assets but the strategy behind Cardinal’s vision for the future.”
This approach allowed DLL to offer financial solutions that aligned with Cardinal’s objectives, ensuring a sustainable path forward.
“Automation is incredibly complex, and we wanted a partner who could challenge our thinking, and share their expertise,” adds Brendon. “DLL’s global footprint and local relevance have been invaluable to us.”
Like any transformation, the implementation of automation at Cardinal was not without its challenges.
“The real hurdle was change management,” says Brendon. “Shifting from a traditional logistics environment to one that’s heavily automated requires a new mindset. Suddenly, we have
engineers and technicians on our payroll alongside our store workers and drivers – it’s a shift in how we operate and integrate.”
Steven adds that one of DLL’s key roles was providing expertise to help Cardinal navigate these challenges.
“While automation is exciting, it’s not without risk. We were able to guide Cardinal through the complexities and tap into the experience of our global asset management team to provide insight into the equipment throughout its expected lifespan,” he says.
In terms of tangible benefits, Brendon highlights several key performance indicators (KPIs) that have already improved due to automation.
“Order output has increased by up to 400 per cent, and we’ve seen much more resilience in managing volume spikes, which is always a challenge in logistics,” he says.
Automation has reduced the pressure on staff, eliminated the need for overtime during peak periods, and improved overall business efficiency.
“Sustainability is important in our development, with key initiatives like rooftop solar panels, battery storage, and recycled plastic pallets leading the way. We’re also exploring fully compostable stretch wrap and harnessing power regeneration in our ASRS cranes for greater efficiency. As our site ramps up, we’re excited to unlock the full potential of these innovations and share our journey towards a greener future.” Brendon says.
Cardinal has ambitious plans for further enhancing its capabilities.
“We have future sites in mind, but beyond that, automation is going to help us integrate various supply chain partners more effectively,” says Brendon.
He believes there’s a global demand for more efficient supply chains, and Cardinal is committed to playing a role in optimising the food supply chain in New Zealand.
“We’ve been working with Cardinal for over two years, and this project showcases the strength of our value proposition,” adds Steven. “We’ve been able to leverage our global expertise and offer bespoke financial solutions tailored to Cardinal’s needs.”
Cardinal’s journey into automation is a testament to the company’s commitment to innovation and efficiency.
The partnership with DLL has played a crucial role in ensuring that this journey is not only successful but sustainable in the long run.
“Automation is changing the identity of our business,” says Brendon. “This isn’t just about one warehouse – it’s about integrating automation into the fabric of Cardinal Logistics and setting us up for the future.”
As Cardinal continues to roll out automation across its network, the collaboration with DLL will remain central to its strategy.
Both Brendon and Steven are confident this partnership will serve as a model for others in the industry, showcasing what is possible when logistics companies and financial experts come together to drive innovation.
“We see this as a long-term partnership with Cardinal, one that will keep advancing as they embrace a future where automation plays a bigger role in their operations,” says Steven. “This is an incredibly exciting period for the industry, and we are inspired by the transformative impact that the right financial solution can have on our clients.”■
Michael Lawrence from Toll Healthcare outlines the company’s strategic advancements in healthcare logistics and consultancy, showcasing its approach to national and global healthcare needs.
Toll Healthcare is redefining global supply chain solutions with its expansive network and innovative approach. Headquartered in Melbourne and Singapore, Toll operates in more than 150 countries, supported by a team of 16,000 professionals.
The company caters to more than 20,000 clients worldwide, delivering end-to-end logistics services. Backed by Japan Post, Toll continues to enhance its capabilities and address complex supply chain challenges, underscoring its commitment to excellence and growth in the logistics industry.
Toll Healthcare is distinguishing itself with its focus on healthcare logistics, offering end-to-end solutions in Australia and beyond. In Australia, the company handles everything from
product warehousing to distribution for a range of medical products, including nutritional supplements, cold chain vaccines, and scheduled drugs.
Other value-added services include specialised secondary assembly solutions, product labelling, and kitting. Toll also provides a cost-effective, validated, and sustainable reverse logistics delivery solution that enables shipments to be reinspected and reused, relieving end-user customers of having to deal with medical disposal.
Globally, Toll Healthcare leverages its forwarding network to manage international supply chains, employing multimodal transport solutions. Its global capabilities are notably active in Asia, with operations in countries like Singapore, India, and China.
