Dematic automates South West
Healthcare's logistics hub
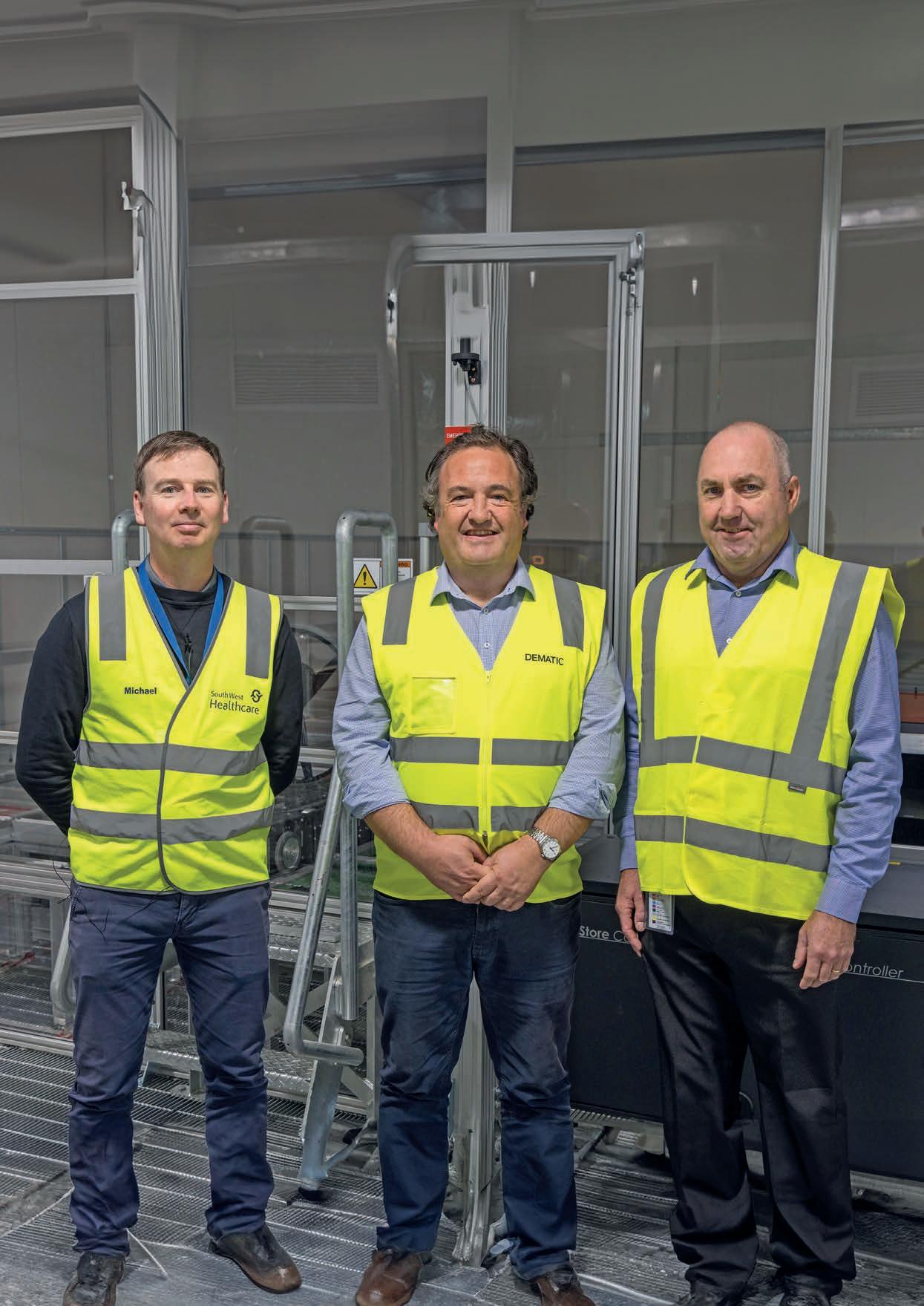
MAKING IT GREEN
Prological explores sustainability at MEGATRANS Körber on planning for the peak season
MEETING DEMANDS
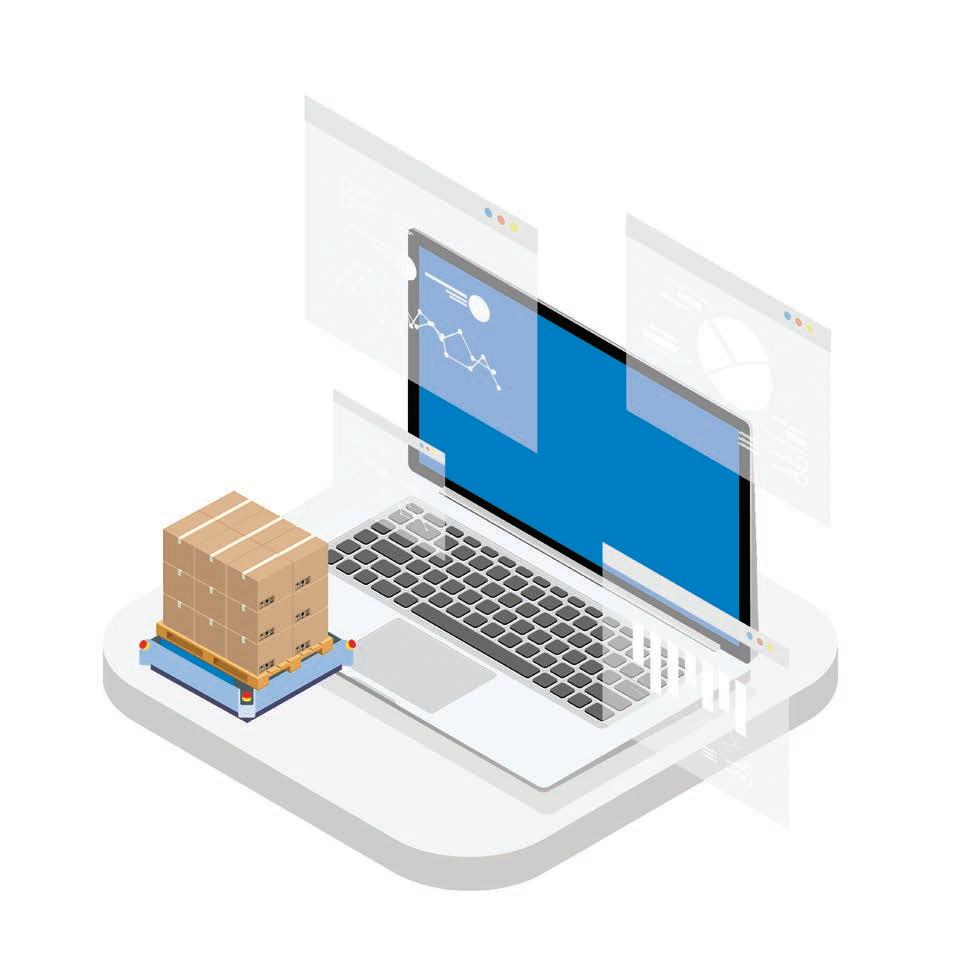
Dematic automates South West
Healthcare's logistics hub
MAKING IT GREEN
Prological explores sustainability at MEGATRANS Körber on planning for the peak season
MEETING DEMANDS
The new 2024 Gartner® Magic Quadrant™ for Warehouse Management Systems is out and for the 6th year in a row, Körber has been named a Leader.
Scan the QR code to get your free copy of the report and discover why Körber stands out among the competition. koerber-supplychain-software.com
Scan for your free copy of the report
MHD Supply Chain Solutions is published by Prime Creative Media
379 Docklands Drive, Docklands VIC 3008
Telephone: (+61) 03 9690 8766
Website: www.primecreative.com.au
CEO: John Murphy
Chief Operating Officer: Christine Clancy
Managing Editor: Mike Wheeler
Editor: Phillip Hazell
Assistant Editor: Joseph Misuraca
Journalist: Mannat Chawla
Business Development Manager: William Jenkin
Design Production Manager: Michelle Weston
Art Director: Blake Storey
Graphic Designers: Danielle Harris, Jacqueline Buckmaster
Client Success Manager: Janine Clements
FOR ADVERTISING OPTIONS
Contact: William Jenkin william.jenkin@primecreative.com.au
SUBSCRIBE
Australian Subscription Rates (inc GST) 1yr (11 issues) for $99.00 2yrs (22 issues) for $179.00
To subscribe and to view other overseas rates visit: www.mhdsupplychain.com.au or Email: subscriptions@primecreative.com.au
ACKNOWLEDGEMENT
MHD Supply Chain Solutions magazine is recognised by the Australian Supply Chain Institute, the Chartered Institute of Logistics and Transport Australia, the Supply Chain and Logistics Association of Australia and the Singapore Logistics and Supply Chain Management Society.
ARTICLES
All articles submitted for publication become the property of the publisher. The Editor reserves the right to adjust any article to conform with the magazine format.
COPYRIGHT
MHD magazine is owned by Prime Creative Media. All material in MHD is copyright and no part may be reproduced or copied in any form or by any means (graphic, electronic or mechanical including information and retrieval systems) without written permission of the publisher. The Editor welcomes contributions but reserves the right to accept or reject any material. While every effort has been made to ensure the accuracy of information Prime Creative Media will not accept responsibility for errors or omissions or for any consequences arising from reliance on information published. The opinions expressed in MHD are not necessarily the opinions of, or endorsed by the publisher unless otherwise stated.
As I step into the role of editor, I’ve had the privilege of immersing myself in the dynamic and ever-evolving supply chain sector.
It’s been a fascinating journey, learning first-hand about the innovative developments that are shaping the future of this industry.
In this edition of MHD Supply Chain Solutions, we take a closer look at how digitisation is transforming the supply chain industry.
As we explore the theme of “digitising operations with AI, data, and cybersecurity,” we can see how automation, smart data usage, and security measures are essential for the future of global logistics and trade.
The cover story features Dematic’s automation of Southwest Healthcare’s Warrnambool facility, where the implementation of the AutoStore GTP system is a game-changer.
By enhancing capacity, improving accuracy, and driving operational efficiency, this innovation reflects the broader industry shift towards technology-driven solutions.
With the increasing reliance on digital systems, cybersecurity is becoming more than just a precaution; it’s a necessity.
In recent months, we’ve seen other major developments highlighting the critical importance of resilient supply chains.
The MoU between Australia, the United Kingdom, and the United States is a step forward.
The formation of the AustraliaUnited Kingdom-United States Supply Chain Resilience Cooperation Group will enhance our ability to manage disruptions to critical supply chains, starting with telecommunications.
Closer to home, Victoria’s top exporters were celebrated at the 45th Governor of Victoria Export Awards, demonstrating the power of local businesses in the global marketplace.
These awards are a reminder of the critical role exports play in Australia’s economy, contributing billions and supporting hundreds of thousands of jobs.
Initiatives like these, alongside cutting-edge infrastructure such as Sydney’s Western International Airport and Avalon Airport’s new freight facility, are key to unlocking greater trade potential, especially as the demand for faster, more efficient e-commerce logistics continues to surge.
The development of the 24-hour Cargo Precinct at Western Sydney Airport, which will increase Sydney’s air cargo capacity by 33 per cent, and Avalon Airport’s new $8 million freight processing facility, are clear indicators of Australia’s commitment to futureproofing supply chains.
These projects not only drive economic growth but also highlight the critical role supply chains play in connecting Australian businesses with global markets, from advanced technology exporters to small businesses going global.
As we move forward, the adoption of AI, data analytics, and advanced cybersecurity measures will underpin the next era of supply chain management. These tools are no longer just innovations but necessities for ensuring efficiency, safety, and resilience in our increasingly interconnected world.
As supply chain managers, business owners, and logistics professionals, these advancements offer practical tools to optimise operations, protect data, and stay competitive. It’s an exciting time for the industry, and I’m thrilled to share how these innovations are shaping the future of supply chain management with you.
Phillip Hazell Editor, MHD Supply Chain Solutions
Known for market leading Toyota forklifts and warehouse equipment, Toyota Material Handling is also proud to o er an unparalleled range of products suitable for Australian businesses. With a huge range of forklifts, elevated work platforms, scrubbers and sweepers, Taylor-Dunn electric vehicles, plus Huski skid steers, scissor lifts, and mini excavators available, chances are we’ve got the equipment that will suit. So, if you’re looking to buy hard working, fully backed equipment for your business, Toyota Material Handling has all you need to add value to your operation. That’s the Toyota Advantage.
12 Dematic automates Southwest Healthcare’s Victorian facility
17 Logical Outlook on achieving sustainability with MEGATRANS panel discussion
20 Körber explains the benefits of leveraging technology for peak season challenges
32 EnerSys minimising costs by utilising data
23 Linde introduces FleetFOCUS for monitoring materials handling equipment
26 Toyota supplying Remedy Drinks with forklift solutions
29 BHD opens its first Queensland-based DC
35 Airstack Intralogistics and CIMC Pteris Global introduce ALUS
39 Falcon Autotech provides advanced automated solutions for e-commerce demand
42 CEVA Logistics expands its footprint by venturing into new sectors
44 Terre Property works with Flinders Port Holdings on South Australian project
46 Kuehne + Nagel collaborate with LEGO Group on Victorian fulfilment centre
EVENTS, AND REGULARS 03 Ed letter
Industry News
MEGATRANS
ASCI courses
SCLAA News 56 People on the Move 58 Product Showcase
DHL Express has announced price increases that will take effect on January 1, 2025. The average increase in will be approximately 4.9 per cent on its published tariff.
