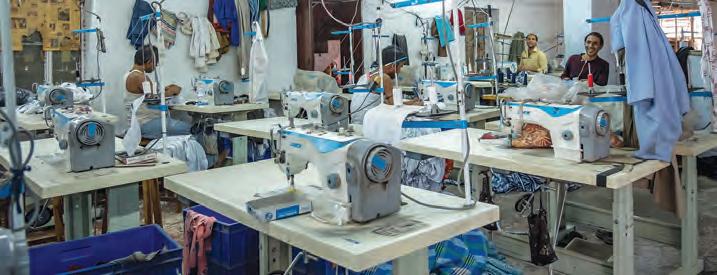
12 minute read
Industry Associations
from MHD November 21
by Prime Group
MODERN SLAVERY IN THE SUPPLY CHAIN
MHD asks Nicholas Bernhardt, Informed 365 CEO about modern slavery – and learns why awareness is key to halting its influence over global supply chains.
WHAT IS MODERN SLAVERY?
It’s something that a lot of people think only happened hundreds of years ago. But it’s more prevalent today than it was yesterday and it will be more prevalent tomorrow than today. By my explanation, modern slavery is forcing someone to do something they do not want to do. The technical definition involves slavery, servitude, human trafficking, forced labour, debt bondage, forced marriage, child labour and the sale or exploitation of children.
WHY IS THE PROBLEM GETTING WORSE?
There’s a lot of money to be had in it, which is the biggest problem. Slave labour is the second highest grossing criminal activity behind the drug trade. The COVID-19 pandemic has also pushed vulnerable people into more desperate situations – when people are desperate, they’ll take on labour they typically wouldn’t.
HOW IS INFORMED365 HELPING CURB THE PROBLEM?
Informed 365 is an Australian based ESG (Environment Social Governance) tech solution that helps companies visualise, monitor, track and engage with their supply chain. Larger companies often have thousands of suppliers so we help engage with the suppliers efficiently without materially adding to the workload. The collected data then underpins a modern slavery statement.
WHAT IS THE MODERN SLAVERY ACT?
The Modern Slavery Act requires entities based, or operating, in Australia, which have an annual consolidated revenue of more than $100 million, to report annually on the risks of modern slavery in their operations and supply chains, and actions to address those risks.
Forty million people are estimated to be engaged in modern slavery.
These organisations are required to submit modern slavery statements, describing the risks of modern slavery in the operations and supply chains. The statements must also include information about actions taken to address those risks.
WHAT ARE THE PENALTIES FOR MODERN SLAVERY BEING A PART OF A COMPANY’S SUPPLY CHAIN?
With the current legislation, there are no penalties for anyone that a doesn’t submit, puts false data into or makes up a statement. As there are no penalties some statements can look like fancy marketing brochures. I believe that penalties for non-conformance would help drive positive change.
HOW DOES AUSTRALIA COMPARE TO THE REST OF THE WORLD?
According to the Global Slavery Index, there were approximately 15,000 people living in “conditions of modern slavery” in Australia five years ago.
Globally there is an estimated 40 million people engaged in modern slavery. About two thirds of the global slave trade occurs in the Asia-Pacific. Some of Australia’s biggest trading partners, including China, Malaysia, Indonesia and Thailand, and are host to some of the most egregious crimes. Modern slavery is usually found in deeper tiers of suppliers.
HOW CAN BUSINESSES BE BETTER?
Half of the battle is awareness and allowing people to know there is a problem. No one’s perfect – even the laptop I’m talking on has probably got components that are based on slavery. Businesses will go a long way by simply addressing it. Internal training is important to pair with talking to suppliers to improve the visibility of a supply chain.
GOALS FOR INFORMED 365 GOING FORWARD
If I’m glass half full, I would say the analogy is health and safety. For example 30 or 40 years ago, health and safety equipment like high-vis vests and boots were almost optional in certain industries and now they have become the norm.
I’m hoping that by building more awareness and providing better data to companies we turn ethical sourcing into the ethos of businesses so they look into the environmental and social aspects of their procurement process as well as the price and location.