“Our strategy is to establish healthcare as a standalone vertical for Toll on a global scale,” says
Michael Lawrence, General Manager –Healthcare, Toll Group.
“With the full backing of Japan Post, we have secured the commitment to invest in and expand our healthcare capabilities worldwide. This includes investments in new facilities across Australia, from Queensland to Melbourne and Perth, creating a fully compliant, national network. This robust infrastructure and technology enables us to grow and adapt our solutions as needed. Our goal is to solidify our position as a leader in healthcare logistics within the next five years.”
Locally, Toll Healthcare’s approach includes strategic partnerships, such as its collaboration with CSL Business, where it has designed and built a facility integrated into CSL’s supply chain. This partnership exemplifies its approach to organic and inorganic
Toll Healthcare’s core strength is its capability to handle mission-critical operations. Images: Toll Healthcare.
growth through mergers, acquisitions, and joint ventures.
One of Toll Healthcare’s strengths is its capability to handle mission-critical operations. With a 24/7 service offering, the company can rapidly respond to urgent medical needs, including the distribution of life-saving vaccines and other time-sensitive medical products.
“Our 24/7 service offering ensures we can handle time-critical demands efficiently,” says Michael.
“Whether it’s for federal and state government immunisation programs, emergency anti-venom, or vaccines for outbreaks, we are equipped to deploy our entire team and infrastructure rapidly.”
The company can dispatch products within half an hour of an order and is prepared to respond to urgent situations, day or night. It also played a pivotal role in the successful rollout of a $90-million meningococcal B vaccination program, which became the largest state-funded initiative in Queensland’s history.
The program aimed to protect children by distributing vaccines across schools. Leveraging its advanced national network and facilities, Toll Healthcare ensured the timely and efficient delivery of these critical vaccines, highlighting its expertise and commitment to high-impact public health initiatives.
Toll offers advanced intermodal solutions for healthcare logistics, integrating planes, trains, trucks, and ships to meet diverse needs. By combining transport modes, Toll delivers flexible, cost-effective solutions tailored to budget and schedule.
With expert teams ensuring smooth transitions and handling various freight types, Toll services include crossdocking, warehousing, distribution, and pick and pack. Its multimodal approach optimises logistics for maximum efficiency.
“Toll has strategically positioned its warehouse network along the East and West Coasts, allowing it to keep products close to customers and ensuring quicker turnarounds,” adds Michael.
“This network reduces distribution risks by avoiding single points of failure and supports our lifepreserving clients by enabling timely deliveries to patients. For instance, our Queensland warehouse ensures rapid access to ferries and flights, allowing us to reach remote communities, like those in the farreaching Thursday Islands, with minimal delay.”
Another aspect of Toll Healthcare’s service offering is its consultancy in supply chain optimisation. Its approach involves tailored solutions for each client, including designing and constructing facilities or optimising existing ones.
This consultancy has become a key component of the business in the past 12 to 18 months, reflecting a broader trend of customers seeking integrated supply chain solutions.
“We treat each customer as a unique opportunity, diving deep to understand their challenges, opportunities, and growth potential,” says Michael.
“Our team conducts comprehensive network studies – analysing everything from manufacturing to international trade lanes and transit hubs – to model the most effective operating solutions.
“From customer service, quality and compliance, safety, and people management, we offer everything
Toll offers advanced intermodal solutions for healthcare logistics.
through our consultancy service.”
The company’s global technology roadmap integrates AI, machine learning, and digitisation, with a focus on business intelligence and analytics to convert data into insights.
Toll’s Singapore-based centre of excellence tests technologies like automation and voice recognition to boost efficiency and throughput. The company can scale technology investments effectively. Operating under a sovereign cloud agreement, it maintains a secure, locally managed network for government and defence applications.
Looking ahead, Toll Healthcare is preparing for an increase in demand driven by population growth and technological advancements. The company is focused on adapting to these changes by investing in technology and infrastructure, ensuring it can meet future challenges and opportunities in healthcare logistics.
“As we face new challenges and vulnerabilities in global supply chains, our key differentiator is that we own and manage our networks, investing in them to guide our customers through future changes and challenges,” says Michael.
Toll Healthcare is set for growth through strategic investments and logistics solutions. By focusing on expanding capabilities and using technology, it is positioned to play a key role in the future of healthcare logistics and consultancy. ■
Wayne Boxshall, Country Manager, Visy Logistics, talks about how the Australian packaging, recycling, and logistics company is working on its growth trajectory.