“We are committed to delivering stable and dependable services globally despite the ongoing impact of geopolitical dynamics and supply chain disruptions on the logistics landscape,” said Phil Corcoran, Managing Director, DHL Express Australia and Papua New Guinea.
Prices are adjusted on an annual basis by DHL Express, taking into consideration inflation and currency dynamics as well as administrative costs related to regulatory and security measures.
National and international authorities regularly update these measures in the more than 220 countries and territories that DHL Express serves. Depending on local conditions, price adjustments will vary from country to country. ■
The Australian Government will open applications to Round 1 of the Quad Clean Energy Supply Chain Diversification Program in November 2024.
Grants will fund research and development projects and feasibility studies to develop more diverse solar photovoltaic, hydrogen electrolyser
and battery supply chains. Projects must be delivered as joint projects between Australian and Indo-Pacific organisations.
The Australian Government has committed A$50 million to this program. Up to A$25 million will be available under this round, with grants ranging from A$100,000 to A$2.5 million.
The program was announced by the Quad – Australia, India, Japan and the United States – at the 2023 Leaders’ Summit. It supports the implementation of the Quad Principles on Clean Energy Supply Chains – a foundation for engagement in clean energy supply chains in the IndoPacific. ■
Justin Carnaby Head of Logistics, AS Colour
When AS Colour started out, the trend was for tight tees and baggy pants. But while clothing fashion trends come and go, the trend that doesn’t change is that customers want their orders delivered on time and accurately.
Dematic’s Multishuttle Goods-to-Person (GTP) fulfilment system enables AS Colour to process orders with higher productivity, faster and with increased accuracy, down to the sequence of items in the package.
As a result, AS Colour has seen a big increase in sales as customers see how fast and accurately their orders reach them.
Learn more at dematic.com/as-colour
Melbourne Airport moved 205 million tonnes of freight in 2022, valued at $22 billion. Image: anek.soowannaphoom@ shutterstock.com.
Coles has officially opened its first Customer Fulfilment Centre (CFC) in Victoria, bringing together world-class technology and automation to enhance the shopping experience for Coles Online customers in greater Melbourne.
Located just over 20 kilometres west of Melbourne’s CBD, the Truganina CFC was opened on 20 September by the Victorian Acting Premier Tim Pallas MP, Coles Group Chairman James Graham and Coles Group CEO Leah Weckert. It’s the first of two CFCs to launch this year as part of a $400 million partnership with a global leader in online grocery transformation, Ocado.
Once fully operational, the modern facility will deliver an enhanced shopping experience for online customers – with better availability, fewer substitutions, an increased range of products and improvements in the shelf-life of staples like mince and milk.
“The transition from a local, storebased fulfilment model to a central, world-class facility will enable us to better serve the greater Melbourne region, home to more than five million people,” says Leah Weckert, Chief Executive Officer, Coles.
The Victorian CFC’s delivery catchment will span the growing Melbourne region from Ballan in the west across to Bunyip in the east, and from Beveridge in the north down to the Mornington Peninsula.
The Truganina site has a footprint of more than 87,000 square metres and can hold three million units of stock while having the ability to process more than 10,000 customer orders per day when running at full capacity.
The site features a centralised hub, known as ‘The Hive’, where a fleet of more than 700 bots will fulfil a customer order containing 50 items in just five minutes, while an artificial intelligence ‘air traffic’ control system will oversee the bots as they move around giant 3D grids, transporting containers of grocery items to be packed and delivered by Coles team members.
The CFC will employ more than 1,000 team members, including drivers and fulfilment roles that will use hightech packing equipment, and there will be a fleet of more than 200 home delivery vans specially designed with dual compartments to ensure fresher products while reducing emissions and
a side door to make it easier and safer for delivery drivers to unload.
“The opening of this CFC is the result of a five-year partnership with Ocado, whose world-class experience is helping Coles to innovate and meet the changing needs of our customers,” says Coles Group Chairman James Graham.
The Truganina CFC features of the build include a two-megawatt solar installation, sensor lighting, a water recycling system, and 100% recycling of cardboard.
The official opening of Truganina will be followed next month by a second CFC site in Wetherill Park, New South Wales.
The Truganina CFC is proudly named Brungilo Curran, meaning Stringybark Gum Tree. The site of the Truganina CFC — Brungilo Curran — is home to the Bunurong People.
Coles recognises the importance of developing a relationship with the people of Bunurong Country, where Coles has established operations. The name and associated artwork at the Truganina CFC were developed through consultation with the local Bunurong community and local artist Kobi Sainty. ■
Online shoppers and businesses in the Greater Geelong area and Melbourne’s west can expect quicker deliveries to their doorsteps, with a new dedicated freight processing facility coming to Avalon Airport – backed by the Allan Labor Government.
Minister for Jobs and Industry
Natalie Hutchins announced a new $8 million facility will boost freight processing and handling at Avalon Airport, with packages set to be processed at a much faster rate.
In the financial year ending June 2023, Avalon Airport handled over 10,000 tonnes of cargo from 52 aircraft. Once operational, the new 24/7 freight facility will be able to process over 100,000 tonnes of cargo each year including both domestic and international freight.
The facility will be equipped with advanced scanning technology, making it one of the first airports in Australia to comply with the new Border Force security screening standards.
The new facility will halve the number of trucks that are currently transporting freight between Avalon Airport and Melbourne Airport with more packages and parcels going out directly from Avalon.
On track to open in 2025, the new facility will create six new direct jobs and hundreds of flow-on jobs in cargo handling, warehousing and distribution.
“This new facility at Avalon Airport will create jobs, attract new businesses, get trucks off the road and expand trade and commerce opportunities for the whole region,” says Natalie Hutchins, Minister for Jobs and Industry.
The new freight processing centre is part of the Greater Avalon Employment Precinct and will bolster its role as an economic hub for the surrounding areas. The Avalon Airport Industrial Precinct is already home to distribution centres for large businesses such as Australia Post, Cotton On and Petstock.
The freight and logistics industry keeps our state moving and employs more than 260,000 Victorians.
“The establishment of this stateof-the-art freight processing facility will strengthen Melbourne Avalon Airport’s role as a critical logistics hub and the creation of a multi-modal hub for Victoria. This investment ensures we can meet the growing demands of e-commerce and trade, driving efficiency and creating new jobs in the region,” says Ari Suss, CEO Melbourne Avalon Airport. ■
In a major boost for Australia’s critical supply chains, construction of an integrated 24-hour Cargo Precinct is taking flight at Sydney’s new international airport, with both Qantas Group and Menzies Aviation signing up to operate at the premier precinct.
The new hub at Western Sydney International (Nancy-Bird Walton) Airport (WSI) will increase Sydney’s air cargo capacity by around 33 per cent upon opening and provide dedicated access via the upgraded Northern Road and proximity to growing freight and logistics centres at Kemps Creek and the Aerotropolis.
“The airport continued to create high-value job opportunities for Western Sydney locals, with the Cargo Precinct expected to support up to 2,000 jobs during construction and more than 19,000 direct and indirect jobs across the precinct and connected supply chains, upon opening, each year,” says Simon Hickey, WSI CEO.
“We’re pleased to welcome two top-tier operators, Qantas Freight and Menzies, to Sydney’s new, integrated Cargo Precinct that will enable direct connectivity between freighters, the terminal and road transport.
Qantas Group is our first freight
airline to sign up to our 24-hour Cargo Precinct, which will provide unparalleled opportunities for farmers, manufacturers and other exporters to grow their businesses.”
The new hub will also be capable of facilitating Qantas’ transformed freighter fleet of new and upgraded Airbus A321 and A330 aircraft.
“We’re already responding to growing market demands, including significant spikes in e-commerce purchases initially prompted by changing spending habits during the COVID-19 pandemic, by increasing the airport’s opening air cargo capacity,” Simon said.
“We’ve secured external financing of $805.4 million to develop the infrastructure for a stand-alone futureproof Cargo Precinct and our Business Precinct to meet business and customer needs now and for decades to come.
This additional funding will support the development of roadways, taxiways and buildings to maximise the value of the airport over the long-term. In turn, this will deliver more socioeconomic benefits like jobs for the people of Western Sydney and beyond, and a greater financial return for all Australian taxpayers.”
World-leading airport services partner Menzies Aviation, which currently handles more than two million tonnes of cargo globally each year, was another fantastic addition to WSI’s Cargo Precinct.
“In a strong signal of the precinct’s critical cargo capacity and future growth opportunities, Menzies has signed a long-term lease with WSI that will see the business operate a facility over the next two decades, specialising in pharmaceutical and cool chain products handling as well as e-commerce and heavy cargo services,” Simon added.
The construction of the precinct –which will include up to 75,000 square metres of warehousing and be capable of servicing eight wide-body aircraft at any one time – began earlier this year and remains on track for cargo operations to commence in 2026.
While WSI’s construction partner is responsible for delivering a range of aeronautical and precinct infrastructure works, the gradual fit-out of the warehouse facilities will be carried out by precinct partners to ensure the layout and design is fitfor-purpose and meets their individual customer’s needs. ■
South West Healthcare, based in Warrnambool, Victoria, is a key provider of healthcare services to communities across Southwest Victoria. As a healthcare hub, the organisation operates several campuses, including the Warrnambool Base Hospital, as well as smaller facilities in Camperdown, Lismore, Hamilton, and Portland. Serving this area requires a sophisticated logistics network capable of ensuring timely delivery of essential medical supplies, linen, food, and equipment to 13 hospitals in the region.
“We provide more than 150 medical, nursing, mental health, allied health and community health services to the 110,000 people who live across the Southwest of Victoria and in Warrnambool, one of the fastestgrowing regional cities in Victoria,” says Michael Farley, Construction Project Manager at South West Healthcare. “We are also the region’s largest employer, with 2158 people working for South West Healthcare across various locations.”
The increasing population in the region, coupled with ageing infrastructure at the Warrnambool Base Hospital, created an urgent need for a modernised logistics system that could handle the demands of today, while being flexible enough to accommodate future growth. South West Healthcare recognised that its Regional Logistics Distribution Centre (RLDC) in Warrnambool required an upgrade to address these challenges.
Faced with growing demand, the need for more storage capacity, and the constraints of outdated facilities, the entity embarked on a project to build a state-of-the-art RLDC. The organisation turned to Dematic for a solution that would not only meet the region’s immediate supply chain needs but would also future-proof operations for years to come.
The new RLDC allowed for South West Health’s laundry and supply and
logistics services to move from its original location at the Warrnambool Base hospital campus to make way for the Victorian Government funded Warrnambool Base Hospital redevelopment project. This project freed up space for vital health services within a new multi-storey clinical services building at the existing hospital site.
At the core of the challenge for South West Healthcare was a lack of space. The distribution centre’s existing facilities were limited in size.
According to Michael, the RLDC was becoming increasingly stretched as the healthcare needs of the region continued to grow.
“Warrnambool and the surrounding region are growing rapidly,” says Michael. “Our logistics facility, which once met our needs, was simply no longer large enough to handle the increased demand. We needed to build a larger warehouse and adopt a more modern approach to logistics to keep up with the region’s growth.”
Previously, the logistics team had to place frequent orders for highusage items, which not only created inefficiencies in procurement but
also increased the risk of stock shortages. The warehouse operated with traditional shelving and manual picking systems, which were not equipped to handle the high volume of orders and stock rotations necessary to support 13 hospitals across the region.
“Our old facility couldn’t store more than a week’s worth of stock for many high-usage items,” says Shane Grundy, Warehouse Logistics Manager. “This meant we had to reorder frequently and handle the same goods multiple times, increasing the workload for our staff and the chance of errors.”
Compounding these space and operational challenges was the need for the RLDC to serve as a critical part of the redevelopment plan for the Warrnambool Base Hospital. It has to act as a logistics hub, as well as support the base hospital and other regional facilities while new clinical service buildings, including emergency departments and operating theatres, were being constructed.
To address these challenges, South West Healthcare sought a solution that could increase storage capacity, improve order accuracy, and reduce the time spent handling stock. After an evaluation process, Dematic’s AutoStore goods-toperson (GTP) system emerged as the choice for the RLDC’s modernisation efforts.
“Once we understood that AutoStore was the right solution for our needs, Dematic’s presentation really stood out,” says Michael. “Their ability to service regional Victoria and their commitment to a five-year maintenance contract, gave us confidence that they were the right partner for this project.”
The Dematic solution requires up to 80 per cent less space than a traditional manual racking layout, which needs wide aisles for forklifts and personnel. AutoStore totesstack vertically, eliminating the need for clear aisles.
The AutoStore solution is a highdensity storage system that maximises the use of vertical space, allowing more goods to be stored in a smaller footprint. It utilises robots that move through a storage grid to retrieve totes and deliver them to ergonomic pick stations.
Items required to fulfil orders arrive from the AutoStore storage system to the GTP workstations when they are needed. Operators then build orders at the ergonomically designed, high-rate workstations efficiently and safely.
This automation eliminates the need for manual stock handling and reduces the risk of errors.
“One of the key benefits of the AutoStore system is its ability to store more items in a much smaller space,” explains Terry Jamieson, Business Development Manager at Dematic. “For South West Healthcare, this was critical. The laundry services at the RLDC needed to expand, so reducing the footprint of the storage facility was essential to making space for other functions.”