If it becomes the standard way of doing business, people will spend money with other ethical businesses, and that in turn will start pushing the bad operators out of the market. ■
ASCI UPDATE
The latest information and updates from the Australasian Supply Chain Institute.
UPCOMING EVENTS AND PROGRAMS
2021
ASCI Annual General Meeting
6 November 2021 11.30am - 1.00pm Online ASCI members can register your virtual attendance to ASCI Annual General Meeting as a guest.
FIRST QUARTER OF 2022
APICS CPIM Part 1 (Basics of Supply Chain Management) - Online Certification Review
1 February 2022 to 12 April 2022 7.00pm - 9.00pm (please check when registering time for AEST or AEDT i.e. daylight saving) 11 sessions | online This 11-week short course is the first module of the APICS Certified in Planning & Inventory Management which is a designation held by over 130,000 supply chain practitioners around the world.
APICS CSCP - Online Certification Review
7 February 2022 to 6 June 2022 7.00pm - 9.30pm 16 sessions | online Eight modules delivered over 16 weeks. The APICS Certified Supply Chain Professional (CSCP) program arms you with end-to-end supply chain knowledge to help you and your business remain competitive in today’s economy. Boost your confidence in supply chain management and master the skills needed to bring new ideas to suppliers, plants, and distributors while improving customer satisfaction. With a CSCP Certification, you’ll gain valuable experience to effectively manage global supply chain efforts and implement essential concepts and strategies to improve day-to-day operations.
APICS CPIM Part 2 - Online Certification Review
17 February 2022 to 2 June 2022 7.00pm - 9.30pm 16 sessions | online This 16-week course covering eight modules, is the second part of the APICS Certified in Planning and Inventory Management which is a designation. It is a requirement that all students have completed CPIM Part 1 prior to commencing the course, please see ‘What’s on’ on our website to enrol in Part 1. The final exam is optional, however if passed with Part 1 certificate, allows participants to obtain their CPIM certificate.
APICS Certified in Logistics, Transport and Distribution (CLTD) - Online Certification Review
2 March 2022 to 25 May 2022 6.30pm - 9.30pm 13 sessions | online Certified in Logistics, Transportation and Distribution (CLTD) proves an in-depth understanding of how to streamline logistics, transportation and distribution including order management, distribution inventory management and warehouse management.
For more information, visit www.asci. org.au/events
ASCI CORPORATE MEMBERSHIP
ASCI corporate membership is available for any group, organisation, industry body institution or business that wants to join ASCI and demonstrate its commitment to best practice and excellence, whilst ensuring its team’s proficiency in the supply chain industry.
ASCI membership provides access to professional pathways including complimentary practitioner registrations, global best practice knowledge, industry involvement and networks.
ASCI corporate members receive individual benefits for employees, including ASCI plus VIP prices for certifications, courses, complimentary tours and networking events and early bird releases.
For more information or to become a member visit ASCI website www.asci.org. au or contact enquiries@ asci.org.au.
Join ASCI and take the steps towards your professional career pathway now and for 2022. Membership starts at $275 with concessions available upon evidence of your employment situation or membership to another association. For more information on membership benefits please visit www.asci.org.au/join.
Clearly understanding, specifying and recording a customer’s needs is essential for supply chain professionals.