Over the past 18 months, Visy Logistics has undergone foundational changes to enhance its logistics and supply chain capabilities.
“It has been about getting the basics right,” says Wayne Boxshall, Country Manager, Visy Logistics.
“Like many companies, we did what we had to do to get through the pandemic, and now it’s time to refine our processes and structures.”
This period saw a focus on internal operational improvements, along with the recruitment of new talent and the restructuring of teams to bolster the company’s expertise in third-party logistics.
Visy Logistics’ expansion has not only been about internal improvements. The company has launched several new operations, including additional large warehousing and transport facilities in Sydney, Melbourne, and Adelaide.
These facilities cater to a variety of needs, from brewery supplies to plastic resins, highlighting Visy Logistics versatility in handling diverse logistics requirements.
Automation and advanced systems play a crucial role in the competitive logistics market. Visy Logistics has been at the forefront of adopting these technologies to streamline operations.
“We are incorporating two Warehouse Management Systems (WMS) and Transportation Management Systems (TMS) across our operations,” says Wayne.
“We’re also installing an Automated Storage and Retrieval System (ASRS) at our new Brisbane glass plant.”
in its warehouses. This technology is useful in handling large items like paper reels, a niche that not all logistics companies cater for, or are set up to carry out, has given us unique insights and capabilities in this area,” says Wayne.
This expertise allows the company to offer end-to-end solutions that seamlessly integrate production and logistics.
Visy prides itself on its ability to provide logistics solutions tailored to client needs. The company’s five divisions – Metro, Line Haul, Intermodal, Global Forwarding, and Bulk – offer a range of services.
“Our Metro division handles national warehousing and local and intrastate transport,” says Wayne.
“Line Haul focuses on long-distance
is noteworthy. In collaboration with the Wagga Wagga City Council, Visy has developed a rail terminal in the city that facilitates the efficient transport of goods by rail. This project is part of Visy Logistics broader strategy to expand its intermodal operations across major cities.
For clients looking for international logistics, Visy Logistics’ Global Forwarding division offers expertise in imports, exports, and customs clearance.
The Bulk division, a newer addition, specialises in handling materials like limestone and sand using pneumatic tankers and tippers.
Under the initiative “Logistics Done Differently,” Visy Logistics aims to set itself apart in the market.
“We leverage 75 years of supply chain know-how from Visy Industries,” says Wayne.
“This extensive experience allows us to understand customer requirements deeply and to offer innovative solutions.”
Visy Logistics focuses on delivering end-to-end supply chain processes, reducing costs, and improving efficiency.
A notable example of Visy Logistics
end-to-end capabilities is its partnership with Mission Foods. Visy manages the entire supply chain for Mission Foods, from sourcing cornflour in California to delivering the final product in Australia.
“We handle everything except the ocean freight and stevedoring, offering a seamless and efficient service,” adds Wayne.
This model exemplifies Visy Logistics’ ability to provide a comprehensive logistics solution, simplifying operations for its clients.
Sustainability is a core value at Visy, reflecting the company’s commitment to responsible business practices.
“We are focusing on initiatives like reducing empty runs, installing solar panels on our warehouses, and introducing electric vehicles in our fleet,” says Wayne.
The company recently launched its first electric van in Adelaide, which is used for delivering wine, showcasing its commitment to reducing carbon emissions.
Visy Logistics sustainability efforts are driven by the high standards set by
Visy Industries, renowned for its circular economy practices.
“Visy Industries has a strong sustainability record, and we are working hard to match that in our logistics operations,” adds Wayne.
The company is exploring further innovations in electric and hybrid vehicle technology and is committed to expanding its use of renewable energy sources.
Looking ahead, the company is poised for further growth and innovation. It plans to expand its intermodal operations and enhance its technological infrastructure to support more efficient and scalable logistics solutions.
“There’s a real drive to grow this business, and we’re excited about the future,” says Wayne.
“Our focus is on leveraging our strengths and continuing to innovate in how we deliver value to our clients.”
With a solid foundation in place, a commitment to sustainability, and a focus on technological innovation, Visy Logistics is well positioned to continue its growth trajectory and set new standards in the logistics industry. ■
A specialist industrial packaging company based in Australia and New Zealand, Aurora Process Solutions, tells MHD about its latest pallet-related innovations.
urora Process Solutions, through its partnership with Robopack, is leading the charge in transforming how companies wrap their pallets, making the process more efficient and sustainable.