The system’s modular design also provides flexibility for future expansion, allowing South West Healthcare to easily add more robots and pick stations, or increase the size of the modular storage grid as demand grows.
The service provider also chose Dematic’s selective pallet racking, ColbyRACK, for storing bulky items that weren’t suitable for the AutoStore GTP system. Designed, engineered, and manufactured by Dematic’s Australian team, ColbyRACK meets rigorous Australian standards.
Installing the AutoStore GTP system was a complex process, particularly due to its integration with South West Healthcare’s existing Oracle-based ordering system. However, Dematic’s project team worked closely with South West Healthcare to ensure that the installation was as seamless as possible.
“The biggest challenge we faced during the installation was integrating the AutoStore system with our Oracle ordering system,” says Michael. “It was a highly complex task, but Dematic’s Software Engineering team worked diligently to ensure that the integration was smooth and effective.”
Despite these technical challenges, the overall installation process was completed on schedule, and Dematic provided extensive training to ensure that South West Healthcare’s staff could operate the system efficiently.
“The training provided by Dematic was top-notch,” says Shane. “Our team was excited to learn the new system, and they adapted to it quickly. The AutoStore system has not only improved our operations but has also provided an opportunity for staff development as they get to work with cutting-edge technology.”
Since the implementation of the AutoStore GTP system, South West Healthcare has seen significant improvements in its supply chain operations. The system has provided a range of benefits, including:
1. Dramatically Increased Storage Capacity
One of the most immediate benefits of the AutoStore GTP system was the increase in storage capacity. The RLDC now holds up to 6500 totes, allowing South West Healthcare to store six to eight weeks’ worth of stock for high-usage items, compared to the one-week capacity in the previous facility. This increase in capacity has reduced the need for frequent reordering and has allowed the warehouse team to focus on more value-added tasks.
“We’ve increased our stock holdings by nearly $200,000,” says Shane. “That means our purchasing team can focus on strategic tasks rather than spending time reordering the same products every week. We’ve also been able to reduce backorders and improve our service levels across the region.”
2. Improved Accuracy and Reduced Errors
The AutoStore GTP system has greatly improved order accuracy by automating the picking process. In the previous system, staff manually picked items from shelves using paper-based picking slips, which created the potential for errors. With AutoStore, the correct product is automatically delivered to the pick station, reducing the chance of human error.
“The system has virtually eliminated picking errors,” explains Shane. “Now, the right product comes directly to the operator, which has significantly improved the accuracy of our orders and made the entire picking process much more efficient.”
3. Optimised Space Utilisation
The high-density design of the AutoStore GTP system has allowed South West Healthcare to maximise the use of available space, freeing up room for the expansion of other critical services. By consolidating storage into a smaller footprint, the RLDC has been able to accommodate the growing needs of its laundry services, which are essential for supporting hospitals in the region.
“One of the major benefits of the AutoStore system is that it reduced the footprint required for storage,” says Terry. “This allowed South West Healthcare to allocate more space to other essential functions, such as the laundry, which is critical to the operation of hospitals in the region.”
4. Futureproofed and Scalable
The modular design of the AutoStore GTP system ensures South West Healthcare can easily expand the system in the future as demand increases. The RLDC has the option to add more robots, increase the size of the storage grid, or add additional pick or replenishment stations as needed.
“The system is designed to grow with us,” says Shane. “While we’re not planning any immediate expansions, it’s comforting to know that we have the flexibility to increase capacity if the demand continues to grow in the coming years.”
5. Faster Turnaround Times and Improved Service
The streamlined operations provided by the AutoStore GTP system have enabled South West Healthcare to improve its
“Dematic’s project team worked closely with South West Healthcare to ensure the AutoStore GTP system installation seamless.
service levels. Orders from regional healthcare facilities are now processed and delivered more quickly, with same day delivery for Warrnambool Base Hospital and next-day delivery for other regional campuses becoming the norm for most items.
“We’ve seen a significant improvement in our order fulfilment times,” says Shane. “The system processes orders much more efficiently, allowing us to get supplies to our hospitals faster. This has been a huge benefit for the region, particularly in emergencies when time is of the essence.”
The partnership between South West Healthcare and Dematic has been a key factor in the success of the project. Dematic provided ongoing support throughout the installation and continues to deliver maintenance and remote IT support to ensure the system operates smoothly.
“Dematic’s commitment to supporting regional Victoria was a big reason we chose them as our partner,” says Michael. “Their team has been fantastic to work with, and their ongoing support has been instrumental in ensuring that the system continues to run efficiently.”
Dematic’s Victoria-based service team provides regular maintenance visits every three months, checking the system to ensure it is functioning as expected. Additionally, remote IT support is available 24/7 to address any issues that arise, allowing the RLDC to operate with minimal downtime.
“Dematic’s support has been excellent,” adds Shane. “Whenever we’ve had an issue, they’ve responded quickly.”
The implementation of Dematic’s AutoStore GTP system has successfully transformed South West Healthcare’s RLDC into a modern, efficient, and future-proof operation. By overcoming space constraints, improving accuracy, and streamlining processes, the new system has enabled South West Healthcare to meet the increasing demands of the region’s healthcare facilities while ensuring long-term scalability.
“Our partnership with South West Healthcare demonstrates how automation can be tailored to meet specific needs and challenges. We’re proud to have delivered a solution that not only meets today’s demands but is also ready to scale for the future,” says Terry.
South West Healthcare will continue providing exceptional service to its healthcare partners across the region, supported by a robust and flexible supply chain infrastructure.
“The AutoStore system has been a game-changer for our operations. The technology is cutting-edge, the support has been excellent, and our staff are excited to work with such a modern system. We’re better equipped than ever to meet the demands of our region,” explains Shane.
Dematic’s AutoStore GTP system has proven to be the ideal solution, offering both immediate improvements and long-term sustainability, ensuring that South West Healthcare can continue to deliver vital services efficiently and reliably.
As the region continues to grow, South West Healthcare’s RLDC will continue to highlight the benefits of strategic automation in the healthcare logistics space.
“We needed a solution that would allow us to manage today’s needs while preparing for the future,” says Michael.
“Dematic’s AutoStore system has exceeded our expectations in terms of efficiency, scalability, and service, allowing us to provide the best possible care for the region’s healthcare facilities.” ■
On Day 2 of MEGATRANS, Peter Jones, Managing Director, Prological, moderated a panel called
Sincreasingly important focus for businesses globally, but achieving tangible results requires navigating complex challenges.
At the 2024 MEGATRANS Expo, industry leaders gathered for a panel discussion titled Beyond Good Intentions: How to Move from Ambition to Action in Supply Chain Sustainability.
Sponsored by Prological, this session offered an exploration of how sustainability goals can be implemented in Australian supply chains, drawing on both local insights and international best practices.
Peter Jones, Managing Director and Founder of Prological, moderated the panel and kicked off the discussion
“Sustainability is now on the agenda of every business we speak with,” says Peter.
“The challenge is taking the global ambitions of large corporations and figuring out how to make them work in the Australian context. There’s often a gap between what’s being asked and what’s achievable here.”
The country’s unique geography, regulatory environment, and economic conditions mean that what works elsewhere may not be as easily implemented.
The panellists shared examples of attempts to bridge this gap, including Global Express’s recent $200 million grant to trial electric vehicles (EVs) in metropolitan Australia, marking a step forward in sustainable logistics.
Richard Phillips, Head of Supply Chain at JLL, highlighted how industrial real estate plays a central role in the sustainability conversation.
“In industrial real estate, we’re faced with a bit of an oxymoron,” explains Richard.
“The process of building warehouses inherently involves tearing up greenfield land and generating massive amounts of embodied carbon. About 80 per cent of the carbon footprint of a building is generated during the construction phase, so there’s a limit to how much we can improve its sustainability once it’s built.”
He points out that in Europe, sustainability has become a key consideration in industrial developments, with initiatives like carbon-neutral buildings being
implemented. However, he admits that replicating such models in Australia presents commercial challenges.
“It’s about finding a balance between what’s financially viable and what’s environmentally sustainable,” says Richard.
“We’re seeing innovations like solar panels becoming standard in new developments, but the cost of green materials like concrete and steel is still prohibitive for most developers.”
Despite these barriers, Richard remains optimistic about the future, suggesting that industrial sites could soon play a role in electricity production.
“We’ve started to hear discussions about installing wind turbines on industrial properties, following examples from Europe. It’s still early days, but this could be part of the long-term solution for making industrial developments more sustainable,” he says.
Andrew Newman, Director at Victoria’s Department of Transport and Planning, emphasised the government’s role in supporting industry efforts to decarbonise the freight sector.
“Government is on a journey as well,” says Andrew. “We’ve set highlevel targets, like achieving net zero by 2050, but now we’re beginning to dig into what needs to happen in transport to make that a reality.”
One of the key challenges, he explains, is the long lifespan of heavy vehicles in Australia.
“The average truck is on the road for about 15 to 16 years, so a truck bought today will still be in use in 2045. We need to encourage the uptake of EVs and other low-emission vehicles now if we want to reach our targets,” says Andrew.
He also emphasised the importance of aligning public policy with private investment to drive meaningful change.
“Governments need to send clear signals to industry that there’s a commercial benefit to investing in sustainable technologies.”
Dr Eamon McGinn, Partner at Deloitte Access Economics, added that in the transport sector, sustainability goals don’t always have to come at the expense of commercial success.
“There’s actually an overlap between financial and environmental sustainability in transport,” says Eamon.
“For example, some technologies, like EVs, can offer lower operating costs and improved reliability over time, which helps both the bottom line and the environment.”
However, Eamon warns that businesses should be realistic about the pace of change.
set ambitious sustainability targets a few years ago are now delaying those targets, because they’re realising just how difficult it is to achieve them,” he said. “The focus should be on achieving smaller, incremental wins rather than aiming for an overnight transformation.”
Throughout the discussion, the panellists stressed the need for practical, achievable solutions. Peter highlighted that many businesses focus on symbolic gestures rather than meaningful change.
with a beehive or two and call it an environmental initiative, but that’s not enough,” he says. “We need to think bigger, like using industrial roofs for solar panels or providing charging stations for EVs.”
adding that while the challenges are considerable, progress was being made.
to cover the entire roof of a new industrial building with solar panels,” he said. “That’s a real step forward, but we need to keep pushing the boundaries and looking for new opportunities to integrate sustainability into the design and operation of these facilities.”
One of the less obvious drivers of sustainability supply chains is the availability of capital.
“It’s not always the Australian customer or developer pushing for sustainability,” explains Richard. “Often, it’s the global investors providing the capital who are setting strict sustainability criteria. They’re mandating that developments meet certain environmental standards, whether or not the local market is ready for it.”
This international pressure is forcing Australian developers to adopt sustainable practices, even if the immediate financial return isn’t clear.
ANTHONY BEAVIS, MANAGING DIRECTOR ANZ AT KÖRBER SUPPLY CHAIN SOFTWARE
From Black Friday to Christmas Eve, every year peak season tests the limits of supply chains worldwide. As consumer expectations soar, companies must evolve their supply chain strategies to stay competitive. Here we explore how organisations can leverage technology to meet the challenges ahead.
Today’s consumers, particularly younger generations, have redefined the meaning of convenience and consumer loyalty. Körber‘s 2023 State of Shipping and Returns survey found that 90 per cent of respondents are less likely to buy from a brand again after a poor online shopping experience, while 29 per cent say they are increasingly willing to share a negative review online. These expectations are pushing retailers to unprecedented levels of agility.
A steep rise in expectations is happening alongside a revolution in the digital marketplace. Platforms like TikTok Shop are introducing new dimensions of virality to online shopping, further amplifying the pressure on supply chains. In this high-stakes arena, agility and innovation in warehouse operations are no longer optional – they’re essential for survival.
Forward-thinking organisations are distinguishing themselves through
strategic investments in smart technology and setting new standards in customer service and operational efficiency.
THE FUTURE OF FULFILLMENT: PROXIMITY, FLEXIBILITY, AND INNOVATION
In response to these rising expectations, many companies are adopting a proximity strategy, moving products closer to the end customer. This approach is manifesting in two
primary forms: micro-fulfillment centres and leveraging existing brickand-mortar stores.
The debate between Buy Online Pick Up In Store (BOPIS) and microfulfillment strategies continues to evolve. While micro-fulfillment centres in urban areas present a compelling long-term solution, many retailers are finding their brick-andmortar stores to be a viable mid-term alternative. However, the ultimate goal remains clear: doorstep delivery.
One thing for certain is that the future of retail lies in operational hybridity – stores that can seamlessly transition between traditional shopping and fulfillment centres will have the flexibility to meet consumers on their terms, wherever they may be.
Technology is also increasingly imperative, but a strong and reliable team of people remains essential to achieving new levels of efficiency. One innovative approach when it comes to engaging employees, is the gamification of warehouse management.
By introducing elements of game design into the work environment, companies can boost employee engagement and productivity. A recent report from WorkhumanGallup reveal that gamification can decrease turnover and reduce absenteeism by an impressive 81 per cent, while also lowering the risk of quality defects by 41 per cent.
Moreover, the transition from legacy systems to more adaptable warehouse management software is accelerating in fulfilment strategies. The use of Autonomous Mobile Robots (AMRs) is also increasing in warehouses worldwide, not only reducing reliance on manual labour but also introducing unprecedented flexibility into operations.