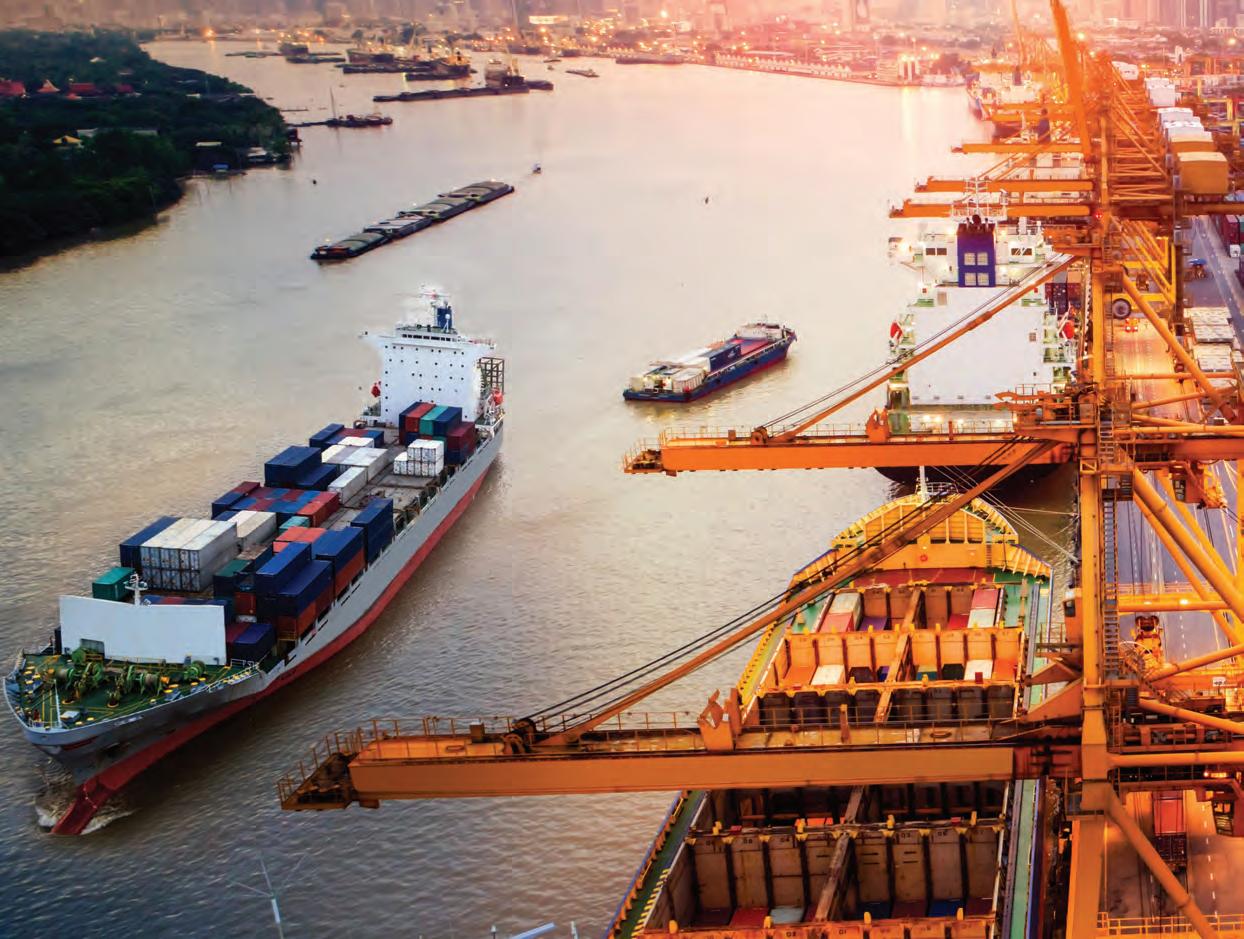
NOTHING TO SEE HERE
Mark Healing from the Supply Chain & Logistics Association of Australia explains why keeping certain interactions with customers to a minimum is an important skill for supply chain practitioners.
As an operational Supply Chain practitioner, I often suggest that if we do our job right, we are invisible to our customer base. If we do not, they want to know every step of our process and why. The customer’s expectation is that their goods or services are available when and how they want them. Sometimes, that expectation is based on a specified scope and timings or alternatively, an implied understanding built on repetition, trust and relationships.
In other words, our customer’s level of expectation is intrinsic in our everyday dealings with them.
HOW DOES THE “INVISIBLE” HAPPEN? THROUGH:
• Interaction with the customer. • Working with them, understanding, clarifying, specifying and recording their needs. • Understanding the individuals within their team technically, personally and emotionally. • Mutually agreeing on an outcome.
The kicker here, is that it must be workable for you as well.
I witnessed an example of this on a recent vacation in Far North Queensland. My wife and I needed to be collected from Cairns Train Station for our Trip to Kuranda on the Sky rail. I watched the bus driver: • Arrive a few minutes prior to arranged time. • Greet all passengers and tick them off his list. • Call ahead to other passengers being collected and suggest they make their way to their collection point.