Pallet wrapping might seem like a minor aspect of the supply chain, but Braden Goddin, Marketing Manager at Aurora Process Solutions, emphasises that it’s an area ripe for optimisation.
“The key way our pallet wrappers contribute to reducing cost per pallet is by utilising software and mechanical innovations designed to minimise the amount of wrap used, without compromising load containment,” explains Braden.
A central feature of Robopack’s pallet wrappers is the pre-stretch function.
“Pre-stretching the film can extend it from 150 per cent up to 400 per cent, allowing businesses to get more coverage out of each roll,” adds Braden.
This not only reduces the amount of wrap required but also translates to cost savings over time.
“The majority of the market doesn’t realise how much money they’re leaving on the table by not using this technology,” he says.
The intelligence of the Robopack systems also plays a crucial role.
“One distinctive feature of our wrapping technology is the Human Machine Interface (HMI) that allows users to optimise their pallet wrap recipe,” says Braden.
This adaptability means that the system can cater to variable loads, strengthening certain areas of the pallet more than others as needed.
“Whether you’re dealing with heavy industrial loads, corrosive environments, or chilled logistics, our wrappers offer a solution that’s tailored specifically to your needs,” he adds.
For businesses handling thousands of
A central feature of Robopack’s pallet wrappers is the pre-stretch function.
pallets annually, even a small percentage of film savings per pallet can add up to financial benefits. These savings extend beyond just cost.
“By optimising the use of plastic film, you can achieve up to a 60 per cent reduction in your carbon footprint, which is a win for both the environment and your bottom line,” says Braden.
As sustainability becomes a higher priority across industries, Aurora Process Solutions is also pioneering
the use of new paper pallet wrap technology.
“It’s an exciting development that reduces the reliance on polyethylene, thus lowering a company’s carbon footprint,” says Braden.
The paper used is no ordinary paper; it’s engineered to stretch up to 15 per cent while remaining 100 per cent recyclable.
“Despite initial expectations, the statistics from Robopack show that this paper wrap can provide up to 40 per cent better load stability than conventional plastic wraps,” adds Braden.
This not only enhances the security of the pallet load but also offers a substantial environmental benefit.
One unique advantage of paper wrapping that Braden highlights is its potential as a marketing tool.
“You can print directly onto the paper, offering branding opportunities for businesses, especially those in retail applications,” explains Braden.
“This adds another layer of value, on top of the environmental benefits”
Switching to paper wrap does require a specific type of wrapper, and Robopack’s PW series is designed precisely for this purpose.
“These wrappers hold larger reels of consumable material, which means
fewer changeovers, less downtime, and ultimately, more efficiency,” says Braden.
This feature is beneficial for semi-automatic and automatic wrapping lines, where minimising manual intervention can lead to productivity gains.
Reducing the environmental impact of pallet wrapping is another area where Aurora Process Solutions excels.
“There are two main ways we help businesses lower their carbon footprint per pallet,” says Braden.
First, by using the correct type of wrap in conjunction with a pre-stretch function, companies can reduce the amount of polyethylene used.
“This directly reduces the volume of plastic waste, cutting down your carbon footprint,” explains Braden.
Second, the shift to paper wrapping offers an even more dramatic reduction.
“By replacing polyethylene with paper, businesses can make a substantial impact on their carbon calculations,” he adds.
The feedback from customers who have switched to Aurora Process Solutions’ pallet wrappers has been positive.
“The most common response we get is one of surprise at how immediate and tangible the savings are after a site visit from our technicians,” says Braden.
Many businesses are unaware of how much the pallet wrapping process can be optimised until they experience it firsthand.
“People often overlook pallet wrapping as an area for cost-saving, but once it’s optimised, the financial benefits are clear,” he adds.
As the industry continues to evolve towards greener supply chains, the role of pallet wrapping technology is set to expand.
“Paper wrap is a massive step in the right direction, and the technology is only going to improve from here,” says Braden. He envisions future developments
in engineered papers with enhanced moisture resistance, making paper wrapping applicable to an even broader range of logistics chains.
Beyond paper, there are other exciting technologies on the horizon.
“Pallet layer adhesive, which locks the layers of products on a pallet together, is another area seeing growth,” explains Braden.