AMRs are more affordable than traditional automation and easy to scale once in place, supporting either long-term growth or short-term seasonality.
Creating meaningful connections between software solutions is crucial for building resilient and costeffective supply chains. While supply
chains have increasingly adopted planning platforms, execution and fulfilment often remain fragmented. The key to overcoming this challenge lies in the seamless integration of Order Management Systems (OMS), Warehouse Management Systems (WMS), and Transportation Management Systems (TMS).
This integration creates a unified ecosystem where each component of the supply chain communicates effectively. The result is a more agile operation, capable of rapid responses to disruptions and changes in demand. Whether adapting to sudden shifts in consumer behaviour or managing supply shortages, an integrated system provides the flexibility needed to maintain continuity while optimising costs.
One of the most significant advantages of connecting OMS, WMS, and TMS is the enhanced visibility and real-time insights they provide. An integrated systems addresses the common challenge of a lack of transparency and delayed information head on by leveraging data from across the supply chain in concert. This visibility enables quick, informed decision-making and helps identify potential issues before they escalate, resulting in smoother operations, improved costeffectiveness, and enhanced customer satisfaction.
The integration of OMS, WMS, and TMS expands optimisation capabilities beyond traditional silos.
Boosting employee engagement and productivity with game design elements.
In today’s global market, where demand fluctuates and supply chain disruptions can range from raw material shortages to blocked shipping canals, this flexibility is invaluable.
The final mile of delivery often presents the most complex and costintensive challenges in the supply chain. Once again, the integration of OMS, WMS, and TMS ensures that this critical phase is optimised for both resilience and cost-effectiveness.
With detailed tracking and optimisation tools, companies can manage final mile deliveries with precision. This capability ensures timely and reliable delivery while controlling expenses. Moreover, it provides the added efficiency needed to react swiftly when something goes wrong – an important advantage in an era where customer expectations for fast, affordable delivery are at an all-time high.
As we navigate the challenges of labour shortages and evolving consumer expectations, the path to success in peak season management lies in embracing technological integration, leveraging real-time data, and maintaining the flexibility to meet customers where they are. Supply chain leaders who use these strategies will do more than just cope with peak season this year - they’ll also drive innovation and gain a competitive edge in the market. ■
Businesses are embracing digital solutions to enhance their operations. As technology advances, modern logistics systems continuously collect and analyse data, using it to optimise complex warehouse and transportation processes.
Forklift trucks are becoming increasingly autonomous due to advanced sensors, making fleet management and real-time data access crucial.
“Fleet management provides vital insights into your equipment’s operation, ultimately improving safety, efficiency, and productivity while ensuring compliance with government regulations,” says Stuart Hitchens, National Fleet Contract Manager at Linde Material Handling Australia.
One such solution leading the charge in this area is Linde’s FleetFOCUS, a fleet management system designed to help businesses optimise their material handling operations. It provides a top-of-the-range Workplace Health and Safety (WHS) solution, allowing real-time communication between
businesses, their fleets, and their operators.
FleetFOCUS is a tool designed to give businesses control over their resources. The system facilitates realtime monitoring and management of fleets, providing the insights needed to enhance operational efficiency.
Businesses can monitor daily equipment usage, identify under- or over-utilised vehicles, observe driving patterns, control vehicle access, and review WHS compliance in real time.
FleetFOCUS isn’t just about visibility. It’s about intelligent management –businesses can take control and make informed decisions to ensure that their fleets are operating at optimal levels.
FleetFOCUS offers several benefits to businesses, each targeting key aspects of fleet management and operational efficiency:
• Optimised Fleet Utilisation – It enables businesses to identify
and address fleet utilisation and operational issues before they affect the bottom line. By analysing equipment usage, businesses can adjust their resources to where they are needed most.
• Workplace Safety Transformation – Safety is paramount in material handling operations, and FleetFOCUS plays a crucial role in monitoring forklift usage and identifying infrastructure damage. The system enhances workplace safety by providing immediate feedback on operator behaviour and equipment conditions.
• Access to Real-Time Information –FleetFOCUS continuously collects and organises data, allowing 24/7 access to fleet information through an online portal. This real-time access ensures that decision-makers are always informed and able to act quickly.
• Cost Savings – By identifying overused or underused equipment, businesses can optimise resource allocation.
One of FleetFOCUS’s strengths is its reliable Wi-Fi and GPRS (3G and 4G) connectivity.
• Customised Solutions – The system can be tailored to meet a company’s unique equipment and operational needs, and integrates with existing security systems, allowing operators to use a single card or fob for access.
Intelligent features include customisable firmware, shock reporting, preoperational questionnaires, driver access control, electronic tag-out systems, and GPS tracking.
• Reprogrammable Firmware – FleetFOCUS can adapt and customise software to meet unique requirements. With efficient two-way messaging, it enables seamless communication between drivers and supervisors. The system is also designed to support a range of security cards and fobs, making integration smooth and efficient.
• Shock Reporting – a standout feature, which helps businesses ensure safe operation following vehicle shocks. Any shocks that exceed the predetermined level automatically reduce the vehicle to ‘limp’ mode, and the supervisor must reset the unit, ensuring accountability and WHS compliance.
• Pre-Operational Questionnaires – it includes a customisable preoperational questionnaire that drivers must complete before using the equipment. These questions can be tailored to specific sites or vehicle types and ensure that each operator confirms the equipment is safe to use before operation.
• Driver Access Control – access can be limited to authorised personnel only. The system accommodates security
cards, fobs, or pin codes, further enhancing security and operational control.
• Electronic Tag Out for Unsafe Vehicle – FleetFOCUS also includes an electronic tag-out feature that allows supervisors to lock out unsafe vehicles, ensuring that only qualified personnel can move them to safe locations.
• GPS Tracking - GPS comes as standard in FleetFOCUS, providing businesses with a powerful tool to monitor the movement and location of their equipment.
One of FleetFOCUS’s major strengths is its reliable Wi-Fi and GPRS (3G and 4G) connectivity, allowing seamless fleet management even in large or complex environments.
“Our system was the first Australian fleet management solution with dual Wi-Fi and GPRS connectivity, ensuring uninterrupted data access,” explains Stuart.
The system also features memory card backup in the event of a network loss, ensuring that data is always preserved and automatically updated when the connection is re-established.
FleetFOCUS offers up to 30 realtime reports, providing businesses with critical data to identify areas for continuous improvement. “These reports enable informed decisionmaking, helping businesses optimise battery consumption, monitor hardware conditions, and track operator licensing,” adds Stuart.
The system’s interactive dashboard offers real-time updates on impacts, battery charge, and operator checks,
eliminating the need to log into multiple systems or wait for email reports.
FleetFOCUS doesn’t just collect data for the sake of it – it uses data to drive real improvements in fleet operations.
“FleetFOCUS utilises data from forklifts to monitor hydraulic traction and driver presence, helping businesses see how their equipment is being used,” says Stuart.
This allows companies to identify inefficiencies, such as using an expensive reach truck for tasks that a more cost-effective pallet jack could handle.
These data-driven insights also extend to operational decisions. For instance, if data shows that equipment is only being used during certain times of the year, businesses can adjust their fleets accordingly.
“FleetFOCUS gives businesses the information they need to manage their fleet effectively, ensuring they don’t overspend on equipment that’s not being fully utilised,” explains Stuart.
FleetFOCUS helps businesses reduce costs. By identifying underutilised equipment and highlighting opportunities for resource reallocation, the system ensures that businesses are making the most of their assets.
“It’s all about optimising resources, not just adding more equipment unnecessarily,” says Stuart.
The system’s customisation capabilities also make it a highly flexible solution. Pre-operational checks can be tailored to specific equipment models, while the data collected from each piece of equipment can be used to tailor future fleet strategies.
“We’re constantly receiving feedback from our customers, and we use that to improve the system,” explains Stuart.
As FleetFOCUS is developed locally, any changes or improvements specifically made by Linde, or our fleet management partner are rolled out quickly and free of charge to all users. ■
Australian beverage manufacturer Remedy Drinks has steadily and successfully built its business using the help of battery-electric Toyota Material Handling forklifts to distribute its products.
Over the past decade, Australian beverage company, Remedy Drinks, has rapidly expanded its operations, with its distinctive kombucha becoming a household name.
As the company scaled up, one crucial factor in its success has been its reliance on Toyota Material Handling Australia’s (TMHA) battery-electric forklifts.
These vehicles have played an essential role in Remedy’s ability to meet growing demand while maintaining sustainable practices and high operational efficiency.
Founded in 2012 by Sarah and Emmet Condon, Remedy Drinks emerged as a healthier alternative to sugary soft drinks. Its home-brewed kombucha, made from 100 per cent natural ingredients with no added sugar, gained popularity among health-conscious consumers.
The company has expanded its product range to include Sodaly natural soft drinks, Kick Natural energy drinks, miniature energy shots, and apple cider vinegar-based beverages.
What started as a small operation in Melbourne’s south-eastern suburbs has now grown into a thriving business. Remedy Drinks occupies a large dual warehouse and production facility in Dandenong South, where demand for its products continues to soar.
Throughout this journey, Remedy has relied heavily on its partnership
with TMHA, which dates back to the company’s first forklift – a secondhand Toyota unit.
Today, Remedy’s material handling fleet includes eight reach forklifts and four counterbalance forklifts, all powered by electric battery technology.
These battery-electric forklifts are at the heart of Remedy’s distribution operations, offering the dual benefits of efficiency and sustainability. Zero emissions during operation mean the forklifts align perfectly with Remedy’s commitment to environmentally friendly practices.
Ryan Stark, Remedy Drinks’ Warehouse Manager, attributes much of the company’s logistical success to these forklifts.
“The warehouse and logistics team’s primary role is to ensure our product is delivered to our customers and knowing that our equipment on-site can do that is our number one priority,” says Ryan.
“It’s great to know that putting our pallets into racking, loading trucks, and picking orders, our equipment can do that and does it reliably.”
Reliability is key to Remedy’s operations, and Ryan is quick to praise the performance of TMHA’s forklifts. Over the years, the partnership between the companies has strengthened, with both working closely to ensure the forklifts are always performing optimally.
“From an operational perspective, they are an easy vehicle to operate,” says Ryan. “They have all the bells and whistles that I think are required on a forklift, particularly from a safety perspective.”
The user-friendly design of Toyota’s
forklifts has proven invaluable to the Remedy team. With intuitive controls and a suite of safety features – these machines are built to maximise both productivity and operator safety.
This is important in a fast-paced production and logistics environment like Remedy Drinks, where safety and efficiency go hand in hand.
In addition to the forklifts themselves, TMHA has provided Remedy Drinks with advanced fleet management tools, including the I_Site telematics system. This technology allows the company to monitor and optimise its forklift fleet in real time. For Ryan, the introduction of I_Site has been a game-changer.
“In particular, the I_Site software for us is huge, as we’re able to have live data in terms of collisions,” explains Ryan.
By eliminating the need for manual checklists and paper-based tracking systems, I_Site has streamlined many of the processes in Remedy’s warehouse.
“You’re doing away with manual checklists and books on the forklifts – that’s all done through the I_Site software, which is a huge thing,” adds Ryan.
Enhancing safety with proximitylinked speed limiting
Safety is a top priority for Remedy Drinks, and TMHA’s forklifts come equipped with safety technologies. One such feature is proximity-linked speed limiting, which automatically reduces the speed of the forklifts in certain areas of the warehouse.
This is particularly useful in zones with high pedestrian traffic, such as the production area, where forklifts must navigate around workers.
“Some of our production forklifts have speed limiters on them,” says Ryan. “Once they move from the
warehouse to the production area, the speed is limited.
“There’s more pedestrian traffic in production, and there’s a little more interaction between forklifts and pedestrians, so this safety feature is invaluable.”
By automating these safety controls, Remedy can ensure the wellbeing of its employees while maintaining smooth and efficient operations.
Remedy’s long-standing relationship with TMHA has been nurtured by Grant Owen, TMHA’s Area Sales Manager, who has been with the company since Remedy first purchased its second-hand forklift.
Over the years, Grant has facilitated Remedy’s forklift needs, from its first new purchase – a pair of Toyota RRE140 reach forklifts – to its ongoing expansion.
As Remedy Drinks continues to grow, securing contracts with major retailers such as Coles and Woolworths, the company’s material handling needs have evolved. Yet, the partnership with TMHA remains steadfast, with TMHA providing the equipment and support required to keep pace with Remedy’s rapid growth.
Remedy Drinks shows no signs of slowing down. With plans to continue expanding, the company is confident that TMHA’s range of equipment will continue to meet its needs.
“Knowing that we’ve got a relationship with a supplier that has a large variety of equipment, we know we can stay with TMHA as our supplier,” says Ryan.
“If we need to have new equipment on site, with the range that Toyota has, we know we’re not going to be in a situation where we can’t get a specific piece of equipment. We can rest assured that TMHA will probably have it in some form.”
For Remedy, this long-term partnership with TMHA ensures that its warehouse operations can scale with the business.
“It allows us to stay within one brand, which obviously helps with our servicing and our relationship. We can get the equipment that we really need to run the warehouse,” adds Ryan.
Sustainability has always been a key part of Remedy Drinks’ philosophy, and the use of battery-electric forklifts has allowed the company to maintain its eco-friendly approach.
By choosing electric forklifts that produce zero emissions during operation, Remedy is not only reducing its carbon footprint but also contributing to a cleaner, greener logistics operation.