• Advise passengers of all the next steps whilst driving to the next collection point. • Collect three other groups along the way whilst battling traffic and fielding general questions. • Communicate with Sky Rail Station as to how many passengers he had and his estimated time of arrival. • Answer all questions and provide extra information on where to sit and what to expect so as passengers would get a better experience once on board the Sky Rail.
We arrived at the Sky Rail Station, the driver’s colleagues met and directed us to our respective cable cars via the ticket booths, and within minutes we were sitting in the cable car enjoying the view. Expectations met and exceeded!
This is just a simple example of managing customer expectations as well as streamlining your internal process. Most of the passengers were oblivious to the driver’s skill of seamlessly making it happen with the minimum of fuss – invisible!
I was impressed in the way the driver set some of these expectations with his imparting of information. The customer at times does not know what they may want or need. This is where the intrinsic knowledge you have of your customer base and your product can add value to their expectation. This will also reinforce the relationship with them and provide an avenue for return business with them.
So, I challenge you - what is your “invisible”? These may be hard to recall as you are doing them that well you don’t even know you are doing them! Now that you’ve done that, it is the “visible” that I would like you to concentrate on.
Be brave and reach out to your customer and establish where you are not meeting their expectation and only then, respectfully share where they aren’t meeting yours. Rest assured you will be working on the “visible” continuously, but I can assure you that if your customer is aware of your interest, they will reward you with the detail to enable these to become just another part of your “invisible”. ■
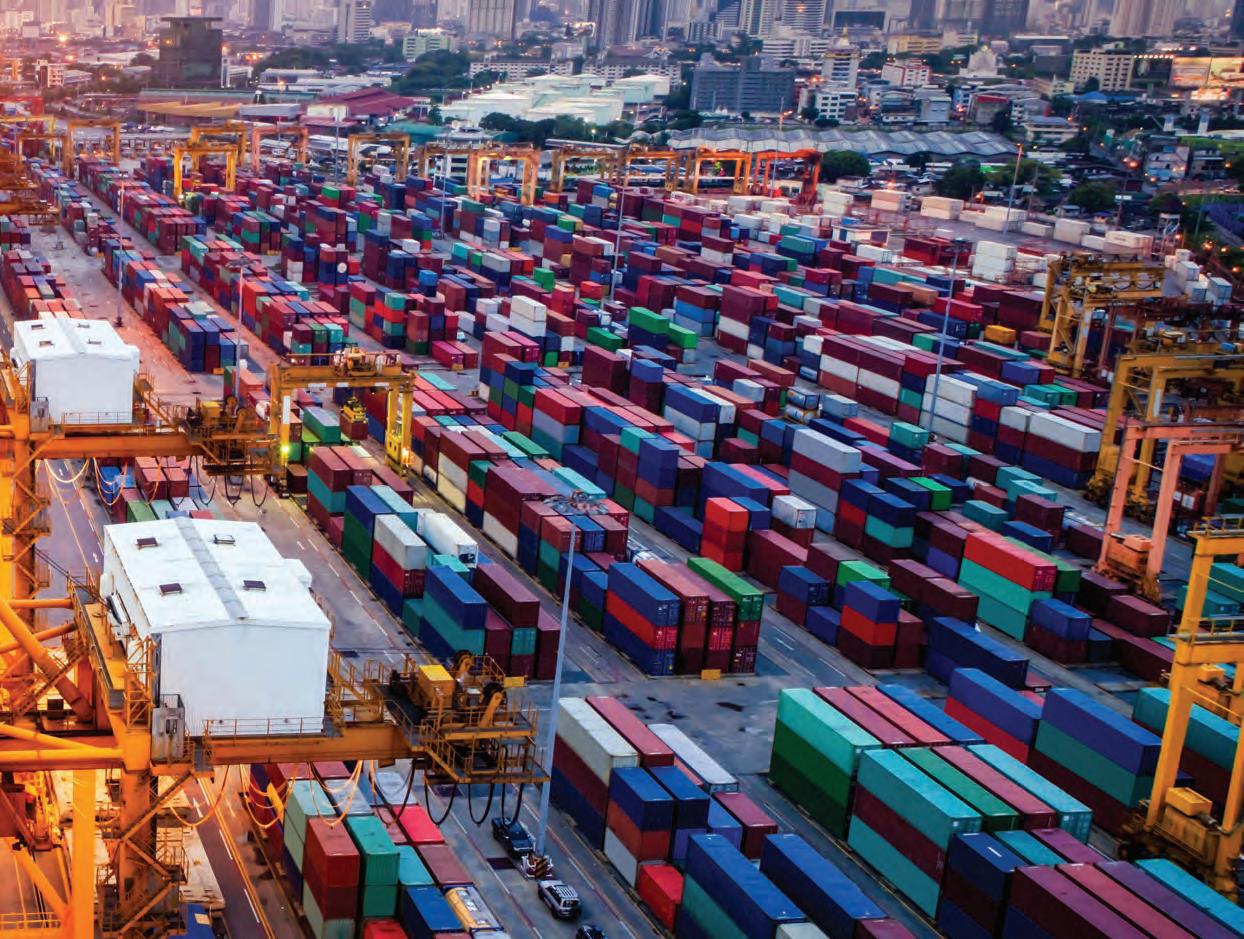
AUSTRALIA’S SUPPLY CHAIN PATH OUT OF LOCKDOWN