“This quick-release adhesive means you don’t need as much wrap to secure a load, further reducing plastic use.”
Additionally, anti-slip sheets, which increase pallet stability, are becoming more common, helping reduce the amount of wrap required.
Recycling is another crucial aspect of the future.
“We’re seeing more development in closed-loop recycling programs for retrieving and recycling plastic consumables from pallets,” says Braden.
“While there’s still a long way to go, progress is being made, giving companies more options for responsibly managing their waste.”
Aurora Process Solutions is not just focused on delivering pallet wrapping technology; the company has broader goals for the Australian and New Zealand markets.
“We’ve been growing year on year, and we’re looking to increase our footprint across Australasia,” says Braden.
Aurora’s strength lies in its ability to scout global innovations in packaging
Aurora Process Solutions is pioneering the use of new paper pallet wrap technology. Images: Aurora Process Solutions
automation and bring them to the local market.
“There are different methods of pallet wrapping, such as rotary arm and ring wrapping that are used widely around the world but are less common here,” explains Braden.
“These methods offer advantages, and we’d like to see them adopted more in Australia and New Zealand.”
By introducing these advanced technologies, Aurora aims to help ANZ businesses compete more effectively on the global stage.
While pallet wrapping is a focus, the company offers more.
“We are specialists in industrial packaging, handling everything from the moment our clients finish manufacturing their product,” says Braden.
This includes filling the packaging, closing it, conveying it, palletising it, wrapping or hooding it, and beyond.
Aurora provides individual pieces of equipment as well as integrated process lines.
“We manufacture, integrate, install, train, and service – essentially offering a full end-to-end, turnkey solution for industrial packaging,” adds Braden.
As the industry shifts towards more sustainable practices, the company is offering innovative, cost-effective, and environmentally friendly pallet wrapping solutions that meet the needs of today’s businesses. ■
A municipal works, civil and commercial construction event.
17-18 September 2025,
In September 2025, a new event will be landing at the Melbourne Convention and Exhibition Centre. Converge will bring together leading decision makers in the Municipal Works, Civil and Commercial Construction space, to share the tools, ideas and technologies that are shaping these sectors.
Australia’s supply chain industry faces a severe skills shortage. To combat this, SCLAA has partnered with WiseTech Academy offering specialised courses to upskill the industry.
Australia is experiencing a severe skills shortage that threatens its capacity to meet the growing demands of freight movement.
Approximately 1.2 million people ensure successful freight movement across the supply chain, with the industry projected to see substantial growth over the next five years. The pandemic intensified the need for the timely delivery of essential goods, highlighting the critical role of a robust and well-staffed supply chain.
However, the sector faces immediate and long-term challenges, including an unsustainable deficit of skilled labour and a downward trend in vocational education and training. Structural issues, including limited awareness of career opportunities and an aging workforce further exacerbate the problem. This has led to a severe disparity between industry needs and available skills, impacting the efficiency and effectiveness of freight operations.
Addressing these challenges requires a multifaceted approach to upskill and reskill the existing workforce while attracting new talent to the industry.
and integrating new IT skills, such as data management, machine learning, and cyber security, into continuous training programs is crucial to enhancing technical capabilities and ensuring the workforce can keep pace with digital innovation and supply chain automation.
By focusing on these areas, the industry can not only fill immediate vacancies but also prepare for future demands and technological shifts. Additionally, promoting awareness about the diverse career pathways and opportunities within the logistics sector can attract a broader talent pool. Strategic collaboration with educational partners is required to increase core competencies, which will help bridge the skills gap. Engaging with schools, universities, and training providers to develop targeted programs can create a pipeline of skilled workers ready to enter the logistics field. This involves not just technical training but also soft skills development, which is essential for managing modern, technologydriven supply chains.
To support this vital transformation, the Supply Chain and Logistics
partnered with WiseTech Academy to assist with upskilling individuals in our industry.
WiseTech Academy is a supplier of practical and innovative learning programs, offering specialised courses in supply chain logistics and corporate compliance. The curriculum is designed to address the specific needs of the supply chain logistics sector, ensuring that workers are equipped with the latest knowledge and skills. This partnership provides SCLAA Corporate Members with access to online courses at a discounted rate. By leveraging this partnership, companies can accelerate their teams’ growth, enhance workplace productivity, and manage corporate risk more effectively. This collaboration helps mitigate the skills shortage and is one of the many benefits available to SCLAA Corporate Members.