This focus on sustainability is something TMHA shares, as the company continues to innovate with electric powertrains and eco-friendly technologies in its material handling solutions.
With both companies aligned on the importance of reducing their
environmental impact, the partnership between Remedy Drinks and TMHA is one that will continue to thrive as the industry moves towards a more sustainable future.
As Remedy Drinks continues to grow, it can do so with confidence, knowing that TMHA will be there to provide the equipment and support it needs to succeed.
For Ryan and his team, the partnership with TMHA is more than just about forklifts – it’s about ensuring that the company’s logistics are always running smoothly and sustainably, allowing Remedy to focus on what it does best: brewing great-tasting, healthy beverages. ■
Racking is designed for storing long or bulky items.
BHD Storage Solutions has opened its first Queensland distribution centre, BHD QLD, to enhance operational efficiency and customer service in a region ripe for growth.
n the world of industrial warehousing, BHD Storage Solutions has emerged as a key player since its inception in the early 2000s. With a mission to revolutionise warehouse fit outs, BHD began its journey by offering modular pallet racking systems.
Over the years, it has expanded its portfolio to include cantilever racking, shelving, and customised storage solutions.
“As the market evolved, BHD adapted by integrating advanced technologies and automation into its fit outs designs, optimising space and enhancing operational efficiency,” says Jason Lovett, Sales Manager, BHD QLD.
“By the 2010s, BHD Storage Solutions was known for its commitment to quality and customer service. We embrace sustainability by incorporating eco-friendly materials and energyefficient practices in our warehouse designs.”
BHD offers expert support from
initial consultation to installation, tailoring each project to clients’ needs.
Committed to innovation, the company helps businesses enhance storage capabilities and streamline operations, solidifying its reputation as a trusted partner in industrial warehouse fit outs.
In September 2024, BHD took a step forward with opening its new facility in Slacks Creek, Queensland, just 20 minutes south of Brisbane.
“This strategic move is not just about expanding physical space; it’s about enhancing operational efficiency and customer service in a region ripe for growth,” says Jason.
The facility is designed to reduce transport lead times, enabling faster delivery and better access to storage solutions. It aims to streamline logistics, enabling BHD QLD to respond more rapidly to customer needs
while minimising costs associated with transportation. By establishing a local presence, the company can provide faster turnaround times for both storage services and support, ultimately enhancing the customer experience.
Additionally, this expansion aligns with BHD’s commitment to sustainability. The new facility incorporates energy-efficient technologies, reducing the environmental impact of its operations.
“As BHD continues to grow, our investment in Queensland underscores our commitment to meeting the evolving demands of businesses while supporting local economic development,” says Jason.
“With the opening of our Slacks Creek facility, we are well-positioned to deliver innovative, cost-effective, and timely storage solutions, reinforcing our status as a key player in the industry.”
pallet racking and cantilever racking, each tailored for specific applications.
Pallet racking is suitable for warehouses and distribution centres, providing an efficient way to store pallets of goods. Its adjustable shelves allow for flexibility, accommodating various product sizes and weights. This system maximises vertical space, enhancing inventory management and accessibility.
Cantilever racking is ideal for storing long or bulky items such as pipes, timber, and plasterboard. Its open design allows for easy loading and unloading while eliminating the need for vertical supports at the front of the rack. Cantilever racks can be configured in single or double-sided setups, optimising space in both small and large facilities.
“Our diverse storage solutions ensure that businesses can effectively manage their inventory while improving operational efficiency,” says Jason.
need for interstate transport, businesses
Additionally, the local presence allows for better inventory management, reducing the need for excess stock that often accumulates due to long lead times. This streamlined approach minimises holding costs and optimises warehouse space.
Businesses also benefit from reduced handling and transfer costs associated with interstate logistics, further contributing to overall savings. By consolidating operations in Queensland, BHD QLD enables its clients to operate more efficiently, allowing them to allocate resources to other critical areas of their business.
BHD QLD offers end-to-end project support, ensuring a smooth transition from initial design to final installation. The process begins with consultations to assess client needs, storage requirements, and operational
goals. This critical first step sets the foundation for tailored design solutions, where detailed layout plans are created, and appropriate storage systems are selected, all while ensuring compliance with safety standards.
Following the design phase, the team helps clients choose high-quality materials and equipment that align with their budget and operational needs. This is followed by the dedicated project managers, who then take charge of overseeing timelines and coordinating with stakeholders to align every aspect with the client’s expectations.
The installation team then executes the plan with precision, adhering to industry best practices. After installation, BHD QLD continues to support clients with training, maintenance services, and necessary adjustments, ensuring optimal performance of the storage solutions tailored to their specific needs.
“Our clients consistently highlight the positive impact of BHD QLD’s local presence, reporting reductions in freight costs and delivery times that enhance their operational efficiency,” explains Jason.
“Clients also appreciate the ease of communication with our local team, which enables faster response times and personalised support for smoother project management. Furthermore, our tailored solutions, informed by local market knowledge, help businesses enhance efficiency and productivity.”
At BHD QLD, a commitment to continuous improvement drives its operations. Understanding the evolving business landscape and client needs, it actively seeks feedback and maintains open communication to ensure its solutions remain effective.
“With a focus on advanced analytics, sustainable practices, and refined design strategies, BHD QLD tries to stay ahead of industry developments,” says Jason.
“We also invest in ongoing training and development, equipping our staff with the skills needed to meet new challenges.”
As the company embraces the future, it remains committed to driving success for its clients, solidifying its position as a key player in industrial warehouse fit outs. Visit - www.bhdqld.com.au. ■
Falcon Autotech is a global intralogistics automation solutions company. With over 10 years of experience, Falcon has worked with some of the most innovative brands in E-Commerce, CEP, Fashion, Food/FMCG, Auto and Pharmaceutical Industries.
CONTACT US:
Email: salesenquiry@falconautoonline.com Website: www.falconautotech.com
Harold Vanasse from EnerSys shares insights on addressing the evolving challenges of optimising material handling equipment in modern operational environments.
Fconstant pressure to maintain and increase throughput, even as resource constraints challenge these efforts,” says Harold Vanasse, Global Senior Director of Sales Enablement at EnerSys. “As a result, many managers are shifting their focus from the initial price of equipment to the total cost of ownership (TCO) over its service life.”
A study conducted by Sapio Research revealed that 63 per cent of those responsible for obtaining material handling equipment are more concerned with total lifetime ownership costs than with the initial purchase price. Labour, hardware, and downtime costs associated with equipment maintenance, repair, and replacement remain concerns.
Facility and fleet managers now seek opportunities to improve operational efficiency by evaluating how equipment power systems affect their overall TCO.
While many managers are exploring capital
management systems, and advanced technologies, they are often surprised to find that meaningful improvements can be achieved by optimising the power sources for their material handling equipment.
However, achieving these efficiencies requires a partner that understands the relationship between power needs and operational requirements.
At EnerSys, the process begins with advanced tools that leverage operational data to optimise equipment operation.
One of these tools is EnSite modelling software, an EnerSys product that simulates how different power systems will perform in a facility before any investment is made.
This approach allows managers to make informed decisions about batteries and chargers, ensuring their equipment is powered optimally for both current and future needs.
In many facilities, fleet managers
hand calculations or spreadsheets – to compare batteries and chargers.
However, with the ever-increasing complexity of technologies and the high volume of operational data, these methods often fall short.
Even intricate spreadsheets cannot accurately account for the variables involved, reducing them to little more than a “best guess” for a critical decision.
EnerSys takes a scientific approach, using computer simulation technology to conduct an application assessment. EnSite modelling software allows for a multi-dimensional analysis, testing the performance of various battery and charger combinations in a virtual environment.
This not only saves time and money but also ensures the system is neither underpowered nor oversized, providing just the right amount of power for the operation.
“The software can even account for fluctuations in facility throughput due to seasonality or varying requirements
between multiple locations,” says Harold.
By simulating these changes, EnerSys can predict how power system performance will be affected, ensuring consistent throughput regardless of operational shifts. In addition, EnSite modelling software provides return on investment (ROI) projections, helping managers justify their power system selection to internal stakeholders.
As more companies face pressure to improve their sustainability efforts, many are considering a shift from internal combustion-powered equipment to battery-powered alternatives.
EnerSys helps ease this transition by using EnSite modelling software to estimate the carbon footprint reductions associated with the switch.
By analysing current fuel usage and projecting electricity equivalents, the software can quantify the sustainability impact of moving to battery-powered equipment, helping companies meet their environmental goals without sacrificing operational efficiency.
“Achieving true optimisation of equipment power systems requires access to a broad range of options,” says Harold.
“Facilities often vary in terms of equipment usage patterns, shift profiles, and the nature of the operations themselves, leading to different power requirements.
“For example, a reach truck used to pick items from high shelves has different power needs than a pallet jack used for loading semi-trailers. Even within the same facility, different departments may require varying power capacities.”
EnerSys provides a portfolio of battery and charger options, ensuring the right solution is available for every scenario.
“Working with a vendor that only offers one type of battery technology can severely limit a facility’s ability to optimise its power system,” explains Harold.
“In some cases, a hybrid approach
– using different battery technologies across departments or equipment types – offers the best solution.”
Unfortunately, many fleet managers make power system decisions based on limited options from a singletechnology provider.
This can lead to either underpowered equipment that disrupts operations or overpowered, overpriced systems that provide more capacity than necessary.
To avoid these pitfalls, EnerSys offers a range of solutions, from Ironclad flooded lead-acid batteries to NexSys Thin Plate Pure Lead (TPPL) batteries and robust Lithium-ion options like NexSys iON batteries.
This array ensures that every facility can find the perfect fit for its unique power demands.
Once the optimal power system has been implemented, routine monitoring and managing of the fleet’s power usage is essential to achieving long-term efficiency.
This step is often overlooked, but it plays a critical role in reducing TCO,” says Harold.
“EnerSys offers Wi-iQ battery monitoring devices that track key parameters such as power usage, temperature, and operator charging behaviour.
“This data is transformed into
actionable intelligence, allowing fleet managers to maximise battery service life and protect equipment from unnecessary wear.”
The data collected by Wi-iQ devices also assists the EnerSys service team in maintaining peak battery performance.
With more than 550 authorised service technicians globally available around the clock, EnerSys provides support, including installation, maintenance, repair, and fleet monitoring services.
This ensures consistent equipment uptime, keeping operations running smoothly.
For facility managers looking to optimise their operations and reduce TCO, EnerSys offers a tailored, data-driven approach. By leveraging advanced tools like EnSite modelling software and Wi-iQ battery monitoring devices, EnerSys provides power solutions that align with both operational needs and sustainability goals.
“Managers should explore these opportunities to improve efficiency and minimise ownership costs,” says Harold.
EnerSys can help facilities achieve true power optimisation with its range of technologies and service support. ■
Henry Hui, who works closely with CIMC Pteris Global, talks about introducing automatic loading and unloading solutions in Australia.
As the demand for automation grows across the globe, CIMC Pteris Global is setting its sights on Australia. Known for its expertise in automated logistics, the company is entering the Australian market for Automatic Loading and Unloading Systems (ALUS).
With a well-established reputation in automation and logistics, CIMC Pteris Global is prepared to meet the unique demands of the Australian industry.
CIMC Pteris Global has long been a player in the automatic logistics sector, with a track record of innovation and operational efficiency. As it ventures into the Australian market, the company aims to tailor its solutions to meet the needs of local businesses.
“Our strategy is to leverage our extensive expertise in logistics and manufacturing operations, enhancing productivity and reducing costs for Australian businesses,” says Henry Hui, Director of Airstack Intralogistics and CIMC Pteris Global collaborator.
“We plan to work closely with local partners and stakeholders to ensure that our systems are seamlessly adapted to the unique demands of the Australian market. This means offering scalable solutions that can integrate smoothly into existing supply chains.”
E-commerce has boomed in Australia, particularly in the wake of the COVID pandemic, creating new challenges for logistics and retail sectors.
Speed has become a critical factor for consumers, and businesses are
increasingly seeking automation to meet these growing demands.
Automated loading and unloading systems, such as those provided by CIMC Pteris Global, offer a solution to streamline logistics and warehousing processes.
Henry emphasises the importance of speed in today’s market.
“E-commerce is all about how fast you can get products to consumers,” he says. “Automated systems play a crucial role in this process, allowing businesses to move goods more quickly and efficiently. Whether it’s unloading containers or getting products onto shelves, speed is critical, and automation is a key driver of this efficiency.”
“With our automated systems, companies can reduce the need for manual labour, which not only improves safety but also increases productivity.
“The high costs of labour and the ongoing workforce shortages in Australia make automation an attractive option for businesses looking to maintain competitiveness.”
Australia’s size presents a unique set of challenges for any logistics solution. With distribution centres spread across major cities and remote regions, automation systems must be versatile and reliable under diverse conditions.
CIMC Pteris Global recognises this challenge and has developed adaptable solutions to meet the needs of businesses operating in different environments.
“While the majority of demand will likely come from major cities and distribution centres, where freight volumes are high, we are also developing solutions that can be scaled for use in remote regions,” says Henry.
“Our systems are designed to handle the complexities of Australian logistics, ensuring that businesses, regardless of location, can benefit from automation.
“Automation will be particularly valuable for medium to large firms that have high freight volumes.
“By eliminating the need for manual unloading and loading, these systems can enhance safety and efficiency. While remote areas may not have the same volume as urban centres, we believe automation will still play a role as logistics systems evolve.”