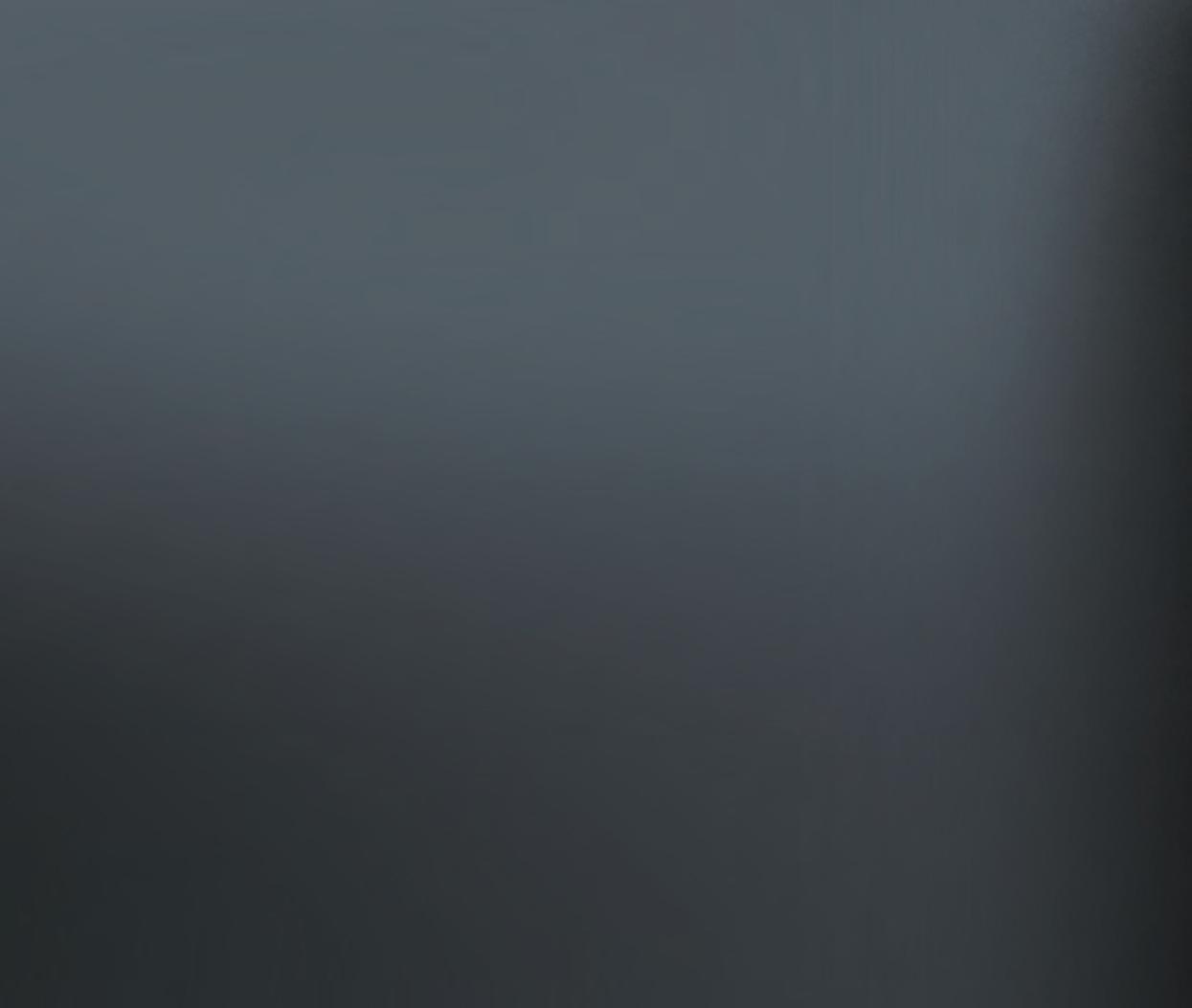
The Australian Logistics Council writes the last 18 months has taught us that early planning measures and national consistency are critical to minimising the impact on the supply chain.
The last 18 months has taught us that early planning measures and national consistency are critical to minimising the impact on the supply chain. Industry needs a pragmatic and clear path forward from health officials to ensure that essential goods and services can continue to be delivered to increasingly expectant consumers.
The inconsistent application of the national freight protocol and the understandably cautious approach by state health officials has had a big impact on supply chain organisations and their employees. The industry has managed to keep the economy moving despite a myriad of permits, rules, testing and vaccination requirements.
As vaccination rates increase across the country and state premiers publicise their intentions of lifting lockdowns, we need health departments to engage with industry and finalise their planning. As we’ve seen from international examples, “living with the virus” means there will be inevitable outbreaks that spread through the community into supply chain networks.
While only some states are declaring plans to reopen, similar approaches will undoubtedly be adopted in all jurisdictions across Australia in the coming months. This means that industry needs leadership from the National Cabinet process to avoid inconsistency, confusion, and further disruptions as we begin the journey to Covid-normal.
The on-going pandemic has seen the unsung heroes of the supply chain resiliently adapting to ever-changing requirements to meet compliance demands, resulting in operational challenges, confusion, and frustration.
By prioritising consultation and collaboration with industry, coupled with 18 months of experience and a considered risk management plan, the National Cabinet can put in place a clear and practical path out of lockdown that includes the critical supply chain network across Australia.