Take advantage of this opportunity to fast-track your team’s development and secure the future of your supply chain operations. By prioritising education and continuous improvement, the industry can build a stronger, more resilient supply chain
The Frank Vale Award recognises outstanding young professionals in the Australian cold chain industry.
Akey highlight at the RWTA 82nd Conference and Exhibition was the Frank Vale contestants presenting to the attendees, where the final decision on the winner was made and presented at the Gala Dinner.
Noah Heldt from Linfox exemplifies remarkable leadership qualities and innovative approaches within the cold
chain sector, setting a high standard for future aspirants. The RWTA is proud to announce the conclusion of the 30th Frank Vale Award, marking three decades of recognising outstanding achievements in the cold chain industry. The Frank Vale Award has been awarded annually since 1993 to acknowledge talented young
people within the industry, who are 35 years of age or younger, have worked in the cold chain industry for a minimum of three years, and who have demonstrated to their employers that they have the potential to become future leaders, and make a positive contribution to the development of the cold chain industry. ■
The RWTA’s 82nd Conference and Exhibition kicked off at Montalto Winery, followed by three days of insightful talks, panels, and industry highlights.
The RWTA held their 82nd Conference and Exhibition this year with the first function at Mornington Peninsula at Montalto Winery. With a record number of attendees, the weather was perfect, clear and a sensational kick-off to the next three days. This event was followed up by the welcome dinner at RACV Cape Schanck that evening.
Monday heralded the beginning of the conference in earnest; speakers, tech talks and a panel were the order of the day. Topics covered ranged from t ransport updates in Victoria, inclusion and diversity, energy-saving activities, automation, and a deep dive into Setpoint
3 Degrees and how it can positively affect the cold chain worldwide. The highlight of the day was the four Frank Vale contestants presenting to the attendees, where the final decision on the winner was made and announced at the Gala Dinner the next day.
Tuesday heralded a full lineup of speakers, finishing with the eagerly awaited Gala Dinner. Speakers included Rob Edwards, The Health Presenter, who gave a presentation on how to improve health. There was also an update on the Discretionary Mutual Fund ensuring excellent savings on insurance. After that, a fast-paced Blockchain presentation took place
followed by an innovative company presentation on sustainable packaging and insulation.
CBRE gave an overview of property space in Australia, followed by a panel to delve into the subject.
Construction updates, EBAs, Unions and construction were a moving feast. Sixty years of Performance Panels updates in Australia on sustainability and efficiency- it’s all about setting the standard in the industry.
A powerhouse presentation was the last of formal proceedings for the day on legislation, best practices and industrial relations to leave the crowd on a high. ■
Our breakthrough new range of pallet wrappers deliver real cost reduction per pallet and an extra level of performance.
Book a free on-site review and analysis of your current pallet wrapping performance
NZ 0800 55 77 33
AU 1800 318 019 hello@aurora-process.com
• Intelligent technology to get the best load containment whilst reducing your wrap usage.
• Unusually shaped loads, unstable or light loads, sharp edges, and loads in cold or hygiene zones – we’ve got it covered.
• Full range of performance wrap and pallet consumables - specified by process technicians not stationary suppliers.
• Fully installed and serviced.
Ask us about paper wrapping options too.
Classes will be conducted from 9 am to 5 pm via Zoom on 26-27 November 2024.
Join the upcoming Production Planning & Control 2-Day Course to learn the processes, tools, techniques and performance measures for production planning and control excellence, which will take place on 26-27 November 2024.
This workshop will provide an understanding of why Integrated Planning & Control techniques were added to our knowledge as we learnt about the different behaviour of DC finished goods, Finished Items at the Manufacturing sites and Manufactured & Purchased items, as well as items that experience repetition where simplicity in execution is paramount. Additionally, planning at the aggregate level through S&OP will also be addressed not just detailed planning.
Accountabilities and cross-functional links will be discussed to enable you to assess the quality of your current processes against checklists. Although
Image: ASCI/Canva
based tool. The other two checklists provided for free will be the fundamental checklist and a checklist focused more on behaviours rather than processes.
Relevant performance measures will be presented to ensure companies are
9 am to 5 pm Sydney Time, totalling 16 training hours. Participants will join via Zoom.
ASCI members can register for $1,950, while non-members can register for $2,350. ■
Classes will be conducted from 9 am to 5 pm on 29-30 October 2024.