“There are several factors we need to take into consideration when designing the system for our clients” adds Jimmy, Marketing Manager from CIMC Pteris Global. “First, we need to assess the possible safety risks during the operation of the automatic loading system, such as mechanical or electrical issues, and their potential consequences; ensuring operator safety through proper training and emergency response skills. Second, the system’s ability to function reliably in various conditions, including different temperatures, humidity levels, and dust, as well as its performance with different types of cargo and loading scenarios.
Last but not least, the automatic loading system needs to be designed to accommodate various vehicle sizes and loading needs, ensuring it works effectively in all scenarios.”
High labour costs and workforce shortages are two of the most pressing issues faced by Australian businesses.
Automation offers a way to mitigate these challenges by reducing the need for manual labour and improving operational efficiency.
CIMC Pteris Global’s ALUS solutions
are designed to help businesses overcome these issues while maintaining cost effectiveness.
“Our systems offer a fully automated solution, which means there’s no need for operators to manually load or unload containers,” says Henry.
“This not only saves costs but also improves safety by reducing the risk of workplace accidents. Companies can run these systems continuously without the limitations of manual labour.
“When you invest in automation, you’re not just reducing labour costs –you’re also improving energy efficiency.
“Automation brings a range of benefits to the table, including the ability to operate 24/7. Businesses won’t have to deal with the unpredictability of manual labour, such as absenteeism or scheduling conflicts.”
While automation offers clear benefits, the initial investment cost can be a barrier for many small to medium
enterprises (SMEs) in Australia.
To address this concern, CIMC Pteris Global is focused on demonstrating the long-term return on investment (ROI) of its systems.
The company plans to use case studies from its successful implementations in other markets, particularly in China, to highlight the cost-saving potential of automation.
“It’s important to show businesses that the upfront cost of automation is an investment in the future,” explains Henry.
“We’ve seen this in China, where companies that have adopted our systems have realised savings in labour and operational costs over time. By showcasing these case studies, we can provide Australian businesses with the evidence they need to see the longterm value of our solutions.”
Henry also sees opportunities for automation in the food and beverage
sector, where handling perishable goods requires speed and precision.
Automating the loading and unloading process ensures that products are moved quickly, reducing the risk of spoilage and maintaining quality.
“Automation in the food and beverage industry is particularly valuable because it helps businesses maintain the integrity of their products,” says Henry.
“By automating these processes, companies can ensure that goods are handled safely and efficiently, meeting both regulatory requirements and consumer expectations.”
Henry is optimistic about the future of ALUS in Australia. As businesses increasingly recognise the benefits of automation, demand for these systems is expected to grow.
Henry agrees that while the technology is still relatively new in Australia, it has the potential to change logistics and warehousing operations across the country.
“The future of logistics is automation,” adds Henry. “As more businesses adopt these systems, we expect to see improvements in efficiency and cost savings. At CIMC Pteris Global, we are committed to supporting Australian industries in their journey towards automation by providing innovative, reliable, and adaptable solutions.
“We believe that automated systems will become a standard part of the logistics and manufacturing landscape in Australia. By partnering with local businesses and adapting our solutions to their specific needs, we are confident that we can help drive this transformation.” ■
Purpose built industrial/bulk storage facility with flexibility for specific commodity uses.
Close proximity to major rail and road transportation routes.
Access to Port infrastructure and potential for direct rail loading.
Leverage off a South Australian port with National and Global reach.
New fulfilment centre
Located in Truganina, Victoria, spanning 26,500 square meters.
Storage capacity
Can hold up to 26,000 pallets.
Customer reach
Serves both the LEGO Group’s B2C and B2B business in Australia and New Zealand.
Advanced automation
Includes carton-reducing technology to minimize packaging and waste.
Sustainability features
+ Dual 100kW solar panel system to reduce electricity consumption and contribute excess power to the grid.
+ Water-saving technologies for on-site amenities and irrigation.
+ Achieved a 5 -star Green Star Rating from the Green Building Council of Australia.
au.kuehne-nagel.com
As e-Commerce reshapes logistics, Chris Josey, Regional Head ANZ, talks about how Falcon Autotech is leveraging advanced automation solutions and meeting evolving demands.
The rapid growth of e-Commerce is reshaping the logistics and supply chain landscape in the Australia and New Zealand (ANZ) region, bringing both challenges and opportunities. As consumers increasingly opt for online shopping, eCommerce providers must enhance speed and efficiency, prompting innovations in technology, warehousing, and last-mile delivery to meet customer expectations.
This shift not only opens avenues for growth but also introduces complexities such as scarcity of space inside warehouses, operator fatigue due to productivity pressure, and meeting strict SLAs from customers.
Falcon Autotech, established in 2012, is at the forefront of warehouse automation solutions, addressing the challenges and opportunities arising from the rapid growth of e-commerce.
The company specialises in advanced technologies like robotics, conveying,
and profiling, helping logistics providers enhance speed and efficiency while navigating increased competition and evolving consumer expectations.
The surge in online shopping has led to demand for efficient logistics solutions. With consumers expecting faster and more flexible delivery options, logistics networks are feeling the strain.
The complexity of managing inventory, warehousing, and transportation has intensified, leading to operational bottlenecks and rising costs. Last-mile delivery has emerged as a challenge.
Reverse logistics, which involves managing product returns, has also gained prominence. Efficiently handling these returns is essential not just for customer satisfaction but also for costeffectiveness.
“Falcon Autotech is in the process of installing an ASRS system to enhance
reverse logistics. While it’s not solely for e-commerce, the flexibility of sortation and automation allows us to tailor solutions that meet various operational needs,” adds Chris.
Furthermore, the demand for additional warehouse space close to population centres has surged, presenting challenges in terms of locating suitable properties and the high costs associated with leasing or constructing new facilities.
An issue compounding these challenges is the labour shortage in the logistics sector, along with the continuously increasing salaries of the warehouse operators
“The industry is facing transport and delivery challenges due to a shortage of labour resources, which is impacting customer service,” says Chris Josey, Regional Head ANZ, Falcon Autotech.
“This challenge results in reduced response times, making it difficult to offer a personalised service. As a result,
we’ve seen an increased reliance on automation technology as organisations strive to keep costs down and maintain sustainability and viability in the market.”
Rising costs pose a challenge for e-Commerce businesses, squeezing profit margins and complicating competition. Several factors contribute to these escalating expenses.
“One of the biggest challenges we face is supply chain disruptions due to our reliance on imported products,” says Chris.
“Frequent updates about shipping issues from geopolitical events or natural disasters have become common. The rise in shipping costs during COVID added to inflationary pressures, and many organisations, especially in 3PL and e-Commerce, struggle to manage how they receive and restock goods efficiently.”
Additionally, last-mile delivery challenges present hurdles, as fuel costs and driver shortages inflate delivery expenses, particularly in rural areas.
Companies with resilient supply chains can adapt more effectively to challenges, maintaining consistent service and gaining an advantage over competitors.
Disruptions can harm a company’s reputation and erode customer trust, so maintaining a resilient supply chain is vital for protecting brand image.
“Diversification with plans A, B, and C
is essential, and leveraging technology, predictive analytics, automation, and partnerships can enhance supply chain resilience and prepare organisations for future challenges,” adds Chris.
Falcon Autotech products help supply chain management by offering realtime visibility for proactive disruption identification and predictive analytics for demand forecasting and inventory optimisation.
They also support scalability through the automation of warehouse operations and logistics, improving efficiency while reducing reliance on manual labour. This design approach enables organisations to invest in technology that grows with its needs.
“Falcon’s technology eliminates repetitive tasks, reducing operator fatigue and enhancing health and safety,” says Chris.
“Designed with environmental sustainability in mind, our systems minimise power draw – shutting down when not in use. We’re also introducing friction wheel technology to our sortation solutions to further cut operational costs. Our automatic storage and retrieval systems maximise free airspace and floor space, efficiently shrinking warehouse footprints based on product profiles.”
Falcon Autotech offers a range of intralogistics automation solutions designed to tackle the challenges posed by labour shortages in the e-commerce sector. Its robotic picking and sorting systems automate repetitive tasks,
enhancing accuracy and efficiency while minimising reliance on manual labour.
Additionally, Automated Storage and Retrieval Systems (AS/RS) optimise warehouse space and reduce the need for manual handling of goods.
To increase overall efficiency, Falcon’s conveyor systems streamline the movement of products within warehouses, enhancing throughput, while high-speed sortation systems automate package sorting to accelerate order fulfilment. Pick-to-Light and Put-to-Light systems further guide workers to the correct locations, improving accuracy and reducing errors, subsequently improving productivity
Falcon Autotech also provides dimensioning and weighing systems that capture precise product data, eliminating manual errors and enhancing inventory management. Its barcode scanning and verification systems ensure accuracy and mitigate the risk of mis-shipments.
With modular designs, Falcon’s solutions allow for easy scalability, and their ability to integrate with existing warehouse management systems (WMS) ensures a flexible automation solution.
As the e-Commerce landscape evolves, Falcon Autotech is poised to innovate and adapt. Key trends, such as increased personalisation and the rise of omnichannel retail, necessitate advanced automation that integrates seamlessly with AI-driven insights for tailored customer experiences.
Additionally, the focus on sustainability drives Falcon to develop energy-efficient solutions and partner with eco-conscious providers. The growth of social commerce and demand for rapid delivery times further emphasise the need for optimised fulfilment processes, a space where Falcon excels with high-speed sortation and automated storage systems.
By investing in R&D and embracing technologies like AI and Machine Learning, Falcon Autotech will continue to refine its offerings, ensuring it meets the changing needs of its customers while promoting sustainable practices. By staying attuned to market demands, Falcon is not just responding to trends but actively shaping the future of e-Commerce logistics. ■
Proud Sponsor of the 2024 MHD Mercury Awards
Our extensive range of products and services ensures we deliver quality solutions for a wide variety of motion applications.
Industries include but not limited to:
• Food and Beverage
• Manufacturing
• Logistics
• Wastewater
• Agricultural
• Mining
sew-eurodrive.com.au
Products and Services include:
• Gearmotors and Gear Units
• Motors
• Decentralised
• Mechanical Variable Speed Drives
• Heavy Industrial Solutions
• Product Life Cycle Services
• Online Support
• Custom Engineered Drive Solutions
• ...and many more!
CEVA Logistics is a leading supply chain and logistics provider that leverages its strengths across multiple sectors to meet evolving market demands while prioritising sustainability and innovation.
CEVA has a large global footprint, covering 170 countries, including Australia and New Zealand.
“In Australia and New Zealand, we have over 50 facilities, spanning approximately 730,000 square metres,” says Guy Meredith, Managing Director of CEVA Logistics in Australia and New Zealand.
This network allows CEVA to connect businesses all over the world, reaching new markets with the ease of one single provider. CEVA’s solutions are tailormade and thanks to a strong culture of innovation and expanding expertise, CEVA is able to provide logistics solutions to a range of industries, including automotive, industrial, technology, consumer & retail, healthcare, luxury and more.
“In addition to our warehouses, we operate manned and unmanned depots
around the country, primarily serving utilities and telecoms infrastructure accounts,” says Guy.
This blend of facilities strengthens CEVA’s end-to-end capabilities, offering warehousing alongside ground transport.
“Seventy percent of our contract logistics customers rely on our transport services, which reinforces our position as a full-service provider,” he adds.
Recently, CEVA has further enhanced its capabilities in consumer and retail, and e-commerce, offering omnichannel solutions for both business-to-business (B2B) and business-to-consumer (B2C) services.
A key factor in CEVA’s continued growth is its strategic acquisitions. The 2022 acquisition of Ingram Micro Commerce and Lifecycle Services (CLS) strengthened CEVA’s presence in the technology and eCommerce sectors.
More recently, CEVA’s parent company, CMA CGM Group, has recently completed its acquisition of Bolloré Logistics.
Guy highlights the synergy between these acquisitions and its existing operations.
“There’s limited overlap, which creates good synergies. We’ve integrated these new capabilities seamlessly into our broader operations,” he says.
With these expansions, CEVA continues to grow its operational footprint, aiming to bring on between 30,000 and 40,000 square metres of additional warehouse space annually.
“Our Kemps Creek facility became operational in January, and more recently, we opened our first site at Lockwood Road nearby,” adds Guy.
“We’re expecting a second facility in Lockwood to come on board early next year.”
Sustainability is at the core of CEVA’s operations. Guided by the CMA CGM Group’s goal of achieving net-zero carbon emissions by 2050, the company’s contract logistics division is leading the way in sustainable practices.
“We’re excited to say that 100 per cent of the lighting in our warehouses is LED and we have renewable energy and waste management programs in place,” explains Guy.
A standout example of CEVA’s commitment to sustainability is its
new Kemps Creek warehouse located in Western Sydney.
This state-of-the-art facility, positioned strategically near the Western Sydney Airport, incorporates numerous green technologies.
“We’re very proud of this site,” says Guy. “It features temperature control, translucent roofing to reduce lighting needs, and rainwater harvesting from the roof.”
Additionally, the Kemps Creek facility has 1,510 solar panels installed on the roof, generating 230 kilowatts of photovoltaic power. The site is also equipped with six to eight electric vehicle charging points and technology to optimise energy usage and monitor temperature control.
“Each new site we open builds on the lessons we’ve learned from previous facilities, continuously enhancing our sustainability measures,” says Guy.