The path could include creating a risk management profile in consultation with governments and industry, assisting to increase compliance whilst reducing administrative burden.
As community and government risk appetite for opening the economy grows, alongside increase in community vaccination rates, risk management approaches need to also adapt.
A national industry safety management system could include: • Ensuring freight and supply chain workers have completed appropriate
inductions and training to ensure workers understand and follow
COVID safe practices • Promotion of vaccination to the workforce • Regular COVID safe communications • Use of government funded Rapid
Antigen Testing where appropriate as a proactive measure to limit workplace transmission • Workforce ‘bubbles’ and regular deep cleaning of premises.
The path also needs to include a national approach to the management of close and casual contacts for fully vaccinated employees. Australia’s supply chain cannot weather large cohorts of the workforce being stood down in isolation as a result of being a close or casual contact.
ALC suggests the path for vaccinated employees exposed to COVID positive contacts should be to isolate until a negative PCR test result is returned. However, they should not have to isolate for 14 days as per the current requirement in most jurisdictions. Government funded Rapid Antigen Testing could be administered as a replacement for isolating at the start of each shift, as a proactive measure.
Finally, as more of the economy opens up, the requirement for permits for interstate and intrastate freight movements will need to be reconsidered. If a business has an approved COVID safe plan and adequate staff safety measures in place, this should remove this administrative requirement.
National planning and alignment are needed now to allow supply chain businesses to plan, adjust, and optimise their operations to continue to meet community needs.