Join the upcoming Master Planning & Material Requirements Planning (MRP) 2-day course to improve the key processes that enable effective inventory management and higher levels of customer service, which will take place on 29-30 October 2024.
By attending this workshop, people will learn how to improve individual processes and link them effectively to the relevant internal or external process, develop an effective five-step IBP process supported by the MPS and key IBP performance measures
to ensure accountability throughout the organisation. They will also identify the purpose of MPS & DRP, and implement safety stock strategies using simple Pareto, complex Pareto and statistically derived safety stocks for improved customer service.
This course is suitable for managing directors of small firms and their direct reports, S&OP/ERP project team members, personnel from: demand management, order entry, customer service, IT staff, master schedulers, production planners, inventory
controllers, distributions planners, capacity planners, purchasing personnel and key middle managers involved in the pre-S&OP meetings, ie. Demand, Supply and Partnership/ Integrated Reconciliation/Pre-S&OP steps.
Classes are conducted daily, from 9 am to 5 pm Sydney Time, totalling 16 training hours. Participants will join via Zoom.
ASCI members can register for $1,950, while non-members can register for $2,350. ■
Registration for the ASCI Supply Chain Sustainability Series 2024 is now open.
Swisslog automated warehouse solutions ‘scalable, flexible Vectura stacker crane for high bay warehouse automation reduces energy consumption of pallet warehouse operations by up to 25 per cent, thanks to features including regenerative energy design for optimal use of cycles. With an outstanding 99.7 per cent availability, and providing a solution reliability with over 50 years of continuous improvement behind it, Swedish-designed Vectura performs equally well in temperatures as low as -30°C in a frozen food warehouse, or in ambient environments as high as +50°C. Proven in more than 600 customer installations, and operating at heights up to 50m, Vectura’s single-mast design reduces cost and uses less space, setting the standard for innovative design for pallet cranes in high-bay warehouses. It achieves very high storage density, with single to multi deep reach, in high buildings and, where land space is limited.
For more information visit www.swisslog.com/en-au
Global cube storage company AutoStore introduces its latest capability, the Grid and Vending Machine solution, designed to simplify warehousing automation. The ConveyorPort is a workstation in its simplest form, where Bins are dropped on a conveyor and transferred to an opening outside of the Grid. Smart covering and sensors ensure operator safety. The CarouselPort is designed to work with the operator, in harmony with Robots to ensure the next Bin is always ready. The workstation operates with three rotating arms, each holding one bin tray. The Vending Machine solution includes various Robots and chargers, as well as a dummy display unit, and a grid structure with 60 Bins.
For more information visit www.autostoresystem.com
The ECE series truck stands out among low-level order pickers due to its innovative features tailored for accessibility, efficiency, and operator comfort. Its height-adjustable steering wheel, known as the “jetPILOT,” ensures accessibility for operators of various heights, making it inclusive for everyone. The operator-oriented working space ensures all necessary equipment, such as scanners, shrink wrap, and documents, are conveniently within reach. Furthermore, the truck can be customised with cutting-edge technology to enable semi-automation in warehouse operations, with the possibility of integrating with Warehouse Management Systems (WMS) based on customer requirements. Experience the difference with the ECE series truck today and elevate your warehouse operations to new heights. To learn more about how our innovative features and customisable options can streamline your workflow and enhance operator satisfaction, visit our website.
ifm Track and Trace Gate is the complete solution for your automated and transparent logistics in your incoming and outgoing goods processes. By directly transferring all goods flows to the IT level, you can organise the inter-locking of production, inventory, and suppliers more efficiently than ever before.
For more information visit www.ifm.com/au/en
A monthly wrap up of the latest appointments in the supply chain, materials handling and logistics industry.
TOLL GROUP APPOINTS NEW BDM
Toll Group welcomes Frank Cotronea as the new Business Development Manager for its Government and Defence business. With more than 30 years of experience in downstream and midstream oil and gas, Frank has excelled in relationship management, pricing strategies, and end-to-end delivery of growth initiatives.
Robert Mackowiak has joined Kardex as Director of New Business Remstar, ANZ. Bringing 16 plus years of expertise in Executive Leadership, Engineering Management, Operations Strategy, Procurement and Supply Chain Planning, Robert is set to lead the team and drive dynamic growth across the region.
Do you have career news to share? Email Joseph Misuraca at Joseph.Misuraca@primecreative.com.au to be featured.