CEVA’s commitment to sustainability has not gone unnoticed. In 2023, the company received the Environmental Excellence Award at the Australian Supply Chain and Logistics Awards, recognising its efforts in sustainable warehousing practices.
In 2024, the company emerged as the winner for the Sustainable Initiative Award at the MHD Mercury Awards Ceremony. CEVA’s procurement team played an important role in the project with the aim of reducing CO2 emissions.
“The goal was to reduce 4,000 tonnes of CO2 emissions annually through aggressive recycling measures that divert waste to landfill,” says Guy.
“By partnering with a waste management company, we’ve implemented monitoring and reporting at each site, and we’ve seen recycling conversion rates improve from as low as 45 per cent to over 80 per cent in just 12 months.
“These efforts align with CEVA’s broader focus on minimising its environmental impact. We prioritise sourcing packaging materials with high recycled content, and where possible, using biodegradable alternatives.”
The integration of Bolloré Logistics has bolstered CEVA’s freight management
capabilities, particularly in sectors like healthcare, fragrance, cosmetics, luxury goods and aerospace.
“These industries are highly focused on sustainability and corporate social responsibility (CSR),” says Guy.
With the Bolloré acquisition, CEVA has become one of the top five logistics providers globally in terms of air and ocean volumes.
The acquisition has also introduced new freight management services and allowed the company to explore scope three carbon reduction strategies, which focus on emissions generated throughout the supply chain.
Australian and New Zealand customers can expect a range of new solutions as a result of the Bolloré acquisition.
“We’re enhancing our domestic transportation offerings and expanding our Trans-Tasman solutions,” says Guy. “We’re also strengthening our end-toend services, from customs clearance and warehouse management to domestic delivery.”
These solutions provide customers with seamless, integrated services across the supply chain.
“Our ability to manage everything from air and ocean freight to warehousing and domestic transportation is an advantage,” adds Guy.
In an increasingly digital world, CEVA is also investing in artificial intelligence (AI) and cybersecurity to stay competitive.
“We inherit robust cybersecurity measures from our parent company, the CMA CGM Group, including intrusion detection and cyber vigilance,” says Guy.
On the AI front, CEVA is implementing innovative solutions across its operations. For instance, in its fashion retail division, it has introduced a labour planning model that uses historical data to optimise staffing and performance management.
“This not only improves costeffectiveness but also helps us utilise our resources more efficiently,” explains Guy.
CEVA is also leveraging smart camera technology to automate scanning and reduce errors in kitting operations for our technology customers. In New Zealand, the company uses demand planning systems to assist with product launches and reposition inventory based on demand.
Globally, CEVA is driving AI innovation, developing tools for dynamic predictive visibility and realtime container tracking.
The company’s digital platform, myCEVA, helps customers balance cost, speed, and emissions, while the Green Ocean program focuses on reducing carbon emissions across ocean freight operations.
As CEVA Logistics continues to expand its footprint and enhance its sustainability initiatives, the company remains committed to delivering innovative, customer-focused solutions. ■
Flinders Port Holdings John Ranaldo and Terre Property Partners’ Mark Brammy explain their joint efforts in developing the South Australian Bulk Commodity Storage facility.
Fmake a leap in South Australia’s trade infrastructure with the development of a new bulk commodity storage facility at the Inner Harbour East precinct.
This project is more than just an upgrade – it’s a milestone in the company’s long-term vision, closely aligned with its Masterplan designed to enhance both import and export capabilities for South Australia.
John Ranaldo, Executive General Manager - Commercial at Flinders Port Holdings, and Mark Brammy, Chief Executive Officer at Terre Property Partners, share insights into how this development fits into the Group’s broader strategy.
In 2020, Flinders Port Holdings commissioned a long-term Masterplan to guide decisions around port and land side infrastructure development. The new bulk commodity shed project is being developed in collaboration with Terre Property Partners.
John explains that the company’s long-term ownership of port and land infrastructure is necessary to its strategic planning.
“Our long-term Masterplan is designed to ensure we make wellinformed decisions for the future of South Australia’s trade and logistics capabilities,” he says.
The Inner Harbour East precinct
was identified as a key opportunity for facilitating bulk commodity imports and exports.
“We’ve been developing Inner Harbour East since 2011 and have invested over $100 million in infrastructure there,” John says.
“This new bulk commodity shed is another major step in transforming the precinct into a world-class trade location.”
“The planning approval process is straighforward. It’s a local council planning consent issued by the City of Port Adelaide given the site is compliant with industrial and port-related activity use,” adds Mark.
The new facility is tailored to meet the growing demand for bulk commodities in South Australia, particularly from sectors like mining and manufacturing. John highlights the increasing pipeline of mining activities in the state, particularly in magnetite iron ore and copper.
“South Australia’s resource sector is thriving, and we believe this facility will be instrumental in supporting that growth,” he says.
However, the focus is not just on exports. John emphasises the importance of supporting the state’s import needs as well.
“Our Masterplan identified that we can’t focus solely on exports. The bulk commodity shed will initially cater to customers importing essential materials such as fertiliser and soda ash, which are crucial for industries like mining and glass manufacturing,” he explains.
Mark points out that Terre Property’s experience, having previously developed two nearby fertiliser storage facilities, gives it a distinct advantage.
“We’ve developed facilities for Incitec Pivot Fertilisers and Wengfu Fertilisers, so we understand both the planning and operational requirements for prospective tenants,” he says.
This expertise is reflected in the design, particularly in accommodating bulk commodity storage.
The facility is being engineered to support high floor loadings and large stockpiles.
“We’re implementing a ground improvement strategy to support an 80 kPa floor loading, allowing stockpiles up
to 10 metres,” explains Mark.
He also addresses the challenges of storing corrosive materials like fertiliser.
“The building requires epoxy paint treatments on steel and timber LVLs instead of steel purlins to ensure the facility’s longevity,” he adds.
John is enthusiastic about the role this facility will play in improving supply chain resilience.
“Resilience in the supply chain means having the capacity and bandwidth to support short-term peaks in volume,” he says.
The Inner Harbour East precinct has already seen the development of other commodity storage facilities, and the new shed will add further capacity to handle increasing trade volumes.
“This precinct has the potential to become a world-class hub for bulk commodities. By adding this new facility, we’re not just boosting capacity – we’re also improving operational efficiency and creating flexibility to accommodate future growth,” says John.
Efficiency is a key design principle for the new bulk commodity storage facility. John reveals that the facility will be constructed with the capability to include a conveyor system that facilitates direct transfer of commodities from ship to shed.
“While the conveyor system isn’t part of the initial construction, we’ve been very clear with our design consultants that it’s something we want to add in the future. This will reduce manual handling and transport time, making the entire operation more efficient,” he explains.
In addition to this, Flinders Port Holdings is conducting a feasibility study on integrating a conveyor system across multiple sheds in the precinct, linking them directly to Berth 29.
“This would create a seamless flow of goods from ship to storage, greatly enhancing operational efficiency across the precinct,” says John.
Flinders Port Holdings is exploring the potential to expand the rail infrastructure within the precinct. Currently, the rail spur into Berth 29 is limited to
400-metre-long trains.
John explains that the Group is investigating options to acquire additional land and develop a rail loop that could accommodate longer trains.
“Completing the rail loop would reduce downtime and improve the overall efficiency of not just this shed but the entire precinct,” he says.
“We’ve enjoyed working with Terre Property over the past year to bring this project to fruition. We’re now approaching the final decision points within Flinders Port Holdings that will allow us to start construction early in 2025.”
Flinders Port Holdings will meet the needs of South Australia’s trade sector. The project will be completed in Q1 2026 and will align with key agricultural seasons, targeting pre-commitment from tenants.
“We are offering spaces ranging from 4000 to 22,000 square metres, with flexibility in division walls and location,” says Mark.
Mark sees this development as part of a broader strategy.
“Our long-term vision is aligned with the port’s ability to attract new users and provide an integrated end-to-end solution,” he says. “It’s one thing to have a port user, but they need storage, and that’s where we come in.”
The new bulk commodity storage facility is a component of the company’s strategy to support both imports and exports, improve supply chain resilience, and enhance operational efficiency.
Terre Property’s efforts are set to strengthen the port’s capabilities and provide infrastructure for South Australia’s bulk commodity sector.
As construction plans move forward, the Inner Harbour East precinct is set to become a world-class hub for bulk commodity trade, benefiting the state for upcoming decades. ■
The LEGO Group has opened a sustainable, automated fulfilment centre in Truganina to serve the Australia and New Zealand markets.
Kuehne+Nagel is a specialist in Contract logistics, such as freight forwarding and supply chain management.
Based in Switzerland, the company offers a range of services, including sea, air, and road freight, fulfilment, warehousing, and customs clearance. It also focuses on digital solutions to optimise logistics processes, provide real-time shipment visibility, and enhance operational efficiency.
In Australia, the company’s operations are integrated into the global network, focusing on transport visibility, customs clearance, and digital logistics solutions to enhance supply chain efficiency.
Earlier this year, the company was named a leader in Gartner’s 2024 Magic Quadrant for Third-Party Logistics (3PL) globally, recognised for its ability to execute and its visionary leadership.
The company was recognised for its range of specialised logistics offerings, a global footprint with expanded facilities, and a deep understanding
of market trends, including trade patterns, digital ecosystems, and sustainability.
Gartner also praised Kuehne+Nagel’s commitment to innovation and customer service.
Ultimately, the company serves multiple industries like aerospace, automotive, healthcare, and high-tech sectors.
“Gartner’s evaluation confirms our steadfast commitment and inventive mindset with which our teams worldwide support our customers’ needs,” says Kuehne+Nagel, CEO Stefan Paul.
“Our Roadmap 2026 underscores our dedication to delivering an unparalleled customer experience in the industry.”
Recently, the LEGO Group has expanded its partnership with Kuehne+Nagel by opening a new fulfilment centre in Truganina, located in Australia’s southeastern state of Victoria.
Spanning 26,500 square metres and equipped with a storage capacity of 26,000 pallets, the new fulfilment centre is designed to serve LEGO’s customers for both B2C and B2B across Australia and New Zealand.
The facility leverages cutting-edge automation to optimise operational processes while adhering to sustainability.
The automation aspects are designed with sustainability in mind, featuring state-of-the-art, carton-reducing technology to minimise packaging and waste.
The facility also integrates a dual 100kW solar panel system to reduce electricity consumption and contribute excess power back to the grid.
Water saving technologies support on-site amenities and irrigation for the surrounding plants and trees.
The fulfilment centre has achieved a 5-star Green Star Rating, which signifies ‘Australian excellence’ in sustainable building practices according to the Green Building Council of Australia (GBCA) standards.
“We are delighted to partner with Kuehne+Nagel as our new logistics partner in the Australian market,” says Troy Taylor, Vice President and General Manager for LEGO Australia.
“This new world-class fulfilment centre in Truganina will allow us to continue with our expansion plans for this very important market as we strive to reach more kids and adults with our iconic LEGO bricks.”
“This project showcases our growth strategy and dedication to expanding our footprint and fulfilment model in the Pacific and strengthening our partnership with the LEGO Group,” says Francis Murugan, Managing Director for Kuehne+Nagel Australia.
“Beyond being a fulfilment centre, it is a hub of efficiency, innovation, and sustainability, equipped with the latest technologies, automation, and ecofriendly practices.” ■
MEGATRANS 2024 showcased industry innovations while addressing sustainability and collaboration, charting a progressive path for supply chain and logistics.
Hosted by Prime Creative Media, MEGATRANS 2024 was a landmark event in the supply chain and logistics industry brought together key stakeholders to explore the future of the industry. Held at the Melbourne Exhibition and Convention Centre on September 18-19, 2024, the event served as a platform for industry leaders and innovators to engage in discussions on pressing challenges and opportunities.
From sustainability to technological advancements, the event highlighted the interconnectedness of various sectors, fostering collaboration and knowledge sharing.
With a robust lineup of speakers, panel discussions, and networking opportunities, the event aimed to shape the direction of the industry as it navigates a rapidly evolving landscape.
The event was kickstarted by the Victorian Transport Association (VTA), which hosted its official opening breakfast.
VTA CEO Peter Anderson set the stage for the morning, emphasising the pressing logistics challenges that the industry faces and the need for collective action and innovation.
“The supply chain is connected. We can’t think in silos,” says Peter.
The breakfast event’s sponsor, Zurich Resilience Solutions’s Peter Johannson, Principal Risk Engineer, delivered an insightful speech on resilience in the face of climate change, cyber threats, and technological advancements.
“Businesses are now being electrified as they deploy artificial intelligence solutions,” says Peter.
He noted that social engineering is integral to companies improving
their operations and that to achieve Scope 3, they should look at supply chain mapping, governance, and risk management.
“The human element is also important. We should aim to have well, happy, and resilient employees,” he says.
The Victorian Minister for Roads & Road Safety and Ports and Freight, Melissa Horne, also addressed the audience, outlining Victorian government projects that are set to reshape the logistics landscape.
She highlighted the West Gate Tunnel, scheduled to open in 2025, and the North-East Link, both of which promise to enhance freight efficiency.
“My role is to work with the VTA as a facilitator for a sustainable and productive freight sector,” says Melissa.
In an era where the demand for skilled labour continues to rise, Horne also celebrated the success of the Truck
Driver Program, which has trained nearly 400 heavy vehicle drivers since its inception.
“Twenty-five per cent of the drivers trained so far have been women,” Melissa added.