Our path out of lockdown hinges on achieving a national and harmonised approach. Getting the path right will be a little bumpy but ultimately manageable. However, getting it wrong could mean a rocky road to freedom. ■
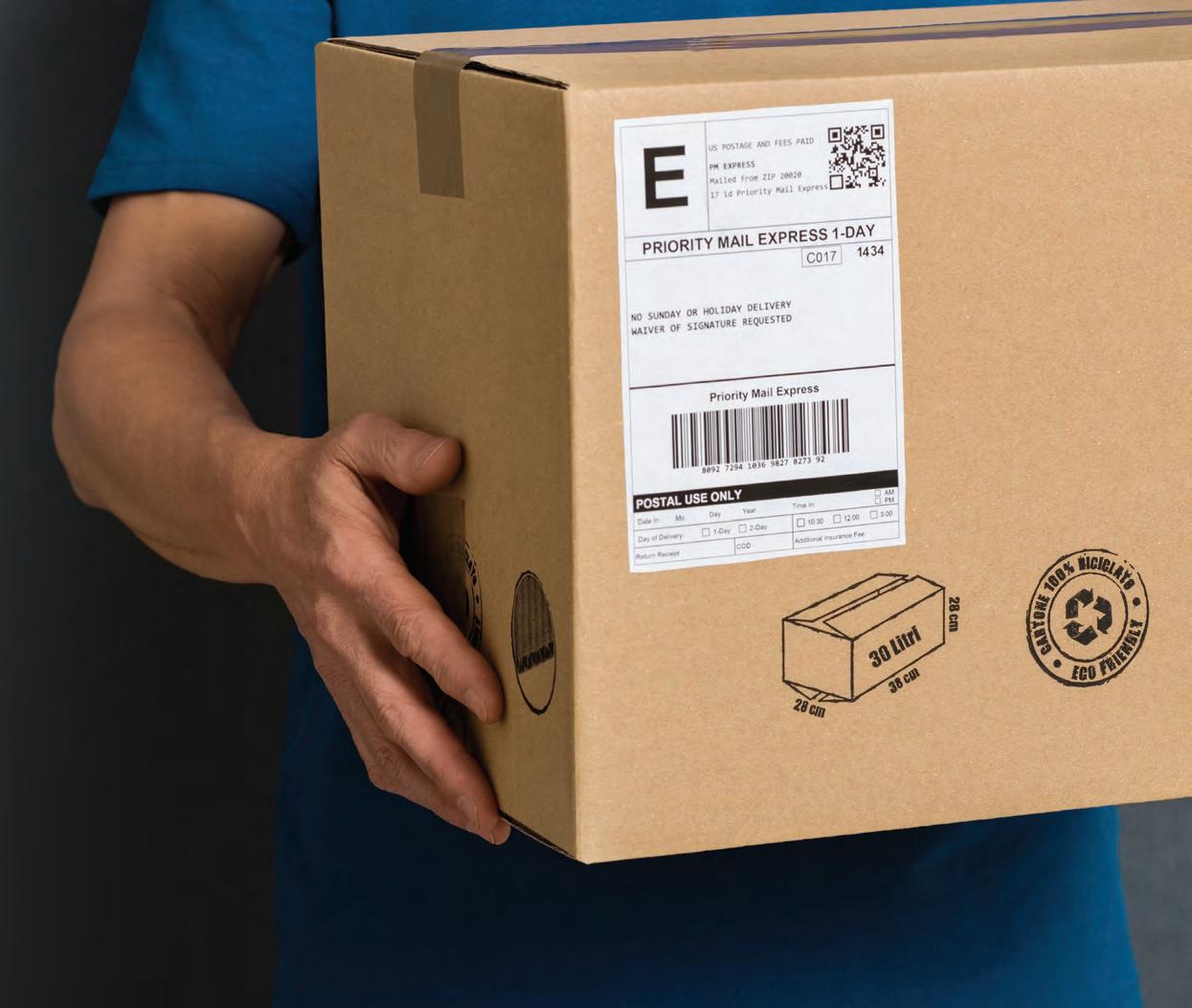