John Murphy, CEO, Prime Creative Media, rounded out the morning’s speeches with a clarion call for collaboration.
“The future of the sustainable supply chain provides both opportunities and challenges as we work towards reducing our carbon footprint,” says John.
The breakfast was only the beginning of a dynamic day at MEGATRANS 2024 when the show floor opened to thousands of attendees. Visitors explored the latest innovations and engaged with industry leaders, setting the stage for conversations and connections.
The conference featured a series of sessions that delved deeper into specific industry challenges and innovations.
One such session, sponsored by OneStop, focused on enhancing visibility and efficiency within the interconnected supply chain. This was followed by a discussion by Toll Group on “Creating the Sustainable Fleet of the Future,” where experts tackled the pressing need for decarbonising logistics fleets.
Post-lunch discussions included a seminar titled “Sustainability and Safety in Supply Chain,” where the panel discussed how automation and digitisation are paving the way for greener operations. The session on “Decarbonising International Shipping & Transport” offered insights into achieving net-zero commitments by 2050 – a challenge that requires concerted efforts across the sector.
Day two of MEGATRANS 2024 continued to foster collaboration, with discussions on the integration of in-warehouse and on-the-road fleets, moving from ambition to action in supply chain sustainability, and leveraging telematics for efficiency gains.
“We think that the transport industry is a key market for us,” says Adam Duncan, General Manager of Sales at Adaptalift.
“We’ve had good feedback from all our team that have worked on
the stand. It’s been positive, good engagement from some potential customers, and we look forward to following up the leads.”
One of the event’s partners, the Supply Chain and Logistics Association of Australia (SCLAA) held a lineup of seminars. This included open remarks from Stephen Lakey, Director, SCLAA, followed by seminars named Trust in Supply Chain Technologies, Eco-Innovation: Driving Profits and Planetary Health, A Fresh Perspective on Inventory Management for Supply Chain Efficiency, Integrating Sustainability and ESG into Supply Chain Management for Competitive Advantage, and Simplifying International Shipping and Transport.
MEGATRANS was more than just a gathering; it was a pivotal moment for industry leaders to confront the evolving challenges in logistics and supply chain management.
“It’s about brand recognition in this space for us,” says Richard Boothey, Business Development Manager, Kärcher.
“The exposure that we’ve got out of it has been great. We’ve had a steady flow of traffic and a lot of interest in products, particularly the robotics side of the business. It’s overall been a positive experience.”
“This year’s event has exceeded the footfall seen at the last MEGATRANS, which speaks volumes about the industry’s enthusiasm,” says Lauren Chartres, Show Director.
“The positive feedback from attendees signalled a strong desire for continued dialogue and innovation in the logistics sector.”
MEGATRANS 2024 has set a new benchmark for engagement and innovation in the logistics sector. With record attendance and meaningful dialogue, the event was a collective commitment to sustainability, technology, and resilience, ensuring a dynamic future for the industry.
The Mercury Awards were held at the Melbourne Convention Centre on the night of September 18th. They celebrated achievements in the logistics and supply chain industry and were sponsored by SEW EURODRIVE. The event emphasised innovation and sustainability, showcasing both established industry leaders and emerging talents across sectors from warehousing to sea freight.
Merging with the Australian Bulk Handling Awards, the gala offered enhanced visibility and networking opportunities for attendees.
Award winners included Allotrac for Supply Chain Innovator of the Year, Skilled Materials Handling for Best Technology Application, CEVA Logistics for Sustainability Initiative Award, Machship for Freight Transport Solution of the Year, Dr. Elsie Hooi for Contribution to Industry Award, and Silk Logistics for the MHD Sustainable Warehouse Award. ■
A municipal works, civil and commercial construction event.
17-18 September 2025, MCEC
In September 2025, a new event will be landing at the Melbourne Convention and Exhibition Centre. Converge will bring together leading decision makers in the Municipal Works, Civil and Commercial Construction space, to share the tools, ideas and technologies that are shaping these sectors.
The pricing for the course for ASCI members is $995 and for the non-members is $1,395.
The Australasian Supply Chain Institute has an upcoming Accurate & Balanced Inventory
1-Day Course on 3 December that will benefit you and your team. The key features of attending include:
ü Learn to balance inventories using Excel.
ü Implement an effective sales forecasting process.
ü Understand data accuracy requirements for computer-based management system.
ü Eliminate annual stock takes and discuss efficient cycle count approaches.
This course is ideal for practitioners in medium to large businesses involved in inventory management, sales forecasting, warehouse staff, sales planning, demand management, and more.
The course will cover topics including Integrated Planning & Control, Record Accuracy, Cycle Counting, Safety Stock approaches, Managing New Products & Deletions, and more.
Date: 3 December 2024
Time: 9 am to 5 pm Sydney Time
Duration: 8 training hours
Platform: Zoom
Points: Participants will earn 8 CPD points for certification maintenance
To register or for more information, please visit the ASCI website.
This course is ideal for practitioners in medium to large businesses involved in inventory management | Image: ASCI
The price for the course for ASCI members is $2,999 and for non-members is $3,399.
If you want to improve your organisation’s supply chain performance, you need knowledgeable operators, supervisors, and leaders who understand global standards.
The Supply Chain Operations Reference (SCOR) model is the leading supply chain standard that is comprehensive, universally accepted, and open access. By using SCOR, you can assess and improve your company’s supply chain, which leads to better business performance. The
latest version, SCOR DS, has undergone a significant update to include sustainability standards and the digital body of knowledge.
This modern framework shifts from a linear supply chain model to a more synchronous network, leading to improved business performance. More than 5,000 organisations worldwide have used SCOR to improve their supply chains, resulting in improved operations, faster digital transformation, reduced IT expenses, and ongoing profit improvement.
Course Dates & Duration
• 6 - 7 November 2024
• 7:00 am - 3:00 pm Sydney Time
• Prerequisite: Work experience in supply chain
Must be an ASCM Member to sign up for the course. Prices include online courses and learning materials (digital only) but not ASCM membership.
Attendees will receive a certificate of completion after the class and can accrue 14 CPD points towards the maintenance of their professional registration.
Classes will be conducted daily, from 9 am to 5 pm Sydney Time, totalling 16 training hours. Participants can join via Zoom.
Join the upcoming Production Planning & Control 2-Day Course to learn the processes, tools, techniques and performance measures for production planning & control excellence, which will take place on 26-27 November 2024. This workshop will provide an understanding of why Integrated Planning & Control techniques were added to our knowledge as we learnt about the different behaviour of DC finished goods, Finished Items at the
Manufacturing sites & Manufactured & Purchased items, as well as items that experience repetition where simplicity in execution is paramount. In addition to this, planning at the aggregate level through S&OP will also be addressed.
Accountabilities and crossfunctional links will be discussed to enable you to assess the quality of your current processes. Although participants will receive three checklists, the focus for this class will
be the Tom Wallace self-assessment, an Excel-based tool. The other two checklists provided free will be the Fundamental checklist, and a checklist focused more on behaviours. Relevant performance measures will be presented to ensure companies are using the correct measures and the correct formula.
ASCI members can register for $1,950, while non-members can register for $2,350.
The course will take place on 26-27 November 2024
Stay ahead of the curve in logistics, warehousing, and supply chain management. MHD Supply Chain Solutions Magazine offers the latest trends, thought leadership, and actionable insights you need to drive your business forward.
Unlock the ideas, information, and strategies that are shaping the future of supply chain management—only available to MHD subscribers. Don’t miss out on the critical insights that can give your business the edge.
• One-year subscription: $99 for 11 issues
• Two-year subscription: $179 for 22 issues
• Auto-renew subscription: $95 per year Scan to subscribe
Contact: subscriptions@primecreative.com.au
Visit: mhdsupplychain.com.au/subscribe/
The Supply Chain and Logistics Association of Australia (SCLAA) has made a strategic move that will enhance its member resources, networking, and professional development opportunities.
The Supply Chain and Logistics Association of Australia (SCLAA) has acquired Supply Chain Partners.
This acquisition is set to bolster the offerings of both associations, providing enhanced resources, connectivity, networking opportunities, professional development for its members, and a centralised industry marketplace for services and products.
Supply Chain Partners, founded by Dr Sharyn Grant offers a range of tools designed to help supply chain professionals improve and transform various aspects of their businesses. Members benefit from an online community hub, providing the ability to directly communicate with a network of supply chain experts.
A digital directory allows individuals to build professional profiles and businesses
to create storefronts showcasing their brands and services. Additionally, the platform features an industry-specific job board, allowing members to either promote job opportunities or apply directly for roles within the supply chain and logistics sector.
This acquisition, instigated by SCLAA Chair Sue Tomic, with the support of the SCLAA Board, is not just a step forward for the association but a leap towards fulfilling the growing demands of its members. By integrating Supply Chain Partners’ digital capabilities with SCLAA’s established reputation and expansive network, the association can now offer its members a more dynamic and comprehensive experience. This strengthens both associations’ offerings, creating a more robust network and suite of services for their combined membership base.
By merging with Supply Chain Partners, SCLAA is positioning itself to better serve the community, offering seamless, digital-first opportunities for networking, professional development, and business growth.
“In response to feedback from
SCLAA members and industry alike, who expressed a need for an online community hub and a more direct way to network with peers beyond in-person events, we have delivered a
“This acquisition represents a new chapter for both associations, and there is a palpable sense of excitement about the future. The SCLAA looks forward to taking both associations to
As the SCLAA continues to evolve, this acquisition is just the beginning of more member-focused initiatives aimed at enhancing the experience for professionals across the supply chain
A monthly wrap up of the latest appointments in the supply chain, materials handling and logistics industry.
Jason Lovett has been appointed Sales Manager for BHD QLD as of July 2024. Jason brings a wealth of experience with over ten years in the racking industry and five years in freight forwarding. He prides himself on delivering highlevel customer service, demonstrating loyalty, and maintaining integrity in all his dealings. Beyond his professional commitments, Jason is passionate about playing the guitar, enjoying music, and exploring culinary arts.
Toll Group has appointed Steve Roughsedge as the new General Manager for Contingency and Sustainment in its Government and Defence business. Steve brings more than 15 years of experience in logistics, IT, and aviation and has previously worked with Toll for over six years in various leadership roles. In his new position, he will focus on ensuring safety, quality, security and service for Toll’s Government and Defence customers whilst leading critical and transformative industry projects.
KARDEX’S AUTOSTORE DESIGN & ENGINEERING MANAGER
Warren Jones has recently joined the Kardex AutoStore. With more than 10 years of experience in design and project engineering across various industries – including intralogistics, consulting, and nuclear technology – Warren has a strong background in optimising operations, improving distribution processes, and implementing efficient strategies. In his latest role, he designed and supported the delivery of AutoStore systems to further enhance Kardex’s capability to improve logistics services and drive operational improvement.
Do you have career news to share? Email Mannat Chawla at mannat.chawla@primecreative.com.au to be featured.
Swisslog automated warehouse solutions ‘scalable, flexible Vectura stacker crane for high bay warehouse automation reduces energy consumption of pallet warehouse operations by up to 25 per cent, thanks to features including regenerative energy design for optimal use of cycles. With an outstanding 99.7 per cent availability, and providing a solution reliability with over 50 years of continuous improvement behind it, Swedish-designed Vectura performs equally well in temperatures as low as -30°C in a frozen food warehouse, or in ambient environments as high as +50°C. Proven in more than 600 customer installations, and operating at heights up to 50m, Vectura’s single-mast design reduces cost and uses less space, setting the standard for innovative design for pallet cranes in high-bay warehouses. It achieves very high storage density, with single to multi deep reach, in high buildings and, where land space is limited.
For more information visit www.swisslog.com/en-au
The Bin-to-Picker AMR solution from Dematic streamlines order fulfilment with advanced storage and retrieval, and Goods-to-Person technologies. This system comprises autonomous mobile robots (AMRs) that transport storage totes directly to pickers, streamlining the picking process, significantly boosting efficiency, and maximising accuracy. Designed to address labour challenges and rising customer expectations, it offers unparalleled flexibility and scalability. Dematic ensures long-term success with comprehensive support, including maintenance, repairs, and future upgrades. By leveraging their industry expertise and wide range of solutions, Dematic delivers tailored systems that optimise business operations, providing a premium experience for clients and their customers.
For more information, visit www.dematic.com and search for the impressive Radial Europe case study.
The ECE series truck stands out among low-level order pickers due to its innovative features tailored for accessibility, efficiency, and operator comfort. Its height-adjustable steering wheel, known as the “jetPILOT,” ensures accessibility for operators of various heights, making it inclusive for everyone. The operator-oriented working space ensures all necessary equipment, such as scanners, shrink wrap, and documents, are conveniently within reach. Furthermore, the truck can be customised with cutting-edge technology to enable semi-automation in warehouse operations, with the possibility of integrating with Warehouse Management Systems (WMS) based on customer requirements. Experience the difference with the ECE series truck today and elevate your warehouse operations to new heights. To learn more about how our innovative features and customisable options can streamline your workflow and enhance operator satisfaction, visit our website.
For more information visit: www.jungheinrich.com.au
ifm Track and Trace Gate is the complete solution for your automated and transparent logistics in your incoming and outgoing goods processes. By directly transferring all goods flows to the IT level, you can organise the inter-locking of production, inventory, and suppliers more efficiently than ever before.
For more information visit www.ifm.com/au/en